Biomass Report: Densification, Variables, and Feedstock Analysis
VerifiedAdded on 2020/03/16
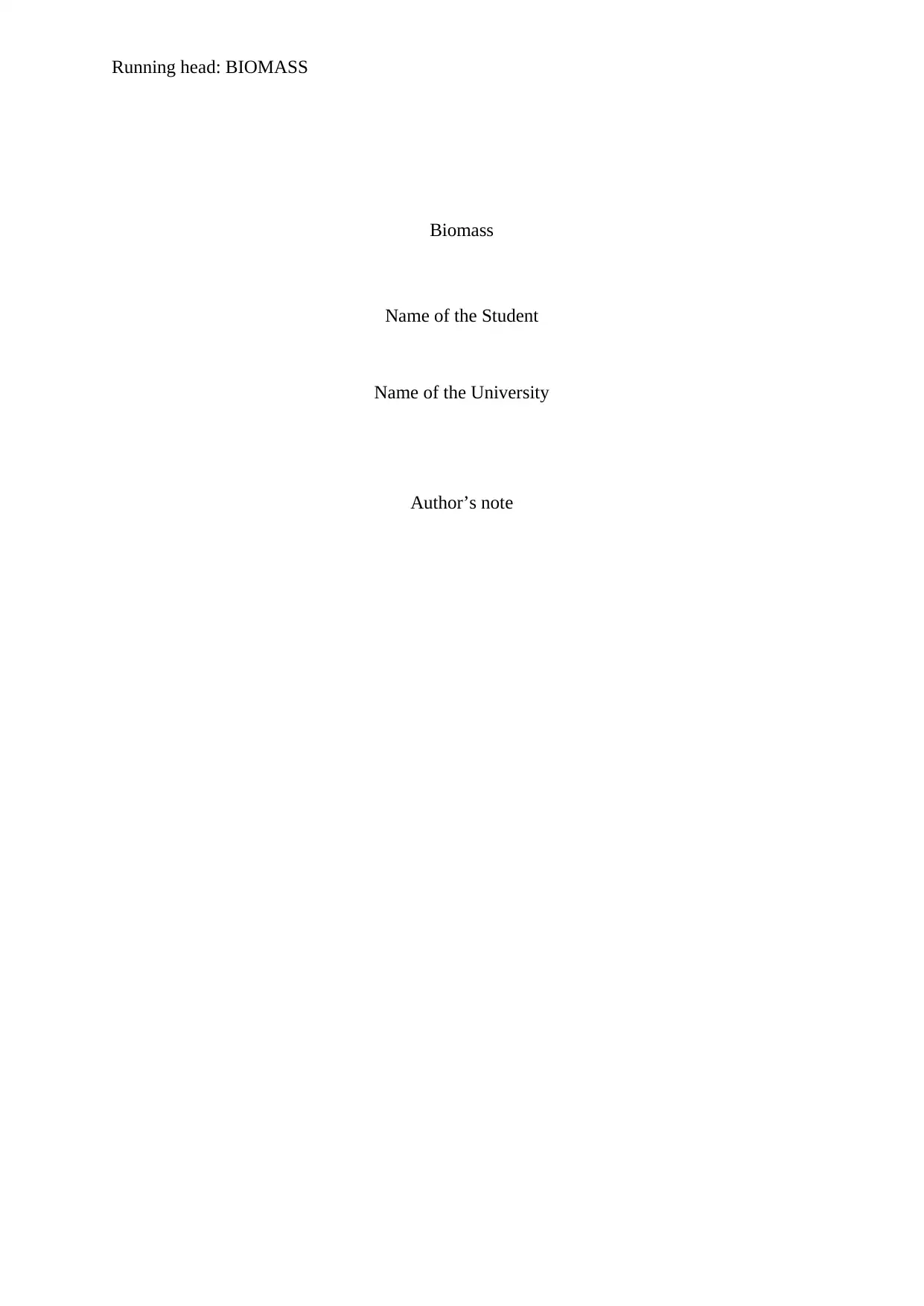
Biomass
Name of the Student
Name of the University
Author’s note
Paraphrase This Document
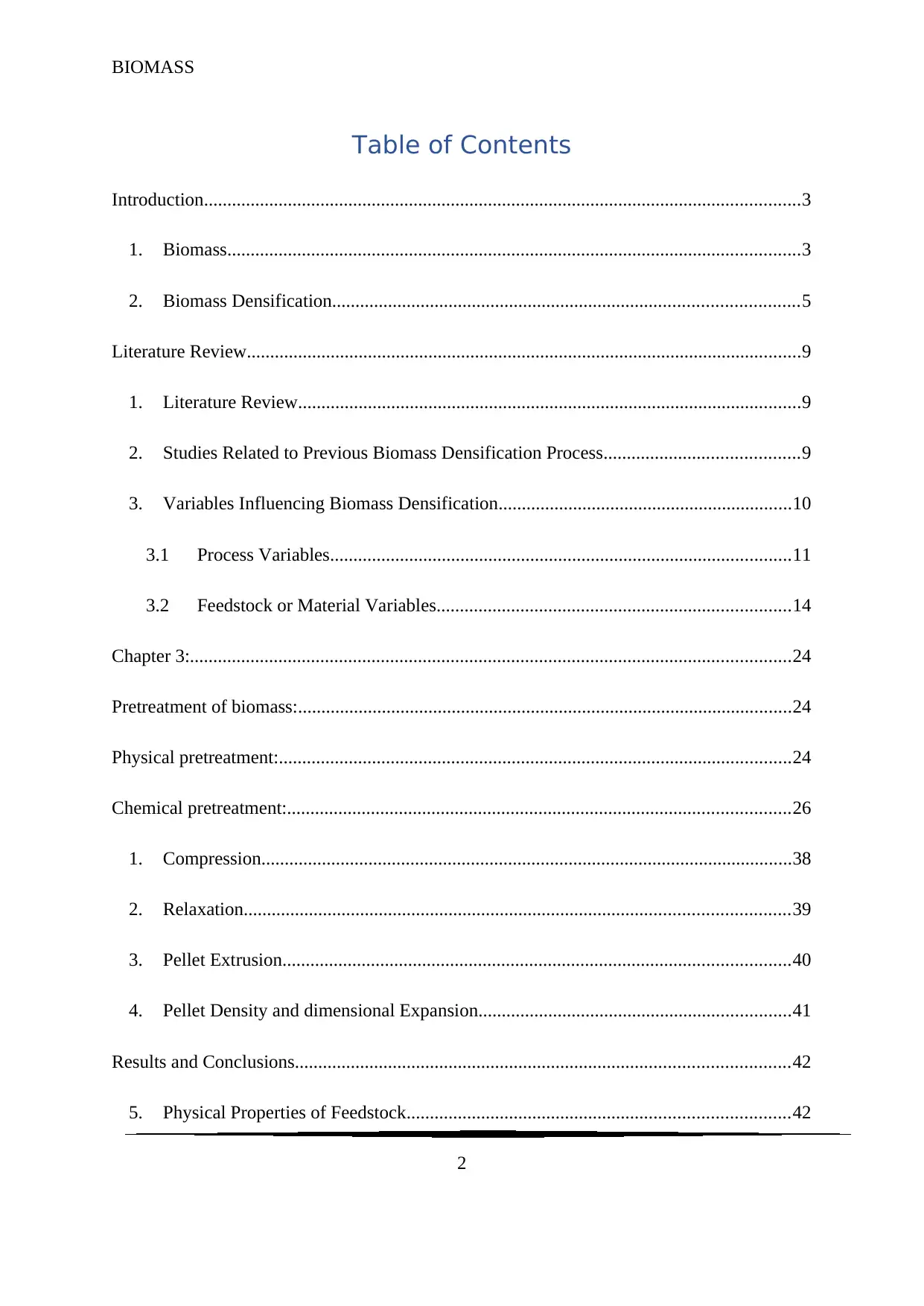
Table of Contents
Introduction................................................................................................................................3
1. Biomass...........................................................................................................................3
2. Biomass Densification....................................................................................................5
Literature Review.......................................................................................................................9
1. Literature Review............................................................................................................9
2. Studies Related to Previous Biomass Densification Process..........................................9
3. Variables Influencing Biomass Densification...............................................................10
3.1 Process Variables...................................................................................................11
3.2 Feedstock or Material Variables............................................................................14
Chapter 3:.................................................................................................................................24
Pretreatment of biomass:..........................................................................................................24
Physical pretreatment:..............................................................................................................24
Chemical pretreatment:............................................................................................................26
1. Compression..................................................................................................................38
2. Relaxation.....................................................................................................................39
3. Pellet Extrusion.............................................................................................................40
4. Pellet Density and dimensional Expansion...................................................................41
Results and Conclusions..........................................................................................................42
5. Physical Properties of Feedstock..................................................................................42
2
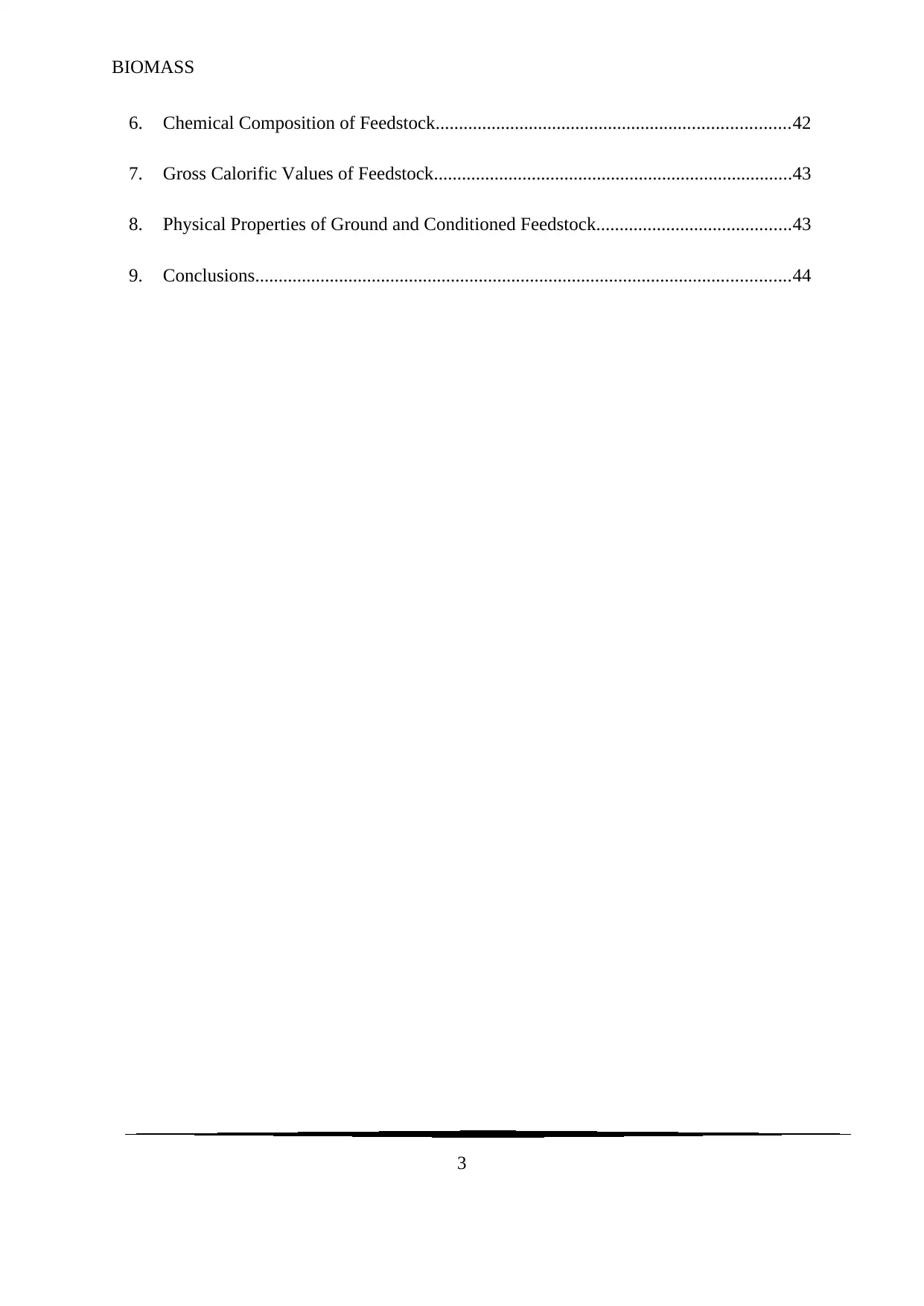
6. Chemical Composition of Feedstock............................................................................42
7. Gross Calorific Values of Feedstock.............................................................................43
8. Physical Properties of Ground and Conditioned Feedstock..........................................43
9. Conclusions...................................................................................................................44
3
⊘ This is a preview!⊘
Do you want full access?
Subscribe today to unlock all pages.

Trusted by 1+ million students worldwide
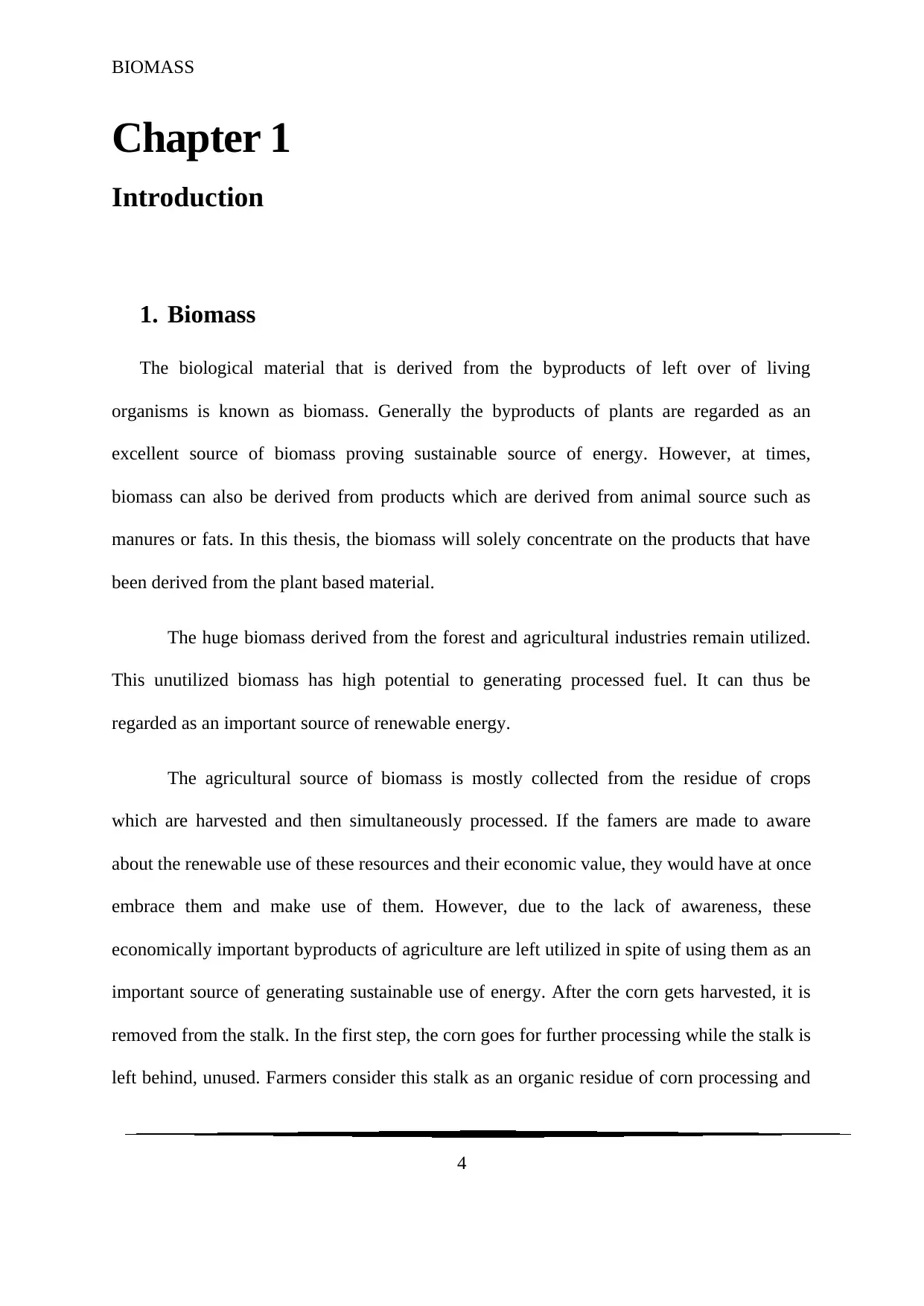
Chapter 1
Introduction
1. Biomass
The biological material that is derived from the byproducts of left over of living
organisms is known as biomass. Generally the byproducts of plants are regarded as an
excellent source of biomass proving sustainable source of energy. However, at times,
biomass can also be derived from products which are derived from animal source such as
manures or fats. In this thesis, the biomass will solely concentrate on the products that have
been derived from the plant based material.
The huge biomass derived from the forest and agricultural industries remain utilized.
This unutilized biomass has high potential to generating processed fuel. It can thus be
regarded as an important source of renewable energy.
The agricultural source of biomass is mostly collected from the residue of crops
which are harvested and then simultaneously processed. If the famers are made to aware
about the renewable use of these resources and their economic value, they would have at once
embrace them and make use of them. However, due to the lack of awareness, these
economically important byproducts of agriculture are left utilized in spite of using them as an
important source of generating sustainable use of energy. After the corn gets harvested, it is
removed from the stalk. In the first step, the corn goes for further processing while the stalk is
left behind, unused. Farmers consider this stalk as an organic residue of corn processing and
4
Paraphrase This Document
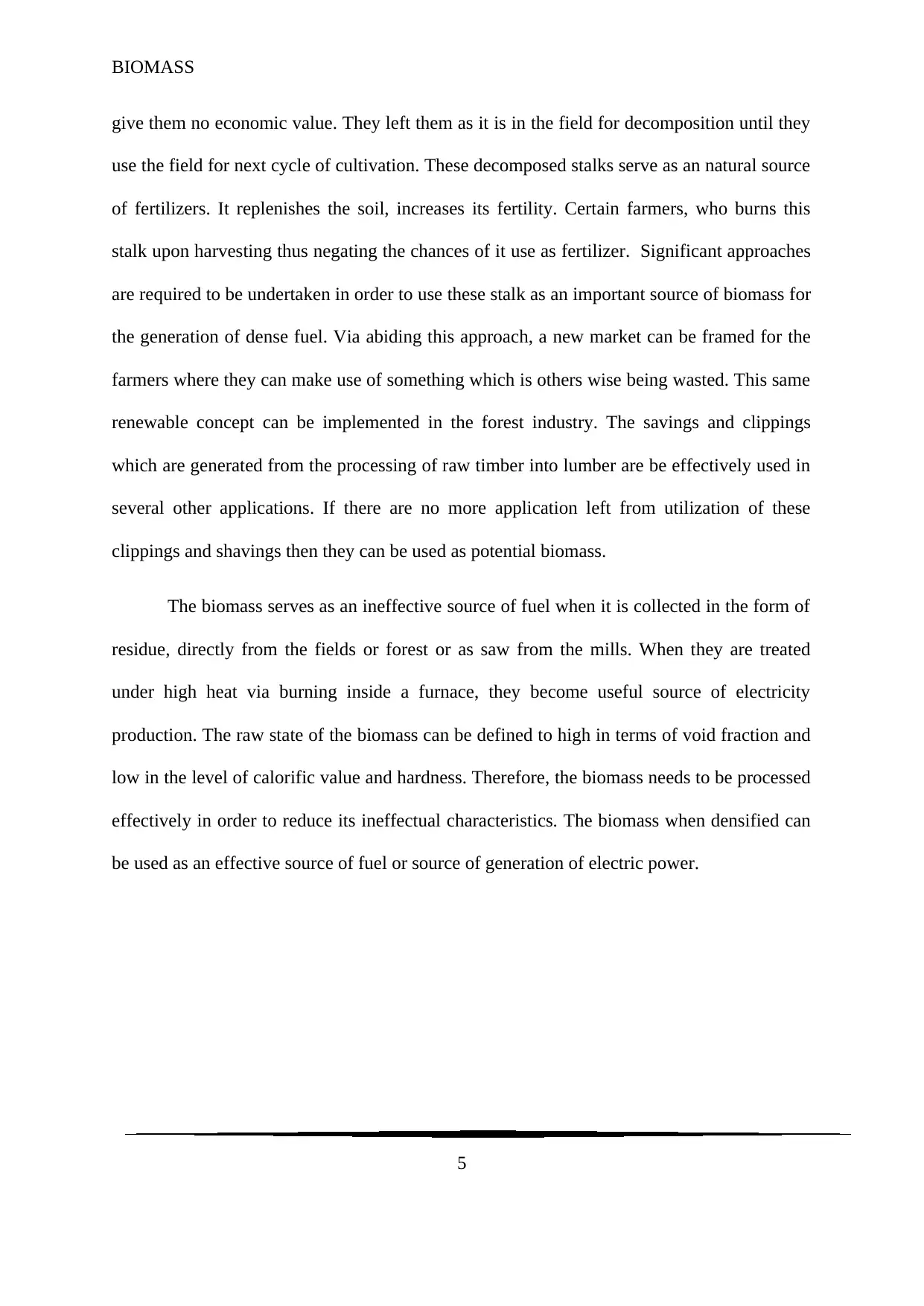
give them no economic value. They left them as it is in the field for decomposition until they
use the field for next cycle of cultivation. These decomposed stalks serve as an natural source
of fertilizers. It replenishes the soil, increases its fertility. Certain farmers, who burns this
stalk upon harvesting thus negating the chances of it use as fertilizer. Significant approaches
are required to be undertaken in order to use these stalk as an important source of biomass for
the generation of dense fuel. Via abiding this approach, a new market can be framed for the
farmers where they can make use of something which is others wise being wasted. This same
renewable concept can be implemented in the forest industry. The savings and clippings
which are generated from the processing of raw timber into lumber are be effectively used in
several other applications. If there are no more application left from utilization of these
clippings and shavings then they can be used as potential biomass.
The biomass serves as an ineffective source of fuel when it is collected in the form of
residue, directly from the fields or forest or as saw from the mills. When they are treated
under high heat via burning inside a furnace, they become useful source of electricity
production. The raw state of the biomass can be defined to high in terms of void fraction and
low in the level of calorific value and hardness. Therefore, the biomass needs to be processed
effectively in order to reduce its ineffectual characteristics. The biomass when densified can
be used as an effective source of fuel or source of generation of electric power.
5
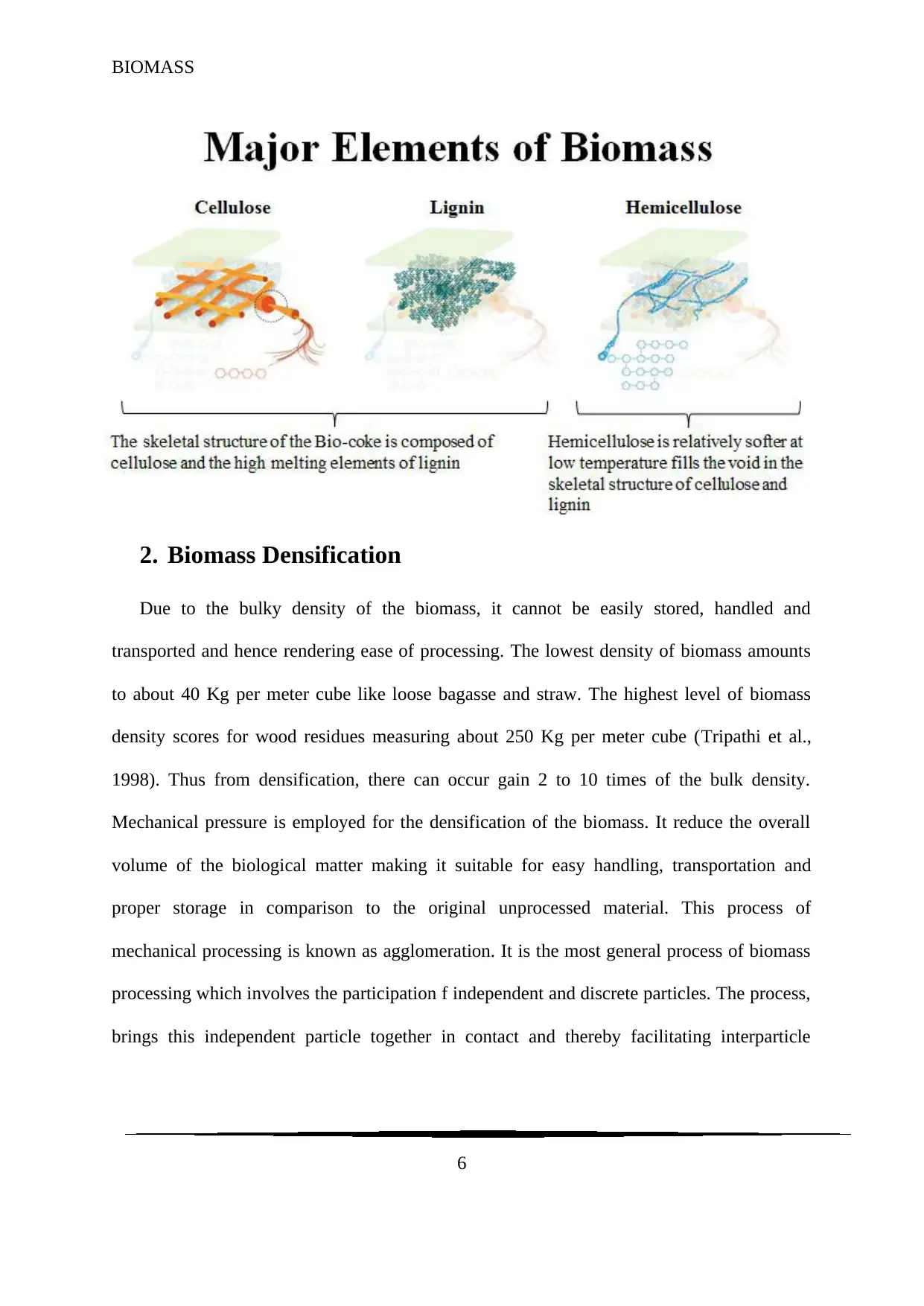
2. Biomass Densification
Due to the bulky density of the biomass, it cannot be easily stored, handled and
transported and hence rendering ease of processing. The lowest density of biomass amounts
to about 40 Kg per meter cube like loose bagasse and straw. The highest level of biomass
density scores for wood residues measuring about 250 Kg per meter cube (Tripathi et al.,
1998). Thus from densification, there can occur gain 2 to 10 times of the bulk density.
Mechanical pressure is employed for the densification of the biomass. It reduce the overall
volume of the biological matter making it suitable for easy handling, transportation and
proper storage in comparison to the original unprocessed material. This process of
mechanical processing is known as agglomeration. It is the most general process of biomass
processing which involves the participation f independent and discrete particles. The process,
brings this independent particle together in contact and thereby facilitating interparticle
6
⊘ This is a preview!⊘
Do you want full access?
Subscribe today to unlock all pages.

