Lean Process Reengineering in Textile Industry
VerifiedAdded on 2022/12/12
|42
|15619
|451
AI Summary
This study focuses on developing a plan for implementing Lean Production methods in the textile industry to reduce waste. It discusses the diagnosis of key issues, value stream analysis, and prioritization of tools. The aim is to improve efficiency and eliminate practices that do not add value.
Contribute Materials
Your contribution can guide someone’s learning journey. Share your
documents today.
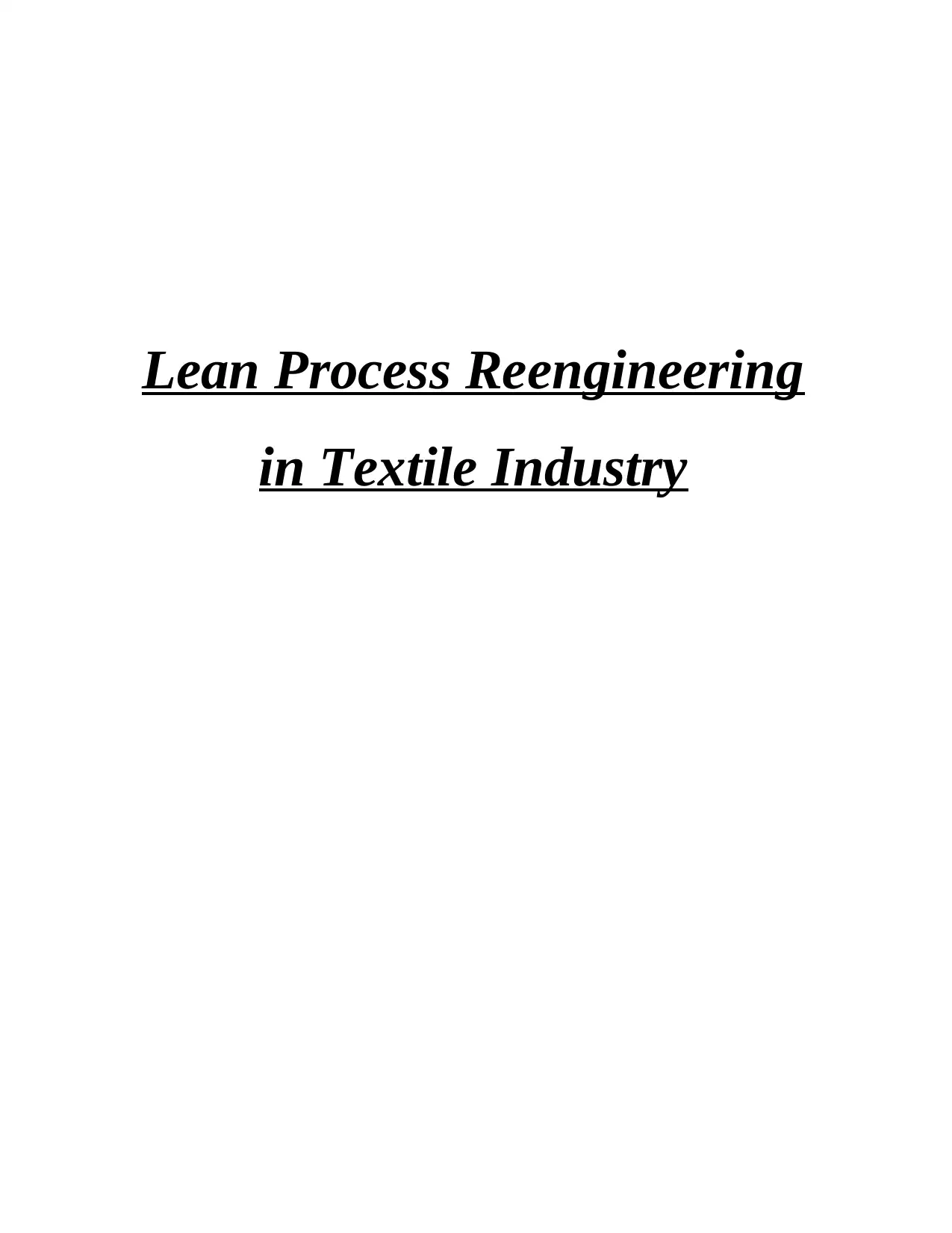
Lean Process Reengineering
in Textile Industry
in Textile Industry
Secure Best Marks with AI Grader
Need help grading? Try our AI Grader for instant feedback on your assignments.
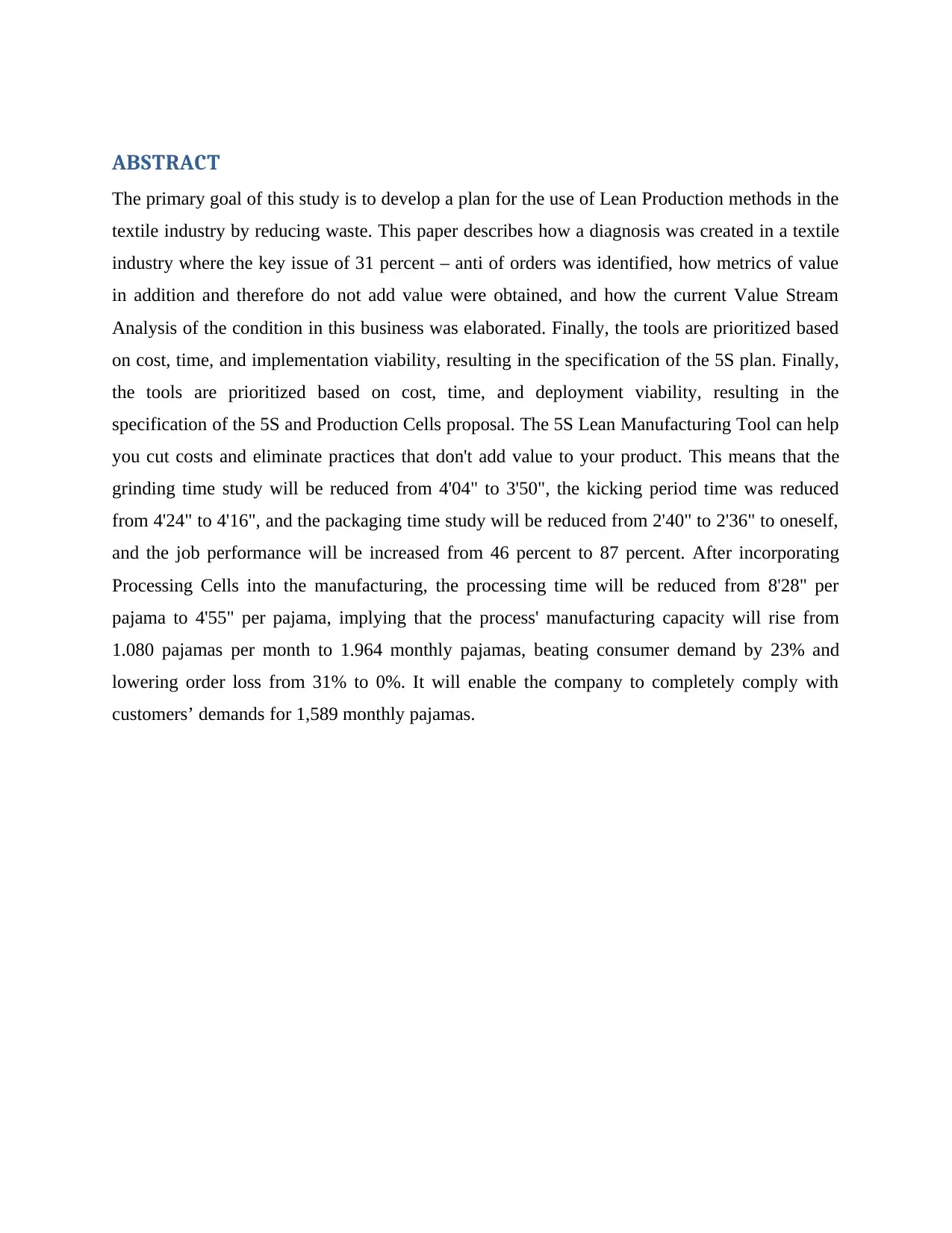
ABSTRACT
The primary goal of this study is to develop a plan for the use of Lean Production methods in the
textile industry by reducing waste. This paper describes how a diagnosis was created in a textile
industry where the key issue of 31 percent – anti of orders was identified, how metrics of value
in addition and therefore do not add value were obtained, and how the current Value Stream
Analysis of the condition in this business was elaborated. Finally, the tools are prioritized based
on cost, time, and implementation viability, resulting in the specification of the 5S plan. Finally,
the tools are prioritized based on cost, time, and deployment viability, resulting in the
specification of the 5S and Production Cells proposal. The 5S Lean Manufacturing Tool can help
you cut costs and eliminate practices that don't add value to your product. This means that the
grinding time study will be reduced from 4'04" to 3'50", the kicking period time was reduced
from 4'24" to 4'16", and the packaging time study will be reduced from 2'40" to 2'36" to oneself,
and the job performance will be increased from 46 percent to 87 percent. After incorporating
Processing Cells into the manufacturing, the processing time will be reduced from 8'28" per
pajama to 4'55" per pajama, implying that the process' manufacturing capacity will rise from
1.080 pajamas per month to 1.964 monthly pajamas, beating consumer demand by 23% and
lowering order loss from 31% to 0%. It will enable the company to completely comply with
customers’ demands for 1,589 monthly pajamas.
The primary goal of this study is to develop a plan for the use of Lean Production methods in the
textile industry by reducing waste. This paper describes how a diagnosis was created in a textile
industry where the key issue of 31 percent – anti of orders was identified, how metrics of value
in addition and therefore do not add value were obtained, and how the current Value Stream
Analysis of the condition in this business was elaborated. Finally, the tools are prioritized based
on cost, time, and implementation viability, resulting in the specification of the 5S plan. Finally,
the tools are prioritized based on cost, time, and deployment viability, resulting in the
specification of the 5S and Production Cells proposal. The 5S Lean Manufacturing Tool can help
you cut costs and eliminate practices that don't add value to your product. This means that the
grinding time study will be reduced from 4'04" to 3'50", the kicking period time was reduced
from 4'24" to 4'16", and the packaging time study will be reduced from 2'40" to 2'36" to oneself,
and the job performance will be increased from 46 percent to 87 percent. After incorporating
Processing Cells into the manufacturing, the processing time will be reduced from 8'28" per
pajama to 4'55" per pajama, implying that the process' manufacturing capacity will rise from
1.080 pajamas per month to 1.964 monthly pajamas, beating consumer demand by 23% and
lowering order loss from 31% to 0%. It will enable the company to completely comply with
customers’ demands for 1,589 monthly pajamas.
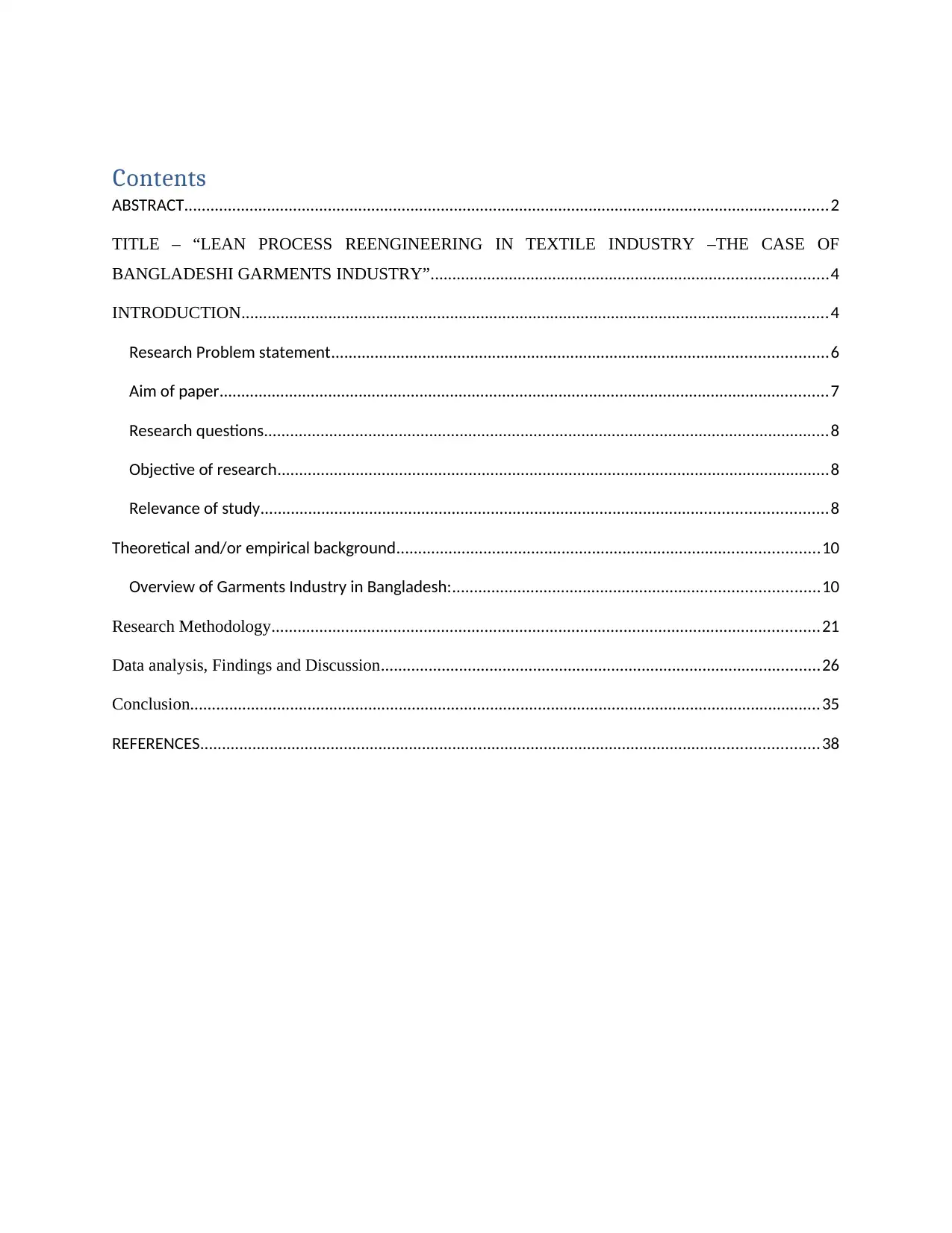
Contents
ABSTRACT....................................................................................................................................................2
TITLE – “LEAN PROCESS REENGINEERING IN TEXTILE INDUSTRY –THE CASE OF
BANGLADESHI GARMENTS INDUSTRY”...........................................................................................4
INTRODUCTION.......................................................................................................................................4
Research Problem statement..................................................................................................................6
Aim of paper............................................................................................................................................7
Research questions..................................................................................................................................8
Objective of research...............................................................................................................................8
Relevance of study..................................................................................................................................8
Theoretical and/or empirical background.................................................................................................10
Overview of Garments Industry in Bangladesh:....................................................................................10
Research Methodology..............................................................................................................................21
Data analysis, Findings and Discussion.....................................................................................................26
Conclusion.................................................................................................................................................35
REFERENCES..............................................................................................................................................38
ABSTRACT....................................................................................................................................................2
TITLE – “LEAN PROCESS REENGINEERING IN TEXTILE INDUSTRY –THE CASE OF
BANGLADESHI GARMENTS INDUSTRY”...........................................................................................4
INTRODUCTION.......................................................................................................................................4
Research Problem statement..................................................................................................................6
Aim of paper............................................................................................................................................7
Research questions..................................................................................................................................8
Objective of research...............................................................................................................................8
Relevance of study..................................................................................................................................8
Theoretical and/or empirical background.................................................................................................10
Overview of Garments Industry in Bangladesh:....................................................................................10
Research Methodology..............................................................................................................................21
Data analysis, Findings and Discussion.....................................................................................................26
Conclusion.................................................................................................................................................35
REFERENCES..............................................................................................................................................38
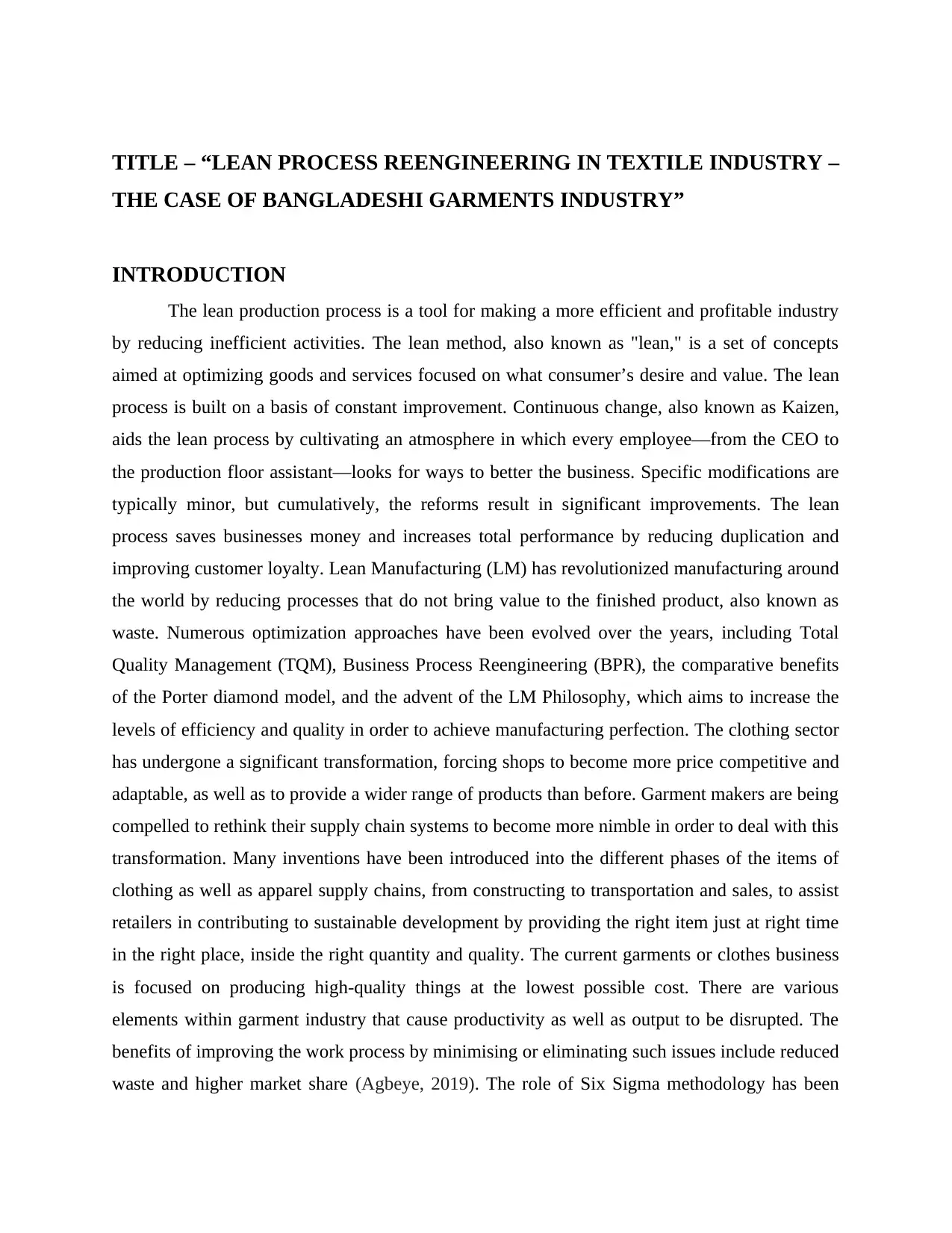
TITLE – “LEAN PROCESS REENGINEERING IN TEXTILE INDUSTRY –
THE CASE OF BANGLADESHI GARMENTS INDUSTRY”
INTRODUCTION
The lean production process is a tool for making a more efficient and profitable industry
by reducing inefficient activities. The lean method, also known as "lean," is a set of concepts
aimed at optimizing goods and services focused on what consumer’s desire and value. The lean
process is built on a basis of constant improvement. Continuous change, also known as Kaizen,
aids the lean process by cultivating an atmosphere in which every employee—from the CEO to
the production floor assistant—looks for ways to better the business. Specific modifications are
typically minor, but cumulatively, the reforms result in significant improvements. The lean
process saves businesses money and increases total performance by reducing duplication and
improving customer loyalty. Lean Manufacturing (LM) has revolutionized manufacturing around
the world by reducing processes that do not bring value to the finished product, also known as
waste. Numerous optimization approaches have been evolved over the years, including Total
Quality Management (TQM), Business Process Reengineering (BPR), the comparative benefits
of the Porter diamond model, and the advent of the LM Philosophy, which aims to increase the
levels of efficiency and quality in order to achieve manufacturing perfection. The clothing sector
has undergone a significant transformation, forcing shops to become more price competitive and
adaptable, as well as to provide a wider range of products than before. Garment makers are being
compelled to rethink their supply chain systems to become more nimble in order to deal with this
transformation. Many inventions have been introduced into the different phases of the items of
clothing as well as apparel supply chains, from constructing to transportation and sales, to assist
retailers in contributing to sustainable development by providing the right item just at right time
in the right place, inside the right quantity and quality. The current garments or clothes business
is focused on producing high-quality things at the lowest possible cost. There are various
elements within garment industry that cause productivity as well as output to be disrupted. The
benefits of improving the work process by minimising or eliminating such issues include reduced
waste and higher market share (Agbeye, 2019). The role of Six Sigma methodology has been
THE CASE OF BANGLADESHI GARMENTS INDUSTRY”
INTRODUCTION
The lean production process is a tool for making a more efficient and profitable industry
by reducing inefficient activities. The lean method, also known as "lean," is a set of concepts
aimed at optimizing goods and services focused on what consumer’s desire and value. The lean
process is built on a basis of constant improvement. Continuous change, also known as Kaizen,
aids the lean process by cultivating an atmosphere in which every employee—from the CEO to
the production floor assistant—looks for ways to better the business. Specific modifications are
typically minor, but cumulatively, the reforms result in significant improvements. The lean
process saves businesses money and increases total performance by reducing duplication and
improving customer loyalty. Lean Manufacturing (LM) has revolutionized manufacturing around
the world by reducing processes that do not bring value to the finished product, also known as
waste. Numerous optimization approaches have been evolved over the years, including Total
Quality Management (TQM), Business Process Reengineering (BPR), the comparative benefits
of the Porter diamond model, and the advent of the LM Philosophy, which aims to increase the
levels of efficiency and quality in order to achieve manufacturing perfection. The clothing sector
has undergone a significant transformation, forcing shops to become more price competitive and
adaptable, as well as to provide a wider range of products than before. Garment makers are being
compelled to rethink their supply chain systems to become more nimble in order to deal with this
transformation. Many inventions have been introduced into the different phases of the items of
clothing as well as apparel supply chains, from constructing to transportation and sales, to assist
retailers in contributing to sustainable development by providing the right item just at right time
in the right place, inside the right quantity and quality. The current garments or clothes business
is focused on producing high-quality things at the lowest possible cost. There are various
elements within garment industry that cause productivity as well as output to be disrupted. The
benefits of improving the work process by minimising or eliminating such issues include reduced
waste and higher market share (Agbeye, 2019). The role of Six Sigma methodology has been
Secure Best Marks with AI Grader
Need help grading? Try our AI Grader for instant feedback on your assignments.
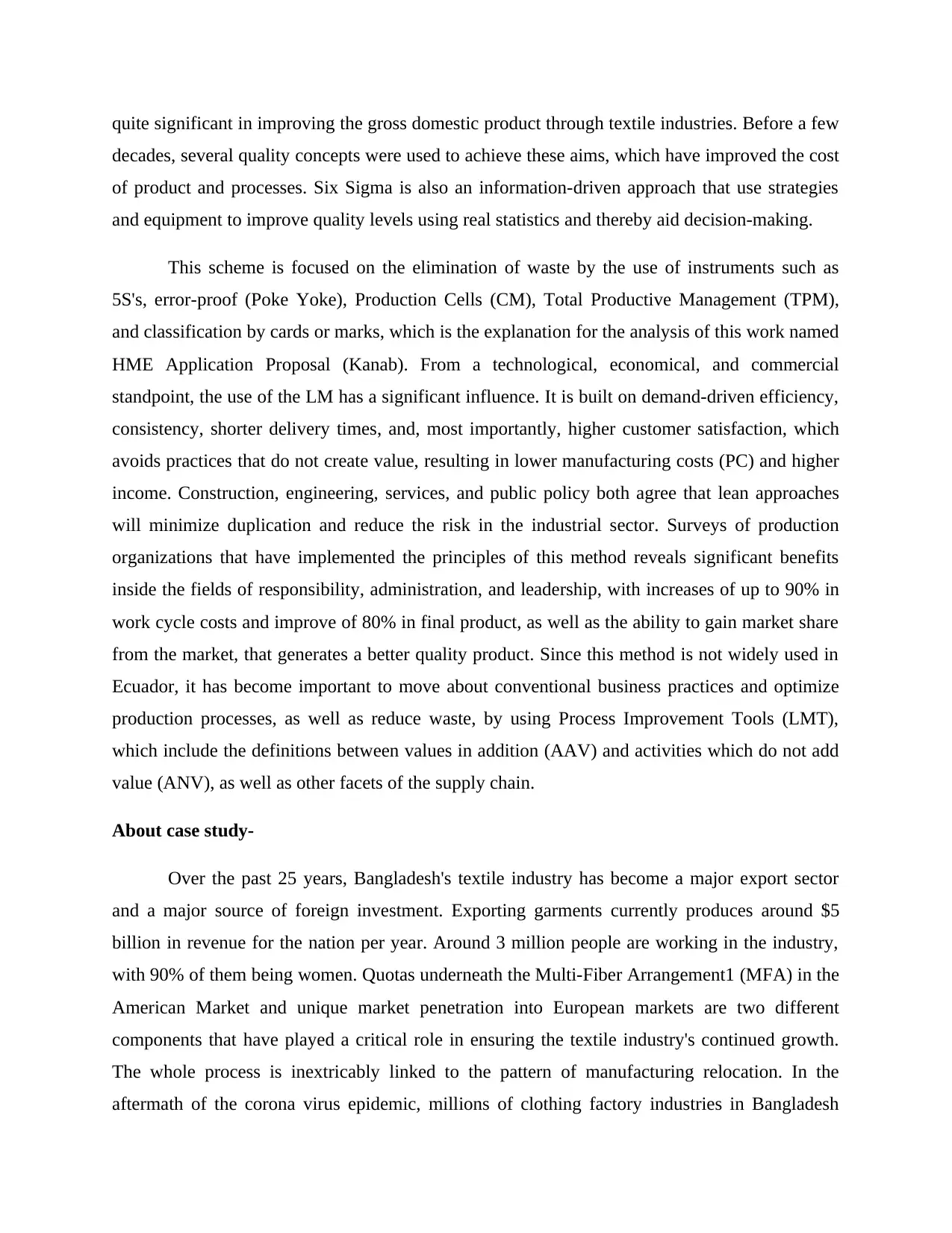
quite significant in improving the gross domestic product through textile industries. Before a few
decades, several quality concepts were used to achieve these aims, which have improved the cost
of product and processes. Six Sigma is also an information-driven approach that use strategies
and equipment to improve quality levels using real statistics and thereby aid decision-making.
This scheme is focused on the elimination of waste by the use of instruments such as
5S's, error-proof (Poke Yoke), Production Cells (CM), Total Productive Management (TPM),
and classification by cards or marks, which is the explanation for the analysis of this work named
HME Application Proposal (Kanab). From a technological, economical, and commercial
standpoint, the use of the LM has a significant influence. It is built on demand-driven efficiency,
consistency, shorter delivery times, and, most importantly, higher customer satisfaction, which
avoids practices that do not create value, resulting in lower manufacturing costs (PC) and higher
income. Construction, engineering, services, and public policy both agree that lean approaches
will minimize duplication and reduce the risk in the industrial sector. Surveys of production
organizations that have implemented the principles of this method reveals significant benefits
inside the fields of responsibility, administration, and leadership, with increases of up to 90% in
work cycle costs and improve of 80% in final product, as well as the ability to gain market share
from the market, that generates a better quality product. Since this method is not widely used in
Ecuador, it has become important to move about conventional business practices and optimize
production processes, as well as reduce waste, by using Process Improvement Tools (LMT),
which include the definitions between values in addition (AAV) and activities which do not add
value (ANV), as well as other facets of the supply chain.
About case study-
Over the past 25 years, Bangladesh's textile industry has become a major export sector
and a major source of foreign investment. Exporting garments currently produces around $5
billion in revenue for the nation per year. Around 3 million people are working in the industry,
with 90% of them being women. Quotas underneath the Multi-Fiber Arrangement1 (MFA) in the
American Market and unique market penetration into European markets are two different
components that have played a critical role in ensuring the textile industry's continued growth.
The whole process is inextricably linked to the pattern of manufacturing relocation. In the
aftermath of the corona virus epidemic, millions of clothing factory industries in Bangladesh
decades, several quality concepts were used to achieve these aims, which have improved the cost
of product and processes. Six Sigma is also an information-driven approach that use strategies
and equipment to improve quality levels using real statistics and thereby aid decision-making.
This scheme is focused on the elimination of waste by the use of instruments such as
5S's, error-proof (Poke Yoke), Production Cells (CM), Total Productive Management (TPM),
and classification by cards or marks, which is the explanation for the analysis of this work named
HME Application Proposal (Kanab). From a technological, economical, and commercial
standpoint, the use of the LM has a significant influence. It is built on demand-driven efficiency,
consistency, shorter delivery times, and, most importantly, higher customer satisfaction, which
avoids practices that do not create value, resulting in lower manufacturing costs (PC) and higher
income. Construction, engineering, services, and public policy both agree that lean approaches
will minimize duplication and reduce the risk in the industrial sector. Surveys of production
organizations that have implemented the principles of this method reveals significant benefits
inside the fields of responsibility, administration, and leadership, with increases of up to 90% in
work cycle costs and improve of 80% in final product, as well as the ability to gain market share
from the market, that generates a better quality product. Since this method is not widely used in
Ecuador, it has become important to move about conventional business practices and optimize
production processes, as well as reduce waste, by using Process Improvement Tools (LMT),
which include the definitions between values in addition (AAV) and activities which do not add
value (ANV), as well as other facets of the supply chain.
About case study-
Over the past 25 years, Bangladesh's textile industry has become a major export sector
and a major source of foreign investment. Exporting garments currently produces around $5
billion in revenue for the nation per year. Around 3 million people are working in the industry,
with 90% of them being women. Quotas underneath the Multi-Fiber Arrangement1 (MFA) in the
American Market and unique market penetration into European markets are two different
components that have played a critical role in ensuring the textile industry's continued growth.
The whole process is inextricably linked to the pattern of manufacturing relocation. In the
aftermath of the corona virus epidemic, millions of clothing factory industries in Bangladesh
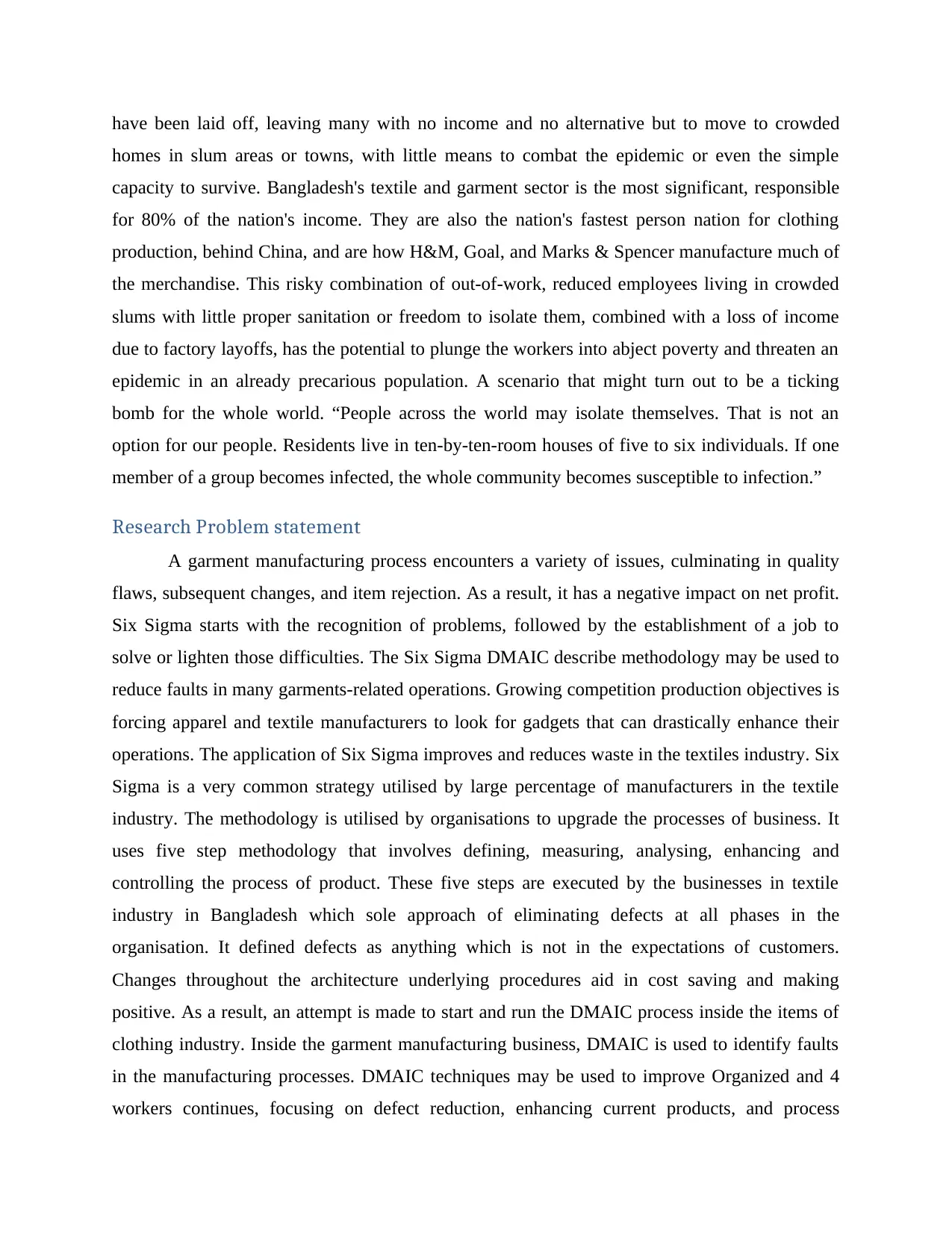
have been laid off, leaving many with no income and no alternative but to move to crowded
homes in slum areas or towns, with little means to combat the epidemic or even the simple
capacity to survive. Bangladesh's textile and garment sector is the most significant, responsible
for 80% of the nation's income. They are also the nation's fastest person nation for clothing
production, behind China, and are how H&M, Goal, and Marks & Spencer manufacture much of
the merchandise. This risky combination of out-of-work, reduced employees living in crowded
slums with little proper sanitation or freedom to isolate them, combined with a loss of income
due to factory layoffs, has the potential to plunge the workers into abject poverty and threaten an
epidemic in an already precarious population. A scenario that might turn out to be a ticking
bomb for the whole world. “People across the world may isolate themselves. That is not an
option for our people. Residents live in ten-by-ten-room houses of five to six individuals. If one
member of a group becomes infected, the whole community becomes susceptible to infection.”
Research Problem statement
A garment manufacturing process encounters a variety of issues, culminating in quality
flaws, subsequent changes, and item rejection. As a result, it has a negative impact on net profit.
Six Sigma starts with the recognition of problems, followed by the establishment of a job to
solve or lighten those difficulties. The Six Sigma DMAIC describe methodology may be used to
reduce faults in many garments-related operations. Growing competition production objectives is
forcing apparel and textile manufacturers to look for gadgets that can drastically enhance their
operations. The application of Six Sigma improves and reduces waste in the textiles industry. Six
Sigma is a very common strategy utilised by large percentage of manufacturers in the textile
industry. The methodology is utilised by organisations to upgrade the processes of business. It
uses five step methodology that involves defining, measuring, analysing, enhancing and
controlling the process of product. These five steps are executed by the businesses in textile
industry in Bangladesh which sole approach of eliminating defects at all phases in the
organisation. It defined defects as anything which is not in the expectations of customers.
