Cost Accounting - Direct cost and Indirect cost
Added on 2022-09-02
30 Pages7186 Words23 Views
COST ACCOUNTING
Chapter 2 (Garrison)
A cost object is anything for which cost data are desired- including products,
customers, jobs and organizational subunits. A cost object is an item that a
company wants to measure separately. For purposes of assigning costs to
costs objects, costs are classified as either direct cost or indirect cost.
Classifications of cost
Cost
classificati
on
Assigning
costs to cost
objects
Direct (Easily traceable)
Indirect (Cannot be traced
easily)
For
manufacturin
g companies
Manufacturing Direct materials
Direct labour
Manufacturinf overhead
Non-manufacturing Selling
Administrative
Preparing
financial
statements
product costs
(inventoriable)
Period costs (expensed)
Cost behavior
in response to
change in
activity
Variable cost
Fixed cost
Mixed cost
making
decisions
Differential costs (differs
between alternatives
Sunk cost (should be
ignored)
Opportunity cost (Foregone
benefit)
Chapter 2 (Garrison)
A cost object is anything for which cost data are desired- including products,
customers, jobs and organizational subunits. A cost object is an item that a
company wants to measure separately. For purposes of assigning costs to
costs objects, costs are classified as either direct cost or indirect cost.
Classifications of cost
Cost
classificati
on
Assigning
costs to cost
objects
Direct (Easily traceable)
Indirect (Cannot be traced
easily)
For
manufacturin
g companies
Manufacturing Direct materials
Direct labour
Manufacturinf overhead
Non-manufacturing Selling
Administrative
Preparing
financial
statements
product costs
(inventoriable)
Period costs (expensed)
Cost behavior
in response to
change in
activity
Variable cost
Fixed cost
Mixed cost
making
decisions
Differential costs (differs
between alternatives
Sunk cost (should be
ignored)
Opportunity cost (Foregone
benefit)
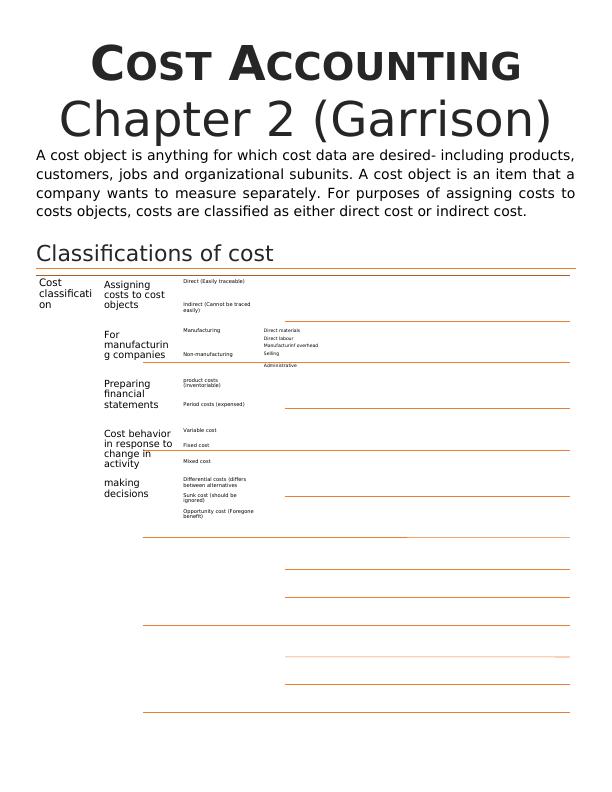
Assigning costs to cost objects
Direct cost: A direct cost is a cost that can be easily and conveniently
traced to a specified cost object. A direct cost is a price that is directly
related to the production of a certain good or service. A direct cost can be
linked to a cost object such as a service, product, or department. The two
basic categories of expenses or prices that businesses might incur are direct
and indirect charges. Direct expenses are frequently variable costs, which
means they change with production levels like inventory.
Direct costs are expenses that your business can completely
attribute to the production of a product. The costs are easily
connected to only one project. Direct costs are not allocated, which
means they are not divided among many departments or projects.