Trusted by 1+ million students worldwide
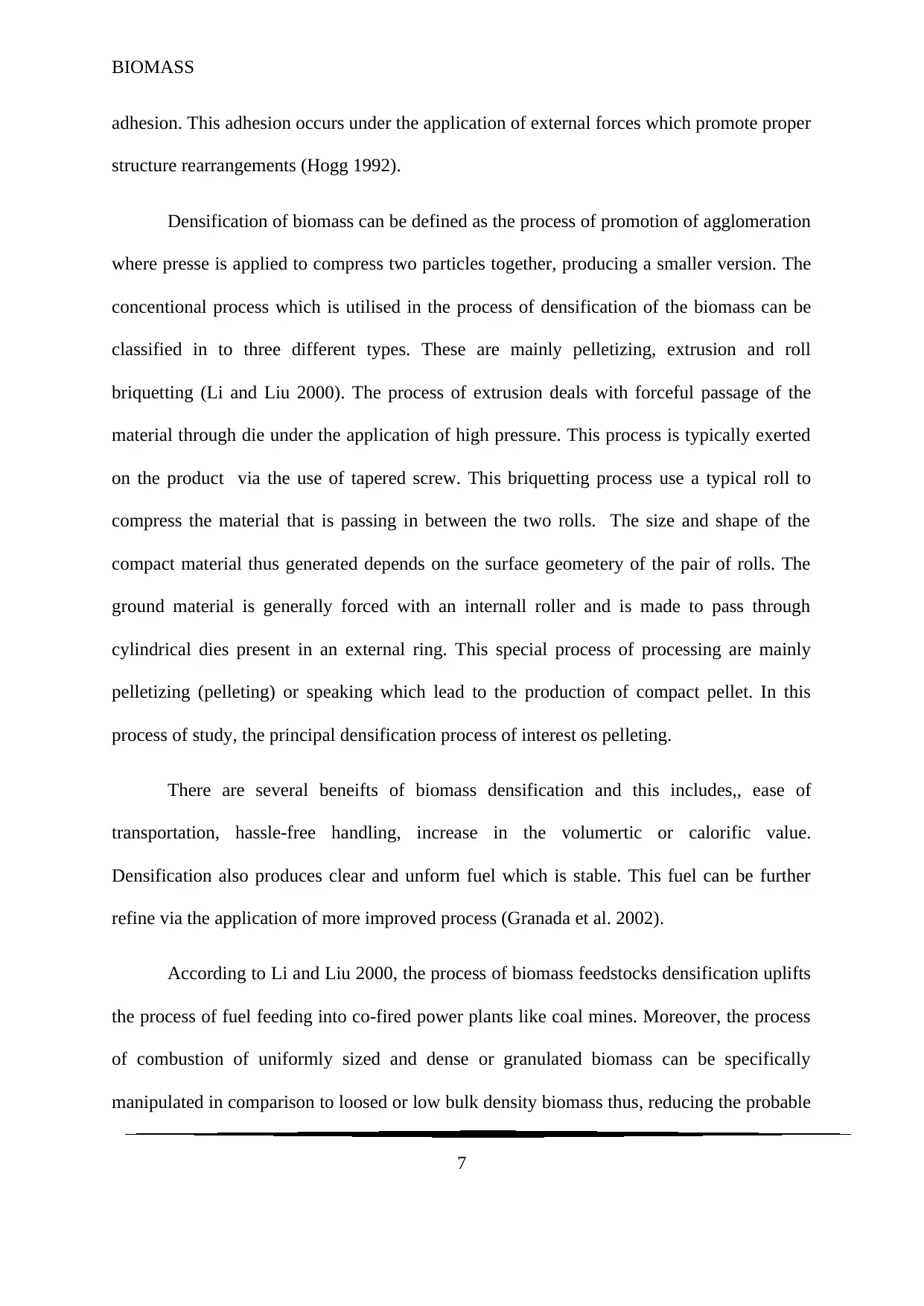
adhesion. This adhesion occurs under the application of external forces which promote proper
structure rearrangements (Hogg 1992).
Densification of biomass can be defined as the process of promotion of agglomeration
where presse is applied to compress two particles together, producing a smaller version. The
concentional process which is utilised in the process of densification of the biomass can be
classified in to three different types. These are mainly pelletizing, extrusion and roll
briquetting (Li and Liu 2000). The process of extrusion deals with forceful passage of the
material through die under the application of high pressure. This process is typically exerted
on the product via the use of tapered screw. This briquetting process use a typical roll to
compress the material that is passing in between the two rolls. The size and shape of the
compact material thus generated depends on the surface geometery of the pair of rolls. The
ground material is generally forced with an internall roller and is made to pass through
cylindrical dies present in an external ring. This special process of processing are mainly
pelletizing (pelleting) or speaking which lead to the production of compact pellet. In this
process of study, the principal densification process of interest os pelleting.
There are several beneifts of biomass densification and this includes,, ease of
transportation, hassle-free handling, increase in the volumertic or calorific value.
Densification also produces clear and unform fuel which is stable. This fuel can be further
refine via the application of more improved process (Granada et al. 2002).
According to Li and Liu 2000, the process of biomass feedstocks densification uplifts
the process of fuel feeding into co-fired power plants like coal mines. Moreover, the process
of combustion of uniformly sized and dense or granulated biomass can be specifically
manipulated in comparison to loosed or low bulk density biomass thus, reducing the probable
7
Paraphrase This Document
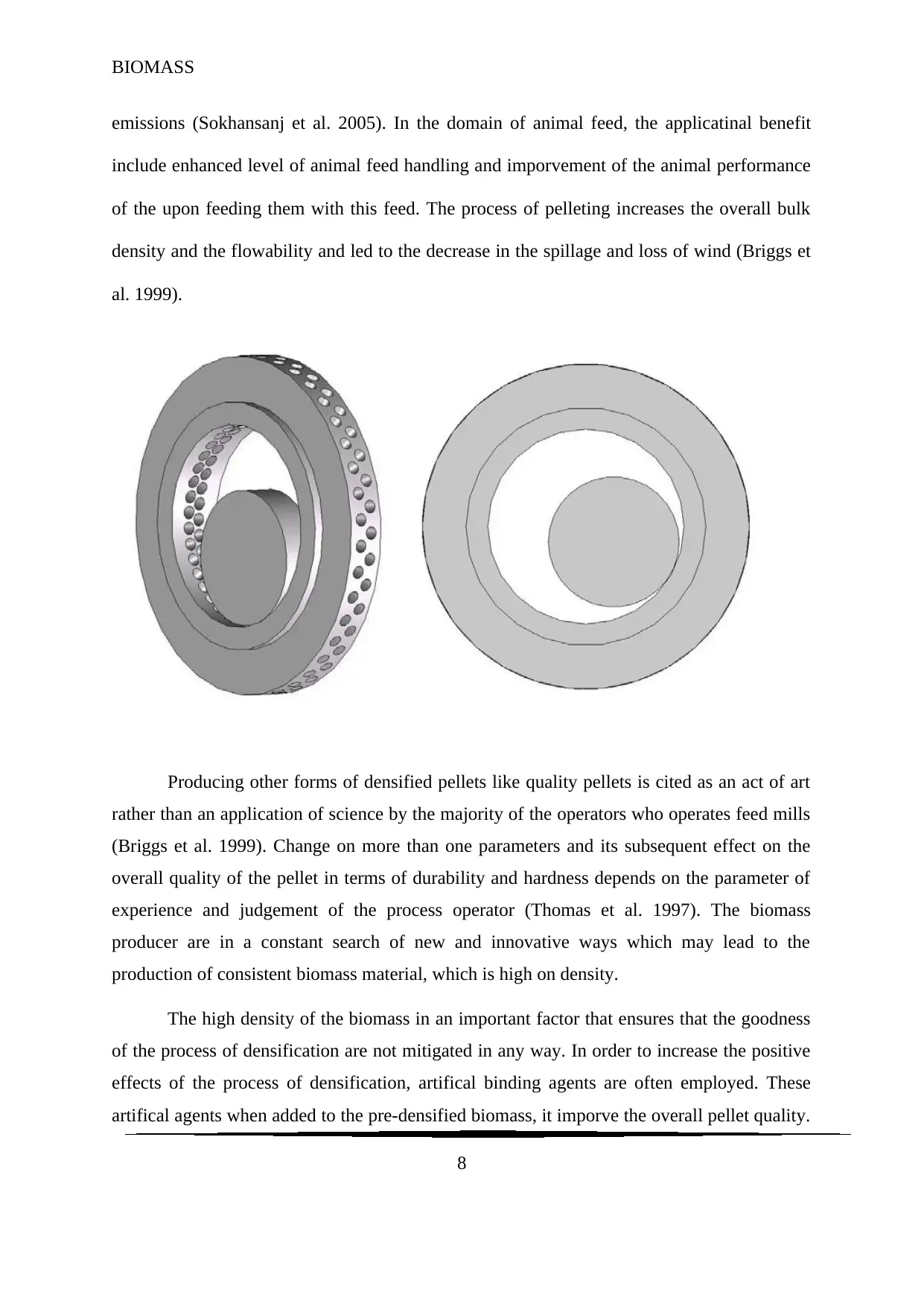
emissions (Sokhansanj et al. 2005). In the domain of animal feed, the applicatinal benefit
include enhanced level of animal feed handling and imporvement of the animal performance
of the upon feeding them with this feed. The process of pelleting increases the overall bulk
density and the flowability and led to the decrease in the spillage and loss of wind (Briggs et
al. 1999).
Producing other forms of densified pellets like quality pellets is cited as an act of art
rather than an application of science by the majority of the operators who operates feed mills
(Briggs et al. 1999). Change on more than one parameters and its subsequent effect on the
overall quality of the pellet in terms of durability and hardness depends on the parameter of
experience and judgement of the process operator (Thomas et al. 1997). The biomass
producer are in a constant search of new and innovative ways which may lead to the
production of consistent biomass material, which is high on density.
The high density of the biomass in an important factor that ensures that the goodness
of the process of densification are not mitigated in any way. In order to increase the positive
effects of the process of densification, artifical binding agents are often employed. These
artifical agents when added to the pre-densified biomass, it imporve the overall pellet quality.
8
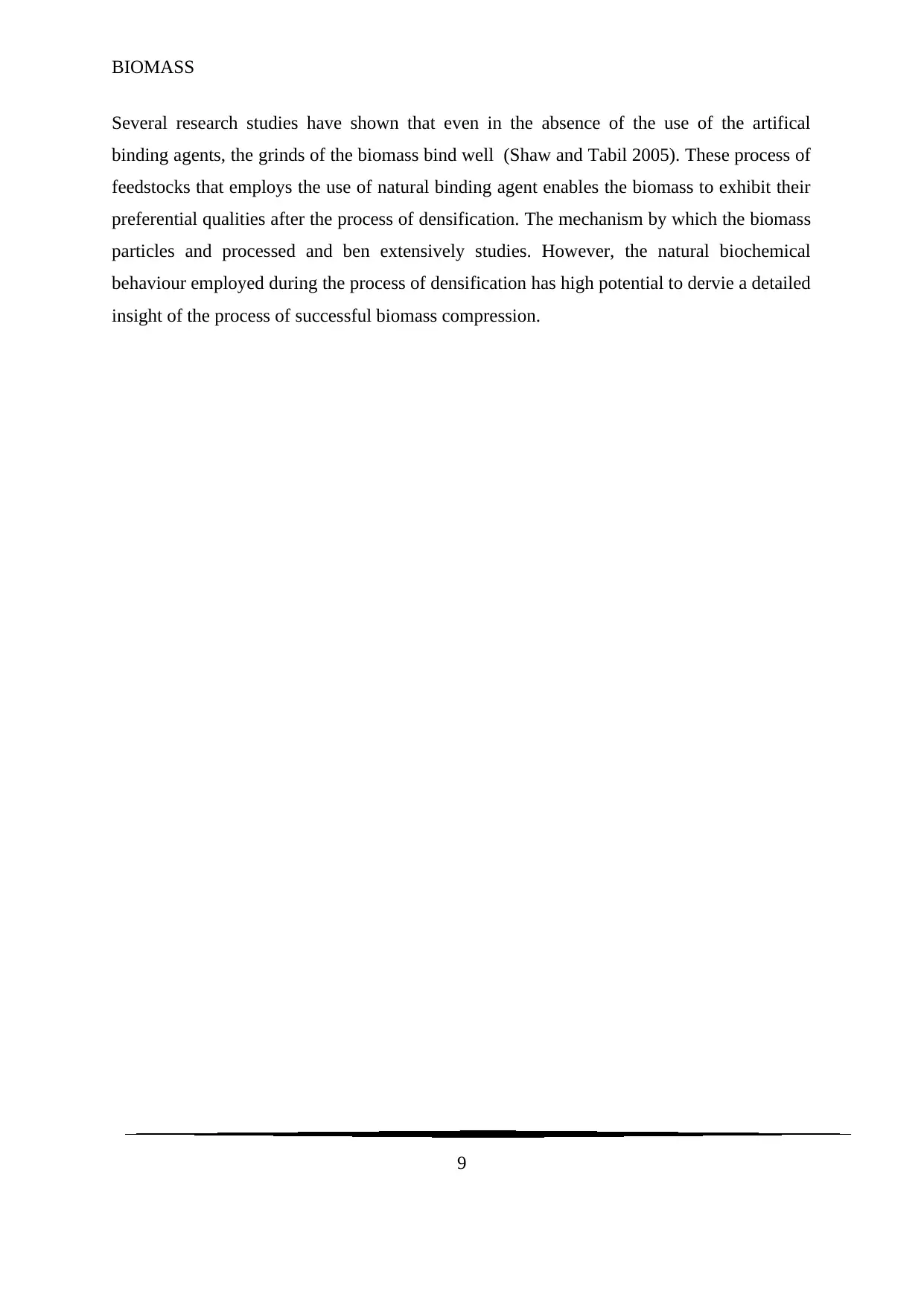
Several research studies have shown that even in the absence of the use of the artifical
binding agents, the grinds of the biomass bind well (Shaw and Tabil 2005). These process of
feedstocks that employs the use of natural binding agent enables the biomass to exhibit their
preferential qualities after the process of densification. The mechanism by which the biomass
particles and processed and ben extensively studies. However, the natural biochemical
behaviour employed during the process of densification has high potential to dervie a detailed
insight of the process of successful biomass compression.
9
⊘ This is a preview!⊘
Do you want full access?
Subscribe today to unlock all pages.

Trusted by 1+ million students worldwide
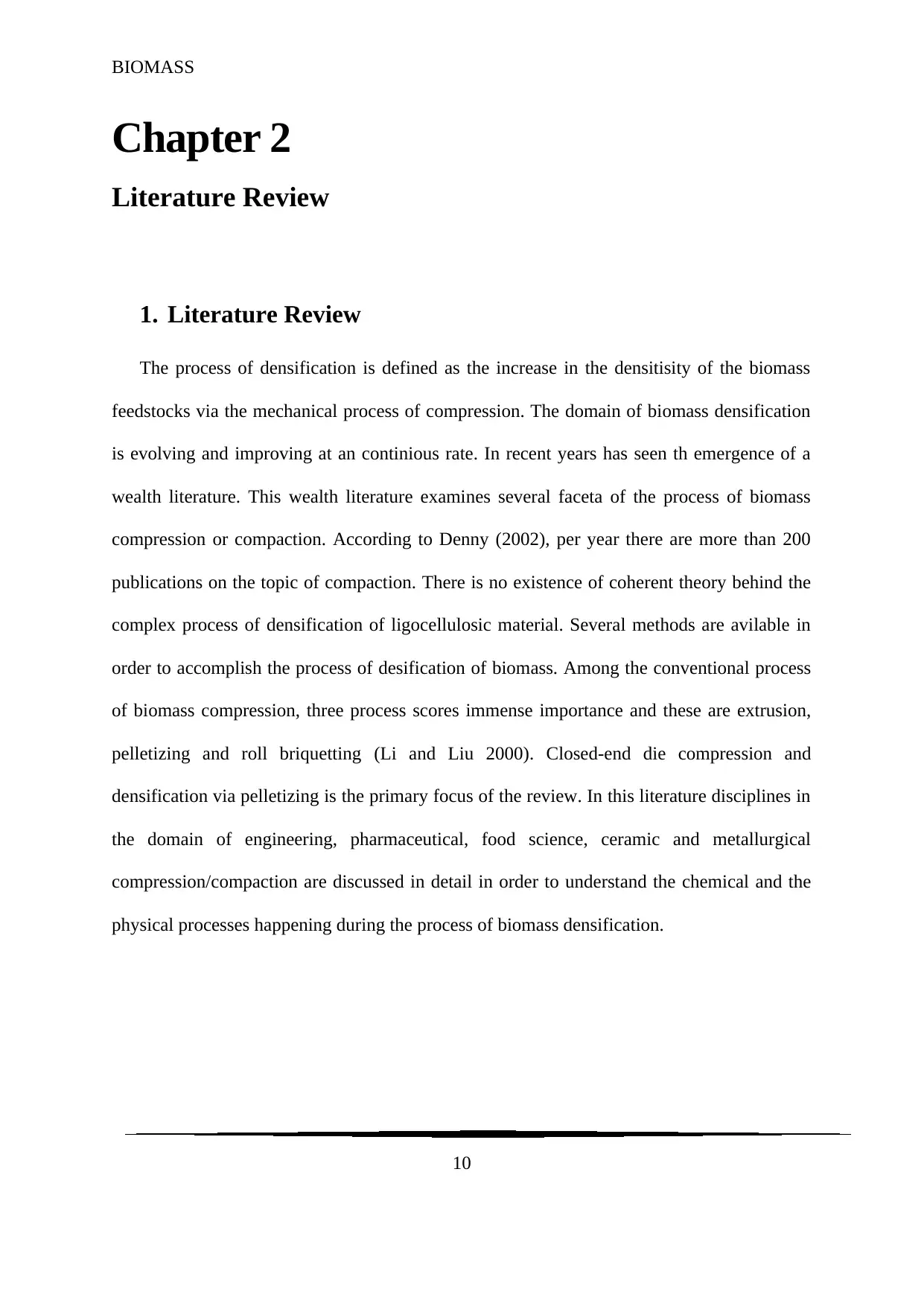
Chapter 2
Literature Review
1. Literature Review
The process of densification is defined as the increase in the densitisity of the biomass
feedstocks via the mechanical process of compression. The domain of biomass densification
is evolving and improving at an continious rate. In recent years has seen th emergence of a
wealth literature. This wealth literature examines several faceta of the process of biomass
compression or compaction. According to Denny (2002), per year there are more than 200
publications on the topic of compaction. There is no existence of coherent theory behind the
complex process of densification of ligocellulosic material. Several methods are avilable in
order to accomplish the process of desification of biomass. Among the conventional process
of biomass compression, three process scores immense importance and these are extrusion,
pelletizing and roll briquetting (Li and Liu 2000). Closed-end die compression and
densification via pelletizing is the primary focus of the review. In this literature disciplines in
the domain of engineering, pharmaceutical, food science, ceramic and metallurgical
compression/compaction are discussed in detail in order to understand the chemical and the
physical processes happening during the process of biomass densification.
10
Paraphrase This Document
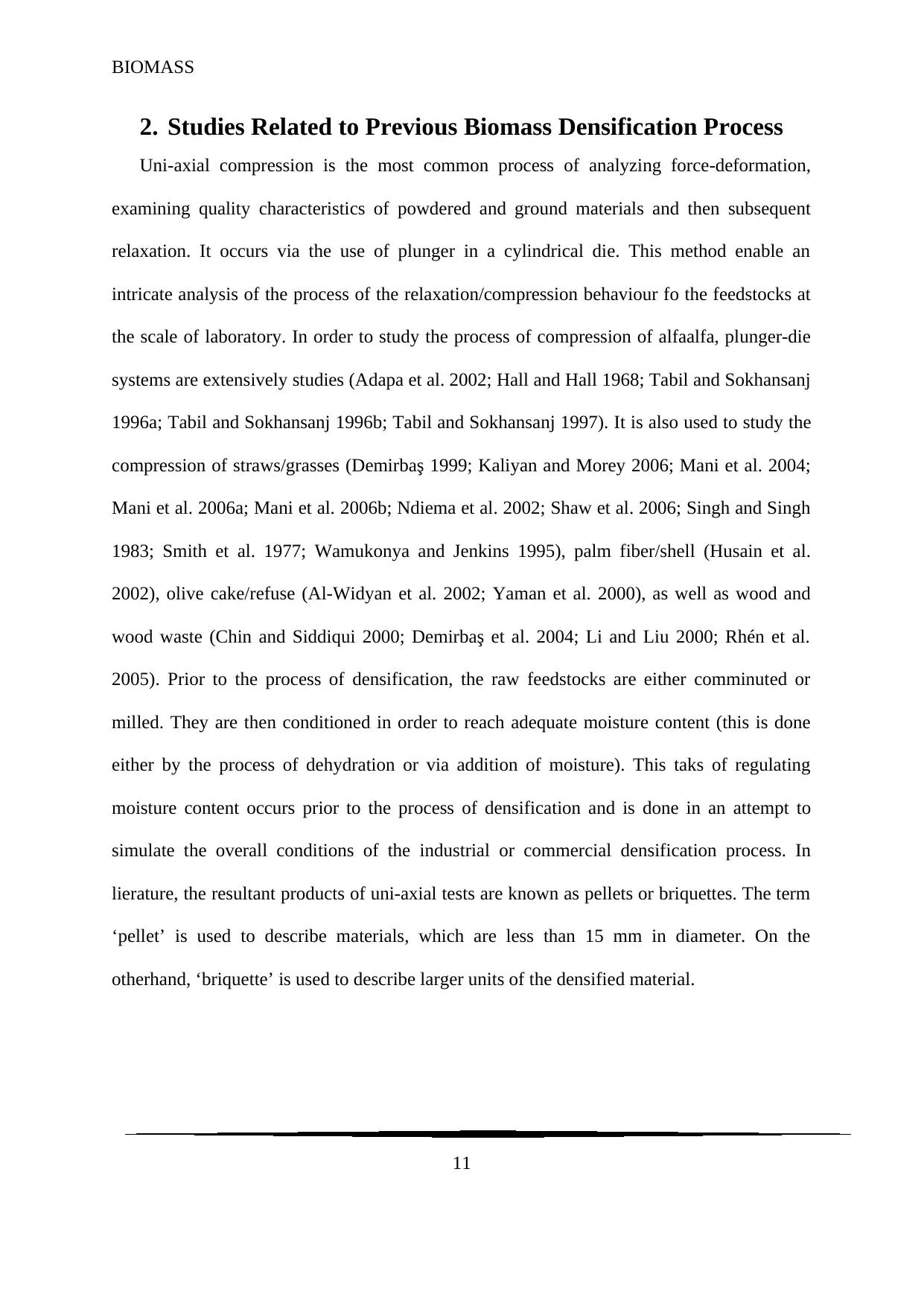
2. Studies Related to Previous Biomass Densification Process
Uni-axial compression is the most common process of analyzing force-deformation,
examining quality characteristics of powdered and ground materials and then subsequent
relaxation. It occurs via the use of plunger in a cylindrical die. This method enable an
intricate analysis of the process of the relaxation/compression behaviour fo the feedstocks at
the scale of laboratory. In order to study the process of compression of alfaalfa, plunger-die
systems are extensively studies (Adapa et al. 2002; Hall and Hall 1968; Tabil and Sokhansanj
1996a; Tabil and Sokhansanj 1996b; Tabil and Sokhansanj 1997). It is also used to study the
compression of straws/grasses (Demirbaş 1999; Kaliyan and Morey 2006; Mani et al. 2004;
Mani et al. 2006a; Mani et al. 2006b; Ndiema et al. 2002; Shaw et al. 2006; Singh and Singh
1983; Smith et al. 1977; Wamukonya and Jenkins 1995), palm fiber/shell (Husain et al.
2002), olive cake/refuse (Al-Widyan et al. 2002; Yaman et al. 2000), as well as wood and
wood waste (Chin and Siddiqui 2000; Demirbaş et al. 2004; Li and Liu 2000; Rhén et al.
2005). Prior to the process of densification, the raw feedstocks are either comminuted or
milled. They are then conditioned in order to reach adequate moisture content (this is done
either by the process of dehydration or via addition of moisture). This taks of regulating
moisture content occurs prior to the process of densification and is done in an attempt to
simulate the overall conditions of the industrial or commercial densification process. In
lierature, the resultant products of uni-axial tests are known as pellets or briquettes. The term
‘pellet’ is used to describe materials, which are less than 15 mm in diameter. On the
otherhand, ‘briquette’ is used to describe larger units of the densified material.
11
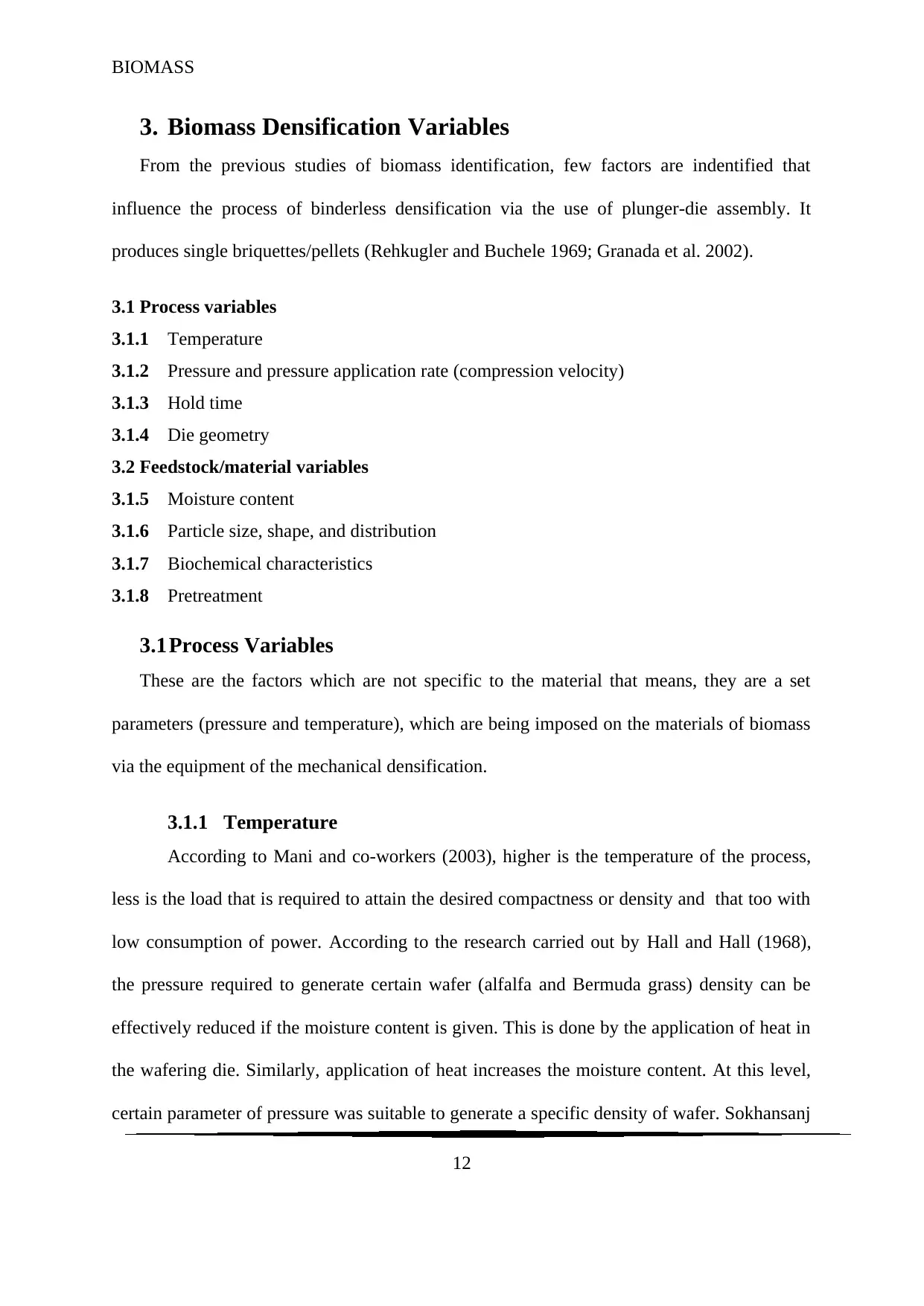
3. Biomass Densification Variables
From the previous studies of biomass identification, few factors are indentified that
influence the process of binderless densification via the use of plunger-die assembly. It
produces single briquettes/pellets (Rehkugler and Buchele 1969; Granada et al. 2002).
3.1 Process variables
3.1.1 Temperature
3.1.2 Pressure and pressure application rate (compression velocity)
3.1.3 Hold time
3.1.4 Die geometry
3.2 Feedstock/material variables
3.1.5 Moisture content
3.1.6 Particle size, shape, and distribution
3.1.7 Biochemical characteristics
3.1.8 Pretreatment
3.1Process Variables
These are the factors which are not specific to the material that means, they are a set
parameters (pressure and temperature), which are being imposed on the materials of biomass
via the equipment of the mechanical densification.
3.1.1 Temperature
According to Mani and co-workers (2003), higher is the temperature of the process,
less is the load that is required to attain the desired compactness or density and that too with
low consumption of power. According to the research carried out by Hall and Hall (1968),
the pressure required to generate certain wafer (alfalfa and Bermuda grass) density can be
effectively reduced if the moisture content is given. This is done by the application of heat in
the wafering die. Similarly, application of heat increases the moisture content. At this level,
certain parameter of pressure was suitable to generate a specific density of wafer. Sokhansanj
12
⊘ This is a preview!⊘
Do you want full access?
Subscribe today to unlock all pages.

