Financial Performance Management
VerifiedAdded on  2022/12/28
|11
|2529
|52
AI Summary
This document discusses financial performance management and its importance in business. It covers topics such as overhead absorption rate, cost per unit, and allocation of overheads. It also explores the benefits of activity-based costing and sensitivity analysis. Additionally, it explains how zero-based budgeting can help balance business expenditures.
Contribute Materials
Your contribution can guide someone’s learning journey. Share your
documents today.
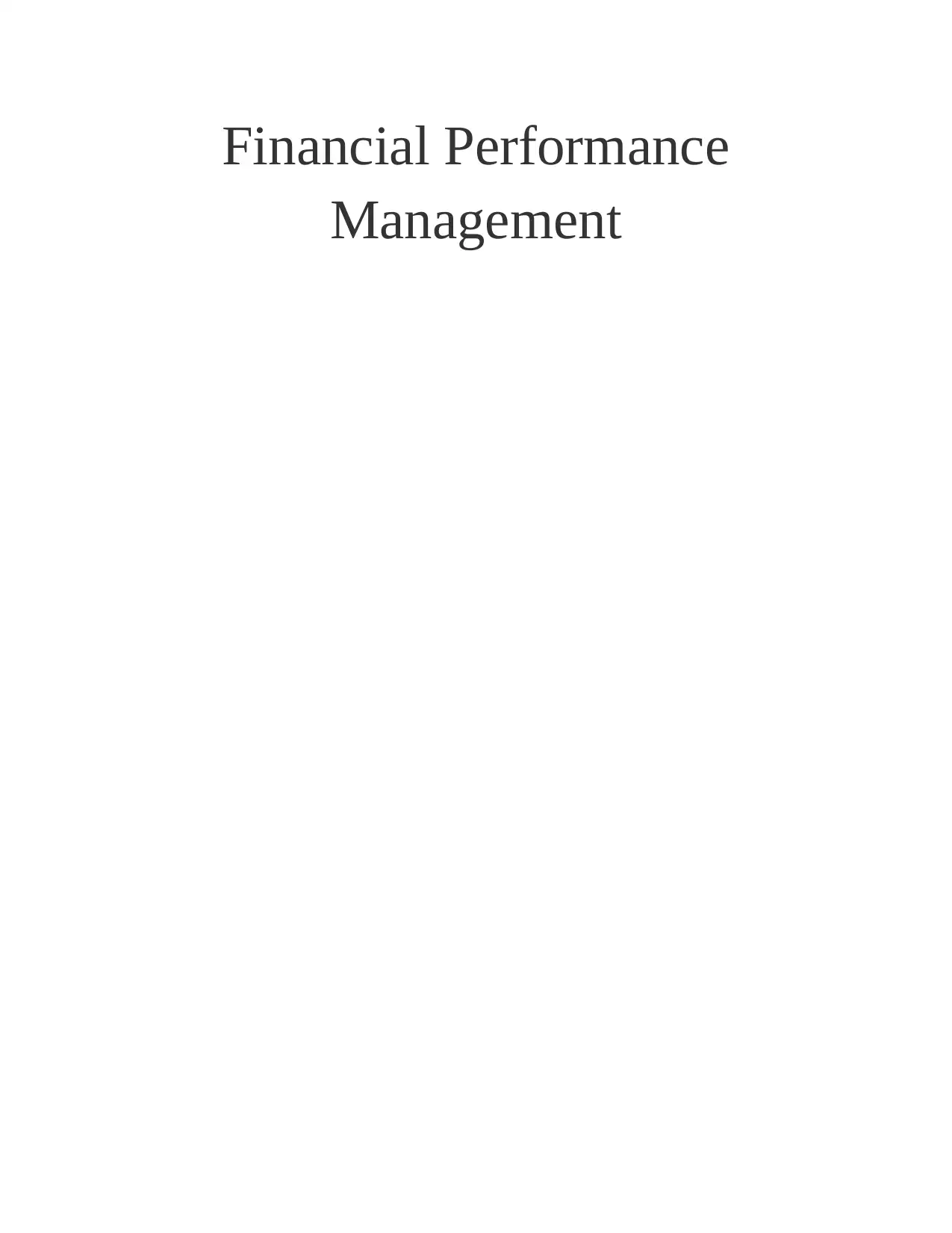
Financial Performance
Management
Management
Secure Best Marks with AI Grader
Need help grading? Try our AI Grader for instant feedback on your assignments.
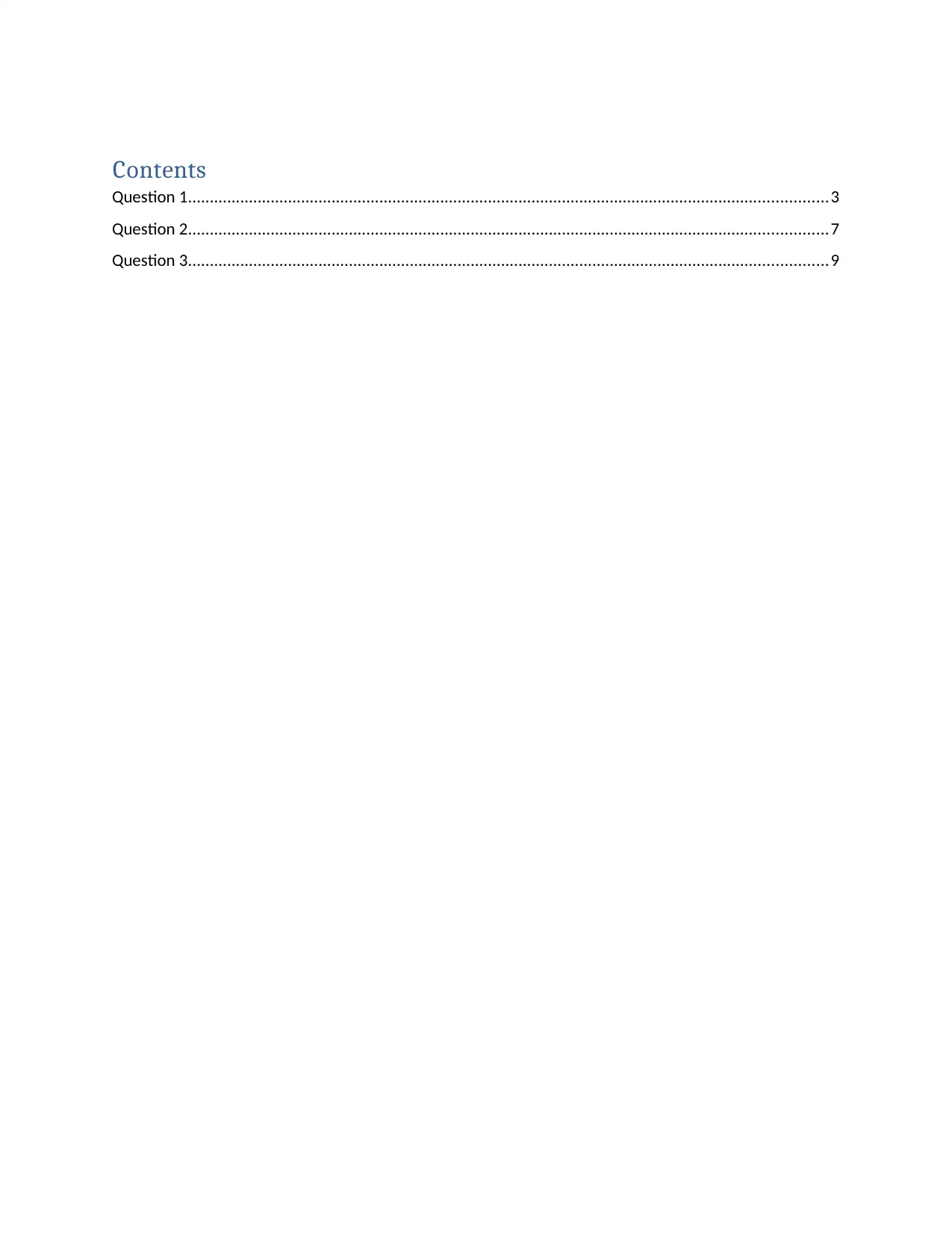
Contents
Question 1...................................................................................................................................................3
Question 2...................................................................................................................................................7
Question 3...................................................................................................................................................9
Question 1...................................................................................................................................................3
