Lean Manufacturing Implementation and Analysis for Acme Machining
VerifiedAdded on 2023/01/18
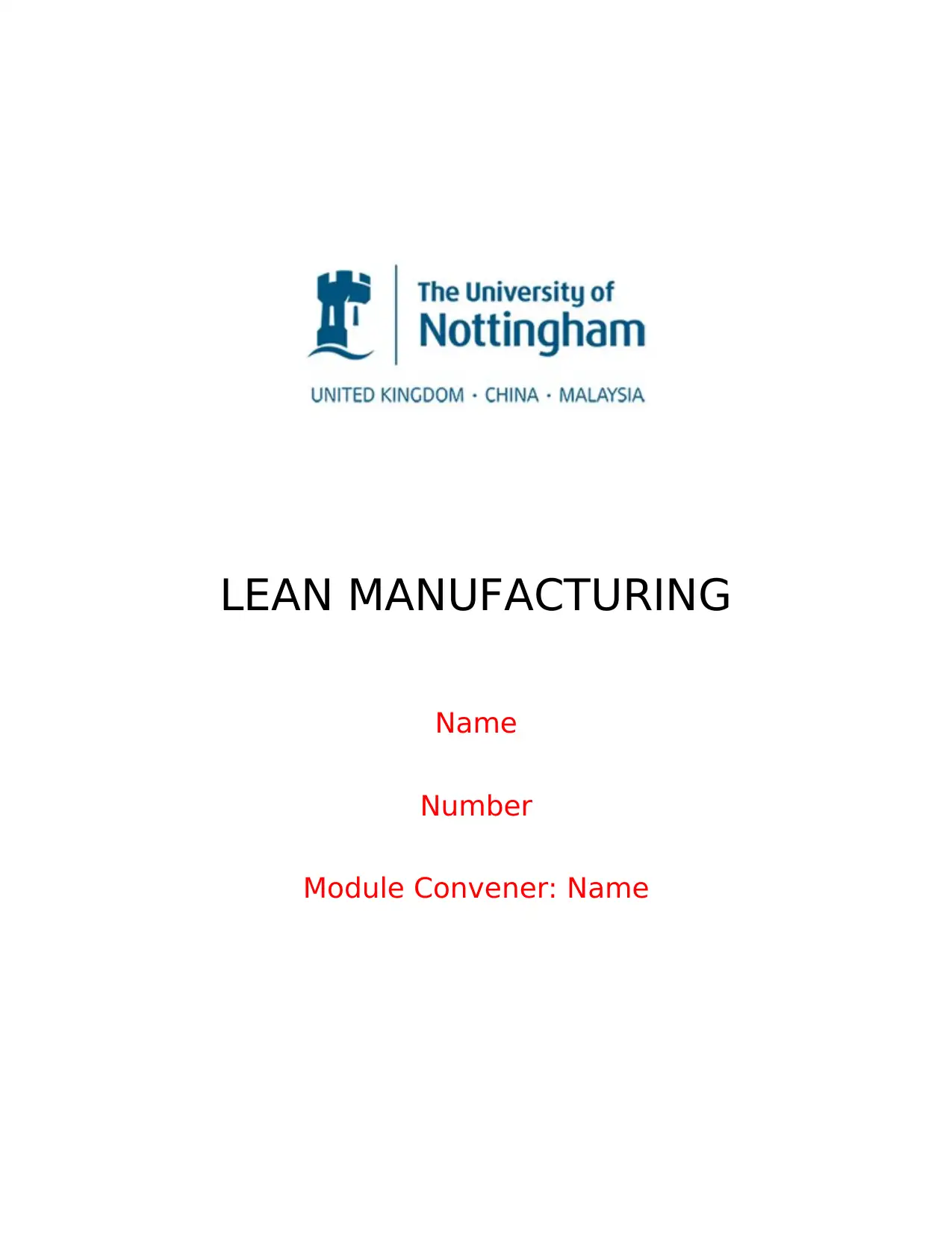
Name
Number
Module Convener: Name
Paraphrase This Document
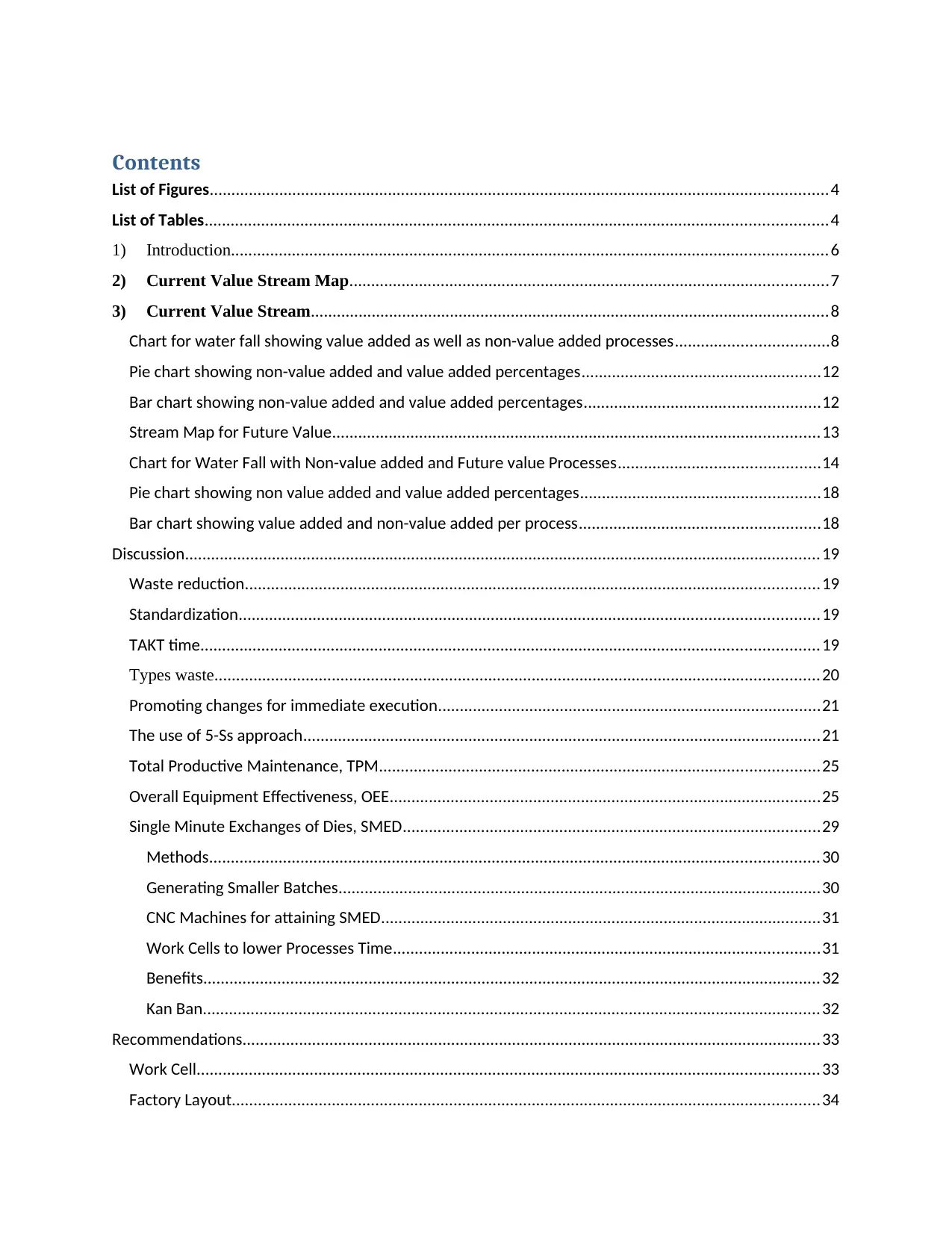
List of Figures..............................................................................................................................................4
List of Tables...............................................................................................................................................4
1) Introduction.........................................................................................................................................6
2) Current Value Stream Map..............................................................................................................7
3) Current Value Stream.......................................................................................................................8
Chart for water fall showing value added as well as non-value added processes...................................8
Pie chart showing non-value added and value added percentages.......................................................12
Bar chart showing non-value added and value added percentages......................................................12
Stream Map for Future Value................................................................................................................13
Chart for Water Fall with Non-value added and Future value Processes..............................................14
Pie chart showing non value added and value added percentages.......................................................18
Bar chart showing value added and non-value added per process.......................................................18
Discussion..................................................................................................................................................19
Waste reduction....................................................................................................................................19
Standardization.....................................................................................................................................19
TAKT time..............................................................................................................................................19
Types waste...........................................................................................................................................20
Promoting changes for immediate execution........................................................................................21
The use of 5-Ss approach.......................................................................................................................21
Total Productive Maintenance, TPM.....................................................................................................25
Overall Equipment Effectiveness, OEE...................................................................................................25
Single Minute Exchanges of Dies, SMED................................................................................................29
Methods............................................................................................................................................30
Generating Smaller Batches...............................................................................................................30
CNC Machines for attaining SMED.....................................................................................................31
Work Cells to lower Processes Time..................................................................................................31
Benefits..............................................................................................................................................32
Kan Ban..............................................................................................................................................32
Recommendations.....................................................................................................................................33
Work Cell...............................................................................................................................................33
Factory Layout.......................................................................................................................................34
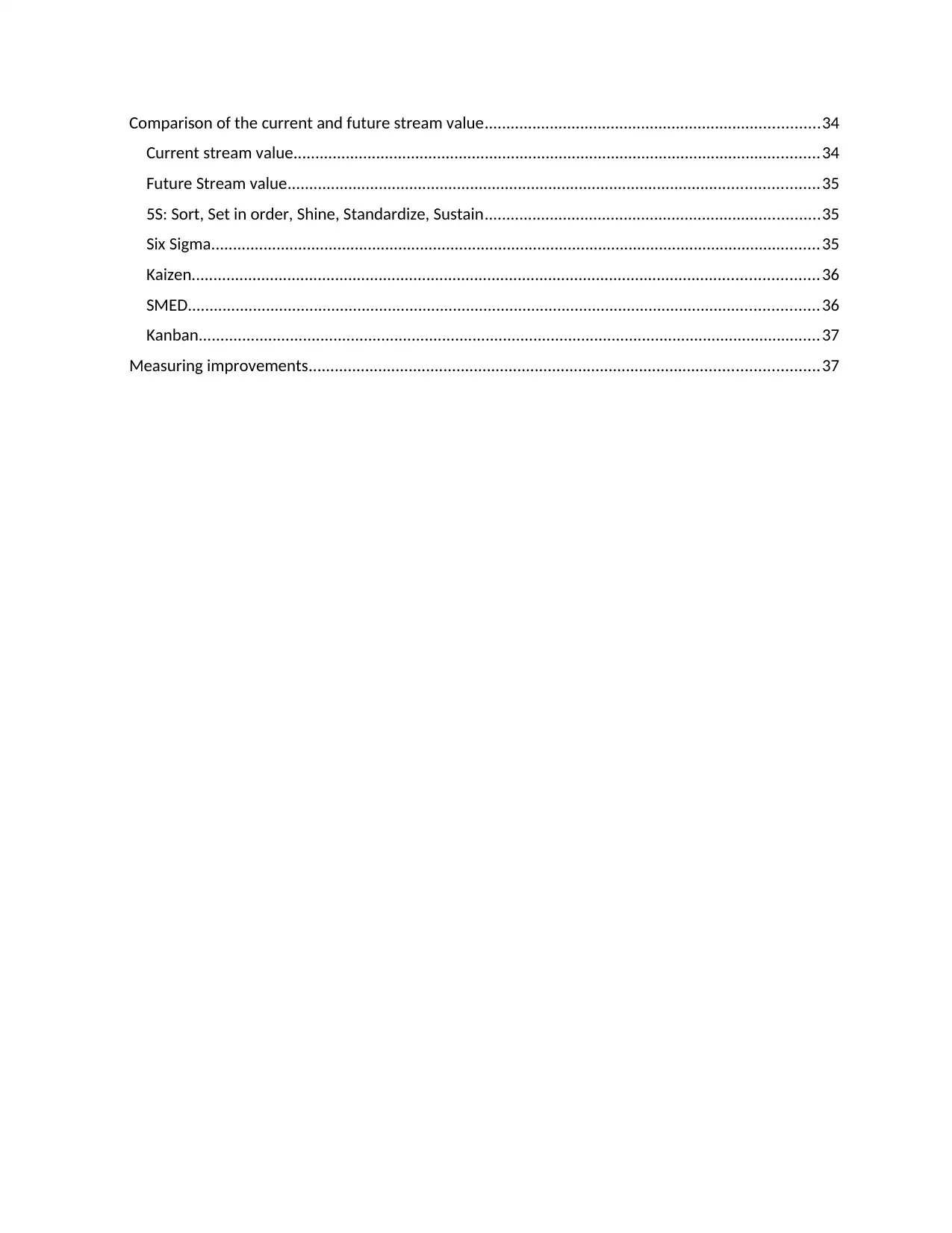
Current stream value.........................................................................................................................34
Future Stream value..........................................................................................................................35
5S: Sort, Set in order, Shine, Standardize, Sustain.............................................................................35
Six Sigma............................................................................................................................................35
Kaizen................................................................................................................................................36
SMED.................................................................................................................................................36
Kanban...............................................................................................................................................37
Measuring improvements.....................................................................................................................37
⊘ This is a preview!⊘
Do you want full access?
Subscribe today to unlock all pages.

Trusted by 1+ million students worldwide
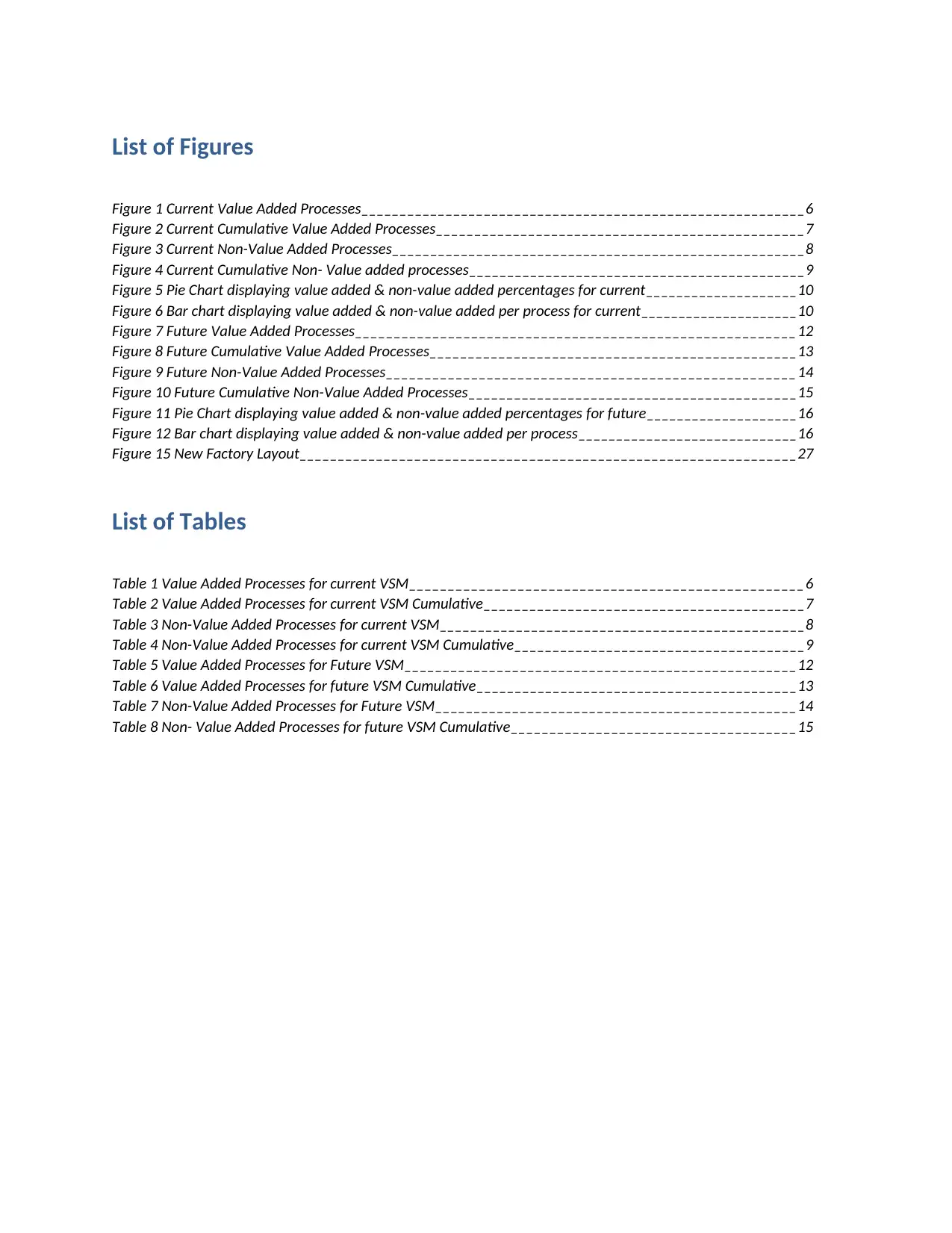
Figure 1 Current Value Added Processes__________________________________________________________6
Figure 2 Current Cumulative Value Added Processes________________________________________________7
Figure 3 Current Non-Value Added Processes______________________________________________________8
Figure 4 Current Cumulative Non- Value added processes____________________________________________9
Figure 5 Pie Chart displaying value added & non-value added percentages for current____________________10
Figure 6 Bar chart displaying value added & non-value added per process for current_____________________10
Figure 7 Future Value Added Processes_________________________________________________________12
Figure 8 Future Cumulative Value Added Processes________________________________________________13
Figure 9 Future Non-Value Added Processes_____________________________________________________14
Figure 10 Future Cumulative Non-Value Added Processes___________________________________________15
Figure 11 Pie Chart displaying value added & non-value added percentages for future____________________16
Figure 12 Bar chart displaying value added & non-value added per process_____________________________16
Figure 15 New Factory Layout_________________________________________________________________27
List of Tables
Table 1 Value Added Processes for current VSM___________________________________________________6
Table 2 Value Added Processes for current VSM Cumulative__________________________________________7
Table 3 Non-Value Added Processes for current VSM________________________________________________8
Table 4 Non-Value Added Processes for current VSM Cumulative______________________________________9
Table 5 Value Added Processes for Future VSM___________________________________________________12
Table 6 Value Added Processes for future VSM Cumulative__________________________________________13
Table 7 Non-Value Added Processes for Future VSM_______________________________________________14
Table 8 Non- Value Added Processes for future VSM Cumulative_____________________________________15
Paraphrase This Document
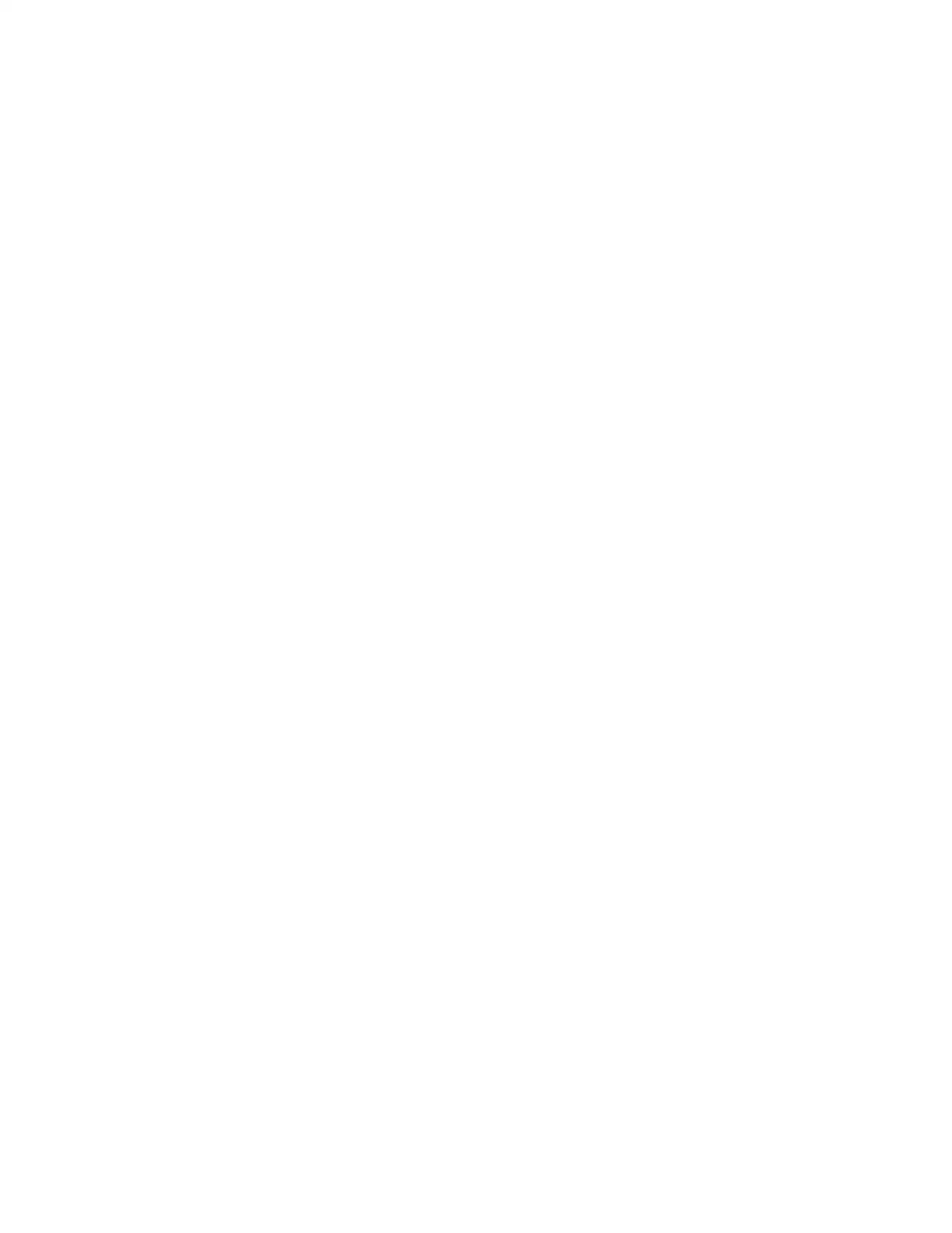
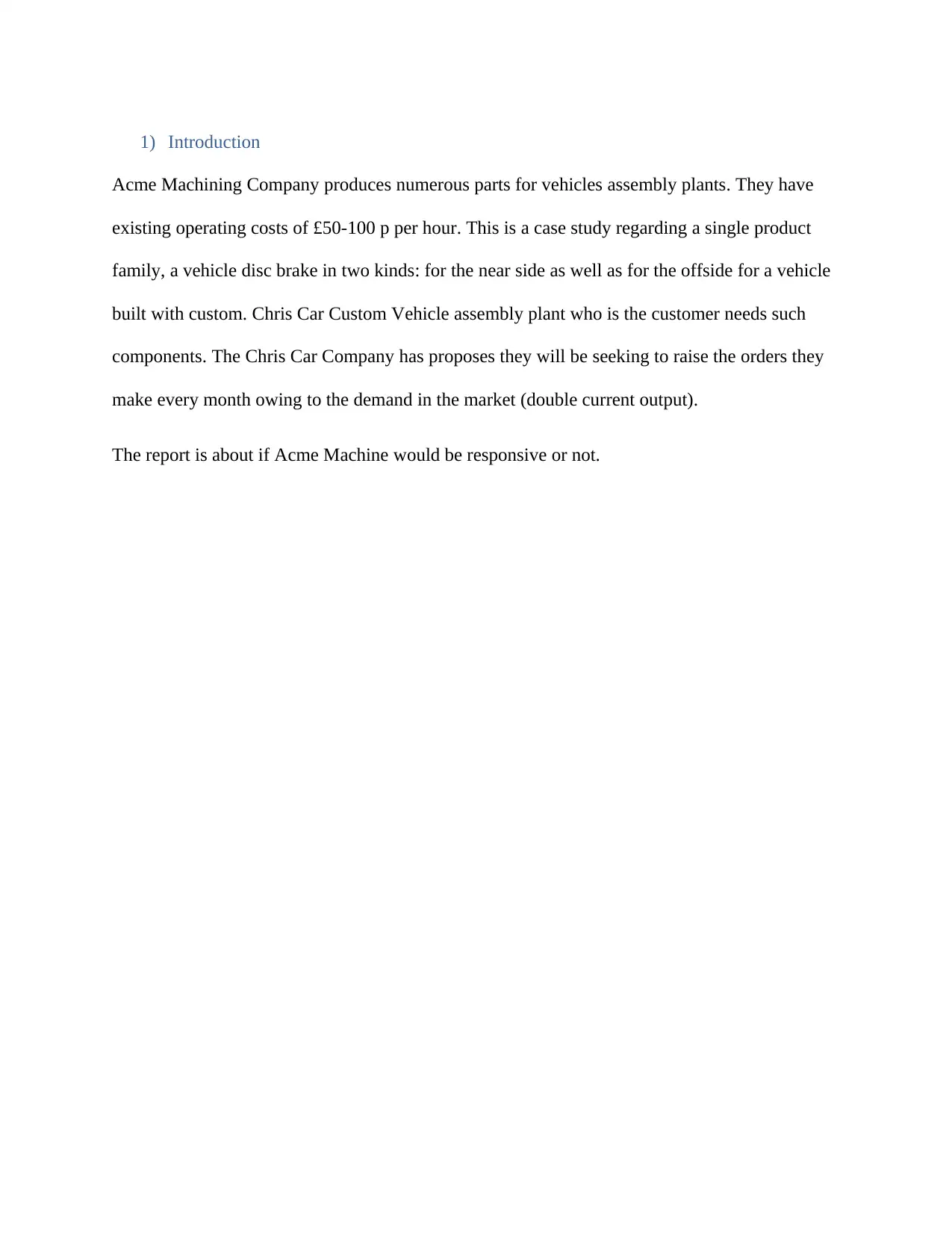
Acme Machining Company produces numerous parts for vehicles assembly plants. They have
existing operating costs of £50-100 p per hour. This is a case study regarding a single product
family, a vehicle disc brake in two kinds: for the near side as well as for the offside for a vehicle
built with custom. Chris Car Custom Vehicle assembly plant who is the customer needs such
components. The Chris Car Company has proposes they will be seeking to raise the orders they
make every month owing to the demand in the market (double current output).
The report is about if Acme Machine would be responsive or not.
⊘ This is a preview!⊘
Do you want full access?
Subscribe today to unlock all pages.

