Investigating the Effect of Nanoclay on Concrete Mechanical Properties
VerifiedAdded on 2020/04/01
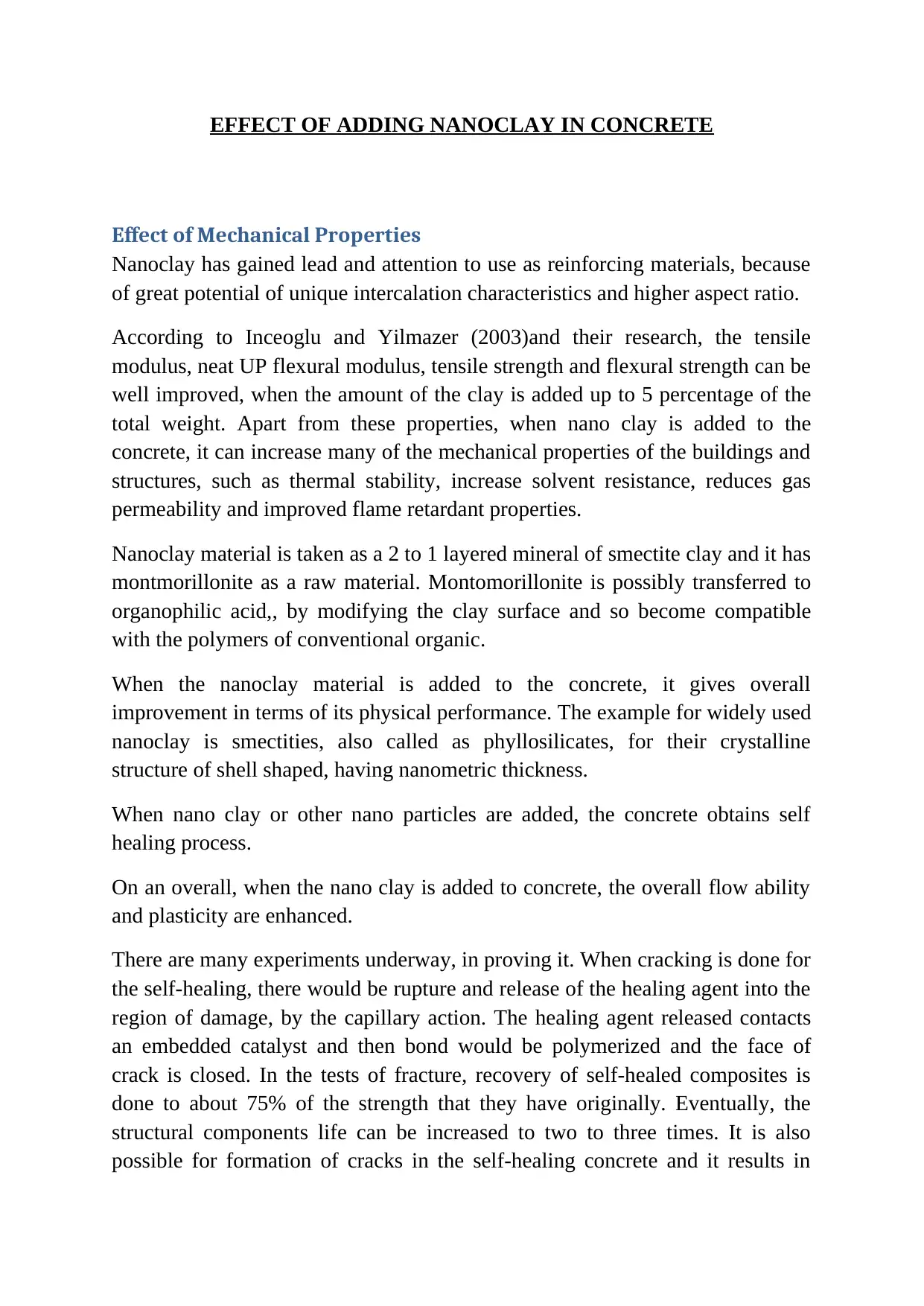
Effect of Mechanical Properties
Nanoclay has gained lead and attention to use as reinforcing materials, because
of great potential of unique intercalation characteristics and higher aspect ratio.
According to Inceoglu and Yilmazer (2003)and their research, the tensile
modulus, neat UP flexural modulus, tensile strength and flexural strength can be
well improved, when the amount of the clay is added up to 5 percentage of the
total weight. Apart from these properties, when nano clay is added to the
concrete, it can increase many of the mechanical properties of the buildings and
structures, such as thermal stability, increase solvent resistance, reduces gas
permeability and improved flame retardant properties.
Nanoclay material is taken as a 2 to 1 layered mineral of smectite clay and it has
montmorillonite as a raw material. Montomorillonite is possibly transferred to
organophilic acid,, by modifying the clay surface and so become compatible
with the polymers of conventional organic.
When the nanoclay material is added to the concrete, it gives overall
improvement in terms of its physical performance. The example for widely used
nanoclay is smectities, also called as phyllosilicates, for their crystalline
structure of shell shaped, having nanometric thickness.
When nano clay or other nano particles are added, the concrete obtains self
healing process.
On an overall, when the nano clay is added to concrete, the overall flow ability
and plasticity are enhanced.
There are many experiments underway, in proving it. When cracking is done for
the self-healing, there would be rupture and release of the healing agent into the
region of damage, by the capillary action. The healing agent released contacts
an embedded catalyst and then bond would be polymerized and the face of
crack is closed. In the tests of fracture, recovery of self-healed composites is
done to about 75% of the strength that they have originally. Eventually, the
structural components life can be increased to two to three times. It is also
possible for formation of cracks in the self-healing concrete and it results in
Paraphrase This Document
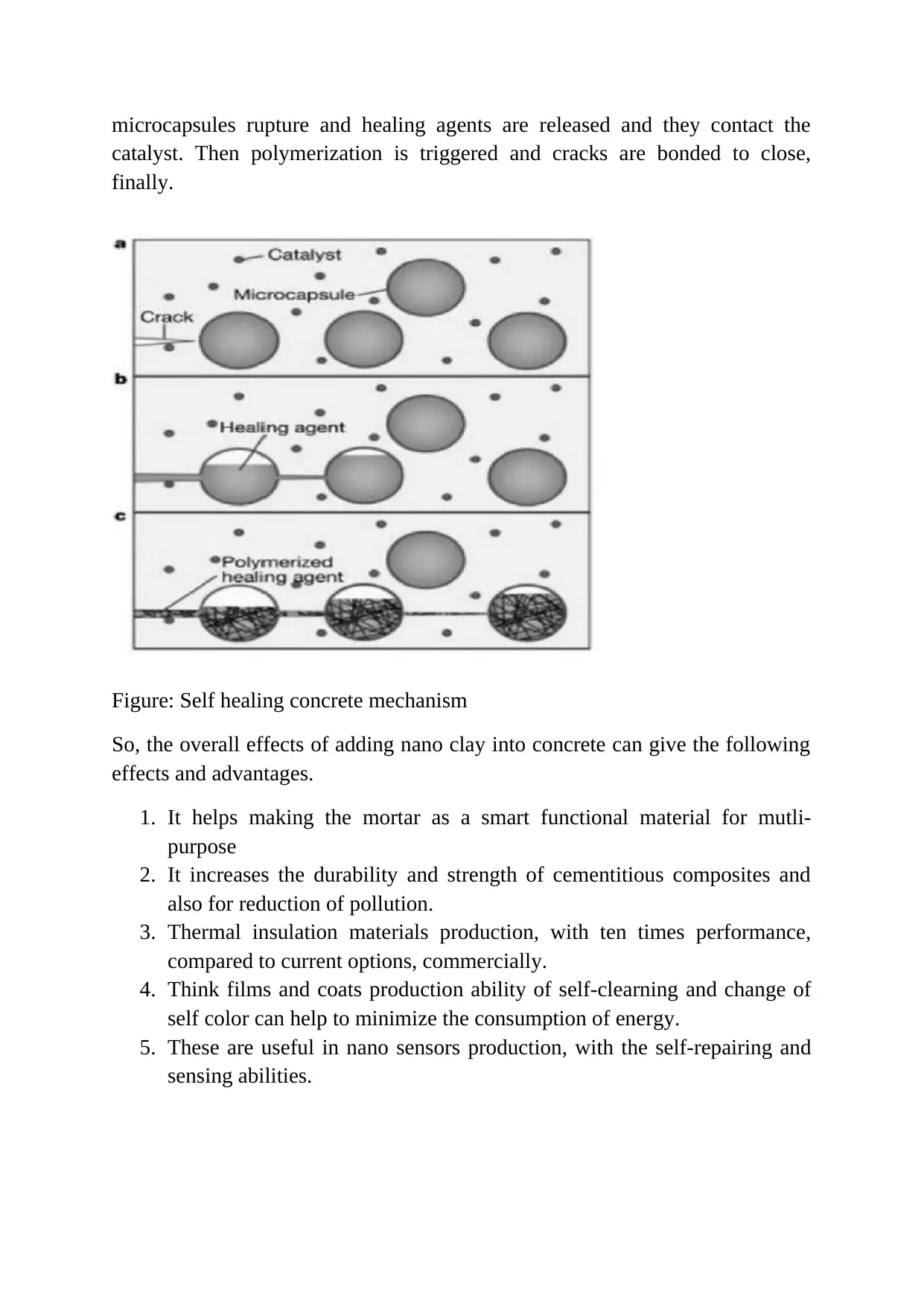
catalyst. Then polymerization is triggered and cracks are bonded to close,
finally.
Figure: Self healing concrete mechanism
So, the overall effects of adding nano clay into concrete can give the following
effects and advantages.
1. It helps making the mortar as a smart functional material for mutli-
purpose
2. It increases the durability and strength of cementitious composites and
also for reduction of pollution.
3. Thermal insulation materials production, with ten times performance,
compared to current options, commercially.
4. Think films and coats production ability of self-clearning and change of
self color can help to minimize the consumption of energy.
5. These are useful in nano sensors production, with the self-repairing and
sensing abilities.
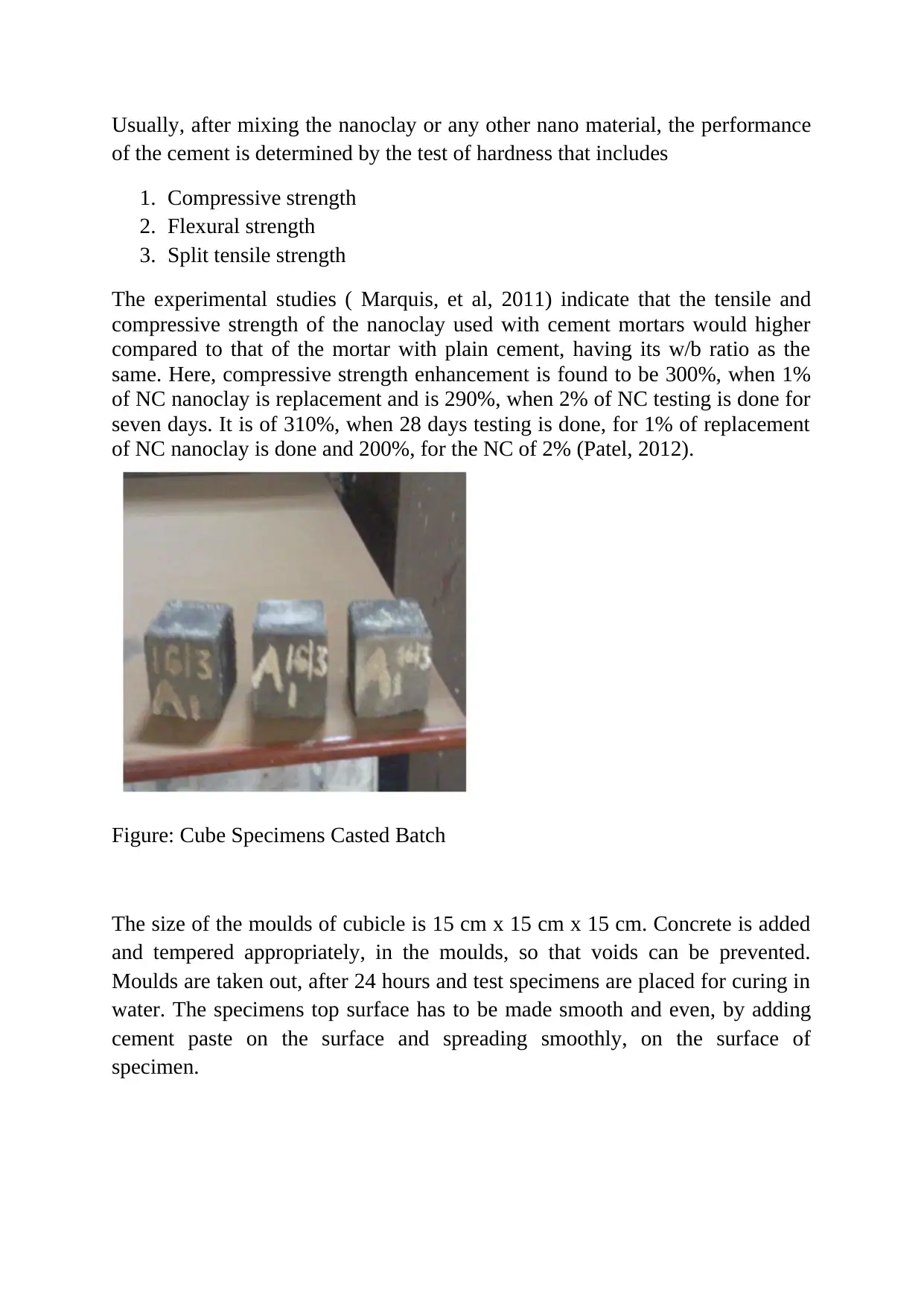
of the cement is determined by the test of hardness that includes
1. Compressive strength
2. Flexural strength
3. Split tensile strength
The experimental studies ( Marquis, et al, 2011) indicate that the tensile and
compressive strength of the nanoclay used with cement mortars would higher
compared to that of the mortar with plain cement, having its w/b ratio as the
same. Here, compressive strength enhancement is found to be 300%, when 1%
of NC nanoclay is replacement and is 290%, when 2% of NC testing is done for
seven days. It is of 310%, when 28 days testing is done, for 1% of replacement
of NC nanoclay is done and 200%, for the NC of 2% (Patel, 2012).
Figure: Cube Specimens Casted Batch
The size of the moulds of cubicle is 15 cm x 15 cm x 15 cm. Concrete is added
and tempered appropriately, in the moulds, so that voids can be prevented.
Moulds are taken out, after 24 hours and test specimens are placed for curing in
water. The specimens top surface has to be made smooth and even, by adding
cement paste on the surface and spreading smoothly, on the surface of
specimen.
⊘ This is a preview!⊘
Do you want full access?
Subscribe today to unlock all pages.

Trusted by 1+ million students worldwide
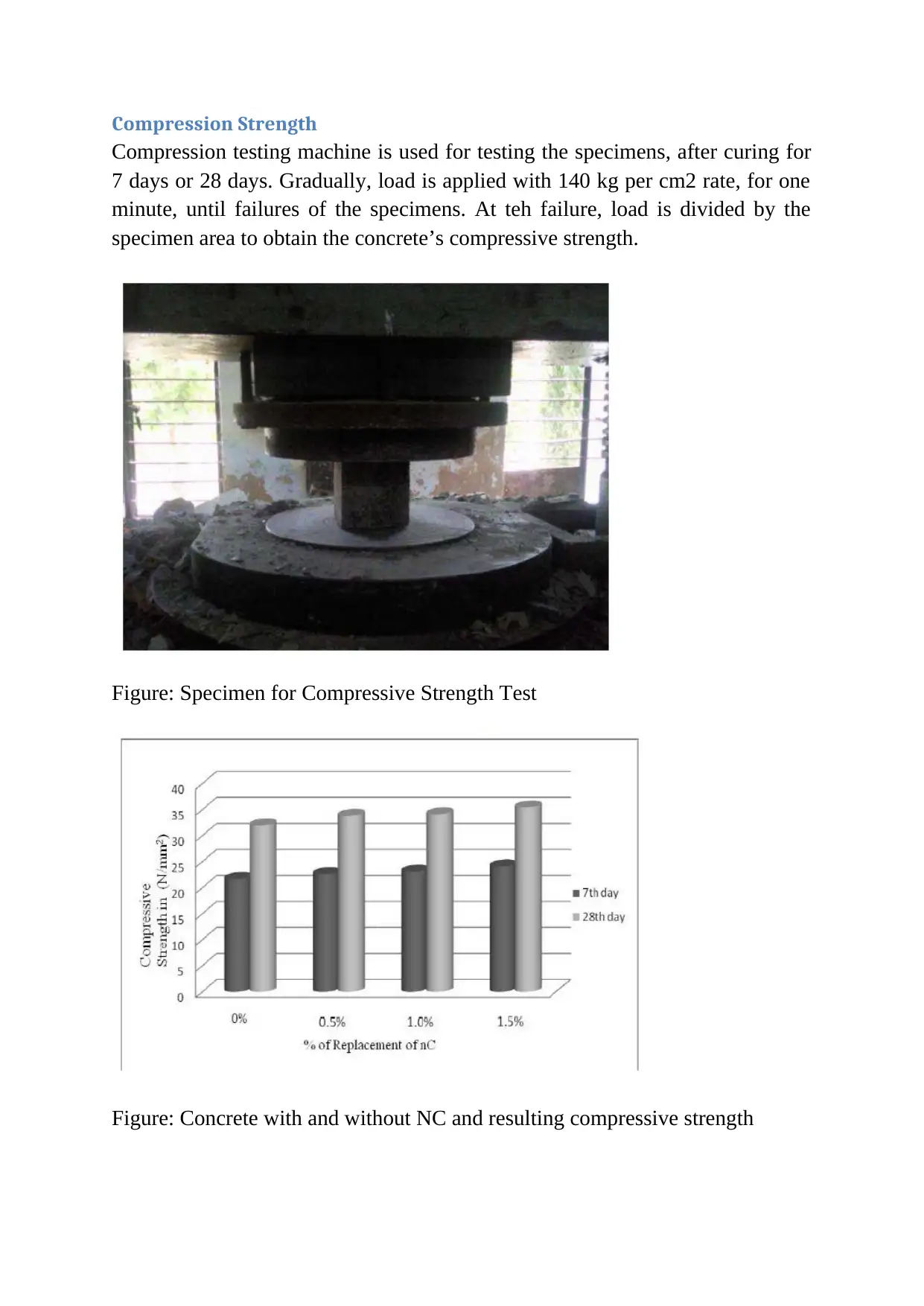
Compression testing machine is used for testing the specimens, after curing for
7 days or 28 days. Gradually, load is applied with 140 kg per cm2 rate, for one
minute, until failures of the specimens. At teh failure, load is divided by the
specimen area to obtain the concrete’s compressive strength.
