Lean Project Management: Current State Map for Manufacturing Quality
VerifiedAdded on  2023/01/20
|15
|3489
|27
AI Summary
This document provides an overview of lean project management and focuses on developing a current state map for manufacturing quality. It discusses the critical to quality parameters and the importance of organizational project management.
Contribute Materials
Your contribution can guide someone’s learning journey. Share your
documents today.
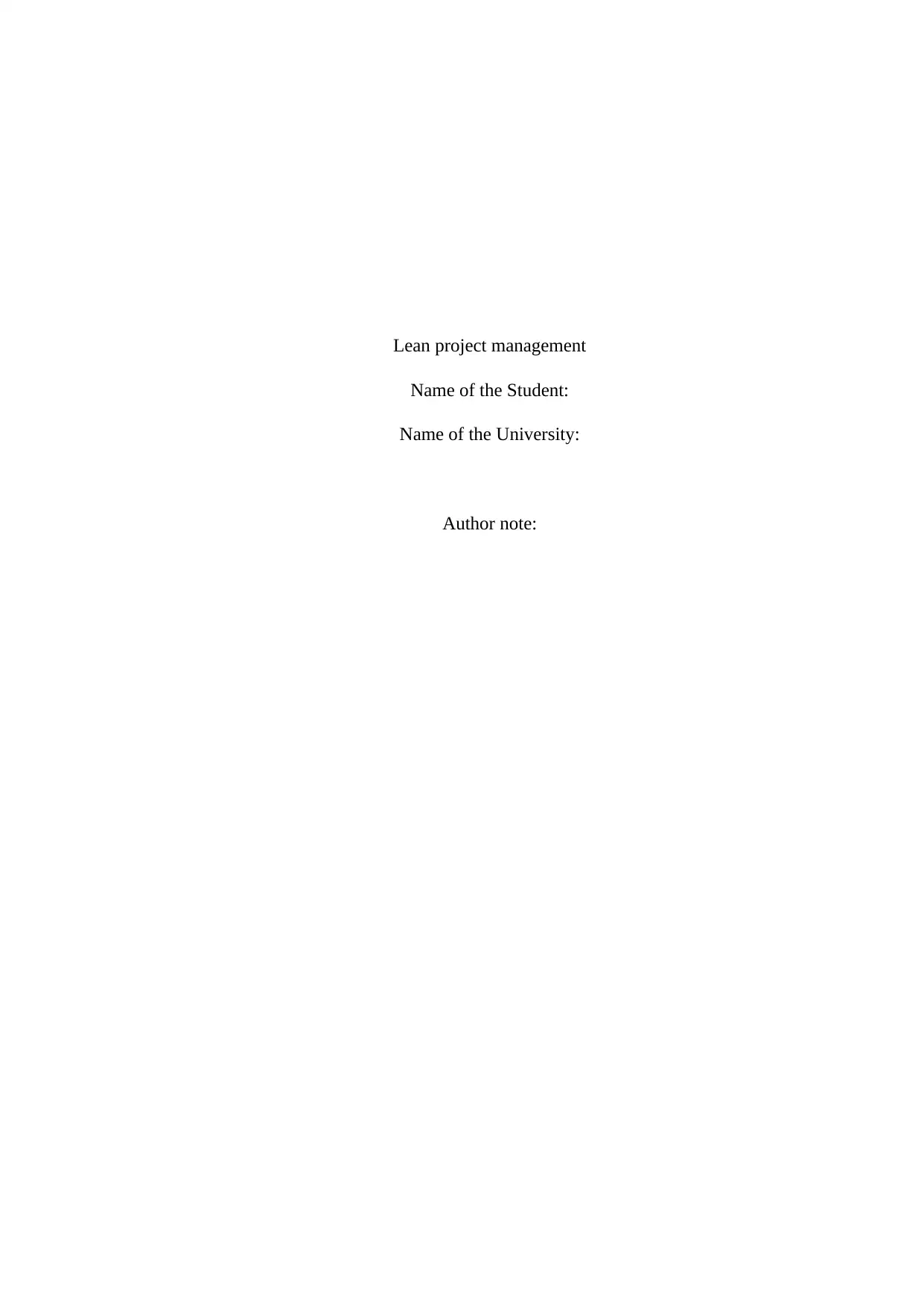
Lean project management
Name of the Student:
Name of the University:
Author note:
Name of the Student:
Name of the University:
Author note:
Secure Best Marks with AI Grader
Need help grading? Try our AI Grader for instant feedback on your assignments.
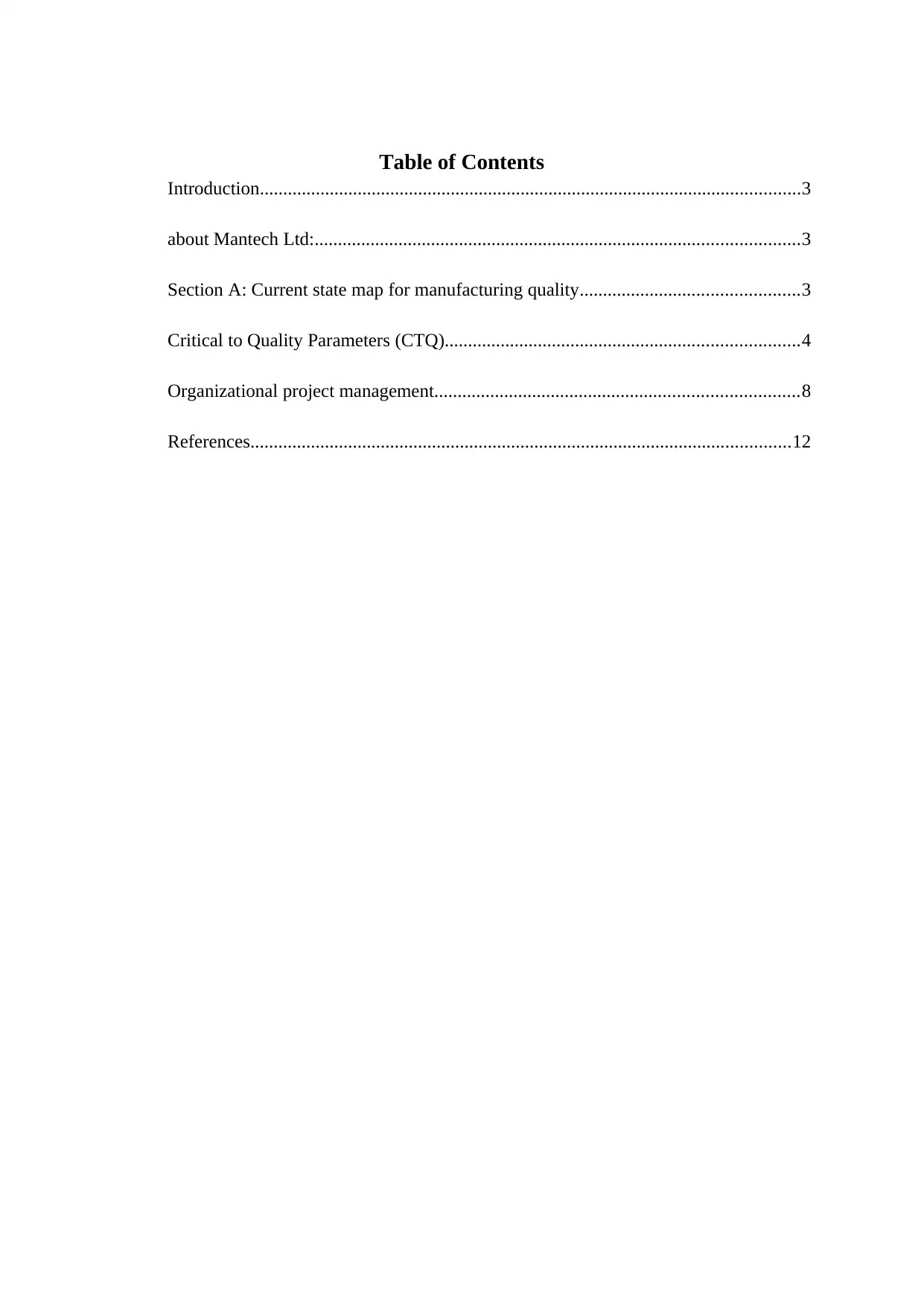
Table of Contents
Introduction....................................................................................................................3
about Mantech Ltd:........................................................................................................3
Section A: Current state map for manufacturing quality...............................................3
Critical to Quality Parameters (CTQ)............................................................................4
Organizational project management..............................................................................8
References....................................................................................................................12
Introduction....................................................................................................................3
about Mantech Ltd:........................................................................................................3
Section A: Current state map for manufacturing quality...............................................3
Critical to Quality Parameters (CTQ)............................................................................4
Organizational project management..............................................................................8
References....................................................................................................................12
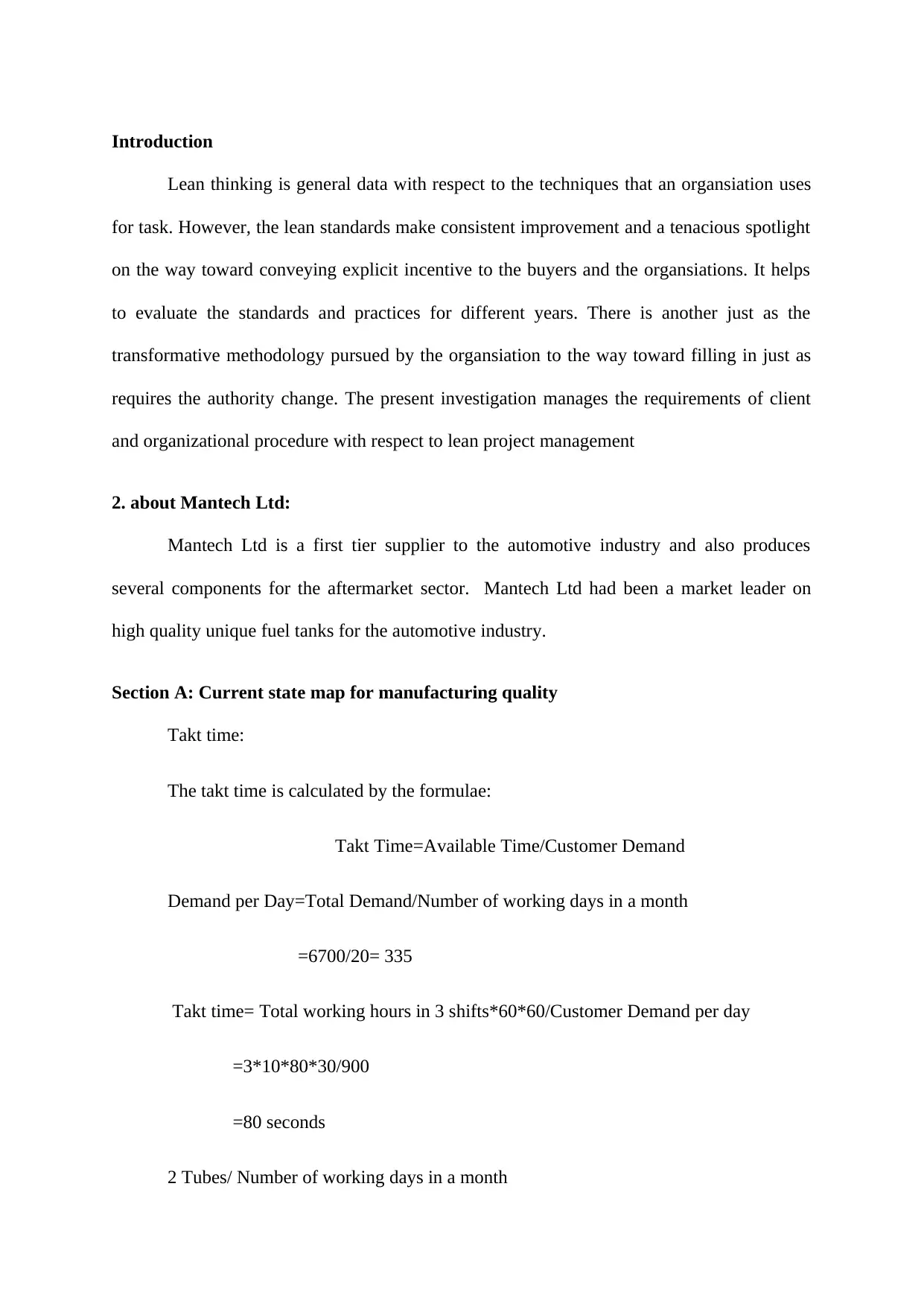
Introduction
Lean thinking is general data with respect to the techniques that an organsiation uses
for task. However, the lean standards make consistent improvement and a tenacious spotlight
on the way toward conveying explicit incentive to the buyers and the organsiations. It helps
to evaluate the standards and practices for different years. There is another just as the
transformative methodology pursued by the organsiation to the way toward filling in just as
requires the authority change. The present investigation manages the requirements of client
and organizational procedure with respect to lean project management
2. about Mantech Ltd:
Mantech Ltd is a first tier supplier to the automotive industry and also produces
several components for the aftermarket sector. Mantech Ltd had been a market leader on
high quality unique fuel tanks for the automotive industry.
