Australian Paper: Aligning Lean Six Sigma for Sustainability
VerifiedAdded on 2023/06/10
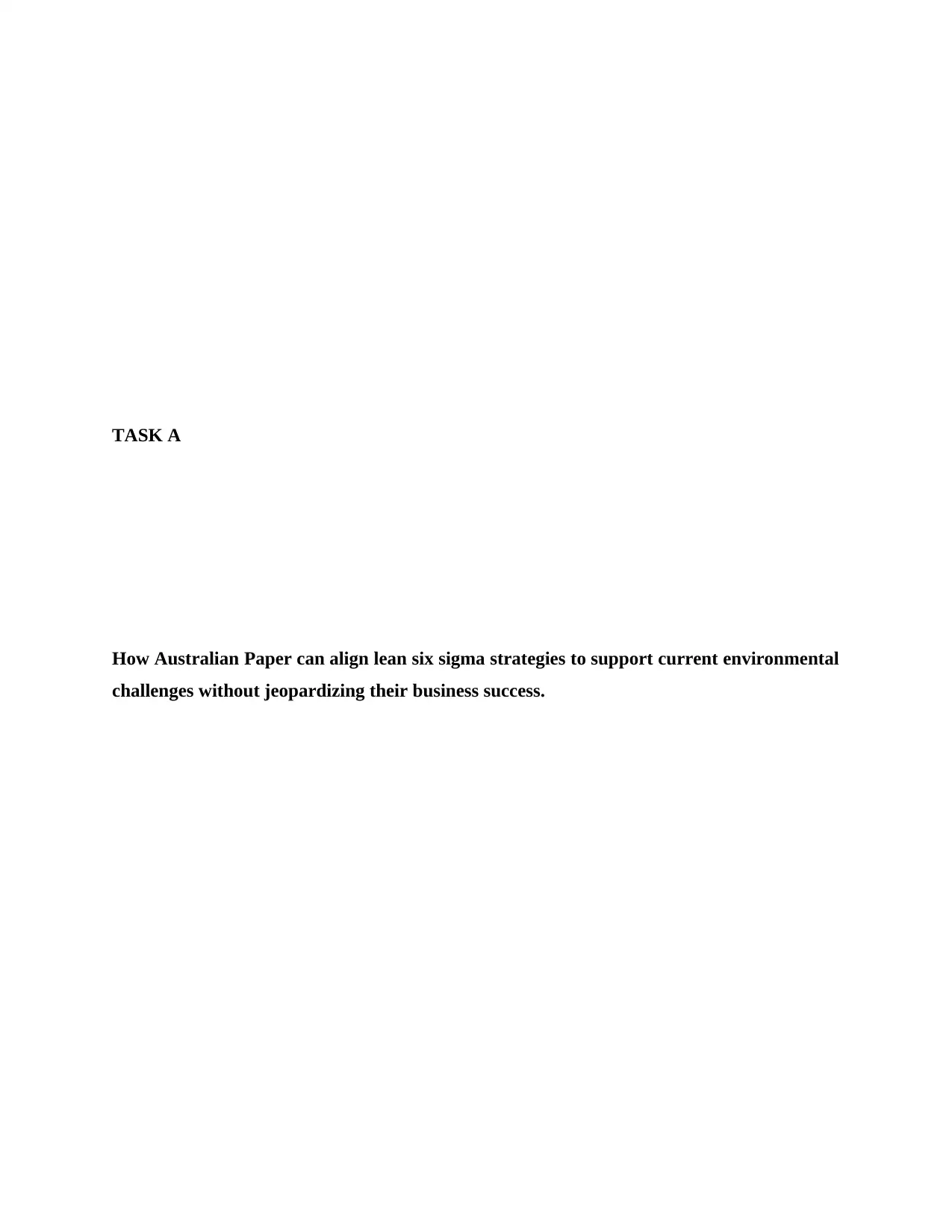
How Australian Paper can align lean six sigma strategies to support current environmental
challenges without jeopardizing their business success.
Paraphrase This Document
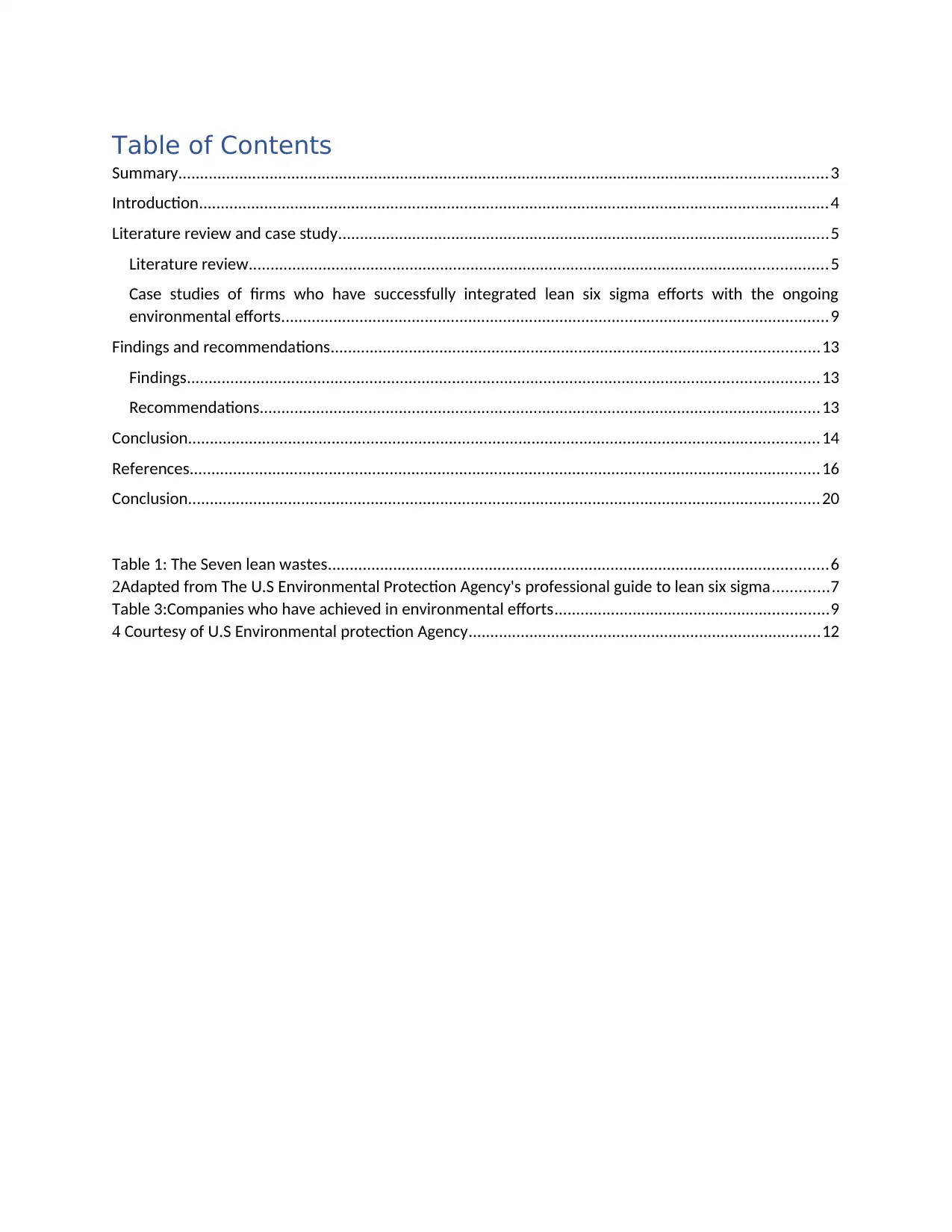
Summary.....................................................................................................................................................3
Introduction.................................................................................................................................................4
Literature review and case study.................................................................................................................5
Literature review.....................................................................................................................................5
Case studies of firms who have successfully integrated lean six sigma efforts with the ongoing
environmental efforts..............................................................................................................................9
Findings and recommendations................................................................................................................13
Findings.................................................................................................................................................13
Recommendations.................................................................................................................................13
Conclusion.................................................................................................................................................14
References.................................................................................................................................................16
Conclusion.................................................................................................................................................20
Table 1: The Seven lean wastes...................................................................................................................6
2Adapted from The U.S Environmental Protection Agency's professional guide to lean six sigma.............7
Table 3:Companies who have achieved in environmental efforts...............................................................9
4 Courtesy of U.S Environmental protection Agency.................................................................................12
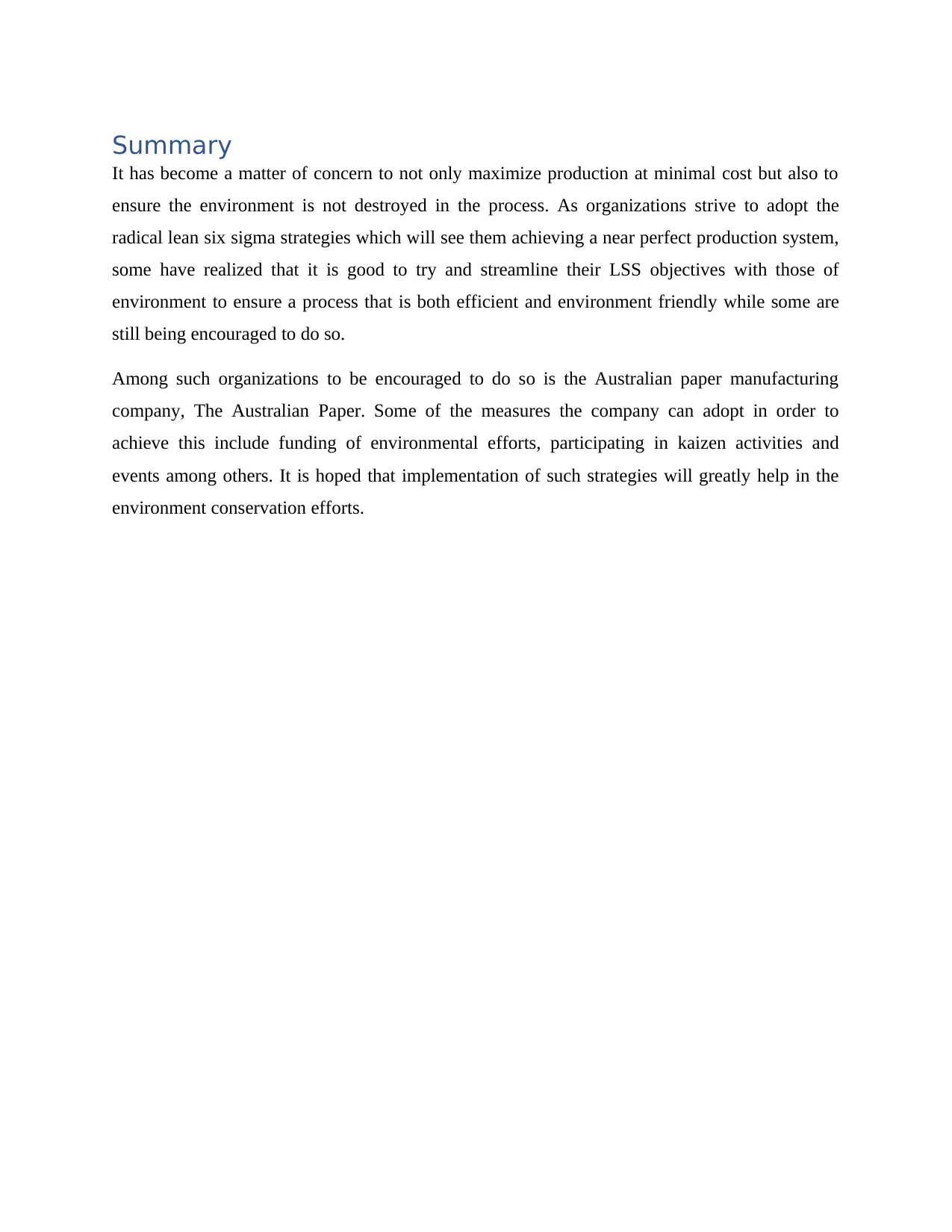
It has become a matter of concern to not only maximize production at minimal cost but also to
ensure the environment is not destroyed in the process. As organizations strive to adopt the
radical lean six sigma strategies which will see them achieving a near perfect production system,
some have realized that it is good to try and streamline their LSS objectives with those of
environment to ensure a process that is both efficient and environment friendly while some are
still being encouraged to do so.
