Improving Supply Chain at IKEA
VerifiedAdded on 2023/01/05
|11
|2740
|79
AI Summary
This report focuses on the case study of IKEA and evaluates the issues in its supply chain. It provides recommendations to improve the supply chain and a project plan. Subject: Supply Chain Management
Contribute Materials
Your contribution can guide someone’s learning journey. Share your
documents today.
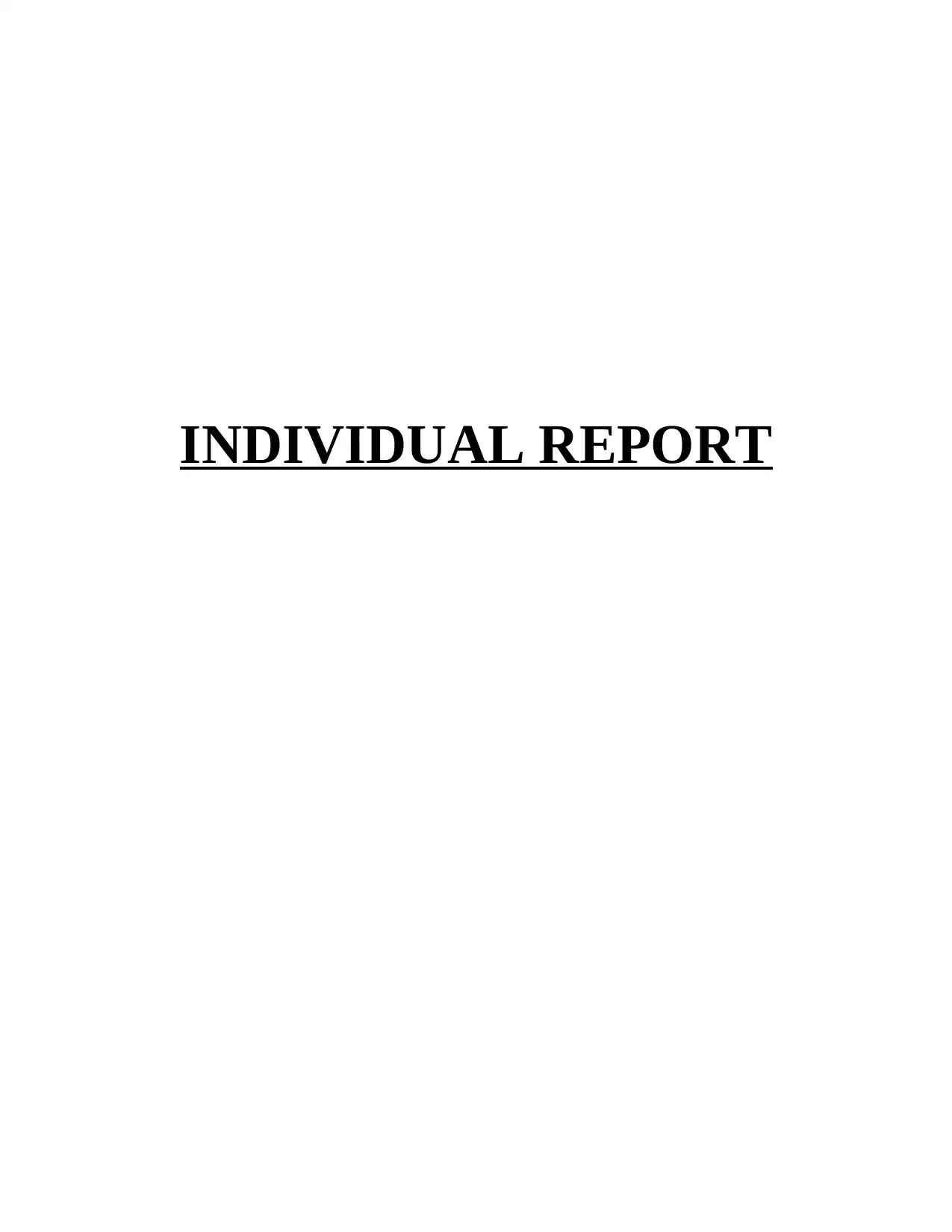
INDIVIDUAL REPORT
Secure Best Marks with AI Grader
Need help grading? Try our AI Grader for instant feedback on your assignments.
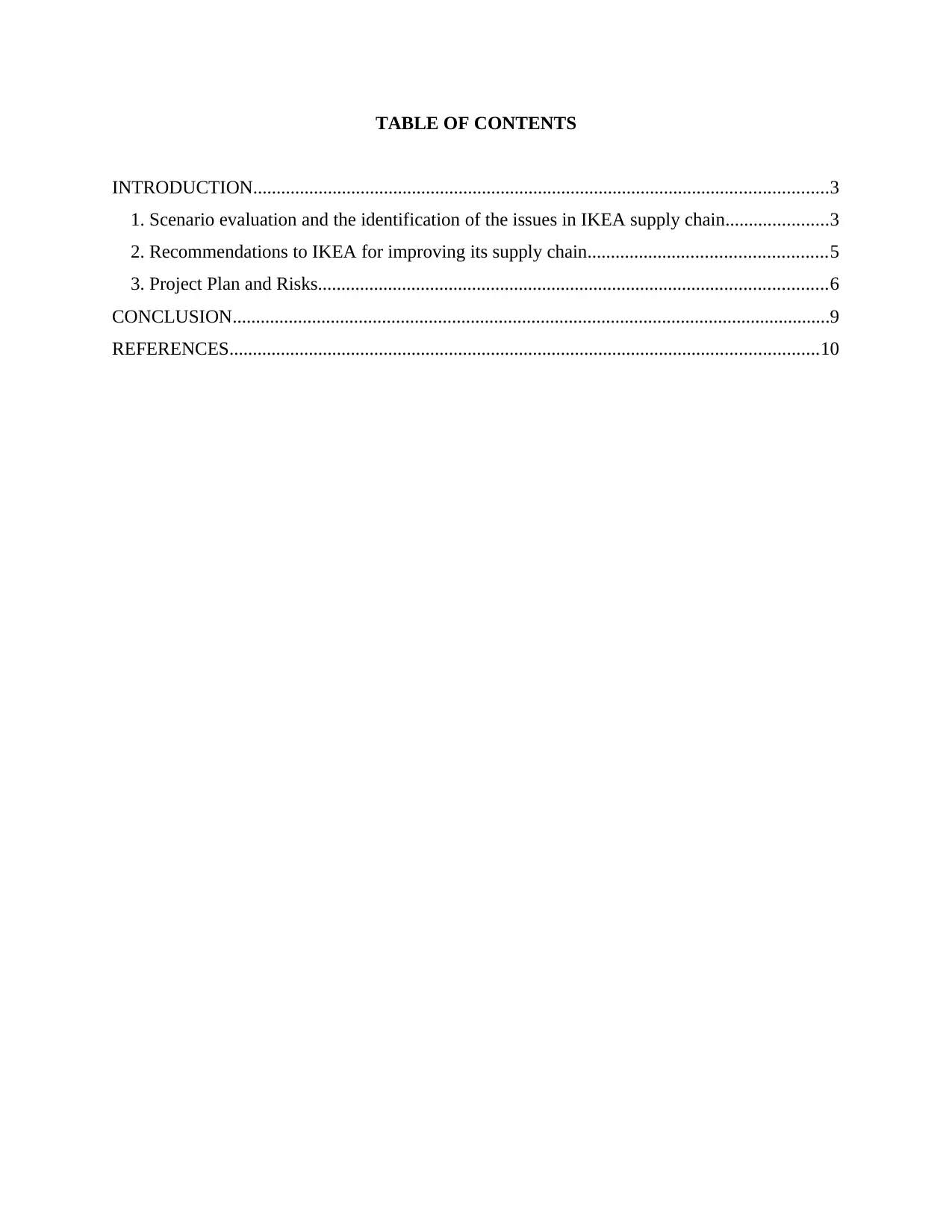
TABLE OF CONTENTS
INTRODUCTION...........................................................................................................................3
1. Scenario evaluation and the identification of the issues in IKEA supply chain......................3
2. Recommendations to IKEA for improving its supply chain...................................................5
3. Project Plan and Risks.............................................................................................................6
CONCLUSION................................................................................................................................9
REFERENCES..............................................................................................................................10
INTRODUCTION...........................................................................................................................3
1. Scenario evaluation and the identification of the issues in IKEA supply chain......................3
2. Recommendations to IKEA for improving its supply chain...................................................5
3. Project Plan and Risks.............................................................................................................6
CONCLUSION................................................................................................................................9
REFERENCES..............................................................................................................................10
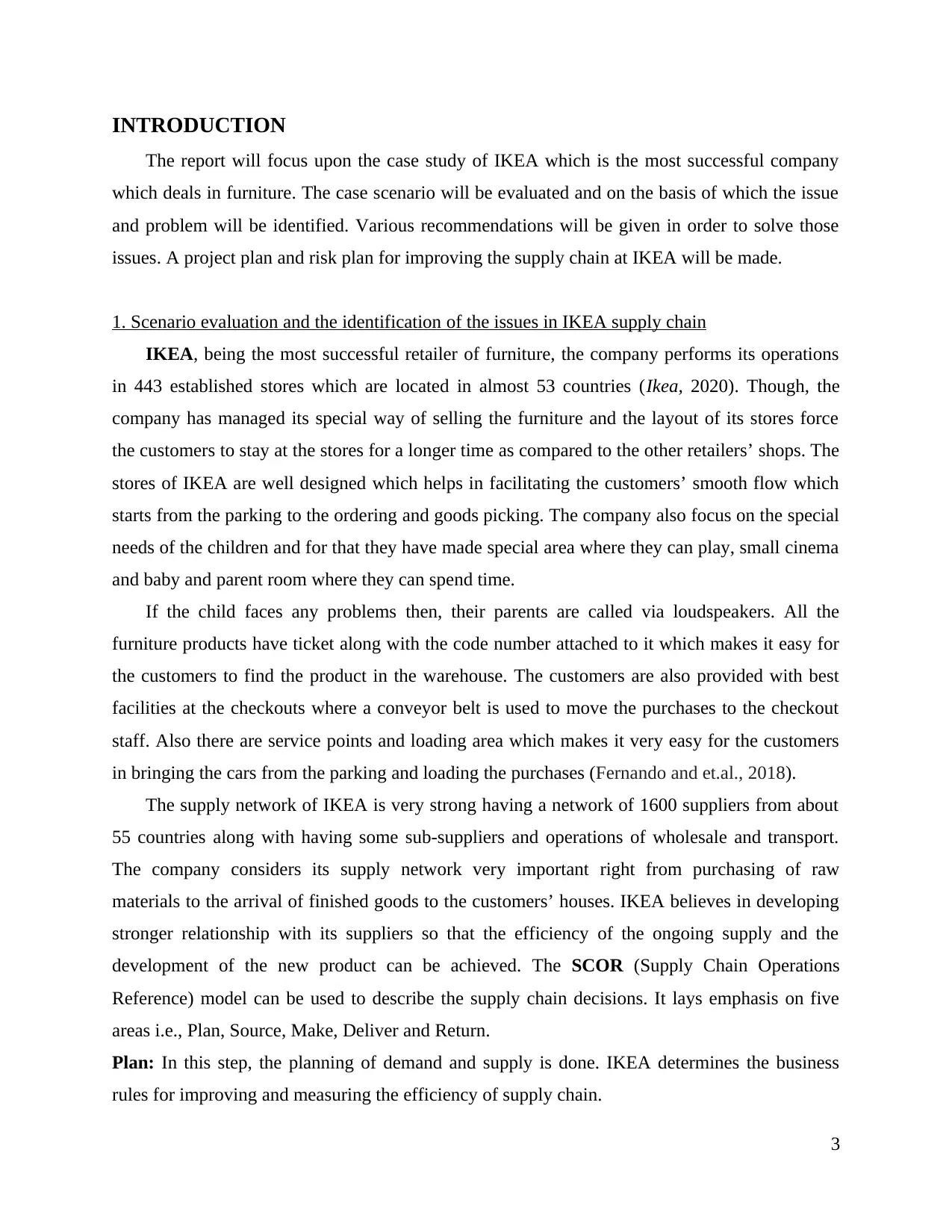
INTRODUCTION
The report will focus upon the case study of IKEA which is the most successful company
which deals in furniture. The case scenario will be evaluated and on the basis of which the issue
and problem will be identified. Various recommendations will be given in order to solve those
issues. A project plan and risk plan for improving the supply chain at IKEA will be made.
1. Scenario evaluation and the identification of the issues in IKEA supply chain
IKEA, being the most successful retailer of furniture, the company performs its operations
in 443 established stores which are located in almost 53 countries (Ikea, 2020). Though, the
company has managed its special way of selling the furniture and the layout of its stores force
the customers to stay at the stores for a longer time as compared to the other retailers’ shops. The
stores of IKEA are well designed which helps in facilitating the customers’ smooth flow which
starts from the parking to the ordering and goods picking. The company also focus on the special
needs of the children and for that they have made special area where they can play, small cinema
and baby and parent room where they can spend time.
If the child faces any problems then, their parents are called via loudspeakers. All the
furniture products have ticket along with the code number attached to it which makes it easy for
the customers to find the product in the warehouse. The customers are also provided with best
