Laser Cladding Materials
32 Pages8841 Words144 Views
Added on 2023-04-20
About This Document
This paper discusses laser cladding system and its usage in creating bonding between different metals. It explores the principles and processes of laser cladding technology, specifically focusing on aluminium alloy and magnesium alloy laser cladding. The paper also highlights the industrial applications of laser cladding.
Laser Cladding Materials
Added on 2023-04-20
ShareRelated Documents
Running head: LASER CLADDING MATERIALS
LASER CLADDING MATERIALS
Name of the Student
Name of the University
Author Note
LASER CLADDING MATERIALS
Name of the Student
Name of the University
Author Note
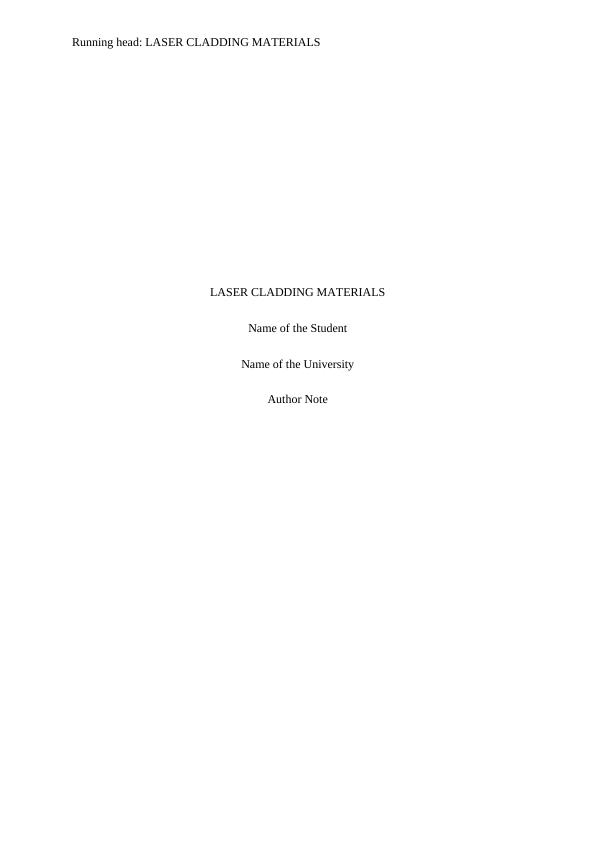
2LASER CLADDING MATERIALS
Table of Contents
Introduction and synopsis:.........................................................................................................3
Principles and processes:............................................................................................................5
Twin Beam Laser Cladding Technology:..............................................................................7
Laser cladding as an automated process:...............................................................................8
Laser cladding process by magnesium alloy:.......................................................................13
Aluminium alloy laser cladding process:.............................................................................14
Laser Cladding of Titanium Alloys......................................................................................16
Laser Cladding of Cobalt Alloys..........................................................................................18
Industrial Application:.............................................................................................................24
Summary and Conclusion:.......................................................................................................27
Bibliography:............................................................................................................................30
Table of Contents
Introduction and synopsis:.........................................................................................................3
Principles and processes:............................................................................................................5
Twin Beam Laser Cladding Technology:..............................................................................7
Laser cladding as an automated process:...............................................................................8
Laser cladding process by magnesium alloy:.......................................................................13
Aluminium alloy laser cladding process:.............................................................................14
Laser Cladding of Titanium Alloys......................................................................................16
Laser Cladding of Cobalt Alloys..........................................................................................18
Industrial Application:.............................................................................................................24
Summary and Conclusion:.......................................................................................................27
