Fundamental of Project Management
VerifiedAdded on 2023/01/12
|20
|4626
|78
AI Summary
This project report consists of a case study of Automation Futures Plc or AF Plc; in which the company has taken a contract to install an automation plant for its client company TTF PLC (Train manufacturing client). This report will discuss about good contracts terms and conditions and what essential points should be mentioned in the contract.
Contribute Materials
Your contribution can guide someone’s learning journey. Share your
documents today.
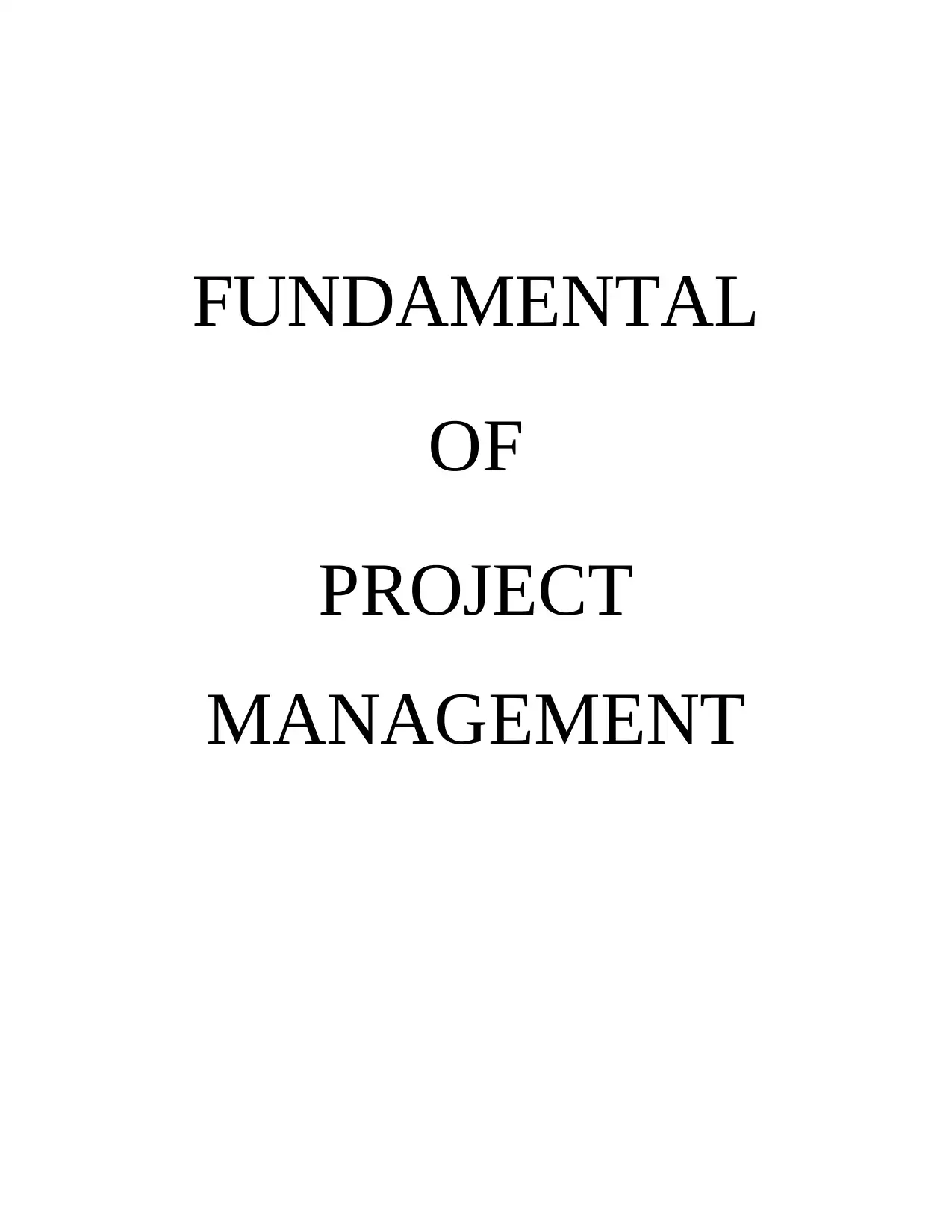
FUNDAMENTAL
OF
PROJECT
MANAGEMENT
OF
PROJECT
MANAGEMENT
Secure Best Marks with AI Grader
Need help grading? Try our AI Grader for instant feedback on your assignments.
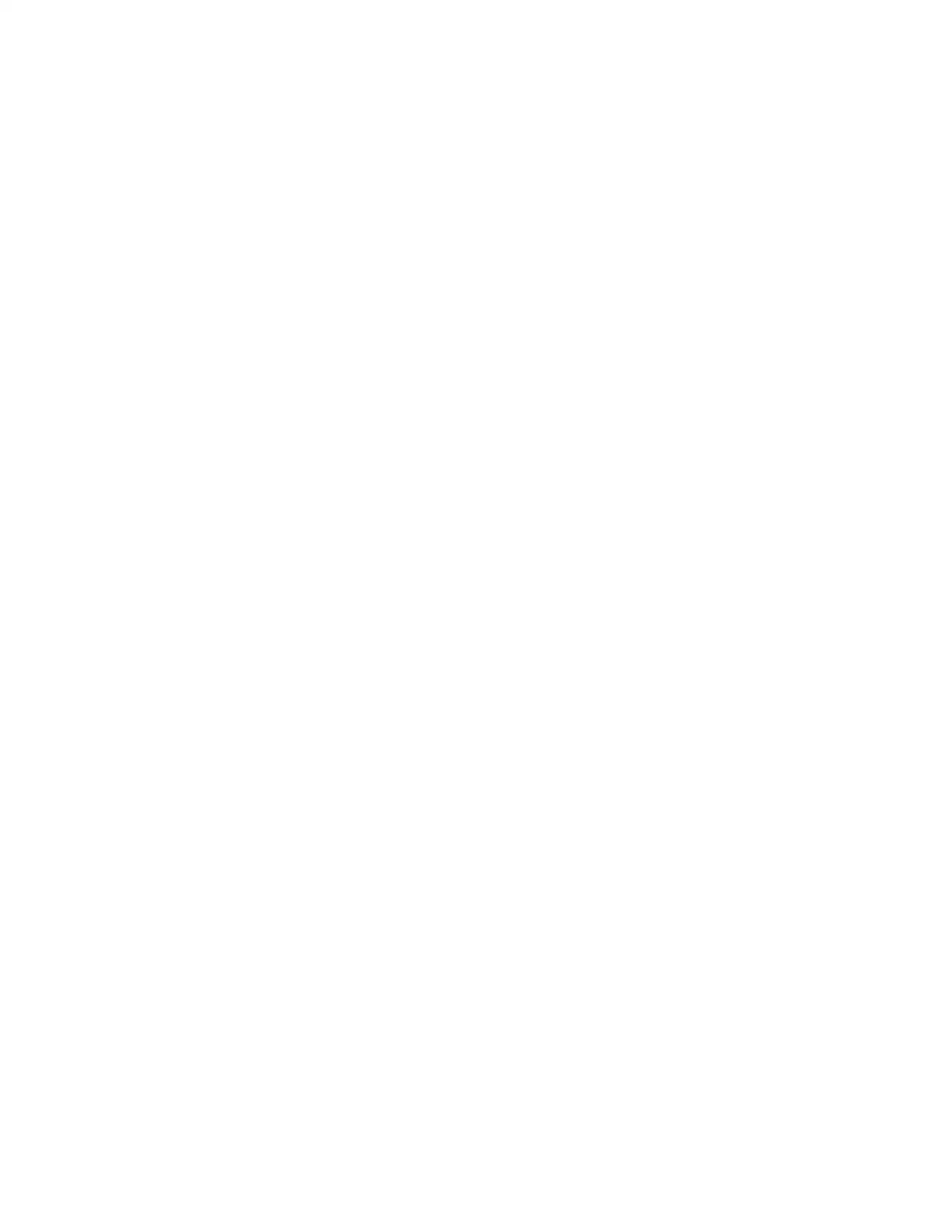
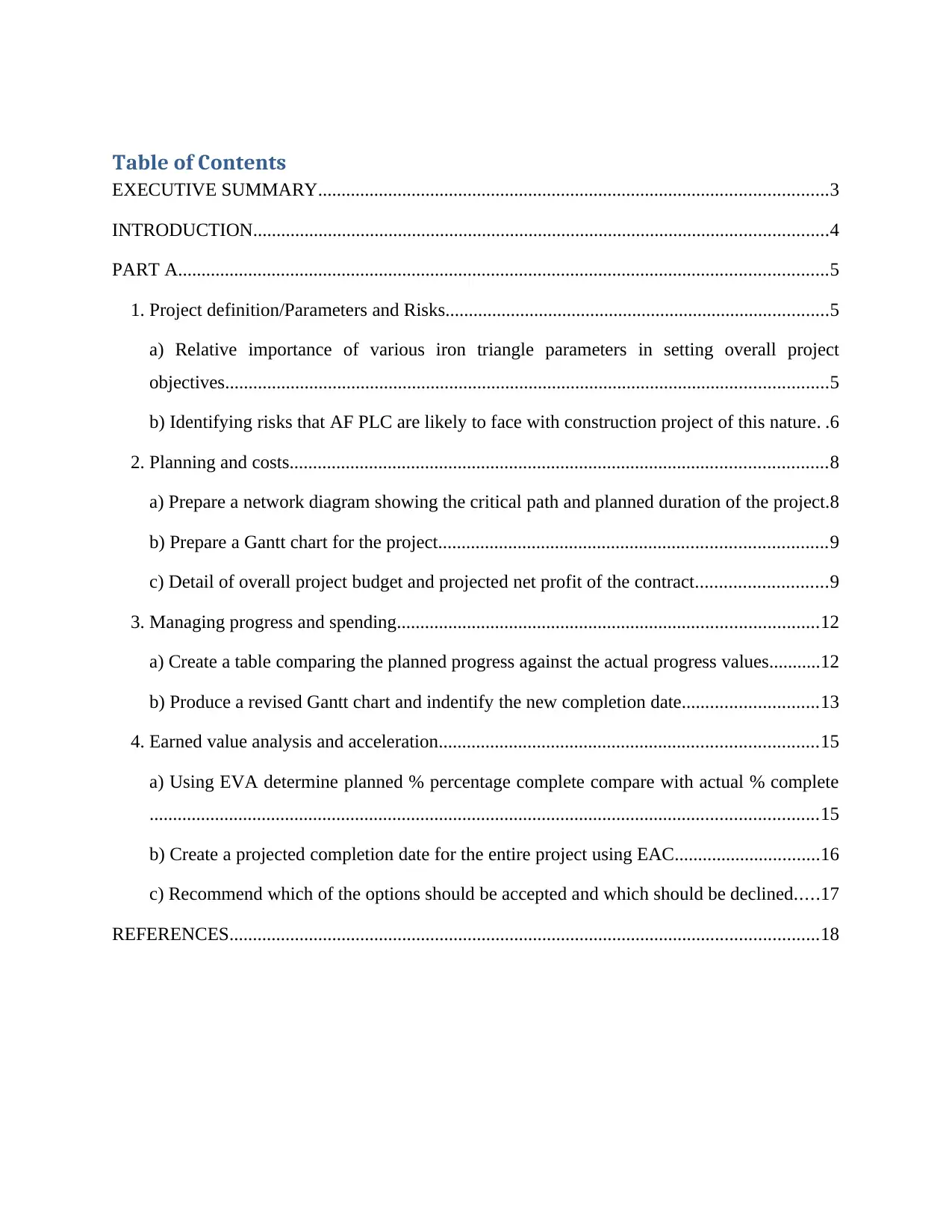
Table of Contents
EXECUTIVE SUMMARY.............................................................................................................3
INTRODUCTION...........................................................................................................................4
PART A...........................................................................................................................................5
1. Project definition/Parameters and Risks..................................................................................5
a) Relative importance of various iron triangle parameters in setting overall project
objectives.................................................................................................................................5
b) Identifying risks that AF PLC are likely to face with construction project of this nature. .6
2. Planning and costs...................................................................................................................8
a) Prepare a network diagram showing the critical path and planned duration of the project.8
b) Prepare a Gantt chart for the project...................................................................................9
c) Detail of overall project budget and projected net profit of the contract............................9
3. Managing progress and spending..........................................................................................12
a) Create a table comparing the planned progress against the actual progress values...........12
b) Produce a revised Gantt chart and indentify the new completion date.............................13
4. Earned value analysis and acceleration.................................................................................15
a) Using EVA determine planned % percentage complete compare with actual % complete
...............................................................................................................................................15
b) Create a projected completion date for the entire project using EAC...............................16
c) Recommend which of the options should be accepted and which should be declined.....17
REFERENCES..............................................................................................................................18
EXECUTIVE SUMMARY.............................................................................................................3
INTRODUCTION...........................................................................................................................4
PART A...........................................................................................................................................5
1. Project definition/Parameters and Risks..................................................................................5
a) Relative importance of various iron triangle parameters in setting overall project
objectives.................................................................................................................................5
b) Identifying risks that AF PLC are likely to face with construction project of this nature. .6
2. Planning and costs...................................................................................................................8
a) Prepare a network diagram showing the critical path and planned duration of the project.8
b) Prepare a Gantt chart for the project...................................................................................9
c) Detail of overall project budget and projected net profit of the contract............................9
3. Managing progress and spending..........................................................................................12
a) Create a table comparing the planned progress against the actual progress values...........12
b) Produce a revised Gantt chart and indentify the new completion date.............................13
4. Earned value analysis and acceleration.................................................................................15
a) Using EVA determine planned % percentage complete compare with actual % complete
...............................................................................................................................................15
b) Create a projected completion date for the entire project using EAC...............................16
c) Recommend which of the options should be accepted and which should be declined.....17
REFERENCES..............................................................................................................................18
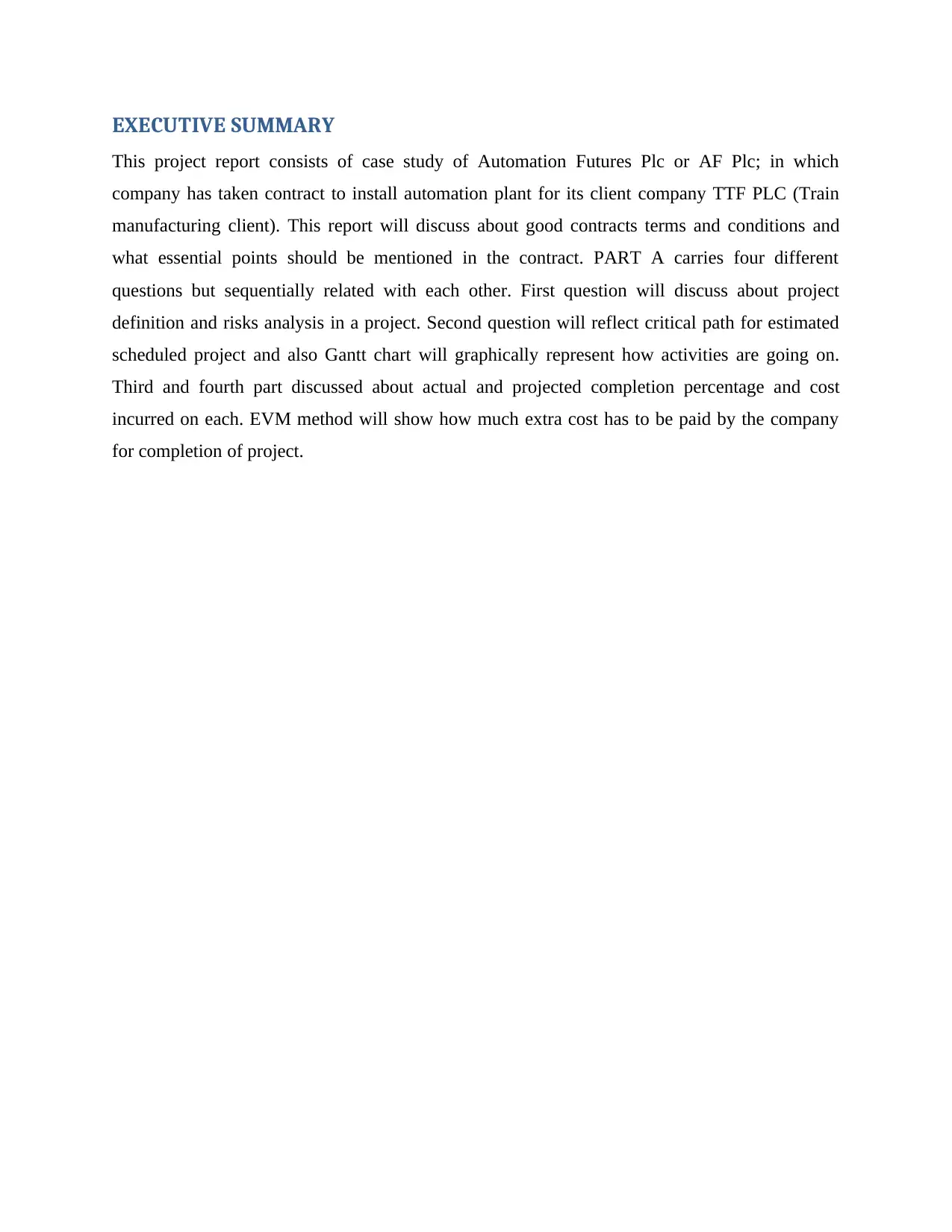
EXECUTIVE SUMMARY
This project report consists of case study of Automation Futures Plc or AF Plc; in which
company has taken contract to install automation plant for its client company TTF PLC (Train
manufacturing client). This report will discuss about good contracts terms and conditions and
what essential points should be mentioned in the contract. PART A carries four different
questions but sequentially related with each other. First question will discuss about project
definition and risks analysis in a project. Second question will reflect critical path for estimated
scheduled project and also Gantt chart will graphically represent how activities are going on.
