Effect of Welding Heat on Weldment Corrosion of Stainless Steel
VerifiedAdded on 2020/03/16
|9
|1634
|340
Report
AI Summary
This report presents a comprehensive analysis of the effect of welding heat on weldment corrosion in austenitic and ferritic stainless steel. The project, conducted at UTS Broadway, investigates the impact of various welding techniques, including Gas Tungsten Arc Welding (GTAW) and Friction Stir ...
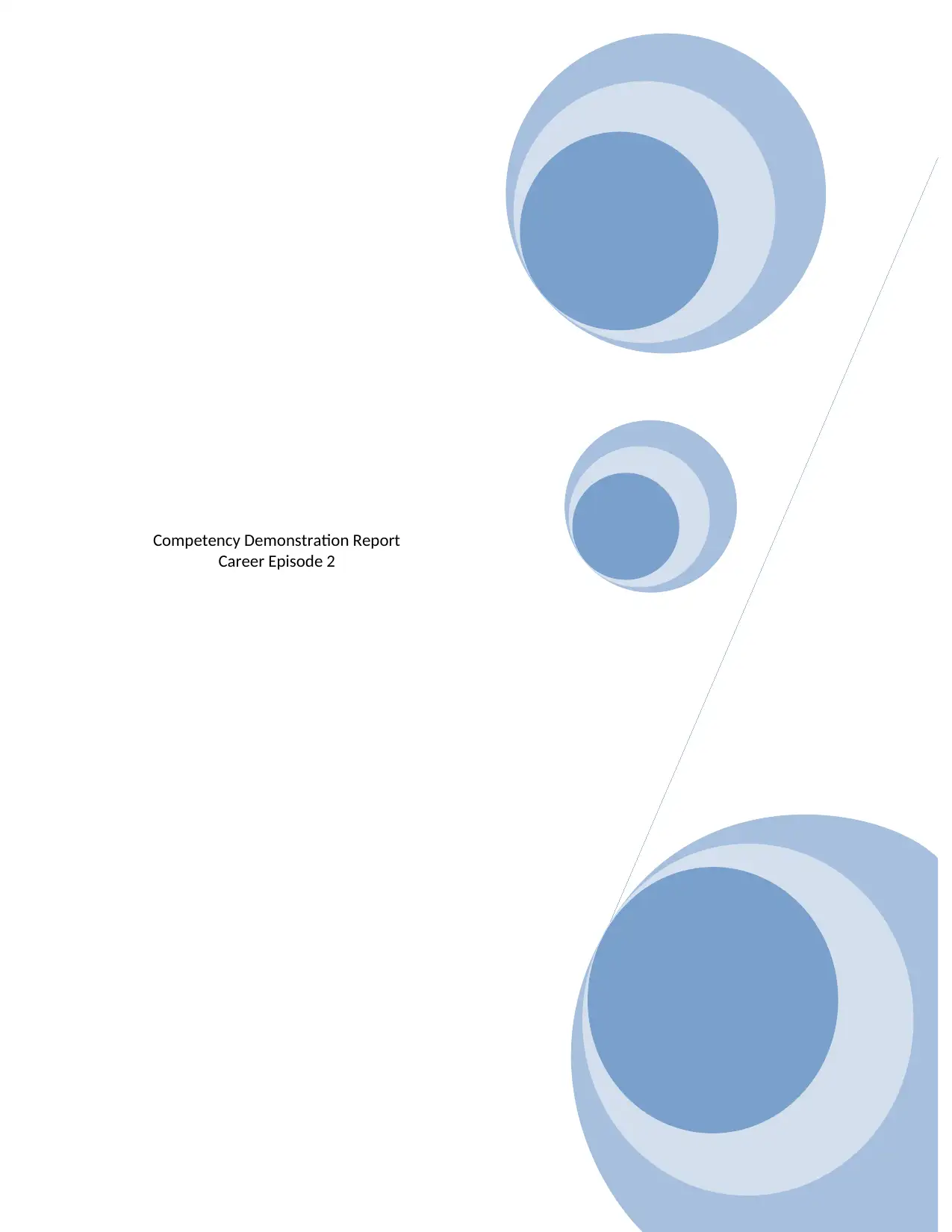
Competency Demonstration Report
Career Episode 2
Career Episode 2
Paraphrase This Document
Need a fresh take? Get an instant paraphrase of this document with our AI Paraphraser
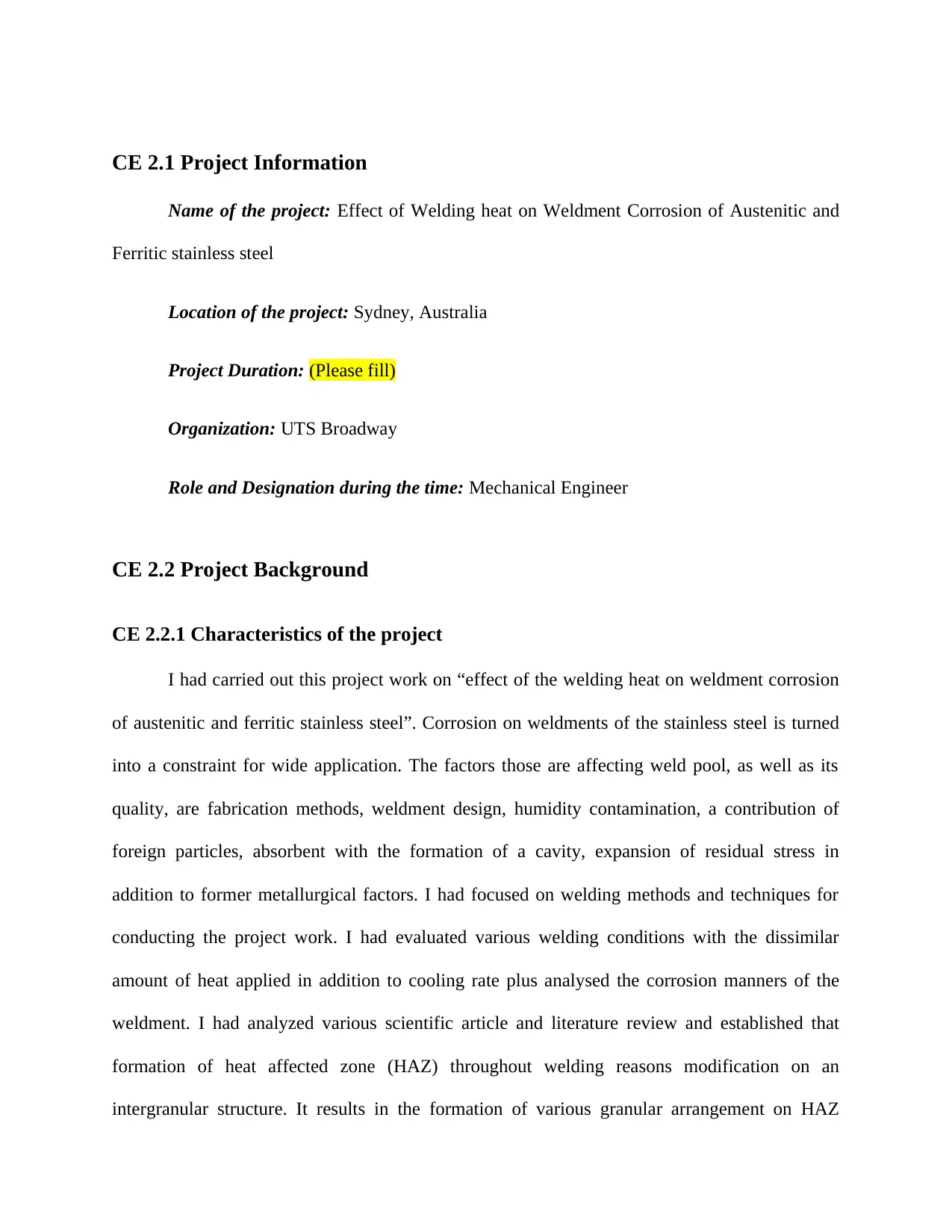
CE 2.1 Project Information
Name of the project: Effect of Welding heat on Weldment Corrosion of Austenitic and
Ferritic stainless steel
Location of the project: Sydney, Australia
Project Duration: (Please fill)
Organization: UTS Broadway
Role and Designation during the time: Mechanical Engineer
CE 2.2 Project Background
CE 2.2.1 Characteristics of the project
I had carried out this project work on “effect of the welding heat on weldment corrosion
of austenitic and ferritic stainless steel”. Corrosion on weldments of the stainless steel is turned
into a constraint for wide application. The factors those are affecting weld pool, as well as its
quality, are fabrication methods, weldment design, humidity contamination, a contribution of
foreign particles, absorbent with the formation of a cavity, expansion of residual stress in
addition to former metallurgical factors. I had focused on welding methods and techniques for
conducting the project work. I had evaluated various welding conditions with the dissimilar
amount of heat applied in addition to cooling rate plus analysed the corrosion manners of the
