Financial Performance Management
VerifiedAdded on  2022/12/28
|12
|2724
|75
AI Summary
This document provides a comprehensive study on financial performance management. It includes calculations of cost per product, evaluation of different costing approaches, and the benefits of activity-based costing. It also discusses the importance of sensitivity analysis in coping with uncertainty. Additionally, it covers the calculation of variances and the problems with the current system of assessing the performance of the production manager. Lastly, it compares zero-based budgeting and incremental budgeting.
Contribute Materials
Your contribution can guide someone’s learning journey. Share your
documents today.
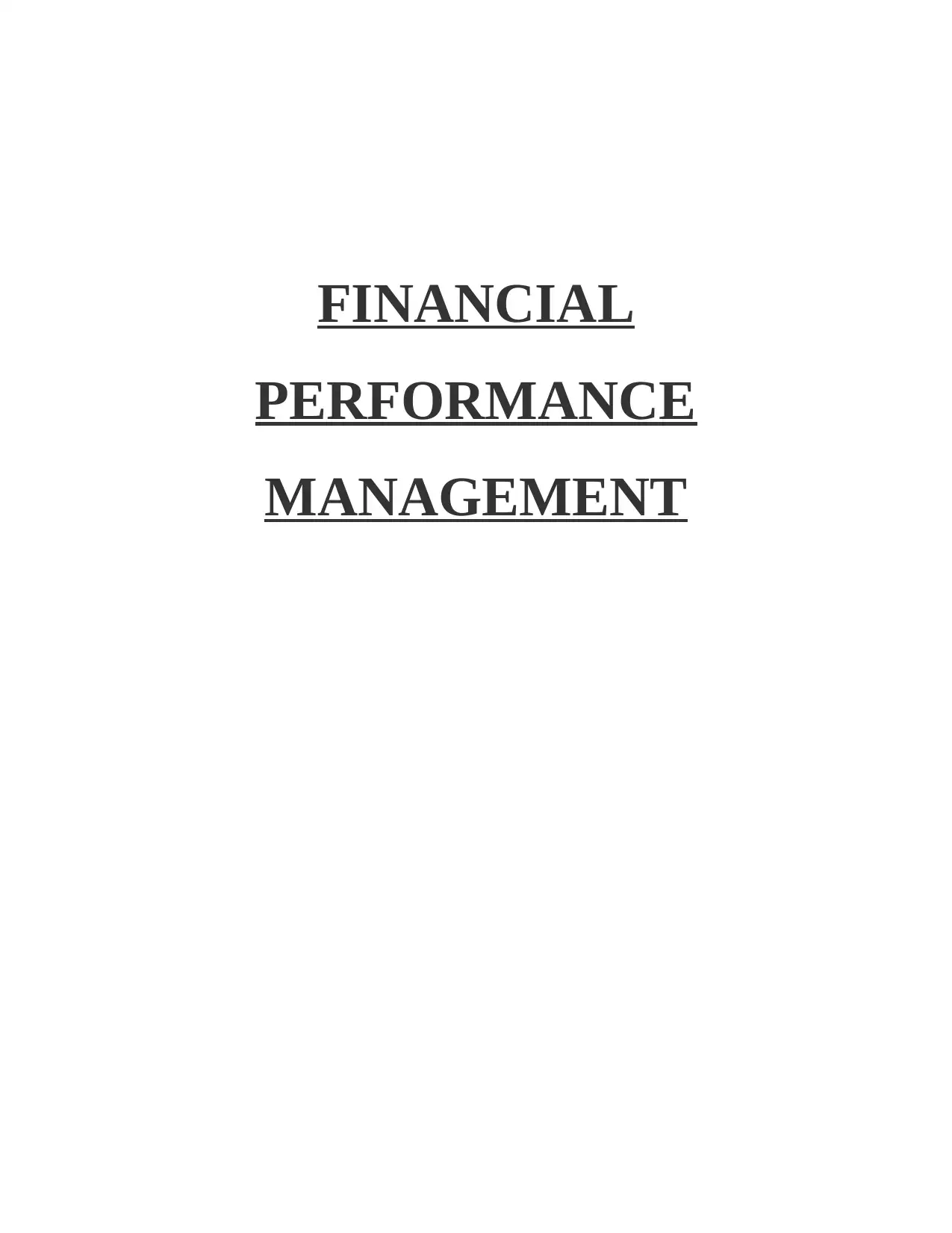
FINANCIAL
PERFORMANCE
MANAGEMENT
PERFORMANCE
MANAGEMENT
Secure Best Marks with AI Grader
Need help grading? Try our AI Grader for instant feedback on your assignments.
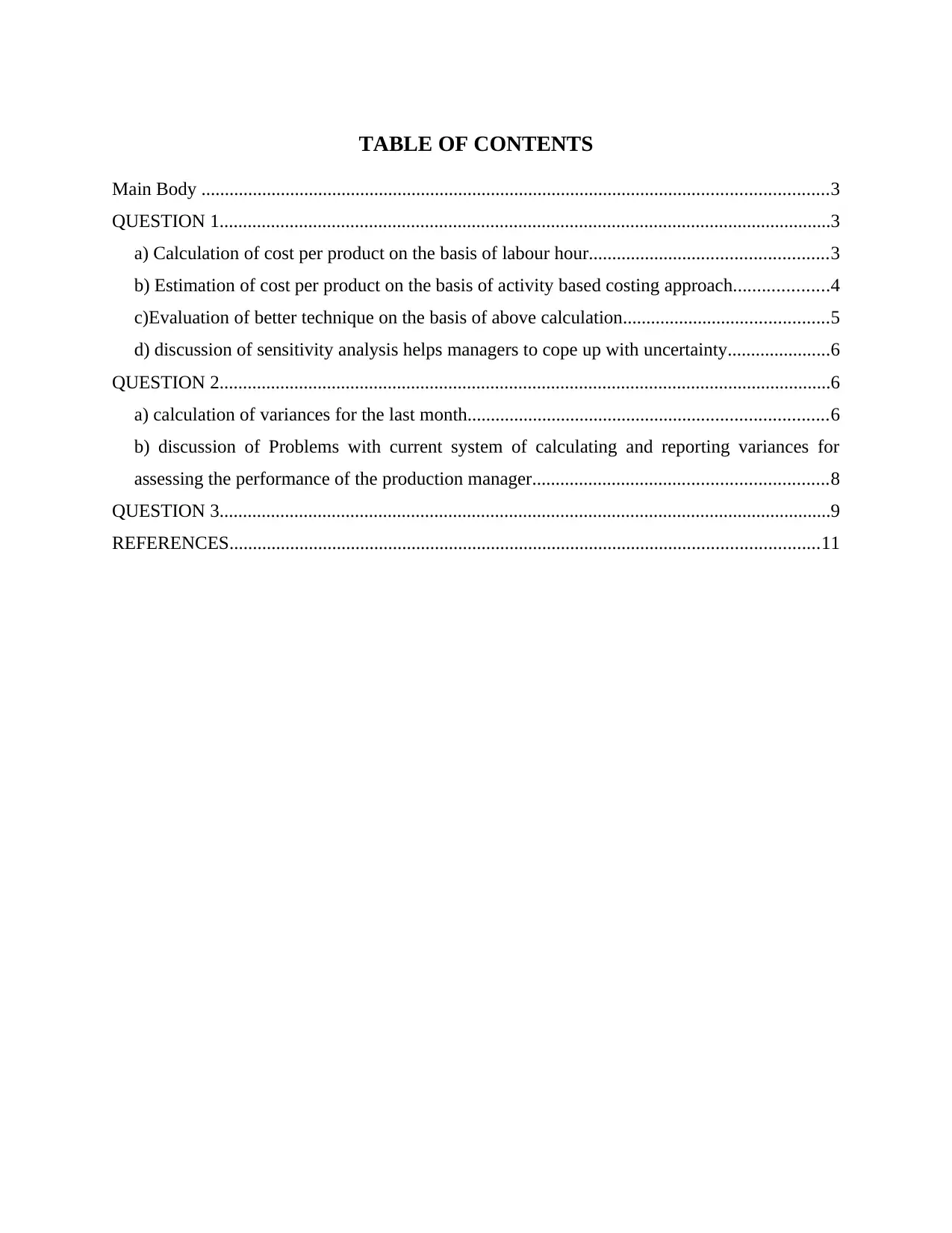
TABLE OF CONTENTS
Main Body ......................................................................................................................................3
QUESTION 1...................................................................................................................................3
a) Calculation of cost per product on the basis of labour hour...................................................3
b) Estimation of cost per product on the basis of activity based costing approach....................4
c)Evaluation of better technique on the basis of above calculation............................................5
d) discussion of sensitivity analysis helps managers to cope up with uncertainty......................6
QUESTION 2...................................................................................................................................6
a) calculation of variances for the last month.............................................................................6
b) discussion of Problems with current system of calculating and reporting variances for
assessing the performance of the production manager...............................................................8
QUESTION 3...................................................................................................................................9
REFERENCES..............................................................................................................................11
Main Body ......................................................................................................................................3
QUESTION 1...................................................................................................................................3
a) Calculation of cost per product on the basis of labour hour...................................................3
b) Estimation of cost per product on the basis of activity based costing approach....................4
c)Evaluation of better technique on the basis of above calculation............................................5
d) discussion of sensitivity analysis helps managers to cope up with uncertainty......................6
QUESTION 2...................................................................................................................................6
a) calculation of variances for the last month.............................................................................6
