Building Cost Estimation Factors
VerifiedAdded on 2020/02/24
|7
|1596
|79
AI Summary
The assignment delves into the crucial aspects of building cost estimation. It emphasizes how material quality, availability (influenced by procurement delays), and fluctuating prices significantly impact early-stage construction costs. The document further examines various estimation methods, highlighting the Storey Enclosure Method's accuracy but limited application in complex designs.
Contribute Materials
Your contribution can guide someone’s learning journey. Share your
documents today.
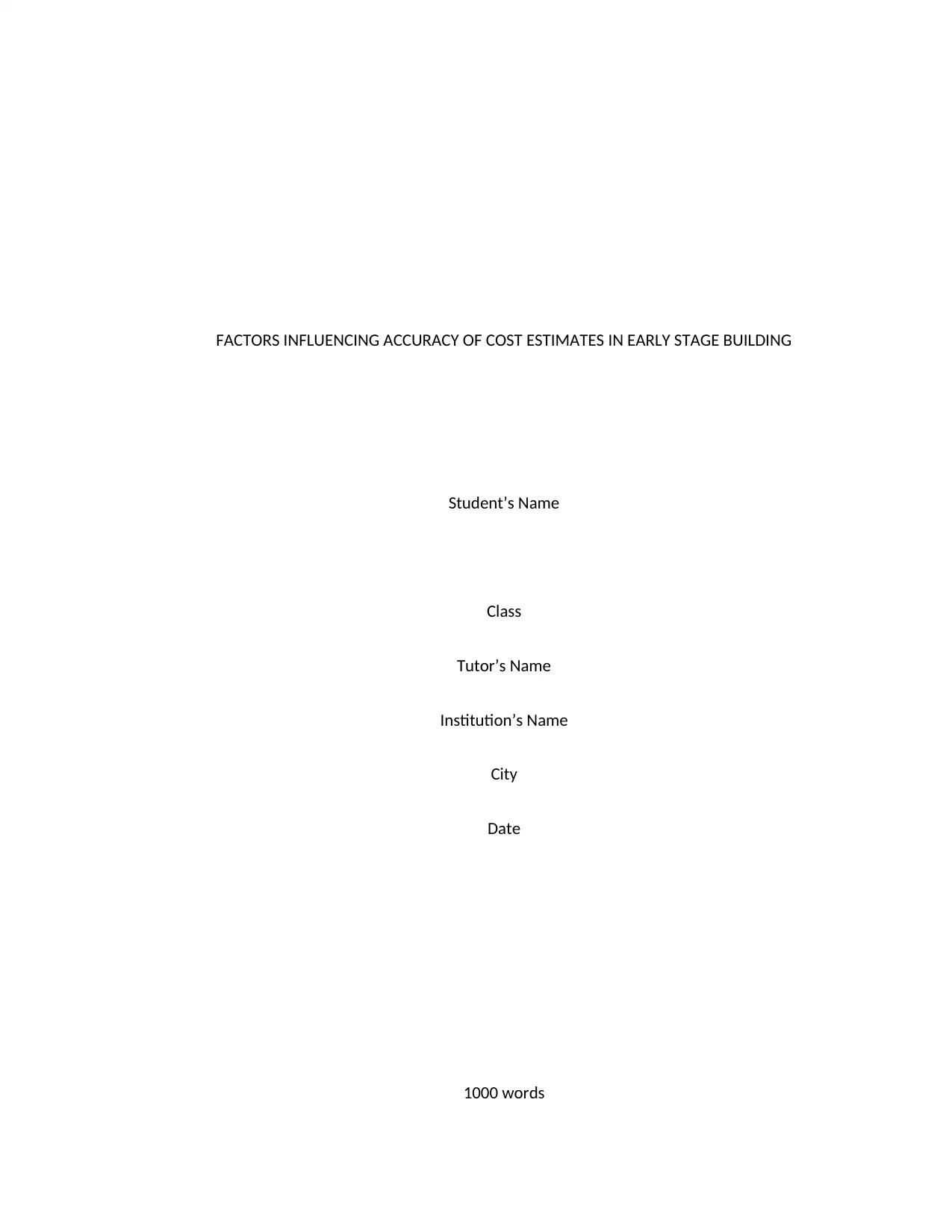
FACTORS INFLUENCING ACCURACY OF COST ESTIMATES IN EARLY STAGE BUILDING
Student’s Name
Class
Tutor’s Name
Institution’s Name
City
Date
1000 words
Student’s Name
Class
Tutor’s Name
Institution’s Name
City
Date
1000 words
Secure Best Marks with AI Grader
Need help grading? Try our AI Grader for instant feedback on your assignments.
