Evaluating Alternative Sands for Geotechnical Engineering Projects
VerifiedAdded on 2023/01/19
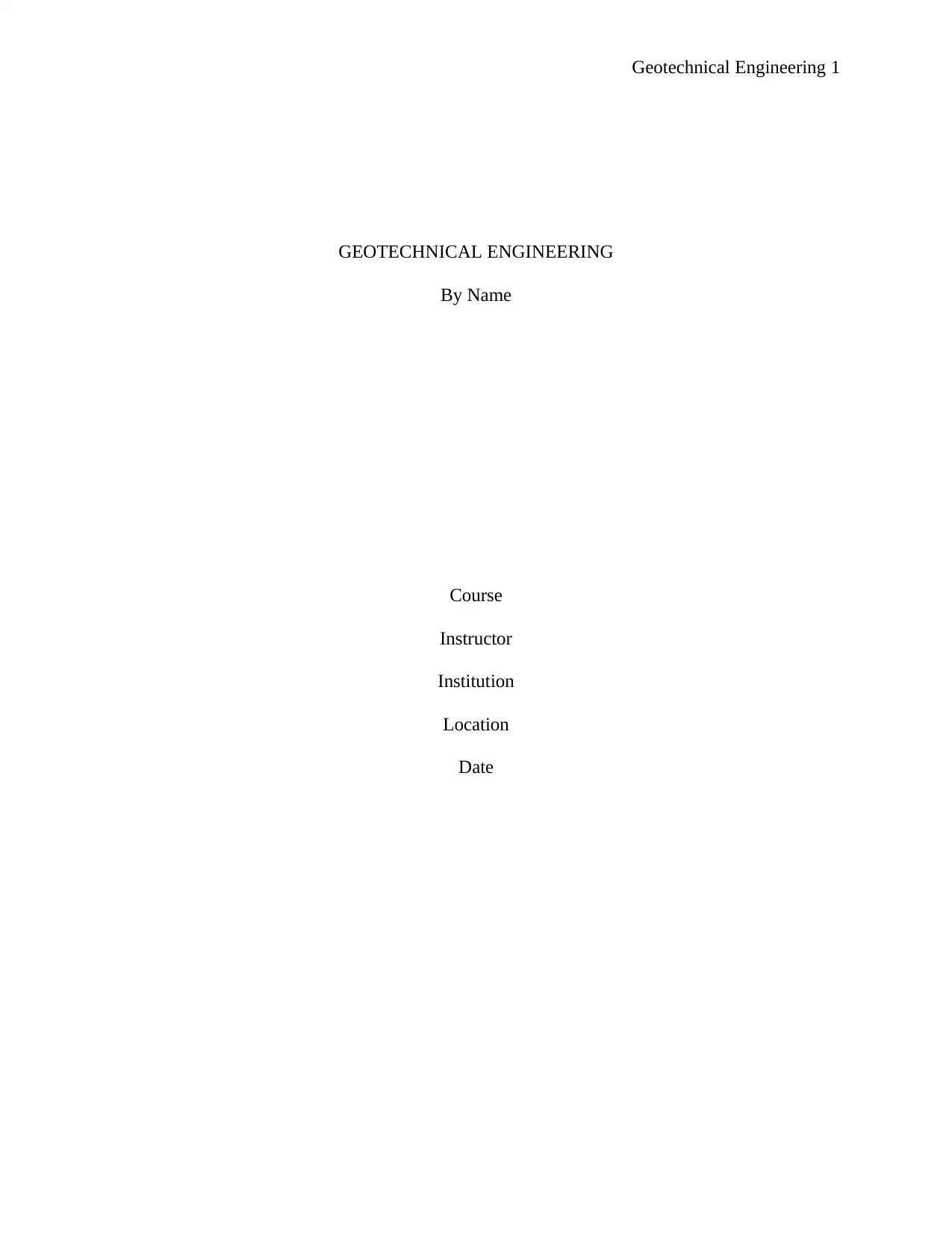
GEOTECHNICAL ENGINEERING
By Name
Course
Instructor
Institution
Location
Date
Paraphrase This Document
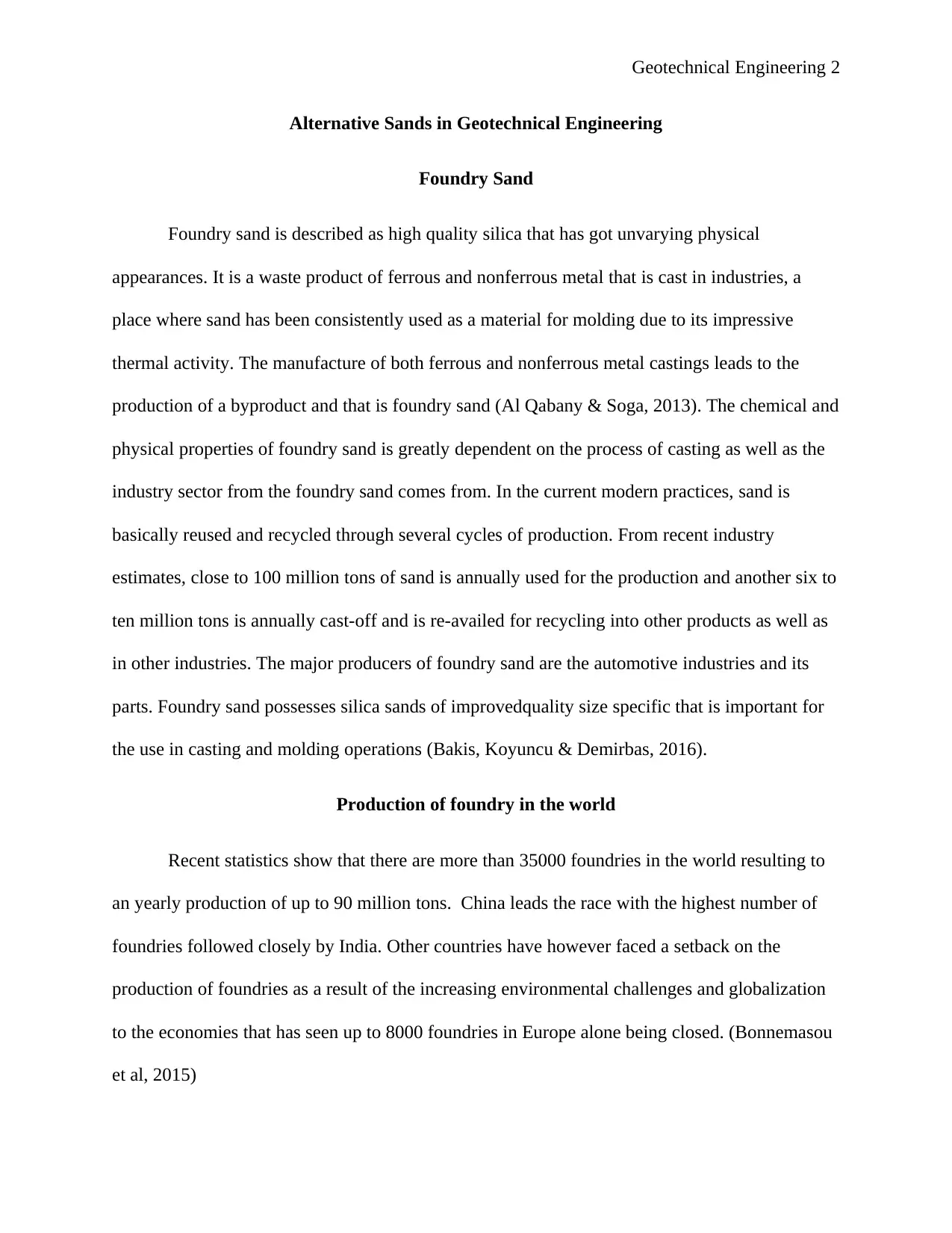
Alternative Sands in Geotechnical Engineering
Foundry Sand
Foundry sand is described as high quality silica that has got unvarying physical
appearances. It is a waste product of ferrous and nonferrous metal that is cast in industries, a
place where sand has been consistently used as a material for molding due to its impressive
thermal activity. The manufacture of both ferrous and nonferrous metal castings leads to the
production of a byproduct and that is foundry sand (Al Qabany & Soga, 2013). The chemical and
physical properties of foundry sand is greatly dependent on the process of casting as well as the
industry sector from the foundry sand comes from. In the current modern practices, sand is
basically reused and recycled through several cycles of production. From recent industry
estimates, close to 100 million tons of sand is annually used for the production and another six to
ten million tons is annually cast-off and is re-availed for recycling into other products as well as
in other industries. The major producers of foundry sand are the automotive industries and its
parts. Foundry sand possesses silica sands of improvedquality size specific that is important for
the use in casting and molding operations (Bakis, Koyuncu & Demirbas, 2016).
Production of foundry in the world
Recent statistics show that there are more than 35000 foundries in the world resulting to
an yearly production of up to 90 million tons. China leads the race with the highest number of
foundries followed closely by India. Other countries have however faced a setback on the
production of foundries as a result of the increasing environmental challenges and globalization
to the economies that has seen up to 8000 foundries in Europe alone being closed. (Bonnemasou
et al, 2015)
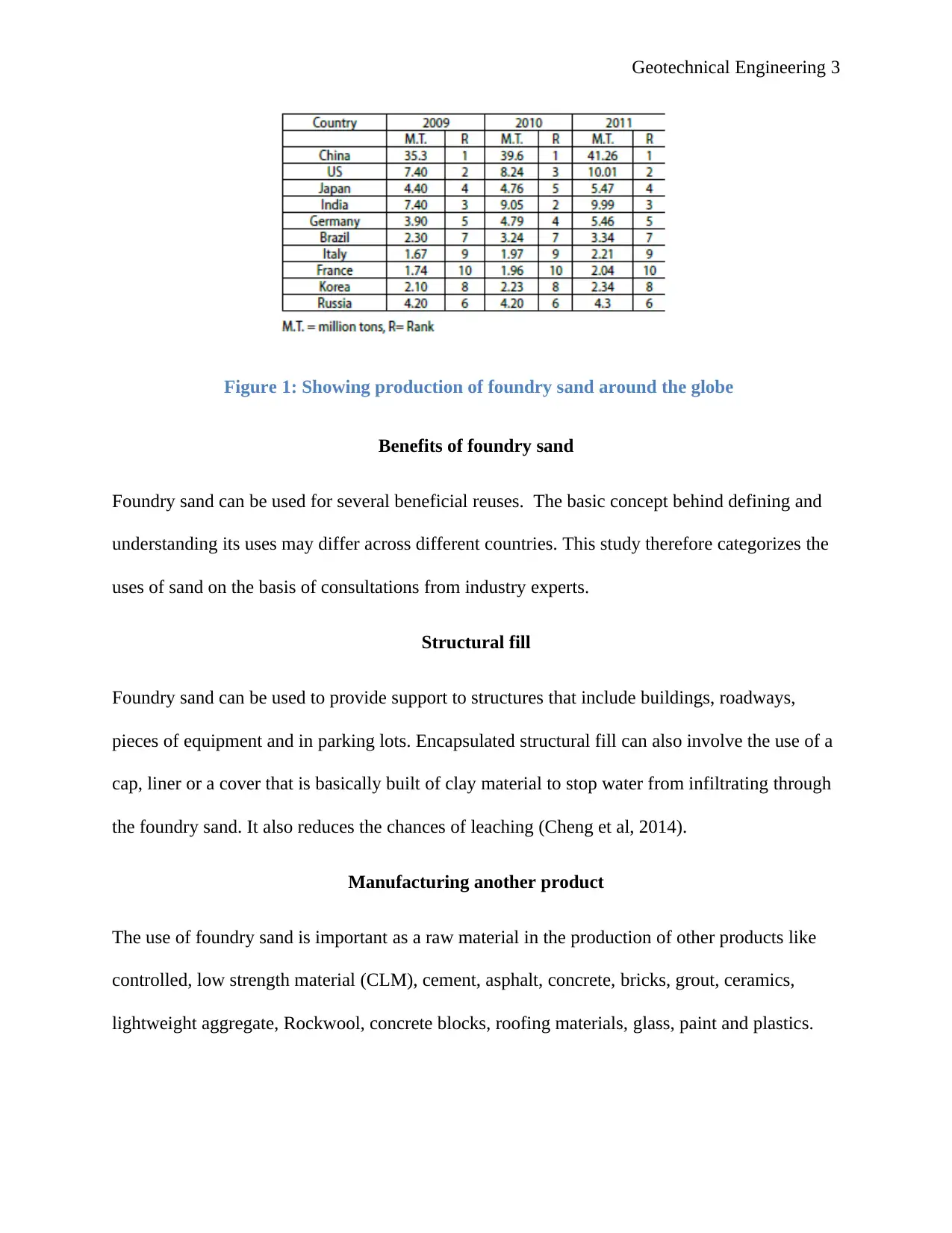
Figure 1: Showing production of foundry sand around the globe
Benefits of foundry sand
Foundry sand can be used for several beneficial reuses. The basic concept behind defining and
understanding its uses may differ across different countries. This study therefore categorizes the
uses of sand on the basis of consultations from industry experts.
Structural fill
Foundry sand can be used to provide support to structures that include buildings, roadways,
pieces of equipment and in parking lots. Encapsulated structural fill can also involve the use of a
cap, liner or a cover that is basically built of clay material to stop water from infiltrating through
the foundry sand. It also reduces the chances of leaching (Cheng et al, 2014).
Manufacturing another product
The use of foundry sand is important as a raw material in the production of other products like
controlled, low strength material (CLM), cement, asphalt, concrete, bricks, grout, ceramics,
lightweight aggregate, Rockwool, concrete blocks, roofing materials, glass, paint and plastics.
⊘ This is a preview!⊘
Do you want full access?
Subscribe today to unlock all pages.

Trusted by 1+ million students worldwide
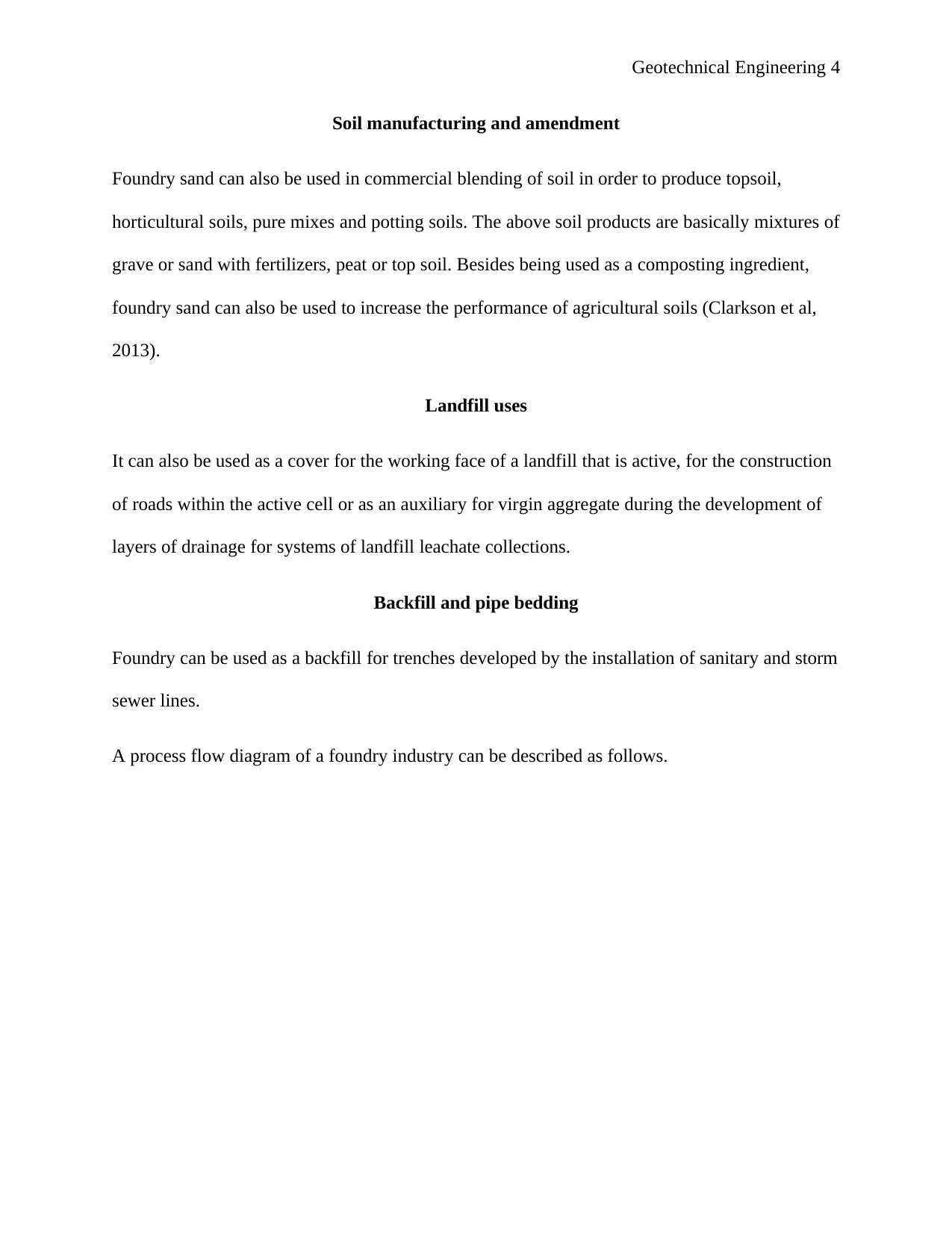
Soil manufacturing and amendment
Foundry sand can also be used in commercial blending of soil in order to produce topsoil,
horticultural soils, pure mixes and potting soils. The above soil products are basically mixtures of
grave or sand with fertilizers, peat or top soil. Besides being used as a composting ingredient,
foundry sand can also be used to increase the performance of agricultural soils (Clarkson et al,
2013).
Landfill uses
It can also be used as a cover for the working face of a landfill that is active, for the construction
of roads within the active cell or as an auxiliary for virgin aggregate during the development of
layers of drainage for systems of landfill leachate collections.
Backfill and pipe bedding
Foundry can be used as a backfill for trenches developed by the installation of sanitary and storm
sewer lines.
A process flow diagram of a foundry industry can be described as follows.
Paraphrase This Document
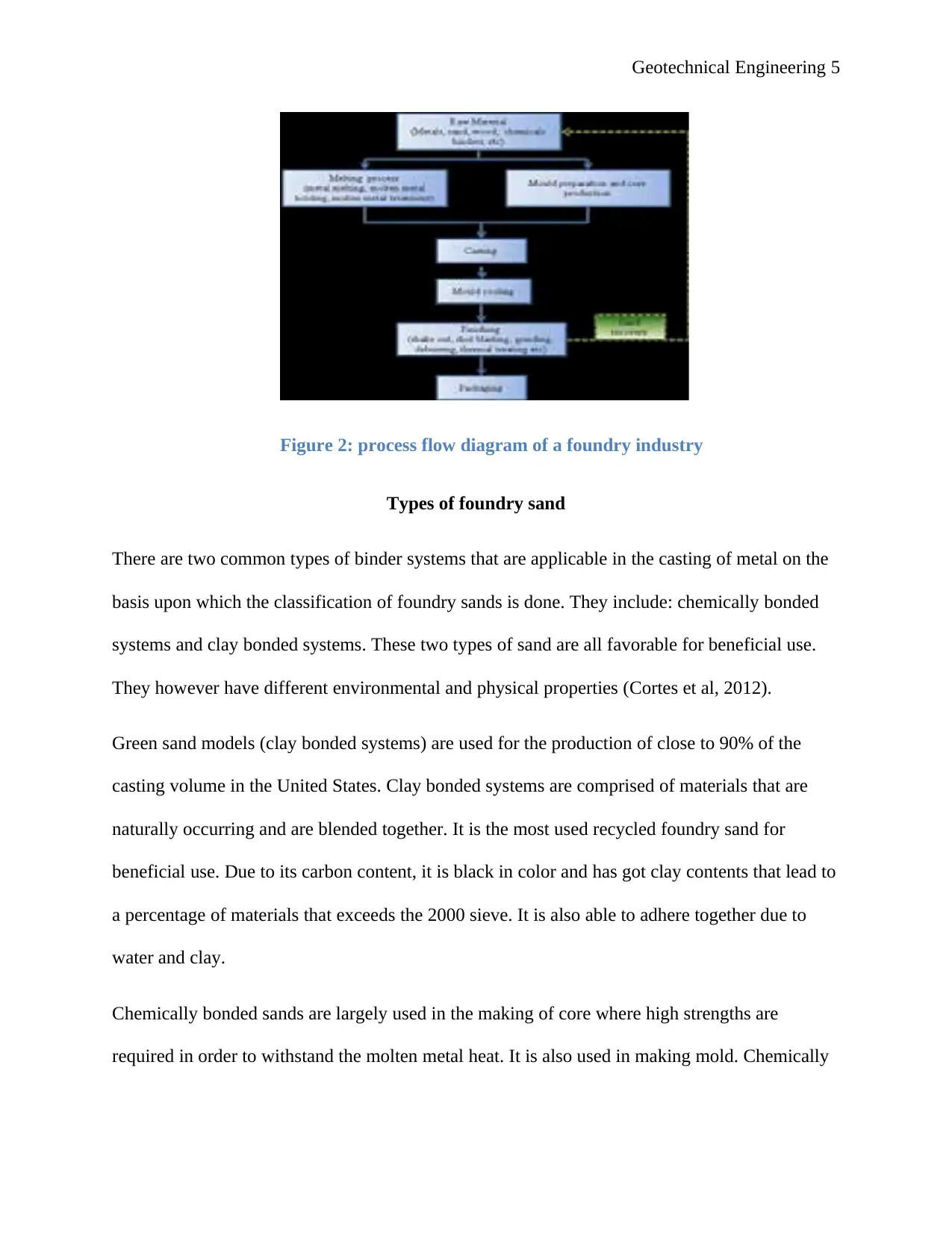
Figure 2: process flow diagram of a foundry industry
Types of foundry sand
There are two common types of binder systems that are applicable in the casting of metal on the
basis upon which the classification of foundry sands is done. They include: chemically bonded
systems and clay bonded systems. These two types of sand are all favorable for beneficial use.
They however have different environmental and physical properties (Cortes et al, 2012).
