Energy Efficiency Opportunities in Automotive Assembly Process
VerifiedAdded on  2023/03/17
|13
|3269
|25
AI Summary
This review explores the energy efficiency opportunities in the automotive assembly process. It discusses the major energy-consuming processes and ways to improve energy efficiency. The review also highlights the importance of minimizing energy consumption while maintaining productivity. Various strategies and measures are suggested to achieve energy efficiency in automotive manufacturing.
Contribute Materials
Your contribution can guide someone’s learning journey. Share your
documents today.
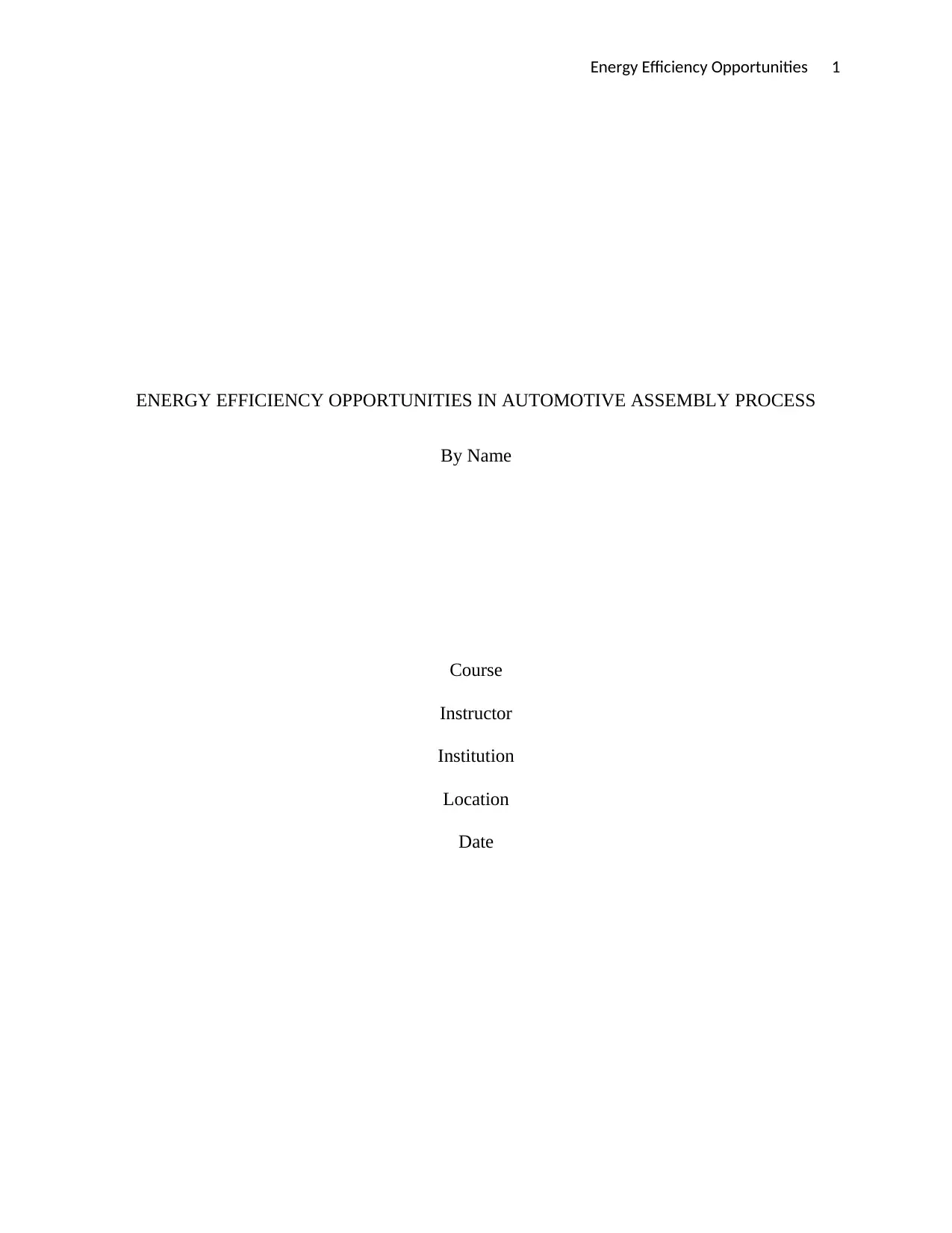
Energy Efficiency Opportunities 1
ENERGY EFFICIENCY OPPORTUNITIES IN AUTOMOTIVE ASSEMBLY PROCESS
By Name
Course
Instructor
Institution
Location
Date
ENERGY EFFICIENCY OPPORTUNITIES IN AUTOMOTIVE ASSEMBLY PROCESS
By Name
Course
Instructor
Institution
Location
Date
Secure Best Marks with AI Grader
Need help grading? Try our AI Grader for instant feedback on your assignments.
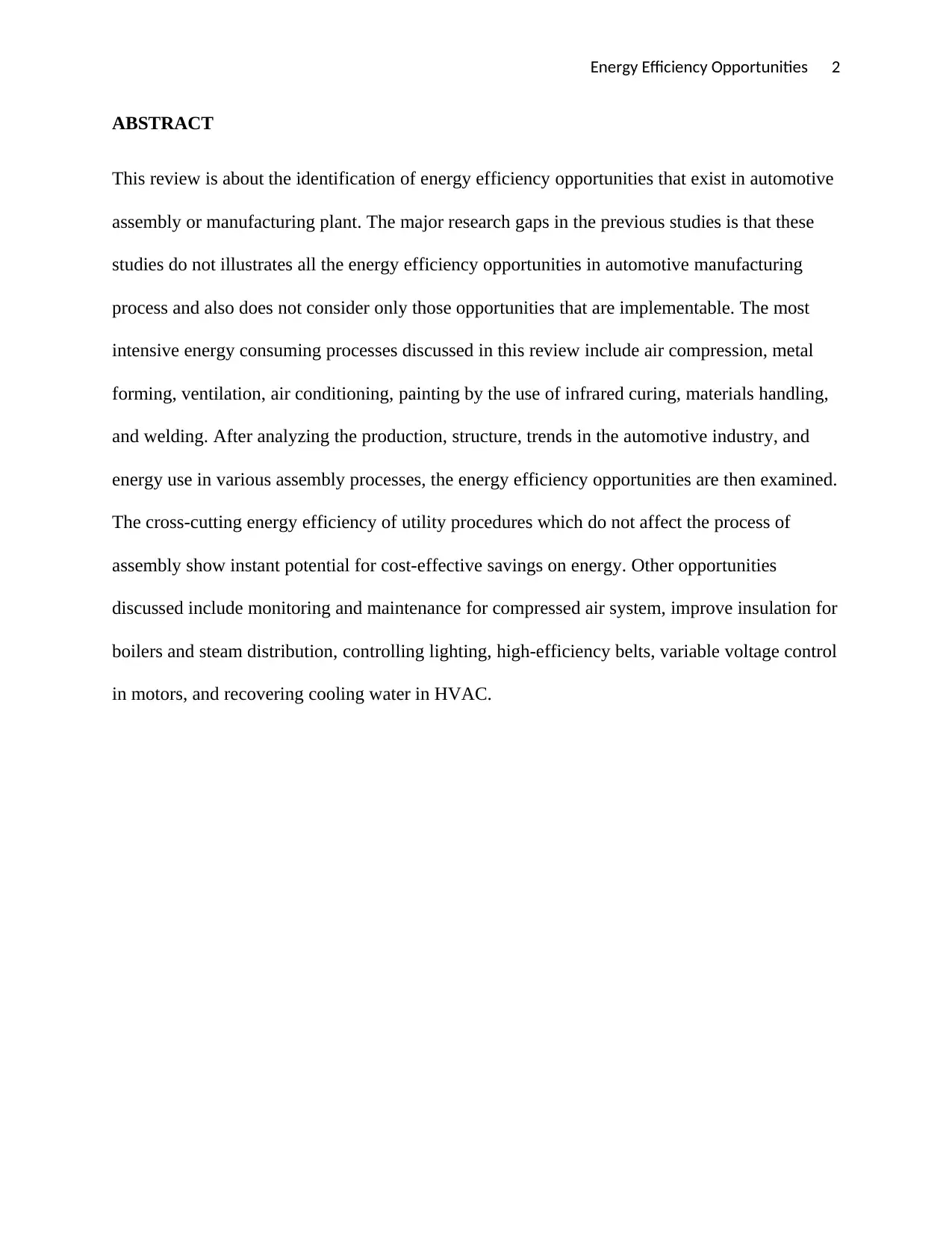
Energy Efficiency Opportunities 2
ABSTRACT
This review is about the identification of energy efficiency opportunities that exist in automotive
assembly or manufacturing plant. The major research gaps in the previous studies is that these
studies do not illustrates all the energy efficiency opportunities in automotive manufacturing
process and also does not consider only those opportunities that are implementable. The most
intensive energy consuming processes discussed in this review include air compression, metal
forming, ventilation, air conditioning, painting by the use of infrared curing, materials handling,
and welding. After analyzing the production, structure, trends in the automotive industry, and
energy use in various assembly processes, the energy efficiency opportunities are then examined.
The cross-cutting energy efficiency of utility procedures which do not affect the process of
assembly show instant potential for cost-effective savings on energy. Other opportunities
discussed include monitoring and maintenance for compressed air system, improve insulation for
boilers and steam distribution, controlling lighting, high-efficiency belts, variable voltage control
in motors, and recovering cooling water in HVAC.
ABSTRACT
This review is about the identification of energy efficiency opportunities that exist in automotive
assembly or manufacturing plant. The major research gaps in the previous studies is that these
studies do not illustrates all the energy efficiency opportunities in automotive manufacturing
process and also does not consider only those opportunities that are implementable. The most
intensive energy consuming processes discussed in this review include air compression, metal
forming, ventilation, air conditioning, painting by the use of infrared curing, materials handling,
and welding. After analyzing the production, structure, trends in the automotive industry, and
energy use in various assembly processes, the energy efficiency opportunities are then examined.
The cross-cutting energy efficiency of utility procedures which do not affect the process of
assembly show instant potential for cost-effective savings on energy. Other opportunities
discussed include monitoring and maintenance for compressed air system, improve insulation for
boilers and steam distribution, controlling lighting, high-efficiency belts, variable voltage control
in motors, and recovering cooling water in HVAC.