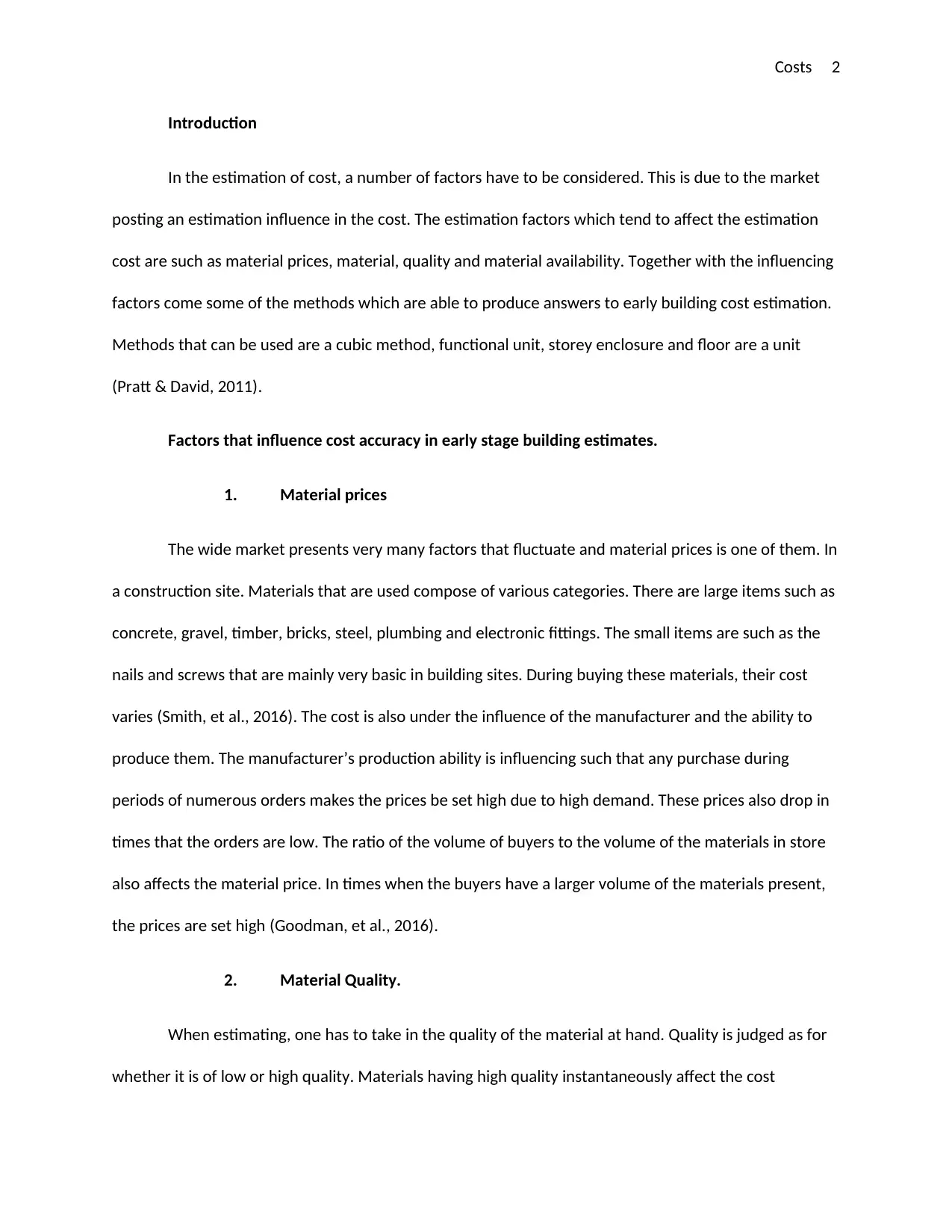
Costs 2
Introduction
In the estimation of cost, a number of factors have to be considered. This is due to the market
posting an estimation influence in the cost. The estimation factors which tend to affect the estimation
cost are such as material prices, material, quality and material availability. Together with the influencing
factors come some of the methods which are able to produce answers to early building cost estimation.
Methods that can be used are a cubic method, functional unit, storey enclosure and floor are a unit
(Pratt & David, 2011).
Factors that influence cost accuracy in early stage building estimates.
1. Material prices
The wide market presents very many factors that fluctuate and material prices is one of them. In
a construction site. Materials that are used compose of various categories. There are large items such as
concrete, gravel, timber, bricks, steel, plumbing and electronic fittings. The small items are such as the
nails and screws that are mainly very basic in building sites. During buying these materials, their cost
varies (Smith, et al., 2016). The cost is also under the influence of the manufacturer and the ability to
produce them. The manufacturer’s production ability is influencing such that any purchase during
periods of numerous orders makes the prices be set high due to high demand. These prices also drop in
times that the orders are low. The ratio of the volume of buyers to the volume of the materials in store
also affects the material price. In times when the buyers have a larger volume of the materials present,
the prices are set high (Goodman, et al., 2016).
2. Material Quality.
When estimating, one has to take in the quality of the material at hand. Quality is judged as for
whether it is of low or high quality. Materials having high quality instantaneously affect the cost
Introduction
In the estimation of cost, a number of factors have to be considered. This is due to the market
posting an estimation influence in the cost. The estimation factors which tend to affect the estimation
cost are such as material prices, material, quality and material availability. Together with the influencing
factors come some of the methods which are able to produce answers to early building cost estimation.
Methods that can be used are a cubic method, functional unit, storey enclosure and floor are a unit
(Pratt & David, 2011).
Factors that influence cost accuracy in early stage building estimates.
1. Material prices
The wide market presents very many factors that fluctuate and material prices is one of them. In
a construction site. Materials that are used compose of various categories. There are large items such as
concrete, gravel, timber, bricks, steel, plumbing and electronic fittings. The small items are such as the
nails and screws that are mainly very basic in building sites. During buying these materials, their cost
varies (Smith, et al., 2016). The cost is also under the influence of the manufacturer and the ability to
produce them. The manufacturer’s production ability is influencing such that any purchase during
periods of numerous orders makes the prices be set high due to high demand. These prices also drop in
times that the orders are low. The ratio of the volume of buyers to the volume of the materials in store
also affects the material price. In times when the buyers have a larger volume of the materials present,
the prices are set high (Goodman, et al., 2016).