Third and fourth part discussed about actual and projected completion percentage and cost
incurred on each. EVM method will show how much extra cost has to be paid by the company
for completion of project.
This project report consists of case study of Automation Futures Plc or AF Plc; in which
company has taken contract to install automation plant for its client company TTF PLC (Train
manufacturing client). This report will discuss about good contracts terms and conditions and
what essential points should be mentioned in the contract. PART A carries four different
questions but sequentially related with each other. First question will discuss about project
definition and risks analysis in a project. Second question will reflect critical path for estimated
scheduled project and also Gantt chart will graphically represent how activities are going on.
Third and fourth part discussed about actual and projected completion percentage and cost
incurred on each. EVM method will show how much extra cost has to be paid by the company
for completion of project.
Secure Best Marks with AI Grader
Need help grading? Try our AI Grader for instant feedback on your assignments.
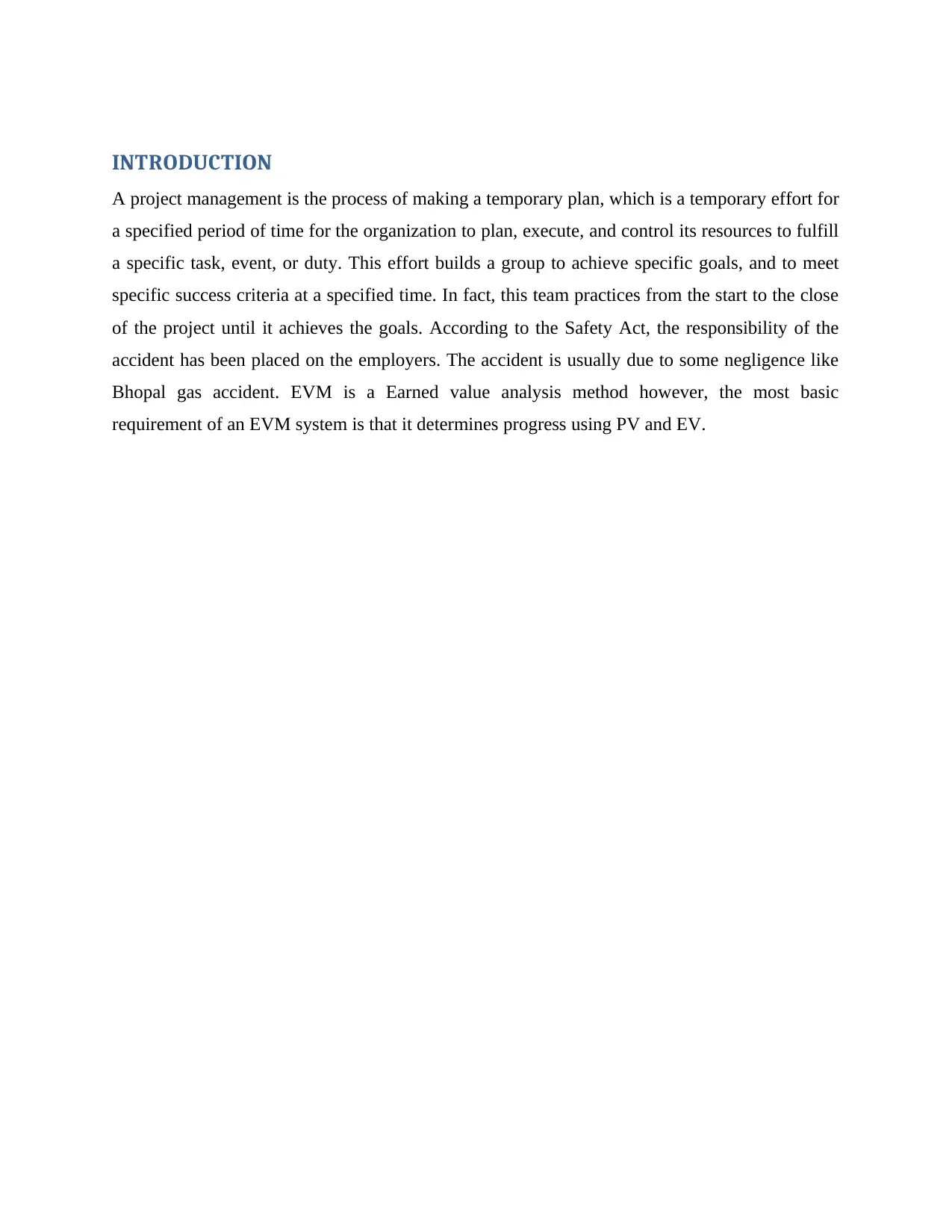
INTRODUCTION
A project management is the process of making a temporary plan, which is a temporary effort for
a specified period of time for the organization to plan, execute, and control its resources to fulfill
a specific task, event, or duty. This effort builds a group to achieve specific goals, and to meet
specific success criteria at a specified time. In fact, this team practices from the start to the close
of the project until it achieves the goals. According to the Safety Act, the responsibility of the
accident has been placed on the employers. The accident is usually due to some negligence like
Bhopal gas accident. EVM is a Earned value analysis method however, the most basic
requirement of an EVM system is that it determines progress using PV and EV.
A project management is the process of making a temporary plan, which is a temporary effort for
a specified period of time for the organization to plan, execute, and control its resources to fulfill
a specific task, event, or duty. This effort builds a group to achieve specific goals, and to meet
specific success criteria at a specified time. In fact, this team practices from the start to the close
of the project until it achieves the goals. According to the Safety Act, the responsibility of the
accident has been placed on the employers. The accident is usually due to some negligence like
Bhopal gas accident. EVM is a Earned value analysis method however, the most basic
requirement of an EVM system is that it determines progress using PV and EV.
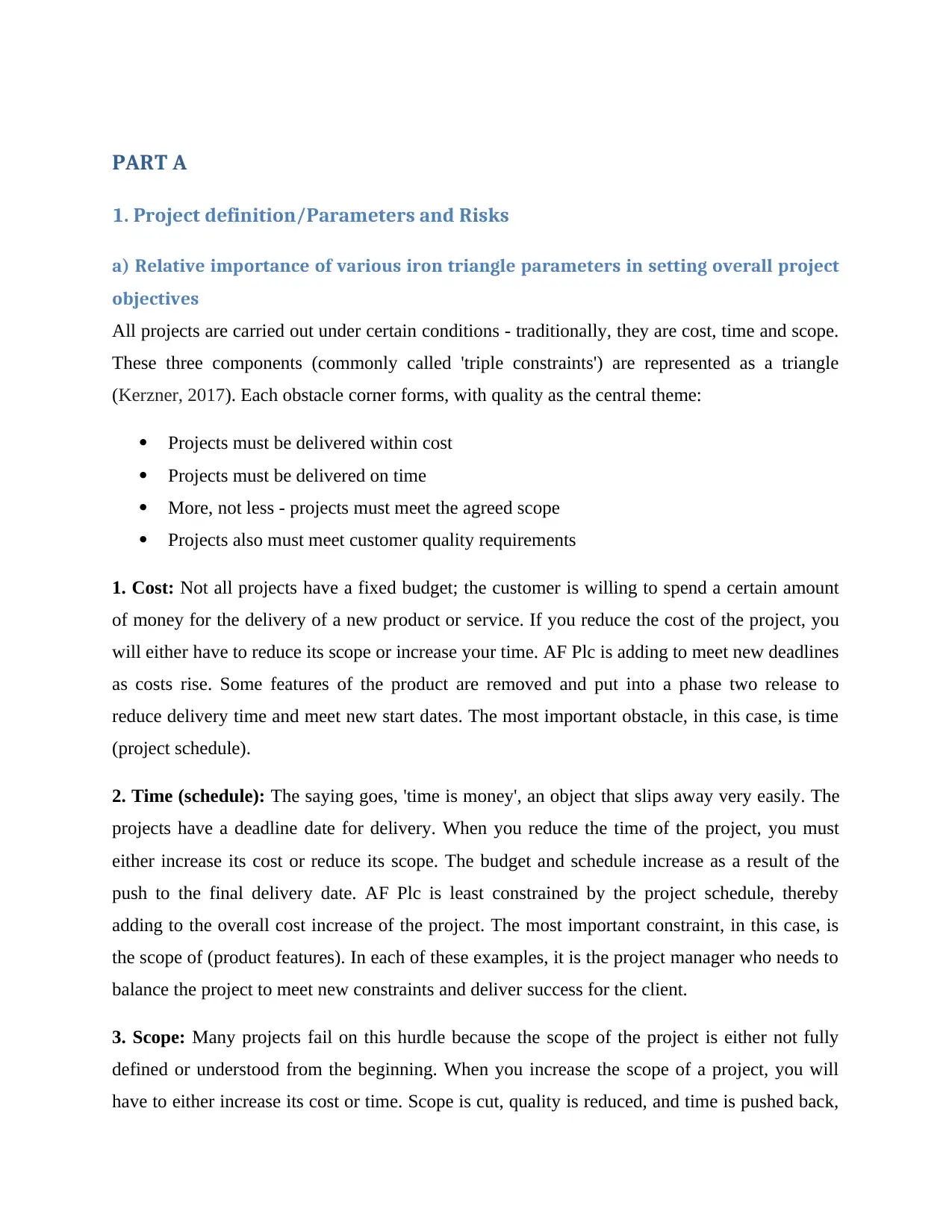
PART A
1. Project definition/Parameters and Risks
a) Relative importance of various iron triangle parameters in setting overall project
objectives
All projects are carried out under certain conditions - traditionally, they are cost, time and scope.
These three components (commonly called 'triple constraints') are represented as a triangle
(Kerzner, 2017). Each obstacle corner forms, with quality as the central theme:
Projects must be delivered within cost
Projects must be delivered on time
More, not less - projects must meet the agreed scope
Projects also must meet customer quality requirements
1. Cost: Not all projects have a fixed budget; the customer is willing to spend a certain amount
of money for the delivery of a new product or service. If you reduce the cost of the project, you
will either have to reduce its scope or increase your time. AF Plc is adding to meet new deadlines
as costs rise. Some features of the product are removed and put into a phase two release to
reduce delivery time and meet new start dates. The most important obstacle, in this case, is time
(project schedule).