Trusted by 1+ million students worldwide
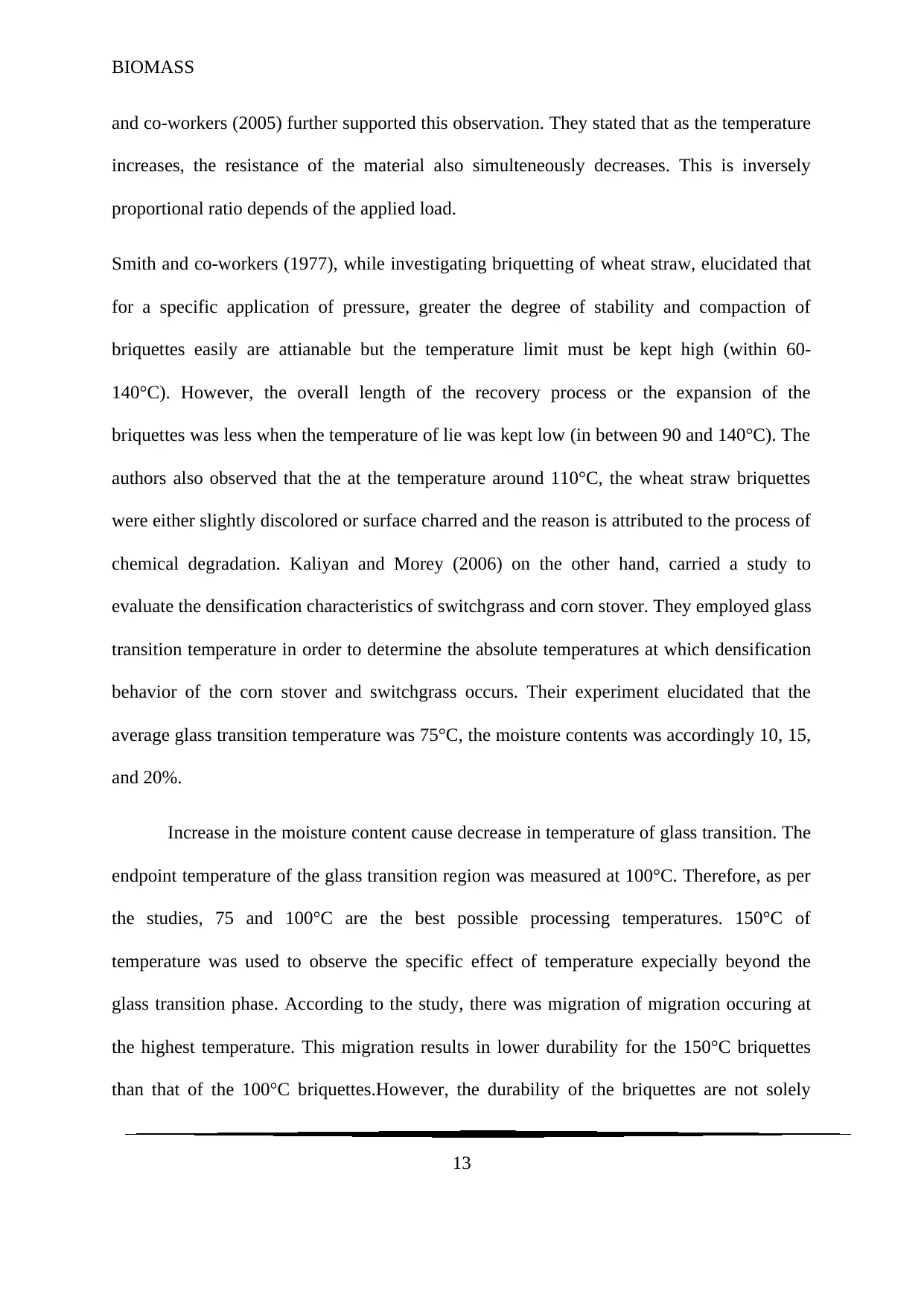
and co-workers (2005) further supported this observation. They stated that as the temperature
increases, the resistance of the material also simulteneously decreases. This is inversely
proportional ratio depends of the applied load.
Smith and co-workers (1977), while investigating briquetting of wheat straw, elucidated that
for a specific application of pressure, greater the degree of stability and compaction of
briquettes easily are attianable but the temperature limit must be kept high (within 60-
140°C). However, the overall length of the recovery process or the expansion of the
briquettes was less when the temperature of lie was kept low (in between 90 and 140°C). The
authors also observed that the at the temperature around 110°C, the wheat straw briquettes
were either slightly discolored or surface charred and the reason is attributed to the process of
chemical degradation. Kaliyan and Morey (2006) on the other hand, carried a study to
evaluate the densification characteristics of switchgrass and corn stover. They employed glass
transition temperature in order to determine the absolute temperatures at which densification
behavior of the corn stover and switchgrass occurs. Their experiment elucidated that the
average glass transition temperature was 75°C, the moisture contents was accordingly 10, 15,
and 20%.
Increase in the moisture content cause decrease in temperature of glass transition. The
endpoint temperature of the glass transition region was measured at 100°C. Therefore, as per
the studies, 75 and 100°C are the best possible processing temperatures. 150°C of
temperature was used to observe the specific effect of temperature expecially beyond the
glass transition phase. According to the study, there was migration of migration occuring at
the highest temperature. This migration results in lower durability for the 150°C briquettes
than that of the 100°C briquettes.However, the durability of the briquettes are not solely
13
Paraphrase This Document
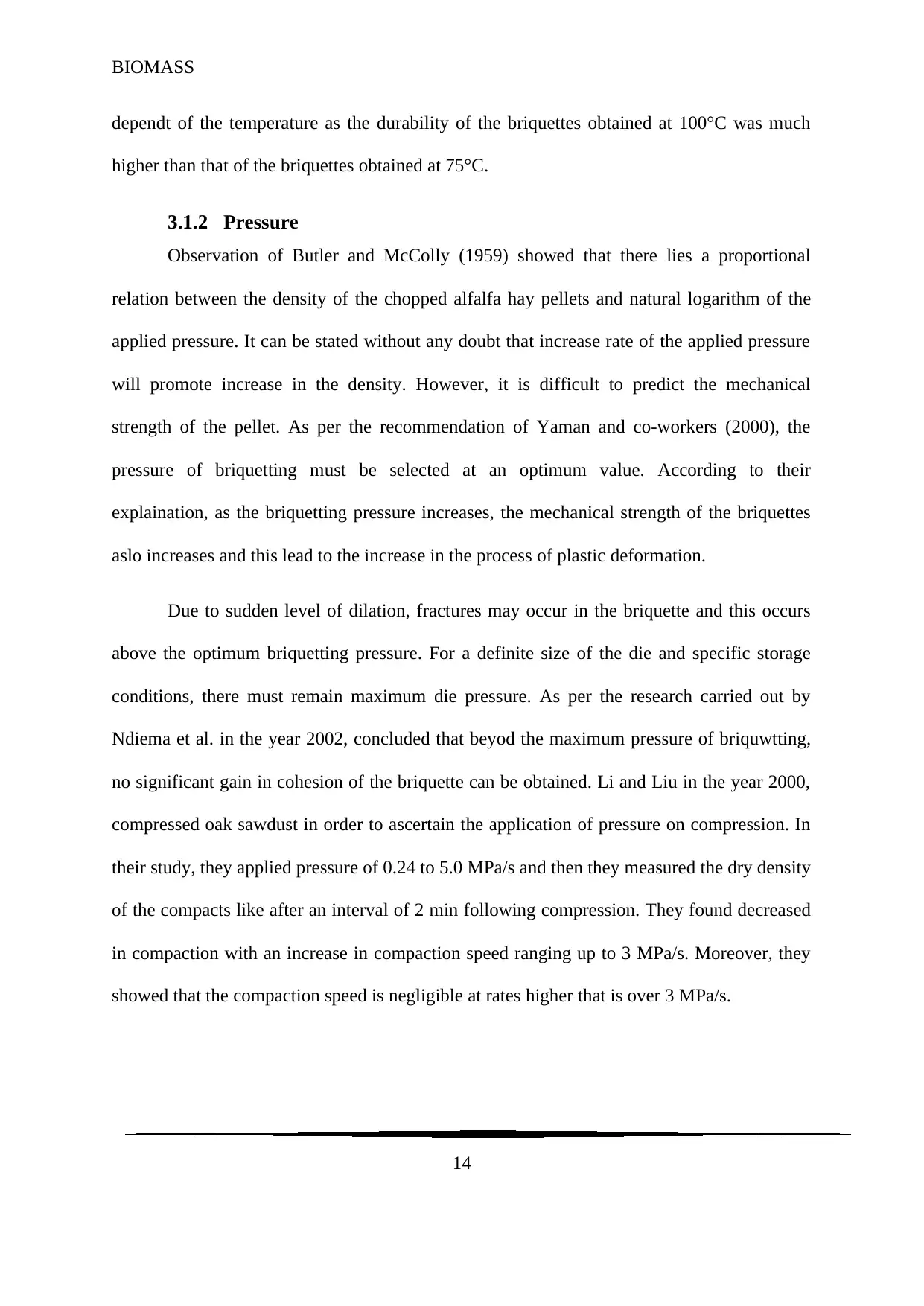
dependt of the temperature as the durability of the briquettes obtained at 100°C was much
higher than that of the briquettes obtained at 75°C.
3.1.2 Pressure
Observation of Butler and McColly (1959) showed that there lies a proportional
relation between the density of the chopped alfalfa hay pellets and natural logarithm of the
applied pressure. It can be stated without any doubt that increase rate of the applied pressure
will promote increase in the density. However, it is difficult to predict the mechanical
strength of the pellet. As per the recommendation of Yaman and co-workers (2000), the
pressure of briquetting must be selected at an optimum value. According to their
explaination, as the briquetting pressure increases, the mechanical strength of the briquettes
aslo increases and this lead to the increase in the process of plastic deformation.
Due to sudden level of dilation, fractures may occur in the briquette and this occurs
above the optimum briquetting pressure. For a definite size of the die and specific storage
conditions, there must remain maximum die pressure. As per the research carried out by
Ndiema et al. in the year 2002, concluded that beyod the maximum pressure of briquwtting,
no significant gain in cohesion of the briquette can be obtained. Li and Liu in the year 2000,
compressed oak sawdust in order to ascertain the application of pressure on compression. In
their study, they applied pressure of 0.24 to 5.0 MPa/s and then they measured the dry density
of the compacts like after an interval of 2 min following compression. They found decreased
in compaction with an increase in compaction speed ranging up to 3 MPa/s. Moreover, they
showed that the compaction speed is negligible at rates higher that is over 3 MPa/s.
14
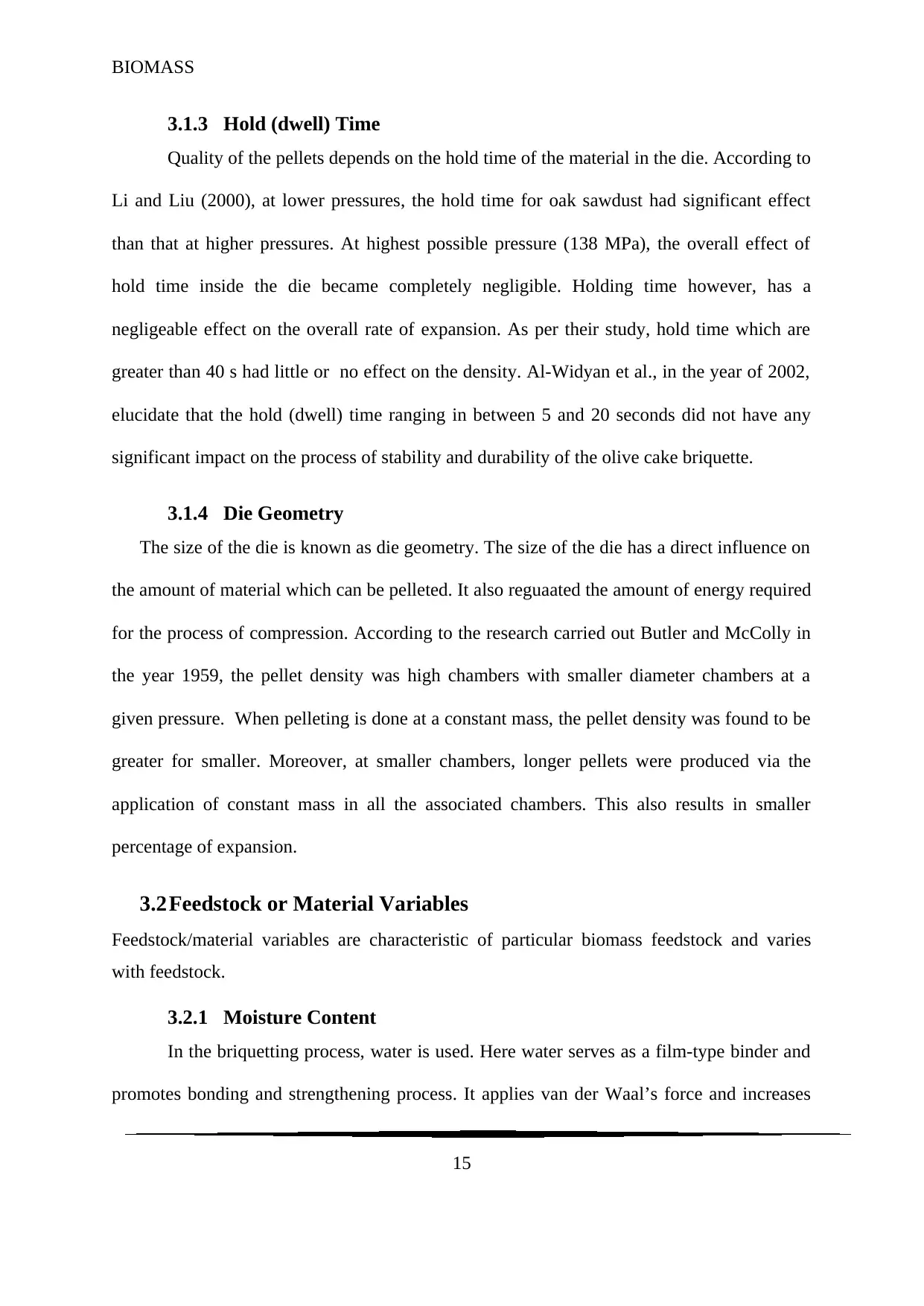
3.1.3 Hold (dwell) Time
Quality of the pellets depends on the hold time of the material in the die. According to
Li and Liu (2000), at lower pressures, the hold time for oak sawdust had significant effect
than that at higher pressures. At highest possible pressure (138 MPa), the overall effect of
hold time inside the die became completely negligible. Holding time however, has a
negligeable effect on the overall rate of expansion. As per their study, hold time which are
greater than 40 s had little or no effect on the density. Al-Widyan et al., in the year of 2002,
elucidate that the hold (dwell) time ranging in between 5 and 20 seconds did not have any
significant impact on the process of stability and durability of the olive cake briquette.
3.1.4 Die Geometry
The size of the die is known as die geometry. The size of the die has a direct influence on
the amount of material which can be pelleted. It also reguaated the amount of energy required
for the process of compression. According to the research carried out Butler and McColly in
the year 1959, the pellet density was high chambers with smaller diameter chambers at a
given pressure. When pelleting is done at a constant mass, the pellet density was found to be
greater for smaller. Moreover, at smaller chambers, longer pellets were produced via the
application of constant mass in all the associated chambers. This also results in smaller
percentage of expansion.
3.2Feedstock or Material Variables
Feedstock/material variables are characteristic of particular biomass feedstock and varies
with feedstock.
3.2.1 Moisture Content
In the briquetting process, water is used. Here water serves as a film-type binder and
promotes bonding and strengthening process. It applies van der Waal’s force and increases
15
⊘ This is a preview!⊘
Do you want full access?
Subscribe today to unlock all pages.

Trusted by 1+ million students worldwide
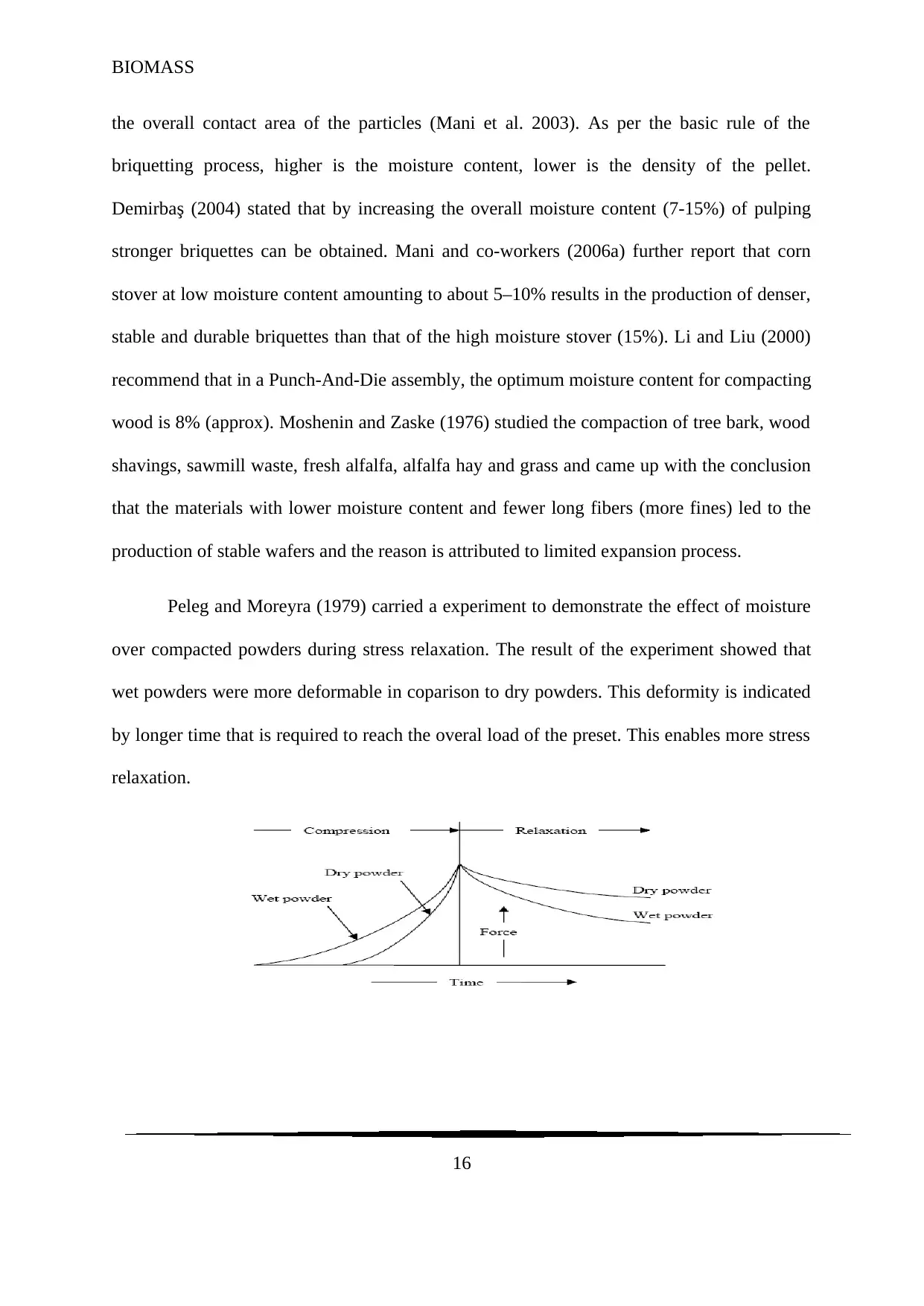
the overall contact area of the particles (Mani et al. 2003). As per the basic rule of the
briquetting process, higher is the moisture content, lower is the density of the pellet.
Demirbaş (2004) stated that by increasing the overall moisture content (7-15%) of pulping
stronger briquettes can be obtained. Mani and co-workers (2006a) further report that corn
stover at low moisture content amounting to about 5–10% results in the production of denser,
stable and durable briquettes than that of the high moisture stover (15%). Li and Liu (2000)
recommend that in a Punch-And-Die assembly, the optimum moisture content for compacting
wood is 8% (approx). Moshenin and Zaske (1976) studied the compaction of tree bark, wood
shavings, sawmill waste, fresh alfalfa, alfalfa hay and grass and came up with the conclusion
that the materials with lower moisture content and fewer long fibers (more fines) led to the
production of stable wafers and the reason is attributed to limited expansion process.
Peleg and Moreyra (1979) carried a experiment to demonstrate the effect of moisture
over compacted powders during stress relaxation. The result of the experiment showed that
wet powders were more deformable in coparison to dry powders. This deformity is indicated
by longer time that is required to reach the overal load of the preset. This enables more stress
relaxation.
16
Paraphrase This Document
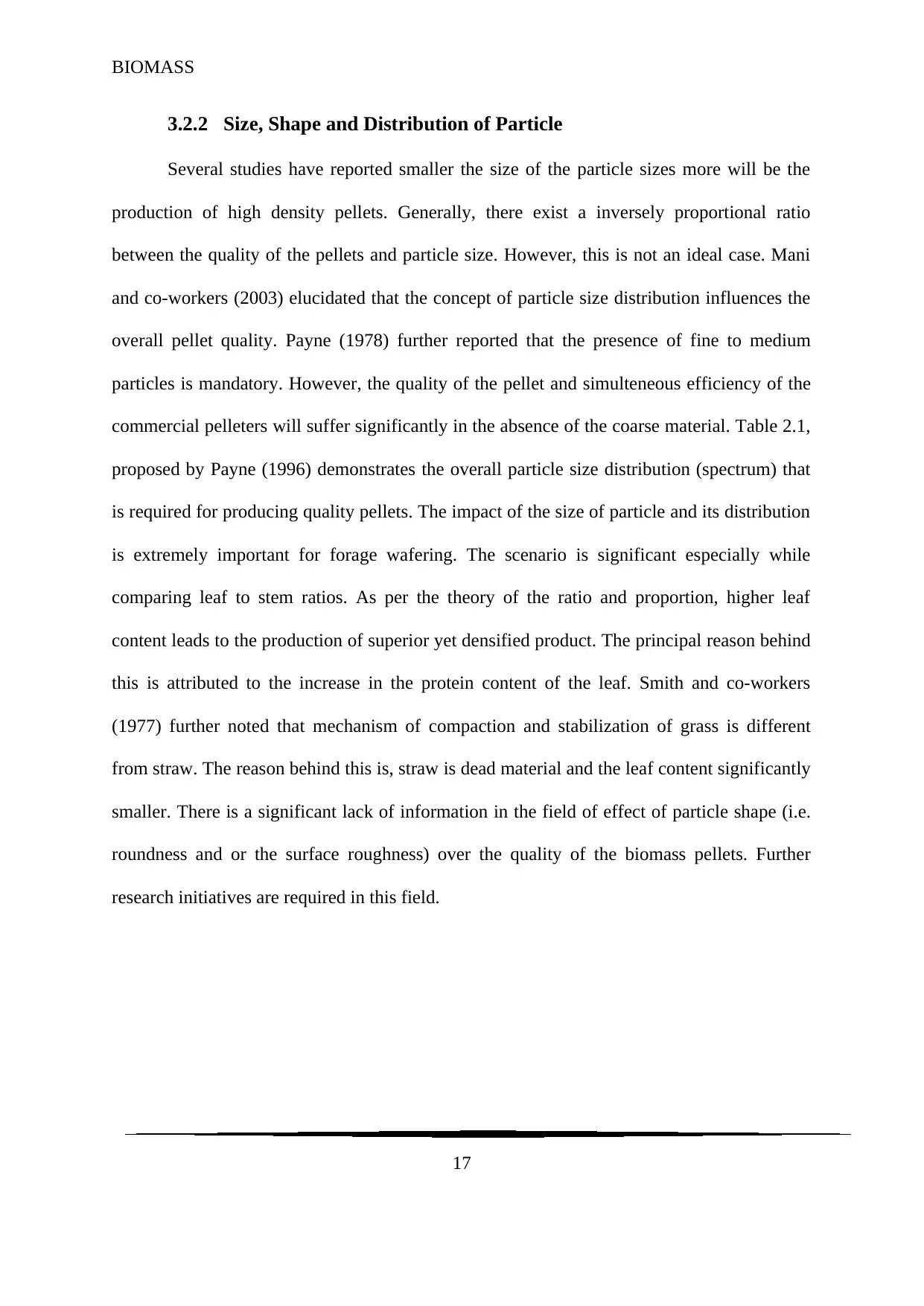
3.2.2 Size, Shape and Distribution of Particle
Several studies have reported smaller the size of the particle sizes more will be the
production of high density pellets. Generally, there exist a inversely proportional ratio
between the quality of the pellets and particle size. However, this is not an ideal case. Mani
and co-workers (2003) elucidated that the concept of particle size distribution influences the
overall pellet quality. Payne (1978) further reported that the presence of fine to medium
particles is mandatory. However, the quality of the pellet and simulteneous efficiency of the
commercial pelleters will suffer significantly in the absence of the coarse material. Table 2.1,
proposed by Payne (1996) demonstrates the overall particle size distribution (spectrum) that
is required for producing quality pellets. The impact of the size of particle and its distribution
is extremely important for forage wafering. The scenario is significant especially while
comparing leaf to stem ratios. As per the theory of the ratio and proportion, higher leaf
content leads to the production of superior yet densified product. The principal reason behind
this is attributed to the increase in the protein content of the leaf. Smith and co-workers
(1977) further noted that mechanism of compaction and stabilization of grass is different
from straw. The reason behind this is, straw is dead material and the leaf content significantly
smaller. There is a significant lack of information in the field of effect of particle shape (i.e.
roundness and or the surface roughness) over the quality of the biomass pellets. Further
research initiatives are required in this field.
17
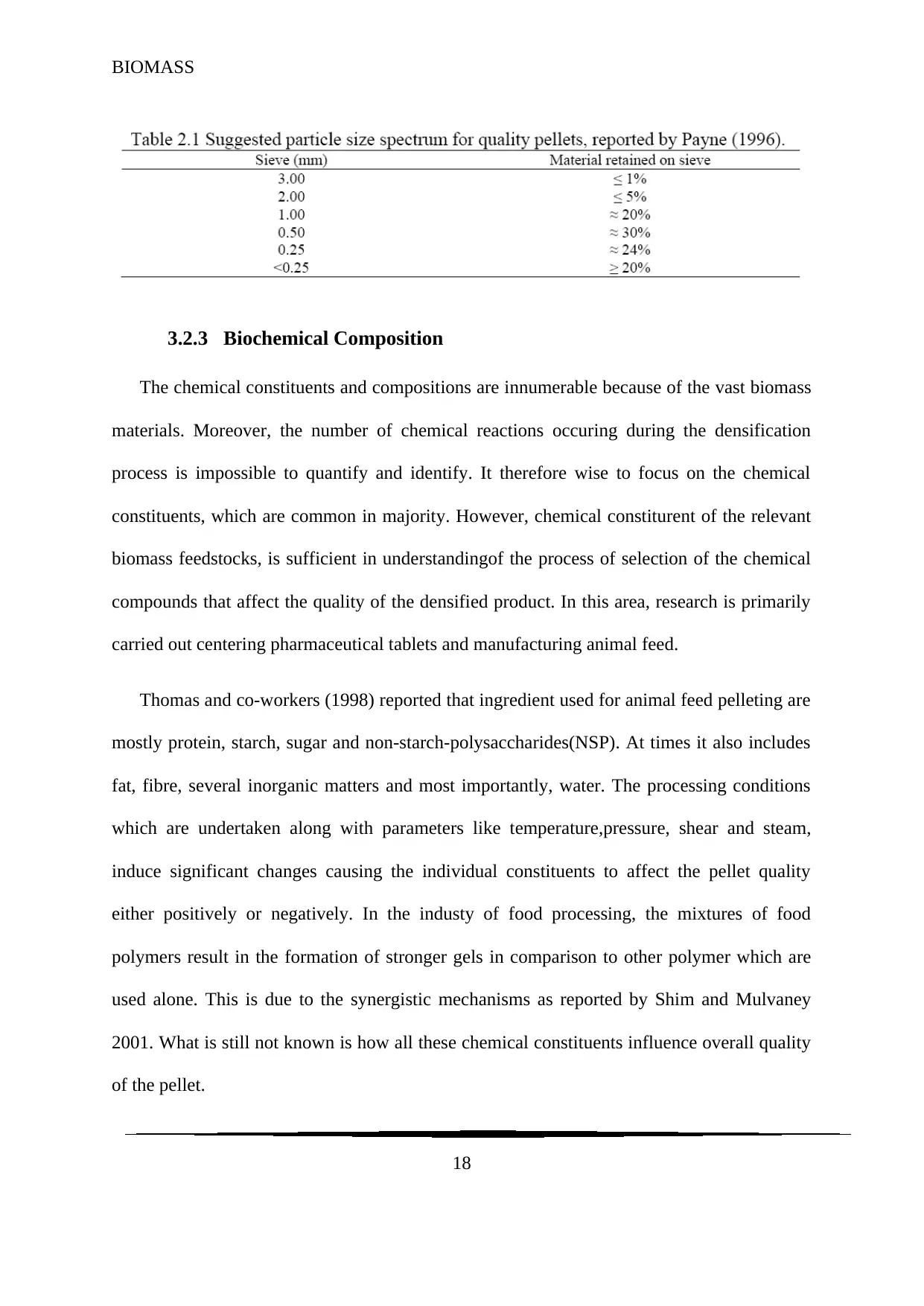
3.2.3 Biochemical Composition
The chemical constituents and compositions are innumerable because of the vast biomass
materials. Moreover, the number of chemical reactions occuring during the densification
process is impossible to quantify and identify. It therefore wise to focus on the chemical
constituents, which are common in majority. However, chemical constiturent of the relevant
biomass feedstocks, is sufficient in understandingof the process of selection of the chemical
compounds that affect the quality of the densified product. In this area, research is primarily
carried out centering pharmaceutical tablets and manufacturing animal feed.
Thomas and co-workers (1998) reported that ingredient used for animal feed pelleting are
mostly protein, starch, sugar and non-starch-polysaccharides(NSP). At times it also includes
fat, fibre, several inorganic matters and most importantly, water. The processing conditions
which are undertaken along with parameters like temperature,pressure, shear and steam,
induce significant changes causing the individual constituents to affect the pellet quality
either positively or negatively. In the industy of food processing, the mixtures of food
polymers result in the formation of stronger gels in comparison to other polymer which are
used alone. This is due to the synergistic mechanisms as reported by Shim and Mulvaney
2001. What is still not known is how all these chemical constituents influence overall quality
of the pellet.
18
⊘ This is a preview!⊘
Do you want full access?
Subscribe today to unlock all pages.