Figure: Specimen for Compressive Strength Test
Figure: Concrete with and without NC and resulting compressive strength
Paraphrase This Document
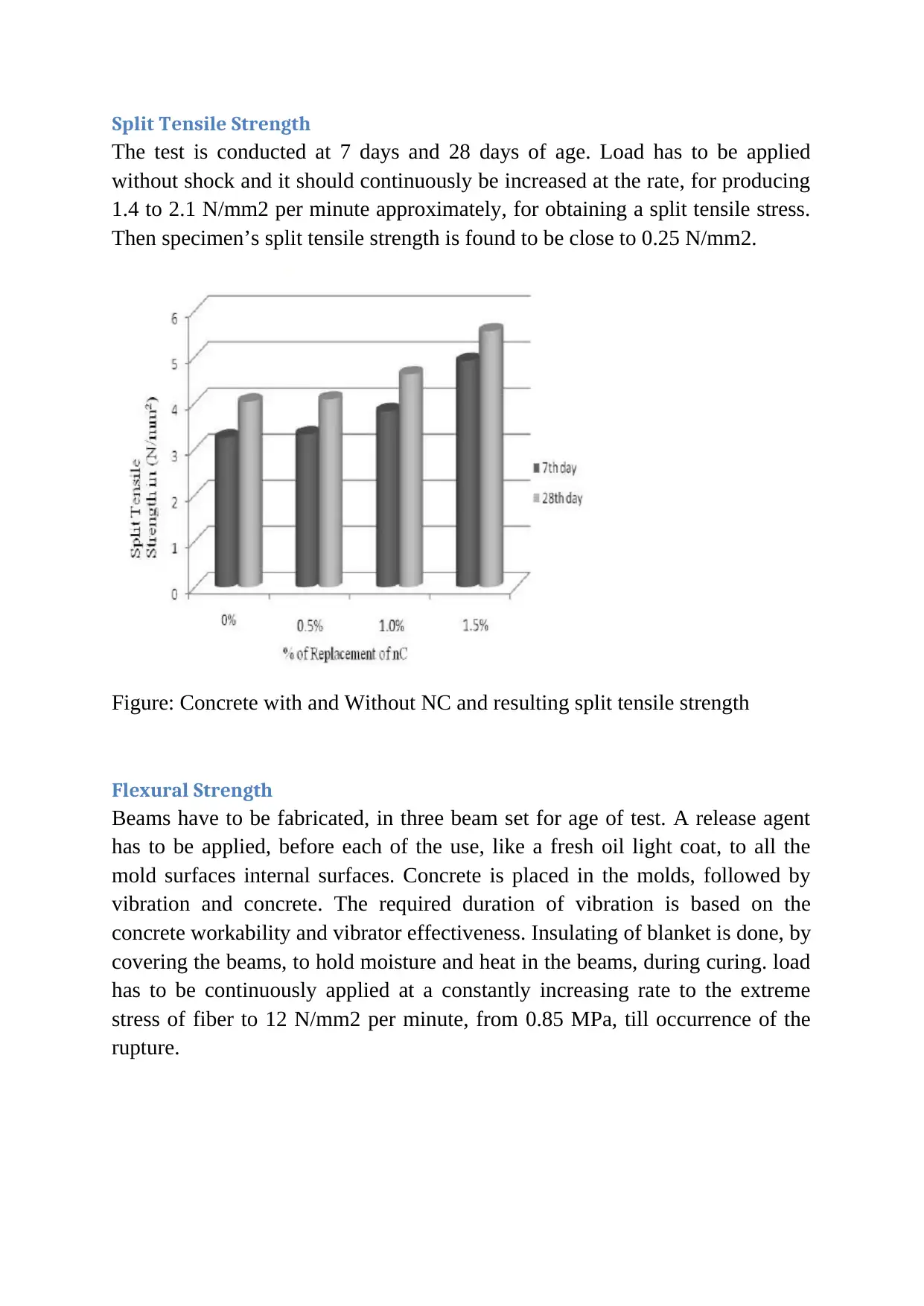
The test is conducted at 7 days and 28 days of age. Load has to be applied
without shock and it should continuously be increased at the rate, for producing
1.4 to 2.1 N/mm2 per minute approximately, for obtaining a split tensile stress.
Then specimen’s split tensile strength is found to be close to 0.25 N/mm2.
Figure: Concrete with and Without NC and resulting split tensile strength
Flexural Strength
Beams have to be fabricated, in three beam set for age of test. A release agent
has to be applied, before each of the use, like a fresh oil light coat, to all the
mold surfaces internal surfaces. Concrete is placed in the molds, followed by
vibration and concrete. The required duration of vibration is based on the
concrete workability and vibrator effectiveness. Insulating of blanket is done, by
covering the beams, to hold moisture and heat in the beams, during curing. load
has to be continuously applied at a constantly increasing rate to the extreme
stress of fiber to 12 N/mm2 per minute, from 0.85 MPa, till occurrence of the
rupture.
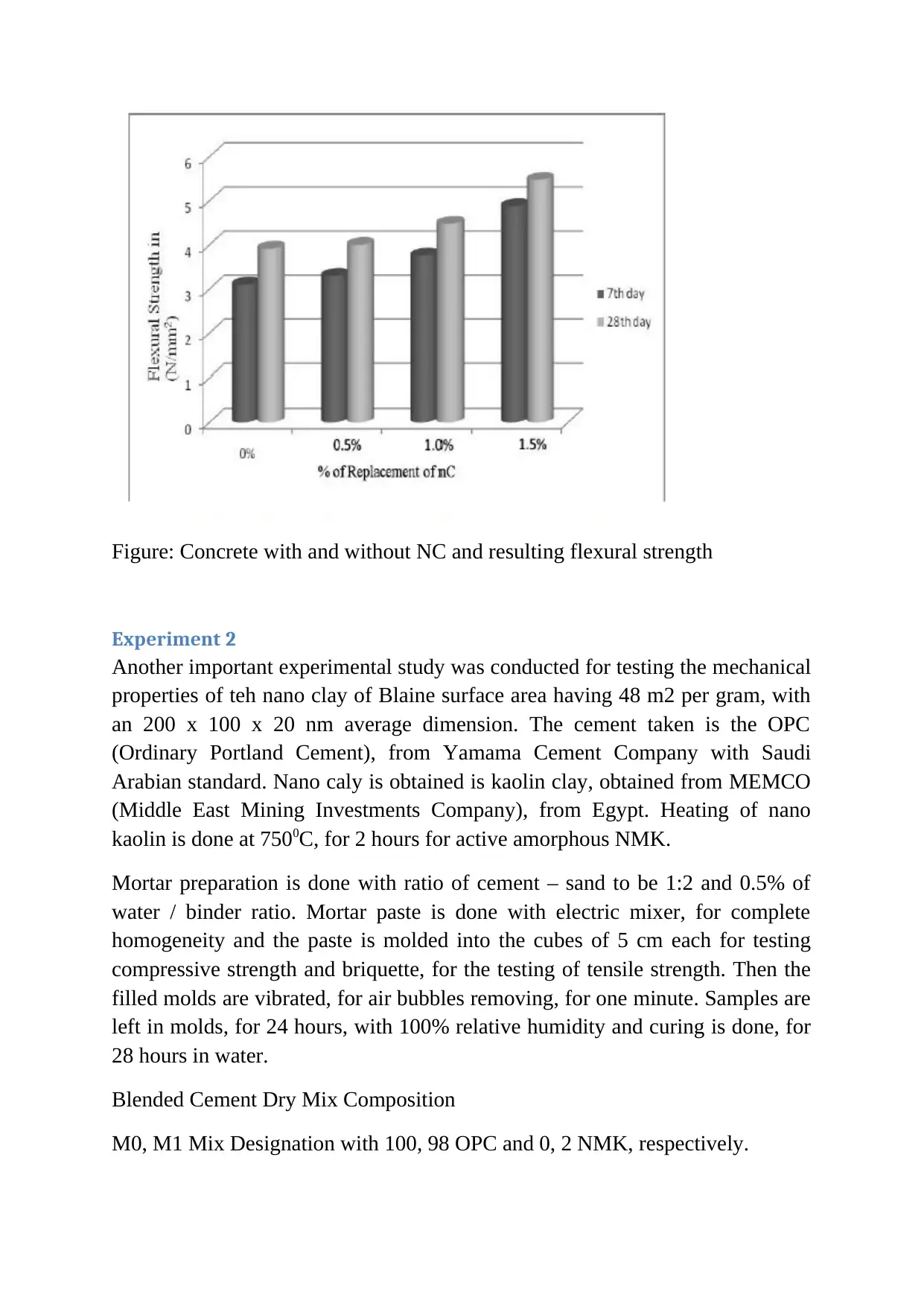
Experiment 2
Another important experimental study was conducted for testing the mechanical
properties of teh nano clay of Blaine surface area having 48 m2 per gram, with
an 200 x 100 x 20 nm average dimension. The cement taken is the OPC
(Ordinary Portland Cement), from Yamama Cement Company with Saudi
Arabian standard. Nano caly is obtained is kaolin clay, obtained from MEMCO
(Middle East Mining Investments Company), from Egypt. Heating of nano
kaolin is done at 7500C, for 2 hours for active amorphous NMK.
Mortar preparation is done with ratio of cement – sand to be 1:2 and 0.5% of
water / binder ratio. Mortar paste is done with electric mixer, for complete
homogeneity and the paste is molded into the cubes of 5 cm each for testing
compressive strength and briquette, for the testing of tensile strength. Then the
filled molds are vibrated, for air bubbles removing, for one minute. Samples are
left in molds, for 24 hours, with 100% relative humidity and curing is done, for
28 hours in water.
Blended Cement Dry Mix Composition
M0, M1 Mix Designation with 100, 98 OPC and 0, 2 NMK, respectively.
⊘ This is a preview!⊘
Do you want full access?
Subscribe today to unlock all pages.

Trusted by 1+ million students worldwide
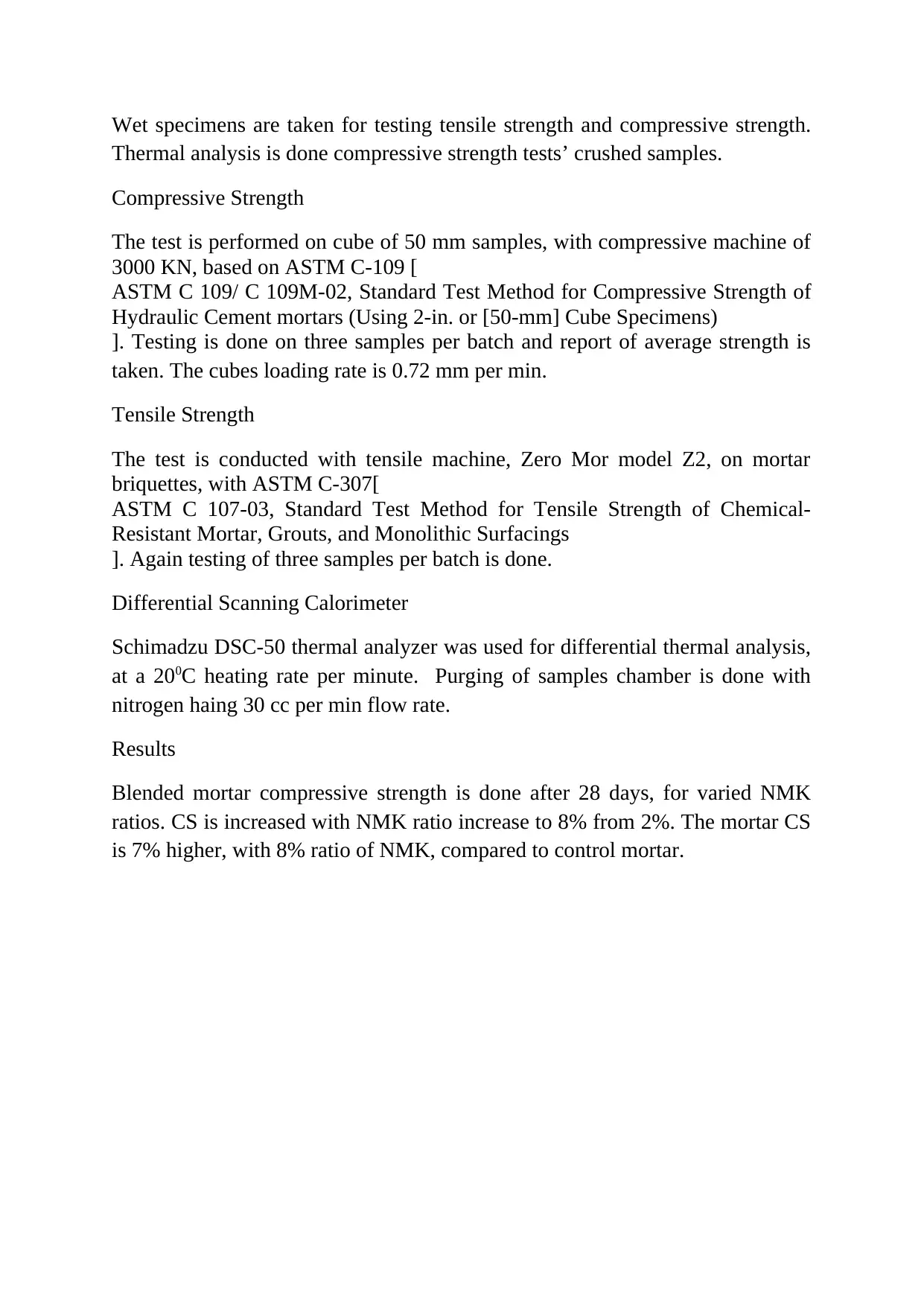
Thermal analysis is done compressive strength tests’ crushed samples.
Compressive Strength
The test is performed on cube of 50 mm samples, with compressive machine of
3000 KN, based on ASTM C-109 [
ASTM C 109/ C 109M-02, Standard Test Method for Compressive Strength of
Hydraulic Cement mortars (Using 2-in. or [50-mm] Cube Specimens)
]. Testing is done on three samples per batch and report of average strength is
taken. The cubes loading rate is 0.72 mm per min.
Tensile Strength
The test is conducted with tensile machine, Zero Mor model Z2, on mortar
briquettes, with ASTM C-307[
ASTM C 107-03, Standard Test Method for Tensile Strength of Chemical-
Resistant Mortar, Grouts, and Monolithic Surfacings
]. Again testing of three samples per batch is done.
Differential Scanning Calorimeter
Schimadzu DSC-50 thermal analyzer was used for differential thermal analysis,
at a 200C heating rate per minute. Purging of samples chamber is done with
nitrogen haing 30 cc per min flow rate.
Results
Blended mortar compressive strength is done after 28 days, for varied NMK
ratios. CS is increased with NMK ratio increase to 8% from 2%. The mortar CS
is 7% higher, with 8% ratio of NMK, compared to control mortar.
Paraphrase This Document
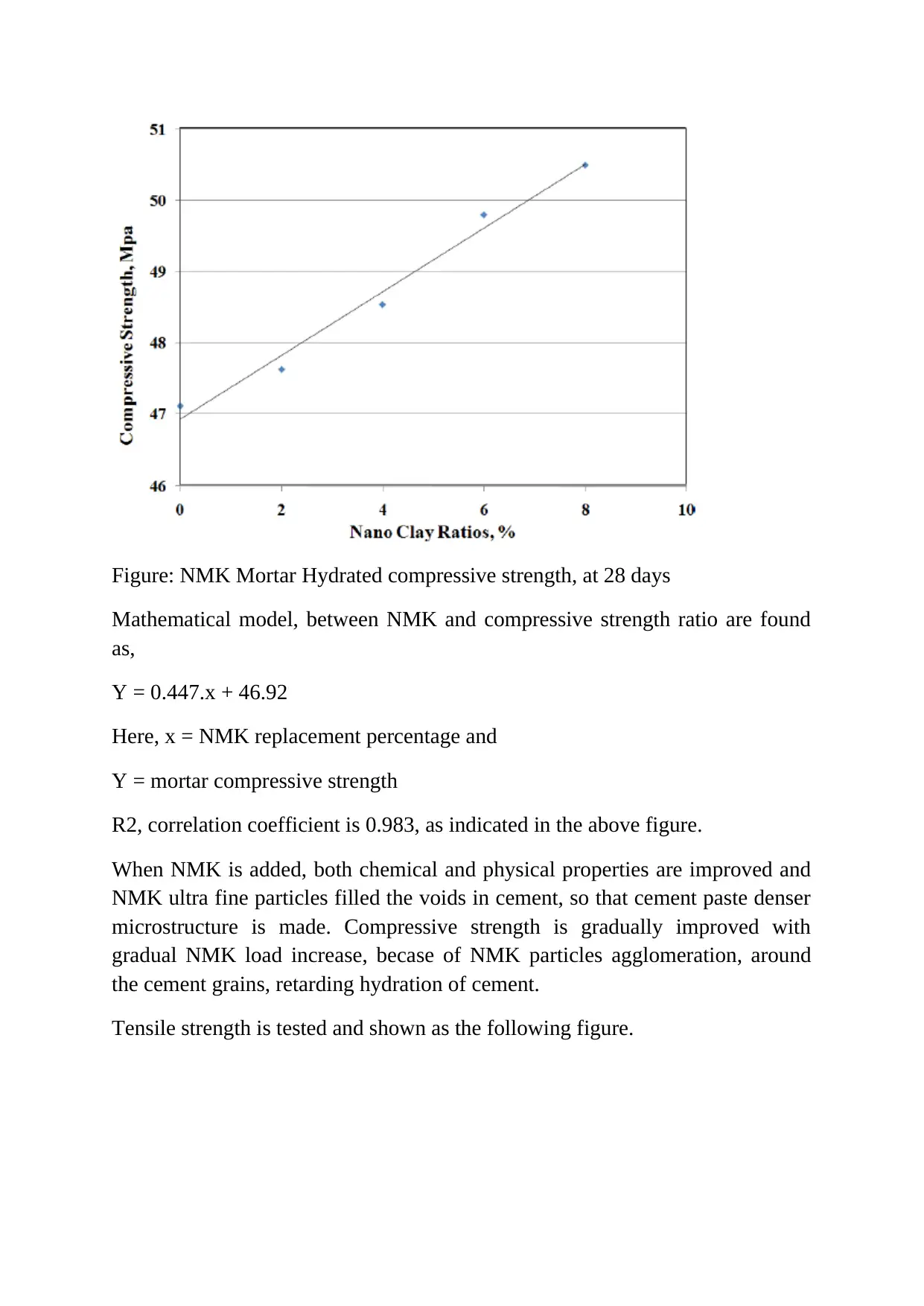
Mathematical model, between NMK and compressive strength ratio are found
as,
Y = 0.447.x + 46.92
Here, x = NMK replacement percentage and
Y = mortar compressive strength
R2, correlation coefficient is 0.983, as indicated in the above figure.
When NMK is added, both chemical and physical properties are improved and
NMK ultra fine particles filled the voids in cement, so that cement paste denser
microstructure is made. Compressive strength is gradually improved with
gradual NMK load increase, becase of NMK particles agglomeration, around
the cement grains, retarding hydration of cement.
Tensile strength is tested and shown as the following figure.
