Lean Manufacturing- Farm Machinery International Case Analysis 2022
Added on 2022-09-10
6 Pages1518 Words24 Views
Lean Manufacturing- Farm Machinery International Case
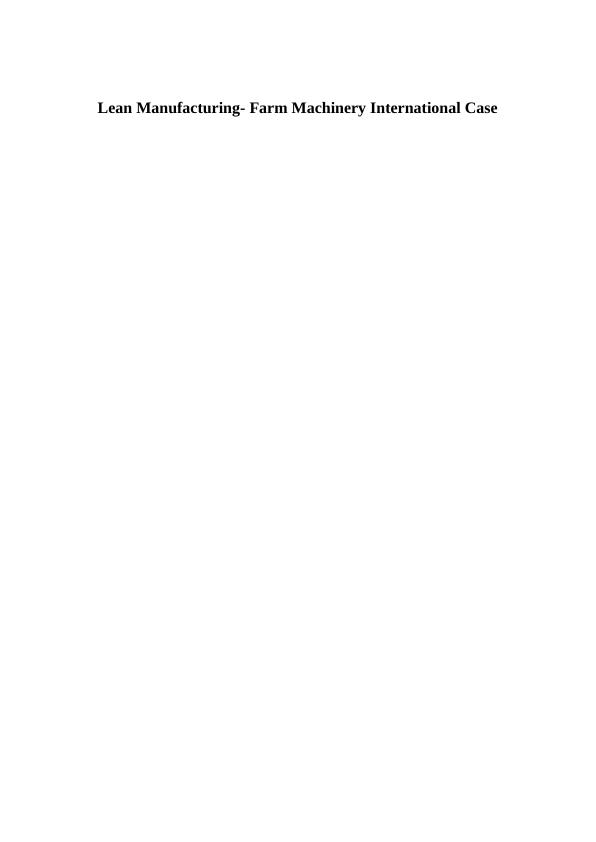
Background
FEI is an international agricultural machinery manufacturer that makes among others things, a
hydraulic control lever. At present, the company’s production is set such that it takes at least 27 days
for a hydraulic control lever to pass through the factory until it is ready for shipping to customers.
Because of this production lead time, FEI now gives customers a 60 day lead time. Customers have
a demand of 24000 hydraulic control levers with order sizes varying between 20 and 200 pieces; the
average order size is 50 pieces. Five units are packed in each box and several shipments are made
daily by truck to various customers and every customer order varies in terms of configuration and
quantity. The mix of the hydraulic lever configurations can be changed to a maximum of two weeks
before the date of shipping. The manufacturing process entails cutting the tubes, welding both ends
of the tube, flash removal, painting done by contractor, assembly, before delivery. This paper
discusses the FEI case in the context of lean manufacturing, a systematic production method with its
roots in Japan at Toyota Motors. The objective of lean is to minimize waste in manufacturing while
maintaining or improving productivity, and seeking ways by which continuous improvements can
be made (Suhardi, Anisa and Laksono, 2019).
The current value stream map
FEI is an international agricultural machinery manufacturer that makes among others things, a
hydraulic control lever. At present, the company’s production is set such that it takes at least 27 days
for a hydraulic control lever to pass through the factory until it is ready for shipping to customers.
Because of this production lead time, FEI now gives customers a 60 day lead time. Customers have
a demand of 24000 hydraulic control levers with order sizes varying between 20 and 200 pieces; the
average order size is 50 pieces. Five units are packed in each box and several shipments are made
daily by truck to various customers and every customer order varies in terms of configuration and
quantity. The mix of the hydraulic lever configurations can be changed to a maximum of two weeks
before the date of shipping. The manufacturing process entails cutting the tubes, welding both ends
of the tube, flash removal, painting done by contractor, assembly, before delivery. This paper
discusses the FEI case in the context of lean manufacturing, a systematic production method with its
roots in Japan at Toyota Motors. The objective of lean is to minimize waste in manufacturing while
maintaining or improving productivity, and seeking ways by which continuous improvements can
be made (Suhardi, Anisa and Laksono, 2019).
The current value stream map

The above system results in an item taking at least 27 days to go through the production process and
be ready for delivery to the customer. After a review following the lean principles, the pull is seen
as being the demand which is 24000 pieces of hydraulic levers per month. This means the average
daily demand for the finished units is 1200 and while there is no known demand mix from
customers, this figure represents a rough demand estimate.
Cutting
The analysis shows that the problem lies in the number of units of products that start the process.
The cutting, though a manual process with a single operator, results in 3800 pieces of tubes being
cut every day, against a demand requirement of just about 1200 units. This means the production is
three times higher than the demand, so there is definitely going to be a backlog (Rahman, Sharif and
Esa, 2013). As such, this analysis recommends that the cutting process should have just a single
shift of eight hours with a one hour break. In the event of changes to product types and considering
the changeover times, the step can have overtime to cater for any additional orders. This will help
reduce the inventory of cut parts to 2 days.