Trusted by 1+ million students worldwide
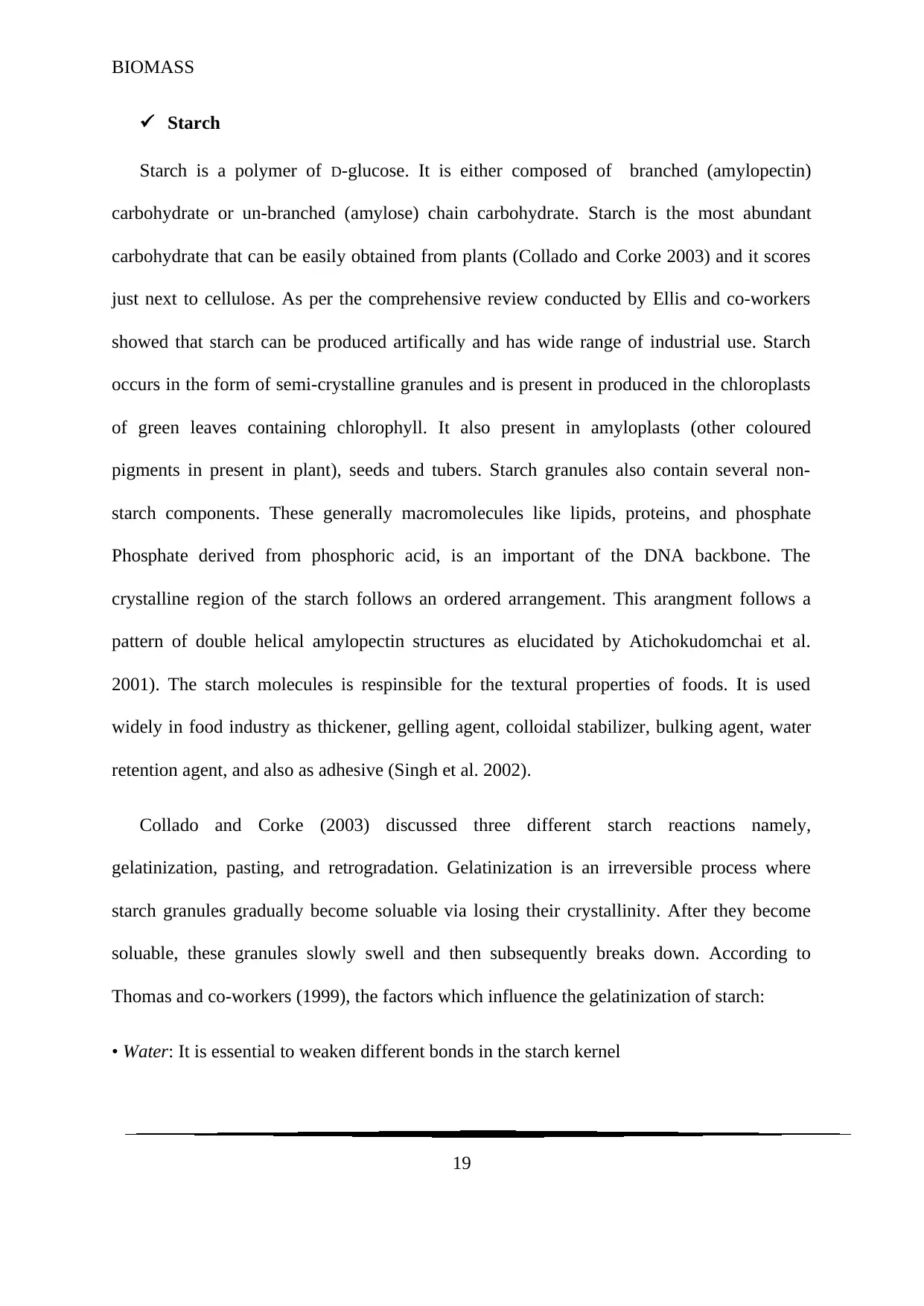
Starch
Starch is a polymer of D-glucose. It is either composed of branched (amylopectin)
carbohydrate or un-branched (amylose) chain carbohydrate. Starch is the most abundant
carbohydrate that can be easily obtained from plants (Collado and Corke 2003) and it scores
just next to cellulose. As per the comprehensive review conducted by Ellis and co-workers
showed that starch can be produced artifically and has wide range of industrial use. Starch
occurs in the form of semi-crystalline granules and is present in produced in the chloroplasts
of green leaves containing chlorophyll. It also present in amyloplasts (other coloured
pigments in present in plant), seeds and tubers. Starch granules also contain several non-
starch components. These generally macromolecules like lipids, proteins, and phosphate
Phosphate derived from phosphoric acid, is an important of the DNA backbone. The
crystalline region of the starch follows an ordered arrangement. This arangment follows a
pattern of double helical amylopectin structures as elucidated by Atichokudomchai et al.
2001). The starch molecules is respinsible for the textural properties of foods. It is used
widely in food industry as thickener, gelling agent, colloidal stabilizer, bulking agent, water
retention agent, and also as adhesive (Singh et al. 2002).
Collado and Corke (2003) discussed three different starch reactions namely,
gelatinization, pasting, and retrogradation. Gelatinization is an irreversible process where
starch granules gradually become soluable via losing their crystallinity. After they become
soluable, these granules slowly swell and then subsequently breaks down. According to
Thomas and co-workers (1999), the factors which influence the gelatinization of starch:
• Water: It is essential to weaken different bonds in the starch kernel
19
Paraphrase This Document
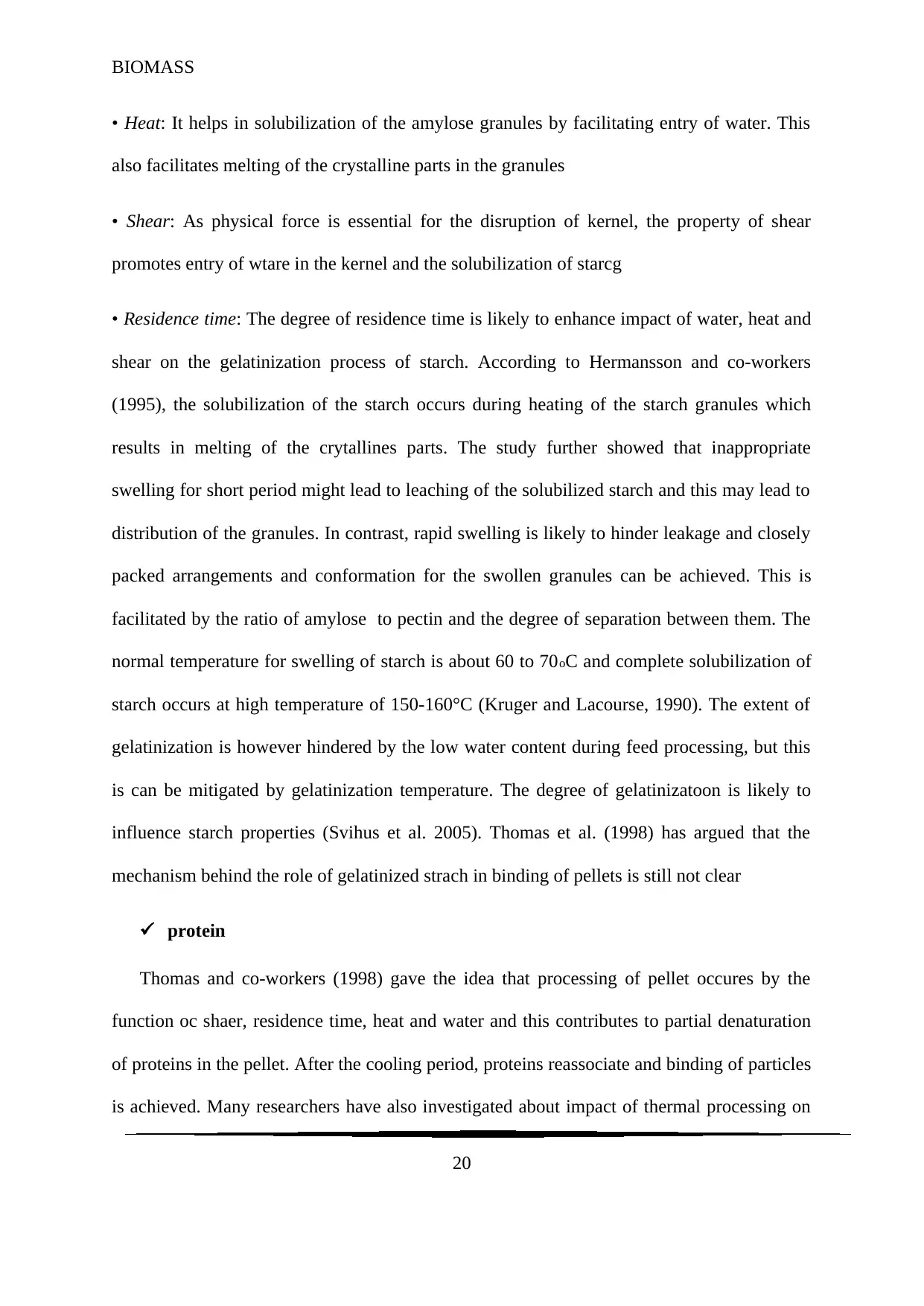
• Heat: It helps in solubilization of the amylose granules by facilitating entry of water. This
also facilitates melting of the crystalline parts in the granules
• Shear: As physical force is essential for the disruption of kernel, the property of shear
promotes entry of wtare in the kernel and the solubilization of starcg
• Residence time: The degree of residence time is likely to enhance impact of water, heat and
shear on the gelatinization process of starch. According to Hermansson and co-workers
(1995), the solubilization of the starch occurs during heating of the starch granules which
results in melting of the crytallines parts. The study further showed that inappropriate
swelling for short period might lead to leaching of the solubilized starch and this may lead to
distribution of the granules. In contrast, rapid swelling is likely to hinder leakage and closely
packed arrangements and conformation for the swollen granules can be achieved. This is
facilitated by the ratio of amylose to pectin and the degree of separation between them. The
normal temperature for swelling of starch is about 60 to 70oC and complete solubilization of
starch occurs at high temperature of 150-160°C (Kruger and Lacourse, 1990). The extent of
gelatinization is however hindered by the low water content during feed processing, but this
is can be mitigated by gelatinization temperature. The degree of gelatinizatoon is likely to
influence starch properties (Svihus et al. 2005). Thomas et al. (1998) has argued that the
mechanism behind the role of gelatinized strach in binding of pellets is still not clear
protein
Thomas and co-workers (1998) gave the idea that processing of pellet occures by the
function oc shaer, residence time, heat and water and this contributes to partial denaturation
of proteins in the pellet. After the cooling period, proteins reassociate and binding of particles
is achieved. Many researchers have also investigated about impact of thermal processing on
20
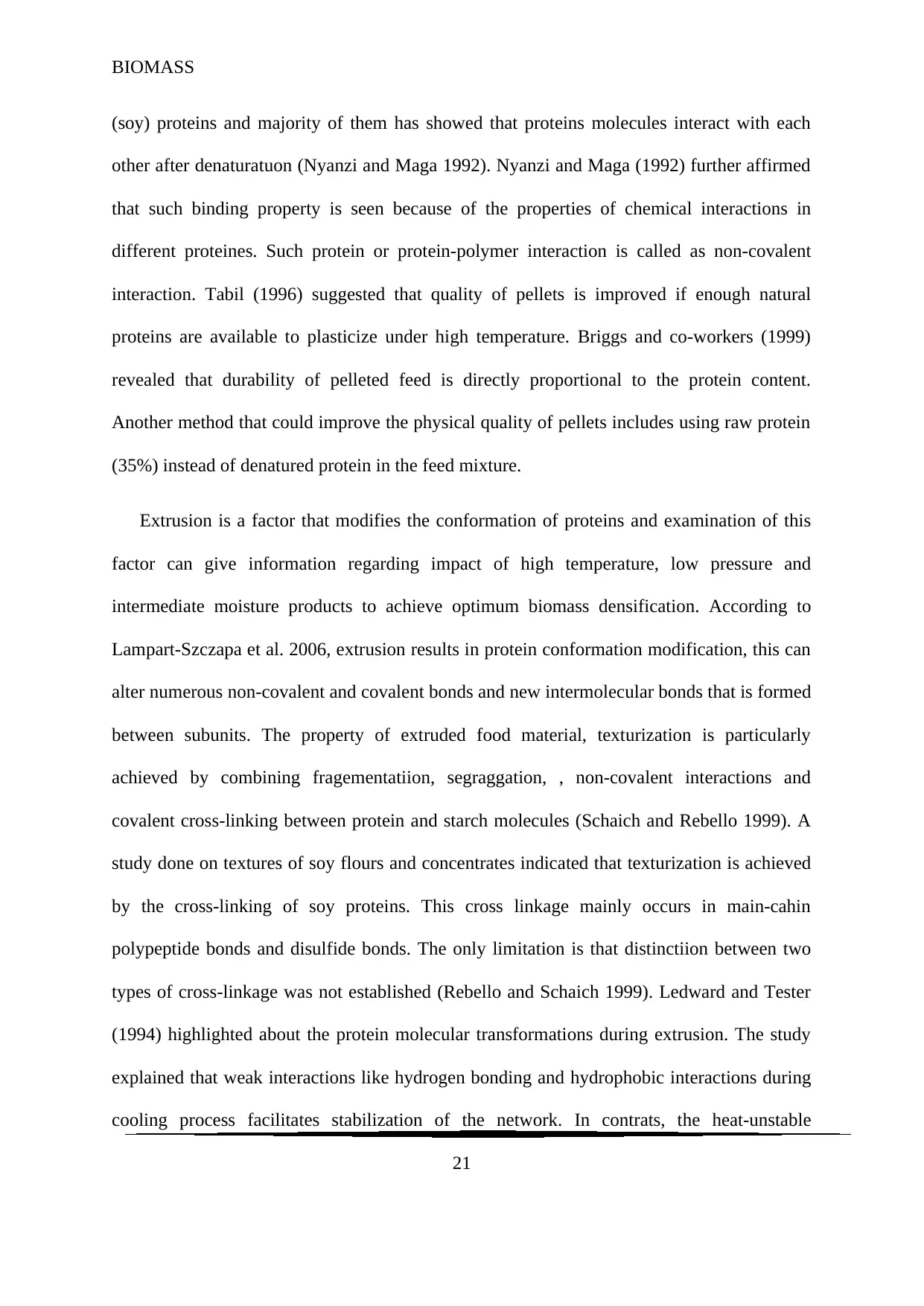
(soy) proteins and majority of them has showed that proteins molecules interact with each
other after denaturatuon (Nyanzi and Maga 1992). Nyanzi and Maga (1992) further affirmed
that such binding property is seen because of the properties of chemical interactions in
different proteines. Such protein or protein-polymer interaction is called as non-covalent
interaction. Tabil (1996) suggested that quality of pellets is improved if enough natural
proteins are available to plasticize under high temperature. Briggs and co-workers (1999)
revealed that durability of pelleted feed is directly proportional to the protein content.
Another method that could improve the physical quality of pellets includes using raw protein
(35%) instead of denatured protein in the feed mixture.
Extrusion is a factor that modifies the conformation of proteins and examination of this
factor can give information regarding impact of high temperature, low pressure and
intermediate moisture products to achieve optimum biomass densification. According to
Lampart-Szczapa et al. 2006, extrusion results in protein conformation modification, this can
alter numerous non-covalent and covalent bonds and new intermolecular bonds that is formed
between subunits. The property of extruded food material, texturization is particularly
achieved by combining fragementatiion, segraggation, , non-covalent interactions and
covalent cross-linking between protein and starch molecules (Schaich and Rebello 1999). A
study done on textures of soy flours and concentrates indicated that texturization is achieved
by the cross-linking of soy proteins. This cross linkage mainly occurs in main-cahin
polypeptide bonds and disulfide bonds. The only limitation is that distinctiion between two
types of cross-linkage was not established (Rebello and Schaich 1999). Ledward and Tester
(1994) highlighted about the protein molecular transformations during extrusion. The study
explained that weak interactions like hydrogen bonding and hydrophobic interactions during
cooling process facilitates stabilization of the network. In contrats, the heat-unstable
21
⊘ This is a preview!⊘
Do you want full access?
Subscribe today to unlock all pages.

Trusted by 1+ million students worldwide
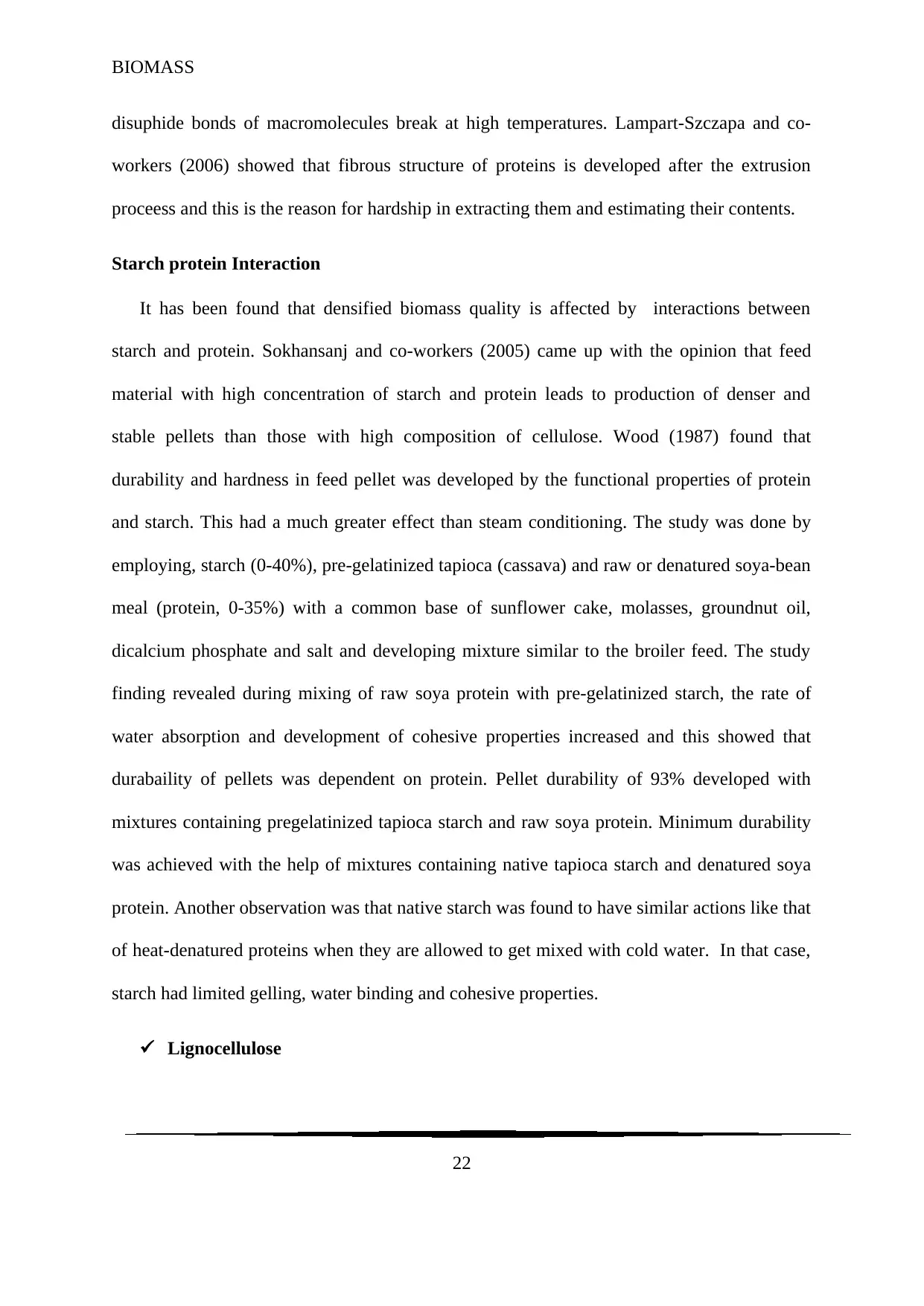
disuphide bonds of macromolecules break at high temperatures. Lampart-Szczapa and co-
workers (2006) showed that fibrous structure of proteins is developed after the extrusion
proceess and this is the reason for hardship in extracting them and estimating their contents.
Starch protein Interaction
It has been found that densified biomass quality is affected by interactions between
starch and protein. Sokhansanj and co-workers (2005) came up with the opinion that feed
material with high concentration of starch and protein leads to production of denser and
stable pellets than those with high composition of cellulose. Wood (1987) found that
durability and hardness in feed pellet was developed by the functional properties of protein
and starch. This had a much greater effect than steam conditioning. The study was done by
employing, starch (0-40%), pre-gelatinized tapioca (cassava) and raw or denatured soya-bean
meal (protein, 0-35%) with a common base of sunflower cake, molasses, groundnut oil,
dicalcium phosphate and salt and developing mixture similar to the broiler feed. The study
finding revealed during mixing of raw soya protein with pre-gelatinized starch, the rate of
water absorption and development of cohesive properties increased and this showed that
durabaility of pellets was dependent on protein. Pellet durability of 93% developed with
mixtures containing pregelatinized tapioca starch and raw soya protein. Minimum durability
was achieved with the help of mixtures containing native tapioca starch and denatured soya
protein. Another observation was that native starch was found to have similar actions like that
of heat-denatured proteins when they are allowed to get mixed with cold water. In that case,
starch had limited gelling, water binding and cohesive properties.
Lignocellulose
22
Paraphrase This Document
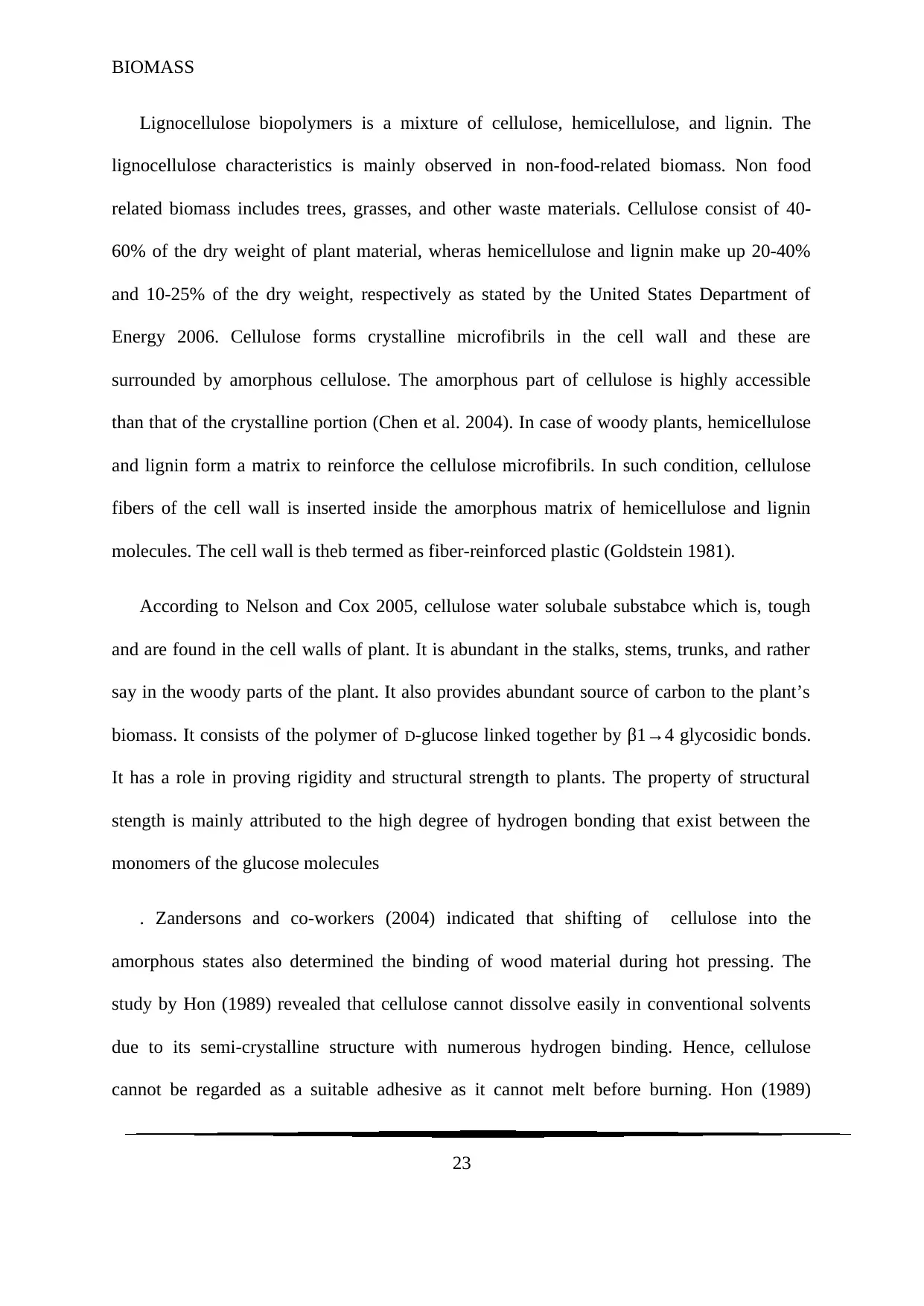
Lignocellulose biopolymers is a mixture of cellulose, hemicellulose, and lignin. The
lignocellulose characteristics is mainly observed in non-food-related biomass. Non food
related biomass includes trees, grasses, and other waste materials. Cellulose consist of 40-
60% of the dry weight of plant material, wheras hemicellulose and lignin make up 20-40%
and 10-25% of the dry weight, respectively as stated by the United States Department of
Energy 2006. Cellulose forms crystalline microfibrils in the cell wall and these are
surrounded by amorphous cellulose. The amorphous part of cellulose is highly accessible
than that of the crystalline portion (Chen et al. 2004). In case of woody plants, hemicellulose
and lignin form a matrix to reinforce the cellulose microfibrils. In such condition, cellulose
fibers of the cell wall is inserted inside the amorphous matrix of hemicellulose and lignin
molecules. The cell wall is theb termed as fiber-reinforced plastic (Goldstein 1981).
According to Nelson and Cox 2005, cellulose water solubale substabce which is, tough
and are found in the cell walls of plant. It is abundant in the stalks, stems, trunks, and rather
say in the woody parts of the plant. It also provides abundant source of carbon to the plant’s
biomass. It consists of the polymer of D-glucose linked together by β1→4 glycosidic bonds.
It has a role in proving rigidity and structural strength to plants. The property of structural
stength is mainly attributed to the high degree of hydrogen bonding that exist between the
monomers of the glucose molecules
. Zandersons and co-workers (2004) indicated that shifting of cellulose into the
amorphous states also determined the binding of wood material during hot pressing. The
study by Hon (1989) revealed that cellulose cannot dissolve easily in conventional solvents
due to its semi-crystalline structure with numerous hydrogen binding. Hence, cellulose
cannot be regarded as a suitable adhesive as it cannot melt before burning. Hon (1989)
23
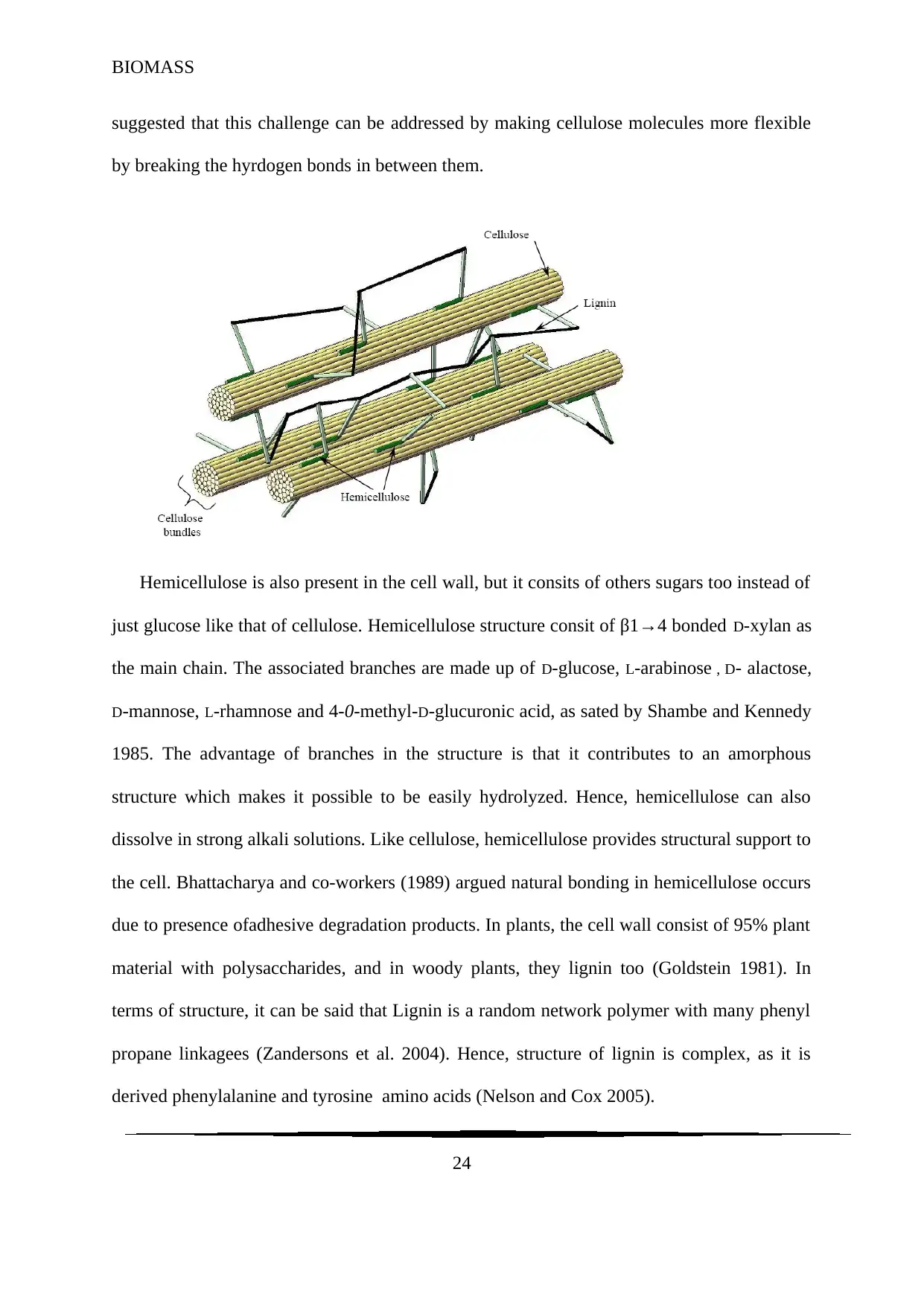
suggested that this challenge can be addressed by making cellulose molecules more flexible
by breaking the hyrdogen bonds in between them.
Hemicellulose is also present in the cell wall, but it consits of others sugars too instead of
just glucose like that of cellulose. Hemicellulose structure consit of β1→4 bonded D-xylan as
the main chain. The associated branches are made up of D-glucose, L-arabinose , D- alactose,
D-mannose, L-rhamnose and 4-0-methyl-D-glucuronic acid, as sated by Shambe and Kennedy
1985. The advantage of branches in the structure is that it contributes to an amorphous
structure which makes it possible to be easily hydrolyzed. Hence, hemicellulose can also
dissolve in strong alkali solutions. Like cellulose, hemicellulose provides structural support to
the cell. Bhattacharya and co-workers (1989) argued natural bonding in hemicellulose occurs
due to presence ofadhesive degradation products. In plants, the cell wall consist of 95% plant
material with polysaccharides, and in woody plants, they lignin too (Goldstein 1981). In
terms of structure, it can be said that Lignin is a random network polymer with many phenyl
propane linkagees (Zandersons et al. 2004). Hence, structure of lignin is complex, as it is
derived phenylalanine and tyrosine amino acids (Nelson and Cox 2005).
24
⊘ This is a preview!⊘
Do you want full access?
Subscribe today to unlock all pages.