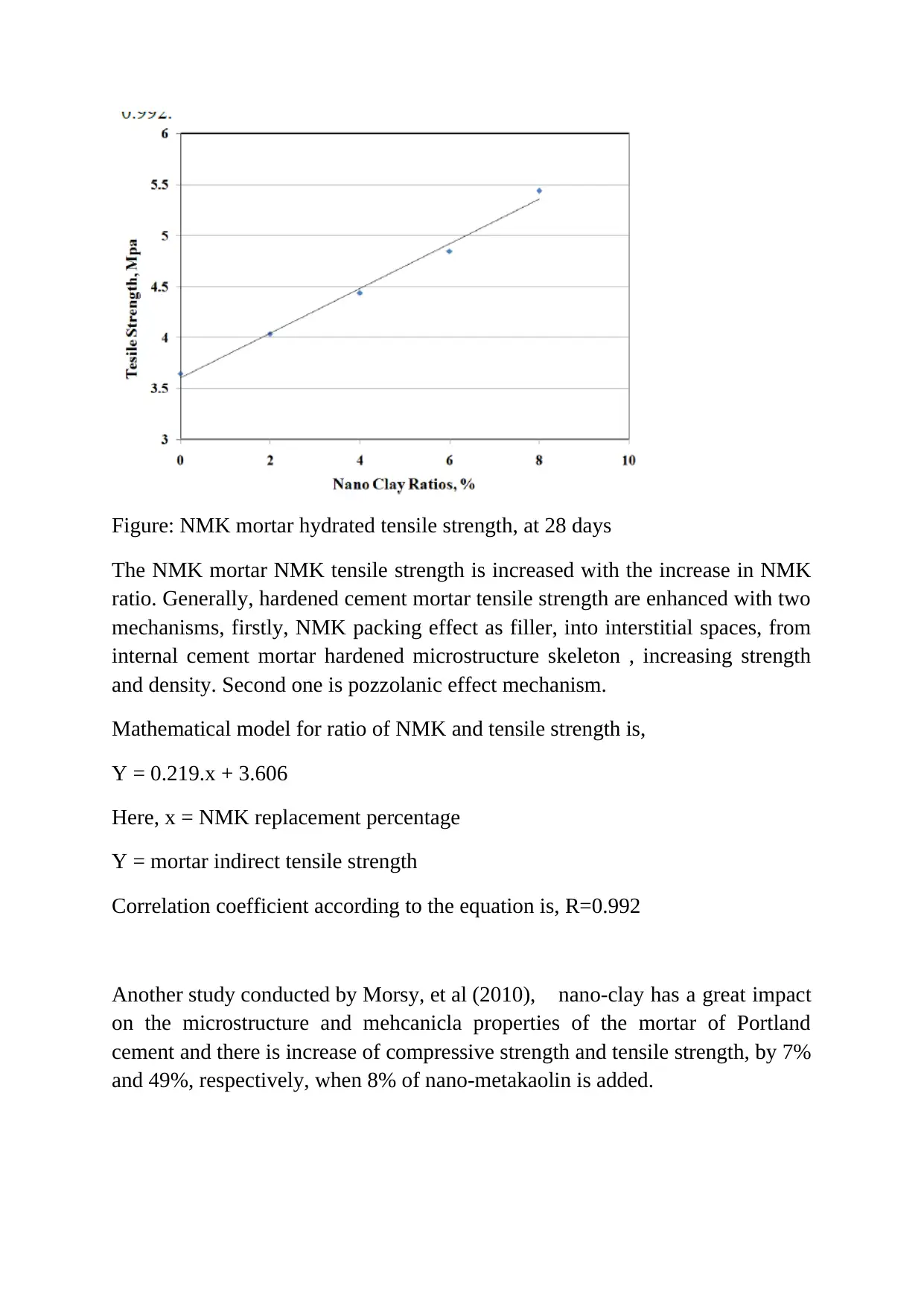
The NMK mortar NMK tensile strength is increased with the increase in NMK
ratio. Generally, hardened cement mortar tensile strength are enhanced with two
mechanisms, firstly, NMK packing effect as filler, into interstitial spaces, from
internal cement mortar hardened microstructure skeleton , increasing strength
and density. Second one is pozzolanic effect mechanism.
Mathematical model for ratio of NMK and tensile strength is,
Y = 0.219.x + 3.606
Here, x = NMK replacement percentage
Y = mortar indirect tensile strength
Correlation coefficient according to the equation is, R=0.992
Another study conducted by Morsy, et al (2010), nano-clay has a great impact
on the microstructure and mehcanicla properties of the mortar of Portland
cement and there is increase of compressive strength and tensile strength, by 7%
and 49%, respectively, when 8% of nano-metakaolin is added.
⊘ This is a preview!⊘
Do you want full access?
Subscribe today to unlock all pages.

Trusted by 1+ million students worldwide
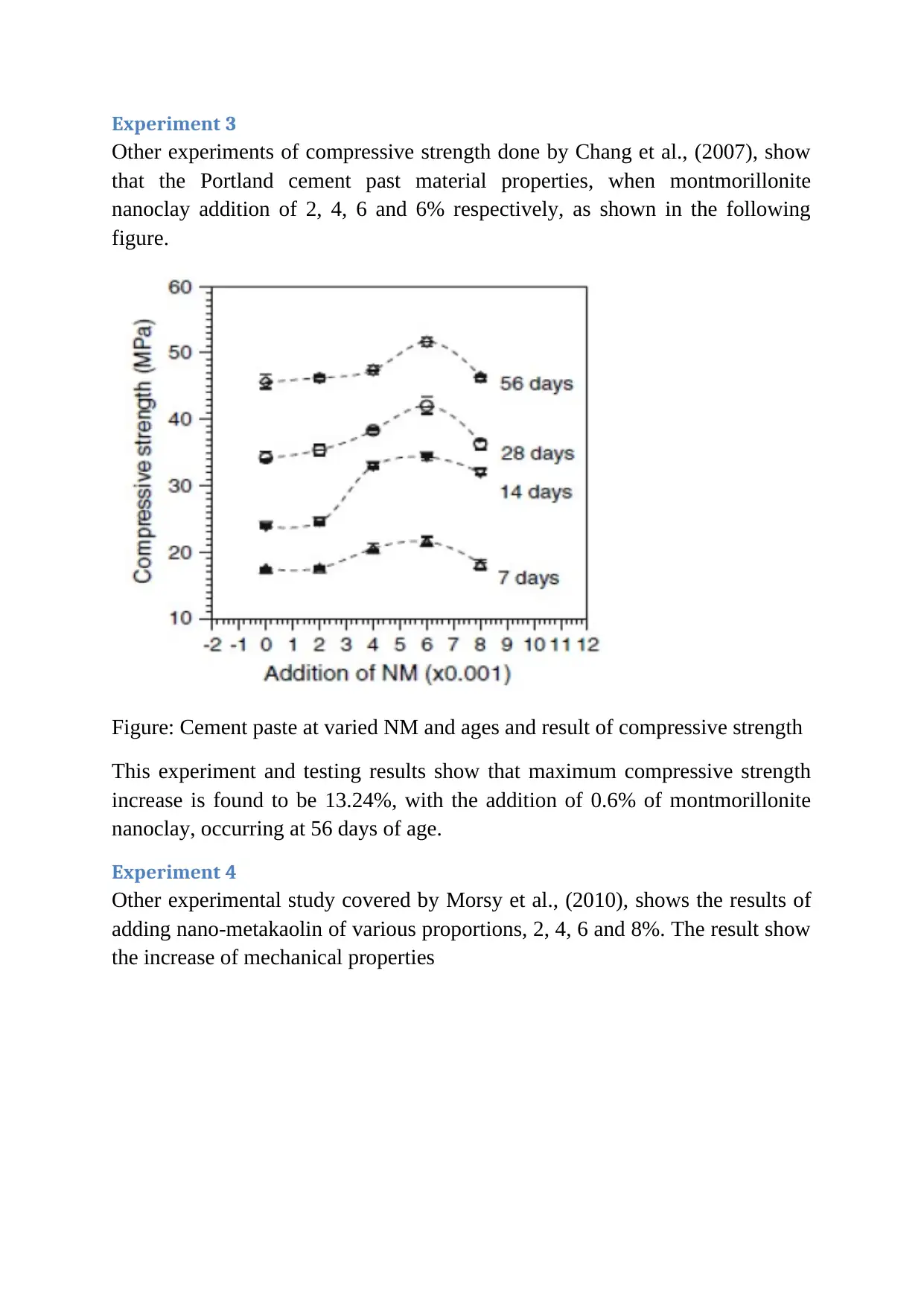
Other experiments of compressive strength done by Chang et al., (2007), show
that the Portland cement past material properties, when montmorillonite
nanoclay addition of 2, 4, 6 and 6% respectively, as shown in the following
figure.
Figure: Cement paste at varied NM and ages and result of compressive strength
This experiment and testing results show that maximum compressive strength
increase is found to be 13.24%, with the addition of 0.6% of montmorillonite
nanoclay, occurring at 56 days of age.
Experiment 4
Other experimental study covered by Morsy et al., (2010), shows the results of
adding nano-metakaolin of various proportions, 2, 4, 6 and 8%. The result show
the increase of mechanical properties
Paraphrase This Document
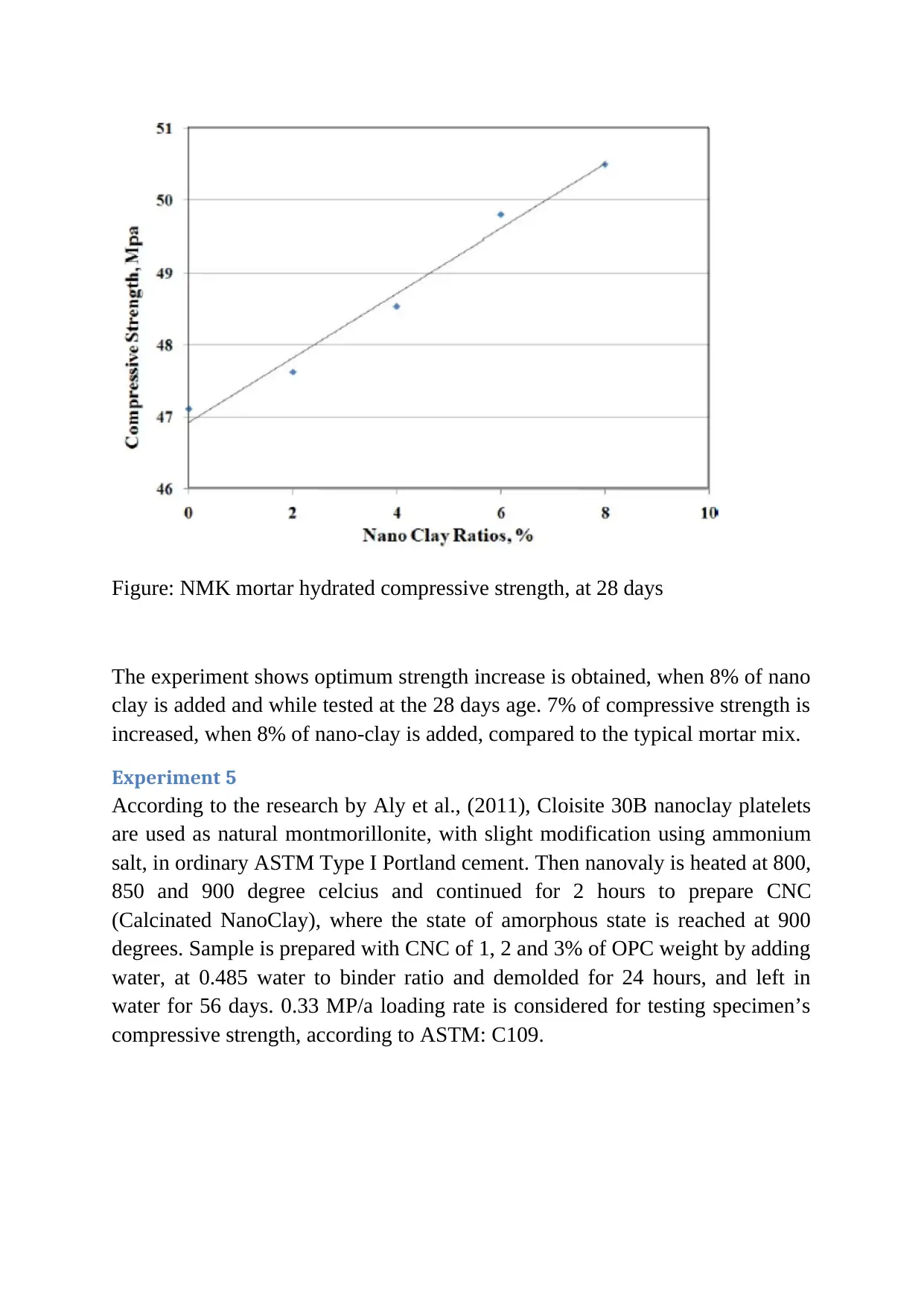
The experiment shows optimum strength increase is obtained, when 8% of nano
clay is added and while tested at the 28 days age. 7% of compressive strength is
increased, when 8% of nano-clay is added, compared to the typical mortar mix.
Experiment 5
According to the research by Aly et al., (2011), Cloisite 30B nanoclay platelets
are used as natural montmorillonite, with slight modification using ammonium
salt, in ordinary ASTM Type I Portland cement. Then nanovaly is heated at 800,
850 and 900 degree celcius and continued for 2 hours to prepare CNC
(Calcinated NanoClay), where the state of amorphous state is reached at 900
degrees. Sample is prepared with CNC of 1, 2 and 3% of OPC weight by adding
water, at 0.485 water to binder ratio and demolded for 24 hours, and left in
water for 56 days. 0.33 MP/a loading rate is considered for testing specimen’s
compressive strength, according to ASTM: C109.
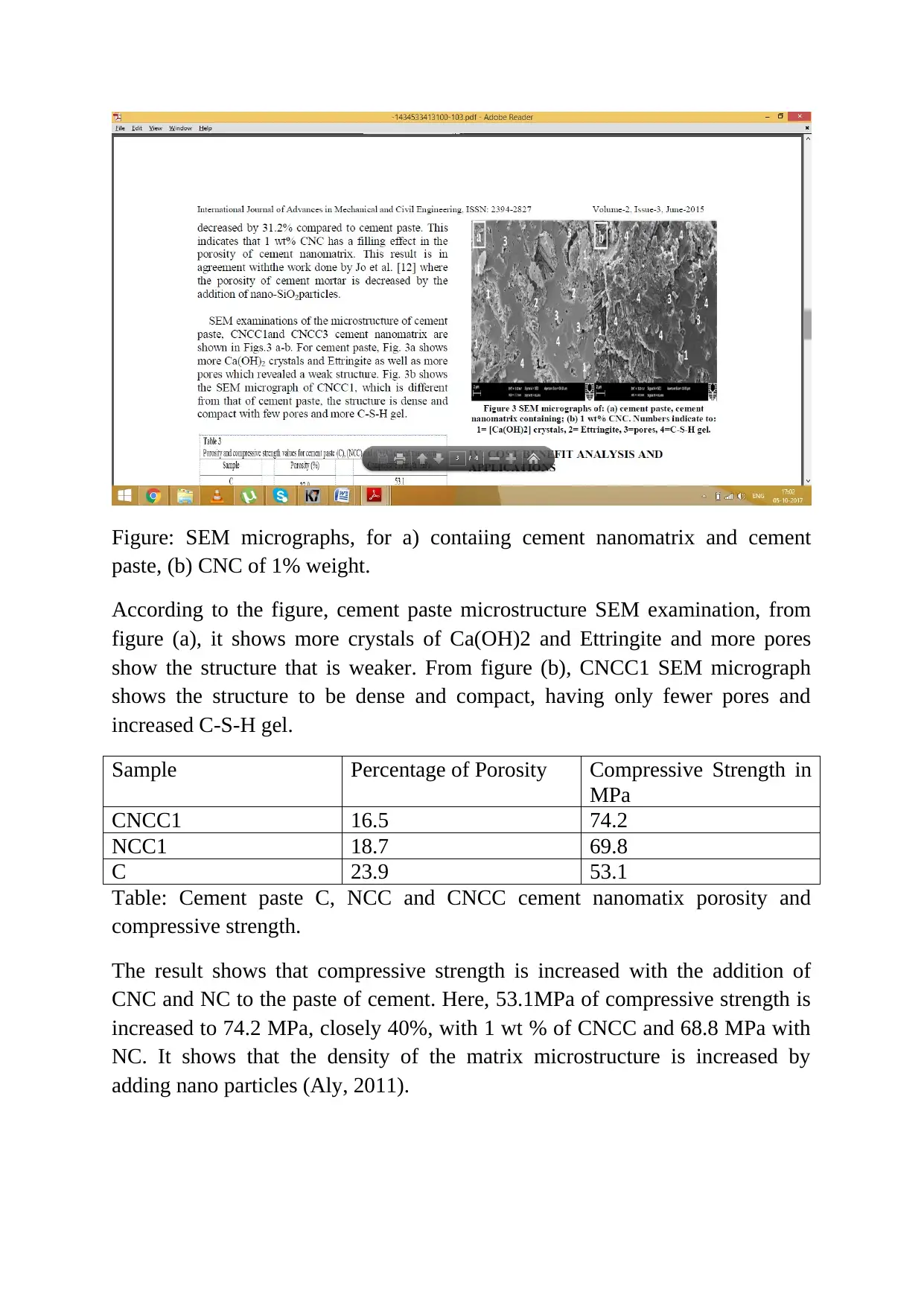
paste, (b) CNC of 1% weight.
According to the figure, cement paste microstructure SEM examination, from
figure (a), it shows more crystals of Ca(OH)2 and Ettringite and more pores
show the structure that is weaker. From figure (b), CNCC1 SEM micrograph
shows the structure to be dense and compact, having only fewer pores and
increased C-S-H gel.
Sample Percentage of Porosity Compressive Strength in
MPa
CNCC1 16.5 74.2
NCC1 18.7 69.8
C 23.9 53.1
Table: Cement paste C, NCC and CNCC cement nanomatix porosity and
compressive strength.
The result shows that compressive strength is increased with the addition of
CNC and NC to the paste of cement. Here, 53.1MPa of compressive strength is
increased to 74.2 MPa, closely 40%, with 1 wt % of CNCC and 68.8 MPa with
NC. It shows that the density of the matrix microstructure is increased by
adding nano particles (Aly, 2011).
⊘ This is a preview!⊘
Do you want full access?
Subscribe today to unlock all pages.

Trusted by 1+ million students worldwide
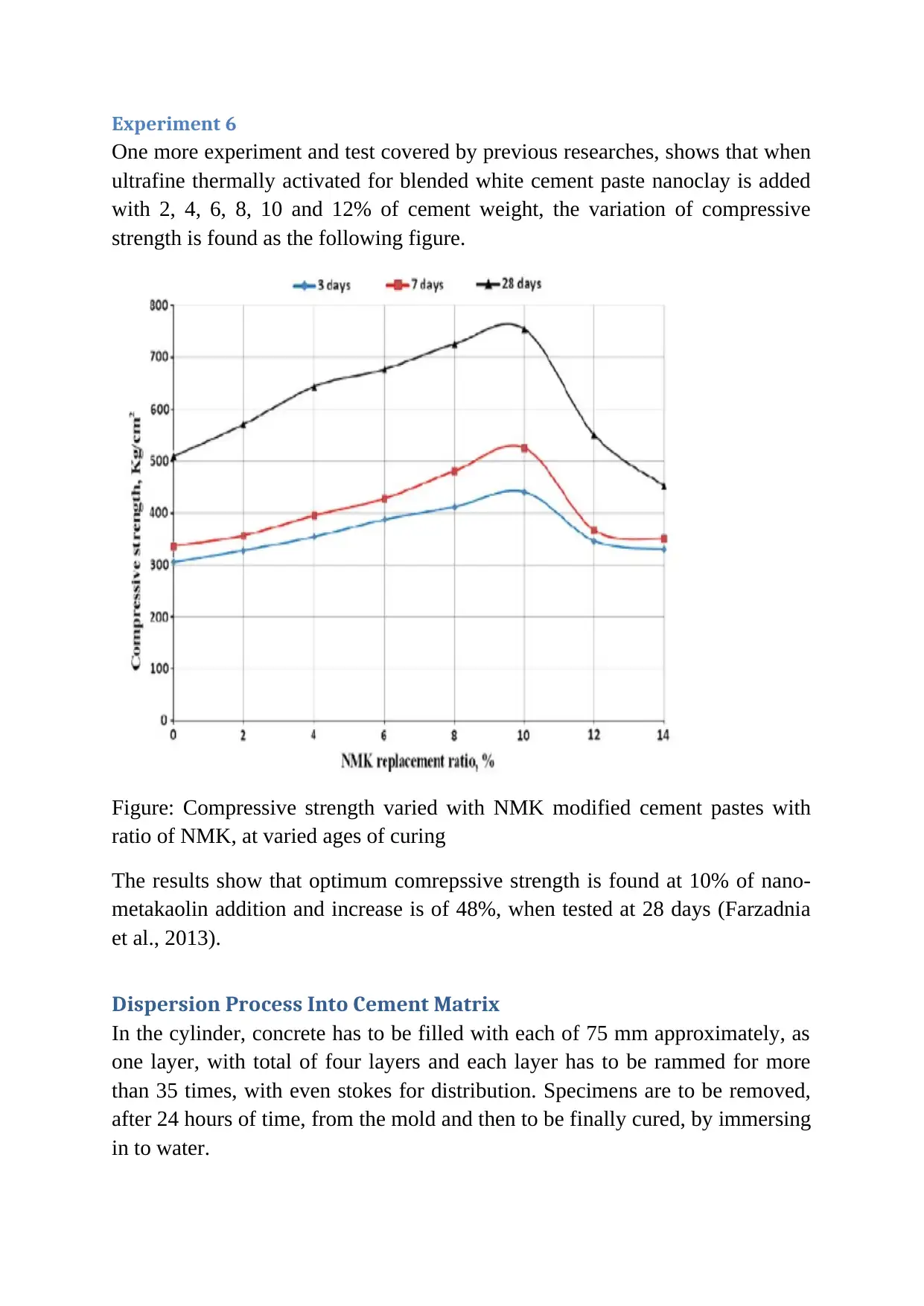
One more experiment and test covered by previous researches, shows that when
ultrafine thermally activated for blended white cement paste nanoclay is added
with 2, 4, 6, 8, 10 and 12% of cement weight, the variation of compressive
strength is found as the following figure.