2. Time (schedule): The saying goes, 'time is money', an object that slips away very easily. The
projects have a deadline date for delivery. When you reduce the time of the project, you must
either increase its cost or reduce its scope. The budget and schedule increase as a result of the
push to the final delivery date. AF Plc is least constrained by the project schedule, thereby
adding to the overall cost increase of the project. The most important constraint, in this case, is
the scope of (product features). In each of these examples, it is the project manager who needs to
balance the project to meet new constraints and deliver success for the client.
3. Scope: Many projects fail on this hurdle because the scope of the project is either not fully
defined or understood from the beginning. When you increase the scope of a project, you will
have to either increase its cost or time. Scope is cut, quality is reduced, and time is pushed back,
1. Project definition/Parameters and Risks
a) Relative importance of various iron triangle parameters in setting overall project
objectives
All projects are carried out under certain conditions - traditionally, they are cost, time and scope.
These three components (commonly called 'triple constraints') are represented as a triangle
(Kerzner, 2017). Each obstacle corner forms, with quality as the central theme:
Projects must be delivered within cost
Projects must be delivered on time
More, not less - projects must meet the agreed scope
Projects also must meet customer quality requirements
1. Cost: Not all projects have a fixed budget; the customer is willing to spend a certain amount
of money for the delivery of a new product or service. If you reduce the cost of the project, you
will either have to reduce its scope or increase your time. AF Plc is adding to meet new deadlines
as costs rise. Some features of the product are removed and put into a phase two release to
reduce delivery time and meet new start dates. The most important obstacle, in this case, is time
(project schedule).
2. Time (schedule): The saying goes, 'time is money', an object that slips away very easily. The
projects have a deadline date for delivery. When you reduce the time of the project, you must
either increase its cost or reduce its scope. The budget and schedule increase as a result of the
push to the final delivery date. AF Plc is least constrained by the project schedule, thereby
adding to the overall cost increase of the project. The most important constraint, in this case, is
the scope of (product features). In each of these examples, it is the project manager who needs to
balance the project to meet new constraints and deliver success for the client.
3. Scope: Many projects fail on this hurdle because the scope of the project is either not fully
defined or understood from the beginning. When you increase the scope of a project, you will
have to either increase its cost or time. Scope is cut, quality is reduced, and time is pushed back,
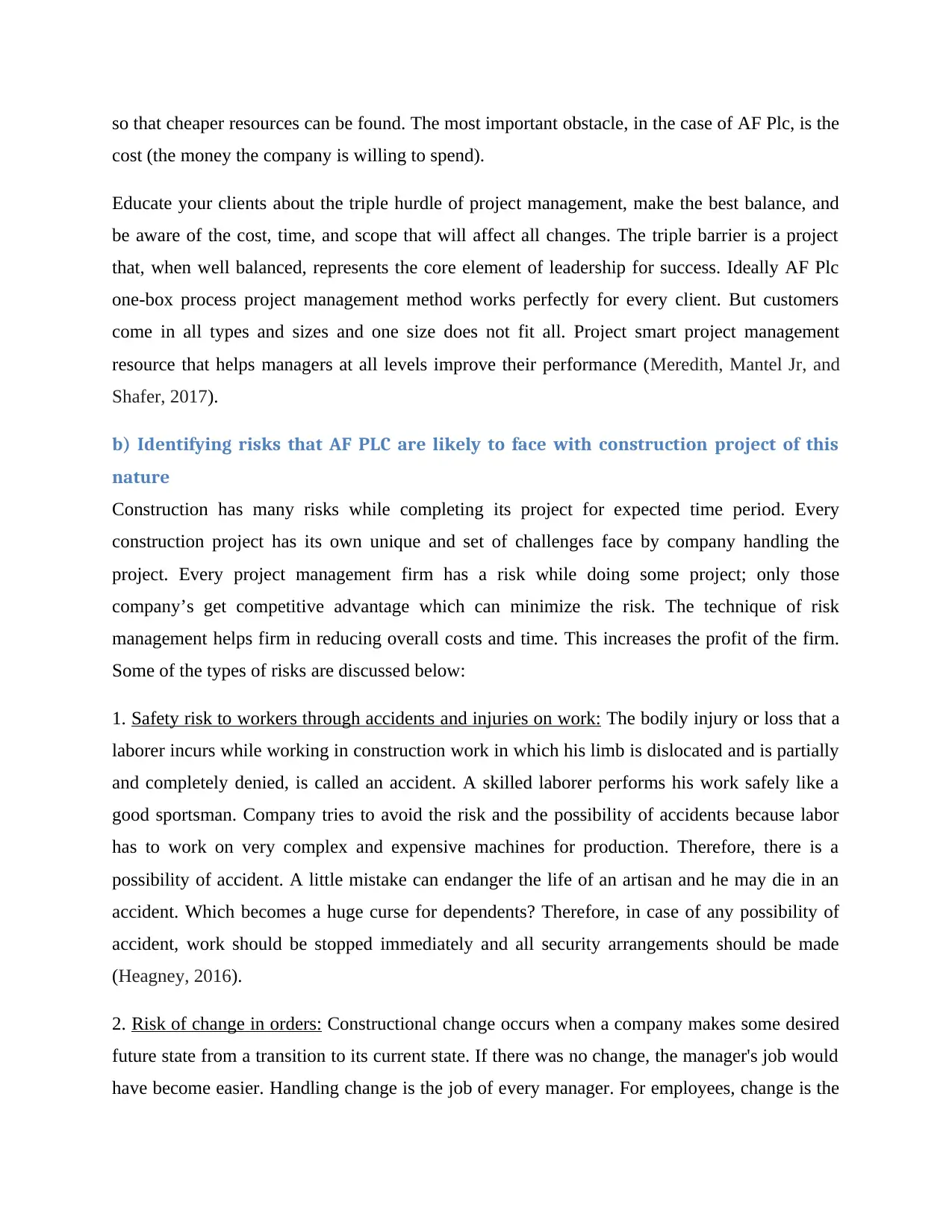
so that cheaper resources can be found. The most important obstacle, in the case of AF Plc, is the
cost (the money the company is willing to spend).
Educate your clients about the triple hurdle of project management, make the best balance, and
be aware of the cost, time, and scope that will affect all changes. The triple barrier is a project
that, when well balanced, represents the core element of leadership for success. Ideally AF Plc
one-box process project management method works perfectly for every client. But customers
come in all types and sizes and one size does not fit all. Project smart project management
resource that helps managers at all levels improve their performance (Meredith, Mantel Jr, and
Shafer, 2017).
b) Identifying risks that AF PLC are likely to face with construction project of this
nature
Construction has many risks while completing its project for expected time period. Every
construction project has its own unique and set of challenges face by company handling the
project. Every project management firm has a risk while doing some project; only those
company’s get competitive advantage which can minimize the risk. The technique of risk
management helps firm in reducing overall costs and time. This increases the profit of the firm.
Some of the types of risks are discussed below:
1. Safety risk to workers through accidents and injuries on work: The bodily injury or loss that a
laborer incurs while working in construction work in which his limb is dislocated and is partially
and completely denied, is called an accident. A skilled laborer performs his work safely like a
good sportsman. Company tries to avoid the risk and the possibility of accidents because labor
has to work on very complex and expensive machines for production. Therefore, there is a
possibility of accident. A little mistake can endanger the life of an artisan and he may die in an
accident. Which becomes a huge curse for dependents? Therefore, in case of any possibility of
accident, work should be stopped immediately and all security arrangements should be made
(Heagney, 2016).
2. Risk of change in orders: Constructional change occurs when a company makes some desired
future state from a transition to its current state. If there was no change, the manager's job would
have become easier. Handling change is the job of every manager. For employees, change is the
cost (the money the company is willing to spend).
Educate your clients about the triple hurdle of project management, make the best balance, and
be aware of the cost, time, and scope that will affect all changes. The triple barrier is a project
that, when well balanced, represents the core element of leadership for success. Ideally AF Plc
one-box process project management method works perfectly for every client. But customers
come in all types and sizes and one size does not fit all. Project smart project management
resource that helps managers at all levels improve their performance (Meredith, Mantel Jr, and
Shafer, 2017).
b) Identifying risks that AF PLC are likely to face with construction project of this
nature
Construction has many risks while completing its project for expected time period. Every
construction project has its own unique and set of challenges face by company handling the
project. Every project management firm has a risk while doing some project; only those
company’s get competitive advantage which can minimize the risk. The technique of risk
management helps firm in reducing overall costs and time. This increases the profit of the firm.
Some of the types of risks are discussed below:
1. Safety risk to workers through accidents and injuries on work: The bodily injury or loss that a
laborer incurs while working in construction work in which his limb is dislocated and is partially
and completely denied, is called an accident. A skilled laborer performs his work safely like a
good sportsman. Company tries to avoid the risk and the possibility of accidents because labor
has to work on very complex and expensive machines for production. Therefore, there is a
possibility of accident. A little mistake can endanger the life of an artisan and he may die in an
accident. Which becomes a huge curse for dependents? Therefore, in case of any possibility of
accident, work should be stopped immediately and all security arrangements should be made
(Heagney, 2016).
2. Risk of change in orders: Constructional change occurs when a company makes some desired
future state from a transition to its current state. If there was no change, the manager's job would
have become easier. Handling change is the job of every manager. For employees, change is the
Paraphrase This Document
Need a fresh take? Get an instant paraphrase of this document with our AI Paraphraser
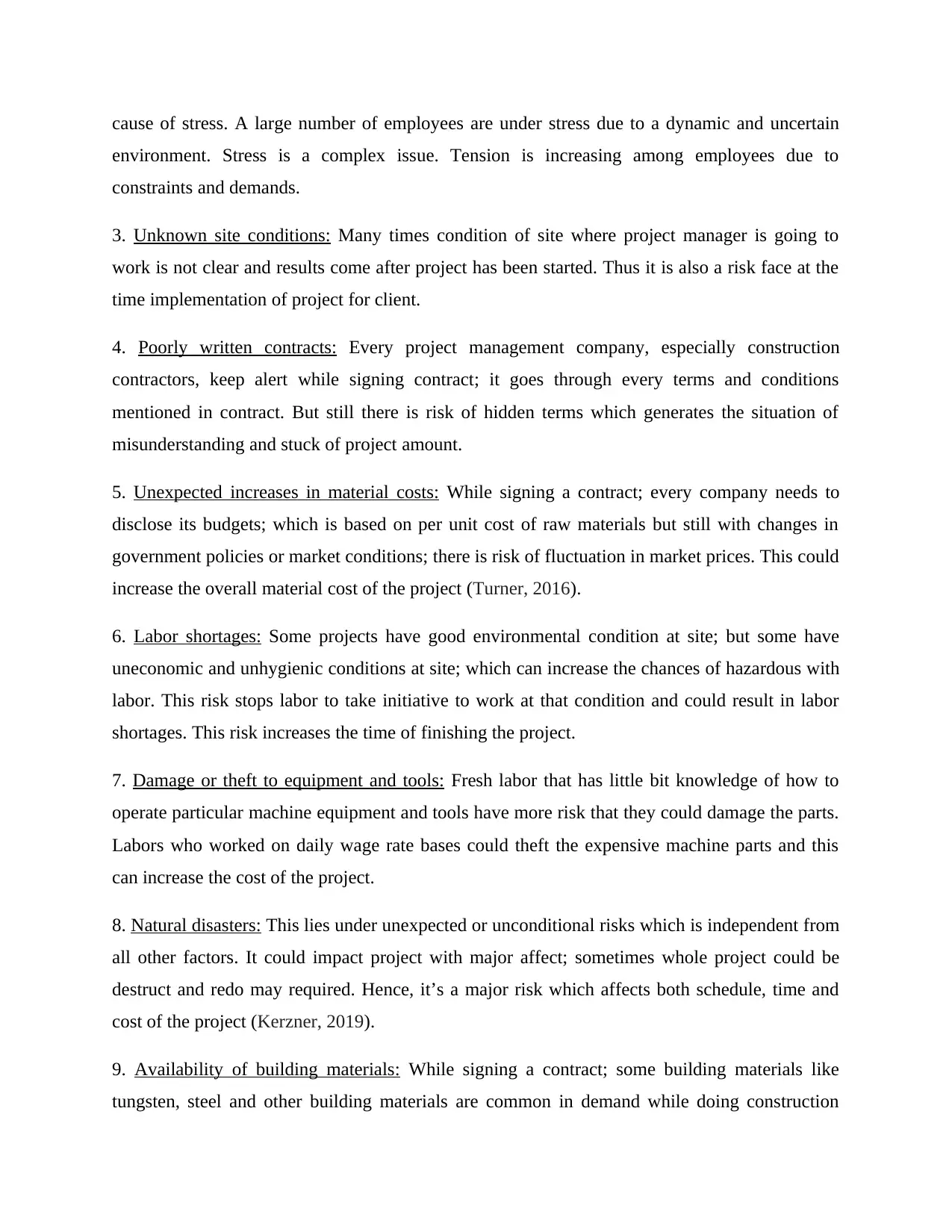
cause of stress. A large number of employees are under stress due to a dynamic and uncertain
environment. Stress is a complex issue. Tension is increasing among employees due to
constraints and demands.
3. Unknown site conditions: Many times condition of site where project manager is going to
work is not clear and results come after project has been started. Thus it is also a risk face at the
time implementation of project for client.
4. Poorly written contracts: Every project management company, especially construction
contractors, keep alert while signing contract; it goes through every terms and conditions
mentioned in contract. But still there is risk of hidden terms which generates the situation of
misunderstanding and stuck of project amount.
5. Unexpected increases in material costs: While signing a contract; every company needs to
disclose its budgets; which is based on per unit cost of raw materials but still with changes in
government policies or market conditions; there is risk of fluctuation in market prices. This could
increase the overall material cost of the project (Turner, 2016).
6. Labor shortages: Some projects have good environmental condition at site; but some have
uneconomic and unhygienic conditions at site; which can increase the chances of hazardous with
labor. This risk stops labor to take initiative to work at that condition and could result in labor
shortages. This risk increases the time of finishing the project.