Bibliography:............................................................................................................................30
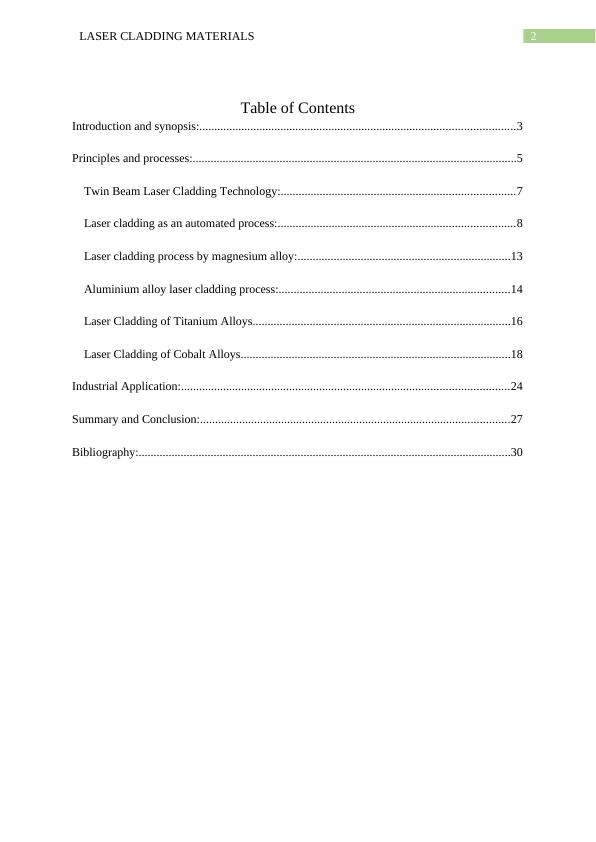
3LASER CLADDING MATERIALS
Introduction and synopsis:
This paper aims to discuss about laser cladding system and the usage of this technique
for creating bonding together different types of metals. Laser cladding technique is very
much useful in the process of explosive welding. The laser cladding is used as it provides
various types of advantages. The main advantages of the laser cladding are the high cooling
rate, well adapted manufacturing, material flexibility and low dilution which makes the laser
cladding process very much efficient in overall cladding process. In this paper the main
principles and the processes of laser cladding technology will be evaluated. Aluminium alloy
laser cladding process is one of the important process of the laser cladding process. Thus in
this paper the process about the aluminium laser cladding is discussed. In the further
evaluation laser cladding process for the magnesium has been discussed thoroughly.
Currently this laser cladding process having several applications in the industrial area and this
industrial application is also discussed in this paper.
The cladding is the process of creating bonding between two dissimilar metals. The
cladding process is totally from the process of gluing or welding. In this method two different
metals are fasten together. In this cladding process laser cladding is one of the most important
method. This laser cladding method is depositing of material by which wire feedstock
material or the powdered material is melted and it is consolidated by a laser for fabrication
process. The laser cladding process involves localized fusion in small areas and the mixing
motion is very strong in the melting container, thus the material gradient can be designed at
microstructure level. The different capability of mixing two or more powder types and the
controlled feedback rate each of flow of powder in the process makes the laser cladding
method an efficient method for mixing heterogeneous materials or for the materials those are
functionally graded. The laser cladding is mainly used for improving the mechanical
Introduction and synopsis:
This paper aims to discuss about laser cladding system and the usage of this technique
for creating bonding together different types of metals. Laser cladding technique is very
much useful in the process of explosive welding. The laser cladding is used as it provides
various types of advantages. The main advantages of the laser cladding are the high cooling
rate, well adapted manufacturing, material flexibility and low dilution which makes the laser
cladding process very much efficient in overall cladding process. In this paper the main
principles and the processes of laser cladding technology will be evaluated. Aluminium alloy
laser cladding process is one of the important process of the laser cladding process. Thus in
this paper the process about the aluminium laser cladding is discussed. In the further
evaluation laser cladding process for the magnesium has been discussed thoroughly.
Currently this laser cladding process having several applications in the industrial area and this
industrial application is also discussed in this paper.
