Laser Cladding Materials: Processes, Applications, and Advancements
VerifiedAdded on 2023/04/20
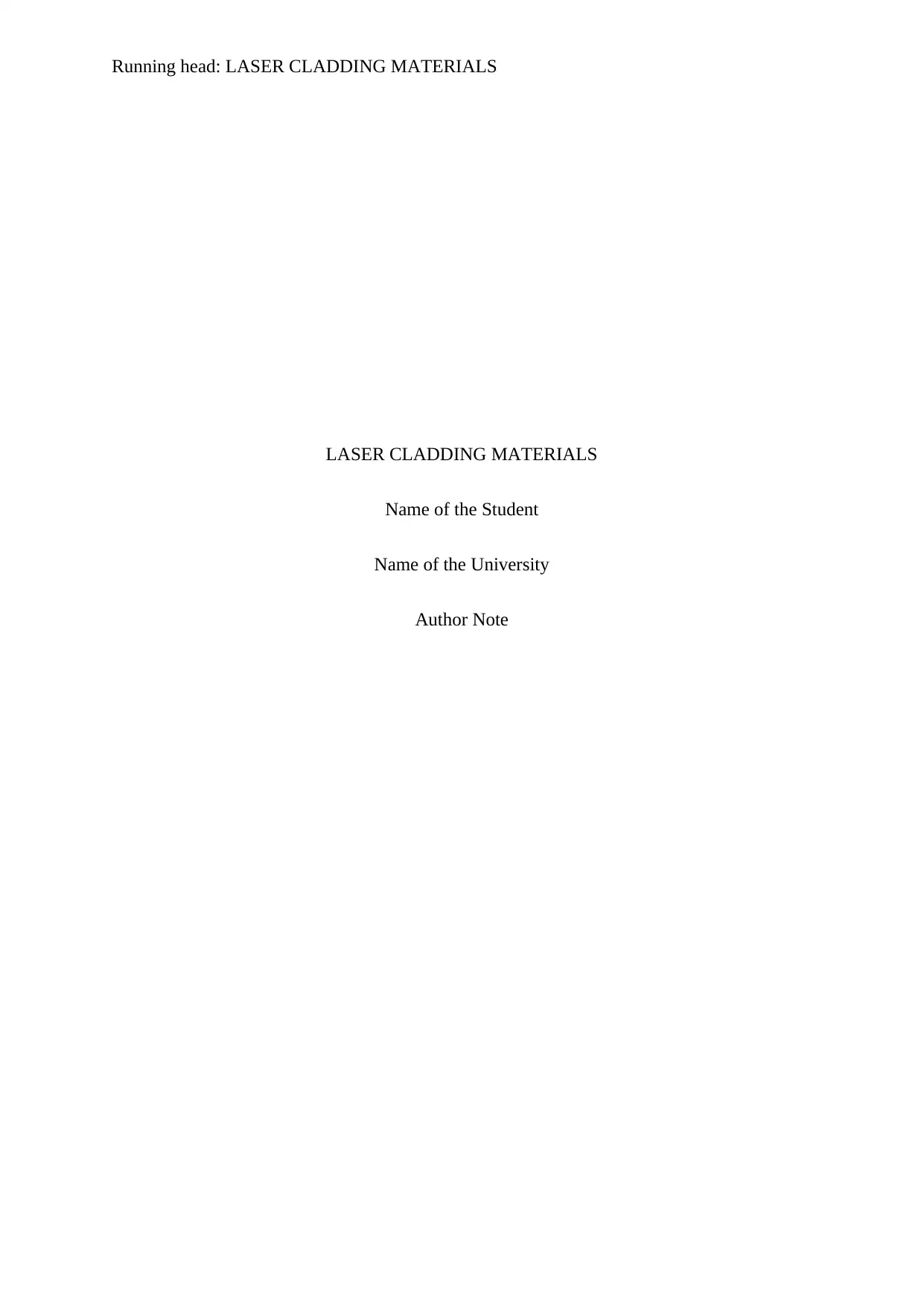
LASER CLADDING MATERIALS
Name of the Student
Name of the University
Author Note
Paraphrase This Document
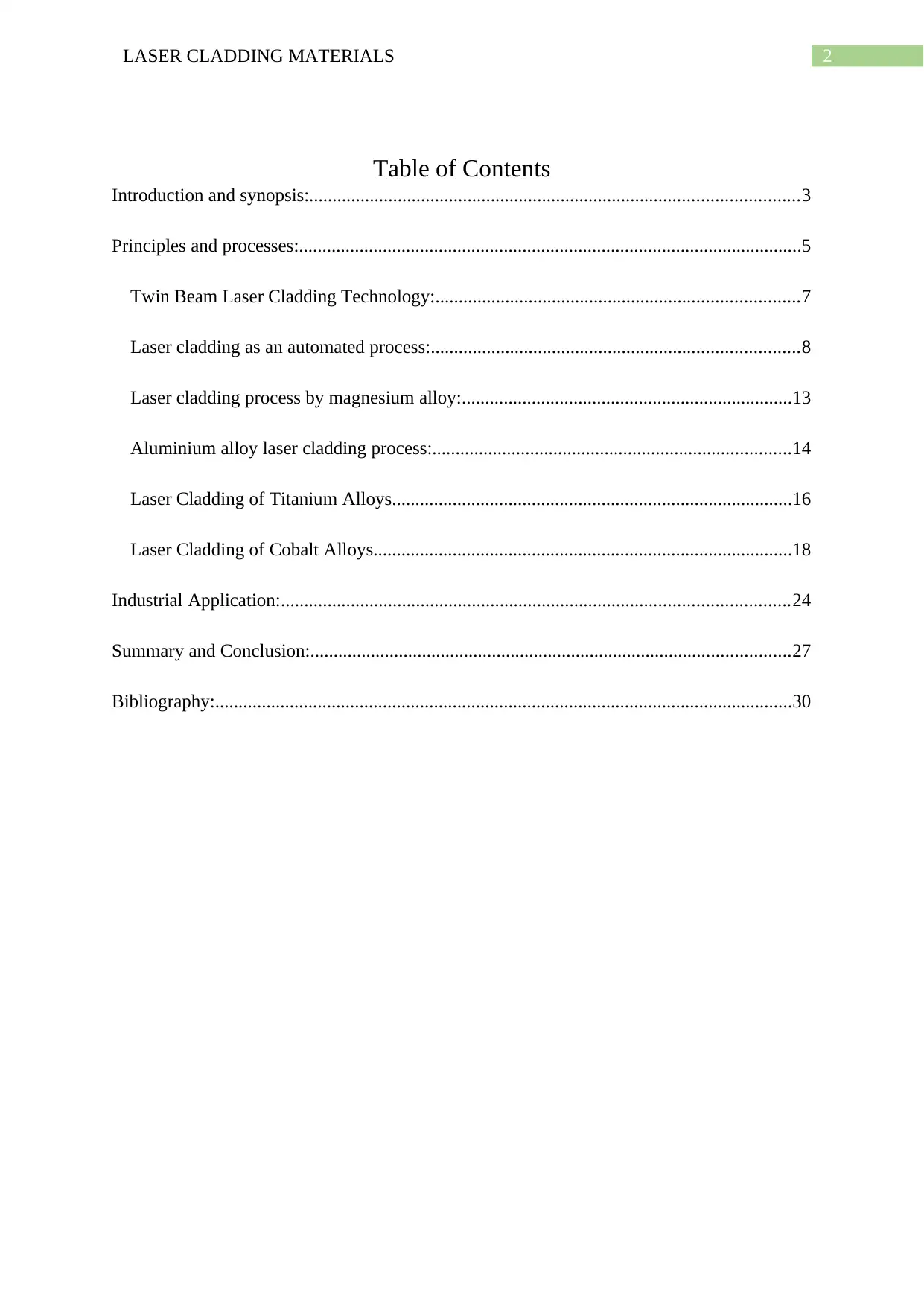
Table of Contents
Introduction and synopsis:.........................................................................................................3
Principles and processes:............................................................................................................5
Twin Beam Laser Cladding Technology:..............................................................................7
Laser cladding as an automated process:...............................................................................8
Laser cladding process by magnesium alloy:.......................................................................13
Aluminium alloy laser cladding process:.............................................................................14
Laser Cladding of Titanium Alloys......................................................................................16
Laser Cladding of Cobalt Alloys..........................................................................................18
Industrial Application:.............................................................................................................24
Summary and Conclusion:.......................................................................................................27
Bibliography:............................................................................................................................30
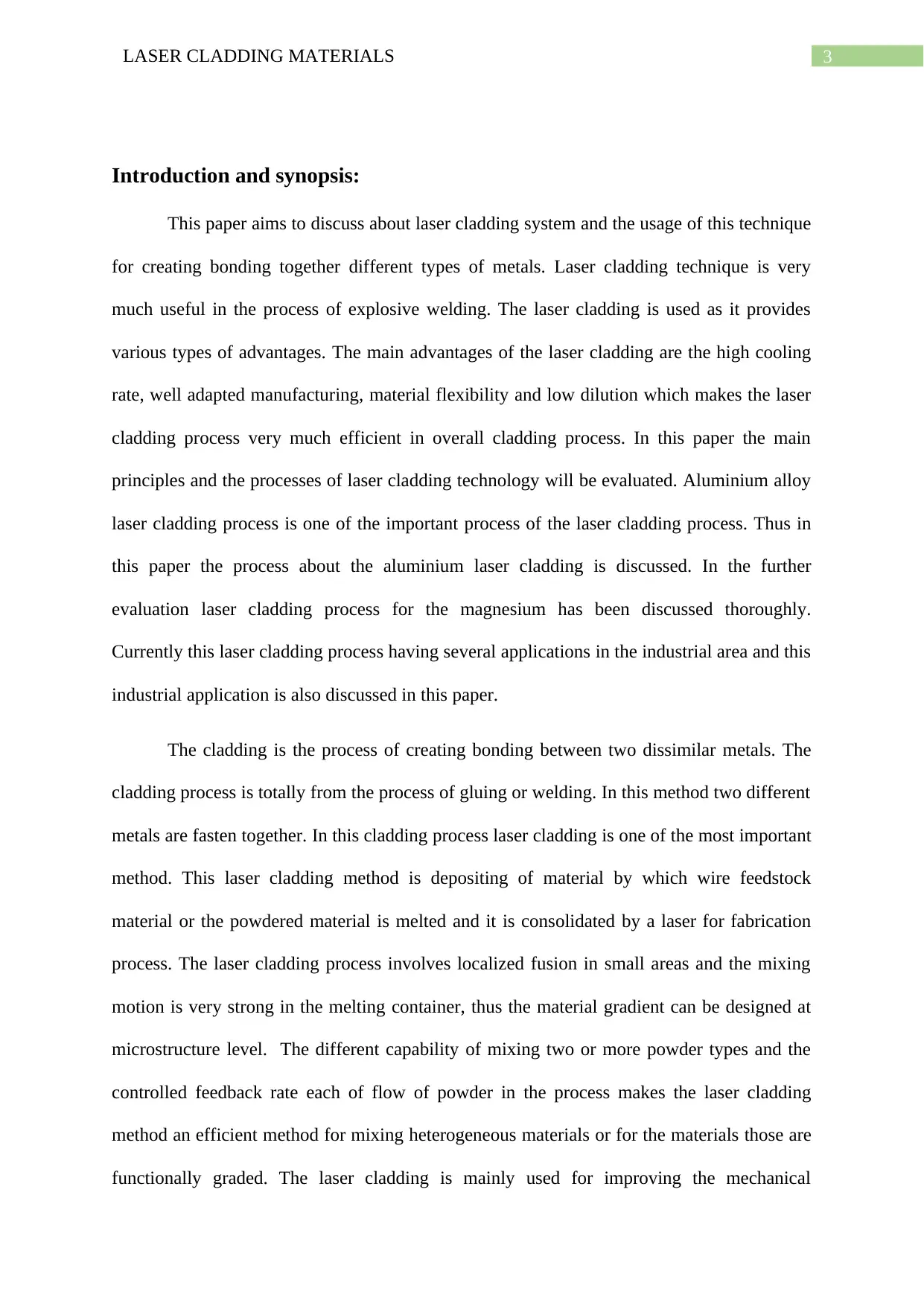
Introduction and synopsis:
This paper aims to discuss about laser cladding system and the usage of this technique
for creating bonding together different types of metals. Laser cladding technique is very
much useful in the process of explosive welding. The laser cladding is used as it provides
various types of advantages. The main advantages of the laser cladding are the high cooling
rate, well adapted manufacturing, material flexibility and low dilution which makes the laser
cladding process very much efficient in overall cladding process. In this paper the main
principles and the processes of laser cladding technology will be evaluated. Aluminium alloy
laser cladding process is one of the important process of the laser cladding process. Thus in
this paper the process about the aluminium laser cladding is discussed. In the further
evaluation laser cladding process for the magnesium has been discussed thoroughly.
Currently this laser cladding process having several applications in the industrial area and this
industrial application is also discussed in this paper.
The cladding is the process of creating bonding between two dissimilar metals. The
cladding process is totally from the process of gluing or welding. In this method two different
metals are fasten together. In this cladding process laser cladding is one of the most important
method. This laser cladding method is depositing of material by which wire feedstock
material or the powdered material is melted and it is consolidated by a laser for fabrication
process. The laser cladding process involves localized fusion in small areas and the mixing
motion is very strong in the melting container, thus the material gradient can be designed at
microstructure level. The different capability of mixing two or more powder types and the
controlled feedback rate each of flow of powder in the process makes the laser cladding
method an efficient method for mixing heterogeneous materials or for the materials those are
functionally graded. The laser cladding is mainly used for improving the mechanical
⊘ This is a preview!⊘
Do you want full access?
Subscribe today to unlock all pages.

Trusted by 1+ million students worldwide
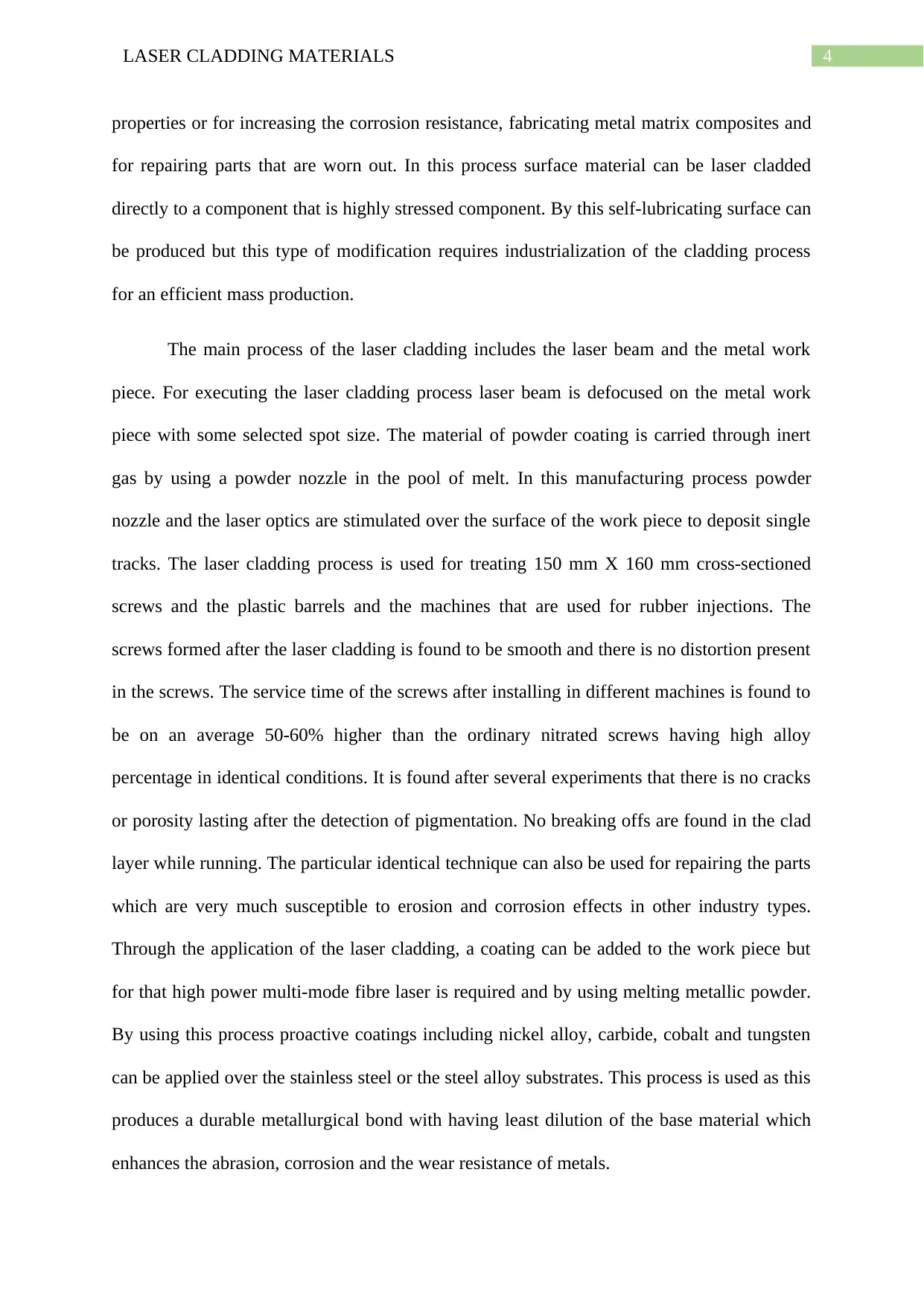
properties or for increasing the corrosion resistance, fabricating metal matrix composites and
for repairing parts that are worn out. In this process surface material can be laser cladded
directly to a component that is highly stressed component. By this self-lubricating surface can
be produced but this type of modification requires industrialization of the cladding process
for an efficient mass production.
The main process of the laser cladding includes the laser beam and the metal work
piece. For executing the laser cladding process laser beam is defocused on the metal work
piece with some selected spot size. The material of powder coating is carried through inert
gas by using a powder nozzle in the pool of melt. In this manufacturing process powder
nozzle and the laser optics are stimulated over the surface of the work piece to deposit single
tracks. The laser cladding process is used for treating 150 mm X 160 mm cross-sectioned
screws and the plastic barrels and the machines that are used for rubber injections. The
screws formed after the laser cladding is found to be smooth and there is no distortion present
in the screws. The service time of the screws after installing in different machines is found to
be on an average 50-60% higher than the ordinary nitrated screws having high alloy
percentage in identical conditions. It is found after several experiments that there is no cracks
or porosity lasting after the detection of pigmentation. No breaking offs are found in the clad
layer while running. The particular identical technique can also be used for repairing the parts
which are very much susceptible to erosion and corrosion effects in other industry types.
Through the application of the laser cladding, a coating can be added to the work piece but
for that high power multi-mode fibre laser is required and by using melting metallic powder.
By using this process proactive coatings including nickel alloy, carbide, cobalt and tungsten
can be applied over the stainless steel or the steel alloy substrates. This process is used as this
produces a durable metallurgical bond with having least dilution of the base material which
enhances the abrasion, corrosion and the wear resistance of metals.