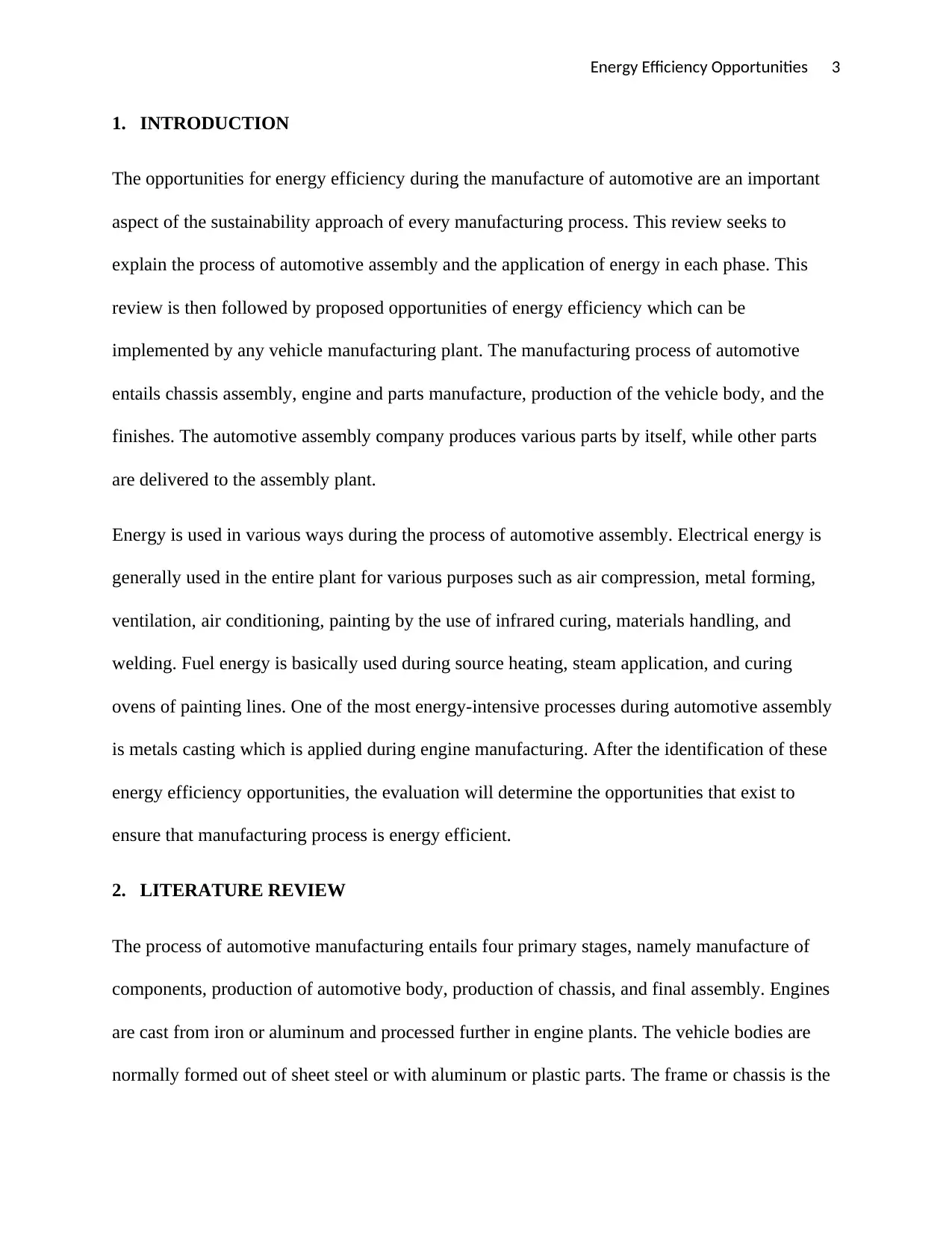
Energy Efficiency Opportunities 3
1. INTRODUCTION
The opportunities for energy efficiency during the manufacture of automotive are an important
aspect of the sustainability approach of every manufacturing process. This review seeks to
explain the process of automotive assembly and the application of energy in each phase. This
review is then followed by proposed opportunities of energy efficiency which can be
implemented by any vehicle manufacturing plant. The manufacturing process of automotive
entails chassis assembly, engine and parts manufacture, production of the vehicle body, and the
finishes. The automotive assembly company produces various parts by itself, while other parts
are delivered to the assembly plant.
Energy is used in various ways during the process of automotive assembly. Electrical energy is
generally used in the entire plant for various purposes such as air compression, metal forming,
ventilation, air conditioning, painting by the use of infrared curing, materials handling, and
welding. Fuel energy is basically used during source heating, steam application, and curing
ovens of painting lines. One of the most energy-intensive processes during automotive assembly
is metals casting which is applied during engine manufacturing. After the identification of these
energy efficiency opportunities, the evaluation will determine the opportunities that exist to
ensure that manufacturing process is energy efficient.
2. LITERATURE REVIEW
The process of automotive manufacturing entails four primary stages, namely manufacture of
components, production of automotive body, production of chassis, and final assembly. Engines
are cast from iron or aluminum and processed further in engine plants. The vehicle bodies are
normally formed out of sheet steel or with aluminum or plastic parts. The frame or chassis is the
1. INTRODUCTION
The opportunities for energy efficiency during the manufacture of automotive are an important
aspect of the sustainability approach of every manufacturing process. This review seeks to
explain the process of automotive assembly and the application of energy in each phase. This
review is then followed by proposed opportunities of energy efficiency which can be
implemented by any vehicle manufacturing plant. The manufacturing process of automotive
entails chassis assembly, engine and parts manufacture, production of the vehicle body, and the
finishes. The automotive assembly company produces various parts by itself, while other parts
are delivered to the assembly plant.
Energy is used in various ways during the process of automotive assembly. Electrical energy is
generally used in the entire plant for various purposes such as air compression, metal forming,
ventilation, air conditioning, painting by the use of infrared curing, materials handling, and
welding. Fuel energy is basically used during source heating, steam application, and curing
ovens of painting lines. One of the most energy-intensive processes during automotive assembly
is metals casting which is applied during engine manufacturing. After the identification of these
energy efficiency opportunities, the evaluation will determine the opportunities that exist to
ensure that manufacturing process is energy efficient.
2. LITERATURE REVIEW
The process of automotive manufacturing entails four primary stages, namely manufacture of
components, production of automotive body, production of chassis, and final assembly. Engines
are cast from iron or aluminum and processed further in engine plants. The vehicle bodies are
normally formed out of sheet steel or with aluminum or plastic parts. The frame or chassis is the
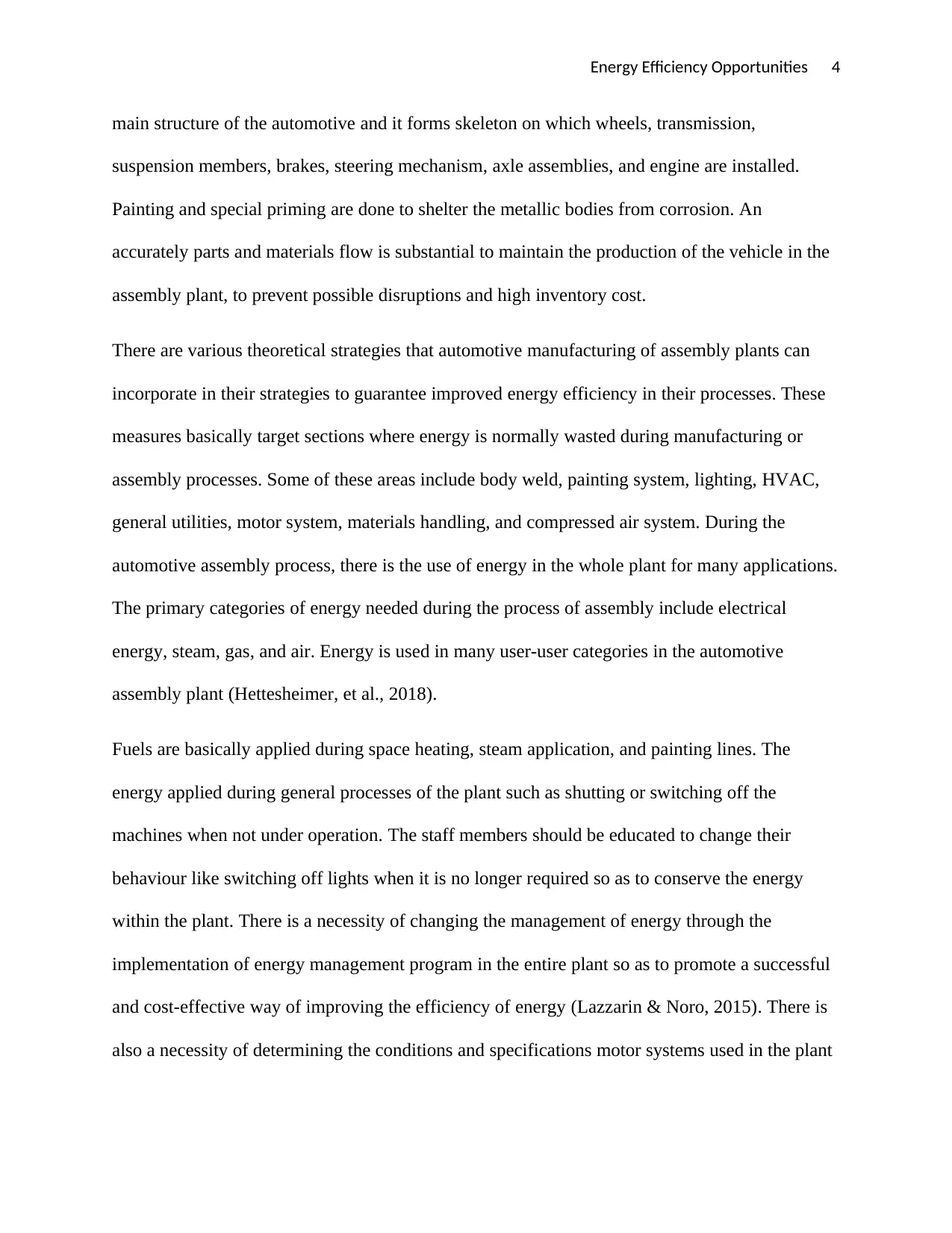
Energy Efficiency Opportunities 4
main structure of the automotive and it forms skeleton on which wheels, transmission,
suspension members, brakes, steering mechanism, axle assemblies, and engine are installed.
