Guided Gear Design for an Escalator
VerifiedAdded on 2019/09/16
|4
|1215
|572
Project
AI Summary
Design a gearbox system for an escalator, considering its components, constraints, and requirements. The task involves estimating loads imposed on the escalator, calculating torque required from the gearbox, determining gear forces, assessing face width of gears, checking preliminary estimates, suggesting modifications if necessary, and listing assumptions.
Contribute Materials
Your contribution can guide someone’s learning journey. Share your
documents today.
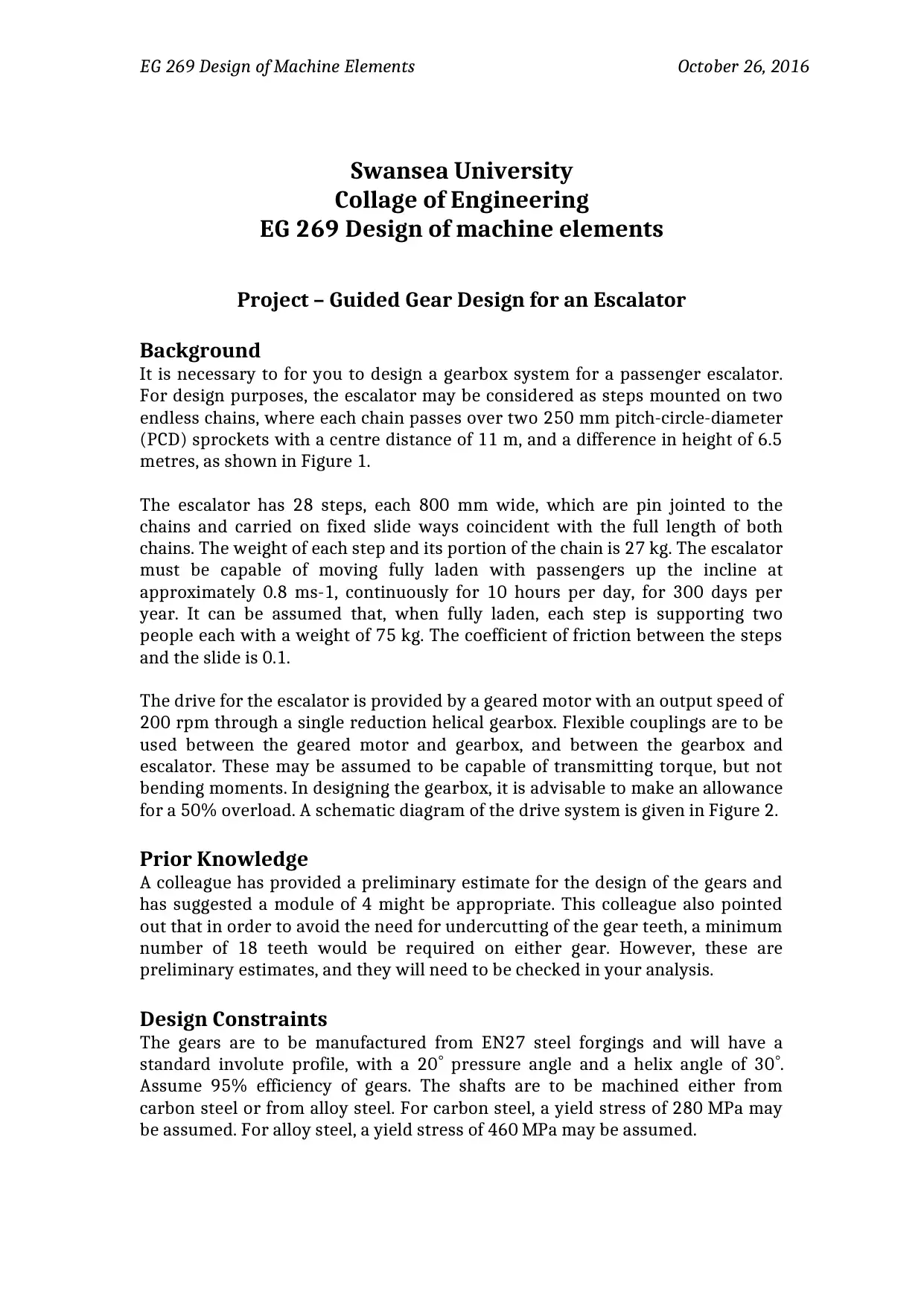
EG 269 Design of Machine Elements October 26, 2016
Swansea University
Collage of Engineering
EG 269 Design of machine elements
Project – Guided Gear Design for an Escalator
Background
It is necessary to for you to design a gearbox system for a passenger escalator.
