Applying Lean Project Management to Improve PEW Ltd's Performance
VerifiedAdded on 2023/06/04
|15
|3864
|134
Case Study
AI Summary
This case study analyzes the challenges faced by Precision Engineering Works (PEW) Pvt. Ltd., a company specializing in plastic molding parts for the telecommunication industry. The company is experiencing a decline in its customer base and profitability due to increased competition from new...
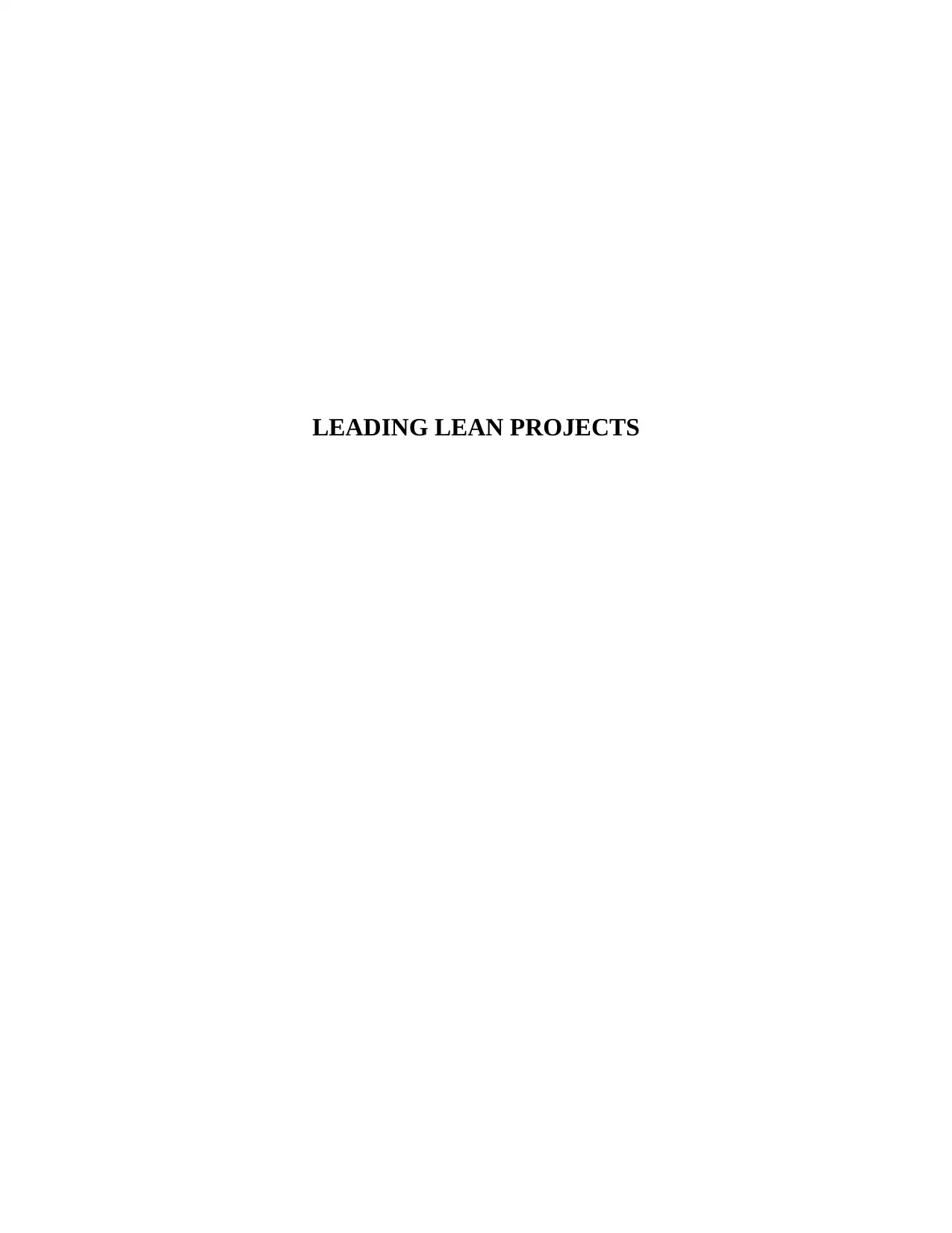
LEADING LEAN PROJECTS
Paraphrase This Document
Need a fresh take? Get an instant paraphrase of this document with our AI Paraphraser
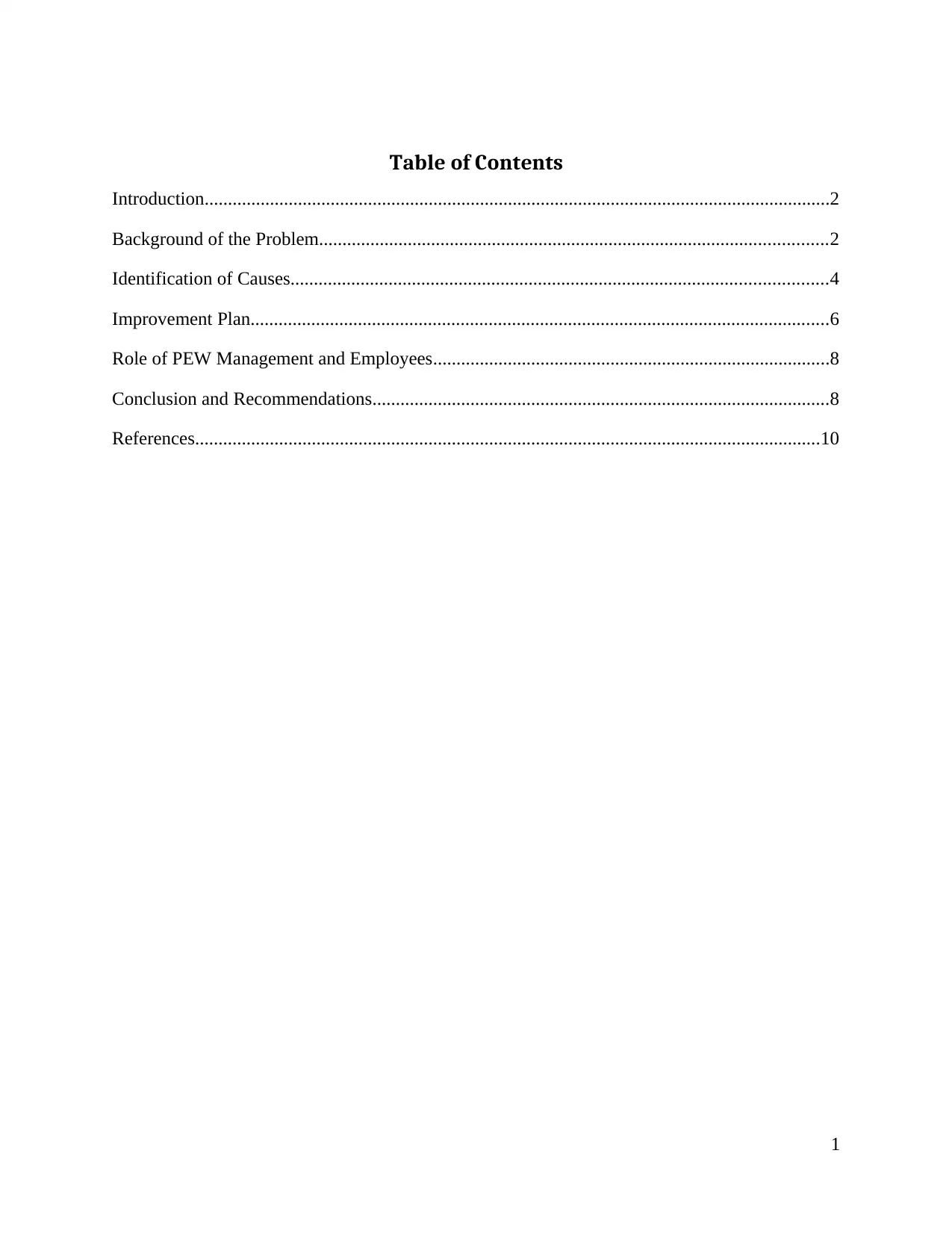
Table of Contents
Introduction......................................................................................................................................2
Background of the Problem.............................................................................................................2
Identification of Causes...................................................................................................................4
Improvement Plan............................................................................................................................6
Role of PEW Management and Employees.....................................................................................8
Conclusion and Recommendations..................................................................................................8
References......................................................................................................................................10
1
Introduction......................................................................................................................................2
Background of the Problem.............................................................................................................2
Identification of Causes...................................................................................................................4
Improvement Plan............................................................................................................................6
Role of PEW Management and Employees.....................................................................................8
Conclusion and Recommendations..................................................................................................8
References......................................................................................................................................10
1
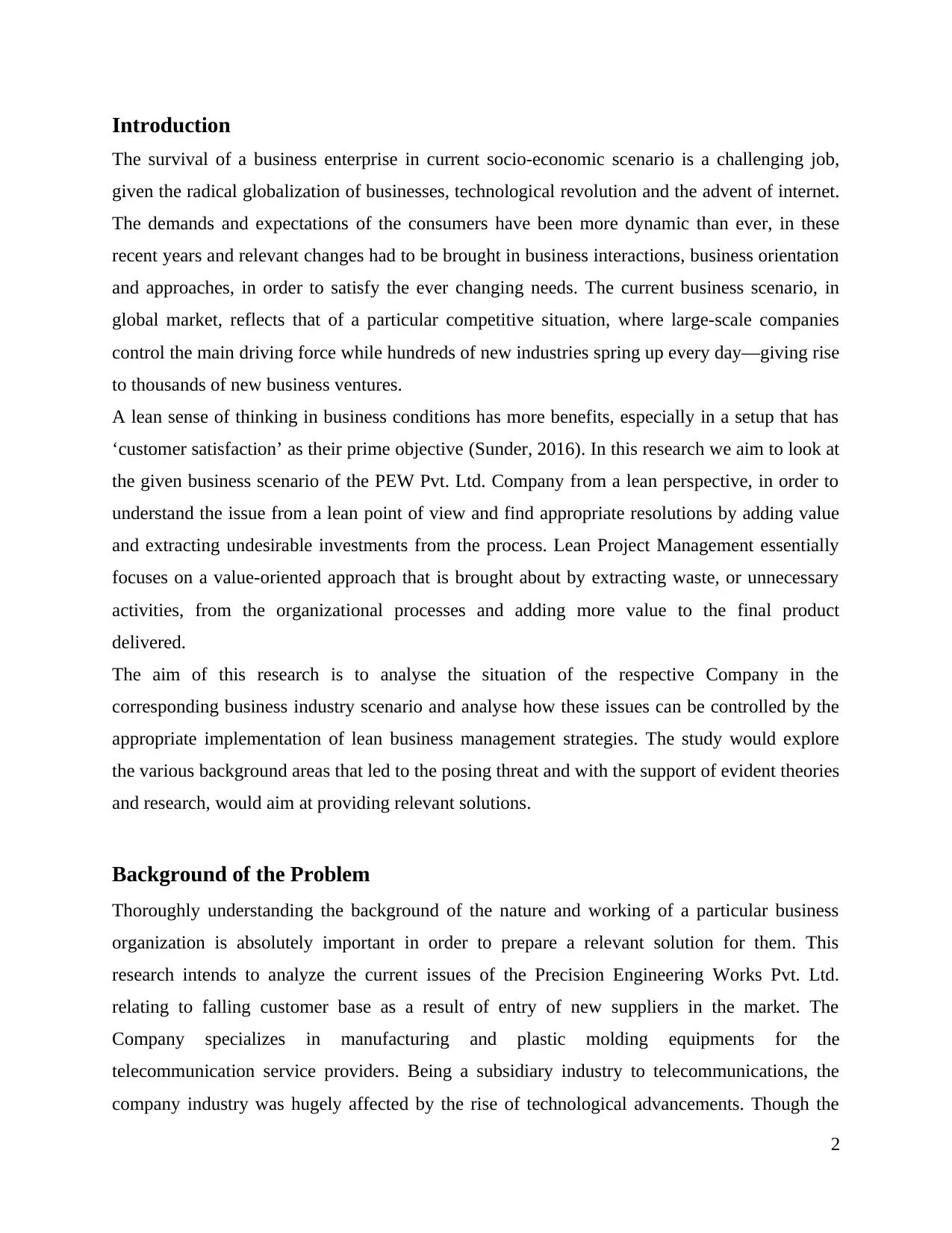
Introduction
The survival of a business enterprise in current socio-economic scenario is a challenging job,
given the radical globalization of businesses, technological revolution and the advent of internet.
