CFD Analysis: Fluid Flow in Rectangular Pipe and Vehicle Models
VerifiedAdded on 2023/04/22
|24
|3839
|238
Report
AI Summary
This report presents a comprehensive CFD (Computational Fluid Dynamics) analysis, focusing on fluid flow simulations in various engineering applications. It begins with an overview of the objectives, including the comparison of fluid velocity and pressure in rectangular pipes, and the visualization of streamline and contour flows. The introduction covers CFD applications in civil, environmental, and naval engineering, particularly in the context of automobile and engine design. The methodology section details the step-by-step procedure using ANSYS software, including CAD model creation, mesh settings, boundary conditions, and solution methods. The report also discusses the finite element method and spectral method, comparing their approaches to solving partial differential equations. Furthermore, it covers the application of CFD in creating vehicle models, with and without spoilers, and outlines the process of meshing the model for accurate simulation results. The report also includes a discussion on the advantages and disadvantages of CFD, along with references for further reading.
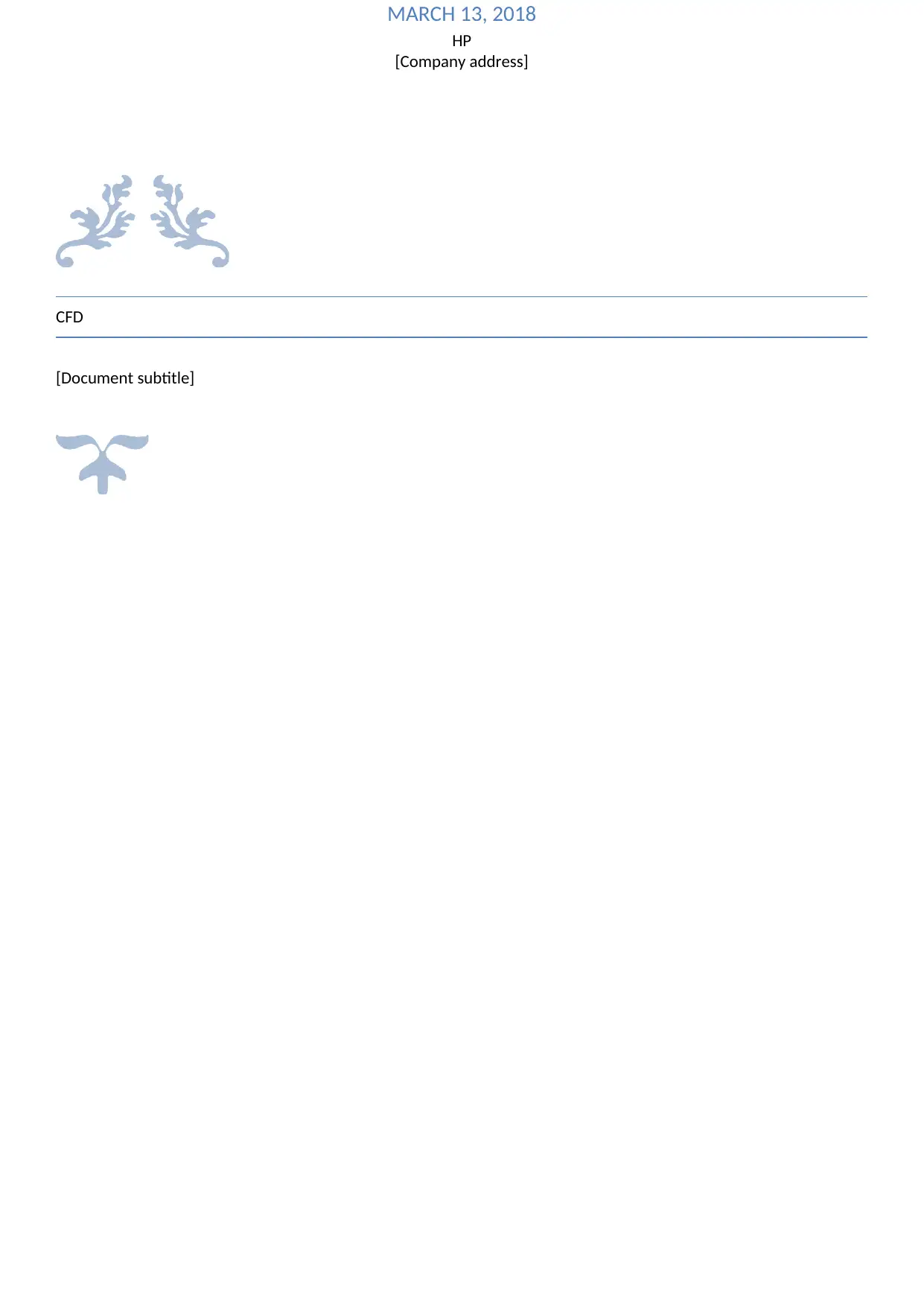
CFD
[Document subtitle]
MARCH 13, 2018
HP
[Company address]
[Document subtitle]
MARCH 13, 2018
HP
[Company address]
Secure Best Marks with AI Grader
Need help grading? Try our AI Grader for instant feedback on your assignments.
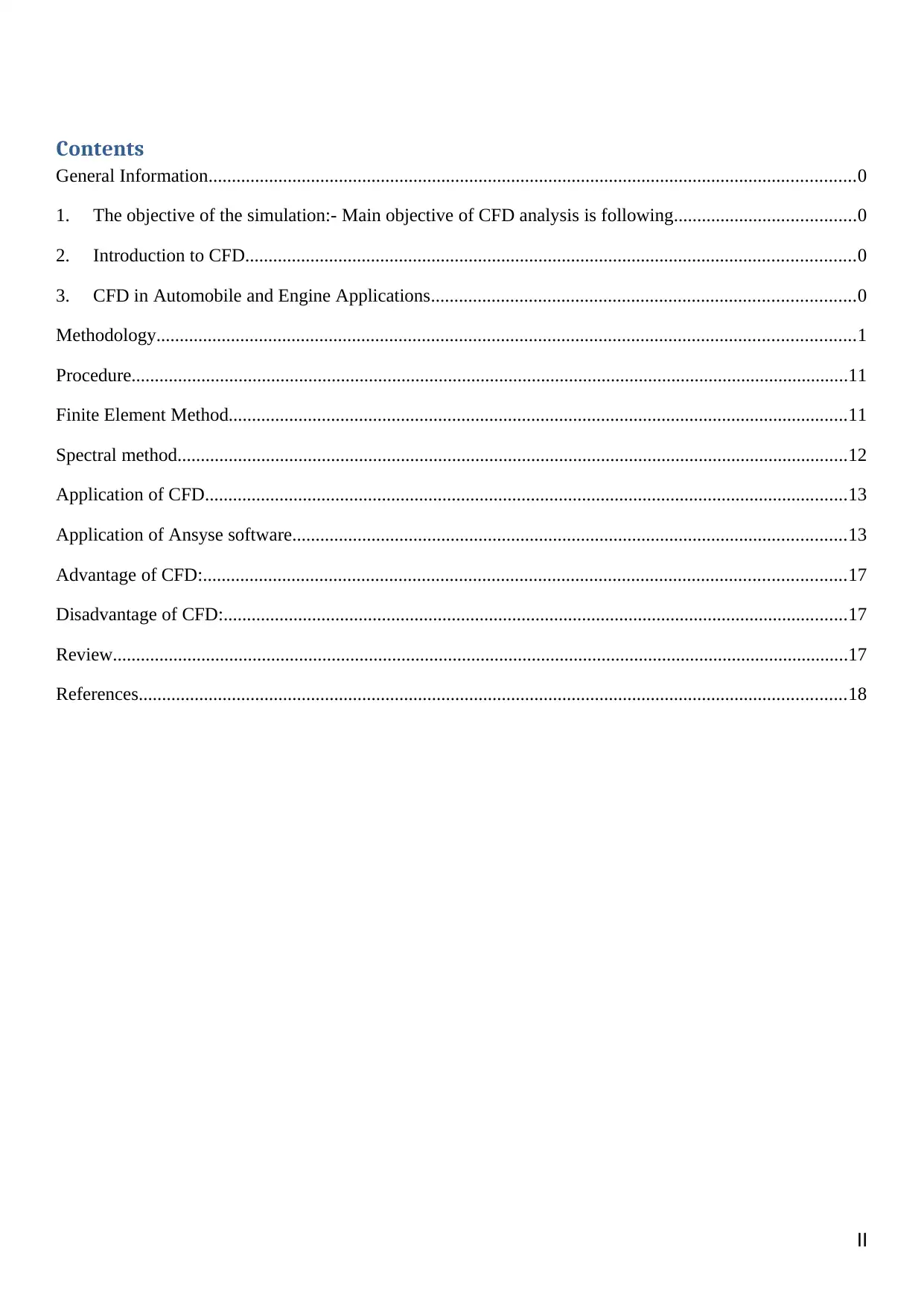
Contents
General Information...........................................................................................................................................0
1. The objective of the simulation:- Main objective of CFD analysis is following.......................................0
2. Introduction to CFD...................................................................................................................................0
3. CFD in Automobile and Engine Applications...........................................................................................0
Methodology......................................................................................................................................................1
Procedure..........................................................................................................................................................11
Finite Element Method.....................................................................................................................................11
Spectral method................................................................................................................................................12
Application of CFD..........................................................................................................................................13
Application of Ansyse software.......................................................................................................................13
Advantage of CFD:..........................................................................................................................................17
Disadvantage of CFD:......................................................................................................................................17
Review..............................................................................................................................................................17
References........................................................................................................................................................18
II
General Information...........................................................................................................................................0
1. The objective of the simulation:- Main objective of CFD analysis is following.......................................0
2. Introduction to CFD...................................................................................................................................0
3. CFD in Automobile and Engine Applications...........................................................................................0
Methodology......................................................................................................................................................1
Procedure..........................................................................................................................................................11
Finite Element Method.....................................................................................................................................11
Spectral method................................................................................................................................................12
Application of CFD..........................................................................................................................................13
Application of Ansyse software.......................................................................................................................13
Advantage of CFD:..........................................................................................................................................17
Disadvantage of CFD:......................................................................................................................................17
Review..............................................................................................................................................................17
References........................................................................................................................................................18
II
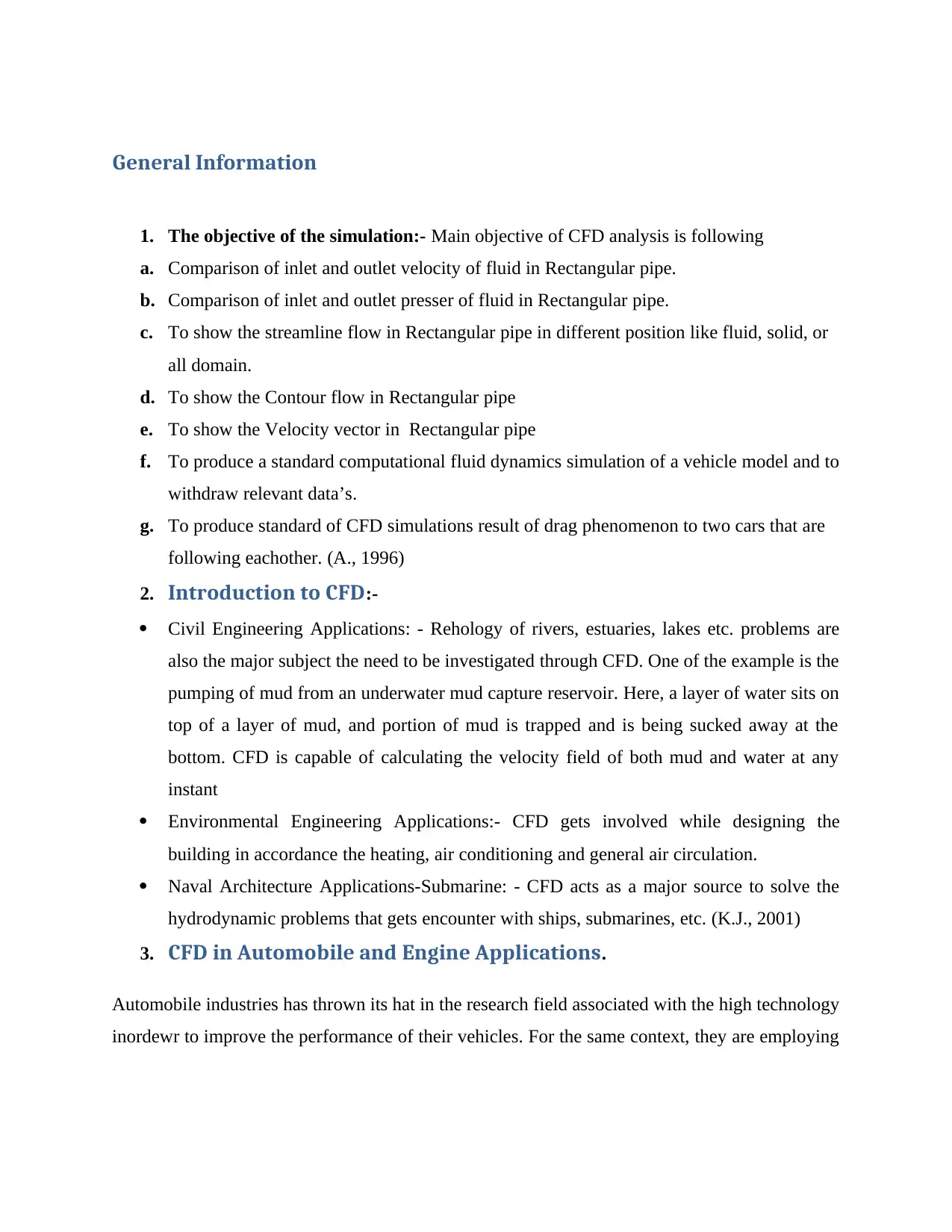
General Information
1. The objective of the simulation:- Main objective of CFD analysis is following
a. Comparison of inlet and outlet velocity of fluid in Rectangular pipe.
b. Comparison of inlet and outlet presser of fluid in Rectangular pipe.
c. To show the streamline flow in Rectangular pipe in different position like fluid, solid, or
all domain.
d. To show the Contour flow in Rectangular pipe
e. To show the Velocity vector in Rectangular pipe
f. To produce a standard computational fluid dynamics simulation of a vehicle model and to
withdraw relevant data’s.
g. To produce standard of CFD simulations result of drag phenomenon to two cars that are
following eachother. (A., 1996)
2. Introduction to CFD:-
Civil Engineering Applications: - Rehology of rivers, estuaries, lakes etc. problems are
also the major subject the need to be investigated through CFD. One of the example is the
pumping of mud from an underwater mud capture reservoir. Here, a layer of water sits on
top of a layer of mud, and portion of mud is trapped and is being sucked away at the
bottom. CFD is capable of calculating the velocity field of both mud and water at any
instant
Environmental Engineering Applications:- CFD gets involved while designing the
building in accordance the heating, air conditioning and general air circulation.