Green sand models (clay bonded systems) are used for the production of close to 90% of the
casting volume in the United States. Clay bonded systems are comprised of materials that are
naturally occurring and are blended together. It is the most used recycled foundry sand for
beneficial use. Due to its carbon content, it is black in color and has got clay contents that lead to
a percentage of materials that exceeds the 2000 sieve. It is also able to adhere together due to
water and clay.
Chemically bonded sands are largely used in the making of core where high strengths are
required in order to withstand the molten metal heat. It is also used in making mold. Chemically
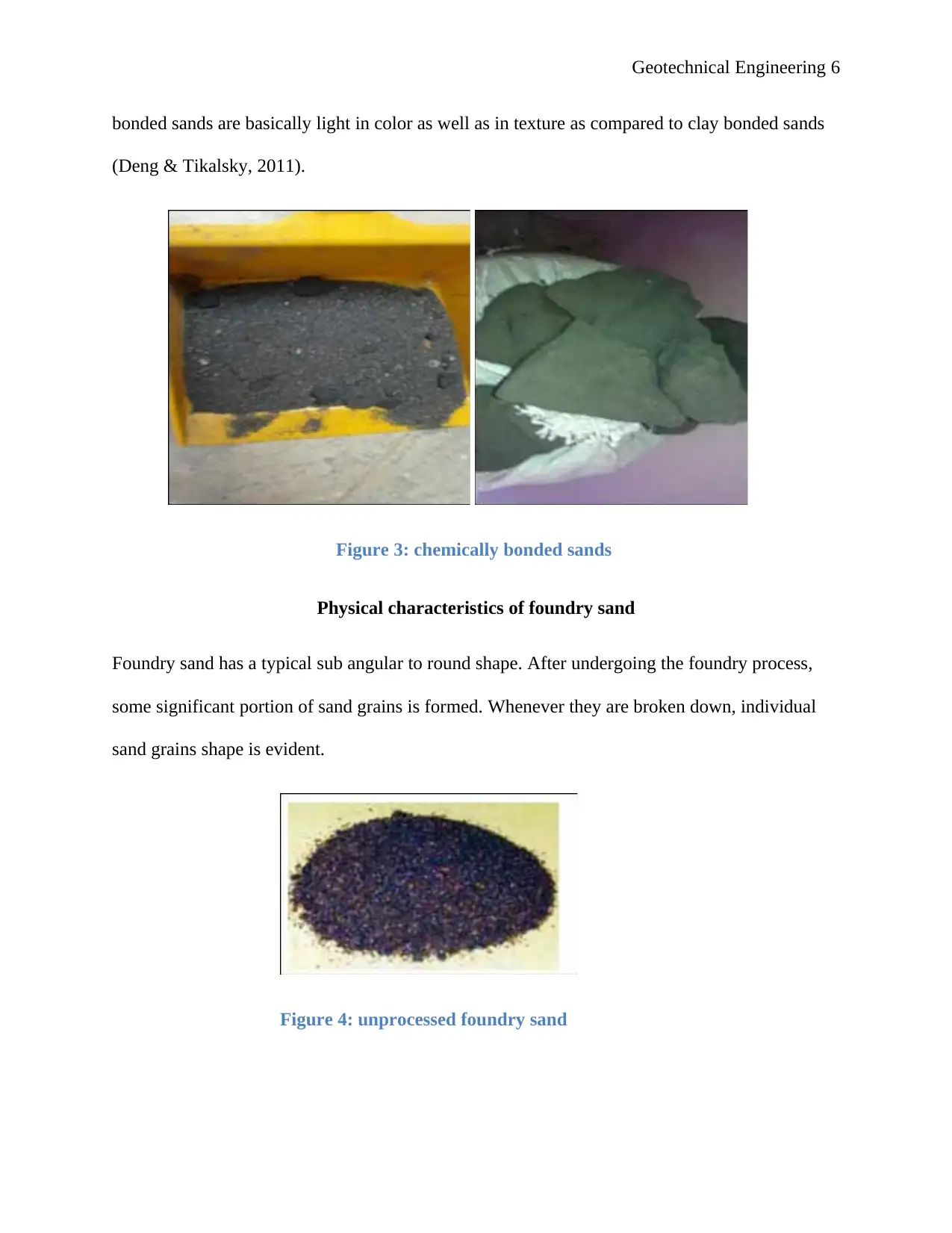
bonded sands are basically light in color as well as in texture as compared to clay bonded sands
(Deng & Tikalsky, 2011).
Figure 3: chemically bonded sands
Physical characteristics of foundry sand
Foundry sand has a typical sub angular to round shape. After undergoing the foundry process,
some significant portion of sand grains is formed. Whenever they are broken down, individual
sand grains shape is evident.
Figure 4: unprocessed foundry sand
⊘ This is a preview!⊘
Do you want full access?
Subscribe today to unlock all pages.

Trusted by 1+ million students worldwide
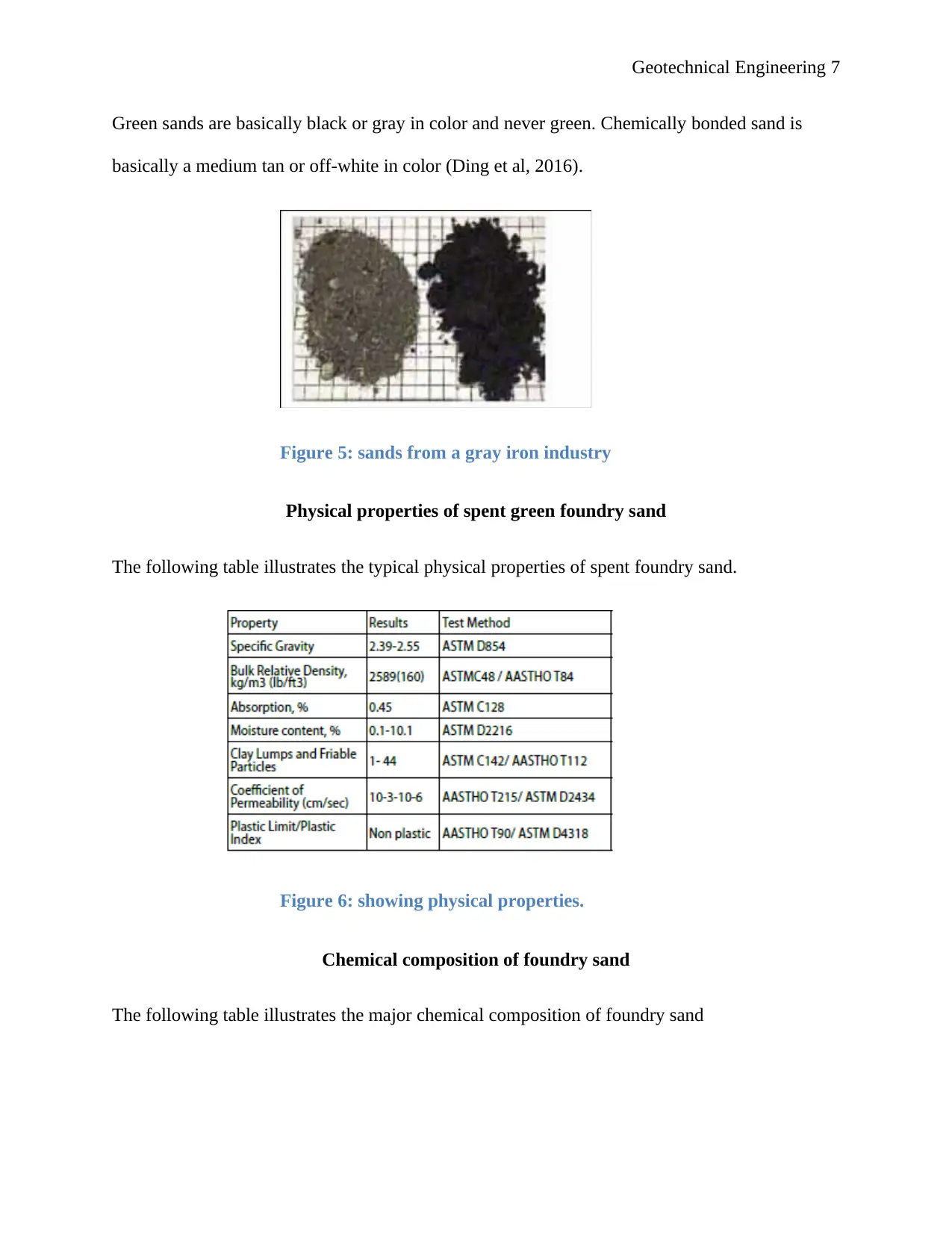
Green sands are basically black or gray in color and never green. Chemically bonded sand is
basically a medium tan or off-white in color (Ding et al, 2016).
Figure 5: sands from a gray iron industry
Physical properties of spent green foundry sand
The following table illustrates the typical physical properties of spent foundry sand.
Figure 6: showing physical properties.
Chemical composition of foundry sand
The following table illustrates the major chemical composition of foundry sand
Paraphrase This Document
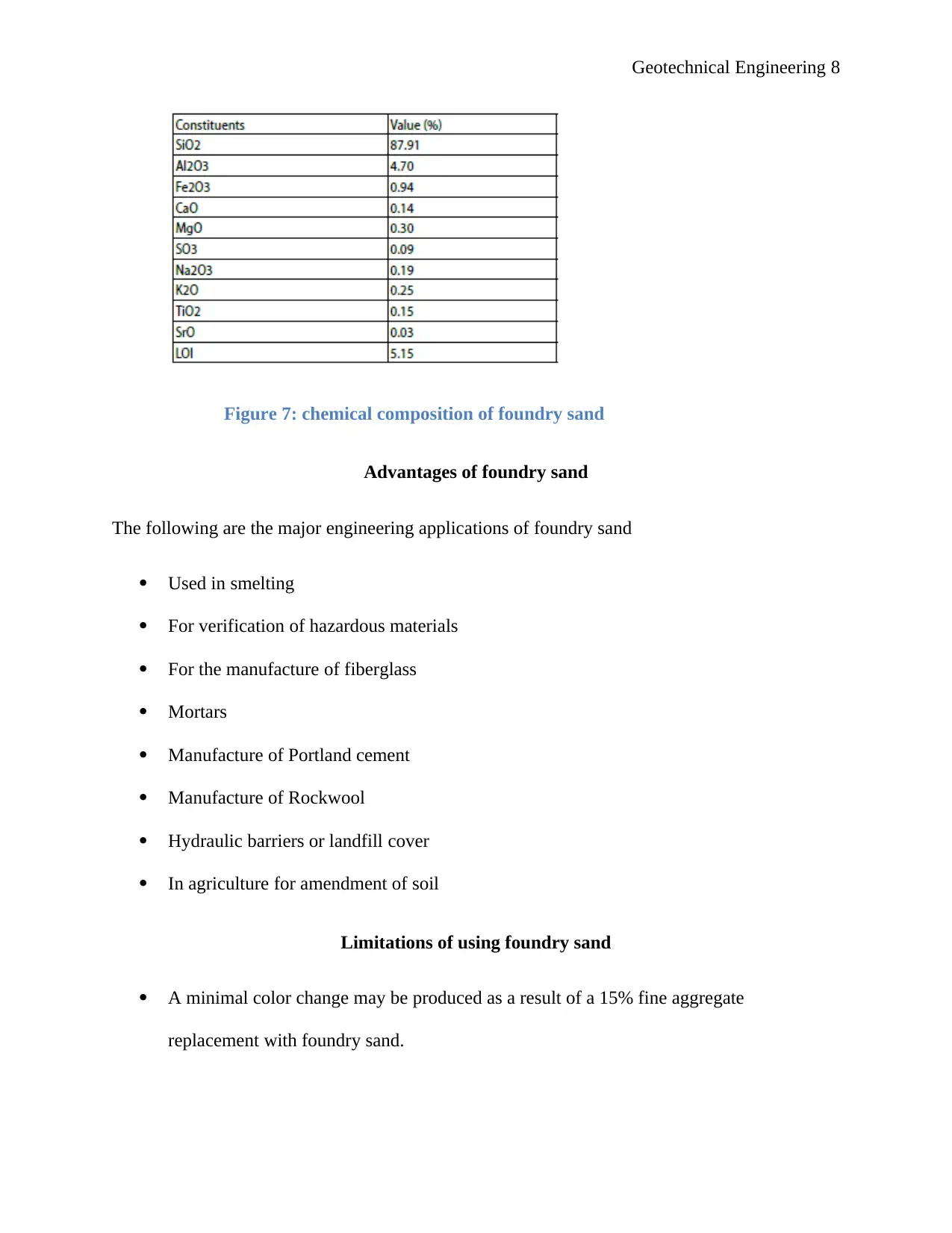
Figure 7: chemical composition of foundry sand
Advantages of foundry sand
The following are the major engineering applications of foundry sand
Used in smelting
For verification of hazardous materials
For the manufacture of fiberglass
Mortars
Manufacture of Portland cement
Manufacture of Rockwool
Hydraulic barriers or landfill cover
In agriculture for amendment of soil
Limitations of using foundry sand
A minimal color change may be produced as a result of a 15% fine aggregate
replacement with foundry sand.
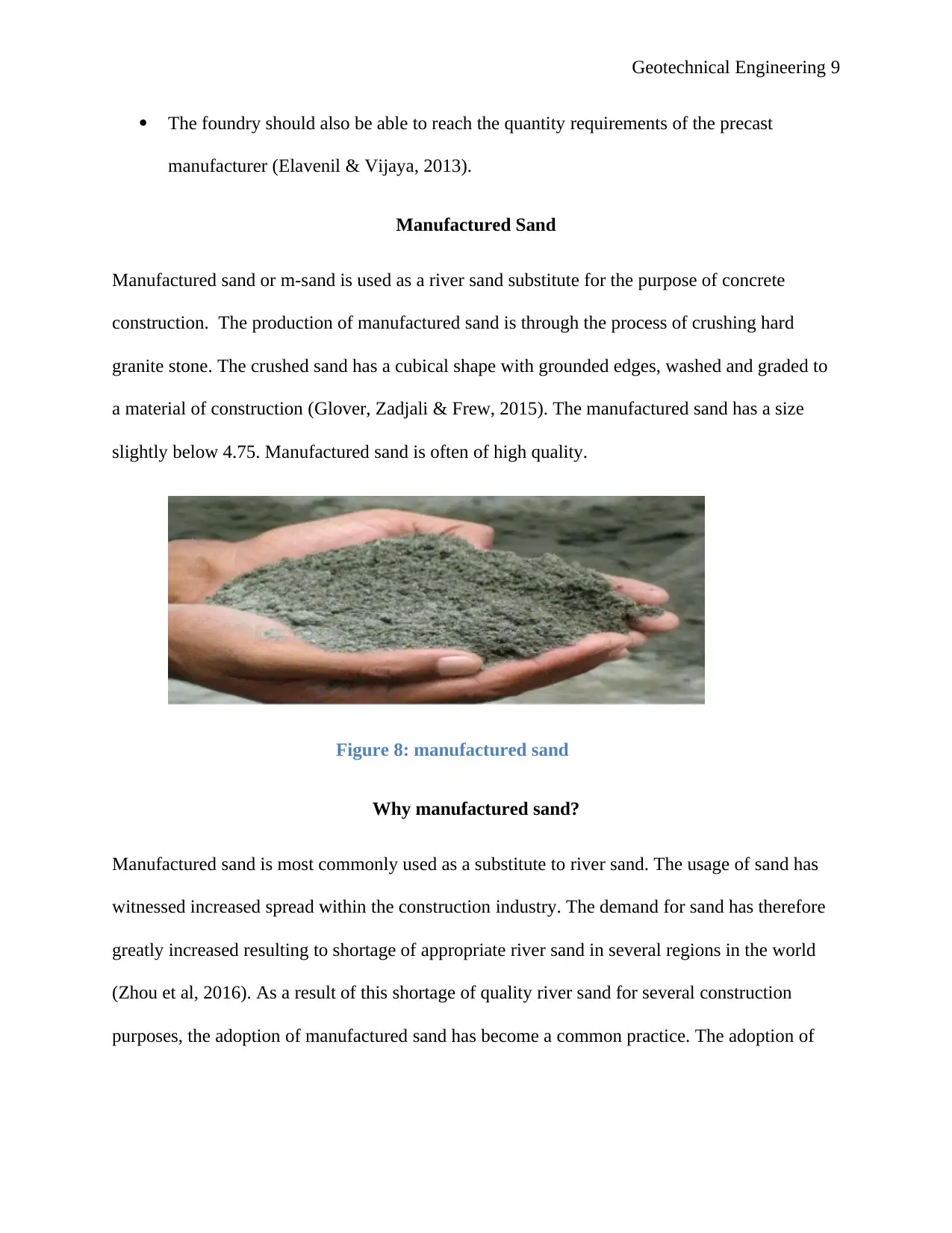
The foundry should also be able to reach the quantity requirements of the precast
manufacturer (Elavenil & Vijaya, 2013).
Manufactured Sand
Manufactured sand or m-sand is used as a river sand substitute for the purpose of concrete
construction. The production of manufactured sand is through the process of crushing hard
granite stone. The crushed sand has a cubical shape with grounded edges, washed and graded to
a material of construction (Glover, Zadjali & Frew, 2015). The manufactured sand has a size
slightly below 4.75. Manufactured sand is often of high quality.
Figure 8: manufactured sand
Why manufactured sand?
Manufactured sand is most commonly used as a substitute to river sand. The usage of sand has
witnessed increased spread within the construction industry. The demand for sand has therefore
greatly increased resulting to shortage of appropriate river sand in several regions in the world
(Zhou et al, 2016). As a result of this shortage of quality river sand for several construction
purposes, the adoption of manufactured sand has become a common practice. The adoption of
⊘ This is a preview!⊘
Do you want full access?
Subscribe today to unlock all pages.

Trusted by 1+ million students worldwide
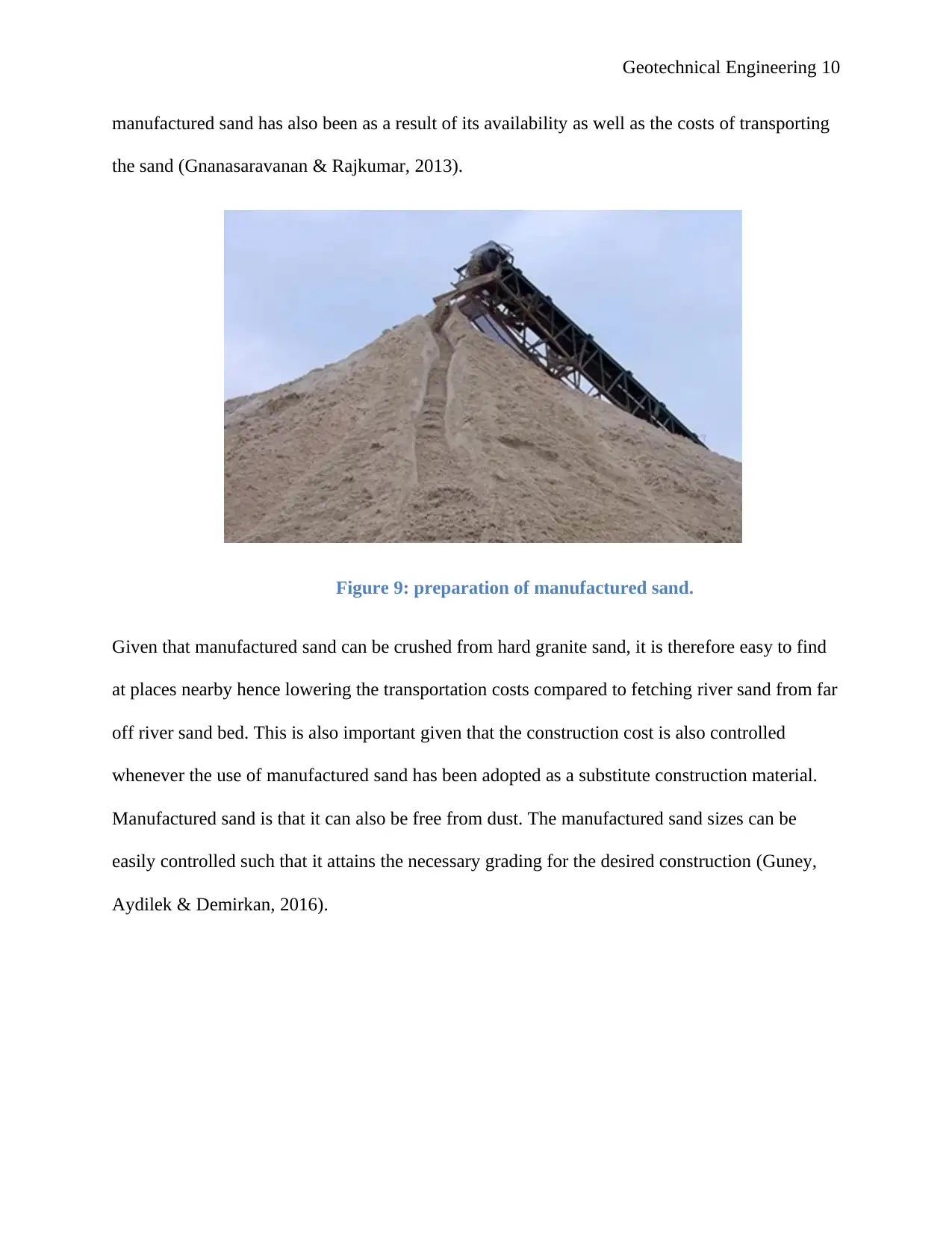
manufactured sand has also been as a result of its availability as well as the costs of transporting
the sand (Gnanasaravanan & Rajkumar, 2013).
Figure 9: preparation of manufactured sand.
Given that manufactured sand can be crushed from hard granite sand, it is therefore easy to find
at places nearby hence lowering the transportation costs compared to fetching river sand from far
off river sand bed. This is also important given that the construction cost is also controlled
whenever the use of manufactured sand has been adopted as a substitute construction material.
Manufactured sand is that it can also be free from dust. The manufactured sand sizes can be
easily controlled such that it attains the necessary grading for the desired construction (Guney,
Aydilek & Demirkan, 2016).
