Inventory Control System
Added on 2023-01-23
8 Pages1400 Words95 Views
INVENTORY CONTROL SYSTEM
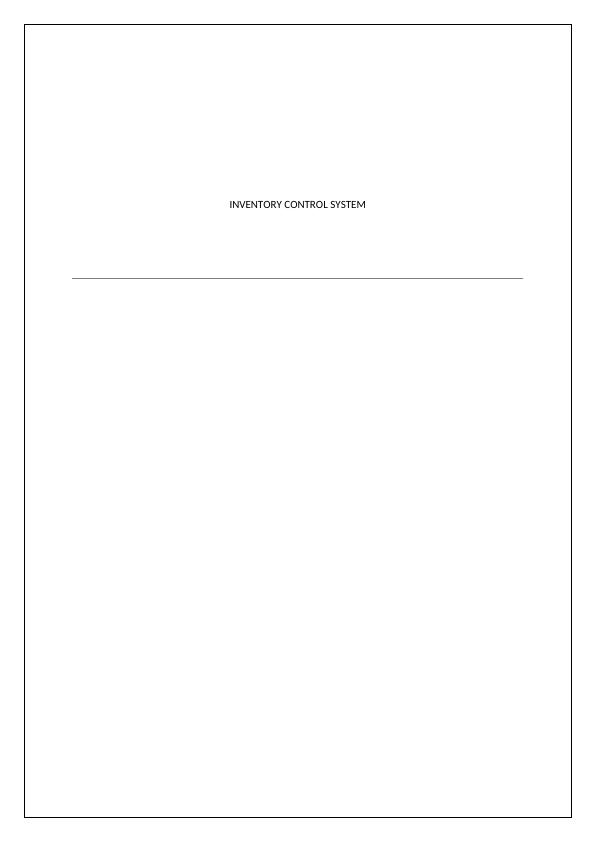
Question 1
Selling price P = $30
Cost C = $12
Salvage value G = 0
Shortage or underage cost Cu = P-C = 30-12 =$18
Excess or overstocking cost Co = C- G = 12-0 = $12
Critical ratio = Cu / (Cu + Co) = 18/(18+12) = 0.60
The critical ratio 0.60 falls in the batch number 5.
Batches Probability Cumulative probability Shortage Overage
0
1 0.03 0.03 4
2 0.09 0.12 3
3 0.11 0.23 2
4 0.17 0.40 1
5 0.22 0.62 0 0
6 0.16 0.78 1 0
7 0.13 0.91 2 0
8 0.05 0.96 3 0
9 0.04 1.00 4 0
Therefore, the optimal number of trees to cut Q = 5 Batches = 5*100 = 500 Trees.
Average demand = (1*0.03) +
(2*0.09)+(3*0.11)+(4*0.17)+(5*0.22)+(6*0.16)+(7*0.13)+(8*0.05)+(9*0.04) = 4.95
Expected shortage = (0*0.03) +
(0*0.09)+(0*0.11)+(0*0.17)+(0*0.22)+(1*0.16)+(2*0.13)+(3*0.05)+(4*0.04) = 0.73
Expected sales = Average demand - Expected shortage = 4.95-0.73 = 4.22
Expected overage = 5-4.22 = 0.78
Expected revenue = (30*4.22 + 0.78*0)*100 = $12660
Expected cost = 12*5*100= $6000
Expected profit = 12660 – 6000 = $6660
Question 2
Mean demand = 9.5 units a month
Lead time = 1 month
Shortage cost = $140 a unit a month
1
Selling price P = $30
Cost C = $12
Salvage value G = 0
Shortage or underage cost Cu = P-C = 30-12 =$18
Excess or overstocking cost Co = C- G = 12-0 = $12
Critical ratio = Cu / (Cu + Co) = 18/(18+12) = 0.60
The critical ratio 0.60 falls in the batch number 5.
Batches Probability Cumulative probability Shortage Overage
0
1 0.03 0.03 4
2 0.09 0.12 3
3 0.11 0.23 2
4 0.17 0.40 1
5 0.22 0.62 0 0
6 0.16 0.78 1 0
7 0.13 0.91 2 0
8 0.05 0.96 3 0
9 0.04 1.00 4 0
Therefore, the optimal number of trees to cut Q = 5 Batches = 5*100 = 500 Trees.
