Framework for Engaging Facilities Management in Design with BIM
VerifiedAdded on 2022/11/13
|9
|6014
|150
Report
AI Summary
This research article from Hindawi Publishing Corporation explores the integration of Facilities Management (FM) into the design stage of building projects using Building Information Modeling (BIM). The authors propose a framework to incorporate FM considerations early in the design process, aiming to reduce maintenance efforts and life cycle costs. The study highlights the benefits of BIM, such as its ability to act as a visual model and database throughout the building lifecycle, facilitating space planning and energy analysis. A case study demonstrates how BIM can be used to design facility managers’ travel paths in the maintenance process, leading to significant cost reductions. The paper emphasizes the importance of considering FM aspects, such as maintenance and repair, energy management, and commissioning, during the design phase. The framework also addresses the need for interoperability between different FM software systems. The research suggests that early engagement of FM through BIM can improve collaboration, optimize building plans, and streamline the integration of FM data, leading to a more efficient and cost-effective building lifecycle. The article covers the use of BIM for various aspects of FM, including maintenance, energy management and commissioning.
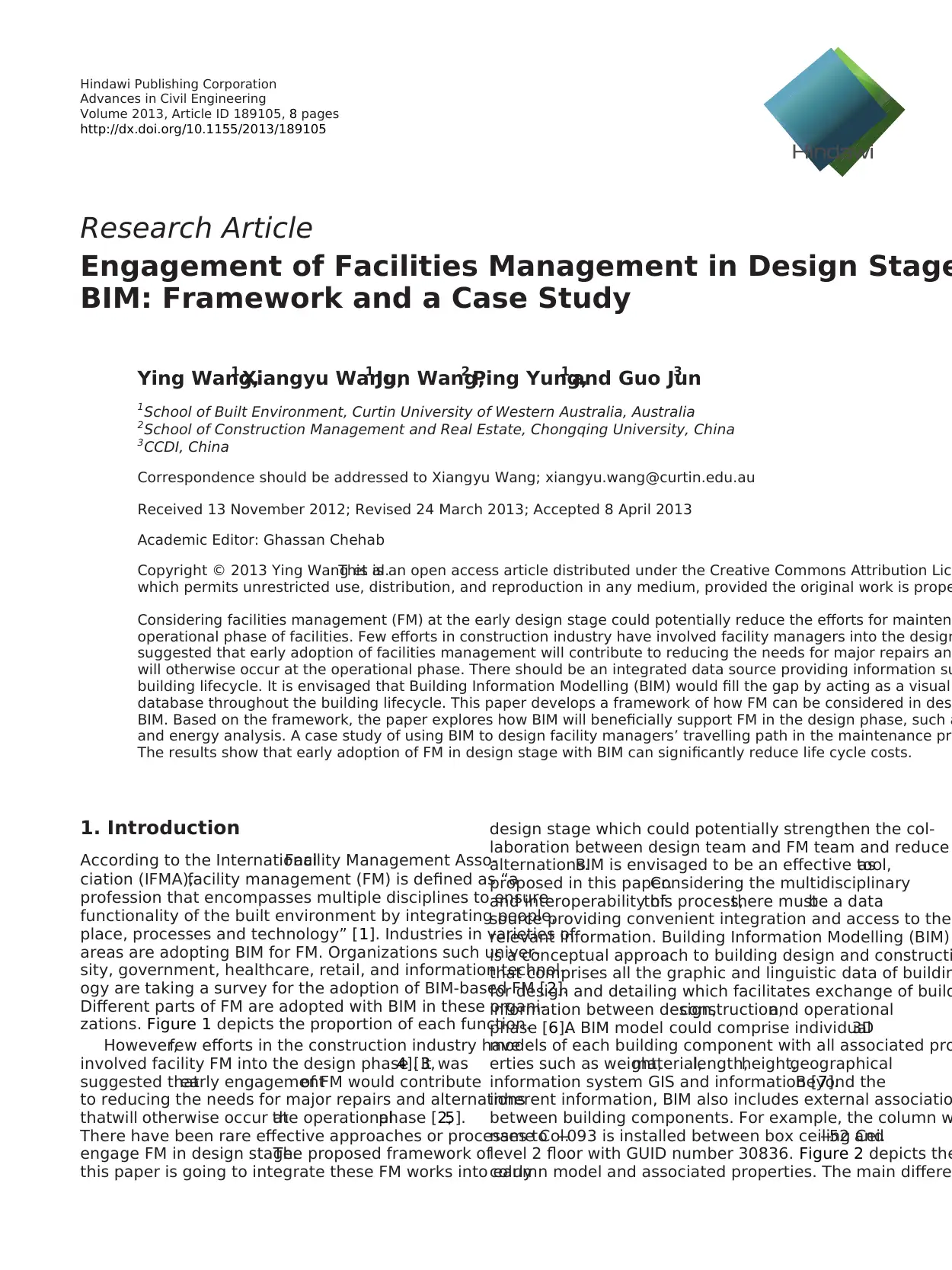
Hindawi Publishing Corporation
Advances in Civil Engineering
Volume 2013, Article ID 189105, 8 pages
http://dx.doi.org/10.1155/2013/189105
Research Article
Engagement of Facilities Management in Design Stage
BIM: Framework and a Case Study
Ying Wang,1 Xiangyu Wang,1 Jun Wang,2 Ping Yung,1 and Guo Jun3
1School of Built Environment, Curtin University of Western Australia, Australia
2School of Construction Management and Real Estate, Chongqing University, China
3CCDI, China
Correspondence should be addressed to Xiangyu Wang; xiangyu.wang@curtin.edu.au
Received 13 November 2012; Revised 24 March 2013; Accepted 8 April 2013
Academic Editor: Ghassan Chehab
Copyright © 2013 Ying Wang et al.This is an open access article distributed under the Creative Commons Attribution Lice
which permits unrestricted use, distribution, and reproduction in any medium, provided the original work is prope
Considering facilities management (FM) at the early design stage could potentially reduce the efforts for maintena
operational phase of facilities. Few efforts in construction industry have involved facility managers into the design
suggested that early adoption of facilities management will contribute to reducing the needs for major repairs an
will otherwise occur at the operational phase. There should be an integrated data source providing information su
building lifecycle. It is envisaged that Building Information Modelling (BIM) would fill the gap by acting as a visual
database throughout the building lifecycle. This paper develops a framework of how FM can be considered in desi
BIM. Based on the framework, the paper explores how BIM will beneficially support FM in the design phase, such a
and energy analysis. A case study of using BIM to design facility managers’ travelling path in the maintenance pro
The results show that early adoption of FM in design stage with BIM can significantly reduce life cycle costs.
1. Introduction
According to the InternationalFacility Management Asso-
ciation (IFMA),facility management (FM) is defined as “a
profession that encompasses multiple disciplines to ensure
functionality of the built environment by integrating people,
place, processes and technology” [1]. Industries in varieties of
areas are adopting BIM for FM. Organizations such univer-
sity, government, healthcare, retail, and information technol-
ogy are taking a survey for the adoption of BIM-based FM [2].
Different parts of FM are adopted with BIM in these organi-
zations. Figure 1 depicts the proportion of each function.
However,few efforts in the construction industry have
involved facility FM into the design phase [3,4]. It was
suggested thatearly engagementof FM would contribute
to reducing the needs for major repairs and alternations
thatwill otherwise occur atthe operationalphase [2,5].
There have been rare effective approaches or processes to
engage FM in design stage.The proposed framework of
this paper is going to integrate these FM works into early
design stage which could potentially strengthen the col-
laboration between design team and FM team and reduce
alternations.BIM is envisaged to be an effective tool,as
proposed in this paper.Considering the multidisciplinary
and interoperability ofthis process,there mustbe a data
source providing convenient integration and access to the
relevant information. Building Information Modelling (BIM)
is a conceptual approach to building design and constructi
that comprises all the graphic and linguistic data of buildin
for design and detailing which facilitates exchange of build
information between design,construction,and operational
phase [6].A BIM model could comprise individual3D
models of each building component with all associated pro
erties such as weight,material,length,height,geographical
information system GIS and information [7].Beyond the
inherent information, BIM also includes external associatio
between building components. For example, the column w
name Col.−093 is installed between box ceiling Cei.−52 and
level 2 floor with GUID number 30836. Figure 2 depicts the
column model and associated properties. The main differe
Advances in Civil Engineering
Volume 2013, Article ID 189105, 8 pages
http://dx.doi.org/10.1155/2013/189105
Research Article
Engagement of Facilities Management in Design Stage
BIM: Framework and a Case Study
Ying Wang,1 Xiangyu Wang,1 Jun Wang,2 Ping Yung,1 and Guo Jun3
1School of Built Environment, Curtin University of Western Australia, Australia
2School of Construction Management and Real Estate, Chongqing University, China
3CCDI, China
Correspondence should be addressed to Xiangyu Wang; xiangyu.wang@curtin.edu.au
Received 13 November 2012; Revised 24 March 2013; Accepted 8 April 2013
Academic Editor: Ghassan Chehab
Copyright © 2013 Ying Wang et al.This is an open access article distributed under the Creative Commons Attribution Lice
which permits unrestricted use, distribution, and reproduction in any medium, provided the original work is prope
Considering facilities management (FM) at the early design stage could potentially reduce the efforts for maintena
operational phase of facilities. Few efforts in construction industry have involved facility managers into the design
suggested that early adoption of facilities management will contribute to reducing the needs for major repairs an
will otherwise occur at the operational phase. There should be an integrated data source providing information su
building lifecycle. It is envisaged that Building Information Modelling (BIM) would fill the gap by acting as a visual
database throughout the building lifecycle. This paper develops a framework of how FM can be considered in desi
BIM. Based on the framework, the paper explores how BIM will beneficially support FM in the design phase, such a
and energy analysis. A case study of using BIM to design facility managers’ travelling path in the maintenance pro
The results show that early adoption of FM in design stage with BIM can significantly reduce life cycle costs.
1. Introduction
According to the InternationalFacility Management Asso-
ciation (IFMA),facility management (FM) is defined as “a
profession that encompasses multiple disciplines to ensure
functionality of the built environment by integrating people,
place, processes and technology” [1]. Industries in varieties of
areas are adopting BIM for FM. Organizations such univer-
sity, government, healthcare, retail, and information technol-
ogy are taking a survey for the adoption of BIM-based FM [2].
Different parts of FM are adopted with BIM in these organi-
zations. Figure 1 depicts the proportion of each function.
However,few efforts in the construction industry have
involved facility FM into the design phase [3,4]. It was
suggested thatearly engagementof FM would contribute
to reducing the needs for major repairs and alternations
thatwill otherwise occur atthe operationalphase [2,5].