Among such organizations to be encouraged to do so is the Australian paper manufacturing
company, The Australian Paper. Some of the measures the company can adopt in order to
achieve this include funding of environmental efforts, participating in kaizen activities and
events among others. It is hoped that implementation of such strategies will greatly help in the
environment conservation efforts.
⊘ This is a preview!⊘
Do you want full access?
Subscribe today to unlock all pages.

Trusted by 1+ million students worldwide
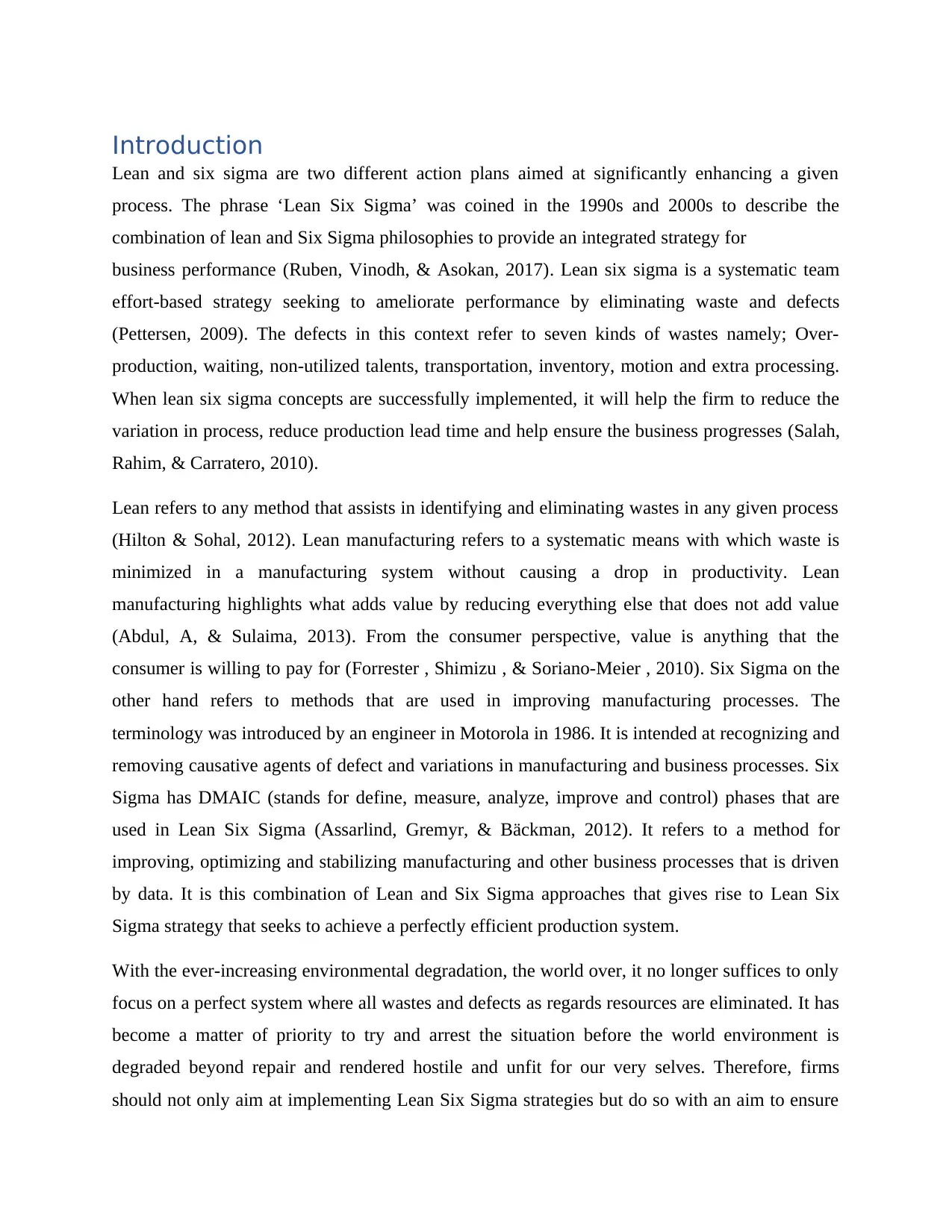
Lean and six sigma are two different action plans aimed at significantly enhancing a given
process. The phrase ‘Lean Six Sigma’ was coined in the 1990s and 2000s to describe the
combination of lean and Six Sigma philosophies to provide an integrated strategy for
business performance (Ruben, Vinodh, & Asokan, 2017). Lean six sigma is a systematic team
effort-based strategy seeking to ameliorate performance by eliminating waste and defects
(Pettersen, 2009). The defects in this context refer to seven kinds of wastes namely; Over-
production, waiting, non-utilized talents, transportation, inventory, motion and extra processing.
When lean six sigma concepts are successfully implemented, it will help the firm to reduce the
variation in process, reduce production lead time and help ensure the business progresses (Salah,
Rahim, & Carratero, 2010).
Lean refers to any method that assists in identifying and eliminating wastes in any given process
(Hilton & Sohal, 2012). Lean manufacturing refers to a systematic means with which waste is
minimized in a manufacturing system without causing a drop in productivity. Lean
manufacturing highlights what adds value by reducing everything else that does not add value
(Abdul, A, & Sulaima, 2013). From the consumer perspective, value is anything that the
consumer is willing to pay for (Forrester , Shimizu , & Soriano-Meier , 2010). Six Sigma on the
other hand refers to methods that are used in improving manufacturing processes. The
terminology was introduced by an engineer in Motorola in 1986. It is intended at recognizing and
removing causative agents of defect and variations in manufacturing and business processes. Six
Sigma has DMAIC (stands for define, measure, analyze, improve and control) phases that are
used in Lean Six Sigma (Assarlind, Gremyr, & Bäckman, 2012). It refers to a method for
improving, optimizing and stabilizing manufacturing and other business processes that is driven
by data. It is this combination of Lean and Six Sigma approaches that gives rise to Lean Six
Sigma strategy that seeks to achieve a perfectly efficient production system.
With the ever-increasing environmental degradation, the world over, it no longer suffices to only
focus on a perfect system where all wastes and defects as regards resources are eliminated. It has
become a matter of priority to try and arrest the situation before the world environment is
degraded beyond repair and rendered hostile and unfit for our very selves. Therefore, firms
should not only aim at implementing Lean Six Sigma strategies but do so with an aim to ensure
Paraphrase This Document
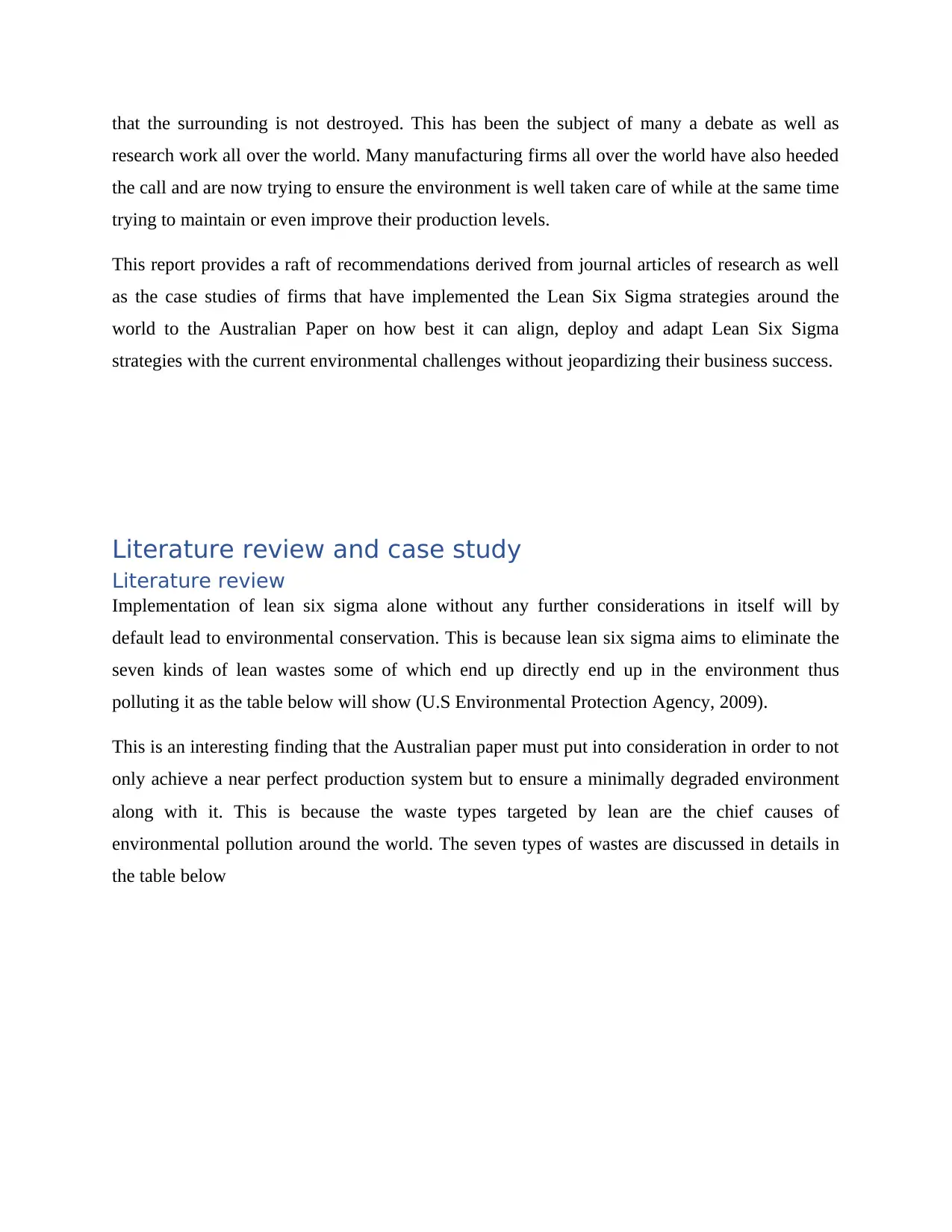
research work all over the world. Many manufacturing firms all over the world have also heeded
the call and are now trying to ensure the environment is well taken care of while at the same time
trying to maintain or even improve their production levels.
This report provides a raft of recommendations derived from journal articles of research as well
as the case studies of firms that have implemented the Lean Six Sigma strategies around the
world to the Australian Paper on how best it can align, deploy and adapt Lean Six Sigma
strategies with the current environmental challenges without jeopardizing their business success.
Literature review and case study
Literature review
Implementation of lean six sigma alone without any further considerations in itself will by
default lead to environmental conservation. This is because lean six sigma aims to eliminate the
seven kinds of lean wastes some of which end up directly end up in the environment thus
polluting it as the table below will show (U.S Environmental Protection Agency, 2009).