Average demand = (1*0.03) +
(2*0.09)+(3*0.11)+(4*0.17)+(5*0.22)+(6*0.16)+(7*0.13)+(8*0.05)+(9*0.04) = 4.95
Expected shortage = (0*0.03) +
(0*0.09)+(0*0.11)+(0*0.17)+(0*0.22)+(1*0.16)+(2*0.13)+(3*0.05)+(4*0.04) = 0.73
Expected sales = Average demand - Expected shortage = 4.95-0.73 = 4.22
Expected overage = 5-4.22 = 0.78
Expected revenue = (30*4.22 + 0.78*0)*100 = $12660
Expected cost = 12*5*100= $6000
Expected profit = 12660 – 6000 = $6660
Question 2
Mean demand = 9.5 units a month
Lead time = 1 month
Shortage cost = $140 a unit a month
1
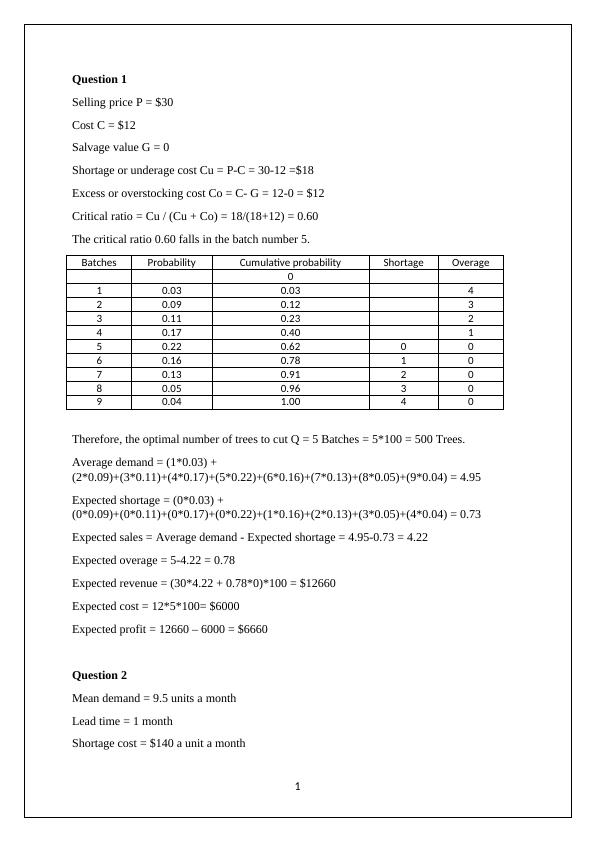
Reorder cost = $50
Holding cost = $6 a unit a month
Optimal value for order quantity =?
Reorder level =?
Now,
Optimal value for order quantity = Sqrt (2*Demand* Shortage cost /Holding cost)
Optimal value for order quantity = Sqrt (2*9.5*140/6) = 21.05 units
Further,
Reorder point = Demand per day * Lead time = 9.5*1 = 9.5
Question 3
Mean demand = 220 units a week
Standard deviation = 25 units
Constant lead time = 2 weeks
Each unit cost = $7.50 a week to store
Service level = 95%
Reorder cost = $400 per order
Unit cost = $100
This is the probabilistic model where the demand is variable and lead time is constant.
Now,
ROP = (Mean demand * Lead time) + (Z* standard deviation of demand per day* sqrt (Lead
time)
The z value for 95% service level assuming normal distribution = 1.65 (Normal Table)
ROP = (220 * 2) + (1.65*25* sqrt (2))
ROP = 440 + 58.34 = 498.34 or 498
Safety stock = (Z* standard deviation of demand per day* sqrt (Lead time) = (1.65*25* sqrt
(2)) = 58.34 or 58
Therefore, the ROP would be 498 and safety stock would be 58 approximately.
The ABC Company would follow the practice to maintain the ROP as 498 and safety stock as
58.
Total annual cost = (200*100/52)+(298*400) = $11,9584
2
Holding cost = $6 a unit a month
Optimal value for order quantity =?
Reorder level =?
Now,
Optimal value for order quantity = Sqrt (2*Demand* Shortage cost /Holding cost)
Optimal value for order quantity = Sqrt (2*9.5*140/6) = 21.05 units
Further,
Reorder point = Demand per day * Lead time = 9.5*1 = 9.5
Question 3
Mean demand = 220 units a week
Standard deviation = 25 units
Constant lead time = 2 weeks
Each unit cost = $7.50 a week to store
Service level = 95%
Reorder cost = $400 per order
Unit cost = $100
This is the probabilistic model where the demand is variable and lead time is constant.
