Engineering Mechanics | Report
Added on 2022-09-18
14 Pages2338 Words36 Views
ENGINEERING MECHANICS
By Name
Course
Instructor
Institution
Location
Date
By Name
Course
Instructor
Institution
Location
Date
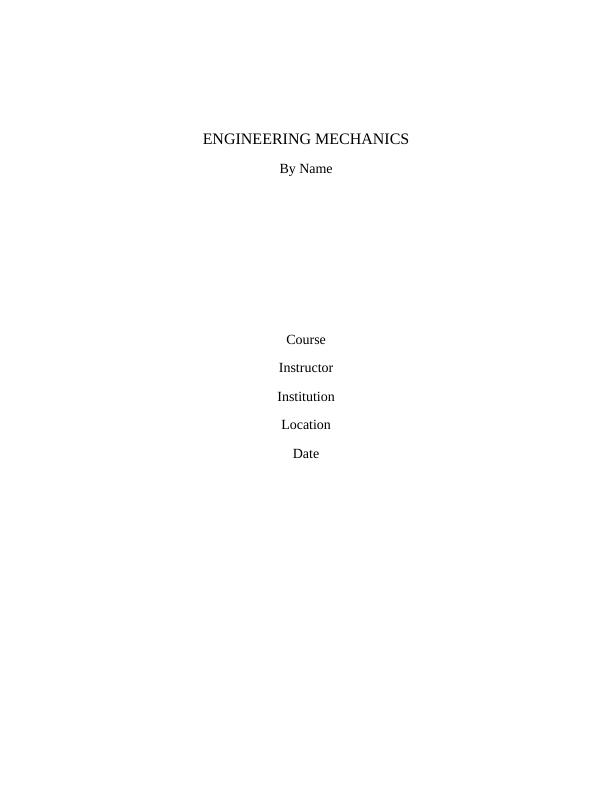
INTRODUCTION
Shaft has been considered as a component very vital in every machine and mechanical systems.
Nearly in all transmission of power in the shaft components, the primary part is shaft. Its design
must therefore be as efficient as possible for effective working of the machine. The conventional
procedure of shaft design therefore has its own benefits. The design of shafts is therefore done
for various conditions of loading. The prime causes of failure in the case of the shaft are the
discontinuities since they cause fracture. In most cases especially practical applications, the
design of shaft must be done for the combined loadings (Sim, Moon and Jeon 2018).
RESULTS AND DISCUSSION
Loading cases to be considered during shaft design:
As a rotating member, it provides rotation axis while transmitting power or the motion itself. The
rotating transmission parts have exposure to possibly two types of loading:
Bending from the transverse loads at the sheaves, gears and sprockets.
The next type of load is the torsion due to the torque being transmitted.
The occurrence of these loads usually take place in combination since the toque being
transmitted maybe related to the forces at the teeth of the sprockets, gears all of which are
usually attached to the shaft. Both bending and torque loads may vary with time or be constant. It
is also possible to consider axial loading on the shaft (SoltanRezaee, et al.2018). This is because
is because its occurrence will be dependent on the coupling or joining arrangement of the shaft
for example when coupling is done by the use of the helical or worm gear. Although it can be
neglected but its consideration will give more accurate design of shaft.
Shaft has been considered as a component very vital in every machine and mechanical systems.
Nearly in all transmission of power in the shaft components, the primary part is shaft. Its design
must therefore be as efficient as possible for effective working of the machine. The conventional
procedure of shaft design therefore has its own benefits. The design of shafts is therefore done
for various conditions of loading. The prime causes of failure in the case of the shaft are the
discontinuities since they cause fracture. In most cases especially practical applications, the
design of shaft must be done for the combined loadings (Sim, Moon and Jeon 2018).
RESULTS AND DISCUSSION
Loading cases to be considered during shaft design:
As a rotating member, it provides rotation axis while transmitting power or the motion itself. The
rotating transmission parts have exposure to possibly two types of loading:
Bending from the transverse loads at the sheaves, gears and sprockets.
The next type of load is the torsion due to the torque being transmitted.
The occurrence of these loads usually take place in combination since the toque being
transmitted maybe related to the forces at the teeth of the sprockets, gears all of which are
usually attached to the shaft. Both bending and torque loads may vary with time or be constant. It
is also possible to consider axial loading on the shaft (SoltanRezaee, et al.2018). This is because
is because its occurrence will be dependent on the coupling or joining arrangement of the shaft
for example when coupling is done by the use of the helical or worm gear. Although it can be
neglected but its consideration will give more accurate design of shaft.
