Load Moment Indicator System with Sensor Model in Crane
VerifiedAdded on 2022/09/01
|8
|2428
|34
AI Summary
Contribute Materials
Your contribution can guide someone’s learning journey. Share your
documents today.
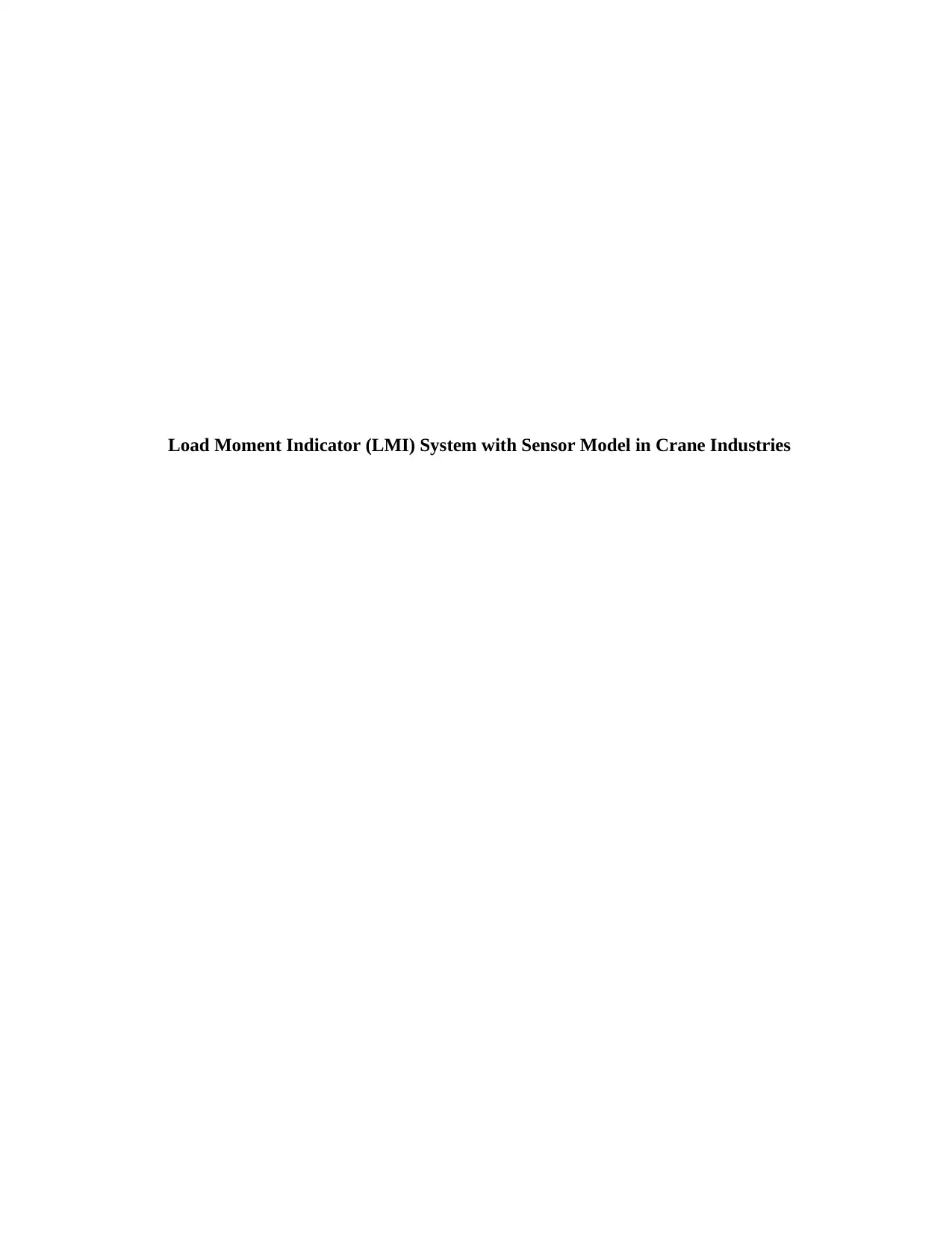
Load Moment Indicator (LMI) System with Sensor Model in Crane Industries
Secure Best Marks with AI Grader
Need help grading? Try our AI Grader for instant feedback on your assignments.
