Design Project: Blanking Die Set for Stainless Steel Sheet
VerifiedAdded on 2023/04/10
|35
|3206
|291
AI Summary
This document provides a detailed analysis of the design process for a blanking die set used to blank two letters from a stainless steel sheet. It covers background information on the blanking process, the problem statement, design constraints and specifications, design approach, and the stress analysis and cost analysis of the design. The document also includes engineering drawings and material selection information.
Contribute Materials
Your contribution can guide someone’s learning journey. Share your
documents today.
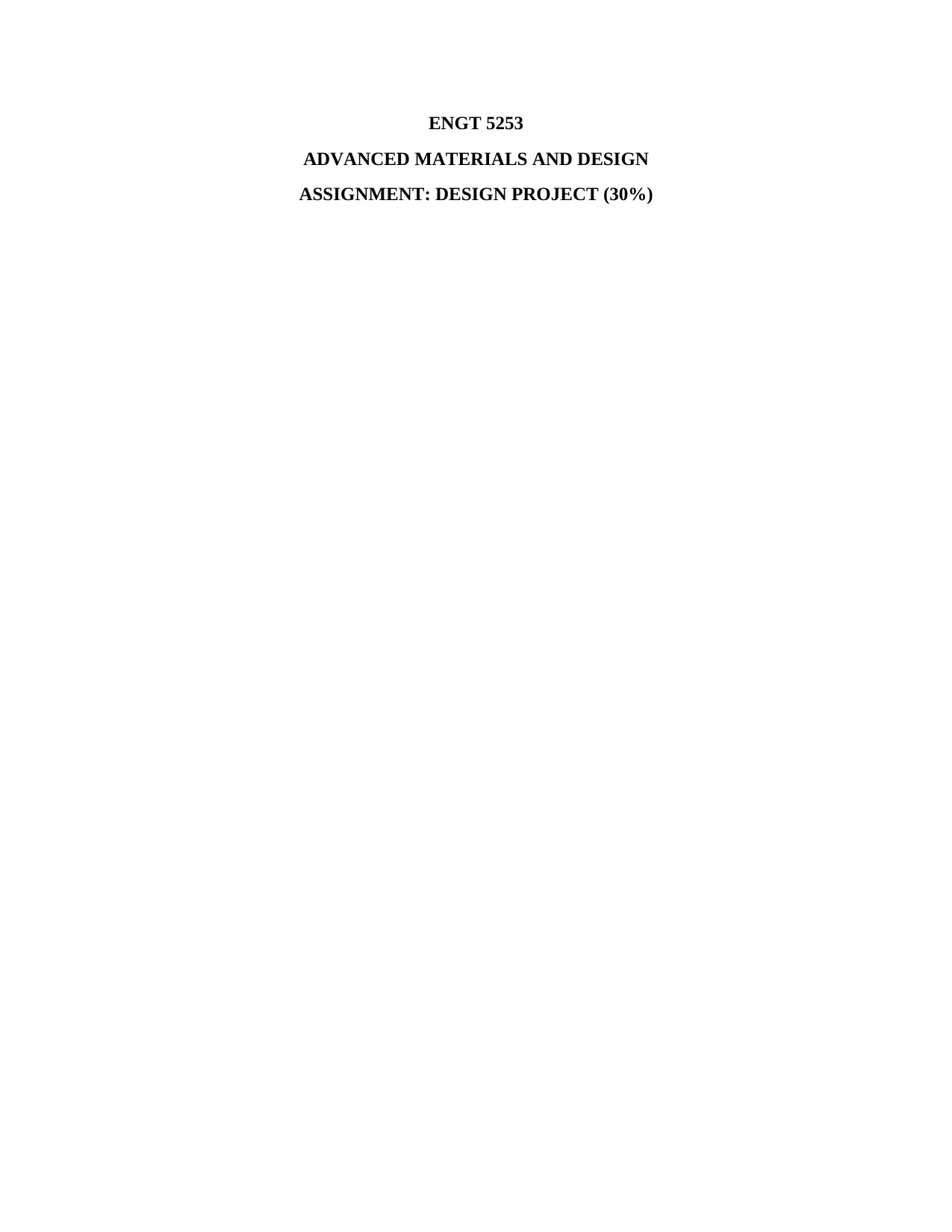
ENGT 5253
ADVANCED MATERIALS AND DESIGN
ASSIGNMENT: DESIGN PROJECT (30%)
ADVANCED MATERIALS AND DESIGN
ASSIGNMENT: DESIGN PROJECT (30%)
Secure Best Marks with AI Grader
Need help grading? Try our AI Grader for instant feedback on your assignments.
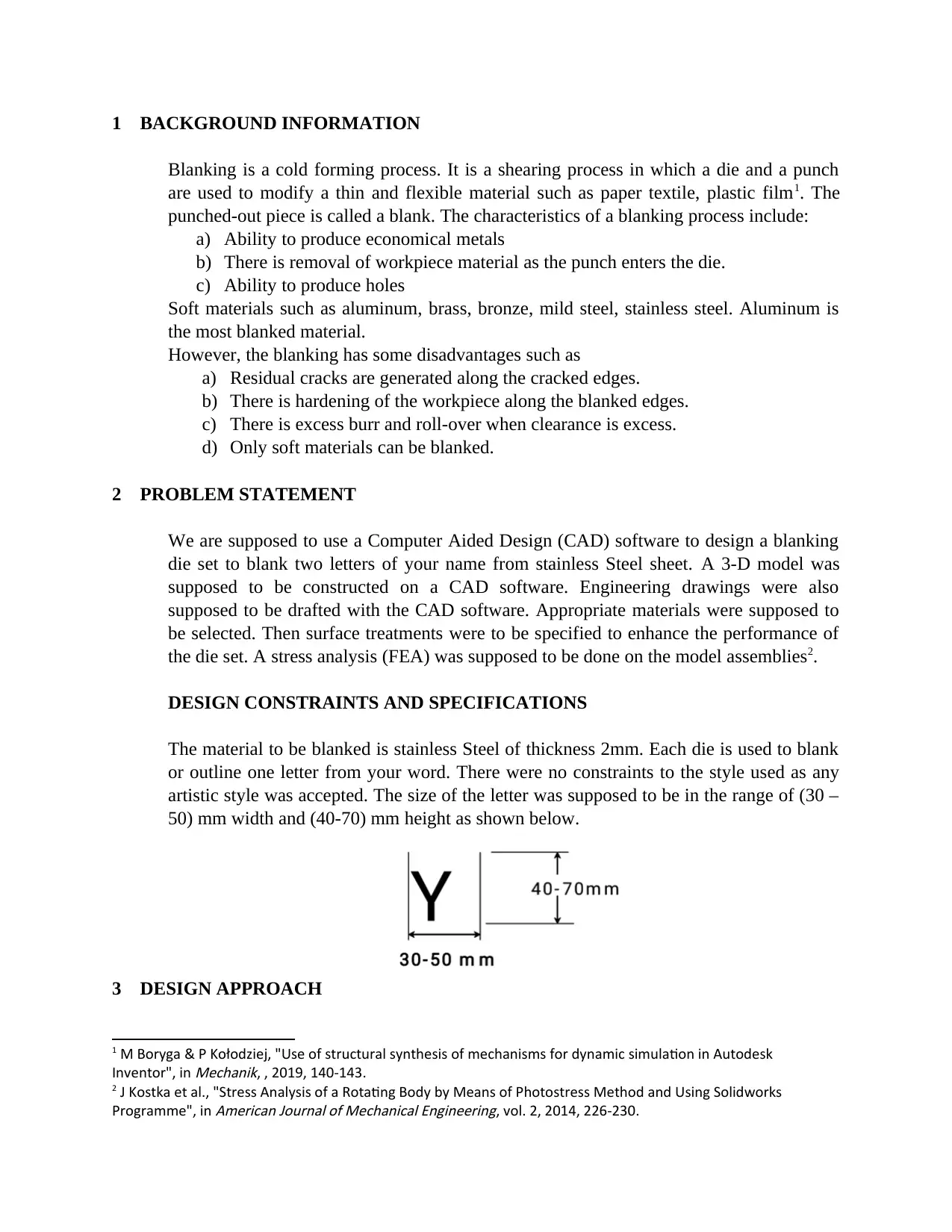
1 BACKGROUND INFORMATION
Blanking is a cold forming process. It is a shearing process in which a die and a punch
are used to modify a thin and flexible material such as paper textile, plastic film1. The
punched-out piece is called a blank. The characteristics of a blanking process include:
a) Ability to produce economical metals
b) There is removal of workpiece material as the punch enters the die.
c) Ability to produce holes
Soft materials such as aluminum, brass, bronze, mild steel, stainless steel. Aluminum is
the most blanked material.
However, the blanking has some disadvantages such as
a) Residual cracks are generated along the cracked edges.
b) There is hardening of the workpiece along the blanked edges.
c) There is excess burr and roll-over when clearance is excess.
d) Only soft materials can be blanked.
2 PROBLEM STATEMENT
We are supposed to use a Computer Aided Design (CAD) software to design a blanking
die set to blank two letters of your name from stainless Steel sheet. A 3-D model was
supposed to be constructed on a CAD software. Engineering drawings were also
supposed to be drafted with the CAD software. Appropriate materials were supposed to
be selected. Then surface treatments were to be specified to enhance the performance of
the die set. A stress analysis (FEA) was supposed to be done on the model assemblies2.
DESIGN CONSTRAINTS AND SPECIFICATIONS
The material to be blanked is stainless Steel of thickness 2mm. Each die is used to blank
or outline one letter from your word. There were no constraints to the style used as any
artistic style was accepted. The size of the letter was supposed to be in the range of (30 –
50) mm width and (40-70) mm height as shown below.
3 DESIGN APPROACH
1 M Boryga & P Kołodziej, "Use of structural synthesis of mechanisms for dynamic simulation in Autodesk
Inventor", in
Mechanik, , 2019, 140-143.
2 J Kostka et al., "Stress Analysis of a Rotating Body by Means of Photostress Method and Using Solidworks
Programme", in
American Journal of Mechanical Engineering, vol. 2, 2014, 226-230.
Blanking is a cold forming process. It is a shearing process in which a die and a punch
are used to modify a thin and flexible material such as paper textile, plastic film1. The
punched-out piece is called a blank. The characteristics of a blanking process include:
a) Ability to produce economical metals
b) There is removal of workpiece material as the punch enters the die.
c) Ability to produce holes
Soft materials such as aluminum, brass, bronze, mild steel, stainless steel. Aluminum is
the most blanked material.
However, the blanking has some disadvantages such as
a) Residual cracks are generated along the cracked edges.
b) There is hardening of the workpiece along the blanked edges.
c) There is excess burr and roll-over when clearance is excess.
d) Only soft materials can be blanked.
2 PROBLEM STATEMENT
We are supposed to use a Computer Aided Design (CAD) software to design a blanking
die set to blank two letters of your name from stainless Steel sheet. A 3-D model was
supposed to be constructed on a CAD software. Engineering drawings were also
supposed to be drafted with the CAD software. Appropriate materials were supposed to
be selected. Then surface treatments were to be specified to enhance the performance of
the die set. A stress analysis (FEA) was supposed to be done on the model assemblies2.
DESIGN CONSTRAINTS AND SPECIFICATIONS
The material to be blanked is stainless Steel of thickness 2mm. Each die is used to blank
or outline one letter from your word. There were no constraints to the style used as any
artistic style was accepted. The size of the letter was supposed to be in the range of (30 –
50) mm width and (40-70) mm height as shown below.
3 DESIGN APPROACH
1 M Boryga & P Kołodziej, "Use of structural synthesis of mechanisms for dynamic simulation in Autodesk
Inventor", in
Mechanik, , 2019, 140-143.
2 J Kostka et al., "Stress Analysis of a Rotating Body by Means of Photostress Method and Using Solidworks
Programme", in
American Journal of Mechanical Engineering, vol. 2, 2014, 226-230.
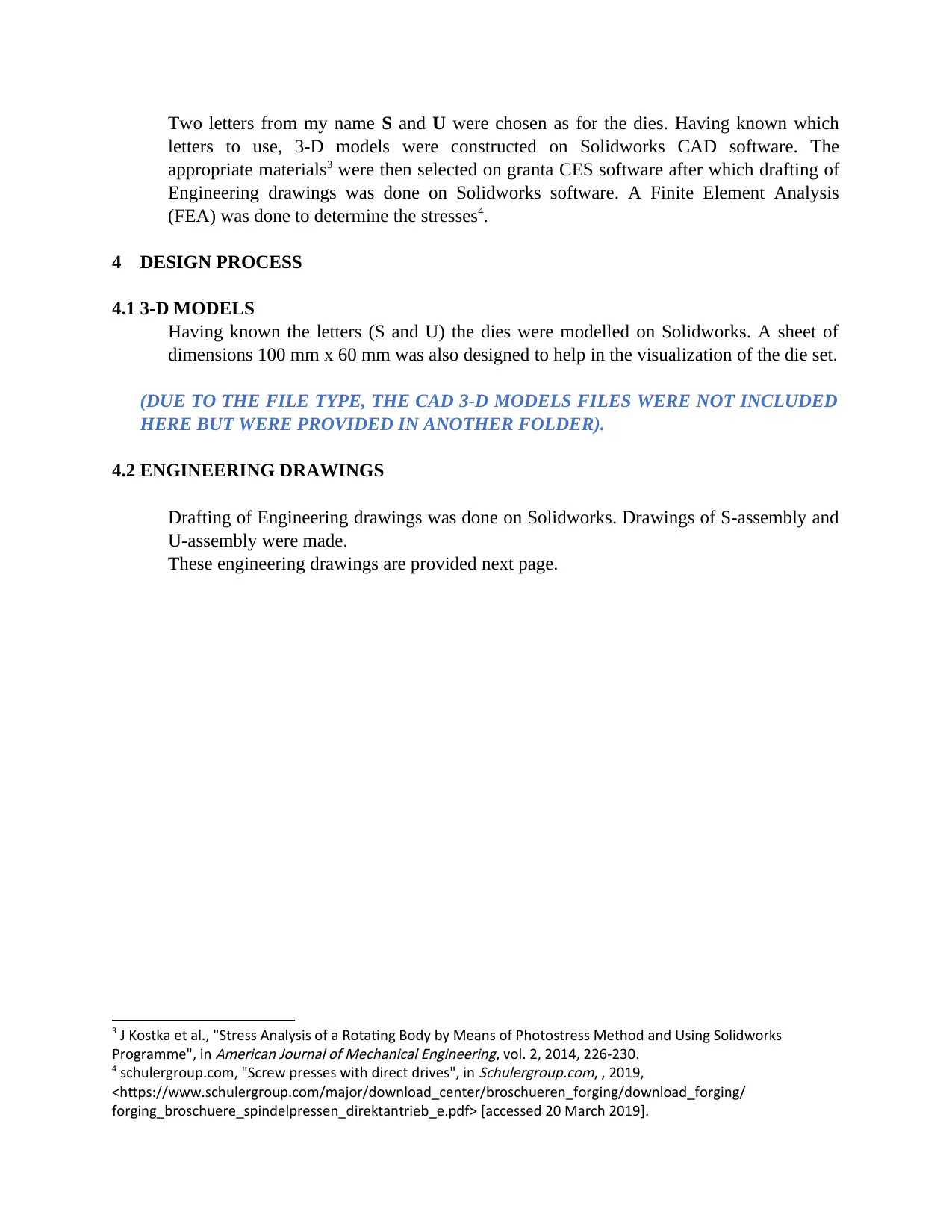
Two letters from my name S and U were chosen as for the dies. Having known which
letters to use, 3-D models were constructed on Solidworks CAD software. The
appropriate materials3 were then selected on granta CES software after which drafting of
Engineering drawings was done on Solidworks software. A Finite Element Analysis
(FEA) was done to determine the stresses4.
4 DESIGN PROCESS
4.1 3-D MODELS
Having known the letters (S and U) the dies were modelled on Solidworks. A sheet of
dimensions 100 mm x 60 mm was also designed to help in the visualization of the die set.
(DUE TO THE FILE TYPE, THE CAD 3-D MODELS FILES WERE NOT INCLUDED
HERE BUT WERE PROVIDED IN ANOTHER FOLDER).
4.2 ENGINEERING DRAWINGS
Drafting of Engineering drawings was done on Solidworks. Drawings of S-assembly and
U-assembly were made.
These engineering drawings are provided next page.
3 J Kostka et al., "Stress Analysis of a Rotating Body by Means of Photostress Method and Using Solidworks
Programme", in
American Journal of Mechanical Engineering, vol. 2, 2014, 226-230.
4 schulergroup.com, "Screw presses with direct drives", in
Schulergroup.com, , 2019,
<https://www.schulergroup.com/major/download_center/broschueren_forging/download_forging/
forging_broschuere_spindelpressen_direktantrieb_e.pdf> [accessed 20 March 2019].
letters to use, 3-D models were constructed on Solidworks CAD software. The
appropriate materials3 were then selected on granta CES software after which drafting of
Engineering drawings was done on Solidworks software. A Finite Element Analysis
(FEA) was done to determine the stresses4.
4 DESIGN PROCESS
4.1 3-D MODELS
Having known the letters (S and U) the dies were modelled on Solidworks. A sheet of
dimensions 100 mm x 60 mm was also designed to help in the visualization of the die set.
(DUE TO THE FILE TYPE, THE CAD 3-D MODELS FILES WERE NOT INCLUDED
HERE BUT WERE PROVIDED IN ANOTHER FOLDER).
4.2 ENGINEERING DRAWINGS
Drafting of Engineering drawings was done on Solidworks. Drawings of S-assembly and
U-assembly were made.
These engineering drawings are provided next page.
3 J Kostka et al., "Stress Analysis of a Rotating Body by Means of Photostress Method and Using Solidworks
Programme", in
American Journal of Mechanical Engineering, vol. 2, 2014, 226-230.
4 schulergroup.com, "Screw presses with direct drives", in
Schulergroup.com, , 2019,
<https://www.schulergroup.com/major/download_center/broschueren_forging/download_forging/
forging_broschuere_spindelpressen_direktantrieb_e.pdf> [accessed 20 March 2019].
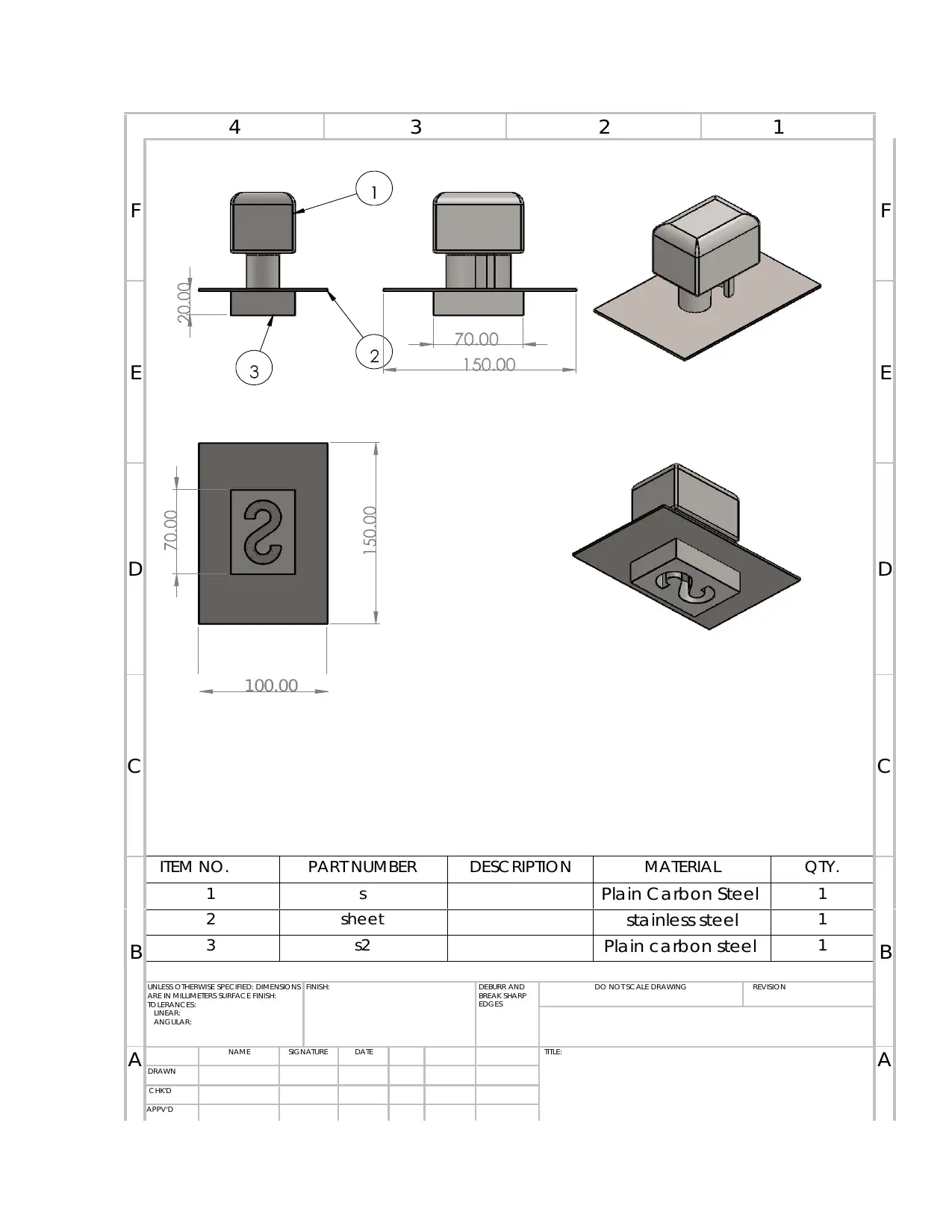
4 3 2 1
F F
E E
D D
C
100.00
C
B
ITEM NO. PART NUMBER DESC RIPTION MATERIAL QTY.
