Low Impact Manufacturing: Analysis of Energy Utilization in Cheddar Cheese Manufacturing
VerifiedAdded on 2023/04/24
|13
|2577
|225
AI Summary
This report aims at analyzing energy utilization in five processes that consume most of the energy in the manufacture of cheddar cheese. The purpose of this analysis is so as to determine energy efficiency of the cheddar cheese manufacturing facility and identify ways of improving it and reducing energy costs. A total of 35MJ of energy is used in manufacturing 1kg of cheddar cheese. Out of this, 43% of the energy is lost and only 57% s used. This shows that there is great potential of improving energy efficiency in manufacturing processes of cheddar cheese. Renewable energy technologies is one of the most suitable techniques that can be used to improve energy efficiency in various manufacturing processes of cheddar cheese.
Contribute Materials
Your contribution can guide someone’s learning journey. Share your
documents today.
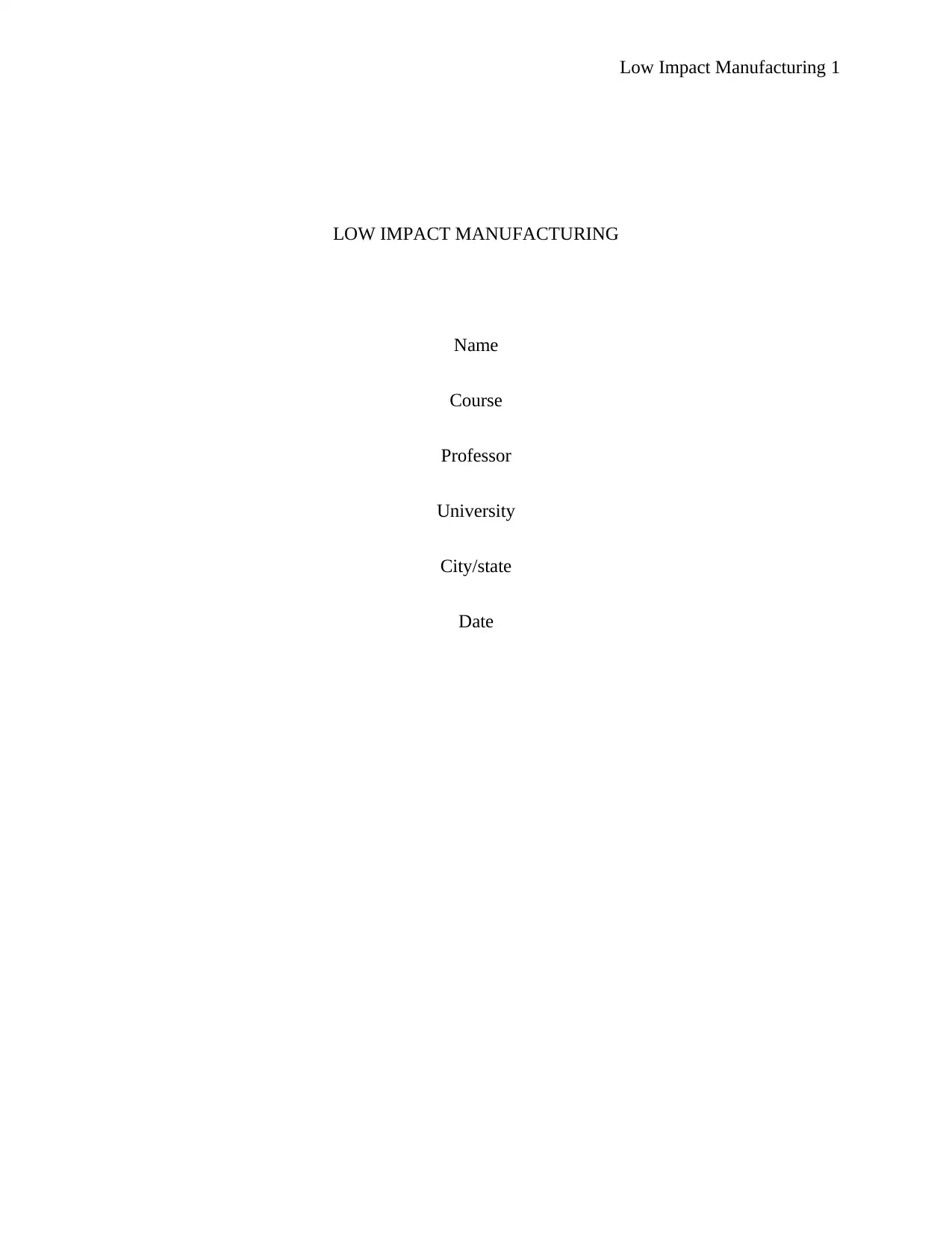
Low Impact Manufacturing 1
LOW IMPACT MANUFACTURING
Name
Course
Professor
University
City/state
Date
LOW IMPACT MANUFACTURING
Name
Course
Professor
University
City/state
Date
Secure Best Marks with AI Grader
Need help grading? Try our AI Grader for instant feedback on your assignments.
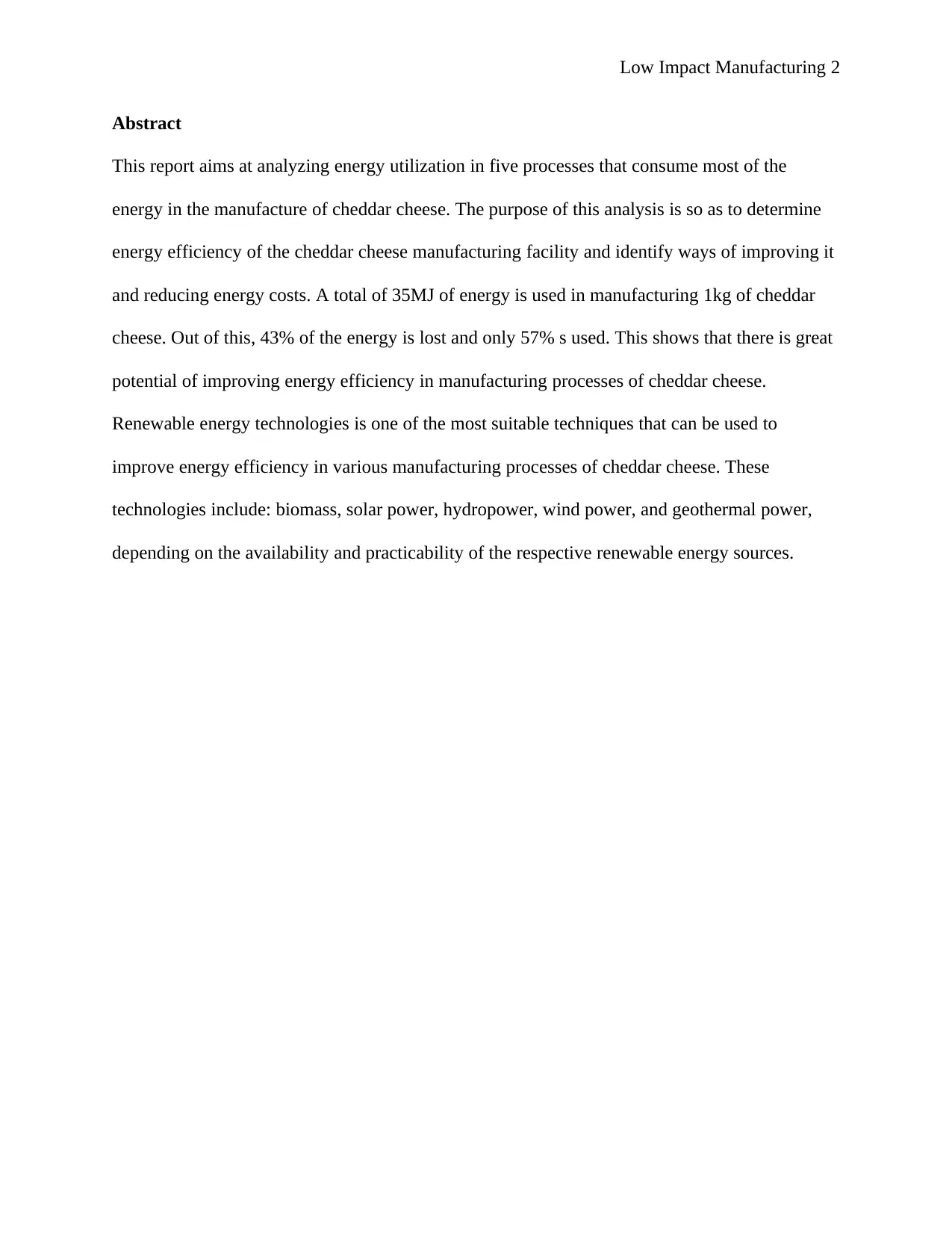
Low Impact Manufacturing 2
Abstract
This report aims at analyzing energy utilization in five processes that consume most of the
energy in the manufacture of cheddar cheese. The purpose of this analysis is so as to determine
energy efficiency of the cheddar cheese manufacturing facility and identify ways of improving it
and reducing energy costs. A total of 35MJ of energy is used in manufacturing 1kg of cheddar
cheese. Out of this, 43% of the energy is lost and only 57% s used. This shows that there is great
potential of improving energy efficiency in manufacturing processes of cheddar cheese.