b) discussion of Problems with current system of calculating and reporting variances for
assessing the performance of the production manager...............................................................8
QUESTION 3...................................................................................................................................9
REFERENCES..............................................................................................................................11

Main Body
QUESTION 1
a) Calculation of cost per product on the basis of labour hour
Lipstick Lip-balm Lip-gloss
Units 30000 35000 3000
Sales 660000 910000 72000
Material Cost 150000 350000 30000
Labour Cost 450000 350000 30000
Overhead Costs 124698.795 96987.952 8313.253
(Based on Labour Hours)
724698.795 796987.952 68313.253
Net Profit/ Loss -64698.795 113012.048 3686.747
Cost per product 24.16 22.77 22.77
Total Cost per product Lipstick Lip-balm Lip-gloss
Selling Price 22 26 24
Cost per product 24.16 22.77 22.77
Profit/Loss per product -2.16 3.23 1.23
Calculation of Absorption
rate based on labour hours
Setup Costs 120000
Receiving Costs 30000
Despatch 15000
Machining 65000
Total 230000
1.3855421687
QUESTION 1
a) Calculation of cost per product on the basis of labour hour
Lipstick Lip-balm Lip-gloss
Units 30000 35000 3000
Sales 660000 910000 72000
Material Cost 150000 350000 30000
Labour Cost 450000 350000 30000
Overhead Costs 124698.795 96987.952 8313.253
(Based on Labour Hours)
724698.795 796987.952 68313.253
Net Profit/ Loss -64698.795 113012.048 3686.747
Cost per product 24.16 22.77 22.77
Total Cost per product Lipstick Lip-balm Lip-gloss
Selling Price 22 26 24
Cost per product 24.16 22.77 22.77
Profit/Loss per product -2.16 3.23 1.23
Calculation of Absorption
rate based on labour hours
Setup Costs 120000
Receiving Costs 30000
Despatch 15000
Machining 65000
Total 230000
1.3855421687
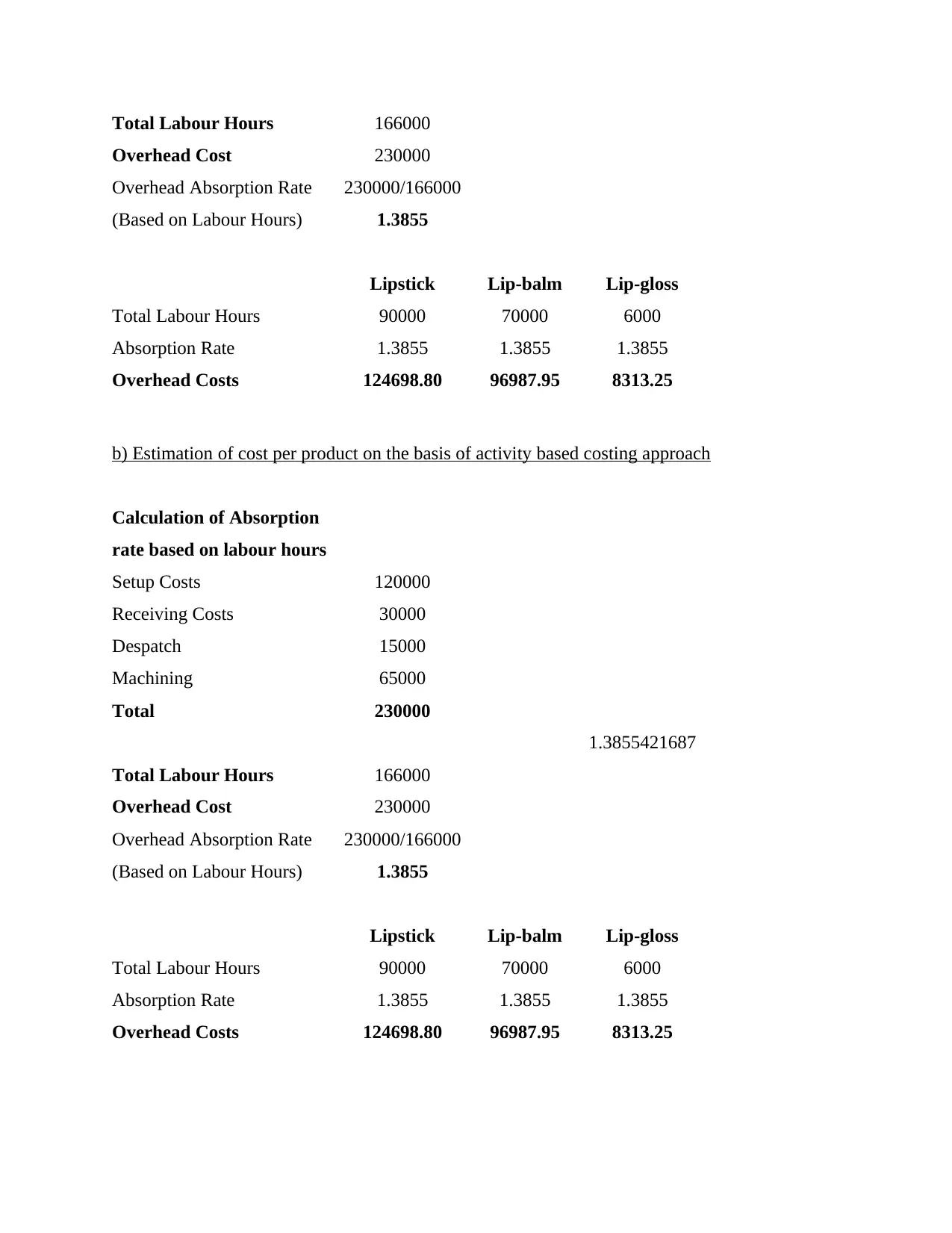
Total Labour Hours 166000
Overhead Cost 230000
Overhead Absorption Rate 230000/166000
(Based on Labour Hours) 1.3855
Lipstick Lip-balm Lip-gloss
Total Labour Hours 90000 70000 6000
Absorption Rate 1.3855 1.3855 1.3855
Overhead Costs 124698.80 96987.95 8313.25
b) Estimation of cost per product on the basis of activity based costing approach
Calculation of Absorption
rate based on labour hours
Setup Costs 120000
Receiving Costs 30000
Despatch 15000
Machining 65000
Total 230000
1.3855421687
Total Labour Hours 166000
Overhead Cost 230000
Overhead Absorption Rate 230000/166000
(Based on Labour Hours) 1.3855
Lipstick Lip-balm Lip-gloss
Total Labour Hours 90000 70000 6000
Absorption Rate 1.3855 1.3855 1.3855
Overhead Costs 124698.80 96987.95 8313.25
Overhead Cost 230000
Overhead Absorption Rate 230000/166000
(Based on Labour Hours) 1.3855
Lipstick Lip-balm Lip-gloss
Total Labour Hours 90000 70000 6000
Absorption Rate 1.3855 1.3855 1.3855
Overhead Costs 124698.80 96987.95 8313.25
b) Estimation of cost per product on the basis of activity based costing approach
Calculation of Absorption
rate based on labour hours
Setup Costs 120000
Receiving Costs 30000
Despatch 15000
Machining 65000
Total 230000
1.3855421687
Total Labour Hours 166000
Overhead Cost 230000
Overhead Absorption Rate 230000/166000
(Based on Labour Hours) 1.3855
Lipstick Lip-balm Lip-gloss
Total Labour Hours 90000 70000 6000
Absorption Rate 1.3855 1.3855 1.3855
Overhead Costs 124698.80 96987.95 8313.25
Secure Best Marks with AI Grader
Need help grading? Try our AI Grader for instant feedback on your assignments.
