Geological Survey of Three Drilled Holes - Desklib
Added on 2022-10-12
11 Pages2491 Words106 Views
GEOLOGICAL SURVEY OF THREE DRILLED HOLES
INTRODUCTION
In this report file we will study about the structure of drilled holes, different types of rocks
found in the holes, understand the requirements of the project of investigation of the site,
types of load exerted on and sustained by the rocks, designing and construction issues of a
hole to be drilled.
TYPES OF ROCKS
There are different types of rocks found I the excavation process of drilling holes in Australia
are Uluru Rock; found in the northern territory also known as Ayers Rock these are huge
sandstone rocks and covers around 3.3 square kilometres, and also 9.4 kilometres around its
base with a height rises about 345 metres above the plain fields, The Kata Tjuta; this rock is
also found in the northern territories and is rounded with the 28 domes with Mt. Olga as the
highest peak around 546 metres above the plain fields, Karlwe Karlwe rock also known as
Devil’s Marbles is also found in northern territory near Wauchope and are often termed as
sacred stones by Aboringinal Dreaming and are said to be the fossilised eggs of the serpent of
rainbow, Mount Augustus also named as Burringurah is double the size of Uluru; a combined
structure of sandstone and conglomerate was formed due to the uplift of an ancient seabed
around 1000 million years old settled on the bed of granite rock around 1650 million years
old, Wave Rock is also very old about 2700 million years was formed by the dissolving and
re-deposition of chemicals in the granite is shaped as a curved cliff faced structure around 15
metres high and 110 metres long, Bald Rock is an isolated rock hill; the largest exposed
granite surface was emplaced by the uplift and erosion that removed the surrounded
sediments and the surrounded metamorphic rocks and due to the resistance from the weather
changes, and many more types of rocks (Ga.gov.au, 2019).
EXCAVATION AND ITS PROCEDURE
The excavation is a work which involves the removal of soil or rocks from a site to form an
open face, a hole or cavity using tools, machinery or explosives. The excavation process is
carried out by following the code of practice for excavation at the working site in spite of the
depth of the hole. The excavation processes to be carried out connected to a construction is
INTRODUCTION
In this report file we will study about the structure of drilled holes, different types of rocks
found in the holes, understand the requirements of the project of investigation of the site,
types of load exerted on and sustained by the rocks, designing and construction issues of a
hole to be drilled.
TYPES OF ROCKS
There are different types of rocks found I the excavation process of drilling holes in Australia
are Uluru Rock; found in the northern territory also known as Ayers Rock these are huge
sandstone rocks and covers around 3.3 square kilometres, and also 9.4 kilometres around its
base with a height rises about 345 metres above the plain fields, The Kata Tjuta; this rock is
also found in the northern territories and is rounded with the 28 domes with Mt. Olga as the
highest peak around 546 metres above the plain fields, Karlwe Karlwe rock also known as
Devil’s Marbles is also found in northern territory near Wauchope and are often termed as
sacred stones by Aboringinal Dreaming and are said to be the fossilised eggs of the serpent of
rainbow, Mount Augustus also named as Burringurah is double the size of Uluru; a combined
structure of sandstone and conglomerate was formed due to the uplift of an ancient seabed
around 1000 million years old settled on the bed of granite rock around 1650 million years
old, Wave Rock is also very old about 2700 million years was formed by the dissolving and
re-deposition of chemicals in the granite is shaped as a curved cliff faced structure around 15
metres high and 110 metres long, Bald Rock is an isolated rock hill; the largest exposed
granite surface was emplaced by the uplift and erosion that removed the surrounded
sediments and the surrounded metamorphic rocks and due to the resistance from the weather
changes, and many more types of rocks (Ga.gov.au, 2019).
