Industrial Engineering: Study Material and Solved Assignments
VerifiedAdded on 2023/04/10
|30
|7444
|295
AI Summary
Desklib offers study material and solved assignments for Industrial Engineering. Explore various topics such as sources of information, personal and team skills, professional development, safety requirements, financial requirements, and more.
Contribute Materials
Your contribution can guide someone’s learning journey. Share your
documents today.
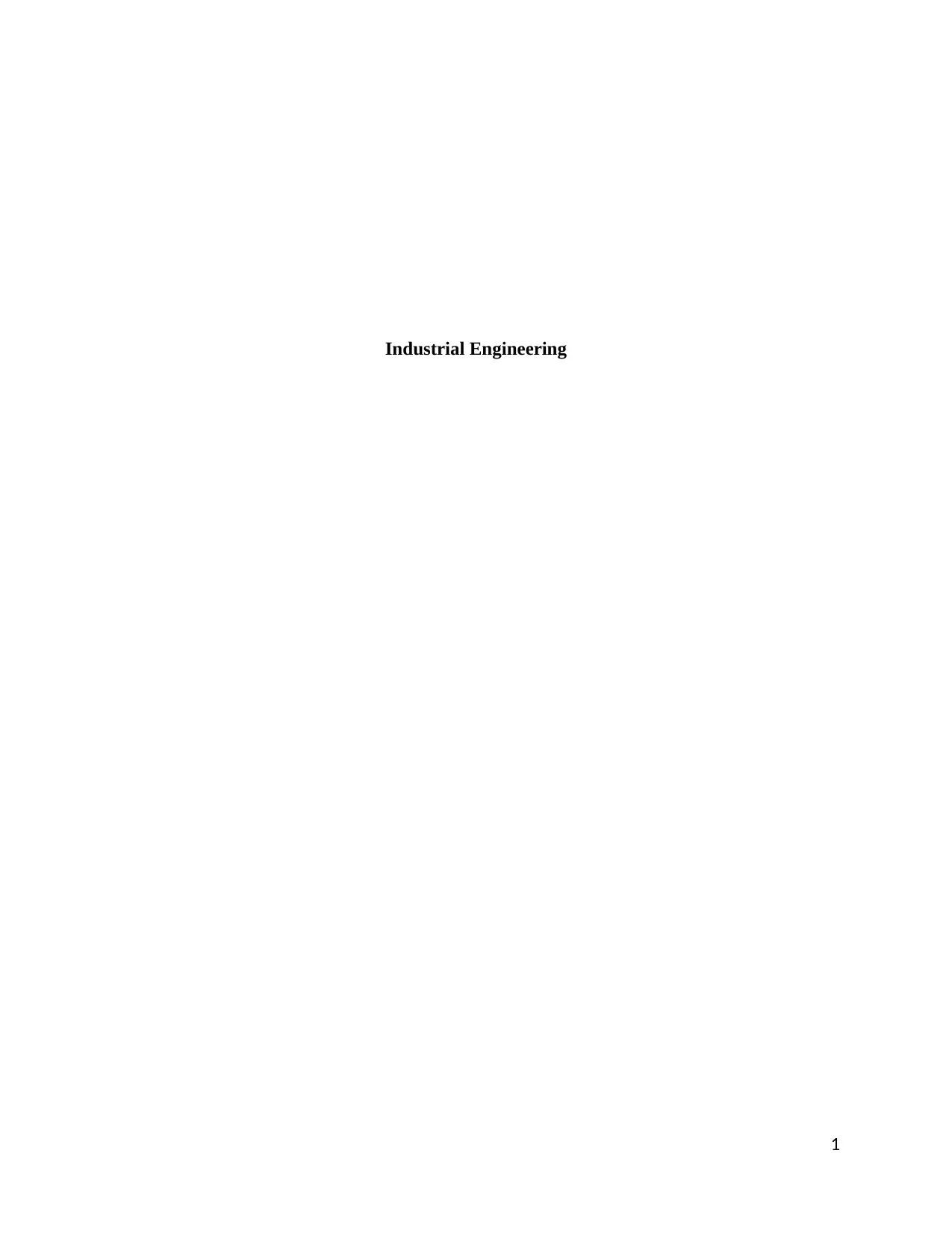
Industrial Engineering
1
1
Secure Best Marks with AI Grader
Need help grading? Try our AI Grader for instant feedback on your assignments.
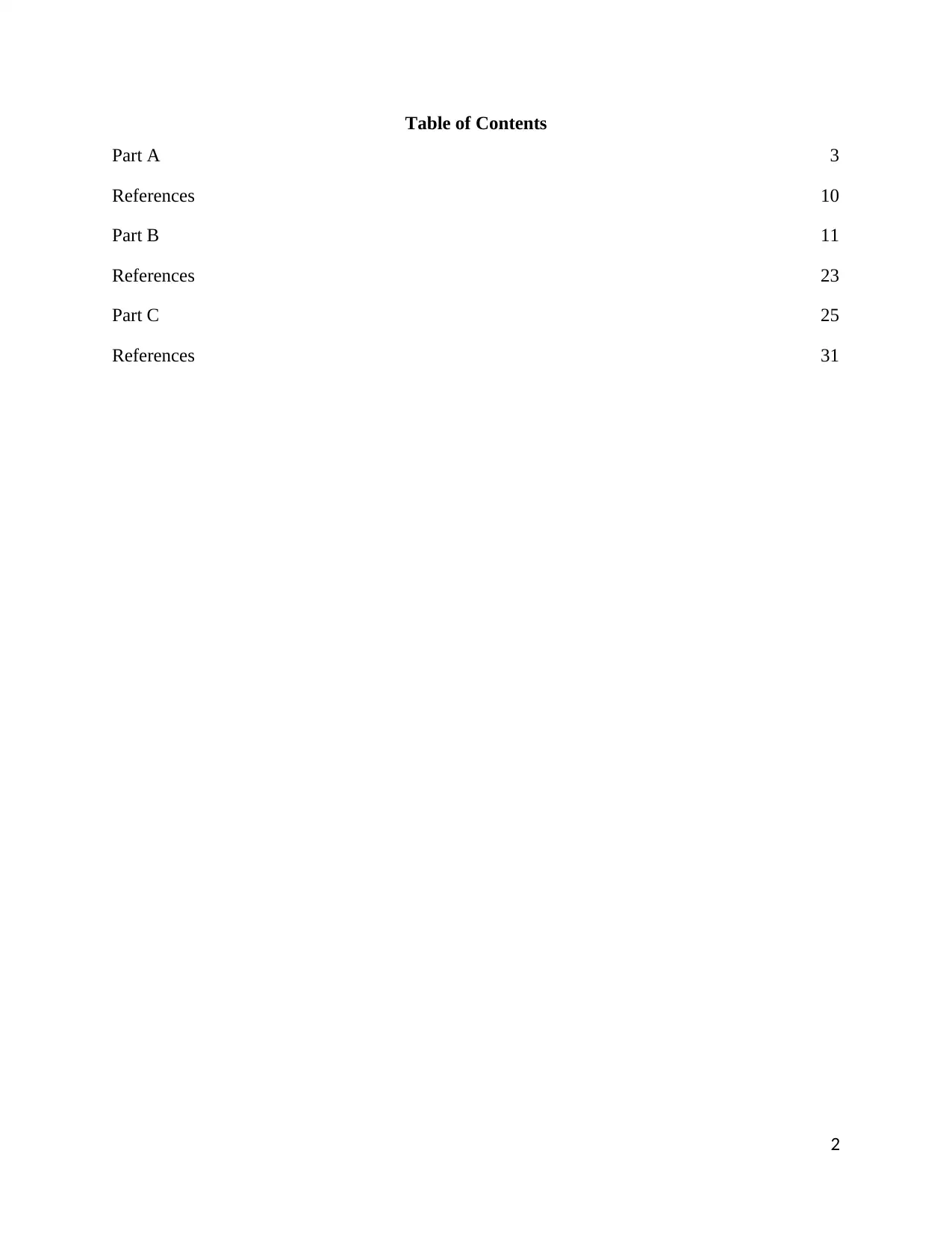
Table of Contents
Part A 3
References 10
Part B 11
References 23
Part C 25
References 31
2
Part A 3
References 10
Part B 11
References 23
Part C 25
References 31
2
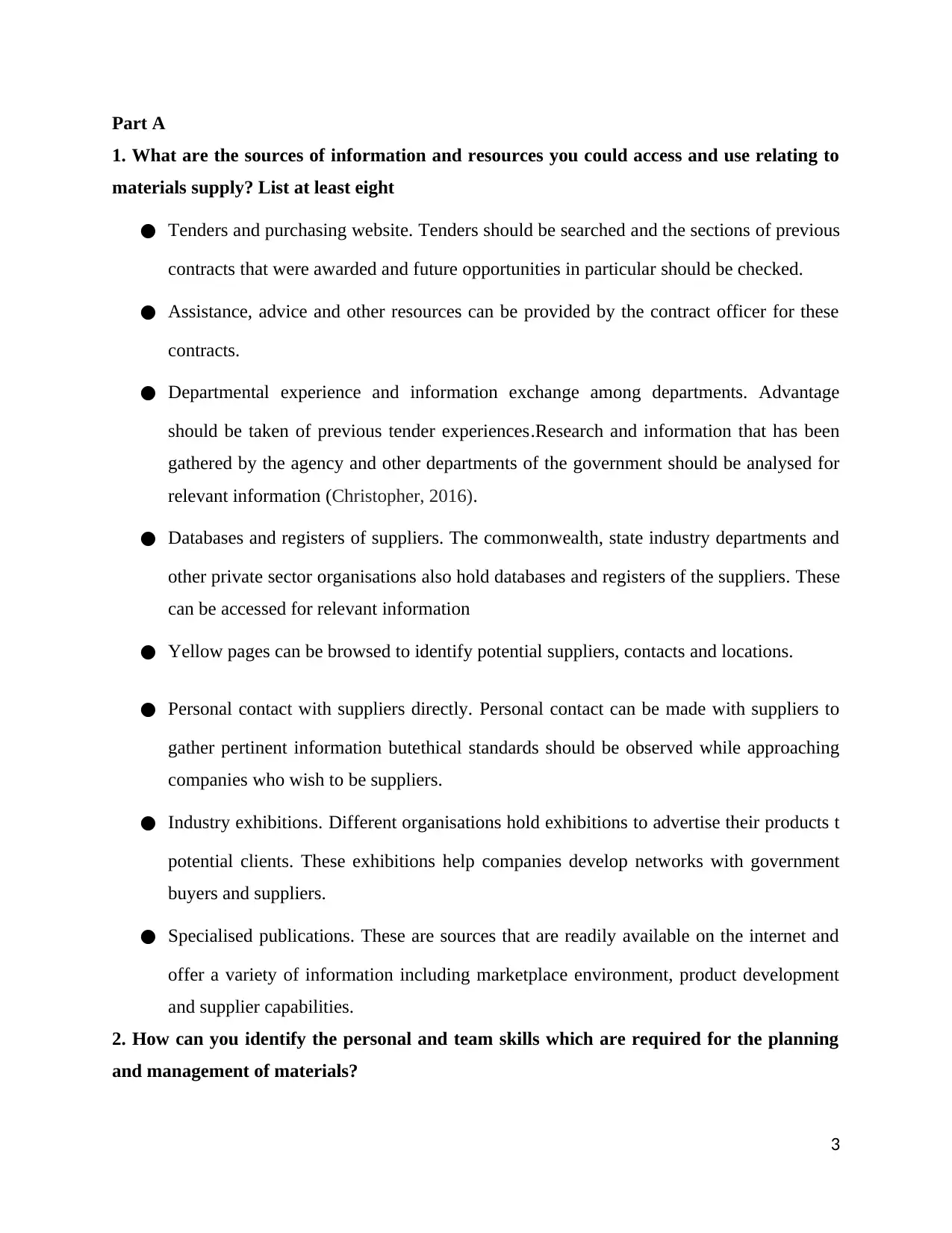
Part A
1. What are the sources of information and resources you could access and use relating to
materials supply? List at least eight
● Tenders and purchasing website. Tenders should be searched and the sections of previous
contracts that were awarded and future opportunities in particular should be checked.
● Assistance, advice and other resources can be provided by the contract officer for these
contracts.
● Departmental experience and information exchange among departments. Advantage
should be taken of previous tender experiences.Research and information that has been
gathered by the agency and other departments of the government should be analysed for
relevant information (Christopher, 2016).
● Databases and registers of suppliers. The commonwealth, state industry departments and
other private sector organisations also hold databases and registers of the suppliers. These
can be accessed for relevant information
● Yellow pages can be browsed to identify potential suppliers, contacts and locations.
● Personal contact with suppliers directly. Personal contact can be made with suppliers to
gather pertinent information butethical standards should be observed while approaching
companies who wish to be suppliers.
● Industry exhibitions. Different organisations hold exhibitions to advertise their products t
potential clients. These exhibitions help companies develop networks with government
buyers and suppliers.
● Specialised publications. These are sources that are readily available on the internet and
offer a variety of information including marketplace environment, product development
and supplier capabilities.
2. How can you identify the personal and team skills which are required for the planning
and management of materials?
3
1. What are the sources of information and resources you could access and use relating to
materials supply? List at least eight
● Tenders and purchasing website. Tenders should be searched and the sections of previous
contracts that were awarded and future opportunities in particular should be checked.
● Assistance, advice and other resources can be provided by the contract officer for these
contracts.
● Departmental experience and information exchange among departments. Advantage
should be taken of previous tender experiences.Research and information that has been
gathered by the agency and other departments of the government should be analysed for
relevant information (Christopher, 2016).
● Databases and registers of suppliers. The commonwealth, state industry departments and
other private sector organisations also hold databases and registers of the suppliers. These
can be accessed for relevant information
● Yellow pages can be browsed to identify potential suppliers, contacts and locations.
● Personal contact with suppliers directly. Personal contact can be made with suppliers to
gather pertinent information butethical standards should be observed while approaching
companies who wish to be suppliers.
● Industry exhibitions. Different organisations hold exhibitions to advertise their products t
potential clients. These exhibitions help companies develop networks with government
buyers and suppliers.
● Specialised publications. These are sources that are readily available on the internet and
offer a variety of information including marketplace environment, product development
and supplier capabilities.
2. How can you identify the personal and team skills which are required for the planning
and management of materials?
3
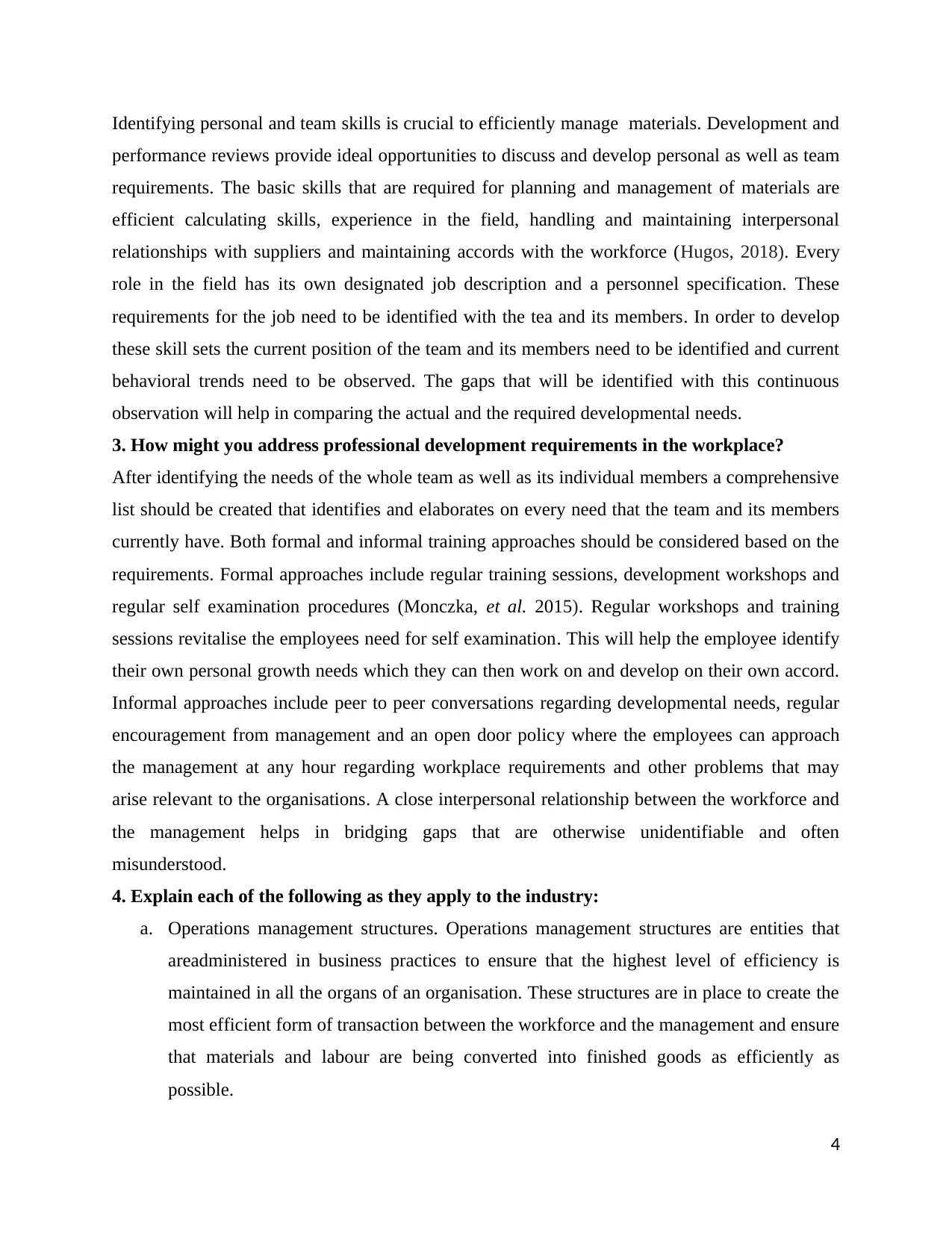
Identifying personal and team skills is crucial to efficiently manage materials. Development and
performance reviews provide ideal opportunities to discuss and develop personal as well as team
requirements. The basic skills that are required for planning and management of materials are
efficient calculating skills, experience in the field, handling and maintaining interpersonal
relationships with suppliers and maintaining accords with the workforce (Hugos, 2018). Every
role in the field has its own designated job description and a personnel specification. These
requirements for the job need to be identified with the tea and its members. In order to develop
these skill sets the current position of the team and its members need to be identified and current
behavioral trends need to be observed. The gaps that will be identified with this continuous
observation will help in comparing the actual and the required developmental needs.
3. How might you address professional development requirements in the workplace?
After identifying the needs of the whole team as well as its individual members a comprehensive
list should be created that identifies and elaborates on every need that the team and its members
currently have. Both formal and informal training approaches should be considered based on the
requirements. Formal approaches include regular training sessions, development workshops and
regular self examination procedures (Monczka, et al. 2015). Regular workshops and training
sessions revitalise the employees need for self examination. This will help the employee identify
their own personal growth needs which they can then work on and develop on their own accord.
Informal approaches include peer to peer conversations regarding developmental needs, regular
encouragement from management and an open door policy where the employees can approach
the management at any hour regarding workplace requirements and other problems that may
arise relevant to the organisations. A close interpersonal relationship between the workforce and
the management helps in bridging gaps that are otherwise unidentifiable and often
misunderstood.
4. Explain each of the following as they apply to the industry:
a. Operations management structures. Operations management structures are entities that
areadministered in business practices to ensure that the highest level of efficiency is
maintained in all the organs of an organisation. These structures are in place to create the
most efficient form of transaction between the workforce and the management and ensure
that materials and labour are being converted into finished goods as efficiently as
possible.
4
performance reviews provide ideal opportunities to discuss and develop personal as well as team
requirements. The basic skills that are required for planning and management of materials are
efficient calculating skills, experience in the field, handling and maintaining interpersonal
relationships with suppliers and maintaining accords with the workforce (Hugos, 2018). Every
role in the field has its own designated job description and a personnel specification. These
requirements for the job need to be identified with the tea and its members. In order to develop
these skill sets the current position of the team and its members need to be identified and current
behavioral trends need to be observed. The gaps that will be identified with this continuous
observation will help in comparing the actual and the required developmental needs.
3. How might you address professional development requirements in the workplace?
After identifying the needs of the whole team as well as its individual members a comprehensive
list should be created that identifies and elaborates on every need that the team and its members
currently have. Both formal and informal training approaches should be considered based on the
requirements. Formal approaches include regular training sessions, development workshops and
regular self examination procedures (Monczka, et al. 2015). Regular workshops and training
sessions revitalise the employees need for self examination. This will help the employee identify
their own personal growth needs which they can then work on and develop on their own accord.
Informal approaches include peer to peer conversations regarding developmental needs, regular
encouragement from management and an open door policy where the employees can approach
the management at any hour regarding workplace requirements and other problems that may
arise relevant to the organisations. A close interpersonal relationship between the workforce and
the management helps in bridging gaps that are otherwise unidentifiable and often
misunderstood.
4. Explain each of the following as they apply to the industry:
a. Operations management structures. Operations management structures are entities that
areadministered in business practices to ensure that the highest level of efficiency is
maintained in all the organs of an organisation. These structures are in place to create the
most efficient form of transaction between the workforce and the management and ensure
that materials and labour are being converted into finished goods as efficiently as
possible.
4
Secure Best Marks with AI Grader
Need help grading? Try our AI Grader for instant feedback on your assignments.
