Inlet Plenum: Importance and Research Findings
VerifiedAdded on 2023/06/12
|21
|6463
|166
AI Summary
This research paper focuses on the importance of inlet plenum in engines and its ability to determine the transport scenario of the fuel/air mixture that gets in the engine cylinders. The paper also discusses various research findings related to inlet plenum.
Contribute Materials
Your contribution can guide someone’s learning journey. Share your
documents today.
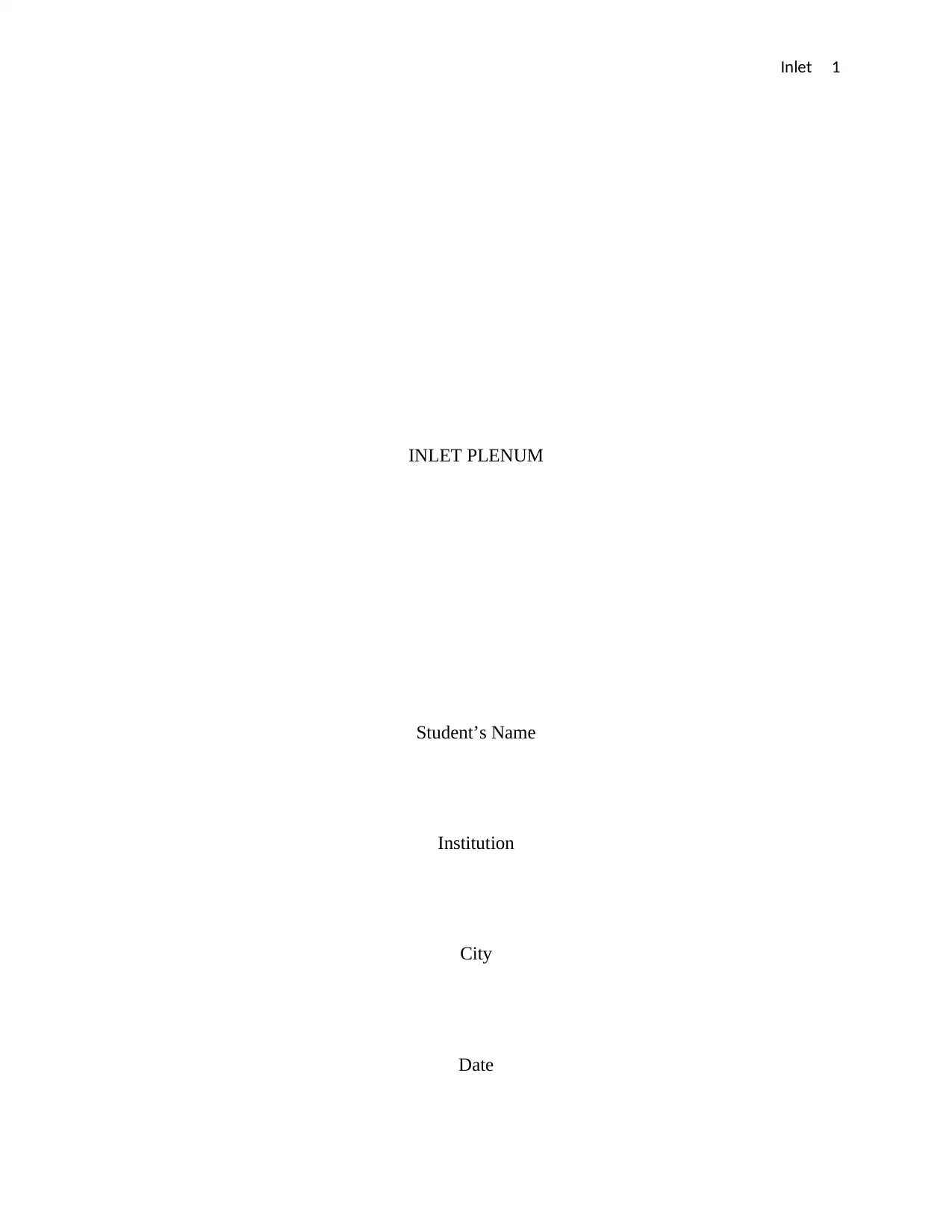
Inlet 1
INLET PLENUM
Student’s Name
Institution
City
Date
INLET PLENUM
Student’s Name
Institution
City
Date
Secure Best Marks with AI Grader
Need help grading? Try our AI Grader for instant feedback on your assignments.
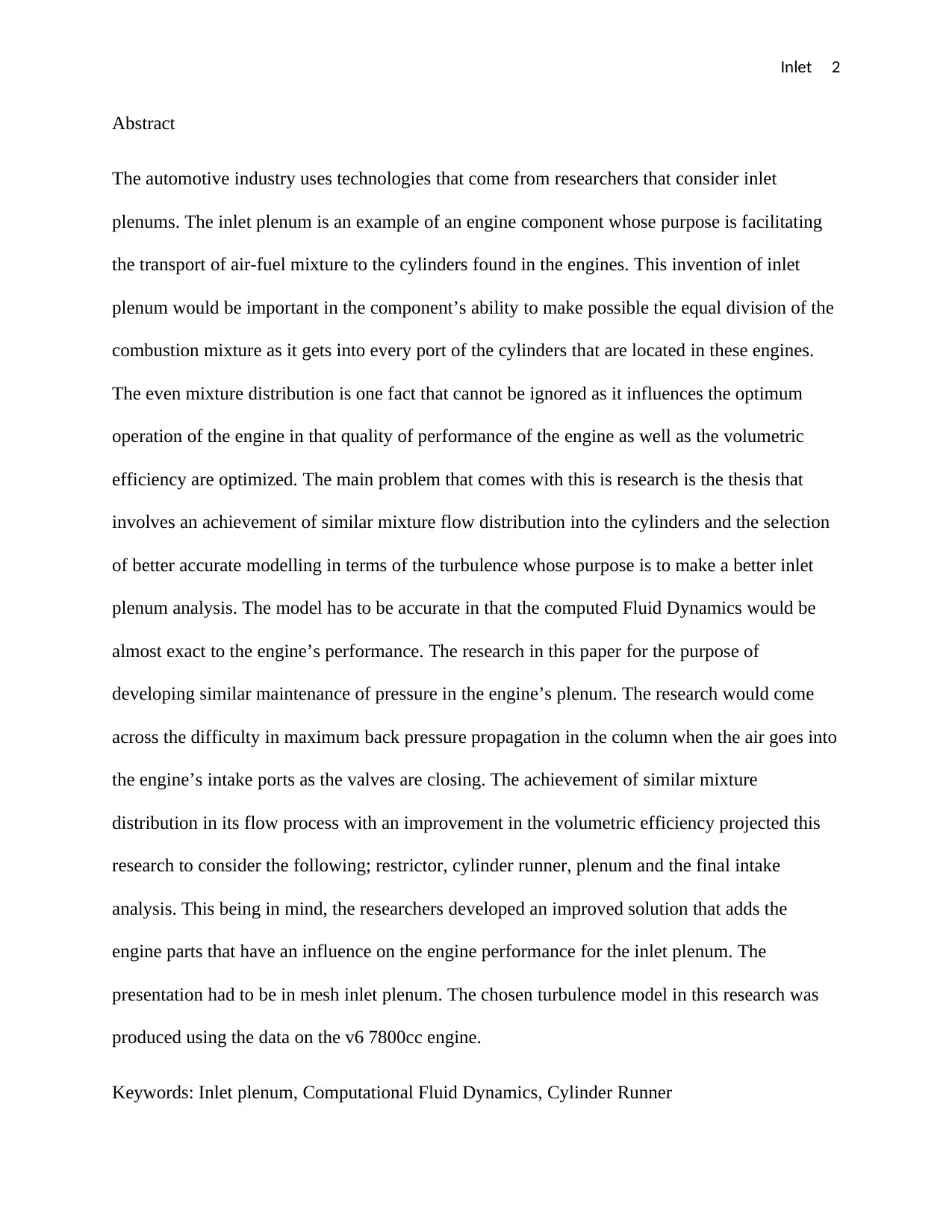
Inlet 2
Abstract
The automotive industry uses technologies that come from researchers that consider inlet
plenums. The inlet plenum is an example of an engine component whose purpose is facilitating
the transport of air-fuel mixture to the cylinders found in the engines. This invention of inlet
plenum would be important in the component’s ability to make possible the equal division of the
combustion mixture as it gets into every port of the cylinders that are located in these engines.
The even mixture distribution is one fact that cannot be ignored as it influences the optimum
operation of the engine in that quality of performance of the engine as well as the volumetric
efficiency are optimized. The main problem that comes with this is research is the thesis that
involves an achievement of similar mixture flow distribution into the cylinders and the selection
of better accurate modelling in terms of the turbulence whose purpose is to make a better inlet
plenum analysis. The model has to be accurate in that the computed Fluid Dynamics would be
almost exact to the engine’s performance. The research in this paper for the purpose of
developing similar maintenance of pressure in the engine’s plenum. The research would come
across the difficulty in maximum back pressure propagation in the column when the air goes into
the engine’s intake ports as the valves are closing. The achievement of similar mixture
distribution in its flow process with an improvement in the volumetric efficiency projected this
research to consider the following; restrictor, cylinder runner, plenum and the final intake
analysis. This being in mind, the researchers developed an improved solution that adds the
engine parts that have an influence on the engine performance for the inlet plenum. The
presentation had to be in mesh inlet plenum. The chosen turbulence model in this research was
produced using the data on the v6 7800cc engine.
Keywords: Inlet plenum, Computational Fluid Dynamics, Cylinder Runner
Abstract
The automotive industry uses technologies that come from researchers that consider inlet
plenums. The inlet plenum is an example of an engine component whose purpose is facilitating
the transport of air-fuel mixture to the cylinders found in the engines. This invention of inlet
plenum would be important in the component’s ability to make possible the equal division of the
combustion mixture as it gets into every port of the cylinders that are located in these engines.
The even mixture distribution is one fact that cannot be ignored as it influences the optimum
operation of the engine in that quality of performance of the engine as well as the volumetric
efficiency are optimized. The main problem that comes with this is research is the thesis that
involves an achievement of similar mixture flow distribution into the cylinders and the selection
of better accurate modelling in terms of the turbulence whose purpose is to make a better inlet
plenum analysis. The model has to be accurate in that the computed Fluid Dynamics would be
almost exact to the engine’s performance. The research in this paper for the purpose of
developing similar maintenance of pressure in the engine’s plenum. The research would come
across the difficulty in maximum back pressure propagation in the column when the air goes into
the engine’s intake ports as the valves are closing. The achievement of similar mixture
distribution in its flow process with an improvement in the volumetric efficiency projected this
research to consider the following; restrictor, cylinder runner, plenum and the final intake
analysis. This being in mind, the researchers developed an improved solution that adds the
engine parts that have an influence on the engine performance for the inlet plenum. The
presentation had to be in mesh inlet plenum. The chosen turbulence model in this research was
produced using the data on the v6 7800cc engine.
Keywords: Inlet plenum, Computational Fluid Dynamics, Cylinder Runner
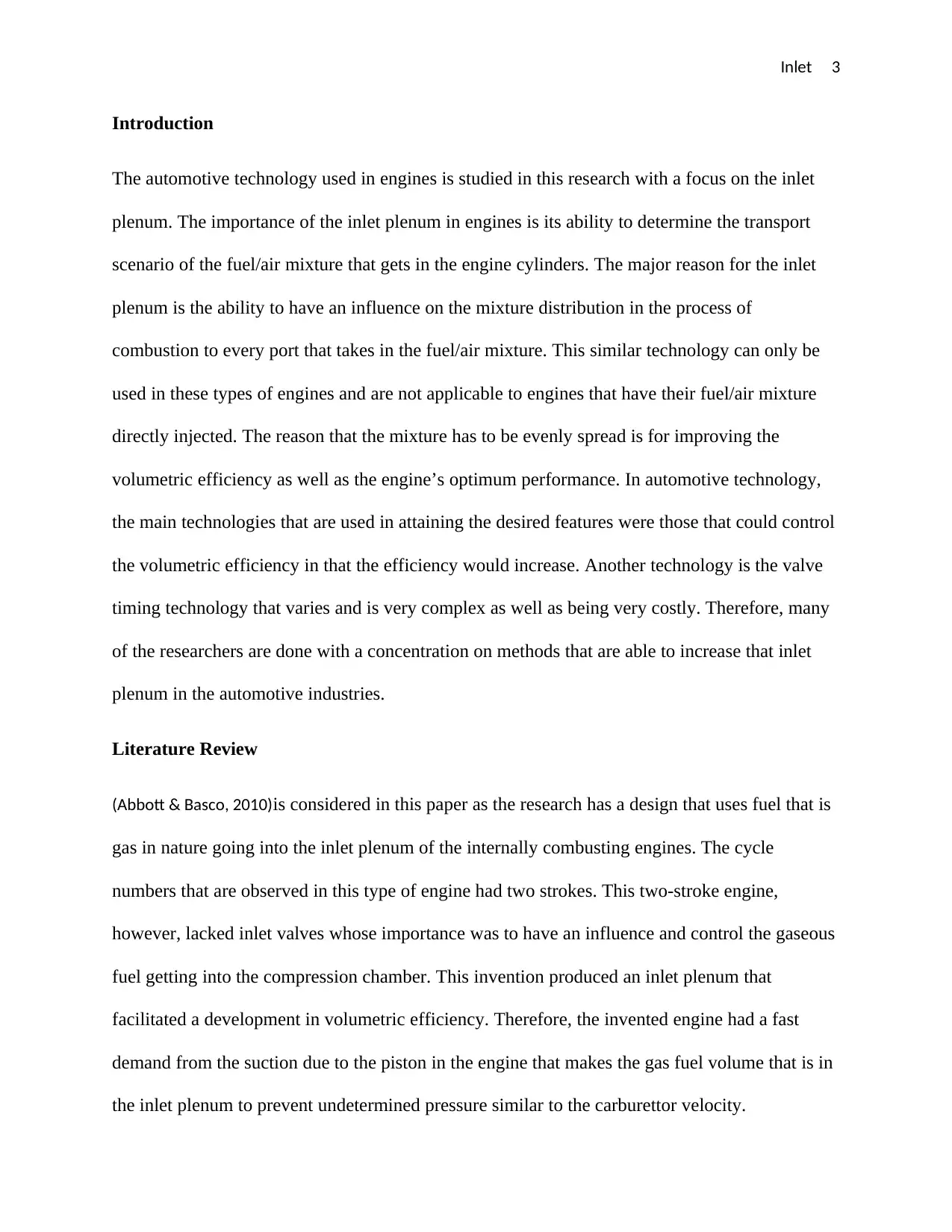
Inlet 3
Introduction
The automotive technology used in engines is studied in this research with a focus on the inlet
plenum. The importance of the inlet plenum in engines is its ability to determine the transport
scenario of the fuel/air mixture that gets in the engine cylinders. The major reason for the inlet
plenum is the ability to have an influence on the mixture distribution in the process of
combustion to every port that takes in the fuel/air mixture. This similar technology can only be
used in these types of engines and are not applicable to engines that have their fuel/air mixture
directly injected. The reason that the mixture has to be evenly spread is for improving the
volumetric efficiency as well as the engine’s optimum performance. In automotive technology,
the main technologies that are used in attaining the desired features were those that could control
the volumetric efficiency in that the efficiency would increase. Another technology is the valve
timing technology that varies and is very complex as well as being very costly. Therefore, many
of the researchers are done with a concentration on methods that are able to increase that inlet
plenum in the automotive industries.
Literature Review
(Abbott & Basco, 2010)is considered in this paper as the research has a design that uses fuel that is
gas in nature going into the inlet plenum of the internally combusting engines. The cycle
numbers that are observed in this type of engine had two strokes. This two-stroke engine,
however, lacked inlet valves whose importance was to have an influence and control the gaseous
fuel getting into the compression chamber. This invention produced an inlet plenum that
facilitated a development in volumetric efficiency. Therefore, the invented engine had a fast
demand from the suction due to the piston in the engine that makes the gas fuel volume that is in
the inlet plenum to prevent undetermined pressure similar to the carburettor velocity.
Introduction
The automotive technology used in engines is studied in this research with a focus on the inlet
plenum. The importance of the inlet plenum in engines is its ability to determine the transport
scenario of the fuel/air mixture that gets in the engine cylinders. The major reason for the inlet
plenum is the ability to have an influence on the mixture distribution in the process of
combustion to every port that takes in the fuel/air mixture. This similar technology can only be
used in these types of engines and are not applicable to engines that have their fuel/air mixture
directly injected. The reason that the mixture has to be evenly spread is for improving the
volumetric efficiency as well as the engine’s optimum performance. In automotive technology,
the main technologies that are used in attaining the desired features were those that could control
the volumetric efficiency in that the efficiency would increase. Another technology is the valve
timing technology that varies and is very complex as well as being very costly. Therefore, many
of the researchers are done with a concentration on methods that are able to increase that inlet
plenum in the automotive industries.