Question 2...................................................................................................................................................7
Question 3...................................................................................................................................................9
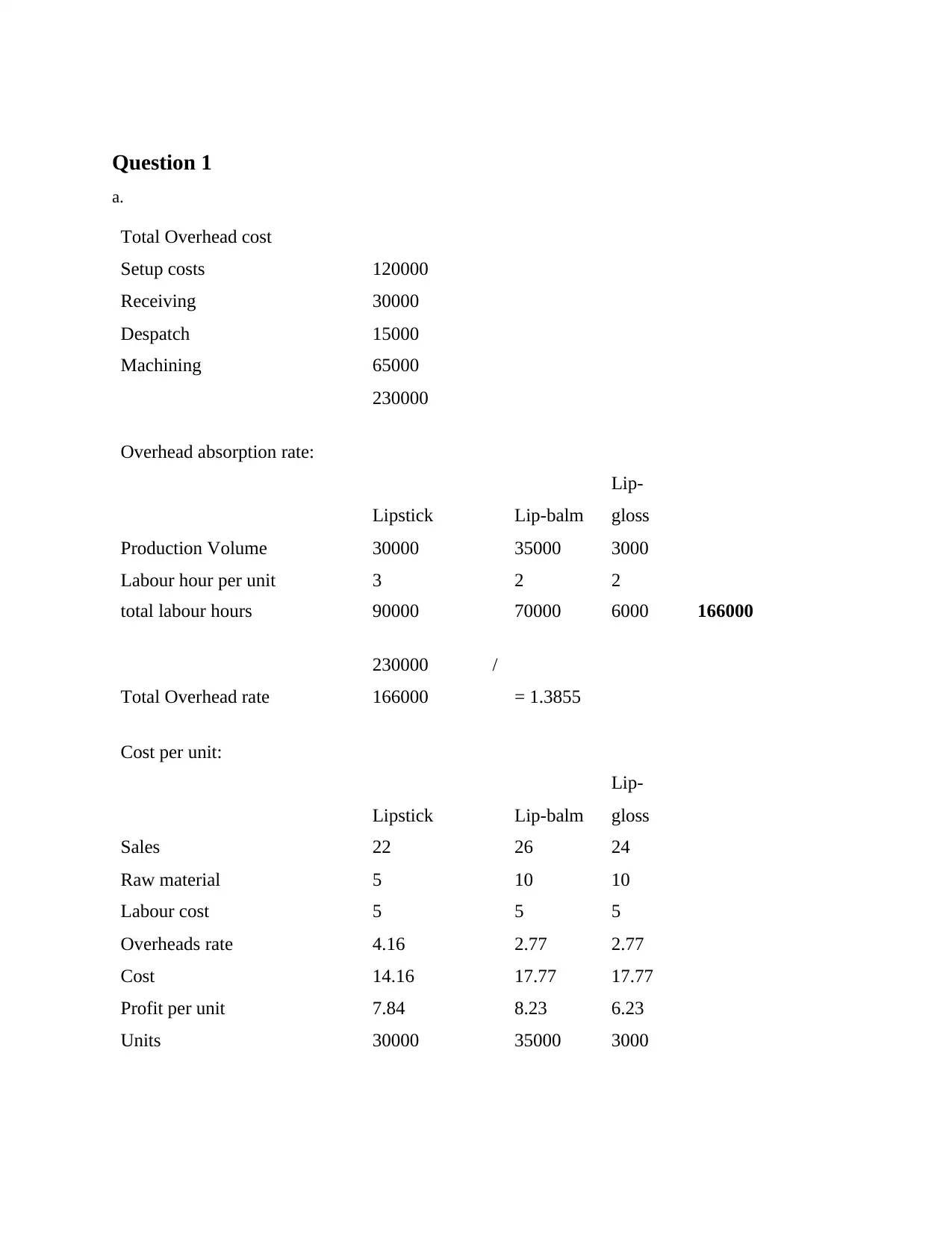
Question 1
a.
Total Overhead cost
Setup costs 120000
Receiving 30000
Despatch 15000
Machining 65000
230000
Overhead absorption rate:
Lipstick Lip-balm
Lip-
gloss
Production Volume 30000 35000 3000
Labour hour per unit 3 2 2
total labour hours 90000 70000 6000 166000
Total Overhead rate
230000 /
166000 = 1.3855
Cost per unit:
Lipstick Lip-balm
Lip-
gloss
Sales 22 26 24
Raw material 5 10 10
Labour cost 5 5 5
Overheads rate 4.16 2.77 2.77
Cost 14.16 17.77 17.77
Profit per unit 7.84 8.23 6.23
Units 30000 35000 3000
a.
Total Overhead cost
Setup costs 120000
Receiving 30000
Despatch 15000
Machining 65000
230000
Overhead absorption rate:
Lipstick Lip-balm
Lip-
gloss
Production Volume 30000 35000 3000
Labour hour per unit 3 2 2
total labour hours 90000 70000 6000 166000
Total Overhead rate
230000 /
166000 = 1.3855
Cost per unit:
Lipstick Lip-balm
Lip-
gloss
Sales 22 26 24
Raw material 5 10 10
Labour cost 5 5 5
Overheads rate 4.16 2.77 2.77
Cost 14.16 17.77 17.77
Profit per unit 7.84 8.23 6.23
Units 30000 35000 3000
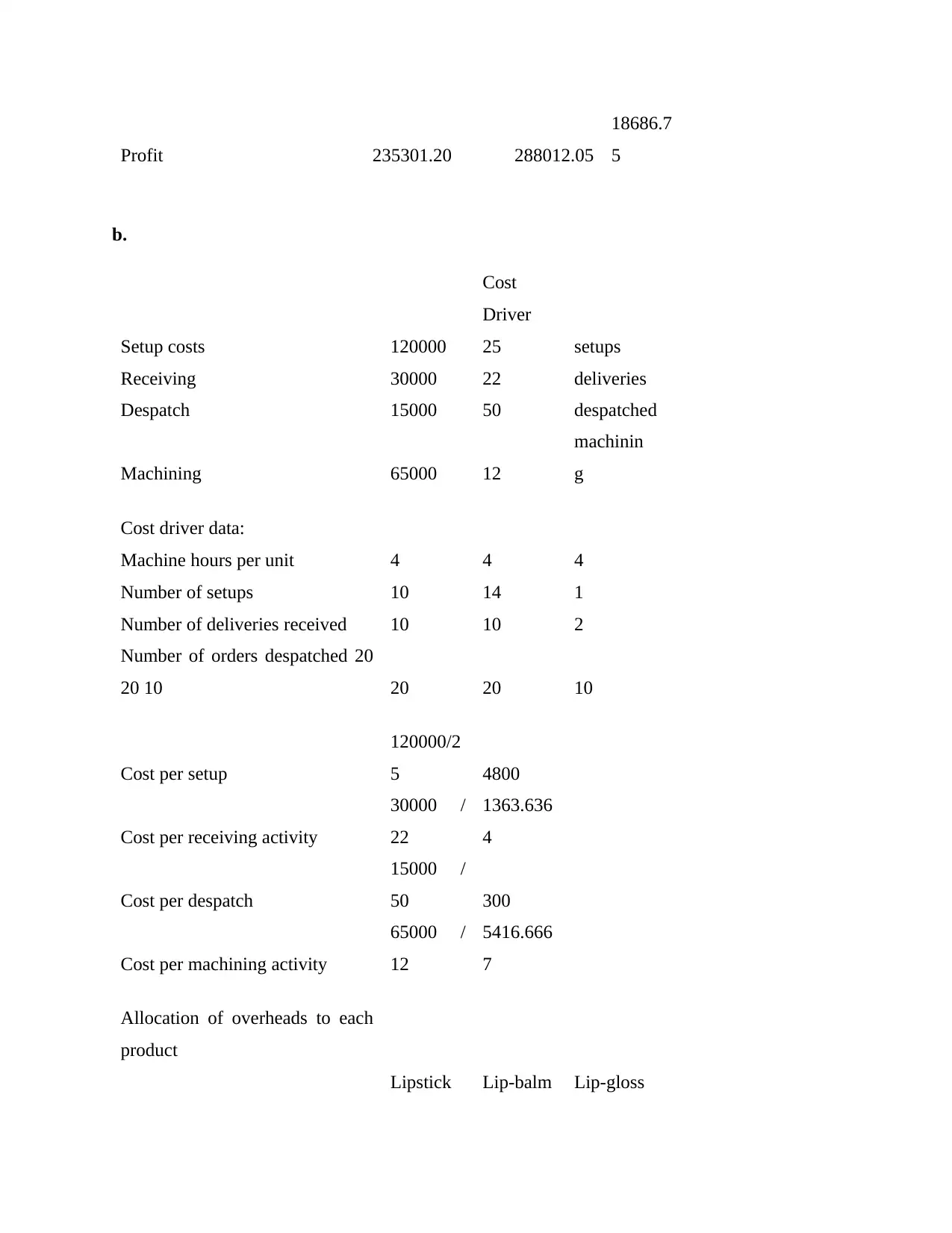
Profit 235301.20 288012.05
18686.7
5
b.