B
1 s Plain C arbon Steel 1
2 sheet stainless steel 1
3 s2 Plain carbon steel 1
UNLESS OTHERWISE SPECIFIED: DIMENSIONS
ARE IN MILLIMETERS SURFAC E FINISH:
TO LERANC ES:
LINEAR:
ANGULAR:
FINISH: DEBURR AND
BREAK SHARP
EDGES
DO NOT SC ALE DRAWING REVISION
A NAME SIGNATURE DATE TITLE:
ADRAWN
C HK'D
APPV'D
F F
E E
D D
C
100.00
C
B
ITEM NO. PART NUMBER DESC RIPTION MATERIAL QTY.
B
1 s Plain C arbon Steel 1
2 sheet stainless steel 1
3 s2 Plain carbon steel 1
UNLESS OTHERWISE SPECIFIED: DIMENSIONS
ARE IN MILLIMETERS SURFAC E FINISH:
TO LERANC ES:
LINEAR:
ANGULAR:
FINISH: DEBURR AND
BREAK SHARP
EDGES
DO NOT SC ALE DRAWING REVISION
A NAME SIGNATURE DATE TITLE:
ADRAWN
C HK'D
APPV'D
Secure Best Marks with AI Grader
Need help grading? Try our AI Grader for instant feedback on your assignments.
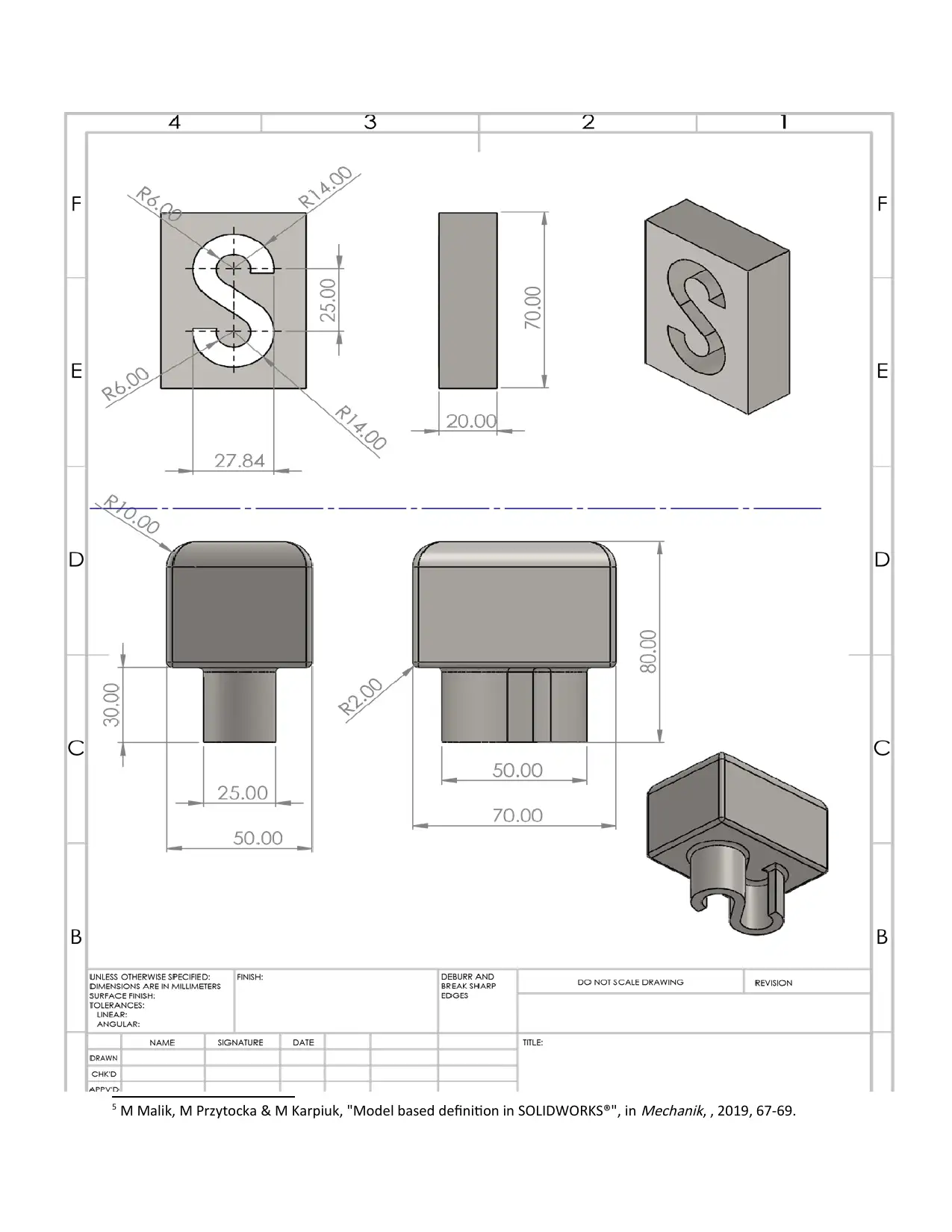
5 M Malik, M Przytocka & M Karpiuk, "Model based definition in SOLIDWORKS®", in
Mechanik, , 2019, 67-69.
Mechanik, , 2019, 67-69.
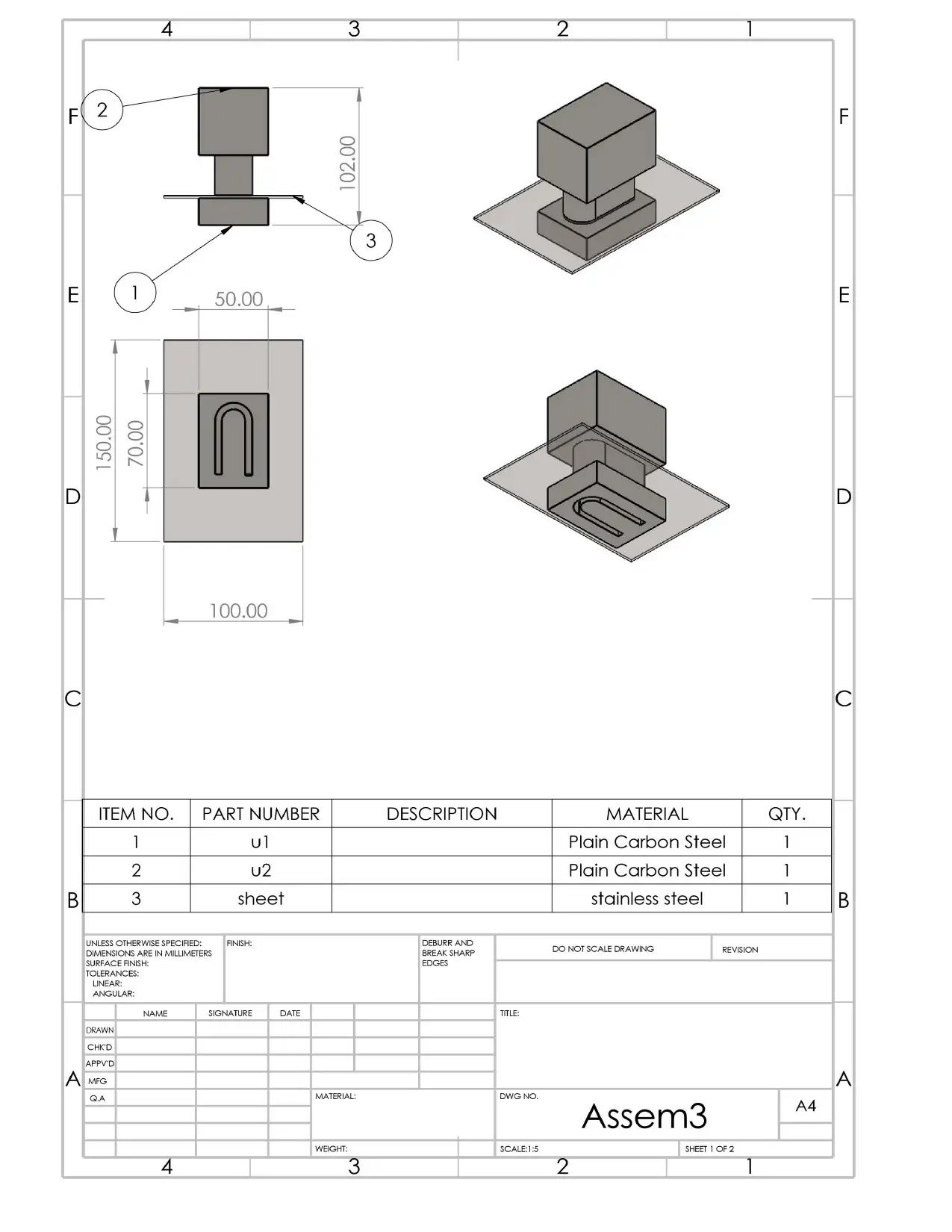
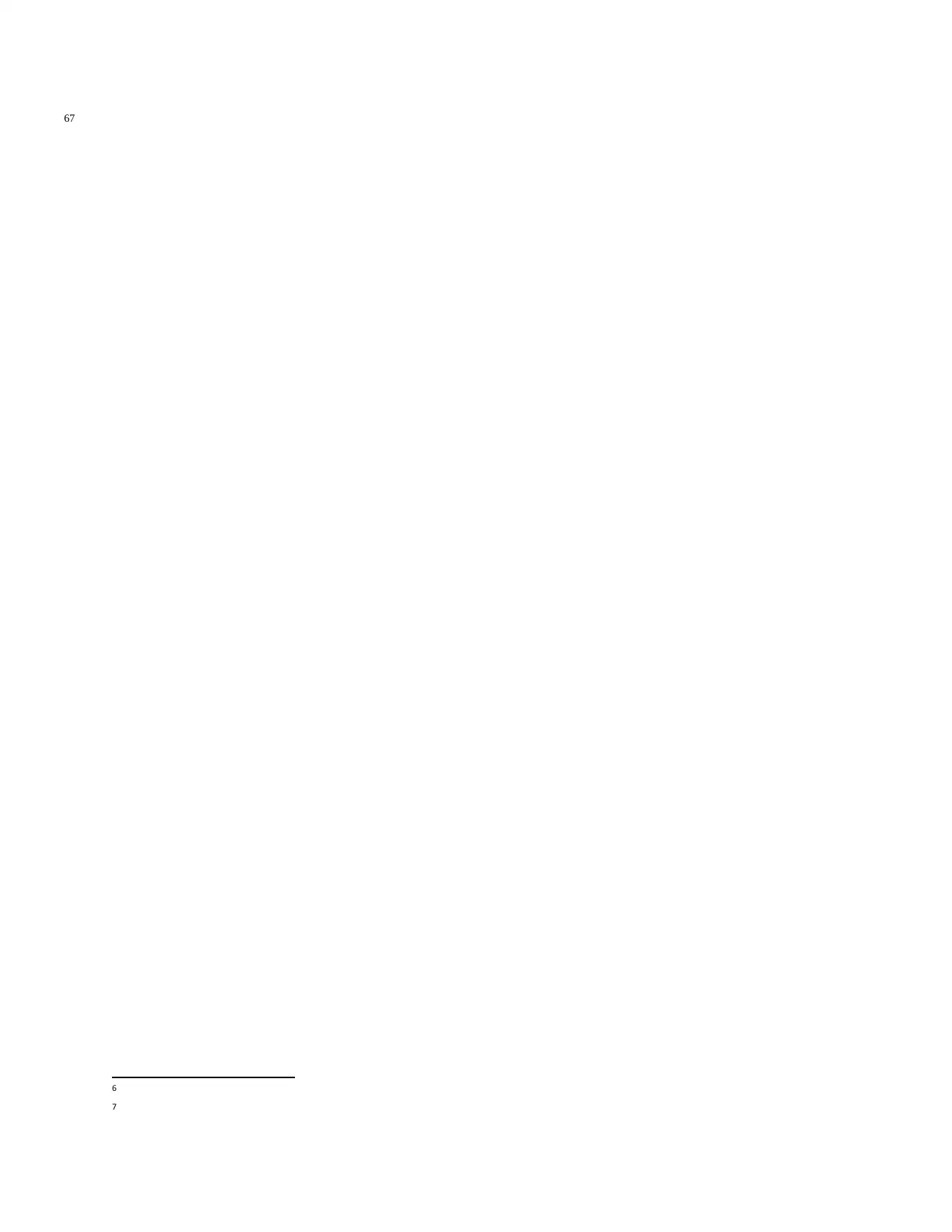
67
6
7
6
7
Paraphrase This Document
Need a fresh take? Get an instant paraphrase of this document with our AI Paraphraser
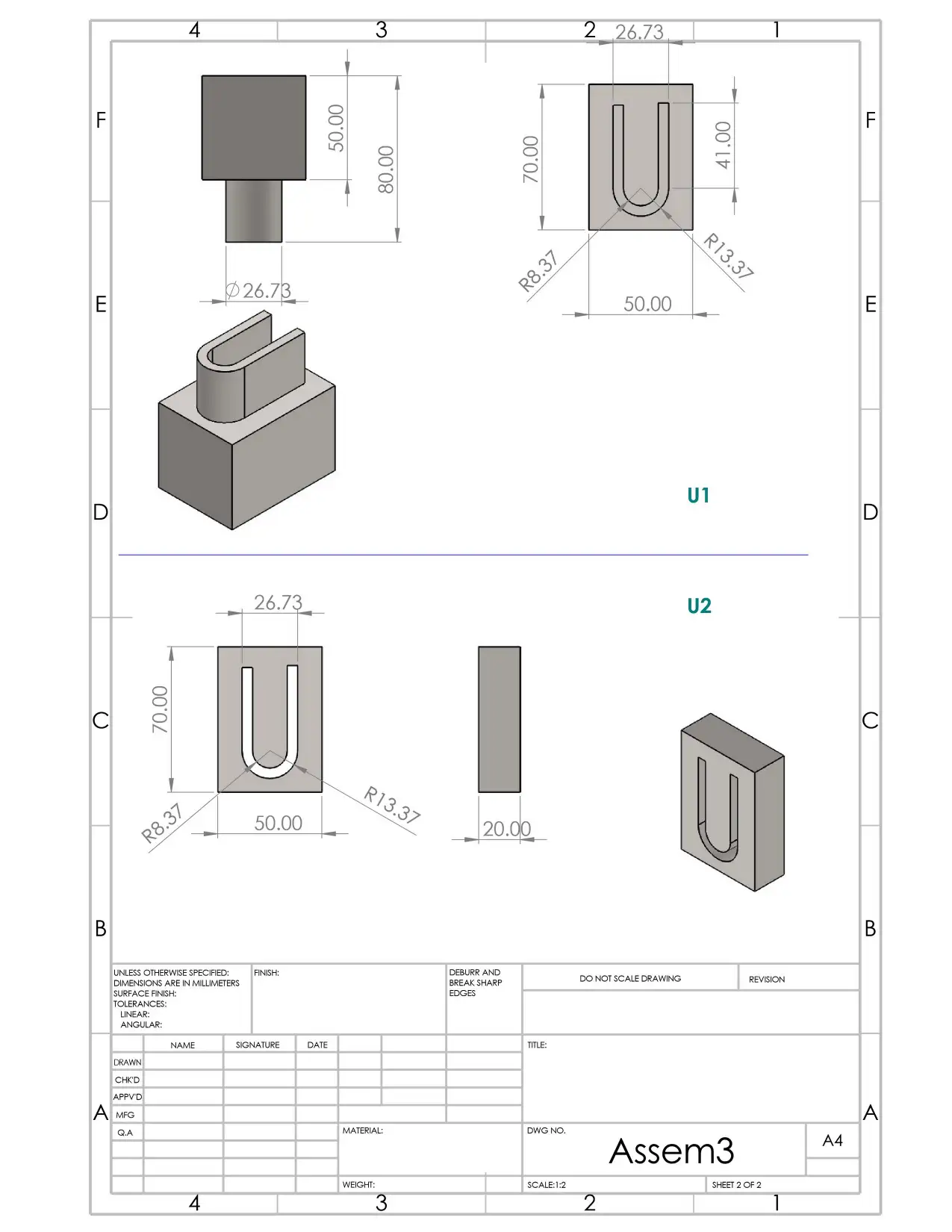
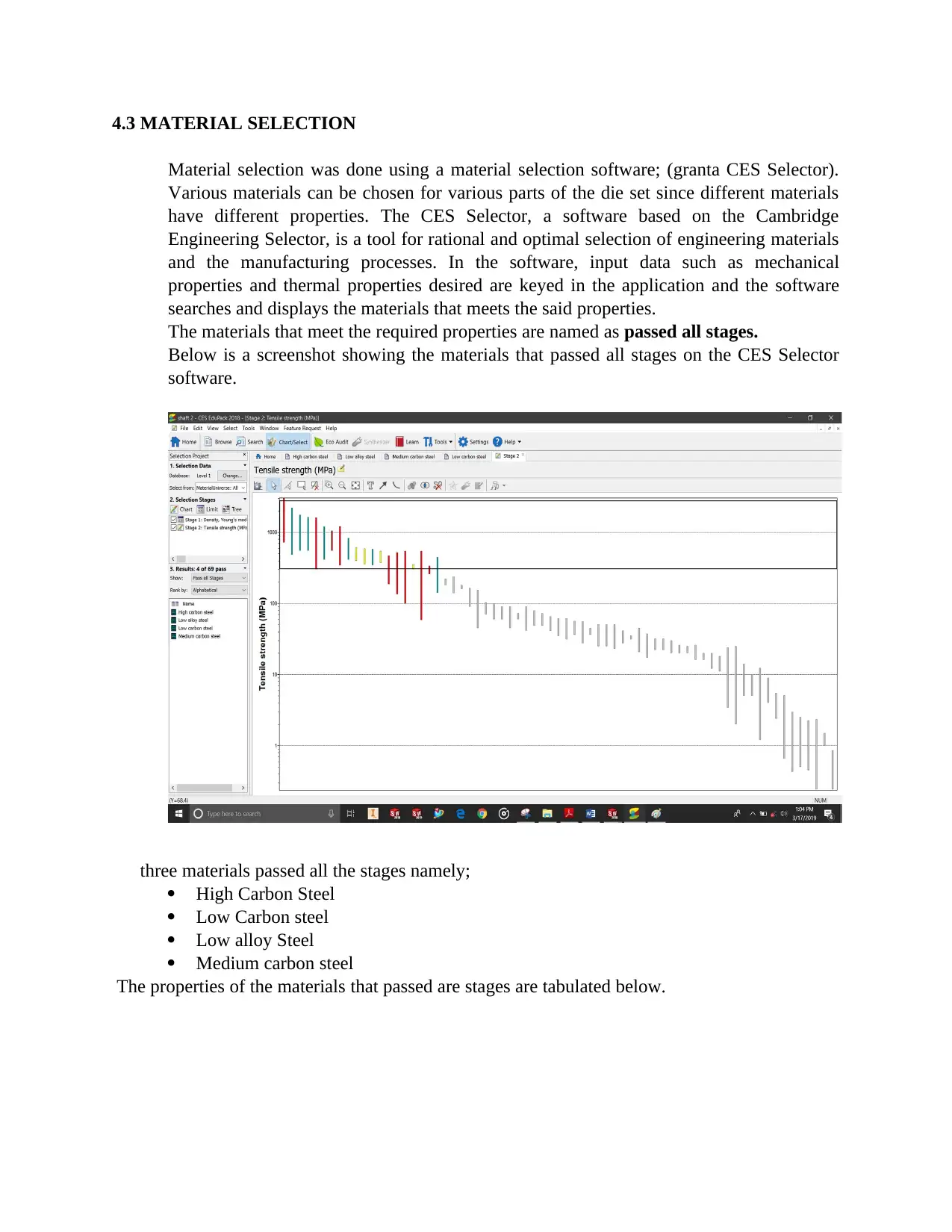
4.3 MATERIAL SELECTION
Material selection was done using a material selection software; (granta CES Selector).
Various materials can be chosen for various parts of the die set since different materials
have different properties. The CES Selector, a software based on the Cambridge
Engineering Selector, is a tool for rational and optimal selection of engineering materials
and the manufacturing processes. In the software, input data such as mechanical
properties and thermal properties desired are keyed in the application and the software
searches and displays the materials that meets the said properties.
The materials that meet the required properties are named as passed all stages.
Below is a screenshot showing the materials that passed all stages on the CES Selector
software.
three materials passed all the stages namely;
High Carbon Steel
Low Carbon steel
Low alloy Steel
Medium carbon steel
The properties of the materials that passed are stages are tabulated below.
Material selection was done using a material selection software; (granta CES Selector).
Various materials can be chosen for various parts of the die set since different materials
have different properties. The CES Selector, a software based on the Cambridge
Engineering Selector, is a tool for rational and optimal selection of engineering materials
and the manufacturing processes. In the software, input data such as mechanical
properties and thermal properties desired are keyed in the application and the software
searches and displays the materials that meets the said properties.
The materials that meet the required properties are named as passed all stages.
Below is a screenshot showing the materials that passed all stages on the CES Selector
software.
three materials passed all the stages namely;
High Carbon Steel
Low Carbon steel
Low alloy Steel
Medium carbon steel
The properties of the materials that passed are stages are tabulated below.