Renewable energy technologies is one of the most suitable techniques that can be used to
improve energy efficiency in various manufacturing processes of cheddar cheese. These
technologies include: biomass, solar power, hydropower, wind power, and geothermal power,
depending on the availability and practicability of the respective renewable energy sources.
Abstract
This report aims at analyzing energy utilization in five processes that consume most of the
energy in the manufacture of cheddar cheese. The purpose of this analysis is so as to determine
energy efficiency of the cheddar cheese manufacturing facility and identify ways of improving it
and reducing energy costs. A total of 35MJ of energy is used in manufacturing 1kg of cheddar
cheese. Out of this, 43% of the energy is lost and only 57% s used. This shows that there is great
potential of improving energy efficiency in manufacturing processes of cheddar cheese.
Renewable energy technologies is one of the most suitable techniques that can be used to
improve energy efficiency in various manufacturing processes of cheddar cheese. These
technologies include: biomass, solar power, hydropower, wind power, and geothermal power,
depending on the availability and practicability of the respective renewable energy sources.
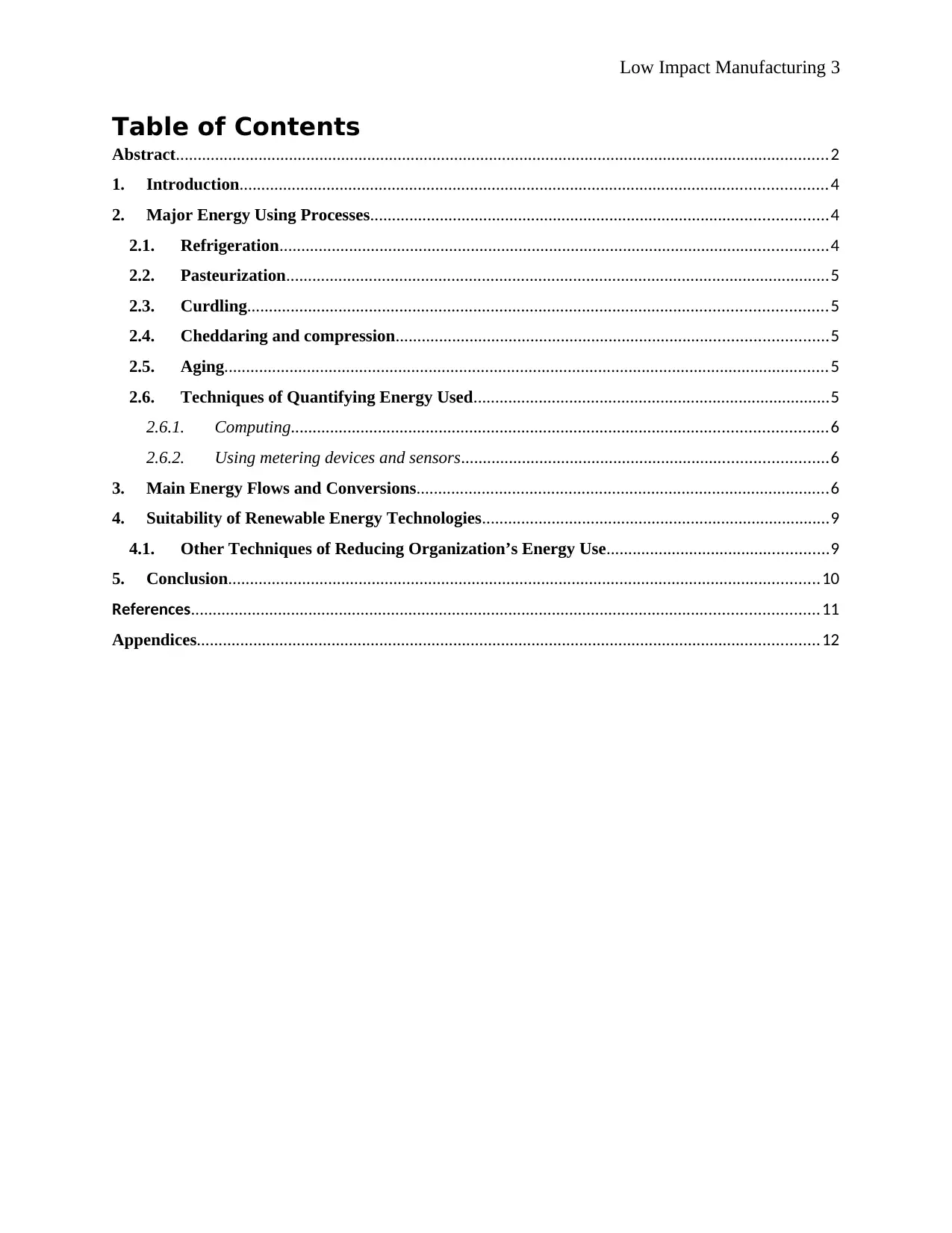
Low Impact Manufacturing 3
Table of Contents
Abstract......................................................................................................................................................2
1. Introduction.......................................................................................................................................4
2. Major Energy Using Processes.........................................................................................................4
2.1. Refrigeration..............................................................................................................................4
2.2. Pasteurization.............................................................................................................................5
2.3. Curdling.....................................................................................................................................5
2.4. Cheddaring and compression...................................................................................................5
2.5. Aging...........................................................................................................................................5
2.6. Techniques of Quantifying Energy Used..................................................................................5
2.6.1. Computing...........................................................................................................................6
2.6.2. Using metering devices and sensors....................................................................................6
3. Main Energy Flows and Conversions...............................................................................................6
4. Suitability of Renewable Energy Technologies................................................................................9
4.1. Other Techniques of Reducing Organization’s Energy Use...................................................9
5. Conclusion........................................................................................................................................10
References................................................................................................................................................11
Appendices...............................................................................................................................................12
Table of Contents
Abstract......................................................................................................................................................2
1. Introduction.......................................................................................................................................4
2. Major Energy Using Processes.........................................................................................................4
2.1. Refrigeration..............................................................................................................................4
2.2. Pasteurization.............................................................................................................................5
2.3. Curdling.....................................................................................................................................5
2.4. Cheddaring and compression...................................................................................................5
2.5. Aging...........................................................................................................................................5
2.6. Techniques of Quantifying Energy Used..................................................................................5
2.6.1. Computing...........................................................................................................................6
2.6.2. Using metering devices and sensors....................................................................................6
3. Main Energy Flows and Conversions...............................................................................................6
4. Suitability of Renewable Energy Technologies................................................................................9
4.1. Other Techniques of Reducing Organization’s Energy Use...................................................9
5. Conclusion........................................................................................................................................10
References................................................................................................................................................11
Appendices...............................................................................................................................................12
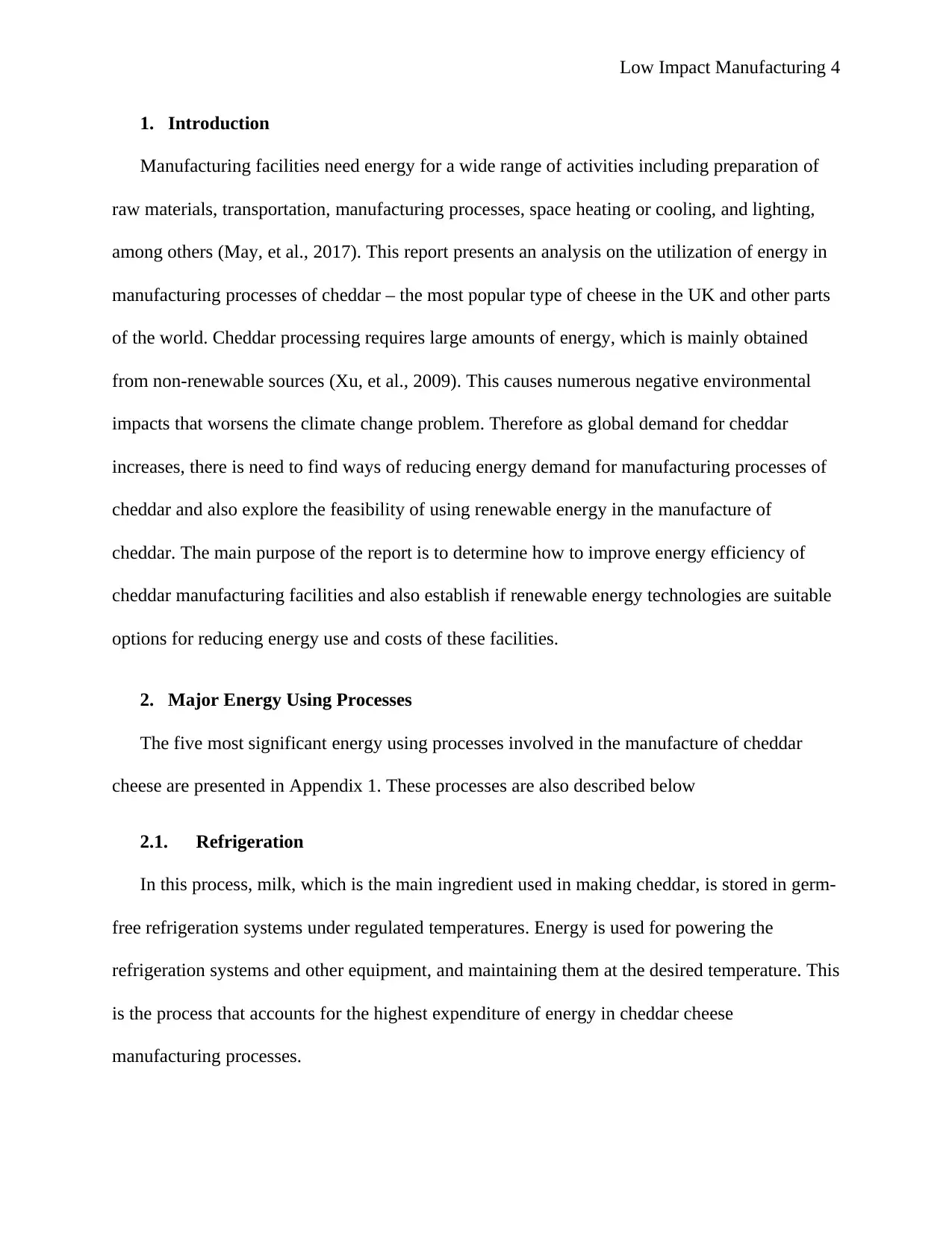
Low Impact Manufacturing 4
1. Introduction
Manufacturing facilities need energy for a wide range of activities including preparation of
raw materials, transportation, manufacturing processes, space heating or cooling, and lighting,
among others (May, et al., 2017). This report presents an analysis on the utilization of energy in
manufacturing processes of cheddar – the most popular type of cheese in the UK and other parts
of the world. Cheddar processing requires large amounts of energy, which is mainly obtained
from non-renewable sources (Xu, et al., 2009). This causes numerous negative environmental
impacts that worsens the climate change problem. Therefore as global demand for cheddar
increases, there is need to find ways of reducing energy demand for manufacturing processes of
cheddar and also explore the feasibility of using renewable energy in the manufacture of
cheddar. The main purpose of the report is to determine how to improve energy efficiency of
cheddar manufacturing facilities and also establish if renewable energy technologies are suitable
options for reducing energy use and costs of these facilities.
