Risk Assessment and Mitigation in Industrial Plants: A Study
VerifiedAdded on 2023/06/03
|12
|5048
|492
Report
AI Summary
This report provides a comprehensive analysis of risk management in industrial plants, focusing on the identification, assessment, and mitigation of various hazards. The study begins with a detailed definition of risk and hazard, followed by an exploration of common risks in industrial settings, includin...
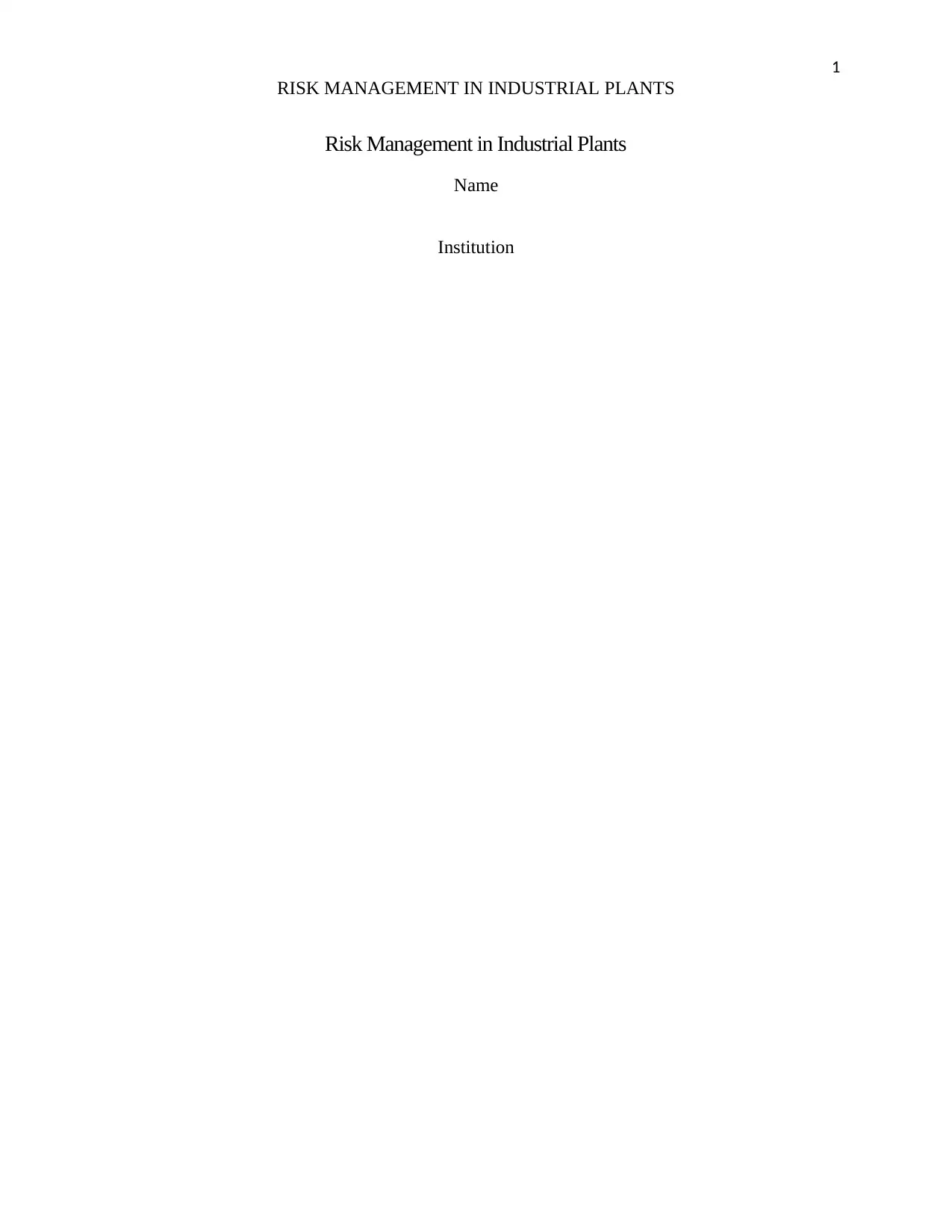
1
RISK MANAGEMENT IN INDUSTRIAL PLANTS
Risk Management in Industrial Plants
Name
Institution
RISK MANAGEMENT IN INDUSTRIAL PLANTS
Risk Management in Industrial Plants
Name
Institution
Paraphrase This Document
Need a fresh take? Get an instant paraphrase of this document with our AI Paraphraser
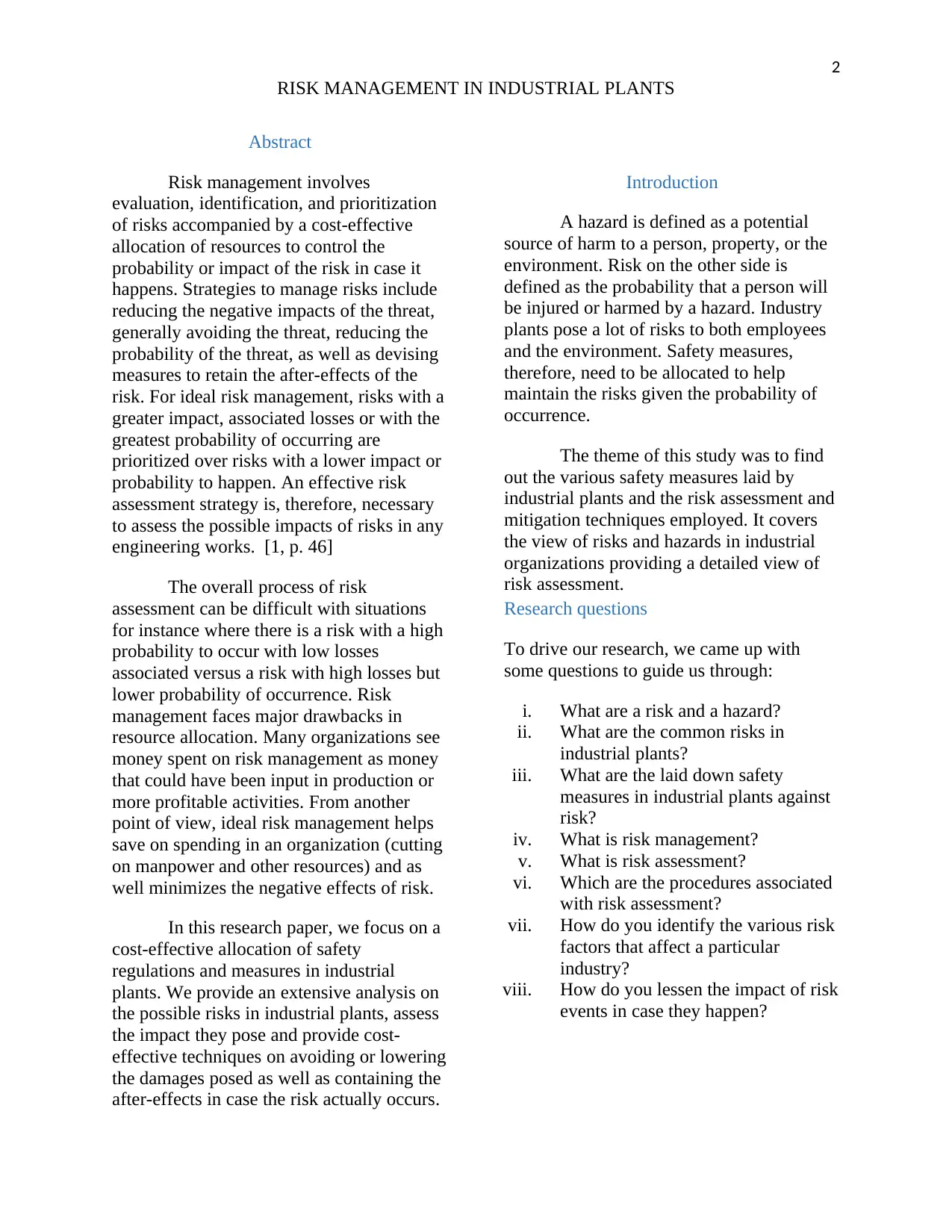
2
RISK MANAGEMENT IN INDUSTRIAL PLANTS
Abstract
Risk management involves
evaluation, identification, and prioritization
of risks accompanied by a cost-effective
allocation of resources to control the
probability or impact of the risk in case it
happens. Strategies to manage risks include
reducing the negative impacts of the threat,
generally avoiding the threat, reducing the
probability of the threat, as well as devising
measures to retain the after-effects of the
risk. For ideal risk management, risks with a
greater impact, associated losses or with the
greatest probability of occurring are
prioritized over risks with a lower impact or
probability to happen. An effective risk
assessment strategy is, therefore, necessary
to assess the possible impacts of risks in any
engineering works. [1, p. 46]
The overall process of risk
assessment can be difficult with situations
for instance where there is a risk with a high
probability to occur with low losses
associated versus a risk with high losses but
lower probability of occurrence. Risk
management faces major drawbacks in
resource allocation. Many organizations see
money spent on risk management as money
that could have been input in production or
more profitable activities. From another
point of view, ideal risk management helps
save on spending in an organization (cutting
on manpower and other resources) and as
well minimizes the negative effects of risk.
In this research paper, we focus on a
cost-effective allocation of safety
regulations and measures in industrial
plants. We provide an extensive analysis on
the possible risks in industrial plants, assess
the impact they pose and provide cost-
effective techniques on avoiding or lowering
the damages posed as well as containing the
after-effects in case the risk actually occurs.
Introduction
A hazard is defined as a potential
source of harm to a person, property, or the
environment. Risk on the other side is
defined as the probability that a person will
be injured or harmed by a hazard. Industry
plants pose a lot of risks to both employees
and the environment. Safety measures,
therefore, need to be allocated to help
maintain the risks given the probability of
occurrence.
The theme of this study was to find
out the various safety measures laid by
industrial plants and the risk assessment and
mitigation techniques employed. It covers
the view of risks and hazards in industrial
organizations providing a detailed view of
risk assessment.
Research questions
To drive our research, we came up with
some questions to guide us through:
i. What are a risk and a hazard?
ii. What are the common risks in
industrial plants?
iii. What are the laid down safety
measures in industrial plants against
risk?
iv. What is risk management?
v. What is risk assessment?
vi. Which are the procedures associated
with risk assessment?
vii. How do you identify the various risk
factors that affect a particular
industry?
viii. How do you lessen the impact of risk
events in case they happen?
RISK MANAGEMENT IN INDUSTRIAL PLANTS
Abstract
Risk management involves
evaluation, identification, and prioritization
of risks accompanied by a cost-effective
allocation of resources to control the
probability or impact of the risk in case it
happens. Strategies to manage risks include
reducing the negative impacts of the threat,
generally avoiding the threat, reducing the
probability of the threat, as well as devising
measures to retain the after-effects of the
risk. For ideal risk management, risks with a
greater impact, associated losses or with the
greatest probability of occurring are
prioritized over risks with a lower impact or
probability to happen. An effective risk
assessment strategy is, therefore, necessary
to assess the possible impacts of risks in any
engineering works. [1, p. 46]
The overall process of risk
assessment can be difficult with situations
for instance where there is a risk with a high
probability to occur with low losses
associated versus a risk with high losses but
lower probability of occurrence. Risk
management faces major drawbacks in
resource allocation. Many organizations see
money spent on risk management as money
that could have been input in production or
more profitable activities. From another
point of view, ideal risk management helps
save on spending in an organization (cutting
on manpower and other resources) and as
well minimizes the negative effects of risk.