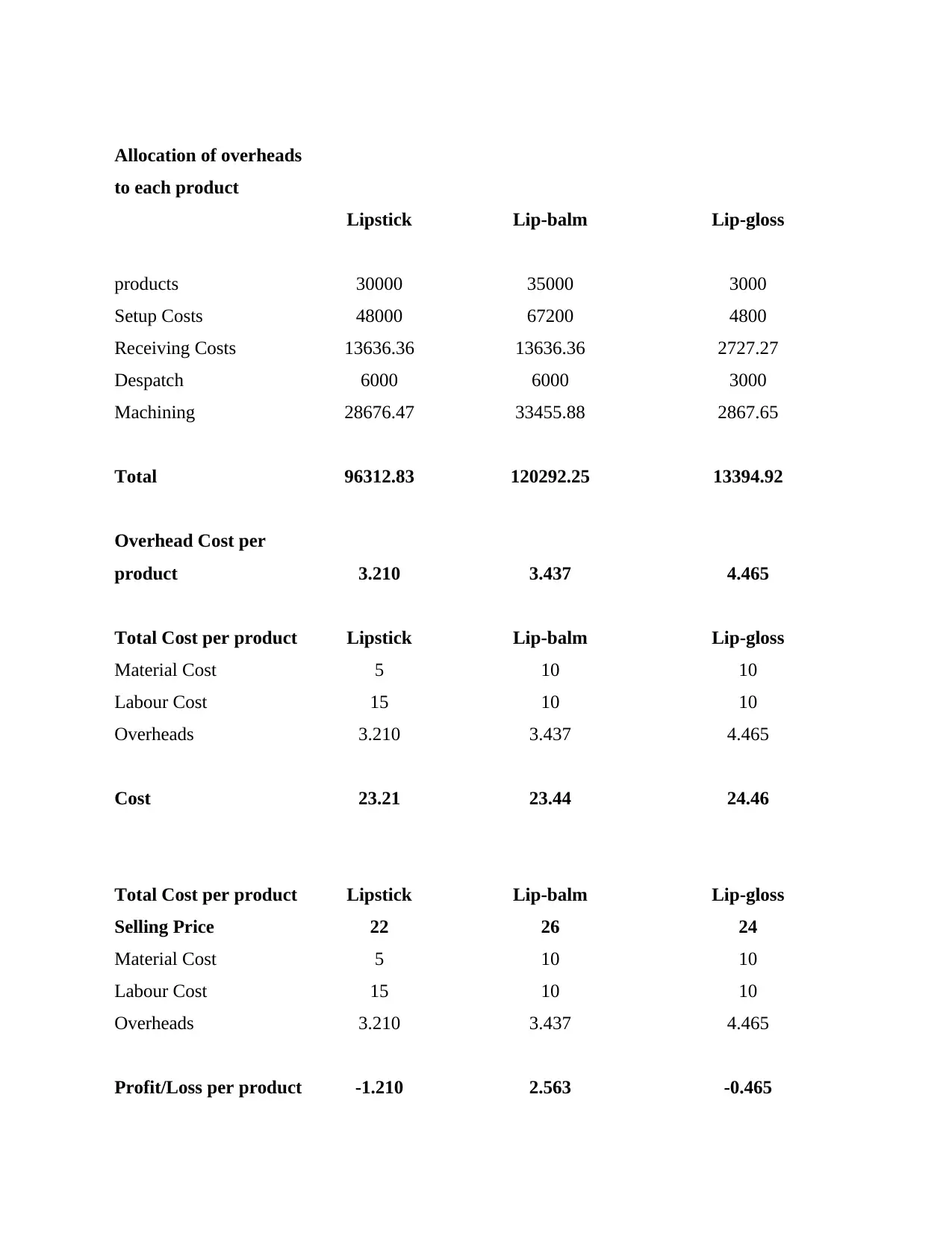
Allocation of overheads
to each product
Lipstick Lip-balm Lip-gloss
products 30000 35000 3000
Setup Costs 48000 67200 4800
Receiving Costs 13636.36 13636.36 2727.27
Despatch 6000 6000 3000
Machining 28676.47 33455.88 2867.65
Total 96312.83 120292.25 13394.92
Overhead Cost per
product 3.210 3.437 4.465
Total Cost per product Lipstick Lip-balm Lip-gloss
Material Cost 5 10 10
Labour Cost 15 10 10
Overheads 3.210 3.437 4.465
Cost 23.21 23.44 24.46
Total Cost per product Lipstick Lip-balm Lip-gloss
Selling Price 22 26 24
Material Cost 5 10 10
Labour Cost 15 10 10
Overheads 3.210 3.437 4.465
Profit/Loss per product -1.210 2.563 -0.465
to each product
Lipstick Lip-balm Lip-gloss
products 30000 35000 3000
Setup Costs 48000 67200 4800
Receiving Costs 13636.36 13636.36 2727.27
Despatch 6000 6000 3000
Machining 28676.47 33455.88 2867.65
Total 96312.83 120292.25 13394.92
Overhead Cost per
product 3.210 3.437 4.465
Total Cost per product Lipstick Lip-balm Lip-gloss
Material Cost 5 10 10
Labour Cost 15 10 10
Overheads 3.210 3.437 4.465
Cost 23.21 23.44 24.46
Total Cost per product Lipstick Lip-balm Lip-gloss
Selling Price 22 26 24
Material Cost 5 10 10
Labour Cost 15 10 10
Overheads 3.210 3.437 4.465
Profit/Loss per product -1.210 2.563 -0.465
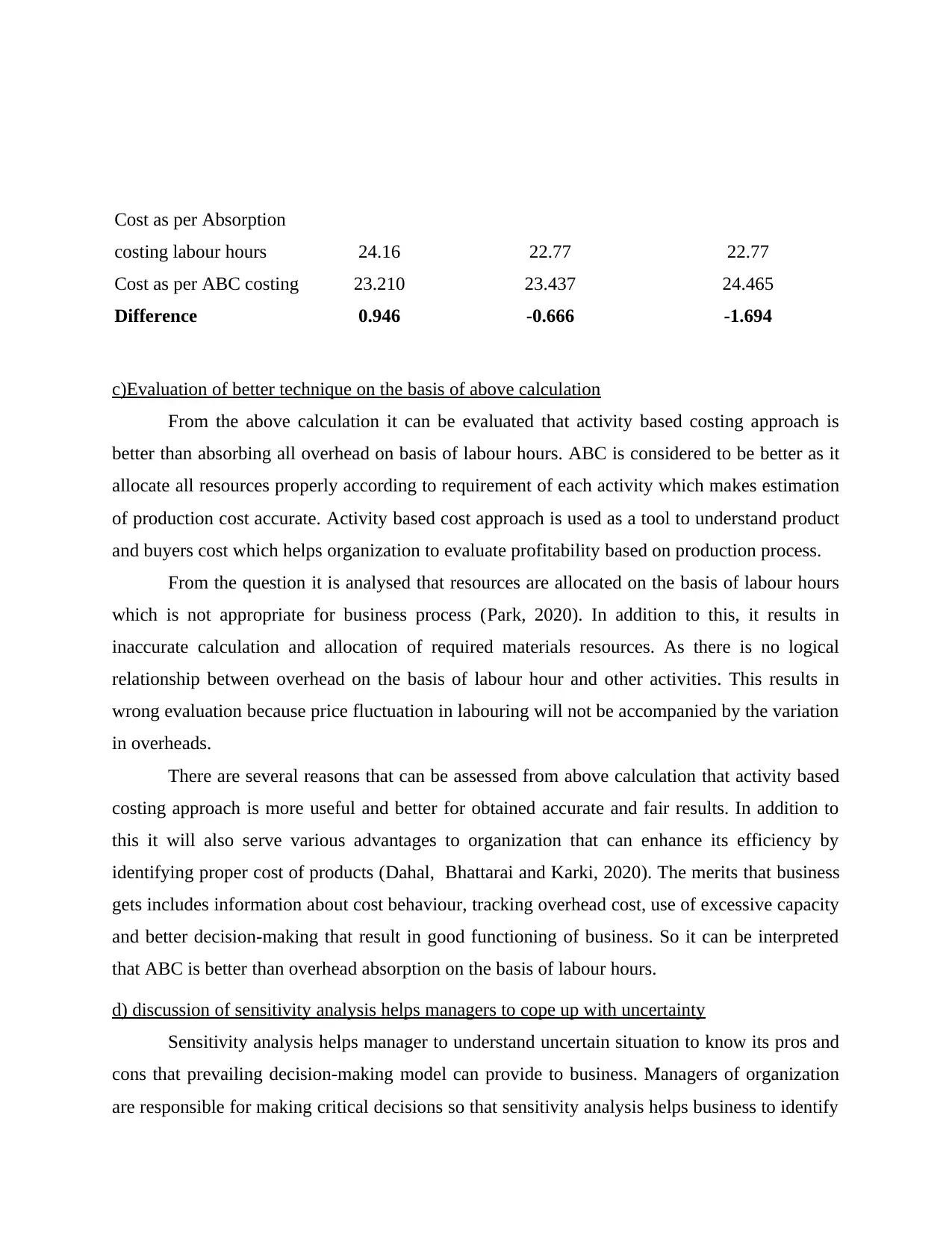
Cost as per Absorption
costing labour hours 24.16 22.77 22.77
Cost as per ABC costing 23.210 23.437 24.465
Difference 0.946 -0.666 -1.694
c)Evaluation of better technique on the basis of above calculation
From the above calculation it can be evaluated that activity based costing approach is
better than absorbing all overhead on basis of labour hours. ABC is considered to be better as it
allocate all resources properly according to requirement of each activity which makes estimation
of production cost accurate. Activity based cost approach is used as a tool to understand product
and buyers cost which helps organization to evaluate profitability based on production process.