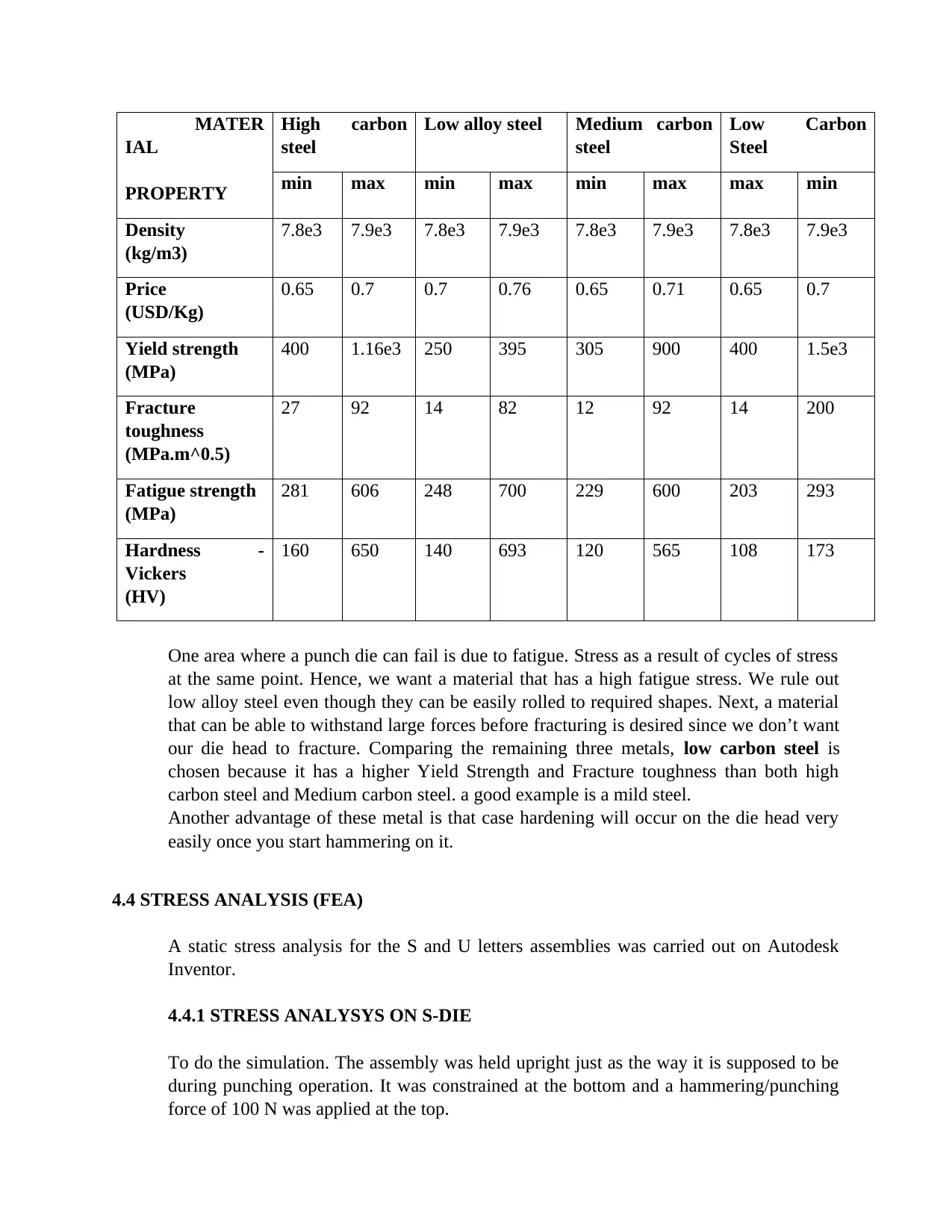
MATER
IAL
PROPERTY
High carbon
steel
Low alloy steel Medium carbon
steel
Low Carbon
Steel
min max min max min max max min
Density
(kg/m3)
7.8e3 7.9e3 7.8e3 7.9e3 7.8e3 7.9e3 7.8e3 7.9e3
Price
(USD/Kg)
0.65 0.7 0.7 0.76 0.65 0.71 0.65 0.7
Yield strength
(MPa)
400 1.16e3 250 395 305 900 400 1.5e3
Fracture
toughness
(MPa.m^0.5)
27 92 14 82 12 92 14 200
Fatigue strength
(MPa)
281 606 248 700 229 600 203 293
Hardness -
Vickers
(HV)
160 650 140 693 120 565 108 173
One area where a punch die can fail is due to fatigue. Stress as a result of cycles of stress
at the same point. Hence, we want a material that has a high fatigue stress. We rule out
low alloy steel even though they can be easily rolled to required shapes. Next, a material
that can be able to withstand large forces before fracturing is desired since we don’t want
our die head to fracture. Comparing the remaining three metals, low carbon steel is
chosen because it has a higher Yield Strength and Fracture toughness than both high
carbon steel and Medium carbon steel. a good example is a mild steel.
Another advantage of these metal is that case hardening will occur on the die head very
easily once you start hammering on it.
4.4 STRESS ANALYSIS (FEA)
A static stress analysis for the S and U letters assemblies was carried out on Autodesk
Inventor.
4.4.1 STRESS ANALYSYS ON S-DIE
To do the simulation. The assembly was held upright just as the way it is supposed to be
during punching operation. It was constrained at the bottom and a hammering/punching
force of 100 N was applied at the top.
IAL
PROPERTY
High carbon
steel
Low alloy steel Medium carbon
steel
Low Carbon
Steel
min max min max min max max min
Density
(kg/m3)
7.8e3 7.9e3 7.8e3 7.9e3 7.8e3 7.9e3 7.8e3 7.9e3
Price
(USD/Kg)
0.65 0.7 0.7 0.76 0.65 0.71 0.65 0.7
Yield strength
(MPa)
400 1.16e3 250 395 305 900 400 1.5e3
Fracture
toughness
(MPa.m^0.5)
27 92 14 82 12 92 14 200
Fatigue strength
(MPa)
281 606 248 700 229 600 203 293
Hardness -
Vickers
(HV)
160 650 140 693 120 565 108 173
One area where a punch die can fail is due to fatigue. Stress as a result of cycles of stress
at the same point. Hence, we want a material that has a high fatigue stress. We rule out
low alloy steel even though they can be easily rolled to required shapes. Next, a material
that can be able to withstand large forces before fracturing is desired since we don’t want
our die head to fracture. Comparing the remaining three metals, low carbon steel is
chosen because it has a higher Yield Strength and Fracture toughness than both high
carbon steel and Medium carbon steel. a good example is a mild steel.
Another advantage of these metal is that case hardening will occur on the die head very
easily once you start hammering on it.
4.4 STRESS ANALYSIS (FEA)
A static stress analysis for the S and U letters assemblies was carried out on Autodesk
Inventor.
4.4.1 STRESS ANALYSYS ON S-DIE
To do the simulation. The assembly was held upright just as the way it is supposed to be
during punching operation. It was constrained at the bottom and a hammering/punching
force of 100 N was applied at the top.
Secure Best Marks with AI Grader
Need help grading? Try our AI Grader for instant feedback on your assignments.
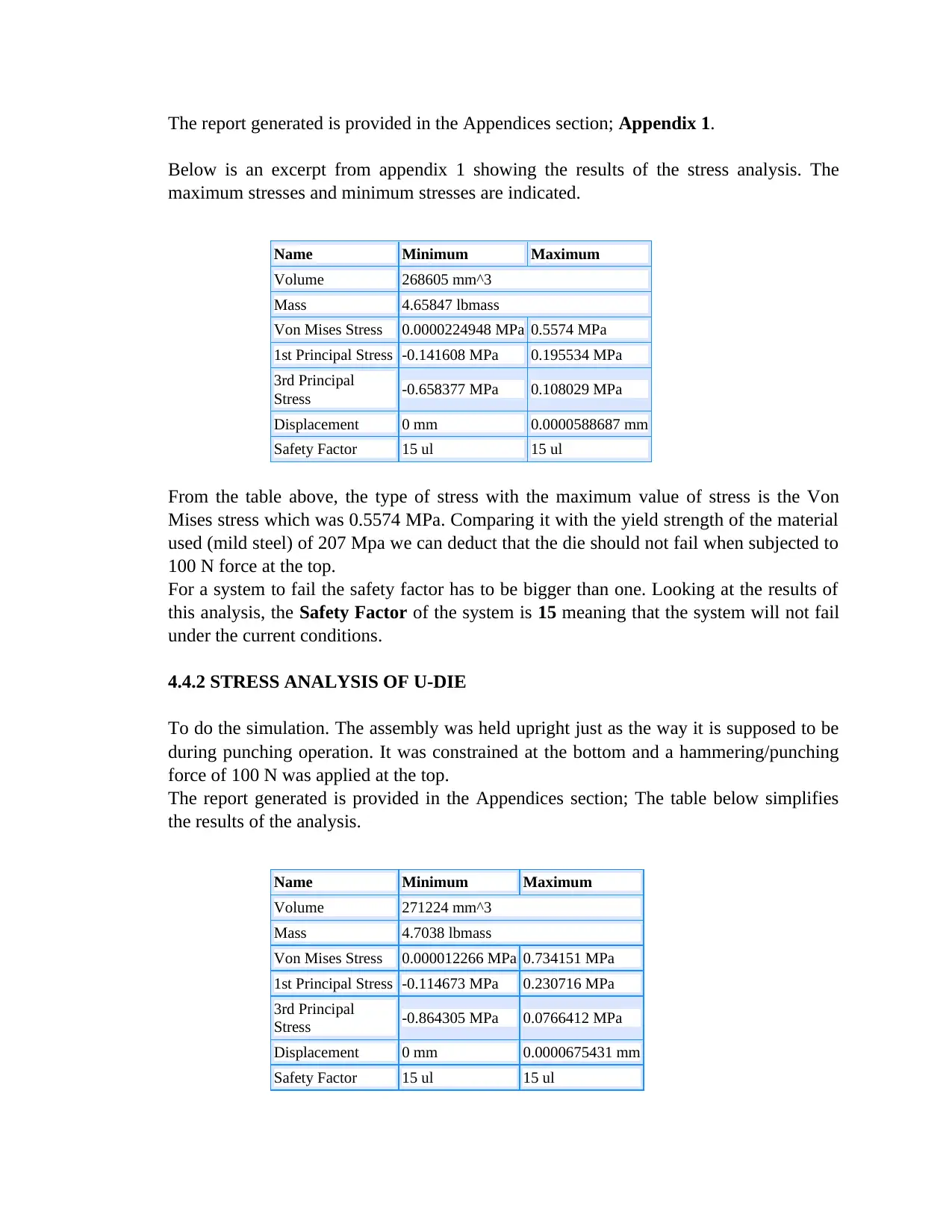
The report generated is provided in the Appendices section; Appendix 1.
Below is an excerpt from appendix 1 showing the results of the stress analysis. The
maximum stresses and minimum stresses are indicated.
Name Minimum Maximum
Volume 268605 mm^3
Mass 4.65847 lbmass
Von Mises Stress 0.0000224948 MPa 0.5574 MPa
1st Principal Stress -0.141608 MPa 0.195534 MPa
3rd Principal
Stress -0.658377 MPa 0.108029 MPa
Displacement 0 mm 0.0000588687 mm
Safety Factor 15 ul 15 ul
From the table above, the type of stress with the maximum value of stress is the Von
Mises stress which was 0.5574 MPa. Comparing it with the yield strength of the material
used (mild steel) of 207 Mpa we can deduct that the die should not fail when subjected to
100 N force at the top.
For a system to fail the safety factor has to be bigger than one. Looking at the results of
this analysis, the Safety Factor of the system is 15 meaning that the system will not fail
under the current conditions.
4.4.2 STRESS ANALYSIS OF U-DIE
To do the simulation. The assembly was held upright just as the way it is supposed to be
during punching operation. It was constrained at the bottom and a hammering/punching
force of 100 N was applied at the top.
The report generated is provided in the Appendices section; The table below simplifies
the results of the analysis.
Name Minimum Maximum
Volume 271224 mm^3
Mass 4.7038 lbmass
Von Mises Stress 0.000012266 MPa 0.734151 MPa
1st Principal Stress -0.114673 MPa 0.230716 MPa
3rd Principal
Stress -0.864305 MPa 0.0766412 MPa
Displacement 0 mm 0.0000675431 mm
Safety Factor 15 ul 15 ul
Below is an excerpt from appendix 1 showing the results of the stress analysis. The
maximum stresses and minimum stresses are indicated.
Name Minimum Maximum
Volume 268605 mm^3
Mass 4.65847 lbmass
Von Mises Stress 0.0000224948 MPa 0.5574 MPa
1st Principal Stress -0.141608 MPa 0.195534 MPa
3rd Principal
Stress -0.658377 MPa 0.108029 MPa
Displacement 0 mm 0.0000588687 mm
Safety Factor 15 ul 15 ul
From the table above, the type of stress with the maximum value of stress is the Von
Mises stress which was 0.5574 MPa. Comparing it with the yield strength of the material
used (mild steel) of 207 Mpa we can deduct that the die should not fail when subjected to
100 N force at the top.
For a system to fail the safety factor has to be bigger than one. Looking at the results of
this analysis, the Safety Factor of the system is 15 meaning that the system will not fail
under the current conditions.
4.4.2 STRESS ANALYSIS OF U-DIE
To do the simulation. The assembly was held upright just as the way it is supposed to be
during punching operation. It was constrained at the bottom and a hammering/punching
force of 100 N was applied at the top.
The report generated is provided in the Appendices section; The table below simplifies
the results of the analysis.
Name Minimum Maximum
Volume 271224 mm^3
Mass 4.7038 lbmass
Von Mises Stress 0.000012266 MPa 0.734151 MPa
1st Principal Stress -0.114673 MPa 0.230716 MPa
3rd Principal
Stress -0.864305 MPa 0.0766412 MPa
Displacement 0 mm 0.0000675431 mm
Safety Factor 15 ul 15 ul
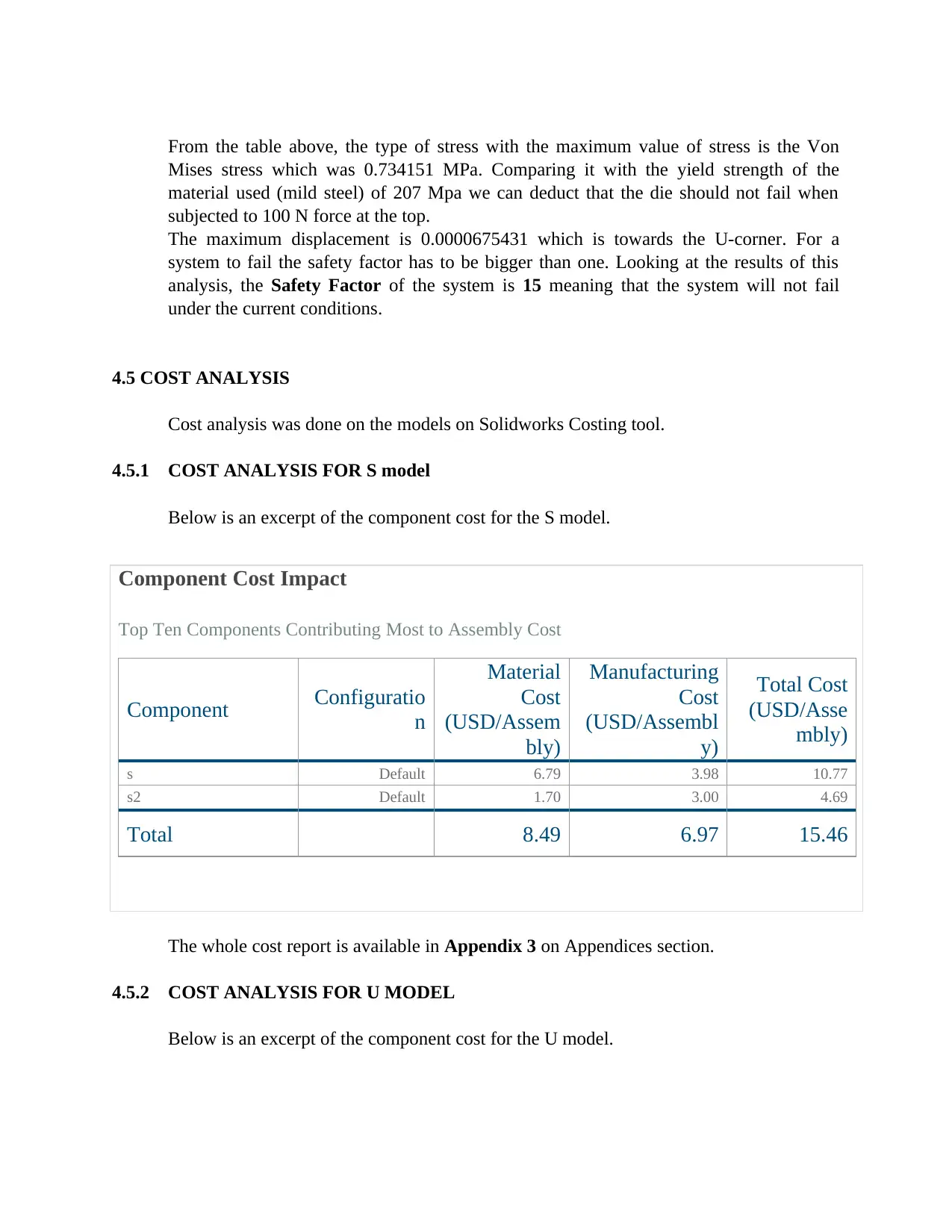
From the table above, the type of stress with the maximum value of stress is the Von
Mises stress which was 0.734151 MPa. Comparing it with the yield strength of the
material used (mild steel) of 207 Mpa we can deduct that the die should not fail when
subjected to 100 N force at the top.
The maximum displacement is 0.0000675431 which is towards the U-corner. For a
system to fail the safety factor has to be bigger than one. Looking at the results of this
analysis, the Safety Factor of the system is 15 meaning that the system will not fail
under the current conditions.
4.5 COST ANALYSIS
Cost analysis was done on the models on Solidworks Costing tool.
4.5.1 COST ANALYSIS FOR S model
Below is an excerpt of the component cost for the S model.
Component Cost Impact
Top Ten Components Contributing Most to Assembly Cost
Component Configuratio
n
Material
Cost
(USD/Assem
bly)
Manufacturing
Cost
(USD/Assembl
y)
Total Cost
(USD/Asse
mbly)
s Default 6.79 3.98 10.77
s2 Default 1.70 3.00 4.69
Total 8.49 6.97 15.46
The whole cost report is available in Appendix 3 on Appendices section.
4.5.2 COST ANALYSIS FOR U MODEL
Below is an excerpt of the component cost for the U model.
Mises stress which was 0.734151 MPa. Comparing it with the yield strength of the
material used (mild steel) of 207 Mpa we can deduct that the die should not fail when
subjected to 100 N force at the top.
The maximum displacement is 0.0000675431 which is towards the U-corner. For a
system to fail the safety factor has to be bigger than one. Looking at the results of this
analysis, the Safety Factor of the system is 15 meaning that the system will not fail
under the current conditions.
4.5 COST ANALYSIS
Cost analysis was done on the models on Solidworks Costing tool.
4.5.1 COST ANALYSIS FOR S model
Below is an excerpt of the component cost for the S model.
Component Cost Impact
Top Ten Components Contributing Most to Assembly Cost
Component Configuratio
n
Material
Cost
(USD/Assem
bly)
Manufacturing
Cost
(USD/Assembl
y)
Total Cost
(USD/Asse
mbly)
s Default 6.79 3.98 10.77
s2 Default 1.70 3.00 4.69
Total 8.49 6.97 15.46
The whole cost report is available in Appendix 3 on Appendices section.
4.5.2 COST ANALYSIS FOR U MODEL
Below is an excerpt of the component cost for the U model.
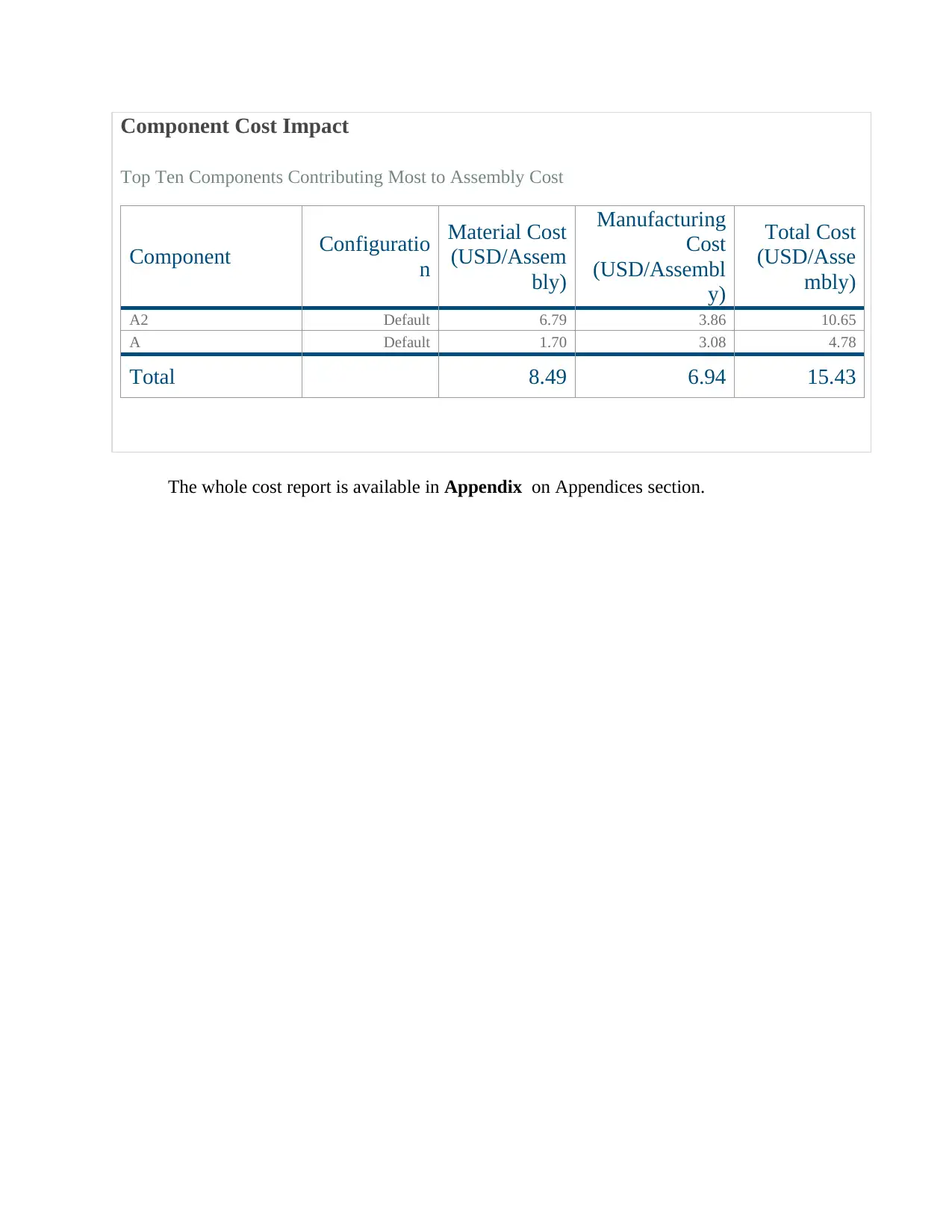
Component Cost Impact
Top Ten Components Contributing Most to Assembly Cost
Component Configuratio
n
Material Cost
(USD/Assem
bly)
Manufacturing
Cost
(USD/Assembl
y)
Total Cost
(USD/Asse
mbly)
A2 Default 6.79 3.86 10.65
A Default 1.70 3.08 4.78
Total 8.49 6.94 15.43
The whole cost report is available in Appendix on Appendices section.