In this research paper, we focus on a
cost-effective allocation of safety
regulations and measures in industrial
plants. We provide an extensive analysis on
the possible risks in industrial plants, assess
the impact they pose and provide cost-
effective techniques on avoiding or lowering
the damages posed as well as containing the
after-effects in case the risk actually occurs.
Introduction
A hazard is defined as a potential
source of harm to a person, property, or the
environment. Risk on the other side is
defined as the probability that a person will
be injured or harmed by a hazard. Industry
plants pose a lot of risks to both employees
and the environment. Safety measures,
therefore, need to be allocated to help
maintain the risks given the probability of
occurrence.
The theme of this study was to find
out the various safety measures laid by
industrial plants and the risk assessment and
mitigation techniques employed. It covers
the view of risks and hazards in industrial
organizations providing a detailed view of
risk assessment.
Research questions
To drive our research, we came up with
some questions to guide us through:
i. What are a risk and a hazard?
ii. What are the common risks in
industrial plants?
iii. What are the laid down safety
measures in industrial plants against
risk?
iv. What is risk management?
v. What is risk assessment?
vi. Which are the procedures associated
with risk assessment?
vii. How do you identify the various risk
factors that affect a particular
industry?
viii. How do you lessen the impact of risk
events in case they happen?
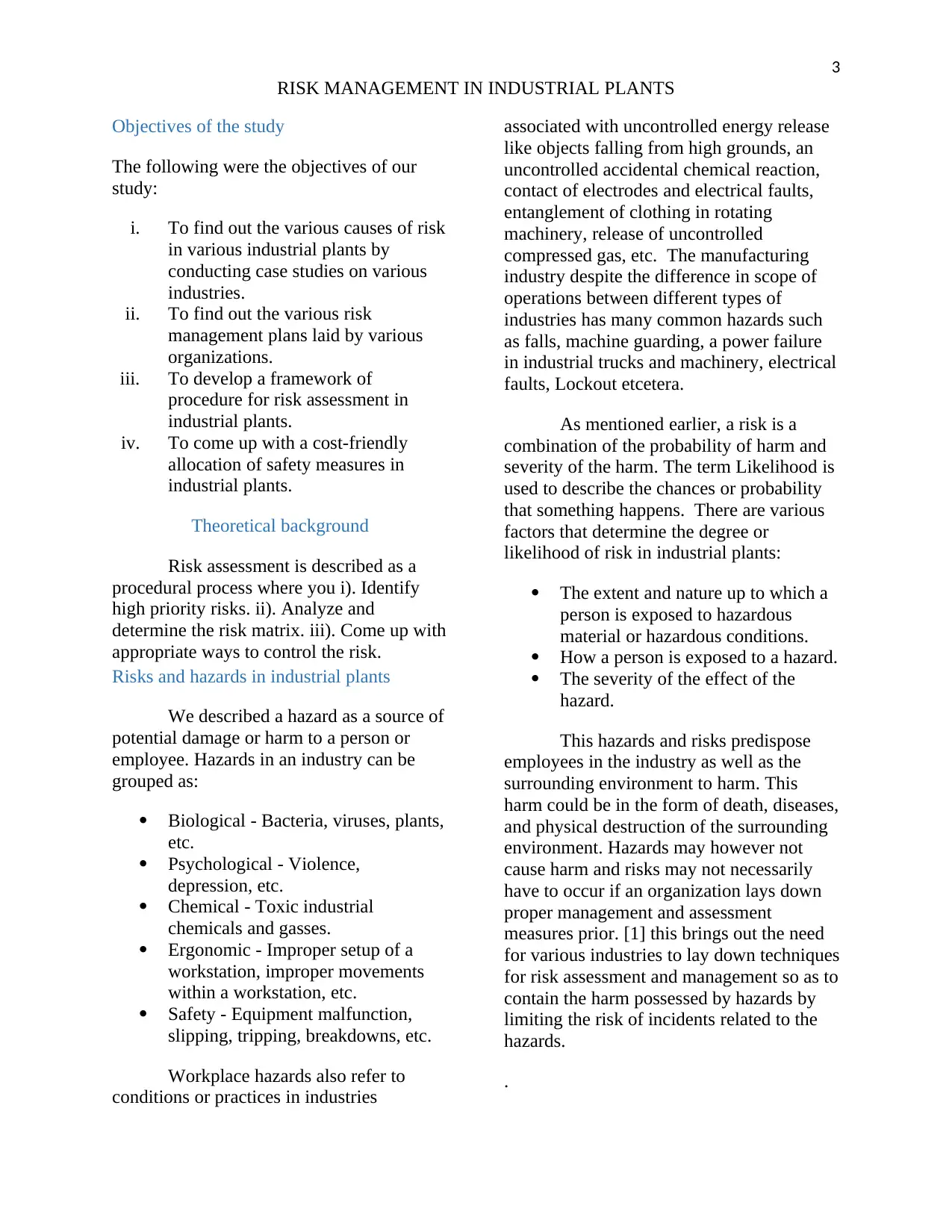
3
RISK MANAGEMENT IN INDUSTRIAL PLANTS
Objectives of the study
The following were the objectives of our
study:
i. To find out the various causes of risk
in various industrial plants by
conducting case studies on various
industries.
ii. To find out the various risk
management plans laid by various
organizations.
iii. To develop a framework of
procedure for risk assessment in
industrial plants.
iv. To come up with a cost-friendly
allocation of safety measures in
industrial plants.
Theoretical background
Risk assessment is described as a
procedural process where you i). Identify
high priority risks. ii). Analyze and
determine the risk matrix. iii). Come up with
appropriate ways to control the risk.
Risks and hazards in industrial plants
We described a hazard as a source of
potential damage or harm to a person or
employee. Hazards in an industry can be
grouped as:
Biological - Bacteria, viruses, plants,
etc.
Psychological - Violence,
depression, etc.
Chemical - Toxic industrial
chemicals and gasses.
Ergonomic - Improper setup of a
workstation, improper movements
within a workstation, etc.
Safety - Equipment malfunction,
slipping, tripping, breakdowns, etc.
Workplace hazards also refer to
conditions or practices in industries
associated with uncontrolled energy release
like objects falling from high grounds, an
uncontrolled accidental chemical reaction,
contact of electrodes and electrical faults,
entanglement of clothing in rotating
machinery, release of uncontrolled
compressed gas, etc. The manufacturing
industry despite the difference in scope of
operations between different types of
industries has many common hazards such
as falls, machine guarding, a power failure
in industrial trucks and machinery, electrical
faults, Lockout etcetera.
As mentioned earlier, a risk is a
combination of the probability of harm and
severity of the harm. The term Likelihood is
used to describe the chances or probability
that something happens. There are various
factors that determine the degree or
likelihood of risk in industrial plants:
The extent and nature up to which a
person is exposed to hazardous
material or hazardous conditions.
How a person is exposed to a hazard.
The severity of the effect of the
hazard.
This hazards and risks predispose
employees in the industry as well as the
surrounding environment to harm. This
harm could be in the form of death, diseases,
and physical destruction of the surrounding
environment. Hazards may however not
cause harm and risks may not necessarily
have to occur if an organization lays down
proper management and assessment
measures prior. [1] this brings out the need
for various industries to lay down techniques
for risk assessment and management so as to
contain the harm possessed by hazards by
limiting the risk of incidents related to the
hazards.
.
RISK MANAGEMENT IN INDUSTRIAL PLANTS
Objectives of the study
The following were the objectives of our
study:
i. To find out the various causes of risk
in various industrial plants by
conducting case studies on various
industries.
ii. To find out the various risk
management plans laid by various
organizations.
iii. To develop a framework of
procedure for risk assessment in
industrial plants.
iv. To come up with a cost-friendly
allocation of safety measures in
industrial plants.
Theoretical background
Risk assessment is described as a
procedural process where you i). Identify
high priority risks. ii). Analyze and
determine the risk matrix. iii). Come up with
appropriate ways to control the risk.
Risks and hazards in industrial plants
We described a hazard as a source of
potential damage or harm to a person or
employee. Hazards in an industry can be
grouped as:
Biological - Bacteria, viruses, plants,
etc.
Psychological - Violence,
depression, etc.
Chemical - Toxic industrial
chemicals and gasses.
Ergonomic - Improper setup of a
workstation, improper movements
within a workstation, etc.
Safety - Equipment malfunction,
slipping, tripping, breakdowns, etc.
Workplace hazards also refer to
conditions or practices in industries
associated with uncontrolled energy release
like objects falling from high grounds, an
uncontrolled accidental chemical reaction,
contact of electrodes and electrical faults,
entanglement of clothing in rotating
machinery, release of uncontrolled
compressed gas, etc. The manufacturing
industry despite the difference in scope of
operations between different types of
industries has many common hazards such
as falls, machine guarding, a power failure
in industrial trucks and machinery, electrical
faults, Lockout etcetera.
As mentioned earlier, a risk is a
combination of the probability of harm and
severity of the harm. The term Likelihood is
used to describe the chances or probability
that something happens. There are various
factors that determine the degree or
likelihood of risk in industrial plants:
The extent and nature up to which a
person is exposed to hazardous
material or hazardous conditions.
How a person is exposed to a hazard.
The severity of the effect of the
hazard.
This hazards and risks predispose
employees in the industry as well as the
surrounding environment to harm. This
harm could be in the form of death, diseases,
and physical destruction of the surrounding
environment. Hazards may however not
cause harm and risks may not necessarily
have to occur if an organization lays down
proper management and assessment
measures prior. [1] this brings out the need
for various industries to lay down techniques
for risk assessment and management so as to
contain the harm possessed by hazards by
limiting the risk of incidents related to the
hazards.
.
⊘ This is a preview!⊘
Do you want full access?
Subscribe today to unlock all pages.