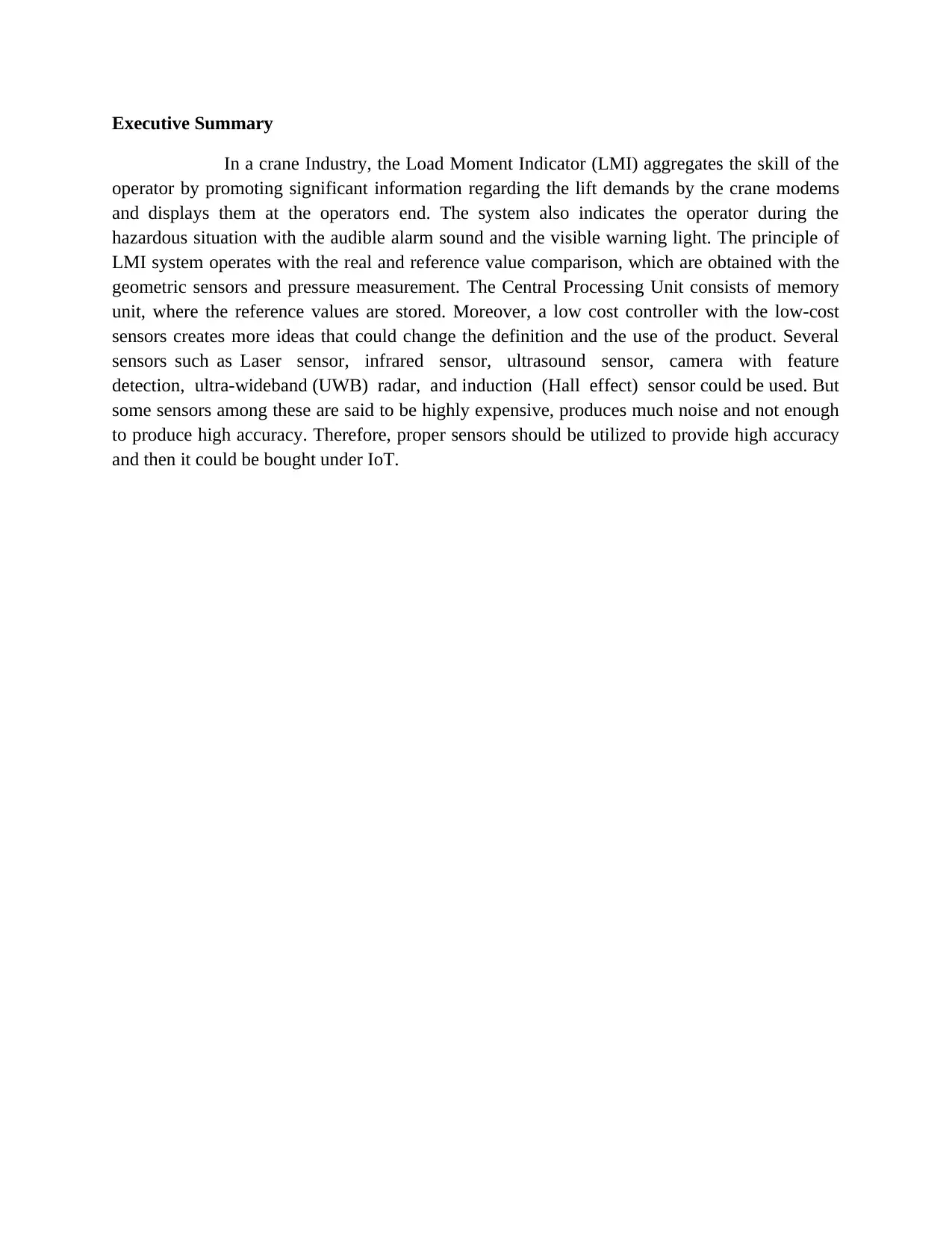
Executive Summary
In a crane Industry, the Load Moment Indicator (LMI) aggregates the skill of the
operator by promoting significant information regarding the lift demands by the crane modems
and displays them at the operators end. The system also indicates the operator during the
hazardous situation with the audible alarm sound and the visible warning light. The principle of
LMI system operates with the real and reference value comparison, which are obtained with the
geometric sensors and pressure measurement. The Central Processing Unit consists of memory
unit, where the reference values are stored. Moreover, a low cost controller with the low-cost
sensors creates more ideas that could change the definition and the use of the product. Several
sensors such as Laser sensor, infrared sensor, ultrasound sensor, camera with feature
detection, ultra-wideband (UWB) radar, and induction (Hall effect) sensor could be used. But
some sensors among these are said to be highly expensive, produces much noise and not enough
to produce high accuracy. Therefore, proper sensors should be utilized to provide high accuracy
and then it could be bought under IoT.