Top Ten Components Contributing Most to Assembly Cost
Component Configuratio
n
Material Cost
(USD/Assem
bly)
Manufacturing
Cost
(USD/Assembl
y)
Total Cost
(USD/Asse
mbly)
A2 Default 6.79 3.86 10.65
A Default 1.70 3.08 4.78
Total 8.49 6.94 15.43
The whole cost report is available in Appendix on Appendices section.
Paraphrase This Document
Need a fresh take? Get an instant paraphrase of this document with our AI Paraphraser
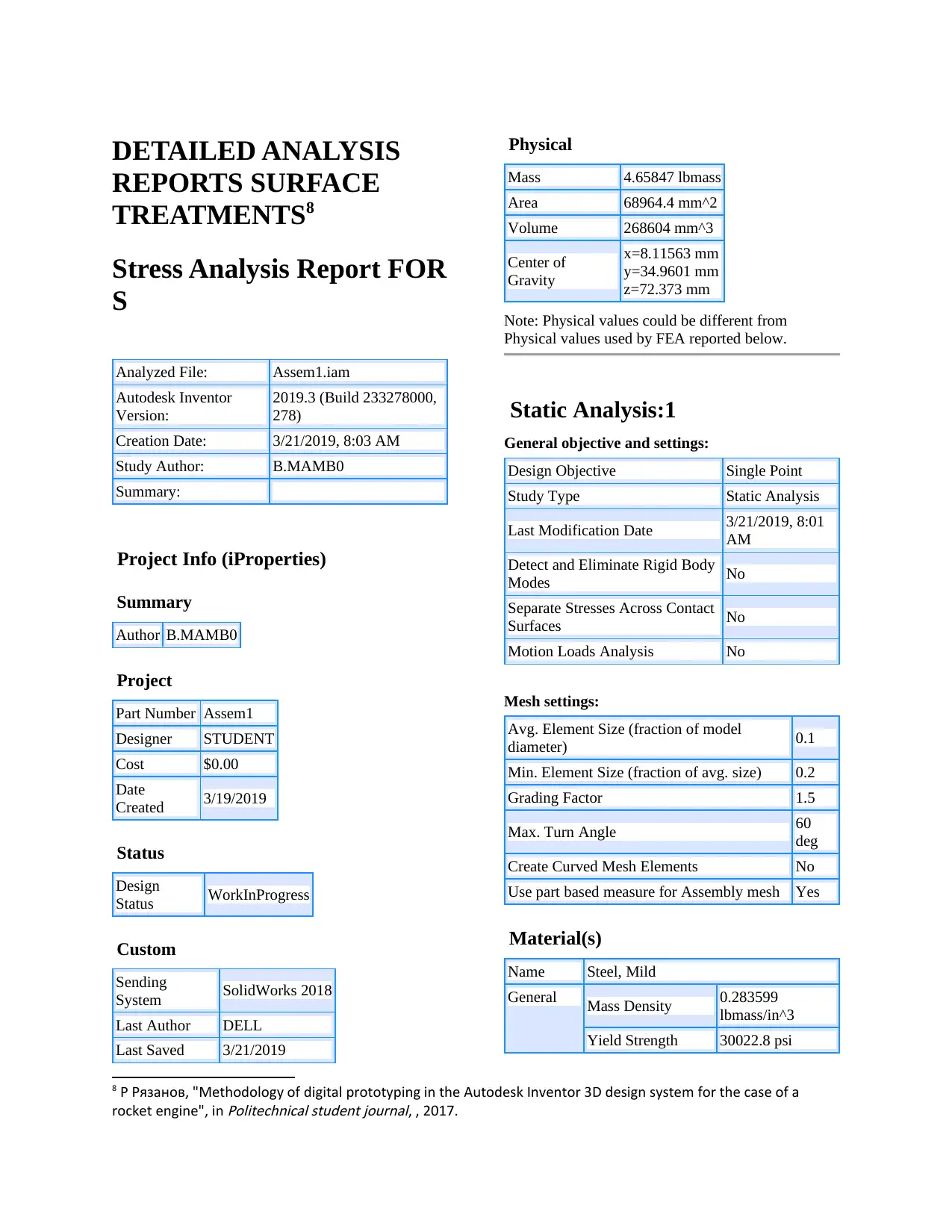
DETAILED ANALYSIS
REPORTS SURFACE
TREATMENTS8
Stress Analysis Report FOR
S
Analyzed File: Assem1.iam
Autodesk Inventor
Version:
2019.3 (Build 233278000,
278)
Creation Date: 3/21/2019, 8:03 AM
Study Author: B.MAMB0
Summary:
Project Info (iProperties)
Summary
Author B.MAMB0
Project
Part Number Assem1
Designer STUDENT
Cost $0.00
Date
Created 3/19/2019
Status
Design
Status WorkInProgress
Custom
Sending
System SolidWorks 2018
Last Author DELL
Last Saved 3/21/2019
Physical
Mass 4.65847 lbmass
Area 68964.4 mm^2
Volume 268604 mm^3
Center of
Gravity
x=8.11563 mm
y=34.9601 mm
z=72.373 mm
Note: Physical values could be different from
Physical values used by FEA reported below.
Static Analysis:1
General objective and settings:
Design Objective Single Point
Study Type Static Analysis
Last Modification Date 3/21/2019, 8:01
AM
Detect and Eliminate Rigid Body
Modes No
Separate Stresses Across Contact
Surfaces No
Motion Loads Analysis No
Mesh settings:
Avg. Element Size (fraction of model
diameter) 0.1
Min. Element Size (fraction of avg. size) 0.2
Grading Factor 1.5
Max. Turn Angle 60
deg
Create Curved Mesh Elements No
Use part based measure for Assembly mesh Yes
Material(s)
Name Steel, Mild
General Mass Density 0.283599
lbmass/in^3
Yield Strength 30022.8 psi
8 Р Рязанов, "Methodology of digital prototyping in the Autodesk Inventor 3D design system for the case of a
rocket engine", in
Politechnical student journal, , 2017.
REPORTS SURFACE
TREATMENTS8
Stress Analysis Report FOR
S
Analyzed File: Assem1.iam
Autodesk Inventor
Version:
2019.3 (Build 233278000,
278)
Creation Date: 3/21/2019, 8:03 AM
Study Author: B.MAMB0
Summary:
Project Info (iProperties)
Summary
Author B.MAMB0
Project
Part Number Assem1
Designer STUDENT
Cost $0.00
Date
Created 3/19/2019
Status
Design
Status WorkInProgress
Custom
Sending
System SolidWorks 2018
Last Author DELL
Last Saved 3/21/2019
Physical
Mass 4.65847 lbmass
Area 68964.4 mm^2
Volume 268604 mm^3
Center of
Gravity
x=8.11563 mm
y=34.9601 mm
z=72.373 mm
Note: Physical values could be different from
Physical values used by FEA reported below.
Static Analysis:1
General objective and settings:
Design Objective Single Point
Study Type Static Analysis
Last Modification Date 3/21/2019, 8:01
AM
Detect and Eliminate Rigid Body
Modes No
Separate Stresses Across Contact
Surfaces No
Motion Loads Analysis No
Mesh settings:
Avg. Element Size (fraction of model
diameter) 0.1
Min. Element Size (fraction of avg. size) 0.2
Grading Factor 1.5
Max. Turn Angle 60
deg
Create Curved Mesh Elements No
Use part based measure for Assembly mesh Yes
Material(s)
Name Steel, Mild
General Mass Density 0.283599
lbmass/in^3
Yield Strength 30022.8 psi
8 Р Рязанов, "Methodology of digital prototyping in the Autodesk Inventor 3D design system for the case of a
rocket engine", in
Politechnical student journal, , 2017.
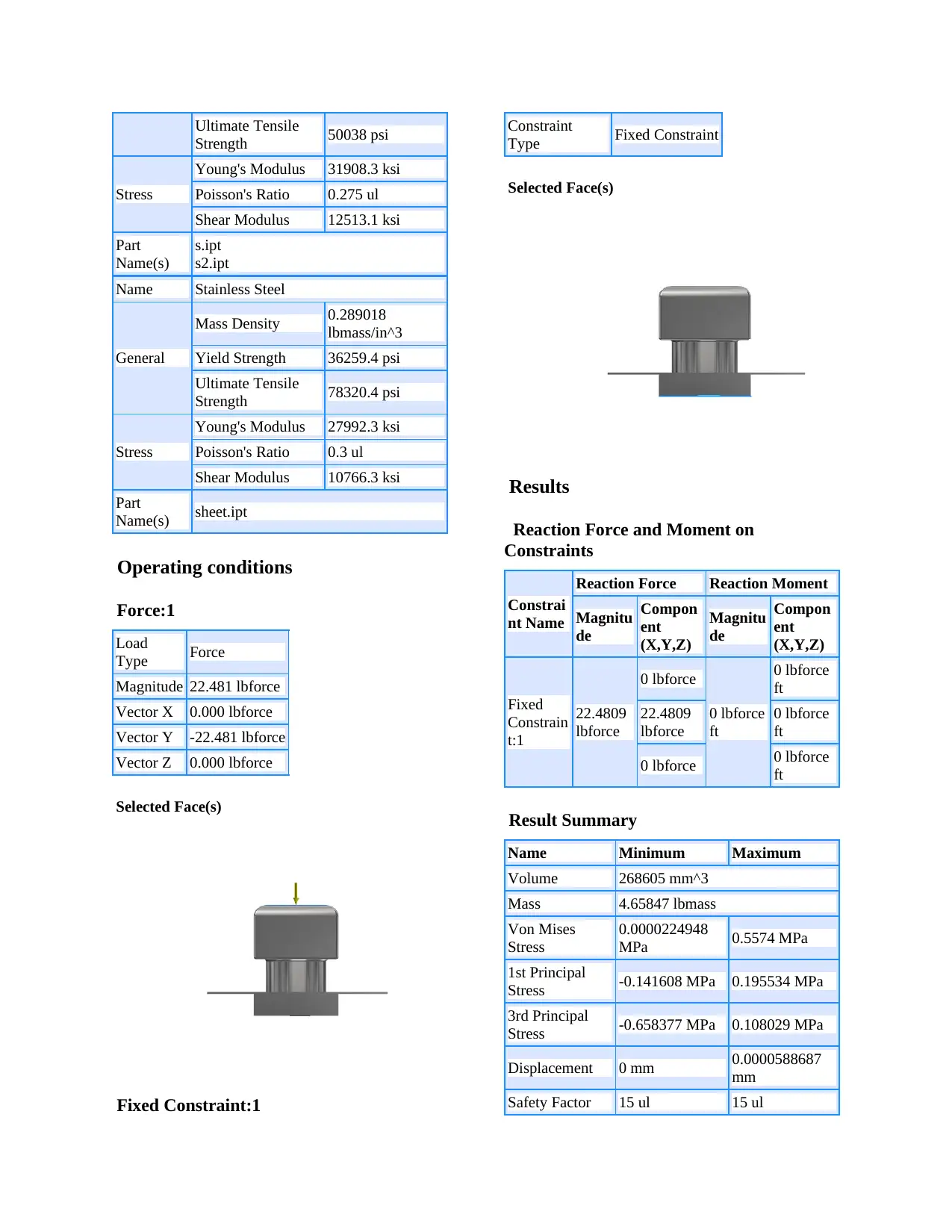
Ultimate Tensile
Strength 50038 psi
Stress
Young's Modulus 31908.3 ksi
Poisson's Ratio 0.275 ul
Shear Modulus 12513.1 ksi
Part
Name(s)
s.ipt
s2.ipt
Name Stainless Steel
General
Mass Density 0.289018
lbmass/in^3
Yield Strength 36259.4 psi
Ultimate Tensile
Strength 78320.4 psi
Stress
Young's Modulus 27992.3 ksi
Poisson's Ratio 0.3 ul
Shear Modulus 10766.3 ksi
Part
Name(s) sheet.ipt
Operating conditions
Force:1
Load
Type Force
Magnitude 22.481 lbforce
Vector X 0.000 lbforce
Vector Y -22.481 lbforce
Vector Z 0.000 lbforce
Selected Face(s)
Fixed Constraint:1
Constraint
Type Fixed Constraint
Selected Face(s)
Results
Reaction Force and Moment on
Constraints
Constrai
nt Name
Reaction Force Reaction Moment
Magnitu
de
Compon
ent
(X,Y,Z)
Magnitu
de
Compon
ent
(X,Y,Z)
Fixed
Constrain
t:1
22.4809
lbforce
0 lbforce
0 lbforce
ft
0 lbforce
ft
22.4809
lbforce
0 lbforce
ft
0 lbforce 0 lbforce
ft
Result Summary
Name Minimum Maximum
Volume 268605 mm^3
Mass 4.65847 lbmass
Von Mises
Stress
0.0000224948
MPa 0.5574 MPa
1st Principal
Stress -0.141608 MPa 0.195534 MPa
3rd Principal
Stress -0.658377 MPa 0.108029 MPa
Displacement 0 mm 0.0000588687
mm
Safety Factor 15 ul 15 ul
Strength 50038 psi
Stress
Young's Modulus 31908.3 ksi
Poisson's Ratio 0.275 ul
Shear Modulus 12513.1 ksi
Part
Name(s)
s.ipt
s2.ipt
Name Stainless Steel
General
Mass Density 0.289018
lbmass/in^3
Yield Strength 36259.4 psi
Ultimate Tensile
Strength 78320.4 psi
Stress
Young's Modulus 27992.3 ksi
Poisson's Ratio 0.3 ul
Shear Modulus 10766.3 ksi
Part
Name(s) sheet.ipt
Operating conditions
Force:1
Load
Type Force
Magnitude 22.481 lbforce
Vector X 0.000 lbforce
Vector Y -22.481 lbforce
Vector Z 0.000 lbforce
Selected Face(s)
Fixed Constraint:1
Constraint
Type Fixed Constraint
Selected Face(s)
Results
Reaction Force and Moment on
Constraints
Constrai
nt Name
Reaction Force Reaction Moment
Magnitu
de
Compon
ent
(X,Y,Z)
Magnitu
de
Compon
ent
(X,Y,Z)
Fixed
Constrain
t:1
22.4809
lbforce
0 lbforce
0 lbforce
ft
0 lbforce
ft
22.4809
lbforce
0 lbforce
ft
0 lbforce 0 lbforce
ft
Result Summary
Name Minimum Maximum
Volume 268605 mm^3
Mass 4.65847 lbmass
Von Mises
Stress
0.0000224948
MPa 0.5574 MPa
1st Principal
Stress -0.141608 MPa 0.195534 MPa
3rd Principal
Stress -0.658377 MPa 0.108029 MPa
Displacement 0 mm 0.0000588687
mm
Safety Factor 15 ul 15 ul
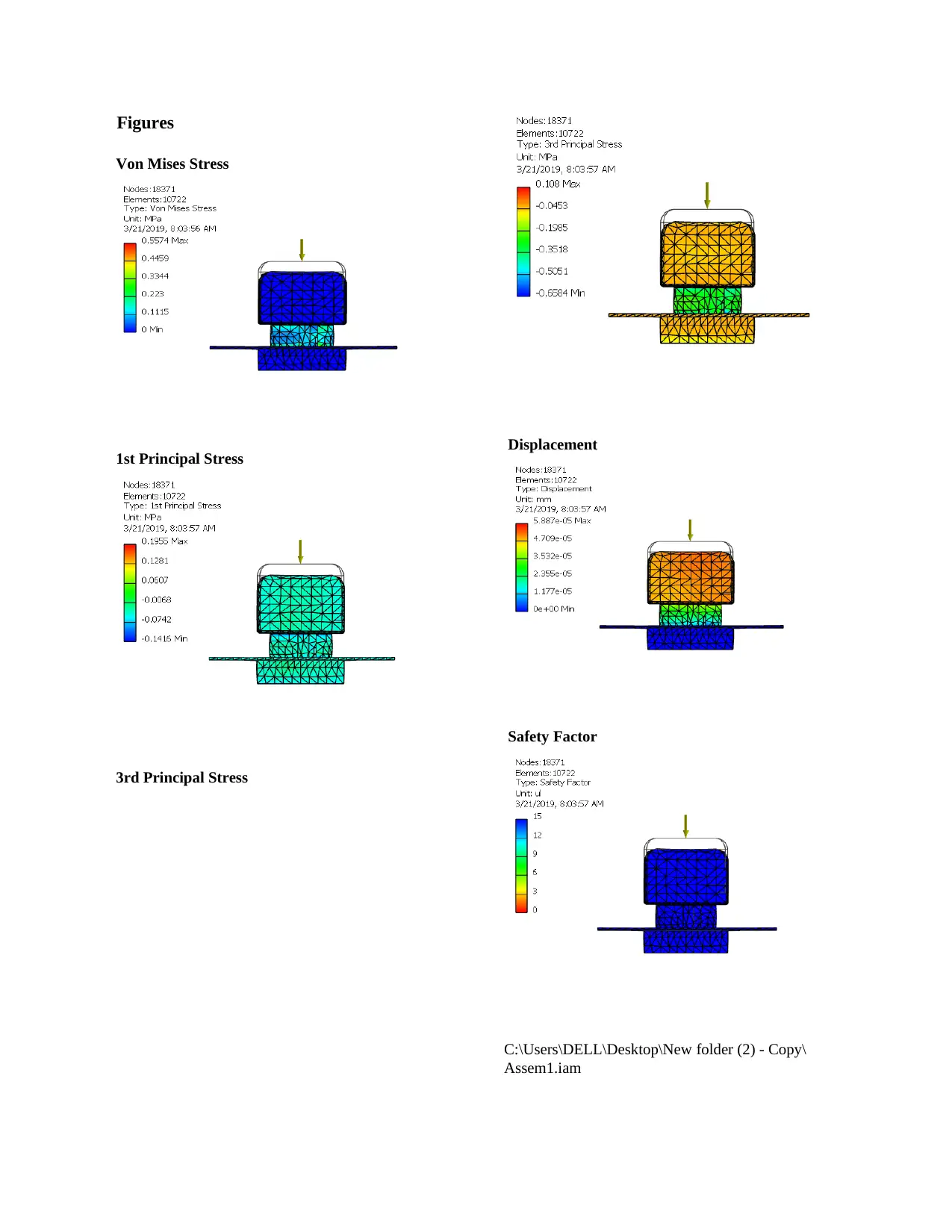
Figures
Von Mises Stress
1st Principal Stress
3rd Principal Stress
Displacement
Safety Factor
C:\Users\DELL\Desktop\New folder (2) - Copy\
Assem1.iam
Von Mises Stress
1st Principal Stress
3rd Principal Stress
Displacement
Safety Factor
C:\Users\DELL\Desktop\New folder (2) - Copy\
Assem1.iam
Secure Best Marks with AI Grader
Need help grading? Try our AI Grader for instant feedback on your assignments.
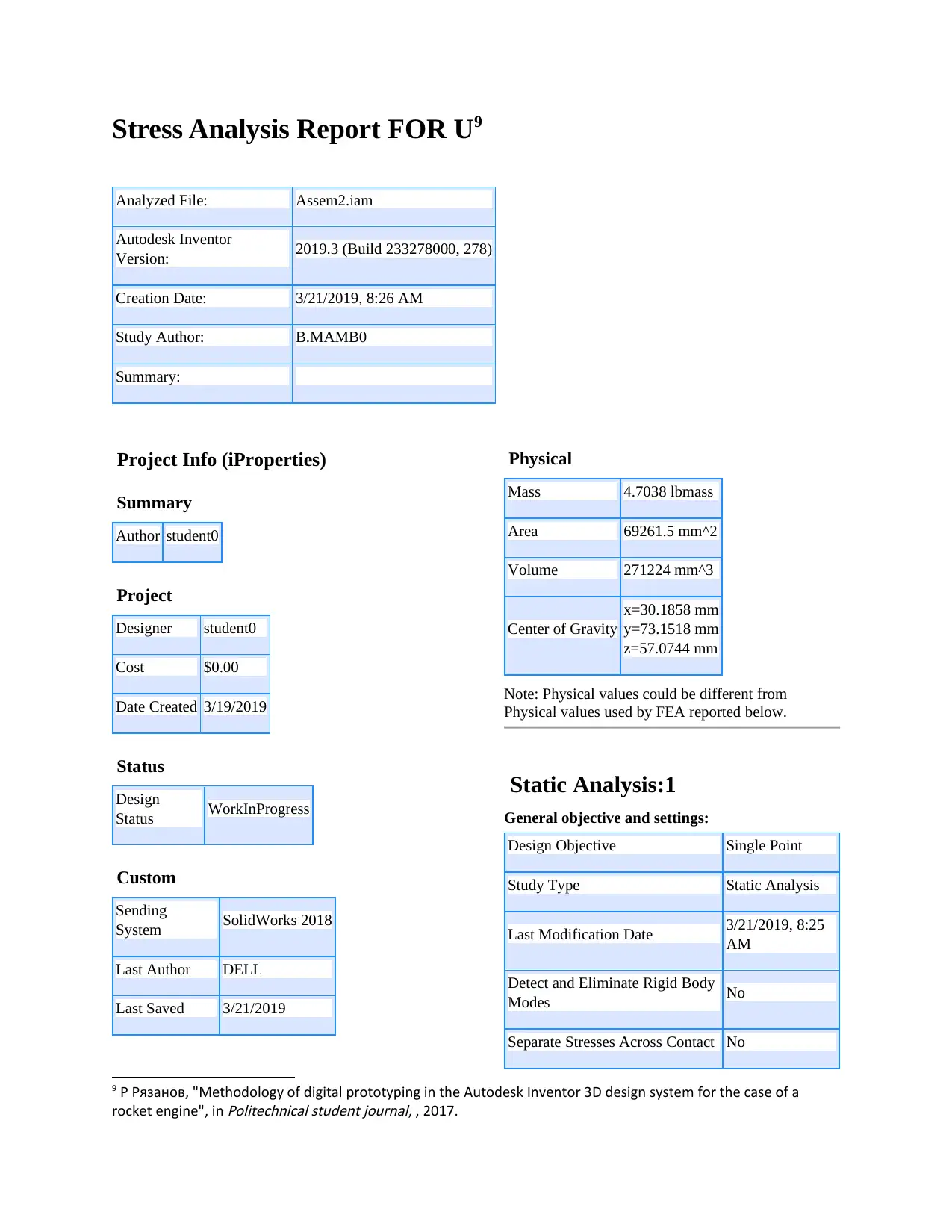
Stress Analysis Report FOR U9
Analyzed File: Assem2.iam
Autodesk Inventor
Version: 2019.3 (Build 233278000, 278)
Creation Date: 3/21/2019, 8:26 AM
Study Author: B.MAMB0
Summary:
Project Info (iProperties)
Summary
Author student0
Project
Designer student0
Cost $0.00
Date Created 3/19/2019
Status
Design
Status WorkInProgress
Custom
Sending
System SolidWorks 2018
Last Author DELL
Last Saved 3/21/2019
Physical
Mass 4.7038 lbmass
Area 69261.5 mm^2
Volume 271224 mm^3
Center of Gravity
x=30.1858 mm
y=73.1518 mm
z=57.0744 mm
Note: Physical values could be different from
Physical values used by FEA reported below.