Cost
Driver
Setup costs 120000 25 setups
Receiving 30000 22 deliveries
Despatch 15000 50 despatched
Machining 65000 12
machinin
g
Cost driver data:
Machine hours per unit 4 4 4
Number of setups 10 14 1
Number of deliveries received 10 10 2
Number of orders despatched 20
20 10 20 20 10
Cost per setup
120000/2
5 4800
Cost per receiving activity
30000 /
22
1363.636
4
Cost per despatch
15000 /
50 300
Cost per machining activity
65000 /
12
5416.666
7
Allocation of overheads to each
product
Lipstick Lip-balm Lip-gloss
18686.7
5
b.
Cost
Driver
Setup costs 120000 25 setups
Receiving 30000 22 deliveries
Despatch 15000 50 despatched
Machining 65000 12
machinin
g
Cost driver data:
Machine hours per unit 4 4 4
Number of setups 10 14 1
Number of deliveries received 10 10 2
Number of orders despatched 20
20 10 20 20 10
Cost per setup
120000/2
5 4800
Cost per receiving activity
30000 /
22
1363.636
4
Cost per despatch
15000 /
50 300
Cost per machining activity
65000 /
12
5416.666
7
Allocation of overheads to each
product
Lipstick Lip-balm Lip-gloss
Secure Best Marks with AI Grader
Need help grading? Try our AI Grader for instant feedback on your assignments.
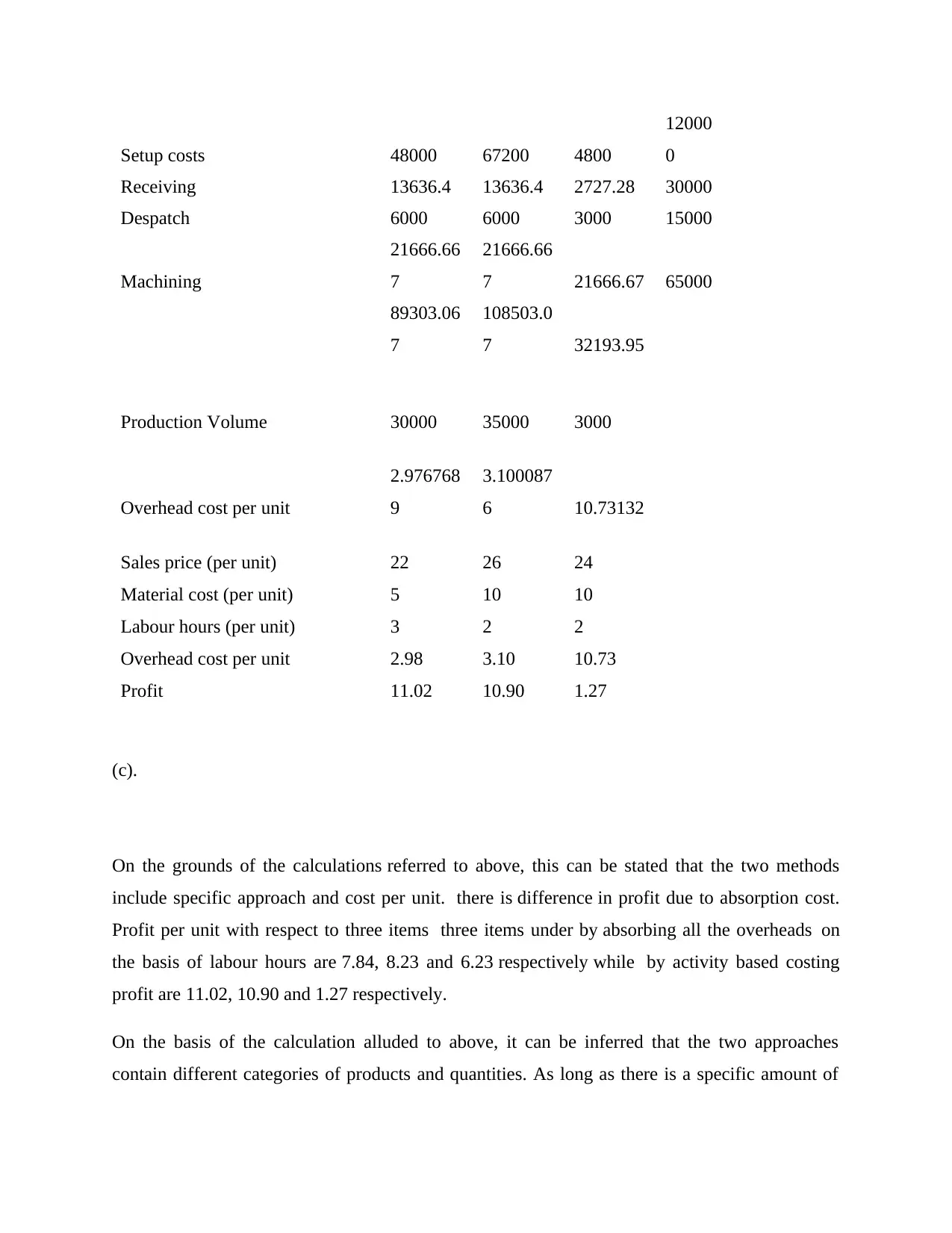
Setup costs 48000 67200 4800
12000
0
Receiving 13636.4 13636.4 2727.28 30000
Despatch 6000 6000 3000 15000
Machining
21666.66
7
21666.66
7 21666.67 65000
89303.06
7
108503.0
7 32193.95
Production Volume 30000 35000 3000
Overhead cost per unit
2.976768
9
3.100087
6 10.73132
Sales price (per unit) 22 26 24
Material cost (per unit) 5 10 10
Labour hours (per unit) 3 2 2
Overhead cost per unit 2.98 3.10 10.73
Profit 11.02 10.90 1.27
(c).
On the grounds of the calculations referred to above, this can be stated that the two methods
include specific approach and cost per unit. there is difference in profit due to absorption cost.
Profit per unit with respect to three items three items under by absorbing all the overheads on
the basis of labour hours are 7.84, 8.23 and 6.23 respectively while by activity based costing
profit are 11.02, 10.90 and 1.27 respectively.
On the basis of the calculation alluded to above, it can be inferred that the two approaches
contain different categories of products and quantities. As long as there is a specific amount of
12000
0
Receiving 13636.4 13636.4 2727.28 30000
Despatch 6000 6000 3000 15000
Machining
21666.66
7
21666.66
7 21666.67 65000
89303.06
7
108503.0
7 32193.95
Production Volume 30000 35000 3000
Overhead cost per unit
2.976768
9
3.100087
6 10.73132
Sales price (per unit) 22 26 24
Material cost (per unit) 5 10 10
Labour hours (per unit) 3 2 2
Overhead cost per unit 2.98 3.10 10.73
Profit 11.02 10.90 1.27
(c).
On the grounds of the calculations referred to above, this can be stated that the two methods
include specific approach and cost per unit. there is difference in profit due to absorption cost.
Profit per unit with respect to three items three items under by absorbing all the overheads on
the basis of labour hours are 7.84, 8.23 and 6.23 respectively while by activity based costing
profit are 11.02, 10.90 and 1.27 respectively.