Paraphrase This Document
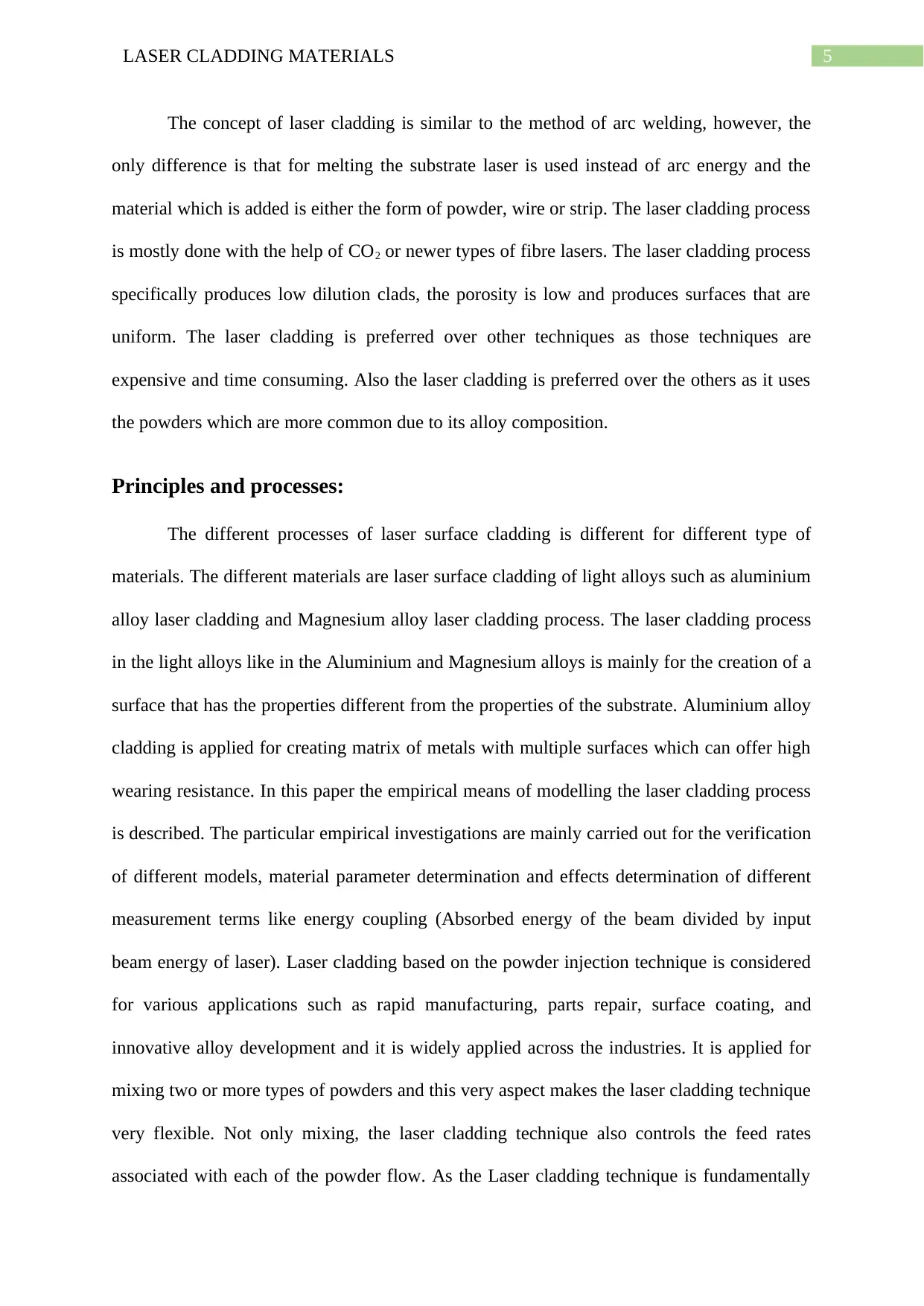
The concept of laser cladding is similar to the method of arc welding, however, the
only difference is that for melting the substrate laser is used instead of arc energy and the
material which is added is either the form of powder, wire or strip. The laser cladding process
is mostly done with the help of CO2 or newer types of fibre lasers. The laser cladding process
specifically produces low dilution clads, the porosity is low and produces surfaces that are
uniform. The laser cladding is preferred over other techniques as those techniques are
expensive and time consuming. Also the laser cladding is preferred over the others as it uses
the powders which are more common due to its alloy composition.
Principles and processes:
The different processes of laser surface cladding is different for different type of
materials. The different materials are laser surface cladding of light alloys such as aluminium
alloy laser cladding and Magnesium alloy laser cladding process. The laser cladding process
in the light alloys like in the Aluminium and Magnesium alloys is mainly for the creation of a
surface that has the properties different from the properties of the substrate. Aluminium alloy
cladding is applied for creating matrix of metals with multiple surfaces which can offer high
wearing resistance. In this paper the empirical means of modelling the laser cladding process
is described. The particular empirical investigations are mainly carried out for the verification
of different models, material parameter determination and effects determination of different
measurement terms like energy coupling (Absorbed energy of the beam divided by input
beam energy of laser). Laser cladding based on the powder injection technique is considered
for various applications such as rapid manufacturing, parts repair, surface coating, and
innovative alloy development and it is widely applied across the industries. It is applied for
mixing two or more types of powders and this very aspect makes the laser cladding technique
very flexible. Not only mixing, the laser cladding technique also controls the feed rates
associated with each of the powder flow. As the Laser cladding technique is fundamentally
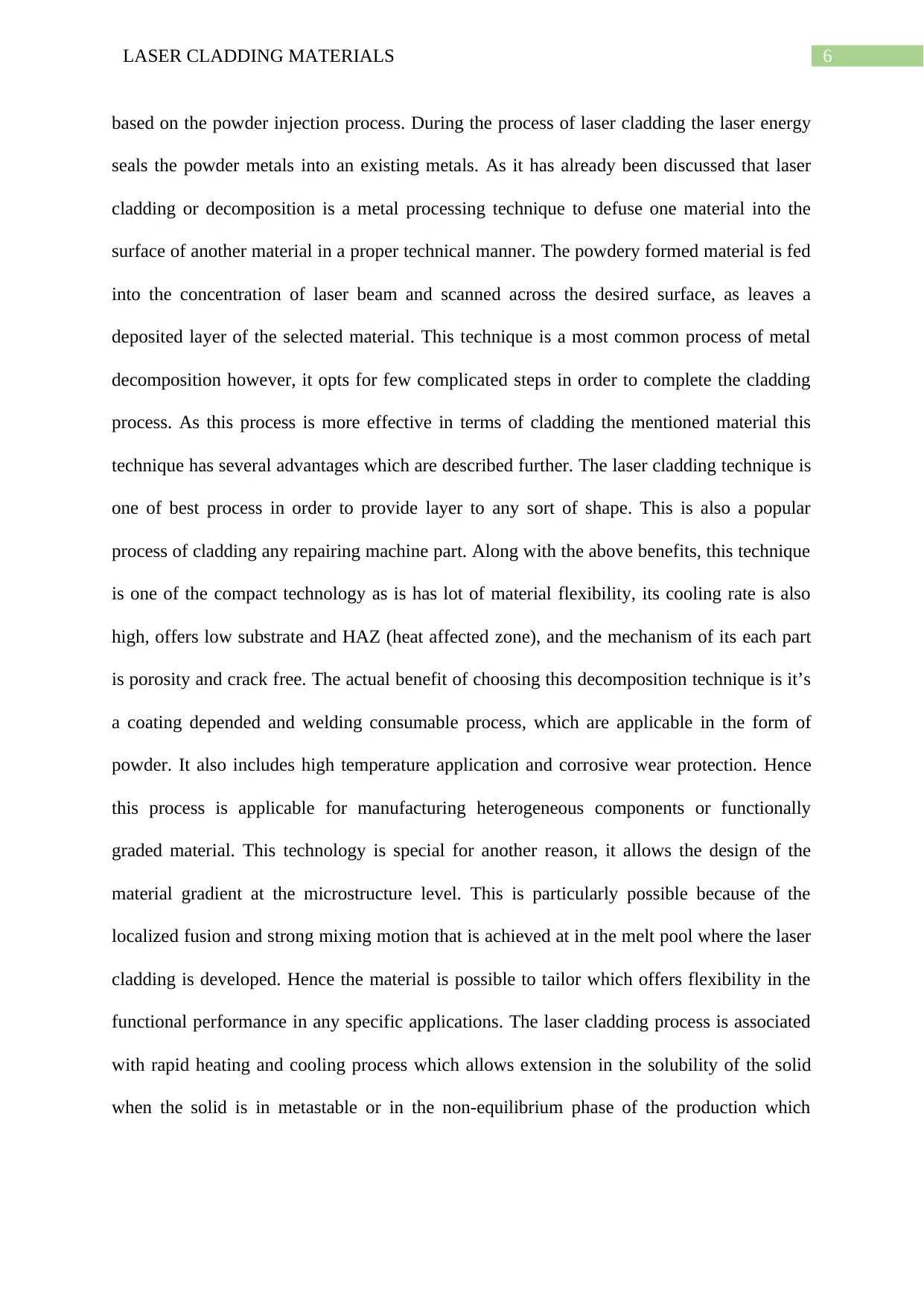
based on the powder injection process. During the process of laser cladding the laser energy
seals the powder metals into an existing metals. As it has already been discussed that laser
cladding or decomposition is a metal processing technique to defuse one material into the
surface of another material in a proper technical manner. The powdery formed material is fed
into the concentration of laser beam and scanned across the desired surface, as leaves a
deposited layer of the selected material. This technique is a most common process of metal
decomposition however, it opts for few complicated steps in order to complete the cladding
process. As this process is more effective in terms of cladding the mentioned material this
technique has several advantages which are described further. The laser cladding technique is
one of best process in order to provide layer to any sort of shape. This is also a popular
process of cladding any repairing machine part. Along with the above benefits, this technique
is one of the compact technology as is has lot of material flexibility, its cooling rate is also
high, offers low substrate and HAZ (heat affected zone), and the mechanism of its each part
is porosity and crack free. The actual benefit of choosing this decomposition technique is it’s
a coating depended and welding consumable process, which are applicable in the form of
powder. It also includes high temperature application and corrosive wear protection. Hence
this process is applicable for manufacturing heterogeneous components or functionally
graded material. This technology is special for another reason, it allows the design of the
material gradient at the microstructure level. This is particularly possible because of the
localized fusion and strong mixing motion that is achieved at in the melt pool where the laser
cladding is developed. Hence the material is possible to tailor which offers flexibility in the
functional performance in any specific applications. The laser cladding process is associated
with rapid heating and cooling process which allows extension in the solubility of the solid
when the solid is in metastable or in the non-equilibrium phase of the production which
⊘ This is a preview!⊘
Do you want full access?
Subscribe today to unlock all pages.

Trusted by 1+ million students worldwide
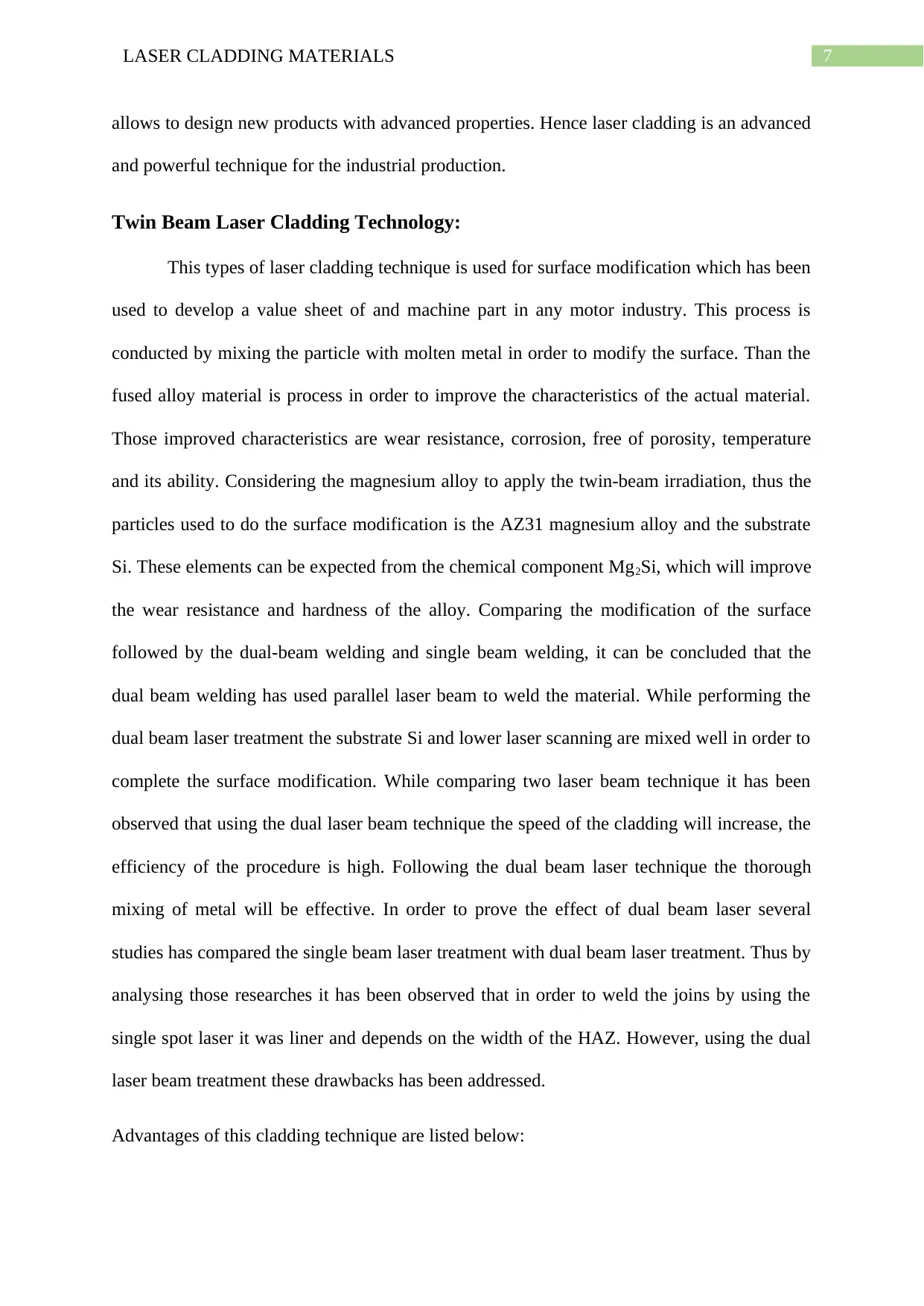
allows to design new products with advanced properties. Hence laser cladding is an advanced
and powerful technique for the industrial production.
Twin Beam Laser Cladding Technology:
This types of laser cladding technique is used for surface modification which has been
used to develop a value sheet of and machine part in any motor industry. This process is
conducted by mixing the particle with molten metal in order to modify the surface. Than the
fused alloy material is process in order to improve the characteristics of the actual material.
Those improved characteristics are wear resistance, corrosion, free of porosity, temperature
and its ability. Considering the magnesium alloy to apply the twin-beam irradiation, thus the
particles used to do the surface modification is the AZ31 magnesium alloy and the substrate
Si. These elements can be expected from the chemical component Mg2Si, which will improve
the wear resistance and hardness of the alloy. Comparing the modification of the surface
followed by the dual-beam welding and single beam welding, it can be concluded that the
dual beam welding has used parallel laser beam to weld the material. While performing the
dual beam laser treatment the substrate Si and lower laser scanning are mixed well in order to
complete the surface modification. While comparing two laser beam technique it has been
observed that using the dual laser beam technique the speed of the cladding will increase, the
efficiency of the procedure is high. Following the dual beam laser technique the thorough
mixing of metal will be effective. In order to prove the effect of dual beam laser several
studies has compared the single beam laser treatment with dual beam laser treatment. Thus by
analysing those researches it has been observed that in order to weld the joins by using the
single spot laser it was liner and depends on the width of the HAZ. However, using the dual
laser beam treatment these drawbacks has been addressed.
Advantages of this cladding technique are listed below:
Paraphrase This Document
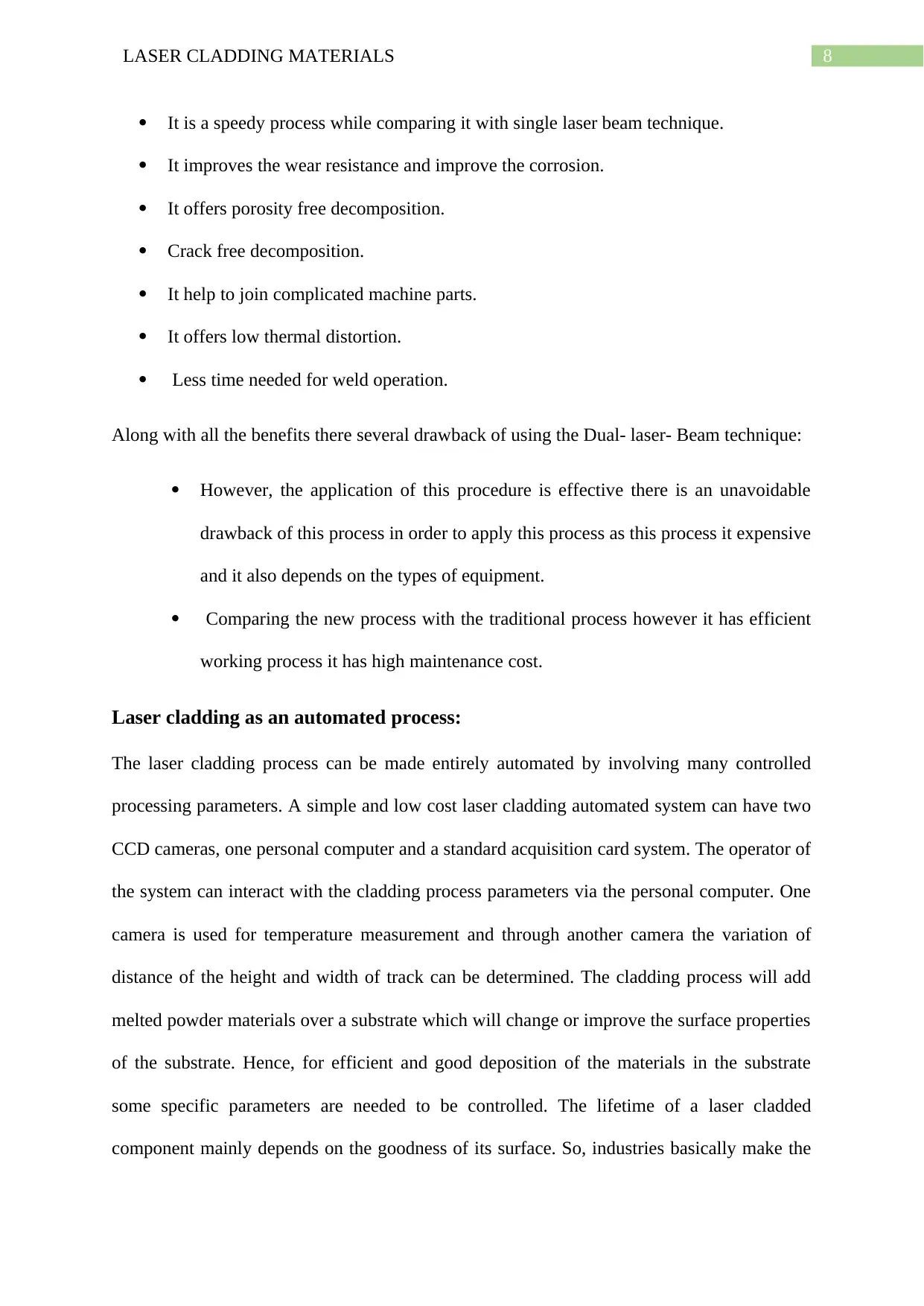
It is a speedy process while comparing it with single laser beam technique.