There have been rare effective approaches or processes to
engage FM in design stage.The proposed framework of
this paper is going to integrate these FM works into early
design stage which could potentially strengthen the col-
laboration between design team and FM team and reduce
alternations.BIM is envisaged to be an effective tool,as
proposed in this paper.Considering the multidisciplinary
and interoperability ofthis process,there mustbe a data
source providing convenient integration and access to the
relevant information. Building Information Modelling (BIM)
is a conceptual approach to building design and constructi
that comprises all the graphic and linguistic data of buildin
for design and detailing which facilitates exchange of build
information between design,construction,and operational
phase [6].A BIM model could comprise individual3D
models of each building component with all associated pro
erties such as weight,material,length,height,geographical
information system GIS and information [7].Beyond the
inherent information, BIM also includes external associatio
between building components. For example, the column w
name Col.−093 is installed between box ceiling Cei.−52 and
level 2 floor with GUID number 30836. Figure 2 depicts the
column model and associated properties. The main differe
Paraphrase This Document
Need a fresh take? Get an instant paraphrase of this document with our AI Paraphraser
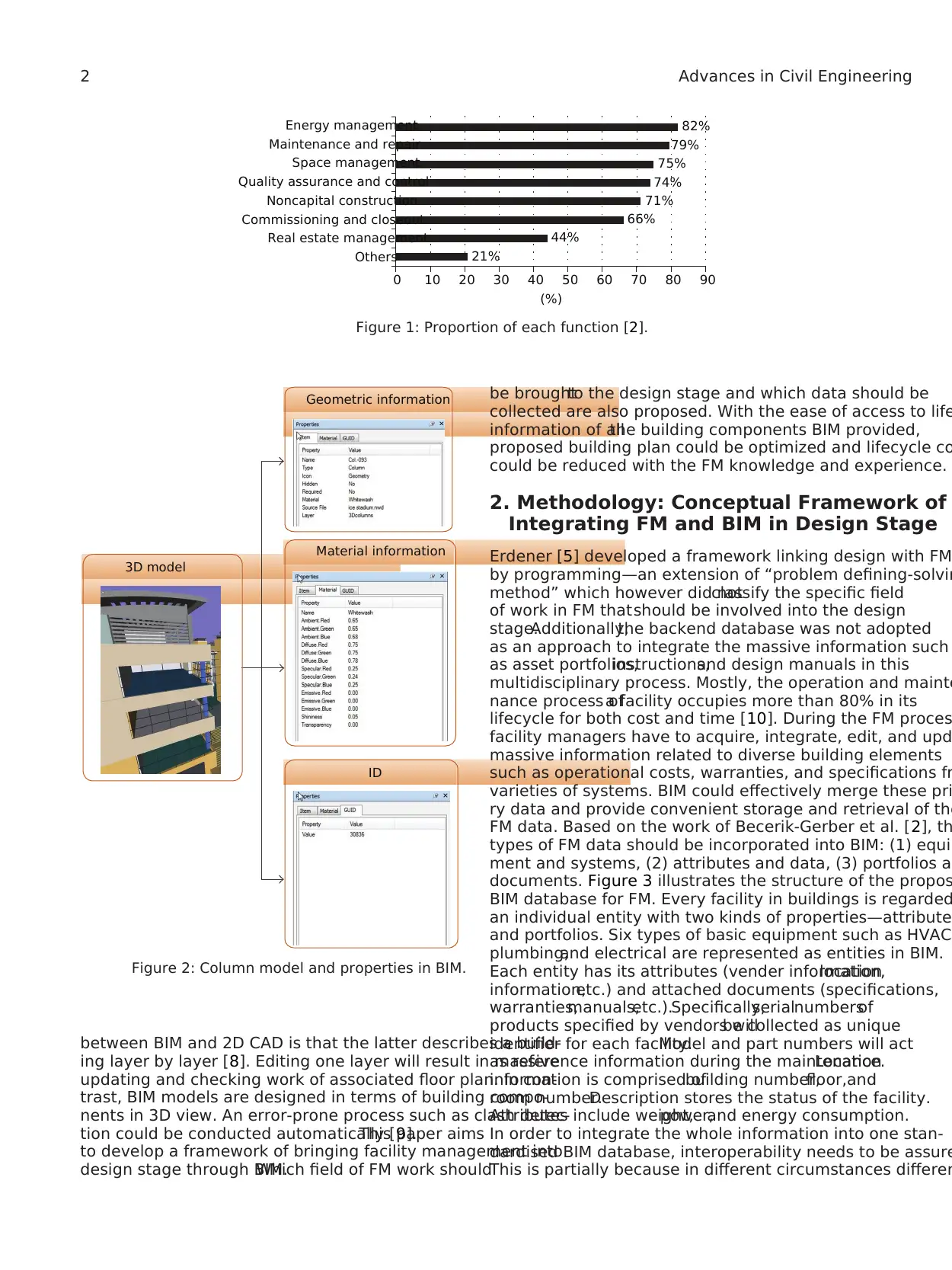
2 Advances in Civil Engineering
0 10 20 30 40 50 60 70 80 90
(%)
82%
79%
75%
74%
71%
66%
44%
21%
Energy management
Maintenance and repair
Space management
Quality assurance and control
Noncapital construction
Real estate management
Others
Commissioning and closeout
Figure 1: Proportion of each function [2].
3D model
Geometric information
Material information
ID
Figure 2: Column model and properties in BIM.
between BIM and 2D CAD is that the latter describes a build-
ing layer by layer [8]. Editing one layer will result in massive
updating and checking work of associated floor plan. In con-
trast, BIM models are designed in terms of building compo-
nents in 3D view. An error-prone process such as clash detec-
tion could be conducted automatically [9].This paper aims
to develop a framework of bringing facility management into
design stage through BIM.Which field of FM work should
be broughtto the design stage and which data should be
collected are also proposed. With the ease of access to life
information of allthe building components BIM provided,
proposed building plan could be optimized and lifecycle co
could be reduced with the FM knowledge and experience.
2. Methodology: Conceptual Framework of
Integrating FM and BIM in Design Stage
Erdener [5] developed a framework linking design with FM
by programming—an extension of “problem defining-solvin
method” which however did notclassify the specific field
of work in FM thatshould be involved into the design
stage.Additionally,the backend database was not adopted
as an approach to integrate the massive information such
as asset portfolios,instructions,and design manuals in this
multidisciplinary process. Mostly, the operation and mainte
nance process ofa facility occupies more than 80% in its
lifecycle for both cost and time [10]. During the FM proces
facility managers have to acquire, integrate, edit, and upd
massive information related to diverse building elements
such as operational costs, warranties, and specifications fr
varieties of systems. BIM could effectively merge these pri
ry data and provide convenient storage and retrieval of the
FM data. Based on the work of Becerik-Gerber et al. [2], th
types of FM data should be incorporated into BIM: (1) equip
ment and systems, (2) attributes and data, (3) portfolios an
documents. Figure 3 illustrates the structure of the propos
BIM database for FM. Every facility in buildings is regarded
an individual entity with two kinds of properties—attributes
and portfolios. Six types of basic equipment such as HVAC,
plumbing,and electrical are represented as entities in BIM.
Each entity has its attributes (vender information,location
information,etc.) and attached documents (specifications,
warranties,manuals,etc.).Specifically,serialnumbersof
products specified by vendors willbe collected as unique
identifier for each facility.Model and part numbers will act
as reference information during the maintenance.Location
information is comprised ofbuilding number,floor,and
room number.Description stores the status of the facility.
Attributes include weight,power,and energy consumption.
In order to integrate the whole information into one stan-
dardised BIM database, interoperability needs to be assure
This is partially because in different circumstances differen
0 10 20 30 40 50 60 70 80 90
(%)
82%
79%
75%
74%
71%
66%
44%
21%
Energy management
Maintenance and repair
Space management
Quality assurance and control
Noncapital construction
Real estate management
Others
Commissioning and closeout
Figure 1: Proportion of each function [2].
3D model
Geometric information
Material information
ID
Figure 2: Column model and properties in BIM.
between BIM and 2D CAD is that the latter describes a build-
ing layer by layer [8]. Editing one layer will result in massive
updating and checking work of associated floor plan. In con-
trast, BIM models are designed in terms of building compo-
nents in 3D view. An error-prone process such as clash detec-
tion could be conducted automatically [9].This paper aims
to develop a framework of bringing facility management into
design stage through BIM.Which field of FM work should
be broughtto the design stage and which data should be
collected are also proposed. With the ease of access to life
information of allthe building components BIM provided,
proposed building plan could be optimized and lifecycle co
could be reduced with the FM knowledge and experience.
2. Methodology: Conceptual Framework of
Integrating FM and BIM in Design Stage
Erdener [5] developed a framework linking design with FM
by programming—an extension of “problem defining-solvin
method” which however did notclassify the specific field
of work in FM thatshould be involved into the design
stage.Additionally,the backend database was not adopted
as an approach to integrate the massive information such
as asset portfolios,instructions,and design manuals in this
multidisciplinary process. Mostly, the operation and mainte
nance process ofa facility occupies more than 80% in its
lifecycle for both cost and time [10]. During the FM proces
facility managers have to acquire, integrate, edit, and upd
massive information related to diverse building elements
such as operational costs, warranties, and specifications fr
varieties of systems. BIM could effectively merge these pri
ry data and provide convenient storage and retrieval of the
FM data. Based on the work of Becerik-Gerber et al. [2], th
types of FM data should be incorporated into BIM: (1) equip
ment and systems, (2) attributes and data, (3) portfolios an
documents. Figure 3 illustrates the structure of the propos
BIM database for FM. Every facility in buildings is regarded
an individual entity with two kinds of properties—attributes
and portfolios. Six types of basic equipment such as HVAC,
plumbing,and electrical are represented as entities in BIM.
Each entity has its attributes (vender information,location
information,etc.) and attached documents (specifications,
warranties,manuals,etc.).Specifically,serialnumbersof
products specified by vendors willbe collected as unique
identifier for each facility.Model and part numbers will act
as reference information during the maintenance.Location
information is comprised ofbuilding number,floor,and
room number.Description stores the status of the facility.
Attributes include weight,power,and energy consumption.
In order to integrate the whole information into one stan-
dardised BIM database, interoperability needs to be assure
This is partially because in different circumstances differen
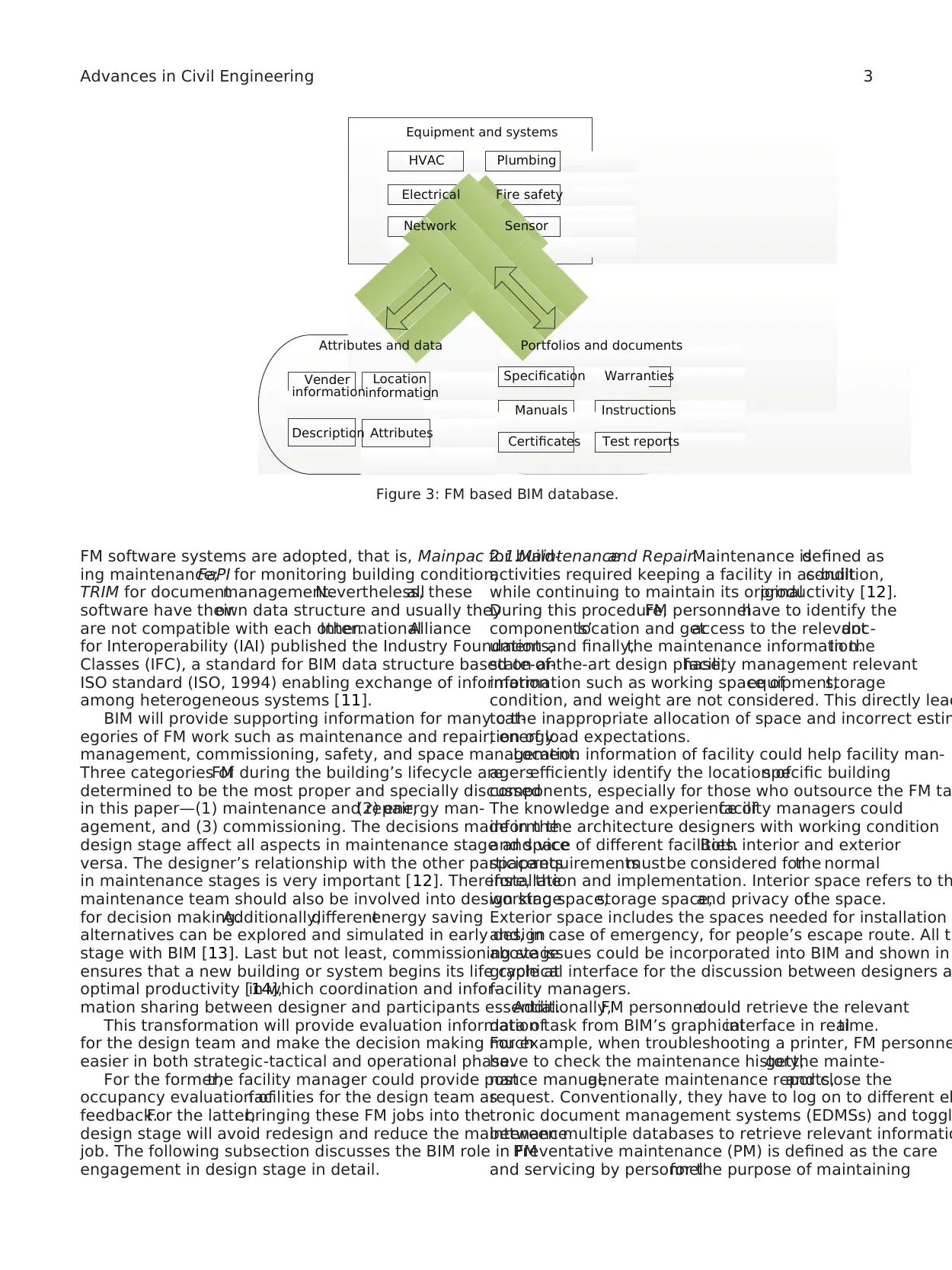
Advances in Civil Engineering 3
Equipment and systems
Portfolios and documents
Specification
Manuals
Certificates
HVAC Plumbing
Electrical
Network
Fire safety
Sensor
Attributes and data
Vender
AttributesDescription
Warranties
Instructions
Test reports
information Location
information
Figure 3: FM based BIM database.