Section A: Current state map for manufacturing quality
Takt time:
The takt time is calculated by the formulae:
Takt Time=Available Time/Customer Demand
Demand per Day=Total Demand/Number of working days in a month
=6700/20= 335
Takt time= Total working hours in 3 shifts*60*60/Customer Demand per day
=3*10*80*30/900
=80 seconds
2 Tubes/ Number of working days in a month
Lean thinking is general data with respect to the techniques that an organsiation uses
for task. However, the lean standards make consistent improvement and a tenacious spotlight
on the way toward conveying explicit incentive to the buyers and the organsiations. It helps
to evaluate the standards and practices for different years. There is another just as the
transformative methodology pursued by the organsiation to the way toward filling in just as
requires the authority change. The present investigation manages the requirements of client
and organizational procedure with respect to lean project management
2. about Mantech Ltd:
Mantech Ltd is a first tier supplier to the automotive industry and also produces
several components for the aftermarket sector. Mantech Ltd had been a market leader on
high quality unique fuel tanks for the automotive industry.
Section A: Current state map for manufacturing quality
Takt time:
The takt time is calculated by the formulae:
Takt Time=Available Time/Customer Demand
Demand per Day=Total Demand/Number of working days in a month
=6700/20= 335
Takt time= Total working hours in 3 shifts*60*60/Customer Demand per day
=3*10*80*30/900
=80 seconds
2 Tubes/ Number of working days in a month
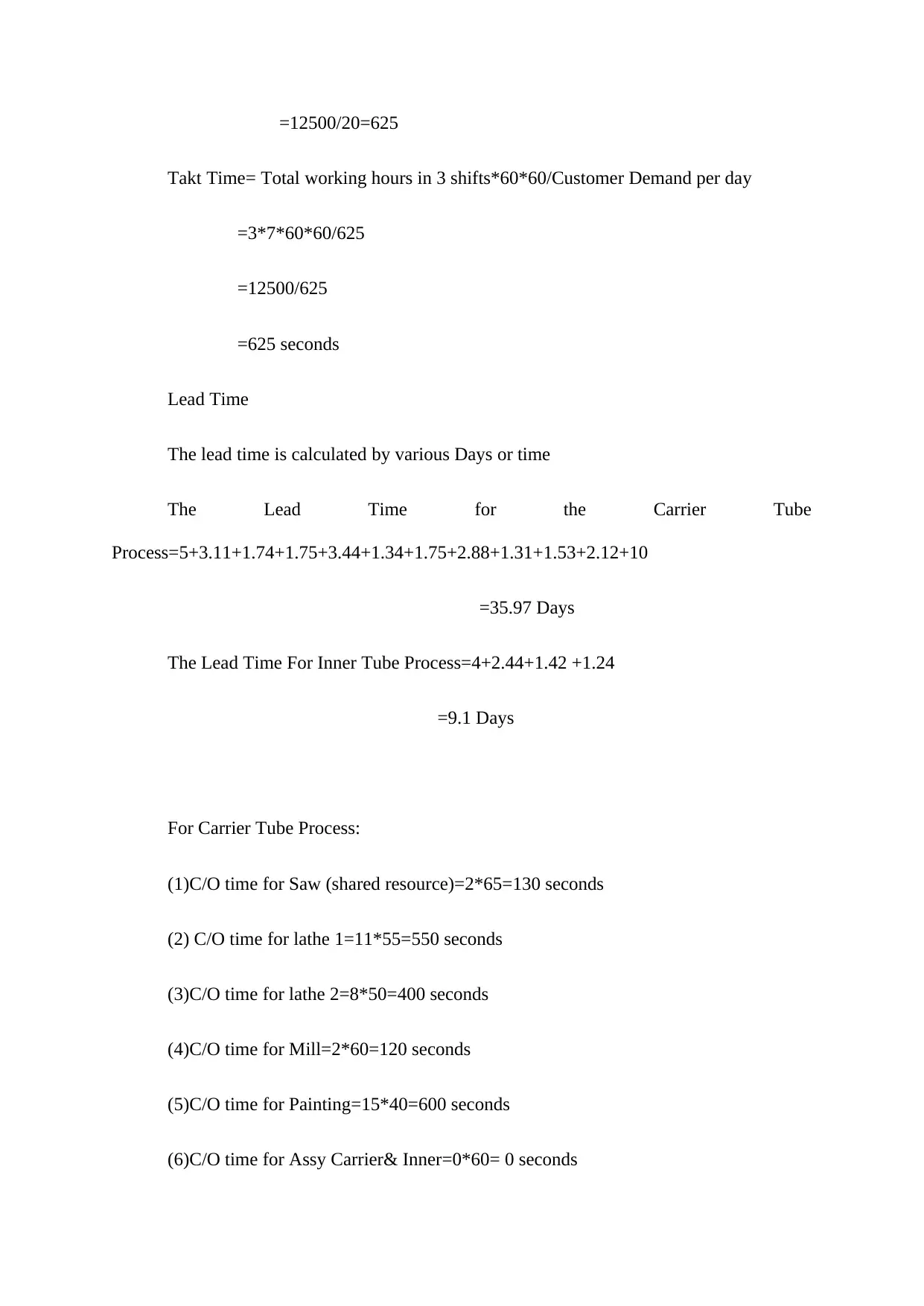
=12500/20=625
Takt Time= Total working hours in 3 shifts*60*60/Customer Demand per day
=3*7*60*60/625
=12500/625
=625 seconds
Lead Time
The lead time is calculated by various Days or time
The Lead Time for the Carrier Tube
Process=5+3.11+1.74+1.75+3.44+1.34+1.75+2.88+1.31+1.53+2.12+10
=35.97 Days
The Lead Time For Inner Tube Process=4+2.44+1.42 +1.24
=9.1 Days
For Carrier Tube Process:
(1)C/O time for Saw (shared resource)=2*65=130 seconds
(2) C/O time for lathe 1=11*55=550 seconds
(3)C/O time for lathe 2=8*50=400 seconds
(4)C/O time for Mill=2*60=120 seconds
(5)C/O time for Painting=15*40=600 seconds
(6)C/O time for Assy Carrier& Inner=0*60= 0 seconds
Takt Time= Total working hours in 3 shifts*60*60/Customer Demand per day
=3*7*60*60/625
=12500/625
=625 seconds
Lead Time
The lead time is calculated by various Days or time
The Lead Time for the Carrier Tube
Process=5+3.11+1.74+1.75+3.44+1.34+1.75+2.88+1.31+1.53+2.12+10
=35.97 Days
The Lead Time For Inner Tube Process=4+2.44+1.42 +1.24
=9.1 Days
For Carrier Tube Process:
(1)C/O time for Saw (shared resource)=2*65=130 seconds
(2) C/O time for lathe 1=11*55=550 seconds
(3)C/O time for lathe 2=8*50=400 seconds
(4)C/O time for Mill=2*60=120 seconds
(5)C/O time for Painting=15*40=600 seconds
(6)C/O time for Assy Carrier& Inner=0*60= 0 seconds
Secure Best Marks with AI Grader
Need help grading? Try our AI Grader for instant feedback on your assignments.