From the question it is analysed that resources are allocated on the basis of labour hours
which is not appropriate for business process (Park, 2020). In addition to this, it results in
inaccurate calculation and allocation of required materials resources. As there is no logical
relationship between overhead on the basis of labour hour and other activities. This results in
wrong evaluation because price fluctuation in labouring will not be accompanied by the variation
in overheads.
There are several reasons that can be assessed from above calculation that activity based
costing approach is more useful and better for obtained accurate and fair results. In addition to
this it will also serve various advantages to organization that can enhance its efficiency by
identifying proper cost of products (Dahal, Bhattarai and Karki, 2020). The merits that business
gets includes information about cost behaviour, tracking overhead cost, use of excessive capacity
and better decision-making that result in good functioning of business. So it can be interpreted
that ABC is better than overhead absorption on the basis of labour hours.
d) discussion of sensitivity analysis helps managers to cope up with uncertainty
Sensitivity analysis helps manager to understand uncertain situation to know its pros and
cons that prevailing decision-making model can provide to business. Managers of organization
are responsible for making critical decisions so that sensitivity analysis helps business to identify
costing labour hours 24.16 22.77 22.77
Cost as per ABC costing 23.210 23.437 24.465
Difference 0.946 -0.666 -1.694
c)Evaluation of better technique on the basis of above calculation
From the above calculation it can be evaluated that activity based costing approach is
better than absorbing all overhead on basis of labour hours. ABC is considered to be better as it
allocate all resources properly according to requirement of each activity which makes estimation
of production cost accurate. Activity based cost approach is used as a tool to understand product
and buyers cost which helps organization to evaluate profitability based on production process.
From the question it is analysed that resources are allocated on the basis of labour hours
which is not appropriate for business process (Park, 2020). In addition to this, it results in
inaccurate calculation and allocation of required materials resources. As there is no logical
relationship between overhead on the basis of labour hour and other activities. This results in
wrong evaluation because price fluctuation in labouring will not be accompanied by the variation
in overheads.
There are several reasons that can be assessed from above calculation that activity based
costing approach is more useful and better for obtained accurate and fair results. In addition to
this it will also serve various advantages to organization that can enhance its efficiency by
identifying proper cost of products (Dahal, Bhattarai and Karki, 2020). The merits that business
gets includes information about cost behaviour, tracking overhead cost, use of excessive capacity
and better decision-making that result in good functioning of business. So it can be interpreted
that ABC is better than overhead absorption on the basis of labour hours.
d) discussion of sensitivity analysis helps managers to cope up with uncertainty
Sensitivity analysis helps manager to understand uncertain situation to know its pros and
cons that prevailing decision-making model can provide to business. Managers of organization
are responsible for making critical decisions so that sensitivity analysis helps business to identify
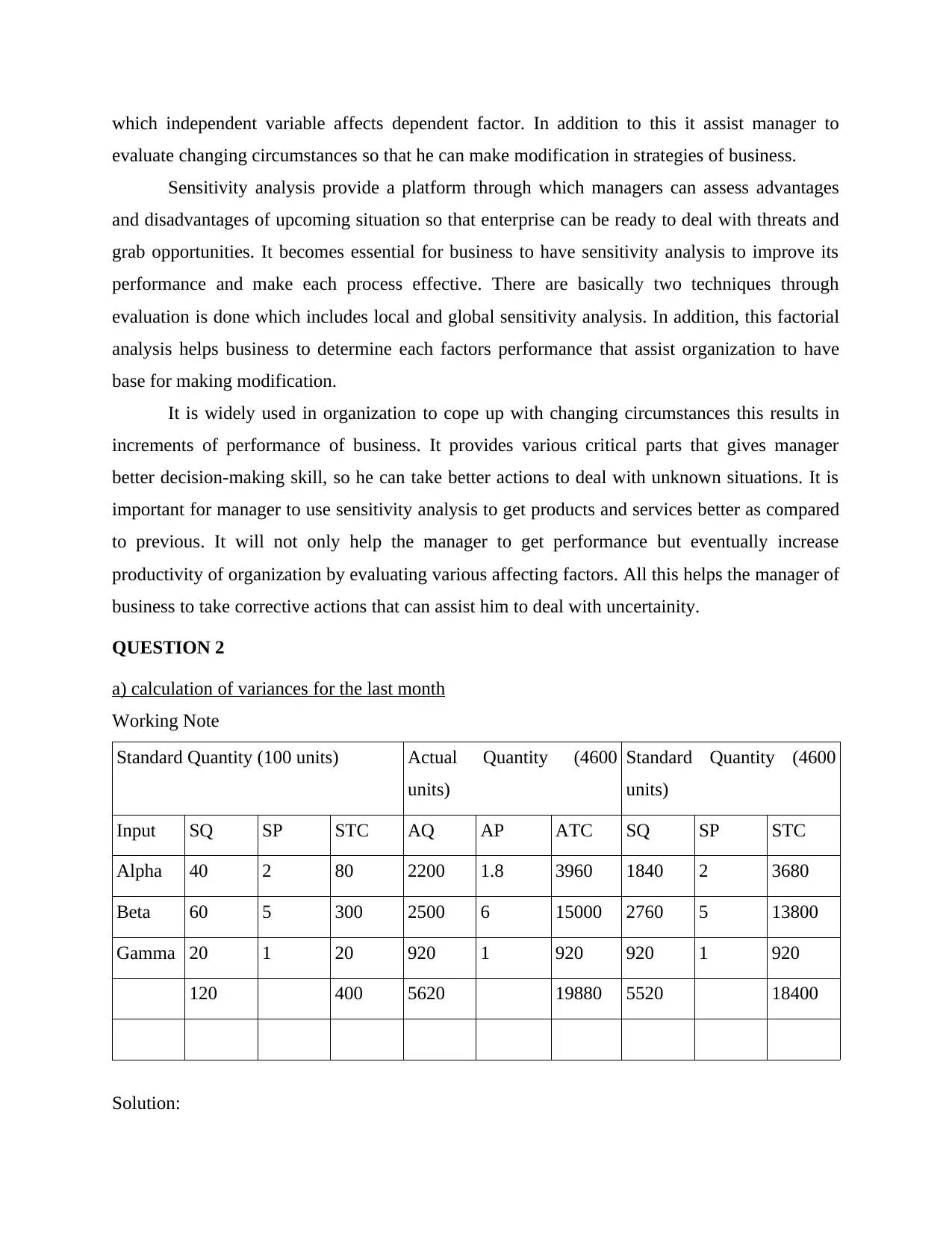
which independent variable affects dependent factor. In addition to this it assist manager to
evaluate changing circumstances so that he can make modification in strategies of business.
Sensitivity analysis provide a platform through which managers can assess advantages
and disadvantages of upcoming situation so that enterprise can be ready to deal with threats and
grab opportunities. It becomes essential for business to have sensitivity analysis to improve its
performance and make each process effective. There are basically two techniques through
evaluation is done which includes local and global sensitivity analysis. In addition, this factorial
analysis helps business to determine each factors performance that assist organization to have
base for making modification.
It is widely used in organization to cope up with changing circumstances this results in
increments of performance of business. It provides various critical parts that gives manager
better decision-making skill, so he can take better actions to deal with unknown situations. It is
important for manager to use sensitivity analysis to get products and services better as compared
to previous. It will not only help the manager to get performance but eventually increase
productivity of organization by evaluating various affecting factors. All this helps the manager of
business to take corrective actions that can assist him to deal with uncertainity.
QUESTION 2
a) calculation of variances for the last month
Working Note
Standard Quantity (100 units) Actual Quantity (4600
units)
Standard Quantity (4600
units)
Input SQ SP STC AQ AP ATC SQ SP STC
Alpha 40 2 80 2200 1.8 3960 1840 2 3680
Beta 60 5 300 2500 6 15000 2760 5 13800
Gamma 20 1 20 920 1 920 920 1 920
120 400 5620 19880 5520 18400
Solution:
evaluate changing circumstances so that he can make modification in strategies of business.
Sensitivity analysis provide a platform through which managers can assess advantages
and disadvantages of upcoming situation so that enterprise can be ready to deal with threats and
grab opportunities. It becomes essential for business to have sensitivity analysis to improve its
performance and make each process effective. There are basically two techniques through
evaluation is done which includes local and global sensitivity analysis. In addition, this factorial
analysis helps business to determine each factors performance that assist organization to have
base for making modification.
