Finite Element Analysis of a Stiffened Plate
VerifiedAdded on 2020/05/28
|15
|1164
|75
AI Summary
The assignment delves into finite element analysis of a stiffened plate. It involves creating and analyzing different models in Abaqus to investigate static, dynamic, and modal responses under various loading scenarios, including variable pressure and impact loads. Students will explore concepts such as frequency analysis, damping methods (direct and Rayleigh), and explicit dynamics simulations. The assignment requires applying specific material properties and plasticity considerations for certain cases.
Contribute Materials
Your contribution can guide someone’s learning journey. Share your
documents today.
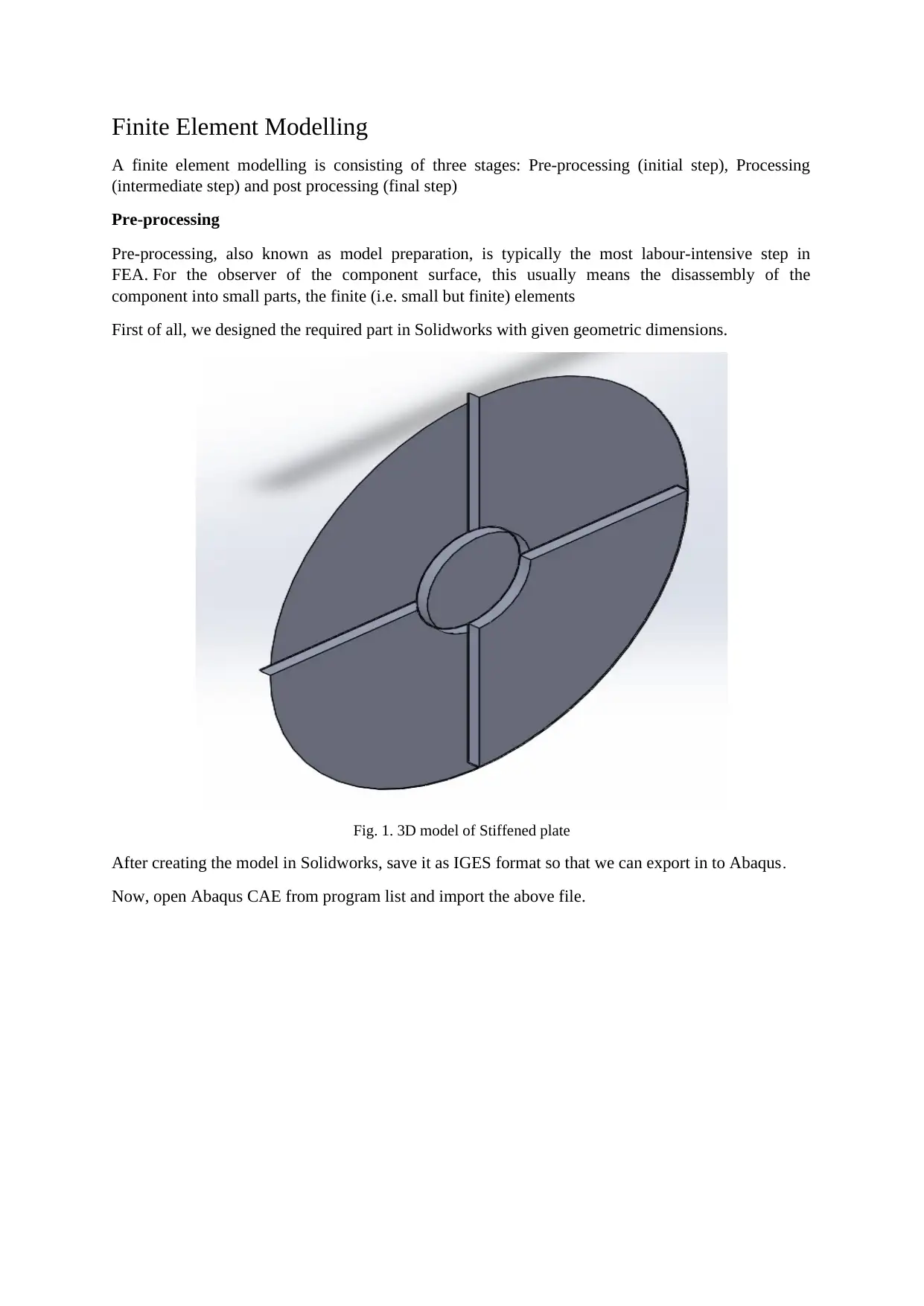
Finite Element Modelling
A finite element modelling is consisting of three stages: Pre-processing (initial step), Processing
(intermediate step) and post processing (final step)
Pre-processing
Pre-processing, also known as model preparation, is typically the most labour-intensive step in
FEA. For the observer of the component surface, this usually means the disassembly of the
component into small parts, the finite (i.e. small but finite) elements
First of all, we designed the required part in Solidworks with given geometric dimensions.
Fig. 1. 3D model of Stiffened plate
After creating the model in Solidworks, save it as IGES format so that we can export in to Abaqus.
Now, open Abaqus CAE from program list and import the above file.
A finite element modelling is consisting of three stages: Pre-processing (initial step), Processing
(intermediate step) and post processing (final step)
Pre-processing
Pre-processing, also known as model preparation, is typically the most labour-intensive step in
FEA. For the observer of the component surface, this usually means the disassembly of the
component into small parts, the finite (i.e. small but finite) elements
First of all, we designed the required part in Solidworks with given geometric dimensions.
Fig. 1. 3D model of Stiffened plate
After creating the model in Solidworks, save it as IGES format so that we can export in to Abaqus.
Now, open Abaqus CAE from program list and import the above file.
Secure Best Marks with AI Grader
Need help grading? Try our AI Grader for instant feedback on your assignments.
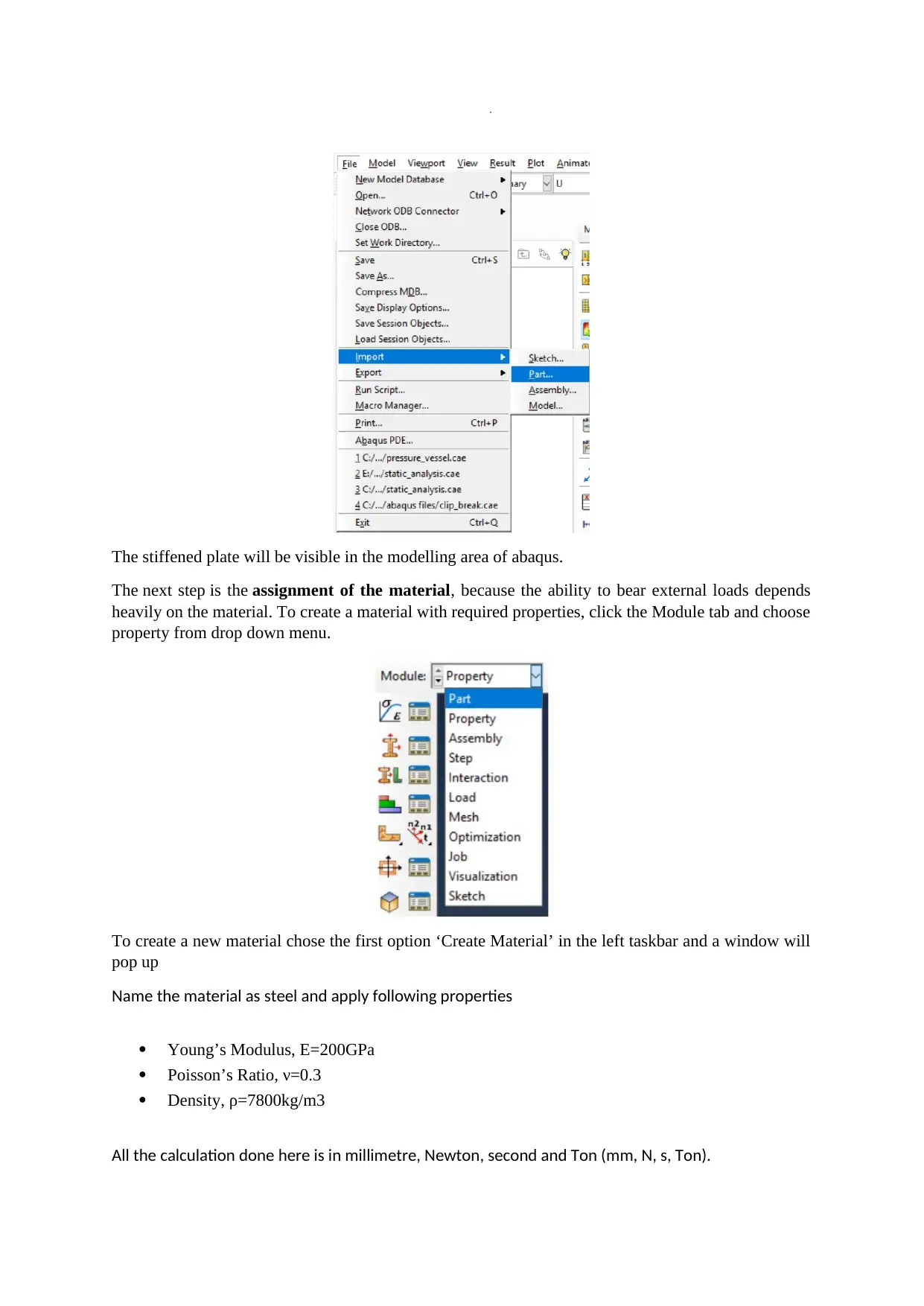
The stiffened plate will be visible in the modelling area of abaqus.