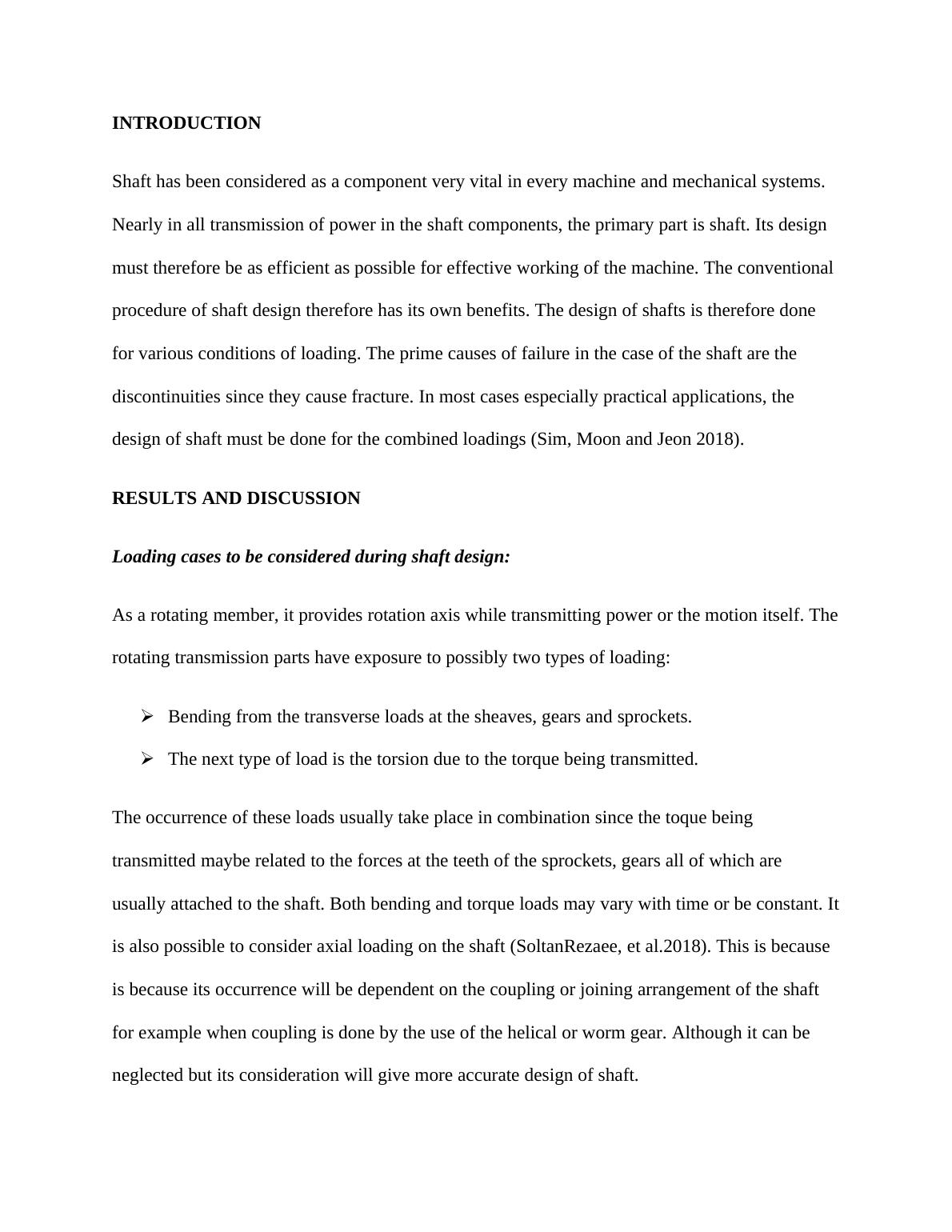
Material for tube section
In order for the tube to effectively perform its functions, it must meet the following
requirements:
Very good properties of welding
Higher durability and torsional strength
High accuracy in terms of geometry. This extends to roundness and eccentricity
Excellent condition of the surface
High values of strength (Gong et al.2018).
In order for the above requirements to be met, a tough material preferably Aluminium Alloy is
chosen. This is because it is known to exhibit good weldability, light weight and well s resistance
to corrosion.
Stress transformation and rupture
Through transformation effects, stress rupture will take place at the end of tertiary creep stage.
This implies that through transformation of stress, the tube’s load carrying capacity will drop to
the level of applied stress hence leading to the failure. The torsional stress transformation will
therefore cause fracture to occur diagonally (Wotzak 2017).