Painting and special priming are done to shelter the metallic bodies from corrosion. An
accurately parts and materials flow is substantial to maintain the production of the vehicle in the
assembly plant, to prevent possible disruptions and high inventory cost.
There are various theoretical strategies that automotive manufacturing of assembly plants can
incorporate in their strategies to guarantee improved energy efficiency in their processes. These
measures basically target sections where energy is normally wasted during manufacturing or
assembly processes. Some of these areas include body weld, painting system, lighting, HVAC,
general utilities, motor system, materials handling, and compressed air system. During the
automotive assembly process, there is the use of energy in the whole plant for many applications.
The primary categories of energy needed during the process of assembly include electrical
energy, steam, gas, and air. Energy is used in many user-user categories in the automotive
assembly plant (Hettesheimer, et al., 2018).
Fuels are basically applied during space heating, steam application, and painting lines. The
energy applied during general processes of the plant such as shutting or switching off the
machines when not under operation. The staff members should be educated to change their
behaviour like switching off lights when it is no longer required so as to conserve the energy
within the plant. There is a necessity of changing the management of energy through the
implementation of energy management program in the entire plant so as to promote a successful
and cost-effective way of improving the efficiency of energy (Lazzarin & Noro, 2015). There is
also a necessity of determining the conditions and specifications motor systems used in the plant
main structure of the automotive and it forms skeleton on which wheels, transmission,
suspension members, brakes, steering mechanism, axle assemblies, and engine are installed.
Painting and special priming are done to shelter the metallic bodies from corrosion. An
accurately parts and materials flow is substantial to maintain the production of the vehicle in the
assembly plant, to prevent possible disruptions and high inventory cost.
There are various theoretical strategies that automotive manufacturing of assembly plants can
incorporate in their strategies to guarantee improved energy efficiency in their processes. These
measures basically target sections where energy is normally wasted during manufacturing or
assembly processes. Some of these areas include body weld, painting system, lighting, HVAC,
general utilities, motor system, materials handling, and compressed air system. During the
automotive assembly process, there is the use of energy in the whole plant for many applications.
The primary categories of energy needed during the process of assembly include electrical
energy, steam, gas, and air. Energy is used in many user-user categories in the automotive
assembly plant (Hettesheimer, et al., 2018).
Fuels are basically applied during space heating, steam application, and painting lines. The
energy applied during general processes of the plant such as shutting or switching off the
machines when not under operation. The staff members should be educated to change their
behaviour like switching off lights when it is no longer required so as to conserve the energy
within the plant. There is a necessity of changing the management of energy through the
implementation of energy management program in the entire plant so as to promote a successful
and cost-effective way of improving the efficiency of energy (Lazzarin & Noro, 2015). There is
also a necessity of determining the conditions and specifications motor systems used in the plant
Secure Best Marks with AI Grader
Need help grading? Try our AI Grader for instant feedback on your assignments.
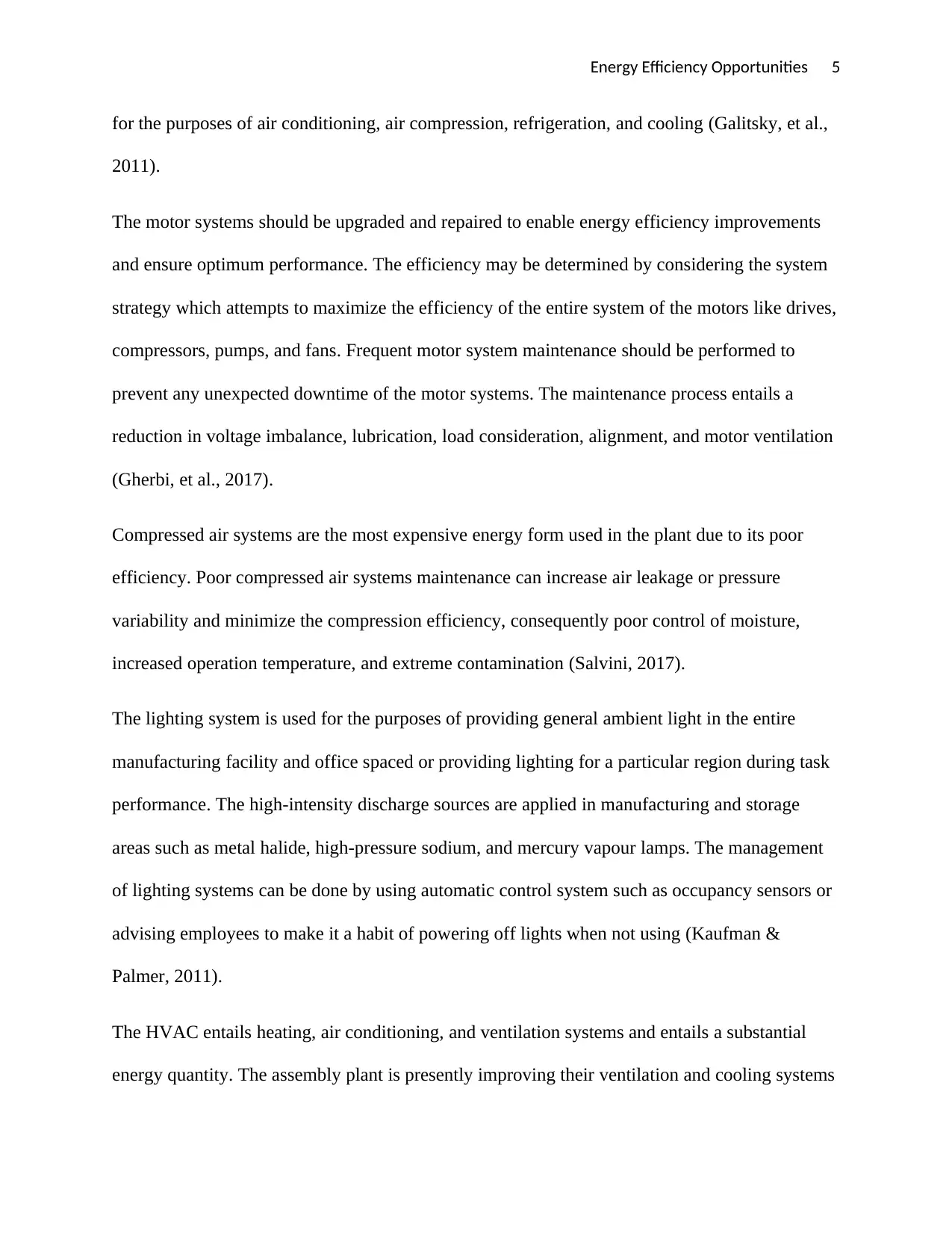
Energy Efficiency Opportunities 5
for the purposes of air conditioning, air compression, refrigeration, and cooling (Galitsky, et al.,
2011).
The motor systems should be upgraded and repaired to enable energy efficiency improvements
and ensure optimum performance. The efficiency may be determined by considering the system
strategy which attempts to maximize the efficiency of the entire system of the motors like drives,
compressors, pumps, and fans. Frequent motor system maintenance should be performed to
prevent any unexpected downtime of the motor systems. The maintenance process entails a
reduction in voltage imbalance, lubrication, load consideration, alignment, and motor ventilation
(Gherbi, et al., 2017).
Compressed air systems are the most expensive energy form used in the plant due to its poor
efficiency. Poor compressed air systems maintenance can increase air leakage or pressure
variability and minimize the compression efficiency, consequently poor control of moisture,
increased operation temperature, and extreme contamination (Salvini, 2017).
The lighting system is used for the purposes of providing general ambient light in the entire
manufacturing facility and office spaced or providing lighting for a particular region during task
performance. The high-intensity discharge sources are applied in manufacturing and storage
areas such as metal halide, high-pressure sodium, and mercury vapour lamps. The management
of lighting systems can be done by using automatic control system such as occupancy sensors or
advising employees to make it a habit of powering off lights when not using (Kaufman &
Palmer, 2011).
The HVAC entails heating, air conditioning, and ventilation systems and entails a substantial
energy quantity. The assembly plant is presently improving their ventilation and cooling systems
for the purposes of air conditioning, air compression, refrigeration, and cooling (Galitsky, et al.,
2011).
The motor systems should be upgraded and repaired to enable energy efficiency improvements
and ensure optimum performance. The efficiency may be determined by considering the system
strategy which attempts to maximize the efficiency of the entire system of the motors like drives,
compressors, pumps, and fans. Frequent motor system maintenance should be performed to
prevent any unexpected downtime of the motor systems. The maintenance process entails a
reduction in voltage imbalance, lubrication, load consideration, alignment, and motor ventilation
(Gherbi, et al., 2017).
Compressed air systems are the most expensive energy form used in the plant due to its poor
efficiency. Poor compressed air systems maintenance can increase air leakage or pressure
variability and minimize the compression efficiency, consequently poor control of moisture,
increased operation temperature, and extreme contamination (Salvini, 2017).
The lighting system is used for the purposes of providing general ambient light in the entire
manufacturing facility and office spaced or providing lighting for a particular region during task
performance. The high-intensity discharge sources are applied in manufacturing and storage
areas such as metal halide, high-pressure sodium, and mercury vapour lamps. The management
of lighting systems can be done by using automatic control system such as occupancy sensors or
advising employees to make it a habit of powering off lights when not using (Kaufman &
Palmer, 2011).