2. Material Quality.
When estimating, one has to take in the quality of the material at hand. Quality is judged as for
whether it is of low or high quality. Materials having high quality instantaneously affect the cost
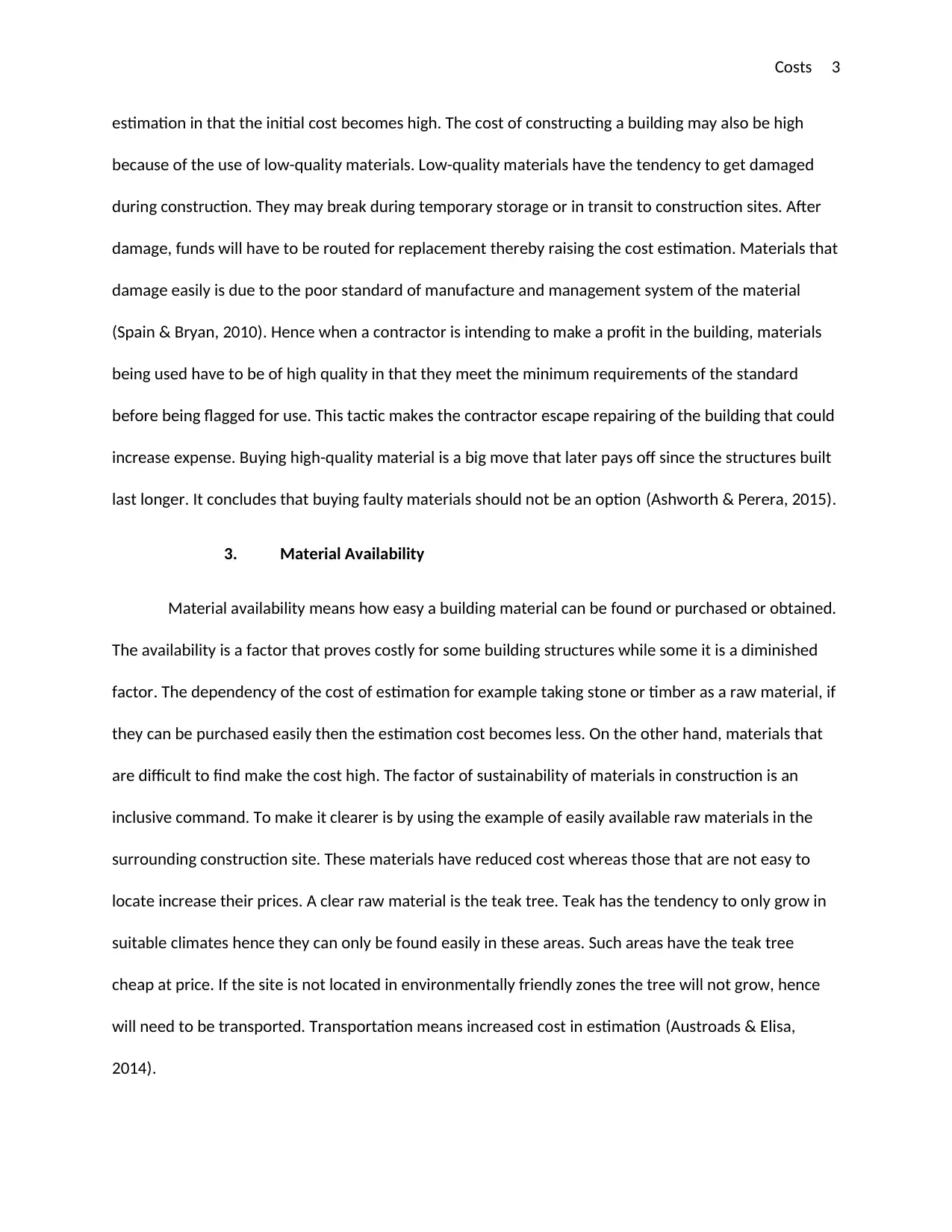
Costs 3
estimation in that the initial cost becomes high. The cost of constructing a building may also be high
because of the use of low-quality materials. Low-quality materials have the tendency to get damaged
during construction. They may break during temporary storage or in transit to construction sites. After
damage, funds will have to be routed for replacement thereby raising the cost estimation. Materials that
damage easily is due to the poor standard of manufacture and management system of the material
(Spain & Bryan, 2010). Hence when a contractor is intending to make a profit in the building, materials
being used have to be of high quality in that they meet the minimum requirements of the standard
before being flagged for use. This tactic makes the contractor escape repairing of the building that could
increase expense. Buying high-quality material is a big move that later pays off since the structures built
last longer. It concludes that buying faulty materials should not be an option (Ashworth & Perera, 2015).
3. Material Availability
Material availability means how easy a building material can be found or purchased or obtained.