For design purposes, the escalator may be considered as steps mounted on two
endless chains, where each chain passes over two 250 mm pitch-circle-diameter
(PCD) sprockets with a centre distance of 11 m, and a difference in height of 6.5
metres, as shown in Figure 1.
The escalator has 28 steps, each 800 mm wide, which are pin jointed to the
chains and carried on fixed slide ways coincident with the full length of both
chains. The weight of each step and its portion of the chain is 27 kg. The escalator
must be capable of moving fully laden with passengers up the incline at
approximately 0.8 ms-1, continuously for 10 hours per day, for 300 days per
year. It can be assumed that, when fully laden, each step is supporting two
people each with a weight of 75 kg. The coefficient of friction between the steps
and the slide is 0.1.
The drive for the escalator is provided by a geared motor with an output speed of
200 rpm through a single reduction helical gearbox. Flexible couplings are to be
used between the geared motor and gearbox, and between the gearbox and
escalator. These may be assumed to be capable of transmitting torque, but not
bending moments. In designing the gearbox, it is advisable to make an allowance
for a 50% overload. A schematic diagram of the drive system is given in Figure 2.
Prior Knowledge
A colleague has provided a preliminary estimate for the design of the gears and
has suggested a module of 4 might be appropriate. This colleague also pointed
out that in order to avoid the need for undercutting of the gear teeth, a minimum
number of 18 teeth would be required on either gear. However, these are
preliminary estimates, and they will need to be checked in your analysis.
Design Constraints
The gears are to be manufactured from EN27 steel forgings and will have a
standard involute profile, with a 20 pressure angle and a helix angle of 30.
Assume 95% efficiency of gears. The shafts are to be machined either from
carbon steel or from alloy steel. For carbon steel, a yield stress of 280 MPa may
be assumed. For alloy steel, a yield stress of 460 MPa may be assumed.
Swansea University
Collage of Engineering
EG 269 Design of machine elements
Project – Guided Gear Design for an Escalator
Background
It is necessary to for you to design a gearbox system for a passenger escalator.
For design purposes, the escalator may be considered as steps mounted on two
endless chains, where each chain passes over two 250 mm pitch-circle-diameter
(PCD) sprockets with a centre distance of 11 m, and a difference in height of 6.5
metres, as shown in Figure 1.
The escalator has 28 steps, each 800 mm wide, which are pin jointed to the
chains and carried on fixed slide ways coincident with the full length of both
chains. The weight of each step and its portion of the chain is 27 kg. The escalator
must be capable of moving fully laden with passengers up the incline at
approximately 0.8 ms-1, continuously for 10 hours per day, for 300 days per
year. It can be assumed that, when fully laden, each step is supporting two
people each with a weight of 75 kg. The coefficient of friction between the steps
and the slide is 0.1.
The drive for the escalator is provided by a geared motor with an output speed of
200 rpm through a single reduction helical gearbox. Flexible couplings are to be
used between the geared motor and gearbox, and between the gearbox and
escalator. These may be assumed to be capable of transmitting torque, but not
bending moments. In designing the gearbox, it is advisable to make an allowance
for a 50% overload. A schematic diagram of the drive system is given in Figure 2.