The next step is the assignment of the material, because the ability to bear external loads depends
heavily on the material. To create a material with required properties, click the Module tab and choose
property from drop down menu.
To create a new material chose the first option ‘Create Material’ in the left taskbar and a window will
pop up
Name the material as steel and apply following properties
Young’s Modulus, E=200GPa
Poisson’s Ratio, ν=0.3
Density, ρ=7800kg/m3
All the calculation done here is in millimetre, Newton, second and Ton (mm, N, s, Ton).
The next step is the assignment of the material, because the ability to bear external loads depends
heavily on the material. To create a material with required properties, click the Module tab and choose
property from drop down menu.
To create a new material chose the first option ‘Create Material’ in the left taskbar and a window will
pop up
Name the material as steel and apply following properties
Young’s Modulus, E=200GPa
Poisson’s Ratio, ν=0.3
Density, ρ=7800kg/m3
All the calculation done here is in millimetre, Newton, second and Ton (mm, N, s, Ton).
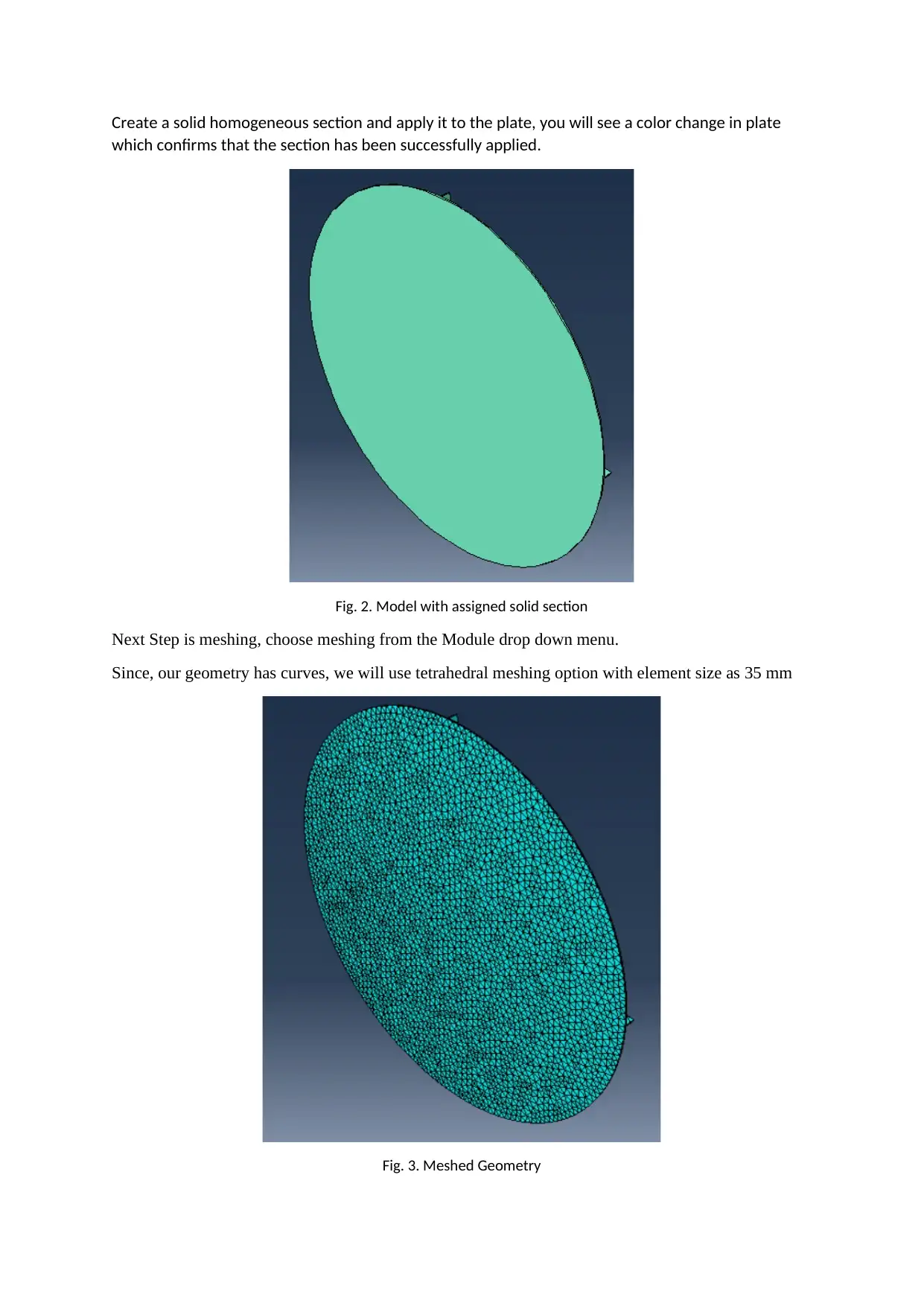
Create a solid homogeneous section and apply it to the plate, you will see a color change in plate
which confirms that the section has been successfully applied.
Fig. 2. Model with assigned solid section
Next Step is meshing, choose meshing from the Module drop down menu.
Since, our geometry has curves, we will use tetrahedral meshing option with element size as 35 mm
Fig. 3. Meshed Geometry
which confirms that the section has been successfully applied.
Fig. 2. Model with assigned solid section
Next Step is meshing, choose meshing from the Module drop down menu.