Trusted by 1+ million students worldwide
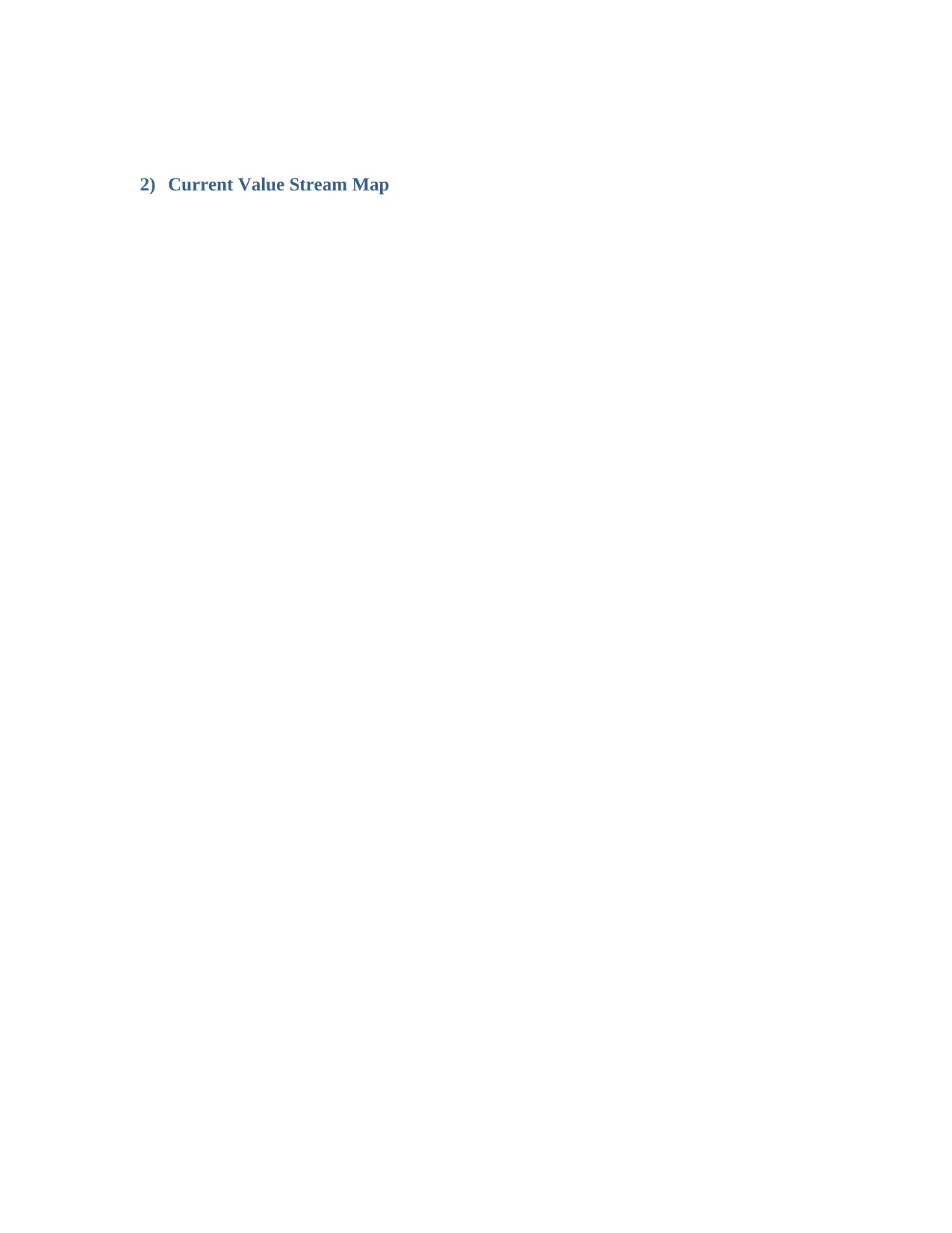
Paraphrase This Document
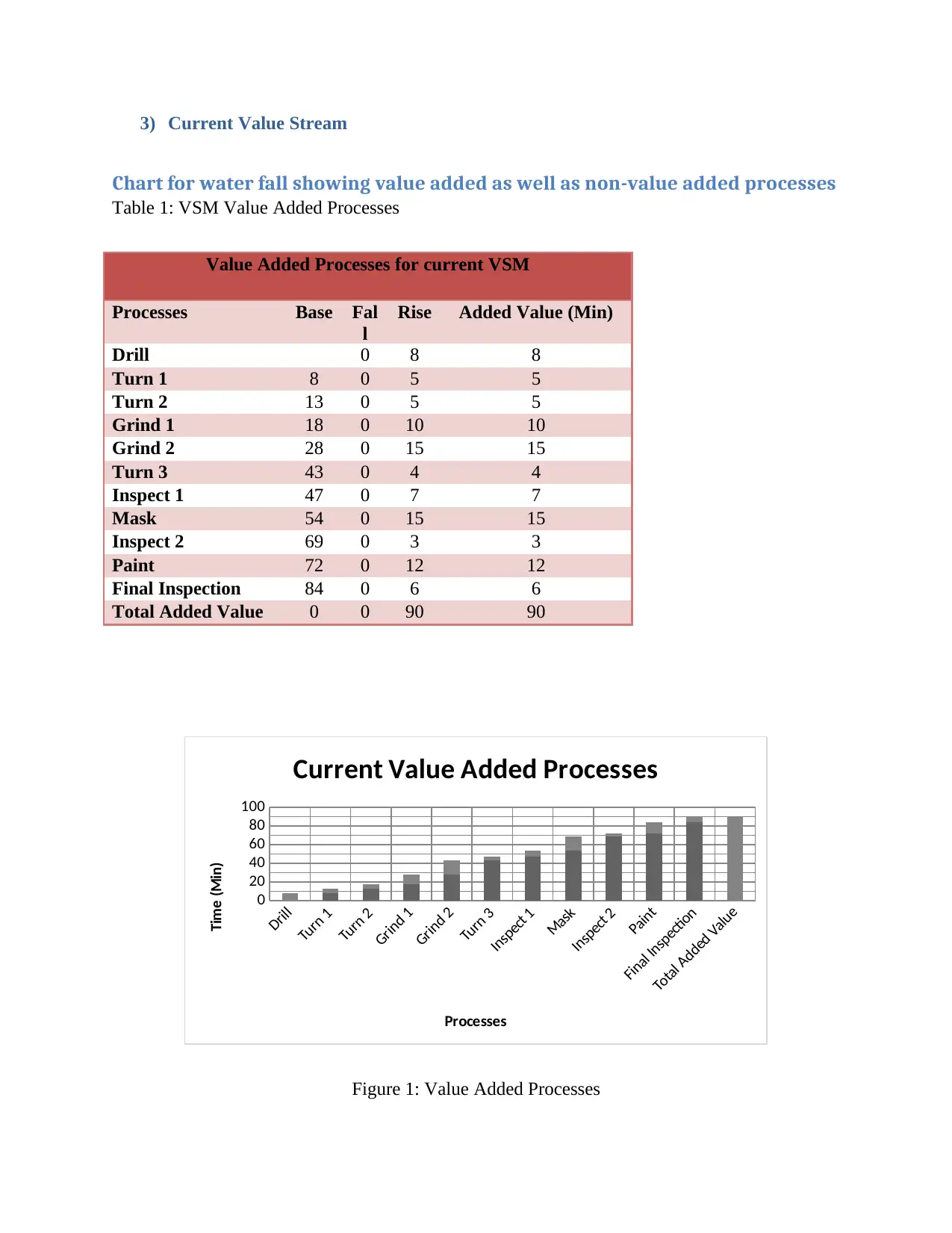
Chart for water fall showing value added as well as non-value added processes
Table 1: VSM Value Added Processes
Value Added Processes for current VSM
Processes Base Fal
l
Rise Added Value (Min)
Drill 0 8 8
Turn 1 8 0 5 5
Turn 2 13 0 5 5
Grind 1 18 0 10 10
Grind 2 28 0 15 15
Turn 3 43 0 4 4
Inspect 1 47 0 7 7
Mask 54 0 15 15
Inspect 2 69 0 3 3
Paint 72 0 12 12
Final Inspection 84 0 6 6
Total Added Value 0 0 90 90
Drill
Turn 1
Turn 2
Grind 1
Grind 2
Turn 3
Inspect 1
Mask
Inspect 2
Paint
Final Inspection
Total Added Value
0
20
40
60
80
100
Current Value Added Processes
Processes
Time (Min)
Figure 1: Value Added Processes
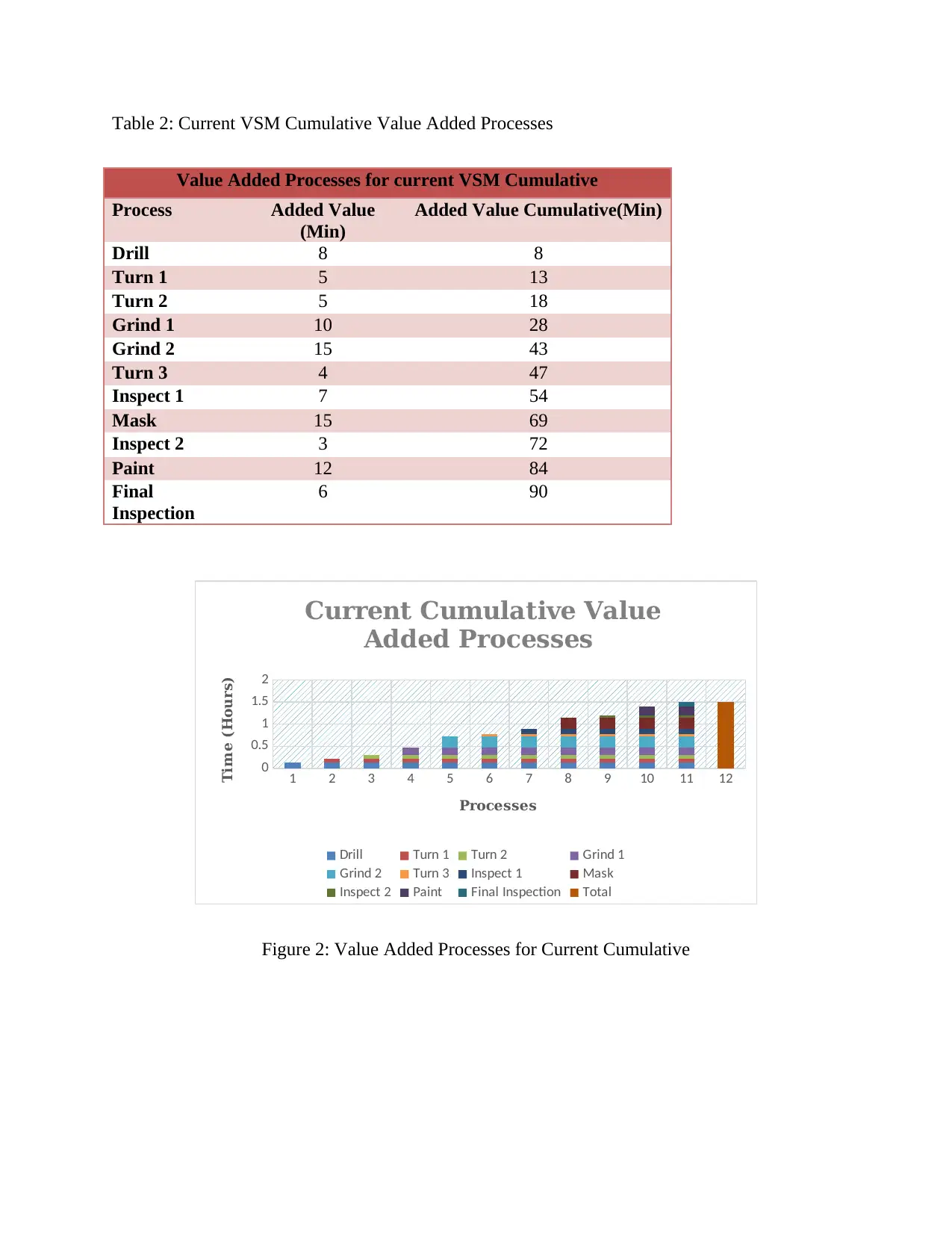
Value Added Processes for current VSM Cumulative
Process Added Value
(Min)
Added Value Cumulative(Min)
Drill 8 8
Turn 1 5 13
Turn 2 5 18
Grind 1 10 28
Grind 2 15 43
Turn 3 4 47
Inspect 1 7 54
Mask 15 69
Inspect 2 3 72
Paint 12 84
Final
Inspection
6 90
1 2 3 4 5 6 7 8 9 10 11 12
0
0.5
1
1.5
2
Current Cumulative Value
Added Processes
Drill Turn 1 Turn 2 Grind 1
Grind 2 Turn 3 Inspect 1 Mask
Inspect 2 Paint Final Inspection Total
Processes
Time (Hours)
Figure 2: Value Added Processes for Current Cumulative
⊘ This is a preview!⊘
Do you want full access?
Subscribe today to unlock all pages.