Literature Review
(Abbott & Basco, 2010)is considered in this paper as the research has a design that uses fuel that is
gas in nature going into the inlet plenum of the internally combusting engines. The cycle
numbers that are observed in this type of engine had two strokes. This two-stroke engine,
however, lacked inlet valves whose importance was to have an influence and control the gaseous
fuel getting into the compression chamber. This invention produced an inlet plenum that
facilitated a development in volumetric efficiency. Therefore, the invented engine had a fast
demand from the suction due to the piston in the engine that makes the gas fuel volume that is in
the inlet plenum to prevent undetermined pressure similar to the carburettor velocity.
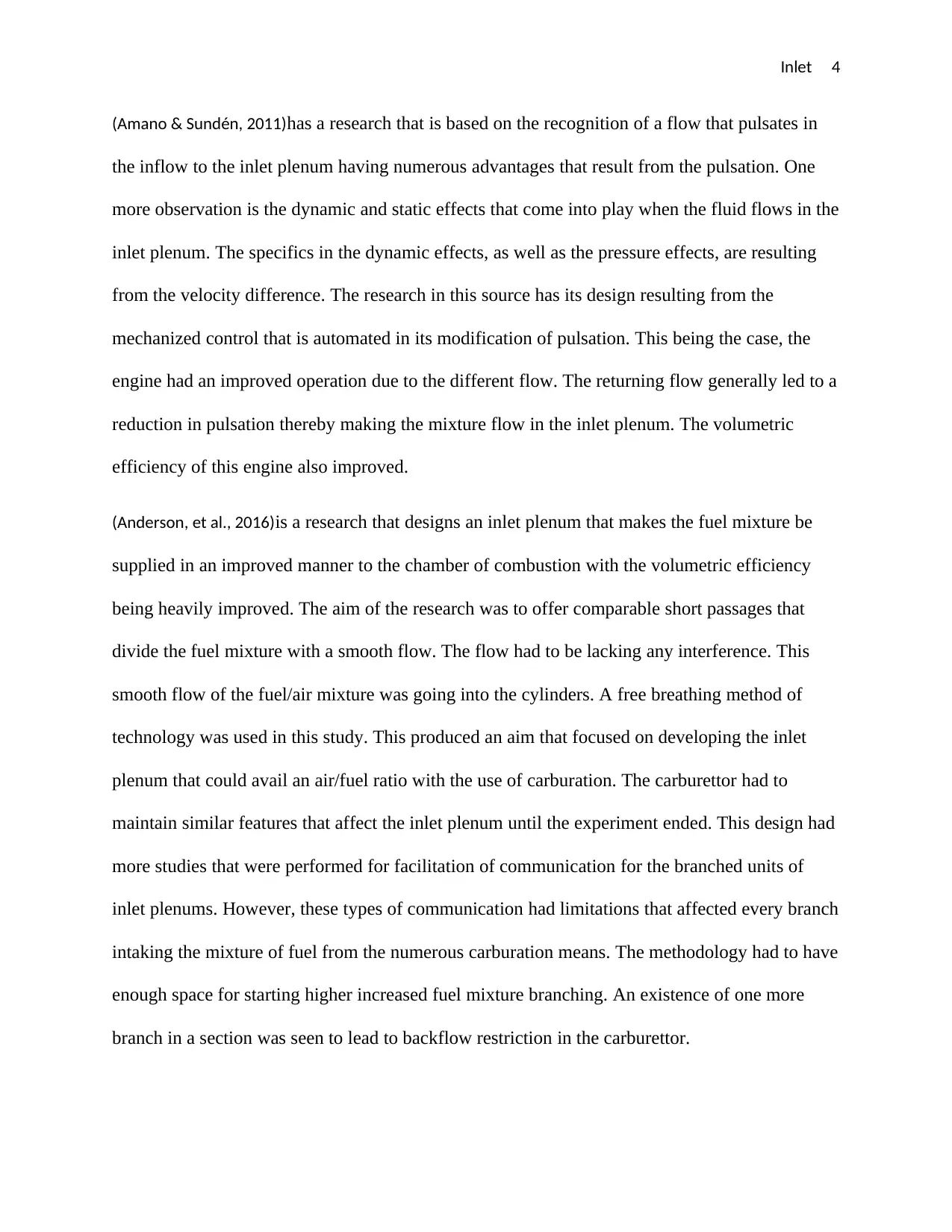
Inlet 4
(Amano & Sundén, 2011)has a research that is based on the recognition of a flow that pulsates in
the inflow to the inlet plenum having numerous advantages that result from the pulsation. One
more observation is the dynamic and static effects that come into play when the fluid flows in the
inlet plenum. The specifics in the dynamic effects, as well as the pressure effects, are resulting
from the velocity difference. The research in this source has its design resulting from the
mechanized control that is automated in its modification of pulsation. This being the case, the
engine had an improved operation due to the different flow. The returning flow generally led to a
reduction in pulsation thereby making the mixture flow in the inlet plenum. The volumetric
efficiency of this engine also improved.
(Anderson, et al., 2016)is a research that designs an inlet plenum that makes the fuel mixture be
supplied in an improved manner to the chamber of combustion with the volumetric efficiency
being heavily improved. The aim of the research was to offer comparable short passages that
divide the fuel mixture with a smooth flow. The flow had to be lacking any interference. This
smooth flow of the fuel/air mixture was going into the cylinders. A free breathing method of
technology was used in this study. This produced an aim that focused on developing the inlet
plenum that could avail an air/fuel ratio with the use of carburation. The carburettor had to
maintain similar features that affect the inlet plenum until the experiment ended. This design had
more studies that were performed for facilitation of communication for the branched units of
inlet plenums. However, these types of communication had limitations that affected every branch
intaking the mixture of fuel from the numerous carburation means. The methodology had to have
enough space for starting higher increased fuel mixture branching. An existence of one more
branch in a section was seen to lead to backflow restriction in the carburettor.
(Amano & Sundén, 2011)has a research that is based on the recognition of a flow that pulsates in
the inflow to the inlet plenum having numerous advantages that result from the pulsation. One
more observation is the dynamic and static effects that come into play when the fluid flows in the
inlet plenum. The specifics in the dynamic effects, as well as the pressure effects, are resulting
from the velocity difference. The research in this source has its design resulting from the
mechanized control that is automated in its modification of pulsation. This being the case, the
engine had an improved operation due to the different flow. The returning flow generally led to a
reduction in pulsation thereby making the mixture flow in the inlet plenum. The volumetric
efficiency of this engine also improved.
(Anderson, et al., 2016)is a research that designs an inlet plenum that makes the fuel mixture be
supplied in an improved manner to the chamber of combustion with the volumetric efficiency
being heavily improved. The aim of the research was to offer comparable short passages that
divide the fuel mixture with a smooth flow. The flow had to be lacking any interference. This
smooth flow of the fuel/air mixture was going into the cylinders. A free breathing method of
technology was used in this study. This produced an aim that focused on developing the inlet
plenum that could avail an air/fuel ratio with the use of carburation. The carburettor had to
maintain similar features that affect the inlet plenum until the experiment ended. This design had
more studies that were performed for facilitation of communication for the branched units of
inlet plenums. However, these types of communication had limitations that affected every branch
intaking the mixture of fuel from the numerous carburation means. The methodology had to have
enough space for starting higher increased fuel mixture branching. An existence of one more
branch in a section was seen to lead to backflow restriction in the carburettor.
Secure Best Marks with AI Grader
Need help grading? Try our AI Grader for instant feedback on your assignments.
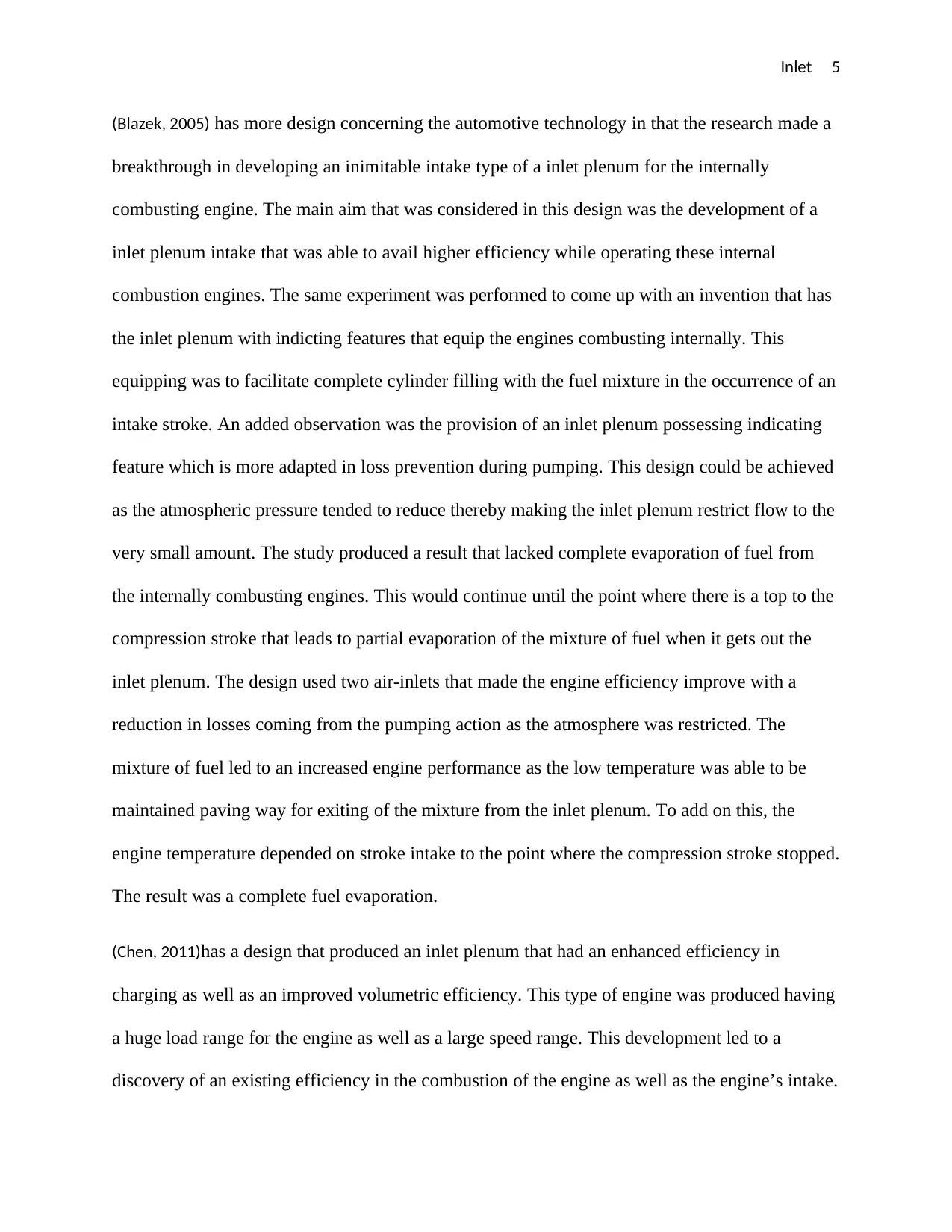
Inlet 5
(Blazek, 2005) has more design concerning the automotive technology in that the research made a
breakthrough in developing an inimitable intake type of a inlet plenum for the internally
combusting engine. The main aim that was considered in this design was the development of a
inlet plenum intake that was able to avail higher efficiency while operating these internal
combustion engines. The same experiment was performed to come up with an invention that has
the inlet plenum with indicting features that equip the engines combusting internally. This
equipping was to facilitate complete cylinder filling with the fuel mixture in the occurrence of an
intake stroke. An added observation was the provision of an inlet plenum possessing indicating
feature which is more adapted in loss prevention during pumping. This design could be achieved
as the atmospheric pressure tended to reduce thereby making the inlet plenum restrict flow to the
very small amount. The study produced a result that lacked complete evaporation of fuel from
the internally combusting engines. This would continue until the point where there is a top to the
compression stroke that leads to partial evaporation of the mixture of fuel when it gets out the
inlet plenum. The design used two air-inlets that made the engine efficiency improve with a
reduction in losses coming from the pumping action as the atmosphere was restricted. The
mixture of fuel led to an increased engine performance as the low temperature was able to be
maintained paving way for exiting of the mixture from the inlet plenum. To add on this, the
engine temperature depended on stroke intake to the point where the compression stroke stopped.
The result was a complete fuel evaporation.
(Chen, 2011)has a design that produced an inlet plenum that had an enhanced efficiency in
charging as well as an improved volumetric efficiency. This type of engine was produced having
a huge load range for the engine as well as a large speed range. This development led to a
discovery of an existing efficiency in the combustion of the engine as well as the engine’s intake.
(Blazek, 2005) has more design concerning the automotive technology in that the research made a
breakthrough in developing an inimitable intake type of a inlet plenum for the internally
combusting engine. The main aim that was considered in this design was the development of a
inlet plenum intake that was able to avail higher efficiency while operating these internal
combustion engines. The same experiment was performed to come up with an invention that has
the inlet plenum with indicting features that equip the engines combusting internally. This
equipping was to facilitate complete cylinder filling with the fuel mixture in the occurrence of an
intake stroke. An added observation was the provision of an inlet plenum possessing indicating
feature which is more adapted in loss prevention during pumping. This design could be achieved
as the atmospheric pressure tended to reduce thereby making the inlet plenum restrict flow to the
very small amount. The study produced a result that lacked complete evaporation of fuel from
the internally combusting engines. This would continue until the point where there is a top to the
compression stroke that leads to partial evaporation of the mixture of fuel when it gets out the
inlet plenum. The design used two air-inlets that made the engine efficiency improve with a
reduction in losses coming from the pumping action as the atmosphere was restricted. The
mixture of fuel led to an increased engine performance as the low temperature was able to be
maintained paving way for exiting of the mixture from the inlet plenum. To add on this, the
engine temperature depended on stroke intake to the point where the compression stroke stopped.
The result was a complete fuel evaporation.
(Chen, 2011)has a design that produced an inlet plenum that had an enhanced efficiency in
charging as well as an improved volumetric efficiency. This type of engine was produced having
a huge load range for the engine as well as a large speed range. This development led to a
discovery of an existing efficiency in the combustion of the engine as well as the engine’s intake.
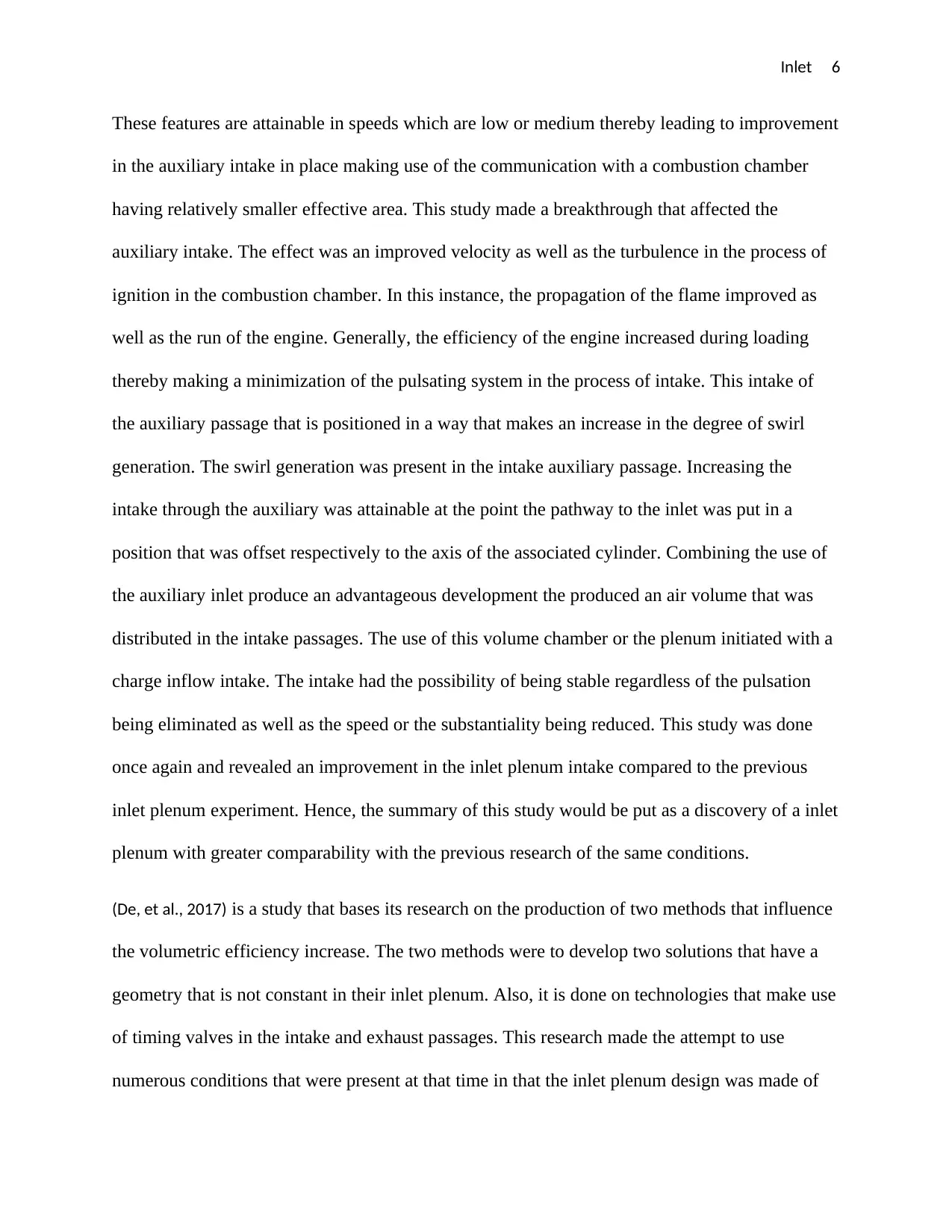
Inlet 6
These features are attainable in speeds which are low or medium thereby leading to improvement
in the auxiliary intake in place making use of the communication with a combustion chamber
having relatively smaller effective area. This study made a breakthrough that affected the
auxiliary intake. The effect was an improved velocity as well as the turbulence in the process of
ignition in the combustion chamber. In this instance, the propagation of the flame improved as
well as the run of the engine. Generally, the efficiency of the engine increased during loading
thereby making a minimization of the pulsating system in the process of intake. This intake of
the auxiliary passage that is positioned in a way that makes an increase in the degree of swirl
generation. The swirl generation was present in the intake auxiliary passage. Increasing the
intake through the auxiliary was attainable at the point the pathway to the inlet was put in a
position that was offset respectively to the axis of the associated cylinder. Combining the use of
the auxiliary inlet produce an advantageous development the produced an air volume that was
distributed in the intake passages. The use of this volume chamber or the plenum initiated with a
charge inflow intake. The intake had the possibility of being stable regardless of the pulsation
being eliminated as well as the speed or the substantiality being reduced. This study was done
once again and revealed an improvement in the inlet plenum intake compared to the previous
inlet plenum experiment. Hence, the summary of this study would be put as a discovery of a inlet
plenum with greater comparability with the previous research of the same conditions.
