Implementing Lean Manufacturing Systems
VerifiedAdded on 2020/10/23
|30
|11054
|137
AI Summary
The provided assignment is a review of lean manufacturing implementation techniques. It includes various references to academic papers and books on the topic. The content covers value stream mapping, one piece flow, kanban process, quality control, and standardized work as key methods for implementing lean manufacturing systems. The references are from reputable sources such as journals, conferences, and books. This assignment is suitable for students in business or industrial engineering programs who need to understand the fundamentals of lean manufacturing and its implementation methods.
Contribute Materials
Your contribution can guide someone’s learning journey. Share your
documents today.

IMPROVEMENT OF THE
OUTSOURCING PROCESSES
THROUGH THE APPLICATION OF
METHODS OF LEAN
MANAGEMENT AT THE SHIPPING
COMPANY HENDRICKS GMBH
AND CO.
OUTSOURCING PROCESSES
THROUGH THE APPLICATION OF
METHODS OF LEAN
MANAGEMENT AT THE SHIPPING
COMPANY HENDRICKS GMBH
AND CO.
Secure Best Marks with AI Grader
Need help grading? Try our AI Grader for instant feedback on your assignments.

TABLE OF CONTENTS
TOPIC ............................................................................................................................................................................1
INTRODUCTION..........................................................................................................................................................1
Problem Statement...............................................................................................................................................1
Objective of Study...............................................................................................................................................2
Procedure of Study...............................................................................................................................................2
ANALYSIS OF LEAN MANAGEMENT.....................................................................................................................4
Lean Management................................................................................................................................................4
Muda (Waste)......................................................................................................................................................5
5's for Lean Culture.............................................................................................................................................6
Plan Do Check Act Cycle....................................................................................................................................8
Standardization..................................................................................................................................................10
First in, first out lean management....................................................................................................................13
One-piece Flow..................................................................................................................................................14
Kanban...............................................................................................................................................................14
Kaizen................................................................................................................................................................15
Poka Yoke..........................................................................................................................................................17
Quality Features failure mode and influence analysis.......................................................................................18
Value Stream Mapping......................................................................................................................................19
PRESENTATION OF COMPANY..............................................................................................................................21
REVIEW OF SELECTED METHODS OF LEAN MANAGEMENT........................................................................22
Value Stream Mapping......................................................................................................................................22
Lean and quality techniques..............................................................................................................................23
TARGET STATE.........................................................................................................................................................25
Improvement of cooperation:.............................................................................................................................25
Transparency and Independence .......................................................................................................................25
Optimization of warehousing and storage space usage....................................................................................26
Value Stream......................................................................................................................................................27
IMPLEMENTATION PLAN ......................................................................................................................................28
Implementation of value stream mapping ........................................................................................................28
Implementation of Muda (Waste)......................................................................................................................29
Implementation of Poka Yuke...........................................................................................................................30
CONCLUSION.............................................................................................................................................................31
REFERENCES..............................................................................................................................................................33
TOPIC ............................................................................................................................................................................1
INTRODUCTION..........................................................................................................................................................1
Problem Statement...............................................................................................................................................1
Objective of Study...............................................................................................................................................2
Procedure of Study...............................................................................................................................................2
ANALYSIS OF LEAN MANAGEMENT.....................................................................................................................4
Lean Management................................................................................................................................................4
Muda (Waste)......................................................................................................................................................5
5's for Lean Culture.............................................................................................................................................6
Plan Do Check Act Cycle....................................................................................................................................8
Standardization..................................................................................................................................................10
First in, first out lean management....................................................................................................................13
One-piece Flow..................................................................................................................................................14
Kanban...............................................................................................................................................................14
Kaizen................................................................................................................................................................15
Poka Yoke..........................................................................................................................................................17
Quality Features failure mode and influence analysis.......................................................................................18
Value Stream Mapping......................................................................................................................................19
PRESENTATION OF COMPANY..............................................................................................................................21
REVIEW OF SELECTED METHODS OF LEAN MANAGEMENT........................................................................22
Value Stream Mapping......................................................................................................................................22
Lean and quality techniques..............................................................................................................................23
TARGET STATE.........................................................................................................................................................25
Improvement of cooperation:.............................................................................................................................25
Transparency and Independence .......................................................................................................................25
Optimization of warehousing and storage space usage....................................................................................26
Value Stream......................................................................................................................................................27
IMPLEMENTATION PLAN ......................................................................................................................................28
Implementation of value stream mapping ........................................................................................................28
Implementation of Muda (Waste)......................................................................................................................29
Implementation of Poka Yuke...........................................................................................................................30
CONCLUSION.............................................................................................................................................................31
REFERENCES..............................................................................................................................................................33

TOPIC
“To explore the improvement measures of outsourcing processes through the application of methods of
lean management at shipping: A case study on Spedition Hendricks GmbH and Co. KG”
INTRODUCTION
Spedition Hendricks GmbH and Co. KG, the company on which this research is based, is a service provider
for Zuma Beach Trading Limited. Zuma, meanwhile, is a textile wholesaler. The exchange between these two
organizations occurs via seek and airway. However, in order to make the exchange process effective, the companies
employ a system of numbering to every batch in order to prevent the risk of theft or loss. Lean management plays an
important role in shipping activities as it helps firms reduce the risk of product mis-management during exchange
and transportation. Frequently, it is this system which helps organizations to enhance the value of their products by
continuously improvising their commodity as per market trends. (Dave, Kubler and Koskela, 2015). This strategy
seeks the attention of firms selling old products in order to minimize waste and optimize its resources.
There are various methods, including value stream mapping and the one-piece flow PDCA cycle, which
can companies in managing the smooth flow of shipping and outsourcing processes (Standardized Work: The
Foundation for Kaizen, 2017). This study seeks to analyze the different methods which can assist scholars in
establishing improvement measures within the functions of Hendricks GmbH and Co. KG. The organization was
founded in 1972 by Eduard Hendricks. Initially, the firm operated using normal functions. However, owing to its
continuous success, it managed to implement critical functions and business processes. Thus, in just a few years, the
firm progressed from being a small organization to a medium size business function. Accordingly, the philosophy of
the entity is focused on providing buyer satisfaction. As such, the key functions of the enterprise aim to deliver high
quality service which is able to meet the changing trends and demands of its customers.
Problem Statement
Outsourcing and service provision are the riskiest management functions of any organisation because they
relate to risks of loss, wastage, and theft, amongst other things. Every transportation lot comprises 900 to 1,000
items. These items continually change as per market trends and consumer preferences. Further to this, the company
numbers every article in each batch in order to limit the likelihood of it being lost of stolen. It has been ascertained
that there are numerous items in stock which become obsolete due to either changing trends or mismanagement. In
accordance with this, it has been identified that the firm is lacking in its lean management. Because of this, KG is
unable to enhance the value of its products, which is impacts on its overall business process. Thus, as per the
problem analysis, it has been determined that it is important for the firm to improve its shipping management in
order to achieve a competitive advantage.
Aim
“To explore the improvement measures of outsourcing processes through the application of methods of
lean management at shipping: A case study on Spedition Hendricks GmbH and Co. KG”
“To explore the improvement measures of outsourcing processes through the application of methods of
lean management at shipping: A case study on Spedition Hendricks GmbH and Co. KG”
INTRODUCTION
Spedition Hendricks GmbH and Co. KG, the company on which this research is based, is a service provider
for Zuma Beach Trading Limited. Zuma, meanwhile, is a textile wholesaler. The exchange between these two
organizations occurs via seek and airway. However, in order to make the exchange process effective, the companies
employ a system of numbering to every batch in order to prevent the risk of theft or loss. Lean management plays an
important role in shipping activities as it helps firms reduce the risk of product mis-management during exchange
and transportation. Frequently, it is this system which helps organizations to enhance the value of their products by
continuously improvising their commodity as per market trends. (Dave, Kubler and Koskela, 2015). This strategy
seeks the attention of firms selling old products in order to minimize waste and optimize its resources.
There are various methods, including value stream mapping and the one-piece flow PDCA cycle, which
can companies in managing the smooth flow of shipping and outsourcing processes (Standardized Work: The
Foundation for Kaizen, 2017). This study seeks to analyze the different methods which can assist scholars in
establishing improvement measures within the functions of Hendricks GmbH and Co. KG. The organization was
founded in 1972 by Eduard Hendricks. Initially, the firm operated using normal functions. However, owing to its
continuous success, it managed to implement critical functions and business processes. Thus, in just a few years, the
firm progressed from being a small organization to a medium size business function. Accordingly, the philosophy of
the entity is focused on providing buyer satisfaction. As such, the key functions of the enterprise aim to deliver high
quality service which is able to meet the changing trends and demands of its customers.
Problem Statement
Outsourcing and service provision are the riskiest management functions of any organisation because they
relate to risks of loss, wastage, and theft, amongst other things. Every transportation lot comprises 900 to 1,000
items. These items continually change as per market trends and consumer preferences. Further to this, the company
numbers every article in each batch in order to limit the likelihood of it being lost of stolen. It has been ascertained
that there are numerous items in stock which become obsolete due to either changing trends or mismanagement. In
accordance with this, it has been identified that the firm is lacking in its lean management. Because of this, KG is
unable to enhance the value of its products, which is impacts on its overall business process. Thus, as per the
problem analysis, it has been determined that it is important for the firm to improve its shipping management in
order to achieve a competitive advantage.
Aim
“To explore the improvement measures of outsourcing processes through the application of methods of
lean management at shipping: A case study on Spedition Hendricks GmbH and Co. KG”

Objectives of Study
To assess the application of methods of lean management
To evaluate the methods of lean management in relation to shipping
To identify improvements in the management system of the shipping activities of KG
The motive behind this study is to define the application of lean management, which assists in improving
logical company functions in order to keep a check on productivity, technological advancement, shipping functions,
dealing of products and to stand out from the competition. Utilizing appropriate tools and methods could help the
enterprise to develop potential growth with regard to its to competitors across the globe.
Procedure of Study
In order to establish a smooth flow for study, the focus of the scholar is to first determine an appropriate
structure and procedure which will be followed consistently throughout. Accordingly, the structure of this
dissertation is as follows:
Introduction: In this chapter, the researcher will summarize the problem statement. This will help in
developing a critical understanding of the title of study. Furthermore, in this section of the dissertation, the focus of
the scholar is on framing the aims and objectives of the research with the help of the instructions of the company and
the problem statement. Defining the core motives of the dissertation within this chapter will assist the scholar in
delivering a smooth flow of investigation on the basis of the aims and objectives.
Analysis of lean management: This chapter focuses on developing knowledge regarding the key concerns
of the objectives, such as standardization 5 S, FIFO, one piece flow, kanban and so forth. Further to this, in order to
summarize these terms, the researcher will explore various online articles and journals. This chapter will be focused
on secondary information, which will help the scholar in extracting reliable information.
Presentation of the company: This is a crucial part of the study because it will facilitate an understanding
of key functions and areas of the firm, such as its outsourcing process, shipping management and warehouse areas.
Detailing organizational information is a core aspect which helps the scholar to deliver effective and reliable data
collection and analysis for the implementation plan. Thus, it could be proposed that presenting the company‘s
information in this chapter of the dissertation will help in understanding the problem statement and ascertaining
improvement measures.
Reviewing the selected methods of lean management: In this chapter, the scholar aims to analyze the
effectiveness of the methods selected for lean management within Spedition Hendricks GmbH and Co. KG.
Reviewing the chosen themes plays an important role as it helps the company in determining the effectiveness of
tools in accordance with the problem statement. However, in this chapter, the researcher will focus on evaluating the
applicability of the chosen lean management methods in order to improve the outsourcing and shipping governance
of the organization.
Target State: This chapter will be focused on targeting the chosen method of lean management in
accordance with the review. insofar as this is concerned, only a few tools will be targeted, in accordance with the
problem statement of the company and the implementation measures. This chapter of study will be focused on the
To assess the application of methods of lean management
To evaluate the methods of lean management in relation to shipping
To identify improvements in the management system of the shipping activities of KG
The motive behind this study is to define the application of lean management, which assists in improving
logical company functions in order to keep a check on productivity, technological advancement, shipping functions,
dealing of products and to stand out from the competition. Utilizing appropriate tools and methods could help the
enterprise to develop potential growth with regard to its to competitors across the globe.
Procedure of Study
In order to establish a smooth flow for study, the focus of the scholar is to first determine an appropriate
structure and procedure which will be followed consistently throughout. Accordingly, the structure of this
dissertation is as follows:
Introduction: In this chapter, the researcher will summarize the problem statement. This will help in
developing a critical understanding of the title of study. Furthermore, in this section of the dissertation, the focus of
the scholar is on framing the aims and objectives of the research with the help of the instructions of the company and
the problem statement. Defining the core motives of the dissertation within this chapter will assist the scholar in
delivering a smooth flow of investigation on the basis of the aims and objectives.
Analysis of lean management: This chapter focuses on developing knowledge regarding the key concerns
of the objectives, such as standardization 5 S, FIFO, one piece flow, kanban and so forth. Further to this, in order to
summarize these terms, the researcher will explore various online articles and journals. This chapter will be focused
on secondary information, which will help the scholar in extracting reliable information.
Presentation of the company: This is a crucial part of the study because it will facilitate an understanding
of key functions and areas of the firm, such as its outsourcing process, shipping management and warehouse areas.
Detailing organizational information is a core aspect which helps the scholar to deliver effective and reliable data
collection and analysis for the implementation plan. Thus, it could be proposed that presenting the company‘s
information in this chapter of the dissertation will help in understanding the problem statement and ascertaining
improvement measures.
Reviewing the selected methods of lean management: In this chapter, the scholar aims to analyze the
effectiveness of the methods selected for lean management within Spedition Hendricks GmbH and Co. KG.
Reviewing the chosen themes plays an important role as it helps the company in determining the effectiveness of
tools in accordance with the problem statement. However, in this chapter, the researcher will focus on evaluating the
applicability of the chosen lean management methods in order to improve the outsourcing and shipping governance
of the organization.
Target State: This chapter will be focused on targeting the chosen method of lean management in
accordance with the review. insofar as this is concerned, only a few tools will be targeted, in accordance with the
problem statement of the company and the implementation measures. This chapter of study will be focused on the
Secure Best Marks with AI Grader
Need help grading? Try our AI Grader for instant feedback on your assignments.