EXCAVATION AND ITS PROCEDURE
The excavation is a work which involves the removal of soil or rocks from a site to form an
open face, a hole or cavity using tools, machinery or explosives. The excavation process is
carried out by following the code of practice for excavation at the working site in spite of the
depth of the hole. The excavation processes to be carried out connected to a construction is
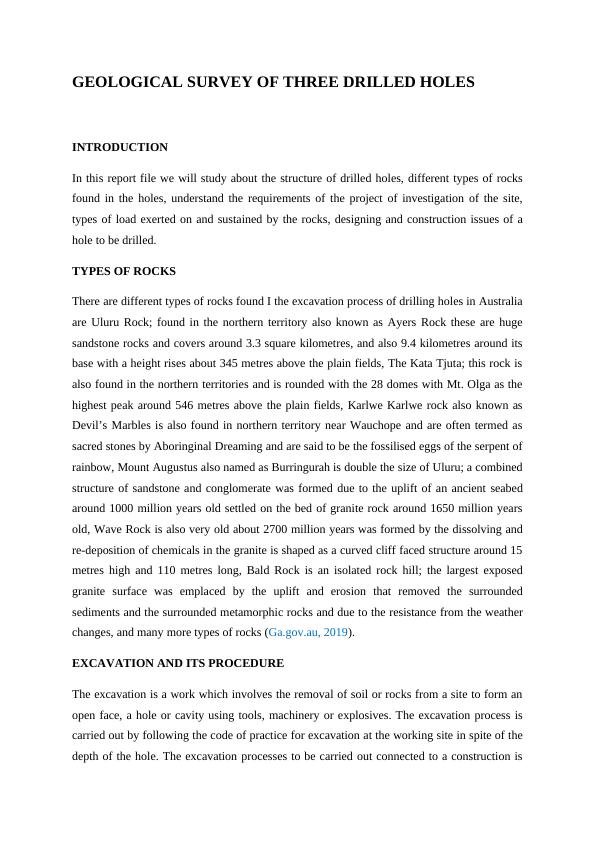
termed as high risk construction work if it is done in or near a shaft or trench with depth more
than 1.5 metres or a tunnel. These specific duties do not apply on a mine or bore where water
law is applied. The excavation procedure has some general requirements as; drilling,
trenching, levelling, digging, driving of pegs into the ground, etc. (Day, 2017). It is to be
understood that no excavation or penetration process should undergo at places adjacent to any
structural unit that could affect the structural integrity of the building. Before starting
excavation process the sites should be inspected thoroughly for stability and signs of collapse
on daily basis and after every blast operation, after an unexpected fall of support, after heavy
rainfall, after the usage of vibrating machines being used in close proximity.
RISK MANAGEMENT
According to the regulation 34-38 made by Excavation Works Department in the code of
practice in Australia can be stated as (Excavation Work code of practice, 2015):
To identify reasonable hazards that can be foreseen and could give the rise to the risks
in excavation.
To determine and eliminate the risks which is practically reasonable.
To maintain and implement control measures to counter control measures.
The code of practice explains the guidelines for managing risks by identifying risks,
accessing the risks, implementing measures for controlling and maintaining the effect of
control methodologies.
For controlling risks, level of safety gained from the control measures should be known by
the inspection and analysis of the measures that could be ranked according to highest safety
to lowest safety always aiming to eliminate a hazard. If the risks are not completely
eliminated then following steps should be taken (Excavation Work code of practice, 2015):
1) By substituting - use of excavator than manual methods to break rocks.
2) By Isolating - make concrete barriers to separate pedestrians and powered mobile
plant to eliminate risk of collision.
3) By introducing Engineering Controls – use of advanced methods like benching,
battering or shoring the sides of the excavation to eliminate the possibilities of failure
of ground or boundaries of the excavated site.
than 1.5 metres or a tunnel. These specific duties do not apply on a mine or bore where water
law is applied. The excavation procedure has some general requirements as; drilling,
trenching, levelling, digging, driving of pegs into the ground, etc. (Day, 2017). It is to be
understood that no excavation or penetration process should undergo at places adjacent to any
structural unit that could affect the structural integrity of the building. Before starting
excavation process the sites should be inspected thoroughly for stability and signs of collapse
on daily basis and after every blast operation, after an unexpected fall of support, after heavy
rainfall, after the usage of vibrating machines being used in close proximity.
RISK MANAGEMENT
According to the regulation 34-38 made by Excavation Works Department in the code of
practice in Australia can be stated as (Excavation Work code of practice, 2015):
To identify reasonable hazards that can be foreseen and could give the rise to the risks
in excavation.
To determine and eliminate the risks which is practically reasonable.
To maintain and implement control measures to counter control measures.
The code of practice explains the guidelines for managing risks by identifying risks,
accessing the risks, implementing measures for controlling and maintaining the effect of
control methodologies.
For controlling risks, level of safety gained from the control measures should be known by
the inspection and analysis of the measures that could be ranked according to highest safety
to lowest safety always aiming to eliminate a hazard. If the risks are not completely
eliminated then following steps should be taken (Excavation Work code of practice, 2015):
1) By substituting - use of excavator than manual methods to break rocks.
2) By Isolating - make concrete barriers to separate pedestrians and powered mobile
plant to eliminate risk of collision.
3) By introducing Engineering Controls – use of advanced methods like benching,
battering or shoring the sides of the excavation to eliminate the possibilities of failure
of ground or boundaries of the excavated site.