The cladding is the process of creating bonding between two dissimilar metals. The
cladding process is totally from the process of gluing or welding. In this method two different
metals are fasten together. In this cladding process laser cladding is one of the most important
method. This laser cladding method is depositing of material by which wire feedstock
material or the powdered material is melted and it is consolidated by a laser for fabrication
process. The laser cladding process involves localized fusion in small areas and the mixing
motion is very strong in the melting container, thus the material gradient can be designed at
microstructure level. The different capability of mixing two or more powder types and the
controlled feedback rate each of flow of powder in the process makes the laser cladding
method an efficient method for mixing heterogeneous materials or for the materials those are
functionally graded. The laser cladding is mainly used for improving the mechanical
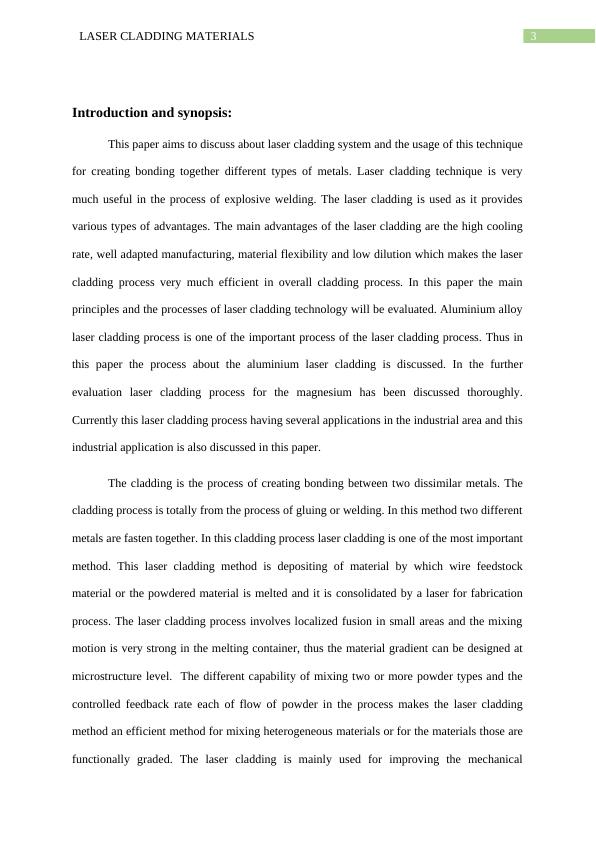
4LASER CLADDING MATERIALS
properties or for increasing the corrosion resistance, fabricating metal matrix composites and
for repairing parts that are worn out. In this process surface material can be laser cladded
directly to a component that is highly stressed component. By this self-lubricating surface can
be produced but this type of modification requires industrialization of the cladding process
for an efficient mass production.
The main process of the laser cladding includes the laser beam and the metal work
piece. For executing the laser cladding process laser beam is defocused on the metal work
piece with some selected spot size. The material of powder coating is carried through inert
gas by using a powder nozzle in the pool of melt. In this manufacturing process powder
nozzle and the laser optics are stimulated over the surface of the work piece to deposit single
tracks. The laser cladding process is used for treating 150 mm X 160 mm cross-sectioned
screws and the plastic barrels and the machines that are used for rubber injections. The
screws formed after the laser cladding is found to be smooth and there is no distortion present
in the screws. The service time of the screws after installing in different machines is found to
be on an average 50-60% higher than the ordinary nitrated screws having high alloy
percentage in identical conditions. It is found after several experiments that there is no cracks
or porosity lasting after the detection of pigmentation. No breaking offs are found in the clad
layer while running. The particular identical technique can also be used for repairing the parts
which are very much susceptible to erosion and corrosion effects in other industry types.
Through the application of the laser cladding, a coating can be added to the work piece but
for that high power multi-mode fibre laser is required and by using melting metallic powder.
By using this process proactive coatings including nickel alloy, carbide, cobalt and tungsten
can be applied over the stainless steel or the steel alloy substrates. This process is used as this
produces a durable metallurgical bond with having least dilution of the base material which
enhances the abrasion, corrosion and the wear resistance of metals.
properties or for increasing the corrosion resistance, fabricating metal matrix composites and
for repairing parts that are worn out. In this process surface material can be laser cladded
directly to a component that is highly stressed component. By this self-lubricating surface can
be produced but this type of modification requires industrialization of the cladding process
for an efficient mass production.
The main process of the laser cladding includes the laser beam and the metal work
piece. For executing the laser cladding process laser beam is defocused on the metal work
piece with some selected spot size. The material of powder coating is carried through inert
gas by using a powder nozzle in the pool of melt. In this manufacturing process powder
nozzle and the laser optics are stimulated over the surface of the work piece to deposit single
tracks. The laser cladding process is used for treating 150 mm X 160 mm cross-sectioned
screws and the plastic barrels and the machines that are used for rubber injections. The
screws formed after the laser cladding is found to be smooth and there is no distortion present
in the screws. The service time of the screws after installing in different machines is found to
be on an average 50-60% higher than the ordinary nitrated screws having high alloy
percentage in identical conditions. It is found after several experiments that there is no cracks
or porosity lasting after the detection of pigmentation. No breaking offs are found in the clad
layer while running. The particular identical technique can also be used for repairing the parts
which are very much susceptible to erosion and corrosion effects in other industry types.