7. Damage or theft to equipment and tools: Fresh labor that has little bit knowledge of how to
operate particular machine equipment and tools have more risk that they could damage the parts.
Labors who worked on daily wage rate bases could theft the expensive machine parts and this
can increase the cost of the project.
8. Natural disasters: This lies under unexpected or unconditional risks which is independent from
all other factors. It could impact project with major affect; sometimes whole project could be
destruct and redo may required. Hence, it’s a major risk which affects both schedule, time and
cost of the project (Kerzner, 2019).
9. Availability of building materials: While signing a contract; some building materials like
tungsten, steel and other building materials are common in demand while doing construction
environment. Stress is a complex issue. Tension is increasing among employees due to
constraints and demands.
3. Unknown site conditions: Many times condition of site where project manager is going to
work is not clear and results come after project has been started. Thus it is also a risk face at the
time implementation of project for client.
4. Poorly written contracts: Every project management company, especially construction
contractors, keep alert while signing contract; it goes through every terms and conditions
mentioned in contract. But still there is risk of hidden terms which generates the situation of
misunderstanding and stuck of project amount.
5. Unexpected increases in material costs: While signing a contract; every company needs to
disclose its budgets; which is based on per unit cost of raw materials but still with changes in
government policies or market conditions; there is risk of fluctuation in market prices. This could
increase the overall material cost of the project (Turner, 2016).
6. Labor shortages: Some projects have good environmental condition at site; but some have
uneconomic and unhygienic conditions at site; which can increase the chances of hazardous with
labor. This risk stops labor to take initiative to work at that condition and could result in labor
shortages. This risk increases the time of finishing the project.
7. Damage or theft to equipment and tools: Fresh labor that has little bit knowledge of how to
operate particular machine equipment and tools have more risk that they could damage the parts.
Labors who worked on daily wage rate bases could theft the expensive machine parts and this
can increase the cost of the project.
8. Natural disasters: This lies under unexpected or unconditional risks which is independent from
all other factors. It could impact project with major affect; sometimes whole project could be
destruct and redo may required. Hence, it’s a major risk which affects both schedule, time and
cost of the project (Kerzner, 2019).
9. Availability of building materials: While signing a contract; some building materials like
tungsten, steel and other building materials are common in demand while doing construction
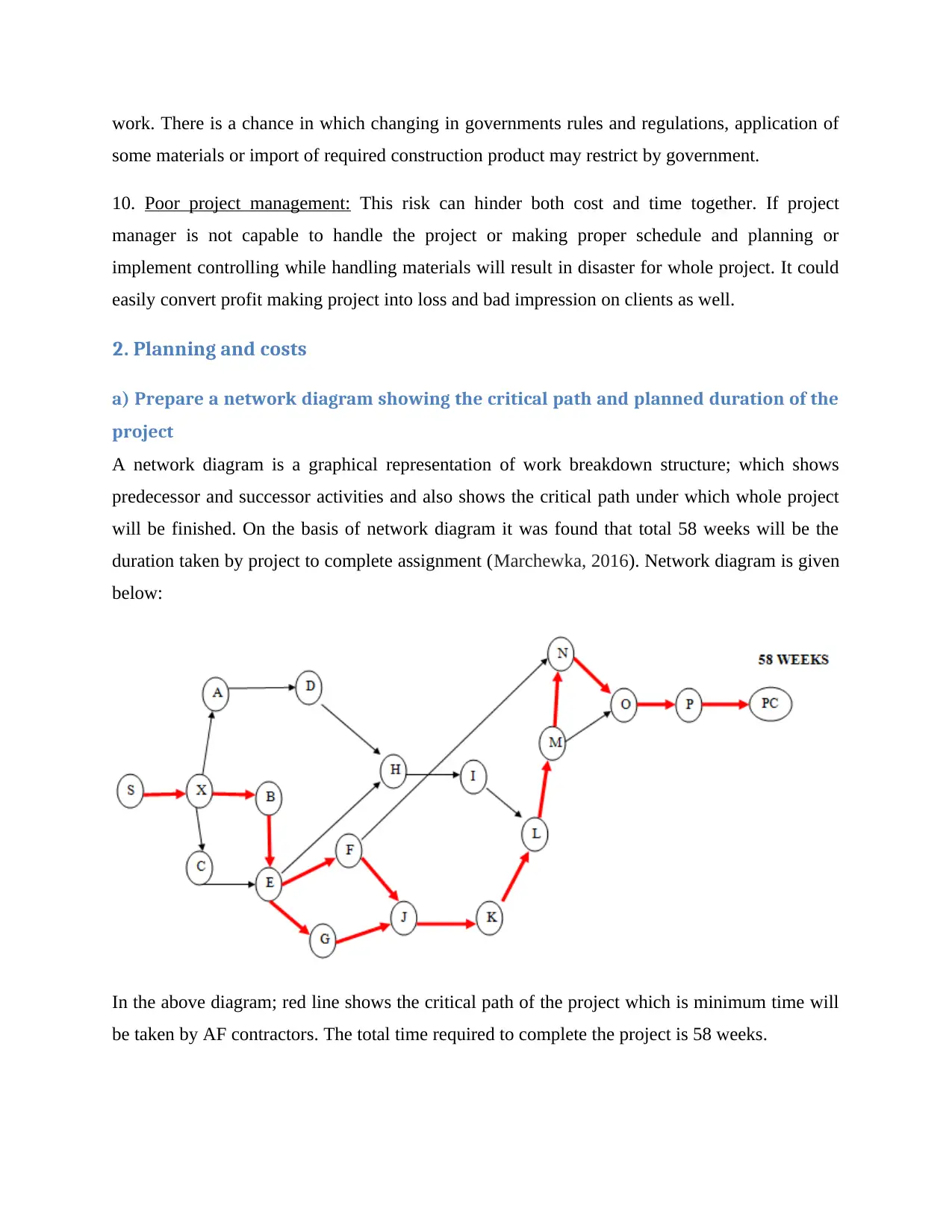
work. There is a chance in which changing in governments rules and regulations, application of
some materials or import of required construction product may restrict by government.
10. Poor project management: This risk can hinder both cost and time together. If project
manager is not capable to handle the project or making proper schedule and planning or
implement controlling while handling materials will result in disaster for whole project. It could
easily convert profit making project into loss and bad impression on clients as well.
2. Planning and costs
a) Prepare a network diagram showing the critical path and planned duration of the
project
A network diagram is a graphical representation of work breakdown structure; which shows
predecessor and successor activities and also shows the critical path under which whole project
will be finished. On the basis of network diagram it was found that total 58 weeks will be the
duration taken by project to complete assignment (Marchewka, 2016). Network diagram is given
below:
In the above diagram; red line shows the critical path of the project which is minimum time will
be taken by AF contractors. The total time required to complete the project is 58 weeks.
some materials or import of required construction product may restrict by government.
10. Poor project management: This risk can hinder both cost and time together. If project
manager is not capable to handle the project or making proper schedule and planning or
implement controlling while handling materials will result in disaster for whole project. It could
easily convert profit making project into loss and bad impression on clients as well.
2. Planning and costs
a) Prepare a network diagram showing the critical path and planned duration of the
project
A network diagram is a graphical representation of work breakdown structure; which shows
predecessor and successor activities and also shows the critical path under which whole project
will be finished. On the basis of network diagram it was found that total 58 weeks will be the
duration taken by project to complete assignment (Marchewka, 2016). Network diagram is given
below:
In the above diagram; red line shows the critical path of the project which is minimum time will
be taken by AF contractors. The total time required to complete the project is 58 weeks.
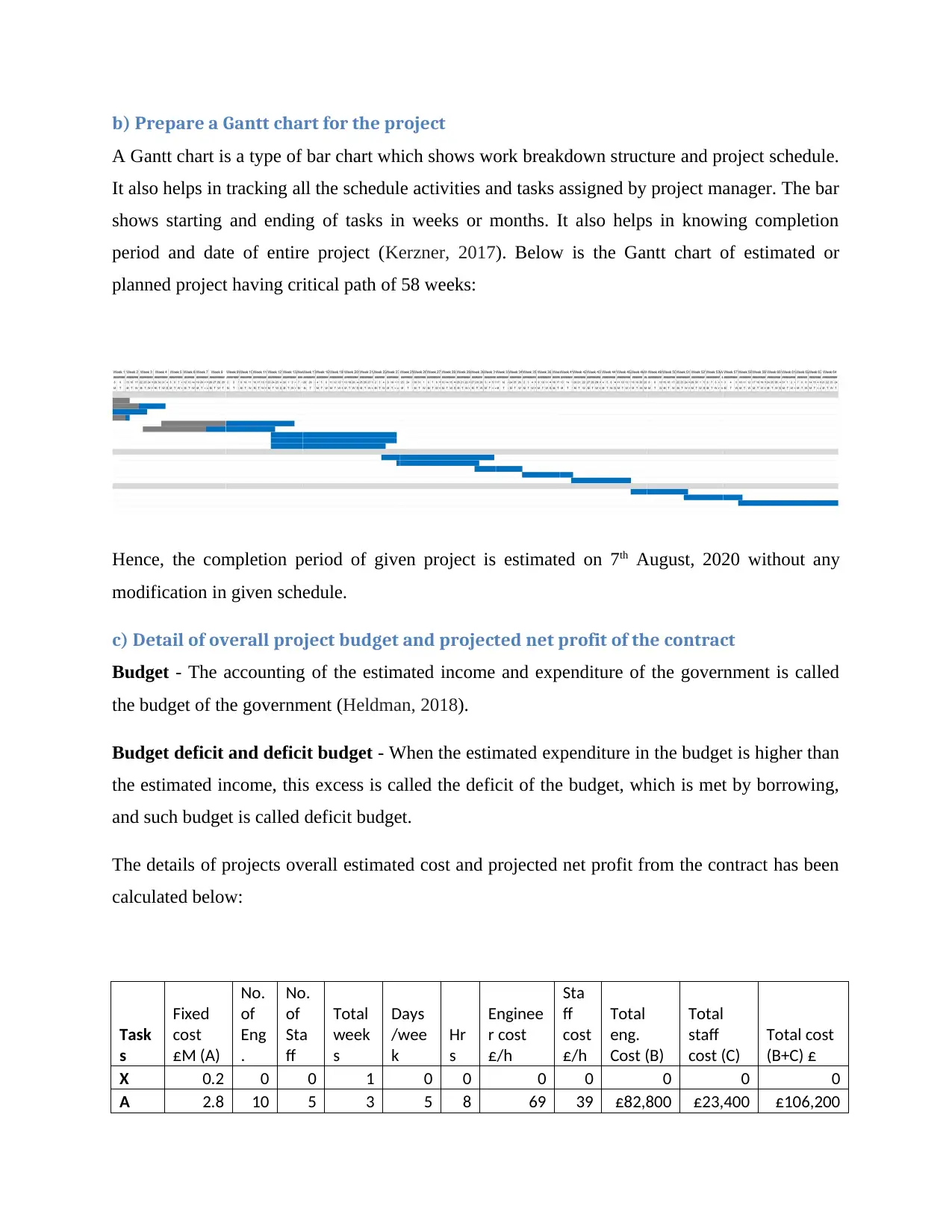
b) Prepare a Gantt chart for the project
A Gantt chart is a type of bar chart which shows work breakdown structure and project schedule.
It also helps in tracking all the schedule activities and tasks assigned by project manager. The bar
shows starting and ending of tasks in weeks or months. It also helps in knowing completion
period and date of entire project (Kerzner, 2017). Below is the Gantt chart of estimated or
planned project having critical path of 58 weeks:
Hence, the completion period of given project is estimated on 7th August, 2020 without any
modification in given schedule.
c) Detail of overall project budget and projected net profit of the contract
Budget - The accounting of the estimated income and expenditure of the government is called
the budget of the government (Heldman, 2018).
Budget deficit and deficit budget - When the estimated expenditure in the budget is higher than
the estimated income, this excess is called the deficit of the budget, which is met by borrowing,
and such budget is called deficit budget.
The details of projects overall estimated cost and projected net profit from the contract has been
calculated below:
Task
s
Fixed
cost
£M (A)
No.
of
Eng
.
No.
of
Sta
ff
Total
week
s
Days
/wee
k
Hr
s
Enginee
r cost
£/h
Sta
ff
cost
£/h
Total
eng.
Cost (B)
Total
staff
cost (C)
Total cost
(B+C) £
X 0.2 0 0 1 0 0 0 0 0 0 0
A 2.8 10 5 3 5 8 69 39 £82,800 £23,400 £106,200
A Gantt chart is a type of bar chart which shows work breakdown structure and project schedule.
It also helps in tracking all the schedule activities and tasks assigned by project manager. The bar
shows starting and ending of tasks in weeks or months. It also helps in knowing completion
period and date of entire project (Kerzner, 2017). Below is the Gantt chart of estimated or
planned project having critical path of 58 weeks:
Hence, the completion period of given project is estimated on 7th August, 2020 without any
modification in given schedule.
c) Detail of overall project budget and projected net profit of the contract
Budget - The accounting of the estimated income and expenditure of the government is called
the budget of the government (Heldman, 2018).
Budget deficit and deficit budget - When the estimated expenditure in the budget is higher than
the estimated income, this excess is called the deficit of the budget, which is met by borrowing,
and such budget is called deficit budget.
The details of projects overall estimated cost and projected net profit from the contract has been
calculated below:
Task
s
Fixed
cost
£M (A)
No.
of
Eng
.
No.
of
Sta
ff
Total
week
s
Days
/wee
k
Hr
s
Enginee
r cost
£/h
Sta
ff
cost
£/h
Total
eng.
Cost (B)
Total
staff
cost (C)
Total cost
(B+C) £
X 0.2 0 0 1 0 0 0 0 0 0 0
A 2.8 10 5 3 5 8 69 39 £82,800 £23,400 £106,200
Secure Best Marks with AI Grader
Need help grading? Try our AI Grader for instant feedback on your assignments.