(De, et al., 2017) is a study that bases its research on the production of two methods that influence
the volumetric efficiency increase. The two methods were to develop two solutions that have a
geometry that is not constant in their inlet plenum. Also, it is done on technologies that make use
of timing valves in the intake and exhaust passages. This research made the attempt to use
numerous conditions that were present at that time in that the inlet plenum design was made of
These features are attainable in speeds which are low or medium thereby leading to improvement
in the auxiliary intake in place making use of the communication with a combustion chamber
having relatively smaller effective area. This study made a breakthrough that affected the
auxiliary intake. The effect was an improved velocity as well as the turbulence in the process of
ignition in the combustion chamber. In this instance, the propagation of the flame improved as
well as the run of the engine. Generally, the efficiency of the engine increased during loading
thereby making a minimization of the pulsating system in the process of intake. This intake of
the auxiliary passage that is positioned in a way that makes an increase in the degree of swirl
generation. The swirl generation was present in the intake auxiliary passage. Increasing the
intake through the auxiliary was attainable at the point the pathway to the inlet was put in a
position that was offset respectively to the axis of the associated cylinder. Combining the use of
the auxiliary inlet produce an advantageous development the produced an air volume that was
distributed in the intake passages. The use of this volume chamber or the plenum initiated with a
charge inflow intake. The intake had the possibility of being stable regardless of the pulsation
being eliminated as well as the speed or the substantiality being reduced. This study was done
once again and revealed an improvement in the inlet plenum intake compared to the previous
inlet plenum experiment. Hence, the summary of this study would be put as a discovery of a inlet
plenum with greater comparability with the previous research of the same conditions.
(De, et al., 2017) is a study that bases its research on the production of two methods that influence
the volumetric efficiency increase. The two methods were to develop two solutions that have a
geometry that is not constant in their inlet plenum. Also, it is done on technologies that make use
of timing valves in the intake and exhaust passages. This research made the attempt to use
numerous conditions that were present at that time in that the inlet plenum design was made of
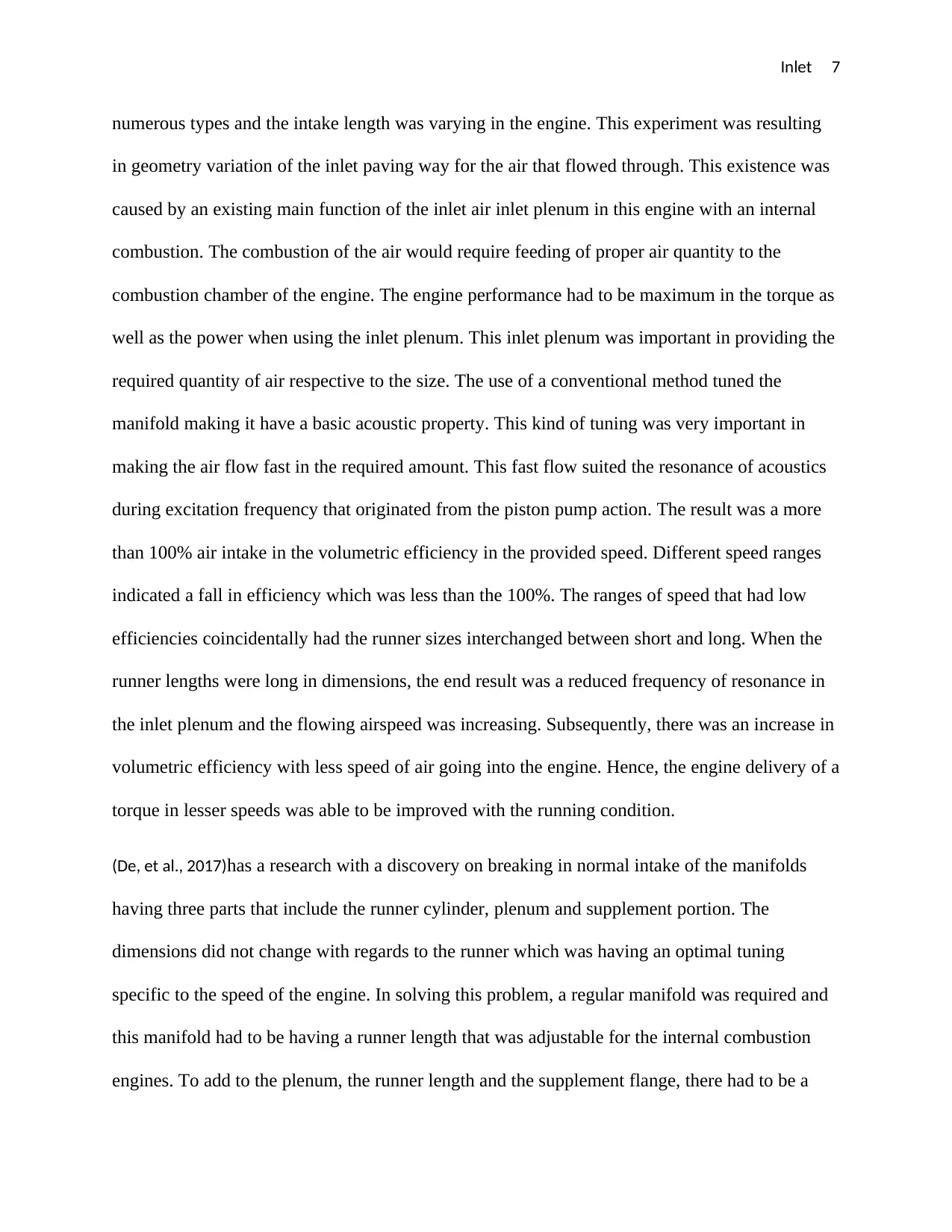
Inlet 7
numerous types and the intake length was varying in the engine. This experiment was resulting
in geometry variation of the inlet paving way for the air that flowed through. This existence was
caused by an existing main function of the inlet air inlet plenum in this engine with an internal
combustion. The combustion of the air would require feeding of proper air quantity to the
combustion chamber of the engine. The engine performance had to be maximum in the torque as
well as the power when using the inlet plenum. This inlet plenum was important in providing the
required quantity of air respective to the size. The use of a conventional method tuned the
manifold making it have a basic acoustic property. This kind of tuning was very important in
making the air flow fast in the required amount. This fast flow suited the resonance of acoustics
during excitation frequency that originated from the piston pump action. The result was a more
than 100% air intake in the volumetric efficiency in the provided speed. Different speed ranges
indicated a fall in efficiency which was less than the 100%. The ranges of speed that had low
efficiencies coincidentally had the runner sizes interchanged between short and long. When the
runner lengths were long in dimensions, the end result was a reduced frequency of resonance in
the inlet plenum and the flowing airspeed was increasing. Subsequently, there was an increase in
volumetric efficiency with less speed of air going into the engine. Hence, the engine delivery of a
torque in lesser speeds was able to be improved with the running condition.
(De, et al., 2017)has a research with a discovery on breaking in normal intake of the manifolds
having three parts that include the runner cylinder, plenum and supplement portion. The
dimensions did not change with regards to the runner which was having an optimal tuning
specific to the speed of the engine. In solving this problem, a regular manifold was required and
this manifold had to be having a runner length that was adjustable for the internal combustion
engines. To add to the plenum, the runner length and the supplement flange, there had to be a
numerous types and the intake length was varying in the engine. This experiment was resulting
in geometry variation of the inlet paving way for the air that flowed through. This existence was
caused by an existing main function of the inlet air inlet plenum in this engine with an internal
combustion. The combustion of the air would require feeding of proper air quantity to the
combustion chamber of the engine. The engine performance had to be maximum in the torque as
well as the power when using the inlet plenum. This inlet plenum was important in providing the
required quantity of air respective to the size. The use of a conventional method tuned the
manifold making it have a basic acoustic property. This kind of tuning was very important in
making the air flow fast in the required amount. This fast flow suited the resonance of acoustics
during excitation frequency that originated from the piston pump action. The result was a more
than 100% air intake in the volumetric efficiency in the provided speed. Different speed ranges
indicated a fall in efficiency which was less than the 100%. The ranges of speed that had low
efficiencies coincidentally had the runner sizes interchanged between short and long. When the
runner lengths were long in dimensions, the end result was a reduced frequency of resonance in
the inlet plenum and the flowing airspeed was increasing. Subsequently, there was an increase in
volumetric efficiency with less speed of air going into the engine. Hence, the engine delivery of a
torque in lesser speeds was able to be improved with the running condition.
(De, et al., 2017)has a research with a discovery on breaking in normal intake of the manifolds
having three parts that include the runner cylinder, plenum and supplement portion. The
dimensions did not change with regards to the runner which was having an optimal tuning
specific to the speed of the engine. In solving this problem, a regular manifold was required and
this manifold had to be having a runner length that was adjustable for the internal combustion
engines. To add to the plenum, the runner length and the supplement flange, there had to be a
Paraphrase This Document
Need a fresh take? Get an instant paraphrase of this document with our AI Paraphraser
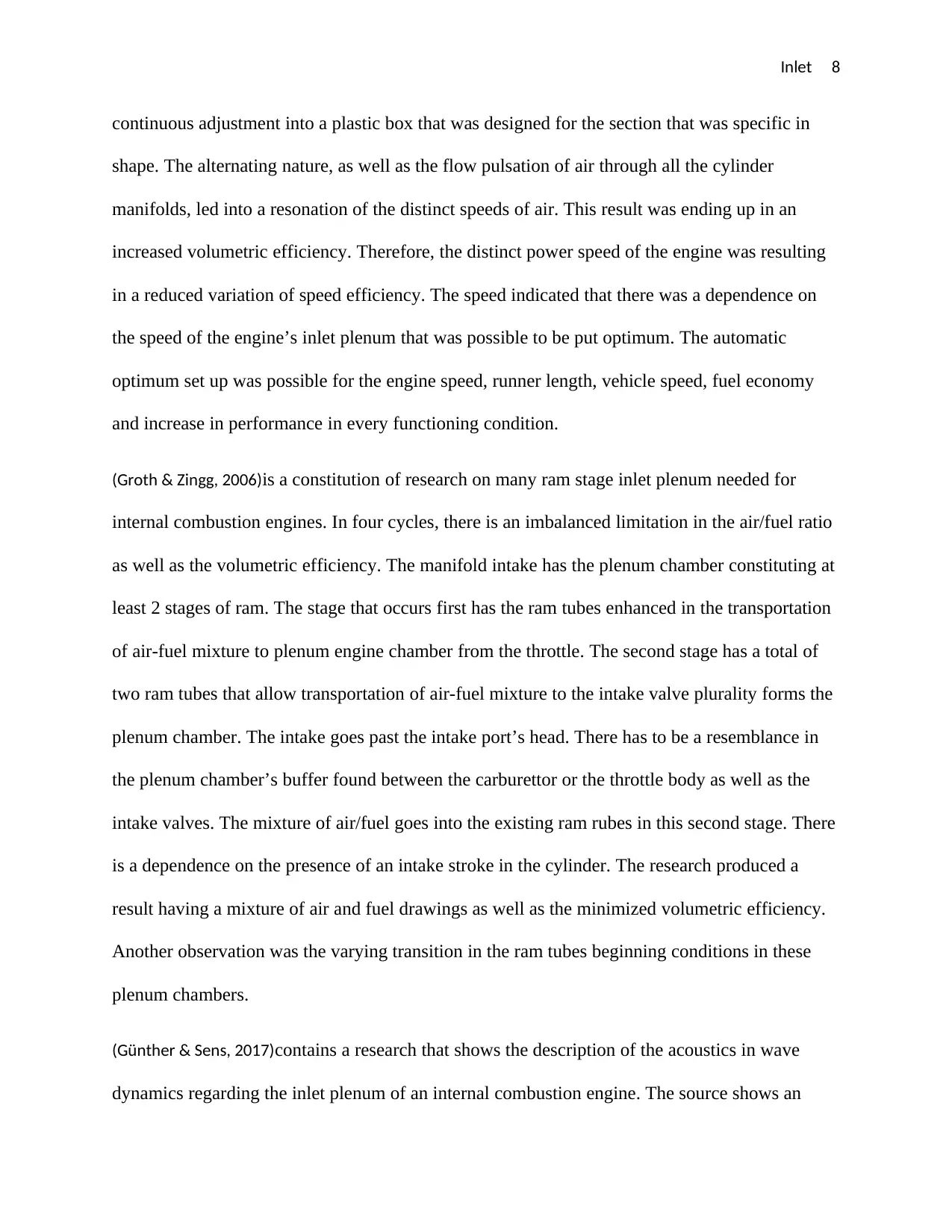
Inlet 8
continuous adjustment into a plastic box that was designed for the section that was specific in
shape. The alternating nature, as well as the flow pulsation of air through all the cylinder
manifolds, led into a resonation of the distinct speeds of air. This result was ending up in an
increased volumetric efficiency. Therefore, the distinct power speed of the engine was resulting
in a reduced variation of speed efficiency. The speed indicated that there was a dependence on
the speed of the engine’s inlet plenum that was possible to be put optimum. The automatic
optimum set up was possible for the engine speed, runner length, vehicle speed, fuel economy
and increase in performance in every functioning condition.
(Groth & Zingg, 2006)is a constitution of research on many ram stage inlet plenum needed for
internal combustion engines. In four cycles, there is an imbalanced limitation in the air/fuel ratio
as well as the volumetric efficiency. The manifold intake has the plenum chamber constituting at
least 2 stages of ram. The stage that occurs first has the ram tubes enhanced in the transportation
of air-fuel mixture to plenum engine chamber from the throttle. The second stage has a total of
two ram tubes that allow transportation of air-fuel mixture to the intake valve plurality forms the
plenum chamber. The intake goes past the intake port’s head. There has to be a resemblance in
the plenum chamber’s buffer found between the carburettor or the throttle body as well as the
intake valves. The mixture of air/fuel goes into the existing ram rubes in this second stage. There
is a dependence on the presence of an intake stroke in the cylinder. The research produced a
result having a mixture of air and fuel drawings as well as the minimized volumetric efficiency.
Another observation was the varying transition in the ram tubes beginning conditions in these
plenum chambers.
(Günther & Sens, 2017)contains a research that shows the description of the acoustics in wave
dynamics regarding the inlet plenum of an internal combustion engine. The source shows an
continuous adjustment into a plastic box that was designed for the section that was specific in
shape. The alternating nature, as well as the flow pulsation of air through all the cylinder
manifolds, led into a resonation of the distinct speeds of air. This result was ending up in an
increased volumetric efficiency. Therefore, the distinct power speed of the engine was resulting
in a reduced variation of speed efficiency. The speed indicated that there was a dependence on
the speed of the engine’s inlet plenum that was possible to be put optimum. The automatic
optimum set up was possible for the engine speed, runner length, vehicle speed, fuel economy
and increase in performance in every functioning condition.