facilities at the checkouts where a conveyor belt is used to move the purchases to the checkout
staff. Also there are service points and loading area which makes it very easy for the customers
in bringing the cars from the parking and loading the purchases (Fernando and et.al., 2018).
The supply network of IKEA is very strong having a network of 1600 suppliers from about
55 countries along with having some sub-suppliers and operations of wholesale and transport.
The company considers its supply network very important right from purchasing of raw
materials to the arrival of finished goods to the customers’ houses. IKEA believes in developing
stronger relationship with its suppliers so that the efficiency of the ongoing supply and the
development of the new product can be achieved. The SCOR (Supply Chain Operations
Reference) model can be used to describe the supply chain decisions. It lays emphasis on five
areas i.e., Plan, Source, Make, Deliver and Return.
Plan: In this step, the planning of demand and supply is done. IKEA determines the business
rules for improving and measuring the efficiency of supply chain.
3
The report will focus upon the case study of IKEA which is the most successful company
which deals in furniture. The case scenario will be evaluated and on the basis of which the issue
and problem will be identified. Various recommendations will be given in order to solve those
issues. A project plan and risk plan for improving the supply chain at IKEA will be made.
1. Scenario evaluation and the identification of the issues in IKEA supply chain
IKEA, being the most successful retailer of furniture, the company performs its operations
in 443 established stores which are located in almost 53 countries (Ikea, 2020). Though, the
company has managed its special way of selling the furniture and the layout of its stores force
the customers to stay at the stores for a longer time as compared to the other retailers’ shops. The
stores of IKEA are well designed which helps in facilitating the customers’ smooth flow which
starts from the parking to the ordering and goods picking. The company also focus on the special
needs of the children and for that they have made special area where they can play, small cinema
and baby and parent room where they can spend time.
If the child faces any problems then, their parents are called via loudspeakers. All the
furniture products have ticket along with the code number attached to it which makes it easy for
the customers to find the product in the warehouse. The customers are also provided with best
facilities at the checkouts where a conveyor belt is used to move the purchases to the checkout
staff. Also there are service points and loading area which makes it very easy for the customers
in bringing the cars from the parking and loading the purchases (Fernando and et.al., 2018).
The supply network of IKEA is very strong having a network of 1600 suppliers from about
55 countries along with having some sub-suppliers and operations of wholesale and transport.
The company considers its supply network very important right from purchasing of raw
materials to the arrival of finished goods to the customers’ houses. IKEA believes in developing
stronger relationship with its suppliers so that the efficiency of the ongoing supply and the
development of the new product can be achieved. The SCOR (Supply Chain Operations
Reference) model can be used to describe the supply chain decisions. It lays emphasis on five
areas i.e., Plan, Source, Make, Deliver and Return.
Plan: In this step, the planning of demand and supply is done. IKEA determines the business
rules for improving and measuring the efficiency of supply chain.
