Lean Six Sigma Applications in Process Improvement
VerifiedAdded on 2020/03/16
|27
|3212
|435
AI Summary
This assignment delves into the practical application of Lean Six Sigma principles within a process improvement framework. Students are tasked with utilizing various tools such as process mapping, causal analysis, Voice of the Customer (VOC) matrices, and Critical to Quality (CTQ) trees to analyze and enhance processes. The assignment emphasizes identifying root causes of problems, understanding customer expectations, and aligning process improvements with customer needs.
Contribute Materials
Your contribution can guide someone’s learning journey. Share your
documents today.
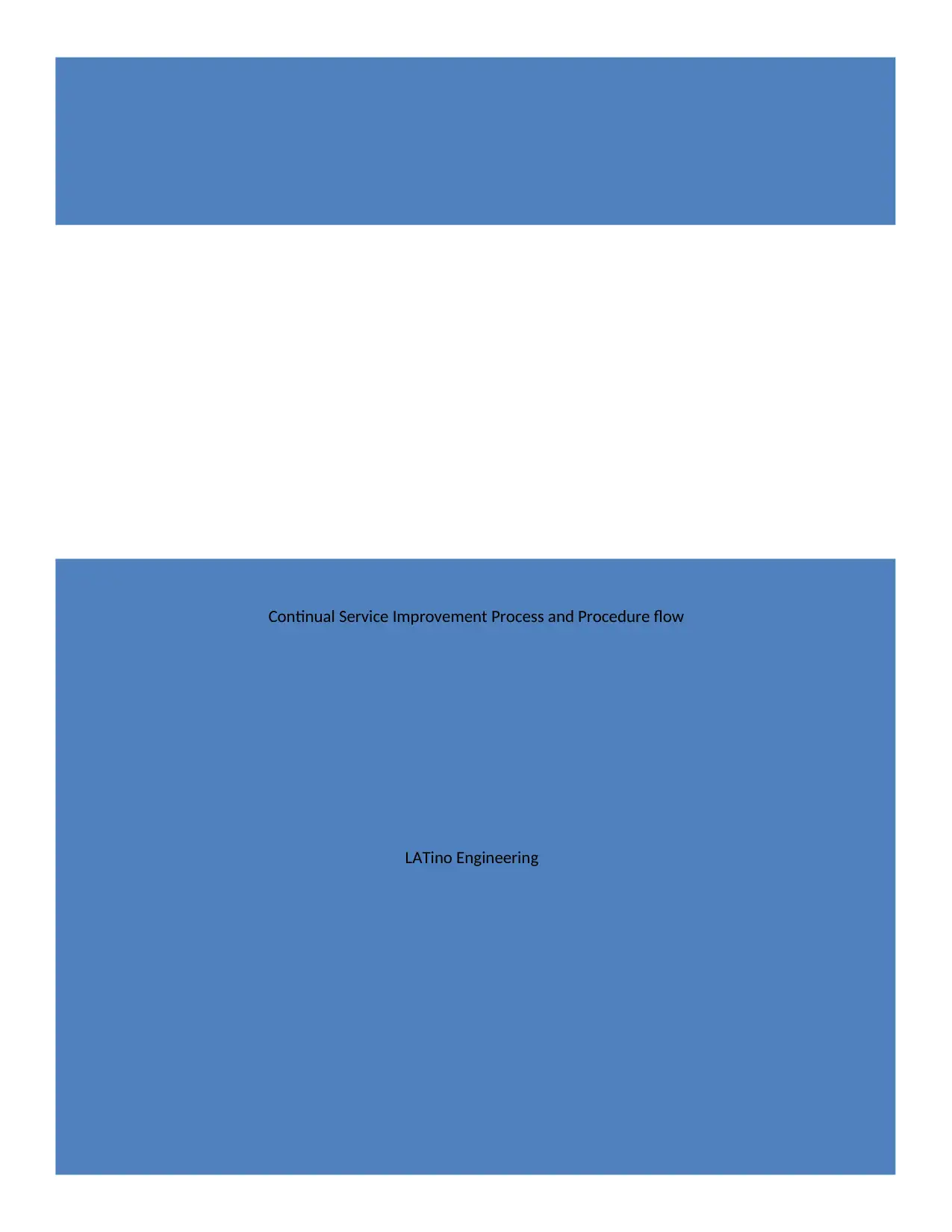
Continual Service Improvement Process and Procedure flow
LATino Engineering
LATino Engineering
Secure Best Marks with AI Grader
Need help grading? Try our AI Grader for instant feedback on your assignments.
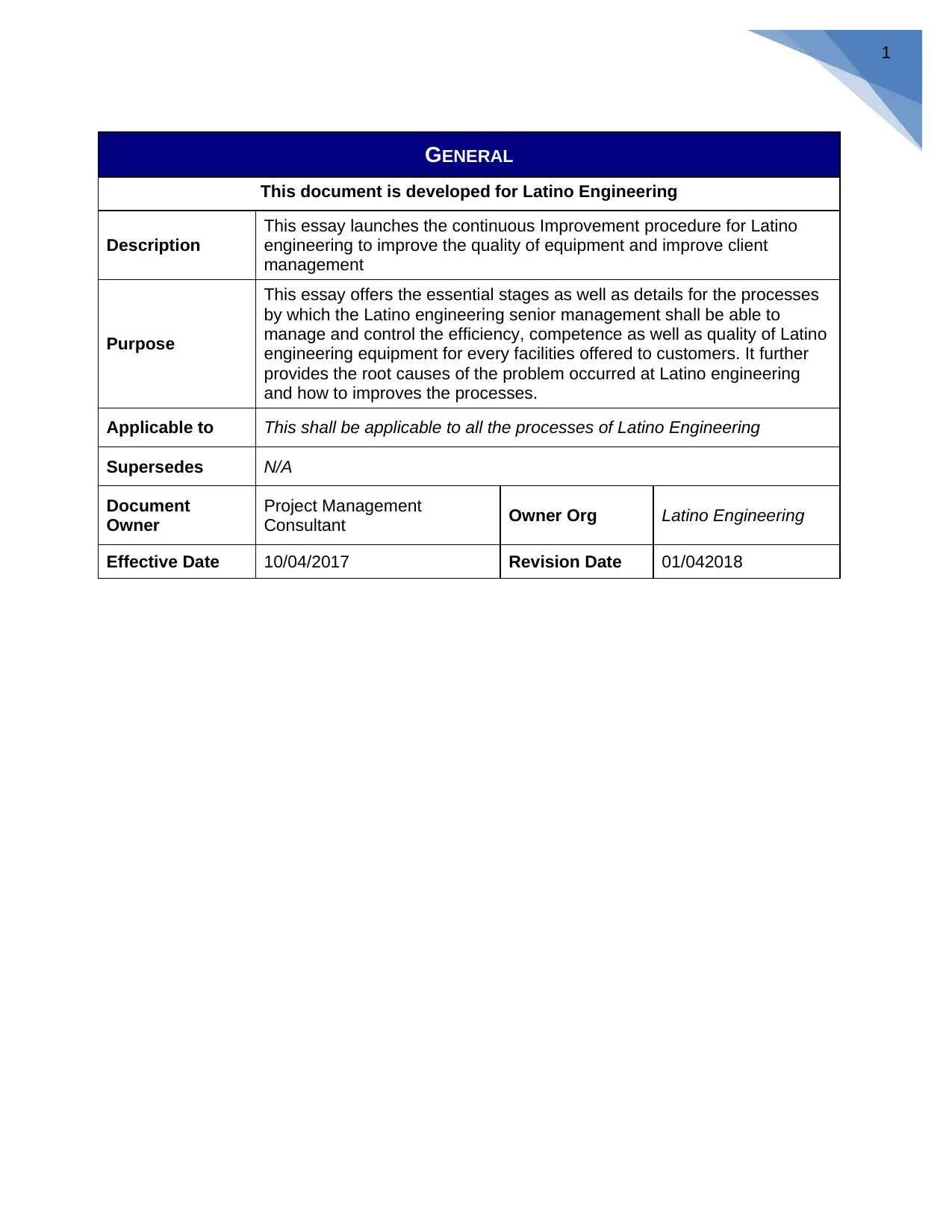
GENERAL
This document is developed for Latino Engineering
Description
This essay launches the continuous Improvement procedure for Latino
engineering to improve the quality of equipment and improve client
management
Purpose
This essay offers the essential stages as well as details for the processes
by which the Latino engineering senior management shall be able to
manage and control the efficiency, competence as well as quality of Latino
engineering equipment for every facilities offered to customers. It further
provides the root causes of the problem occurred at Latino engineering
and how to improves the processes.
Applicable to This shall be applicable to all the processes of Latino Engineering
Supersedes N/A
Document
Owner
Project Management
Consultant Owner Org Latino Engineering
Effective Date 10/04/2017 Revision Date 01/042018
1
This document is developed for Latino Engineering
Description
This essay launches the continuous Improvement procedure for Latino
engineering to improve the quality of equipment and improve client
management
Purpose
This essay offers the essential stages as well as details for the processes
by which the Latino engineering senior management shall be able to
manage and control the efficiency, competence as well as quality of Latino
engineering equipment for every facilities offered to customers. It further
provides the root causes of the problem occurred at Latino engineering
and how to improves the processes.
Applicable to This shall be applicable to all the processes of Latino Engineering
Supersedes N/A
Document
Owner
Project Management
Consultant Owner Org Latino Engineering
Effective Date 10/04/2017 Revision Date 01/042018
1
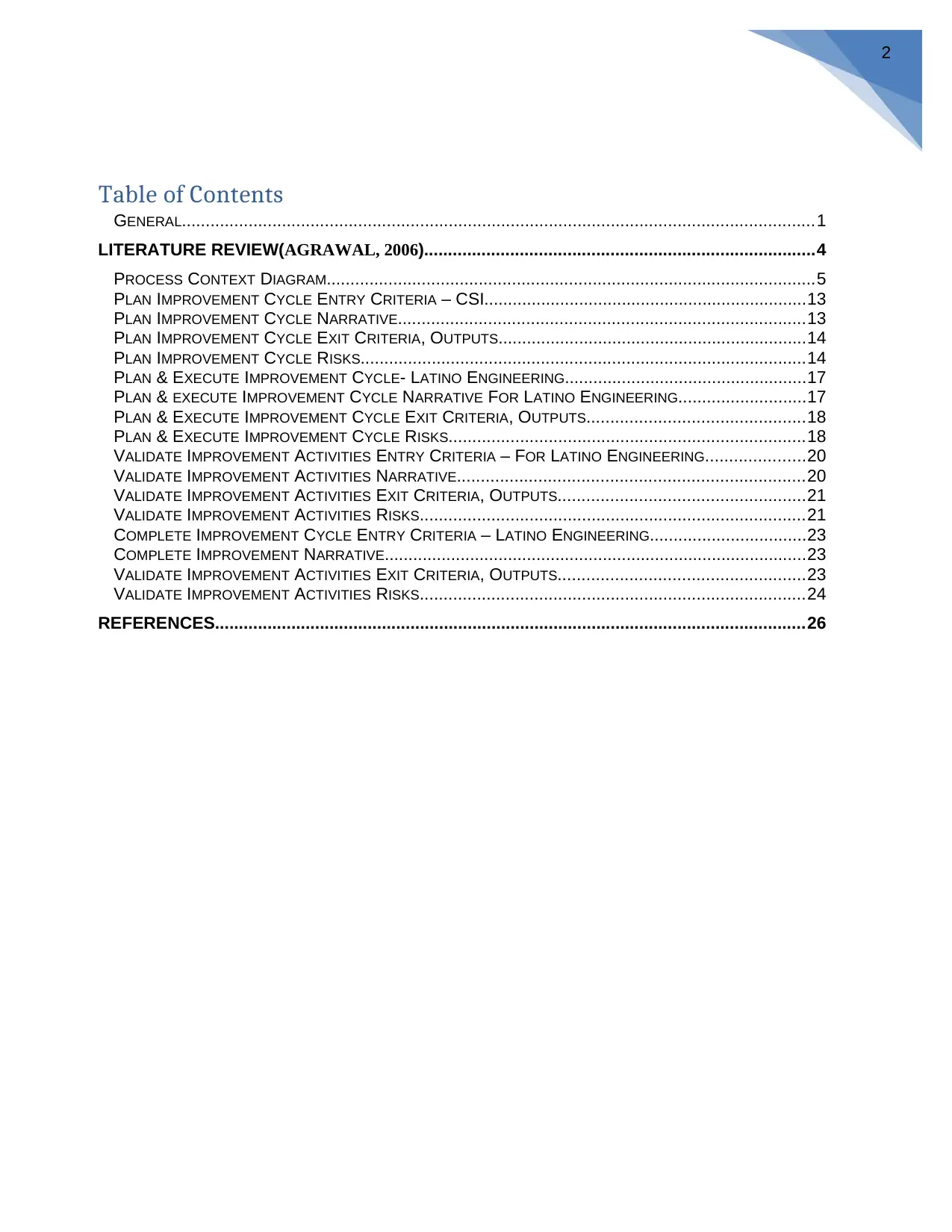
Table of Contents
GENERAL.....................................................................................................................................1
LITERATURE REVIEW(AGRAWAL, 2006)..................................................................................4
PROCESS CONTEXT DIAGRAM.......................................................................................................5
PLAN IMPROVEMENT CYCLE ENTRY CRITERIA – CSI....................................................................13
PLAN IMPROVEMENT CYCLE NARRATIVE......................................................................................13
PLAN IMPROVEMENT CYCLE EXIT CRITERIA, OUTPUTS.................................................................14
PLAN IMPROVEMENT CYCLE RISKS..............................................................................................14
PLAN & EXECUTE IMPROVEMENT CYCLE- LATINO ENGINEERING...................................................17
PLAN & EXECUTE IMPROVEMENT CYCLE NARRATIVE FOR LATINO ENGINEERING...........................17
PLAN & EXECUTE IMPROVEMENT CYCLE EXIT CRITERIA, OUTPUTS..............................................18
PLAN & EXECUTE IMPROVEMENT CYCLE RISKS...........................................................................18
VALIDATE IMPROVEMENT ACTIVITIES ENTRY CRITERIA – FOR LATINO ENGINEERING.....................20
VALIDATE IMPROVEMENT ACTIVITIES NARRATIVE.........................................................................20
VALIDATE IMPROVEMENT ACTIVITIES EXIT CRITERIA, OUTPUTS....................................................21
VALIDATE IMPROVEMENT ACTIVITIES RISKS.................................................................................21
COMPLETE IMPROVEMENT CYCLE ENTRY CRITERIA – LATINO ENGINEERING.................................23
COMPLETE IMPROVEMENT NARRATIVE.........................................................................................23
VALIDATE IMPROVEMENT ACTIVITIES EXIT CRITERIA, OUTPUTS....................................................23
VALIDATE IMPROVEMENT ACTIVITIES RISKS.................................................................................24
REFERENCES............................................................................................................................26
2
GENERAL.....................................................................................................................................1
LITERATURE REVIEW(AGRAWAL, 2006)..................................................................................4
PROCESS CONTEXT DIAGRAM.......................................................................................................5
PLAN IMPROVEMENT CYCLE ENTRY CRITERIA – CSI....................................................................13
PLAN IMPROVEMENT CYCLE NARRATIVE......................................................................................13
PLAN IMPROVEMENT CYCLE EXIT CRITERIA, OUTPUTS.................................................................14
PLAN IMPROVEMENT CYCLE RISKS..............................................................................................14
PLAN & EXECUTE IMPROVEMENT CYCLE- LATINO ENGINEERING...................................................17
PLAN & EXECUTE IMPROVEMENT CYCLE NARRATIVE FOR LATINO ENGINEERING...........................17
PLAN & EXECUTE IMPROVEMENT CYCLE EXIT CRITERIA, OUTPUTS..............................................18
PLAN & EXECUTE IMPROVEMENT CYCLE RISKS...........................................................................18
VALIDATE IMPROVEMENT ACTIVITIES ENTRY CRITERIA – FOR LATINO ENGINEERING.....................20
VALIDATE IMPROVEMENT ACTIVITIES NARRATIVE.........................................................................20
VALIDATE IMPROVEMENT ACTIVITIES EXIT CRITERIA, OUTPUTS....................................................21
VALIDATE IMPROVEMENT ACTIVITIES RISKS.................................................................................21
COMPLETE IMPROVEMENT CYCLE ENTRY CRITERIA – LATINO ENGINEERING.................................23
COMPLETE IMPROVEMENT NARRATIVE.........................................................................................23
VALIDATE IMPROVEMENT ACTIVITIES EXIT CRITERIA, OUTPUTS....................................................23
VALIDATE IMPROVEMENT ACTIVITIES RISKS.................................................................................24
REFERENCES............................................................................................................................26
2
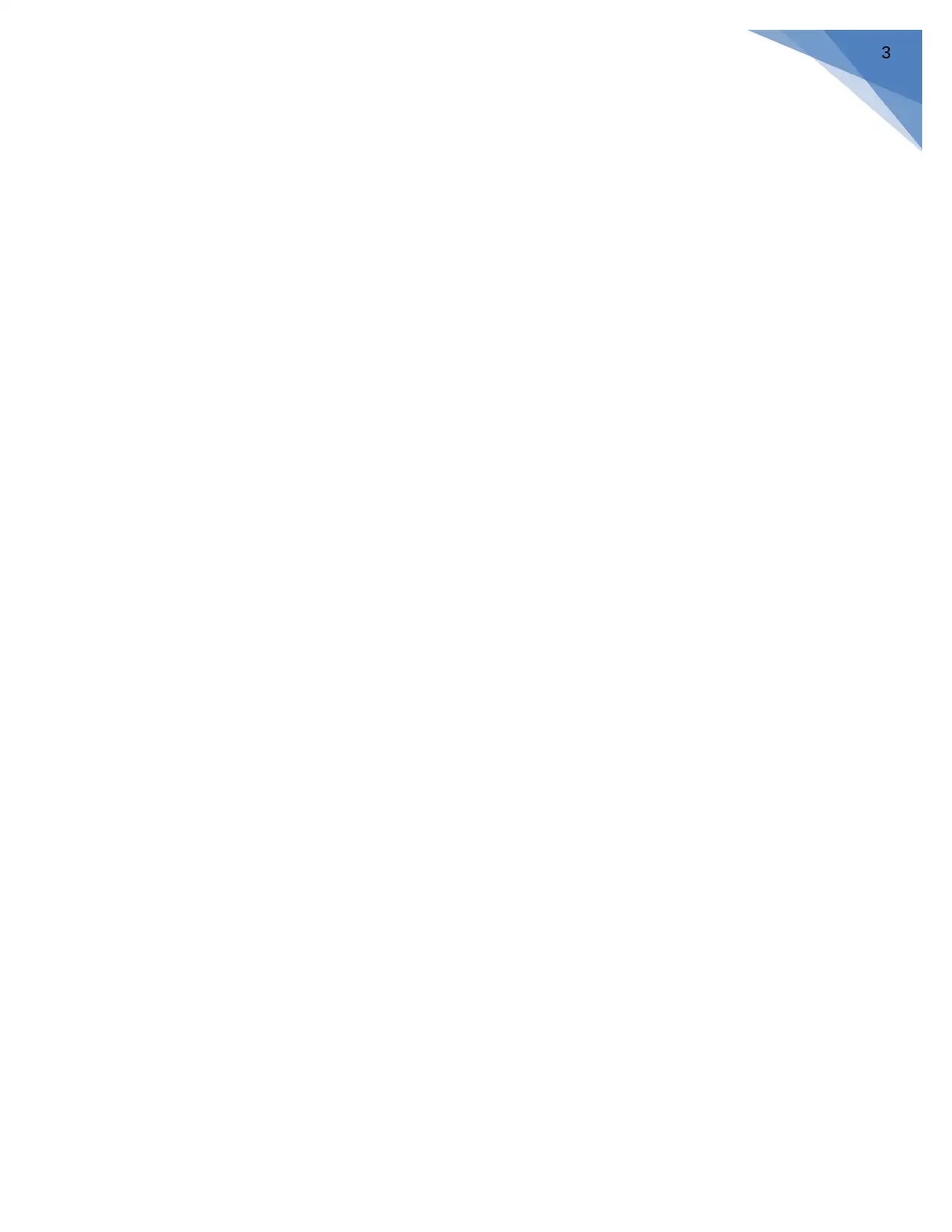
3
Secure Best Marks with AI Grader
Need help grading? Try our AI Grader for instant feedback on your assignments.