weldment. I had analyzed various scientific article and literature review and established that
formation of heat affected zone (HAZ) throughout welding reasons modification on an
intergranular structure. It results in the formation of various granular arrangement on HAZ
Name of the project: Effect of Welding heat on Weldment Corrosion of Austenitic and
Ferritic stainless steel
Location of the project: Sydney, Australia
Project Duration: (Please fill)
Organization: UTS Broadway
Role and Designation during the time: Mechanical Engineer
CE 2.2 Project Background
CE 2.2.1 Characteristics of the project
I had carried out this project work on “effect of the welding heat on weldment corrosion
of austenitic and ferritic stainless steel”. Corrosion on weldments of the stainless steel is turned
into a constraint for wide application. The factors those are affecting weld pool, as well as its
quality, are fabrication methods, weldment design, humidity contamination, a contribution of
foreign particles, absorbent with the formation of a cavity, expansion of residual stress in
addition to former metallurgical factors. I had focused on welding methods and techniques for
conducting the project work. I had evaluated various welding conditions with the dissimilar
amount of heat applied in addition to cooling rate plus analysed the corrosion manners of the
weldment. I had analyzed various scientific article and literature review and established that
formation of heat affected zone (HAZ) throughout welding reasons modification on an
intergranular structure. It results in the formation of various granular arrangement on HAZ
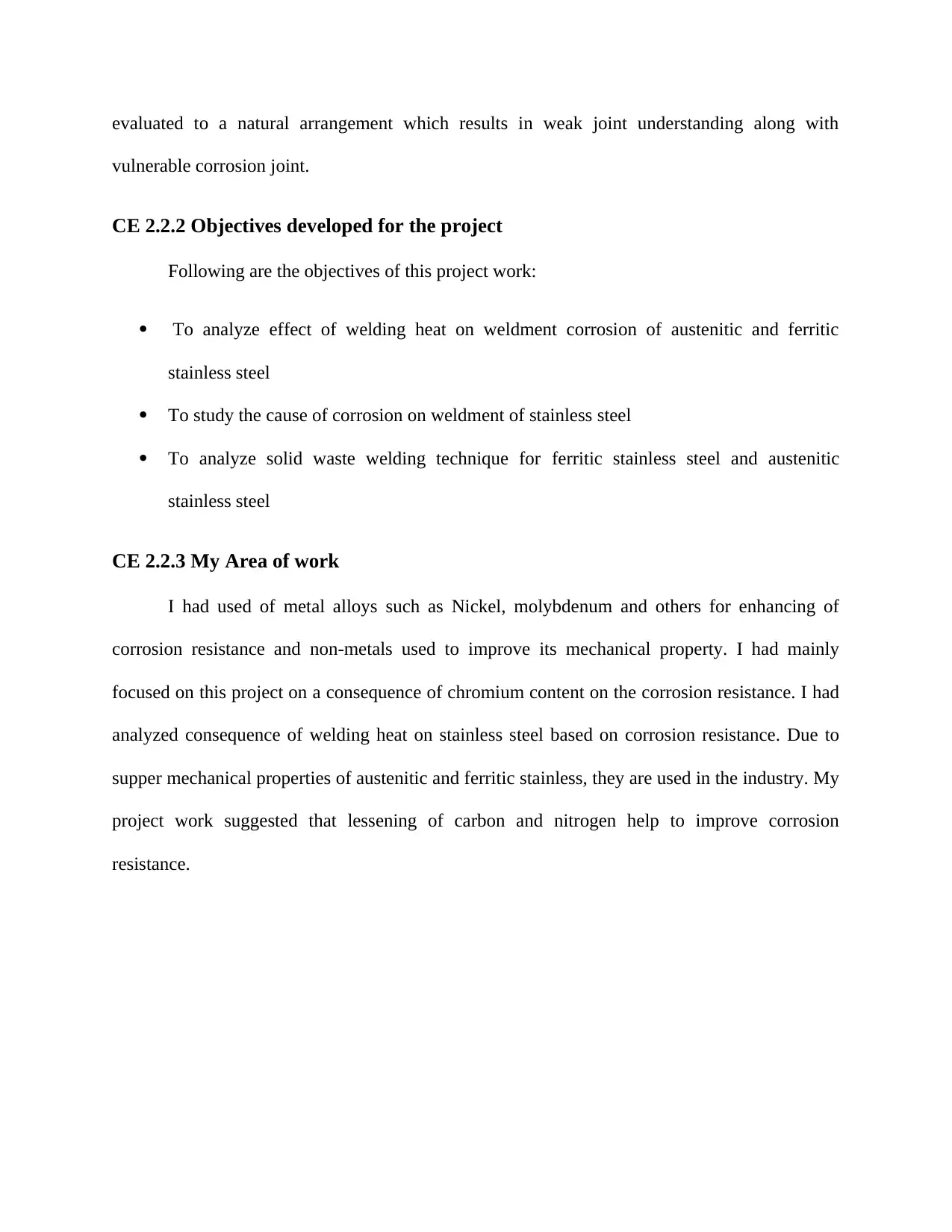
evaluated to a natural arrangement which results in weak joint understanding along with
vulnerable corrosion joint.