Trusted by 1+ million students worldwide
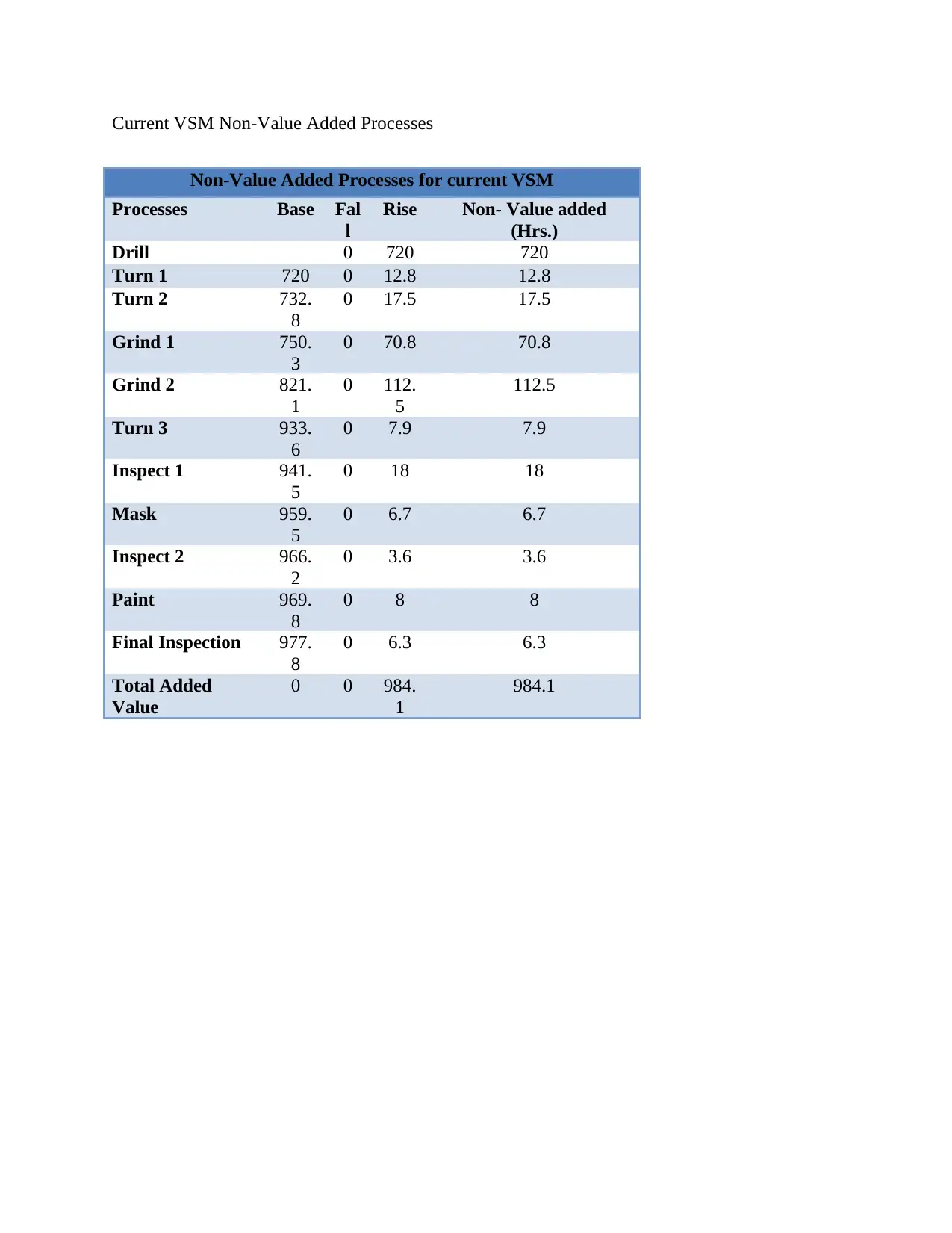
Non-Value Added Processes for current VSM
Processes Base Fal
l
Rise Non- Value added
(Hrs.)
Drill 0 720 720
Turn 1 720 0 12.8 12.8
Turn 2 732.
8
0 17.5 17.5
Grind 1 750.
3
0 70.8 70.8
Grind 2 821.
1
0 112.
5
112.5
Turn 3 933.
6
0 7.9 7.9
Inspect 1 941.
5
0 18 18
Mask 959.
5
0 6.7 6.7
Inspect 2 966.
2
0 3.6 3.6
Paint 969.
8
0 8 8
Final Inspection 977.
8
0 6.3 6.3
Total Added
Value
0 0 984.
1
984.1
Paraphrase This Document
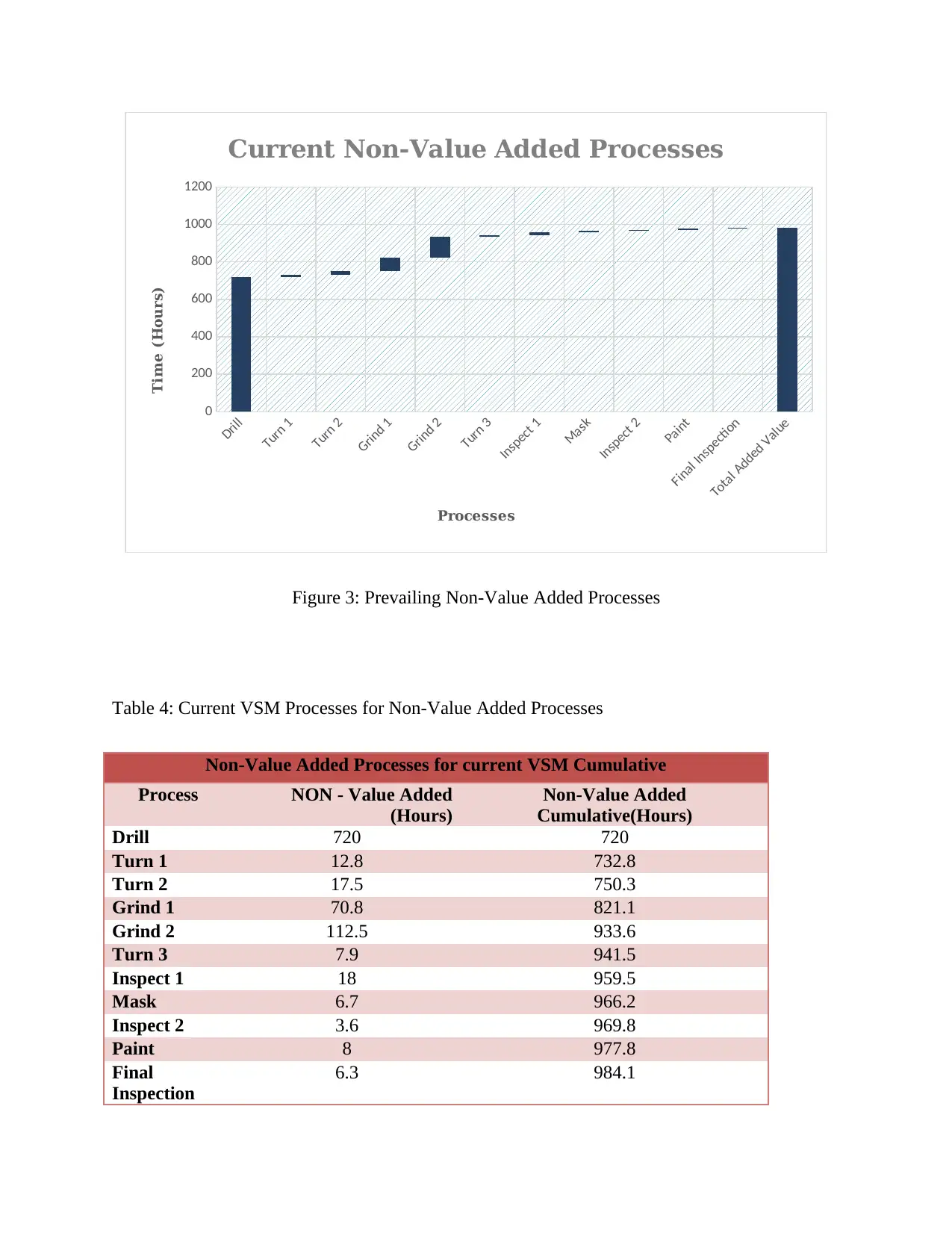
Turn 1
Turn 2
Grind 1
Grind 2
Turn 3
Inspect 1
Mask
Inspect 2
Paint
Final Inspection
Total Added Value
0
200
400
600
800
1000
1200
Current Non-Value Added Processes
Processes
Time (Hours)
Figure 3: Prevailing Non-Value Added Processes
Table 4: Current VSM Processes for Non-Value Added Processes
Non-Value Added Processes for current VSM Cumulative
Process NON - Value Added
(Hours)
Non-Value Added
Cumulative(Hours)
Drill 720 720
Turn 1 12.8 732.8
Turn 2 17.5 750.3
Grind 1 70.8 821.1
Grind 2 112.5 933.6
Turn 3 7.9 941.5
Inspect 1 18 959.5
Mask 6.7 966.2
Inspect 2 3.6 969.8
Paint 8 977.8
Final
Inspection
6.3 984.1
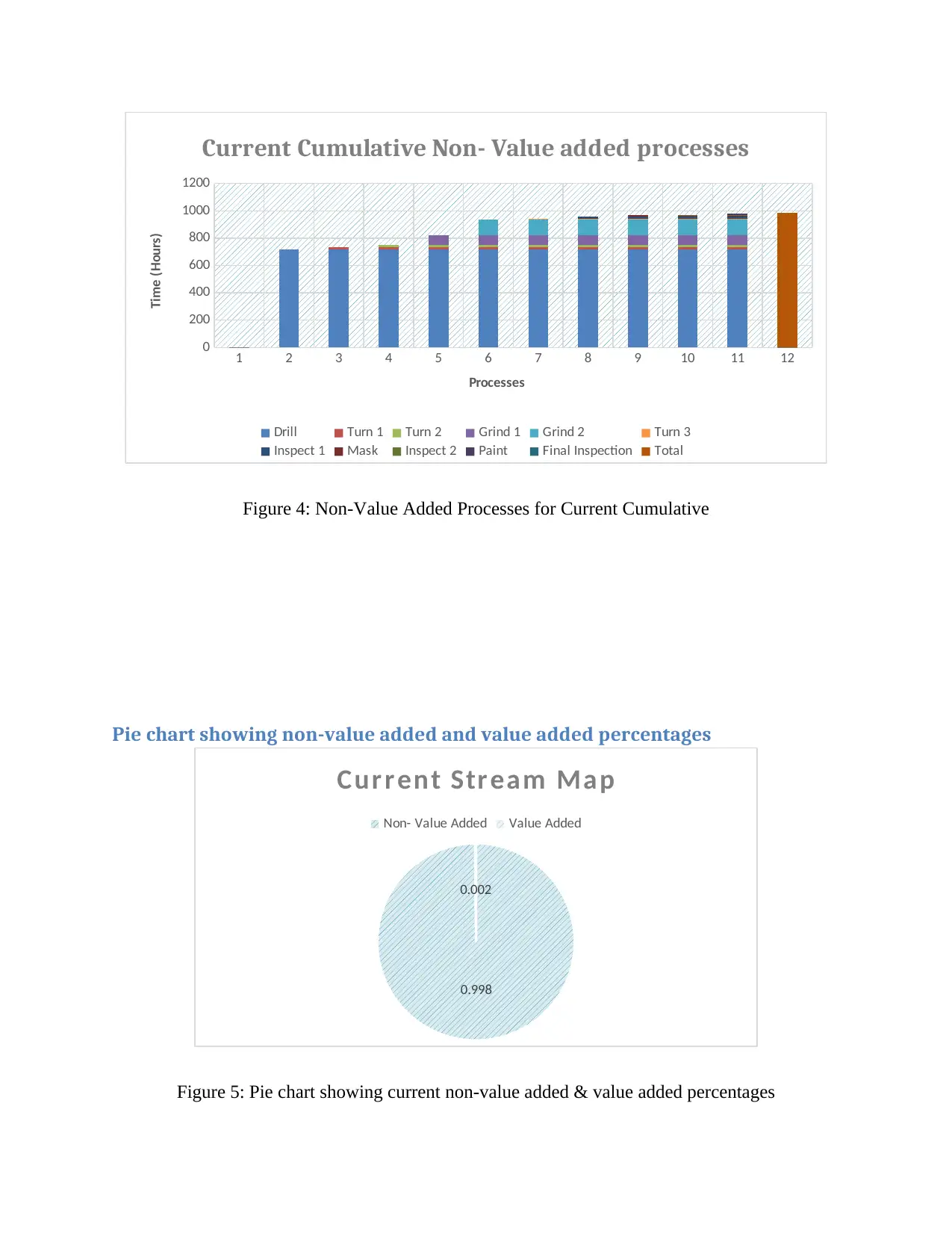
0
200
400
600
800
1000
1200
Current Cumulative Non- Value added processes
Drill Turn 1 Turn 2 Grind 1 Grind 2 Turn 3
Inspect 1 Mask Inspect 2 Paint Final Inspection Total
Processes
Time (Hours)
Figure 4: Non-Value Added Processes for Current Cumulative
Pie chart showing non-value added and value added percentages
0.998
0.002
Cur rent Str eam Map
Non- Value Added Value Added
Figure 5: Pie chart showing current non-value added & value added percentages
⊘ This is a preview!⊘
Do you want full access?
Subscribe today to unlock all pages.

Trusted by 1+ million students worldwide
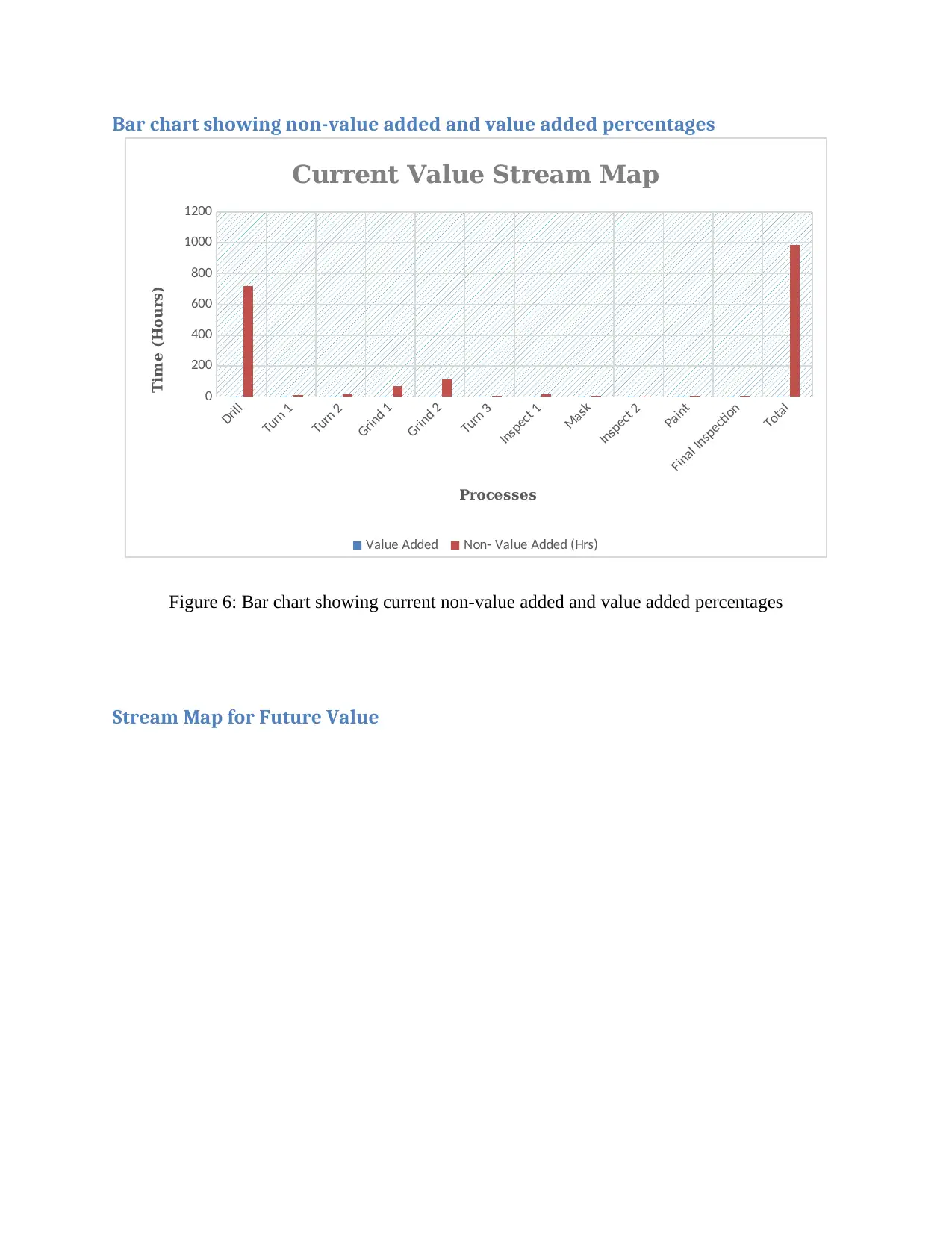
Drill
Turn 1
Turn 2
Grind 1
Grind 2
Turn 3
Inspect 1
Mask
Inspect 2
Paint
Final Inspection
Total
0
200
400
600
800
1000
1200
Current Value Stream Map
Value Added Non- Value Added (Hrs)
Processes
Time (Hours)
Figure 6: Bar chart showing current non-value added and value added percentages
Stream Map for Future Value
Paraphrase This Document
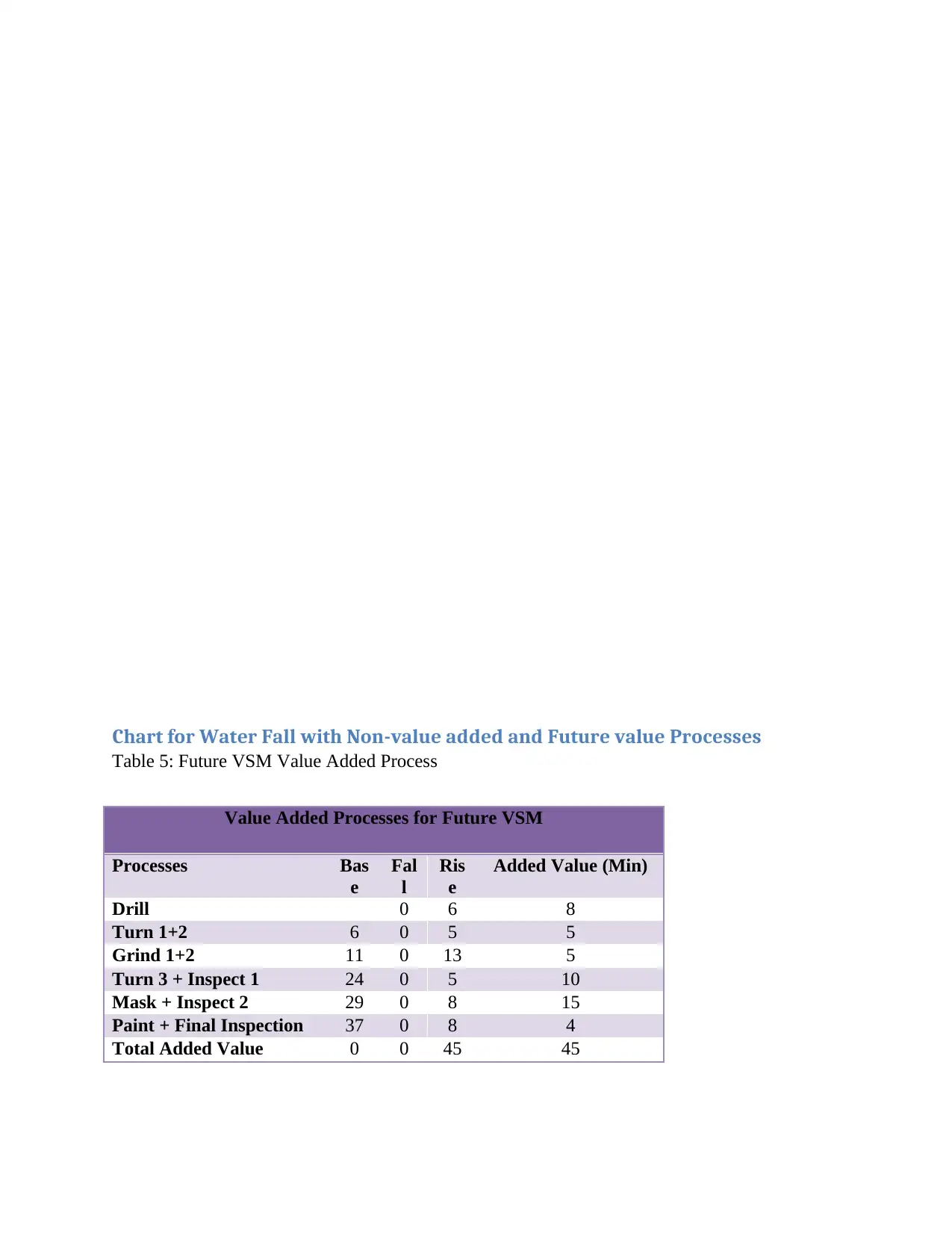
Table 5: Future VSM Value Added Process
Value Added Processes for Future VSM
Processes Bas
e
Fal
l
Ris
e
Added Value (Min)
Drill 0 6 8
Turn 1+2 6 0 5 5
Grind 1+2 11 0 13 5
Turn 3 + Inspect 1 24 0 5 10
Mask + Inspect 2 29 0 8 15
Paint + Final Inspection 37 0 8 4
Total Added Value 0 0 45 45

Table 6: Future VSM Cumulative Value Added Processes
Value Added Processes for future VSM Cumulative
Processes Added Value
(Min)
Added Value Cumulative
(Min)
Drill 6 6
Turn 1+2 5 11
Grind 1+2 13 24
Turn 3 + Inspect 1 5 29
Mask + Inspect 2 8 37
Paint + Final
Inspection
8 45
Total Added Value 0 45
⊘ This is a preview!⊘
Do you want full access?
Subscribe today to unlock all pages.