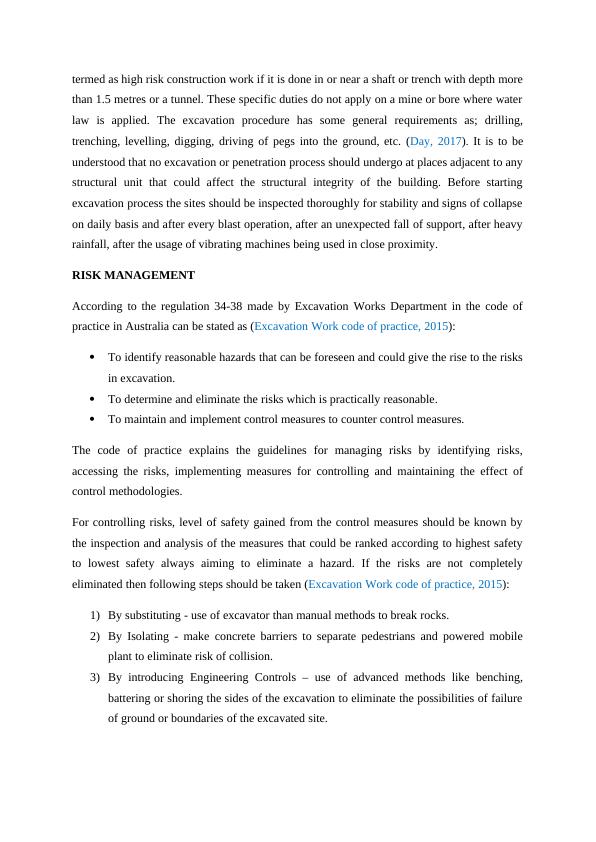
GUIDELINES FOR EXCAVATION SUPPORT
The functions to provide support to the excavation field to support and retain earth and
adjacent structures from falling are illustrated as:
a. The Earth Retention type (contains support wall like sheet pile, diaphragm wall, etc.).
b. Bracing Support type (either internal or external bracing like rakers, struts) that
supports the earth retention type.
The types of support required in excavation are (Zumrawi and El-Amin, 2016):
i. Diaphragm Wall is a continuous support wall made of concrete that is excavated in
place in accordance with the loads from retained soil and water. These walls are
designed on the basis of bending moments and shears resulting from lateral pressures
acting on the wall. These loads should be considered while designing the wall to
support vertical loads.
ii. Sheet Piling; a vertical steel shapes driven into the ground interconnected with each
other to support lateral loads, to form a continuous wall. The wall gets structural
strength from the sheets itself.
iii. Slurry Wall; a substantiated and continuous wall formed by filling a series of discrete
trenches with tremic concrete. The slurry is used to prevent collapsing of trench
during excavation for slurry wall preparation, this wall retain soil and groundwater at
the exterior wall and allows the excavation and removal of soil from inside.
iv. Preloaded Bracing; creates a tight fit between the supporting elements by reducing
shoring deflection and ground settlement during excavation, where feasible struts
should be applied in preload condition at 50% design loads to gain proper bearing
between supporting material.
LNG Site
The project site is a huge LNG facility (Woodside, 2019) whose data for three drilled holes
are provided. Australia is on the verge to cross LNG export capacity, Qatar was at the first
position. Now Australia is going to be the world’s largest liquefied natural gas (LNG)
exporter outshining Qatar, according to the data provided by Australia’s Department of
industry, innovation and science (DIIS).
The functions to provide support to the excavation field to support and retain earth and
adjacent structures from falling are illustrated as:
a. The Earth Retention type (contains support wall like sheet pile, diaphragm wall, etc.).
b. Bracing Support type (either internal or external bracing like rakers, struts) that
supports the earth retention type.
The types of support required in excavation are (Zumrawi and El-Amin, 2016):
i. Diaphragm Wall is a continuous support wall made of concrete that is excavated in
place in accordance with the loads from retained soil and water. These walls are
designed on the basis of bending moments and shears resulting from lateral pressures
acting on the wall. These loads should be considered while designing the wall to
support vertical loads.
ii. Sheet Piling; a vertical steel shapes driven into the ground interconnected with each
other to support lateral loads, to form a continuous wall. The wall gets structural
strength from the sheets itself.
iii. Slurry Wall; a substantiated and continuous wall formed by filling a series of discrete
trenches with tremic concrete. The slurry is used to prevent collapsing of trench
during excavation for slurry wall preparation, this wall retain soil and groundwater at
the exterior wall and allows the excavation and removal of soil from inside.
iv. Preloaded Bracing; creates a tight fit between the supporting elements by reducing
shoring deflection and ground settlement during excavation, where feasible struts
should be applied in preload condition at 50% design loads to gain proper bearing
between supporting material.
LNG Site
The project site is a huge LNG facility (Woodside, 2019) whose data for three drilled holes
are provided. Australia is on the verge to cross LNG export capacity, Qatar was at the first
position. Now Australia is going to be the world’s largest liquefied natural gas (LNG)
exporter outshining Qatar, according to the data provided by Australia’s Department of
industry, innovation and science (DIIS).