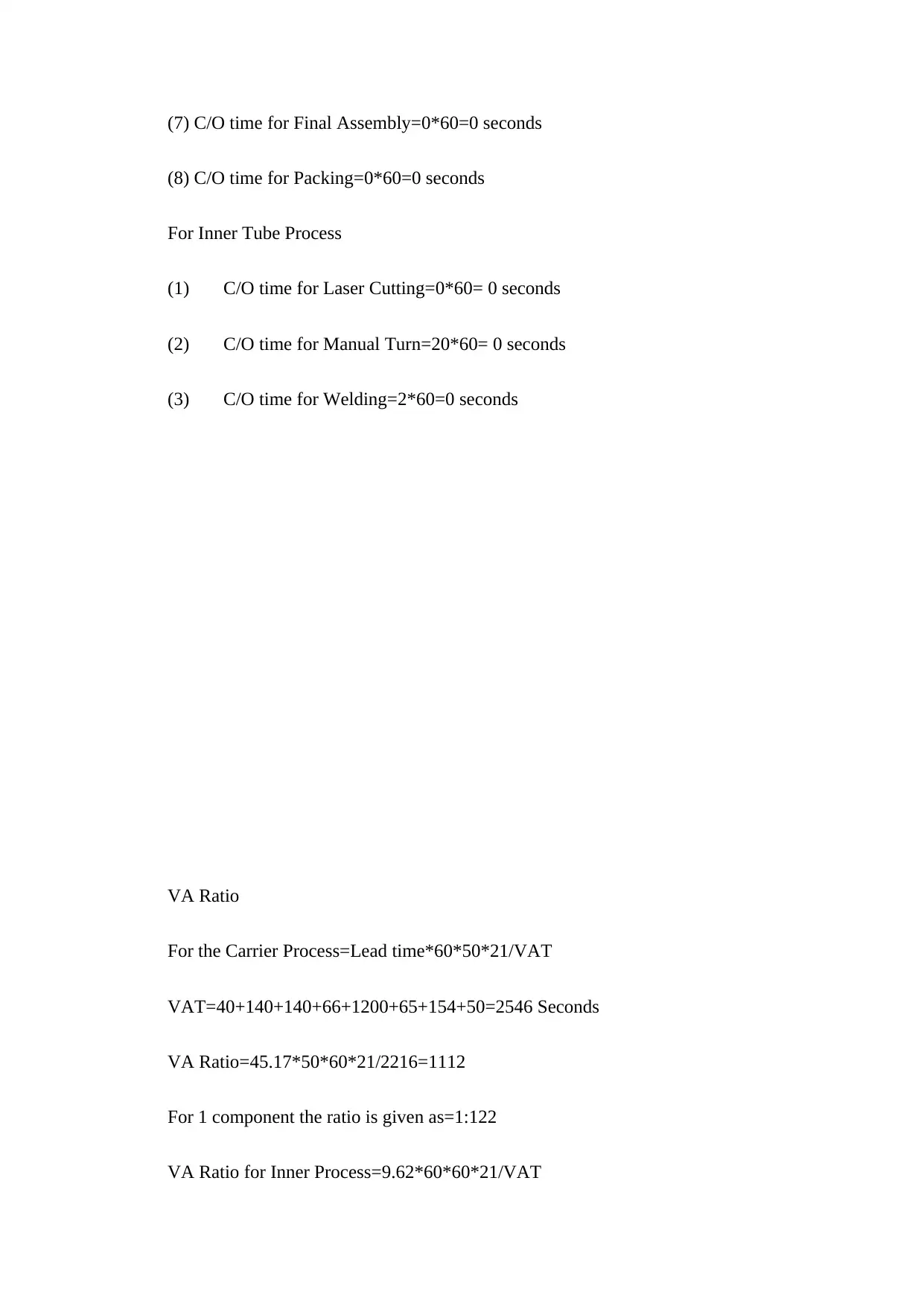
(7) C/O time for Final Assembly=0*60=0 seconds
(8) C/O time for Packing=0*60=0 seconds
For Inner Tube Process
(1) C/O time for Laser Cutting=0*60= 0 seconds
(2) C/O time for Manual Turn=20*60= 0 seconds
(3) C/O time for Welding=2*60=0 seconds
VA Ratio
For the Carrier Process=Lead time*60*50*21/VAT
VAT=40+140+140+66+1200+65+154+50=2546 Seconds
VA Ratio=45.17*50*60*21/2216=1112
For 1 component the ratio is given as=1:122
VA Ratio for Inner Process=9.62*60*60*21/VAT
(8) C/O time for Packing=0*60=0 seconds
For Inner Tube Process
(1) C/O time for Laser Cutting=0*60= 0 seconds
(2) C/O time for Manual Turn=20*60= 0 seconds
(3) C/O time for Welding=2*60=0 seconds
VA Ratio
For the Carrier Process=Lead time*60*50*21/VAT
VAT=40+140+140+66+1200+65+154+50=2546 Seconds
VA Ratio=45.17*50*60*21/2216=1112
For 1 component the ratio is given as=1:122
VA Ratio for Inner Process=9.62*60*60*21/VAT
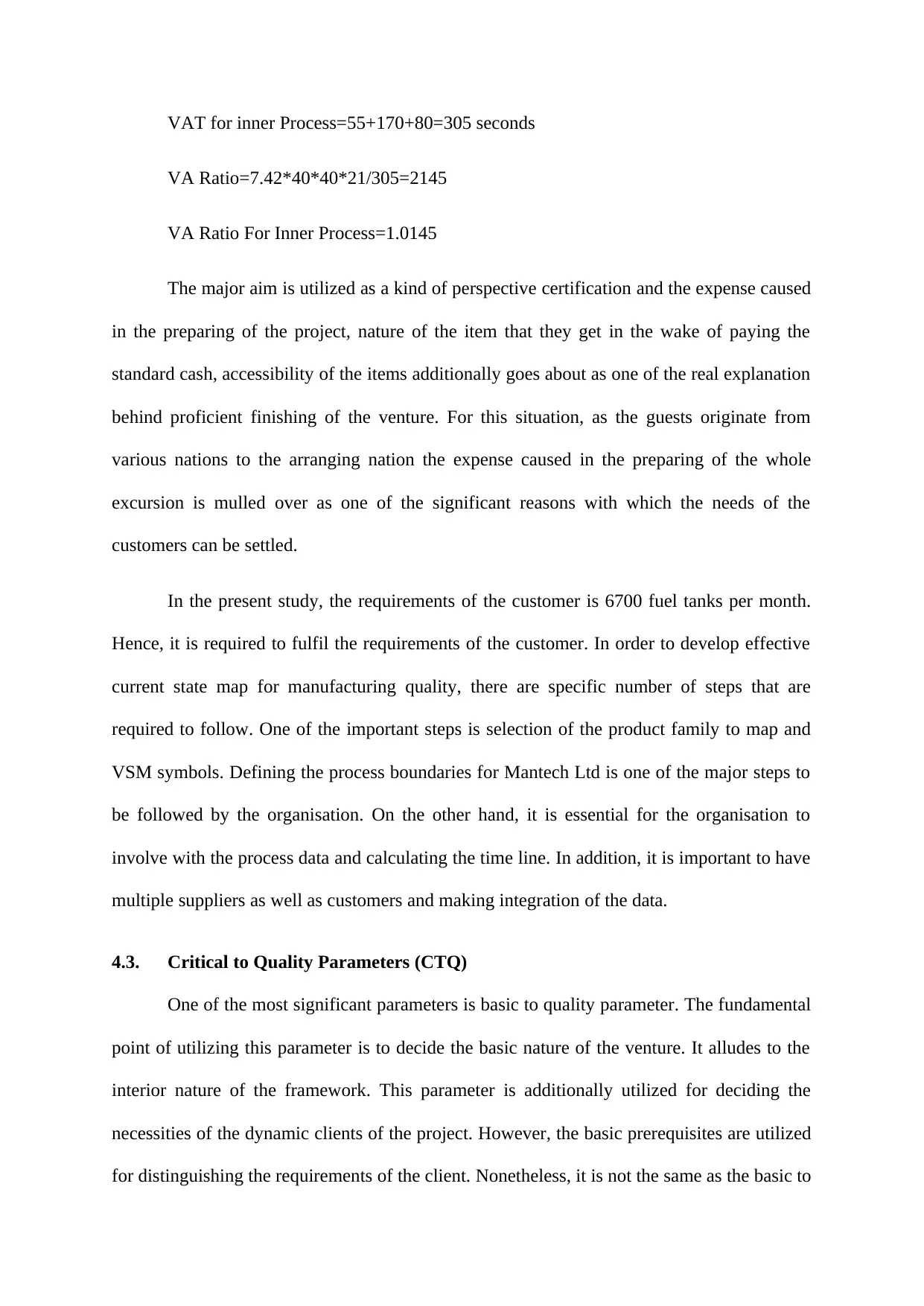
VAT for inner Process=55+170+80=305 seconds
VA Ratio=7.42*40*40*21/305=2145
VA Ratio For Inner Process=1.0145
The major aim is utilized as a kind of perspective certification and the expense caused
in the preparing of the project, nature of the item that they get in the wake of paying the
standard cash, accessibility of the items additionally goes about as one of the real explanation
behind proficient finishing of the venture. For this situation, as the guests originate from
various nations to the arranging nation the expense caused in the preparing of the whole
excursion is mulled over as one of the significant reasons with which the needs of the
customers can be settled.
In the present study, the requirements of the customer is 6700 fuel tanks per month.
Hence, it is required to fulfil the requirements of the customer. In order to develop effective
current state map for manufacturing quality, there are specific number of steps that are
required to follow. One of the important steps is selection of the product family to map and
VSM symbols. Defining the process boundaries for Mantech Ltd is one of the major steps to
be followed by the organisation. On the other hand, it is essential for the organisation to
involve with the process data and calculating the time line. In addition, it is important to have
multiple suppliers as well as customers and making integration of the data.
4.3. Critical to Quality Parameters (CTQ)
One of the most significant parameters is basic to quality parameter. The fundamental
point of utilizing this parameter is to decide the basic nature of the venture. It alludes to the
interior nature of the framework. This parameter is additionally utilized for deciding the
necessities of the dynamic clients of the project. However, the basic prerequisites are utilized
for distinguishing the requirements of the client. Nonetheless, it is not the same as the basic to
VA Ratio=7.42*40*40*21/305=2145
VA Ratio For Inner Process=1.0145
The major aim is utilized as a kind of perspective certification and the expense caused
in the preparing of the project, nature of the item that they get in the wake of paying the
standard cash, accessibility of the items additionally goes about as one of the real explanation
behind proficient finishing of the venture. For this situation, as the guests originate from
various nations to the arranging nation the expense caused in the preparing of the whole
excursion is mulled over as one of the significant reasons with which the needs of the
customers can be settled.
In the present study, the requirements of the customer is 6700 fuel tanks per month.
Hence, it is required to fulfil the requirements of the customer. In order to develop effective
current state map for manufacturing quality, there are specific number of steps that are
required to follow. One of the important steps is selection of the product family to map and
VSM symbols. Defining the process boundaries for Mantech Ltd is one of the major steps to
be followed by the organisation. On the other hand, it is essential for the organisation to
involve with the process data and calculating the time line. In addition, it is important to have
multiple suppliers as well as customers and making integration of the data.