limited aspects and methods such as improvement of cooperation, transparency and Independence, optimization of
warehousing and storage space usage.
Implementation plan: This chapter of the dissertation will be related to the chosen methods of lean
management and their implementation within the shipping and outsourcing functions of the company. However, it
will also help in evaluating and summarizing the learning of the overall research with regards to the business process
of KG. Implementing changes in the organization will develop understanding of the importance of change and the
effectiveness of lean management methods., To emphasize its significance, the researcher will break the plan into
steps. Step wise process will assist the scholar in making clear description of change and implementation measures
with regard to choices.
Conclusion: The conclusion will summarize the findings of the data collection, data analysis and change
process. This is important as it allows the scholar an opportunity to define the overall information included in the
study. To make the conclusion effective, the scholar will focus on separating it into paragraphs related to each
chapter. This segregation of findings will assist the researcher in developing a clear and systematic understanding of
the overall information.
ANALYSIS OF LEAN MANAGEMENT
Lean Management
According to Tandler, 2013, lean management plays a crucial role in managing successful business
functions because it helps firms to deliver functions in the same direction in order to serve customer demands and to
maintain a competitive advantages. It helps enterprises to achieve their purpose of delivering consumer satisfaction.
Furthermore, it has been it has been identified that lean management is a set of values and principles which assist
companies in enhancing their product values at every possible step. In accordance with the enhancement of goods, it
can be said that products are the asset to organisation. Therefore, it is essential for organisation to manage lean
which is related to improving production function, manufacturing process. Further, change management, supply
chain issue, technological advancement and employee turnoverb are another concern of lean management of
organisation. Lean management, with its 5 elementary principles, is known to offer significant benefits to
manufacturing firms. These five principles are value, the value stream, flow, pull and perfection.
Forbes and Ahmed, 2010, stated that it is important for transportation and logistics firms to manage
standardization, quality, cost effectiveness and growth. In accordance with this, to manage lean, it is important for
firms to follow certain rules. These can include the necessity of the organization’s work to be highly specific in
relation to sequence, timing, outcome and content. Further to this, it is important for management to maintain an
effective customer supplier connection in order to minimize the chances of waste and to maintain cost effectiveness
within business functions. Establishing a connection with buyers is an important process since it is this that drives
consumers’ perceptions of their products and services. Further, deriving path way of every logistic and shipping
functions helps company in managing direct and simple management functions which is also beneficial in
maintaining the cost effectiveness of business functions. In contrast, Uygun and Wagner, 2011, stated that
implenting and following rules is the lean plan which helps logistics and transportation companies to easily manage
warehousing and storage space usage.
Implementation plan: This chapter of the dissertation will be related to the chosen methods of lean
management and their implementation within the shipping and outsourcing functions of the company. However, it
will also help in evaluating and summarizing the learning of the overall research with regards to the business process
of KG. Implementing changes in the organization will develop understanding of the importance of change and the
effectiveness of lean management methods., To emphasize its significance, the researcher will break the plan into
steps. Step wise process will assist the scholar in making clear description of change and implementation measures
with regard to choices.
Conclusion: The conclusion will summarize the findings of the data collection, data analysis and change
process. This is important as it allows the scholar an opportunity to define the overall information included in the
study. To make the conclusion effective, the scholar will focus on separating it into paragraphs related to each
chapter. This segregation of findings will assist the researcher in developing a clear and systematic understanding of
the overall information.
ANALYSIS OF LEAN MANAGEMENT
Lean Management
According to Tandler, 2013, lean management plays a crucial role in managing successful business
functions because it helps firms to deliver functions in the same direction in order to serve customer demands and to
maintain a competitive advantages. It helps enterprises to achieve their purpose of delivering consumer satisfaction.
Furthermore, it has been it has been identified that lean management is a set of values and principles which assist
companies in enhancing their product values at every possible step. In accordance with the enhancement of goods, it
can be said that products are the asset to organisation. Therefore, it is essential for organisation to manage lean
which is related to improving production function, manufacturing process. Further, change management, supply
chain issue, technological advancement and employee turnoverb are another concern of lean management of
organisation. Lean management, with its 5 elementary principles, is known to offer significant benefits to
manufacturing firms. These five principles are value, the value stream, flow, pull and perfection.
Forbes and Ahmed, 2010, stated that it is important for transportation and logistics firms to manage
standardization, quality, cost effectiveness and growth. In accordance with this, to manage lean, it is important for
firms to follow certain rules. These can include the necessity of the organization’s work to be highly specific in
relation to sequence, timing, outcome and content. Further to this, it is important for management to maintain an
effective customer supplier connection in order to minimize the chances of waste and to maintain cost effectiveness
within business functions. Establishing a connection with buyers is an important process since it is this that drives
consumers’ perceptions of their products and services. Further, deriving path way of every logistic and shipping
functions helps company in managing direct and simple management functions which is also beneficial in
maintaining the cost effectiveness of business functions. In contrast, Uygun and Wagner, 2011, stated that
implenting and following rules is the lean plan which helps logistics and transportation companies to easily manage

their products and services. This can aid them in minimizing waste and optimising use of their resources and
working as per changing trends.
However, the author explores the rule relating to improvement measures and managing continuous change.
The scholar believes that whilst this is a predominantly scientific method, it can also be an effective technique for
logical and transformation firms. This method establishes safe management functions with regards to dynamic
market trends. Likewise, the shipping and exchange services of Spedition Hendricks GmbH and Co. KG and Zuma
Beach Trading are focused on marking; employing a technique whereby they label all their batches at the time of
exchange in order to prevent risk of waste, loss or theft. To make the labelling specific to them, the firm also enables
with article number to items at the time of individual packaging. On the other hand, the present application and
management styles of company end up wasting old garments due to changing trends. Therefore, to mitigate this
issue, the firm needs to implement the use of lean management, as this offers different applications of managing safe
products and logistic services, like value stream mapping 5S. Thus, it could be suggested that implementing lean
could assist the firm in managing their product waste due to changing trends and changing articles constantly.
Kaizen
Martin and Osterling, 2014, noted that Kaizen is tool for lean management which assists the organization in
instances where the improvement of a firm is related to its employees’ motivation empowerment and collective
efforts. This tool allows the organization to set measures for improvement with the aim of enhancing employee
efficiency, incremental changes and reducing the manual workload in manufacturing processes and so on. Kaizen
manages change from top level of the organization (the CEO) down to the bottom (assembly line worker). However,
can be an especially effective process when employed in the context of logistical and purchasing services. In
addition to this, it helps management in setting cross-sectional boundaries in the supply chain, which serves to
remove the chance of overlapping and missing goods which are supplied in batches.
working as per changing trends.
However, the author explores the rule relating to improvement measures and managing continuous change.
The scholar believes that whilst this is a predominantly scientific method, it can also be an effective technique for
logical and transformation firms. This method establishes safe management functions with regards to dynamic
market trends. Likewise, the shipping and exchange services of Spedition Hendricks GmbH and Co. KG and Zuma
Beach Trading are focused on marking; employing a technique whereby they label all their batches at the time of
exchange in order to prevent risk of waste, loss or theft. To make the labelling specific to them, the firm also enables
with article number to items at the time of individual packaging. On the other hand, the present application and
management styles of company end up wasting old garments due to changing trends. Therefore, to mitigate this
issue, the firm needs to implement the use of lean management, as this offers different applications of managing safe
products and logistic services, like value stream mapping 5S. Thus, it could be suggested that implementing lean
could assist the firm in managing their product waste due to changing trends and changing articles constantly.
Kaizen
Martin and Osterling, 2014, noted that Kaizen is tool for lean management which assists the organization in
instances where the improvement of a firm is related to its employees’ motivation empowerment and collective
efforts. This tool allows the organization to set measures for improvement with the aim of enhancing employee
efficiency, incremental changes and reducing the manual workload in manufacturing processes and so on. Kaizen
manages change from top level of the organization (the CEO) down to the bottom (assembly line worker). However,
can be an especially effective process when employed in the context of logistical and purchasing services. In
addition to this, it helps management in setting cross-sectional boundaries in the supply chain, which serves to
remove the chance of overlapping and missing goods which are supplied in batches.

Through analysis of Illustration 7, it is reasonable to suggest that the Kaizen model may
help a company to implement continuous improvement, where the process is cyclical and the
focus of management is on determining the root causes of their problems. Further, for the
problems, alternative solutions are predicted and tested as per organizational functioning.
Illustration 1: Kaizen
Source: (Keyte and Locher, 2016.)
help a company to implement continuous improvement, where the process is cyclical and the
focus of management is on determining the root causes of their problems. Further, for the
problems, alternative solutions are predicted and tested as per organizational functioning.
Illustration 1: Kaizen
Source: (Keyte and Locher, 2016.)
Paraphrase This Document
Need a fresh take? Get an instant paraphrase of this document with our AI Paraphraser

Following this, the best alternative will be implemented and work will be carried out in a
standardized way. This will help to highlight problems and mis-management. However, with
completely process and analysis the business aims at developing counter measures for overall
improvement. Hence, from this discussion, it can be concluded that the model offers a long-term
approach by helping the enterprise in achieving small and incremental changes. It is beneficial
for both employees and management. The process is considered effective for logistics and
transportation processes because it assists in improving the quality and efficiency of outsourcing
firms.
Muda (Waste)
According to Yamamoto and Bellgran, 2010, the term lean manufacturing was first
proposed by Womack, Jones in their book “The Machine That Changed the World” which was
launched in 1991. In its original incarnation, the term came about as a refusal to accept waste.
Similarly, Muda is a Japanese term that denotes waste. However, the mechanism of Muda is
based on seven different types of waste, which are outlined below:
Over processing: It is common for logistics and transportation services to manufacture
extra products in order to minimize defects.
Waiting: Waiting for the production of goods is a step which impacts the cost
effectiveness of business operations and hampers the smooth flow of logistic activities.
Over production: This is related to waste, where the goods produced are greater than
customer demand. Over production of products leads to waste and disrupts production
activities of other batches.
Transportation: This is related to the movement of products from one place to another.
Of course, this is a core the function of organizations and cannot be stopped.
Transportation can cause various types of waste, through defects, loss and delays.
Inventory: Inventory relates to raw materials, work in progress and the processing of
finished products. However, management of inventory plays a crucial role in managing
waste because it is directly linked to resources.
Motion: This is the movement of goods from one place to another. However, movement
of goods within the context of logistic is related to bulk transfers, which holds the
potential for waste.
standardized way. This will help to highlight problems and mis-management. However, with
completely process and analysis the business aims at developing counter measures for overall
improvement. Hence, from this discussion, it can be concluded that the model offers a long-term
approach by helping the enterprise in achieving small and incremental changes. It is beneficial
for both employees and management. The process is considered effective for logistics and
transportation processes because it assists in improving the quality and efficiency of outsourcing
firms.
Muda (Waste)
According to Yamamoto and Bellgran, 2010, the term lean manufacturing was first
proposed by Womack, Jones in their book “The Machine That Changed the World” which was
launched in 1991. In its original incarnation, the term came about as a refusal to accept waste.
Similarly, Muda is a Japanese term that denotes waste. However, the mechanism of Muda is
based on seven different types of waste, which are outlined below:
Over processing: It is common for logistics and transportation services to manufacture
extra products in order to minimize defects.
Waiting: Waiting for the production of goods is a step which impacts the cost
effectiveness of business operations and hampers the smooth flow of logistic activities.
Over production: This is related to waste, where the goods produced are greater than
customer demand. Over production of products leads to waste and disrupts production
activities of other batches.
Transportation: This is related to the movement of products from one place to another.
Of course, this is a core the function of organizations and cannot be stopped.
Transportation can cause various types of waste, through defects, loss and delays.
Inventory: Inventory relates to raw materials, work in progress and the processing of
finished products. However, management of inventory plays a crucial role in managing
waste because it is directly linked to resources.
Motion: This is the movement of goods from one place to another. However, movement
of goods within the context of logistic is related to bulk transfers, which holds the
potential for waste.