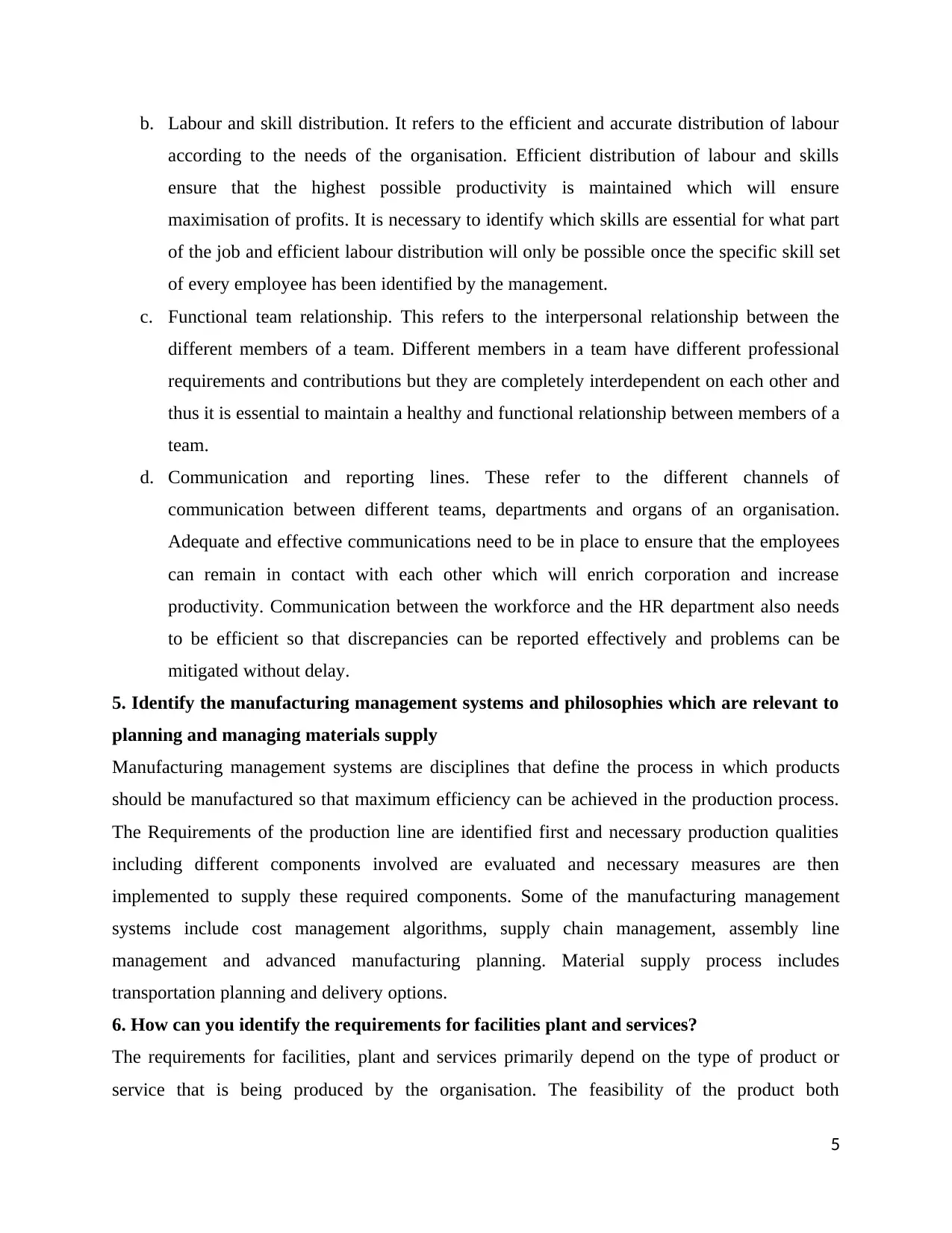
b. Labour and skill distribution. It refers to the efficient and accurate distribution of labour
according to the needs of the organisation. Efficient distribution of labour and skills
ensure that the highest possible productivity is maintained which will ensure
maximisation of profits. It is necessary to identify which skills are essential for what part
of the job and efficient labour distribution will only be possible once the specific skill set
of every employee has been identified by the management.
c. Functional team relationship. This refers to the interpersonal relationship between the
different members of a team. Different members in a team have different professional
requirements and contributions but they are completely interdependent on each other and
thus it is essential to maintain a healthy and functional relationship between members of a
team.
d. Communication and reporting lines. These refer to the different channels of
communication between different teams, departments and organs of an organisation.
Adequate and effective communications need to be in place to ensure that the employees
can remain in contact with each other which will enrich corporation and increase
productivity. Communication between the workforce and the HR department also needs
to be efficient so that discrepancies can be reported effectively and problems can be
mitigated without delay.
5. Identify the manufacturing management systems and philosophies which are relevant to
planning and managing materials supply
Manufacturing management systems are disciplines that define the process in which products
should be manufactured so that maximum efficiency can be achieved in the production process.
The Requirements of the production line are identified first and necessary production qualities
including different components involved are evaluated and necessary measures are then
implemented to supply these required components. Some of the manufacturing management
systems include cost management algorithms, supply chain management, assembly line
management and advanced manufacturing planning. Material supply process includes
transportation planning and delivery options.
6. How can you identify the requirements for facilities plant and services?
The requirements for facilities, plant and services primarily depend on the type of product or
service that is being produced by the organisation. The feasibility of the product both
5
according to the needs of the organisation. Efficient distribution of labour and skills
ensure that the highest possible productivity is maintained which will ensure
maximisation of profits. It is necessary to identify which skills are essential for what part
of the job and efficient labour distribution will only be possible once the specific skill set
of every employee has been identified by the management.
c. Functional team relationship. This refers to the interpersonal relationship between the
different members of a team. Different members in a team have different professional
requirements and contributions but they are completely interdependent on each other and
thus it is essential to maintain a healthy and functional relationship between members of a
team.
d. Communication and reporting lines. These refer to the different channels of
communication between different teams, departments and organs of an organisation.
Adequate and effective communications need to be in place to ensure that the employees
can remain in contact with each other which will enrich corporation and increase
productivity. Communication between the workforce and the HR department also needs
to be efficient so that discrepancies can be reported effectively and problems can be
mitigated without delay.
5. Identify the manufacturing management systems and philosophies which are relevant to
planning and managing materials supply
Manufacturing management systems are disciplines that define the process in which products
should be manufactured so that maximum efficiency can be achieved in the production process.
The Requirements of the production line are identified first and necessary production qualities
including different components involved are evaluated and necessary measures are then
implemented to supply these required components. Some of the manufacturing management
systems include cost management algorithms, supply chain management, assembly line
management and advanced manufacturing planning. Material supply process includes
transportation planning and delivery options.
6. How can you identify the requirements for facilities plant and services?
The requirements for facilities, plant and services primarily depend on the type of product or
service that is being produced by the organisation. The feasibility of the product both
5
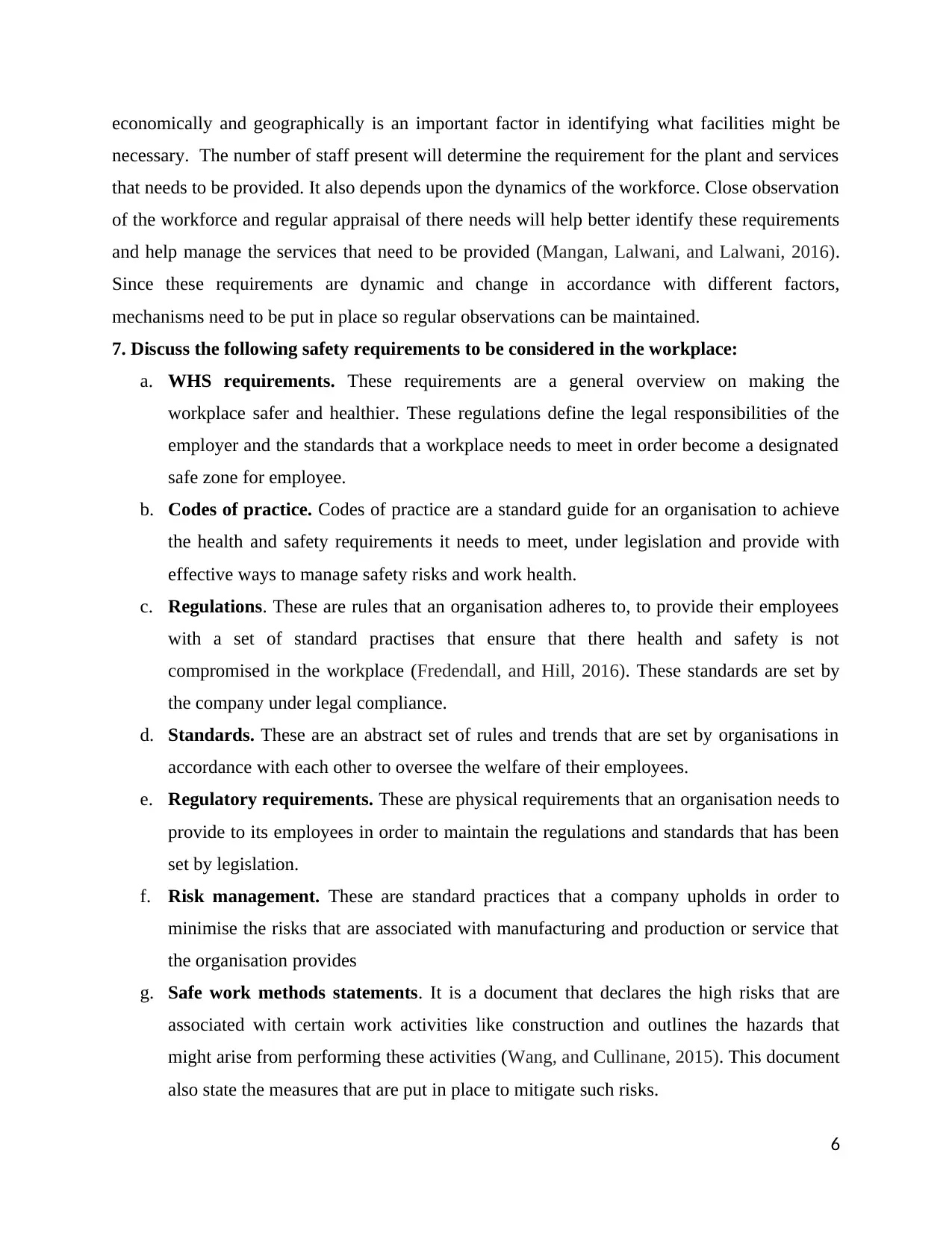
economically and geographically is an important factor in identifying what facilities might be
necessary. The number of staff present will determine the requirement for the plant and services
that needs to be provided. It also depends upon the dynamics of the workforce. Close observation
of the workforce and regular appraisal of there needs will help better identify these requirements
and help manage the services that need to be provided (Mangan, Lalwani, and Lalwani, 2016).
Since these requirements are dynamic and change in accordance with different factors,
mechanisms need to be put in place so regular observations can be maintained.
7. Discuss the following safety requirements to be considered in the workplace:
a. WHS requirements. These requirements are a general overview on making the
workplace safer and healthier. These regulations define the legal responsibilities of the
employer and the standards that a workplace needs to meet in order become a designated
safe zone for employee.
b. Codes of practice. Codes of practice are a standard guide for an organisation to achieve
the health and safety requirements it needs to meet, under legislation and provide with
effective ways to manage safety risks and work health.
c. Regulations. These are rules that an organisation adheres to, to provide their employees
with a set of standard practises that ensure that there health and safety is not
compromised in the workplace (Fredendall, and Hill, 2016). These standards are set by
the company under legal compliance.
d. Standards. These are an abstract set of rules and trends that are set by organisations in
accordance with each other to oversee the welfare of their employees.
e. Regulatory requirements. These are physical requirements that an organisation needs to
provide to its employees in order to maintain the regulations and standards that has been
set by legislation.
f. Risk management. These are standard practices that a company upholds in order to
minimise the risks that are associated with manufacturing and production or service that
the organisation provides
g. Safe work methods statements. It is a document that declares the high risks that are
associated with certain work activities like construction and outlines the hazards that
might arise from performing these activities (Wang, and Cullinane, 2015). This document
also state the measures that are put in place to mitigate such risks.
6
necessary. The number of staff present will determine the requirement for the plant and services
that needs to be provided. It also depends upon the dynamics of the workforce. Close observation
of the workforce and regular appraisal of there needs will help better identify these requirements
and help manage the services that need to be provided (Mangan, Lalwani, and Lalwani, 2016).
Since these requirements are dynamic and change in accordance with different factors,
mechanisms need to be put in place so regular observations can be maintained.
7. Discuss the following safety requirements to be considered in the workplace:
a. WHS requirements. These requirements are a general overview on making the
workplace safer and healthier. These regulations define the legal responsibilities of the
employer and the standards that a workplace needs to meet in order become a designated
safe zone for employee.
b. Codes of practice. Codes of practice are a standard guide for an organisation to achieve
the health and safety requirements it needs to meet, under legislation and provide with
effective ways to manage safety risks and work health.
c. Regulations. These are rules that an organisation adheres to, to provide their employees
with a set of standard practises that ensure that there health and safety is not
compromised in the workplace (Fredendall, and Hill, 2016). These standards are set by
the company under legal compliance.
d. Standards. These are an abstract set of rules and trends that are set by organisations in
accordance with each other to oversee the welfare of their employees.
e. Regulatory requirements. These are physical requirements that an organisation needs to
provide to its employees in order to maintain the regulations and standards that has been
set by legislation.
f. Risk management. These are standard practices that a company upholds in order to
minimise the risks that are associated with manufacturing and production or service that
the organisation provides
g. Safe work methods statements. It is a document that declares the high risks that are
associated with certain work activities like construction and outlines the hazards that
might arise from performing these activities (Wang, and Cullinane, 2015). This document
also state the measures that are put in place to mitigate such risks.
6
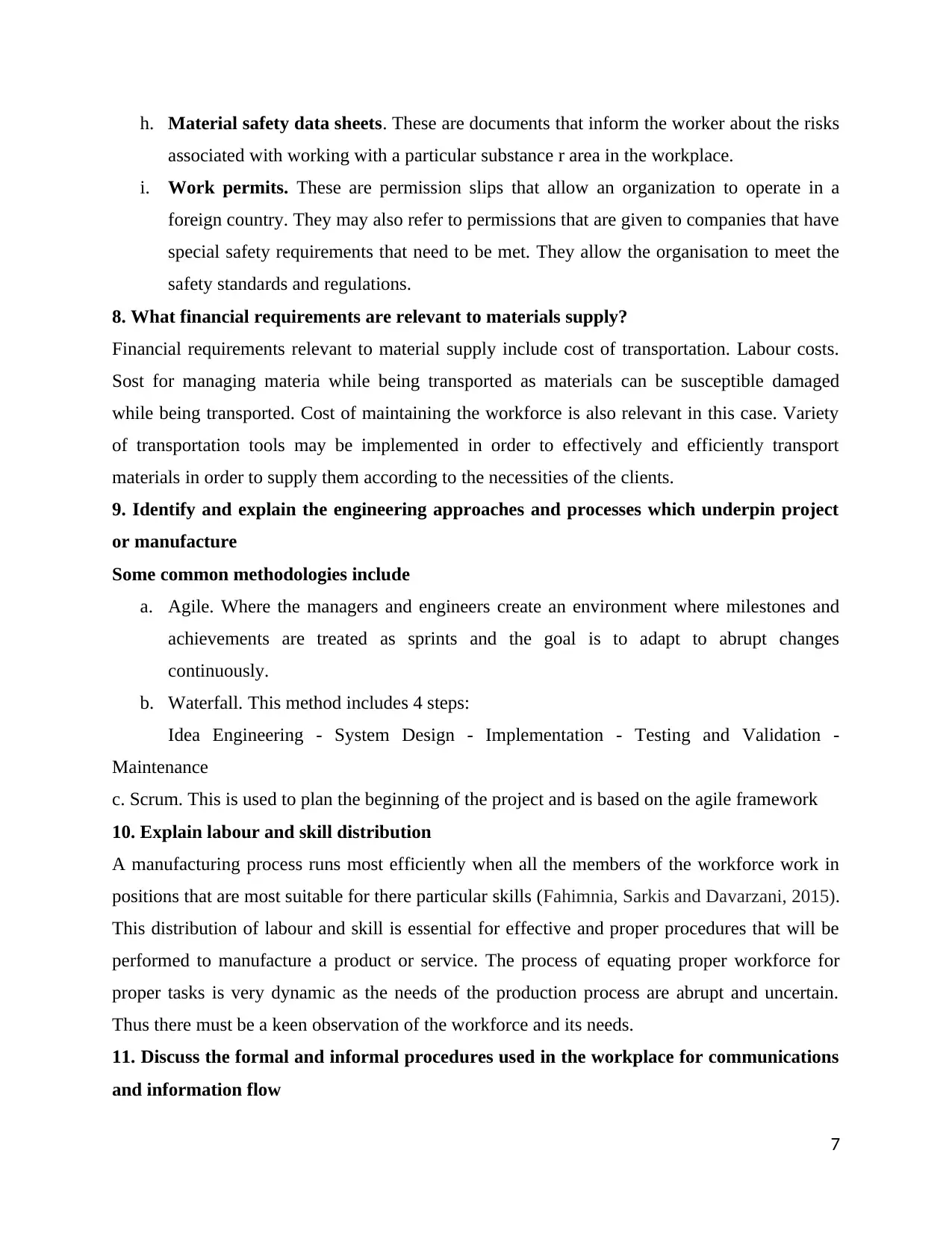
h. Material safety data sheets. These are documents that inform the worker about the risks
associated with working with a particular substance r area in the workplace.
i. Work permits. These are permission slips that allow an organization to operate in a
foreign country. They may also refer to permissions that are given to companies that have
special safety requirements that need to be met. They allow the organisation to meet the
safety standards and regulations.
8. What financial requirements are relevant to materials supply?
Financial requirements relevant to material supply include cost of transportation. Labour costs.
Sost for managing materia while being transported as materials can be susceptible damaged
while being transported. Cost of maintaining the workforce is also relevant in this case. Variety
of transportation tools may be implemented in order to effectively and efficiently transport
materials in order to supply them according to the necessities of the clients.
9. Identify and explain the engineering approaches and processes which underpin project
or manufacture
Some common methodologies include
a. Agile. Where the managers and engineers create an environment where milestones and
achievements are treated as sprints and the goal is to adapt to abrupt changes
continuously.
b. Waterfall. This method includes 4 steps:
Idea Engineering - System Design - Implementation - Testing and Validation -
Maintenance
c. Scrum. This is used to plan the beginning of the project and is based on the agile framework
10. Explain labour and skill distribution
A manufacturing process runs most efficiently when all the members of the workforce work in
positions that are most suitable for there particular skills (Fahimnia, Sarkis and Davarzani, 2015).
This distribution of labour and skill is essential for effective and proper procedures that will be
performed to manufacture a product or service. The process of equating proper workforce for
proper tasks is very dynamic as the needs of the production process are abrupt and uncertain.
Thus there must be a keen observation of the workforce and its needs.
11. Discuss the formal and informal procedures used in the workplace for communications
and information flow
7
associated with working with a particular substance r area in the workplace.
i. Work permits. These are permission slips that allow an organization to operate in a
foreign country. They may also refer to permissions that are given to companies that have
special safety requirements that need to be met. They allow the organisation to meet the
safety standards and regulations.
8. What financial requirements are relevant to materials supply?
Financial requirements relevant to material supply include cost of transportation. Labour costs.
Sost for managing materia while being transported as materials can be susceptible damaged
while being transported. Cost of maintaining the workforce is also relevant in this case. Variety
of transportation tools may be implemented in order to effectively and efficiently transport
materials in order to supply them according to the necessities of the clients.
9. Identify and explain the engineering approaches and processes which underpin project
or manufacture
Some common methodologies include
a. Agile. Where the managers and engineers create an environment where milestones and
achievements are treated as sprints and the goal is to adapt to abrupt changes
continuously.
b. Waterfall. This method includes 4 steps:
Idea Engineering - System Design - Implementation - Testing and Validation -
Maintenance
c. Scrum. This is used to plan the beginning of the project and is based on the agile framework
10. Explain labour and skill distribution
A manufacturing process runs most efficiently when all the members of the workforce work in
positions that are most suitable for there particular skills (Fahimnia, Sarkis and Davarzani, 2015).
This distribution of labour and skill is essential for effective and proper procedures that will be
performed to manufacture a product or service. The process of equating proper workforce for
proper tasks is very dynamic as the needs of the production process are abrupt and uncertain.
Thus there must be a keen observation of the workforce and its needs.
11. Discuss the formal and informal procedures used in the workplace for communications
and information flow
7
Paraphrase This Document
Need a fresh take? Get an instant paraphrase of this document with our AI Paraphraser
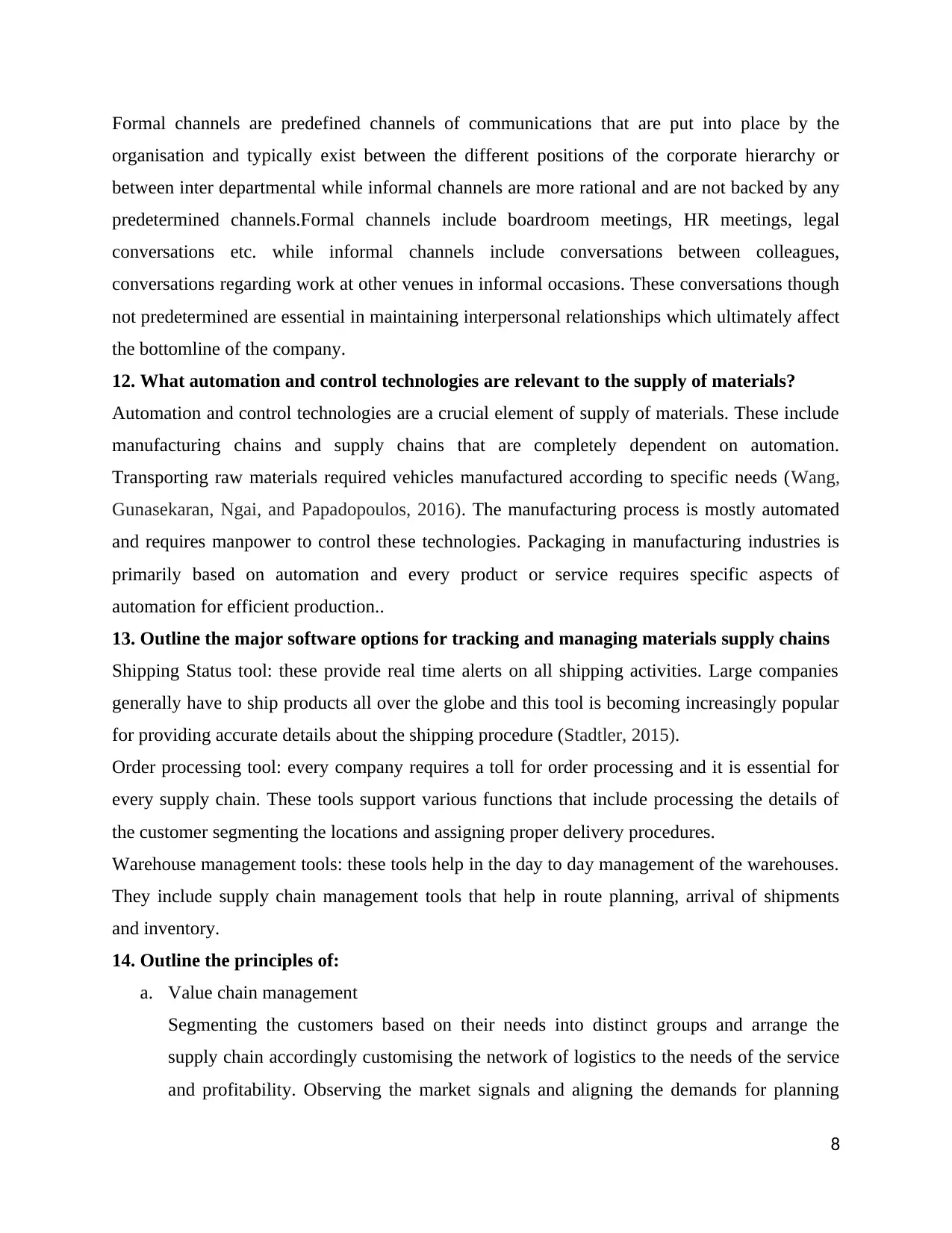
Formal channels are predefined channels of communications that are put into place by the
organisation and typically exist between the different positions of the corporate hierarchy or
between inter departmental while informal channels are more rational and are not backed by any
predetermined channels.Formal channels include boardroom meetings, HR meetings, legal
conversations etc. while informal channels include conversations between colleagues,
conversations regarding work at other venues in informal occasions. These conversations though
not predetermined are essential in maintaining interpersonal relationships which ultimately affect
the bottomline of the company.