Trusted by 1+ million students worldwide
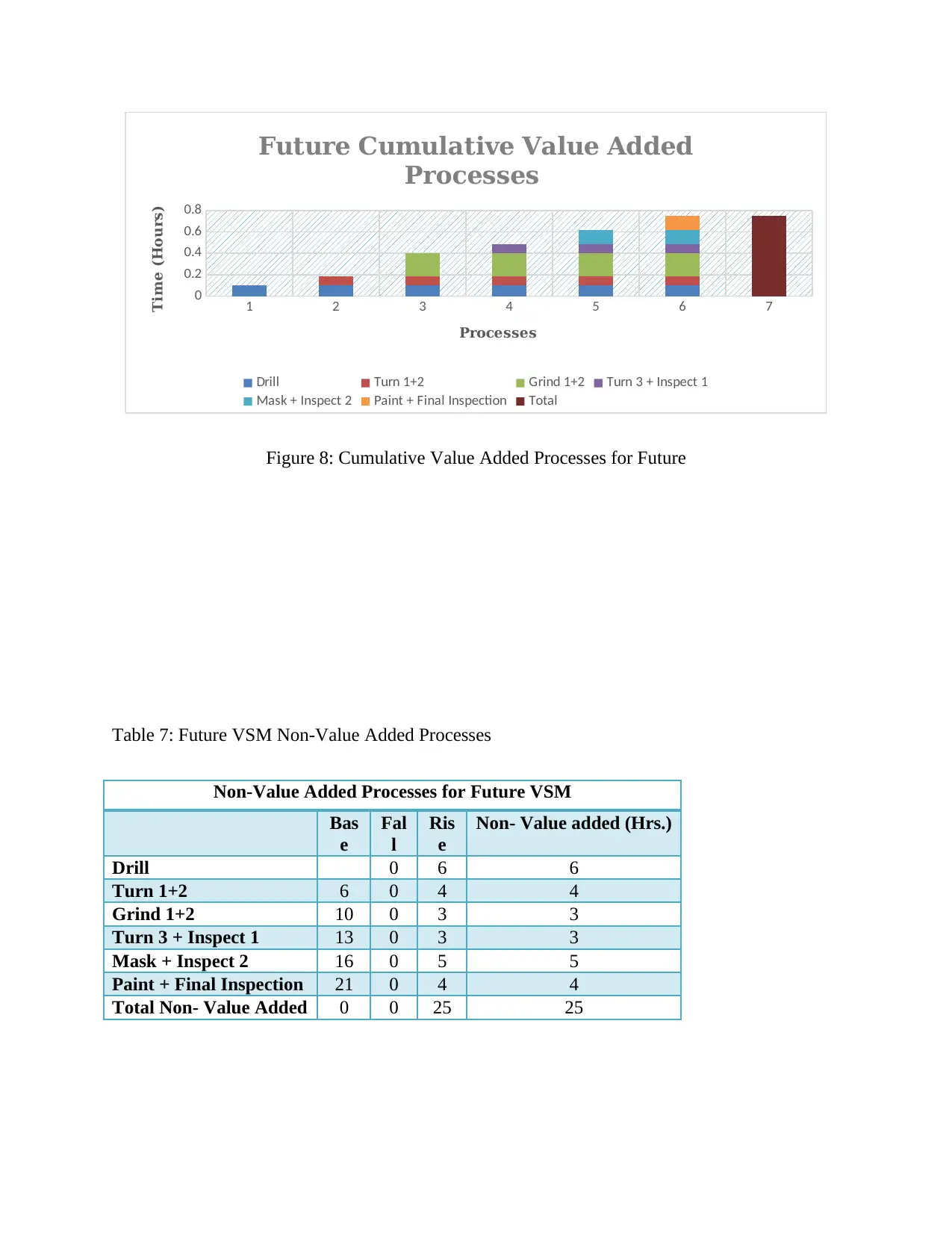
0
0.2
0.4
0.6
0.8
Future Cumulative Value Added
Processes
Drill Turn 1+2 Grind 1+2 Turn 3 + Inspect 1
Mask + Inspect 2 Paint + Final Inspection Total
Processes
Time (Hours)
Figure 8: Cumulative Value Added Processes for Future
Table 7: Future VSM Non-Value Added Processes
Non-Value Added Processes for Future VSM
Bas
e
Fal
l
Ris
e
Non- Value added (Hrs.)
Drill 0 6 6
Turn 1+2 6 0 4 4
Grind 1+2 10 0 3 3
Turn 3 + Inspect 1 13 0 3 3
Mask + Inspect 2 16 0 5 5
Paint + Final Inspection 21 0 4 4
Total Non- Value Added 0 0 25 25
Paraphrase This Document
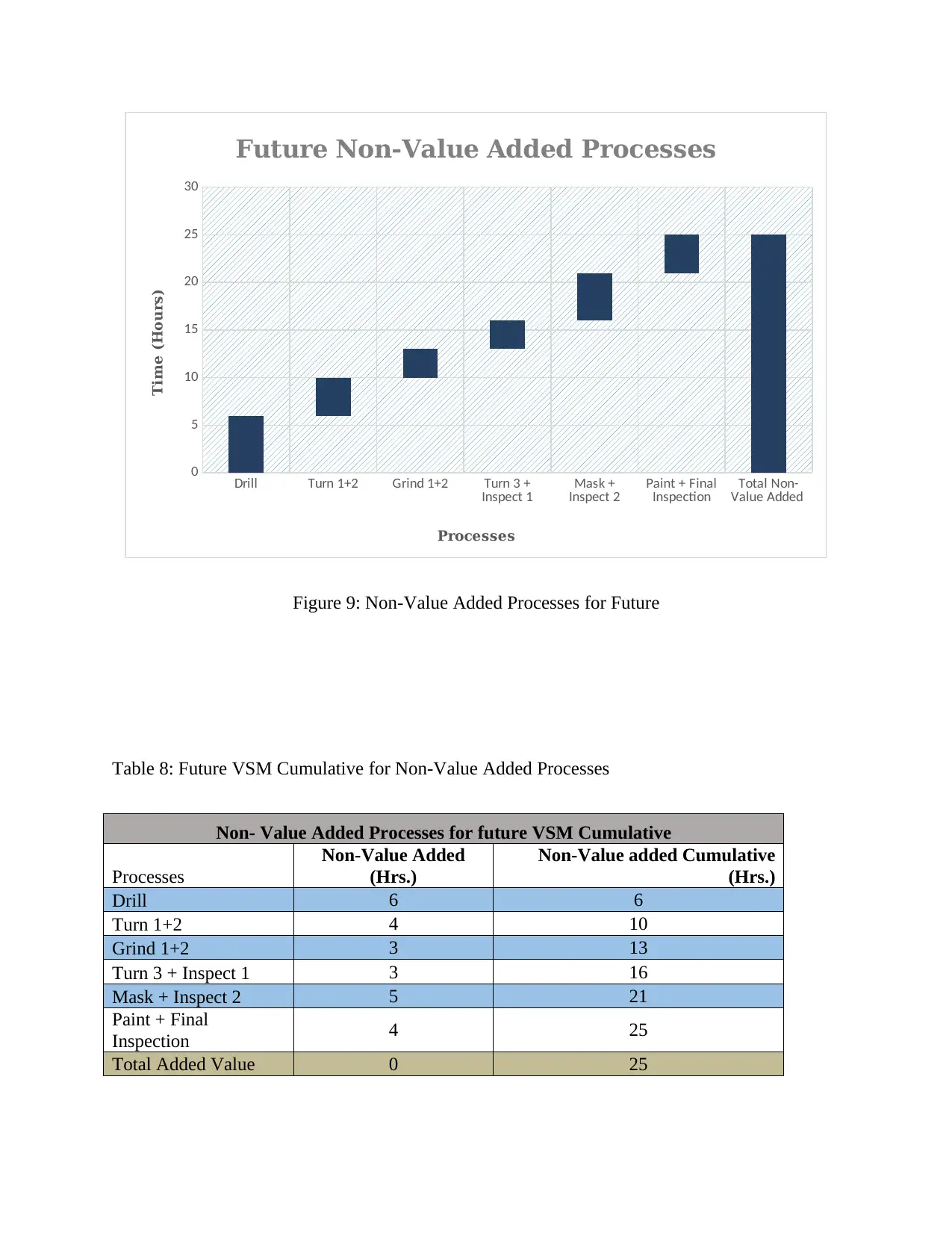
Inspect 1 Mask +
Inspect 2 Paint + Final
Inspection Total Non-
Value Added
0
5
10
15
20
25
30
Future Non-Value Added Processes
Processes
Time (Hours)
Figure 9: Non-Value Added Processes for Future
Table 8: Future VSM Cumulative for Non-Value Added Processes
Non- Value Added Processes for future VSM Cumulative
Processes
Non-Value Added
(Hrs.)
Non-Value added Cumulative
(Hrs.)
Drill 6 6
Turn 1+2 4 10
Grind 1+2 3 13
Turn 3 + Inspect 1 3 16
Mask + Inspect 2 5 21
Paint + Final
Inspection 4 25
Total Added Value 0 25
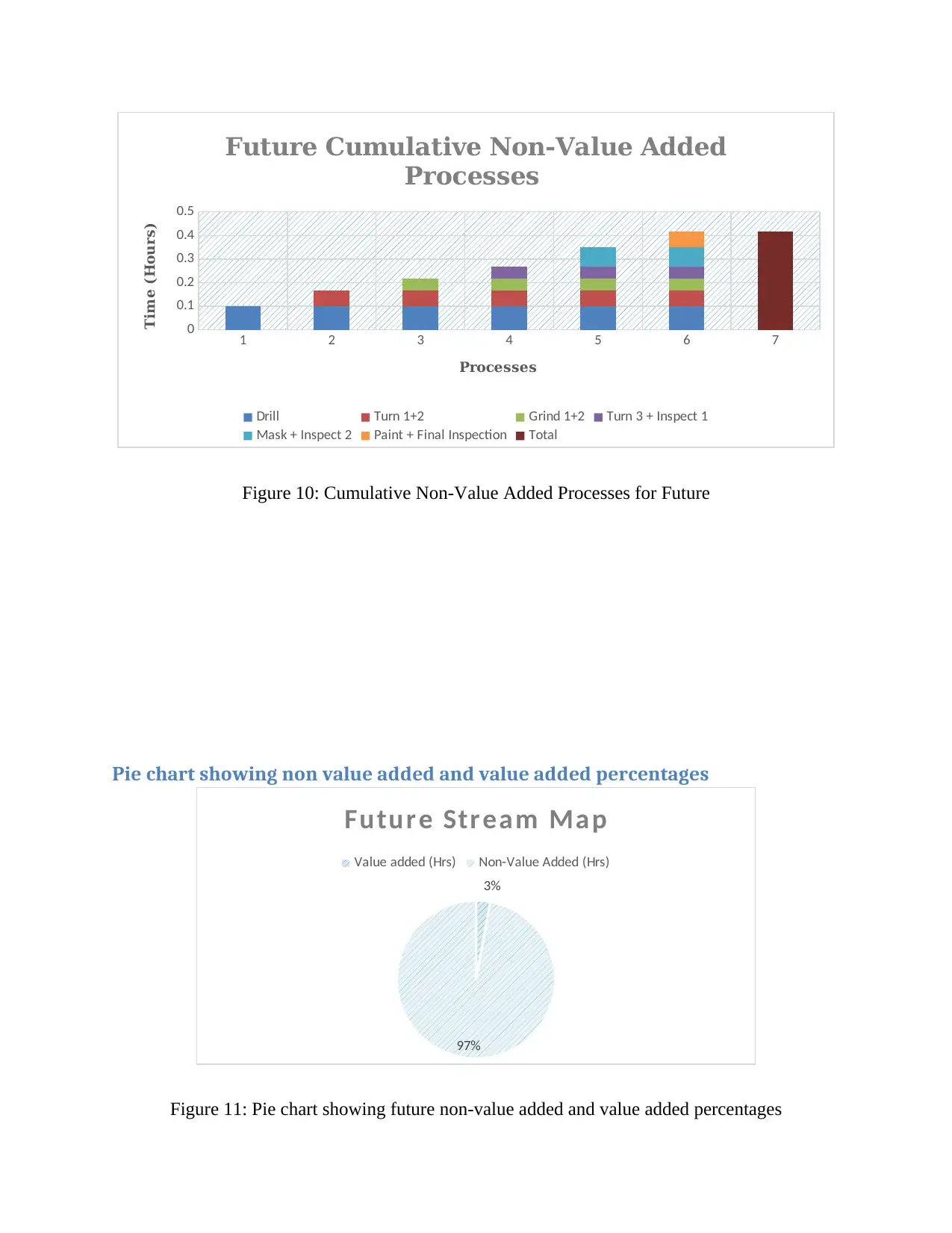
0
0.1
0.2
0.3
0.4
0.5
Future Cumulative Non-Value Added
Processes
Drill Turn 1+2 Grind 1+2 Turn 3 + Inspect 1
Mask + Inspect 2 Paint + Final Inspection Total
Processes
Time (Hours)
Figure 10: Cumulative Non-Value Added Processes for Future
Pie chart showing non value added and value added percentages
3%
97%
Future Stream Map
Value added (Hrs) Non-Value Added (Hrs)
Figure 11: Pie chart showing future non-value added and value added percentages
⊘ This is a preview!⊘
Do you want full access?
Subscribe today to unlock all pages.

Trusted by 1+ million students worldwide
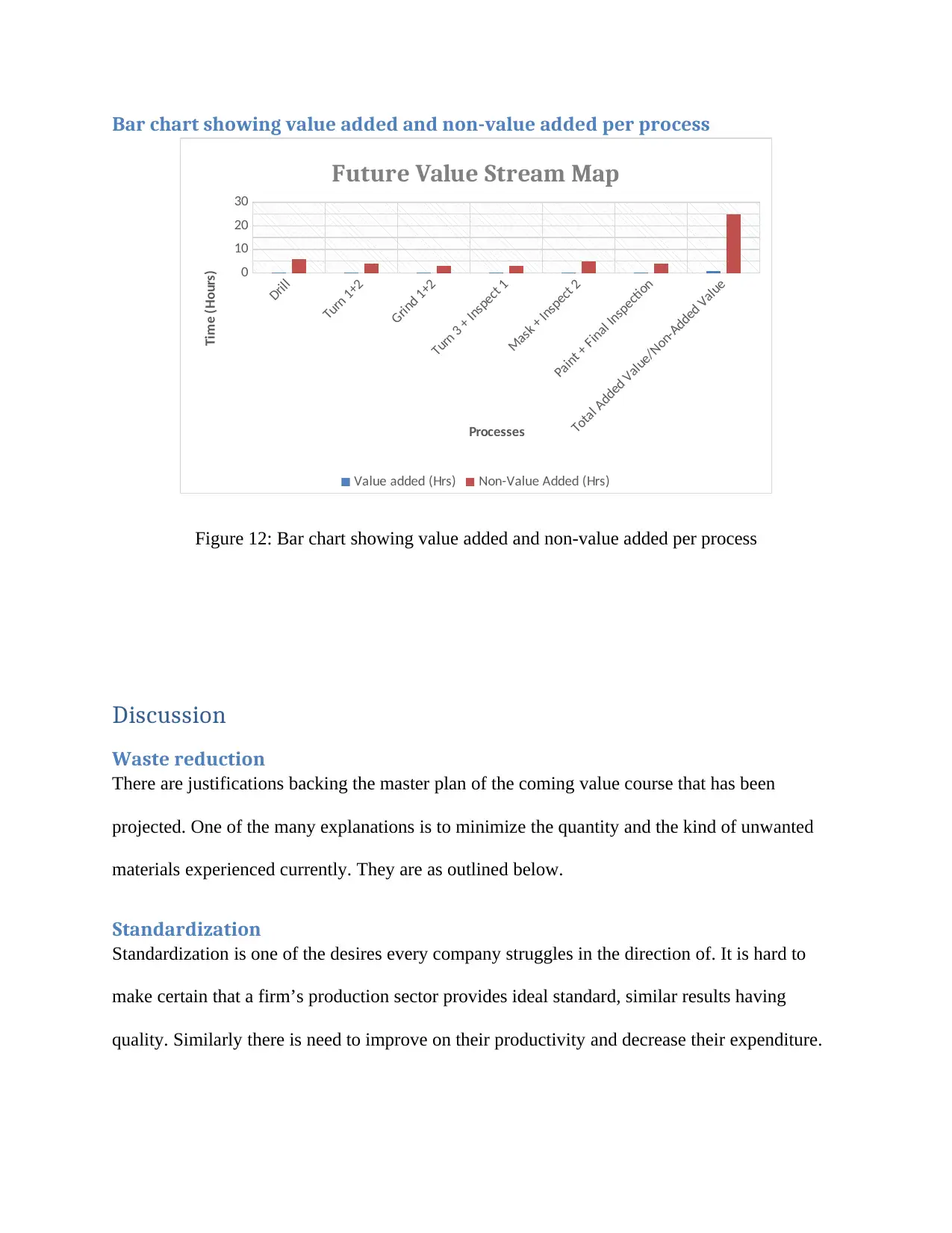
Drill
Turn 1+2
Grind 1+2
Turn 3 + Inspect 1
Mask + Inspect 2
Paint + Final Inspection
Total Added Value/Non-Added Value
0
10
20
30
Future Value Stream Map
Value added (Hrs) Non-Value Added (Hrs)
Processes
Time (Hours)
Figure 12: Bar chart showing value added and non-value added per process
Discussion
Waste reduction
There are justifications backing the master plan of the coming value course that has been
projected. One of the many explanations is to minimize the quantity and the kind of unwanted
materials experienced currently. They are as outlined below.
Standardization
Standardization is one of the desires every company struggles in the direction of. It is hard to
make certain that a firm’s production sector provides ideal standard, similar results having
quality. Similarly there is need to improve on their productivity and decrease their expenditure.
Paraphrase This Document
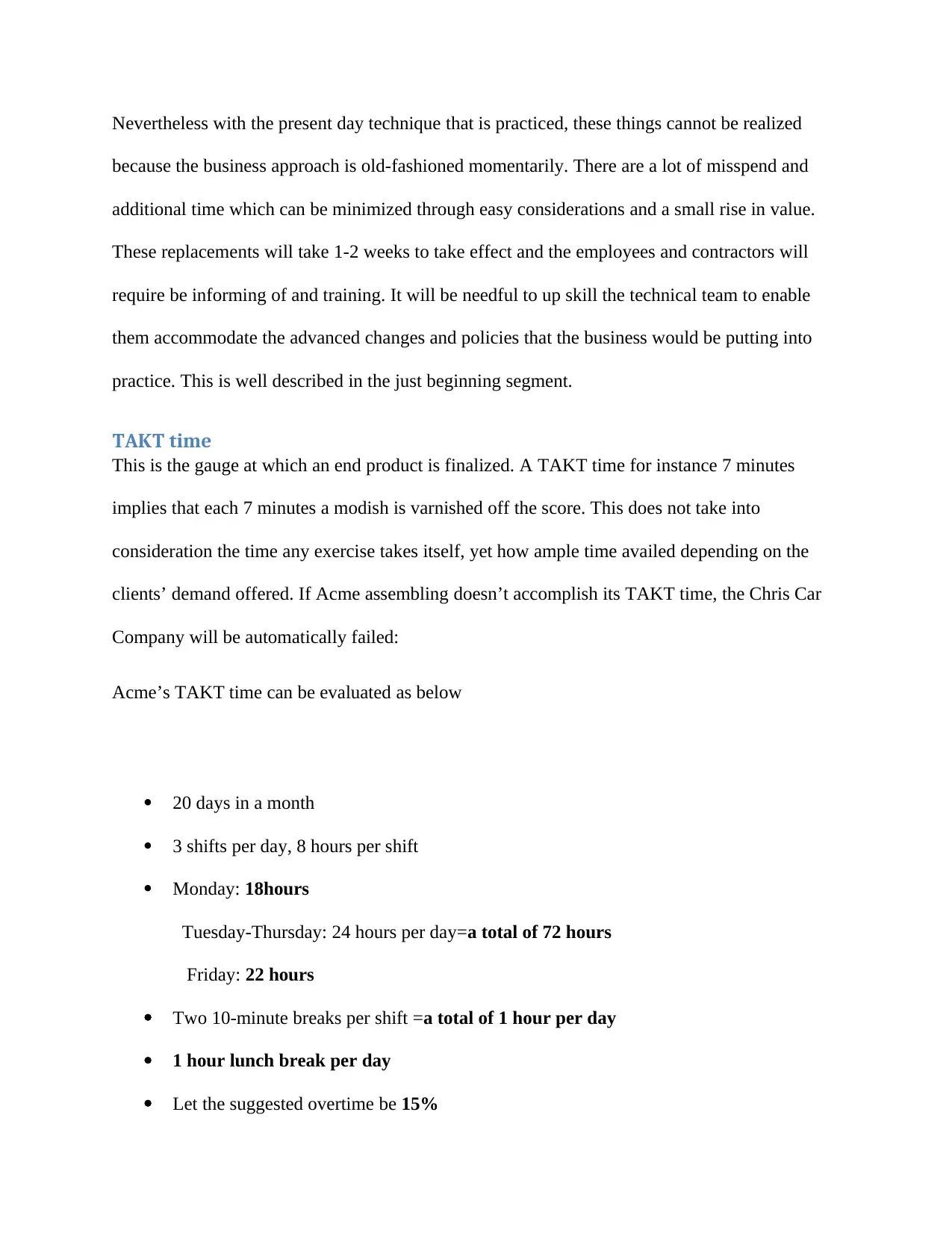
because the business approach is old-fashioned momentarily. There are a lot of misspend and
additional time which can be minimized through easy considerations and a small rise in value.
These replacements will take 1-2 weeks to take effect and the employees and contractors will
require be informing of and training. It will be needful to up skill the technical team to enable
them accommodate the advanced changes and policies that the business would be putting into
practice. This is well described in the just beginning segment.
TAKT time
This is the gauge at which an end product is finalized. A TAKT time for instance 7 minutes
implies that each 7 minutes a modish is varnished off the score. This does not take into
consideration the time any exercise takes itself, yet how ample time availed depending on the
clients’ demand offered. If Acme assembling doesn’t accomplish its TAKT time, the Chris Car
Company will be automatically failed:
Acme’s TAKT time can be evaluated as below
20 days in a month
3 shifts per day, 8 hours per shift
Monday: 18hours
Tuesday-Thursday: 24 hours per day=a total of 72 hours
Friday: 22 hours
Two 10-minute breaks per shift =a total of 1 hour per day
1 hour lunch break per day
Let the suggested overtime be 15%
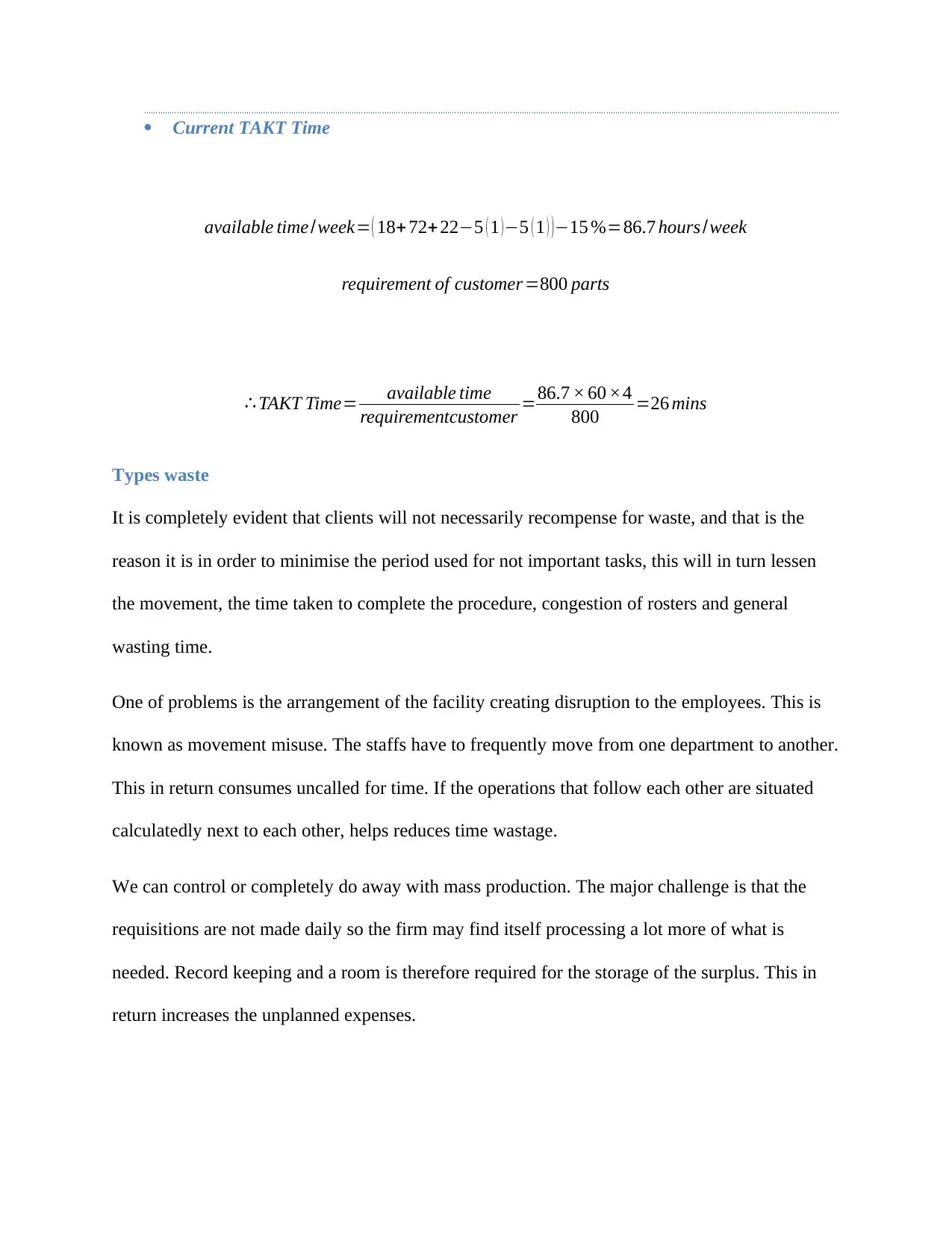
available time/week= ( 18+ 72+22−5 ( 1 )−5 ( 1 ) )−15 %=86.7 hours /week
requirement of customer =800 parts
∴ TAKT Time= available time
requirementcustomer =86.7 × 60 ×4
800 =26 mins
Types waste
It is completely evident that clients will not necessarily recompense for waste, and that is the
reason it is in order to minimise the period used for not important tasks, this will in turn lessen
the movement, the time taken to complete the procedure, congestion of rosters and general
wasting time.
One of problems is the arrangement of the facility creating disruption to the employees. This is
known as movement misuse. The staffs have to frequently move from one department to another.
This in return consumes uncalled for time. If the operations that follow each other are situated
calculatedly next to each other, helps reduces time wastage.
We can control or completely do away with mass production. The major challenge is that the
requisitions are not made daily so the firm may find itself processing a lot more of what is
needed. Record keeping and a room is therefore required for the storage of the surplus. This in
return increases the unplanned expenses.
⊘ This is a preview!⊘
Do you want full access?
Subscribe today to unlock all pages.