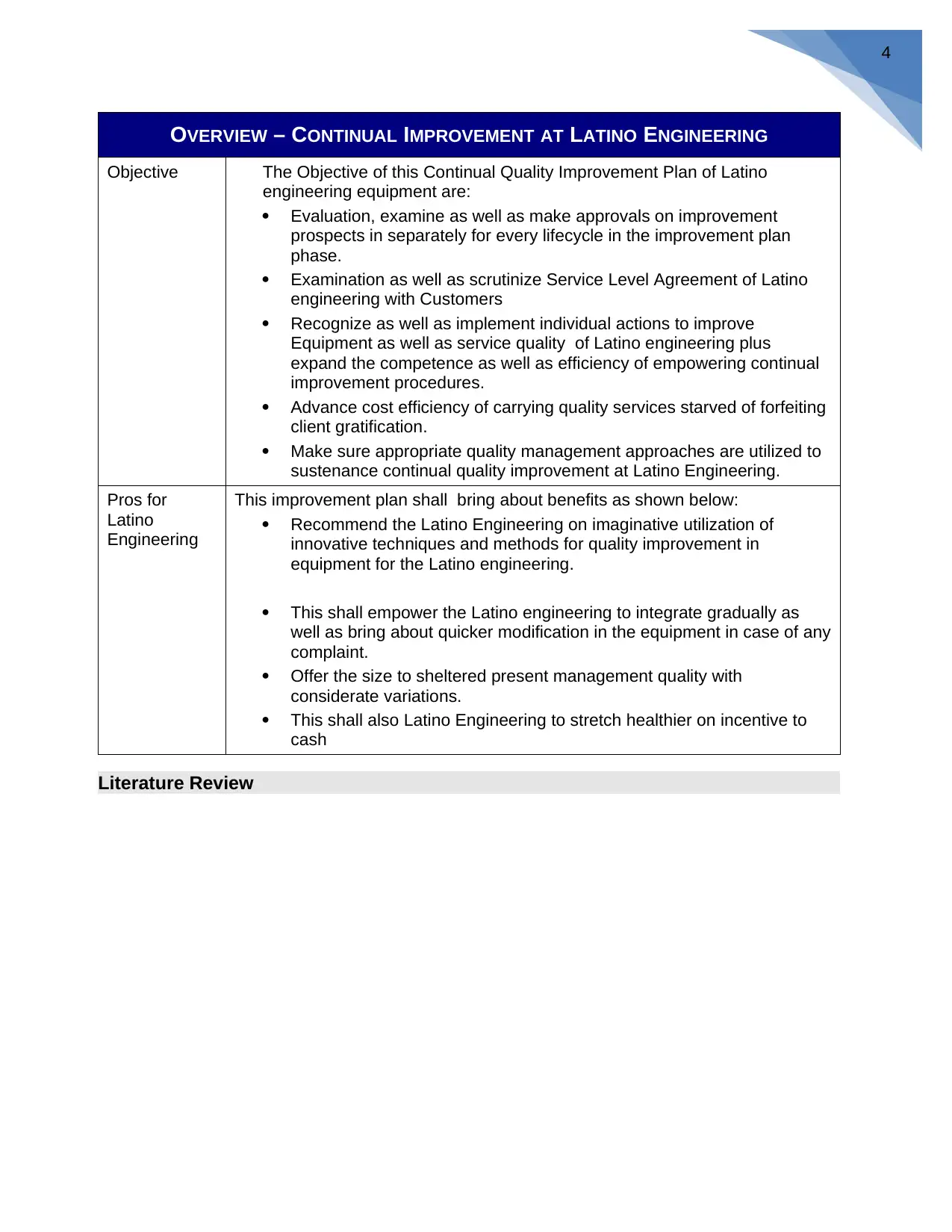
OVERVIEW – CONTINUAL IMPROVEMENT AT LATINO ENGINEERING
Objective The Objective of this Continual Quality Improvement Plan of Latino
engineering equipment are:
Evaluation, examine as well as make approvals on improvement
prospects in separately for every lifecycle in the improvement plan
phase.
Examination as well as scrutinize Service Level Agreement of Latino
engineering with Customers
Recognize as well as implement individual actions to improve
Equipment as well as service quality of Latino engineering plus
expand the competence as well as efficiency of empowering continual
improvement procedures.
Advance cost efficiency of carrying quality services starved of forfeiting
client gratification.
Make sure appropriate quality management approaches are utilized to
sustenance continual quality improvement at Latino Engineering.
Pros for
Latino
Engineering
This improvement plan shall bring about benefits as shown below:
Recommend the Latino Engineering on imaginative utilization of
innovative techniques and methods for quality improvement in
equipment for the Latino engineering.
This shall empower the Latino engineering to integrate gradually as
well as bring about quicker modification in the equipment in case of any
complaint.
Offer the size to sheltered present management quality with
considerate variations.
This shall also Latino Engineering to stretch healthier on incentive to
cash
Literature Review
4
Objective The Objective of this Continual Quality Improvement Plan of Latino
engineering equipment are:
Evaluation, examine as well as make approvals on improvement
prospects in separately for every lifecycle in the improvement plan
phase.
Examination as well as scrutinize Service Level Agreement of Latino
engineering with Customers
Recognize as well as implement individual actions to improve
Equipment as well as service quality of Latino engineering plus
expand the competence as well as efficiency of empowering continual
improvement procedures.
Advance cost efficiency of carrying quality services starved of forfeiting
client gratification.
Make sure appropriate quality management approaches are utilized to
sustenance continual quality improvement at Latino Engineering.
Pros for
Latino
Engineering
This improvement plan shall bring about benefits as shown below:
Recommend the Latino Engineering on imaginative utilization of
innovative techniques and methods for quality improvement in
equipment for the Latino engineering.
This shall empower the Latino engineering to integrate gradually as
well as bring about quicker modification in the equipment in case of any
complaint.
Offer the size to sheltered present management quality with
considerate variations.
This shall also Latino Engineering to stretch healthier on incentive to
cash
Literature Review
4
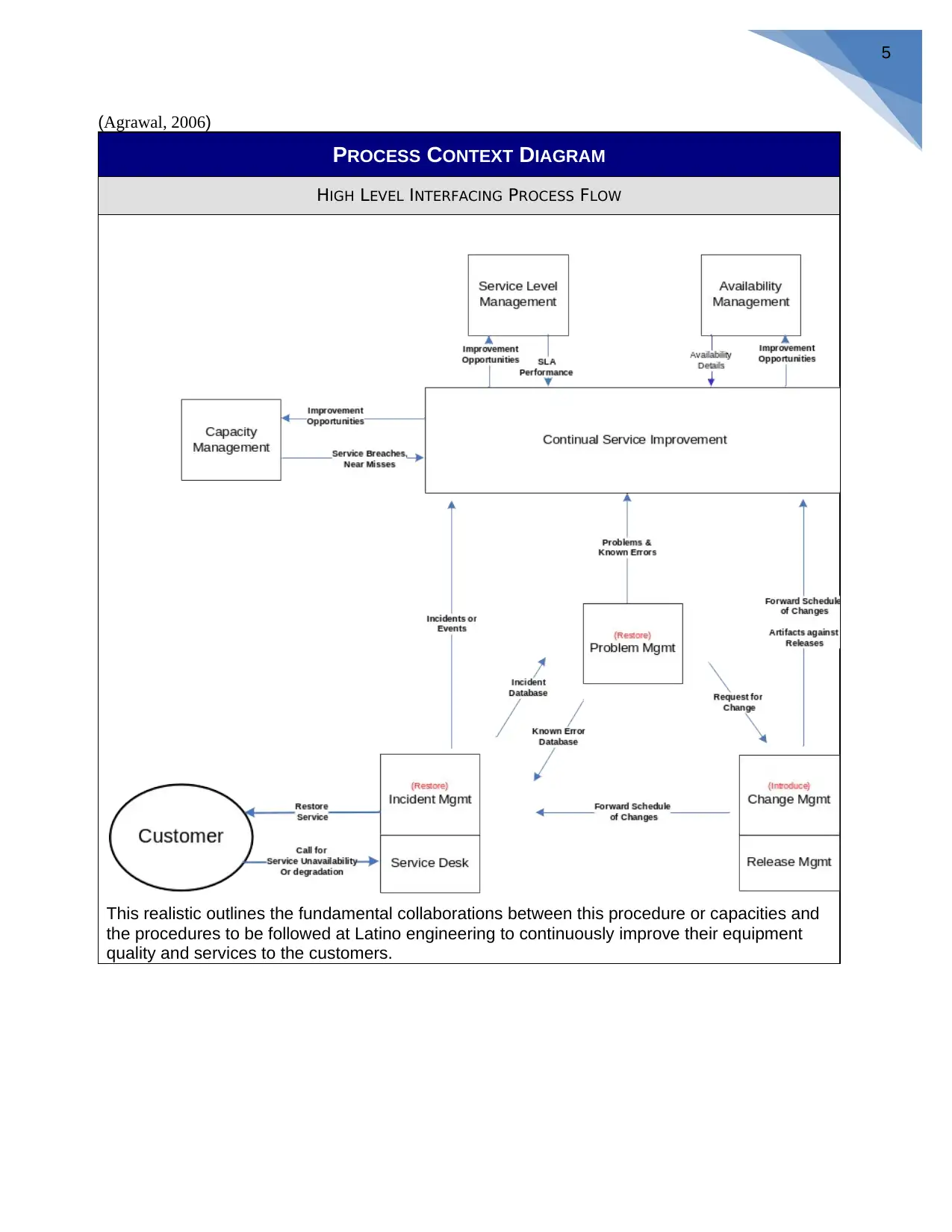
(Agrawal, 2006)
PROCESS CONTEXT DIAGRAM
HIGH LEVEL INTERFACING PROCESS FLOW
This realistic outlines the fundamental collaborations between this procedure or capacities and
the procedures to be followed at Latino engineering to continuously improve their equipment
quality and services to the customers.
5
PROCESS CONTEXT DIAGRAM
HIGH LEVEL INTERFACING PROCESS FLOW
This realistic outlines the fundamental collaborations between this procedure or capacities and
the procedures to be followed at Latino engineering to continuously improve their equipment
quality and services to the customers.