CE 2.2.2 Objectives developed for the project
Following are the objectives of this project work:
To analyze effect of welding heat on weldment corrosion of austenitic and ferritic
stainless steel
To study the cause of corrosion on weldment of stainless steel
To analyze solid waste welding technique for ferritic stainless steel and austenitic
stainless steel
CE 2.2.3 My Area of work
I had used of metal alloys such as Nickel, molybdenum and others for enhancing of
corrosion resistance and non-metals used to improve its mechanical property. I had mainly
focused on this project on a consequence of chromium content on the corrosion resistance. I had
analyzed consequence of welding heat on stainless steel based on corrosion resistance. Due to
supper mechanical properties of austenitic and ferritic stainless, they are used in the industry. My
project work suggested that lessening of carbon and nitrogen help to improve corrosion
resistance.
vulnerable corrosion joint.
CE 2.2.2 Objectives developed for the project
Following are the objectives of this project work:
To analyze effect of welding heat on weldment corrosion of austenitic and ferritic
stainless steel
To study the cause of corrosion on weldment of stainless steel
To analyze solid waste welding technique for ferritic stainless steel and austenitic
stainless steel
CE 2.2.3 My Area of work
I had used of metal alloys such as Nickel, molybdenum and others for enhancing of
corrosion resistance and non-metals used to improve its mechanical property. I had mainly
focused on this project on a consequence of chromium content on the corrosion resistance. I had
analyzed consequence of welding heat on stainless steel based on corrosion resistance. Due to
supper mechanical properties of austenitic and ferritic stainless, they are used in the industry. My
project work suggested that lessening of carbon and nitrogen help to improve corrosion
resistance.
⊘ This is a preview!⊘
Do you want full access?
Subscribe today to unlock all pages.

Trusted by 1+ million students worldwide
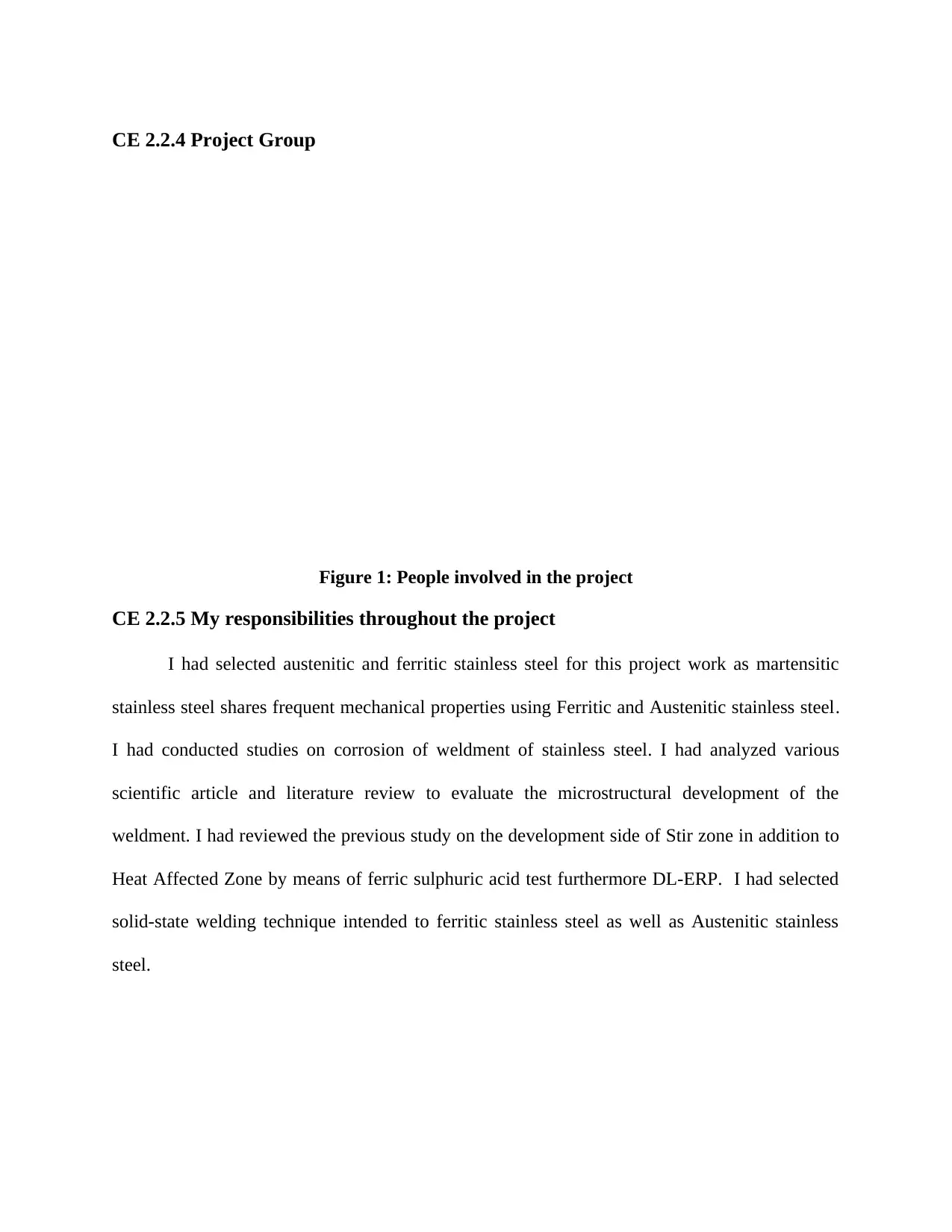
CE 2.2.4 Project Group
Figure 1: People involved in the project
CE 2.2.5 My responsibilities throughout the project
I had selected austenitic and ferritic stainless steel for this project work as martensitic
stainless steel shares frequent mechanical properties using Ferritic and Austenitic stainless steel.