FM software systems are adopted, that is, Mainpac for build-
ing maintenance;FaPI for monitoring building condition;
TRIM for documentmanagement.Nevertheless,all these
software have theirown data structure and usually they
are not compatible with each other.InternationalAlliance
for Interoperability (IAI) published the Industry Foundation
Classes (IFC), a standard for BIM data structure based on an
ISO standard (ISO, 1994) enabling exchange of information
among heterogeneous systems [11].
BIM will provide supporting information for many cat-
egories of FM work such as maintenance and repair, energy
management, commissioning, safety, and space management.
Three categories ofFM during the building’s lifecycle are
determined to be the most proper and specially discussed
in this paper—(1) maintenance and repair,(2) energy man-
agement, and (3) commissioning. The decisions made in the
design stage affect all aspects in maintenance stage and vice
versa. The designer’s relationship with the other participants
in maintenance stages is very important [12]. Therefore, the
maintenance team should also be involved into design stage
for decision making.Additionally,differentenergy saving
alternatives can be explored and simulated in early design
stage with BIM [13]. Last but not least, commissioning stage
ensures that a new building or system begins its life cycle at
optimal productivity [14],in which coordination and infor-
mation sharing between designer and participants essential.
This transformation will provide evaluation information
for the design team and make the decision making much
easier in both strategic-tactical and operational phase.
For the former,the facility manager could provide post
occupancy evaluation offacilities for the design team as
feedback.For the latter,bringing these FM jobs into the
design stage will avoid redesign and reduce the maintenance
job. The following subsection discusses the BIM role in FM
engagement in design stage in detail.
2.1.Maintenanceand Repair.Maintenance isdefined as
activities required keeping a facility in as-builtcondition,
while continuing to maintain its originalproductivity [12].
During this procedure,FM personnelhave to identify the
components’location and getaccess to the relevantdoc-
uments,and finally,the maintenance information.In the
state-of-the-art design phase,facility management relevant
information such as working space ofequipment,storage
condition, and weight are not considered. This directly lead
to the inappropriate allocation of space and incorrect estim
tion of load expectations.
Location information of facility could help facility man-
agersefficiently identify the location ofspecific building
components, especially for those who outsource the FM ta
The knowledge and experience offacility managers could
inform the architecture designers with working condition
and space of different facilities.Both interior and exterior
spacerequirementsmustbe considered forthe normal
installation and implementation. Interior space refers to th
working space,storage space,and privacy ofthe space.
Exterior space includes the spaces needed for installation
and, in case of emergency, for people’s escape route. All th
above issues could be incorporated into BIM and shown in
graphical interface for the discussion between designers a
facility managers.
Additionally,FM personnelcould retrieve the relevant
data oftask from BIM’s graphicalinterface in realtime.
For example, when troubleshooting a printer, FM personne
have to check the maintenance history,getthe mainte-
nance manual,generate maintenance reports,and close the
request. Conventionally, they have to log on to different el
tronic document management systems (EDMSs) and toggl
between multiple databases to retrieve relevant informatio
Preventative maintenance (PM) is defined as the care
and servicing by personnelfor the purpose of maintaining
Equipment and systems
Portfolios and documents
Specification
Manuals
Certificates
HVAC Plumbing
Electrical
Network
Fire safety
Sensor
Attributes and data
Vender
AttributesDescription
Warranties
Instructions
Test reports
information Location
information
Figure 3: FM based BIM database.
FM software systems are adopted, that is, Mainpac for build-
ing maintenance;FaPI for monitoring building condition;
TRIM for documentmanagement.Nevertheless,all these
software have theirown data structure and usually they
are not compatible with each other.InternationalAlliance
for Interoperability (IAI) published the Industry Foundation
Classes (IFC), a standard for BIM data structure based on an
ISO standard (ISO, 1994) enabling exchange of information
among heterogeneous systems [11].
BIM will provide supporting information for many cat-
egories of FM work such as maintenance and repair, energy
management, commissioning, safety, and space management.
Three categories ofFM during the building’s lifecycle are
determined to be the most proper and specially discussed
in this paper—(1) maintenance and repair,(2) energy man-
agement, and (3) commissioning. The decisions made in the
design stage affect all aspects in maintenance stage and vice
versa. The designer’s relationship with the other participants
in maintenance stages is very important [12]. Therefore, the
maintenance team should also be involved into design stage
for decision making.Additionally,differentenergy saving
alternatives can be explored and simulated in early design
stage with BIM [13]. Last but not least, commissioning stage
ensures that a new building or system begins its life cycle at
optimal productivity [14],in which coordination and infor-
mation sharing between designer and participants essential.
This transformation will provide evaluation information
for the design team and make the decision making much
easier in both strategic-tactical and operational phase.
For the former,the facility manager could provide post
occupancy evaluation offacilities for the design team as
feedback.For the latter,bringing these FM jobs into the
design stage will avoid redesign and reduce the maintenance
job. The following subsection discusses the BIM role in FM
engagement in design stage in detail.
2.1.Maintenanceand Repair.Maintenance isdefined as
activities required keeping a facility in as-builtcondition,
while continuing to maintain its originalproductivity [12].
During this procedure,FM personnelhave to identify the
components’location and getaccess to the relevantdoc-
uments,and finally,the maintenance information.In the
state-of-the-art design phase,facility management relevant
information such as working space ofequipment,storage
condition, and weight are not considered. This directly lead
to the inappropriate allocation of space and incorrect estim
tion of load expectations.
Location information of facility could help facility man-
agersefficiently identify the location ofspecific building
components, especially for those who outsource the FM ta
The knowledge and experience offacility managers could
inform the architecture designers with working condition
and space of different facilities.Both interior and exterior
spacerequirementsmustbe considered forthe normal
installation and implementation. Interior space refers to th
working space,storage space,and privacy ofthe space.
Exterior space includes the spaces needed for installation
and, in case of emergency, for people’s escape route. All th
above issues could be incorporated into BIM and shown in
graphical interface for the discussion between designers a
facility managers.
Additionally,FM personnelcould retrieve the relevant
data oftask from BIM’s graphicalinterface in realtime.
For example, when troubleshooting a printer, FM personne
have to check the maintenance history,getthe mainte-
nance manual,generate maintenance reports,and close the
request. Conventionally, they have to log on to different el
tronic document management systems (EDMSs) and toggl
between multiple databases to retrieve relevant informatio
Preventative maintenance (PM) is defined as the care
and servicing by personnelfor the purpose of maintaining
You're viewing a preview
Unlock full access by subscribing today!
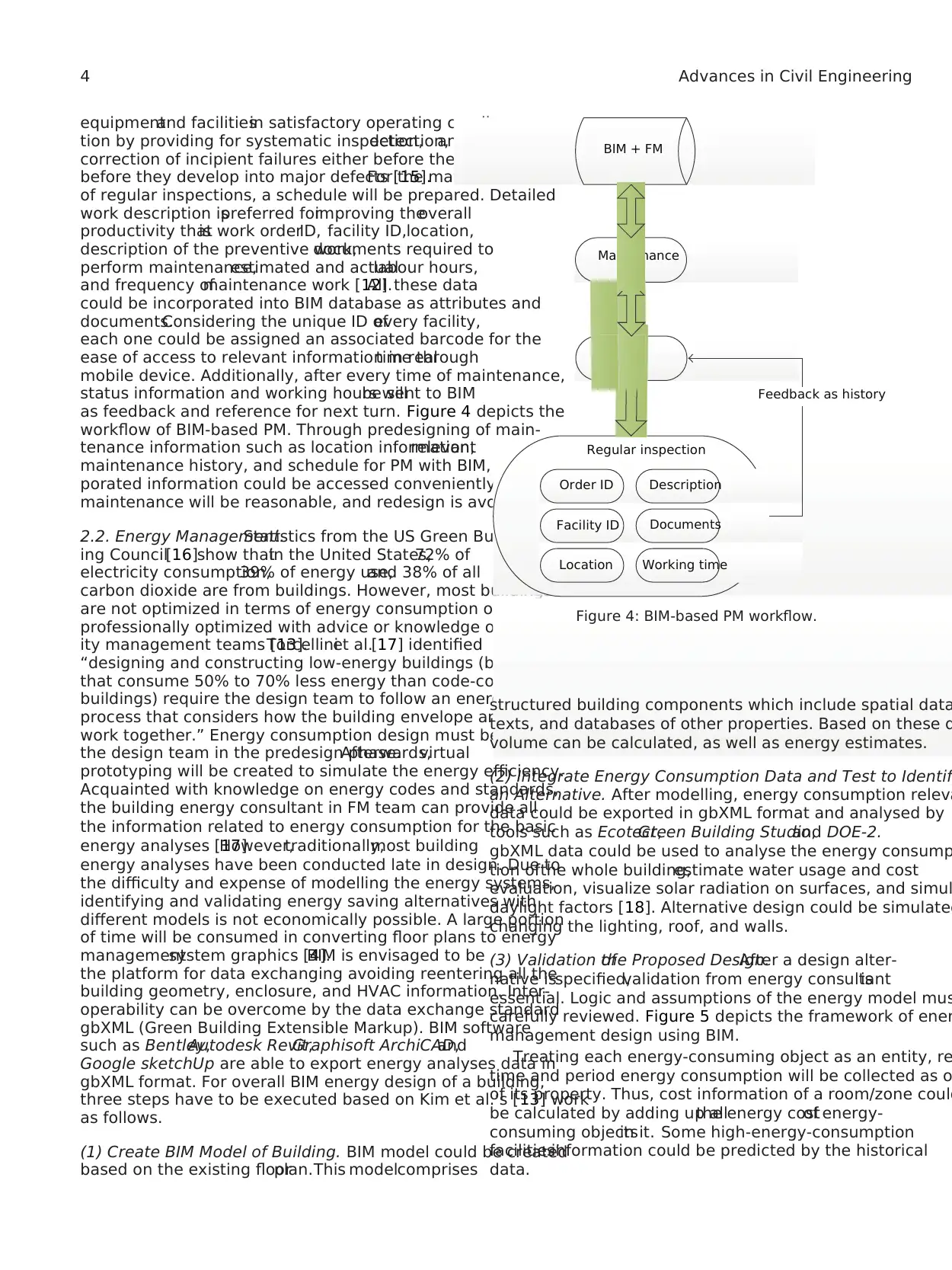
4 Advances in Civil Engineering
equipmentand facilitiesin satisfactory operating condi-
tion by providing for systematic inspection,detection,and
correction of incipient failures either before they occur or
before they develop into major defects [15].For the matter
of regular inspections, a schedule will be prepared. Detailed
work description ispreferred forimproving theoverall
productivity thatis work orderID, facility ID,location,
description of the preventive work,documents required to
perform maintenance,estimated and actuallabour hours,
and frequency ofmaintenance work [12].All these data
could be incorporated into BIM database as attributes and
documents.Considering the unique ID ofevery facility,
each one could be assigned an associated barcode for the
ease of access to relevant information in realtime through
mobile device. Additionally, after every time of maintenance,
status information and working hours willbe sent to BIM
as feedback and reference for next turn. Figure 4 depicts the
workflow of BIM-based PM. Through predesigning of main-
tenance information such as location information,relevant
maintenance history, and schedule for PM with BIM, incor-
porated information could be accessed conveniently. Future
maintenance will be reasonable, and redesign is avoided.