On the basis of the calculation alluded to above, it can be inferred that the two approaches
contain different categories of products and quantities. As long as there is a specific amount of
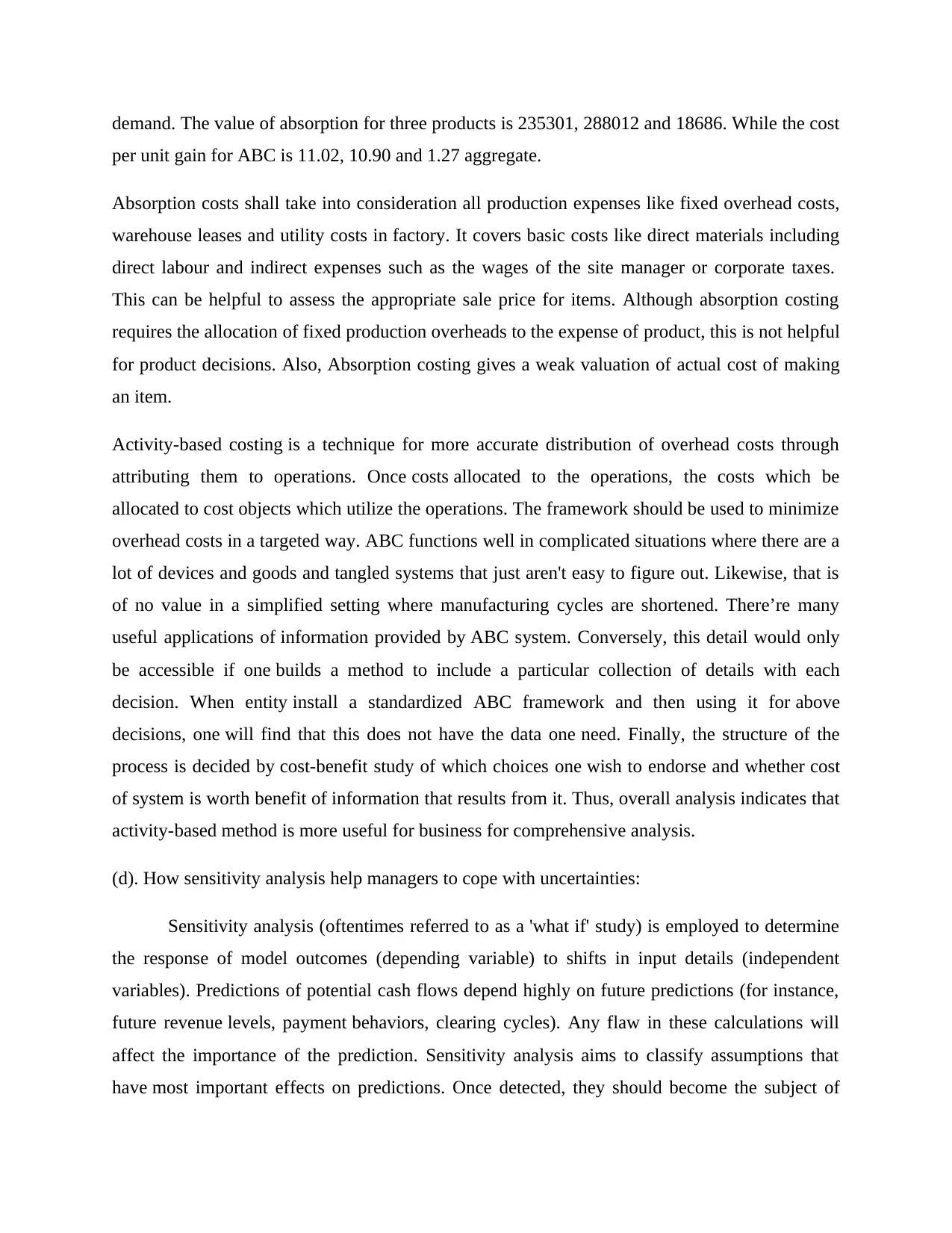
demand. The value of absorption for three products is 235301, 288012 and 18686. While the cost
per unit gain for ABC is 11.02, 10.90 and 1.27 aggregate.
Absorption costs shall take into consideration all production expenses like fixed overhead costs,
warehouse leases and utility costs in factory. It covers basic costs like direct materials including
direct labour and indirect expenses such as the wages of the site manager or corporate taxes.
This can be helpful to assess the appropriate sale price for items. Although absorption costing
requires the allocation of fixed production overheads to the expense of product, this is not helpful
for product decisions. Also, Absorption costing gives a weak valuation of actual cost of making
an item.
Activity-based costing is a technique for more accurate distribution of overhead costs through
attributing them to operations. Once costs allocated to the operations, the costs which be
allocated to cost objects which utilize the operations. The framework should be used to minimize
overhead costs in a targeted way. ABC functions well in complicated situations where there are a
lot of devices and goods and tangled systems that just aren't easy to figure out. Likewise, that is
of no value in a simplified setting where manufacturing cycles are shortened. There’re many
useful applications of information provided by ABC system. Conversely, this detail would only
be accessible if one builds a method to include a particular collection of details with each
decision. When entity install a standardized ABC framework and then using it for above
decisions, one will find that this does not have the data one need. Finally, the structure of the
process is decided by cost-benefit study of which choices one wish to endorse and whether cost
of system is worth benefit of information that results from it. Thus, overall analysis indicates that
activity-based method is more useful for business for comprehensive analysis.
(d). How sensitivity analysis help managers to cope with uncertainties:
Sensitivity analysis (oftentimes referred to as a 'what if' study) is employed to determine
the response of model outcomes (depending variable) to shifts in input details (independent
variables). Predictions of potential cash flows depend highly on future predictions (for instance,
future revenue levels, payment behaviors, clearing cycles). Any flaw in these calculations will
affect the importance of the prediction. Sensitivity analysis aims to classify assumptions that
have most important effects on predictions. Once detected, they should become the subject of
per unit gain for ABC is 11.02, 10.90 and 1.27 aggregate.
Absorption costs shall take into consideration all production expenses like fixed overhead costs,
warehouse leases and utility costs in factory. It covers basic costs like direct materials including
direct labour and indirect expenses such as the wages of the site manager or corporate taxes.
This can be helpful to assess the appropriate sale price for items. Although absorption costing
requires the allocation of fixed production overheads to the expense of product, this is not helpful
for product decisions. Also, Absorption costing gives a weak valuation of actual cost of making
an item.
Activity-based costing is a technique for more accurate distribution of overhead costs through
attributing them to operations. Once costs allocated to the operations, the costs which be
allocated to cost objects which utilize the operations. The framework should be used to minimize
overhead costs in a targeted way. ABC functions well in complicated situations where there are a
lot of devices and goods and tangled systems that just aren't easy to figure out. Likewise, that is
of no value in a simplified setting where manufacturing cycles are shortened. There’re many
useful applications of information provided by ABC system. Conversely, this detail would only
be accessible if one builds a method to include a particular collection of details with each
decision. When entity install a standardized ABC framework and then using it for above
decisions, one will find that this does not have the data one need. Finally, the structure of the
process is decided by cost-benefit study of which choices one wish to endorse and whether cost
of system is worth benefit of information that results from it. Thus, overall analysis indicates that
activity-based method is more useful for business for comprehensive analysis.