5
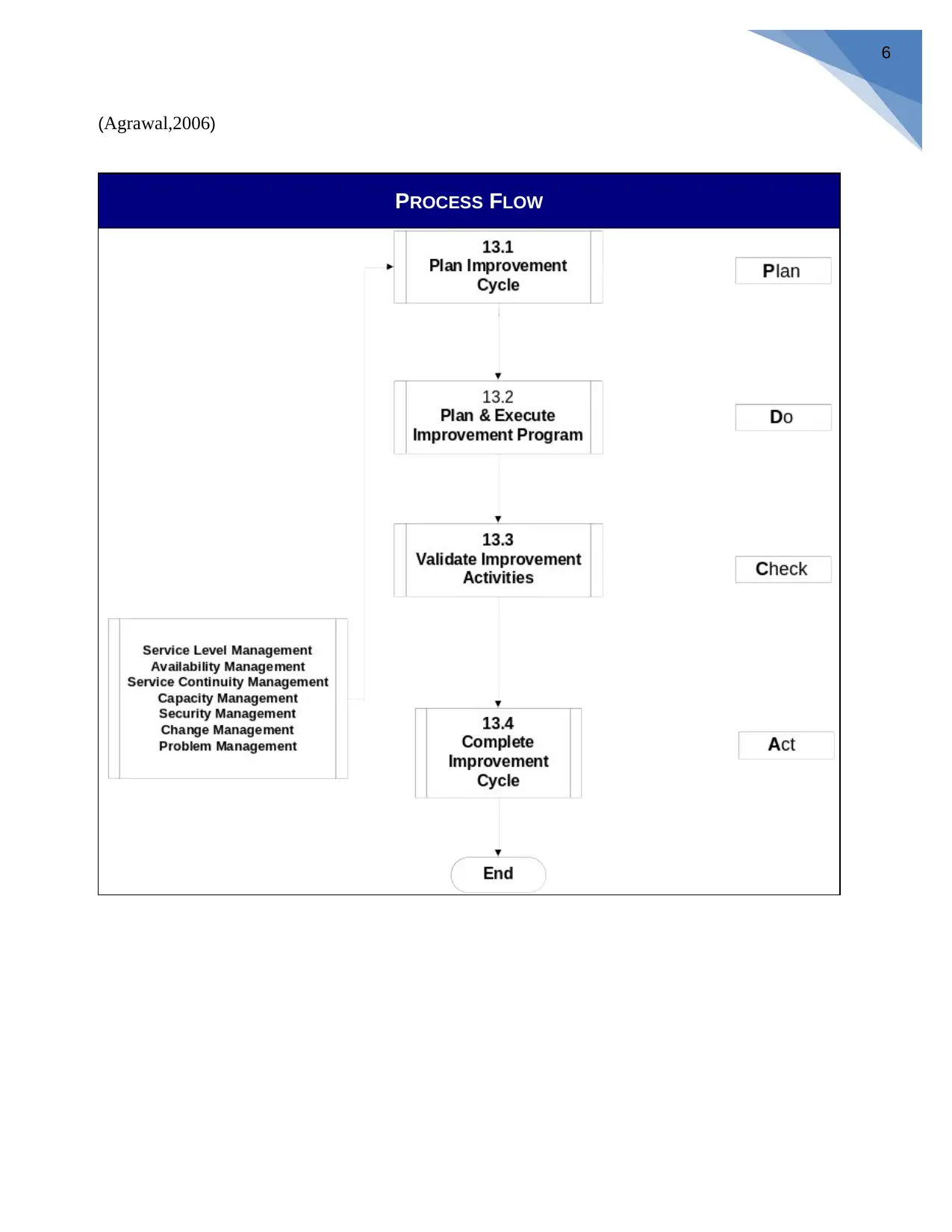
(Agrawal,2006)
PROCESS FLOW
6
PROCESS FLOW
6
Paraphrase This Document
Need a fresh take? Get an instant paraphrase of this document with our AI Paraphraser
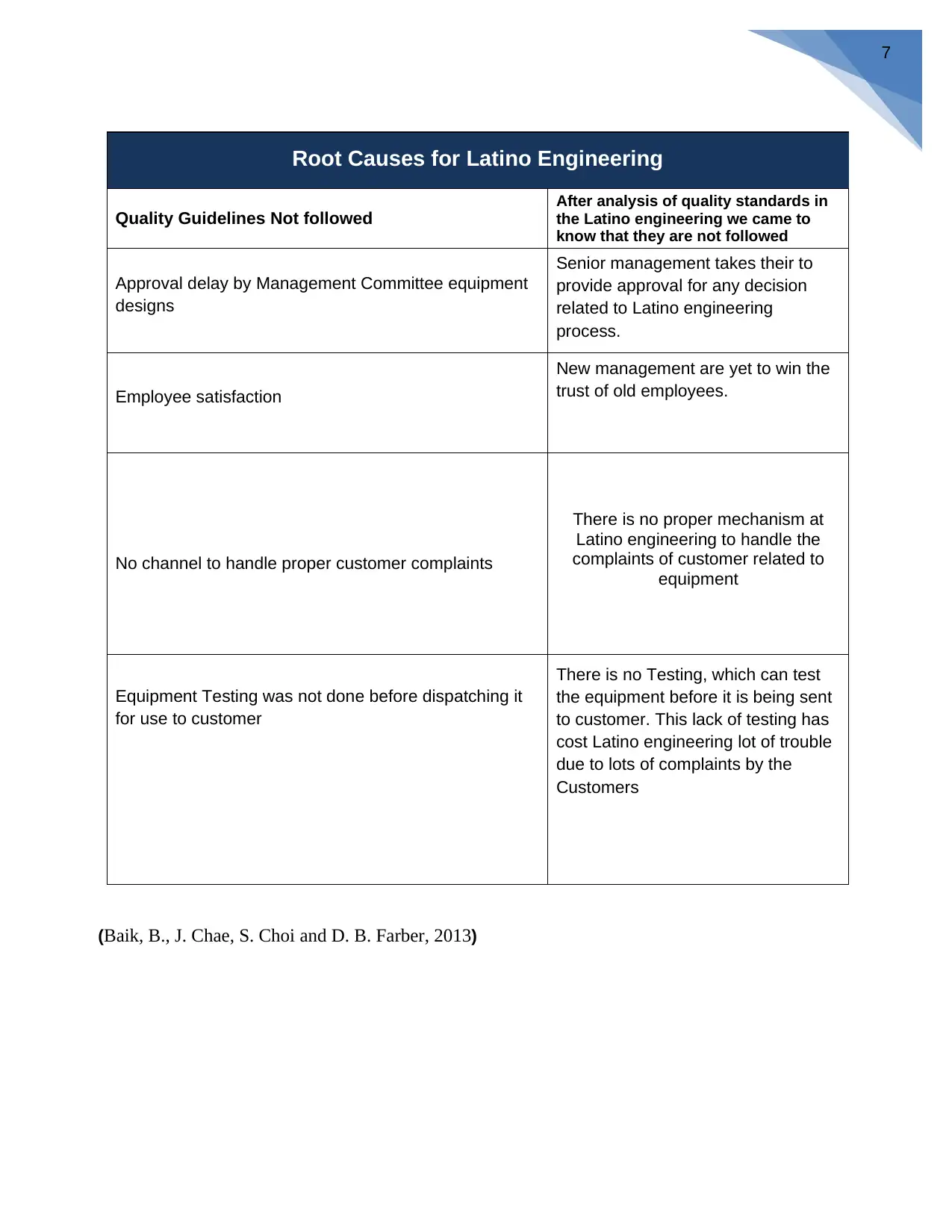
Root Causes for Latino Engineering
Quality Guidelines Not followed
After analysis of quality standards in
the Latino engineering we came to
know that they are not followed
Approval delay by Management Committee equipment
designs
Senior management takes their to
provide approval for any decision
related to Latino engineering
process.
Employee satisfaction
New management are yet to win the
trust of old employees.
No channel to handle proper customer complaints
There is no proper mechanism at
Latino engineering to handle the
complaints of customer related to
equipment
Equipment Testing was not done before dispatching it
for use to customer
There is no Testing, which can test
the equipment before it is being sent
to customer. This lack of testing has
cost Latino engineering lot of trouble
due to lots of complaints by the
Customers
(Baik, B., J. Chae, S. Choi and D. B. Farber, 2013)
7
Quality Guidelines Not followed
After analysis of quality standards in
the Latino engineering we came to
know that they are not followed
Approval delay by Management Committee equipment
designs
Senior management takes their to
provide approval for any decision
related to Latino engineering
process.
Employee satisfaction
New management are yet to win the
trust of old employees.
No channel to handle proper customer complaints
There is no proper mechanism at
Latino engineering to handle the
complaints of customer related to
equipment
Equipment Testing was not done before dispatching it
for use to customer
There is no Testing, which can test
the equipment before it is being sent
to customer. This lack of testing has
cost Latino engineering lot of trouble
due to lots of complaints by the
Customers
(Baik, B., J. Chae, S. Choi and D. B. Farber, 2013)
7
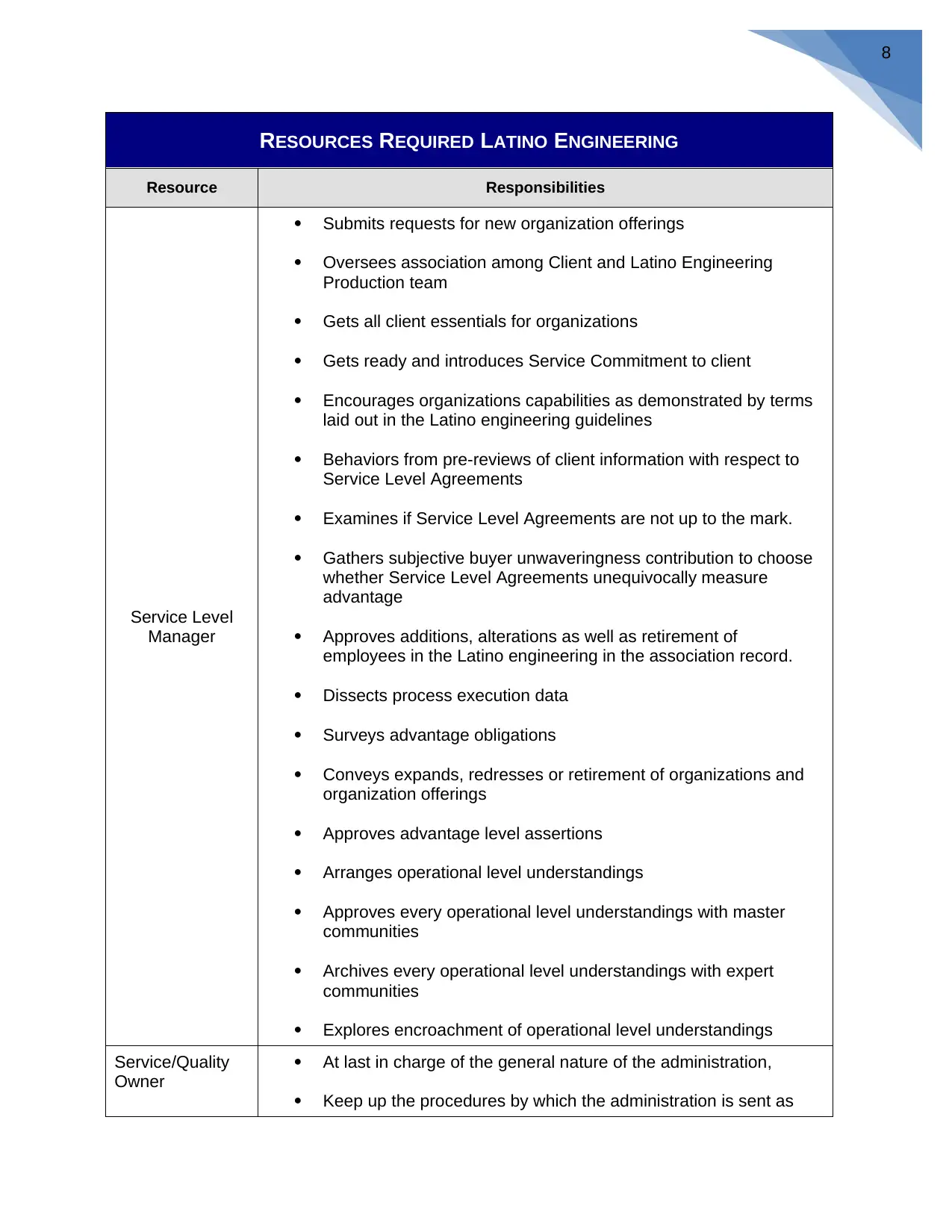
RESOURCES REQUIRED LATINO ENGINEERING
Resource Responsibilities
Service Level
Manager
Submits requests for new organization offerings
Oversees association among Client and Latino Engineering
Production team
Gets all client essentials for organizations
Gets ready and introduces Service Commitment to client
Encourages organizations capabilities as demonstrated by terms
laid out in the Latino engineering guidelines
Behaviors from pre-reviews of client information with respect to
Service Level Agreements
Examines if Service Level Agreements are not up to the mark.
Gathers subjective buyer unwaveringness contribution to choose
whether Service Level Agreements unequivocally measure
advantage
Approves additions, alterations as well as retirement of
employees in the Latino engineering in the association record.
Dissects process execution data
Surveys advantage obligations
Conveys expands, redresses or retirement of organizations and
organization offerings
Approves advantage level assertions
Arranges operational level understandings
Approves every operational level understandings with master
communities
Archives every operational level understandings with expert
communities
Explores encroachment of operational level understandings
Service/Quality
Owner
At last in charge of the general nature of the administration,
Keep up the procedures by which the administration is sent as
8
Resource Responsibilities
Service Level
Manager
Submits requests for new organization offerings
Oversees association among Client and Latino Engineering
Production team
Gets all client essentials for organizations
Gets ready and introduces Service Commitment to client
Encourages organizations capabilities as demonstrated by terms
laid out in the Latino engineering guidelines
Behaviors from pre-reviews of client information with respect to
Service Level Agreements
Examines if Service Level Agreements are not up to the mark.
Gathers subjective buyer unwaveringness contribution to choose
whether Service Level Agreements unequivocally measure
advantage
Approves additions, alterations as well as retirement of
employees in the Latino engineering in the association record.
Dissects process execution data
Surveys advantage obligations
Conveys expands, redresses or retirement of organizations and
organization offerings
Approves advantage level assertions
Arranges operational level understandings
Approves every operational level understandings with master
communities
Archives every operational level understandings with expert
communities
Explores encroachment of operational level understandings
Service/Quality
Owner
At last in charge of the general nature of the administration,
Keep up the procedures by which the administration is sent as
8
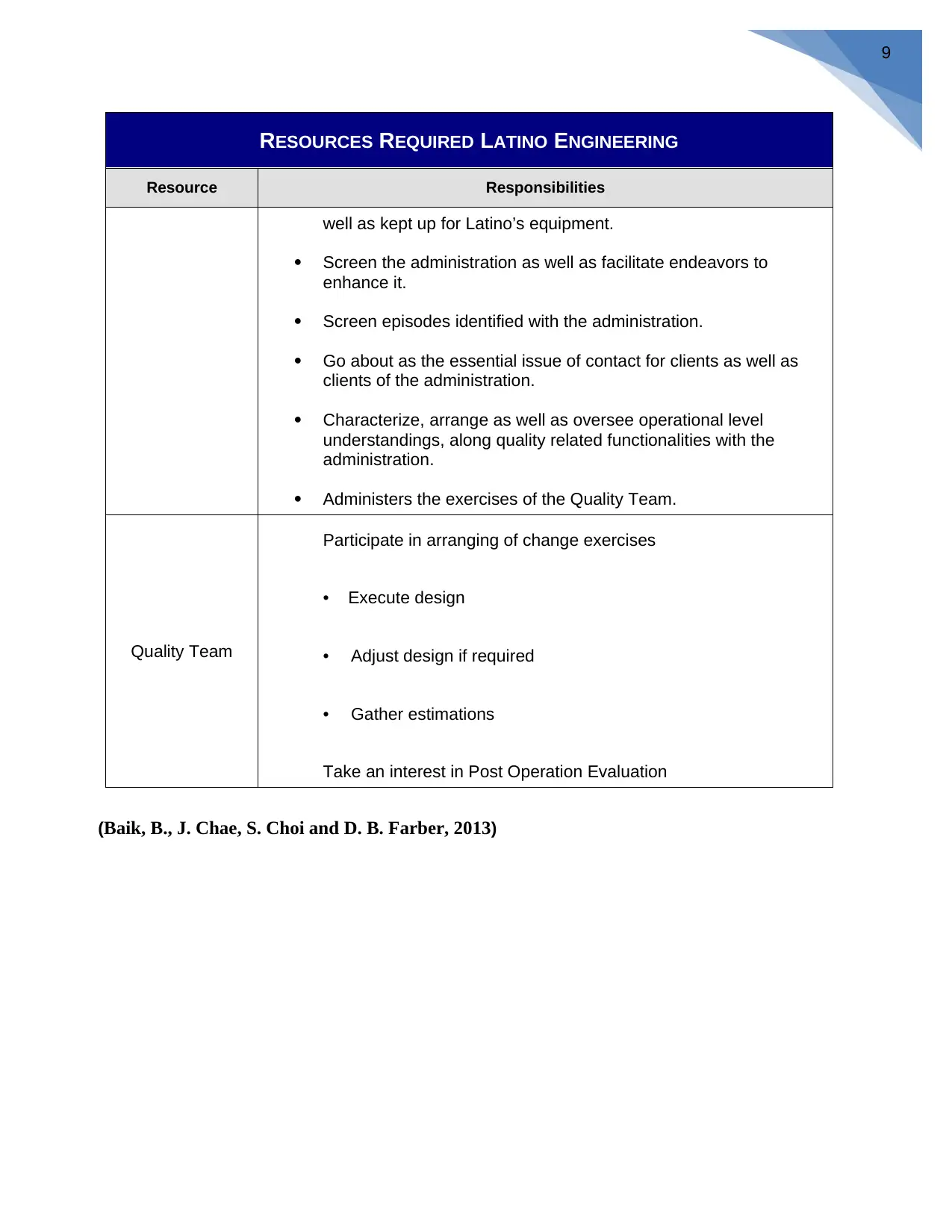
RESOURCES REQUIRED LATINO ENGINEERING
Resource Responsibilities
well as kept up for Latino’s equipment.
Screen the administration as well as facilitate endeavors to
enhance it.
Screen episodes identified with the administration.
Go about as the essential issue of contact for clients as well as
clients of the administration.
Characterize, arrange as well as oversee operational level
understandings, along quality related functionalities with the
administration.
Administers the exercises of the Quality Team.
Quality Team
Participate in arranging of change exercises
• Execute design
• Adjust design if required
• Gather estimations
Take an interest in Post Operation Evaluation
(Baik, B., J. Chae, S. Choi and D. B. Farber, 2013)
9
Resource Responsibilities
well as kept up for Latino’s equipment.
Screen the administration as well as facilitate endeavors to
enhance it.
Screen episodes identified with the administration.
Go about as the essential issue of contact for clients as well as
clients of the administration.
Characterize, arrange as well as oversee operational level
understandings, along quality related functionalities with the
administration.
Administers the exercises of the Quality Team.
Quality Team
Participate in arranging of change exercises
• Execute design
• Adjust design if required
• Gather estimations
Take an interest in Post Operation Evaluation
(Baik, B., J. Chae, S. Choi and D. B. Farber, 2013)
9
Secure Best Marks with AI Grader
Need help grading? Try our AI Grader for instant feedback on your assignments.