The demands and expectations of the consumers have been more dynamic than ever, in these
recent years and relevant changes had to be brought in business interactions, business orientation
and approaches, in order to satisfy the ever changing needs. The current business scenario, in
global market, reflects that of a particular competitive situation, where large-scale companies
control the main driving force while hundreds of new industries spring up every day—giving rise
to thousands of new business ventures.
A lean sense of thinking in business conditions has more benefits, especially in a setup that has
‘customer satisfaction’ as their prime objective (Sunder, 2016). In this research we aim to look at
the given business scenario of the PEW Pvt. Ltd. Company from a lean perspective, in order to
understand the issue from a lean point of view and find appropriate resolutions by adding value
and extracting undesirable investments from the process. Lean Project Management essentially
focuses on a value-oriented approach that is brought about by extracting waste, or unnecessary
activities, from the organizational processes and adding more value to the final product
delivered.
The aim of this research is to analyse the situation of the respective Company in the
corresponding business industry scenario and analyse how these issues can be controlled by the
appropriate implementation of lean business management strategies. The study would explore
the various background areas that led to the posing threat and with the support of evident theories
and research, would aim at providing relevant solutions.
Background of the Problem
Thoroughly understanding the background of the nature and working of a particular business
organization is absolutely important in order to prepare a relevant solution for them. This
research intends to analyze the current issues of the Precision Engineering Works Pvt. Ltd.
relating to falling customer base as a result of entry of new suppliers in the market. The
Company specializes in manufacturing and plastic molding equipments for the
telecommunication service providers. Being a subsidiary industry to telecommunications, the
company industry was hugely affected by the rise of technological advancements. Though the
2
The survival of a business enterprise in current socio-economic scenario is a challenging job,
given the radical globalization of businesses, technological revolution and the advent of internet.
The demands and expectations of the consumers have been more dynamic than ever, in these
recent years and relevant changes had to be brought in business interactions, business orientation
and approaches, in order to satisfy the ever changing needs. The current business scenario, in
global market, reflects that of a particular competitive situation, where large-scale companies
control the main driving force while hundreds of new industries spring up every day—giving rise
to thousands of new business ventures.
A lean sense of thinking in business conditions has more benefits, especially in a setup that has
‘customer satisfaction’ as their prime objective (Sunder, 2016). In this research we aim to look at
the given business scenario of the PEW Pvt. Ltd. Company from a lean perspective, in order to
understand the issue from a lean point of view and find appropriate resolutions by adding value
and extracting undesirable investments from the process. Lean Project Management essentially
focuses on a value-oriented approach that is brought about by extracting waste, or unnecessary
activities, from the organizational processes and adding more value to the final product
delivered.
The aim of this research is to analyse the situation of the respective Company in the
corresponding business industry scenario and analyse how these issues can be controlled by the
appropriate implementation of lean business management strategies. The study would explore
the various background areas that led to the posing threat and with the support of evident theories
and research, would aim at providing relevant solutions.
Background of the Problem
Thoroughly understanding the background of the nature and working of a particular business
organization is absolutely important in order to prepare a relevant solution for them. This
research intends to analyze the current issues of the Precision Engineering Works Pvt. Ltd.
relating to falling customer base as a result of entry of new suppliers in the market. The
Company specializes in manufacturing and plastic molding equipments for the
telecommunication service providers. Being a subsidiary industry to telecommunications, the
company industry was hugely affected by the rise of technological advancements. Though the
2
⊘ This is a preview!⊘
Do you want full access?
Subscribe today to unlock all pages.

Trusted by 1+ million students worldwide
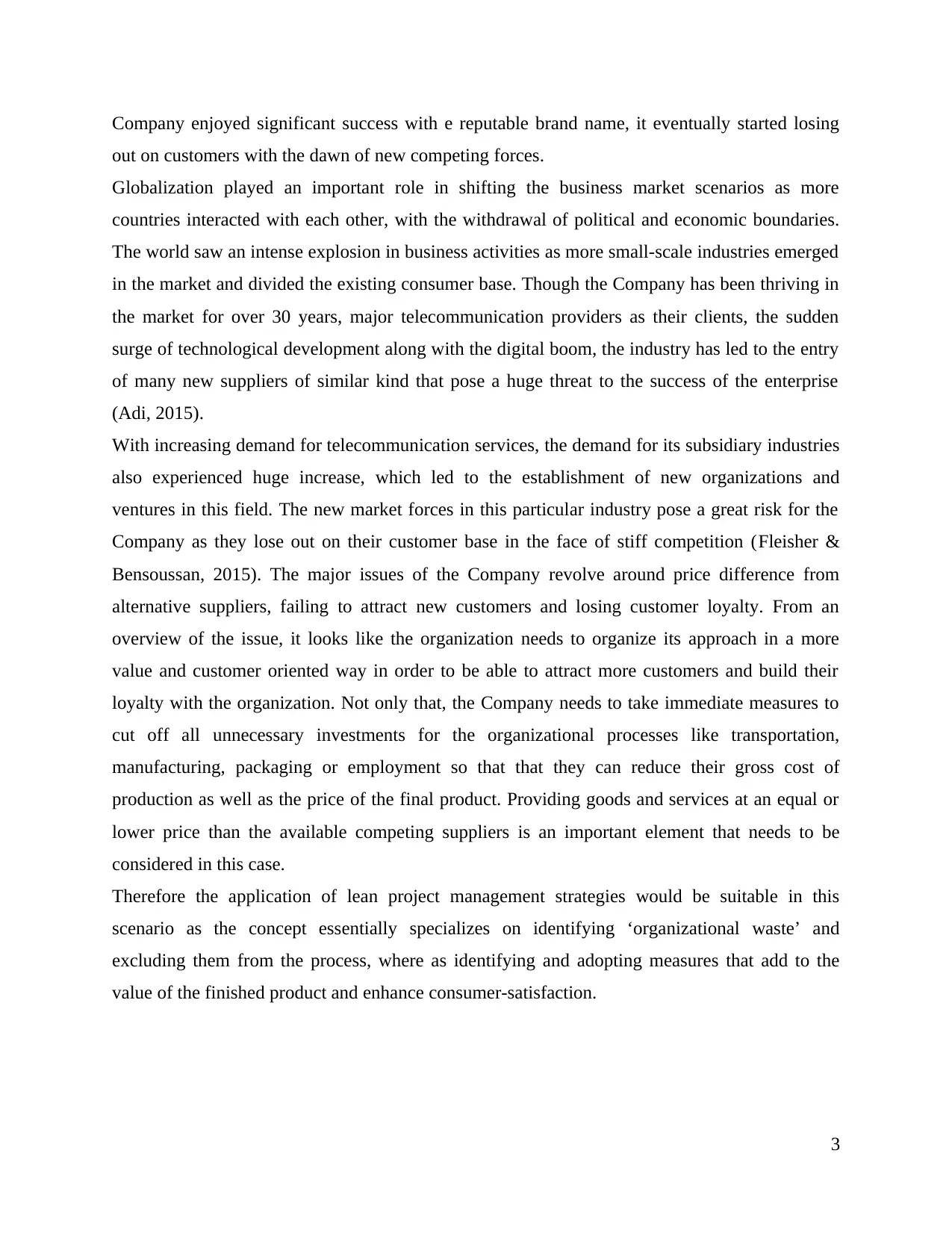
Company enjoyed significant success with e reputable brand name, it eventually started losing
out on customers with the dawn of new competing forces.
Globalization played an important role in shifting the business market scenarios as more
countries interacted with each other, with the withdrawal of political and economic boundaries.
The world saw an intense explosion in business activities as more small-scale industries emerged
in the market and divided the existing consumer base. Though the Company has been thriving in
the market for over 30 years, major telecommunication providers as their clients, the sudden
surge of technological development along with the digital boom, the industry has led to the entry
of many new suppliers of similar kind that pose a huge threat to the success of the enterprise
(Adi, 2015).
With increasing demand for telecommunication services, the demand for its subsidiary industries
also experienced huge increase, which led to the establishment of new organizations and
ventures in this field. The new market forces in this particular industry pose a great risk for the
Company as they lose out on their customer base in the face of stiff competition (Fleisher &
Bensoussan, 2015). The major issues of the Company revolve around price difference from
alternative suppliers, failing to attract new customers and losing customer loyalty. From an
overview of the issue, it looks like the organization needs to organize its approach in a more
value and customer oriented way in order to be able to attract more customers and build their
loyalty with the organization. Not only that, the Company needs to take immediate measures to
cut off all unnecessary investments for the organizational processes like transportation,
manufacturing, packaging or employment so that that they can reduce their gross cost of
production as well as the price of the final product. Providing goods and services at an equal or
lower price than the available competing suppliers is an important element that needs to be
considered in this case.
Therefore the application of lean project management strategies would be suitable in this
scenario as the concept essentially specializes on identifying ‘organizational waste’ and
excluding them from the process, where as identifying and adopting measures that add to the
value of the finished product and enhance consumer-satisfaction.
3
out on customers with the dawn of new competing forces.
Globalization played an important role in shifting the business market scenarios as more
countries interacted with each other, with the withdrawal of political and economic boundaries.
The world saw an intense explosion in business activities as more small-scale industries emerged
in the market and divided the existing consumer base. Though the Company has been thriving in
the market for over 30 years, major telecommunication providers as their clients, the sudden
surge of technological development along with the digital boom, the industry has led to the entry
of many new suppliers of similar kind that pose a huge threat to the success of the enterprise
(Adi, 2015).
With increasing demand for telecommunication services, the demand for its subsidiary industries
also experienced huge increase, which led to the establishment of new organizations and
ventures in this field. The new market forces in this particular industry pose a great risk for the
Company as they lose out on their customer base in the face of stiff competition (Fleisher &
Bensoussan, 2015). The major issues of the Company revolve around price difference from
alternative suppliers, failing to attract new customers and losing customer loyalty. From an
overview of the issue, it looks like the organization needs to organize its approach in a more
value and customer oriented way in order to be able to attract more customers and build their
loyalty with the organization. Not only that, the Company needs to take immediate measures to
cut off all unnecessary investments for the organizational processes like transportation,
manufacturing, packaging or employment so that that they can reduce their gross cost of
production as well as the price of the final product. Providing goods and services at an equal or
lower price than the available competing suppliers is an important element that needs to be
considered in this case.