2.2. Energy Management.Statistics from the US Green Build-
ing Council[16]show thatin the United States,72% of
electricity consumption,39% of energy use,and 38% of all
carbon dioxide are from buildings. However, most buildings
are not optimized in terms of energy consumption or not
professionally optimized with advice or knowledge of facil-
ity management teams [13].Torcelliniet al.[17] identified
“designing and constructing low-energy buildings (buildings
that consume 50% to 70% less energy than code-compliant
buildings) require the design team to follow an energy-design
process that considers how the building envelope and systems
work together.” Energy consumption design must be set by
the design team in the predesign phase.Afterwards,virtual
prototyping will be created to simulate the energy efficiency.
Acquainted with knowledge on energy codes and standards,
the building energy consultant in FM team can provide all
the information related to energy consumption for the basic
energy analyses [17].However,traditionally,most building
energy analyses have been conducted late in design. Due to
the difficulty and expense of modelling the energy systems,
identifying and validating energy saving alternatives with
different models is not economically possible. A large portion
of time will be consumed in converting floor plans to energy
managementsystem graphics [4].BIM is envisaged to be
the platform for data exchanging avoiding reentering all the
building geometry, enclosure, and HVAC information. Inter-
operability can be overcome by the data exchange standard
gbXML (Green Building Extensible Markup). BIM software
such as Bentley,Autodesk Revit,Graphisoft ArchiCAD,and
Google sketchUp are able to export energy analyses data in
gbXML format. For overall BIM energy design of a building,
three steps have to be executed based on Kim et al.’s [13] work
as follows.
(1) Create BIM Model of Building. BIM model could be created
based on the existing floorplan.This modelcomprises
BIM + FM
Maintenance
PM
Feedback as history
Regular inspection
Order ID
Facility ID
Location
Description
Working time
Documents
Figure 4: BIM-based PM workflow.
structured building components which include spatial data
texts, and databases of other properties. Based on these d
volume can be calculated, as well as energy estimates.
(2) Integrate Energy Consumption Data and Test to Identif
an Alternative. After modelling, energy consumption releva
data could be exported in gbXML format and analysed by
tools such as Ecotect,Green Building Studio,and DOE-2.
gbXML data could be used to analyse the energy consump
tion ofthe whole building,estimate water usage and cost
evaluation, visualize solar radiation on surfaces, and simul
daylight factors [18]. Alternative design could be simulated
changing the lighting, roof, and walls.
(3) Validation ofthe Proposed Design.After a design alter-
native isspecified,validation from energy consultantis
essential. Logic and assumptions of the energy model mus
carefully reviewed. Figure 5 depicts the framework of ener
management design using BIM.
Treating each energy-consuming object as an entity, re
time and period energy consumption will be collected as o
of its property. Thus, cost information of a room/zone could
be calculated by adding up allthe energy costof energy-
consuming objectsin it. Some high-energy-consumption
facilities’information could be predicted by the historical
data.
equipmentand facilitiesin satisfactory operating condi-
tion by providing for systematic inspection,detection,and
correction of incipient failures either before they occur or
before they develop into major defects [15].For the matter
of regular inspections, a schedule will be prepared. Detailed
work description ispreferred forimproving theoverall
productivity thatis work orderID, facility ID,location,
description of the preventive work,documents required to
perform maintenance,estimated and actuallabour hours,
and frequency ofmaintenance work [12].All these data
could be incorporated into BIM database as attributes and
documents.Considering the unique ID ofevery facility,
each one could be assigned an associated barcode for the
ease of access to relevant information in realtime through
mobile device. Additionally, after every time of maintenance,
status information and working hours willbe sent to BIM
as feedback and reference for next turn. Figure 4 depicts the
workflow of BIM-based PM. Through predesigning of main-
tenance information such as location information,relevant
maintenance history, and schedule for PM with BIM, incor-
porated information could be accessed conveniently. Future
maintenance will be reasonable, and redesign is avoided.
2.2. Energy Management.Statistics from the US Green Build-
ing Council[16]show thatin the United States,72% of
electricity consumption,39% of energy use,and 38% of all
carbon dioxide are from buildings. However, most buildings
are not optimized in terms of energy consumption or not
professionally optimized with advice or knowledge of facil-
ity management teams [13].Torcelliniet al.[17] identified
“designing and constructing low-energy buildings (buildings
that consume 50% to 70% less energy than code-compliant
buildings) require the design team to follow an energy-design
process that considers how the building envelope and systems
work together.” Energy consumption design must be set by
the design team in the predesign phase.Afterwards,virtual
prototyping will be created to simulate the energy efficiency.
Acquainted with knowledge on energy codes and standards,
the building energy consultant in FM team can provide all
the information related to energy consumption for the basic
energy analyses [17].However,traditionally,most building
energy analyses have been conducted late in design. Due to
the difficulty and expense of modelling the energy systems,
identifying and validating energy saving alternatives with
different models is not economically possible. A large portion
of time will be consumed in converting floor plans to energy
managementsystem graphics [4].BIM is envisaged to be
the platform for data exchanging avoiding reentering all the
building geometry, enclosure, and HVAC information. Inter-
operability can be overcome by the data exchange standard
gbXML (Green Building Extensible Markup). BIM software
such as Bentley,Autodesk Revit,Graphisoft ArchiCAD,and
Google sketchUp are able to export energy analyses data in
gbXML format. For overall BIM energy design of a building,
three steps have to be executed based on Kim et al.’s [13] work
as follows.
(1) Create BIM Model of Building. BIM model could be created
based on the existing floorplan.This modelcomprises
BIM + FM
Maintenance
PM
Feedback as history
Regular inspection
Order ID
Facility ID
Location
Description
Working time
Documents
Figure 4: BIM-based PM workflow.
structured building components which include spatial data
texts, and databases of other properties. Based on these d
volume can be calculated, as well as energy estimates.
(2) Integrate Energy Consumption Data and Test to Identif
an Alternative. After modelling, energy consumption releva
data could be exported in gbXML format and analysed by
tools such as Ecotect,Green Building Studio,and DOE-2.
gbXML data could be used to analyse the energy consump
tion ofthe whole building,estimate water usage and cost
evaluation, visualize solar radiation on surfaces, and simul
daylight factors [18]. Alternative design could be simulated
changing the lighting, roof, and walls.
(3) Validation ofthe Proposed Design.After a design alter-
native isspecified,validation from energy consultantis
essential. Logic and assumptions of the energy model mus
carefully reviewed. Figure 5 depicts the framework of ener
management design using BIM.
Treating each energy-consuming object as an entity, re
time and period energy consumption will be collected as o
of its property. Thus, cost information of a room/zone could
be calculated by adding up allthe energy costof energy-
consuming objectsin it. Some high-energy-consumption
facilities’information could be predicted by the historical
data.
Paraphrase This Document
Need a fresh take? Get an instant paraphrase of this document with our AI Paraphraser
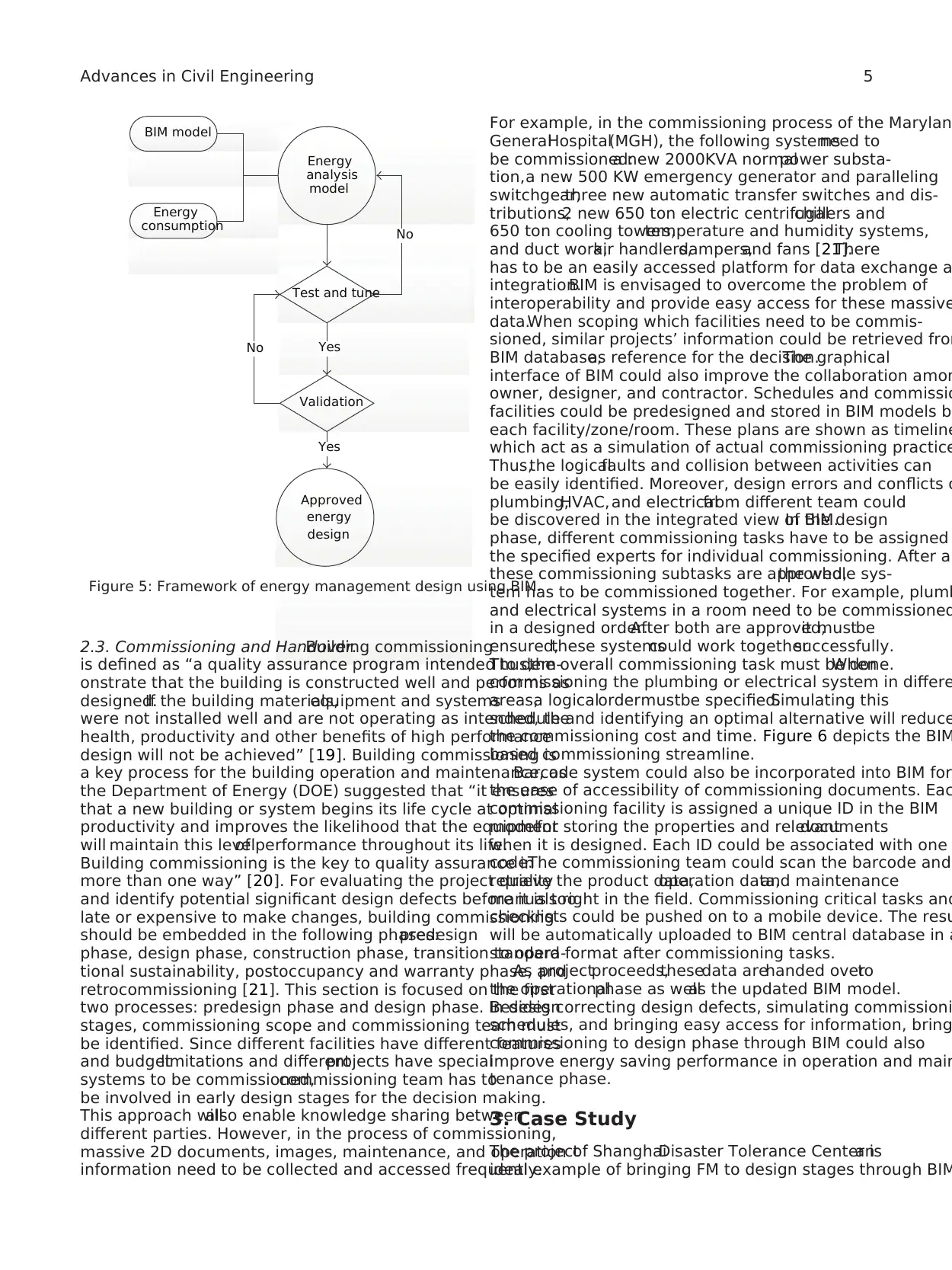
Advances in Civil Engineering 5
BIM model
Energy
consumption
No
Energy
analysis
model
Test and tune
Yes
No
Validation
Approved
energy
design
Yes
Figure 5: Framework of energy management design using BIM.
2.3. Commissioning and Handover.Building commissioning
is defined as “a quality assurance program intended to dem-
onstrate that the building is constructed well and performs as
designed.If the building materials,equipment and systems
were not installed well and are not operating as intended, the
health, productivity and other benefits of high performance
design will not be achieved” [19]. Building commissioning is
a key process for the building operation and maintenance, as
the Department of Energy (DOE) suggested that “it ensures
that a new building or system begins its life cycle at optimal
productivity and improves the likelihood that the equipment
will maintain this levelof performance throughout its life.