Defects: Defect is a situation which occurs when goods are distributed to consumers.
Though it occurs during transit, the defective products are ultimately waste which is
attributable to the firm because buyers will not purchase damaged goods. Thus, this is the
situation most applicable to Spedition Hendricks GmbH and Co. KG
As per the views of Österman and Fundin (2014), who suggested that lean thinking which
is based on banishing waste and creating wealth for the organization. In keeping with this, it
could be said that it is important for the organization to consider a lean thinking approach. This
will comprise factors including specific value, value stream, flow, pull and perform. All these
factors of lean thinking focus on growth and competitive advantage. This approach can assist
companies in considering the practical aspects of lean management. In addition, the author stated
that the concepts of fundamental lean thinking help enterprises in enabling the use of different
stages with regards to improvement processes.
5's for Lean Culture
According to Ansah, Sorooshian and Mustafa, 2016, 5's of lean management reflects the
culture of the workplace. 5's denotes the five primary phases which need to considered for
managing an effective and productive work environment. It is this strategy which assists
companies in establishing the orderly flow of management and business operations. Furthermore,
it is considered an effective technique within logistics and transportation functions, because it
helps to eliminate waste and establish a smooth and systematic flow of organizational functions.
Implementing tool for lean culture assists the enterprise in managing effective workflow, with
optimum utilization of resources. The author discussed about functions and detailed use of 5's
tool differently which is described below:
Sort: Sorting is the most common part of the lean approach, where an organization
focuses on dividing activities according to their workplace categorical distribution. In
this, the focus of the firm is to reduce the pressure of the work in progress in order to
minimize waste. Insofar as this is concerned, logistics firms use red tagging to specify the
location of particular items.
Set in order: Setting in order is used to specify a series of steps in continuous order. This
strategy helps the business in removing disruption in systematic order management. It
acts as a pillar to organizational functions and is beneficial to the firm as it helps them to
establish the phase of every procedure and action.
Though it occurs during transit, the defective products are ultimately waste which is
attributable to the firm because buyers will not purchase damaged goods. Thus, this is the
situation most applicable to Spedition Hendricks GmbH and Co. KG
As per the views of Österman and Fundin (2014), who suggested that lean thinking which
is based on banishing waste and creating wealth for the organization. In keeping with this, it
could be said that it is important for the organization to consider a lean thinking approach. This
will comprise factors including specific value, value stream, flow, pull and perform. All these
factors of lean thinking focus on growth and competitive advantage. This approach can assist
companies in considering the practical aspects of lean management. In addition, the author stated
that the concepts of fundamental lean thinking help enterprises in enabling the use of different
stages with regards to improvement processes.
5's for Lean Culture
According to Ansah, Sorooshian and Mustafa, 2016, 5's of lean management reflects the
culture of the workplace. 5's denotes the five primary phases which need to considered for
managing an effective and productive work environment. It is this strategy which assists
companies in establishing the orderly flow of management and business operations. Furthermore,
it is considered an effective technique within logistics and transportation functions, because it
helps to eliminate waste and establish a smooth and systematic flow of organizational functions.
Implementing tool for lean culture assists the enterprise in managing effective workflow, with
optimum utilization of resources. The author discussed about functions and detailed use of 5's
tool differently which is described below:
Sort: Sorting is the most common part of the lean approach, where an organization
focuses on dividing activities according to their workplace categorical distribution. In
this, the focus of the firm is to reduce the pressure of the work in progress in order to
minimize waste. Insofar as this is concerned, logistics firms use red tagging to specify the
location of particular items.
Set in order: Setting in order is used to specify a series of steps in continuous order. This
strategy helps the business in removing disruption in systematic order management. It
acts as a pillar to organizational functions and is beneficial to the firm as it helps them to
establish the phase of every procedure and action.

Shine: This relates to the workplace environment, for which it is the responsibility of the
firm to ensure a safe and productive environment by managing the workplace
relationships of the employees and the employer. Shine helps the firm to maintain a
positive working environment through continuous working and by implementing
preventive measures.
Standardize: This is related to improvement measures, where the firm aims at
scheduling improvement guidelines in order to minimize the chances of a relapse. In this
strategy, the organization aims to set a priority for managing changes in order to reduce
the chance of misconceptions and mis-management of programs.
Sustain: This S of lean culture is related to the establishment of discipline within
activities which are related to the workplace environment, stock management, inventory
management, production, transport, waste and productivity. However, sustainability in
organizations is connected to communication, specification of activities, structure, time,
knowledge, training and rewards and recognition.
Thus, in accordance with 5's methodology within the context of lean initiative, it has been
determined that it is a plan which helps the firm in setting effective techniques for maintaining a
positive and productive work environment.
One-piece flow
Tandler, 2013, identified that a one-piece flow system can help an organization to
manage its services and function in order to become lean. The flow in this strategy is related to
eliminating large amount of Muda that is waste out of organization. The functions in this process
goes in u shape, where information flows from one person to another as per their responsibility
and authority. This system of lean management helps the enterprise to manage overlapping of
activities, ways, over processing and over-production. Moreover, it is considered a careful way
of working and managing business operations.
firm to ensure a safe and productive environment by managing the workplace
relationships of the employees and the employer. Shine helps the firm to maintain a
positive working environment through continuous working and by implementing
preventive measures.
Standardize: This is related to improvement measures, where the firm aims at
scheduling improvement guidelines in order to minimize the chances of a relapse. In this
strategy, the organization aims to set a priority for managing changes in order to reduce
the chance of misconceptions and mis-management of programs.
Sustain: This S of lean culture is related to the establishment of discipline within
activities which are related to the workplace environment, stock management, inventory
management, production, transport, waste and productivity. However, sustainability in
organizations is connected to communication, specification of activities, structure, time,
knowledge, training and rewards and recognition.
Thus, in accordance with 5's methodology within the context of lean initiative, it has been
determined that it is a plan which helps the firm in setting effective techniques for maintaining a
positive and productive work environment.
One-piece flow
Tandler, 2013, identified that a one-piece flow system can help an organization to
manage its services and function in order to become lean. The flow in this strategy is related to
eliminating large amount of Muda that is waste out of organization. The functions in this process
goes in u shape, where information flows from one person to another as per their responsibility
and authority. This system of lean management helps the enterprise to manage overlapping of
activities, ways, over processing and over-production. Moreover, it is considered a careful way
of working and managing business operations.
Secure Best Marks with AI Grader
Need help grading? Try our AI Grader for instant feedback on your assignments.

In accordance with the one-piece flow system, it has been determined that it can be an
effective tool for lean management, because it offers a step-wise process in which the firm
derives the components of activities the in initial step in order to avoid the chance of confusion
and waste. Furthermore, the steps comprise a shift in activities from workstation to workstation,
as per assembly line flow. Hence, the flow ends at the final processing and at the production
stage where the goods are ready to meet customer demands.
Kanban
Uygun and Wagner, 2011, proposed that the Kanban approach is established in
organizations for the purposes of continuous, incremental and evolutionary changes. Kanban is a
Japanese word which reflects card or label. The approach is consumer-centric, and allows the
consumer to pull the products they want from the company, according to their needs and wants.
This approach is effective in lean management because it helps the firm to minimize waste by
only producing limited products which meet the buyer’s requirements. Thus, it negates the need
for production of large volumes of products, which again minimizes waste and helps in
establishing lean business activities. Additional to this, as outlined in Illustration 6 below, it
could be suggested that the Kanban model helps organizations to maintain a positive relationship
with their customers as this approach to lean helps the firm to enhance its products and services
in accordance with their customers’ needs.
Illustration 3: One piece flow
effective tool for lean management, because it offers a step-wise process in which the firm
derives the components of activities the in initial step in order to avoid the chance of confusion
and waste. Furthermore, the steps comprise a shift in activities from workstation to workstation,
as per assembly line flow. Hence, the flow ends at the final processing and at the production
stage where the goods are ready to meet customer demands.
Kanban
Uygun and Wagner, 2011, proposed that the Kanban approach is established in
organizations for the purposes of continuous, incremental and evolutionary changes. Kanban is a
Japanese word which reflects card or label. The approach is consumer-centric, and allows the
consumer to pull the products they want from the company, according to their needs and wants.
This approach is effective in lean management because it helps the firm to minimize waste by
only producing limited products which meet the buyer’s requirements. Thus, it negates the need
for production of large volumes of products, which again minimizes waste and helps in
establishing lean business activities. Additional to this, as outlined in Illustration 6 below, it
could be suggested that the Kanban model helps organizations to maintain a positive relationship
with their customers as this approach to lean helps the firm to enhance its products and services
in accordance with their customers’ needs.
Illustration 3: One piece flow

As demonstrated by Yamamoto and Bellgran’s (2010) model, Kanban establishes a cyclic
process for managing consumers’ needs and wants. This Kanban cycle comprises limited work in
progress, managing flow, explicit policies for managing ethical flow, feedback loops,
improvement measures and visualization of changes.
Quality features failure mode and influence analysis
Singh, Garg and Sharma, 2011, discussed failure mode and influence evaluation, which
are types of Failure modes and effects analysis (FMEA) a system which is related to the global
level services of an organisation. Further to that, there is a design which is related to internal the
business environment, its components and sub system. Additionally, there is a process which
relates to the manufacturing and assembly line production system that can assist in eliminating
the waste activities and proper utilisation of resources. Apart from, this there is a component
which is related to services and business operations. Lastly, the software component relates to
the software functions of management.
Illustration 4: Kanban process of lean management
Source: (Yamamoto and Bellgran, 2010)
process for managing consumers’ needs and wants. This Kanban cycle comprises limited work in
progress, managing flow, explicit policies for managing ethical flow, feedback loops,
improvement measures and visualization of changes.
Quality features failure mode and influence analysis
Singh, Garg and Sharma, 2011, discussed failure mode and influence evaluation, which
are types of Failure modes and effects analysis (FMEA) a system which is related to the global
level services of an organisation. Further to that, there is a design which is related to internal the
business environment, its components and sub system. Additionally, there is a process which
relates to the manufacturing and assembly line production system that can assist in eliminating
the waste activities and proper utilisation of resources. Apart from, this there is a component
which is related to services and business operations. Lastly, the software component relates to
the software functions of management.
Illustration 4: Kanban process of lean management
Source: (Yamamoto and Bellgran, 2010)

Faulkner and Badurdeen, 2014 proposed that quality measures play an important role in
initiating and promoting product requirements at production level in order to reduce the chances
of failures during processing. Analysis of customer quality requirements for meeting their
demands, it is importnat for the organisation to have proper information flow in organisation to
reduce mis-communication and interaction gap in every department of organisation. However,
the above illustration demonstrates the three paths for quality measures, on the basis of action
that is designing of changes, processing of changes, proofing of errors, establishing control,
analysing mistakes and setting changed standards and procedures. This specification sof model
assit in improving business process minimizing waste and errors.
Value Stream Mapping
As Tyagi, Choudhary and Yang, 2015 comment, value stream mapping is a lean tool
which can be used to detail every step of business functions within an organization. It is
particularly useful for managing waste, time and setting improvement measures. It is also an
important tool to organisations because it helps to determine the series of steps which need to be
Illustration 5: Quality- One FMEA three path model
Source: (Gurumurthy and Kodali, 2011)
initiating and promoting product requirements at production level in order to reduce the chances
of failures during processing. Analysis of customer quality requirements for meeting their
demands, it is importnat for the organisation to have proper information flow in organisation to
reduce mis-communication and interaction gap in every department of organisation. However,
the above illustration demonstrates the three paths for quality measures, on the basis of action
that is designing of changes, processing of changes, proofing of errors, establishing control,
analysing mistakes and setting changed standards and procedures. This specification sof model
assit in improving business process minimizing waste and errors.
Value Stream Mapping
As Tyagi, Choudhary and Yang, 2015 comment, value stream mapping is a lean tool
which can be used to detail every step of business functions within an organization. It is
particularly useful for managing waste, time and setting improvement measures. It is also an
important tool to organisations because it helps to determine the series of steps which need to be
Illustration 5: Quality- One FMEA three path model
Source: (Gurumurthy and Kodali, 2011)
Paraphrase This Document
Need a fresh take? Get an instant paraphrase of this document with our AI Paraphraser