Trusted by 1+ million students worldwide
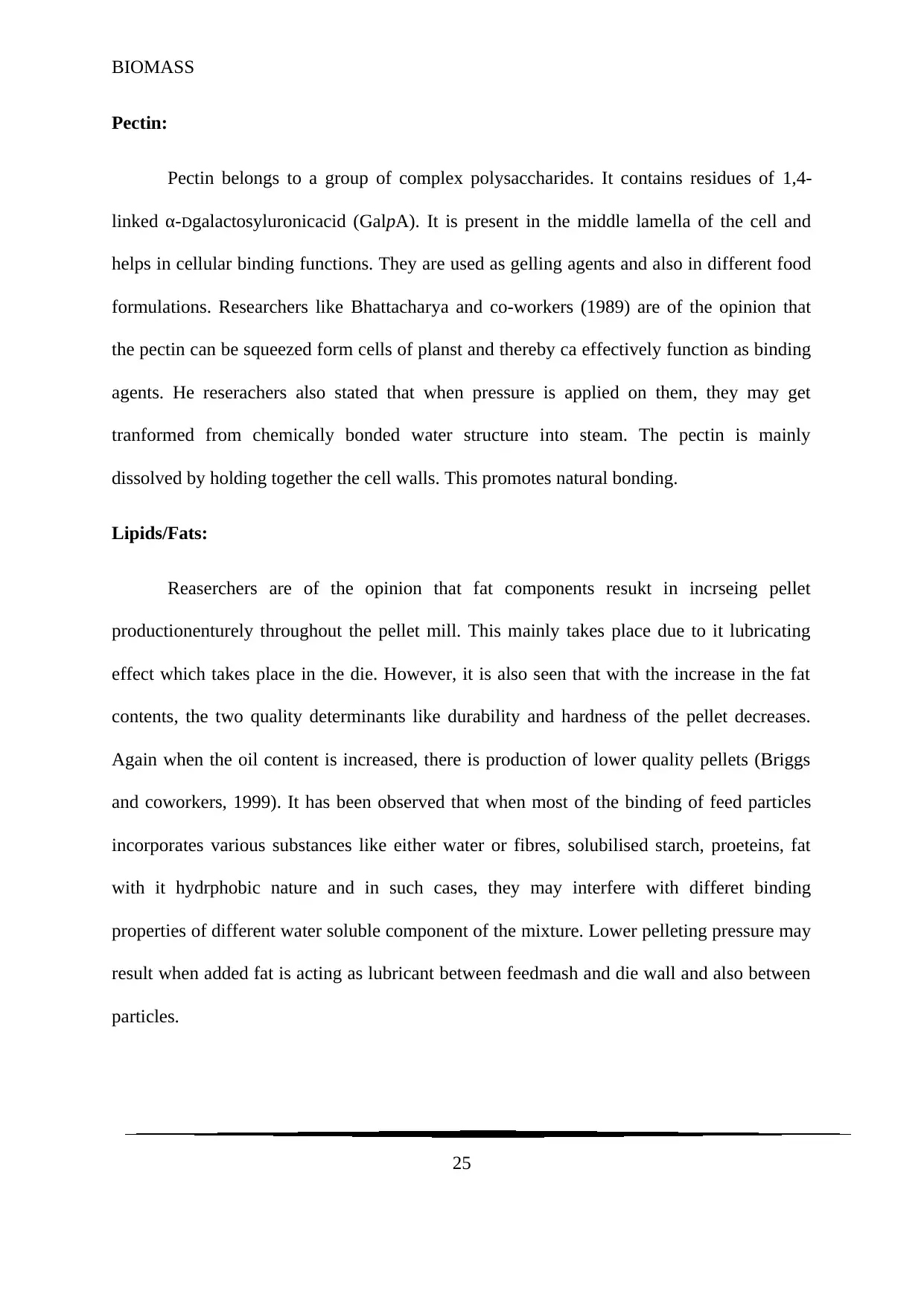
Pectin:
Pectin belongs to a group of complex polysaccharides. It contains residues of 1,4-
linked α-Dgalactosyluronicacid (GalpA). It is present in the middle lamella of the cell and
helps in cellular binding functions. They are used as gelling agents and also in different food
formulations. Researchers like Bhattacharya and co-workers (1989) are of the opinion that
the pectin can be squeezed form cells of planst and thereby ca effectively function as binding
agents. He reserachers also stated that when pressure is applied on them, they may get
tranformed from chemically bonded water structure into steam. The pectin is mainly
dissolved by holding together the cell walls. This promotes natural bonding.
Lipids/Fats:
Reaserchers are of the opinion that fat components resukt in incrseing pellet
productionenturely throughout the pellet mill. This mainly takes place due to it lubricating
effect which takes place in the die. However, it is also seen that with the increase in the fat
contents, the two quality determinants like durability and hardness of the pellet decreases.
Again when the oil content is increased, there is production of lower quality pellets (Briggs
and coworkers, 1999). It has been observed that when most of the binding of feed particles
incorporates various substances like either water or fibres, solubilised starch, proeteins, fat
with it hydrphobic nature and in such cases, they may interfere with differet binding
properties of different water soluble component of the mixture. Lower pelleting pressure may
result when added fat is acting as lubricant between feedmash and die wall and also between
particles.
25
Paraphrase This Document
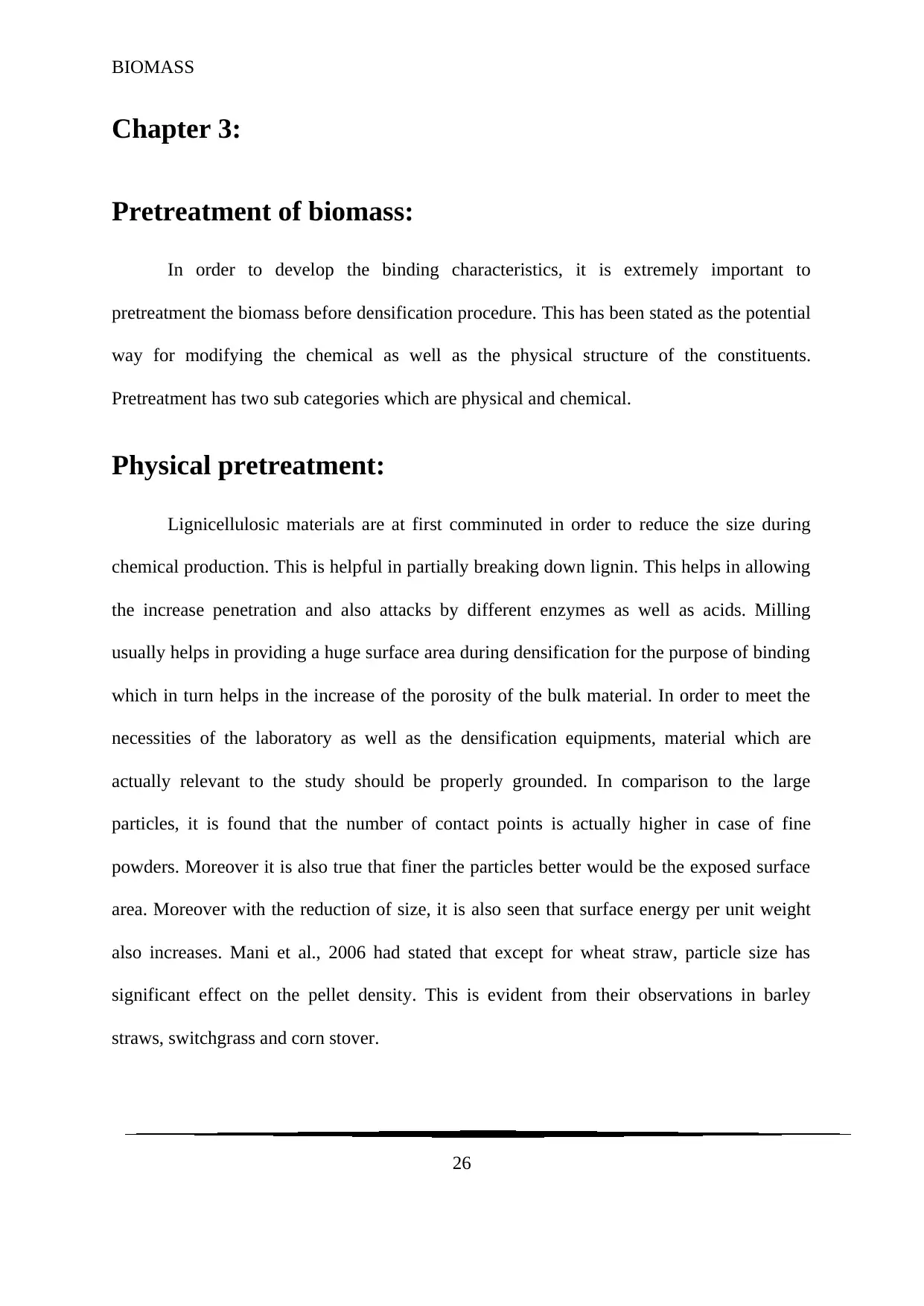
Chapter 3:
Pretreatment of biomass:
In order to develop the binding characteristics, it is extremely important to
pretreatment the biomass before densification procedure. This has been stated as the potential
way for modifying the chemical as well as the physical structure of the constituents.
Pretreatment has two sub categories which are physical and chemical.
Physical pretreatment:
Lignicellulosic materials are at first comminuted in order to reduce the size during
chemical production. This is helpful in partially breaking down lignin. This helps in allowing
the increase penetration and also attacks by different enzymes as well as acids. Milling
usually helps in providing a huge surface area during densification for the purpose of binding
which in turn helps in the increase of the porosity of the bulk material. In order to meet the
necessities of the laboratory as well as the densification equipments, material which are
actually relevant to the study should be properly grounded. In comparison to the large
particles, it is found that the number of contact points is actually higher in case of fine
powders. Moreover it is also true that finer the particles better would be the exposed surface
area. Moreover with the reduction of size, it is also seen that surface energy per unit weight
also increases. Mani et al., 2006 had stated that except for wheat straw, particle size has
significant effect on the pellet density. This is evident from their observations in barley
straws, switchgrass and corn stover.
26
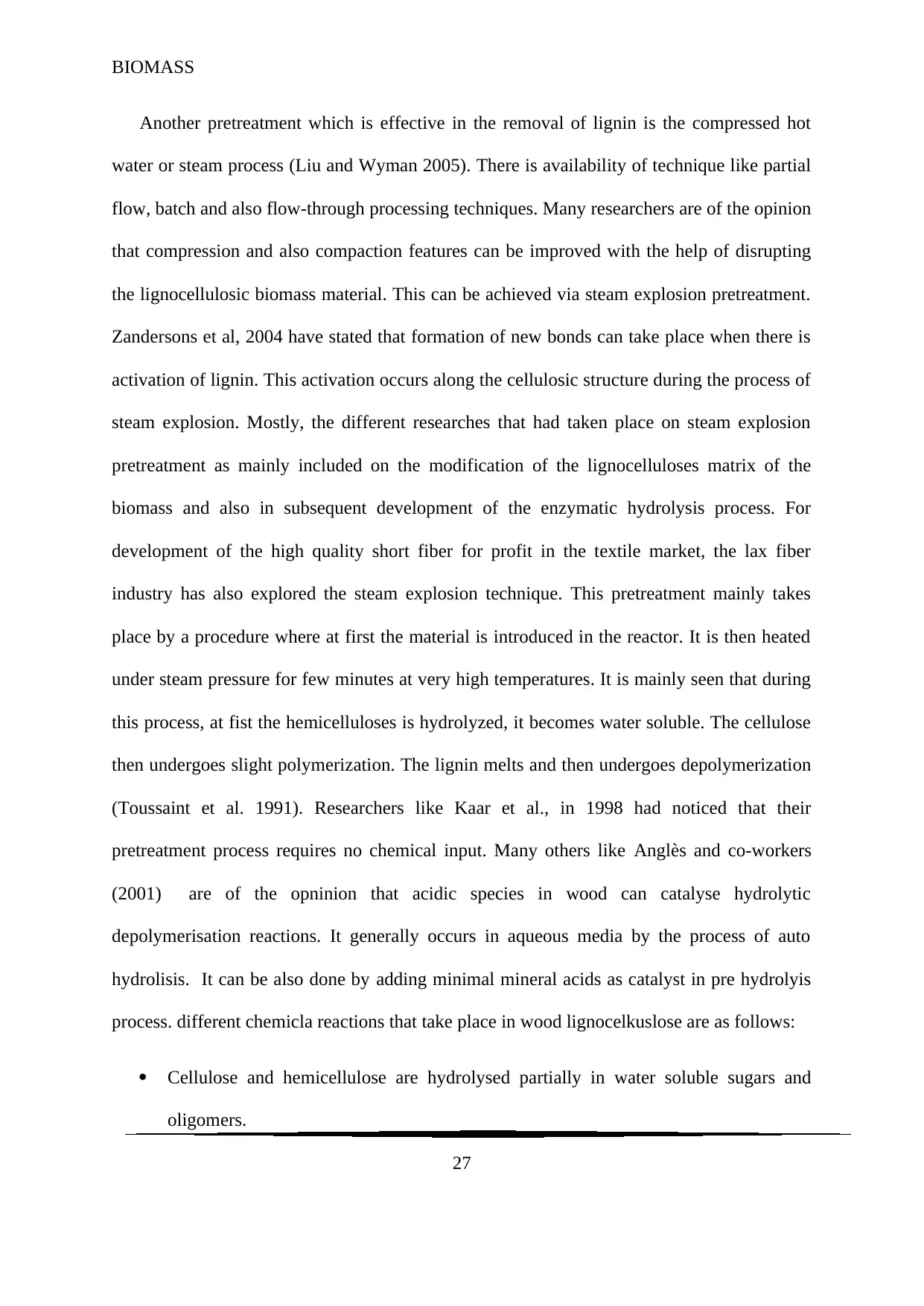
Another pretreatment which is effective in the removal of lignin is the compressed hot
water or steam process (Liu and Wyman 2005). There is availability of technique like partial
flow, batch and also flow-through processing techniques. Many researchers are of the opinion
that compression and also compaction features can be improved with the help of disrupting
the lignocellulosic biomass material. This can be achieved via steam explosion pretreatment.
Zandersons et al, 2004 have stated that formation of new bonds can take place when there is
activation of lignin. This activation occurs along the cellulosic structure during the process of
steam explosion. Mostly, the different researches that had taken place on steam explosion
pretreatment as mainly included on the modification of the lignocelluloses matrix of the
biomass and also in subsequent development of the enzymatic hydrolysis process. For
development of the high quality short fiber for profit in the textile market, the lax fiber
industry has also explored the steam explosion technique. This pretreatment mainly takes
place by a procedure where at first the material is introduced in the reactor. It is then heated
under steam pressure for few minutes at very high temperatures. It is mainly seen that during
this process, at fist the hemicelluloses is hydrolyzed, it becomes water soluble. The cellulose
then undergoes slight polymerization. The lignin melts and then undergoes depolymerization
(Toussaint et al. 1991). Researchers like Kaar et al., in 1998 had noticed that their
pretreatment process requires no chemical input. Many others like Anglès and co-workers
(2001) are of the opninion that acidic species in wood can catalyse hydrolytic
depolymerisation reactions. It generally occurs in aqueous media by the process of auto
hydrolisis. It can be also done by adding minimal mineral acids as catalyst in pre hydrolyis
process. different chemicla reactions that take place in wood lignocelkuslose are as follows:
Cellulose and hemicellulose are hydrolysed partially in water soluble sugars and
oligomers.
27
⊘ This is a preview!⊘
Do you want full access?
Subscribe today to unlock all pages.

Trusted by 1+ million students worldwide
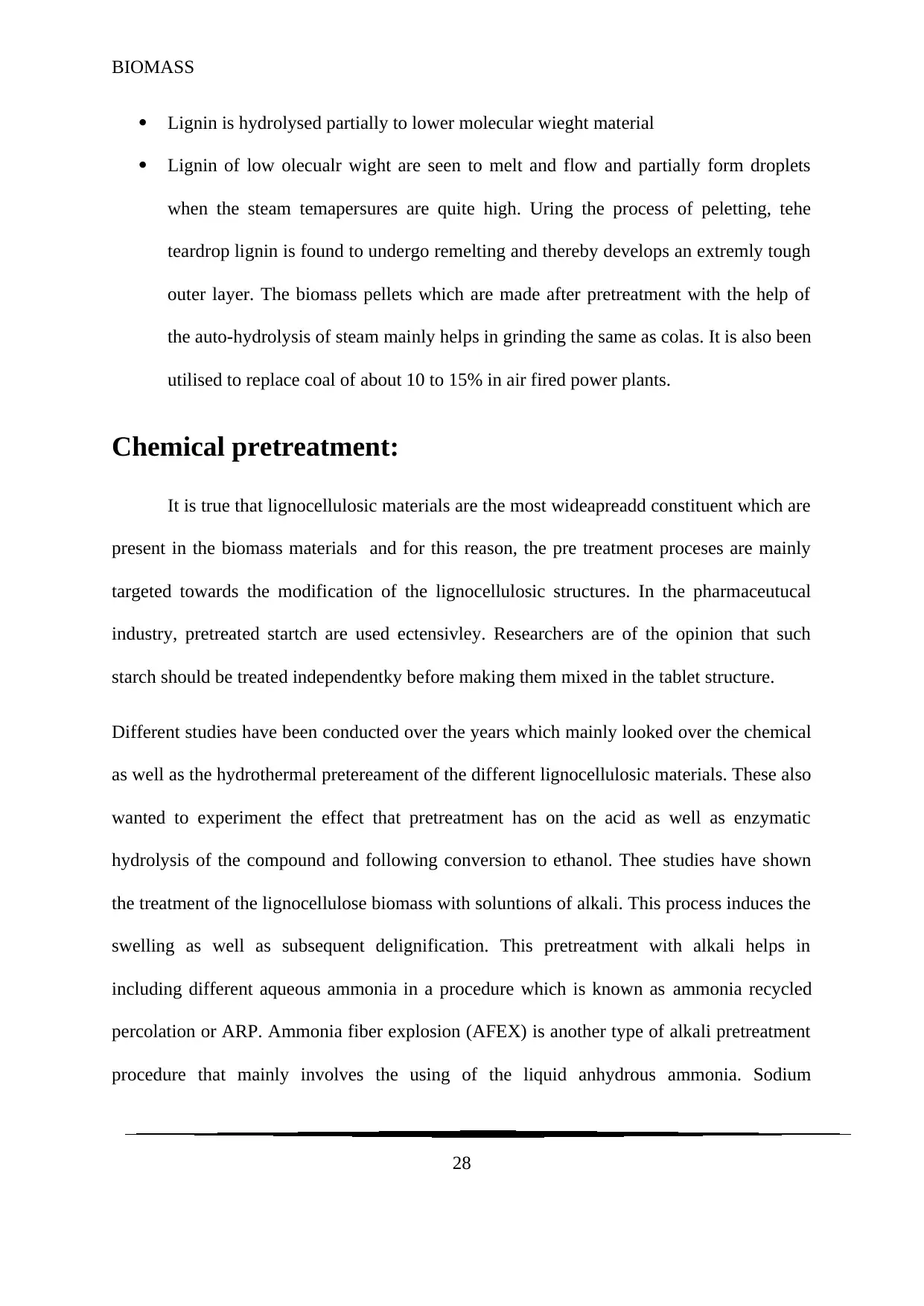
Lignin is hydrolysed partially to lower molecular wieght material
Lignin of low olecualr wight are seen to melt and flow and partially form droplets
when the steam temapersures are quite high. Uring the process of peletting, tehe
teardrop lignin is found to undergo remelting and thereby develops an extremly tough
outer layer. The biomass pellets which are made after pretreatment with the help of
the auto-hydrolysis of steam mainly helps in grinding the same as colas. It is also been
utilised to replace coal of about 10 to 15% in air fired power plants.
Chemical pretreatment:
It is true that lignocellulosic materials are the most wideapreadd constituent which are
present in the biomass materials and for this reason, the pre treatment proceses are mainly
targeted towards the modification of the lignocellulosic structures. In the pharmaceutucal
industry, pretreated startch are used ectensivley. Researchers are of the opinion that such
starch should be treated independentky before making them mixed in the tablet structure.
Different studies have been conducted over the years which mainly looked over the chemical
as well as the hydrothermal pretereament of the different lignocellulosic materials. These also
wanted to experiment the effect that pretreatment has on the acid as well as enzymatic
hydrolysis of the compound and following conversion to ethanol. Thee studies have shown
the treatment of the lignocellulose biomass with soluntions of alkali. This process induces the
swelling as well as subsequent delignification. This pretreatment with alkali helps in
including different aqueous ammonia in a procedure which is known as ammonia recycled
percolation or ARP. Ammonia fiber explosion (AFEX) is another type of alkali pretreatment
procedure that mainly involves the using of the liquid anhydrous ammonia. Sodium
28
Paraphrase This Document
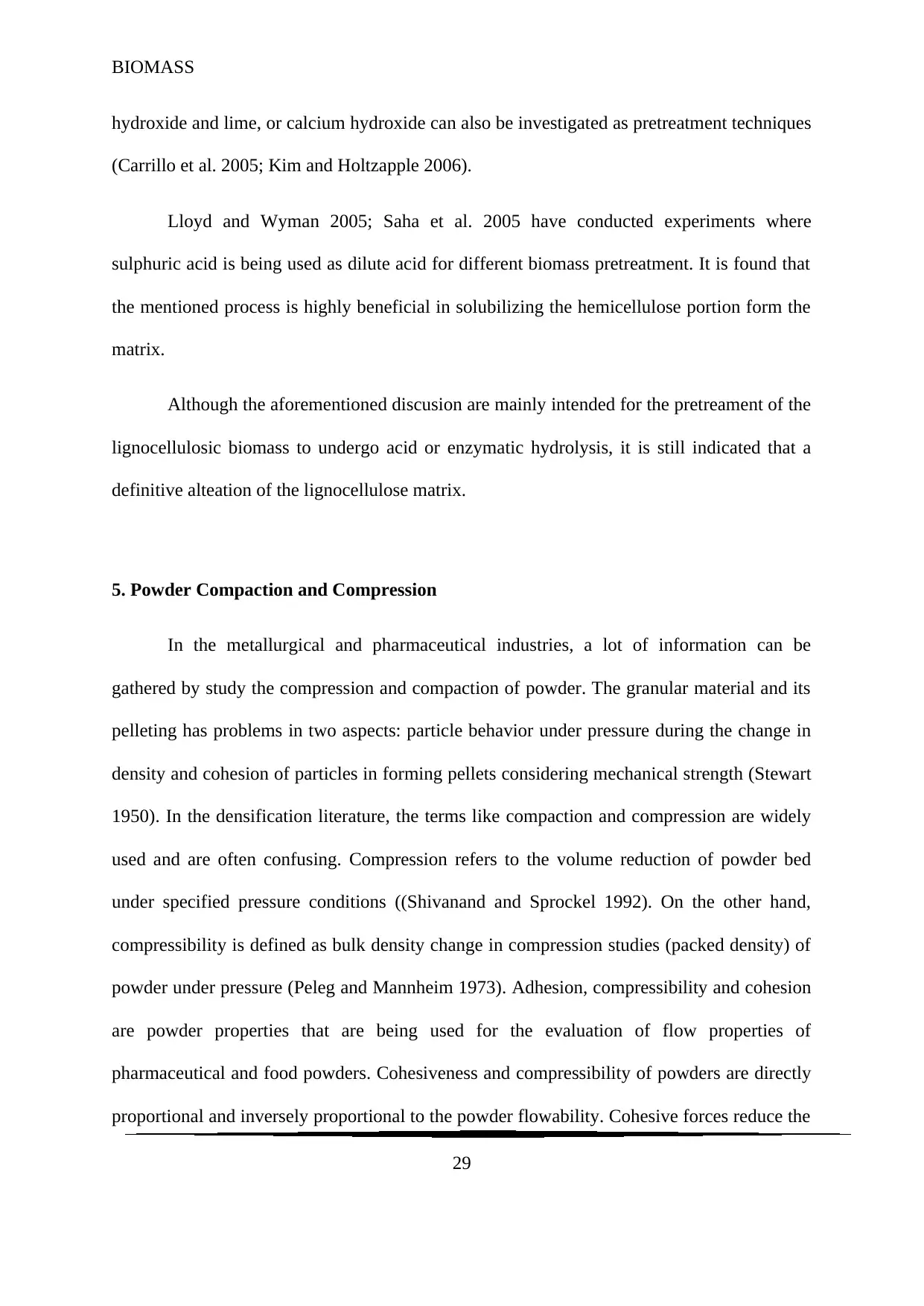
hydroxide and lime, or calcium hydroxide can also be investigated as pretreatment techniques
(Carrillo et al. 2005; Kim and Holtzapple 2006).
Lloyd and Wyman 2005; Saha et al. 2005 have conducted experiments where
sulphuric acid is being used as dilute acid for different biomass pretreatment. It is found that
the mentioned process is highly beneficial in solubilizing the hemicellulose portion form the
matrix.
Although the aforementioned discusion are mainly intended for the pretreament of the
lignocellulosic biomass to undergo acid or enzymatic hydrolysis, it is still indicated that a
definitive alteation of the lignocellulose matrix.
5. Powder Compaction and Compression
In the metallurgical and pharmaceutical industries, a lot of information can be
gathered by study the compression and compaction of powder. The granular material and its
pelleting has problems in two aspects: particle behavior under pressure during the change in
density and cohesion of particles in forming pellets considering mechanical strength (Stewart
1950). In the densification literature, the terms like compaction and compression are widely
used and are often confusing. Compression refers to the volume reduction of powder bed
under specified pressure conditions ((Shivanand and Sprockel 1992). On the other hand,
compressibility is defined as bulk density change in compression studies (packed density) of
powder under pressure (Peleg and Mannheim 1973). Adhesion, compressibility and cohesion
are powder properties that are being used for the evaluation of flow properties of
pharmaceutical and food powders. Cohesiveness and compressibility of powders are directly
proportional and inversely proportional to the powder flowability. Cohesive forces reduce the
29
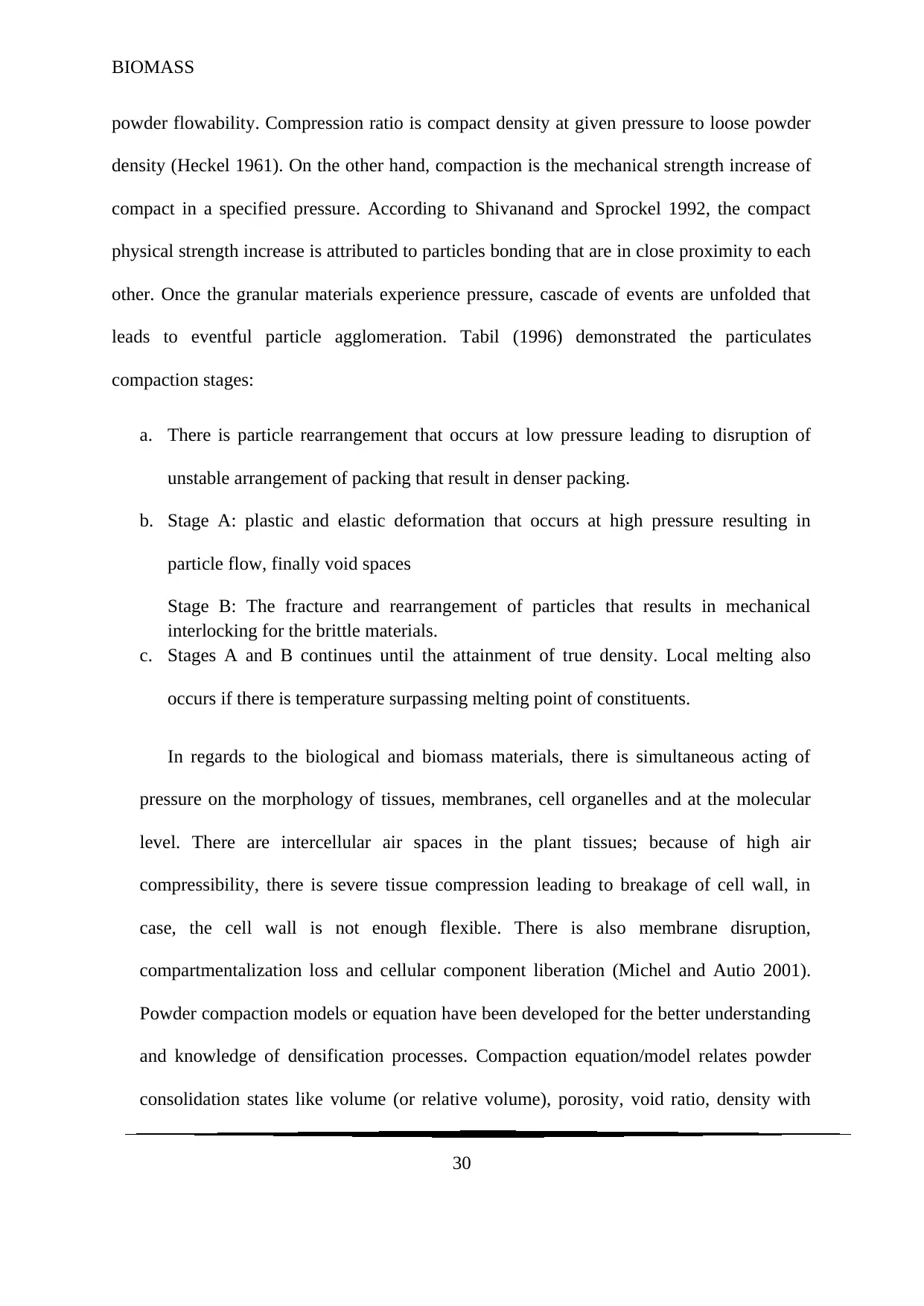
powder flowability. Compression ratio is compact density at given pressure to loose powder
density (Heckel 1961). On the other hand, compaction is the mechanical strength increase of
compact in a specified pressure. According to Shivanand and Sprockel 1992, the compact
physical strength increase is attributed to particles bonding that are in close proximity to each
other. Once the granular materials experience pressure, cascade of events are unfolded that
leads to eventful particle agglomeration. Tabil (1996) demonstrated the particulates
compaction stages:
a. There is particle rearrangement that occurs at low pressure leading to disruption of
unstable arrangement of packing that result in denser packing.
b. Stage A: plastic and elastic deformation that occurs at high pressure resulting in
particle flow, finally void spaces
Stage B: The fracture and rearrangement of particles that results in mechanical
interlocking for the brittle materials.
c. Stages A and B continues until the attainment of true density. Local melting also
occurs if there is temperature surpassing melting point of constituents.
In regards to the biological and biomass materials, there is simultaneous acting of
pressure on the morphology of tissues, membranes, cell organelles and at the molecular
level. There are intercellular air spaces in the plant tissues; because of high air
compressibility, there is severe tissue compression leading to breakage of cell wall, in
case, the cell wall is not enough flexible. There is also membrane disruption,
compartmentalization loss and cellular component liberation (Michel and Autio 2001).
Powder compaction models or equation have been developed for the better understanding
and knowledge of densification processes. Compaction equation/model relates powder
consolidation states like volume (or relative volume), porosity, void ratio, density with
30
⊘ This is a preview!⊘
Do you want full access?
Subscribe today to unlock all pages.