It improves the wear resistance and improve the corrosion.
It offers porosity free decomposition.
Crack free decomposition.
It help to join complicated machine parts.
It offers low thermal distortion.
Less time needed for weld operation.
Along with all the benefits there several drawback of using the Dual- laser- Beam technique:
However, the application of this procedure is effective there is an unavoidable
drawback of this process in order to apply this process as this process it expensive
and it also depends on the types of equipment.
Comparing the new process with the traditional process however it has efficient
working process it has high maintenance cost.
Laser cladding as an automated process:
The laser cladding process can be made entirely automated by involving many controlled
processing parameters. A simple and low cost laser cladding automated system can have two
CCD cameras, one personal computer and a standard acquisition card system. The operator of
the system can interact with the cladding process parameters via the personal computer. One
camera is used for temperature measurement and through another camera the variation of
distance of the height and width of track can be determined. The cladding process will add
melted powder materials over a substrate which will change or improve the surface properties
of the substrate. Hence, for efficient and good deposition of the materials in the substrate
some specific parameters are needed to be controlled. The lifetime of a laser cladded
component mainly depends on the goodness of its surface. So, industries basically make the
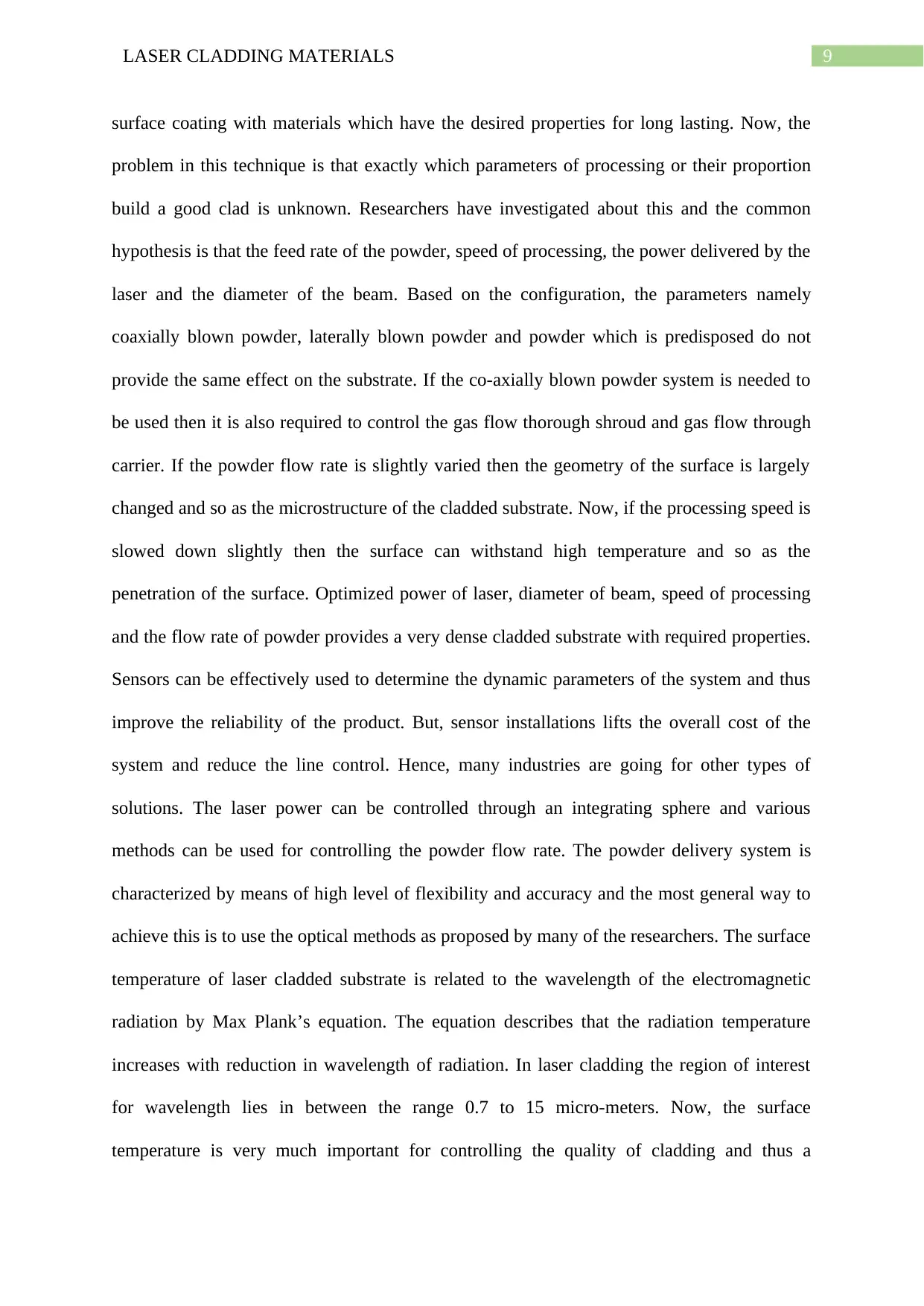
surface coating with materials which have the desired properties for long lasting. Now, the
problem in this technique is that exactly which parameters of processing or their proportion
build a good clad is unknown. Researchers have investigated about this and the common
hypothesis is that the feed rate of the powder, speed of processing, the power delivered by the
laser and the diameter of the beam. Based on the configuration, the parameters namely
coaxially blown powder, laterally blown powder and powder which is predisposed do not
provide the same effect on the substrate. If the co-axially blown powder system is needed to
be used then it is also required to control the gas flow thorough shroud and gas flow through
carrier. If the powder flow rate is slightly varied then the geometry of the surface is largely
changed and so as the microstructure of the cladded substrate. Now, if the processing speed is
slowed down slightly then the surface can withstand high temperature and so as the
penetration of the surface. Optimized power of laser, diameter of beam, speed of processing
and the flow rate of powder provides a very dense cladded substrate with required properties.
Sensors can be effectively used to determine the dynamic parameters of the system and thus
improve the reliability of the product. But, sensor installations lifts the overall cost of the
system and reduce the line control. Hence, many industries are going for other types of
solutions. The laser power can be controlled through an integrating sphere and various
methods can be used for controlling the powder flow rate. The powder delivery system is
characterized by means of high level of flexibility and accuracy and the most general way to
achieve this is to use the optical methods as proposed by many of the researchers. The surface
temperature of laser cladded substrate is related to the wavelength of the electromagnetic
radiation by Max Plank’s equation. The equation describes that the radiation temperature
increases with reduction in wavelength of radiation. In laser cladding the region of interest
for wavelength lies in between the range 0.7 to 15 micro-meters. Now, the surface
temperature is very much important for controlling the quality of cladding and thus a
⊘ This is a preview!⊘
Do you want full access?
Subscribe today to unlock all pages.

Trusted by 1+ million students worldwide
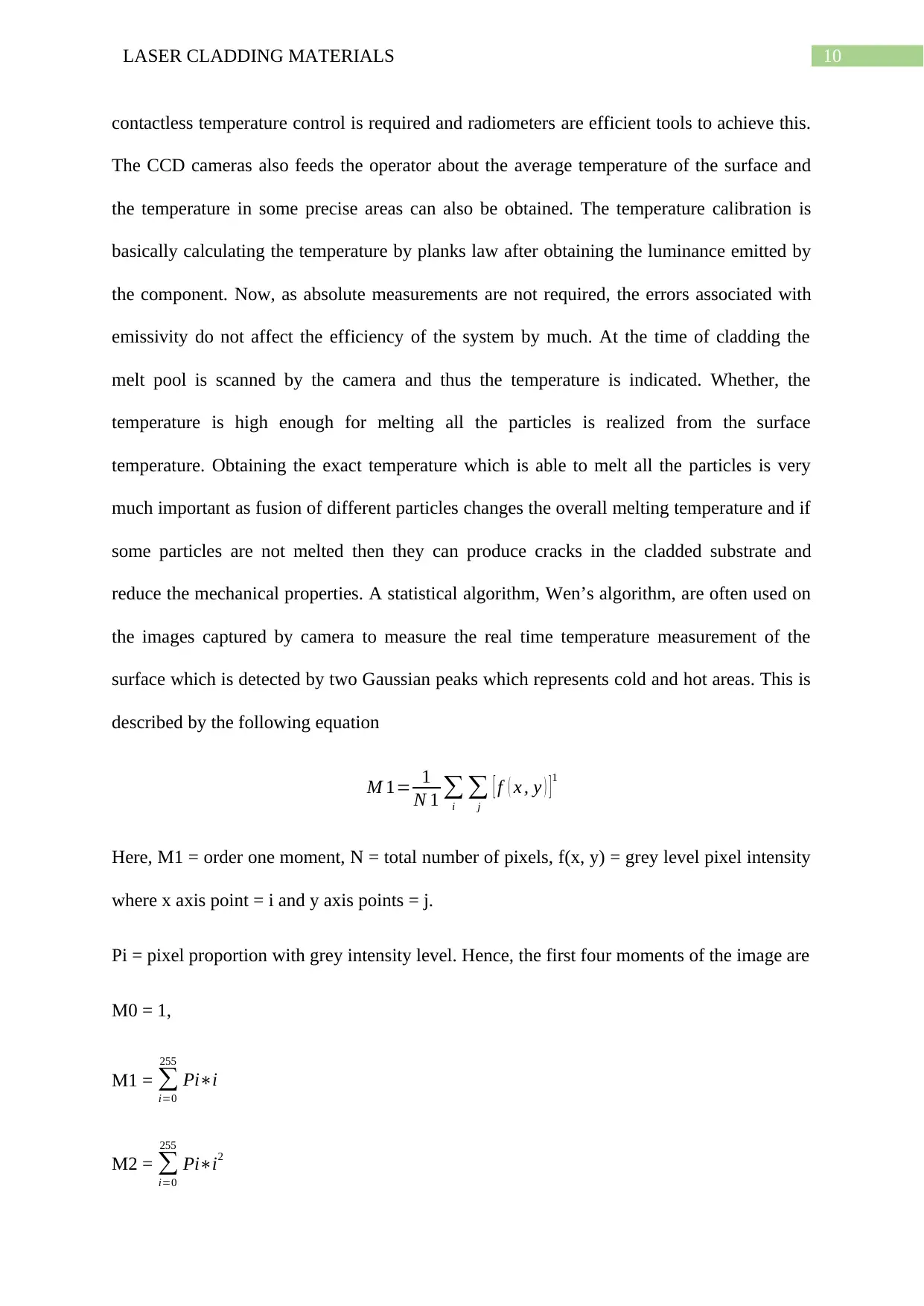
contactless temperature control is required and radiometers are efficient tools to achieve this.
The CCD cameras also feeds the operator about the average temperature of the surface and
the temperature in some precise areas can also be obtained. The temperature calibration is
basically calculating the temperature by planks law after obtaining the luminance emitted by
the component. Now, as absolute measurements are not required, the errors associated with
emissivity do not affect the efficiency of the system by much. At the time of cladding the
melt pool is scanned by the camera and thus the temperature is indicated. Whether, the
temperature is high enough for melting all the particles is realized from the surface
temperature. Obtaining the exact temperature which is able to melt all the particles is very
much important as fusion of different particles changes the overall melting temperature and if
some particles are not melted then they can produce cracks in the cladded substrate and
reduce the mechanical properties. A statistical algorithm, Wen’s algorithm, are often used on
the images captured by camera to measure the real time temperature measurement of the
surface which is detected by two Gaussian peaks which represents cold and hot areas. This is
described by the following equation
M 1= 1
N 1 ∑
i
∑
j
[ f ( x , y ) ]1
Here, M1 = order one moment, N = total number of pixels, f(x, y) = grey level pixel intensity
where x axis point = i and y axis points = j.
Pi = pixel proportion with grey intensity level. Hence, the first four moments of the image are
M0 = 1,
M1 = ∑
i=0
255
Pi∗i
M2 = ∑
i=0
255
Pi∗i2
Paraphrase This Document

M3 = ∑
i=0
255
Pi∗i3
The grey image has only two populations 1 and 0 which are denoted by Z1 and Z2. Now, the
proportion of grey level Z1 is q1 and the proportion of grey level Z2 is q2. Now, applying the
statistical momentum conservation rule the linear equation that are needed to be solved
becomes
M 0=q 1∗z 10 + q 2∗z 20
M 1=q 1∗z 11+q 2∗z 21
M 2=q 1∗z 12 +q 2∗z 22
M 3=q 1∗z 13 +q 2∗z 23
By, solving above equations the solutions of Z1 and Z2 can be obtained from the following
equation.
Z2 +C 1∗Z +C 0=0
Now, by knowing q1 and q2 the Wen’s threshold can be found when the value of the
reparation function is equal to q1. Now, after obtaining the wen’s threshold the average grey
level is calculated from the following equation.
G=
( ∑
i=We n' s threshold
255
Gi∗Nbi )
∑
i=We n' s threshold
255
Nbi
Gi = grey level i
Nbi = pixel numbers having the value of level equal to i.
The temperature histogram is shown below.
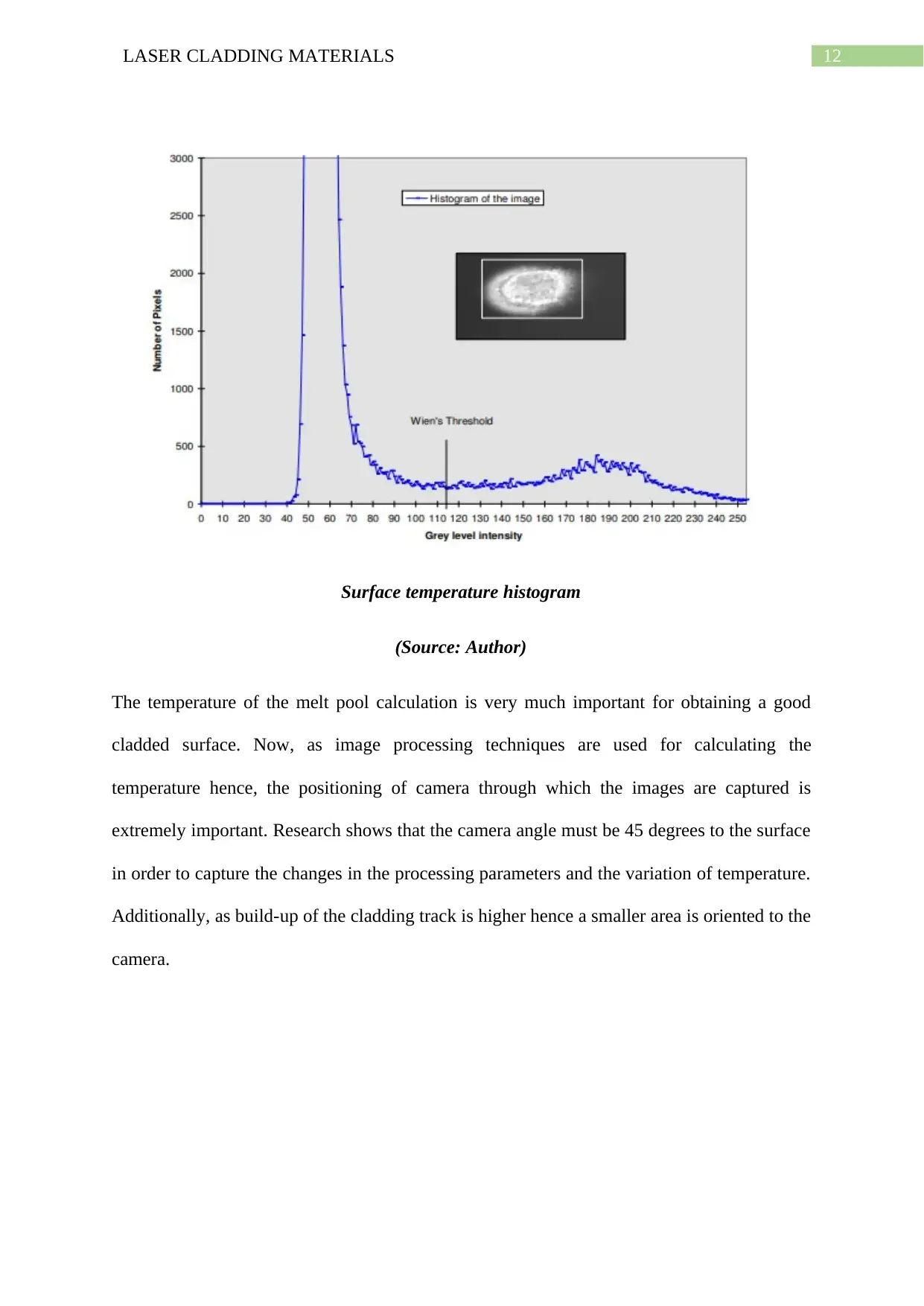
Surface temperature histogram
(Source: Author)
The temperature of the melt pool calculation is very much important for obtaining a good
cladded surface. Now, as image processing techniques are used for calculating the
temperature hence, the positioning of camera through which the images are captured is
extremely important. Research shows that the camera angle must be 45 degrees to the surface
in order to capture the changes in the processing parameters and the variation of temperature.
Additionally, as build-up of the cladding track is higher hence a smaller area is oriented to the
camera.
⊘ This is a preview!⊘
Do you want full access?
Subscribe today to unlock all pages.