taken. For example, in logistic business there are numerous goods which are wasted due to over-
processing, defects and changing trends. Value stream mapping can establish certain
standardsfor the production and transfer of goods. Monitoring the entire process of a firm helps
management to minimize waste and errors. Identification of a problem at an initial level through
mapping can assist in delivering continuous improvement in services and business management.
From the above illustration, it is clear that this model could assist the firm in delivering
an effective flow of information and materials in order to avoid confusion and errors. In this type
of mapping, production control is connected with two specific determinants that is supplier and
customer where supplier of organisation. Further, the process is related to process A, B, C and
shipping. However, shipping is ultimately related to the customer. Every section in the material
flow is segregated with the time and percentage of management functions. This percentage
distribution of materials helps the company to manage waste which is created due to over
processing and over production. Vinodh, Ruben and Asokan, 2016, discussed the production
Illustration 6: Value Stream Mapping
Source: (Moreira, Alves and Sousa, 2010)
processing, defects and changing trends. Value stream mapping can establish certain
standardsfor the production and transfer of goods. Monitoring the entire process of a firm helps
management to minimize waste and errors. Identification of a problem at an initial level through
mapping can assist in delivering continuous improvement in services and business management.
From the above illustration, it is clear that this model could assist the firm in delivering
an effective flow of information and materials in order to avoid confusion and errors. In this type
of mapping, production control is connected with two specific determinants that is supplier and
customer where supplier of organisation. Further, the process is related to process A, B, C and
shipping. However, shipping is ultimately related to the customer. Every section in the material
flow is segregated with the time and percentage of management functions. This percentage
distribution of materials helps the company to manage waste which is created due to over
processing and over production. Vinodh, Ruben and Asokan, 2016, discussed the production
Illustration 6: Value Stream Mapping
Source: (Moreira, Alves and Sousa, 2010)

control and its segregation, which are also limited by timeframes like suppliers and the
production shares system of weekly orders, whereas buyer’s and production shares system of
monthly orders. This segregation of departments and function on the basis of time constraints
offers the best mechanism for business outsourcing, logistic, transportation in overlapping
functions and information. Thus, from the illustration it can be concluded that the process leads
to step-by-step with a time ladder.
PRESENTATION OF COMPANY
Hendricks Internationale Spedition GmbH & Co. KG is a logistic and service provider
was founded in 1972 by Edurad Hendrick in Germany. The firm started off as a transport
services company in the Rhine-Ruhr region. However, to achieve a competitive position in the
market, the entrepreneur added complex changes in order to expand business functions and
services. With the addition of new services, the firm broke new ground and enjoyed success,
which helped them to establish a prominent position as a small and medium size enterprise.
The successful implementation of changes within the current enterprise has allowed it to
become a leading logistic and service provider, which works for textile wholesaler Zuma on a
regular basis. However, owing to continuous improvement the company has gained expertise in
logistic market services like cargo handling, sea freight, air and transportation. The management
has consolidated its success by managing continuous changes in operations and supply chain
management.
Today. the firm is spread across 100,000 square meters of logistic space, and has 242
employees. In accordance with logistic functions, the company is able generate earnings of more
than 44 million euros a year. it has been noted that the firm and its services are consumer-
centered, and therefore focus on serving meeting buyer satisfaction by maintaining high quality
services.
The philosophy followed by Hendricks Internationale Spedition GmbH & Co. KG is
based on meeting consumer demand and promoting cost transparency amongst purchasers in
order to establish a stable market position. This, in turn allows them to secure a leading and
competitive position within outbound and logistic services. In addition to this, the management
of the company offers flexible working to employees and involvement in decision making.
Moreover, the business is focused on empowering workers. Insofar as this is concerned, the
production shares system of weekly orders, whereas buyer’s and production shares system of
monthly orders. This segregation of departments and function on the basis of time constraints
offers the best mechanism for business outsourcing, logistic, transportation in overlapping
functions and information. Thus, from the illustration it can be concluded that the process leads
to step-by-step with a time ladder.
PRESENTATION OF COMPANY
Hendricks Internationale Spedition GmbH & Co. KG is a logistic and service provider
was founded in 1972 by Edurad Hendrick in Germany. The firm started off as a transport
services company in the Rhine-Ruhr region. However, to achieve a competitive position in the
market, the entrepreneur added complex changes in order to expand business functions and
services. With the addition of new services, the firm broke new ground and enjoyed success,
which helped them to establish a prominent position as a small and medium size enterprise.
The successful implementation of changes within the current enterprise has allowed it to
become a leading logistic and service provider, which works for textile wholesaler Zuma on a
regular basis. However, owing to continuous improvement the company has gained expertise in
logistic market services like cargo handling, sea freight, air and transportation. The management
has consolidated its success by managing continuous changes in operations and supply chain
management.
Today. the firm is spread across 100,000 square meters of logistic space, and has 242
employees. In accordance with logistic functions, the company is able generate earnings of more
than 44 million euros a year. it has been noted that the firm and its services are consumer-
centered, and therefore focus on serving meeting buyer satisfaction by maintaining high quality
services.
The philosophy followed by Hendricks Internationale Spedition GmbH & Co. KG is
based on meeting consumer demand and promoting cost transparency amongst purchasers in
order to establish a stable market position. This, in turn allows them to secure a leading and
competitive position within outbound and logistic services. In addition to this, the management
of the company offers flexible working to employees and involvement in decision making.
Moreover, the business is focused on empowering workers. Insofar as this is concerned, the

enterprise encourages employees to participate in change, improvisation and the modification of
any service or plan.
The responsibility of Spedition GmbH & Co. KG is based on satisfying internal and
external stakeholders, because these are the key individuals who share the interests of the
organization and its products and services. Accordingly, to establish social benefits, the
objective of the business is to optimize its resources. Further to this, they also endeavor to use
renewable resources in order to prevent scarcity of natural resources, which are limited. Also,
depletion of natural resources can impact on environmental and climatic stability. Thus, the
responsible functioning of management is focused on corporate governance, which aims at
following socially responsible practices.
The problem statement of research which has been discovered through study, states that
Spedition Hendricks GmbH & Co. KG is a service provider for ZUMA BEACH TRADING
LTD. Zuma is a textile wholesaler. However, KG receives an every day delivery from them via
various distribution channels. Every batch contains 900 to 1000 items and every article is
individually numbered. Due to over production, processing and caging consumer trends, there
are various goods which are becoming obsolete. Any dead stock counts as waste, and leads to
wastage of resources. Further, this Muda of stock is impacting on the cost effectiveness of
organization. Thus, in accordance with problems and mis-management it is important to establish
lean management systems to prevent waste and errors in operational activities.
REVIEW OF SELECTED METHODS OF LEAN MANAGEMENT
In accordance to presentation of company and its services with Zuma, the textile
wholesaler it has been identified that it is important for the firm establishing lean management in
order to prevent Muda (Chen, Li and Shady, 2010). However, from the above discussion of
various lean manufacturing and management models by different types of lean managment
which can be nefifical for Spedition Hendricks GmbH & Co. KG, , it has been implied that there
are few strategies whiich can assist in managing the improvement measures for outsourcing
process with the help of lean application of methods. In accordance with the overall discussion
and analysis, few models of lean are considered relevant for outsourcing process of firm are as
follows:
any service or plan.
The responsibility of Spedition GmbH & Co. KG is based on satisfying internal and
external stakeholders, because these are the key individuals who share the interests of the
organization and its products and services. Accordingly, to establish social benefits, the
objective of the business is to optimize its resources. Further to this, they also endeavor to use
renewable resources in order to prevent scarcity of natural resources, which are limited. Also,
depletion of natural resources can impact on environmental and climatic stability. Thus, the
responsible functioning of management is focused on corporate governance, which aims at
following socially responsible practices.
The problem statement of research which has been discovered through study, states that
Spedition Hendricks GmbH & Co. KG is a service provider for ZUMA BEACH TRADING
LTD. Zuma is a textile wholesaler. However, KG receives an every day delivery from them via
various distribution channels. Every batch contains 900 to 1000 items and every article is
individually numbered. Due to over production, processing and caging consumer trends, there
are various goods which are becoming obsolete. Any dead stock counts as waste, and leads to
wastage of resources. Further, this Muda of stock is impacting on the cost effectiveness of
organization. Thus, in accordance with problems and mis-management it is important to establish
lean management systems to prevent waste and errors in operational activities.
REVIEW OF SELECTED METHODS OF LEAN MANAGEMENT
In accordance to presentation of company and its services with Zuma, the textile
wholesaler it has been identified that it is important for the firm establishing lean management in
order to prevent Muda (Chen, Li and Shady, 2010). However, from the above discussion of
various lean manufacturing and management models by different types of lean managment
which can be nefifical for Spedition Hendricks GmbH & Co. KG, , it has been implied that there
are few strategies whiich can assist in managing the improvement measures for outsourcing
process with the help of lean application of methods. In accordance with the overall discussion
and analysis, few models of lean are considered relevant for outsourcing process of firm are as
follows:
Secure Best Marks with AI Grader
Need help grading? Try our AI Grader for instant feedback on your assignments.

Value Stream Mapping
This model could potentially assist the firm in managing their material and information
flow in a proportionate direction. This can assist the firm in managing systematic management
and functioning of logistic operations. This is an effective model for GmbH & Co. KG., because
it focuses on working within time constraints and with a systematic flow of operations. The
model is segregated into two sections: logistic operations and daily plans, where logistic
functions are related to the suppliers and customers of the company. However, the flow between
logistics is related to material flow, which needs to be of the approved quality and best possible
cost.
The daily plan of a logistic value stream is first processed for bulk picking, where a pick
list is managed, generally in two shifts. The second process relates to the picking of items to
another level for checking (Shields, 2016). Checking bulk stock helps the company to make
detailed records of every article in the batch. In the third stage, the picked items are rechecked in
order to maintain appropriate records and details of the packed items. This stage allows
organizations to analyze each and every article in order to prevent theft, loss, scarcity and waste
of resources. After checking every product, the process moves to the next step, which is packing.
The process of two shifts continues in every step, in order to manage workload. However, after
individually packing articles, the stock is packed as a whole. Thus, after overall packaging, the
stock goes for accounting check and shipment of goods. Overall, the process of packing is the
system which requires rework and therefore consumers major time according to every other
processing.
The last processing is shipment of goods through interface, which comprises time and
leads to waste. However, the value stream mapping is a mechanism which designs the overall
process and activity according to their time consumption in activities of Spedition Hendricks
GmbH & Co. KG, (Singh, Garg and Grewal, 2010). Thus, the segregation of activities according
to their timing helps to reduce waste during interface. Hence, it could be stated that value the
streaming process helps and leads business operation in relation to time.
Lean and quality techniques
Lean and quality techniques play an important role in the management of logistic
operations, as they help the firm to manage mistakes and errors when performing operational
functions. Poke Yoke is a management method which can assist in managing systematic
This model could potentially assist the firm in managing their material and information
flow in a proportionate direction. This can assist the firm in managing systematic management
and functioning of logistic operations. This is an effective model for GmbH & Co. KG., because
it focuses on working within time constraints and with a systematic flow of operations. The
model is segregated into two sections: logistic operations and daily plans, where logistic
functions are related to the suppliers and customers of the company. However, the flow between
logistics is related to material flow, which needs to be of the approved quality and best possible
cost.
The daily plan of a logistic value stream is first processed for bulk picking, where a pick
list is managed, generally in two shifts. The second process relates to the picking of items to
another level for checking (Shields, 2016). Checking bulk stock helps the company to make
detailed records of every article in the batch. In the third stage, the picked items are rechecked in
order to maintain appropriate records and details of the packed items. This stage allows
organizations to analyze each and every article in order to prevent theft, loss, scarcity and waste
of resources. After checking every product, the process moves to the next step, which is packing.
The process of two shifts continues in every step, in order to manage workload. However, after
individually packing articles, the stock is packed as a whole. Thus, after overall packaging, the
stock goes for accounting check and shipment of goods. Overall, the process of packing is the
system which requires rework and therefore consumers major time according to every other
processing.
The last processing is shipment of goods through interface, which comprises time and
leads to waste. However, the value stream mapping is a mechanism which designs the overall
process and activity according to their time consumption in activities of Spedition Hendricks
GmbH & Co. KG, (Singh, Garg and Grewal, 2010). Thus, the segregation of activities according
to their timing helps to reduce waste during interface. Hence, it could be stated that value the
streaming process helps and leads business operation in relation to time.
Lean and quality techniques
Lean and quality techniques play an important role in the management of logistic
operations, as they help the firm to manage mistakes and errors when performing operational
functions. Poke Yoke is a management method which can assist in managing systematic