Paraphrase This Document
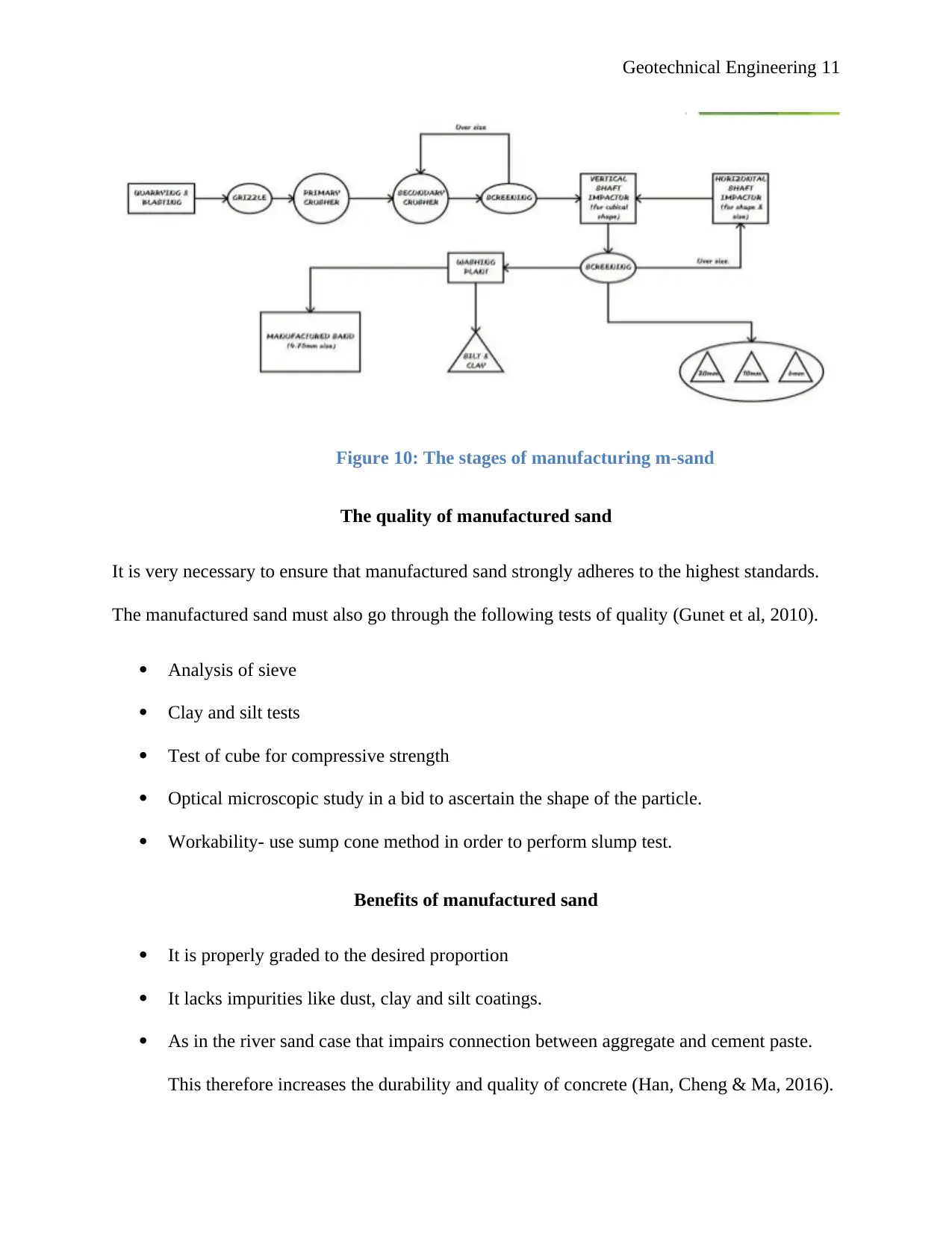
Figure 10: The stages of manufacturing m-sand
The quality of manufactured sand
It is very necessary to ensure that manufactured sand strongly adheres to the highest standards.
The manufactured sand must also go through the following tests of quality (Gunet et al, 2010).
Analysis of sieve
Clay and silt tests
Test of cube for compressive strength
Optical microscopic study in a bid to ascertain the shape of the particle.
Workability- use sump cone method in order to perform slump test.
Benefits of manufactured sand
It is properly graded to the desired proportion
It lacks impurities like dust, clay and silt coatings.
As in the river sand case that impairs connection between aggregate and cement paste.
This therefore increases the durability and quality of concrete (Han, Cheng & Ma, 2016).
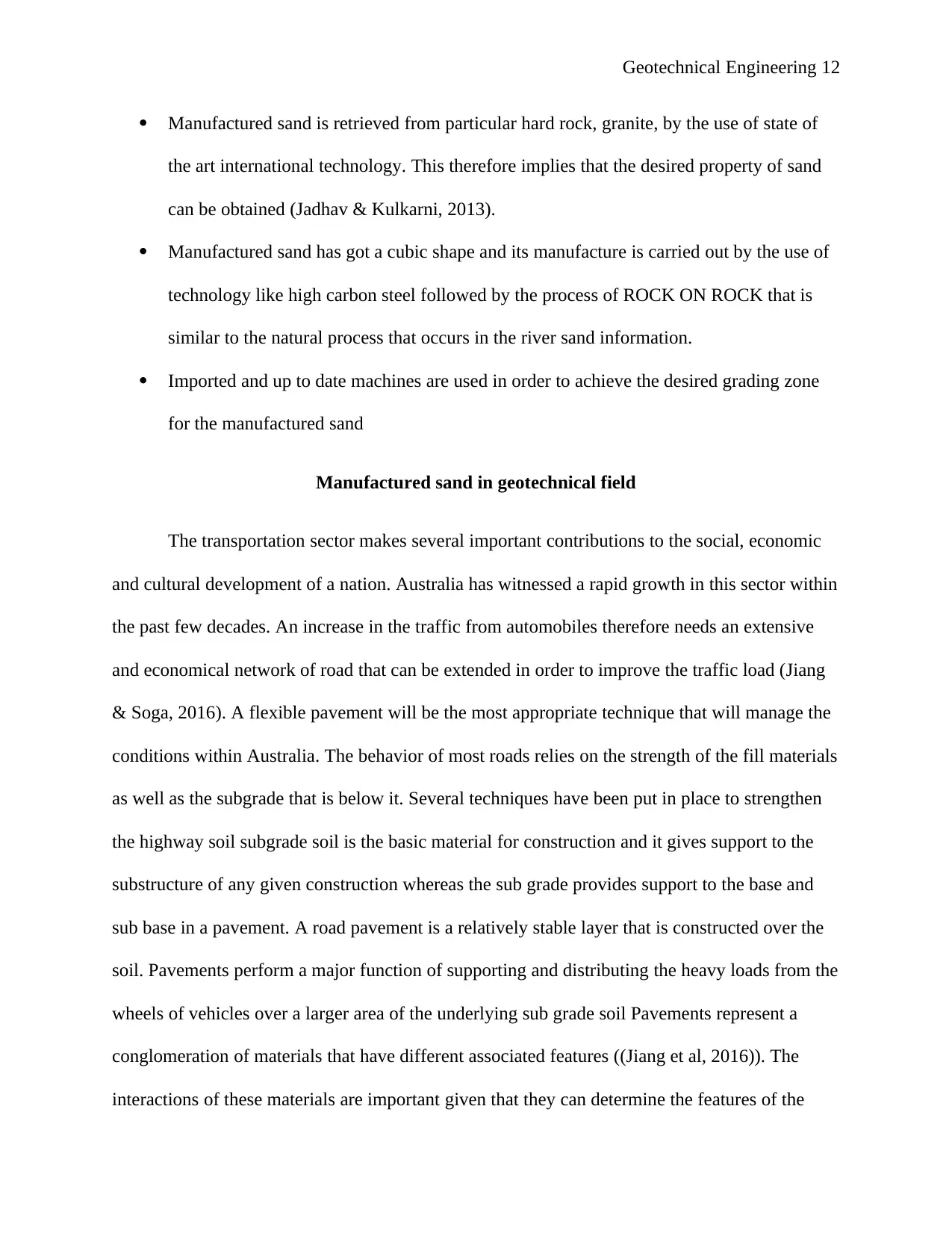
Manufactured sand is retrieved from particular hard rock, granite, by the use of state of
the art international technology. This therefore implies that the desired property of sand
can be obtained (Jadhav & Kulkarni, 2013).
Manufactured sand has got a cubic shape and its manufacture is carried out by the use of
technology like high carbon steel followed by the process of ROCK ON ROCK that is
similar to the natural process that occurs in the river sand information.
Imported and up to date machines are used in order to achieve the desired grading zone
for the manufactured sand
Manufactured sand in geotechnical field
The transportation sector makes several important contributions to the social, economic
and cultural development of a nation. Australia has witnessed a rapid growth in this sector within
the past few decades. An increase in the traffic from automobiles therefore needs an extensive
and economical network of road that can be extended in order to improve the traffic load (Jiang
& Soga, 2016). A flexible pavement will be the most appropriate technique that will manage the
conditions within Australia. The behavior of most roads relies on the strength of the fill materials
as well as the subgrade that is below it. Several techniques have been put in place to strengthen
the highway soil subgrade soil is the basic material for construction and it gives support to the
substructure of any given construction whereas the sub grade provides support to the base and
sub base in a pavement. A road pavement is a relatively stable layer that is constructed over the
soil. Pavements perform a major function of supporting and distributing the heavy loads from the
wheels of vehicles over a larger area of the underlying sub grade soil Pavements represent a
conglomeration of materials that have different associated features ((Jiang et al, 2016)). The
interactions of these materials are important given that they can determine the features of the
⊘ This is a preview!⊘
Do you want full access?
Subscribe today to unlock all pages.

Trusted by 1+ million students worldwide
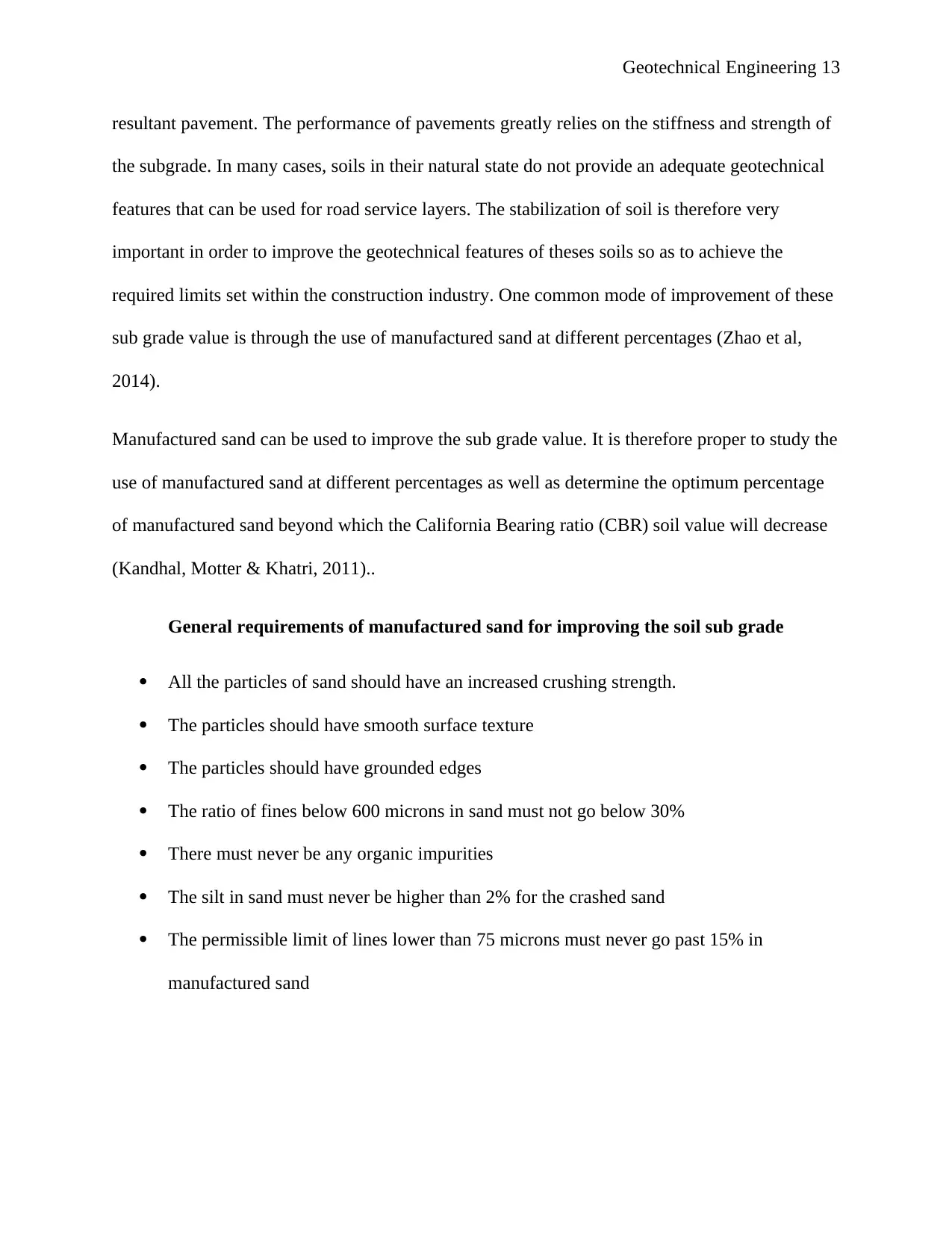
resultant pavement. The performance of pavements greatly relies on the stiffness and strength of
the subgrade. In many cases, soils in their natural state do not provide an adequate geotechnical
features that can be used for road service layers. The stabilization of soil is therefore very
important in order to improve the geotechnical features of theses soils so as to achieve the
required limits set within the construction industry. One common mode of improvement of these
sub grade value is through the use of manufactured sand at different percentages (Zhao et al,
2014).
Manufactured sand can be used to improve the sub grade value. It is therefore proper to study the
use of manufactured sand at different percentages as well as determine the optimum percentage
of manufactured sand beyond which the California Bearing ratio (CBR) soil value will decrease
(Kandhal, Motter & Khatri, 2011)..
General requirements of manufactured sand for improving the soil sub grade
All the particles of sand should have an increased crushing strength.
The particles should have smooth surface texture
The particles should have grounded edges
The ratio of fines below 600 microns in sand must not go below 30%
There must never be any organic impurities
The silt in sand must never be higher than 2% for the crashed sand
The permissible limit of lines lower than 75 microns must never go past 15% in
manufactured sand
Paraphrase This Document
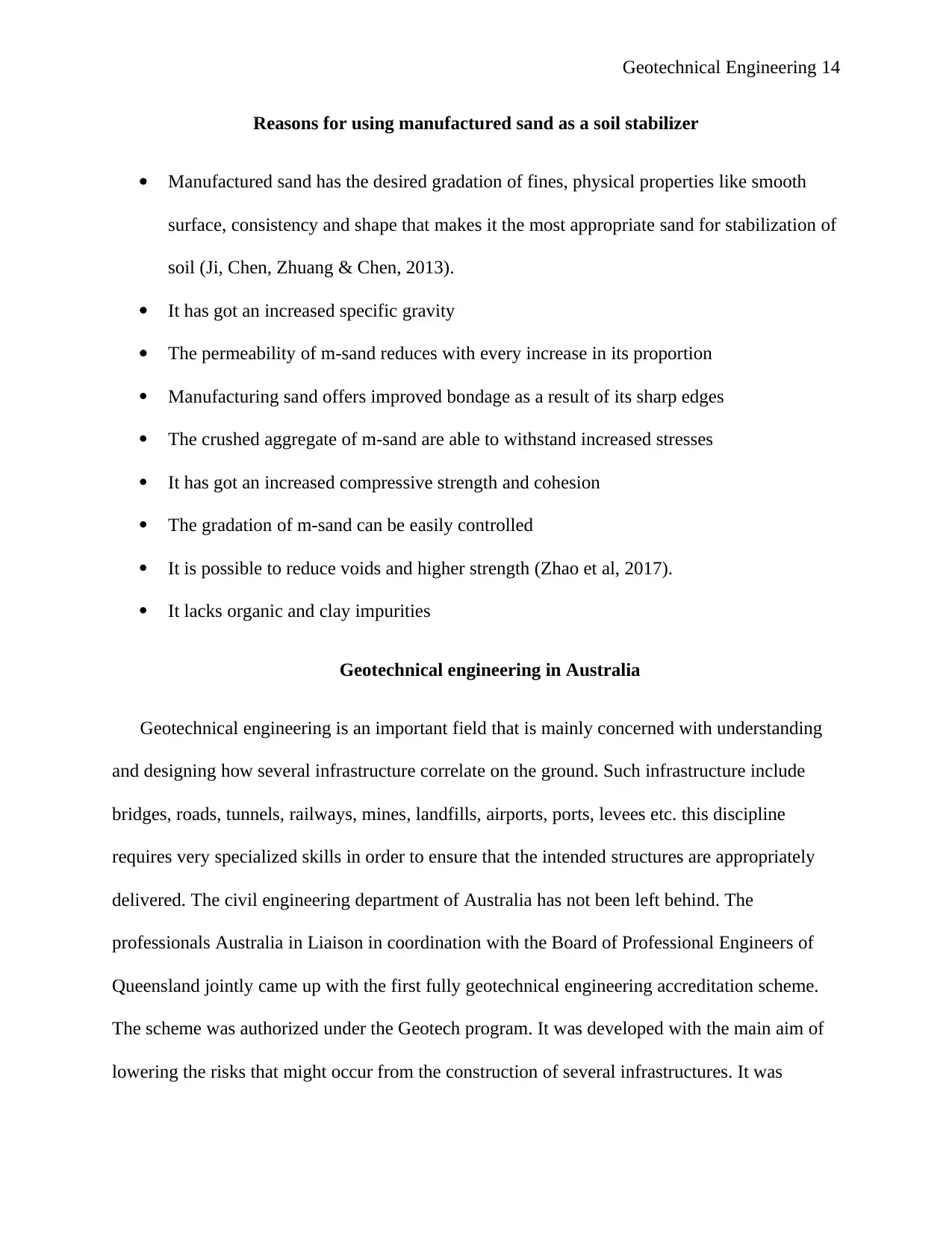
Reasons for using manufactured sand as a soil stabilizer
Manufactured sand has the desired gradation of fines, physical properties like smooth
surface, consistency and shape that makes it the most appropriate sand for stabilization of
soil (Ji, Chen, Zhuang & Chen, 2013).
It has got an increased specific gravity
The permeability of m-sand reduces with every increase in its proportion
Manufacturing sand offers improved bondage as a result of its sharp edges
The crushed aggregate of m-sand are able to withstand increased stresses
It has got an increased compressive strength and cohesion
The gradation of m-sand can be easily controlled
It is possible to reduce voids and higher strength (Zhao et al, 2017).
It lacks organic and clay impurities
Geotechnical engineering in Australia
Geotechnical engineering is an important field that is mainly concerned with understanding
and designing how several infrastructure correlate on the ground. Such infrastructure include
bridges, roads, tunnels, railways, mines, landfills, airports, ports, levees etc. this discipline
requires very specialized skills in order to ensure that the intended structures are appropriately
delivered. The civil engineering department of Australia has not been left behind. The
professionals Australia in Liaison in coordination with the Board of Professional Engineers of
Queensland jointly came up with the first fully geotechnical engineering accreditation scheme.
The scheme was authorized under the Geotech program. It was developed with the main aim of
lowering the risks that might occur from the construction of several infrastructures. It was
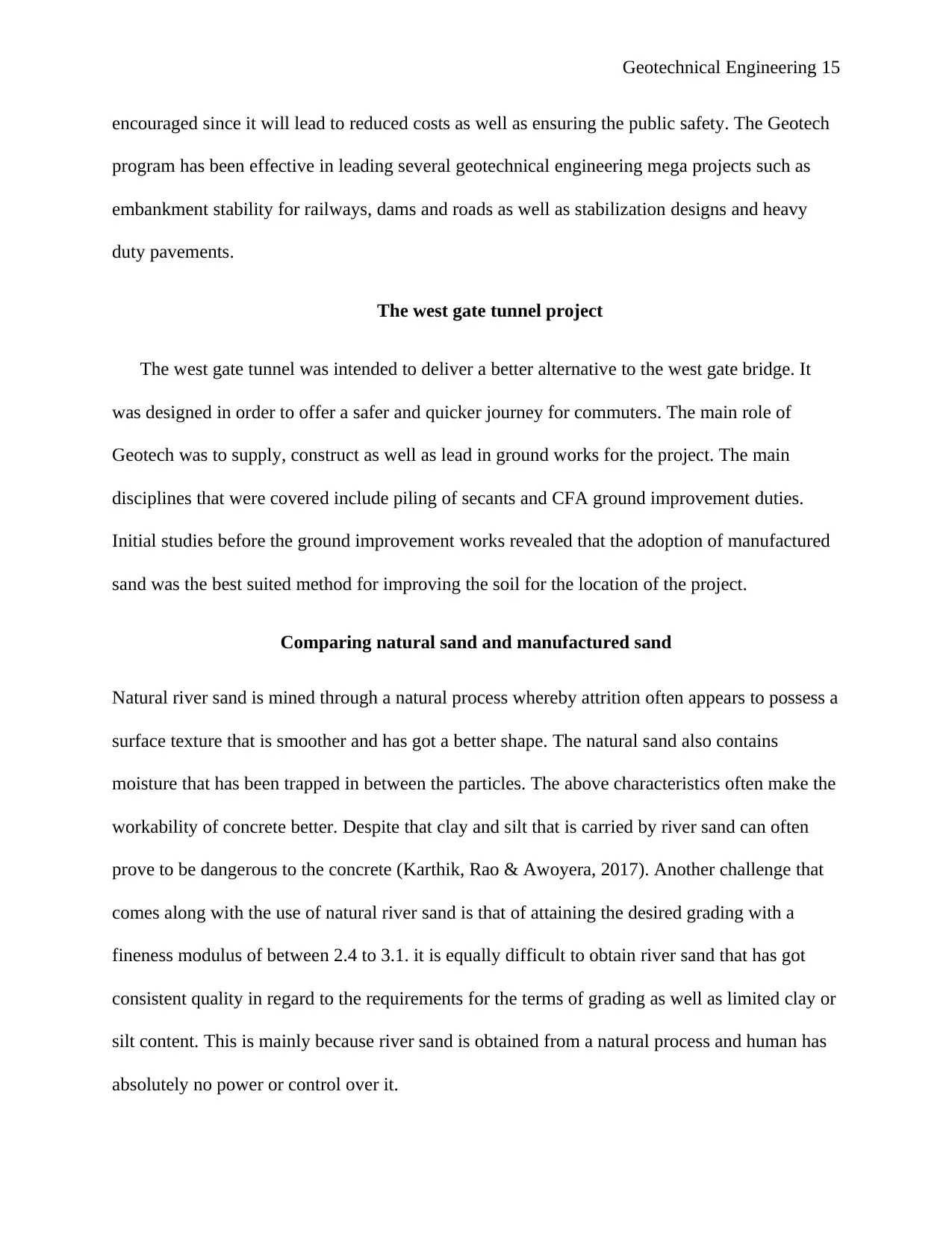
encouraged since it will lead to reduced costs as well as ensuring the public safety. The Geotech
program has been effective in leading several geotechnical engineering mega projects such as
embankment stability for railways, dams and roads as well as stabilization designs and heavy
duty pavements.