Changes throughout the architecture underlying procedures aid in cost saving and making
positive. As a result, an attempt is made to start and run the DMAIC process inside the items of
clothing industry. Inside the garment manufacturing business, DMAIC is used to identify faults
in the manufacturing processes. DMAIC techniques may be used to improve Organized and 4
workers continues, focusing on defect reduction, enhancing current products, and process
homes in slum areas or towns, with little means to combat the epidemic or even the simple
capacity to survive. Bangladesh's textile and garment sector is the most significant, responsible
for 80% of the nation's income. They are also the nation's fastest person nation for clothing
production, behind China, and are how H&M, Goal, and Marks & Spencer manufacture much of
the merchandise. This risky combination of out-of-work, reduced employees living in crowded
slums with little proper sanitation or freedom to isolate them, combined with a loss of income
due to factory layoffs, has the potential to plunge the workers into abject poverty and threaten an
epidemic in an already precarious population. A scenario that might turn out to be a ticking
bomb for the whole world. “People across the world may isolate themselves. That is not an
option for our people. Residents live in ten-by-ten-room houses of five to six individuals. If one
member of a group becomes infected, the whole community becomes susceptible to infection.”
Research Problem statement
A garment manufacturing process encounters a variety of issues, culminating in quality
flaws, subsequent changes, and item rejection. As a result, it has a negative impact on net profit.
Six Sigma starts with the recognition of problems, followed by the establishment of a job to
solve or lighten those difficulties. The Six Sigma DMAIC describe methodology may be used to
reduce faults in many garments-related operations. Growing competition production objectives is
forcing apparel and textile manufacturers to look for gadgets that can drastically enhance their
operations. The application of Six Sigma improves and reduces waste in the textiles industry. Six
Sigma is a very common strategy utilised by large percentage of manufacturers in the textile
industry. The methodology is utilised by organisations to upgrade the processes of business. It
uses five step methodology that involves defining, measuring, analysing, enhancing and
controlling the process of product. These five steps are executed by the businesses in textile
industry in Bangladesh which sole approach of eliminating defects at all phases in the
organisation. It defined defects as anything which is not in the expectations of customers.
Changes throughout the architecture underlying procedures aid in cost saving and making
positive. As a result, an attempt is made to start and run the DMAIC process inside the items of
clothing industry. Inside the garment manufacturing business, DMAIC is used to identify faults
in the manufacturing processes. DMAIC techniques may be used to improve Organized and 4
workers continues, focusing on defect reduction, enhancing current products, and process
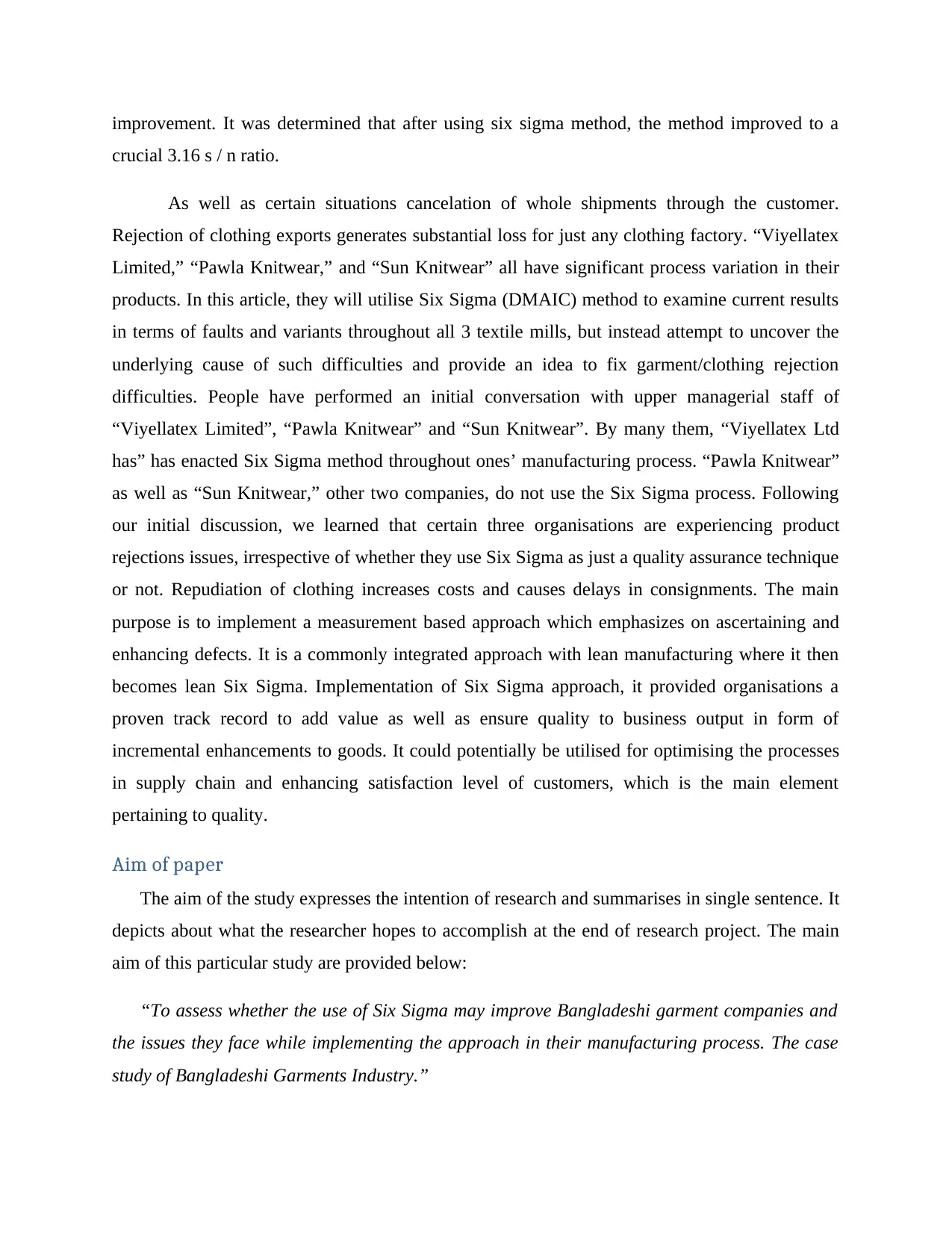
improvement. It was determined that after using six sigma method, the method improved to a
crucial 3.16 s / n ratio.
As well as certain situations cancelation of whole shipments through the customer.
Rejection of clothing exports generates substantial loss for just any clothing factory. “Viyellatex
Limited,” “Pawla Knitwear,” and “Sun Knitwear” all have significant process variation in their
products. In this article, they will utilise Six Sigma (DMAIC) method to examine current results
in terms of faults and variants throughout all 3 textile mills, but instead attempt to uncover the
underlying cause of such difficulties and provide an idea to fix garment/clothing rejection
difficulties. People have performed an initial conversation with upper managerial staff of
“Viyellatex Limited”, “Pawla Knitwear” and “Sun Knitwear”. By many them, “Viyellatex Ltd
has” has enacted Six Sigma method throughout ones’ manufacturing process. “Pawla Knitwear”
as well as “Sun Knitwear,” other two companies, do not use the Six Sigma process. Following
our initial discussion, we learned that certain three organisations are experiencing product
rejections issues, irrespective of whether they use Six Sigma as just a quality assurance technique
or not. Repudiation of clothing increases costs and causes delays in consignments. The main
purpose is to implement a measurement based approach which emphasizes on ascertaining and
enhancing defects. It is a commonly integrated approach with lean manufacturing where it then
becomes lean Six Sigma. Implementation of Six Sigma approach, it provided organisations a
proven track record to add value as well as ensure quality to business output in form of
incremental enhancements to goods. It could potentially be utilised for optimising the processes
in supply chain and enhancing satisfaction level of customers, which is the main element
pertaining to quality.
Aim of paper
The aim of the study expresses the intention of research and summarises in single sentence. It
depicts about what the researcher hopes to accomplish at the end of research project. The main
aim of this particular study are provided below:
“To assess whether the use of Six Sigma may improve Bangladeshi garment companies and
the issues they face while implementing the approach in their manufacturing process. The case
study of Bangladeshi Garments Industry.”
crucial 3.16 s / n ratio.
As well as certain situations cancelation of whole shipments through the customer.
Rejection of clothing exports generates substantial loss for just any clothing factory. “Viyellatex
Limited,” “Pawla Knitwear,” and “Sun Knitwear” all have significant process variation in their
products. In this article, they will utilise Six Sigma (DMAIC) method to examine current results
in terms of faults and variants throughout all 3 textile mills, but instead attempt to uncover the
underlying cause of such difficulties and provide an idea to fix garment/clothing rejection
difficulties. People have performed an initial conversation with upper managerial staff of
“Viyellatex Limited”, “Pawla Knitwear” and “Sun Knitwear”. By many them, “Viyellatex Ltd
has” has enacted Six Sigma method throughout ones’ manufacturing process. “Pawla Knitwear”
as well as “Sun Knitwear,” other two companies, do not use the Six Sigma process. Following
our initial discussion, we learned that certain three organisations are experiencing product
rejections issues, irrespective of whether they use Six Sigma as just a quality assurance technique
or not. Repudiation of clothing increases costs and causes delays in consignments. The main
purpose is to implement a measurement based approach which emphasizes on ascertaining and
enhancing defects. It is a commonly integrated approach with lean manufacturing where it then
becomes lean Six Sigma. Implementation of Six Sigma approach, it provided organisations a
proven track record to add value as well as ensure quality to business output in form of
incremental enhancements to goods. It could potentially be utilised for optimising the processes
in supply chain and enhancing satisfaction level of customers, which is the main element
pertaining to quality.
Aim of paper
The aim of the study expresses the intention of research and summarises in single sentence. It
depicts about what the researcher hopes to accomplish at the end of research project. The main
aim of this particular study are provided below:
“To assess whether the use of Six Sigma may improve Bangladeshi garment companies and
the issues they face while implementing the approach in their manufacturing process. The case
study of Bangladeshi Garments Industry.”
Paraphrase This Document
Need a fresh take? Get an instant paraphrase of this document with our AI Paraphraser
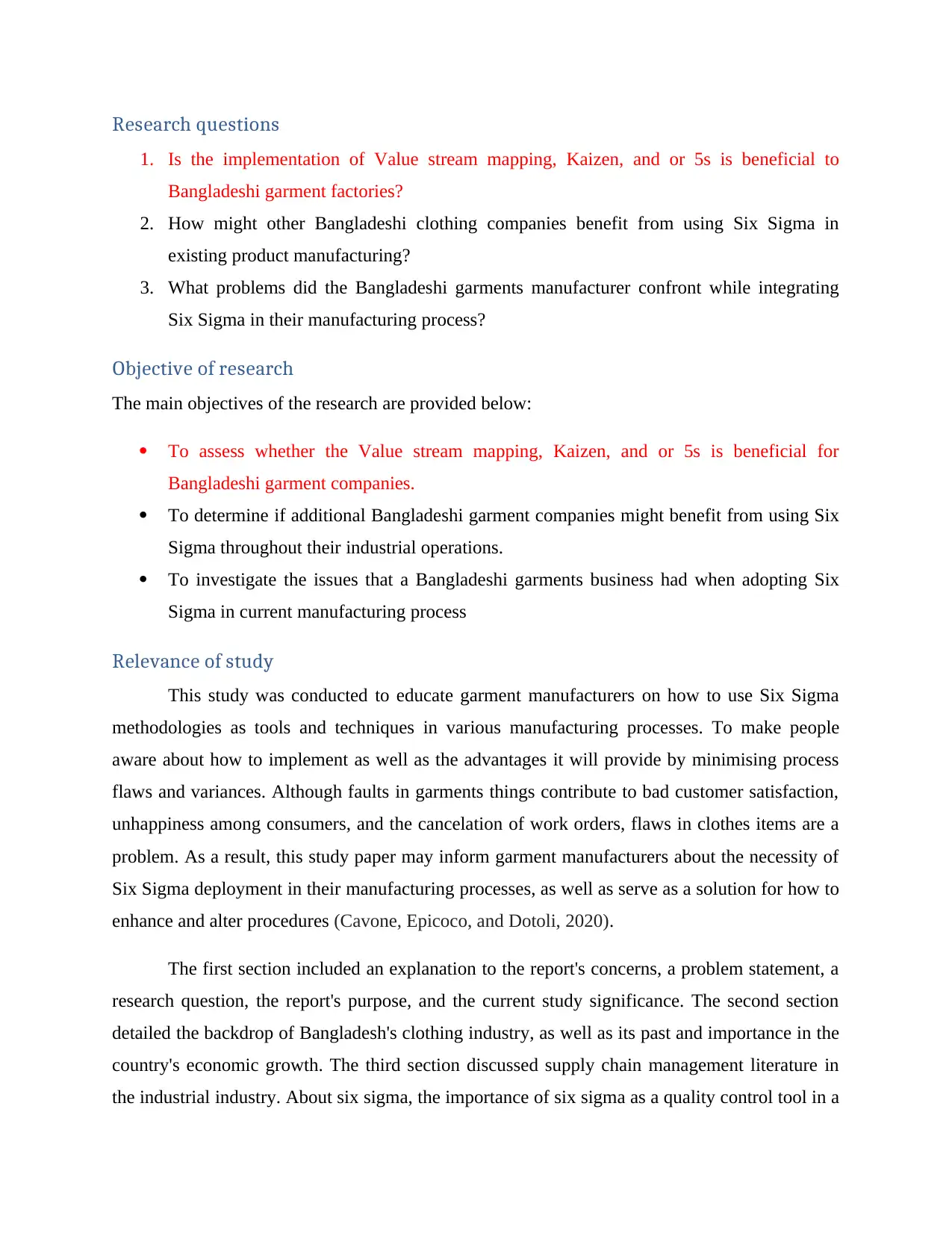
Research questions
1. Is the implementation of Value stream mapping, Kaizen, and or 5s is beneficial to
Bangladeshi garment factories?
2. How might other Bangladeshi clothing companies benefit from using Six Sigma in
existing product manufacturing?
3. What problems did the Bangladeshi garments manufacturer confront while integrating
Six Sigma in their manufacturing process?
Objective of research
The main objectives of the research are provided below:
To assess whether the Value stream mapping, Kaizen, and or 5s is beneficial for
Bangladeshi garment companies.
To determine if additional Bangladeshi garment companies might benefit from using Six
Sigma throughout their industrial operations.
To investigate the issues that a Bangladeshi garments business had when adopting Six
Sigma in current manufacturing process
Relevance of study
This study was conducted to educate garment manufacturers on how to use Six Sigma
methodologies as tools and techniques in various manufacturing processes. To make people
aware about how to implement as well as the advantages it will provide by minimising process
flaws and variances. Although faults in garments things contribute to bad customer satisfaction,
unhappiness among consumers, and the cancelation of work orders, flaws in clothes items are a
problem. As a result, this study paper may inform garment manufacturers about the necessity of
Six Sigma deployment in their manufacturing processes, as well as serve as a solution for how to
enhance and alter procedures (Cavone, Epicoco, and Dotoli, 2020).
The first section included an explanation to the report's concerns, a problem statement, a
research question, the report's purpose, and the current study significance. The second section
detailed the backdrop of Bangladesh's clothing industry, as well as its past and importance in the
country's economic growth. The third section discussed supply chain management literature in
the industrial industry. About six sigma, the importance of six sigma as a quality control tool in a
1. Is the implementation of Value stream mapping, Kaizen, and or 5s is beneficial to
Bangladeshi garment factories?
2. How might other Bangladeshi clothing companies benefit from using Six Sigma in
existing product manufacturing?
3. What problems did the Bangladeshi garments manufacturer confront while integrating
Six Sigma in their manufacturing process?
Objective of research
The main objectives of the research are provided below:
To assess whether the Value stream mapping, Kaizen, and or 5s is beneficial for
Bangladeshi garment companies.
To determine if additional Bangladeshi garment companies might benefit from using Six
Sigma throughout their industrial operations.
To investigate the issues that a Bangladeshi garments business had when adopting Six
Sigma in current manufacturing process
Relevance of study
This study was conducted to educate garment manufacturers on how to use Six Sigma
methodologies as tools and techniques in various manufacturing processes. To make people
aware about how to implement as well as the advantages it will provide by minimising process
flaws and variances. Although faults in garments things contribute to bad customer satisfaction,
unhappiness among consumers, and the cancelation of work orders, flaws in clothes items are a
problem. As a result, this study paper may inform garment manufacturers about the necessity of
Six Sigma deployment in their manufacturing processes, as well as serve as a solution for how to
enhance and alter procedures (Cavone, Epicoco, and Dotoli, 2020).
The first section included an explanation to the report's concerns, a problem statement, a
research question, the report's purpose, and the current study significance. The second section
detailed the backdrop of Bangladesh's clothing industry, as well as its past and importance in the
country's economic growth. The third section discussed supply chain management literature in
the industrial industry. About six sigma, the importance of six sigma as a quality control tool in a
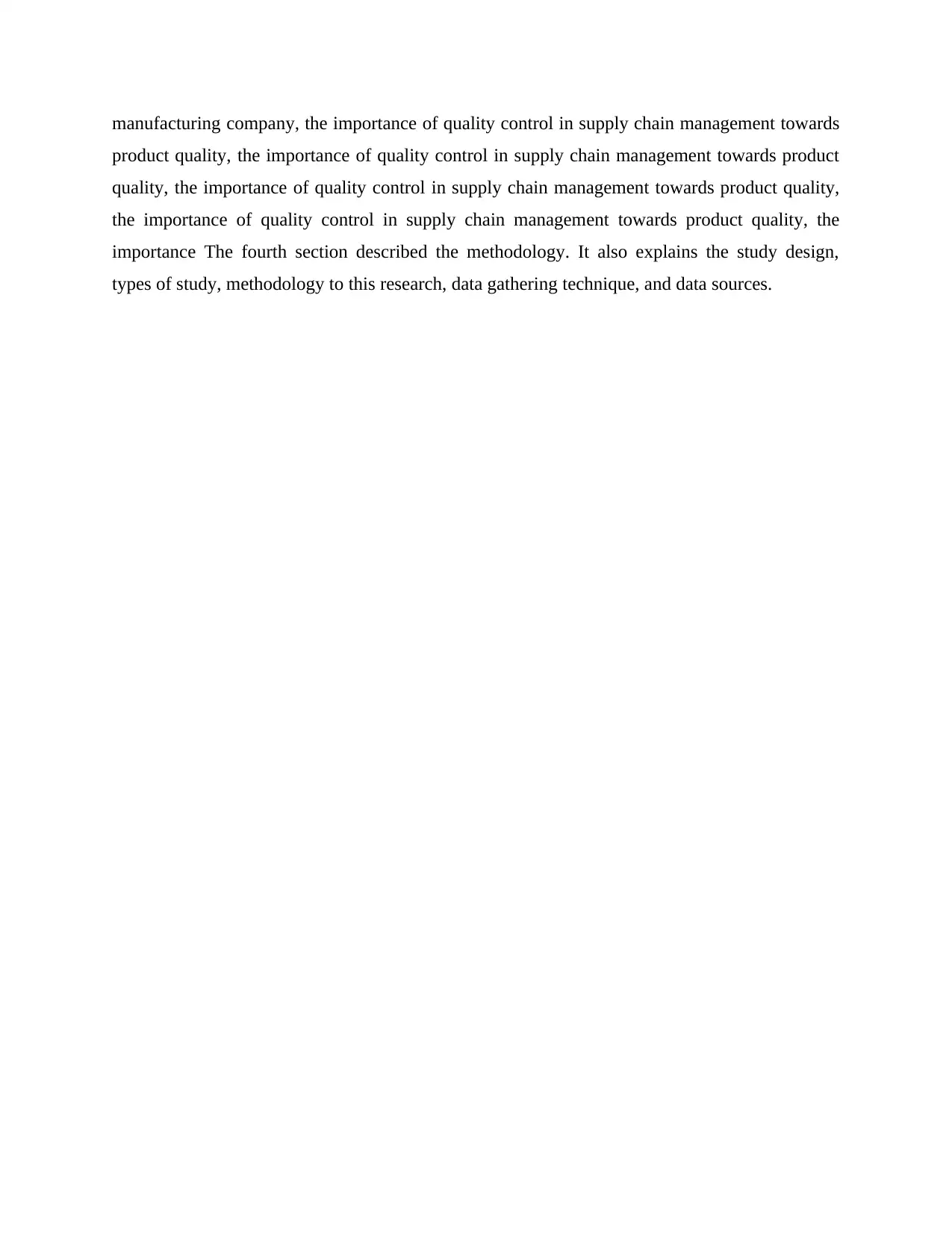
manufacturing company, the importance of quality control in supply chain management towards
product quality, the importance of quality control in supply chain management towards product
quality, the importance of quality control in supply chain management towards product quality,
the importance of quality control in supply chain management towards product quality, the
importance The fourth section described the methodology. It also explains the study design,
types of study, methodology to this research, data gathering technique, and data sources.
product quality, the importance of quality control in supply chain management towards product
quality, the importance of quality control in supply chain management towards product quality,
the importance of quality control in supply chain management towards product quality, the
importance The fourth section described the methodology. It also explains the study design,
types of study, methodology to this research, data gathering technique, and data sources.
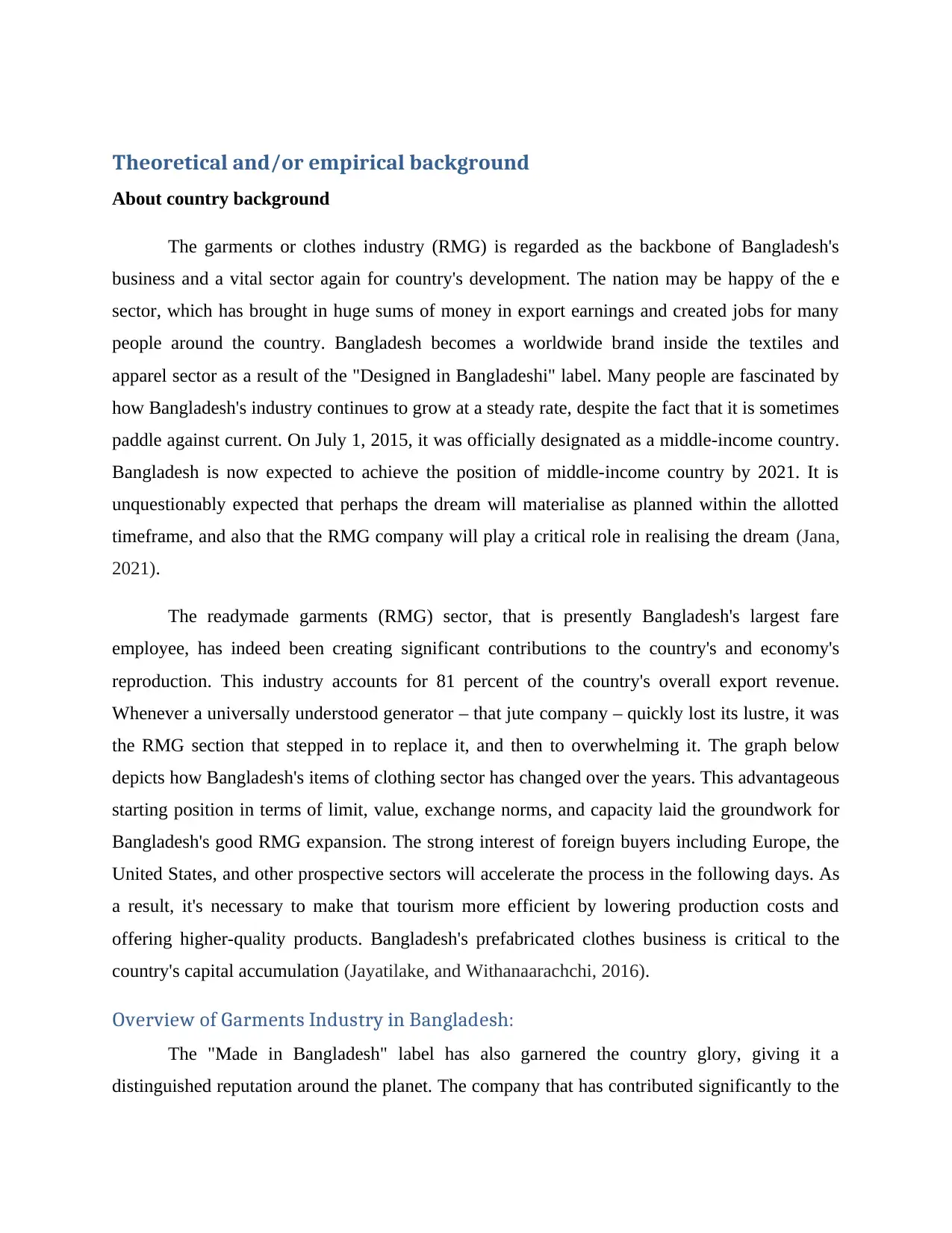
Theoretical and/or empirical background
About country background
The garments or clothes industry (RMG) is regarded as the backbone of Bangladesh's
business and a vital sector again for country's development. The nation may be happy of the e
sector, which has brought in huge sums of money in export earnings and created jobs for many
people around the country. Bangladesh becomes a worldwide brand inside the textiles and
apparel sector as a result of the "Designed in Bangladeshi" label. Many people are fascinated by
how Bangladesh's industry continues to grow at a steady rate, despite the fact that it is sometimes
paddle against current. On July 1, 2015, it was officially designated as a middle-income country.
Bangladesh is now expected to achieve the position of middle-income country by 2021. It is
unquestionably expected that perhaps the dream will materialise as planned within the allotted
timeframe, and also that the RMG company will play a critical role in realising the dream (Jana,
2021).
The readymade garments (RMG) sector, that is presently Bangladesh's largest fare
employee, has indeed been creating significant contributions to the country's and economy's
reproduction. This industry accounts for 81 percent of the country's overall export revenue.
Whenever a universally understood generator – that jute company – quickly lost its lustre, it was
the RMG section that stepped in to replace it, and then to overwhelming it. The graph below
depicts how Bangladesh's items of clothing sector has changed over the years. This advantageous
starting position in terms of limit, value, exchange norms, and capacity laid the groundwork for
Bangladesh's good RMG expansion. The strong interest of foreign buyers including Europe, the
United States, and other prospective sectors will accelerate the process in the following days. As
a result, it's necessary to make that tourism more efficient by lowering production costs and
offering higher-quality products. Bangladesh's prefabricated clothes business is critical to the
country's capital accumulation (Jayatilake, and Withanaarachchi, 2016).
Overview of Garments Industry in Bangladesh:
The "Made in Bangladesh" label has also garnered the country glory, giving it a
distinguished reputation around the planet. The company that has contributed significantly to the
About country background
The garments or clothes industry (RMG) is regarded as the backbone of Bangladesh's
business and a vital sector again for country's development. The nation may be happy of the e
sector, which has brought in huge sums of money in export earnings and created jobs for many
people around the country. Bangladesh becomes a worldwide brand inside the textiles and
apparel sector as a result of the "Designed in Bangladeshi" label. Many people are fascinated by
how Bangladesh's industry continues to grow at a steady rate, despite the fact that it is sometimes
paddle against current. On July 1, 2015, it was officially designated as a middle-income country.
Bangladesh is now expected to achieve the position of middle-income country by 2021. It is
unquestionably expected that perhaps the dream will materialise as planned within the allotted
timeframe, and also that the RMG company will play a critical role in realising the dream (Jana,
2021).
The readymade garments (RMG) sector, that is presently Bangladesh's largest fare
employee, has indeed been creating significant contributions to the country's and economy's
reproduction. This industry accounts for 81 percent of the country's overall export revenue.
Whenever a universally understood generator – that jute company – quickly lost its lustre, it was
the RMG section that stepped in to replace it, and then to overwhelming it. The graph below
depicts how Bangladesh's items of clothing sector has changed over the years. This advantageous
starting position in terms of limit, value, exchange norms, and capacity laid the groundwork for
Bangladesh's good RMG expansion. The strong interest of foreign buyers including Europe, the
United States, and other prospective sectors will accelerate the process in the following days. As
a result, it's necessary to make that tourism more efficient by lowering production costs and
offering higher-quality products. Bangladesh's prefabricated clothes business is critical to the
country's capital accumulation (Jayatilake, and Withanaarachchi, 2016).
Overview of Garments Industry in Bangladesh:
The "Made in Bangladesh" label has also garnered the country glory, giving it a
distinguished reputation around the planet. The company that has contributed significantly to the
Secure Best Marks with AI Grader
Need help grading? Try our AI Grader for instant feedback on your assignments.
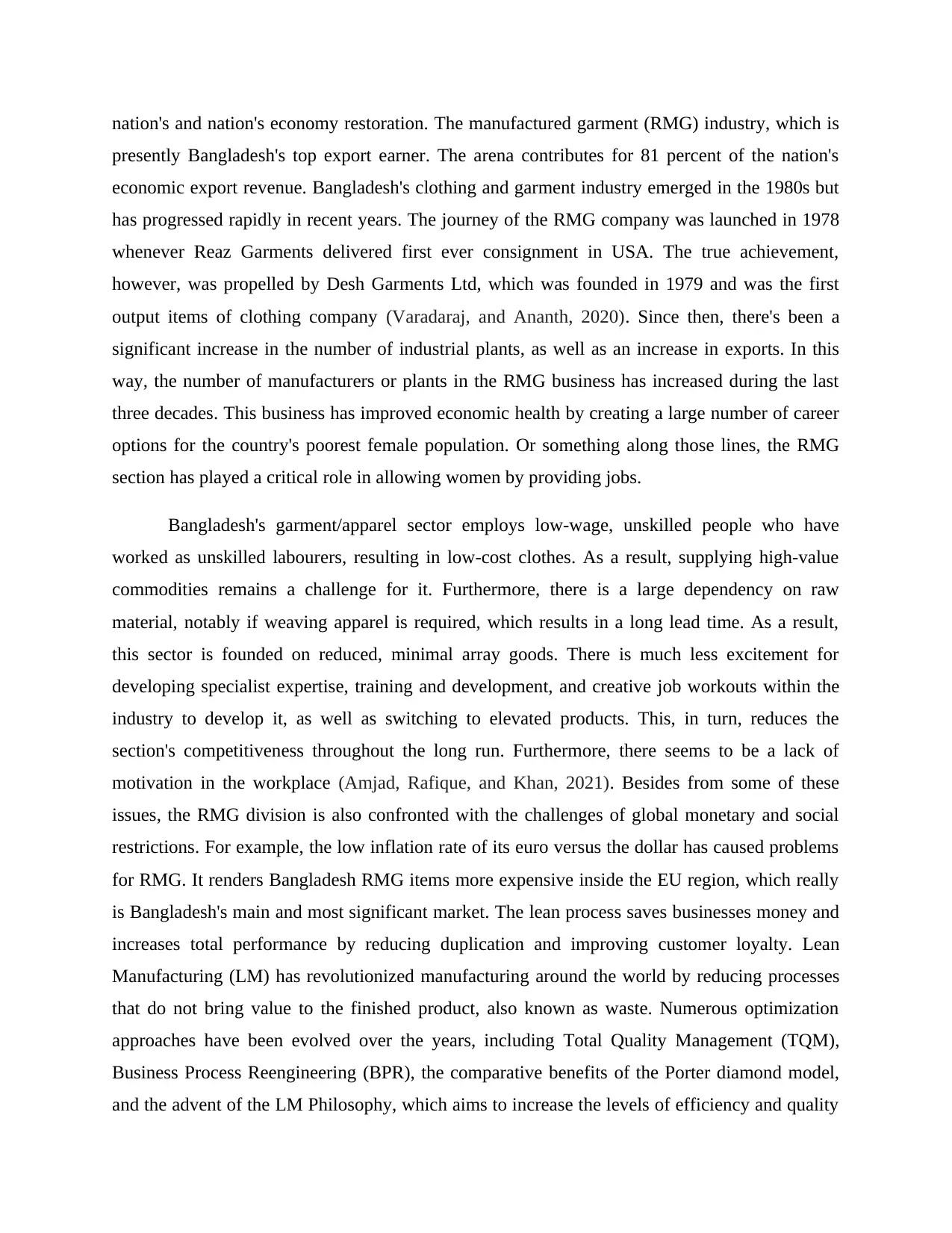
nation's and nation's economy restoration. The manufactured garment (RMG) industry, which is
presently Bangladesh's top export earner. The arena contributes for 81 percent of the nation's
economic export revenue. Bangladesh's clothing and garment industry emerged in the 1980s but
has progressed rapidly in recent years. The journey of the RMG company was launched in 1978
whenever Reaz Garments delivered first ever consignment in USA. The true achievement,
however, was propelled by Desh Garments Ltd, which was founded in 1979 and was the first
output items of clothing company (Varadaraj, and Ananth, 2020). Since then, there's been a
significant increase in the number of industrial plants, as well as an increase in exports. In this
way, the number of manufacturers or plants in the RMG business has increased during the last
three decades. This business has improved economic health by creating a large number of career
options for the country's poorest female population. Or something along those lines, the RMG
section has played a critical role in allowing women by providing jobs.
Bangladesh's garment/apparel sector employs low-wage, unskilled people who have
worked as unskilled labourers, resulting in low-cost clothes. As a result, supplying high-value
commodities remains a challenge for it. Furthermore, there is a large dependency on raw
material, notably if weaving apparel is required, which results in a long lead time. As a result,
this sector is founded on reduced, minimal array goods. There is much less excitement for
developing specialist expertise, training and development, and creative job workouts within the
industry to develop it, as well as switching to elevated products. This, in turn, reduces the
section's competitiveness throughout the long run. Furthermore, there seems to be a lack of
motivation in the workplace (Amjad, Rafique, and Khan, 2021). Besides from some of these
issues, the RMG division is also confronted with the challenges of global monetary and social
restrictions. For example, the low inflation rate of its euro versus the dollar has caused problems
for RMG. It renders Bangladesh RMG items more expensive inside the EU region, which really
is Bangladesh's main and most significant market. The lean process saves businesses money and
increases total performance by reducing duplication and improving customer loyalty. Lean
Manufacturing (LM) has revolutionized manufacturing around the world by reducing processes
that do not bring value to the finished product, also known as waste. Numerous optimization
approaches have been evolved over the years, including Total Quality Management (TQM),
Business Process Reengineering (BPR), the comparative benefits of the Porter diamond model,
and the advent of the LM Philosophy, which aims to increase the levels of efficiency and quality
presently Bangladesh's top export earner. The arena contributes for 81 percent of the nation's
economic export revenue. Bangladesh's clothing and garment industry emerged in the 1980s but
has progressed rapidly in recent years. The journey of the RMG company was launched in 1978
whenever Reaz Garments delivered first ever consignment in USA. The true achievement,
however, was propelled by Desh Garments Ltd, which was founded in 1979 and was the first
output items of clothing company (Varadaraj, and Ananth, 2020). Since then, there's been a
significant increase in the number of industrial plants, as well as an increase in exports. In this
way, the number of manufacturers or plants in the RMG business has increased during the last
three decades. This business has improved economic health by creating a large number of career
options for the country's poorest female population. Or something along those lines, the RMG
section has played a critical role in allowing women by providing jobs.