Figure: Compressive strength varied with NMK modified cement pastes with
ratio of NMK, at varied ages of curing
The results show that optimum comrepssive strength is found at 10% of nano-
metakaolin addition and increase is of 48%, when tested at 28 days (Farzadnia
et al., 2013).
Dispersion Process Into Cement Matrix
In the cylinder, concrete has to be filled with each of 75 mm approximately, as
one layer, with total of four layers and each layer has to be rammed for more
than 35 times, with even stokes for distribution. Specimens are to be removed,
after 24 hours of time, from the mold and then to be finally cured, by immersing
in to water.
Paraphrase This Document
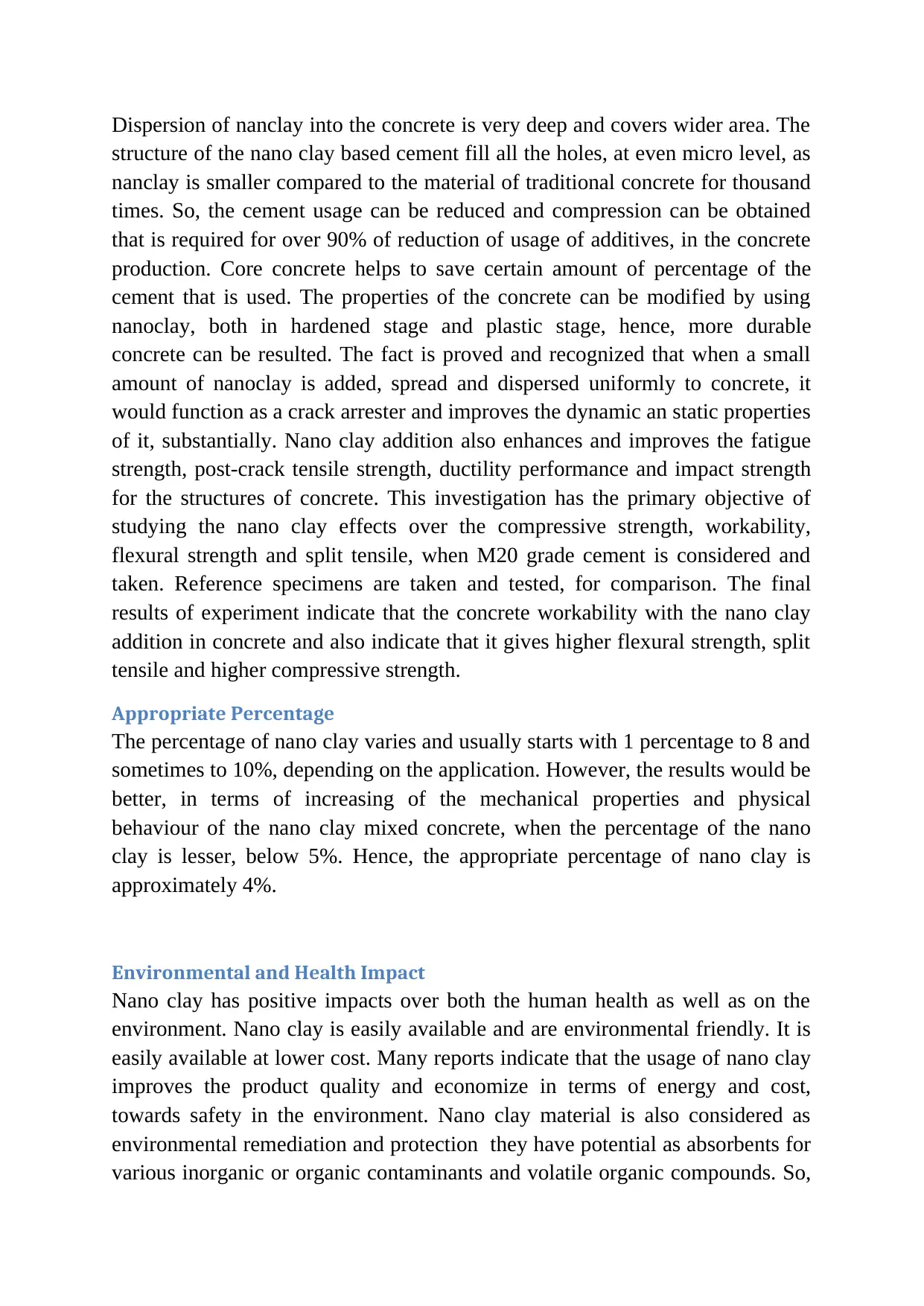
structure of the nano clay based cement fill all the holes, at even micro level, as
nanclay is smaller compared to the material of traditional concrete for thousand
times. So, the cement usage can be reduced and compression can be obtained
that is required for over 90% of reduction of usage of additives, in the concrete
production. Core concrete helps to save certain amount of percentage of the
cement that is used. The properties of the concrete can be modified by using
nanoclay, both in hardened stage and plastic stage, hence, more durable
concrete can be resulted. The fact is proved and recognized that when a small
amount of nanoclay is added, spread and dispersed uniformly to concrete, it
would function as a crack arrester and improves the dynamic an static properties
of it, substantially. Nano clay addition also enhances and improves the fatigue
strength, post-crack tensile strength, ductility performance and impact strength
for the structures of concrete. This investigation has the primary objective of
studying the nano clay effects over the compressive strength, workability,
flexural strength and split tensile, when M20 grade cement is considered and
taken. Reference specimens are taken and tested, for comparison. The final
results of experiment indicate that the concrete workability with the nano clay
addition in concrete and also indicate that it gives higher flexural strength, split
tensile and higher compressive strength.
Appropriate Percentage
The percentage of nano clay varies and usually starts with 1 percentage to 8 and
sometimes to 10%, depending on the application. However, the results would be
better, in terms of increasing of the mechanical properties and physical
behaviour of the nano clay mixed concrete, when the percentage of the nano
clay is lesser, below 5%. Hence, the appropriate percentage of nano clay is
approximately 4%.
Environmental and Health Impact
Nano clay has positive impacts over both the human health as well as on the
environment. Nano clay is easily available and are environmental friendly. It is
easily available at lower cost. Many reports indicate that the usage of nano clay
improves the product quality and economize in terms of energy and cost,
towards safety in the environment. Nano clay material is also considered as
environmental remediation and protection they have potential as absorbents for
various inorganic or organic contaminants and volatile organic compounds. So,
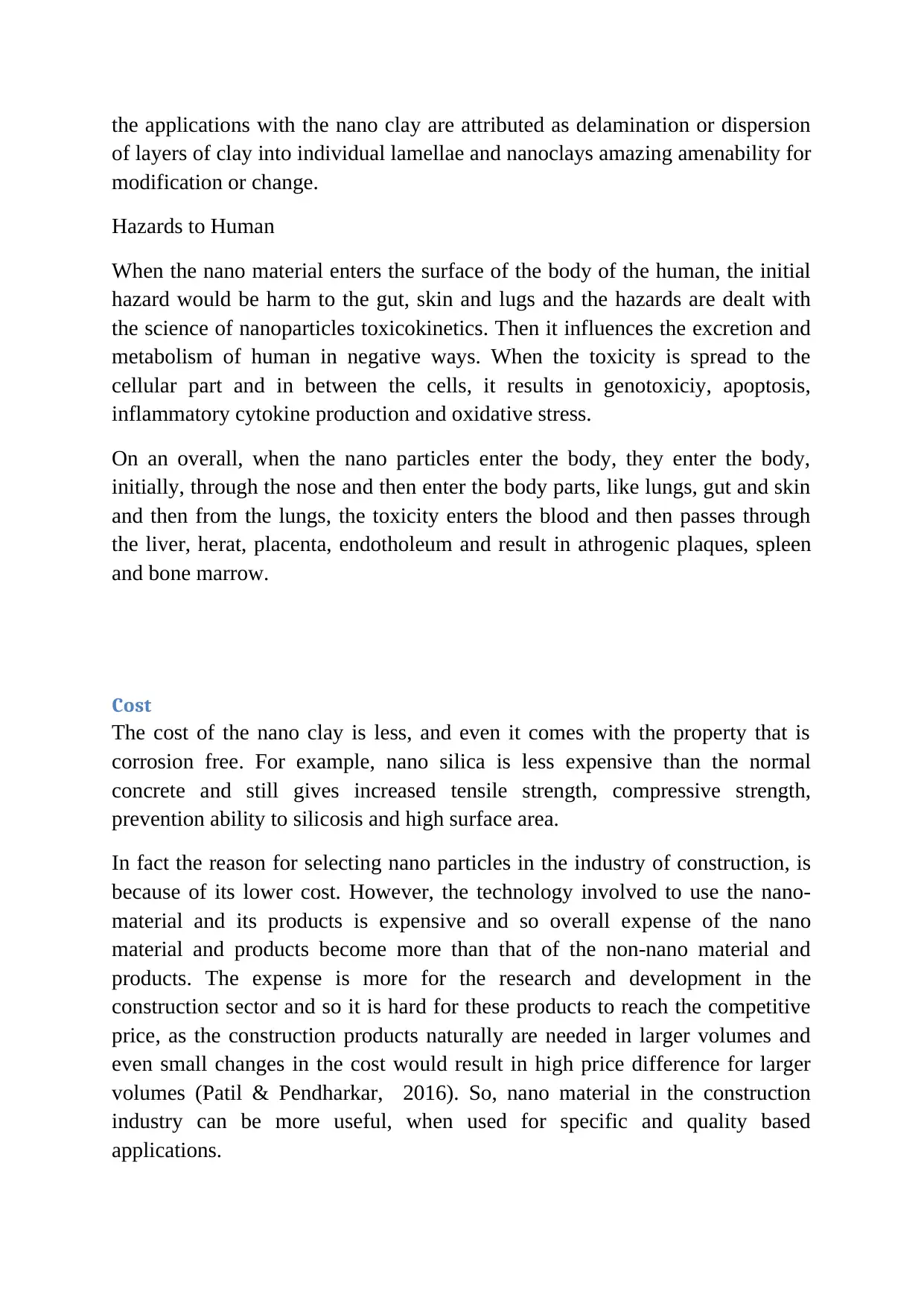
of layers of clay into individual lamellae and nanoclays amazing amenability for
modification or change.
Hazards to Human
When the nano material enters the surface of the body of the human, the initial
hazard would be harm to the gut, skin and lugs and the hazards are dealt with
the science of nanoparticles toxicokinetics. Then it influences the excretion and
metabolism of human in negative ways. When the toxicity is spread to the
cellular part and in between the cells, it results in genotoxiciy, apoptosis,
inflammatory cytokine production and oxidative stress.
On an overall, when the nano particles enter the body, they enter the body,
initially, through the nose and then enter the body parts, like lungs, gut and skin
and then from the lungs, the toxicity enters the blood and then passes through
the liver, herat, placenta, endotholeum and result in athrogenic plaques, spleen
and bone marrow.
Cost
The cost of the nano clay is less, and even it comes with the property that is
corrosion free. For example, nano silica is less expensive than the normal
concrete and still gives increased tensile strength, compressive strength,
prevention ability to silicosis and high surface area.
In fact the reason for selecting nano particles in the industry of construction, is
because of its lower cost. However, the technology involved to use the nano-
material and its products is expensive and so overall expense of the nano
material and products become more than that of the non-nano material and
products. The expense is more for the research and development in the
construction sector and so it is hard for these products to reach the competitive
price, as the construction products naturally are needed in larger volumes and
even small changes in the cost would result in high price difference for larger
volumes (Patil & Pendharkar, 2016). So, nano material in the construction
industry can be more useful, when used for specific and quality based
applications.
⊘ This is a preview!⊘
Do you want full access?
Subscribe today to unlock all pages.

Trusted by 1+ million students worldwide
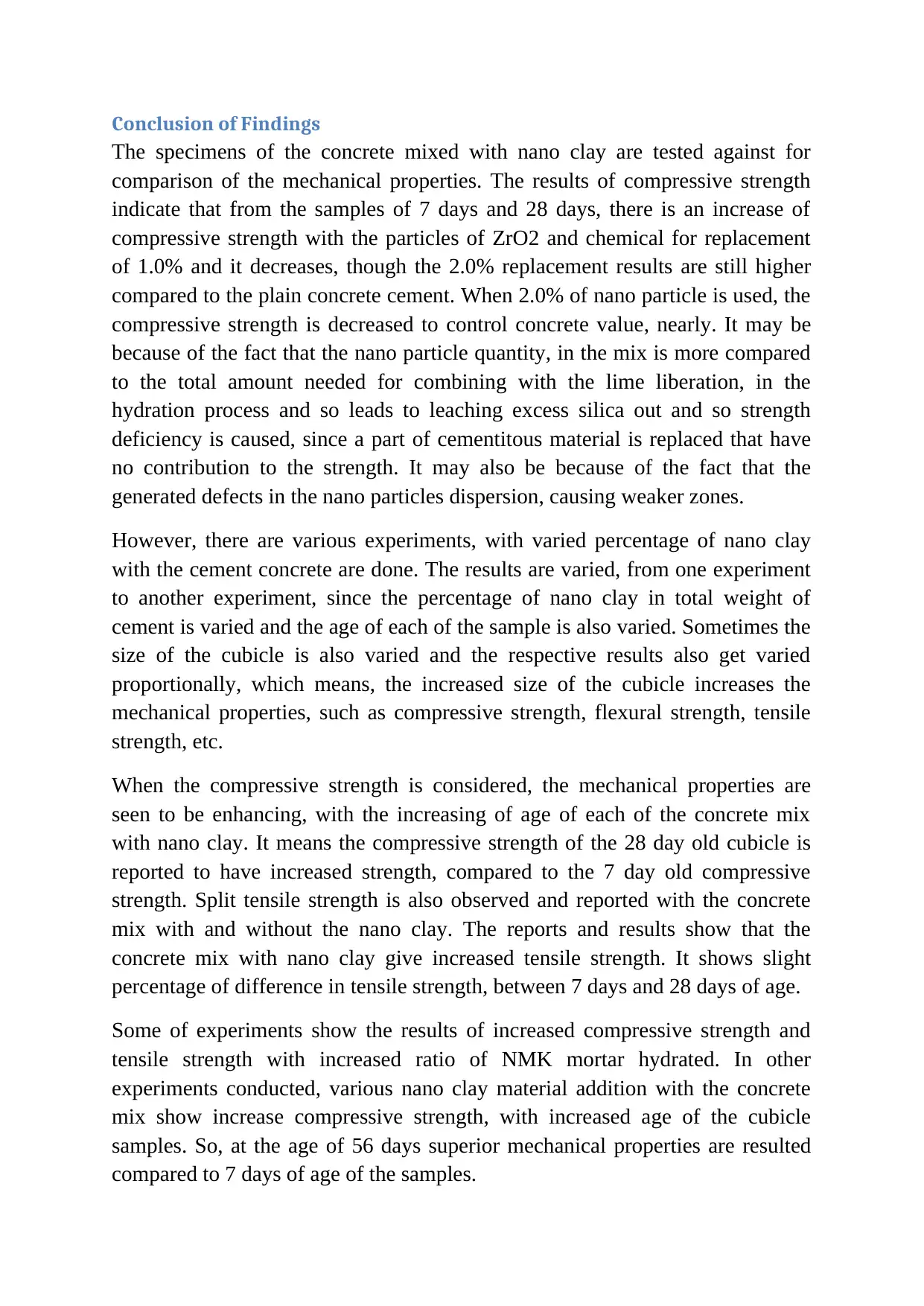
The specimens of the concrete mixed with nano clay are tested against for
comparison of the mechanical properties. The results of compressive strength
indicate that from the samples of 7 days and 28 days, there is an increase of
compressive strength with the particles of ZrO2 and chemical for replacement
of 1.0% and it decreases, though the 2.0% replacement results are still higher
compared to the plain concrete cement. When 2.0% of nano particle is used, the
compressive strength is decreased to control concrete value, nearly. It may be
because of the fact that the nano particle quantity, in the mix is more compared
to the total amount needed for combining with the lime liberation, in the
hydration process and so leads to leaching excess silica out and so strength
deficiency is caused, since a part of cementitous material is replaced that have
no contribution to the strength. It may also be because of the fact that the
generated defects in the nano particles dispersion, causing weaker zones.
However, there are various experiments, with varied percentage of nano clay
with the cement concrete are done. The results are varied, from one experiment
to another experiment, since the percentage of nano clay in total weight of
cement is varied and the age of each of the sample is also varied. Sometimes the
size of the cubicle is also varied and the respective results also get varied
proportionally, which means, the increased size of the cubicle increases the
mechanical properties, such as compressive strength, flexural strength, tensile
strength, etc.
When the compressive strength is considered, the mechanical properties are
seen to be enhancing, with the increasing of age of each of the concrete mix
with nano clay. It means the compressive strength of the 28 day old cubicle is
reported to have increased strength, compared to the 7 day old compressive
strength. Split tensile strength is also observed and reported with the concrete
mix with and without the nano clay. The reports and results show that the
concrete mix with nano clay give increased tensile strength. It shows slight
percentage of difference in tensile strength, between 7 days and 28 days of age.
Some of experiments show the results of increased compressive strength and
tensile strength with increased ratio of NMK mortar hydrated. In other
experiments conducted, various nano clay material addition with the concrete
mix show increase compressive strength, with increased age of the cubicle
samples. So, at the age of 56 days superior mechanical properties are resulted
compared to 7 days of age of the samples.