Trusted by 1+ million students worldwide
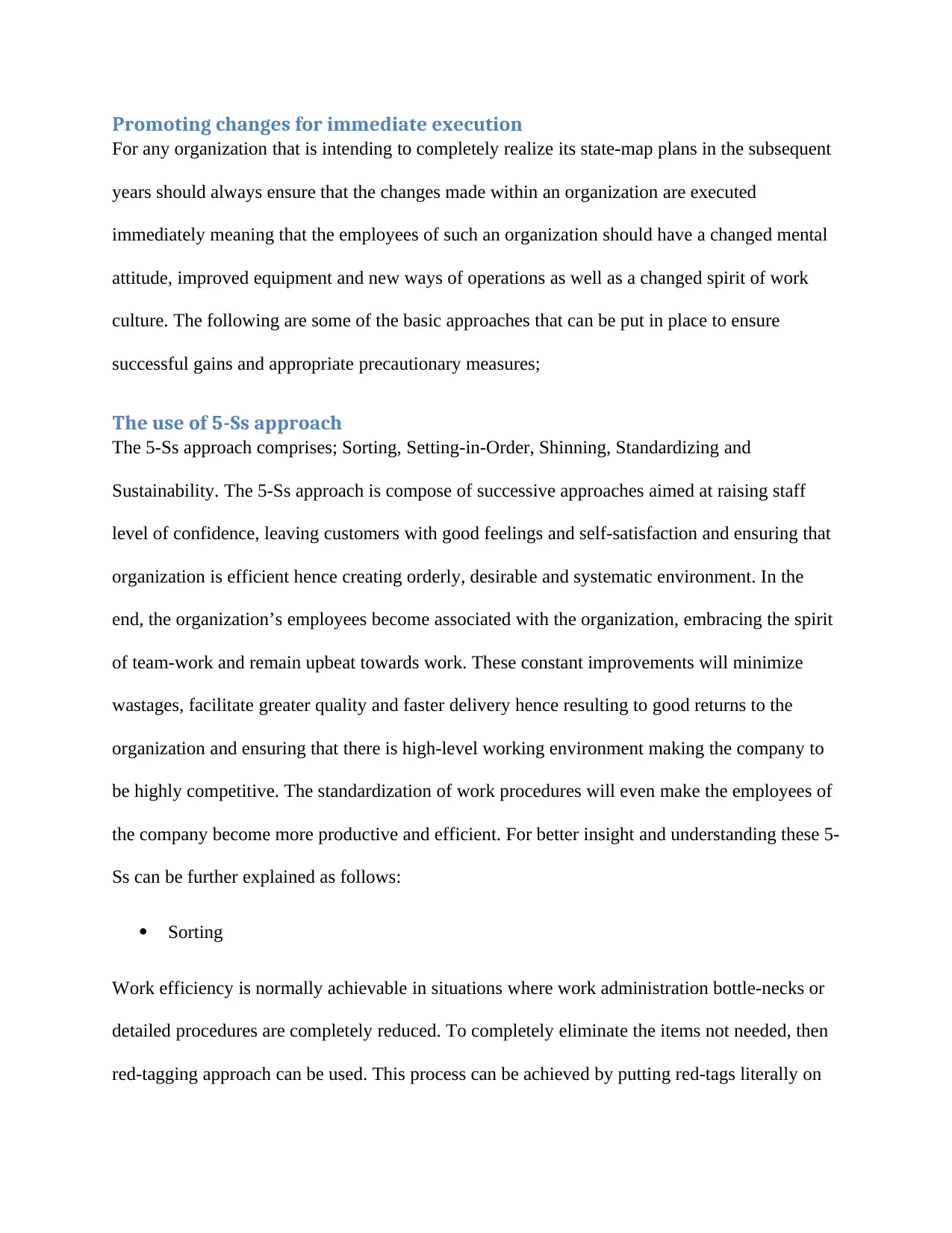
For any organization that is intending to completely realize its state-map plans in the subsequent
years should always ensure that the changes made within an organization are executed
immediately meaning that the employees of such an organization should have a changed mental
attitude, improved equipment and new ways of operations as well as a changed spirit of work
culture. The following are some of the basic approaches that can be put in place to ensure
successful gains and appropriate precautionary measures;
The use of 5-Ss approach
The 5-Ss approach comprises; Sorting, Setting-in-Order, Shinning, Standardizing and
Sustainability. The 5-Ss approach is compose of successive approaches aimed at raising staff
level of confidence, leaving customers with good feelings and self-satisfaction and ensuring that
organization is efficient hence creating orderly, desirable and systematic environment. In the
end, the organization’s employees become associated with the organization, embracing the spirit
of team-work and remain upbeat towards work. These constant improvements will minimize
wastages, facilitate greater quality and faster delivery hence resulting to good returns to the
organization and ensuring that there is high-level working environment making the company to
be highly competitive. The standardization of work procedures will even make the employees of
the company become more productive and efficient. For better insight and understanding these 5-
Ss can be further explained as follows:
Sorting
Work efficiency is normally achievable in situations where work administration bottle-necks or
detailed procedures are completely reduced. To completely eliminate the items not needed, then
red-tagging approach can be used. This process can be achieved by putting red-tags literally on
Paraphrase This Document
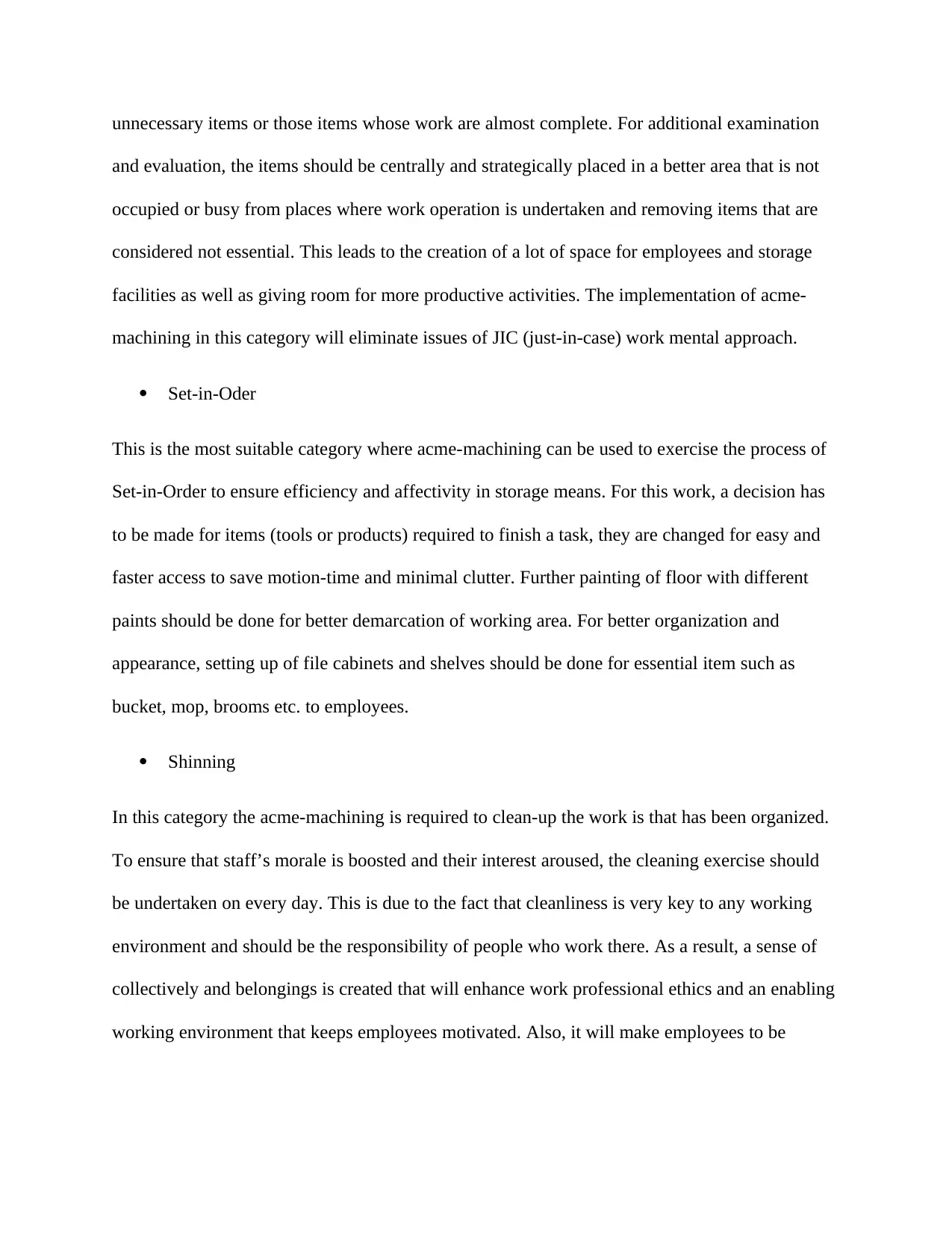
and evaluation, the items should be centrally and strategically placed in a better area that is not
occupied or busy from places where work operation is undertaken and removing items that are
considered not essential. This leads to the creation of a lot of space for employees and storage
facilities as well as giving room for more productive activities. The implementation of acme-
machining in this category will eliminate issues of JIC (just-in-case) work mental approach.
Set-in-Oder
This is the most suitable category where acme-machining can be used to exercise the process of
Set-in-Order to ensure efficiency and affectivity in storage means. For this work, a decision has
to be made for items (tools or products) required to finish a task, they are changed for easy and
faster access to save motion-time and minimal clutter. Further painting of floor with different
paints should be done for better demarcation of working area. For better organization and
appearance, setting up of file cabinets and shelves should be done for essential item such as
bucket, mop, brooms etc. to employees.
Shinning
In this category the acme-machining is required to clean-up the work is that has been organized.
To ensure that staff’s morale is boosted and their interest aroused, the cleaning exercise should
be undertaken on every day. This is due to the fact that cleanliness is very key to any working
environment and should be the responsibility of people who work there. As a result, a sense of
collectively and belongings is created that will enhance work professional ethics and an enabling
working environment that keeps employees motivated. Also, it will make employees to be
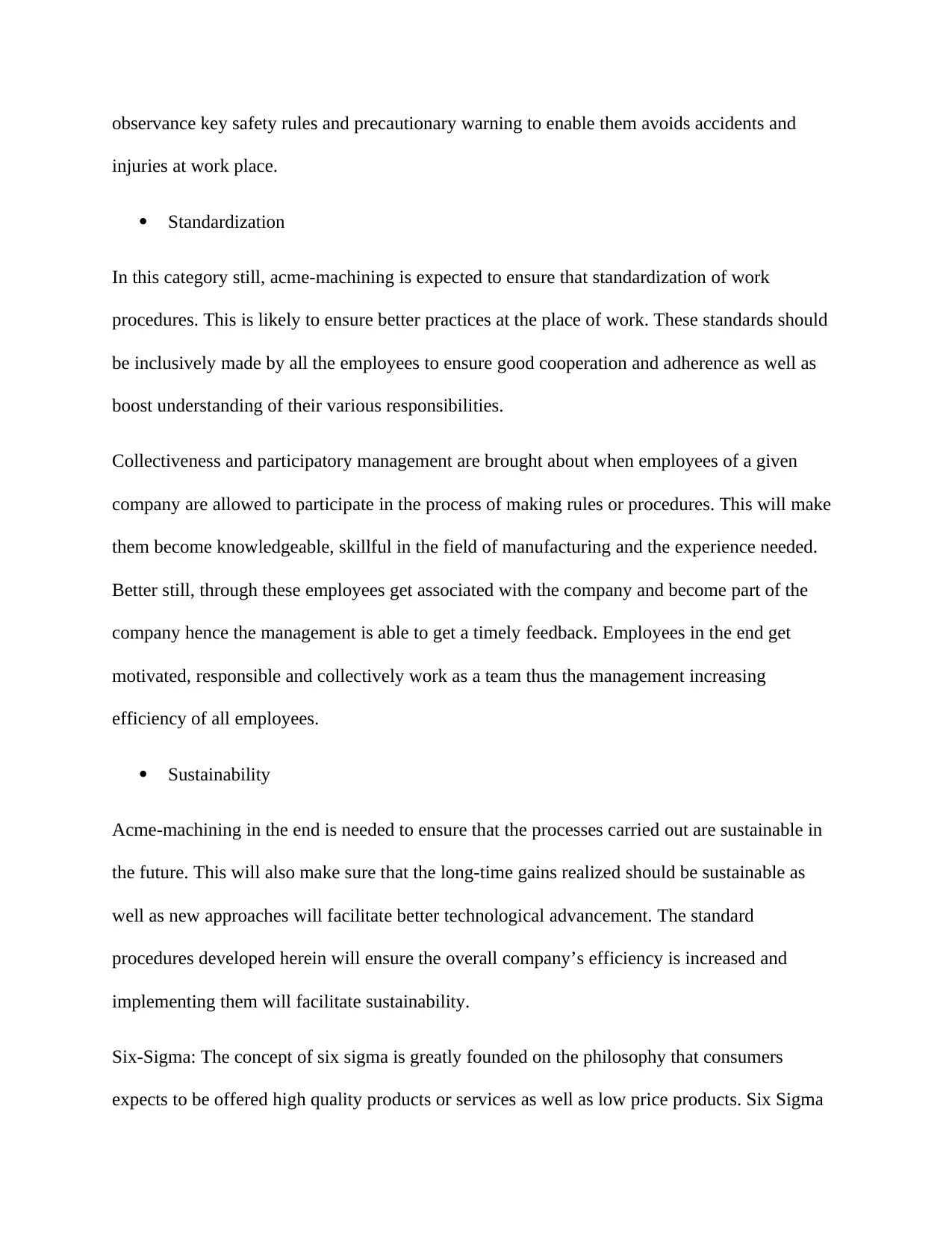
injuries at work place.
Standardization
In this category still, acme-machining is expected to ensure that standardization of work
procedures. This is likely to ensure better practices at the place of work. These standards should
be inclusively made by all the employees to ensure good cooperation and adherence as well as
boost understanding of their various responsibilities.
Collectiveness and participatory management are brought about when employees of a given
company are allowed to participate in the process of making rules or procedures. This will make
them become knowledgeable, skillful in the field of manufacturing and the experience needed.
Better still, through these employees get associated with the company and become part of the
company hence the management is able to get a timely feedback. Employees in the end get
motivated, responsible and collectively work as a team thus the management increasing
efficiency of all employees.
Sustainability
Acme-machining in the end is needed to ensure that the processes carried out are sustainable in
the future. This will also make sure that the long-time gains realized should be sustainable as
well as new approaches will facilitate better technological advancement. The standard
procedures developed herein will ensure the overall company’s efficiency is increased and
implementing them will facilitate sustainability.
Six-Sigma: The concept of six sigma is greatly founded on the philosophy that consumers
expects to be offered high quality products or services as well as low price products. Six Sigma
⊘ This is a preview!⊘
Do you want full access?
Subscribe today to unlock all pages.