Bangladesh's garment/apparel sector employs low-wage, unskilled people who have
worked as unskilled labourers, resulting in low-cost clothes. As a result, supplying high-value
commodities remains a challenge for it. Furthermore, there is a large dependency on raw
material, notably if weaving apparel is required, which results in a long lead time. As a result,
this sector is founded on reduced, minimal array goods. There is much less excitement for
developing specialist expertise, training and development, and creative job workouts within the
industry to develop it, as well as switching to elevated products. This, in turn, reduces the
section's competitiveness throughout the long run. Furthermore, there seems to be a lack of
motivation in the workplace (Amjad, Rafique, and Khan, 2021). Besides from some of these
issues, the RMG division is also confronted with the challenges of global monetary and social
restrictions. For example, the low inflation rate of its euro versus the dollar has caused problems
for RMG. It renders Bangladesh RMG items more expensive inside the EU region, which really
is Bangladesh's main and most significant market. The lean process saves businesses money and
increases total performance by reducing duplication and improving customer loyalty. Lean
Manufacturing (LM) has revolutionized manufacturing around the world by reducing processes
that do not bring value to the finished product, also known as waste. Numerous optimization
approaches have been evolved over the years, including Total Quality Management (TQM),
Business Process Reengineering (BPR), the comparative benefits of the Porter diamond model,
and the advent of the LM Philosophy, which aims to increase the levels of efficiency and quality
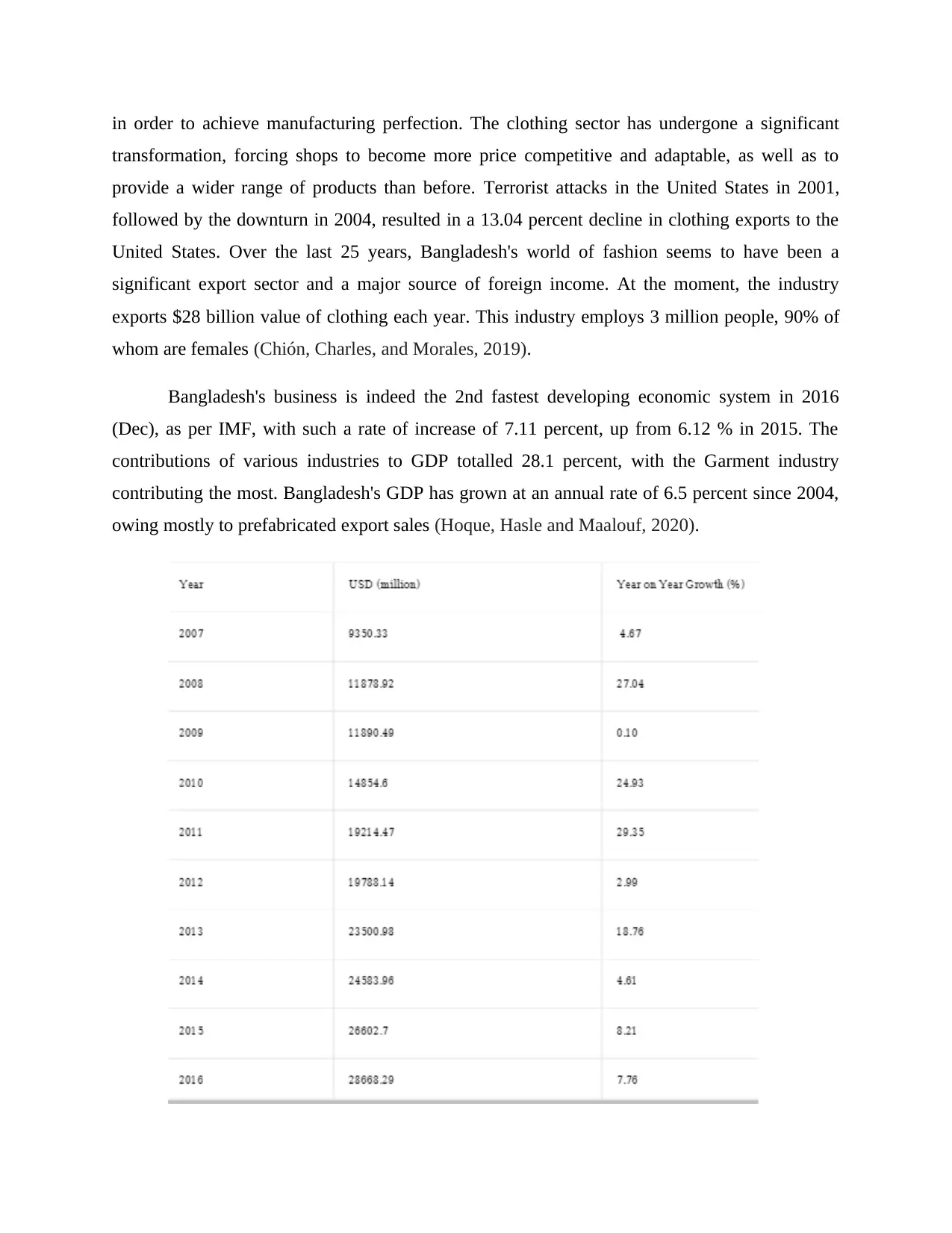
in order to achieve manufacturing perfection. The clothing sector has undergone a significant
transformation, forcing shops to become more price competitive and adaptable, as well as to
provide a wider range of products than before. Terrorist attacks in the United States in 2001,
followed by the downturn in 2004, resulted in a 13.04 percent decline in clothing exports to the
United States. Over the last 25 years, Bangladesh's world of fashion seems to have been a
significant export sector and a major source of foreign income. At the moment, the industry
exports $28 billion value of clothing each year. This industry employs 3 million people, 90% of
whom are females (Chión, Charles, and Morales, 2019).
Bangladesh's business is indeed the 2nd fastest developing economic system in 2016
(Dec), as per IMF, with such a rate of increase of 7.11 percent, up from 6.12 % in 2015. The
contributions of various industries to GDP totalled 28.1 percent, with the Garment industry
contributing the most. Bangladesh's GDP has grown at an annual rate of 6.5 percent since 2004,
owing mostly to prefabricated export sales (Hoque, Hasle and Maalouf, 2020).
transformation, forcing shops to become more price competitive and adaptable, as well as to
provide a wider range of products than before. Terrorist attacks in the United States in 2001,
followed by the downturn in 2004, resulted in a 13.04 percent decline in clothing exports to the
United States. Over the last 25 years, Bangladesh's world of fashion seems to have been a
significant export sector and a major source of foreign income. At the moment, the industry
exports $28 billion value of clothing each year. This industry employs 3 million people, 90% of
whom are females (Chión, Charles, and Morales, 2019).
Bangladesh's business is indeed the 2nd fastest developing economic system in 2016
(Dec), as per IMF, with such a rate of increase of 7.11 percent, up from 6.12 % in 2015. The
contributions of various industries to GDP totalled 28.1 percent, with the Garment industry
contributing the most. Bangladesh's GDP has grown at an annual rate of 6.5 percent since 2004,
owing mostly to prefabricated export sales (Hoque, Hasle and Maalouf, 2020).
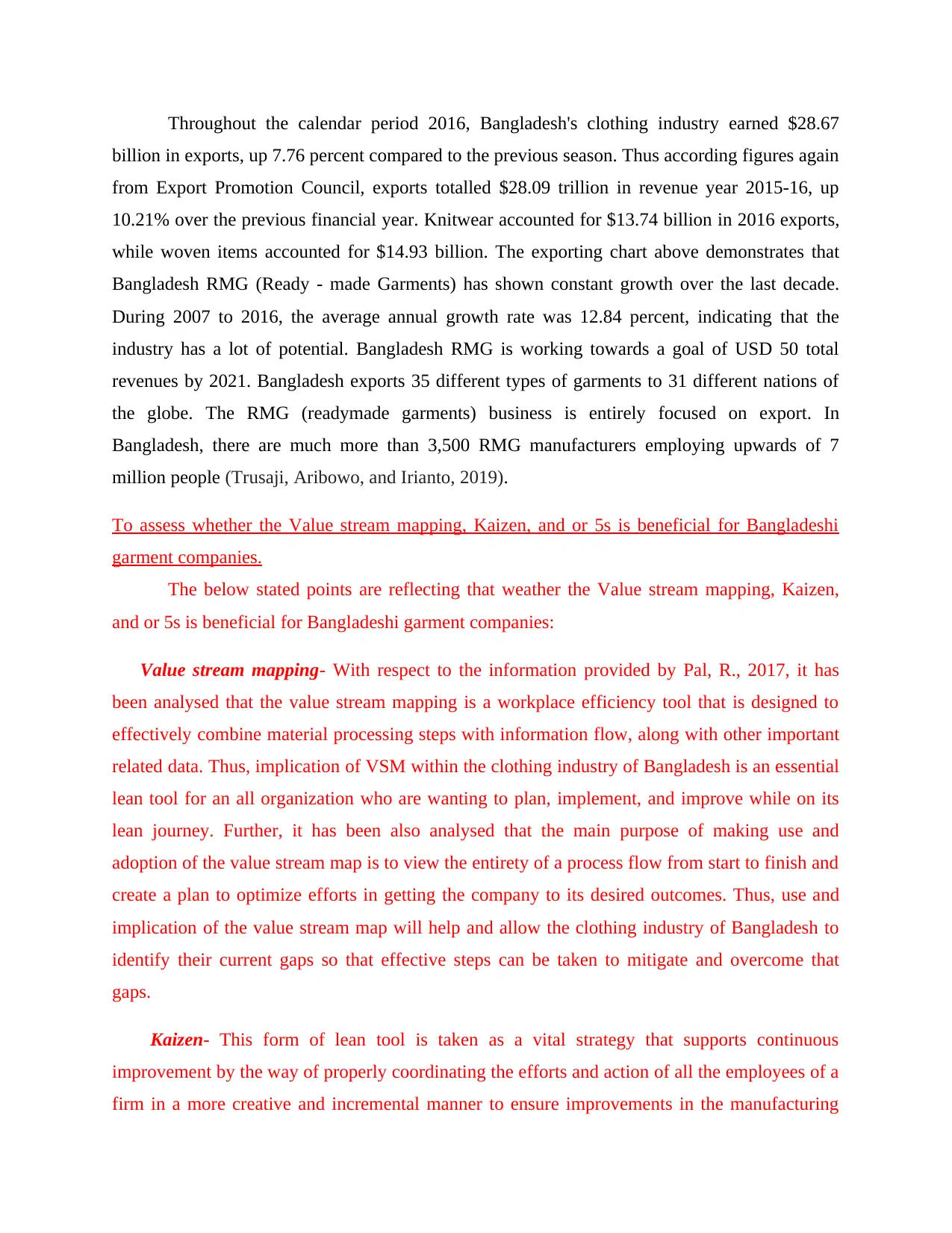
Throughout the calendar period 2016, Bangladesh's clothing industry earned $28.67
billion in exports, up 7.76 percent compared to the previous season. Thus according figures again
from Export Promotion Council, exports totalled $28.09 trillion in revenue year 2015-16, up
10.21% over the previous financial year. Knitwear accounted for $13.74 billion in 2016 exports,
while woven items accounted for $14.93 billion. The exporting chart above demonstrates that
Bangladesh RMG (Ready - made Garments) has shown constant growth over the last decade.
During 2007 to 2016, the average annual growth rate was 12.84 percent, indicating that the
industry has a lot of potential. Bangladesh RMG is working towards a goal of USD 50 total
revenues by 2021. Bangladesh exports 35 different types of garments to 31 different nations of
the globe. The RMG (readymade garments) business is entirely focused on export. In
Bangladesh, there are much more than 3,500 RMG manufacturers employing upwards of 7
million people (Trusaji, Aribowo, and Irianto, 2019).
To assess whether the Value stream mapping, Kaizen, and or 5s is beneficial for Bangladeshi
garment companies.
The below stated points are reflecting that weather the Value stream mapping, Kaizen,
and or 5s is beneficial for Bangladeshi garment companies:
Value stream mapping- With respect to the information provided by Pal, R., 2017, it has
been analysed that the value stream mapping is a workplace efficiency tool that is designed to
effectively combine material processing steps with information flow, along with other important
related data. Thus, implication of VSM within the clothing industry of Bangladesh is an essential
lean tool for an all organization who are wanting to plan, implement, and improve while on its
lean journey. Further, it has been also analysed that the main purpose of making use and
adoption of the value stream map is to view the entirety of a process flow from start to finish and
create a plan to optimize efforts in getting the company to its desired outcomes. Thus, use and
implication of the value stream map will help and allow the clothing industry of Bangladesh to
identify their current gaps so that effective steps can be taken to mitigate and overcome that
gaps.
Kaizen- This form of lean tool is taken as a vital strategy that supports continuous
improvement by the way of properly coordinating the efforts and action of all the employees of a
firm in a more creative and incremental manner to ensure improvements in the manufacturing
billion in exports, up 7.76 percent compared to the previous season. Thus according figures again
from Export Promotion Council, exports totalled $28.09 trillion in revenue year 2015-16, up
10.21% over the previous financial year. Knitwear accounted for $13.74 billion in 2016 exports,
while woven items accounted for $14.93 billion. The exporting chart above demonstrates that
Bangladesh RMG (Ready - made Garments) has shown constant growth over the last decade.
During 2007 to 2016, the average annual growth rate was 12.84 percent, indicating that the
industry has a lot of potential. Bangladesh RMG is working towards a goal of USD 50 total
revenues by 2021. Bangladesh exports 35 different types of garments to 31 different nations of
the globe. The RMG (readymade garments) business is entirely focused on export. In
Bangladesh, there are much more than 3,500 RMG manufacturers employing upwards of 7
million people (Trusaji, Aribowo, and Irianto, 2019).
To assess whether the Value stream mapping, Kaizen, and or 5s is beneficial for Bangladeshi
garment companies.
The below stated points are reflecting that weather the Value stream mapping, Kaizen,
and or 5s is beneficial for Bangladeshi garment companies:
Value stream mapping- With respect to the information provided by Pal, R., 2017, it has
been analysed that the value stream mapping is a workplace efficiency tool that is designed to
effectively combine material processing steps with information flow, along with other important
related data. Thus, implication of VSM within the clothing industry of Bangladesh is an essential
lean tool for an all organization who are wanting to plan, implement, and improve while on its
lean journey. Further, it has been also analysed that the main purpose of making use and
adoption of the value stream map is to view the entirety of a process flow from start to finish and
create a plan to optimize efforts in getting the company to its desired outcomes. Thus, use and
implication of the value stream map will help and allow the clothing industry of Bangladesh to
identify their current gaps so that effective steps can be taken to mitigate and overcome that
gaps.
Kaizen- This form of lean tool is taken as a vital strategy that supports continuous
improvement by the way of properly coordinating the efforts and action of all the employees of a
firm in a more creative and incremental manner to ensure improvements in the manufacturing
Paraphrase This Document
Need a fresh take? Get an instant paraphrase of this document with our AI Paraphraser
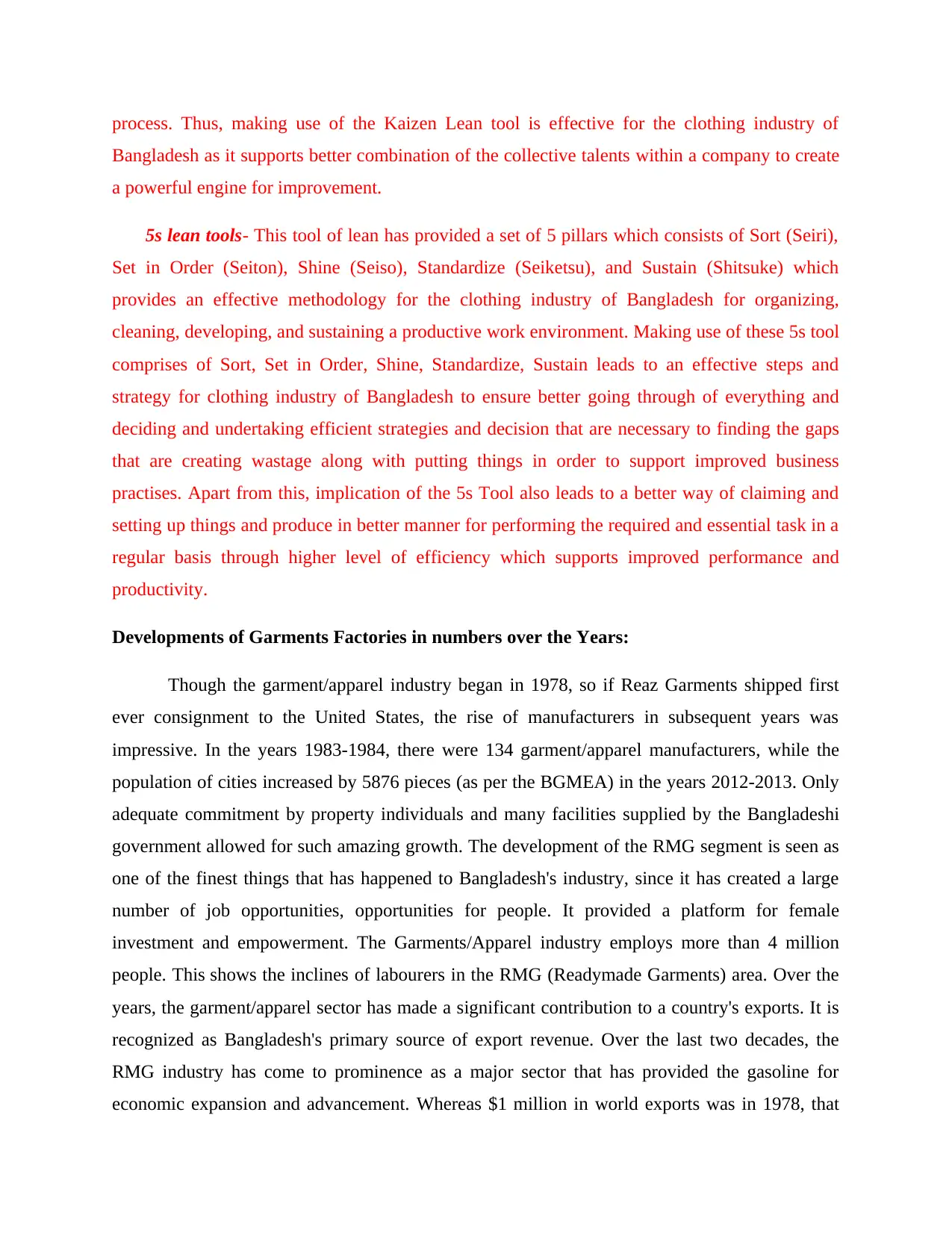
process. Thus, making use of the Kaizen Lean tool is effective for the clothing industry of
Bangladesh as it supports better combination of the collective talents within a company to create
a powerful engine for improvement.
5s lean tools- This tool of lean has provided a set of 5 pillars which consists of Sort (Seiri),
Set in Order (Seiton), Shine (Seiso), Standardize (Seiketsu), and Sustain (Shitsuke) which
provides an effective methodology for the clothing industry of Bangladesh for organizing,
cleaning, developing, and sustaining a productive work environment. Making use of these 5s tool
comprises of Sort, Set in Order, Shine, Standardize, Sustain leads to an effective steps and
strategy for clothing industry of Bangladesh to ensure better going through of everything and
deciding and undertaking efficient strategies and decision that are necessary to finding the gaps
that are creating wastage along with putting things in order to support improved business
practises. Apart from this, implication of the 5s Tool also leads to a better way of claiming and
setting up things and produce in better manner for performing the required and essential task in a
regular basis through higher level of efficiency which supports improved performance and
productivity.
Developments of Garments Factories in numbers over the Years:
Though the garment/apparel industry began in 1978, so if Reaz Garments shipped first
ever consignment to the United States, the rise of manufacturers in subsequent years was
impressive. In the years 1983-1984, there were 134 garment/apparel manufacturers, while the
population of cities increased by 5876 pieces (as per the BGMEA) in the years 2012-2013. Only
adequate commitment by property individuals and many facilities supplied by the Bangladeshi
government allowed for such amazing growth. The development of the RMG segment is seen as
one of the finest things that has happened to Bangladesh's industry, since it has created a large
number of job opportunities, opportunities for people. It provided a platform for female
investment and empowerment. The Garments/Apparel industry employs more than 4 million
people. This shows the inclines of labourers in the RMG (Readymade Garments) area. Over the
years, the garment/apparel sector has made a significant contribution to a country's exports. It is
recognized as Bangladesh's primary source of export revenue. Over the last two decades, the
RMG industry has come to prominence as a major sector that has provided the gasoline for
economic expansion and advancement. Whereas $1 million in world exports was in 1978, that
Bangladesh as it supports better combination of the collective talents within a company to create
a powerful engine for improvement.
5s lean tools- This tool of lean has provided a set of 5 pillars which consists of Sort (Seiri),
Set in Order (Seiton), Shine (Seiso), Standardize (Seiketsu), and Sustain (Shitsuke) which
provides an effective methodology for the clothing industry of Bangladesh for organizing,
cleaning, developing, and sustaining a productive work environment. Making use of these 5s tool
comprises of Sort, Set in Order, Shine, Standardize, Sustain leads to an effective steps and
strategy for clothing industry of Bangladesh to ensure better going through of everything and
deciding and undertaking efficient strategies and decision that are necessary to finding the gaps
that are creating wastage along with putting things in order to support improved business
practises. Apart from this, implication of the 5s Tool also leads to a better way of claiming and
setting up things and produce in better manner for performing the required and essential task in a
regular basis through higher level of efficiency which supports improved performance and
productivity.
Developments of Garments Factories in numbers over the Years:
Though the garment/apparel industry began in 1978, so if Reaz Garments shipped first
ever consignment to the United States, the rise of manufacturers in subsequent years was
impressive. In the years 1983-1984, there were 134 garment/apparel manufacturers, while the
population of cities increased by 5876 pieces (as per the BGMEA) in the years 2012-2013. Only
adequate commitment by property individuals and many facilities supplied by the Bangladeshi
government allowed for such amazing growth. The development of the RMG segment is seen as
one of the finest things that has happened to Bangladesh's industry, since it has created a large
number of job opportunities, opportunities for people. It provided a platform for female
investment and empowerment. The Garments/Apparel industry employs more than 4 million
people. This shows the inclines of labourers in the RMG (Readymade Garments) area. Over the
years, the garment/apparel sector has made a significant contribution to a country's exports. It is
recognized as Bangladesh's primary source of export revenue. Over the last two decades, the
RMG industry has come to prominence as a major sector that has provided the gasoline for
economic expansion and advancement. Whereas $1 million in world exports was in 1978, that
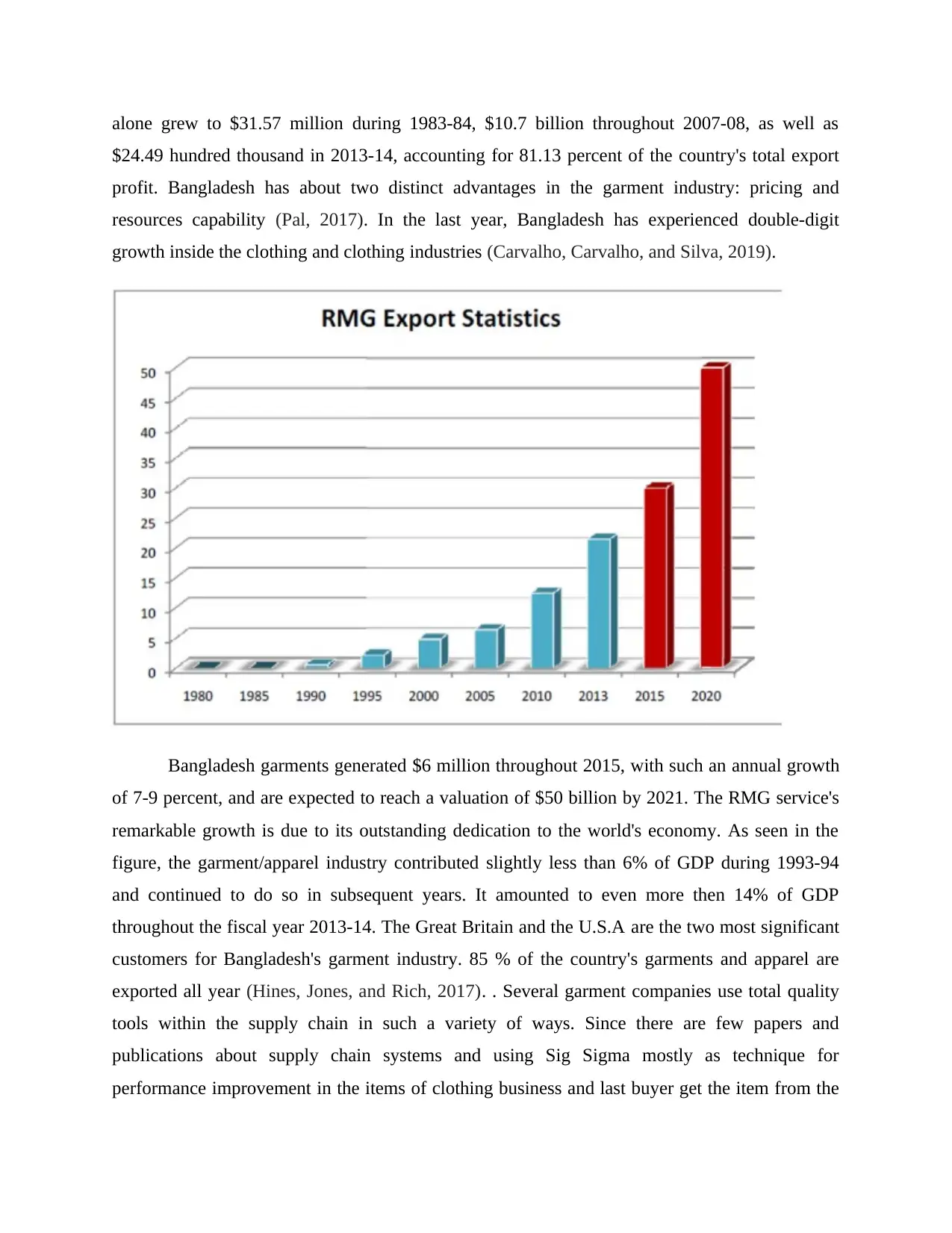
alone grew to $31.57 million during 1983-84, $10.7 billion throughout 2007-08, as well as
$24.49 hundred thousand in 2013-14, accounting for 81.13 percent of the country's total export
profit. Bangladesh has about two distinct advantages in the garment industry: pricing and
resources capability (Pal, 2017). In the last year, Bangladesh has experienced double-digit
growth inside the clothing and clothing industries (Carvalho, Carvalho, and Silva, 2019).
Bangladesh garments generated $6 million throughout 2015, with such an annual growth
of 7-9 percent, and are expected to reach a valuation of $50 billion by 2021. The RMG service's
remarkable growth is due to its outstanding dedication to the world's economy. As seen in the
figure, the garment/apparel industry contributed slightly less than 6% of GDP during 1993-94
and continued to do so in subsequent years. It amounted to even more then 14% of GDP
throughout the fiscal year 2013-14. The Great Britain and the U.S.A are the two most significant
customers for Bangladesh's garment industry. 85 % of the country's garments and apparel are
exported all year (Hines, Jones, and Rich, 2017). . Several garment companies use total quality
tools within the supply chain in such a variety of ways. Since there are few papers and
publications about supply chain systems and using Sig Sigma mostly as technique for
performance improvement in the items of clothing business and last buyer get the item from the
$24.49 hundred thousand in 2013-14, accounting for 81.13 percent of the country's total export
profit. Bangladesh has about two distinct advantages in the garment industry: pricing and
resources capability (Pal, 2017). In the last year, Bangladesh has experienced double-digit
growth inside the clothing and clothing industries (Carvalho, Carvalho, and Silva, 2019).
Bangladesh garments generated $6 million throughout 2015, with such an annual growth
of 7-9 percent, and are expected to reach a valuation of $50 billion by 2021. The RMG service's
remarkable growth is due to its outstanding dedication to the world's economy. As seen in the
figure, the garment/apparel industry contributed slightly less than 6% of GDP during 1993-94
and continued to do so in subsequent years. It amounted to even more then 14% of GDP
throughout the fiscal year 2013-14. The Great Britain and the U.S.A are the two most significant
customers for Bangladesh's garment industry. 85 % of the country's garments and apparel are
exported all year (Hines, Jones, and Rich, 2017). . Several garment companies use total quality
tools within the supply chain in such a variety of ways. Since there are few papers and
publications about supply chain systems and using Sig Sigma mostly as technique for
performance improvement in the items of clothing business and last buyer get the item from the
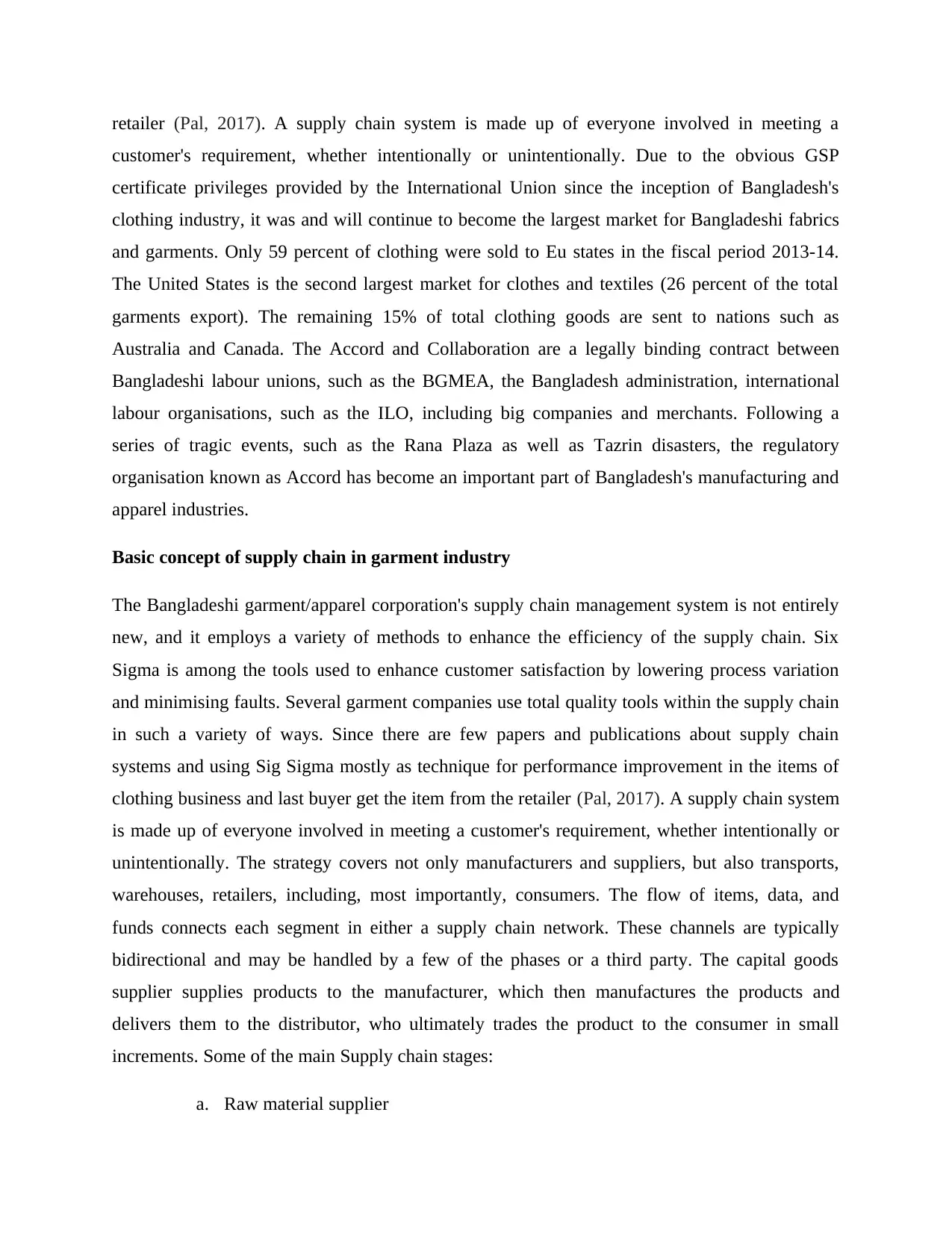
retailer (Pal, 2017). A supply chain system is made up of everyone involved in meeting a
customer's requirement, whether intentionally or unintentionally. Due to the obvious GSP
certificate privileges provided by the International Union since the inception of Bangladesh's
clothing industry, it was and will continue to become the largest market for Bangladeshi fabrics
and garments. Only 59 percent of clothing were sold to Eu states in the fiscal period 2013-14.
The United States is the second largest market for clothes and textiles (26 percent of the total
garments export). The remaining 15% of total clothing goods are sent to nations such as
Australia and Canada. The Accord and Collaboration are a legally binding contract between
Bangladeshi labour unions, such as the BGMEA, the Bangladesh administration, international
labour organisations, such as the ILO, including big companies and merchants. Following a
series of tragic events, such as the Rana Plaza as well as Tazrin disasters, the regulatory
organisation known as Accord has become an important part of Bangladesh's manufacturing and
apparel industries.
Basic concept of supply chain in garment industry
The Bangladeshi garment/apparel corporation's supply chain management system is not entirely
new, and it employs a variety of methods to enhance the efficiency of the supply chain. Six
Sigma is among the tools used to enhance customer satisfaction by lowering process variation
and minimising faults. Several garment companies use total quality tools within the supply chain
in such a variety of ways. Since there are few papers and publications about supply chain
systems and using Sig Sigma mostly as technique for performance improvement in the items of
clothing business and last buyer get the item from the retailer (Pal, 2017). A supply chain system
is made up of everyone involved in meeting a customer's requirement, whether intentionally or
unintentionally. The strategy covers not only manufacturers and suppliers, but also transports,
warehouses, retailers, including, most importantly, consumers. The flow of items, data, and
funds connects each segment in either a supply chain network. These channels are typically
bidirectional and may be handled by a few of the phases or a third party. The capital goods
supplier supplies products to the manufacturer, which then manufactures the products and
delivers them to the distributor, who ultimately trades the product to the consumer in small
increments. Some of the main Supply chain stages:
a. Raw material supplier
customer's requirement, whether intentionally or unintentionally. Due to the obvious GSP
certificate privileges provided by the International Union since the inception of Bangladesh's
clothing industry, it was and will continue to become the largest market for Bangladeshi fabrics
and garments. Only 59 percent of clothing were sold to Eu states in the fiscal period 2013-14.
The United States is the second largest market for clothes and textiles (26 percent of the total
garments export). The remaining 15% of total clothing goods are sent to nations such as
Australia and Canada. The Accord and Collaboration are a legally binding contract between
Bangladeshi labour unions, such as the BGMEA, the Bangladesh administration, international
labour organisations, such as the ILO, including big companies and merchants. Following a
series of tragic events, such as the Rana Plaza as well as Tazrin disasters, the regulatory
organisation known as Accord has become an important part of Bangladesh's manufacturing and
apparel industries.
Basic concept of supply chain in garment industry
The Bangladeshi garment/apparel corporation's supply chain management system is not entirely
new, and it employs a variety of methods to enhance the efficiency of the supply chain. Six
Sigma is among the tools used to enhance customer satisfaction by lowering process variation
and minimising faults. Several garment companies use total quality tools within the supply chain
in such a variety of ways. Since there are few papers and publications about supply chain
systems and using Sig Sigma mostly as technique for performance improvement in the items of
clothing business and last buyer get the item from the retailer (Pal, 2017). A supply chain system
is made up of everyone involved in meeting a customer's requirement, whether intentionally or
unintentionally. The strategy covers not only manufacturers and suppliers, but also transports,
warehouses, retailers, including, most importantly, consumers. The flow of items, data, and
funds connects each segment in either a supply chain network. These channels are typically
bidirectional and may be handled by a few of the phases or a third party. The capital goods
supplier supplies products to the manufacturer, which then manufactures the products and
delivers them to the distributor, who ultimately trades the product to the consumer in small
increments. Some of the main Supply chain stages:
a. Raw material supplier
Secure Best Marks with AI Grader
Need help grading? Try our AI Grader for instant feedback on your assignments.
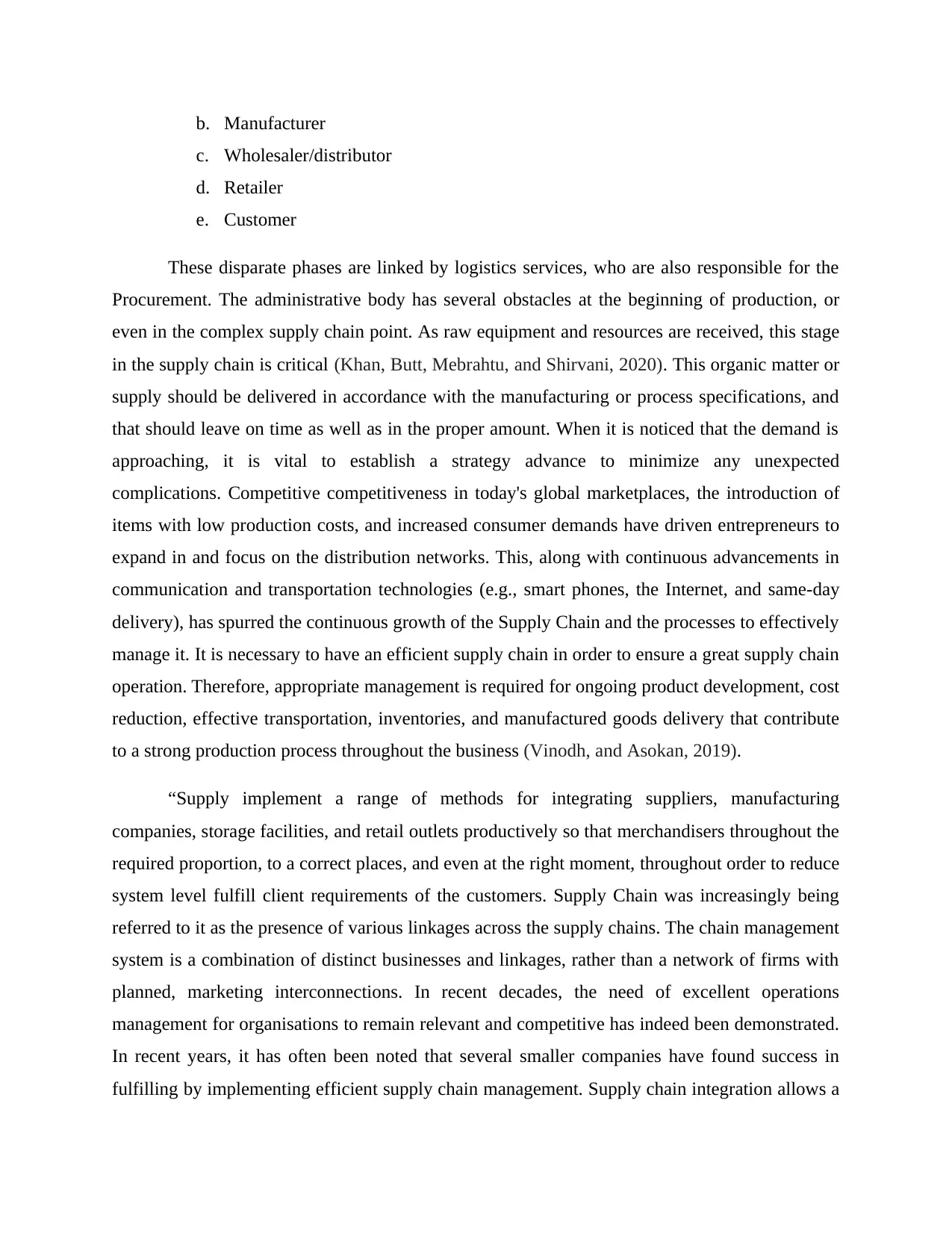
b. Manufacturer
c. Wholesaler/distributor
d. Retailer
e. Customer
These disparate phases are linked by logistics services, who are also responsible for the
Procurement. The administrative body has several obstacles at the beginning of production, or
even in the complex supply chain point. As raw equipment and resources are received, this stage
in the supply chain is critical (Khan, Butt, Mebrahtu, and Shirvani, 2020). This organic matter or
supply should be delivered in accordance with the manufacturing or process specifications, and
that should leave on time as well as in the proper amount. When it is noticed that the demand is
approaching, it is vital to establish a strategy advance to minimize any unexpected
complications. Competitive competitiveness in today's global marketplaces, the introduction of
items with low production costs, and increased consumer demands have driven entrepreneurs to
expand in and focus on the distribution networks. This, along with continuous advancements in
communication and transportation technologies (e.g., smart phones, the Internet, and same-day
delivery), has spurred the continuous growth of the Supply Chain and the processes to effectively
manage it. It is necessary to have an efficient supply chain in order to ensure a great supply chain
operation. Therefore, appropriate management is required for ongoing product development, cost
reduction, effective transportation, inventories, and manufactured goods delivery that contribute
to a strong production process throughout the business (Vinodh, and Asokan, 2019).