Trusted by 1+ million students worldwide
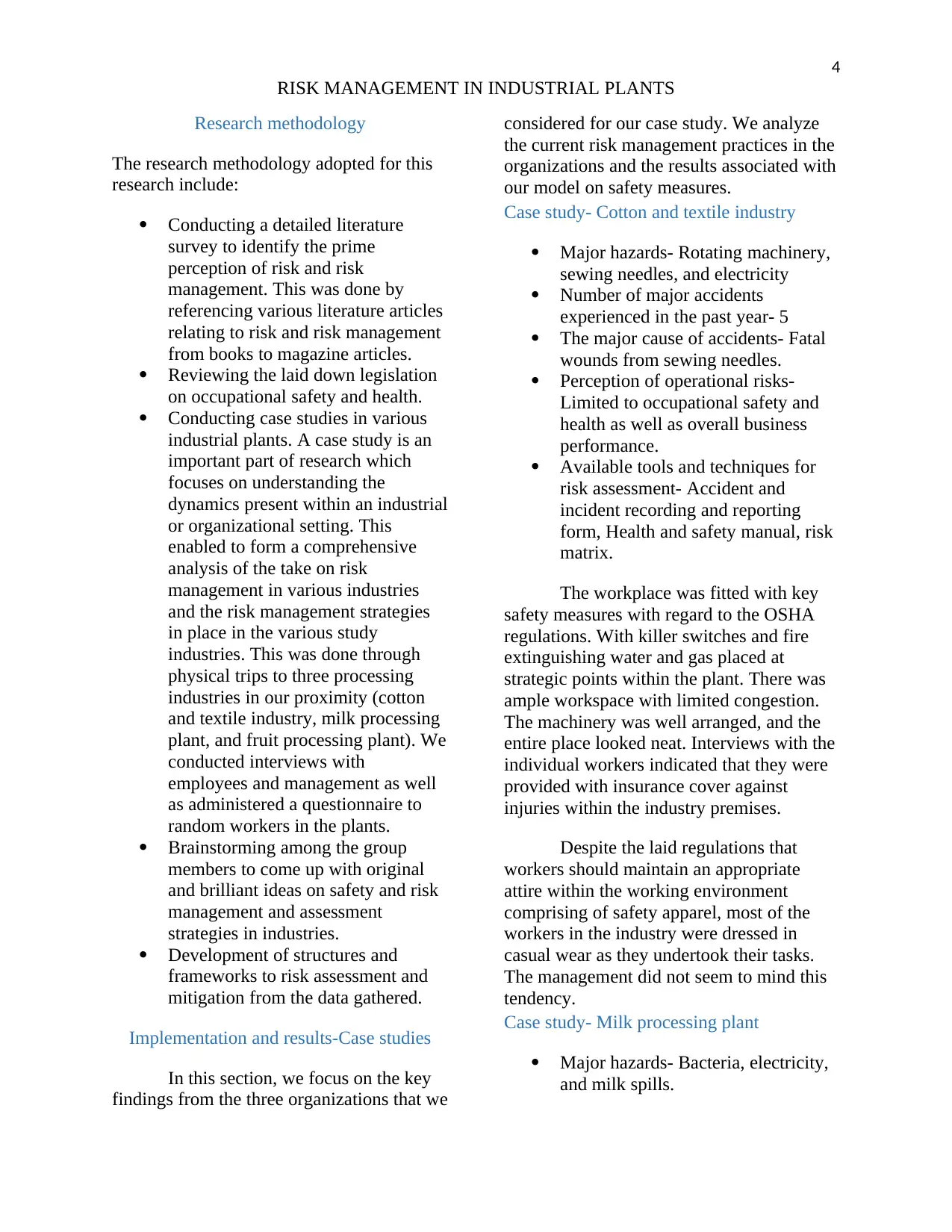
4
RISK MANAGEMENT IN INDUSTRIAL PLANTS
Research methodology
The research methodology adopted for this
research include:
Conducting a detailed literature
survey to identify the prime
perception of risk and risk
management. This was done by
referencing various literature articles
relating to risk and risk management
from books to magazine articles.
Reviewing the laid down legislation
on occupational safety and health.
Conducting case studies in various
industrial plants. A case study is an
important part of research which
focuses on understanding the
dynamics present within an industrial
or organizational setting. This
enabled to form a comprehensive
analysis of the take on risk
management in various industries
and the risk management strategies
in place in the various study
industries. This was done through
physical trips to three processing
industries in our proximity (cotton
and textile industry, milk processing
plant, and fruit processing plant). We
conducted interviews with
employees and management as well
as administered a questionnaire to
random workers in the plants.
Brainstorming among the group
members to come up with original
and brilliant ideas on safety and risk
management and assessment
strategies in industries.
Development of structures and
frameworks to risk assessment and
mitigation from the data gathered.
Implementation and results-Case studies
In this section, we focus on the key
findings from the three organizations that we
considered for our case study. We analyze
the current risk management practices in the
organizations and the results associated with
our model on safety measures.
Case study- Cotton and textile industry
Major hazards- Rotating machinery,
sewing needles, and electricity
Number of major accidents
experienced in the past year- 5
The major cause of accidents- Fatal
wounds from sewing needles.
Perception of operational risks-
Limited to occupational safety and
health as well as overall business
performance.
Available tools and techniques for
risk assessment- Accident and
incident recording and reporting
form, Health and safety manual, risk
matrix.
The workplace was fitted with key
safety measures with regard to the OSHA
regulations. With killer switches and fire
extinguishing water and gas placed at
strategic points within the plant. There was
ample workspace with limited congestion.
The machinery was well arranged, and the
entire place looked neat. Interviews with the
individual workers indicated that they were
provided with insurance cover against
injuries within the industry premises.
Despite the laid regulations that
workers should maintain an appropriate
attire within the working environment
comprising of safety apparel, most of the
workers in the industry were dressed in
casual wear as they undertook their tasks.
The management did not seem to mind this
tendency.
Case study- Milk processing plant
Major hazards- Bacteria, electricity,
and milk spills.
RISK MANAGEMENT IN INDUSTRIAL PLANTS
Research methodology
The research methodology adopted for this
research include:
Conducting a detailed literature
survey to identify the prime
perception of risk and risk
management. This was done by
referencing various literature articles
relating to risk and risk management
from books to magazine articles.
Reviewing the laid down legislation
on occupational safety and health.
Conducting case studies in various
industrial plants. A case study is an
important part of research which
focuses on understanding the
dynamics present within an industrial
or organizational setting. This
enabled to form a comprehensive
analysis of the take on risk
management in various industries
and the risk management strategies
in place in the various study
industries. This was done through
physical trips to three processing
industries in our proximity (cotton
and textile industry, milk processing
plant, and fruit processing plant). We
conducted interviews with
employees and management as well
as administered a questionnaire to
random workers in the plants.
Brainstorming among the group
members to come up with original
and brilliant ideas on safety and risk
management and assessment
strategies in industries.
Development of structures and
frameworks to risk assessment and
mitigation from the data gathered.
Implementation and results-Case studies
In this section, we focus on the key
findings from the three organizations that we
considered for our case study. We analyze
the current risk management practices in the
organizations and the results associated with
our model on safety measures.
Case study- Cotton and textile industry
Major hazards- Rotating machinery,
sewing needles, and electricity
Number of major accidents
experienced in the past year- 5
The major cause of accidents- Fatal
wounds from sewing needles.
Perception of operational risks-
Limited to occupational safety and
health as well as overall business
performance.
Available tools and techniques for
risk assessment- Accident and
incident recording and reporting
form, Health and safety manual, risk
matrix.
The workplace was fitted with key
safety measures with regard to the OSHA
regulations. With killer switches and fire
extinguishing water and gas placed at
strategic points within the plant. There was
ample workspace with limited congestion.
The machinery was well arranged, and the
entire place looked neat. Interviews with the
individual workers indicated that they were
provided with insurance cover against
injuries within the industry premises.
Despite the laid regulations that
workers should maintain an appropriate
attire within the working environment
comprising of safety apparel, most of the
workers in the industry were dressed in
casual wear as they undertook their tasks.
The management did not seem to mind this
tendency.
Case study- Milk processing plant
Major hazards- Bacteria, electricity,
and milk spills.
Paraphrase This Document
Need a fresh take? Get an instant paraphrase of this document with our AI Paraphraser
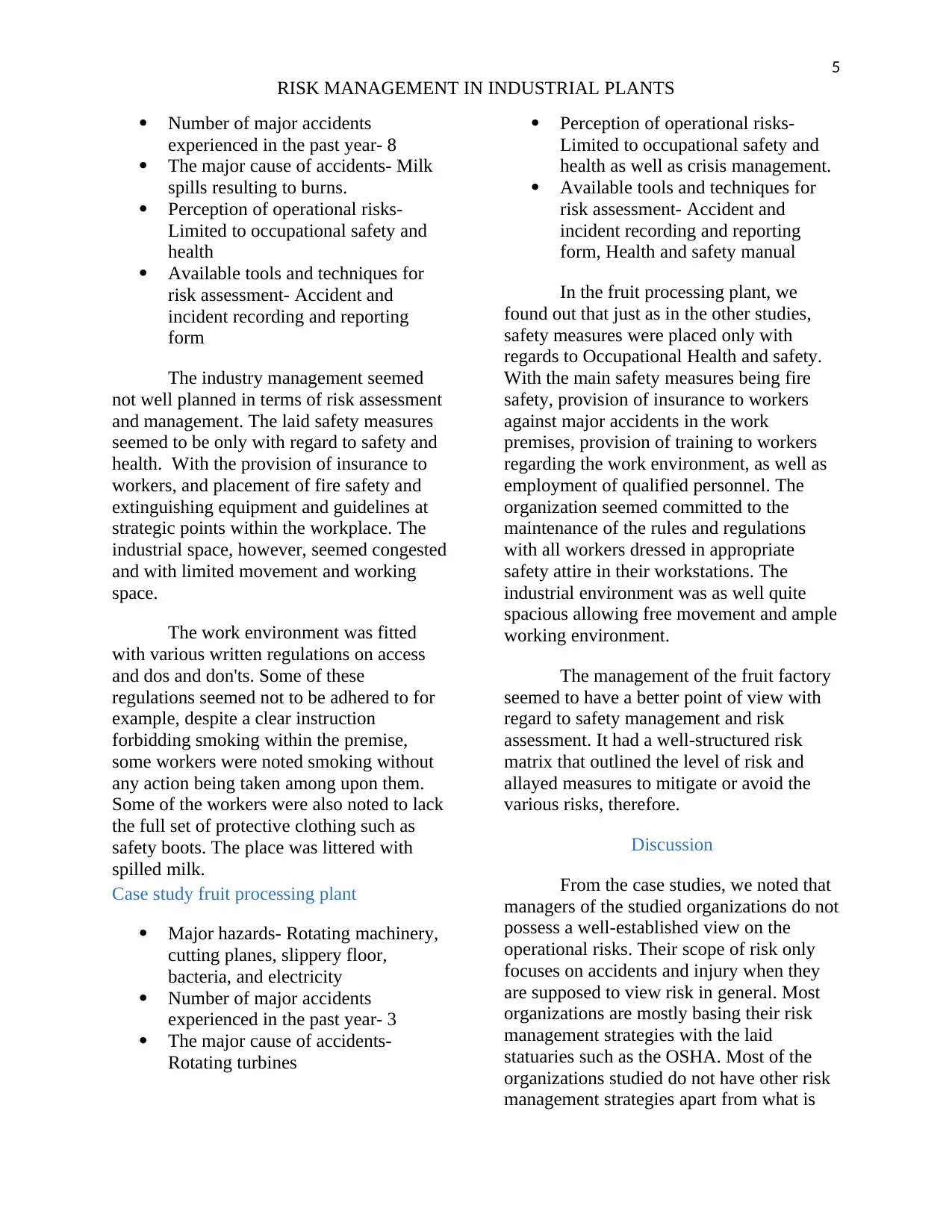
5
RISK MANAGEMENT IN INDUSTRIAL PLANTS
Number of major accidents
experienced in the past year- 8
The major cause of accidents- Milk
spills resulting to burns.
Perception of operational risks-
Limited to occupational safety and
health
Available tools and techniques for
risk assessment- Accident and
incident recording and reporting
form
The industry management seemed
not well planned in terms of risk assessment
and management. The laid safety measures
seemed to be only with regard to safety and
health. With the provision of insurance to
workers, and placement of fire safety and
extinguishing equipment and guidelines at
strategic points within the workplace. The
industrial space, however, seemed congested
and with limited movement and working
space.
The work environment was fitted
with various written regulations on access
and dos and don'ts. Some of these
regulations seemed not to be adhered to for
example, despite a clear instruction
forbidding smoking within the premise,
some workers were noted smoking without
any action being taken among upon them.
Some of the workers were also noted to lack
the full set of protective clothing such as
safety boots. The place was littered with
spilled milk.
Case study fruit processing plant
Major hazards- Rotating machinery,
cutting planes, slippery floor,
bacteria, and electricity
Number of major accidents
experienced in the past year- 3
The major cause of accidents-
Rotating turbines
Perception of operational risks-
Limited to occupational safety and
health as well as crisis management.
Available tools and techniques for
risk assessment- Accident and
incident recording and reporting
form, Health and safety manual
In the fruit processing plant, we
found out that just as in the other studies,
safety measures were placed only with
regards to Occupational Health and safety.