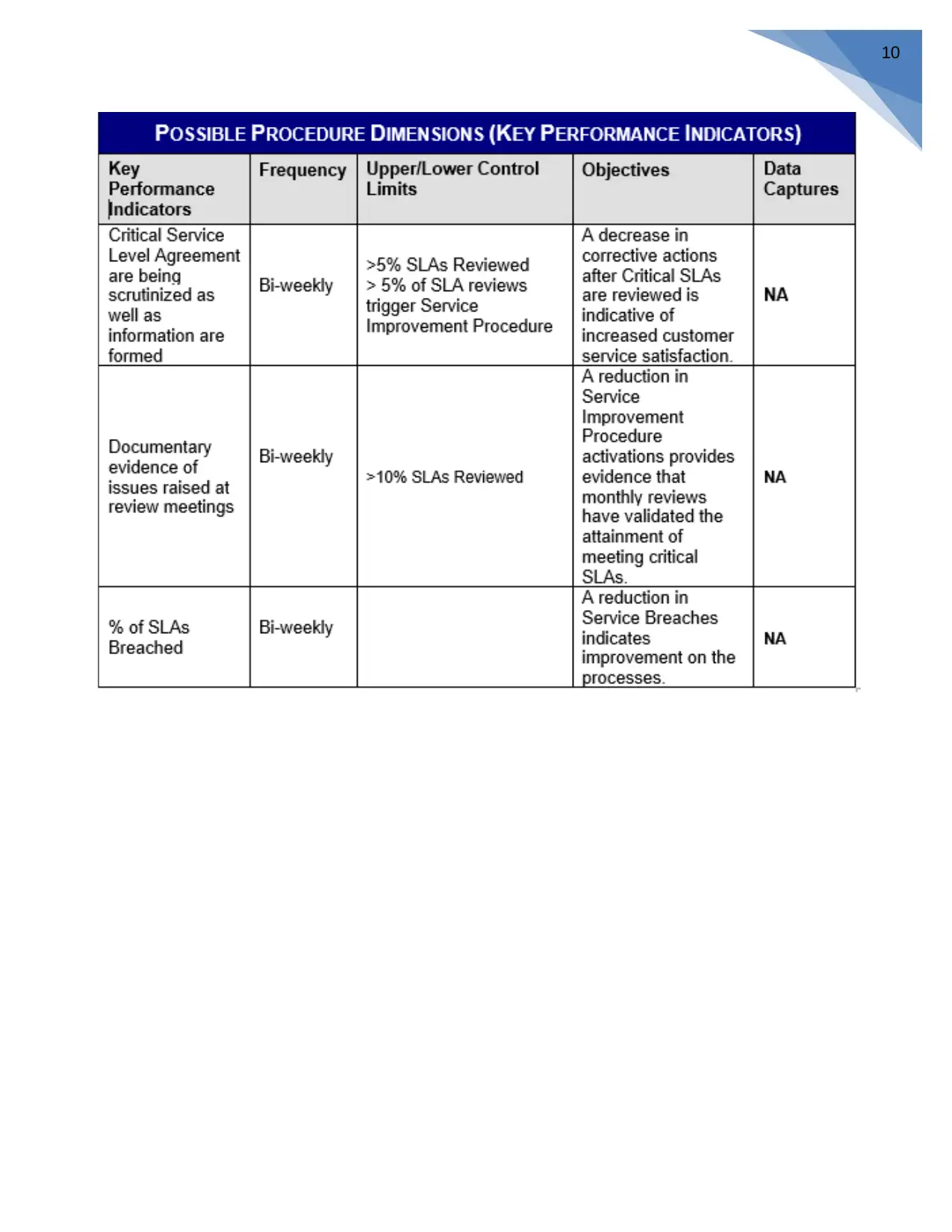
10
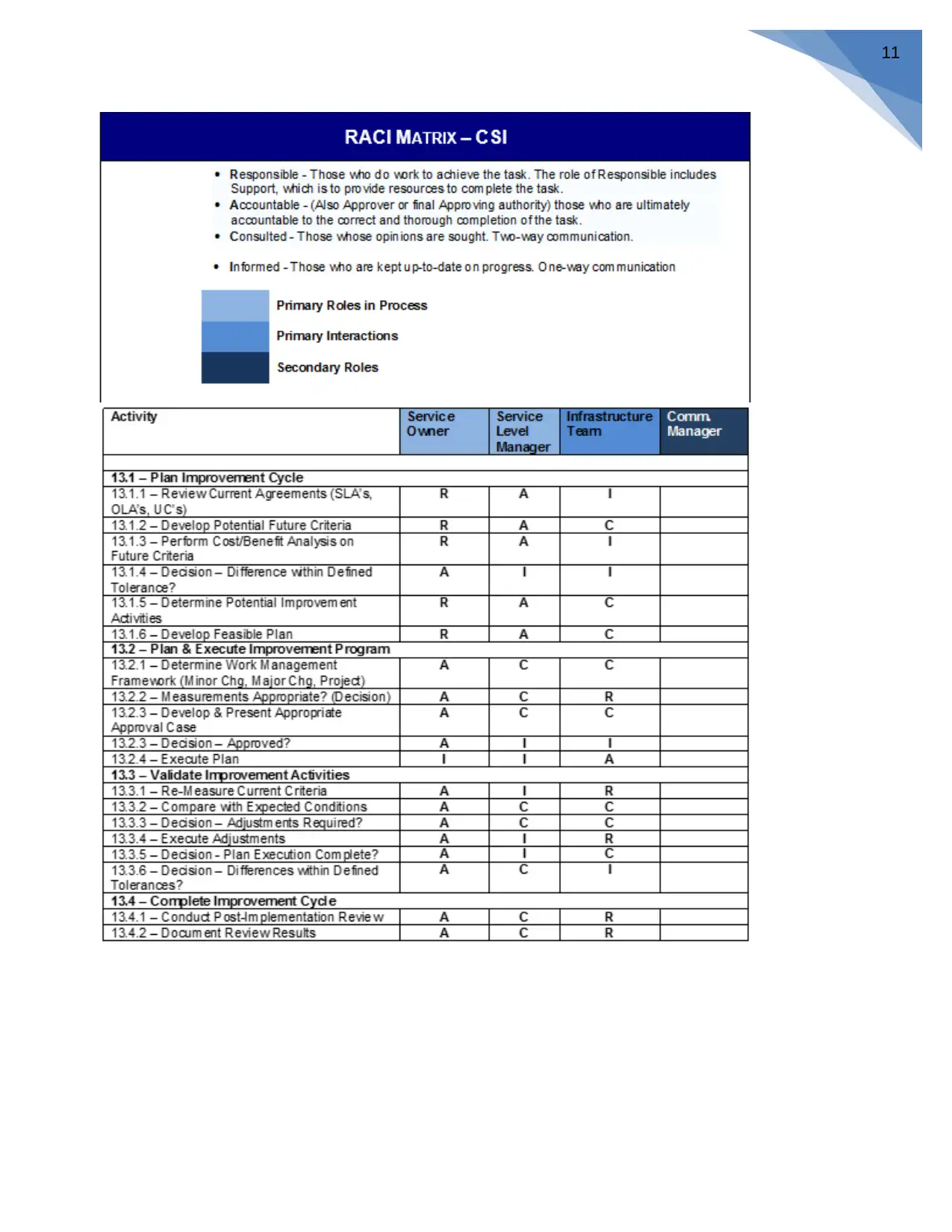
11
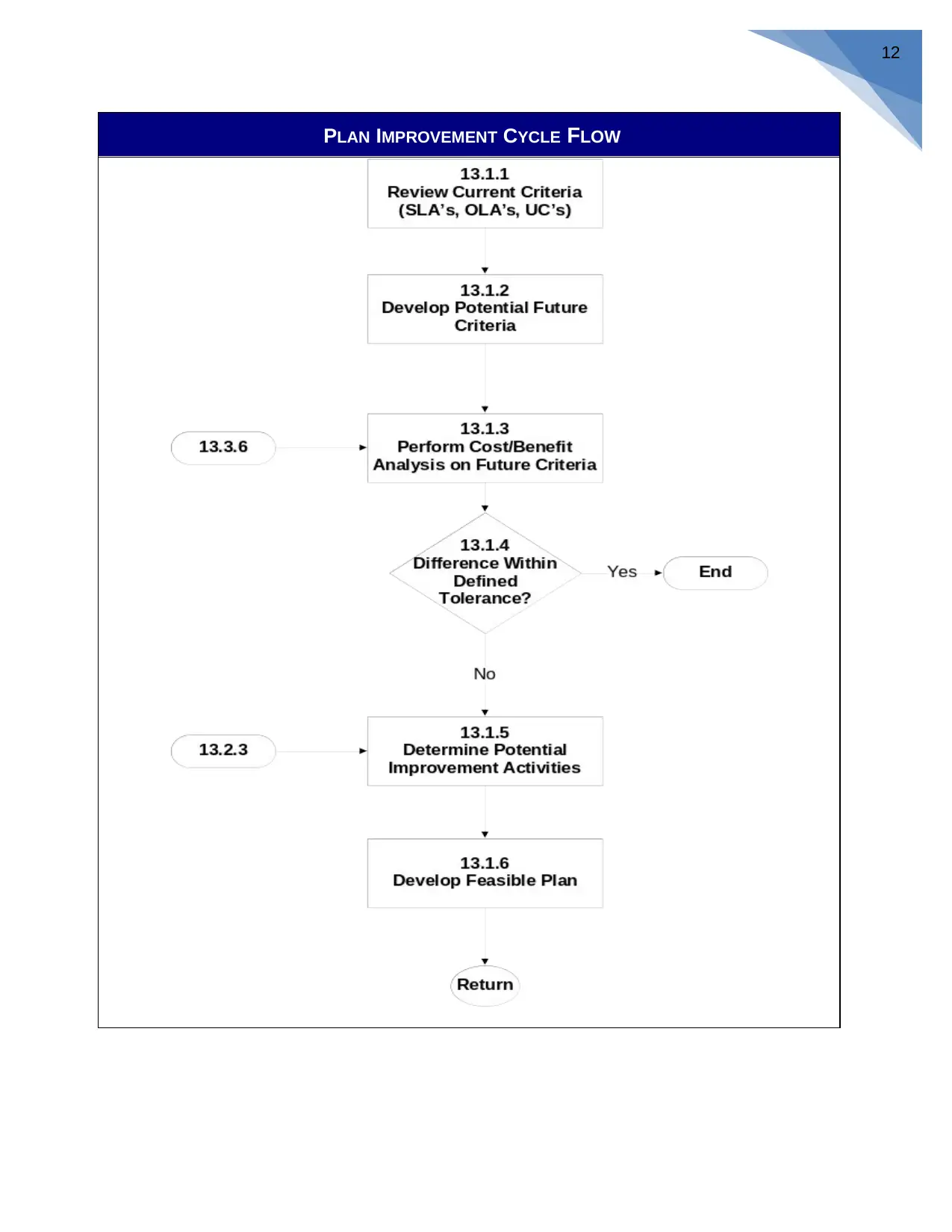
PLAN IMPROVEMENT CYCLE FLOW
12
12
Paraphrase This Document
Need a fresh take? Get an instant paraphrase of this document with our AI Paraphraser
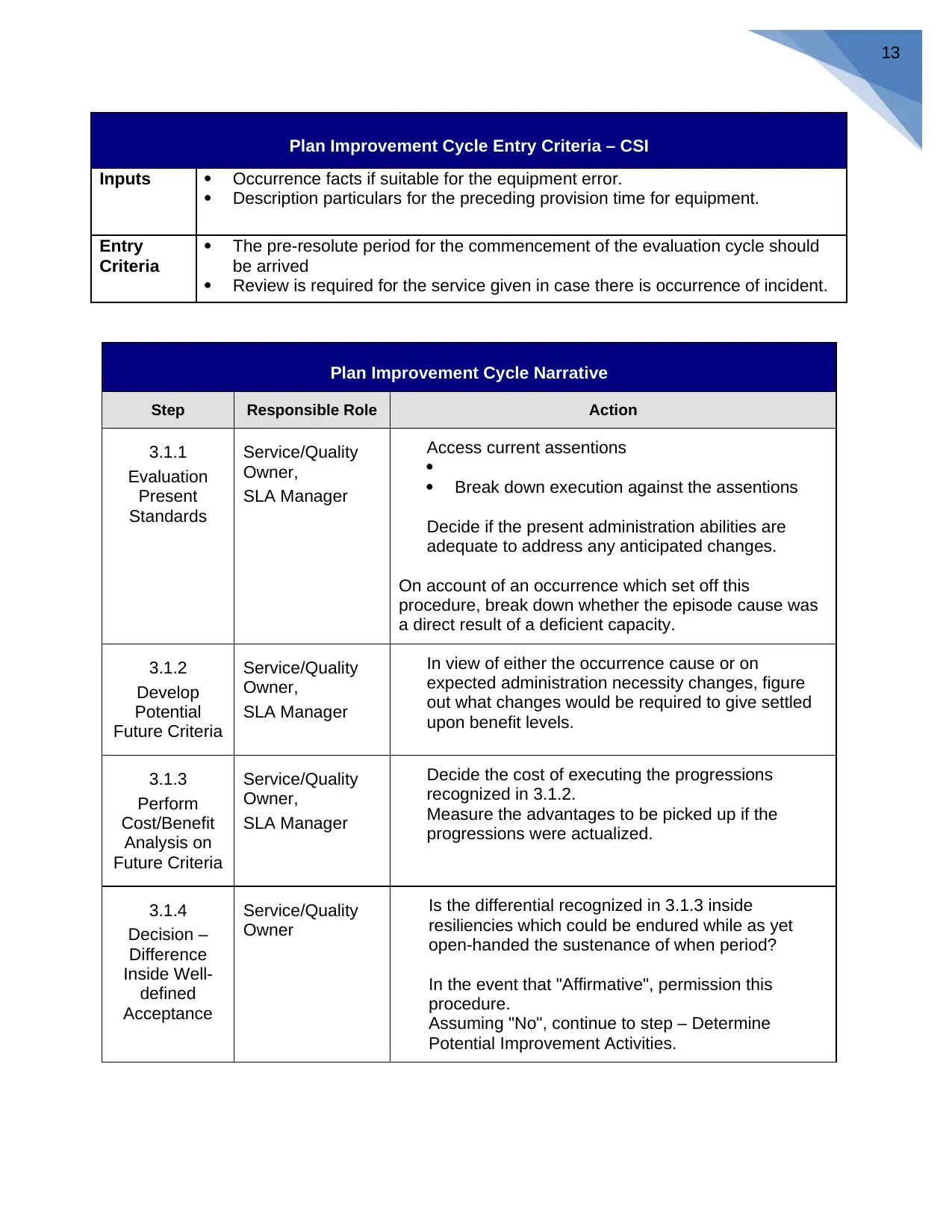
Plan Improvement Cycle Entry Criteria – CSI
Inputs Occurrence facts if suitable for the equipment error.
Description particulars for the preceding provision time for equipment.
Entry
Criteria
The pre-resolute period for the commencement of the evaluation cycle should
be arrived
Review is required for the service given in case there is occurrence of incident.
Plan Improvement Cycle Narrative
Step Responsible Role Action
3.1.1
Evaluation
Present
Standards
Service/Quality
Owner,
SLA Manager
Access current assentions
Break down execution against the assentions
Decide if the present administration abilities are
adequate to address any anticipated changes.
On account of an occurrence which set off this
procedure, break down whether the episode cause was
a direct result of a deficient capacity.
3.1.2
Develop
Potential
Future Criteria
Service/Quality
Owner,
SLA Manager
In view of either the occurrence cause or on
expected administration necessity changes, figure
out what changes would be required to give settled
upon benefit levels.
3.1.3
Perform
Cost/Benefit
Analysis on
Future Criteria
Service/Quality
Owner,
SLA Manager
Decide the cost of executing the progressions
recognized in 3.1.2.
Measure the advantages to be picked up if the
progressions were actualized.
3.1.4
Decision –
Difference
Inside Well-
defined
Acceptance
Service/Quality
Owner
Is the differential recognized in 3.1.3 inside
resiliencies which could be endured while as yet
open-handed the sustenance of when period?
In the event that "Affirmative", permission this
procedure.
Assuming "No", continue to step – Determine
Potential Improvement Activities.
13
Inputs Occurrence facts if suitable for the equipment error.
Description particulars for the preceding provision time for equipment.
Entry
Criteria
The pre-resolute period for the commencement of the evaluation cycle should
be arrived
Review is required for the service given in case there is occurrence of incident.
Plan Improvement Cycle Narrative
Step Responsible Role Action
3.1.1
Evaluation
Present
Standards
Service/Quality
Owner,
SLA Manager
Access current assentions
Break down execution against the assentions
Decide if the present administration abilities are
adequate to address any anticipated changes.
On account of an occurrence which set off this
procedure, break down whether the episode cause was
a direct result of a deficient capacity.
3.1.2
Develop
Potential
Future Criteria
Service/Quality
Owner,
SLA Manager
In view of either the occurrence cause or on
expected administration necessity changes, figure
out what changes would be required to give settled
upon benefit levels.
3.1.3
Perform
Cost/Benefit
Analysis on
Future Criteria
Service/Quality
Owner,
SLA Manager
Decide the cost of executing the progressions
recognized in 3.1.2.
Measure the advantages to be picked up if the
progressions were actualized.
3.1.4
Decision –
Difference
Inside Well-
defined
Acceptance
Service/Quality
Owner
Is the differential recognized in 3.1.3 inside
resiliencies which could be endured while as yet
open-handed the sustenance of when period?
In the event that "Affirmative", permission this
procedure.
Assuming "No", continue to step – Determine
Potential Improvement Activities.