“Supply implement a range of methods for integrating suppliers, manufacturing
companies, storage facilities, and retail outlets productively so that merchandisers throughout the
required proportion, to a correct places, and even at the right moment, throughout order to reduce
system level fulfill client requirements of the customers. Supply Chain was increasingly being
referred to it as the presence of various linkages across the supply chains. The chain management
system is a combination of distinct businesses and linkages, rather than a network of firms with
planned, marketing interconnections. In recent decades, the need of excellent operations
management for organisations to remain relevant and competitive has indeed been demonstrated.
In recent years, it has often been noted that several smaller companies have found success in
fulfilling by implementing efficient supply chain management. Supply chain integration allows a
c. Wholesaler/distributor
d. Retailer
e. Customer
These disparate phases are linked by logistics services, who are also responsible for the
Procurement. The administrative body has several obstacles at the beginning of production, or
even in the complex supply chain point. As raw equipment and resources are received, this stage
in the supply chain is critical (Khan, Butt, Mebrahtu, and Shirvani, 2020). This organic matter or
supply should be delivered in accordance with the manufacturing or process specifications, and
that should leave on time as well as in the proper amount. When it is noticed that the demand is
approaching, it is vital to establish a strategy advance to minimize any unexpected
complications. Competitive competitiveness in today's global marketplaces, the introduction of
items with low production costs, and increased consumer demands have driven entrepreneurs to
expand in and focus on the distribution networks. This, along with continuous advancements in
communication and transportation technologies (e.g., smart phones, the Internet, and same-day
delivery), has spurred the continuous growth of the Supply Chain and the processes to effectively
manage it. It is necessary to have an efficient supply chain in order to ensure a great supply chain
operation. Therefore, appropriate management is required for ongoing product development, cost
reduction, effective transportation, inventories, and manufactured goods delivery that contribute
to a strong production process throughout the business (Vinodh, and Asokan, 2019).
“Supply implement a range of methods for integrating suppliers, manufacturing
companies, storage facilities, and retail outlets productively so that merchandisers throughout the
required proportion, to a correct places, and even at the right moment, throughout order to reduce
system level fulfill client requirements of the customers. Supply Chain was increasingly being
referred to it as the presence of various linkages across the supply chains. The chain management
system is a combination of distinct businesses and linkages, rather than a network of firms with
planned, marketing interconnections. In recent decades, the need of excellent operations
management for organisations to remain relevant and competitive has indeed been demonstrated.
In recent years, it has often been noted that several smaller companies have found success in
fulfilling by implementing efficient supply chain management. Supply chain integration allows a
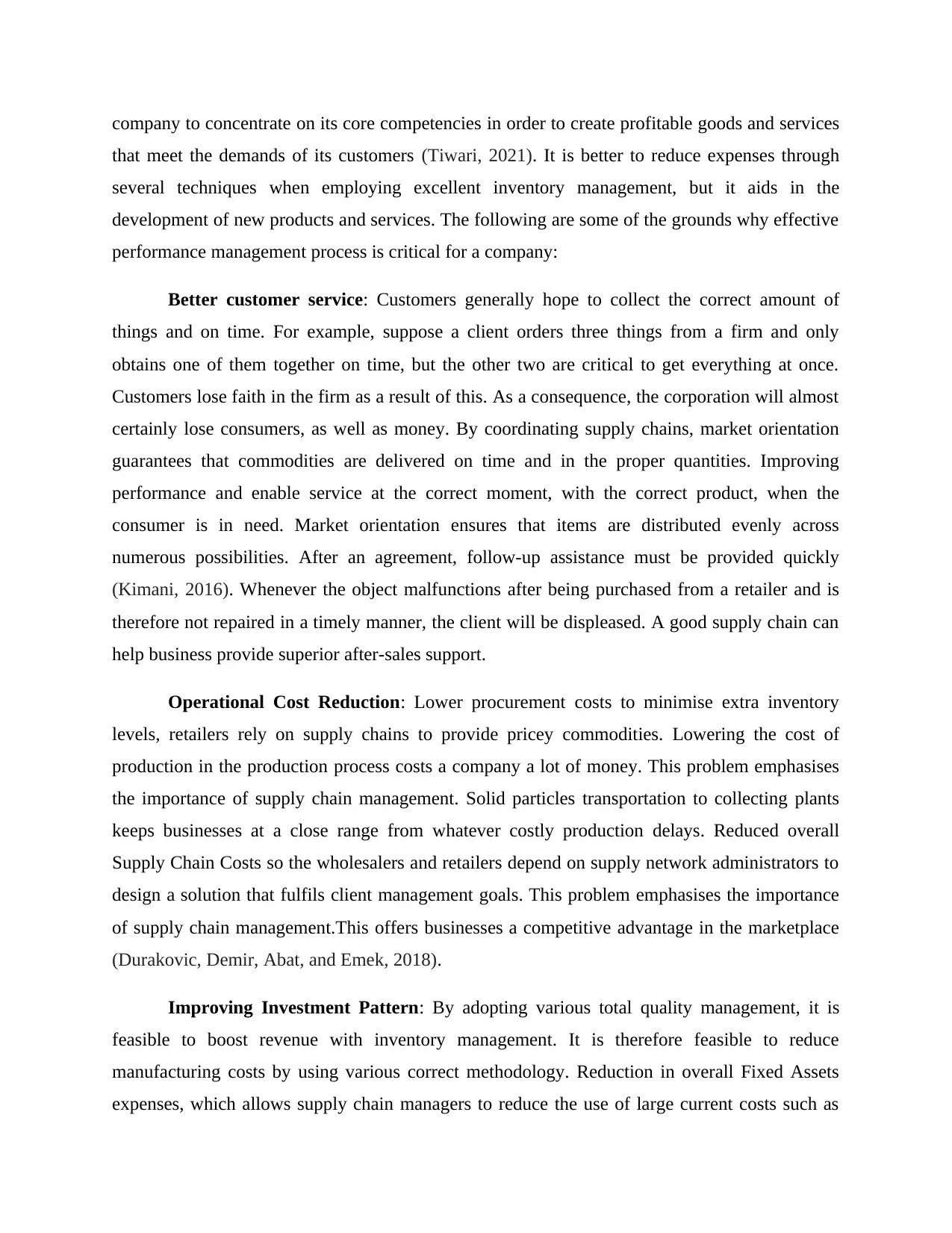
company to concentrate on its core competencies in order to create profitable goods and services
that meet the demands of its customers (Tiwari, 2021). It is better to reduce expenses through
several techniques when employing excellent inventory management, but it aids in the
development of new products and services. The following are some of the grounds why effective
performance management process is critical for a company:
Better customer service: Customers generally hope to collect the correct amount of
things and on time. For example, suppose a client orders three things from a firm and only
obtains one of them together on time, but the other two are critical to get everything at once.
Customers lose faith in the firm as a result of this. As a consequence, the corporation will almost
certainly lose consumers, as well as money. By coordinating supply chains, market orientation
guarantees that commodities are delivered on time and in the proper quantities. Improving
performance and enable service at the correct moment, with the correct product, when the
consumer is in need. Market orientation ensures that items are distributed evenly across
numerous possibilities. After an agreement, follow-up assistance must be provided quickly
(Kimani, 2016). Whenever the object malfunctions after being purchased from a retailer and is
therefore not repaired in a timely manner, the client will be displeased. A good supply chain can
help business provide superior after-sales support.
Operational Cost Reduction: Lower procurement costs to minimise extra inventory
levels, retailers rely on supply chains to provide pricey commodities. Lowering the cost of
production in the production process costs a company a lot of money. This problem emphasises
the importance of supply chain management. Solid particles transportation to collecting plants
keeps businesses at a close range from whatever costly production delays. Reduced overall
Supply Chain Costs so the wholesalers and retailers depend on supply network administrators to
design a solution that fulfils client management goals. This problem emphasises the importance
of supply chain management.This offers businesses a competitive advantage in the marketplace
(Durakovic, Demir, Abat, and Emek, 2018).
Improving Investment Pattern: By adopting various total quality management, it is
feasible to boost revenue with inventory management. It is therefore feasible to reduce
manufacturing costs by using various correct methodology. Reduction in overall Fixed Assets
expenses, which allows supply chain managers to reduce the use of large current costs such as
that meet the demands of its customers (Tiwari, 2021). It is better to reduce expenses through
several techniques when employing excellent inventory management, but it aids in the
development of new products and services. The following are some of the grounds why effective
performance management process is critical for a company:
Better customer service: Customers generally hope to collect the correct amount of
things and on time. For example, suppose a client orders three things from a firm and only
obtains one of them together on time, but the other two are critical to get everything at once.
Customers lose faith in the firm as a result of this. As a consequence, the corporation will almost
certainly lose consumers, as well as money. By coordinating supply chains, market orientation
guarantees that commodities are delivered on time and in the proper quantities. Improving
performance and enable service at the correct moment, with the correct product, when the
consumer is in need. Market orientation ensures that items are distributed evenly across
numerous possibilities. After an agreement, follow-up assistance must be provided quickly
(Kimani, 2016). Whenever the object malfunctions after being purchased from a retailer and is
therefore not repaired in a timely manner, the client will be displeased. A good supply chain can
help business provide superior after-sales support.
Operational Cost Reduction: Lower procurement costs to minimise extra inventory
levels, retailers rely on supply chains to provide pricey commodities. Lowering the cost of
production in the production process costs a company a lot of money. This problem emphasises
the importance of supply chain management. Solid particles transportation to collecting plants
keeps businesses at a close range from whatever costly production delays. Reduced overall
Supply Chain Costs so the wholesalers and retailers depend on supply network administrators to
design a solution that fulfils client management goals. This problem emphasises the importance
of supply chain management.This offers businesses a competitive advantage in the marketplace
(Durakovic, Demir, Abat, and Emek, 2018).
Improving Investment Pattern: By adopting various total quality management, it is
feasible to boost revenue with inventory management. It is therefore feasible to reduce
manufacturing costs by using various correct methodology. Reduction in overall Fixed Assets
expenses, which allows supply chain managers to reduce the use of large current costs such as
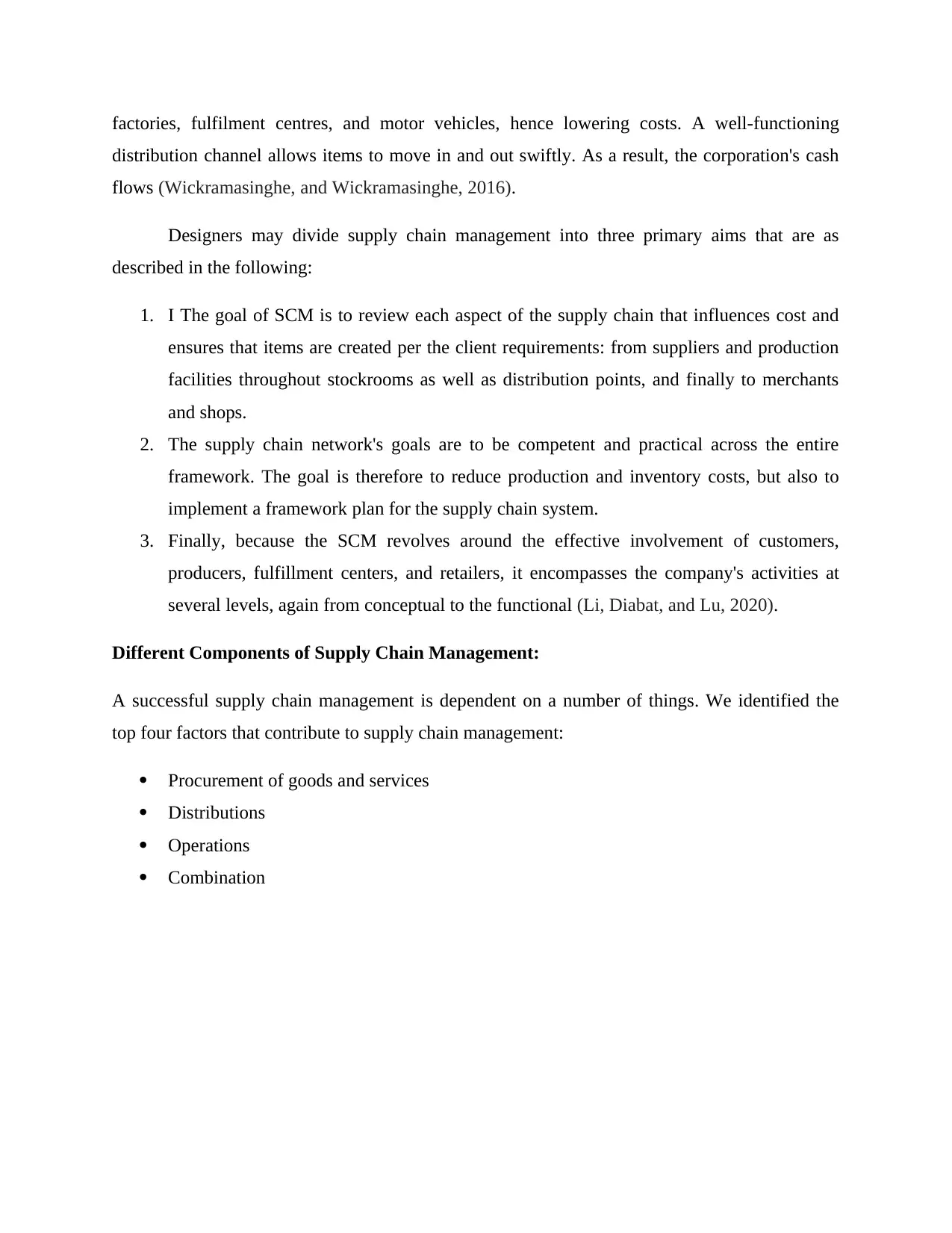
factories, fulfilment centres, and motor vehicles, hence lowering costs. A well-functioning
distribution channel allows items to move in and out swiftly. As a result, the corporation's cash
flows (Wickramasinghe, and Wickramasinghe, 2016).
Designers may divide supply chain management into three primary aims that are as
described in the following:
1. I The goal of SCM is to review each aspect of the supply chain that influences cost and
ensures that items are created per the client requirements: from suppliers and production
facilities throughout stockrooms as well as distribution points, and finally to merchants
and shops.
2. The supply chain network's goals are to be competent and practical across the entire
framework. The goal is therefore to reduce production and inventory costs, but also to
implement a framework plan for the supply chain system.
3. Finally, because the SCM revolves around the effective involvement of customers,
producers, fulfillment centers, and retailers, it encompasses the company's activities at
several levels, again from conceptual to the functional (Li, Diabat, and Lu, 2020).
Different Components of Supply Chain Management:
A successful supply chain management is dependent on a number of things. We identified the
top four factors that contribute to supply chain management:
Procurement of goods and services
Distributions
Operations
Combination
distribution channel allows items to move in and out swiftly. As a result, the corporation's cash
flows (Wickramasinghe, and Wickramasinghe, 2016).
Designers may divide supply chain management into three primary aims that are as
described in the following:
1. I The goal of SCM is to review each aspect of the supply chain that influences cost and
ensures that items are created per the client requirements: from suppliers and production
facilities throughout stockrooms as well as distribution points, and finally to merchants
and shops.
2. The supply chain network's goals are to be competent and practical across the entire
framework. The goal is therefore to reduce production and inventory costs, but also to
implement a framework plan for the supply chain system.
3. Finally, because the SCM revolves around the effective involvement of customers,
producers, fulfillment centers, and retailers, it encompasses the company's activities at
several levels, again from conceptual to the functional (Li, Diabat, and Lu, 2020).
Different Components of Supply Chain Management:
A successful supply chain management is dependent on a number of things. We identified the
top four factors that contribute to supply chain management:
Procurement of goods and services
Distributions
Operations
Combination
Paraphrase This Document
Need a fresh take? Get an instant paraphrase of this document with our AI Paraphraser
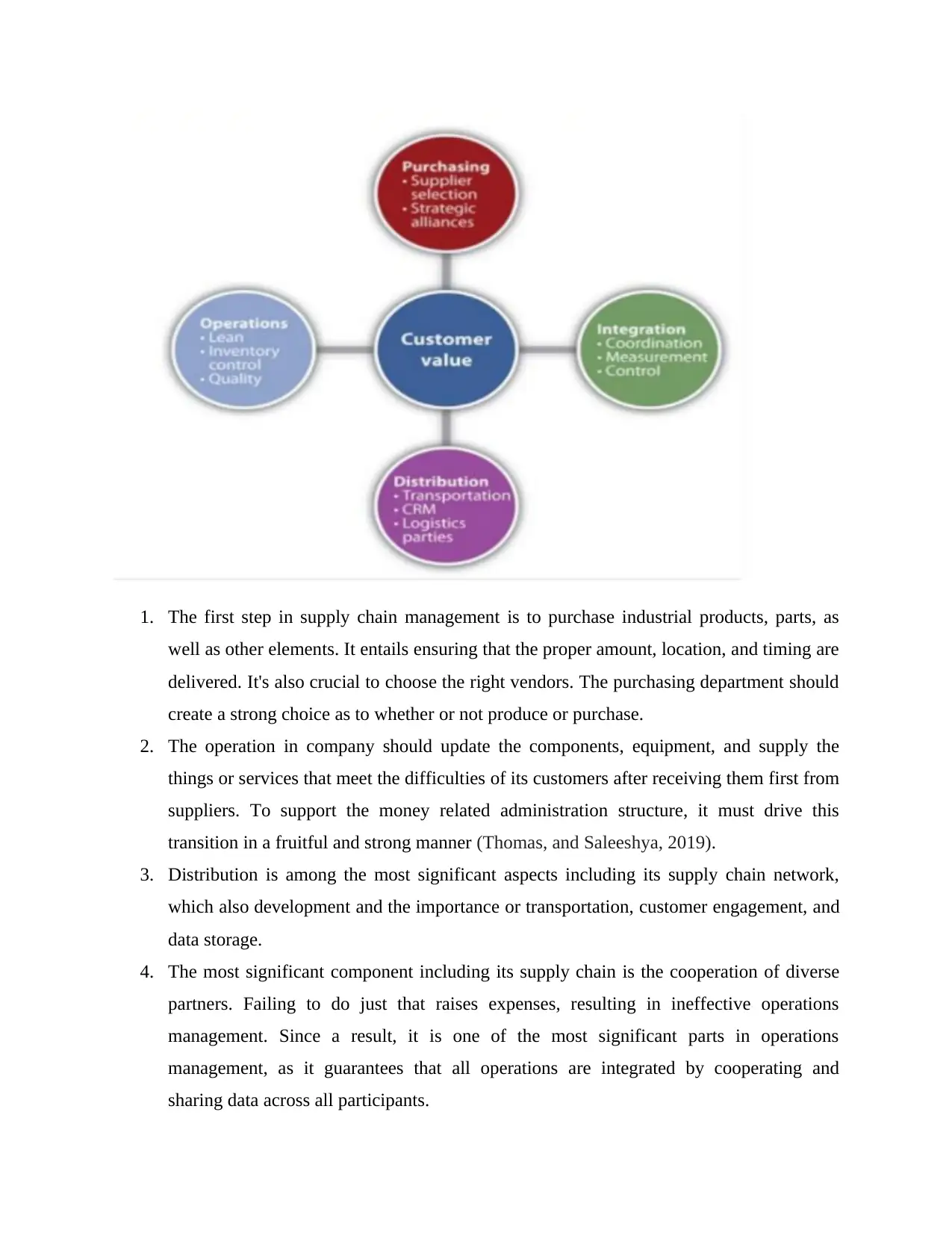
1. The first step in supply chain management is to purchase industrial products, parts, as
well as other elements. It entails ensuring that the proper amount, location, and timing are
delivered. It's also crucial to choose the right vendors. The purchasing department should
create a strong choice as to whether or not produce or purchase.
2. The operation in company should update the components, equipment, and supply the
things or services that meet the difficulties of its customers after receiving them first from
suppliers. To support the money related administration structure, it must drive this
transition in a fruitful and strong manner (Thomas, and Saleeshya, 2019).
3. Distribution is among the most significant aspects including its supply chain network,
which also development and the importance or transportation, customer engagement, and
data storage.
4. The most significant component including its supply chain is the cooperation of diverse
partners. Failing to do just that raises expenses, resulting in ineffective operations
management. Since a result, it is one of the most significant parts in operations
management, as it guarantees that all operations are integrated by cooperating and
sharing data across all participants.
well as other elements. It entails ensuring that the proper amount, location, and timing are
delivered. It's also crucial to choose the right vendors. The purchasing department should
create a strong choice as to whether or not produce or purchase.
2. The operation in company should update the components, equipment, and supply the
things or services that meet the difficulties of its customers after receiving them first from
suppliers. To support the money related administration structure, it must drive this
transition in a fruitful and strong manner (Thomas, and Saleeshya, 2019).
3. Distribution is among the most significant aspects including its supply chain network,
which also development and the importance or transportation, customer engagement, and
data storage.
4. The most significant component including its supply chain is the cooperation of diverse
partners. Failing to do just that raises expenses, resulting in ineffective operations
management. Since a result, it is one of the most significant parts in operations
management, as it guarantees that all operations are integrated by cooperating and
sharing data across all participants.
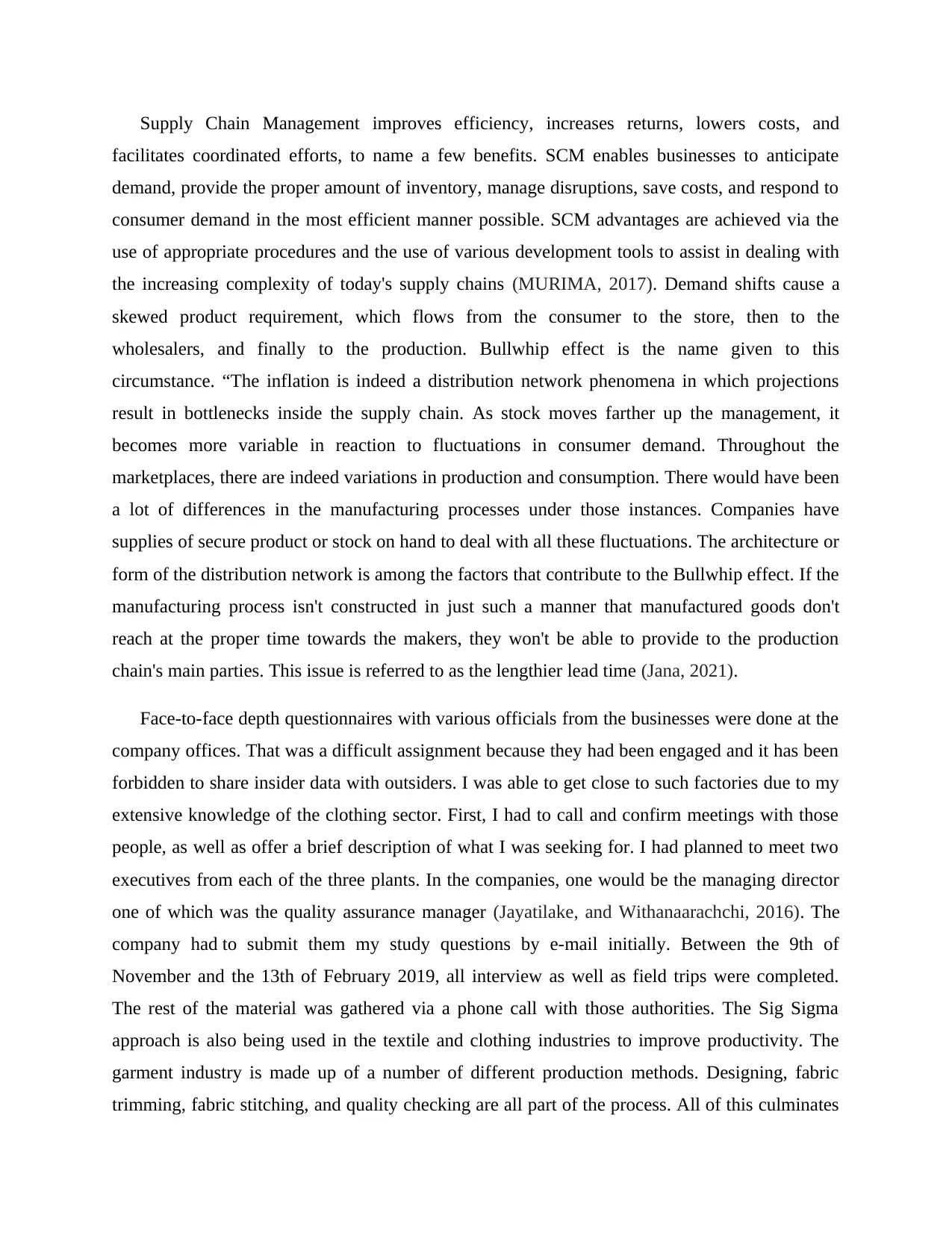
Supply Chain Management improves efficiency, increases returns, lowers costs, and
facilitates coordinated efforts, to name a few benefits. SCM enables businesses to anticipate
demand, provide the proper amount of inventory, manage disruptions, save costs, and respond to
consumer demand in the most efficient manner possible. SCM advantages are achieved via the
use of appropriate procedures and the use of various development tools to assist in dealing with
the increasing complexity of today's supply chains (MURIMA, 2017). Demand shifts cause a
skewed product requirement, which flows from the consumer to the store, then to the
wholesalers, and finally to the production. Bullwhip effect is the name given to this
circumstance. “The inflation is indeed a distribution network phenomena in which projections
result in bottlenecks inside the supply chain. As stock moves farther up the management, it
becomes more variable in reaction to fluctuations in consumer demand. Throughout the
marketplaces, there are indeed variations in production and consumption. There would have been
a lot of differences in the manufacturing processes under those instances. Companies have
supplies of secure product or stock on hand to deal with all these fluctuations. The architecture or
form of the distribution network is among the factors that contribute to the Bullwhip effect. If the
manufacturing process isn't constructed in just such a manner that manufactured goods don't
reach at the proper time towards the makers, they won't be able to provide to the production
chain's main parties. This issue is referred to as the lengthier lead time (Jana, 2021).
Face-to-face depth questionnaires with various officials from the businesses were done at the
company offices. That was a difficult assignment because they had been engaged and it has been
forbidden to share insider data with outsiders. I was able to get close to such factories due to my
extensive knowledge of the clothing sector. First, I had to call and confirm meetings with those
people, as well as offer a brief description of what I was seeking for. I had planned to meet two
executives from each of the three plants. In the companies, one would be the managing director
one of which was the quality assurance manager (Jayatilake, and Withanaarachchi, 2016). The
company had to submit them my study questions by e-mail initially. Between the 9th of
November and the 13th of February 2019, all interview as well as field trips were completed.
The rest of the material was gathered via a phone call with those authorities. The Sig Sigma
approach is also being used in the textile and clothing industries to improve productivity. The
garment industry is made up of a number of different production methods. Designing, fabric
trimming, fabric stitching, and quality checking are all part of the process. All of this culminates
facilitates coordinated efforts, to name a few benefits. SCM enables businesses to anticipate
demand, provide the proper amount of inventory, manage disruptions, save costs, and respond to
consumer demand in the most efficient manner possible. SCM advantages are achieved via the
use of appropriate procedures and the use of various development tools to assist in dealing with
the increasing complexity of today's supply chains (MURIMA, 2017). Demand shifts cause a
skewed product requirement, which flows from the consumer to the store, then to the
wholesalers, and finally to the production. Bullwhip effect is the name given to this
circumstance. “The inflation is indeed a distribution network phenomena in which projections
result in bottlenecks inside the supply chain. As stock moves farther up the management, it
becomes more variable in reaction to fluctuations in consumer demand. Throughout the
marketplaces, there are indeed variations in production and consumption. There would have been
a lot of differences in the manufacturing processes under those instances. Companies have
supplies of secure product or stock on hand to deal with all these fluctuations. The architecture or
form of the distribution network is among the factors that contribute to the Bullwhip effect. If the
manufacturing process isn't constructed in just such a manner that manufactured goods don't
reach at the proper time towards the makers, they won't be able to provide to the production
chain's main parties. This issue is referred to as the lengthier lead time (Jana, 2021).
Face-to-face depth questionnaires with various officials from the businesses were done at the
company offices. That was a difficult assignment because they had been engaged and it has been
forbidden to share insider data with outsiders. I was able to get close to such factories due to my
extensive knowledge of the clothing sector. First, I had to call and confirm meetings with those
people, as well as offer a brief description of what I was seeking for. I had planned to meet two
executives from each of the three plants. In the companies, one would be the managing director
one of which was the quality assurance manager (Jayatilake, and Withanaarachchi, 2016). The
company had to submit them my study questions by e-mail initially. Between the 9th of
November and the 13th of February 2019, all interview as well as field trips were completed.
The rest of the material was gathered via a phone call with those authorities. The Sig Sigma
approach is also being used in the textile and clothing industries to improve productivity. The
garment industry is made up of a number of different production methods. Designing, fabric
trimming, fabric stitching, and quality checking are all part of the process. All of this culminates
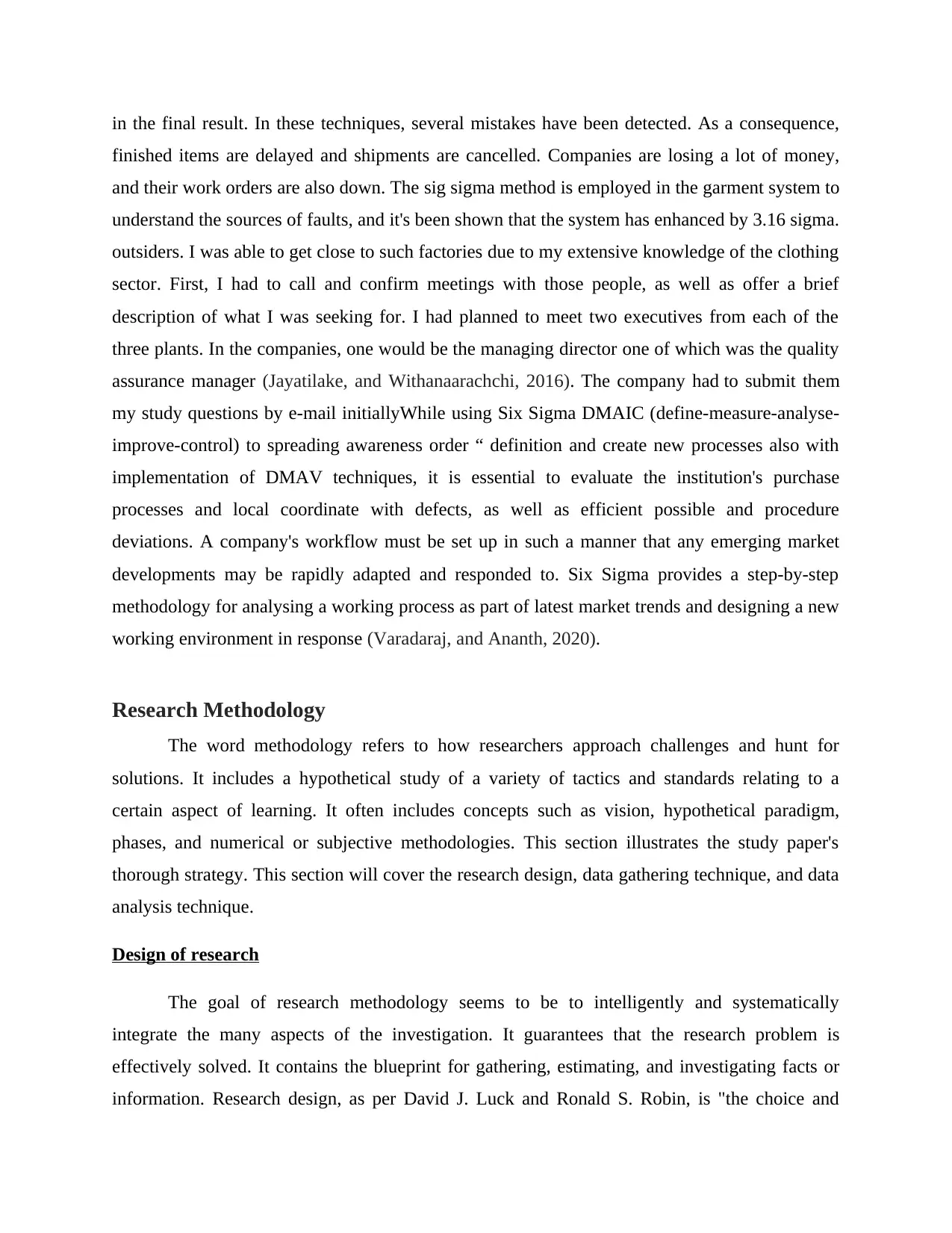
in the final result. In these techniques, several mistakes have been detected. As a consequence,
finished items are delayed and shipments are cancelled. Companies are losing a lot of money,
and their work orders are also down. The sig sigma method is employed in the garment system to
understand the sources of faults, and it's been shown that the system has enhanced by 3.16 sigma.
outsiders. I was able to get close to such factories due to my extensive knowledge of the clothing
sector. First, I had to call and confirm meetings with those people, as well as offer a brief
description of what I was seeking for. I had planned to meet two executives from each of the
three plants. In the companies, one would be the managing director one of which was the quality
assurance manager (Jayatilake, and Withanaarachchi, 2016). The company had to submit them
my study questions by e-mail initiallyWhile using Six Sigma DMAIC (define-measure-analyse-
improve-control) to spreading awareness order “ definition and create new processes also with
implementation of DMAV techniques, it is essential to evaluate the institution's purchase
processes and local coordinate with defects, as well as efficient possible and procedure
deviations. A company's workflow must be set up in such a manner that any emerging market
developments may be rapidly adapted and responded to. Six Sigma provides a step-by-step
methodology for analysing a working process as part of latest market trends and designing a new
working environment in response (Varadaraj, and Ananth, 2020).
Research Methodology
The word methodology refers to how researchers approach challenges and hunt for
solutions. It includes a hypothetical study of a variety of tactics and standards relating to a
certain aspect of learning. It often includes concepts such as vision, hypothetical paradigm,
phases, and numerical or subjective methodologies. This section illustrates the study paper's
thorough strategy. This section will cover the research design, data gathering technique, and data
analysis technique.