2. Major Energy Using Processes
The five most significant energy using processes involved in the manufacture of cheddar
cheese are presented in Appendix 1. These processes are also described below
2.1. Refrigeration
In this process, milk, which is the main ingredient used in making cheddar, is stored in germ-
free refrigeration systems under regulated temperatures. Energy is used for powering the
refrigeration systems and other equipment, and maintaining them at the desired temperature. This
is the process that accounts for the highest expenditure of energy in cheddar cheese
manufacturing processes.
1. Introduction
Manufacturing facilities need energy for a wide range of activities including preparation of
raw materials, transportation, manufacturing processes, space heating or cooling, and lighting,
among others (May, et al., 2017). This report presents an analysis on the utilization of energy in
manufacturing processes of cheddar – the most popular type of cheese in the UK and other parts
of the world. Cheddar processing requires large amounts of energy, which is mainly obtained
from non-renewable sources (Xu, et al., 2009). This causes numerous negative environmental
impacts that worsens the climate change problem. Therefore as global demand for cheddar
increases, there is need to find ways of reducing energy demand for manufacturing processes of
cheddar and also explore the feasibility of using renewable energy in the manufacture of
cheddar. The main purpose of the report is to determine how to improve energy efficiency of
cheddar manufacturing facilities and also establish if renewable energy technologies are suitable
options for reducing energy use and costs of these facilities.
2. Major Energy Using Processes
The five most significant energy using processes involved in the manufacture of cheddar
cheese are presented in Appendix 1. These processes are also described below
2.1. Refrigeration
In this process, milk, which is the main ingredient used in making cheddar, is stored in germ-
free refrigeration systems under regulated temperatures. Energy is used for powering the
refrigeration systems and other equipment, and maintaining them at the desired temperature. This
is the process that accounts for the highest expenditure of energy in cheddar cheese
manufacturing processes.
Secure Best Marks with AI Grader
Need help grading? Try our AI Grader for instant feedback on your assignments.
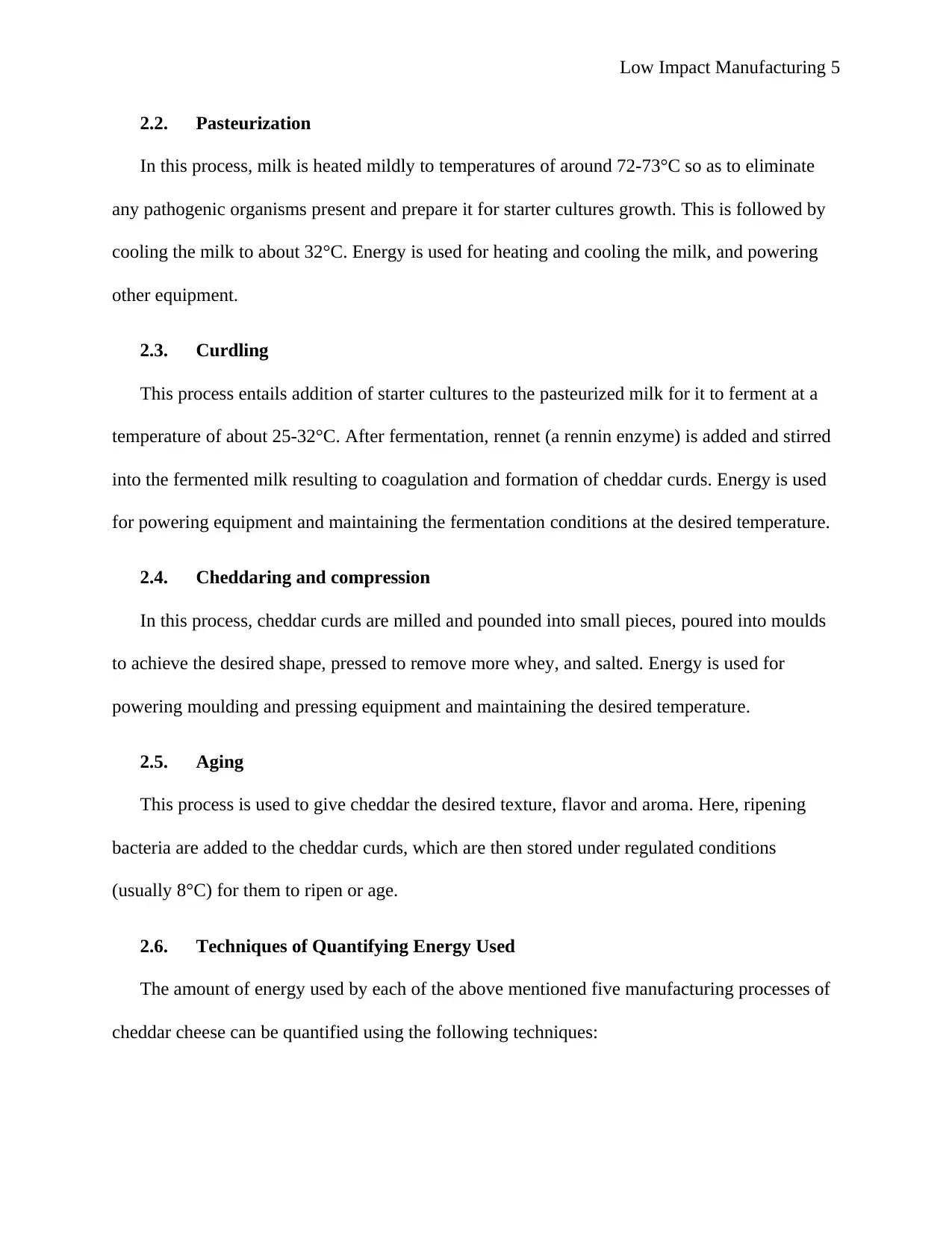
Low Impact Manufacturing 5
2.2. Pasteurization
In this process, milk is heated mildly to temperatures of around 72-73°C so as to eliminate
any pathogenic organisms present and prepare it for starter cultures growth. This is followed by
cooling the milk to about 32°C. Energy is used for heating and cooling the milk, and powering
other equipment.
2.3. Curdling
This process entails addition of starter cultures to the pasteurized milk for it to ferment at a
temperature of about 25-32°C. After fermentation, rennet (a rennin enzyme) is added and stirred
into the fermented milk resulting to coagulation and formation of cheddar curds. Energy is used
for powering equipment and maintaining the fermentation conditions at the desired temperature.
2.4. Cheddaring and compression
In this process, cheddar curds are milled and pounded into small pieces, poured into moulds
to achieve the desired shape, pressed to remove more whey, and salted. Energy is used for
powering moulding and pressing equipment and maintaining the desired temperature.
2.5. Aging
This process is used to give cheddar the desired texture, flavor and aroma. Here, ripening
bacteria are added to the cheddar curds, which are then stored under regulated conditions
(usually 8°C) for them to ripen or age.
2.6. Techniques of Quantifying Energy Used
The amount of energy used by each of the above mentioned five manufacturing processes of
cheddar cheese can be quantified using the following techniques:
2.2. Pasteurization
In this process, milk is heated mildly to temperatures of around 72-73°C so as to eliminate
any pathogenic organisms present and prepare it for starter cultures growth. This is followed by
cooling the milk to about 32°C. Energy is used for heating and cooling the milk, and powering
other equipment.