Building commissioning is the key to quality assurance in
more than one way” [20]. For evaluating the project quality
and identify potential significant design defects before it is too
late or expensive to make changes, building commissioning
should be embedded in the following phases:predesign
phase, design phase, construction phase, transition to opera-
tional sustainability, postoccupancy and warranty phase, and
retrocommissioning [21]. This section is focused on the first
two processes: predesign phase and design phase. In design
stages, commissioning scope and commissioning team must
be identified. Since different facilities have different features
and budgetlimitations and differentprojects have special
systems to be commissioned,commissioning team has to
be involved in early design stages for the decision making.
This approach willalso enable knowledge sharing between
different parties. However, in the process of commissioning,
massive 2D documents, images, maintenance, and operation
information need to be collected and accessed frequently.
For example, in the commissioning process of the Marylan
GeneralHospital(MGH), the following systemsneed to
be commissioned:a new 2000KVA normalpower substa-
tion,a new 500 KW emergency generator and paralleling
switchgear,three new automatic transfer switches and dis-
tributions,2 new 650 ton electric centrifugalchillers and
650 ton cooling towers,temperature and humidity systems,
and duct work,air handlers,dampers,and fans [21].There
has to be an easily accessed platform for data exchange a
integration.BIM is envisaged to overcome the problem of
interoperability and provide easy access for these massive
data.When scoping which facilities need to be commis-
sioned, similar projects’ information could be retrieved from
BIM database,as reference for the decision.The graphical
interface of BIM could also improve the collaboration amon
owner, designer, and contractor. Schedules and commissio
facilities could be predesigned and stored in BIM models by
each facility/zone/room. These plans are shown as timeline
which act as a simulation of actual commissioning practice
Thus,the logicalfaults and collision between activities can
be easily identified. Moreover, design errors and conflicts o
plumbing,HVAC, and electricalfrom different team could
be discovered in the integrated view of BIM.In the design
phase, different commissioning tasks have to be assigned
the specified experts for individual commissioning. After al
these commissioning subtasks are approved,the whole sys-
tem has to be commissioned together. For example, plumb
and electrical systems in a room need to be commissioned
in a designed order.After both are approved,it mustbe
ensured,these systemscould work togethersuccessfully.
Thus,the overall commissioning task must be done.When
commissioning the plumbing or electrical system in differe
areas,a logicalordermustbe specified.Simulating this
schedule and identifying an optimal alternative will reduce
the commissioning cost and time. Figure 6 depicts the BIM
based commissioning streamline.
Barcode system could also be incorporated into BIM for
the ease of accessibility of commissioning documents. Eac
commissioning facility is assigned a unique ID in the BIM
modelfor storing the properties and relevantdocuments
when it is designed. Each ID could be associated with one
code.The commissioning team could scan the barcode and
retrieve the product data,operation data,and maintenance
manuals right in the field. Commissioning critical tasks and
checklists could be pushed on to a mobile device. The resu
will be automatically uploaded to BIM central database in a
standard format after commissioning tasks.
As projectproceeds,thesedata arehanded overto
the operationalphase as wellas the updated BIM model.
Besides correcting design defects, simulating commissioni
schedules, and bringing easy access for information, bring
commissioning to design phase through BIM could also
improve energy saving performance in operation and main
tenance phase.
3. Case Study
The projectof ShanghaiDisaster Tolerance Center isan
ideal example of bringing FM to design stages through BIM
BIM model
Energy
consumption
No
Energy
analysis
model
Test and tune
Yes
No
Validation
Approved
energy
design
Yes
Figure 5: Framework of energy management design using BIM.
2.3. Commissioning and Handover.Building commissioning
is defined as “a quality assurance program intended to dem-
onstrate that the building is constructed well and performs as
designed.If the building materials,equipment and systems
were not installed well and are not operating as intended, the
health, productivity and other benefits of high performance
design will not be achieved” [19]. Building commissioning is
a key process for the building operation and maintenance, as
the Department of Energy (DOE) suggested that “it ensures
that a new building or system begins its life cycle at optimal
productivity and improves the likelihood that the equipment
will maintain this levelof performance throughout its life.
Building commissioning is the key to quality assurance in
more than one way” [20]. For evaluating the project quality
and identify potential significant design defects before it is too
late or expensive to make changes, building commissioning
should be embedded in the following phases:predesign
phase, design phase, construction phase, transition to opera-
tional sustainability, postoccupancy and warranty phase, and
retrocommissioning [21]. This section is focused on the first
two processes: predesign phase and design phase. In design
stages, commissioning scope and commissioning team must
be identified. Since different facilities have different features
and budgetlimitations and differentprojects have special
systems to be commissioned,commissioning team has to
be involved in early design stages for the decision making.
This approach willalso enable knowledge sharing between
different parties. However, in the process of commissioning,
massive 2D documents, images, maintenance, and operation
information need to be collected and accessed frequently.
For example, in the commissioning process of the Marylan
GeneralHospital(MGH), the following systemsneed to
be commissioned:a new 2000KVA normalpower substa-
tion,a new 500 KW emergency generator and paralleling
switchgear,three new automatic transfer switches and dis-
tributions,2 new 650 ton electric centrifugalchillers and
650 ton cooling towers,temperature and humidity systems,
and duct work,air handlers,dampers,and fans [21].There
has to be an easily accessed platform for data exchange a
integration.BIM is envisaged to overcome the problem of
interoperability and provide easy access for these massive
data.When scoping which facilities need to be commis-
sioned, similar projects’ information could be retrieved from
BIM database,as reference for the decision.The graphical
interface of BIM could also improve the collaboration amon
owner, designer, and contractor. Schedules and commissio
facilities could be predesigned and stored in BIM models by
each facility/zone/room. These plans are shown as timeline
which act as a simulation of actual commissioning practice
Thus,the logicalfaults and collision between activities can
be easily identified. Moreover, design errors and conflicts o
plumbing,HVAC, and electricalfrom different team could
be discovered in the integrated view of BIM.In the design
phase, different commissioning tasks have to be assigned
the specified experts for individual commissioning. After al
these commissioning subtasks are approved,the whole sys-
tem has to be commissioned together. For example, plumb
and electrical systems in a room need to be commissioned
in a designed order.After both are approved,it mustbe
ensured,these systemscould work togethersuccessfully.
Thus,the overall commissioning task must be done.When
commissioning the plumbing or electrical system in differe
areas,a logicalordermustbe specified.Simulating this
schedule and identifying an optimal alternative will reduce
the commissioning cost and time. Figure 6 depicts the BIM
based commissioning streamline.
Barcode system could also be incorporated into BIM for
the ease of accessibility of commissioning documents. Eac
commissioning facility is assigned a unique ID in the BIM
modelfor storing the properties and relevantdocuments
when it is designed. Each ID could be associated with one
code.The commissioning team could scan the barcode and
retrieve the product data,operation data,and maintenance
manuals right in the field. Commissioning critical tasks and
checklists could be pushed on to a mobile device. The resu
will be automatically uploaded to BIM central database in a
standard format after commissioning tasks.
As projectproceeds,thesedata arehanded overto
the operationalphase as wellas the updated BIM model.
Besides correcting design defects, simulating commissioni
schedules, and bringing easy access for information, bring
commissioning to design phase through BIM could also
improve energy saving performance in operation and main
tenance phase.
3. Case Study
The projectof ShanghaiDisaster Tolerance Center isan
ideal example of bringing FM to design stages through BIM
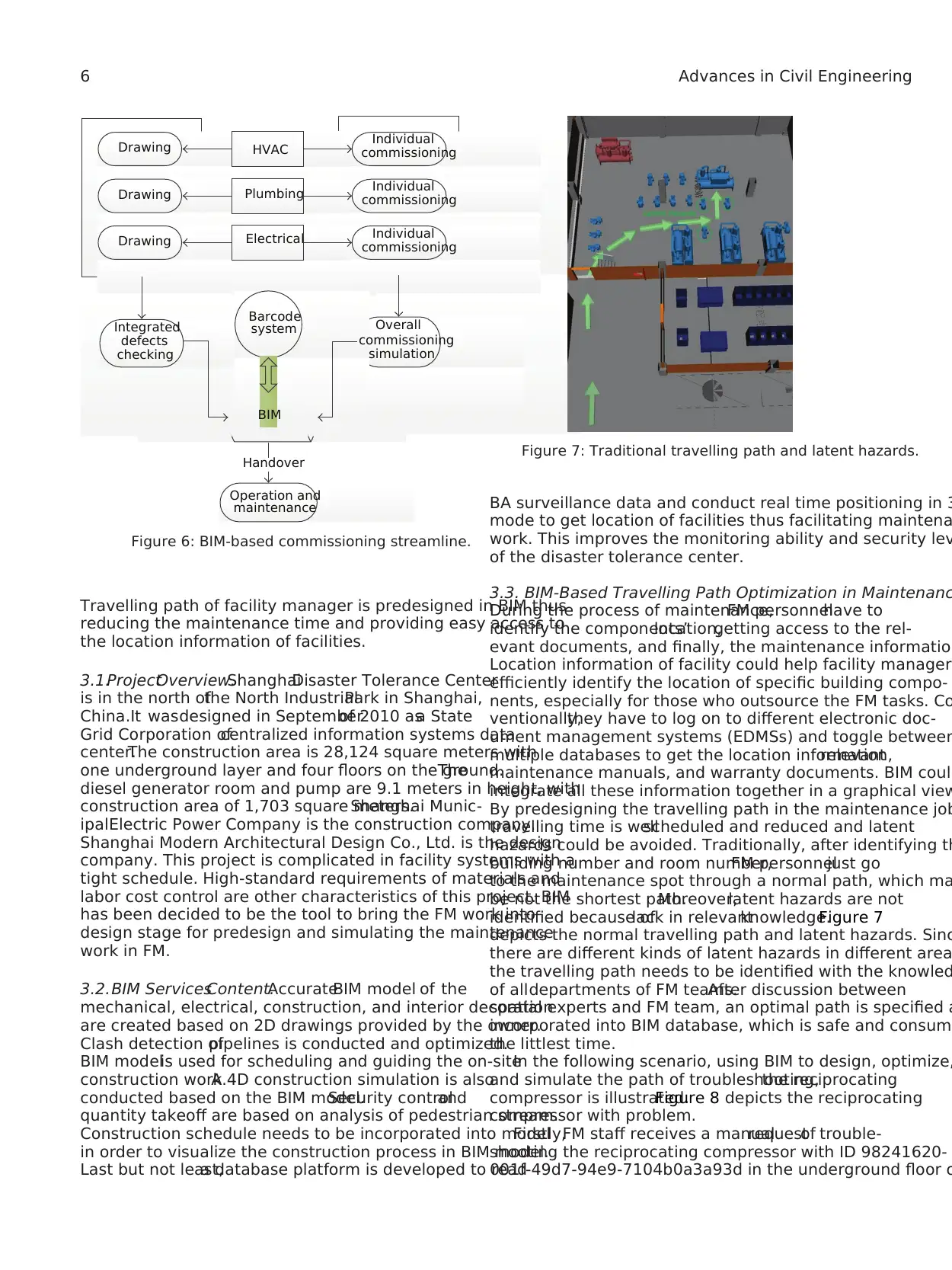
6 Advances in Civil Engineering
Drawing HVAC Individual
commissioning
Drawing Plumbing
Drawing Electrical
Barcode
system Overall
commissioning
simulation
Integrated
defects
checking
BIM
Handover
Operation and
maintenance
Individual
commissioning
Individual
commissioning
Figure 6: BIM-based commissioning streamline.
Travelling path of facility manager is predesigned in BIM thus
reducing the maintenance time and providing easy access to
the location information of facilities.