13
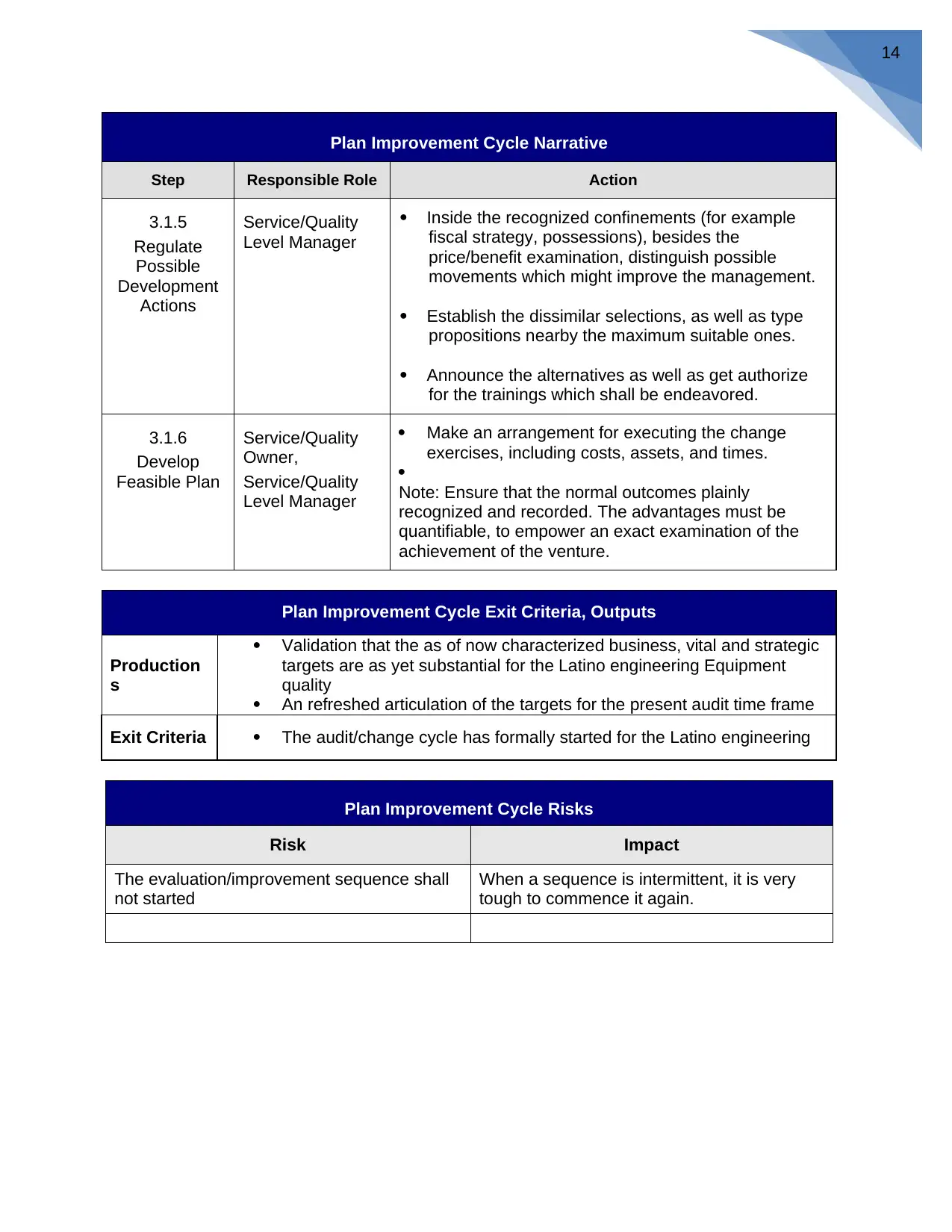
Plan Improvement Cycle Narrative
Step Responsible Role Action
3.1.5
Regulate
Possible
Development
Actions
Service/Quality
Level Manager
Inside the recognized confinements (for example
fiscal strategy, possessions), besides the
price/benefit examination, distinguish possible
movements which might improve the management.
Establish the dissimilar selections, as well as type
propositions nearby the maximum suitable ones.
Announce the alternatives as well as get authorize
for the trainings which shall be endeavored.
3.1.6
Develop
Feasible Plan
Service/Quality
Owner,
Service/Quality
Level Manager
Make an arrangement for executing the change
exercises, including costs, assets, and times.
Note: Ensure that the normal outcomes plainly
recognized and recorded. The advantages must be
quantifiable, to empower an exact examination of the
achievement of the venture.
Plan Improvement Cycle Exit Criteria, Outputs
Production
s
Validation that the as of now characterized business, vital and strategic
targets are as yet substantial for the Latino engineering Equipment
quality
An refreshed articulation of the targets for the present audit time frame
Exit Criteria The audit/change cycle has formally started for the Latino engineering
Plan Improvement Cycle Risks
Risk Impact
The evaluation/improvement sequence shall
not started
When a sequence is intermittent, it is very
tough to commence it again.
14
Step Responsible Role Action
3.1.5
Regulate
Possible
Development
Actions
Service/Quality
Level Manager
Inside the recognized confinements (for example
fiscal strategy, possessions), besides the
price/benefit examination, distinguish possible
movements which might improve the management.
Establish the dissimilar selections, as well as type
propositions nearby the maximum suitable ones.
Announce the alternatives as well as get authorize
for the trainings which shall be endeavored.
3.1.6
Develop
Feasible Plan
Service/Quality
Owner,
Service/Quality
Level Manager
Make an arrangement for executing the change
exercises, including costs, assets, and times.
Note: Ensure that the normal outcomes plainly
recognized and recorded. The advantages must be
quantifiable, to empower an exact examination of the
achievement of the venture.
Plan Improvement Cycle Exit Criteria, Outputs
Production
s
Validation that the as of now characterized business, vital and strategic
targets are as yet substantial for the Latino engineering Equipment
quality
An refreshed articulation of the targets for the present audit time frame
Exit Criteria The audit/change cycle has formally started for the Latino engineering
Plan Improvement Cycle Risks
Risk Impact
The evaluation/improvement sequence shall
not started
When a sequence is intermittent, it is very
tough to commence it again.
14
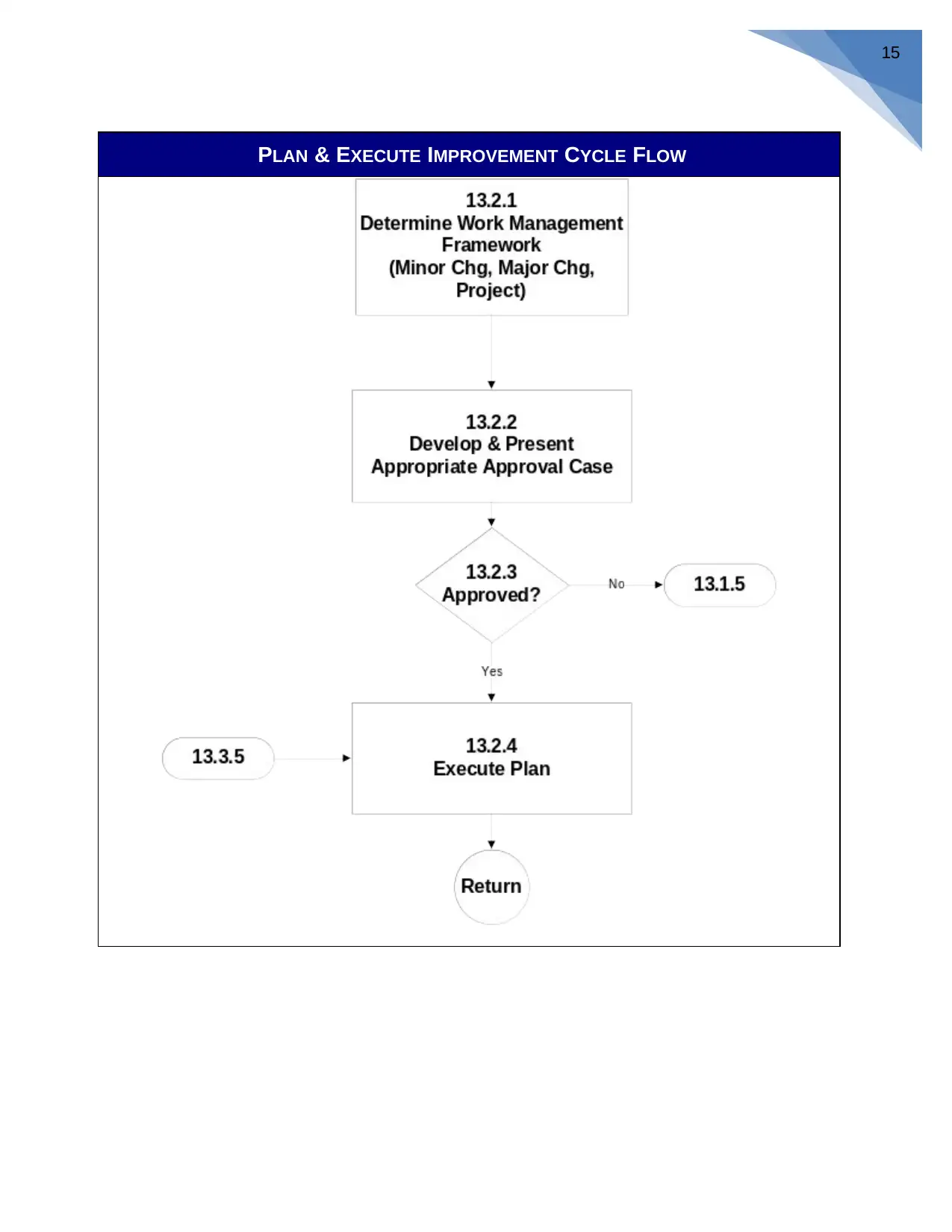
PLAN & EXECUTE IMPROVEMENT CYCLE FLOW
15
15
Secure Best Marks with AI Grader
Need help grading? Try our AI Grader for instant feedback on your assignments.
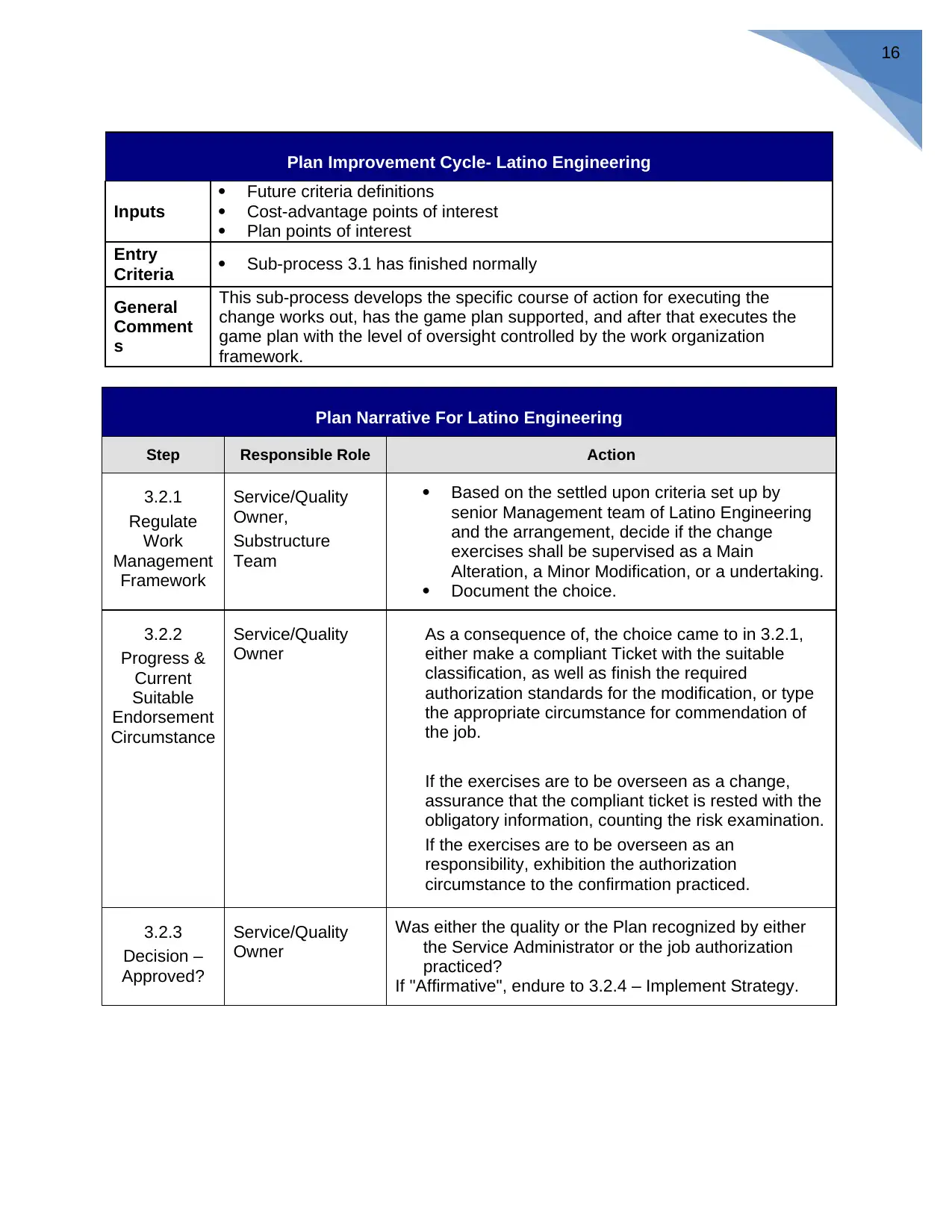
Plan Improvement Cycle- Latino Engineering
Inputs
Future criteria definitions
Cost-advantage points of interest
Plan points of interest
Entry
Criteria Sub-process 3.1 has finished normally
General
Comment
s
This sub-process develops the specific course of action for executing the
change works out, has the game plan supported, and after that executes the
game plan with the level of oversight controlled by the work organization
framework.
Plan Narrative For Latino Engineering
Step Responsible Role Action
3.2.1
Regulate
Work
Management
Framework
Service/Quality
Owner,
Substructure
Team
Based on the settled upon criteria set up by
senior Management team of Latino Engineering
and the arrangement, decide if the change
exercises shall be supervised as a Main
Alteration, a Minor Modification, or a undertaking.
Document the choice.
3.2.2
Progress &
Current
Suitable
Endorsement
Circumstance
Service/Quality
Owner
As a consequence of, the choice came to in 3.2.1,
either make a compliant Ticket with the suitable
classification, as well as finish the required
authorization standards for the modification, or type
the appropriate circumstance for commendation of
the job.
If the exercises are to be overseen as a change,
assurance that the compliant ticket is rested with the
obligatory information, counting the risk examination.
If the exercises are to be overseen as an
responsibility, exhibition the authorization
circumstance to the confirmation practiced.
3.2.3
Decision –
Approved?
Service/Quality
Owner
Was either the quality or the Plan recognized by either
the Service Administrator or the job authorization
practiced?
If "Affirmative", endure to 3.2.4 – Implement Strategy.
16
Inputs
Future criteria definitions
Cost-advantage points of interest
Plan points of interest
Entry
Criteria Sub-process 3.1 has finished normally
General
Comment
s
This sub-process develops the specific course of action for executing the
change works out, has the game plan supported, and after that executes the
game plan with the level of oversight controlled by the work organization
framework.
Plan Narrative For Latino Engineering
Step Responsible Role Action
3.2.1
Regulate
Work
Management
Framework
Service/Quality
Owner,
Substructure
Team
Based on the settled upon criteria set up by
senior Management team of Latino Engineering
and the arrangement, decide if the change
exercises shall be supervised as a Main
Alteration, a Minor Modification, or a undertaking.
Document the choice.
3.2.2
Progress &
Current
Suitable
Endorsement
Circumstance
Service/Quality
Owner
As a consequence of, the choice came to in 3.2.1,
either make a compliant Ticket with the suitable
classification, as well as finish the required
authorization standards for the modification, or type
the appropriate circumstance for commendation of
the job.
If the exercises are to be overseen as a change,
assurance that the compliant ticket is rested with the
obligatory information, counting the risk examination.
If the exercises are to be overseen as an
responsibility, exhibition the authorization
circumstance to the confirmation practiced.
3.2.3
Decision –
Approved?
Service/Quality
Owner
Was either the quality or the Plan recognized by either
the Service Administrator or the job authorization
practiced?
If "Affirmative", endure to 3.2.4 – Implement Strategy.