3
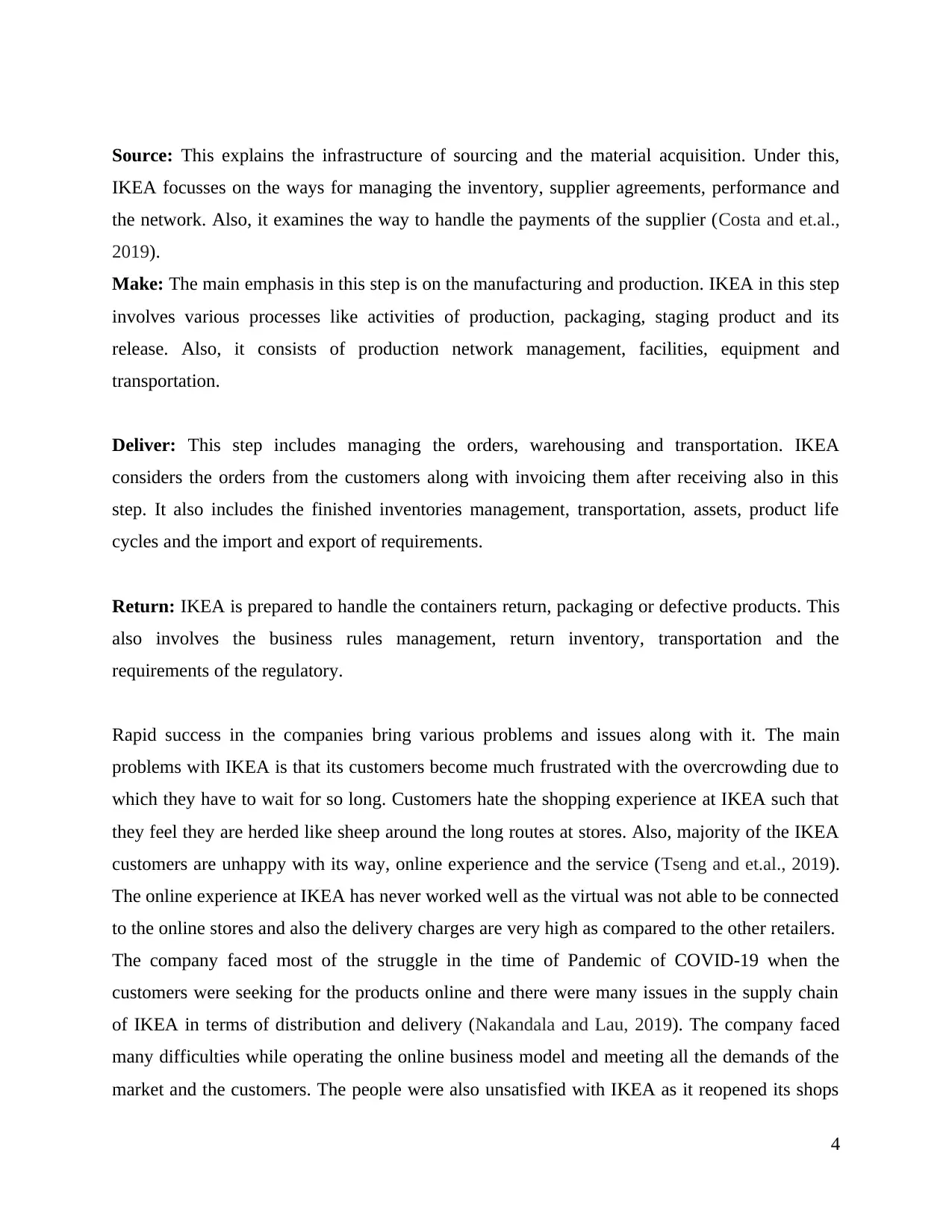
Source: This explains the infrastructure of sourcing and the material acquisition. Under this,
IKEA focusses on the ways for managing the inventory, supplier agreements, performance and
the network. Also, it examines the way to handle the payments of the supplier (Costa and et.al.,
2019).
Make: The main emphasis in this step is on the manufacturing and production. IKEA in this step
involves various processes like activities of production, packaging, staging product and its
release. Also, it consists of production network management, facilities, equipment and
transportation.
Deliver: This step includes managing the orders, warehousing and transportation. IKEA
considers the orders from the customers along with invoicing them after receiving also in this
step. It also includes the finished inventories management, transportation, assets, product life
cycles and the import and export of requirements.
Return: IKEA is prepared to handle the containers return, packaging or defective products. This
also involves the business rules management, return inventory, transportation and the
requirements of the regulatory.
Rapid success in the companies bring various problems and issues along with it. The main
problems with IKEA is that its customers become much frustrated with the overcrowding due to
which they have to wait for so long. Customers hate the shopping experience at IKEA such that
they feel they are herded like sheep around the long routes at stores. Also, majority of the IKEA
customers are unhappy with its way, online experience and the service (Tseng and et.al., 2019).
The online experience at IKEA has never worked well as the virtual was not able to be connected
to the online stores and also the delivery charges are very high as compared to the other retailers.
The company faced most of the struggle in the time of Pandemic of COVID-19 when the
customers were seeking for the products online and there were many issues in the supply chain
of IKEA in terms of distribution and delivery (Nakandala and Lau, 2019). The company faced
many difficulties while operating the online business model and meeting all the demands of the
market and the customers. The people were also unsatisfied with IKEA as it reopened its shops
4
IKEA focusses on the ways for managing the inventory, supplier agreements, performance and
the network. Also, it examines the way to handle the payments of the supplier (Costa and et.al.,
2019).
Make: The main emphasis in this step is on the manufacturing and production. IKEA in this step
involves various processes like activities of production, packaging, staging product and its
release. Also, it consists of production network management, facilities, equipment and
transportation.
Deliver: This step includes managing the orders, warehousing and transportation. IKEA
considers the orders from the customers along with invoicing them after receiving also in this
step. It also includes the finished inventories management, transportation, assets, product life
cycles and the import and export of requirements.
Return: IKEA is prepared to handle the containers return, packaging or defective products. This
also involves the business rules management, return inventory, transportation and the
requirements of the regulatory.
Rapid success in the companies bring various problems and issues along with it. The main
problems with IKEA is that its customers become much frustrated with the overcrowding due to
which they have to wait for so long. Customers hate the shopping experience at IKEA such that
they feel they are herded like sheep around the long routes at stores. Also, majority of the IKEA
customers are unhappy with its way, online experience and the service (Tseng and et.al., 2019).
The online experience at IKEA has never worked well as the virtual was not able to be connected
to the online stores and also the delivery charges are very high as compared to the other retailers.
The company faced most of the struggle in the time of Pandemic of COVID-19 when the
customers were seeking for the products online and there were many issues in the supply chain
of IKEA in terms of distribution and delivery (Nakandala and Lau, 2019). The company faced
many difficulties while operating the online business model and meeting all the demands of the
market and the customers. The people were also unsatisfied with IKEA as it reopened its shops
4
Secure Best Marks with AI Grader
Need help grading? Try our AI Grader for instant feedback on your assignments.