Through the application of the laser cladding, a coating can be added to the work piece but
for that high power multi-mode fibre laser is required and by using melting metallic powder.
By using this process proactive coatings including nickel alloy, carbide, cobalt and tungsten
can be applied over the stainless steel or the steel alloy substrates. This process is used as this
produces a durable metallurgical bond with having least dilution of the base material which
enhances the abrasion, corrosion and the wear resistance of metals.
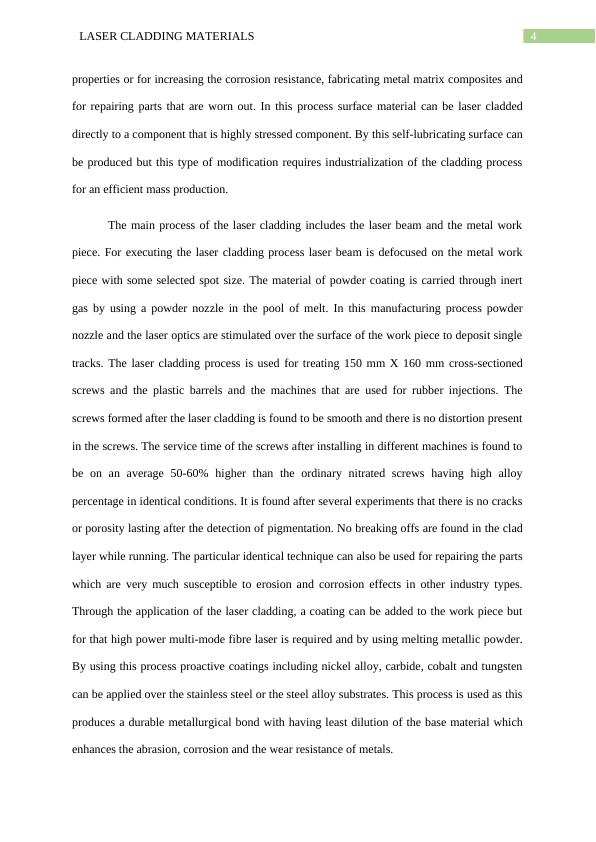
5LASER CLADDING MATERIALS
The concept of laser cladding is similar to the method of arc welding, however, the
only difference is that for melting the substrate laser is used instead of arc energy and the
material which is added is either the form of powder, wire or strip. The laser cladding process
is mostly done with the help of CO2 or newer types of fibre lasers. The laser cladding process
specifically produces low dilution clads, the porosity is low and produces surfaces that are
uniform. The laser cladding is preferred over other techniques as those techniques are
expensive and time consuming. Also the laser cladding is preferred over the others as it uses
the powders which are more common due to its alloy composition.
Principles and processes:
The different processes of laser surface cladding is different for different type of
materials. The different materials are laser surface cladding of light alloys such as aluminium
alloy laser cladding and Magnesium alloy laser cladding process. The laser cladding process
in the light alloys like in the Aluminium and Magnesium alloys is mainly for the creation of a
surface that has the properties different from the properties of the substrate. Aluminium alloy
cladding is applied for creating matrix of metals with multiple surfaces which can offer high
wearing resistance. In this paper the empirical means of modelling the laser cladding process
is described. The particular empirical investigations are mainly carried out for the verification
of different models, material parameter determination and effects determination of different
measurement terms like energy coupling (Absorbed energy of the beam divided by input
beam energy of laser). Laser cladding based on the powder injection technique is considered
for various applications such as rapid manufacturing, parts repair, surface coating, and
innovative alloy development and it is widely applied across the industries. It is applied for
mixing two or more types of powders and this very aspect makes the laser cladding technique
very flexible. Not only mixing, the laser cladding technique also controls the feed rates
associated with each of the powder flow. As the Laser cladding technique is fundamentally
The concept of laser cladding is similar to the method of arc welding, however, the
only difference is that for melting the substrate laser is used instead of arc energy and the
material which is added is either the form of powder, wire or strip. The laser cladding process
is mostly done with the help of CO2 or newer types of fibre lasers. The laser cladding process
specifically produces low dilution clads, the porosity is low and produces surfaces that are
uniform. The laser cladding is preferred over other techniques as those techniques are
expensive and time consuming. Also the laser cladding is preferred over the others as it uses
the powders which are more common due to its alloy composition.