16
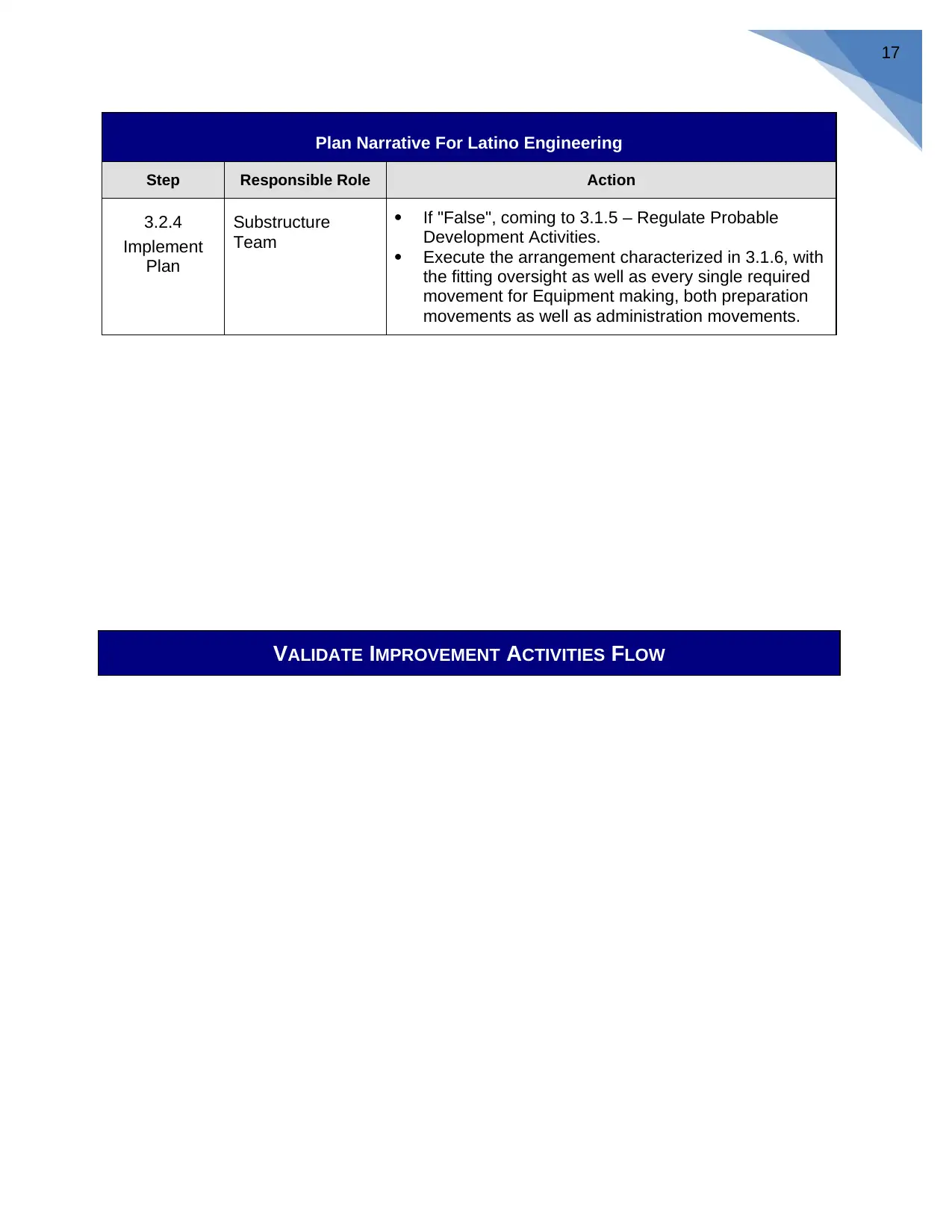
Plan Narrative For Latino Engineering
Step Responsible Role Action
3.2.4
Implement
Plan
Substructure
Team
If "False", coming to 3.1.5 – Regulate Probable
Development Activities.
Execute the arrangement characterized in 3.1.6, with
the fitting oversight as well as every single required
movement for Equipment making, both preparation
movements as well as administration movements.
VALIDATE IMPROVEMENT ACTIVITIES FLOW
17
Step Responsible Role Action
3.2.4
Implement
Plan
Substructure
Team
If "False", coming to 3.1.5 – Regulate Probable
Development Activities.
Execute the arrangement characterized in 3.1.6, with
the fitting oversight as well as every single required
movement for Equipment making, both preparation
movements as well as administration movements.
VALIDATE IMPROVEMENT ACTIVITIES FLOW
17
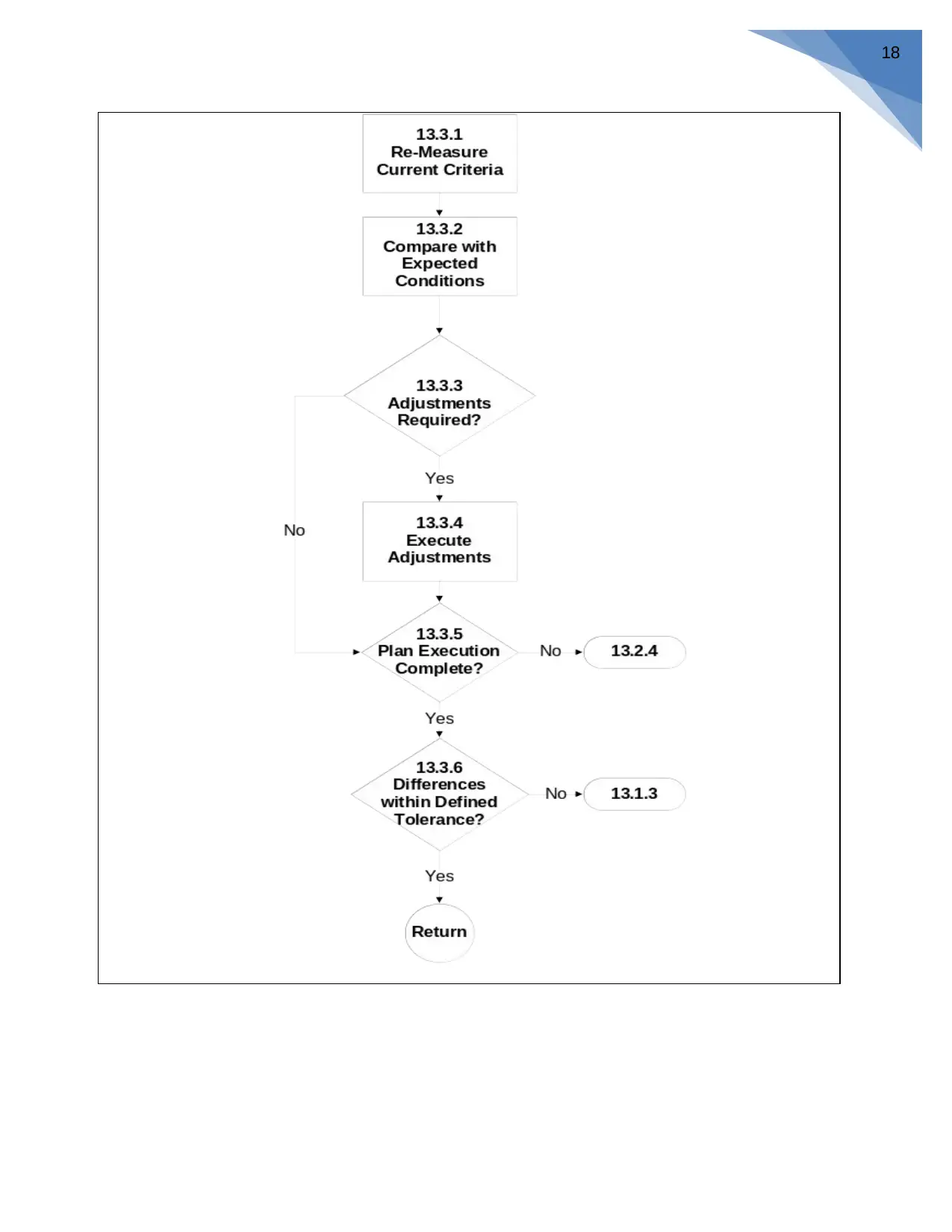
18
Paraphrase This Document
Need a fresh take? Get an instant paraphrase of this document with our AI Paraphraser
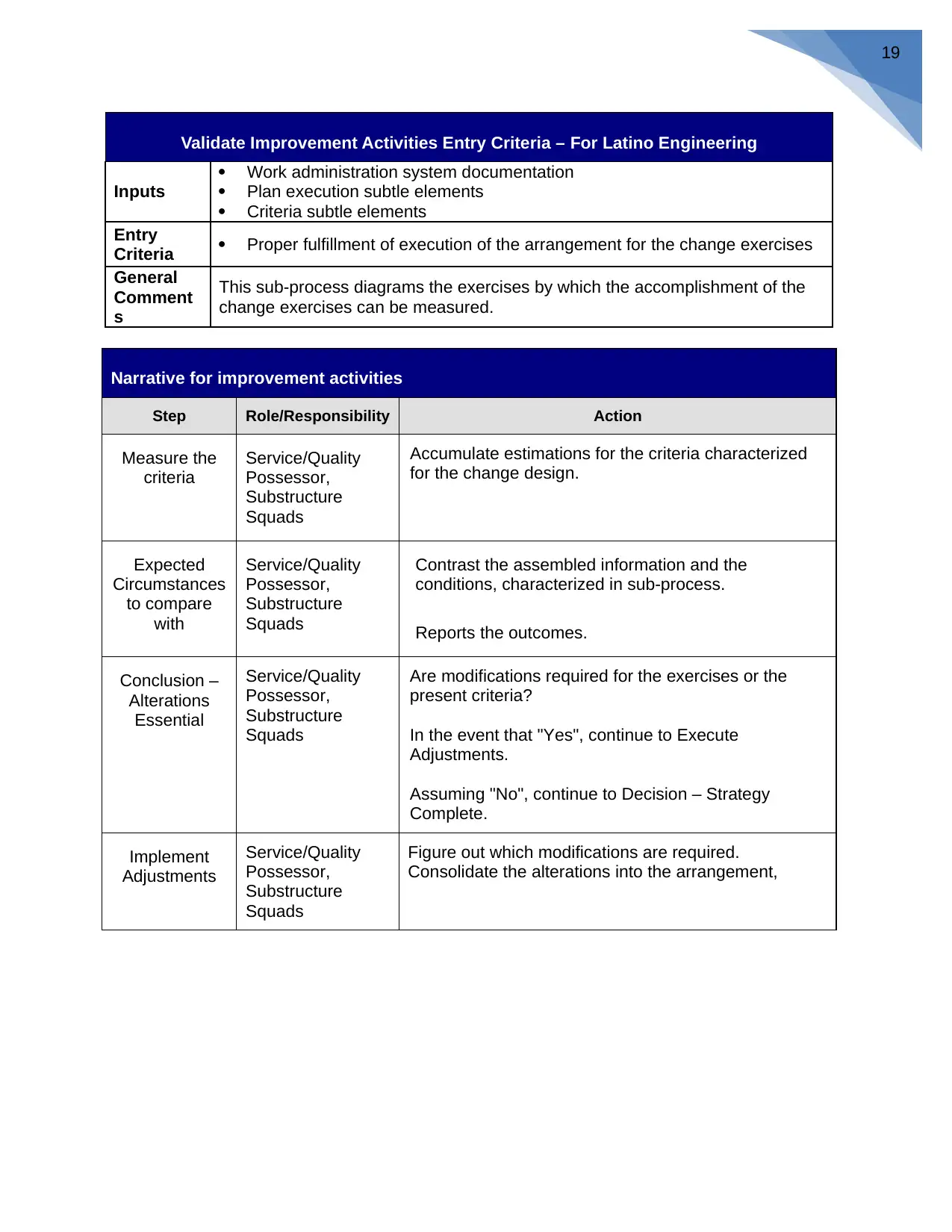
Validate Improvement Activities Entry Criteria – For Latino Engineering
Inputs
Work administration system documentation
Plan execution subtle elements
Criteria subtle elements
Entry
Criteria Proper fulfillment of execution of the arrangement for the change exercises
General
Comment
s
This sub-process diagrams the exercises by which the accomplishment of the
change exercises can be measured.
Narrative for improvement activities
Step Role/Responsibility Action
Measure the
criteria
Service/Quality
Possessor,
Substructure
Squads
Accumulate estimations for the criteria characterized
for the change design.
Expected
Circumstances
to compare
with
Service/Quality
Possessor,
Substructure
Squads
Contrast the assembled information and the
conditions, characterized in sub-process.
Reports the outcomes.
Conclusion –
Alterations
Essential
Service/Quality
Possessor,
Substructure
Squads
Are modifications required for the exercises or the
present criteria?
In the event that "Yes", continue to Execute
Adjustments.
Assuming "No", continue to Decision – Strategy
Complete.
Implement
Adjustments
Service/Quality
Possessor,
Substructure
Squads
Figure out which modifications are required.
Consolidate the alterations into the arrangement,
19
Inputs
Work administration system documentation
Plan execution subtle elements
Criteria subtle elements
Entry
Criteria Proper fulfillment of execution of the arrangement for the change exercises
General
Comment
s
This sub-process diagrams the exercises by which the accomplishment of the
change exercises can be measured.
Narrative for improvement activities
Step Role/Responsibility Action
Measure the
criteria
Service/Quality
Possessor,
Substructure
Squads
Accumulate estimations for the criteria characterized
for the change design.
Expected
Circumstances
to compare
with
Service/Quality
Possessor,
Substructure
Squads
Contrast the assembled information and the
conditions, characterized in sub-process.
Reports the outcomes.
Conclusion –
Alterations
Essential
Service/Quality
Possessor,
Substructure
Squads
Are modifications required for the exercises or the
present criteria?
In the event that "Yes", continue to Execute
Adjustments.
Assuming "No", continue to Decision – Strategy
Complete.
Implement
Adjustments
Service/Quality
Possessor,
Substructure
Squads
Figure out which modifications are required.
Consolidate the alterations into the arrangement,
19
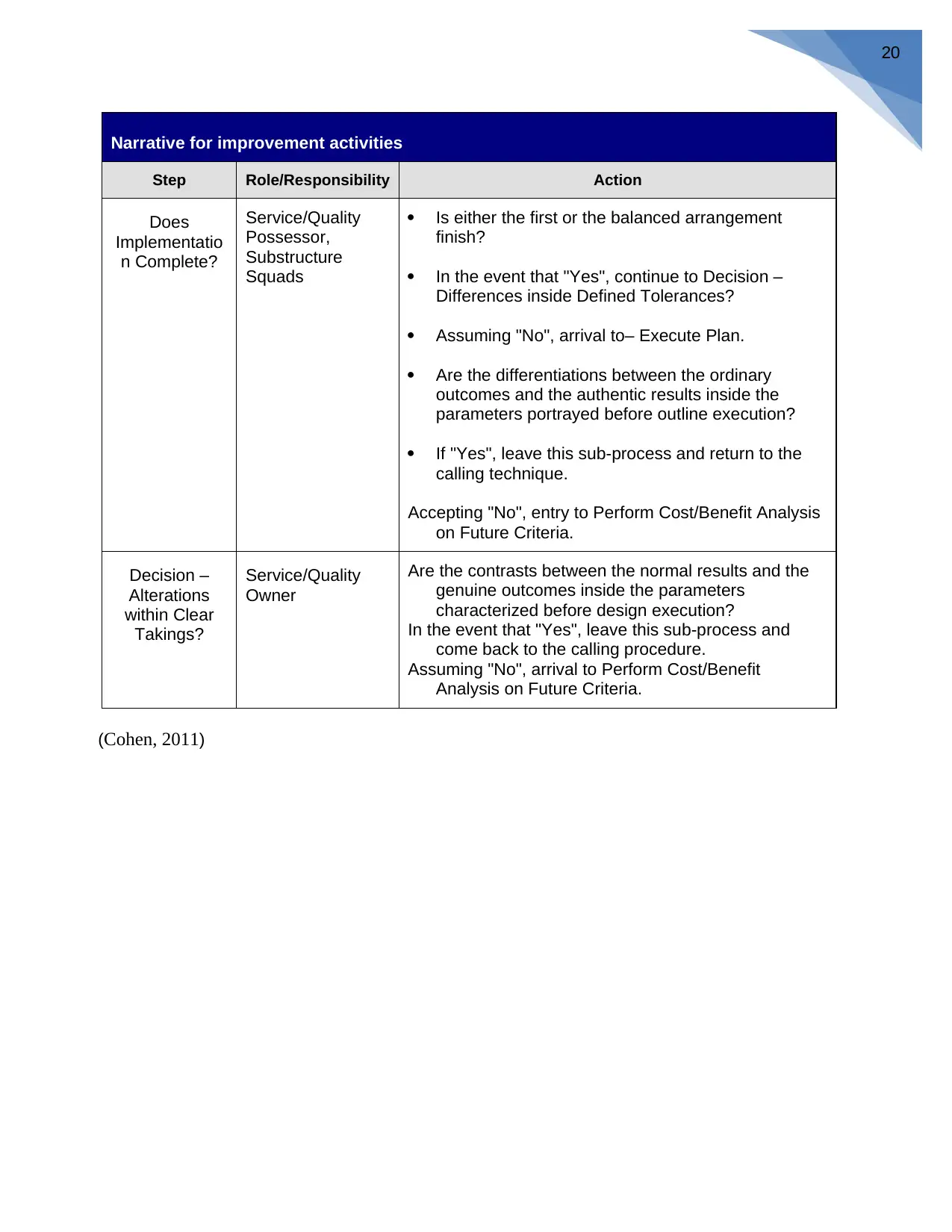
Narrative for improvement activities
Step Role/Responsibility Action
Does
Implementatio
n Complete?
Service/Quality
Possessor,
Substructure
Squads
Is either the first or the balanced arrangement
finish?
In the event that "Yes", continue to Decision –
Differences inside Defined Tolerances?
Assuming "No", arrival to– Execute Plan.
Are the differentiations between the ordinary
outcomes and the authentic results inside the
parameters portrayed before outline execution?
If "Yes", leave this sub-process and return to the
calling technique.
Accepting "No", entry to Perform Cost/Benefit Analysis
on Future Criteria.
Decision –
Alterations
within Clear
Takings?
Service/Quality
Owner
Are the contrasts between the normal results and the
genuine outcomes inside the parameters
characterized before design execution?
In the event that "Yes", leave this sub-process and
come back to the calling procedure.
Assuming "No", arrival to Perform Cost/Benefit
Analysis on Future Criteria.
(Cohen, 2011)
20
Step Role/Responsibility Action
Does
Implementatio
n Complete?
Service/Quality
Possessor,
Substructure
Squads
Is either the first or the balanced arrangement
finish?
In the event that "Yes", continue to Decision –
Differences inside Defined Tolerances?
Assuming "No", arrival to– Execute Plan.