Paraphrase This Document
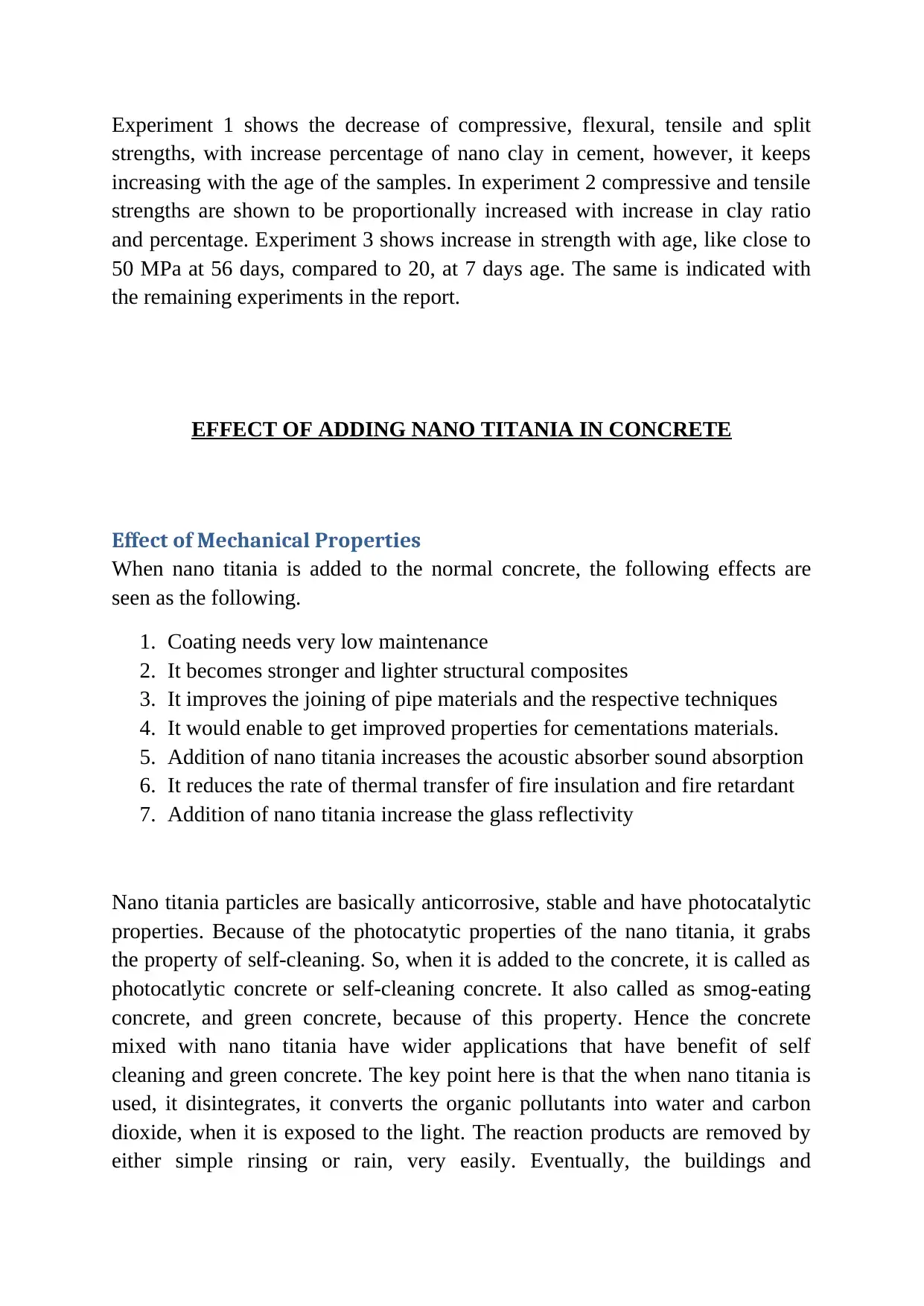
strengths, with increase percentage of nano clay in cement, however, it keeps
increasing with the age of the samples. In experiment 2 compressive and tensile
strengths are shown to be proportionally increased with increase in clay ratio
and percentage. Experiment 3 shows increase in strength with age, like close to
50 MPa at 56 days, compared to 20, at 7 days age. The same is indicated with
the remaining experiments in the report.
EFFECT OF ADDING NANO TITANIA IN CONCRETE
Effect of Mechanical Properties
When nano titania is added to the normal concrete, the following effects are
seen as the following.
1. Coating needs very low maintenance
2. It becomes stronger and lighter structural composites
3. It improves the joining of pipe materials and the respective techniques
4. It would enable to get improved properties for cementations materials.
5. Addition of nano titania increases the acoustic absorber sound absorption
6. It reduces the rate of thermal transfer of fire insulation and fire retardant
7. Addition of nano titania increase the glass reflectivity
Nano titania particles are basically anticorrosive, stable and have photocatalytic
properties. Because of the photocatytic properties of the nano titania, it grabs
the property of self-cleaning. So, when it is added to the concrete, it is called as
photocatlytic concrete or self-cleaning concrete. It also called as smog-eating
concrete, and green concrete, because of this property. Hence the concrete
mixed with nano titania have wider applications that have benefit of self
cleaning and green concrete. The key point here is that the when nano titania is
used, it disintegrates, it converts the organic pollutants into water and carbon
dioxide, when it is exposed to the light. The reaction products are removed by
either simple rinsing or rain, very easily. Eventually, the buildings and
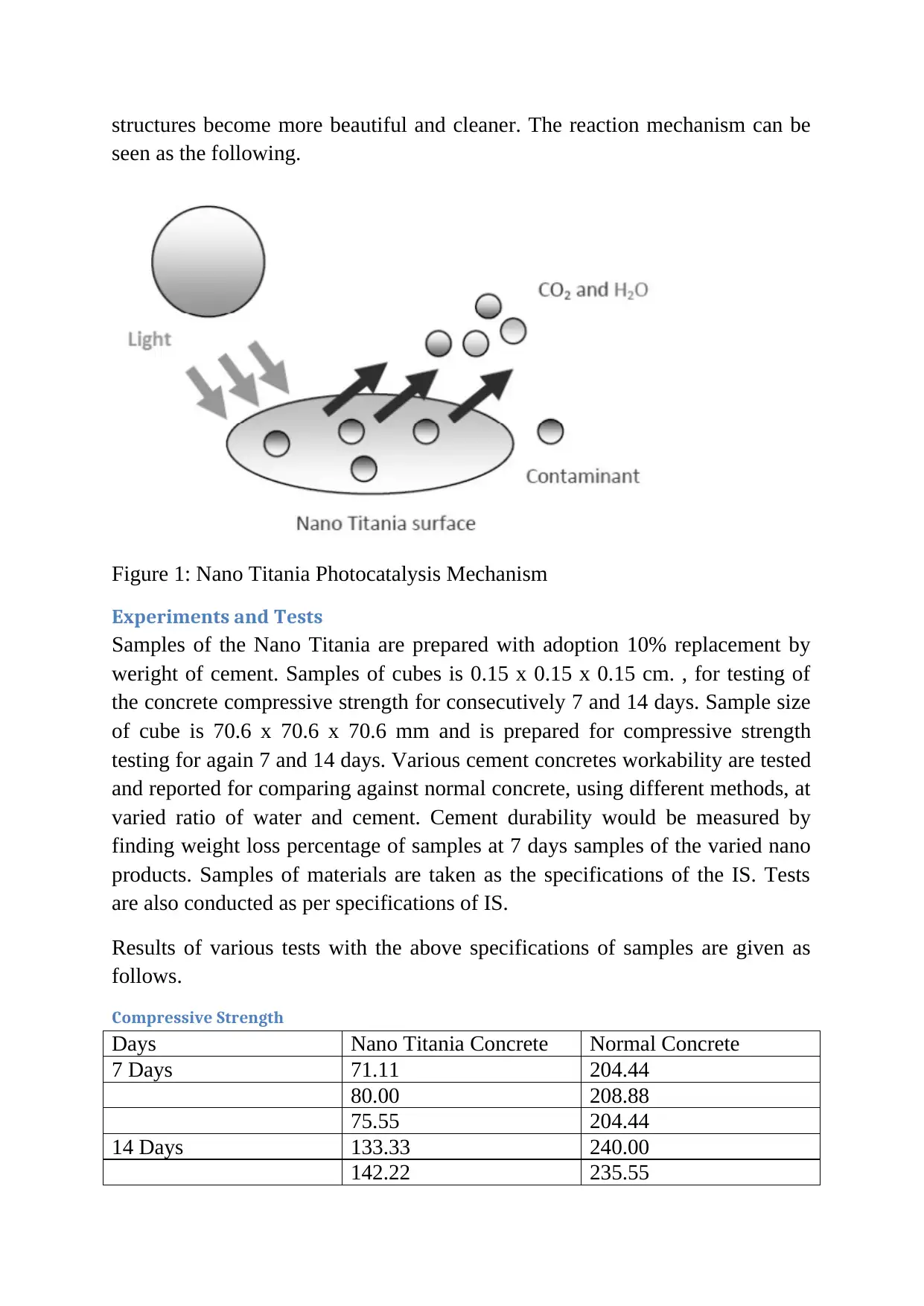
seen as the following.
Figure 1: Nano Titania Photocatalysis Mechanism
Experiments and Tests
Samples of the Nano Titania are prepared with adoption 10% replacement by
weright of cement. Samples of cubes is 0.15 x 0.15 x 0.15 cm. , for testing of
the concrete compressive strength for consecutively 7 and 14 days. Sample size
of cube is 70.6 x 70.6 x 70.6 mm and is prepared for compressive strength
testing for again 7 and 14 days. Various cement concretes workability are tested
and reported for comparing against normal concrete, using different methods, at
varied ratio of water and cement. Cement durability would be measured by
finding weight loss percentage of samples at 7 days samples of the varied nano
products. Samples of materials are taken as the specifications of the IS. Tests
are also conducted as per specifications of IS.
Results of various tests with the above specifications of samples are given as
follows.
Compressive Strength
Days Nano Titania Concrete Normal Concrete
7 Days 71.11 204.44
80.00 208.88
75.55 204.44
14 Days 133.33 240.00
142.22 235.55
⊘ This is a preview!⊘
Do you want full access?
Subscribe today to unlock all pages.

Trusted by 1+ million students worldwide
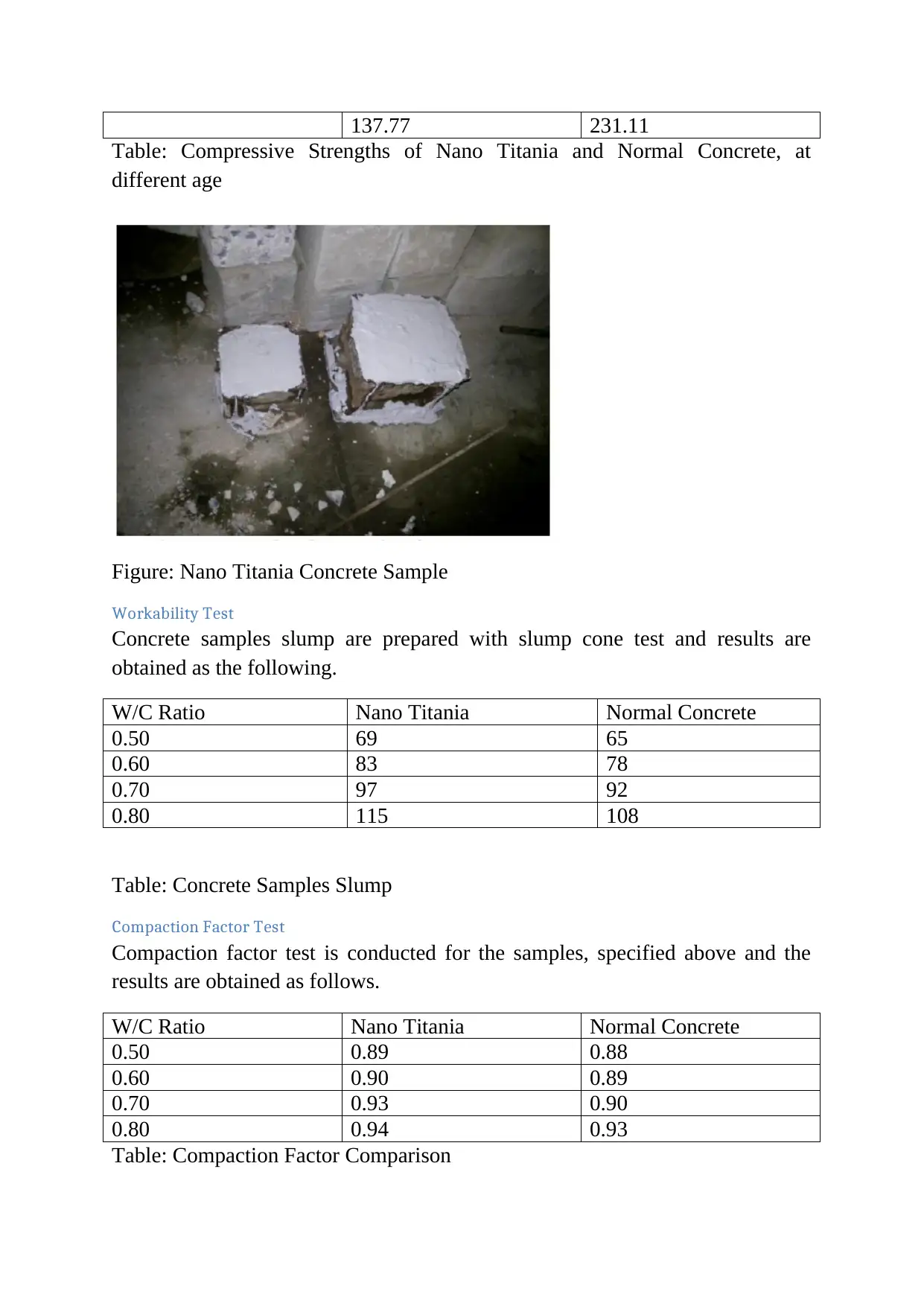
Table: Compressive Strengths of Nano Titania and Normal Concrete, at
different age
Figure: Nano Titania Concrete Sample
Workability Test
Concrete samples slump are prepared with slump cone test and results are
obtained as the following.
W/C Ratio Nano Titania Normal Concrete
0.50 69 65
0.60 83 78
0.70 97 92
0.80 115 108
Table: Concrete Samples Slump
Compaction Factor Test
Compaction factor test is conducted for the samples, specified above and the
results are obtained as follows.
W/C Ratio Nano Titania Normal Concrete
0.50 0.89 0.88
0.60 0.90 0.89
0.70 0.93 0.90
0.80 0.94 0.93
Table: Compaction Factor Comparison
Paraphrase This Document
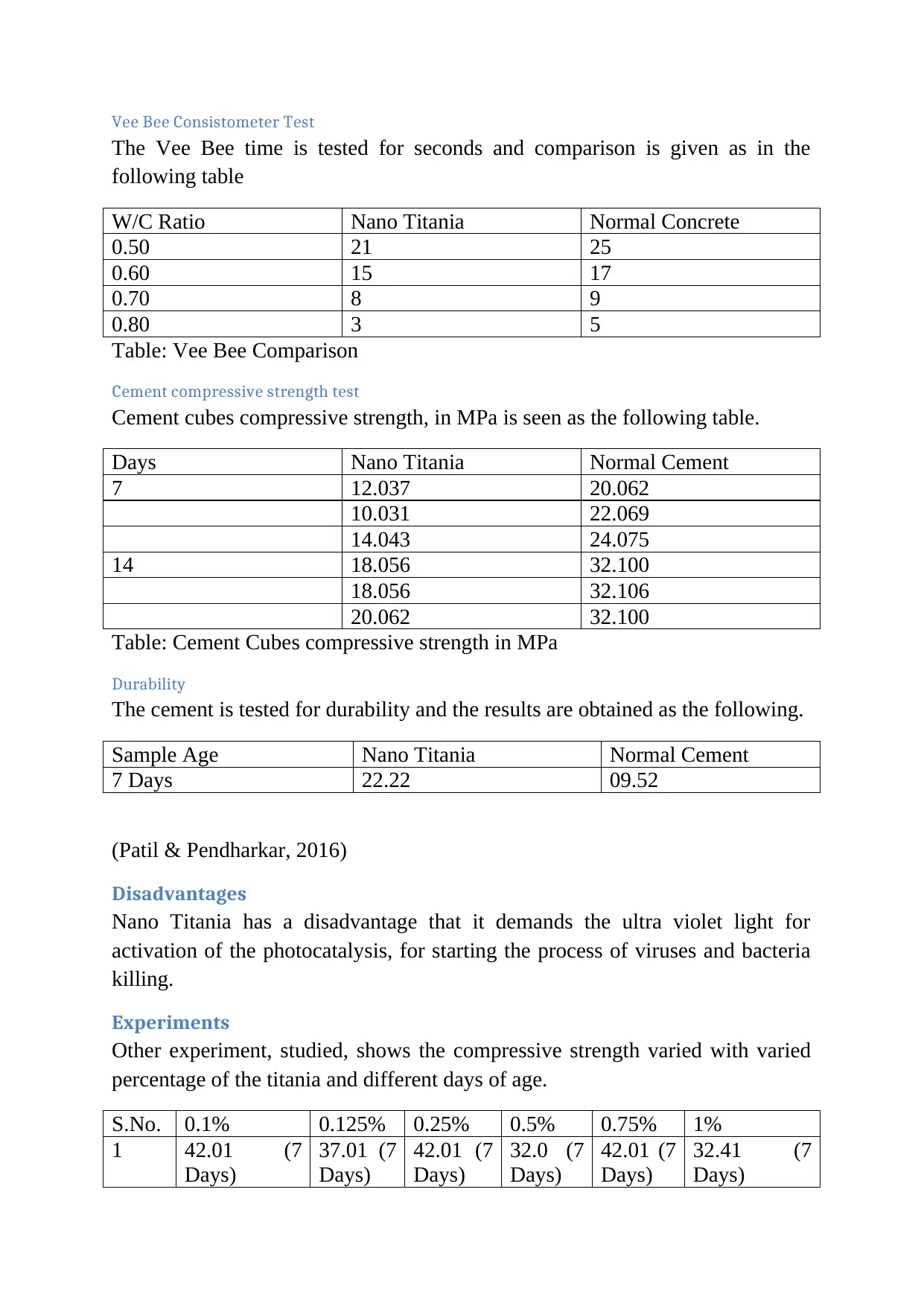
The Vee Bee time is tested for seconds and comparison is given as in the
following table
W/C Ratio Nano Titania Normal Concrete
0.50 21 25
0.60 15 17
0.70 8 9
0.80 3 5
Table: Vee Bee Comparison
Cement compressive strength test
Cement cubes compressive strength, in MPa is seen as the following table.
Days Nano Titania Normal Cement
7 12.037 20.062
10.031 22.069
14.043 24.075
14 18.056 32.100
18.056 32.106
20.062 32.100
Table: Cement Cubes compressive strength in MPa
Durability
The cement is tested for durability and the results are obtained as the following.
Sample Age Nano Titania Normal Cement
7 Days 22.22 09.52
(Patil & Pendharkar, 2016)
Disadvantages
Nano Titania has a disadvantage that it demands the ultra violet light for
activation of the photocatalysis, for starting the process of viruses and bacteria
killing.
Experiments
Other experiment, studied, shows the compressive strength varied with varied
percentage of the titania and different days of age.