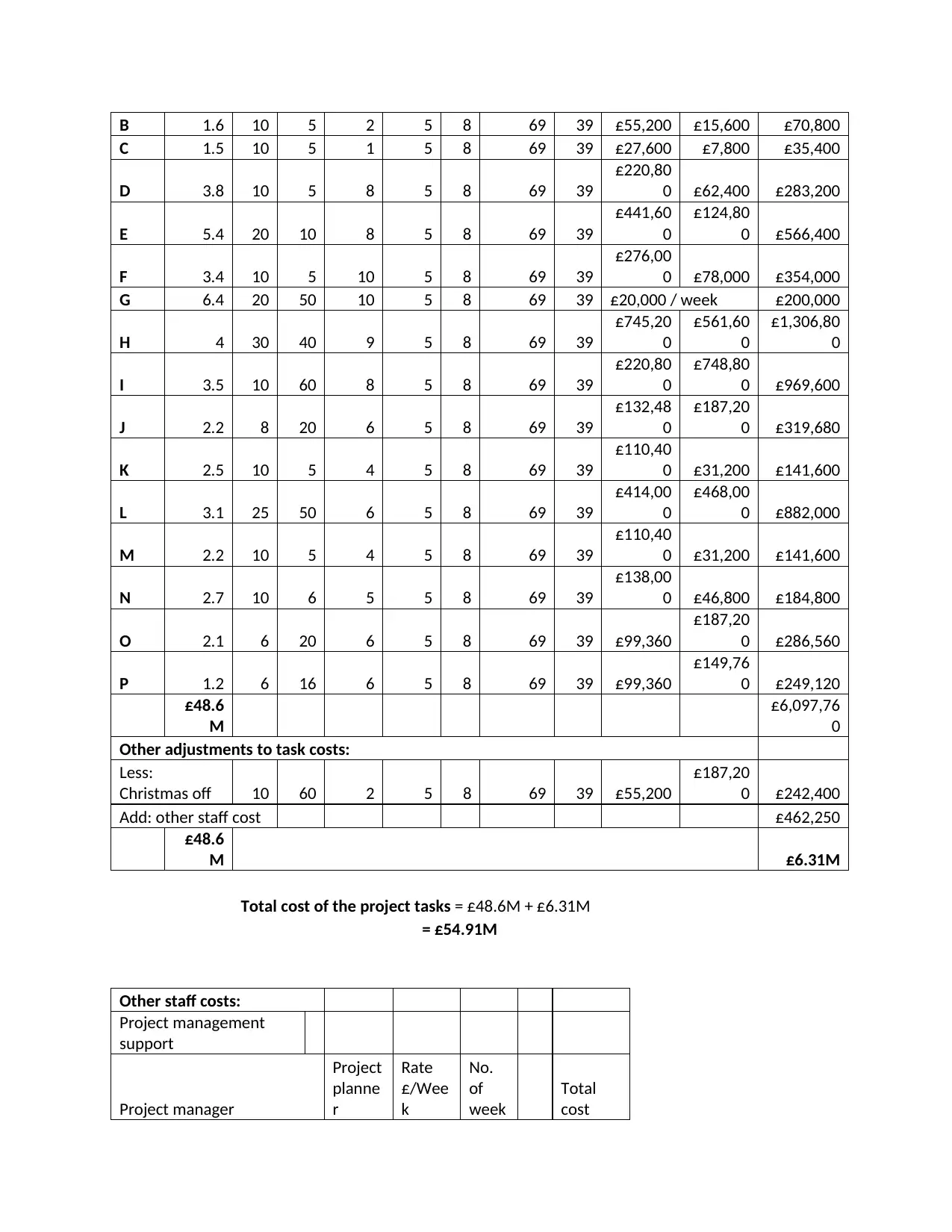
B 1.6 10 5 2 5 8 69 39 £55,200 £15,600 £70,800
C 1.5 10 5 1 5 8 69 39 £27,600 £7,800 £35,400
D 3.8 10 5 8 5 8 69 39
£220,80
0 £62,400 £283,200
E 5.4 20 10 8 5 8 69 39
£441,60
0
£124,80
0 £566,400
F 3.4 10 5 10 5 8 69 39
£276,00
0 £78,000 £354,000
G 6.4 20 50 10 5 8 69 39 £20,000 / week £200,000
H 4 30 40 9 5 8 69 39
£745,20
0
£561,60
0
£1,306,80
0
I 3.5 10 60 8 5 8 69 39
£220,80
0
£748,80
0 £969,600
J 2.2 8 20 6 5 8 69 39
£132,48
0
£187,20
0 £319,680
K 2.5 10 5 4 5 8 69 39
£110,40
0 £31,200 £141,600
L 3.1 25 50 6 5 8 69 39
£414,00
0
£468,00
0 £882,000
M 2.2 10 5 4 5 8 69 39
£110,40
0 £31,200 £141,600
N 2.7 10 6 5 5 8 69 39
£138,00
0 £46,800 £184,800
O 2.1 6 20 6 5 8 69 39 £99,360
£187,20
0 £286,560
P 1.2 6 16 6 5 8 69 39 £99,360
£149,76
0 £249,120
£48.6
M
£6,097,76
0
Other adjustments to task costs:
Less:
Christmas off 10 60 2 5 8 69 39 £55,200
£187,20
0 £242,400
Add: other staff cost £462,250
£48.6
M £6.31M
Total cost of the project tasks = £48.6M + £6.31M
= £54.91M
Other staff costs:
Project management
support
Project manager
Project
planne
r
Rate
£/Wee
k
No.
of
week
Total
cost
C 1.5 10 5 1 5 8 69 39 £27,600 £7,800 £35,400
D 3.8 10 5 8 5 8 69 39
£220,80
0 £62,400 £283,200
E 5.4 20 10 8 5 8 69 39
£441,60
0
£124,80
0 £566,400
F 3.4 10 5 10 5 8 69 39
£276,00
0 £78,000 £354,000
G 6.4 20 50 10 5 8 69 39 £20,000 / week £200,000
H 4 30 40 9 5 8 69 39
£745,20
0
£561,60
0
£1,306,80
0
I 3.5 10 60 8 5 8 69 39
£220,80
0
£748,80
0 £969,600
J 2.2 8 20 6 5 8 69 39
£132,48
0
£187,20
0 £319,680
K 2.5 10 5 4 5 8 69 39
£110,40
0 £31,200 £141,600
L 3.1 25 50 6 5 8 69 39
£414,00
0
£468,00
0 £882,000
M 2.2 10 5 4 5 8 69 39
£110,40
0 £31,200 £141,600
N 2.7 10 6 5 5 8 69 39
£138,00
0 £46,800 £184,800
O 2.1 6 20 6 5 8 69 39 £99,360
£187,20
0 £286,560
P 1.2 6 16 6 5 8 69 39 £99,360
£149,76
0 £249,120
£48.6
M
£6,097,76
0
Other adjustments to task costs:
Less:
Christmas off 10 60 2 5 8 69 39 £55,200
£187,20
0 £242,400
Add: other staff cost £462,250
£48.6
M £6.31M
Total cost of the project tasks = £48.6M + £6.31M
= £54.91M
Other staff costs:
Project management
support
Project manager
Project
planne
r
Rate
£/Wee
k
No.
of
week
Total
cost
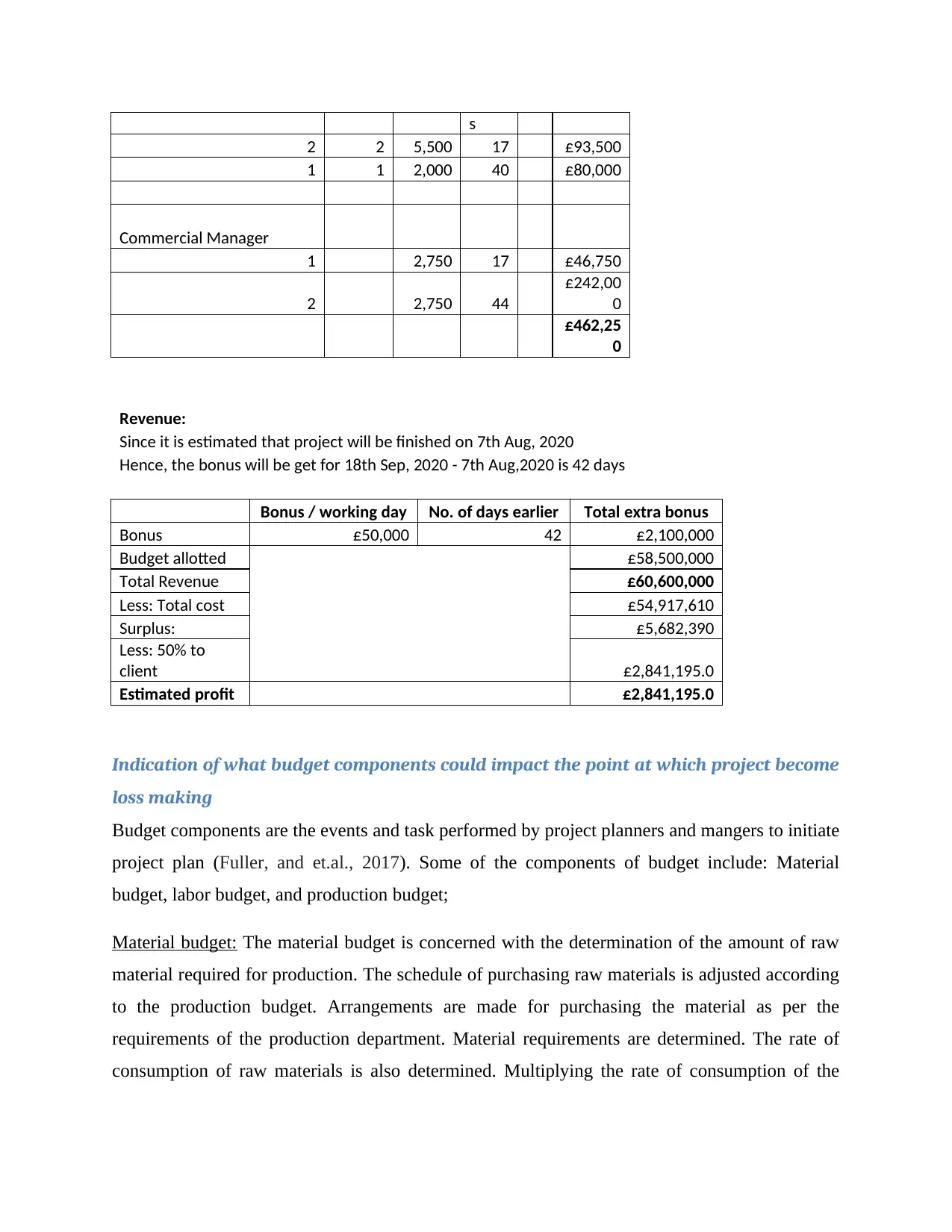
s
2 2 5,500 17 £93,500
1 1 2,000 40 £80,000
Commercial Manager
1 2,750 17 £46,750
2 2,750 44
£242,00
0
£462,25
0
Revenue:
Since it is estimated that project will be finished on 7th Aug, 2020
Hence, the bonus will be get for 18th Sep, 2020 - 7th Aug,2020 is 42 days
Bonus / working day No. of days earlier Total extra bonus
Bonus £50,000 42 £2,100,000
Budget allotted £58,500,000
Total Revenue £60,600,000
Less: Total cost £54,917,610
Surplus: £5,682,390
Less: 50% to
client £2,841,195.0
Estimated profit £2,841,195.0
Indication of what budget components could impact the point at which project become
loss making
Budget components are the events and task performed by project planners and mangers to initiate
project plan (Fuller, and et.al., 2017). Some of the components of budget include: Material
budget, labor budget, and production budget;
Material budget: The material budget is concerned with the determination of the amount of raw
material required for production. The schedule of purchasing raw materials is adjusted according
to the production budget. Arrangements are made for purchasing the material as per the
requirements of the production department. Material requirements are determined. The rate of
consumption of raw materials is also determined. Multiplying the rate of consumption of the
2 2 5,500 17 £93,500
1 1 2,000 40 £80,000
Commercial Manager
1 2,750 17 £46,750
2 2,750 44
£242,00
0
£462,25
0
Revenue:
Since it is estimated that project will be finished on 7th Aug, 2020
Hence, the bonus will be get for 18th Sep, 2020 - 7th Aug,2020 is 42 days
Bonus / working day No. of days earlier Total extra bonus
Bonus £50,000 42 £2,100,000
Budget allotted £58,500,000
Total Revenue £60,600,000
Less: Total cost £54,917,610
Surplus: £5,682,390
Less: 50% to
client £2,841,195.0
Estimated profit £2,841,195.0
Indication of what budget components could impact the point at which project become
loss making
Budget components are the events and task performed by project planners and mangers to initiate
project plan (Fuller, and et.al., 2017). Some of the components of budget include: Material
budget, labor budget, and production budget;
Material budget: The material budget is concerned with the determination of the amount of raw
material required for production. The schedule of purchasing raw materials is adjusted according
to the production budget. Arrangements are made for purchasing the material as per the
requirements of the production department. Material requirements are determined. The rate of
consumption of raw materials is also determined. Multiplying the rate of consumption of the
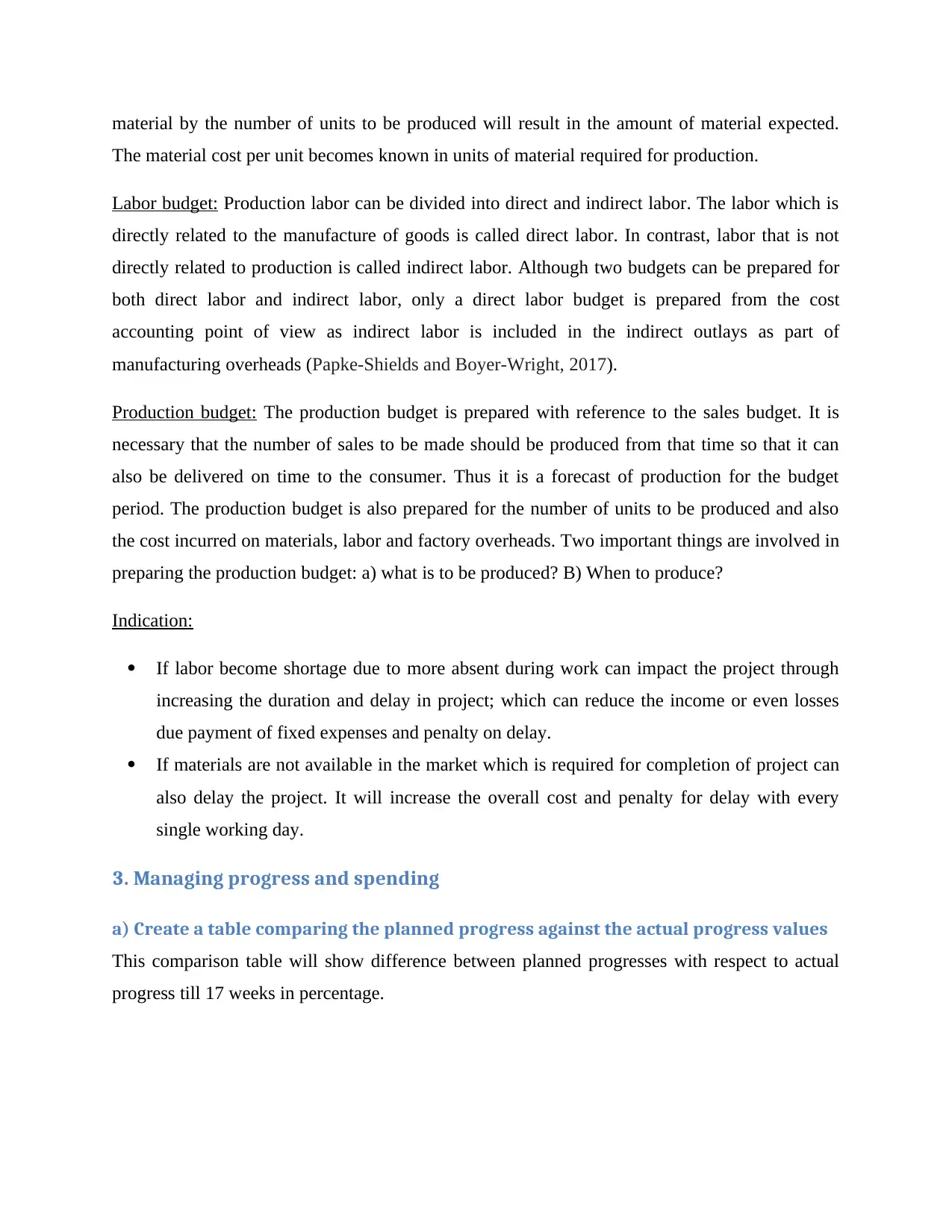
material by the number of units to be produced will result in the amount of material expected.
