Financial Performance Management: Costing and Budgeting Analysis
VerifiedAdded on 2022/12/28
|9
|1888
|63
Homework Assignment
AI Summary
This assignment provides a comprehensive analysis of financial performance management. It begins with a detailed examination of absorption costing and activity-based costing (ABC), comparing their applications and implications on product costing and profitability. The solution includes calculation...
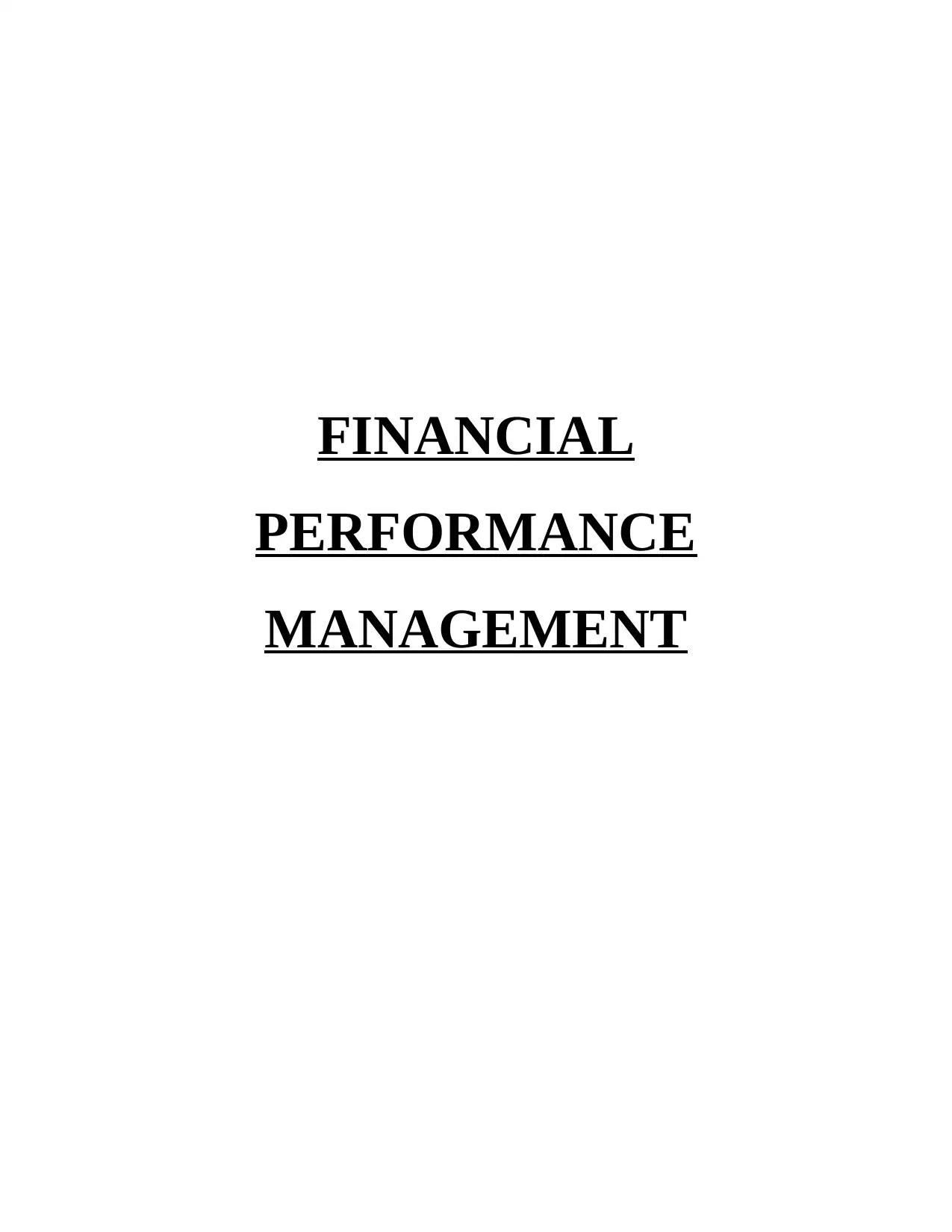
FINANCIAL
PERFORMANCE
MANAGEMENT
PERFORMANCE
MANAGEMENT
Paraphrase This Document
Need a fresh take? Get an instant paraphrase of this document with our AI Paraphraser
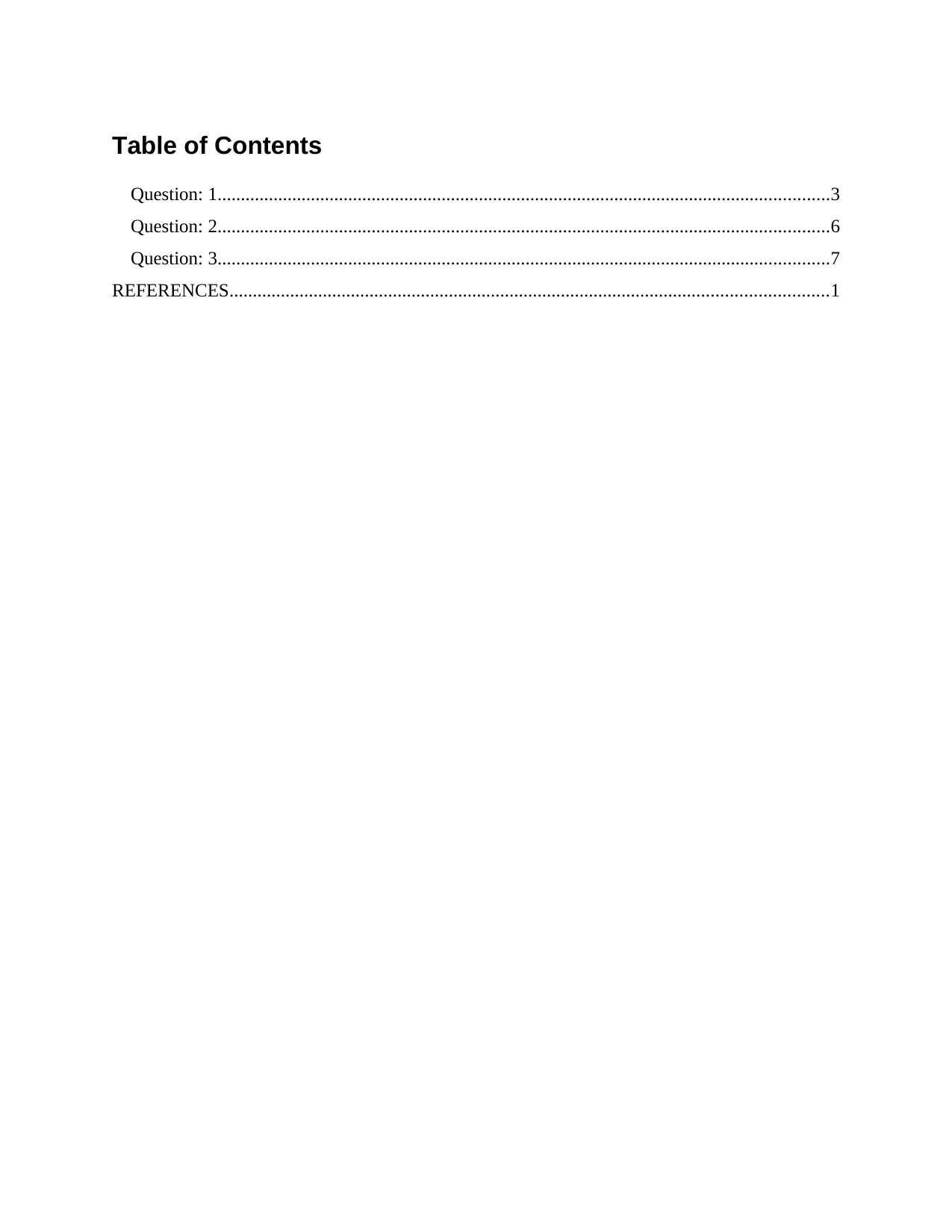
Table of Contents
Question: 1...................................................................................................................................3
Question: 2...................................................................................................................................6
Question: 3...................................................................................................................................7
REFERENCES................................................................................................................................1
Question: 1...................................................................................................................................3
Question: 2...................................................................................................................................6
Question: 3...................................................................................................................................7
REFERENCES................................................................................................................................1