4.3. Critical to Quality Parameters (CTQ)
One of the most significant parameters is basic to quality parameter. The fundamental
point of utilizing this parameter is to decide the basic nature of the venture. It alludes to the
interior nature of the framework. This parameter is additionally utilized for deciding the
necessities of the dynamic clients of the project. However, the basic prerequisites are utilized
for distinguishing the requirements of the client. Nonetheless, it is not the same as the basic to
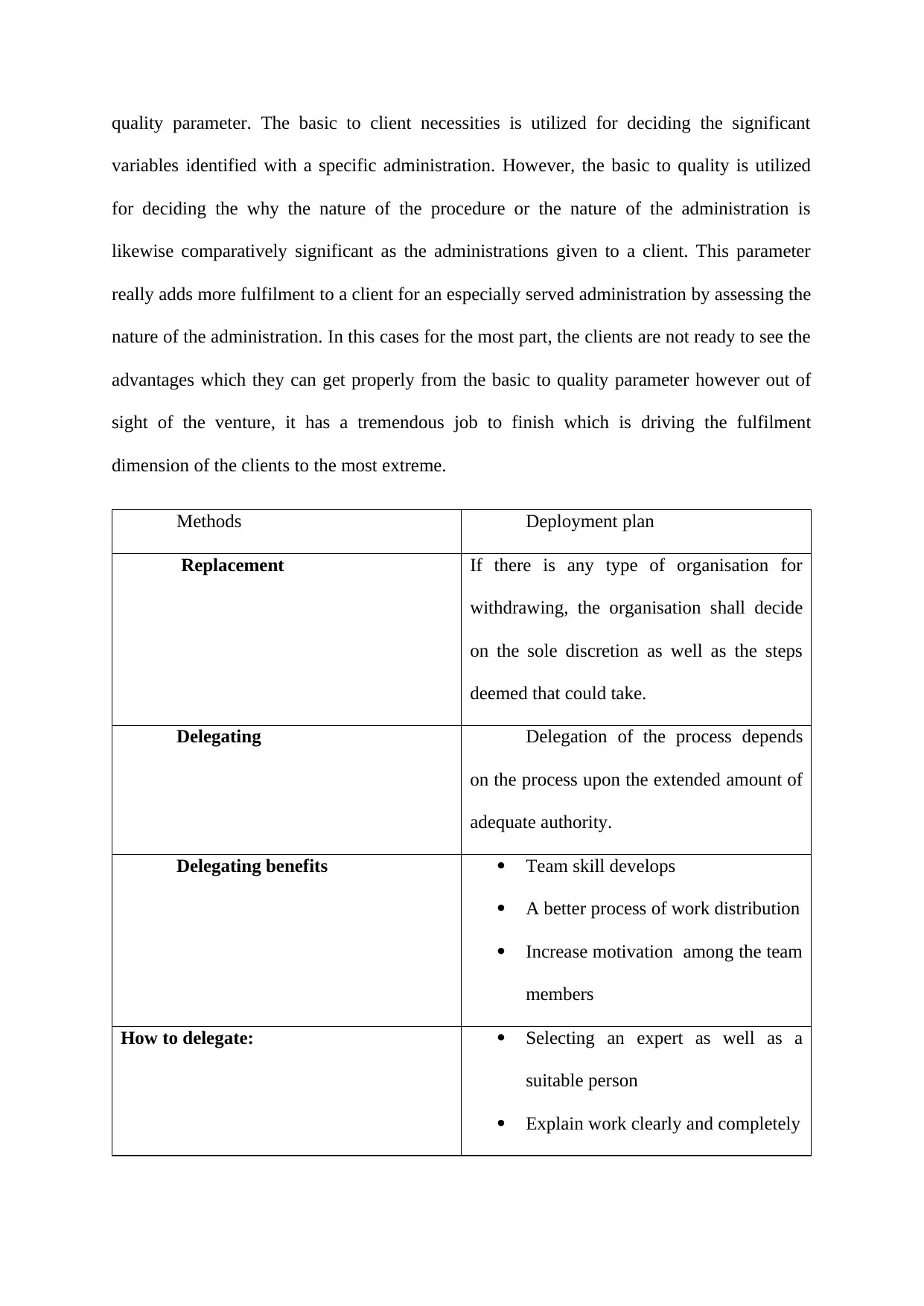
quality parameter. The basic to client necessities is utilized for deciding the significant
variables identified with a specific administration. However, the basic to quality is utilized
for deciding the why the nature of the procedure or the nature of the administration is
likewise comparatively significant as the administrations given to a client. This parameter
really adds more fulfilment to a client for an especially served administration by assessing the
nature of the administration. In this cases for the most part, the clients are not ready to see the
advantages which they can get properly from the basic to quality parameter however out of
sight of the venture, it has a tremendous job to finish which is driving the fulfilment
dimension of the clients to the most extreme.
Methods Deployment plan
Replacement If there is any type of organisation for
withdrawing, the organisation shall decide
on the sole discretion as well as the steps
deemed that could take.
Delegating Delegation of the process depends
on the process upon the extended amount of
adequate authority.
Delegating benefits ď‚· Team skill develops
ď‚· A better process of work distribution
ď‚· Increase motivation among the team
members
How to delegate: ď‚· Selecting an expert as well as a
suitable person
ď‚· Explain work clearly and completely
variables identified with a specific administration. However, the basic to quality is utilized
for deciding the why the nature of the procedure or the nature of the administration is
likewise comparatively significant as the administrations given to a client. This parameter
really adds more fulfilment to a client for an especially served administration by assessing the
nature of the administration. In this cases for the most part, the clients are not ready to see the
advantages which they can get properly from the basic to quality parameter however out of
sight of the venture, it has a tremendous job to finish which is driving the fulfilment
dimension of the clients to the most extreme.
Methods Deployment plan
Replacement If there is any type of organisation for
withdrawing, the organisation shall decide
on the sole discretion as well as the steps
deemed that could take.
Delegating Delegation of the process depends
on the process upon the extended amount of
adequate authority.
Delegating benefits ď‚· Team skill develops
ď‚· A better process of work distribution
ď‚· Increase motivation among the team
members
How to delegate: ď‚· Selecting an expert as well as a
suitable person
ď‚· Explain work clearly and completely
Paraphrase This Document
Need a fresh take? Get an instant paraphrase of this document with our AI Paraphraser
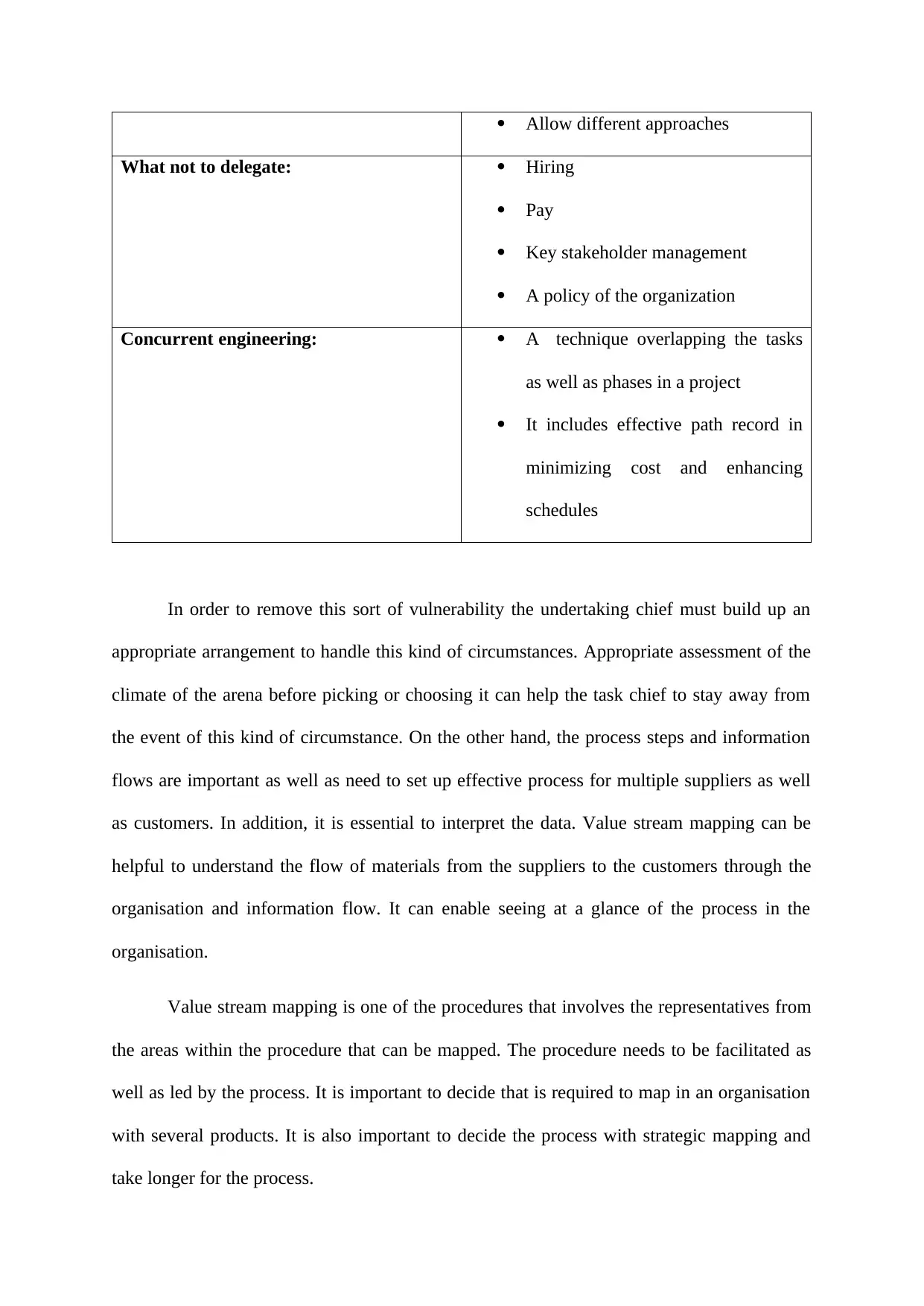
ď‚· Allow different approaches
What not to delegate: ď‚· Hiring
ď‚· Pay
ď‚· Key stakeholder management
ď‚· A policy of the organization
Concurrent engineering: ď‚· A technique overlapping the tasks
as well as phases in a project
ď‚· It includes effective path record in
minimizing cost and enhancing
schedules
In order to remove this sort of vulnerability the undertaking chief must build up an
appropriate arrangement to handle this kind of circumstances. Appropriate assessment of the
climate of the arena before picking or choosing it can help the task chief to stay away from
the event of this kind of circumstance. On the other hand, the process steps and information
flows are important as well as need to set up effective process for multiple suppliers as well
as customers. In addition, it is essential to interpret the data. Value stream mapping can be
helpful to understand the flow of materials from the suppliers to the customers through the
organisation and information flow. It can enable seeing at a glance of the process in the
organisation.
Value stream mapping is one of the procedures that involves the representatives from
the areas within the procedure that can be mapped. The procedure needs to be facilitated as
well as led by the process. It is important to decide that is required to map in an organisation
with several products. It is also important to decide the process with strategic mapping and
take longer for the process.
What not to delegate: ď‚· Hiring
ď‚· Pay
ď‚· Key stakeholder management
ď‚· A policy of the organization
Concurrent engineering: ď‚· A technique overlapping the tasks
as well as phases in a project
ď‚· It includes effective path record in
minimizing cost and enhancing
schedules
In order to remove this sort of vulnerability the undertaking chief must build up an
appropriate arrangement to handle this kind of circumstances. Appropriate assessment of the
climate of the arena before picking or choosing it can help the task chief to stay away from
the event of this kind of circumstance. On the other hand, the process steps and information
flows are important as well as need to set up effective process for multiple suppliers as well
as customers. In addition, it is essential to interpret the data. Value stream mapping can be
helpful to understand the flow of materials from the suppliers to the customers through the
organisation and information flow. It can enable seeing at a glance of the process in the
organisation.
Value stream mapping is one of the procedures that involves the representatives from
the areas within the procedure that can be mapped. The procedure needs to be facilitated as
well as led by the process. It is important to decide that is required to map in an organisation
with several products. It is also important to decide the process with strategic mapping and
take longer for the process.