Trusted by 1+ million students worldwide
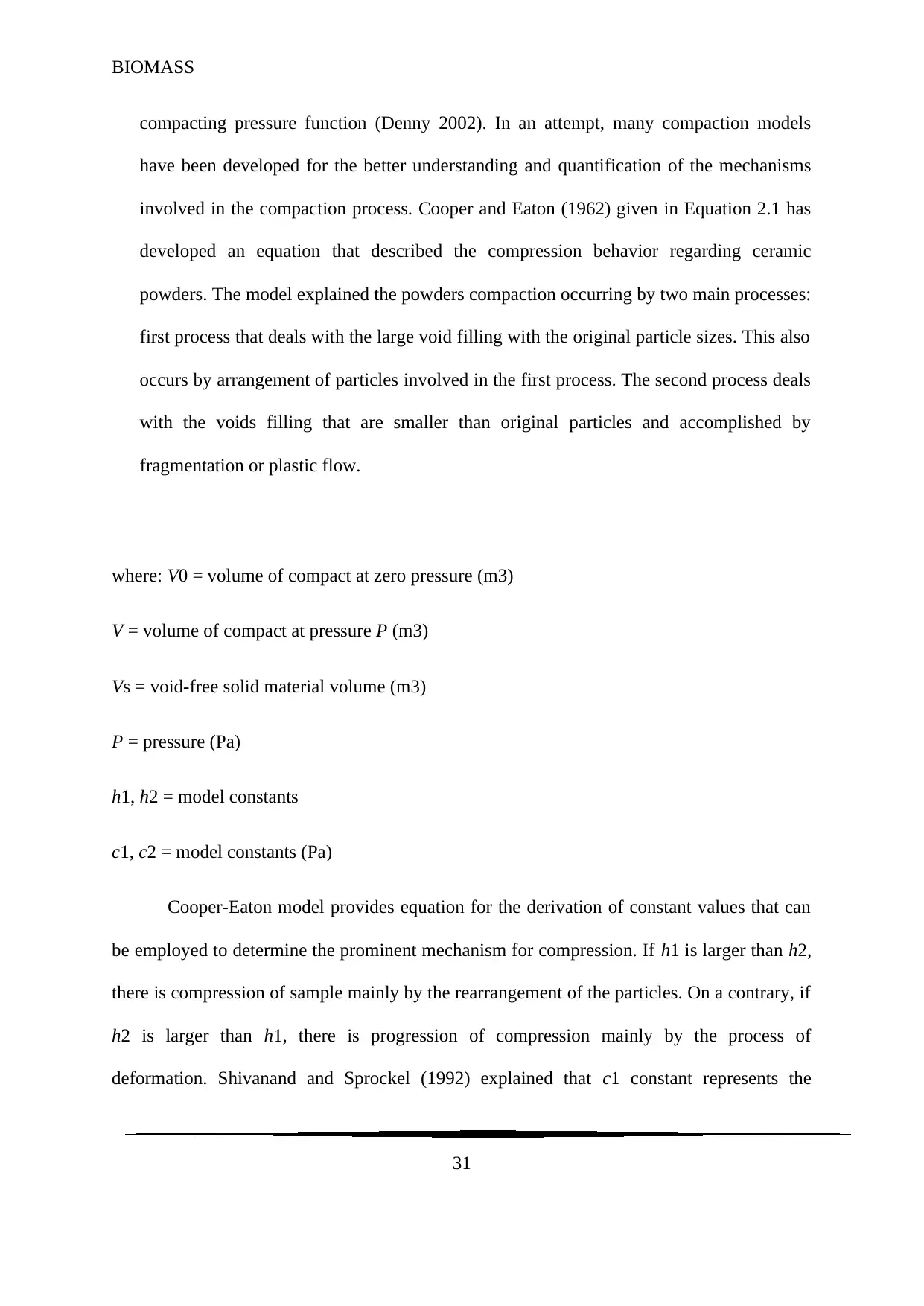
compacting pressure function (Denny 2002). In an attempt, many compaction models
have been developed for the better understanding and quantification of the mechanisms
involved in the compaction process. Cooper and Eaton (1962) given in Equation 2.1 has
developed an equation that described the compression behavior regarding ceramic
powders. The model explained the powders compaction occurring by two main processes:
first process that deals with the large void filling with the original particle sizes. This also
occurs by arrangement of particles involved in the first process. The second process deals
with the voids filling that are smaller than original particles and accomplished by
fragmentation or plastic flow.
where: V0 = volume of compact at zero pressure (m3)
V = volume of compact at pressure P (m3)
Vs = void-free solid material volume (m3)
P = pressure (Pa)
h1, h2 = model constants
c1, c2 = model constants (Pa)
Cooper-Eaton model provides equation for the derivation of constant values that can
be employed to determine the prominent mechanism for compression. If h1 is larger than h2,
there is compression of sample mainly by the rearrangement of the particles. On a contrary, if
h2 is larger than h1, there is progression of compression mainly by the process of
deformation. Shivanand and Sprockel (1992) explained that c1 constant represents the
31
Paraphrase This Document
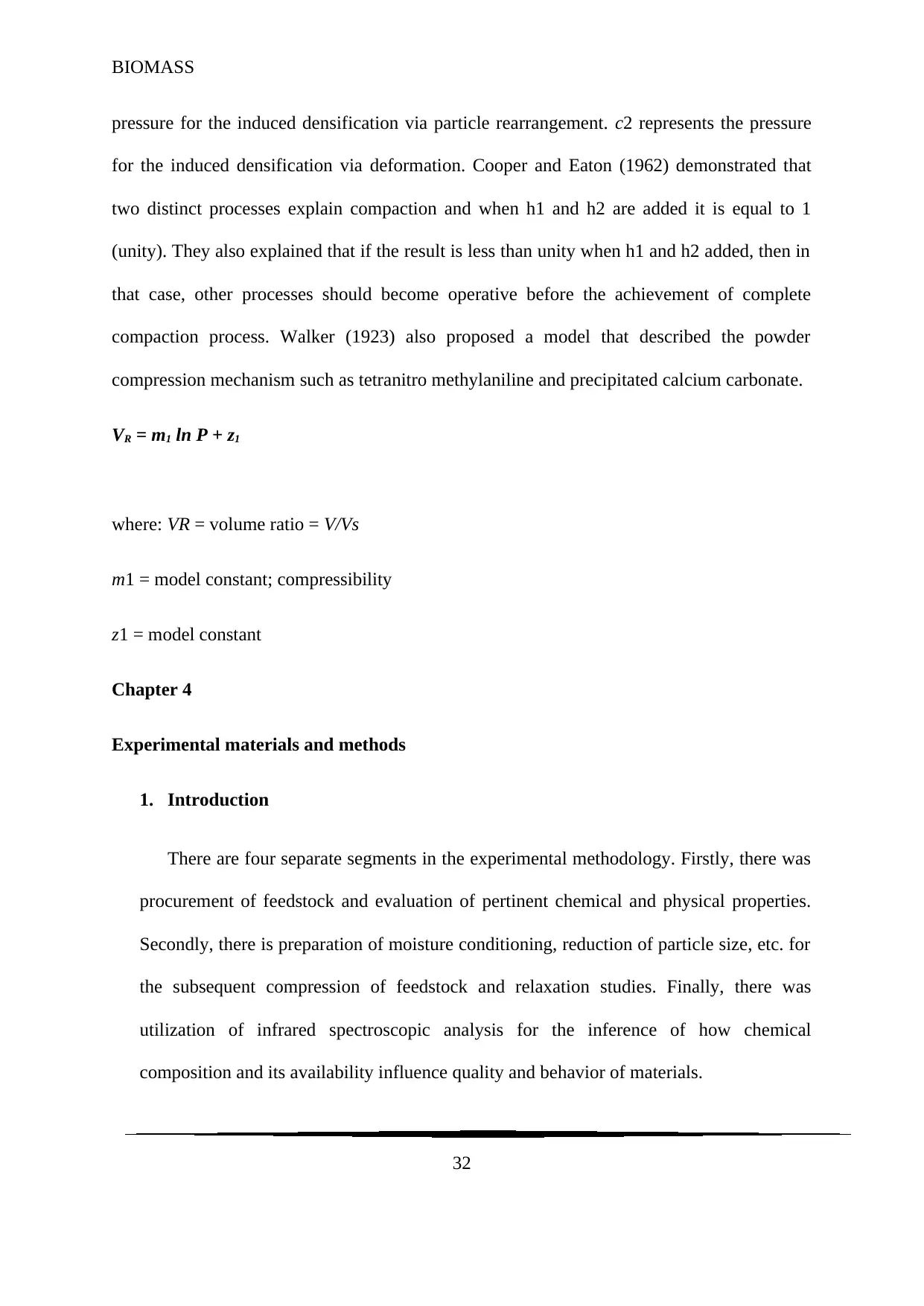
pressure for the induced densification via particle rearrangement. c2 represents the pressure
for the induced densification via deformation. Cooper and Eaton (1962) demonstrated that
two distinct processes explain compaction and when h1 and h2 are added it is equal to 1
(unity). They also explained that if the result is less than unity when h1 and h2 added, then in
that case, other processes should become operative before the achievement of complete
compaction process. Walker (1923) also proposed a model that described the powder
compression mechanism such as tetranitro methylaniline and precipitated calcium carbonate.
VR = m1 ln P + z1
where: VR = volume ratio = V/Vs
m1 = model constant; compressibility
z1 = model constant
Chapter 4
Experimental materials and methods
1. Introduction
There are four separate segments in the experimental methodology. Firstly, there was
procurement of feedstock and evaluation of pertinent chemical and physical properties.
Secondly, there is preparation of moisture conditioning, reduction of particle size, etc. for
the subsequent compression of feedstock and relaxation studies. Finally, there was
utilization of infrared spectroscopic analysis for the inference of how chemical
composition and its availability influence quality and behavior of materials.
32
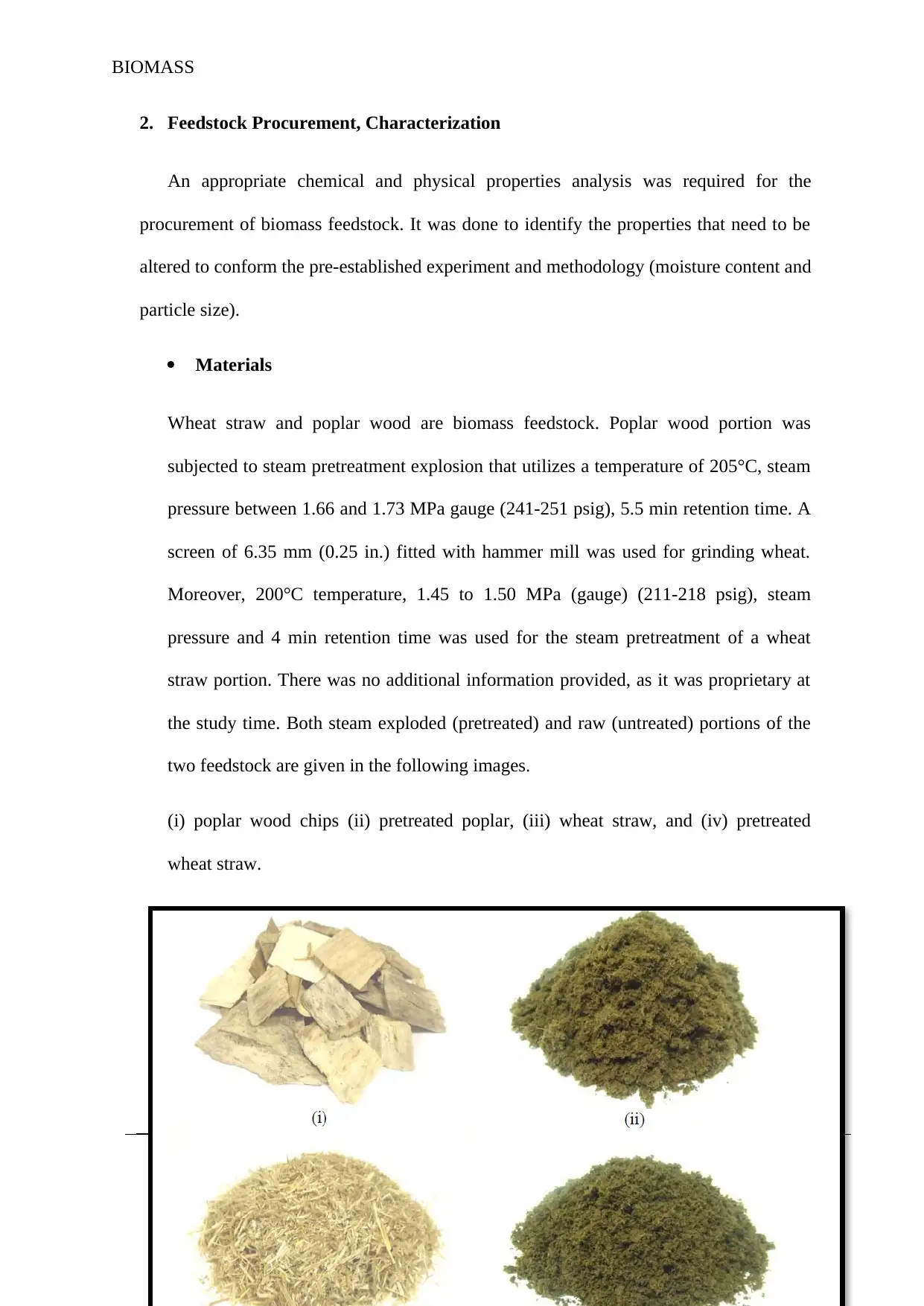
2. Feedstock Procurement, Characterization
An appropriate chemical and physical properties analysis was required for the
procurement of biomass feedstock. It was done to identify the properties that need to be
altered to conform the pre-established experiment and methodology (moisture content and
particle size).
Materials
Wheat straw and poplar wood are biomass feedstock. Poplar wood portion was
subjected to steam pretreatment explosion that utilizes a temperature of 205°C, steam
pressure between 1.66 and 1.73 MPa gauge (241-251 psig), 5.5 min retention time. A
screen of 6.35 mm (0.25 in.) fitted with hammer mill was used for grinding wheat.
Moreover, 200°C temperature, 1.45 to 1.50 MPa (gauge) (211-218 psig), steam
pressure and 4 min retention time was used for the steam pretreatment of a wheat
straw portion. There was no additional information provided, as it was proprietary at
the study time. Both steam exploded (pretreated) and raw (untreated) portions of the
two feedstock are given in the following images.
(i) poplar wood chips (ii) pretreated poplar, (iii) wheat straw, and (iv) pretreated
wheat straw.
33
⊘ This is a preview!⊘
Do you want full access?
Subscribe today to unlock all pages.