In a crane Industry, the Load Moment Indicator (LMI) aggregates the skill of the
operator by promoting significant information regarding the lift demands by the crane modems
and displays them at the operators end. The system also indicates the operator during the
hazardous situation with the audible alarm sound and the visible warning light. The principle of
LMI system operates with the real and reference value comparison, which are obtained with the
geometric sensors and pressure measurement. The Central Processing Unit consists of memory
unit, where the reference values are stored. Moreover, a low cost controller with the low-cost
sensors creates more ideas that could change the definition and the use of the product. Several
sensors such as Laser sensor, infrared sensor, ultrasound sensor, camera with feature
detection, ultra-wideband (UWB) radar, and induction (Hall effect) sensor could be used. But
some sensors among these are said to be highly expensive, produces much noise and not enough
to produce high accuracy. Therefore, proper sensors should be utilized to provide high accuracy
and then it could be bought under IoT.
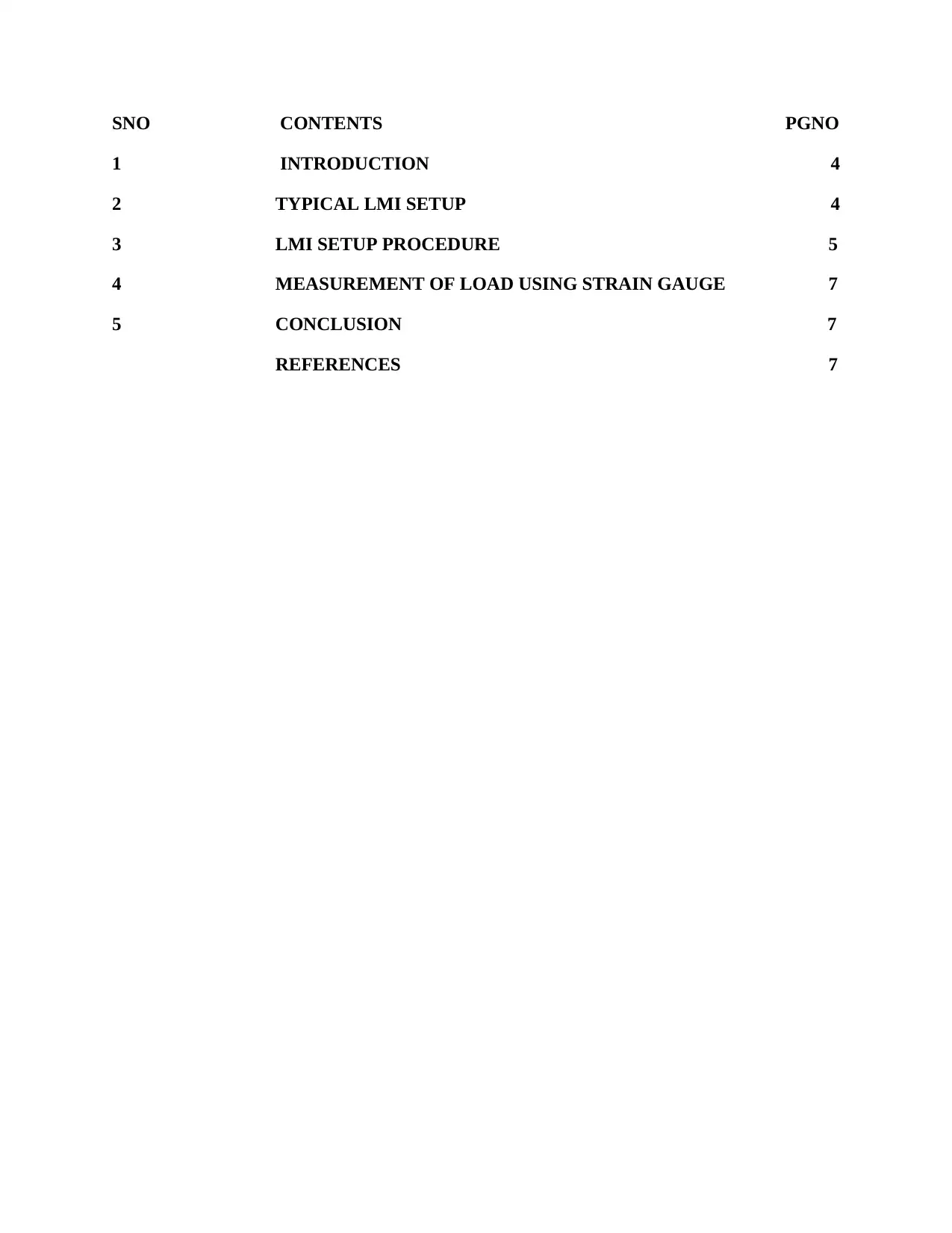
SNO CONTENTS PGNO
1 INTRODUCTION 4
2 TYPICAL LMI SETUP 4
3 LMI SETUP PROCEDURE 5
4 MEASUREMENT OF LOAD USING STRAIN GAUGE 7
5 CONCLUSION 7
REFERENCES 7
1 INTRODUCTION 4
2 TYPICAL LMI SETUP 4
3 LMI SETUP PROCEDURE 5
4 MEASUREMENT OF LOAD USING STRAIN GAUGE 7
5 CONCLUSION 7
REFERENCES 7
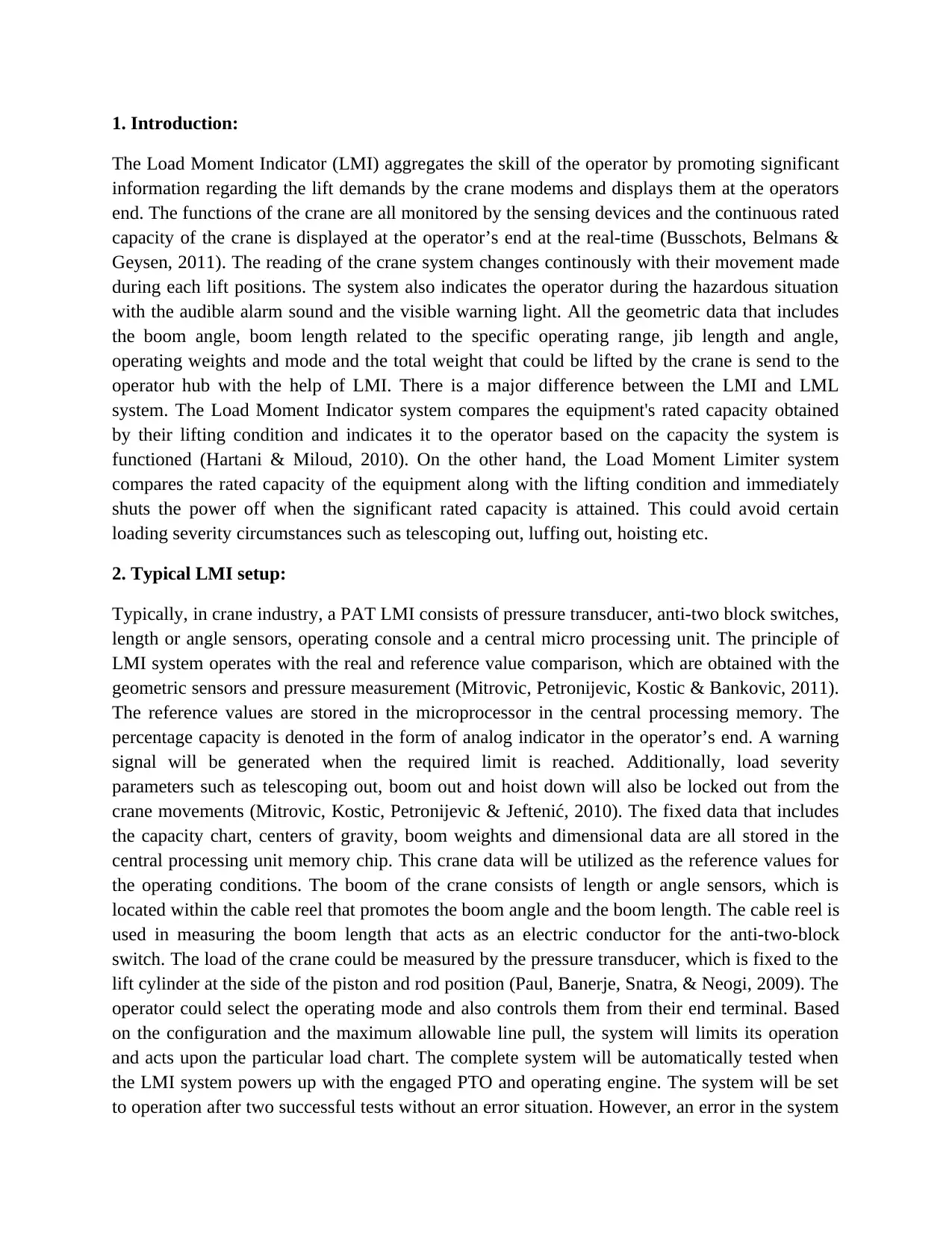
1. Introduction:
The Load Moment Indicator (LMI) aggregates the skill of the operator by promoting significant
information regarding the lift demands by the crane modems and displays them at the operators
end. The functions of the crane are all monitored by the sensing devices and the continuous rated
capacity of the crane is displayed at the operator’s end at the real-time (Busschots, Belmans &
Geysen, 2011). The reading of the crane system changes continously with their movement made