The west gate tunnel project
The west gate tunnel was intended to deliver a better alternative to the west gate bridge. It
was designed in order to offer a safer and quicker journey for commuters. The main role of
Geotech was to supply, construct as well as lead in ground works for the project. The main
disciplines that were covered include piling of secants and CFA ground improvement duties.
Initial studies before the ground improvement works revealed that the adoption of manufactured
sand was the best suited method for improving the soil for the location of the project.
Comparing natural sand and manufactured sand
Natural river sand is mined through a natural process whereby attrition often appears to possess a
surface texture that is smoother and has got a better shape. The natural sand also contains
moisture that has been trapped in between the particles. The above characteristics often make the
workability of concrete better. Despite that clay and silt that is carried by river sand can often
prove to be dangerous to the concrete (Karthik, Rao & Awoyera, 2017). Another challenge that
comes along with the use of natural river sand is that of attaining the desired grading with a
fineness modulus of between 2.4 to 3.1. it is equally difficult to obtain river sand that has got
consistent quality in regard to the requirements for the terms of grading as well as limited clay or
silt content. This is mainly because river sand is obtained from a natural process and human has
absolutely no power or control over it.
⊘ This is a preview!⊘
Do you want full access?
Subscribe today to unlock all pages.

Trusted by 1+ million students worldwide
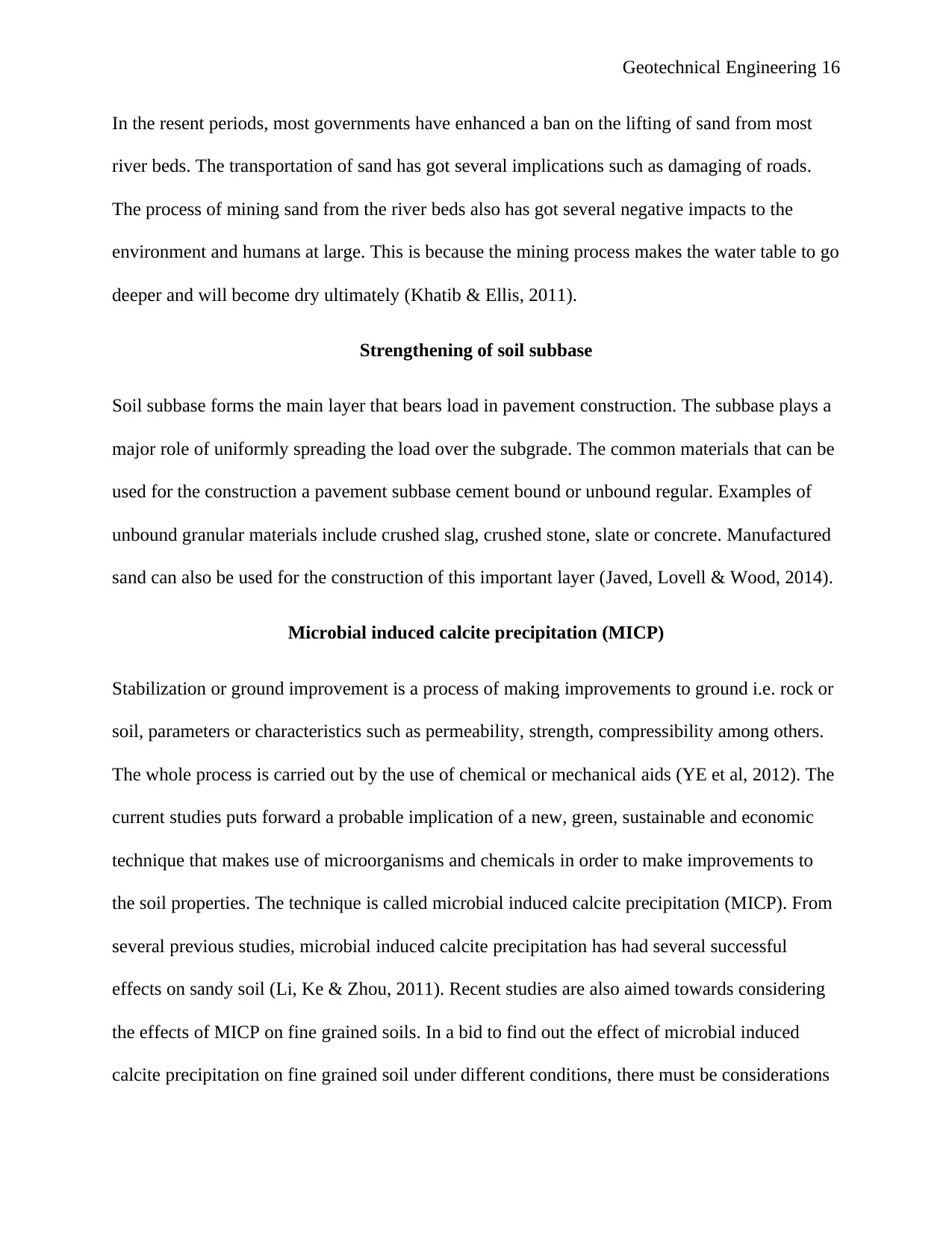
In the resent periods, most governments have enhanced a ban on the lifting of sand from most
river beds. The transportation of sand has got several implications such as damaging of roads.
The process of mining sand from the river beds also has got several negative impacts to the
environment and humans at large. This is because the mining process makes the water table to go
deeper and will become dry ultimately (Khatib & Ellis, 2011).
Strengthening of soil subbase
Soil subbase forms the main layer that bears load in pavement construction. The subbase plays a
major role of uniformly spreading the load over the subgrade. The common materials that can be
used for the construction a pavement subbase cement bound or unbound regular. Examples of
unbound granular materials include crushed slag, crushed stone, slate or concrete. Manufactured
sand can also be used for the construction of this important layer (Javed, Lovell & Wood, 2014).
Microbial induced calcite precipitation (MICP)
Stabilization or ground improvement is a process of making improvements to ground i.e. rock or
soil, parameters or characteristics such as permeability, strength, compressibility among others.
The whole process is carried out by the use of chemical or mechanical aids (YE et al, 2012). The
current studies puts forward a probable implication of a new, green, sustainable and economic
technique that makes use of microorganisms and chemicals in order to make improvements to
the soil properties. The technique is called microbial induced calcite precipitation (MICP). From
several previous studies, microbial induced calcite precipitation has had several successful
effects on sandy soil (Li, Ke & Zhou, 2011). Recent studies are also aimed towards considering
the effects of MICP on fine grained soils. In a bid to find out the effect of microbial induced
calcite precipitation on fine grained soil under different conditions, there must be considerations
Paraphrase This Document
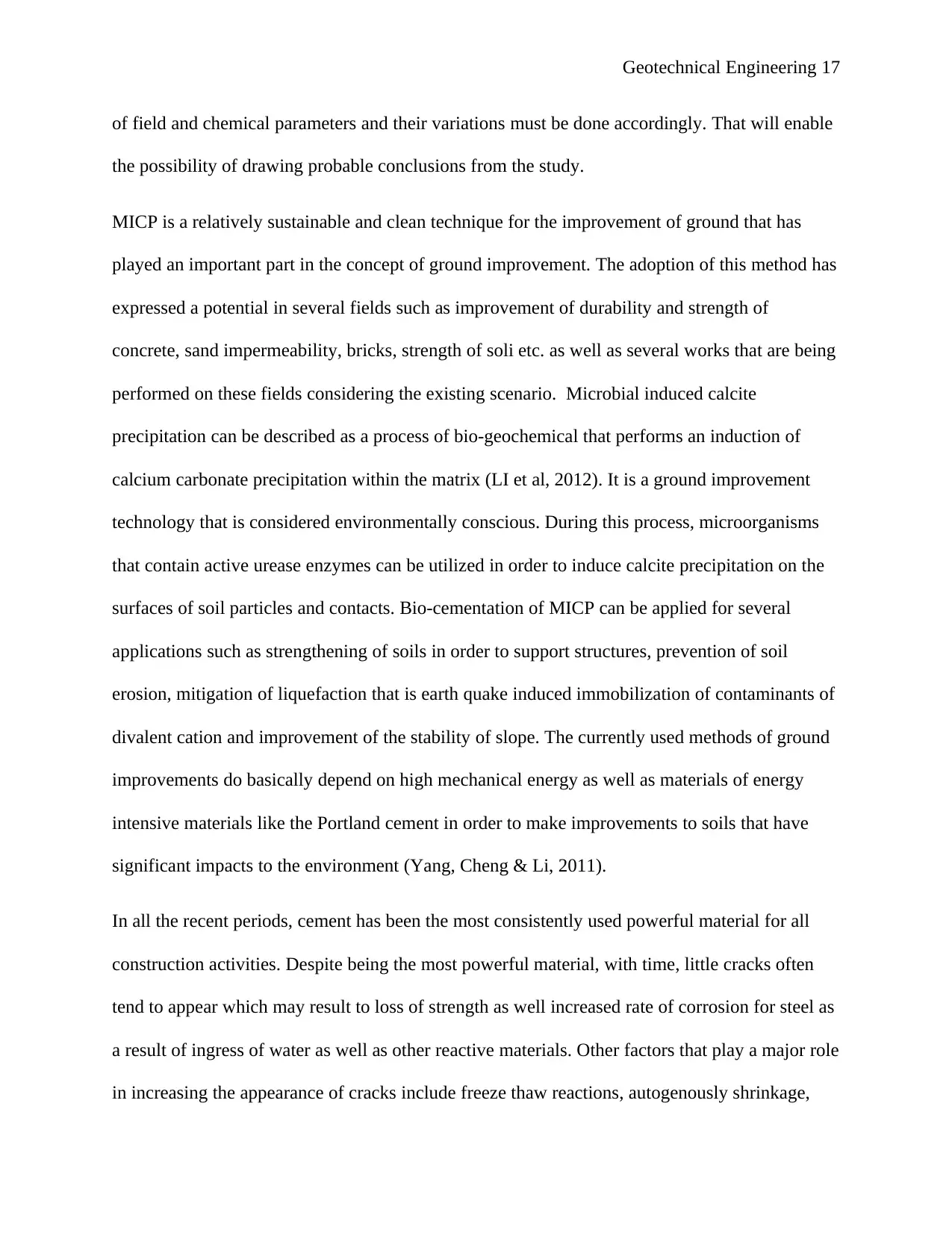
of field and chemical parameters and their variations must be done accordingly. That will enable
the possibility of drawing probable conclusions from the study.
MICP is a relatively sustainable and clean technique for the improvement of ground that has
played an important part in the concept of ground improvement. The adoption of this method has
expressed a potential in several fields such as improvement of durability and strength of
concrete, sand impermeability, bricks, strength of soli etc. as well as several works that are being
performed on these fields considering the existing scenario. Microbial induced calcite
precipitation can be described as a process of bio-geochemical that performs an induction of
calcium carbonate precipitation within the matrix (LI et al, 2012). It is a ground improvement
technology that is considered environmentally conscious. During this process, microorganisms
that contain active urease enzymes can be utilized in order to induce calcite precipitation on the
surfaces of soil particles and contacts. Bio-cementation of MICP can be applied for several
applications such as strengthening of soils in order to support structures, prevention of soil
erosion, mitigation of liquefaction that is earth quake induced immobilization of contaminants of
divalent cation and improvement of the stability of slope. The currently used methods of ground
improvements do basically depend on high mechanical energy as well as materials of energy
intensive materials like the Portland cement in order to make improvements to soils that have
significant impacts to the environment (Yang, Cheng & Li, 2011).
In all the recent periods, cement has been the most consistently used powerful material for all
construction activities. Despite being the most powerful material, with time, little cracks often
tend to appear which may result to loss of strength as well increased rate of corrosion for steel as
a result of ingress of water as well as other reactive materials. Other factors that play a major role
in increasing the appearance of cracks include freeze thaw reactions, autogenously shrinkage,
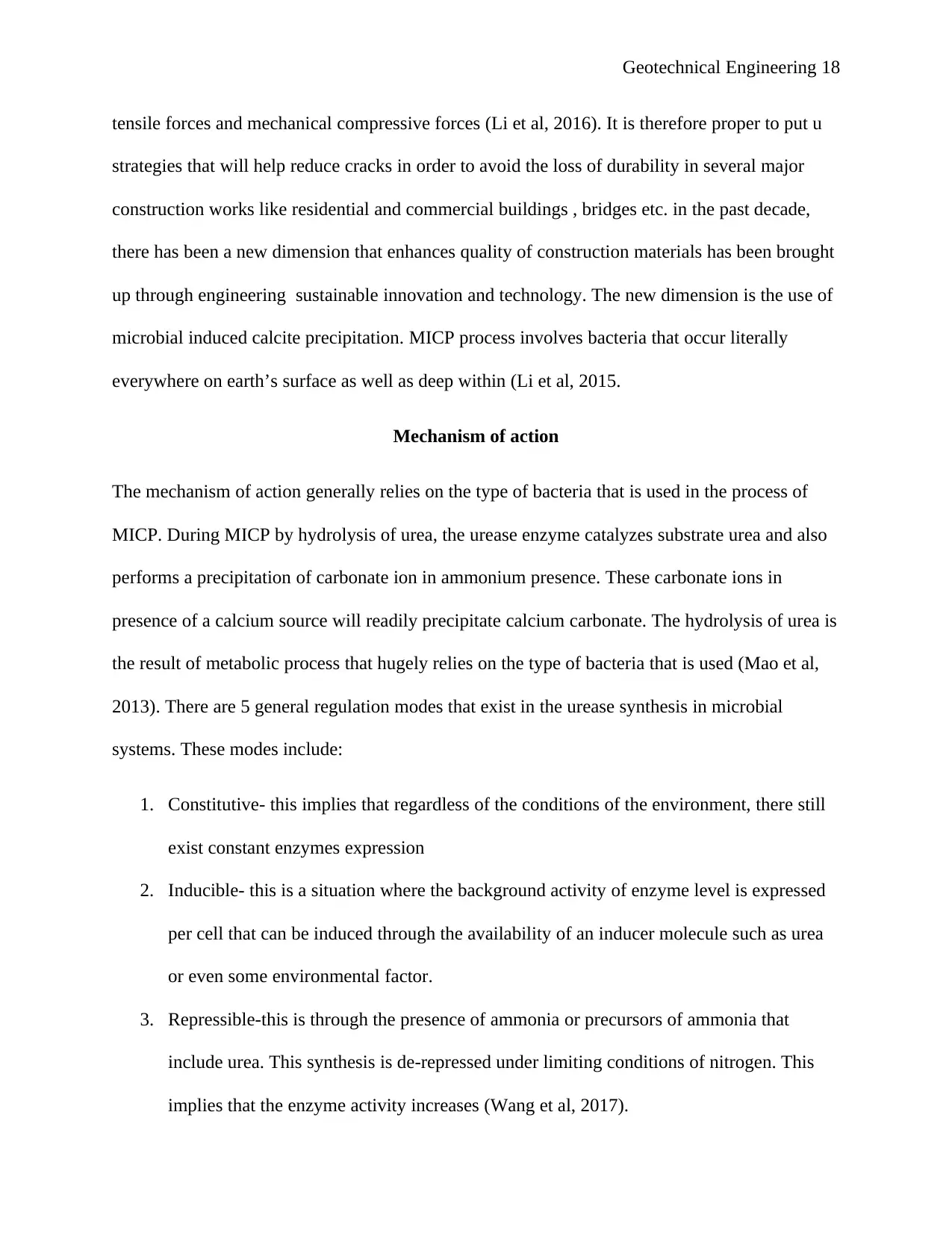
tensile forces and mechanical compressive forces (Li et al, 2016). It is therefore proper to put u
strategies that will help reduce cracks in order to avoid the loss of durability in several major
construction works like residential and commercial buildings , bridges etc. in the past decade,
there has been a new dimension that enhances quality of construction materials has been brought
up through engineering sustainable innovation and technology. The new dimension is the use of
microbial induced calcite precipitation. MICP process involves bacteria that occur literally
everywhere on earth’s surface as well as deep within (Li et al, 2015.
Mechanism of action
The mechanism of action generally relies on the type of bacteria that is used in the process of
MICP. During MICP by hydrolysis of urea, the urease enzyme catalyzes substrate urea and also
performs a precipitation of carbonate ion in ammonium presence. These carbonate ions in
presence of a calcium source will readily precipitate calcium carbonate. The hydrolysis of urea is
the result of metabolic process that hugely relies on the type of bacteria that is used (Mao et al,
2013). There are 5 general regulation modes that exist in the urease synthesis in microbial
systems. These modes include:
1. Constitutive- this implies that regardless of the conditions of the environment, there still
exist constant enzymes expression
2. Inducible- this is a situation where the background activity of enzyme level is expressed
per cell that can be induced through the availability of an inducer molecule such as urea
or even some environmental factor.
3. Repressible-this is through the presence of ammonia or precursors of ammonia that
include urea. This synthesis is de-repressed under limiting conditions of nitrogen. This
implies that the enzyme activity increases (Wang et al, 2017).
⊘ This is a preview!⊘
Do you want full access?
Subscribe today to unlock all pages.

Trusted by 1+ million students worldwide
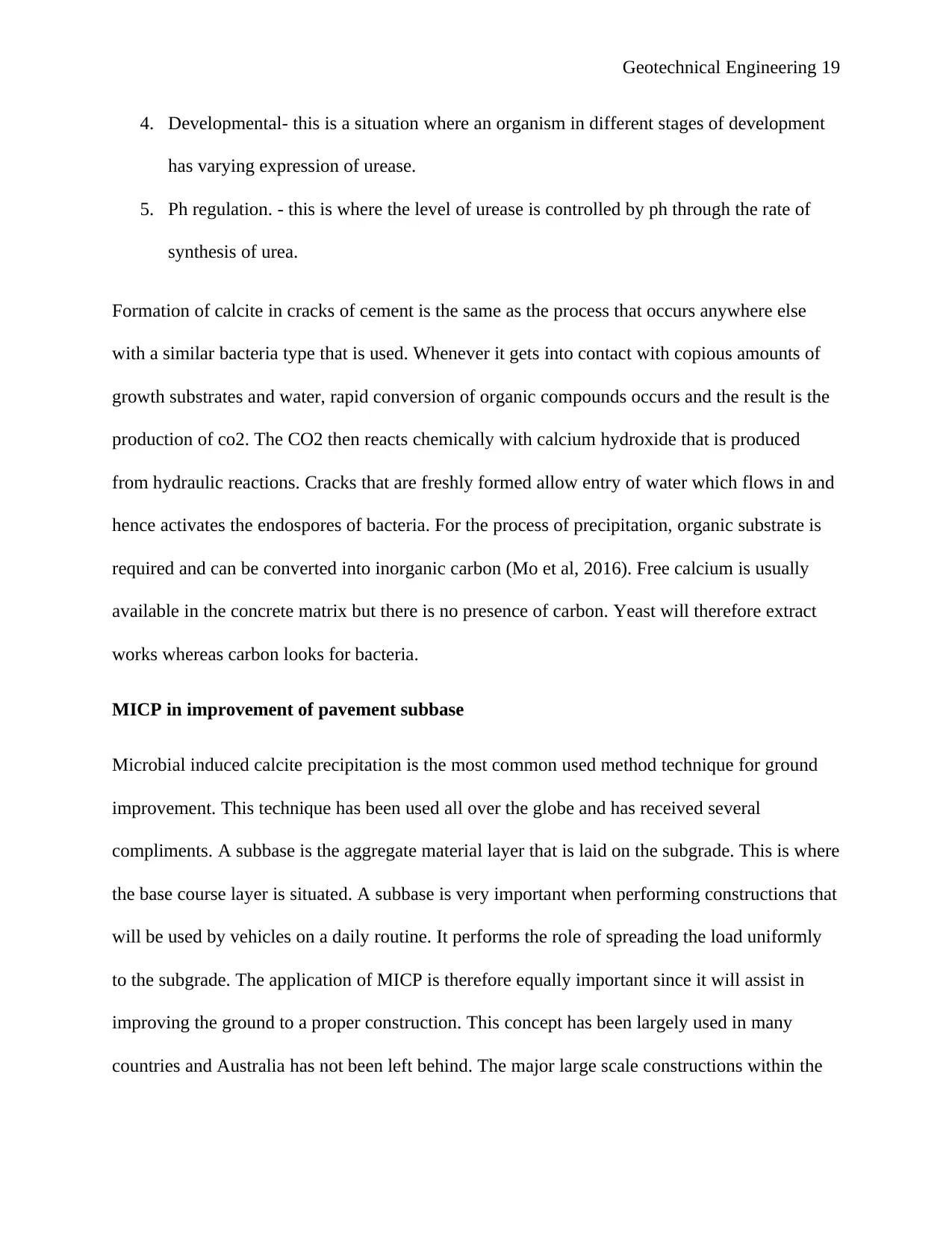
4. Developmental- this is a situation where an organism in different stages of development
has varying expression of urease.
5. Ph regulation. - this is where the level of urease is controlled by ph through the rate of
synthesis of urea.
Formation of calcite in cracks of cement is the same as the process that occurs anywhere else
with a similar bacteria type that is used. Whenever it gets into contact with copious amounts of
growth substrates and water, rapid conversion of organic compounds occurs and the result is the
production of co2. The CO2 then reacts chemically with calcium hydroxide that is produced
from hydraulic reactions. Cracks that are freshly formed allow entry of water which flows in and
hence activates the endospores of bacteria. For the process of precipitation, organic substrate is
required and can be converted into inorganic carbon (Mo et al, 2016). Free calcium is usually
available in the concrete matrix but there is no presence of carbon. Yeast will therefore extract
works whereas carbon looks for bacteria.