12. What automation and control technologies are relevant to the supply of materials?
Automation and control technologies are a crucial element of supply of materials. These include
manufacturing chains and supply chains that are completely dependent on automation.
Transporting raw materials required vehicles manufactured according to specific needs (Wang,
Gunasekaran, Ngai, and Papadopoulos, 2016). The manufacturing process is mostly automated
and requires manpower to control these technologies. Packaging in manufacturing industries is
primarily based on automation and every product or service requires specific aspects of
automation for efficient production..
13. Outline the major software options for tracking and managing materials supply chains
Shipping Status tool: these provide real time alerts on all shipping activities. Large companies
generally have to ship products all over the globe and this tool is becoming increasingly popular
for providing accurate details about the shipping procedure (Stadtler, 2015).
Order processing tool: every company requires a toll for order processing and it is essential for
every supply chain. These tools support various functions that include processing the details of
the customer segmenting the locations and assigning proper delivery procedures.
Warehouse management tools: these tools help in the day to day management of the warehouses.
They include supply chain management tools that help in route planning, arrival of shipments
and inventory.
14. Outline the principles of:
a. Value chain management
Segmenting the customers based on their needs into distinct groups and arrange the
supply chain accordingly customising the network of logistics to the needs of the service
and profitability. Observing the market signals and aligning the demands for planning
8
organisation and typically exist between the different positions of the corporate hierarchy or
between inter departmental while informal channels are more rational and are not backed by any
predetermined channels.Formal channels include boardroom meetings, HR meetings, legal
conversations etc. while informal channels include conversations between colleagues,
conversations regarding work at other venues in informal occasions. These conversations though
not predetermined are essential in maintaining interpersonal relationships which ultimately affect
the bottomline of the company.
12. What automation and control technologies are relevant to the supply of materials?
Automation and control technologies are a crucial element of supply of materials. These include
manufacturing chains and supply chains that are completely dependent on automation.
Transporting raw materials required vehicles manufactured according to specific needs (Wang,
Gunasekaran, Ngai, and Papadopoulos, 2016). The manufacturing process is mostly automated
and requires manpower to control these technologies. Packaging in manufacturing industries is
primarily based on automation and every product or service requires specific aspects of
automation for efficient production..
13. Outline the major software options for tracking and managing materials supply chains
Shipping Status tool: these provide real time alerts on all shipping activities. Large companies
generally have to ship products all over the globe and this tool is becoming increasingly popular
for providing accurate details about the shipping procedure (Stadtler, 2015).
Order processing tool: every company requires a toll for order processing and it is essential for
every supply chain. These tools support various functions that include processing the details of
the customer segmenting the locations and assigning proper delivery procedures.
Warehouse management tools: these tools help in the day to day management of the warehouses.
They include supply chain management tools that help in route planning, arrival of shipments
and inventory.
14. Outline the principles of:
a. Value chain management
Segmenting the customers based on their needs into distinct groups and arrange the
supply chain accordingly customising the network of logistics to the needs of the service
and profitability. Observing the market signals and aligning the demands for planning
8
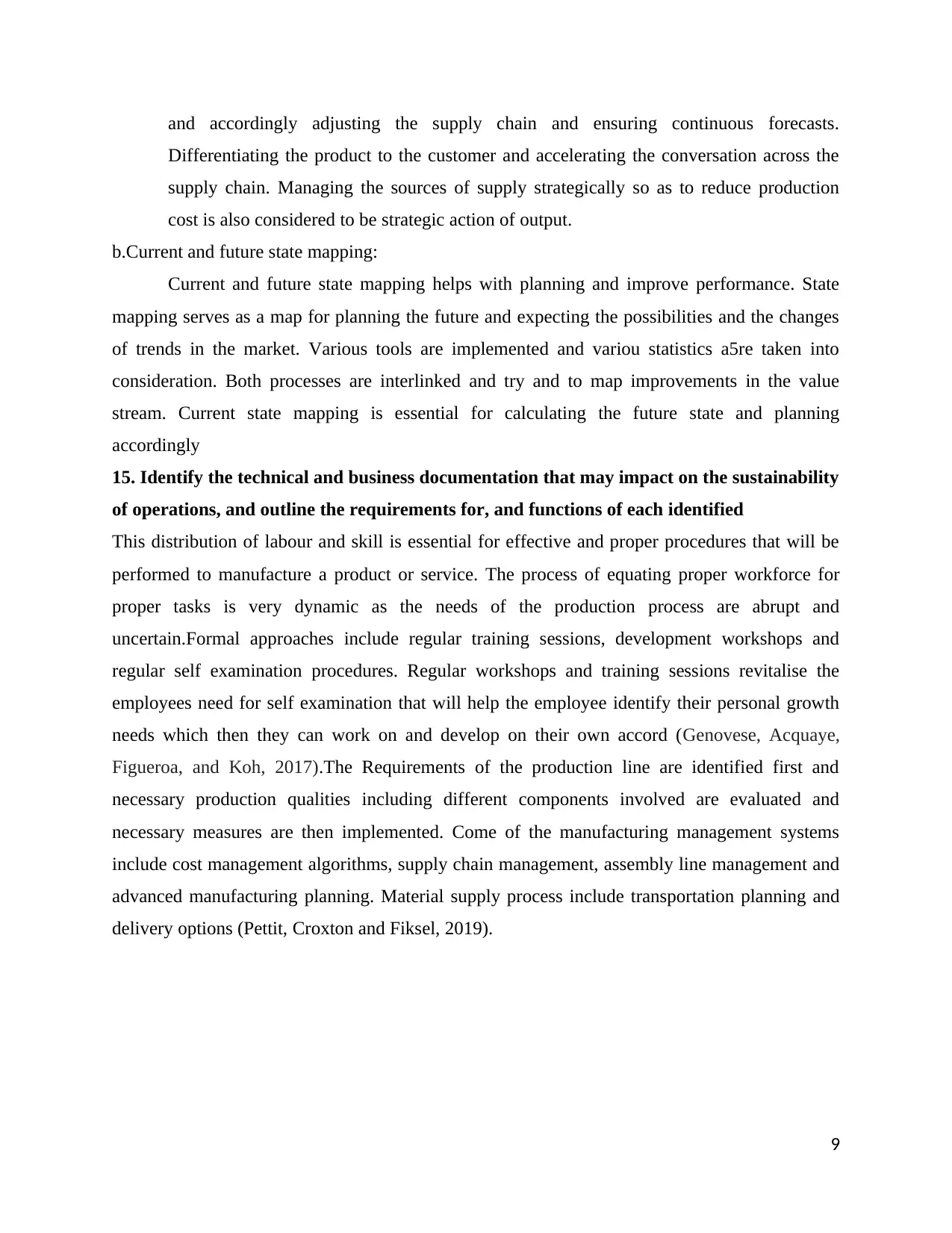
and accordingly adjusting the supply chain and ensuring continuous forecasts.
Differentiating the product to the customer and accelerating the conversation across the
supply chain. Managing the sources of supply strategically so as to reduce production
cost is also considered to be strategic action of output.
b.Current and future state mapping:
Current and future state mapping helps with planning and improve performance. State
mapping serves as a map for planning the future and expecting the possibilities and the changes
of trends in the market. Various tools are implemented and variou statistics a5re taken into
consideration. Both processes are interlinked and try and to map improvements in the value
stream. Current state mapping is essential for calculating the future state and planning
accordingly
15. Identify the technical and business documentation that may impact on the sustainability
of operations, and outline the requirements for, and functions of each identified
This distribution of labour and skill is essential for effective and proper procedures that will be
performed to manufacture a product or service. The process of equating proper workforce for
proper tasks is very dynamic as the needs of the production process are abrupt and
uncertain.Formal approaches include regular training sessions, development workshops and
regular self examination procedures. Regular workshops and training sessions revitalise the
employees need for self examination that will help the employee identify their personal growth
needs which then they can work on and develop on their own accord (Genovese, Acquaye,
Figueroa, and Koh, 2017).The Requirements of the production line are identified first and
necessary production qualities including different components involved are evaluated and
necessary measures are then implemented. Come of the manufacturing management systems
include cost management algorithms, supply chain management, assembly line management and
advanced manufacturing planning. Material supply process include transportation planning and
delivery options (Pettit, Croxton and Fiksel, 2019).
9
Differentiating the product to the customer and accelerating the conversation across the
supply chain. Managing the sources of supply strategically so as to reduce production
cost is also considered to be strategic action of output.
b.Current and future state mapping:
Current and future state mapping helps with planning and improve performance. State
mapping serves as a map for planning the future and expecting the possibilities and the changes
of trends in the market. Various tools are implemented and variou statistics a5re taken into
consideration. Both processes are interlinked and try and to map improvements in the value
stream. Current state mapping is essential for calculating the future state and planning
accordingly
15. Identify the technical and business documentation that may impact on the sustainability
of operations, and outline the requirements for, and functions of each identified
This distribution of labour and skill is essential for effective and proper procedures that will be
performed to manufacture a product or service. The process of equating proper workforce for
proper tasks is very dynamic as the needs of the production process are abrupt and
uncertain.Formal approaches include regular training sessions, development workshops and
regular self examination procedures. Regular workshops and training sessions revitalise the
employees need for self examination that will help the employee identify their personal growth
needs which then they can work on and develop on their own accord (Genovese, Acquaye,
Figueroa, and Koh, 2017).The Requirements of the production line are identified first and
necessary production qualities including different components involved are evaluated and
necessary measures are then implemented. Come of the manufacturing management systems
include cost management algorithms, supply chain management, assembly line management and
advanced manufacturing planning. Material supply process include transportation planning and
delivery options (Pettit, Croxton and Fiksel, 2019).
9
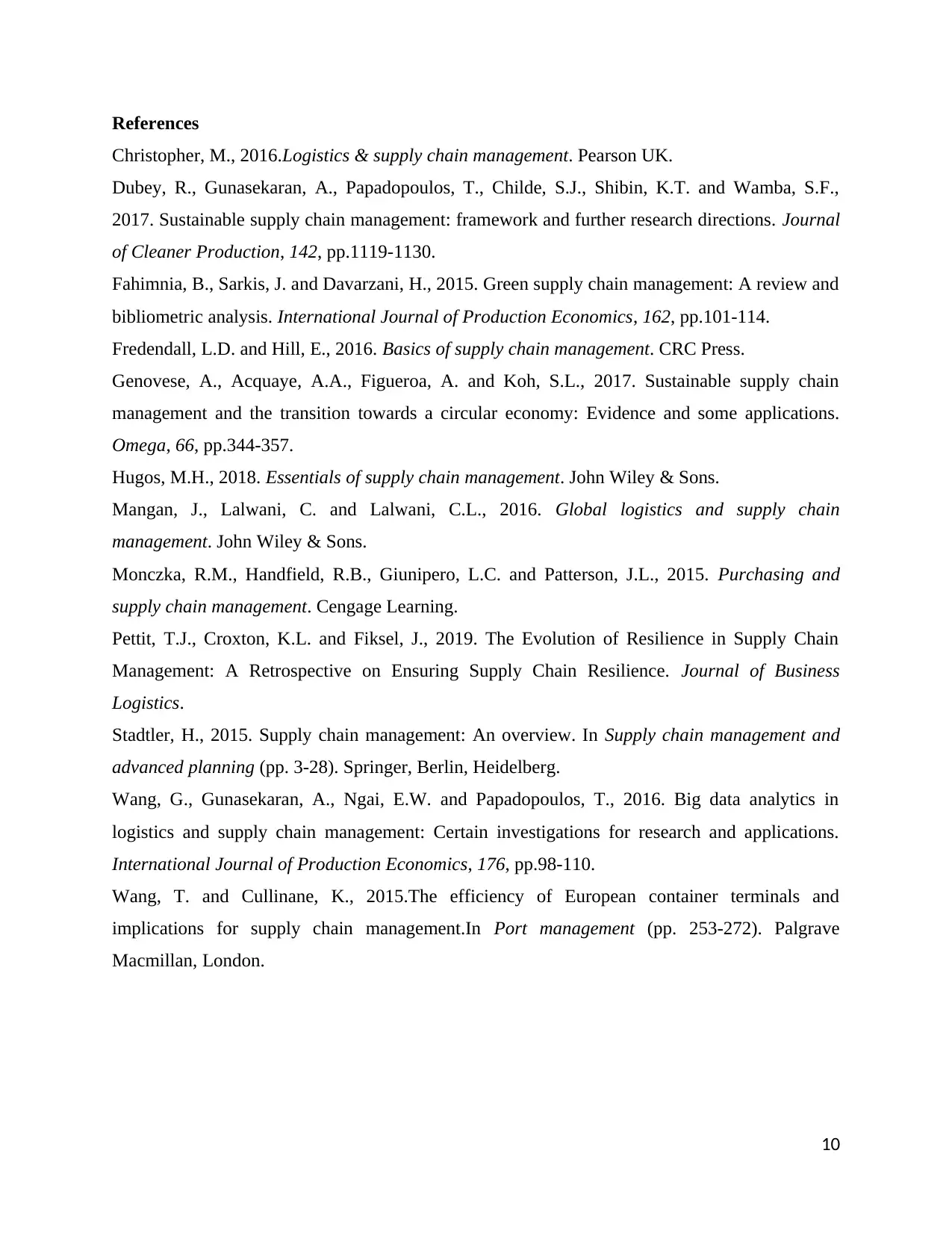
References
Christopher, M., 2016.Logistics & supply chain management. Pearson UK.
Dubey, R., Gunasekaran, A., Papadopoulos, T., Childe, S.J., Shibin, K.T. and Wamba, S.F.,
2017. Sustainable supply chain management: framework and further research directions. Journal
of Cleaner Production, 142, pp.1119-1130.
Fahimnia, B., Sarkis, J. and Davarzani, H., 2015. Green supply chain management: A review and
bibliometric analysis. International Journal of Production Economics, 162, pp.101-114.
Fredendall, L.D. and Hill, E., 2016. Basics of supply chain management. CRC Press.
Genovese, A., Acquaye, A.A., Figueroa, A. and Koh, S.L., 2017. Sustainable supply chain
management and the transition towards a circular economy: Evidence and some applications.
Omega, 66, pp.344-357.
Hugos, M.H., 2018. Essentials of supply chain management. John Wiley & Sons.
Mangan, J., Lalwani, C. and Lalwani, C.L., 2016. Global logistics and supply chain
management. John Wiley & Sons.
Monczka, R.M., Handfield, R.B., Giunipero, L.C. and Patterson, J.L., 2015. Purchasing and
supply chain management. Cengage Learning.
Pettit, T.J., Croxton, K.L. and Fiksel, J., 2019. The Evolution of Resilience in Supply Chain
Management: A Retrospective on Ensuring Supply Chain Resilience. Journal of Business
Logistics.
Stadtler, H., 2015. Supply chain management: An overview. In Supply chain management and
advanced planning (pp. 3-28). Springer, Berlin, Heidelberg.
Wang, G., Gunasekaran, A., Ngai, E.W. and Papadopoulos, T., 2016. Big data analytics in
logistics and supply chain management: Certain investigations for research and applications.
International Journal of Production Economics, 176, pp.98-110.
Wang, T. and Cullinane, K., 2015.The efficiency of European container terminals and
implications for supply chain management.In Port management (pp. 253-272). Palgrave
Macmillan, London.
10
Christopher, M., 2016.Logistics & supply chain management. Pearson UK.
Dubey, R., Gunasekaran, A., Papadopoulos, T., Childe, S.J., Shibin, K.T. and Wamba, S.F.,
2017. Sustainable supply chain management: framework and further research directions. Journal
of Cleaner Production, 142, pp.1119-1130.
Fahimnia, B., Sarkis, J. and Davarzani, H., 2015. Green supply chain management: A review and
bibliometric analysis. International Journal of Production Economics, 162, pp.101-114.
Fredendall, L.D. and Hill, E., 2016. Basics of supply chain management. CRC Press.
Genovese, A., Acquaye, A.A., Figueroa, A. and Koh, S.L., 2017. Sustainable supply chain
management and the transition towards a circular economy: Evidence and some applications.
Omega, 66, pp.344-357.
Hugos, M.H., 2018. Essentials of supply chain management. John Wiley & Sons.
Mangan, J., Lalwani, C. and Lalwani, C.L., 2016. Global logistics and supply chain
management. John Wiley & Sons.
Monczka, R.M., Handfield, R.B., Giunipero, L.C. and Patterson, J.L., 2015. Purchasing and
supply chain management. Cengage Learning.
Pettit, T.J., Croxton, K.L. and Fiksel, J., 2019. The Evolution of Resilience in Supply Chain
Management: A Retrospective on Ensuring Supply Chain Resilience. Journal of Business
Logistics.
Stadtler, H., 2015. Supply chain management: An overview. In Supply chain management and
advanced planning (pp. 3-28). Springer, Berlin, Heidelberg.
Wang, G., Gunasekaran, A., Ngai, E.W. and Papadopoulos, T., 2016. Big data analytics in
logistics and supply chain management: Certain investigations for research and applications.
International Journal of Production Economics, 176, pp.98-110.
Wang, T. and Cullinane, K., 2015.The efficiency of European container terminals and
implications for supply chain management.In Port management (pp. 253-272). Palgrave
Macmillan, London.
10
Secure Best Marks with AI Grader
Need help grading? Try our AI Grader for instant feedback on your assignments.
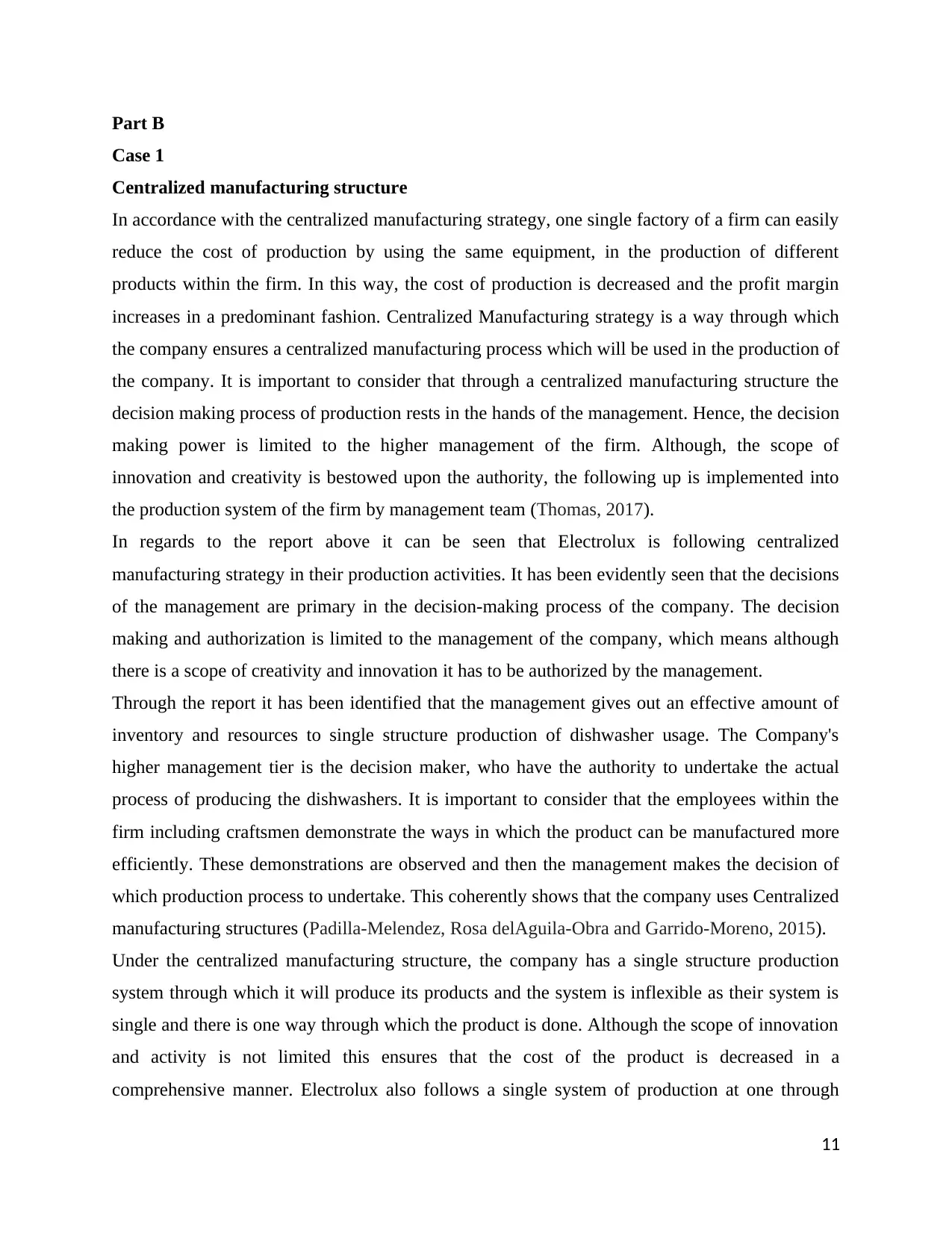
Part B
Case 1
Centralized manufacturing structure
In accordance with the centralized manufacturing strategy, one single factory of a firm can easily
reduce the cost of production by using the same equipment, in the production of different
products within the firm. In this way, the cost of production is decreased and the profit margin
increases in a predominant fashion. Centralized Manufacturing strategy is a way through which
the company ensures a centralized manufacturing process which will be used in the production of
the company. It is important to consider that through a centralized manufacturing structure the
decision making process of production rests in the hands of the management. Hence, the decision
making power is limited to the higher management of the firm. Although, the scope of
innovation and creativity is bestowed upon the authority, the following up is implemented into
the production system of the firm by management team (Thomas, 2017).
In regards to the report above it can be seen that Electrolux is following centralized
manufacturing strategy in their production activities. It has been evidently seen that the decisions
of the management are primary in the decision-making process of the company. The decision
making and authorization is limited to the management of the company, which means although
there is a scope of creativity and innovation it has to be authorized by the management.
Through the report it has been identified that the management gives out an effective amount of
inventory and resources to single structure production of dishwasher usage. The Company's
higher management tier is the decision maker, who have the authority to undertake the actual
process of producing the dishwashers. It is important to consider that the employees within the
firm including craftsmen demonstrate the ways in which the product can be manufactured more
efficiently. These demonstrations are observed and then the management makes the decision of
which production process to undertake. This coherently shows that the company uses Centralized
manufacturing structures (Padilla-Melendez, Rosa delAguila-Obra and Garrido-Moreno, 2015).