processes by reducing mistakes and errors. It is particularly effective for Spedition Hendricks
GmbH & Co. KG. It helps in preventing mistakes at the initial level that is just after process.
After process the mechanism offers the which is called mistakes for the model assist in setting
prior preventive measure (Chen, Li and Shady, 2010). However, there are certain situations
where mistakes and errors are not visible at the level of processing. This model assist in setting
defection which is related to detecting mistakes not as errors but as defects which eliminates the
use of certain commodity. The continuous process of analysis helps the firm in forming an
assembly line of production functions, which is beneficial in maintaining the quality of goods
and services. Thus, it could be suggested that the Poke Yoke Mechanism can help in lean
management, but it can also assist in lean manufacturing, which is related to the quality of
logistic services.
Aside from this, in relation to the logistics services and operations of Spedition Hendricks
GmbH & Co. KG, it has been identified that the mechanism of the Muda model could help the
firm in lean management in order to maintain efficiency and effectiveness of its goods and
services. It is the responsibility of the firm to ensure the best quality services and good for the
customer. In terms of quality, it is essential for the firm to manage the qualitative aspect of its
services, which can be done through the lean management tool that is Muda (Singh, Garg and
Grewal, 2010). Muda is a Japanese term, and represents waste. Therefore it demonstrates an
effective mechanism for assisting the logistic firm in managing its waste activities through the
management of 7 types of waste within the organization. With the help of over-processing, the
firm will be able to analyze the limits at which the production needs to stopped in order to
prevent waste of resources. Establishing control over waste will also assist management in
monitoring resources and quality.
Waiting time impacts on the cost efficiency of firms. This could hinder the quality
management of Spedition Hendricks GmbH & Co. KG. This step of the model will help in
implementing the management of assembly lines in order to reduce waiting system for batches
with the help of this model the firm will be able to frame step wise process in order to remove
hindrance of functions which leads to wastage of resources. The operation will be settled
according to batch and in order of activities (Palmer, 2011). On the other hand, over-production
is a major cause wastage of resources, which impacts quality and leads to waste. Therefore, in
accordance to product management team will be able to analyze the consumer demand and goods
GmbH & Co. KG. It helps in preventing mistakes at the initial level that is just after process.
After process the mechanism offers the which is called mistakes for the model assist in setting
prior preventive measure (Chen, Li and Shady, 2010). However, there are certain situations
where mistakes and errors are not visible at the level of processing. This model assist in setting
defection which is related to detecting mistakes not as errors but as defects which eliminates the
use of certain commodity. The continuous process of analysis helps the firm in forming an
assembly line of production functions, which is beneficial in maintaining the quality of goods
and services. Thus, it could be suggested that the Poke Yoke Mechanism can help in lean
management, but it can also assist in lean manufacturing, which is related to the quality of
logistic services.
Aside from this, in relation to the logistics services and operations of Spedition Hendricks
GmbH & Co. KG, it has been identified that the mechanism of the Muda model could help the
firm in lean management in order to maintain efficiency and effectiveness of its goods and
services. It is the responsibility of the firm to ensure the best quality services and good for the
customer. In terms of quality, it is essential for the firm to manage the qualitative aspect of its
services, which can be done through the lean management tool that is Muda (Singh, Garg and
Grewal, 2010). Muda is a Japanese term, and represents waste. Therefore it demonstrates an
effective mechanism for assisting the logistic firm in managing its waste activities through the
management of 7 types of waste within the organization. With the help of over-processing, the
firm will be able to analyze the limits at which the production needs to stopped in order to
prevent waste of resources. Establishing control over waste will also assist management in
monitoring resources and quality.
Waiting time impacts on the cost efficiency of firms. This could hinder the quality
management of Spedition Hendricks GmbH & Co. KG. This step of the model will help in
implementing the management of assembly lines in order to reduce waiting system for batches
with the help of this model the firm will be able to frame step wise process in order to remove
hindrance of functions which leads to wastage of resources. The operation will be settled
according to batch and in order of activities (Palmer, 2011). On the other hand, over-production
is a major cause wastage of resources, which impacts quality and leads to waste. Therefore, in
accordance to product management team will be able to analyze the consumer demand and goods

requirement. The coordination between supply and production will assist the company in
reducing waste and making optimizing its use of resources. Thus, using Muda it could be stated
that the Spedition Hendricks GmbH & Co. KG, will be able to control waste over the 7 stages of
over-processing, production, wait, inventory, transportation and motion (Sundar, Balaji and
Kumar, 2014). Hence, this lean management will help the company in reducing waste and
controlling quality in order to serve customers with its premium products and services.
Improvement of cooperation:
Improvement in working conditions or in cooperation is necessary to implement all
logistical processes in the manufacturing industry. Organization can result in increased
productivity and competitiveness with the help of Poka Yoke, as discussed above in this study
(Conger, 2015). This has introduced many company benefits. Poka Yoke helps companies to
avoid mistakes within business processes. Higher levels of productivity and better workplace
action will help to enhance the skills of employees as well as the overall production level. With
the help of proper implementation process of logistic managment will make output better and
productive . These types of manual practices or action plans addressed the in corrective part of
the organization. Group cooperation prevents future uncertainty (D’Andreamatteo Ianni and
Sargiacomo, 2015). Spedition Hendricks Gmbh and Co. KG derive benefits from different terms
to introduce an effective maintenance process. Moreover, it brings new opportunities for the
company to gain the adequate activities and reduce the waste of their products. Poka Yoke is the
concentric term of lean manufacturing that helps to provide opportunities to work in cooperation
or at a group level.
The process can be both effective and challenging deoending on the way in which it is
implemented in the overall process. Kanban, by contrast, is another process for effectively
managing logistic systems, whilst also controllong overall processes of waste and ineffective
manufacturing systems. The main purpose of this is to enhance the overall improvements and
improve areas where cooperation is lacking within the logistic operations of Spedition Hendricks
GmbH & Co. KG, (Greiner, 2015). This also helps to control the unwanted activities within the
system. Cooperation is essential to organizations, as it proffers benefits in terms of work quality
and efficient outputs.
reducing waste and making optimizing its use of resources. Thus, using Muda it could be stated
that the Spedition Hendricks GmbH & Co. KG, will be able to control waste over the 7 stages of
over-processing, production, wait, inventory, transportation and motion (Sundar, Balaji and
Kumar, 2014). Hence, this lean management will help the company in reducing waste and
controlling quality in order to serve customers with its premium products and services.
Improvement of cooperation:
Improvement in working conditions or in cooperation is necessary to implement all
logistical processes in the manufacturing industry. Organization can result in increased
productivity and competitiveness with the help of Poka Yoke, as discussed above in this study
(Conger, 2015). This has introduced many company benefits. Poka Yoke helps companies to
avoid mistakes within business processes. Higher levels of productivity and better workplace
action will help to enhance the skills of employees as well as the overall production level. With
the help of proper implementation process of logistic managment will make output better and
productive . These types of manual practices or action plans addressed the in corrective part of
the organization. Group cooperation prevents future uncertainty (D’Andreamatteo Ianni and
Sargiacomo, 2015). Spedition Hendricks Gmbh and Co. KG derive benefits from different terms
to introduce an effective maintenance process. Moreover, it brings new opportunities for the
company to gain the adequate activities and reduce the waste of their products. Poka Yoke is the
concentric term of lean manufacturing that helps to provide opportunities to work in cooperation
or at a group level.
The process can be both effective and challenging deoending on the way in which it is
implemented in the overall process. Kanban, by contrast, is another process for effectively
managing logistic systems, whilst also controllong overall processes of waste and ineffective
manufacturing systems. The main purpose of this is to enhance the overall improvements and
improve areas where cooperation is lacking within the logistic operations of Spedition Hendricks
GmbH & Co. KG, (Greiner, 2015). This also helps to control the unwanted activities within the
system. Cooperation is essential to organizations, as it proffers benefits in terms of work quality
and efficient outputs.
Paraphrase This Document
Need a fresh take? Get an instant paraphrase of this document with our AI Paraphraser

Transparency and Independence
Effective approaches and models of logistic managment will help to enhance the
transparency level of work through company can esaily manage their stock and warehousing
process. It helps to confirm the better opportunity and growth. Transparency of work refers to
optimum productivity., and is a productive element of accountability in the area of company
independence. This helps to assure better enviornment and improvising nature of the work that
affect overall outcome performances.. Overall, it could bring new changes and better
opportunities to Spedition Hendricks Gmbh and Co. KG in order to process all the work in a
systematic manner. All the models of lean management offer better output results and growth.
Overall, outcomes of the approaches of logistic managment that will help organisation to assure
the better storemaking work. Overall, it provides new challenges and growth can be undertaken
by the company for the purposes of expansion. It has been the subject of discussion and
empirical research, both in developed and developing countries (Heizer, 2016). Based on this
management task, the company needs to be productive and maintain a productive nature of
growth in order to develop the best possible action plan. With the help of the proposed lean
management models and approaches including Kanban, Kaizen and Poka Yoke will help to
manager of Spedition Hendricks GmbH & Co. KG, to gain knowlde over stock and raw material.
Company should adopt the lean managment theories and target goals in order to implement
warehosuing work and proper stock maintenance.. Ultimately, this promotes better opportunities
for work.
The main target of the company is to achieve its goals. Moreover, it brings new
opportunity and growth. In order to achieve the company goals that are to avoid wastage and
improper activity in the overall management which brings new managment targets. This helps to
enable managment goals and proper implemntation process that helps to bring better flow of
stock maintenace. Moreover, it brings new opportunity and growth for Spedition Hendricks
GmbH & Co. KG, which will helps the firm in maintaining better transperancy level in working
performance (Hoffman, 2017). The Kaizen model can help companies to achieve lean
management, which assists in instances where improvements relate to employees and goals.
Transparency of processes tends to lead to better functions and offer opportunities for growth.
Aside from this, it can improve work performance.
Effective approaches and models of logistic managment will help to enhance the
transparency level of work through company can esaily manage their stock and warehousing
process. It helps to confirm the better opportunity and growth. Transparency of work refers to
optimum productivity., and is a productive element of accountability in the area of company
independence. This helps to assure better enviornment and improvising nature of the work that
affect overall outcome performances.. Overall, it could bring new changes and better
opportunities to Spedition Hendricks Gmbh and Co. KG in order to process all the work in a
systematic manner. All the models of lean management offer better output results and growth.
Overall, outcomes of the approaches of logistic managment that will help organisation to assure
the better storemaking work. Overall, it provides new challenges and growth can be undertaken
by the company for the purposes of expansion. It has been the subject of discussion and
empirical research, both in developed and developing countries (Heizer, 2016). Based on this
management task, the company needs to be productive and maintain a productive nature of
growth in order to develop the best possible action plan. With the help of the proposed lean
management models and approaches including Kanban, Kaizen and Poka Yoke will help to
manager of Spedition Hendricks GmbH & Co. KG, to gain knowlde over stock and raw material.
Company should adopt the lean managment theories and target goals in order to implement
warehosuing work and proper stock maintenance.. Ultimately, this promotes better opportunities
for work.
The main target of the company is to achieve its goals. Moreover, it brings new
opportunity and growth. In order to achieve the company goals that are to avoid wastage and
improper activity in the overall management which brings new managment targets. This helps to
enable managment goals and proper implemntation process that helps to bring better flow of
stock maintenace. Moreover, it brings new opportunity and growth for Spedition Hendricks
GmbH & Co. KG, which will helps the firm in maintaining better transperancy level in working
performance (Hoffman, 2017). The Kaizen model can help companies to achieve lean
management, which assists in instances where improvements relate to employees and goals.
Transparency of processes tends to lead to better functions and offer opportunities for growth.
Aside from this, it can improve work performance.