Since, our geometry has curves, we will use tetrahedral meshing option with element size as 35 mm
Fig. 3. Meshed Geometry
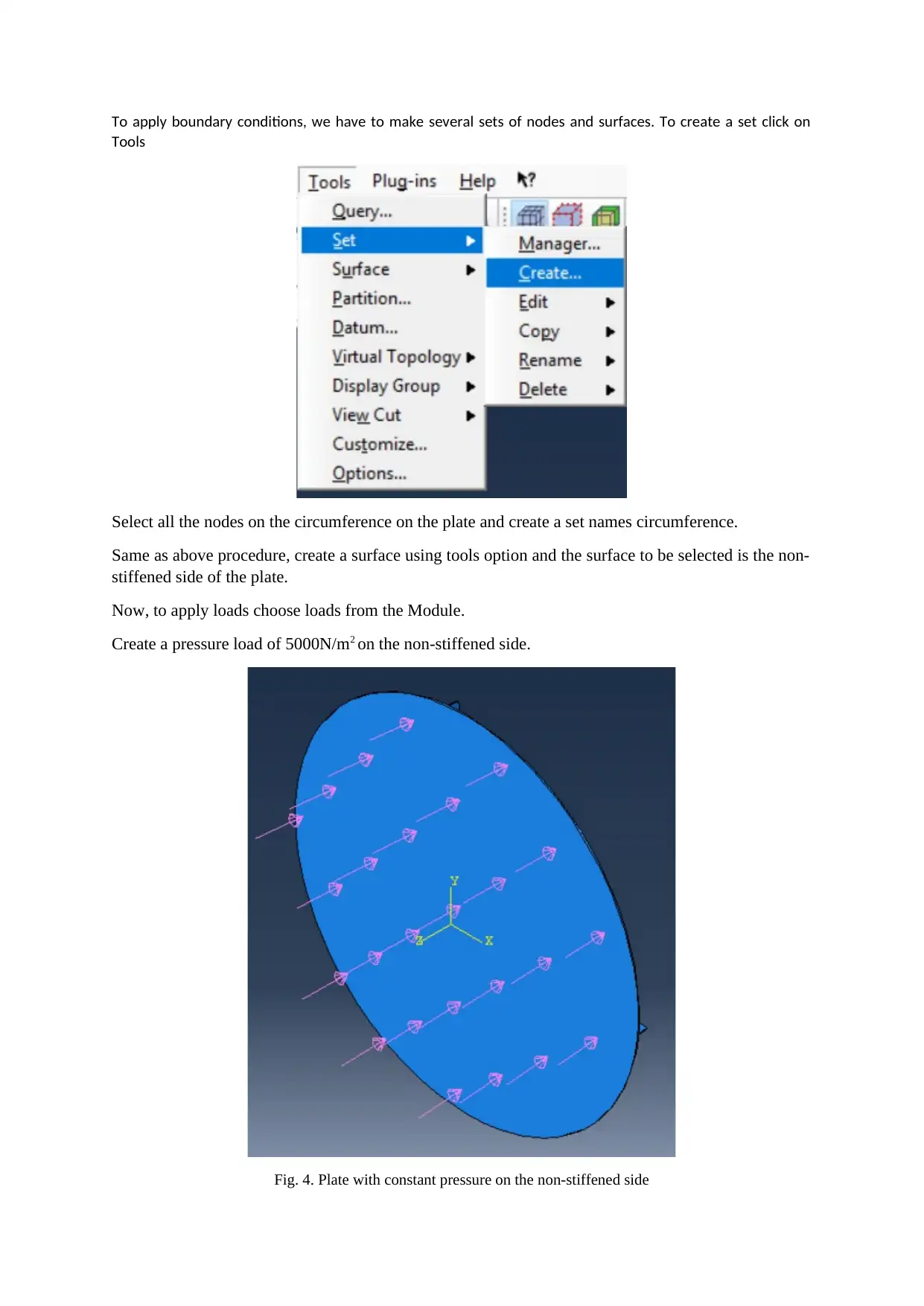
To apply boundary conditions, we have to make several sets of nodes and surfaces. To create a set click on
Tools
Select all the nodes on the circumference on the plate and create a set names circumference.
Same as above procedure, create a surface using tools option and the surface to be selected is the non-
stiffened side of the plate.
Now, to apply loads choose loads from the Module.
Create a pressure load of 5000N/m2 on the non-stiffened side.
Fig. 4. Plate with constant pressure on the non-stiffened side
Tools
Select all the nodes on the circumference on the plate and create a set names circumference.
Same as above procedure, create a surface using tools option and the surface to be selected is the non-
stiffened side of the plate.
Now, to apply loads choose loads from the Module.
Create a pressure load of 5000N/m2 on the non-stiffened side.
Fig. 4. Plate with constant pressure on the non-stiffened side
Secure Best Marks with AI Grader
Need help grading? Try our AI Grader for instant feedback on your assignments.
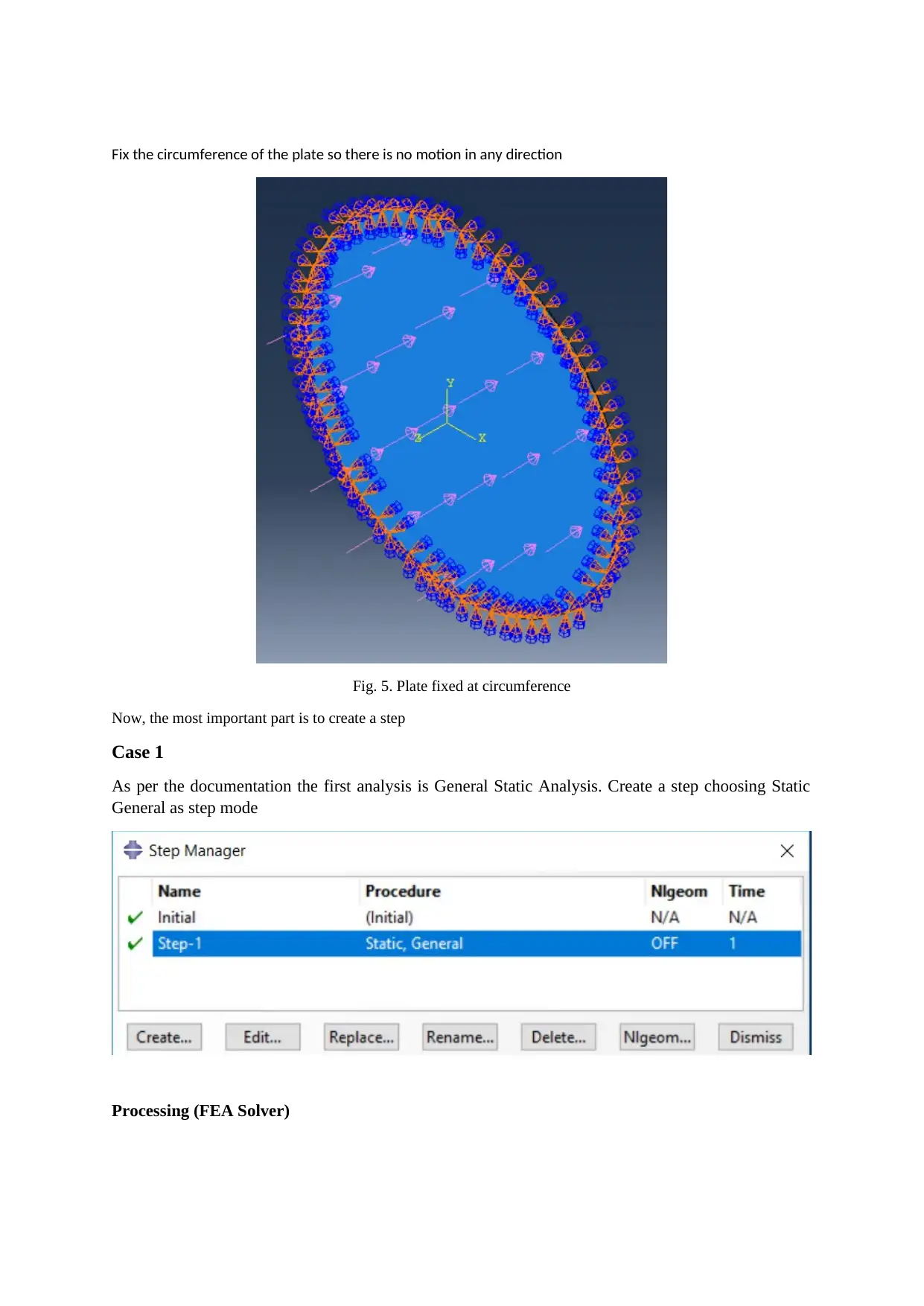
Fix the circumference of the plate so there is no motion in any direction
Fig. 5. Plate fixed at circumference
Now, the most important part is to create a step
Case 1
As per the documentation the first analysis is General Static Analysis. Create a step choosing Static
General as step mode
Processing (FEA Solver)
Fig. 5. Plate fixed at circumference
Now, the most important part is to create a step
Case 1
As per the documentation the first analysis is General Static Analysis. Create a step choosing Static
General as step mode
Processing (FEA Solver)
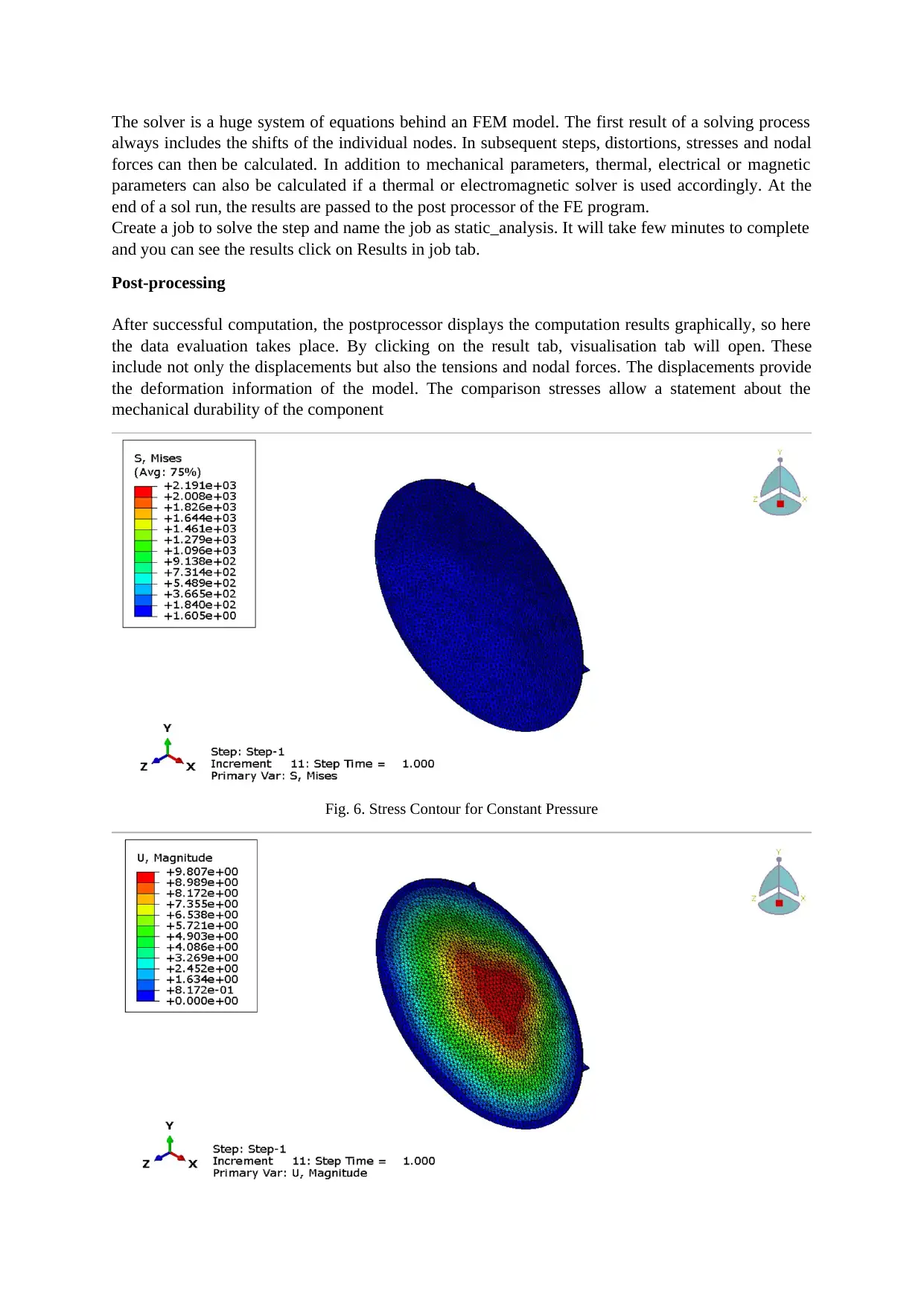
The solver is a huge system of equations behind an FEM model. The first result of a solving process
always includes the shifts of the individual nodes. In subsequent steps, distortions, stresses and nodal
forces can then be calculated. In addition to mechanical parameters, thermal, electrical or magnetic