MICP in improvement of pavement subbase
Microbial induced calcite precipitation is the most common used method technique for ground
improvement. This technique has been used all over the globe and has received several
compliments. A subbase is the aggregate material layer that is laid on the subgrade. This is where
the base course layer is situated. A subbase is very important when performing constructions that
will be used by vehicles on a daily routine. It performs the role of spreading the load uniformly
to the subgrade. The application of MICP is therefore equally important since it will assist in
improving the ground to a proper construction. This concept has been largely used in many
countries and Australia has not been left behind. The major large scale constructions within the
Paraphrase This Document
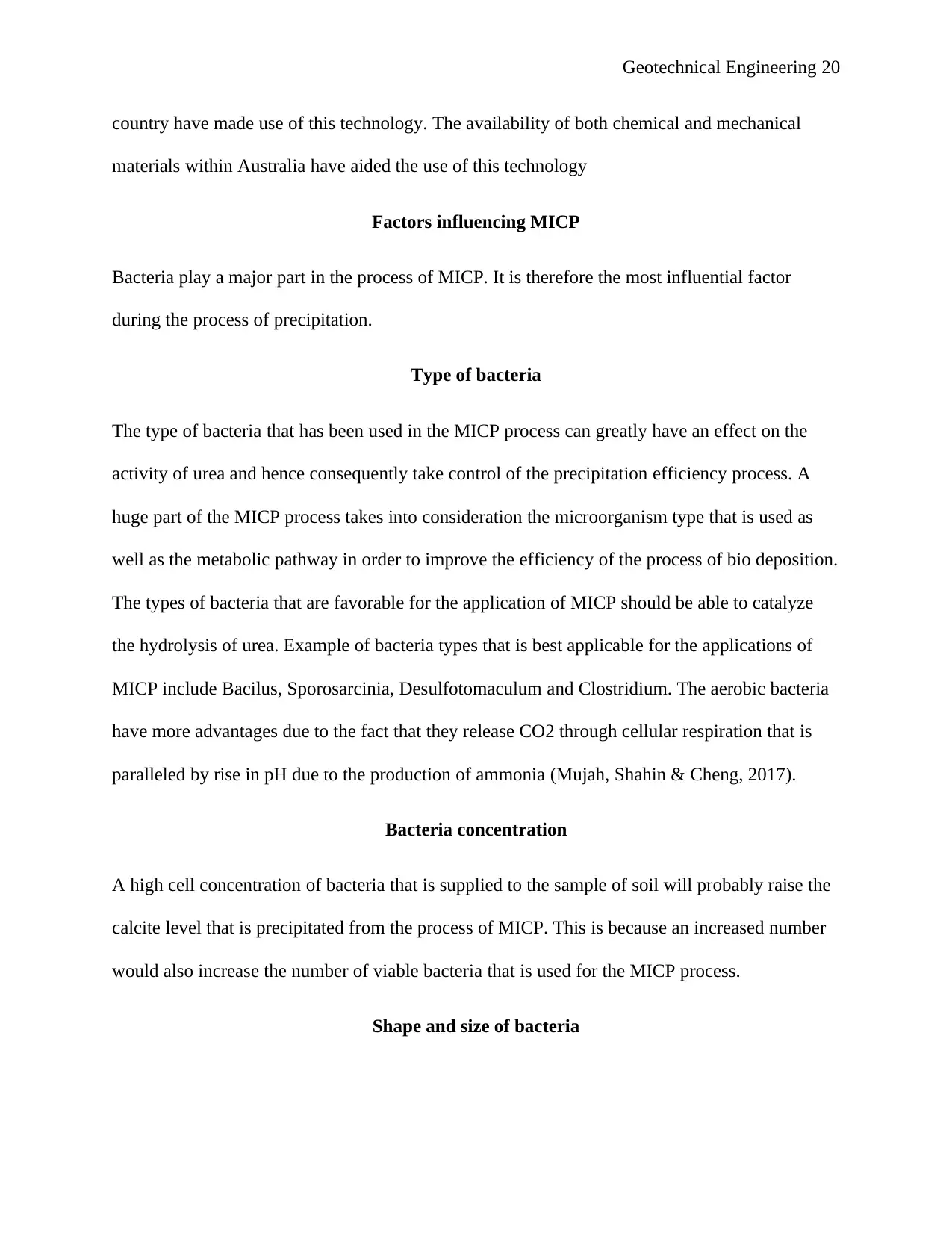
country have made use of this technology. The availability of both chemical and mechanical
materials within Australia have aided the use of this technology
Factors influencing MICP
Bacteria play a major part in the process of MICP. It is therefore the most influential factor
during the process of precipitation.
Type of bacteria
The type of bacteria that has been used in the MICP process can greatly have an effect on the
activity of urea and hence consequently take control of the precipitation efficiency process. A
huge part of the MICP process takes into consideration the microorganism type that is used as
well as the metabolic pathway in order to improve the efficiency of the process of bio deposition.
The types of bacteria that are favorable for the application of MICP should be able to catalyze
the hydrolysis of urea. Example of bacteria types that is best applicable for the applications of
MICP include Bacilus, Sporosarcinia, Desulfotomaculum and Clostridium. The aerobic bacteria
have more advantages due to the fact that they release CO2 through cellular respiration that is
paralleled by rise in pH due to the production of ammonia (Mujah, Shahin & Cheng, 2017).
Bacteria concentration
A high cell concentration of bacteria that is supplied to the sample of soil will probably raise the
calcite level that is precipitated from the process of MICP. This is because an increased number
would also increase the number of viable bacteria that is used for the MICP process.
Shape and size of bacteria
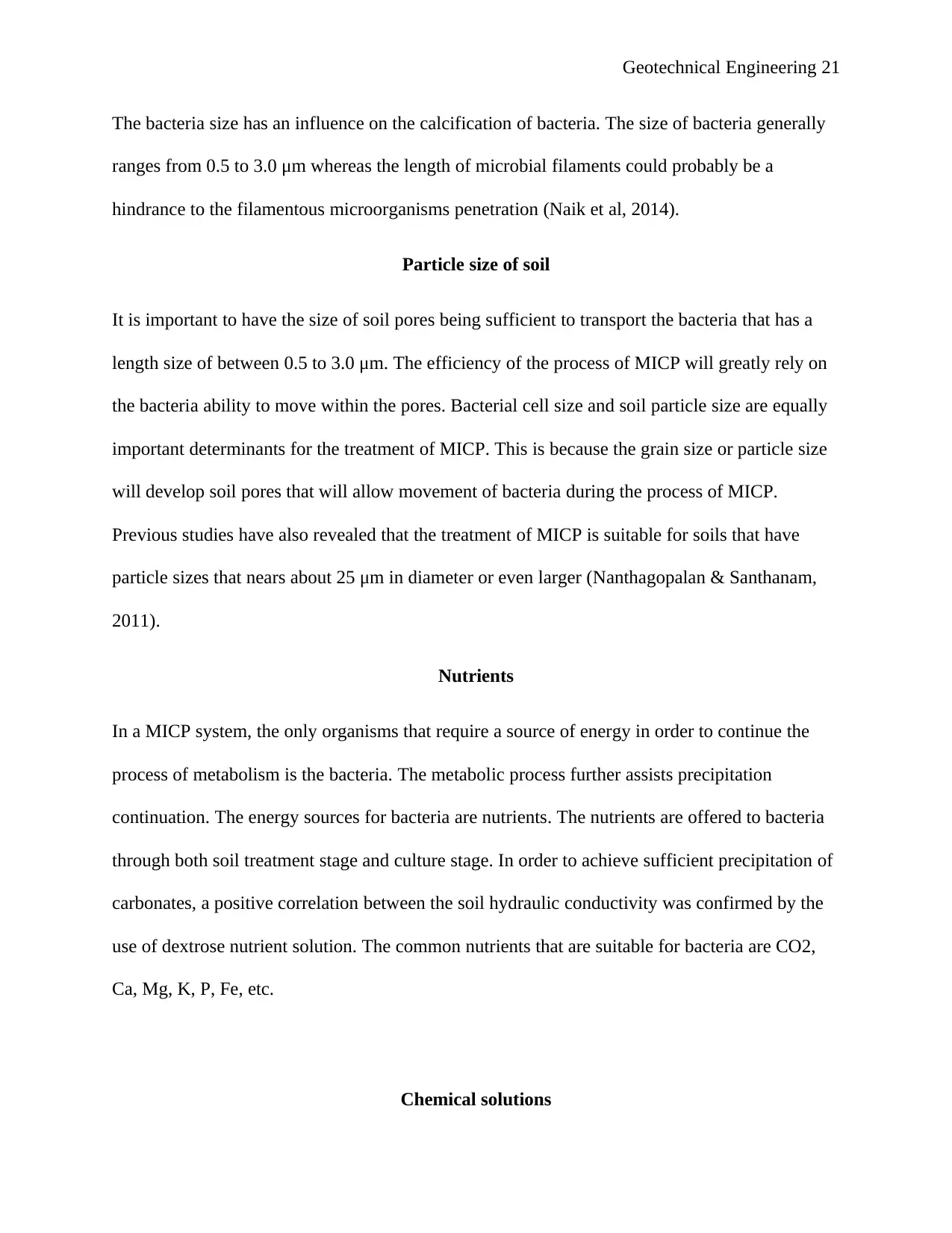
The bacteria size has an influence on the calcification of bacteria. The size of bacteria generally
ranges from 0.5 to 3.0 μm whereas the length of microbial filaments could probably be a
hindrance to the filamentous microorganisms penetration (Naik et al, 2014).
Particle size of soil
It is important to have the size of soil pores being sufficient to transport the bacteria that has a
length size of between 0.5 to 3.0 μm. The efficiency of the process of MICP will greatly rely on
the bacteria ability to move within the pores. Bacterial cell size and soil particle size are equally
important determinants for the treatment of MICP. This is because the grain size or particle size
will develop soil pores that will allow movement of bacteria during the process of MICP.
Previous studies have also revealed that the treatment of MICP is suitable for soils that have
particle sizes that nears about 25 μm in diameter or even larger (Nanthagopalan & Santhanam,
2011).
Nutrients
In a MICP system, the only organisms that require a source of energy in order to continue the
process of metabolism is the bacteria. The metabolic process further assists precipitation
continuation. The energy sources for bacteria are nutrients. The nutrients are offered to bacteria
through both soil treatment stage and culture stage. In order to achieve sufficient precipitation of
carbonates, a positive correlation between the soil hydraulic conductivity was confirmed by the
use of dextrose nutrient solution. The common nutrients that are suitable for bacteria are CO2,
Ca, Mg, K, P, Fe, etc.
Chemical solutions
⊘ This is a preview!⊘
Do you want full access?
Subscribe today to unlock all pages.

Trusted by 1+ million students worldwide
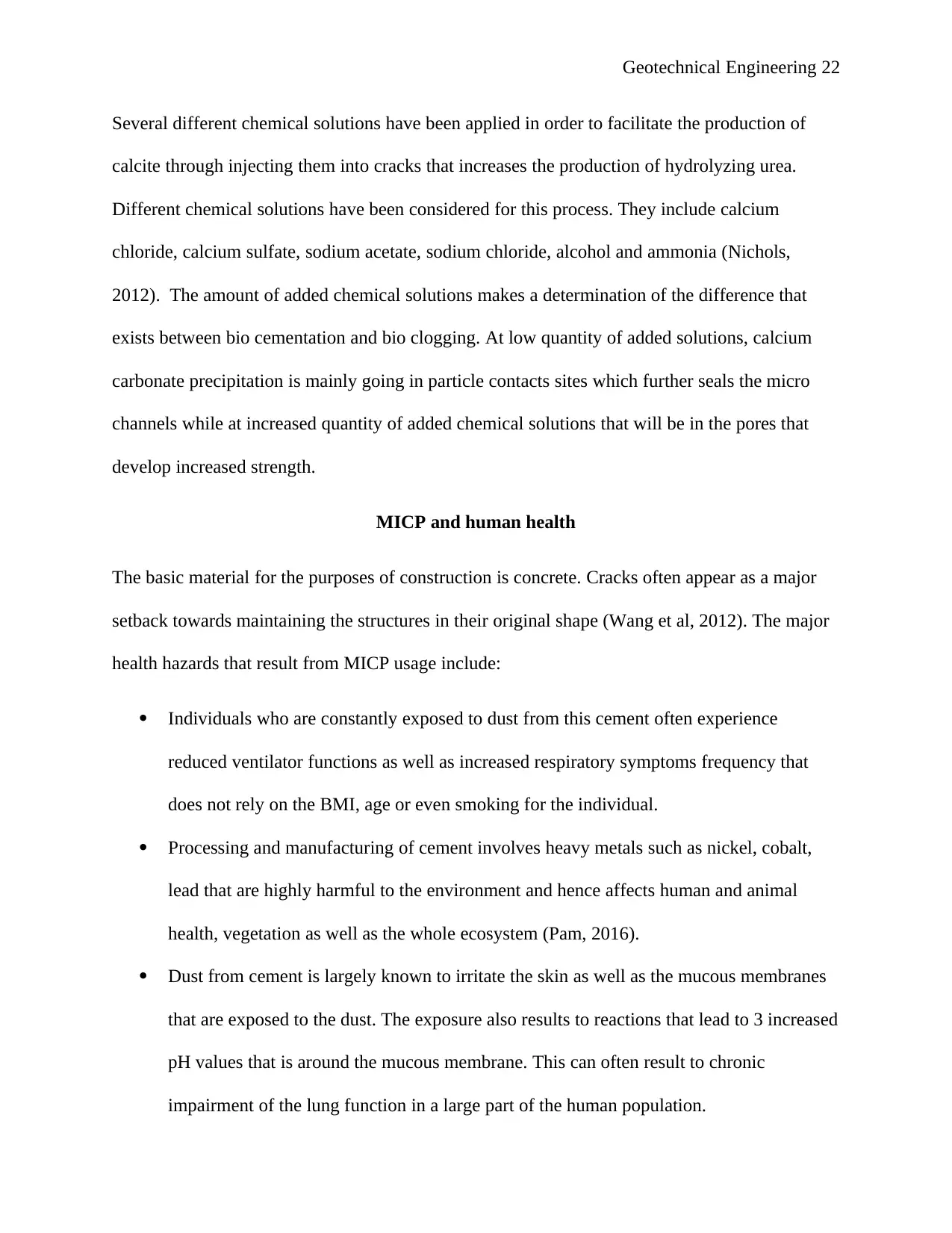
Several different chemical solutions have been applied in order to facilitate the production of
calcite through injecting them into cracks that increases the production of hydrolyzing urea.
Different chemical solutions have been considered for this process. They include calcium
chloride, calcium sulfate, sodium acetate, sodium chloride, alcohol and ammonia (Nichols,
2012). The amount of added chemical solutions makes a determination of the difference that
exists between bio cementation and bio clogging. At low quantity of added solutions, calcium
carbonate precipitation is mainly going in particle contacts sites which further seals the micro
channels while at increased quantity of added chemical solutions that will be in the pores that
develop increased strength.
MICP and human health
The basic material for the purposes of construction is concrete. Cracks often appear as a major
setback towards maintaining the structures in their original shape (Wang et al, 2012). The major
health hazards that result from MICP usage include:
Individuals who are constantly exposed to dust from this cement often experience
reduced ventilator functions as well as increased respiratory symptoms frequency that
does not rely on the BMI, age or even smoking for the individual.
Processing and manufacturing of cement involves heavy metals such as nickel, cobalt,
lead that are highly harmful to the environment and hence affects human and animal
health, vegetation as well as the whole ecosystem (Pam, 2016).
Dust from cement is largely known to irritate the skin as well as the mucous membranes
that are exposed to the dust. The exposure also results to reactions that lead to 3 increased
pH values that is around the mucous membrane. This can often result to chronic
impairment of the lung function in a large part of the human population.
Paraphrase This Document
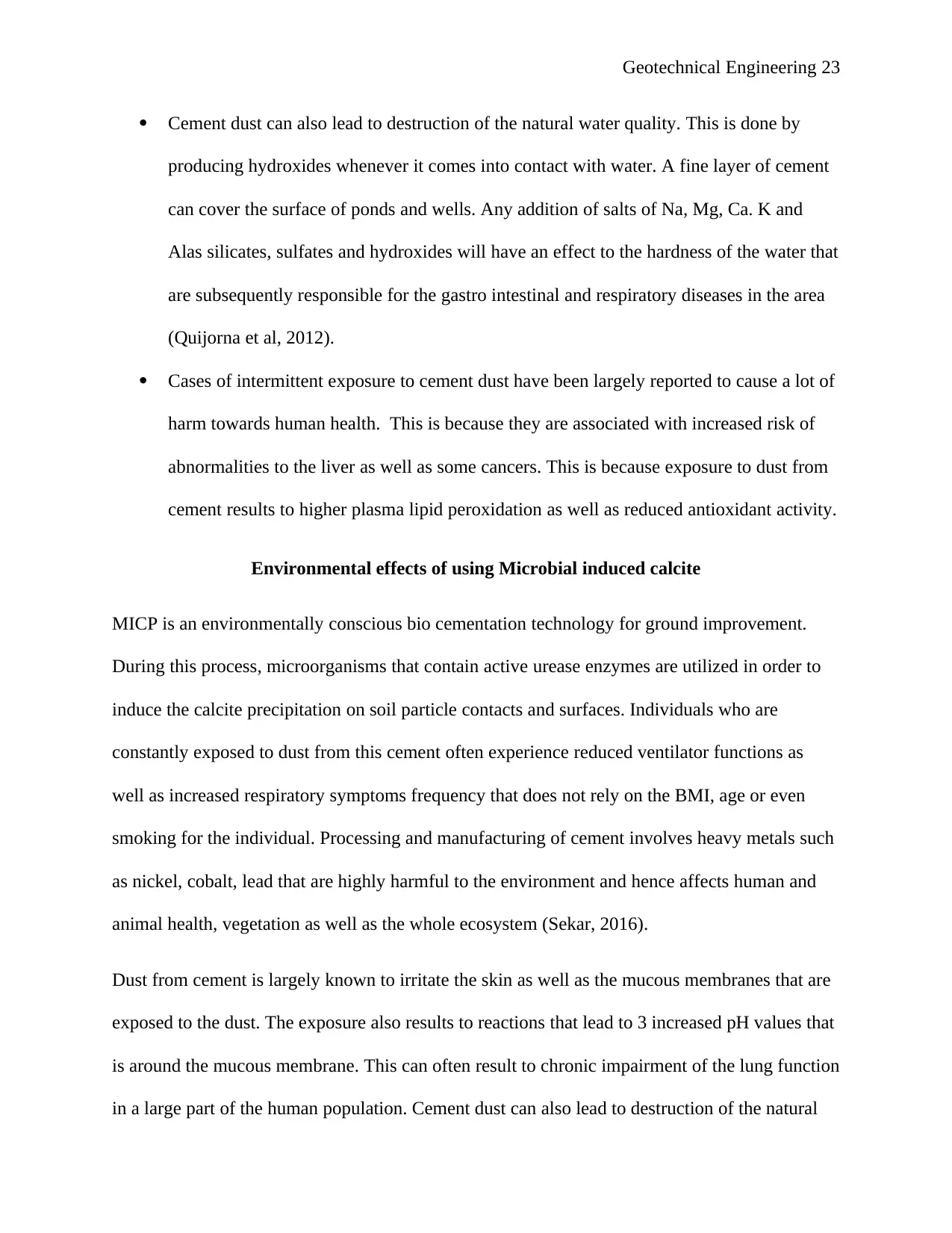
Cement dust can also lead to destruction of the natural water quality. This is done by
producing hydroxides whenever it comes into contact with water. A fine layer of cement
can cover the surface of ponds and wells. Any addition of salts of Na, Mg, Ca. K and
Alas silicates, sulfates and hydroxides will have an effect to the hardness of the water that
are subsequently responsible for the gastro intestinal and respiratory diseases in the area
(Quijorna et al, 2012).
Cases of intermittent exposure to cement dust have been largely reported to cause a lot of
harm towards human health. This is because they are associated with increased risk of
abnormalities to the liver as well as some cancers. This is because exposure to dust from
cement results to higher plasma lipid peroxidation as well as reduced antioxidant activity.
Environmental effects of using Microbial induced calcite
MICP is an environmentally conscious bio cementation technology for ground improvement.
During this process, microorganisms that contain active urease enzymes are utilized in order to
induce the calcite precipitation on soil particle contacts and surfaces. Individuals who are
constantly exposed to dust from this cement often experience reduced ventilator functions as
well as increased respiratory symptoms frequency that does not rely on the BMI, age or even
smoking for the individual. Processing and manufacturing of cement involves heavy metals such
as nickel, cobalt, lead that are highly harmful to the environment and hence affects human and
animal health, vegetation as well as the whole ecosystem (Sekar, 2016).