Principles and processes:
The different processes of laser surface cladding is different for different type of
materials. The different materials are laser surface cladding of light alloys such as aluminium
alloy laser cladding and Magnesium alloy laser cladding process. The laser cladding process
in the light alloys like in the Aluminium and Magnesium alloys is mainly for the creation of a
surface that has the properties different from the properties of the substrate. Aluminium alloy
cladding is applied for creating matrix of metals with multiple surfaces which can offer high
wearing resistance. In this paper the empirical means of modelling the laser cladding process
is described. The particular empirical investigations are mainly carried out for the verification
of different models, material parameter determination and effects determination of different
measurement terms like energy coupling (Absorbed energy of the beam divided by input
beam energy of laser). Laser cladding based on the powder injection technique is considered
for various applications such as rapid manufacturing, parts repair, surface coating, and
innovative alloy development and it is widely applied across the industries. It is applied for
mixing two or more types of powders and this very aspect makes the laser cladding technique
very flexible. Not only mixing, the laser cladding technique also controls the feed rates
associated with each of the powder flow. As the Laser cladding technique is fundamentally
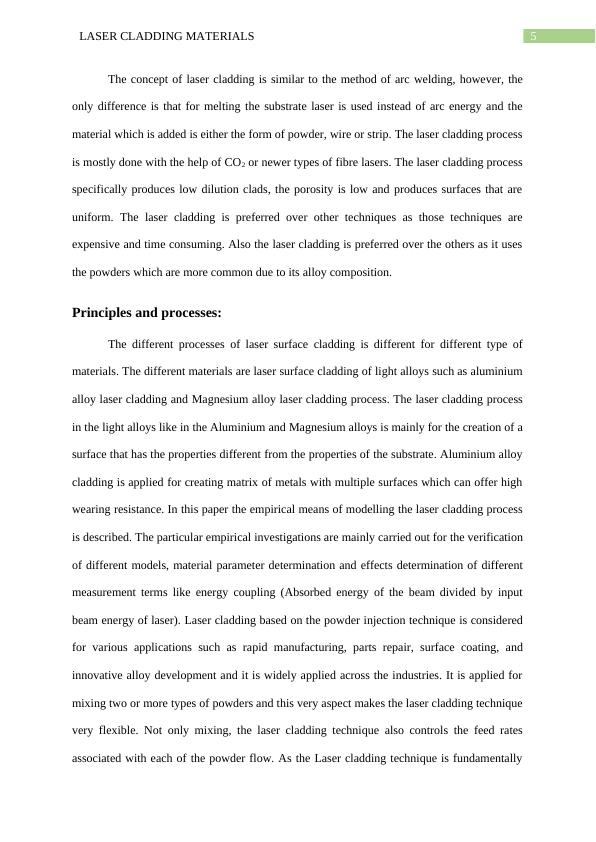
6LASER CLADDING MATERIALS
based on the powder injection process. During the process of laser cladding the laser energy
seals the powder metals into an existing metals. As it has already been discussed that laser
cladding or decomposition is a metal processing technique to defuse one material into the
surface of another material in a proper technical manner. The powdery formed material is fed
into the concentration of laser beam and scanned across the desired surface, as leaves a
deposited layer of the selected material. This technique is a most common process of metal
decomposition however, it opts for few complicated steps in order to complete the cladding
process. As this process is more effective in terms of cladding the mentioned material this
technique has several advantages which are described further. The laser cladding technique is
one of best process in order to provide layer to any sort of shape. This is also a popular
process of cladding any repairing machine part. Along with the above benefits, this technique
is one of the compact technology as is has lot of material flexibility, its cooling rate is also
high, offers low substrate and HAZ (heat affected zone), and the mechanism of its each part
is porosity and crack free. The actual benefit of choosing this decomposition technique is it’s
a coating depended and welding consumable process, which are applicable in the form of
powder. It also includes high temperature application and corrosive wear protection. Hence
this process is applicable for manufacturing heterogeneous components or functionally
graded material. This technology is special for another reason, it allows the design of the
material gradient at the microstructure level. This is particularly possible because of the