S.No. 0.1% 0.125% 0.25% 0.5% 0.75% 1%
1 42.01 (7
Days)
37.01 (7
Days)
42.01 (7
Days)
32.0 (7
Days)
42.01 (7
Days)
32.41 (7
Days)
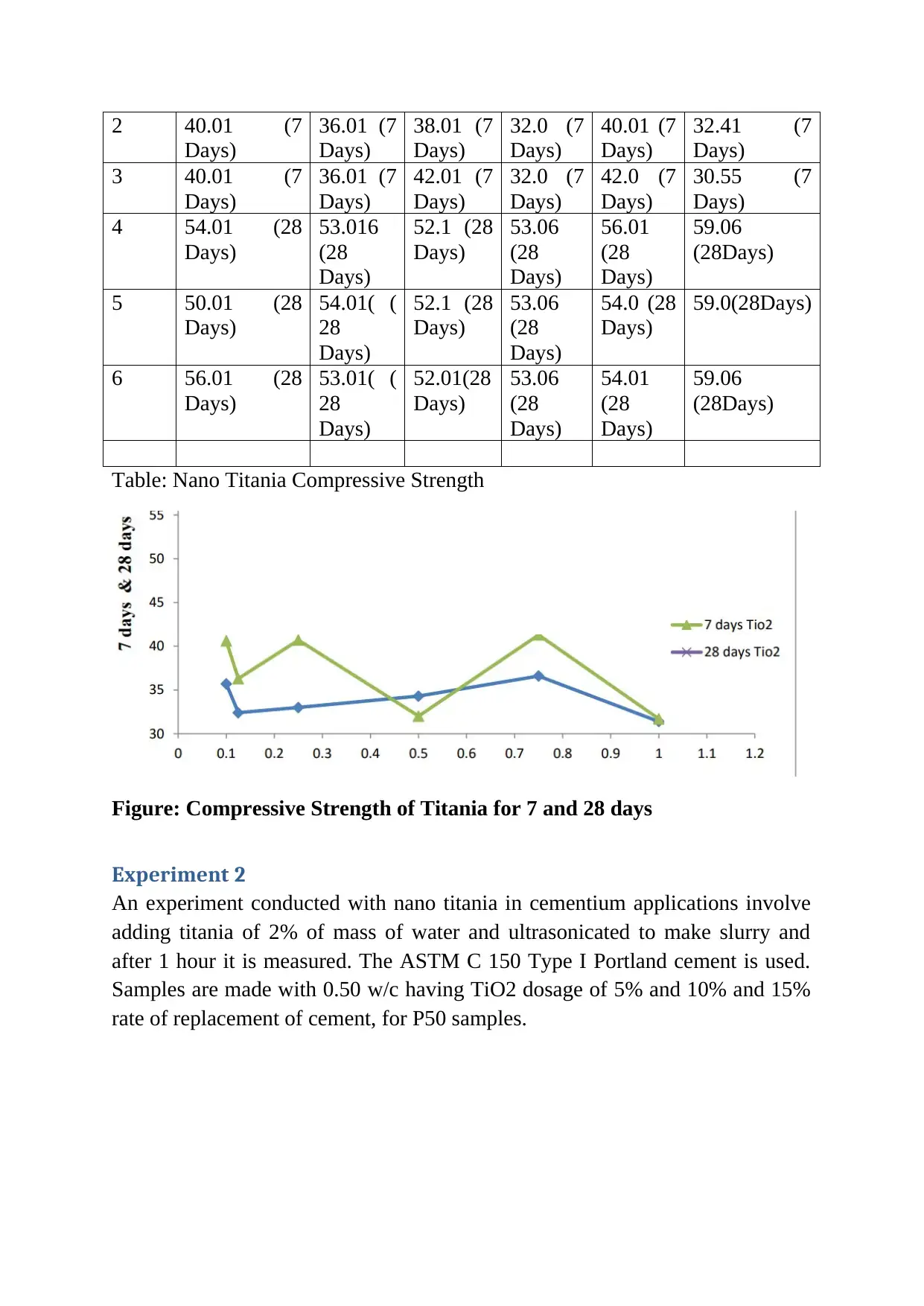
Days)
36.01 (7
Days)
38.01 (7
Days)
32.0 (7
Days)
40.01 (7
Days)
32.41 (7
Days)
3 40.01 (7
Days)
36.01 (7
Days)
42.01 (7
Days)
32.0 (7
Days)
42.0 (7
Days)
30.55 (7
Days)
4 54.01 (28
Days)
53.016
(28
Days)
52.1 (28
Days)
53.06
(28
Days)
56.01
(28
Days)
59.06
(28Days)
5 50.01 (28
Days)
54.01( (
28
Days)
52.1 (28
Days)
53.06
(28
Days)
54.0 (28
Days)
59.0(28Days)
6 56.01 (28
Days)
53.01( (
28
Days)
52.01(28
Days)
53.06
(28
Days)
54.01
(28
Days)
59.06
(28Days)
Table: Nano Titania Compressive Strength
Figure: Compressive Strength of Titania for 7 and 28 days
Experiment 2
An experiment conducted with nano titania in cementium applications involve
adding titania of 2% of mass of water and ultrasonicated to make slurry and
after 1 hour it is measured. The ASTM C 150 Type I Portland cement is used.
Samples are made with 0.50 w/c having TiO2 dosage of 5% and 10% and 15%
rate of replacement of cement, for P50 samples.
⊘ This is a preview!⊘
Do you want full access?
Subscribe today to unlock all pages.

Trusted by 1+ million students worldwide
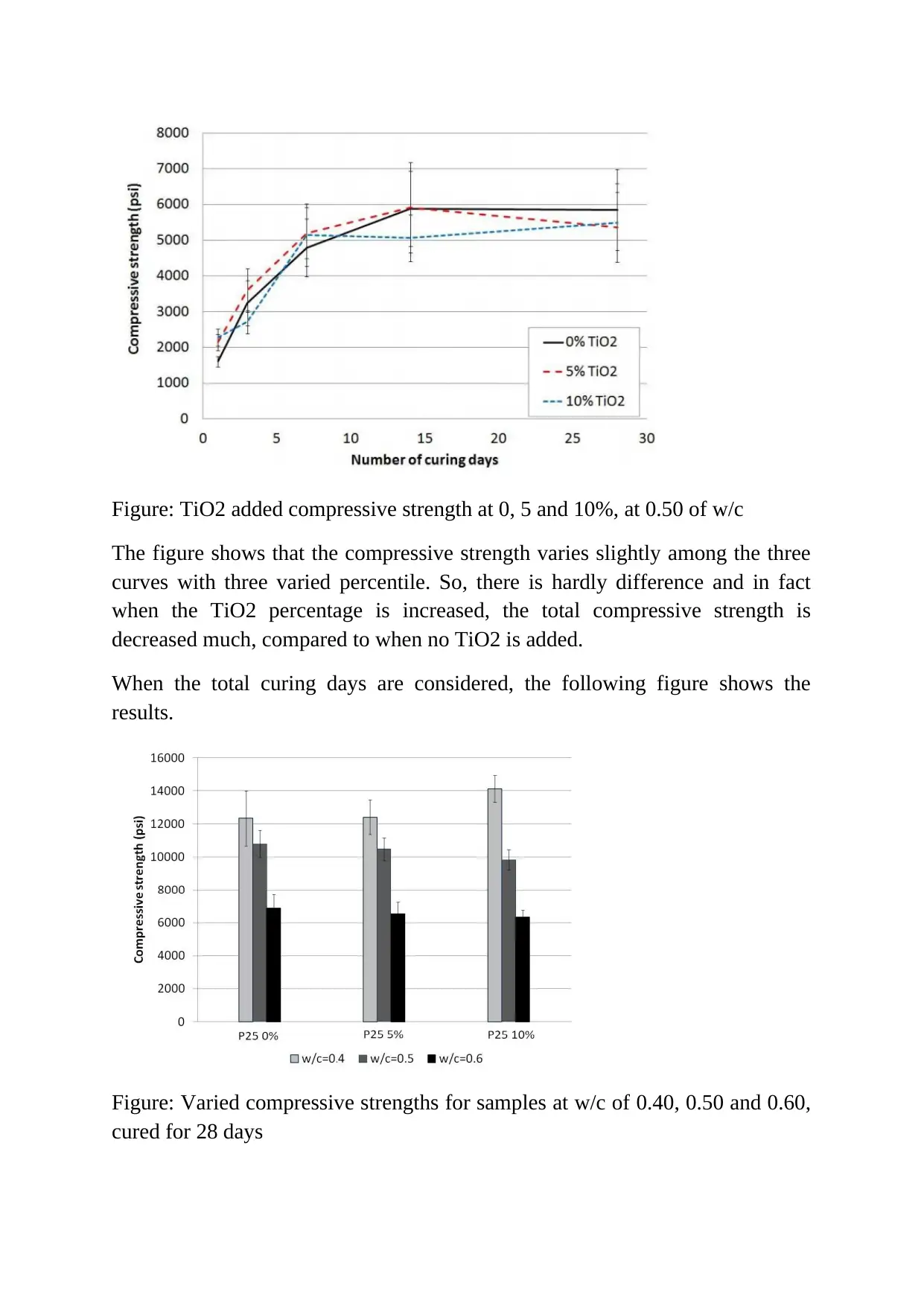
The figure shows that the compressive strength varies slightly among the three
curves with three varied percentile. So, there is hardly difference and in fact
when the TiO2 percentage is increased, the total compressive strength is
decreased much, compared to when no TiO2 is added.
When the total curing days are considered, the following figure shows the
results.
Figure: Varied compressive strengths for samples at w/c of 0.40, 0.50 and 0.60,
cured for 28 days
Paraphrase This Document
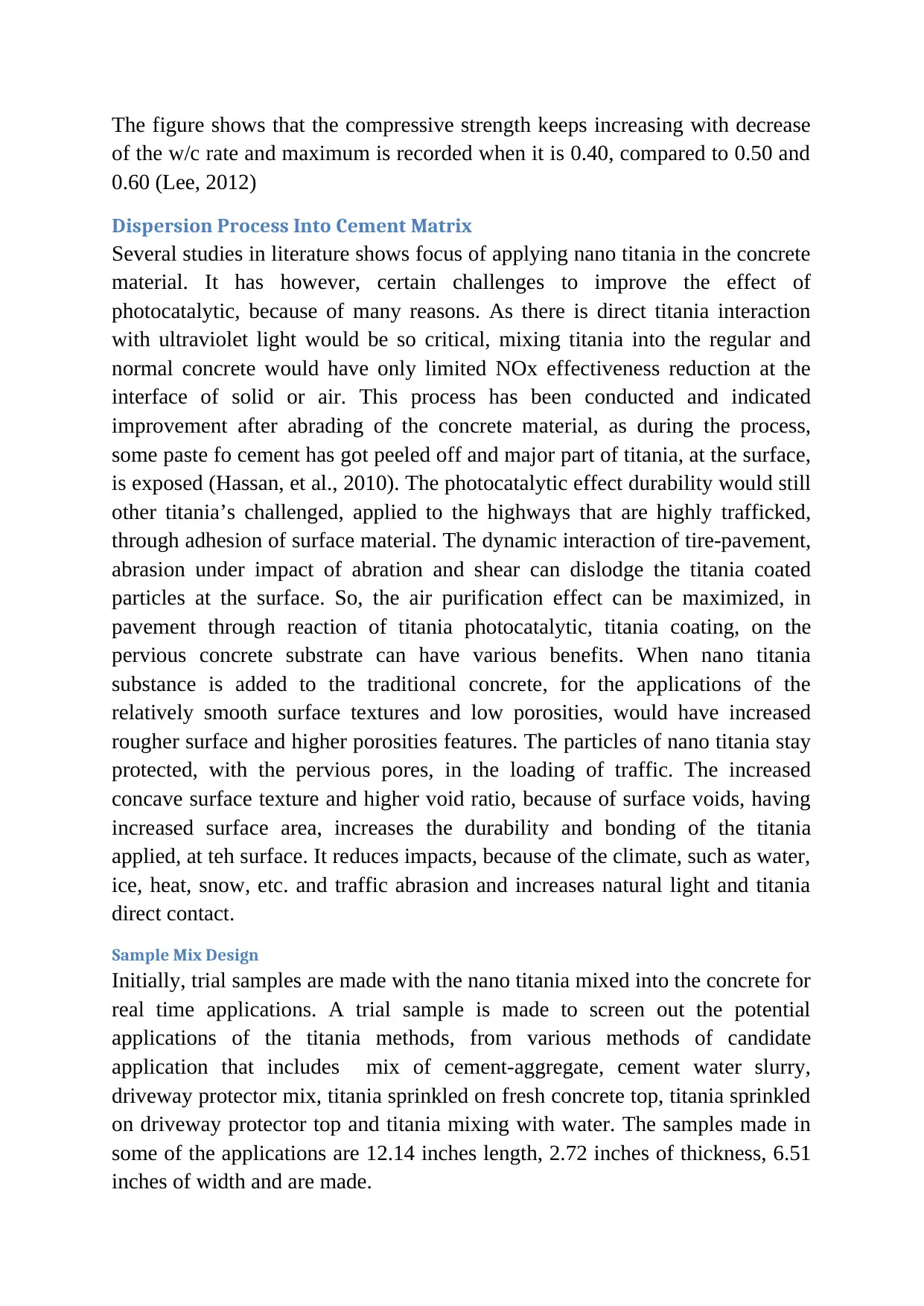
of the w/c rate and maximum is recorded when it is 0.40, compared to 0.50 and
0.60 (Lee, 2012)
Dispersion Process Into Cement Matrix
Several studies in literature shows focus of applying nano titania in the concrete
material. It has however, certain challenges to improve the effect of
photocatalytic, because of many reasons. As there is direct titania interaction
with ultraviolet light would be so critical, mixing titania into the regular and
normal concrete would have only limited NOx effectiveness reduction at the
interface of solid or air. This process has been conducted and indicated
improvement after abrading of the concrete material, as during the process,
some paste fo cement has got peeled off and major part of titania, at the surface,
is exposed (Hassan, et al., 2010). The photocatalytic effect durability would still
other titania’s challenged, applied to the highways that are highly trafficked,
through adhesion of surface material. The dynamic interaction of tire-pavement,
abrasion under impact of abration and shear can dislodge the titania coated
particles at the surface. So, the air purification effect can be maximized, in
pavement through reaction of titania photocatalytic, titania coating, on the
pervious concrete substrate can have various benefits. When nano titania
substance is added to the traditional concrete, for the applications of the
relatively smooth surface textures and low porosities, would have increased
rougher surface and higher porosities features. The particles of nano titania stay
protected, with the pervious pores, in the loading of traffic. The increased
concave surface texture and higher void ratio, because of surface voids, having
increased surface area, increases the durability and bonding of the titania
applied, at teh surface. It reduces impacts, because of the climate, such as water,
ice, heat, snow, etc. and traffic abrasion and increases natural light and titania
direct contact.
Sample Mix Design
Initially, trial samples are made with the nano titania mixed into the concrete for
real time applications. A trial sample is made to screen out the potential
applications of the titania methods, from various methods of candidate
application that includes mix of cement-aggregate, cement water slurry,
driveway protector mix, titania sprinkled on fresh concrete top, titania sprinkled
on driveway protector top and titania mixing with water. The samples made in
some of the applications are 12.14 inches length, 2.72 inches of thickness, 6.51
inches of width and are made.
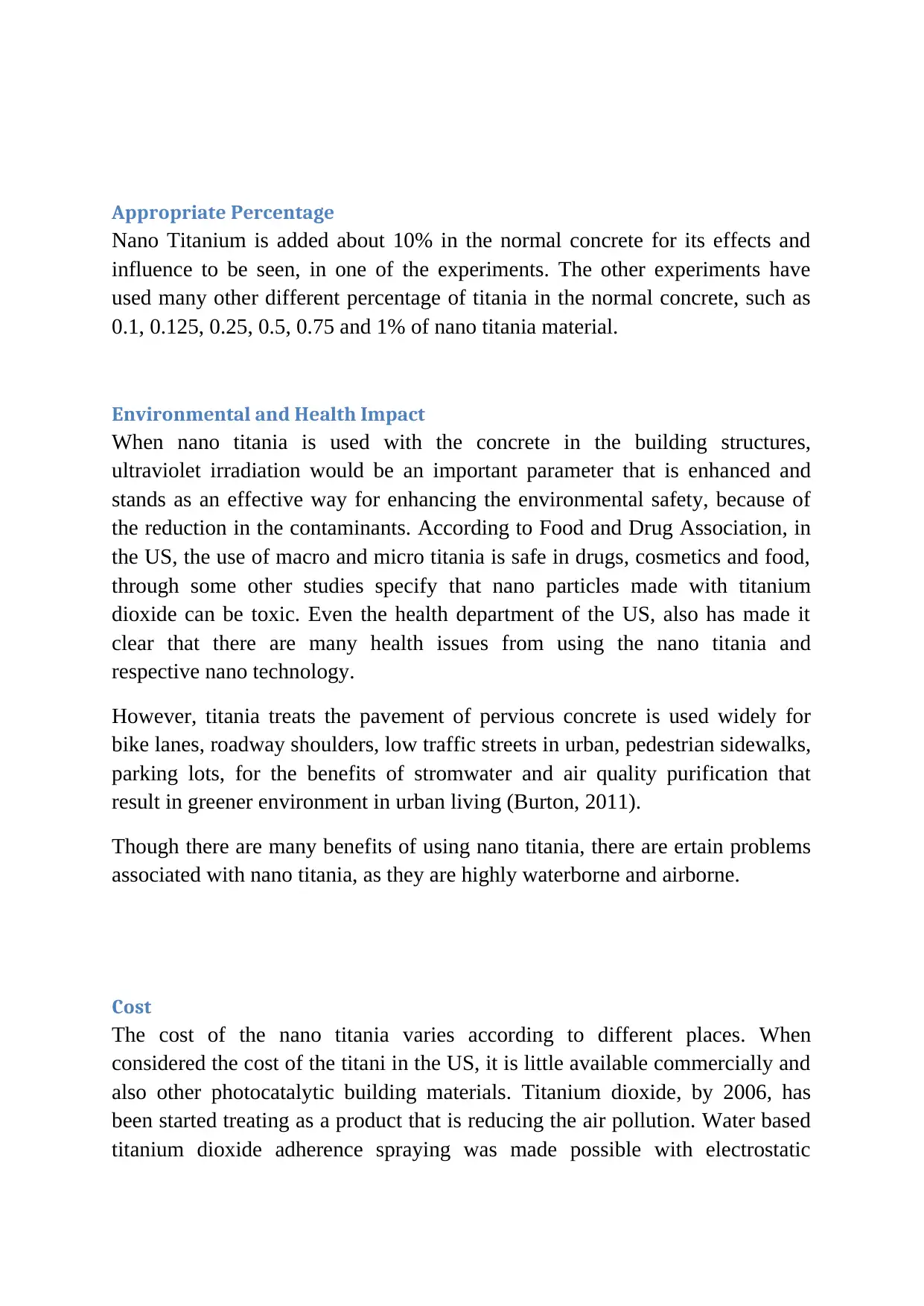
Nano Titanium is added about 10% in the normal concrete for its effects and
influence to be seen, in one of the experiments. The other experiments have
used many other different percentage of titania in the normal concrete, such as
0.1, 0.125, 0.25, 0.5, 0.75 and 1% of nano titania material.
Environmental and Health Impact
When nano titania is used with the concrete in the building structures,
ultraviolet irradiation would be an important parameter that is enhanced and
stands as an effective way for enhancing the environmental safety, because of
the reduction in the contaminants. According to Food and Drug Association, in
the US, the use of macro and micro titania is safe in drugs, cosmetics and food,
through some other studies specify that nano particles made with titanium
dioxide can be toxic. Even the health department of the US, also has made it
clear that there are many health issues from using the nano titania and
respective nano technology.
However, titania treats the pavement of pervious concrete is used widely for
bike lanes, roadway shoulders, low traffic streets in urban, pedestrian sidewalks,
parking lots, for the benefits of stromwater and air quality purification that
result in greener environment in urban living (Burton, 2011).
Though there are many benefits of using nano titania, there are ertain problems
associated with nano titania, as they are highly waterborne and airborne.