Static Analysis:1
General objective and settings:
Design Objective Single Point
Study Type Static Analysis
Last Modification Date 3/21/2019, 8:25
AM
Detect and Eliminate Rigid Body
Modes No
Separate Stresses Across Contact No
9 Р Рязанов, "Methodology of digital prototyping in the Autodesk Inventor 3D design system for the case of a
rocket engine", in
Politechnical student journal, , 2017.
Analyzed File: Assem2.iam
Autodesk Inventor
Version: 2019.3 (Build 233278000, 278)
Creation Date: 3/21/2019, 8:26 AM
Study Author: B.MAMB0
Summary:
Project Info (iProperties)
Summary
Author student0
Project
Designer student0
Cost $0.00
Date Created 3/19/2019
Status
Design
Status WorkInProgress
Custom
Sending
System SolidWorks 2018
Last Author DELL
Last Saved 3/21/2019
Physical
Mass 4.7038 lbmass
Area 69261.5 mm^2
Volume 271224 mm^3
Center of Gravity
x=30.1858 mm
y=73.1518 mm
z=57.0744 mm
Note: Physical values could be different from
Physical values used by FEA reported below.
Static Analysis:1
General objective and settings:
Design Objective Single Point
Study Type Static Analysis
Last Modification Date 3/21/2019, 8:25
AM
Detect and Eliminate Rigid Body
Modes No
Separate Stresses Across Contact No
9 Р Рязанов, "Methodology of digital prototyping in the Autodesk Inventor 3D design system for the case of a
rocket engine", in
Politechnical student journal, , 2017.
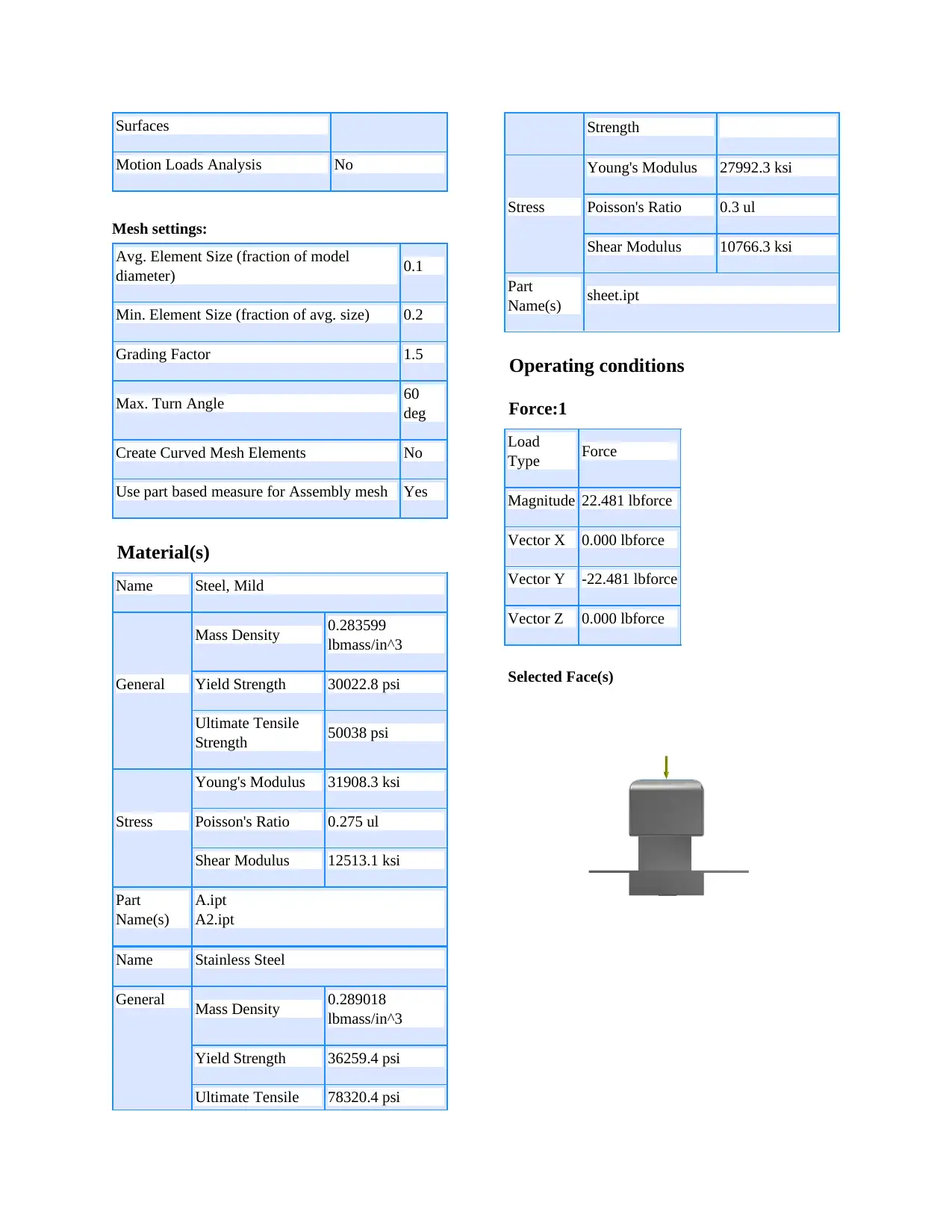
Surfaces
Motion Loads Analysis No
Mesh settings:
Avg. Element Size (fraction of model
diameter) 0.1
Min. Element Size (fraction of avg. size) 0.2
Grading Factor 1.5
Max. Turn Angle 60
deg
Create Curved Mesh Elements No
Use part based measure for Assembly mesh Yes
Material(s)
Name Steel, Mild
General
Mass Density 0.283599
lbmass/in^3
Yield Strength 30022.8 psi
Ultimate Tensile
Strength 50038 psi
Stress
Young's Modulus 31908.3 ksi
Poisson's Ratio 0.275 ul
Shear Modulus 12513.1 ksi
Part
Name(s)
A.ipt
A2.ipt
Name Stainless Steel
General Mass Density 0.289018
lbmass/in^3
Yield Strength 36259.4 psi
Ultimate Tensile 78320.4 psi
Strength
Stress
Young's Modulus 27992.3 ksi
Poisson's Ratio 0.3 ul
Shear Modulus 10766.3 ksi
Part
Name(s) sheet.ipt
Operating conditions
Force:1
Load
Type Force
Magnitude 22.481 lbforce
Vector X 0.000 lbforce
Vector Y -22.481 lbforce
Vector Z 0.000 lbforce
Selected Face(s)
Motion Loads Analysis No
Mesh settings:
Avg. Element Size (fraction of model
diameter) 0.1
Min. Element Size (fraction of avg. size) 0.2
Grading Factor 1.5
Max. Turn Angle 60
deg
Create Curved Mesh Elements No
Use part based measure for Assembly mesh Yes
Material(s)
Name Steel, Mild
General
Mass Density 0.283599
lbmass/in^3
Yield Strength 30022.8 psi
Ultimate Tensile
Strength 50038 psi
Stress
Young's Modulus 31908.3 ksi
Poisson's Ratio 0.275 ul
Shear Modulus 12513.1 ksi
Part
Name(s)
A.ipt
A2.ipt
Name Stainless Steel
General Mass Density 0.289018
lbmass/in^3
Yield Strength 36259.4 psi
Ultimate Tensile 78320.4 psi
Strength
Stress
Young's Modulus 27992.3 ksi
Poisson's Ratio 0.3 ul
Shear Modulus 10766.3 ksi
Part
Name(s) sheet.ipt
Operating conditions
Force:1
Load
Type Force
Magnitude 22.481 lbforce
Vector X 0.000 lbforce
Vector Y -22.481 lbforce
Vector Z 0.000 lbforce
Selected Face(s)
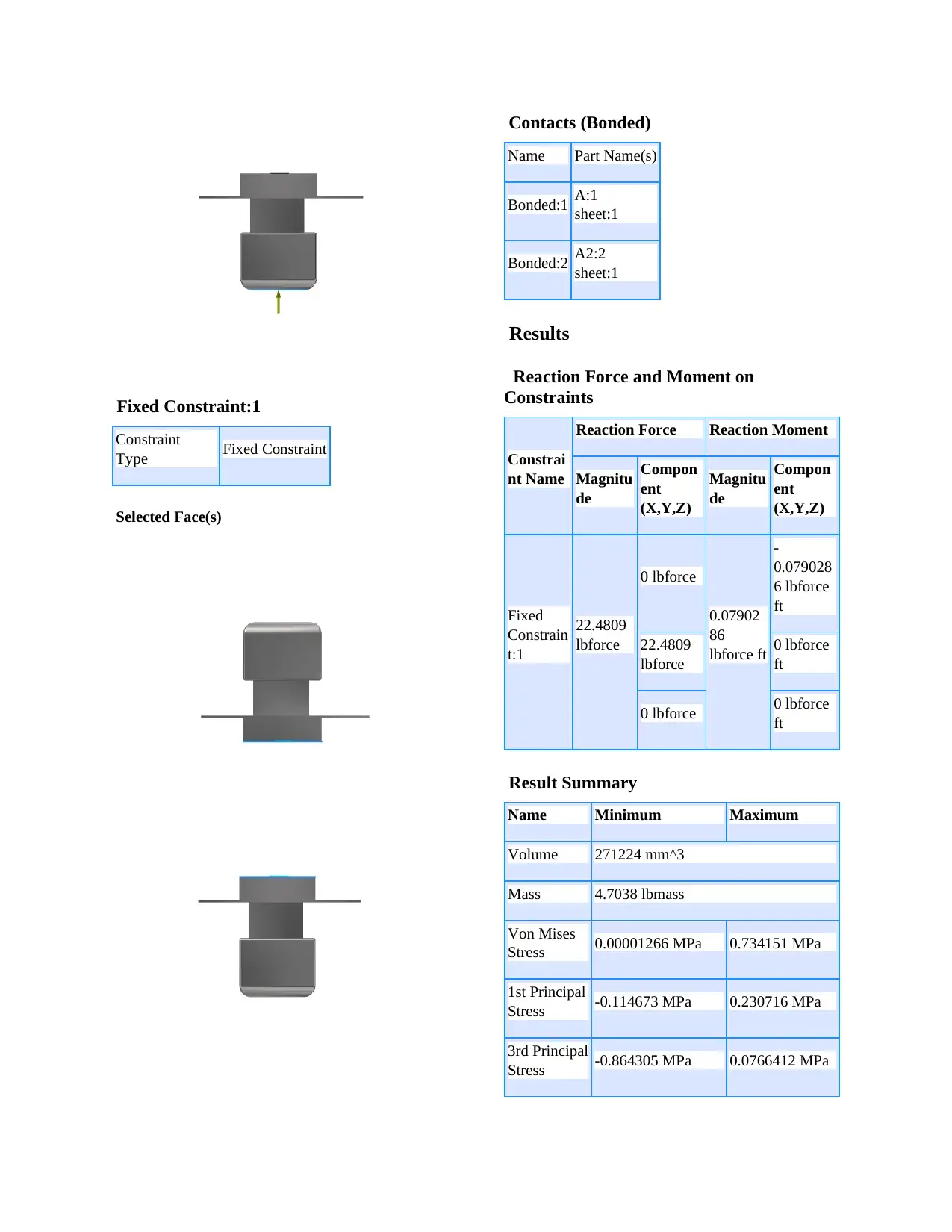
Fixed Constraint:1
Constraint
Type Fixed Constraint
Selected Face(s)
Contacts (Bonded)
Name Part Name(s)
Bonded:1 A:1
sheet:1
Bonded:2 A2:2
sheet:1
Results
Reaction Force and Moment on
Constraints
Constrai
nt Name
Reaction Force Reaction Moment
Magnitu
de
Compon
ent
(X,Y,Z)
Magnitu
de
Compon
ent
(X,Y,Z)
Fixed
Constrain
t:1
22.4809
lbforce
0 lbforce
0.07902
86
lbforce ft
-
0.079028
6 lbforce
ft
22.4809
lbforce
0 lbforce
ft
0 lbforce 0 lbforce
ft
Result Summary
Name Minimum Maximum
Volume 271224 mm^3