during each lift positions. The system also indicates the operator during the hazardous situation
with the audible alarm sound and the visible warning light. All the geometric data that includes
the boom angle, boom length related to the specific operating range, jib length and angle,
operating weights and mode and the total weight that could be lifted by the crane is send to the
operator hub with the help of LMI. There is a major difference between the LMI and LML
system. The Load Moment Indicator system compares the equipment's rated capacity obtained
by their lifting condition and indicates it to the operator based on the capacity the system is
functioned (Hartani & Miloud, 2010). On the other hand, the Load Moment Limiter system
compares the rated capacity of the equipment along with the lifting condition and immediately
shuts the power off when the significant rated capacity is attained. This could avoid certain
loading severity circumstances such as telescoping out, luffing out, hoisting etc.
2. Typical LMI setup:
Typically, in crane industry, a PAT LMI consists of pressure transducer, anti-two block switches,
length or angle sensors, operating console and a central micro processing unit. The principle of
LMI system operates with the real and reference value comparison, which are obtained with the
geometric sensors and pressure measurement (Mitrovic, Petronijevic, Kostic & Bankovic, 2011).
The reference values are stored in the microprocessor in the central processing memory. The
percentage capacity is denoted in the form of analog indicator in the operator’s end. A warning
signal will be generated when the required limit is reached. Additionally, load severity
parameters such as telescoping out, boom out and hoist down will also be locked out from the
crane movements (Mitrovic, Kostic, Petronijevic & Jeftenić, 2010). The fixed data that includes
the capacity chart, centers of gravity, boom weights and dimensional data are all stored in the