Naval Architecture Applications-Submarine: - CFD acts as a major source to solve the
hydrodynamic problems that gets encounter with ships, submarines, etc. (K.J., 2001)
3. CFD in Automobile and Engine Applications.
Automobile industries has thrown its hat in the research field associated with the high technology
inordewr to improve the performance of their vehicles. For the same context, they are employing
1. The objective of the simulation:- Main objective of CFD analysis is following
a. Comparison of inlet and outlet velocity of fluid in Rectangular pipe.
b. Comparison of inlet and outlet presser of fluid in Rectangular pipe.
c. To show the streamline flow in Rectangular pipe in different position like fluid, solid, or
all domain.
d. To show the Contour flow in Rectangular pipe
e. To show the Velocity vector in Rectangular pipe
f. To produce a standard computational fluid dynamics simulation of a vehicle model and to
withdraw relevant data’s.
g. To produce standard of CFD simulations result of drag phenomenon to two cars that are
following eachother. (A., 1996)
2. Introduction to CFD:-
Civil Engineering Applications: - Rehology of rivers, estuaries, lakes etc. problems are
also the major subject the need to be investigated through CFD. One of the example is the
pumping of mud from an underwater mud capture reservoir. Here, a layer of water sits on
top of a layer of mud, and portion of mud is trapped and is being sucked away at the
bottom. CFD is capable of calculating the velocity field of both mud and water at any
instant
Environmental Engineering Applications:- CFD gets involved while designing the
building in accordance the heating, air conditioning and general air circulation.
Naval Architecture Applications-Submarine: - CFD acts as a major source to solve the
hydrodynamic problems that gets encounter with ships, submarines, etc. (K.J., 2001)
3. CFD in Automobile and Engine Applications.
Automobile industries has thrown its hat in the research field associated with the high technology
inordewr to improve the performance of their vehicles. For the same context, they are employing
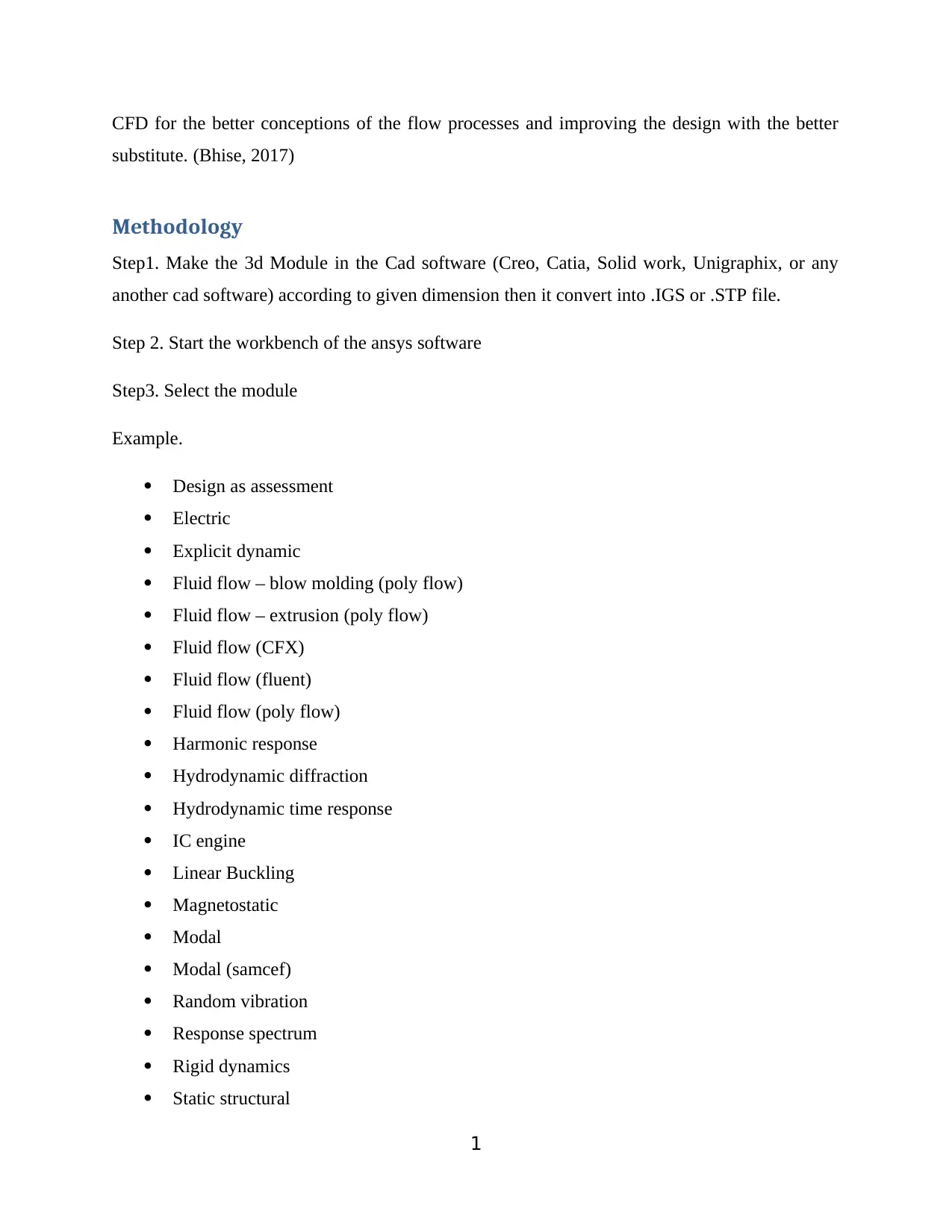
CFD for the better conceptions of the flow processes and improving the design with the better
substitute. (Bhise, 2017)
Methodology
Step1. Make the 3d Module in the Cad software (Creo, Catia, Solid work, Unigraphix, or any
another cad software) according to given dimension then it convert into .IGS or .STP file.
Step 2. Start the workbench of the ansys software
Step3. Select the module
Example.
Design as assessment
Electric
Explicit dynamic
Fluid flow – blow molding (poly flow)
Fluid flow – extrusion (poly flow)
Fluid flow (CFX)
Fluid flow (fluent)
Fluid flow (poly flow)
Harmonic response
Hydrodynamic diffraction
Hydrodynamic time response
IC engine
Linear Buckling
Magnetostatic
Modal
Modal (samcef)
Random vibration
Response spectrum
Rigid dynamics
Static structural
1
substitute. (Bhise, 2017)
Methodology
Step1. Make the 3d Module in the Cad software (Creo, Catia, Solid work, Unigraphix, or any
another cad software) according to given dimension then it convert into .IGS or .STP file.
Step 2. Start the workbench of the ansys software
Step3. Select the module
Example.
Design as assessment
Electric
Explicit dynamic
Fluid flow – blow molding (poly flow)
Fluid flow – extrusion (poly flow)
Fluid flow (CFX)
Fluid flow (fluent)
Fluid flow (poly flow)
Harmonic response
Hydrodynamic diffraction
Hydrodynamic time response
IC engine
Linear Buckling
Magnetostatic
Modal
Modal (samcef)
Random vibration
Response spectrum
Rigid dynamics
Static structural
1
Secure Best Marks with AI Grader
Need help grading? Try our AI Grader for instant feedback on your assignments.
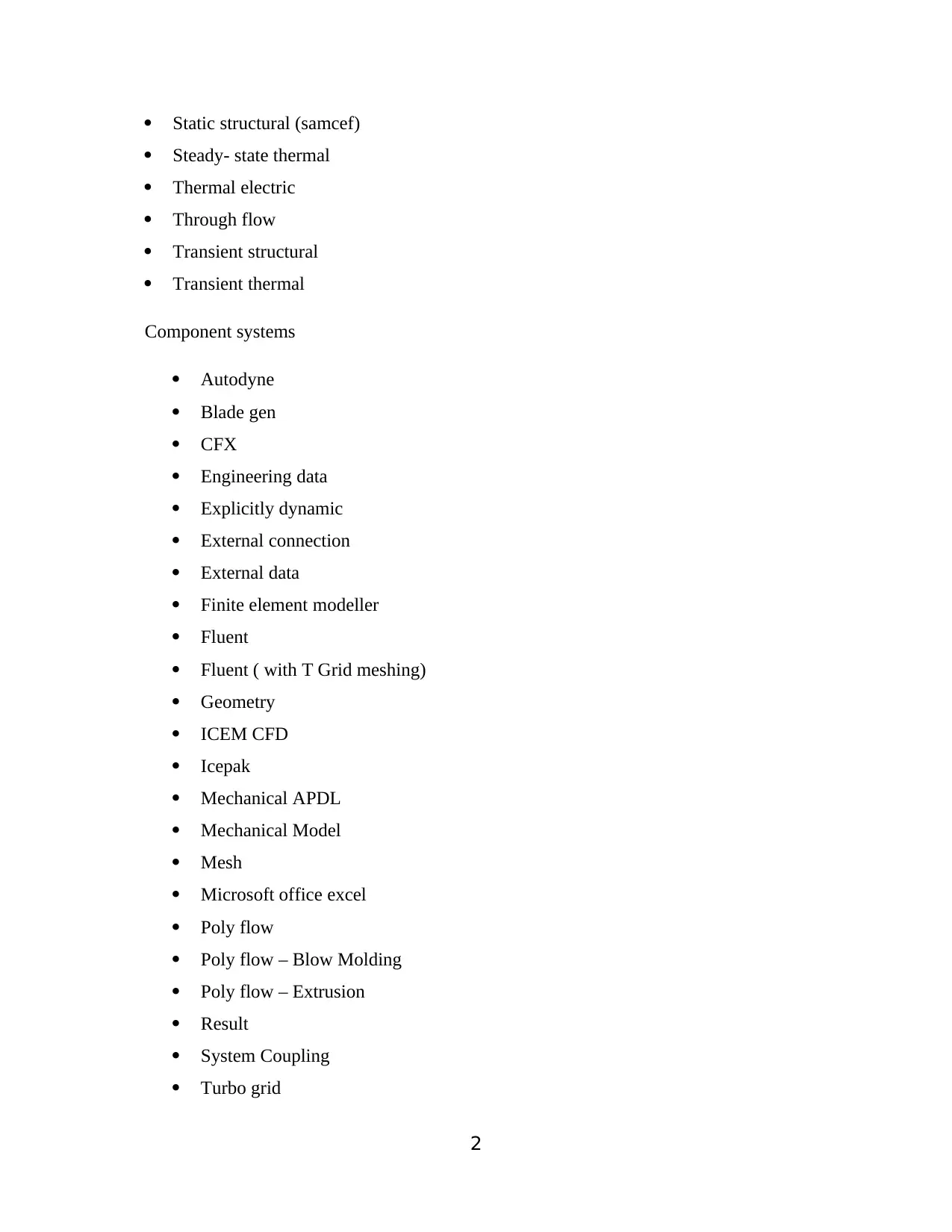
Static structural (samcef)
Steady- state thermal