Calculations
Parameters given;
A torque of 1100 N.m
Diameter of 42 mm
The material used yield stress of is 450 MPa.
In order for the tube to effectively perform its functions, it must meet the following
requirements:
Very good properties of welding
Higher durability and torsional strength
High accuracy in terms of geometry. This extends to roundness and eccentricity
Excellent condition of the surface
High values of strength (Gong et al.2018).
In order for the above requirements to be met, a tough material preferably Aluminium Alloy is
chosen. This is because it is known to exhibit good weldability, light weight and well s resistance
to corrosion.
Stress transformation and rupture
Through transformation effects, stress rupture will take place at the end of tertiary creep stage.
This implies that through transformation of stress, the tube’s load carrying capacity will drop to
the level of applied stress hence leading to the failure. The torsional stress transformation will
therefore cause fracture to occur diagonally (Wotzak 2017).
Calculations
Parameters given;
A torque of 1100 N.m
Diameter of 42 mm
The material used yield stress of is 450 MPa.
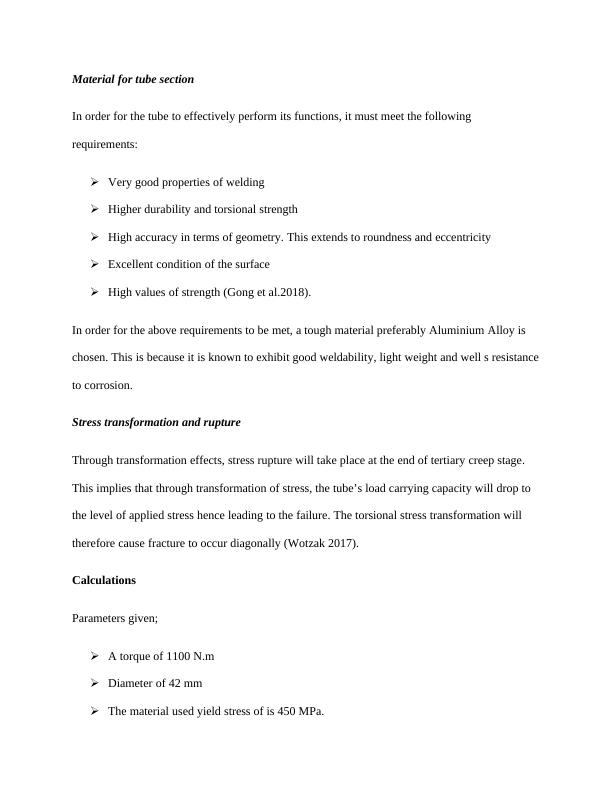
Part I
It is obvious that maximum shear stress is usually a function of the wall thickness.
Taking the formula (Morgan, et al.2018)
Sketch;
It is obvious that maximum shear stress is usually a function of the wall thickness.
Taking the formula (Morgan, et al.2018)
Sketch;
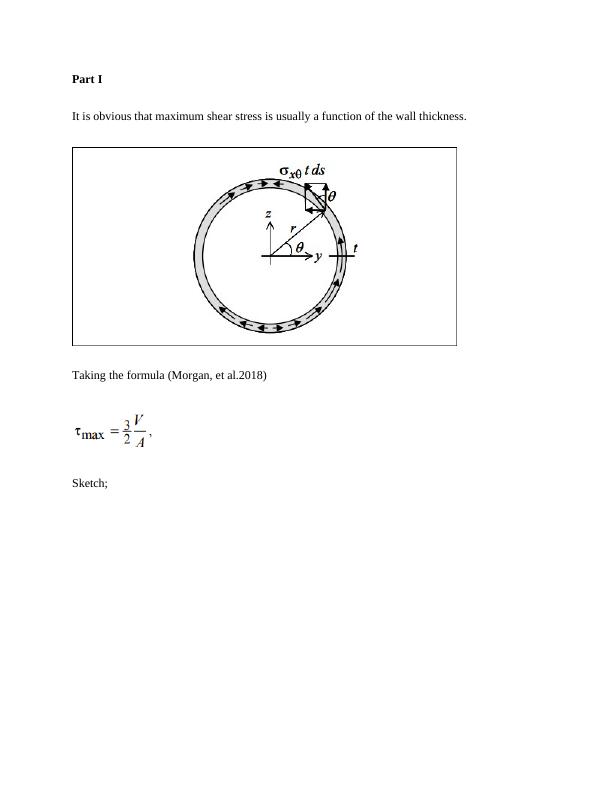
End of preview
Want to access all the pages? Upload your documents or become a member.