(Groth & Zingg, 2006)is a constitution of research on many ram stage inlet plenum needed for
internal combustion engines. In four cycles, there is an imbalanced limitation in the air/fuel ratio
as well as the volumetric efficiency. The manifold intake has the plenum chamber constituting at
least 2 stages of ram. The stage that occurs first has the ram tubes enhanced in the transportation
of air-fuel mixture to plenum engine chamber from the throttle. The second stage has a total of
two ram tubes that allow transportation of air-fuel mixture to the intake valve plurality forms the
plenum chamber. The intake goes past the intake port’s head. There has to be a resemblance in
the plenum chamber’s buffer found between the carburettor or the throttle body as well as the
intake valves. The mixture of air/fuel goes into the existing ram rubes in this second stage. There
is a dependence on the presence of an intake stroke in the cylinder. The research produced a
result having a mixture of air and fuel drawings as well as the minimized volumetric efficiency.
Another observation was the varying transition in the ram tubes beginning conditions in these
plenum chambers.
(Günther & Sens, 2017)contains a research that shows the description of the acoustics in wave
dynamics regarding the inlet plenum of an internal combustion engine. The source shows an
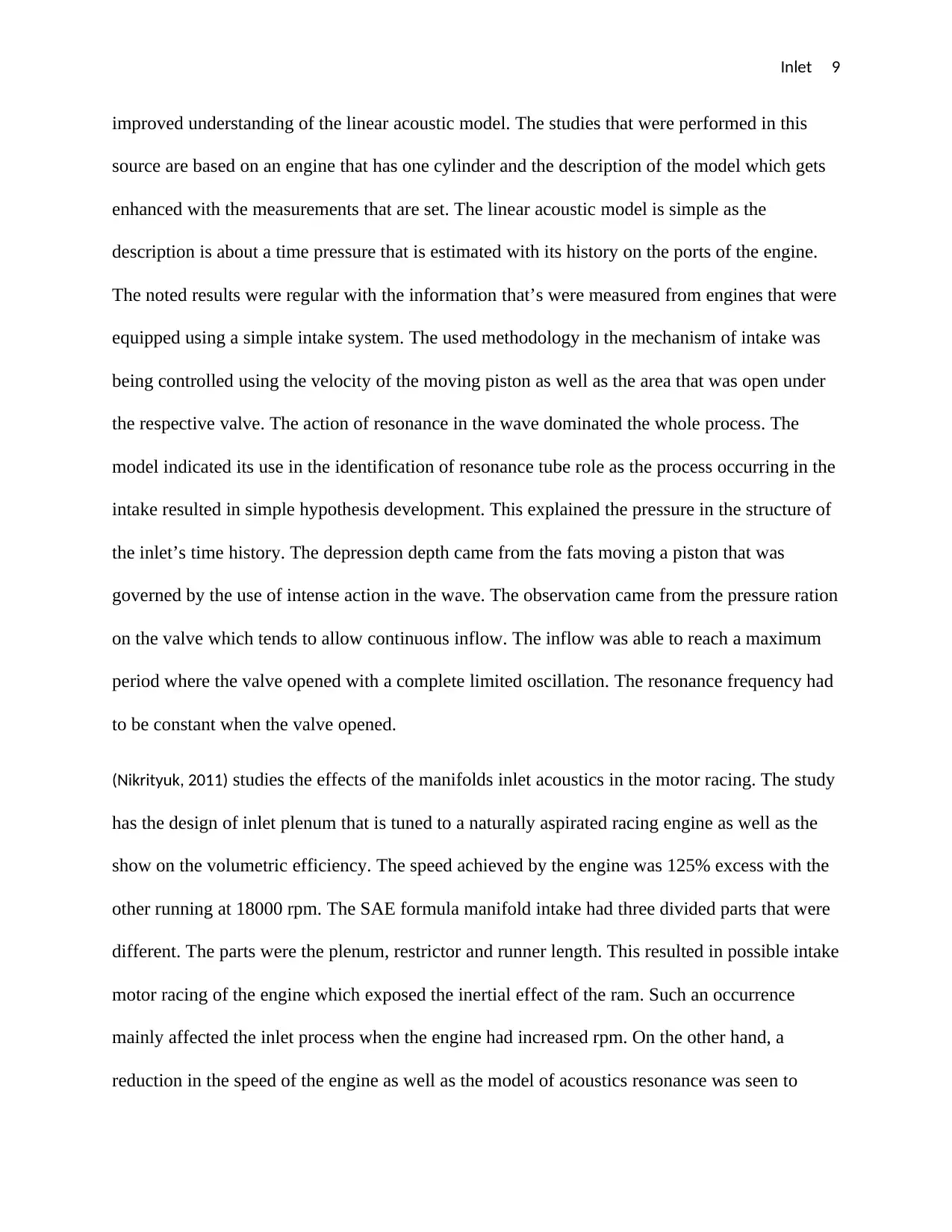
Inlet 9
improved understanding of the linear acoustic model. The studies that were performed in this
source are based on an engine that has one cylinder and the description of the model which gets
enhanced with the measurements that are set. The linear acoustic model is simple as the
description is about a time pressure that is estimated with its history on the ports of the engine.
The noted results were regular with the information that’s were measured from engines that were
equipped using a simple intake system. The used methodology in the mechanism of intake was
being controlled using the velocity of the moving piston as well as the area that was open under
the respective valve. The action of resonance in the wave dominated the whole process. The
model indicated its use in the identification of resonance tube role as the process occurring in the
intake resulted in simple hypothesis development. This explained the pressure in the structure of
the inlet’s time history. The depression depth came from the fats moving a piston that was
governed by the use of intense action in the wave. The observation came from the pressure ration
on the valve which tends to allow continuous inflow. The inflow was able to reach a maximum
period where the valve opened with a complete limited oscillation. The resonance frequency had
to be constant when the valve opened.
(Nikrityuk, 2011) studies the effects of the manifolds inlet acoustics in the motor racing. The study
has the design of inlet plenum that is tuned to a naturally aspirated racing engine as well as the
show on the volumetric efficiency. The speed achieved by the engine was 125% excess with the
other running at 18000 rpm. The SAE formula manifold intake had three divided parts that were
different. The parts were the plenum, restrictor and runner length. This resulted in possible intake
motor racing of the engine which exposed the inertial effect of the ram. Such an occurrence
mainly affected the inlet process when the engine had increased rpm. On the other hand, a
reduction in the speed of the engine as well as the model of acoustics resonance was seen to
improved understanding of the linear acoustic model. The studies that were performed in this
source are based on an engine that has one cylinder and the description of the model which gets
enhanced with the measurements that are set. The linear acoustic model is simple as the
description is about a time pressure that is estimated with its history on the ports of the engine.
The noted results were regular with the information that’s were measured from engines that were
equipped using a simple intake system. The used methodology in the mechanism of intake was
being controlled using the velocity of the moving piston as well as the area that was open under
the respective valve. The action of resonance in the wave dominated the whole process. The
model indicated its use in the identification of resonance tube role as the process occurring in the
intake resulted in simple hypothesis development. This explained the pressure in the structure of
the inlet’s time history. The depression depth came from the fats moving a piston that was
governed by the use of intense action in the wave. The observation came from the pressure ration
on the valve which tends to allow continuous inflow. The inflow was able to reach a maximum
period where the valve opened with a complete limited oscillation. The resonance frequency had
to be constant when the valve opened.
(Nikrityuk, 2011) studies the effects of the manifolds inlet acoustics in the motor racing. The study
has the design of inlet plenum that is tuned to a naturally aspirated racing engine as well as the
show on the volumetric efficiency. The speed achieved by the engine was 125% excess with the
other running at 18000 rpm. The SAE formula manifold intake had three divided parts that were
different. The parts were the plenum, restrictor and runner length. This resulted in possible intake
motor racing of the engine which exposed the inertial effect of the ram. Such an occurrence
mainly affected the inlet process when the engine had increased rpm. On the other hand, a
reduction in the speed of the engine as well as the model of acoustics resonance was seen to
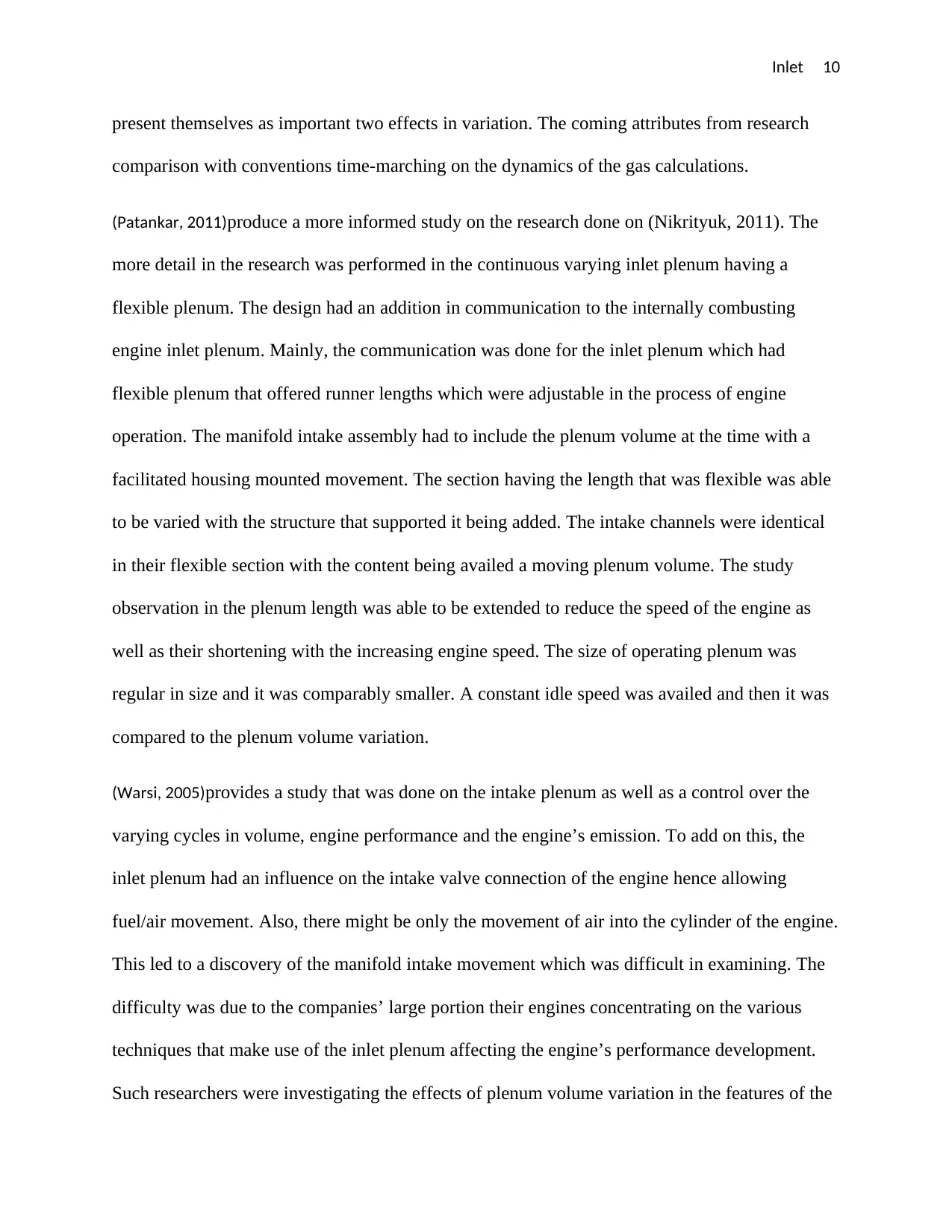
Inlet 10
present themselves as important two effects in variation. The coming attributes from research
comparison with conventions time-marching on the dynamics of the gas calculations.
(Patankar, 2011)produce a more informed study on the research done on (Nikrityuk, 2011). The
more detail in the research was performed in the continuous varying inlet plenum having a
flexible plenum. The design had an addition in communication to the internally combusting
engine inlet plenum. Mainly, the communication was done for the inlet plenum which had
flexible plenum that offered runner lengths which were adjustable in the process of engine
operation. The manifold intake assembly had to include the plenum volume at the time with a
facilitated housing mounted movement. The section having the length that was flexible was able
to be varied with the structure that supported it being added. The intake channels were identical
in their flexible section with the content being availed a moving plenum volume. The study
observation in the plenum length was able to be extended to reduce the speed of the engine as
well as their shortening with the increasing engine speed. The size of operating plenum was
regular in size and it was comparably smaller. A constant idle speed was availed and then it was
compared to the plenum volume variation.
(Warsi, 2005)provides a study that was done on the intake plenum as well as a control over the
varying cycles in volume, engine performance and the engine’s emission. To add on this, the
inlet plenum had an influence on the intake valve connection of the engine hence allowing
fuel/air movement. Also, there might be only the movement of air into the cylinder of the engine.
This led to a discovery of the manifold intake movement which was difficult in examining. The
difficulty was due to the companies’ large portion their engines concentrating on the various
techniques that make use of the inlet plenum affecting the engine’s performance development.
Such researchers were investigating the effects of plenum volume variation in the features of the
present themselves as important two effects in variation. The coming attributes from research
comparison with conventions time-marching on the dynamics of the gas calculations.
(Patankar, 2011)produce a more informed study on the research done on (Nikrityuk, 2011). The
more detail in the research was performed in the continuous varying inlet plenum having a
flexible plenum. The design had an addition in communication to the internally combusting
engine inlet plenum. Mainly, the communication was done for the inlet plenum which had
flexible plenum that offered runner lengths which were adjustable in the process of engine
operation. The manifold intake assembly had to include the plenum volume at the time with a
facilitated housing mounted movement. The section having the length that was flexible was able
to be varied with the structure that supported it being added. The intake channels were identical
in their flexible section with the content being availed a moving plenum volume. The study
observation in the plenum length was able to be extended to reduce the speed of the engine as
well as their shortening with the increasing engine speed. The size of operating plenum was
regular in size and it was comparably smaller. A constant idle speed was availed and then it was
compared to the plenum volume variation.
(Warsi, 2005)provides a study that was done on the intake plenum as well as a control over the
varying cycles in volume, engine performance and the engine’s emission. To add on this, the
inlet plenum had an influence on the intake valve connection of the engine hence allowing
fuel/air movement. Also, there might be only the movement of air into the cylinder of the engine.
This led to a discovery of the manifold intake movement which was difficult in examining. The
difficulty was due to the companies’ large portion their engines concentrating on the various
techniques that make use of the inlet plenum affecting the engine’s performance development.
Such researchers were investigating the effects of plenum volume variation in the features of the
Secure Best Marks with AI Grader
Need help grading? Try our AI Grader for instant feedback on your assignments.
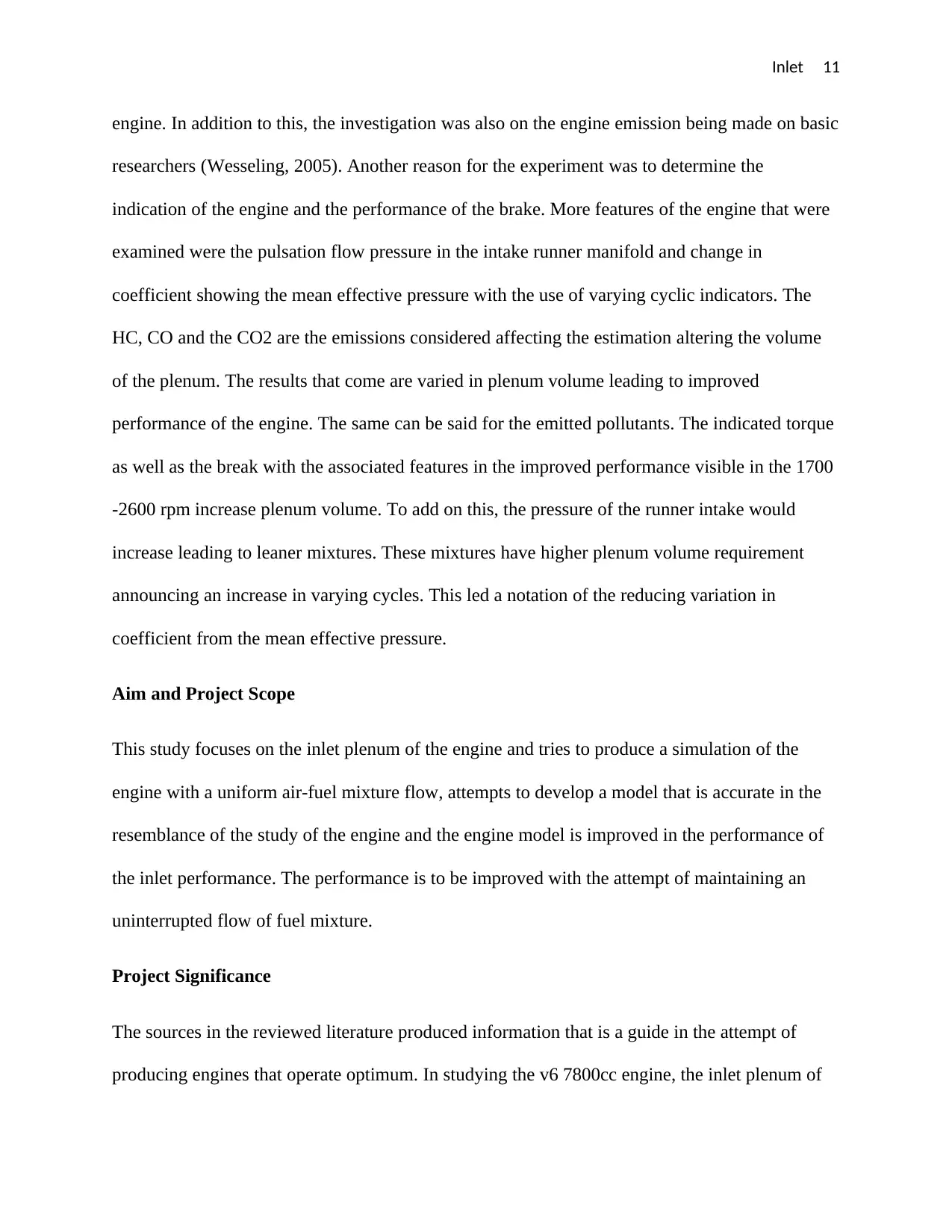
Inlet 11
engine. In addition to this, the investigation was also on the engine emission being made on basic
researchers (Wesseling, 2005). Another reason for the experiment was to determine the
indication of the engine and the performance of the brake. More features of the engine that were
examined were the pulsation flow pressure in the intake runner manifold and change in
coefficient showing the mean effective pressure with the use of varying cyclic indicators. The
HC, CO and the CO2 are the emissions considered affecting the estimation altering the volume
of the plenum. The results that come are varied in plenum volume leading to improved
performance of the engine. The same can be said for the emitted pollutants. The indicated torque
as well as the break with the associated features in the improved performance visible in the 1700
-2600 rpm increase plenum volume. To add on this, the pressure of the runner intake would
increase leading to leaner mixtures. These mixtures have higher plenum volume requirement
announcing an increase in varying cycles. This led a notation of the reducing variation in
coefficient from the mean effective pressure.