localized fusion and strong mixing motion that is achieved at in the melt pool where the laser
cladding is developed. Hence the material is possible to tailor which offers flexibility in the
functional performance in any specific applications. The laser cladding process is associated
with rapid heating and cooling process which allows extension in the solubility of the solid
when the solid is in metastable or in the non-equilibrium phase of the production which
based on the powder injection process. During the process of laser cladding the laser energy
seals the powder metals into an existing metals. As it has already been discussed that laser
cladding or decomposition is a metal processing technique to defuse one material into the
surface of another material in a proper technical manner. The powdery formed material is fed
into the concentration of laser beam and scanned across the desired surface, as leaves a
deposited layer of the selected material. This technique is a most common process of metal
decomposition however, it opts for few complicated steps in order to complete the cladding
process. As this process is more effective in terms of cladding the mentioned material this
technique has several advantages which are described further. The laser cladding technique is
one of best process in order to provide layer to any sort of shape. This is also a popular
process of cladding any repairing machine part. Along with the above benefits, this technique
is one of the compact technology as is has lot of material flexibility, its cooling rate is also
high, offers low substrate and HAZ (heat affected zone), and the mechanism of its each part
is porosity and crack free. The actual benefit of choosing this decomposition technique is it’s
a coating depended and welding consumable process, which are applicable in the form of
powder. It also includes high temperature application and corrosive wear protection. Hence
this process is applicable for manufacturing heterogeneous components or functionally
graded material. This technology is special for another reason, it allows the design of the
material gradient at the microstructure level. This is particularly possible because of the
localized fusion and strong mixing motion that is achieved at in the melt pool where the laser
cladding is developed. Hence the material is possible to tailor which offers flexibility in the
functional performance in any specific applications. The laser cladding process is associated
with rapid heating and cooling process which allows extension in the solubility of the solid
when the solid is in metastable or in the non-equilibrium phase of the production which
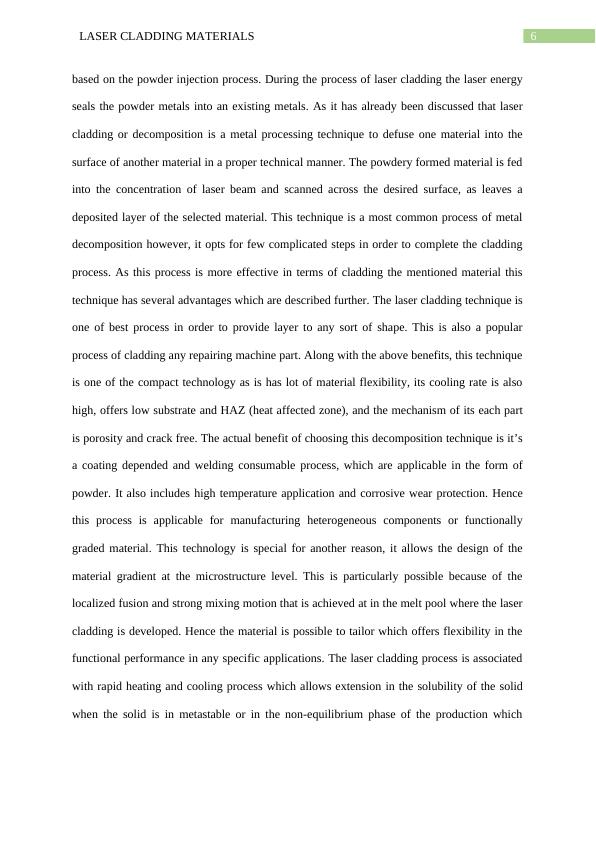
7LASER CLADDING MATERIALS
allows to design new products with advanced properties. Hence laser cladding is an advanced
and powerful technique for the industrial production.
Twin Beam Laser Cladding Technology:
This types of laser cladding technique is used for surface modification which has been
used to develop a value sheet of and machine part in any motor industry. This process is
conducted by mixing the particle with molten metal in order to modify the surface. Than the
fused alloy material is process in order to improve the characteristics of the actual material.