Dust from cement is largely known to irritate the skin as well as the mucous membranes that are
exposed to the dust. The exposure also results to reactions that lead to 3 increased pH values that
is around the mucous membrane. This can often result to chronic impairment of the lung function
in a large part of the human population. Cement dust can also lead to destruction of the natural
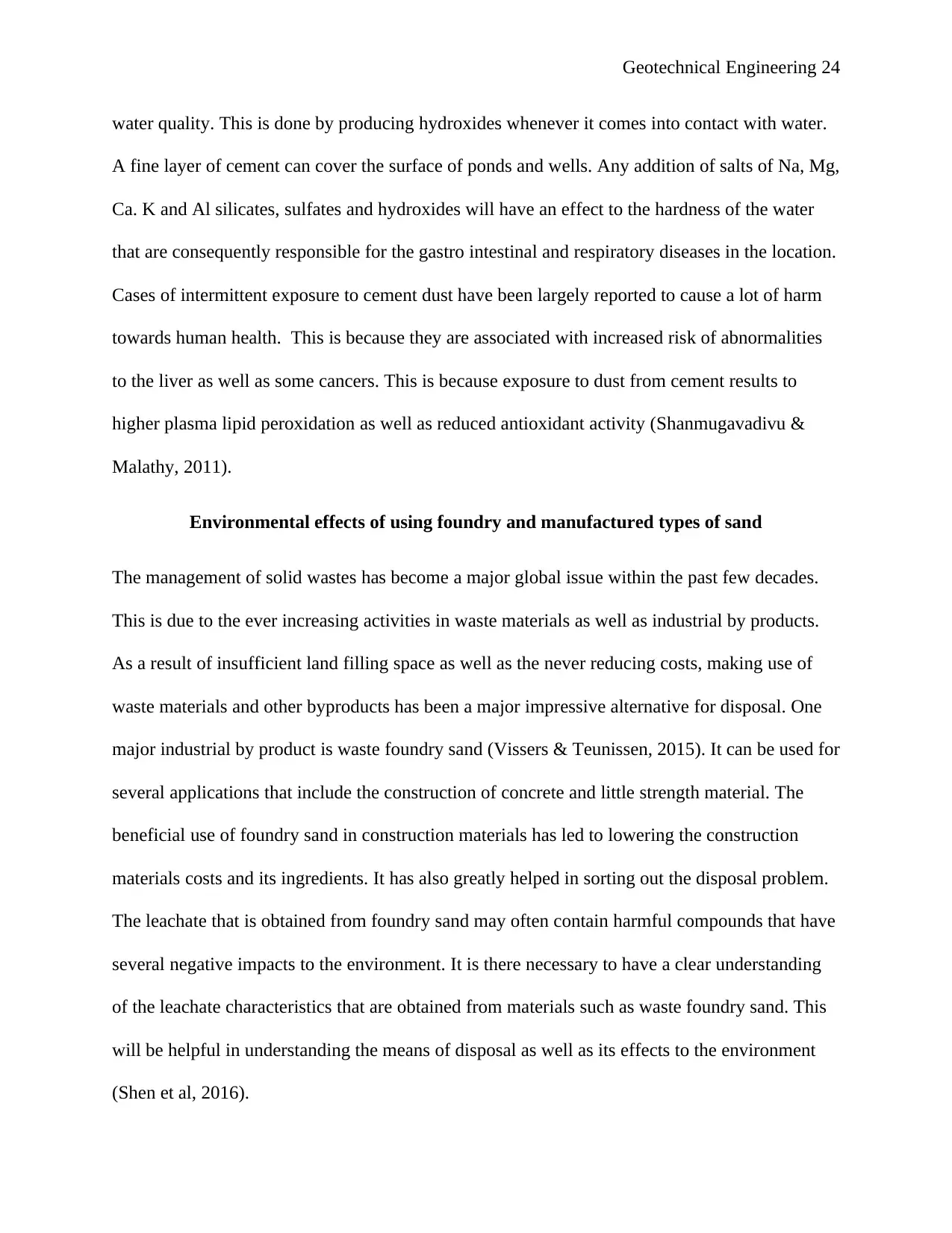
water quality. This is done by producing hydroxides whenever it comes into contact with water.
A fine layer of cement can cover the surface of ponds and wells. Any addition of salts of Na, Mg,
Ca. K and Al silicates, sulfates and hydroxides will have an effect to the hardness of the water
that are consequently responsible for the gastro intestinal and respiratory diseases in the location.
Cases of intermittent exposure to cement dust have been largely reported to cause a lot of harm
towards human health. This is because they are associated with increased risk of abnormalities
to the liver as well as some cancers. This is because exposure to dust from cement results to
higher plasma lipid peroxidation as well as reduced antioxidant activity (Shanmugavadivu &
Malathy, 2011).
Environmental effects of using foundry and manufactured types of sand
The management of solid wastes has become a major global issue within the past few decades.
This is due to the ever increasing activities in waste materials as well as industrial by products.
As a result of insufficient land filling space as well as the never reducing costs, making use of
waste materials and other byproducts has been a major impressive alternative for disposal. One
major industrial by product is waste foundry sand (Vissers & Teunissen, 2015). It can be used for
several applications that include the construction of concrete and little strength material. The
beneficial use of foundry sand in construction materials has led to lowering the construction
materials costs and its ingredients. It has also greatly helped in sorting out the disposal problem.
The leachate that is obtained from foundry sand may often contain harmful compounds that have
several negative impacts to the environment. It is there necessary to have a clear understanding
of the leachate characteristics that are obtained from materials such as waste foundry sand. This
will be helpful in understanding the means of disposal as well as its effects to the environment
(Shen et al, 2016).
⊘ This is a preview!⊘
Do you want full access?
Subscribe today to unlock all pages.

Trusted by 1+ million students worldwide
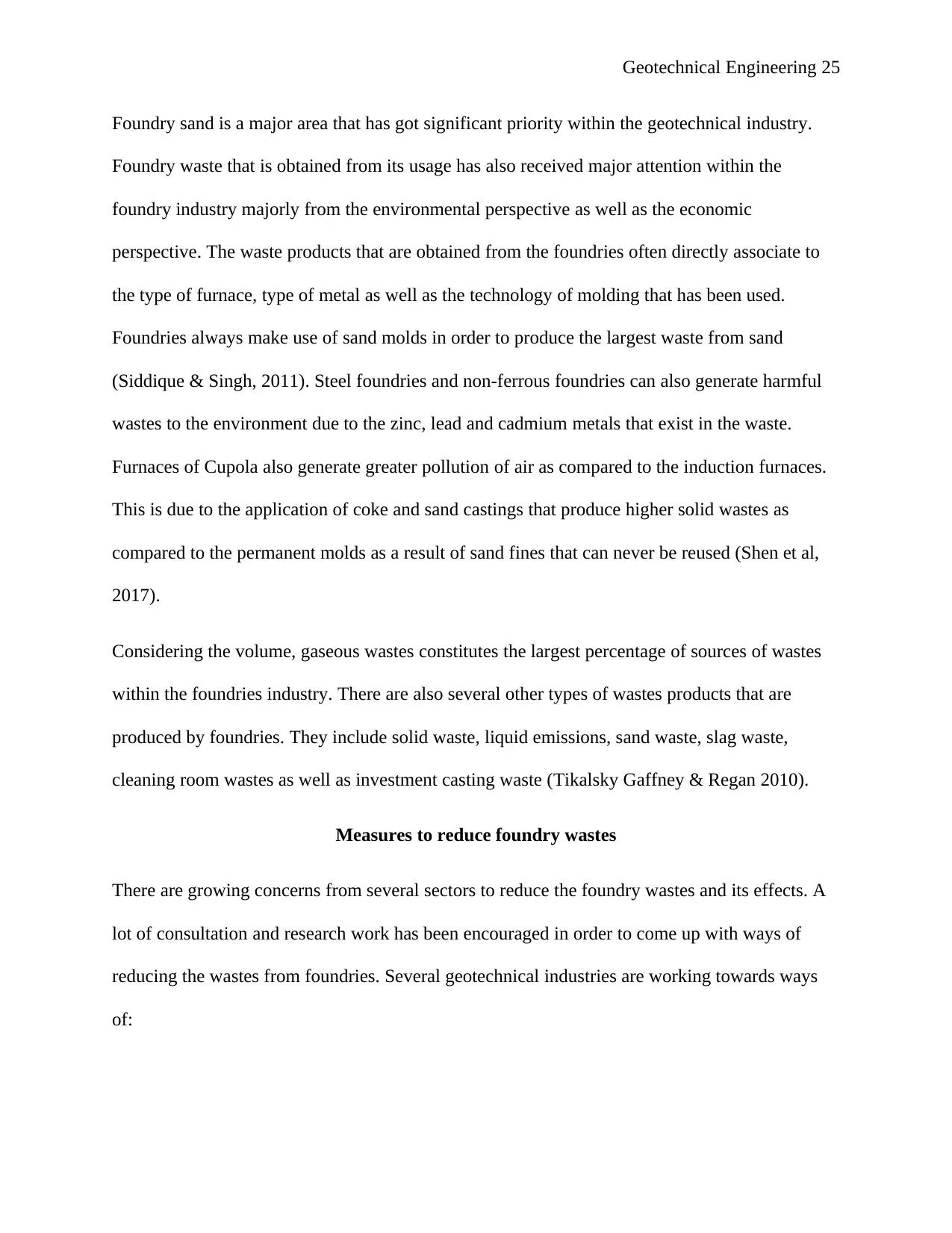
Foundry sand is a major area that has got significant priority within the geotechnical industry.
Foundry waste that is obtained from its usage has also received major attention within the
foundry industry majorly from the environmental perspective as well as the economic
perspective. The waste products that are obtained from the foundries often directly associate to
the type of furnace, type of metal as well as the technology of molding that has been used.
Foundries always make use of sand molds in order to produce the largest waste from sand
(Siddique & Singh, 2011). Steel foundries and non-ferrous foundries can also generate harmful
wastes to the environment due to the zinc, lead and cadmium metals that exist in the waste.
Furnaces of Cupola also generate greater pollution of air as compared to the induction furnaces.
This is due to the application of coke and sand castings that produce higher solid wastes as
compared to the permanent molds as a result of sand fines that can never be reused (Shen et al,
2017).
Considering the volume, gaseous wastes constitutes the largest percentage of sources of wastes
within the foundries industry. There are also several other types of wastes products that are
produced by foundries. They include solid waste, liquid emissions, sand waste, slag waste,
cleaning room wastes as well as investment casting waste (Tikalsky Gaffney & Regan 2010).
Measures to reduce foundry wastes
There are growing concerns from several sectors to reduce the foundry wastes and its effects. A
lot of consultation and research work has been encouraged in order to come up with ways of
reducing the wastes from foundries. Several geotechnical industries are working towards ways
of:
Paraphrase This Document
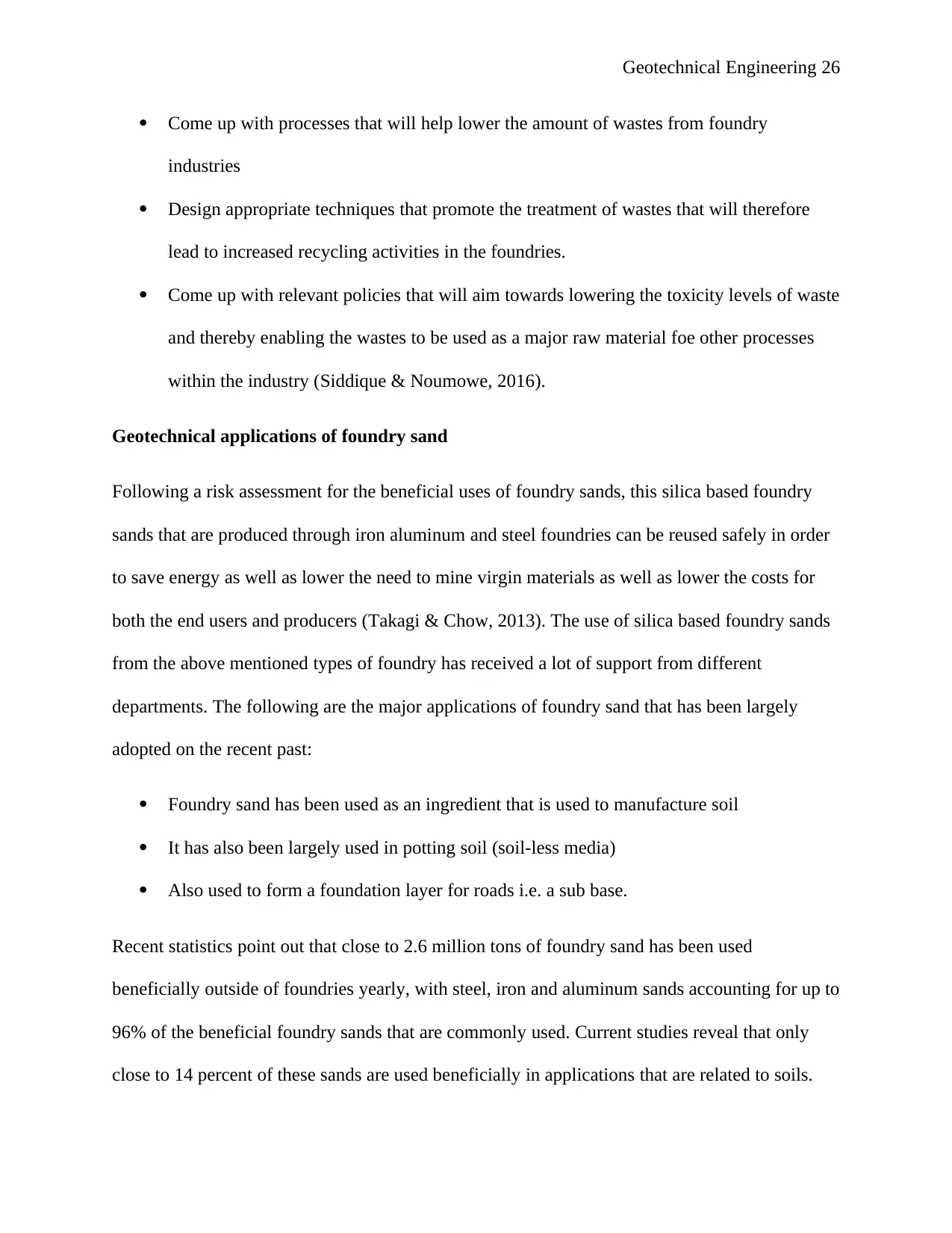
Come up with processes that will help lower the amount of wastes from foundry
industries
Design appropriate techniques that promote the treatment of wastes that will therefore
lead to increased recycling activities in the foundries.
Come up with relevant policies that will aim towards lowering the toxicity levels of waste
and thereby enabling the wastes to be used as a major raw material foe other processes
within the industry (Siddique & Noumowe, 2016).
Geotechnical applications of foundry sand
Following a risk assessment for the beneficial uses of foundry sands, this silica based foundry
sands that are produced through iron aluminum and steel foundries can be reused safely in order
to save energy as well as lower the need to mine virgin materials as well as lower the costs for
both the end users and producers (Takagi & Chow, 2013). The use of silica based foundry sands
from the above mentioned types of foundry has received a lot of support from different
departments. The following are the major applications of foundry sand that has been largely
adopted on the recent past:
Foundry sand has been used as an ingredient that is used to manufacture soil
It has also been largely used in potting soil (soil-less media)
Also used to form a foundation layer for roads i.e. a sub base.
Recent statistics point out that close to 2.6 million tons of foundry sand has been used
beneficially outside of foundries yearly, with steel, iron and aluminum sands accounting for up to
96% of the beneficial foundry sands that are commonly used. Current studies reveal that only
close to 14 percent of these sands are used beneficially in applications that are related to soils.
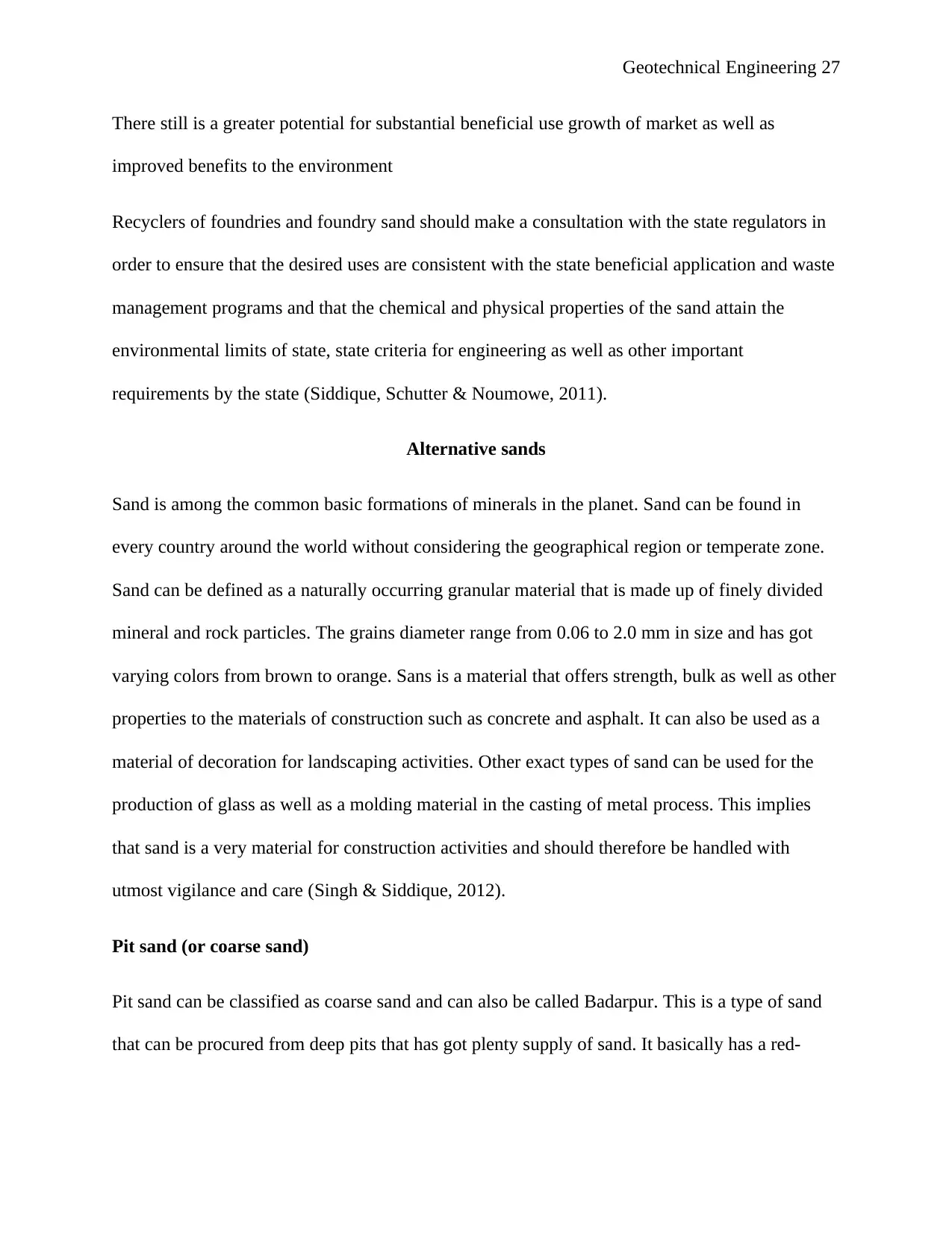
There still is a greater potential for substantial beneficial use growth of market as well as
improved benefits to the environment
Recyclers of foundries and foundry sand should make a consultation with the state regulators in
order to ensure that the desired uses are consistent with the state beneficial application and waste
management programs and that the chemical and physical properties of the sand attain the
environmental limits of state, state criteria for engineering as well as other important
requirements by the state (Siddique, Schutter & Noumowe, 2011).
Alternative sands
Sand is among the common basic formations of minerals in the planet. Sand can be found in
every country around the world without considering the geographical region or temperate zone.
Sand can be defined as a naturally occurring granular material that is made up of finely divided
mineral and rock particles. The grains diameter range from 0.06 to 2.0 mm in size and has got
varying colors from brown to orange. Sans is a material that offers strength, bulk as well as other
properties to the materials of construction such as concrete and asphalt. It can also be used as a
material of decoration for landscaping activities. Other exact types of sand can be used for the
production of glass as well as a molding material in the casting of metal process. This implies
that sand is a very material for construction activities and should therefore be handled with
utmost vigilance and care (Singh & Siddique, 2012).
Pit sand (or coarse sand)
Pit sand can be classified as coarse sand and can also be called Badarpur. This is a type of sand
that can be procured from deep pits that has got plenty supply of sand. It basically has a red-
⊘ This is a preview!⊘
Do you want full access?
Subscribe today to unlock all pages.

Trusted by 1+ million students worldwide
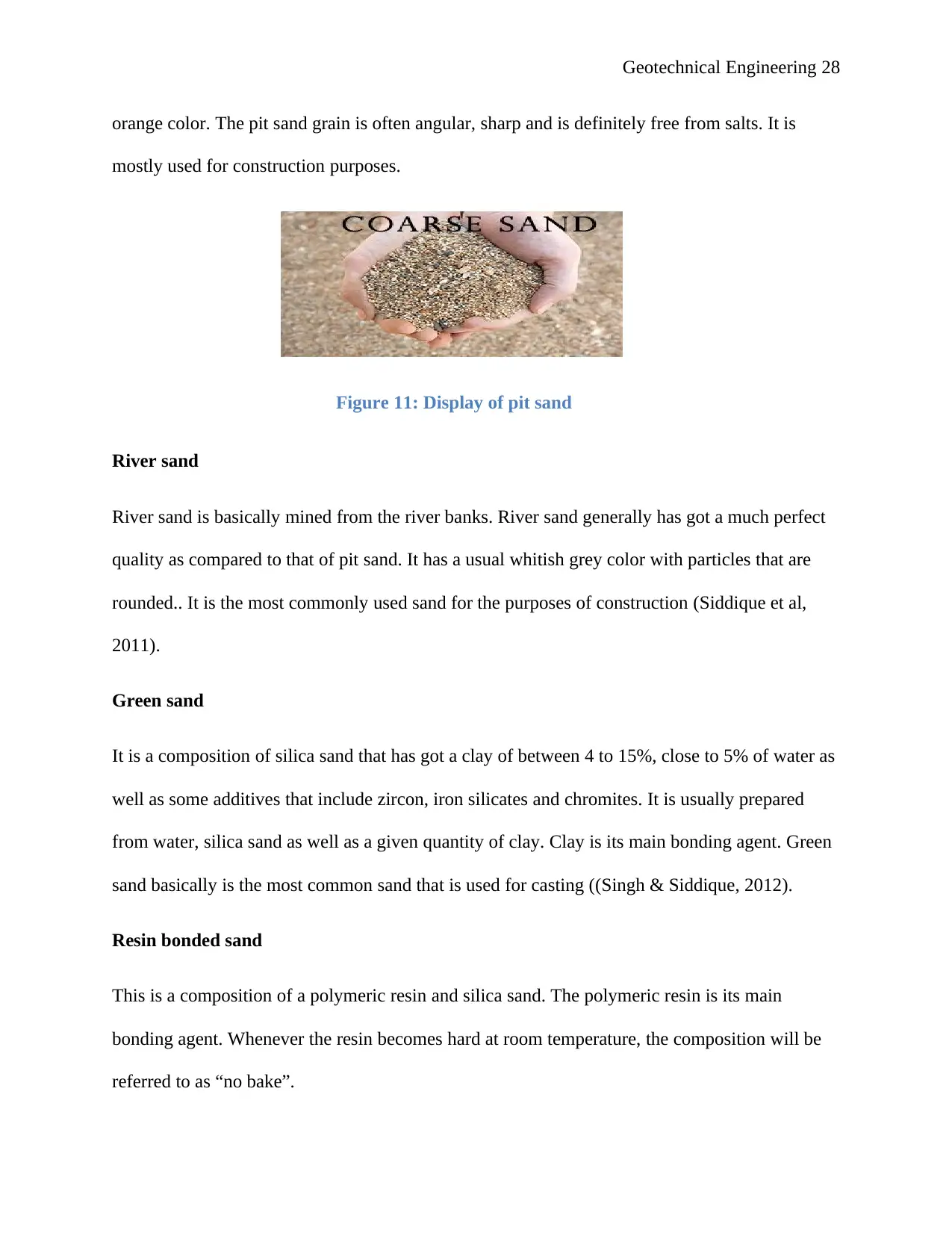
orange color. The pit sand grain is often angular, sharp and is definitely free from salts. It is
mostly used for construction purposes.