Trusted by 1+ million students worldwide
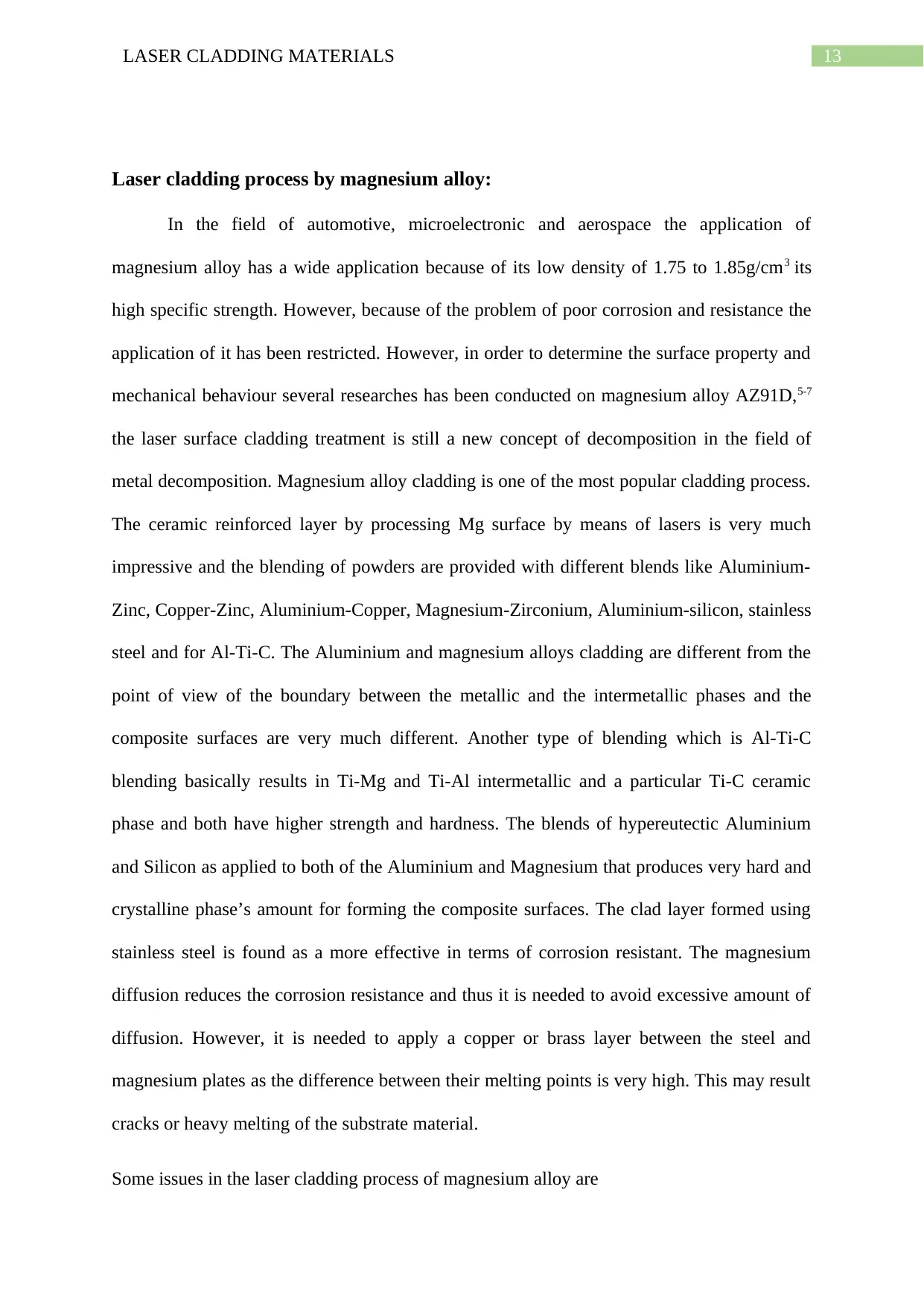
Laser cladding process by magnesium alloy:
In the field of automotive, microelectronic and aerospace the application of
magnesium alloy has a wide application because of its low density of 1.75 to 1.85g/cm3 its
high specific strength. However, because of the problem of poor corrosion and resistance the
application of it has been restricted. However, in order to determine the surface property and
mechanical behaviour several researches has been conducted on magnesium alloy AZ91D,5-7
the laser surface cladding treatment is still a new concept of decomposition in the field of
metal decomposition. Magnesium alloy cladding is one of the most popular cladding process.
The ceramic reinforced layer by processing Mg surface by means of lasers is very much
impressive and the blending of powders are provided with different blends like Aluminium-
Zinc, Copper-Zinc, Aluminium-Copper, Magnesium-Zirconium, Aluminium-silicon, stainless
steel and for Al-Ti-C. The Aluminium and magnesium alloys cladding are different from the
point of view of the boundary between the metallic and the intermetallic phases and the
composite surfaces are very much different. Another type of blending which is Al-Ti-C
blending basically results in Ti-Mg and Ti-Al intermetallic and a particular Ti-C ceramic
phase and both have higher strength and hardness. The blends of hypereutectic Aluminium
and Silicon as applied to both of the Aluminium and Magnesium that produces very hard and
crystalline phase’s amount for forming the composite surfaces. The clad layer formed using
stainless steel is found as a more effective in terms of corrosion resistant. The magnesium
diffusion reduces the corrosion resistance and thus it is needed to avoid excessive amount of
diffusion. However, it is needed to apply a copper or brass layer between the steel and
magnesium plates as the difference between their melting points is very high. This may result
cracks or heavy melting of the substrate material.
Some issues in the laser cladding process of magnesium alloy are
Paraphrase This Document
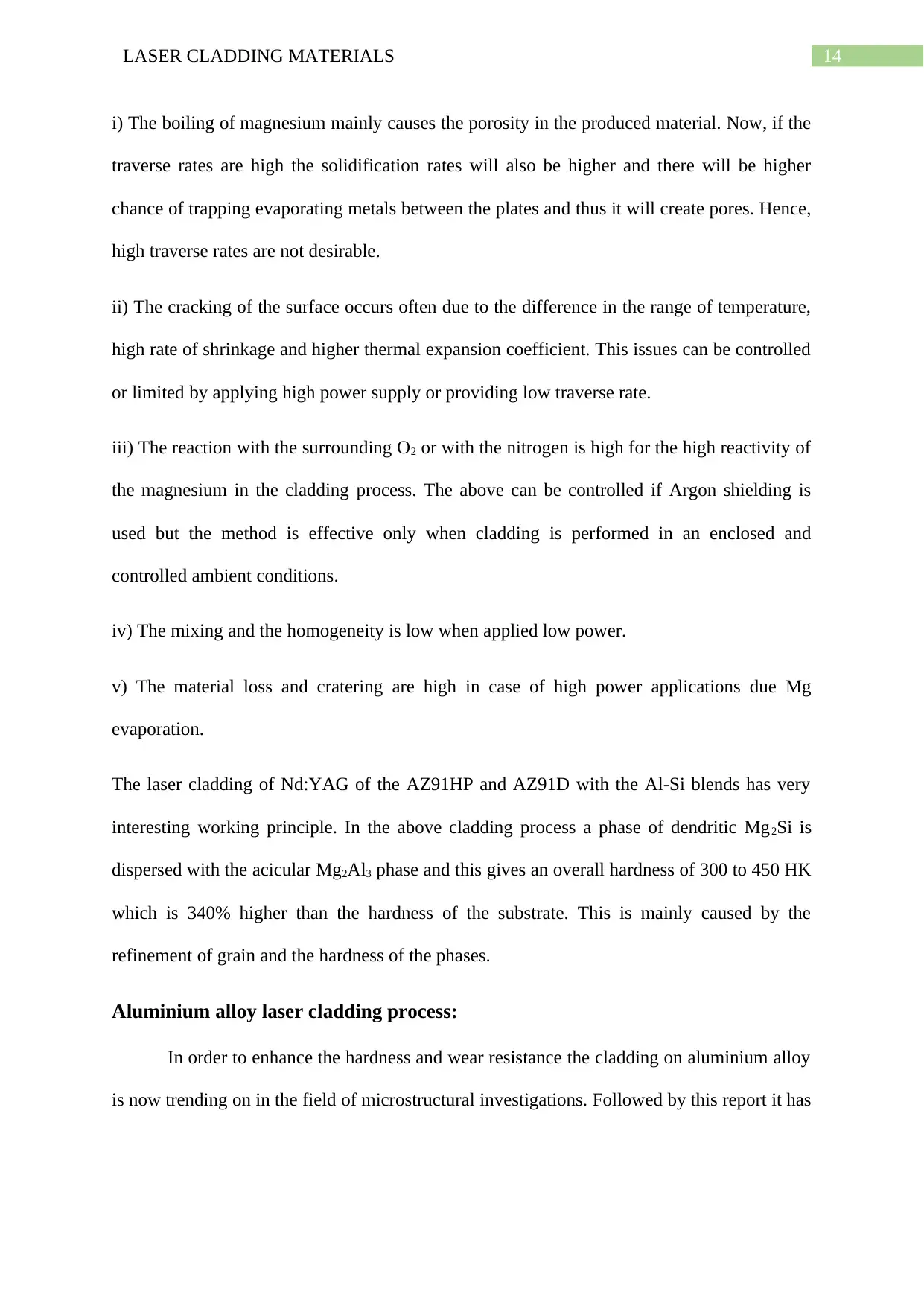
i) The boiling of magnesium mainly causes the porosity in the produced material. Now, if the
traverse rates are high the solidification rates will also be higher and there will be higher
chance of trapping evaporating metals between the plates and thus it will create pores. Hence,
high traverse rates are not desirable.
ii) The cracking of the surface occurs often due to the difference in the range of temperature,
high rate of shrinkage and higher thermal expansion coefficient. This issues can be controlled
or limited by applying high power supply or providing low traverse rate.
iii) The reaction with the surrounding O2 or with the nitrogen is high for the high reactivity of
the magnesium in the cladding process. The above can be controlled if Argon shielding is
used but the method is effective only when cladding is performed in an enclosed and
controlled ambient conditions.
iv) The mixing and the homogeneity is low when applied low power.
v) The material loss and cratering are high in case of high power applications due Mg
evaporation.
The laser cladding of Nd:YAG of the AZ91HP and AZ91D with the Al-Si blends has very
interesting working principle. In the above cladding process a phase of dendritic Mg2Si is
dispersed with the acicular Mg2Al3 phase and this gives an overall hardness of 300 to 450 HK
which is 340% higher than the hardness of the substrate. This is mainly caused by the
refinement of grain and the hardness of the phases.
Aluminium alloy laser cladding process:
In order to enhance the hardness and wear resistance the cladding on aluminium alloy
is now trending on in the field of microstructural investigations. Followed by this report it has
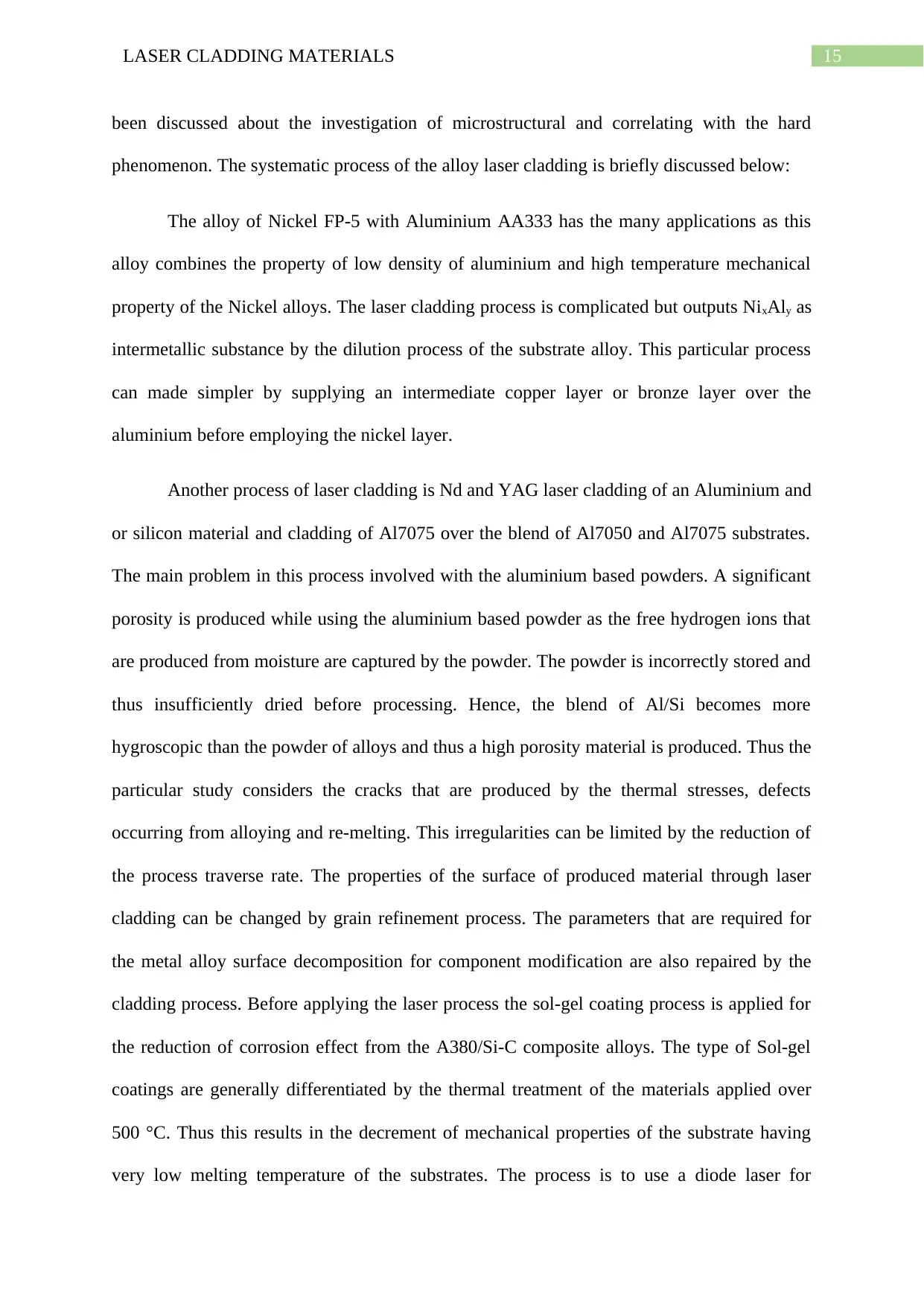
been discussed about the investigation of microstructural and correlating with the hard
phenomenon. The systematic process of the alloy laser cladding is briefly discussed below:
The alloy of Nickel FP-5 with Aluminium AA333 has the many applications as this
alloy combines the property of low density of aluminium and high temperature mechanical
property of the Nickel alloys. The laser cladding process is complicated but outputs NixAly as
intermetallic substance by the dilution process of the substrate alloy. This particular process
can made simpler by supplying an intermediate copper layer or bronze layer over the
aluminium before employing the nickel layer.
Another process of laser cladding is Nd and YAG laser cladding of an Aluminium and
or silicon material and cladding of Al7075 over the blend of Al7050 and Al7075 substrates.
The main problem in this process involved with the aluminium based powders. A significant
porosity is produced while using the aluminium based powder as the free hydrogen ions that
are produced from moisture are captured by the powder. The powder is incorrectly stored and
thus insufficiently dried before processing. Hence, the blend of Al/Si becomes more
hygroscopic than the powder of alloys and thus a high porosity material is produced. Thus the
particular study considers the cracks that are produced by the thermal stresses, defects
occurring from alloying and re-melting. This irregularities can be limited by the reduction of
the process traverse rate. The properties of the surface of produced material through laser
cladding can be changed by grain refinement process. The parameters that are required for
the metal alloy surface decomposition for component modification are also repaired by the
cladding process. Before applying the laser process the sol-gel coating process is applied for
the reduction of corrosion effect from the A380/Si-C composite alloys. The type of Sol-gel
coatings are generally differentiated by the thermal treatment of the materials applied over
500 °C. Thus this results in the decrement of mechanical properties of the substrate having
very low melting temperature of the substrates. The process is to use a diode laser for
⊘ This is a preview!⊘
Do you want full access?
Subscribe today to unlock all pages.

Trusted by 1+ million students worldwide
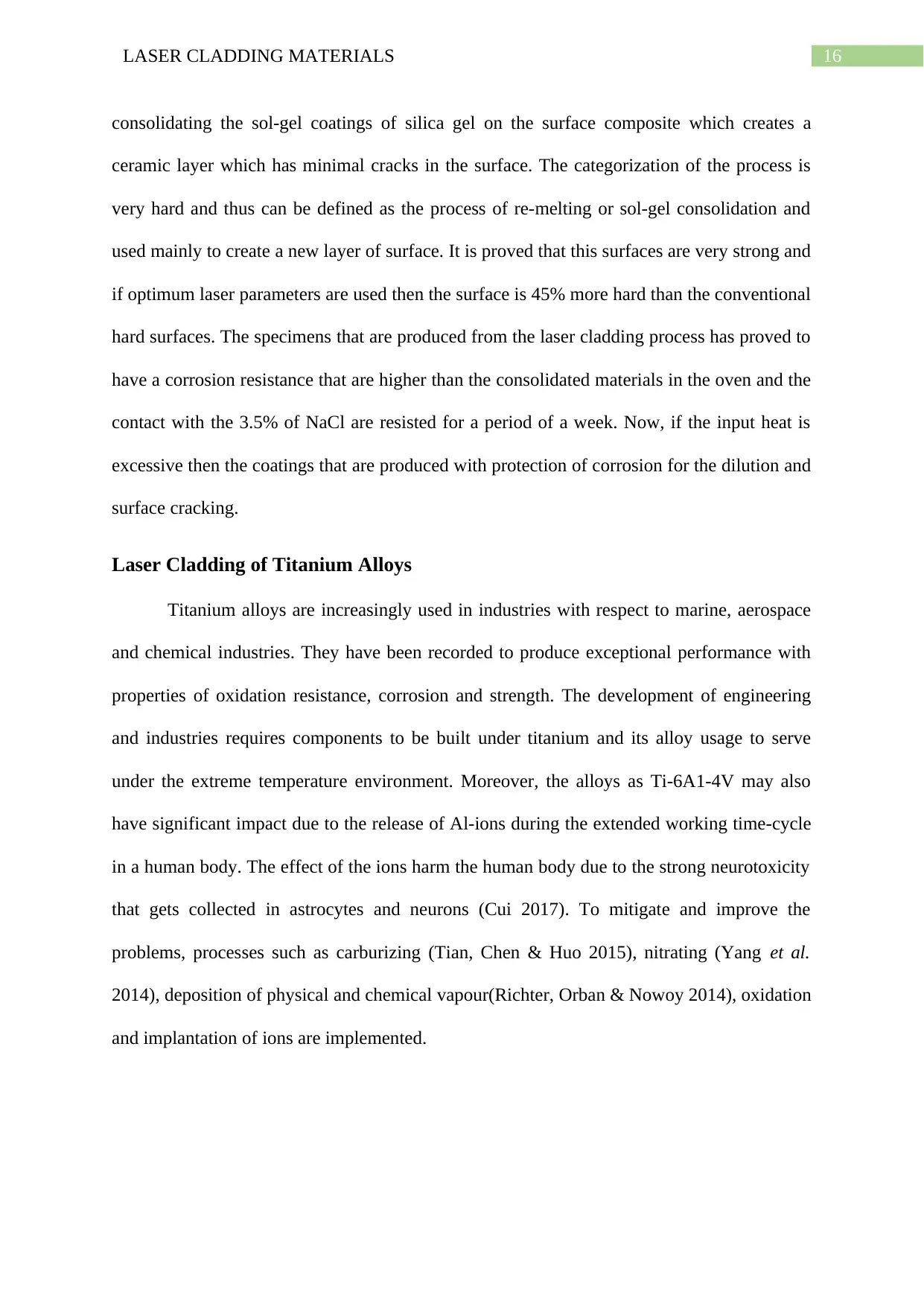
consolidating the sol-gel coatings of silica gel on the surface composite which creates a
ceramic layer which has minimal cracks in the surface. The categorization of the process is
very hard and thus can be defined as the process of re-melting or sol-gel consolidation and
used mainly to create a new layer of surface. It is proved that this surfaces are very strong and
if optimum laser parameters are used then the surface is 45% more hard than the conventional
hard surfaces. The specimens that are produced from the laser cladding process has proved to
have a corrosion resistance that are higher than the consolidated materials in the oven and the
contact with the 3.5% of NaCl are resisted for a period of a week. Now, if the input heat is
excessive then the coatings that are produced with protection of corrosion for the dilution and
surface cracking.