Those improved characteristics are wear resistance, corrosion, free of porosity, temperature
and its ability. Considering the magnesium alloy to apply the twin-beam irradiation, thus the
particles used to do the surface modification is the AZ31 magnesium alloy and the substrate
Si. These elements can be expected from the chemical component Mg2Si, which will improve
the wear resistance and hardness of the alloy. Comparing the modification of the surface
followed by the dual-beam welding and single beam welding, it can be concluded that the
dual beam welding has used parallel laser beam to weld the material. While performing the
dual beam laser treatment the substrate Si and lower laser scanning are mixed well in order to
complete the surface modification. While comparing two laser beam technique it has been
observed that using the dual laser beam technique the speed of the cladding will increase, the
efficiency of the procedure is high. Following the dual beam laser technique the thorough
mixing of metal will be effective. In order to prove the effect of dual beam laser several
studies has compared the single beam laser treatment with dual beam laser treatment. Thus by
analysing those researches it has been observed that in order to weld the joins by using the
single spot laser it was liner and depends on the width of the HAZ. However, using the dual
laser beam treatment these drawbacks has been addressed.
Advantages of this cladding technique are listed below:
allows to design new products with advanced properties. Hence laser cladding is an advanced
and powerful technique for the industrial production.
Twin Beam Laser Cladding Technology:
This types of laser cladding technique is used for surface modification which has been
used to develop a value sheet of and machine part in any motor industry. This process is
conducted by mixing the particle with molten metal in order to modify the surface. Than the
fused alloy material is process in order to improve the characteristics of the actual material.
Those improved characteristics are wear resistance, corrosion, free of porosity, temperature
and its ability. Considering the magnesium alloy to apply the twin-beam irradiation, thus the
particles used to do the surface modification is the AZ31 magnesium alloy and the substrate
Si. These elements can be expected from the chemical component Mg2Si, which will improve
the wear resistance and hardness of the alloy. Comparing the modification of the surface
followed by the dual-beam welding and single beam welding, it can be concluded that the
dual beam welding has used parallel laser beam to weld the material. While performing the
dual beam laser treatment the substrate Si and lower laser scanning are mixed well in order to
complete the surface modification. While comparing two laser beam technique it has been
observed that using the dual laser beam technique the speed of the cladding will increase, the
efficiency of the procedure is high. Following the dual beam laser technique the thorough
mixing of metal will be effective. In order to prove the effect of dual beam laser several
studies has compared the single beam laser treatment with dual beam laser treatment. Thus by
analysing those researches it has been observed that in order to weld the joins by using the
single spot laser it was liner and depends on the width of the HAZ. However, using the dual
laser beam treatment these drawbacks has been addressed.
Advantages of this cladding technique are listed below:
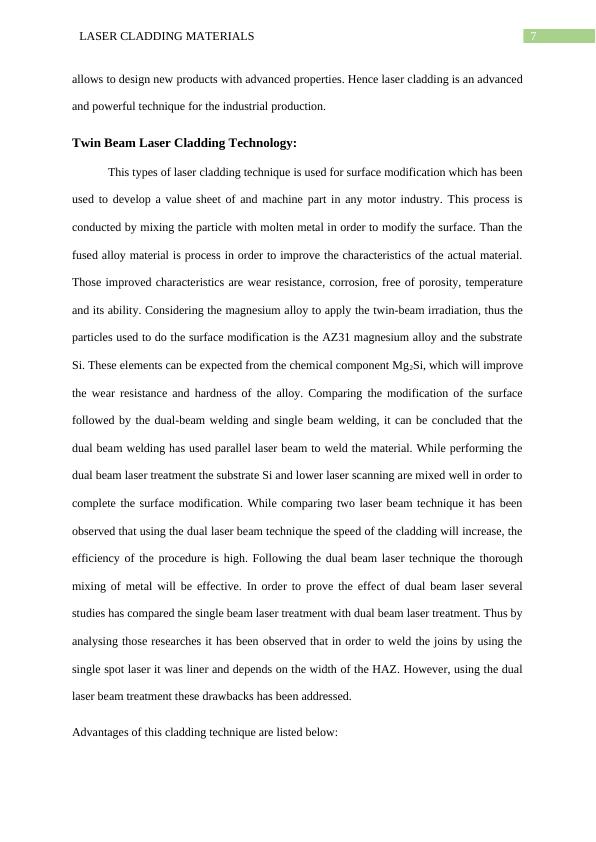
8LASER CLADDING MATERIALS
It is a speedy process while comparing it with single laser beam technique.
It improves the wear resistance and improve the corrosion.
It offers porosity free decomposition.
Crack free decomposition.
It help to join complicated machine parts.
It offers low thermal distortion.
Less time needed for weld operation.
Along with all the benefits there several drawback of using the Dual- laser- Beam technique:
However, the application of this procedure is effective there is an unavoidable
drawback of this process in order to apply this process as this process it expensive
and it also depends on the types of equipment.