parameters can also be calculated if a thermal or electromagnetic solver is used accordingly. At the
end of a sol run, the results are passed to the post processor of the FE program.
Create a job to solve the step and name the job as static_analysis. It will take few minutes to complete
and you can see the results click on Results in job tab.
Post-processing
After successful computation, the postprocessor displays the computation results graphically, so here
the data evaluation takes place. By clicking on the result tab, visualisation tab will open. These
include not only the displacements but also the tensions and nodal forces. The displacements provide
the deformation information of the model. The comparison stresses allow a statement about the
mechanical durability of the component
Fig. 6. Stress Contour for Constant Pressure
always includes the shifts of the individual nodes. In subsequent steps, distortions, stresses and nodal
forces can then be calculated. In addition to mechanical parameters, thermal, electrical or magnetic
parameters can also be calculated if a thermal or electromagnetic solver is used accordingly. At the
end of a sol run, the results are passed to the post processor of the FE program.
Create a job to solve the step and name the job as static_analysis. It will take few minutes to complete
and you can see the results click on Results in job tab.
Post-processing
After successful computation, the postprocessor displays the computation results graphically, so here
the data evaluation takes place. By clicking on the result tab, visualisation tab will open. These
include not only the displacements but also the tensions and nodal forces. The displacements provide
the deformation information of the model. The comparison stresses allow a statement about the
mechanical durability of the component
Fig. 6. Stress Contour for Constant Pressure
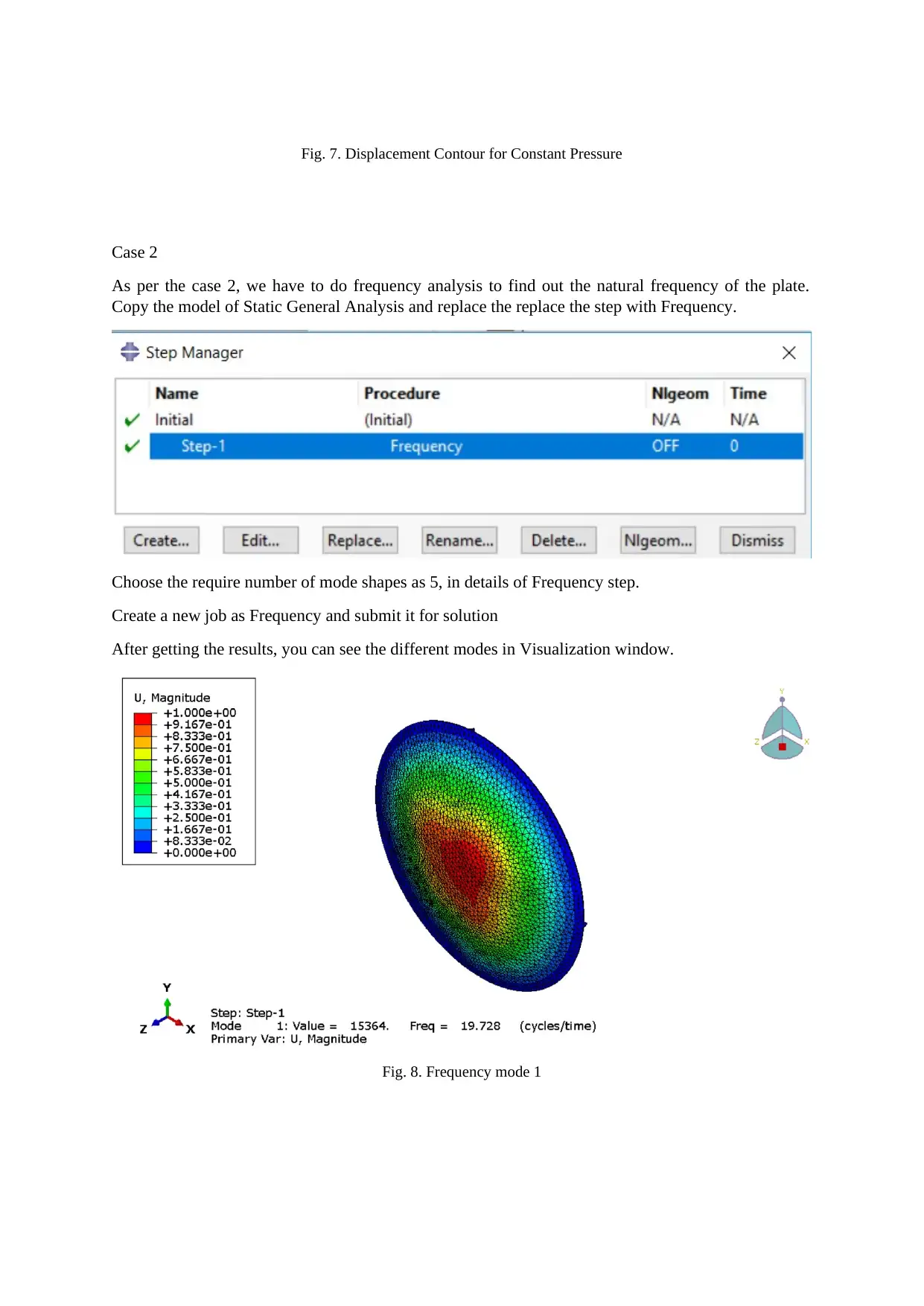
Fig. 7. Displacement Contour for Constant Pressure
Case 2
As per the case 2, we have to do frequency analysis to find out the natural frequency of the plate.