The availability is a factor that proves costly for some building structures while some it is a diminished
factor. The dependency of the cost of estimation for example taking stone or timber as a raw material, if
they can be purchased easily then the estimation cost becomes less. On the other hand, materials that
are difficult to find make the cost high. The factor of sustainability of materials in construction is an
inclusive command. To make it clearer is by using the example of easily available raw materials in the
surrounding construction site. These materials have reduced cost whereas those that are not easy to
locate increase their prices. A clear raw material is the teak tree. Teak has the tendency to only grow in
suitable climates hence they can only be found easily in these areas. Such areas have the teak tree
cheap at price. If the site is not located in environmentally friendly zones the tree will not grow, hence
will need to be transported. Transportation means increased cost in estimation (Austroads & Elisa,
2014).
estimation in that the initial cost becomes high. The cost of constructing a building may also be high
because of the use of low-quality materials. Low-quality materials have the tendency to get damaged
during construction. They may break during temporary storage or in transit to construction sites. After
damage, funds will have to be routed for replacement thereby raising the cost estimation. Materials that
damage easily is due to the poor standard of manufacture and management system of the material
(Spain & Bryan, 2010). Hence when a contractor is intending to make a profit in the building, materials
being used have to be of high quality in that they meet the minimum requirements of the standard
before being flagged for use. This tactic makes the contractor escape repairing of the building that could
increase expense. Buying high-quality material is a big move that later pays off since the structures built
last longer. It concludes that buying faulty materials should not be an option (Ashworth & Perera, 2015).
3. Material Availability
Material availability means how easy a building material can be found or purchased or obtained.
The availability is a factor that proves costly for some building structures while some it is a diminished
factor. The dependency of the cost of estimation for example taking stone or timber as a raw material, if
they can be purchased easily then the estimation cost becomes less. On the other hand, materials that
are difficult to find make the cost high. The factor of sustainability of materials in construction is an
inclusive command. To make it clearer is by using the example of easily available raw materials in the
surrounding construction site. These materials have reduced cost whereas those that are not easy to
locate increase their prices. A clear raw material is the teak tree. Teak has the tendency to only grow in
suitable climates hence they can only be found easily in these areas. Such areas have the teak tree
cheap at price. If the site is not located in environmentally friendly zones the tree will not grow, hence
will need to be transported. Transportation means increased cost in estimation (Austroads & Elisa,
2014).
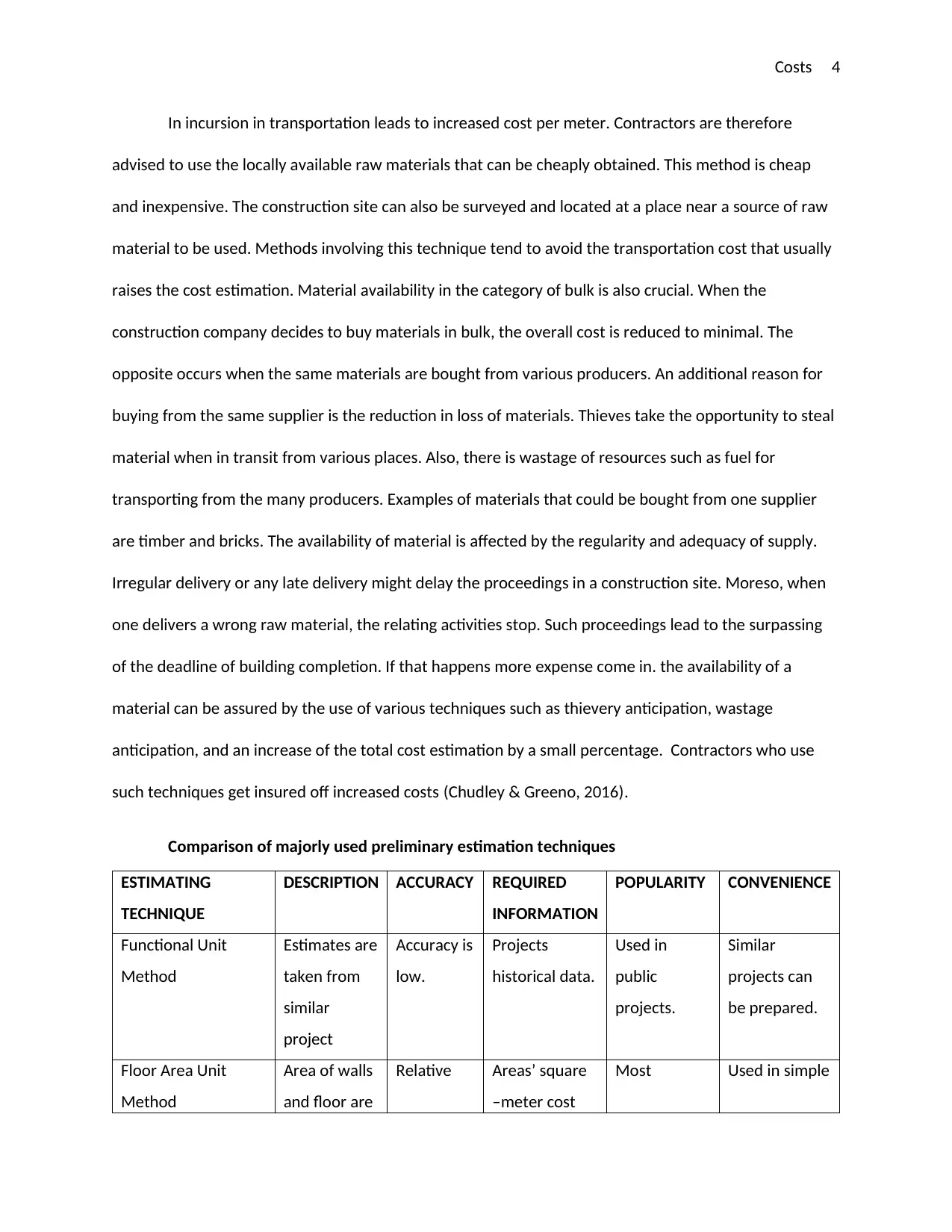
Costs 4
In incursion in transportation leads to increased cost per meter. Contractors are therefore
advised to use the locally available raw materials that can be cheaply obtained. This method is cheap
and inexpensive. The construction site can also be surveyed and located at a place near a source of raw
material to be used. Methods involving this technique tend to avoid the transportation cost that usually
raises the cost estimation. Material availability in the category of bulk is also crucial. When the
construction company decides to buy materials in bulk, the overall cost is reduced to minimal. The
opposite occurs when the same materials are bought from various producers. An additional reason for
buying from the same supplier is the reduction in loss of materials. Thieves take the opportunity to steal
material when in transit from various places. Also, there is wastage of resources such as fuel for
transporting from the many producers. Examples of materials that could be bought from one supplier
are timber and bricks. The availability of material is affected by the regularity and adequacy of supply.