3.1.ProjectOverview.ShanghaiDisaster Tolerance Center
is in the north ofthe North IndustrialPark in Shanghai,
China.It wasdesigned in Septemberof 2010 asa State
Grid Corporation ofcentralized information systems data
center.The construction area is 28,124 square meters with
one underground layer and four floors on the ground.The
diesel generator room and pump are 9.1 meters in height, with
construction area of 1,703 square meters.Shanghai Munic-
ipalElectric Power Company is the construction company.
Shanghai Modern Architectural Design Co., Ltd. is the design
company. This project is complicated in facility systems with a
tight schedule. High-standard requirements of materials and
labor cost control are other characteristics of this project. BIM
has been decided to be the tool to bring the FM work into
design stage for predesign and simulating the maintenance
work in FM.
3.2.BIM ServicesContent.AccurateBIM model of the
mechanical, electrical, construction, and interior decoration
are created based on 2D drawings provided by the owner.
Clash detection ofpipelines is conducted and optimized.
BIM modelis used for scheduling and guiding the on-site
construction work.A 4D construction simulation is also
conducted based on the BIM model.Security controland
quantity takeoff are based on analysis of pedestrian stream.
Construction schedule needs to be incorporated into model
in order to visualize the construction process in BIM model.
Last but not least,a database platform is developed to read
Figure 7: Traditional travelling path and latent hazards.
BA surveillance data and conduct real time positioning in 3
mode to get location of facilities thus facilitating maintena
work. This improves the monitoring ability and security lev
of the disaster tolerance center.
3.3. BIM-Based Travelling Path Optimization in Maintenanc
During the process of maintenance,FM personnelhave to
identify the components’location,getting access to the rel-
evant documents, and finally, the maintenance information
Location information of facility could help facility managers
efficiently identify the location of specific building compo-
nents, especially for those who outsource the FM tasks. Co
ventionally,they have to log on to different electronic doc-
ument management systems (EDMSs) and toggle between
multiple databases to get the location information,relevant
maintenance manuals, and warranty documents. BIM could
integrate all these information together in a graphical view
By predesigning the travelling path in the maintenance job
travelling time is wellscheduled and reduced and latent
hazards could be avoided. Traditionally, after identifying th
building number and room number,FM personneljust go
to the maintenance spot through a normal path, which ma
be not the shortest path.Moreover,latent hazards are not
identified because oflack in relevantknowledge.Figure 7
depicts the normal travelling path and latent hazards. Sinc
there are different kinds of latent hazards in different area
the travelling path needs to be identified with the knowled
of alldepartments of FM teams.After discussion between
spatial experts and FM team, an optimal path is specified a
incorporated into BIM database, which is safe and consume
the littlest time.
In the following scenario, using BIM to design, optimize,
and simulate the path of troubleshooting,the reciprocating
compressor is illustrated.Figure 8 depicts the reciprocating
compressor with problem.
Firstly,FM staff receives a manualrequestof trouble-
shooting the reciprocating compressor with ID 98241620-
001f-49d7-94e9-7104b0a3a93d in the underground floor o
Drawing HVAC Individual
commissioning
Drawing Plumbing
Drawing Electrical
Barcode
system Overall
commissioning
simulation
Integrated
defects
checking
BIM
Handover
Operation and
maintenance
Individual
commissioning
Individual
commissioning
Figure 6: BIM-based commissioning streamline.
Travelling path of facility manager is predesigned in BIM thus
reducing the maintenance time and providing easy access to
the location information of facilities.
3.1.ProjectOverview.ShanghaiDisaster Tolerance Center
is in the north ofthe North IndustrialPark in Shanghai,
China.It wasdesigned in Septemberof 2010 asa State
Grid Corporation ofcentralized information systems data
center.The construction area is 28,124 square meters with
one underground layer and four floors on the ground.The
diesel generator room and pump are 9.1 meters in height, with
construction area of 1,703 square meters.Shanghai Munic-
ipalElectric Power Company is the construction company.
Shanghai Modern Architectural Design Co., Ltd. is the design
company. This project is complicated in facility systems with a
tight schedule. High-standard requirements of materials and
labor cost control are other characteristics of this project. BIM
has been decided to be the tool to bring the FM work into
design stage for predesign and simulating the maintenance
work in FM.
3.2.BIM ServicesContent.AccurateBIM model of the
mechanical, electrical, construction, and interior decoration
are created based on 2D drawings provided by the owner.
Clash detection ofpipelines is conducted and optimized.
BIM modelis used for scheduling and guiding the on-site
construction work.A 4D construction simulation is also
conducted based on the BIM model.Security controland
quantity takeoff are based on analysis of pedestrian stream.
Construction schedule needs to be incorporated into model
in order to visualize the construction process in BIM model.
Last but not least,a database platform is developed to read
Figure 7: Traditional travelling path and latent hazards.
BA surveillance data and conduct real time positioning in 3
mode to get location of facilities thus facilitating maintena
work. This improves the monitoring ability and security lev
of the disaster tolerance center.
3.3. BIM-Based Travelling Path Optimization in Maintenanc
During the process of maintenance,FM personnelhave to
identify the components’location,getting access to the rel-
evant documents, and finally, the maintenance information
Location information of facility could help facility managers
efficiently identify the location of specific building compo-
nents, especially for those who outsource the FM tasks. Co
ventionally,they have to log on to different electronic doc-
ument management systems (EDMSs) and toggle between
multiple databases to get the location information,relevant
maintenance manuals, and warranty documents. BIM could
integrate all these information together in a graphical view
By predesigning the travelling path in the maintenance job
travelling time is wellscheduled and reduced and latent
hazards could be avoided. Traditionally, after identifying th
building number and room number,FM personneljust go
to the maintenance spot through a normal path, which ma
be not the shortest path.Moreover,latent hazards are not
identified because oflack in relevantknowledge.Figure 7
depicts the normal travelling path and latent hazards. Sinc
there are different kinds of latent hazards in different area
the travelling path needs to be identified with the knowled
of alldepartments of FM teams.After discussion between
spatial experts and FM team, an optimal path is specified a
incorporated into BIM database, which is safe and consume
the littlest time.
In the following scenario, using BIM to design, optimize,
and simulate the path of troubleshooting,the reciprocating
compressor is illustrated.Figure 8 depicts the reciprocating
compressor with problem.
Firstly,FM staff receives a manualrequestof trouble-
shooting the reciprocating compressor with ID 98241620-
001f-49d7-94e9-7104b0a3a93d in the underground floor o
You're viewing a preview
Unlock full access by subscribing today!
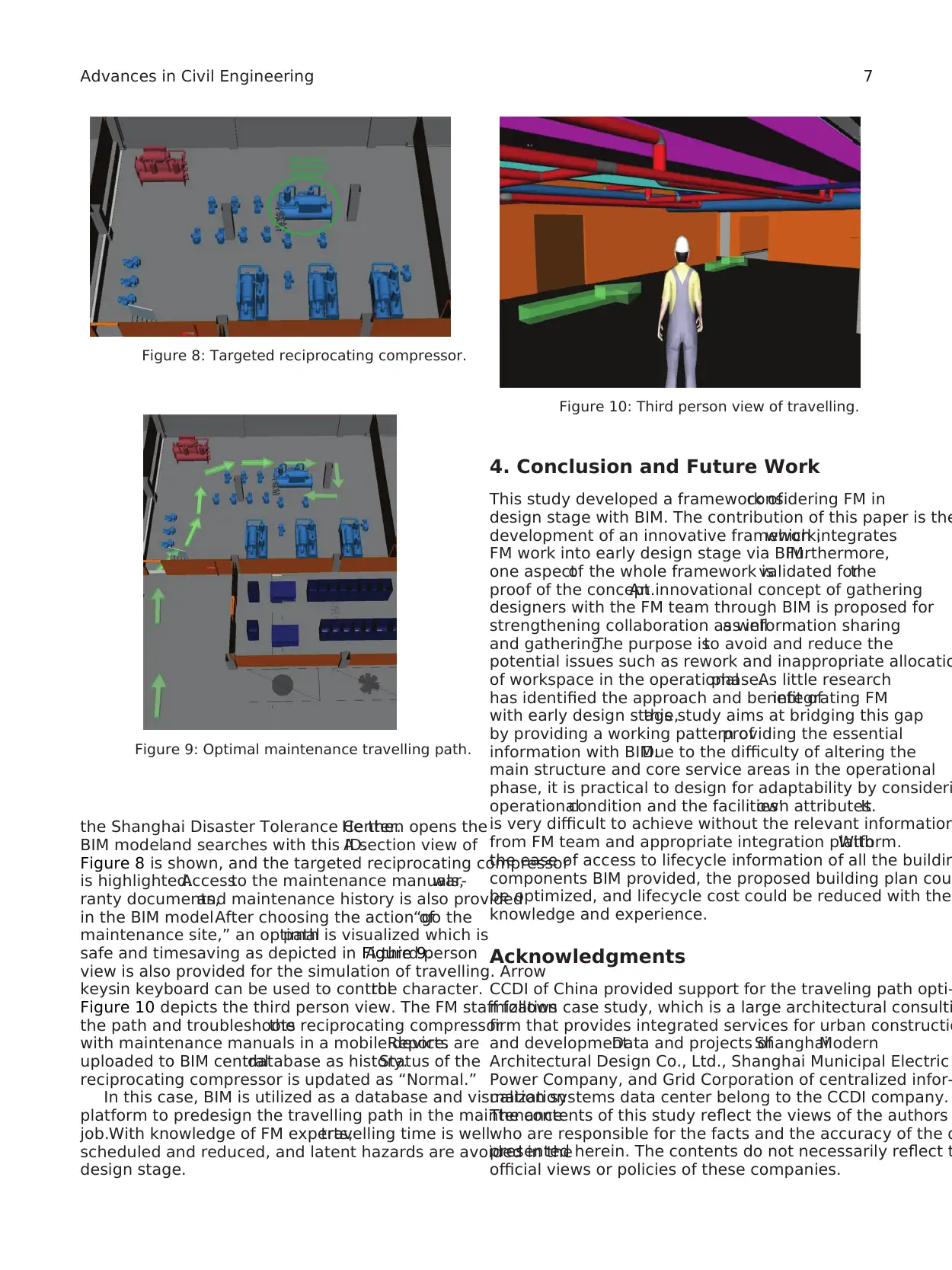
Advances in Civil Engineering 7
Figure 8: Targeted reciprocating compressor.
Figure 9: Optimal maintenance travelling path.
the Shanghai Disaster Tolerance Center.He then opens the
BIM modeland searches with this ID.A section view of
Figure 8 is shown, and the targeted reciprocating compressor
is highlighted.Accessto the maintenance manuals,war-
ranty documents,and maintenance history is also provided
in the BIM model.After choosing the action of“go the
maintenance site,” an optimalpath is visualized which is
safe and timesaving as depicted in Figure 9.A third person
view is also provided for the simulation of travelling. Arrow
keysin keyboard can be used to controlthe character.
Figure 10 depicts the third person view. The FM staff follows
the path and troubleshootsthe reciprocating compressor
with maintenance manuals in a mobile device.Reports are
uploaded to BIM centraldatabase as history.Status of the
reciprocating compressor is updated as “Normal.”
In this case, BIM is utilized as a database and visualization
platform to predesign the travelling path in the maintenance
job.With knowledge of FM experts,travelling time is well
scheduled and reduced, and latent hazards are avoided in the
design stage.
Figure 10: Third person view of travelling.
4. Conclusion and Future Work
This study developed a framework ofconsidering FM in
design stage with BIM. The contribution of this paper is the
development of an innovative framework,which integrates
FM work into early design stage via BIM.Furthermore,
one aspectof the whole framework isvalidated forthe
proof of the concept.An innovational concept of gathering
designers with the FM team through BIM is proposed for
strengthening collaboration as wellas information sharing
and gathering.The purpose isto avoid and reduce the
potential issues such as rework and inappropriate allocatio
of workspace in the operationalphase.As little research
has identified the approach and benefit ofintegrating FM
with early design stage,this study aims at bridging this gap
by providing a working pattern ofproviding the essential
information with BIM.Due to the difficulty of altering the
main structure and core service areas in the operational
phase, it is practical to design for adaptability by consideri
operationalcondition and the facilities’own attributes.It
is very difficult to achieve without the relevant information
from FM team and appropriate integration platform.With
the ease of access to lifecycle information of all the buildin
components BIM provided, the proposed building plan coul
be optimized, and lifecycle cost could be reduced with the
knowledge and experience.