Laser Cladding of Titanium Alloys
Titanium alloys are increasingly used in industries with respect to marine, aerospace
and chemical industries. They have been recorded to produce exceptional performance with
properties of oxidation resistance, corrosion and strength. The development of engineering
and industries requires components to be built under titanium and its alloy usage to serve
under the extreme temperature environment. Moreover, the alloys as Ti-6A1-4V may also
have significant impact due to the release of Al-ions during the extended working time-cycle
in a human body. The effect of the ions harm the human body due to the strong neurotoxicity
that gets collected in astrocytes and neurons (Cui 2017). To mitigate and improve the
problems, processes such as carburizing (Tian, Chen & Huo 2015), nitrating (Yang et al.
2014), deposition of physical and chemical vapour(Richter, Orban & Nowoy 2014), oxidation
and implantation of ions are implemented.
Paraphrase This Document
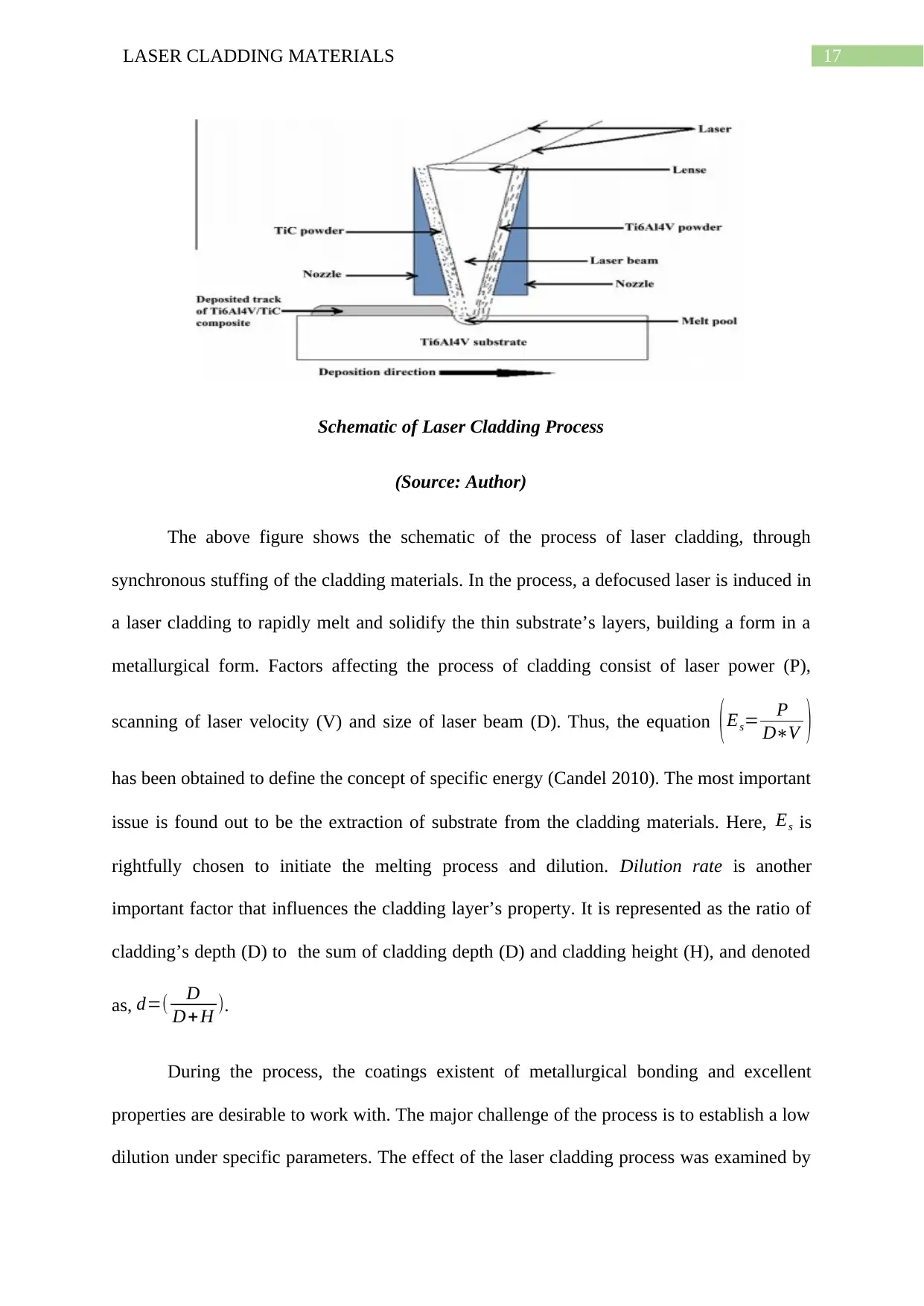
Schematic of Laser Cladding Process
(Source: Author)
The above figure shows the schematic of the process of laser cladding, through
synchronous stuffing of the cladding materials. In the process, a defocused laser is induced in
a laser cladding to rapidly melt and solidify the thin substrate’s layers, building a form in a
metallurgical form. Factors affecting the process of cladding consist of laser power (P),
scanning of laser velocity (V) and size of laser beam (D). Thus, the equation ( Es= P
D∗V )
has been obtained to define the concept of specific energy (Candel 2010). The most important
issue is found out to be the extraction of substrate from the cladding materials. Here, Es is
rightfully chosen to initiate the melting process and dilution. Dilution rate is another
important factor that influences the cladding layer’s property. It is represented as the ratio of
cladding’s depth (D) to the sum of cladding depth (D) and cladding height (H), and denoted
as, d=( D
D+H ).
During the process, the coatings existent of metallurgical bonding and excellent
properties are desirable to work with. The major challenge of the process is to establish a low
dilution under specific parameters. The effect of the laser cladding process was examined by
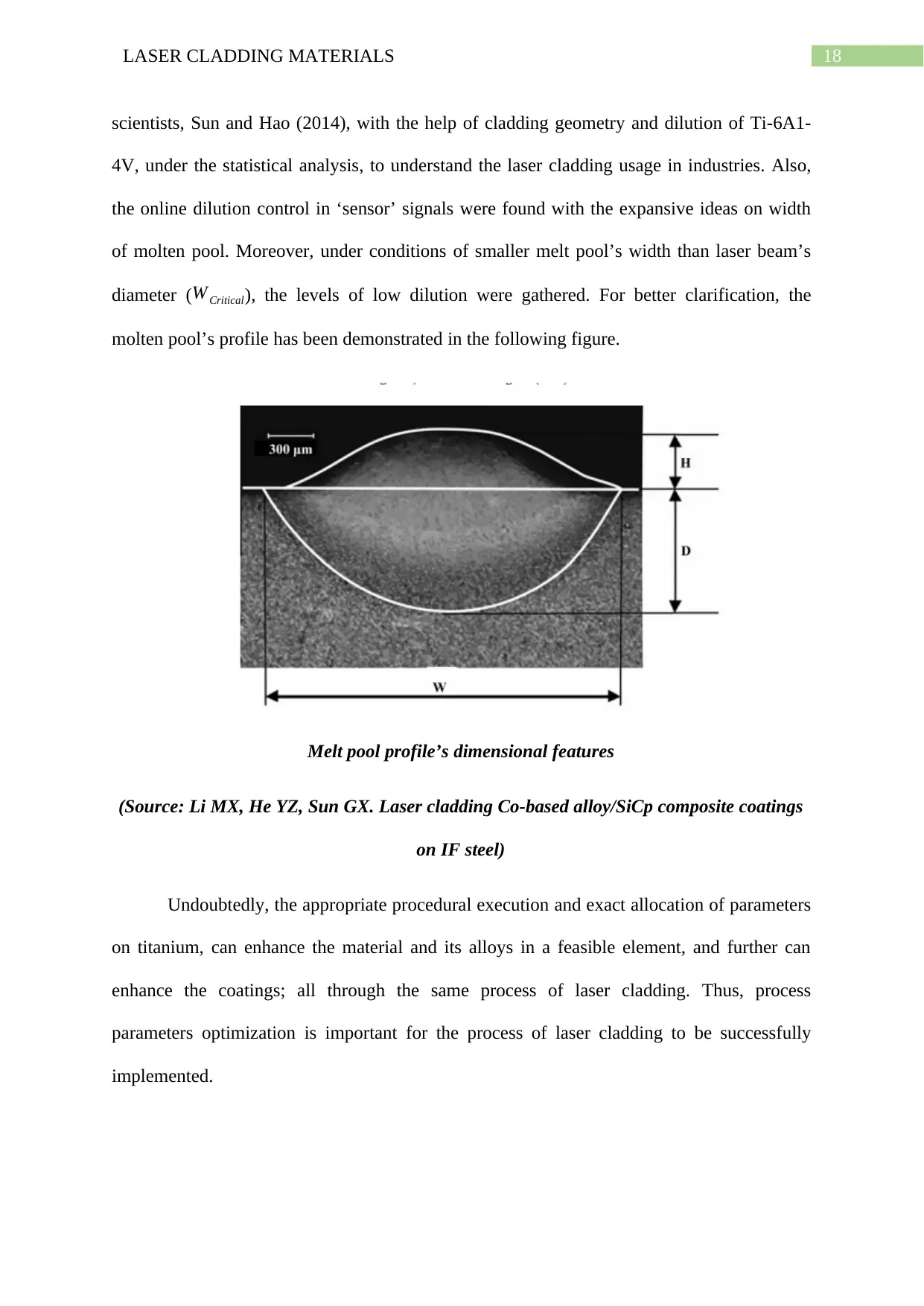
scientists, Sun and Hao (2014), with the help of cladding geometry and dilution of Ti-6A1-
4V, under the statistical analysis, to understand the laser cladding usage in industries. Also,
the online dilution control in ‘sensor’ signals were found with the expansive ideas on width
of molten pool. Moreover, under conditions of smaller melt pool’s width than laser beam’s
diameter (W Critical), the levels of low dilution were gathered. For better clarification, the
molten pool’s profile has been demonstrated in the following figure.
Melt pool profile’s dimensional features
(Source: Li MX, He YZ, Sun GX. Laser cladding Co-based alloy/SiCp composite coatings
on IF steel)
Undoubtedly, the appropriate procedural execution and exact allocation of parameters
on titanium, can enhance the material and its alloys in a feasible element, and further can
enhance the coatings; all through the same process of laser cladding. Thus, process
parameters optimization is important for the process of laser cladding to be successfully
implemented.
⊘ This is a preview!⊘
Do you want full access?
Subscribe today to unlock all pages.

Trusted by 1+ million students worldwide
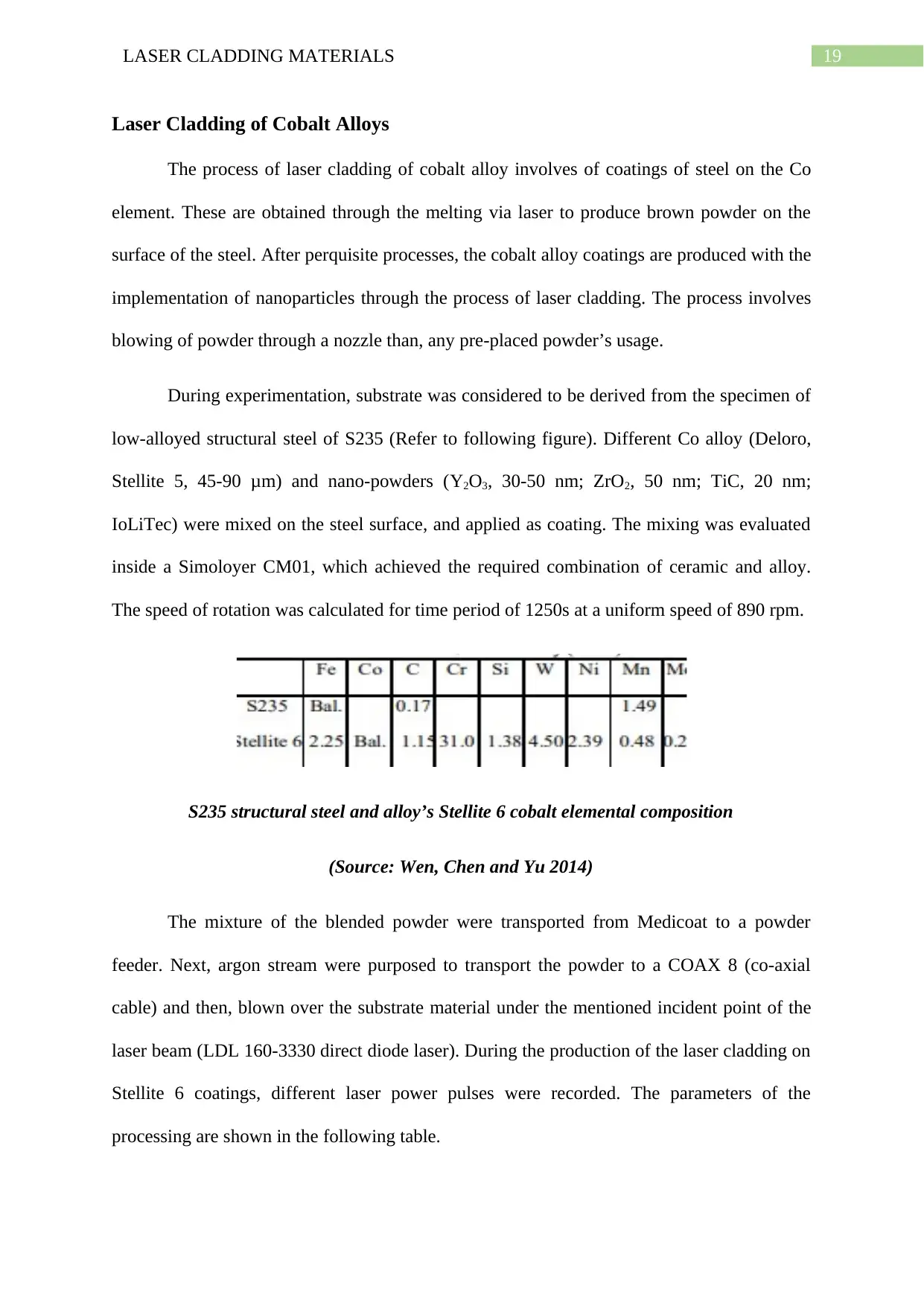
Laser Cladding of Cobalt Alloys
The process of laser cladding of cobalt alloy involves of coatings of steel on the Co
element. These are obtained through the melting via laser to produce brown powder on the
surface of the steel. After perquisite processes, the cobalt alloy coatings are produced with the
implementation of nanoparticles through the process of laser cladding. The process involves
blowing of powder through a nozzle than, any pre-placed powder’s usage.
During experimentation, substrate was considered to be derived from the specimen of
low-alloyed structural steel of S235 (Refer to following figure). Different Co alloy (Deloro,
Stellite 5, 45-90 μm) and nano-powders (Y2O3, 30-50 nm; ZrO2, 50 nm; TiC, 20 nm;
IoLiTec) were mixed on the steel surface, and applied as coating. The mixing was evaluated
inside a Simoloyer CM01, which achieved the required combination of ceramic and alloy.
The speed of rotation was calculated for time period of 1250s at a uniform speed of 890 rpm.
S235 structural steel and alloy’s Stellite 6 cobalt elemental composition
(Source: Wen, Chen and Yu 2014)
The mixture of the blended powder were transported from Medicoat to a powder
feeder. Next, argon stream were purposed to transport the powder to a COAX 8 (co-axial
cable) and then, blown over the substrate material under the mentioned incident point of the
laser beam (LDL 160-3330 direct diode laser). During the production of the laser cladding on
Stellite 6 coatings, different laser power pulses were recorded. The parameters of the
processing are shown in the following table.
Paraphrase This Document
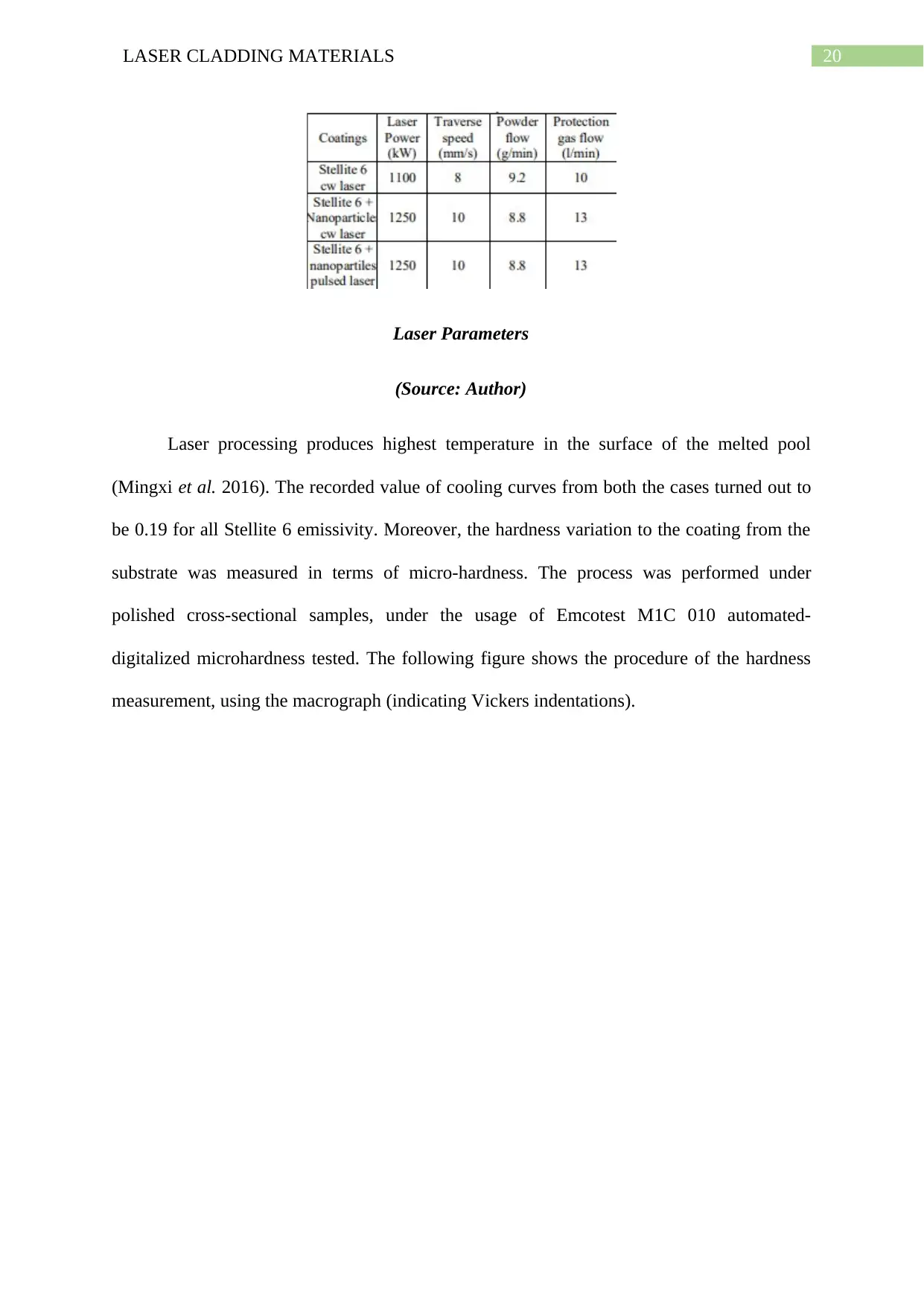
Laser Parameters
(Source: Author)
Laser processing produces highest temperature in the surface of the melted pool
(Mingxi et al. 2016). The recorded value of cooling curves from both the cases turned out to
be 0.19 for all Stellite 6 emissivity. Moreover, the hardness variation to the coating from the
substrate was measured in terms of micro-hardness. The process was performed under
polished cross-sectional samples, under the usage of Emcotest M1C 010 automated-
digitalized microhardness tested. The following figure shows the procedure of the hardness
measurement, using the macrograph (indicating Vickers indentations).