Irregular delivery or any late delivery might delay the proceedings in a construction site. Moreso, when
one delivers a wrong raw material, the relating activities stop. Such proceedings lead to the surpassing
of the deadline of building completion. If that happens more expense come in. the availability of a
material can be assured by the use of various techniques such as thievery anticipation, wastage
anticipation, and an increase of the total cost estimation by a small percentage. Contractors who use
such techniques get insured off increased costs (Chudley & Greeno, 2016).
Comparison of majorly used preliminary estimation techniques
ESTIMATING
TECHNIQUE
DESCRIPTION ACCURACY REQUIRED
INFORMATION
POPULARITY CONVENIENCE
Functional Unit
Method
Estimates are
taken from
similar
project
Accuracy is
low.
Projects
historical data.
Used in
public
projects.
Similar
projects can
be prepared.
Floor Area Unit
Method
Area of walls
and floor are
Relative Areas’ square
–meter cost
Most Used in simple
In incursion in transportation leads to increased cost per meter. Contractors are therefore
advised to use the locally available raw materials that can be cheaply obtained. This method is cheap
and inexpensive. The construction site can also be surveyed and located at a place near a source of raw
material to be used. Methods involving this technique tend to avoid the transportation cost that usually
raises the cost estimation. Material availability in the category of bulk is also crucial. When the
construction company decides to buy materials in bulk, the overall cost is reduced to minimal. The
opposite occurs when the same materials are bought from various producers. An additional reason for
buying from the same supplier is the reduction in loss of materials. Thieves take the opportunity to steal
material when in transit from various places. Also, there is wastage of resources such as fuel for
transporting from the many producers. Examples of materials that could be bought from one supplier
are timber and bricks. The availability of material is affected by the regularity and adequacy of supply.
Irregular delivery or any late delivery might delay the proceedings in a construction site. Moreso, when
one delivers a wrong raw material, the relating activities stop. Such proceedings lead to the surpassing
of the deadline of building completion. If that happens more expense come in. the availability of a
material can be assured by the use of various techniques such as thievery anticipation, wastage
anticipation, and an increase of the total cost estimation by a small percentage. Contractors who use
such techniques get insured off increased costs (Chudley & Greeno, 2016).
Comparison of majorly used preliminary estimation techniques
ESTIMATING
TECHNIQUE
DESCRIPTION ACCURACY REQUIRED
INFORMATION
POPULARITY CONVENIENCE
Functional Unit
Method
Estimates are
taken from
similar
project
Accuracy is
low.
Projects
historical data.
Used in
public
projects.
Similar
projects can
be prepared.
Floor Area Unit
Method
Area of walls
and floor are
Relative Areas’ square
–meter cost
Most Used in simple
Secure Best Marks with AI Grader
Need help grading? Try our AI Grader for instant feedback on your assignments.