Cost
The cost of the nano titania varies according to different places. When
considered the cost of the titani in the US, it is little available commercially and
also other photocatalytic building materials. Titanium dioxide, by 2006, has
been started treating as a product that is reducing the air pollution. Water based
titanium dioxide adherence spraying was made possible with electrostatic
⊘ This is a preview!⊘
Do you want full access?
Subscribe today to unlock all pages.

Trusted by 1+ million students worldwide
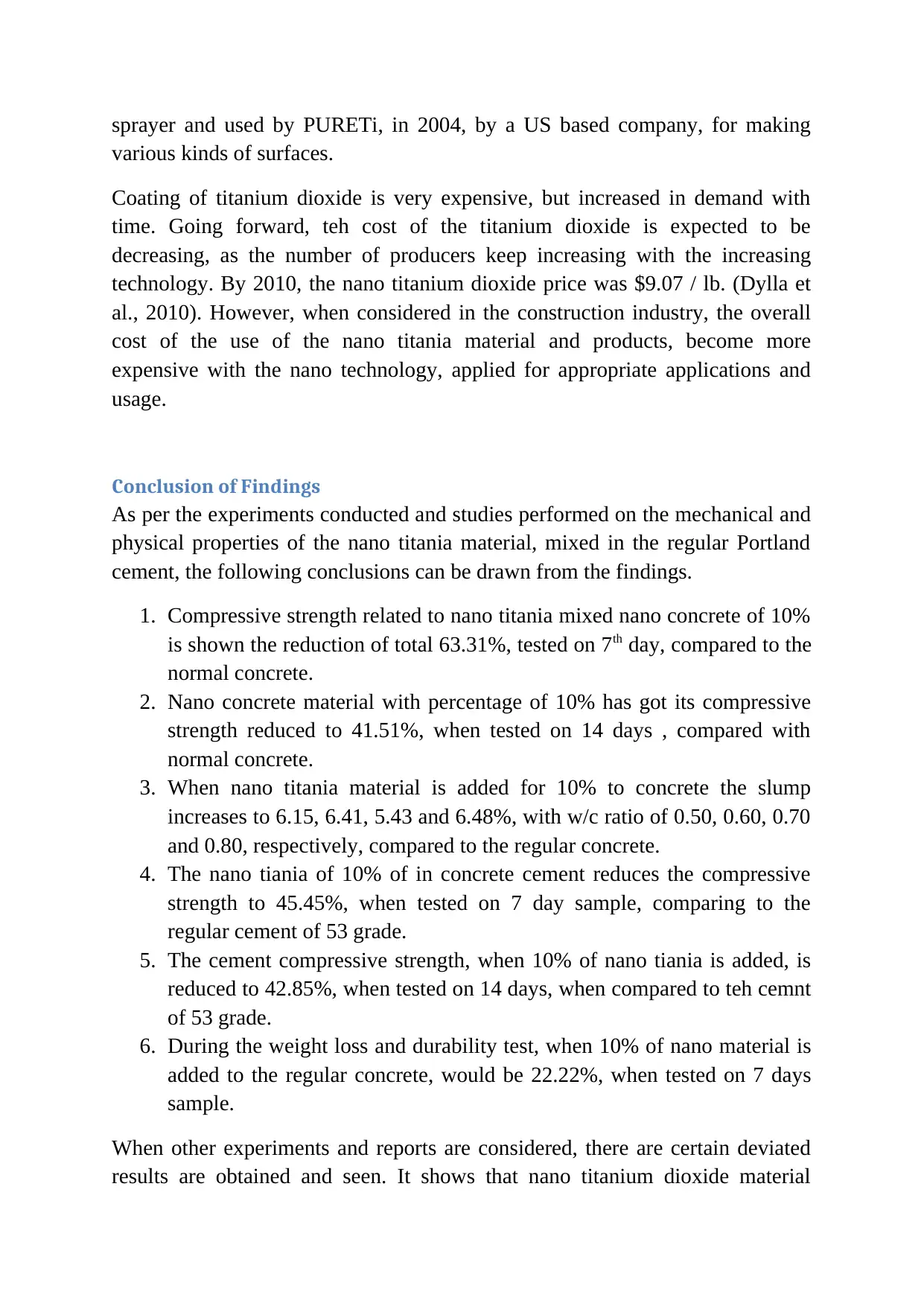
various kinds of surfaces.
Coating of titanium dioxide is very expensive, but increased in demand with
time. Going forward, teh cost of the titanium dioxide is expected to be
decreasing, as the number of producers keep increasing with the increasing
technology. By 2010, the nano titanium dioxide price was $9.07 / lb. (Dylla et
al., 2010). However, when considered in the construction industry, the overall
cost of the use of the nano titania material and products, become more
expensive with the nano technology, applied for appropriate applications and
usage.
Conclusion of Findings
As per the experiments conducted and studies performed on the mechanical and
physical properties of the nano titania material, mixed in the regular Portland
cement, the following conclusions can be drawn from the findings.
1. Compressive strength related to nano titania mixed nano concrete of 10%
is shown the reduction of total 63.31%, tested on 7th day, compared to the
normal concrete.
2. Nano concrete material with percentage of 10% has got its compressive
strength reduced to 41.51%, when tested on 14 days , compared with
normal concrete.
3. When nano titania material is added for 10% to concrete the slump
increases to 6.15, 6.41, 5.43 and 6.48%, with w/c ratio of 0.50, 0.60, 0.70
and 0.80, respectively, compared to the regular concrete.
4. The nano tiania of 10% of in concrete cement reduces the compressive
strength to 45.45%, when tested on 7 day sample, comparing to the
regular cement of 53 grade.
5. The cement compressive strength, when 10% of nano tiania is added, is
reduced to 42.85%, when tested on 14 days, when compared to teh cemnt
of 53 grade.
6. During the weight loss and durability test, when 10% of nano material is
added to the regular concrete, would be 22.22%, when tested on 7 days
sample.
When other experiments and reports are considered, there are certain deviated
results are obtained and seen. It shows that nano titanium dioxide material
Paraphrase This Document
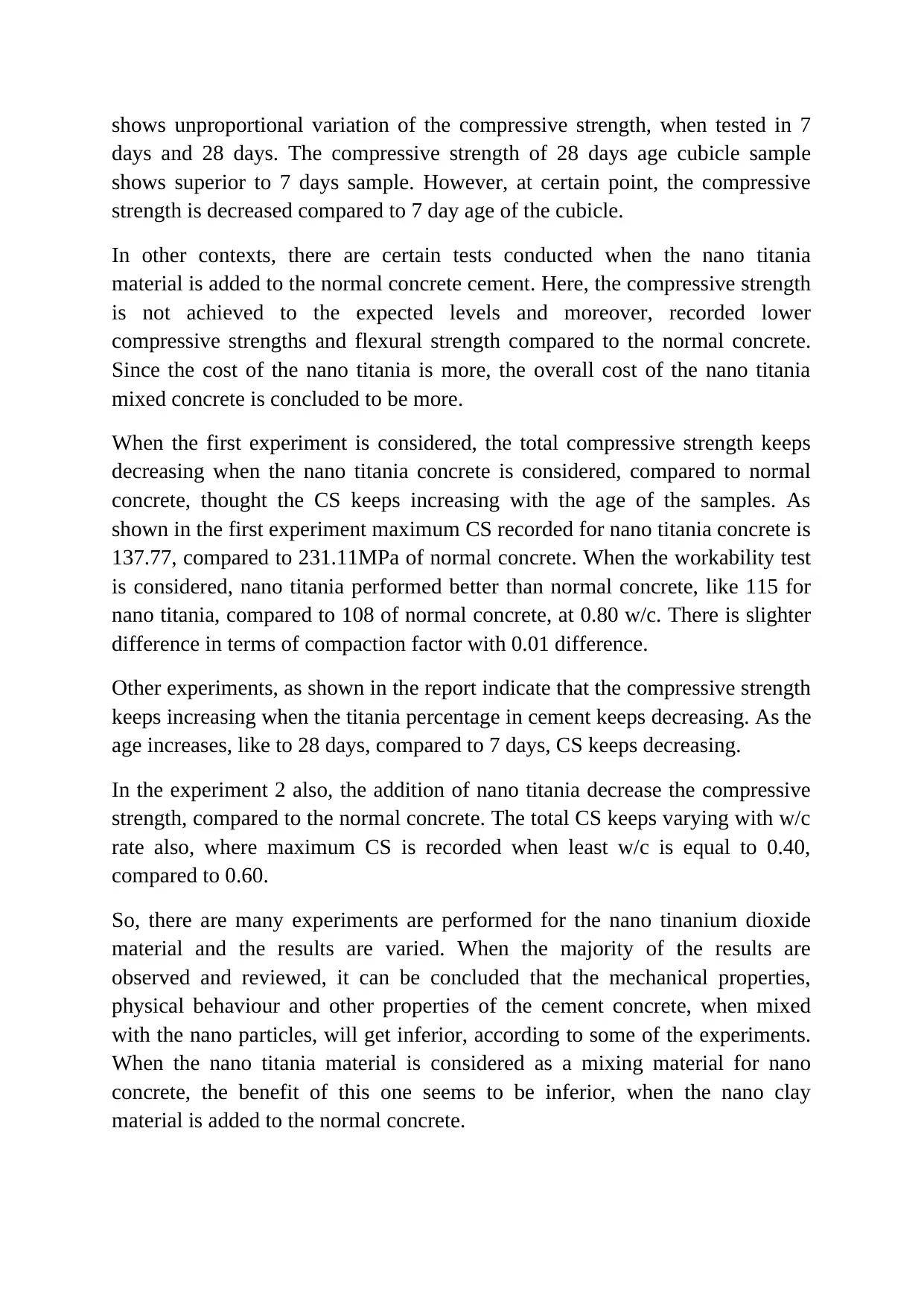
days and 28 days. The compressive strength of 28 days age cubicle sample
shows superior to 7 days sample. However, at certain point, the compressive
strength is decreased compared to 7 day age of the cubicle.
In other contexts, there are certain tests conducted when the nano titania
material is added to the normal concrete cement. Here, the compressive strength
is not achieved to the expected levels and moreover, recorded lower
compressive strengths and flexural strength compared to the normal concrete.
Since the cost of the nano titania is more, the overall cost of the nano titania
mixed concrete is concluded to be more.
When the first experiment is considered, the total compressive strength keeps
decreasing when the nano titania concrete is considered, compared to normal
concrete, thought the CS keeps increasing with the age of the samples. As
shown in the first experiment maximum CS recorded for nano titania concrete is
137.77, compared to 231.11MPa of normal concrete. When the workability test
is considered, nano titania performed better than normal concrete, like 115 for
nano titania, compared to 108 of normal concrete, at 0.80 w/c. There is slighter
difference in terms of compaction factor with 0.01 difference.
Other experiments, as shown in the report indicate that the compressive strength
keeps increasing when the titania percentage in cement keeps decreasing. As the
age increases, like to 28 days, compared to 7 days, CS keeps decreasing.
In the experiment 2 also, the addition of nano titania decrease the compressive
strength, compared to the normal concrete. The total CS keeps varying with w/c
rate also, where maximum CS is recorded when least w/c is equal to 0.40,
compared to 0.60.
So, there are many experiments are performed for the nano tinanium dioxide
material and the results are varied. When the majority of the results are
observed and reviewed, it can be concluded that the mechanical properties,
physical behaviour and other properties of the cement concrete, when mixed
with the nano particles, will get inferior, according to some of the experiments.
When the nano titania material is considered as a mixing material for nano
concrete, the benefit of this one seems to be inferior, when the nano clay
material is added to the normal concrete.
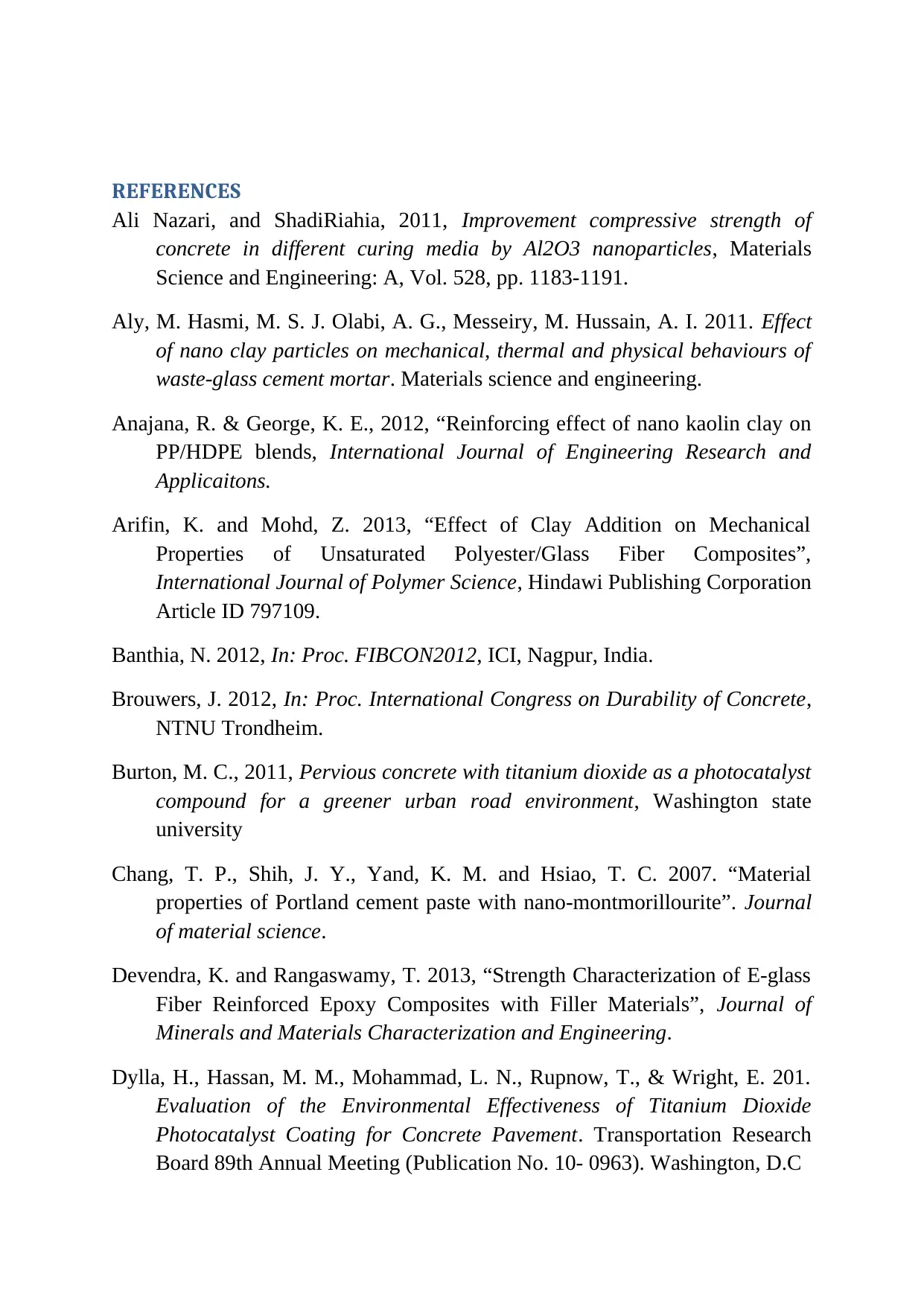
Ali Nazari, and ShadiRiahia, 2011, Improvement compressive strength of
concrete in different curing media by Al2O3 nanoparticles, Materials
Science and Engineering: A, Vol. 528, pp. 1183-1191.
Aly, M. Hasmi, M. S. J. Olabi, A. G., Messeiry, M. Hussain, A. I. 2011. Effect
of nano clay particles on mechanical, thermal and physical behaviours of
waste-glass cement mortar. Materials science and engineering.
Anajana, R. & George, K. E., 2012, “Reinforcing effect of nano kaolin clay on
PP/HDPE blends, International Journal of Engineering Research and
Applicaitons.
Arifin, K. and Mohd, Z. 2013, “Effect of Clay Addition on Mechanical
Properties of Unsaturated Polyester/Glass Fiber Composites”,
International Journal of Polymer Science, Hindawi Publishing Corporation
Article ID 797109.
Banthia, N. 2012, In: Proc. FIBCON2012, ICI, Nagpur, India.
Brouwers, J. 2012, In: Proc. International Congress on Durability of Concrete,
NTNU Trondheim.
Burton, M. C., 2011, Pervious concrete with titanium dioxide as a photocatalyst
compound for a greener urban road environment, Washington state
university
Chang, T. P., Shih, J. Y., Yand, K. M. and Hsiao, T. C. 2007. “Material
properties of Portland cement paste with nano-montmorillourite”. Journal
of material science.
Devendra, K. and Rangaswamy, T. 2013, “Strength Characterization of E-glass
Fiber Reinforced Epoxy Composites with Filler Materials”, Journal of
Minerals and Materials Characterization and Engineering.
Dylla, H., Hassan, M. M., Mohammad, L. N., Rupnow, T., & Wright, E. 201.
Evaluation of the Environmental Effectiveness of Titanium Dioxide
Photocatalyst Coating for Concrete Pavement. Transportation Research
Board 89th Annual Meeting (Publication No. 10- 0963). Washington, D.C
⊘ This is a preview!⊘
Do you want full access?
Subscribe today to unlock all pages.

Trusted by 1+ million students worldwide
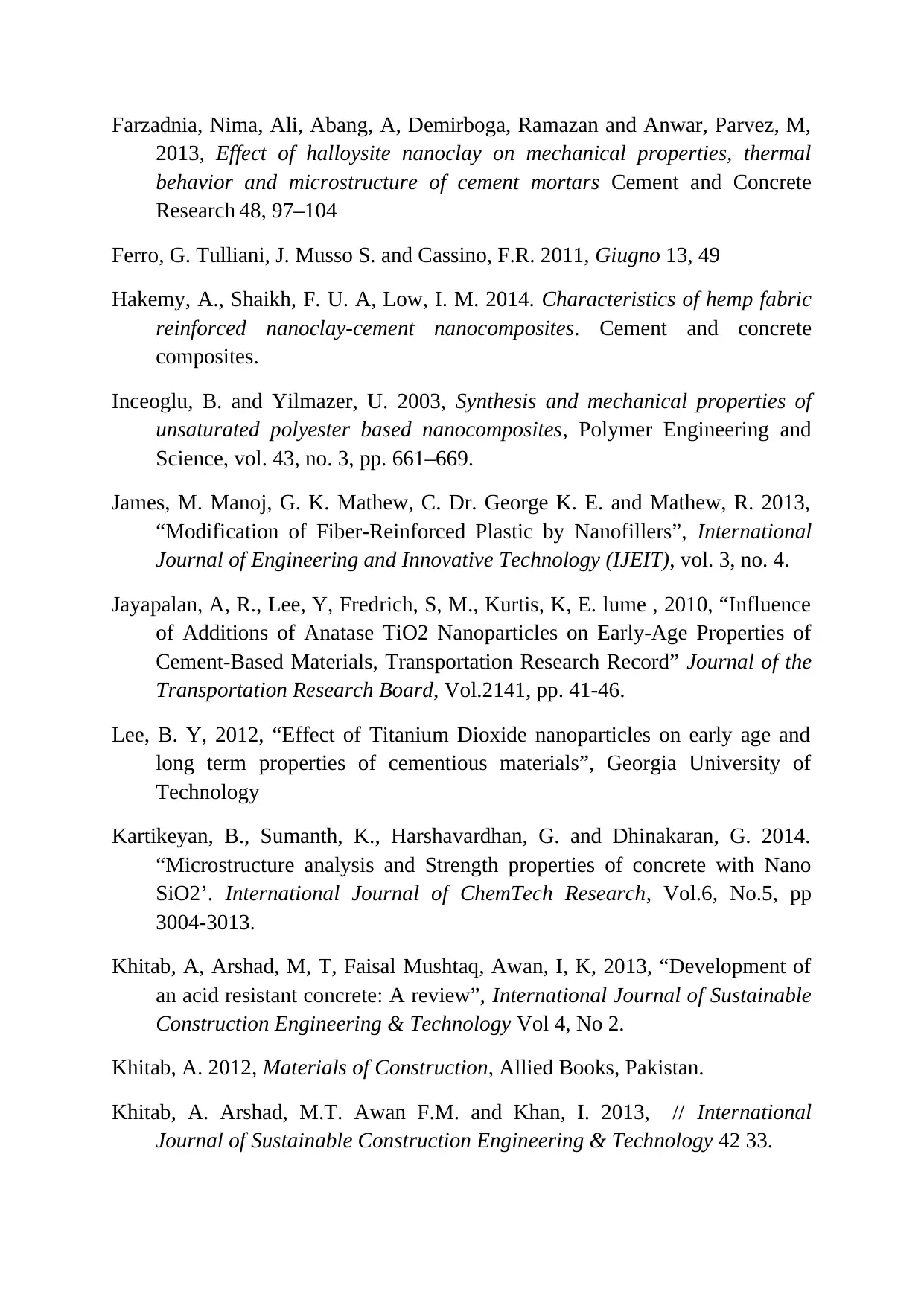
2013, Effect of halloysite nanoclay on mechanical properties, thermal
behavior and microstructure of cement mortars Cement and Concrete
Research 48, 97–104
Ferro, G. Tulliani, J. Musso S. and Cassino, F.R. 2011, Giugno 13, 49
Hakemy, A., Shaikh, F. U. A, Low, I. M. 2014. Characteristics of hemp fabric
reinforced nanoclay-cement nanocomposites. Cement and concrete
composites.