Welding 1 and 2
This section will also have a reduced workload and does not need two shifts as the new number of
produced cut tubes can all be welded on both sides in a single shift. Alternatively, the step can have
a single welding station working two shifts to complete all welding (for both ends). The inventory
time is then reduced to just one day
De-Flashing workstation
This section will require two shifts to handle all the welded parts as the new total required work
time only is 14 and a half hours, taking into consideration changeover and the possibility of changes
to requirements, the two shifts are more than sufficient to handle all the work and still have
sufficient breaks. The inventory time is then reduced to just one day
Painting
This is a bottleneck in the system and determines the throughput for this system (Hannola and
Myller, 2012); it requires two days to paint the parts, based on the previous value stream map. At
the moment, the workload has been reduced by two thirds, meaning that the painter, working at
present rates, will require less than a day to complete the work. The inventory time is then reduced
to just one day
Connector assembly
Given the required time to assemble each part of 195 seconds, the step will still require two shifts
with the current staff to work on the now reduced workload but will complete the entire arriving
batch within a day. This means the inventory time is now reduced to just over one day, so we
assume two days.
be ready for delivery to the customer. After a review following the lean principles, the pull is seen
as being the demand which is 24000 pieces of hydraulic levers per month. This means the average
daily demand for the finished units is 1200 and while there is no known demand mix from
customers, this figure represents a rough demand estimate.
Cutting
The analysis shows that the problem lies in the number of units of products that start the process.
The cutting, though a manual process with a single operator, results in 3800 pieces of tubes being
cut every day, against a demand requirement of just about 1200 units. This means the production is
three times higher than the demand, so there is definitely going to be a backlog (Rahman, Sharif and
Esa, 2013). As such, this analysis recommends that the cutting process should have just a single
shift of eight hours with a one hour break. In the event of changes to product types and considering
the changeover times, the step can have overtime to cater for any additional orders. This will help
reduce the inventory of cut parts to 2 days.
Welding 1 and 2
This section will also have a reduced workload and does not need two shifts as the new number of
produced cut tubes can all be welded on both sides in a single shift. Alternatively, the step can have
a single welding station working two shifts to complete all welding (for both ends). The inventory
time is then reduced to just one day
De-Flashing workstation
This section will require two shifts to handle all the welded parts as the new total required work
time only is 14 and a half hours, taking into consideration changeover and the possibility of changes
to requirements, the two shifts are more than sufficient to handle all the work and still have
sufficient breaks. The inventory time is then reduced to just one day
Painting
This is a bottleneck in the system and determines the throughput for this system (Hannola and
Myller, 2012); it requires two days to paint the parts, based on the previous value stream map. At
the moment, the workload has been reduced by two thirds, meaning that the painter, working at
present rates, will require less than a day to complete the work. The inventory time is then reduced
to just one day
Connector assembly
Given the required time to assemble each part of 195 seconds, the step will still require two shifts
with the current staff to work on the now reduced workload but will complete the entire arriving
batch within a day. This means the inventory time is now reduced to just over one day, so we
assume two days.
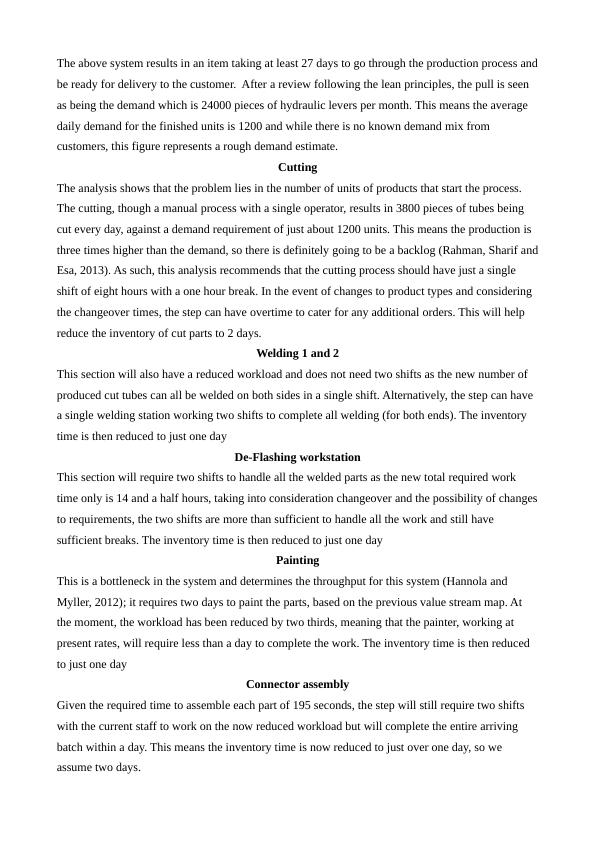
End of preview
Want to access all the pages? Upload your documents or become a member.
Related Documents
Manufacturing of Lean Assignment 2022lg...
|11
|1958
|23
Lean Manufacturing Case Study 2022lg...
|6
|1352
|19
Assignment | How do you present a value stream map?lg...
|16
|3247
|45
Assignment | What Is Process Mapping ?lg...
|14
|2966
|24