It is widely used in organization to cope up with changing circumstances this results in
increments of performance of business. It provides various critical parts that gives manager
better decision-making skill, so he can take better actions to deal with unknown situations. It is
important for manager to use sensitivity analysis to get products and services better as compared
to previous. It will not only help the manager to get performance but eventually increase
productivity of organization by evaluating various affecting factors. All this helps the manager of
business to take corrective actions that can assist him to deal with uncertainity.
QUESTION 2
a) calculation of variances for the last month
Working Note
Standard Quantity (100 units) Actual Quantity (4600
units)
Standard Quantity (4600
units)
Input SQ SP STC AQ AP ATC SQ SP STC
Alpha 40 2 80 2200 1.8 3960 1840 2 3680
Beta 60 5 300 2500 6 15000 2760 5 13800
Gamma 20 1 20 920 1 920 920 1 920
120 400 5620 19880 5520 18400
Solution:
Paraphrase This Document
Need a fresh take? Get an instant paraphrase of this document with our AI Paraphraser
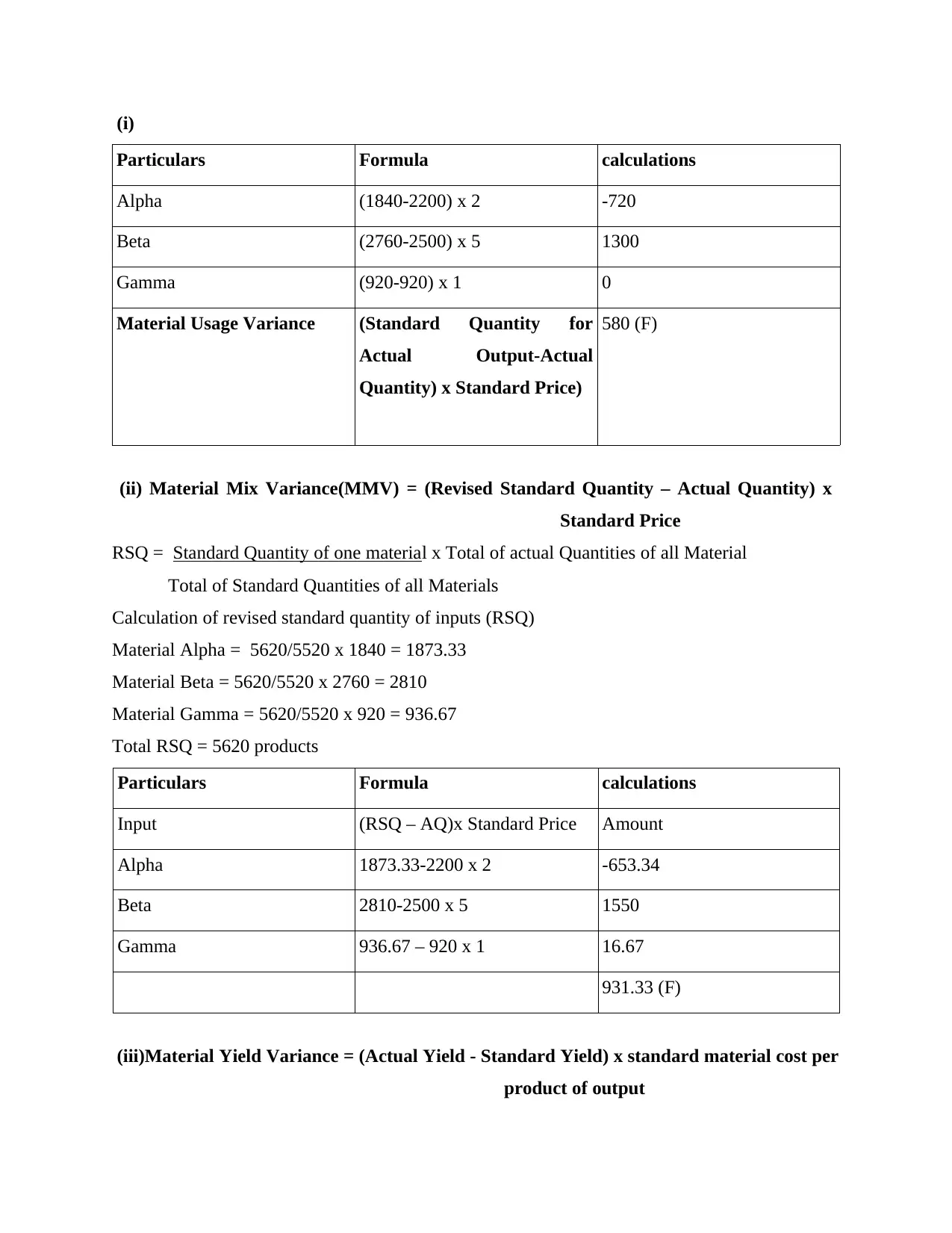
(i)
Particulars Formula calculations
Alpha (1840-2200) x 2 -720
Beta (2760-2500) x 5 1300
Gamma (920-920) x 1 0
Material Usage Variance (Standard Quantity for
Actual Output-Actual
Quantity) x Standard Price)
580 (F)
(ii) Material Mix Variance(MMV) = (Revised Standard Quantity – Actual Quantity) x
Standard Price
RSQ = Standard Quantity of one material x Total of actual Quantities of all Material
Total of Standard Quantities of all Materials
Calculation of revised standard quantity of inputs (RSQ)
Material Alpha = 5620/5520 x 1840 = 1873.33
Material Beta = 5620/5520 x 2760 = 2810
Material Gamma = 5620/5520 x 920 = 936.67
Total RSQ = 5620 products
Particulars Formula calculations
Input (RSQ – AQ)x Standard Price Amount
Alpha 1873.33-2200 x 2 -653.34
Beta 2810-2500 x 5 1550
Gamma 936.67 – 920 x 1 16.67
931.33 (F)
(iii)Material Yield Variance = (Actual Yield - Standard Yield) x standard material cost per
product of output
Particulars Formula calculations
Alpha (1840-2200) x 2 -720
Beta (2760-2500) x 5 1300
Gamma (920-920) x 1 0
Material Usage Variance (Standard Quantity for
Actual Output-Actual
Quantity) x Standard Price)
580 (F)
(ii) Material Mix Variance(MMV) = (Revised Standard Quantity – Actual Quantity) x
Standard Price
RSQ = Standard Quantity of one material x Total of actual Quantities of all Material
Total of Standard Quantities of all Materials
Calculation of revised standard quantity of inputs (RSQ)
Material Alpha = 5620/5520 x 1840 = 1873.33
Material Beta = 5620/5520 x 2760 = 2810
Material Gamma = 5620/5520 x 920 = 936.67
Total RSQ = 5620 products
Particulars Formula calculations
Input (RSQ – AQ)x Standard Price Amount
Alpha 1873.33-2200 x 2 -653.34
Beta 2810-2500 x 5 1550
Gamma 936.67 – 920 x 1 16.67
931.33 (F)
(iii)Material Yield Variance = (Actual Yield - Standard Yield) x standard material cost per
product of output
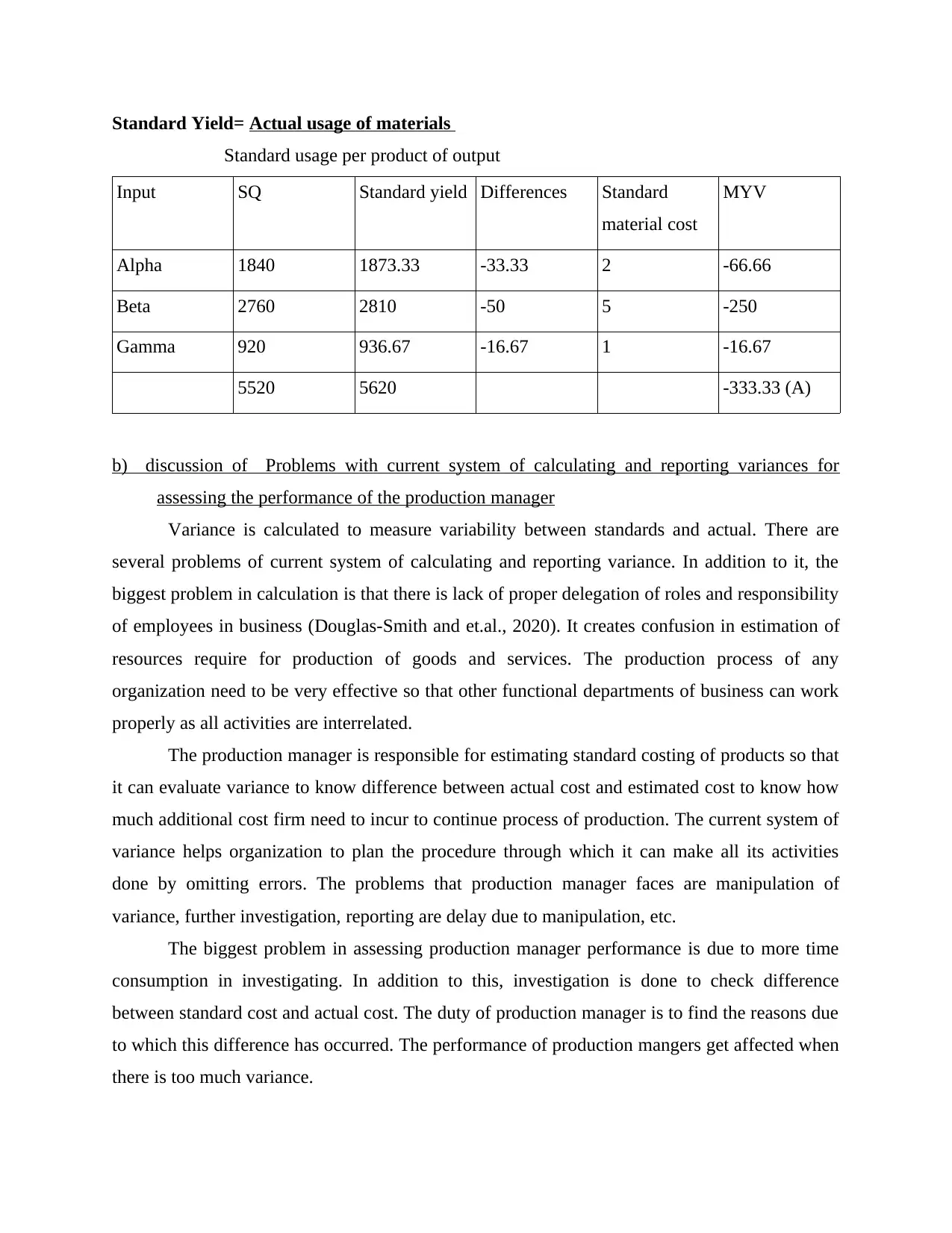
Standard Yield= Actual usage of materials
Standard usage per product of output
Input SQ Standard yield Differences Standard
material cost
MYV
Alpha 1840 1873.33 -33.33 2 -66.66
Beta 2760 2810 -50 5 -250
Gamma 920 936.67 -16.67 1 -16.67
5520 5620 -333.33 (A)
b) discussion of Problems with current system of calculating and reporting variances for
assessing the performance of the production manager
Variance is calculated to measure variability between standards and actual. There are
several problems of current system of calculating and reporting variance. In addition to it, the
biggest problem in calculation is that there is lack of proper delegation of roles and responsibility