2.3. Curdling
This process entails addition of starter cultures to the pasteurized milk for it to ferment at a
temperature of about 25-32°C. After fermentation, rennet (a rennin enzyme) is added and stirred
into the fermented milk resulting to coagulation and formation of cheddar curds. Energy is used
for powering equipment and maintaining the fermentation conditions at the desired temperature.
2.4. Cheddaring and compression
In this process, cheddar curds are milled and pounded into small pieces, poured into moulds
to achieve the desired shape, pressed to remove more whey, and salted. Energy is used for
powering moulding and pressing equipment and maintaining the desired temperature.
2.5. Aging
This process is used to give cheddar the desired texture, flavor and aroma. Here, ripening
bacteria are added to the cheddar curds, which are then stored under regulated conditions
(usually 8°C) for them to ripen or age.
2.6. Techniques of Quantifying Energy Used
The amount of energy used by each of the above mentioned five manufacturing processes of
cheddar cheese can be quantified using the following techniques:
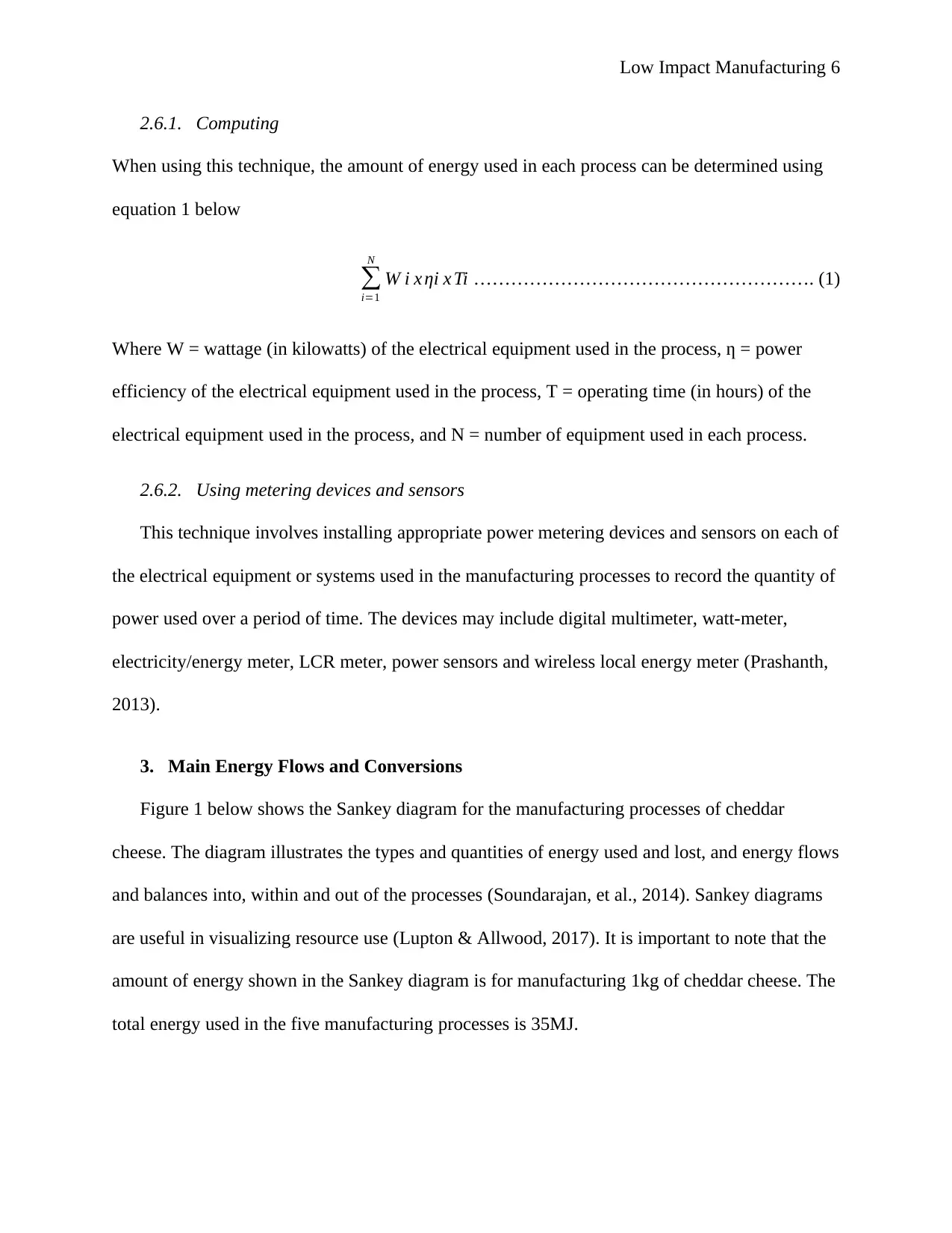
Low Impact Manufacturing 6
2.6.1. Computing
When using this technique, the amount of energy used in each process can be determined using
equation 1 below
∑
i=1
N
W i x ƞi x Ti ………………………………………………. (1)
Where W = wattage (in kilowatts) of the electrical equipment used in the process, ƞ = power
efficiency of the electrical equipment used in the process, T = operating time (in hours) of the
electrical equipment used in the process, and N = number of equipment used in each process.
2.6.2. Using metering devices and sensors
This technique involves installing appropriate power metering devices and sensors on each of
the electrical equipment or systems used in the manufacturing processes to record the quantity of
power used over a period of time. The devices may include digital multimeter, watt-meter,
electricity/energy meter, LCR meter, power sensors and wireless local energy meter (Prashanth,
2013).
3. Main Energy Flows and Conversions
Figure 1 below shows the Sankey diagram for the manufacturing processes of cheddar
cheese. The diagram illustrates the types and quantities of energy used and lost, and energy flows
and balances into, within and out of the processes (Soundarajan, et al., 2014). Sankey diagrams
are useful in visualizing resource use (Lupton & Allwood, 2017). It is important to note that the
amount of energy shown in the Sankey diagram is for manufacturing 1kg of cheddar cheese. The
total energy used in the five manufacturing processes is 35MJ.
2.6.1. Computing
When using this technique, the amount of energy used in each process can be determined using
equation 1 below
∑
i=1
N
W i x ƞi x Ti ………………………………………………. (1)
Where W = wattage (in kilowatts) of the electrical equipment used in the process, ƞ = power
efficiency of the electrical equipment used in the process, T = operating time (in hours) of the
electrical equipment used in the process, and N = number of equipment used in each process.
2.6.2. Using metering devices and sensors
This technique involves installing appropriate power metering devices and sensors on each of
the electrical equipment or systems used in the manufacturing processes to record the quantity of
power used over a period of time. The devices may include digital multimeter, watt-meter,
electricity/energy meter, LCR meter, power sensors and wireless local energy meter (Prashanth,
2013).
3. Main Energy Flows and Conversions
Figure 1 below shows the Sankey diagram for the manufacturing processes of cheddar
cheese. The diagram illustrates the types and quantities of energy used and lost, and energy flows
and balances into, within and out of the processes (Soundarajan, et al., 2014). Sankey diagrams
are useful in visualizing resource use (Lupton & Allwood, 2017). It is important to note that the
amount of energy shown in the Sankey diagram is for manufacturing 1kg of cheddar cheese. The
total energy used in the five manufacturing processes is 35MJ.