This is an interesting finding that the Australian paper must put into consideration in order to not
only achieve a near perfect production system but to ensure a minimally degraded environment
along with it. This is because the waste types targeted by lean are the chief causes of
environmental pollution around the world. The seven types of wastes are discussed in details in
the table below
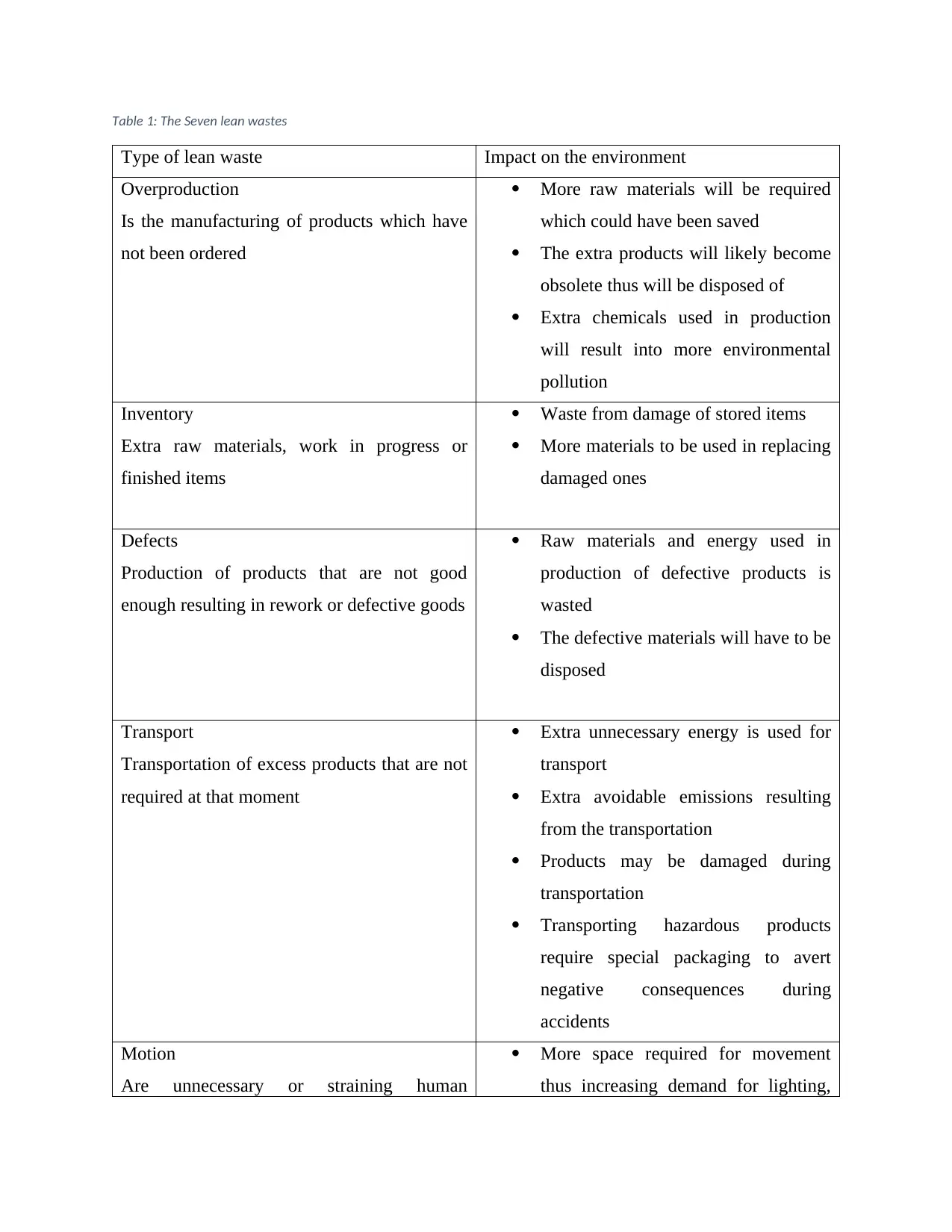
Type of lean waste Impact on the environment
Overproduction
Is the manufacturing of products which have
not been ordered
ï‚· More raw materials will be required
which could have been saved
ï‚· The extra products will likely become
obsolete thus will be disposed of
ï‚· Extra chemicals used in production
will result into more environmental
pollution
Inventory
Extra raw materials, work in progress or
finished items
ï‚· Waste from damage of stored items
ï‚· More materials to be used in replacing
damaged ones
Defects
Production of products that are not good
enough resulting in rework or defective goods
ï‚· Raw materials and energy used in
production of defective products is
wasted
ï‚· The defective materials will have to be
disposed
Transport
Transportation of excess products that are not
required at that moment
ï‚· Extra unnecessary energy is used for
transport
ï‚· Extra avoidable emissions resulting
from the transportation
ï‚· Products may be damaged during
transportation
ï‚· Transporting hazardous products
require special packaging to avert
negative consequences during
accidents
Motion
Are unnecessary or straining human
ï‚· More space required for movement
thus increasing demand for lighting,
⊘ This is a preview!⊘
Do you want full access?
Subscribe today to unlock all pages.

Trusted by 1+ million students worldwide
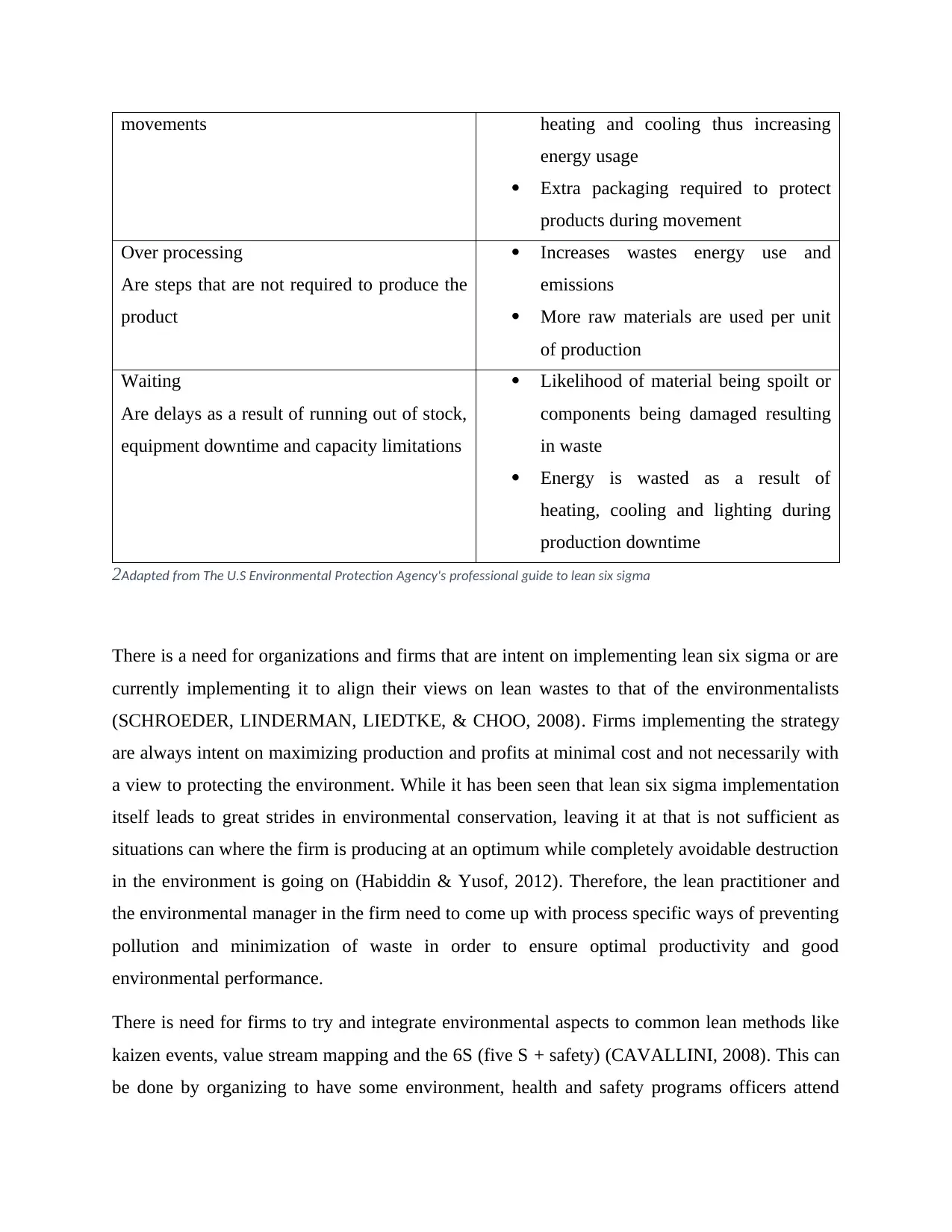
energy usage
ï‚· Extra packaging required to protect
products during movement
Over processing
Are steps that are not required to produce the
product
ï‚· Increases wastes energy use and
emissions
ï‚· More raw materials are used per unit
of production
Waiting
Are delays as a result of running out of stock,
equipment downtime and capacity limitations
ï‚· Likelihood of material being spoilt or
components being damaged resulting
in waste
ï‚· Energy is wasted as a result of
heating, cooling and lighting during
production downtime
2Adapted from The U.S Environmental Protection Agency's professional guide to lean six sigma
There is a need for organizations and firms that are intent on implementing lean six sigma or are
currently implementing it to align their views on lean wastes to that of the environmentalists
(SCHROEDER, LINDERMAN, LIEDTKE, & CHOO, 2008). Firms implementing the strategy
are always intent on maximizing production and profits at minimal cost and not necessarily with
a view to protecting the environment. While it has been seen that lean six sigma implementation
itself leads to great strides in environmental conservation, leaving it at that is not sufficient as
situations can where the firm is producing at an optimum while completely avoidable destruction
in the environment is going on (Habiddin & Yusof, 2012). Therefore, the lean practitioner and
the environmental manager in the firm need to come up with process specific ways of preventing
pollution and minimization of waste in order to ensure optimal productivity and good
environmental performance.
There is need for firms to try and integrate environmental aspects to common lean methods like
kaizen events, value stream mapping and the 6S (five S + safety) (CAVALLINI, 2008). This can
be done by organizing to have some environment, health and safety programs officers attend
Paraphrase This Document
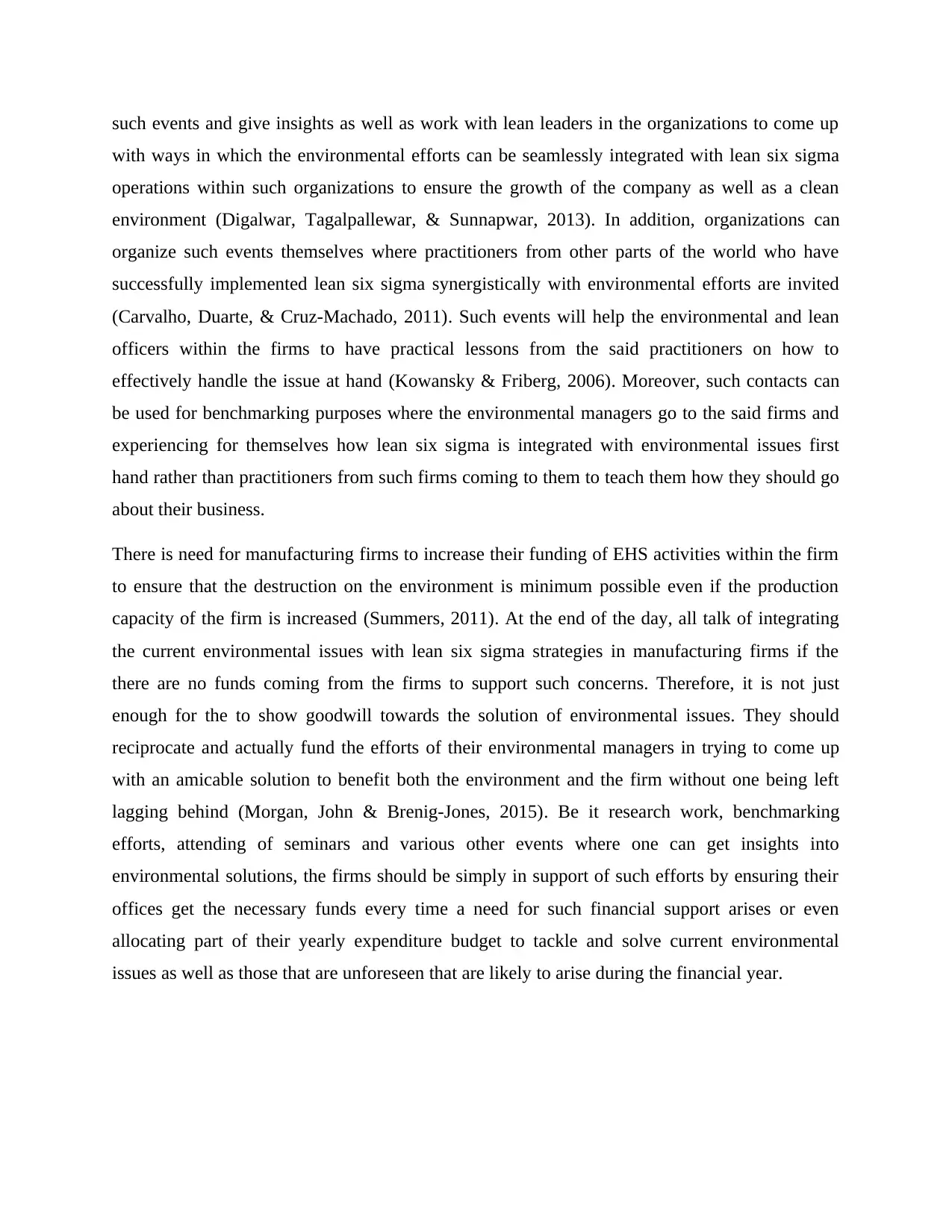
with ways in which the environmental efforts can be seamlessly integrated with lean six sigma
operations within such organizations to ensure the growth of the company as well as a clean
environment (Digalwar, Tagalpallewar, & Sunnapwar, 2013). In addition, organizations can
organize such events themselves where practitioners from other parts of the world who have
successfully implemented lean six sigma synergistically with environmental efforts are invited
(Carvalho, Duarte, & Cruz-Machado, 2011). Such events will help the environmental and lean
officers within the firms to have practical lessons from the said practitioners on how to
effectively handle the issue at hand (Kowansky & Friberg, 2006). Moreover, such contacts can
be used for benchmarking purposes where the environmental managers go to the said firms and
experiencing for themselves how lean six sigma is integrated with environmental issues first
hand rather than practitioners from such firms coming to them to teach them how they should go
about their business.