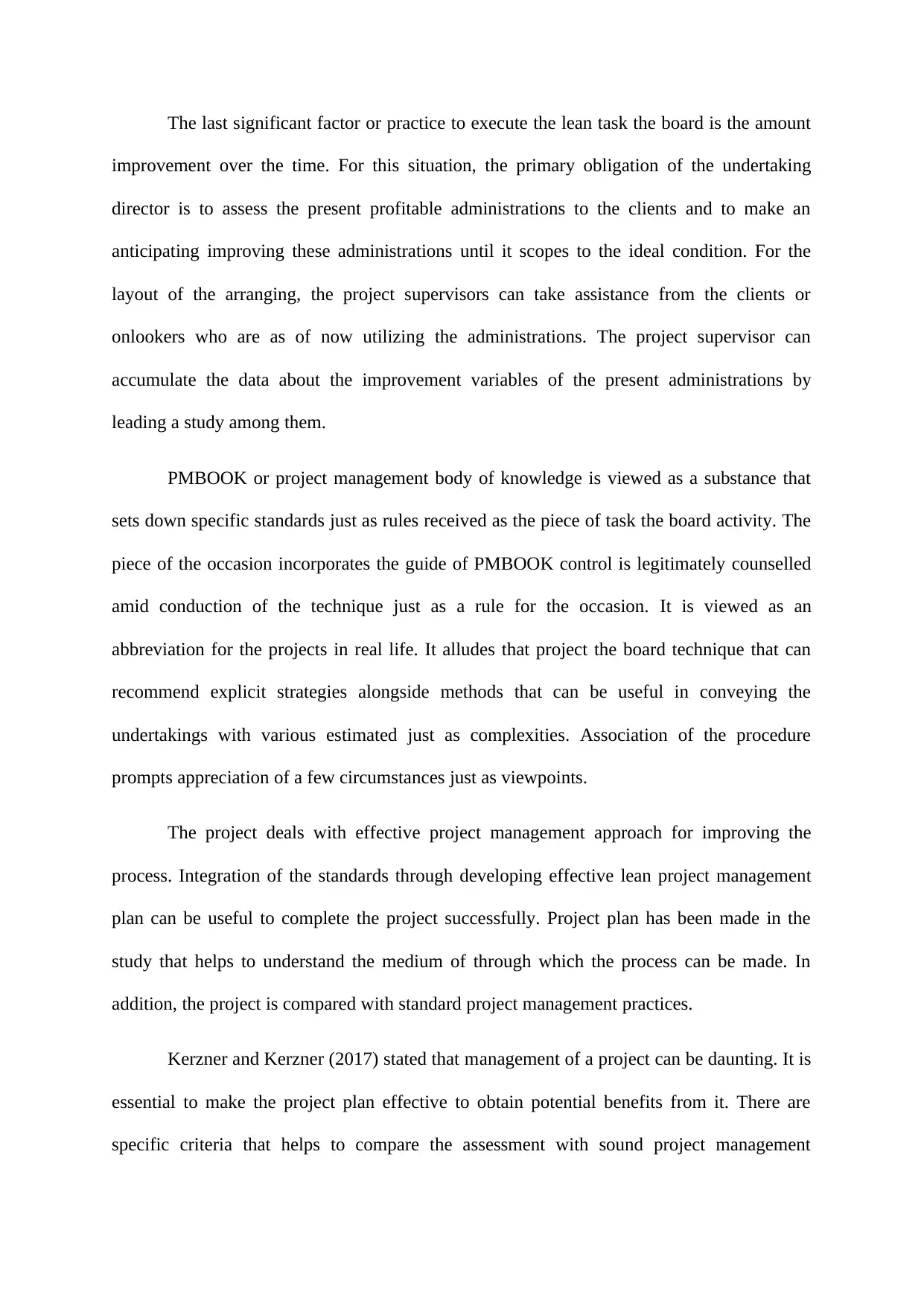
The last significant factor or practice to execute the lean task the board is the amount
improvement over the time. For this situation, the primary obligation of the undertaking
director is to assess the present profitable administrations to the clients and to make an
anticipating improving these administrations until it scopes to the ideal condition. For the
layout of the arranging, the project supervisors can take assistance from the clients or
onlookers who are as of now utilizing the administrations. The project supervisor can
accumulate the data about the improvement variables of the present administrations by
leading a study among them.
PMBOOK or project management body of knowledge is viewed as a substance that
sets down specific standards just as rules received as the piece of task the board activity. The
piece of the occasion incorporates the guide of PMBOOK control is legitimately counselled
amid conduction of the technique just as a rule for the occasion. It is viewed as an
abbreviation for the projects in real life. It alludes that project the board technique that can
recommend explicit strategies alongside methods that can be useful in conveying the
undertakings with various estimated just as complexities. Association of the procedure
prompts appreciation of a few circumstances just as viewpoints.
The project deals with effective project management approach for improving the
process. Integration of the standards through developing effective lean project management
plan can be useful to complete the project successfully. Project plan has been made in the
study that helps to understand the medium of through which the process can be made. In
addition, the project is compared with standard project management practices.
Kerzner and Kerzner (2017) stated that management of a project can be daunting. It is
essential to make the project plan effective to obtain potential benefits from it. There are
specific criteria that helps to compare the assessment with sound project management
improvement over the time. For this situation, the primary obligation of the undertaking
director is to assess the present profitable administrations to the clients and to make an
anticipating improving these administrations until it scopes to the ideal condition. For the
layout of the arranging, the project supervisors can take assistance from the clients or
onlookers who are as of now utilizing the administrations. The project supervisor can
accumulate the data about the improvement variables of the present administrations by
leading a study among them.
PMBOOK or project management body of knowledge is viewed as a substance that
sets down specific standards just as rules received as the piece of task the board activity. The
piece of the occasion incorporates the guide of PMBOOK control is legitimately counselled
amid conduction of the technique just as a rule for the occasion. It is viewed as an
abbreviation for the projects in real life. It alludes that project the board technique that can
recommend explicit strategies alongside methods that can be useful in conveying the
undertakings with various estimated just as complexities. Association of the procedure
prompts appreciation of a few circumstances just as viewpoints.
The project deals with effective project management approach for improving the
process. Integration of the standards through developing effective lean project management
plan can be useful to complete the project successfully. Project plan has been made in the
study that helps to understand the medium of through which the process can be made. In
addition, the project is compared with standard project management practices.
Kerzner and Kerzner (2017) stated that management of a project can be daunting. It is
essential to make the project plan effective to obtain potential benefits from it. There are
specific criteria that helps to compare the assessment with sound project management
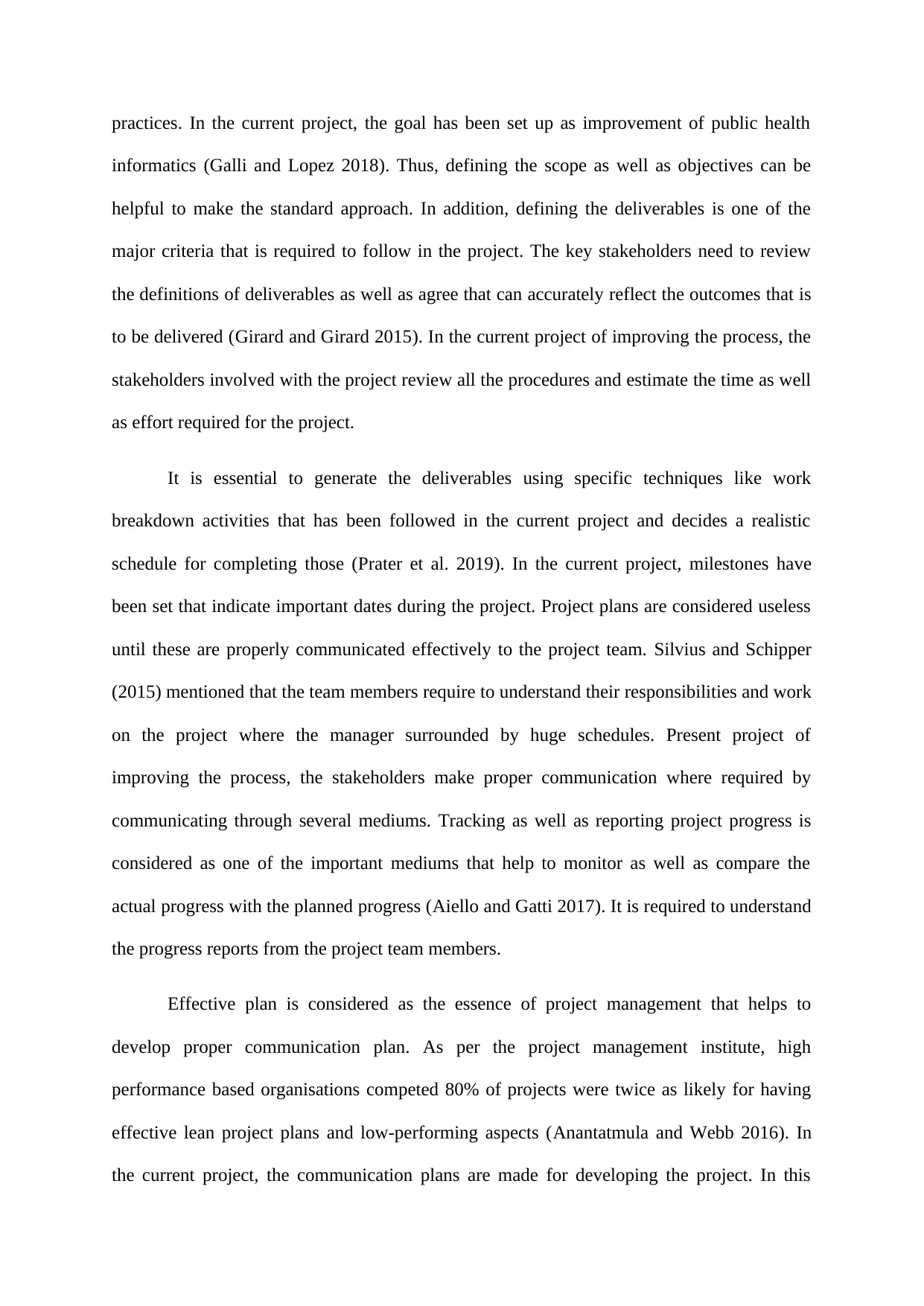
practices. In the current project, the goal has been set up as improvement of public health
informatics (Galli and Lopez 2018). Thus, defining the scope as well as objectives can be
helpful to make the standard approach. In addition, defining the deliverables is one of the
major criteria that is required to follow in the project. The key stakeholders need to review
the definitions of deliverables as well as agree that can accurately reflect the outcomes that is
to be delivered (Girard and Girard 2015). In the current project of improving the process, the
stakeholders involved with the project review all the procedures and estimate the time as well
as effort required for the project.
It is essential to generate the deliverables using specific techniques like work
breakdown activities that has been followed in the current project and decides a realistic
schedule for completing those (Prater et al. 2019). In the current project, milestones have
been set that indicate important dates during the project. Project plans are considered useless
until these are properly communicated effectively to the project team. Silvius and Schipper
(2015) mentioned that the team members require to understand their responsibilities and work
on the project where the manager surrounded by huge schedules. Present project of
improving the process, the stakeholders make proper communication where required by
communicating through several mediums. Tracking as well as reporting project progress is
considered as one of the important mediums that help to monitor as well as compare the
actual progress with the planned progress (Aiello and Gatti 2017). It is required to understand
the progress reports from the project team members.