Design of research
The goal of research methodology seems to be to intelligently and systematically
integrate the many aspects of the investigation. It guarantees that the research problem is
effectively solved. It contains the blueprint for gathering, estimating, and investigating facts or
information. Research design, as per David J. Luck and Ronald S. Robin, is "the choice and
finished items are delayed and shipments are cancelled. Companies are losing a lot of money,
and their work orders are also down. The sig sigma method is employed in the garment system to
understand the sources of faults, and it's been shown that the system has enhanced by 3.16 sigma.
outsiders. I was able to get close to such factories due to my extensive knowledge of the clothing
sector. First, I had to call and confirm meetings with those people, as well as offer a brief
description of what I was seeking for. I had planned to meet two executives from each of the
three plants. In the companies, one would be the managing director one of which was the quality
assurance manager (Jayatilake, and Withanaarachchi, 2016). The company had to submit them
my study questions by e-mail initiallyWhile using Six Sigma DMAIC (define-measure-analyse-
improve-control) to spreading awareness order “ definition and create new processes also with
implementation of DMAV techniques, it is essential to evaluate the institution's purchase
processes and local coordinate with defects, as well as efficient possible and procedure
deviations. A company's workflow must be set up in such a manner that any emerging market
developments may be rapidly adapted and responded to. Six Sigma provides a step-by-step
methodology for analysing a working process as part of latest market trends and designing a new
working environment in response (Varadaraj, and Ananth, 2020).
Research Methodology
The word methodology refers to how researchers approach challenges and hunt for
solutions. It includes a hypothetical study of a variety of tactics and standards relating to a
certain aspect of learning. It often includes concepts such as vision, hypothetical paradigm,
phases, and numerical or subjective methodologies. This section illustrates the study paper's
thorough strategy. This section will cover the research design, data gathering technique, and data
analysis technique.
Design of research
The goal of research methodology seems to be to intelligently and systematically
integrate the many aspects of the investigation. It guarantees that the research problem is
effectively solved. It contains the blueprint for gathering, estimating, and investigating facts or
information. Research design, as per David J. Luck and Ronald S. Robin, is "the choice and
Secure Best Marks with AI Grader
Need help grading? Try our AI Grader for instant feedback on your assignments.
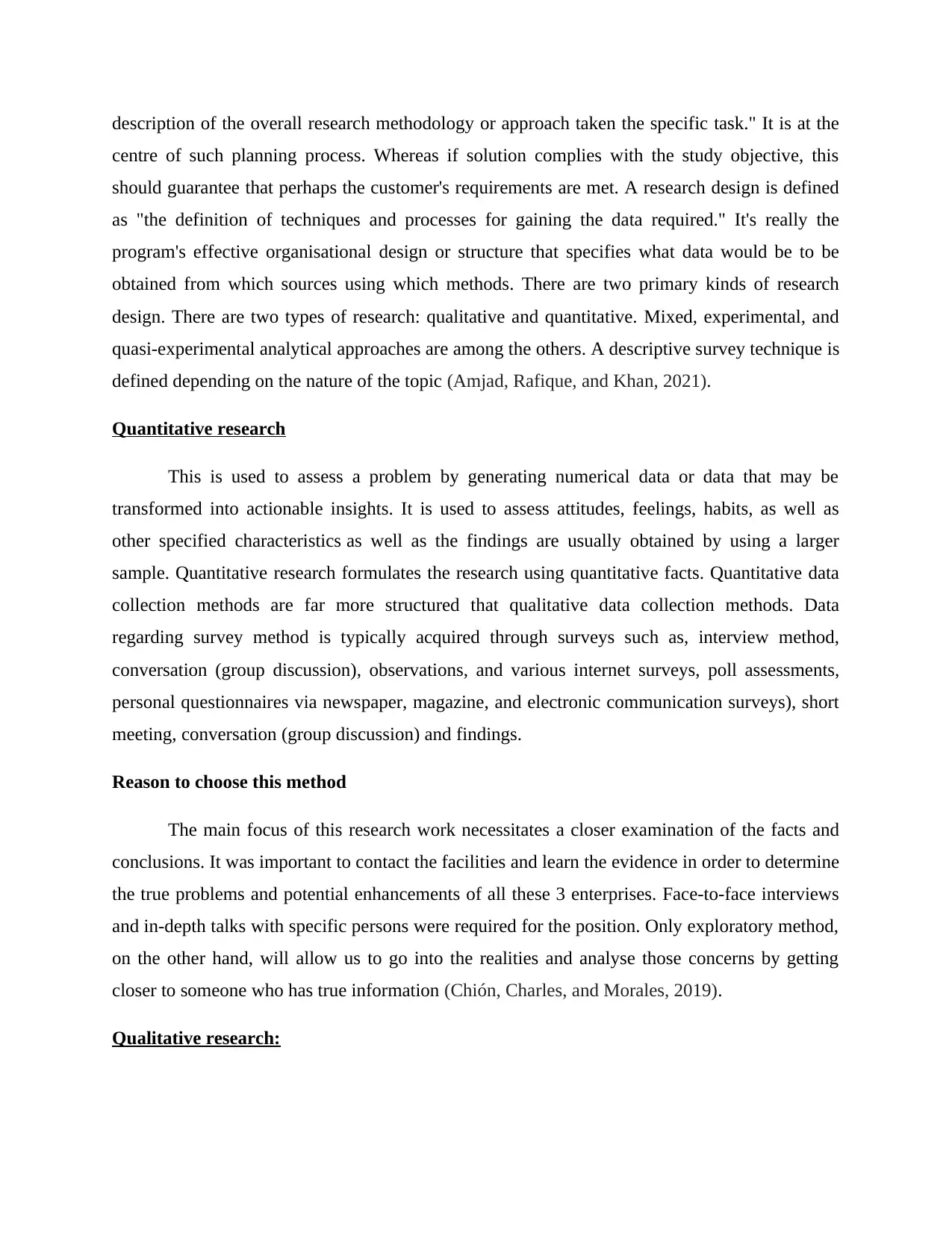
description of the overall research methodology or approach taken the specific task." It is at the
centre of such planning process. Whereas if solution complies with the study objective, this
should guarantee that perhaps the customer's requirements are met. A research design is defined
as "the definition of techniques and processes for gaining the data required." It's really the
program's effective organisational design or structure that specifies what data would be to be
obtained from which sources using which methods. There are two primary kinds of research
design. There are two types of research: qualitative and quantitative. Mixed, experimental, and
quasi-experimental analytical approaches are among the others. A descriptive survey technique is
defined depending on the nature of the topic (Amjad, Rafique, and Khan, 2021).
Quantitative research
This is used to assess a problem by generating numerical data or data that may be
transformed into actionable insights. It is used to assess attitudes, feelings, habits, as well as
other specified characteristics as well as the findings are usually obtained by using a larger
sample. Quantitative research formulates the research using quantitative facts. Quantitative data
collection methods are far more structured that qualitative data collection methods. Data
regarding survey method is typically acquired through surveys such as, interview method,
conversation (group discussion), observations, and various internet surveys, poll assessments,
personal questionnaires via newspaper, magazine, and electronic communication surveys), short
meeting, conversation (group discussion) and findings.
Reason to choose this method
The main focus of this research work necessitates a closer examination of the facts and
conclusions. It was important to contact the facilities and learn the evidence in order to determine
the true problems and potential enhancements of all these 3 enterprises. Face-to-face interviews
and in-depth talks with specific persons were required for the position. Only exploratory method,
on the other hand, will allow us to go into the realities and analyse those concerns by getting
closer to someone who has true information (Chión, Charles, and Morales, 2019).
Qualitative research:
centre of such planning process. Whereas if solution complies with the study objective, this
should guarantee that perhaps the customer's requirements are met. A research design is defined
as "the definition of techniques and processes for gaining the data required." It's really the
program's effective organisational design or structure that specifies what data would be to be
obtained from which sources using which methods. There are two primary kinds of research
design. There are two types of research: qualitative and quantitative. Mixed, experimental, and
quasi-experimental analytical approaches are among the others. A descriptive survey technique is
defined depending on the nature of the topic (Amjad, Rafique, and Khan, 2021).
Quantitative research
This is used to assess a problem by generating numerical data or data that may be
transformed into actionable insights. It is used to assess attitudes, feelings, habits, as well as
other specified characteristics as well as the findings are usually obtained by using a larger
sample. Quantitative research formulates the research using quantitative facts. Quantitative data
collection methods are far more structured that qualitative data collection methods. Data
regarding survey method is typically acquired through surveys such as, interview method,
conversation (group discussion), observations, and various internet surveys, poll assessments,
personal questionnaires via newspaper, magazine, and electronic communication surveys), short
meeting, conversation (group discussion) and findings.
Reason to choose this method
The main focus of this research work necessitates a closer examination of the facts and
conclusions. It was important to contact the facilities and learn the evidence in order to determine
the true problems and potential enhancements of all these 3 enterprises. Face-to-face interviews
and in-depth talks with specific persons were required for the position. Only exploratory method,
on the other hand, will allow us to go into the realities and analyse those concerns by getting
closer to someone who has true information (Chión, Charles, and Morales, 2019).
Qualitative research:
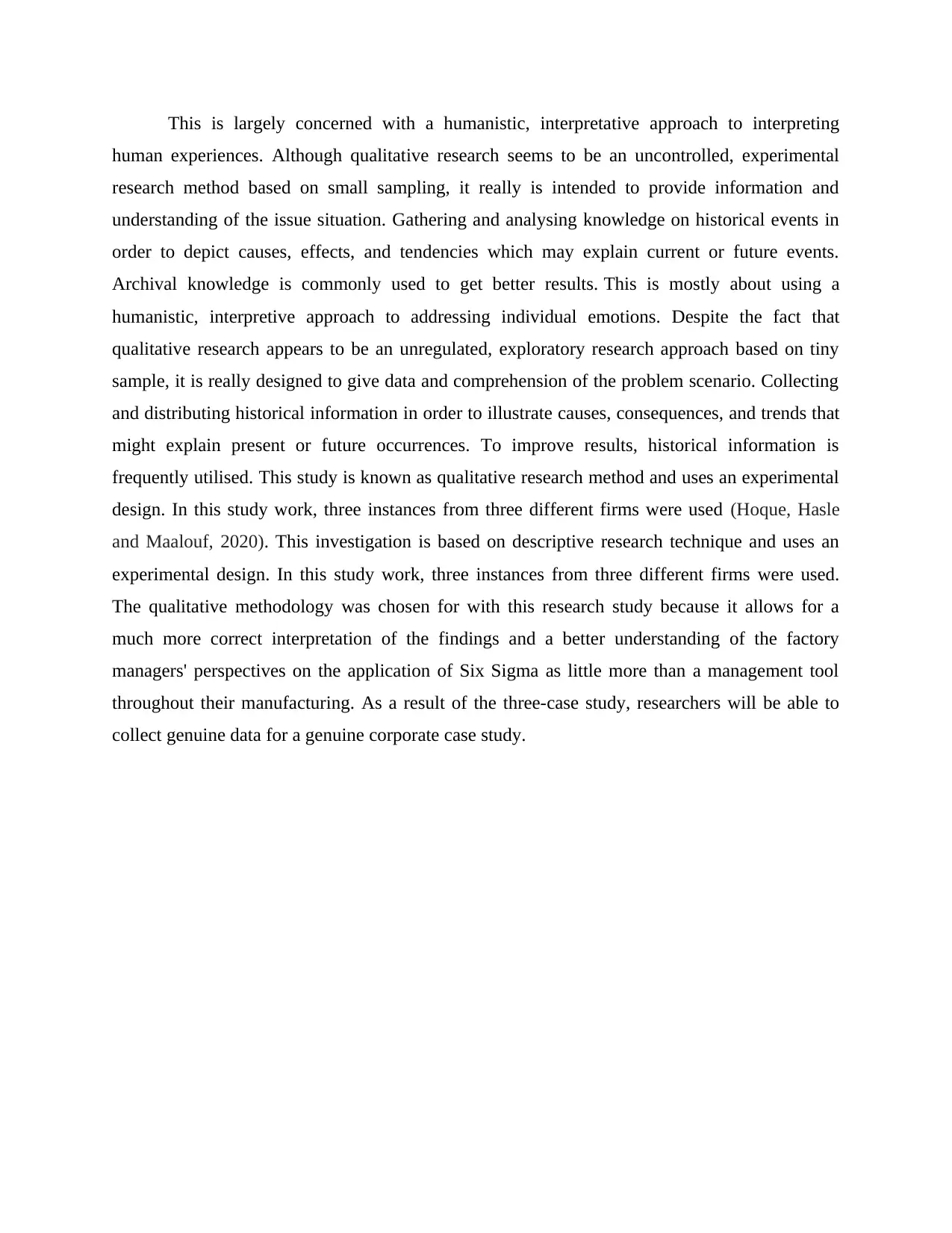
This is largely concerned with a humanistic, interpretative approach to interpreting
human experiences. Although qualitative research seems to be an uncontrolled, experimental
research method based on small sampling, it really is intended to provide information and
understanding of the issue situation. Gathering and analysing knowledge on historical events in
order to depict causes, effects, and tendencies which may explain current or future events.
Archival knowledge is commonly used to get better results. This is mostly about using a
humanistic, interpretive approach to addressing individual emotions. Despite the fact that
qualitative research appears to be an unregulated, exploratory research approach based on tiny
sample, it is really designed to give data and comprehension of the problem scenario. Collecting
and distributing historical information in order to illustrate causes, consequences, and trends that
might explain present or future occurrences. To improve results, historical information is
frequently utilised. This study is known as qualitative research method and uses an experimental
design. In this study work, three instances from three different firms were used (Hoque, Hasle
and Maalouf, 2020). This investigation is based on descriptive research technique and uses an
experimental design. In this study work, three instances from three different firms were used.
The qualitative methodology was chosen for with this research study because it allows for a
much more correct interpretation of the findings and a better understanding of the factory
managers' perspectives on the application of Six Sigma as little more than a management tool
throughout their manufacturing. As a result of the three-case study, researchers will be able to
collect genuine data for a genuine corporate case study.
human experiences. Although qualitative research seems to be an uncontrolled, experimental
research method based on small sampling, it really is intended to provide information and
understanding of the issue situation. Gathering and analysing knowledge on historical events in
order to depict causes, effects, and tendencies which may explain current or future events.
Archival knowledge is commonly used to get better results. This is mostly about using a
humanistic, interpretive approach to addressing individual emotions. Despite the fact that
qualitative research appears to be an unregulated, exploratory research approach based on tiny
sample, it is really designed to give data and comprehension of the problem scenario. Collecting
and distributing historical information in order to illustrate causes, consequences, and trends that
might explain present or future occurrences. To improve results, historical information is
frequently utilised. This study is known as qualitative research method and uses an experimental
design. In this study work, three instances from three different firms were used (Hoque, Hasle
and Maalouf, 2020). This investigation is based on descriptive research technique and uses an
experimental design. In this study work, three instances from three different firms were used.
The qualitative methodology was chosen for with this research study because it allows for a
much more correct interpretation of the findings and a better understanding of the factory
managers' perspectives on the application of Six Sigma as little more than a management tool
throughout their manufacturing. As a result of the three-case study, researchers will be able to
collect genuine data for a genuine corporate case study.
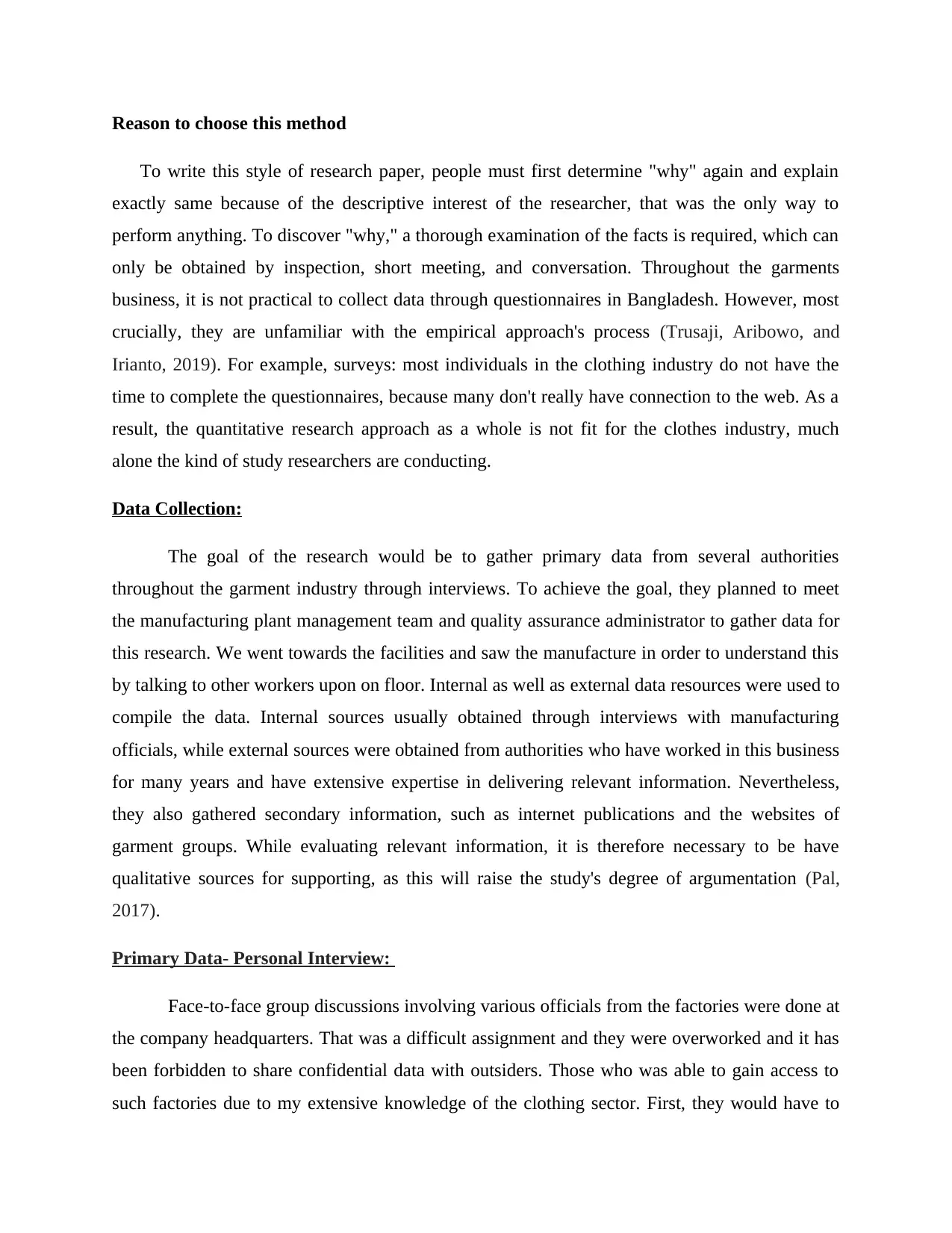
Reason to choose this method
To write this style of research paper, people must first determine "why" again and explain
exactly same because of the descriptive interest of the researcher, that was the only way to
perform anything. To discover "why," a thorough examination of the facts is required, which can
only be obtained by inspection, short meeting, and conversation. Throughout the garments
business, it is not practical to collect data through questionnaires in Bangladesh. However, most
crucially, they are unfamiliar with the empirical approach's process (Trusaji, Aribowo, and
Irianto, 2019). For example, surveys: most individuals in the clothing industry do not have the
time to complete the questionnaires, because many don't really have connection to the web. As a
result, the quantitative research approach as a whole is not fit for the clothes industry, much
alone the kind of study researchers are conducting.
Data Collection:
The goal of the research would be to gather primary data from several authorities
throughout the garment industry through interviews. To achieve the goal, they planned to meet
the manufacturing plant management team and quality assurance administrator to gather data for
this research. We went towards the facilities and saw the manufacture in order to understand this
by talking to other workers upon on floor. Internal as well as external data resources were used to
compile the data. Internal sources usually obtained through interviews with manufacturing
officials, while external sources were obtained from authorities who have worked in this business
for many years and have extensive expertise in delivering relevant information. Nevertheless,
they also gathered secondary information, such as internet publications and the websites of
garment groups. While evaluating relevant information, it is therefore necessary to be have
qualitative sources for supporting, as this will raise the study's degree of argumentation (Pal,
2017).
Primary Data- Personal Interview:
Face-to-face group discussions involving various officials from the factories were done at
the company headquarters. That was a difficult assignment and they were overworked and it has
been forbidden to share confidential data with outsiders. Those who was able to gain access to
such factories due to my extensive knowledge of the clothing sector. First, they would have to
To write this style of research paper, people must first determine "why" again and explain
exactly same because of the descriptive interest of the researcher, that was the only way to
perform anything. To discover "why," a thorough examination of the facts is required, which can
only be obtained by inspection, short meeting, and conversation. Throughout the garments
business, it is not practical to collect data through questionnaires in Bangladesh. However, most
crucially, they are unfamiliar with the empirical approach's process (Trusaji, Aribowo, and
Irianto, 2019). For example, surveys: most individuals in the clothing industry do not have the
time to complete the questionnaires, because many don't really have connection to the web. As a
result, the quantitative research approach as a whole is not fit for the clothes industry, much
alone the kind of study researchers are conducting.
Data Collection:
The goal of the research would be to gather primary data from several authorities
throughout the garment industry through interviews. To achieve the goal, they planned to meet
the manufacturing plant management team and quality assurance administrator to gather data for
this research. We went towards the facilities and saw the manufacture in order to understand this
by talking to other workers upon on floor. Internal as well as external data resources were used to
compile the data. Internal sources usually obtained through interviews with manufacturing
officials, while external sources were obtained from authorities who have worked in this business
for many years and have extensive expertise in delivering relevant information. Nevertheless,
they also gathered secondary information, such as internet publications and the websites of
garment groups. While evaluating relevant information, it is therefore necessary to be have
qualitative sources for supporting, as this will raise the study's degree of argumentation (Pal,
2017).
Primary Data- Personal Interview:
Face-to-face group discussions involving various officials from the factories were done at
the company headquarters. That was a difficult assignment and they were overworked and it has
been forbidden to share confidential data with outsiders. Those who was able to gain access to
such factories due to my extensive knowledge of the clothing sector. First, they would have to
Paraphrase This Document
Need a fresh take? Get an instant paraphrase of this document with our AI Paraphraser
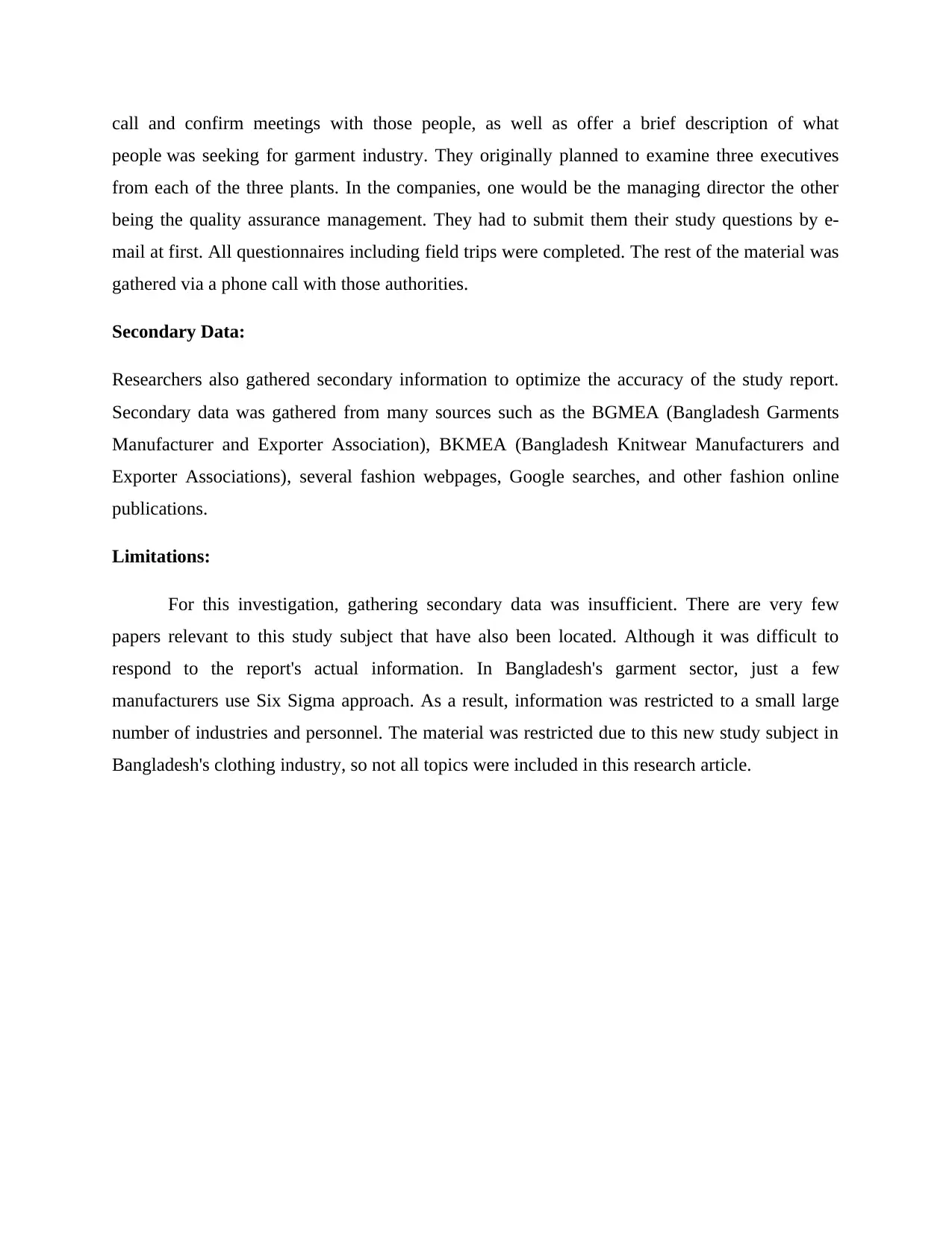
call and confirm meetings with those people, as well as offer a brief description of what
people was seeking for garment industry. They originally planned to examine three executives
from each of the three plants. In the companies, one would be the managing director the other
being the quality assurance management. They had to submit them their study questions by e-
mail at first. All questionnaires including field trips were completed. The rest of the material was
gathered via a phone call with those authorities.
Secondary Data:
Researchers also gathered secondary information to optimize the accuracy of the study report.
Secondary data was gathered from many sources such as the BGMEA (Bangladesh Garments
Manufacturer and Exporter Association), BKMEA (Bangladesh Knitwear Manufacturers and
Exporter Associations), several fashion webpages, Google searches, and other fashion online
publications.
Limitations:
For this investigation, gathering secondary data was insufficient. There are very few
papers relevant to this study subject that have also been located. Although it was difficult to
respond to the report's actual information. In Bangladesh's garment sector, just a few
manufacturers use Six Sigma approach. As a result, information was restricted to a small large
number of industries and personnel. The material was restricted due to this new study subject in
Bangladesh's clothing industry, so not all topics were included in this research article.
people was seeking for garment industry. They originally planned to examine three executives
from each of the three plants. In the companies, one would be the managing director the other
being the quality assurance management. They had to submit them their study questions by e-
mail at first. All questionnaires including field trips were completed. The rest of the material was
gathered via a phone call with those authorities.
Secondary Data:
Researchers also gathered secondary information to optimize the accuracy of the study report.
Secondary data was gathered from many sources such as the BGMEA (Bangladesh Garments
Manufacturer and Exporter Association), BKMEA (Bangladesh Knitwear Manufacturers and
Exporter Associations), several fashion webpages, Google searches, and other fashion online
publications.
Limitations:
For this investigation, gathering secondary data was insufficient. There are very few
papers relevant to this study subject that have also been located. Although it was difficult to
respond to the report's actual information. In Bangladesh's garment sector, just a few
manufacturers use Six Sigma approach. As a result, information was restricted to a small large
number of industries and personnel. The material was restricted due to this new study subject in
Bangladesh's clothing industry, so not all topics were included in this research article.
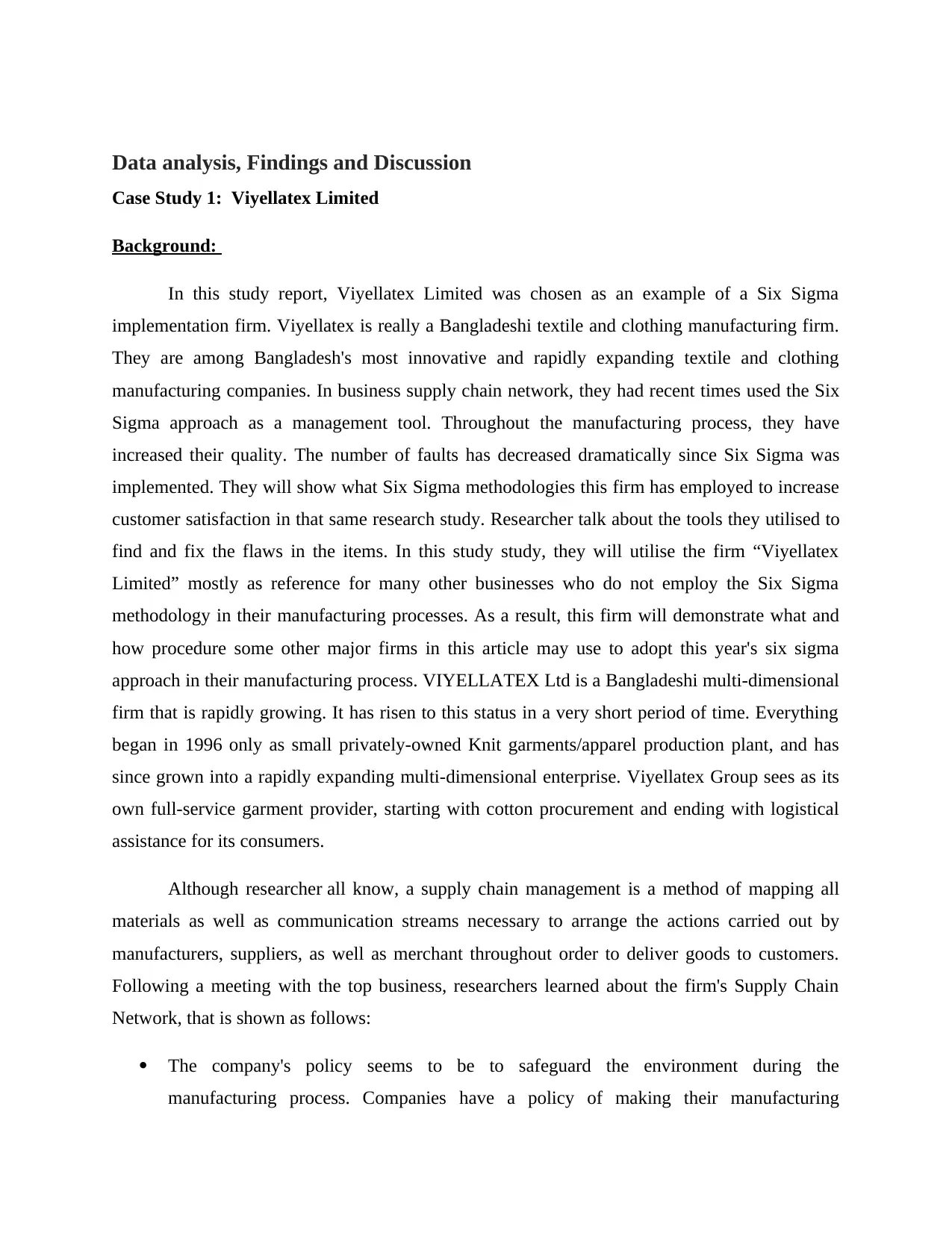
Data analysis, Findings and Discussion
Case Study 1: Viyellatex Limited
Background:
In this study report, Viyellatex Limited was chosen as an example of a Six Sigma
implementation firm. Viyellatex is really a Bangladeshi textile and clothing manufacturing firm.
They are among Bangladesh's most innovative and rapidly expanding textile and clothing
manufacturing companies. In business supply chain network, they had recent times used the Six
Sigma approach as a management tool. Throughout the manufacturing process, they have
increased their quality. The number of faults has decreased dramatically since Six Sigma was
implemented. They will show what Six Sigma methodologies this firm has employed to increase
customer satisfaction in that same research study. Researcher talk about the tools they utilised to
find and fix the flaws in the items. In this study study, they will utilise the firm “Viyellatex
Limited” mostly as reference for many other businesses who do not employ the Six Sigma
methodology in their manufacturing processes. As a result, this firm will demonstrate what and
how procedure some other major firms in this article may use to adopt this year's six sigma
approach in their manufacturing process. VIYELLATEX Ltd is a Bangladeshi multi-dimensional
firm that is rapidly growing. It has risen to this status in a very short period of time. Everything
began in 1996 only as small privately-owned Knit garments/apparel production plant, and has
since grown into a rapidly expanding multi-dimensional enterprise. Viyellatex Group sees as its
own full-service garment provider, starting with cotton procurement and ending with logistical
assistance for its consumers.
Although researcher all know, a supply chain management is a method of mapping all
materials as well as communication streams necessary to arrange the actions carried out by
manufacturers, suppliers, as well as merchant throughout order to deliver goods to customers.
Following a meeting with the top business, researchers learned about the firm's Supply Chain
Network, that is shown as follows:
The company's policy seems to be to safeguard the environment during the
manufacturing process. Companies have a policy of making their manufacturing
Case Study 1: Viyellatex Limited
Background:
In this study report, Viyellatex Limited was chosen as an example of a Six Sigma
implementation firm. Viyellatex is really a Bangladeshi textile and clothing manufacturing firm.
They are among Bangladesh's most innovative and rapidly expanding textile and clothing
manufacturing companies. In business supply chain network, they had recent times used the Six
Sigma approach as a management tool. Throughout the manufacturing process, they have
increased their quality. The number of faults has decreased dramatically since Six Sigma was
implemented. They will show what Six Sigma methodologies this firm has employed to increase
customer satisfaction in that same research study. Researcher talk about the tools they utilised to
find and fix the flaws in the items. In this study study, they will utilise the firm “Viyellatex
Limited” mostly as reference for many other businesses who do not employ the Six Sigma
methodology in their manufacturing processes. As a result, this firm will demonstrate what and
how procedure some other major firms in this article may use to adopt this year's six sigma
approach in their manufacturing process. VIYELLATEX Ltd is a Bangladeshi multi-dimensional
firm that is rapidly growing. It has risen to this status in a very short period of time. Everything
began in 1996 only as small privately-owned Knit garments/apparel production plant, and has
since grown into a rapidly expanding multi-dimensional enterprise. Viyellatex Group sees as its
own full-service garment provider, starting with cotton procurement and ending with logistical
assistance for its consumers.
Although researcher all know, a supply chain management is a method of mapping all
materials as well as communication streams necessary to arrange the actions carried out by
manufacturers, suppliers, as well as merchant throughout order to deliver goods to customers.
Following a meeting with the top business, researchers learned about the firm's Supply Chain
Network, that is shown as follows:
The company's policy seems to be to safeguard the environment during the
manufacturing process. Companies have a policy of making their manufacturing
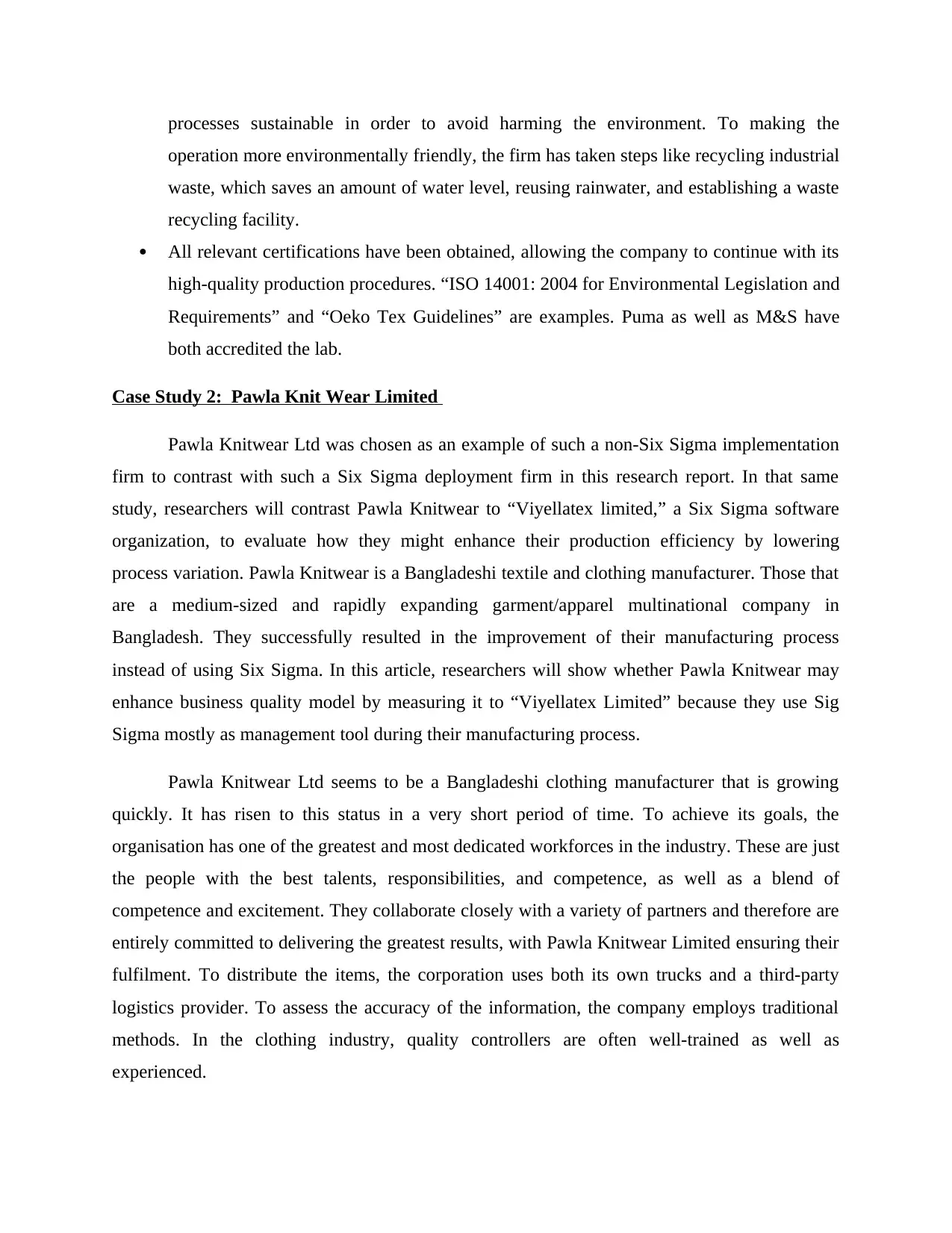
processes sustainable in order to avoid harming the environment. To making the
operation more environmentally friendly, the firm has taken steps like recycling industrial
waste, which saves an amount of water level, reusing rainwater, and establishing a waste
recycling facility.