With the main safety measures being fire
safety, provision of insurance to workers
against major accidents in the work
premises, provision of training to workers
regarding the work environment, as well as
employment of qualified personnel. The
organization seemed committed to the
maintenance of the rules and regulations
with all workers dressed in appropriate
safety attire in their workstations. The
industrial environment was as well quite
spacious allowing free movement and ample
working environment.
The management of the fruit factory
seemed to have a better point of view with
regard to safety management and risk
assessment. It had a well-structured risk
matrix that outlined the level of risk and
allayed measures to mitigate or avoid the
various risks, therefore.
Discussion
From the case studies, we noted that
managers of the studied organizations do not
possess a well-established view on the
operational risks. Their scope of risk only
focuses on accidents and injury when they
are supposed to view risk in general. Most
organizations are mostly basing their risk
management strategies with the laid
statuaries such as the OSHA. Most of the
organizations studied do not have other risk
management strategies apart from what is
RISK MANAGEMENT IN INDUSTRIAL PLANTS
Number of major accidents
experienced in the past year- 8
The major cause of accidents- Milk
spills resulting to burns.
Perception of operational risks-
Limited to occupational safety and
health
Available tools and techniques for
risk assessment- Accident and
incident recording and reporting
form
The industry management seemed
not well planned in terms of risk assessment
and management. The laid safety measures
seemed to be only with regard to safety and
health. With the provision of insurance to
workers, and placement of fire safety and
extinguishing equipment and guidelines at
strategic points within the workplace. The
industrial space, however, seemed congested
and with limited movement and working
space.
The work environment was fitted
with various written regulations on access
and dos and don'ts. Some of these
regulations seemed not to be adhered to for
example, despite a clear instruction
forbidding smoking within the premise,
some workers were noted smoking without
any action being taken among upon them.
Some of the workers were also noted to lack
the full set of protective clothing such as
safety boots. The place was littered with
spilled milk.
Case study fruit processing plant
Major hazards- Rotating machinery,
cutting planes, slippery floor,
bacteria, and electricity
Number of major accidents
experienced in the past year- 3
The major cause of accidents-
Rotating turbines
Perception of operational risks-
Limited to occupational safety and
health as well as crisis management.
Available tools and techniques for
risk assessment- Accident and
incident recording and reporting
form, Health and safety manual
In the fruit processing plant, we
found out that just as in the other studies,
safety measures were placed only with
regards to Occupational Health and safety.
With the main safety measures being fire
safety, provision of insurance to workers
against major accidents in the work
premises, provision of training to workers
regarding the work environment, as well as
employment of qualified personnel. The
organization seemed committed to the
maintenance of the rules and regulations
with all workers dressed in appropriate
safety attire in their workstations. The
industrial environment was as well quite
spacious allowing free movement and ample
working environment.
The management of the fruit factory
seemed to have a better point of view with
regard to safety management and risk
assessment. It had a well-structured risk
matrix that outlined the level of risk and
allayed measures to mitigate or avoid the
various risks, therefore.
Discussion
From the case studies, we noted that
managers of the studied organizations do not
possess a well-established view on the
operational risks. Their scope of risk only
focuses on accidents and injury when they
are supposed to view risk in general. Most
organizations are mostly basing their risk
management strategies with the laid
statuaries such as the OSHA. Most of the
organizations studied do not have other risk
management strategies apart from what is
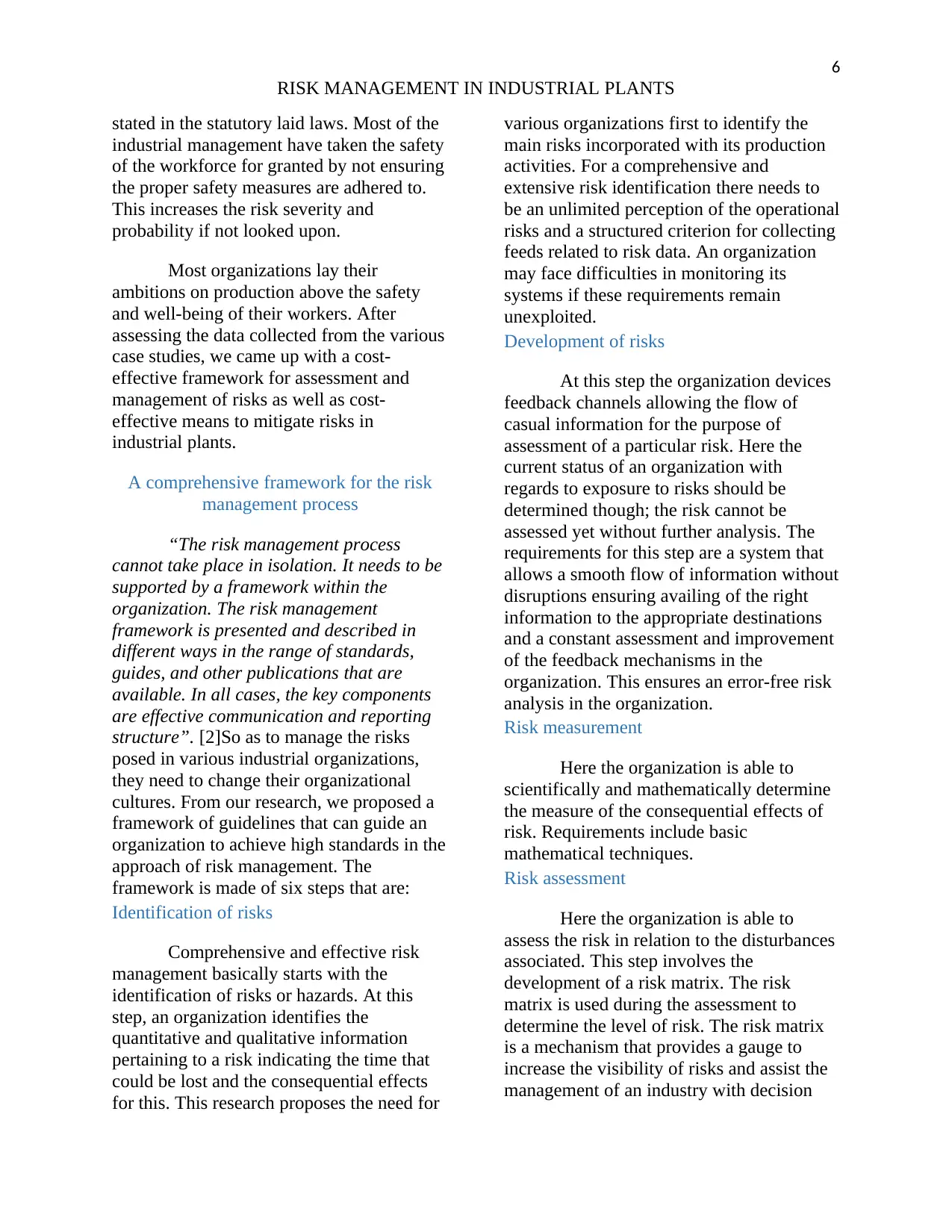
6
RISK MANAGEMENT IN INDUSTRIAL PLANTS
stated in the statutory laid laws. Most of the
industrial management have taken the safety
of the workforce for granted by not ensuring
the proper safety measures are adhered to.
This increases the risk severity and
probability if not looked upon.
Most organizations lay their
ambitions on production above the safety
and well-being of their workers. After
assessing the data collected from the various
case studies, we came up with a cost-
effective framework for assessment and
management of risks as well as cost-
effective means to mitigate risks in
industrial plants.
A comprehensive framework for the risk
management process
“The risk management process
cannot take place in isolation. It needs to be
supported by a framework within the
organization. The risk management
framework is presented and described in
different ways in the range of standards,
guides, and other publications that are
available. In all cases, the key components
are effective communication and reporting
structure”. [2]So as to manage the risks
posed in various industrial organizations,
they need to change their organizational
cultures. From our research, we proposed a
framework of guidelines that can guide an
organization to achieve high standards in the
approach of risk management. The
framework is made of six steps that are:
Identification of risks
Comprehensive and effective risk
management basically starts with the
identification of risks or hazards. At this
step, an organization identifies the
quantitative and qualitative information
pertaining to a risk indicating the time that
could be lost and the consequential effects
for this. This research proposes the need for
various organizations first to identify the
main risks incorporated with its production
activities. For a comprehensive and
extensive risk identification there needs to
be an unlimited perception of the operational
risks and a structured criterion for collecting
feeds related to risk data. An organization
may face difficulties in monitoring its
systems if these requirements remain
unexploited.
Development of risks
At this step the organization devices
feedback channels allowing the flow of
casual information for the purpose of
assessment of a particular risk. Here the
current status of an organization with
regards to exposure to risks should be
determined though; the risk cannot be
assessed yet without further analysis. The
requirements for this step are a system that
allows a smooth flow of information without
disruptions ensuring availing of the right
information to the appropriate destinations
and a constant assessment and improvement
of the feedback mechanisms in the
organization. This ensures an error-free risk
analysis in the organization.
Risk measurement
Here the organization is able to
scientifically and mathematically determine
the measure of the consequential effects of
risk. Requirements include basic
mathematical techniques.
Risk assessment
Here the organization is able to
assess the risk in relation to the disturbances
associated. This step involves the
development of a risk matrix. The risk
matrix is used during the assessment to
determine the level of risk. The risk matrix
is a mechanism that provides a gauge to
increase the visibility of risks and assist the
management of an industry with decision
RISK MANAGEMENT IN INDUSTRIAL PLANTS
stated in the statutory laid laws. Most of the
industrial management have taken the safety
of the workforce for granted by not ensuring
the proper safety measures are adhered to.
This increases the risk severity and
probability if not looked upon.
Most organizations lay their
ambitions on production above the safety
and well-being of their workers. After
assessing the data collected from the various
case studies, we came up with a cost-
effective framework for assessment and
management of risks as well as cost-
effective means to mitigate risks in
industrial plants.
A comprehensive framework for the risk
management process
“The risk management process
cannot take place in isolation. It needs to be
supported by a framework within the
organization. The risk management
framework is presented and described in
different ways in the range of standards,
guides, and other publications that are
available. In all cases, the key components
are effective communication and reporting
structure”. [2]So as to manage the risks
posed in various industrial organizations,
they need to change their organizational
cultures. From our research, we proposed a
framework of guidelines that can guide an
organization to achieve high standards in the
approach of risk management. The
framework is made of six steps that are:
Identification of risks
Comprehensive and effective risk
management basically starts with the
identification of risks or hazards. At this
step, an organization identifies the
quantitative and qualitative information
pertaining to a risk indicating the time that
could be lost and the consequential effects
for this. This research proposes the need for
various organizations first to identify the
main risks incorporated with its production
activities. For a comprehensive and
extensive risk identification there needs to
be an unlimited perception of the operational
risks and a structured criterion for collecting
feeds related to risk data. An organization
may face difficulties in monitoring its
systems if these requirements remain
unexploited.
Development of risks
At this step the organization devices
feedback channels allowing the flow of
casual information for the purpose of
assessment of a particular risk. Here the
current status of an organization with
regards to exposure to risks should be
determined though; the risk cannot be
assessed yet without further analysis. The
requirements for this step are a system that
allows a smooth flow of information without
disruptions ensuring availing of the right
information to the appropriate destinations
and a constant assessment and improvement
of the feedback mechanisms in the
organization. This ensures an error-free risk
analysis in the organization.
Risk measurement
Here the organization is able to
scientifically and mathematically determine
the measure of the consequential effects of
risk. Requirements include basic
mathematical techniques.