of employees in business (Douglas-Smith and et.al., 2020). It creates confusion in estimation of
resources require for production of goods and services. The production process of any
organization need to be very effective so that other functional departments of business can work
properly as all activities are interrelated.
The production manager is responsible for estimating standard costing of products so that
it can evaluate variance to know difference between actual cost and estimated cost to know how
much additional cost firm need to incur to continue process of production. The current system of
variance helps organization to plan the procedure through which it can make all its activities
done by omitting errors. The problems that production manager faces are manipulation of
variance, further investigation, reporting are delay due to manipulation, etc.
The biggest problem in assessing production manager performance is due to more time
consumption in investigating. In addition to this, investigation is done to check difference
between standard cost and actual cost. The duty of production manager is to find the reasons due
to which this difference has occurred. The performance of production mangers get affected when
there is too much variance.
Standard usage per product of output
Input SQ Standard yield Differences Standard
material cost
MYV
Alpha 1840 1873.33 -33.33 2 -66.66
Beta 2760 2810 -50 5 -250
Gamma 920 936.67 -16.67 1 -16.67
5520 5620 -333.33 (A)
b) discussion of Problems with current system of calculating and reporting variances for
assessing the performance of the production manager
Variance is calculated to measure variability between standards and actual. There are
several problems of current system of calculating and reporting variance. In addition to it, the
biggest problem in calculation is that there is lack of proper delegation of roles and responsibility
of employees in business (Douglas-Smith and et.al., 2020). It creates confusion in estimation of
resources require for production of goods and services. The production process of any
organization need to be very effective so that other functional departments of business can work
properly as all activities are interrelated.
The production manager is responsible for estimating standard costing of products so that
it can evaluate variance to know difference between actual cost and estimated cost to know how
much additional cost firm need to incur to continue process of production. The current system of
variance helps organization to plan the procedure through which it can make all its activities
done by omitting errors. The problems that production manager faces are manipulation of
variance, further investigation, reporting are delay due to manipulation, etc.
The biggest problem in assessing production manager performance is due to more time
consumption in investigating. In addition to this, investigation is done to check difference
between standard cost and actual cost. The duty of production manager is to find the reasons due
to which this difference has occurred. The performance of production mangers get affected when
there is too much variance.
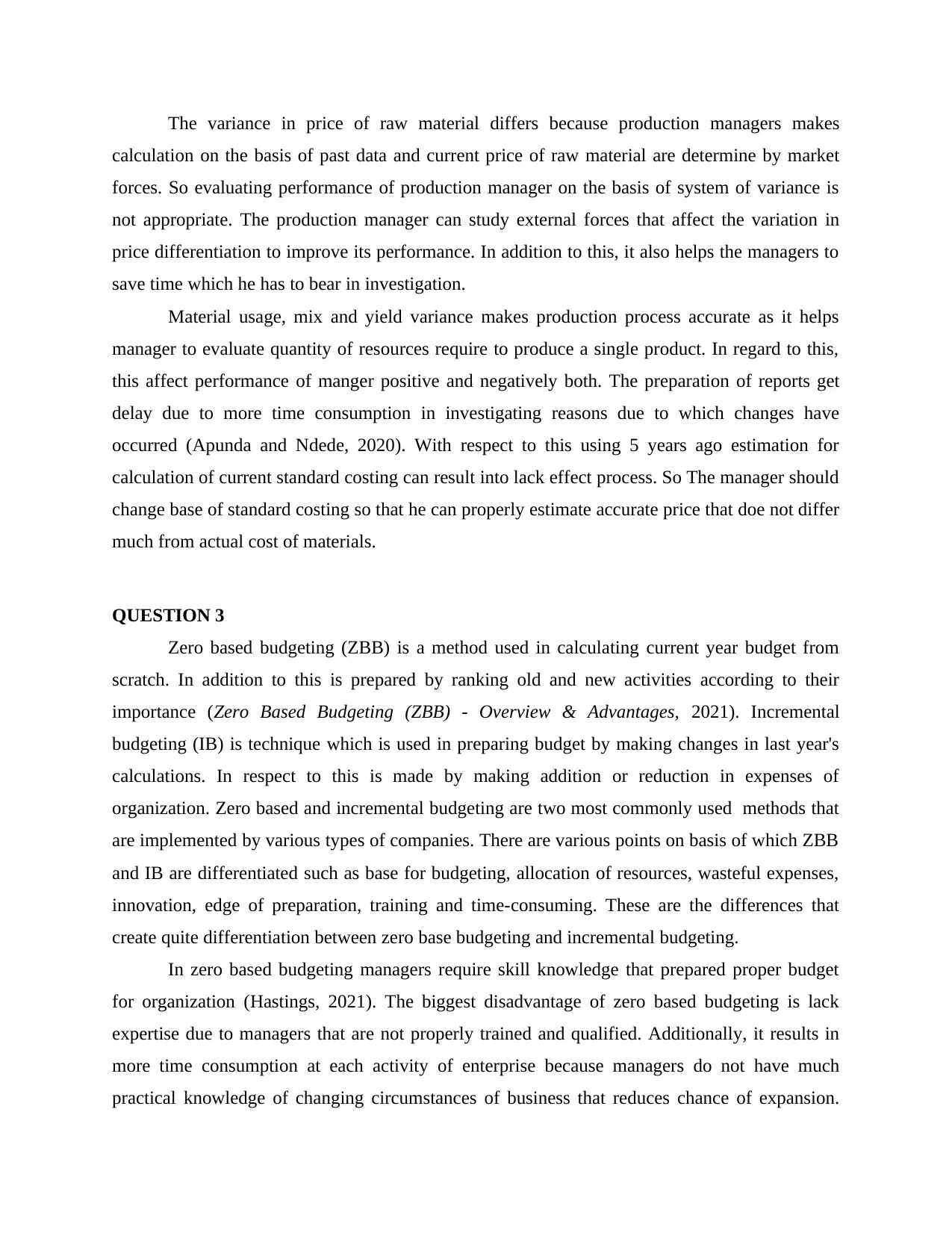
The variance in price of raw material differs because production managers makes
calculation on the basis of past data and current price of raw material are determine by market
forces. So evaluating performance of production manager on the basis of system of variance is
not appropriate. The production manager can study external forces that affect the variation in
price differentiation to improve its performance. In addition to this, it also helps the managers to
save time which he has to bear in investigation.