Effective plan is considered as the essence of project management that helps to
develop proper communication plan. As per the project management institute, high
performance based organisations competed 80% of projects were twice as likely for having
effective lean project plans and low-performing aspects (Anantatmula and Webb 2016). In
the current project, the communication plans are made for developing the project. In this
informatics (Galli and Lopez 2018). Thus, defining the scope as well as objectives can be
helpful to make the standard approach. In addition, defining the deliverables is one of the
major criteria that is required to follow in the project. The key stakeholders need to review
the definitions of deliverables as well as agree that can accurately reflect the outcomes that is
to be delivered (Girard and Girard 2015). In the current project of improving the process, the
stakeholders involved with the project review all the procedures and estimate the time as well
as effort required for the project.
It is essential to generate the deliverables using specific techniques like work
breakdown activities that has been followed in the current project and decides a realistic
schedule for completing those (Prater et al. 2019). In the current project, milestones have
been set that indicate important dates during the project. Project plans are considered useless
until these are properly communicated effectively to the project team. Silvius and Schipper
(2015) mentioned that the team members require to understand their responsibilities and work
on the project where the manager surrounded by huge schedules. Present project of
improving the process, the stakeholders make proper communication where required by
communicating through several mediums. Tracking as well as reporting project progress is
considered as one of the important mediums that help to monitor as well as compare the
actual progress with the planned progress (Aiello and Gatti 2017). It is required to understand
the progress reports from the project team members.
Effective plan is considered as the essence of project management that helps to
develop proper communication plan. As per the project management institute, high
performance based organisations competed 80% of projects were twice as likely for having
effective lean project plans and low-performing aspects (Anantatmula and Webb 2016). In
the current project, the communication plans are made for developing the project. In this
Secure Best Marks with AI Grader
Need help grading? Try our AI Grader for instant feedback on your assignments.
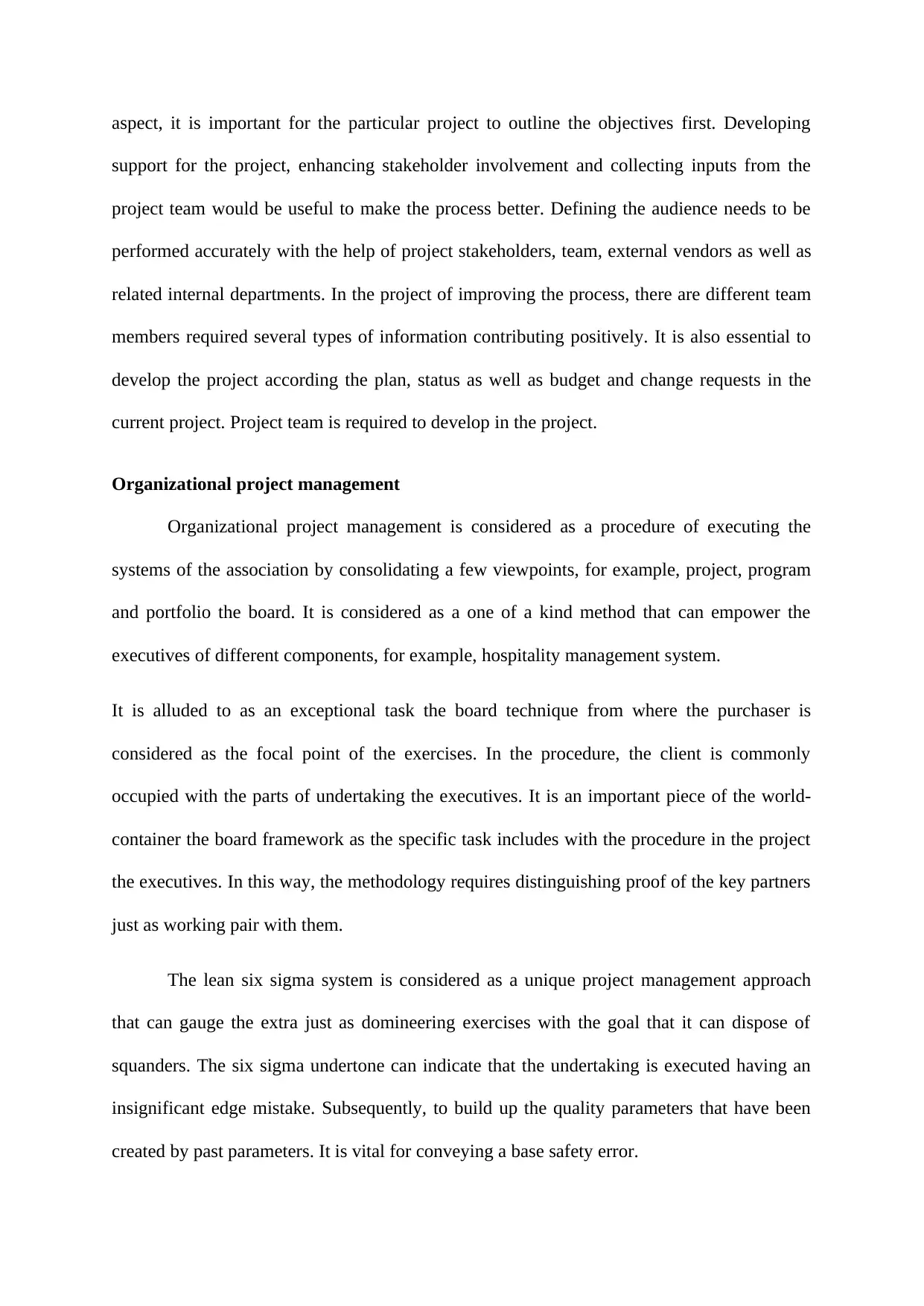
aspect, it is important for the particular project to outline the objectives first. Developing
support for the project, enhancing stakeholder involvement and collecting inputs from the
project team would be useful to make the process better. Defining the audience needs to be
performed accurately with the help of project stakeholders, team, external vendors as well as
related internal departments. In the project of improving the process, there are different team
members required several types of information contributing positively. It is also essential to
develop the project according the plan, status as well as budget and change requests in the
current project. Project team is required to develop in the project.
Organizational project management
Organizational project management is considered as a procedure of executing the
systems of the association by consolidating a few viewpoints, for example, project, program
and portfolio the board. It is considered as a one of a kind method that can empower the
executives of different components, for example, hospitality management system.
It is alluded to as an exceptional task the board technique from where the purchaser is
considered as the focal point of the exercises. In the procedure, the client is commonly
occupied with the parts of undertaking the executives. It is an important piece of the world-
container the board framework as the specific task includes with the procedure in the project
the executives. In this way, the methodology requires distinguishing proof of the key partners
just as working pair with them.
The lean six sigma system is considered as a unique project management approach
that can gauge the extra just as domineering exercises with the goal that it can dispose of
squanders. The six sigma undertone can indicate that the undertaking is executed having an
insignificant edge mistake. Subsequently, to build up the quality parameters that have been
created by past parameters. It is vital for conveying a base safety error.
support for the project, enhancing stakeholder involvement and collecting inputs from the
project team would be useful to make the process better. Defining the audience needs to be
performed accurately with the help of project stakeholders, team, external vendors as well as
related internal departments. In the project of improving the process, there are different team
members required several types of information contributing positively. It is also essential to
develop the project according the plan, status as well as budget and change requests in the
current project. Project team is required to develop in the project.
Organizational project management
Organizational project management is considered as a procedure of executing the
systems of the association by consolidating a few viewpoints, for example, project, program
and portfolio the board. It is considered as a one of a kind method that can empower the
executives of different components, for example, hospitality management system.
It is alluded to as an exceptional task the board technique from where the purchaser is
considered as the focal point of the exercises. In the procedure, the client is commonly
occupied with the parts of undertaking the executives. It is an important piece of the world-
container the board framework as the specific task includes with the procedure in the project
the executives. In this way, the methodology requires distinguishing proof of the key partners
just as working pair with them.
The lean six sigma system is considered as a unique project management approach
that can gauge the extra just as domineering exercises with the goal that it can dispose of
squanders. The six sigma undertone can indicate that the undertaking is executed having an
insignificant edge mistake. Subsequently, to build up the quality parameters that have been
created by past parameters. It is vital for conveying a base safety error.
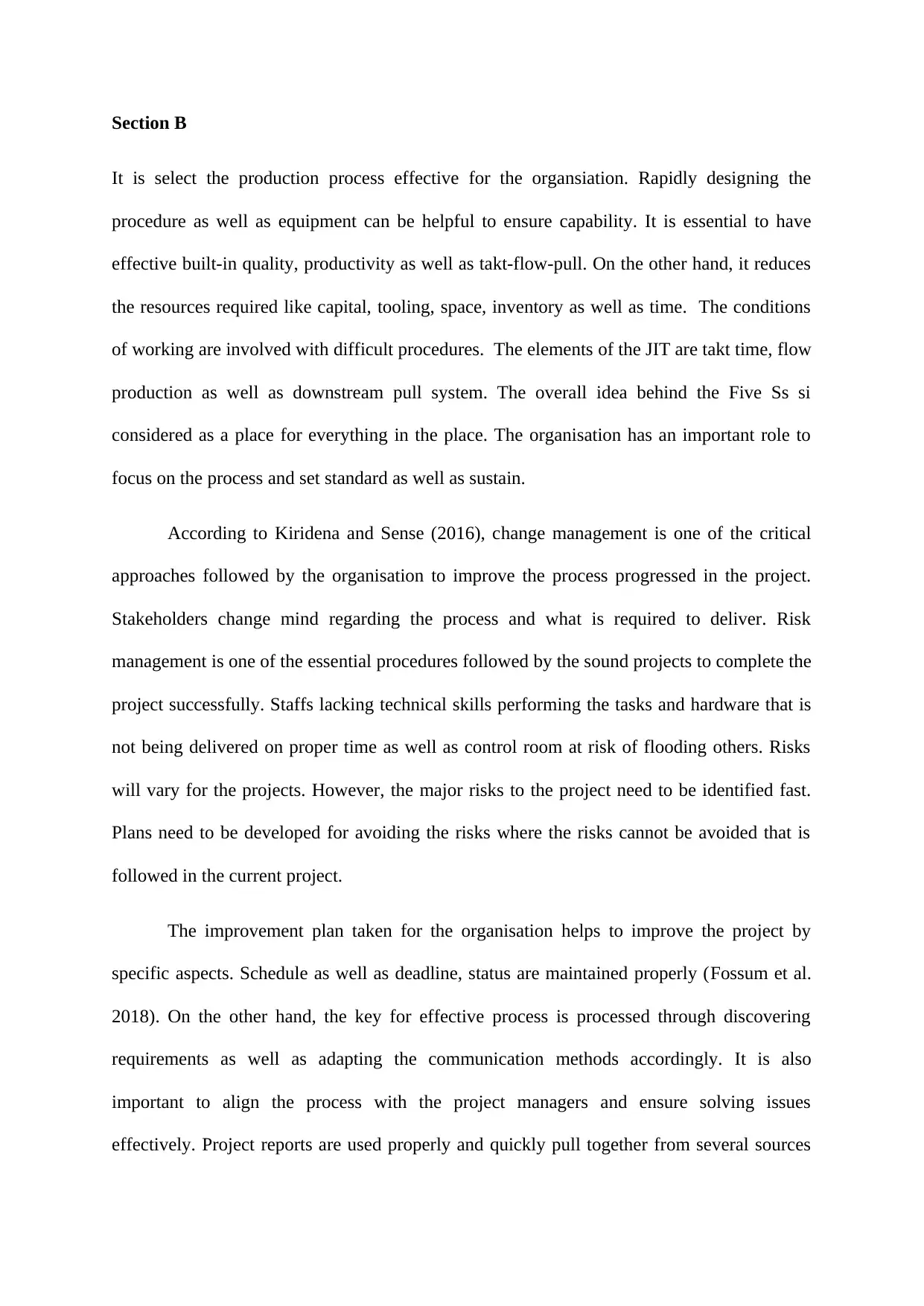
Section B
It is select the production process effective for the organsiation. Rapidly designing the
procedure as well as equipment can be helpful to ensure capability. It is essential to have
effective built-in quality, productivity as well as takt-flow-pull. On the other hand, it reduces
the resources required like capital, tooling, space, inventory as well as time. The conditions
of working are involved with difficult procedures. The elements of the JIT are takt time, flow
production as well as downstream pull system. The overall idea behind the Five Ss si
considered as a place for everything in the place. The organisation has an important role to
focus on the process and set standard as well as sustain.