All relevant certifications have been obtained, allowing the company to continue with its
high-quality production procedures. “ISO 14001: 2004 for Environmental Legislation and
Requirements” and “Oeko Tex Guidelines” are examples. Puma as well as M&S have
both accredited the lab.
Case Study 2: Pawla Knit Wear Limited
Pawla Knitwear Ltd was chosen as an example of such a non-Six Sigma implementation
firm to contrast with such a Six Sigma deployment firm in this research report. In that same
study, researchers will contrast Pawla Knitwear to “Viyellatex limited,” a Six Sigma software
organization, to evaluate how they might enhance their production efficiency by lowering
process variation. Pawla Knitwear is a Bangladeshi textile and clothing manufacturer. Those that
are a medium-sized and rapidly expanding garment/apparel multinational company in
Bangladesh. They successfully resulted in the improvement of their manufacturing process
instead of using Six Sigma. In this article, researchers will show whether Pawla Knitwear may
enhance business quality model by measuring it to “Viyellatex Limited” because they use Sig
Sigma mostly as management tool during their manufacturing process.
Pawla Knitwear Ltd seems to be a Bangladeshi clothing manufacturer that is growing
quickly. It has risen to this status in a very short period of time. To achieve its goals, the
organisation has one of the greatest and most dedicated workforces in the industry. These are just
the people with the best talents, responsibilities, and competence, as well as a blend of
competence and excitement. They collaborate closely with a variety of partners and therefore are
entirely committed to delivering the greatest results, with Pawla Knitwear Limited ensuring their
fulfilment. To distribute the items, the corporation uses both its own trucks and a third-party
logistics provider. To assess the accuracy of the information, the company employs traditional
methods. In the clothing industry, quality controllers are often well-trained as well as
experienced.
operation more environmentally friendly, the firm has taken steps like recycling industrial
waste, which saves an amount of water level, reusing rainwater, and establishing a waste
recycling facility.
All relevant certifications have been obtained, allowing the company to continue with its
high-quality production procedures. “ISO 14001: 2004 for Environmental Legislation and
Requirements” and “Oeko Tex Guidelines” are examples. Puma as well as M&S have
both accredited the lab.
Case Study 2: Pawla Knit Wear Limited
Pawla Knitwear Ltd was chosen as an example of such a non-Six Sigma implementation
firm to contrast with such a Six Sigma deployment firm in this research report. In that same
study, researchers will contrast Pawla Knitwear to “Viyellatex limited,” a Six Sigma software
organization, to evaluate how they might enhance their production efficiency by lowering
process variation. Pawla Knitwear is a Bangladeshi textile and clothing manufacturer. Those that
are a medium-sized and rapidly expanding garment/apparel multinational company in
Bangladesh. They successfully resulted in the improvement of their manufacturing process
instead of using Six Sigma. In this article, researchers will show whether Pawla Knitwear may
enhance business quality model by measuring it to “Viyellatex Limited” because they use Sig
Sigma mostly as management tool during their manufacturing process.
Pawla Knitwear Ltd seems to be a Bangladeshi clothing manufacturer that is growing
quickly. It has risen to this status in a very short period of time. To achieve its goals, the
organisation has one of the greatest and most dedicated workforces in the industry. These are just
the people with the best talents, responsibilities, and competence, as well as a blend of
competence and excitement. They collaborate closely with a variety of partners and therefore are
entirely committed to delivering the greatest results, with Pawla Knitwear Limited ensuring their
fulfilment. To distribute the items, the corporation uses both its own trucks and a third-party
logistics provider. To assess the accuracy of the information, the company employs traditional
methods. In the clothing industry, quality controllers are often well-trained as well as
experienced.
Secure Best Marks with AI Grader
Need help grading? Try our AI Grader for instant feedback on your assignments.
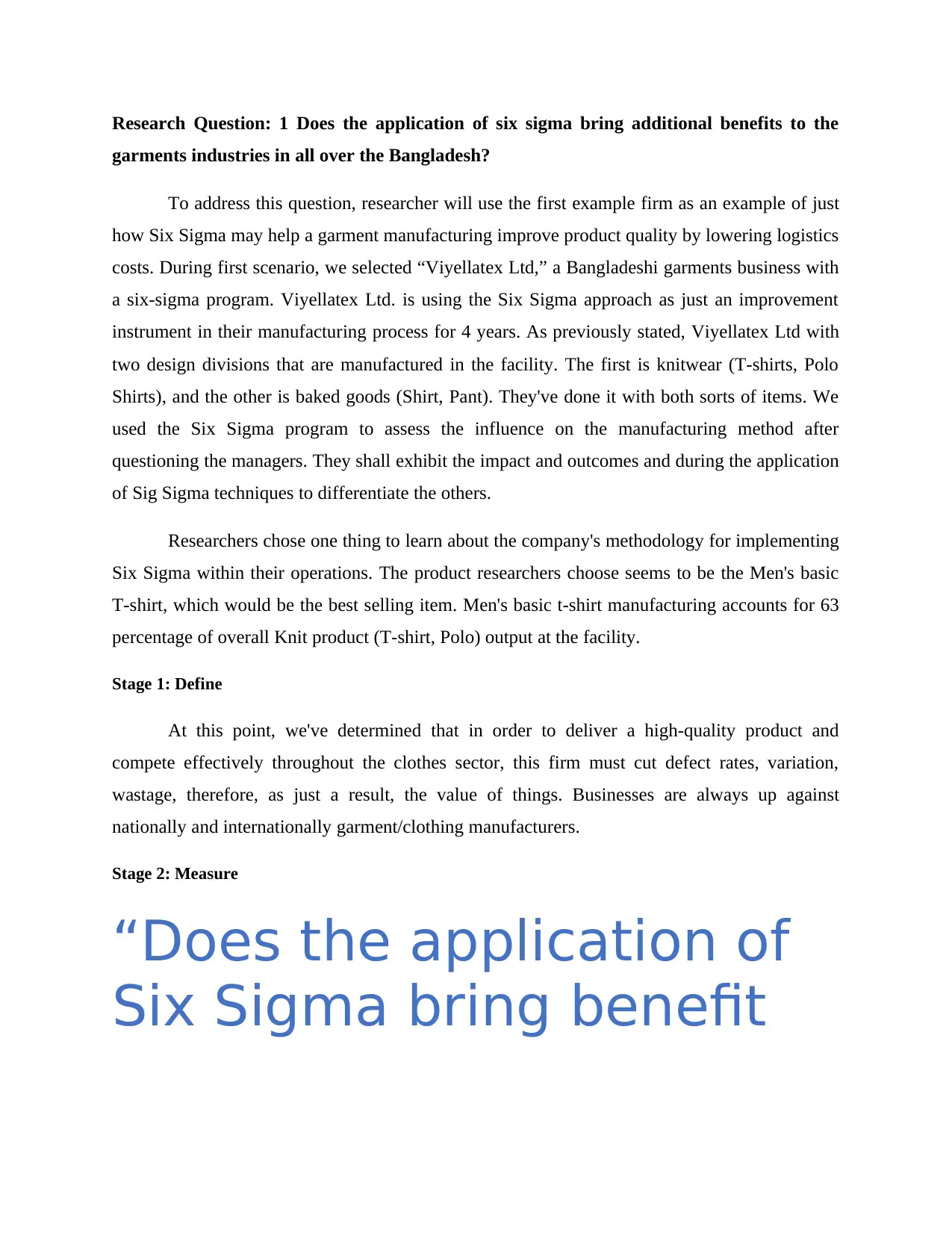
Research Question: 1 Does the application of six sigma bring additional benefits to the
garments industries in all over the Bangladesh?
To address this question, researcher will use the first example firm as an example of just
how Six Sigma may help a garment manufacturing improve product quality by lowering logistics
costs. During first scenario, we selected “Viyellatex Ltd,” a Bangladeshi garments business with
a six-sigma program. Viyellatex Ltd. is using the Six Sigma approach as just an improvement
instrument in their manufacturing process for 4 years. As previously stated, Viyellatex Ltd with
two design divisions that are manufactured in the facility. The first is knitwear (T-shirts, Polo
Shirts), and the other is baked goods (Shirt, Pant). They've done it with both sorts of items. We
used the Six Sigma program to assess the influence on the manufacturing method after
questioning the managers. They shall exhibit the impact and outcomes and during the application
of Sig Sigma techniques to differentiate the others.
Researchers chose one thing to learn about the company's methodology for implementing
Six Sigma within their operations. The product researchers choose seems to be the Men's basic
T-shirt, which would be the best selling item. Men's basic t-shirt manufacturing accounts for 63
percentage of overall Knit product (T-shirt, Polo) output at the facility.
Stage 1: Define
At this point, we've determined that in order to deliver a high-quality product and
compete effectively throughout the clothes sector, this firm must cut defect rates, variation,
wastage, therefore, as just a result, the value of things. Businesses are always up against
nationally and internationally garment/clothing manufacturers.
Stage 2: Measure
“Does the application of
Six Sigma bring benefit
garments industries in all over the Bangladesh?
To address this question, researcher will use the first example firm as an example of just
how Six Sigma may help a garment manufacturing improve product quality by lowering logistics
costs. During first scenario, we selected “Viyellatex Ltd,” a Bangladeshi garments business with
a six-sigma program. Viyellatex Ltd. is using the Six Sigma approach as just an improvement
instrument in their manufacturing process for 4 years. As previously stated, Viyellatex Ltd with
two design divisions that are manufactured in the facility. The first is knitwear (T-shirts, Polo
Shirts), and the other is baked goods (Shirt, Pant). They've done it with both sorts of items. We
used the Six Sigma program to assess the influence on the manufacturing method after
questioning the managers. They shall exhibit the impact and outcomes and during the application
of Sig Sigma techniques to differentiate the others.
Researchers chose one thing to learn about the company's methodology for implementing
Six Sigma within their operations. The product researchers choose seems to be the Men's basic
T-shirt, which would be the best selling item. Men's basic t-shirt manufacturing accounts for 63
percentage of overall Knit product (T-shirt, Polo) output at the facility.
Stage 1: Define
At this point, we've determined that in order to deliver a high-quality product and
compete effectively throughout the clothes sector, this firm must cut defect rates, variation,
wastage, therefore, as just a result, the value of things. Businesses are always up against
nationally and internationally garment/clothing manufacturers.
Stage 2: Measure
“Does the application of
Six Sigma bring benefit
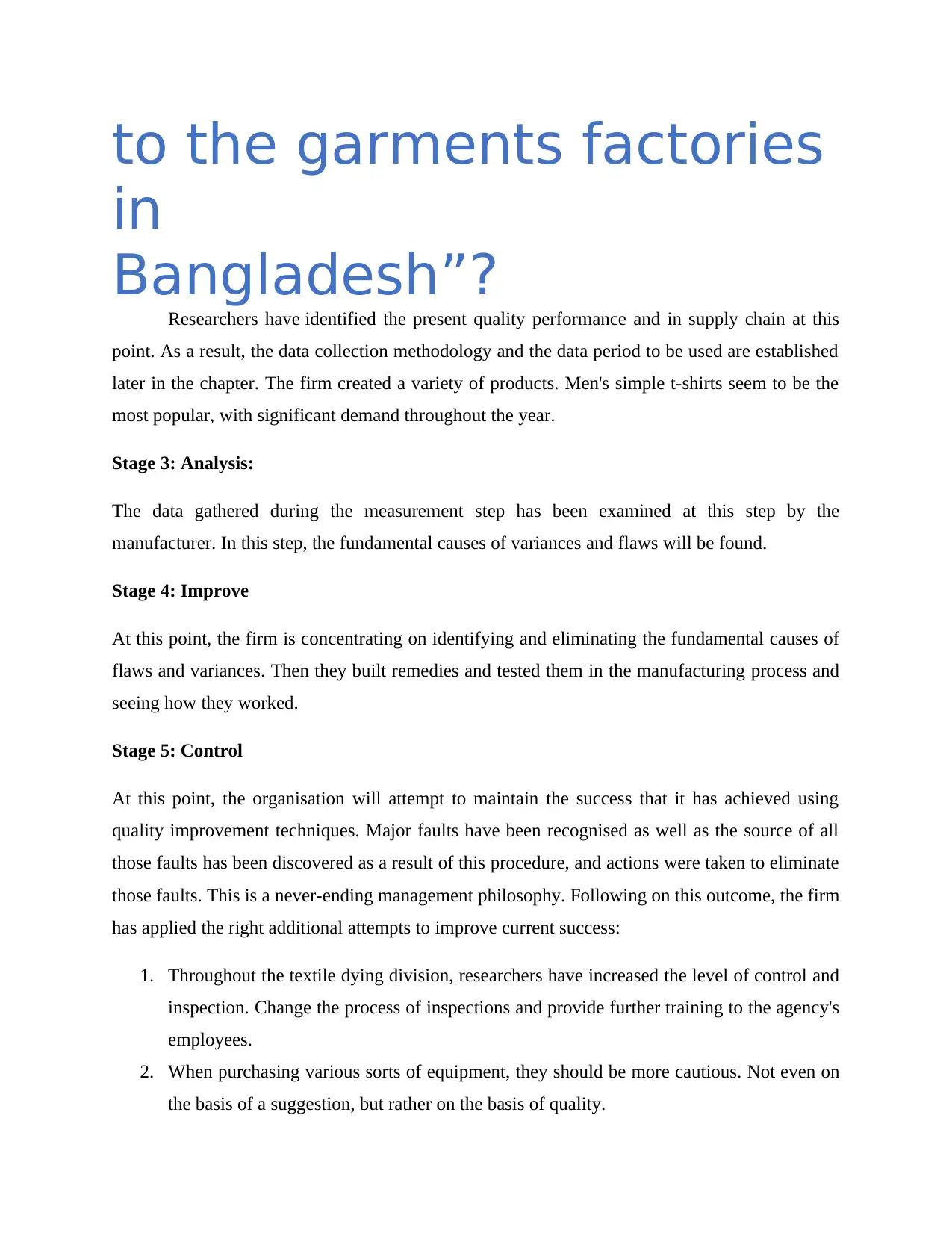
to the garments factories
in
Bangladesh”?
Researchers have identified the present quality performance and in supply chain at this
point. As a result, the data collection methodology and the data period to be used are established
later in the chapter. The firm created a variety of products. Men's simple t-shirts seem to be the
most popular, with significant demand throughout the year.
Stage 3: Analysis:
The data gathered during the measurement step has been examined at this step by the
manufacturer. In this step, the fundamental causes of variances and flaws will be found.
Stage 4: Improve
At this point, the firm is concentrating on identifying and eliminating the fundamental causes of
flaws and variances. Then they built remedies and tested them in the manufacturing process and
seeing how they worked.
Stage 5: Control
At this point, the organisation will attempt to maintain the success that it has achieved using
quality improvement techniques. Major faults have been recognised as well as the source of all
those faults has been discovered as a result of this procedure, and actions were taken to eliminate
those faults. This is a never-ending management philosophy. Following on this outcome, the firm
has applied the right additional attempts to improve current success:
1. Throughout the textile dying division, researchers have increased the level of control and
inspection. Change the process of inspections and provide further training to the agency's
employees.
2. When purchasing various sorts of equipment, they should be more cautious. Not even on
the basis of a suggestion, but rather on the basis of quality.
in
Bangladesh”?
Researchers have identified the present quality performance and in supply chain at this
point. As a result, the data collection methodology and the data period to be used are established
later in the chapter. The firm created a variety of products. Men's simple t-shirts seem to be the
most popular, with significant demand throughout the year.
Stage 3: Analysis:
The data gathered during the measurement step has been examined at this step by the
manufacturer. In this step, the fundamental causes of variances and flaws will be found.
Stage 4: Improve
At this point, the firm is concentrating on identifying and eliminating the fundamental causes of
flaws and variances. Then they built remedies and tested them in the manufacturing process and
seeing how they worked.
Stage 5: Control
At this point, the organisation will attempt to maintain the success that it has achieved using
quality improvement techniques. Major faults have been recognised as well as the source of all
those faults has been discovered as a result of this procedure, and actions were taken to eliminate
those faults. This is a never-ending management philosophy. Following on this outcome, the firm
has applied the right additional attempts to improve current success:
1. Throughout the textile dying division, researchers have increased the level of control and
inspection. Change the process of inspections and provide further training to the agency's
employees.
2. When purchasing various sorts of equipment, they should be more cautious. Not even on
the basis of a suggestion, but rather on the basis of quality.
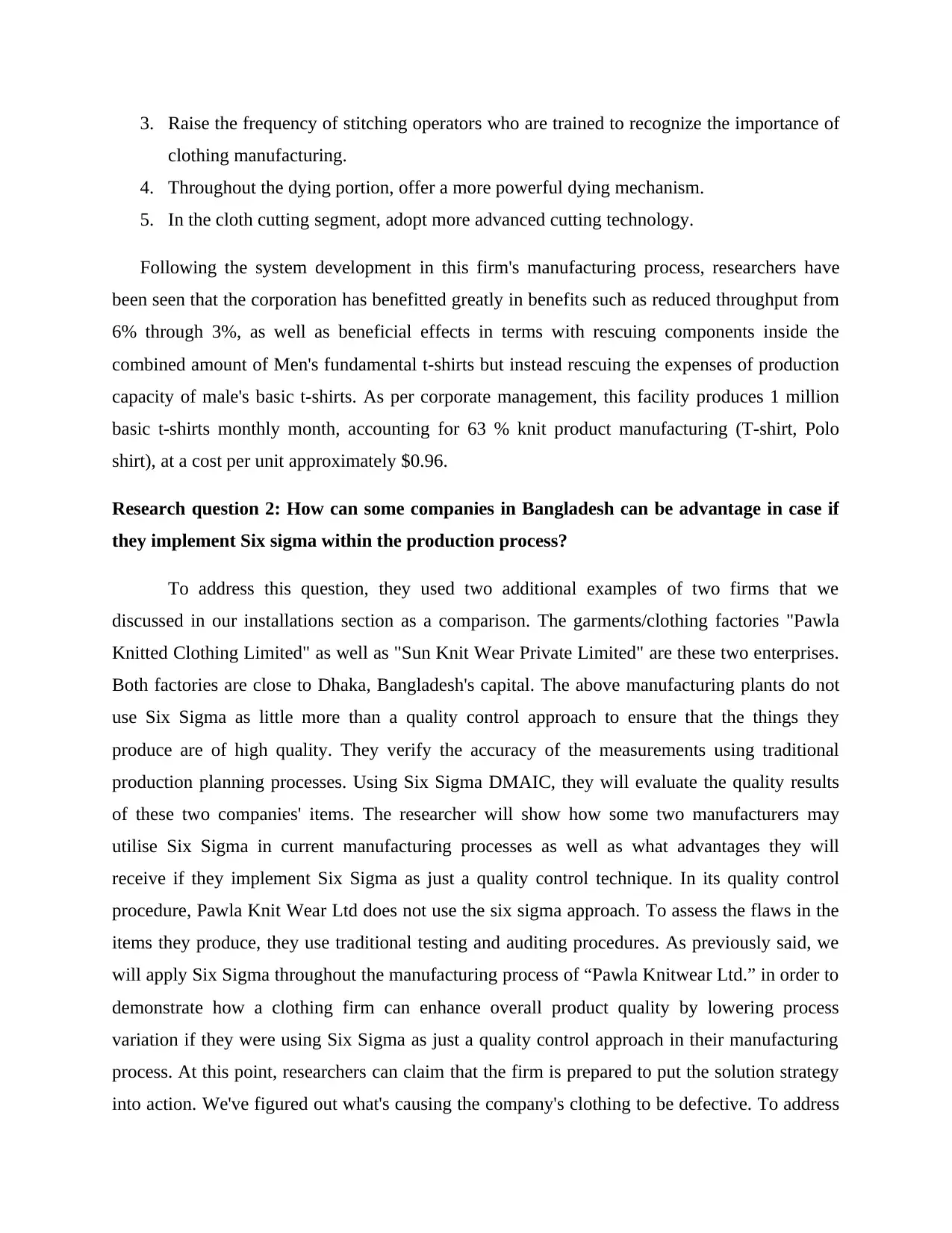
3. Raise the frequency of stitching operators who are trained to recognize the importance of
clothing manufacturing.
4. Throughout the dying portion, offer a more powerful dying mechanism.
5. In the cloth cutting segment, adopt more advanced cutting technology.
Following the system development in this firm's manufacturing process, researchers have
been seen that the corporation has benefitted greatly in benefits such as reduced throughput from
6% through 3%, as well as beneficial effects in terms with rescuing components inside the
combined amount of Men's fundamental t-shirts but instead rescuing the expenses of production
capacity of male's basic t-shirts. As per corporate management, this facility produces 1 million
basic t-shirts monthly month, accounting for 63 % knit product manufacturing (T-shirt, Polo
shirt), at a cost per unit approximately $0.96.
Research question 2: How can some companies in Bangladesh can be advantage in case if
they implement Six sigma within the production process?
To address this question, they used two additional examples of two firms that we
discussed in our installations section as a comparison. The garments/clothing factories "Pawla
Knitted Clothing Limited" as well as "Sun Knit Wear Private Limited" are these two enterprises.
Both factories are close to Dhaka, Bangladesh's capital. The above manufacturing plants do not
use Six Sigma as little more than a quality control approach to ensure that the things they
produce are of high quality. They verify the accuracy of the measurements using traditional
production planning processes. Using Six Sigma DMAIC, they will evaluate the quality results
of these two companies' items. The researcher will show how some two manufacturers may
utilise Six Sigma in current manufacturing processes as well as what advantages they will
receive if they implement Six Sigma as just a quality control technique. In its quality control
procedure, Pawla Knit Wear Ltd does not use the six sigma approach. To assess the flaws in the
items they produce, they use traditional testing and auditing procedures. As previously said, we
will apply Six Sigma throughout the manufacturing process of “Pawla Knitwear Ltd.” in order to
demonstrate how a clothing firm can enhance overall product quality by lowering process
variation if they were using Six Sigma as just a quality control approach in their manufacturing
process. At this point, researchers can claim that the firm is prepared to put the solution strategy
into action. We've figured out what's causing the company's clothing to be defective. To address
clothing manufacturing.
4. Throughout the dying portion, offer a more powerful dying mechanism.
5. In the cloth cutting segment, adopt more advanced cutting technology.
Following the system development in this firm's manufacturing process, researchers have
been seen that the corporation has benefitted greatly in benefits such as reduced throughput from
6% through 3%, as well as beneficial effects in terms with rescuing components inside the
combined amount of Men's fundamental t-shirts but instead rescuing the expenses of production
capacity of male's basic t-shirts. As per corporate management, this facility produces 1 million
basic t-shirts monthly month, accounting for 63 % knit product manufacturing (T-shirt, Polo
shirt), at a cost per unit approximately $0.96.
Research question 2: How can some companies in Bangladesh can be advantage in case if
they implement Six sigma within the production process?
To address this question, they used two additional examples of two firms that we
discussed in our installations section as a comparison. The garments/clothing factories "Pawla
Knitted Clothing Limited" as well as "Sun Knit Wear Private Limited" are these two enterprises.
Both factories are close to Dhaka, Bangladesh's capital. The above manufacturing plants do not
use Six Sigma as little more than a quality control approach to ensure that the things they
produce are of high quality. They verify the accuracy of the measurements using traditional
production planning processes. Using Six Sigma DMAIC, they will evaluate the quality results
of these two companies' items. The researcher will show how some two manufacturers may
utilise Six Sigma in current manufacturing processes as well as what advantages they will
receive if they implement Six Sigma as just a quality control technique. In its quality control
procedure, Pawla Knit Wear Ltd does not use the six sigma approach. To assess the flaws in the
items they produce, they use traditional testing and auditing procedures. As previously said, we
will apply Six Sigma throughout the manufacturing process of “Pawla Knitwear Ltd.” in order to
demonstrate how a clothing firm can enhance overall product quality by lowering process
variation if they were using Six Sigma as just a quality control approach in their manufacturing
process. At this point, researchers can claim that the firm is prepared to put the solution strategy
into action. We've figured out what's causing the company's clothing to be defective. To address
Paraphrase This Document
Need a fresh take? Get an instant paraphrase of this document with our AI Paraphraser
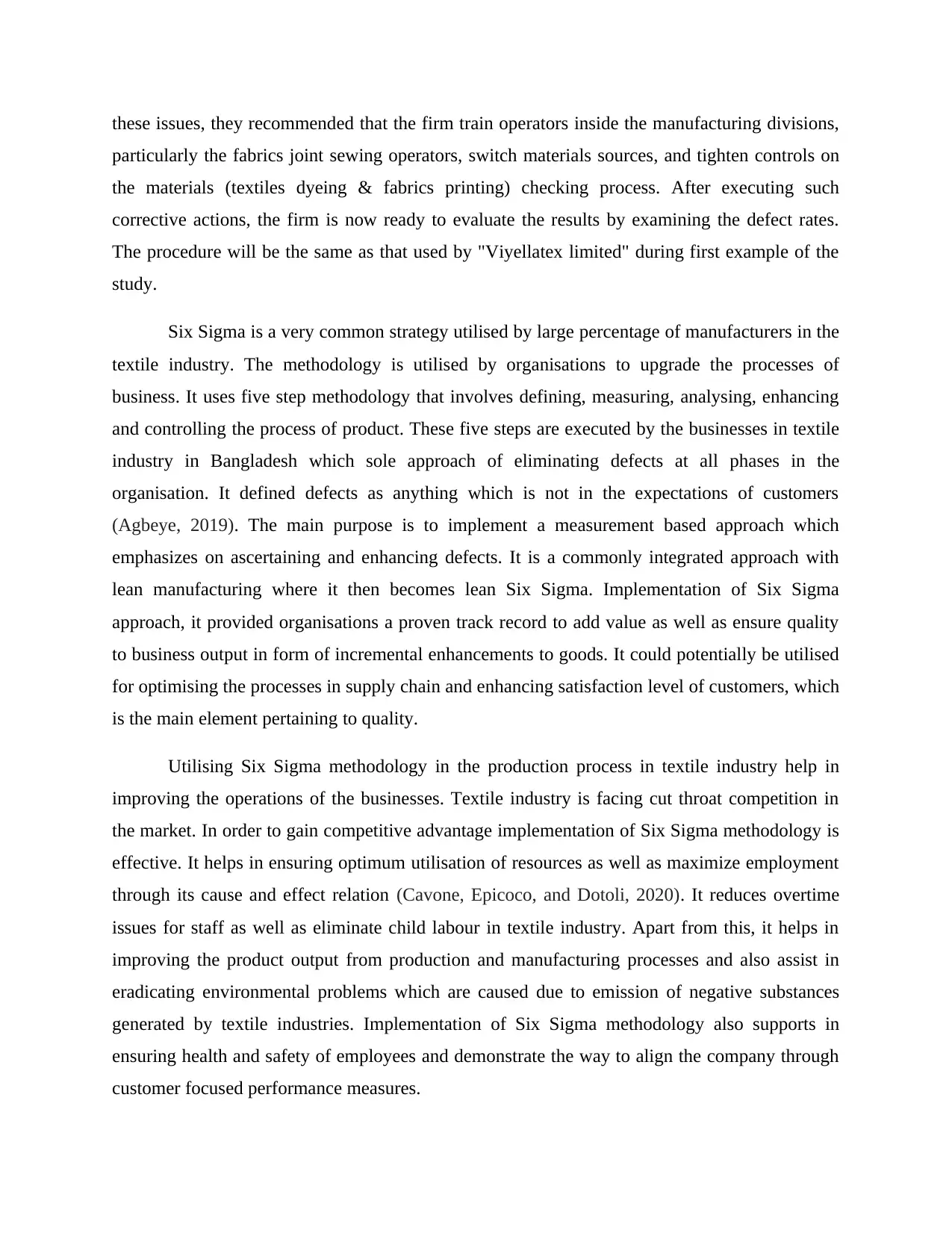
these issues, they recommended that the firm train operators inside the manufacturing divisions,
particularly the fabrics joint sewing operators, switch materials sources, and tighten controls on
the materials (textiles dyeing & fabrics printing) checking process. After executing such
corrective actions, the firm is now ready to evaluate the results by examining the defect rates.
The procedure will be the same as that used by "Viyellatex limited" during first example of the
study.
Six Sigma is a very common strategy utilised by large percentage of manufacturers in the
textile industry. The methodology is utilised by organisations to upgrade the processes of
business. It uses five step methodology that involves defining, measuring, analysing, enhancing
and controlling the process of product. These five steps are executed by the businesses in textile
industry in Bangladesh which sole approach of eliminating defects at all phases in the
organisation. It defined defects as anything which is not in the expectations of customers
(Agbeye, 2019). The main purpose is to implement a measurement based approach which
emphasizes on ascertaining and enhancing defects. It is a commonly integrated approach with
lean manufacturing where it then becomes lean Six Sigma. Implementation of Six Sigma
approach, it provided organisations a proven track record to add value as well as ensure quality
to business output in form of incremental enhancements to goods. It could potentially be utilised
for optimising the processes in supply chain and enhancing satisfaction level of customers, which
is the main element pertaining to quality.
Utilising Six Sigma methodology in the production process in textile industry help in
improving the operations of the businesses. Textile industry is facing cut throat competition in
the market. In order to gain competitive advantage implementation of Six Sigma methodology is
effective. It helps in ensuring optimum utilisation of resources as well as maximize employment
through its cause and effect relation (Cavone, Epicoco, and Dotoli, 2020). It reduces overtime
issues for staff as well as eliminate child labour in textile industry. Apart from this, it helps in
improving the product output from production and manufacturing processes and also assist in
eradicating environmental problems which are caused due to emission of negative substances
generated by textile industries. Implementation of Six Sigma methodology also supports in
ensuring health and safety of employees and demonstrate the way to align the company through
customer focused performance measures.
particularly the fabrics joint sewing operators, switch materials sources, and tighten controls on
the materials (textiles dyeing & fabrics printing) checking process. After executing such
corrective actions, the firm is now ready to evaluate the results by examining the defect rates.
The procedure will be the same as that used by "Viyellatex limited" during first example of the
study.
Six Sigma is a very common strategy utilised by large percentage of manufacturers in the
textile industry. The methodology is utilised by organisations to upgrade the processes of
business. It uses five step methodology that involves defining, measuring, analysing, enhancing
and controlling the process of product. These five steps are executed by the businesses in textile
industry in Bangladesh which sole approach of eliminating defects at all phases in the
organisation. It defined defects as anything which is not in the expectations of customers
(Agbeye, 2019). The main purpose is to implement a measurement based approach which
emphasizes on ascertaining and enhancing defects. It is a commonly integrated approach with
lean manufacturing where it then becomes lean Six Sigma. Implementation of Six Sigma
approach, it provided organisations a proven track record to add value as well as ensure quality
to business output in form of incremental enhancements to goods. It could potentially be utilised
for optimising the processes in supply chain and enhancing satisfaction level of customers, which
is the main element pertaining to quality.
Utilising Six Sigma methodology in the production process in textile industry help in
improving the operations of the businesses. Textile industry is facing cut throat competition in
the market. In order to gain competitive advantage implementation of Six Sigma methodology is
effective. It helps in ensuring optimum utilisation of resources as well as maximize employment
through its cause and effect relation (Cavone, Epicoco, and Dotoli, 2020). It reduces overtime
issues for staff as well as eliminate child labour in textile industry. Apart from this, it helps in
improving the product output from production and manufacturing processes and also assist in
eradicating environmental problems which are caused due to emission of negative substances
generated by textile industries. Implementation of Six Sigma methodology also supports in
ensuring health and safety of employees and demonstrate the way to align the company through
customer focused performance measures.
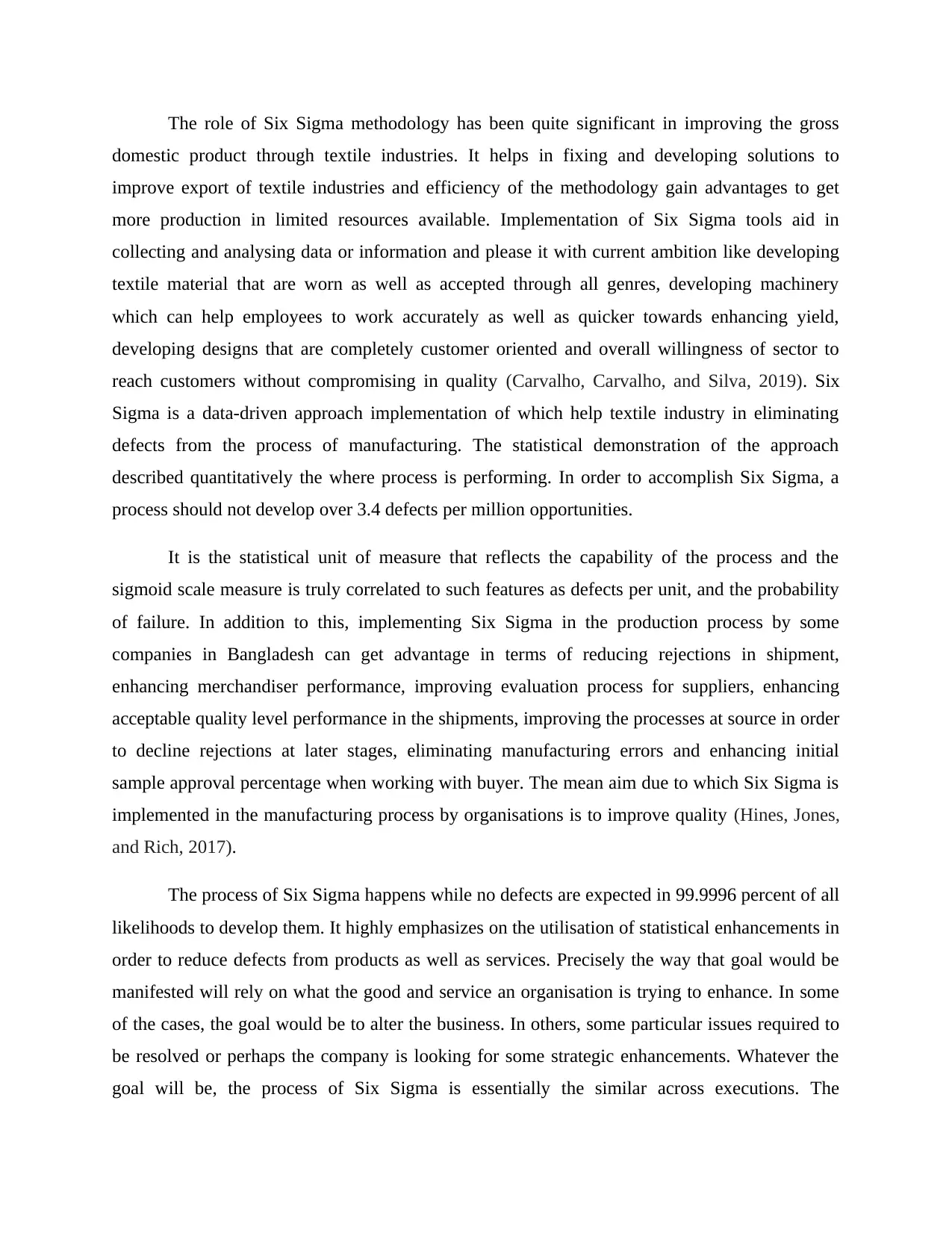
The role of Six Sigma methodology has been quite significant in improving the gross
domestic product through textile industries. It helps in fixing and developing solutions to
improve export of textile industries and efficiency of the methodology gain advantages to get
more production in limited resources available. Implementation of Six Sigma tools aid in
collecting and analysing data or information and please it with current ambition like developing
textile material that are worn as well as accepted through all genres, developing machinery
which can help employees to work accurately as well as quicker towards enhancing yield,
developing designs that are completely customer oriented and overall willingness of sector to
reach customers without compromising in quality (Carvalho, Carvalho, and Silva, 2019). Six
Sigma is a data-driven approach implementation of which help textile industry in eliminating
defects from the process of manufacturing. The statistical demonstration of the approach
described quantitatively the where process is performing. In order to accomplish Six Sigma, a
process should not develop over 3.4 defects per million opportunities.