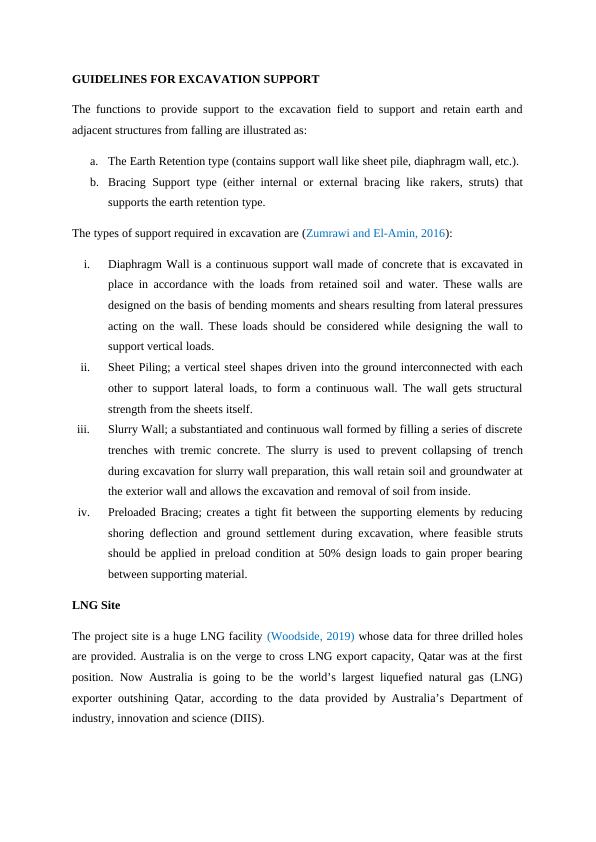
Source: U.S. Energy Information Administration, CEDIGAZ
Australia’s LNG export capacity has increased extensively from 2.6 billion cubic feet per day
in 2011 to more than 11.4 billion cubic feet per day (Bcf/d) in 2019 (Eia.gov, 2019).
Australia’s DIIS gave a forecast for 2020-21 to be increased by 10.8 Bcf/d, after the
successful run up to full capacity of Wheatstone, Ichthys and Prelude floating LNG (FLNG)
projects.
The drilled hole specifications are enlisted in the tables below along with the lithographic
code and rock strength.
Australia’s LNG export capacity has increased extensively from 2.6 billion cubic feet per day
in 2011 to more than 11.4 billion cubic feet per day (Bcf/d) in 2019 (Eia.gov, 2019).
Australia’s DIIS gave a forecast for 2020-21 to be increased by 10.8 Bcf/d, after the
successful run up to full capacity of Wheatstone, Ichthys and Prelude floating LNG (FLNG)
projects.
The drilled hole specifications are enlisted in the tables below along with the lithographic
code and rock strength.
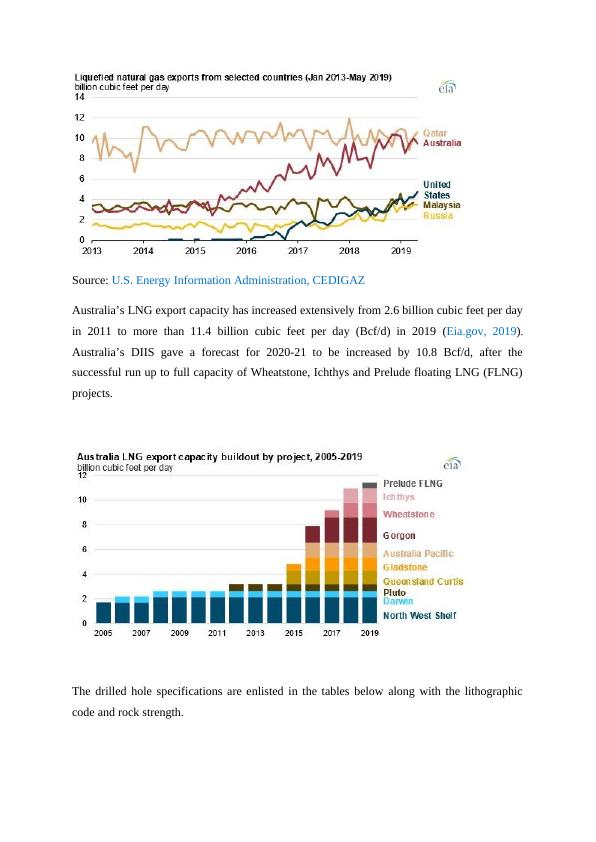
End of preview
Want to access all the pages? Upload your documents or become a member.
Related Documents
Geological Study of Rocks in Merri Creek Catchment Arealg...
|10
|1967
|475