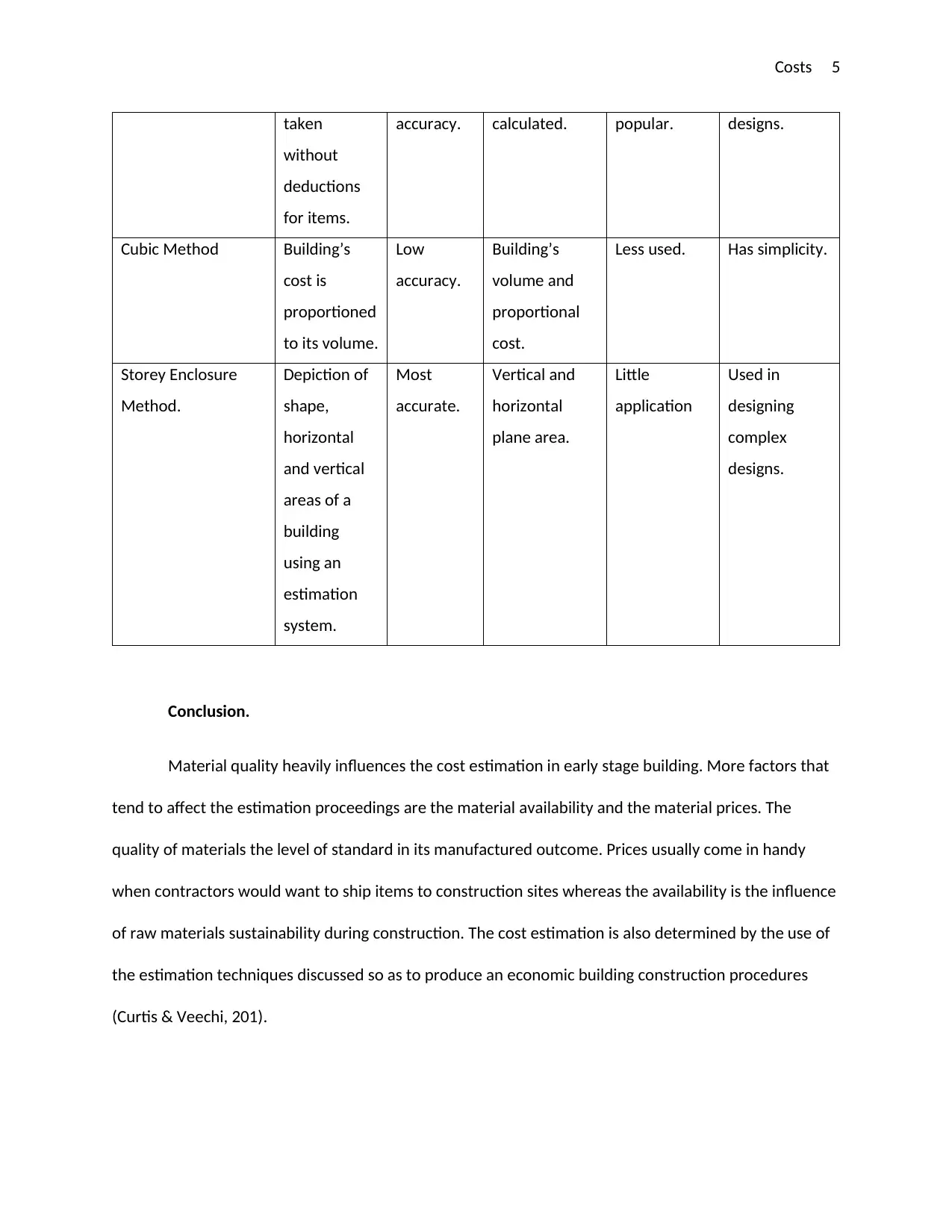
Costs 5
taken
without
deductions
for items.
accuracy. calculated. popular. designs.
Cubic Method Building’s
cost is
proportioned
to its volume.
Low
accuracy.
Building’s
volume and
proportional
cost.
Less used. Has simplicity.
Storey Enclosure
Method.
Depiction of
shape,
horizontal
and vertical
areas of a
building
using an
estimation
system.
Most
accurate.
Vertical and
horizontal
plane area.
Little
application
Used in
designing
complex
designs.
Conclusion.
Material quality heavily influences the cost estimation in early stage building. More factors that
tend to affect the estimation proceedings are the material availability and the material prices. The
quality of materials the level of standard in its manufactured outcome. Prices usually come in handy
when contractors would want to ship items to construction sites whereas the availability is the influence
of raw materials sustainability during construction. The cost estimation is also determined by the use of
the estimation techniques discussed so as to produce an economic building construction procedures
(Curtis & Veechi, 201).
taken
without
deductions
for items.
accuracy. calculated. popular. designs.
Cubic Method Building’s
cost is
proportioned
to its volume.
Low
accuracy.
Building’s
volume and
proportional
cost.
Less used. Has simplicity.
Storey Enclosure
Method.
Depiction of
shape,
horizontal
and vertical
areas of a
building
using an
estimation
system.
Most
accurate.
Vertical and
horizontal
plane area.
Little
application
Used in
designing
complex
designs.
Conclusion.
Material quality heavily influences the cost estimation in early stage building. More factors that
tend to affect the estimation proceedings are the material availability and the material prices. The
quality of materials the level of standard in its manufactured outcome. Prices usually come in handy
when contractors would want to ship items to construction sites whereas the availability is the influence
of raw materials sustainability during construction. The cost estimation is also determined by the use of
the estimation techniques discussed so as to produce an economic building construction procedures
(Curtis & Veechi, 201).