The material cost per unit becomes known in units of material required for production.
Labor budget: Production labor can be divided into direct and indirect labor. The labor which is
directly related to the manufacture of goods is called direct labor. In contrast, labor that is not
directly related to production is called indirect labor. Although two budgets can be prepared for
both direct labor and indirect labor, only a direct labor budget is prepared from the cost
accounting point of view as indirect labor is included in the indirect outlays as part of
manufacturing overheads (Papke-Shields and Boyer-Wright, 2017).
Production budget: The production budget is prepared with reference to the sales budget. It is
necessary that the number of sales to be made should be produced from that time so that it can
also be delivered on time to the consumer. Thus it is a forecast of production for the budget
period. The production budget is also prepared for the number of units to be produced and also
the cost incurred on materials, labor and factory overheads. Two important things are involved in
preparing the production budget: a) what is to be produced? B) When to produce?
Indication:
If labor become shortage due to more absent during work can impact the project through
increasing the duration and delay in project; which can reduce the income or even losses
due payment of fixed expenses and penalty on delay.
If materials are not available in the market which is required for completion of project can
also delay the project. It will increase the overall cost and penalty for delay with every
single working day.
3. Managing progress and spending
a) Create a table comparing the planned progress against the actual progress values
This comparison table will show difference between planned progresses with respect to actual
progress till 17 weeks in percentage.
The material cost per unit becomes known in units of material required for production.
Labor budget: Production labor can be divided into direct and indirect labor. The labor which is
directly related to the manufacture of goods is called direct labor. In contrast, labor that is not
directly related to production is called indirect labor. Although two budgets can be prepared for
both direct labor and indirect labor, only a direct labor budget is prepared from the cost
accounting point of view as indirect labor is included in the indirect outlays as part of
manufacturing overheads (Papke-Shields and Boyer-Wright, 2017).
Production budget: The production budget is prepared with reference to the sales budget. It is
necessary that the number of sales to be made should be produced from that time so that it can
also be delivered on time to the consumer. Thus it is a forecast of production for the budget
period. The production budget is also prepared for the number of units to be produced and also
the cost incurred on materials, labor and factory overheads. Two important things are involved in
preparing the production budget: a) what is to be produced? B) When to produce?
Indication:
If labor become shortage due to more absent during work can impact the project through
increasing the duration and delay in project; which can reduce the income or even losses
due payment of fixed expenses and penalty on delay.
If materials are not available in the market which is required for completion of project can
also delay the project. It will increase the overall cost and penalty for delay with every
single working day.
3. Managing progress and spending
a) Create a table comparing the planned progress against the actual progress values
This comparison table will show difference between planned progresses with respect to actual
progress till 17 weeks in percentage.
Paraphrase This Document
Need a fresh take? Get an instant paraphrase of this document with our AI Paraphraser
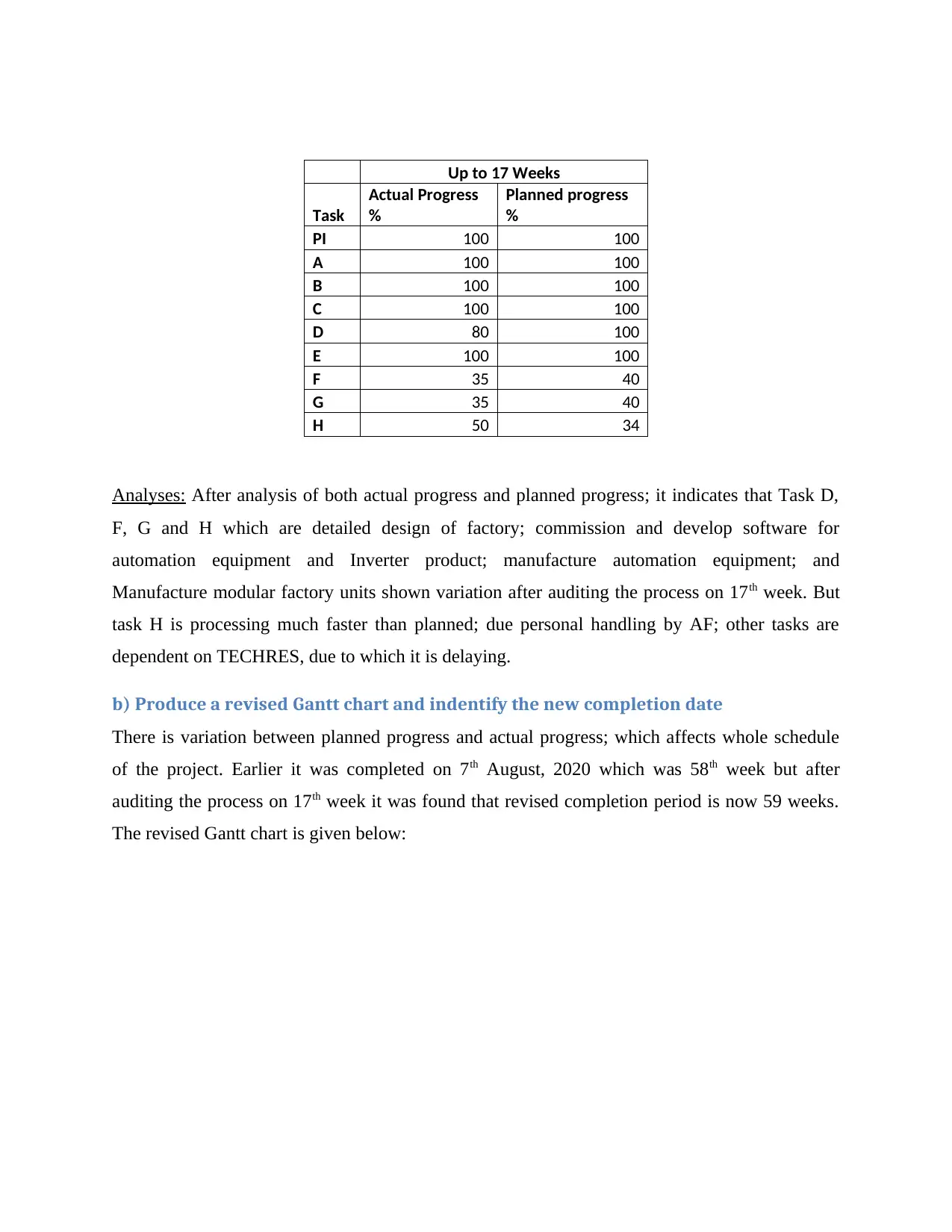
Up to 17 Weeks
Task
Actual Progress
%
Planned progress
%
PI 100 100
A 100 100
B 100 100
C 100 100
D 80 100
E 100 100
F 35 40
G 35 40
H 50 34
Analyses: After analysis of both actual progress and planned progress; it indicates that Task D,
F, G and H which are detailed design of factory; commission and develop software for
automation equipment and Inverter product; manufacture automation equipment; and
Manufacture modular factory units shown variation after auditing the process on 17th week. But
task H is processing much faster than planned; due personal handling by AF; other tasks are
dependent on TECHRES, due to which it is delaying.
b) Produce a revised Gantt chart and indentify the new completion date
There is variation between planned progress and actual progress; which affects whole schedule
of the project. Earlier it was completed on 7th August, 2020 which was 58th week but after
auditing the process on 17th week it was found that revised completion period is now 59 weeks.
The revised Gantt chart is given below:
Task
Actual Progress
%
Planned progress
%
PI 100 100
A 100 100
B 100 100
C 100 100
D 80 100
E 100 100
F 35 40
G 35 40
H 50 34
Analyses: After analysis of both actual progress and planned progress; it indicates that Task D,
F, G and H which are detailed design of factory; commission and develop software for
automation equipment and Inverter product; manufacture automation equipment; and
Manufacture modular factory units shown variation after auditing the process on 17th week. But
task H is processing much faster than planned; due personal handling by AF; other tasks are
dependent on TECHRES, due to which it is delaying.
b) Produce a revised Gantt chart and indentify the new completion date
There is variation between planned progress and actual progress; which affects whole schedule
of the project. Earlier it was completed on 7th August, 2020 which was 58th week but after
auditing the process on 17th week it was found that revised completion period is now 59 weeks.
The revised Gantt chart is given below:
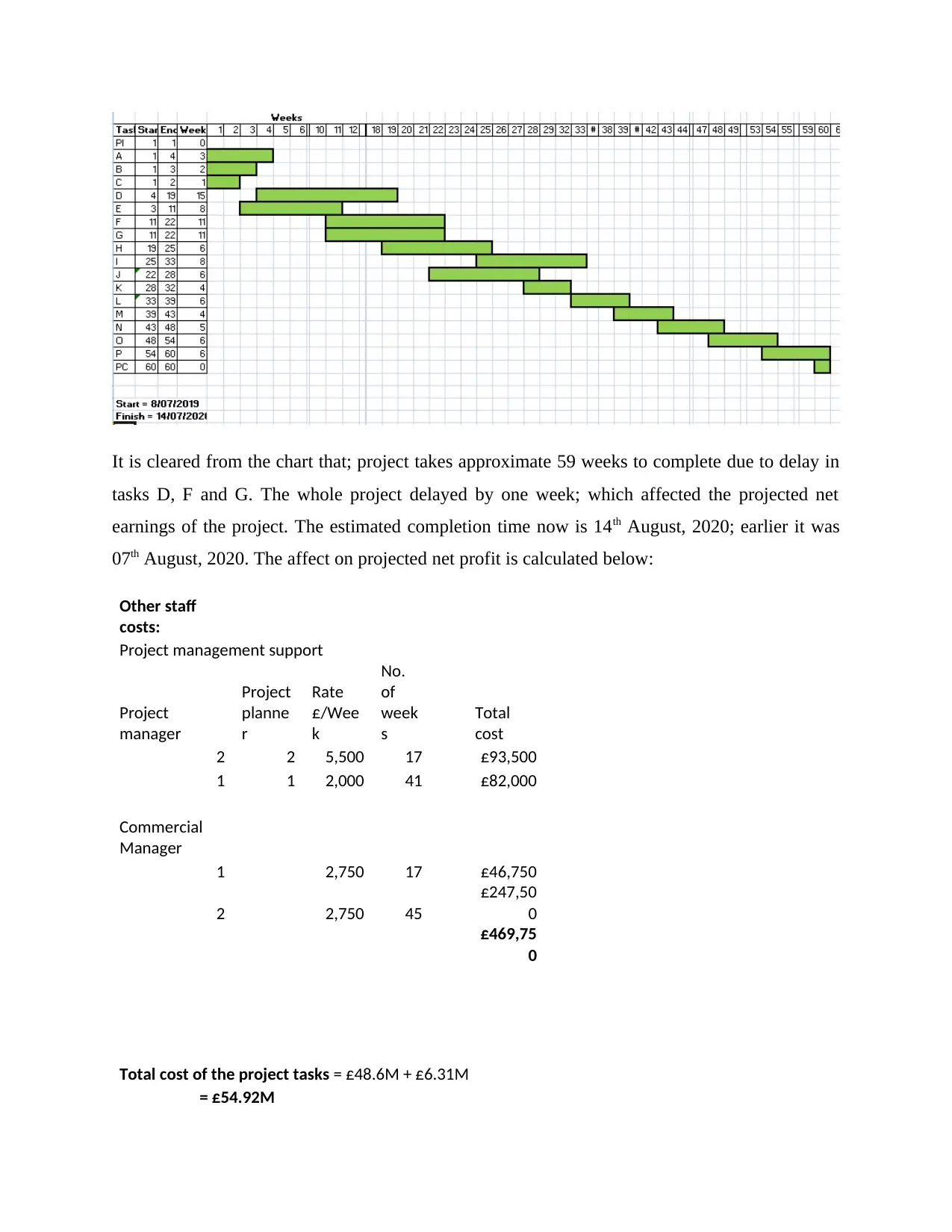
It is cleared from the chart that; project takes approximate 59 weeks to complete due to delay in
tasks D, F and G. The whole project delayed by one week; which affected the projected net
earnings of the project. The estimated completion time now is 14th August, 2020; earlier it was
07th August, 2020. The affect on projected net profit is calculated below:
Other staff
costs:
Project management support
Project
manager
Project
planne
r
Rate
£/Wee
k
No.