Acknowledgments
CCDI of China provided support for the traveling path opti-
mization case study, which is a large architectural consulti
firm that provides integrated services for urban constructio
and development.Data and projects ofShanghaiModern
Architectural Design Co., Ltd., Shanghai Municipal Electric
Power Company, and Grid Corporation of centralized infor-
mation systems data center belong to the CCDI company.
The contents of this study reflect the views of the authors
who are responsible for the facts and the accuracy of the d
presented herein. The contents do not necessarily reflect t
official views or policies of these companies.
Figure 8: Targeted reciprocating compressor.
Figure 9: Optimal maintenance travelling path.
the Shanghai Disaster Tolerance Center.He then opens the
BIM modeland searches with this ID.A section view of
Figure 8 is shown, and the targeted reciprocating compressor
is highlighted.Accessto the maintenance manuals,war-
ranty documents,and maintenance history is also provided
in the BIM model.After choosing the action of“go the
maintenance site,” an optimalpath is visualized which is
safe and timesaving as depicted in Figure 9.A third person
view is also provided for the simulation of travelling. Arrow
keysin keyboard can be used to controlthe character.
Figure 10 depicts the third person view. The FM staff follows
the path and troubleshootsthe reciprocating compressor
with maintenance manuals in a mobile device.Reports are
uploaded to BIM centraldatabase as history.Status of the
reciprocating compressor is updated as “Normal.”
In this case, BIM is utilized as a database and visualization
platform to predesign the travelling path in the maintenance
job.With knowledge of FM experts,travelling time is well
scheduled and reduced, and latent hazards are avoided in the
design stage.
Figure 10: Third person view of travelling.
4. Conclusion and Future Work
This study developed a framework ofconsidering FM in
design stage with BIM. The contribution of this paper is the
development of an innovative framework,which integrates
FM work into early design stage via BIM.Furthermore,
one aspectof the whole framework isvalidated forthe
proof of the concept.An innovational concept of gathering
designers with the FM team through BIM is proposed for
strengthening collaboration as wellas information sharing
and gathering.The purpose isto avoid and reduce the
potential issues such as rework and inappropriate allocatio
of workspace in the operationalphase.As little research
has identified the approach and benefit ofintegrating FM
with early design stage,this study aims at bridging this gap
by providing a working pattern ofproviding the essential
information with BIM.Due to the difficulty of altering the
main structure and core service areas in the operational
phase, it is practical to design for adaptability by consideri
operationalcondition and the facilities’own attributes.It
is very difficult to achieve without the relevant information
from FM team and appropriate integration platform.With
the ease of access to lifecycle information of all the buildin
components BIM provided, the proposed building plan coul
be optimized, and lifecycle cost could be reduced with the
knowledge and experience.
Acknowledgments
CCDI of China provided support for the traveling path opti-
mization case study, which is a large architectural consulti
firm that provides integrated services for urban constructio
and development.Data and projects ofShanghaiModern
Architectural Design Co., Ltd., Shanghai Municipal Electric
Power Company, and Grid Corporation of centralized infor-
mation systems data center belong to the CCDI company.
The contents of this study reflect the views of the authors
who are responsible for the facts and the accuracy of the d
presented herein. The contents do not necessarily reflect t
official views or policies of these companies.
Paraphrase This Document
Need a fresh take? Get an instant paraphrase of this document with our AI Paraphraser
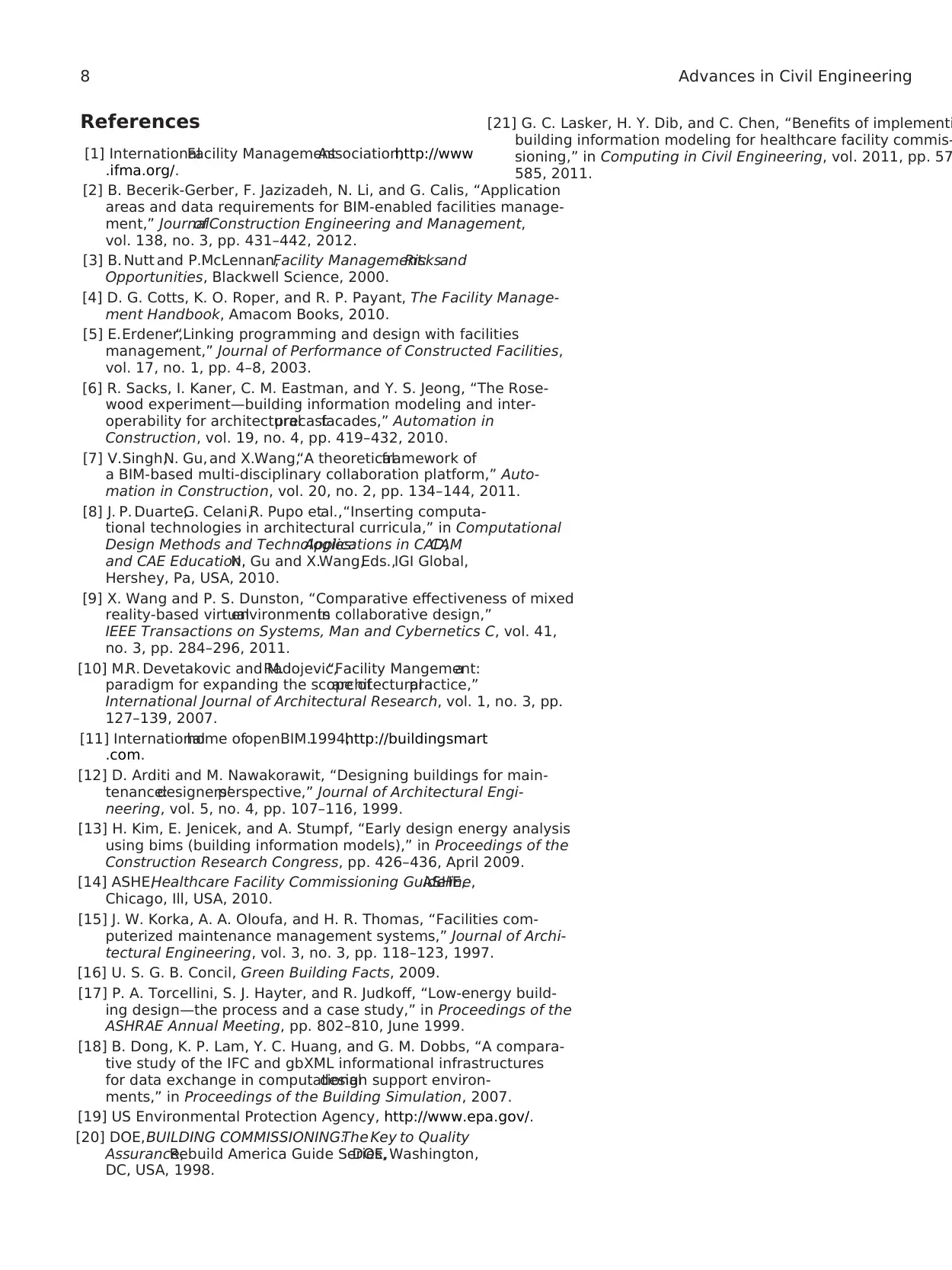
8 Advances in Civil Engineering
References
[1] InternationalFacility ManagementAssociation,http://www
.ifma.org/.
[2] B. Becerik-Gerber, F. Jazizadeh, N. Li, and G. Calis, “Application
areas and data requirements for BIM-enabled facilities manage-
ment,” Journalof Construction Engineering and Management,
vol. 138, no. 3, pp. 431–442, 2012.
[3] B. Nutt and P.McLennan,Facility Management:Risksand
Opportunities, Blackwell Science, 2000.
[4] D. G. Cotts, K. O. Roper, and R. P. Payant, The Facility Manage-
ment Handbook, Amacom Books, 2010.
[5] E.Erdener,“Linking programming and design with facilities
management,” Journal of Performance of Constructed Facilities,
vol. 17, no. 1, pp. 4–8, 2003.
[6] R. Sacks, I. Kaner, C. M. Eastman, and Y. S. Jeong, “The Rose-
wood experiment—building information modeling and inter-
operability for architecturalprecastfacades,” Automation in
Construction, vol. 19, no. 4, pp. 419–432, 2010.
[7] V.Singh,N. Gu, and X.Wang,“A theoreticalframework of
a BIM-based multi-disciplinary collaboration platform,” Auto-
mation in Construction, vol. 20, no. 2, pp. 134–144, 2011.
[8] J. P. Duarte,G. Celani,R. Pupo etal.,“Inserting computa-
tional technologies in architectural curricula,” in Computational
Design Methods and Technologies:Applications in CAD,CAM
and CAE Education,N. Gu and X.Wang,Eds.,IGI Global,
Hershey, Pa, USA, 2010.
[9] X. Wang and P. S. Dunston, “Comparative effectiveness of mixed
reality-based virtualenvironmentsin collaborative design,”
IEEE Transactions on Systems, Man and Cybernetics C, vol. 41,
no. 3, pp. 284–296, 2011.
[10] M.R. Devetakovic and M.Radojevic,“Facility Mangement:a
paradigm for expanding the scope ofarchitecturalpractice,”
International Journal of Architectural Research, vol. 1, no. 3, pp.
127–139, 2007.
[11] Internationalhome ofopenBIM.1994,http://buildingsmart
.com.
[12] D. Arditi and M. Nawakorawit, “Designing buildings for main-
tenance:designers’perspective,” Journal of Architectural Engi-
neering, vol. 5, no. 4, pp. 107–116, 1999.
[13] H. Kim, E. Jenicek, and A. Stumpf, “Early design energy analysis
using bims (building information models),” in Proceedings of the
Construction Research Congress, pp. 426–436, April 2009.
[14] ASHE,Healthcare Facility Commissioning Guideline,ASHE,
Chicago, Ill, USA, 2010.
[15] J. W. Korka, A. A. Oloufa, and H. R. Thomas, “Facilities com-
puterized maintenance management systems,” Journal of Archi-
tectural Engineering, vol. 3, no. 3, pp. 118–123, 1997.
[16] U. S. G. B. Concil, Green Building Facts, 2009.
[17] P. A. Torcellini, S. J. Hayter, and R. Judkoff, “Low-energy build-
ing design—the process and a case study,” in Proceedings of the
ASHRAE Annual Meeting, pp. 802–810, June 1999.
[18] B. Dong, K. P. Lam, Y. C. Huang, and G. M. Dobbs, “A compara-
tive study of the IFC and gbXML informational infrastructures
for data exchange in computationaldesign support environ-
ments,” in Proceedings of the Building Simulation, 2007.
[19] US Environmental Protection Agency, http://www.epa.gov/.
[20] DOE,BUILDING COMMISSIONING:The Key to Quality
Assurance,Rebuild America Guide Series,DOE,Washington,
DC, USA, 1998.
[21] G. C. Lasker, H. Y. Dib, and C. Chen, “Benefits of implementi
building information modeling for healthcare facility commis-
sioning,” in Computing in Civil Engineering, vol. 2011, pp. 57
585, 2011.
References
[1] InternationalFacility ManagementAssociation,http://www
.ifma.org/.
[2] B. Becerik-Gerber, F. Jazizadeh, N. Li, and G. Calis, “Application
areas and data requirements for BIM-enabled facilities manage-
ment,” Journalof Construction Engineering and Management,
vol. 138, no. 3, pp. 431–442, 2012.
[3] B. Nutt and P.McLennan,Facility Management:Risksand
Opportunities, Blackwell Science, 2000.