Trusted by 1+ million students worldwide
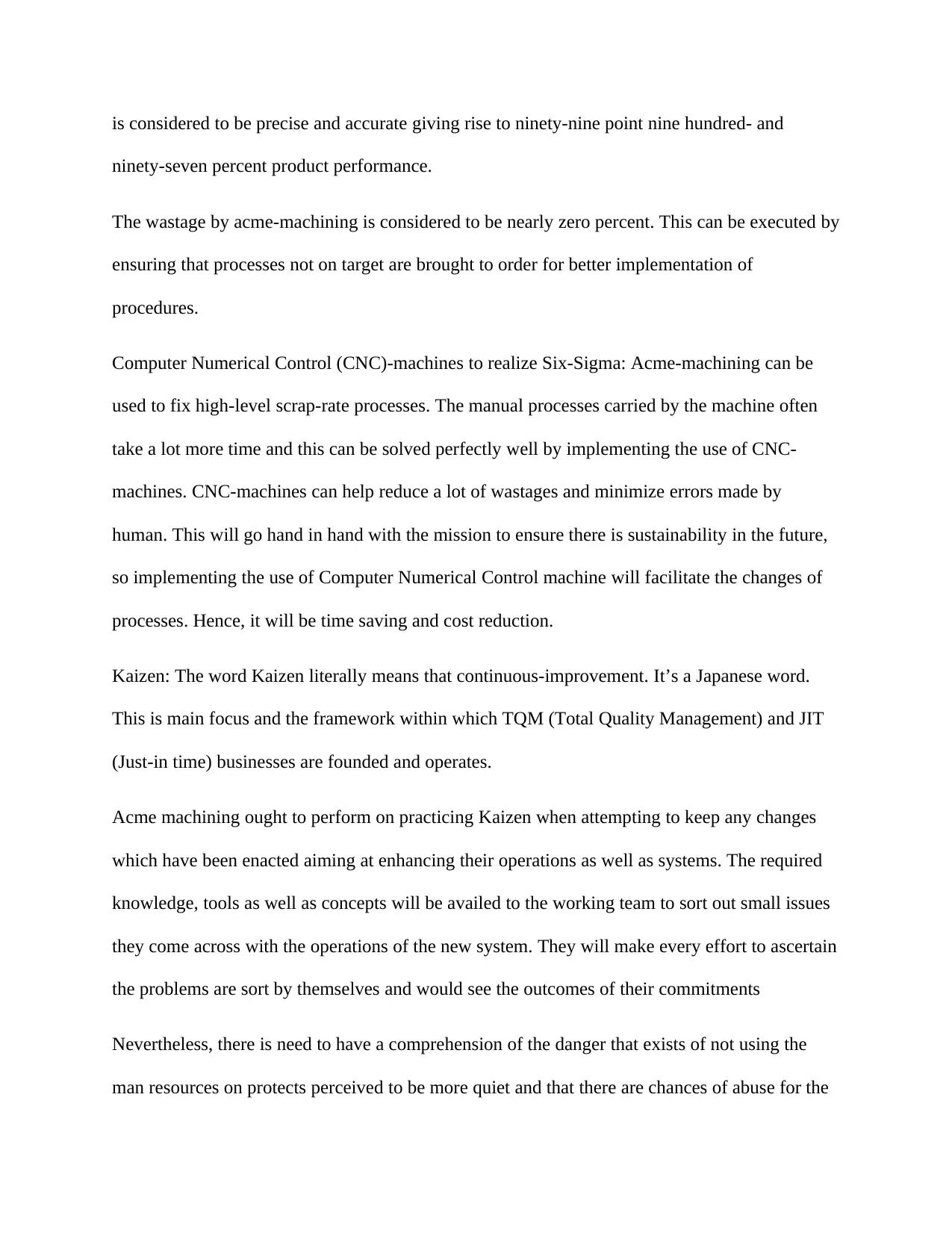
ninety-seven percent product performance.
The wastage by acme-machining is considered to be nearly zero percent. This can be executed by
ensuring that processes not on target are brought to order for better implementation of
procedures.
Computer Numerical Control (CNC)-machines to realize Six-Sigma: Acme-machining can be
used to fix high-level scrap-rate processes. The manual processes carried by the machine often
take a lot more time and this can be solved perfectly well by implementing the use of CNC-
machines. CNC-machines can help reduce a lot of wastages and minimize errors made by
human. This will go hand in hand with the mission to ensure there is sustainability in the future,
so implementing the use of Computer Numerical Control machine will facilitate the changes of
processes. Hence, it will be time saving and cost reduction.
Kaizen: The word Kaizen literally means that continuous-improvement. It’s a Japanese word.
This is main focus and the framework within which TQM (Total Quality Management) and JIT
(Just-in time) businesses are founded and operates.
Acme machining ought to perform on practicing Kaizen when attempting to keep any changes
which have been enacted aiming at enhancing their operations as well as systems. The required
knowledge, tools as well as concepts will be availed to the working team to sort out small issues
they come across with the operations of the new system. They will make every effort to ascertain
the problems are sort by themselves and would see the outcomes of their commitments
Nevertheless, there is need to have a comprehension of the danger that exists of not using the
man resources on protects perceived to be more quiet and that there are chances of abuse for the
Paraphrase This Document
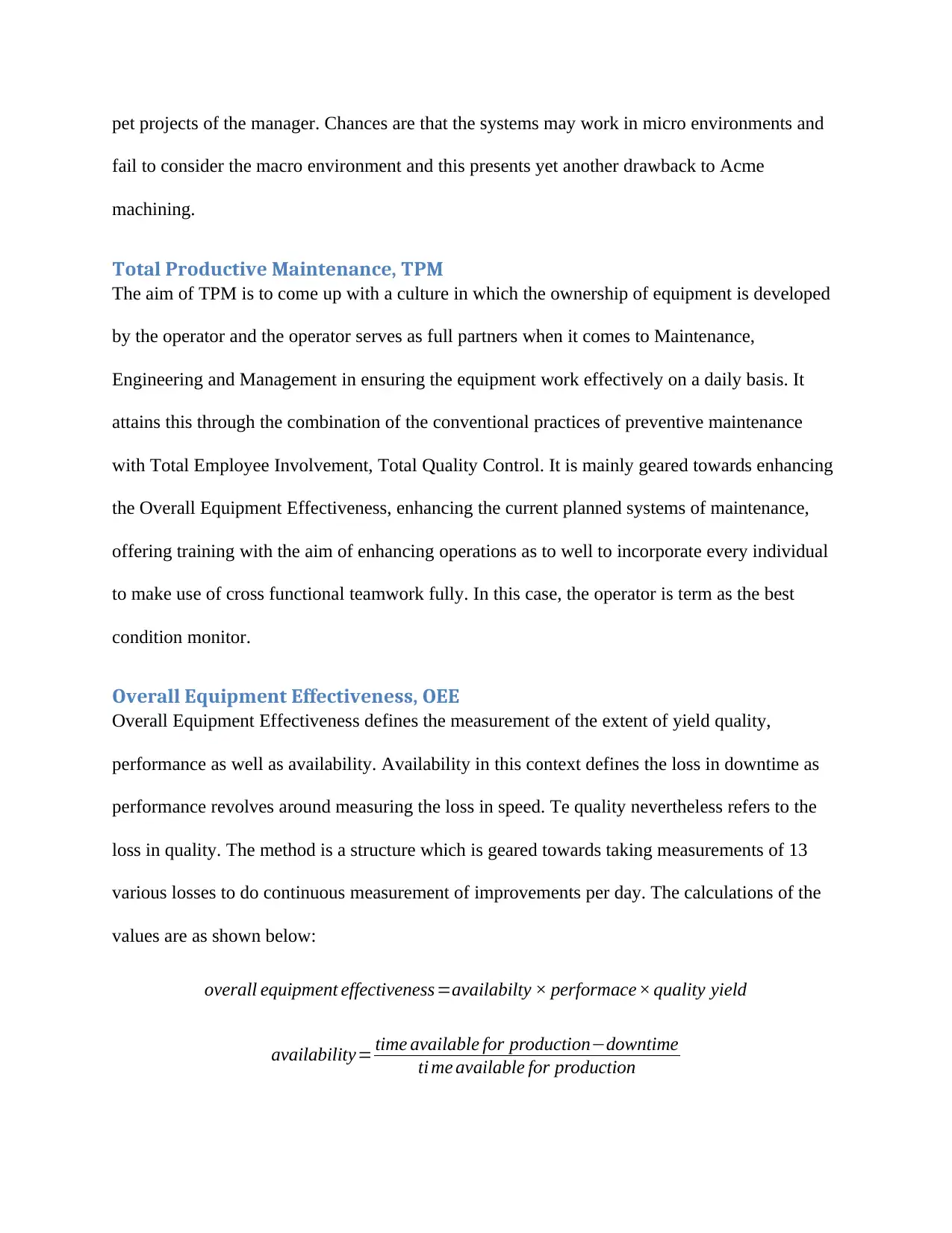
fail to consider the macro environment and this presents yet another drawback to Acme
machining.
Total Productive Maintenance, TPM
The aim of TPM is to come up with a culture in which the ownership of equipment is developed
by the operator and the operator serves as full partners when it comes to Maintenance,
Engineering and Management in ensuring the equipment work effectively on a daily basis. It
attains this through the combination of the conventional practices of preventive maintenance
with Total Employee Involvement, Total Quality Control. It is mainly geared towards enhancing
the Overall Equipment Effectiveness, enhancing the current planned systems of maintenance,
offering training with the aim of enhancing operations as to well to incorporate every individual
to make use of cross functional teamwork fully. In this case, the operator is term as the best
condition monitor.
Overall Equipment Effectiveness, OEE
Overall Equipment Effectiveness defines the measurement of the extent of yield quality,
performance as well as availability. Availability in this context defines the loss in downtime as
performance revolves around measuring the loss in speed. Te quality nevertheless refers to the
loss in quality. The method is a structure which is geared towards taking measurements of 13
various losses to do continuous measurement of improvements per day. The calculations of the
values are as shown below:
overall equipment effectiveness=availabilty × performace× quality yield
availability= time available for production−downtime
ti me available for production
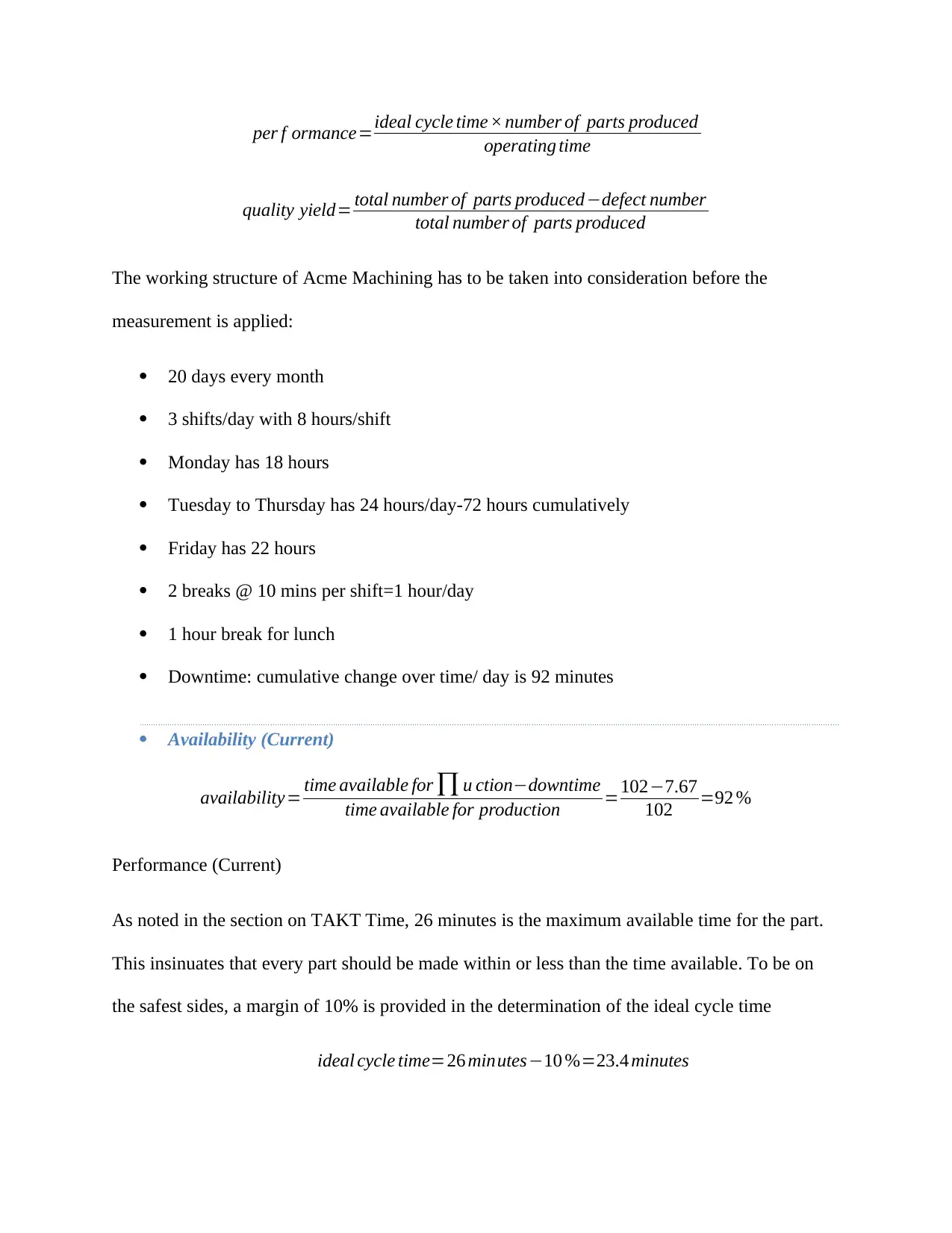
operating time
quality yield= total number of parts produced−defect number
total number of parts produced
The working structure of Acme Machining has to be taken into consideration before the
measurement is applied:
20 days every month
3 shifts/day with 8 hours/shift
Monday has 18 hours
Tuesday to Thursday has 24 hours/day-72 hours cumulatively
Friday has 22 hours
2 breaks @ 10 mins per shift=1 hour/day
1 hour break for lunch
Downtime: cumulative change over time/ day is 92 minutes
Availability (Current)
availability= time available for ∏ u ction−downtime
time available for production =102−7.67
102 =92 %
Performance (Current)
As noted in the section on TAKT Time, 26 minutes is the maximum available time for the part.
This insinuates that every part should be made within or less than the time available. To be on
the safest sides, a margin of 10% is provided in the determination of the ideal cycle time
ideal cycle time=26 minutes−10 %=23.4 minutes
⊘ This is a preview!⊘
Do you want full access?
Subscribe today to unlock all pages.

Trusted by 1+ million students worldwide
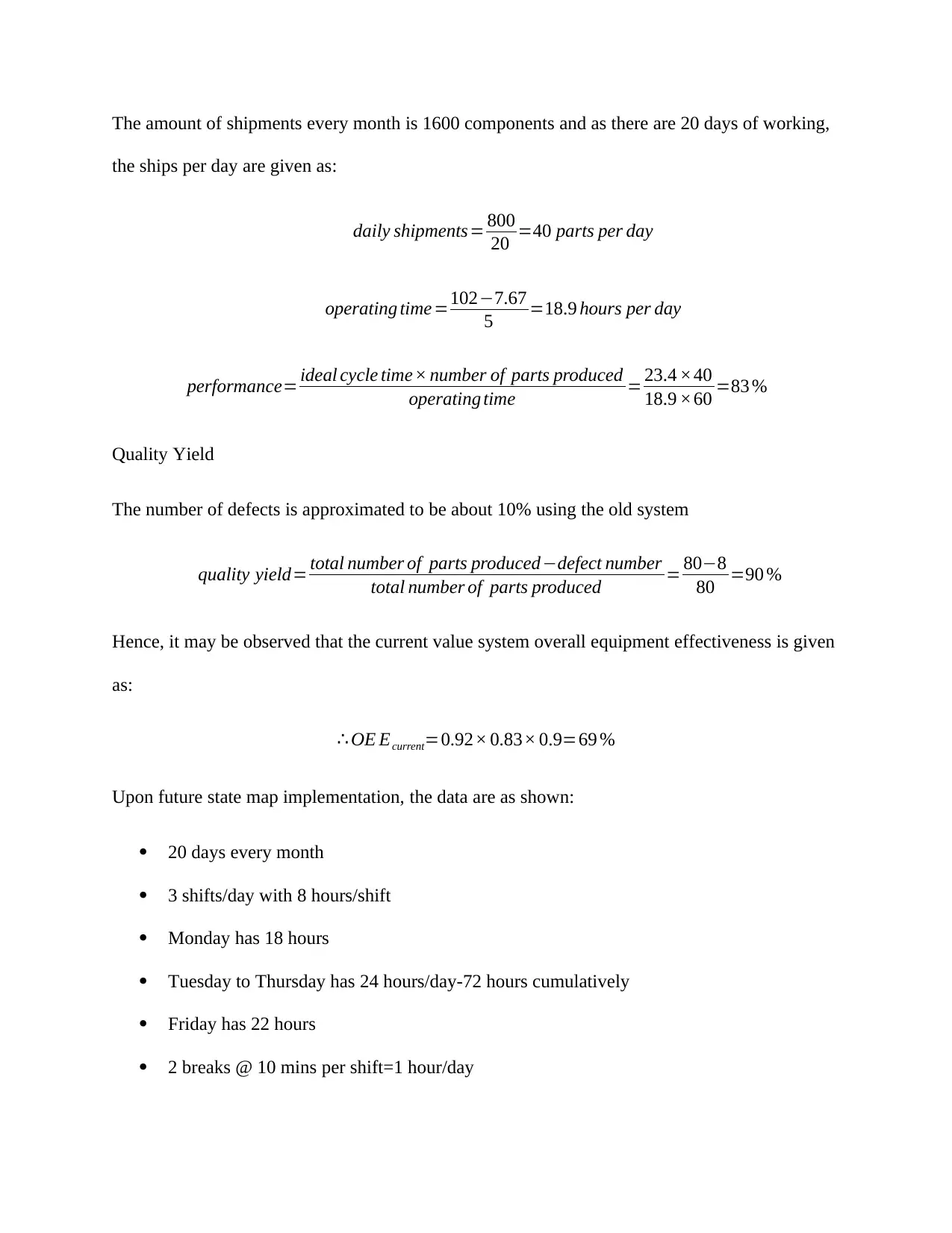
the ships per day are given as:
daily shipments= 800
20 =40 parts per day
operating time=102−7.67
5 =18.9 hours per day
performance= ideal cycle time× number of parts produced
operating time = 23.4 ×40
18.9 ×60 =83 %
Quality Yield
The number of defects is approximated to be about 10% using the old system
quality yield= total number of parts produced−defect number
total number of parts produced = 80−8
80 =90 %
Hence, it may be observed that the current value system overall equipment effectiveness is given
as:
∴ OE Ecurrent=0.92× 0.83× 0.9=69 %
Upon future state map implementation, the data are as shown:
20 days every month
3 shifts/day with 8 hours/shift
Monday has 18 hours
Tuesday to Thursday has 24 hours/day-72 hours cumulatively
Friday has 22 hours
2 breaks @ 10 mins per shift=1 hour/day
Paraphrase This Document
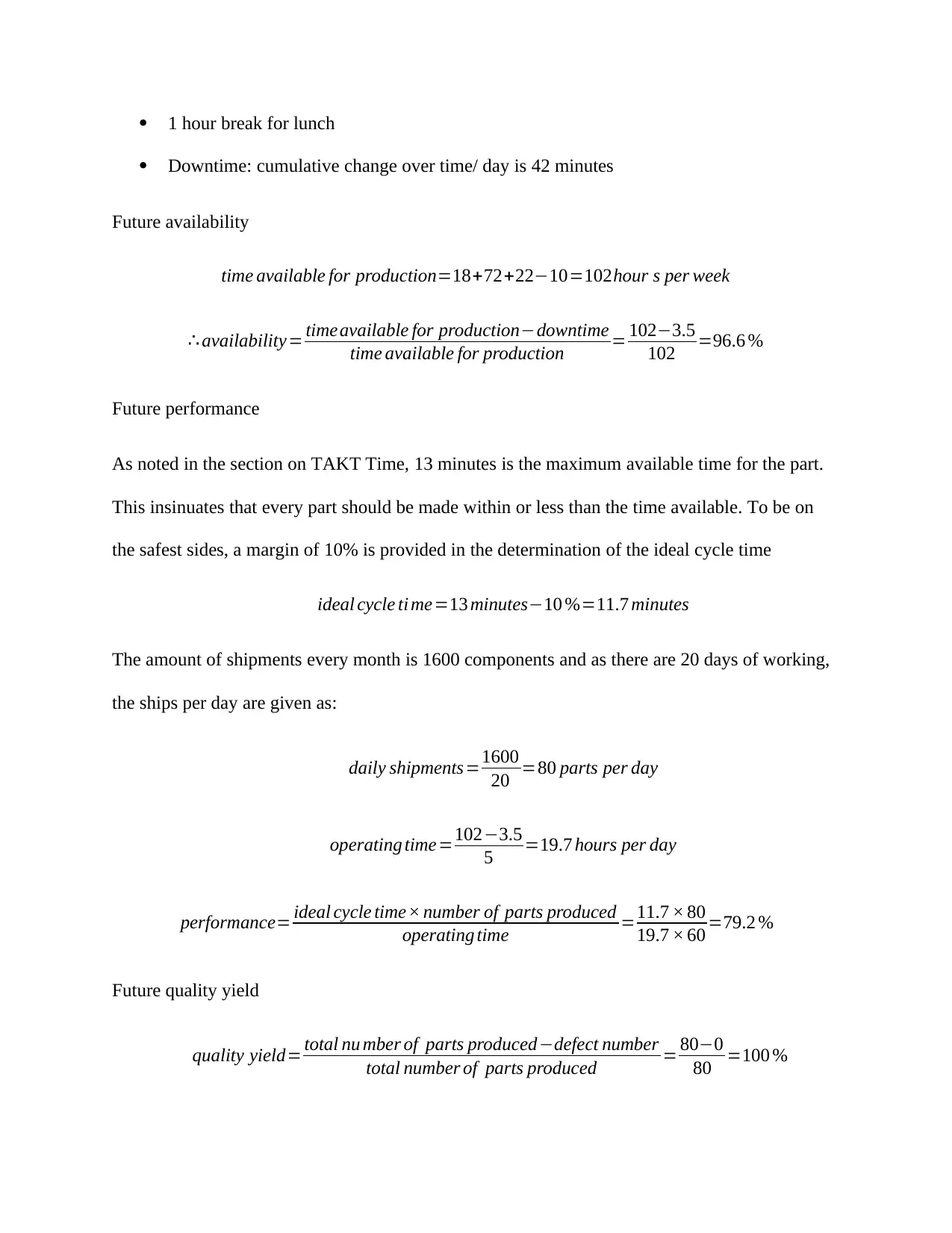
Downtime: cumulative change over time/ day is 42 minutes
Future availability
time available for production=18+72+22−10=102hour s per week
∴ availability= timeavailable for production−downtime
time available for production = 102−3.5
102 =96.6 %
Future performance
As noted in the section on TAKT Time, 13 minutes is the maximum available time for the part.
This insinuates that every part should be made within or less than the time available. To be on
the safest sides, a margin of 10% is provided in the determination of the ideal cycle time
ideal cycle ti me=13 minutes−10 %=11.7 minutes
The amount of shipments every month is 1600 components and as there are 20 days of working,
the ships per day are given as:
daily shipments=1600
20 =80 parts per day
operating time=102−3.5
5 =19.7 hours per day
performance= ideal cycle time× number of parts produced
operating time =11.7 × 80
19.7 × 60 =79.2 %
Future quality yield
quality yield= total nu mber of parts produced−defect number
total number of parts produced = 80−0
80 =100 %
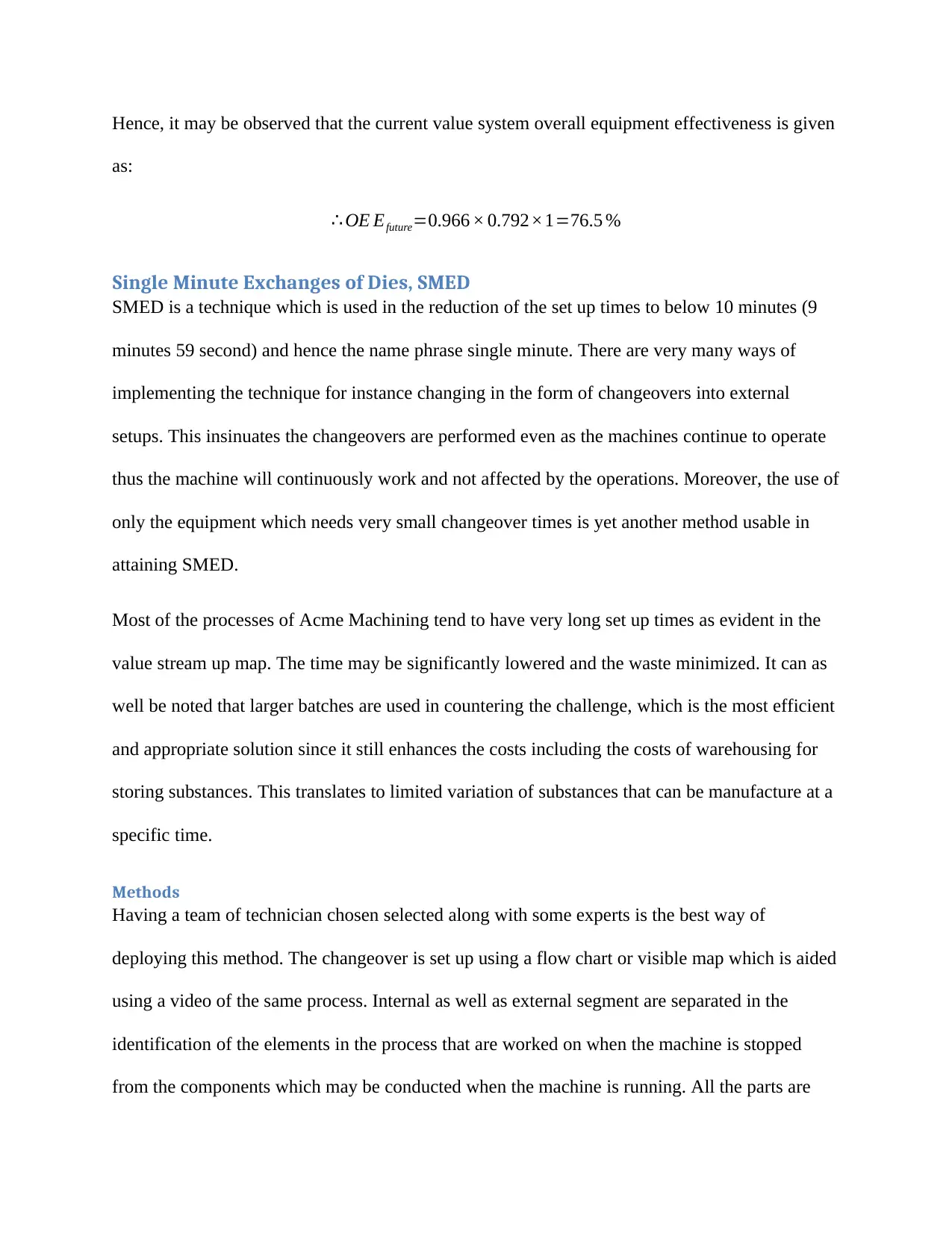
as:
∴ OE Efuture=0.966 × 0.792×1=76.5 %
Single Minute Exchanges of Dies, SMED
SMED is a technique which is used in the reduction of the set up times to below 10 minutes (9
minutes 59 second) and hence the name phrase single minute. There are very many ways of
implementing the technique for instance changing in the form of changeovers into external
setups. This insinuates the changeovers are performed even as the machines continue to operate
thus the machine will continuously work and not affected by the operations. Moreover, the use of
only the equipment which needs very small changeover times is yet another method usable in
attaining SMED.
Most of the processes of Acme Machining tend to have very long set up times as evident in the
value stream up map. The time may be significantly lowered and the waste minimized. It can as
well be noted that larger batches are used in countering the challenge, which is the most efficient
and appropriate solution since it still enhances the costs including the costs of warehousing for
storing substances. This translates to limited variation of substances that can be manufacture at a
specific time.
Methods
Having a team of technician chosen selected along with some experts is the best way of
deploying this method. The changeover is set up using a flow chart or visible map which is aided
using a video of the same process. Internal as well as external segment are separated in the
identification of the elements in the process that are worked on when the machine is stopped
from the components which may be conducted when the machine is running. All the parts are
⊘ This is a preview!⊘
Do you want full access?
Subscribe today to unlock all pages.