Thermal electric
Through flow
Transient structural
Transient thermal
Component systems
Autodyne
Blade gen
CFX
Engineering data
Explicitly dynamic
External connection
External data
Finite element modeller
Fluent
Fluent ( with T Grid meshing)
Geometry
ICEM CFD
Icepak
Mechanical APDL
Mechanical Model
Mesh
Microsoft office excel
Poly flow
Poly flow – Blow Molding
Poly flow – Extrusion
Result
System Coupling
Turbo grid
2
Steady- state thermal
Thermal electric
Through flow
Transient structural
Transient thermal
Component systems
Autodyne
Blade gen
CFX
Engineering data
Explicitly dynamic
External connection
External data
Finite element modeller
Fluent
Fluent ( with T Grid meshing)
Geometry
ICEM CFD
Icepak
Mechanical APDL
Mechanical Model
Mesh
Microsoft office excel
Poly flow
Poly flow – Blow Molding
Poly flow – Extrusion
Result
System Coupling
Turbo grid
2
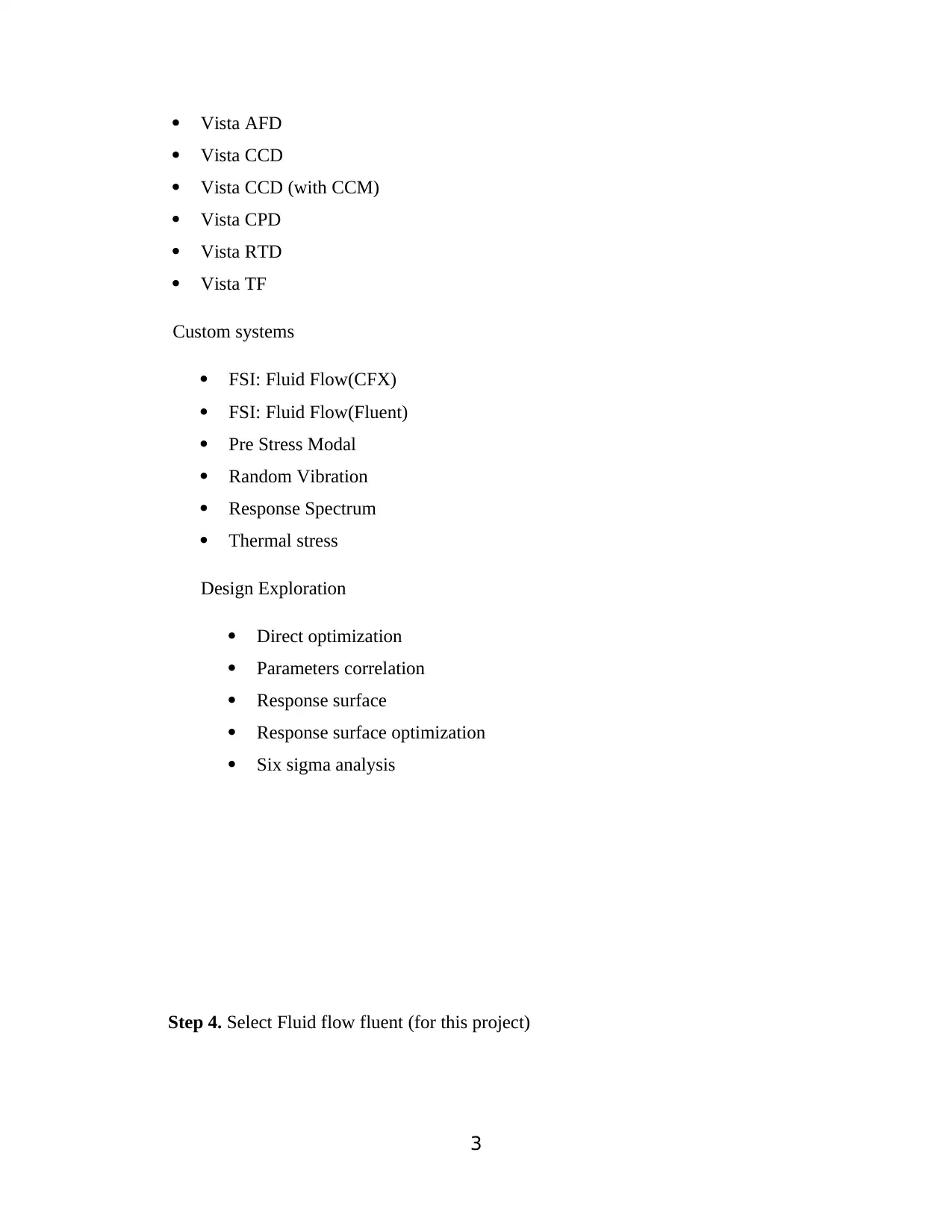
Vista AFD
Vista CCD
Vista CCD (with CCM)
Vista CPD
Vista RTD
Vista TF
Custom systems
FSI: Fluid Flow(CFX)
FSI: Fluid Flow(Fluent)
Pre Stress Modal
Random Vibration
Response Spectrum
Thermal stress
Design Exploration
Direct optimization
Parameters correlation
Response surface
Response surface optimization
Six sigma analysis
Step 4. Select Fluid flow fluent (for this project)
3
Vista CCD
Vista CCD (with CCM)
Vista CPD
Vista RTD
Vista TF
Custom systems
FSI: Fluid Flow(CFX)
FSI: Fluid Flow(Fluent)
Pre Stress Modal
Random Vibration
Response Spectrum
Thermal stress
Design Exploration
Direct optimization
Parameters correlation
Response surface
Response surface optimization
Six sigma analysis
Step 4. Select Fluid flow fluent (for this project)
3
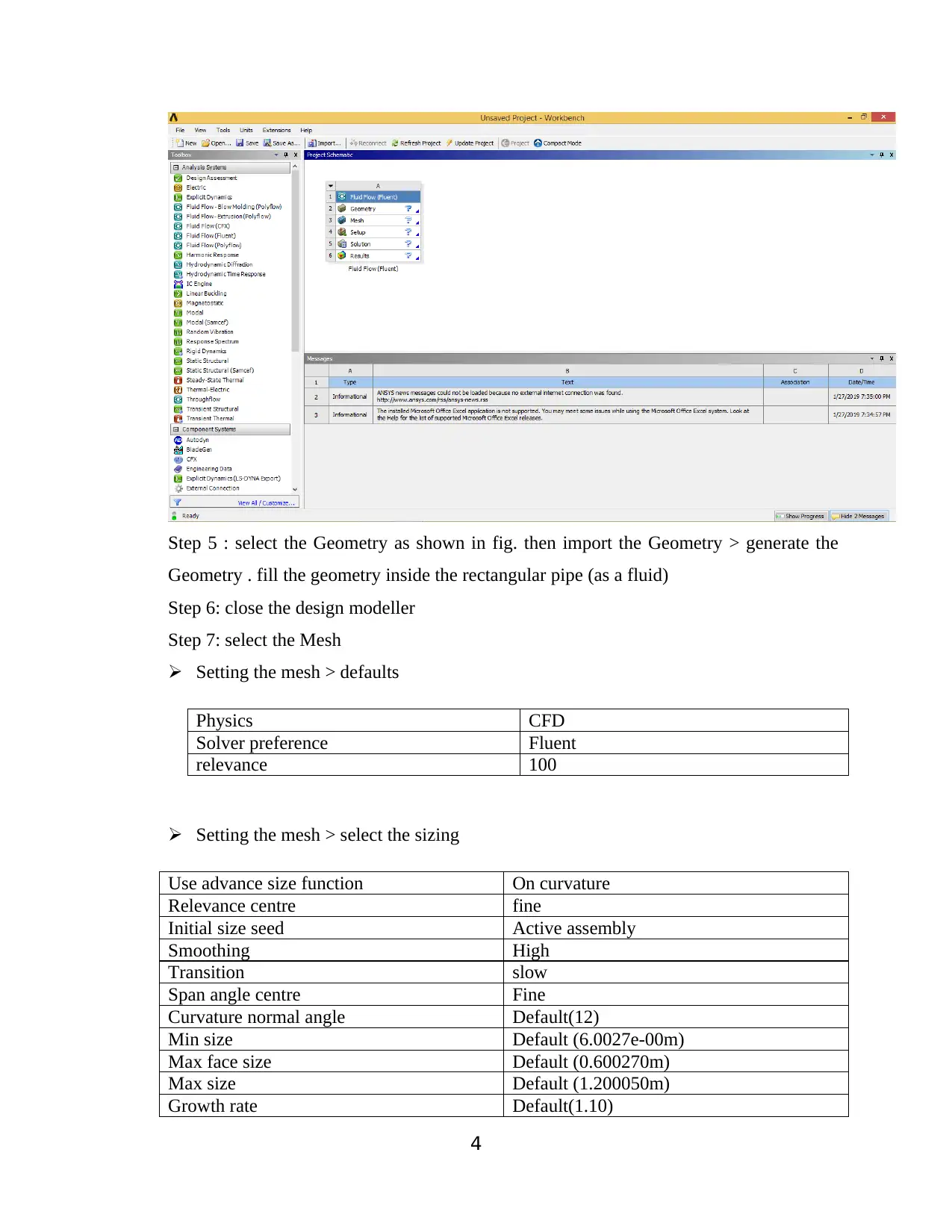
Step 5 : select the Geometry as shown in fig. then import the Geometry > generate the
Geometry . fill the geometry inside the rectangular pipe (as a fluid)
Step 6: close the design modeller
Step 7: select the Mesh
Setting the mesh > defaults
Physics CFD
Solver preference Fluent
relevance 100
Setting the mesh > select the sizing
Use advance size function On curvature
Relevance centre fine
Initial size seed Active assembly
Smoothing High
Transition slow
Span angle centre Fine
Curvature normal angle Default(12)
Min size Default (6.0027e-00m)
Max face size Default (0.600270m)
Max size Default (1.200050m)
Growth rate Default(1.10)
4
Geometry . fill the geometry inside the rectangular pipe (as a fluid)
Step 6: close the design modeller
Step 7: select the Mesh
Setting the mesh > defaults
Physics CFD
Solver preference Fluent
relevance 100
Setting the mesh > select the sizing
Use advance size function On curvature
Relevance centre fine
Initial size seed Active assembly
Smoothing High
Transition slow
Span angle centre Fine
Curvature normal angle Default(12)
Min size Default (6.0027e-00m)
Max face size Default (0.600270m)
Max size Default (1.200050m)
Growth rate Default(1.10)
4
Paraphrase This Document
Need a fresh take? Get an instant paraphrase of this document with our AI Paraphraser
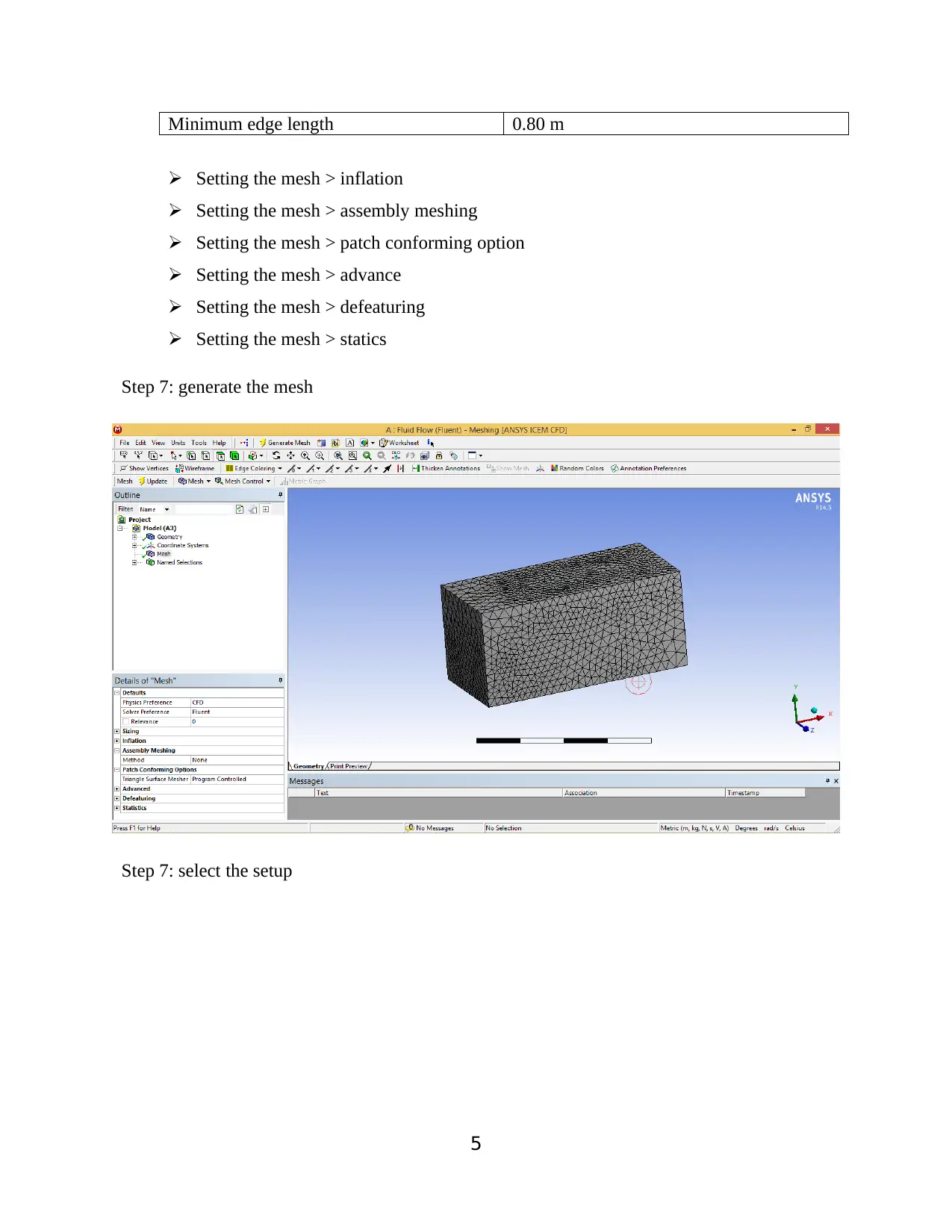
Minimum edge length 0.80 m
Setting the mesh > inflation
Setting the mesh > assembly meshing
Setting the mesh > patch conforming option
Setting the mesh > advance
Setting the mesh > defeaturing
Setting the mesh > statics
Step 7: generate the mesh
Step 7: select the setup
5
Setting the mesh > inflation
Setting the mesh > assembly meshing
Setting the mesh > patch conforming option
Setting the mesh > advance
Setting the mesh > defeaturing
Setting the mesh > statics
Step 7: generate the mesh
Step 7: select the setup
5
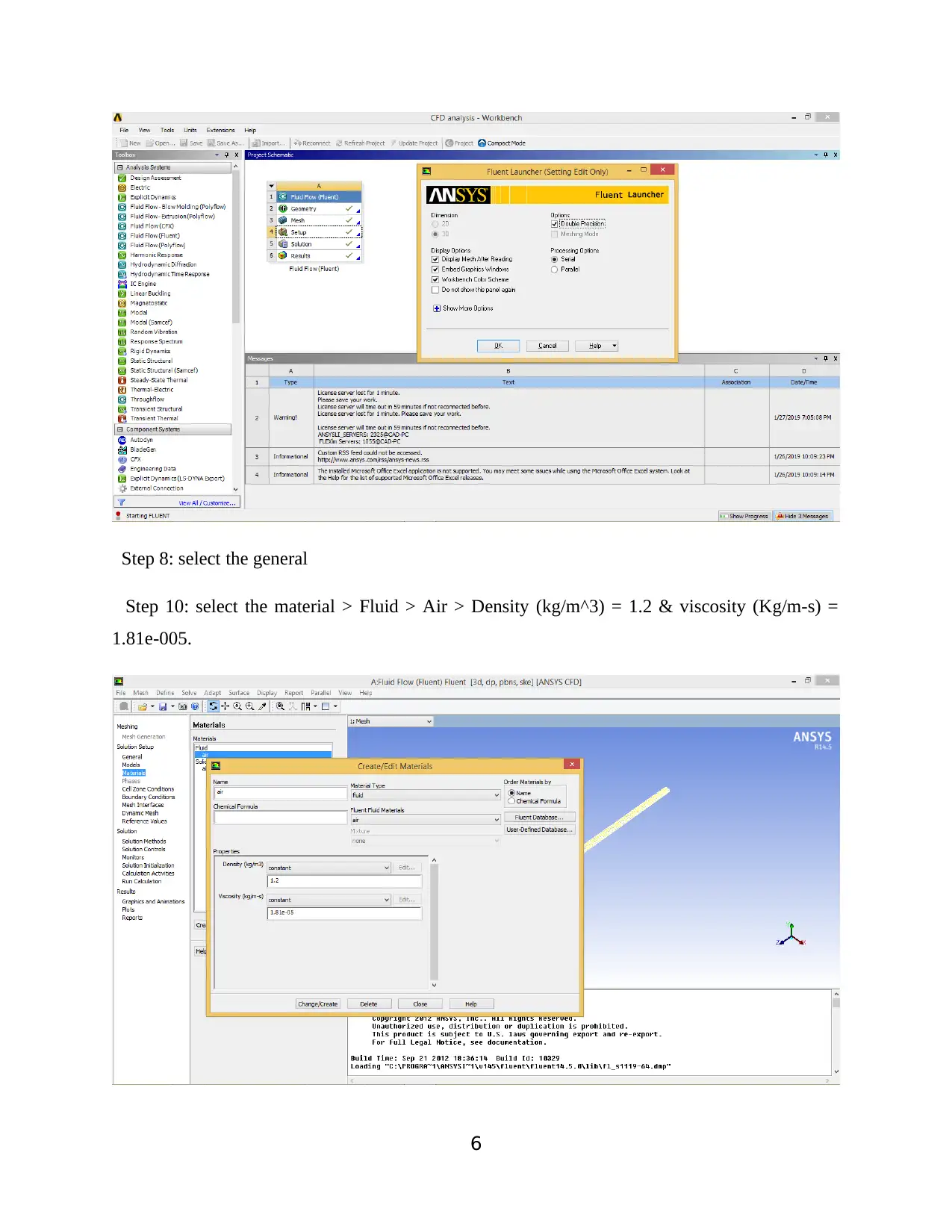
Step 8: select the general
Step 10: select the material > Fluid > Air > Density (kg/m^3) = 1.2 & viscosity (Kg/m-s) =
1.81e-005.
6
Step 10: select the material > Fluid > Air > Density (kg/m^3) = 1.2 & viscosity (Kg/m-s) =
1.81e-005.