I had conducted studies on corrosion of weldment of stainless steel. I had analyzed various
scientific article and literature review to evaluate the microstructural development of the
weldment. I had reviewed the previous study on the development side of Stir zone in addition to
Heat Affected Zone by means of ferric sulphuric acid test furthermore DL-ERP. I had selected
solid-state welding technique intended to ferritic stainless steel as well as Austenitic stainless
steel.
DeanofFacultyHeadofthedepartmentProjectSupervisorMechanicalEngineer
Figure 1: People involved in the project
CE 2.2.5 My responsibilities throughout the project
I had selected austenitic and ferritic stainless steel for this project work as martensitic
stainless steel shares frequent mechanical properties using Ferritic and Austenitic stainless steel.
I had conducted studies on corrosion of weldment of stainless steel. I had analyzed various
scientific article and literature review to evaluate the microstructural development of the
weldment. I had reviewed the previous study on the development side of Stir zone in addition to
Heat Affected Zone by means of ferric sulphuric acid test furthermore DL-ERP. I had selected
solid-state welding technique intended to ferritic stainless steel as well as Austenitic stainless
steel.
DeanofFacultyHeadofthedepartmentProjectSupervisorMechanicalEngineer
Paraphrase This Document
Need a fresh take? Get an instant paraphrase of this document with our AI Paraphraser
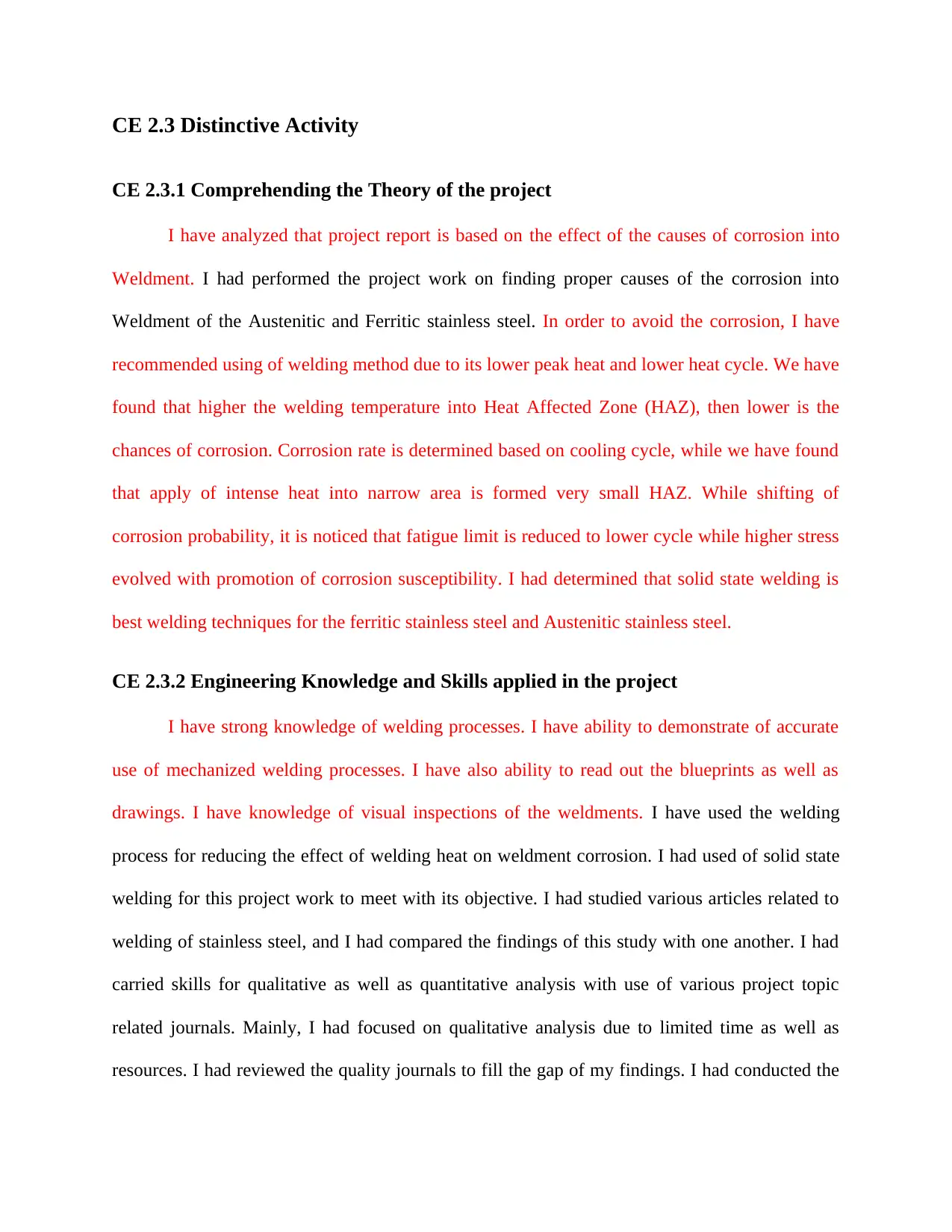
CE 2.3 Distinctive Activity
CE 2.3.1 Comprehending the Theory of the project
I have analyzed that project report is based on the effect of the causes of corrosion into
Weldment. I had performed the project work on finding proper causes of the corrosion into
Weldment of the Austenitic and Ferritic stainless steel. In order to avoid the corrosion, I have
recommended using of welding method due to its lower peak heat and lower heat cycle. We have
found that higher the welding temperature into Heat Affected Zone (HAZ), then lower is the
chances of corrosion. Corrosion rate is determined based on cooling cycle, while we have found
that apply of intense heat into narrow area is formed very small HAZ. While shifting of
corrosion probability, it is noticed that fatigue limit is reduced to lower cycle while higher stress
evolved with promotion of corrosion susceptibility. I had determined that solid state welding is
best welding techniques for the ferritic stainless steel and Austenitic stainless steel.