Material usage, mix and yield variance makes production process accurate as it helps
manager to evaluate quantity of resources require to produce a single product. In regard to this,
this affect performance of manger positive and negatively both. The preparation of reports get
delay due to more time consumption in investigating reasons due to which changes have
occurred (Apunda and Ndede, 2020). With respect to this using 5 years ago estimation for
calculation of current standard costing can result into lack effect process. So The manager should
change base of standard costing so that he can properly estimate accurate price that doe not differ
much from actual cost of materials.
QUESTION 3
Zero based budgeting (ZBB) is a method used in calculating current year budget from
scratch. In addition to this is prepared by ranking old and new activities according to their
importance (Zero Based Budgeting (ZBB) - Overview & Advantages, 2021). Incremental
budgeting (IB) is technique which is used in preparing budget by making changes in last year's
calculations. In respect to this is made by making addition or reduction in expenses of
organization. Zero based and incremental budgeting are two most commonly used methods that
are implemented by various types of companies. There are various points on basis of which ZBB
and IB are differentiated such as base for budgeting, allocation of resources, wasteful expenses,
innovation, edge of preparation, training and time-consuming. These are the differences that
create quite differentiation between zero base budgeting and incremental budgeting.
In zero based budgeting managers require skill knowledge that prepared proper budget
for organization (Hastings, 2021). The biggest disadvantage of zero based budgeting is lack
expertise due to managers that are not properly trained and qualified. Additionally, it results in
more time consumption at each activity of enterprise because managers do not have much
practical knowledge of changing circumstances of business that reduces chance of expansion.
calculation on the basis of past data and current price of raw material are determine by market
forces. So evaluating performance of production manager on the basis of system of variance is
not appropriate. The production manager can study external forces that affect the variation in
price differentiation to improve its performance. In addition to this, it also helps the managers to
save time which he has to bear in investigation.
Material usage, mix and yield variance makes production process accurate as it helps
manager to evaluate quantity of resources require to produce a single product. In regard to this,
this affect performance of manger positive and negatively both. The preparation of reports get
delay due to more time consumption in investigating reasons due to which changes have
occurred (Apunda and Ndede, 2020). With respect to this using 5 years ago estimation for
calculation of current standard costing can result into lack effect process. So The manager should
change base of standard costing so that he can properly estimate accurate price that doe not differ
much from actual cost of materials.
QUESTION 3
Zero based budgeting (ZBB) is a method used in calculating current year budget from
scratch. In addition to this is prepared by ranking old and new activities according to their
importance (Zero Based Budgeting (ZBB) - Overview & Advantages, 2021). Incremental
budgeting (IB) is technique which is used in preparing budget by making changes in last year's
calculations. In respect to this is made by making addition or reduction in expenses of
organization. Zero based and incremental budgeting are two most commonly used methods that
are implemented by various types of companies. There are various points on basis of which ZBB
and IB are differentiated such as base for budgeting, allocation of resources, wasteful expenses,
innovation, edge of preparation, training and time-consuming. These are the differences that
create quite differentiation between zero base budgeting and incremental budgeting.
In zero based budgeting managers require skill knowledge that prepared proper budget
for organization (Hastings, 2021). The biggest disadvantage of zero based budgeting is lack
expertise due to managers that are not properly trained and qualified. Additionally, it results in
more time consumption at each activity of enterprise because managers do not have much
practical knowledge of changing circumstances of business that reduces chance of expansion.
Secure Best Marks with AI Grader
Need help grading? Try our AI Grader for instant feedback on your assignments.
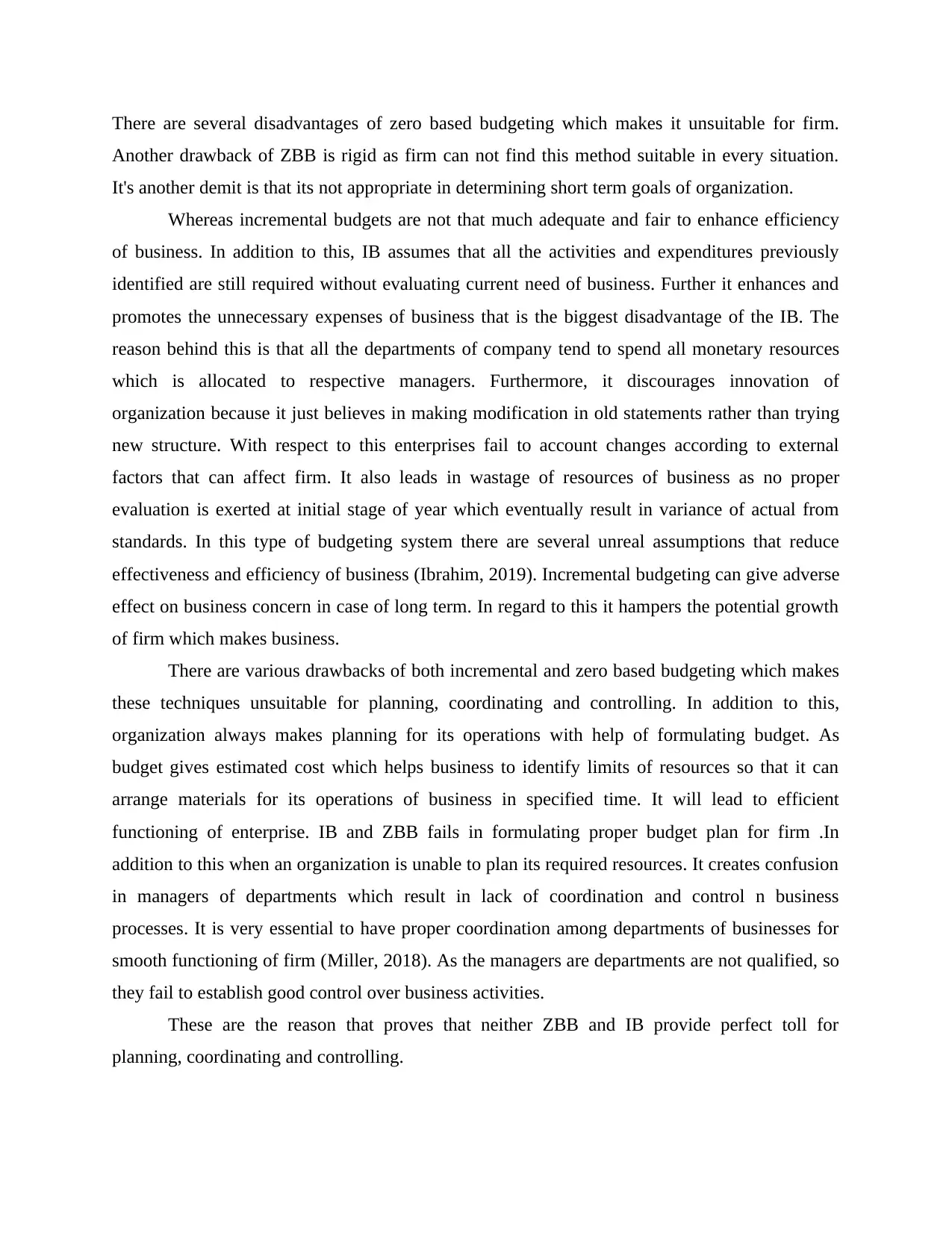
There are several disadvantages of zero based budgeting which makes it unsuitable for firm.
Another drawback of ZBB is rigid as firm can not find this method suitable in every situation.
It's another demit is that its not appropriate in determining short term goals of organization.
Whereas incremental budgets are not that much adequate and fair to enhance efficiency
of business. In addition to this, IB assumes that all the activities and expenditures previously
identified are still required without evaluating current need of business. Further it enhances and
promotes the unnecessary expenses of business that is the biggest disadvantage of the IB. The
reason behind this is that all the departments of company tend to spend all monetary resources
which is allocated to respective managers. Furthermore, it discourages innovation of
organization because it just believes in making modification in old statements rather than trying
new structure. With respect to this enterprises fail to account changes according to external
factors that can affect firm. It also leads in wastage of resources of business as no proper
evaluation is exerted at initial stage of year which eventually result in variance of actual from
standards. In this type of budgeting system there are several unreal assumptions that reduce
effectiveness and efficiency of business (Ibrahim, 2019). Incremental budgeting can give adverse
effect on business concern in case of long term. In regard to this it hampers the potential growth
of firm which makes business.
There are various drawbacks of both incremental and zero based budgeting which makes
these techniques unsuitable for planning, coordinating and controlling. In addition to this,
organization always makes planning for its operations with help of formulating budget. As
budget gives estimated cost which helps business to identify limits of resources so that it can
arrange materials for its operations of business in specified time. It will lead to efficient
functioning of enterprise. IB and ZBB fails in formulating proper budget plan for firm .In
addition to this when an organization is unable to plan its required resources. It creates confusion
in managers of departments which result in lack of coordination and control n business
processes. It is very essential to have proper coordination among departments of businesses for
smooth functioning of firm (Miller, 2018). As the managers are departments are not qualified, so
they fail to establish good control over business activities.