The HVAC entails heating, air conditioning, and ventilation systems and entails a substantial
energy quantity. The assembly plant is presently improving their ventilation and cooling systems
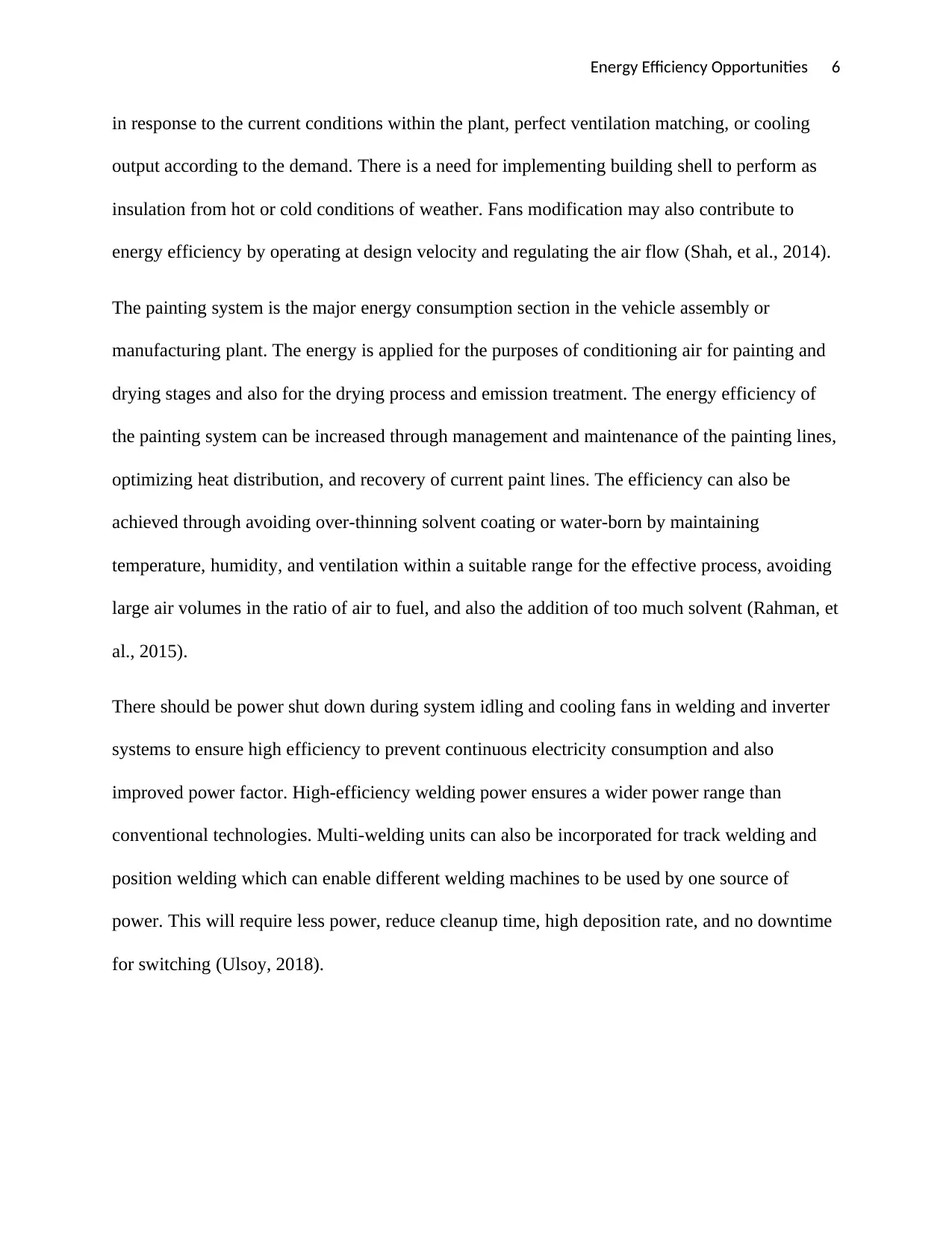
Energy Efficiency Opportunities 6
in response to the current conditions within the plant, perfect ventilation matching, or cooling
output according to the demand. There is a need for implementing building shell to perform as
insulation from hot or cold conditions of weather. Fans modification may also contribute to
energy efficiency by operating at design velocity and regulating the air flow (Shah, et al., 2014).
The painting system is the major energy consumption section in the vehicle assembly or
manufacturing plant. The energy is applied for the purposes of conditioning air for painting and
drying stages and also for the drying process and emission treatment. The energy efficiency of
the painting system can be increased through management and maintenance of the painting lines,
optimizing heat distribution, and recovery of current paint lines. The efficiency can also be
achieved through avoiding over-thinning solvent coating or water-born by maintaining
temperature, humidity, and ventilation within a suitable range for the effective process, avoiding
large air volumes in the ratio of air to fuel, and also the addition of too much solvent (Rahman, et
al., 2015).
There should be power shut down during system idling and cooling fans in welding and inverter
systems to ensure high efficiency to prevent continuous electricity consumption and also
improved power factor. High-efficiency welding power ensures a wider power range than
conventional technologies. Multi-welding units can also be incorporated for track welding and
position welding which can enable different welding machines to be used by one source of
power. This will require less power, reduce cleanup time, high deposition rate, and no downtime
for switching (Ulsoy, 2018).
in response to the current conditions within the plant, perfect ventilation matching, or cooling
output according to the demand. There is a need for implementing building shell to perform as
insulation from hot or cold conditions of weather. Fans modification may also contribute to
energy efficiency by operating at design velocity and regulating the air flow (Shah, et al., 2014).
The painting system is the major energy consumption section in the vehicle assembly or
manufacturing plant. The energy is applied for the purposes of conditioning air for painting and
drying stages and also for the drying process and emission treatment. The energy efficiency of
the painting system can be increased through management and maintenance of the painting lines,
optimizing heat distribution, and recovery of current paint lines. The efficiency can also be
achieved through avoiding over-thinning solvent coating or water-born by maintaining
temperature, humidity, and ventilation within a suitable range for the effective process, avoiding
large air volumes in the ratio of air to fuel, and also the addition of too much solvent (Rahman, et
al., 2015).
There should be power shut down during system idling and cooling fans in welding and inverter
systems to ensure high efficiency to prevent continuous electricity consumption and also
improved power factor. High-efficiency welding power ensures a wider power range than
conventional technologies. Multi-welding units can also be incorporated for track welding and
position welding which can enable different welding machines to be used by one source of
power. This will require less power, reduce cleanup time, high deposition rate, and no downtime
for switching (Ulsoy, 2018).
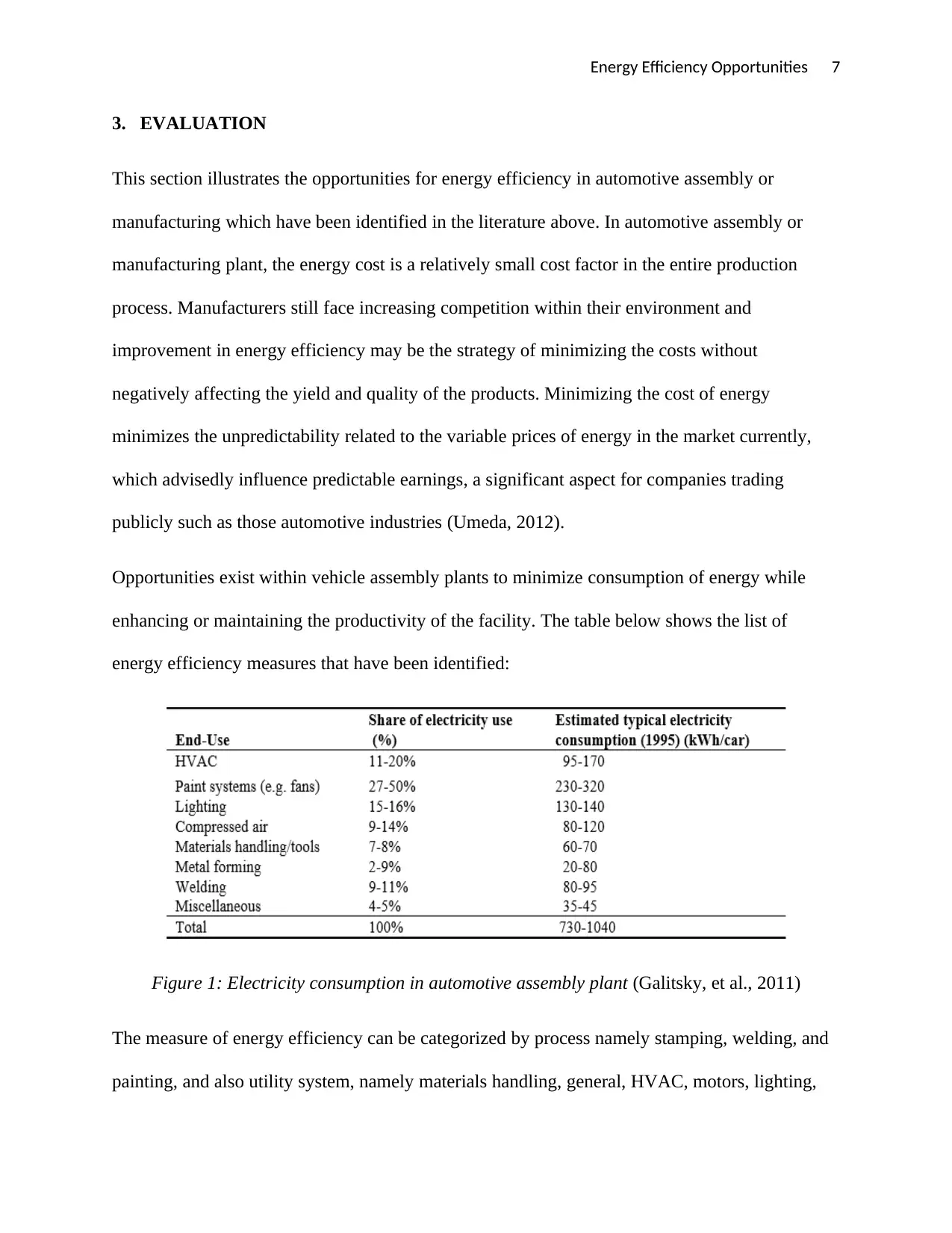
Energy Efficiency Opportunities 7
3. EVALUATION
This section illustrates the opportunities for energy efficiency in automotive assembly or
manufacturing which have been identified in the literature above. In automotive assembly or
manufacturing plant, the energy cost is a relatively small cost factor in the entire production
process. Manufacturers still face increasing competition within their environment and
improvement in energy efficiency may be the strategy of minimizing the costs without
negatively affecting the yield and quality of the products. Minimizing the cost of energy
minimizes the unpredictability related to the variable prices of energy in the market currently,
which advisedly influence predictable earnings, a significant aspect for companies trading
publicly such as those automotive industries (Umeda, 2012).