CE 2.3.2 Engineering Knowledge and Skills applied in the project
I have strong knowledge of welding processes. I have ability to demonstrate of accurate
use of mechanized welding processes. I have also ability to read out the blueprints as well as
drawings. I have knowledge of visual inspections of the weldments. I have used the welding
process for reducing the effect of welding heat on weldment corrosion. I had used of solid state
welding for this project work to meet with its objective. I had studied various articles related to
welding of stainless steel, and I had compared the findings of this study with one another. I had
carried skills for qualitative as well as quantitative analysis with use of various project topic
related journals. Mainly, I had focused on qualitative analysis due to limited time as well as
resources. I had reviewed the quality journals to fill the gap of my findings. I had conducted the
CE 2.3.1 Comprehending the Theory of the project
I have analyzed that project report is based on the effect of the causes of corrosion into
Weldment. I had performed the project work on finding proper causes of the corrosion into
Weldment of the Austenitic and Ferritic stainless steel. In order to avoid the corrosion, I have
recommended using of welding method due to its lower peak heat and lower heat cycle. We have
found that higher the welding temperature into Heat Affected Zone (HAZ), then lower is the
chances of corrosion. Corrosion rate is determined based on cooling cycle, while we have found
that apply of intense heat into narrow area is formed very small HAZ. While shifting of
corrosion probability, it is noticed that fatigue limit is reduced to lower cycle while higher stress
evolved with promotion of corrosion susceptibility. I had determined that solid state welding is
best welding techniques for the ferritic stainless steel and Austenitic stainless steel.
CE 2.3.2 Engineering Knowledge and Skills applied in the project
I have strong knowledge of welding processes. I have ability to demonstrate of accurate
use of mechanized welding processes. I have also ability to read out the blueprints as well as
drawings. I have knowledge of visual inspections of the weldments. I have used the welding
process for reducing the effect of welding heat on weldment corrosion. I had used of solid state
welding for this project work to meet with its objective. I had studied various articles related to
welding of stainless steel, and I had compared the findings of this study with one another. I had
carried skills for qualitative as well as quantitative analysis with use of various project topic
related journals. Mainly, I had focused on qualitative analysis due to limited time as well as
resources. I had reviewed the quality journals to fill the gap of my findings. I had conducted the
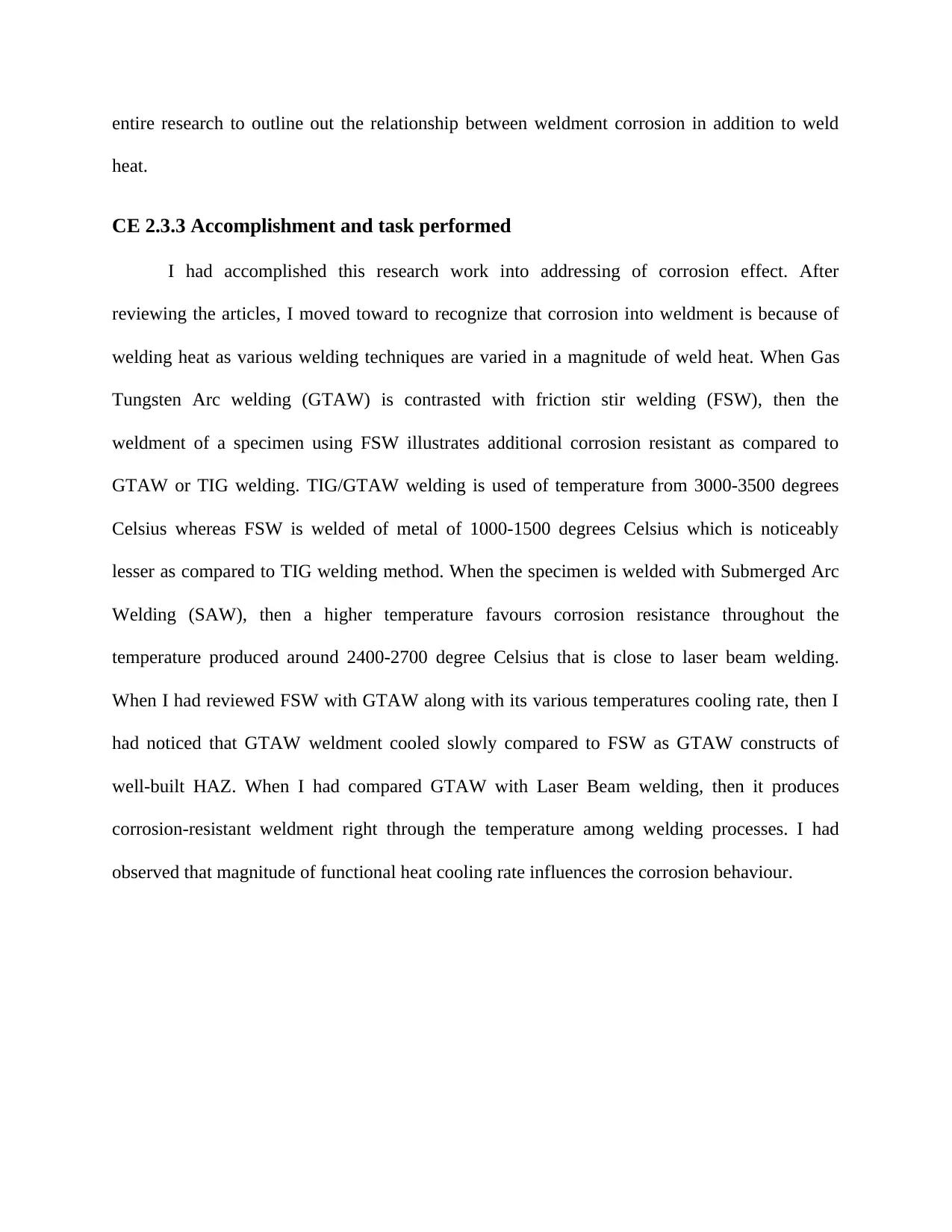
entire research to outline out the relationship between weldment corrosion in addition to weld
heat.