Under the centralized manufacturing structure, the company has a single structure production
system through which it will produce its products and the system is inflexible as their system is
single and there is one way through which the product is done. Although the scope of innovation
and activity is not limited this ensures that the cost of the product is decreased in a
comprehensive manner. Electrolux also follows a single system of production at one through
11
Case 1
Centralized manufacturing structure
In accordance with the centralized manufacturing strategy, one single factory of a firm can easily
reduce the cost of production by using the same equipment, in the production of different
products within the firm. In this way, the cost of production is decreased and the profit margin
increases in a predominant fashion. Centralized Manufacturing strategy is a way through which
the company ensures a centralized manufacturing process which will be used in the production of
the company. It is important to consider that through a centralized manufacturing structure the
decision making process of production rests in the hands of the management. Hence, the decision
making power is limited to the higher management of the firm. Although, the scope of
innovation and creativity is bestowed upon the authority, the following up is implemented into
the production system of the firm by management team (Thomas, 2017).
In regards to the report above it can be seen that Electrolux is following centralized
manufacturing strategy in their production activities. It has been evidently seen that the decisions
of the management are primary in the decision-making process of the company. The decision
making and authorization is limited to the management of the company, which means although
there is a scope of creativity and innovation it has to be authorized by the management.
Through the report it has been identified that the management gives out an effective amount of
inventory and resources to single structure production of dishwasher usage. The Company's
higher management tier is the decision maker, who have the authority to undertake the actual
process of producing the dishwashers. It is important to consider that the employees within the
firm including craftsmen demonstrate the ways in which the product can be manufactured more
efficiently. These demonstrations are observed and then the management makes the decision of
which production process to undertake. This coherently shows that the company uses Centralized
manufacturing structures (Padilla-Melendez, Rosa delAguila-Obra and Garrido-Moreno, 2015).
Under the centralized manufacturing structure, the company has a single structure production
system through which it will produce its products and the system is inflexible as their system is
single and there is one way through which the product is done. Although the scope of innovation
and activity is not limited this ensures that the cost of the product is decreased in a
comprehensive manner. Electrolux also follows a single system of production at one through
11
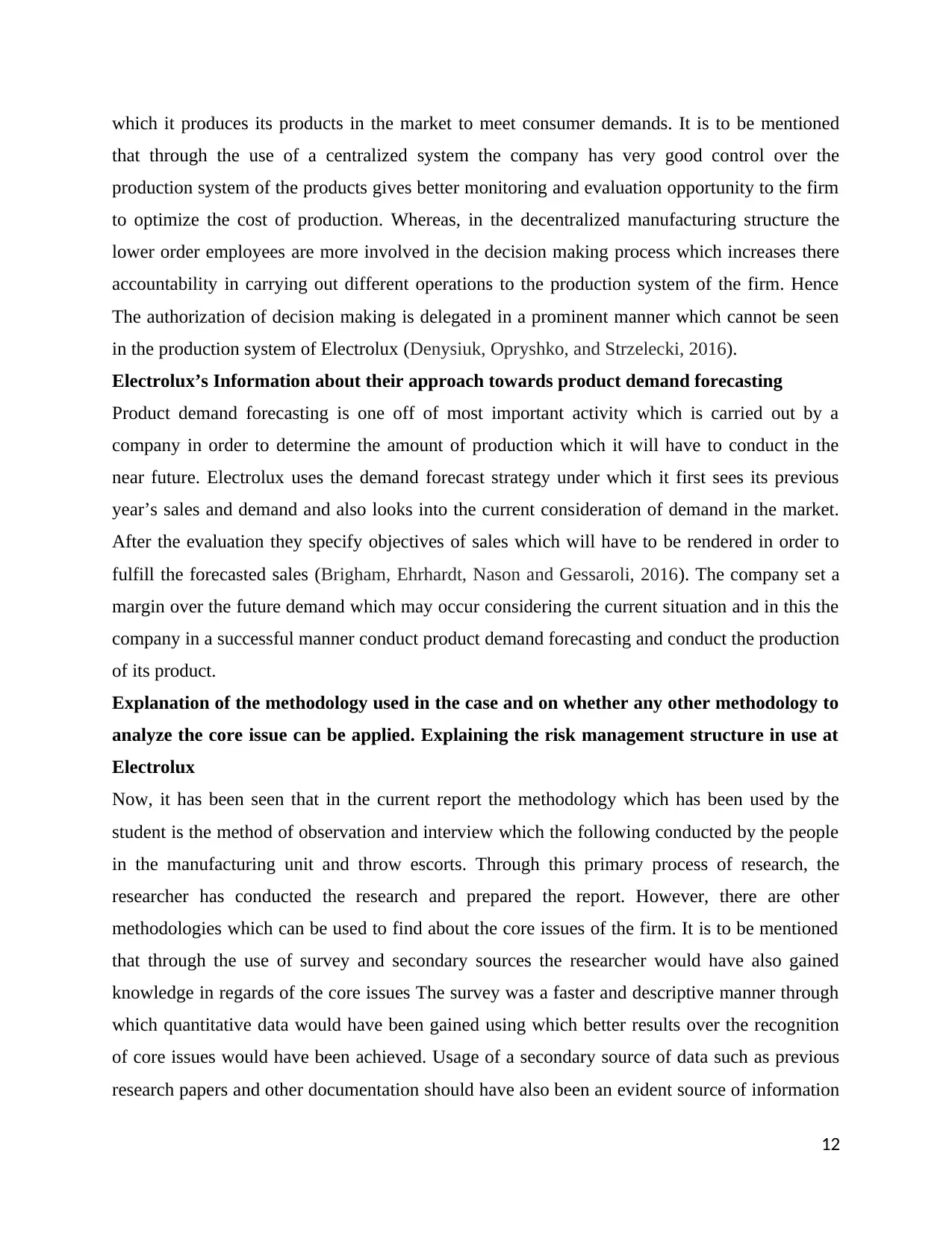
which it produces its products in the market to meet consumer demands. It is to be mentioned
that through the use of a centralized system the company has very good control over the
production system of the products gives better monitoring and evaluation opportunity to the firm
to optimize the cost of production. Whereas, in the decentralized manufacturing structure the
lower order employees are more involved in the decision making process which increases there
accountability in carrying out different operations to the production system of the firm. Hence
The authorization of decision making is delegated in a prominent manner which cannot be seen
in the production system of Electrolux (Denysiuk, Opryshko, and Strzelecki, 2016).
Electrolux’s Information about their approach towards product demand forecasting
Product demand forecasting is one off of most important activity which is carried out by a
company in order to determine the amount of production which it will have to conduct in the
near future. Electrolux uses the demand forecast strategy under which it first sees its previous
year’s sales and demand and also looks into the current consideration of demand in the market.
After the evaluation they specify objectives of sales which will have to be rendered in order to
fulfill the forecasted sales (Brigham, Ehrhardt, Nason and Gessaroli, 2016). The company set a
margin over the future demand which may occur considering the current situation and in this the
company in a successful manner conduct product demand forecasting and conduct the production
of its product.
Explanation of the methodology used in the case and on whether any other methodology to
analyze the core issue can be applied. Explaining the risk management structure in use at
Electrolux
Now, it has been seen that in the current report the methodology which has been used by the
student is the method of observation and interview which the following conducted by the people
in the manufacturing unit and throw escorts. Through this primary process of research, the
researcher has conducted the research and prepared the report. However, there are other
methodologies which can be used to find about the core issues of the firm. It is to be mentioned
that through the use of survey and secondary sources the researcher would have also gained
knowledge in regards of the core issues The survey was a faster and descriptive manner through
which quantitative data would have been gained using which better results over the recognition
of core issues would have been achieved. Usage of a secondary source of data such as previous
research papers and other documentation should have also been an evident source of information
12
that through the use of a centralized system the company has very good control over the
production system of the products gives better monitoring and evaluation opportunity to the firm
to optimize the cost of production. Whereas, in the decentralized manufacturing structure the
lower order employees are more involved in the decision making process which increases there
accountability in carrying out different operations to the production system of the firm. Hence
The authorization of decision making is delegated in a prominent manner which cannot be seen
in the production system of Electrolux (Denysiuk, Opryshko, and Strzelecki, 2016).
Electrolux’s Information about their approach towards product demand forecasting
Product demand forecasting is one off of most important activity which is carried out by a
company in order to determine the amount of production which it will have to conduct in the
near future. Electrolux uses the demand forecast strategy under which it first sees its previous
year’s sales and demand and also looks into the current consideration of demand in the market.
After the evaluation they specify objectives of sales which will have to be rendered in order to
fulfill the forecasted sales (Brigham, Ehrhardt, Nason and Gessaroli, 2016). The company set a
margin over the future demand which may occur considering the current situation and in this the
company in a successful manner conduct product demand forecasting and conduct the production
of its product.
Explanation of the methodology used in the case and on whether any other methodology to
analyze the core issue can be applied. Explaining the risk management structure in use at
Electrolux
Now, it has been seen that in the current report the methodology which has been used by the
student is the method of observation and interview which the following conducted by the people
in the manufacturing unit and throw escorts. Through this primary process of research, the
researcher has conducted the research and prepared the report. However, there are other
methodologies which can be used to find about the core issues of the firm. It is to be mentioned
that through the use of survey and secondary sources the researcher would have also gained
knowledge in regards of the core issues The survey was a faster and descriptive manner through
which quantitative data would have been gained using which better results over the recognition
of core issues would have been achieved. Usage of a secondary source of data such as previous
research papers and other documentation should have also been an evident source of information
12
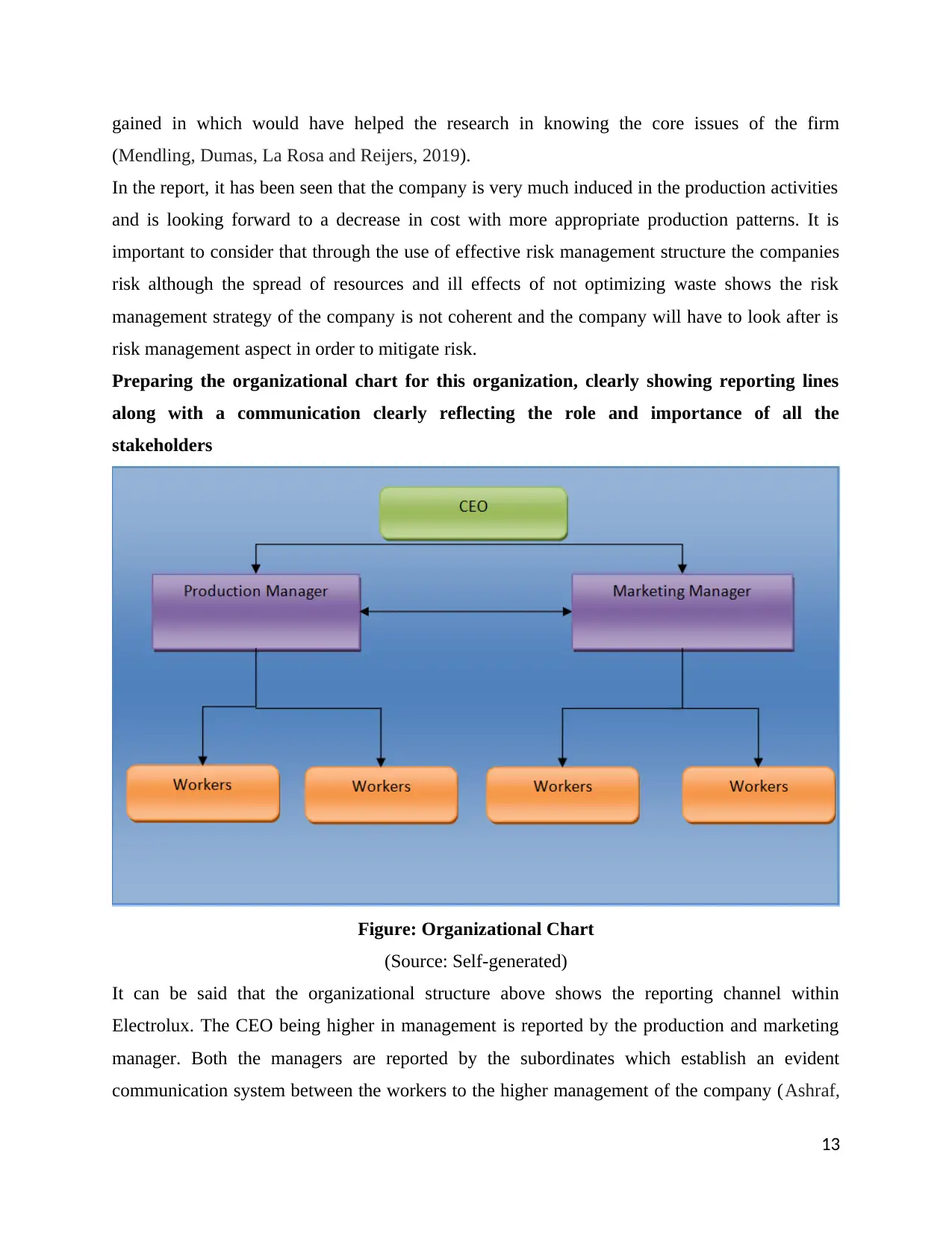
gained in which would have helped the research in knowing the core issues of the firm
(Mendling, Dumas, La Rosa and Reijers, 2019).
In the report, it has been seen that the company is very much induced in the production activities
and is looking forward to a decrease in cost with more appropriate production patterns. It is
important to consider that through the use of effective risk management structure the companies
risk although the spread of resources and ill effects of not optimizing waste shows the risk
management strategy of the company is not coherent and the company will have to look after is
risk management aspect in order to mitigate risk.
Preparing the organizational chart for this organization, clearly showing reporting lines
along with a communication clearly reflecting the role and importance of all the
stakeholders
Figure: Organizational Chart
(Source: Self-generated)
It can be said that the organizational structure above shows the reporting channel within
Electrolux. The CEO being higher in management is reported by the production and marketing
manager. Both the managers are reported by the subordinates which establish an evident
communication system between the workers to the higher management of the company (Ashraf,
13
(Mendling, Dumas, La Rosa and Reijers, 2019).
In the report, it has been seen that the company is very much induced in the production activities
and is looking forward to a decrease in cost with more appropriate production patterns. It is
important to consider that through the use of effective risk management structure the companies
risk although the spread of resources and ill effects of not optimizing waste shows the risk
management strategy of the company is not coherent and the company will have to look after is
risk management aspect in order to mitigate risk.
Preparing the organizational chart for this organization, clearly showing reporting lines
along with a communication clearly reflecting the role and importance of all the
stakeholders
Figure: Organizational Chart
(Source: Self-generated)
It can be said that the organizational structure above shows the reporting channel within
Electrolux. The CEO being higher in management is reported by the production and marketing
manager. Both the managers are reported by the subordinates which establish an evident
communication system between the workers to the higher management of the company (Ashraf,
13
Paraphrase This Document
Need a fresh take? Get an instant paraphrase of this document with our AI Paraphraser
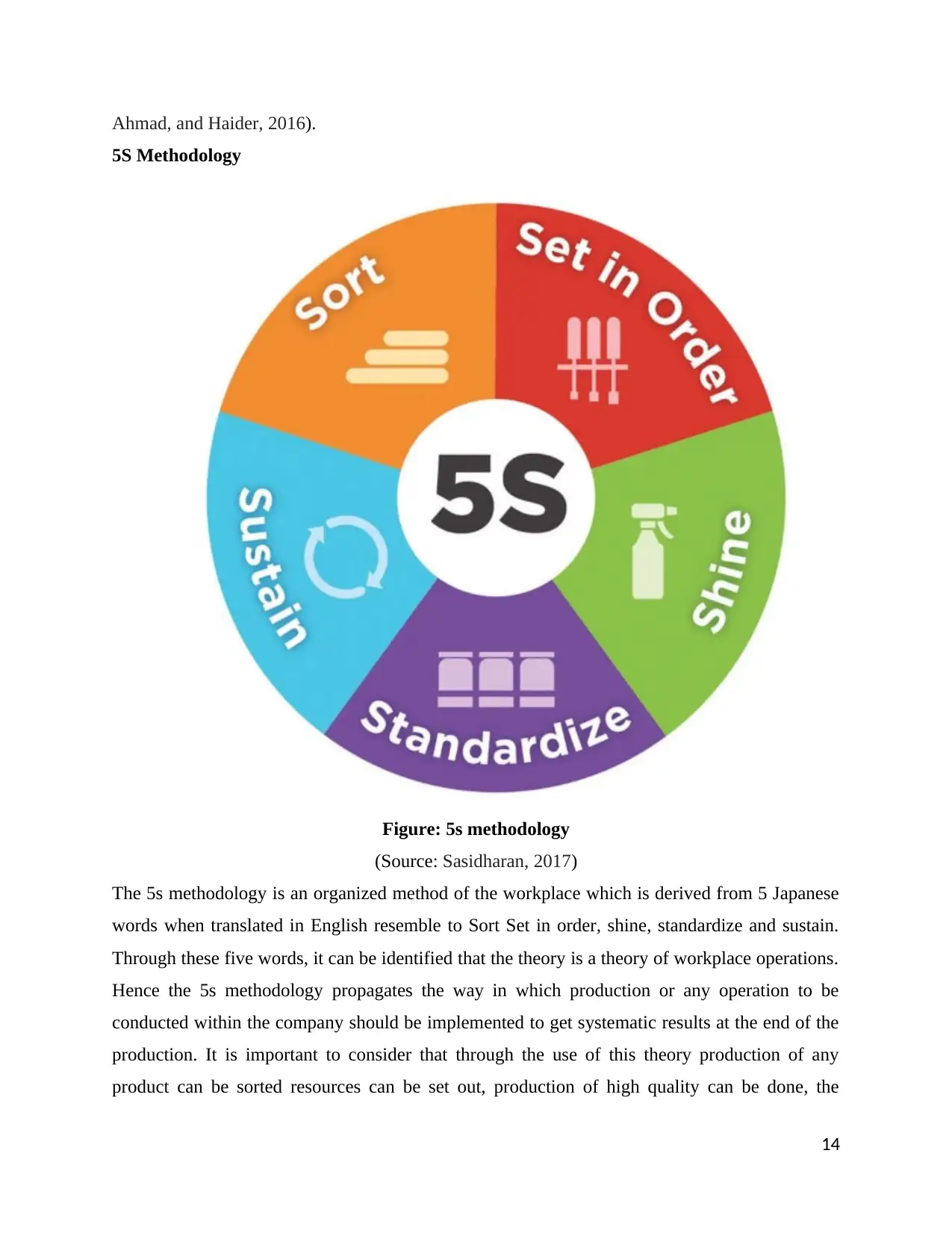
Ahmad, and Haider, 2016).
5S Methodology
Figure: 5s methodology
(Source: Sasidharan, 2017)
The 5s methodology is an organized method of the workplace which is derived from 5 Japanese
words when translated in English resemble to Sort Set in order, shine, standardize and sustain.
Through these five words, it can be identified that the theory is a theory of workplace operations.
Hence the 5s methodology propagates the way in which production or any operation to be
conducted within the company should be implemented to get systematic results at the end of the
production. It is important to consider that through the use of this theory production of any
product can be sorted resources can be set out, production of high quality can be done, the
14
5S Methodology
Figure: 5s methodology
(Source: Sasidharan, 2017)
The 5s methodology is an organized method of the workplace which is derived from 5 Japanese
words when translated in English resemble to Sort Set in order, shine, standardize and sustain.
Through these five words, it can be identified that the theory is a theory of workplace operations.
Hence the 5s methodology propagates the way in which production or any operation to be
conducted within the company should be implemented to get systematic results at the end of the
production. It is important to consider that through the use of this theory production of any
product can be sorted resources can be set out, production of high quality can be done, the
14
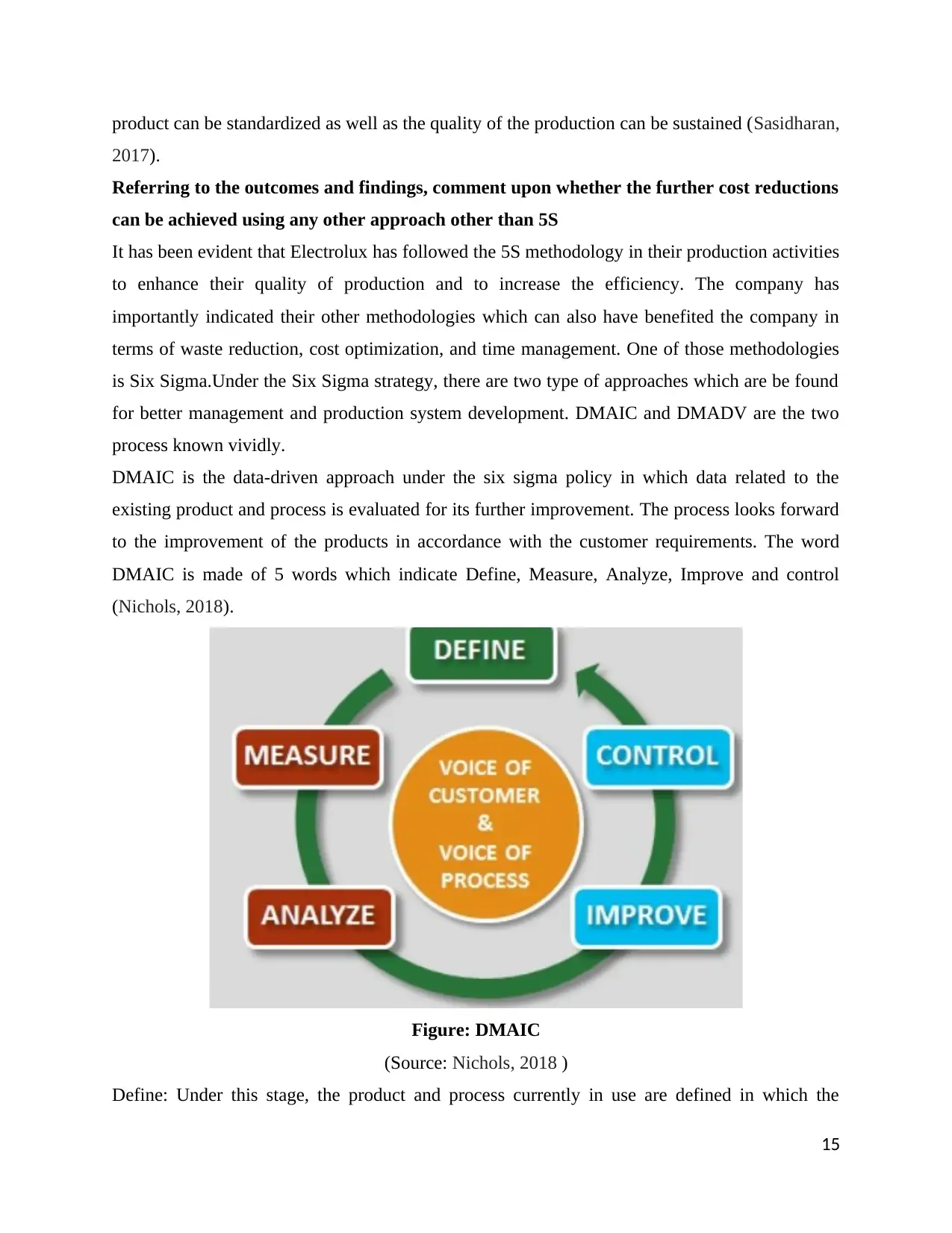
product can be standardized as well as the quality of the production can be sustained (Sasidharan,
2017).