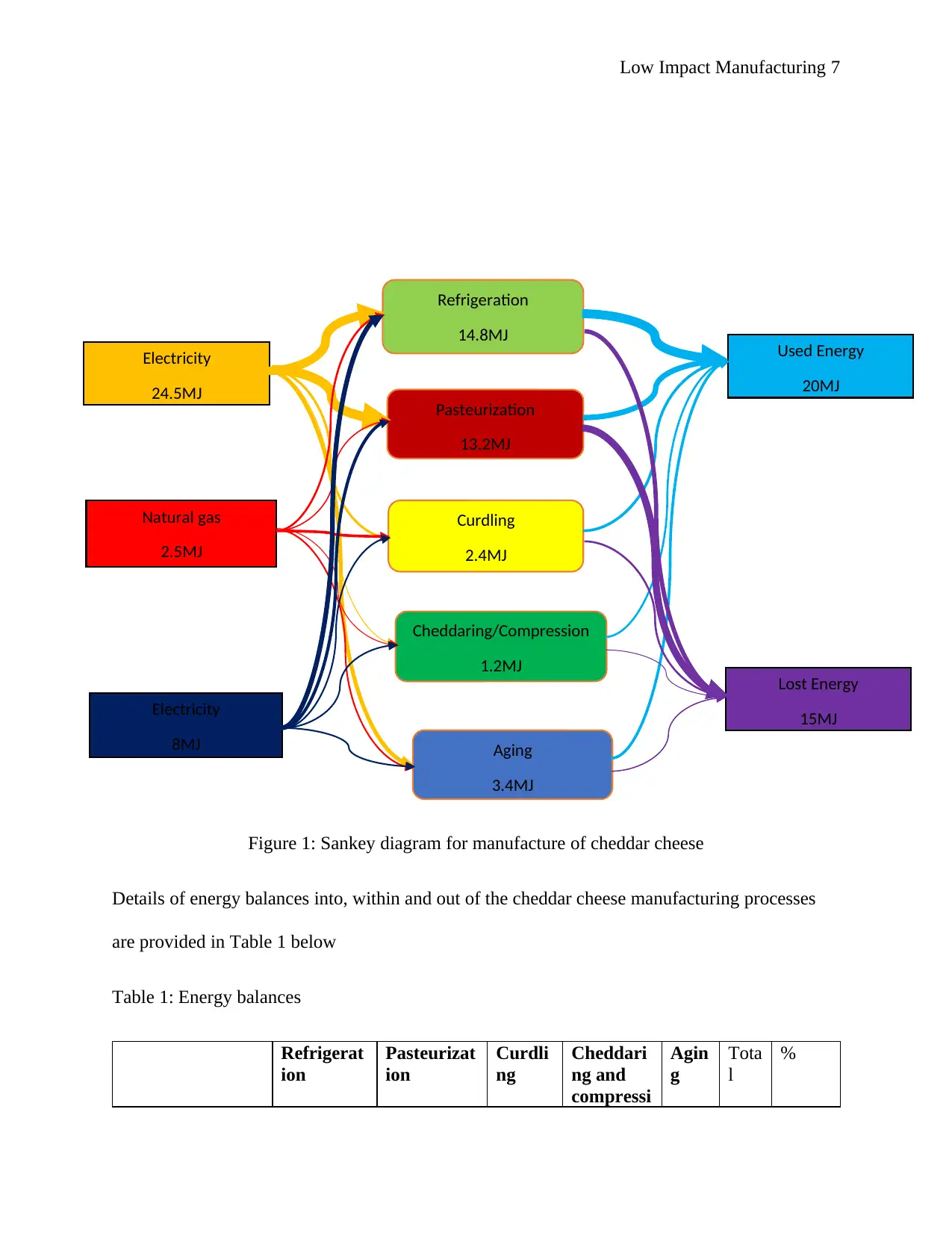
Low Impact Manufacturing 7
Figure 1: Sankey diagram for manufacture of cheddar cheese
Details of energy balances into, within and out of the cheddar cheese manufacturing processes
are provided in Table 1 below
Table 1: Energy balances
Refrigerat
ion
Pasteurizat
ion
Curdli
ng
Cheddari
ng and
compressi
Agin
g
Tota
l
%
Refrigeration
14.8MJ
Aging
3.4MJ
Cheddaring/Compression
1.2MJ
Curdling
2.4MJ
Pasteurization
13.2MJ
Electricity
24.5MJ
Natural gas
2.5MJ
Electricity
8MJ
Used Energy
20MJ
Lost Energy
15MJ
Figure 1: Sankey diagram for manufacture of cheddar cheese
Details of energy balances into, within and out of the cheddar cheese manufacturing processes
are provided in Table 1 below
Table 1: Energy balances
Refrigerat
ion
Pasteurizat
ion
Curdli
ng
Cheddari
ng and
compressi
Agin
g
Tota
l
%
Refrigeration
14.8MJ
Aging
3.4MJ
Cheddaring/Compression
1.2MJ
Curdling
2.4MJ
Pasteurization
13.2MJ
Electricity
24.5MJ
Natural gas
2.5MJ
Electricity
8MJ
Used Energy
20MJ
Lost Energy
15MJ
Paraphrase This Document
Need a fresh take? Get an instant paraphrase of this document with our AI Paraphraser
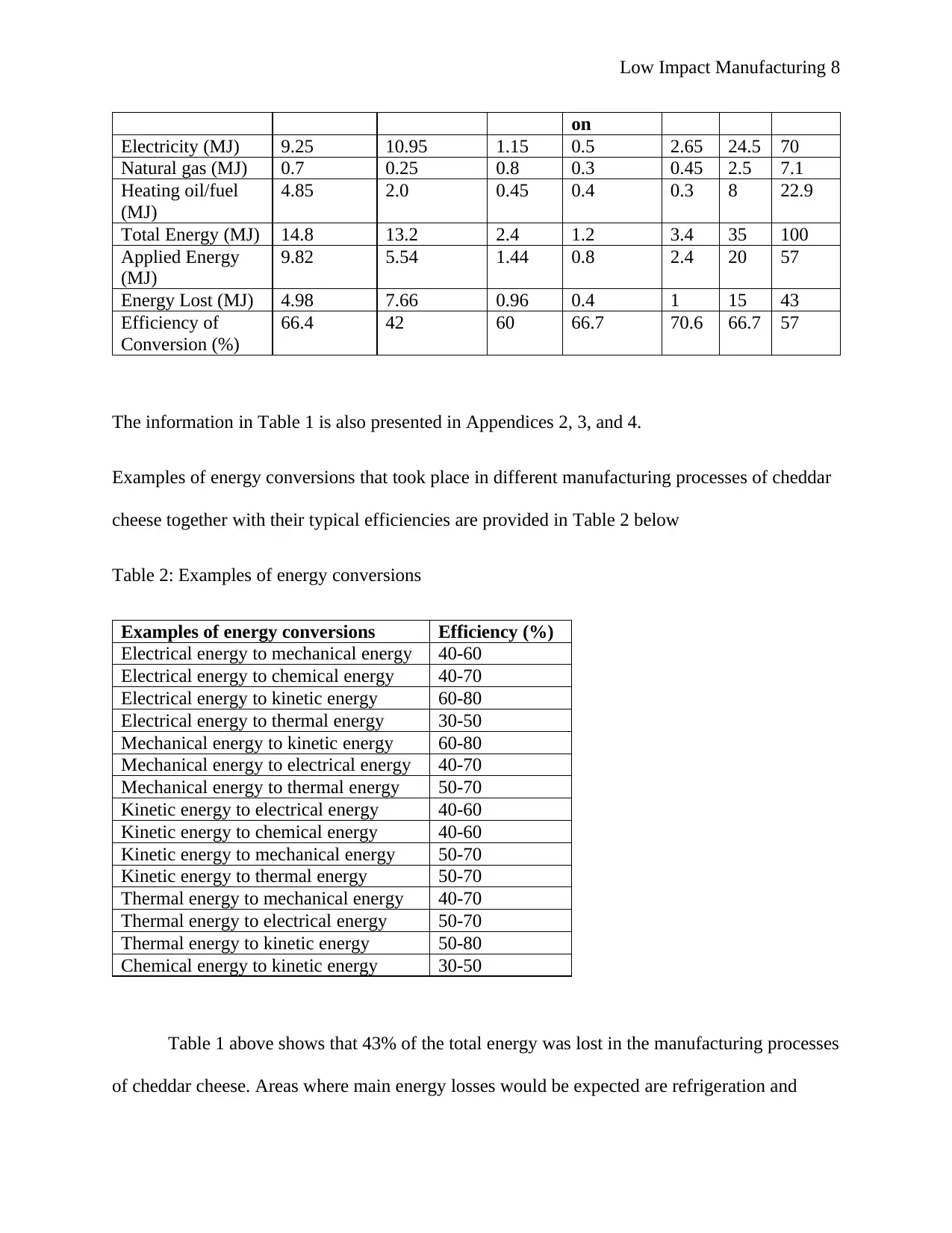
Low Impact Manufacturing 8
on
Electricity (MJ) 9.25 10.95 1.15 0.5 2.65 24.5 70
Natural gas (MJ) 0.7 0.25 0.8 0.3 0.45 2.5 7.1
Heating oil/fuel
(MJ)
4.85 2.0 0.45 0.4 0.3 8 22.9
Total Energy (MJ) 14.8 13.2 2.4 1.2 3.4 35 100
Applied Energy
(MJ)
9.82 5.54 1.44 0.8 2.4 20 57
Energy Lost (MJ) 4.98 7.66 0.96 0.4 1 15 43
Efficiency of
Conversion (%)
66.4 42 60 66.7 70.6 66.7 57
The information in Table 1 is also presented in Appendices 2, 3, and 4.
Examples of energy conversions that took place in different manufacturing processes of cheddar
cheese together with their typical efficiencies are provided in Table 2 below
Table 2: Examples of energy conversions
Examples of energy conversions Efficiency (%)
Electrical energy to mechanical energy 40-60
Electrical energy to chemical energy 40-70
Electrical energy to kinetic energy 60-80
Electrical energy to thermal energy 30-50
Mechanical energy to kinetic energy 60-80
Mechanical energy to electrical energy 40-70
Mechanical energy to thermal energy 50-70
Kinetic energy to electrical energy 40-60
Kinetic energy to chemical energy 40-60
Kinetic energy to mechanical energy 50-70
Kinetic energy to thermal energy 50-70
Thermal energy to mechanical energy 40-70
Thermal energy to electrical energy 50-70
Thermal energy to kinetic energy 50-80
Chemical energy to kinetic energy 30-50
Table 1 above shows that 43% of the total energy was lost in the manufacturing processes
of cheddar cheese. Areas where main energy losses would be expected are refrigeration and
on
Electricity (MJ) 9.25 10.95 1.15 0.5 2.65 24.5 70
Natural gas (MJ) 0.7 0.25 0.8 0.3 0.45 2.5 7.1
Heating oil/fuel
(MJ)
4.85 2.0 0.45 0.4 0.3 8 22.9
Total Energy (MJ) 14.8 13.2 2.4 1.2 3.4 35 100
Applied Energy
(MJ)
9.82 5.54 1.44 0.8 2.4 20 57
Energy Lost (MJ) 4.98 7.66 0.96 0.4 1 15 43
Efficiency of
Conversion (%)
66.4 42 60 66.7 70.6 66.7 57
The information in Table 1 is also presented in Appendices 2, 3, and 4.