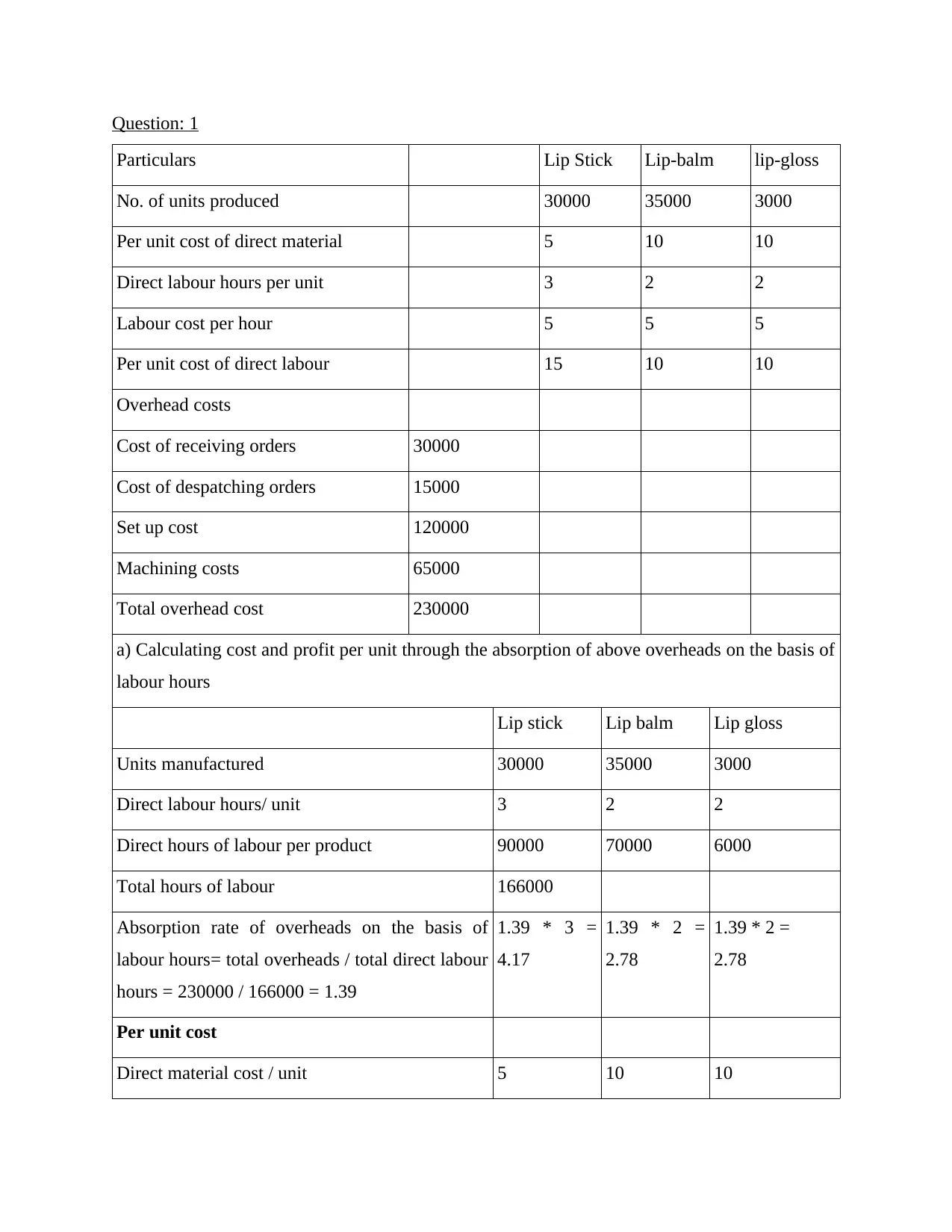
Question: 1
Particulars Lip Stick Lip-balm lip-gloss
No. of units produced 30000 35000 3000
Per unit cost of direct material 5 10 10
Direct labour hours per unit 3 2 2
Labour cost per hour 5 5 5
Per unit cost of direct labour 15 10 10
Overhead costs
Cost of receiving orders 30000
Cost of despatching orders 15000
Set up cost 120000
Machining costs 65000
Total overhead cost 230000
a) Calculating cost and profit per unit through the absorption of above overheads on the basis of
labour hours
Lip stick Lip balm Lip gloss
Units manufactured 30000 35000 3000
Direct labour hours/ unit 3 2 2
Direct hours of labour per product 90000 70000 6000
Total hours of labour 166000
Absorption rate of overheads on the basis of
labour hours= total overheads / total direct labour
hours = 230000 / 166000 = 1.39
1.39 * 3 =
4.17
1.39 * 2 =
2.78
1.39 * 2 =
2.78
Per unit cost
Direct material cost / unit 5 10 10
Particulars Lip Stick Lip-balm lip-gloss
No. of units produced 30000 35000 3000
Per unit cost of direct material 5 10 10
Direct labour hours per unit 3 2 2
Labour cost per hour 5 5 5
Per unit cost of direct labour 15 10 10
Overhead costs
Cost of receiving orders 30000
Cost of despatching orders 15000
Set up cost 120000
Machining costs 65000
Total overhead cost 230000
a) Calculating cost and profit per unit through the absorption of above overheads on the basis of
labour hours
Lip stick Lip balm Lip gloss
Units manufactured 30000 35000 3000
Direct labour hours/ unit 3 2 2
Direct hours of labour per product 90000 70000 6000
Total hours of labour 166000
Absorption rate of overheads on the basis of
labour hours= total overheads / total direct labour
hours = 230000 / 166000 = 1.39
1.39 * 3 =
4.17
1.39 * 2 =
2.78
1.39 * 2 =
2.78
Per unit cost
Direct material cost / unit 5 10 10
You're viewing a preview
Unlock full access by subscribing today!