Risk assessment
Here the organization is able to
assess the risk in relation to the disturbances
associated. This step involves the
development of a risk matrix. The risk
matrix is used during the assessment to
determine the level of risk. The risk matrix
is a mechanism that provides a gauge to
increase the visibility of risks and assist the
management of an industry with decision
⊘ This is a preview!⊘
Do you want full access?
Subscribe today to unlock all pages.

Trusted by 1+ million students worldwide
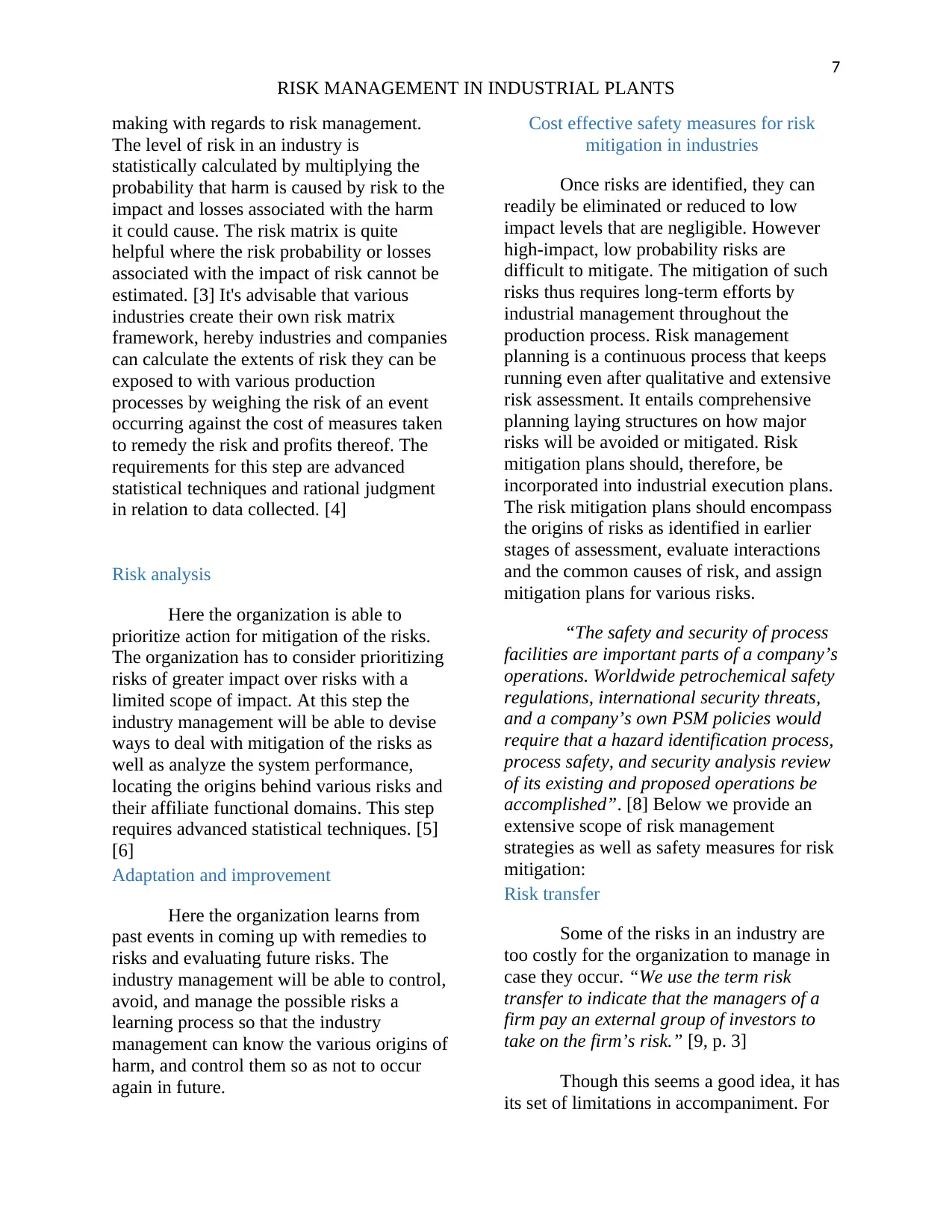
7
RISK MANAGEMENT IN INDUSTRIAL PLANTS
making with regards to risk management.
The level of risk in an industry is
statistically calculated by multiplying the
probability that harm is caused by risk to the
impact and losses associated with the harm
it could cause. The risk matrix is quite
helpful where the risk probability or losses
associated with the impact of risk cannot be
estimated. [3] It's advisable that various
industries create their own risk matrix
framework, hereby industries and companies
can calculate the extents of risk they can be
exposed to with various production
processes by weighing the risk of an event
occurring against the cost of measures taken
to remedy the risk and profits thereof. The
requirements for this step are advanced
statistical techniques and rational judgment
in relation to data collected. [4]
Risk analysis
Here the organization is able to
prioritize action for mitigation of the risks.
The organization has to consider prioritizing
risks of greater impact over risks with a
limited scope of impact. At this step the
industry management will be able to devise
ways to deal with mitigation of the risks as
well as analyze the system performance,
locating the origins behind various risks and
their affiliate functional domains. This step
requires advanced statistical techniques. [5]
[6]
Adaptation and improvement
Here the organization learns from
past events in coming up with remedies to
risks and evaluating future risks. The
industry management will be able to control,
avoid, and manage the possible risks a
learning process so that the industry
management can know the various origins of
harm, and control them so as not to occur
again in future.
Cost effective safety measures for risk
mitigation in industries
Once risks are identified, they can
readily be eliminated or reduced to low
impact levels that are negligible. However
high-impact, low probability risks are
difficult to mitigate. The mitigation of such
risks thus requires long-term efforts by
industrial management throughout the
production process. Risk management
planning is a continuous process that keeps
running even after qualitative and extensive
risk assessment. It entails comprehensive
planning laying structures on how major
risks will be avoided or mitigated. Risk
mitigation plans should, therefore, be
incorporated into industrial execution plans.
The risk mitigation plans should encompass
the origins of risks as identified in earlier
stages of assessment, evaluate interactions
and the common causes of risk, and assign
mitigation plans for various risks.
“The safety and security of process
facilities are important parts of a company’s
operations. Worldwide petrochemical safety
regulations, international security threats,
and a company’s own PSM policies would
require that a hazard identification process,
process safety, and security analysis review
of its existing and proposed operations be
accomplished”. [8] Below we provide an
extensive scope of risk management
strategies as well as safety measures for risk
mitigation:
Risk transfer
Some of the risks in an industry are
too costly for the organization to manage in
case they occur. “We use the term risk
transfer to indicate that the managers of a
firm pay an external group of investors to
take on the firm’s risk.” [9, p. 3]
Though this seems a good idea, it has
its set of limitations in accompaniment. For
RISK MANAGEMENT IN INDUSTRIAL PLANTS
making with regards to risk management.
The level of risk in an industry is
statistically calculated by multiplying the
probability that harm is caused by risk to the
impact and losses associated with the harm
it could cause. The risk matrix is quite
helpful where the risk probability or losses
associated with the impact of risk cannot be
estimated. [3] It's advisable that various
industries create their own risk matrix
framework, hereby industries and companies
can calculate the extents of risk they can be
exposed to with various production
processes by weighing the risk of an event
occurring against the cost of measures taken
to remedy the risk and profits thereof. The
requirements for this step are advanced
statistical techniques and rational judgment
in relation to data collected. [4]
Risk analysis
Here the organization is able to
prioritize action for mitigation of the risks.
The organization has to consider prioritizing
risks of greater impact over risks with a
limited scope of impact. At this step the
industry management will be able to devise
ways to deal with mitigation of the risks as
well as analyze the system performance,
locating the origins behind various risks and
their affiliate functional domains. This step
requires advanced statistical techniques. [5]
[6]
Adaptation and improvement
Here the organization learns from
past events in coming up with remedies to
risks and evaluating future risks. The
industry management will be able to control,
avoid, and manage the possible risks a
learning process so that the industry
management can know the various origins of
harm, and control them so as not to occur
again in future.
Cost effective safety measures for risk
mitigation in industries
Once risks are identified, they can
readily be eliminated or reduced to low
impact levels that are negligible. However
high-impact, low probability risks are
difficult to mitigate. The mitigation of such
risks thus requires long-term efforts by
industrial management throughout the
production process. Risk management
planning is a continuous process that keeps
running even after qualitative and extensive
risk assessment. It entails comprehensive
planning laying structures on how major
risks will be avoided or mitigated. Risk
mitigation plans should, therefore, be
incorporated into industrial execution plans.
The risk mitigation plans should encompass
the origins of risks as identified in earlier
stages of assessment, evaluate interactions
and the common causes of risk, and assign
mitigation plans for various risks.
“The safety and security of process
facilities are important parts of a company’s
operations. Worldwide petrochemical safety
regulations, international security threats,
and a company’s own PSM policies would
require that a hazard identification process,
process safety, and security analysis review
of its existing and proposed operations be
accomplished”. [8] Below we provide an
extensive scope of risk management
strategies as well as safety measures for risk
mitigation:
Risk transfer
Some of the risks in an industry are
too costly for the organization to manage in
case they occur. “We use the term risk
transfer to indicate that the managers of a
firm pay an external group of investors to
take on the firm’s risk.” [9, p. 3]
Though this seems a good idea, it has
its set of limitations in accompaniment. For
Paraphrase This Document
Need a fresh take? Get an instant paraphrase of this document with our AI Paraphraser
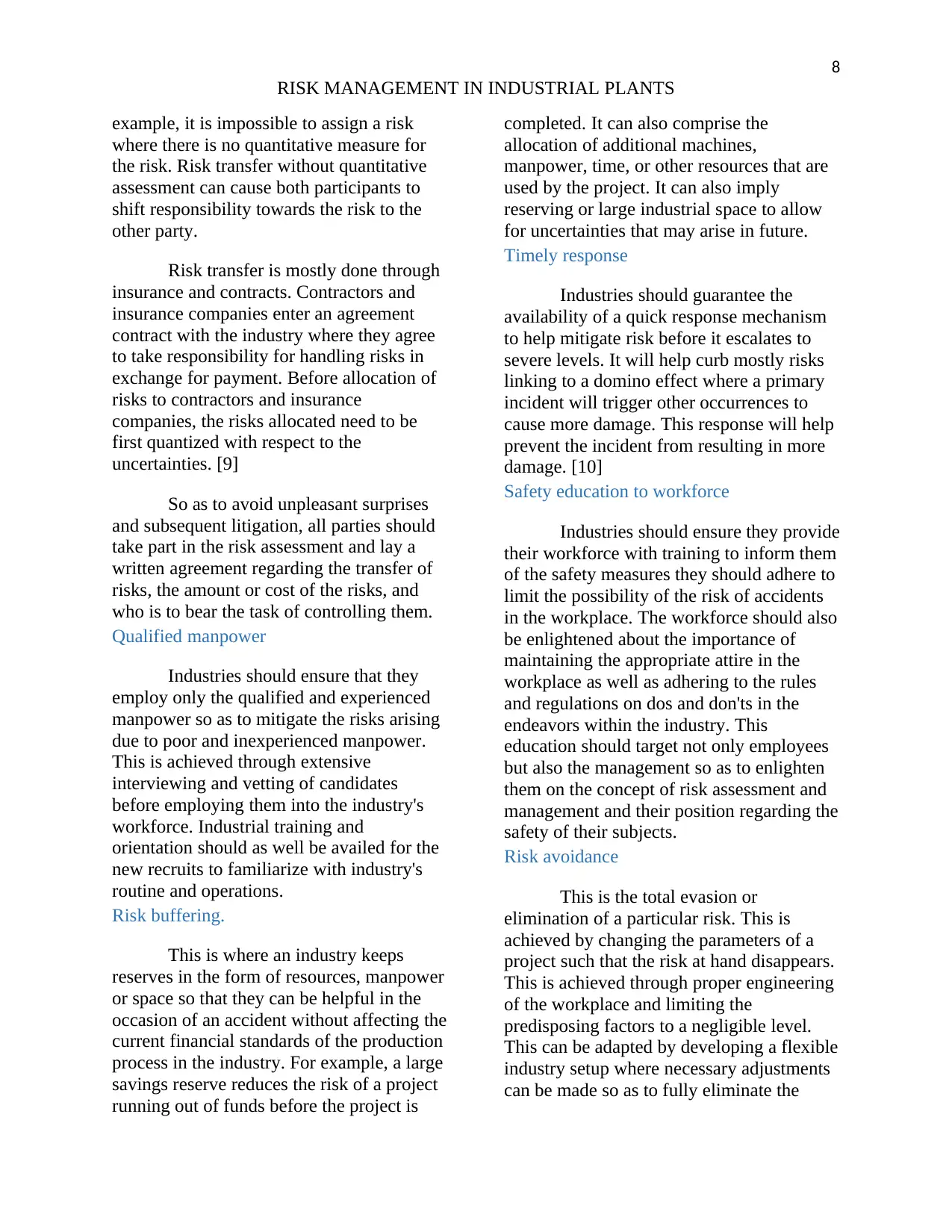
8
RISK MANAGEMENT IN INDUSTRIAL PLANTS
example, it is impossible to assign a risk
where there is no quantitative measure for
the risk. Risk transfer without quantitative
assessment can cause both participants to
shift responsibility towards the risk to the
other party.