Examples of energy conversions that took place in different manufacturing processes of cheddar
cheese together with their typical efficiencies are provided in Table 2 below
Table 2: Examples of energy conversions
Examples of energy conversions Efficiency (%)
Electrical energy to mechanical energy 40-60
Electrical energy to chemical energy 40-70
Electrical energy to kinetic energy 60-80
Electrical energy to thermal energy 30-50
Mechanical energy to kinetic energy 60-80
Mechanical energy to electrical energy 40-70
Mechanical energy to thermal energy 50-70
Kinetic energy to electrical energy 40-60
Kinetic energy to chemical energy 40-60
Kinetic energy to mechanical energy 50-70
Kinetic energy to thermal energy 50-70
Thermal energy to mechanical energy 40-70
Thermal energy to electrical energy 50-70
Thermal energy to kinetic energy 50-80
Chemical energy to kinetic energy 30-50
Table 1 above shows that 43% of the total energy was lost in the manufacturing processes
of cheddar cheese. Areas where main energy losses would be expected are refrigeration and

Low Impact Manufacturing 9
pasteurization. These are processes that mainly involve cooling and heating, which are
susceptible to energy losses.
4. Suitability of Renewable Energy Technologies
The benefits of renewable energy technologies in manufacturing facilities cannot be
overemphasized (Jacobson & Delucchi, 2011). These technologies can significantly lower
energy costs, greenhouse gas emissions (Owusu & Asummadu-Sarkodie, 2016) and other
environmental impacts related to manufacturing processes of cheddar cheese. Biomass is a
suitable option for providing all the energy needed for heating during pasteurization and heating.
The energy needed for various manufacturing processes can also be provided by solar energy
technologies such as concentrating solar energy technology, solar thermal technology, and solar
photovoltaic technology.
Additionally, other renewable energy technologies such as wind energy technology,
geothermal energy technology and hydroelectric technology are also suitable in providing the
needed power for the operations of the facility depending on the availability of their respective
renewable energy sources and the practicability of using them. This means that renewable energy
technologies are suitable for reducing the cost of energy used by the cheddar cheese processing
facility.
4.1. Other Techniques of Reducing Organization’s Energy Use
There are also several other techniques that the organization can use to reduce the amount
and cost of energy used in the facility. Some of these techniques include the following: replace
existing heating and electrical equipment used in each of the manufacturing processes with new
and more energy efficient ones; develop a heat recovery system to recover and reuse lost thermal
pasteurization. These are processes that mainly involve cooling and heating, which are
susceptible to energy losses.
4. Suitability of Renewable Energy Technologies
The benefits of renewable energy technologies in manufacturing facilities cannot be
overemphasized (Jacobson & Delucchi, 2011). These technologies can significantly lower
energy costs, greenhouse gas emissions (Owusu & Asummadu-Sarkodie, 2016) and other
environmental impacts related to manufacturing processes of cheddar cheese. Biomass is a
suitable option for providing all the energy needed for heating during pasteurization and heating.
The energy needed for various manufacturing processes can also be provided by solar energy
technologies such as concentrating solar energy technology, solar thermal technology, and solar
photovoltaic technology.
Additionally, other renewable energy technologies such as wind energy technology,
geothermal energy technology and hydroelectric technology are also suitable in providing the
needed power for the operations of the facility depending on the availability of their respective
renewable energy sources and the practicability of using them. This means that renewable energy
technologies are suitable for reducing the cost of energy used by the cheddar cheese processing
facility.
4.1. Other Techniques of Reducing Organization’s Energy Use
There are also several other techniques that the organization can use to reduce the amount
and cost of energy used in the facility. Some of these techniques include the following: replace
existing heating and electrical equipment used in each of the manufacturing processes with new
and more energy efficient ones; develop a heat recovery system to recover and reuse lost thermal
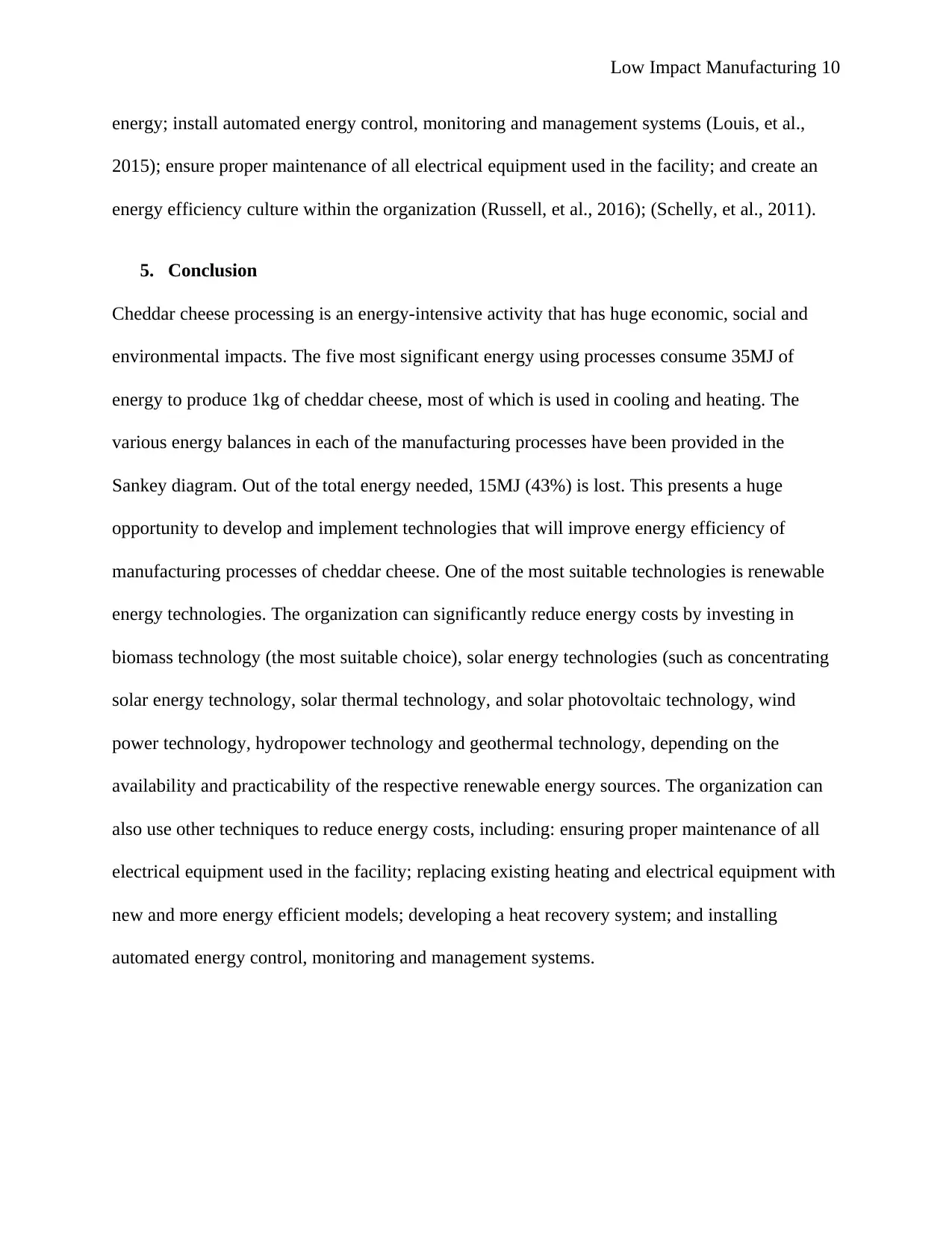
Low Impact Manufacturing 10
energy; install automated energy control, monitoring and management systems (Louis, et al.,
2015); ensure proper maintenance of all electrical equipment used in the facility; and create an
energy efficiency culture within the organization (Russell, et al., 2016); (Schelly, et al., 2011).
5. Conclusion
Cheddar cheese processing is an energy-intensive activity that has huge economic, social and
environmental impacts. The five most significant energy using processes consume 35MJ of
energy to produce 1kg of cheddar cheese, most of which is used in cooling and heating. The
various energy balances in each of the manufacturing processes have been provided in the
Sankey diagram. Out of the total energy needed, 15MJ (43%) is lost. This presents a huge
opportunity to develop and implement technologies that will improve energy efficiency of
manufacturing processes of cheddar cheese. One of the most suitable technologies is renewable
energy technologies. The organization can significantly reduce energy costs by investing in
biomass technology (the most suitable choice), solar energy technologies (such as concentrating
solar energy technology, solar thermal technology, and solar photovoltaic technology, wind
power technology, hydropower technology and geothermal technology, depending on the
availability and practicability of the respective renewable energy sources. The organization can
also use other techniques to reduce energy costs, including: ensuring proper maintenance of all
electrical equipment used in the facility; replacing existing heating and electrical equipment with
new and more energy efficient models; developing a heat recovery system; and installing
automated energy control, monitoring and management systems.
energy; install automated energy control, monitoring and management systems (Louis, et al.,
2015); ensure proper maintenance of all electrical equipment used in the facility; and create an
energy efficiency culture within the organization (Russell, et al., 2016); (Schelly, et al., 2011).