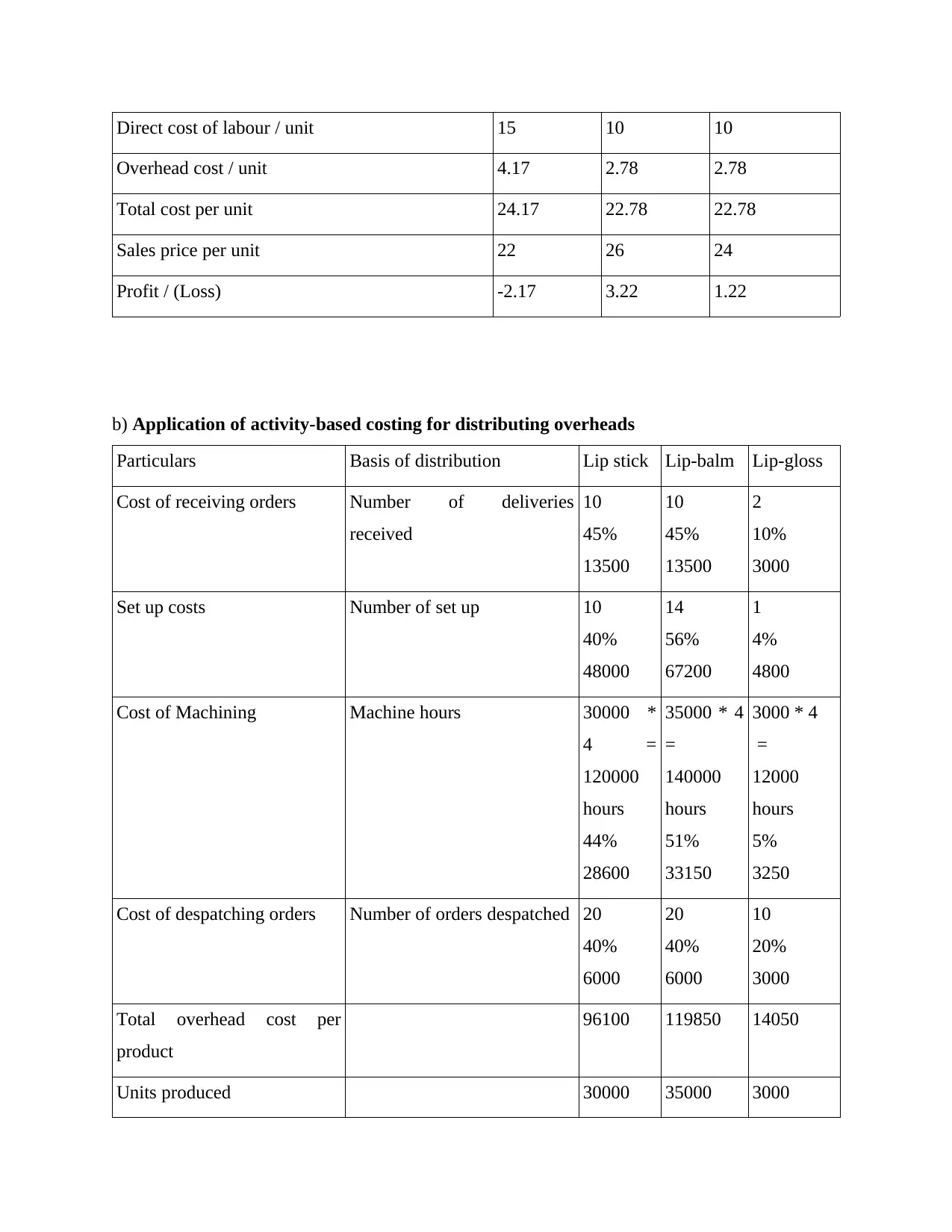
Direct cost of labour / unit 15 10 10
Overhead cost / unit 4.17 2.78 2.78
Total cost per unit 24.17 22.78 22.78
Sales price per unit 22 26 24
Profit / (Loss) -2.17 3.22 1.22
b) Application of activity-based costing for distributing overheads
Particulars Basis of distribution Lip stick Lip-balm Lip-gloss
Cost of receiving orders Number of deliveries
received
10
45%
13500
10
45%
13500
2
10%
3000
Set up costs Number of set up 10
40%
48000
14
56%
67200
1
4%
4800
Cost of Machining Machine hours 30000 *
4 =
120000
hours
44%
28600
35000 * 4
=
140000
hours
51%
33150
3000 * 4
=
12000
hours
5%
3250
Cost of despatching orders Number of orders despatched 20
40%
6000
20
40%
6000
10
20%
3000
Total overhead cost per
product
96100 119850 14050
Units produced 30000 35000 3000
Overhead cost / unit 4.17 2.78 2.78
Total cost per unit 24.17 22.78 22.78
Sales price per unit 22 26 24
Profit / (Loss) -2.17 3.22 1.22
b) Application of activity-based costing for distributing overheads
Particulars Basis of distribution Lip stick Lip-balm Lip-gloss
Cost of receiving orders Number of deliveries
received
10
45%
13500
10
45%
13500
2
10%
3000
Set up costs Number of set up 10
40%
48000
14
56%
67200
1
4%
4800
Cost of Machining Machine hours 30000 *
4 =
120000
hours
44%
28600
35000 * 4
=
140000
hours
51%
33150
3000 * 4
=
12000
hours
5%
3250
Cost of despatching orders Number of orders despatched 20
40%
6000
20
40%
6000
10
20%
3000
Total overhead cost per
product
96100 119850 14050
Units produced 30000 35000 3000
Paraphrase This Document
Need a fresh take? Get an instant paraphrase of this document with our AI Paraphraser
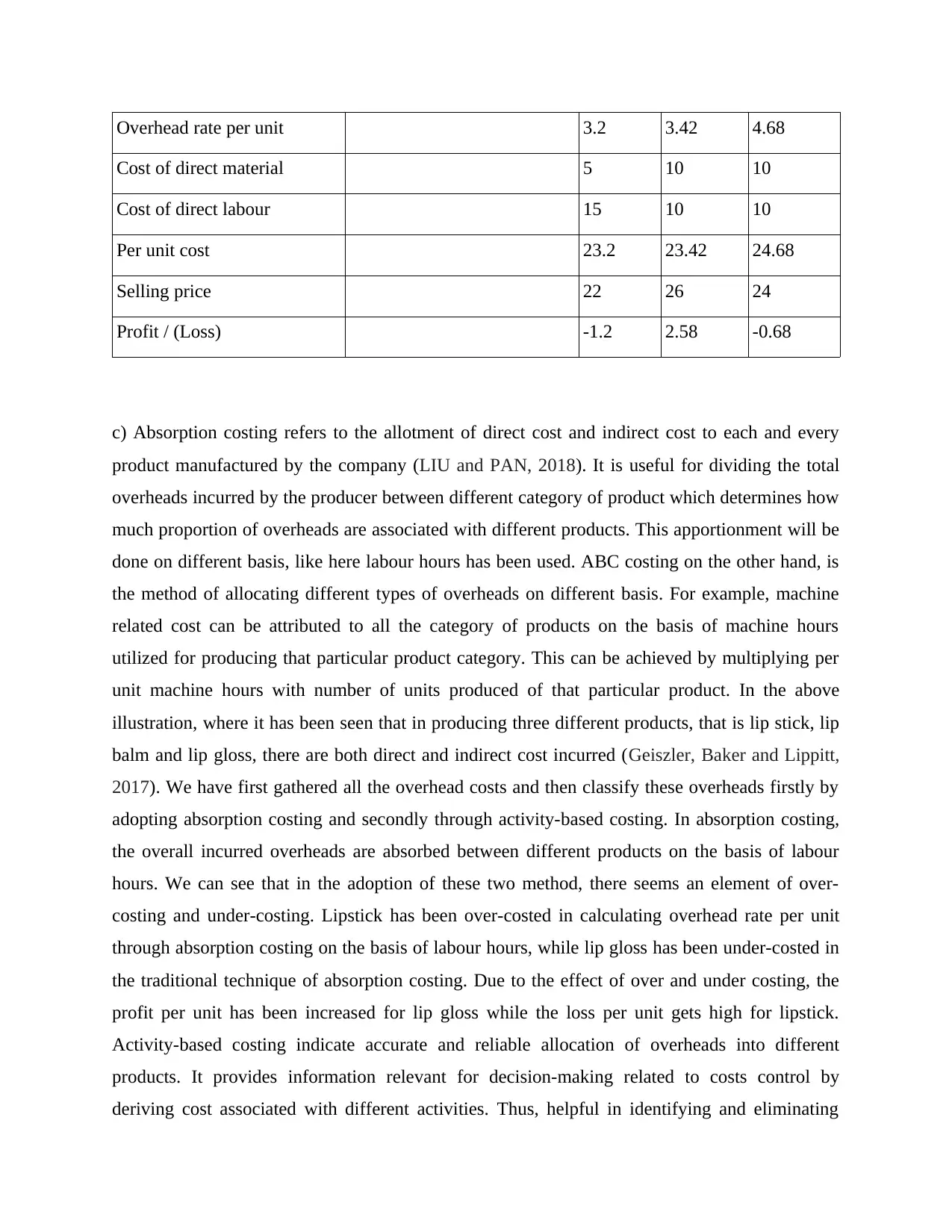
Overhead rate per unit 3.2 3.42 4.68
Cost of direct material 5 10 10
Cost of direct labour 15 10 10
Per unit cost 23.2 23.42 24.68
Selling price 22 26 24
Profit / (Loss) -1.2 2.58 -0.68
c) Absorption costing refers to the allotment of direct cost and indirect cost to each and every
product manufactured by the company (LIU and PAN, 2018). It is useful for dividing the total
overheads incurred by the producer between different category of product which determines how
much proportion of overheads are associated with different products. This apportionment will be
done on different basis, like here labour hours has been used. ABC costing on the other hand, is
the method of allocating different types of overheads on different basis. For example, machine
related cost can be attributed to all the category of products on the basis of machine hours
utilized for producing that particular product category. This can be achieved by multiplying per
unit machine hours with number of units produced of that particular product. In the above
illustration, where it has been seen that in producing three different products, that is lip stick, lip
balm and lip gloss, there are both direct and indirect cost incurred (Geiszler, Baker and Lippitt,