Optimization of warehousing and storage space usage
This is the another mechaninsm for accomplishing better objectives and growth, whilst
delivering improved performance. It can also offer greater work performance levels which can
serve to meet growth and development needs of Spedition Hendricks GmbH & Co. KG. Proper
utilisation of all resources will help to get better opportunity and growth in performance level.
All-in-all, it provides new services and better opportunities for the growth level of work.
Manufacturing is the essential part of the organisation that creates product and services, it is
essential for company to analyse the importance of logistic management and implement proper
models and theories of lean managment (McIvor, 2016). It brings more productive growth and
improved channels for managing the work. Optimizing all warehouses essential resources will
enhance the logistic performance level. Optimization will help to maximize productivity and
target market opportunities. It brings new opportunity to handle logistic issues in better
productive manner. Moreover, optimization of resources gives better objectives and growth to
and giving the best outcome results and productivity level of growth. That helps to take the best
productive manner of growth. Moreover, it will assit the Spedition Hendricks GmbH & Co. KG,
in contributing in the production level of growth (Myerson, 2015). Apart from that, it provides
new skills and opportunities to deliver positive results. It offer better performance and effective
target goals, in addition to improved resource planning and growth. Every warehouse manager
faces challenges in terms of spacial constraints. It gives new valuable growth and task making
performance. Overall, it brings new methods and target goals and productive nature growth.
Overall, growth and challenging nature of task making performance.
Implementing lean management skills and tasks offers new wys of performing.
Warehouses should be managed systematically in terms of presenting task performance goals.
Overall, provides better performance levels and achieves improved services growth. Inventory
efficiency is the strong factor which will assit teh Spedition Hendricks GmbH & Co. KG, in
attaining productive outcomes and having better logistic arrangments.
Value Stream
Value stream it is the leading and value making task performance and goals oriented
work that add more qualitiative work and approches that helps to make better output
performnces. It can offer better performance levels and task-oriented goods and services. This
can grow performance levels (Ptak and Schragenheim, 2016). Moreover, it gives greater
This is the another mechaninsm for accomplishing better objectives and growth, whilst
delivering improved performance. It can also offer greater work performance levels which can
serve to meet growth and development needs of Spedition Hendricks GmbH & Co. KG. Proper
utilisation of all resources will help to get better opportunity and growth in performance level.
All-in-all, it provides new services and better opportunities for the growth level of work.
Manufacturing is the essential part of the organisation that creates product and services, it is
essential for company to analyse the importance of logistic management and implement proper
models and theories of lean managment (McIvor, 2016). It brings more productive growth and
improved channels for managing the work. Optimizing all warehouses essential resources will
enhance the logistic performance level. Optimization will help to maximize productivity and
target market opportunities. It brings new opportunity to handle logistic issues in better
productive manner. Moreover, optimization of resources gives better objectives and growth to
and giving the best outcome results and productivity level of growth. That helps to take the best
productive manner of growth. Moreover, it will assit the Spedition Hendricks GmbH & Co. KG,
in contributing in the production level of growth (Myerson, 2015). Apart from that, it provides
new skills and opportunities to deliver positive results. It offer better performance and effective
target goals, in addition to improved resource planning and growth. Every warehouse manager
faces challenges in terms of spacial constraints. It gives new valuable growth and task making
performance. Overall, it brings new methods and target goals and productive nature growth.
Overall, growth and challenging nature of task making performance.
Implementing lean management skills and tasks offers new wys of performing.
Warehouses should be managed systematically in terms of presenting task performance goals.
Overall, provides better performance levels and achieves improved services growth. Inventory
efficiency is the strong factor which will assit teh Spedition Hendricks GmbH & Co. KG, in
attaining productive outcomes and having better logistic arrangments.
Value Stream
Value stream it is the leading and value making task performance and goals oriented
work that add more qualitiative work and approches that helps to make better output
performnces. It can offer better performance levels and task-oriented goods and services. This
can grow performance levels (Ptak and Schragenheim, 2016). Moreover, it gives greater
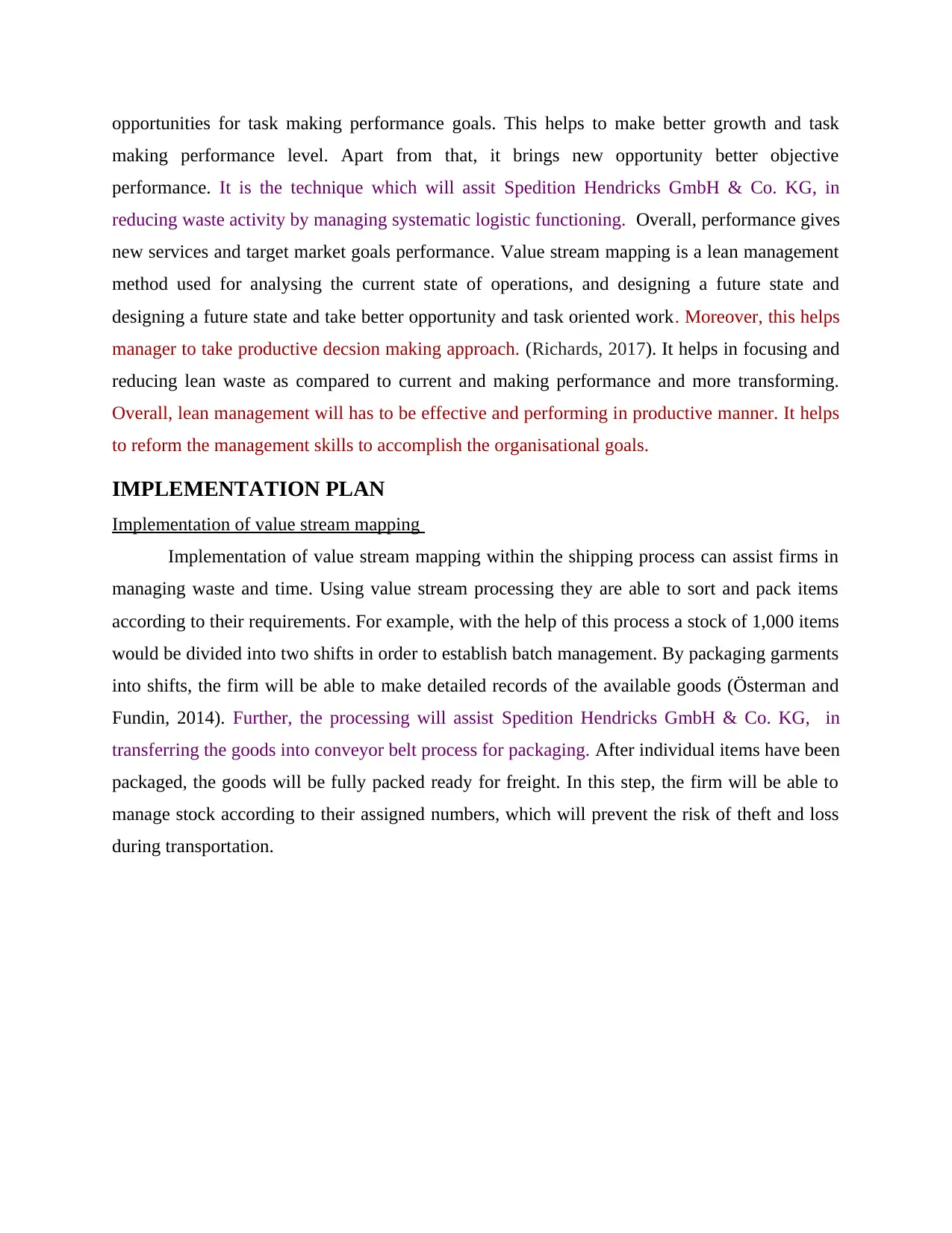
opportunities for task making performance goals. This helps to make better growth and task
making performance level. Apart from that, it brings new opportunity better objective
performance. It is the technique which will assit Spedition Hendricks GmbH & Co. KG, in
reducing waste activity by managing systematic logistic functioning. Overall, performance gives
new services and target market goals performance. Value stream mapping is a lean management
method used for analysing the current state of operations, and designing a future state and
designing a future state and take better opportunity and task oriented work. Moreover, this helps
manager to take productive decsion making approach. (Richards, 2017). It helps in focusing and
reducing lean waste as compared to current and making performance and more transforming.
Overall, lean management will has to be effective and performing in productive manner. It helps
to reform the management skills to accomplish the organisational goals.
IMPLEMENTATION PLAN
Implementation of value stream mapping
Implementation of value stream mapping within the shipping process can assist firms in
managing waste and time. Using value stream processing they are able to sort and pack items
according to their requirements. For example, with the help of this process a stock of 1,000 items
would be divided into two shifts in order to establish batch management. By packaging garments
into shifts, the firm will be able to make detailed records of the available goods (Österman and
Fundin, 2014). Further, the processing will assist Spedition Hendricks GmbH & Co. KG, in
transferring the goods into conveyor belt process for packaging. After individual items have been
packaged, the goods will be fully packed ready for freight. In this step, the firm will be able to
manage stock according to their assigned numbers, which will prevent the risk of theft and loss
during transportation.
making performance level. Apart from that, it brings new opportunity better objective
performance. It is the technique which will assit Spedition Hendricks GmbH & Co. KG, in
reducing waste activity by managing systematic logistic functioning. Overall, performance gives
new services and target market goals performance. Value stream mapping is a lean management
method used for analysing the current state of operations, and designing a future state and
designing a future state and take better opportunity and task oriented work. Moreover, this helps
manager to take productive decsion making approach. (Richards, 2017). It helps in focusing and
reducing lean waste as compared to current and making performance and more transforming.
Overall, lean management will has to be effective and performing in productive manner. It helps
to reform the management skills to accomplish the organisational goals.
IMPLEMENTATION PLAN
Implementation of value stream mapping
Implementation of value stream mapping within the shipping process can assist firms in
managing waste and time. Using value stream processing they are able to sort and pack items
according to their requirements. For example, with the help of this process a stock of 1,000 items
would be divided into two shifts in order to establish batch management. By packaging garments
into shifts, the firm will be able to make detailed records of the available goods (Österman and
Fundin, 2014). Further, the processing will assist Spedition Hendricks GmbH & Co. KG, in
transferring the goods into conveyor belt process for packaging. After individual items have been
packaged, the goods will be fully packed ready for freight. In this step, the firm will be able to
manage stock according to their assigned numbers, which will prevent the risk of theft and loss
during transportation.
Secure Best Marks with AI Grader
Need help grading? Try our AI Grader for instant feedback on your assignments.

The operations team will unload the boxes in a logical order, according to their numbers,
to reduce the chance of confusion and negligence of resources. For example, if there are 200
packages, then the movement of the packages will be set according to the distribution of the
batches in order to reduce the chance of confusion. Here, value stream mapping will benefit
Spedition Hendricks GmbH & Co. KG, by promoting quality control of the goods at the time of
individual packaging (Begam, Swamynathan and Sekkizhar, 2013). This process is time
consuming because it relates to product quality, which directly impacts on the consumers. By
employing this mechanism, the organisation will be able to maintain its logistics as it assists in
recording the repetition of particular items. The individual packaging of items within whole
packages allows the firm to better manage stock availability, which will ultimately help them to
manage dead stock. Lastly, the stock is shifted to the next station and has a system-printed GLS
label applied to them, ready for pickup. The collection and management of stock can be done
overnight in order prevent wasting time, stock management and recognition. The final process is
related to the customer supply, which will be managed with the help of individual stock. Thus,
based on the discussion outlined above, implementation of value steam processes in the context
of Hendricks Internationale Spedition GmbH & Co. KG could encourage lean management
shipping processes.
Illustration 7: Value stream mapping for Spedition Hendricks GmbH & Co. KG.
Source: (Chen, Li and Shady, 2010)
to reduce the chance of confusion and negligence of resources. For example, if there are 200
packages, then the movement of the packages will be set according to the distribution of the
batches in order to reduce the chance of confusion. Here, value stream mapping will benefit
Spedition Hendricks GmbH & Co. KG, by promoting quality control of the goods at the time of
individual packaging (Begam, Swamynathan and Sekkizhar, 2013). This process is time
consuming because it relates to product quality, which directly impacts on the consumers. By
employing this mechanism, the organisation will be able to maintain its logistics as it assists in
recording the repetition of particular items. The individual packaging of items within whole
packages allows the firm to better manage stock availability, which will ultimately help them to
manage dead stock. Lastly, the stock is shifted to the next station and has a system-printed GLS
label applied to them, ready for pickup. The collection and management of stock can be done
overnight in order prevent wasting time, stock management and recognition. The final process is
related to the customer supply, which will be managed with the help of individual stock. Thus,
based on the discussion outlined above, implementation of value steam processes in the context
of Hendricks Internationale Spedition GmbH & Co. KG could encourage lean management
shipping processes.
Illustration 7: Value stream mapping for Spedition Hendricks GmbH & Co. KG.
Source: (Chen, Li and Shady, 2010)