Mass 4.7038 lbmass
Von Mises
Stress 0.00001266 MPa 0.734151 MPa
1st Principal
Stress -0.114673 MPa 0.230716 MPa
3rd Principal
Stress -0.864305 MPa 0.0766412 MPa
Constraint
Type Fixed Constraint
Selected Face(s)
Contacts (Bonded)
Name Part Name(s)
Bonded:1 A:1
sheet:1
Bonded:2 A2:2
sheet:1
Results
Reaction Force and Moment on
Constraints
Constrai
nt Name
Reaction Force Reaction Moment
Magnitu
de
Compon
ent
(X,Y,Z)
Magnitu
de
Compon
ent
(X,Y,Z)
Fixed
Constrain
t:1
22.4809
lbforce
0 lbforce
0.07902
86
lbforce ft
-
0.079028
6 lbforce
ft
22.4809
lbforce
0 lbforce
ft
0 lbforce 0 lbforce
ft
Result Summary
Name Minimum Maximum
Volume 271224 mm^3
Mass 4.7038 lbmass
Von Mises
Stress 0.00001266 MPa 0.734151 MPa
1st Principal
Stress -0.114673 MPa 0.230716 MPa
3rd Principal
Stress -0.864305 MPa 0.0766412 MPa
Paraphrase This Document
Need a fresh take? Get an instant paraphrase of this document with our AI Paraphraser
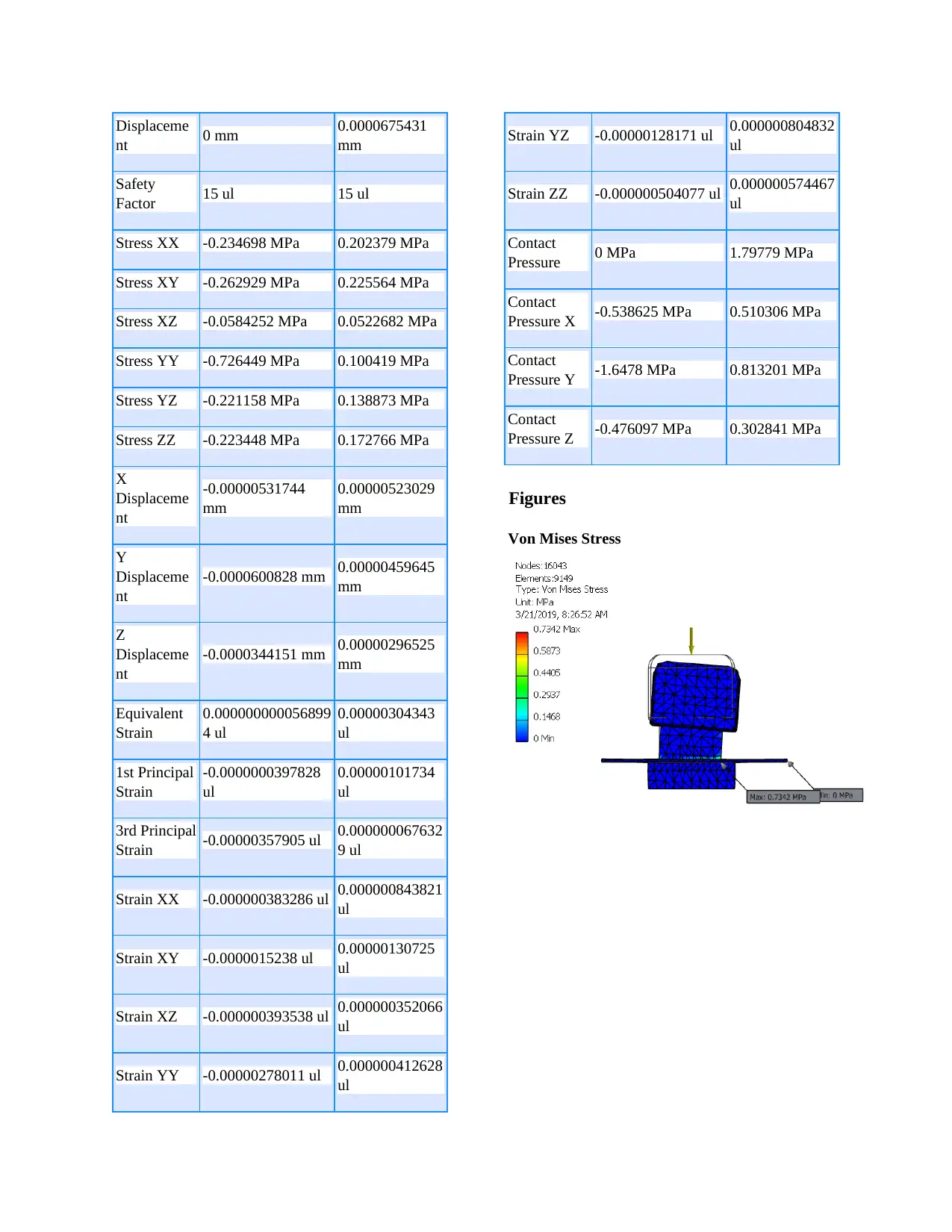
Displaceme
nt 0 mm 0.0000675431
mm
Safety
Factor 15 ul 15 ul
Stress XX -0.234698 MPa 0.202379 MPa
Stress XY -0.262929 MPa 0.225564 MPa
Stress XZ -0.0584252 MPa 0.0522682 MPa
Stress YY -0.726449 MPa 0.100419 MPa
Stress YZ -0.221158 MPa 0.138873 MPa
Stress ZZ -0.223448 MPa 0.172766 MPa
X
Displaceme
nt
-0.00000531744
mm
0.00000523029
mm
Y
Displaceme
nt
-0.0000600828 mm 0.00000459645
mm
Z
Displaceme
nt
-0.0000344151 mm 0.00000296525
mm
Equivalent
Strain
0.000000000056899
4 ul
0.00000304343
ul
1st Principal
Strain
-0.0000000397828
ul
0.00000101734
ul
3rd Principal
Strain -0.00000357905 ul 0.000000067632
9 ul
Strain XX -0.000000383286 ul 0.000000843821
ul
Strain XY -0.0000015238 ul 0.00000130725
ul
Strain XZ -0.000000393538 ul 0.000000352066
ul
Strain YY -0.00000278011 ul 0.000000412628
ul
Strain YZ -0.00000128171 ul 0.000000804832
ul
Strain ZZ -0.000000504077 ul 0.000000574467
ul
Contact
Pressure 0 MPa 1.79779 MPa
Contact
Pressure X -0.538625 MPa 0.510306 MPa
Contact
Pressure Y -1.6478 MPa 0.813201 MPa
Contact
Pressure Z -0.476097 MPa 0.302841 MPa
Figures
Von Mises Stress
nt 0 mm 0.0000675431
mm
Safety
Factor 15 ul 15 ul
Stress XX -0.234698 MPa 0.202379 MPa
Stress XY -0.262929 MPa 0.225564 MPa
Stress XZ -0.0584252 MPa 0.0522682 MPa
Stress YY -0.726449 MPa 0.100419 MPa
Stress YZ -0.221158 MPa 0.138873 MPa
Stress ZZ -0.223448 MPa 0.172766 MPa
X
Displaceme
nt
-0.00000531744
mm
0.00000523029
mm
Y
Displaceme
nt
-0.0000600828 mm 0.00000459645
mm
Z
Displaceme
nt
-0.0000344151 mm 0.00000296525
mm
Equivalent
Strain
0.000000000056899
4 ul
0.00000304343
ul
1st Principal
Strain
-0.0000000397828
ul
0.00000101734
ul
3rd Principal
Strain -0.00000357905 ul 0.000000067632
9 ul
Strain XX -0.000000383286 ul 0.000000843821
ul
Strain XY -0.0000015238 ul 0.00000130725
ul
Strain XZ -0.000000393538 ul 0.000000352066
ul
Strain YY -0.00000278011 ul 0.000000412628
ul
Strain YZ -0.00000128171 ul 0.000000804832
ul
Strain ZZ -0.000000504077 ul 0.000000574467
ul
Contact
Pressure 0 MPa 1.79779 MPa
Contact
Pressure X -0.538625 MPa 0.510306 MPa
Contact
Pressure Y -1.6478 MPa 0.813201 MPa
Contact
Pressure Z -0.476097 MPa 0.302841 MPa
Figures
Von Mises Stress
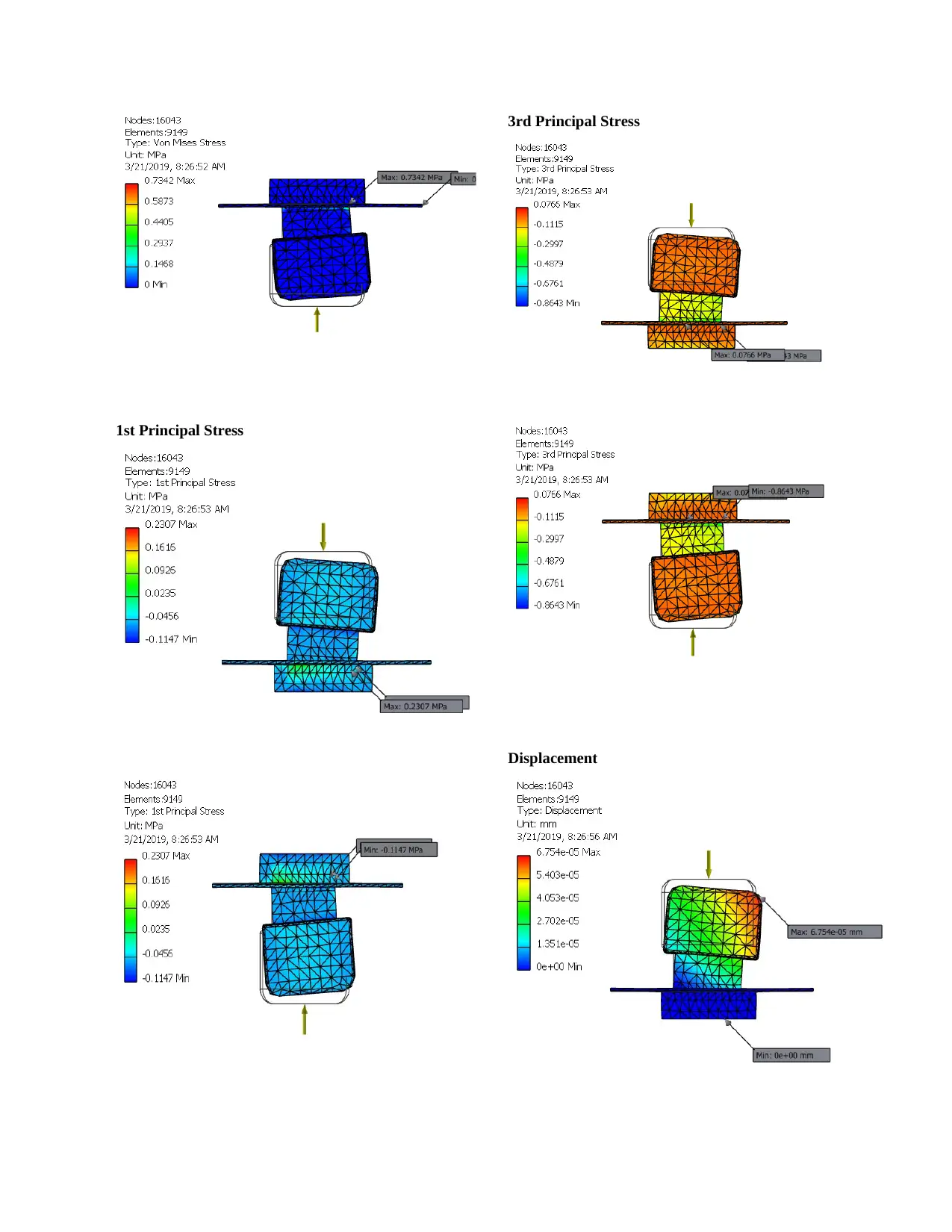
1st Principal Stress
3rd Principal Stress
Displacement
3rd Principal Stress
Displacement
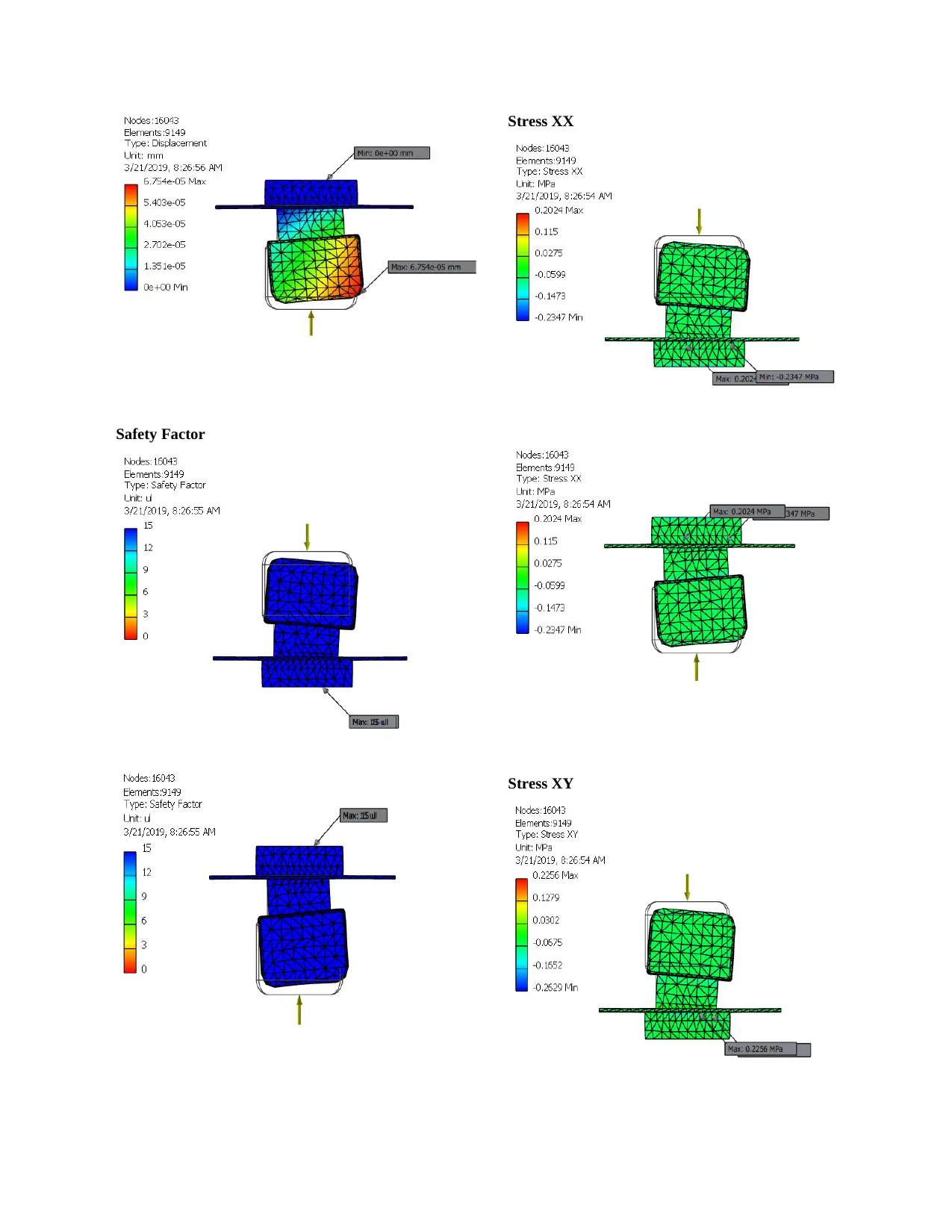
Safety Factor
Stress XX
Stress XY
Stress XX
Stress XY
Secure Best Marks with AI Grader
Need help grading? Try our AI Grader for instant feedback on your assignments.
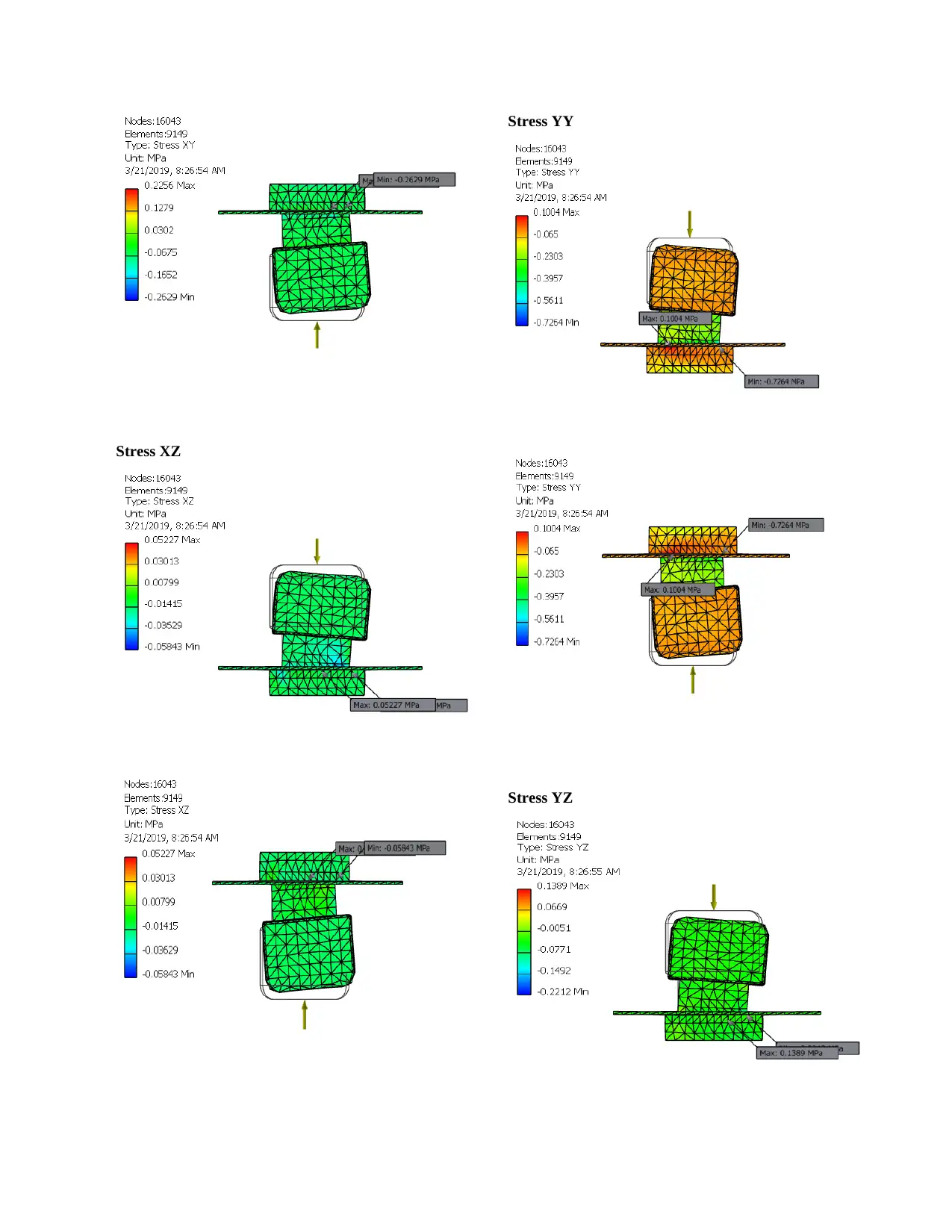
Stress XZ
Stress YY
Stress YZ
Stress YY
Stress YZ
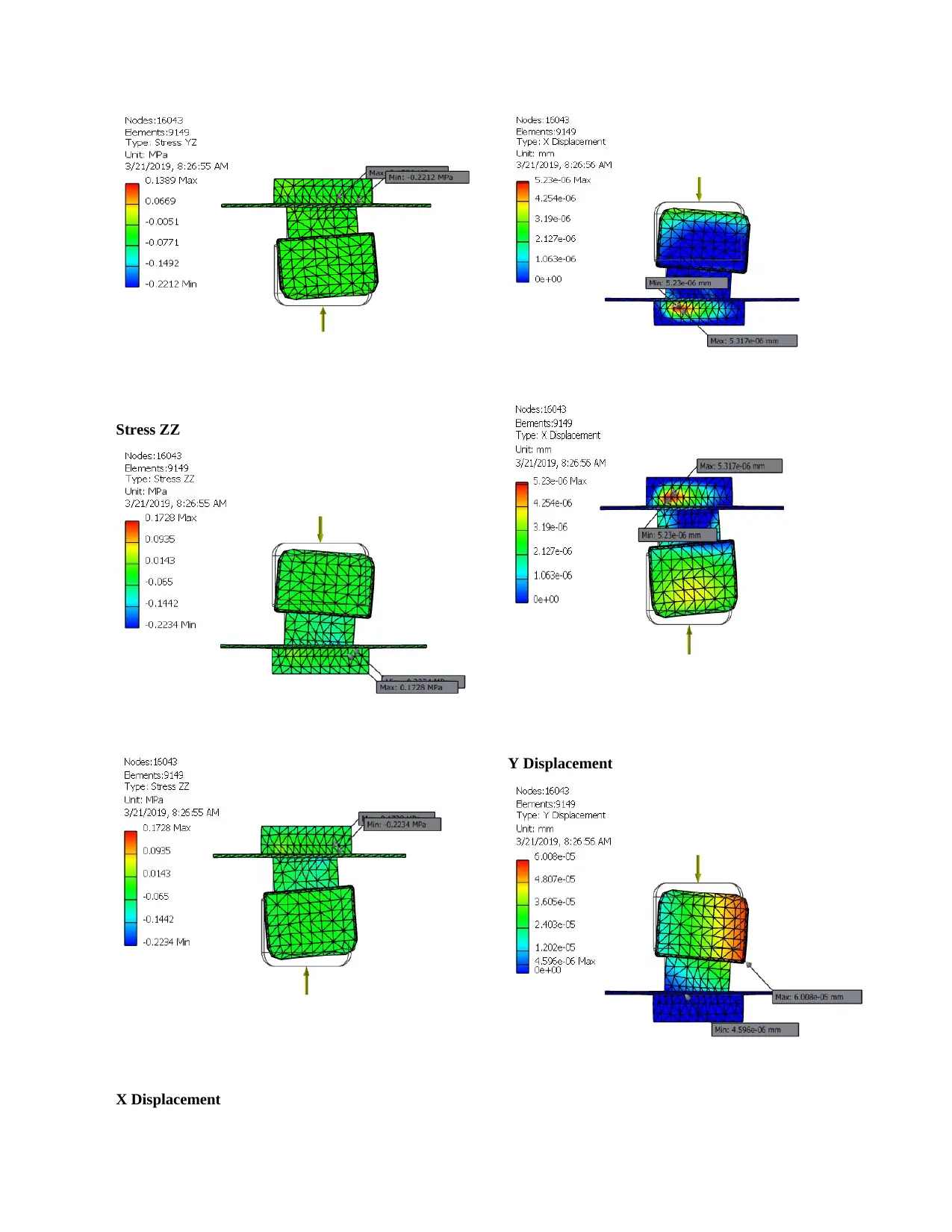
Stress ZZ
X Displacement
Y Displacement
X Displacement
Y Displacement
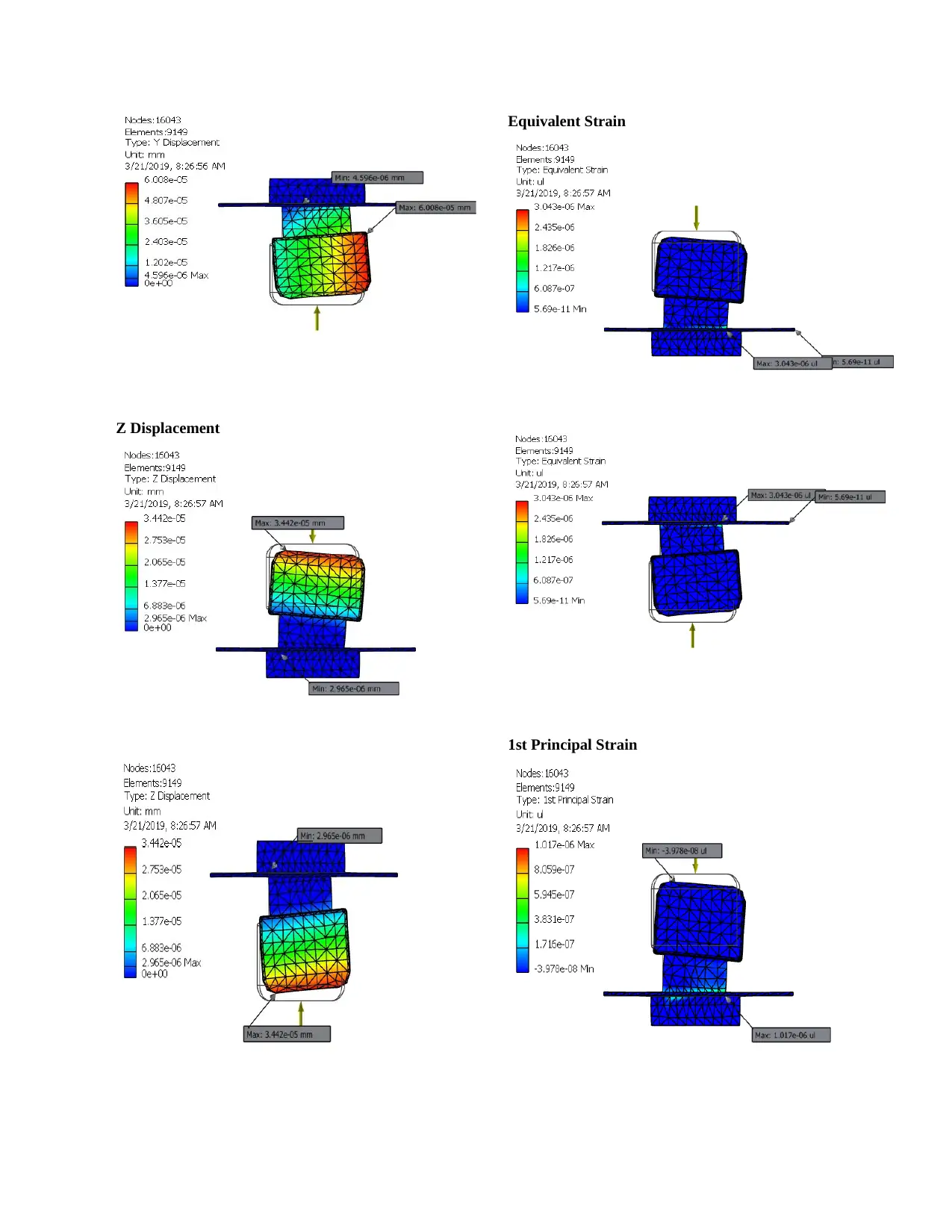
Z Displacement
Equivalent Strain
1st Principal Strain