Trusted by 1+ million students worldwide
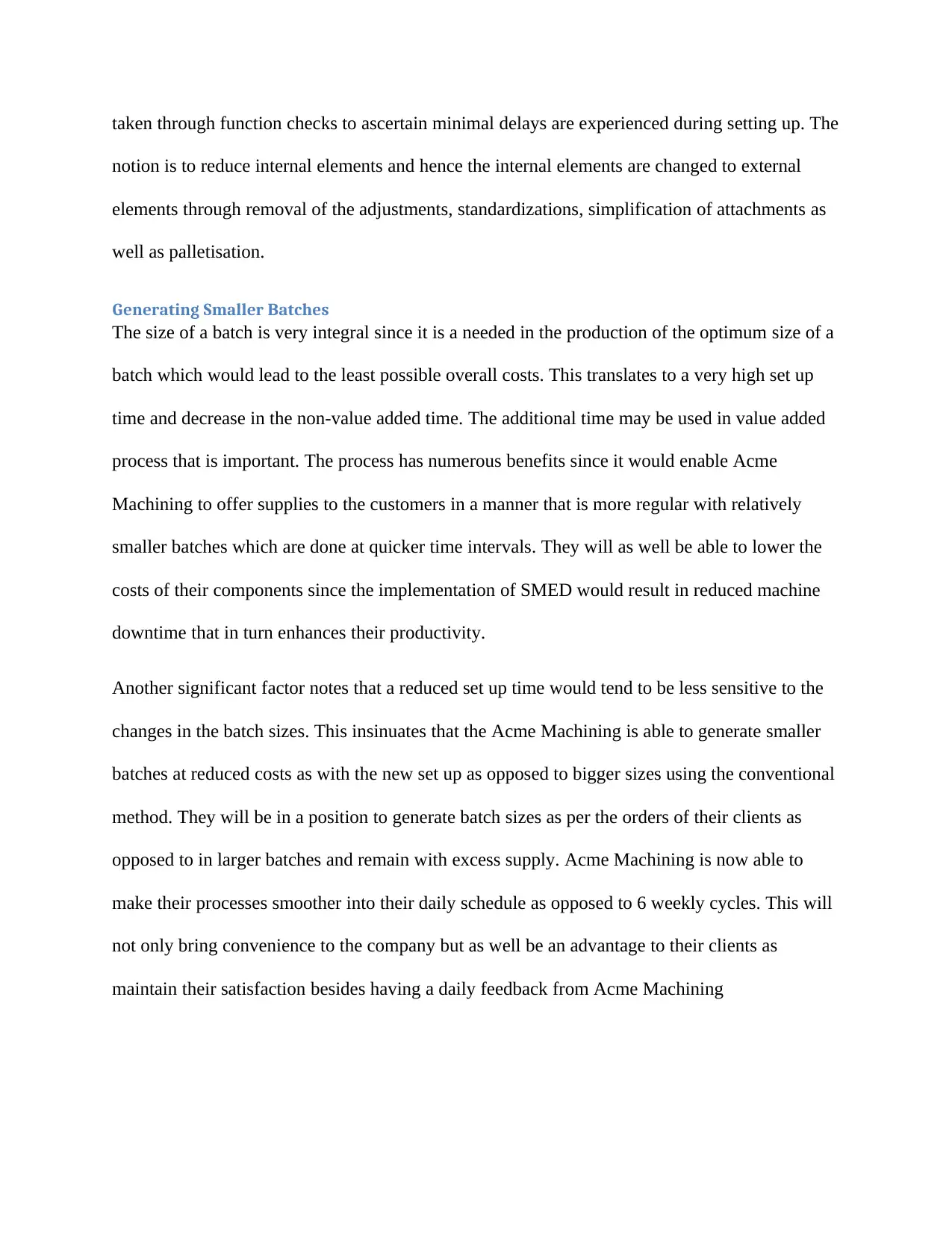
notion is to reduce internal elements and hence the internal elements are changed to external
elements through removal of the adjustments, standardizations, simplification of attachments as
well as palletisation.
Generating Smaller Batches
The size of a batch is very integral since it is a needed in the production of the optimum size of a
batch which would lead to the least possible overall costs. This translates to a very high set up
time and decrease in the non-value added time. The additional time may be used in value added
process that is important. The process has numerous benefits since it would enable Acme
Machining to offer supplies to the customers in a manner that is more regular with relatively
smaller batches which are done at quicker time intervals. They will as well be able to lower the
costs of their components since the implementation of SMED would result in reduced machine
downtime that in turn enhances their productivity.
Another significant factor notes that a reduced set up time would tend to be less sensitive to the
changes in the batch sizes. This insinuates that the Acme Machining is able to generate smaller
batches at reduced costs as with the new set up as opposed to bigger sizes using the conventional
method. They will be in a position to generate batch sizes as per the orders of their clients as
opposed to in larger batches and remain with excess supply. Acme Machining is now able to
make their processes smoother into their daily schedule as opposed to 6 weekly cycles. This will
not only bring convenience to the company but as well be an advantage to their clients as
maintain their satisfaction besides having a daily feedback from Acme Machining
Paraphrase This Document
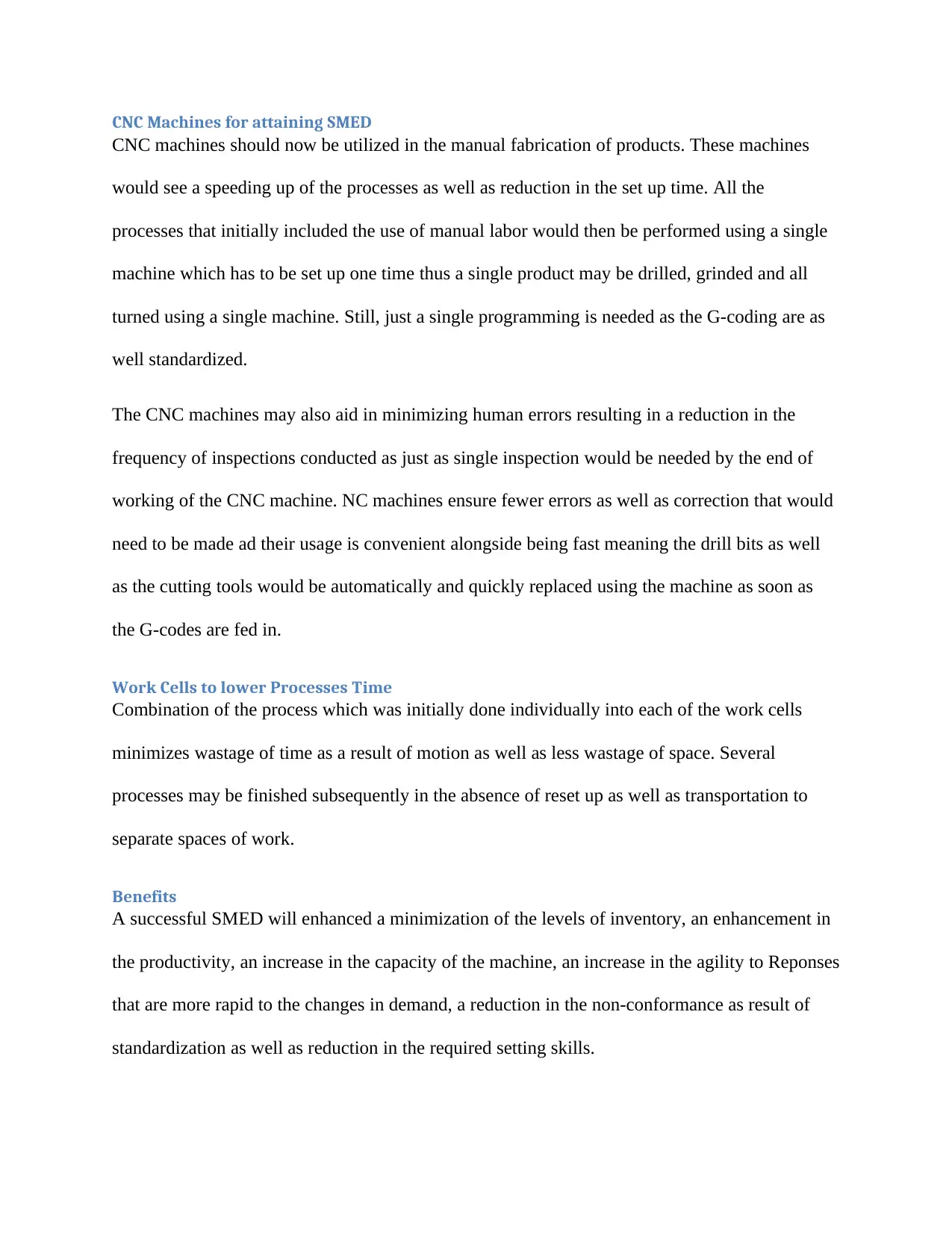
CNC machines should now be utilized in the manual fabrication of products. These machines
would see a speeding up of the processes as well as reduction in the set up time. All the
processes that initially included the use of manual labor would then be performed using a single
machine which has to be set up one time thus a single product may be drilled, grinded and all
turned using a single machine. Still, just a single programming is needed as the G-coding are as
well standardized.
The CNC machines may also aid in minimizing human errors resulting in a reduction in the
frequency of inspections conducted as just as single inspection would be needed by the end of
working of the CNC machine. NC machines ensure fewer errors as well as correction that would
need to be made ad their usage is convenient alongside being fast meaning the drill bits as well
as the cutting tools would be automatically and quickly replaced using the machine as soon as
the G-codes are fed in.
Work Cells to lower Processes Time
Combination of the process which was initially done individually into each of the work cells
minimizes wastage of time as a result of motion as well as less wastage of space. Several
processes may be finished subsequently in the absence of reset up as well as transportation to
separate spaces of work.
Benefits
A successful SMED will enhanced a minimization of the levels of inventory, an enhancement in
the productivity, an increase in the capacity of the machine, an increase in the agility to Reponses
that are more rapid to the changes in demand, a reduction in the non-conformance as result of
standardization as well as reduction in the required setting skills.
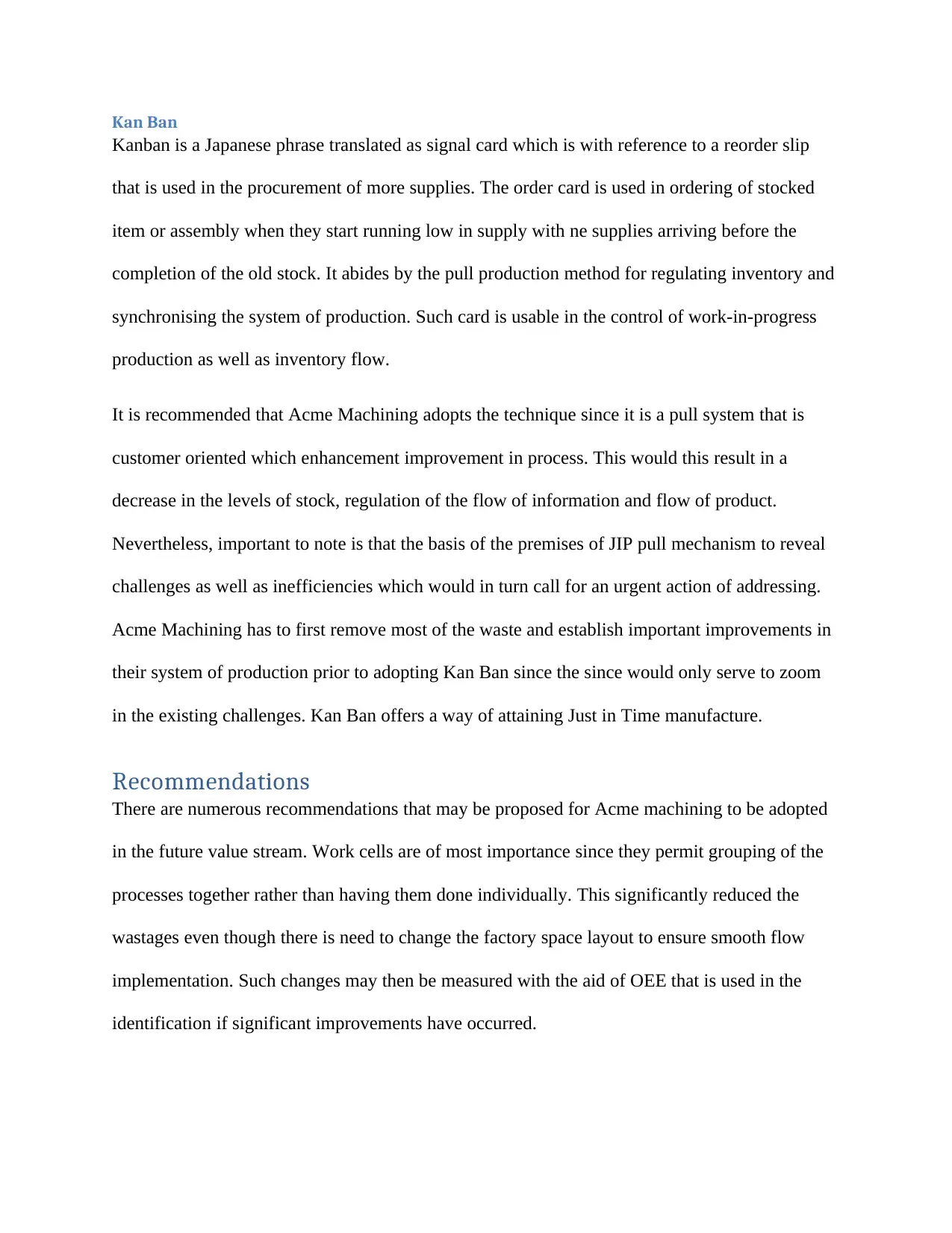
Kanban is a Japanese phrase translated as signal card which is with reference to a reorder slip
that is used in the procurement of more supplies. The order card is used in ordering of stocked
item or assembly when they start running low in supply with ne supplies arriving before the
completion of the old stock. It abides by the pull production method for regulating inventory and
synchronising the system of production. Such card is usable in the control of work-in-progress
production as well as inventory flow.
It is recommended that Acme Machining adopts the technique since it is a pull system that is
customer oriented which enhancement improvement in process. This would this result in a
decrease in the levels of stock, regulation of the flow of information and flow of product.
Nevertheless, important to note is that the basis of the premises of JIP pull mechanism to reveal
challenges as well as inefficiencies which would in turn call for an urgent action of addressing.
Acme Machining has to first remove most of the waste and establish important improvements in
their system of production prior to adopting Kan Ban since the since would only serve to zoom
in the existing challenges. Kan Ban offers a way of attaining Just in Time manufacture.
Recommendations
There are numerous recommendations that may be proposed for Acme machining to be adopted
in the future value stream. Work cells are of most importance since they permit grouping of the
processes together rather than having them done individually. This significantly reduced the
wastages even though there is need to change the factory space layout to ensure smooth flow
implementation. Such changes may then be measured with the aid of OEE that is used in the
identification if significant improvements have occurred.
⊘ This is a preview!⊘
Do you want full access?
Subscribe today to unlock all pages.