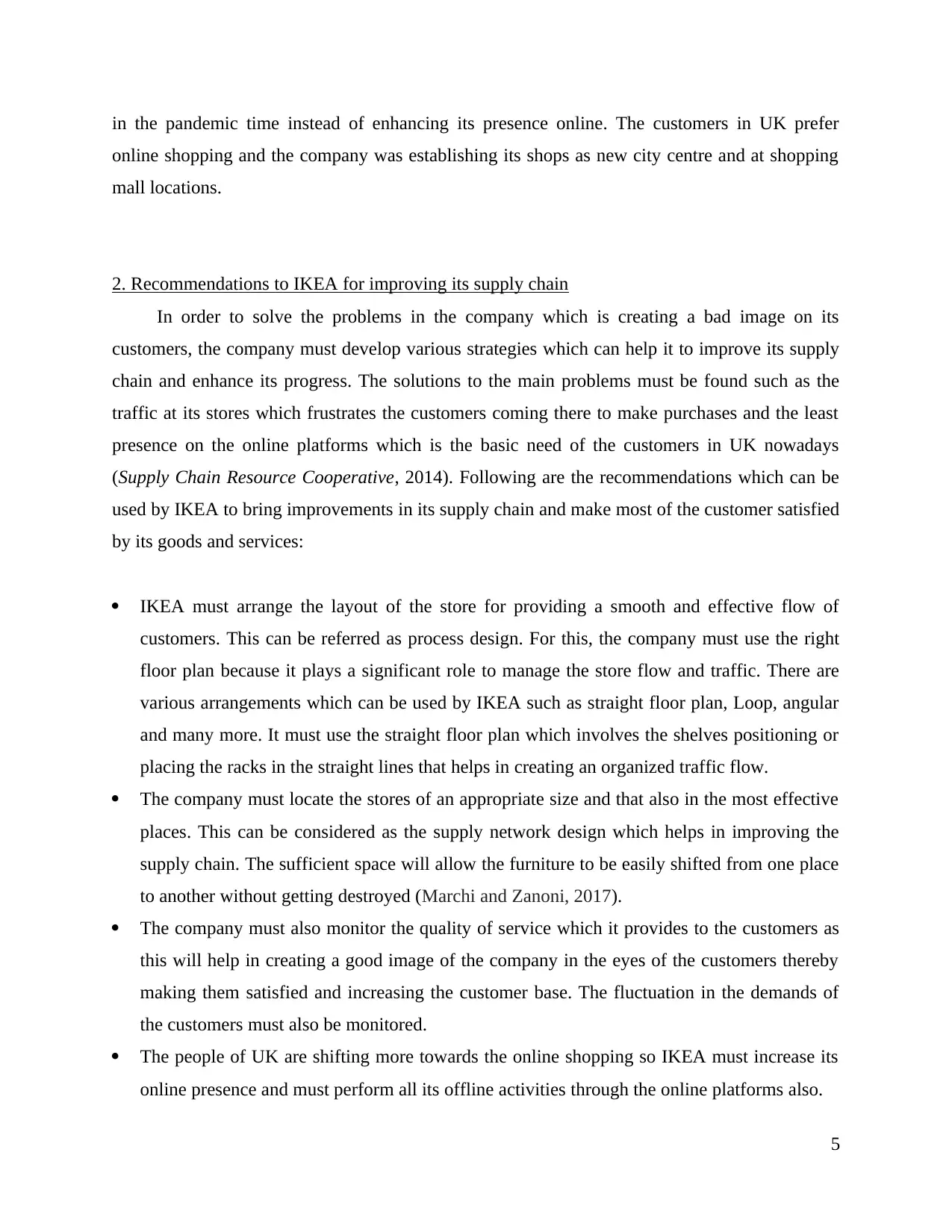
in the pandemic time instead of enhancing its presence online. The customers in UK prefer
online shopping and the company was establishing its shops as new city centre and at shopping
mall locations.
2. Recommendations to IKEA for improving its supply chain
In order to solve the problems in the company which is creating a bad image on its
customers, the company must develop various strategies which can help it to improve its supply
chain and enhance its progress. The solutions to the main problems must be found such as the
traffic at its stores which frustrates the customers coming there to make purchases and the least
presence on the online platforms which is the basic need of the customers in UK nowadays
(Supply Chain Resource Cooperative, 2014). Following are the recommendations which can be
used by IKEA to bring improvements in its supply chain and make most of the customer satisfied
by its goods and services:
IKEA must arrange the layout of the store for providing a smooth and effective flow of
customers. This can be referred as process design. For this, the company must use the right
floor plan because it plays a significant role to manage the store flow and traffic. There are
various arrangements which can be used by IKEA such as straight floor plan, Loop, angular
and many more. It must use the straight floor plan which involves the shelves positioning or
placing the racks in the straight lines that helps in creating an organized traffic flow.
The company must locate the stores of an appropriate size and that also in the most effective
places. This can be considered as the supply network design which helps in improving the
supply chain. The sufficient space will allow the furniture to be easily shifted from one place
to another without getting destroyed (Marchi and Zanoni, 2017).
The company must also monitor the quality of service which it provides to the customers as
this will help in creating a good image of the company in the eyes of the customers thereby
making them satisfied and increasing the customer base. The fluctuation in the demands of
the customers must also be monitored.
The people of UK are shifting more towards the online shopping so IKEA must increase its
online presence and must perform all its offline activities through the online platforms also.
5
online shopping and the company was establishing its shops as new city centre and at shopping
mall locations.
2. Recommendations to IKEA for improving its supply chain
In order to solve the problems in the company which is creating a bad image on its
customers, the company must develop various strategies which can help it to improve its supply
chain and enhance its progress. The solutions to the main problems must be found such as the
traffic at its stores which frustrates the customers coming there to make purchases and the least
presence on the online platforms which is the basic need of the customers in UK nowadays
(Supply Chain Resource Cooperative, 2014). Following are the recommendations which can be
used by IKEA to bring improvements in its supply chain and make most of the customer satisfied
by its goods and services:
IKEA must arrange the layout of the store for providing a smooth and effective flow of
customers. This can be referred as process design. For this, the company must use the right
floor plan because it plays a significant role to manage the store flow and traffic. There are
various arrangements which can be used by IKEA such as straight floor plan, Loop, angular
and many more. It must use the straight floor plan which involves the shelves positioning or
placing the racks in the straight lines that helps in creating an organized traffic flow.
The company must locate the stores of an appropriate size and that also in the most effective
places. This can be considered as the supply network design which helps in improving the
supply chain. The sufficient space will allow the furniture to be easily shifted from one place
to another without getting destroyed (Marchi and Zanoni, 2017).
The company must also monitor the quality of service which it provides to the customers as
this will help in creating a good image of the company in the eyes of the customers thereby
making them satisfied and increasing the customer base. The fluctuation in the demands of
the customers must also be monitored.
The people of UK are shifting more towards the online shopping so IKEA must increase its
online presence and must perform all its offline activities through the online platforms also.
5
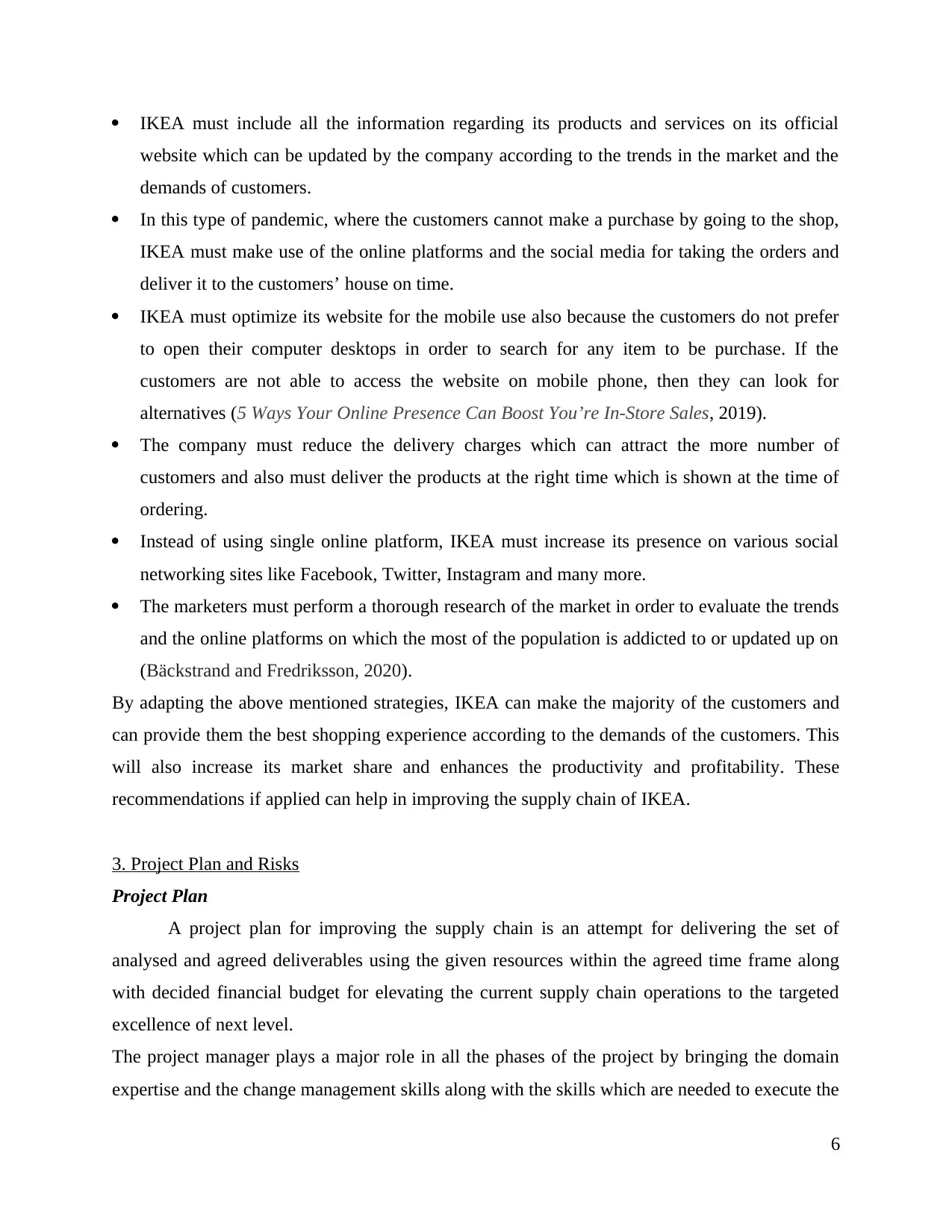
IKEA must include all the information regarding its products and services on its official
website which can be updated by the company according to the trends in the market and the
demands of customers.