According to Kiridena and Sense (2016), change management is one of the critical
approaches followed by the organisation to improve the process progressed in the project.
Stakeholders change mind regarding the process and what is required to deliver. Risk
management is one of the essential procedures followed by the sound projects to complete the
project successfully. Staffs lacking technical skills performing the tasks and hardware that is
not being delivered on proper time as well as control room at risk of flooding others. Risks
will vary for the projects. However, the major risks to the project need to be identified fast.
Plans need to be developed for avoiding the risks where the risks cannot be avoided that is
followed in the current project.
The improvement plan taken for the organisation helps to improve the project by
specific aspects. Schedule as well as deadline, status are maintained properly (Fossum et al.
2018). On the other hand, the key for effective process is processed through discovering
requirements as well as adapting the communication methods accordingly. It is also
important to align the process with the project managers and ensure solving issues
effectively. Project reports are used properly and quickly pull together from several sources
It is select the production process effective for the organsiation. Rapidly designing the
procedure as well as equipment can be helpful to ensure capability. It is essential to have
effective built-in quality, productivity as well as takt-flow-pull. On the other hand, it reduces
the resources required like capital, tooling, space, inventory as well as time. The conditions
of working are involved with difficult procedures. The elements of the JIT are takt time, flow
production as well as downstream pull system. The overall idea behind the Five Ss si
considered as a place for everything in the place. The organisation has an important role to
focus on the process and set standard as well as sustain.
According to Kiridena and Sense (2016), change management is one of the critical
approaches followed by the organisation to improve the process progressed in the project.
Stakeholders change mind regarding the process and what is required to deliver. Risk
management is one of the essential procedures followed by the sound projects to complete the
project successfully. Staffs lacking technical skills performing the tasks and hardware that is
not being delivered on proper time as well as control room at risk of flooding others. Risks
will vary for the projects. However, the major risks to the project need to be identified fast.
Plans need to be developed for avoiding the risks where the risks cannot be avoided that is
followed in the current project.
The improvement plan taken for the organisation helps to improve the project by
specific aspects. Schedule as well as deadline, status are maintained properly (Fossum et al.
2018). On the other hand, the key for effective process is processed through discovering
requirements as well as adapting the communication methods accordingly. It is also
important to align the process with the project managers and ensure solving issues
effectively. Project reports are used properly and quickly pull together from several sources
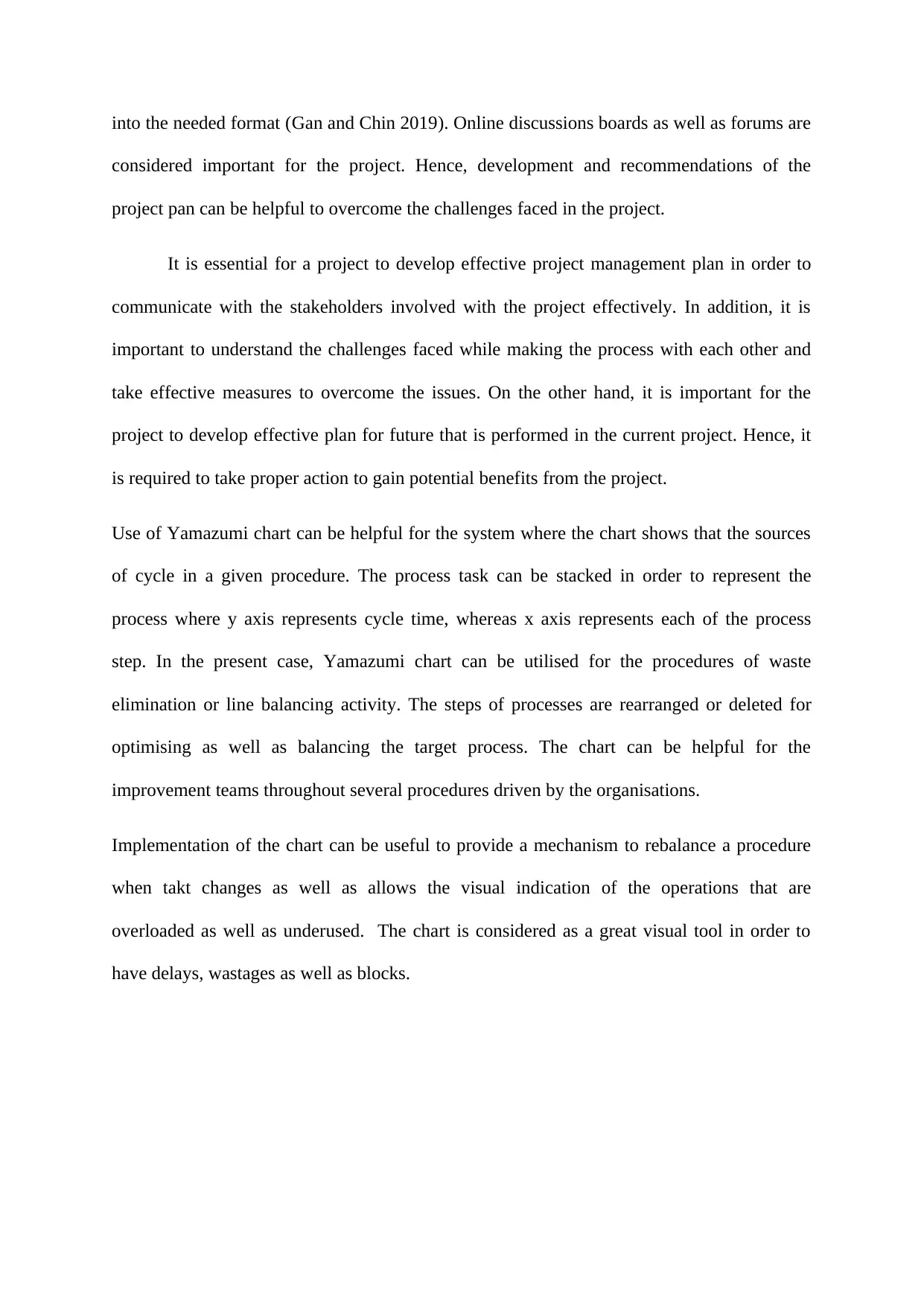
into the needed format (Gan and Chin 2019). Online discussions boards as well as forums are
considered important for the project. Hence, development and recommendations of the
project pan can be helpful to overcome the challenges faced in the project.
It is essential for a project to develop effective project management plan in order to
communicate with the stakeholders involved with the project effectively. In addition, it is
important to understand the challenges faced while making the process with each other and
take effective measures to overcome the issues. On the other hand, it is important for the
project to develop effective plan for future that is performed in the current project. Hence, it
is required to take proper action to gain potential benefits from the project.
Use of Yamazumi chart can be helpful for the system where the chart shows that the sources
of cycle in a given procedure. The process task can be stacked in order to represent the
process where y axis represents cycle time, whereas x axis represents each of the process
step. In the present case, Yamazumi chart can be utilised for the procedures of waste
elimination or line balancing activity. The steps of processes are rearranged or deleted for
optimising as well as balancing the target process. The chart can be helpful for the
improvement teams throughout several procedures driven by the organisations.
Implementation of the chart can be useful to provide a mechanism to rebalance a procedure
when takt changes as well as allows the visual indication of the operations that are
overloaded as well as underused. The chart is considered as a great visual tool in order to
have delays, wastages as well as blocks.
considered important for the project. Hence, development and recommendations of the
project pan can be helpful to overcome the challenges faced in the project.
It is essential for a project to develop effective project management plan in order to
communicate with the stakeholders involved with the project effectively. In addition, it is
important to understand the challenges faced while making the process with each other and
take effective measures to overcome the issues. On the other hand, it is important for the
project to develop effective plan for future that is performed in the current project. Hence, it
is required to take proper action to gain potential benefits from the project.
Use of Yamazumi chart can be helpful for the system where the chart shows that the sources
of cycle in a given procedure. The process task can be stacked in order to represent the
process where y axis represents cycle time, whereas x axis represents each of the process
step. In the present case, Yamazumi chart can be utilised for the procedures of waste
elimination or line balancing activity. The steps of processes are rearranged or deleted for
optimising as well as balancing the target process. The chart can be helpful for the
improvement teams throughout several procedures driven by the organisations.
Implementation of the chart can be useful to provide a mechanism to rebalance a procedure
when takt changes as well as allows the visual indication of the operations that are
overloaded as well as underused. The chart is considered as a great visual tool in order to
have delays, wastages as well as blocks.