Referring to the outcomes and findings, comment upon whether the further cost reductions
can be achieved using any other approach other than 5S
It has been evident that Electrolux has followed the 5S methodology in their production activities
to enhance their quality of production and to increase the efficiency. The company has
importantly indicated their other methodologies which can also have benefited the company in
terms of waste reduction, cost optimization, and time management. One of those methodologies
is Six Sigma.Under the Six Sigma strategy, there are two type of approaches which are be found
for better management and production system development. DMAIC and DMADV are the two
process known vividly.
DMAIC is the data-driven approach under the six sigma policy in which data related to the
existing product and process is evaluated for its further improvement. The process looks forward
to the improvement of the products in accordance with the customer requirements. The word
DMAIC is made of 5 words which indicate Define, Measure, Analyze, Improve and control
(Nichols, 2018).
Figure: DMAIC
(Source: Nichols, 2018 )
Define: Under this stage, the product and process currently in use are defined in which the
15
2017).
Referring to the outcomes and findings, comment upon whether the further cost reductions
can be achieved using any other approach other than 5S
It has been evident that Electrolux has followed the 5S methodology in their production activities
to enhance their quality of production and to increase the efficiency. The company has
importantly indicated their other methodologies which can also have benefited the company in
terms of waste reduction, cost optimization, and time management. One of those methodologies
is Six Sigma.Under the Six Sigma strategy, there are two type of approaches which are be found
for better management and production system development. DMAIC and DMADV are the two
process known vividly.
DMAIC is the data-driven approach under the six sigma policy in which data related to the
existing product and process is evaluated for its further improvement. The process looks forward
to the improvement of the products in accordance with the customer requirements. The word
DMAIC is made of 5 words which indicate Define, Measure, Analyze, Improve and control
(Nichols, 2018).
Figure: DMAIC
(Source: Nichols, 2018 )
Define: Under this stage, the product and process currently in use are defined in which the
15
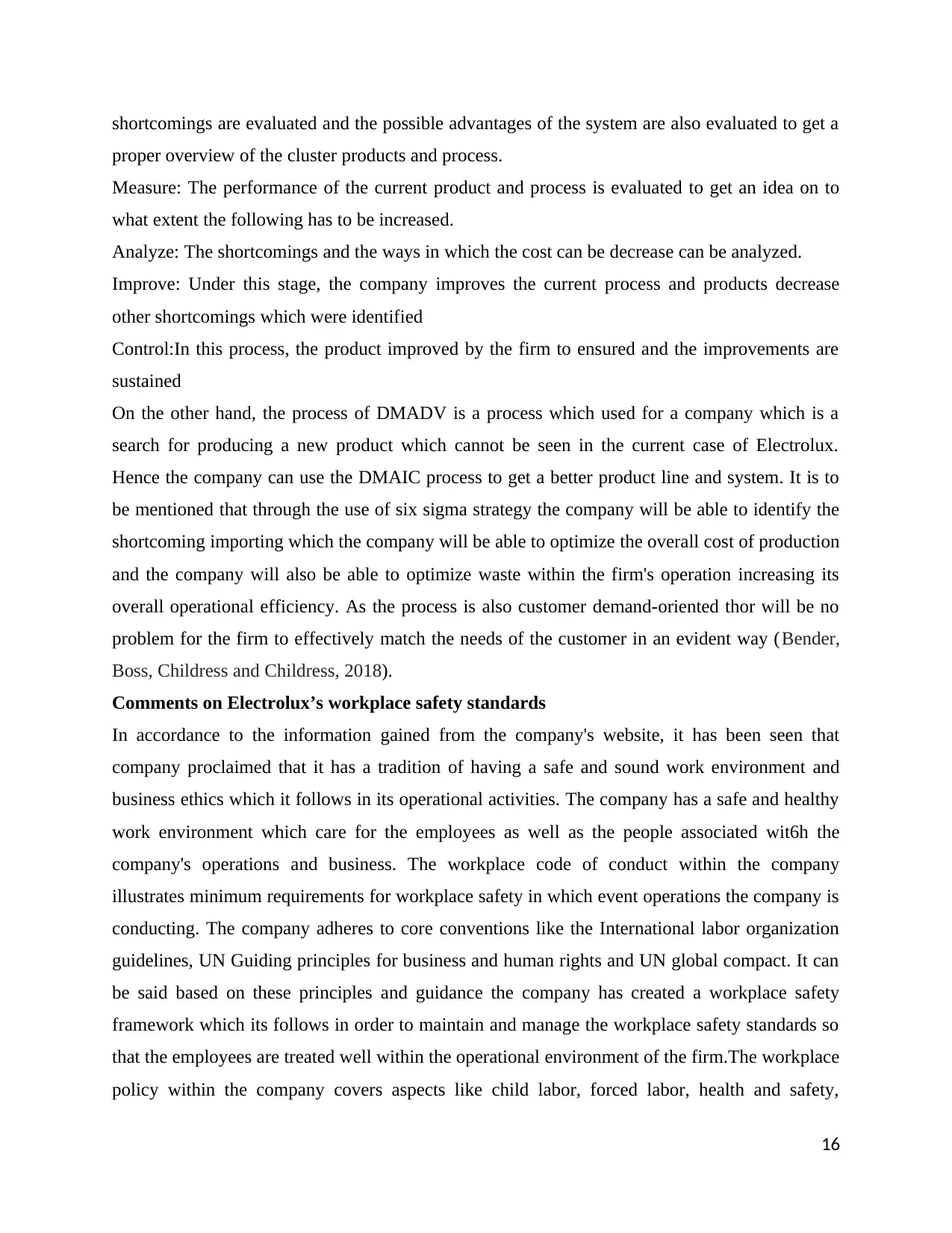
shortcomings are evaluated and the possible advantages of the system are also evaluated to get a
proper overview of the cluster products and process.
Measure: The performance of the current product and process is evaluated to get an idea on to
what extent the following has to be increased.
Analyze: The shortcomings and the ways in which the cost can be decrease can be analyzed.
Improve: Under this stage, the company improves the current process and products decrease
other shortcomings which were identified
Control:In this process, the product improved by the firm to ensured and the improvements are
sustained
On the other hand, the process of DMADV is a process which used for a company which is a
search for producing a new product which cannot be seen in the current case of Electrolux.
Hence the company can use the DMAIC process to get a better product line and system. It is to
be mentioned that through the use of six sigma strategy the company will be able to identify the
shortcoming importing which the company will be able to optimize the overall cost of production
and the company will also be able to optimize waste within the firm's operation increasing its
overall operational efficiency. As the process is also customer demand-oriented thor will be no
problem for the firm to effectively match the needs of the customer in an evident way (Bender,
Boss, Childress and Childress, 2018).
Comments on Electrolux’s workplace safety standards
In accordance to the information gained from the company's website, it has been seen that
company proclaimed that it has a tradition of having a safe and sound work environment and
business ethics which it follows in its operational activities. The company has a safe and healthy
work environment which care for the employees as well as the people associated wit6h the
company's operations and business. The workplace code of conduct within the company
illustrates minimum requirements for workplace safety in which event operations the company is
conducting. The company adheres to core conventions like the International labor organization
guidelines, UN Guiding principles for business and human rights and UN global compact. It can
be said based on these principles and guidance the company has created a workplace safety
framework which its follows in order to maintain and manage the workplace safety standards so
that the employees are treated well within the operational environment of the firm.The workplace
policy within the company covers aspects like child labor, forced labor, health and safety,
16
proper overview of the cluster products and process.
Measure: The performance of the current product and process is evaluated to get an idea on to
what extent the following has to be increased.
Analyze: The shortcomings and the ways in which the cost can be decrease can be analyzed.
Improve: Under this stage, the company improves the current process and products decrease
other shortcomings which were identified
Control:In this process, the product improved by the firm to ensured and the improvements are
sustained
On the other hand, the process of DMADV is a process which used for a company which is a
search for producing a new product which cannot be seen in the current case of Electrolux.
Hence the company can use the DMAIC process to get a better product line and system. It is to
be mentioned that through the use of six sigma strategy the company will be able to identify the
shortcoming importing which the company will be able to optimize the overall cost of production
and the company will also be able to optimize waste within the firm's operation increasing its
overall operational efficiency. As the process is also customer demand-oriented thor will be no
problem for the firm to effectively match the needs of the customer in an evident way (Bender,
Boss, Childress and Childress, 2018).
Comments on Electrolux’s workplace safety standards
In accordance to the information gained from the company's website, it has been seen that
company proclaimed that it has a tradition of having a safe and sound work environment and
business ethics which it follows in its operational activities. The company has a safe and healthy
work environment which care for the employees as well as the people associated wit6h the
company's operations and business. The workplace code of conduct within the company
illustrates minimum requirements for workplace safety in which event operations the company is
conducting. The company adheres to core conventions like the International labor organization
guidelines, UN Guiding principles for business and human rights and UN global compact. It can
be said based on these principles and guidance the company has created a workplace safety
framework which its follows in order to maintain and manage the workplace safety standards so
that the employees are treated well within the operational environment of the firm.The workplace
policy within the company covers aspects like child labor, forced labor, health and safety,
16
Secure Best Marks with AI Grader
Need help grading? Try our AI Grader for instant feedback on your assignments.
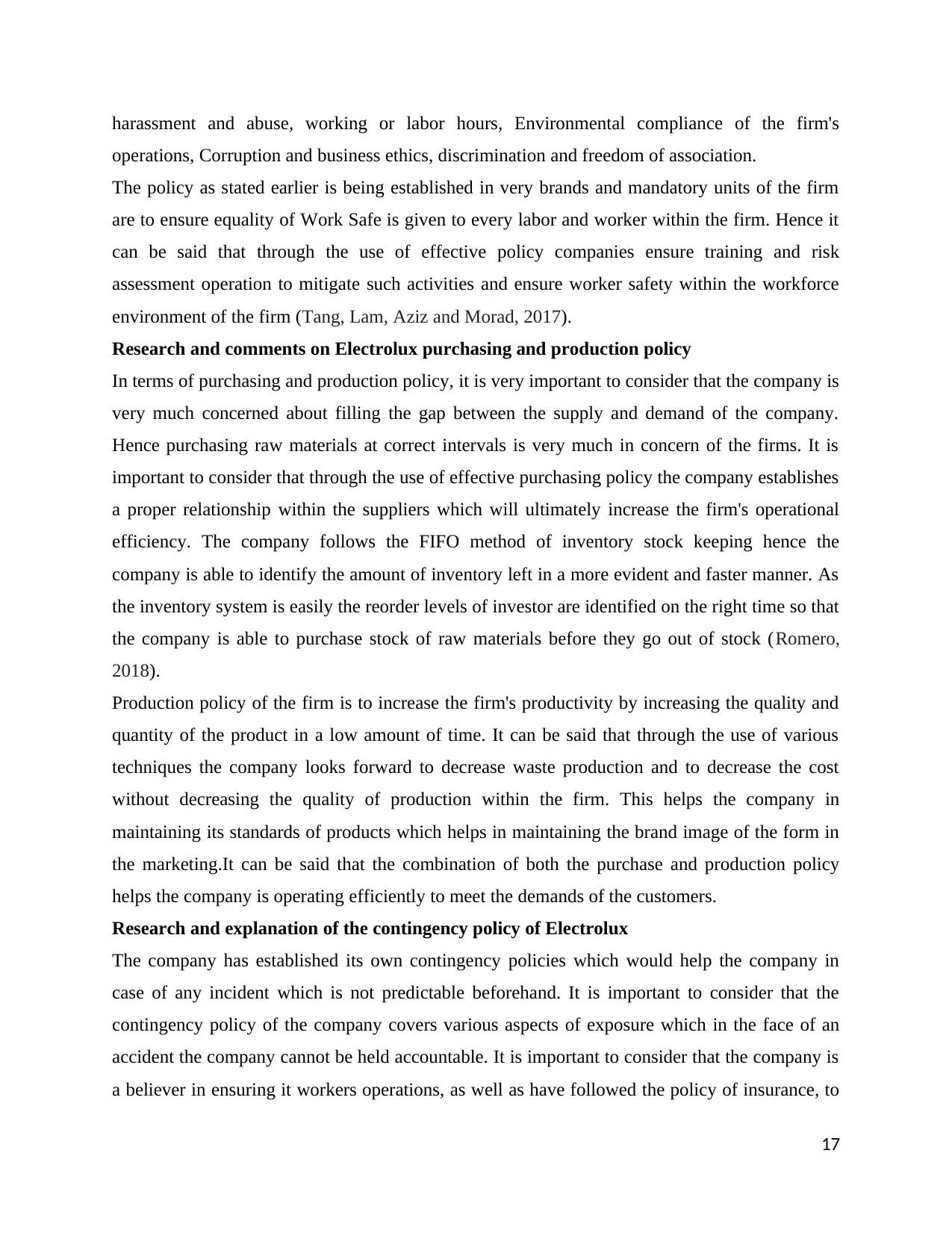
harassment and abuse, working or labor hours, Environmental compliance of the firm's
operations, Corruption and business ethics, discrimination and freedom of association.
The policy as stated earlier is being established in very brands and mandatory units of the firm
are to ensure equality of Work Safe is given to every labor and worker within the firm. Hence it
can be said that through the use of effective policy companies ensure training and risk
assessment operation to mitigate such activities and ensure worker safety within the workforce
environment of the firm (Tang, Lam, Aziz and Morad, 2017).
Research and comments on Electrolux purchasing and production policy
In terms of purchasing and production policy, it is very important to consider that the company is
very much concerned about filling the gap between the supply and demand of the company.
Hence purchasing raw materials at correct intervals is very much in concern of the firms. It is
important to consider that through the use of effective purchasing policy the company establishes
a proper relationship within the suppliers which will ultimately increase the firm's operational
efficiency. The company follows the FIFO method of inventory stock keeping hence the
company is able to identify the amount of inventory left in a more evident and faster manner. As
the inventory system is easily the reorder levels of investor are identified on the right time so that
the company is able to purchase stock of raw materials before they go out of stock (Romero,
2018).
Production policy of the firm is to increase the firm's productivity by increasing the quality and
quantity of the product in a low amount of time. It can be said that through the use of various
techniques the company looks forward to decrease waste production and to decrease the cost
without decreasing the quality of production within the firm. This helps the company in
maintaining its standards of products which helps in maintaining the brand image of the form in
the marketing.It can be said that the combination of both the purchase and production policy
helps the company is operating efficiently to meet the demands of the customers.
Research and explanation of the contingency policy of Electrolux
The company has established its own contingency policies which would help the company in
case of any incident which is not predictable beforehand. It is important to consider that the
contingency policy of the company covers various aspects of exposure which in the face of an
accident the company cannot be held accountable. It is important to consider that the company is
a believer in ensuring it workers operations, as well as have followed the policy of insurance, to
17
operations, Corruption and business ethics, discrimination and freedom of association.
The policy as stated earlier is being established in very brands and mandatory units of the firm
are to ensure equality of Work Safe is given to every labor and worker within the firm. Hence it
can be said that through the use of effective policy companies ensure training and risk
assessment operation to mitigate such activities and ensure worker safety within the workforce
environment of the firm (Tang, Lam, Aziz and Morad, 2017).
Research and comments on Electrolux purchasing and production policy
In terms of purchasing and production policy, it is very important to consider that the company is
very much concerned about filling the gap between the supply and demand of the company.
Hence purchasing raw materials at correct intervals is very much in concern of the firms. It is
important to consider that through the use of effective purchasing policy the company establishes
a proper relationship within the suppliers which will ultimately increase the firm's operational
efficiency. The company follows the FIFO method of inventory stock keeping hence the
company is able to identify the amount of inventory left in a more evident and faster manner. As
the inventory system is easily the reorder levels of investor are identified on the right time so that
the company is able to purchase stock of raw materials before they go out of stock (Romero,
2018).
Production policy of the firm is to increase the firm's productivity by increasing the quality and
quantity of the product in a low amount of time. It can be said that through the use of various
techniques the company looks forward to decrease waste production and to decrease the cost
without decreasing the quality of production within the firm. This helps the company in
maintaining its standards of products which helps in maintaining the brand image of the form in
the marketing.It can be said that the combination of both the purchase and production policy
helps the company is operating efficiently to meet the demands of the customers.
Research and explanation of the contingency policy of Electrolux
The company has established its own contingency policies which would help the company in
case of any incident which is not predictable beforehand. It is important to consider that the
contingency policy of the company covers various aspects of exposure which in the face of an
accident the company cannot be held accountable. It is important to consider that the company is
a believer in ensuring it workers operations, as well as have followed the policy of insurance, to
17
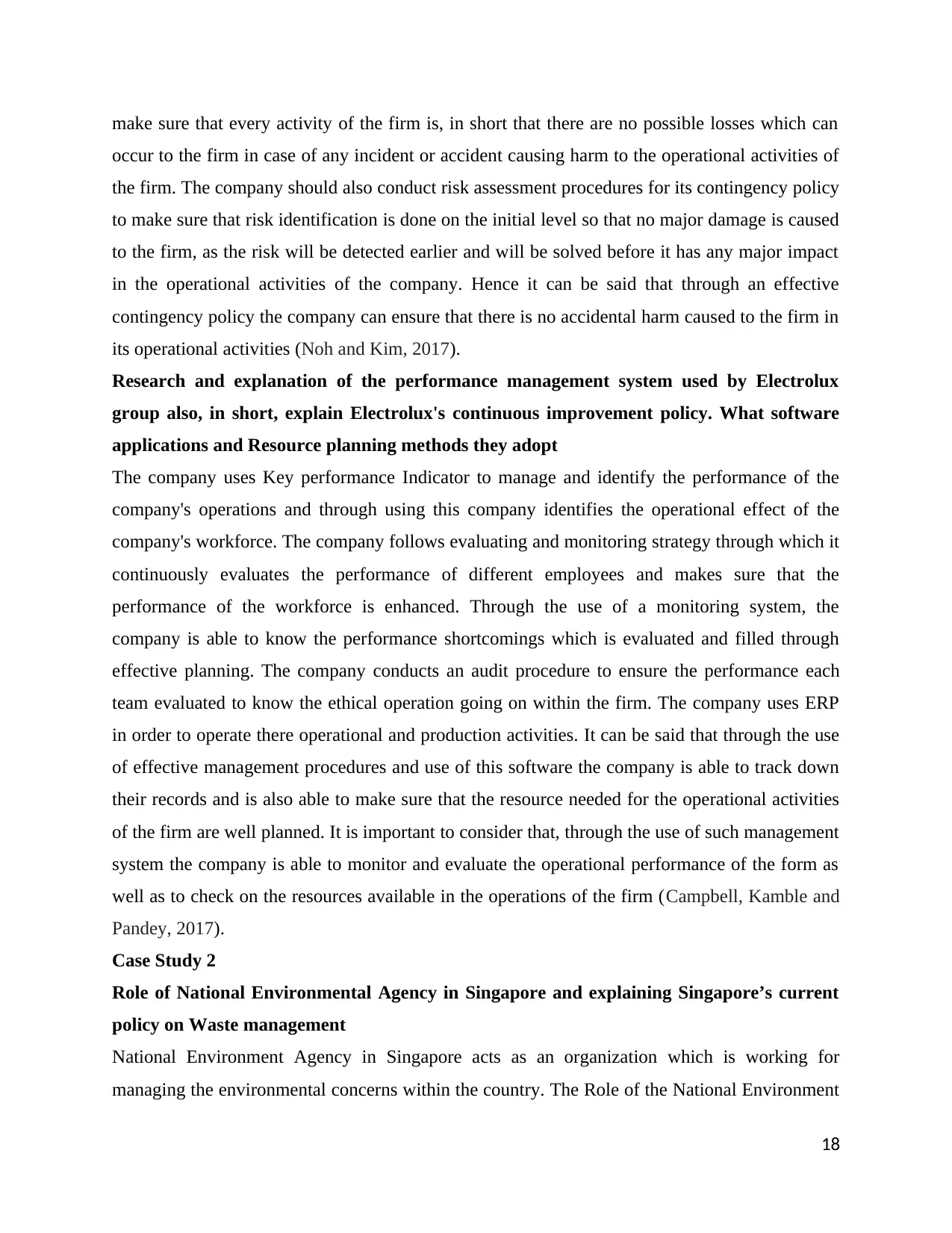
make sure that every activity of the firm is, in short that there are no possible losses which can
occur to the firm in case of any incident or accident causing harm to the operational activities of
the firm. The company should also conduct risk assessment procedures for its contingency policy
to make sure that risk identification is done on the initial level so that no major damage is caused
to the firm, as the risk will be detected earlier and will be solved before it has any major impact
in the operational activities of the company. Hence it can be said that through an effective
contingency policy the company can ensure that there is no accidental harm caused to the firm in
its operational activities (Noh and Kim, 2017).
Research and explanation of the performance management system used by Electrolux
group also, in short, explain Electrolux's continuous improvement policy. What software
applications and Resource planning methods they adopt
The company uses Key performance Indicator to manage and identify the performance of the
company's operations and through using this company identifies the operational effect of the
company's workforce. The company follows evaluating and monitoring strategy through which it
continuously evaluates the performance of different employees and makes sure that the
performance of the workforce is enhanced. Through the use of a monitoring system, the
company is able to know the performance shortcomings which is evaluated and filled through
effective planning. The company conducts an audit procedure to ensure the performance each
team evaluated to know the ethical operation going on within the firm. The company uses ERP
in order to operate there operational and production activities. It can be said that through the use
of effective management procedures and use of this software the company is able to track down
their records and is also able to make sure that the resource needed for the operational activities
of the firm are well planned. It is important to consider that, through the use of such management
system the company is able to monitor and evaluate the operational performance of the form as
well as to check on the resources available in the operations of the firm (Campbell, Kamble and
Pandey, 2017).
Case Study 2
Role of National Environmental Agency in Singapore and explaining Singapore’s current
policy on Waste management
National Environment Agency in Singapore acts as an organization which is working for
managing the environmental concerns within the country. The Role of the National Environment
18
occur to the firm in case of any incident or accident causing harm to the operational activities of
the firm. The company should also conduct risk assessment procedures for its contingency policy
to make sure that risk identification is done on the initial level so that no major damage is caused
to the firm, as the risk will be detected earlier and will be solved before it has any major impact
in the operational activities of the company. Hence it can be said that through an effective
contingency policy the company can ensure that there is no accidental harm caused to the firm in
its operational activities (Noh and Kim, 2017).
Research and explanation of the performance management system used by Electrolux
group also, in short, explain Electrolux's continuous improvement policy. What software
applications and Resource planning methods they adopt
The company uses Key performance Indicator to manage and identify the performance of the
company's operations and through using this company identifies the operational effect of the
company's workforce. The company follows evaluating and monitoring strategy through which it
continuously evaluates the performance of different employees and makes sure that the
performance of the workforce is enhanced. Through the use of a monitoring system, the
company is able to know the performance shortcomings which is evaluated and filled through
effective planning. The company conducts an audit procedure to ensure the performance each
team evaluated to know the ethical operation going on within the firm. The company uses ERP
in order to operate there operational and production activities. It can be said that through the use
of effective management procedures and use of this software the company is able to track down
their records and is also able to make sure that the resource needed for the operational activities
of the firm are well planned. It is important to consider that, through the use of such management
system the company is able to monitor and evaluate the operational performance of the form as
well as to check on the resources available in the operations of the firm (Campbell, Kamble and
Pandey, 2017).