Prior Knowledge
A colleague has provided a preliminary estimate for the design of the gears and
has suggested a module of 4 might be appropriate. This colleague also pointed
out that in order to avoid the need for undercutting of the gear teeth, a minimum
number of 18 teeth would be required on either gear. However, these are
preliminary estimates, and they will need to be checked in your analysis.
Design Constraints
The gears are to be manufactured from EN27 steel forgings and will have a
standard involute profile, with a 20 pressure angle and a helix angle of 30.
Assume 95% efficiency of gears. The shafts are to be machined either from
carbon steel or from alloy steel. For carbon steel, a yield stress of 280 MPa may
be assumed. For alloy steel, a yield stress of 460 MPa may be assumed.
Secure Best Marks with AI Grader
Need help grading? Try our AI Grader for instant feedback on your assignments.

EG 269 Design of Machine Elements October 26, 2016
Description of Task
As part of your design, you will need to undertake the following tasks:
Estimate the loads imposed on the escalator;
Calculate the torque required from the gearbox;
Calculate the gear forces;
Determine the face width of the gears;
Assess whether the preliminary estimates for the gear size are
satisfactory;
Suggest any modifications to the gear design if necessary;
List all assumptions.
Provide concluding remarks for the selected design
You can use and ISO and BS Specification documents (provided) and a data table
(provided) as a guide to help you design of the gears (e.g. face width, module,
Description of Task
As part of your design, you will need to undertake the following tasks:
Estimate the loads imposed on the escalator;
Calculate the torque required from the gearbox;
Calculate the gear forces;
Determine the face width of the gears;
Assess whether the preliminary estimates for the gear size are
satisfactory;
Suggest any modifications to the gear design if necessary;
List all assumptions.
Provide concluding remarks for the selected design
You can use and ISO and BS Specification documents (provided) and a data table
(provided) as a guide to help you design of the gears (e.g. face width, module,

EG 269 Design of Machine Elements October 26, 2016
number of teeth). The design must meet the following constraints to be
considered as optimised
Constraints must satisfy
Diameter of pinion gear (d1) > 2 x Axial pitch (Pa)
Face width of the pinion gear (b) < Diameter of pinion gear (d1)
Actual contact stress (σH) < Allowable contact stress (σHP) (pinion gear)
Actual root bending stress (σF) < Permissible tooth root bending stress
(σFP) (pinion gear)
Actual contact stress (σH) < Allowable contact stress (σHP) (driven wheel)
Actual root bending stress (σF) < Permissible tooth root bending stress
(σFP) (driven wheel)
You will be required to submit a report which describes the design challenges, as
well as the approach that you have taken in designing each of the items. Any
assumptions that you make should be mentioned in your report. The main body
of the report should not exceed 3 pages in length. It would be appropriate to
include a summary of your calculations (table 2) in your report, but detailed
calculations should be attached as an appendix, rather than being included in the
main body of the report.
Assessment
The assessment for this task will be based on a report. The mark that is achieved
for the report will contribute 15% towards your final mark for the EG 269
module. The following criteria will be used to assess the reports:
Final report
Introduction to the overall design task (10%)
Description of the key features of your design and the
rationale for the design choices that have been made (30%)
Design calculations (50%)
Overall quality of report (10%)
Timelines
The project will start on Friday October 28 2016 for this project will be carried
out over 5 weeks of the semester. The deadline for the submission of the report
is 11:00pm on Friday November 25 2016. The following guide is provided to
assist in managing the progress of the project.
Table 1: Suggested Timetable for each Project Task
Week Task
1 Familiarisation with task.
Read the ISO and BS support documentation.
Sketch a body diagram.