Paraphrase This Document
Need a fresh take? Get an instant paraphrase of this document with our AI Paraphraser
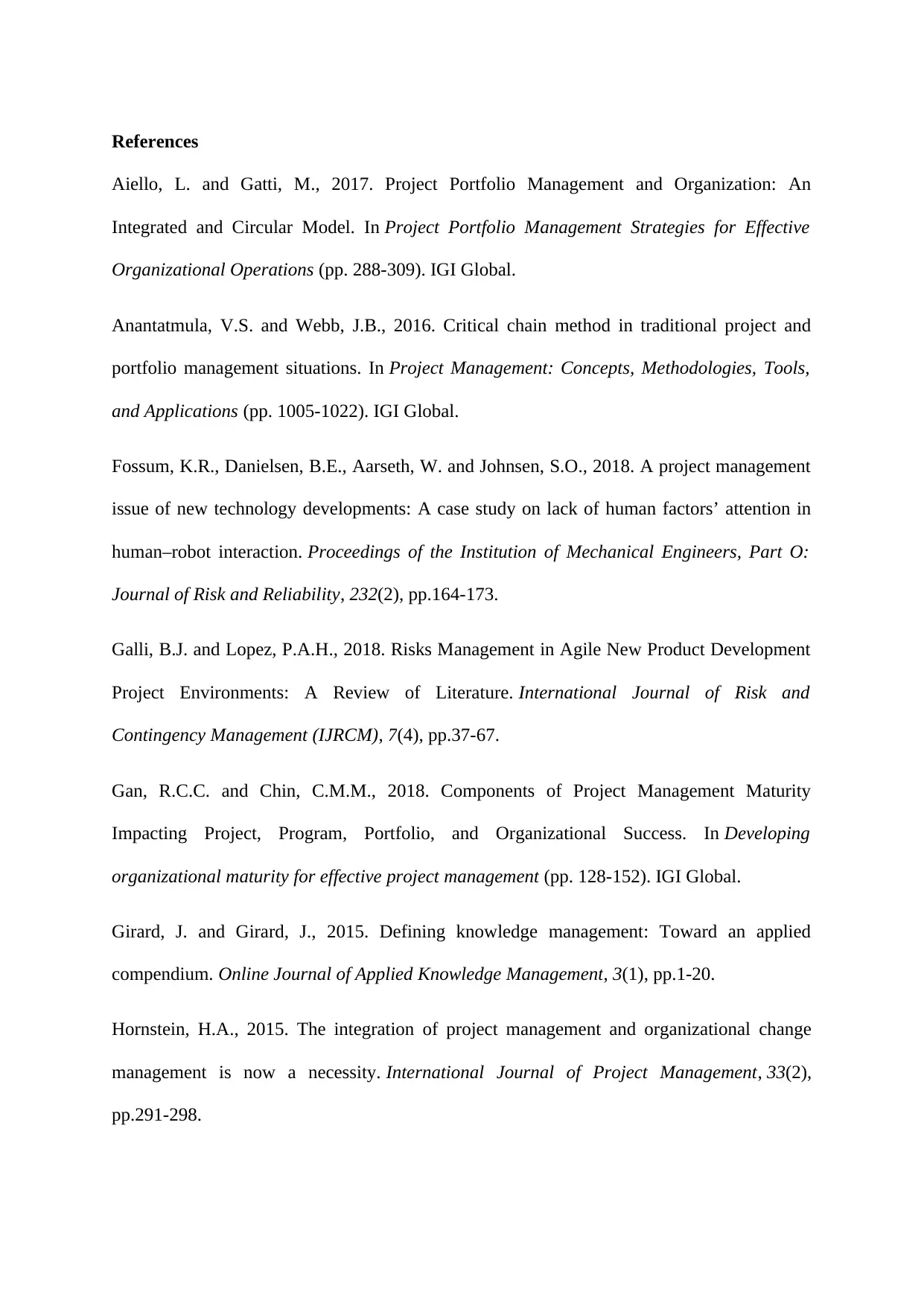
References
Aiello, L. and Gatti, M., 2017. Project Portfolio Management and Organization: An
Integrated and Circular Model. In Project Portfolio Management Strategies for Effective
Organizational Operations (pp. 288-309). IGI Global.
Anantatmula, V.S. and Webb, J.B., 2016. Critical chain method in traditional project and
portfolio management situations. In Project Management: Concepts, Methodologies, Tools,
and Applications (pp. 1005-1022). IGI Global.
Fossum, K.R., Danielsen, B.E., Aarseth, W. and Johnsen, S.O., 2018. A project management
issue of new technology developments: A case study on lack of human factors’ attention in
human–robot interaction. Proceedings of the Institution of Mechanical Engineers, Part O:
Journal of Risk and Reliability, 232(2), pp.164-173.
Galli, B.J. and Lopez, P.A.H., 2018. Risks Management in Agile New Product Development
Project Environments: A Review of Literature. International Journal of Risk and
Contingency Management (IJRCM), 7(4), pp.37-67.
Gan, R.C.C. and Chin, C.M.M., 2018. Components of Project Management Maturity
Impacting Project, Program, Portfolio, and Organizational Success. In Developing
organizational maturity for effective project management (pp. 128-152). IGI Global.
Girard, J. and Girard, J., 2015. Defining knowledge management: Toward an applied
compendium. Online Journal of Applied Knowledge Management, 3(1), pp.1-20.
Hornstein, H.A., 2015. The integration of project management and organizational change
management is now a necessity. International Journal of Project Management, 33(2),
pp.291-298.
Aiello, L. and Gatti, M., 2017. Project Portfolio Management and Organization: An
Integrated and Circular Model. In Project Portfolio Management Strategies for Effective
Organizational Operations (pp. 288-309). IGI Global.
Anantatmula, V.S. and Webb, J.B., 2016. Critical chain method in traditional project and
portfolio management situations. In Project Management: Concepts, Methodologies, Tools,
and Applications (pp. 1005-1022). IGI Global.
Fossum, K.R., Danielsen, B.E., Aarseth, W. and Johnsen, S.O., 2018. A project management
issue of new technology developments: A case study on lack of human factors’ attention in
human–robot interaction. Proceedings of the Institution of Mechanical Engineers, Part O:
Journal of Risk and Reliability, 232(2), pp.164-173.
Galli, B.J. and Lopez, P.A.H., 2018. Risks Management in Agile New Product Development
Project Environments: A Review of Literature. International Journal of Risk and
Contingency Management (IJRCM), 7(4), pp.37-67.
Gan, R.C.C. and Chin, C.M.M., 2018. Components of Project Management Maturity
Impacting Project, Program, Portfolio, and Organizational Success. In Developing
organizational maturity for effective project management (pp. 128-152). IGI Global.
Girard, J. and Girard, J., 2015. Defining knowledge management: Toward an applied
compendium. Online Journal of Applied Knowledge Management, 3(1), pp.1-20.
Hornstein, H.A., 2015. The integration of project management and organizational change
management is now a necessity. International Journal of Project Management, 33(2),
pp.291-298.
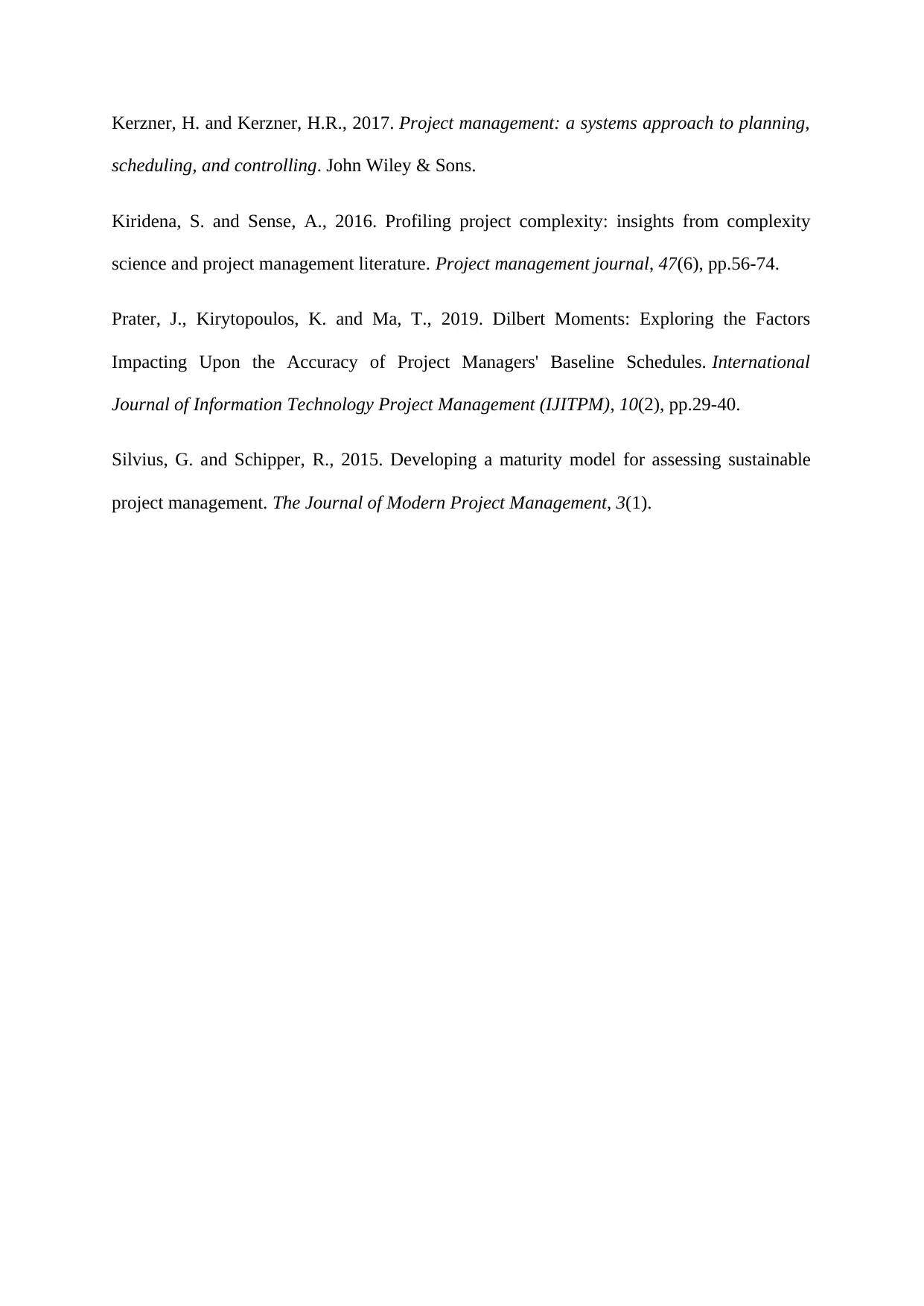
Kerzner, H. and Kerzner, H.R., 2017. Project management: a systems approach to planning,
scheduling, and controlling. John Wiley & Sons.
Kiridena, S. and Sense, A., 2016. Profiling project complexity: insights from complexity
science and project management literature. Project management journal, 47(6), pp.56-74.
Prater, J., Kirytopoulos, K. and Ma, T., 2019. Dilbert Moments: Exploring the Factors
Impacting Upon the Accuracy of Project Managers' Baseline Schedules. International
Journal of Information Technology Project Management (IJITPM), 10(2), pp.29-40.
Silvius, G. and Schipper, R., 2015. Developing a maturity model for assessing sustainable
project management. The Journal of Modern Project Management, 3(1).
scheduling, and controlling. John Wiley & Sons.
Kiridena, S. and Sense, A., 2016. Profiling project complexity: insights from complexity
science and project management literature. Project management journal, 47(6), pp.56-74.
Prater, J., Kirytopoulos, K. and Ma, T., 2019. Dilbert Moments: Exploring the Factors
Impacting Upon the Accuracy of Project Managers' Baseline Schedules. International
Journal of Information Technology Project Management (IJITPM), 10(2), pp.29-40.
Silvius, G. and Schipper, R., 2015. Developing a maturity model for assessing sustainable
project management. The Journal of Modern Project Management, 3(1).
1 out of 15

Your All-in-One AI-Powered Toolkit for Academic Success.
 +13062052269
info@desklib.com
Available 24*7 on WhatsApp / Email
Unlock your academic potential
© 2024  |  Zucol Services PVT LTD  |  All rights reserved.