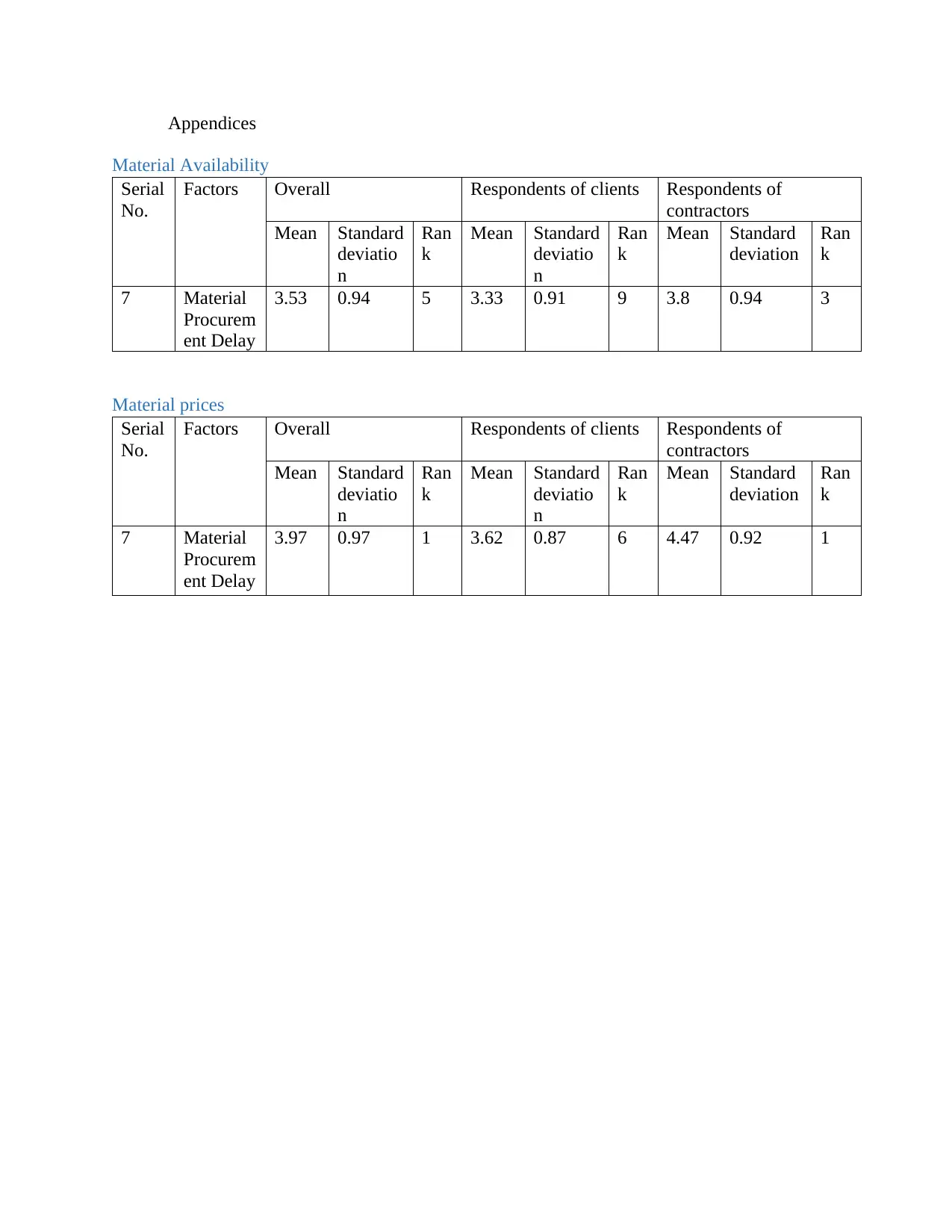
Appendices
Material Availability
Serial
No.
Factors Overall Respondents of clients Respondents of
contractors
Mean Standard
deviatio
n
Ran
k
Mean Standard
deviatio
n
Ran
k
Mean Standard
deviation
Ran
k
7 Material
Procurem
ent Delay
3.53 0.94 5 3.33 0.91 9 3.8 0.94 3
Material prices
Serial
No.
Factors Overall Respondents of clients Respondents of
contractors
Mean Standard
deviatio
n
Ran
k
Mean Standard
deviatio
n
Ran
k
Mean Standard
deviation
Ran
k
7 Material
Procurem
ent Delay
3.97 0.97 1 3.62 0.87 6 4.47 0.92 1
Material Availability
Serial
No.
Factors Overall Respondents of clients Respondents of
contractors
Mean Standard
deviatio
n
Ran
k
Mean Standard
deviatio
n
Ran
k
Mean Standard
deviation
Ran
k
7 Material
Procurem
ent Delay
3.53 0.94 5 3.33 0.91 9 3.8 0.94 3
Material prices
Serial
No.