It is the statistical unit of measure that reflects the capability of the process and the
sigmoid scale measure is truly correlated to such features as defects per unit, and the probability
of failure. In addition to this, implementing Six Sigma in the production process by some
companies in Bangladesh can get advantage in terms of reducing rejections in shipment,
enhancing merchandiser performance, improving evaluation process for suppliers, enhancing
acceptable quality level performance in the shipments, improving the processes at source in order
to decline rejections at later stages, eliminating manufacturing errors and enhancing initial
sample approval percentage when working with buyer. The mean aim due to which Six Sigma is
implemented in the manufacturing process by organisations is to improve quality (Hines, Jones,
and Rich, 2017).
The process of Six Sigma happens while no defects are expected in 99.9996 percent of all
likelihoods to develop them. It highly emphasizes on the utilisation of statistical enhancements in
order to reduce defects from products as well as services. Precisely the way that goal would be
manifested will rely on what the good and service an organisation is trying to enhance. In some
of the cases, the goal would be to alter the business. In others, some particular issues required to
be resolved or perhaps the company is looking for some strategic enhancements. Whatever the
goal will be, the process of Six Sigma is essentially the similar across executions. The
domestic product through textile industries. It helps in fixing and developing solutions to
improve export of textile industries and efficiency of the methodology gain advantages to get
more production in limited resources available. Implementation of Six Sigma tools aid in
collecting and analysing data or information and please it with current ambition like developing
textile material that are worn as well as accepted through all genres, developing machinery
which can help employees to work accurately as well as quicker towards enhancing yield,
developing designs that are completely customer oriented and overall willingness of sector to
reach customers without compromising in quality (Carvalho, Carvalho, and Silva, 2019). Six
Sigma is a data-driven approach implementation of which help textile industry in eliminating
defects from the process of manufacturing. The statistical demonstration of the approach
described quantitatively the where process is performing. In order to accomplish Six Sigma, a
process should not develop over 3.4 defects per million opportunities.
It is the statistical unit of measure that reflects the capability of the process and the
sigmoid scale measure is truly correlated to such features as defects per unit, and the probability
of failure. In addition to this, implementing Six Sigma in the production process by some
companies in Bangladesh can get advantage in terms of reducing rejections in shipment,
enhancing merchandiser performance, improving evaluation process for suppliers, enhancing
acceptable quality level performance in the shipments, improving the processes at source in order
to decline rejections at later stages, eliminating manufacturing errors and enhancing initial
sample approval percentage when working with buyer. The mean aim due to which Six Sigma is
implemented in the manufacturing process by organisations is to improve quality (Hines, Jones,
and Rich, 2017).
The process of Six Sigma happens while no defects are expected in 99.9996 percent of all
likelihoods to develop them. It highly emphasizes on the utilisation of statistical enhancements in
order to reduce defects from products as well as services. Precisely the way that goal would be
manifested will rely on what the good and service an organisation is trying to enhance. In some
of the cases, the goal would be to alter the business. In others, some particular issues required to
be resolved or perhaps the company is looking for some strategic enhancements. Whatever the
goal will be, the process of Six Sigma is essentially the similar across executions. The
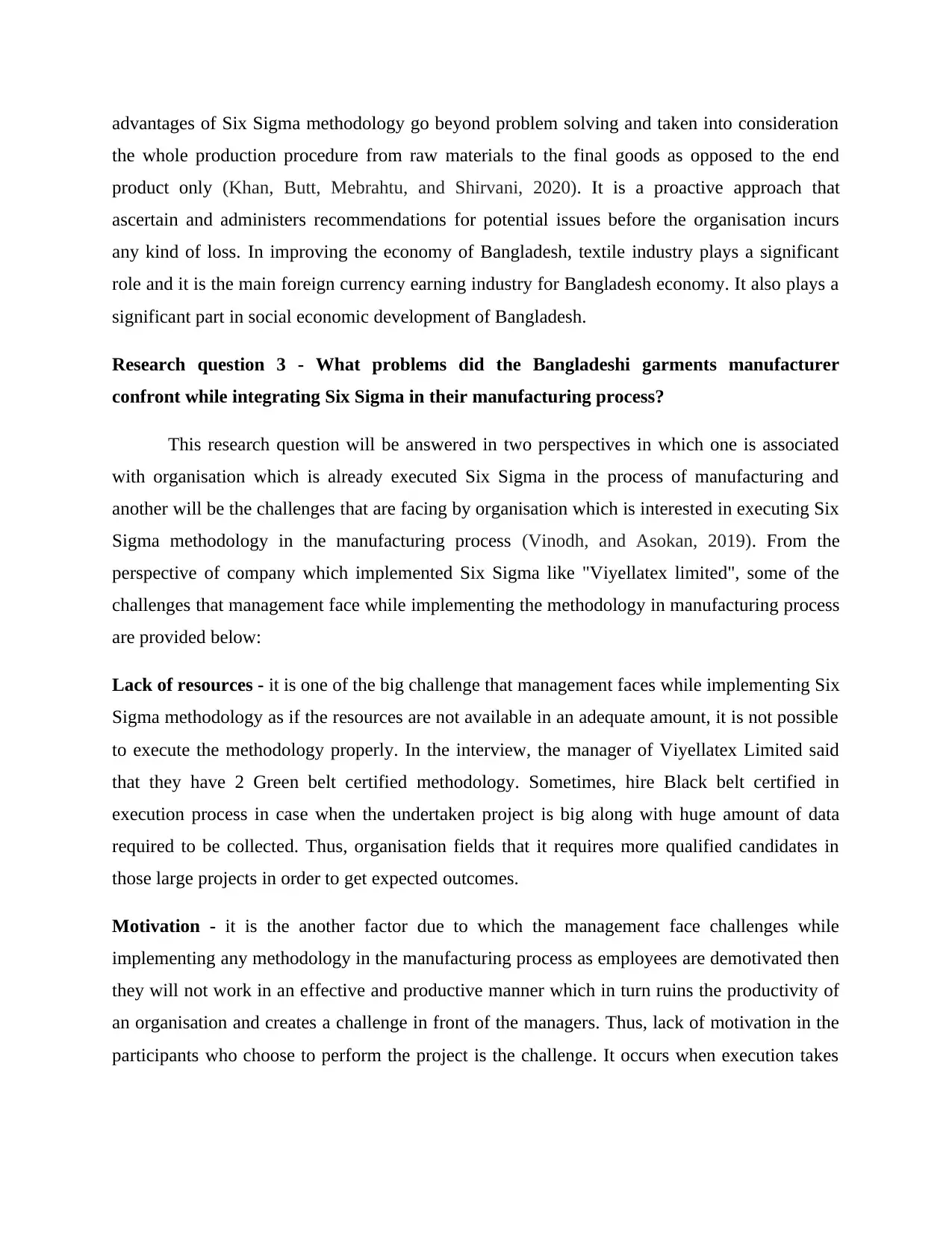
advantages of Six Sigma methodology go beyond problem solving and taken into consideration
the whole production procedure from raw materials to the final goods as opposed to the end
product only (Khan, Butt, Mebrahtu, and Shirvani, 2020). It is a proactive approach that
ascertain and administers recommendations for potential issues before the organisation incurs
any kind of loss. In improving the economy of Bangladesh, textile industry plays a significant
role and it is the main foreign currency earning industry for Bangladesh economy. It also plays a
significant part in social economic development of Bangladesh.
Research question 3 - What problems did the Bangladeshi garments manufacturer
confront while integrating Six Sigma in their manufacturing process?
This research question will be answered in two perspectives in which one is associated
with organisation which is already executed Six Sigma in the process of manufacturing and
another will be the challenges that are facing by organisation which is interested in executing Six
Sigma methodology in the manufacturing process (Vinodh, and Asokan, 2019). From the
perspective of company which implemented Six Sigma like "Viyellatex limited", some of the
challenges that management face while implementing the methodology in manufacturing process
are provided below:
Lack of resources - it is one of the big challenge that management faces while implementing Six
Sigma methodology as if the resources are not available in an adequate amount, it is not possible
to execute the methodology properly. In the interview, the manager of Viyellatex Limited said
that they have 2 Green belt certified methodology. Sometimes, hire Black belt certified in
execution process in case when the undertaken project is big along with huge amount of data
required to be collected. Thus, organisation fields that it requires more qualified candidates in
those large projects in order to get expected outcomes.
Motivation - it is the another factor due to which the management face challenges while
implementing any methodology in the manufacturing process as employees are demotivated then
they will not work in an effective and productive manner which in turn ruins the productivity of
an organisation and creates a challenge in front of the managers. Thus, lack of motivation in the
participants who choose to perform the project is the challenge. It occurs when execution takes
the whole production procedure from raw materials to the final goods as opposed to the end
product only (Khan, Butt, Mebrahtu, and Shirvani, 2020). It is a proactive approach that
ascertain and administers recommendations for potential issues before the organisation incurs
any kind of loss. In improving the economy of Bangladesh, textile industry plays a significant
role and it is the main foreign currency earning industry for Bangladesh economy. It also plays a
significant part in social economic development of Bangladesh.
Research question 3 - What problems did the Bangladeshi garments manufacturer
confront while integrating Six Sigma in their manufacturing process?
This research question will be answered in two perspectives in which one is associated
with organisation which is already executed Six Sigma in the process of manufacturing and
another will be the challenges that are facing by organisation which is interested in executing Six
Sigma methodology in the manufacturing process (Vinodh, and Asokan, 2019). From the
perspective of company which implemented Six Sigma like "Viyellatex limited", some of the
challenges that management face while implementing the methodology in manufacturing process
are provided below:
Lack of resources - it is one of the big challenge that management faces while implementing Six
Sigma methodology as if the resources are not available in an adequate amount, it is not possible
to execute the methodology properly. In the interview, the manager of Viyellatex Limited said
that they have 2 Green belt certified methodology. Sometimes, hire Black belt certified in
execution process in case when the undertaken project is big along with huge amount of data
required to be collected. Thus, organisation fields that it requires more qualified candidates in
those large projects in order to get expected outcomes.
Motivation - it is the another factor due to which the management face challenges while
implementing any methodology in the manufacturing process as employees are demotivated then
they will not work in an effective and productive manner which in turn ruins the productivity of
an organisation and creates a challenge in front of the managers. Thus, lack of motivation in the
participants who choose to perform the project is the challenge. It occurs when execution takes
Secure Best Marks with AI Grader
Need help grading? Try our AI Grader for instant feedback on your assignments.
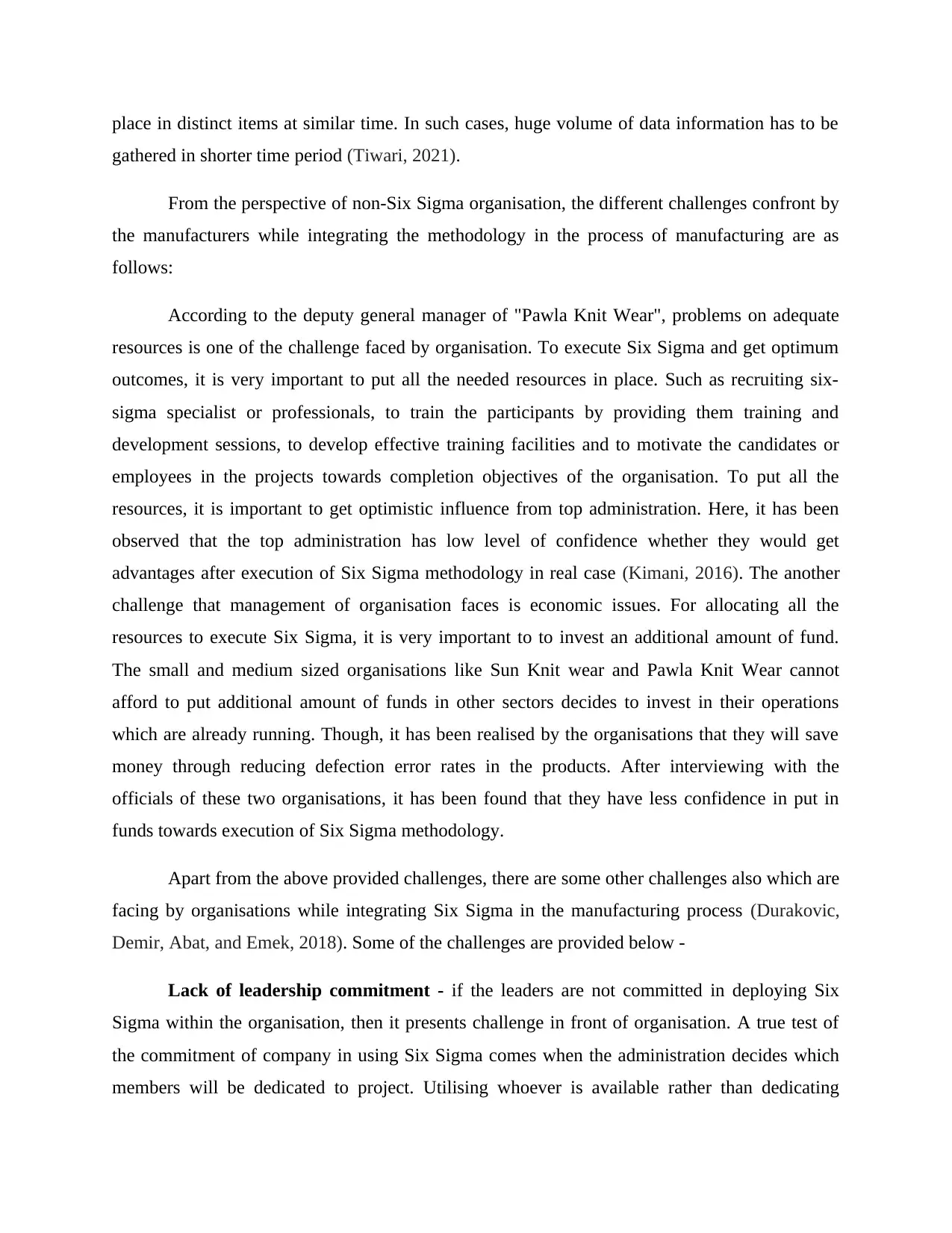
place in distinct items at similar time. In such cases, huge volume of data information has to be
gathered in shorter time period (Tiwari, 2021).
From the perspective of non-Six Sigma organisation, the different challenges confront by
the manufacturers while integrating the methodology in the process of manufacturing are as
follows:
According to the deputy general manager of "Pawla Knit Wear", problems on adequate
resources is one of the challenge faced by organisation. To execute Six Sigma and get optimum
outcomes, it is very important to put all the needed resources in place. Such as recruiting six-
sigma specialist or professionals, to train the participants by providing them training and
development sessions, to develop effective training facilities and to motivate the candidates or
employees in the projects towards completion objectives of the organisation. To put all the
resources, it is important to get optimistic influence from top administration. Here, it has been
observed that the top administration has low level of confidence whether they would get
advantages after execution of Six Sigma methodology in real case (Kimani, 2016). The another
challenge that management of organisation faces is economic issues. For allocating all the
resources to execute Six Sigma, it is very important to to invest an additional amount of fund.
The small and medium sized organisations like Sun Knit wear and Pawla Knit Wear cannot
afford to put additional amount of funds in other sectors decides to invest in their operations
which are already running. Though, it has been realised by the organisations that they will save
money through reducing defection error rates in the products. After interviewing with the
officials of these two organisations, it has been found that they have less confidence in put in
funds towards execution of Six Sigma methodology.
Apart from the above provided challenges, there are some other challenges also which are
facing by organisations while integrating Six Sigma in the manufacturing process (Durakovic,
Demir, Abat, and Emek, 2018). Some of the challenges are provided below -
Lack of leadership commitment - if the leaders are not committed in deploying Six
Sigma within the organisation, then it presents challenge in front of organisation. A true test of
the commitment of company in using Six Sigma comes when the administration decides which
members will be dedicated to project. Utilising whoever is available rather than dedicating
gathered in shorter time period (Tiwari, 2021).
From the perspective of non-Six Sigma organisation, the different challenges confront by
the manufacturers while integrating the methodology in the process of manufacturing are as
follows:
According to the deputy general manager of "Pawla Knit Wear", problems on adequate
resources is one of the challenge faced by organisation. To execute Six Sigma and get optimum
outcomes, it is very important to put all the needed resources in place. Such as recruiting six-
sigma specialist or professionals, to train the participants by providing them training and
development sessions, to develop effective training facilities and to motivate the candidates or
employees in the projects towards completion objectives of the organisation. To put all the
resources, it is important to get optimistic influence from top administration. Here, it has been
observed that the top administration has low level of confidence whether they would get
advantages after execution of Six Sigma methodology in real case (Kimani, 2016). The another
challenge that management of organisation faces is economic issues. For allocating all the
resources to execute Six Sigma, it is very important to to invest an additional amount of fund.
The small and medium sized organisations like Sun Knit wear and Pawla Knit Wear cannot
afford to put additional amount of funds in other sectors decides to invest in their operations
which are already running. Though, it has been realised by the organisations that they will save
money through reducing defection error rates in the products. After interviewing with the
officials of these two organisations, it has been found that they have less confidence in put in
funds towards execution of Six Sigma methodology.
Apart from the above provided challenges, there are some other challenges also which are
facing by organisations while integrating Six Sigma in the manufacturing process (Durakovic,
Demir, Abat, and Emek, 2018). Some of the challenges are provided below -
Lack of leadership commitment - if the leaders are not committed in deploying Six
Sigma within the organisation, then it presents challenge in front of organisation. A true test of
the commitment of company in using Six Sigma comes when the administration decides which
members will be dedicated to project. Utilising whoever is available rather than dedicating
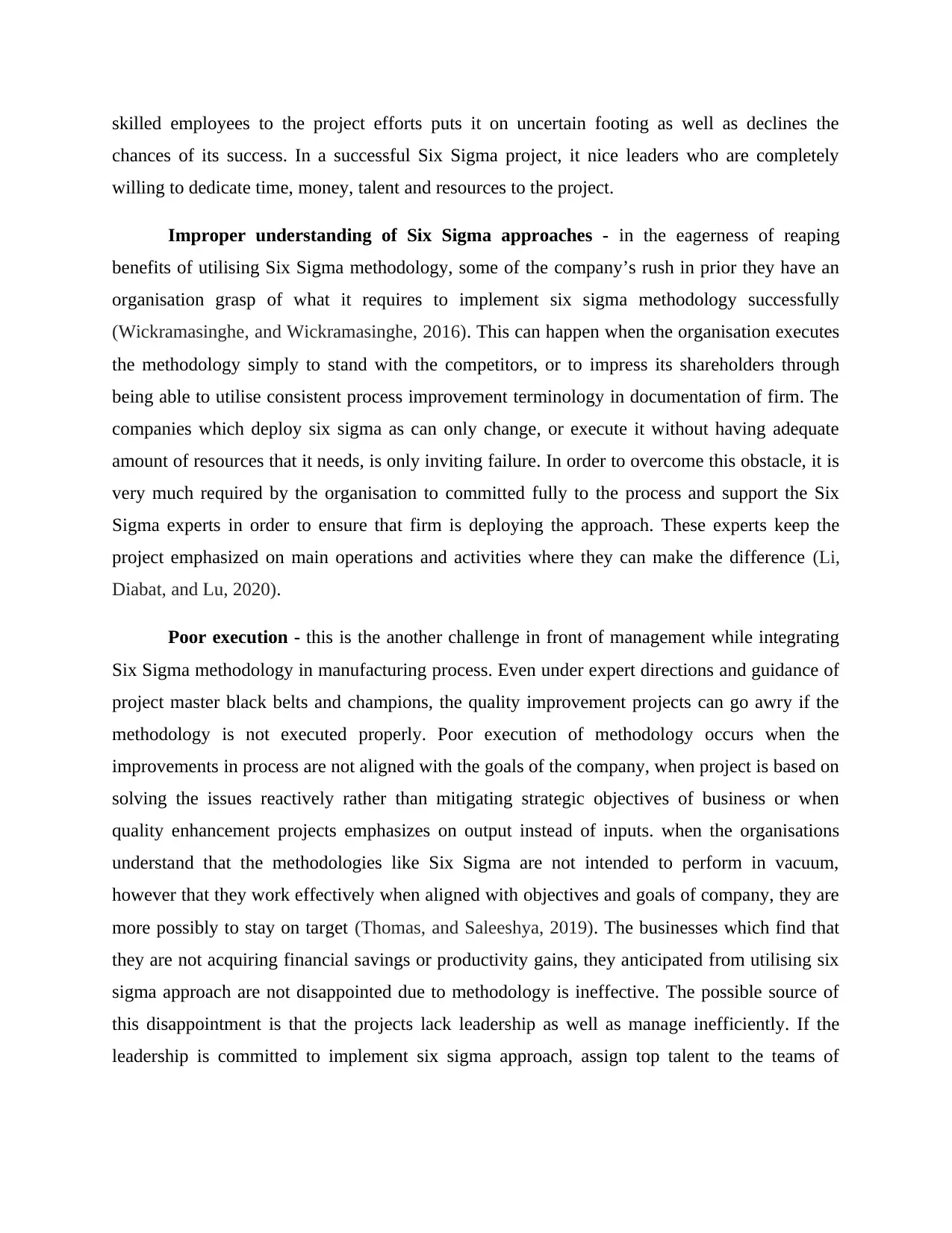
skilled employees to the project efforts puts it on uncertain footing as well as declines the
chances of its success. In a successful Six Sigma project, it nice leaders who are completely
willing to dedicate time, money, talent and resources to the project.
Improper understanding of Six Sigma approaches - in the eagerness of reaping
benefits of utilising Six Sigma methodology, some of the company’s rush in prior they have an
organisation grasp of what it requires to implement six sigma methodology successfully
(Wickramasinghe, and Wickramasinghe, 2016). This can happen when the organisation executes
the methodology simply to stand with the competitors, or to impress its shareholders through
being able to utilise consistent process improvement terminology in documentation of firm. The
companies which deploy six sigma as can only change, or execute it without having adequate
amount of resources that it needs, is only inviting failure. In order to overcome this obstacle, it is
very much required by the organisation to committed fully to the process and support the Six
Sigma experts in order to ensure that firm is deploying the approach. These experts keep the
project emphasized on main operations and activities where they can make the difference (Li,
Diabat, and Lu, 2020).
Poor execution - this is the another challenge in front of management while integrating
Six Sigma methodology in manufacturing process. Even under expert directions and guidance of
project master black belts and champions, the quality improvement projects can go awry if the
methodology is not executed properly. Poor execution of methodology occurs when the
improvements in process are not aligned with the goals of the company, when project is based on
solving the issues reactively rather than mitigating strategic objectives of business or when
quality enhancement projects emphasizes on output instead of inputs. when the organisations
understand that the methodologies like Six Sigma are not intended to perform in vacuum,
however that they work effectively when aligned with objectives and goals of company, they are
more possibly to stay on target (Thomas, and Saleeshya, 2019). The businesses which find that
they are not acquiring financial savings or productivity gains, they anticipated from utilising six
sigma approach are not disappointed due to methodology is ineffective. The possible source of
this disappointment is that the projects lack leadership as well as manage inefficiently. If the
leadership is committed to implement six sigma approach, assign top talent to the teams of
chances of its success. In a successful Six Sigma project, it nice leaders who are completely
willing to dedicate time, money, talent and resources to the project.
Improper understanding of Six Sigma approaches - in the eagerness of reaping
benefits of utilising Six Sigma methodology, some of the company’s rush in prior they have an
organisation grasp of what it requires to implement six sigma methodology successfully
(Wickramasinghe, and Wickramasinghe, 2016). This can happen when the organisation executes
the methodology simply to stand with the competitors, or to impress its shareholders through
being able to utilise consistent process improvement terminology in documentation of firm. The
companies which deploy six sigma as can only change, or execute it without having adequate
amount of resources that it needs, is only inviting failure. In order to overcome this obstacle, it is
very much required by the organisation to committed fully to the process and support the Six
Sigma experts in order to ensure that firm is deploying the approach. These experts keep the
project emphasized on main operations and activities where they can make the difference (Li,
Diabat, and Lu, 2020).
Poor execution - this is the another challenge in front of management while integrating
Six Sigma methodology in manufacturing process. Even under expert directions and guidance of
project master black belts and champions, the quality improvement projects can go awry if the
methodology is not executed properly. Poor execution of methodology occurs when the
improvements in process are not aligned with the goals of the company, when project is based on
solving the issues reactively rather than mitigating strategic objectives of business or when
quality enhancement projects emphasizes on output instead of inputs. when the organisations
understand that the methodologies like Six Sigma are not intended to perform in vacuum,
however that they work effectively when aligned with objectives and goals of company, they are
more possibly to stay on target (Thomas, and Saleeshya, 2019). The businesses which find that
they are not acquiring financial savings or productivity gains, they anticipated from utilising six
sigma approach are not disappointed due to methodology is ineffective. The possible source of
this disappointment is that the projects lack leadership as well as manage inefficiently. If the
leadership is committed to implement six sigma approach, assign top talent to the teams of
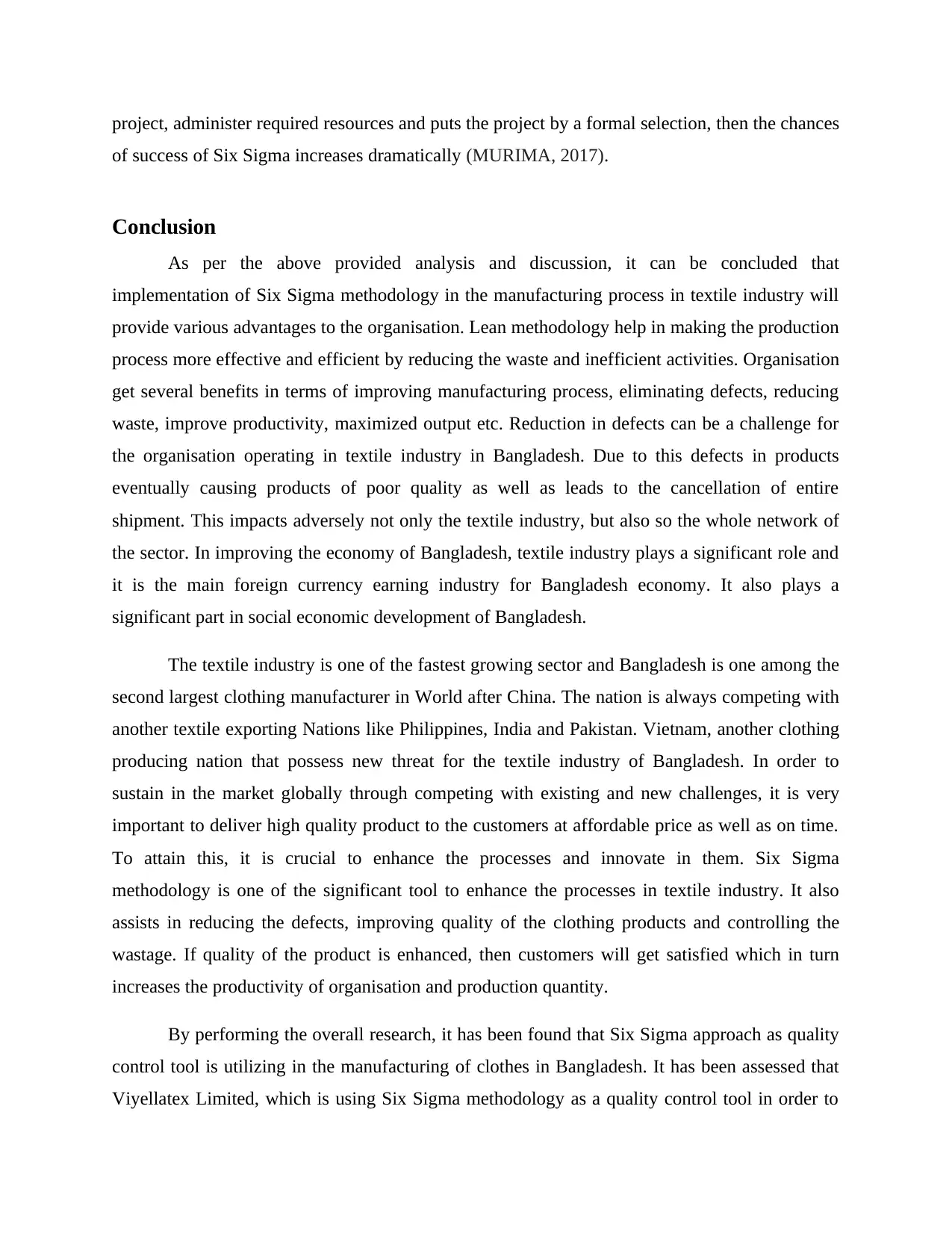
project, administer required resources and puts the project by a formal selection, then the chances
of success of Six Sigma increases dramatically (MURIMA, 2017).
Conclusion
As per the above provided analysis and discussion, it can be concluded that
implementation of Six Sigma methodology in the manufacturing process in textile industry will
provide various advantages to the organisation. Lean methodology help in making the production
process more effective and efficient by reducing the waste and inefficient activities. Organisation
get several benefits in terms of improving manufacturing process, eliminating defects, reducing
waste, improve productivity, maximized output etc. Reduction in defects can be a challenge for
the organisation operating in textile industry in Bangladesh. Due to this defects in products
eventually causing products of poor quality as well as leads to the cancellation of entire
shipment. This impacts adversely not only the textile industry, but also so the whole network of
the sector. In improving the economy of Bangladesh, textile industry plays a significant role and
it is the main foreign currency earning industry for Bangladesh economy. It also plays a
significant part in social economic development of Bangladesh.
The textile industry is one of the fastest growing sector and Bangladesh is one among the
second largest clothing manufacturer in World after China. The nation is always competing with
another textile exporting Nations like Philippines, India and Pakistan. Vietnam, another clothing
producing nation that possess new threat for the textile industry of Bangladesh. In order to
sustain in the market globally through competing with existing and new challenges, it is very
important to deliver high quality product to the customers at affordable price as well as on time.
To attain this, it is crucial to enhance the processes and innovate in them. Six Sigma
methodology is one of the significant tool to enhance the processes in textile industry. It also
assists in reducing the defects, improving quality of the clothing products and controlling the
wastage. If quality of the product is enhanced, then customers will get satisfied which in turn
increases the productivity of organisation and production quantity.
By performing the overall research, it has been found that Six Sigma approach as quality
control tool is utilizing in the manufacturing of clothes in Bangladesh. It has been assessed that
Viyellatex Limited, which is using Six Sigma methodology as a quality control tool in order to
of success of Six Sigma increases dramatically (MURIMA, 2017).
Conclusion
As per the above provided analysis and discussion, it can be concluded that
implementation of Six Sigma methodology in the manufacturing process in textile industry will
provide various advantages to the organisation. Lean methodology help in making the production
process more effective and efficient by reducing the waste and inefficient activities. Organisation
get several benefits in terms of improving manufacturing process, eliminating defects, reducing
waste, improve productivity, maximized output etc. Reduction in defects can be a challenge for
the organisation operating in textile industry in Bangladesh. Due to this defects in products
eventually causing products of poor quality as well as leads to the cancellation of entire
shipment. This impacts adversely not only the textile industry, but also so the whole network of
the sector. In improving the economy of Bangladesh, textile industry plays a significant role and
it is the main foreign currency earning industry for Bangladesh economy. It also plays a
significant part in social economic development of Bangladesh.
The textile industry is one of the fastest growing sector and Bangladesh is one among the
second largest clothing manufacturer in World after China. The nation is always competing with
another textile exporting Nations like Philippines, India and Pakistan. Vietnam, another clothing
producing nation that possess new threat for the textile industry of Bangladesh. In order to
sustain in the market globally through competing with existing and new challenges, it is very
important to deliver high quality product to the customers at affordable price as well as on time.
To attain this, it is crucial to enhance the processes and innovate in them. Six Sigma
methodology is one of the significant tool to enhance the processes in textile industry. It also
assists in reducing the defects, improving quality of the clothing products and controlling the
wastage. If quality of the product is enhanced, then customers will get satisfied which in turn
increases the productivity of organisation and production quantity.
By performing the overall research, it has been found that Six Sigma approach as quality
control tool is utilizing in the manufacturing of clothes in Bangladesh. It has been assessed that
Viyellatex Limited, which is using Six Sigma methodology as a quality control tool in order to
Paraphrase This Document
Need a fresh take? Get an instant paraphrase of this document with our AI Paraphraser
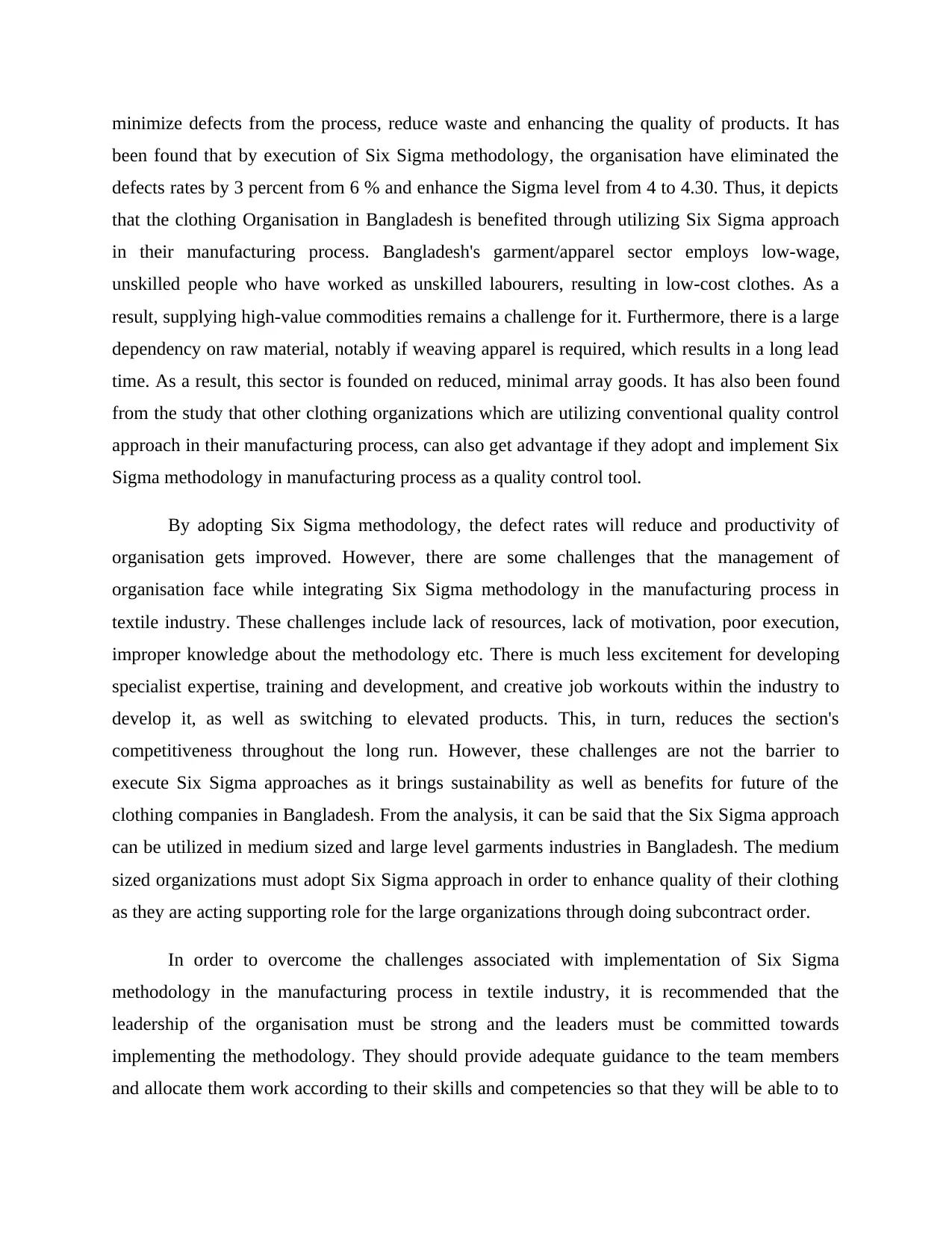
minimize defects from the process, reduce waste and enhancing the quality of products. It has
been found that by execution of Six Sigma methodology, the organisation have eliminated the
defects rates by 3 percent from 6 % and enhance the Sigma level from 4 to 4.30. Thus, it depicts
that the clothing Organisation in Bangladesh is benefited through utilizing Six Sigma approach
in their manufacturing process. Bangladesh's garment/apparel sector employs low-wage,
unskilled people who have worked as unskilled labourers, resulting in low-cost clothes. As a
result, supplying high-value commodities remains a challenge for it. Furthermore, there is a large
dependency on raw material, notably if weaving apparel is required, which results in a long lead
time. As a result, this sector is founded on reduced, minimal array goods. It has also been found
from the study that other clothing organizations which are utilizing conventional quality control
approach in their manufacturing process, can also get advantage if they adopt and implement Six
Sigma methodology in manufacturing process as a quality control tool.