Opportunities exist within vehicle assembly plants to minimize consumption of energy while
enhancing or maintaining the productivity of the facility. The table below shows the list of
energy efficiency measures that have been identified:
Figure 1: Electricity consumption in automotive assembly plant (Galitsky, et al., 2011)
The measure of energy efficiency can be categorized by process namely stamping, welding, and
painting, and also utility system, namely materials handling, general, HVAC, motors, lighting,
3. EVALUATION
This section illustrates the opportunities for energy efficiency in automotive assembly or
manufacturing which have been identified in the literature above. In automotive assembly or
manufacturing plant, the energy cost is a relatively small cost factor in the entire production
process. Manufacturers still face increasing competition within their environment and
improvement in energy efficiency may be the strategy of minimizing the costs without
negatively affecting the yield and quality of the products. Minimizing the cost of energy
minimizes the unpredictability related to the variable prices of energy in the market currently,
which advisedly influence predictable earnings, a significant aspect for companies trading
publicly such as those automotive industries (Umeda, 2012).
Opportunities exist within vehicle assembly plants to minimize consumption of energy while
enhancing or maintaining the productivity of the facility. The table below shows the list of
energy efficiency measures that have been identified:
Figure 1: Electricity consumption in automotive assembly plant (Galitsky, et al., 2011)
The measure of energy efficiency can be categorized by process namely stamping, welding, and
painting, and also utility system, namely materials handling, general, HVAC, motors, lighting,
Paraphrase This Document
Need a fresh take? Get an instant paraphrase of this document with our AI Paraphraser
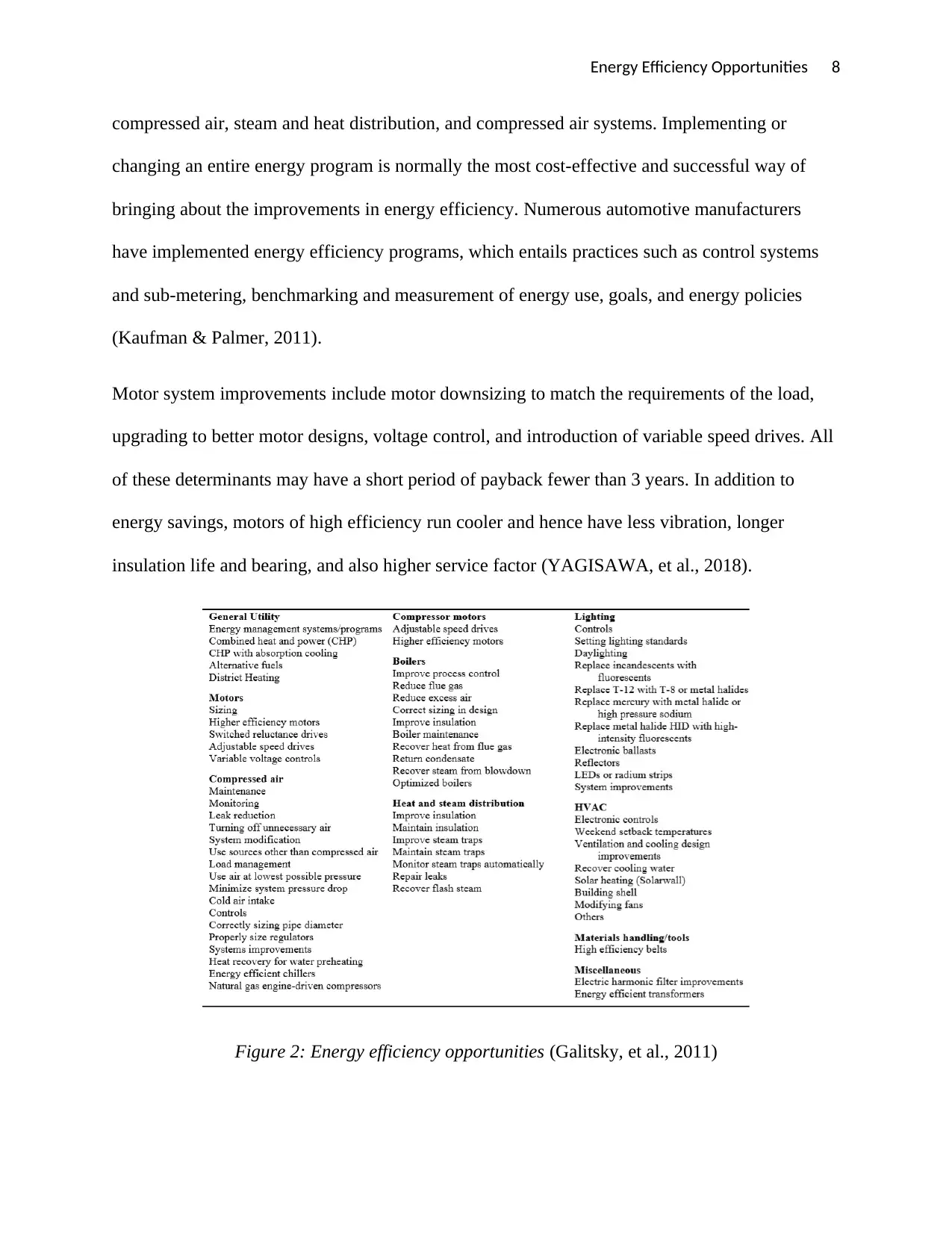
Energy Efficiency Opportunities 8
compressed air, steam and heat distribution, and compressed air systems. Implementing or
changing an entire energy program is normally the most cost-effective and successful way of
bringing about the improvements in energy efficiency. Numerous automotive manufacturers
have implemented energy efficiency programs, which entails practices such as control systems
and sub-metering, benchmarking and measurement of energy use, goals, and energy policies
(Kaufman & Palmer, 2011).
Motor system improvements include motor downsizing to match the requirements of the load,
upgrading to better motor designs, voltage control, and introduction of variable speed drives. All
of these determinants may have a short period of payback fewer than 3 years. In addition to
energy savings, motors of high efficiency run cooler and hence have less vibration, longer
insulation life and bearing, and also higher service factor (YAGISAWA, et al., 2018).
Figure 2: Energy efficiency opportunities (Galitsky, et al., 2011)
compressed air, steam and heat distribution, and compressed air systems. Implementing or
changing an entire energy program is normally the most cost-effective and successful way of
bringing about the improvements in energy efficiency. Numerous automotive manufacturers
have implemented energy efficiency programs, which entails practices such as control systems
and sub-metering, benchmarking and measurement of energy use, goals, and energy policies
(Kaufman & Palmer, 2011).
Motor system improvements include motor downsizing to match the requirements of the load,
upgrading to better motor designs, voltage control, and introduction of variable speed drives. All
of these determinants may have a short period of payback fewer than 3 years. In addition to
energy savings, motors of high efficiency run cooler and hence have less vibration, longer
insulation life and bearing, and also higher service factor (YAGISAWA, et al., 2018).
Figure 2: Energy efficiency opportunities (Galitsky, et al., 2011)
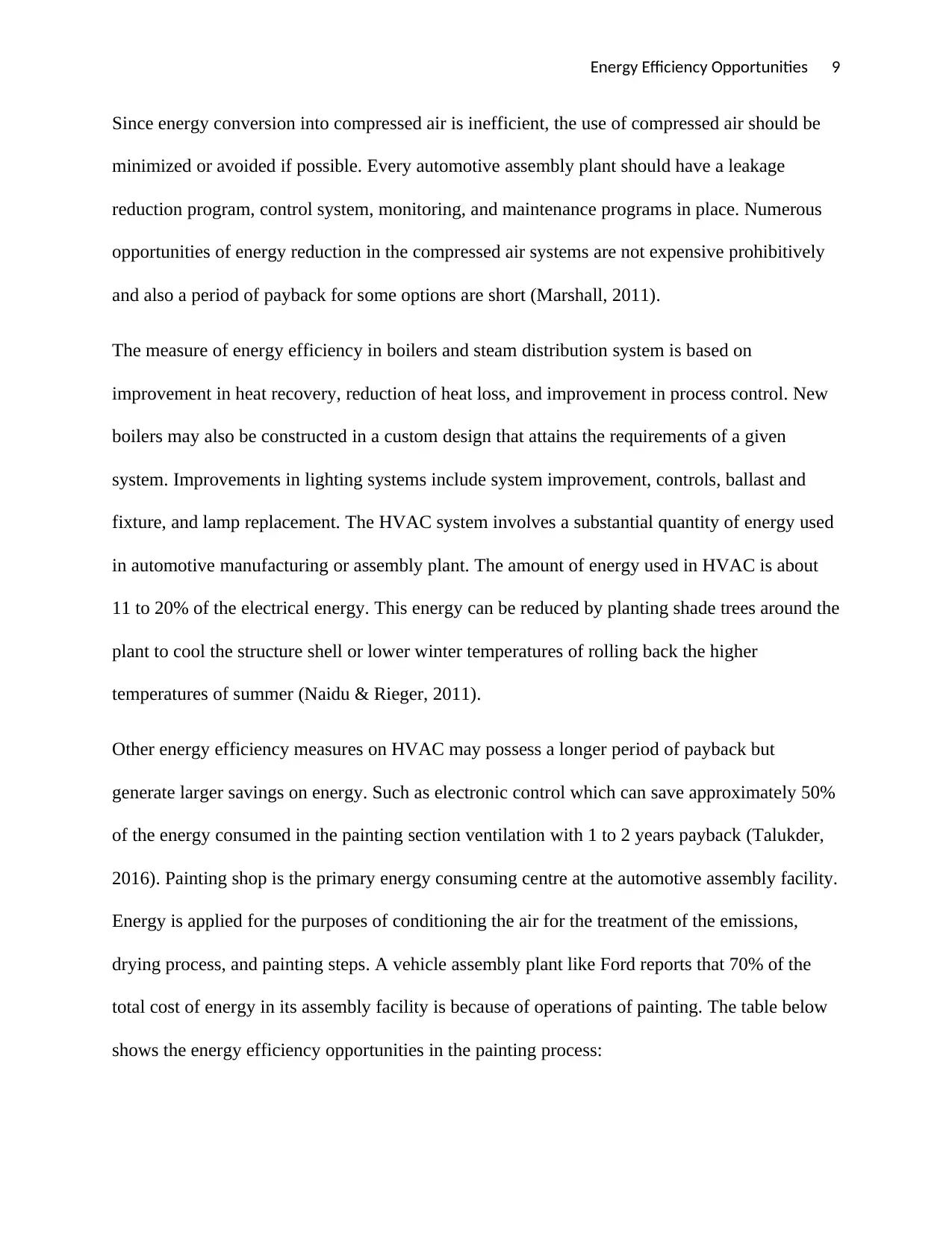
Energy Efficiency Opportunities 9
Since energy conversion into compressed air is inefficient, the use of compressed air should be
minimized or avoided if possible. Every automotive assembly plant should have a leakage
reduction program, control system, monitoring, and maintenance programs in place. Numerous
opportunities of energy reduction in the compressed air systems are not expensive prohibitively
and also a period of payback for some options are short (Marshall, 2011).