Case Study 2
Role of National Environmental Agency in Singapore and explaining Singapore’s current
policy on Waste management
National Environment Agency in Singapore acts as an organization which is working for
managing the environmental concerns within the country. The Role of the National Environment
18
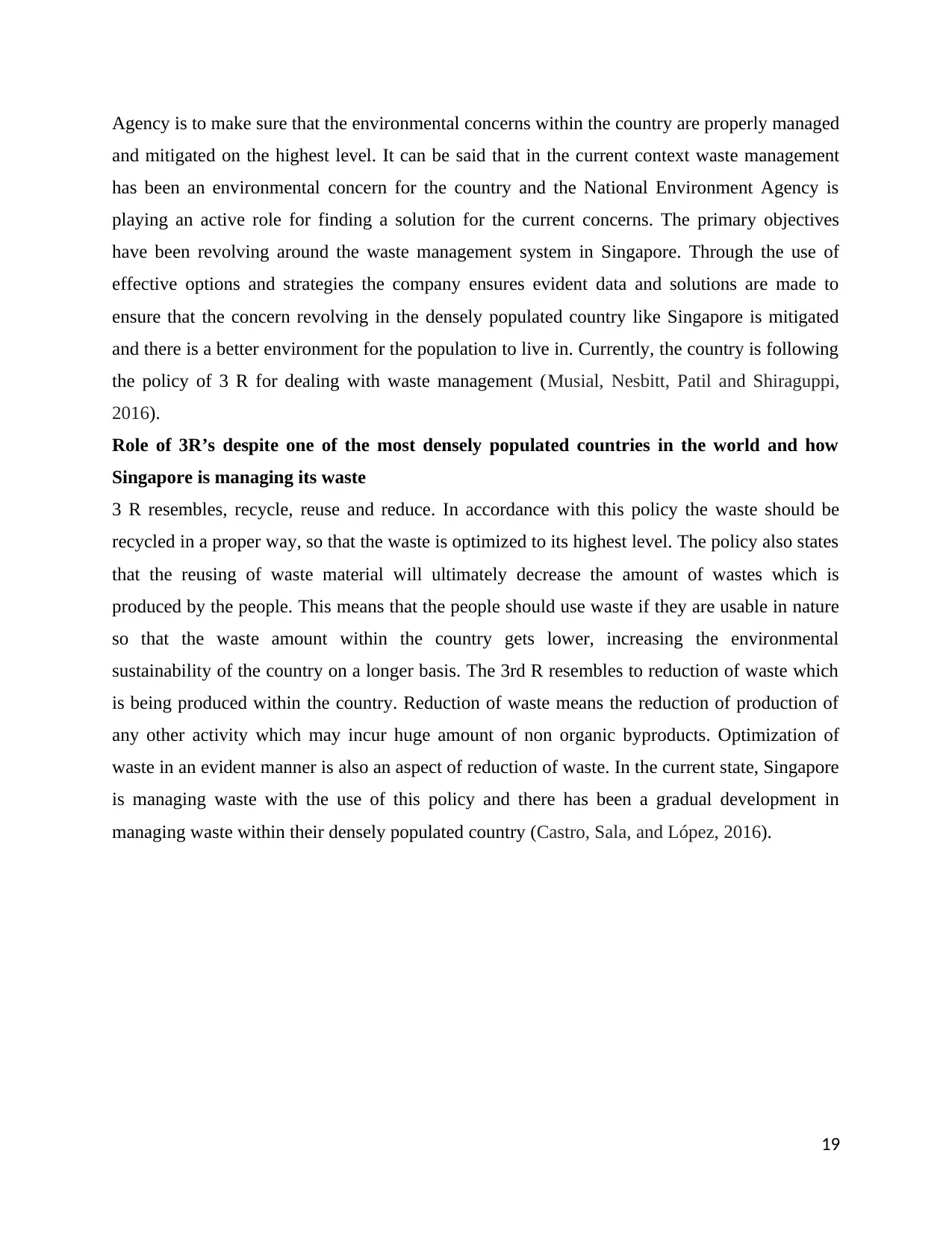
Agency is to make sure that the environmental concerns within the country are properly managed
and mitigated on the highest level. It can be said that in the current context waste management
has been an environmental concern for the country and the National Environment Agency is
playing an active role for finding a solution for the current concerns. The primary objectives
have been revolving around the waste management system in Singapore. Through the use of
effective options and strategies the company ensures evident data and solutions are made to
ensure that the concern revolving in the densely populated country like Singapore is mitigated
and there is a better environment for the population to live in. Currently, the country is following
the policy of 3 R for dealing with waste management (Musial, Nesbitt, Patil and Shiraguppi,
2016).
Role of 3R’s despite one of the most densely populated countries in the world and how
Singapore is managing its waste
3 R resembles, recycle, reuse and reduce. In accordance with this policy the waste should be
recycled in a proper way, so that the waste is optimized to its highest level. The policy also states
that the reusing of waste material will ultimately decrease the amount of wastes which is
produced by the people. This means that the people should use waste if they are usable in nature
so that the waste amount within the country gets lower, increasing the environmental
sustainability of the country on a longer basis. The 3rd R resembles to reduction of waste which
is being produced within the country. Reduction of waste means the reduction of production of
any other activity which may incur huge amount of non organic byproducts. Optimization of
waste in an evident manner is also an aspect of reduction of waste. In the current state, Singapore
is managing waste with the use of this policy and there has been a gradual development in
managing waste within their densely populated country (Castro, Sala, and López, 2016).
19
and mitigated on the highest level. It can be said that in the current context waste management
has been an environmental concern for the country and the National Environment Agency is
playing an active role for finding a solution for the current concerns. The primary objectives
have been revolving around the waste management system in Singapore. Through the use of
effective options and strategies the company ensures evident data and solutions are made to
ensure that the concern revolving in the densely populated country like Singapore is mitigated
and there is a better environment for the population to live in. Currently, the country is following
the policy of 3 R for dealing with waste management (Musial, Nesbitt, Patil and Shiraguppi,
2016).
Role of 3R’s despite one of the most densely populated countries in the world and how
Singapore is managing its waste
3 R resembles, recycle, reuse and reduce. In accordance with this policy the waste should be
recycled in a proper way, so that the waste is optimized to its highest level. The policy also states
that the reusing of waste material will ultimately decrease the amount of wastes which is
produced by the people. This means that the people should use waste if they are usable in nature
so that the waste amount within the country gets lower, increasing the environmental
sustainability of the country on a longer basis. The 3rd R resembles to reduction of waste which
is being produced within the country. Reduction of waste means the reduction of production of
any other activity which may incur huge amount of non organic byproducts. Optimization of
waste in an evident manner is also an aspect of reduction of waste. In the current state, Singapore
is managing waste with the use of this policy and there has been a gradual development in
managing waste within their densely populated country (Castro, Sala, and López, 2016).
19
Paraphrase This Document
Need a fresh take? Get an instant paraphrase of this document with our AI Paraphraser
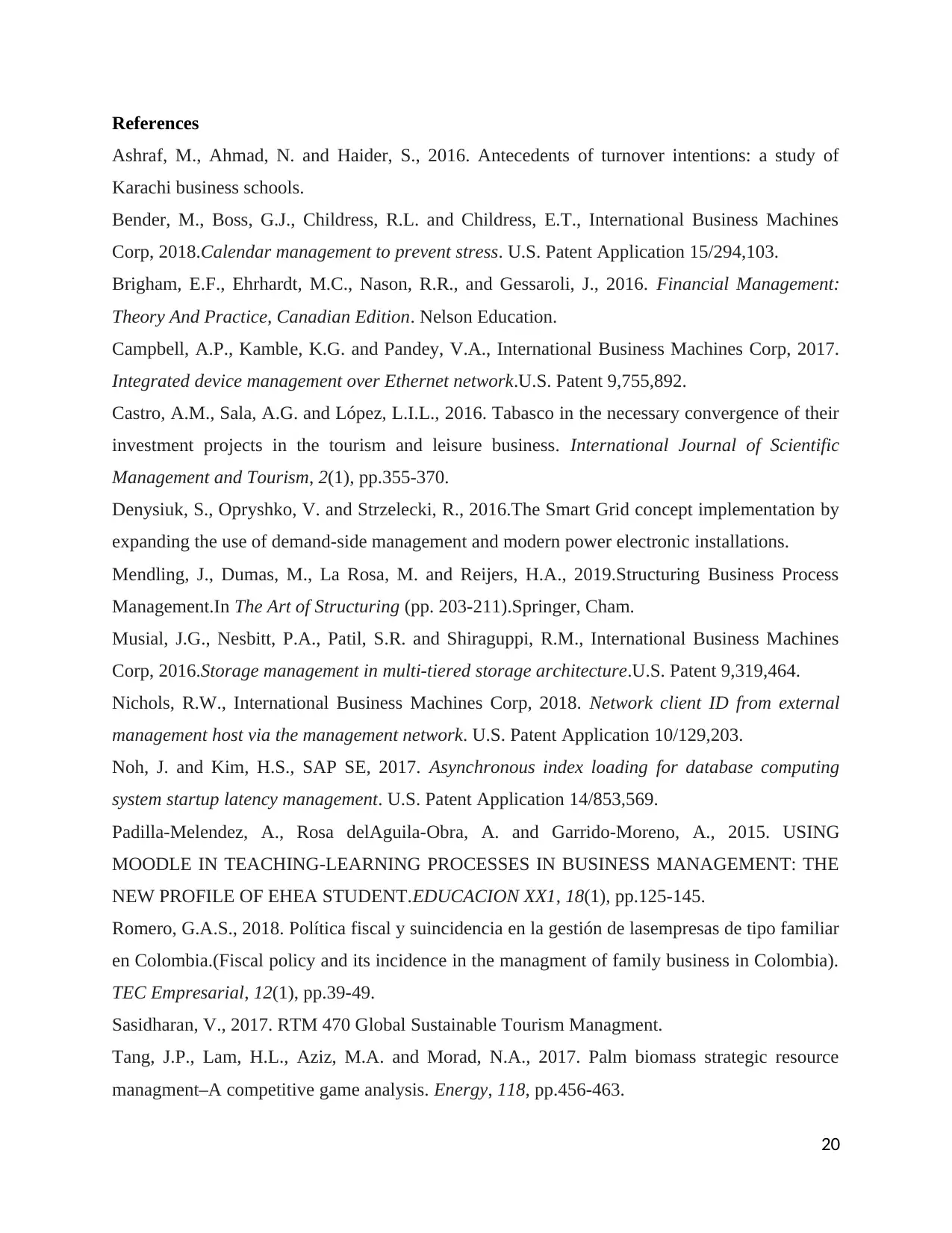
References
Ashraf, M., Ahmad, N. and Haider, S., 2016. Antecedents of turnover intentions: a study of
Karachi business schools.
Bender, M., Boss, G.J., Childress, R.L. and Childress, E.T., International Business Machines
Corp, 2018.Calendar management to prevent stress. U.S. Patent Application 15/294,103.
Brigham, E.F., Ehrhardt, M.C., Nason, R.R., and Gessaroli, J., 2016. Financial Management:
Theory And Practice, Canadian Edition. Nelson Education.
Campbell, A.P., Kamble, K.G. and Pandey, V.A., International Business Machines Corp, 2017.
Integrated device management over Ethernet network.U.S. Patent 9,755,892.
Castro, A.M., Sala, A.G. and López, L.I.L., 2016. Tabasco in the necessary convergence of their
investment projects in the tourism and leisure business. International Journal of Scientific
Management and Tourism, 2(1), pp.355-370.
Denysiuk, S., Opryshko, V. and Strzelecki, R., 2016.The Smart Grid concept implementation by
expanding the use of demand-side management and modern power electronic installations.
Mendling, J., Dumas, M., La Rosa, M. and Reijers, H.A., 2019.Structuring Business Process
Management.In The Art of Structuring (pp. 203-211).Springer, Cham.
Musial, J.G., Nesbitt, P.A., Patil, S.R. and Shiraguppi, R.M., International Business Machines
Corp, 2016.Storage management in multi-tiered storage architecture.U.S. Patent 9,319,464.
Nichols, R.W., International Business Machines Corp, 2018. Network client ID from external
management host via the management network. U.S. Patent Application 10/129,203.
Noh, J. and Kim, H.S., SAP SE, 2017. Asynchronous index loading for database computing
system startup latency management. U.S. Patent Application 14/853,569.
Padilla-Melendez, A., Rosa delAguila-Obra, A. and Garrido-Moreno, A., 2015. USING
MOODLE IN TEACHING-LEARNING PROCESSES IN BUSINESS MANAGEMENT: THE
NEW PROFILE OF EHEA STUDENT.EDUCACION XX1, 18(1), pp.125-145.
Romero, G.A.S., 2018. Política fiscal y suincidencia en la gestión de lasempresas de tipo familiar
en Colombia.(Fiscal policy and its incidence in the managment of family business in Colombia).
TEC Empresarial, 12(1), pp.39-49.
Sasidharan, V., 2017. RTM 470 Global Sustainable Tourism Managment.
Tang, J.P., Lam, H.L., Aziz, M.A. and Morad, N.A., 2017. Palm biomass strategic resource
managment–A competitive game analysis. Energy, 118, pp.456-463.
20
Ashraf, M., Ahmad, N. and Haider, S., 2016. Antecedents of turnover intentions: a study of
Karachi business schools.
Bender, M., Boss, G.J., Childress, R.L. and Childress, E.T., International Business Machines
Corp, 2018.Calendar management to prevent stress. U.S. Patent Application 15/294,103.
Brigham, E.F., Ehrhardt, M.C., Nason, R.R., and Gessaroli, J., 2016. Financial Management:
Theory And Practice, Canadian Edition. Nelson Education.
Campbell, A.P., Kamble, K.G. and Pandey, V.A., International Business Machines Corp, 2017.
Integrated device management over Ethernet network.U.S. Patent 9,755,892.
Castro, A.M., Sala, A.G. and López, L.I.L., 2016. Tabasco in the necessary convergence of their
investment projects in the tourism and leisure business. International Journal of Scientific
Management and Tourism, 2(1), pp.355-370.
Denysiuk, S., Opryshko, V. and Strzelecki, R., 2016.The Smart Grid concept implementation by
expanding the use of demand-side management and modern power electronic installations.
Mendling, J., Dumas, M., La Rosa, M. and Reijers, H.A., 2019.Structuring Business Process
Management.In The Art of Structuring (pp. 203-211).Springer, Cham.
Musial, J.G., Nesbitt, P.A., Patil, S.R. and Shiraguppi, R.M., International Business Machines
Corp, 2016.Storage management in multi-tiered storage architecture.U.S. Patent 9,319,464.
Nichols, R.W., International Business Machines Corp, 2018. Network client ID from external
management host via the management network. U.S. Patent Application 10/129,203.
Noh, J. and Kim, H.S., SAP SE, 2017. Asynchronous index loading for database computing
system startup latency management. U.S. Patent Application 14/853,569.
Padilla-Melendez, A., Rosa delAguila-Obra, A. and Garrido-Moreno, A., 2015. USING
MOODLE IN TEACHING-LEARNING PROCESSES IN BUSINESS MANAGEMENT: THE
NEW PROFILE OF EHEA STUDENT.EDUCACION XX1, 18(1), pp.125-145.
Romero, G.A.S., 2018. Política fiscal y suincidencia en la gestión de lasempresas de tipo familiar
en Colombia.(Fiscal policy and its incidence in the managment of family business in Colombia).
TEC Empresarial, 12(1), pp.39-49.
Sasidharan, V., 2017. RTM 470 Global Sustainable Tourism Managment.
Tang, J.P., Lam, H.L., Aziz, M.A. and Morad, N.A., 2017. Palm biomass strategic resource
managment–A competitive game analysis. Energy, 118, pp.456-463.
20
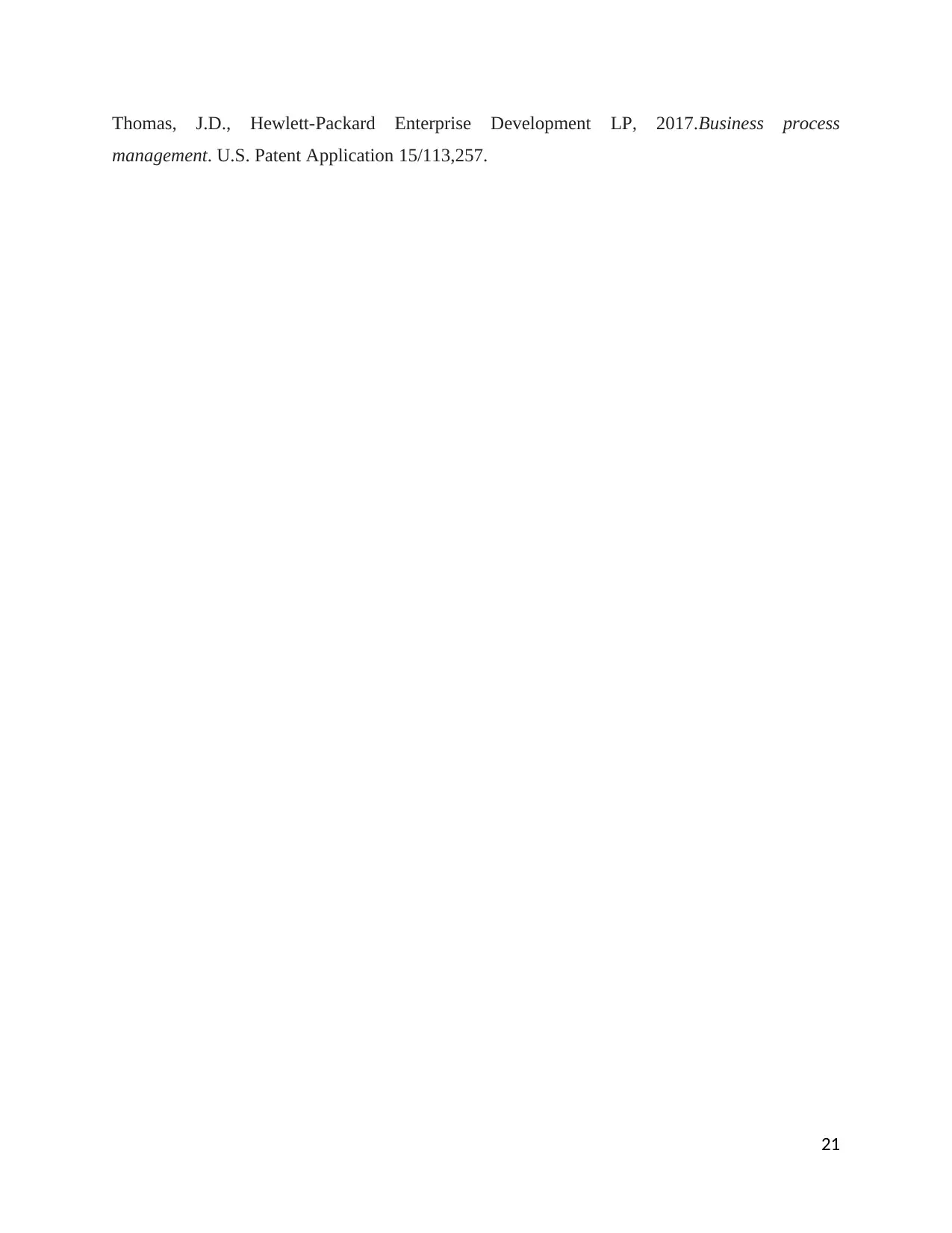
Thomas, J.D., Hewlett-Packard Enterprise Development LP, 2017.Business process
management. U.S. Patent Application 15/113,257.
21
management. U.S. Patent Application 15/113,257.
21
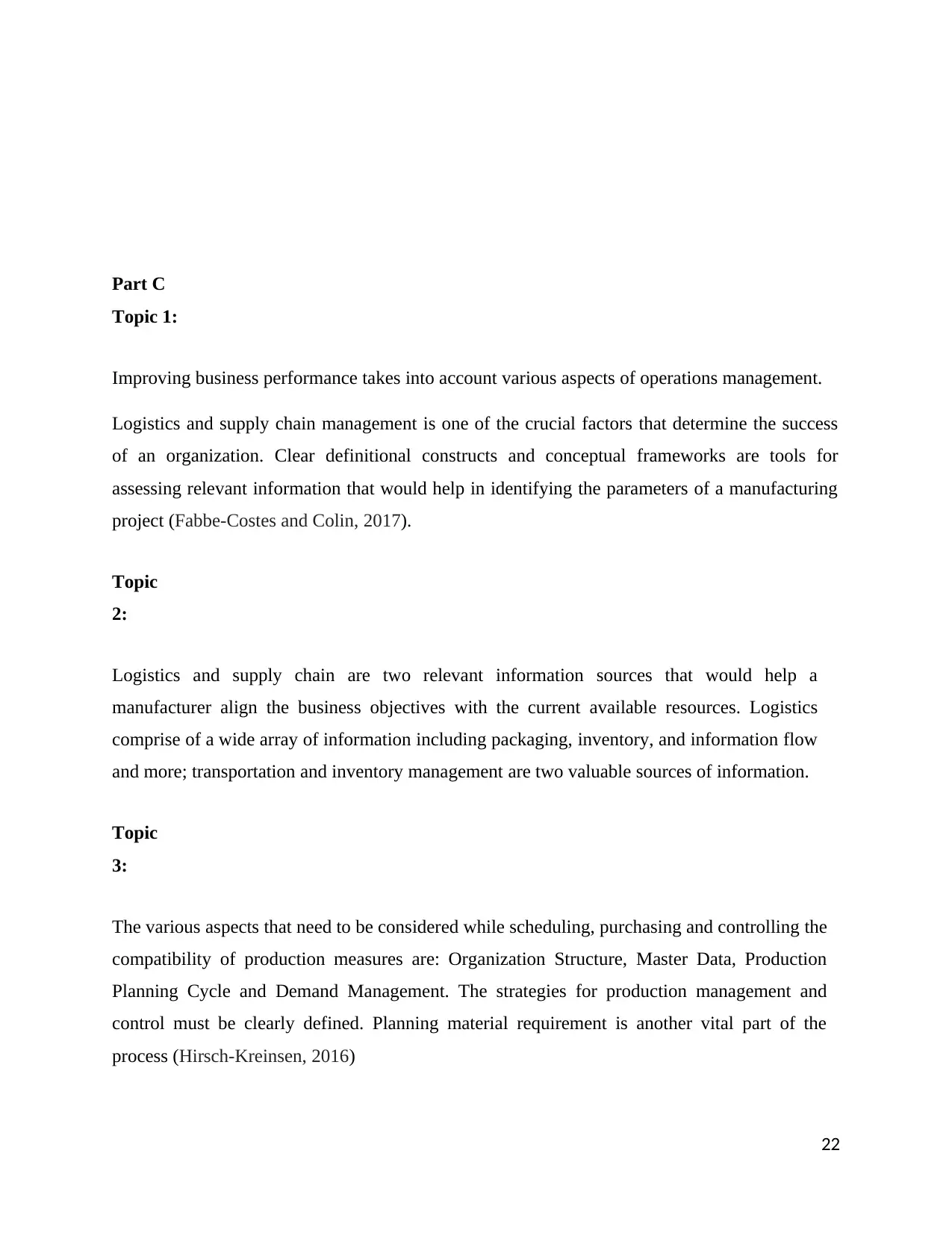
Part C
Topic 1:
Improving business performance takes into account various aspects of operations management.