Estimate loads, friction and torque imposed on the escalator.
number of teeth). The design must meet the following constraints to be
considered as optimised
Constraints must satisfy
Diameter of pinion gear (d1) > 2 x Axial pitch (Pa)
Face width of the pinion gear (b) < Diameter of pinion gear (d1)
Actual contact stress (σH) < Allowable contact stress (σHP) (pinion gear)
Actual root bending stress (σF) < Permissible tooth root bending stress
(σFP) (pinion gear)
Actual contact stress (σH) < Allowable contact stress (σHP) (driven wheel)
Actual root bending stress (σF) < Permissible tooth root bending stress
(σFP) (driven wheel)
You will be required to submit a report which describes the design challenges, as
well as the approach that you have taken in designing each of the items. Any
assumptions that you make should be mentioned in your report. The main body
of the report should not exceed 3 pages in length. It would be appropriate to
include a summary of your calculations (table 2) in your report, but detailed
calculations should be attached as an appendix, rather than being included in the
main body of the report.
Assessment
The assessment for this task will be based on a report. The mark that is achieved
for the report will contribute 15% towards your final mark for the EG 269
module. The following criteria will be used to assess the reports:
Final report
Introduction to the overall design task (10%)
Description of the key features of your design and the
rationale for the design choices that have been made (30%)
Design calculations (50%)
Overall quality of report (10%)
Timelines
The project will start on Friday October 28 2016 for this project will be carried
out over 5 weeks of the semester. The deadline for the submission of the report
is 11:00pm on Friday November 25 2016. The following guide is provided to
assist in managing the progress of the project.
Table 1: Suggested Timetable for each Project Task
Week Task
1 Familiarisation with task.
Read the ISO and BS support documentation.
Sketch a body diagram.
Estimate loads, friction and torque imposed on the escalator.
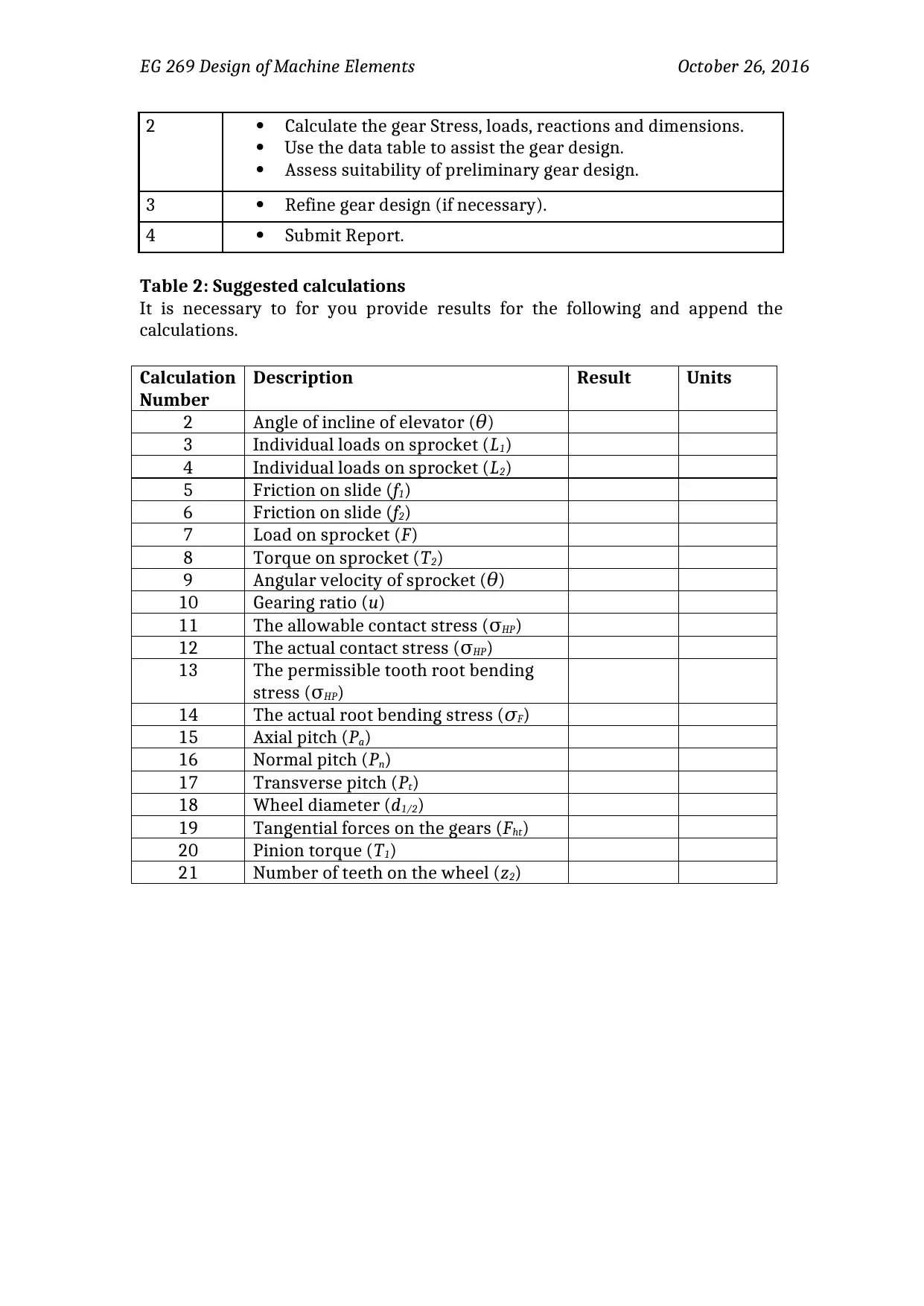
EG 269 Design of Machine Elements October 26, 2016
2 Calculate the gear Stress, loads, reactions and dimensions.