Aim and Project Scope
This study focuses on the inlet plenum of the engine and tries to produce a simulation of the
engine with a uniform air-fuel mixture flow, attempts to develop a model that is accurate in the
resemblance of the study of the engine and the engine model is improved in the performance of
the inlet performance. The performance is to be improved with the attempt of maintaining an
uninterrupted flow of fuel mixture.
Project Significance
The sources in the reviewed literature produced information that is a guide in the attempt of
producing engines that operate optimum. In studying the v6 7800cc engine, the inlet plenum of
engine. In addition to this, the investigation was also on the engine emission being made on basic
researchers (Wesseling, 2005). Another reason for the experiment was to determine the
indication of the engine and the performance of the brake. More features of the engine that were
examined were the pulsation flow pressure in the intake runner manifold and change in
coefficient showing the mean effective pressure with the use of varying cyclic indicators. The
HC, CO and the CO2 are the emissions considered affecting the estimation altering the volume
of the plenum. The results that come are varied in plenum volume leading to improved
performance of the engine. The same can be said for the emitted pollutants. The indicated torque
as well as the break with the associated features in the improved performance visible in the 1700
-2600 rpm increase plenum volume. To add on this, the pressure of the runner intake would
increase leading to leaner mixtures. These mixtures have higher plenum volume requirement
announcing an increase in varying cycles. This led a notation of the reducing variation in
coefficient from the mean effective pressure.
Aim and Project Scope
This study focuses on the inlet plenum of the engine and tries to produce a simulation of the
engine with a uniform air-fuel mixture flow, attempts to develop a model that is accurate in the
resemblance of the study of the engine and the engine model is improved in the performance of
the inlet performance. The performance is to be improved with the attempt of maintaining an
uninterrupted flow of fuel mixture.
Project Significance
The sources in the reviewed literature produced information that is a guide in the attempt of
producing engines that operate optimum. In studying the v6 7800cc engine, the inlet plenum of
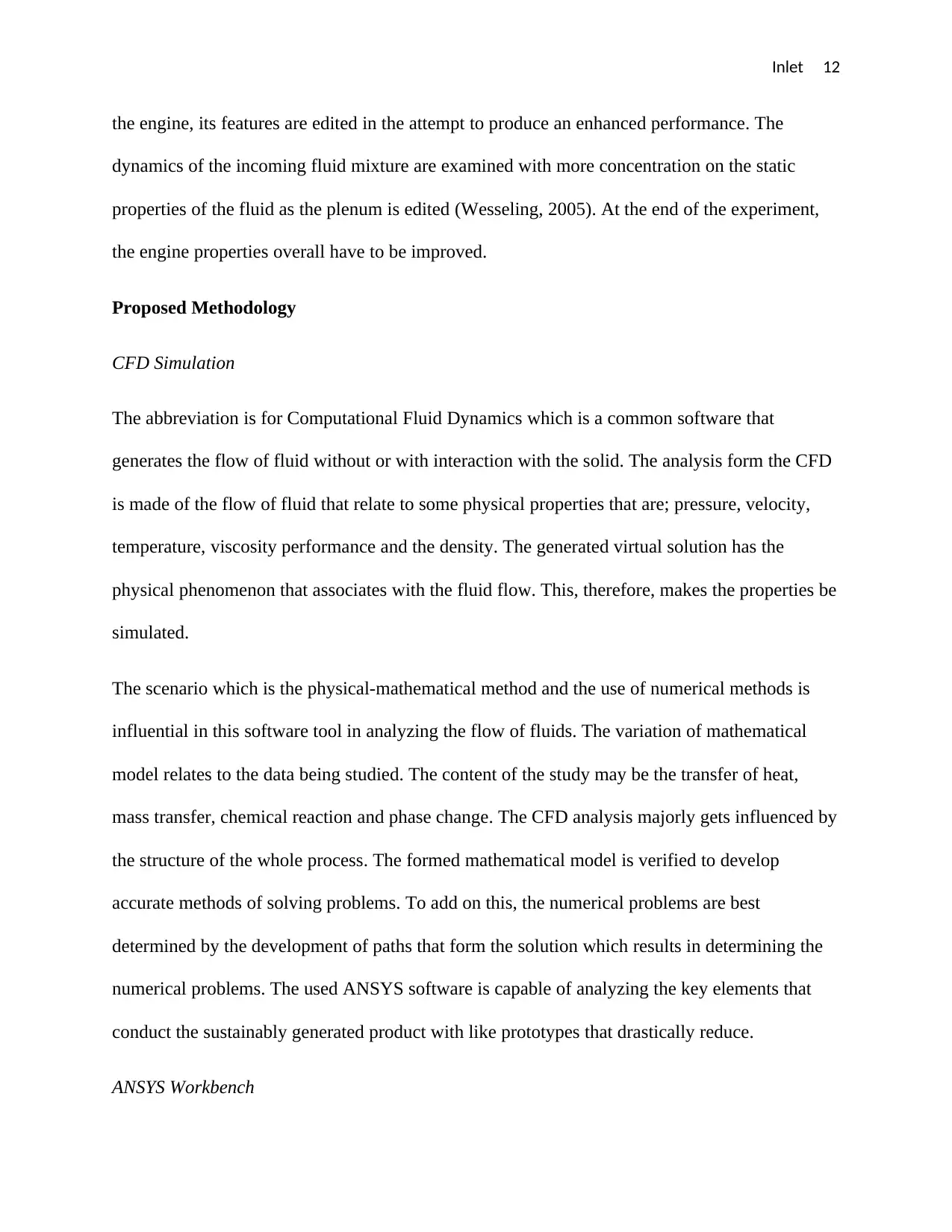
Inlet 12
the engine, its features are edited in the attempt to produce an enhanced performance. The
dynamics of the incoming fluid mixture are examined with more concentration on the static
properties of the fluid as the plenum is edited (Wesseling, 2005). At the end of the experiment,
the engine properties overall have to be improved.
Proposed Methodology
CFD Simulation
The abbreviation is for Computational Fluid Dynamics which is a common software that
generates the flow of fluid without or with interaction with the solid. The analysis form the CFD
is made of the flow of fluid that relate to some physical properties that are; pressure, velocity,
temperature, viscosity performance and the density. The generated virtual solution has the
physical phenomenon that associates with the fluid flow. This, therefore, makes the properties be
simulated.
The scenario which is the physical-mathematical method and the use of numerical methods is
influential in this software tool in analyzing the flow of fluids. The variation of mathematical
model relates to the data being studied. The content of the study may be the transfer of heat,
mass transfer, chemical reaction and phase change. The CFD analysis majorly gets influenced by
the structure of the whole process. The formed mathematical model is verified to develop
accurate methods of solving problems. To add on this, the numerical problems are best
determined by the development of paths that form the solution which results in determining the
numerical problems. The used ANSYS software is capable of analyzing the key elements that
conduct the sustainably generated product with like prototypes that drastically reduce.
ANSYS Workbench
the engine, its features are edited in the attempt to produce an enhanced performance. The
dynamics of the incoming fluid mixture are examined with more concentration on the static
properties of the fluid as the plenum is edited (Wesseling, 2005). At the end of the experiment,
the engine properties overall have to be improved.
Proposed Methodology
CFD Simulation
The abbreviation is for Computational Fluid Dynamics which is a common software that
generates the flow of fluid without or with interaction with the solid. The analysis form the CFD
is made of the flow of fluid that relate to some physical properties that are; pressure, velocity,
temperature, viscosity performance and the density. The generated virtual solution has the
physical phenomenon that associates with the fluid flow. This, therefore, makes the properties be
simulated.
The scenario which is the physical-mathematical method and the use of numerical methods is
influential in this software tool in analyzing the flow of fluids. The variation of mathematical
model relates to the data being studied. The content of the study may be the transfer of heat,
mass transfer, chemical reaction and phase change. The CFD analysis majorly gets influenced by
the structure of the whole process. The formed mathematical model is verified to develop
accurate methods of solving problems. To add on this, the numerical problems are best
determined by the development of paths that form the solution which results in determining the
numerical problems. The used ANSYS software is capable of analyzing the key elements that
conduct the sustainably generated product with like prototypes that drastically reduce.
ANSYS Workbench
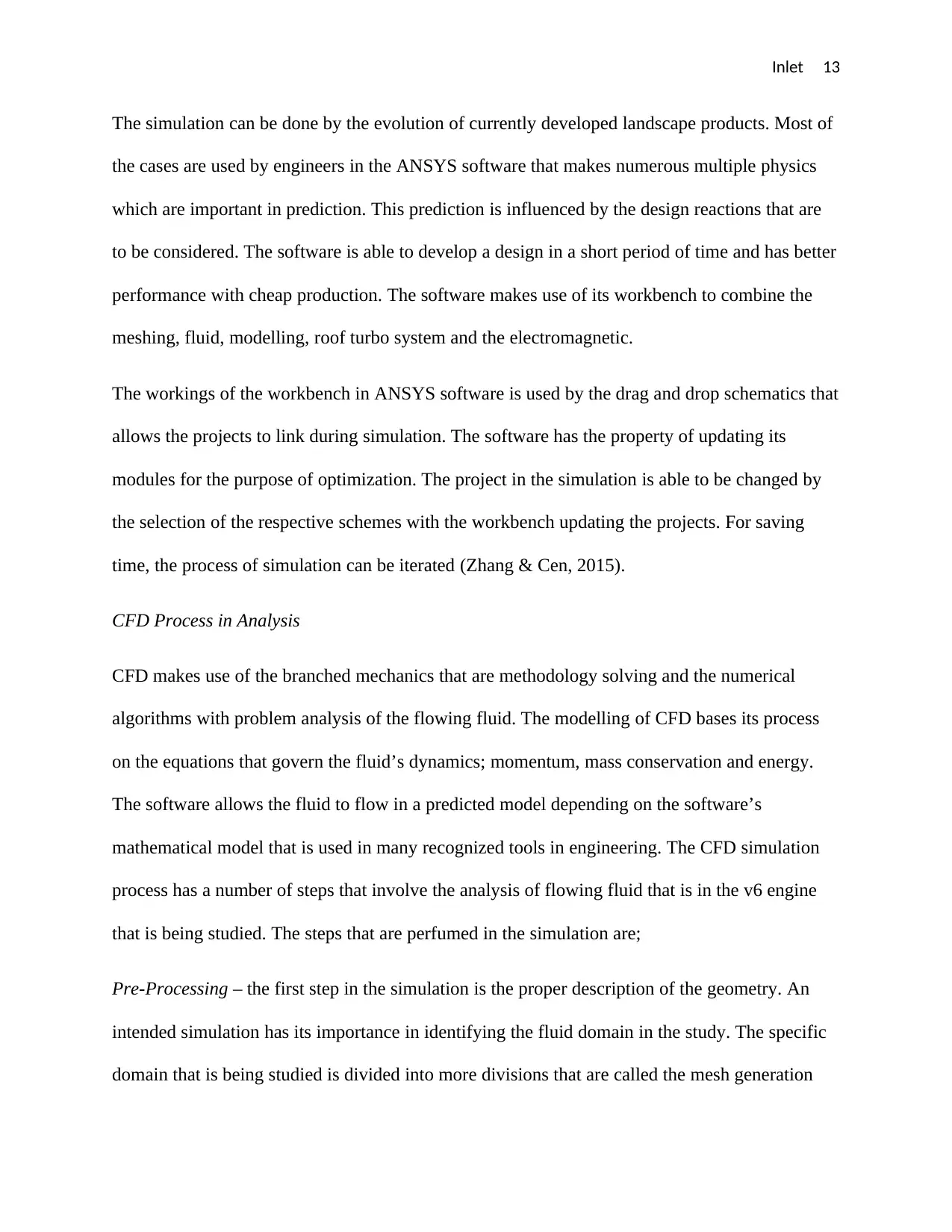
Inlet 13
The simulation can be done by the evolution of currently developed landscape products. Most of
the cases are used by engineers in the ANSYS software that makes numerous multiple physics
which are important in prediction. This prediction is influenced by the design reactions that are
to be considered. The software is able to develop a design in a short period of time and has better
performance with cheap production. The software makes use of its workbench to combine the
meshing, fluid, modelling, roof turbo system and the electromagnetic.
The workings of the workbench in ANSYS software is used by the drag and drop schematics that
allows the projects to link during simulation. The software has the property of updating its
modules for the purpose of optimization. The project in the simulation is able to be changed by
the selection of the respective schemes with the workbench updating the projects. For saving
time, the process of simulation can be iterated (Zhang & Cen, 2015).
CFD Process in Analysis
CFD makes use of the branched mechanics that are methodology solving and the numerical
algorithms with problem analysis of the flowing fluid. The modelling of CFD bases its process
on the equations that govern the fluid’s dynamics; momentum, mass conservation and energy.
The software allows the fluid to flow in a predicted model depending on the software’s
mathematical model that is used in many recognized tools in engineering. The CFD simulation
process has a number of steps that involve the analysis of flowing fluid that is in the v6 engine
that is being studied. The steps that are perfumed in the simulation are;
Pre-Processing – the first step in the simulation is the proper description of the geometry. An
intended simulation has its importance in identifying the fluid domain in the study. The specific
domain that is being studied is divided into more divisions that are called the mesh generation
The simulation can be done by the evolution of currently developed landscape products. Most of
the cases are used by engineers in the ANSYS software that makes numerous multiple physics
which are important in prediction. This prediction is influenced by the design reactions that are
to be considered. The software is able to develop a design in a short period of time and has better
performance with cheap production. The software makes use of its workbench to combine the
meshing, fluid, modelling, roof turbo system and the electromagnetic.
The workings of the workbench in ANSYS software is used by the drag and drop schematics that
allows the projects to link during simulation. The software has the property of updating its
modules for the purpose of optimization. The project in the simulation is able to be changed by
the selection of the respective schemes with the workbench updating the projects. For saving
time, the process of simulation can be iterated (Zhang & Cen, 2015).
CFD Process in Analysis
CFD makes use of the branched mechanics that are methodology solving and the numerical
algorithms with problem analysis of the flowing fluid. The modelling of CFD bases its process
on the equations that govern the fluid’s dynamics; momentum, mass conservation and energy.