Inceoglu, B. and Yilmazer, U. 2003, Synthesis and mechanical properties of
unsaturated polyester based nanocomposites, Polymer Engineering and
Science, vol. 43, no. 3, pp. 661–669.
James, M. Manoj, G. K. Mathew, C. Dr. George K. E. and Mathew, R. 2013,
“Modification of Fiber-Reinforced Plastic by Nanofillers”, International
Journal of Engineering and Innovative Technology (IJEIT), vol. 3, no. 4.
Jayapalan, A, R., Lee, Y, Fredrich, S, M., Kurtis, K, E. lume , 2010, “Influence
of Additions of Anatase TiO2 Nanoparticles on Early-Age Properties of
Cement-Based Materials, Transportation Research Record” Journal of the
Transportation Research Board, Vol.2141, pp. 41-46.
Lee, B. Y, 2012, “Effect of Titanium Dioxide nanoparticles on early age and
long term properties of cementious materials”, Georgia University of
Technology
Kartikeyan, B., Sumanth, K., Harshavardhan, G. and Dhinakaran, G. 2014.
“Microstructure analysis and Strength properties of concrete with Nano
SiO2’. International Journal of ChemTech Research, Vol.6, No.5, pp
3004-3013.
Khitab, A, Arshad, M, T, Faisal Mushtaq, Awan, I, K, 2013, “Development of
an acid resistant concrete: A review”, International Journal of Sustainable
Construction Engineering & Technology Vol 4, No 2.
Khitab, A. 2012, Materials of Construction, Allied Books, Pakistan.
Khitab, A. Arshad, M.T. Awan F.M. and Khan, I. 2013, // International
Journal of Sustainable Construction Engineering & Technology 42 33.
Paraphrase This Document
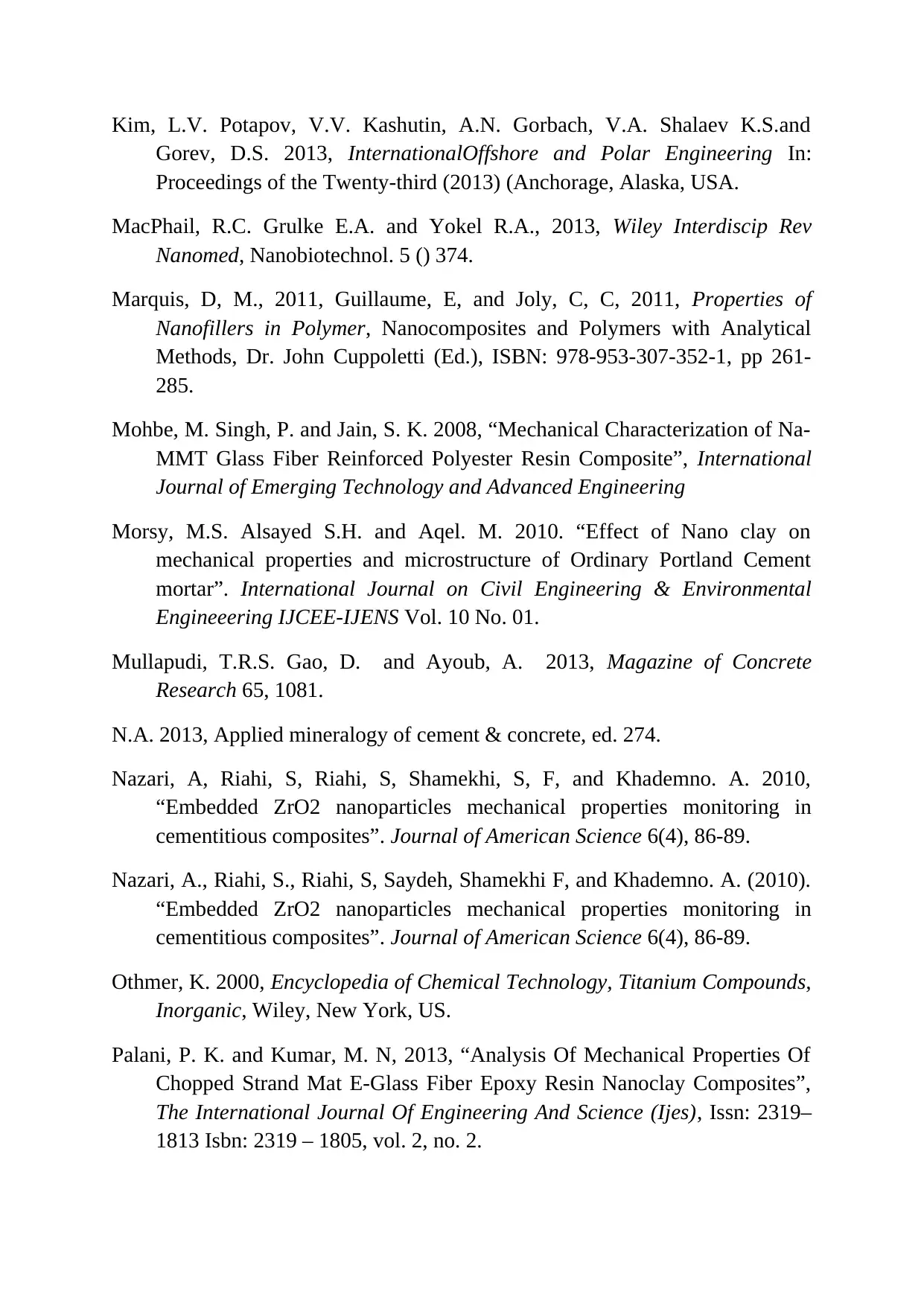
Gorev, D.S. 2013, InternationalOffshore and Polar Engineering In:
Proceedings of the Twenty-third (2013) (Anchorage, Alaska, USA.
MacPhail, R.C. Grulke E.A. and Yokel R.A., 2013, Wiley Interdiscip Rev
Nanomed, Nanobiotechnol. 5 () 374.
Marquis, D, M., 2011, Guillaume, E, and Joly, C, C, 2011, Properties of
Nanofillers in Polymer, Nanocomposites and Polymers with Analytical
Methods, Dr. John Cuppoletti (Ed.), ISBN: 978-953-307-352-1, pp 261-
285.
Mohbe, M. Singh, P. and Jain, S. K. 2008, “Mechanical Characterization of Na-
MMT Glass Fiber Reinforced Polyester Resin Composite”, International
Journal of Emerging Technology and Advanced Engineering
Morsy, M.S. Alsayed S.H. and Aqel. M. 2010. “Effect of Nano clay on
mechanical properties and microstructure of Ordinary Portland Cement
mortar”. International Journal on Civil Engineering & Environmental
Engineeering IJCEE-IJENS Vol. 10 No. 01.
Mullapudi, T.R.S. Gao, D. and Ayoub, A. 2013, Magazine of Concrete
Research 65, 1081.
N.A. 2013, Applied mineralogy of cement & concrete, ed. 274.
Nazari, A, Riahi, S, Riahi, S, Shamekhi, S, F, and Khademno. A. 2010,
“Embedded ZrO2 nanoparticles mechanical properties monitoring in
cementitious composites”. Journal of American Science 6(4), 86-89.
Nazari, A., Riahi, S., Riahi, S, Saydeh, Shamekhi F, and Khademno. A. (2010).
“Embedded ZrO2 nanoparticles mechanical properties monitoring in
cementitious composites”. Journal of American Science 6(4), 86-89.
Othmer, K. 2000, Encyclopedia of Chemical Technology, Titanium Compounds,
Inorganic, Wiley, New York, US.
Palani, P. K. and Kumar, M. N, 2013, “Analysis Of Mechanical Properties Of
Chopped Strand Mat E-Glass Fiber Epoxy Resin Nanoclay Composites”,
The International Journal Of Engineering And Science (Ijes), Issn: 2319–
1813 Isbn: 2319 – 1805, vol. 2, no. 2.
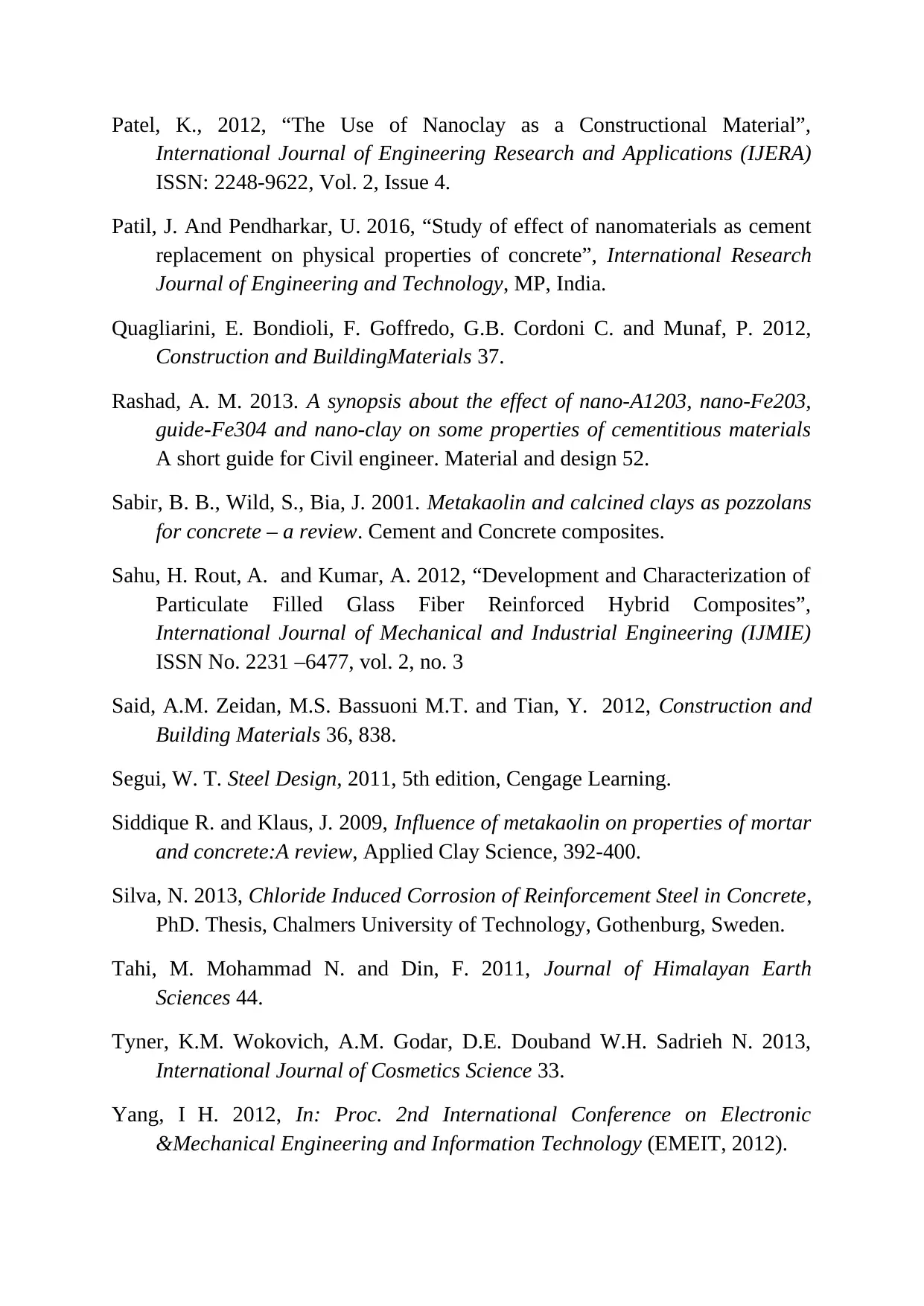
International Journal of Engineering Research and Applications (IJERA)
ISSN: 2248-9622, Vol. 2, Issue 4.
Patil, J. And Pendharkar, U. 2016, “Study of effect of nanomaterials as cement
replacement on physical properties of concrete”, International Research
Journal of Engineering and Technology, MP, India.
Quagliarini, E. Bondioli, F. Goffredo, G.B. Cordoni C. and Munaf, P. 2012,
Construction and BuildingMaterials 37.
Rashad, A. M. 2013. A synopsis about the effect of nano-A1203, nano-Fe203,
guide-Fe304 and nano-clay on some properties of cementitious materials
A short guide for Civil engineer. Material and design 52.
Sabir, B. B., Wild, S., Bia, J. 2001. Metakaolin and calcined clays as pozzolans
for concrete – a review. Cement and Concrete composites.
Sahu, H. Rout, A. and Kumar, A. 2012, “Development and Characterization of
Particulate Filled Glass Fiber Reinforced Hybrid Composites”,
International Journal of Mechanical and Industrial Engineering (IJMIE)
ISSN No. 2231 –6477, vol. 2, no. 3
Said, A.M. Zeidan, M.S. Bassuoni M.T. and Tian, Y. 2012, Construction and
Building Materials 36, 838.
Segui, W. T. Steel Design, 2011, 5th edition, Cengage Learning.
Siddique R. and Klaus, J. 2009, Influence of metakaolin on properties of mortar
and concrete:A review, Applied Clay Science, 392-400.
Silva, N. 2013, Chloride Induced Corrosion of Reinforcement Steel in Concrete,
PhD. Thesis, Chalmers University of Technology, Gothenburg, Sweden.
Tahi, M. Mohammad N. and Din, F. 2011, Journal of Himalayan Earth
Sciences 44.
Tyner, K.M. Wokovich, A.M. Godar, D.E. Douband W.H. Sadrieh N. 2013,
International Journal of Cosmetics Science 33.
Yang, I H. 2012, In: Proc. 2nd International Conference on Electronic
&Mechanical Engineering and Information Technology (EMEIT, 2012).
⊘ This is a preview!⊘
Do you want full access?
Subscribe today to unlock all pages.

Trusted by 1+ million students worldwide
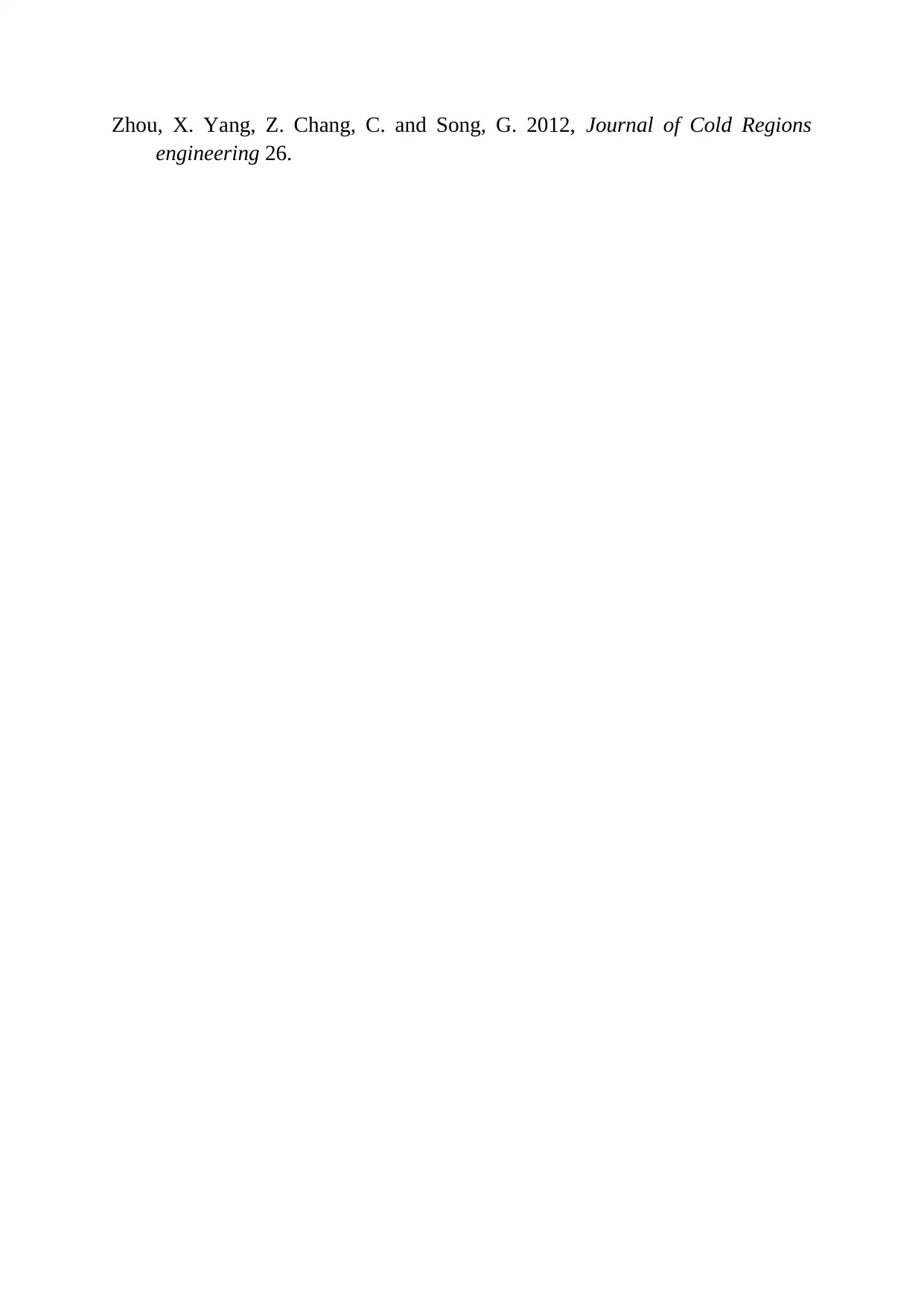
engineering 26.
Related Documents

Your All-in-One AI-Powered Toolkit for Academic Success.
+13062052269
info@desklib.com
Available 24*7 on WhatsApp / Email
© 2024 | Zucol Services PVT LTD | All rights reserved.