Are the differentiations between the ordinary
outcomes and the authentic results inside the
parameters portrayed before outline execution?
If "Yes", leave this sub-process and return to the
calling technique.
Accepting "No", entry to Perform Cost/Benefit Analysis
on Future Criteria.
Decision –
Alterations
within Clear
Takings?
Service/Quality
Owner
Are the contrasts between the normal results and the
genuine outcomes inside the parameters
characterized before design execution?
In the event that "Yes", leave this sub-process and
come back to the calling procedure.
Assuming "No", arrival to Perform Cost/Benefit
Analysis on Future Criteria.
(Cohen, 2011)
20
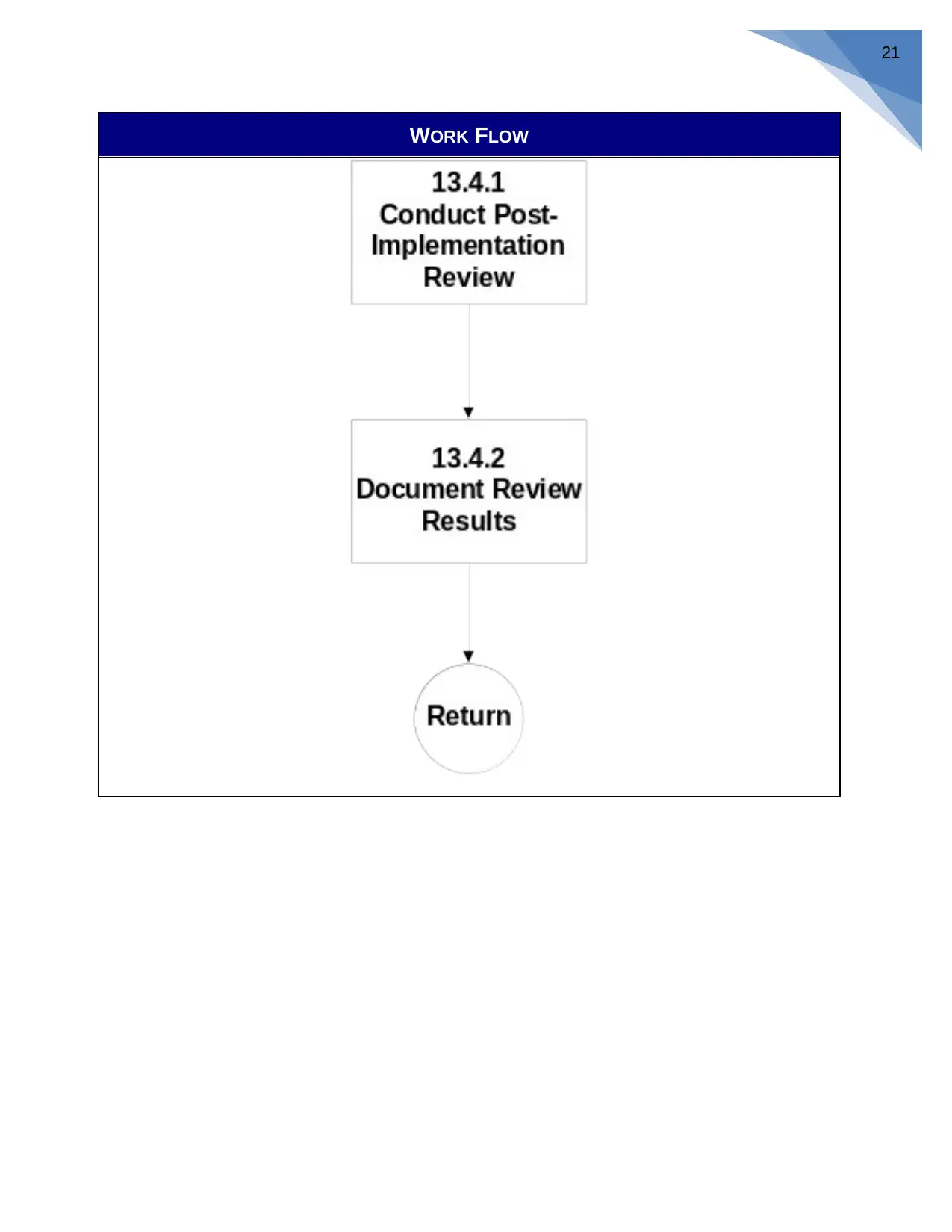
WORK FLOW
21
21
Secure Best Marks with AI Grader
Need help grading? Try our AI Grader for instant feedback on your assignments.
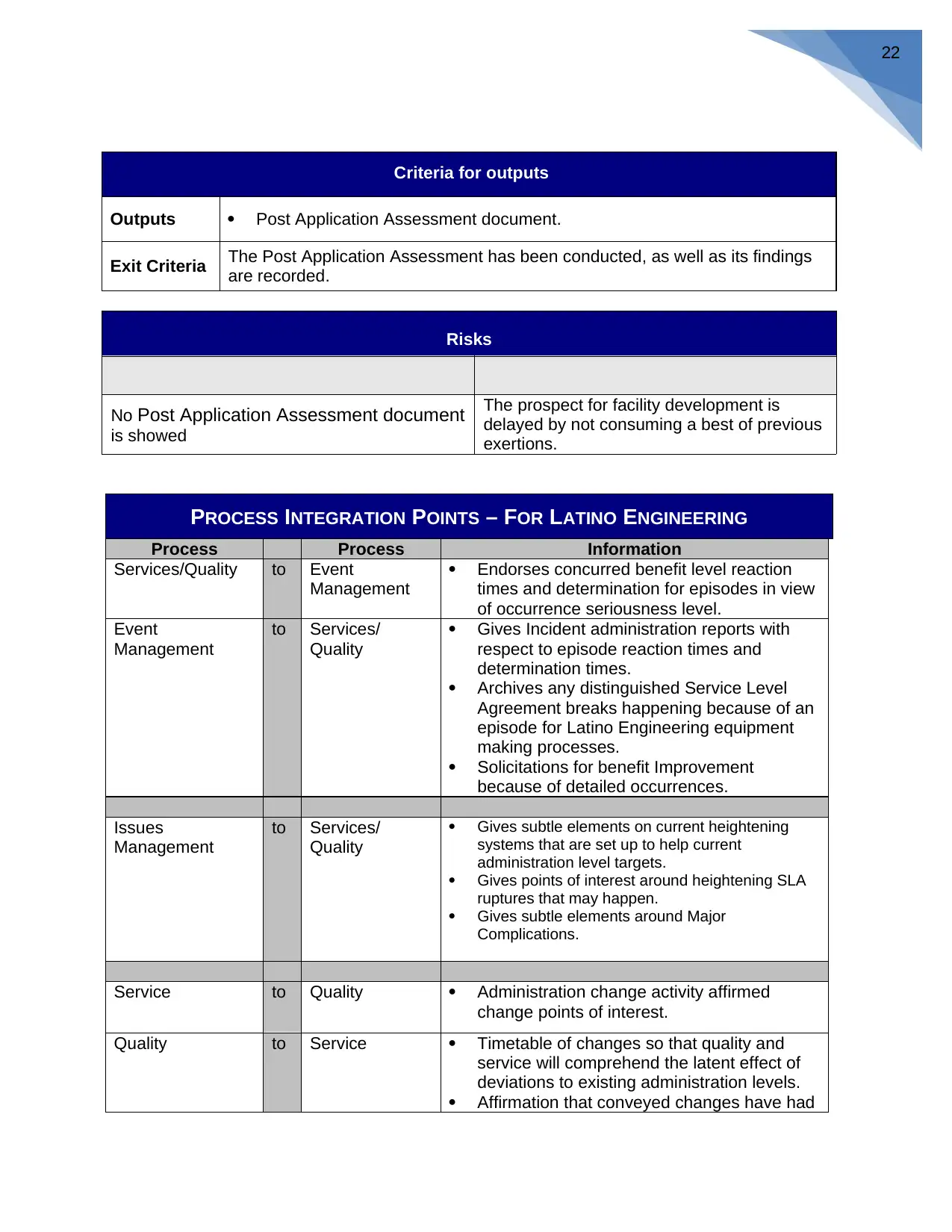
Criteria for outputs
Outputs Post Application Assessment document.
Exit Criteria The Post Application Assessment has been conducted, as well as its findings
are recorded.
Risks
No Post Application Assessment document
is showed
The prospect for facility development is
delayed by not consuming a best of previous
exertions.
PROCESS INTEGRATION POINTS – FOR LATINO ENGINEERING
Process Process Information
Services/Quality to Event
Management
Endorses concurred benefit level reaction
times and determination for episodes in view
of occurrence seriousness level.
Event
Management
to Services/
Quality
Gives Incident administration reports with
respect to episode reaction times and
determination times.
Archives any distinguished Service Level
Agreement breaks happening because of an
episode for Latino Engineering equipment
making processes.
Solicitations for benefit Improvement
because of detailed occurrences.
Issues
Management
to Services/
Quality
Gives subtle elements on current heightening
systems that are set up to help current
administration level targets.
Gives points of interest around heightening SLA
ruptures that may happen.
Gives subtle elements around Major
Complications.
Service to Quality Administration change activity affirmed
change points of interest.
Quality to Service Timetable of changes so that quality and
service will comprehend the latent effect of
deviations to existing administration levels.
Affirmation that conveyed changes have had
22
Outputs Post Application Assessment document.
Exit Criteria The Post Application Assessment has been conducted, as well as its findings
are recorded.
Risks
No Post Application Assessment document
is showed
The prospect for facility development is
delayed by not consuming a best of previous
exertions.
PROCESS INTEGRATION POINTS – FOR LATINO ENGINEERING
Process Process Information
Services/Quality to Event
Management
Endorses concurred benefit level reaction
times and determination for episodes in view
of occurrence seriousness level.
Event
Management
to Services/
Quality
Gives Incident administration reports with
respect to episode reaction times and
determination times.
Archives any distinguished Service Level
Agreement breaks happening because of an
episode for Latino Engineering equipment
making processes.
Solicitations for benefit Improvement
because of detailed occurrences.
Issues
Management
to Services/
Quality
Gives subtle elements on current heightening
systems that are set up to help current
administration level targets.
Gives points of interest around heightening SLA
ruptures that may happen.
Gives subtle elements around Major
Complications.
Service to Quality Administration change activity affirmed
change points of interest.
Quality to Service Timetable of changes so that quality and
service will comprehend the latent effect of
deviations to existing administration levels.
Affirmation that conveyed changes have had
22
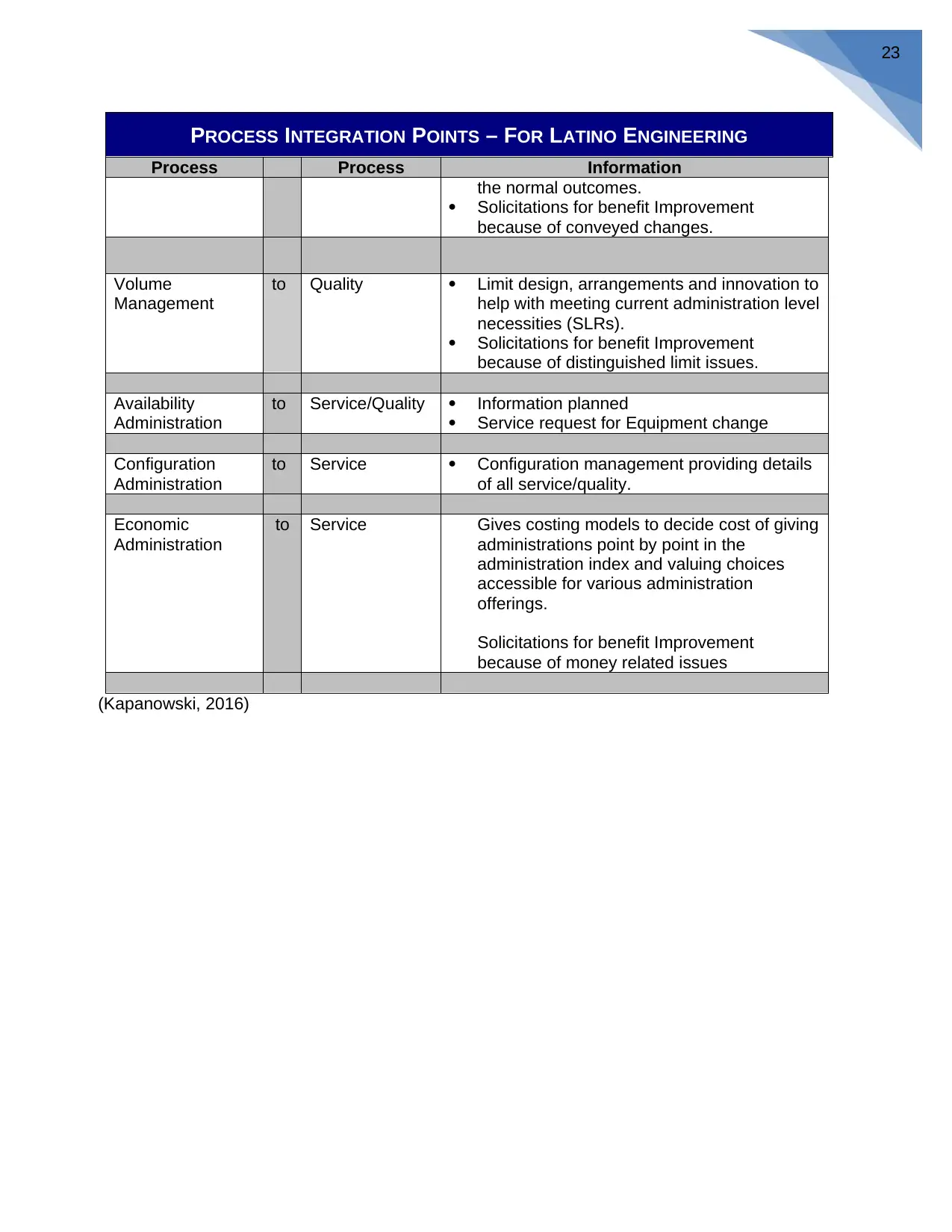
PROCESS INTEGRATION POINTS – FOR LATINO ENGINEERING
Process Process Information
the normal outcomes.
Solicitations for benefit Improvement
because of conveyed changes.
Volume
Management
to Quality Limit design, arrangements and innovation to
help with meeting current administration level
necessities (SLRs).
Solicitations for benefit Improvement
because of distinguished limit issues.
Availability
Administration
to Service/Quality Information planned
Service request for Equipment change
Configuration
Administration
to Service Configuration management providing details
of all service/quality.
Economic
Administration
to Service Gives costing models to decide cost of giving
administrations point by point in the
administration index and valuing choices
accessible for various administration
offerings.
Solicitations for benefit Improvement
because of money related issues
(Kapanowski, 2016)
23
Process Process Information
the normal outcomes.
Solicitations for benefit Improvement
because of conveyed changes.
Volume
Management
to Quality Limit design, arrangements and innovation to
help with meeting current administration level
necessities (SLRs).
Solicitations for benefit Improvement
because of distinguished limit issues.
Availability
Administration
to Service/Quality Information planned
Service request for Equipment change
Configuration
Administration
to Service Configuration management providing details
of all service/quality.
Economic
Administration
to Service Gives costing models to decide cost of giving
administrations point by point in the
administration index and valuing choices
accessible for various administration
offerings.