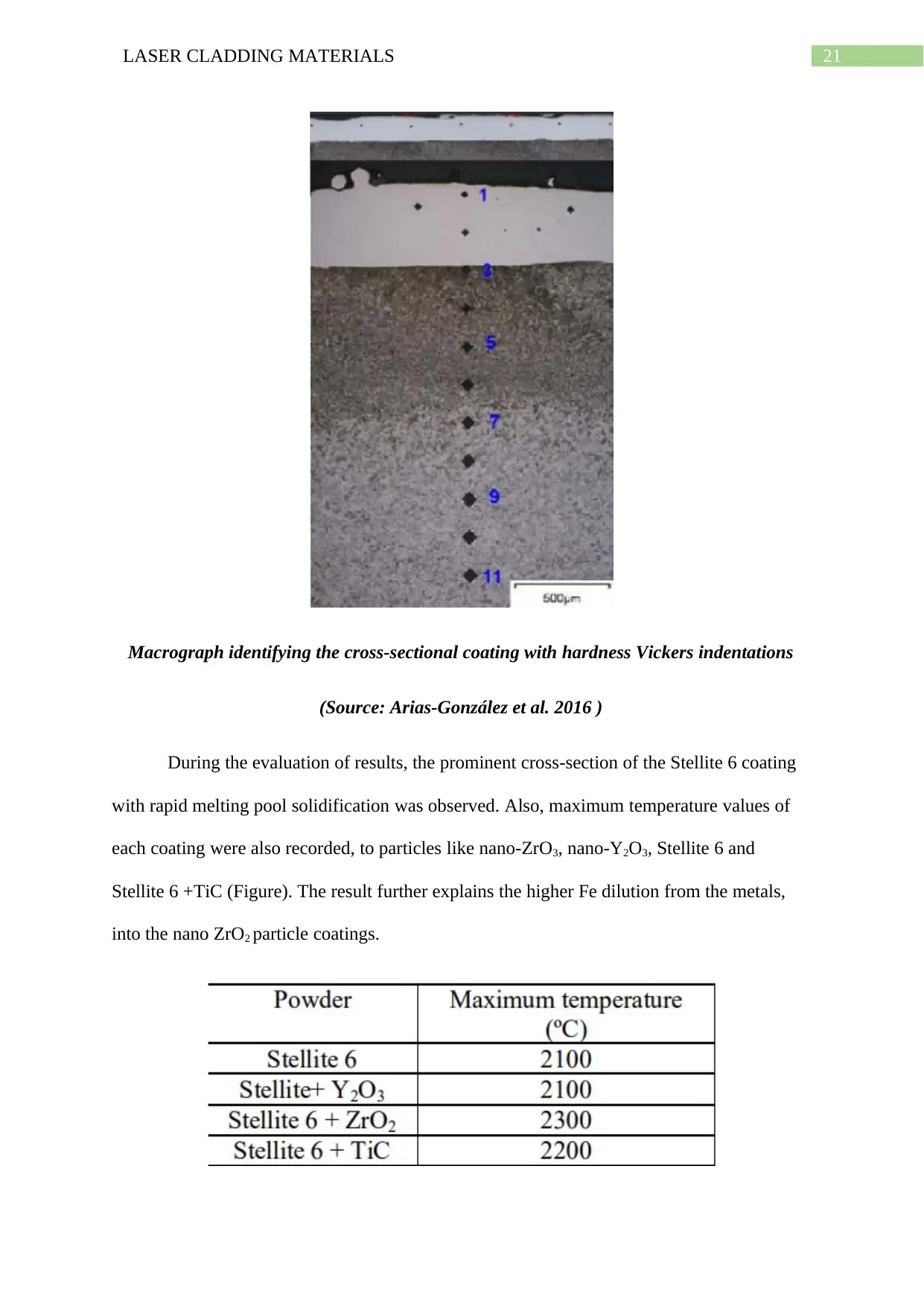
Macrograph identifying the cross-sectional coating with hardness Vickers indentations
(Source: Arias-González et al. 2016 )
During the evaluation of results, the prominent cross-section of the Stellite 6 coating
with rapid melting pool solidification was observed. Also, maximum temperature values of
each coating were also recorded, to particles like nano-ZrO3, nano-Y2O3, Stellite 6 and
Stellite 6 +TiC (Figure). The result further explains the higher Fe dilution from the metals,
into the nano ZrO2 particle coatings.
⊘ This is a preview!⊘
Do you want full access?
Subscribe today to unlock all pages.

Trusted by 1+ million students worldwide

Melt pool surface’s maximum temperature values during coating (as measured by the
pyrometer)
(Source: Author)
After the production of Stellite 6 (under 0.6% of nano-ceramic particles), the
microstructure of the top layer of Stellite 6 is observed to produce 0.55% of nano-Y2O3 layer
of coating (Figure 5). Also, the inter-dendric spaces and dendrites are also obtained,
signifying the alike structure of the Stellite coating and the EDS zone (Figure 6).
Fig 5: Micrographs (SEM) of stellite 6+ Fig 6: Interdentritic zone of Eutectic microstructure
0.55% Y2O3 microstructures
(Source: Shu et al. 2017)
From the above figures, the change of solidification of coating’s microstructure is
observed to change with appropriate insertion of nano-Y2O5. Also, the dendrites along with
the Y2O3 becomes denser and thinner, moving close to the surface. The refinement of
dendrites are primarily caused for the nanoparticles, promoting heterogeneous nucleation.
Again, while working with coating of 0.5% of nano-ZrO2 (Figure 7), the solidification
state is recorded to be different than previously implemented Y2O3.
Paraphrase This Document
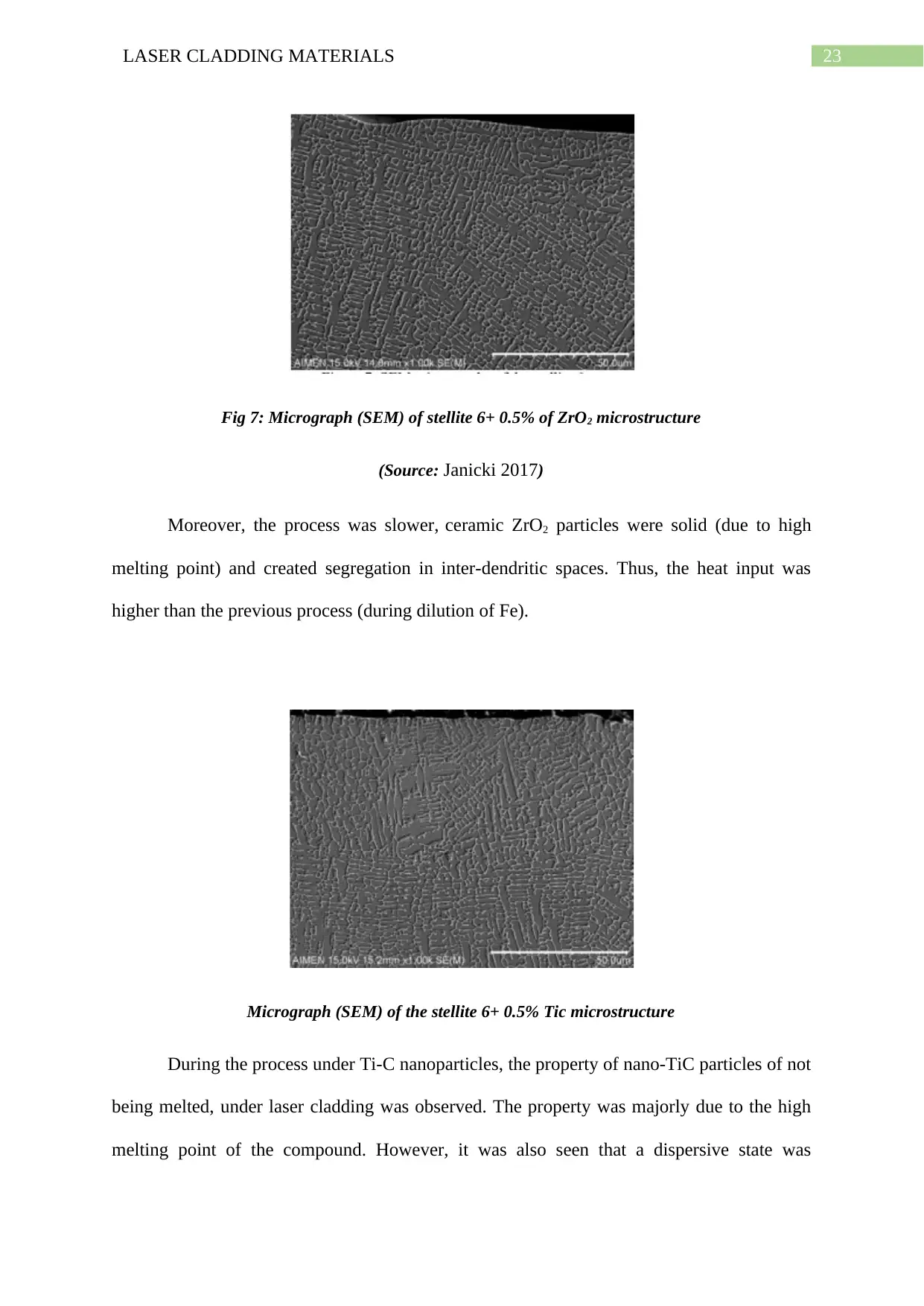
Fig 7: Micrograph (SEM) of stellite 6+ 0.5% of ZrO2 microstructure
(Source: Janicki 2017)
Moreover, the process was slower, ceramic ZrO2 particles were solid (due to high
melting point) and created segregation in inter-dendritic spaces. Thus, the heat input was
higher than the previous process (during dilution of Fe).
Micrograph (SEM) of the stellite 6+ 0.5% Tic microstructure
During the process under Ti-C nanoparticles, the property of nano-TiC particles of not
being melted, under laser cladding was observed. The property was majorly due to the high
melting point of the compound. However, it was also seen that a dispersive state was
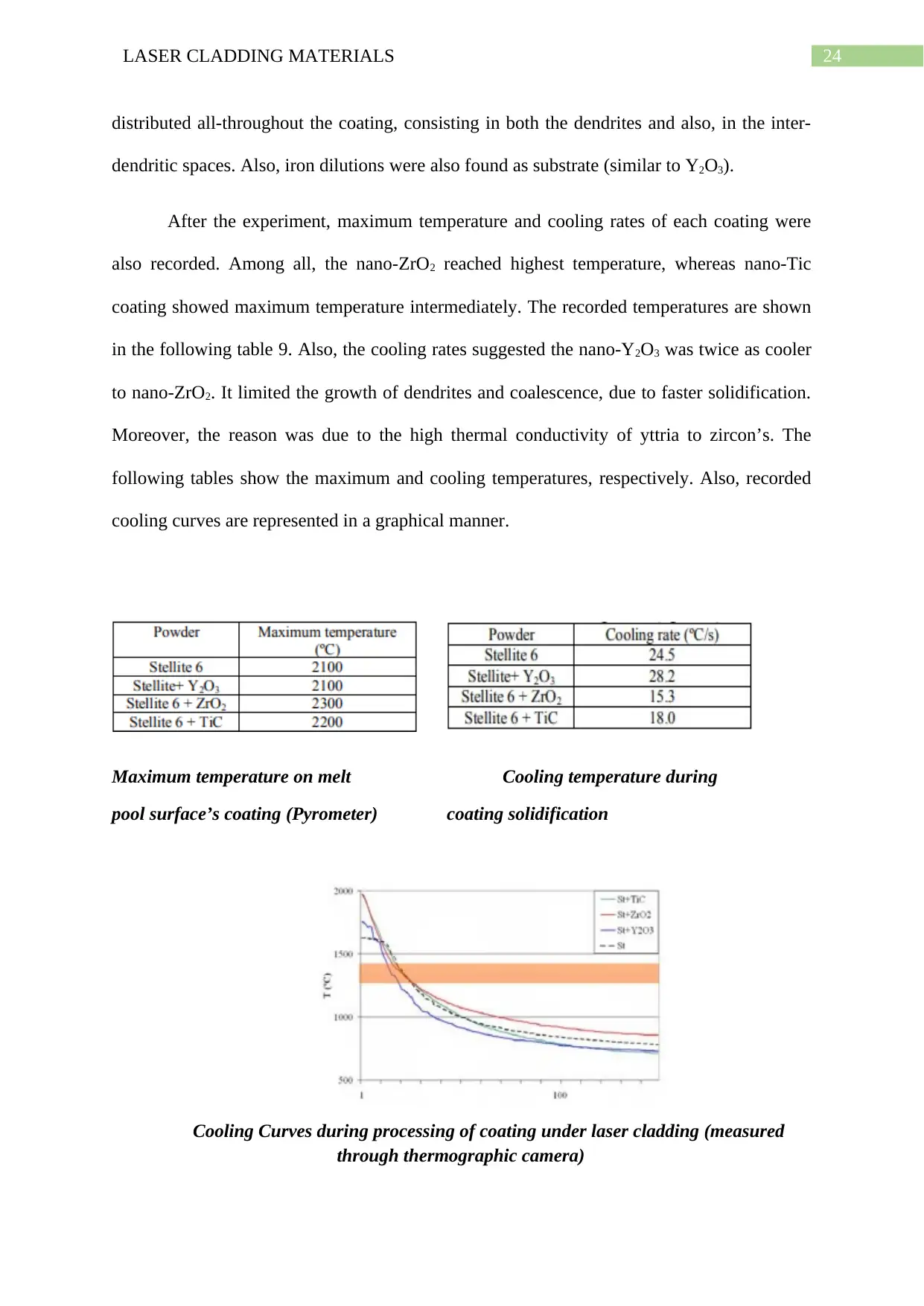
distributed all-throughout the coating, consisting in both the dendrites and also, in the inter-
dendritic spaces. Also, iron dilutions were also found as substrate (similar to Y2O3).
After the experiment, maximum temperature and cooling rates of each coating were
also recorded. Among all, the nano-ZrO2 reached highest temperature, whereas nano-Tic
coating showed maximum temperature intermediately. The recorded temperatures are shown
in the following table 9. Also, the cooling rates suggested the nano-Y2O3 was twice as cooler
to nano-ZrO2. It limited the growth of dendrites and coalescence, due to faster solidification.
Moreover, the reason was due to the high thermal conductivity of yttria to zircon’s. The
following tables show the maximum and cooling temperatures, respectively. Also, recorded
cooling curves are represented in a graphical manner.
Maximum temperature on melt Cooling temperature during
pool surface’s coating (Pyrometer) coating solidification
Cooling Curves during processing of coating under laser cladding (measured
through thermographic camera)
⊘ This is a preview!⊘
Do you want full access?
Subscribe today to unlock all pages.

Trusted by 1+ million students worldwide
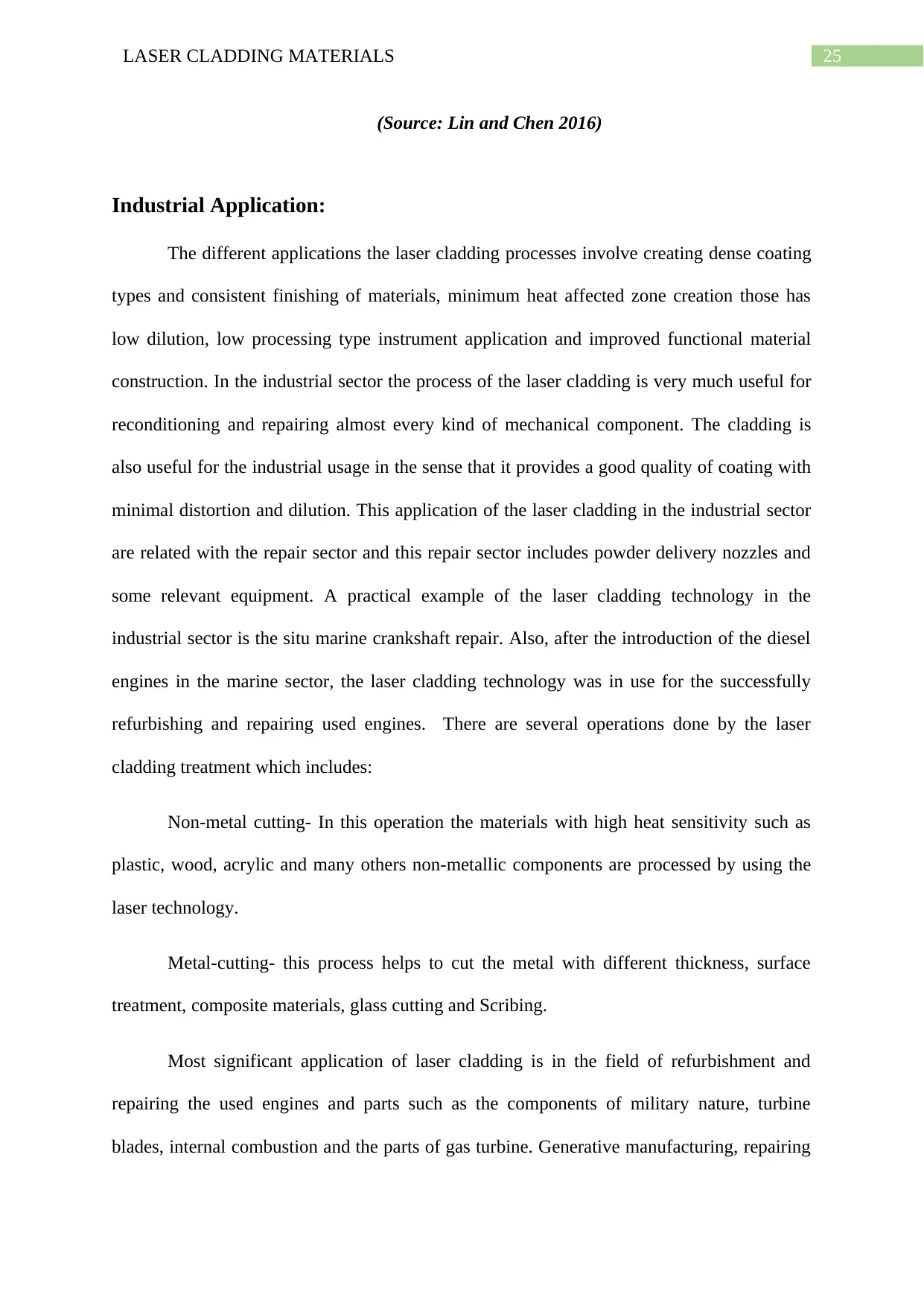
(Source: Lin and Chen 2016)
Industrial Application:
The different applications the laser cladding processes involve creating dense coating
types and consistent finishing of materials, minimum heat affected zone creation those has
low dilution, low processing type instrument application and improved functional material
construction. In the industrial sector the process of the laser cladding is very much useful for
reconditioning and repairing almost every kind of mechanical component. The cladding is
also useful for the industrial usage in the sense that it provides a good quality of coating with
minimal distortion and dilution. This application of the laser cladding in the industrial sector
are related with the repair sector and this repair sector includes powder delivery nozzles and
some relevant equipment. A practical example of the laser cladding technology in the
industrial sector is the situ marine crankshaft repair. Also, after the introduction of the diesel
engines in the marine sector, the laser cladding technology was in use for the successfully
refurbishing and repairing used engines. There are several operations done by the laser
cladding treatment which includes:
Non-metal cutting- In this operation the materials with high heat sensitivity such as
plastic, wood, acrylic and many others non-metallic components are processed by using the
laser technology.