A direct cost can be a fixed cost or variable cost.
An example of a direct cost are the supplies used to make the product. For
example, if you own a printing company, the paper for each project is a
direct cost. The employees who work on the production line are considered
direct labor. Their wages can also be attributed as a direct cost of the
projects.
Indirect cost: Indirect costs are expenses that cannot be traced back to a
single cost object or cost source. During the manufacturing process, items
like products, departments, and customers create costs. These are
considered cost objects because the original manufacturing costs stem from
them. The factory manager’s salary is called a common cost.
Now, consider the sales staff at the company. The sales staff is not
connected to one project. Therefore, their wages are not direct
costs because they cannot be attributed to any one project. Their
wages must be allocated to multiple projects.
Direct cost: A direct cost is a cost that can be easily and conveniently
traced to a specified cost object. A direct cost is a price that is directly
related to the production of a certain good or service. A direct cost can be
linked to a cost object such as a service, product, or department. The two
basic categories of expenses or prices that businesses might incur are direct
and indirect charges. Direct expenses are frequently variable costs, which
means they change with production levels like inventory.
Direct costs are expenses that your business can completely
attribute to the production of a product. The costs are easily
connected to only one project. Direct costs are not allocated, which
means they are not divided among many departments or projects.
A direct cost can be a fixed cost or variable cost.
An example of a direct cost are the supplies used to make the product. For
example, if you own a printing company, the paper for each project is a
direct cost. The employees who work on the production line are considered
direct labor. Their wages can also be attributed as a direct cost of the
projects.
Indirect cost: Indirect costs are expenses that cannot be traced back to a
single cost object or cost source. During the manufacturing process, items
like products, departments, and customers create costs. These are
considered cost objects because the original manufacturing costs stem from
them. The factory manager’s salary is called a common cost.
Now, consider the sales staff at the company. The sales staff is not
connected to one project. Therefore, their wages are not direct
costs because they cannot be attributed to any one project. Their
wages must be allocated to multiple projects.
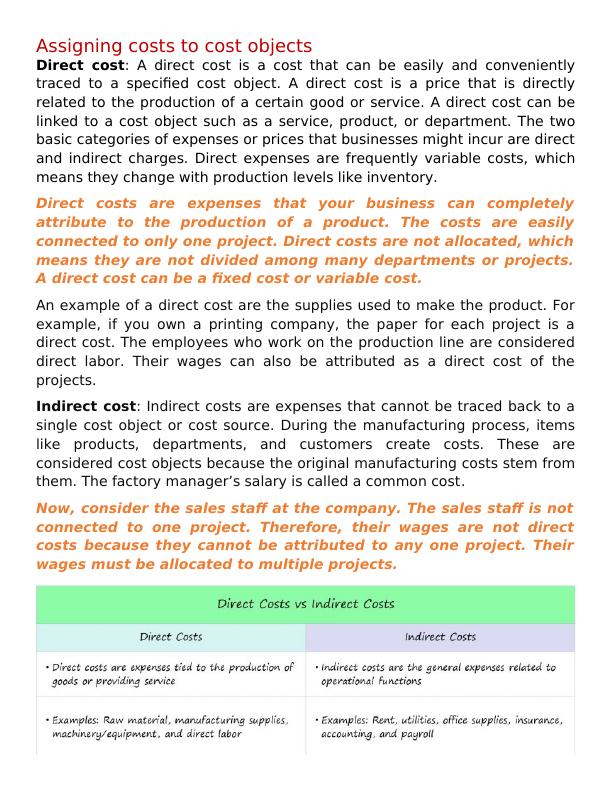
Cost classification for manufacturing companies
Costs may be classified as manufacturing costs and non-manufacturing
costs. This classification is usually used by manufacturing companies.
Manufacturing costs
Most manufacturing companies separate their manufacturing costs into two
direct cost categories, direct-materials and direct labor and in one indirect
cost categories, manufacturing overhead.
Direct materials
Direct labor
Manufacturing overhead
Direct materials: Direct material is the physical items built into a product.