of
week
s
Total
cost
2 2 5,500 17 £93,500
1 1 2,000 41 £82,000
Commercial
Manager
1 2,750 17 £46,750
2 2,750 45
£247,50
0
£469,75
0
Total cost of the project tasks = £48.6M + £6.31M
= £54.92M
tasks D, F and G. The whole project delayed by one week; which affected the projected net
earnings of the project. The estimated completion time now is 14th August, 2020; earlier it was
07th August, 2020. The affect on projected net profit is calculated below:
Other staff
costs:
Project management support
Project
manager
Project
planne
r
Rate
£/Wee
k
No.
of
week
s
Total
cost
2 2 5,500 17 £93,500
1 1 2,000 41 £82,000
Commercial
Manager
1 2,750 17 £46,750
2 2,750 45
£247,50
0
£469,75
0
Total cost of the project tasks = £48.6M + £6.31M
= £54.92M
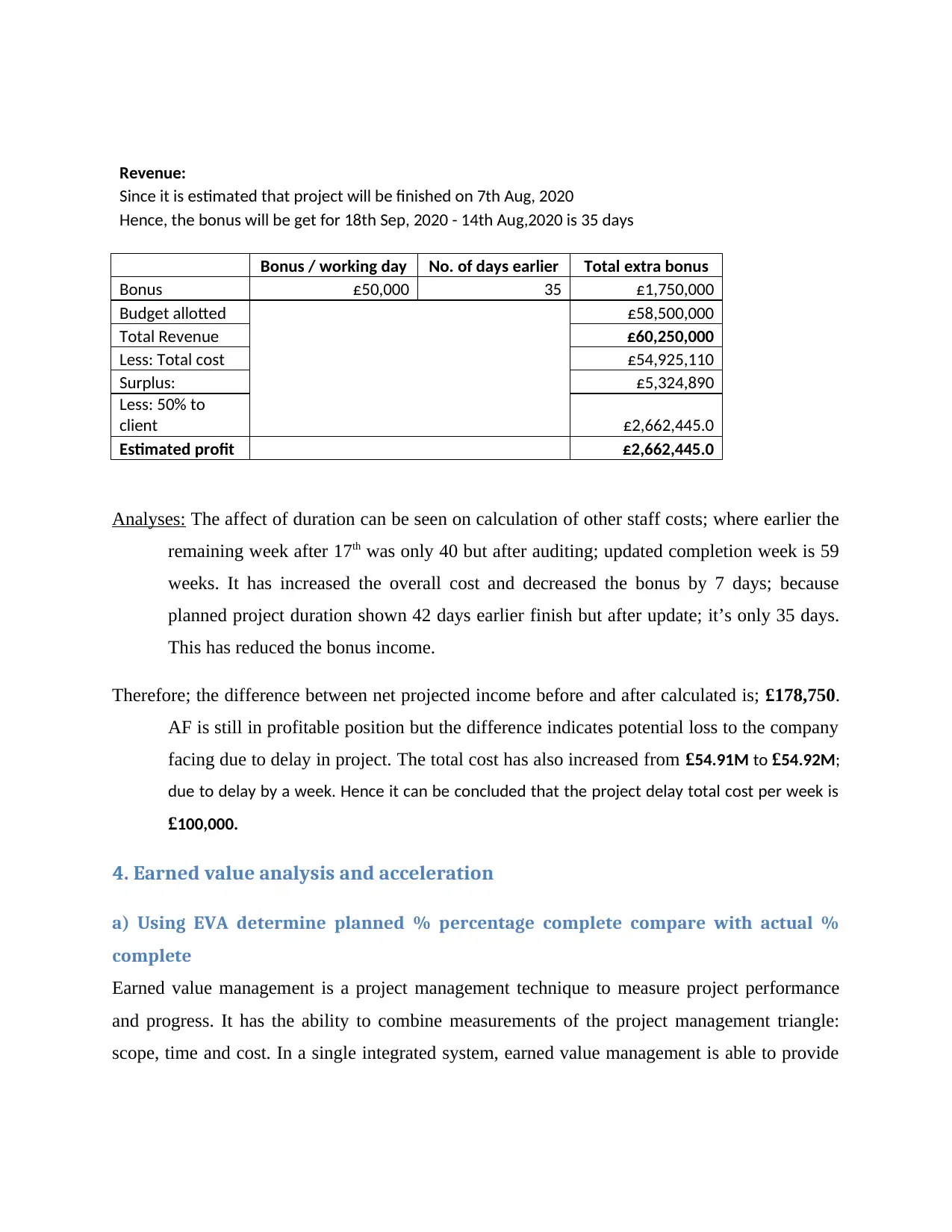
Revenue:
Since it is estimated that project will be finished on 7th Aug, 2020
Hence, the bonus will be get for 18th Sep, 2020 - 14th Aug,2020 is 35 days
Bonus / working day No. of days earlier Total extra bonus
Bonus £50,000 35 £1,750,000
Budget allotted £58,500,000
Total Revenue £60,250,000
Less: Total cost £54,925,110
Surplus: £5,324,890
Less: 50% to
client £2,662,445.0
Estimated profit £2,662,445.0
Analyses: The affect of duration can be seen on calculation of other staff costs; where earlier the
remaining week after 17th was only 40 but after auditing; updated completion week is 59
weeks. It has increased the overall cost and decreased the bonus by 7 days; because
planned project duration shown 42 days earlier finish but after update; it’s only 35 days.
This has reduced the bonus income.
Therefore; the difference between net projected income before and after calculated is; £178,750.
AF is still in profitable position but the difference indicates potential loss to the company
facing due to delay in project. The total cost has also increased from £54.91M to £54.92M;
due to delay by a week. Hence it can be concluded that the project delay total cost per week is
£100,000.
4. Earned value analysis and acceleration
a) Using EVA determine planned % percentage complete compare with actual %
complete
Earned value management is a project management technique to measure project performance
and progress. It has the ability to combine measurements of the project management triangle:
scope, time and cost. In a single integrated system, earned value management is able to provide
Since it is estimated that project will be finished on 7th Aug, 2020
Hence, the bonus will be get for 18th Sep, 2020 - 14th Aug,2020 is 35 days
Bonus / working day No. of days earlier Total extra bonus
Bonus £50,000 35 £1,750,000
Budget allotted £58,500,000
Total Revenue £60,250,000
Less: Total cost £54,925,110
Surplus: £5,324,890
Less: 50% to
client £2,662,445.0
Estimated profit £2,662,445.0
Analyses: The affect of duration can be seen on calculation of other staff costs; where earlier the
remaining week after 17th was only 40 but after auditing; updated completion week is 59
weeks. It has increased the overall cost and decreased the bonus by 7 days; because
planned project duration shown 42 days earlier finish but after update; it’s only 35 days.
This has reduced the bonus income.
Therefore; the difference between net projected income before and after calculated is; £178,750.
AF is still in profitable position but the difference indicates potential loss to the company
facing due to delay in project. The total cost has also increased from £54.91M to £54.92M;
due to delay by a week. Hence it can be concluded that the project delay total cost per week is
£100,000.
4. Earned value analysis and acceleration
a) Using EVA determine planned % percentage complete compare with actual %
complete
Earned value management is a project management technique to measure project performance
and progress. It has the ability to combine measurements of the project management triangle:
scope, time and cost. In a single integrated system, earned value management is able to provide
Secure Best Marks with AI Grader
Need help grading? Try our AI Grader for instant feedback on your assignments.
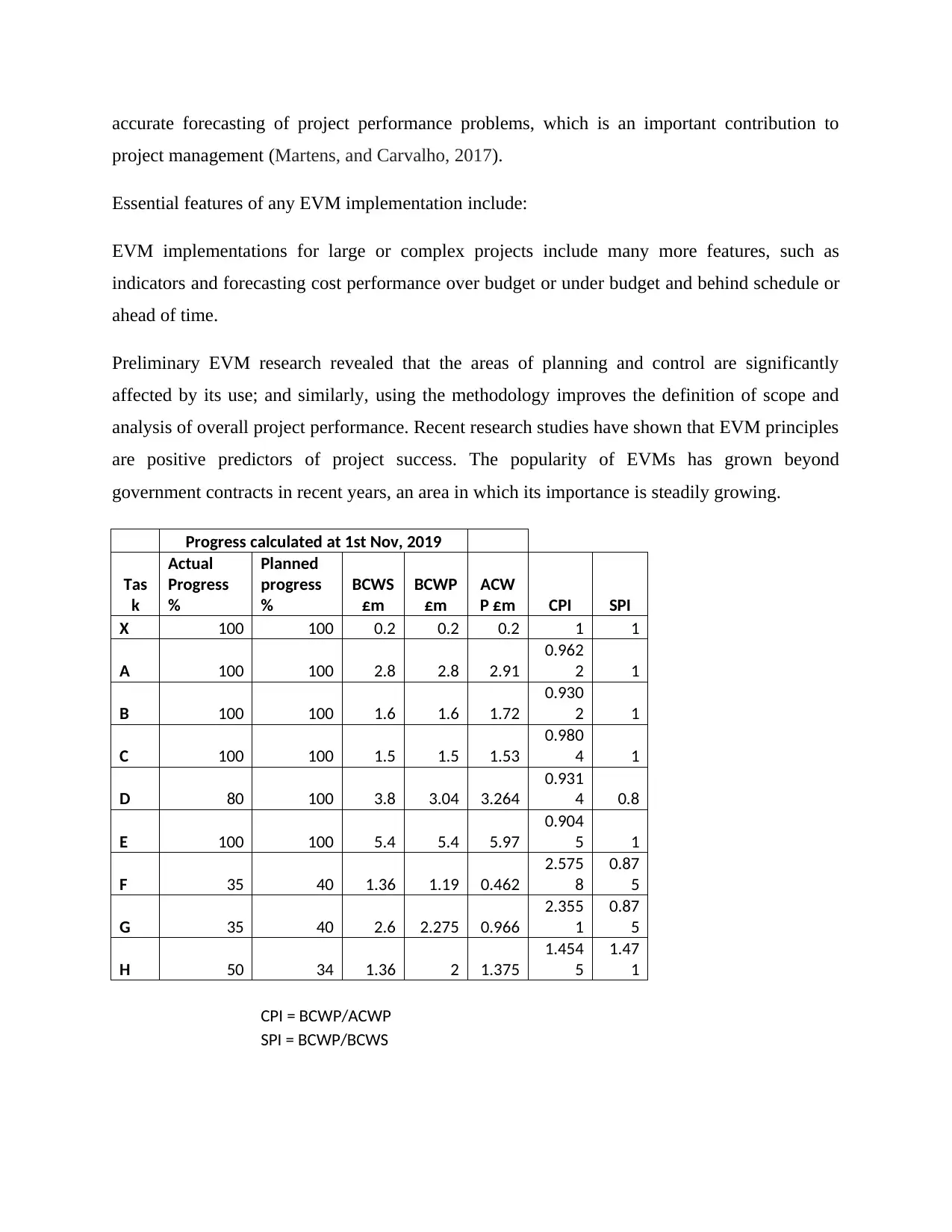
accurate forecasting of project performance problems, which is an important contribution to
project management (Martens, and Carvalho, 2017).
Essential features of any EVM implementation include:
EVM implementations for large or complex projects include many more features, such as
indicators and forecasting cost performance over budget or under budget and behind schedule or
ahead of time.
Preliminary EVM research revealed that the areas of planning and control are significantly
affected by its use; and similarly, using the methodology improves the definition of scope and
analysis of overall project performance. Recent research studies have shown that EVM principles
are positive predictors of project success. The popularity of EVMs has grown beyond
government contracts in recent years, an area in which its importance is steadily growing.
Progress calculated at 1st Nov, 2019
Tas
k
Actual
Progress
%
Planned
progress
%
BCWS
£m
BCWP
£m
ACW
P £m CPI SPI
X 100 100 0.2 0.2 0.2 1 1
A 100 100 2.8 2.8 2.91
0.962
2 1
B 100 100 1.6 1.6 1.72
0.930
2 1
C 100 100 1.5 1.5 1.53
0.980
4 1
D 80 100 3.8 3.04 3.264
0.931
4 0.8
E 100 100 5.4 5.4 5.97
0.904
5 1
F 35 40 1.36 1.19 0.462
2.575
8
0.87
5
G 35 40 2.6 2.275 0.966
2.355
1
0.87
5
H 50 34 1.36 2 1.375
1.454
5
1.47
1
CPI = BCWP/ACWP
SPI = BCWP/BCWS
project management (Martens, and Carvalho, 2017).
Essential features of any EVM implementation include:
EVM implementations for large or complex projects include many more features, such as
indicators and forecasting cost performance over budget or under budget and behind schedule or
ahead of time.
Preliminary EVM research revealed that the areas of planning and control are significantly
affected by its use; and similarly, using the methodology improves the definition of scope and
analysis of overall project performance. Recent research studies have shown that EVM principles
are positive predictors of project success. The popularity of EVMs has grown beyond
government contracts in recent years, an area in which its importance is steadily growing.