Copy the model of Static General Analysis and replace the replace the step with Frequency.
Choose the require number of mode shapes as 5, in details of Frequency step.
Create a new job as Frequency and submit it for solution
After getting the results, you can see the different modes in Visualization window.
Fig. 8. Frequency mode 1
Case 2
As per the case 2, we have to do frequency analysis to find out the natural frequency of the plate.
Copy the model of Static General Analysis and replace the replace the step with Frequency.
Choose the require number of mode shapes as 5, in details of Frequency step.
Create a new job as Frequency and submit it for solution
After getting the results, you can see the different modes in Visualization window.
Fig. 8. Frequency mode 1
Paraphrase This Document
Need a fresh take? Get an instant paraphrase of this document with our AI Paraphraser
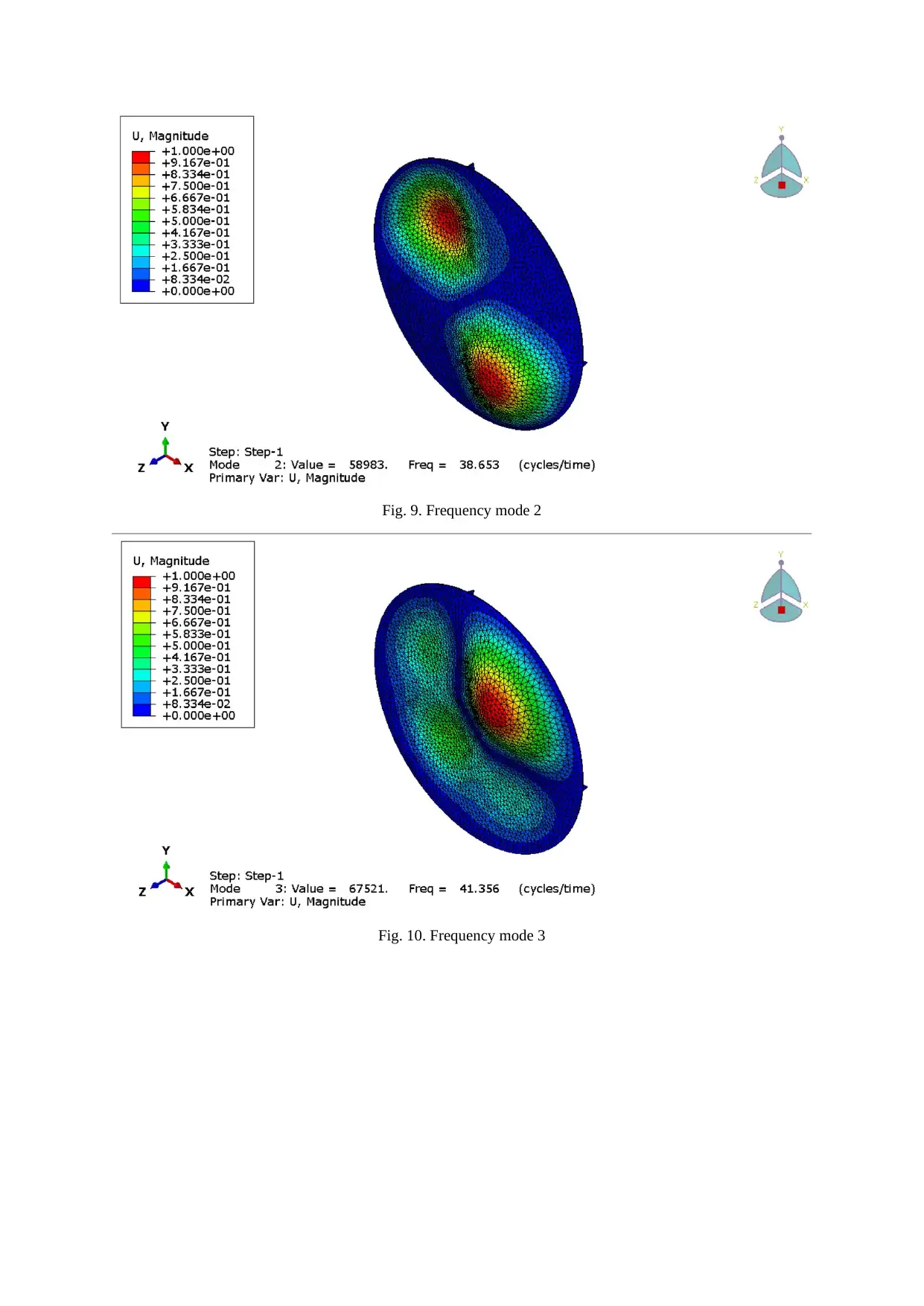
Fig. 9. Frequency mode 2
Fig. 10. Frequency mode 3
Fig. 10. Frequency mode 3
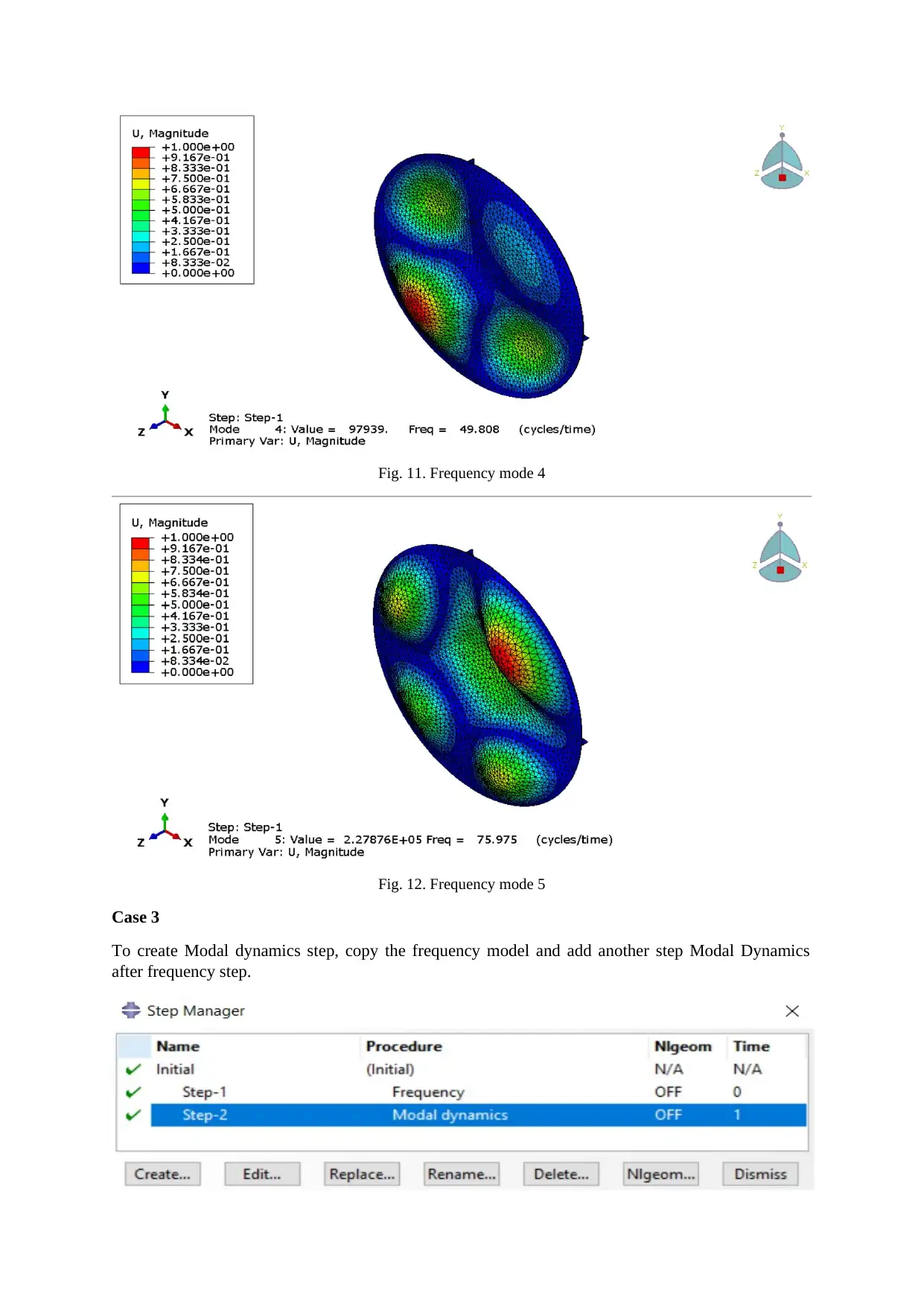
Fig. 11. Frequency mode 4
Fig. 12. Frequency mode 5
Case 3
To create Modal dynamics step, copy the frequency model and add another step Modal Dynamics
after frequency step.