Apart from this, it can be said that to maintain effectivenes sin outsourcing process teh
firm can imp-lement the use of measures such as Spedition Hendricks GmbH & Co. KG, will be
focusing on listing outsourcing activities in order to reduce the chance of maintaining dead stock
which creates huge impact on lean engagement of organization.
Implementation of Muda (Waste)
Spedition Hendricks GmbH & Co. KG, will implement the Muda model to assist the
organization in managing the 7 stages related to resource waste and time that; both of which
hamper the cost effectiveness of business functions. Thus, implementing a waste mechanism will
help the company to exert control over production, which will allow them greater utilization of
stock which remains unused due to changing consumer trends. The limitation production process
is directly linked to processing, which will help with the time management of different activities
and stages in assembly line operational process (Taleghani, 2010). Further, the limited
production process will reduce waiting times for exit activity and batches, which again help the
team in managing cost the effectiveness of goods by delivering them on time and according to
buyers needs and wants. Additionally, managing transportation in batches and with the help of
individuals packaging will allow the firm to maintain appropriate recording of articles, which
helps in regulating defects, losses delays.
Evidently, check over transportation could be of benefit to Spedition Hendricks GmbH &
Co. KG, in terms of stock management, in order to prevent resource waste due to oversupply and
dead stock. In addition, monitoring inventory plays an important role and will assist the
organization in checking their raw materials, work in progress and the processing of finished
products. Nevertheless, reviewing inventory at every stage will help in lean management and
regulating checks over quality of products and services (Rahman, Laosirihongthong and Sohal,
2010). Motion and defects are the two stages which are inter-related, and therefore suitable for
setting improvement measures of outsourcing processes. The application of lean management at
the shipping logistics transfer that is bulk of transfer. This monitoring and reviewing will help
management in analyzing areas which lead to waste of resources and time.
Further, Spedition Hendricks GmbH & Co. KG, will implement monitoring team who
will be responsible for looking at systematic functioning of logistic functions. This team will be
responsible for analyzing loopholes in series of management outsourcing process which can lead
to waste.
firm can imp-lement the use of measures such as Spedition Hendricks GmbH & Co. KG, will be
focusing on listing outsourcing activities in order to reduce the chance of maintaining dead stock
which creates huge impact on lean engagement of organization.
Implementation of Muda (Waste)
Spedition Hendricks GmbH & Co. KG, will implement the Muda model to assist the
organization in managing the 7 stages related to resource waste and time that; both of which
hamper the cost effectiveness of business functions. Thus, implementing a waste mechanism will
help the company to exert control over production, which will allow them greater utilization of
stock which remains unused due to changing consumer trends. The limitation production process
is directly linked to processing, which will help with the time management of different activities
and stages in assembly line operational process (Taleghani, 2010). Further, the limited
production process will reduce waiting times for exit activity and batches, which again help the
team in managing cost the effectiveness of goods by delivering them on time and according to
buyers needs and wants. Additionally, managing transportation in batches and with the help of
individuals packaging will allow the firm to maintain appropriate recording of articles, which
helps in regulating defects, losses delays.
Evidently, check over transportation could be of benefit to Spedition Hendricks GmbH &
Co. KG, in terms of stock management, in order to prevent resource waste due to oversupply and
dead stock. In addition, monitoring inventory plays an important role and will assist the
organization in checking their raw materials, work in progress and the processing of finished
products. Nevertheless, reviewing inventory at every stage will help in lean management and
regulating checks over quality of products and services (Rahman, Laosirihongthong and Sohal,
2010). Motion and defects are the two stages which are inter-related, and therefore suitable for
setting improvement measures of outsourcing processes. The application of lean management at
the shipping logistics transfer that is bulk of transfer. This monitoring and reviewing will help
management in analyzing areas which lead to waste of resources and time.
Further, Spedition Hendricks GmbH & Co. KG, will implement monitoring team who
will be responsible for looking at systematic functioning of logistic functions. This team will be
responsible for analyzing loopholes in series of management outsourcing process which can lead
to waste.

Implementation of Poka Yuke
Poka Yuke offers opportunities to improve the quality of logistic performance. The goal
of manufacturing is to provide value added products in a timely manner. Thus, implementing this
process within the system is much necessary to meet organization goals.
Hence, in accordance with the implementation plan, it can be concluded that it important
for the organization to set improvement measures as per the mechanisms of lean management.
This change will assist the firm in dealing with waste activities which are hampering the quality
of goods. Further to this, it will facilitate easy management of operations in accordance with
assembly line production and management. Finally, implementation will be advantageous to the
enterprise as it will help the company to slowly reduce its problems of stock waste due to
changes in market and consumer trends.
In contrast, for managing lead and customer expectation Spedition Hendricks GmbH &
Co. KG, will be focusing on trial run where the firm will focus on analyzing first outsourcing
ability. This will assist the firm in gaining knowledge over vendor outsourcing, employees and
consumers. It is improvement plan which will helps the organization in deriving suitable
solutions to fulfill expectation of managing land and serving customer satisfaction.
Poka Yuke offers opportunities to improve the quality of logistic performance. The goal
of manufacturing is to provide value added products in a timely manner. Thus, implementing this
process within the system is much necessary to meet organization goals.
Hence, in accordance with the implementation plan, it can be concluded that it important
for the organization to set improvement measures as per the mechanisms of lean management.
This change will assist the firm in dealing with waste activities which are hampering the quality
of goods. Further to this, it will facilitate easy management of operations in accordance with
assembly line production and management. Finally, implementation will be advantageous to the
enterprise as it will help the company to slowly reduce its problems of stock waste due to
changes in market and consumer trends.
In contrast, for managing lead and customer expectation Spedition Hendricks GmbH &
Co. KG, will be focusing on trial run where the firm will focus on analyzing first outsourcing
ability. This will assist the firm in gaining knowledge over vendor outsourcing, employees and
consumers. It is improvement plan which will helps the organization in deriving suitable
solutions to fulfill expectation of managing land and serving customer satisfaction.
Paraphrase This Document
Need a fresh take? Get an instant paraphrase of this document with our AI Paraphraser

CONCLUSION
This dissertation considered the different applications of lean management which are
available to Spedition Hendricks GmbH and Co. KG to improve their shipping functions and
reduce waste. The report developed a critical understanding of lean management and its various
methods, including Muda, 5 s strategy, Poke Yoke and value stream mapping. The research
centered on the study of secondary sources, and explored the practical implementation of the
available approaches in relation to the company and its responsibilities.
The first chapter outlined the aims of the study and identified the existing problems
which have necessitated the later analysis of lean methods. To develop a critical understanding of
the company and its major issues, the thesis first presented a background to the study, where the
aim was to explore the improvement measures of outsourcing processes through the application
of methods of lean management within the context of shipping: A case study on Spedition
Hendricks GmbH and Co. KG. The base of the aim is problem statement from which it has been
outlined that firm lacks in lean management. Further, to prevent waste which is hamper quality
of company’s products and services an also can become turbulence to firm’s objective to attain
competitive advantage.
The secondary phase of the study is based on secondary research in which the researcher
outlined different lean management methods and their implications to companies for improving
functions and management of activities. The secondary sources explored included case studies,
articles, books and journals. In this the scholar outlined about lean management which helps the
firm in establishing functions in one same direction in order to serve customer demands and to
maintain competitive advantage. The discussion in this study outlined about the Muda (waste)
mechanism, which is focused on over-processing, waiting, over-production, transportation,
inventor and motion, defects. In addition to this, it outlined the views of various scholars and
authors on lean culture, which relates to the 7 s of management: sorting of activities, setting
functions in order, shining, which is related to a positive work environment, safety,
standardizing, which is focused on improvising, and sustaining, which is related to stock
management, inventory management, production, transport, waste and productivity.
Apart from this, the discussion of secondary sources was based on value stream mapping,
which is the most effective use of lean management, as it is focused on specific business
This dissertation considered the different applications of lean management which are
available to Spedition Hendricks GmbH and Co. KG to improve their shipping functions and
reduce waste. The report developed a critical understanding of lean management and its various
methods, including Muda, 5 s strategy, Poke Yoke and value stream mapping. The research
centered on the study of secondary sources, and explored the practical implementation of the
available approaches in relation to the company and its responsibilities.
The first chapter outlined the aims of the study and identified the existing problems
which have necessitated the later analysis of lean methods. To develop a critical understanding of
the company and its major issues, the thesis first presented a background to the study, where the
aim was to explore the improvement measures of outsourcing processes through the application
of methods of lean management within the context of shipping: A case study on Spedition
Hendricks GmbH and Co. KG. The base of the aim is problem statement from which it has been
outlined that firm lacks in lean management. Further, to prevent waste which is hamper quality
of company’s products and services an also can become turbulence to firm’s objective to attain
competitive advantage.
The secondary phase of the study is based on secondary research in which the researcher
outlined different lean management methods and their implications to companies for improving
functions and management of activities. The secondary sources explored included case studies,
articles, books and journals. In this the scholar outlined about lean management which helps the
firm in establishing functions in one same direction in order to serve customer demands and to
maintain competitive advantage. The discussion in this study outlined about the Muda (waste)
mechanism, which is focused on over-processing, waiting, over-production, transportation,
inventor and motion, defects. In addition to this, it outlined the views of various scholars and
authors on lean culture, which relates to the 7 s of management: sorting of activities, setting
functions in order, shining, which is related to a positive work environment, safety,
standardizing, which is focused on improvising, and sustaining, which is related to stock
management, inventory management, production, transport, waste and productivity.
Apart from this, the discussion of secondary sources was based on value stream mapping,
which is the most effective use of lean management, as it is focused on specific business

processes according to different activities within limited time constraints in order to establish
control over waste and to monitor the quality of products. The reviews of the scholar concluded
with an evaluation of the Plan Do Check Act Cycle, the Standardization concept, First in, first
out lean management, One-piece Flow, Kanban, Kaizen and Poka Yoke. It was determined that
secondary study was effective because it helps develop a critical understanding of every topic,
with the help of different suggestions and visual representation such as illustrations.
The next phase of the theses explored the company itself. It was noted that Hendricks
Internationale Spedition GmbH & Co. KG is a logistic and service provider founded in 1972 by
Edurad Hendrick in Germany. The firm started on a small scale, but quickly grew. The problem
statement of study has been also derived from the creative activities of both the organization
which arise with shipment. The chapter concluded with the firm’s responsibilities, which is based
on serving satisfaction to internal and external stakeholders. From the presentation, it has been
outlined that the philosophy of the organization is based on serving consumer satisfaction by
maintain quality of products a cost transparency with the help of lean management.
The study concluded with a balanced decision as to which lean management tools should
be implemented by Spedition Hendricks GmbH and Co. KG. The chosen tools were value stream
mapping, Muda and Poka Hoke. However, the reviewed tools were implemented in the
organization with the help of target stated which is based on key consideration of business
including improvements of cooperation. Further, Optimization of warehousing and storage space
usage, value streaming, transparency and independence. Hence, after implementing it can be
concluded that lean management has assisted the firm in setting improvement measures in
activities by setting functions in order to minimize waste and errors.
control over waste and to monitor the quality of products. The reviews of the scholar concluded
with an evaluation of the Plan Do Check Act Cycle, the Standardization concept, First in, first
out lean management, One-piece Flow, Kanban, Kaizen and Poka Yoke. It was determined that
secondary study was effective because it helps develop a critical understanding of every topic,
with the help of different suggestions and visual representation such as illustrations.
The next phase of the theses explored the company itself. It was noted that Hendricks
Internationale Spedition GmbH & Co. KG is a logistic and service provider founded in 1972 by
Edurad Hendrick in Germany. The firm started on a small scale, but quickly grew. The problem
statement of study has been also derived from the creative activities of both the organization
which arise with shipment. The chapter concluded with the firm’s responsibilities, which is based
on serving satisfaction to internal and external stakeholders. From the presentation, it has been
outlined that the philosophy of the organization is based on serving consumer satisfaction by
maintain quality of products a cost transparency with the help of lean management.
The study concluded with a balanced decision as to which lean management tools should
be implemented by Spedition Hendricks GmbH and Co. KG. The chosen tools were value stream
mapping, Muda and Poka Hoke. However, the reviewed tools were implemented in the
organization with the help of target stated which is based on key consideration of business
including improvements of cooperation. Further, Optimization of warehousing and storage space
usage, value streaming, transparency and independence. Hence, after implementing it can be
concluded that lean management has assisted the firm in setting improvement measures in
activities by setting functions in order to minimize waste and errors.