Comparing the new process with the traditional process however it has efficient
working process it has high maintenance cost.
Laser cladding as an automated process:
The laser cladding process can be made entirely automated by involving many controlled
processing parameters. A simple and low cost laser cladding automated system can have two
CCD cameras, one personal computer and a standard acquisition card system. The operator of
the system can interact with the cladding process parameters via the personal computer. One
camera is used for temperature measurement and through another camera the variation of
distance of the height and width of track can be determined. The cladding process will add
melted powder materials over a substrate which will change or improve the surface properties
of the substrate. Hence, for efficient and good deposition of the materials in the substrate
some specific parameters are needed to be controlled. The lifetime of a laser cladded
component mainly depends on the goodness of its surface. So, industries basically make the
It is a speedy process while comparing it with single laser beam technique.
It improves the wear resistance and improve the corrosion.
It offers porosity free decomposition.
Crack free decomposition.
It help to join complicated machine parts.
It offers low thermal distortion.
Less time needed for weld operation.
Along with all the benefits there several drawback of using the Dual- laser- Beam technique:
However, the application of this procedure is effective there is an unavoidable
drawback of this process in order to apply this process as this process it expensive
and it also depends on the types of equipment.
Comparing the new process with the traditional process however it has efficient
working process it has high maintenance cost.
Laser cladding as an automated process:
The laser cladding process can be made entirely automated by involving many controlled
processing parameters. A simple and low cost laser cladding automated system can have two
CCD cameras, one personal computer and a standard acquisition card system. The operator of
the system can interact with the cladding process parameters via the personal computer. One
camera is used for temperature measurement and through another camera the variation of
distance of the height and width of track can be determined. The cladding process will add
melted powder materials over a substrate which will change or improve the surface properties
of the substrate. Hence, for efficient and good deposition of the materials in the substrate
some specific parameters are needed to be controlled. The lifetime of a laser cladded
component mainly depends on the goodness of its surface. So, industries basically make the
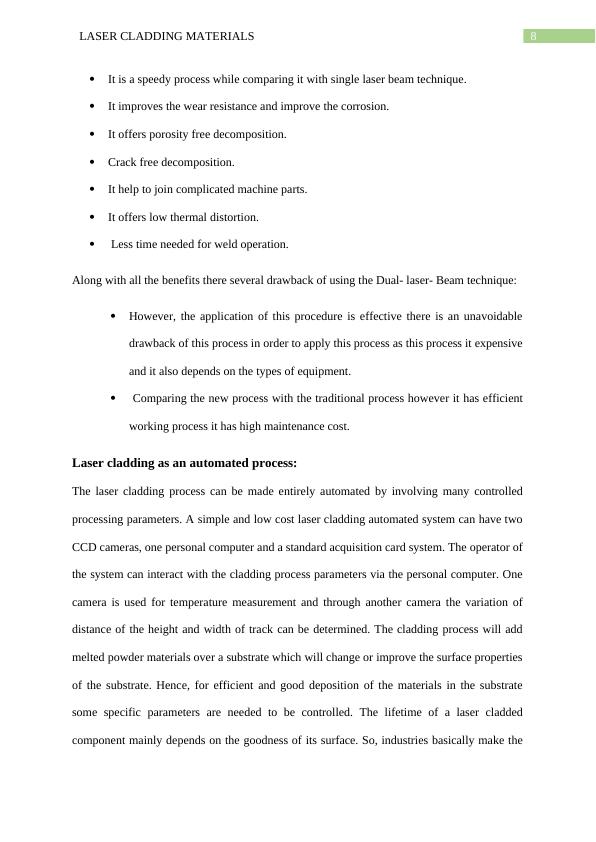
End of preview
Want to access all the pages? Upload your documents or become a member.
Related Documents
Laser Cladding of Cobalt Alloylg...
|17
|1076
|130
Effects Of Laser Scan Speed - Doclg...
|11
|2609
|199
Alloys in Laser Claddinglg...
|37
|8539
|33
Laser Cladding of Cobalt Alloy and Properties of Alloys in Mechanical Engineeringlg...
|38
|8099
|208
Assignment On Literature Plannerlg...
|5
|1601
|31
Adhesive Bonding in Mechanical Engineeringlg...
|30
|2913
|165