Therefore the application of lean project management strategies would be suitable in this
scenario as the concept essentially specializes on identifying ‘organizational waste’ and
excluding them from the process, where as identifying and adopting measures that add to the
value of the finished product and enhance consumer-satisfaction.
3
Paraphrase This Document
Need a fresh take? Get an instant paraphrase of this document with our AI Paraphraser
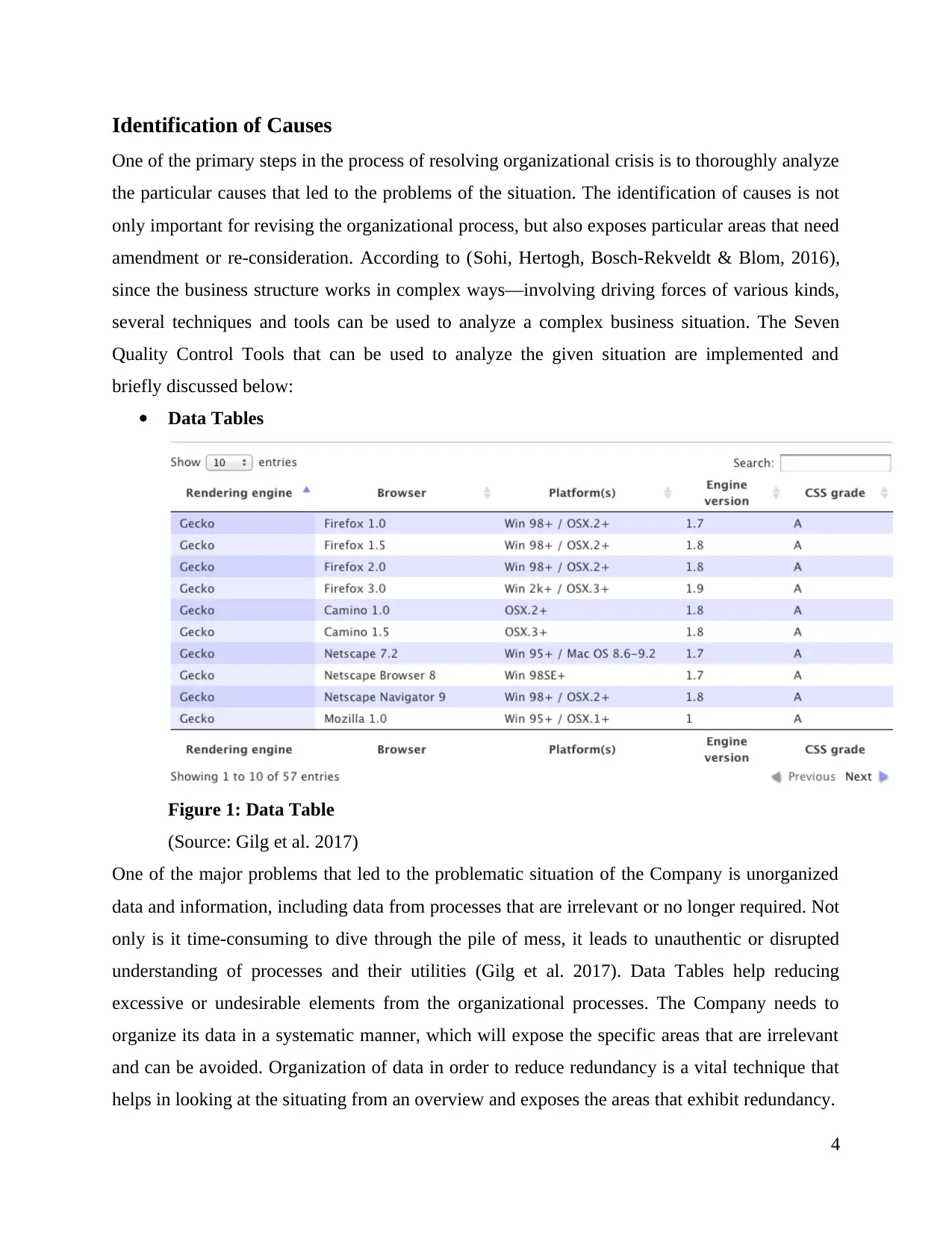
Identification of Causes
One of the primary steps in the process of resolving organizational crisis is to thoroughly analyze
the particular causes that led to the problems of the situation. The identification of causes is not
only important for revising the organizational process, but also exposes particular areas that need
amendment or re-consideration. According to (Sohi, Hertogh, Bosch-Rekveldt & Blom, 2016),
since the business structure works in complex ways—involving driving forces of various kinds,
several techniques and tools can be used to analyze a complex business situation. The Seven
Quality Control Tools that can be used to analyze the given situation are implemented and
briefly discussed below:
Data Tables
Figure 1: Data Table
(Source: Gilg et al. 2017)
One of the major problems that led to the problematic situation of the Company is unorganized
data and information, including data from processes that are irrelevant or no longer required. Not
only is it time-consuming to dive through the pile of mess, it leads to unauthentic or disrupted
understanding of processes and their utilities (Gilg et al. 2017). Data Tables help reducing
excessive or undesirable elements from the organizational processes. The Company needs to
organize its data in a systematic manner, which will expose the specific areas that are irrelevant
and can be avoided. Organization of data in order to reduce redundancy is a vital technique that
helps in looking at the situating from an overview and exposes the areas that exhibit redundancy.
4
One of the primary steps in the process of resolving organizational crisis is to thoroughly analyze
the particular causes that led to the problems of the situation. The identification of causes is not
only important for revising the organizational process, but also exposes particular areas that need
amendment or re-consideration. According to (Sohi, Hertogh, Bosch-Rekveldt & Blom, 2016),
since the business structure works in complex ways—involving driving forces of various kinds,
several techniques and tools can be used to analyze a complex business situation. The Seven
Quality Control Tools that can be used to analyze the given situation are implemented and
briefly discussed below:
Data Tables
Figure 1: Data Table
(Source: Gilg et al. 2017)
One of the major problems that led to the problematic situation of the Company is unorganized
data and information, including data from processes that are irrelevant or no longer required. Not
only is it time-consuming to dive through the pile of mess, it leads to unauthentic or disrupted
understanding of processes and their utilities (Gilg et al. 2017). Data Tables help reducing
excessive or undesirable elements from the organizational processes. The Company needs to
organize its data in a systematic manner, which will expose the specific areas that are irrelevant
and can be avoided. Organization of data in order to reduce redundancy is a vital technique that
helps in looking at the situating from an overview and exposes the areas that exhibit redundancy.
4
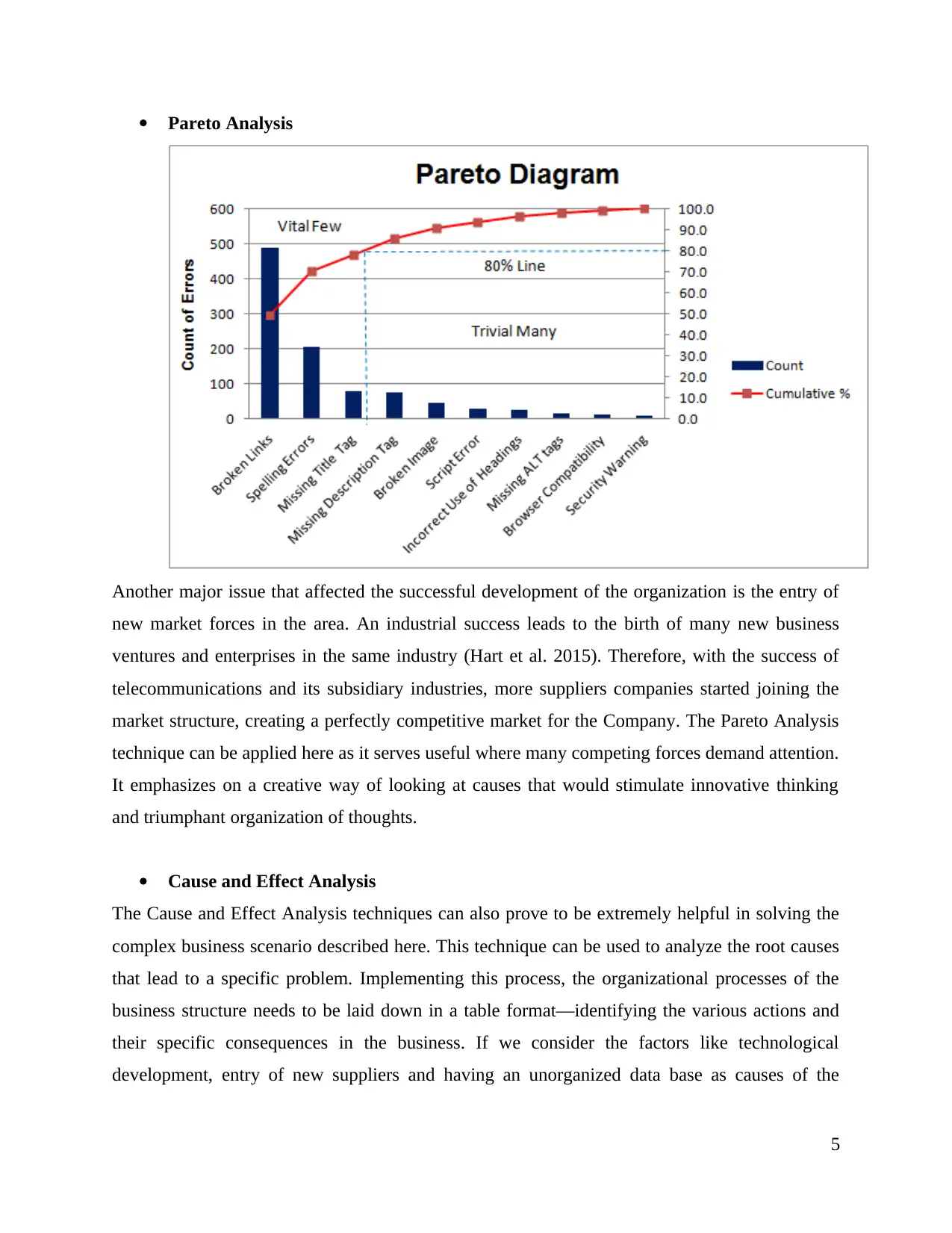
Pareto Analysis
Another major issue that affected the successful development of the organization is the entry of
new market forces in the area. An industrial success leads to the birth of many new business
ventures and enterprises in the same industry (Hart et al. 2015). Therefore, with the success of
telecommunications and its subsidiary industries, more suppliers companies started joining the
market structure, creating a perfectly competitive market for the Company. The Pareto Analysis
technique can be applied here as it serves useful where many competing forces demand attention.
It emphasizes on a creative way of looking at causes that would stimulate innovative thinking
and triumphant organization of thoughts.