Fig. 12. Frequency mode 5
Case 3
To create Modal dynamics step, copy the frequency model and add another step Modal Dynamics
after frequency step.
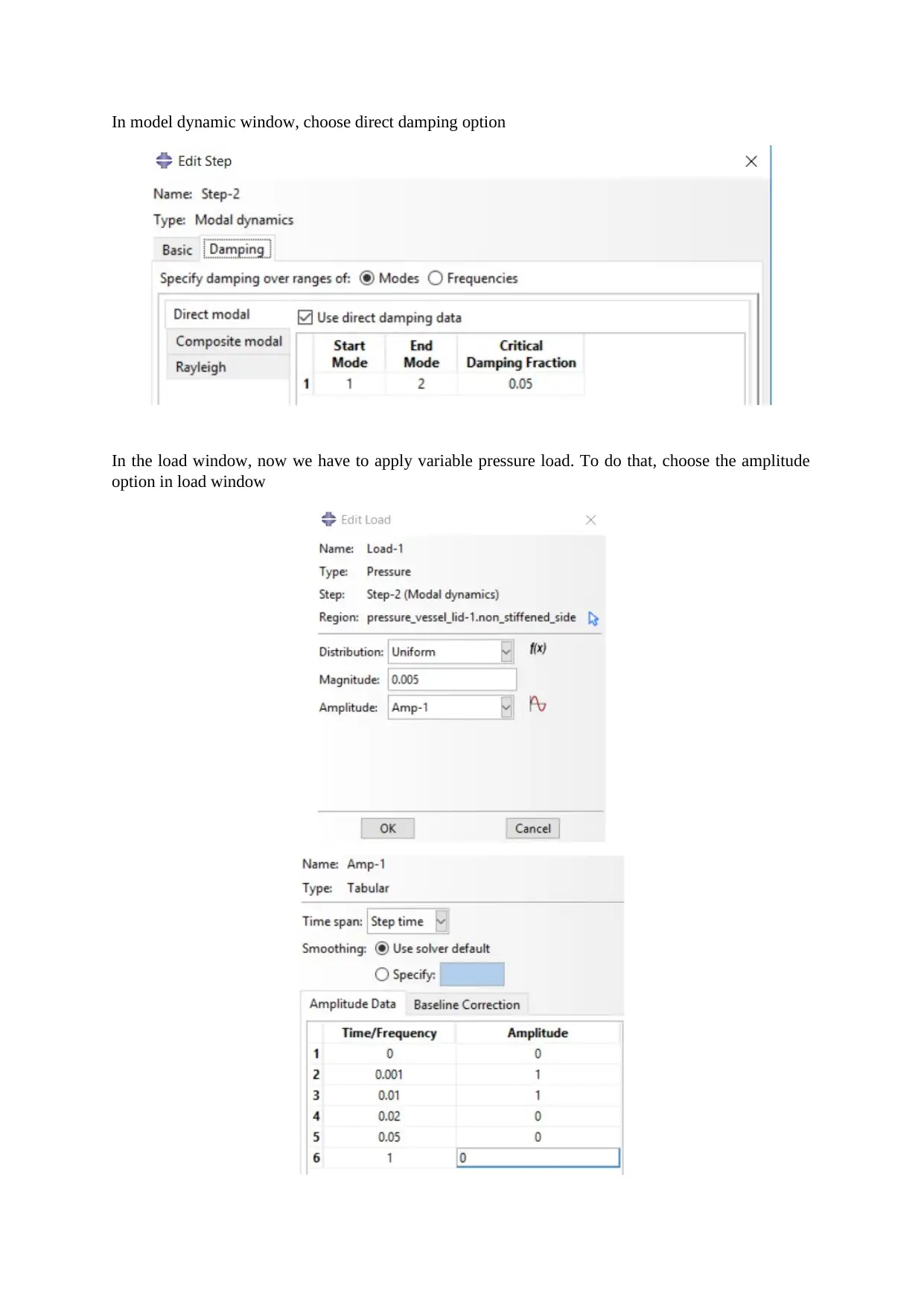
In model dynamic window, choose direct damping option
In the load window, now we have to apply variable pressure load. To do that, choose the amplitude
option in load window
In the load window, now we have to apply variable pressure load. To do that, choose the amplitude
option in load window
Secure Best Marks with AI Grader
Need help grading? Try our AI Grader for instant feedback on your assignments.
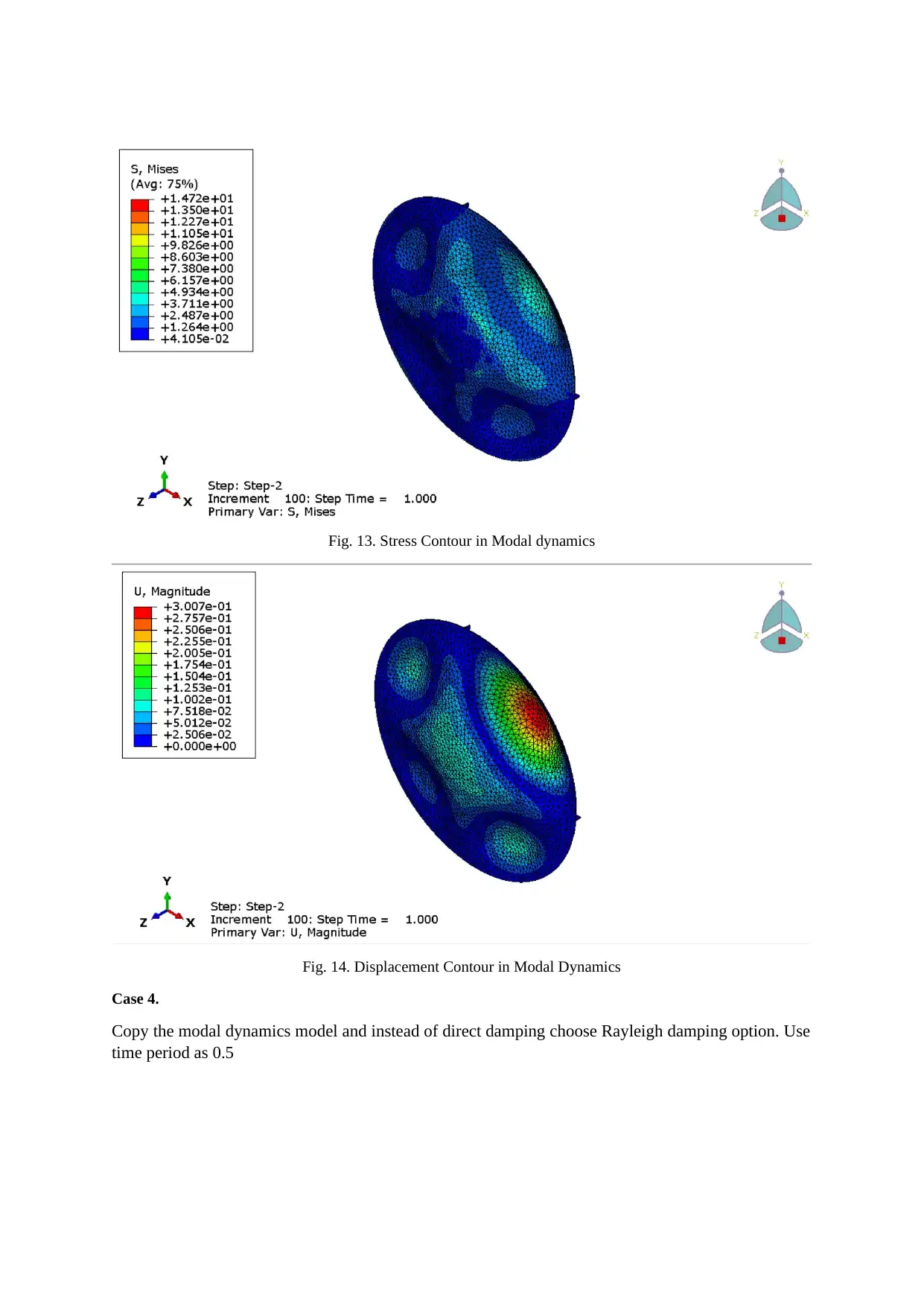
Fig. 13. Stress Contour in Modal dynamics
Fig. 14. Displacement Contour in Modal Dynamics
Case 4.