2017). We have first gathered all the overhead costs and then classify these overheads firstly by
adopting absorption costing and secondly through activity-based costing. In absorption costing,
the overall incurred overheads are absorbed between different products on the basis of labour
hours. We can see that in the adoption of these two method, there seems an element of over-
costing and under-costing. Lipstick has been over-costed in calculating overhead rate per unit
through absorption costing on the basis of labour hours, while lip gloss has been under-costed in
the traditional technique of absorption costing. Due to the effect of over and under costing, the
profit per unit has been increased for lip gloss while the loss per unit gets high for lipstick.
Activity-based costing indicate accurate and reliable allocation of overheads into different
products. It provides information relevant for decision-making related to costs control by
deriving cost associated with different activities. Thus, helpful in identifying and eliminating
Cost of direct material 5 10 10
Cost of direct labour 15 10 10
Per unit cost 23.2 23.42 24.68
Selling price 22 26 24
Profit / (Loss) -1.2 2.58 -0.68
c) Absorption costing refers to the allotment of direct cost and indirect cost to each and every
product manufactured by the company (LIU and PAN, 2018). It is useful for dividing the total
overheads incurred by the producer between different category of product which determines how
much proportion of overheads are associated with different products. This apportionment will be
done on different basis, like here labour hours has been used. ABC costing on the other hand, is
the method of allocating different types of overheads on different basis. For example, machine
related cost can be attributed to all the category of products on the basis of machine hours
utilized for producing that particular product category. This can be achieved by multiplying per
unit machine hours with number of units produced of that particular product. In the above
illustration, where it has been seen that in producing three different products, that is lip stick, lip
balm and lip gloss, there are both direct and indirect cost incurred (Geiszler, Baker and Lippitt,
2017). We have first gathered all the overhead costs and then classify these overheads firstly by
adopting absorption costing and secondly through activity-based costing. In absorption costing,
the overall incurred overheads are absorbed between different products on the basis of labour
hours. We can see that in the adoption of these two method, there seems an element of over-
costing and under-costing. Lipstick has been over-costed in calculating overhead rate per unit
through absorption costing on the basis of labour hours, while lip gloss has been under-costed in
the traditional technique of absorption costing. Due to the effect of over and under costing, the
profit per unit has been increased for lip gloss while the loss per unit gets high for lipstick.