By adopting Six Sigma methodology, the defect rates will reduce and productivity of
organisation gets improved. However, there are some challenges that the management of
organisation face while integrating Six Sigma methodology in the manufacturing process in
textile industry. These challenges include lack of resources, lack of motivation, poor execution,
improper knowledge about the methodology etc. There is much less excitement for developing
specialist expertise, training and development, and creative job workouts within the industry to
develop it, as well as switching to elevated products. This, in turn, reduces the section's
competitiveness throughout the long run. However, these challenges are not the barrier to
execute Six Sigma approaches as it brings sustainability as well as benefits for future of the
clothing companies in Bangladesh. From the analysis, it can be said that the Six Sigma approach
can be utilized in medium sized and large level garments industries in Bangladesh. The medium
sized organizations must adopt Six Sigma approach in order to enhance quality of their clothing
as they are acting supporting role for the large organizations through doing subcontract order.
In order to overcome the challenges associated with implementation of Six Sigma
methodology in the manufacturing process in textile industry, it is recommended that the
leadership of the organisation must be strong and the leaders must be committed towards
implementing the methodology. They should provide adequate guidance to the team members
and allocate them work according to their skills and competencies so that they will be able to to
been found that by execution of Six Sigma methodology, the organisation have eliminated the
defects rates by 3 percent from 6 % and enhance the Sigma level from 4 to 4.30. Thus, it depicts
that the clothing Organisation in Bangladesh is benefited through utilizing Six Sigma approach
in their manufacturing process. Bangladesh's garment/apparel sector employs low-wage,
unskilled people who have worked as unskilled labourers, resulting in low-cost clothes. As a
result, supplying high-value commodities remains a challenge for it. Furthermore, there is a large
dependency on raw material, notably if weaving apparel is required, which results in a long lead
time. As a result, this sector is founded on reduced, minimal array goods. It has also been found
from the study that other clothing organizations which are utilizing conventional quality control
approach in their manufacturing process, can also get advantage if they adopt and implement Six
Sigma methodology in manufacturing process as a quality control tool.
By adopting Six Sigma methodology, the defect rates will reduce and productivity of
organisation gets improved. However, there are some challenges that the management of
organisation face while integrating Six Sigma methodology in the manufacturing process in
textile industry. These challenges include lack of resources, lack of motivation, poor execution,
improper knowledge about the methodology etc. There is much less excitement for developing
specialist expertise, training and development, and creative job workouts within the industry to
develop it, as well as switching to elevated products. This, in turn, reduces the section's
competitiveness throughout the long run. However, these challenges are not the barrier to
execute Six Sigma approaches as it brings sustainability as well as benefits for future of the
clothing companies in Bangladesh. From the analysis, it can be said that the Six Sigma approach
can be utilized in medium sized and large level garments industries in Bangladesh. The medium
sized organizations must adopt Six Sigma approach in order to enhance quality of their clothing
as they are acting supporting role for the large organizations through doing subcontract order.
In order to overcome the challenges associated with implementation of Six Sigma
methodology in the manufacturing process in textile industry, it is recommended that the
leadership of the organisation must be strong and the leaders must be committed towards
implementing the methodology. They should provide adequate guidance to the team members
and allocate them work according to their skills and competencies so that they will be able to to
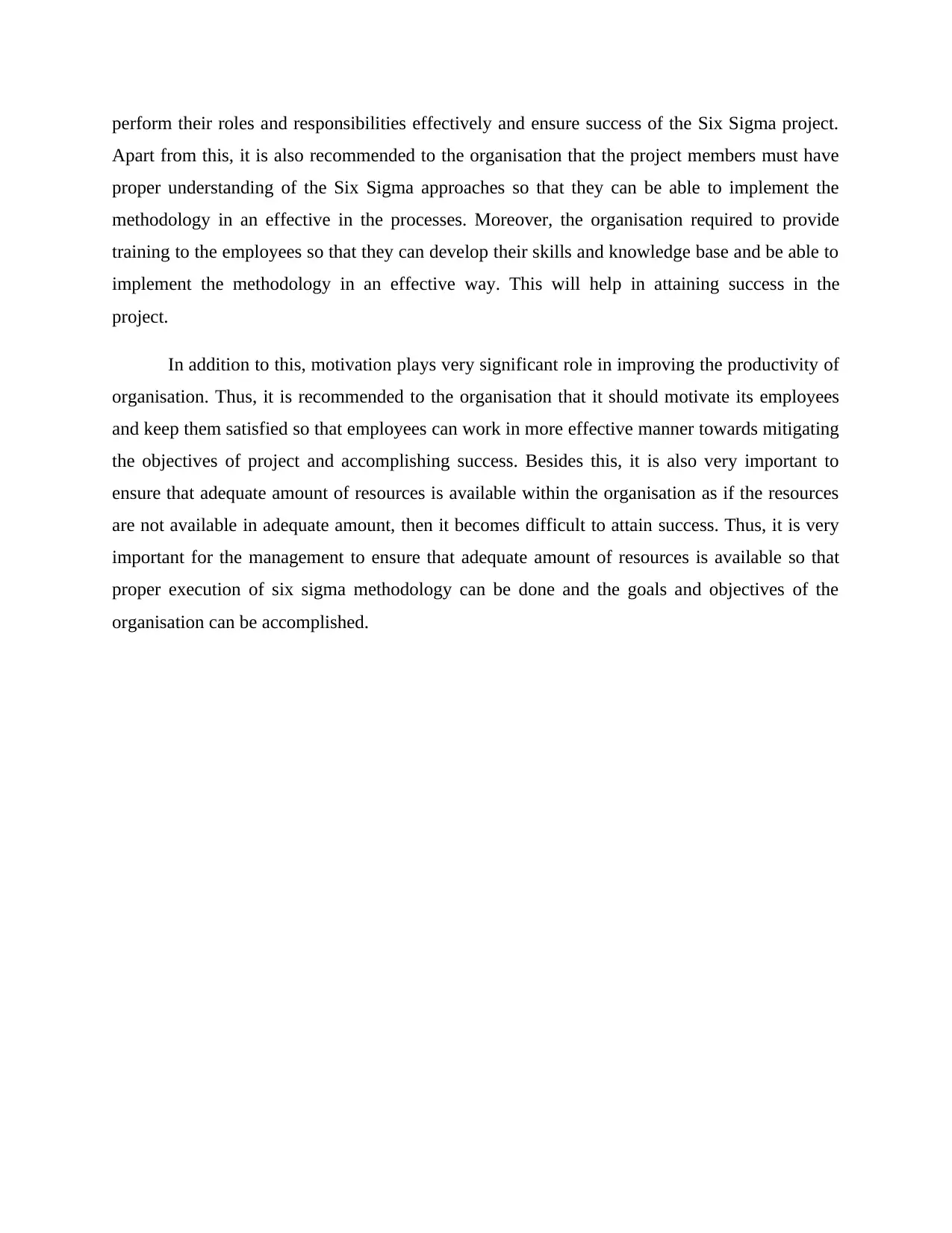
perform their roles and responsibilities effectively and ensure success of the Six Sigma project.
Apart from this, it is also recommended to the organisation that the project members must have
proper understanding of the Six Sigma approaches so that they can be able to implement the
methodology in an effective in the processes. Moreover, the organisation required to provide
training to the employees so that they can develop their skills and knowledge base and be able to
implement the methodology in an effective way. This will help in attaining success in the
project.
In addition to this, motivation plays very significant role in improving the productivity of
organisation. Thus, it is recommended to the organisation that it should motivate its employees
and keep them satisfied so that employees can work in more effective manner towards mitigating
the objectives of project and accomplishing success. Besides this, it is also very important to
ensure that adequate amount of resources is available within the organisation as if the resources
are not available in adequate amount, then it becomes difficult to attain success. Thus, it is very
important for the management to ensure that adequate amount of resources is available so that
proper execution of six sigma methodology can be done and the goals and objectives of the
organisation can be accomplished.
Apart from this, it is also recommended to the organisation that the project members must have
proper understanding of the Six Sigma approaches so that they can be able to implement the
methodology in an effective in the processes. Moreover, the organisation required to provide
training to the employees so that they can develop their skills and knowledge base and be able to
implement the methodology in an effective way. This will help in attaining success in the
project.
In addition to this, motivation plays very significant role in improving the productivity of
organisation. Thus, it is recommended to the organisation that it should motivate its employees
and keep them satisfied so that employees can work in more effective manner towards mitigating
the objectives of project and accomplishing success. Besides this, it is also very important to
ensure that adequate amount of resources is available within the organisation as if the resources
are not available in adequate amount, then it becomes difficult to attain success. Thus, it is very
important for the management to ensure that adequate amount of resources is available so that
proper execution of six sigma methodology can be done and the goals and objectives of the
organisation can be accomplished.
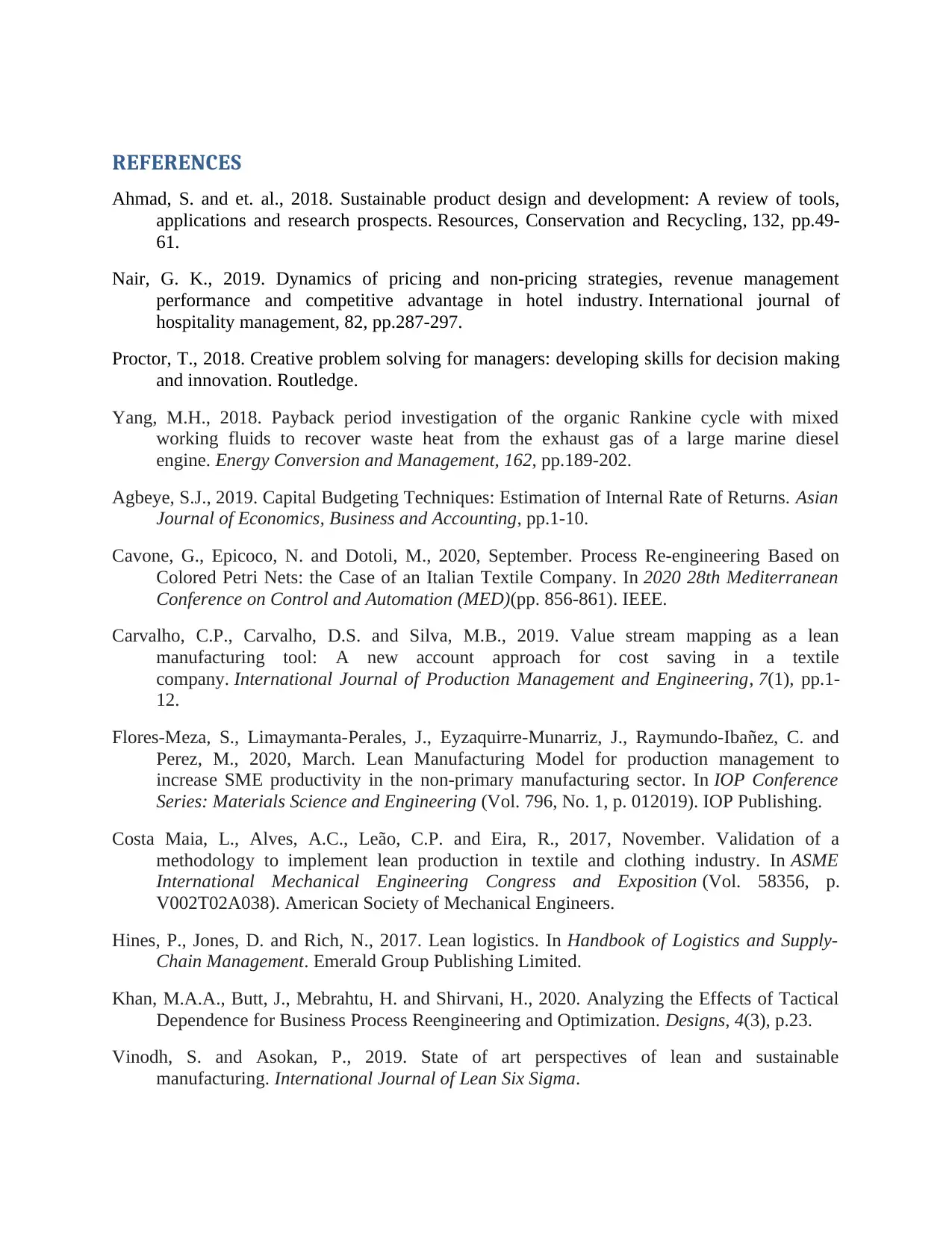
REFERENCES
Ahmad, S. and et. al., 2018. Sustainable product design and development: A review of tools,
applications and research prospects. Resources, Conservation and Recycling, 132, pp.49-
61.
Nair, G. K., 2019. Dynamics of pricing and non-pricing strategies, revenue management
performance and competitive advantage in hotel industry. International journal of
hospitality management, 82, pp.287-297.
Proctor, T., 2018. Creative problem solving for managers: developing skills for decision making
and innovation. Routledge.
Yang, M.H., 2018. Payback period investigation of the organic Rankine cycle with mixed
working fluids to recover waste heat from the exhaust gas of a large marine diesel
engine. Energy Conversion and Management, 162, pp.189-202.
Agbeye, S.J., 2019. Capital Budgeting Techniques: Estimation of Internal Rate of Returns. Asian
Journal of Economics, Business and Accounting, pp.1-10.
Cavone, G., Epicoco, N. and Dotoli, M., 2020, September. Process Re-engineering Based on
Colored Petri Nets: the Case of an Italian Textile Company. In 2020 28th Mediterranean
Conference on Control and Automation (MED)(pp. 856-861). IEEE.
Carvalho, C.P., Carvalho, D.S. and Silva, M.B., 2019. Value stream mapping as a lean
manufacturing tool: A new account approach for cost saving in a textile
company. International Journal of Production Management and Engineering, 7(1), pp.1-
12.
Flores-Meza, S., Limaymanta-Perales, J., Eyzaquirre-Munarriz, J., Raymundo-Ibañez, C. and
Perez, M., 2020, March. Lean Manufacturing Model for production management to
increase SME productivity in the non-primary manufacturing sector. In IOP Conference
Series: Materials Science and Engineering (Vol. 796, No. 1, p. 012019). IOP Publishing.
Costa Maia, L., Alves, A.C., Leão, C.P. and Eira, R., 2017, November. Validation of a
methodology to implement lean production in textile and clothing industry. In ASME
International Mechanical Engineering Congress and Exposition (Vol. 58356, p.
V002T02A038). American Society of Mechanical Engineers.
Hines, P., Jones, D. and Rich, N., 2017. Lean logistics. In Handbook of Logistics and Supply-
Chain Management. Emerald Group Publishing Limited.
Khan, M.A.A., Butt, J., Mebrahtu, H. and Shirvani, H., 2020. Analyzing the Effects of Tactical
Dependence for Business Process Reengineering and Optimization. Designs, 4(3), p.23.
Vinodh, S. and Asokan, P., 2019. State of art perspectives of lean and sustainable
manufacturing. International Journal of Lean Six Sigma.
Ahmad, S. and et. al., 2018. Sustainable product design and development: A review of tools,
applications and research prospects. Resources, Conservation and Recycling, 132, pp.49-
61.
Nair, G. K., 2019. Dynamics of pricing and non-pricing strategies, revenue management
performance and competitive advantage in hotel industry. International journal of
hospitality management, 82, pp.287-297.
Proctor, T., 2018. Creative problem solving for managers: developing skills for decision making
and innovation. Routledge.
Yang, M.H., 2018. Payback period investigation of the organic Rankine cycle with mixed
working fluids to recover waste heat from the exhaust gas of a large marine diesel
engine. Energy Conversion and Management, 162, pp.189-202.
Agbeye, S.J., 2019. Capital Budgeting Techniques: Estimation of Internal Rate of Returns. Asian
Journal of Economics, Business and Accounting, pp.1-10.
Cavone, G., Epicoco, N. and Dotoli, M., 2020, September. Process Re-engineering Based on
Colored Petri Nets: the Case of an Italian Textile Company. In 2020 28th Mediterranean
Conference on Control and Automation (MED)(pp. 856-861). IEEE.
Carvalho, C.P., Carvalho, D.S. and Silva, M.B., 2019. Value stream mapping as a lean
manufacturing tool: A new account approach for cost saving in a textile
company. International Journal of Production Management and Engineering, 7(1), pp.1-
12.
Flores-Meza, S., Limaymanta-Perales, J., Eyzaquirre-Munarriz, J., Raymundo-Ibañez, C. and
Perez, M., 2020, March. Lean Manufacturing Model for production management to
increase SME productivity in the non-primary manufacturing sector. In IOP Conference
Series: Materials Science and Engineering (Vol. 796, No. 1, p. 012019). IOP Publishing.
Costa Maia, L., Alves, A.C., Leão, C.P. and Eira, R., 2017, November. Validation of a
methodology to implement lean production in textile and clothing industry. In ASME
International Mechanical Engineering Congress and Exposition (Vol. 58356, p.
V002T02A038). American Society of Mechanical Engineers.
Hines, P., Jones, D. and Rich, N., 2017. Lean logistics. In Handbook of Logistics and Supply-
Chain Management. Emerald Group Publishing Limited.
Khan, M.A.A., Butt, J., Mebrahtu, H. and Shirvani, H., 2020. Analyzing the Effects of Tactical
Dependence for Business Process Reengineering and Optimization. Designs, 4(3), p.23.
Vinodh, S. and Asokan, P., 2019. State of art perspectives of lean and sustainable
manufacturing. International Journal of Lean Six Sigma.
Secure Best Marks with AI Grader
Need help grading? Try our AI Grader for instant feedback on your assignments.
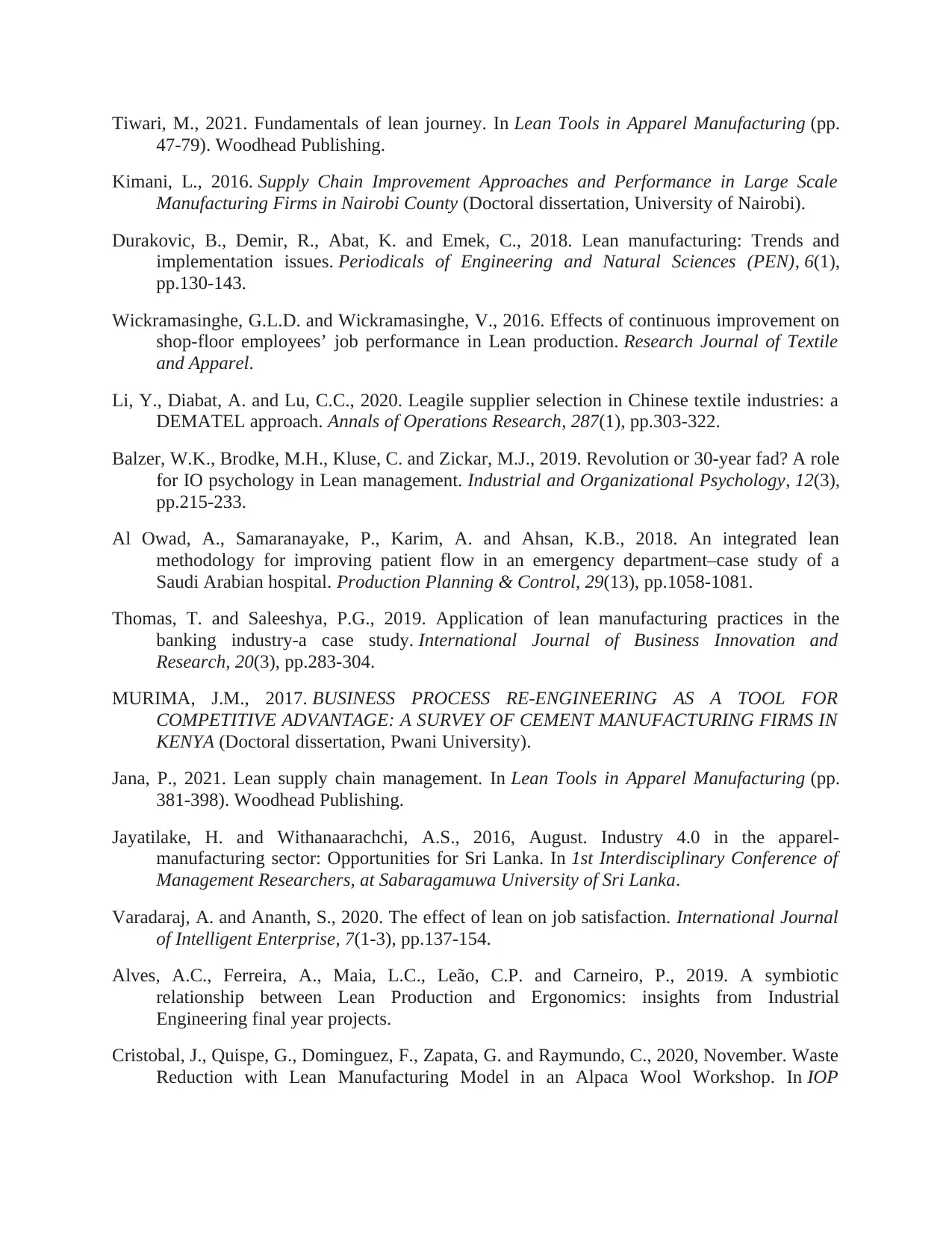
Tiwari, M., 2021. Fundamentals of lean journey. In Lean Tools in Apparel Manufacturing (pp.
47-79). Woodhead Publishing.
Kimani, L., 2016. Supply Chain Improvement Approaches and Performance in Large Scale
Manufacturing Firms in Nairobi County (Doctoral dissertation, University of Nairobi).
Durakovic, B., Demir, R., Abat, K. and Emek, C., 2018. Lean manufacturing: Trends and
implementation issues. Periodicals of Engineering and Natural Sciences (PEN), 6(1),
pp.130-143.
Wickramasinghe, G.L.D. and Wickramasinghe, V., 2016. Effects of continuous improvement on
shop-floor employees’ job performance in Lean production. Research Journal of Textile
and Apparel.
Li, Y., Diabat, A. and Lu, C.C., 2020. Leagile supplier selection in Chinese textile industries: a
DEMATEL approach. Annals of Operations Research, 287(1), pp.303-322.
Balzer, W.K., Brodke, M.H., Kluse, C. and Zickar, M.J., 2019. Revolution or 30-year fad? A role
for IO psychology in Lean management. Industrial and Organizational Psychology, 12(3),
pp.215-233.
Al Owad, A., Samaranayake, P., Karim, A. and Ahsan, K.B., 2018. An integrated lean
methodology for improving patient flow in an emergency department–case study of a
Saudi Arabian hospital. Production Planning & Control, 29(13), pp.1058-1081.
Thomas, T. and Saleeshya, P.G., 2019. Application of lean manufacturing practices in the
banking industry-a case study. International Journal of Business Innovation and
Research, 20(3), pp.283-304.
MURIMA, J.M., 2017. BUSINESS PROCESS RE-ENGINEERING AS A TOOL FOR
COMPETITIVE ADVANTAGE: A SURVEY OF CEMENT MANUFACTURING FIRMS IN
KENYA (Doctoral dissertation, Pwani University).
Jana, P., 2021. Lean supply chain management. In Lean Tools in Apparel Manufacturing (pp.
381-398). Woodhead Publishing.
Jayatilake, H. and Withanaarachchi, A.S., 2016, August. Industry 4.0 in the apparel-
manufacturing sector: Opportunities for Sri Lanka. In 1st Interdisciplinary Conference of
Management Researchers, at Sabaragamuwa University of Sri Lanka.
Varadaraj, A. and Ananth, S., 2020. The effect of lean on job satisfaction. International Journal
of Intelligent Enterprise, 7(1-3), pp.137-154.
Alves, A.C., Ferreira, A., Maia, L.C., Leão, C.P. and Carneiro, P., 2019. A symbiotic
relationship between Lean Production and Ergonomics: insights from Industrial
Engineering final year projects.
Cristobal, J., Quispe, G., Dominguez, F., Zapata, G. and Raymundo, C., 2020, November. Waste
Reduction with Lean Manufacturing Model in an Alpaca Wool Workshop. In IOP
47-79). Woodhead Publishing.
Kimani, L., 2016. Supply Chain Improvement Approaches and Performance in Large Scale
Manufacturing Firms in Nairobi County (Doctoral dissertation, University of Nairobi).
Durakovic, B., Demir, R., Abat, K. and Emek, C., 2018. Lean manufacturing: Trends and
implementation issues. Periodicals of Engineering and Natural Sciences (PEN), 6(1),
pp.130-143.
Wickramasinghe, G.L.D. and Wickramasinghe, V., 2016. Effects of continuous improvement on
shop-floor employees’ job performance in Lean production. Research Journal of Textile
and Apparel.
Li, Y., Diabat, A. and Lu, C.C., 2020. Leagile supplier selection in Chinese textile industries: a
DEMATEL approach. Annals of Operations Research, 287(1), pp.303-322.
Balzer, W.K., Brodke, M.H., Kluse, C. and Zickar, M.J., 2019. Revolution or 30-year fad? A role
for IO psychology in Lean management. Industrial and Organizational Psychology, 12(3),
pp.215-233.
Al Owad, A., Samaranayake, P., Karim, A. and Ahsan, K.B., 2018. An integrated lean
methodology for improving patient flow in an emergency department–case study of a
Saudi Arabian hospital. Production Planning & Control, 29(13), pp.1058-1081.
Thomas, T. and Saleeshya, P.G., 2019. Application of lean manufacturing practices in the
banking industry-a case study. International Journal of Business Innovation and
Research, 20(3), pp.283-304.
MURIMA, J.M., 2017. BUSINESS PROCESS RE-ENGINEERING AS A TOOL FOR
COMPETITIVE ADVANTAGE: A SURVEY OF CEMENT MANUFACTURING FIRMS IN
KENYA (Doctoral dissertation, Pwani University).
Jana, P., 2021. Lean supply chain management. In Lean Tools in Apparel Manufacturing (pp.
381-398). Woodhead Publishing.
Jayatilake, H. and Withanaarachchi, A.S., 2016, August. Industry 4.0 in the apparel-
manufacturing sector: Opportunities for Sri Lanka. In 1st Interdisciplinary Conference of
Management Researchers, at Sabaragamuwa University of Sri Lanka.
Varadaraj, A. and Ananth, S., 2020. The effect of lean on job satisfaction. International Journal
of Intelligent Enterprise, 7(1-3), pp.137-154.
Alves, A.C., Ferreira, A., Maia, L.C., Leão, C.P. and Carneiro, P., 2019. A symbiotic
relationship between Lean Production and Ergonomics: insights from Industrial
Engineering final year projects.
Cristobal, J., Quispe, G., Dominguez, F., Zapata, G. and Raymundo, C., 2020, November. Waste
Reduction with Lean Manufacturing Model in an Alpaca Wool Workshop. In IOP
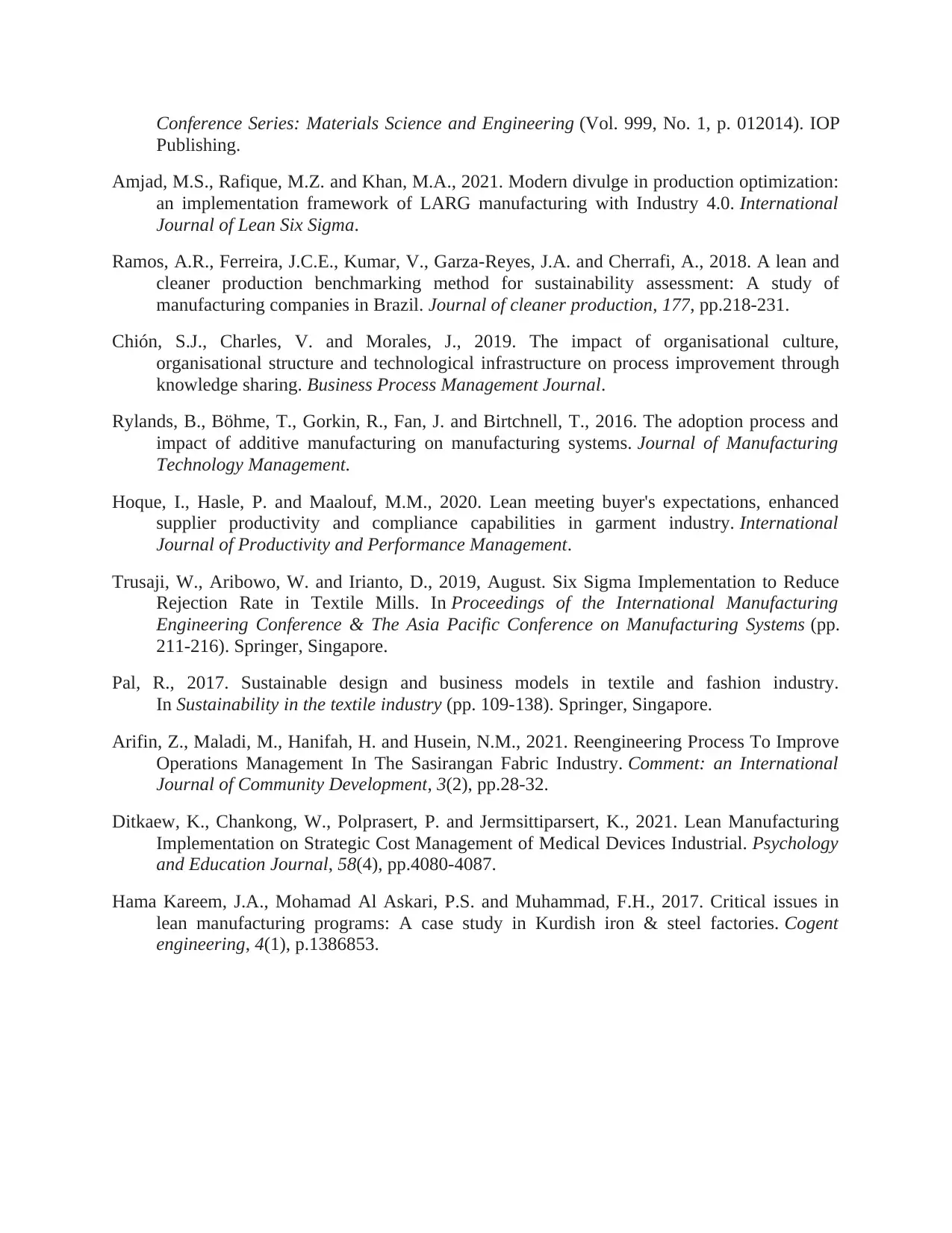
Conference Series: Materials Science and Engineering (Vol. 999, No. 1, p. 012014). IOP
Publishing.
Amjad, M.S., Rafique, M.Z. and Khan, M.A., 2021. Modern divulge in production optimization:
an implementation framework of LARG manufacturing with Industry 4.0. International
Journal of Lean Six Sigma.
Ramos, A.R., Ferreira, J.C.E., Kumar, V., Garza-Reyes, J.A. and Cherrafi, A., 2018. A lean and
cleaner production benchmarking method for sustainability assessment: A study of
manufacturing companies in Brazil. Journal of cleaner production, 177, pp.218-231.
Chión, S.J., Charles, V. and Morales, J., 2019. The impact of organisational culture,
organisational structure and technological infrastructure on process improvement through
knowledge sharing. Business Process Management Journal.
Rylands, B., Böhme, T., Gorkin, R., Fan, J. and Birtchnell, T., 2016. The adoption process and
impact of additive manufacturing on manufacturing systems. Journal of Manufacturing
Technology Management.
Hoque, I., Hasle, P. and Maalouf, M.M., 2020. Lean meeting buyer's expectations, enhanced
supplier productivity and compliance capabilities in garment industry. International
Journal of Productivity and Performance Management.
Trusaji, W., Aribowo, W. and Irianto, D., 2019, August. Six Sigma Implementation to Reduce
Rejection Rate in Textile Mills. In Proceedings of the International Manufacturing
Engineering Conference & The Asia Pacific Conference on Manufacturing Systems (pp.
211-216). Springer, Singapore.
Pal, R., 2017. Sustainable design and business models in textile and fashion industry.
In Sustainability in the textile industry (pp. 109-138). Springer, Singapore.
Arifin, Z., Maladi, M., Hanifah, H. and Husein, N.M., 2021. Reengineering Process To Improve
Operations Management In The Sasirangan Fabric Industry. Comment: an International
Journal of Community Development, 3(2), pp.28-32.
Ditkaew, K., Chankong, W., Polprasert, P. and Jermsittiparsert, K., 2021. Lean Manufacturing
Implementation on Strategic Cost Management of Medical Devices Industrial. Psychology
and Education Journal, 58(4), pp.4080-4087.
Hama Kareem, J.A., Mohamad Al Askari, P.S. and Muhammad, F.H., 2017. Critical issues in
lean manufacturing programs: A case study in Kurdish iron & steel factories. Cogent
engineering, 4(1), p.1386853.
Publishing.
Amjad, M.S., Rafique, M.Z. and Khan, M.A., 2021. Modern divulge in production optimization:
an implementation framework of LARG manufacturing with Industry 4.0. International
Journal of Lean Six Sigma.
Ramos, A.R., Ferreira, J.C.E., Kumar, V., Garza-Reyes, J.A. and Cherrafi, A., 2018. A lean and
cleaner production benchmarking method for sustainability assessment: A study of
manufacturing companies in Brazil. Journal of cleaner production, 177, pp.218-231.
Chión, S.J., Charles, V. and Morales, J., 2019. The impact of organisational culture,
organisational structure and technological infrastructure on process improvement through
knowledge sharing. Business Process Management Journal.
Rylands, B., Böhme, T., Gorkin, R., Fan, J. and Birtchnell, T., 2016. The adoption process and
impact of additive manufacturing on manufacturing systems. Journal of Manufacturing
Technology Management.
Hoque, I., Hasle, P. and Maalouf, M.M., 2020. Lean meeting buyer's expectations, enhanced
supplier productivity and compliance capabilities in garment industry. International
Journal of Productivity and Performance Management.
Trusaji, W., Aribowo, W. and Irianto, D., 2019, August. Six Sigma Implementation to Reduce
Rejection Rate in Textile Mills. In Proceedings of the International Manufacturing
Engineering Conference & The Asia Pacific Conference on Manufacturing Systems (pp.
211-216). Springer, Singapore.
Pal, R., 2017. Sustainable design and business models in textile and fashion industry.
In Sustainability in the textile industry (pp. 109-138). Springer, Singapore.
Arifin, Z., Maladi, M., Hanifah, H. and Husein, N.M., 2021. Reengineering Process To Improve
Operations Management In The Sasirangan Fabric Industry. Comment: an International
Journal of Community Development, 3(2), pp.28-32.
Ditkaew, K., Chankong, W., Polprasert, P. and Jermsittiparsert, K., 2021. Lean Manufacturing
Implementation on Strategic Cost Management of Medical Devices Industrial. Psychology
and Education Journal, 58(4), pp.4080-4087.
Hama Kareem, J.A., Mohamad Al Askari, P.S. and Muhammad, F.H., 2017. Critical issues in
lean manufacturing programs: A case study in Kurdish iron & steel factories. Cogent
engineering, 4(1), p.1386853.
1 out of 42
Related Documents
![[object Object]](/_next/image/?url=%2F_next%2Fstatic%2Fmedia%2Flogo.6d15ce61.png&w=640&q=75)
Your All-in-One AI-Powered Toolkit for Academic Success.
+13062052269
info@desklib.com
Available 24*7 on WhatsApp / Email
Unlock your academic potential
© 2024 | Zucol Services PVT LTD | All rights reserved.