There is need for manufacturing firms to increase their funding of EHS activities within the firm
to ensure that the destruction on the environment is minimum possible even if the production
capacity of the firm is increased (Summers, 2011). At the end of the day, all talk of integrating
the current environmental issues with lean six sigma strategies in manufacturing firms if the
there are no funds coming from the firms to support such concerns. Therefore, it is not just
enough for the to show goodwill towards the solution of environmental issues. They should
reciprocate and actually fund the efforts of their environmental managers in trying to come up
with an amicable solution to benefit both the environment and the firm without one being left
lagging behind (Morgan, John & Brenig-Jones, 2015). Be it research work, benchmarking
efforts, attending of seminars and various other events where one can get insights into
environmental solutions, the firms should be simply in support of such efforts by ensuring their
offices get the necessary funds every time a need for such financial support arises or even
allocating part of their yearly expenditure budget to tackle and solve current environmental
issues as well as those that are unforeseen that are likely to arise during the financial year.
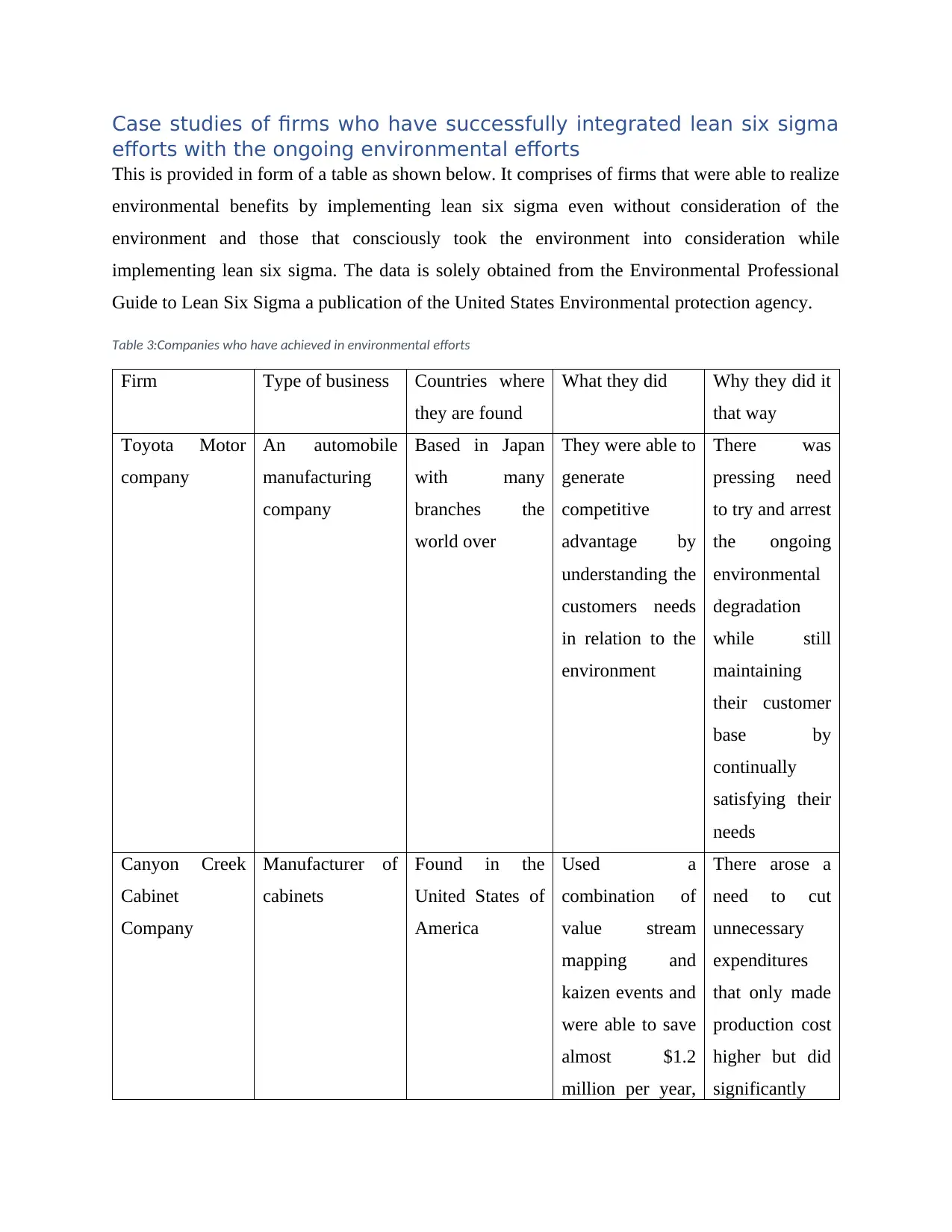
efforts with the ongoing environmental efforts
This is provided in form of a table as shown below. It comprises of firms that were able to realize
environmental benefits by implementing lean six sigma even without consideration of the
environment and those that consciously took the environment into consideration while
implementing lean six sigma. The data is solely obtained from the Environmental Professional
Guide to Lean Six Sigma a publication of the United States Environmental protection agency.
Table 3:Companies who have achieved in environmental efforts
Firm Type of business Countries where
they are found
What they did Why they did it
that way
Toyota Motor
company
An automobile
manufacturing
company
Based in Japan
with many
branches the
world over
They were able to
generate
competitive
advantage by
understanding the
customers needs
in relation to the
environment
There was
pressing need
to try and arrest
the ongoing
environmental
degradation
while still
maintaining
their customer
base by
continually
satisfying their
needs
Canyon Creek
Cabinet
Company
Manufacturer of
cabinets
Found in the
United States of
America
Used a
combination of
value stream
mapping and
kaizen events and
were able to save
almost $1.2
million per year,
There arose a
need to cut
unnecessary
expenditures
that only made
production cost
higher but did
significantly
⊘ This is a preview!⊘
Do you want full access?
Subscribe today to unlock all pages.

Trusted by 1+ million students worldwide
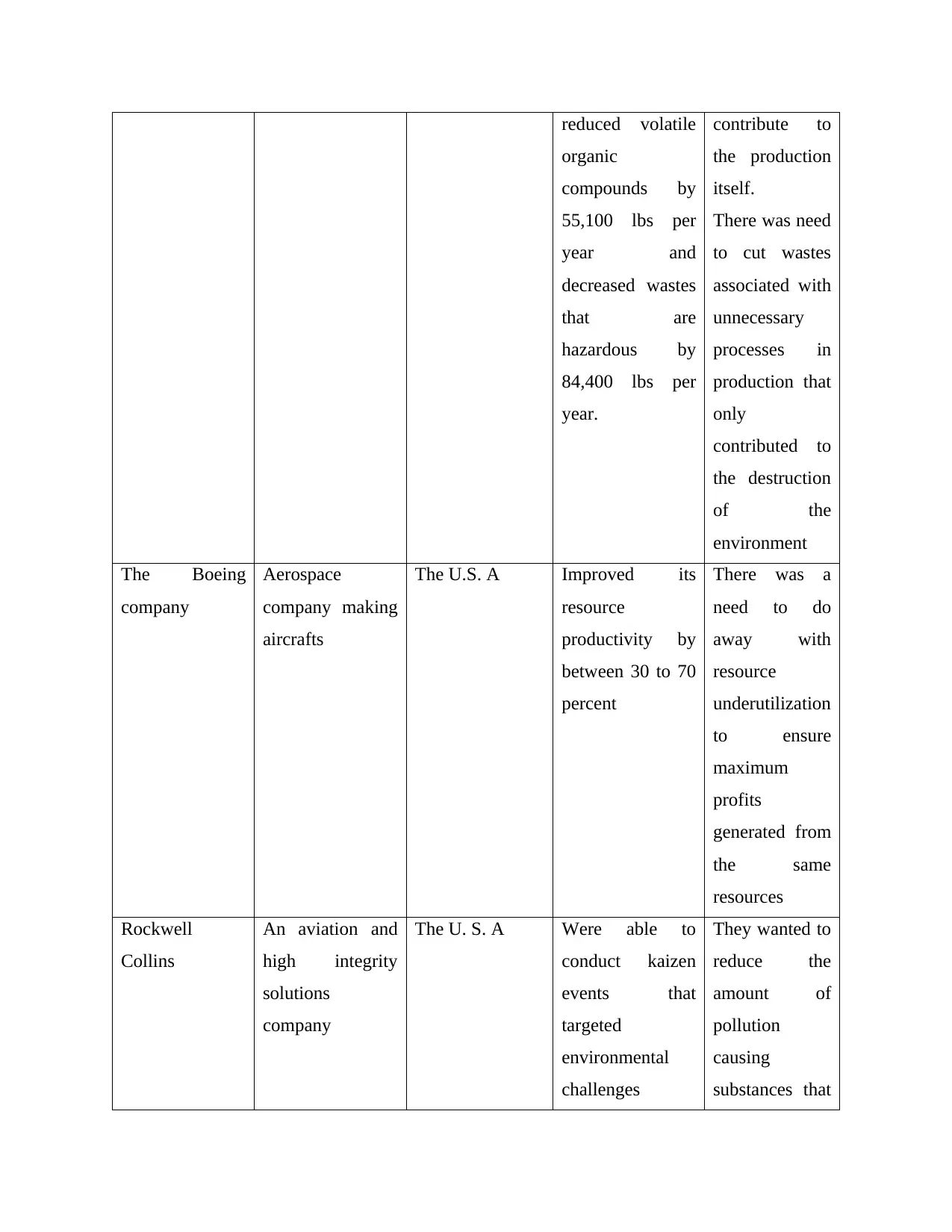
organic
compounds by
55,100 lbs per
year and
decreased wastes
that are
hazardous by
84,400 lbs per
year.
contribute to
the production
itself.