The software allows the fluid to flow in a predicted model depending on the software’s
mathematical model that is used in many recognized tools in engineering. The CFD simulation
process has a number of steps that involve the analysis of flowing fluid that is in the v6 engine
that is being studied. The steps that are perfumed in the simulation are;
Pre-Processing – the first step in the simulation is the proper description of the geometry. An
intended simulation has its importance in identifying the fluid domain in the study. The specific
domain that is being studied is divided into more divisions that are called the mesh generation
Paraphrase This Document
Need a fresh take? Get an instant paraphrase of this document with our AI Paraphraser
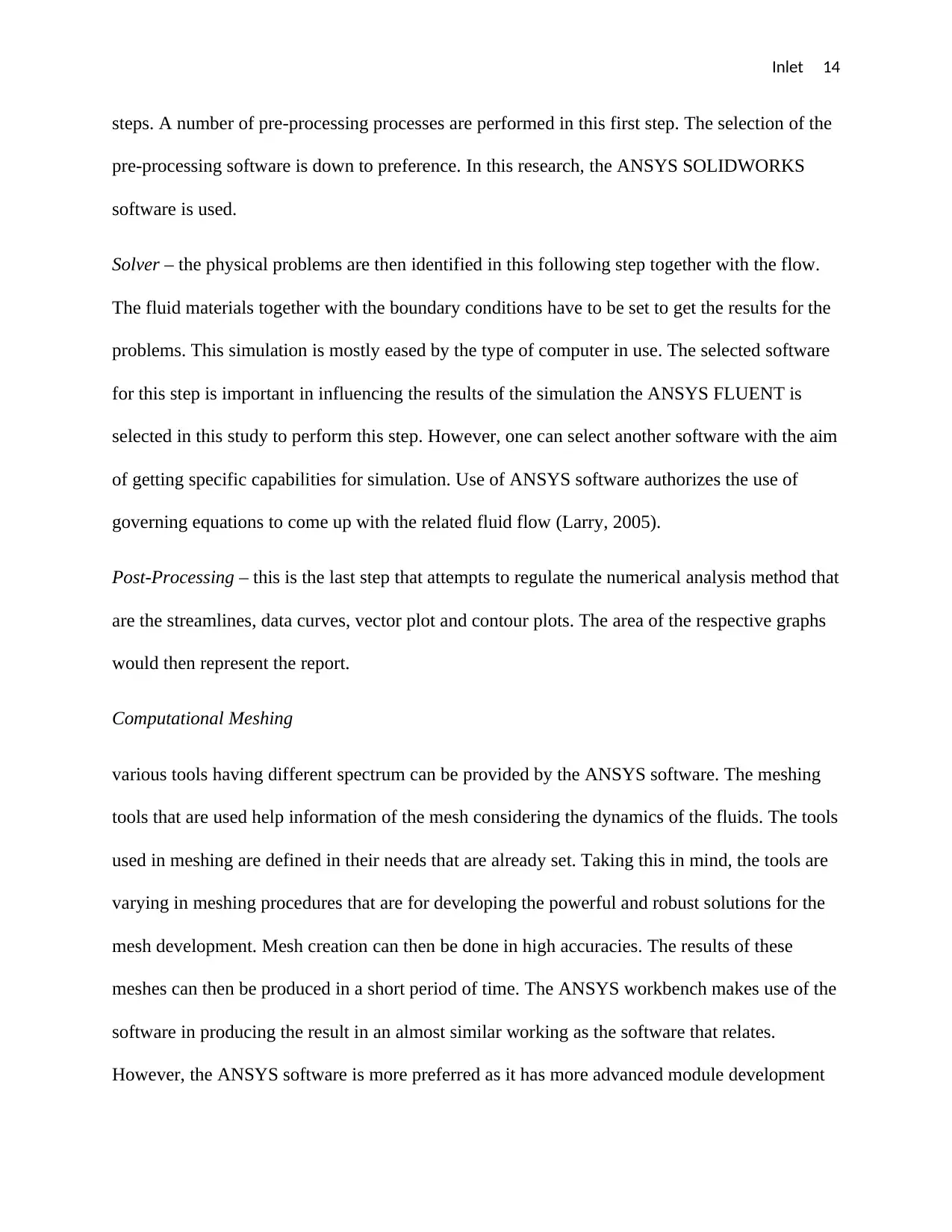
Inlet 14
steps. A number of pre-processing processes are performed in this first step. The selection of the
pre-processing software is down to preference. In this research, the ANSYS SOLIDWORKS
software is used.
Solver – the physical problems are then identified in this following step together with the flow.
The fluid materials together with the boundary conditions have to be set to get the results for the
problems. This simulation is mostly eased by the type of computer in use. The selected software
for this step is important in influencing the results of the simulation the ANSYS FLUENT is
selected in this study to perform this step. However, one can select another software with the aim
of getting specific capabilities for simulation. Use of ANSYS software authorizes the use of
governing equations to come up with the related fluid flow (Larry, 2005).
Post-Processing – this is the last step that attempts to regulate the numerical analysis method that
are the streamlines, data curves, vector plot and contour plots. The area of the respective graphs
would then represent the report.
Computational Meshing
various tools having different spectrum can be provided by the ANSYS software. The meshing
tools that are used help information of the mesh considering the dynamics of the fluids. The tools
used in meshing are defined in their needs that are already set. Taking this in mind, the tools are
varying in meshing procedures that are for developing the powerful and robust solutions for the
mesh development. Mesh creation can then be done in high accuracies. The results of these
meshes can then be produced in a short period of time. The ANSYS workbench makes use of the
software in producing the result in an almost similar working as the software that relates.
However, the ANSYS software is more preferred as it has more advanced module development
steps. A number of pre-processing processes are performed in this first step. The selection of the
pre-processing software is down to preference. In this research, the ANSYS SOLIDWORKS
software is used.
Solver – the physical problems are then identified in this following step together with the flow.
The fluid materials together with the boundary conditions have to be set to get the results for the
problems. This simulation is mostly eased by the type of computer in use. The selected software
for this step is important in influencing the results of the simulation the ANSYS FLUENT is
selected in this study to perform this step. However, one can select another software with the aim
of getting specific capabilities for simulation. Use of ANSYS software authorizes the use of
governing equations to come up with the related fluid flow (Larry, 2005).
Post-Processing – this is the last step that attempts to regulate the numerical analysis method that
are the streamlines, data curves, vector plot and contour plots. The area of the respective graphs
would then represent the report.
Computational Meshing
various tools having different spectrum can be provided by the ANSYS software. The meshing
tools that are used help information of the mesh considering the dynamics of the fluids. The tools
used in meshing are defined in their needs that are already set. Taking this in mind, the tools are
varying in meshing procedures that are for developing the powerful and robust solutions for the
mesh development. Mesh creation can then be done in high accuracies. The results of these
meshes can then be produced in a short period of time. The ANSYS workbench makes use of the
software in producing the result in an almost similar working as the software that relates.
However, the ANSYS software is more preferred as it has more advanced module development
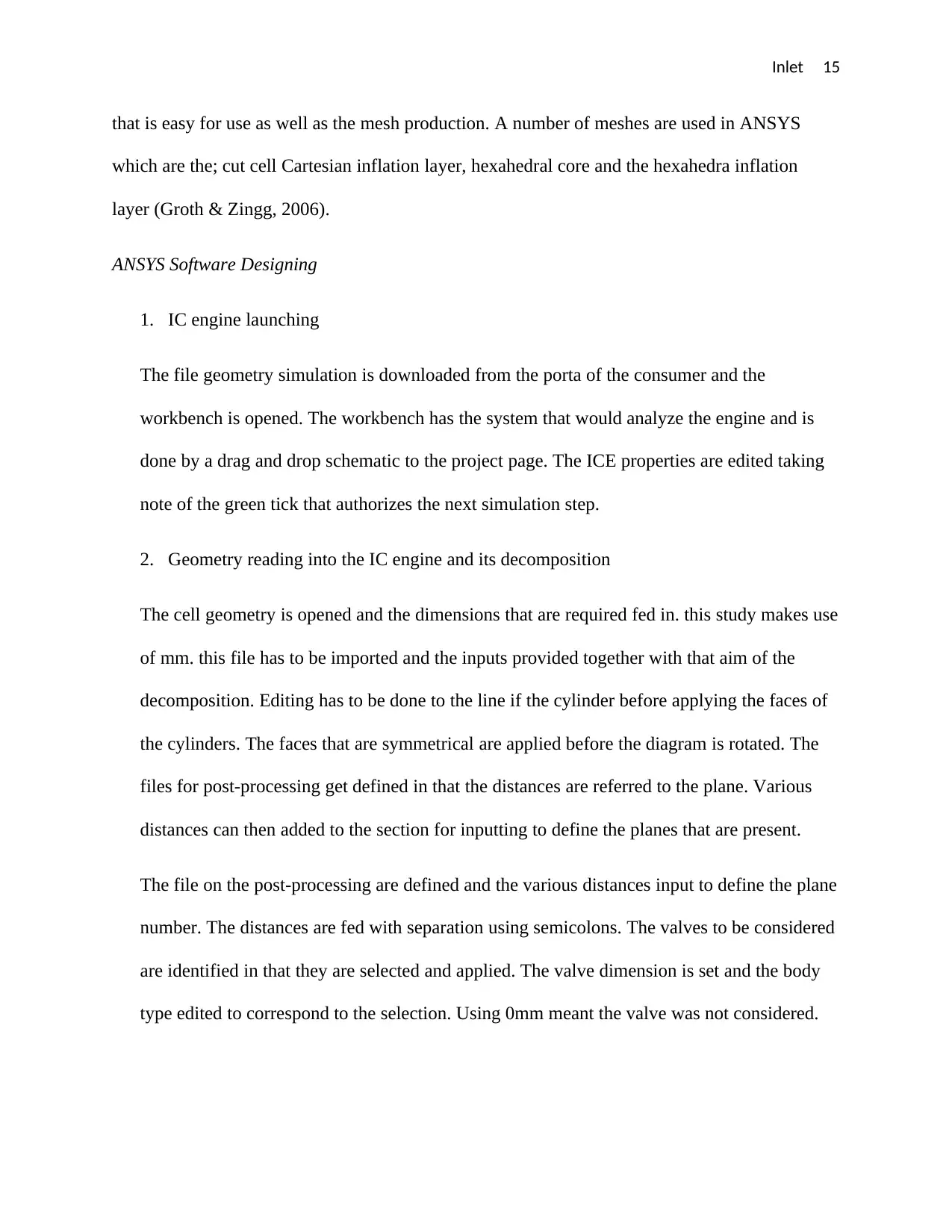
Inlet 15
that is easy for use as well as the mesh production. A number of meshes are used in ANSYS
which are the; cut cell Cartesian inflation layer, hexahedral core and the hexahedra inflation
layer (Groth & Zingg, 2006).
ANSYS Software Designing
1. IC engine launching
The file geometry simulation is downloaded from the porta of the consumer and the
workbench is opened. The workbench has the system that would analyze the engine and is
done by a drag and drop schematic to the project page. The ICE properties are edited taking
note of the green tick that authorizes the next simulation step.
2. Geometry reading into the IC engine and its decomposition
The cell geometry is opened and the dimensions that are required fed in. this study makes use
of mm. this file has to be imported and the inputs provided together with that aim of the
decomposition. Editing has to be done to the line if the cylinder before applying the faces of
the cylinders. The faces that are symmetrical are applied before the diagram is rotated. The
files for post-processing get defined in that the distances are referred to the plane. Various
distances can then added to the section for inputting to define the planes that are present.
The file on the post-processing are defined and the various distances input to define the plane
number. The distances are fed with separation using semicolons. The valves to be considered
are identified in that they are selected and applied. The valve dimension is set and the body
type edited to correspond to the selection. Using 0mm meant the valve was not considered.
that is easy for use as well as the mesh production. A number of meshes are used in ANSYS
which are the; cut cell Cartesian inflation layer, hexahedral core and the hexahedra inflation
layer (Groth & Zingg, 2006).
ANSYS Software Designing
1. IC engine launching
The file geometry simulation is downloaded from the porta of the consumer and the
workbench is opened. The workbench has the system that would analyze the engine and is
done by a drag and drop schematic to the project page. The ICE properties are edited taking
note of the green tick that authorizes the next simulation step.
2. Geometry reading into the IC engine and its decomposition
The cell geometry is opened and the dimensions that are required fed in. this study makes use
of mm. this file has to be imported and the inputs provided together with that aim of the
decomposition. Editing has to be done to the line if the cylinder before applying the faces of
the cylinders. The faces that are symmetrical are applied before the diagram is rotated. The
files for post-processing get defined in that the distances are referred to the plane. Various
distances can then added to the section for inputting to define the planes that are present.
The file on the post-processing are defined and the various distances input to define the plane
number. The distances are fed with separation using semicolons. The valves to be considered
are identified in that they are selected and applied. The valve dimension is set and the body
type edited to correspond to the selection. Using 0mm meant the valve was not considered.
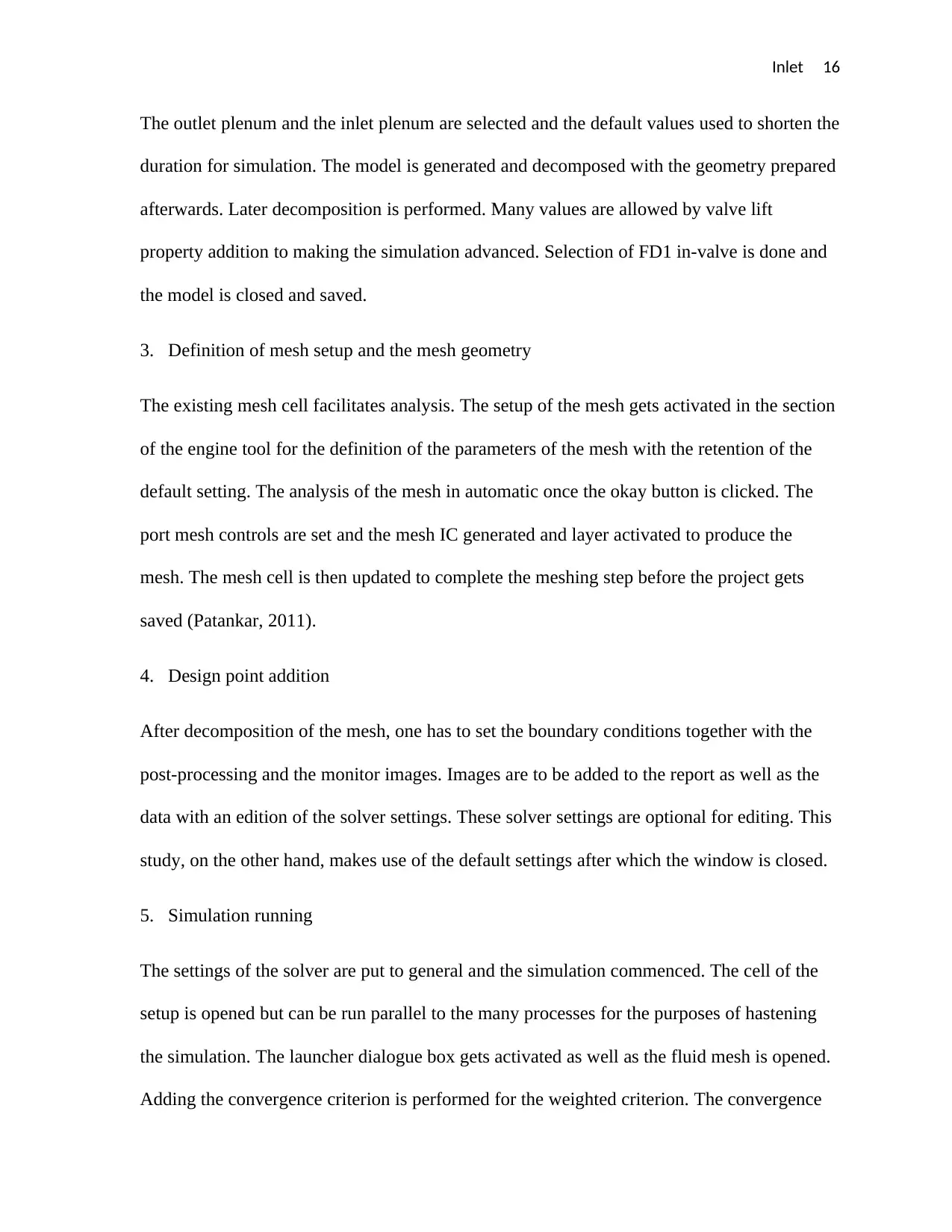
Inlet 16
The outlet plenum and the inlet plenum are selected and the default values used to shorten the
duration for simulation. The model is generated and decomposed with the geometry prepared
afterwards. Later decomposition is performed. Many values are allowed by valve lift
property addition to making the simulation advanced. Selection of FD1 in-valve is done and
the model is closed and saved.
3. Definition of mesh setup and the mesh geometry
The existing mesh cell facilitates analysis. The setup of the mesh gets activated in the section
of the engine tool for the definition of the parameters of the mesh with the retention of the
default setting. The analysis of the mesh in automatic once the okay button is clicked. The
port mesh controls are set and the mesh IC generated and layer activated to produce the
mesh. The mesh cell is then updated to complete the meshing step before the project gets
saved (Patankar, 2011).
4. Design point addition
After decomposition of the mesh, one has to set the boundary conditions together with the
post-processing and the monitor images. Images are to be added to the report as well as the
data with an edition of the solver settings. These solver settings are optional for editing. This
study, on the other hand, makes use of the default settings after which the window is closed.