Risk transfer is mostly done through
insurance and contracts. Contractors and
insurance companies enter an agreement
contract with the industry where they agree
to take responsibility for handling risks in
exchange for payment. Before allocation of
risks to contractors and insurance
companies, the risks allocated need to be
first quantized with respect to the
uncertainties. [9]
So as to avoid unpleasant surprises
and subsequent litigation, all parties should
take part in the risk assessment and lay a
written agreement regarding the transfer of
risks, the amount or cost of the risks, and
who is to bear the task of controlling them.
Qualified manpower
Industries should ensure that they
employ only the qualified and experienced
manpower so as to mitigate the risks arising
due to poor and inexperienced manpower.
This is achieved through extensive
interviewing and vetting of candidates
before employing them into the industry's
workforce. Industrial training and
orientation should as well be availed for the
new recruits to familiarize with industry's
routine and operations.
Risk buffering.
This is where an industry keeps
reserves in the form of resources, manpower
or space so that they can be helpful in the
occasion of an accident without affecting the
current financial standards of the production
process in the industry. For example, a large
savings reserve reduces the risk of a project
running out of funds before the project is
completed. It can also comprise the
allocation of additional machines,
manpower, time, or other resources that are
used by the project. It can also imply
reserving or large industrial space to allow
for uncertainties that may arise in future.
Timely response
Industries should guarantee the
availability of a quick response mechanism
to help mitigate risk before it escalates to
severe levels. It will help curb mostly risks
linking to a domino effect where a primary
incident will trigger other occurrences to
cause more damage. This response will help
prevent the incident from resulting in more
damage. [10]
Safety education to workforce
Industries should ensure they provide
their workforce with training to inform them
of the safety measures they should adhere to
limit the possibility of the risk of accidents
in the workplace. The workforce should also
be enlightened about the importance of
maintaining the appropriate attire in the
workplace as well as adhering to the rules
and regulations on dos and don'ts in the
endeavors within the industry. This
education should target not only employees
but also the management so as to enlighten
them on the concept of risk assessment and
management and their position regarding the
safety of their subjects.
Risk avoidance
This is the total evasion or
elimination of a particular risk. This is
achieved by changing the parameters of a
project such that the risk at hand disappears.
This is achieved through proper engineering
of the workplace and limiting the
predisposing factors to a negligible level.
This can be adapted by developing a flexible
industry setup where necessary adjustments
can be made so as to fully eliminate the
RISK MANAGEMENT IN INDUSTRIAL PLANTS
example, it is impossible to assign a risk
where there is no quantitative measure for
the risk. Risk transfer without quantitative
assessment can cause both participants to
shift responsibility towards the risk to the
other party.
Risk transfer is mostly done through
insurance and contracts. Contractors and
insurance companies enter an agreement
contract with the industry where they agree
to take responsibility for handling risks in
exchange for payment. Before allocation of
risks to contractors and insurance
companies, the risks allocated need to be
first quantized with respect to the
uncertainties. [9]
So as to avoid unpleasant surprises
and subsequent litigation, all parties should
take part in the risk assessment and lay a
written agreement regarding the transfer of
risks, the amount or cost of the risks, and
who is to bear the task of controlling them.
Qualified manpower
Industries should ensure that they
employ only the qualified and experienced
manpower so as to mitigate the risks arising
due to poor and inexperienced manpower.
This is achieved through extensive
interviewing and vetting of candidates
before employing them into the industry's
workforce. Industrial training and
orientation should as well be availed for the
new recruits to familiarize with industry's
routine and operations.
Risk buffering.
This is where an industry keeps
reserves in the form of resources, manpower
or space so that they can be helpful in the
occasion of an accident without affecting the
current financial standards of the production
process in the industry. For example, a large
savings reserve reduces the risk of a project
running out of funds before the project is
completed. It can also comprise the
allocation of additional machines,
manpower, time, or other resources that are
used by the project. It can also imply
reserving or large industrial space to allow
for uncertainties that may arise in future.
Timely response
Industries should guarantee the
availability of a quick response mechanism
to help mitigate risk before it escalates to
severe levels. It will help curb mostly risks
linking to a domino effect where a primary
incident will trigger other occurrences to
cause more damage. This response will help
prevent the incident from resulting in more
damage. [10]
Safety education to workforce
Industries should ensure they provide
their workforce with training to inform them
of the safety measures they should adhere to
limit the possibility of the risk of accidents
in the workplace. The workforce should also
be enlightened about the importance of
maintaining the appropriate attire in the
workplace as well as adhering to the rules
and regulations on dos and don'ts in the
endeavors within the industry. This
education should target not only employees
but also the management so as to enlighten
them on the concept of risk assessment and
management and their position regarding the
safety of their subjects.
Risk avoidance
This is the total evasion or
elimination of a particular risk. This is
achieved by changing the parameters of a
project such that the risk at hand disappears.
This is achieved through proper engineering
of the workplace and limiting the
predisposing factors to a negligible level.
This can be adapted by developing a flexible
industry setup where necessary adjustments
can be made so as to fully eliminate the
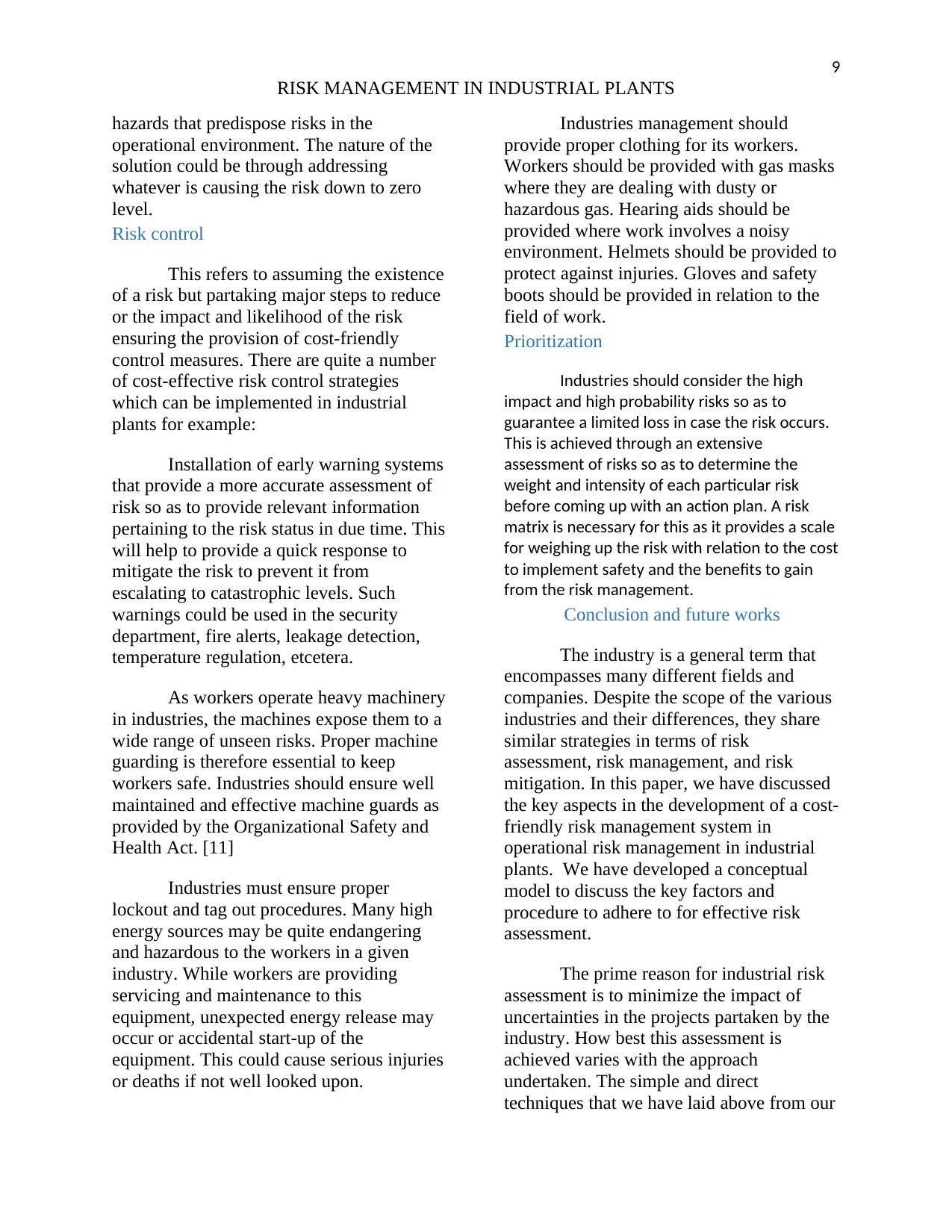
9
RISK MANAGEMENT IN INDUSTRIAL PLANTS
hazards that predispose risks in the
operational environment. The nature of the
solution could be through addressing
whatever is causing the risk down to zero
level.
Risk control
This refers to assuming the existence
of a risk but partaking major steps to reduce
or the impact and likelihood of the risk
ensuring the provision of cost-friendly
control measures. There are quite a number
of cost-effective risk control strategies
which can be implemented in industrial
plants for example:
Installation of early warning systems
that provide a more accurate assessment of
risk so as to provide relevant information
pertaining to the risk status in due time. This
will help to provide a quick response to
mitigate the risk to prevent it from
escalating to catastrophic levels. Such
warnings could be used in the security
department, fire alerts, leakage detection,
temperature regulation, etcetera.