Cause and Effect Analysis
The Cause and Effect Analysis techniques can also prove to be extremely helpful in solving the
complex business scenario described here. This technique can be used to analyze the root causes
that lead to a specific problem. Implementing this process, the organizational processes of the
business structure needs to be laid down in a table format—identifying the various actions and
their specific consequences in the business. If we consider the factors like technological
development, entry of new suppliers and having an unorganized data base as causes of the
5
Another major issue that affected the successful development of the organization is the entry of
new market forces in the area. An industrial success leads to the birth of many new business
ventures and enterprises in the same industry (Hart et al. 2015). Therefore, with the success of
telecommunications and its subsidiary industries, more suppliers companies started joining the
market structure, creating a perfectly competitive market for the Company. The Pareto Analysis
technique can be applied here as it serves useful where many competing forces demand attention.
It emphasizes on a creative way of looking at causes that would stimulate innovative thinking
and triumphant organization of thoughts.
Cause and Effect Analysis
The Cause and Effect Analysis techniques can also prove to be extremely helpful in solving the
complex business scenario described here. This technique can be used to analyze the root causes
that lead to a specific problem. Implementing this process, the organizational processes of the
business structure needs to be laid down in a table format—identifying the various actions and
their specific consequences in the business. If we consider the factors like technological
development, entry of new suppliers and having an unorganized data base as causes of the
5
⊘ This is a preview!⊘
Do you want full access?
Subscribe today to unlock all pages.

Trusted by 1+ million students worldwide
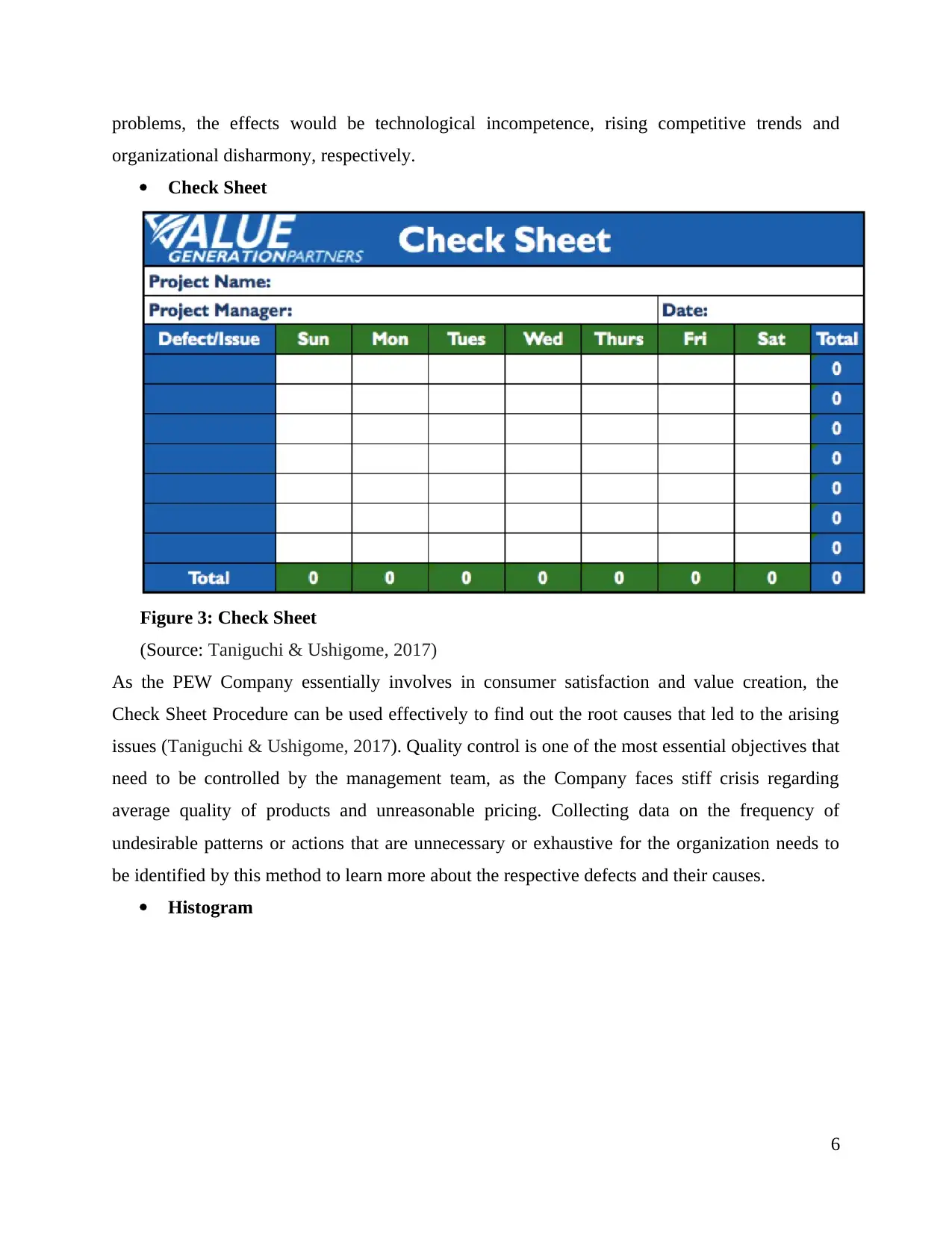
problems, the effects would be technological incompetence, rising competitive trends and
organizational disharmony, respectively.
Check Sheet
Figure 3: Check Sheet
(Source: Taniguchi & Ushigome, 2017)
As the PEW Company essentially involves in consumer satisfaction and value creation, the
Check Sheet Procedure can be used effectively to find out the root causes that led to the arising
issues (Taniguchi & Ushigome, 2017). Quality control is one of the most essential objectives that
need to be controlled by the management team, as the Company faces stiff crisis regarding
average quality of products and unreasonable pricing. Collecting data on the frequency of
undesirable patterns or actions that are unnecessary or exhaustive for the organization needs to
be identified by this method to learn more about the respective defects and their causes.
Histogram
6
organizational disharmony, respectively.
Check Sheet
Figure 3: Check Sheet
(Source: Taniguchi & Ushigome, 2017)
As the PEW Company essentially involves in consumer satisfaction and value creation, the
Check Sheet Procedure can be used effectively to find out the root causes that led to the arising
issues (Taniguchi & Ushigome, 2017). Quality control is one of the most essential objectives that
need to be controlled by the management team, as the Company faces stiff crisis regarding
average quality of products and unreasonable pricing. Collecting data on the frequency of
undesirable patterns or actions that are unnecessary or exhaustive for the organization needs to
be identified by this method to learn more about the respective defects and their causes.
Histogram
6
Paraphrase This Document
Need a fresh take? Get an instant paraphrase of this document with our AI Paraphraser
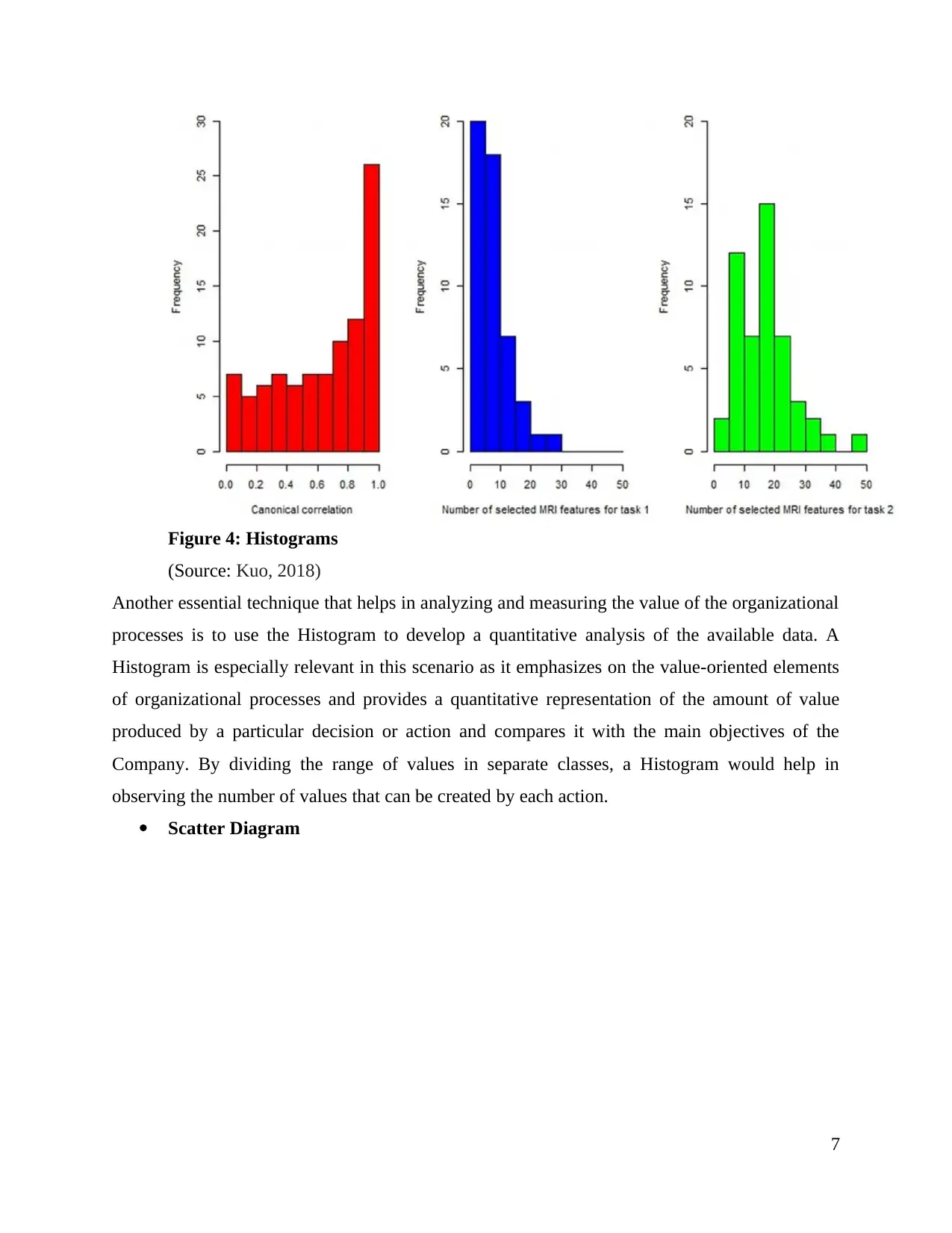
Figure 4: Histograms
(Source: Kuo, 2018)
Another essential technique that helps in analyzing and measuring the value of the organizational
processes is to use the Histogram to develop a quantitative analysis of the available data. A
Histogram is especially relevant in this scenario as it emphasizes on the value-oriented elements
of organizational processes and provides a quantitative representation of the amount of value
produced by a particular decision or action and compares it with the main objectives of the
Company. By dividing the range of values in separate classes, a Histogram would help in
observing the number of values that can be created by each action.
Scatter Diagram
7
(Source: Kuo, 2018)
Another essential technique that helps in analyzing and measuring the value of the organizational
processes is to use the Histogram to develop a quantitative analysis of the available data. A
Histogram is especially relevant in this scenario as it emphasizes on the value-oriented elements
of organizational processes and provides a quantitative representation of the amount of value
produced by a particular decision or action and compares it with the main objectives of the
Company. By dividing the range of values in separate classes, a Histogram would help in
observing the number of values that can be created by each action.