Trusted by 1+ million students worldwide
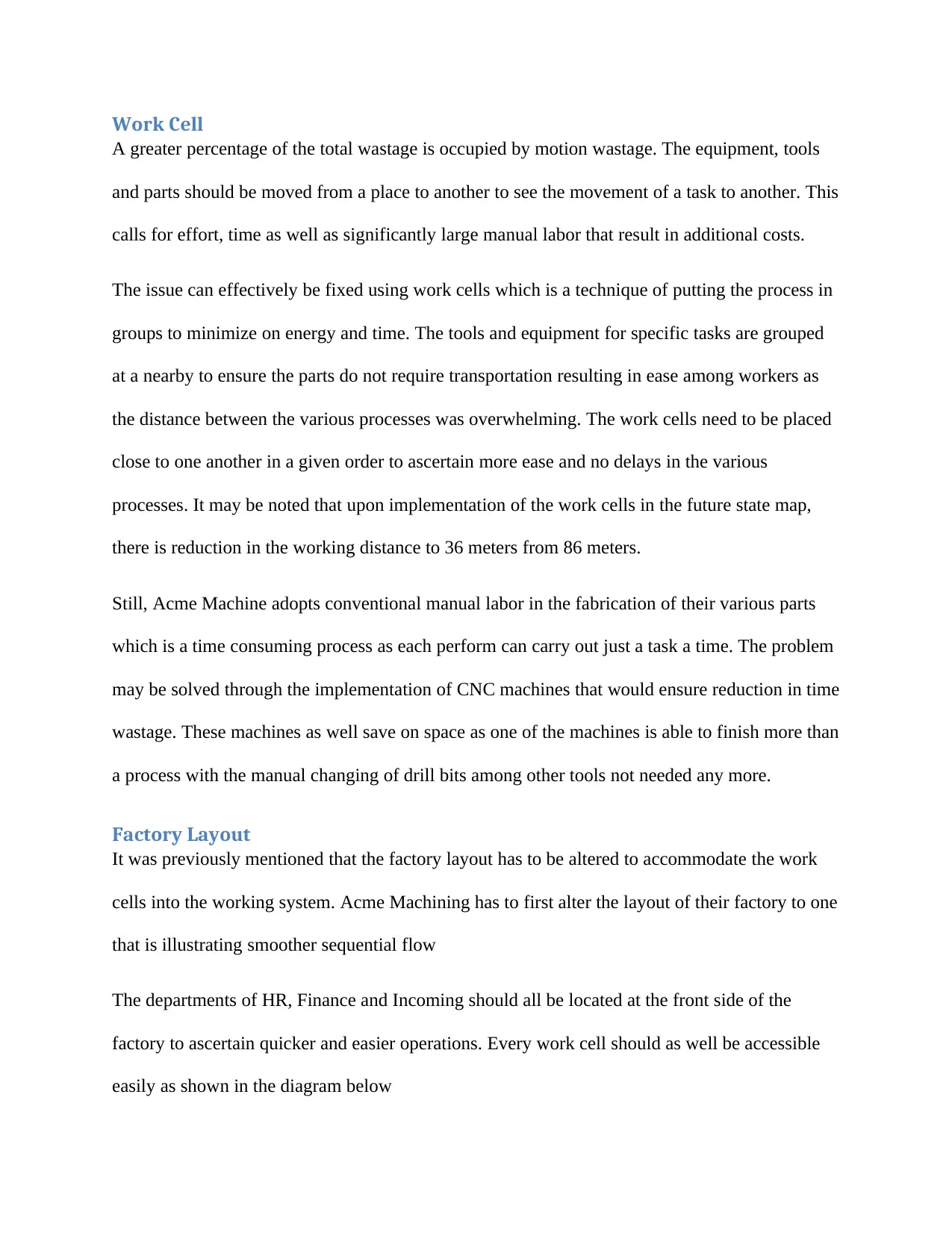
A greater percentage of the total wastage is occupied by motion wastage. The equipment, tools
and parts should be moved from a place to another to see the movement of a task to another. This
calls for effort, time as well as significantly large manual labor that result in additional costs.
The issue can effectively be fixed using work cells which is a technique of putting the process in
groups to minimize on energy and time. The tools and equipment for specific tasks are grouped
at a nearby to ensure the parts do not require transportation resulting in ease among workers as
the distance between the various processes was overwhelming. The work cells need to be placed
close to one another in a given order to ascertain more ease and no delays in the various
processes. It may be noted that upon implementation of the work cells in the future state map,
there is reduction in the working distance to 36 meters from 86 meters.
Still, Acme Machine adopts conventional manual labor in the fabrication of their various parts
which is a time consuming process as each perform can carry out just a task a time. The problem
may be solved through the implementation of CNC machines that would ensure reduction in time
wastage. These machines as well save on space as one of the machines is able to finish more than
a process with the manual changing of drill bits among other tools not needed any more.
Factory Layout
It was previously mentioned that the factory layout has to be altered to accommodate the work
cells into the working system. Acme Machining has to first alter the layout of their factory to one
that is illustrating smoother sequential flow
The departments of HR, Finance and Incoming should all be located at the front side of the
factory to ascertain quicker and easier operations. Every work cell should as well be accessible
easily as shown in the diagram below
Paraphrase This Document
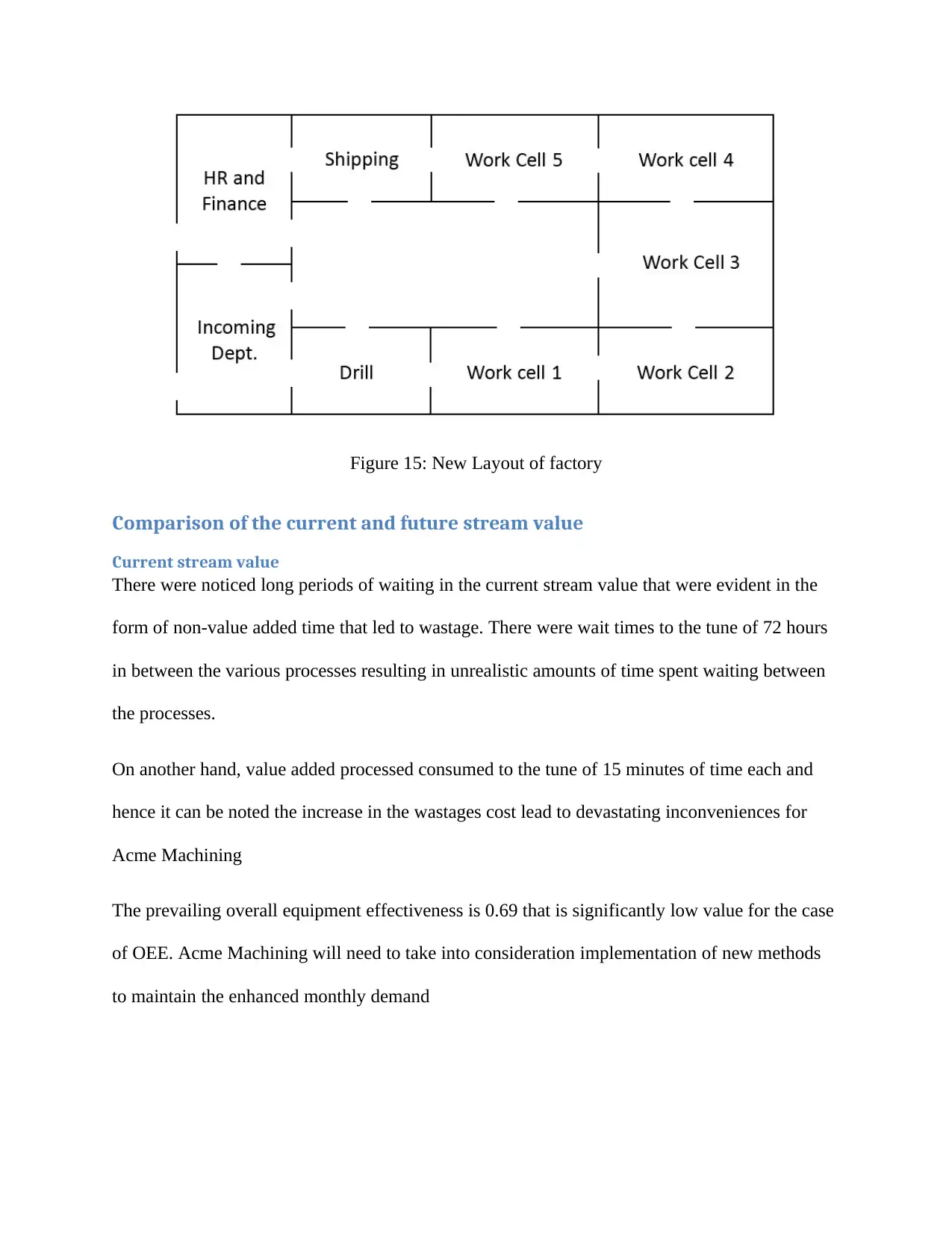
Comparison of the current and future stream value
Current stream value
There were noticed long periods of waiting in the current stream value that were evident in the
form of non-value added time that led to wastage. There were wait times to the tune of 72 hours
in between the various processes resulting in unrealistic amounts of time spent waiting between
the processes.
On another hand, value added processed consumed to the tune of 15 minutes of time each and
hence it can be noted the increase in the wastages cost lead to devastating inconveniences for
Acme Machining
The prevailing overall equipment effectiveness is 0.69 that is significantly low value for the case
of OEE. Acme Machining will need to take into consideration implementation of new methods
to maintain the enhanced monthly demand
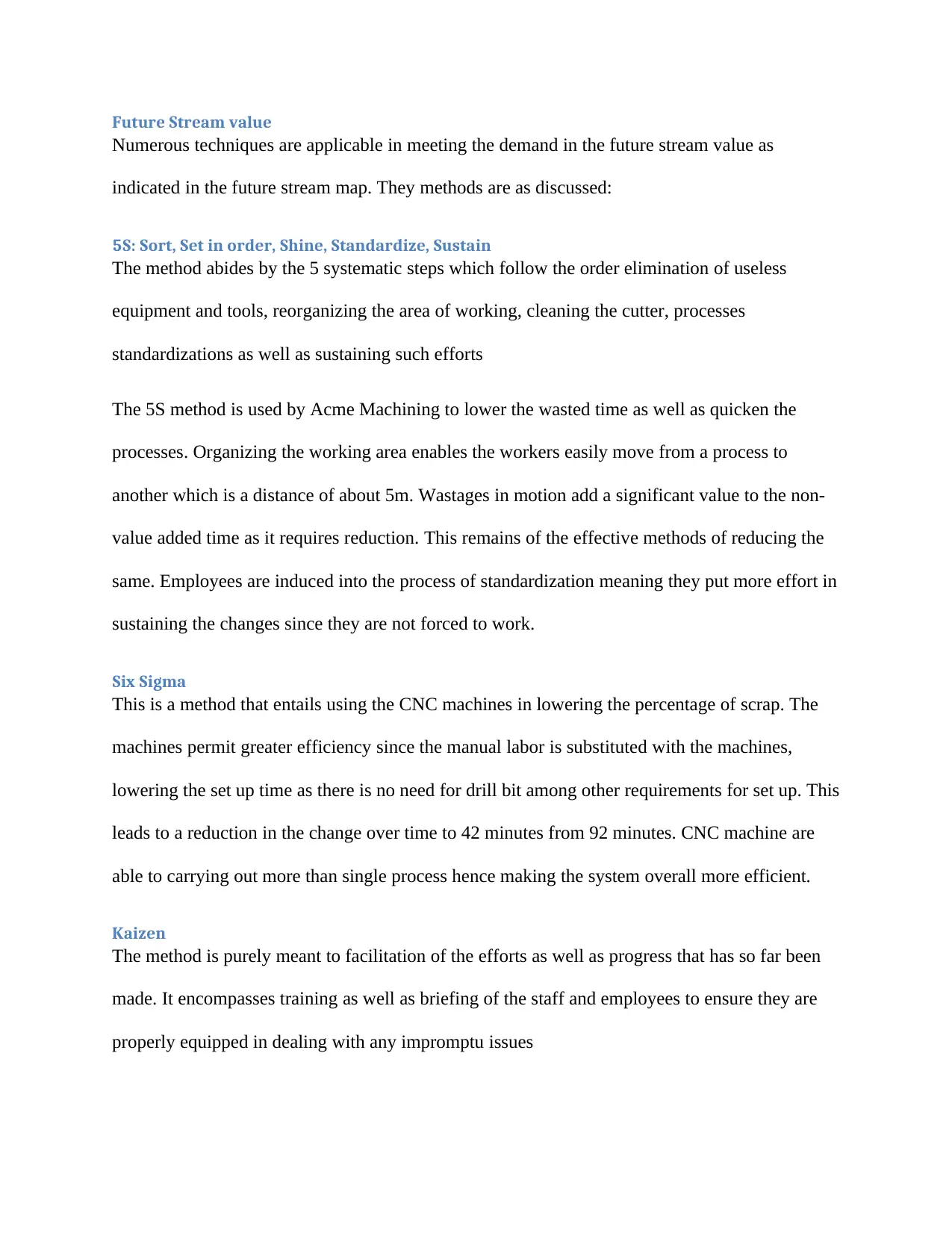
Numerous techniques are applicable in meeting the demand in the future stream value as
indicated in the future stream map. They methods are as discussed:
5S: Sort, Set in order, Shine, Standardize, Sustain
The method abides by the 5 systematic steps which follow the order elimination of useless
equipment and tools, reorganizing the area of working, cleaning the cutter, processes
standardizations as well as sustaining such efforts
The 5S method is used by Acme Machining to lower the wasted time as well as quicken the
processes. Organizing the working area enables the workers easily move from a process to
another which is a distance of about 5m. Wastages in motion add a significant value to the non-
value added time as it requires reduction. This remains of the effective methods of reducing the
same. Employees are induced into the process of standardization meaning they put more effort in
sustaining the changes since they are not forced to work.
Six Sigma
This is a method that entails using the CNC machines in lowering the percentage of scrap. The
machines permit greater efficiency since the manual labor is substituted with the machines,
lowering the set up time as there is no need for drill bit among other requirements for set up. This
leads to a reduction in the change over time to 42 minutes from 92 minutes. CNC machine are
able to carrying out more than single process hence making the system overall more efficient.
Kaizen
The method is purely meant to facilitation of the efforts as well as progress that has so far been
made. It encompasses training as well as briefing of the staff and employees to ensure they are
properly equipped in dealing with any impromptu issues
⊘ This is a preview!⊘
Do you want full access?
Subscribe today to unlock all pages.

Trusted by 1+ million students worldwide
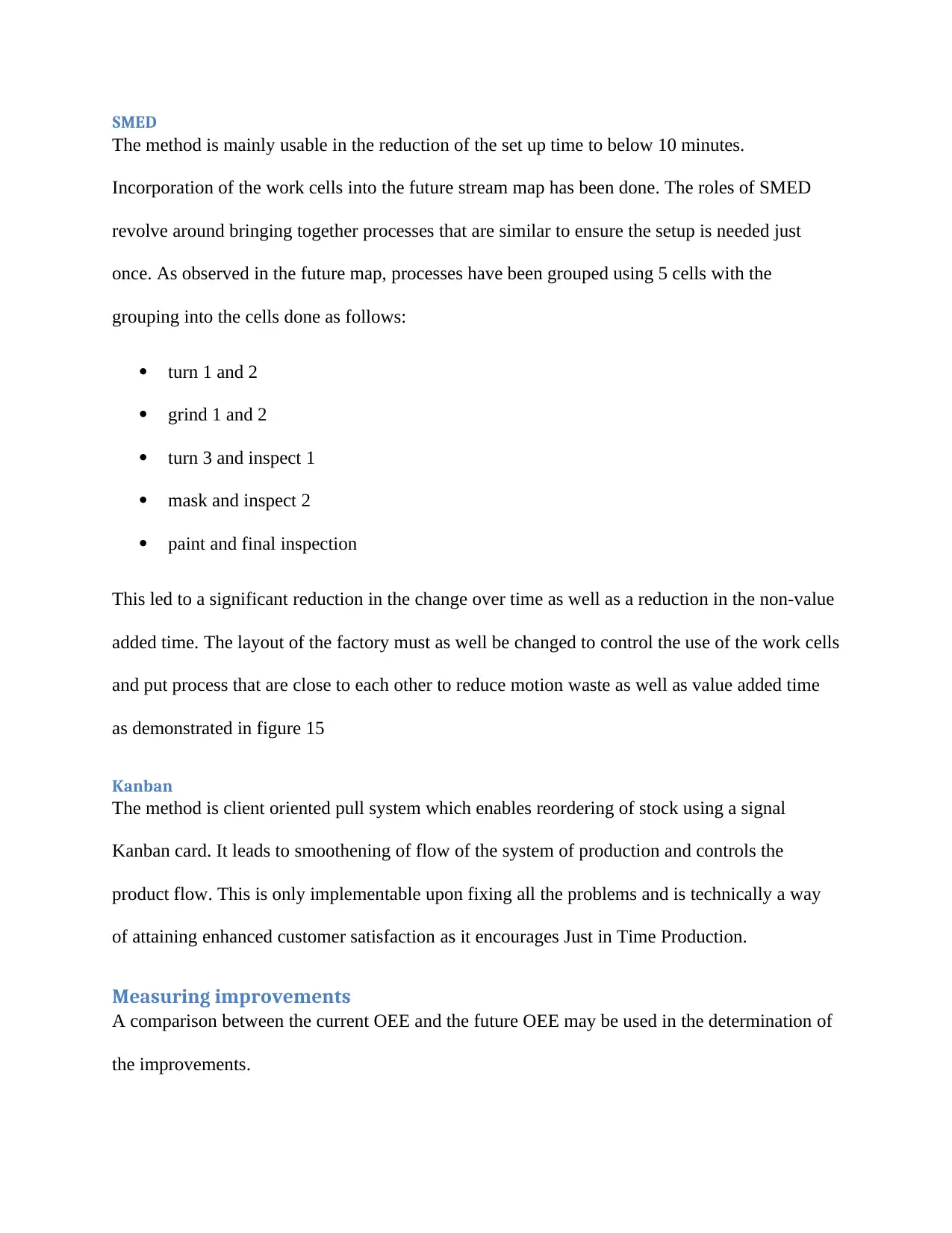
The method is mainly usable in the reduction of the set up time to below 10 minutes.
Incorporation of the work cells into the future stream map has been done. The roles of SMED
revolve around bringing together processes that are similar to ensure the setup is needed just
once. As observed in the future map, processes have been grouped using 5 cells with the
grouping into the cells done as follows:
turn 1 and 2
grind 1 and 2
turn 3 and inspect 1
mask and inspect 2
paint and final inspection
This led to a significant reduction in the change over time as well as a reduction in the non-value
added time. The layout of the factory must as well be changed to control the use of the work cells
and put process that are close to each other to reduce motion waste as well as value added time
as demonstrated in figure 15
Kanban
The method is client oriented pull system which enables reordering of stock using a signal
Kanban card. It leads to smoothening of flow of the system of production and controls the
product flow. This is only implementable upon fixing all the problems and is technically a way
of attaining enhanced customer satisfaction as it encourages Just in Time Production.
Measuring improvements
A comparison between the current OEE and the future OEE may be used in the determination of
the improvements.
Paraphrase This Document
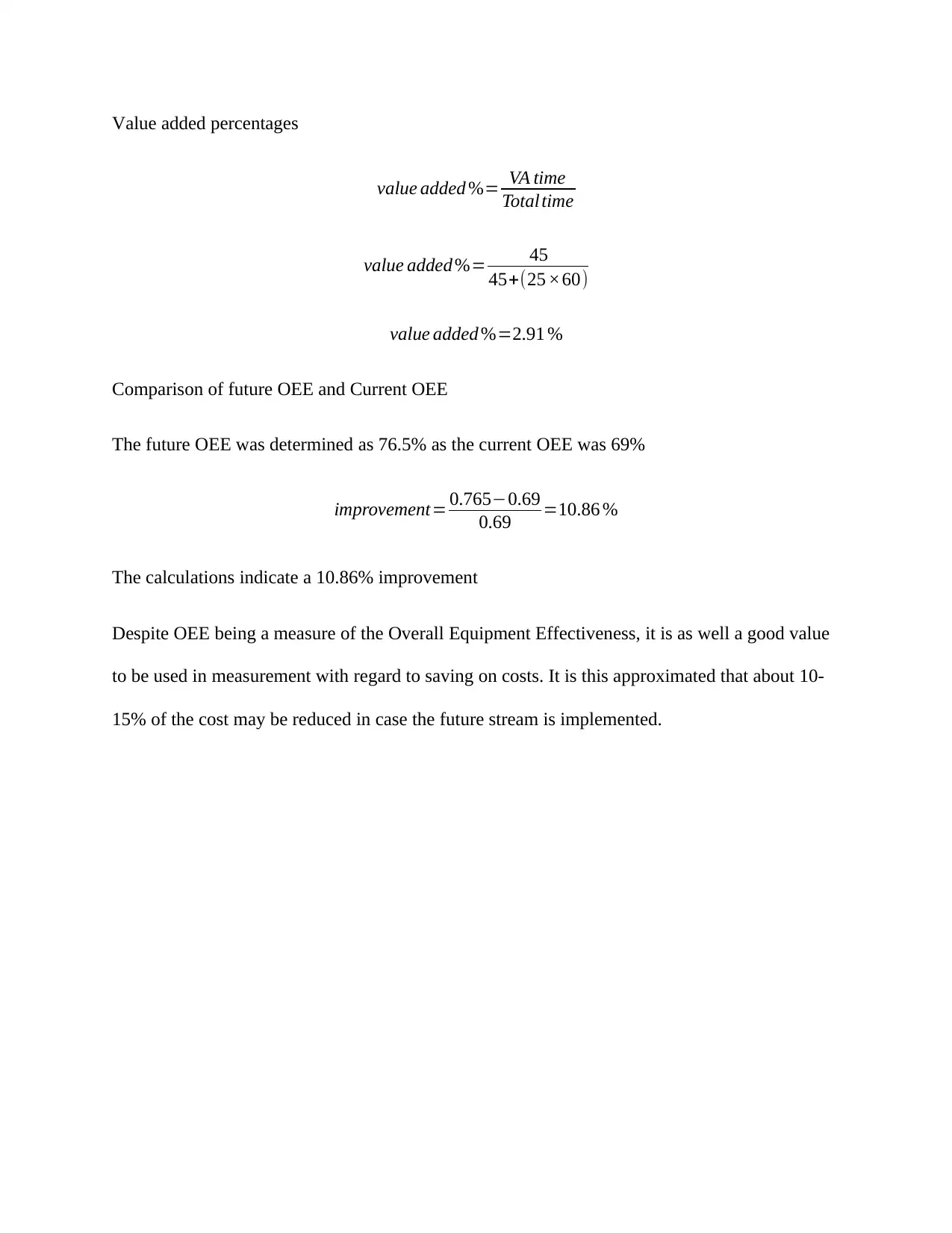
value added %= VA time
Total time
value added %= 45
45+(25 ×60)
value added %=2.91 %
Comparison of future OEE and Current OEE
The future OEE was determined as 76.5% as the current OEE was 69%
improvement= 0.765−0.69
0.69 =10.86 %
The calculations indicate a 10.86% improvement
Despite OEE being a measure of the Overall Equipment Effectiveness, it is as well a good value
to be used in measurement with regard to saving on costs. It is this approximated that about 10-
15% of the cost may be reduced in case the future stream is implemented.
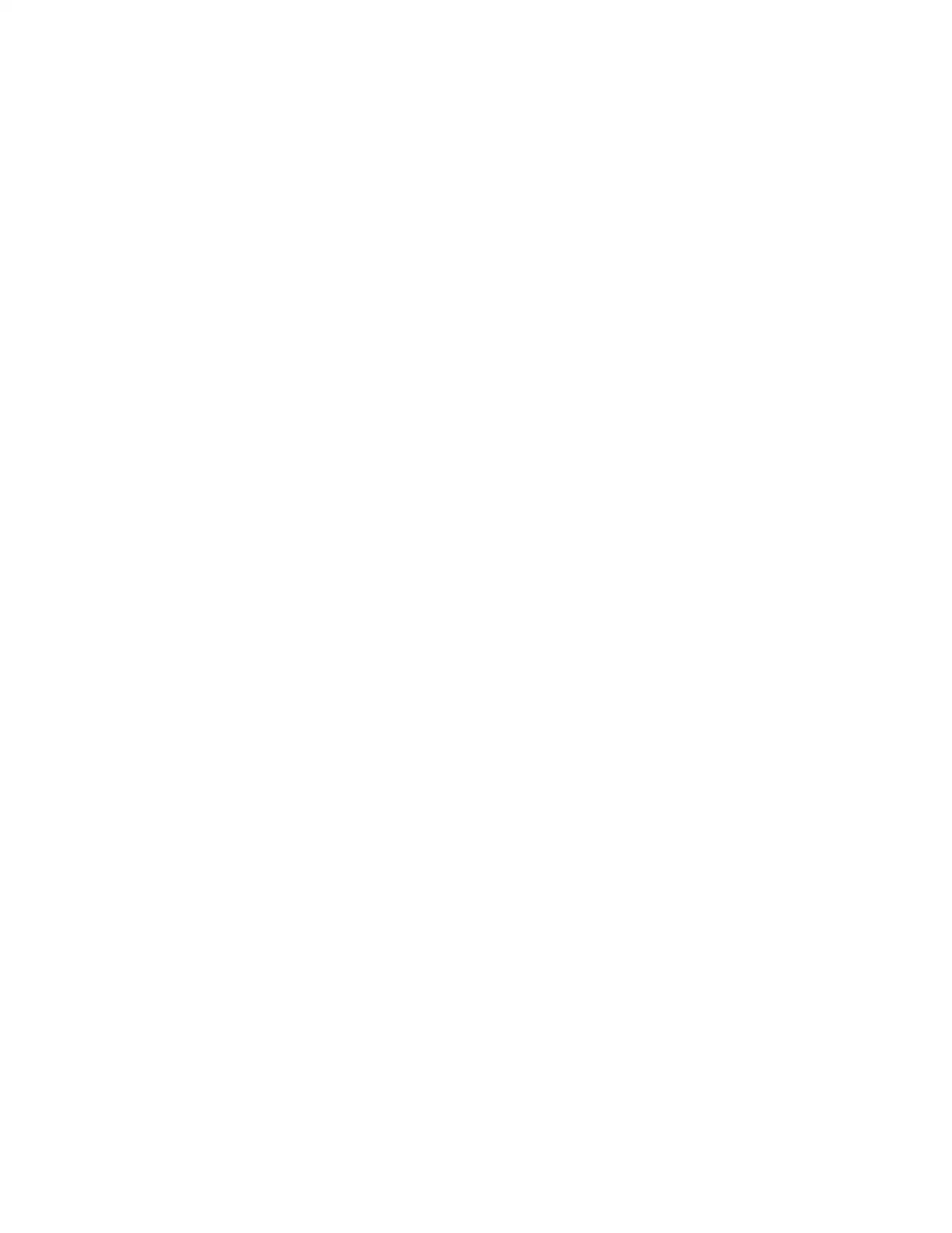
⊘ This is a preview!⊘
Do you want full access?
Subscribe today to unlock all pages.

Trusted by 1+ million students worldwide

Your All-in-One AI-Powered Toolkit for Academic Success.
+13062052269
info@desklib.com
Available 24*7 on WhatsApp / Email
© 2024 | Zucol Services PVT LTD | All rights reserved.