CE 2.3.3 Accomplishment and task performed
I had accomplished this research work into addressing of corrosion effect. After
reviewing the articles, I moved toward to recognize that corrosion into weldment is because of
welding heat as various welding techniques are varied in a magnitude of weld heat. When Gas
Tungsten Arc welding (GTAW) is contrasted with friction stir welding (FSW), then the
weldment of a specimen using FSW illustrates additional corrosion resistant as compared to
GTAW or TIG welding. TIG/GTAW welding is used of temperature from 3000-3500 degrees
Celsius whereas FSW is welded of metal of 1000-1500 degrees Celsius which is noticeably
lesser as compared to TIG welding method. When the specimen is welded with Submerged Arc
Welding (SAW), then a higher temperature favours corrosion resistance throughout the
temperature produced around 2400-2700 degree Celsius that is close to laser beam welding.
When I had reviewed FSW with GTAW along with its various temperatures cooling rate, then I
had noticed that GTAW weldment cooled slowly compared to FSW as GTAW constructs of
well-built HAZ. When I had compared GTAW with Laser Beam welding, then it produces
corrosion-resistant weldment right through the temperature among welding processes. I had
observed that magnitude of functional heat cooling rate influences the corrosion behaviour.
heat.
CE 2.3.3 Accomplishment and task performed
I had accomplished this research work into addressing of corrosion effect. After
reviewing the articles, I moved toward to recognize that corrosion into weldment is because of
welding heat as various welding techniques are varied in a magnitude of weld heat. When Gas
Tungsten Arc welding (GTAW) is contrasted with friction stir welding (FSW), then the
weldment of a specimen using FSW illustrates additional corrosion resistant as compared to
GTAW or TIG welding. TIG/GTAW welding is used of temperature from 3000-3500 degrees
Celsius whereas FSW is welded of metal of 1000-1500 degrees Celsius which is noticeably
lesser as compared to TIG welding method. When the specimen is welded with Submerged Arc
Welding (SAW), then a higher temperature favours corrosion resistance throughout the
temperature produced around 2400-2700 degree Celsius that is close to laser beam welding.
When I had reviewed FSW with GTAW along with its various temperatures cooling rate, then I
had noticed that GTAW weldment cooled slowly compared to FSW as GTAW constructs of
well-built HAZ. When I had compared GTAW with Laser Beam welding, then it produces
corrosion-resistant weldment right through the temperature among welding processes. I had
observed that magnitude of functional heat cooling rate influences the corrosion behaviour.
⊘ This is a preview!⊘
Do you want full access?
Subscribe today to unlock all pages.

Trusted by 1+ million students worldwide
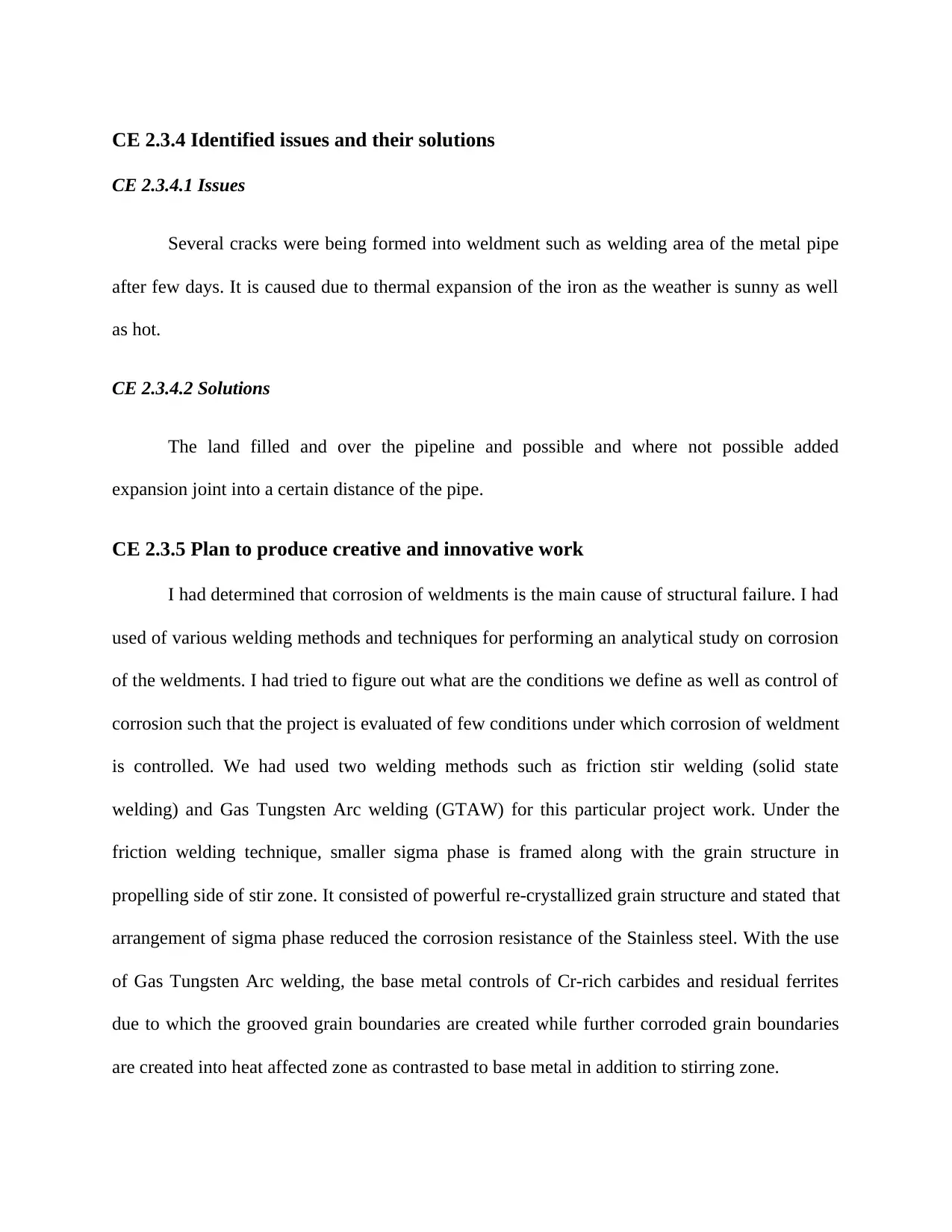
CE 2.3.4 Identified issues and their solutions
CE 2.3.4.1 Issues
Several cracks were being formed into weldment such as welding area of the metal pipe
after few days. It is caused due to thermal expansion of the iron as the weather is sunny as well
as hot.