5. Simulation running
The settings of the solver are put to general and the simulation commenced. The cell of the
setup is opened but can be run parallel to the many processes for the purposes of hastening
the simulation. The launcher dialogue box gets activated as well as the fluid mesh is opened.
Adding the convergence criterion is performed for the weighted criterion. The convergence
The outlet plenum and the inlet plenum are selected and the default values used to shorten the
duration for simulation. The model is generated and decomposed with the geometry prepared
afterwards. Later decomposition is performed. Many values are allowed by valve lift
property addition to making the simulation advanced. Selection of FD1 in-valve is done and
the model is closed and saved.
3. Definition of mesh setup and the mesh geometry
The existing mesh cell facilitates analysis. The setup of the mesh gets activated in the section
of the engine tool for the definition of the parameters of the mesh with the retention of the
default setting. The analysis of the mesh in automatic once the okay button is clicked. The
port mesh controls are set and the mesh IC generated and layer activated to produce the
mesh. The mesh cell is then updated to complete the meshing step before the project gets
saved (Patankar, 2011).
4. Design point addition
After decomposition of the mesh, one has to set the boundary conditions together with the
post-processing and the monitor images. Images are to be added to the report as well as the
data with an edition of the solver settings. These solver settings are optional for editing. This
study, on the other hand, makes use of the default settings after which the window is closed.
5. Simulation running
The settings of the solver are put to general and the simulation commenced. The cell of the
setup is opened but can be run parallel to the many processes for the purposes of hastening
the simulation. The launcher dialogue box gets activated as well as the fluid mesh is opened.
Adding the convergence criterion is performed for the weighted criterion. The convergence
Secure Best Marks with AI Grader
Need help grading? Try our AI Grader for instant feedback on your assignments.
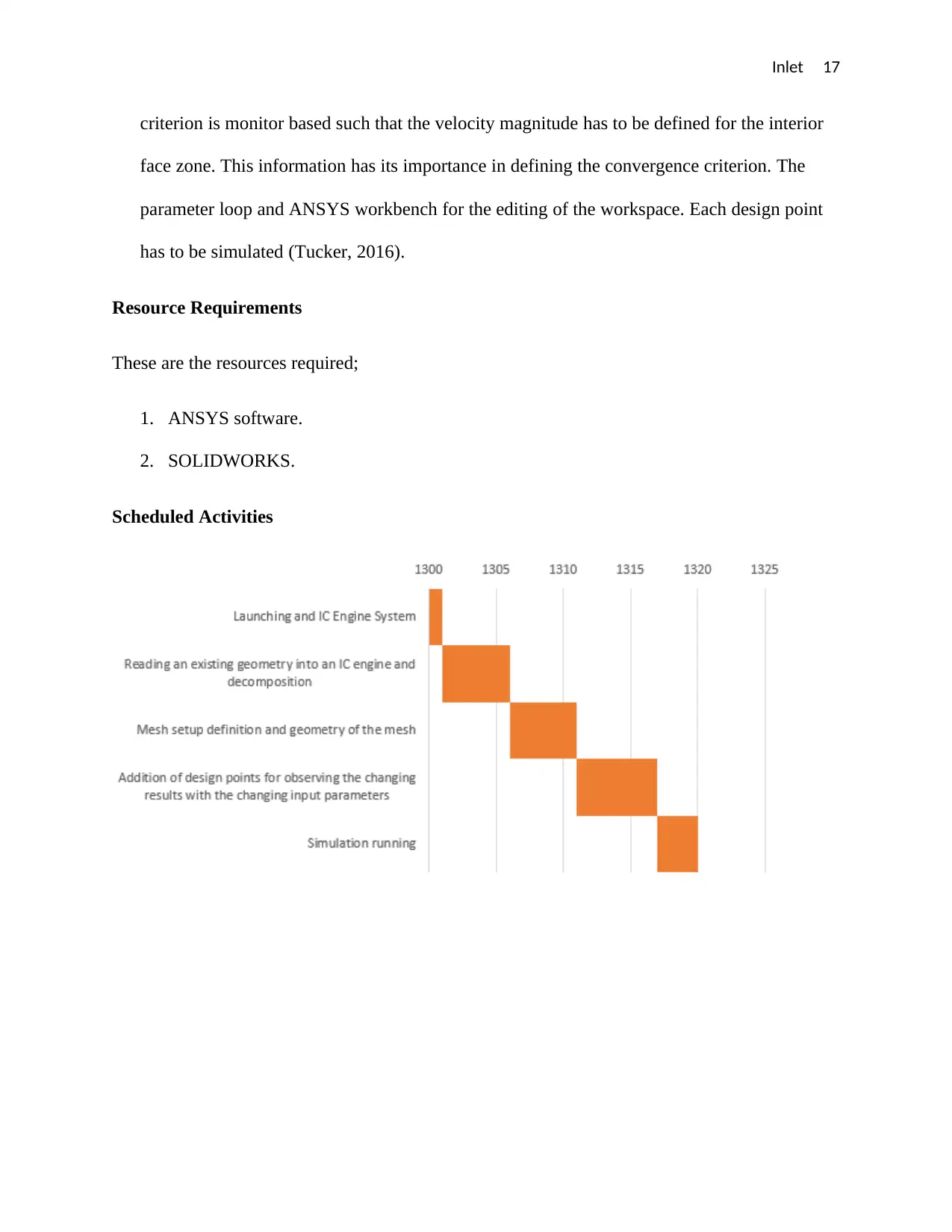
Inlet 17
criterion is monitor based such that the velocity magnitude has to be defined for the interior
face zone. This information has its importance in defining the convergence criterion. The
parameter loop and ANSYS workbench for the editing of the workspace. Each design point
has to be simulated (Tucker, 2016).
Resource Requirements
These are the resources required;
1. ANSYS software.
2. SOLIDWORKS.
Scheduled Activities
criterion is monitor based such that the velocity magnitude has to be defined for the interior
face zone. This information has its importance in defining the convergence criterion. The
parameter loop and ANSYS workbench for the editing of the workspace. Each design point
has to be simulated (Tucker, 2016).
Resource Requirements
These are the resources required;
1. ANSYS software.
2. SOLIDWORKS.
Scheduled Activities
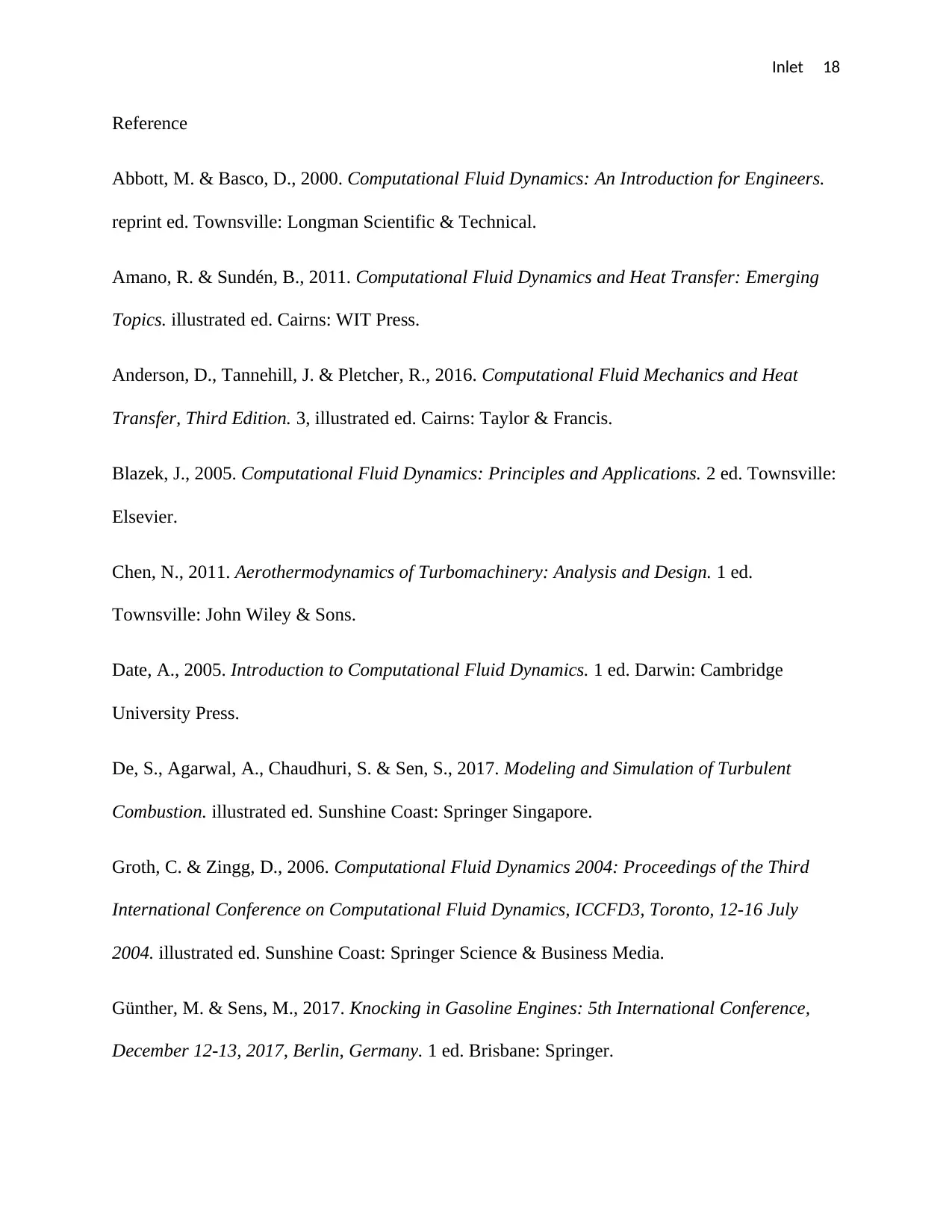
Inlet 18
Reference
Abbott, M. & Basco, D., 2000. Computational Fluid Dynamics: An Introduction for Engineers.
reprint ed. Townsville: Longman Scientific & Technical.
Amano, R. & Sundén, B., 2011. Computational Fluid Dynamics and Heat Transfer: Emerging
Topics. illustrated ed. Cairns: WIT Press.
Anderson, D., Tannehill, J. & Pletcher, R., 2016. Computational Fluid Mechanics and Heat
Transfer, Third Edition. 3, illustrated ed. Cairns: Taylor & Francis.
Blazek, J., 2005. Computational Fluid Dynamics: Principles and Applications. 2 ed. Townsville:
Elsevier.
Chen, N., 2011. Aerothermodynamics of Turbomachinery: Analysis and Design. 1 ed.
Townsville: John Wiley & Sons.
Date, A., 2005. Introduction to Computational Fluid Dynamics. 1 ed. Darwin: Cambridge
University Press.
De, S., Agarwal, A., Chaudhuri, S. & Sen, S., 2017. Modeling and Simulation of Turbulent
Combustion. illustrated ed. Sunshine Coast: Springer Singapore.
Groth, C. & Zingg, D., 2006. Computational Fluid Dynamics 2004: Proceedings of the Third
International Conference on Computational Fluid Dynamics, ICCFD3, Toronto, 12-16 July
2004. illustrated ed. Sunshine Coast: Springer Science & Business Media.
Günther, M. & Sens, M., 2017. Knocking in Gasoline Engines: 5th International Conference,
December 12-13, 2017, Berlin, Germany. 1 ed. Brisbane: Springer.
Reference
Abbott, M. & Basco, D., 2000. Computational Fluid Dynamics: An Introduction for Engineers.
reprint ed. Townsville: Longman Scientific & Technical.
Amano, R. & Sundén, B., 2011. Computational Fluid Dynamics and Heat Transfer: Emerging
Topics. illustrated ed. Cairns: WIT Press.
Anderson, D., Tannehill, J. & Pletcher, R., 2016. Computational Fluid Mechanics and Heat
Transfer, Third Edition. 3, illustrated ed. Cairns: Taylor & Francis.
Blazek, J., 2005. Computational Fluid Dynamics: Principles and Applications. 2 ed. Townsville:
Elsevier.
Chen, N., 2011. Aerothermodynamics of Turbomachinery: Analysis and Design. 1 ed.
Townsville: John Wiley & Sons.
Date, A., 2005. Introduction to Computational Fluid Dynamics. 1 ed. Darwin: Cambridge
University Press.
De, S., Agarwal, A., Chaudhuri, S. & Sen, S., 2017. Modeling and Simulation of Turbulent
Combustion. illustrated ed. Sunshine Coast: Springer Singapore.
Groth, C. & Zingg, D., 2006. Computational Fluid Dynamics 2004: Proceedings of the Third
International Conference on Computational Fluid Dynamics, ICCFD3, Toronto, 12-16 July
2004. illustrated ed. Sunshine Coast: Springer Science & Business Media.
Günther, M. & Sens, M., 2017. Knocking in Gasoline Engines: 5th International Conference,
December 12-13, 2017, Berlin, Germany. 1 ed. Brisbane: Springer.
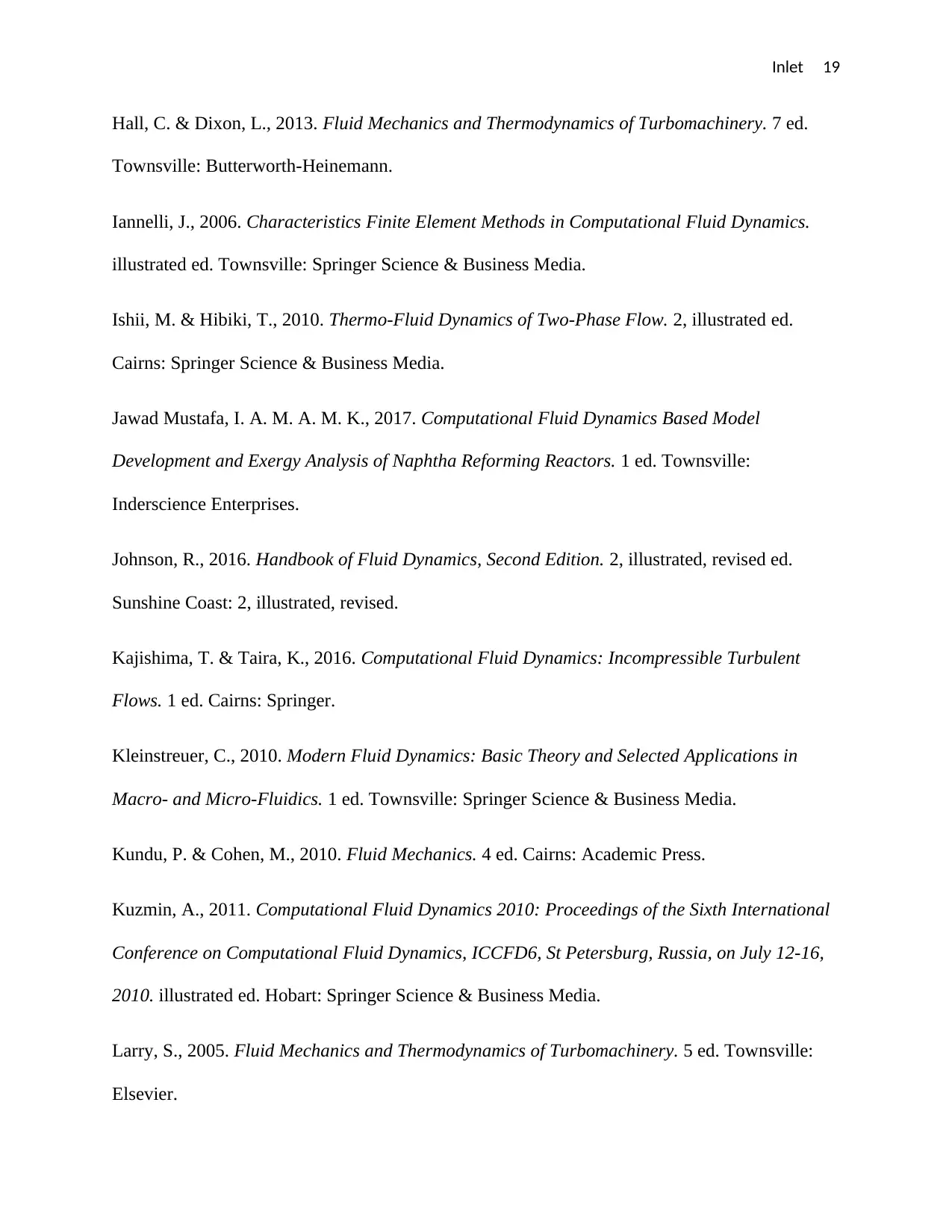
Inlet 19
Hall, C. & Dixon, L., 2013. Fluid Mechanics and Thermodynamics of Turbomachinery. 7 ed.
Townsville: Butterworth-Heinemann.
Iannelli, J., 2006. Characteristics Finite Element Methods in Computational Fluid Dynamics.
illustrated ed. Townsville: Springer Science & Business Media.
Ishii, M. & Hibiki, T., 2010. Thermo-Fluid Dynamics of Two-Phase Flow. 2, illustrated ed.