In this type of pandemic, where the customers cannot make a purchase by going to the shop,
IKEA must make use of the online platforms and the social media for taking the orders and
deliver it to the customers’ house on time.
IKEA must optimize its website for the mobile use also because the customers do not prefer
to open their computer desktops in order to search for any item to be purchase. If the
customers are not able to access the website on mobile phone, then they can look for
alternatives (5 Ways Your Online Presence Can Boost You’re In-Store Sales, 2019).
The company must reduce the delivery charges which can attract the more number of
customers and also must deliver the products at the right time which is shown at the time of
ordering.
Instead of using single online platform, IKEA must increase its presence on various social
networking sites like Facebook, Twitter, Instagram and many more.
The marketers must perform a thorough research of the market in order to evaluate the trends
and the online platforms on which the most of the population is addicted to or updated up on
(Bäckstrand and Fredriksson, 2020).
By adapting the above mentioned strategies, IKEA can make the majority of the customers and
can provide them the best shopping experience according to the demands of the customers. This
will also increase its market share and enhances the productivity and profitability. These
recommendations if applied can help in improving the supply chain of IKEA.
3. Project Plan and Risks
Project Plan
A project plan for improving the supply chain is an attempt for delivering the set of
analysed and agreed deliverables using the given resources within the agreed time frame along
with decided financial budget for elevating the current supply chain operations to the targeted
excellence of next level.
The project manager plays a major role in all the phases of the project by bringing the domain
expertise and the change management skills along with the skills which are needed to execute the
6
website which can be updated by the company according to the trends in the market and the
demands of customers.
In this type of pandemic, where the customers cannot make a purchase by going to the shop,
IKEA must make use of the online platforms and the social media for taking the orders and
deliver it to the customers’ house on time.
IKEA must optimize its website for the mobile use also because the customers do not prefer
to open their computer desktops in order to search for any item to be purchase. If the
customers are not able to access the website on mobile phone, then they can look for
alternatives (5 Ways Your Online Presence Can Boost You’re In-Store Sales, 2019).
The company must reduce the delivery charges which can attract the more number of
customers and also must deliver the products at the right time which is shown at the time of
ordering.
Instead of using single online platform, IKEA must increase its presence on various social
networking sites like Facebook, Twitter, Instagram and many more.
The marketers must perform a thorough research of the market in order to evaluate the trends
and the online platforms on which the most of the population is addicted to or updated up on
(Bäckstrand and Fredriksson, 2020).
By adapting the above mentioned strategies, IKEA can make the majority of the customers and
can provide them the best shopping experience according to the demands of the customers. This
will also increase its market share and enhances the productivity and profitability. These
recommendations if applied can help in improving the supply chain of IKEA.
3. Project Plan and Risks
Project Plan
A project plan for improving the supply chain is an attempt for delivering the set of
analysed and agreed deliverables using the given resources within the agreed time frame along
with decided financial budget for elevating the current supply chain operations to the targeted
excellence of next level.
The project manager plays a major role in all the phases of the project by bringing the domain
expertise and the change management skills along with the skills which are needed to execute the
6
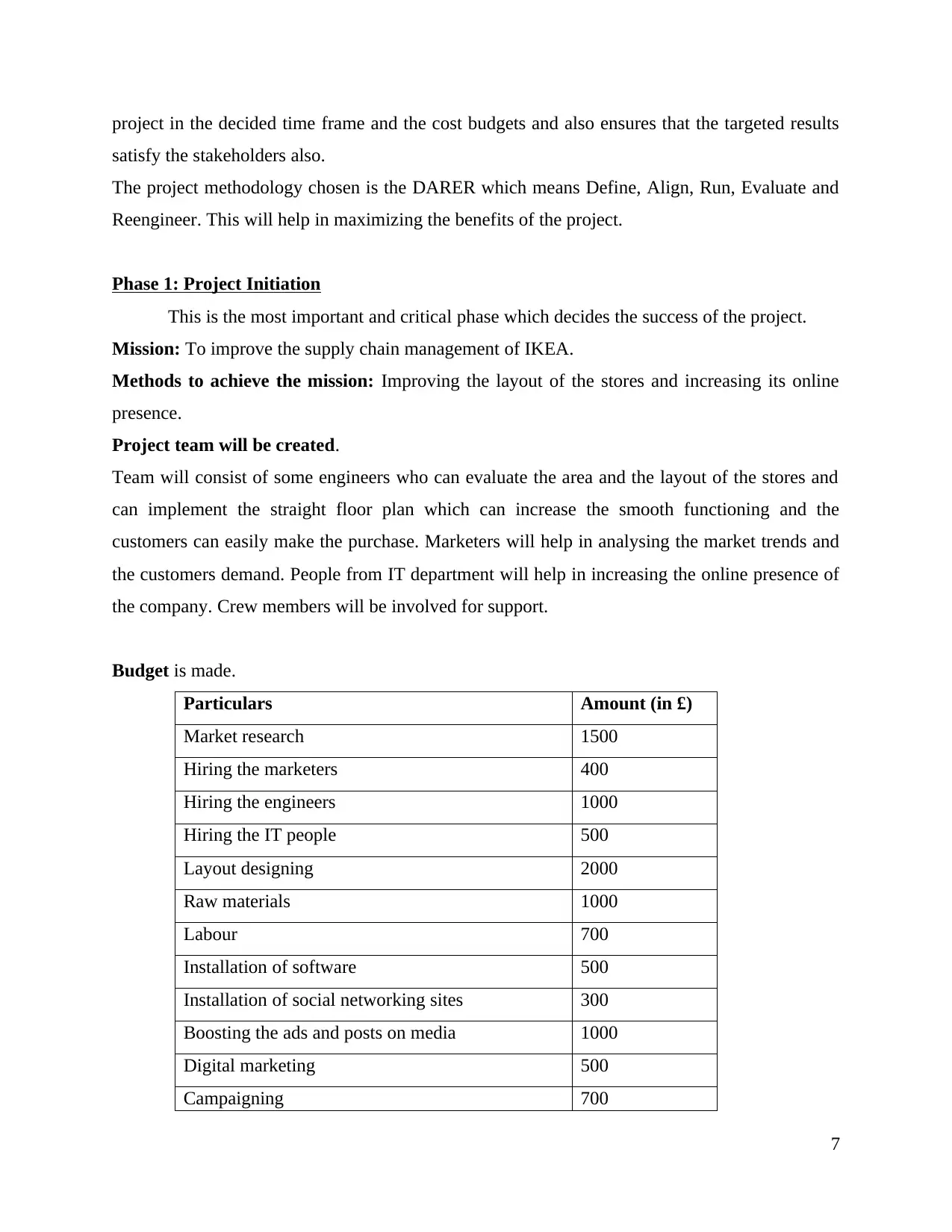
project in the decided time frame and the cost budgets and also ensures that the targeted results
satisfy the stakeholders also.
The project methodology chosen is the DARER which means Define, Align, Run, Evaluate and
Reengineer. This will help in maximizing the benefits of the project.
Phase 1: Project Initiation
This is the most important and critical phase which decides the success of the project.
Mission: To improve the supply chain management of IKEA.