Scatter Diagram
7
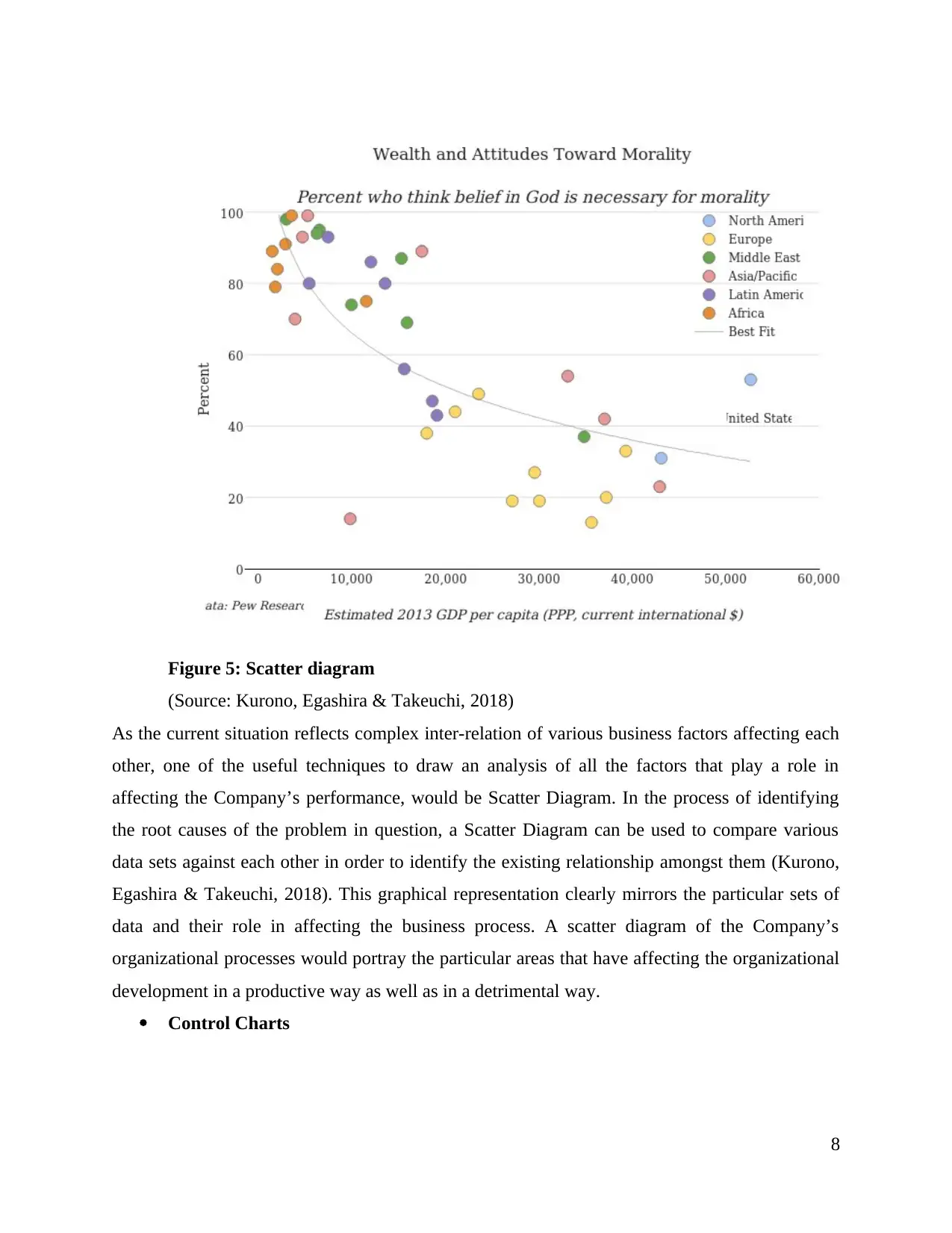
Figure 5: Scatter diagram
(Source: Kurono, Egashira & Takeuchi, 2018)
As the current situation reflects complex inter-relation of various business factors affecting each
other, one of the useful techniques to draw an analysis of all the factors that play a role in
affecting the Company’s performance, would be Scatter Diagram. In the process of identifying
the root causes of the problem in question, a Scatter Diagram can be used to compare various
data sets against each other in order to identify the existing relationship amongst them (Kurono,
Egashira & Takeuchi, 2018). This graphical representation clearly mirrors the particular sets of
data and their role in affecting the business process. A scatter diagram of the Company’s
organizational processes would portray the particular areas that have affecting the organizational
development in a productive way as well as in a detrimental way.
Control Charts
8
(Source: Kurono, Egashira & Takeuchi, 2018)
As the current situation reflects complex inter-relation of various business factors affecting each
other, one of the useful techniques to draw an analysis of all the factors that play a role in
affecting the Company’s performance, would be Scatter Diagram. In the process of identifying
the root causes of the problem in question, a Scatter Diagram can be used to compare various
data sets against each other in order to identify the existing relationship amongst them (Kurono,
Egashira & Takeuchi, 2018). This graphical representation clearly mirrors the particular sets of
data and their role in affecting the business process. A scatter diagram of the Company’s
organizational processes would portray the particular areas that have affecting the organizational
development in a productive way as well as in a detrimental way.
Control Charts
8
⊘ This is a preview!⊘
Do you want full access?
Subscribe today to unlock all pages.

Trusted by 1+ million students worldwide
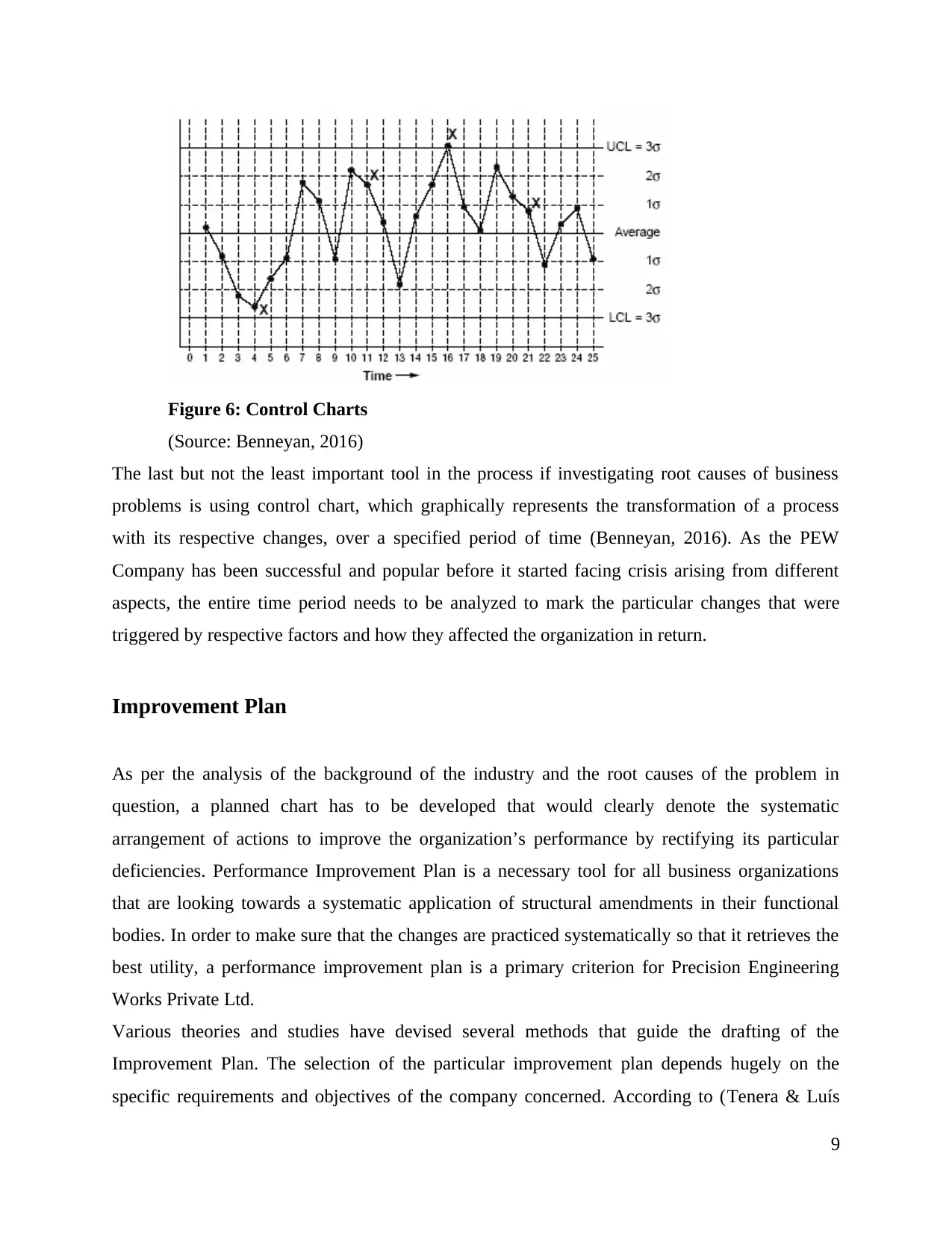
Figure 6: Control Charts
(Source: Benneyan, 2016)
The last but not the least important tool in the process if investigating root causes of business
problems is using control chart, which graphically represents the transformation of a process
with its respective changes, over a specified period of time (Benneyan, 2016). As the PEW
Company has been successful and popular before it started facing crisis arising from different
aspects, the entire time period needs to be analyzed to mark the particular changes that were
triggered by respective factors and how they affected the organization in return.
Improvement Plan
As per the analysis of the background of the industry and the root causes of the problem in
question, a planned chart has to be developed that would clearly denote the systematic
arrangement of actions to improve the organization’s performance by rectifying its particular
deficiencies. Performance Improvement Plan is a necessary tool for all business organizations
that are looking towards a systematic application of structural amendments in their functional
bodies. In order to make sure that the changes are practiced systematically so that it retrieves the
best utility, a performance improvement plan is a primary criterion for Precision Engineering
Works Private Ltd.
Various theories and studies have devised several methods that guide the drafting of the
Improvement Plan. The selection of the particular improvement plan depends hugely on the
specific requirements and objectives of the company concerned. According to (Tenera & Luís
9
(Source: Benneyan, 2016)
The last but not the least important tool in the process if investigating root causes of business
problems is using control chart, which graphically represents the transformation of a process
with its respective changes, over a specified period of time (Benneyan, 2016). As the PEW
Company has been successful and popular before it started facing crisis arising from different
aspects, the entire time period needs to be analyzed to mark the particular changes that were
triggered by respective factors and how they affected the organization in return.
Improvement Plan
As per the analysis of the background of the industry and the root causes of the problem in
question, a planned chart has to be developed that would clearly denote the systematic
arrangement of actions to improve the organization’s performance by rectifying its particular
deficiencies. Performance Improvement Plan is a necessary tool for all business organizations
that are looking towards a systematic application of structural amendments in their functional
bodies. In order to make sure that the changes are practiced systematically so that it retrieves the
best utility, a performance improvement plan is a primary criterion for Precision Engineering
Works Private Ltd.