There was need
to cut wastes
associated with
unnecessary
processes in
production that
only
contributed to
the destruction
of the
environment
The Boeing
company
Aerospace
company making
aircrafts
The U.S. A Improved its
resource
productivity by
between 30 to 70
percent
There was a
need to do
away with
resource
underutilization
to ensure
maximum
profits
generated from
the same
resources
Rockwell
Collins
An aviation and
high integrity
solutions
company
The U. S. A Were able to
conduct kaizen
events that
targeted
environmental
challenges
They wanted to
reduce the
amount of
pollution
causing
substances that
Paraphrase This Document
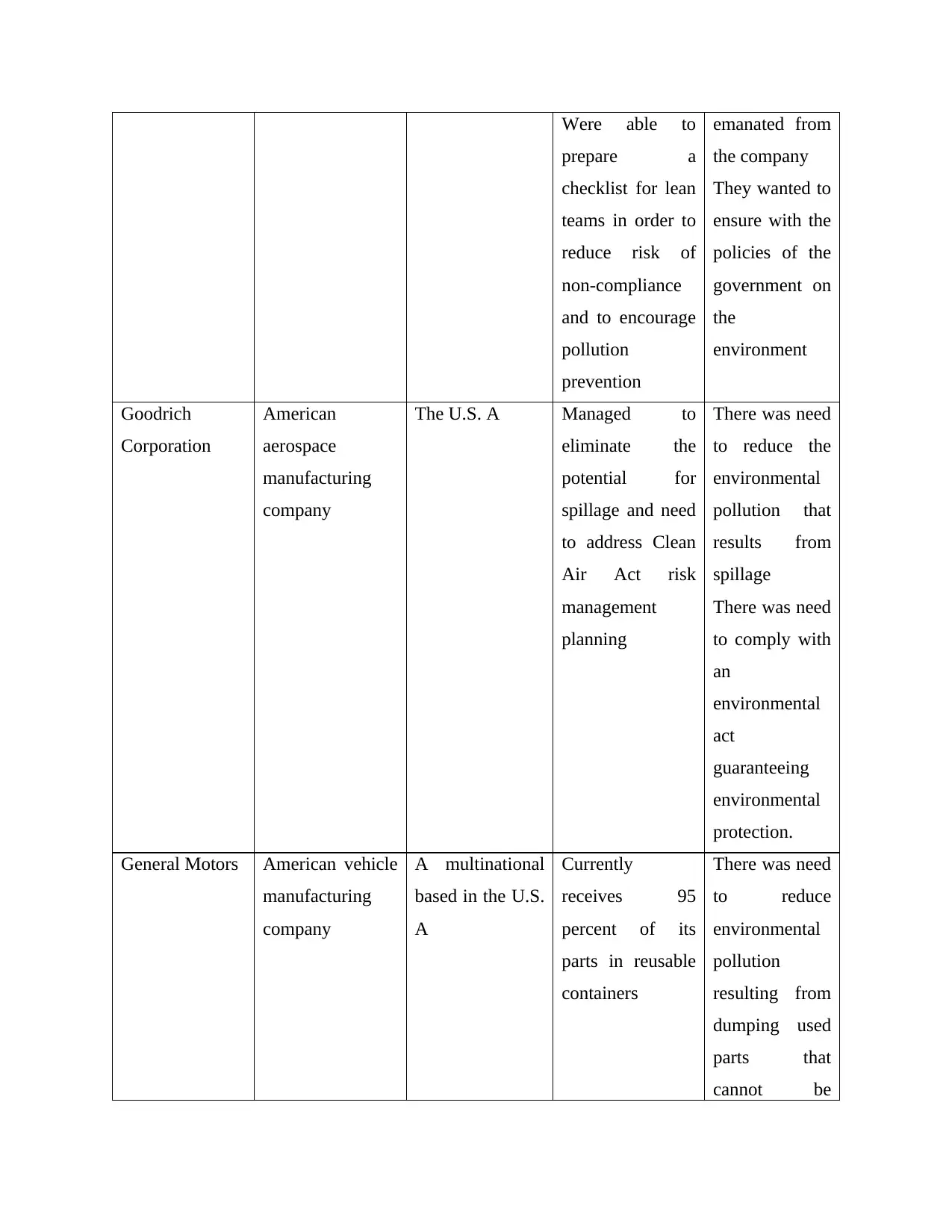
prepare a
checklist for lean
teams in order to
reduce risk of
non-compliance
and to encourage
pollution
prevention
emanated from
the company
They wanted to
ensure with the
policies of the
government on
the
environment
Goodrich
Corporation
American
aerospace
manufacturing
company
The U.S. A Managed to
eliminate the
potential for
spillage and need
to address Clean
Air Act risk
management
planning
There was need
to reduce the
environmental
pollution that
results from
spillage
There was need
to comply with
an
environmental
act
guaranteeing
environmental
protection.
General Motors American vehicle
manufacturing
company
A multinational
based in the U.S.
A
Currently
receives 95
percent of its
parts in reusable
containers
There was need
to reduce
environmental
pollution
resulting from
dumping used
parts that
cannot be
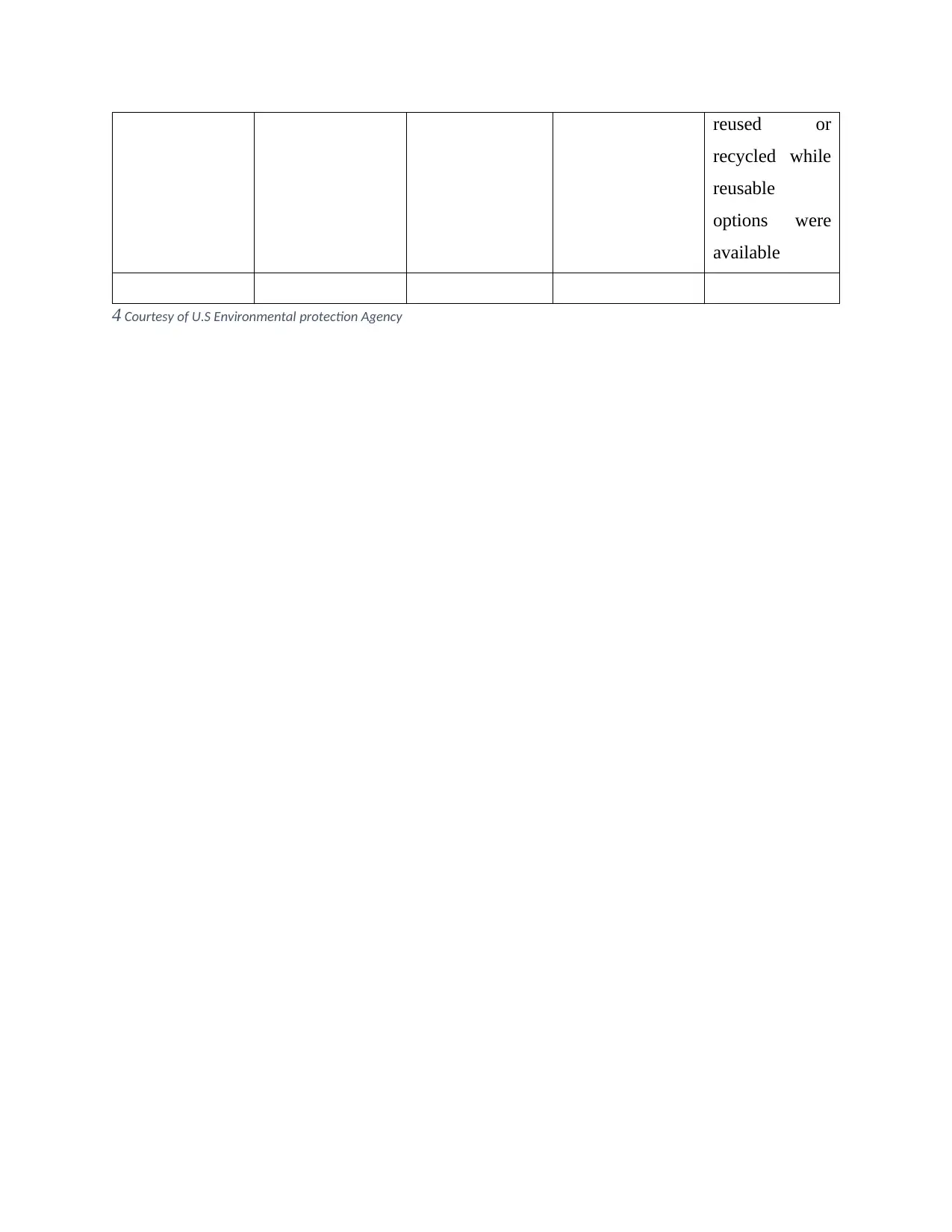
recycled while
reusable
options were
available
4 Courtesy of U.S Environmental protection Agency
⊘ This is a preview!⊘
Do you want full access?
Subscribe today to unlock all pages.

Trusted by 1+ million students worldwide
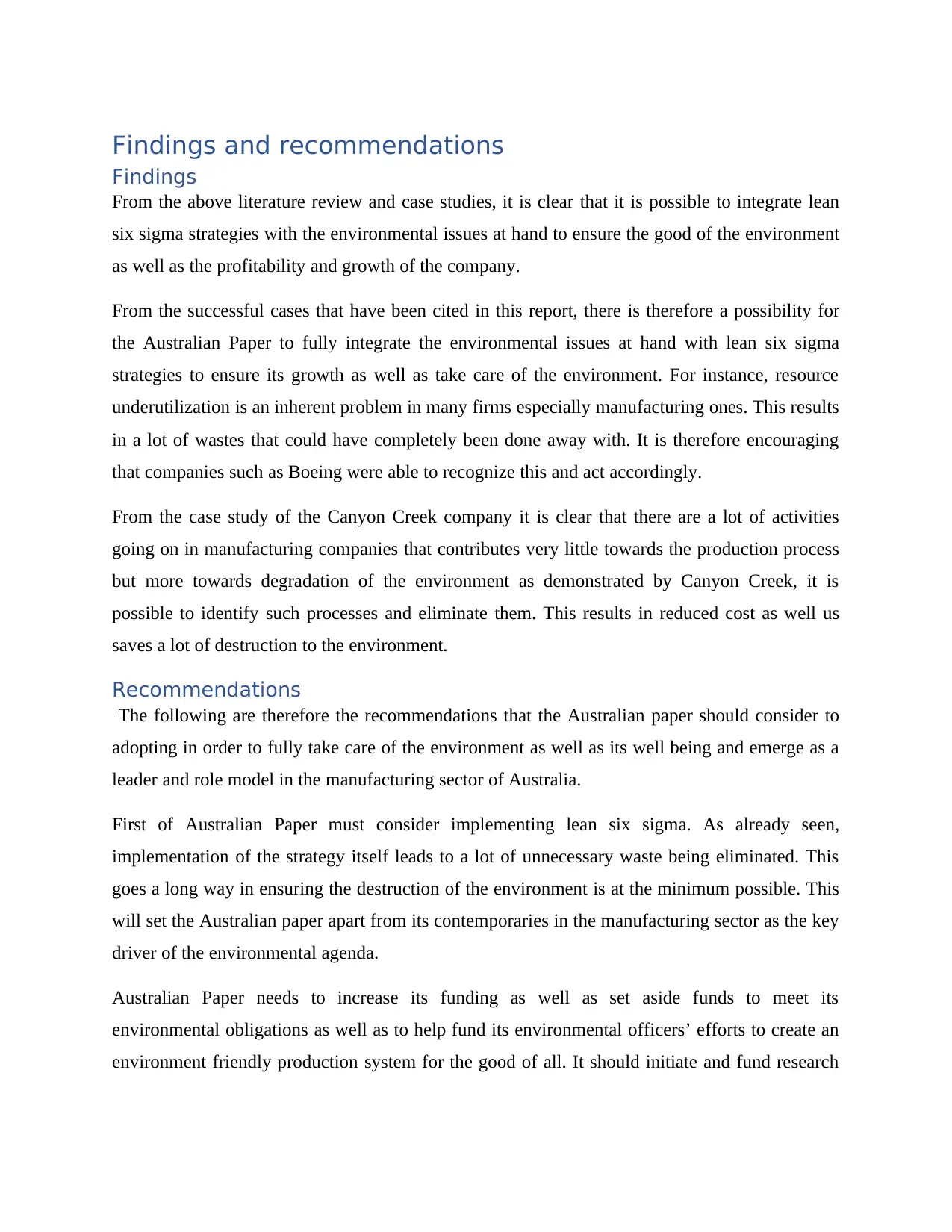
Findings
From the above literature review and case studies, it is clear that it is possible to integrate lean
six sigma strategies with the environmental issues at hand to ensure the good of the environment
as well as the profitability and growth of the company.
From the successful cases that have been cited in this report, there is therefore a possibility for
the Australian Paper to fully integrate the environmental issues at hand with lean six sigma
strategies to ensure its growth as well as take care of the environment. For instance, resource
underutilization is an inherent problem in many firms especially manufacturing ones. This results
in a lot of wastes that could have completely been done away with. It is therefore encouraging
that companies such as Boeing were able to recognize this and act accordingly.