These are the reason that proves that neither ZBB and IB provide perfect toll for
planning, coordinating and controlling.
Another drawback of ZBB is rigid as firm can not find this method suitable in every situation.
It's another demit is that its not appropriate in determining short term goals of organization.
Whereas incremental budgets are not that much adequate and fair to enhance efficiency
of business. In addition to this, IB assumes that all the activities and expenditures previously
identified are still required without evaluating current need of business. Further it enhances and
promotes the unnecessary expenses of business that is the biggest disadvantage of the IB. The
reason behind this is that all the departments of company tend to spend all monetary resources
which is allocated to respective managers. Furthermore, it discourages innovation of
organization because it just believes in making modification in old statements rather than trying
new structure. With respect to this enterprises fail to account changes according to external
factors that can affect firm. It also leads in wastage of resources of business as no proper
evaluation is exerted at initial stage of year which eventually result in variance of actual from
standards. In this type of budgeting system there are several unreal assumptions that reduce
effectiveness and efficiency of business (Ibrahim, 2019). Incremental budgeting can give adverse
effect on business concern in case of long term. In regard to this it hampers the potential growth
of firm which makes business.
There are various drawbacks of both incremental and zero based budgeting which makes
these techniques unsuitable for planning, coordinating and controlling. In addition to this,
organization always makes planning for its operations with help of formulating budget. As
budget gives estimated cost which helps business to identify limits of resources so that it can
arrange materials for its operations of business in specified time. It will lead to efficient
functioning of enterprise. IB and ZBB fails in formulating proper budget plan for firm .In
addition to this when an organization is unable to plan its required resources. It creates confusion
in managers of departments which result in lack of coordination and control n business
processes. It is very essential to have proper coordination among departments of businesses for
smooth functioning of firm (Miller, 2018). As the managers are departments are not qualified, so
they fail to establish good control over business activities.
These are the reason that proves that neither ZBB and IB provide perfect toll for
planning, coordinating and controlling.
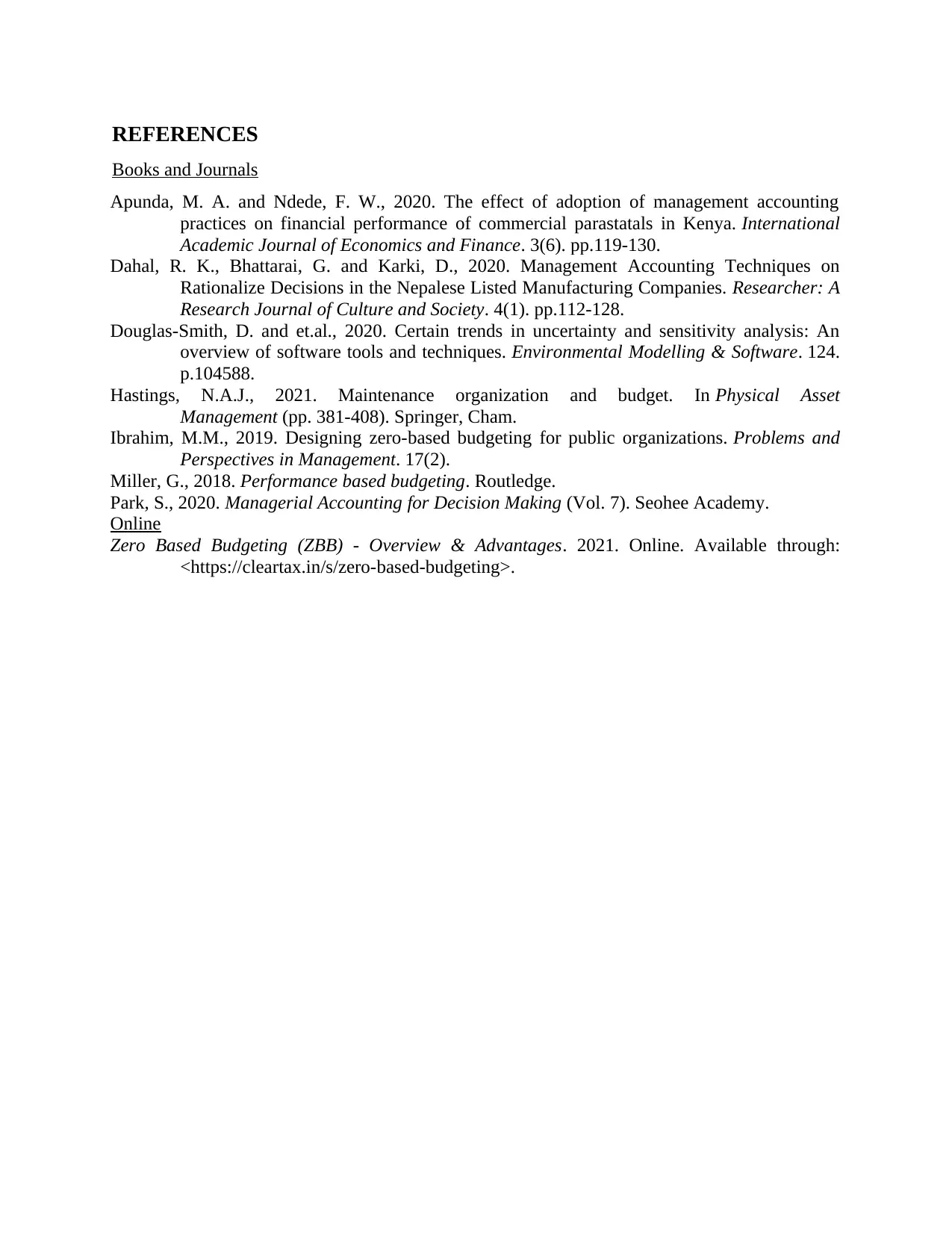
REFERENCES
Books and Journals
Apunda, M. A. and Ndede, F. W., 2020. The effect of adoption of management accounting
practices on financial performance of commercial parastatals in Kenya. International
Academic Journal of Economics and Finance. 3(6). pp.119-130.
Dahal, R. K., Bhattarai, G. and Karki, D., 2020. Management Accounting Techniques on
Rationalize Decisions in the Nepalese Listed Manufacturing Companies. Researcher: A
Research Journal of Culture and Society. 4(1). pp.112-128.
Douglas-Smith, D. and et.al., 2020. Certain trends in uncertainty and sensitivity analysis: An
overview of software tools and techniques. Environmental Modelling & Software. 124.
p.104588.
Hastings, N.A.J., 2021. Maintenance organization and budget. In Physical Asset
Management (pp. 381-408). Springer, Cham.
Ibrahim, M.M., 2019. Designing zero-based budgeting for public organizations. Problems and
Perspectives in Management. 17(2).
Miller, G., 2018. Performance based budgeting. Routledge.
Park, S., 2020. Managerial Accounting for Decision Making (Vol. 7). Seohee Academy.
Online
Zero Based Budgeting (ZBB) - Overview & Advantages. 2021. Online. Available through:
<https://cleartax.in/s/zero-based-budgeting>.
Books and Journals
Apunda, M. A. and Ndede, F. W., 2020. The effect of adoption of management accounting
practices on financial performance of commercial parastatals in Kenya. International
Academic Journal of Economics and Finance. 3(6). pp.119-130.
Dahal, R. K., Bhattarai, G. and Karki, D., 2020. Management Accounting Techniques on
Rationalize Decisions in the Nepalese Listed Manufacturing Companies. Researcher: A
Research Journal of Culture and Society. 4(1). pp.112-128.
Douglas-Smith, D. and et.al., 2020. Certain trends in uncertainty and sensitivity analysis: An
overview of software tools and techniques. Environmental Modelling & Software. 124.
p.104588.
Hastings, N.A.J., 2021. Maintenance organization and budget. In Physical Asset
Management (pp. 381-408). Springer, Cham.
Ibrahim, M.M., 2019. Designing zero-based budgeting for public organizations. Problems and
Perspectives in Management. 17(2).
Miller, G., 2018. Performance based budgeting. Routledge.
Park, S., 2020. Managerial Accounting for Decision Making (Vol. 7). Seohee Academy.
Online
Zero Based Budgeting (ZBB) - Overview & Advantages. 2021. Online. Available through:
<https://cleartax.in/s/zero-based-budgeting>.
1 out of 12
Related Documents
![[object Object]](/_next/image/?url=%2F_next%2Fstatic%2Fmedia%2Flogo.6d15ce61.png&w=640&q=75)
Your All-in-One AI-Powered Toolkit for Academic Success.
 +13062052269
info@desklib.com
Available 24*7 on WhatsApp / Email
Unlock your academic potential
© 2024  |  Zucol Services PVT LTD  |  All rights reserved.