Cairns: Springer Science & Business Media.
Jawad Mustafa, I. A. M. A. M. K., 2017. Computational Fluid Dynamics Based Model
Development and Exergy Analysis of Naphtha Reforming Reactors. 1 ed. Townsville:
Inderscience Enterprises.
Johnson, R., 2016. Handbook of Fluid Dynamics, Second Edition. 2, illustrated, revised ed.
Sunshine Coast: 2, illustrated, revised.
Kajishima, T. & Taira, K., 2016. Computational Fluid Dynamics: Incompressible Turbulent
Flows. 1 ed. Cairns: Springer.
Kleinstreuer, C., 2010. Modern Fluid Dynamics: Basic Theory and Selected Applications in
Macro- and Micro-Fluidics. 1 ed. Townsville: Springer Science & Business Media.
Kundu, P. & Cohen, M., 2010. Fluid Mechanics. 4 ed. Cairns: Academic Press.
Kuzmin, A., 2011. Computational Fluid Dynamics 2010: Proceedings of the Sixth International
Conference on Computational Fluid Dynamics, ICCFD6, St Petersburg, Russia, on July 12-16,
2010. illustrated ed. Hobart: Springer Science & Business Media.
Larry, S., 2005. Fluid Mechanics and Thermodynamics of Turbomachinery. 5 ed. Townsville:
Elsevier.
Hall, C. & Dixon, L., 2013. Fluid Mechanics and Thermodynamics of Turbomachinery. 7 ed.
Townsville: Butterworth-Heinemann.
Iannelli, J., 2006. Characteristics Finite Element Methods in Computational Fluid Dynamics.
illustrated ed. Townsville: Springer Science & Business Media.
Ishii, M. & Hibiki, T., 2010. Thermo-Fluid Dynamics of Two-Phase Flow. 2, illustrated ed.
Cairns: Springer Science & Business Media.
Jawad Mustafa, I. A. M. A. M. K., 2017. Computational Fluid Dynamics Based Model
Development and Exergy Analysis of Naphtha Reforming Reactors. 1 ed. Townsville:
Inderscience Enterprises.
Johnson, R., 2016. Handbook of Fluid Dynamics, Second Edition. 2, illustrated, revised ed.
Sunshine Coast: 2, illustrated, revised.
Kajishima, T. & Taira, K., 2016. Computational Fluid Dynamics: Incompressible Turbulent
Flows. 1 ed. Cairns: Springer.
Kleinstreuer, C., 2010. Modern Fluid Dynamics: Basic Theory and Selected Applications in
Macro- and Micro-Fluidics. 1 ed. Townsville: Springer Science & Business Media.
Kundu, P. & Cohen, M., 2010. Fluid Mechanics. 4 ed. Cairns: Academic Press.
Kuzmin, A., 2011. Computational Fluid Dynamics 2010: Proceedings of the Sixth International
Conference on Computational Fluid Dynamics, ICCFD6, St Petersburg, Russia, on July 12-16,
2010. illustrated ed. Hobart: Springer Science & Business Media.
Larry, S., 2005. Fluid Mechanics and Thermodynamics of Turbomachinery. 5 ed. Townsville:
Elsevier.
Paraphrase This Document
Need a fresh take? Get an instant paraphrase of this document with our AI Paraphraser
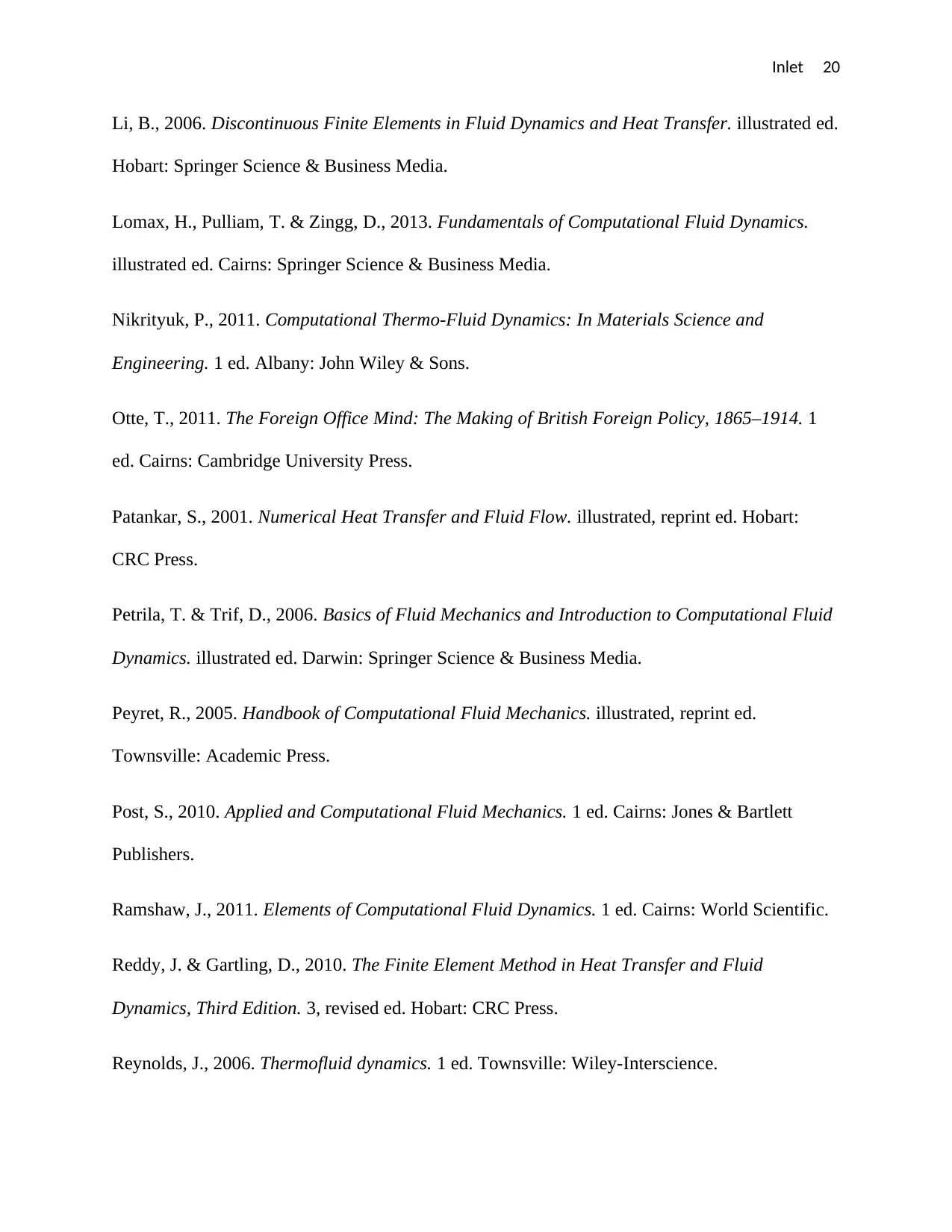
Inlet 20
Li, B., 2006. Discontinuous Finite Elements in Fluid Dynamics and Heat Transfer. illustrated ed.
Hobart: Springer Science & Business Media.
Lomax, H., Pulliam, T. & Zingg, D., 2013. Fundamentals of Computational Fluid Dynamics.
illustrated ed. Cairns: Springer Science & Business Media.
Nikrityuk, P., 2011. Computational Thermo-Fluid Dynamics: In Materials Science and
Engineering. 1 ed. Albany: John Wiley & Sons.
Otte, T., 2011. The Foreign Office Mind: The Making of British Foreign Policy, 1865–1914. 1
ed. Cairns: Cambridge University Press.
Patankar, S., 2001. Numerical Heat Transfer and Fluid Flow. illustrated, reprint ed. Hobart:
CRC Press.
Petrila, T. & Trif, D., 2006. Basics of Fluid Mechanics and Introduction to Computational Fluid
Dynamics. illustrated ed. Darwin: Springer Science & Business Media.
Peyret, R., 2005. Handbook of Computational Fluid Mechanics. illustrated, reprint ed.
Townsville: Academic Press.
Post, S., 2010. Applied and Computational Fluid Mechanics. 1 ed. Cairns: Jones & Bartlett
Publishers.
Ramshaw, J., 2011. Elements of Computational Fluid Dynamics. 1 ed. Cairns: World Scientific.
Reddy, J. & Gartling, D., 2010. The Finite Element Method in Heat Transfer and Fluid
Dynamics, Third Edition. 3, revised ed. Hobart: CRC Press.
Reynolds, J., 2006. Thermofluid dynamics. 1 ed. Townsville: Wiley-Interscience.
Li, B., 2006. Discontinuous Finite Elements in Fluid Dynamics and Heat Transfer. illustrated ed.
Hobart: Springer Science & Business Media.
Lomax, H., Pulliam, T. & Zingg, D., 2013. Fundamentals of Computational Fluid Dynamics.
illustrated ed. Cairns: Springer Science & Business Media.
Nikrityuk, P., 2011. Computational Thermo-Fluid Dynamics: In Materials Science and
Engineering. 1 ed. Albany: John Wiley & Sons.
Otte, T., 2011. The Foreign Office Mind: The Making of British Foreign Policy, 1865–1914. 1
ed. Cairns: Cambridge University Press.
Patankar, S., 2001. Numerical Heat Transfer and Fluid Flow. illustrated, reprint ed. Hobart:
CRC Press.
Petrila, T. & Trif, D., 2006. Basics of Fluid Mechanics and Introduction to Computational Fluid
Dynamics. illustrated ed. Darwin: Springer Science & Business Media.
Peyret, R., 2005. Handbook of Computational Fluid Mechanics. illustrated, reprint ed.
Townsville: Academic Press.
Post, S., 2010. Applied and Computational Fluid Mechanics. 1 ed. Cairns: Jones & Bartlett
Publishers.
Ramshaw, J., 2011. Elements of Computational Fluid Dynamics. 1 ed. Cairns: World Scientific.
Reddy, J. & Gartling, D., 2010. The Finite Element Method in Heat Transfer and Fluid
Dynamics, Third Edition. 3, revised ed. Hobart: CRC Press.
Reynolds, J., 2006. Thermofluid dynamics. 1 ed. Townsville: Wiley-Interscience.
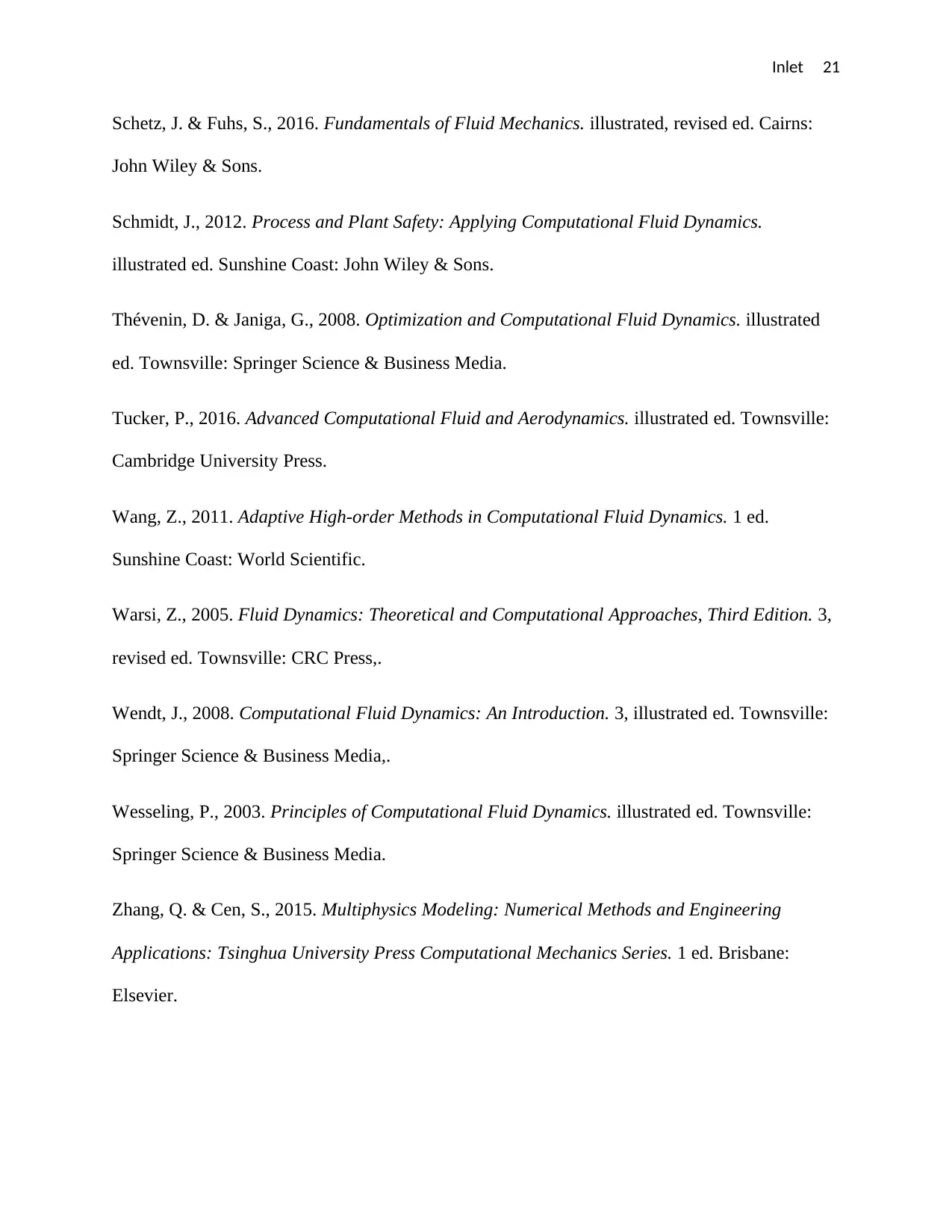
Inlet 21
Schetz, J. & Fuhs, S., 2016. Fundamentals of Fluid Mechanics. illustrated, revised ed. Cairns:
John Wiley & Sons.
Schmidt, J., 2012. Process and Plant Safety: Applying Computational Fluid Dynamics.
illustrated ed. Sunshine Coast: John Wiley & Sons.
Thévenin, D. & Janiga, G., 2008. Optimization and Computational Fluid Dynamics. illustrated
ed. Townsville: Springer Science & Business Media.
Tucker, P., 2016. Advanced Computational Fluid and Aerodynamics. illustrated ed. Townsville:
Cambridge University Press.
Wang, Z., 2011. Adaptive High-order Methods in Computational Fluid Dynamics. 1 ed.
Sunshine Coast: World Scientific.
Warsi, Z., 2005. Fluid Dynamics: Theoretical and Computational Approaches, Third Edition. 3,
revised ed. Townsville: CRC Press,.
Wendt, J., 2008. Computational Fluid Dynamics: An Introduction. 3, illustrated ed. Townsville:
Springer Science & Business Media,.
Wesseling, P., 2003. Principles of Computational Fluid Dynamics. illustrated ed. Townsville:
Springer Science & Business Media.
Zhang, Q. & Cen, S., 2015. Multiphysics Modeling: Numerical Methods and Engineering
Applications: Tsinghua University Press Computational Mechanics Series. 1 ed. Brisbane:
Elsevier.
Schetz, J. & Fuhs, S., 2016. Fundamentals of Fluid Mechanics. illustrated, revised ed. Cairns:
John Wiley & Sons.
Schmidt, J., 2012. Process and Plant Safety: Applying Computational Fluid Dynamics.
illustrated ed. Sunshine Coast: John Wiley & Sons.
Thévenin, D. & Janiga, G., 2008. Optimization and Computational Fluid Dynamics. illustrated
ed. Townsville: Springer Science & Business Media.
Tucker, P., 2016. Advanced Computational Fluid and Aerodynamics. illustrated ed. Townsville:
Cambridge University Press.
Wang, Z., 2011. Adaptive High-order Methods in Computational Fluid Dynamics. 1 ed.
Sunshine Coast: World Scientific.
Warsi, Z., 2005. Fluid Dynamics: Theoretical and Computational Approaches, Third Edition. 3,
revised ed. Townsville: CRC Press,.
Wendt, J., 2008. Computational Fluid Dynamics: An Introduction. 3, illustrated ed. Townsville:
Springer Science & Business Media,.
Wesseling, P., 2003. Principles of Computational Fluid Dynamics. illustrated ed. Townsville:
Springer Science & Business Media.
Zhang, Q. & Cen, S., 2015. Multiphysics Modeling: Numerical Methods and Engineering
Applications: Tsinghua University Press Computational Mechanics Series. 1 ed. Brisbane:
Elsevier.
1 out of 21
Related Documents
![[object Object]](/_next/image/?url=%2F_next%2Fstatic%2Fmedia%2Flogo.6d15ce61.png&w=640&q=75)
Your All-in-One AI-Powered Toolkit for Academic Success.
+13062052269
info@desklib.com
Available 24*7 on WhatsApp / Email
Unlock your academic potential
© 2024 | Zucol Services PVT LTD | All rights reserved.