From the case study of the Canyon Creek company it is clear that there are a lot of activities
going on in manufacturing companies that contributes very little towards the production process
but more towards degradation of the environment as demonstrated by Canyon Creek, it is
possible to identify such processes and eliminate them. This results in reduced cost as well us
saves a lot of destruction to the environment.
Recommendations
The following are therefore the recommendations that the Australian paper should consider to
adopting in order to fully take care of the environment as well as its well being and emerge as a
leader and role model in the manufacturing sector of Australia.
First of Australian Paper must consider implementing lean six sigma. As already seen,
implementation of the strategy itself leads to a lot of unnecessary waste being eliminated. This
goes a long way in ensuring the destruction of the environment is at the minimum possible. This
will set the Australian paper apart from its contemporaries in the manufacturing sector as the key
driver of the environmental agenda.
Australian Paper needs to increase its funding as well as set aside funds to meet its
environmental obligations as well as to help fund its environmental officers’ efforts to create an
environment friendly production system for the good of all. It should initiate and fund research
Paraphrase This Document
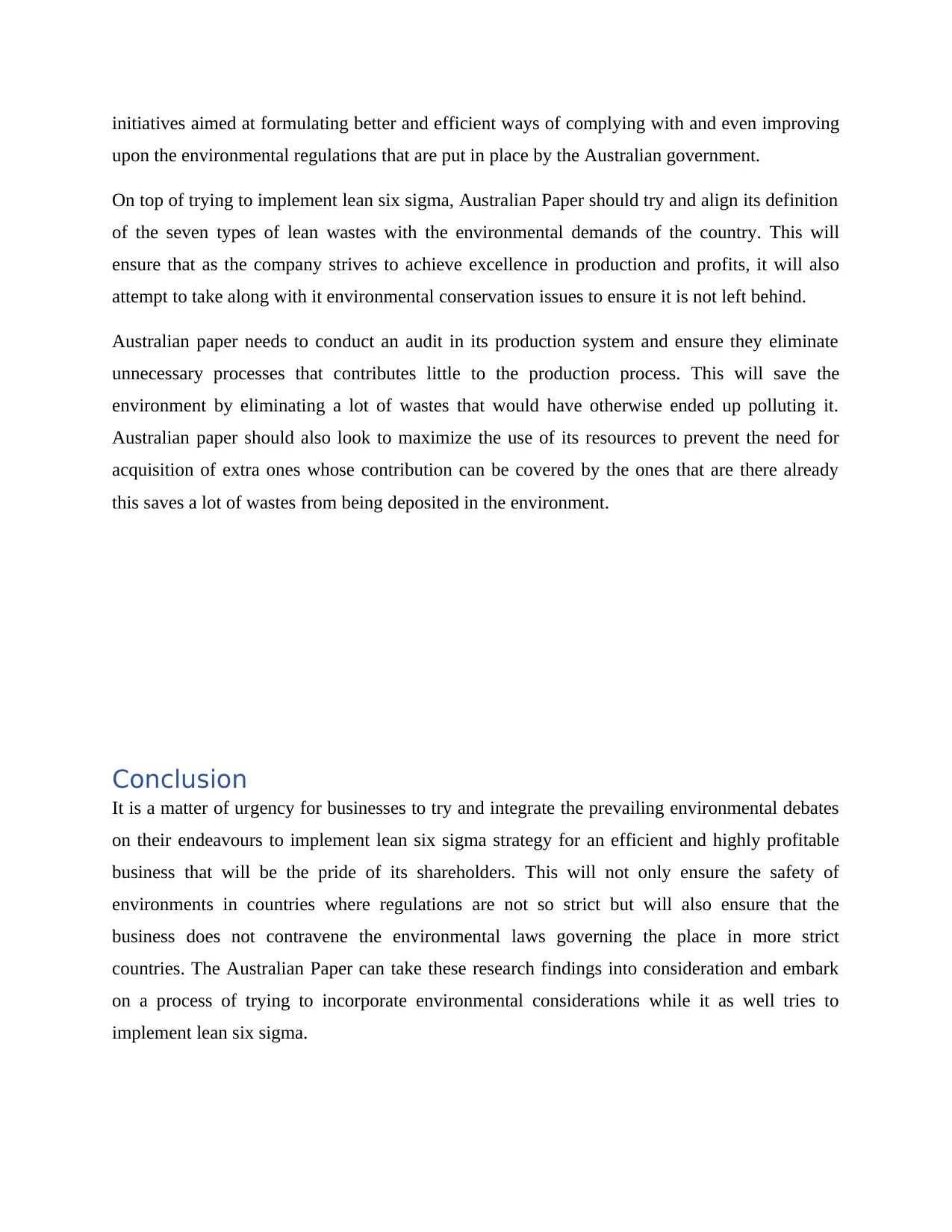
upon the environmental regulations that are put in place by the Australian government.
On top of trying to implement lean six sigma, Australian Paper should try and align its definition
of the seven types of lean wastes with the environmental demands of the country. This will
ensure that as the company strives to achieve excellence in production and profits, it will also
attempt to take along with it environmental conservation issues to ensure it is not left behind.
Australian paper needs to conduct an audit in its production system and ensure they eliminate
unnecessary processes that contributes little to the production process. This will save the
environment by eliminating a lot of wastes that would have otherwise ended up polluting it.
Australian paper should also look to maximize the use of its resources to prevent the need for
acquisition of extra ones whose contribution can be covered by the ones that are there already
this saves a lot of wastes from being deposited in the environment.
Conclusion
It is a matter of urgency for businesses to try and integrate the prevailing environmental debates
on their endeavours to implement lean six sigma strategy for an efficient and highly profitable
business that will be the pride of its shareholders. This will not only ensure the safety of
environments in countries where regulations are not so strict but will also ensure that the
business does not contravene the environmental laws governing the place in more strict
countries. The Australian Paper can take these research findings into consideration and embark
on a process of trying to incorporate environmental considerations while it as well tries to
implement lean six sigma.
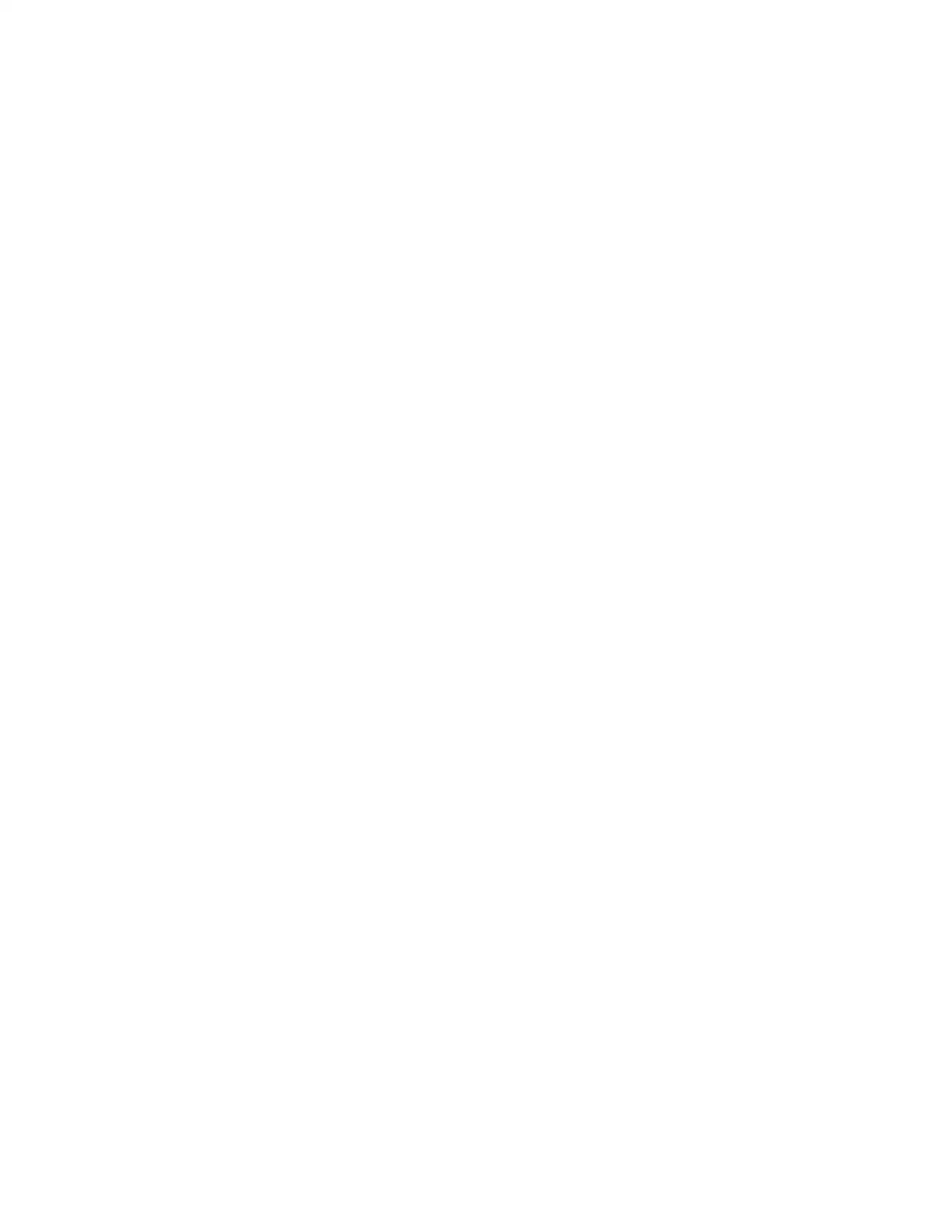
⊘ This is a preview!⊘
Do you want full access?
Subscribe today to unlock all pages.

Trusted by 1+ million students worldwide
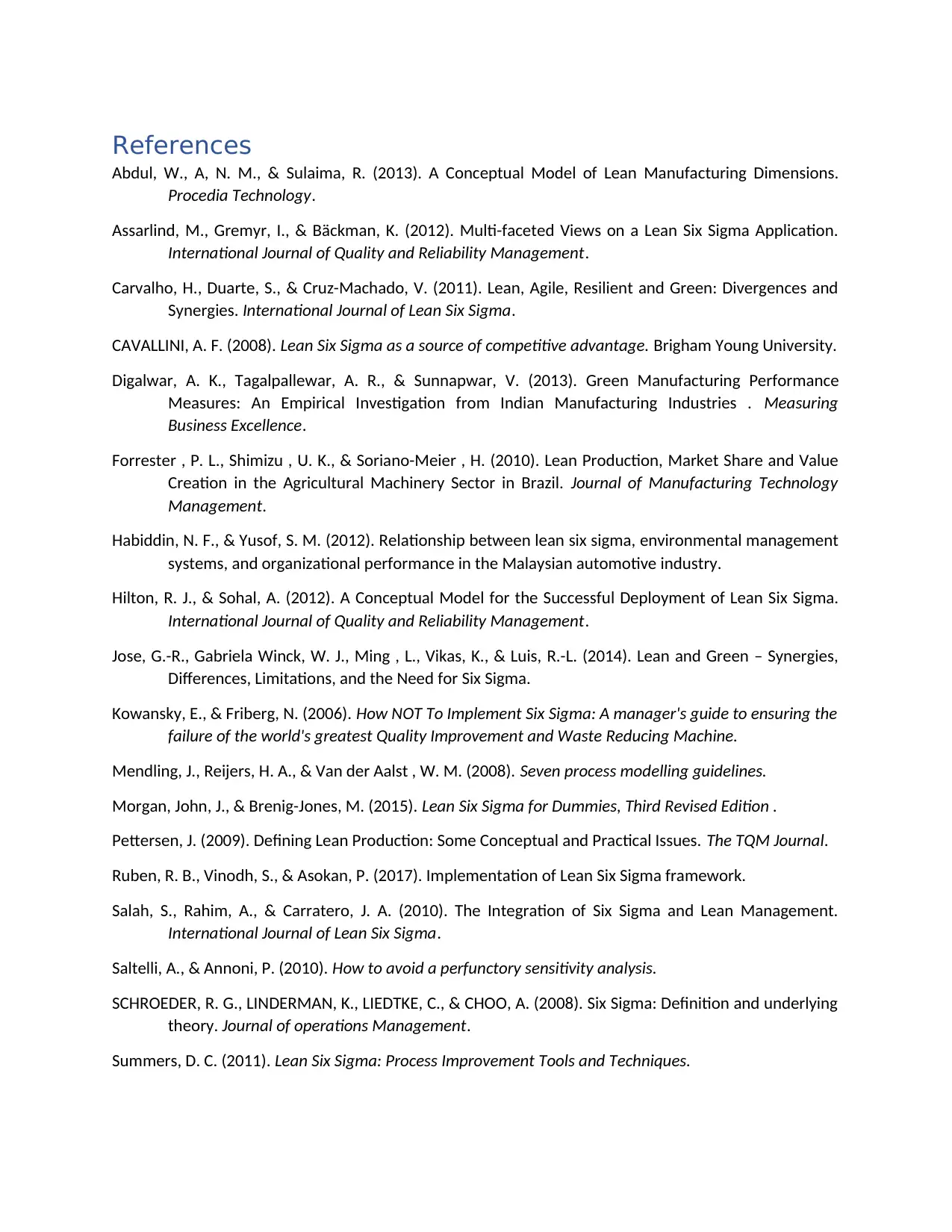
Abdul, W., A, N. M., & Sulaima, R. (2013). A Conceptual Model of Lean Manufacturing Dimensions.