(d). How sensitivity analysis help managers to cope with uncertainties:
Sensitivity analysis (oftentimes referred to as a 'what if' study) is employed to determine
the response of model outcomes (depending variable) to shifts in input details (independent
variables). Predictions of potential cash flows depend highly on future predictions (for instance,
future revenue levels, payment behaviors, clearing cycles). Any flaw in these calculations will
affect the importance of the prediction. Sensitivity analysis aims to classify assumptions that
have most important effects on predictions. Once detected, they should become the subject of
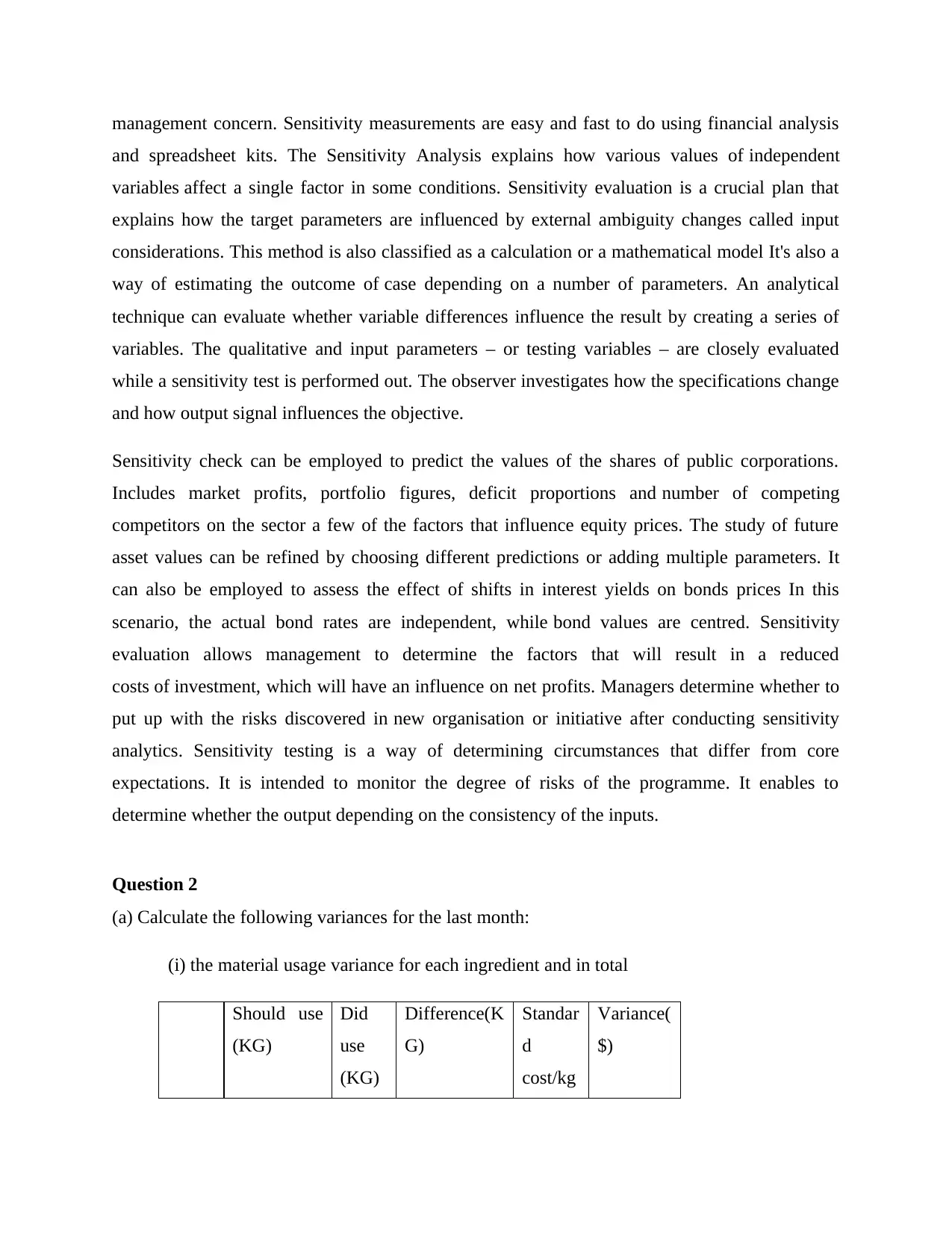
management concern. Sensitivity measurements are easy and fast to do using financial analysis
and spreadsheet kits. The Sensitivity Analysis explains how various values of independent
variables affect a single factor in some conditions. Sensitivity evaluation is a crucial plan that
explains how the target parameters are influenced by external ambiguity changes called input
considerations. This method is also classified as a calculation or a mathematical model It's also a
way of estimating the outcome of case depending on a number of parameters. An analytical
technique can evaluate whether variable differences influence the result by creating a series of
variables. The qualitative and input parameters – or testing variables – are closely evaluated
while a sensitivity test is performed out. The observer investigates how the specifications change
and how output signal influences the objective.
Sensitivity check can be employed to predict the values of the shares of public corporations.
Includes market profits, portfolio figures, deficit proportions and number of competing
competitors on the sector a few of the factors that influence equity prices. The study of future
asset values can be refined by choosing different predictions or adding multiple parameters. It
can also be employed to assess the effect of shifts in interest yields on bonds prices In this
scenario, the actual bond rates are independent, while bond values are centred. Sensitivity
evaluation allows management to determine the factors that will result in a reduced
costs of investment, which will have an influence on net profits. Managers determine whether to
put up with the risks discovered in new organisation or initiative after conducting sensitivity
analytics. Sensitivity testing is a way of determining circumstances that differ from core
expectations. It is intended to monitor the degree of risks of the programme. It enables to
determine whether the output depending on the consistency of the inputs.
Question 2
(a) Calculate the following variances for the last month:
(i) the material usage variance for each ingredient and in total
Should use
(KG)
Did
use
(KG)
Difference(K
G)
Standar
d
cost/kg
Variance(
$)
and spreadsheet kits. The Sensitivity Analysis explains how various values of independent
variables affect a single factor in some conditions. Sensitivity evaluation is a crucial plan that
explains how the target parameters are influenced by external ambiguity changes called input
considerations. This method is also classified as a calculation or a mathematical model It's also a
way of estimating the outcome of case depending on a number of parameters. An analytical
technique can evaluate whether variable differences influence the result by creating a series of
variables. The qualitative and input parameters – or testing variables – are closely evaluated
while a sensitivity test is performed out. The observer investigates how the specifications change
and how output signal influences the objective.
Sensitivity check can be employed to predict the values of the shares of public corporations.
Includes market profits, portfolio figures, deficit proportions and number of competing
competitors on the sector a few of the factors that influence equity prices. The study of future
asset values can be refined by choosing different predictions or adding multiple parameters. It
can also be employed to assess the effect of shifts in interest yields on bonds prices In this
scenario, the actual bond rates are independent, while bond values are centred. Sensitivity
evaluation allows management to determine the factors that will result in a reduced
costs of investment, which will have an influence on net profits. Managers determine whether to
put up with the risks discovered in new organisation or initiative after conducting sensitivity
analytics. Sensitivity testing is a way of determining circumstances that differ from core
expectations. It is intended to monitor the degree of risks of the programme. It enables to
determine whether the output depending on the consistency of the inputs.
Question 2
(a) Calculate the following variances for the last month:
(i) the material usage variance for each ingredient and in total
Should use
(KG)
Did
use
(KG)
Difference(K
G)
Standar
d
cost/kg
Variance(
$)
Paraphrase This Document
Need a fresh take? Get an instant paraphrase of this document with our AI Paraphraser
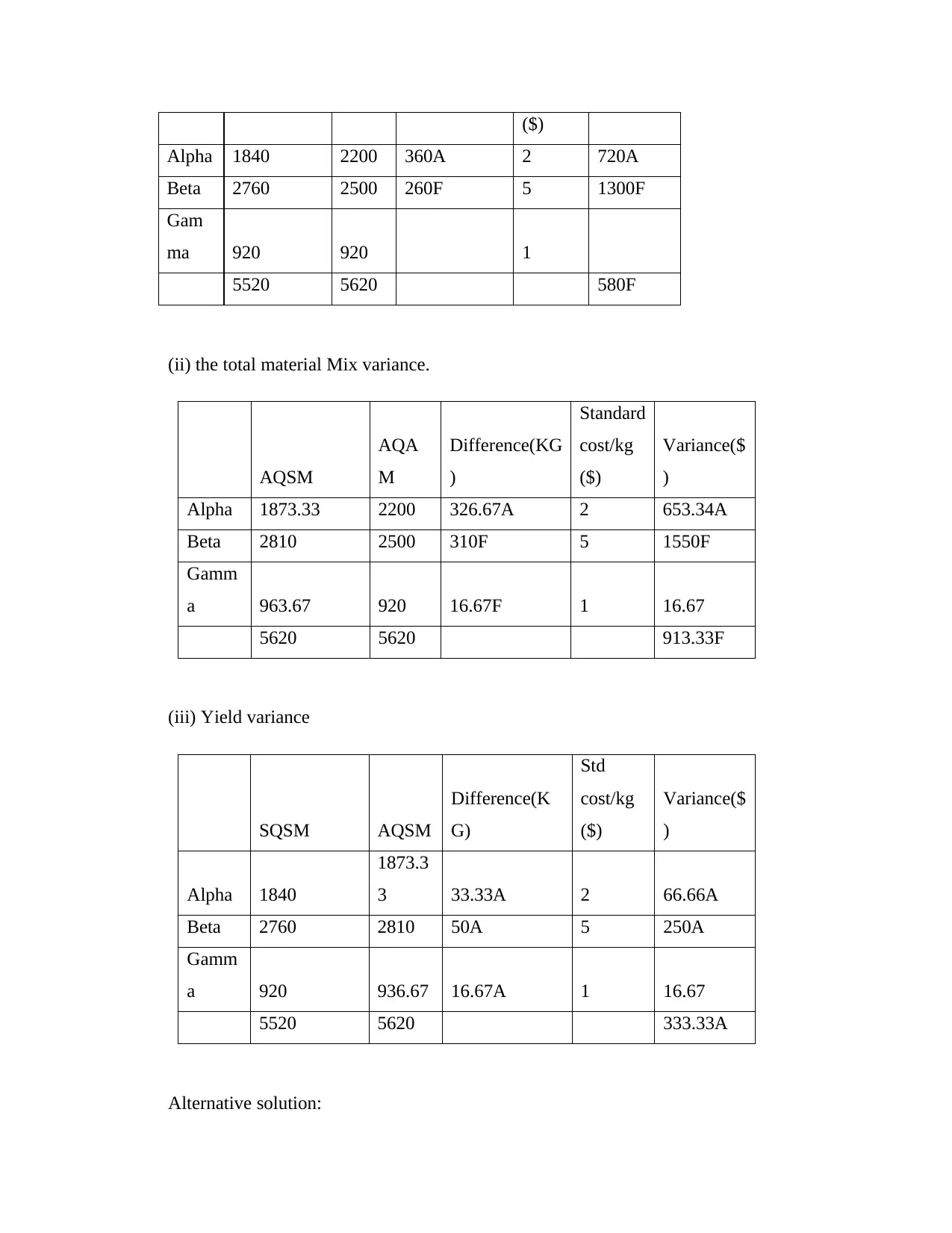
($)
Alpha 1840 2200 360A 2 720A
Beta 2760 2500 260F 5 1300F
Gam
ma 920 920 1
5520 5620 580F
(ii) the total material Mix variance.