Figure 11: Display of pit sand
River sand
River sand is basically mined from the river banks. River sand generally has got a much perfect
quality as compared to that of pit sand. It has a usual whitish grey color with particles that are
rounded.. It is the most commonly used sand for the purposes of construction (Siddique et al,
2011).
Green sand
It is a composition of silica sand that has got a clay of between 4 to 15%, close to 5% of water as
well as some additives that include zircon, iron silicates and chromites. It is usually prepared
from water, silica sand as well as a given quantity of clay. Clay is its main bonding agent. Green
sand basically is the most common sand that is used for casting ((Singh & Siddique, 2012).
Resin bonded sand
This is a composition of a polymeric resin and silica sand. The polymeric resin is its main
bonding agent. Whenever the resin becomes hard at room temperature, the composition will be
referred to as “no bake”.
Paraphrase This Document
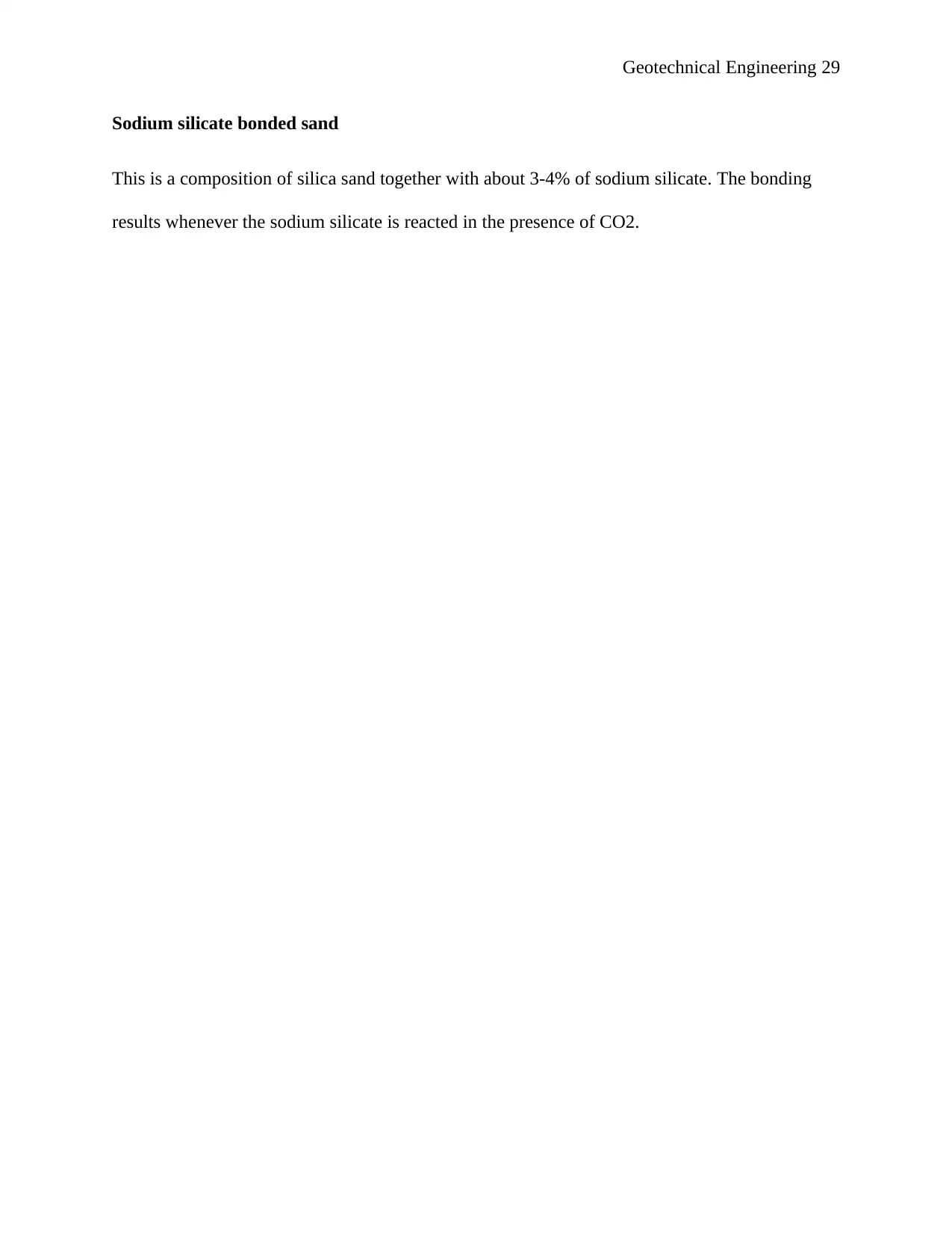
Sodium silicate bonded sand
This is a composition of silica sand together with about 3-4% of sodium silicate. The bonding
results whenever the sodium silicate is reacted in the presence of CO2.
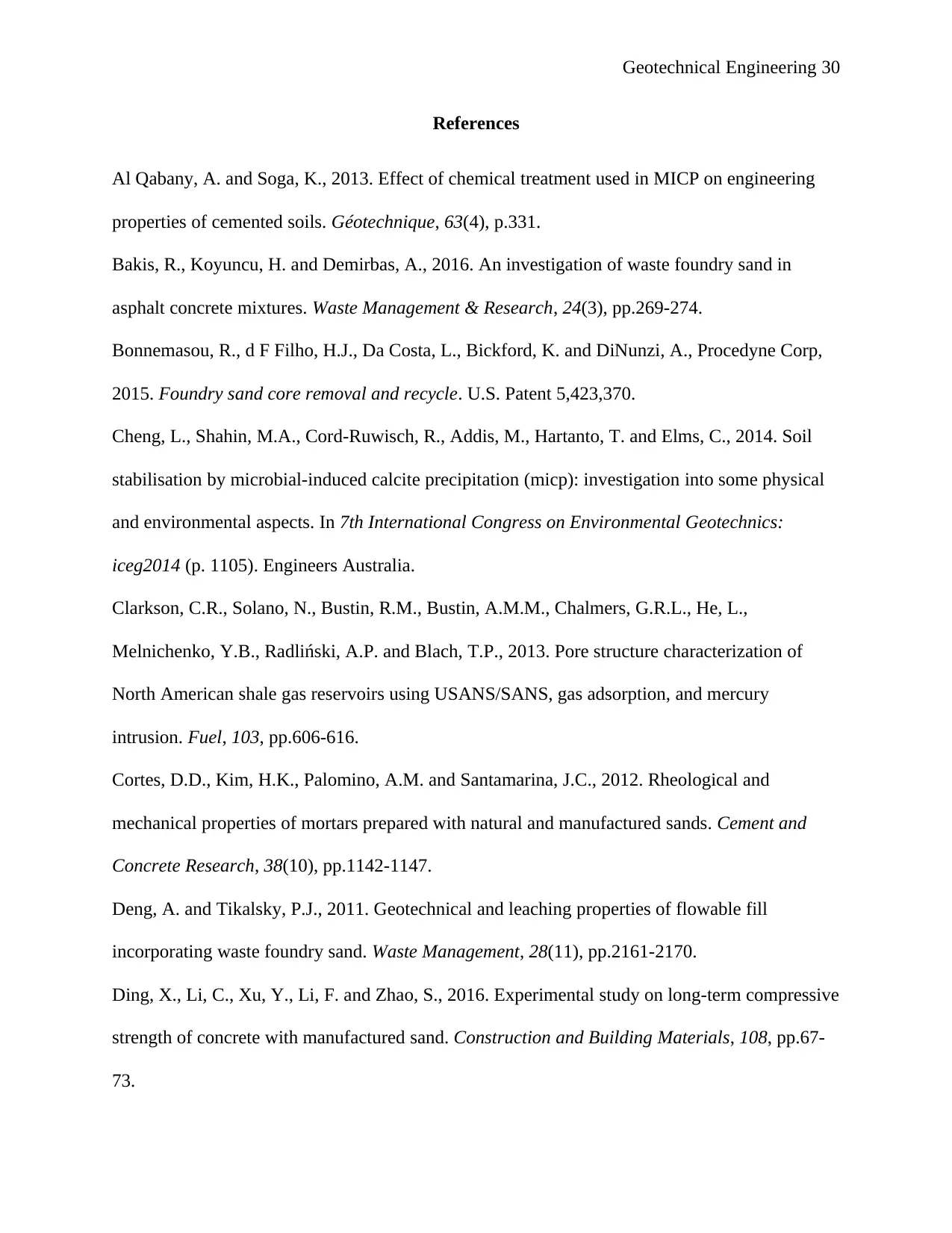
References
Al Qabany, A. and Soga, K., 2013. Effect of chemical treatment used in MICP on engineering
properties of cemented soils. Géotechnique, 63(4), p.331.
Bakis, R., Koyuncu, H. and Demirbas, A., 2016. An investigation of waste foundry sand in
asphalt concrete mixtures. Waste Management & Research, 24(3), pp.269-274.
Bonnemasou, R., d F Filho, H.J., Da Costa, L., Bickford, K. and DiNunzi, A., Procedyne Corp,
2015. Foundry sand core removal and recycle. U.S. Patent 5,423,370.
Cheng, L., Shahin, M.A., Cord-Ruwisch, R., Addis, M., Hartanto, T. and Elms, C., 2014. Soil
stabilisation by microbial-induced calcite precipitation (micp): investigation into some physical
and environmental aspects. In 7th International Congress on Environmental Geotechnics:
iceg2014 (p. 1105). Engineers Australia.
Clarkson, C.R., Solano, N., Bustin, R.M., Bustin, A.M.M., Chalmers, G.R.L., He, L.,
Melnichenko, Y.B., Radliński, A.P. and Blach, T.P., 2013. Pore structure characterization of
North American shale gas reservoirs using USANS/SANS, gas adsorption, and mercury
intrusion. Fuel, 103, pp.606-616.
Cortes, D.D., Kim, H.K., Palomino, A.M. and Santamarina, J.C., 2012. Rheological and
mechanical properties of mortars prepared with natural and manufactured sands. Cement and
Concrete Research, 38(10), pp.1142-1147.
Deng, A. and Tikalsky, P.J., 2011. Geotechnical and leaching properties of flowable fill
incorporating waste foundry sand. Waste Management, 28(11), pp.2161-2170.
Ding, X., Li, C., Xu, Y., Li, F. and Zhao, S., 2016. Experimental study on long-term compressive
strength of concrete with manufactured sand. Construction and Building Materials, 108, pp.67-
73.
⊘ This is a preview!⊘
Do you want full access?
Subscribe today to unlock all pages.

Trusted by 1+ million students worldwide
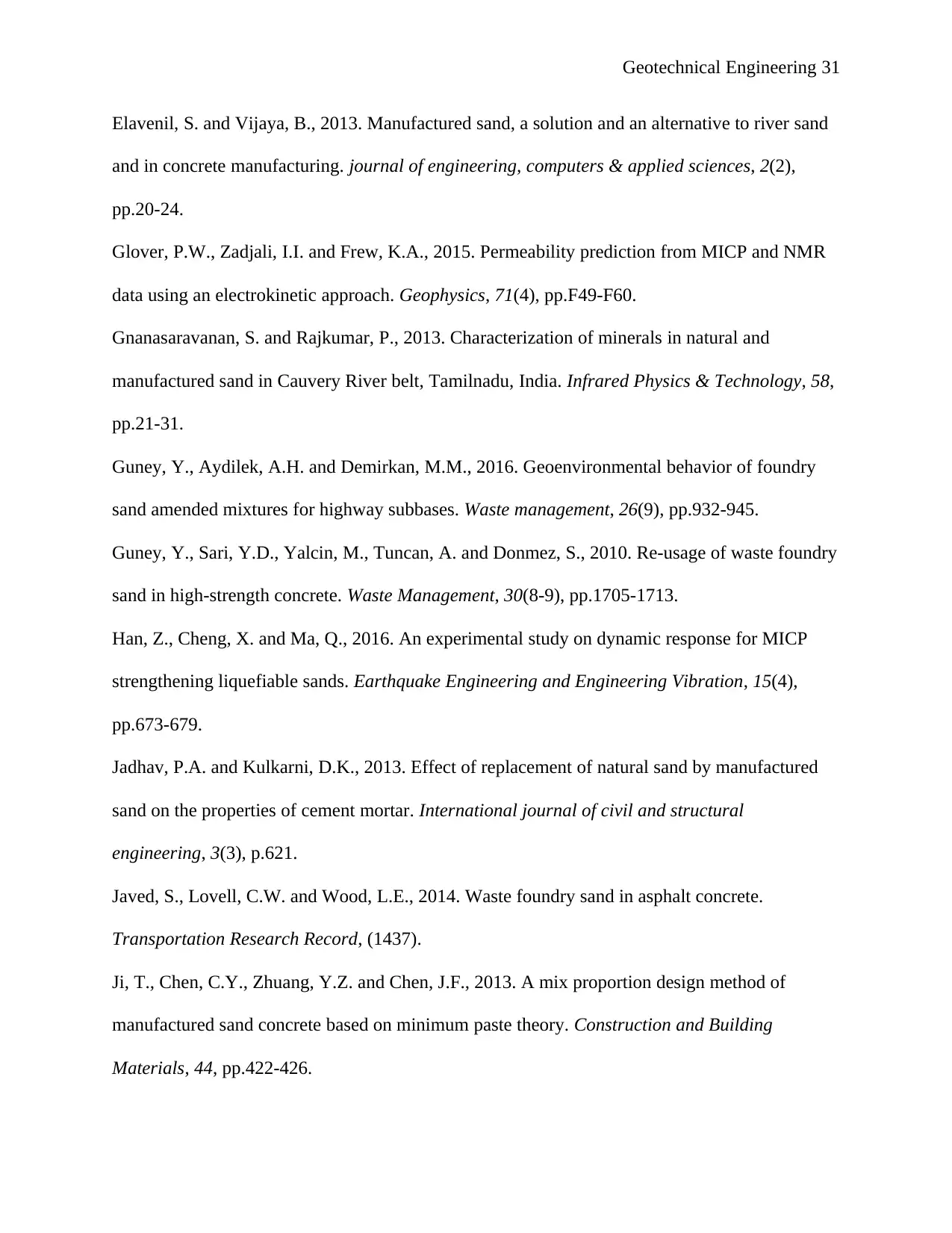
Elavenil, S. and Vijaya, B., 2013. Manufactured sand, a solution and an alternative to river sand
and in concrete manufacturing. journal of engineering, computers & applied sciences, 2(2),
pp.20-24.
Glover, P.W., Zadjali, I.I. and Frew, K.A., 2015. Permeability prediction from MICP and NMR
data using an electrokinetic approach. Geophysics, 71(4), pp.F49-F60.
Gnanasaravanan, S. and Rajkumar, P., 2013. Characterization of minerals in natural and
manufactured sand in Cauvery River belt, Tamilnadu, India. Infrared Physics & Technology, 58,
pp.21-31.
Guney, Y., Aydilek, A.H. and Demirkan, M.M., 2016. Geoenvironmental behavior of foundry
sand amended mixtures for highway subbases. Waste management, 26(9), pp.932-945.
Guney, Y., Sari, Y.D., Yalcin, M., Tuncan, A. and Donmez, S., 2010. Re-usage of waste foundry
sand in high-strength concrete. Waste Management, 30(8-9), pp.1705-1713.
Han, Z., Cheng, X. and Ma, Q., 2016. An experimental study on dynamic response for MICP
strengthening liquefiable sands. Earthquake Engineering and Engineering Vibration, 15(4),
pp.673-679.
Jadhav, P.A. and Kulkarni, D.K., 2013. Effect of replacement of natural sand by manufactured
sand on the properties of cement mortar. International journal of civil and structural
engineering, 3(3), p.621.
Javed, S., Lovell, C.W. and Wood, L.E., 2014. Waste foundry sand in asphalt concrete.
Transportation Research Record, (1437).
Ji, T., Chen, C.Y., Zhuang, Y.Z. and Chen, J.F., 2013. A mix proportion design method of
manufactured sand concrete based on minimum paste theory. Construction and Building
Materials, 44, pp.422-426.
Paraphrase This Document
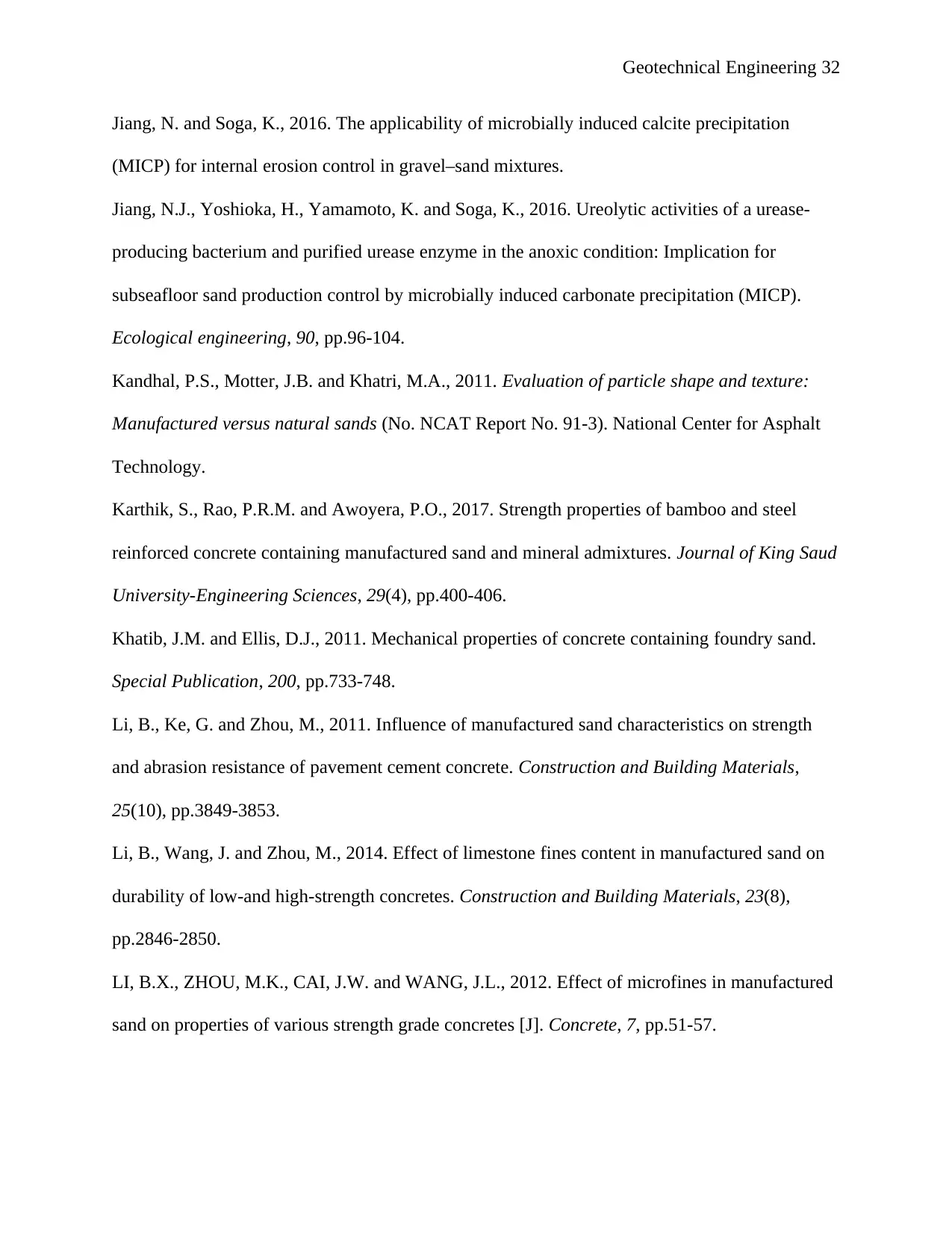
Jiang, N. and Soga, K., 2016. The applicability of microbially induced calcite precipitation
(MICP) for internal erosion control in gravel–sand mixtures.
Jiang, N.J., Yoshioka, H., Yamamoto, K. and Soga, K., 2016. Ureolytic activities of a urease-
producing bacterium and purified urease enzyme in the anoxic condition: Implication for
subseafloor sand production control by microbially induced carbonate precipitation (MICP).
Ecological engineering, 90, pp.96-104.
Kandhal, P.S., Motter, J.B. and Khatri, M.A., 2011. Evaluation of particle shape and texture:
Manufactured versus natural sands (No. NCAT Report No. 91-3). National Center for Asphalt
Technology.
Karthik, S., Rao, P.R.M. and Awoyera, P.O., 2017. Strength properties of bamboo and steel
reinforced concrete containing manufactured sand and mineral admixtures. Journal of King Saud
University-Engineering Sciences, 29(4), pp.400-406.
Khatib, J.M. and Ellis, D.J., 2011. Mechanical properties of concrete containing foundry sand.
Special Publication, 200, pp.733-748.
Li, B., Ke, G. and Zhou, M., 2011. Influence of manufactured sand characteristics on strength
and abrasion resistance of pavement cement concrete. Construction and Building Materials,
25(10), pp.3849-3853.
Li, B., Wang, J. and Zhou, M., 2014. Effect of limestone fines content in manufactured sand on
durability of low-and high-strength concretes. Construction and Building Materials, 23(8),
pp.2846-2850.
LI, B.X., ZHOU, M.K., CAI, J.W. and WANG, J.L., 2012. Effect of microfines in manufactured
sand on properties of various strength grade concretes [J]. Concrete, 7, pp.51-57.