Copy the modal dynamics model and instead of direct damping choose Rayleigh damping option. Use
time period as 0.5
Fig. 14. Displacement Contour in Modal Dynamics
Case 4.
Copy the modal dynamics model and instead of direct damping choose Rayleigh damping option. Use
time period as 0.5
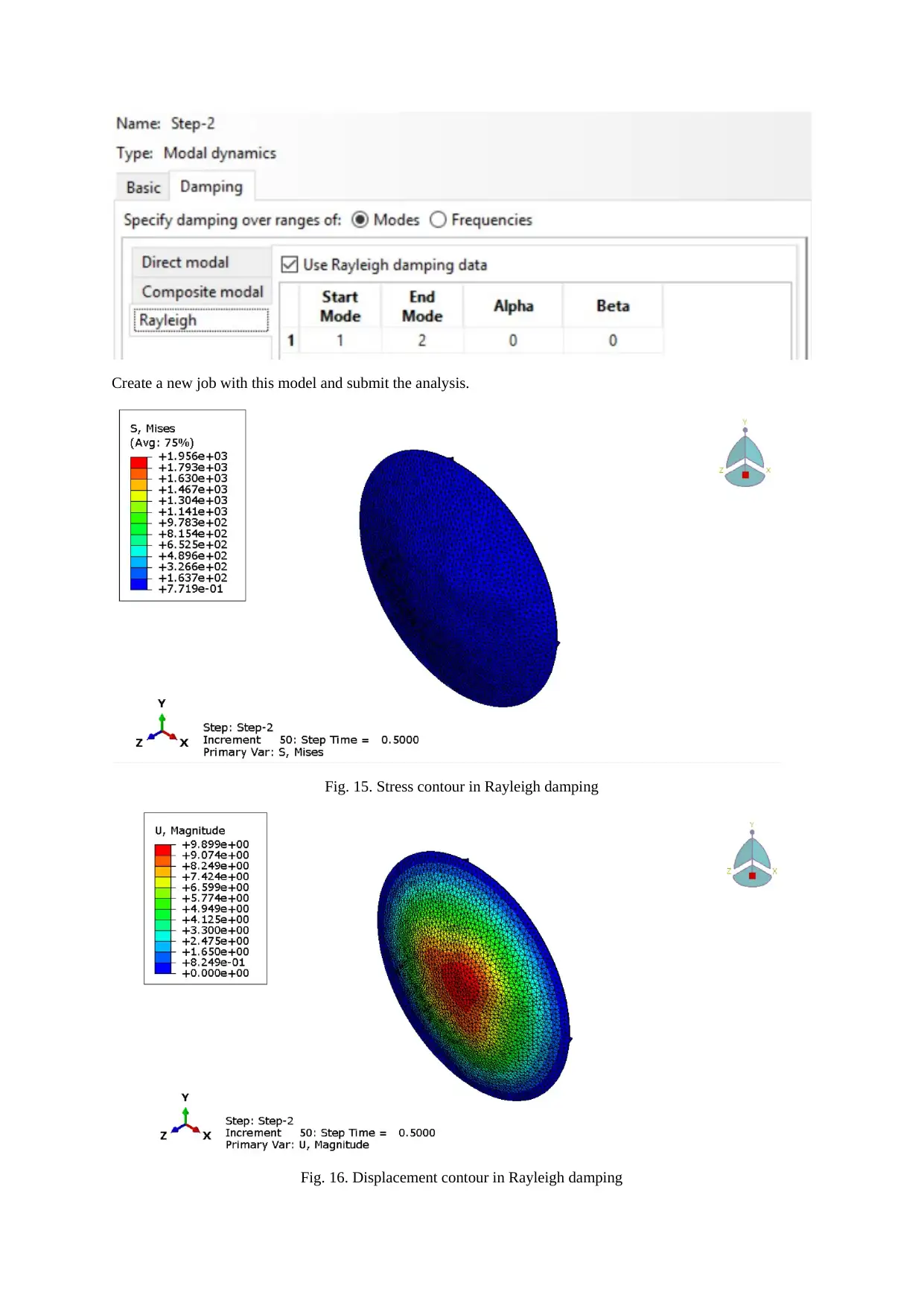
Create a new job with this model and submit the analysis.