Equivalent Strain
1st Principal Strain
Paraphrase This Document
Need a fresh take? Get an instant paraphrase of this document with our AI Paraphraser
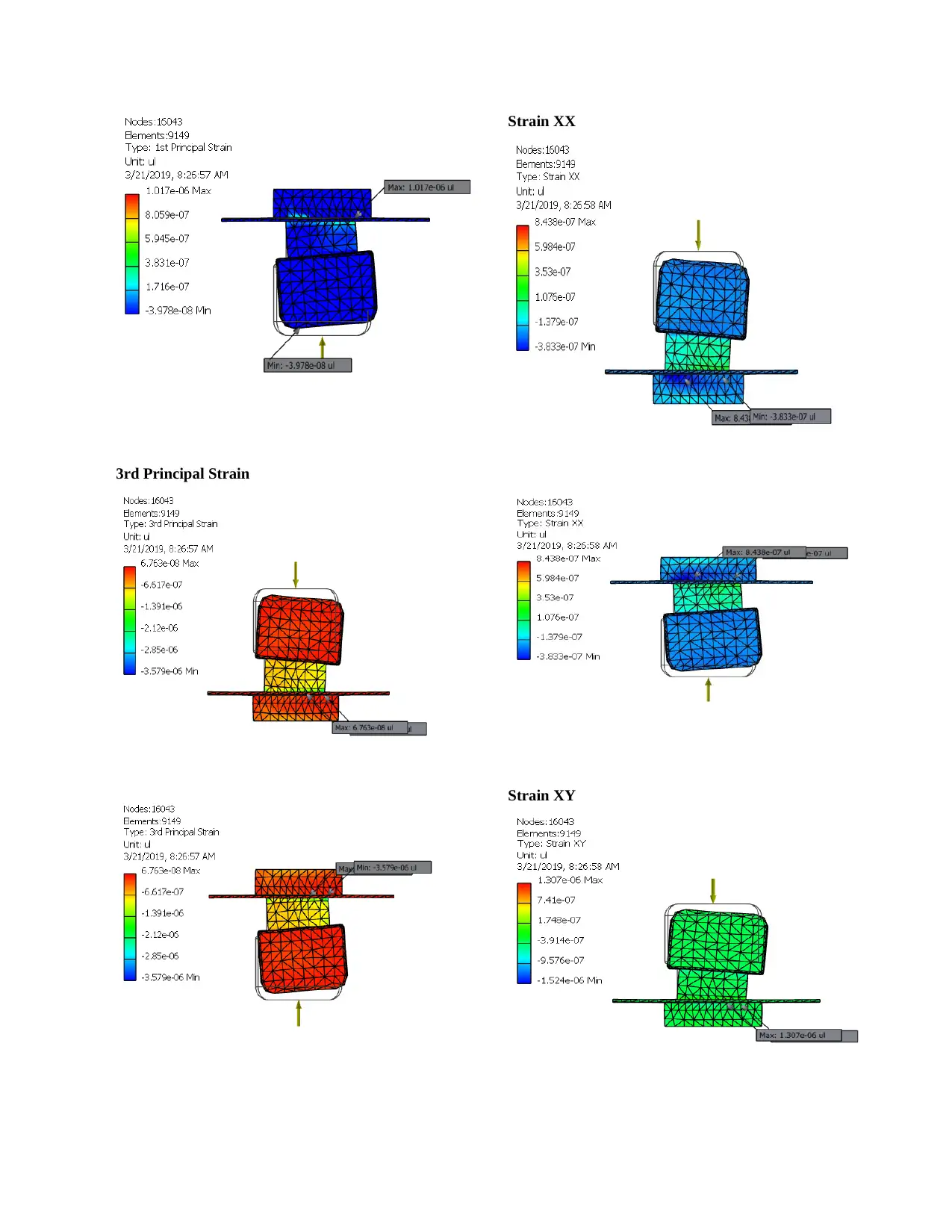
3rd Principal Strain
Strain XX
Strain XY
Strain XX
Strain XY
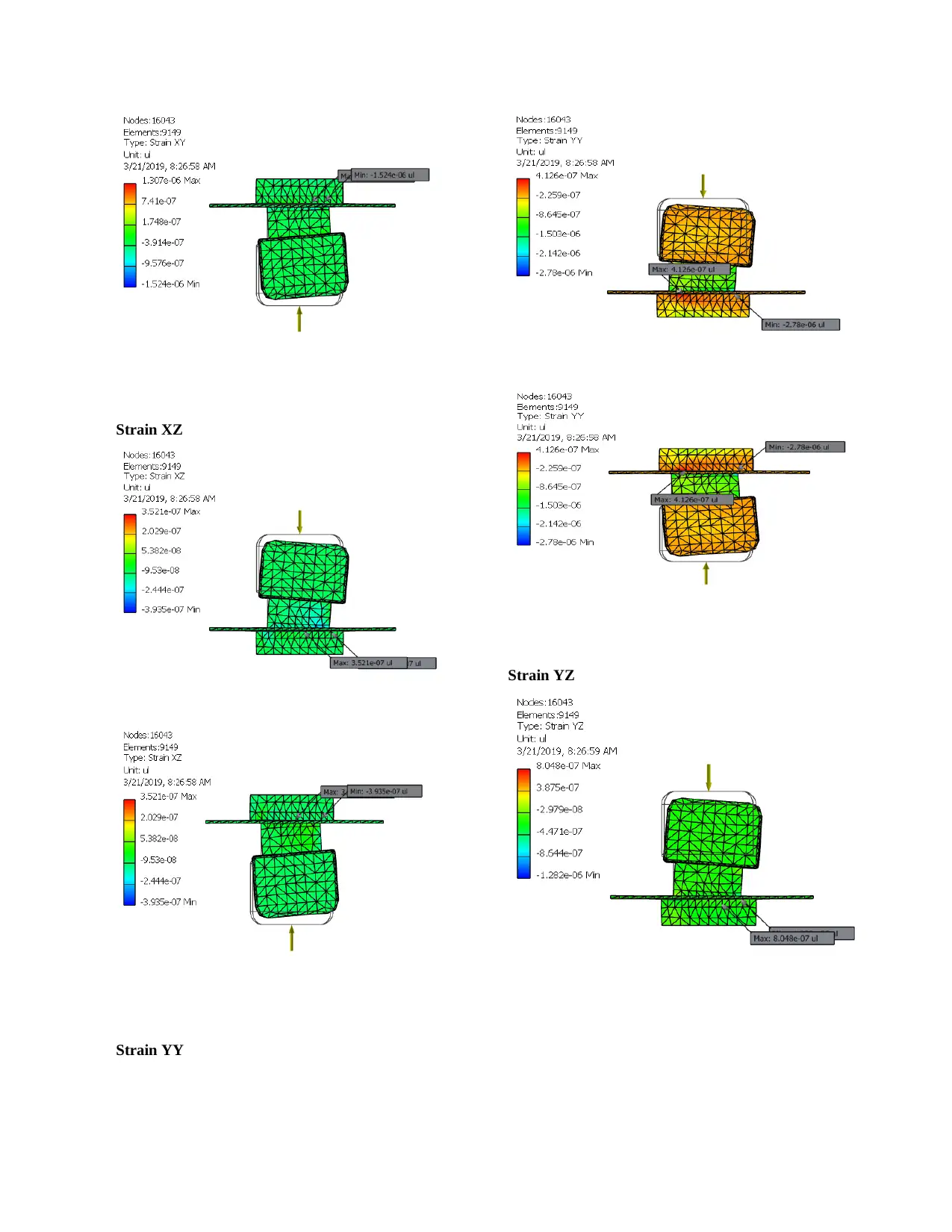
Strain XZ
Strain YY
Strain YZ
Strain YY
Strain YZ
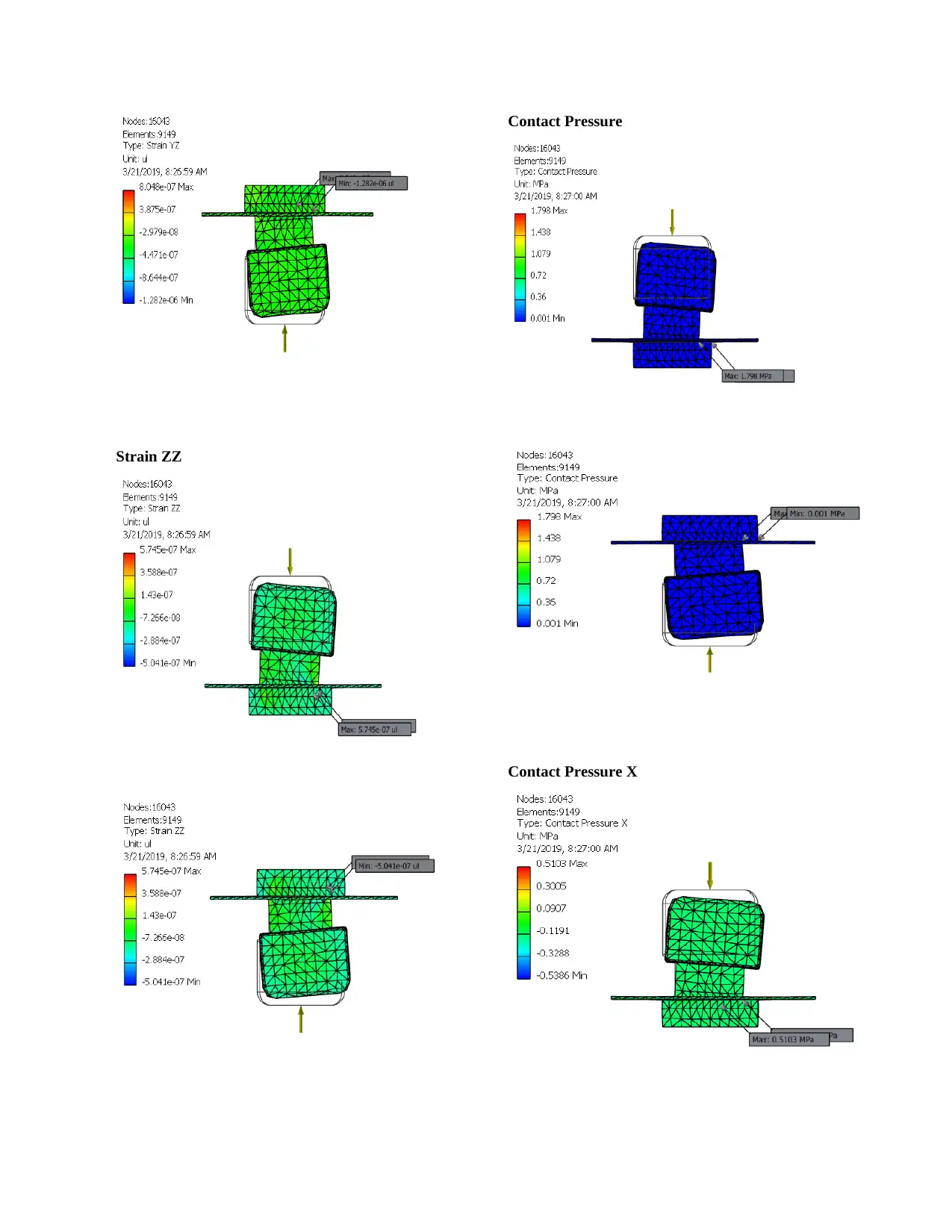
Strain ZZ
Contact Pressure
Contact Pressure X
Contact Pressure
Contact Pressure X
Secure Best Marks with AI Grader
Need help grading? Try our AI Grader for instant feedback on your assignments.
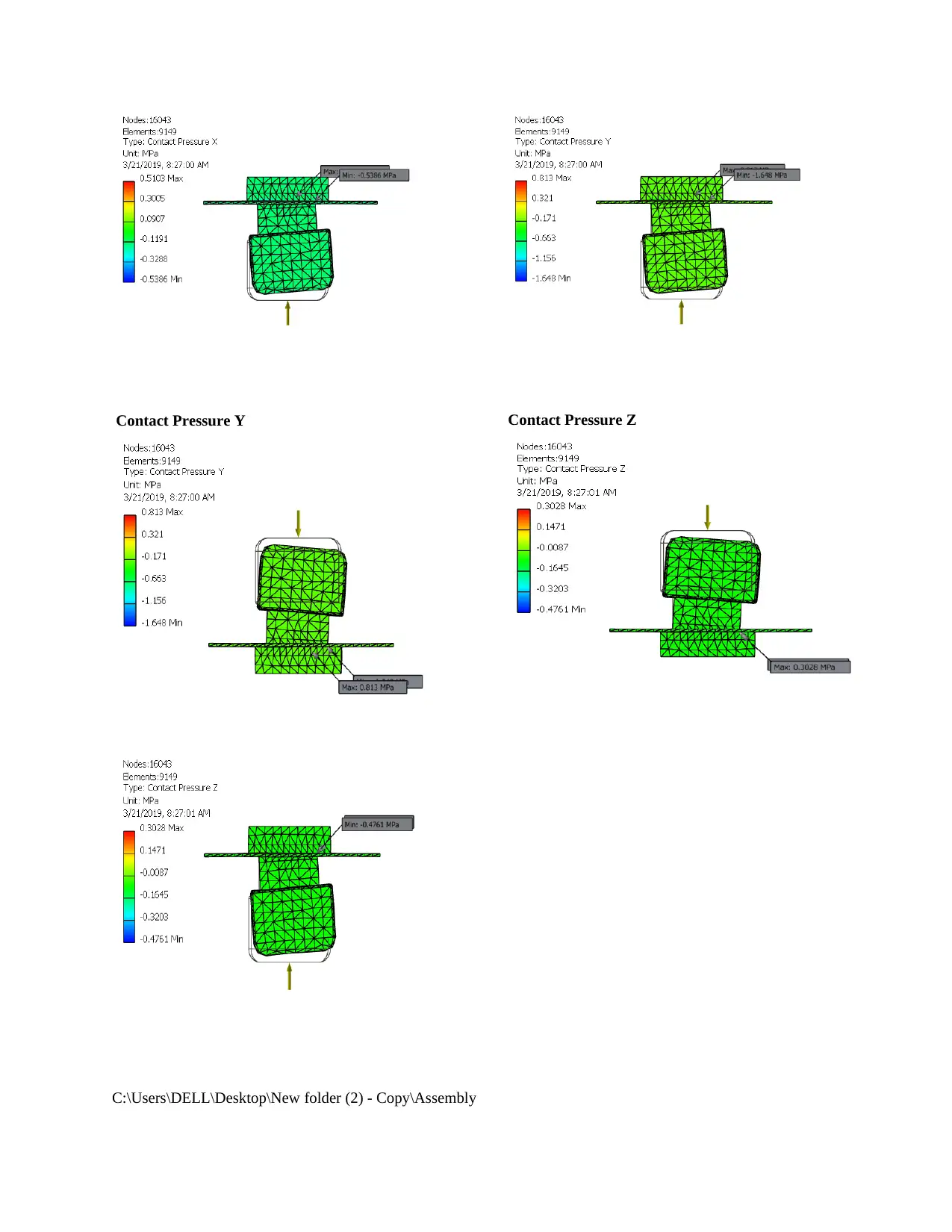
Contact Pressure Y Contact Pressure Z
C:\Users\DELL\Desktop\New folder (2) - Copy\Assembly
C:\Users\DELL\Desktop\New folder (2) - Copy\Assembly
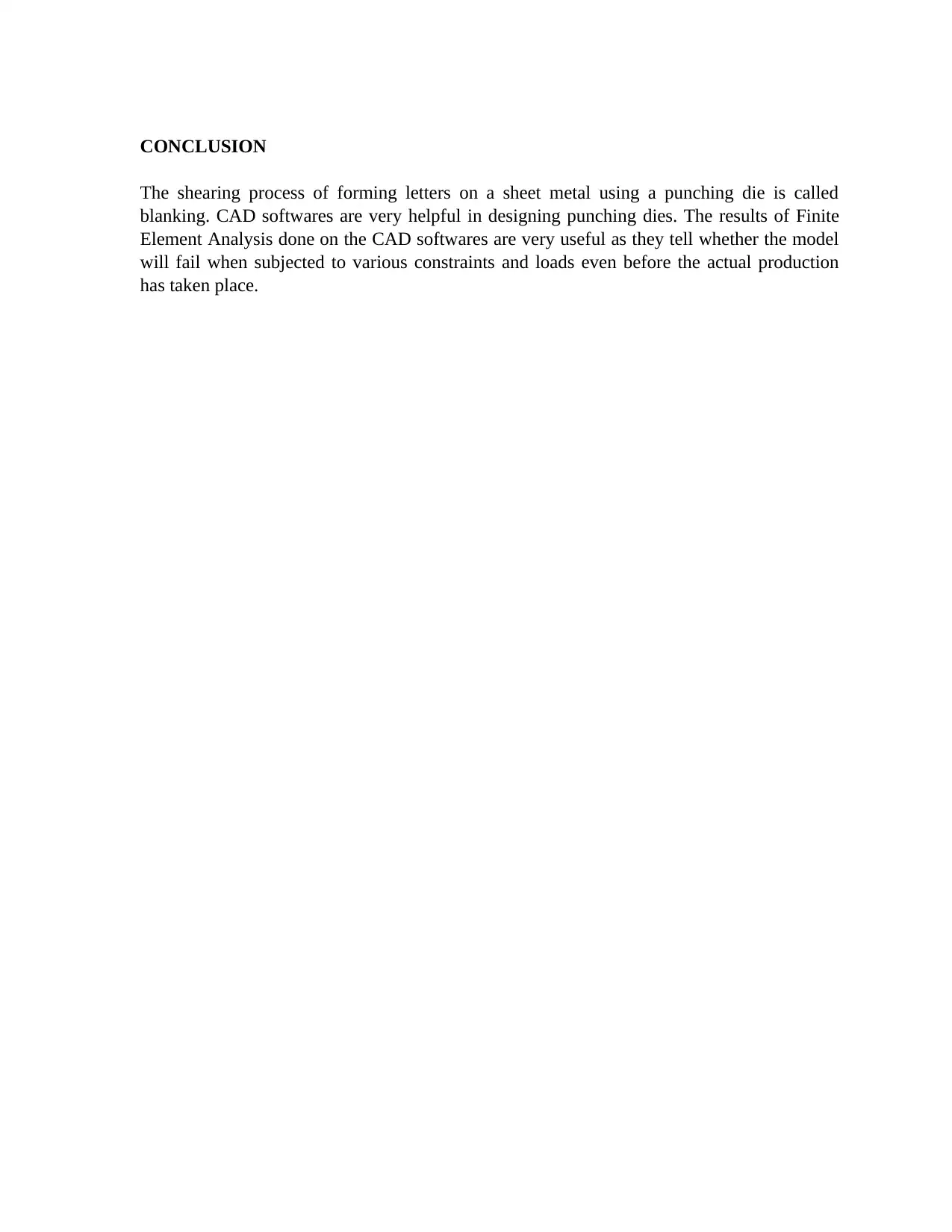
CONCLUSION
The shearing process of forming letters on a sheet metal using a punching die is called
blanking. CAD softwares are very helpful in designing punching dies. The results of Finite
Element Analysis done on the CAD softwares are very useful as they tell whether the model
will fail when subjected to various constraints and loads even before the actual production
has taken place.
The shearing process of forming letters on a sheet metal using a punching die is called
blanking. CAD softwares are very helpful in designing punching dies. The results of Finite
Element Analysis done on the CAD softwares are very useful as they tell whether the model
will fail when subjected to various constraints and loads even before the actual production
has taken place.
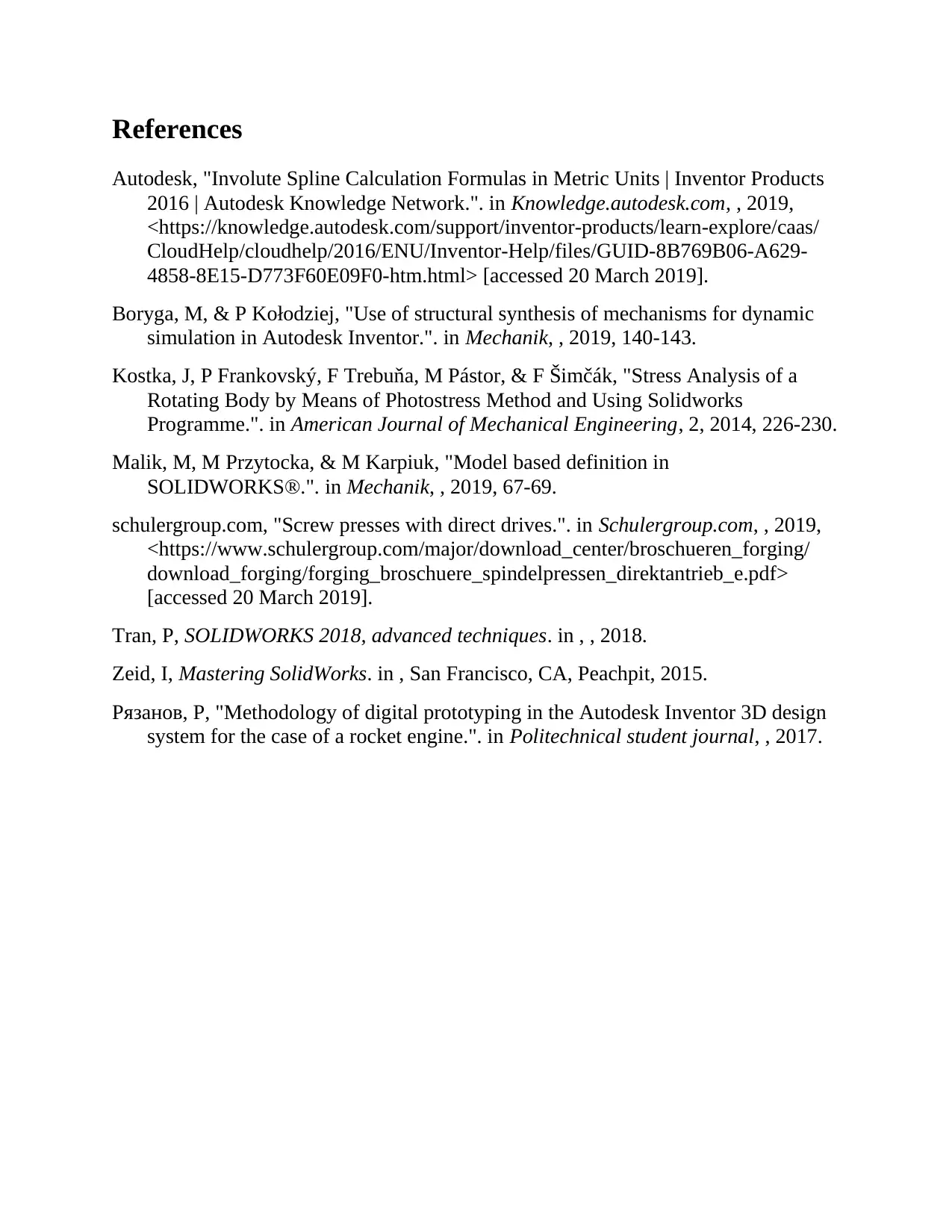
References
Autodesk, "Involute Spline Calculation Formulas in Metric Units | Inventor Products
2016 | Autodesk Knowledge Network.". in Knowledge.autodesk.com, , 2019,
<https://knowledge.autodesk.com/support/inventor-products/learn-explore/caas/
CloudHelp/cloudhelp/2016/ENU/Inventor-Help/files/GUID-8B769B06-A629-
4858-8E15-D773F60E09F0-htm.html> [accessed 20 March 2019].
Boryga, M, & P Kołodziej, "Use of structural synthesis of mechanisms for dynamic
simulation in Autodesk Inventor.". in Mechanik, , 2019, 140-143.
Kostka, J, P Frankovský, F Trebuňa, M Pástor, & F Šimčák, "Stress Analysis of a
Rotating Body by Means of Photostress Method and Using Solidworks
Programme.". in American Journal of Mechanical Engineering, 2, 2014, 226-230.
Malik, M, M Przytocka, & M Karpiuk, "Model based definition in
SOLIDWORKS®.". in Mechanik, , 2019, 67-69.
schulergroup.com, "Screw presses with direct drives.". in Schulergroup.com, , 2019,
<https://www.schulergroup.com/major/download_center/broschueren_forging/
download_forging/forging_broschuere_spindelpressen_direktantrieb_e.pdf>
[accessed 20 March 2019].
Tran, P, SOLIDWORKS 2018, advanced techniques. in , , 2018.
Zeid, I, Mastering SolidWorks. in , San Francisco, CA, Peachpit, 2015.
Рязанов, Р, "Methodology of digital prototyping in the Autodesk Inventor 3D design
system for the case of a rocket engine.". in Politechnical student journal, , 2017.
Autodesk, "Involute Spline Calculation Formulas in Metric Units | Inventor Products
2016 | Autodesk Knowledge Network.". in Knowledge.autodesk.com, , 2019,
<https://knowledge.autodesk.com/support/inventor-products/learn-explore/caas/
CloudHelp/cloudhelp/2016/ENU/Inventor-Help/files/GUID-8B769B06-A629-
4858-8E15-D773F60E09F0-htm.html> [accessed 20 March 2019].
Boryga, M, & P Kołodziej, "Use of structural synthesis of mechanisms for dynamic
simulation in Autodesk Inventor.". in Mechanik, , 2019, 140-143.
Kostka, J, P Frankovský, F Trebuňa, M Pástor, & F Šimčák, "Stress Analysis of a
Rotating Body by Means of Photostress Method and Using Solidworks
Programme.". in American Journal of Mechanical Engineering, 2, 2014, 226-230.