6
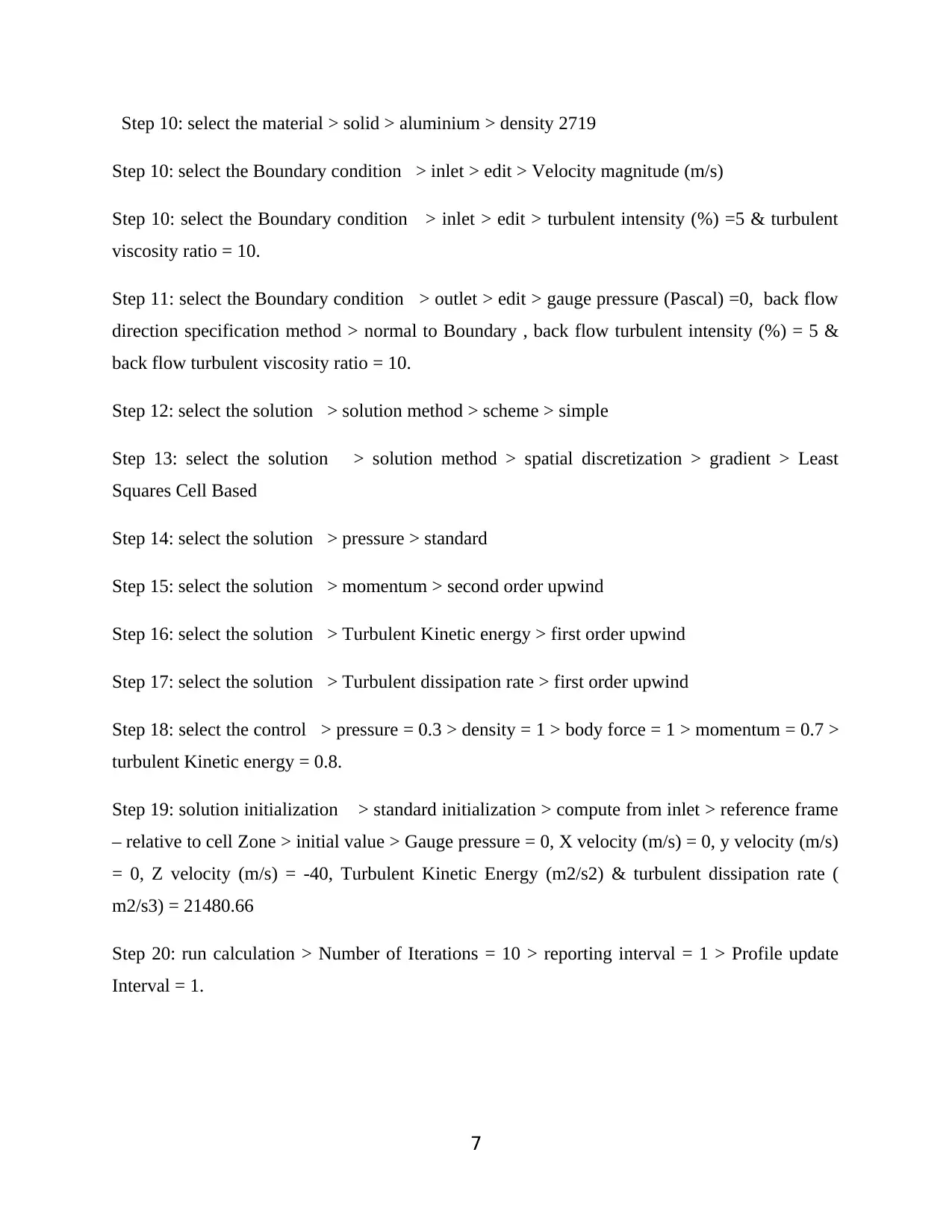
Step 10: select the material > solid > aluminium > density 2719
Step 10: select the Boundary condition > inlet > edit > Velocity magnitude (m/s)
Step 10: select the Boundary condition > inlet > edit > turbulent intensity (%) =5 & turbulent
viscosity ratio = 10.
Step 11: select the Boundary condition > outlet > edit > gauge pressure (Pascal) =0, back flow
direction specification method > normal to Boundary , back flow turbulent intensity (%) = 5 &
back flow turbulent viscosity ratio = 10.
Step 12: select the solution > solution method > scheme > simple
Step 13: select the solution > solution method > spatial discretization > gradient > Least
Squares Cell Based
Step 14: select the solution > pressure > standard
Step 15: select the solution > momentum > second order upwind
Step 16: select the solution > Turbulent Kinetic energy > first order upwind
Step 17: select the solution > Turbulent dissipation rate > first order upwind
Step 18: select the control > pressure = 0.3 > density = 1 > body force = 1 > momentum = 0.7 >
turbulent Kinetic energy = 0.8.
Step 19: solution initialization > standard initialization > compute from inlet > reference frame
– relative to cell Zone > initial value > Gauge pressure = 0, X velocity (m/s) = 0, y velocity (m/s)
= 0, Z velocity (m/s) = -40, Turbulent Kinetic Energy (m2/s2) & turbulent dissipation rate (
m2/s3) = 21480.66
Step 20: run calculation > Number of Iterations = 10 > reporting interval = 1 > Profile update
Interval = 1.
7
Step 10: select the Boundary condition > inlet > edit > Velocity magnitude (m/s)
Step 10: select the Boundary condition > inlet > edit > turbulent intensity (%) =5 & turbulent
viscosity ratio = 10.
Step 11: select the Boundary condition > outlet > edit > gauge pressure (Pascal) =0, back flow
direction specification method > normal to Boundary , back flow turbulent intensity (%) = 5 &
back flow turbulent viscosity ratio = 10.
Step 12: select the solution > solution method > scheme > simple
Step 13: select the solution > solution method > spatial discretization > gradient > Least
Squares Cell Based
Step 14: select the solution > pressure > standard
Step 15: select the solution > momentum > second order upwind
Step 16: select the solution > Turbulent Kinetic energy > first order upwind
Step 17: select the solution > Turbulent dissipation rate > first order upwind
Step 18: select the control > pressure = 0.3 > density = 1 > body force = 1 > momentum = 0.7 >
turbulent Kinetic energy = 0.8.
Step 19: solution initialization > standard initialization > compute from inlet > reference frame
– relative to cell Zone > initial value > Gauge pressure = 0, X velocity (m/s) = 0, y velocity (m/s)
= 0, Z velocity (m/s) = -40, Turbulent Kinetic Energy (m2/s2) & turbulent dissipation rate (
m2/s3) = 21480.66
Step 20: run calculation > Number of Iterations = 10 > reporting interval = 1 > Profile update
Interval = 1.
7
Secure Best Marks with AI Grader
Need help grading? Try our AI Grader for instant feedback on your assignments.

Step 21: result > Graph and Animation
Step 22: result > plots
Step 23: result > reports
Step 24: file > close fluent
Step 25: results > select Stream line > Geometry
Type 3 D streamline
Domains All domain
Start from inlet
sampling Equally spaced
# of point 25
variable velocity
8
Step 22: result > plots
Step 23: result > reports
Step 24: file > close fluent
Step 25: results > select Stream line > Geometry
Type 3 D streamline
Domains All domain
Start from inlet
sampling Equally spaced
# of point 25
variable velocity
8
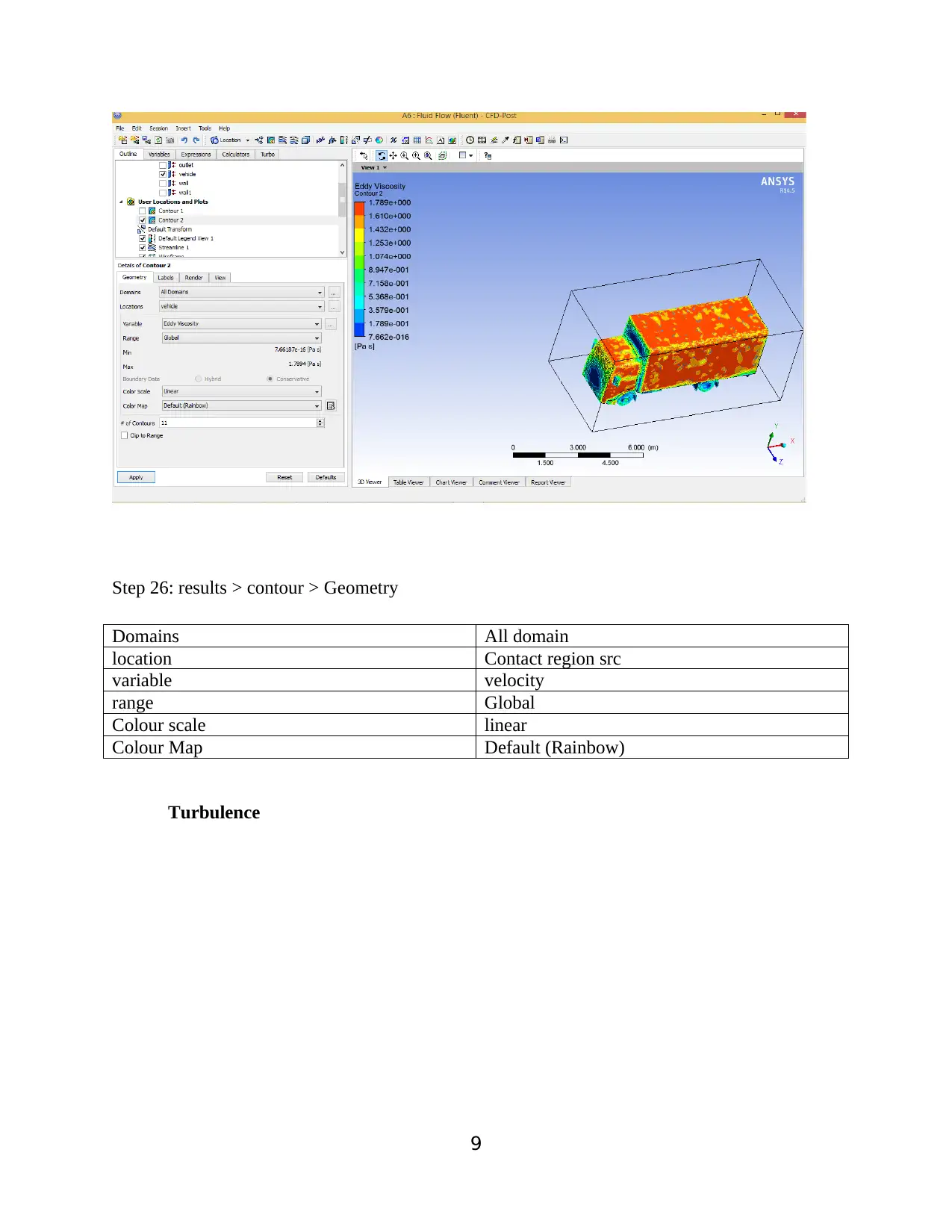
Step 26: results > contour > Geometry
Domains All domain
location Contact region src
variable velocity
range Global
Colour scale linear
Colour Map Default (Rainbow)
Turbulence
9
Domains All domain
location Contact region src
variable velocity
range Global
Colour scale linear
Colour Map Default (Rainbow)
Turbulence
9
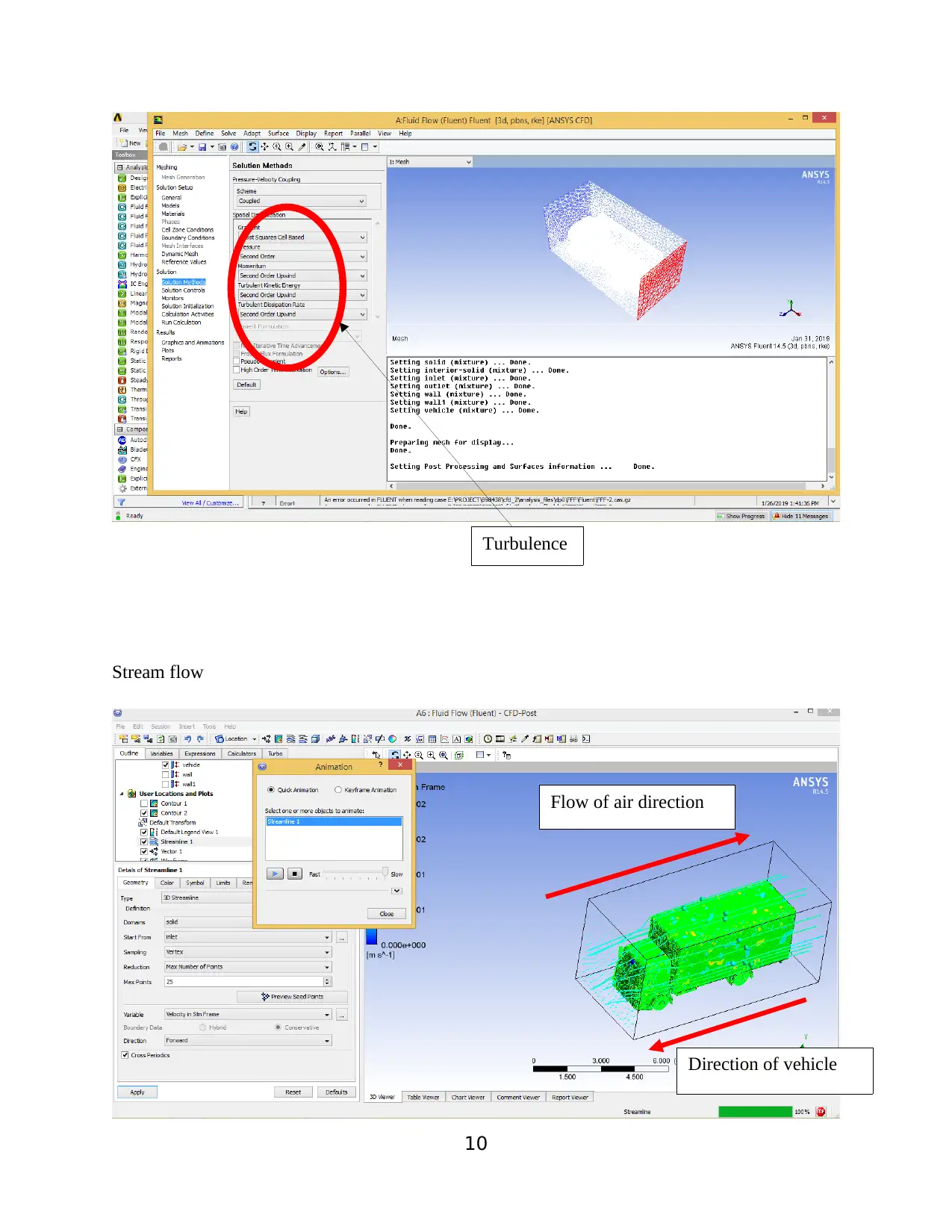
Stream flow
10
Turbulence
Flow of air direction
Direction of vehicle
10
Turbulence
Flow of air direction
Direction of vehicle
Paraphrase This Document
Need a fresh take? Get an instant paraphrase of this document with our AI Paraphraser
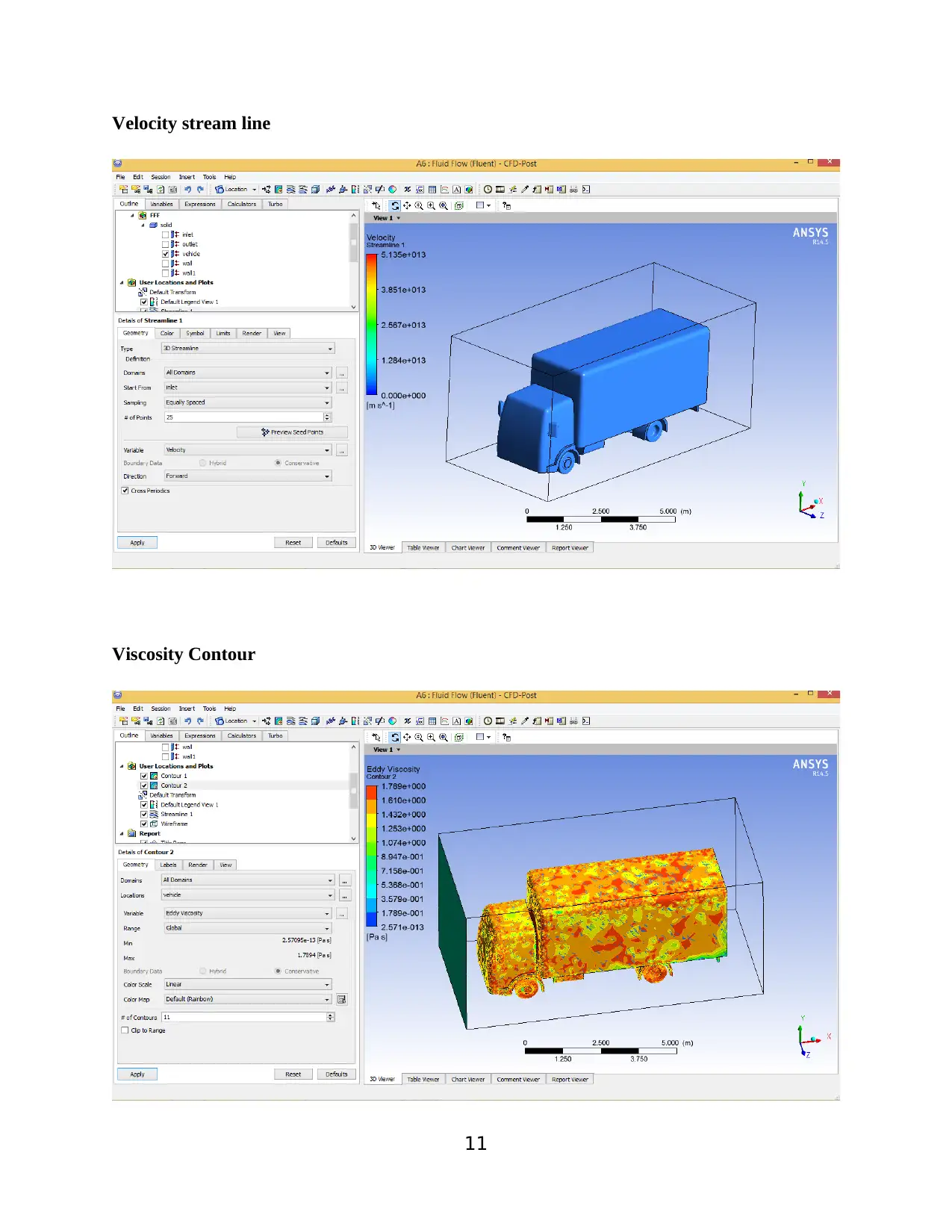
Velocity stream line
Viscosity Contour
11
Viscosity Contour
11
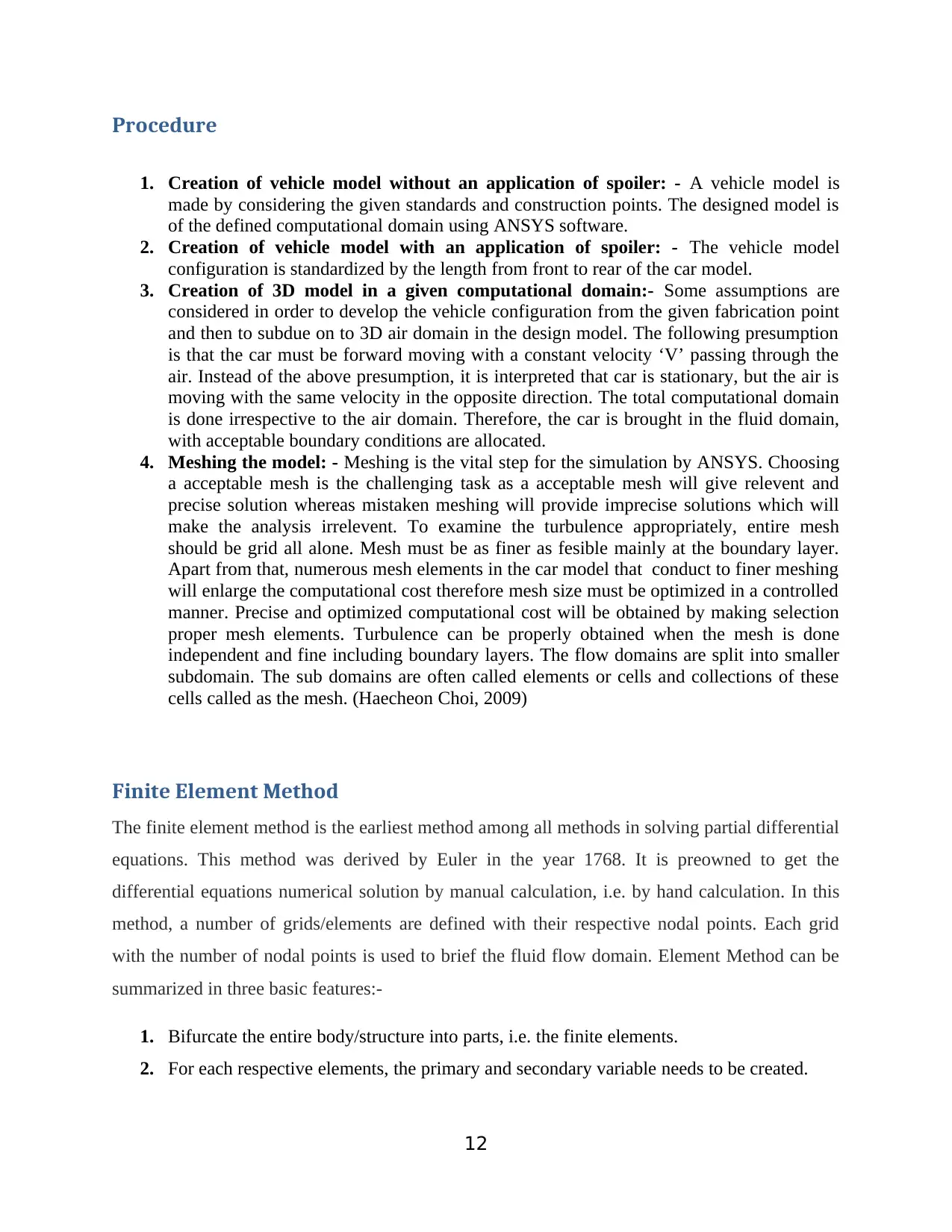
Procedure
1. Creation of vehicle model without an application of spoiler: - A vehicle model is
made by considering the given standards and construction points. The designed model is
of the defined computational domain using ANSYS software.
2. Creation of vehicle model with an application of spoiler: - The vehicle model
configuration is standardized by the length from front to rear of the car model.
3. Creation of 3D model in a given computational domain:- Some assumptions are
considered in order to develop the vehicle configuration from the given fabrication point
and then to subdue on to 3D air domain in the design model. The following presumption
is that the car must be forward moving with a constant velocity ‘V’ passing through the
air. Instead of the above presumption, it is interpreted that car is stationary, but the air is
moving with the same velocity in the opposite direction. The total computational domain
is done irrespective to the air domain. Therefore, the car is brought in the fluid domain,
with acceptable boundary conditions are allocated.
4. Meshing the model: - Meshing is the vital step for the simulation by ANSYS. Choosing
a acceptable mesh is the challenging task as a acceptable mesh will give relevent and
precise solution whereas mistaken meshing will provide imprecise solutions which will
make the analysis irrelevent. To examine the turbulence appropriately, entire mesh
should be grid all alone. Mesh must be as finer as fesible mainly at the boundary layer.
Apart from that, numerous mesh elements in the car model that conduct to finer meshing
will enlarge the computational cost therefore mesh size must be optimized in a controlled
manner. Precise and optimized computational cost will be obtained by making selection
proper mesh elements. Turbulence can be properly obtained when the mesh is done
independent and fine including boundary layers. The flow domains are split into smaller
subdomain. The sub domains are often called elements or cells and collections of these