For example, the direct materials for a baker include flour, eggs,
yeast, sugar, oil, and water. The direct materials concept is used in cost
accounting, where this cost is separately classified in several types of
financial analysis. Direct materials are rolled into the total cost of goods
produced, which is then subdivided into the cost of goods sold (which
appears in the income statement) and ending inventory (which appears in
the balance sheet). The finished product of a company may become raw
material of another company. For example, cement is a finished product for
manufacturers of cement and raw materials for companies involved in
construction business.
Direct labor: Direct labor refers to the salaries and wages paid to workers
directly involved in the manufacture of a specific product or in performing a
service. The work performed must be related to the specific task. For a
business that provides services to its customers, direct labor is the work
performed by the workers who provide the service directly to the
customers, such as auditors, lawyers, and consultants. Examples of direct
labor cost include labor cost of machine operators and painters in a
manufacturing company. Like direct materials, it comprises of a
significant portion of total manufacturing cost.
The sum of direct materials cost and direct labor cost is known as
prime cost. Prime cost = Direct materials cost + Direct labor cost
Manufacturing overhead: Manufacturing costs other than direct materials
and direct labor are categorized as manufacturing overhead cost (also
known as factory overhead costs). They usually include indirect materials,
Costs may be classified as manufacturing costs and non-manufacturing
costs. This classification is usually used by manufacturing companies.
Manufacturing costs
Most manufacturing companies separate their manufacturing costs into two
direct cost categories, direct-materials and direct labor and in one indirect
cost categories, manufacturing overhead.
Direct materials
Direct labor
Manufacturing overhead
Direct materials: Direct material is the physical items built into a product.
For example, the direct materials for a baker include flour, eggs,
yeast, sugar, oil, and water. The direct materials concept is used in cost
accounting, where this cost is separately classified in several types of
financial analysis. Direct materials are rolled into the total cost of goods
produced, which is then subdivided into the cost of goods sold (which
appears in the income statement) and ending inventory (which appears in
the balance sheet). The finished product of a company may become raw
material of another company. For example, cement is a finished product for
manufacturers of cement and raw materials for companies involved in
construction business.
Direct labor: Direct labor refers to the salaries and wages paid to workers
directly involved in the manufacture of a specific product or in performing a
service. The work performed must be related to the specific task. For a
business that provides services to its customers, direct labor is the work
performed by the workers who provide the service directly to the
customers, such as auditors, lawyers, and consultants. Examples of direct
labor cost include labor cost of machine operators and painters in a
manufacturing company. Like direct materials, it comprises of a
significant portion of total manufacturing cost.
The sum of direct materials cost and direct labor cost is known as
prime cost. Prime cost = Direct materials cost + Direct labor cost
Manufacturing overhead: Manufacturing costs other than direct materials
and direct labor are categorized as manufacturing overhead cost (also
known as factory overhead costs). They usually include indirect materials,
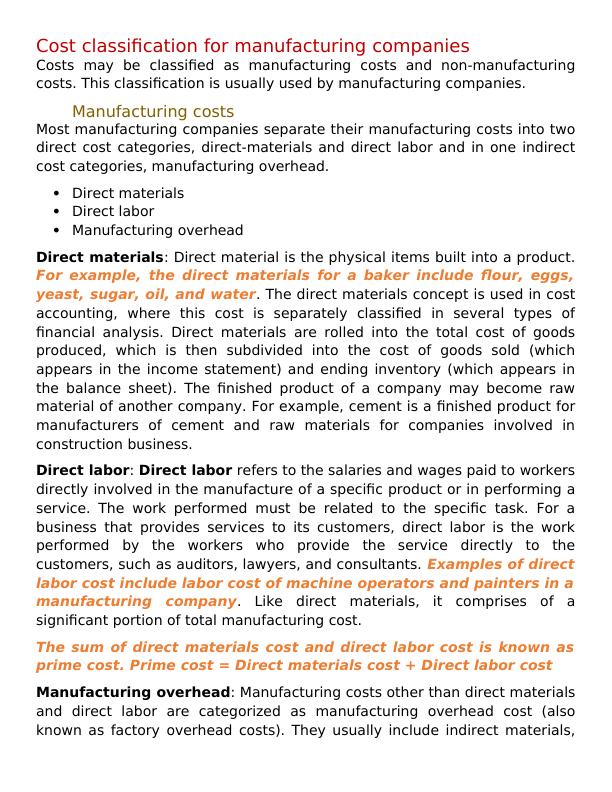
indirect labor, salary of supervisor, lighting, heat and insurance cost of
factory etc. Mostly, manufacturing overhead costs cannot be easily traced
to individual units of finished products. The three types of overhead costs
are:
Fixed: These costs do not change each month. Also, business activity
does not cause these costs to change. Fixed overhead costs include
rent, mortgage, government fees and property taxes.