The measure of energy efficiency in boilers and steam distribution system is based on
improvement in heat recovery, reduction of heat loss, and improvement in process control. New
boilers may also be constructed in a custom design that attains the requirements of a given
system. Improvements in lighting systems include system improvement, controls, ballast and
fixture, and lamp replacement. The HVAC system involves a substantial quantity of energy used
in automotive manufacturing or assembly plant. The amount of energy used in HVAC is about
11 to 20% of the electrical energy. This energy can be reduced by planting shade trees around the
plant to cool the structure shell or lower winter temperatures of rolling back the higher
temperatures of summer (Naidu & Rieger, 2011).
Other energy efficiency measures on HVAC may possess a longer period of payback but
generate larger savings on energy. Such as electronic control which can save approximately 50%
of the energy consumed in the painting section ventilation with 1 to 2 years payback (Talukder,
2016). Painting shop is the primary energy consuming centre at the automotive assembly facility.
Energy is applied for the purposes of conditioning the air for the treatment of the emissions,
drying process, and painting steps. A vehicle assembly plant like Ford reports that 70% of the
total cost of energy in its assembly facility is because of operations of painting. The table below
shows the energy efficiency opportunities in the painting process:
Since energy conversion into compressed air is inefficient, the use of compressed air should be
minimized or avoided if possible. Every automotive assembly plant should have a leakage
reduction program, control system, monitoring, and maintenance programs in place. Numerous
opportunities of energy reduction in the compressed air systems are not expensive prohibitively
and also a period of payback for some options are short (Marshall, 2011).
The measure of energy efficiency in boilers and steam distribution system is based on
improvement in heat recovery, reduction of heat loss, and improvement in process control. New
boilers may also be constructed in a custom design that attains the requirements of a given
system. Improvements in lighting systems include system improvement, controls, ballast and
fixture, and lamp replacement. The HVAC system involves a substantial quantity of energy used
in automotive manufacturing or assembly plant. The amount of energy used in HVAC is about
11 to 20% of the electrical energy. This energy can be reduced by planting shade trees around the
plant to cool the structure shell or lower winter temperatures of rolling back the higher
temperatures of summer (Naidu & Rieger, 2011).
Other energy efficiency measures on HVAC may possess a longer period of payback but
generate larger savings on energy. Such as electronic control which can save approximately 50%
of the energy consumed in the painting section ventilation with 1 to 2 years payback (Talukder,
2016). Painting shop is the primary energy consuming centre at the automotive assembly facility.
Energy is applied for the purposes of conditioning the air for the treatment of the emissions,
drying process, and painting steps. A vehicle assembly plant like Ford reports that 70% of the
total cost of energy in its assembly facility is because of operations of painting. The table below
shows the energy efficiency opportunities in the painting process:
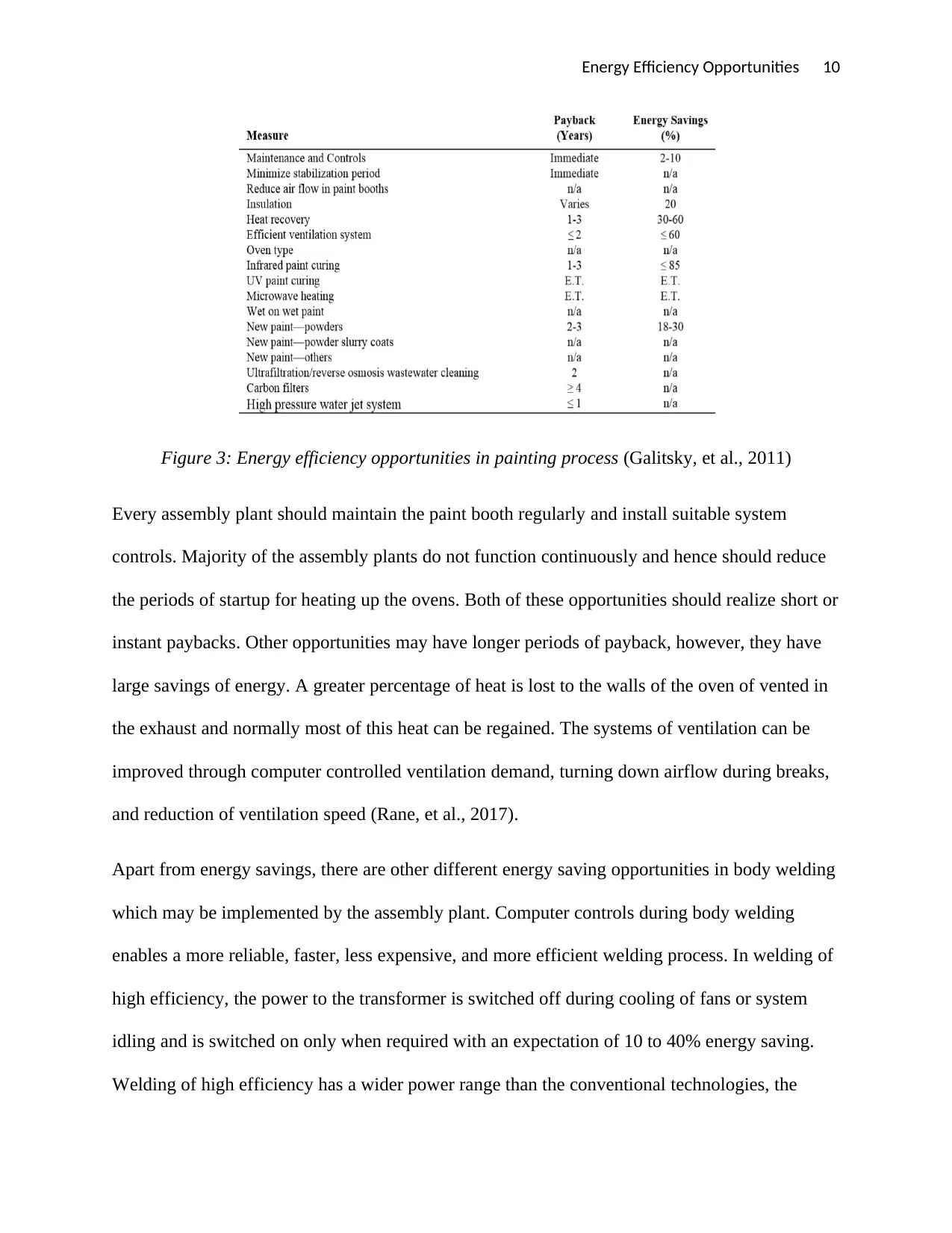
Energy Efficiency Opportunities 10
Figure 3: Energy efficiency opportunities in painting process (Galitsky, et al., 2011)
Every assembly plant should maintain the paint booth regularly and install suitable system
controls. Majority of the assembly plants do not function continuously and hence should reduce
the periods of startup for heating up the ovens. Both of these opportunities should realize short or
instant paybacks. Other opportunities may have longer periods of payback, however, they have
large savings of energy. A greater percentage of heat is lost to the walls of the oven of vented in
the exhaust and normally most of this heat can be regained. The systems of ventilation can be
improved through computer controlled ventilation demand, turning down airflow during breaks,
and reduction of ventilation speed (Rane, et al., 2017).
Apart from energy savings, there are other different energy saving opportunities in body welding
which may be implemented by the assembly plant. Computer controls during body welding
enables a more reliable, faster, less expensive, and more efficient welding process. In welding of
high efficiency, the power to the transformer is switched off during cooling of fans or system
idling and is switched on only when required with an expectation of 10 to 40% energy saving.
Welding of high efficiency has a wider power range than the conventional technologies, the
Figure 3: Energy efficiency opportunities in painting process (Galitsky, et al., 2011)
Every assembly plant should maintain the paint booth regularly and install suitable system
controls. Majority of the assembly plants do not function continuously and hence should reduce
the periods of startup for heating up the ovens. Both of these opportunities should realize short or
instant paybacks. Other opportunities may have longer periods of payback, however, they have
large savings of energy. A greater percentage of heat is lost to the walls of the oven of vented in
the exhaust and normally most of this heat can be regained. The systems of ventilation can be
improved through computer controlled ventilation demand, turning down airflow during breaks,
and reduction of ventilation speed (Rane, et al., 2017).
Apart from energy savings, there are other different energy saving opportunities in body welding
which may be implemented by the assembly plant. Computer controls during body welding
enables a more reliable, faster, less expensive, and more efficient welding process. In welding of
high efficiency, the power to the transformer is switched off during cooling of fans or system
idling and is switched on only when required with an expectation of 10 to 40% energy saving.
Welding of high efficiency has a wider power range than the conventional technologies, the
Secure Best Marks with AI Grader
Need help grading? Try our AI Grader for instant feedback on your assignments.