AQSM
AQA
M
Difference(KG
)
Standard
cost/kg
($)
Variance($
)
Alpha 1873.33 2200 326.67A 2 653.34A
Beta 2810 2500 310F 5 1550F
Gamm
a 963.67 920 16.67F 1 16.67
5620 5620 913.33F
(iii) Yield variance
SQSM AQSM
Difference(K
G)
Std
cost/kg
($)
Variance($
)
Alpha 1840
1873.3
3 33.33A 2 66.66A
Beta 2760 2810 50A 5 250A
Gamm
a 920 936.67 16.67A 1 16.67
5520 5620 333.33A
Alternative solution:
Alpha 1840 2200 360A 2 720A
Beta 2760 2500 260F 5 1300F
Gam
ma 920 920 1
5520 5620 580F
(ii) the total material Mix variance.
AQSM
AQA
M
Difference(KG
)
Standard
cost/kg
($)
Variance($
)
Alpha 1873.33 2200 326.67A 2 653.34A
Beta 2810 2500 310F 5 1550F
Gamm
a 963.67 920 16.67F 1 16.67
5620 5620 913.33F
(iii) Yield variance
SQSM AQSM
Difference(K
G)
Std
cost/kg
($)
Variance($
)
Alpha 1840
1873.3
3 33.33A 2 66.66A
Beta 2760 2810 50A 5 250A
Gamm
a 920 936.67 16.67A 1 16.67
5520 5620 333.33A
Alternative solution:
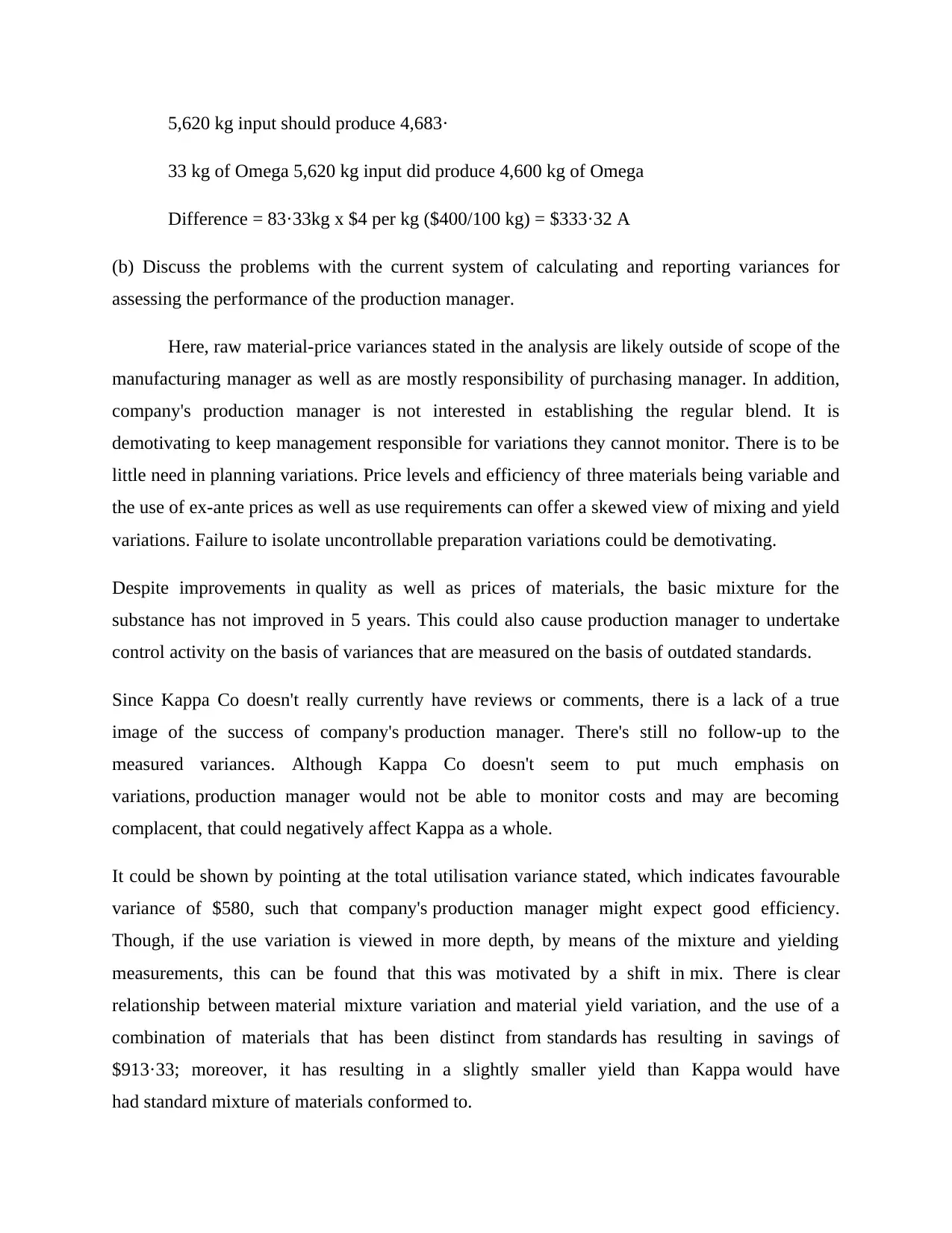
5,620 kg input should produce 4,683·
33 kg of Omega 5,620 kg input did produce 4,600 kg of Omega
Difference = 83·33kg x $4 per kg ($400/100 kg) = $333·32 A
(b) Discuss the problems with the current system of calculating and reporting variances for
assessing the performance of the production manager.
Here, raw material-price variances stated in the analysis are likely outside of scope of the
manufacturing manager as well as are mostly responsibility of purchasing manager. In addition,
company's production manager is not interested in establishing the regular blend. It is
demotivating to keep management responsible for variations they cannot monitor. There is to be
little need in planning variations. Price levels and efficiency of three materials being variable and
the use of ex-ante prices as well as use requirements can offer a skewed view of mixing and yield
variations. Failure to isolate uncontrollable preparation variations could be demotivating.
Despite improvements in quality as well as prices of materials, the basic mixture for the
substance has not improved in 5 years. This could also cause production manager to undertake
control activity on the basis of variances that are measured on the basis of outdated standards.
Since Kappa Co doesn't really currently have reviews or comments, there is a lack of a true
image of the success of company's production manager. There's still no follow-up to the
measured variances. Although Kappa Co doesn't seem to put much emphasis on
variations, production manager would not be able to monitor costs and may are becoming
complacent, that could negatively affect Kappa as a whole.
It could be shown by pointing at the total utilisation variance stated, which indicates favourable
variance of $580, such that company's production manager might expect good efficiency.