Activity-based costing indicate accurate and reliable allocation of overheads into different
products. It provides information relevant for decision-making related to costs control by
deriving cost associated with different activities. Thus, helpful in identifying and eliminating
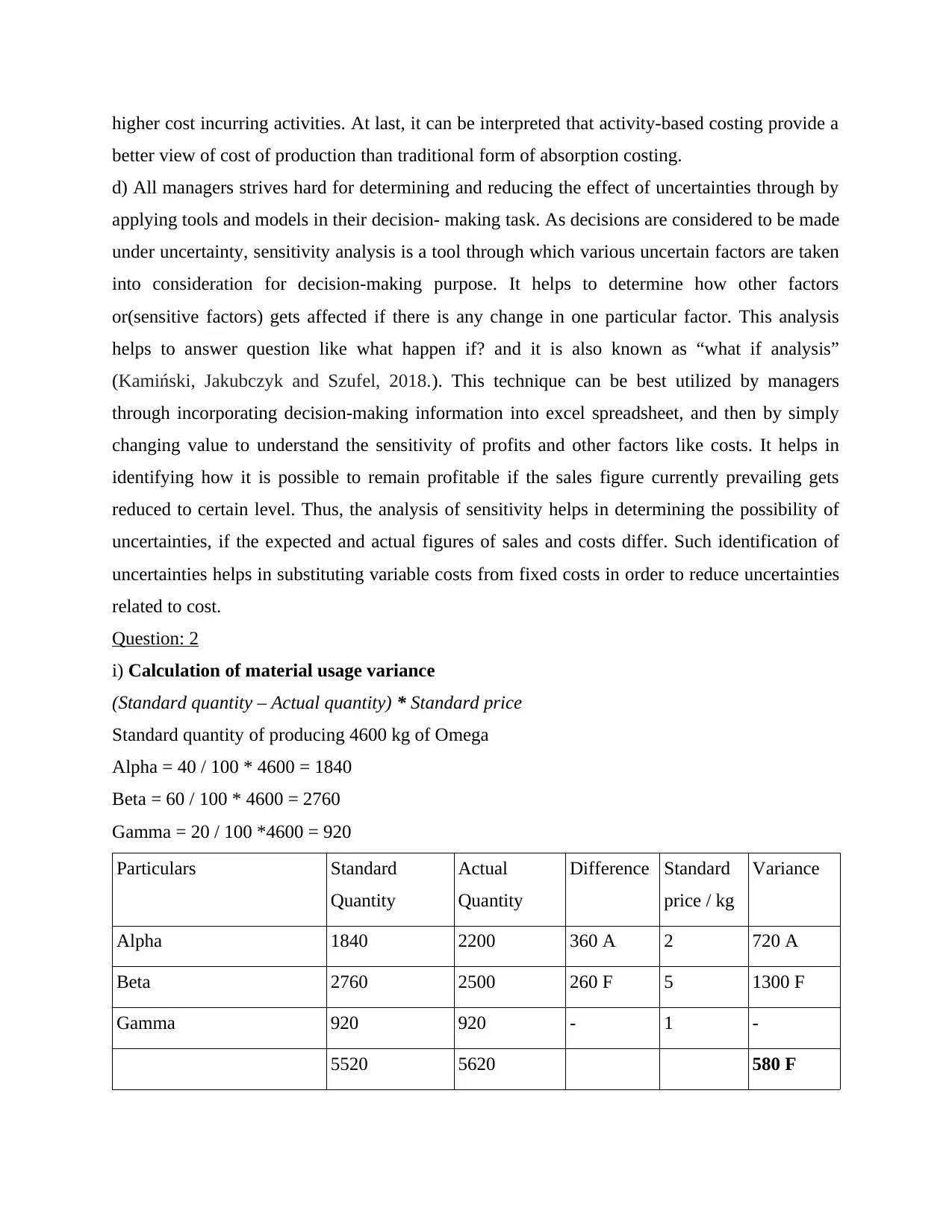
higher cost incurring activities. At last, it can be interpreted that activity-based costing provide a
better view of cost of production than traditional form of absorption costing.
d) All managers strives hard for determining and reducing the effect of uncertainties through by
applying tools and models in their decision- making task. As decisions are considered to be made
under uncertainty, sensitivity analysis is a tool through which various uncertain factors are taken
into consideration for decision-making purpose. It helps to determine how other factors
or(sensitive factors) gets affected if there is any change in one particular factor. This analysis
helps to answer question like what happen if? and it is also known as “what if analysis”
(Kamiński, Jakubczyk and Szufel, 2018.). This technique can be best utilized by managers
through incorporating decision-making information into excel spreadsheet, and then by simply
changing value to understand the sensitivity of profits and other factors like costs. It helps in
identifying how it is possible to remain profitable if the sales figure currently prevailing gets
reduced to certain level. Thus, the analysis of sensitivity helps in determining the possibility of
uncertainties, if the expected and actual figures of sales and costs differ. Such identification of
uncertainties helps in substituting variable costs from fixed costs in order to reduce uncertainties
related to cost.
Question: 2
i) Calculation of material usage variance
(Standard quantity – Actual quantity) * Standard price
Standard quantity of producing 4600 kg of Omega
Alpha = 40 / 100 * 4600 = 1840
Beta = 60 / 100 * 4600 = 2760
Gamma = 20 / 100 *4600 = 920
Particulars Standard
Quantity
Actual
Quantity
Difference Standard
price / kg
Variance
Alpha 1840 2200 360 A 2 720 A
Beta 2760 2500 260 F 5 1300 F
Gamma 920 920 - 1 -
5520 5620 580 F
better view of cost of production than traditional form of absorption costing.
d) All managers strives hard for determining and reducing the effect of uncertainties through by
applying tools and models in their decision- making task. As decisions are considered to be made
under uncertainty, sensitivity analysis is a tool through which various uncertain factors are taken
into consideration for decision-making purpose. It helps to determine how other factors
or(sensitive factors) gets affected if there is any change in one particular factor. This analysis
helps to answer question like what happen if? and it is also known as “what if analysis”
(Kamiński, Jakubczyk and Szufel, 2018.). This technique can be best utilized by managers
through incorporating decision-making information into excel spreadsheet, and then by simply
changing value to understand the sensitivity of profits and other factors like costs. It helps in
identifying how it is possible to remain profitable if the sales figure currently prevailing gets
reduced to certain level. Thus, the analysis of sensitivity helps in determining the possibility of
uncertainties, if the expected and actual figures of sales and costs differ. Such identification of
uncertainties helps in substituting variable costs from fixed costs in order to reduce uncertainties
related to cost.