Trusted by 1+ million students worldwide
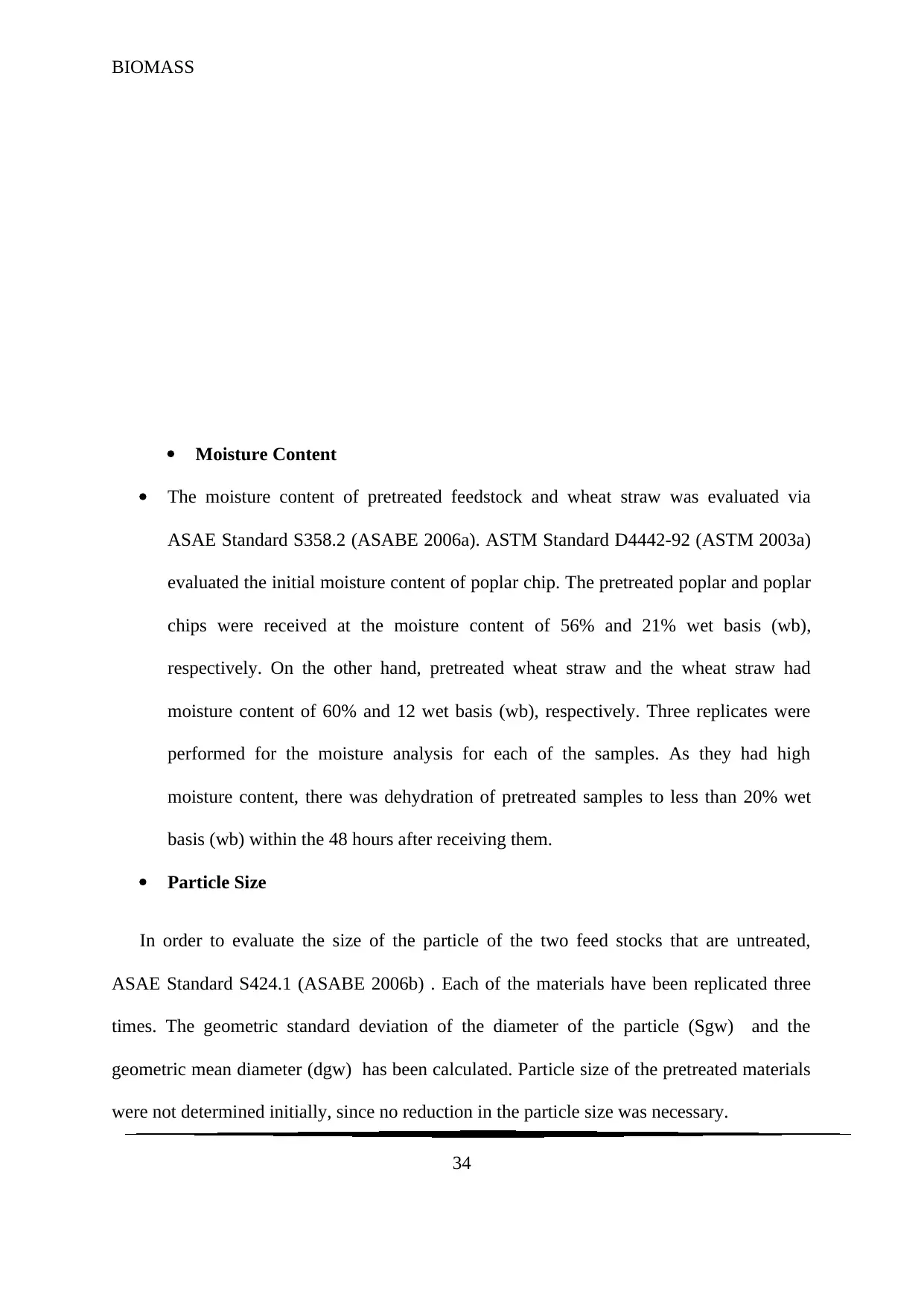
Moisture Content
The moisture content of pretreated feedstock and wheat straw was evaluated via
ASAE Standard S358.2 (ASABE 2006a). ASTM Standard D4442-92 (ASTM 2003a)
evaluated the initial moisture content of poplar chip. The pretreated poplar and poplar
chips were received at the moisture content of 56% and 21% wet basis (wb),
respectively. On the other hand, pretreated wheat straw and the wheat straw had
moisture content of 60% and 12 wet basis (wb), respectively. Three replicates were
performed for the moisture analysis for each of the samples. As they had high
moisture content, there was dehydration of pretreated samples to less than 20% wet
basis (wb) within the 48 hours after receiving them.
Particle Size
In order to evaluate the size of the particle of the two feed stocks that are untreated,
ASAE Standard S424.1 (ASABE 2006b) . Each of the materials have been replicated three
times. The geometric standard deviation of the diameter of the particle (Sgw) and the
geometric mean diameter (dgw) has been calculated. Particle size of the pretreated materials
were not determined initially, since no reduction in the particle size was necessary.
34
Paraphrase This Document
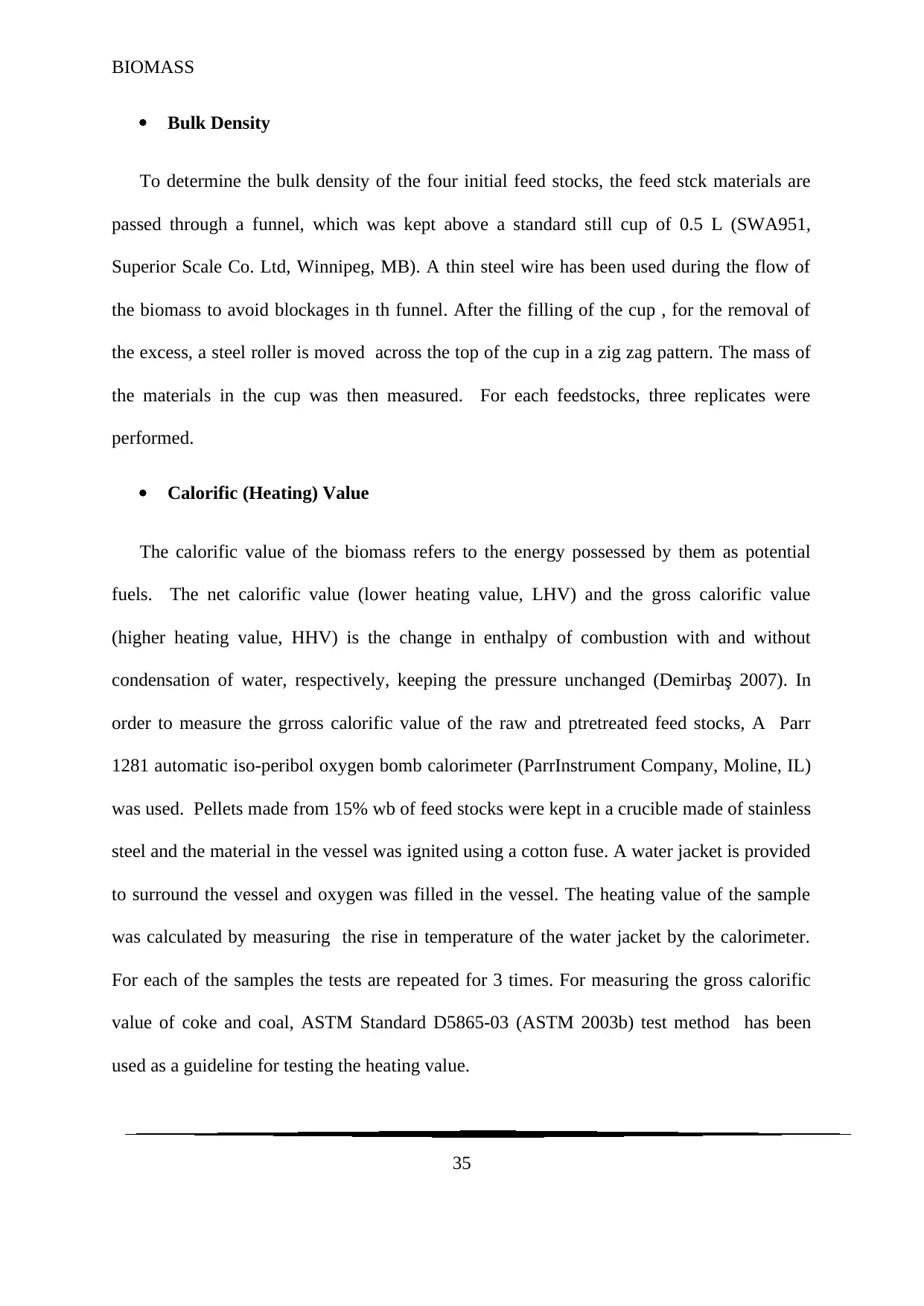
Bulk Density
To determine the bulk density of the four initial feed stocks, the feed stck materials are
passed through a funnel, which was kept above a standard still cup of 0.5 L (SWA951,
Superior Scale Co. Ltd, Winnipeg, MB). A thin steel wire has been used during the flow of
the biomass to avoid blockages in th funnel. After the filling of the cup , for the removal of
the excess, a steel roller is moved across the top of the cup in a zig zag pattern. The mass of
the materials in the cup was then measured. For each feedstocks, three replicates were
performed.
Calorific (Heating) Value
The calorific value of the biomass refers to the energy possessed by them as potential
fuels. The net calorific value (lower heating value, LHV) and the gross calorific value
(higher heating value, HHV) is the change in enthalpy of combustion with and without
condensation of water, respectively, keeping the pressure unchanged (Demirbaş 2007). In
order to measure the grross calorific value of the raw and ptretreated feed stocks, A Parr
1281 automatic iso-peribol oxygen bomb calorimeter (ParrInstrument Company, Moline, IL)
was used. Pellets made from 15% wb of feed stocks were kept in a crucible made of stainless
steel and the material in the vessel was ignited using a cotton fuse. A water jacket is provided
to surround the vessel and oxygen was filled in the vessel. The heating value of the sample
was calculated by measuring the rise in temperature of the water jacket by the calorimeter.
For each of the samples the tests are repeated for 3 times. For measuring the gross calorific
value of coke and coal, ASTM Standard D5865-03 (ASTM 2003b) test method has been
used as a guideline for testing the heating value.
35
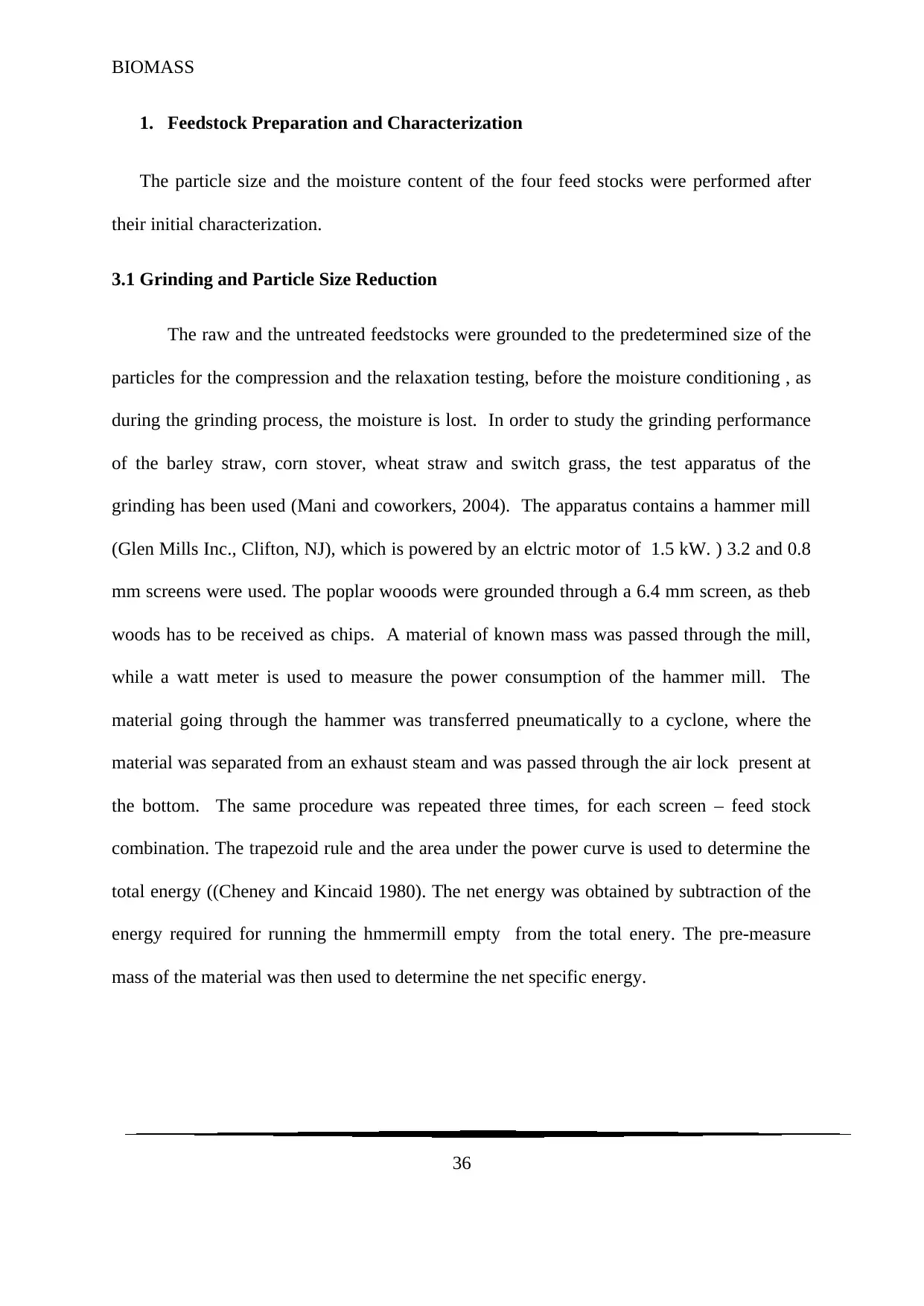
1. Feedstock Preparation and Characterization
The particle size and the moisture content of the four feed stocks were performed after
their initial characterization.
3.1 Grinding and Particle Size Reduction
The raw and the untreated feedstocks were grounded to the predetermined size of the
particles for the compression and the relaxation testing, before the moisture conditioning , as
during the grinding process, the moisture is lost. In order to study the grinding performance
of the barley straw, corn stover, wheat straw and switch grass, the test apparatus of the
grinding has been used (Mani and coworkers, 2004). The apparatus contains a hammer mill
(Glen Mills Inc., Clifton, NJ), which is powered by an elctric motor of 1.5 kW. ) 3.2 and 0.8
mm screens were used. The poplar wooods were grounded through a 6.4 mm screen, as theb
woods has to be received as chips. A material of known mass was passed through the mill,
while a watt meter is used to measure the power consumption of the hammer mill. The
material going through the hammer was transferred pneumatically to a cyclone, where the
material was separated from an exhaust steam and was passed through the air lock present at
the bottom. The same procedure was repeated three times, for each screen – feed stock
combination. The trapezoid rule and the area under the power curve is used to determine the
total energy ((Cheney and Kincaid 1980). The net energy was obtained by subtraction of the
energy required for running the hmmermill empty from the total enery. The pre-measure
mass of the material was then used to determine the net specific energy.
36
⊘ This is a preview!⊘
Do you want full access?
Subscribe today to unlock all pages.

Trusted by 1+ million students worldwide
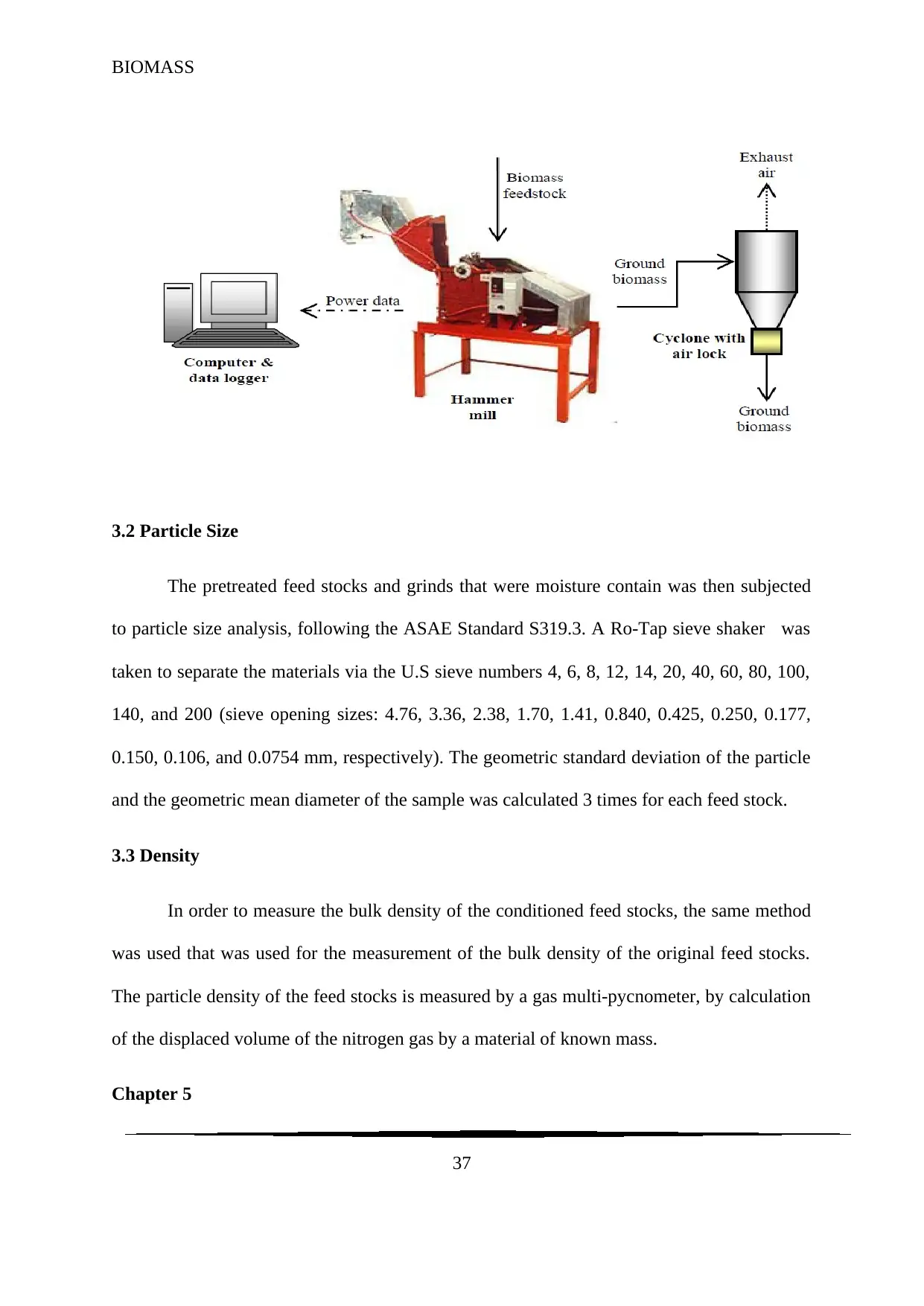
3.2 Particle Size
The pretreated feed stocks and grinds that were moisture contain was then subjected
to particle size analysis, following the ASAE Standard S319.3. A Ro-Tap sieve shaker was
taken to separate the materials via the U.S sieve numbers 4, 6, 8, 12, 14, 20, 40, 60, 80, 100,
140, and 200 (sieve opening sizes: 4.76, 3.36, 2.38, 1.70, 1.41, 0.840, 0.425, 0.250, 0.177,
0.150, 0.106, and 0.0754 mm, respectively). The geometric standard deviation of the particle
and the geometric mean diameter of the sample was calculated 3 times for each feed stock.
3.3 Density
In order to measure the bulk density of the conditioned feed stocks, the same method
was used that was used for the measurement of the bulk density of the original feed stocks.
The particle density of the feed stocks is measured by a gas multi-pycnometer, by calculation
of the displaced volume of the nitrogen gas by a material of known mass.
Chapter 5
37
Paraphrase This Document
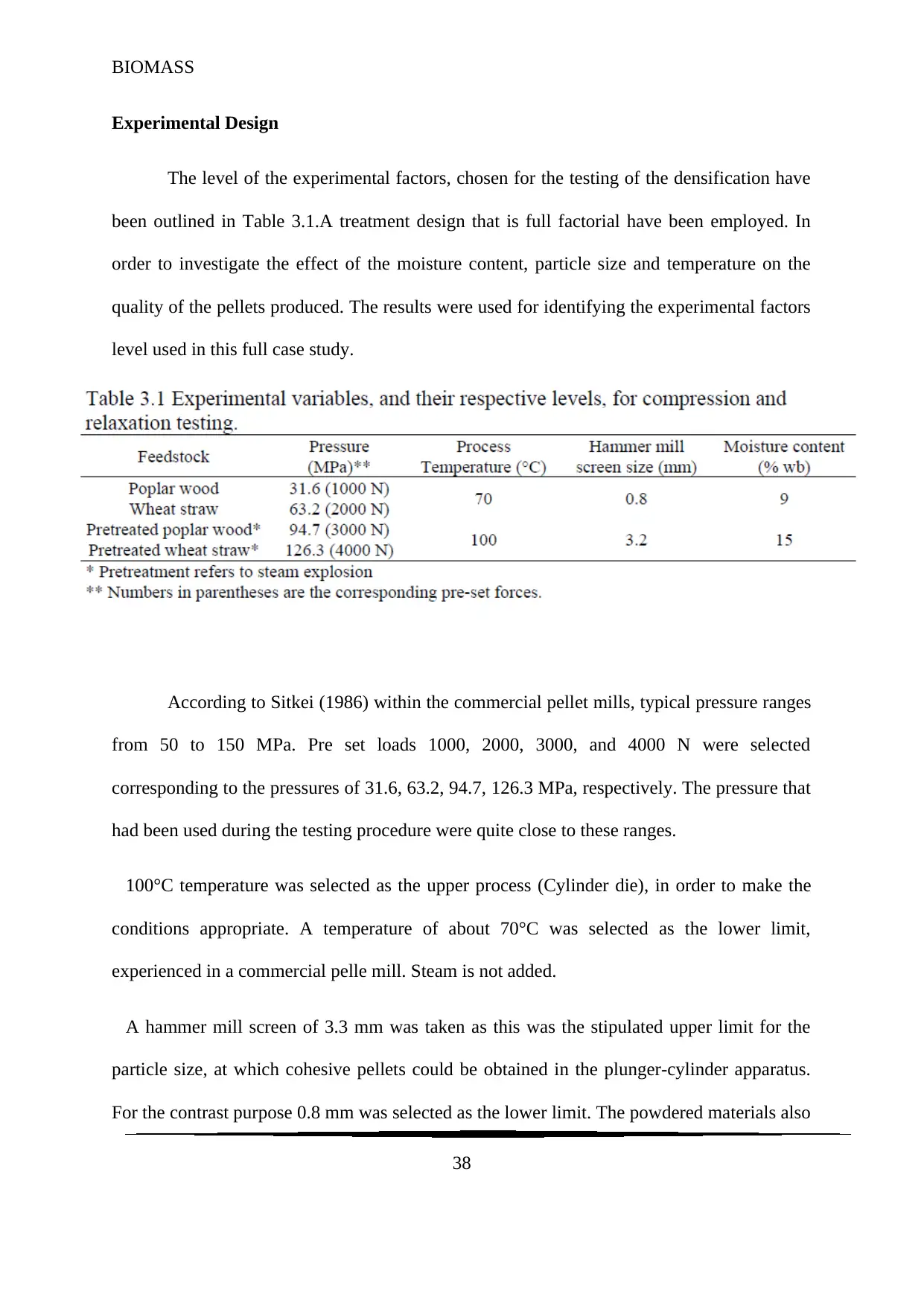
Experimental Design
The level of the experimental factors, chosen for the testing of the densification have
been outlined in Table 3.1.A treatment design that is full factorial have been employed. In
order to investigate the effect of the moisture content, particle size and temperature on the
quality of the pellets produced. The results were used for identifying the experimental factors
level used in this full case study.
According to Sitkei (1986) within the commercial pellet mills, typical pressure ranges
from 50 to 150 MPa. Pre set loads 1000, 2000, 3000, and 4000 N were selected
corresponding to the pressures of 31.6, 63.2, 94.7, 126.3 MPa, respectively. The pressure that
had been used during the testing procedure were quite close to these ranges.
100°C temperature was selected as the upper process (Cylinder die), in order to make the
conditions appropriate. A temperature of about 70°C was selected as the lower limit,
experienced in a commercial pelle mill. Steam is not added.
A hammer mill screen of 3.3 mm was taken as this was the stipulated upper limit for the
particle size, at which cohesive pellets could be obtained in the plunger-cylinder apparatus.
For the contrast purpose 0.8 mm was selected as the lower limit. The powdered materials also
38
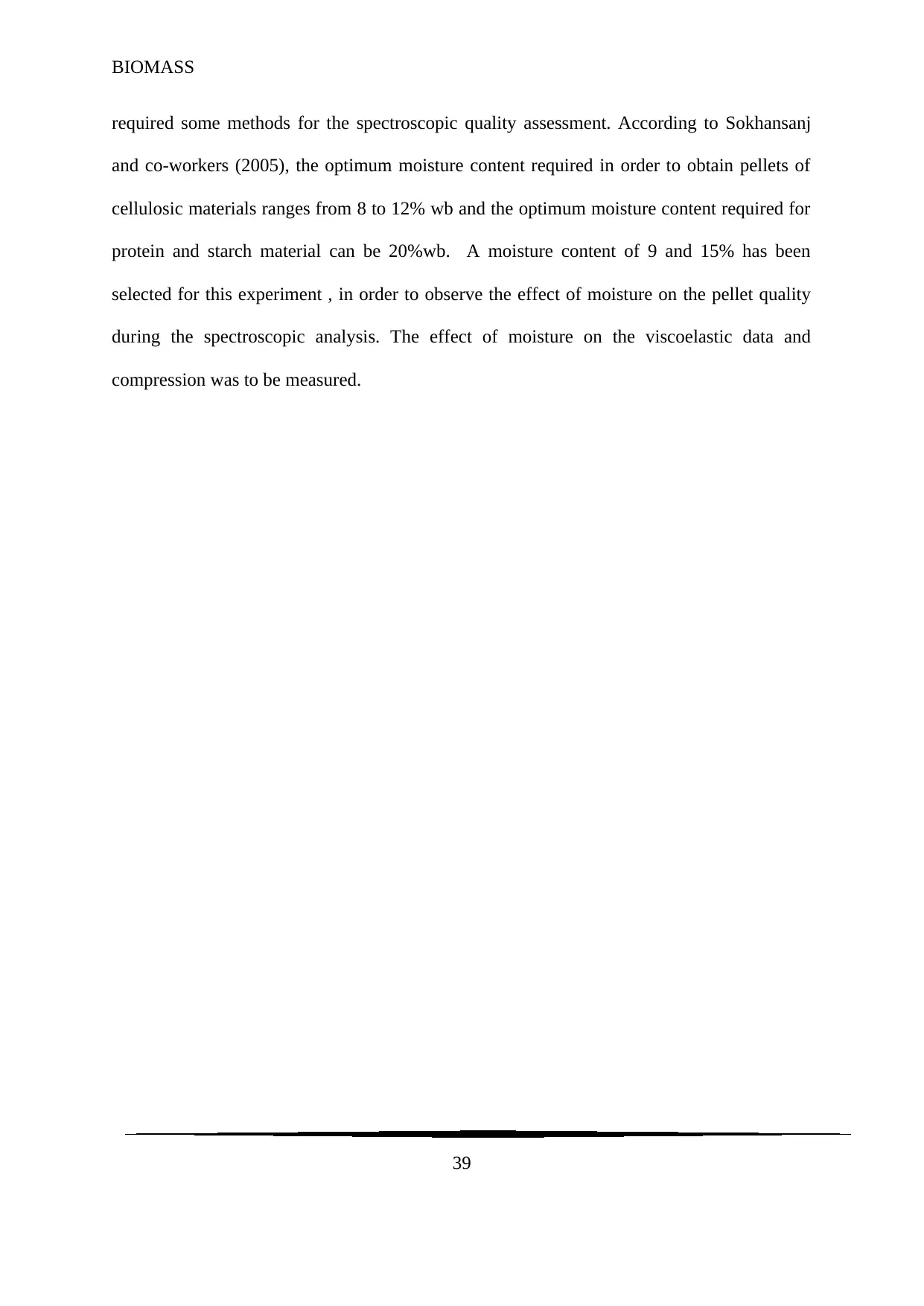
required some methods for the spectroscopic quality assessment. According to Sokhansanj
and co-workers (2005), the optimum moisture content required in order to obtain pellets of
cellulosic materials ranges from 8 to 12% wb and the optimum moisture content required for
protein and starch material can be 20%wb. A moisture content of 9 and 15% has been
selected for this experiment , in order to observe the effect of moisture on the pellet quality
during the spectroscopic analysis. The effect of moisture on the viscoelastic data and
compression was to be measured.
39
⊘ This is a preview!⊘
Do you want full access?
Subscribe today to unlock all pages.