As workers operate heavy machinery
in industries, the machines expose them to a
wide range of unseen risks. Proper machine
guarding is therefore essential to keep
workers safe. Industries should ensure well
maintained and effective machine guards as
provided by the Organizational Safety and
Health Act. [11]
Industries must ensure proper
lockout and tag out procedures. Many high
energy sources may be quite endangering
and hazardous to the workers in a given
industry. While workers are providing
servicing and maintenance to this
equipment, unexpected energy release may
occur or accidental start-up of the
equipment. This could cause serious injuries
or deaths if not well looked upon.
Industries management should
provide proper clothing for its workers.
Workers should be provided with gas masks
where they are dealing with dusty or
hazardous gas. Hearing aids should be
provided where work involves a noisy
environment. Helmets should be provided to
protect against injuries. Gloves and safety
boots should be provided in relation to the
field of work.
Prioritization
Industries should consider the high
impact and high probability risks so as to
guarantee a limited loss in case the risk occurs.
This is achieved through an extensive
assessment of risks so as to determine the
weight and intensity of each particular risk
before coming up with an action plan. A risk
matrix is necessary for this as it provides a scale
for weighing up the risk with relation to the cost
to implement safety and the benefits to gain
from the risk management.
Conclusion and future works
The industry is a general term that
encompasses many different fields and
companies. Despite the scope of the various
industries and their differences, they share
similar strategies in terms of risk
assessment, risk management, and risk
mitigation. In this paper, we have discussed
the key aspects in the development of a cost-
friendly risk management system in
operational risk management in industrial
plants. We have developed a conceptual
model to discuss the key factors and
procedure to adhere to for effective risk
assessment.
The prime reason for industrial risk
assessment is to minimize the impact of
uncertainties in the projects partaken by the
industry. How best this assessment is
achieved varies with the approach
undertaken. The simple and direct
techniques that we have laid above from our
RISK MANAGEMENT IN INDUSTRIAL PLANTS
hazards that predispose risks in the
operational environment. The nature of the
solution could be through addressing
whatever is causing the risk down to zero
level.
Risk control
This refers to assuming the existence
of a risk but partaking major steps to reduce
or the impact and likelihood of the risk
ensuring the provision of cost-friendly
control measures. There are quite a number
of cost-effective risk control strategies
which can be implemented in industrial
plants for example:
Installation of early warning systems
that provide a more accurate assessment of
risk so as to provide relevant information
pertaining to the risk status in due time. This
will help to provide a quick response to
mitigate the risk to prevent it from
escalating to catastrophic levels. Such
warnings could be used in the security
department, fire alerts, leakage detection,
temperature regulation, etcetera.
As workers operate heavy machinery
in industries, the machines expose them to a
wide range of unseen risks. Proper machine
guarding is therefore essential to keep
workers safe. Industries should ensure well
maintained and effective machine guards as
provided by the Organizational Safety and
Health Act. [11]
Industries must ensure proper
lockout and tag out procedures. Many high
energy sources may be quite endangering
and hazardous to the workers in a given
industry. While workers are providing
servicing and maintenance to this
equipment, unexpected energy release may
occur or accidental start-up of the
equipment. This could cause serious injuries
or deaths if not well looked upon.
Industries management should
provide proper clothing for its workers.
Workers should be provided with gas masks
where they are dealing with dusty or
hazardous gas. Hearing aids should be
provided where work involves a noisy
environment. Helmets should be provided to
protect against injuries. Gloves and safety
boots should be provided in relation to the
field of work.
Prioritization
Industries should consider the high
impact and high probability risks so as to
guarantee a limited loss in case the risk occurs.
This is achieved through an extensive
assessment of risks so as to determine the
weight and intensity of each particular risk
before coming up with an action plan. A risk
matrix is necessary for this as it provides a scale
for weighing up the risk with relation to the cost
to implement safety and the benefits to gain
from the risk management.
Conclusion and future works
The industry is a general term that
encompasses many different fields and
companies. Despite the scope of the various
industries and their differences, they share
similar strategies in terms of risk
assessment, risk management, and risk
mitigation. In this paper, we have discussed
the key aspects in the development of a cost-
friendly risk management system in
operational risk management in industrial
plants. We have developed a conceptual
model to discuss the key factors and
procedure to adhere to for effective risk
assessment.
The prime reason for industrial risk
assessment is to minimize the impact of
uncertainties in the projects partaken by the
industry. How best this assessment is
achieved varies with the approach
undertaken. The simple and direct
techniques that we have laid above from our
⊘ This is a preview!⊘
Do you want full access?
Subscribe today to unlock all pages.

Trusted by 1+ million students worldwide
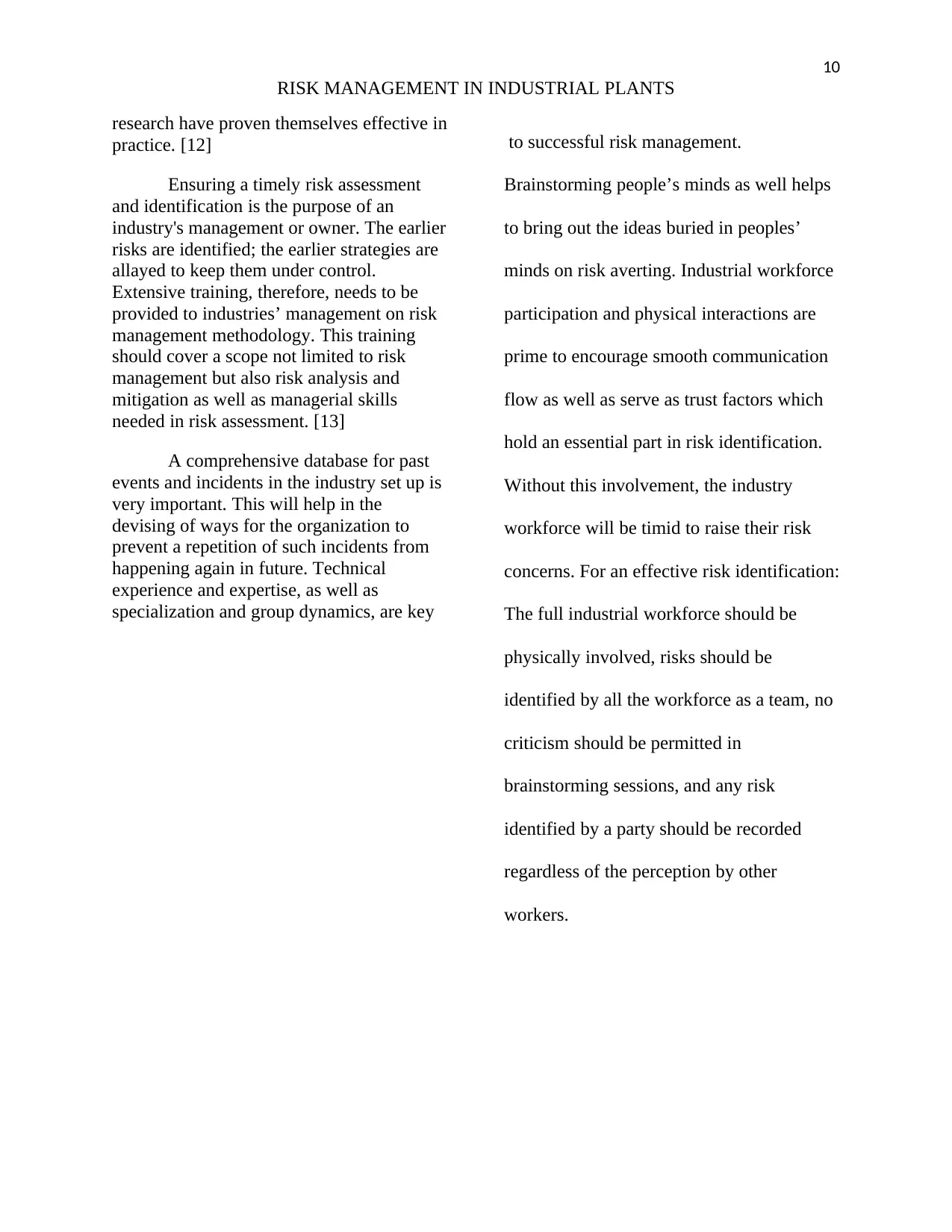
10
RISK MANAGEMENT IN INDUSTRIAL PLANTS
research have proven themselves effective in
practice. [12]
Ensuring a timely risk assessment
and identification is the purpose of an
industry's management or owner. The earlier
risks are identified; the earlier strategies are
allayed to keep them under control.
Extensive training, therefore, needs to be
provided to industries’ management on risk
management methodology. This training
should cover a scope not limited to risk
management but also risk analysis and
mitigation as well as managerial skills
needed in risk assessment. [13]
A comprehensive database for past
events and incidents in the industry set up is
very important. This will help in the
devising of ways for the organization to
prevent a repetition of such incidents from
happening again in future. Technical
experience and expertise, as well as
specialization and group dynamics, are key
to successful risk management.
Brainstorming people’s minds as well helps
to bring out the ideas buried in peoples’
minds on risk averting. Industrial workforce
participation and physical interactions are
prime to encourage smooth communication
flow as well as serve as trust factors which
hold an essential part in risk identification.
Without this involvement, the industry
workforce will be timid to raise their risk
concerns. For an effective risk identification:
The full industrial workforce should be
physically involved, risks should be
identified by all the workforce as a team, no
criticism should be permitted in
brainstorming sessions, and any risk
identified by a party should be recorded
regardless of the perception by other
workers.
RISK MANAGEMENT IN INDUSTRIAL PLANTS
research have proven themselves effective in
practice. [12]
Ensuring a timely risk assessment
and identification is the purpose of an
industry's management or owner. The earlier
risks are identified; the earlier strategies are
allayed to keep them under control.
Extensive training, therefore, needs to be
provided to industries’ management on risk
management methodology. This training
should cover a scope not limited to risk
management but also risk analysis and
mitigation as well as managerial skills
needed in risk assessment. [13]
A comprehensive database for past
events and incidents in the industry set up is
very important. This will help in the
devising of ways for the organization to
prevent a repetition of such incidents from
happening again in future. Technical
experience and expertise, as well as
specialization and group dynamics, are key
to successful risk management.
Brainstorming people’s minds as well helps
to bring out the ideas buried in peoples’
minds on risk averting. Industrial workforce
participation and physical interactions are
prime to encourage smooth communication
flow as well as serve as trust factors which
hold an essential part in risk identification.
Without this involvement, the industry
workforce will be timid to raise their risk
concerns. For an effective risk identification:
The full industrial workforce should be
physically involved, risks should be
identified by all the workforce as a team, no
criticism should be permitted in
brainstorming sessions, and any risk
identified by a party should be recorded
regardless of the perception by other
workers.