Various theories and studies have devised several methods that guide the drafting of the
Improvement Plan. The selection of the particular improvement plan depends hugely on the
specific requirements and objectives of the company concerned. According to (Tenera & Luís
9
Paraphrase This Document
Need a fresh take? Get an instant paraphrase of this document with our AI Paraphraser
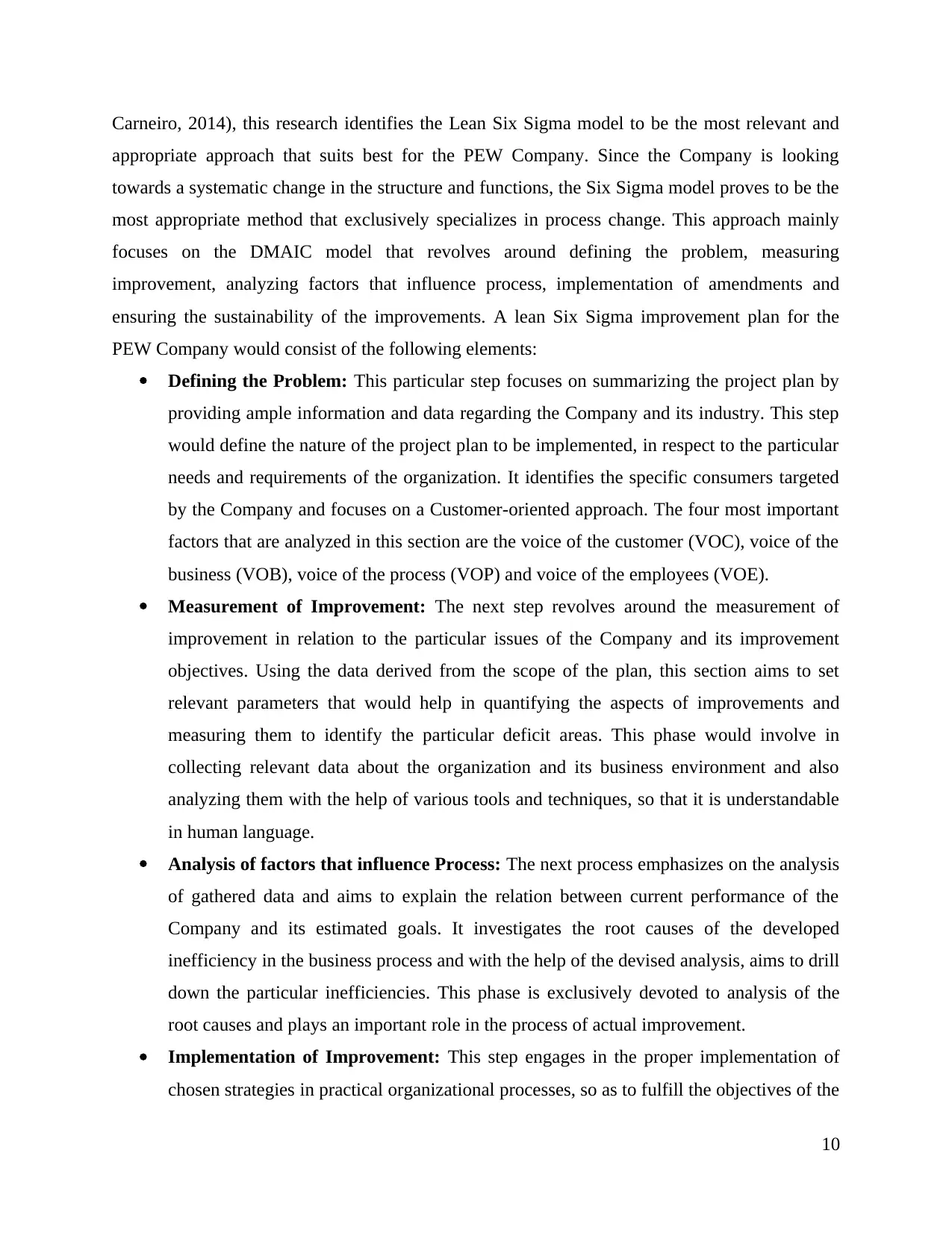
Carneiro, 2014), this research identifies the Lean Six Sigma model to be the most relevant and
appropriate approach that suits best for the PEW Company. Since the Company is looking
towards a systematic change in the structure and functions, the Six Sigma model proves to be the
most appropriate method that exclusively specializes in process change. This approach mainly
focuses on the DMAIC model that revolves around defining the problem, measuring
improvement, analyzing factors that influence process, implementation of amendments and
ensuring the sustainability of the improvements. A lean Six Sigma improvement plan for the
PEW Company would consist of the following elements:
Defining the Problem: This particular step focuses on summarizing the project plan by
providing ample information and data regarding the Company and its industry. This step
would define the nature of the project plan to be implemented, in respect to the particular
needs and requirements of the organization. It identifies the specific consumers targeted
by the Company and focuses on a Customer-oriented approach. The four most important
factors that are analyzed in this section are the voice of the customer (VOC), voice of the
business (VOB), voice of the process (VOP) and voice of the employees (VOE).
Measurement of Improvement: The next step revolves around the measurement of
improvement in relation to the particular issues of the Company and its improvement
objectives. Using the data derived from the scope of the plan, this section aims to set
relevant parameters that would help in quantifying the aspects of improvements and
measuring them to identify the particular deficit areas. This phase would involve in
collecting relevant data about the organization and its business environment and also
analyzing them with the help of various tools and techniques, so that it is understandable
in human language.
Analysis of factors that influence Process: The next process emphasizes on the analysis
of gathered data and aims to explain the relation between current performance of the
Company and its estimated goals. It investigates the root causes of the developed
inefficiency in the business process and with the help of the devised analysis, aims to drill
down the particular inefficiencies. This phase is exclusively devoted to analysis of the
root causes and plays an important role in the process of actual improvement.
Implementation of Improvement: This step engages in the proper implementation of
chosen strategies in practical organizational processes, so as to fulfill the objectives of the
10
appropriate approach that suits best for the PEW Company. Since the Company is looking
towards a systematic change in the structure and functions, the Six Sigma model proves to be the
most appropriate method that exclusively specializes in process change. This approach mainly
focuses on the DMAIC model that revolves around defining the problem, measuring
improvement, analyzing factors that influence process, implementation of amendments and
ensuring the sustainability of the improvements. A lean Six Sigma improvement plan for the
PEW Company would consist of the following elements:
Defining the Problem: This particular step focuses on summarizing the project plan by
providing ample information and data regarding the Company and its industry. This step
would define the nature of the project plan to be implemented, in respect to the particular
needs and requirements of the organization. It identifies the specific consumers targeted
by the Company and focuses on a Customer-oriented approach. The four most important
factors that are analyzed in this section are the voice of the customer (VOC), voice of the
business (VOB), voice of the process (VOP) and voice of the employees (VOE).
Measurement of Improvement: The next step revolves around the measurement of
improvement in relation to the particular issues of the Company and its improvement
objectives. Using the data derived from the scope of the plan, this section aims to set
relevant parameters that would help in quantifying the aspects of improvements and
measuring them to identify the particular deficit areas. This phase would involve in
collecting relevant data about the organization and its business environment and also
analyzing them with the help of various tools and techniques, so that it is understandable
in human language.
Analysis of factors that influence Process: The next process emphasizes on the analysis
of gathered data and aims to explain the relation between current performance of the
Company and its estimated goals. It investigates the root causes of the developed
inefficiency in the business process and with the help of the devised analysis, aims to drill
down the particular inefficiencies. This phase is exclusively devoted to analysis of the
root causes and plays an important role in the process of actual improvement.
Implementation of Improvement: This step engages in the proper implementation of
chosen strategies in practical organizational processes, so as to fulfill the objectives of the
10
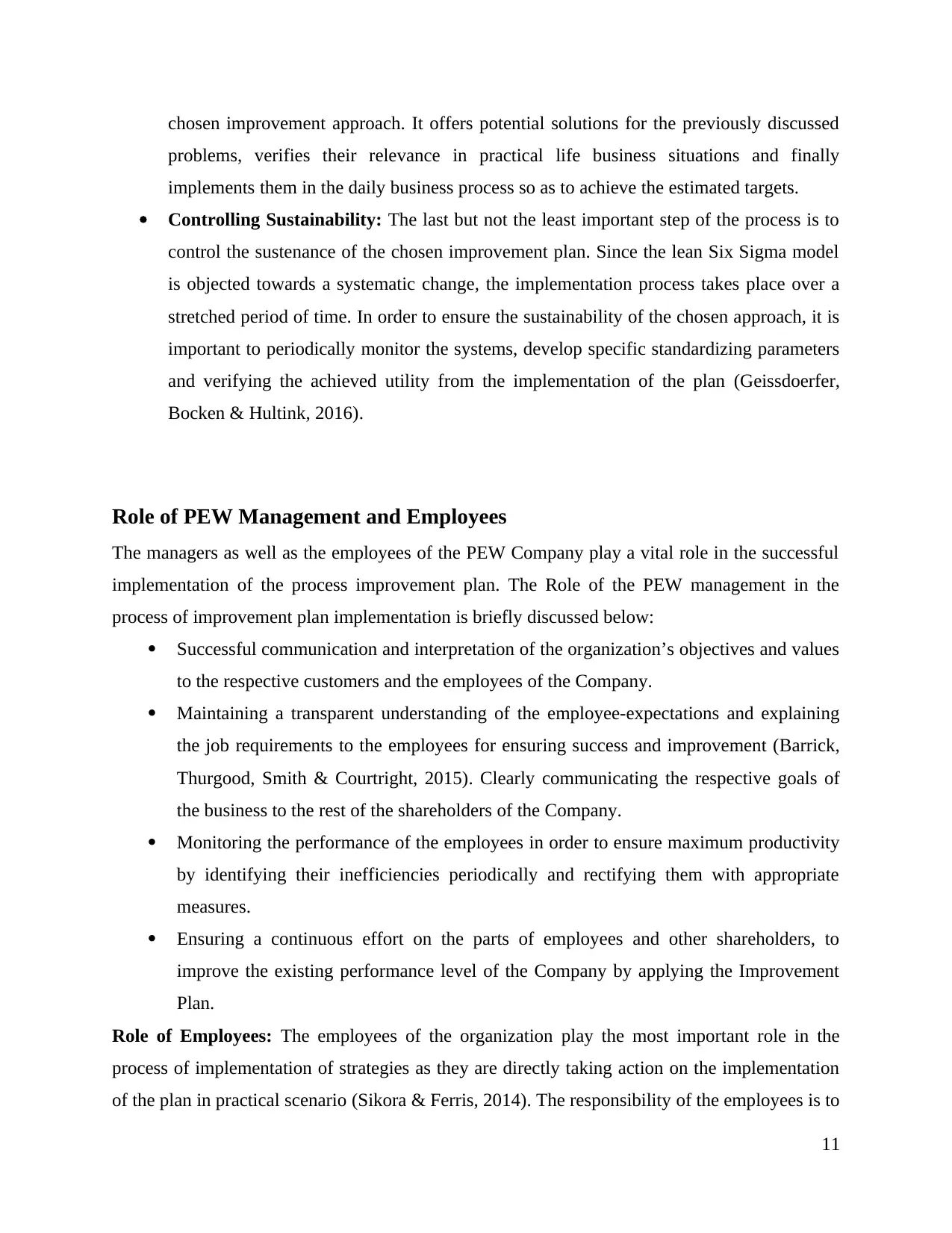
chosen improvement approach. It offers potential solutions for the previously discussed
problems, verifies their relevance in practical life business situations and finally
implements them in the daily business process so as to achieve the estimated targets.