Question: 2
i) Calculation of material usage variance
(Standard quantity – Actual quantity) * Standard price
Standard quantity of producing 4600 kg of Omega
Alpha = 40 / 100 * 4600 = 1840
Beta = 60 / 100 * 4600 = 2760
Gamma = 20 / 100 *4600 = 920
Particulars Standard
Quantity
Actual
Quantity
Difference Standard
price / kg
Variance
Alpha 1840 2200 360 A 2 720 A
Beta 2760 2500 260 F 5 1300 F
Gamma 920 920 - 1 -
5520 5620 580 F
You're viewing a preview
Unlock full access by subscribing today!
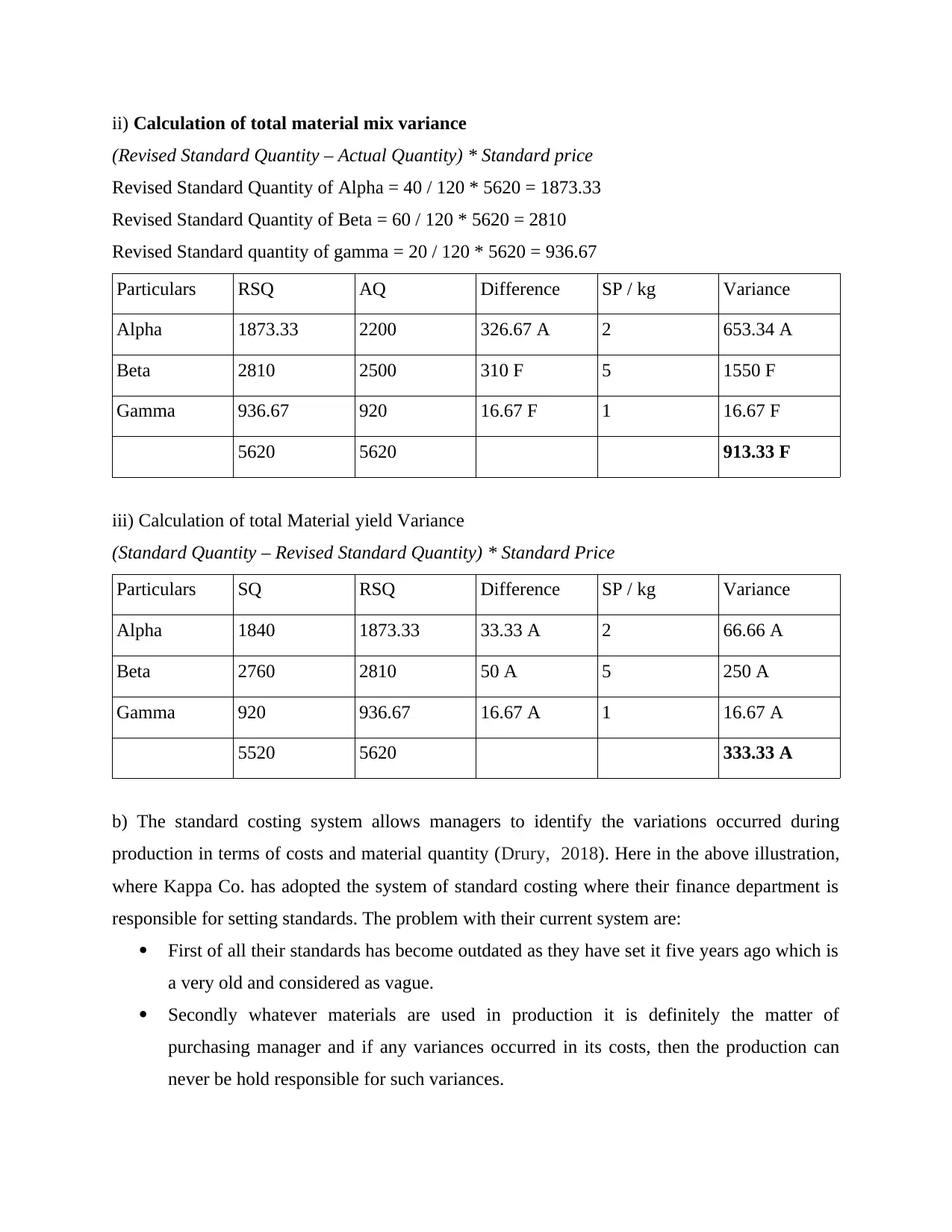
ii) Calculation of total material mix variance
(Revised Standard Quantity – Actual Quantity) * Standard price
Revised Standard Quantity of Alpha = 40 / 120 * 5620 = 1873.33
Revised Standard Quantity of Beta = 60 / 120 * 5620 = 2810
Revised Standard quantity of gamma = 20 / 120 * 5620 = 936.67
Particulars RSQ AQ Difference SP / kg Variance
Alpha 1873.33 2200 326.67 A 2 653.34 A
Beta 2810 2500 310 F 5 1550 F
Gamma 936.67 920 16.67 F 1 16.67 F
5620 5620 913.33 F
iii) Calculation of total Material yield Variance
(Standard Quantity – Revised Standard Quantity) * Standard Price
Particulars SQ RSQ Difference SP / kg Variance
Alpha 1840 1873.33 33.33 A 2 66.66 A
Beta 2760 2810 50 A 5 250 A
Gamma 920 936.67 16.67 A 1 16.67 A
5520 5620 333.33 A
b) The standard costing system allows managers to identify the variations occurred during
production in terms of costs and material quantity (Drury, 2018). Here in the above illustration,
where Kappa Co. has adopted the system of standard costing where their finance department is
responsible for setting standards. The problem with their current system are:
First of all their standards has become outdated as they have set it five years ago which is
a very old and considered as vague.
Secondly whatever materials are used in production it is definitely the matter of
purchasing manager and if any variances occurred in its costs, then the production can
never be hold responsible for such variances.
(Revised Standard Quantity – Actual Quantity) * Standard price
Revised Standard Quantity of Alpha = 40 / 120 * 5620 = 1873.33
Revised Standard Quantity of Beta = 60 / 120 * 5620 = 2810
Revised Standard quantity of gamma = 20 / 120 * 5620 = 936.67
Particulars RSQ AQ Difference SP / kg Variance
Alpha 1873.33 2200 326.67 A 2 653.34 A
Beta 2810 2500 310 F 5 1550 F
Gamma 936.67 920 16.67 F 1 16.67 F
5620 5620 913.33 F
iii) Calculation of total Material yield Variance
(Standard Quantity – Revised Standard Quantity) * Standard Price
Particulars SQ RSQ Difference SP / kg Variance
Alpha 1840 1873.33 33.33 A 2 66.66 A
Beta 2760 2810 50 A 5 250 A
Gamma 920 936.67 16.67 A 1 16.67 A
5520 5620 333.33 A
b) The standard costing system allows managers to identify the variations occurred during
production in terms of costs and material quantity (Drury, 2018). Here in the above illustration,
where Kappa Co. has adopted the system of standard costing where their finance department is
responsible for setting standards. The problem with their current system are:
First of all their standards has become outdated as they have set it five years ago which is
a very old and considered as vague.