Progress calculated at 1st Nov, 2019
Tas
k
Actual
Progress
%
Planned
progress
%
BCWS
£m
BCWP
£m
ACW
P £m CPI SPI
X 100 100 0.2 0.2 0.2 1 1
A 100 100 2.8 2.8 2.91
0.962
2 1
B 100 100 1.6 1.6 1.72
0.930
2 1
C 100 100 1.5 1.5 1.53
0.980
4 1
D 80 100 3.8 3.04 3.264
0.931
4 0.8
E 100 100 5.4 5.4 5.97
0.904
5 1
F 35 40 1.36 1.19 0.462
2.575
8
0.87
5
G 35 40 2.6 2.275 0.966
2.355
1
0.87
5
H 50 34 1.36 2 1.375
1.454
5
1.47
1
CPI = BCWP/ACWP
SPI = BCWP/BCWS
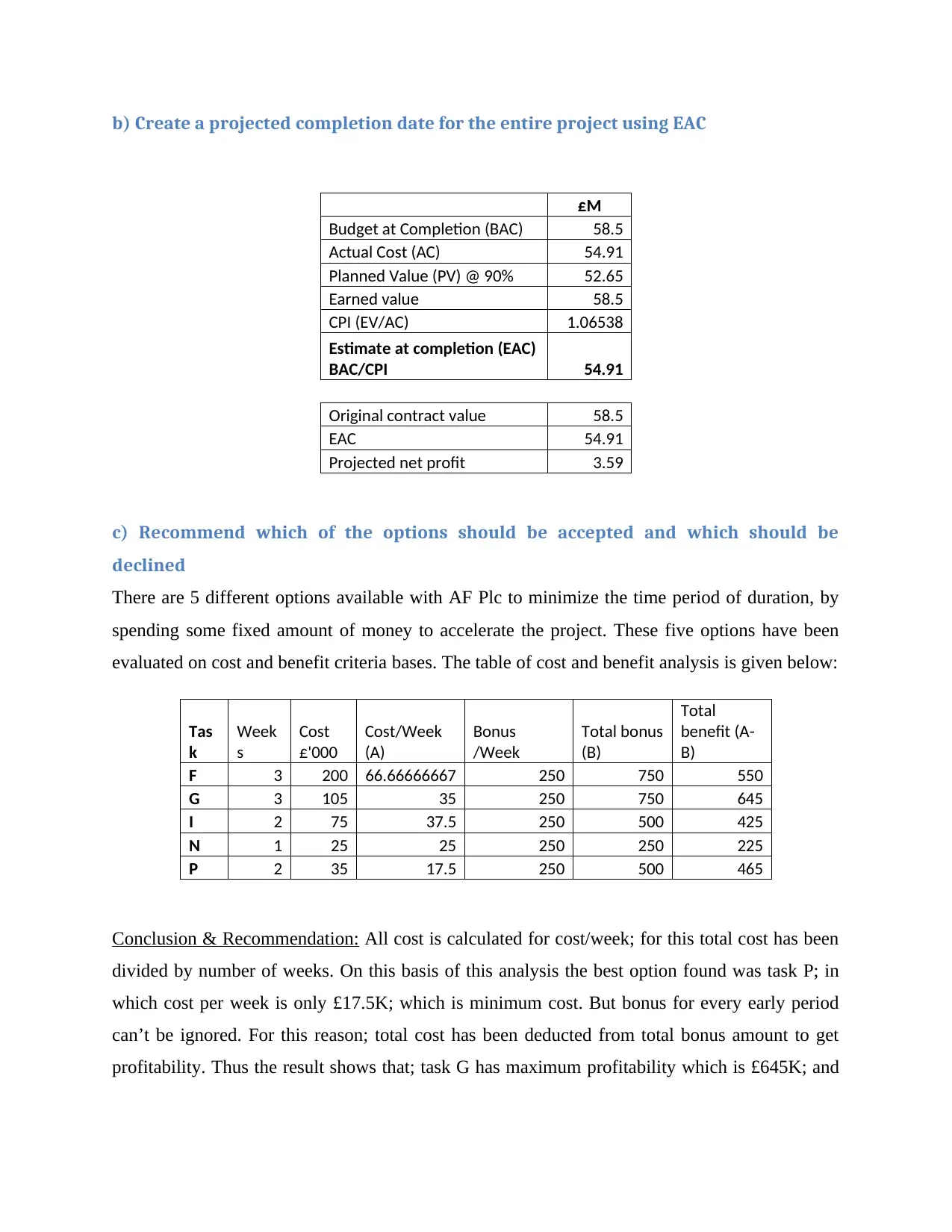
b) Create a projected completion date for the entire project using EAC
£M
Budget at Completion (BAC) 58.5
Actual Cost (AC) 54.91
Planned Value (PV) @ 90% 52.65
Earned value 58.5
CPI (EV/AC) 1.06538
Estimate at completion (EAC)
BAC/CPI 54.91
Original contract value 58.5
EAC 54.91
Projected net profit 3.59
c) Recommend which of the options should be accepted and which should be
declined
There are 5 different options available with AF Plc to minimize the time period of duration, by
spending some fixed amount of money to accelerate the project. These five options have been
evaluated on cost and benefit criteria bases. The table of cost and benefit analysis is given below:
Tas
k
Week
s
Cost
£'000
Cost/Week
(A)
Bonus
/Week
Total bonus
(B)
Total
benefit (A-
B)
F 3 200 66.66666667 250 750 550
G 3 105 35 250 750 645
I 2 75 37.5 250 500 425
N 1 25 25 250 250 225
P 2 35 17.5 250 500 465
Conclusion & Recommendation: All cost is calculated for cost/week; for this total cost has been
divided by number of weeks. On this basis of this analysis the best option found was task P; in
which cost per week is only £17.5K; which is minimum cost. But bonus for every early period
can’t be ignored. For this reason; total cost has been deducted from total bonus amount to get
profitability. Thus the result shows that; task G has maximum profitability which is £645K; and
£M
Budget at Completion (BAC) 58.5
Actual Cost (AC) 54.91
Planned Value (PV) @ 90% 52.65
Earned value 58.5
CPI (EV/AC) 1.06538
Estimate at completion (EAC)
BAC/CPI 54.91
Original contract value 58.5
EAC 54.91
Projected net profit 3.59
c) Recommend which of the options should be accepted and which should be
declined
There are 5 different options available with AF Plc to minimize the time period of duration, by
spending some fixed amount of money to accelerate the project. These five options have been
evaluated on cost and benefit criteria bases. The table of cost and benefit analysis is given below:
Tas
k
Week
s
Cost
£'000
Cost/Week
(A)
Bonus
/Week
Total bonus
(B)
Total
benefit (A-
B)
F 3 200 66.66666667 250 750 550
G 3 105 35 250 750 645
I 2 75 37.5 250 500 425
N 1 25 25 250 250 225
P 2 35 17.5 250 500 465
Conclusion & Recommendation: All cost is calculated for cost/week; for this total cost has been
divided by number of weeks. On this basis of this analysis the best option found was task P; in
which cost per week is only £17.5K; which is minimum cost. But bonus for every early period
can’t be ignored. For this reason; total cost has been deducted from total bonus amount to get
profitability. Thus the result shows that; task G has maximum profitability which is £645K; and

hence on this basis task G will be selected as a acceleration option for the project and rest
alternatives will be rejected.
alternatives will be rejected.
Paraphrase This Document
Need a fresh take? Get an instant paraphrase of this document with our AI Paraphraser
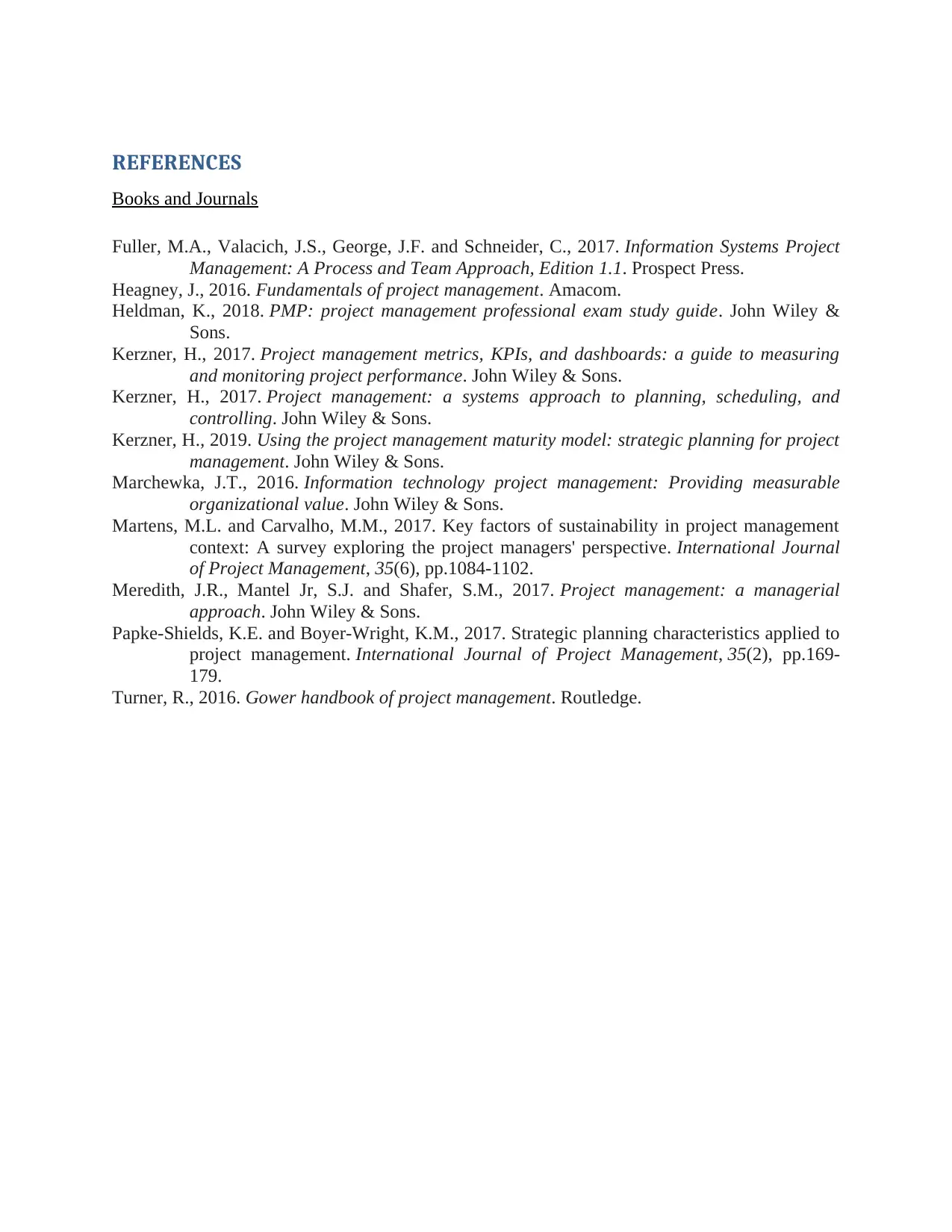
REFERENCES
Books and Journals
Fuller, M.A., Valacich, J.S., George, J.F. and Schneider, C., 2017. Information Systems Project
Management: A Process and Team Approach, Edition 1.1. Prospect Press.
Heagney, J., 2016. Fundamentals of project management. Amacom.
Heldman, K., 2018. PMP: project management professional exam study guide. John Wiley &
Sons.
Kerzner, H., 2017. Project management metrics, KPIs, and dashboards: a guide to measuring
and monitoring project performance. John Wiley & Sons.
Kerzner, H., 2017. Project management: a systems approach to planning, scheduling, and
controlling. John Wiley & Sons.
Kerzner, H., 2019. Using the project management maturity model: strategic planning for project
management. John Wiley & Sons.
Marchewka, J.T., 2016. Information technology project management: Providing measurable
organizational value. John Wiley & Sons.
Martens, M.L. and Carvalho, M.M., 2017. Key factors of sustainability in project management
context: A survey exploring the project managers' perspective. International Journal
of Project Management, 35(6), pp.1084-1102.
Meredith, J.R., Mantel Jr, S.J. and Shafer, S.M., 2017. Project management: a managerial
approach. John Wiley & Sons.
Papke-Shields, K.E. and Boyer-Wright, K.M., 2017. Strategic planning characteristics applied to
project management. International Journal of Project Management, 35(2), pp.169-
179.
Turner, R., 2016. Gower handbook of project management. Routledge.
Books and Journals
Fuller, M.A., Valacich, J.S., George, J.F. and Schneider, C., 2017. Information Systems Project
Management: A Process and Team Approach, Edition 1.1. Prospect Press.
Heagney, J., 2016. Fundamentals of project management. Amacom.
Heldman, K., 2018. PMP: project management professional exam study guide. John Wiley &
Sons.
Kerzner, H., 2017. Project management metrics, KPIs, and dashboards: a guide to measuring
and monitoring project performance. John Wiley & Sons.
Kerzner, H., 2017. Project management: a systems approach to planning, scheduling, and
controlling. John Wiley & Sons.
Kerzner, H., 2019. Using the project management maturity model: strategic planning for project
management. John Wiley & Sons.
Marchewka, J.T., 2016. Information technology project management: Providing measurable
organizational value. John Wiley & Sons.
Martens, M.L. and Carvalho, M.M., 2017. Key factors of sustainability in project management
context: A survey exploring the project managers' perspective. International Journal
of Project Management, 35(6), pp.1084-1102.
Meredith, J.R., Mantel Jr, S.J. and Shafer, S.M., 2017. Project management: a managerial
approach. John Wiley & Sons.
Papke-Shields, K.E. and Boyer-Wright, K.M., 2017. Strategic planning characteristics applied to
project management. International Journal of Project Management, 35(2), pp.169-
179.
Turner, R., 2016. Gower handbook of project management. Routledge.
1 out of 20
Related Documents
![[object Object]](/_next/image/?url=%2F_next%2Fstatic%2Fmedia%2Flogo.6d15ce61.png&w=640&q=75)
Your All-in-One AI-Powered Toolkit for Academic Success.
+13062052269
info@desklib.com
Available 24*7 on WhatsApp / Email
Unlock your academic potential
© 2024 | Zucol Services PVT LTD | All rights reserved.