Logistics and supply chain management is one of the crucial factors that determine the success
of an organization. Clear definitional constructs and conceptual frameworks are tools for
assessing relevant information that would help in identifying the parameters of a manufacturing
project (Fabbe-Costes and Colin, 2017).
Topic
2:
Logistics and supply chain are two relevant information sources that would help a
manufacturer align the business objectives with the current available resources. Logistics
comprise of a wide array of information including packaging, inventory, and information flow
and more; transportation and inventory management are two valuable sources of information.
Topic
3:
The various aspects that need to be considered while scheduling, purchasing and controlling the
compatibility of production measures are: Organization Structure, Master Data, Production
Planning Cycle and Demand Management. The strategies for production management and
control must be clearly defined. Planning material requirement is another vital part of the
process (Hirsch-Kreinsen, 2016)
22
Topic 1:
Improving business performance takes into account various aspects of operations management.
Logistics and supply chain management is one of the crucial factors that determine the success
of an organization. Clear definitional constructs and conceptual frameworks are tools for
assessing relevant information that would help in identifying the parameters of a manufacturing
project (Fabbe-Costes and Colin, 2017).
Topic
2:
Logistics and supply chain are two relevant information sources that would help a
manufacturer align the business objectives with the current available resources. Logistics
comprise of a wide array of information including packaging, inventory, and information flow
and more; transportation and inventory management are two valuable sources of information.
Topic
3:
The various aspects that need to be considered while scheduling, purchasing and controlling the
compatibility of production measures are: Organization Structure, Master Data, Production
Planning Cycle and Demand Management. The strategies for production management and
control must be clearly defined. Planning material requirement is another vital part of the
process (Hirsch-Kreinsen, 2016)
22
Secure Best Marks with AI Grader
Need help grading? Try our AI Grader for instant feedback on your assignments.
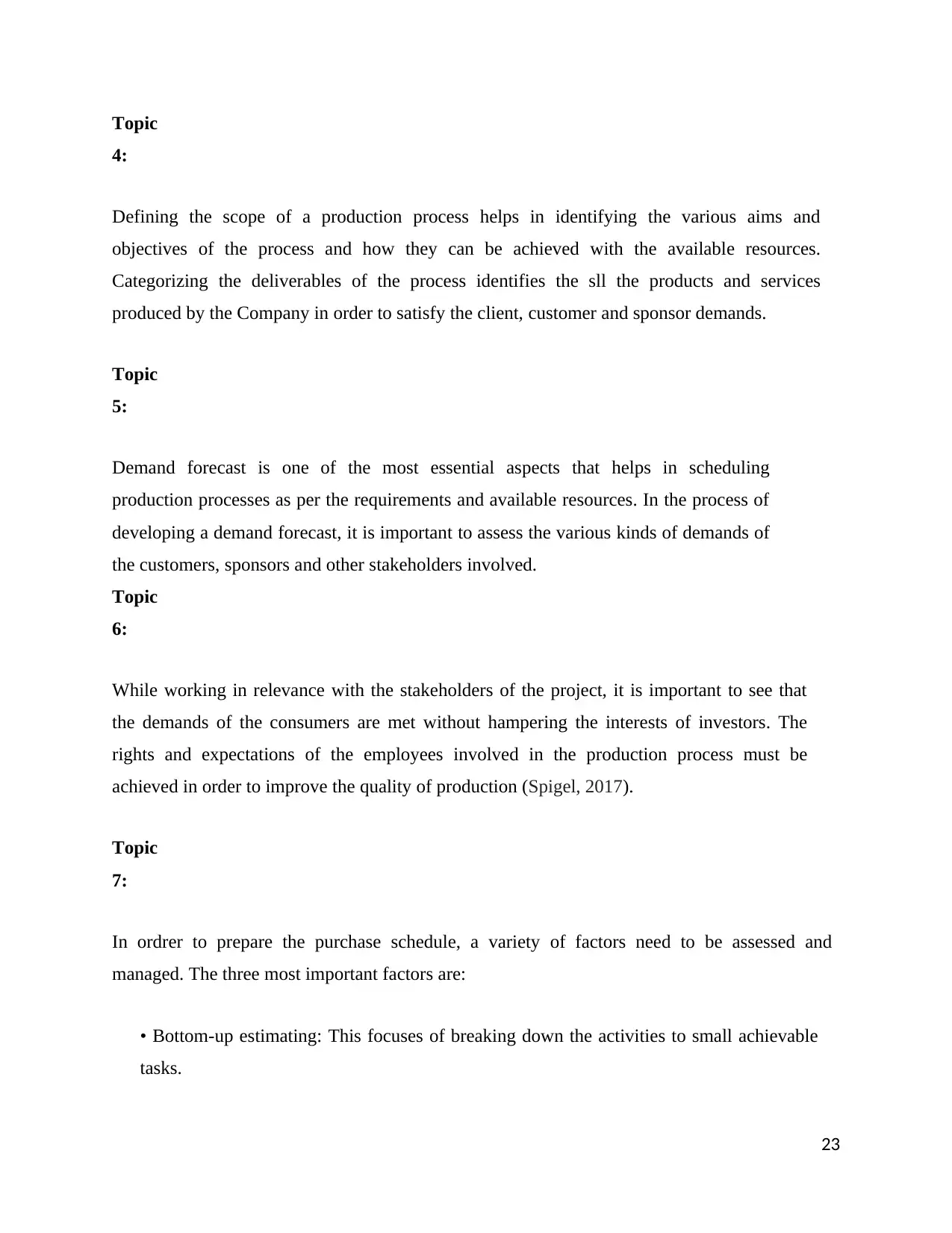
Topic
4:
Defining the scope of a production process helps in identifying the various aims and
objectives of the process and how they can be achieved with the available resources.
Categorizing the deliverables of the process identifies the sll the products and services
produced by the Company in order to satisfy the client, customer and sponsor demands.
Topic
5:
Demand forecast is one of the most essential aspects that helps in scheduling
production processes as per the requirements and available resources. In the process of
developing a demand forecast, it is important to assess the various kinds of demands of
the customers, sponsors and other stakeholders involved.
Topic
6:
While working in relevance with the stakeholders of the project, it is important to see that
the demands of the consumers are met without hampering the interests of investors. The
rights and expectations of the employees involved in the production process must be
achieved in order to improve the quality of production (Spigel, 2017).
Topic
7:
In ordrer to prepare the purchase schedule, a variety of factors need to be assessed and
managed. The three most important factors are:
• Bottom-up estimating: This focuses of breaking down the activities to small achievable
tasks.
23
4:
Defining the scope of a production process helps in identifying the various aims and
objectives of the process and how they can be achieved with the available resources.
Categorizing the deliverables of the process identifies the sll the products and services
produced by the Company in order to satisfy the client, customer and sponsor demands.
Topic
5:
Demand forecast is one of the most essential aspects that helps in scheduling
production processes as per the requirements and available resources. In the process of
developing a demand forecast, it is important to assess the various kinds of demands of
the customers, sponsors and other stakeholders involved.
Topic
6:
While working in relevance with the stakeholders of the project, it is important to see that
the demands of the consumers are met without hampering the interests of investors. The
rights and expectations of the employees involved in the production process must be
achieved in order to improve the quality of production (Spigel, 2017).
Topic
7:
In ordrer to prepare the purchase schedule, a variety of factors need to be assessed and
managed. The three most important factors are:
• Bottom-up estimating: This focuses of breaking down the activities to small achievable
tasks.
23
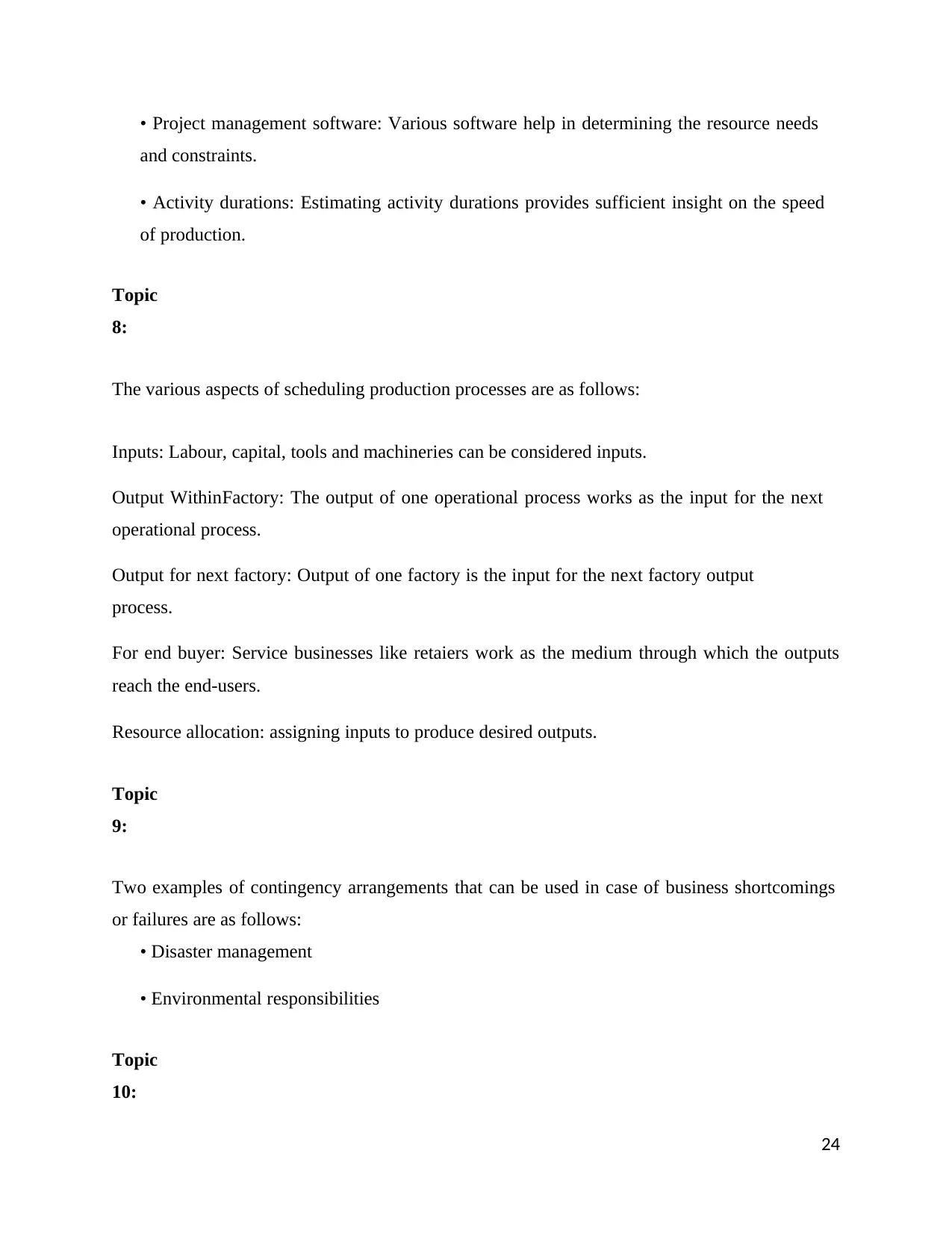
• Project management software: Various software help in determining the resource needs
and constraints.
• Activity durations: Estimating activity durations provides sufficient insight on the speed
of production.
Topic
8:
The various aspects of scheduling production processes are as follows:
Inputs: Labour, capital, tools and machineries can be considered inputs.
Output WithinFactory: The output of one operational process works as the input for the next
operational process.
Output for next factory: Output of one factory is the input for the next factory output
process.
For end buyer: Service businesses like retaiers work as the medium through which the outputs
reach the end-users.
Resource allocation: assigning inputs to produce desired outputs.
Topic
9:
Two examples of contingency arrangements that can be used in case of business shortcomings
or failures are as follows:
• Disaster management
• Environmental responsibilities
Topic
10:
24
and constraints.
• Activity durations: Estimating activity durations provides sufficient insight on the speed
of production.
Topic
8:
The various aspects of scheduling production processes are as follows:
Inputs: Labour, capital, tools and machineries can be considered inputs.
Output WithinFactory: The output of one operational process works as the input for the next
operational process.
Output for next factory: Output of one factory is the input for the next factory output
process.
For end buyer: Service businesses like retaiers work as the medium through which the outputs
reach the end-users.
Resource allocation: assigning inputs to produce desired outputs.
Topic
9:
Two examples of contingency arrangements that can be used in case of business shortcomings
or failures are as follows:
• Disaster management
• Environmental responsibilities
Topic
10:
24
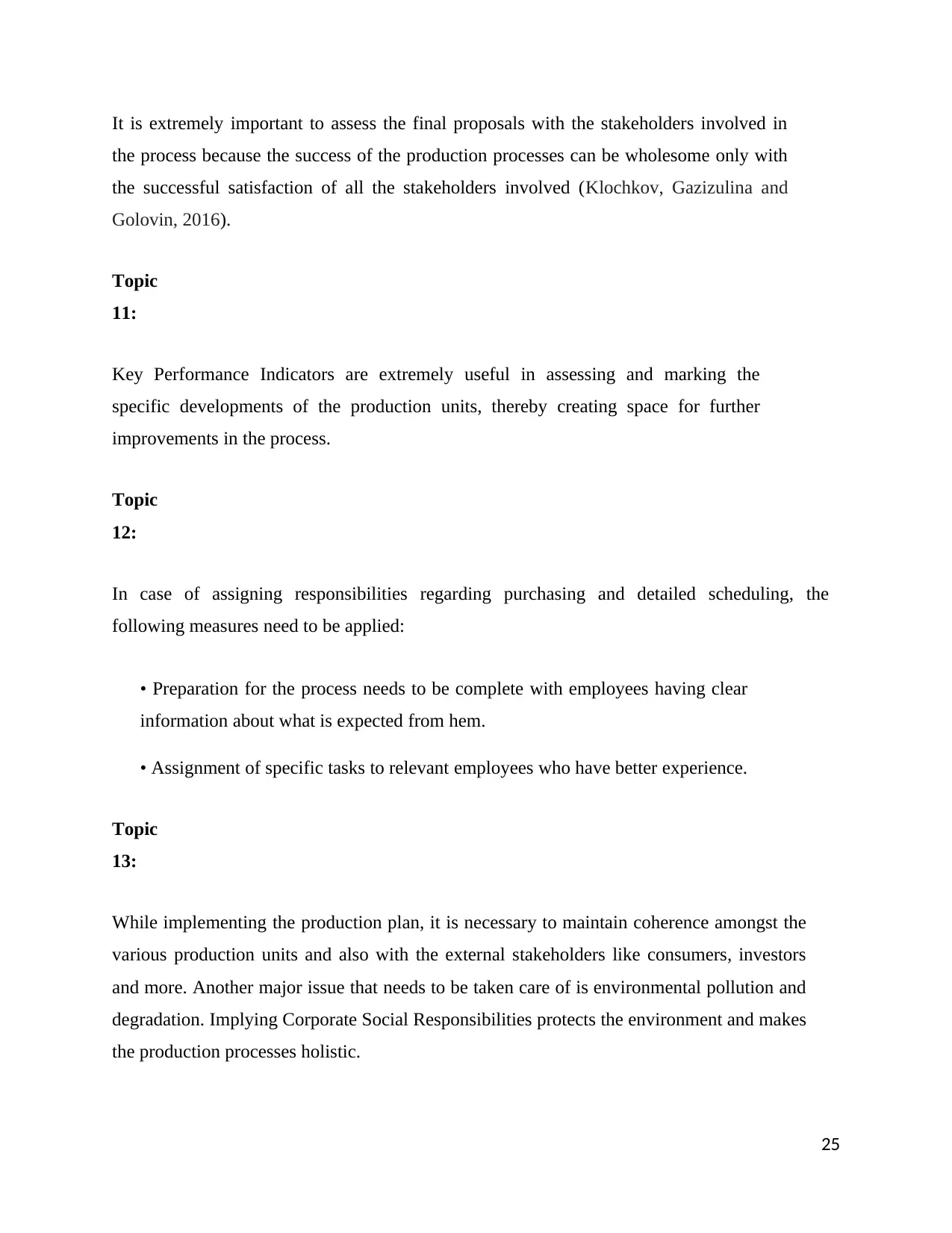
It is extremely important to assess the final proposals with the stakeholders involved in
the process because the success of the production processes can be wholesome only with
the successful satisfaction of all the stakeholders involved (Klochkov, Gazizulina and
Golovin, 2016).
Topic
11:
Key Performance Indicators are extremely useful in assessing and marking the
specific developments of the production units, thereby creating space for further
improvements in the process.
Topic
12:
In case of assigning responsibilities regarding purchasing and detailed scheduling, the
following measures need to be applied:
• Preparation for the process needs to be complete with employees having clear
information about what is expected from hem.
• Assignment of specific tasks to relevant employees who have better experience.
Topic
13:
While implementing the production plan, it is necessary to maintain coherence amongst the
various production units and also with the external stakeholders like consumers, investors
and more. Another major issue that needs to be taken care of is environmental pollution and
degradation. Implying Corporate Social Responsibilities protects the environment and makes
the production processes holistic.
25
the process because the success of the production processes can be wholesome only with
the successful satisfaction of all the stakeholders involved (Klochkov, Gazizulina and
Golovin, 2016).
Topic
11:
Key Performance Indicators are extremely useful in assessing and marking the
specific developments of the production units, thereby creating space for further
improvements in the process.
Topic
12:
In case of assigning responsibilities regarding purchasing and detailed scheduling, the
following measures need to be applied:
• Preparation for the process needs to be complete with employees having clear
information about what is expected from hem.
• Assignment of specific tasks to relevant employees who have better experience.
Topic
13:
While implementing the production plan, it is necessary to maintain coherence amongst the
various production units and also with the external stakeholders like consumers, investors
and more. Another major issue that needs to be taken care of is environmental pollution and
degradation. Implying Corporate Social Responsibilities protects the environment and makes
the production processes holistic.
25
Paraphrase This Document
Need a fresh take? Get an instant paraphrase of this document with our AI Paraphraser
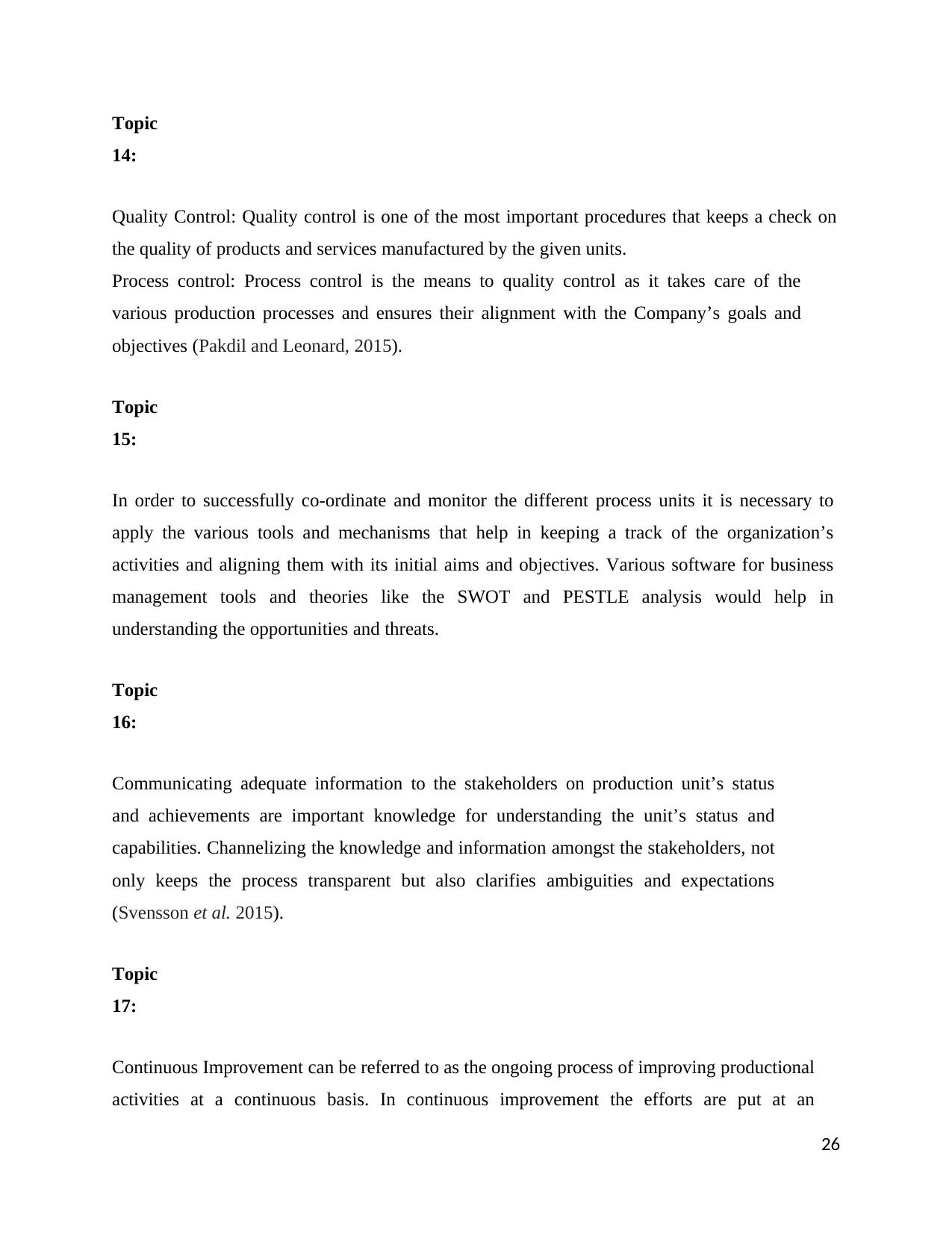
Topic
14:
Quality Control: Quality control is one of the most important procedures that keeps a check on
the quality of products and services manufactured by the given units.
Process control: Process control is the means to quality control as it takes care of the
various production processes and ensures their alignment with the Company’s goals and
objectives (Pakdil and Leonard, 2015).
Topic
15:
In order to successfully co-ordinate and monitor the different process units it is necessary to
apply the various tools and mechanisms that help in keeping a track of the organization’s
activities and aligning them with its initial aims and objectives. Various software for business
management tools and theories like the SWOT and PESTLE analysis would help in
understanding the opportunities and threats.
Topic
16:
Communicating adequate information to the stakeholders on production unit’s status
and achievements are important knowledge for understanding the unit’s status and
capabilities. Channelizing the knowledge and information amongst the stakeholders, not
only keeps the process transparent but also clarifies ambiguities and expectations
(Svensson et al. 2015).