[4] D. G. Cotts, K. O. Roper, and R. P. Payant, The Facility Manage-
ment Handbook, Amacom Books, 2010.
[5] E.Erdener,“Linking programming and design with facilities
management,” Journal of Performance of Constructed Facilities,
vol. 17, no. 1, pp. 4–8, 2003.
[6] R. Sacks, I. Kaner, C. M. Eastman, and Y. S. Jeong, “The Rose-
wood experiment—building information modeling and inter-
operability for architecturalprecastfacades,” Automation in
Construction, vol. 19, no. 4, pp. 419–432, 2010.
[7] V.Singh,N. Gu, and X.Wang,“A theoreticalframework of
a BIM-based multi-disciplinary collaboration platform,” Auto-
mation in Construction, vol. 20, no. 2, pp. 134–144, 2011.
[8] J. P. Duarte,G. Celani,R. Pupo etal.,“Inserting computa-
tional technologies in architectural curricula,” in Computational
Design Methods and Technologies:Applications in CAD,CAM
and CAE Education,N. Gu and X.Wang,Eds.,IGI Global,
Hershey, Pa, USA, 2010.
[9] X. Wang and P. S. Dunston, “Comparative effectiveness of mixed
reality-based virtualenvironmentsin collaborative design,”
IEEE Transactions on Systems, Man and Cybernetics C, vol. 41,
no. 3, pp. 284–296, 2011.
[10] M.R. Devetakovic and M.Radojevic,“Facility Mangement:a
paradigm for expanding the scope ofarchitecturalpractice,”
International Journal of Architectural Research, vol. 1, no. 3, pp.
127–139, 2007.
[11] Internationalhome ofopenBIM.1994,http://buildingsmart
.com.
[12] D. Arditi and M. Nawakorawit, “Designing buildings for main-
tenance:designers’perspective,” Journal of Architectural Engi-
neering, vol. 5, no. 4, pp. 107–116, 1999.
[13] H. Kim, E. Jenicek, and A. Stumpf, “Early design energy analysis
using bims (building information models),” in Proceedings of the
Construction Research Congress, pp. 426–436, April 2009.
[14] ASHE,Healthcare Facility Commissioning Guideline,ASHE,
Chicago, Ill, USA, 2010.
[15] J. W. Korka, A. A. Oloufa, and H. R. Thomas, “Facilities com-
puterized maintenance management systems,” Journal of Archi-
tectural Engineering, vol. 3, no. 3, pp. 118–123, 1997.
[16] U. S. G. B. Concil, Green Building Facts, 2009.
[17] P. A. Torcellini, S. J. Hayter, and R. Judkoff, “Low-energy build-
ing design—the process and a case study,” in Proceedings of the
ASHRAE Annual Meeting, pp. 802–810, June 1999.
[18] B. Dong, K. P. Lam, Y. C. Huang, and G. M. Dobbs, “A compara-
tive study of the IFC and gbXML informational infrastructures
for data exchange in computationaldesign support environ-
ments,” in Proceedings of the Building Simulation, 2007.
[19] US Environmental Protection Agency, http://www.epa.gov/.
[20] DOE,BUILDING COMMISSIONING:The Key to Quality
Assurance,Rebuild America Guide Series,DOE,Washington,
DC, USA, 1998.
[21] G. C. Lasker, H. Y. Dib, and C. Chen, “Benefits of implementi
building information modeling for healthcare facility commis-
sioning,” in Computing in Civil Engineering, vol. 2011, pp. 57
585, 2011.
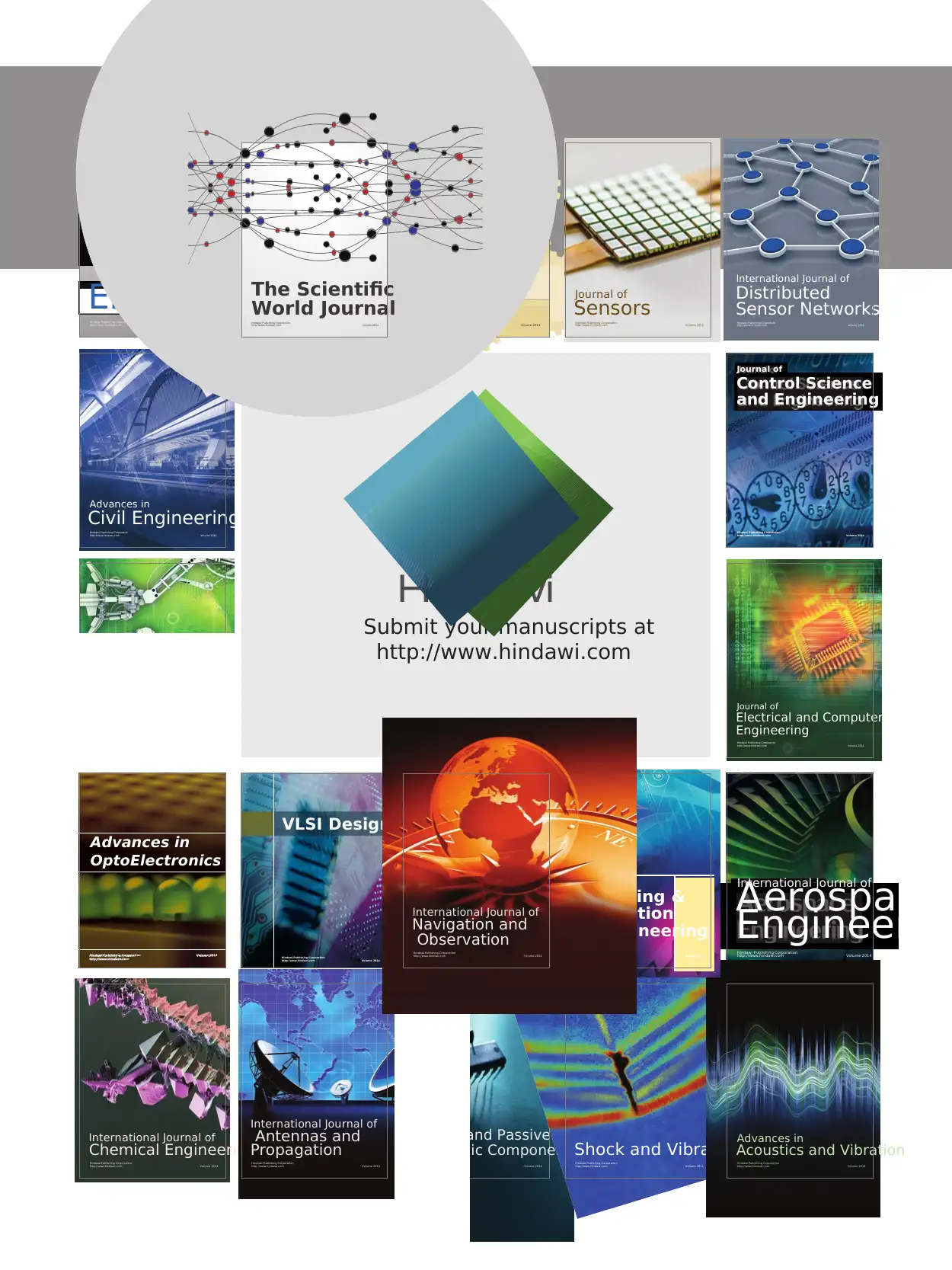
International Journal of
Aerospace
EngineeringHindawi Publishing Corporation
http://www.hindawi.com Volume 2014
Robotics
Journal of
Hindawi Publishing Corporation
http://www.hindawi.com Volume 2014
Hindawi Publishing Corporation
http://www.hindawi.com Volume 2014
Active and Passive
Electronic Components
Control Science
and Engineering
Journal of
Hindawi Publishing Corporation
http://www.hindawi.com Volume 2014
International Journal of
Rotating
Machinery
Hindawi Publishing Corporation
http://www.hindawi.com Volume 2014
Hindawi Publishing Corporation
http://www.hindawi.com
Journal of
Engineering
Volume 2014
Submit your manuscripts at
http://www.hindawi.com
VLSI Design
Hindawi Publishing Corporation
http://www.hindawi.com Volume 201 4
Hindawi Publishing Corporation
http://www.hindawi.com Volume 2014
Shock and Vibration
Hindawi Publishing Corporation
http://www.hindawi.com Volume 2014
Civil Engineering
Advances in
Acoustics and Vibration
Advances in
Hindawi Publishing Corporation
http://www.hindawi.com Volume 2014
Hindawi Publishing Corporation
http://www.hindawi.com Volume 2014
Electrical and Computer
Engineering
Journal of
Advances in
OptoElectronics
Hindawi Publishing Corporation
http://www.hindawi.com
Volume 2014
The Scientific
World JournalHindawi Publishing Corporation
http://www.hindawi.com Volume 2014
Sensors
Journal of
Hindawi Publishing Corporation
http://www.hindawi.com Volume 2014
Modelling &
Simulation
in Engineering
Hindawi Publishing Corporation
http://www.hindawi.com Volume 2014
Hindawi Publishing Corporation
http://www.hindawi.com Volume 2014
Chemical Engineering
International Journal of Antennas and
Propagation
International Journal of
Hindawi Publishing Corporation
http://www.hindawi.com Volume 2014
Hindawi Publishing Corporation
http://www.hindawi.com Volume 2014
Navigation and
Observation
International Journal of
Hindawi Publishing Corporation
http://www.hindawi.com Volume 2014
Distributed
Sensor Networks
International Journal of
Aerospace
EngineeringHindawi Publishing Corporation
http://www.hindawi.com Volume 2014
Robotics
Journal of
Hindawi Publishing Corporation
http://www.hindawi.com Volume 2014
Hindawi Publishing Corporation
http://www.hindawi.com Volume 2014
Active and Passive
Electronic Components
Control Science
and Engineering
Journal of
Hindawi Publishing Corporation
http://www.hindawi.com Volume 2014
International Journal of
Rotating
Machinery
Hindawi Publishing Corporation
http://www.hindawi.com Volume 2014
Hindawi Publishing Corporation
http://www.hindawi.com
Journal of
Engineering
Volume 2014
Submit your manuscripts at
http://www.hindawi.com
VLSI Design
Hindawi Publishing Corporation
http://www.hindawi.com Volume 201 4
Hindawi Publishing Corporation
http://www.hindawi.com Volume 2014
Shock and Vibration
Hindawi Publishing Corporation
http://www.hindawi.com Volume 2014
Civil Engineering
Advances in
Acoustics and Vibration
Advances in
Hindawi Publishing Corporation
http://www.hindawi.com Volume 2014
Hindawi Publishing Corporation
http://www.hindawi.com Volume 2014
Electrical and Computer
Engineering
Journal of
Advances in
OptoElectronics
Hindawi Publishing Corporation
http://www.hindawi.com
Volume 2014
The Scientific
World JournalHindawi Publishing Corporation
http://www.hindawi.com Volume 2014
Sensors
Journal of
Hindawi Publishing Corporation
http://www.hindawi.com Volume 2014
Modelling &
Simulation
in Engineering
Hindawi Publishing Corporation
http://www.hindawi.com Volume 2014
Hindawi Publishing Corporation
http://www.hindawi.com Volume 2014
Chemical Engineering
International Journal of Antennas and
Propagation
International Journal of
Hindawi Publishing Corporation
http://www.hindawi.com Volume 2014
Hindawi Publishing Corporation
http://www.hindawi.com Volume 2014
Navigation and
Observation
International Journal of
Hindawi Publishing Corporation
http://www.hindawi.com Volume 2014
Distributed
Sensor Networks
International Journal of
You're viewing a preview
Unlock full access by subscribing today!
1 out of 9

Your All-in-One AI-Powered Toolkit for Academic Success.
+13062052269
info@desklib.com
Available 24*7 on WhatsApp / Email
Unlock your academic potential
© 2024 | Zucol Services PVT LTD | All rights reserved.