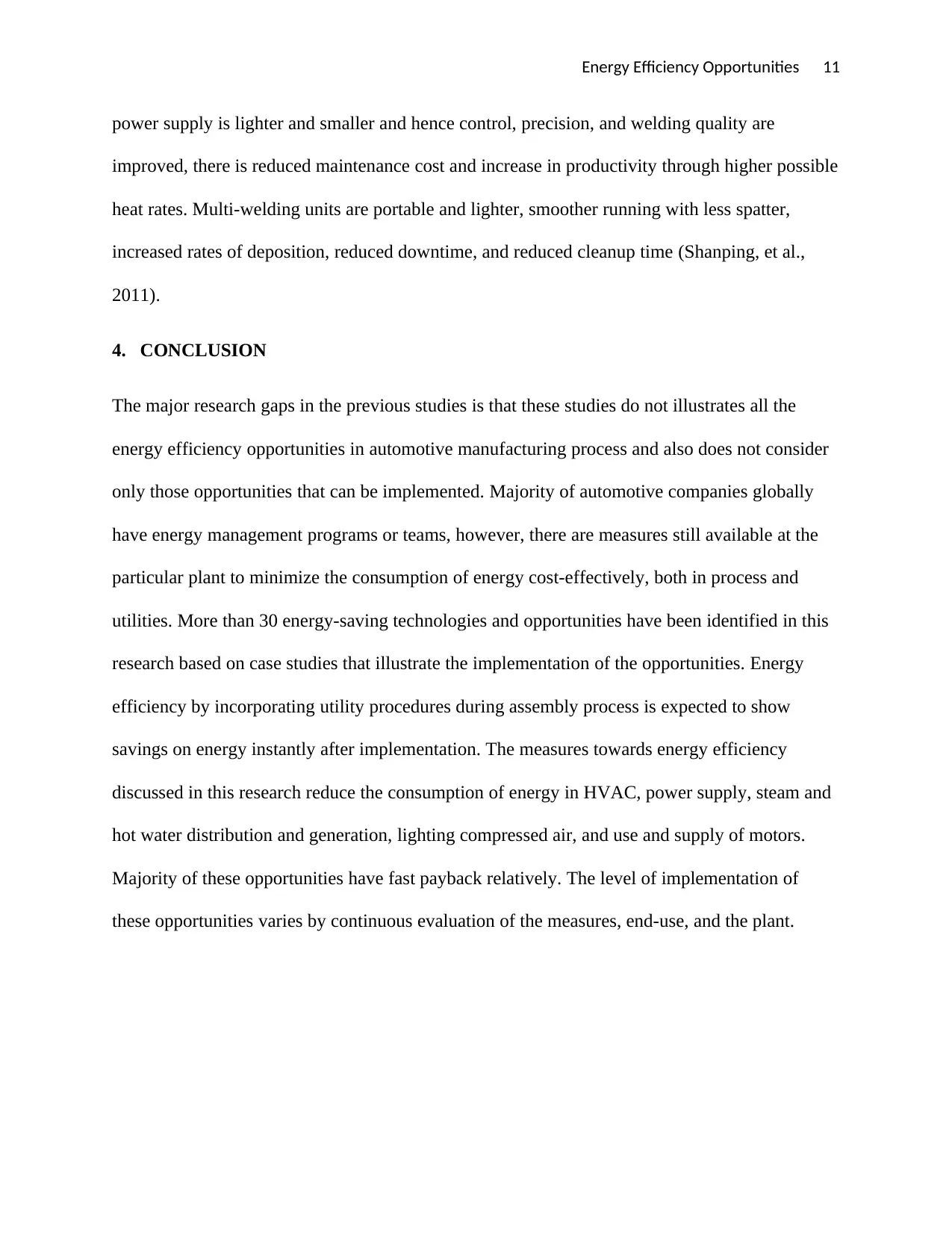
Energy Efficiency Opportunities 11
power supply is lighter and smaller and hence control, precision, and welding quality are
improved, there is reduced maintenance cost and increase in productivity through higher possible
heat rates. Multi-welding units are portable and lighter, smoother running with less spatter,
increased rates of deposition, reduced downtime, and reduced cleanup time (Shanping, et al.,
2011).
4. CONCLUSION
The major research gaps in the previous studies is that these studies do not illustrates all the
energy efficiency opportunities in automotive manufacturing process and also does not consider
only those opportunities that can be implemented. Majority of automotive companies globally
have energy management programs or teams, however, there are measures still available at the
particular plant to minimize the consumption of energy cost-effectively, both in process and
utilities. More than 30 energy-saving technologies and opportunities have been identified in this
research based on case studies that illustrate the implementation of the opportunities. Energy
efficiency by incorporating utility procedures during assembly process is expected to show
savings on energy instantly after implementation. The measures towards energy efficiency
discussed in this research reduce the consumption of energy in HVAC, power supply, steam and
hot water distribution and generation, lighting compressed air, and use and supply of motors.
Majority of these opportunities have fast payback relatively. The level of implementation of
these opportunities varies by continuous evaluation of the measures, end-use, and the plant.
power supply is lighter and smaller and hence control, precision, and welding quality are
improved, there is reduced maintenance cost and increase in productivity through higher possible
heat rates. Multi-welding units are portable and lighter, smoother running with less spatter,
increased rates of deposition, reduced downtime, and reduced cleanup time (Shanping, et al.,
2011).
4. CONCLUSION
The major research gaps in the previous studies is that these studies do not illustrates all the
energy efficiency opportunities in automotive manufacturing process and also does not consider
only those opportunities that can be implemented. Majority of automotive companies globally
have energy management programs or teams, however, there are measures still available at the
particular plant to minimize the consumption of energy cost-effectively, both in process and
utilities. More than 30 energy-saving technologies and opportunities have been identified in this
research based on case studies that illustrate the implementation of the opportunities. Energy
efficiency by incorporating utility procedures during assembly process is expected to show
savings on energy instantly after implementation. The measures towards energy efficiency
discussed in this research reduce the consumption of energy in HVAC, power supply, steam and
hot water distribution and generation, lighting compressed air, and use and supply of motors.
Majority of these opportunities have fast payback relatively. The level of implementation of
these opportunities varies by continuous evaluation of the measures, end-use, and the plant.
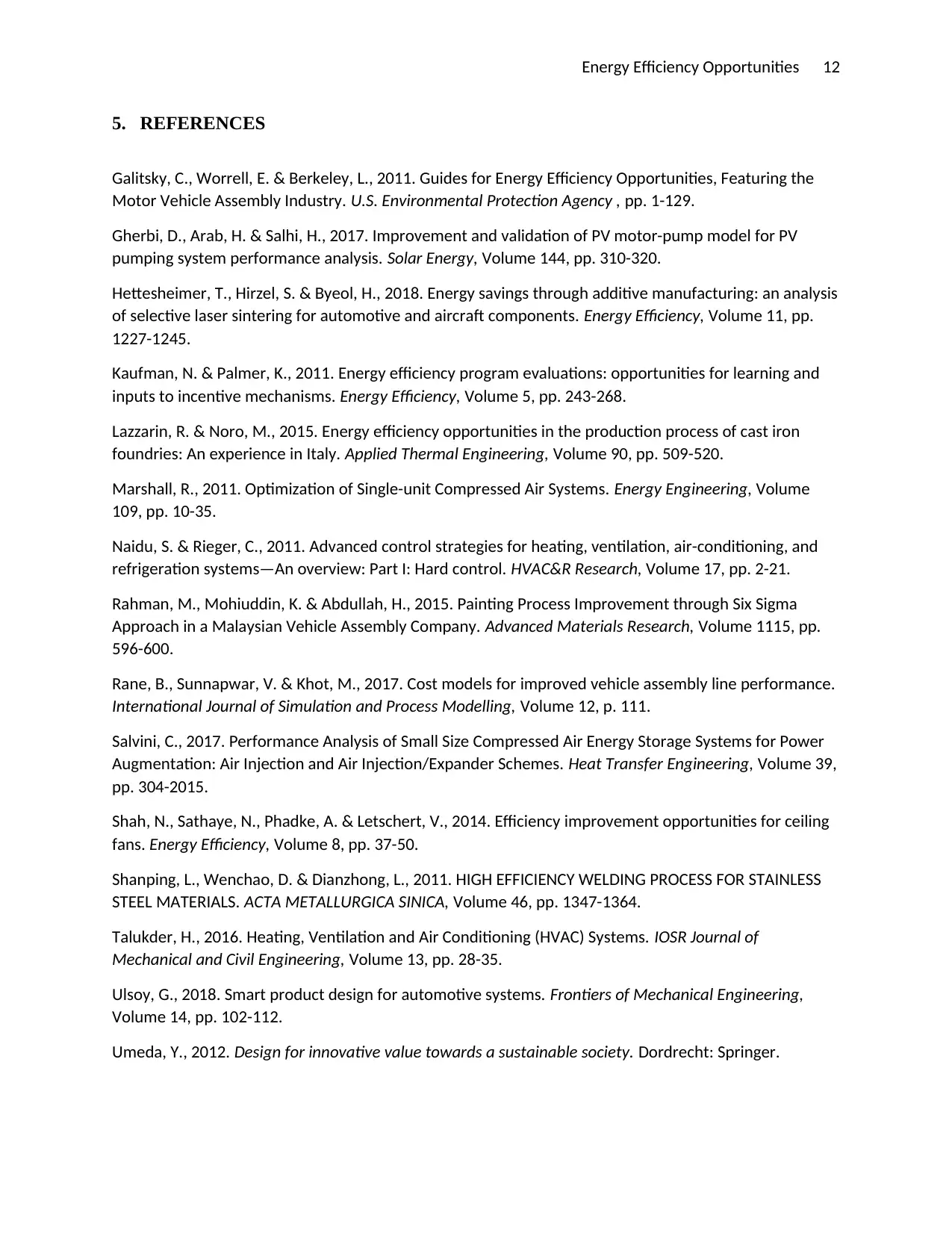
Energy Efficiency Opportunities 12
5. REFERENCES
Galitsky, C., Worrell, E. & Berkeley, L., 2011. Guides for Energy Efficiency Opportunities, Featuring the
Motor Vehicle Assembly Industry. U.S. Environmental Protection Agency , pp. 1-129.
Gherbi, D., Arab, H. & Salhi, H., 2017. Improvement and validation of PV motor-pump model for PV
pumping system performance analysis. Solar Energy, Volume 144, pp. 310-320.
Hettesheimer, T., Hirzel, S. & Byeol, H., 2018. Energy savings through additive manufacturing: an analysis
of selective laser sintering for automotive and aircraft components. Energy Efficiency, Volume 11, pp.