Secondly whatever materials are used in production it is definitely the matter of
purchasing manager and if any variances occurred in its costs, then the production can
never be hold responsible for such variances.
Paraphrase This Document
Need a fresh take? Get an instant paraphrase of this document with our AI Paraphraser
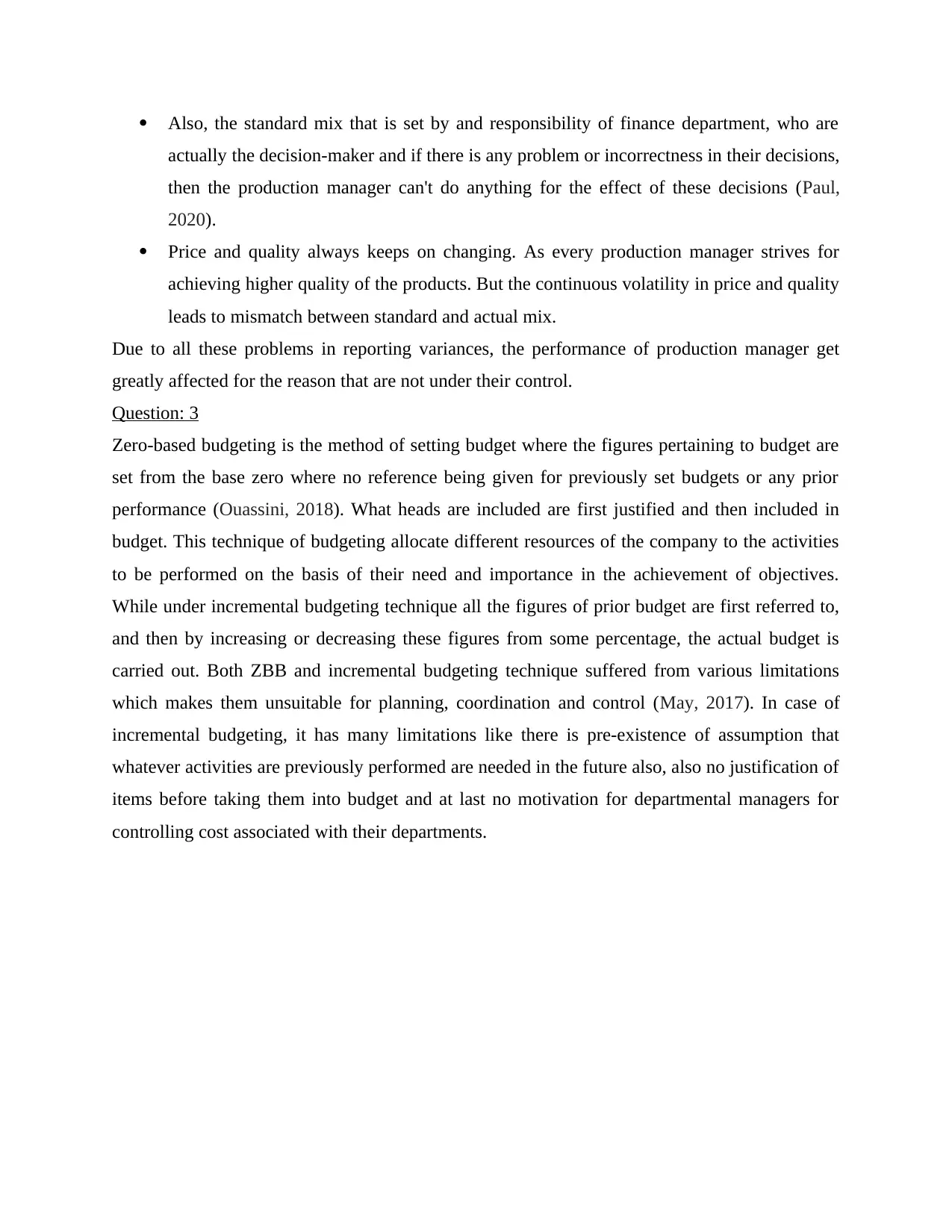
Also, the standard mix that is set by and responsibility of finance department, who are
actually the decision-maker and if there is any problem or incorrectness in their decisions,
then the production manager can't do anything for the effect of these decisions (Paul,
2020).
Price and quality always keeps on changing. As every production manager strives for
achieving higher quality of the products. But the continuous volatility in price and quality
leads to mismatch between standard and actual mix.
Due to all these problems in reporting variances, the performance of production manager get
greatly affected for the reason that are not under their control.
Question: 3
Zero-based budgeting is the method of setting budget where the figures pertaining to budget are
set from the base zero where no reference being given for previously set budgets or any prior
performance (Ouassini, 2018). What heads are included are first justified and then included in
budget. This technique of budgeting allocate different resources of the company to the activities
to be performed on the basis of their need and importance in the achievement of objectives.
While under incremental budgeting technique all the figures of prior budget are first referred to,
and then by increasing or decreasing these figures from some percentage, the actual budget is
carried out. Both ZBB and incremental budgeting technique suffered from various limitations
which makes them unsuitable for planning, coordination and control (May, 2017). In case of
incremental budgeting, it has many limitations like there is pre-existence of assumption that
whatever activities are previously performed are needed in the future also, also no justification of
items before taking them into budget and at last no motivation for departmental managers for
controlling cost associated with their departments.
actually the decision-maker and if there is any problem or incorrectness in their decisions,
then the production manager can't do anything for the effect of these decisions (Paul,
2020).
Price and quality always keeps on changing. As every production manager strives for
achieving higher quality of the products. But the continuous volatility in price and quality
leads to mismatch between standard and actual mix.
Due to all these problems in reporting variances, the performance of production manager get
greatly affected for the reason that are not under their control.
Question: 3
Zero-based budgeting is the method of setting budget where the figures pertaining to budget are
set from the base zero where no reference being given for previously set budgets or any prior
performance (Ouassini, 2018). What heads are included are first justified and then included in
budget. This technique of budgeting allocate different resources of the company to the activities
to be performed on the basis of their need and importance in the achievement of objectives.