Use the data table to assist the gear design.
Assess suitability of preliminary gear design.
3 Refine gear design (if necessary).
4 Submit Report.
Table 2: Suggested calculations
It is necessary to for you provide results for the following and append the
calculations.
Calculation
Number
Description Result Units
2 Angle of incline of elevator (θ)
3 Individual loads on sprocket (L1)
4 Individual loads on sprocket (L2)
5 Friction on slide (f1)
6 Friction on slide (f2)
7 Load on sprocket (F)
8 Torque on sprocket (T2)
9 Angular velocity of sprocket (θ)
10 Gearing ratio (u)
11 The allowable contact stress (σHP)
12 The actual contact stress (σHP)
13 The permissible tooth root bending
stress (σHP)
14 The actual root bending stress (σF)
15 Axial pitch (Pa)
16 Normal pitch (Pn)
17 Transverse pitch (Pt)
18 Wheel diameter (d1/2)
19 Tangential forces on the gears (Fht)
20 Pinion torque (T1)
21 Number of teeth on the wheel (z2)
2 Calculate the gear Stress, loads, reactions and dimensions.
Use the data table to assist the gear design.
Assess suitability of preliminary gear design.
3 Refine gear design (if necessary).
4 Submit Report.
Table 2: Suggested calculations
It is necessary to for you provide results for the following and append the
calculations.
Calculation
Number
Description Result Units
2 Angle of incline of elevator (θ)
3 Individual loads on sprocket (L1)
4 Individual loads on sprocket (L2)
5 Friction on slide (f1)
6 Friction on slide (f2)
7 Load on sprocket (F)
8 Torque on sprocket (T2)
9 Angular velocity of sprocket (θ)
10 Gearing ratio (u)
11 The allowable contact stress (σHP)
12 The actual contact stress (σHP)
13 The permissible tooth root bending
stress (σHP)
14 The actual root bending stress (σF)
15 Axial pitch (Pa)
16 Normal pitch (Pn)
17 Transverse pitch (Pt)
18 Wheel diameter (d1/2)
19 Tangential forces on the gears (Fht)
20 Pinion torque (T1)
21 Number of teeth on the wheel (z2)
1 out of 4
Related Documents
![[object Object]](/_next/image/?url=%2F_next%2Fstatic%2Fmedia%2Flogo.6d15ce61.png&w=640&q=75)
Your All-in-One AI-Powered Toolkit for Academic Success.
+13062052269
info@desklib.com
Available 24*7 on WhatsApp / Email
Unlock your academic potential
© 2024 | Zucol Services PVT LTD | All rights reserved.