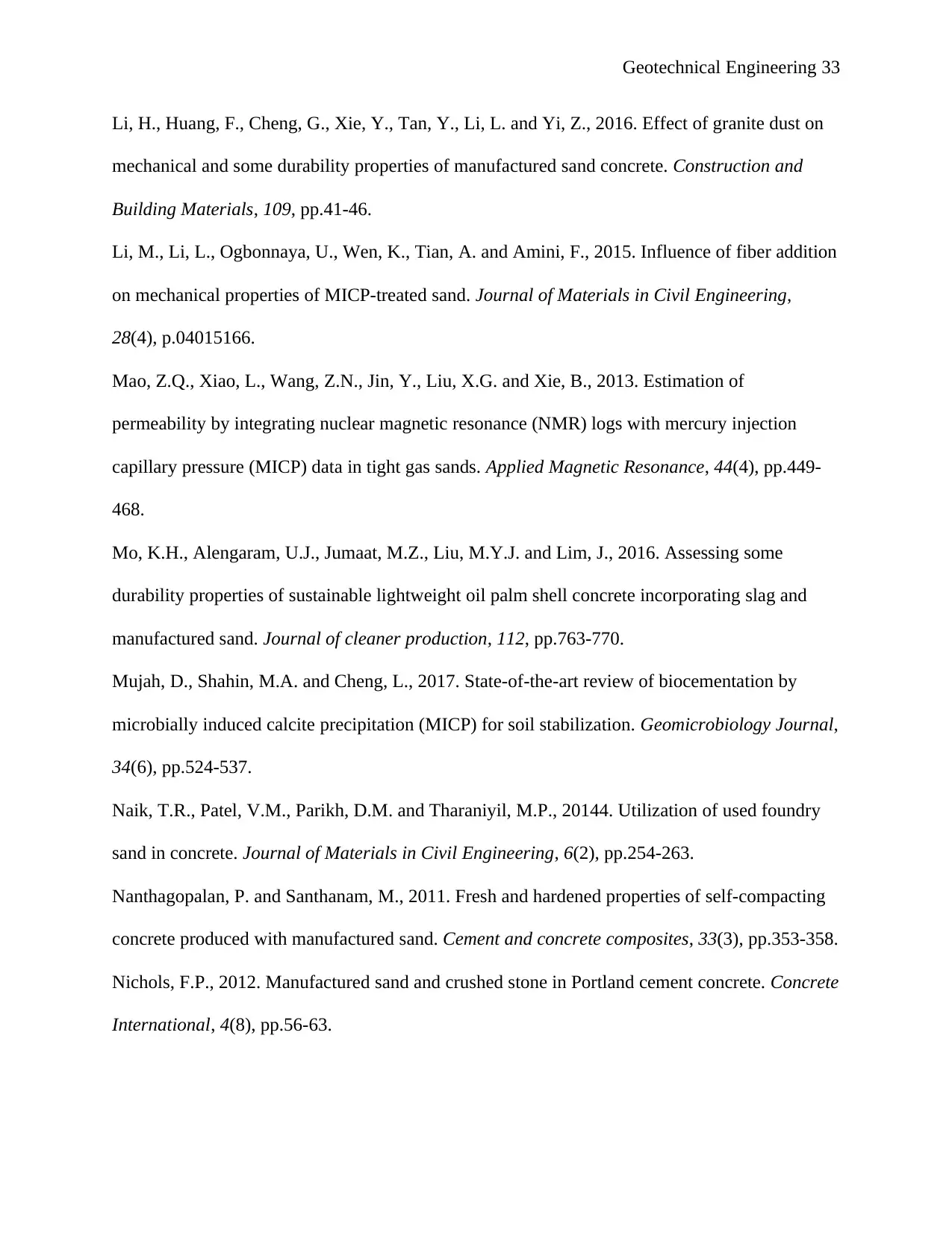
Li, H., Huang, F., Cheng, G., Xie, Y., Tan, Y., Li, L. and Yi, Z., 2016. Effect of granite dust on
mechanical and some durability properties of manufactured sand concrete. Construction and
Building Materials, 109, pp.41-46.
Li, M., Li, L., Ogbonnaya, U., Wen, K., Tian, A. and Amini, F., 2015. Influence of fiber addition
on mechanical properties of MICP-treated sand. Journal of Materials in Civil Engineering,
28(4), p.04015166.
Mao, Z.Q., Xiao, L., Wang, Z.N., Jin, Y., Liu, X.G. and Xie, B., 2013. Estimation of
permeability by integrating nuclear magnetic resonance (NMR) logs with mercury injection
capillary pressure (MICP) data in tight gas sands. Applied Magnetic Resonance, 44(4), pp.449-
468.
Mo, K.H., Alengaram, U.J., Jumaat, M.Z., Liu, M.Y.J. and Lim, J., 2016. Assessing some
durability properties of sustainable lightweight oil palm shell concrete incorporating slag and
manufactured sand. Journal of cleaner production, 112, pp.763-770.
Mujah, D., Shahin, M.A. and Cheng, L., 2017. State-of-the-art review of biocementation by
microbially induced calcite precipitation (MICP) for soil stabilization. Geomicrobiology Journal,
34(6), pp.524-537.
Naik, T.R., Patel, V.M., Parikh, D.M. and Tharaniyil, M.P., 20144. Utilization of used foundry
sand in concrete. Journal of Materials in Civil Engineering, 6(2), pp.254-263.
Nanthagopalan, P. and Santhanam, M., 2011. Fresh and hardened properties of self-compacting
concrete produced with manufactured sand. Cement and concrete composites, 33(3), pp.353-358.
Nichols, F.P., 2012. Manufactured sand and crushed stone in Portland cement concrete. Concrete
International, 4(8), pp.56-63.
⊘ This is a preview!⊘
Do you want full access?
Subscribe today to unlock all pages.

Trusted by 1+ million students worldwide
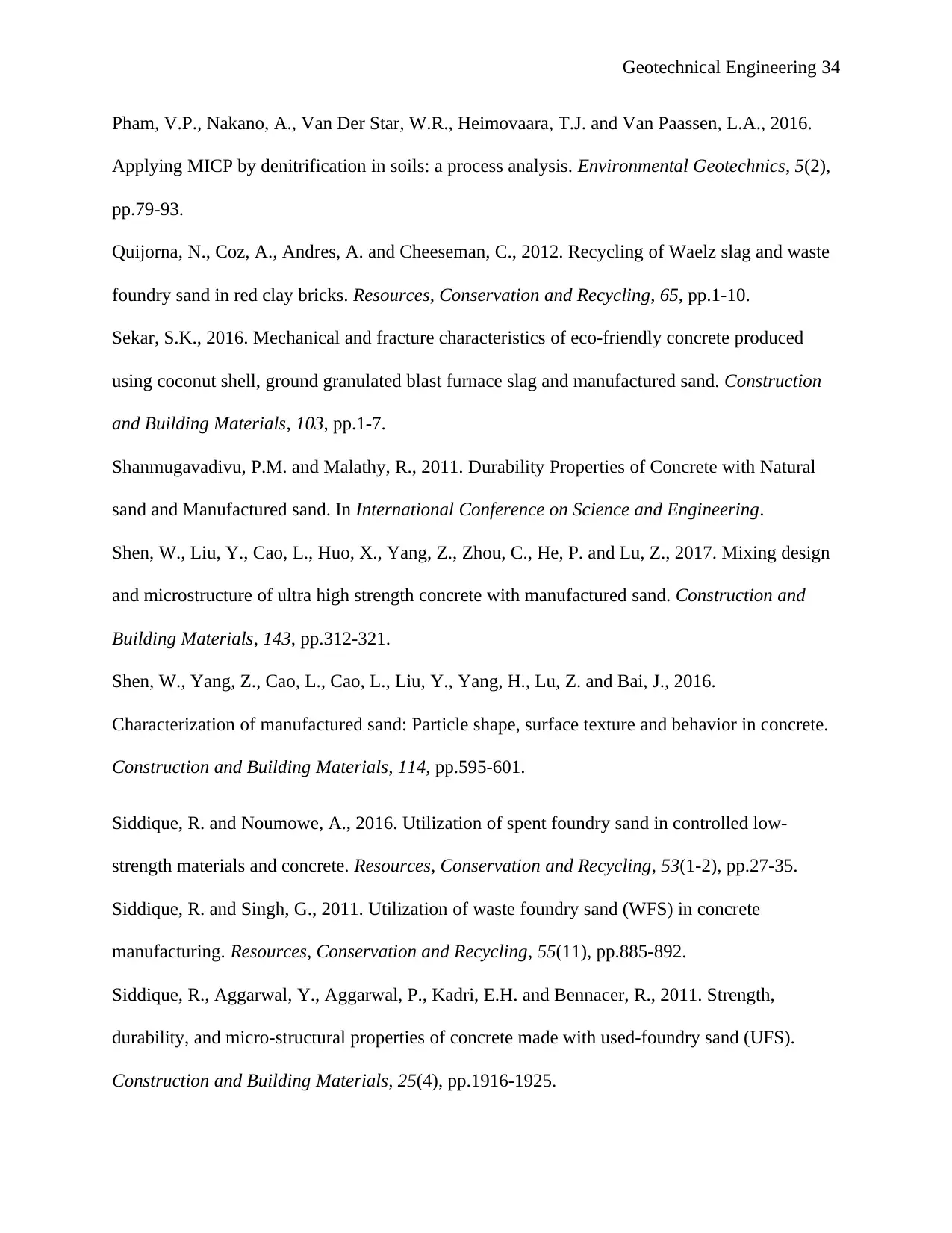
Pham, V.P., Nakano, A., Van Der Star, W.R., Heimovaara, T.J. and Van Paassen, L.A., 2016.
Applying MICP by denitrification in soils: a process analysis. Environmental Geotechnics, 5(2),
pp.79-93.
Quijorna, N., Coz, A., Andres, A. and Cheeseman, C., 2012. Recycling of Waelz slag and waste
foundry sand in red clay bricks. Resources, Conservation and Recycling, 65, pp.1-10.
Sekar, S.K., 2016. Mechanical and fracture characteristics of eco-friendly concrete produced
using coconut shell, ground granulated blast furnace slag and manufactured sand. Construction
and Building Materials, 103, pp.1-7.
Shanmugavadivu, P.M. and Malathy, R., 2011. Durability Properties of Concrete with Natural
sand and Manufactured sand. In International Conference on Science and Engineering.
Shen, W., Liu, Y., Cao, L., Huo, X., Yang, Z., Zhou, C., He, P. and Lu, Z., 2017. Mixing design
and microstructure of ultra high strength concrete with manufactured sand. Construction and
Building Materials, 143, pp.312-321.
Shen, W., Yang, Z., Cao, L., Cao, L., Liu, Y., Yang, H., Lu, Z. and Bai, J., 2016.
Characterization of manufactured sand: Particle shape, surface texture and behavior in concrete.
Construction and Building Materials, 114, pp.595-601.
Siddique, R. and Noumowe, A., 2016. Utilization of spent foundry sand in controlled low-
strength materials and concrete. Resources, Conservation and Recycling, 53(1-2), pp.27-35.
Siddique, R. and Singh, G., 2011. Utilization of waste foundry sand (WFS) in concrete
manufacturing. Resources, Conservation and Recycling, 55(11), pp.885-892.
Siddique, R., Aggarwal, Y., Aggarwal, P., Kadri, E.H. and Bennacer, R., 2011. Strength,
durability, and micro-structural properties of concrete made with used-foundry sand (UFS).
Construction and Building Materials, 25(4), pp.1916-1925.
Paraphrase This Document
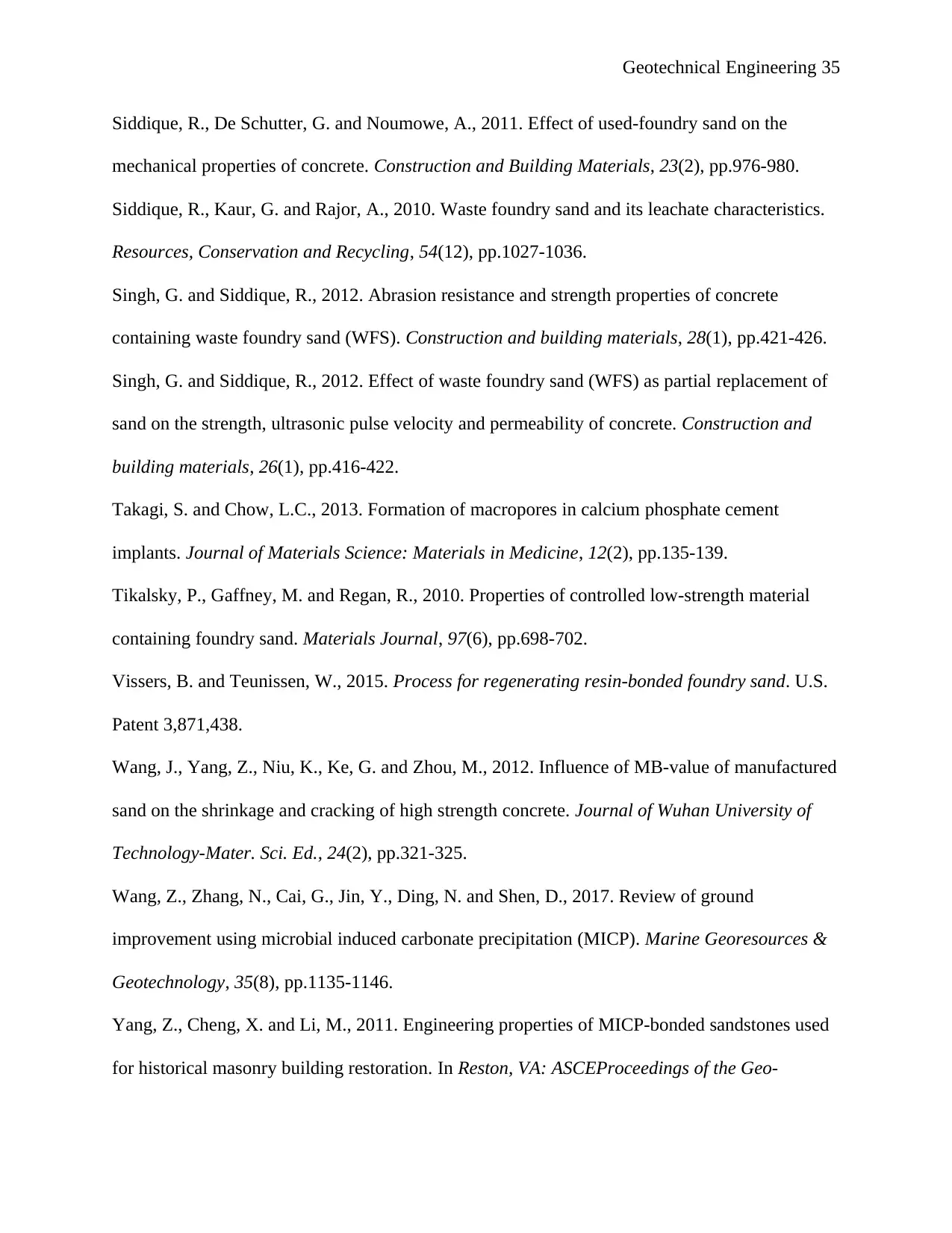
Siddique, R., De Schutter, G. and Noumowe, A., 2011. Effect of used-foundry sand on the
mechanical properties of concrete. Construction and Building Materials, 23(2), pp.976-980.
Siddique, R., Kaur, G. and Rajor, A., 2010. Waste foundry sand and its leachate characteristics.
Resources, Conservation and Recycling, 54(12), pp.1027-1036.
Singh, G. and Siddique, R., 2012. Abrasion resistance and strength properties of concrete
containing waste foundry sand (WFS). Construction and building materials, 28(1), pp.421-426.
Singh, G. and Siddique, R., 2012. Effect of waste foundry sand (WFS) as partial replacement of
sand on the strength, ultrasonic pulse velocity and permeability of concrete. Construction and
building materials, 26(1), pp.416-422.
Takagi, S. and Chow, L.C., 2013. Formation of macropores in calcium phosphate cement
implants. Journal of Materials Science: Materials in Medicine, 12(2), pp.135-139.
Tikalsky, P., Gaffney, M. and Regan, R., 2010. Properties of controlled low-strength material
containing foundry sand. Materials Journal, 97(6), pp.698-702.
Vissers, B. and Teunissen, W., 2015. Process for regenerating resin-bonded foundry sand. U.S.
Patent 3,871,438.
Wang, J., Yang, Z., Niu, K., Ke, G. and Zhou, M., 2012. Influence of MB-value of manufactured
sand on the shrinkage and cracking of high strength concrete. Journal of Wuhan University of
Technology-Mater. Sci. Ed., 24(2), pp.321-325.
Wang, Z., Zhang, N., Cai, G., Jin, Y., Ding, N. and Shen, D., 2017. Review of ground
improvement using microbial induced carbonate precipitation (MICP). Marine Georesources &
Geotechnology, 35(8), pp.1135-1146.
Yang, Z., Cheng, X. and Li, M., 2011. Engineering properties of MICP-bonded sandstones used
for historical masonry building restoration. In Reston, VA: ASCEProceedings of the Geo-
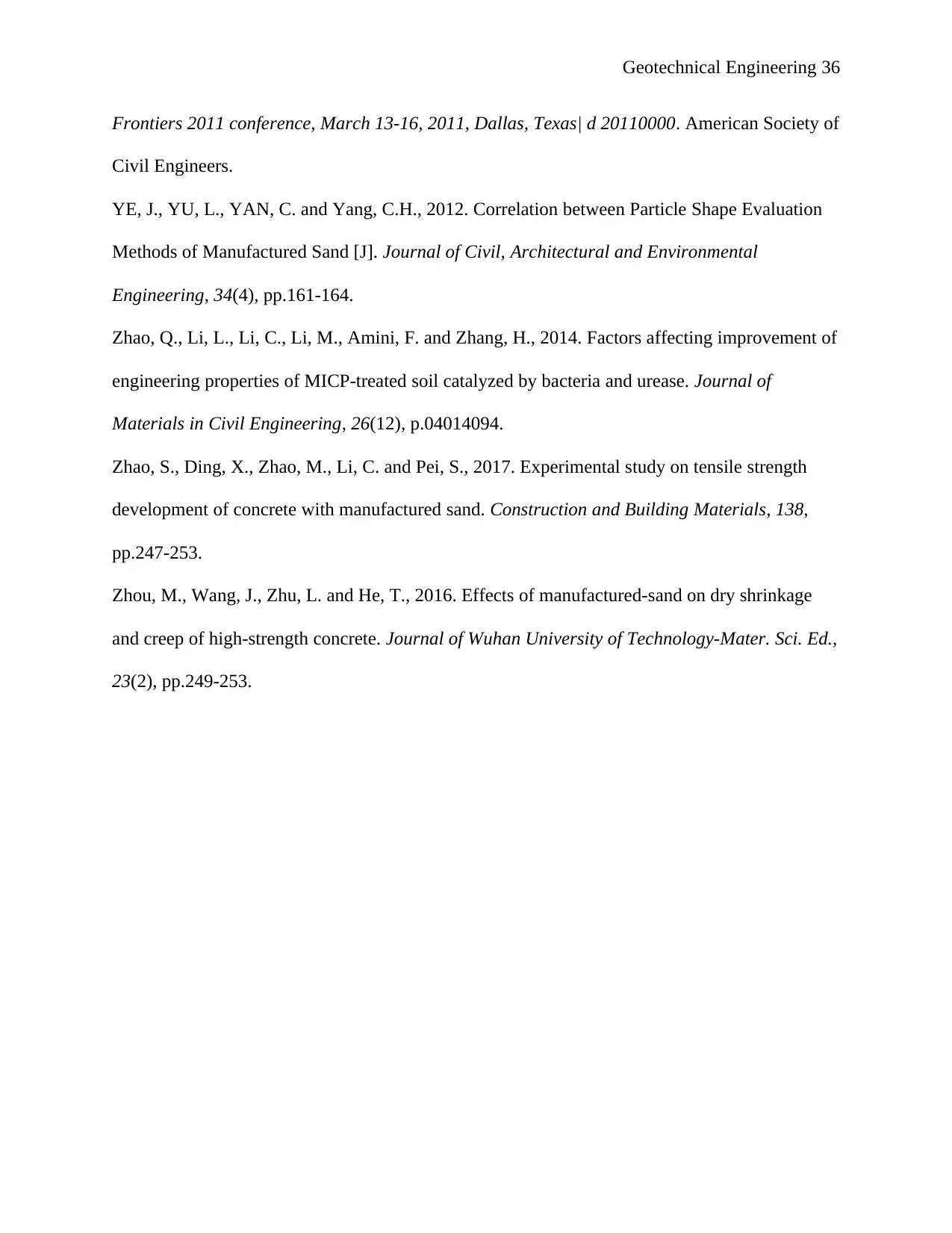
Frontiers 2011 conference, March 13-16, 2011, Dallas, Texas| d 20110000. American Society of
Civil Engineers.
YE, J., YU, L., YAN, C. and Yang, C.H., 2012. Correlation between Particle Shape Evaluation
Methods of Manufactured Sand [J]. Journal of Civil, Architectural and Environmental
Engineering, 34(4), pp.161-164.
Zhao, Q., Li, L., Li, C., Li, M., Amini, F. and Zhang, H., 2014. Factors affecting improvement of
engineering properties of MICP-treated soil catalyzed by bacteria and urease. Journal of
Materials in Civil Engineering, 26(12), p.04014094.
Zhao, S., Ding, X., Zhao, M., Li, C. and Pei, S., 2017. Experimental study on tensile strength
development of concrete with manufactured sand. Construction and Building Materials, 138,
pp.247-253.
Zhou, M., Wang, J., Zhu, L. and He, T., 2016. Effects of manufactured-sand on dry shrinkage
and creep of high-strength concrete. Journal of Wuhan University of Technology-Mater. Sci. Ed.,
23(2), pp.249-253.
⊘ This is a preview!⊘
Do you want full access?
Subscribe today to unlock all pages.

Trusted by 1+ million students worldwide

Your All-in-One AI-Powered Toolkit for Academic Success.
+13062052269
info@desklib.com
Available 24*7 on WhatsApp / Email
© 2024 | Zucol Services PVT LTD | All rights reserved.