CE 2.3.4.2 Solutions
The land filled and over the pipeline and possible and where not possible added
expansion joint into a certain distance of the pipe.
CE 2.3.5 Plan to produce creative and innovative work
I had determined that corrosion of weldments is the main cause of structural failure. I had
used of various welding methods and techniques for performing an analytical study on corrosion
of the weldments. I had tried to figure out what are the conditions we define as well as control of
corrosion such that the project is evaluated of few conditions under which corrosion of weldment
is controlled. We had used two welding methods such as friction stir welding (solid state
welding) and Gas Tungsten Arc welding (GTAW) for this particular project work. Under the
friction welding technique, smaller sigma phase is framed along with the grain structure in
propelling side of stir zone. It consisted of powerful re-crystallized grain structure and stated that
arrangement of sigma phase reduced the corrosion resistance of the Stainless steel. With the use
of Gas Tungsten Arc welding, the base metal controls of Cr-rich carbides and residual ferrites
due to which the grooved grain boundaries are created while further corroded grain boundaries
are created into heat affected zone as contrasted to base metal in addition to stirring zone.
CE 2.3.4.1 Issues
Several cracks were being formed into weldment such as welding area of the metal pipe
after few days. It is caused due to thermal expansion of the iron as the weather is sunny as well
as hot.
CE 2.3.4.2 Solutions
The land filled and over the pipeline and possible and where not possible added
expansion joint into a certain distance of the pipe.
CE 2.3.5 Plan to produce creative and innovative work
I had determined that corrosion of weldments is the main cause of structural failure. I had
used of various welding methods and techniques for performing an analytical study on corrosion
of the weldments. I had tried to figure out what are the conditions we define as well as control of
corrosion such that the project is evaluated of few conditions under which corrosion of weldment
is controlled. We had used two welding methods such as friction stir welding (solid state
welding) and Gas Tungsten Arc welding (GTAW) for this particular project work. Under the
friction welding technique, smaller sigma phase is framed along with the grain structure in
propelling side of stir zone. It consisted of powerful re-crystallized grain structure and stated that
arrangement of sigma phase reduced the corrosion resistance of the Stainless steel. With the use
of Gas Tungsten Arc welding, the base metal controls of Cr-rich carbides and residual ferrites
due to which the grooved grain boundaries are created while further corroded grain boundaries
are created into heat affected zone as contrasted to base metal in addition to stirring zone.
Paraphrase This Document
Need a fresh take? Get an instant paraphrase of this document with our AI Paraphraser
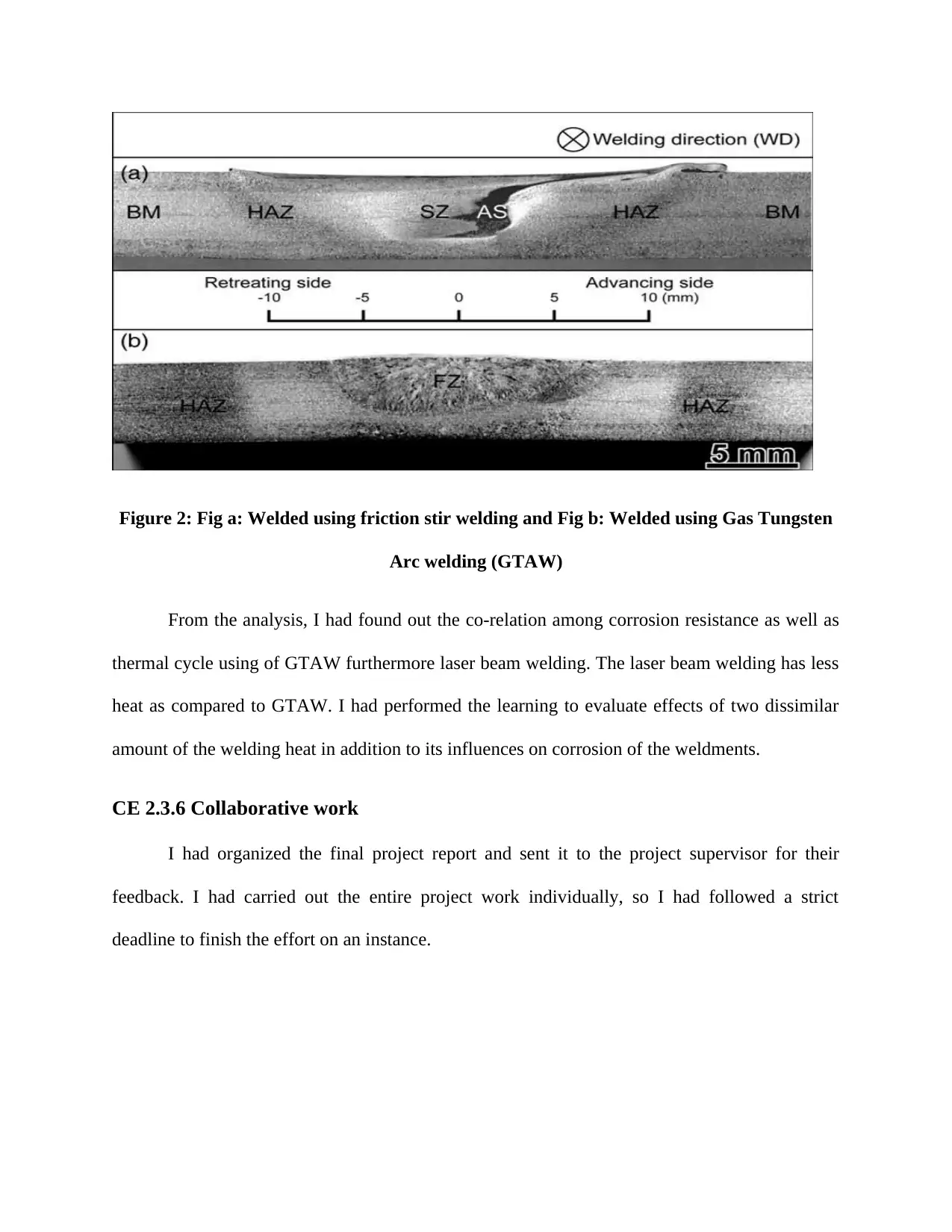
Figure 2: Fig a: Welded using friction stir welding and Fig b: Welded using Gas Tungsten
Arc welding (GTAW)
From the analysis, I had found out the co-relation among corrosion resistance as well as
thermal cycle using of GTAW furthermore laser beam welding. The laser beam welding has less
heat as compared to GTAW. I had performed the learning to evaluate effects of two dissimilar
amount of the welding heat in addition to its influences on corrosion of the weldments.