cells called as the mesh. (Haecheon Choi, 2009)
Finite Element Method
The finite element method is the earliest method among all methods in solving partial differential
equations. This method was derived by Euler in the year 1768. It is preowned to get the
differential equations numerical solution by manual calculation, i.e. by hand calculation. In this
method, a number of grids/elements are defined with their respective nodal points. Each grid
with the number of nodal points is used to brief the fluid flow domain. Element Method can be
summarized in three basic features:-
1. Bifurcate the entire body/structure into parts, i.e. the finite elements.
2. For each respective elements, the primary and secondary variable needs to be created.
12
1. Creation of vehicle model without an application of spoiler: - A vehicle model is
made by considering the given standards and construction points. The designed model is
of the defined computational domain using ANSYS software.
2. Creation of vehicle model with an application of spoiler: - The vehicle model
configuration is standardized by the length from front to rear of the car model.
3. Creation of 3D model in a given computational domain:- Some assumptions are
considered in order to develop the vehicle configuration from the given fabrication point
and then to subdue on to 3D air domain in the design model. The following presumption
is that the car must be forward moving with a constant velocity ‘V’ passing through the
air. Instead of the above presumption, it is interpreted that car is stationary, but the air is
moving with the same velocity in the opposite direction. The total computational domain
is done irrespective to the air domain. Therefore, the car is brought in the fluid domain,
with acceptable boundary conditions are allocated.
4. Meshing the model: - Meshing is the vital step for the simulation by ANSYS. Choosing
a acceptable mesh is the challenging task as a acceptable mesh will give relevent and
precise solution whereas mistaken meshing will provide imprecise solutions which will
make the analysis irrelevent. To examine the turbulence appropriately, entire mesh
should be grid all alone. Mesh must be as finer as fesible mainly at the boundary layer.
Apart from that, numerous mesh elements in the car model that conduct to finer meshing
will enlarge the computational cost therefore mesh size must be optimized in a controlled
manner. Precise and optimized computational cost will be obtained by making selection
proper mesh elements. Turbulence can be properly obtained when the mesh is done
independent and fine including boundary layers. The flow domains are split into smaller
subdomain. The sub domains are often called elements or cells and collections of these
cells called as the mesh. (Haecheon Choi, 2009)
Finite Element Method
The finite element method is the earliest method among all methods in solving partial differential
equations. This method was derived by Euler in the year 1768. It is preowned to get the
differential equations numerical solution by manual calculation, i.e. by hand calculation. In this
method, a number of grids/elements are defined with their respective nodal points. Each grid
with the number of nodal points is used to brief the fluid flow domain. Element Method can be
summarized in three basic features:-
1. Bifurcate the entire body/structure into parts, i.e. the finite elements.
2. For each respective elements, the primary and secondary variable needs to be created.
12
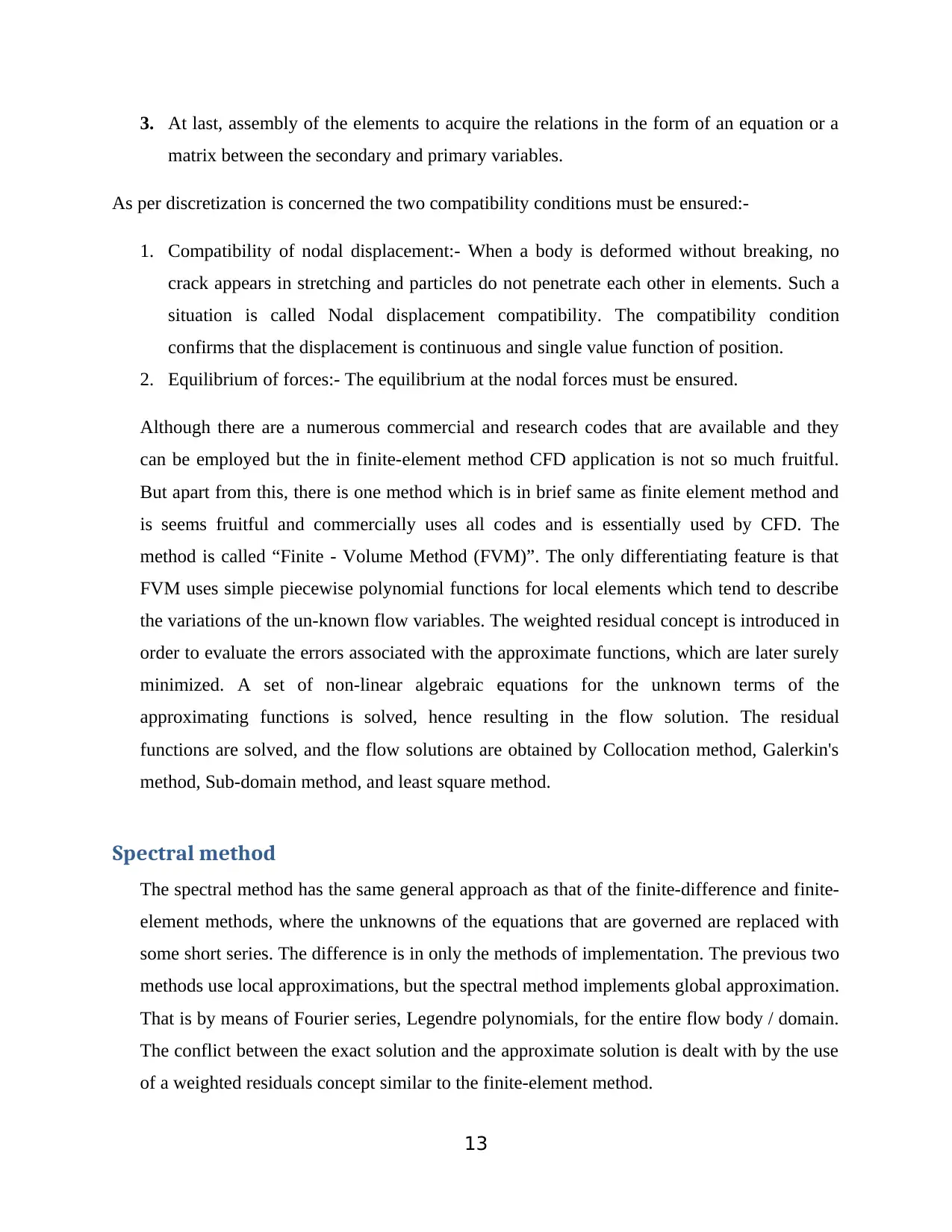
3. At last, assembly of the elements to acquire the relations in the form of an equation or a
matrix between the secondary and primary variables.
As per discretization is concerned the two compatibility conditions must be ensured:-
1. Compatibility of nodal displacement:- When a body is deformed without breaking, no
crack appears in stretching and particles do not penetrate each other in elements. Such a
situation is called Nodal displacement compatibility. The compatibility condition
confirms that the displacement is continuous and single value function of position.
2. Equilibrium of forces:- The equilibrium at the nodal forces must be ensured.
Although there are a numerous commercial and research codes that are available and they
can be employed but the in finite-element method CFD application is not so much fruitful.
But apart from this, there is one method which is in brief same as finite element method and
is seems fruitful and commercially uses all codes and is essentially used by CFD. The
method is called “Finite - Volume Method (FVM)”. The only differentiating feature is that
FVM uses simple piecewise polynomial functions for local elements which tend to describe
the variations of the un-known flow variables. The weighted residual concept is introduced in
order to evaluate the errors associated with the approximate functions, which are later surely
minimized. A set of non-linear algebraic equations for the unknown terms of the
approximating functions is solved, hence resulting in the flow solution. The residual
functions are solved, and the flow solutions are obtained by Collocation method, Galerkin's
method, Sub-domain method, and least square method.
Spectral method
The spectral method has the same general approach as that of the finite-difference and finite-
element methods, where the unknowns of the equations that are governed are replaced with
some short series. The difference is in only the methods of implementation. The previous two
methods use local approximations, but the spectral method implements global approximation.
That is by means of Fourier series, Legendre polynomials, for the entire flow body / domain.
The conflict between the exact solution and the approximate solution is dealt with by the use
of a weighted residuals concept similar to the finite-element method.
13
matrix between the secondary and primary variables.
As per discretization is concerned the two compatibility conditions must be ensured:-
1. Compatibility of nodal displacement:- When a body is deformed without breaking, no
crack appears in stretching and particles do not penetrate each other in elements. Such a
situation is called Nodal displacement compatibility. The compatibility condition
confirms that the displacement is continuous and single value function of position.