Solicitations for benefit Improvement
because of money related issues
(Kapanowski, 2016)
23
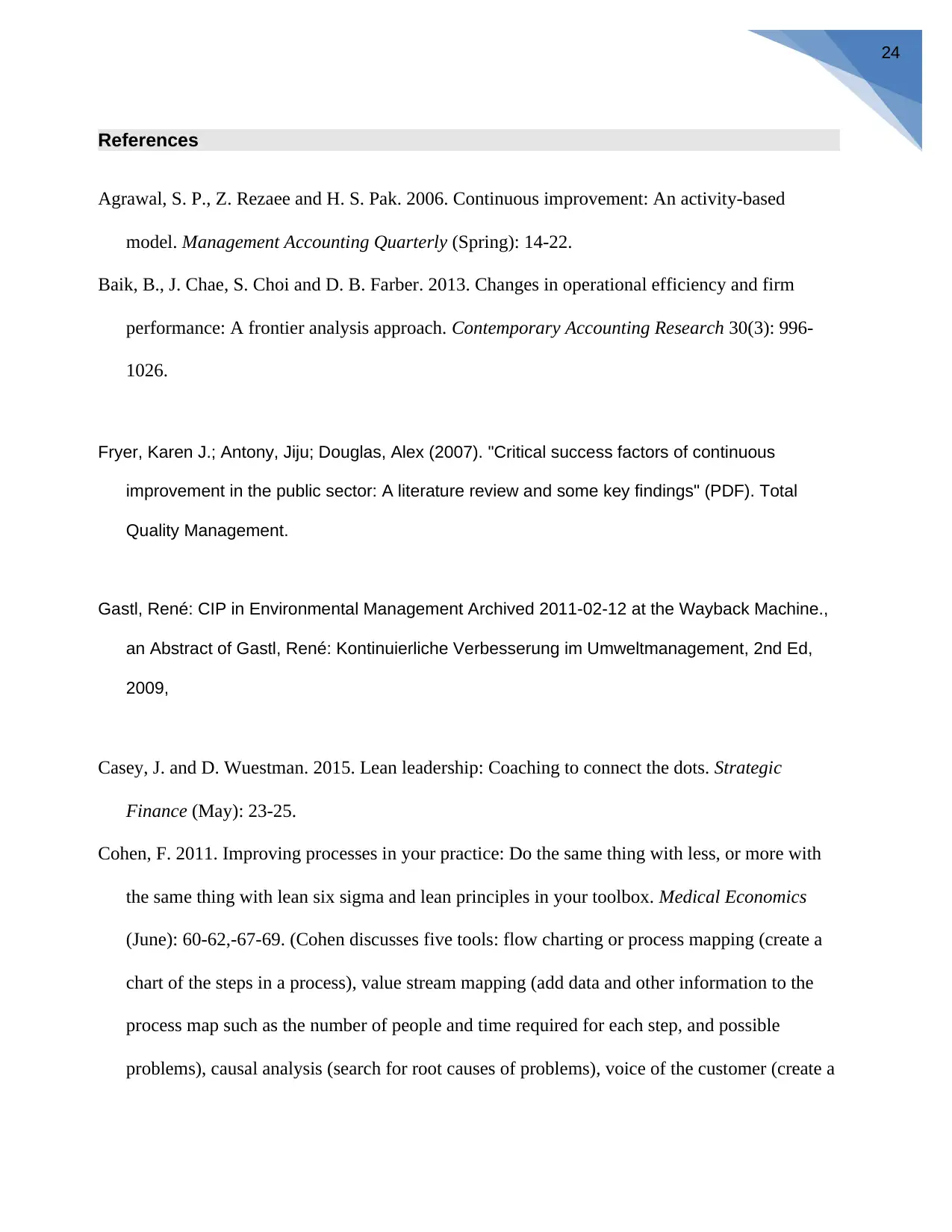
References
Agrawal, S. P., Z. Rezaee and H. S. Pak. 2006. Continuous improvement: An activity-based
model. Management Accounting Quarterly (Spring): 14-22.
Baik, B., J. Chae, S. Choi and D. B. Farber. 2013. Changes in operational efficiency and firm
performance: A frontier analysis approach. Contemporary Accounting Research 30(3): 996-
1026.
Fryer, Karen J.; Antony, Jiju; Douglas, Alex (2007). "Critical success factors of continuous
improvement in the public sector: A literature review and some key findings" (PDF). Total
Quality Management.
Gastl, René: CIP in Environmental Management Archived 2011-02-12 at the Wayback Machine.,
an Abstract of Gastl, René: Kontinuierliche Verbesserung im Umweltmanagement, 2nd Ed,
2009,
Casey, J. and D. Wuestman. 2015. Lean leadership: Coaching to connect the dots. Strategic
Finance (May): 23-25.
Cohen, F. 2011. Improving processes in your practice: Do the same thing with less, or more with
the same thing with lean six sigma and lean principles in your toolbox. Medical Economics
(June): 60-62,-67-69. (Cohen discusses five tools: flow charting or process mapping (create a
chart of the steps in a process), value stream mapping (add data and other information to the
process map such as the number of people and time required for each step, and possible
problems), causal analysis (search for root causes of problems), voice of the customer (create a
24
Agrawal, S. P., Z. Rezaee and H. S. Pak. 2006. Continuous improvement: An activity-based
model. Management Accounting Quarterly (Spring): 14-22.
Baik, B., J. Chae, S. Choi and D. B. Farber. 2013. Changes in operational efficiency and firm
performance: A frontier analysis approach. Contemporary Accounting Research 30(3): 996-
1026.
Fryer, Karen J.; Antony, Jiju; Douglas, Alex (2007). "Critical success factors of continuous
improvement in the public sector: A literature review and some key findings" (PDF). Total
Quality Management.
Gastl, René: CIP in Environmental Management Archived 2011-02-12 at the Wayback Machine.,
an Abstract of Gastl, René: Kontinuierliche Verbesserung im Umweltmanagement, 2nd Ed,
2009,
Casey, J. and D. Wuestman. 2015. Lean leadership: Coaching to connect the dots. Strategic
Finance (May): 23-25.
Cohen, F. 2011. Improving processes in your practice: Do the same thing with less, or more with
the same thing with lean six sigma and lean principles in your toolbox. Medical Economics
(June): 60-62,-67-69. (Cohen discusses five tools: flow charting or process mapping (create a
chart of the steps in a process), value stream mapping (add data and other information to the
process map such as the number of people and time required for each step, and possible
problems), causal analysis (search for root causes of problems), voice of the customer (create a
24
Paraphrase This Document
Need a fresh take? Get an instant paraphrase of this document with our AI Paraphraser
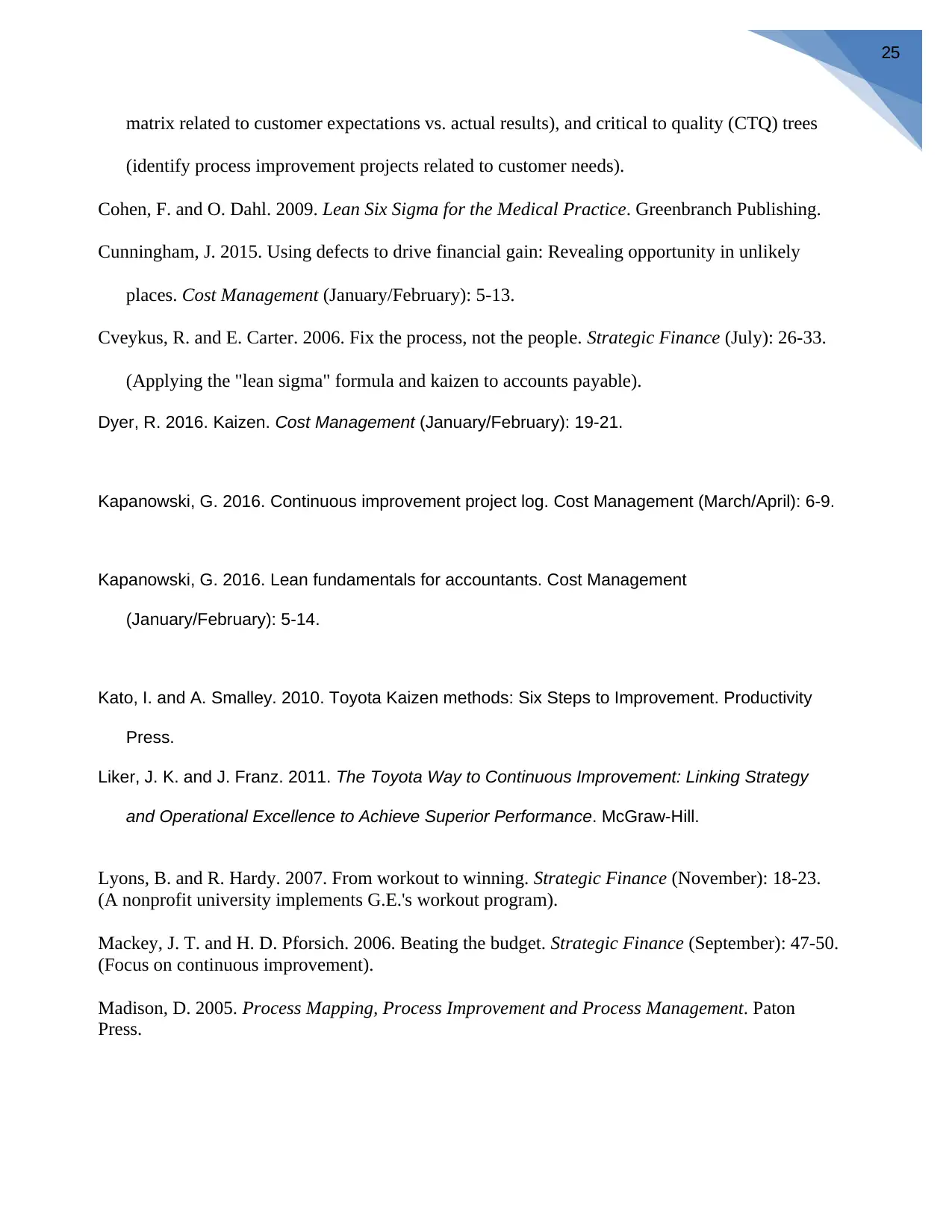
matrix related to customer expectations vs. actual results), and critical to quality (CTQ) trees
(identify process improvement projects related to customer needs).
Cohen, F. and O. Dahl. 2009. Lean Six Sigma for the Medical Practice. Greenbranch Publishing.
Cunningham, J. 2015. Using defects to drive financial gain: Revealing opportunity in unlikely
places. Cost Management (January/February): 5-13.
Cveykus, R. and E. Carter. 2006. Fix the process, not the people. Strategic Finance (July): 26-33.
(Applying the "lean sigma" formula and kaizen to accounts payable).
Dyer, R. 2016. Kaizen. Cost Management (January/February): 19-21.
Kapanowski, G. 2016. Continuous improvement project log. Cost Management (March/April): 6-9.
Kapanowski, G. 2016. Lean fundamentals for accountants. Cost Management
(January/February): 5-14.
Kato, I. and A. Smalley. 2010. Toyota Kaizen methods: Six Steps to Improvement. Productivity
Press.
Liker, J. K. and J. Franz. 2011. The Toyota Way to Continuous Improvement: Linking Strategy
and Operational Excellence to Achieve Superior Performance. McGraw-Hill.
Lyons, B. and R. Hardy. 2007. From workout to winning. Strategic Finance (November): 18-23.
(A nonprofit university implements G.E.'s workout program).
Mackey, J. T. and H. D. Pforsich. 2006. Beating the budget. Strategic Finance (September): 47-50.
(Focus on continuous improvement).
Madison, D. 2005. Process Mapping, Process Improvement and Process Management. Paton
Press.
25
(identify process improvement projects related to customer needs).
Cohen, F. and O. Dahl. 2009. Lean Six Sigma for the Medical Practice. Greenbranch Publishing.
Cunningham, J. 2015. Using defects to drive financial gain: Revealing opportunity in unlikely
places. Cost Management (January/February): 5-13.
Cveykus, R. and E. Carter. 2006. Fix the process, not the people. Strategic Finance (July): 26-33.
(Applying the "lean sigma" formula and kaizen to accounts payable).
Dyer, R. 2016. Kaizen. Cost Management (January/February): 19-21.
Kapanowski, G. 2016. Continuous improvement project log. Cost Management (March/April): 6-9.
Kapanowski, G. 2016. Lean fundamentals for accountants. Cost Management
(January/February): 5-14.
Kato, I. and A. Smalley. 2010. Toyota Kaizen methods: Six Steps to Improvement. Productivity
Press.
Liker, J. K. and J. Franz. 2011. The Toyota Way to Continuous Improvement: Linking Strategy
and Operational Excellence to Achieve Superior Performance. McGraw-Hill.
Lyons, B. and R. Hardy. 2007. From workout to winning. Strategic Finance (November): 18-23.
(A nonprofit university implements G.E.'s workout program).
Mackey, J. T. and H. D. Pforsich. 2006. Beating the budget. Strategic Finance (September): 47-50.
(Focus on continuous improvement).
Madison, D. 2005. Process Mapping, Process Improvement and Process Management. Paton
Press.
25
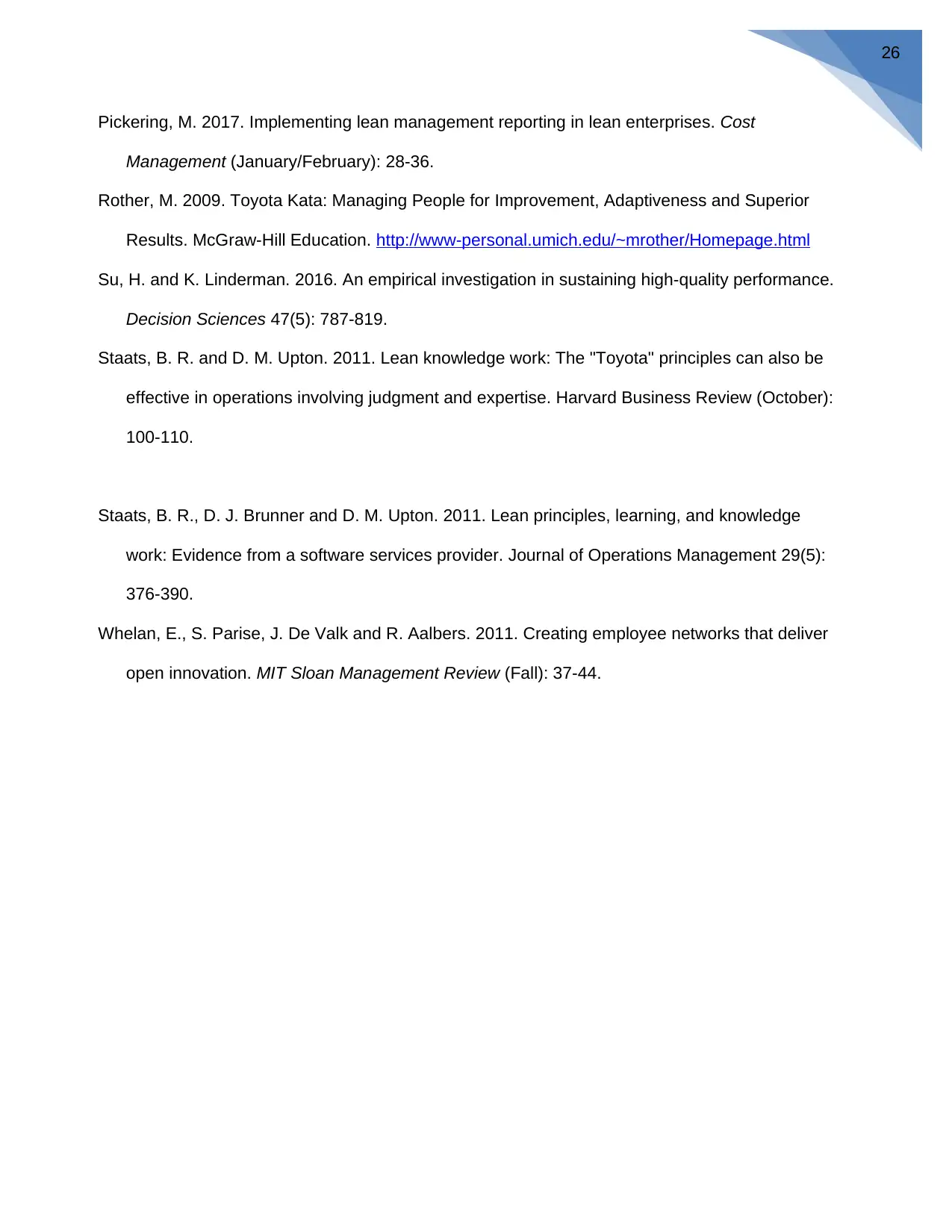
Pickering, M. 2017. Implementing lean management reporting in lean enterprises. Cost
Management (January/February): 28-36.
Rother, M. 2009. Toyota Kata: Managing People for Improvement, Adaptiveness and Superior
Results. McGraw-Hill Education. http://www-personal.umich.edu/~mrother/Homepage.html
Su, H. and K. Linderman. 2016. An empirical investigation in sustaining high-quality performance.
Decision Sciences 47(5): 787-819.
Staats, B. R. and D. M. Upton. 2011. Lean knowledge work: The "Toyota" principles can also be
effective in operations involving judgment and expertise. Harvard Business Review (October):
100-110.
Staats, B. R., D. J. Brunner and D. M. Upton. 2011. Lean principles, learning, and knowledge
work: Evidence from a software services provider. Journal of Operations Management 29(5):
376-390.
Whelan, E., S. Parise, J. De Valk and R. Aalbers. 2011. Creating employee networks that deliver
open innovation. MIT Sloan Management Review (Fall): 37-44.
26
Management (January/February): 28-36.
Rother, M. 2009. Toyota Kata: Managing People for Improvement, Adaptiveness and Superior
Results. McGraw-Hill Education. http://www-personal.umich.edu/~mrother/Homepage.html
Su, H. and K. Linderman. 2016. An empirical investigation in sustaining high-quality performance.
Decision Sciences 47(5): 787-819.
Staats, B. R. and D. M. Upton. 2011. Lean knowledge work: The "Toyota" principles can also be
effective in operations involving judgment and expertise. Harvard Business Review (October):
100-110.
Staats, B. R., D. J. Brunner and D. M. Upton. 2011. Lean principles, learning, and knowledge
work: Evidence from a software services provider. Journal of Operations Management 29(5):
376-390.
Whelan, E., S. Parise, J. De Valk and R. Aalbers. 2011. Creating employee networks that deliver
open innovation. MIT Sloan Management Review (Fall): 37-44.
26
1 out of 27
Related Documents
![[object Object]](/_next/image/?url=%2F_next%2Fstatic%2Fmedia%2Flogo.6d15ce61.png&w=640&q=75)
Your All-in-One AI-Powered Toolkit for Academic Success.
+13062052269
info@desklib.com
Available 24*7 on WhatsApp / Email
Unlock your academic potential
© 2024 | Zucol Services PVT LTD | All rights reserved.