Controlling Sustainability: The last but not the least important step of the process is to
control the sustenance of the chosen improvement plan. Since the lean Six Sigma model
is objected towards a systematic change, the implementation process takes place over a
stretched period of time. In order to ensure the sustainability of the chosen approach, it is
important to periodically monitor the systems, develop specific standardizing parameters
and verifying the achieved utility from the implementation of the plan (Geissdoerfer,
Bocken & Hultink, 2016).
Role of PEW Management and Employees
The managers as well as the employees of the PEW Company play a vital role in the successful
implementation of the process improvement plan. The Role of the PEW management in the
process of improvement plan implementation is briefly discussed below:
Successful communication and interpretation of the organization’s objectives and values
to the respective customers and the employees of the Company.
Maintaining a transparent understanding of the employee-expectations and explaining
the job requirements to the employees for ensuring success and improvement (Barrick,
Thurgood, Smith & Courtright, 2015). Clearly communicating the respective goals of
the business to the rest of the shareholders of the Company.
Monitoring the performance of the employees in order to ensure maximum productivity
by identifying their inefficiencies periodically and rectifying them with appropriate
measures.
Ensuring a continuous effort on the parts of employees and other shareholders, to
improve the existing performance level of the Company by applying the Improvement
Plan.
Role of Employees: The employees of the organization play the most important role in the
process of implementation of strategies as they are directly taking action on the implementation
of the plan in practical scenario (Sikora & Ferris, 2014). The responsibility of the employees is to
11
problems, verifies their relevance in practical life business situations and finally
implements them in the daily business process so as to achieve the estimated targets.
Controlling Sustainability: The last but not the least important step of the process is to
control the sustenance of the chosen improvement plan. Since the lean Six Sigma model
is objected towards a systematic change, the implementation process takes place over a
stretched period of time. In order to ensure the sustainability of the chosen approach, it is
important to periodically monitor the systems, develop specific standardizing parameters
and verifying the achieved utility from the implementation of the plan (Geissdoerfer,
Bocken & Hultink, 2016).
Role of PEW Management and Employees
The managers as well as the employees of the PEW Company play a vital role in the successful
implementation of the process improvement plan. The Role of the PEW management in the
process of improvement plan implementation is briefly discussed below:
Successful communication and interpretation of the organization’s objectives and values
to the respective customers and the employees of the Company.
Maintaining a transparent understanding of the employee-expectations and explaining
the job requirements to the employees for ensuring success and improvement (Barrick,
Thurgood, Smith & Courtright, 2015). Clearly communicating the respective goals of
the business to the rest of the shareholders of the Company.
Monitoring the performance of the employees in order to ensure maximum productivity
by identifying their inefficiencies periodically and rectifying them with appropriate
measures.
Ensuring a continuous effort on the parts of employees and other shareholders, to
improve the existing performance level of the Company by applying the Improvement
Plan.
Role of Employees: The employees of the organization play the most important role in the
process of implementation of strategies as they are directly taking action on the implementation
of the plan in practical scenario (Sikora & Ferris, 2014). The responsibility of the employees is to
11
⊘ This is a preview!⊘
Do you want full access?
Subscribe today to unlock all pages.

Trusted by 1+ million students worldwide
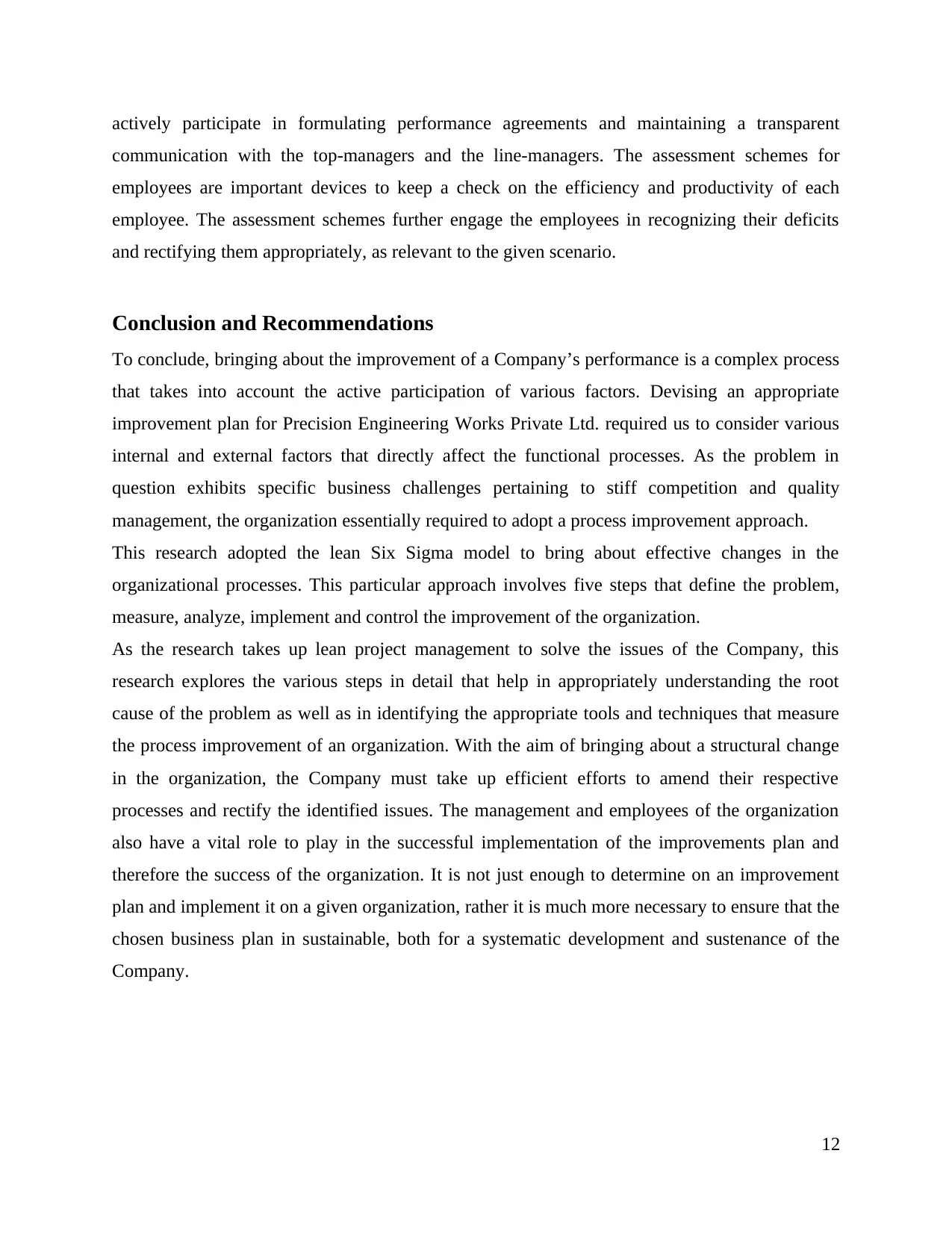
actively participate in formulating performance agreements and maintaining a transparent
communication with the top-managers and the line-managers. The assessment schemes for
employees are important devices to keep a check on the efficiency and productivity of each
employee. The assessment schemes further engage the employees in recognizing their deficits
and rectifying them appropriately, as relevant to the given scenario.
Conclusion and Recommendations
To conclude, bringing about the improvement of a Company’s performance is a complex process
that takes into account the active participation of various factors. Devising an appropriate
improvement plan for Precision Engineering Works Private Ltd. required us to consider various
internal and external factors that directly affect the functional processes. As the problem in
question exhibits specific business challenges pertaining to stiff competition and quality
management, the organization essentially required to adopt a process improvement approach.
This research adopted the lean Six Sigma model to bring about effective changes in the
organizational processes. This particular approach involves five steps that define the problem,
measure, analyze, implement and control the improvement of the organization.
As the research takes up lean project management to solve the issues of the Company, this
research explores the various steps in detail that help in appropriately understanding the root
cause of the problem as well as in identifying the appropriate tools and techniques that measure
the process improvement of an organization. With the aim of bringing about a structural change
in the organization, the Company must take up efficient efforts to amend their respective
processes and rectify the identified issues. The management and employees of the organization
also have a vital role to play in the successful implementation of the improvements plan and
therefore the success of the organization. It is not just enough to determine on an improvement
plan and implement it on a given organization, rather it is much more necessary to ensure that the
chosen business plan in sustainable, both for a systematic development and sustenance of the
Company.
12
communication with the top-managers and the line-managers. The assessment schemes for
employees are important devices to keep a check on the efficiency and productivity of each
employee. The assessment schemes further engage the employees in recognizing their deficits
and rectifying them appropriately, as relevant to the given scenario.
Conclusion and Recommendations
To conclude, bringing about the improvement of a Company’s performance is a complex process
that takes into account the active participation of various factors. Devising an appropriate
improvement plan for Precision Engineering Works Private Ltd. required us to consider various
internal and external factors that directly affect the functional processes. As the problem in
question exhibits specific business challenges pertaining to stiff competition and quality
management, the organization essentially required to adopt a process improvement approach.
This research adopted the lean Six Sigma model to bring about effective changes in the
organizational processes. This particular approach involves five steps that define the problem,
measure, analyze, implement and control the improvement of the organization.
As the research takes up lean project management to solve the issues of the Company, this
research explores the various steps in detail that help in appropriately understanding the root
cause of the problem as well as in identifying the appropriate tools and techniques that measure
the process improvement of an organization. With the aim of bringing about a structural change
in the organization, the Company must take up efficient efforts to amend their respective
processes and rectify the identified issues. The management and employees of the organization
also have a vital role to play in the successful implementation of the improvements plan and
therefore the success of the organization. It is not just enough to determine on an improvement
plan and implement it on a given organization, rather it is much more necessary to ensure that the
chosen business plan in sustainable, both for a systematic development and sustenance of the
Company.
12
Paraphrase This Document
Need a fresh take? Get an instant paraphrase of this document with our AI Paraphraser

References
Adi, B. (2015). An Evaluation of the Nigerian telecommunication industry competitiveness:
Application of Porter’s five forces model. World, 5(3). Retrieved from:
http://www.wjsspapers.com/static/documents/September/2015/2.%20Bongo.pdf
Barrick, M. R., Thurgood, G. R., Smith, T. A., & Courtright, S. H. (2015). Collective
organizational engagement: Linking motivational antecedents, strategic implementation,
and firm performance. Academy of Management journal, 58(1), 111-135. DOI:
https://doi.org/10.5465/amj.2013.0227
Benneyan, J. C. (2016). Design and Use of g-Type Control Charts for Industry and Healthcare:
SPC Charts for Hospital Infections and Adverse Events. Retrieved from
https://www.coe.neu.edu/healthcare/pdfs/publications/C31.%20Design%20of
%20geometric%20charts,%20IEMS%201999.pdf
Fleisher, C. S., & Bensoussan, B. E. (2015). Business and competitive analysis: effective
application of new and classic methods. FT Press. Retrieved from:
http://www.academia.edu/download/30356361/bca_overview.pdf
Geissdoerfer, M., Bocken, N. M., & Hultink, E. J. (2016). Design thinking to enhance the
sustainable business modelling process–A workshop based on a value mapping
process. Journal of Cleaner Production, 135, 1218-1232. DOI:
https://doi.org/10.1016/j.jclepro.2016.07.020
Gilg, J., Methven, S., Casula, A., Castledine, C., MacNeill, S. J., Ford, D., ... & Mallett, T.