Metal-cutting- this process helps to cut the metal with different thickness, surface
treatment, composite materials, glass cutting and Scribing.
Most significant application of laser cladding is in the field of refurbishment and
repairing the used engines and parts such as the components of military nature, turbine
blades, internal combustion and the parts of gas turbine. Generative manufacturing, repairing
Paraphrase This Document
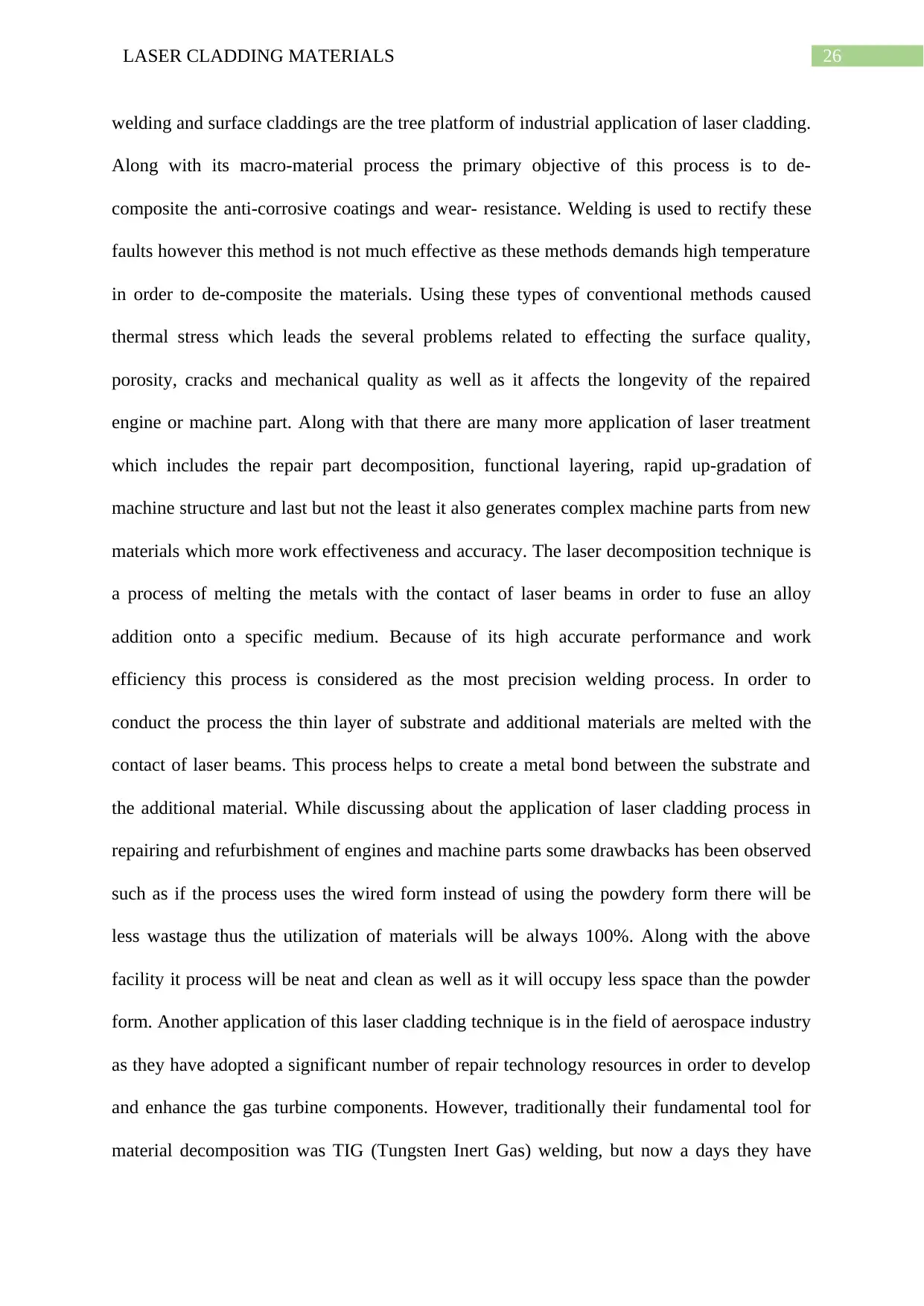
welding and surface claddings are the tree platform of industrial application of laser cladding.
Along with its macro-material process the primary objective of this process is to de-
composite the anti-corrosive coatings and wear- resistance. Welding is used to rectify these
faults however this method is not much effective as these methods demands high temperature
in order to de-composite the materials. Using these types of conventional methods caused
thermal stress which leads the several problems related to effecting the surface quality,
porosity, cracks and mechanical quality as well as it affects the longevity of the repaired
engine or machine part. Along with that there are many more application of laser treatment
which includes the repair part decomposition, functional layering, rapid up-gradation of
machine structure and last but not the least it also generates complex machine parts from new
materials which more work effectiveness and accuracy. The laser decomposition technique is
a process of melting the metals with the contact of laser beams in order to fuse an alloy
addition onto a specific medium. Because of its high accurate performance and work
efficiency this process is considered as the most precision welding process. In order to
conduct the process the thin layer of substrate and additional materials are melted with the
contact of laser beams. This process helps to create a metal bond between the substrate and
the additional material. While discussing about the application of laser cladding process in
repairing and refurbishment of engines and machine parts some drawbacks has been observed
such as if the process uses the wired form instead of using the powdery form there will be
less wastage thus the utilization of materials will be always 100%. Along with the above
facility it process will be neat and clean as well as it will occupy less space than the powder
form. Another application of this laser cladding technique is in the field of aerospace industry
as they have adopted a significant number of repair technology resources in order to develop
and enhance the gas turbine components. However, traditionally their fundamental tool for
material decomposition was TIG (Tungsten Inert Gas) welding, but now a days they have
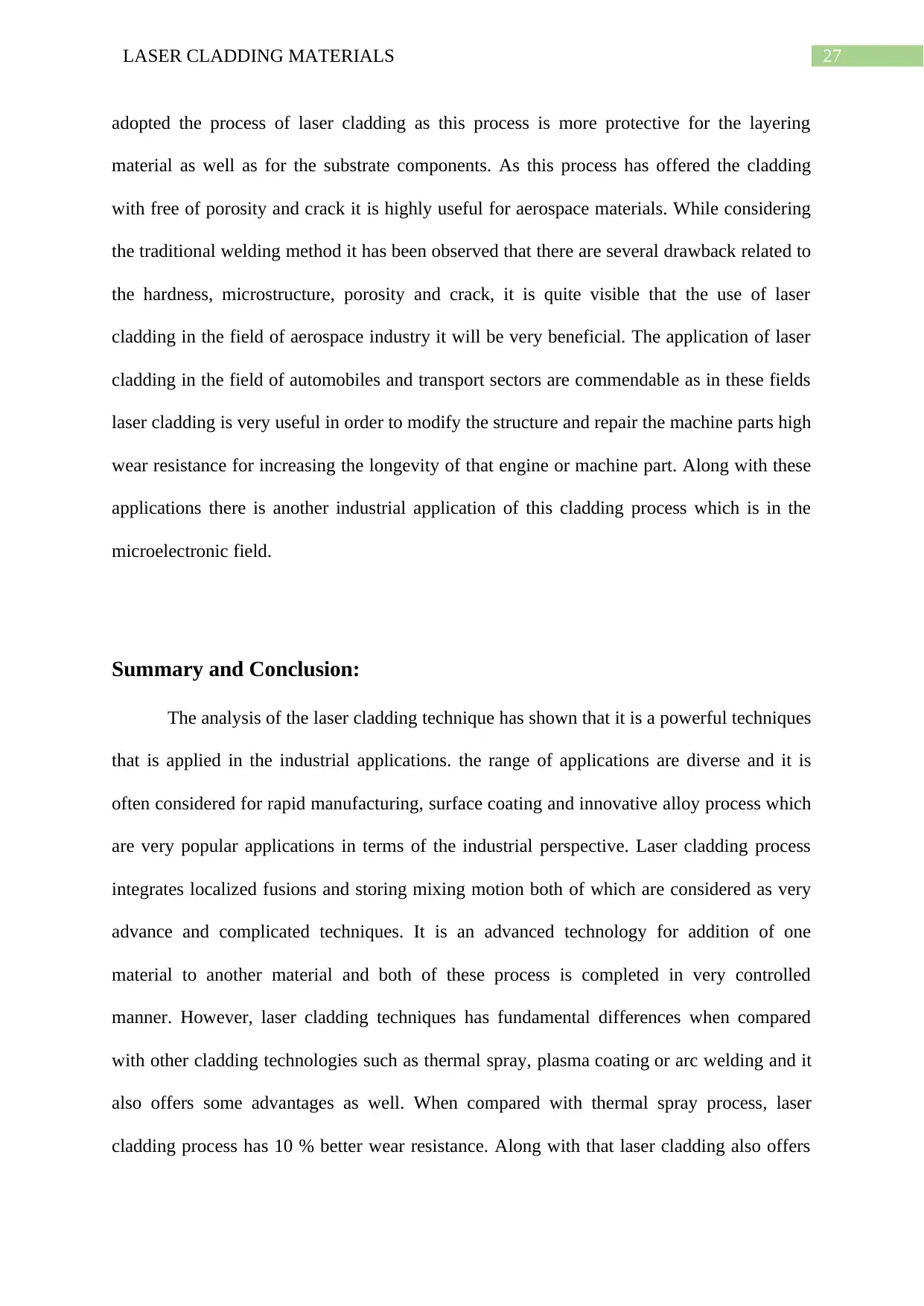
adopted the process of laser cladding as this process is more protective for the layering
material as well as for the substrate components. As this process has offered the cladding
with free of porosity and crack it is highly useful for aerospace materials. While considering
the traditional welding method it has been observed that there are several drawback related to
the hardness, microstructure, porosity and crack, it is quite visible that the use of laser
cladding in the field of aerospace industry it will be very beneficial. The application of laser
cladding in the field of automobiles and transport sectors are commendable as in these fields
laser cladding is very useful in order to modify the structure and repair the machine parts high
wear resistance for increasing the longevity of that engine or machine part. Along with these
applications there is another industrial application of this cladding process which is in the
microelectronic field.
Summary and Conclusion:
The analysis of the laser cladding technique has shown that it is a powerful techniques
that is applied in the industrial applications. the range of applications are diverse and it is
often considered for rapid manufacturing, surface coating and innovative alloy process which
are very popular applications in terms of the industrial perspective. Laser cladding process
integrates localized fusions and storing mixing motion both of which are considered as very
advance and complicated techniques. It is an advanced technology for addition of one
material to another material and both of these process is completed in very controlled
manner. However, laser cladding techniques has fundamental differences when compared
with other cladding technologies such as thermal spray, plasma coating or arc welding and it
also offers some advantages as well. When compared with thermal spray process, laser
cladding process has 10 % better wear resistance. Along with that laser cladding also offers
⊘ This is a preview!⊘
Do you want full access?
Subscribe today to unlock all pages.

Trusted by 1+ million students worldwide
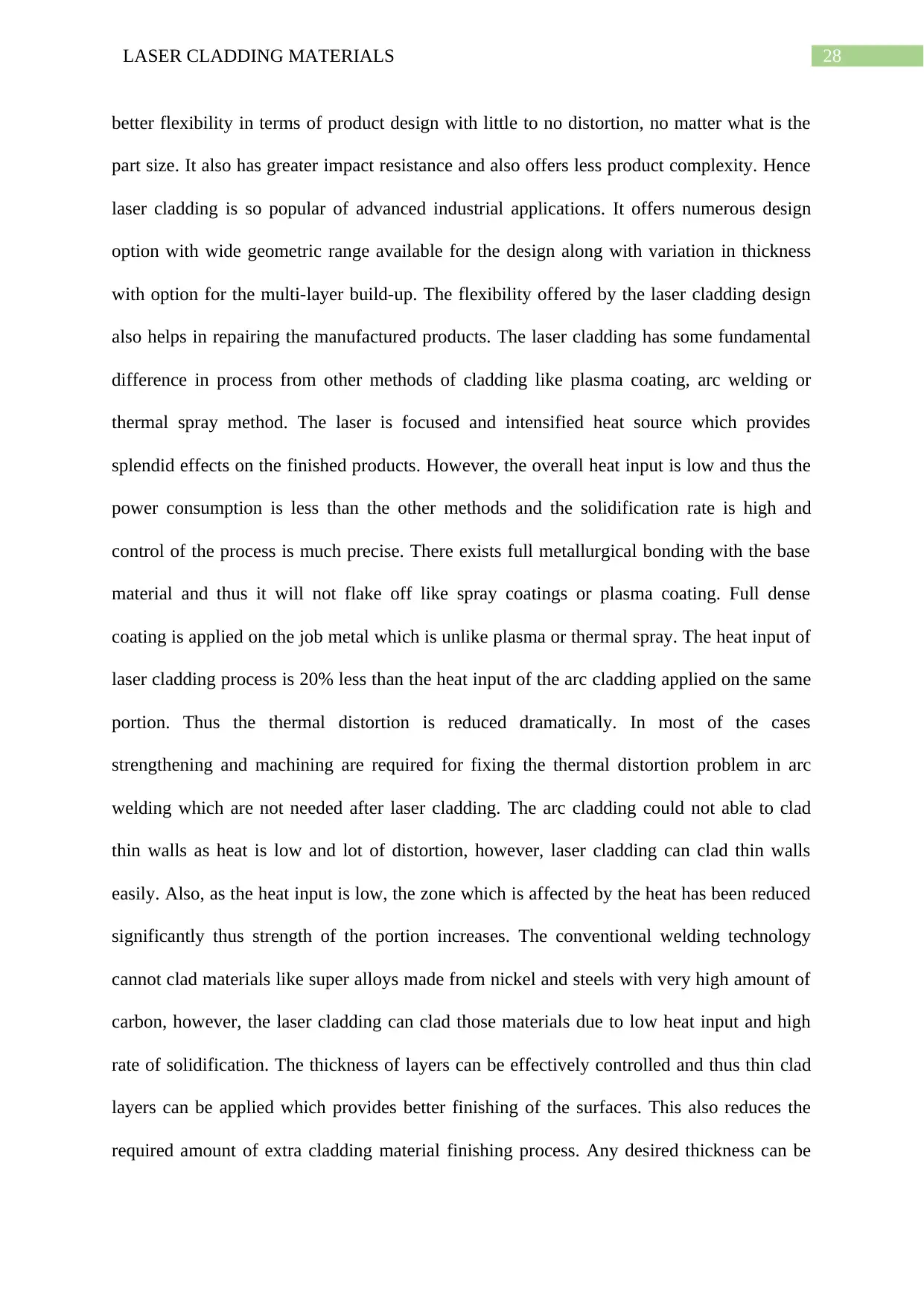
better flexibility in terms of product design with little to no distortion, no matter what is the
part size. It also has greater impact resistance and also offers less product complexity. Hence
laser cladding is so popular of advanced industrial applications. It offers numerous design
option with wide geometric range available for the design along with variation in thickness
with option for the multi-layer build-up. The flexibility offered by the laser cladding design
also helps in repairing the manufactured products. The laser cladding has some fundamental
difference in process from other methods of cladding like plasma coating, arc welding or
thermal spray method. The laser is focused and intensified heat source which provides
splendid effects on the finished products. However, the overall heat input is low and thus the
power consumption is less than the other methods and the solidification rate is high and
control of the process is much precise. There exists full metallurgical bonding with the base
material and thus it will not flake off like spray coatings or plasma coating. Full dense
coating is applied on the job metal which is unlike plasma or thermal spray. The heat input of
laser cladding process is 20% less than the heat input of the arc cladding applied on the same
portion. Thus the thermal distortion is reduced dramatically. In most of the cases
strengthening and machining are required for fixing the thermal distortion problem in arc
welding which are not needed after laser cladding. The arc cladding could not able to clad
thin walls as heat is low and lot of distortion, however, laser cladding can clad thin walls
easily. Also, as the heat input is low, the zone which is affected by the heat has been reduced
significantly thus strength of the portion increases. The conventional welding technology
cannot clad materials like super alloys made from nickel and steels with very high amount of
carbon, however, the laser cladding can clad those materials due to low heat input and high
rate of solidification. The thickness of layers can be effectively controlled and thus thin clad
layers can be applied which provides better finishing of the surfaces. This also reduces the
required amount of extra cladding material finishing process. Any desired thickness can be
Paraphrase This Document
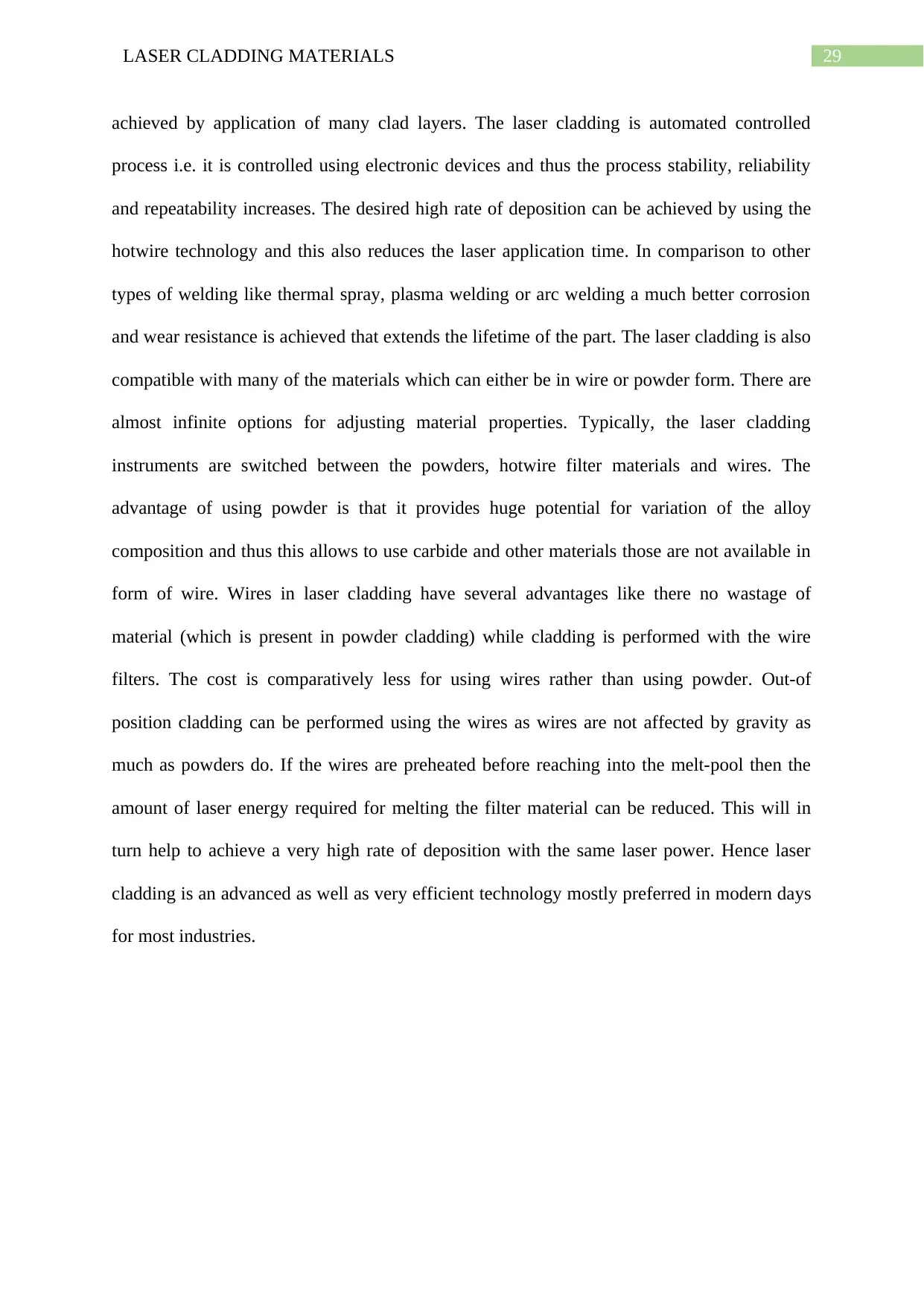
achieved by application of many clad layers. The laser cladding is automated controlled
process i.e. it is controlled using electronic devices and thus the process stability, reliability
and repeatability increases. The desired high rate of deposition can be achieved by using the
hotwire technology and this also reduces the laser application time. In comparison to other
types of welding like thermal spray, plasma welding or arc welding a much better corrosion
and wear resistance is achieved that extends the lifetime of the part. The laser cladding is also
compatible with many of the materials which can either be in wire or powder form. There are
almost infinite options for adjusting material properties. Typically, the laser cladding
instruments are switched between the powders, hotwire filter materials and wires. The
advantage of using powder is that it provides huge potential for variation of the alloy
composition and thus this allows to use carbide and other materials those are not available in
form of wire. Wires in laser cladding have several advantages like there no wastage of
material (which is present in powder cladding) while cladding is performed with the wire
filters. The cost is comparatively less for using wires rather than using powder. Out-of
position cladding can be performed using the wires as wires are not affected by gravity as
much as powders do. If the wires are preheated before reaching into the melt-pool then the
amount of laser energy required for melting the filter material can be reduced. This will in
turn help to achieve a very high rate of deposition with the same laser power. Hence laser
cladding is an advanced as well as very efficient technology mostly preferred in modern days
for most industries.