Factors Overall Respondents of clients Respondents of
contractors
Mean Standard
deviatio
n
Ran
k
Mean Standard
deviatio
n
Ran
k
Mean Standard
deviation
Ran
k
7 Material
Procurem
ent Delay
3.97 0.97 1 3.62 0.87 6 4.47 0.92 1
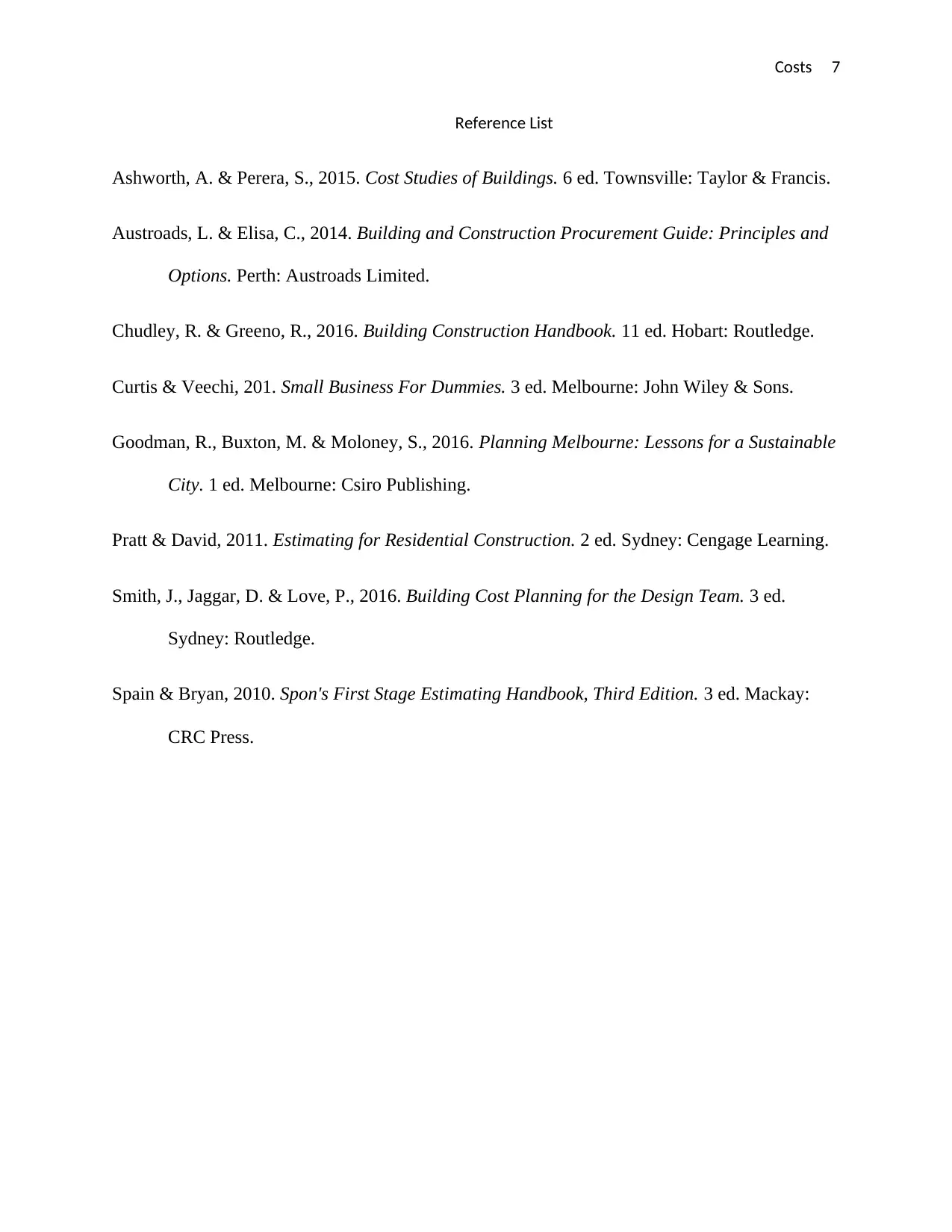
Costs 7
Reference List
Ashworth, A. & Perera, S., 2015. Cost Studies of Buildings. 6 ed. Townsville: Taylor & Francis.
Austroads, L. & Elisa, C., 2014. Building and Construction Procurement Guide: Principles and
Options. Perth: Austroads Limited.
Chudley, R. & Greeno, R., 2016. Building Construction Handbook. 11 ed. Hobart: Routledge.
Curtis & Veechi, 201. Small Business For Dummies. 3 ed. Melbourne: John Wiley & Sons.
Goodman, R., Buxton, M. & Moloney, S., 2016. Planning Melbourne: Lessons for a Sustainable
City. 1 ed. Melbourne: Csiro Publishing.
Pratt & David, 2011. Estimating for Residential Construction. 2 ed. Sydney: Cengage Learning.
Smith, J., Jaggar, D. & Love, P., 2016. Building Cost Planning for the Design Team. 3 ed.
Sydney: Routledge.
Spain & Bryan, 2010. Spon's First Stage Estimating Handbook, Third Edition. 3 ed. Mackay:
CRC Press.
Reference List
Ashworth, A. & Perera, S., 2015. Cost Studies of Buildings. 6 ed. Townsville: Taylor & Francis.
Austroads, L. & Elisa, C., 2014. Building and Construction Procurement Guide: Principles and
Options. Perth: Austroads Limited.
Chudley, R. & Greeno, R., 2016. Building Construction Handbook. 11 ed. Hobart: Routledge.
Curtis & Veechi, 201. Small Business For Dummies. 3 ed. Melbourne: John Wiley & Sons.
Goodman, R., Buxton, M. & Moloney, S., 2016. Planning Melbourne: Lessons for a Sustainable
City. 1 ed. Melbourne: Csiro Publishing.
Pratt & David, 2011. Estimating for Residential Construction. 2 ed. Sydney: Cengage Learning.
Smith, J., Jaggar, D. & Love, P., 2016. Building Cost Planning for the Design Team. 3 ed.
Sydney: Routledge.
Spain & Bryan, 2010. Spon's First Stage Estimating Handbook, Third Edition. 3 ed. Mackay:
CRC Press.
1 out of 7
Related Documents
![[object Object]](/_next/image/?url=%2F_next%2Fstatic%2Fmedia%2Flogo.6d15ce61.png&w=640&q=75)
Your All-in-One AI-Powered Toolkit for Academic Success.
+13062052269
info@desklib.com
Available 24*7 on WhatsApp / Email
Unlock your academic potential
© 2024 | Zucol Services PVT LTD | All rights reserved.