Variable: These are costs that can change with production output.
These items include some operational utilities such as electric, gas and
trash service. Output can also impact shipping costs, maintenance
situations, legal fees and advertising.
Semi-variable: These items might change over time with increased or
decreased business activity. Business activities may determine the
initial costs but over time, as activity changes, these costs may
increase or decrease. Some examples of semi-variable costs may
include operational utilities, rent or leasing and insurance.
The sum of direct labor cost and manufacturing overhead cost is
known as conversion cost. Conversion cost = Direct labor cost +
Manufacturing overhead cost.
Non-manufacturing costs
Non-manufacturing costs are further divided into the following categories:
Marketing and selling costs
Administrative costs
Examples of marketing and selling costs include advertising costs, order
taking costs and salaries of sales persons etc. Examples of administrative
costs include salaries of executives, accounting costs, and general
administration costs etc.
Selling costs include all costs that are incurred to secure customer orders
and get the finished product to the customer. These costs are sometimes
called as order-getting and order-filling costs.
Administrative costs include all costs associated with the general
management of an organization rather than with manufacturing or selling.
Examples of administrative costs include executive compensation, general
accounting, pubic relations and similar costs.
factory etc. Mostly, manufacturing overhead costs cannot be easily traced
to individual units of finished products. The three types of overhead costs
are:
Fixed: These costs do not change each month. Also, business activity
does not cause these costs to change. Fixed overhead costs include
rent, mortgage, government fees and property taxes.
Variable: These are costs that can change with production output.
These items include some operational utilities such as electric, gas and
trash service. Output can also impact shipping costs, maintenance
situations, legal fees and advertising.
Semi-variable: These items might change over time with increased or
decreased business activity. Business activities may determine the
initial costs but over time, as activity changes, these costs may
increase or decrease. Some examples of semi-variable costs may
include operational utilities, rent or leasing and insurance.
The sum of direct labor cost and manufacturing overhead cost is
known as conversion cost. Conversion cost = Direct labor cost +
Manufacturing overhead cost.
Non-manufacturing costs
Non-manufacturing costs are further divided into the following categories:
Marketing and selling costs
Administrative costs
Examples of marketing and selling costs include advertising costs, order
taking costs and salaries of sales persons etc. Examples of administrative
costs include salaries of executives, accounting costs, and general
administration costs etc.
Selling costs include all costs that are incurred to secure customer orders
and get the finished product to the customer. These costs are sometimes
called as order-getting and order-filling costs.
Administrative costs include all costs associated with the general
management of an organization rather than with manufacturing or selling.
Examples of administrative costs include executive compensation, general
accounting, pubic relations and similar costs.