Procedia Technology.
Assarlind, M., Gremyr, I., & Bäckman, K. (2012). Multi-faceted Views on a Lean Six Sigma Application.
International Journal of Quality and Reliability Management.
Carvalho, H., Duarte, S., & Cruz-Machado, V. (2011). Lean, Agile, Resilient and Green: Divergences and
Synergies. International Journal of Lean Six Sigma.
CAVALLINI, A. F. (2008). Lean Six Sigma as a source of competitive advantage. Brigham Young University.
Digalwar, A. K., Tagalpallewar, A. R., & Sunnapwar, V. (2013). Green Manufacturing Performance
Measures: An Empirical Investigation from Indian Manufacturing Industries . Measuring
Business Excellence.
Forrester , P. L., Shimizu , U. K., & Soriano-Meier , H. (2010). Lean Production, Market Share and Value
Creation in the Agricultural Machinery Sector in Brazil. Journal of Manufacturing Technology
Management.
Habiddin, N. F., & Yusof, S. M. (2012). Relationship between lean six sigma, environmental management
systems, and organizational performance in the Malaysian automotive industry.
Hilton, R. J., & Sohal, A. (2012). A Conceptual Model for the Successful Deployment of Lean Six Sigma.
International Journal of Quality and Reliability Management.
Jose, G.-R., Gabriela Winck, W. J., Ming , L., Vikas, K., & Luis, R.-L. (2014). Lean and Green – Synergies,
Differences, Limitations, and the Need for Six Sigma.
Kowansky, E., & Friberg, N. (2006). How NOT To Implement Six Sigma: A manager's guide to ensuring the
failure of the world's greatest Quality Improvement and Waste Reducing Machine.
Mendling, J., Reijers, H. A., & Van der Aalst , W. M. (2008). Seven process modelling guidelines.
Morgan, John, J., & Brenig-Jones, M. (2015). Lean Six Sigma for Dummies, Third Revised Edition .
Pettersen, J. (2009). Defining Lean Production: Some Conceptual and Practical Issues. The TQM Journal.
Ruben, R. B., Vinodh, S., & Asokan, P. (2017). Implementation of Lean Six Sigma framework.
Salah, S., Rahim, A., & Carratero, J. A. (2010). The Integration of Six Sigma and Lean Management.
International Journal of Lean Six Sigma.
Saltelli, A., & Annoni, P. (2010). How to avoid a perfunctory sensitivity analysis.
SCHROEDER, R. G., LINDERMAN, K., LIEDTKE, C., & CHOO, A. (2008). Six Sigma: Definition and underlying
theory. Journal of operations Management.
Summers, D. C. (2011). Lean Six Sigma: Process Improvement Tools and Techniques.
Paraphrase This Document
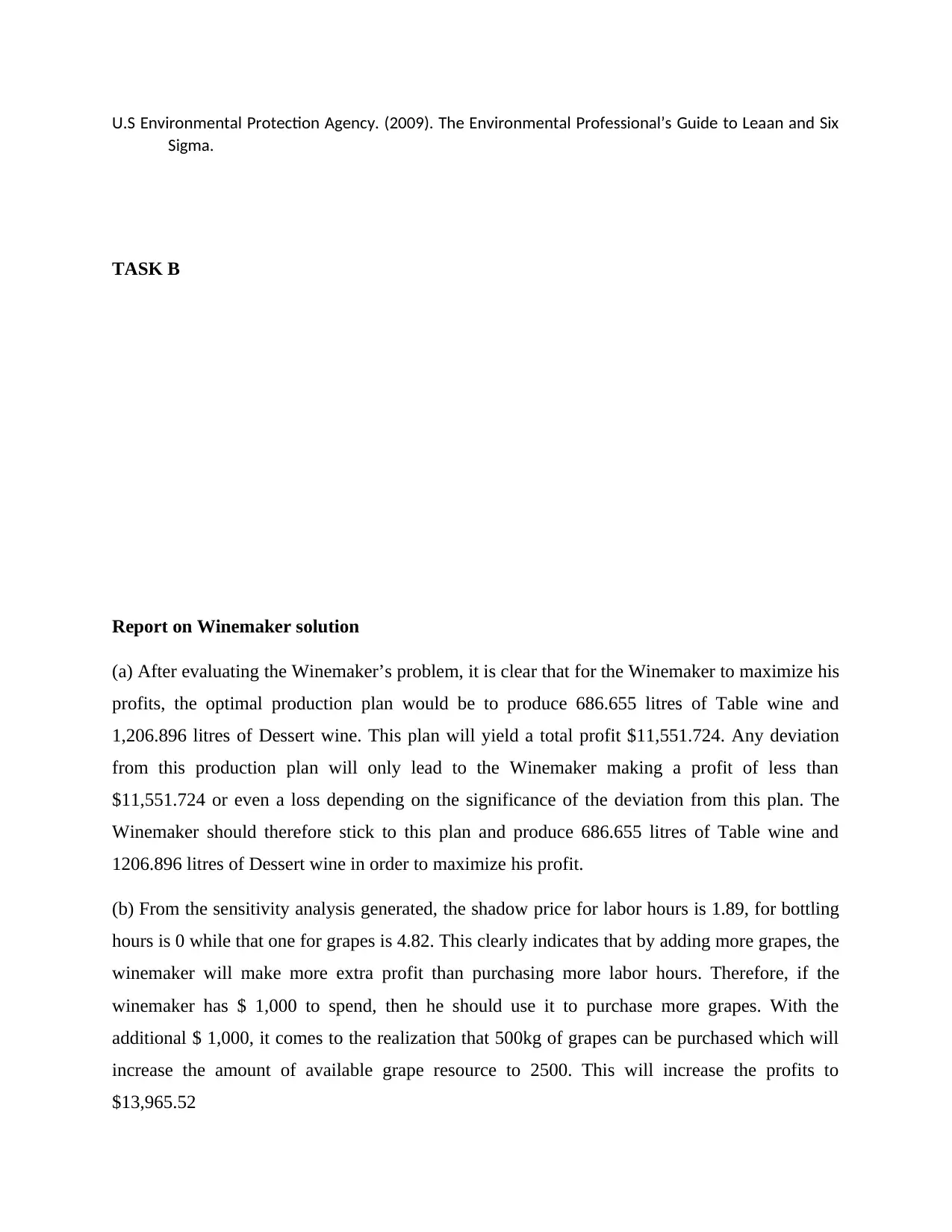
Sigma.
TASK B
Report on Winemaker solution
(a) After evaluating the Winemaker’s problem, it is clear that for the Winemaker to maximize his
profits, the optimal production plan would be to produce 686.655 litres of Table wine and
1,206.896 litres of Dessert wine. This plan will yield a total profit $11,551.724. Any deviation
from this production plan will only lead to the Winemaker making a profit of less than
$11,551.724 or even a loss depending on the significance of the deviation from this plan. The
Winemaker should therefore stick to this plan and produce 686.655 litres of Table wine and
1206.896 litres of Dessert wine in order to maximize his profit.
(b) From the sensitivity analysis generated, the shadow price for labor hours is 1.89, for bottling
hours is 0 while that one for grapes is 4.82. This clearly indicates that by adding more grapes, the
winemaker will make more extra profit than purchasing more labor hours. Therefore, if the
winemaker has $ 1,000 to spend, then he should use it to purchase more grapes. With the
additional $ 1,000, it comes to the realization that 500kg of grapes can be purchased which will
increase the amount of available grape resource to 2500. This will increase the profits to
$13,965.52

litres for Dessert wine, The Winemaker cannot afford to produce 686.655 litres of Table wine
and 1206.896 litres of Dessert wine as this will result in losses because some litres of wine will
not be sold. After factoring in this new information and using it in the maximization problem for
the Winemaker it comes to the realization that the Winemaker should produce 600 litres Table
wine and also 600 litres of Dessert wine because this is the production plan that will lead to a
maximum possible profit of $7,800. Any other production plan will likely lead to profits but not
the maximum.
(d) If the Winemaker were to concentrate on producing only one type of wine with the promise
that the market demand for that particular type of wine will tripple, then he should concentrate
on producing table wine. This is because production of table wine alone with the available
resources leads to a profit of $10,667. If the Winemaker were to concentrate on producing
Dessert wine, he would only make a profit of $8,333. This is clearly less than the profit of
$10,667 that he would obtain from production of Table wine. Since the Winemaker is looking to
maximize his profit, he should therefore choose a production plan that ensures that he actually
maximizes the said profits. This production plan turns out to be the production of Table wine.
Methods
Seven step modelling process
Where the objective function is first defined, followed by gathering the data (data was already
provided in this case), data is the prepared for modelling, then variables are selected and
transformed, then the model is processed and evaluated then validated and finally implemented.
The purpose of this report is to provide a recommendation on the final step, that is
implementation of the model to the company (Mendling, Reijers, & Van der Aalst , 2008). All
the other six parts have been done in the excel sheet that will accompany this report
Sensitivity analysis
⊘ This is a preview!⊘
Do you want full access?
Subscribe today to unlock all pages.