Topic
17:
Continuous Improvement can be referred to as the ongoing process of improving productional
activities at a continuous basis. In continuous improvement the efforts are put at an
26
14:
Quality Control: Quality control is one of the most important procedures that keeps a check on
the quality of products and services manufactured by the given units.
Process control: Process control is the means to quality control as it takes care of the
various production processes and ensures their alignment with the Company’s goals and
objectives (Pakdil and Leonard, 2015).
Topic
15:
In order to successfully co-ordinate and monitor the different process units it is necessary to
apply the various tools and mechanisms that help in keeping a track of the organization’s
activities and aligning them with its initial aims and objectives. Various software for business
management tools and theories like the SWOT and PESTLE analysis would help in
understanding the opportunities and threats.
Topic
16:
Communicating adequate information to the stakeholders on production unit’s status
and achievements are important knowledge for understanding the unit’s status and
capabilities. Channelizing the knowledge and information amongst the stakeholders, not
only keeps the process transparent but also clarifies ambiguities and expectations
(Svensson et al. 2015).
Topic
17:
Continuous Improvement can be referred to as the ongoing process of improving productional
activities at a continuous basis. In continuous improvement the efforts are put at an
26
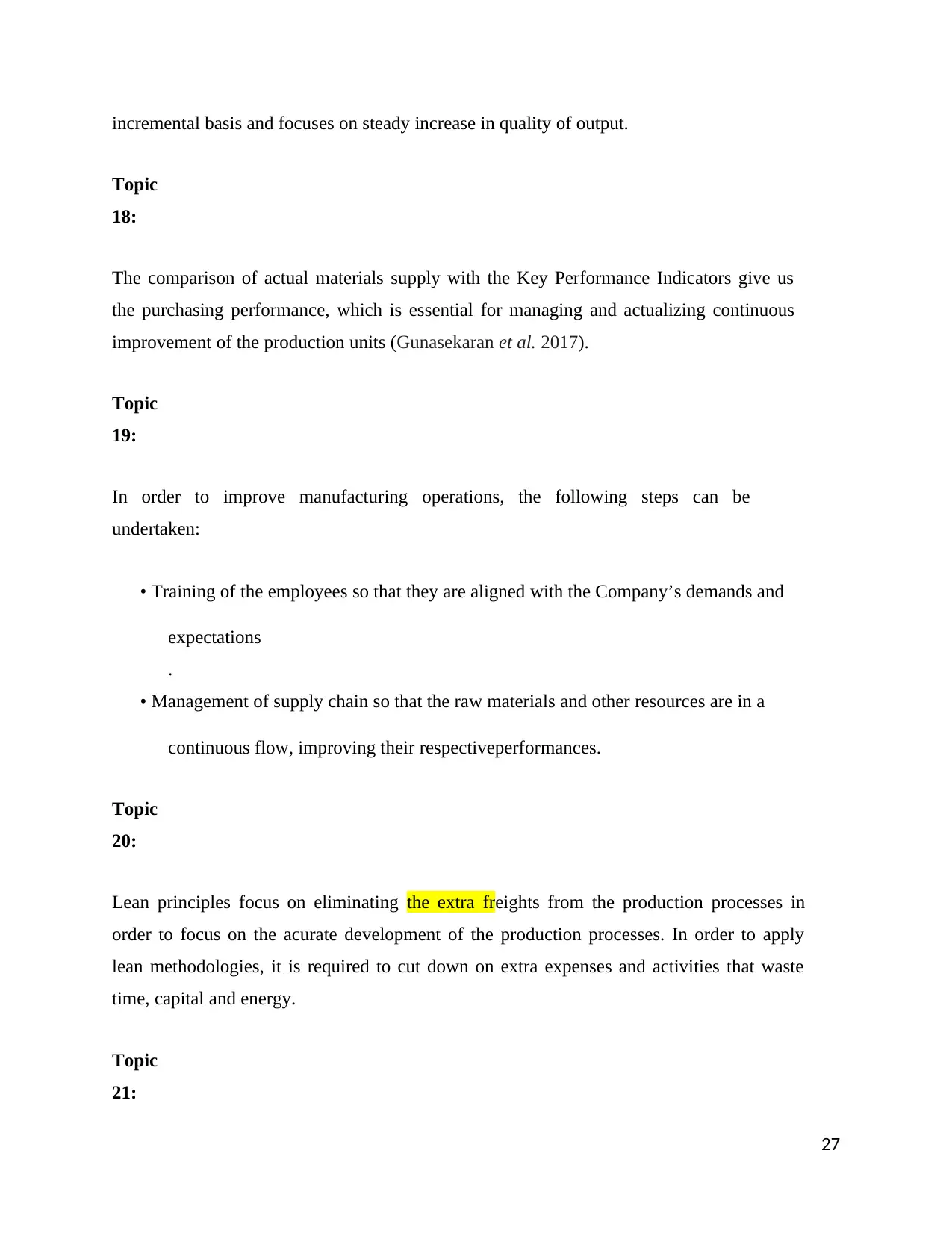
incremental basis and focuses on steady increase in quality of output.
Topic
18:
The comparison of actual materials supply with the Key Performance Indicators give us
the purchasing performance, which is essential for managing and actualizing continuous
improvement of the production units (Gunasekaran et al. 2017).
Topic
19:
In order to improve manufacturing operations, the following steps can be
undertaken:
• Training of the employees so that they are aligned with the Company’s demands and
expectations
.
• Management of supply chain so that the raw materials and other resources are in a
continuous flow, improving their respectiveperformances.
Topic
20:
Lean principles focus on eliminating the extra freights from the production processes in
order to focus on the acurate development of the production processes. In order to apply
lean methodologies, it is required to cut down on extra expenses and activities that waste
time, capital and energy.
Topic
21:
27
Topic
18:
The comparison of actual materials supply with the Key Performance Indicators give us
the purchasing performance, which is essential for managing and actualizing continuous
improvement of the production units (Gunasekaran et al. 2017).
Topic
19:
In order to improve manufacturing operations, the following steps can be
undertaken:
• Training of the employees so that they are aligned with the Company’s demands and
expectations
.
• Management of supply chain so that the raw materials and other resources are in a
continuous flow, improving their respectiveperformances.
Topic
20:
Lean principles focus on eliminating the extra freights from the production processes in
order to focus on the acurate development of the production processes. In order to apply
lean methodologies, it is required to cut down on extra expenses and activities that waste
time, capital and energy.
Topic
21:
27
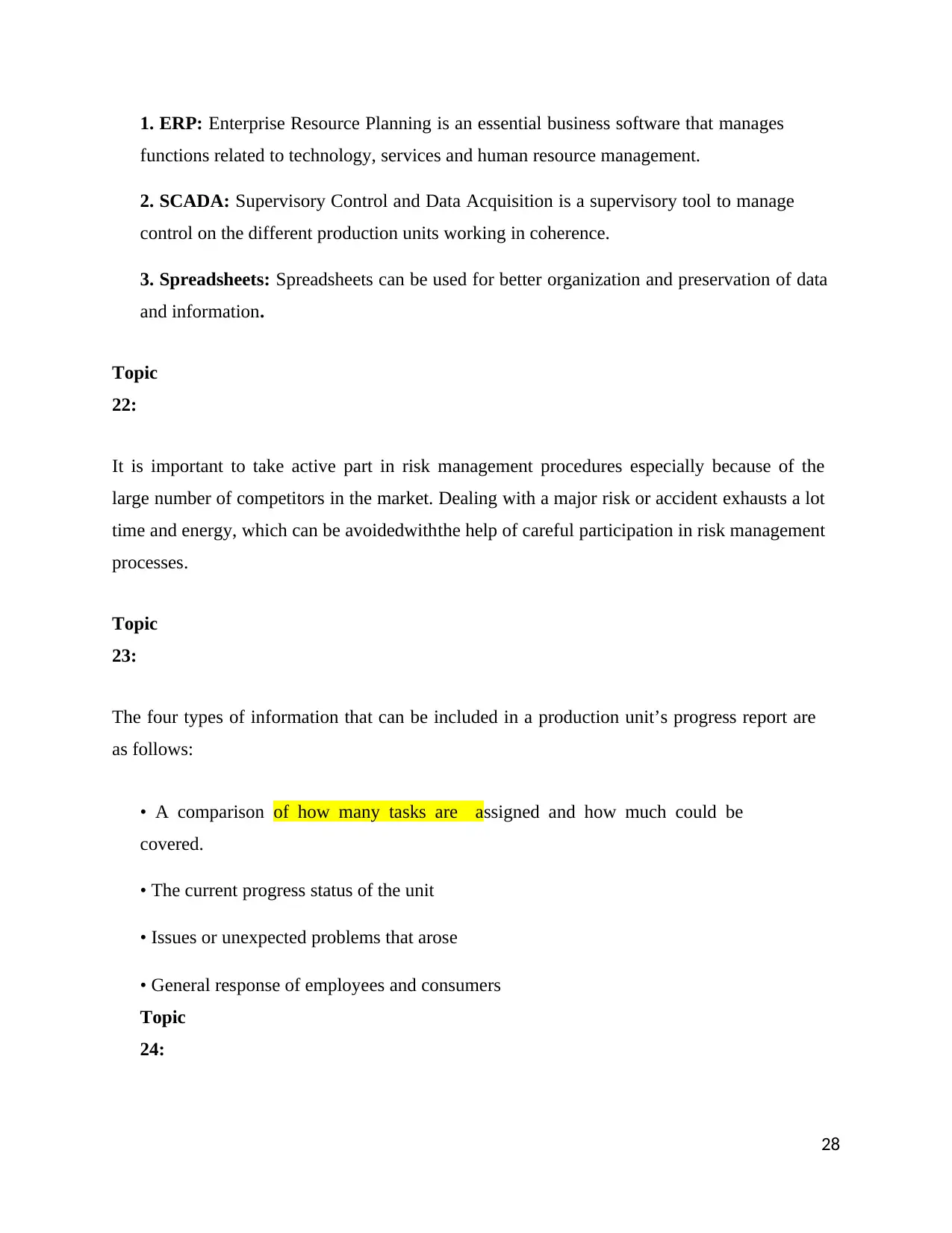
1. ERP: Enterprise Resource Planning is an essential business software that manages
functions related to technology, services and human resource management.
2. SCADA: Supervisory Control and Data Acquisition is a supervisory tool to manage
control on the different production units working in coherence.
3. Spreadsheets: Spreadsheets can be used for better organization and preservation of data
and information.
Topic
22:
It is important to take active part in risk management procedures especially because of the
large number of competitors in the market. Dealing with a major risk or accident exhausts a lot
time and energy, which can be avoidedwiththe help of careful participation in risk management
processes.
Topic
23:
The four types of information that can be included in a production unit’s progress report are
as follows:
• A comparison of how many tasks are assigned and how much could be
covered.
• The current progress status of the unit
• Issues or unexpected problems that arose
• General response of employees and consumers
Topic
24:
28
functions related to technology, services and human resource management.
2. SCADA: Supervisory Control and Data Acquisition is a supervisory tool to manage
control on the different production units working in coherence.
3. Spreadsheets: Spreadsheets can be used for better organization and preservation of data
and information.
Topic
22:
It is important to take active part in risk management procedures especially because of the
large number of competitors in the market. Dealing with a major risk or accident exhausts a lot
time and energy, which can be avoidedwiththe help of careful participation in risk management
processes.
Topic
23:
The four types of information that can be included in a production unit’s progress report are
as follows:
• A comparison of how many tasks are assigned and how much could be
covered.
• The current progress status of the unit
• Issues or unexpected problems that arose
• General response of employees and consumers
Topic
24:
28
Secure Best Marks with AI Grader
Need help grading? Try our AI Grader for instant feedback on your assignments.
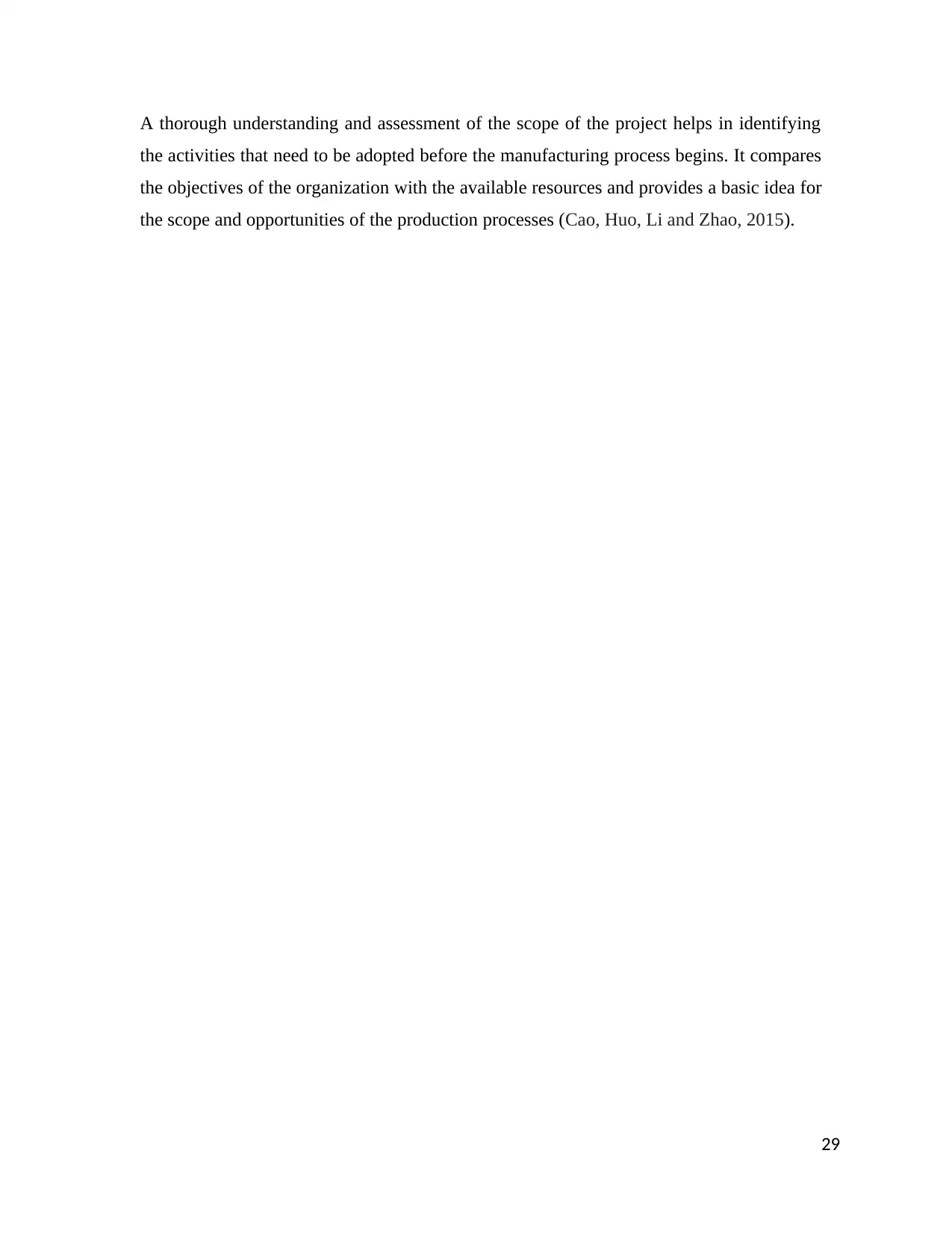
A thorough understanding and assessment of the scope of the project helps in identifying
the activities that need to be adopted before the manufacturing process begins. It compares
the objectives of the organization with the available resources and provides a basic idea for
the scope and opportunities of the production processes (Cao, Huo, Li and Zhao, 2015).
29
the activities that need to be adopted before the manufacturing process begins. It compares
the objectives of the organization with the available resources and provides a basic idea for
the scope and opportunities of the production processes (Cao, Huo, Li and Zhao, 2015).
29
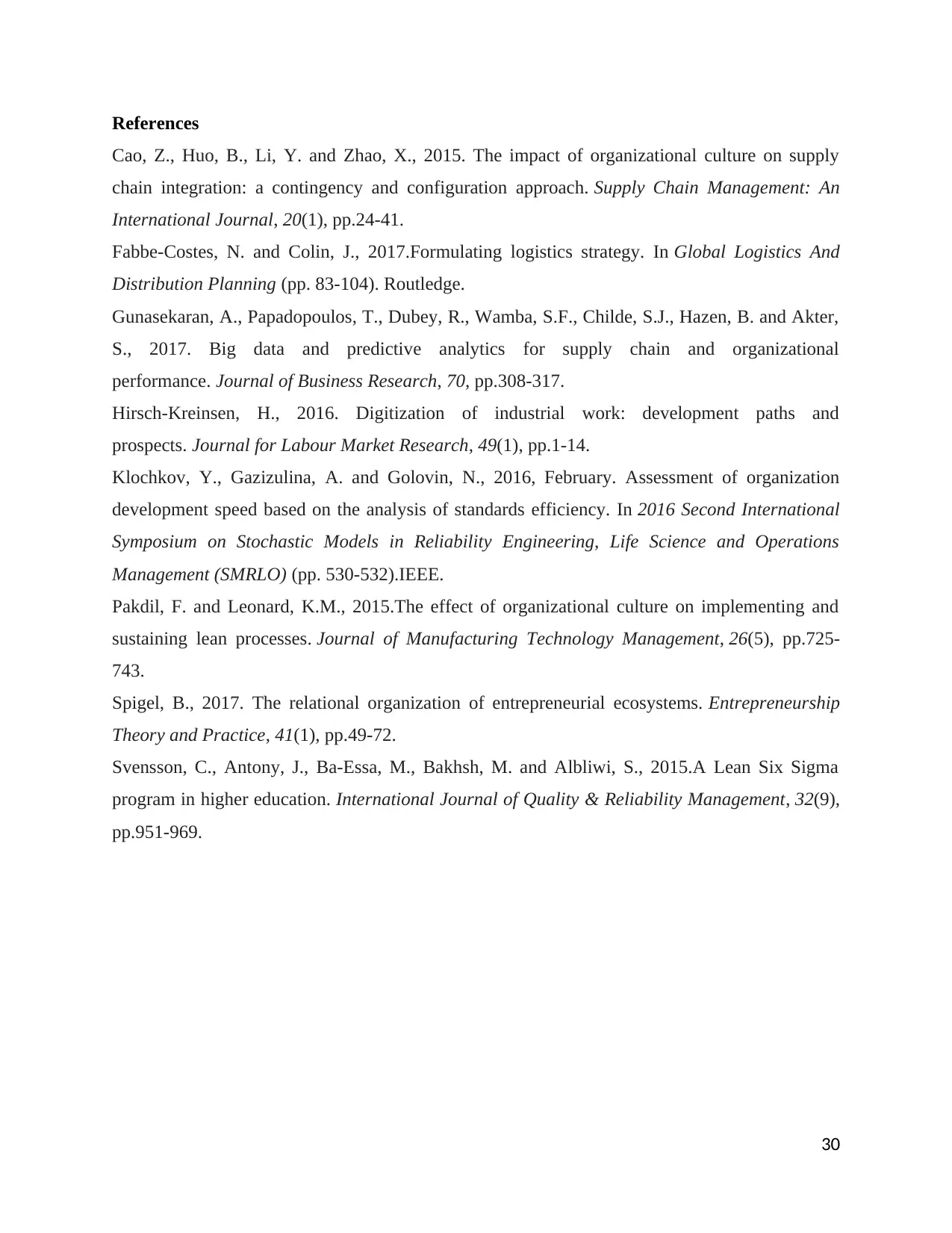
References
Cao, Z., Huo, B., Li, Y. and Zhao, X., 2015. The impact of organizational culture on supply
chain integration: a contingency and configuration approach. Supply Chain Management: An
International Journal, 20(1), pp.24-41.
Fabbe-Costes, N. and Colin, J., 2017.Formulating logistics strategy. In Global Logistics And
Distribution Planning (pp. 83-104). Routledge.
Gunasekaran, A., Papadopoulos, T., Dubey, R., Wamba, S.F., Childe, S.J., Hazen, B. and Akter,
S., 2017. Big data and predictive analytics for supply chain and organizational
performance. Journal of Business Research, 70, pp.308-317.
Hirsch-Kreinsen, H., 2016. Digitization of industrial work: development paths and
prospects. Journal for Labour Market Research, 49(1), pp.1-14.
Klochkov, Y., Gazizulina, A. and Golovin, N., 2016, February. Assessment of organization
development speed based on the analysis of standards efficiency. In 2016 Second International
Symposium on Stochastic Models in Reliability Engineering, Life Science and Operations
Management (SMRLO) (pp. 530-532).IEEE.
Pakdil, F. and Leonard, K.M., 2015.The effect of organizational culture on implementing and
sustaining lean processes. Journal of Manufacturing Technology Management, 26(5), pp.725-
743.
Spigel, B., 2017. The relational organization of entrepreneurial ecosystems. Entrepreneurship
Theory and Practice, 41(1), pp.49-72.
Svensson, C., Antony, J., Ba-Essa, M., Bakhsh, M. and Albliwi, S., 2015.A Lean Six Sigma
program in higher education. International Journal of Quality & Reliability Management, 32(9),
pp.951-969.
30
Cao, Z., Huo, B., Li, Y. and Zhao, X., 2015. The impact of organizational culture on supply
chain integration: a contingency and configuration approach. Supply Chain Management: An
International Journal, 20(1), pp.24-41.
Fabbe-Costes, N. and Colin, J., 2017.Formulating logistics strategy. In Global Logistics And
Distribution Planning (pp. 83-104). Routledge.
Gunasekaran, A., Papadopoulos, T., Dubey, R., Wamba, S.F., Childe, S.J., Hazen, B. and Akter,
S., 2017. Big data and predictive analytics for supply chain and organizational
performance. Journal of Business Research, 70, pp.308-317.
Hirsch-Kreinsen, H., 2016. Digitization of industrial work: development paths and
prospects. Journal for Labour Market Research, 49(1), pp.1-14.
Klochkov, Y., Gazizulina, A. and Golovin, N., 2016, February. Assessment of organization
development speed based on the analysis of standards efficiency. In 2016 Second International
Symposium on Stochastic Models in Reliability Engineering, Life Science and Operations
Management (SMRLO) (pp. 530-532).IEEE.
Pakdil, F. and Leonard, K.M., 2015.The effect of organizational culture on implementing and
sustaining lean processes. Journal of Manufacturing Technology Management, 26(5), pp.725-
743.
Spigel, B., 2017. The relational organization of entrepreneurial ecosystems. Entrepreneurship
Theory and Practice, 41(1), pp.49-72.
Svensson, C., Antony, J., Ba-Essa, M., Bakhsh, M. and Albliwi, S., 2015.A Lean Six Sigma
program in higher education. International Journal of Quality & Reliability Management, 32(9),
pp.951-969.
30
1 out of 30
Related Documents

Your All-in-One AI-Powered Toolkit for Academic Success.
+13062052269
info@desklib.com
Available 24*7 on WhatsApp / Email
Unlock your academic potential
© 2024 | Zucol Services PVT LTD | All rights reserved.