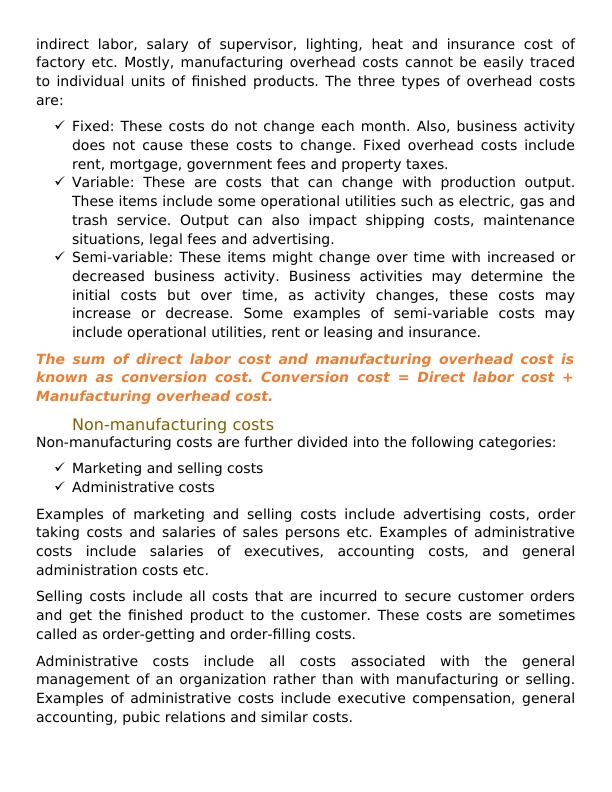
Cost classifications for preparing financial statements
When preparing a balance sheet and an income statement, companies need
to classify their costs as product cost and period cost. To understand the
differences between product cost and period costs, we must first discuss the
matching principle from financial accounting. The matching principle is
based on the accrual concept the costs incurred to generate a particular
revenue should be recognized as expenses in the same period that the
revenue is recognized. Matching Principle is a common accounting concept.
Under this, a company should report an expense in the income statement in
the same period when it earns the revenue.
Product costs
Product cost refers to the costs incurred to create a product. These costs
include direct labor, direct materials, consumable production supplies, and
factory overhead. Product cost can also be considered the cost of the labor
required to deliver a service to a customer. The cost of a product on a unit
basis is typically derived by compiling the costs associated with a batch of
units that were produced as a group, and dividing by the number of units
manufactured. The calculation is:
(Total direct labor + Total direct materials + Consumable supplies
+ Total allocated overhead) ÷ Total number of units = Product unit
cost
These costs are also known as inventoriable costs.
Period costs
Period costs are costs that cannot be capitalized on a company’s balance
sheet. In other words, they are expensed in the period incurred and appear
on the income statement. Period costs are also called period expenses. In
managerial and cost accounting, period costs refer to costs that are not tied
to or related to the production of inventory. Examples include selling,
general and administrative (SG&A) expenses, marketing expenses, CEO
salary, and rent expense relating to a corporate office. The costs are not
related to the production of inventory and are therefore expensed in the
period incurred. In short, all costs that are not involved in the production of
a product (product costs) are period costs.
Prime cost and conversion cost
When preparing a balance sheet and an income statement, companies need
to classify their costs as product cost and period cost. To understand the
differences between product cost and period costs, we must first discuss the
matching principle from financial accounting. The matching principle is
based on the accrual concept the costs incurred to generate a particular
revenue should be recognized as expenses in the same period that the
revenue is recognized. Matching Principle is a common accounting concept.
Under this, a company should report an expense in the income statement in
the same period when it earns the revenue.
Product costs
Product cost refers to the costs incurred to create a product. These costs
include direct labor, direct materials, consumable production supplies, and
factory overhead. Product cost can also be considered the cost of the labor
required to deliver a service to a customer. The cost of a product on a unit
basis is typically derived by compiling the costs associated with a batch of
units that were produced as a group, and dividing by the number of units
manufactured. The calculation is:
(Total direct labor + Total direct materials + Consumable supplies
+ Total allocated overhead) ÷ Total number of units = Product unit
cost
These costs are also known as inventoriable costs.
Period costs
Period costs are costs that cannot be capitalized on a company’s balance
sheet. In other words, they are expensed in the period incurred and appear
on the income statement. Period costs are also called period expenses. In
managerial and cost accounting, period costs refer to costs that are not tied
to or related to the production of inventory. Examples include selling,
general and administrative (SG&A) expenses, marketing expenses, CEO
salary, and rent expense relating to a corporate office. The costs are not
related to the production of inventory and are therefore expensed in the
period incurred. In short, all costs that are not involved in the production of
a product (product costs) are period costs.