Trusted by 1+ million students worldwide
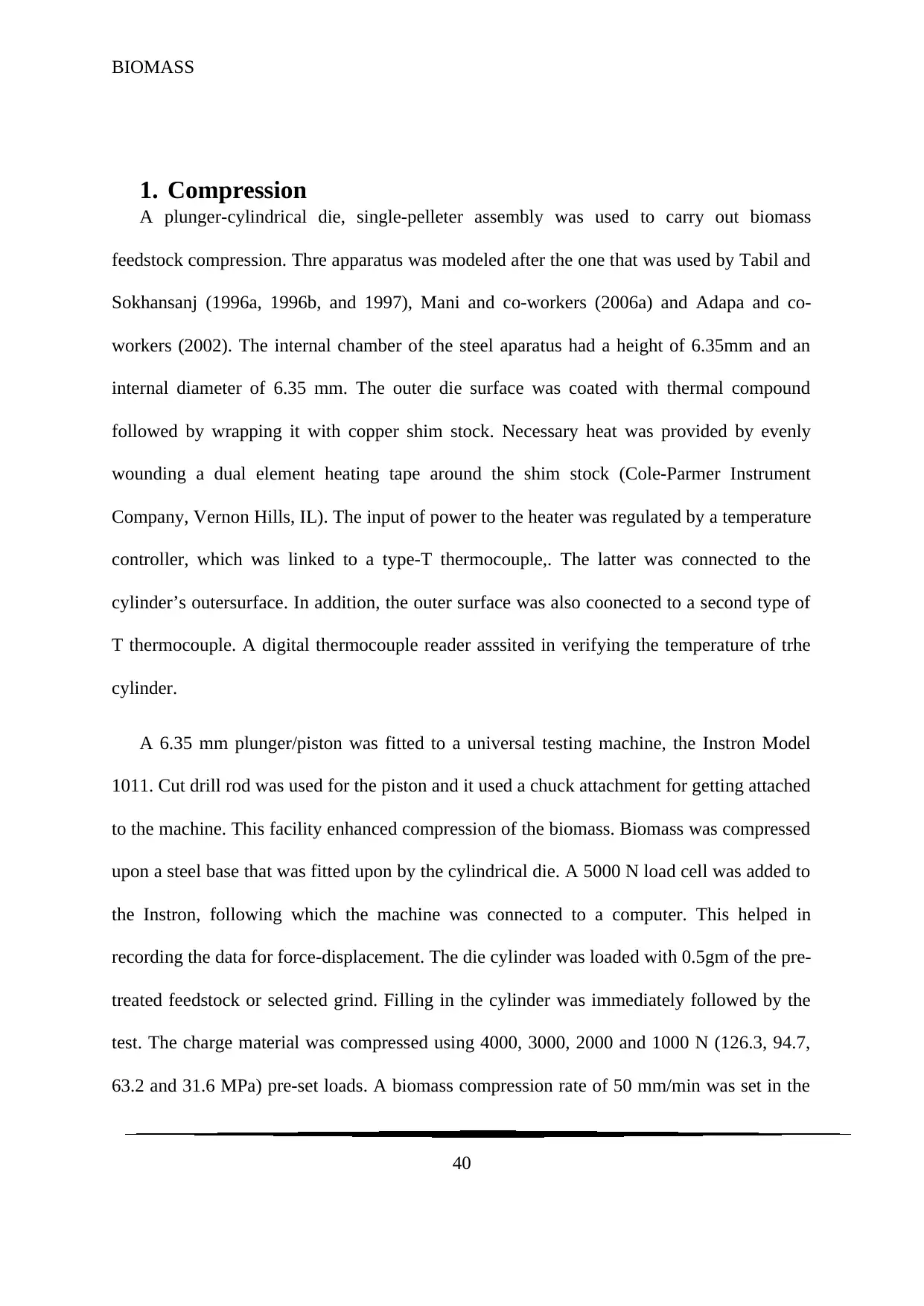
1. Compression
A plunger-cylindrical die, single-pelleter assembly was used to carry out biomass
feedstock compression. Thre apparatus was modeled after the one that was used by Tabil and
Sokhansanj (1996a, 1996b, and 1997), Mani and co-workers (2006a) and Adapa and co-
workers (2002). The internal chamber of the steel aparatus had a height of 6.35mm and an
internal diameter of 6.35 mm. The outer die surface was coated with thermal compound
followed by wrapping it with copper shim stock. Necessary heat was provided by evenly
wounding a dual element heating tape around the shim stock (Cole-Parmer Instrument
Company, Vernon Hills, IL). The input of power to the heater was regulated by a temperature
controller, which was linked to a type-T thermocouple,. The latter was connected to the
cylinder’s outersurface. In addition, the outer surface was also coonected to a second type of
T thermocouple. A digital thermocouple reader asssited in verifying the temperature of trhe
cylinder.
A 6.35 mm plunger/piston was fitted to a universal testing machine, the Instron Model
1011. Cut drill rod was used for the piston and it used a chuck attachment for getting attached
to the machine. This facility enhanced compression of the biomass. Biomass was compressed
upon a steel base that was fitted upon by the cylindrical die. A 5000 N load cell was added to
the Instron, following which the machine was connected to a computer. This helped in
recording the data for force-displacement. The die cylinder was loaded with 0.5gm of the pre-
treated feedstock or selected grind. Filling in the cylinder was immediately followed by the
test. The charge material was compressed using 4000, 3000, 2000 and 1000 N (126.3, 94.7,
63.2 and 31.6 MPa) pre-set loads. A biomass compression rate of 50 mm/min was set in the
40
Paraphrase This Document
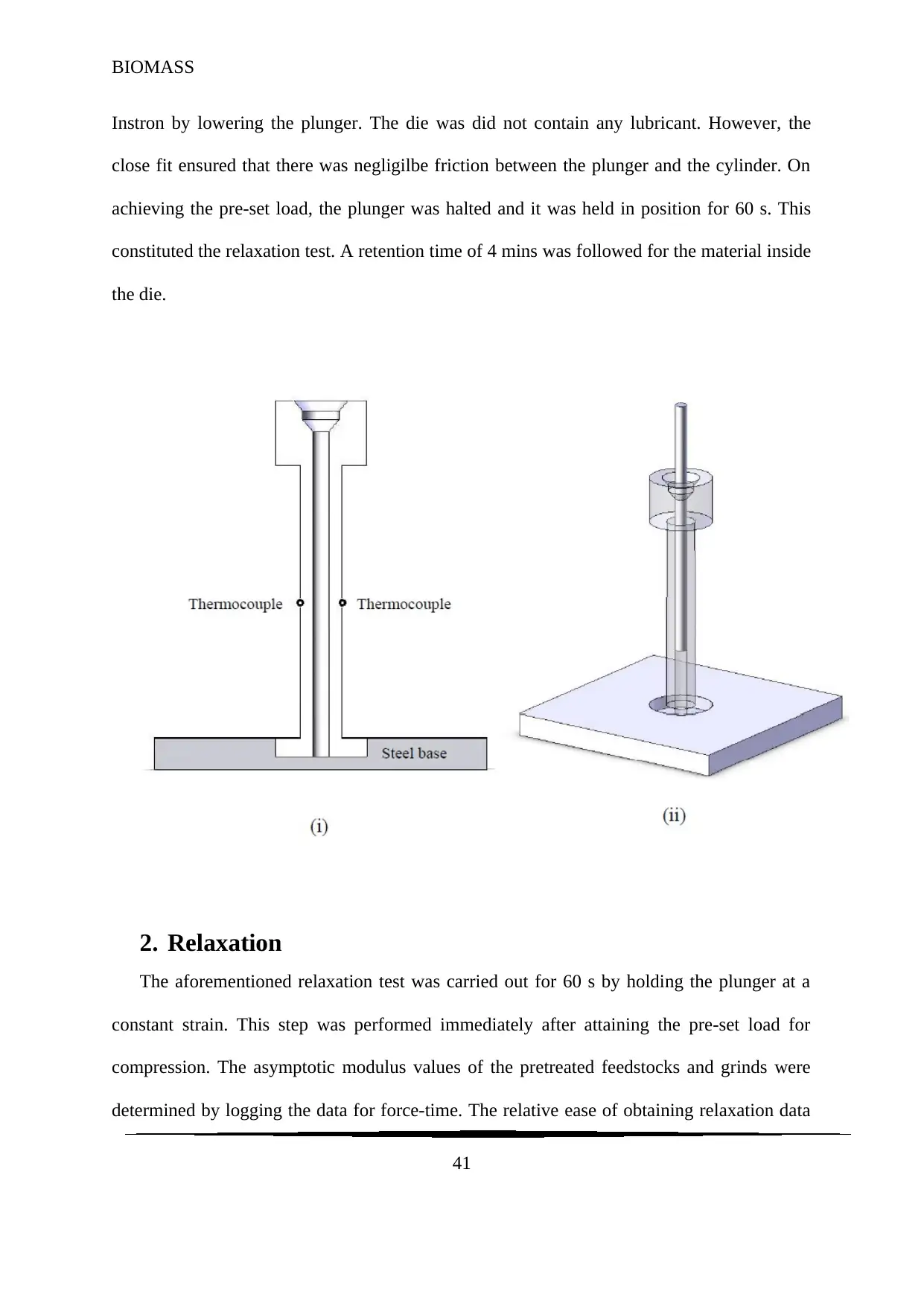
Instron by lowering the plunger. The die was did not contain any lubricant. However, the
close fit ensured that there was negligilbe friction between the plunger and the cylinder. On
achieving the pre-set load, the plunger was halted and it was held in position for 60 s. This
constituted the relaxation test. A retention time of 4 mins was followed for the material inside
the die.
2. Relaxation
The aforementioned relaxation test was carried out for 60 s by holding the plunger at a
constant strain. This step was performed immediately after attaining the pre-set load for
compression. The asymptotic modulus values of the pretreated feedstocks and grinds were
determined by logging the data for force-time. The relative ease of obtaining relaxation data
41
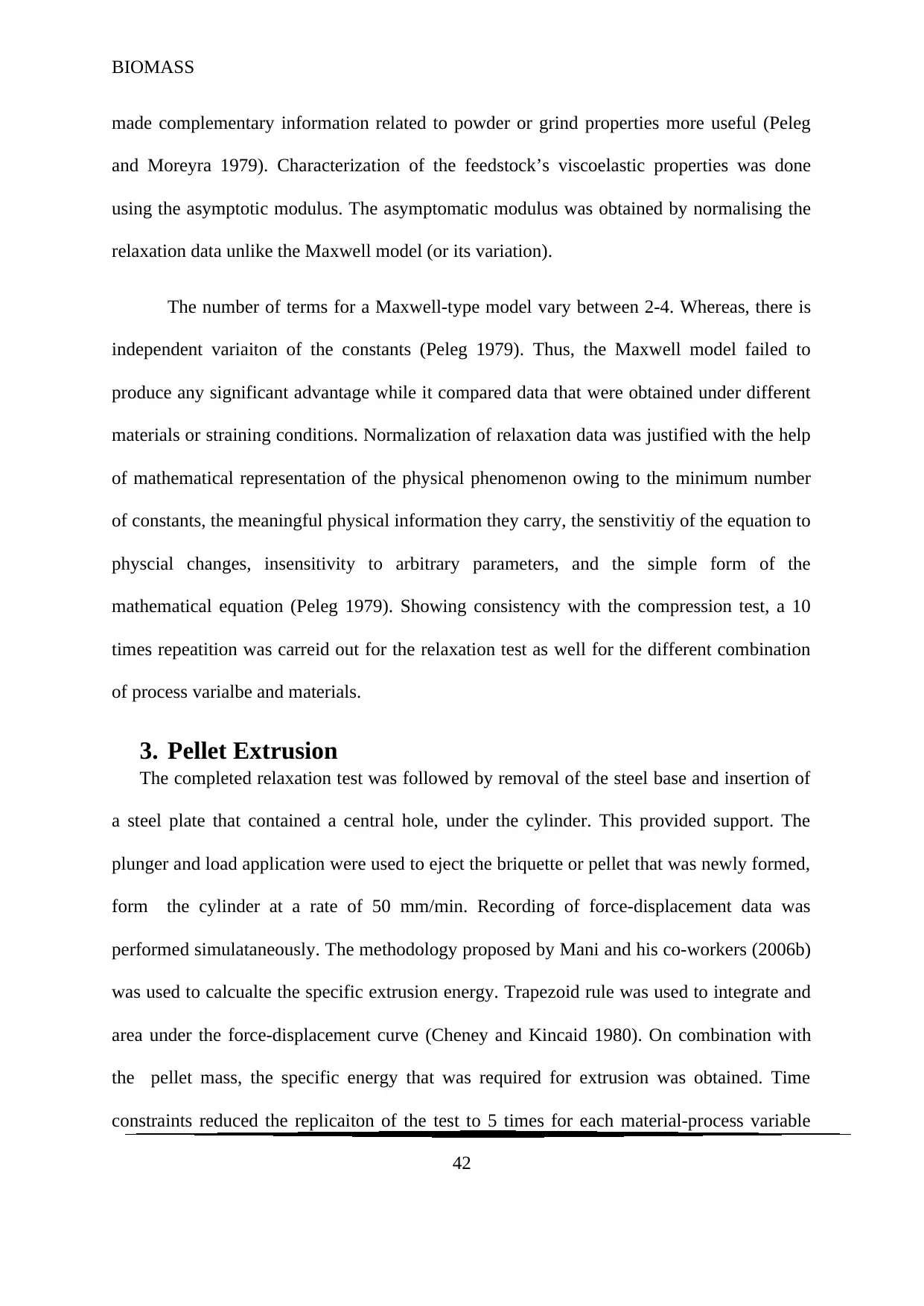
made complementary information related to powder or grind properties more useful (Peleg
and Moreyra 1979). Characterization of the feedstock’s viscoelastic properties was done
using the asymptotic modulus. The asymptomatic modulus was obtained by normalising the
relaxation data unlike the Maxwell model (or its variation).
The number of terms for a Maxwell-type model vary between 2-4. Whereas, there is
independent variaiton of the constants (Peleg 1979). Thus, the Maxwell model failed to
produce any significant advantage while it compared data that were obtained under different
materials or straining conditions. Normalization of relaxation data was justified with the help
of mathematical representation of the physical phenomenon owing to the minimum number
of constants, the meaningful physical information they carry, the senstivitiy of the equation to
physcial changes, insensitivity to arbitrary parameters, and the simple form of the
mathematical equation (Peleg 1979). Showing consistency with the compression test, a 10
times repeatition was carreid out for the relaxation test as well for the different combination
of process varialbe and materials.
3. Pellet Extrusion
The completed relaxation test was followed by removal of the steel base and insertion of
a steel plate that contained a central hole, under the cylinder. This provided support. The
plunger and load application were used to eject the briquette or pellet that was newly formed,
form the cylinder at a rate of 50 mm/min. Recording of force-displacement data was
performed simulataneously. The methodology proposed by Mani and his co-workers (2006b)
was used to calcualte the specific extrusion energy. Trapezoid rule was used to integrate and
area under the force-displacement curve (Cheney and Kincaid 1980). On combination with
the pellet mass, the specific energy that was required for extrusion was obtained. Time
constraints reduced the replicaiton of the test to 5 times for each material-process variable
42
⊘ This is a preview!⊘
Do you want full access?
Subscribe today to unlock all pages.

Trusted by 1+ million students worldwide
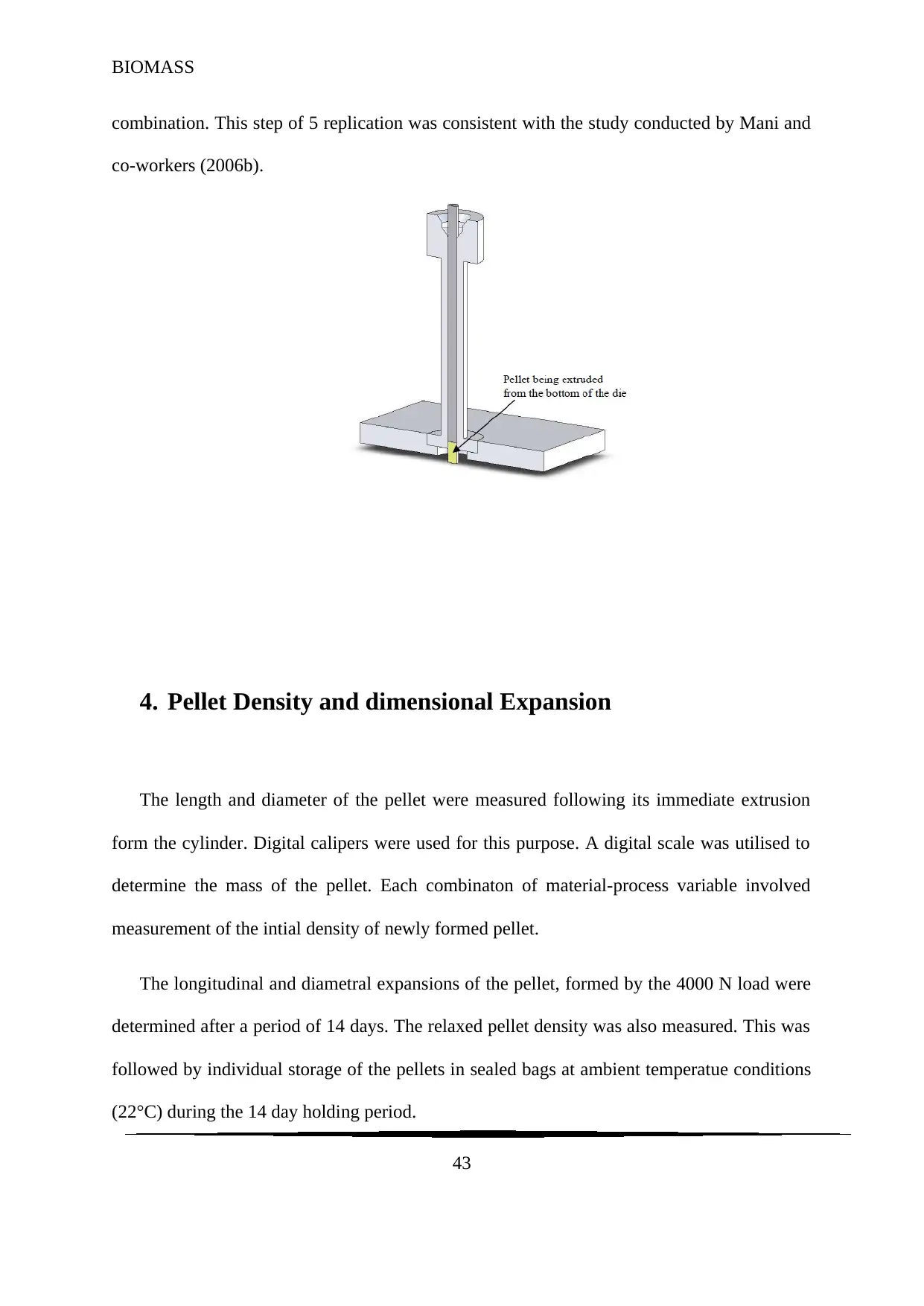
combination. This step of 5 replication was consistent with the study conducted by Mani and
co-workers (2006b).
4. Pellet Density and dimensional Expansion
The length and diameter of the pellet were measured following its immediate extrusion
form the cylinder. Digital calipers were used for this purpose. A digital scale was utilised to
determine the mass of the pellet. Each combinaton of material-process variable involved
measurement of the intial density of newly formed pellet.
The longitudinal and diametral expansions of the pellet, formed by the 4000 N load were
determined after a period of 14 days. The relaxed pellet density was also measured. This was
followed by individual storage of the pellets in sealed bags at ambient temperatue conditions
(22°C) during the 14 day holding period.
43
Paraphrase This Document
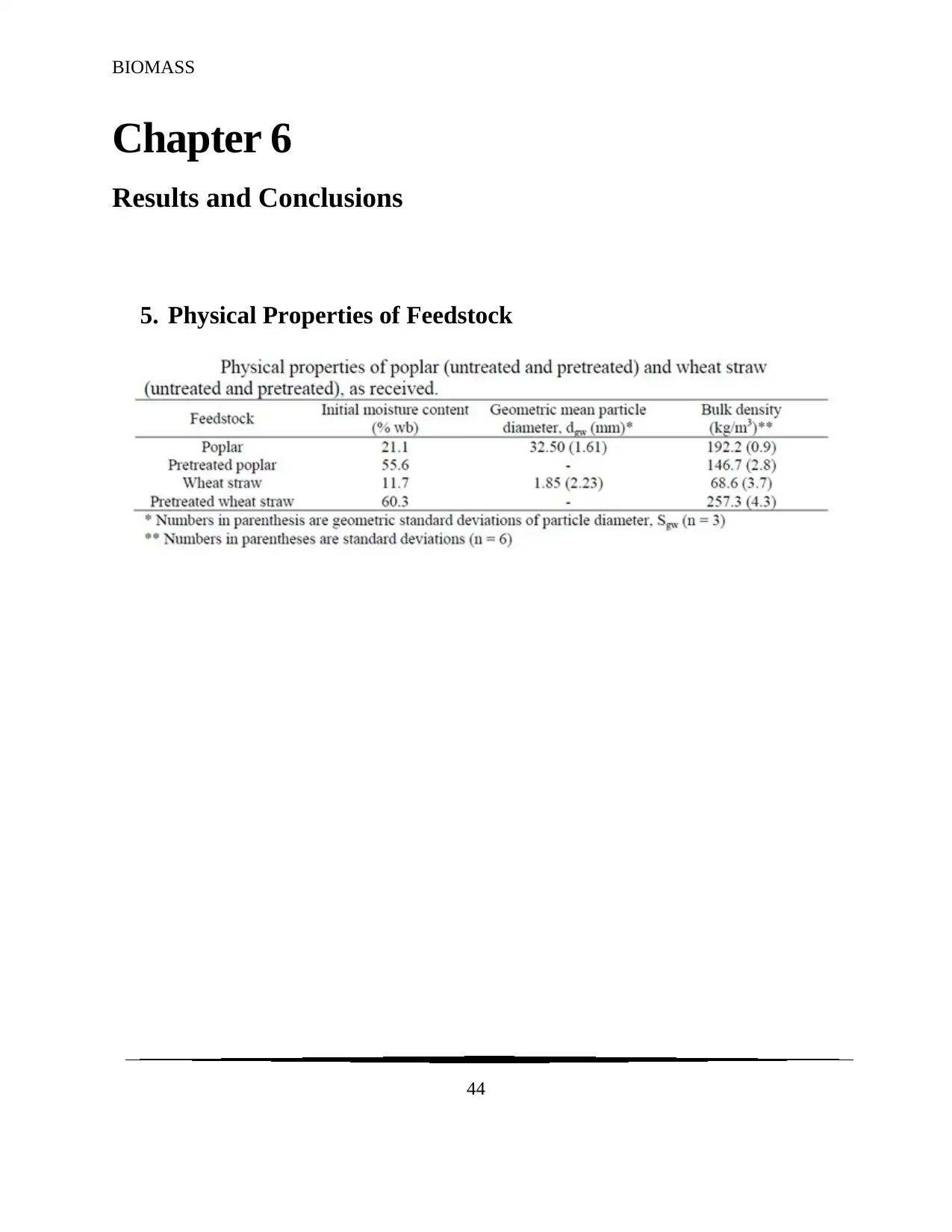
Chapter 6
Results and Conclusions
5. Physical Properties of Feedstock
44
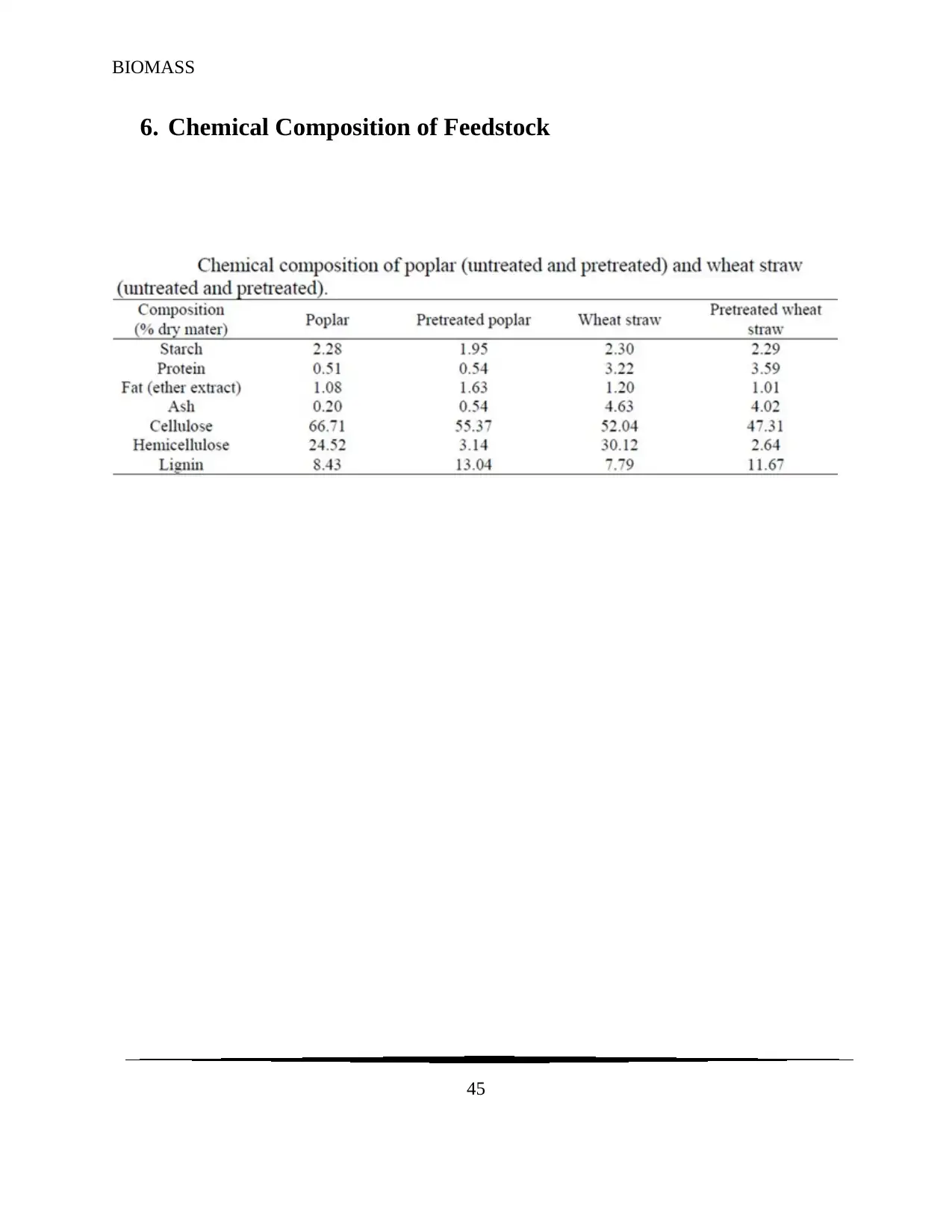
6. Chemical Composition of Feedstock
45
⊘ This is a preview!⊘
Do you want full access?
Subscribe today to unlock all pages.

Trusted by 1+ million students worldwide
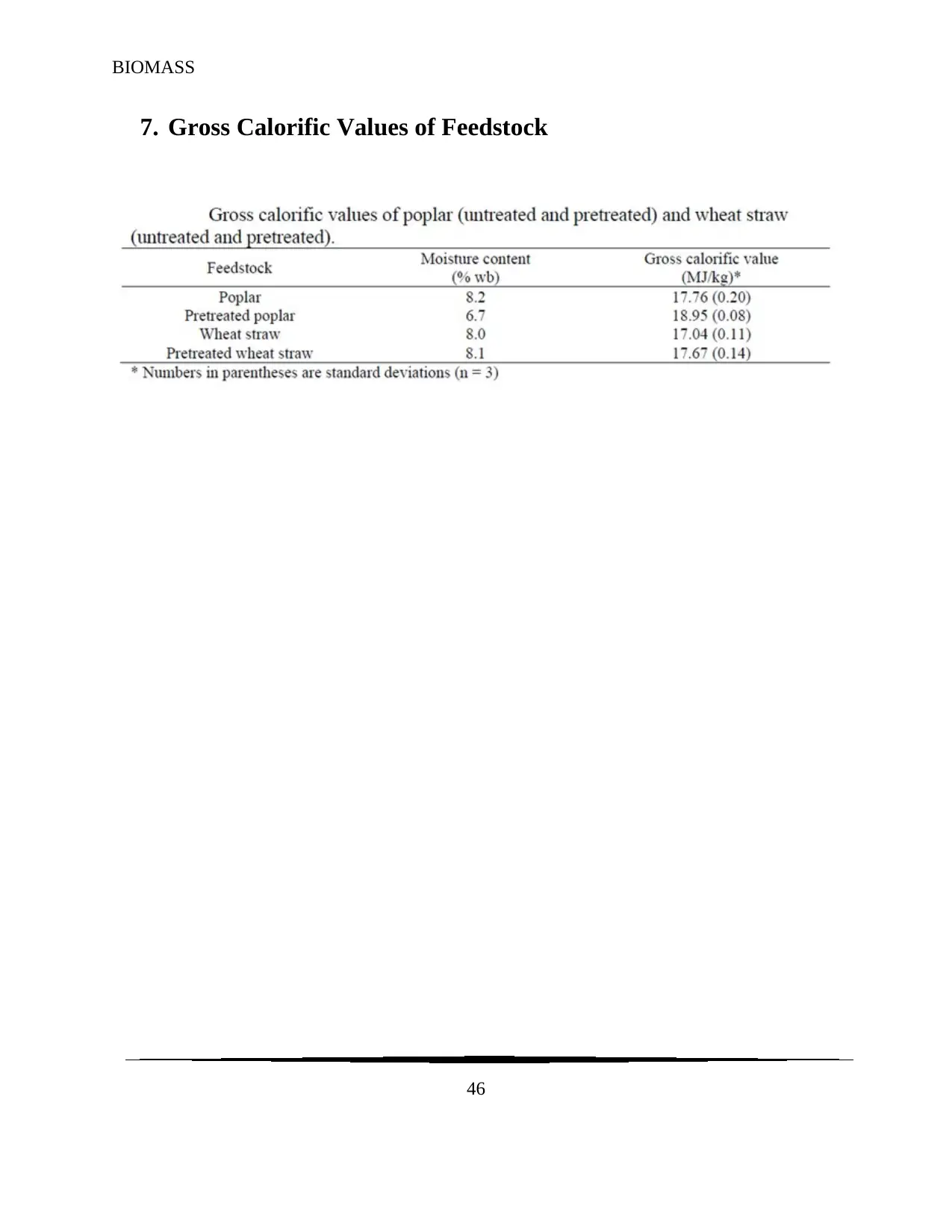
7. Gross Calorific Values of Feedstock
46
Paraphrase This Document
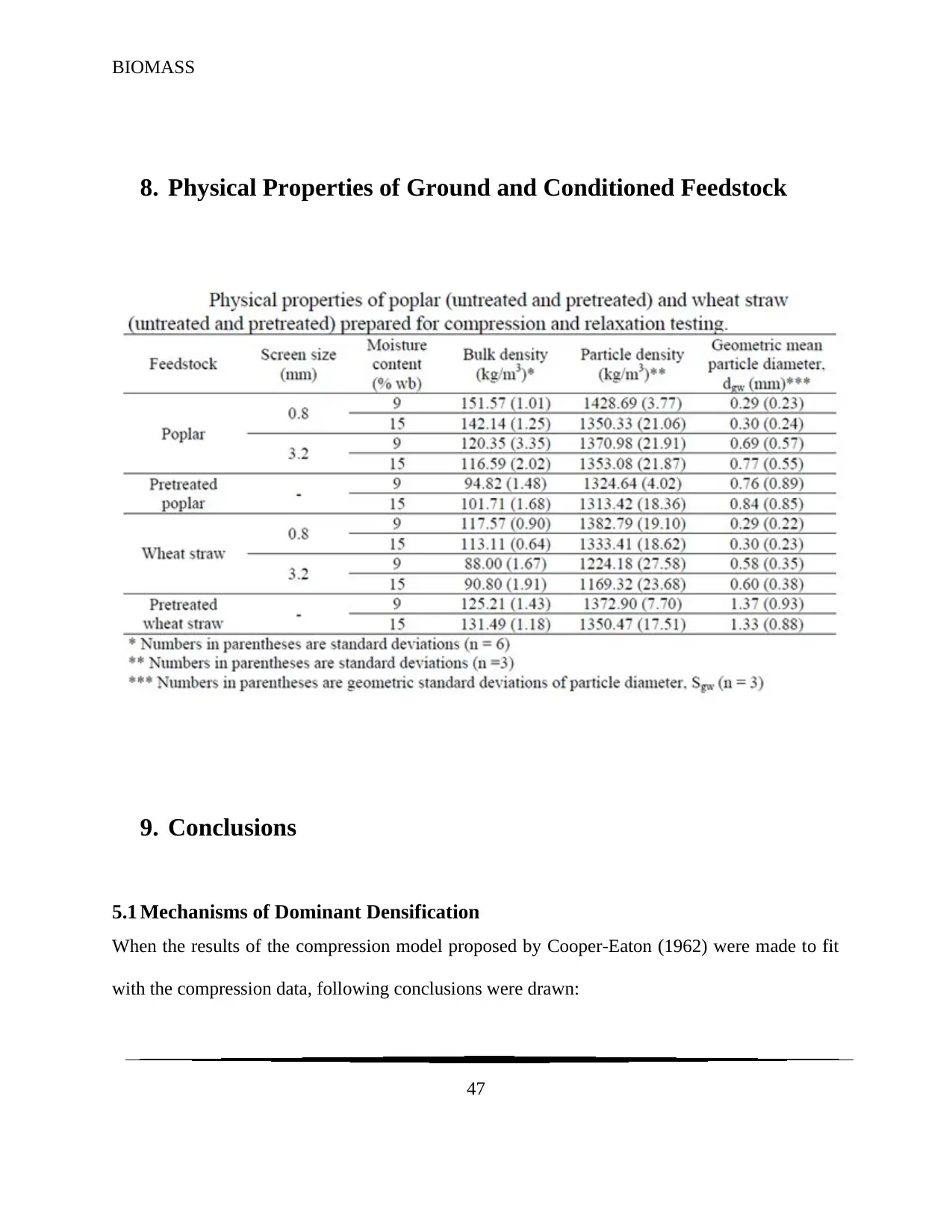
8. Physical Properties of Ground and Conditioned Feedstock
9. Conclusions
5.1 Mechanisms of Dominant Densification
When the results of the compression model proposed by Cooper-Eaton (1962) were made to fit
with the compression data, following conclusions were drawn:
47

Your All-in-One AI-Powered Toolkit for Academic Success.
+13062052269
info@desklib.com
Available 24*7 on WhatsApp / Email
© 2024 | Zucol Services PVT LTD | All rights reserved.