1227-1245.
Kaufman, N. & Palmer, K., 2011. Energy efficiency program evaluations: opportunities for learning and
inputs to incentive mechanisms. Energy Efficiency, Volume 5, pp. 243-268.
Lazzarin, R. & Noro, M., 2015. Energy efficiency opportunities in the production process of cast iron
foundries: An experience in Italy. Applied Thermal Engineering, Volume 90, pp. 509-520.
Marshall, R., 2011. Optimization of Single-unit Compressed Air Systems. Energy Engineering, Volume
109, pp. 10-35.
Naidu, S. & Rieger, C., 2011. Advanced control strategies for heating, ventilation, air-conditioning, and
refrigeration systems—An overview: Part I: Hard control. HVAC&R Research, Volume 17, pp. 2-21.
Rahman, M., Mohiuddin, K. & Abdullah, H., 2015. Painting Process Improvement through Six Sigma
Approach in a Malaysian Vehicle Assembly Company. Advanced Materials Research, Volume 1115, pp.
596-600.
Rane, B., Sunnapwar, V. & Khot, M., 2017. Cost models for improved vehicle assembly line performance.
International Journal of Simulation and Process Modelling, Volume 12, p. 111.
Salvini, C., 2017. Performance Analysis of Small Size Compressed Air Energy Storage Systems for Power
Augmentation: Air Injection and Air Injection/Expander Schemes. Heat Transfer Engineering, Volume 39,
pp. 304-2015.
Shah, N., Sathaye, N., Phadke, A. & Letschert, V., 2014. Efficiency improvement opportunities for ceiling
fans. Energy Efficiency, Volume 8, pp. 37-50.
Shanping, L., Wenchao, D. & Dianzhong, L., 2011. HIGH EFFICIENCY WELDING PROCESS FOR STAINLESS
STEEL MATERIALS. ACTA METALLURGICA SINICA, Volume 46, pp. 1347-1364.
Talukder, H., 2016. Heating, Ventilation and Air Conditioning (HVAC) Systems. IOSR Journal of
Mechanical and Civil Engineering, Volume 13, pp. 28-35.
Ulsoy, G., 2018. Smart product design for automotive systems. Frontiers of Mechanical Engineering,
Volume 14, pp. 102-112.
Umeda, Y., 2012. Design for innovative value towards a sustainable society. Dordrecht: Springer.
5. REFERENCES
Galitsky, C., Worrell, E. & Berkeley, L., 2011. Guides for Energy Efficiency Opportunities, Featuring the
Motor Vehicle Assembly Industry. U.S. Environmental Protection Agency , pp. 1-129.
Gherbi, D., Arab, H. & Salhi, H., 2017. Improvement and validation of PV motor-pump model for PV
pumping system performance analysis. Solar Energy, Volume 144, pp. 310-320.
Hettesheimer, T., Hirzel, S. & Byeol, H., 2018. Energy savings through additive manufacturing: an analysis
of selective laser sintering for automotive and aircraft components. Energy Efficiency, Volume 11, pp.
1227-1245.
Kaufman, N. & Palmer, K., 2011. Energy efficiency program evaluations: opportunities for learning and
inputs to incentive mechanisms. Energy Efficiency, Volume 5, pp. 243-268.
Lazzarin, R. & Noro, M., 2015. Energy efficiency opportunities in the production process of cast iron
foundries: An experience in Italy. Applied Thermal Engineering, Volume 90, pp. 509-520.
Marshall, R., 2011. Optimization of Single-unit Compressed Air Systems. Energy Engineering, Volume
109, pp. 10-35.
Naidu, S. & Rieger, C., 2011. Advanced control strategies for heating, ventilation, air-conditioning, and
refrigeration systems—An overview: Part I: Hard control. HVAC&R Research, Volume 17, pp. 2-21.
Rahman, M., Mohiuddin, K. & Abdullah, H., 2015. Painting Process Improvement through Six Sigma
Approach in a Malaysian Vehicle Assembly Company. Advanced Materials Research, Volume 1115, pp.
596-600.
Rane, B., Sunnapwar, V. & Khot, M., 2017. Cost models for improved vehicle assembly line performance.
International Journal of Simulation and Process Modelling, Volume 12, p. 111.
Salvini, C., 2017. Performance Analysis of Small Size Compressed Air Energy Storage Systems for Power
Augmentation: Air Injection and Air Injection/Expander Schemes. Heat Transfer Engineering, Volume 39,
pp. 304-2015.
Shah, N., Sathaye, N., Phadke, A. & Letschert, V., 2014. Efficiency improvement opportunities for ceiling
fans. Energy Efficiency, Volume 8, pp. 37-50.
Shanping, L., Wenchao, D. & Dianzhong, L., 2011. HIGH EFFICIENCY WELDING PROCESS FOR STAINLESS
STEEL MATERIALS. ACTA METALLURGICA SINICA, Volume 46, pp. 1347-1364.
Talukder, H., 2016. Heating, Ventilation and Air Conditioning (HVAC) Systems. IOSR Journal of
Mechanical and Civil Engineering, Volume 13, pp. 28-35.
Ulsoy, G., 2018. Smart product design for automotive systems. Frontiers of Mechanical Engineering,
Volume 14, pp. 102-112.
Umeda, Y., 2012. Design for innovative value towards a sustainable society. Dordrecht: Springer.
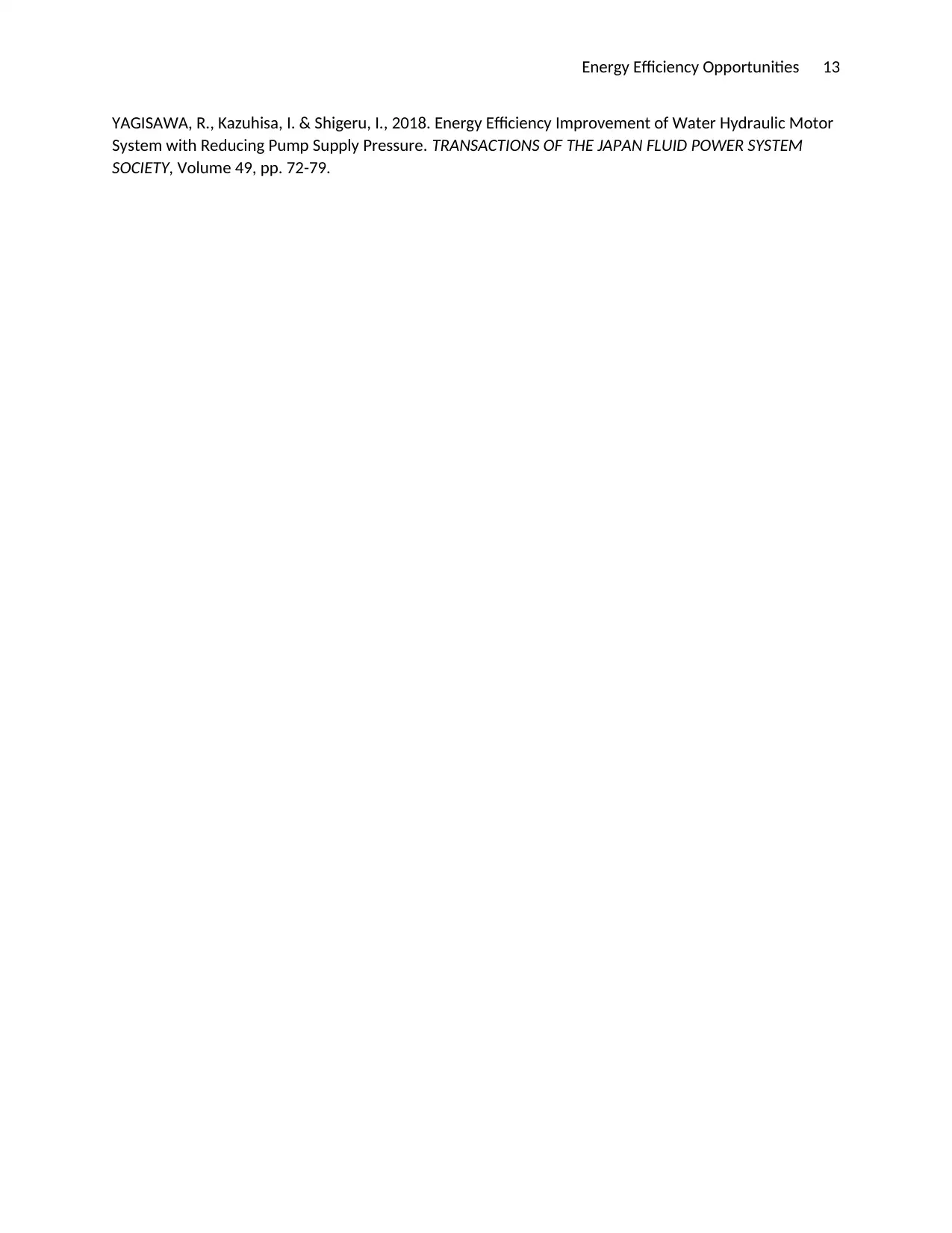
Energy Efficiency Opportunities 13
YAGISAWA, R., Kazuhisa, I. & Shigeru, I., 2018. Energy Efficiency Improvement of Water Hydraulic Motor
System with Reducing Pump Supply Pressure. TRANSACTIONS OF THE JAPAN FLUID POWER SYSTEM
SOCIETY, Volume 49, pp. 72-79.
YAGISAWA, R., Kazuhisa, I. & Shigeru, I., 2018. Energy Efficiency Improvement of Water Hydraulic Motor
System with Reducing Pump Supply Pressure. TRANSACTIONS OF THE JAPAN FLUID POWER SYSTEM
SOCIETY, Volume 49, pp. 72-79.
1 out of 13
![[object Object]](/_next/image/?url=%2F_next%2Fstatic%2Fmedia%2Flogo.6d15ce61.png&w=640&q=75)
Your All-in-One AI-Powered Toolkit for Academic Success.
 +13062052269
info@desklib.com
Available 24*7 on WhatsApp / Email
Unlock your academic potential
© 2024  |  Zucol Services PVT LTD  |  All rights reserved.