Paraphrase This Document
Need a fresh take? Get an instant paraphrase of this document with our AI Paraphraser
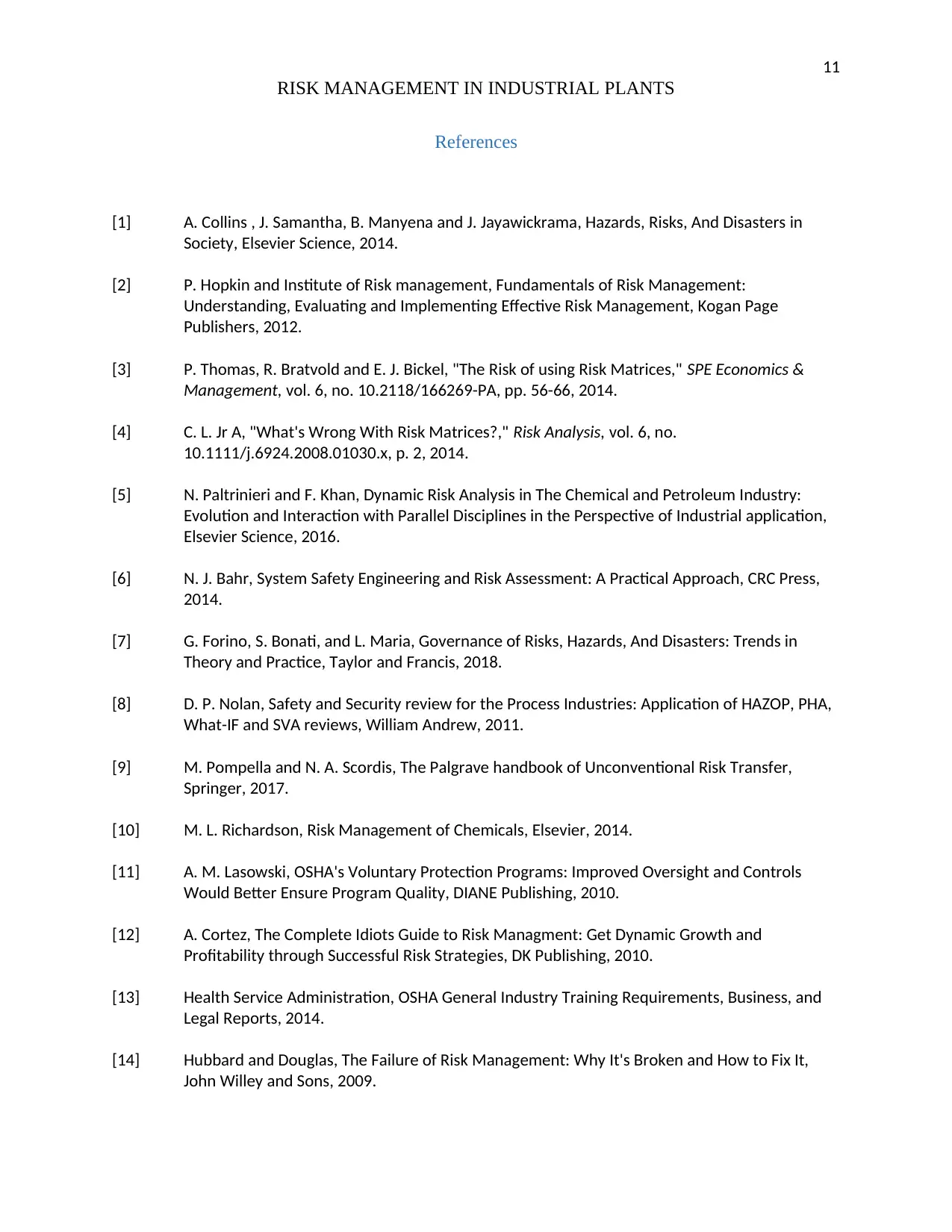
11
RISK MANAGEMENT IN INDUSTRIAL PLANTS
References
[1] A. Collins , J. Samantha, B. Manyena and J. Jayawickrama, Hazards, Risks, And Disasters in
Society, Elsevier Science, 2014.
[2] P. Hopkin and Institute of Risk management, Fundamentals of Risk Management:
Understanding, Evaluating and Implementing Effective Risk Management, Kogan Page
Publishers, 2012.
[3] P. Thomas, R. Bratvold and E. J. Bickel, "The Risk of using Risk Matrices," SPE Economics &
Management, vol. 6, no. 10.2118/166269-PA, pp. 56-66, 2014.
[4] C. L. Jr A, "What's Wrong With Risk Matrices?," Risk Analysis, vol. 6, no.
10.1111/j.6924.2008.01030.x, p. 2, 2014.
[5] N. Paltrinieri and F. Khan, Dynamic Risk Analysis in The Chemical and Petroleum Industry:
Evolution and Interaction with Parallel Disciplines in the Perspective of Industrial application,
Elsevier Science, 2016.
[6] N. J. Bahr, System Safety Engineering and Risk Assessment: A Practical Approach, CRC Press,
2014.
[7] G. Forino, S. Bonati, and L. Maria, Governance of Risks, Hazards, And Disasters: Trends in
Theory and Practice, Taylor and Francis, 2018.
[8] D. P. Nolan, Safety and Security review for the Process Industries: Application of HAZOP, PHA,
What-IF and SVA reviews, William Andrew, 2011.
[9] M. Pompella and N. A. Scordis, The Palgrave handbook of Unconventional Risk Transfer,
Springer, 2017.
[10] M. L. Richardson, Risk Management of Chemicals, Elsevier, 2014.
[11] A. M. Lasowski, OSHA's Voluntary Protection Programs: Improved Oversight and Controls
Would Better Ensure Program Quality, DIANE Publishing, 2010.
[12] A. Cortez, The Complete Idiots Guide to Risk Managment: Get Dynamic Growth and
Profitability through Successful Risk Strategies, DK Publishing, 2010.
[13] Health Service Administration, OSHA General Industry Training Requirements, Business, and
Legal Reports, 2014.
[14] Hubbard and Douglas, The Failure of Risk Management: Why It's Broken and How to Fix It,
John Willey and Sons, 2009.
RISK MANAGEMENT IN INDUSTRIAL PLANTS
References
[1] A. Collins , J. Samantha, B. Manyena and J. Jayawickrama, Hazards, Risks, And Disasters in
Society, Elsevier Science, 2014.
[2] P. Hopkin and Institute of Risk management, Fundamentals of Risk Management:
Understanding, Evaluating and Implementing Effective Risk Management, Kogan Page
Publishers, 2012.
[3] P. Thomas, R. Bratvold and E. J. Bickel, "The Risk of using Risk Matrices," SPE Economics &
Management, vol. 6, no. 10.2118/166269-PA, pp. 56-66, 2014.
[4] C. L. Jr A, "What's Wrong With Risk Matrices?," Risk Analysis, vol. 6, no.
10.1111/j.6924.2008.01030.x, p. 2, 2014.
[5] N. Paltrinieri and F. Khan, Dynamic Risk Analysis in The Chemical and Petroleum Industry:
Evolution and Interaction with Parallel Disciplines in the Perspective of Industrial application,
Elsevier Science, 2016.
[6] N. J. Bahr, System Safety Engineering and Risk Assessment: A Practical Approach, CRC Press,
2014.
[7] G. Forino, S. Bonati, and L. Maria, Governance of Risks, Hazards, And Disasters: Trends in
Theory and Practice, Taylor and Francis, 2018.
[8] D. P. Nolan, Safety and Security review for the Process Industries: Application of HAZOP, PHA,
What-IF and SVA reviews, William Andrew, 2011.
[9] M. Pompella and N. A. Scordis, The Palgrave handbook of Unconventional Risk Transfer,
Springer, 2017.
[10] M. L. Richardson, Risk Management of Chemicals, Elsevier, 2014.
[11] A. M. Lasowski, OSHA's Voluntary Protection Programs: Improved Oversight and Controls
Would Better Ensure Program Quality, DIANE Publishing, 2010.
[12] A. Cortez, The Complete Idiots Guide to Risk Managment: Get Dynamic Growth and
Profitability through Successful Risk Strategies, DK Publishing, 2010.
[13] Health Service Administration, OSHA General Industry Training Requirements, Business, and
Legal Reports, 2014.
[14] Hubbard and Douglas, The Failure of Risk Management: Why It's Broken and How to Fix It,
John Willey and Sons, 2009.
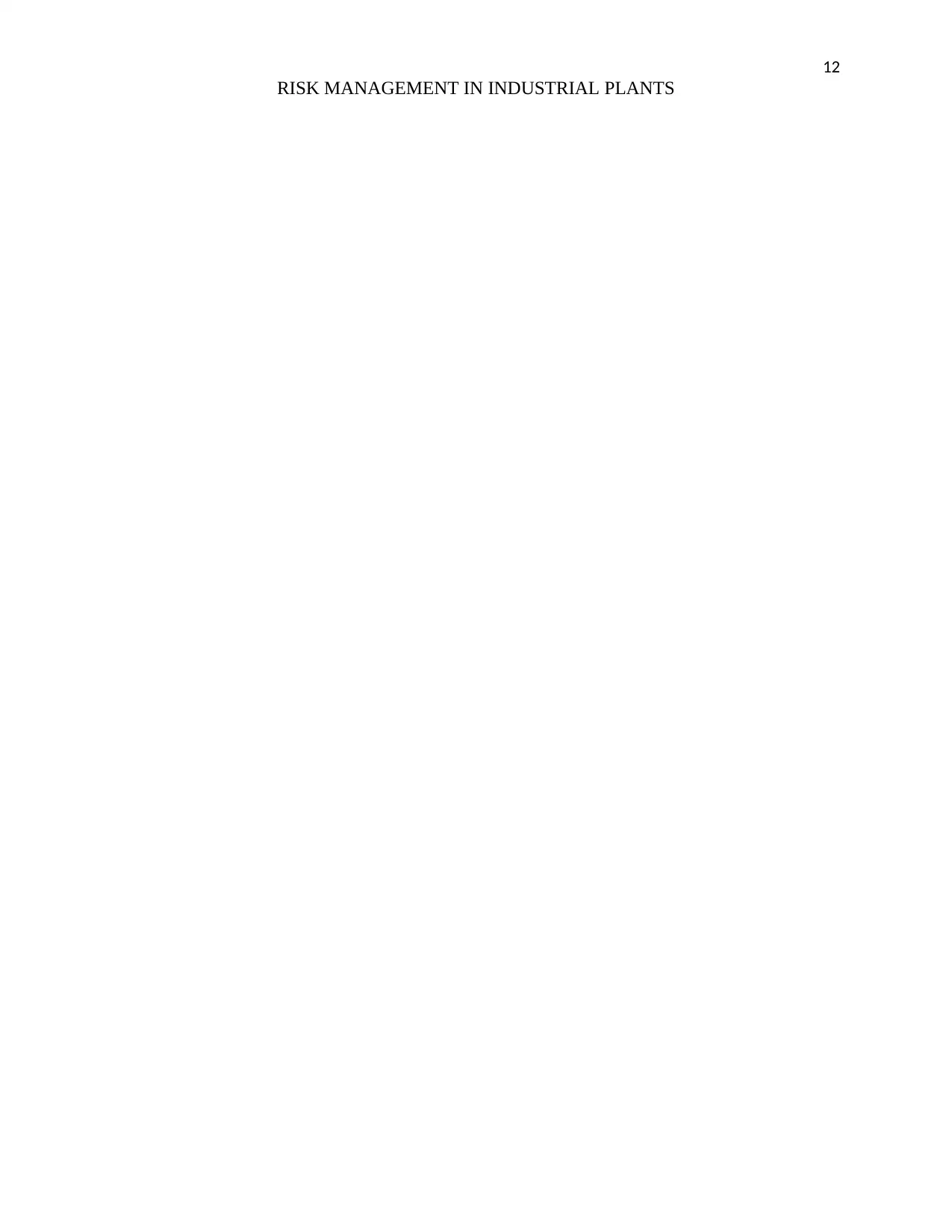
12
RISK MANAGEMENT IN INDUSTRIAL PLANTS
RISK MANAGEMENT IN INDUSTRIAL PLANTS
⊘ This is a preview!⊘
Do you want full access?
Subscribe today to unlock all pages.

Trusted by 1+ million students worldwide
1 out of 12
Related Documents

Your All-in-One AI-Powered Toolkit for Academic Success.
+13062052269
info@desklib.com
Available 24*7 on WhatsApp / Email
Unlock your academic potential
© 2024 | Zucol Services PVT LTD | All rights reserved.