REFERENCES
Books and Journals
Ansah, R.H., Sorooshian, S. and Mustafa, S.B., 2016. Lean construction: an effective approach for project
management. ARPN Journal of Engineering and Applied Sciences. 11(3). pp.1607-1612.
Begam, M.S., Swamynathan, R. and Sekkizhar, J., 2013. Current trends on lean management–A review.
International Journal of lean thinking. 4(2). pp.15-21.
Chen, J.C., Li, Y. and Shady, B.D., 2010. From value stream mapping toward a lean/sigma continuous improvement
process: an industrial case study. International Journal of Production Research. 48(4). pp.1069-1086.
Conger, S., 2015. Six sigma and business process management. In Handbook on Business Process Management
1 (pp. 127-146). Springer, Berlin, Heidelberg.
D’Andreamatteo, A., Ianni, L. and Sargiacomo, M., 2015. Lean in healthcare: A comprehensive review. Health
policy. 119(9). pp.1197-1209.
Dave, B., Kubler, S. and Koskela, L., 2015. Intelligent products: shifting the production control logic in construction
(with Lean and BIM). In Proceedings of the 23rd Annual Conference of the International Group for
Lean Construction. Perth, Australia, 29-31 July 2015. International Group for Lean Construction.
Faulkner, W. and Badurdeen, F., 2014. Sustainable Value Stream Mapping (Sus-VSM): methodology to visualize
and assess manufacturing sustainability performance. Journal of cleaner production, 85, pp.8-18.
Forbes, L.H. and Ahmed, S.M., 2010. Modern construction: lean project delivery and integrated practices. Crc
Press.
Freytag, P.V. and Evald, M.R., 2016. Implementation of lean in the elderly care sector; how does it affect the
behaviour of the organisation members?. 7 Challenging traditional leadership behaviors in a distributed
and ambiguous knowledge-intensive work environment. p.47.
Greiner, M., 2015. A comparison of lean management in the automotive and telecommunications sectors.
Gurumurthy, A. and Kodali, R., 2011. Design of lean manufacturing systems using value stream mapping with
simulation: a case study. Journal of Manufacturing Technology Management. 22(4). pp.444-473.
Heizer, J., 2016. Operations Management, 11/e. Pearson Education India.
Hoffman, K. L., 2017. Improving the Effectiveness of Forensic DNA Testing Services through the Application of
Lean Principles. Forensic Science Policy & Management: An International Journal. 8(1-2). pp.47-54.
Keyte, B. and Locher, D.A., 2016. The complete lean enterprise: Value stream mapping for administrative and
office processes. Productivity Press.
Martin, K. and Osterling, M., 2014. Value stream mapping. Estados Unidos de América: Shingo Institute.
McIvor, R., 2016. An analysis of the application of process improvement techniques in business process
outsourcing. International Journal of Quality & Reliability Management. 33(3). pp.321-343.
Meza, D. and Jeong, K.Y., 2013. Measuring efficiency of lean six sigma project implementation using data
envelopment analysis at NASA. Journal of Industrial Engineering and Management. 6(2). pp.401.
Moreira, F., Alves, A.C. and Sousa, R.M., 2010. Towards eco-efficient lean production systems. In Balanced
Automation Systems for Future Manufacturing Networks (pp. 100-108). Springer, Berlin, Heidelberg.
28
Books and Journals
Ansah, R.H., Sorooshian, S. and Mustafa, S.B., 2016. Lean construction: an effective approach for project
management. ARPN Journal of Engineering and Applied Sciences. 11(3). pp.1607-1612.
Begam, M.S., Swamynathan, R. and Sekkizhar, J., 2013. Current trends on lean management–A review.
International Journal of lean thinking. 4(2). pp.15-21.
Chen, J.C., Li, Y. and Shady, B.D., 2010. From value stream mapping toward a lean/sigma continuous improvement
process: an industrial case study. International Journal of Production Research. 48(4). pp.1069-1086.
Conger, S., 2015. Six sigma and business process management. In Handbook on Business Process Management
1 (pp. 127-146). Springer, Berlin, Heidelberg.
D’Andreamatteo, A., Ianni, L. and Sargiacomo, M., 2015. Lean in healthcare: A comprehensive review. Health
policy. 119(9). pp.1197-1209.
Dave, B., Kubler, S. and Koskela, L., 2015. Intelligent products: shifting the production control logic in construction
(with Lean and BIM). In Proceedings of the 23rd Annual Conference of the International Group for
Lean Construction. Perth, Australia, 29-31 July 2015. International Group for Lean Construction.
Faulkner, W. and Badurdeen, F., 2014. Sustainable Value Stream Mapping (Sus-VSM): methodology to visualize
and assess manufacturing sustainability performance. Journal of cleaner production, 85, pp.8-18.
Forbes, L.H. and Ahmed, S.M., 2010. Modern construction: lean project delivery and integrated practices. Crc
Press.
Freytag, P.V. and Evald, M.R., 2016. Implementation of lean in the elderly care sector; how does it affect the
behaviour of the organisation members?. 7 Challenging traditional leadership behaviors in a distributed
and ambiguous knowledge-intensive work environment. p.47.
Greiner, M., 2015. A comparison of lean management in the automotive and telecommunications sectors.
Gurumurthy, A. and Kodali, R., 2011. Design of lean manufacturing systems using value stream mapping with
simulation: a case study. Journal of Manufacturing Technology Management. 22(4). pp.444-473.
Heizer, J., 2016. Operations Management, 11/e. Pearson Education India.
Hoffman, K. L., 2017. Improving the Effectiveness of Forensic DNA Testing Services through the Application of
Lean Principles. Forensic Science Policy & Management: An International Journal. 8(1-2). pp.47-54.
Keyte, B. and Locher, D.A., 2016. The complete lean enterprise: Value stream mapping for administrative and
office processes. Productivity Press.
Martin, K. and Osterling, M., 2014. Value stream mapping. Estados Unidos de América: Shingo Institute.
McIvor, R., 2016. An analysis of the application of process improvement techniques in business process
outsourcing. International Journal of Quality & Reliability Management. 33(3). pp.321-343.
Meza, D. and Jeong, K.Y., 2013. Measuring efficiency of lean six sigma project implementation using data
envelopment analysis at NASA. Journal of Industrial Engineering and Management. 6(2). pp.401.
Moreira, F., Alves, A.C. and Sousa, R.M., 2010. Towards eco-efficient lean production systems. In Balanced
Automation Systems for Future Manufacturing Networks (pp. 100-108). Springer, Berlin, Heidelberg.
28
Secure Best Marks with AI Grader
Need help grading? Try our AI Grader for instant feedback on your assignments.

Myerson, P. A., 2015. Supply chain and logistics management made easy: methods and applications for planning,
operations, integration, control and improvement, and network design. Pearson Education.
Österman, C. and Fundin, A., 2014. Exploring approaches how to measure a lean process. Organizacija. 47(3).
pp.132-142.
Palmer, V.S., 2011. Inventory management KAIZEN. In Engineering Management for Applied Technology, 2001.
EMAT 2001. Proceedings. 2nd International Workshop on (pp. 55-56). IEEE.
Potente, T., Jasinski, T. and Wolff, B., 2013. Productivity Increase through Industrialization of Overhead in Cyber-
Physical Production Systems. In Advanced Materials Research. Trans Tech Publications. (Vol. 769, pp.
359-366).
Ptak, C. A. and Schragenheim, E., 2016. ERP: tools, techniques, and applications for integrating the supply chain.
Crc Press.
Rahani, A.R. and Al-Ashraf, M., 2012. Production flow analysis through value stream mapping: a lean
manufacturing process case study. Procedia Engineering. 41. pp.1727-1734.
Rahman, S., Laosirihongthong, T. and Sohal, A.S., 2010. Impact of lean strategy on operational performance: a
study of Thai manufacturing companies. Journal of manufacturing technology management. 21(7).
pp.839-852.
Richards, G., 2017. Warehouse management: a complete guide to improving efficiency and minimizing costs in the
modern warehouse. Kogan Page Publishers.
Roosen, T.J. and Pons, D.J., 2013. Environmentally lean production: the development and incorporation of an
environmental impact index into value stream mapping. Journal of Industrial Engineering. 2013.
Shields, H., 2016. Attacking Lean Wastes. Quality Progress. 39(8). pp.78.
Singh, B., Garg, S.K. and Grewal, C., 2010. Lean implementation and its benefits to production industry.
International journal of lean six sigma. 1(2). pp.157-168.
Singh, B., Garg, S.K. and Sharma, S.K., 2011. Value stream mapping: literature review and implications for Indian
industry. The International Journal of Advanced Manufacturing Technology. 53(5-8). pp.799-809.
Sundar, R., Balaji, A.N. and Kumar, R.S., 2014. A review on lean manufacturing implementation techniques.
Procedia Engineering. 97. pp.1875-1885.
Taleghani, M., 2010. Key factors for implementing the lean manufacturing system. Journal of American science.
6(7). pp.287-291.
Tandler, S.M., 2013. Bedeutung eines Supply Chain Safety Managements für lean-agile Supply Chains. In Supply
Chain Safety Management. Springer Gabler, Wiesbaden. (pp. 1-13).
Theory and Taleghani, M., 2010. Key factors for implementing the lean manufacturing system. Journal of American
science. 6(7). pp.287-291.
Tyagi, S., Choudhary, A. and Yang, K., 2015. Value stream mapping to reduce the lead-time of a product
development process. International Journal of Production Economics. 160. pp.202-212.
29
operations, integration, control and improvement, and network design. Pearson Education.
Österman, C. and Fundin, A., 2014. Exploring approaches how to measure a lean process. Organizacija. 47(3).
pp.132-142.
Palmer, V.S., 2011. Inventory management KAIZEN. In Engineering Management for Applied Technology, 2001.
EMAT 2001. Proceedings. 2nd International Workshop on (pp. 55-56). IEEE.
Potente, T., Jasinski, T. and Wolff, B., 2013. Productivity Increase through Industrialization of Overhead in Cyber-
Physical Production Systems. In Advanced Materials Research. Trans Tech Publications. (Vol. 769, pp.
359-366).
Ptak, C. A. and Schragenheim, E., 2016. ERP: tools, techniques, and applications for integrating the supply chain.
Crc Press.
Rahani, A.R. and Al-Ashraf, M., 2012. Production flow analysis through value stream mapping: a lean
manufacturing process case study. Procedia Engineering. 41. pp.1727-1734.
Rahman, S., Laosirihongthong, T. and Sohal, A.S., 2010. Impact of lean strategy on operational performance: a
study of Thai manufacturing companies. Journal of manufacturing technology management. 21(7).
pp.839-852.
Richards, G., 2017. Warehouse management: a complete guide to improving efficiency and minimizing costs in the
modern warehouse. Kogan Page Publishers.
Roosen, T.J. and Pons, D.J., 2013. Environmentally lean production: the development and incorporation of an
environmental impact index into value stream mapping. Journal of Industrial Engineering. 2013.
Shields, H., 2016. Attacking Lean Wastes. Quality Progress. 39(8). pp.78.
Singh, B., Garg, S.K. and Grewal, C., 2010. Lean implementation and its benefits to production industry.
International journal of lean six sigma. 1(2). pp.157-168.
Singh, B., Garg, S.K. and Sharma, S.K., 2011. Value stream mapping: literature review and implications for Indian
industry. The International Journal of Advanced Manufacturing Technology. 53(5-8). pp.799-809.
Sundar, R., Balaji, A.N. and Kumar, R.S., 2014. A review on lean manufacturing implementation techniques.
Procedia Engineering. 97. pp.1875-1885.
Taleghani, M., 2010. Key factors for implementing the lean manufacturing system. Journal of American science.
6(7). pp.287-291.
Tandler, S.M., 2013. Bedeutung eines Supply Chain Safety Managements für lean-agile Supply Chains. In Supply
Chain Safety Management. Springer Gabler, Wiesbaden. (pp. 1-13).
Theory and Taleghani, M., 2010. Key factors for implementing the lean manufacturing system. Journal of American
science. 6(7). pp.287-291.
Tyagi, S., Choudhary, A. and Yang, K., 2015. Value stream mapping to reduce the lead-time of a product
development process. International Journal of Production Economics. 160. pp.202-212.
29

Uygun, Y. and Wagner, S.U., 2011. Guidelines for human-based implementation of lean production. In Proceedings
of 44th CIRP International Conference on Manufacturing Systems-New Worlds of Manufacturing.
Omnipress: Madison, Wisconsin.
Vinodh, S., Ruben, R.B. and Asokan, P., 2016. Life cycle assessment integrated value stream mapping framework
to ensure sustainable manufacturing: a case study. Clean Technologies and Environmental Policy. 18(1).
pp.279-295.
Yamamoto, Y. and Bellgran, M., 2010. Fundamental mindset that drives improvements towards lean production.
Assembly Automation. 30(2). pp.124-130.
Zokaei, K., Lovins, H. and Hines, P., 2016. Creating a lean and green business system: techniques for improving
profits and sustainability. Productivity Press.
Online
Practice on FiFo Lanes – How Does FiFo Work in Lean Manufacturing?. 2014. [Online]. Available through:
<https://www.allaboutlean.com/fifo-lane/>.
Standardized Work: The Foundation for Kaizen. 2017. [Online]. Available through:
<https://www.lean.org/Workshops/WorkshopDescription.cfm?WorkshopId=20>.
30
of 44th CIRP International Conference on Manufacturing Systems-New Worlds of Manufacturing.
Omnipress: Madison, Wisconsin.
Vinodh, S., Ruben, R.B. and Asokan, P., 2016. Life cycle assessment integrated value stream mapping framework
to ensure sustainable manufacturing: a case study. Clean Technologies and Environmental Policy. 18(1).
pp.279-295.
Yamamoto, Y. and Bellgran, M., 2010. Fundamental mindset that drives improvements towards lean production.
Assembly Automation. 30(2). pp.124-130.
Zokaei, K., Lovins, H. and Hines, P., 2016. Creating a lean and green business system: techniques for improving
profits and sustainability. Productivity Press.
Online
Practice on FiFo Lanes – How Does FiFo Work in Lean Manufacturing?. 2014. [Online]. Available through:
<https://www.allaboutlean.com/fifo-lane/>.
Standardized Work: The Foundation for Kaizen. 2017. [Online]. Available through:
<https://www.lean.org/Workshops/WorkshopDescription.cfm?WorkshopId=20>.
30
1 out of 30
![[object Object]](/_next/image/?url=%2F_next%2Fstatic%2Fmedia%2Flogo.6d15ce61.png&w=640&q=75)
Your All-in-One AI-Powered Toolkit for Academic Success.
+13062052269
info@desklib.com
Available 24*7 on WhatsApp / Email
Unlock your academic potential
© 2024 | Zucol Services PVT LTD | All rights reserved.