Now,
ROP = (Mean demand * Lead time) + (Z* standard deviation of demand per day* sqrt (Lead
time)
The z value for 95% service level assuming normal distribution = 1.65 (Normal Table)
ROP = (220 * 2) + (1.65*25* sqrt (2))
ROP = 440 + 58.34 = 498.34 or 498
Safety stock = (Z* standard deviation of demand per day* sqrt (Lead time) = (1.65*25* sqrt
(2)) = 58.34 or 58
Therefore, the ROP would be 498 and safety stock would be 58 approximately.
The ABC Company would follow the practice to maintain the ROP as 498 and safety stock as
58.
Total annual cost = (200*100/52)+(298*400) = $11,9584
2
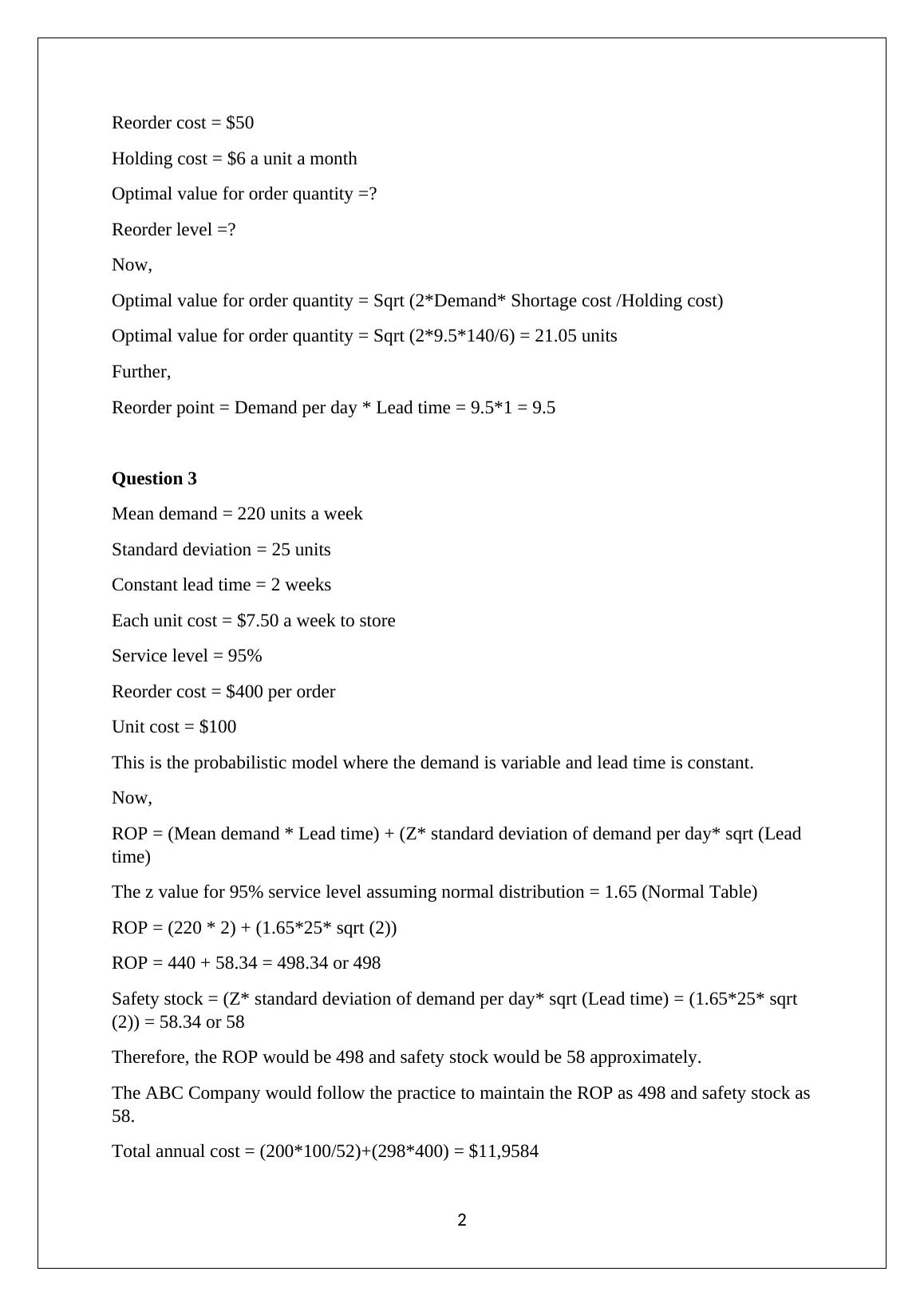
End of preview
Want to access all the pages? Upload your documents or become a member.
Related Documents
Inventory Control Systemlg...
|12
|1266
|95
Value of Stock and Profit Calculationlg...
|11
|2775
|37