Trusted by 1+ million students worldwide
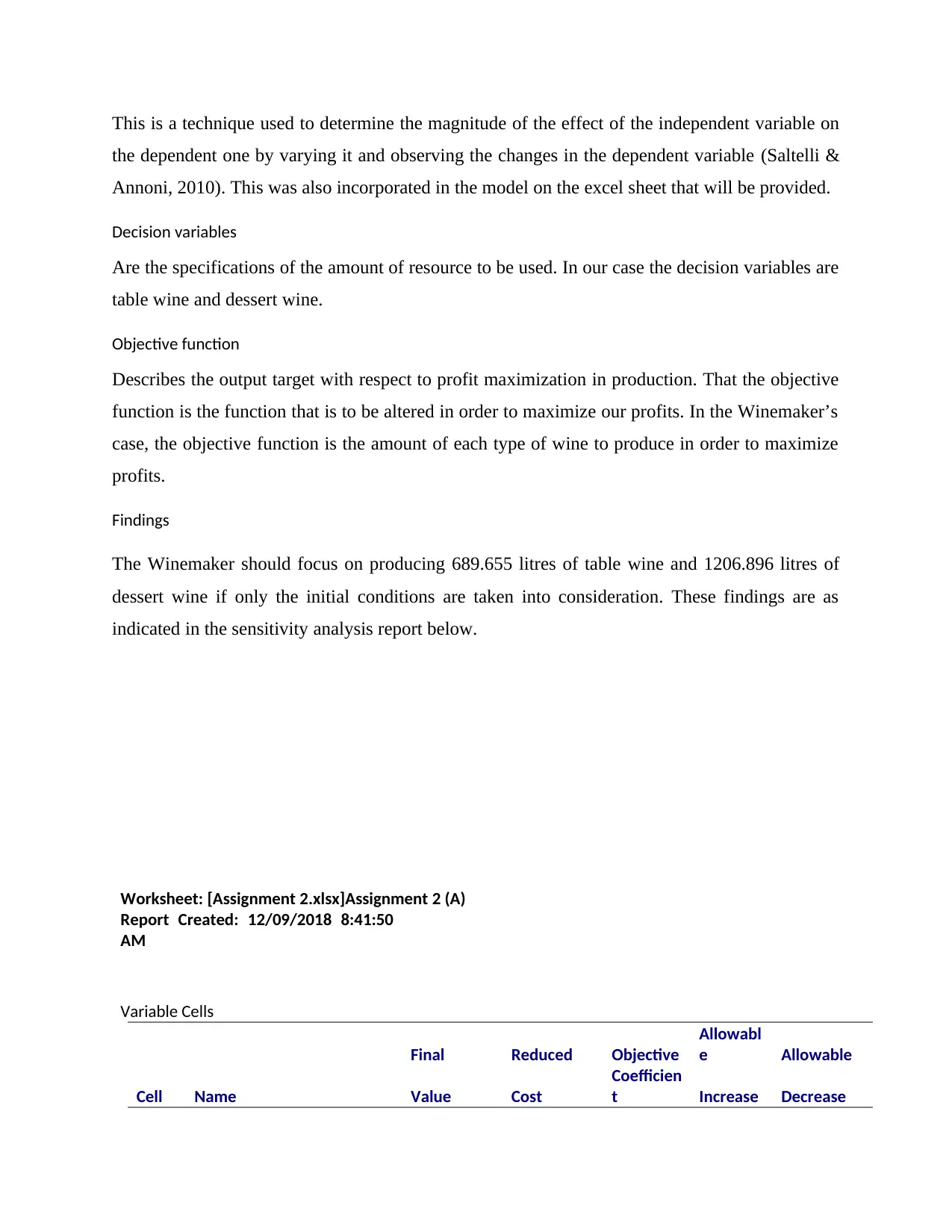
the dependent one by varying it and observing the changes in the dependent variable (Saltelli &
Annoni, 2010). This was also incorporated in the model on the excel sheet that will be provided.
Decision variables
Are the specifications of the amount of resource to be used. In our case the decision variables are
table wine and dessert wine.
Objective function
Describes the output target with respect to profit maximization in production. That the objective
function is the function that is to be altered in order to maximize our profits. In the Winemaker’s
case, the objective function is the amount of each type of wine to produce in order to maximize
profits.
Findings
The Winemaker should focus on producing 689.655 litres of table wine and 1206.896 litres of
dessert wine if only the initial conditions are taken into consideration. These findings are as
indicated in the sensitivity analysis report below.
Worksheet: [Assignment 2.xlsx]Assignment 2 (A)
Report Created: 12/09/2018 8:41:50
AM
Variable Cells
Final Reduced Objective
Allowabl
e Allowable
Cell Name Value Cost
Coefficien
t Increase Decrease
Paraphrase This Document
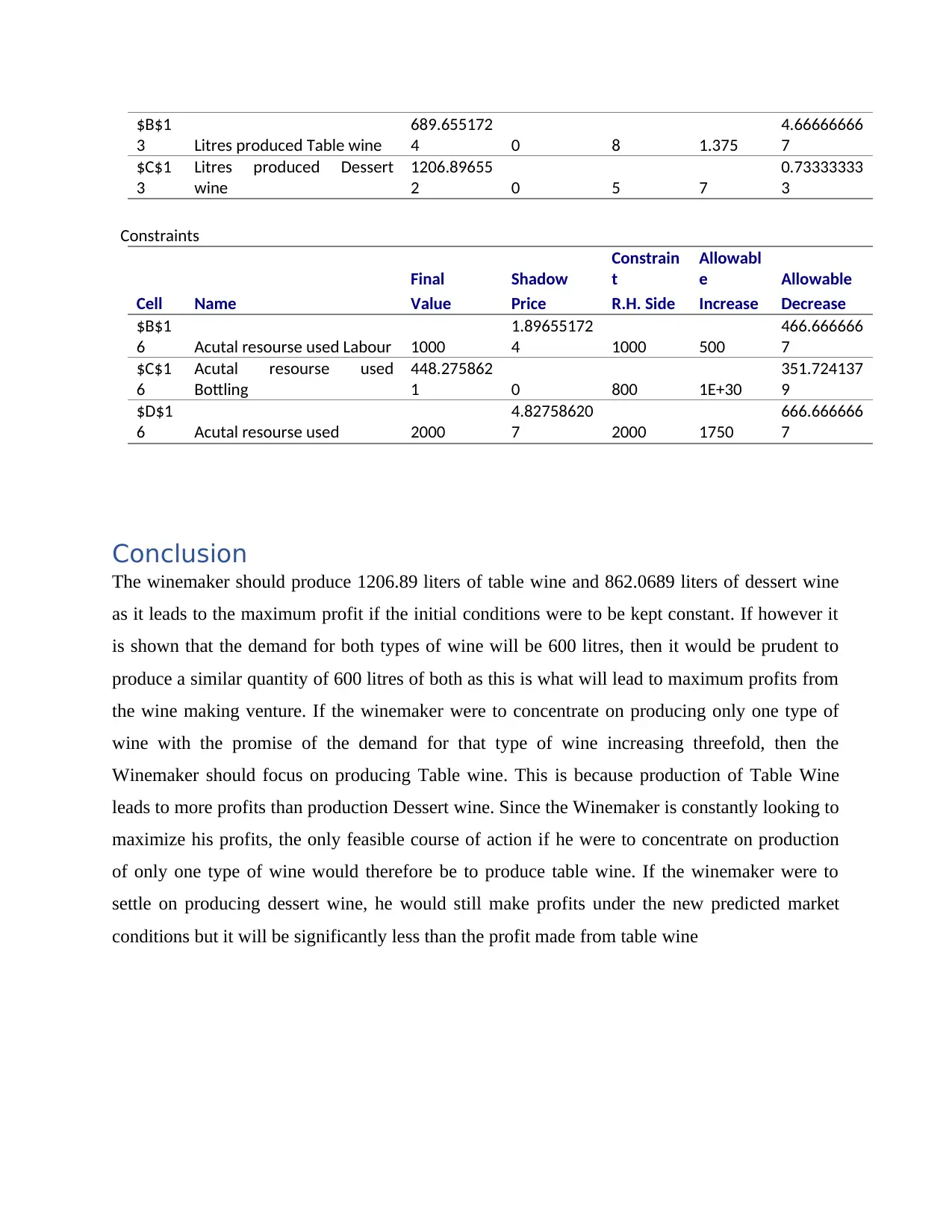
3 Litres produced Table wine
689.655172
4 0 8 1.375
4.66666666
7
$C$1
3
Litres produced Dessert
wine
1206.89655
2 0 5 7
0.73333333
3
Constraints
Final Shadow
Constrain
t
Allowabl
e Allowable
Cell Name Value Price R.H. Side Increase Decrease
$B$1
6 Acutal resourse used Labour 1000
1.89655172
4 1000 500
466.666666
7
$C$1
6
Acutal resourse used
Bottling
448.275862
1 0 800 1E+30
351.724137
9
$D$1
6 Acutal resourse used 2000
4.82758620
7 2000 1750
666.666666
7
Conclusion
The winemaker should produce 1206.89 liters of table wine and 862.0689 liters of dessert wine
as it leads to the maximum profit if the initial conditions were to be kept constant. If however it
is shown that the demand for both types of wine will be 600 litres, then it would be prudent to
produce a similar quantity of 600 litres of both as this is what will lead to maximum profits from
the wine making venture. If the winemaker were to concentrate on producing only one type of
wine with the promise of the demand for that type of wine increasing threefold, then the
Winemaker should focus on producing Table wine. This is because production of Table Wine
leads to more profits than production Dessert wine. Since the Winemaker is constantly looking to
maximize his profits, the only feasible course of action if he were to concentrate on production
of only one type of wine would therefore be to produce table wine. If the winemaker were to
settle on producing dessert wine, he would still make profits under the new predicted market
conditions but it will be significantly less than the profit made from table wine
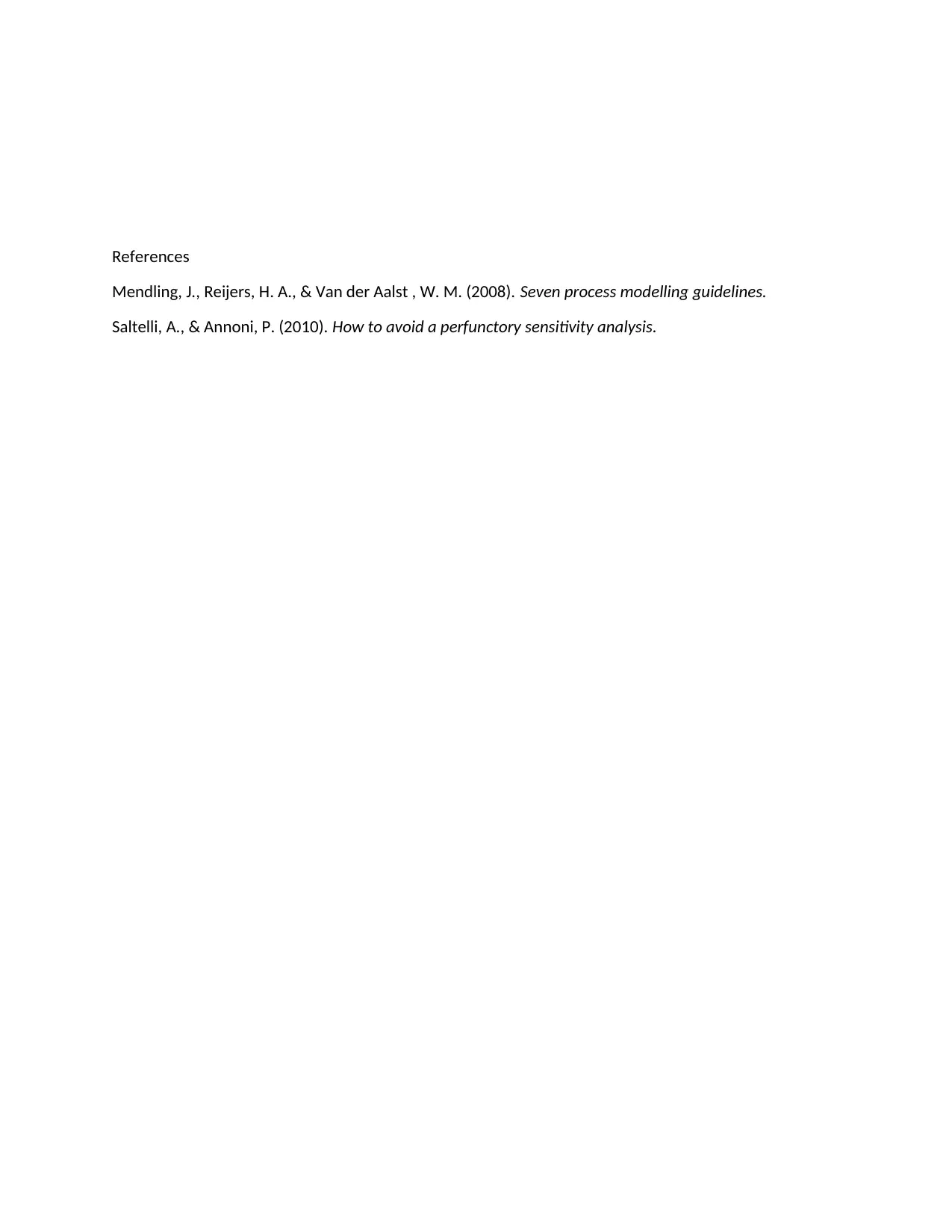
Mendling, J., Reijers, H. A., & Van der Aalst , W. M. (2008). Seven process modelling guidelines.
Saltelli, A., & Annoni, P. (2010). How to avoid a perfunctory sensitivity analysis.
⊘ This is a preview!⊘
Do you want full access?
Subscribe today to unlock all pages.

Trusted by 1+ million students worldwide
Related Documents

Your All-in-One AI-Powered Toolkit for Academic Success.
+13062052269
info@desklib.com
Available 24*7 on WhatsApp / Email
© 2024 | Zucol Services PVT LTD | All rights reserved.