Though, if the use variation is viewed in more depth, by means of the mixture and yielding
measurements, this can be found that this was motivated by a shift in mix. There is clear
relationship between material mixture variation and material yield variation, and the use of a
combination of materials that has been distinct from standards has resulting in savings of
$913·33; moreover, it has resulting in a slightly smaller yield than Kappa would have
had standard mixture of materials conformed to.
33 kg of Omega 5,620 kg input did produce 4,600 kg of Omega
Difference = 83·33kg x $4 per kg ($400/100 kg) = $333·32 A
(b) Discuss the problems with the current system of calculating and reporting variances for
assessing the performance of the production manager.
Here, raw material-price variances stated in the analysis are likely outside of scope of the
manufacturing manager as well as are mostly responsibility of purchasing manager. In addition,
company's production manager is not interested in establishing the regular blend. It is
demotivating to keep management responsible for variations they cannot monitor. There is to be
little need in planning variations. Price levels and efficiency of three materials being variable and
the use of ex-ante prices as well as use requirements can offer a skewed view of mixing and yield
variations. Failure to isolate uncontrollable preparation variations could be demotivating.
Despite improvements in quality as well as prices of materials, the basic mixture for the
substance has not improved in 5 years. This could also cause production manager to undertake
control activity on the basis of variances that are measured on the basis of outdated standards.
Since Kappa Co doesn't really currently have reviews or comments, there is a lack of a true
image of the success of company's production manager. There's still no follow-up to the
measured variances. Although Kappa Co doesn't seem to put much emphasis on
variations, production manager would not be able to monitor costs and may are becoming
complacent, that could negatively affect Kappa as a whole.
It could be shown by pointing at the total utilisation variance stated, which indicates favourable
variance of $580, such that company's production manager might expect good efficiency.
Though, if the use variation is viewed in more depth, by means of the mixture and yielding
measurements, this can be found that this was motivated by a shift in mix. There is clear
relationship between material mixture variation and material yield variation, and the use of a
combination of materials that has been distinct from standards has resulting in savings of
$913·33; moreover, it has resulting in a slightly smaller yield than Kappa would have
had standard mixture of materials conformed to.
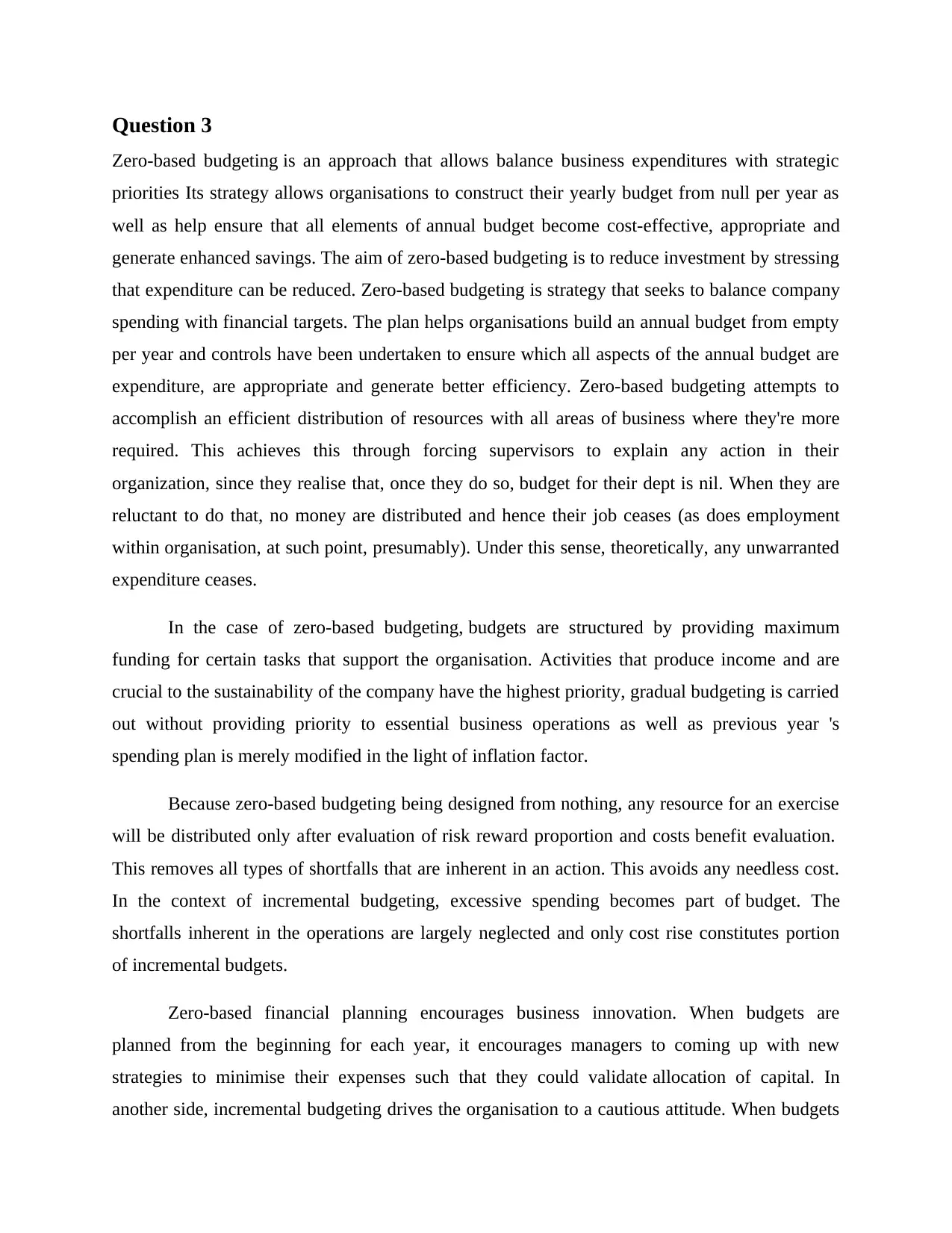
Question 3
Zero-based budgeting is an approach that allows balance business expenditures with strategic
priorities Its strategy allows organisations to construct their yearly budget from null per year as
well as help ensure that all elements of annual budget become cost-effective, appropriate and
generate enhanced savings. The aim of zero-based budgeting is to reduce investment by stressing
that expenditure can be reduced. Zero-based budgeting is strategy that seeks to balance company
spending with financial targets. The plan helps organisations build an annual budget from empty
per year and controls have been undertaken to ensure which all aspects of the annual budget are
expenditure, are appropriate and generate better efficiency. Zero-based budgeting attempts to
accomplish an efficient distribution of resources with all areas of business where they're more
required. This achieves this through forcing supervisors to explain any action in their
organization, since they realise that, once they do so, budget for their dept is nil. When they are
reluctant to do that, no money are distributed and hence their job ceases (as does employment
within organisation, at such point, presumably). Under this sense, theoretically, any unwarranted
expenditure ceases.
In the case of zero-based budgeting, budgets are structured by providing maximum
funding for certain tasks that support the organisation. Activities that produce income and are
crucial to the sustainability of the company have the highest priority, gradual budgeting is carried
out without providing priority to essential business operations as well as previous year 's
spending plan is merely modified in the light of inflation factor.
Because zero-based budgeting being designed from nothing, any resource for an exercise
will be distributed only after evaluation of risk reward proportion and costs benefit evaluation.
This removes all types of shortfalls that are inherent in an action. This avoids any needless cost.
In the context of incremental budgeting, excessive spending becomes part of budget. The
shortfalls inherent in the operations are largely neglected and only cost rise constitutes portion
of incremental budgets.
Zero-based financial planning encourages business innovation. When budgets are
planned from the beginning for each year, it encourages managers to coming up with new
strategies to minimise their expenses such that they could validate allocation of capital. In
another side, incremental budgeting drives the organisation to a cautious attitude. When budgets
Zero-based budgeting is an approach that allows balance business expenditures with strategic
priorities Its strategy allows organisations to construct their yearly budget from null per year as
well as help ensure that all elements of annual budget become cost-effective, appropriate and
generate enhanced savings. The aim of zero-based budgeting is to reduce investment by stressing
that expenditure can be reduced. Zero-based budgeting is strategy that seeks to balance company
spending with financial targets. The plan helps organisations build an annual budget from empty
per year and controls have been undertaken to ensure which all aspects of the annual budget are
expenditure, are appropriate and generate better efficiency. Zero-based budgeting attempts to
accomplish an efficient distribution of resources with all areas of business where they're more
required. This achieves this through forcing supervisors to explain any action in their
organization, since they realise that, once they do so, budget for their dept is nil. When they are
reluctant to do that, no money are distributed and hence their job ceases (as does employment
within organisation, at such point, presumably). Under this sense, theoretically, any unwarranted
expenditure ceases.