5. Conclusion
Cheddar cheese processing is an energy-intensive activity that has huge economic, social and
environmental impacts. The five most significant energy using processes consume 35MJ of
energy to produce 1kg of cheddar cheese, most of which is used in cooling and heating. The
various energy balances in each of the manufacturing processes have been provided in the
Sankey diagram. Out of the total energy needed, 15MJ (43%) is lost. This presents a huge
opportunity to develop and implement technologies that will improve energy efficiency of
manufacturing processes of cheddar cheese. One of the most suitable technologies is renewable
energy technologies. The organization can significantly reduce energy costs by investing in
biomass technology (the most suitable choice), solar energy technologies (such as concentrating
solar energy technology, solar thermal technology, and solar photovoltaic technology, wind
power technology, hydropower technology and geothermal technology, depending on the
availability and practicability of the respective renewable energy sources. The organization can
also use other techniques to reduce energy costs, including: ensuring proper maintenance of all
electrical equipment used in the facility; replacing existing heating and electrical equipment with
new and more energy efficient models; developing a heat recovery system; and installing
automated energy control, monitoring and management systems.
Secure Best Marks with AI Grader
Need help grading? Try our AI Grader for instant feedback on your assignments.
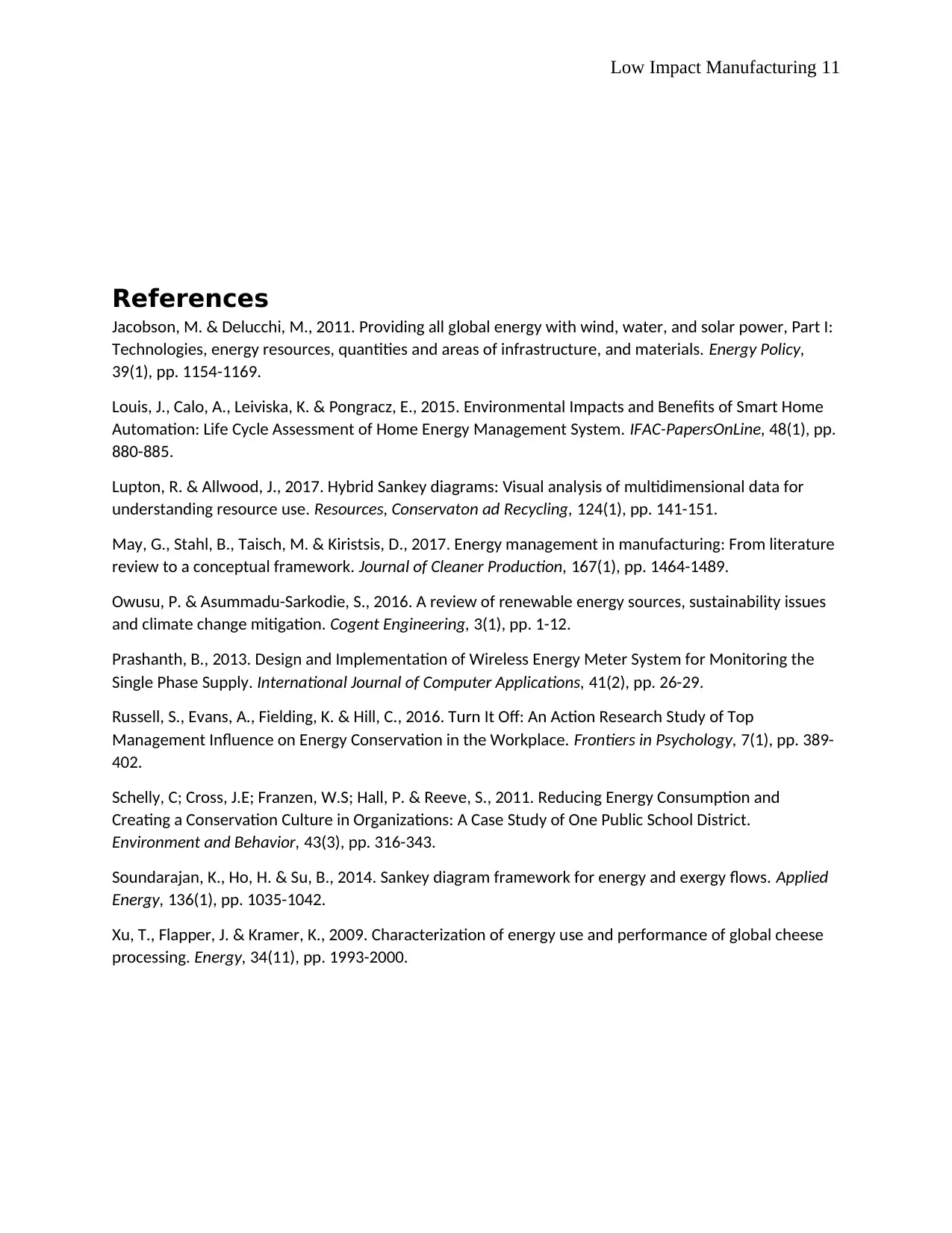
Low Impact Manufacturing 11
References
Jacobson, M. & Delucchi, M., 2011. Providing all global energy with wind, water, and solar power, Part I:
Technologies, energy resources, quantities and areas of infrastructure, and materials. Energy Policy,
39(1), pp. 1154-1169.
Louis, J., Calo, A., Leiviska, K. & Pongracz, E., 2015. Environmental Impacts and Benefits of Smart Home
Automation: Life Cycle Assessment of Home Energy Management System. IFAC-PapersOnLine, 48(1), pp.
880-885.
Lupton, R. & Allwood, J., 2017. Hybrid Sankey diagrams: Visual analysis of multidimensional data for
understanding resource use. Resources, Conservaton ad Recycling, 124(1), pp. 141-151.
May, G., Stahl, B., Taisch, M. & Kiristsis, D., 2017. Energy management in manufacturing: From literature
review to a conceptual framework. Journal of Cleaner Production, 167(1), pp. 1464-1489.
Owusu, P. & Asummadu-Sarkodie, S., 2016. A review of renewable energy sources, sustainability issues
and climate change mitigation. Cogent Engineering, 3(1), pp. 1-12.
Prashanth, B., 2013. Design and Implementation of Wireless Energy Meter System for Monitoring the
Single Phase Supply. International Journal of Computer Applications, 41(2), pp. 26-29.
Russell, S., Evans, A., Fielding, K. & Hill, C., 2016. Turn It Off: An Action Research Study of Top
Management Influence on Energy Conservation in the Workplace. Frontiers in Psychology, 7(1), pp. 389-
402.
Schelly, C; Cross, J.E; Franzen, W.S; Hall, P. & Reeve, S., 2011. Reducing Energy Consumption and
Creating a Conservation Culture in Organizations: A Case Study of One Public School District.
Environment and Behavior, 43(3), pp. 316-343.
Soundarajan, K., Ho, H. & Su, B., 2014. Sankey diagram framework for energy and exergy flows. Applied
Energy, 136(1), pp. 1035-1042.
Xu, T., Flapper, J. & Kramer, K., 2009. Characterization of energy use and performance of global cheese
processing. Energy, 34(11), pp. 1993-2000.
References
Jacobson, M. & Delucchi, M., 2011. Providing all global energy with wind, water, and solar power, Part I:
Technologies, energy resources, quantities and areas of infrastructure, and materials. Energy Policy,
39(1), pp. 1154-1169.
Louis, J., Calo, A., Leiviska, K. & Pongracz, E., 2015. Environmental Impacts and Benefits of Smart Home
Automation: Life Cycle Assessment of Home Energy Management System. IFAC-PapersOnLine, 48(1), pp.
880-885.
Lupton, R. & Allwood, J., 2017. Hybrid Sankey diagrams: Visual analysis of multidimensional data for
understanding resource use. Resources, Conservaton ad Recycling, 124(1), pp. 141-151.
May, G., Stahl, B., Taisch, M. & Kiristsis, D., 2017. Energy management in manufacturing: From literature
review to a conceptual framework. Journal of Cleaner Production, 167(1), pp. 1464-1489.
Owusu, P. & Asummadu-Sarkodie, S., 2016. A review of renewable energy sources, sustainability issues
and climate change mitigation. Cogent Engineering, 3(1), pp. 1-12.
Prashanth, B., 2013. Design and Implementation of Wireless Energy Meter System for Monitoring the
Single Phase Supply. International Journal of Computer Applications, 41(2), pp. 26-29.
Russell, S., Evans, A., Fielding, K. & Hill, C., 2016. Turn It Off: An Action Research Study of Top
Management Influence on Energy Conservation in the Workplace. Frontiers in Psychology, 7(1), pp. 389-
402.
Schelly, C; Cross, J.E; Franzen, W.S; Hall, P. & Reeve, S., 2011. Reducing Energy Consumption and
Creating a Conservation Culture in Organizations: A Case Study of One Public School District.
Environment and Behavior, 43(3), pp. 316-343.
Soundarajan, K., Ho, H. & Su, B., 2014. Sankey diagram framework for energy and exergy flows. Applied
Energy, 136(1), pp. 1035-1042.
Xu, T., Flapper, J. & Kramer, K., 2009. Characterization of energy use and performance of global cheese
processing. Energy, 34(11), pp. 1993-2000.