Methods to achieve the mission: Improving the layout of the stores and increasing its online
presence.
Project team will be created.
Team will consist of some engineers who can evaluate the area and the layout of the stores and
can implement the straight floor plan which can increase the smooth functioning and the
customers can easily make the purchase. Marketers will help in analysing the market trends and
the customers demand. People from IT department will help in increasing the online presence of
the company. Crew members will be involved for support.
Budget is made.
Particulars Amount (in £)
Market research 1500
Hiring the marketers 400
Hiring the engineers 1000
Hiring the IT people 500
Layout designing 2000
Raw materials 1000
Labour 700
Installation of software 500
Installation of social networking sites 300
Boosting the ads and posts on media 1000
Digital marketing 500
Campaigning 700
7
satisfy the stakeholders also.
The project methodology chosen is the DARER which means Define, Align, Run, Evaluate and
Reengineer. This will help in maximizing the benefits of the project.
Phase 1: Project Initiation
This is the most important and critical phase which decides the success of the project.
Mission: To improve the supply chain management of IKEA.
Methods to achieve the mission: Improving the layout of the stores and increasing its online
presence.
Project team will be created.
Team will consist of some engineers who can evaluate the area and the layout of the stores and
can implement the straight floor plan which can increase the smooth functioning and the
customers can easily make the purchase. Marketers will help in analysing the market trends and
the customers demand. People from IT department will help in increasing the online presence of
the company. Crew members will be involved for support.
Budget is made.
Particulars Amount (in £)
Market research 1500
Hiring the marketers 400
Hiring the engineers 1000
Hiring the IT people 500
Layout designing 2000
Raw materials 1000
Labour 700
Installation of software 500
Installation of social networking sites 300
Boosting the ads and posts on media 1000
Digital marketing 500
Campaigning 700
7
Paraphrase This Document
Need a fresh take? Get an instant paraphrase of this document with our AI Paraphraser
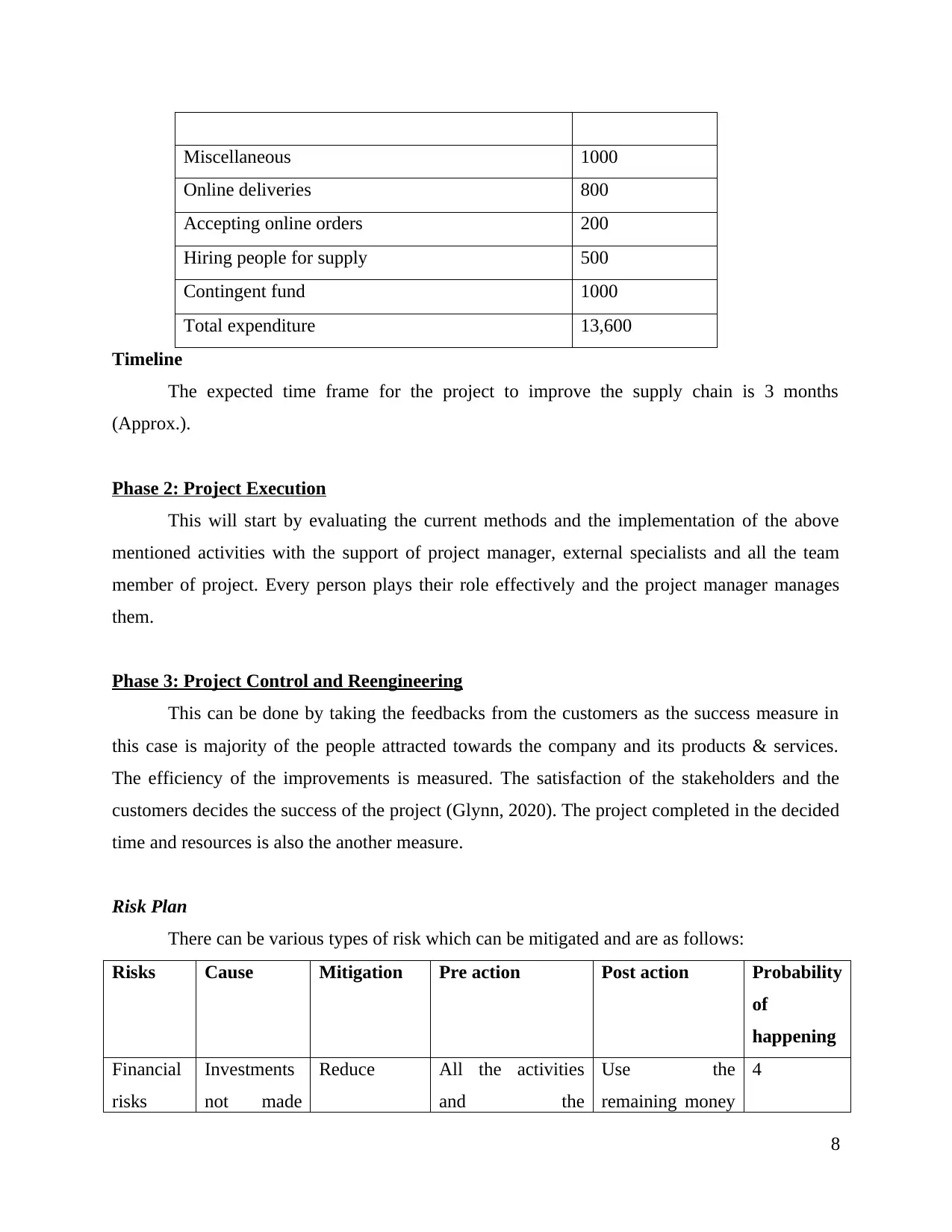
Miscellaneous 1000
Online deliveries 800
Accepting online orders 200
Hiring people for supply 500
Contingent fund 1000
Total expenditure 13,600
Timeline
The expected time frame for the project to improve the supply chain is 3 months
(Approx.).
Phase 2: Project Execution
This will start by evaluating the current methods and the implementation of the above
mentioned activities with the support of project manager, external specialists and all the team
member of project. Every person plays their role effectively and the project manager manages
them.
Phase 3: Project Control and Reengineering
This can be done by taking the feedbacks from the customers as the success measure in
this case is majority of the people attracted towards the company and its products & services.
The efficiency of the improvements is measured. The satisfaction of the stakeholders and the
customers decides the success of the project (Glynn, 2020). The project completed in the decided
time and resources is also the another measure.
Risk Plan
There can be various types of risk which can be mitigated and are as follows:
Risks Cause Mitigation Pre action Post action Probability
of
happening
Financial
risks
Investments
not made
Reduce All the activities
and the
Use the
remaining money
4
8
Online deliveries 800
Accepting online orders 200
Hiring people for supply 500
Contingent fund 1000
Total expenditure 13,600
Timeline
The expected time frame for the project to improve the supply chain is 3 months
(Approx.).
Phase 2: Project Execution
This will start by evaluating the current methods and the implementation of the above
mentioned activities with the support of project manager, external specialists and all the team
member of project. Every person plays their role effectively and the project manager manages
them.
Phase 3: Project Control and Reengineering
This can be done by taking the feedbacks from the customers as the success measure in
this case is majority of the people attracted towards the company and its products & services.
The efficiency of the improvements is measured. The satisfaction of the stakeholders and the
customers decides the success of the project (Glynn, 2020). The project completed in the decided
time and resources is also the another measure.