While under incremental budgeting technique all the figures of prior budget are first referred to,
and then by increasing or decreasing these figures from some percentage, the actual budget is
carried out. Both ZBB and incremental budgeting technique suffered from various limitations
which makes them unsuitable for planning, coordination and control (May, 2017). In case of
incremental budgeting, it has many limitations like there is pre-existence of assumption that
whatever activities are previously performed are needed in the future also, also no justification of
items before taking them into budget and at last no motivation for departmental managers for
controlling cost associated with their departments.
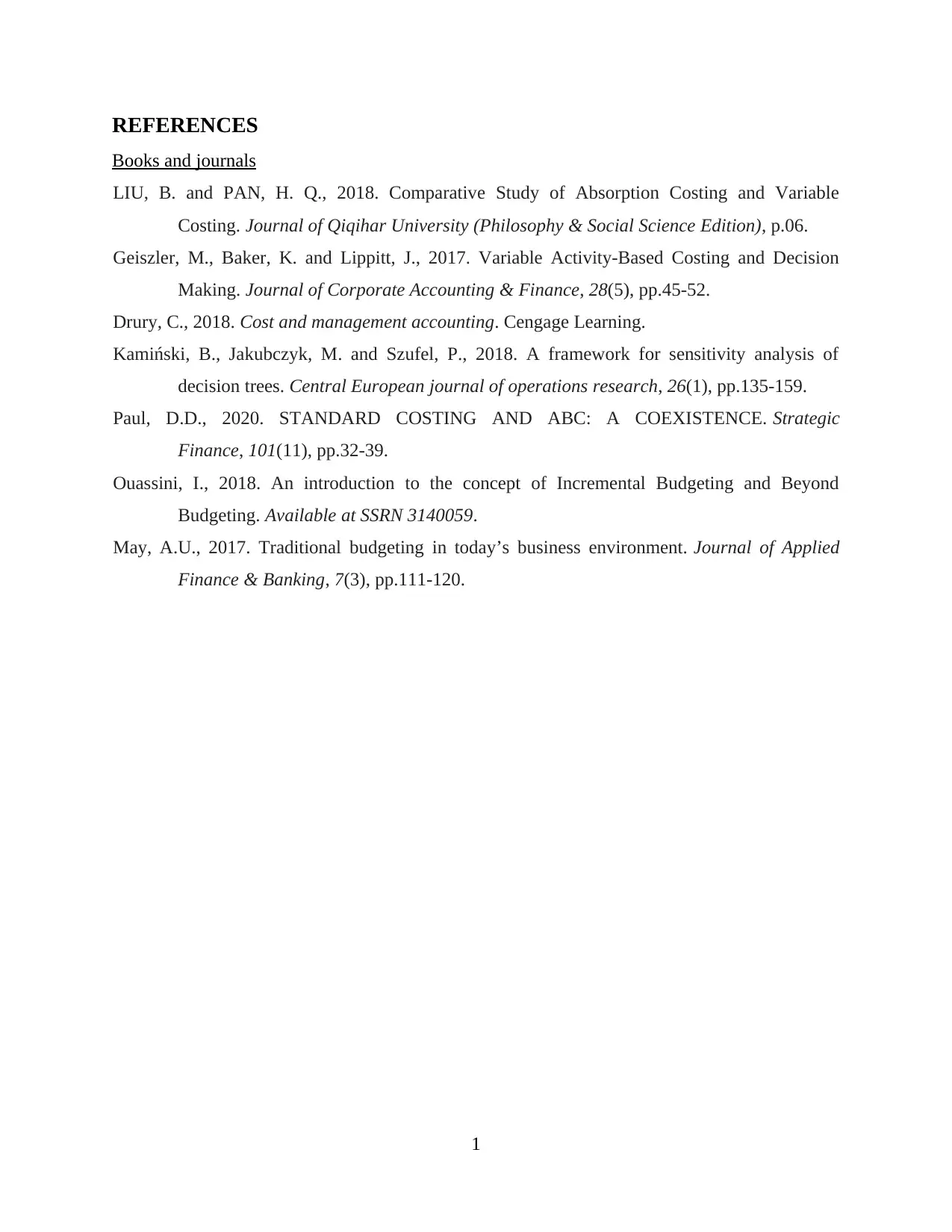
REFERENCES
Books and journals
LIU, B. and PAN, H. Q., 2018. Comparative Study of Absorption Costing and Variable
Costing. Journal of Qiqihar University (Philosophy & Social Science Edition), p.06.
Geiszler, M., Baker, K. and Lippitt, J., 2017. Variable Activity‐Based Costing and Decision
Making. Journal of Corporate Accounting & Finance, 28(5), pp.45-52.
Drury, C., 2018. Cost and management accounting. Cengage Learning.
Kamiński, B., Jakubczyk, M. and Szufel, P., 2018. A framework for sensitivity analysis of
decision trees. Central European journal of operations research, 26(1), pp.135-159.
Paul, D.D., 2020. STANDARD COSTING AND ABC: A COEXISTENCE. Strategic
Finance, 101(11), pp.32-39.
Ouassini, I., 2018. An introduction to the concept of Incremental Budgeting and Beyond
Budgeting. Available at SSRN 3140059.
May, A.U., 2017. Traditional budgeting in today’s business environment. Journal of Applied
Finance & Banking, 7(3), pp.111-120.
1
Books and journals
LIU, B. and PAN, H. Q., 2018. Comparative Study of Absorption Costing and Variable
Costing. Journal of Qiqihar University (Philosophy & Social Science Edition), p.06.
Geiszler, M., Baker, K. and Lippitt, J., 2017. Variable Activity‐Based Costing and Decision
Making. Journal of Corporate Accounting & Finance, 28(5), pp.45-52.
Drury, C., 2018. Cost and management accounting. Cengage Learning.
Kamiński, B., Jakubczyk, M. and Szufel, P., 2018. A framework for sensitivity analysis of
decision trees. Central European journal of operations research, 26(1), pp.135-159.
Paul, D.D., 2020. STANDARD COSTING AND ABC: A COEXISTENCE. Strategic
Finance, 101(11), pp.32-39.
Ouassini, I., 2018. An introduction to the concept of Incremental Budgeting and Beyond
Budgeting. Available at SSRN 3140059.
May, A.U., 2017. Traditional budgeting in today’s business environment. Journal of Applied
Finance & Banking, 7(3), pp.111-120.
1
You're viewing a preview
Unlock full access by subscribing today!
1 out of 9
Related Documents

Your All-in-One AI-Powered Toolkit for Academic Success.
+13062052269
info@desklib.com
Available 24*7 on WhatsApp / Email
Unlock your academic potential
© 2024 | Zucol Services PVT LTD | All rights reserved.