Malik, M, M Przytocka, & M Karpiuk, "Model based definition in
SOLIDWORKS®.". in Mechanik, , 2019, 67-69.
schulergroup.com, "Screw presses with direct drives.". in Schulergroup.com, , 2019,
<https://www.schulergroup.com/major/download_center/broschueren_forging/
download_forging/forging_broschuere_spindelpressen_direktantrieb_e.pdf>
[accessed 20 March 2019].
Tran, P, SOLIDWORKS 2018, advanced techniques. in , , 2018.
Zeid, I, Mastering SolidWorks. in , San Francisco, CA, Peachpit, 2015.
Рязанов, Р, "Methodology of digital prototyping in the Autodesk Inventor 3D design
system for the case of a rocket engine.". in Politechnical student journal, , 2017.
Paraphrase This Document
Need a fresh take? Get an instant paraphrase of this document with our AI Paraphraser
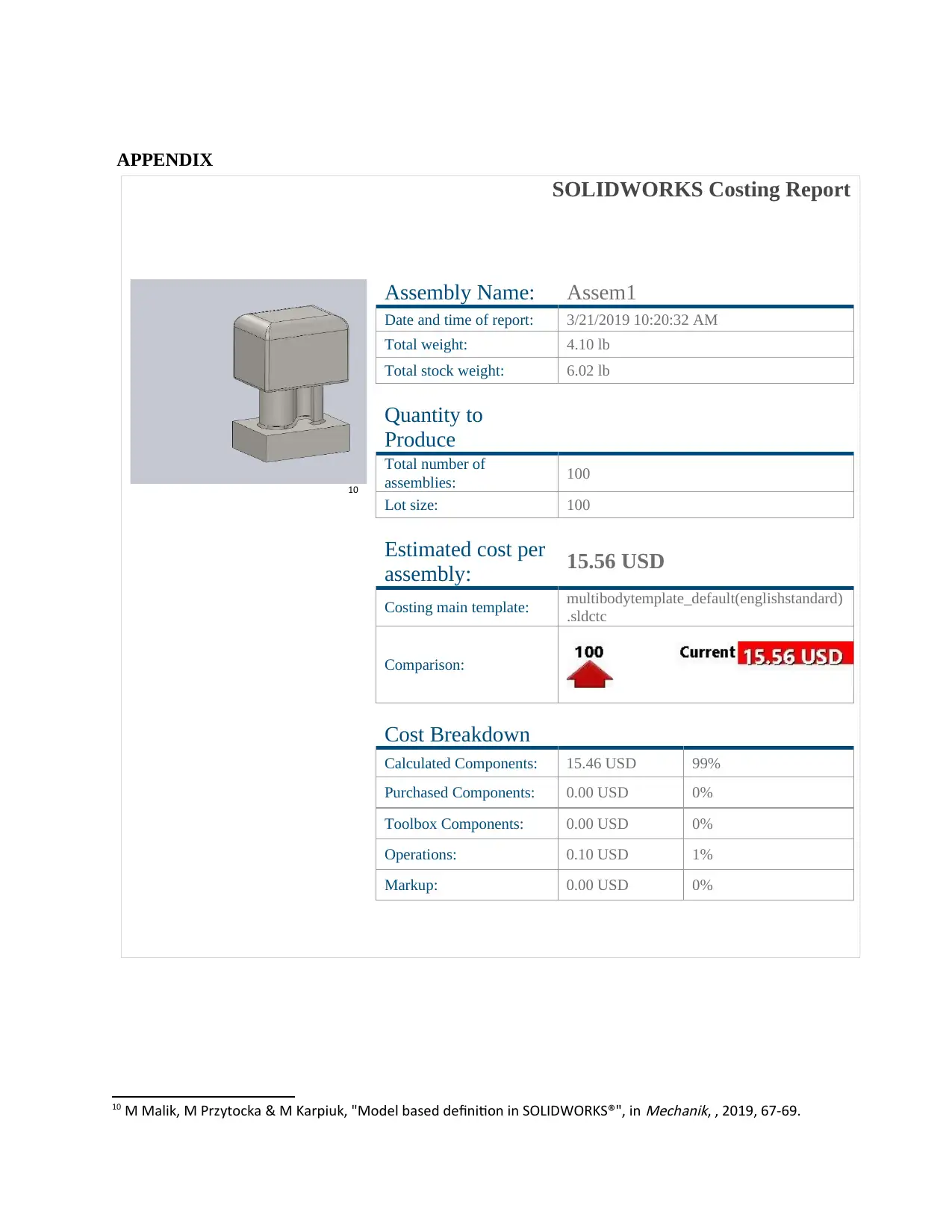
APPENDIX
SOLIDWORKS Costing Report
10
Assembly Name: Assem1
Date and time of report: 3/21/2019 10:20:32 AM
Total weight: 4.10 lb
Total stock weight: 6.02 lb
Quantity to
Produce
Total number of
assemblies: 100
Lot size: 100
Estimated cost per
assembly: 15.56 USD
Costing main template: multibodytemplate_default(englishstandard)
.sldctc
Comparison:
Cost Breakdown
Calculated Components: 15.46 USD 99%
Purchased Components: 0.00 USD 0%
Toolbox Components: 0.00 USD 0%
Operations: 0.10 USD 1%
Markup: 0.00 USD 0%
10 M Malik, M Przytocka & M Karpiuk, "Model based definition in SOLIDWORKS®", in
Mechanik, , 2019, 67-69.
SOLIDWORKS Costing Report
10
Assembly Name: Assem1
Date and time of report: 3/21/2019 10:20:32 AM
Total weight: 4.10 lb
Total stock weight: 6.02 lb
Quantity to
Produce
Total number of
assemblies: 100
Lot size: 100
Estimated cost per
assembly: 15.56 USD
Costing main template: multibodytemplate_default(englishstandard)
.sldctc
Comparison:
Cost Breakdown
Calculated Components: 15.46 USD 99%
Purchased Components: 0.00 USD 0%
Toolbox Components: 0.00 USD 0%
Operations: 0.10 USD 1%
Markup: 0.00 USD 0%
10 M Malik, M Przytocka & M Karpiuk, "Model based definition in SOLIDWORKS®", in
Mechanik, , 2019, 67-69.
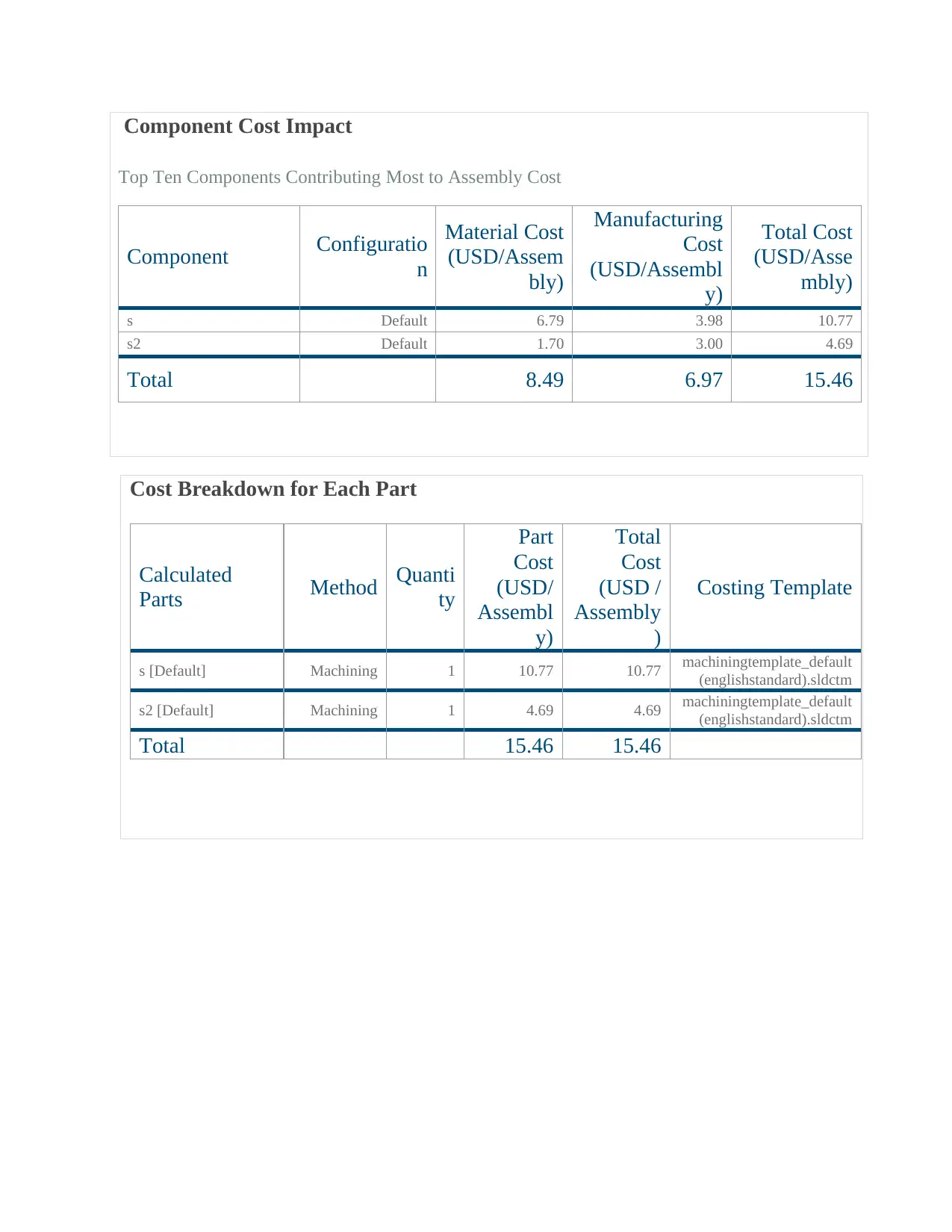
Component Cost Impact
Top Ten Components Contributing Most to Assembly Cost
Component Configuratio
n
Material Cost
(USD/Assem
bly)
Manufacturing
Cost
(USD/Assembl
y)
Total Cost
(USD/Asse
mbly)
s Default 6.79 3.98 10.77
s2 Default 1.70 3.00 4.69
Total 8.49 6.97 15.46
Cost Breakdown for Each Part
Calculated
Parts Method Quanti
ty
Part
Cost
(USD/
Assembl
y)
Total
Cost
(USD /
Assembly
)
Costing Template
s [Default] Machining 1 10.77 10.77 machiningtemplate_default
(englishstandard).sldctm
s2 [Default] Machining 1 4.69 4.69 machiningtemplate_default
(englishstandard).sldctm
Total 15.46 15.46
Top Ten Components Contributing Most to Assembly Cost
Component Configuratio
n
Material Cost
(USD/Assem
bly)
Manufacturing
Cost
(USD/Assembl
y)
Total Cost
(USD/Asse
mbly)
s Default 6.79 3.98 10.77
s2 Default 1.70 3.00 4.69
Total 8.49 6.97 15.46
Cost Breakdown for Each Part
Calculated
Parts Method Quanti
ty
Part
Cost
(USD/
Assembl
y)
Total
Cost
(USD /
Assembly
)
Costing Template
s [Default] Machining 1 10.77 10.77 machiningtemplate_default
(englishstandard).sldctm
s2 [Default] Machining 1 4.69 4.69 machiningtemplate_default
(englishstandard).sldctm
Total 15.46 15.46
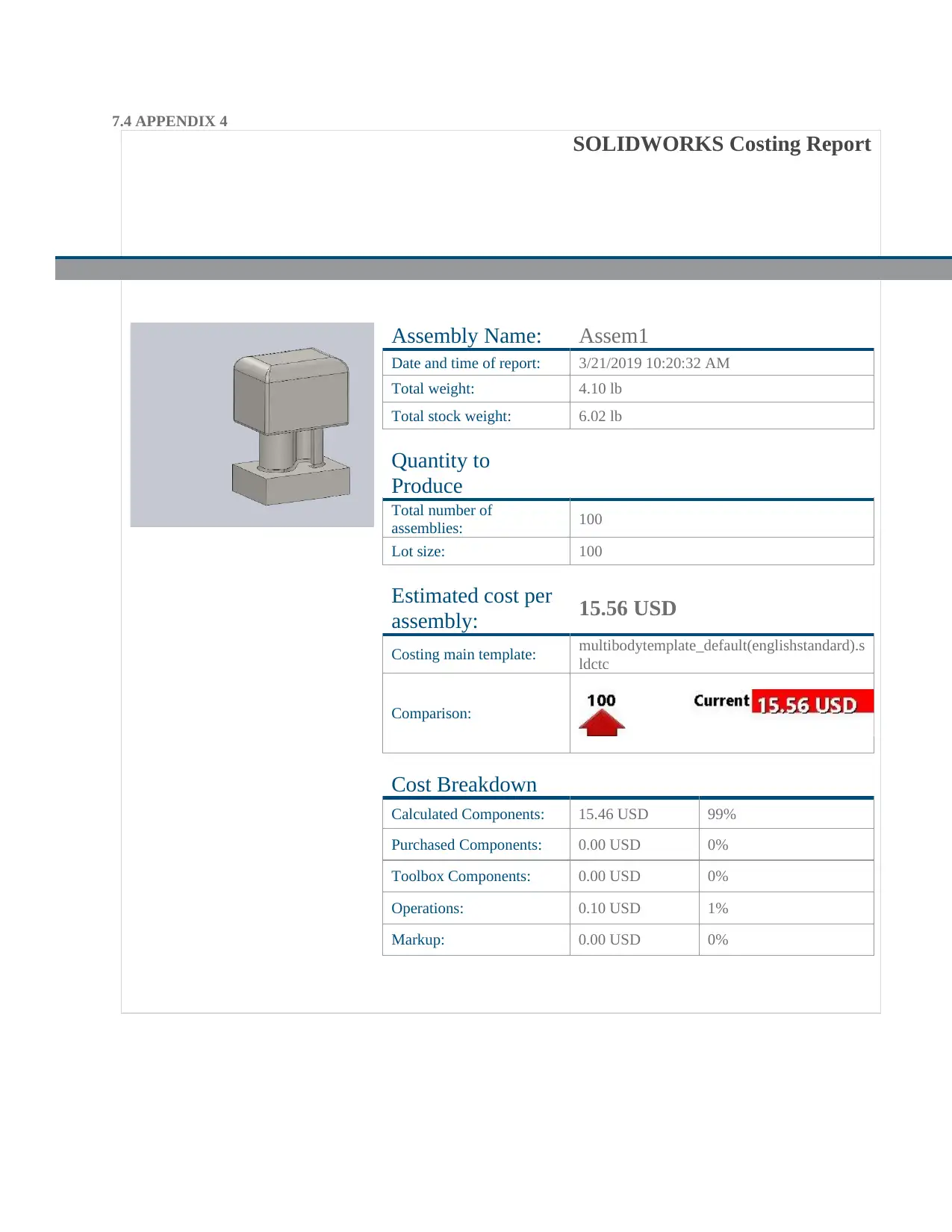
7.4 APPENDIX 4
SOLIDWORKS Costing Report
Assembly Name: Assem1
Date and time of report: 3/21/2019 10:20:32 AM
Total weight: 4.10 lb
Total stock weight: 6.02 lb
Quantity to
Produce
Total number of
assemblies: 100
Lot size: 100
Estimated cost per
assembly: 15.56 USD
Costing main template: multibodytemplate_default(englishstandard).s
ldctc
Comparison:
Cost Breakdown
Calculated Components: 15.46 USD 99%
Purchased Components: 0.00 USD 0%
Toolbox Components: 0.00 USD 0%
Operations: 0.10 USD 1%
Markup: 0.00 USD 0%
SOLIDWORKS Costing Report
Assembly Name: Assem1
Date and time of report: 3/21/2019 10:20:32 AM
Total weight: 4.10 lb
Total stock weight: 6.02 lb
Quantity to
Produce
Total number of
assemblies: 100
Lot size: 100
Estimated cost per
assembly: 15.56 USD
Costing main template: multibodytemplate_default(englishstandard).s
ldctc
Comparison:
Cost Breakdown
Calculated Components: 15.46 USD 99%
Purchased Components: 0.00 USD 0%
Toolbox Components: 0.00 USD 0%
Operations: 0.10 USD 1%
Markup: 0.00 USD 0%
Secure Best Marks with AI Grader
Need help grading? Try our AI Grader for instant feedback on your assignments.
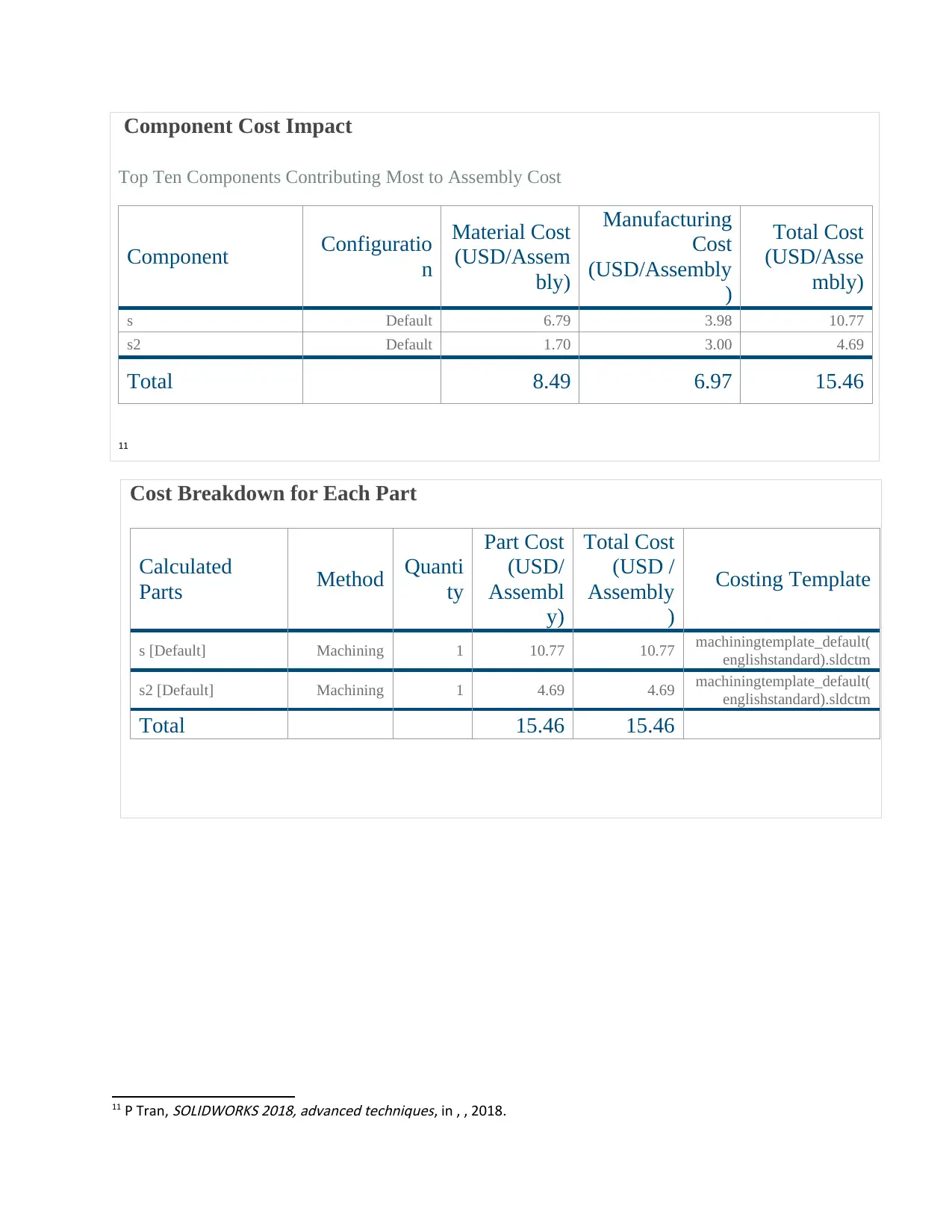
Component Cost Impact
Top Ten Components Contributing Most to Assembly Cost
Component Configuratio
n
Material Cost
(USD/Assem
bly)
Manufacturing
Cost
(USD/Assembly
)
Total Cost
(USD/Asse
mbly)
s Default 6.79 3.98 10.77
s2 Default 1.70 3.00 4.69
Total 8.49 6.97 15.46
11
Cost Breakdown for Each Part
Calculated
Parts Method Quanti
ty
Part Cost
(USD/
Assembl
y)
Total Cost
(USD /
Assembly
)
Costing Template
s [Default] Machining 1 10.77 10.77 machiningtemplate_default(
englishstandard).sldctm
s2 [Default] Machining 1 4.69 4.69 machiningtemplate_default(
englishstandard).sldctm
Total 15.46 15.46
11 P Tran,
SOLIDWORKS 2018, advanced techniques, in , , 2018.
Top Ten Components Contributing Most to Assembly Cost
Component Configuratio
n
Material Cost
(USD/Assem
bly)
Manufacturing
Cost
(USD/Assembly
)
Total Cost
(USD/Asse
mbly)
s Default 6.79 3.98 10.77
s2 Default 1.70 3.00 4.69
Total 8.49 6.97 15.46
11
Cost Breakdown for Each Part
Calculated
Parts Method Quanti
ty
Part Cost
(USD/
Assembl
y)
Total Cost
(USD /
Assembly
)
Costing Template
s [Default] Machining 1 10.77 10.77 machiningtemplate_default(
englishstandard).sldctm
s2 [Default] Machining 1 4.69 4.69 machiningtemplate_default(
englishstandard).sldctm
Total 15.46 15.46
11 P Tran,
SOLIDWORKS 2018, advanced techniques, in , , 2018.
1 out of 35
Related Documents
![[object Object]](/_next/image/?url=%2F_next%2Fstatic%2Fmedia%2Flogo.6d15ce61.png&w=640&q=75)
Your All-in-One AI-Powered Toolkit for Academic Success.
+13062052269
info@desklib.com
Available 24*7 on WhatsApp / Email
Unlock your academic potential
© 2024 | Zucol Services PVT LTD | All rights reserved.