Risk Plan
There can be various types of risk which can be mitigated and are as follows:
Risks Cause Mitigation Pre action Post action Probability
of
happening
Financial
risks
Investments
not made
Reduce All the activities
and the
Use the
remaining money
4
8
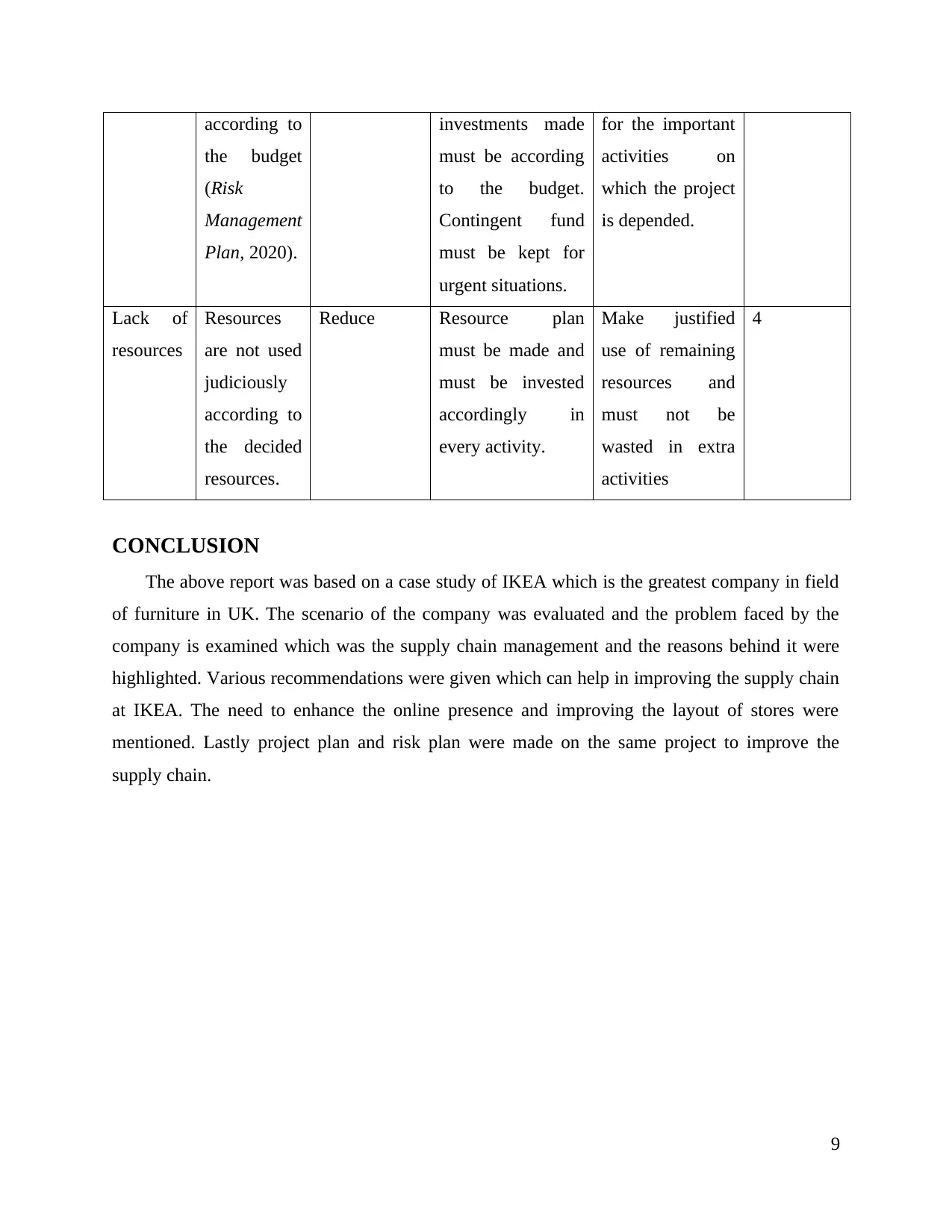
according to
the budget
(Risk
Management
Plan, 2020).
investments made
must be according
to the budget.
Contingent fund
must be kept for
urgent situations.
for the important
activities on
which the project
is depended.
Lack of
resources
Resources
are not used
judiciously
according to
the decided
resources.
Reduce Resource plan
must be made and
must be invested
accordingly in
every activity.
Make justified
use of remaining
resources and
must not be
wasted in extra
activities
4
CONCLUSION
The above report was based on a case study of IKEA which is the greatest company in field
of furniture in UK. The scenario of the company was evaluated and the problem faced by the
company is examined which was the supply chain management and the reasons behind it were
highlighted. Various recommendations were given which can help in improving the supply chain
at IKEA. The need to enhance the online presence and improving the layout of stores were
mentioned. Lastly project plan and risk plan were made on the same project to improve the
supply chain.
9
the budget
(Risk
Management
Plan, 2020).
investments made
must be according
to the budget.
Contingent fund
must be kept for
urgent situations.
for the important
activities on
which the project
is depended.
Lack of
resources
Resources
are not used
judiciously
according to
the decided
resources.
Reduce Resource plan
must be made and
must be invested
accordingly in
every activity.
Make justified
use of remaining
resources and
must not be
wasted in extra
activities
4
CONCLUSION
The above report was based on a case study of IKEA which is the greatest company in field
of furniture in UK. The scenario of the company was evaluated and the problem faced by the
company is examined which was the supply chain management and the reasons behind it were
highlighted. Various recommendations were given which can help in improving the supply chain
at IKEA. The need to enhance the online presence and improving the layout of stores were
mentioned. Lastly project plan and risk plan were made on the same project to improve the
supply chain.
9
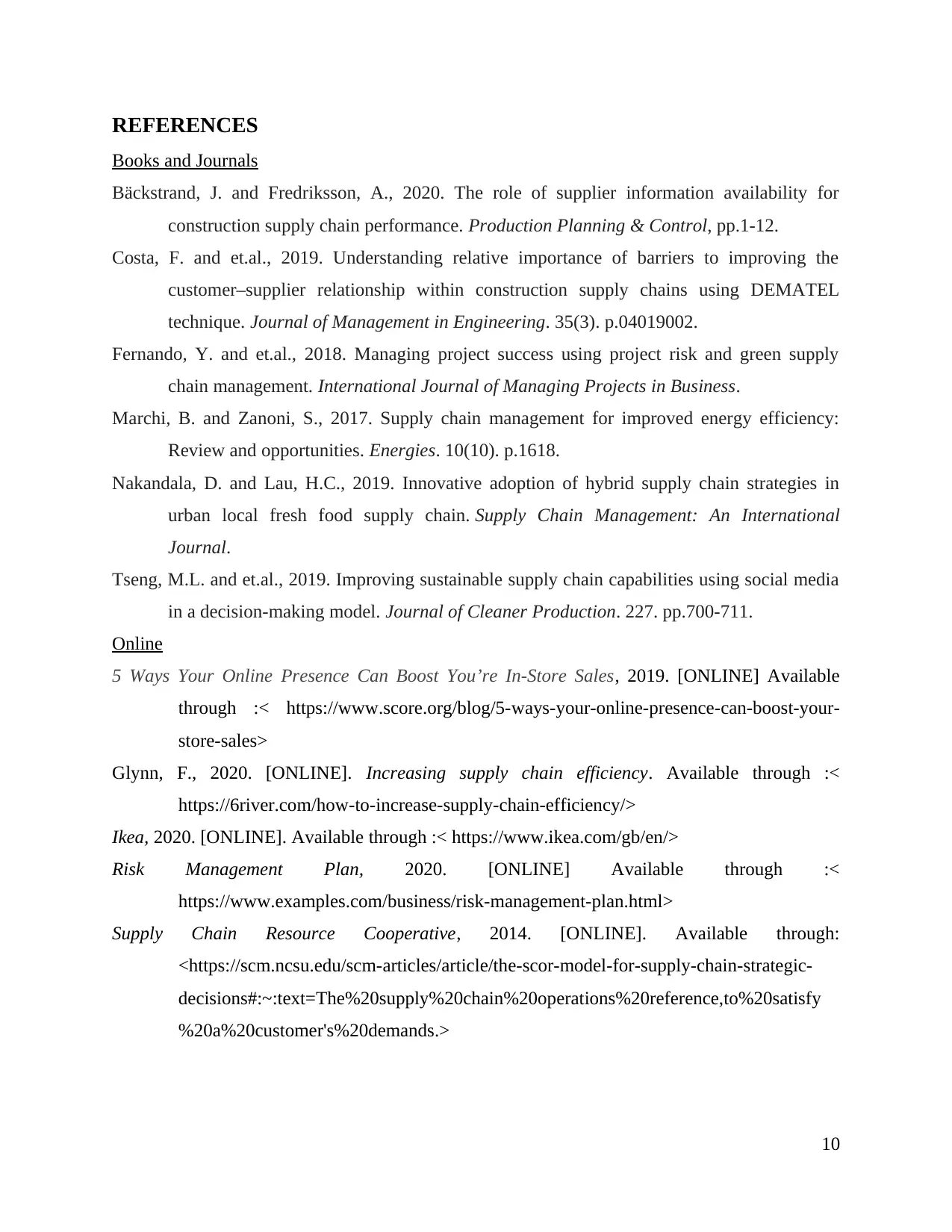
REFERENCES
Books and Journals
Bäckstrand, J. and Fredriksson, A., 2020. The role of supplier information availability for
construction supply chain performance. Production Planning & Control, pp.1-12.