Prime cost and conversion cost

Prime costs are the sum of direct material costs and
direct labor costs. Conversion cost is the sum of direct
labor costs and manufacturing overhead.
Cost classifications for predicting cost behavior
Variable cost
Variable costs are expenses that vary in proportion to the volume of goods
or services that a business produces. In other words, they are costs that
vary depending on the volume of activity. The costs increase as the volume
of activities increases and decrease as the volume of activities decreases.
For a cost to be variable, it must be variable with respect to something. That
something is its activity based. An activity base is a measure of whatever
causes the incurrence of a variable cost. A activity base is sometimes
referred to as a cost driver.
Fixed cost
The term fixed cost refers to a cost that does not change with an increase or
decrease in the number of goods or services produced or sold. Fixed costs
are expenses that have to be paid by a company, independent of any
specific business activities. This means fixed costs are generally indirect, in
that they don't apply to a company's production of any goods or services.
Let us say, in a milk factory, the monthly payments for the
phone lines and security system and the monthly rent for the
facilities are fixed costs as they do not change according to
how much milk the factory produces. On the other hand, the
factory’s wage costs are variable as it will need to hire more
workers if the production increases. An analytical formula can
track the relationship between fixed cost and variable cost in
management accounting. It is important to know how total
costs are divided between the two types of costs. The division
of the costs is critical, and forecasting the earnings generated
by various changes in unit sales affects future planned
marketing campaigns. Discretionary fixed costs usually come
about from decisions made by management to spend on
certain fixed cost items. Examples of discretionary costs
include advertising, machinery maintenance, and research and
development (R&D) expenditures.
Committed fixed costs represent organizational investments with a
multiyear planning horizon that cannot be significantly reduced
direct labor costs. Conversion cost is the sum of direct
labor costs and manufacturing overhead.
Cost classifications for predicting cost behavior
Variable cost
Variable costs are expenses that vary in proportion to the volume of goods
or services that a business produces. In other words, they are costs that
vary depending on the volume of activity. The costs increase as the volume
of activities increases and decrease as the volume of activities decreases.
For a cost to be variable, it must be variable with respect to something. That
something is its activity based. An activity base is a measure of whatever
causes the incurrence of a variable cost. A activity base is sometimes
referred to as a cost driver.
Fixed cost
The term fixed cost refers to a cost that does not change with an increase or
decrease in the number of goods or services produced or sold. Fixed costs
are expenses that have to be paid by a company, independent of any
specific business activities. This means fixed costs are generally indirect, in
that they don't apply to a company's production of any goods or services.
Let us say, in a milk factory, the monthly payments for the
phone lines and security system and the monthly rent for the
facilities are fixed costs as they do not change according to
how much milk the factory produces. On the other hand, the
factory’s wage costs are variable as it will need to hire more
workers if the production increases. An analytical formula can
track the relationship between fixed cost and variable cost in
management accounting. It is important to know how total
costs are divided between the two types of costs. The division
of the costs is critical, and forecasting the earnings generated
by various changes in unit sales affects future planned
marketing campaigns. Discretionary fixed costs usually come
about from decisions made by management to spend on
certain fixed cost items. Examples of discretionary costs
include advertising, machinery maintenance, and research and
development (R&D) expenditures.
Committed fixed costs represent organizational investments with a
multiyear planning horizon that cannot be significantly reduced

End of preview
Want to access all the pages? Upload your documents or become a member.
Related Documents
Meaning of Production Costlg...
|19
|4629
|38
Management and Cost Accounting - Doclg...
|8
|1642
|26
Production Cost and Its Calculation - Deskliblg...
|19
|4816
|229
Using Cost Information for Budgeting and Forecasting in the Management Accountinglg...
|18
|4731
|226
MANAGEMENT ACCOUNTING FOR COSTS AND CONTROLSlg...
|7
|1263
|424
Managerial Accounting: Traditional Costing vs Activity Based Costinglg...
|10
|1859
|185