2. Equilibrium of forces:- The equilibrium at the nodal forces must be ensured.
Although there are a numerous commercial and research codes that are available and they
can be employed but the in finite-element method CFD application is not so much fruitful.
But apart from this, there is one method which is in brief same as finite element method and
is seems fruitful and commercially uses all codes and is essentially used by CFD. The
method is called “Finite - Volume Method (FVM)”. The only differentiating feature is that
FVM uses simple piecewise polynomial functions for local elements which tend to describe
the variations of the un-known flow variables. The weighted residual concept is introduced in
order to evaluate the errors associated with the approximate functions, which are later surely
minimized. A set of non-linear algebraic equations for the unknown terms of the
approximating functions is solved, hence resulting in the flow solution. The residual
functions are solved, and the flow solutions are obtained by Collocation method, Galerkin's
method, Sub-domain method, and least square method.
Spectral method
The spectral method has the same general approach as that of the finite-difference and finite-
element methods, where the unknowns of the equations that are governed are replaced with
some short series. The difference is in only the methods of implementation. The previous two
methods use local approximations, but the spectral method implements global approximation.
That is by means of Fourier series, Legendre polynomials, for the entire flow body / domain.
The conflict between the exact solution and the approximate solution is dealt with by the use
of a weighted residuals concept similar to the finite-element method.
13
Secure Best Marks with AI Grader
Need help grading? Try our AI Grader for instant feedback on your assignments.
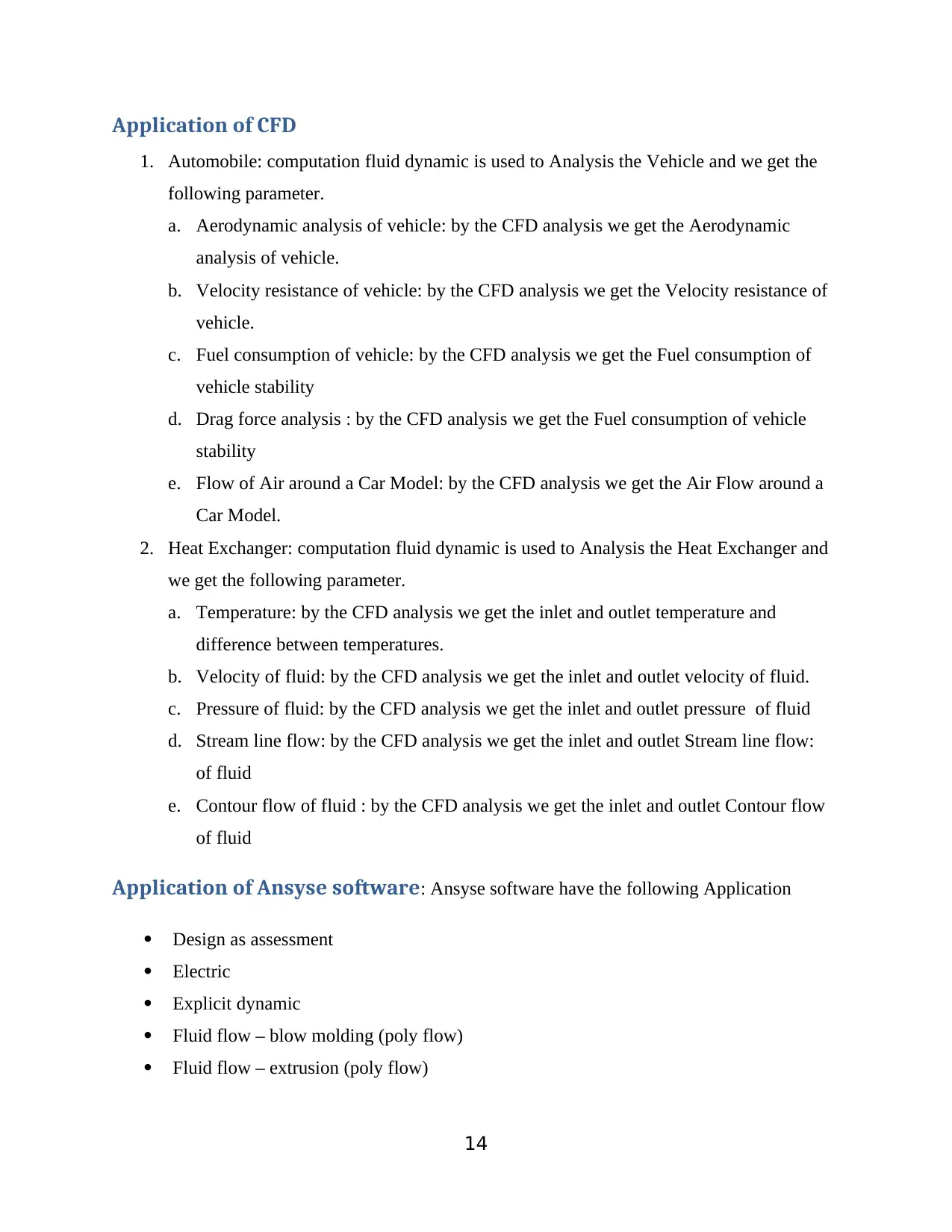
Application of CFD
1. Automobile: computation fluid dynamic is used to Analysis the Vehicle and we get the
following parameter.
a. Aerodynamic analysis of vehicle: by the CFD analysis we get the Aerodynamic
analysis of vehicle.
b. Velocity resistance of vehicle: by the CFD analysis we get the Velocity resistance of
vehicle.
c. Fuel consumption of vehicle: by the CFD analysis we get the Fuel consumption of
vehicle stability
d. Drag force analysis : by the CFD analysis we get the Fuel consumption of vehicle
stability
e. Flow of Air around a Car Model: by the CFD analysis we get the Air Flow around a
Car Model.
2. Heat Exchanger: computation fluid dynamic is used to Analysis the Heat Exchanger and
we get the following parameter.
a. Temperature: by the CFD analysis we get the inlet and outlet temperature and
difference between temperatures.
b. Velocity of fluid: by the CFD analysis we get the inlet and outlet velocity of fluid.
c. Pressure of fluid: by the CFD analysis we get the inlet and outlet pressure of fluid
d. Stream line flow: by the CFD analysis we get the inlet and outlet Stream line flow:
of fluid
e. Contour flow of fluid : by the CFD analysis we get the inlet and outlet Contour flow
of fluid
Application of Ansyse software: Ansyse software have the following Application
Design as assessment
Electric
Explicit dynamic
Fluid flow – blow molding (poly flow)
Fluid flow – extrusion (poly flow)
14
1. Automobile: computation fluid dynamic is used to Analysis the Vehicle and we get the
following parameter.
a. Aerodynamic analysis of vehicle: by the CFD analysis we get the Aerodynamic
analysis of vehicle.
b. Velocity resistance of vehicle: by the CFD analysis we get the Velocity resistance of
vehicle.
c. Fuel consumption of vehicle: by the CFD analysis we get the Fuel consumption of
vehicle stability
d. Drag force analysis : by the CFD analysis we get the Fuel consumption of vehicle
stability
e. Flow of Air around a Car Model: by the CFD analysis we get the Air Flow around a
Car Model.
2. Heat Exchanger: computation fluid dynamic is used to Analysis the Heat Exchanger and
we get the following parameter.
a. Temperature: by the CFD analysis we get the inlet and outlet temperature and
difference between temperatures.
b. Velocity of fluid: by the CFD analysis we get the inlet and outlet velocity of fluid.
c. Pressure of fluid: by the CFD analysis we get the inlet and outlet pressure of fluid
d. Stream line flow: by the CFD analysis we get the inlet and outlet Stream line flow:
of fluid
e. Contour flow of fluid : by the CFD analysis we get the inlet and outlet Contour flow
of fluid
Application of Ansyse software: Ansyse software have the following Application
Design as assessment
Electric
Explicit dynamic
Fluid flow – blow molding (poly flow)
Fluid flow – extrusion (poly flow)
14
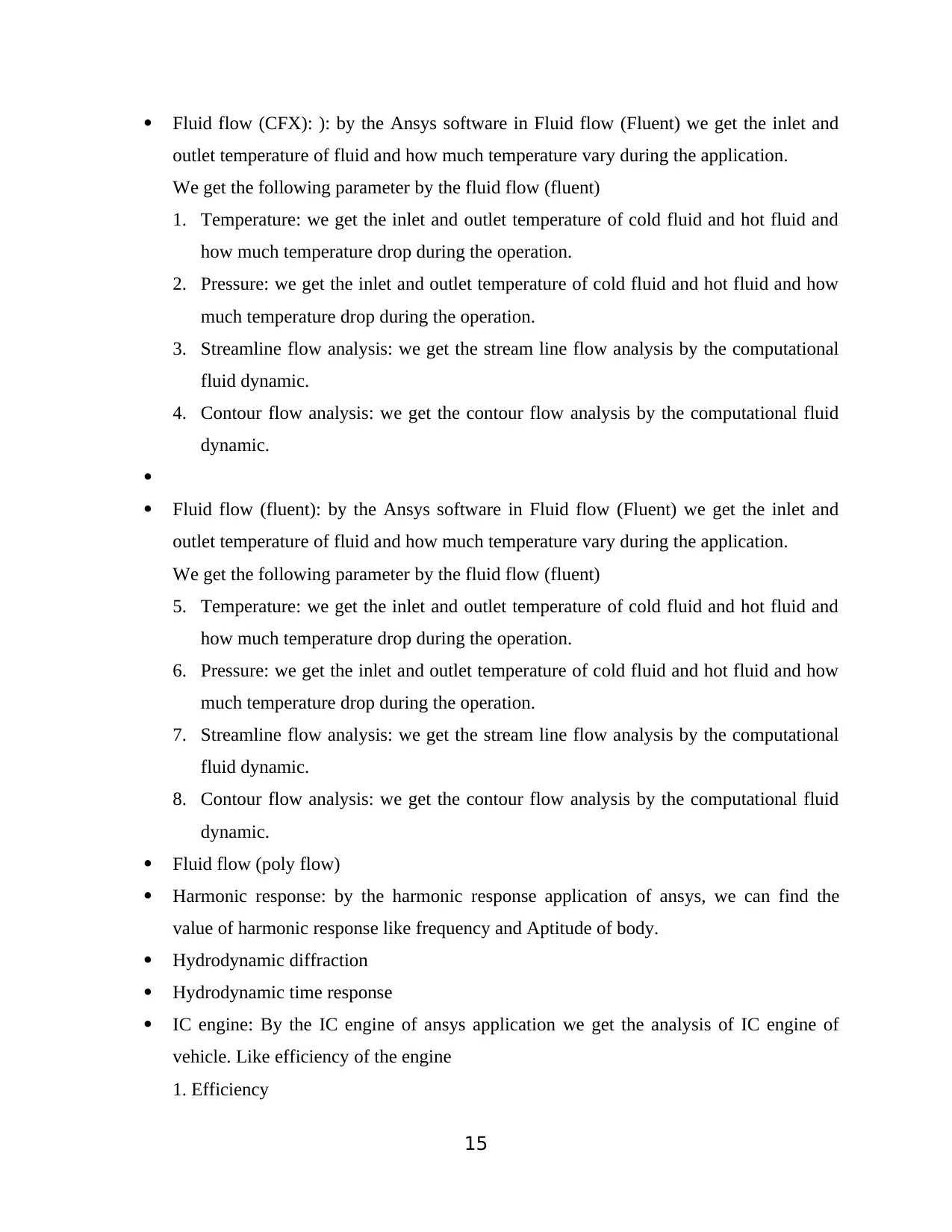
Fluid flow (CFX): ): by the Ansys software in Fluid flow (Fluent) we get the inlet and
outlet temperature of fluid and how much temperature vary during the application.
We get the following parameter by the fluid flow (fluent)
1. Temperature: we get the inlet and outlet temperature of cold fluid and hot fluid and
how much temperature drop during the operation.
2. Pressure: we get the inlet and outlet temperature of cold fluid and hot fluid and how
much temperature drop during the operation.
3. Streamline flow analysis: we get the stream line flow analysis by the computational
fluid dynamic.
4. Contour flow analysis: we get the contour flow analysis by the computational fluid
dynamic.
Fluid flow (fluent): by the Ansys software in Fluid flow (Fluent) we get the inlet and
outlet temperature of fluid and how much temperature vary during the application.
We get the following parameter by the fluid flow (fluent)
5. Temperature: we get the inlet and outlet temperature of cold fluid and hot fluid and
how much temperature drop during the operation.
6. Pressure: we get the inlet and outlet temperature of cold fluid and hot fluid and how
much temperature drop during the operation.
7. Streamline flow analysis: we get the stream line flow analysis by the computational
fluid dynamic.
8. Contour flow analysis: we get the contour flow analysis by the computational fluid
dynamic.
Fluid flow (poly flow)
Harmonic response: by the harmonic response application of ansys, we can find the
value of harmonic response like frequency and Aptitude of body.
Hydrodynamic diffraction
Hydrodynamic time response
IC engine: By the IC engine of ansys application we get the analysis of IC engine of
vehicle. Like efficiency of the engine
1. Efficiency
15
outlet temperature of fluid and how much temperature vary during the application.
We get the following parameter by the fluid flow (fluent)
1. Temperature: we get the inlet and outlet temperature of cold fluid and hot fluid and
how much temperature drop during the operation.
2. Pressure: we get the inlet and outlet temperature of cold fluid and hot fluid and how
much temperature drop during the operation.
3. Streamline flow analysis: we get the stream line flow analysis by the computational
fluid dynamic.
4. Contour flow analysis: we get the contour flow analysis by the computational fluid
dynamic.
Fluid flow (fluent): by the Ansys software in Fluid flow (Fluent) we get the inlet and
outlet temperature of fluid and how much temperature vary during the application.
We get the following parameter by the fluid flow (fluent)
5. Temperature: we get the inlet and outlet temperature of cold fluid and hot fluid and
how much temperature drop during the operation.
6. Pressure: we get the inlet and outlet temperature of cold fluid and hot fluid and how
much temperature drop during the operation.
7. Streamline flow analysis: we get the stream line flow analysis by the computational
fluid dynamic.
8. Contour flow analysis: we get the contour flow analysis by the computational fluid
dynamic.
Fluid flow (poly flow)
Harmonic response: by the harmonic response application of ansys, we can find the
value of harmonic response like frequency and Aptitude of body.