Costa, F. and et.al., 2019. Understanding relative importance of barriers to improving the
customer–supplier relationship within construction supply chains using DEMATEL
technique. Journal of Management in Engineering. 35(3). p.04019002.
Fernando, Y. and et.al., 2018. Managing project success using project risk and green supply
chain management. International Journal of Managing Projects in Business.
Marchi, B. and Zanoni, S., 2017. Supply chain management for improved energy efficiency:
Review and opportunities. Energies. 10(10). p.1618.
Nakandala, D. and Lau, H.C., 2019. Innovative adoption of hybrid supply chain strategies in
urban local fresh food supply chain. Supply Chain Management: An International
Journal.
Tseng, M.L. and et.al., 2019. Improving sustainable supply chain capabilities using social media
in a decision-making model. Journal of Cleaner Production. 227. pp.700-711.
Online
5 Ways Your Online Presence Can Boost You’re In-Store Sales, 2019. [ONLINE] Available
through :< https://www.score.org/blog/5-ways-your-online-presence-can-boost-your-
store-sales>
Glynn, F., 2020. [ONLINE]. Increasing supply chain efficiency. Available through :<
https://6river.com/how-to-increase-supply-chain-efficiency/>
Ikea, 2020. [ONLINE]. Available through :< https://www.ikea.com/gb/en/>
Risk Management Plan, 2020. [ONLINE] Available through :<
https://www.examples.com/business/risk-management-plan.html>
Supply Chain Resource Cooperative, 2014. [ONLINE]. Available through:
<https://scm.ncsu.edu/scm-articles/article/the-scor-model-for-supply-chain-strategic-
decisions#:~:text=The%20supply%20chain%20operations%20reference,to%20satisfy
%20a%20customer's%20demands.>
10
Books and Journals
Bäckstrand, J. and Fredriksson, A., 2020. The role of supplier information availability for
construction supply chain performance. Production Planning & Control, pp.1-12.
Costa, F. and et.al., 2019. Understanding relative importance of barriers to improving the
customer–supplier relationship within construction supply chains using DEMATEL
technique. Journal of Management in Engineering. 35(3). p.04019002.
Fernando, Y. and et.al., 2018. Managing project success using project risk and green supply
chain management. International Journal of Managing Projects in Business.
Marchi, B. and Zanoni, S., 2017. Supply chain management for improved energy efficiency:
Review and opportunities. Energies. 10(10). p.1618.
Nakandala, D. and Lau, H.C., 2019. Innovative adoption of hybrid supply chain strategies in
urban local fresh food supply chain. Supply Chain Management: An International
Journal.
Tseng, M.L. and et.al., 2019. Improving sustainable supply chain capabilities using social media
in a decision-making model. Journal of Cleaner Production. 227. pp.700-711.
Online
5 Ways Your Online Presence Can Boost You’re In-Store Sales, 2019. [ONLINE] Available
through :< https://www.score.org/blog/5-ways-your-online-presence-can-boost-your-
store-sales>
Glynn, F., 2020. [ONLINE]. Increasing supply chain efficiency. Available through :<
https://6river.com/how-to-increase-supply-chain-efficiency/>
Ikea, 2020. [ONLINE]. Available through :< https://www.ikea.com/gb/en/>
Risk Management Plan, 2020. [ONLINE] Available through :<
https://www.examples.com/business/risk-management-plan.html>
Supply Chain Resource Cooperative, 2014. [ONLINE]. Available through:
<https://scm.ncsu.edu/scm-articles/article/the-scor-model-for-supply-chain-strategic-
decisions#:~:text=The%20supply%20chain%20operations%20reference,to%20satisfy
%20a%20customer's%20demands.>
10
Secure Best Marks with AI Grader
Need help grading? Try our AI Grader for instant feedback on your assignments.
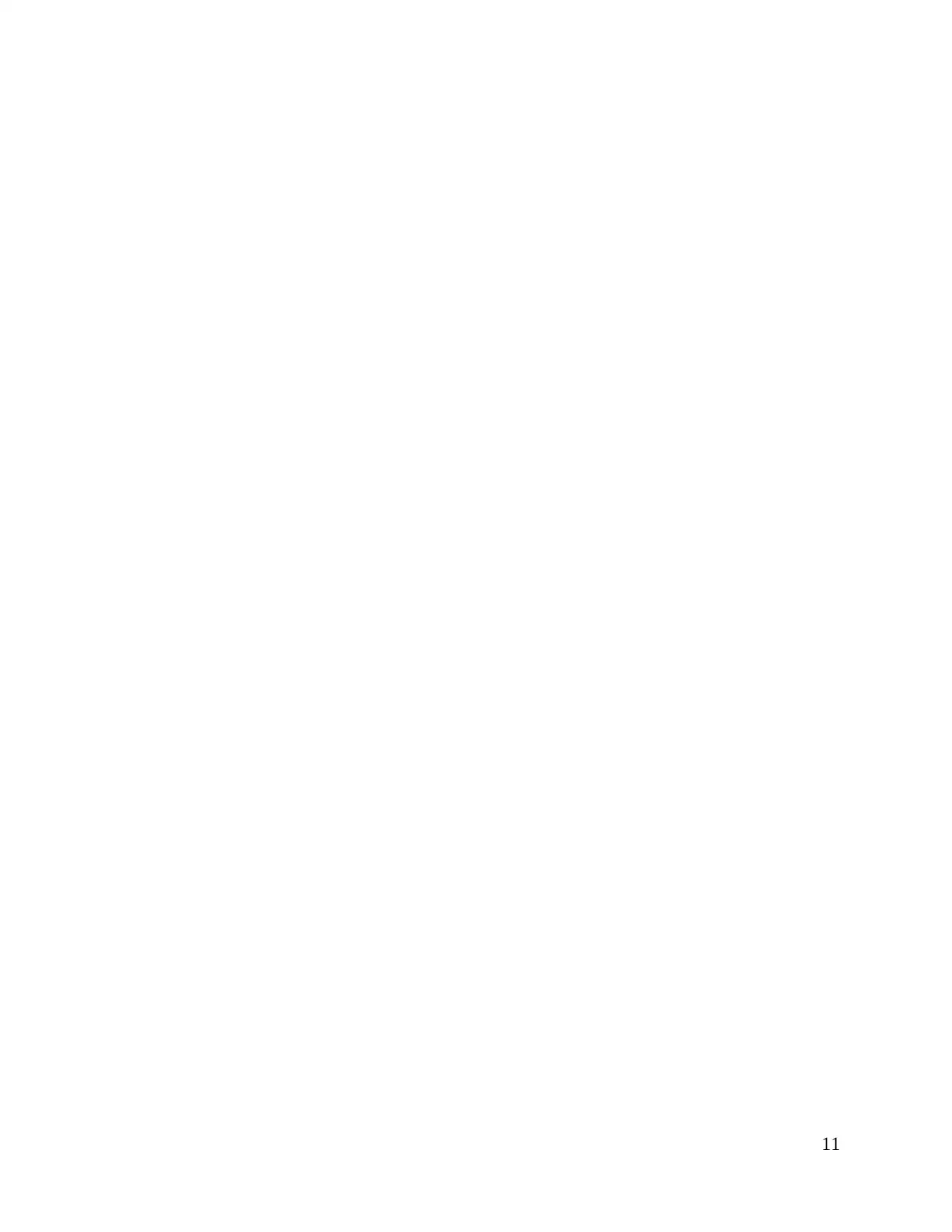
11
1 out of 11
Related Documents
![[object Object]](/_next/image/?url=%2F_next%2Fstatic%2Fmedia%2Flogo.6d15ce61.png&w=640&q=75)
Your All-in-One AI-Powered Toolkit for Academic Success.
+13062052269
info@desklib.com
Available 24*7 on WhatsApp / Email
Unlock your academic potential
© 2024 | Zucol Services PVT LTD | All rights reserved.