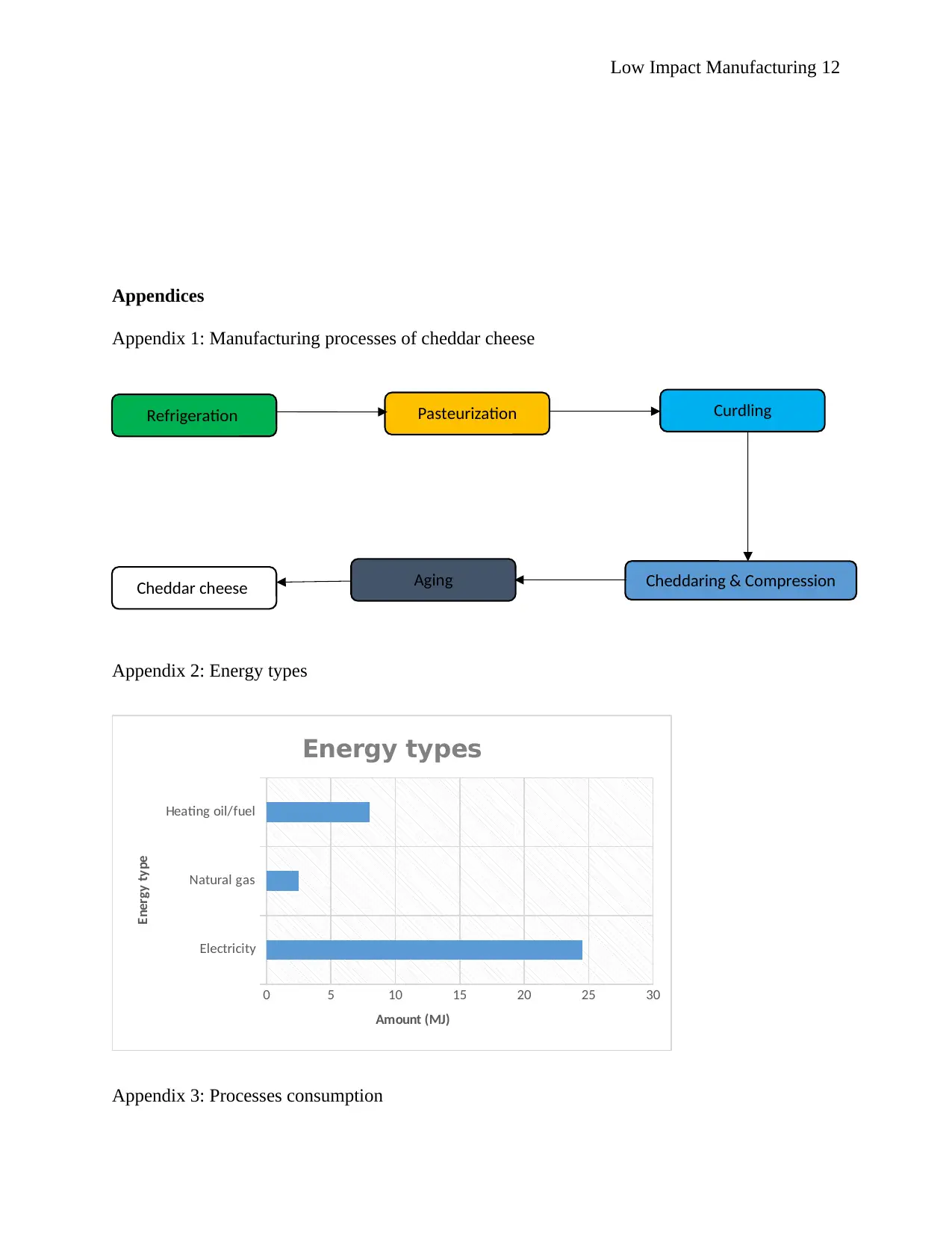
Low Impact Manufacturing 12
Appendices
Appendix 1: Manufacturing processes of cheddar cheese
Appendix 2: Energy types
Electricity
Natural gas
Heating oil/fuel
0 5 10 15 20 25 30
Energy types
Amount (MJ)
Energy type
Appendix 3: Processes consumption
Refrigeration Pasteurization Curdling
Cheddaring & CompressionAgingCheddar cheese
Appendices
Appendix 1: Manufacturing processes of cheddar cheese
Appendix 2: Energy types
Electricity
Natural gas
Heating oil/fuel
0 5 10 15 20 25 30
Energy types
Amount (MJ)
Energy type
Appendix 3: Processes consumption
Refrigeration Pasteurization Curdling
Cheddaring & CompressionAgingCheddar cheese
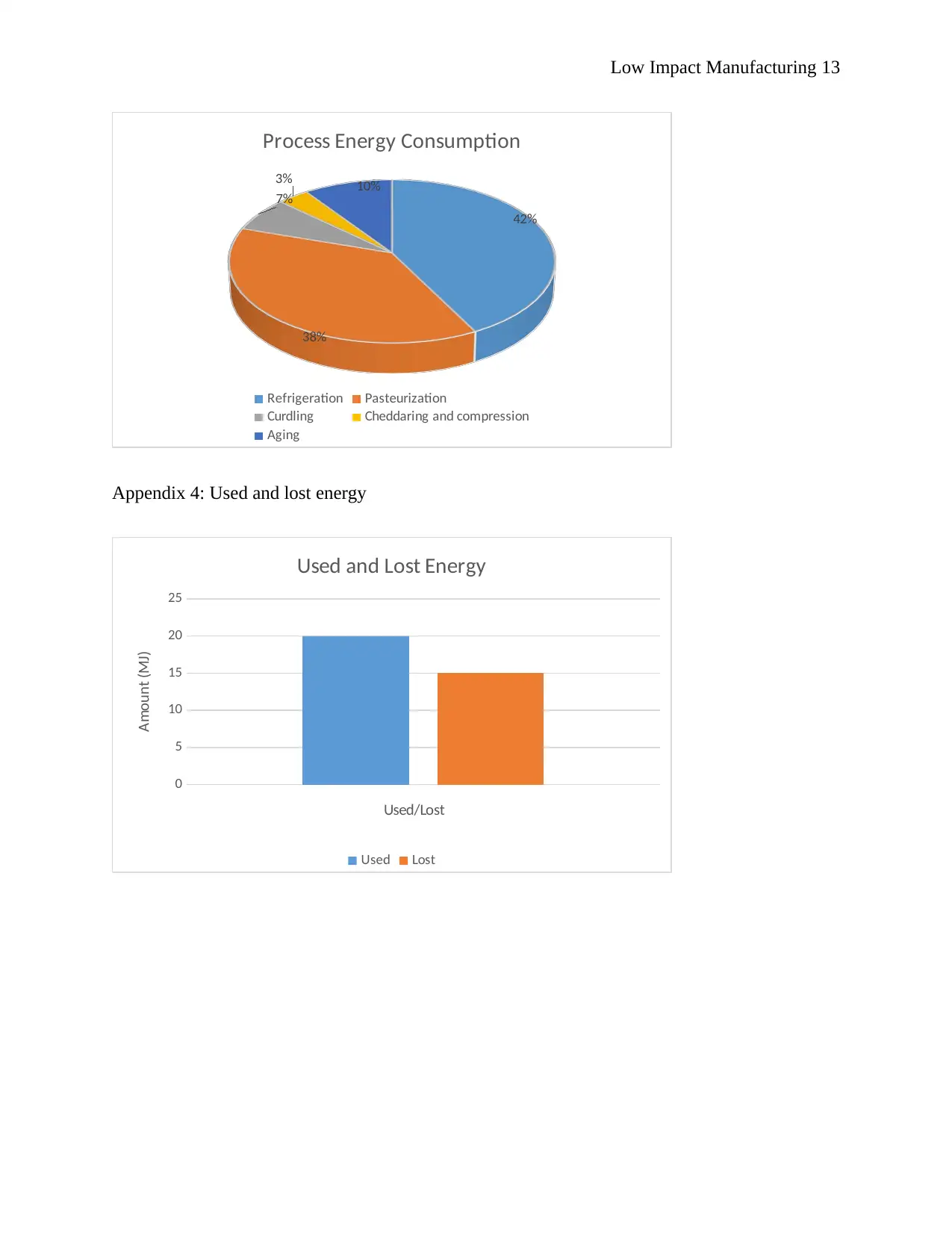
Low Impact Manufacturing 13
42%
38%
7%
3% 10%
Process Energy Consumption
Refrigeration Pasteurization
Curdling Cheddaring and compression
Aging
Appendix 4: Used and lost energy
0
5
10
15
20
25
Used and Lost Energy
Used Lost
Used/Lost
Amount (MJ)
42%
38%
7%
3% 10%
Process Energy Consumption
Refrigeration Pasteurization
Curdling Cheddaring and compression
Aging
Appendix 4: Used and lost energy
0
5
10
15
20
25
Used and Lost Energy
Used Lost
Used/Lost
Amount (MJ)
1 out of 13
Related Documents
![[object Object]](/_next/image/?url=%2F_next%2Fstatic%2Fmedia%2Flogo.6d15ce61.png&w=640&q=75)
Your All-in-One AI-Powered Toolkit for Academic Success.
+13062052269
info@desklib.com
Available 24*7 on WhatsApp / Email
Unlock your academic potential
© 2024 | Zucol Services PVT LTD | All rights reserved.