Hydrodynamic diffraction
Hydrodynamic time response
IC engine: By the IC engine of ansys application we get the analysis of IC engine of
vehicle. Like efficiency of the engine
1. Efficiency
15
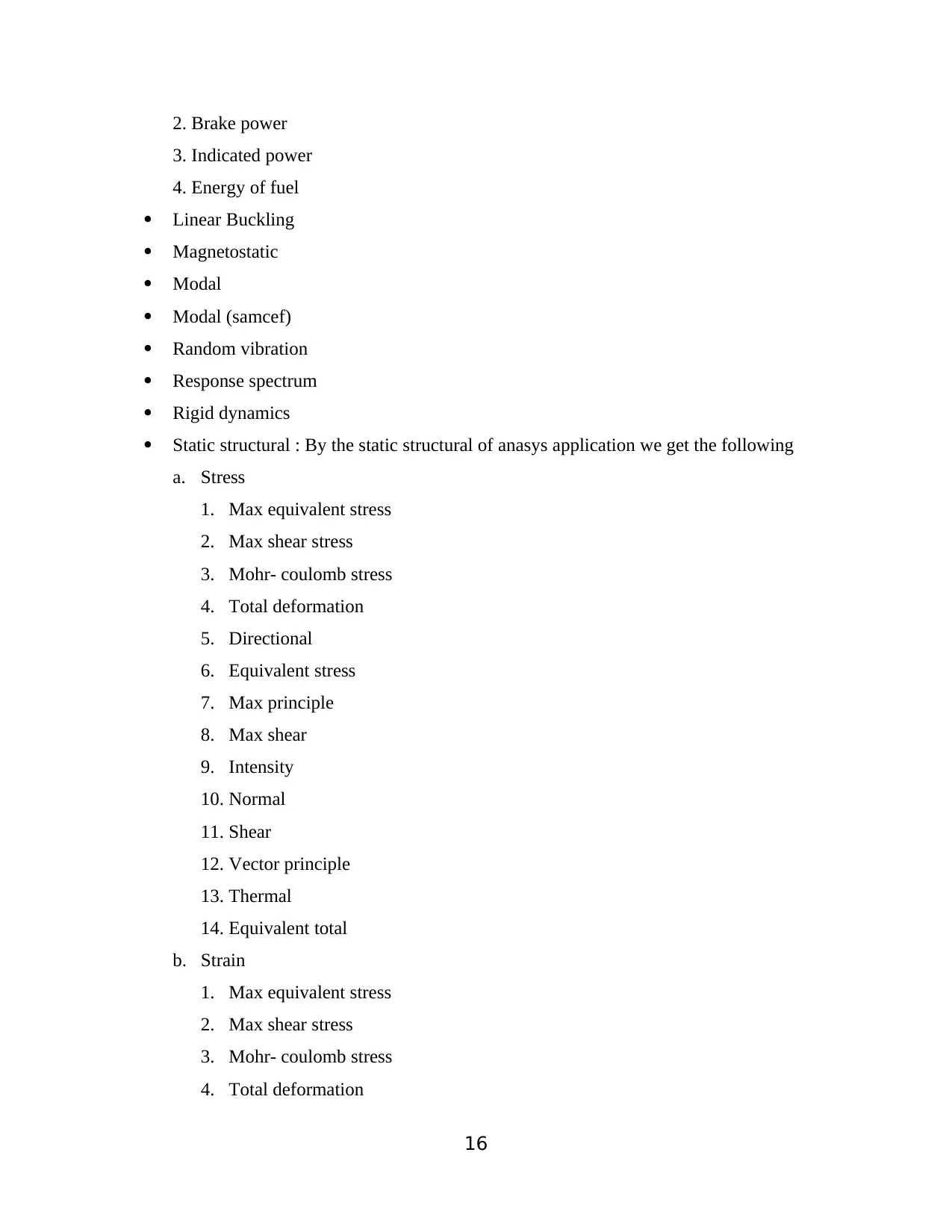
2. Brake power
3. Indicated power
4. Energy of fuel
Linear Buckling
Magnetostatic
Modal
Modal (samcef)
Random vibration
Response spectrum
Rigid dynamics
Static structural : By the static structural of anasys application we get the following
a. Stress
1. Max equivalent stress
2. Max shear stress
3. Mohr- coulomb stress
4. Total deformation
5. Directional
6. Equivalent stress
7. Max principle
8. Max shear
9. Intensity
10. Normal
11. Shear
12. Vector principle
13. Thermal
14. Equivalent total
b. Strain
1. Max equivalent stress
2. Max shear stress
3. Mohr- coulomb stress
4. Total deformation
16
3. Indicated power
4. Energy of fuel
Linear Buckling
Magnetostatic
Modal
Modal (samcef)
Random vibration
Response spectrum
Rigid dynamics
Static structural : By the static structural of anasys application we get the following
a. Stress
1. Max equivalent stress
2. Max shear stress
3. Mohr- coulomb stress
4. Total deformation
5. Directional
6. Equivalent stress
7. Max principle
8. Max shear
9. Intensity
10. Normal
11. Shear
12. Vector principle
13. Thermal
14. Equivalent total
b. Strain
1. Max equivalent stress
2. Max shear stress
3. Mohr- coulomb stress
4. Total deformation
16
Paraphrase This Document
Need a fresh take? Get an instant paraphrase of this document with our AI Paraphraser
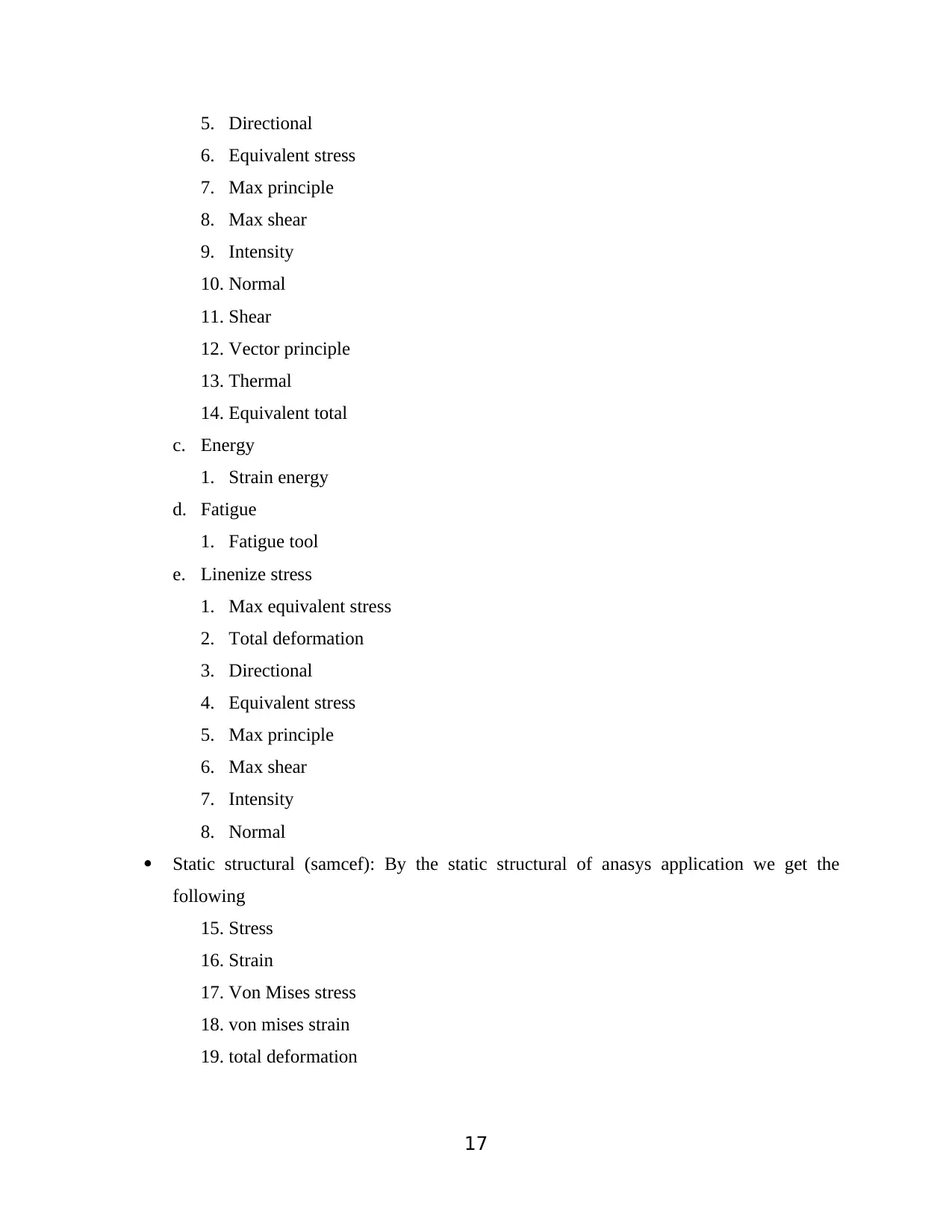
5. Directional
6. Equivalent stress
7. Max principle
8. Max shear
9. Intensity
10. Normal
11. Shear
12. Vector principle
13. Thermal
14. Equivalent total
c. Energy
1. Strain energy
d. Fatigue
1. Fatigue tool
e. Linenize stress
1. Max equivalent stress
2. Total deformation
3. Directional
4. Equivalent stress
5. Max principle
6. Max shear
7. Intensity
8. Normal
Static structural (samcef): By the static structural of anasys application we get the
following
15. Stress
16. Strain
17. Von Mises stress
18. von mises strain
19. total deformation
17
6. Equivalent stress
7. Max principle
8. Max shear
9. Intensity
10. Normal
11. Shear
12. Vector principle
13. Thermal
14. Equivalent total
c. Energy
1. Strain energy
d. Fatigue
1. Fatigue tool
e. Linenize stress
1. Max equivalent stress
2. Total deformation
3. Directional
4. Equivalent stress
5. Max principle
6. Max shear
7. Intensity
8. Normal
Static structural (samcef): By the static structural of anasys application we get the
following
15. Stress
16. Strain
17. Von Mises stress
18. von mises strain
19. total deformation
17
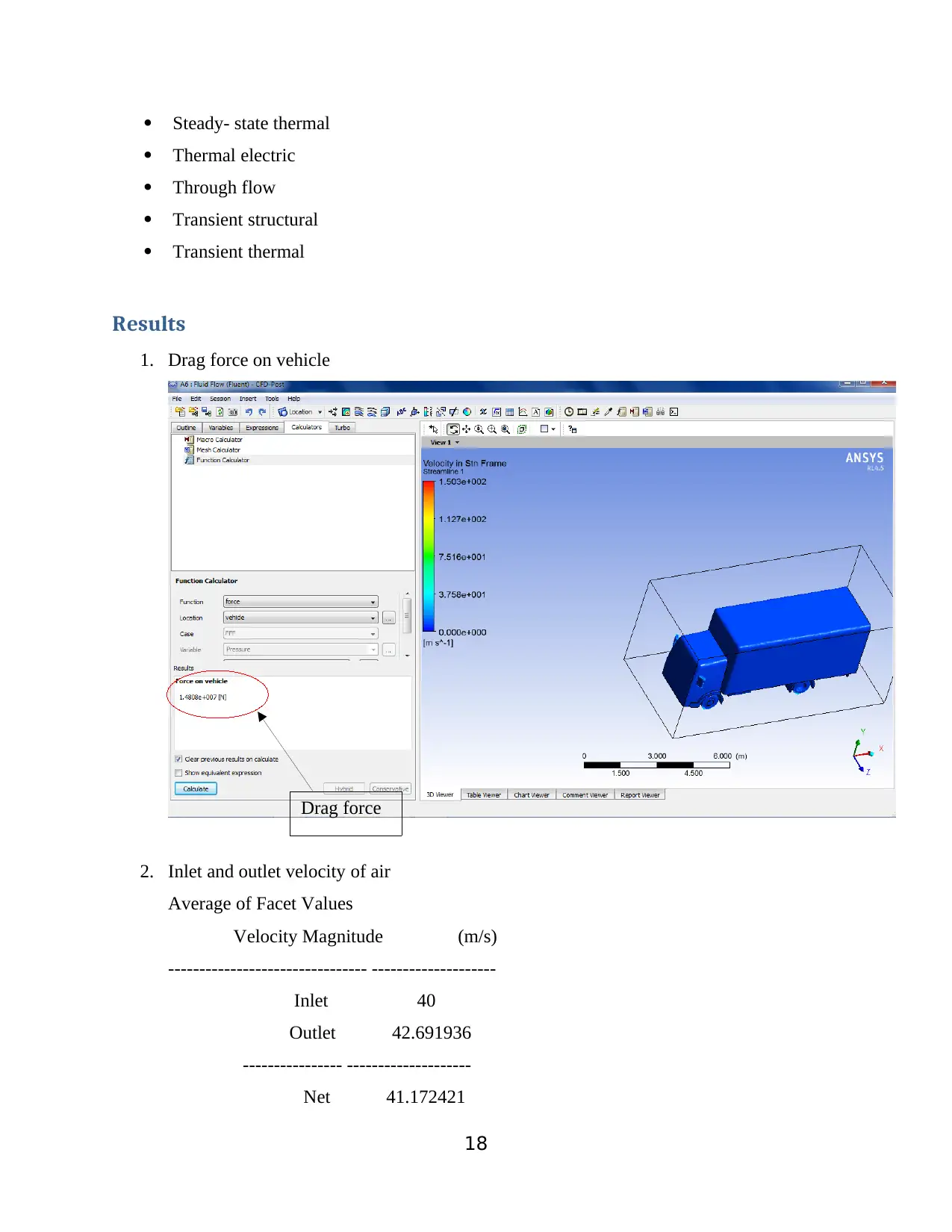
Steady- state thermal
Thermal electric
Through flow
Transient structural
Transient thermal
Results
1. Drag force on vehicle
2. Inlet and outlet velocity of air
Average of Facet Values
Velocity Magnitude (m/s)
-------------------------------- --------------------
Inlet 40
Outlet 42.691936
---------------- --------------------
Net 41.172421
18
Drag force
Thermal electric
Through flow
Transient structural
Transient thermal
Results
1. Drag force on vehicle
2. Inlet and outlet velocity of air
Average of Facet Values
Velocity Magnitude (m/s)
-------------------------------- --------------------
Inlet 40
Outlet 42.691936
---------------- --------------------
Net 41.172421
18
Drag force
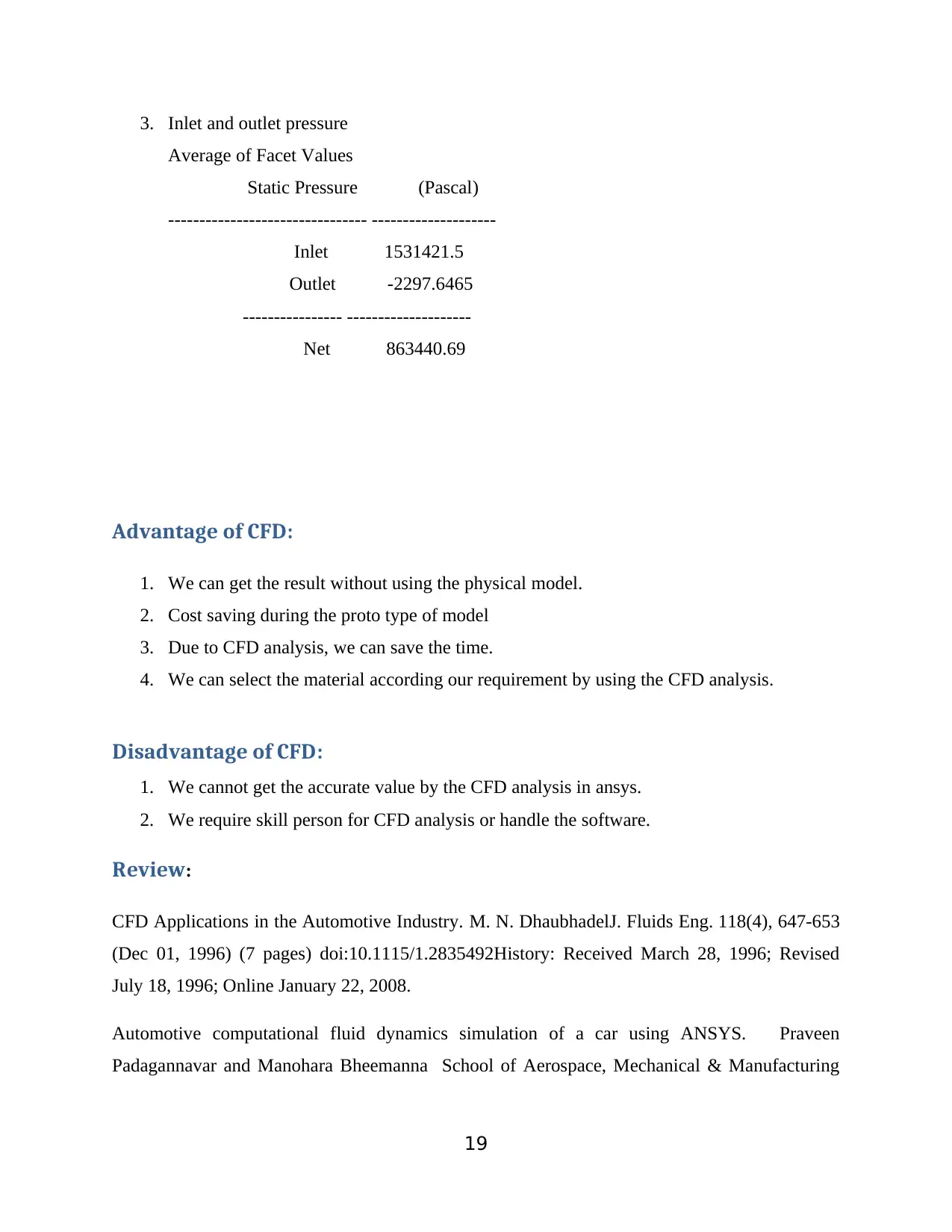
3. Inlet and outlet pressure
Average of Facet Values
Static Pressure (Pascal)
-------------------------------- --------------------
Inlet 1531421.5
Outlet -2297.6465
---------------- --------------------
Net 863440.69
Advantage of CFD:
1. We can get the result without using the physical model.
2. Cost saving during the proto type of model
3. Due to CFD analysis, we can save the time.
4. We can select the material according our requirement by using the CFD analysis.
Disadvantage of CFD:
1. We cannot get the accurate value by the CFD analysis in ansys.
2. We require skill person for CFD analysis or handle the software.
Review:
CFD Applications in the Automotive Industry. M. N. DhaubhadelJ. Fluids Eng. 118(4), 647-653
(Dec 01, 1996) (7 pages) doi:10.1115/1.2835492History: Received March 28, 1996; Revised
July 18, 1996; Online January 22, 2008.
Automotive computational fluid dynamics simulation of a car using ANSYS. Praveen
Padagannavar and Manohara Bheemanna School of Aerospace, Mechanical & Manufacturing
19
Average of Facet Values
Static Pressure (Pascal)
-------------------------------- --------------------
Inlet 1531421.5
Outlet -2297.6465
---------------- --------------------
Net 863440.69
Advantage of CFD:
1. We can get the result without using the physical model.
2. Cost saving during the proto type of model
3. Due to CFD analysis, we can save the time.
4. We can select the material according our requirement by using the CFD analysis.
Disadvantage of CFD:
1. We cannot get the accurate value by the CFD analysis in ansys.
2. We require skill person for CFD analysis or handle the software.
Review:
CFD Applications in the Automotive Industry. M. N. DhaubhadelJ. Fluids Eng. 118(4), 647-653
(Dec 01, 1996) (7 pages) doi:10.1115/1.2835492History: Received March 28, 1996; Revised
July 18, 1996; Online January 22, 2008.
Automotive computational fluid dynamics simulation of a car using ANSYS. Praveen
Padagannavar and Manohara Bheemanna School of Aerospace, Mechanical & Manufacturing
19
Secure Best Marks with AI Grader
Need help grading? Try our AI Grader for instant feedback on your assignments.
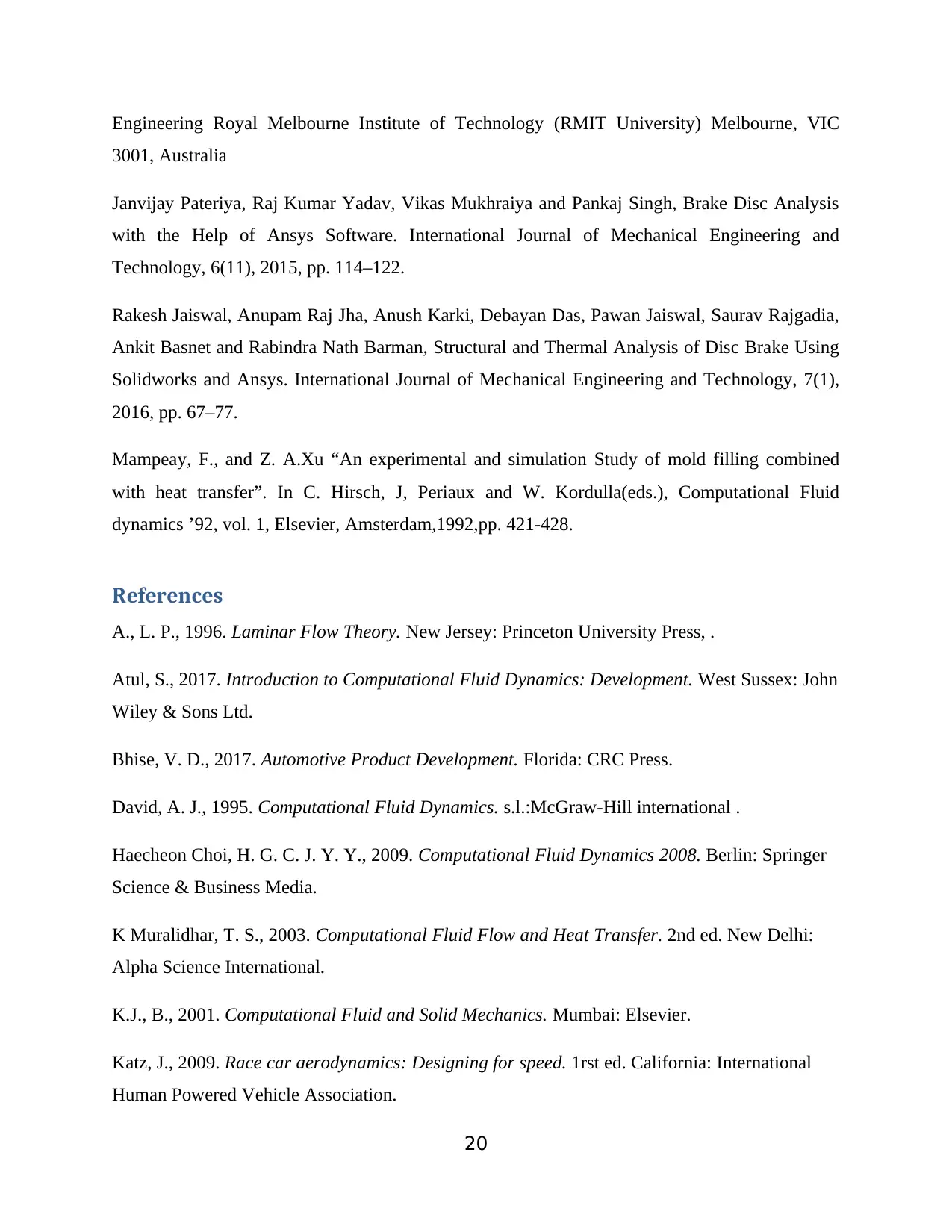
Engineering Royal Melbourne Institute of Technology (RMIT University) Melbourne, VIC
3001, Australia
Janvijay Pateriya, Raj Kumar Yadav, Vikas Mukhraiya and Pankaj Singh, Brake Disc Analysis
with the Help of Ansys Software. International Journal of Mechanical Engineering and
Technology, 6(11), 2015, pp. 114–122.
Rakesh Jaiswal, Anupam Raj Jha, Anush Karki, Debayan Das, Pawan Jaiswal, Saurav Rajgadia,
Ankit Basnet and Rabindra Nath Barman, Structural and Thermal Analysis of Disc Brake Using
Solidworks and Ansys. International Journal of Mechanical Engineering and Technology, 7(1),
2016, pp. 67–77.
Mampeay, F., and Z. A.Xu “An experimental and simulation Study of mold filling combined
with heat transfer”. In C. Hirsch, J, Periaux and W. Kordulla(eds.), Computational Fluid
dynamics ’92, vol. 1, Elsevier, Amsterdam,1992,pp. 421-428.
References
A., L. P., 1996. Laminar Flow Theory. New Jersey: Princeton University Press, .
Atul, S., 2017. Introduction to Computational Fluid Dynamics: Development. West Sussex: John
Wiley & Sons Ltd.
Bhise, V. D., 2017. Automotive Product Development. Florida: CRC Press.
David, A. J., 1995. Computational Fluid Dynamics. s.l.:McGraw-Hill international .
Haecheon Choi, H. G. C. J. Y. Y., 2009. Computational Fluid Dynamics 2008. Berlin: Springer
Science & Business Media.
K Muralidhar, T. S., 2003. Computational Fluid Flow and Heat Transfer. 2nd ed. New Delhi:
Alpha Science International.
K.J., B., 2001. Computational Fluid and Solid Mechanics. Mumbai: Elsevier.
Katz, J., 2009. Race car aerodynamics: Designing for speed. 1rst ed. California: International
Human Powered Vehicle Association.
20
3001, Australia
Janvijay Pateriya, Raj Kumar Yadav, Vikas Mukhraiya and Pankaj Singh, Brake Disc Analysis
with the Help of Ansys Software. International Journal of Mechanical Engineering and
Technology, 6(11), 2015, pp. 114–122.
Rakesh Jaiswal, Anupam Raj Jha, Anush Karki, Debayan Das, Pawan Jaiswal, Saurav Rajgadia,
Ankit Basnet and Rabindra Nath Barman, Structural and Thermal Analysis of Disc Brake Using
Solidworks and Ansys. International Journal of Mechanical Engineering and Technology, 7(1),
2016, pp. 67–77.
Mampeay, F., and Z. A.Xu “An experimental and simulation Study of mold filling combined
with heat transfer”. In C. Hirsch, J, Periaux and W. Kordulla(eds.), Computational Fluid
dynamics ’92, vol. 1, Elsevier, Amsterdam,1992,pp. 421-428.
References
A., L. P., 1996. Laminar Flow Theory. New Jersey: Princeton University Press, .
Atul, S., 2017. Introduction to Computational Fluid Dynamics: Development. West Sussex: John
Wiley & Sons Ltd.
Bhise, V. D., 2017. Automotive Product Development. Florida: CRC Press.
David, A. J., 1995. Computational Fluid Dynamics. s.l.:McGraw-Hill international .
Haecheon Choi, H. G. C. J. Y. Y., 2009. Computational Fluid Dynamics 2008. Berlin: Springer
Science & Business Media.
K Muralidhar, T. S., 2003. Computational Fluid Flow and Heat Transfer. 2nd ed. New Delhi:
Alpha Science International.
K.J., B., 2001. Computational Fluid and Solid Mechanics. Mumbai: Elsevier.
Katz, J., 2009. Race car aerodynamics: Designing for speed. 1rst ed. California: International
Human Powered Vehicle Association.
20
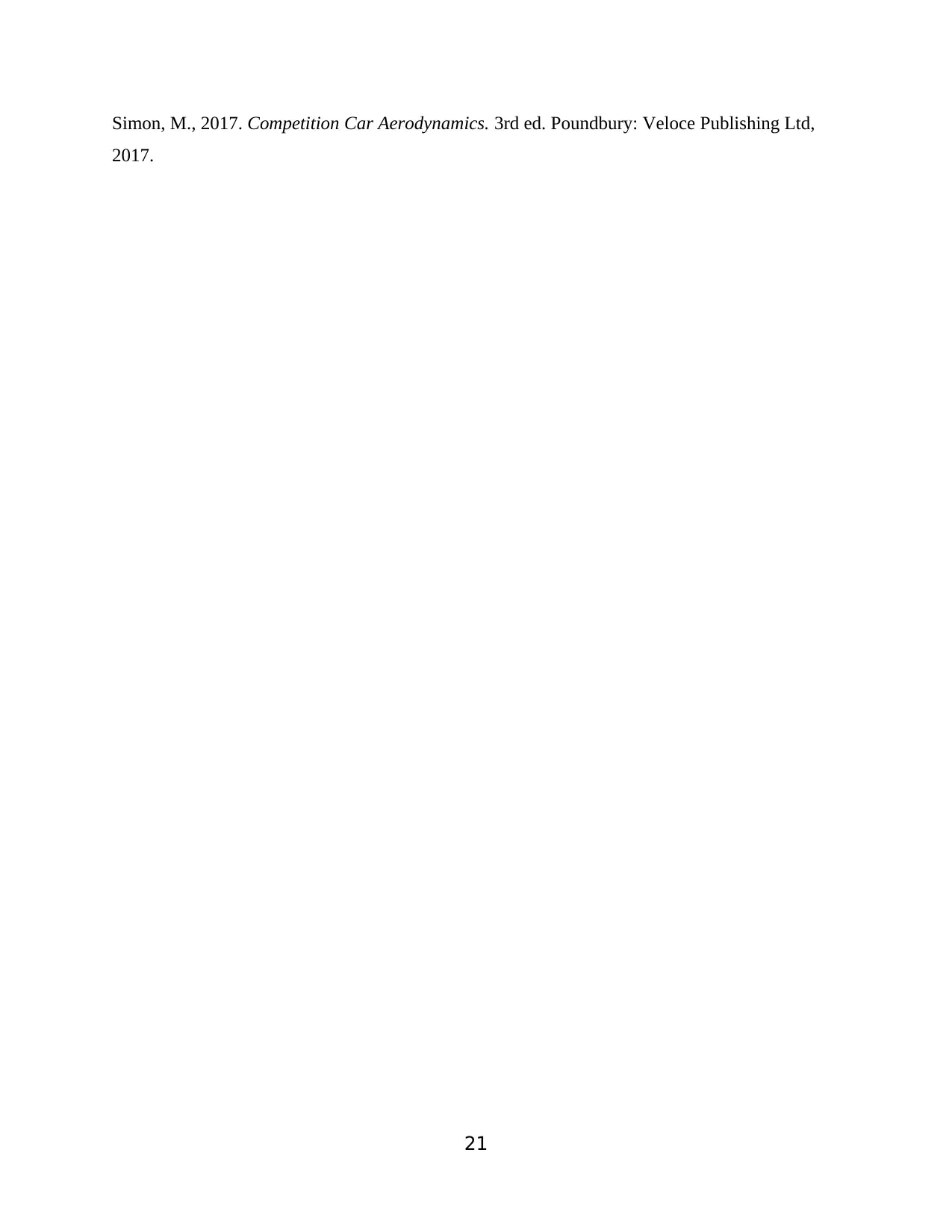
Simon, M., 2017. Competition Car Aerodynamics. 3rd ed. Poundbury: Veloce Publishing Ltd,
2017.
21
2017.
21
1 out of 24
Related Documents

Your All-in-One AI-Powered Toolkit for Academic Success.
+13062052269
info@desklib.com
Available 24*7 on WhatsApp / Email
Unlock your academic potential
© 2024 | Zucol Services PVT LTD | All rights reserved.