CE 2.3.6 Collaborative work
I had organized the final project report and sent it to the project supervisor for their
feedback. I had carried out the entire project work individually, so I had followed a strict
deadline to finish the effort on an instance.
Arc welding (GTAW)
From the analysis, I had found out the co-relation among corrosion resistance as well as
thermal cycle using of GTAW furthermore laser beam welding. The laser beam welding has less
heat as compared to GTAW. I had performed the learning to evaluate effects of two dissimilar
amount of the welding heat in addition to its influences on corrosion of the weldments.
CE 2.3.6 Collaborative work
I had organized the final project report and sent it to the project supervisor for their
feedback. I had carried out the entire project work individually, so I had followed a strict
deadline to finish the effort on an instance.
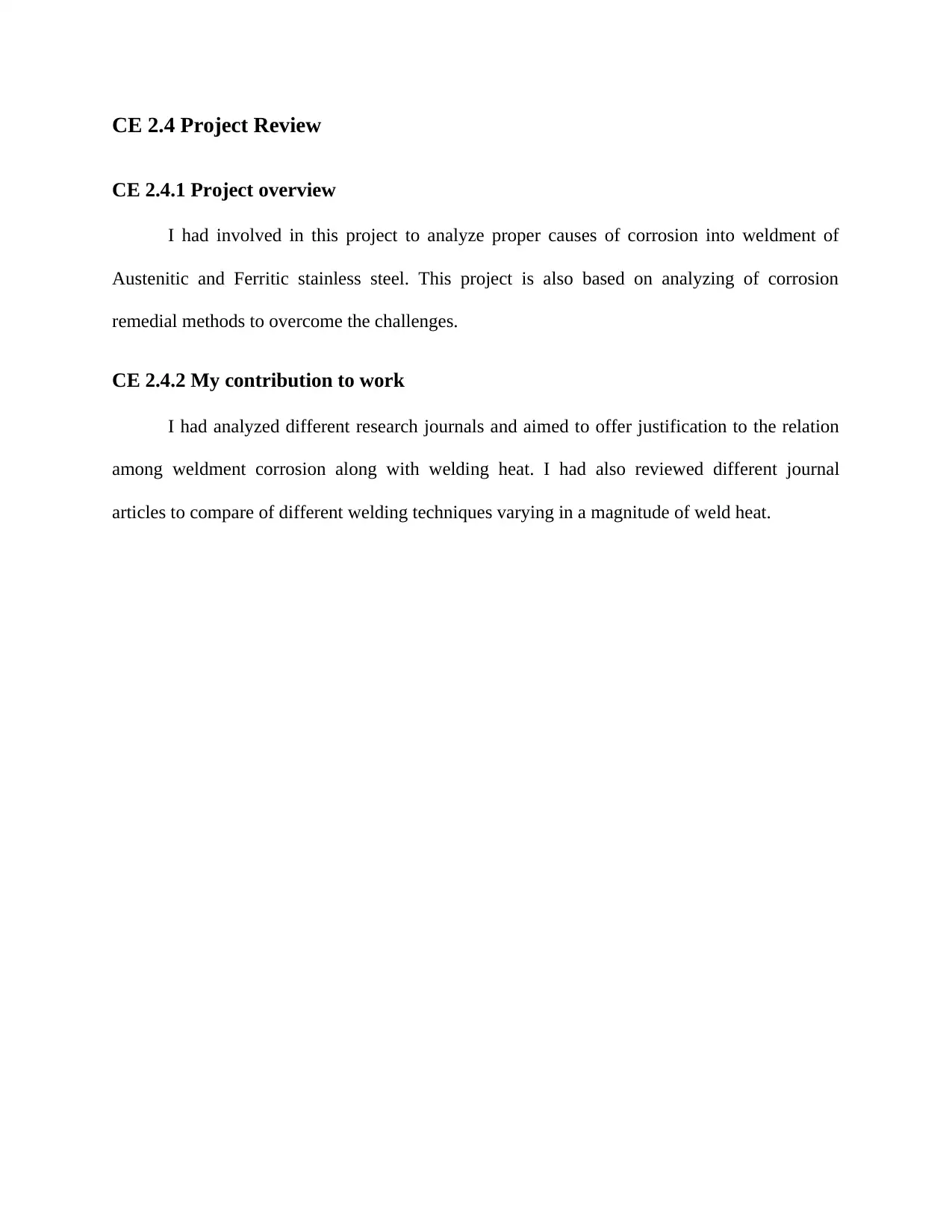
CE 2.4 Project Review
CE 2.4.1 Project overview
I had involved in this project to analyze proper causes of corrosion into weldment of
Austenitic and Ferritic stainless steel. This project is also based on analyzing of corrosion
remedial methods to overcome the challenges.
CE 2.4.2 My contribution to work
I had analyzed different research journals and aimed to offer justification to the relation
among weldment corrosion along with welding heat. I had also reviewed different journal
articles to compare of different welding techniques varying in a magnitude of weld heat.
CE 2.4.1 Project overview
I had involved in this project to analyze proper causes of corrosion into weldment of
Austenitic and Ferritic stainless steel. This project is also based on analyzing of corrosion
remedial methods to overcome the challenges.
CE 2.4.2 My contribution to work
I had analyzed different research journals and aimed to offer justification to the relation
among weldment corrosion along with welding heat. I had also reviewed different journal
articles to compare of different welding techniques varying in a magnitude of weld heat.
⊘ This is a preview!⊘
Do you want full access?
Subscribe today to unlock all pages.

Trusted by 1+ million students worldwide
1 out of 9
Related Documents

Your All-in-One AI-Powered Toolkit for Academic Success.
+13062052269
info@desklib.com
Available 24*7 on WhatsApp / Email
Unlock your academic potential
© 2024 | Zucol Services PVT LTD | All rights reserved.