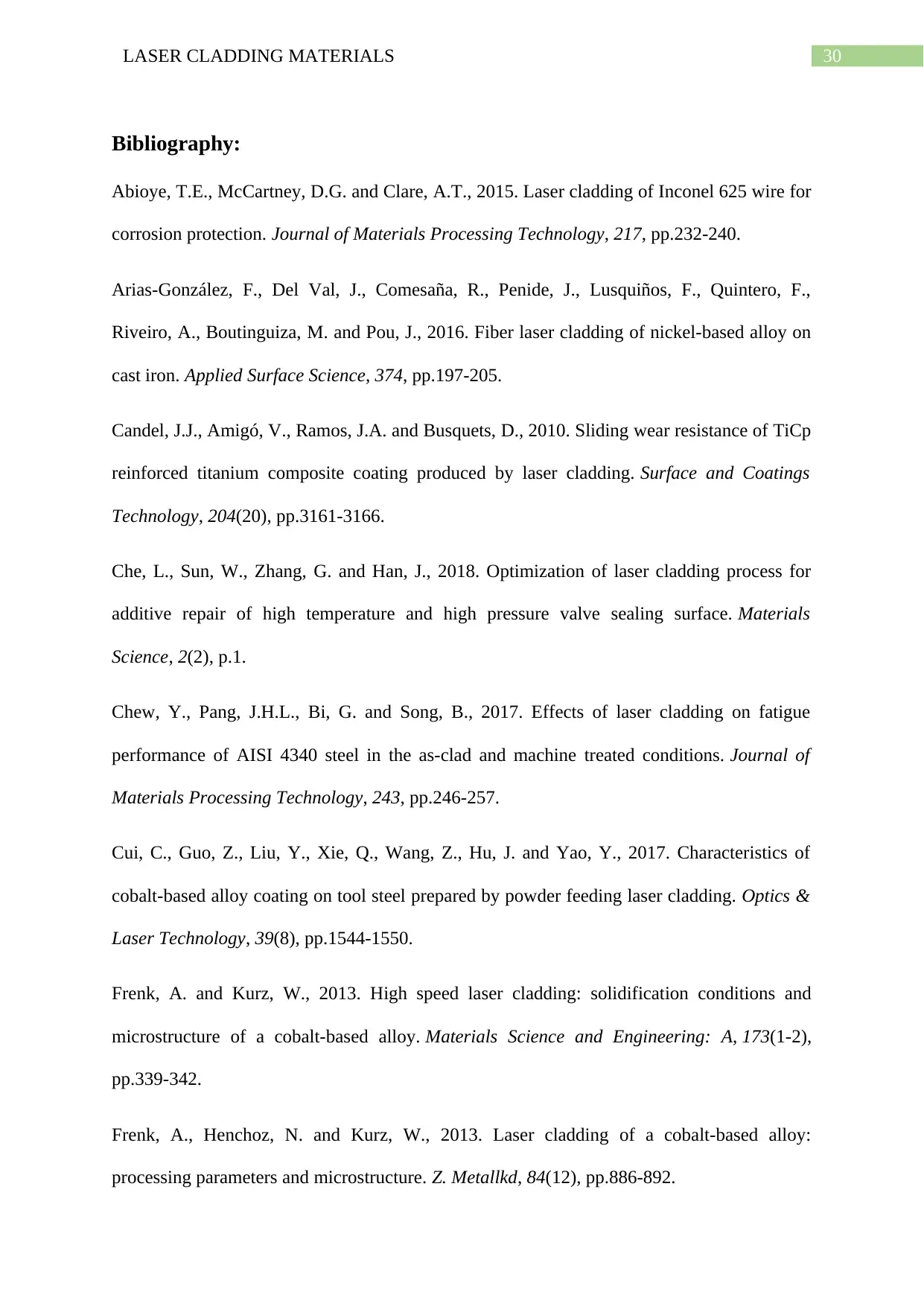
Bibliography:
Abioye, T.E., McCartney, D.G. and Clare, A.T., 2015. Laser cladding of Inconel 625 wire for
corrosion protection. Journal of Materials Processing Technology, 217, pp.232-240.
Arias-González, F., Del Val, J., Comesaña, R., Penide, J., Lusquiños, F., Quintero, F.,
Riveiro, A., Boutinguiza, M. and Pou, J., 2016. Fiber laser cladding of nickel-based alloy on
cast iron. Applied Surface Science, 374, pp.197-205.
Candel, J.J., Amigó, V., Ramos, J.A. and Busquets, D., 2010. Sliding wear resistance of TiCp
reinforced titanium composite coating produced by laser cladding. Surface and Coatings
Technology, 204(20), pp.3161-3166.
Che, L., Sun, W., Zhang, G. and Han, J., 2018. Optimization of laser cladding process for
additive repair of high temperature and high pressure valve sealing surface. Materials
Science, 2(2), p.1.
Chew, Y., Pang, J.H.L., Bi, G. and Song, B., 2017. Effects of laser cladding on fatigue
performance of AISI 4340 steel in the as-clad and machine treated conditions. Journal of
Materials Processing Technology, 243, pp.246-257.
Cui, C., Guo, Z., Liu, Y., Xie, Q., Wang, Z., Hu, J. and Yao, Y., 2017. Characteristics of
cobalt-based alloy coating on tool steel prepared by powder feeding laser cladding. Optics &
Laser Technology, 39(8), pp.1544-1550.
Frenk, A. and Kurz, W., 2013. High speed laser cladding: solidification conditions and
microstructure of a cobalt-based alloy. Materials Science and Engineering: A, 173(1-2),
pp.339-342.
Frenk, A., Henchoz, N. and Kurz, W., 2013. Laser cladding of a cobalt-based alloy:
processing parameters and microstructure. Z. Metallkd, 84(12), pp.886-892.
⊘ This is a preview!⊘
Do you want full access?
Subscribe today to unlock all pages.

Trusted by 1+ million students worldwide
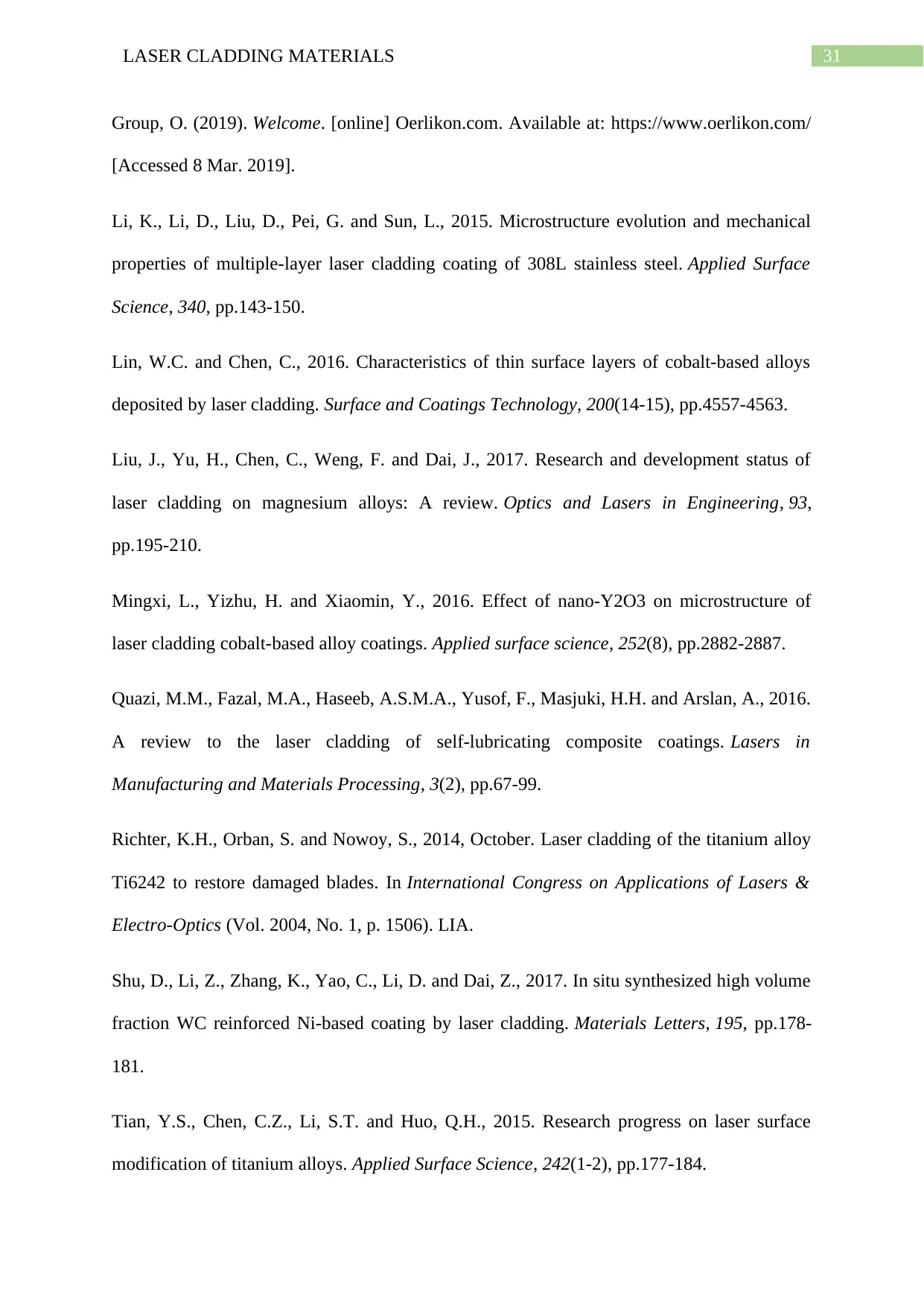
Group, O. (2019). Welcome. [online] Oerlikon.com. Available at: https://www.oerlikon.com/
[Accessed 8 Mar. 2019].
Li, K., Li, D., Liu, D., Pei, G. and Sun, L., 2015. Microstructure evolution and mechanical
properties of multiple-layer laser cladding coating of 308L stainless steel. Applied Surface
Science, 340, pp.143-150.
Lin, W.C. and Chen, C., 2016. Characteristics of thin surface layers of cobalt-based alloys
deposited by laser cladding. Surface and Coatings Technology, 200(14-15), pp.4557-4563.
Liu, J., Yu, H., Chen, C., Weng, F. and Dai, J., 2017. Research and development status of
laser cladding on magnesium alloys: A review. Optics and Lasers in Engineering, 93,
pp.195-210.
Mingxi, L., Yizhu, H. and Xiaomin, Y., 2016. Effect of nano-Y2O3 on microstructure of
laser cladding cobalt-based alloy coatings. Applied surface science, 252(8), pp.2882-2887.
Quazi, M.M., Fazal, M.A., Haseeb, A.S.M.A., Yusof, F., Masjuki, H.H. and Arslan, A., 2016.
A review to the laser cladding of self-lubricating composite coatings. Lasers in
Manufacturing and Materials Processing, 3(2), pp.67-99.
Richter, K.H., Orban, S. and Nowoy, S., 2014, October. Laser cladding of the titanium alloy
Ti6242 to restore damaged blades. In International Congress on Applications of Lasers &
Electro-Optics (Vol. 2004, No. 1, p. 1506). LIA.
Shu, D., Li, Z., Zhang, K., Yao, C., Li, D. and Dai, Z., 2017. In situ synthesized high volume
fraction WC reinforced Ni-based coating by laser cladding. Materials Letters, 195, pp.178-
181.
Tian, Y.S., Chen, C.Z., Li, S.T. and Huo, Q.H., 2015. Research progress on laser surface
modification of titanium alloys. Applied Surface Science, 242(1-2), pp.177-184.
Paraphrase This Document
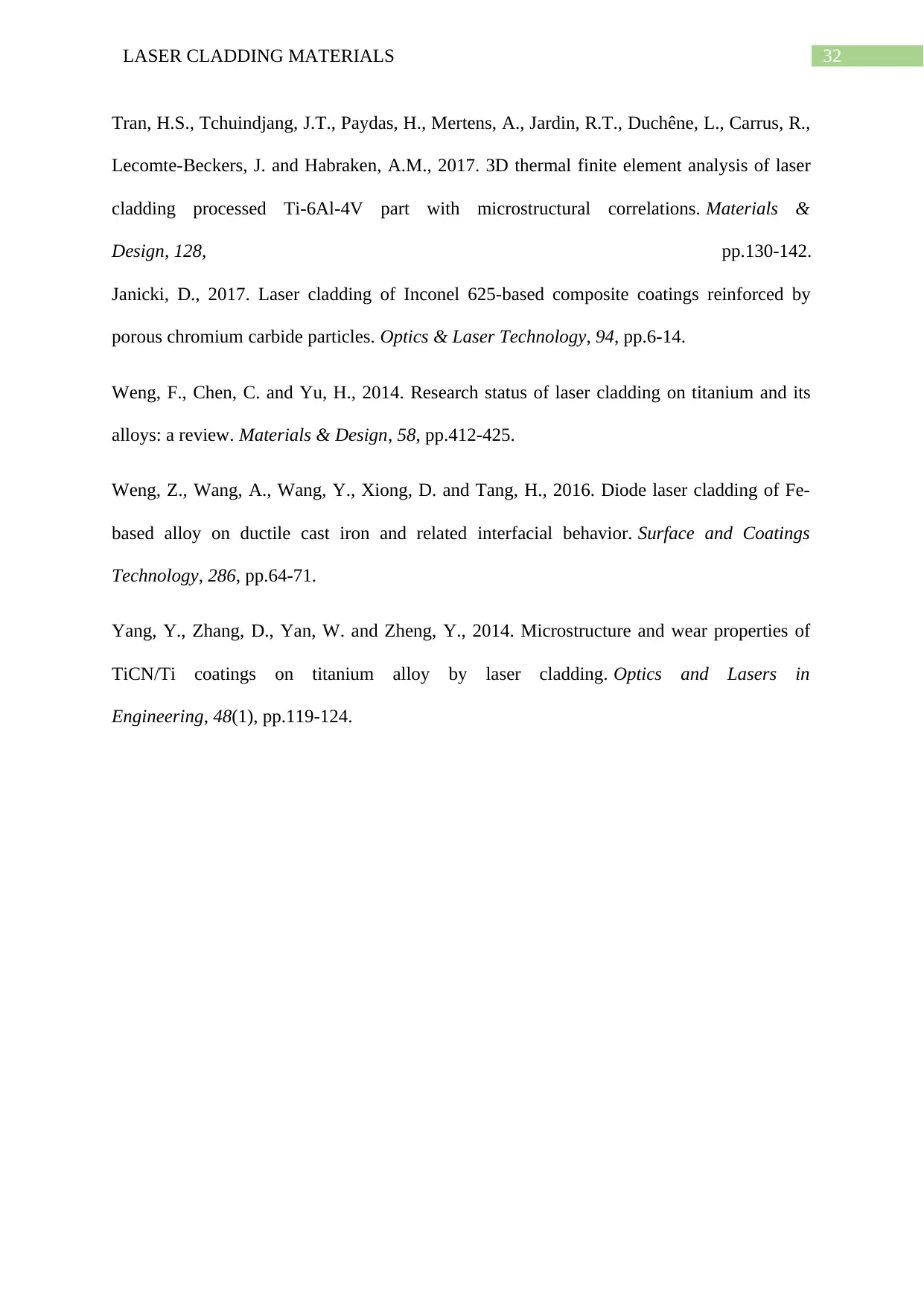
Tran, H.S., Tchuindjang, J.T., Paydas, H., Mertens, A., Jardin, R.T., Duchêne, L., Carrus, R.,
Lecomte-Beckers, J. and Habraken, A.M., 2017. 3D thermal finite element analysis of laser
cladding processed Ti-6Al-4V part with microstructural correlations. Materials &
Design, 128, pp.130-142.
Janicki, D., 2017. Laser cladding of Inconel 625-based composite coatings reinforced by
porous chromium carbide particles. Optics & Laser Technology, 94, pp.6-14.
Weng, F., Chen, C. and Yu, H., 2014. Research status of laser cladding on titanium and its
alloys: a review. Materials & Design, 58, pp.412-425.
Weng, Z., Wang, A., Wang, Y., Xiong, D. and Tang, H., 2016. Diode laser cladding of Fe-
based alloy on ductile cast iron and related interfacial behavior. Surface and Coatings
Technology, 286, pp.64-71.
Yang, Y., Zhang, D., Yan, W. and Zheng, Y., 2014. Microstructure and wear properties of
TiCN/Ti coatings on titanium alloy by laser cladding. Optics and Lasers in
Engineering, 48(1), pp.119-124.
Related Documents

Your All-in-One AI-Powered Toolkit for Academic Success.
+13062052269
info@desklib.com
Available 24*7 on WhatsApp / Email
© 2024 | Zucol Services PVT LTD | All rights reserved.