Fig. 15. Stress contour in Rayleigh damping
Fig. 16. Displacement contour in Rayleigh damping
Fig. 15. Stress contour in Rayleigh damping
Fig. 16. Displacement contour in Rayleigh damping
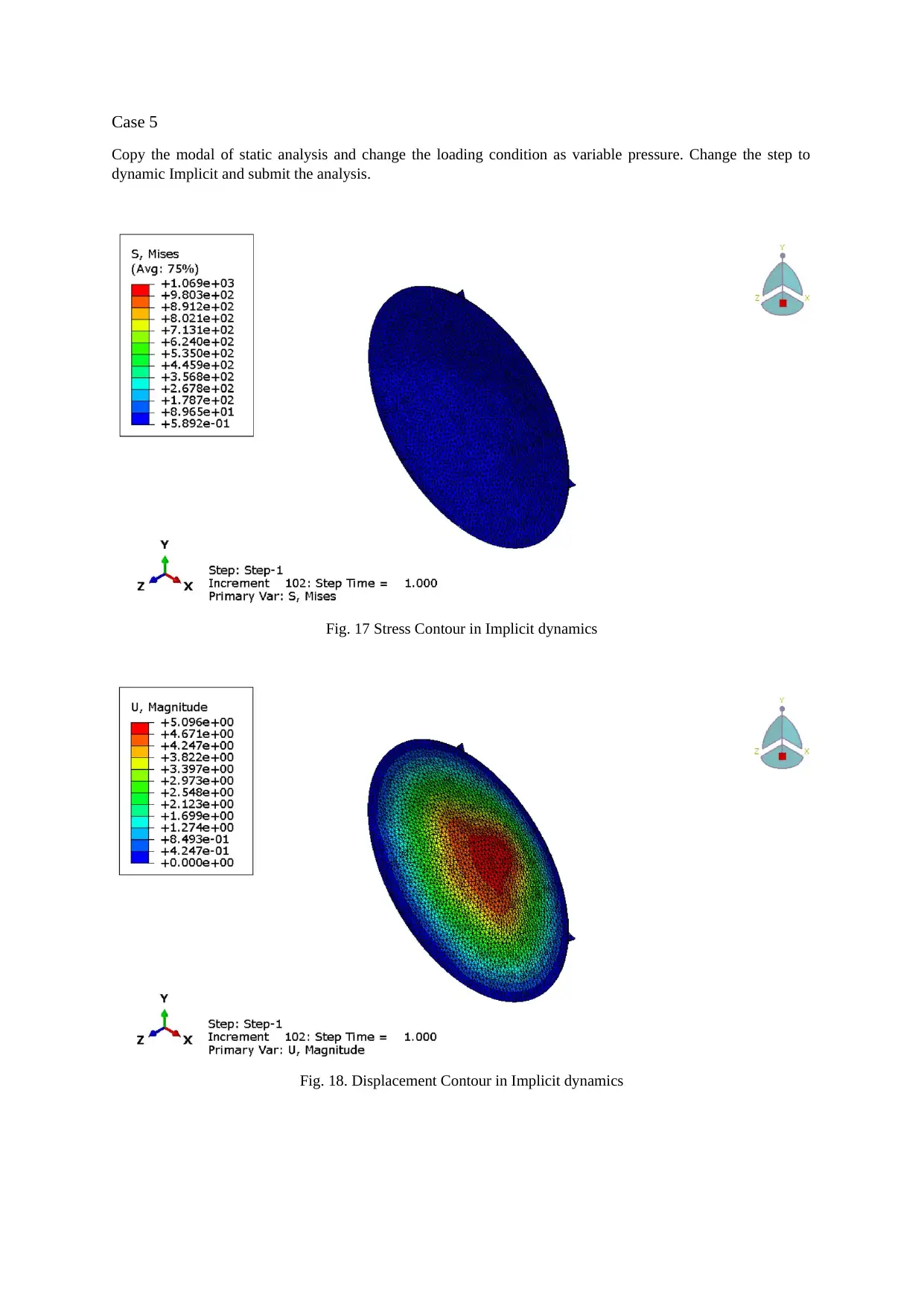
Case 5
Copy the modal of static analysis and change the loading condition as variable pressure. Change the step to
dynamic Implicit and submit the analysis.
Fig. 17 Stress Contour in Implicit dynamics
Fig. 18. Displacement Contour in Implicit dynamics
Copy the modal of static analysis and change the loading condition as variable pressure. Change the step to
dynamic Implicit and submit the analysis.
Fig. 17 Stress Contour in Implicit dynamics
Fig. 18. Displacement Contour in Implicit dynamics
Paraphrase This Document
Need a fresh take? Get an instant paraphrase of this document with our AI Paraphraser

Case 4
Copy the above model and replace the step as Explicit dynamics. Change the pressure in the loading
window as 100000N/m2. There are also some changes in material properties, to add those changes add
plasticity to the material properties as per the following table
Fig. 19. Stress contour for Explicit dynamics
Copy the above model and replace the step as Explicit dynamics. Change the pressure in the loading
window as 100000N/m2. There are also some changes in material properties, to add those changes add
plasticity to the material properties as per the following table
Fig. 19. Stress contour for Explicit dynamics
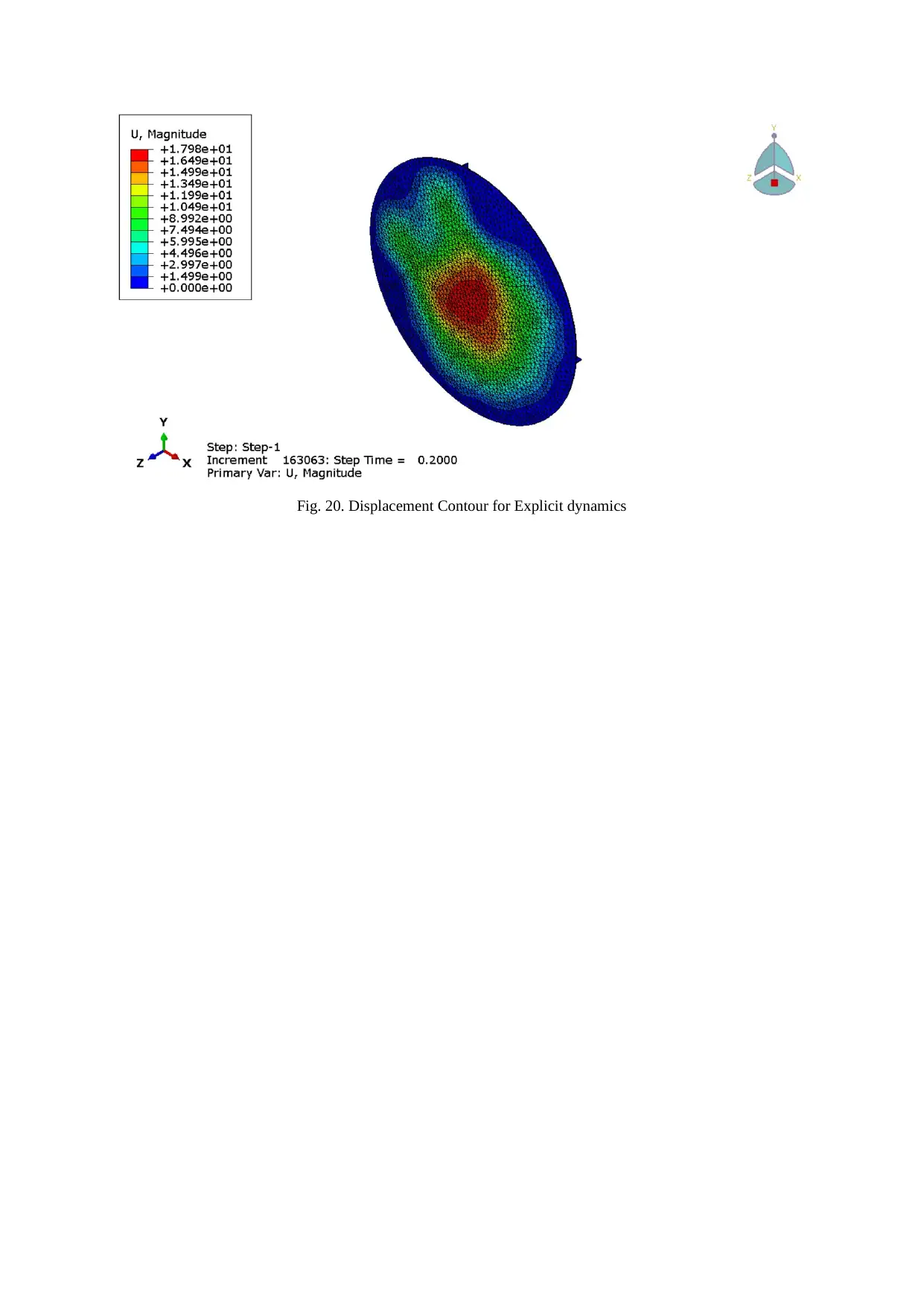
Fig. 20. Displacement Contour for Explicit dynamics
Copy the above model and replace the step as Explicit dynamics. Change the pressure in the loading
window as 100000N/m2. There are also some changes in material properties, to add those changes add
plasticity to the material properties as per the following table
Copy the above model and replace the step as Explicit dynamics. Change the pressure in the loading
window as 100000N/m2. There are also some changes in material properties, to add those changes add
plasticity to the material properties as per the following table
Copy the above model and replace the step as Explicit dynamics. Change the pressure in the loading
window as 100000N/m2. There are also some changes in material properties, to add those changes add
plasticity to the material properties as per the following table
Copy the above model and replace the step as Explicit dynamics. Change the pressure in the loading
window as 100000N/m2. There are also some changes in material properties, to add those changes add
plasticity to the material properties as per the following table
1 out of 15
Related Documents
![[object Object]](/_next/image/?url=%2F_next%2Fstatic%2Fmedia%2Flogo.6d15ce61.png&w=640&q=75)
Your All-in-One AI-Powered Toolkit for Academic Success.
+13062052269
info@desklib.com
Available 24*7 on WhatsApp / Email
Unlock your academic potential
© 2024 | Zucol Services PVT LTD | All rights reserved.