In the case of zero-based budgeting, budgets are structured by providing maximum
funding for certain tasks that support the organisation. Activities that produce income and are
crucial to the sustainability of the company have the highest priority, gradual budgeting is carried
out without providing priority to essential business operations as well as previous year 's
spending plan is merely modified in the light of inflation factor.
Because zero-based budgeting being designed from nothing, any resource for an exercise
will be distributed only after evaluation of risk reward proportion and costs benefit evaluation.
This removes all types of shortfalls that are inherent in an action. This avoids any needless cost.
In the context of incremental budgeting, excessive spending becomes part of budget. The
shortfalls inherent in the operations are largely neglected and only cost rise constitutes portion
of incremental budgets.
Zero-based financial planning encourages business innovation. When budgets are
planned from the beginning for each year, it encourages managers to coming up with new
strategies to minimise their expenses such that they could validate allocation of capital. In
another side, incremental budgeting drives the organisation to a cautious attitude. When budgets
Secure Best Marks with AI Grader
Need help grading? Try our AI Grader for instant feedback on your assignments.
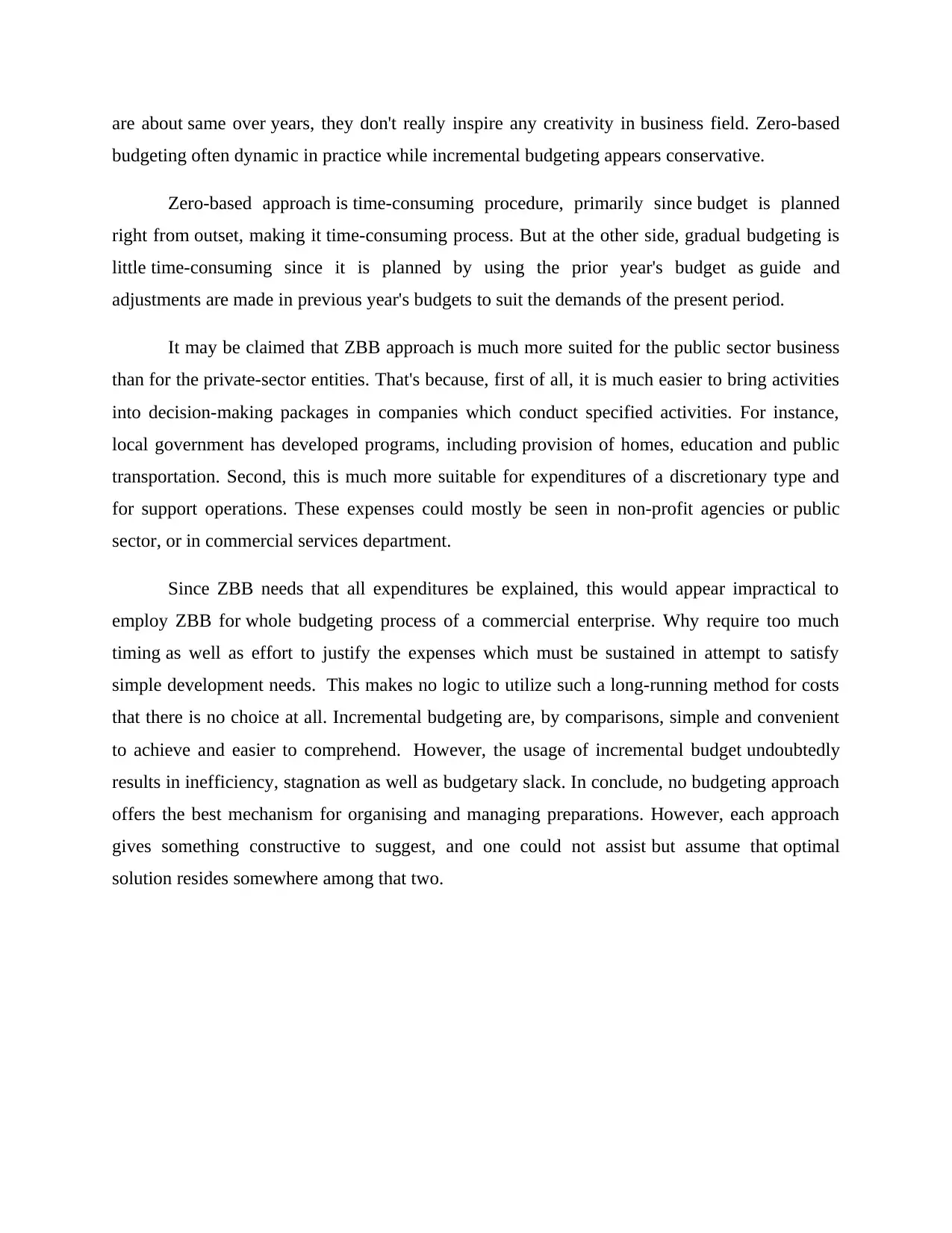
are about same over years, they don't really inspire any creativity in business field. Zero-based
budgeting often dynamic in practice while incremental budgeting appears conservative.
Zero-based approach is time-consuming procedure, primarily since budget is planned
right from outset, making it time-consuming process. But at the other side, gradual budgeting is
little time-consuming since it is planned by using the prior year's budget as guide and
adjustments are made in previous year's budgets to suit the demands of the present period.
It may be claimed that ZBB approach is much more suited for the public sector business
than for the private-sector entities. That's because, first of all, it is much easier to bring activities
into decision-making packages in companies which conduct specified activities. For instance,
local government has developed programs, including provision of homes, education and public
transportation. Second, this is much more suitable for expenditures of a discretionary type and
for support operations. These expenses could mostly be seen in non-profit agencies or public
sector, or in commercial services department.
Since ZBB needs that all expenditures be explained, this would appear impractical to
employ ZBB for whole budgeting process of a commercial enterprise. Why require too much
timing as well as effort to justify the expenses which must be sustained in attempt to satisfy
simple development needs. This makes no logic to utilize such a long-running method for costs
that there is no choice at all. Incremental budgeting are, by comparisons, simple and convenient
to achieve and easier to comprehend. However, the usage of incremental budget undoubtedly
results in inefficiency, stagnation as well as budgetary slack. In conclude, no budgeting approach
offers the best mechanism for organising and managing preparations. However, each approach
gives something constructive to suggest, and one could not assist but assume that optimal
solution resides somewhere among that two.
budgeting often dynamic in practice while incremental budgeting appears conservative.
Zero-based approach is time-consuming procedure, primarily since budget is planned
right from outset, making it time-consuming process. But at the other side, gradual budgeting is
little time-consuming since it is planned by using the prior year's budget as guide and
adjustments are made in previous year's budgets to suit the demands of the present period.
It may be claimed that ZBB approach is much more suited for the public sector business
than for the private-sector entities. That's because, first of all, it is much easier to bring activities
into decision-making packages in companies which conduct specified activities. For instance,
local government has developed programs, including provision of homes, education and public
transportation. Second, this is much more suitable for expenditures of a discretionary type and
for support operations. These expenses could mostly be seen in non-profit agencies or public
sector, or in commercial services department.
Since ZBB needs that all expenditures be explained, this would appear impractical to
employ ZBB for whole budgeting process of a commercial enterprise. Why require too much
timing as well as effort to justify the expenses which must be sustained in attempt to satisfy
simple development needs. This makes no logic to utilize such a long-running method for costs
that there is no choice at all. Incremental budgeting are, by comparisons, simple and convenient
to achieve and easier to comprehend. However, the usage of incremental budget undoubtedly
results in inefficiency, stagnation as well as budgetary slack. In conclude, no budgeting approach
offers the best mechanism for organising and managing preparations. However, each approach
gives something constructive to suggest, and one could not assist but assume that optimal
solution resides somewhere among that two.
1 out of 11
Related Documents
![[object Object]](/_next/image/?url=%2F_next%2Fstatic%2Fmedia%2Flogo.6d15ce61.png&w=640&q=75)
Your All-in-One AI-Powered Toolkit for Academic Success.
 +13062052269
info@desklib.com
Available 24*7 on WhatsApp / Email
Unlock your academic potential
© 2024  |  Zucol Services PVT LTD  |  All rights reserved.