(2017). UK Renal Registry 19th Annual Report: Appendix K Renal Centre Names and
Abbreviations used in the Figures and Data Tables. Nephron, 137(Suppl. 1), 405-406.
Doi: 10.1159/000481388
Hart, Y., Sheftel, H., Hausser, J., Szekely, P., Ben-Moshe, N. B., Korem, Y., ... & Alon, U.
(2015). Inferring biological tasks using Pareto analysis of high-dimensional data. Nature
methods, 12(3), 233. Retrieved from https://www.nature.com/articles/nmeth.3254
Kuo, S. S. (2018). U.S. Patent Application No. 15/797,269. Retrieved from
https://patents.google.com/patent/US20180067741A1/en?oq=Kuo%2c+S.+S.+(2018).
+U.S.+Patent+Application+No.+15%2f797%2c269
13
Adi, B. (2015). An Evaluation of the Nigerian telecommunication industry competitiveness:
Application of Porter’s five forces model. World, 5(3). Retrieved from:
http://www.wjsspapers.com/static/documents/September/2015/2.%20Bongo.pdf
Barrick, M. R., Thurgood, G. R., Smith, T. A., & Courtright, S. H. (2015). Collective
organizational engagement: Linking motivational antecedents, strategic implementation,
and firm performance. Academy of Management journal, 58(1), 111-135. DOI:
https://doi.org/10.5465/amj.2013.0227
Benneyan, J. C. (2016). Design and Use of g-Type Control Charts for Industry and Healthcare:
SPC Charts for Hospital Infections and Adverse Events. Retrieved from
https://www.coe.neu.edu/healthcare/pdfs/publications/C31.%20Design%20of
%20geometric%20charts,%20IEMS%201999.pdf
Fleisher, C. S., & Bensoussan, B. E. (2015). Business and competitive analysis: effective
application of new and classic methods. FT Press. Retrieved from:
http://www.academia.edu/download/30356361/bca_overview.pdf
Geissdoerfer, M., Bocken, N. M., & Hultink, E. J. (2016). Design thinking to enhance the
sustainable business modelling process–A workshop based on a value mapping
process. Journal of Cleaner Production, 135, 1218-1232. DOI:
https://doi.org/10.1016/j.jclepro.2016.07.020
Gilg, J., Methven, S., Casula, A., Castledine, C., MacNeill, S. J., Ford, D., ... & Mallett, T.
(2017). UK Renal Registry 19th Annual Report: Appendix K Renal Centre Names and
Abbreviations used in the Figures and Data Tables. Nephron, 137(Suppl. 1), 405-406.
Doi: 10.1159/000481388
Hart, Y., Sheftel, H., Hausser, J., Szekely, P., Ben-Moshe, N. B., Korem, Y., ... & Alon, U.
(2015). Inferring biological tasks using Pareto analysis of high-dimensional data. Nature
methods, 12(3), 233. Retrieved from https://www.nature.com/articles/nmeth.3254
Kuo, S. S. (2018). U.S. Patent Application No. 15/797,269. Retrieved from
https://patents.google.com/patent/US20180067741A1/en?oq=Kuo%2c+S.+S.+(2018).
+U.S.+Patent+Application+No.+15%2f797%2c269
13
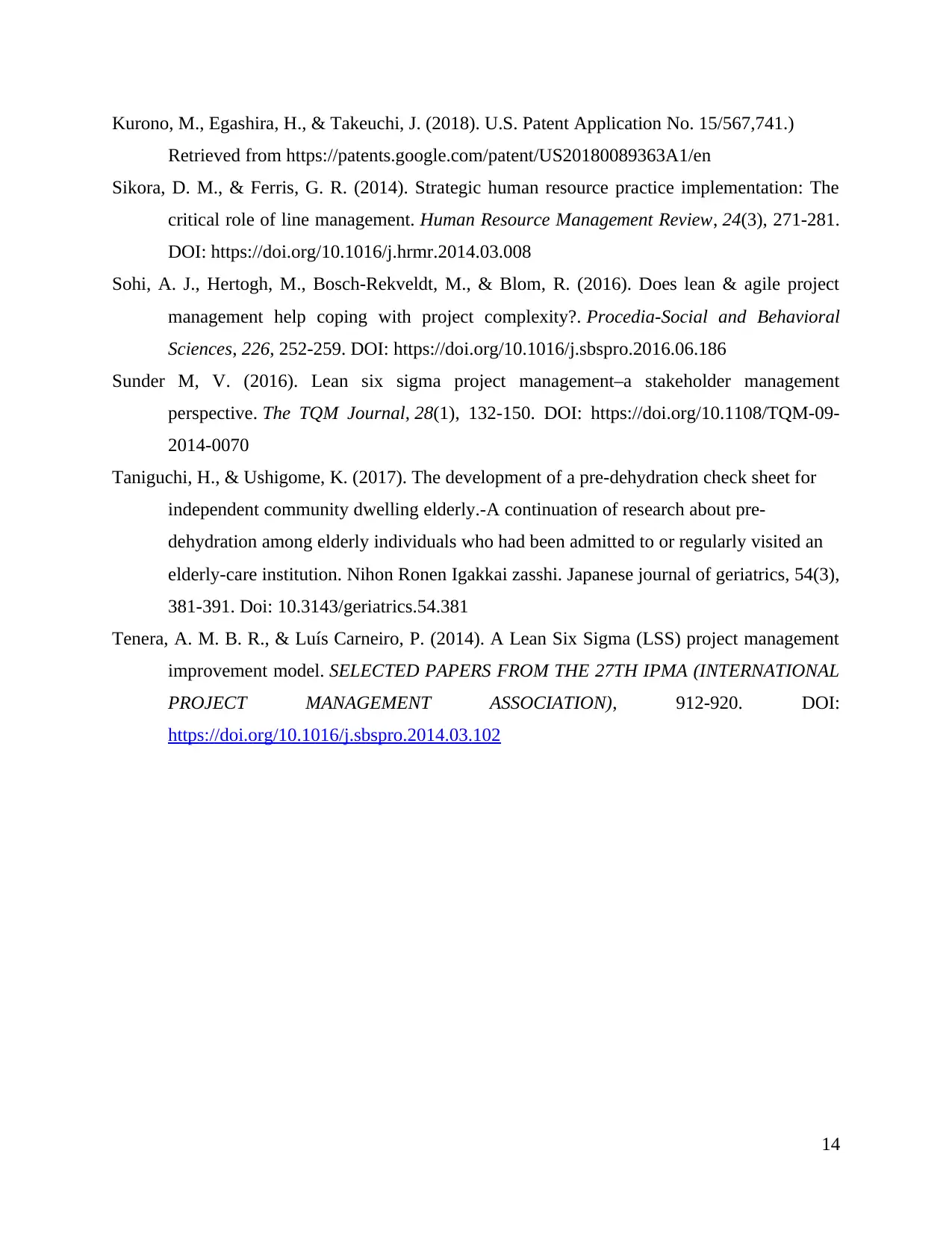
Kurono, M., Egashira, H., & Takeuchi, J. (2018). U.S. Patent Application No. 15/567,741.)
Retrieved from https://patents.google.com/patent/US20180089363A1/en
Sikora, D. M., & Ferris, G. R. (2014). Strategic human resource practice implementation: The
critical role of line management. Human Resource Management Review, 24(3), 271-281.
DOI: https://doi.org/10.1016/j.hrmr.2014.03.008
Sohi, A. J., Hertogh, M., Bosch-Rekveldt, M., & Blom, R. (2016). Does lean & agile project
management help coping with project complexity?. Procedia-Social and Behavioral
Sciences, 226, 252-259. DOI: https://doi.org/10.1016/j.sbspro.2016.06.186
Sunder M, V. (2016). Lean six sigma project management–a stakeholder management
perspective. The TQM Journal, 28(1), 132-150. DOI: https://doi.org/10.1108/TQM-09-
2014-0070
Taniguchi, H., & Ushigome, K. (2017). The development of a pre-dehydration check sheet for
independent community dwelling elderly.-A continuation of research about pre-
dehydration among elderly individuals who had been admitted to or regularly visited an
elderly-care institution. Nihon Ronen Igakkai zasshi. Japanese journal of geriatrics, 54(3),
381-391. Doi: 10.3143/geriatrics.54.381
Tenera, A. M. B. R., & Luís Carneiro, P. (2014). A Lean Six Sigma (LSS) project management
improvement model. SELECTED PAPERS FROM THE 27TH IPMA (INTERNATIONAL
PROJECT MANAGEMENT ASSOCIATION), 912-920. DOI:
https://doi.org/10.1016/j.sbspro.2014.03.102
14
Retrieved from https://patents.google.com/patent/US20180089363A1/en
Sikora, D. M., & Ferris, G. R. (2014). Strategic human resource practice implementation: The
critical role of line management. Human Resource Management Review, 24(3), 271-281.
DOI: https://doi.org/10.1016/j.hrmr.2014.03.008
Sohi, A. J., Hertogh, M., Bosch-Rekveldt, M., & Blom, R. (2016). Does lean & agile project
management help coping with project complexity?. Procedia-Social and Behavioral
Sciences, 226, 252-259. DOI: https://doi.org/10.1016/j.sbspro.2016.06.186
Sunder M, V. (2016). Lean six sigma project management–a stakeholder management
perspective. The TQM Journal, 28(1), 132-150. DOI: https://doi.org/10.1108/TQM-09-
2014-0070
Taniguchi, H., & Ushigome, K. (2017). The development of a pre-dehydration check sheet for
independent community dwelling elderly.-A continuation of research about pre-
dehydration among elderly individuals who had been admitted to or regularly visited an
elderly-care institution. Nihon Ronen Igakkai zasshi. Japanese journal of geriatrics, 54(3),
381-391. Doi: 10.3143/geriatrics.54.381
Tenera, A. M. B. R., & Luís Carneiro, P. (2014). A Lean Six Sigma (LSS) project management
improvement model. SELECTED PAPERS FROM THE 27TH IPMA (INTERNATIONAL
PROJECT MANAGEMENT ASSOCIATION), 912-920. DOI:
https://doi.org/10.1016/j.sbspro.2014.03.102
14
⊘ This is a preview!⊘
Do you want full access?
Subscribe today to unlock all pages.

Trusted by 1+ million students worldwide
1 out of 15
Related Documents

Your All-in-One AI-Powered Toolkit for Academic Success.
+13062052269
info@desklib.com
Available 24*7 on WhatsApp / Email
Unlock your academic potential
© 2024 | Zucol Services PVT LTD | All rights reserved.