central processing unit memory chip. This crane data will be utilized as the reference values for
the operating conditions. The boom of the crane consists of length or angle sensors, which is
located within the cable reel that promotes the boom angle and the boom length. The cable reel is
used in measuring the boom length that acts as an electric conductor for the anti-two-block
switch. The load of the crane could be measured by the pressure transducer, which is fixed to the
lift cylinder at the side of the piston and rod position (Paul, Banerje, Snatra, & Neogi, 2009). The
operator could select the operating mode and also controls them from their end terminal. Based
on the configuration and the maximum allowable line pull, the system will limits its operation
and acts upon the particular load chart. The complete system will be automatically tested when
the LMI system powers up with the engaged PTO and operating engine. The system will be set
to operation after two successful tests without an error situation. However, an error in the system
The Load Moment Indicator (LMI) aggregates the skill of the operator by promoting significant
information regarding the lift demands by the crane modems and displays them at the operators
end. The functions of the crane are all monitored by the sensing devices and the continuous rated
capacity of the crane is displayed at the operator’s end at the real-time (Busschots, Belmans &
Geysen, 2011). The reading of the crane system changes continously with their movement made
during each lift positions. The system also indicates the operator during the hazardous situation
with the audible alarm sound and the visible warning light. All the geometric data that includes
the boom angle, boom length related to the specific operating range, jib length and angle,
operating weights and mode and the total weight that could be lifted by the crane is send to the
operator hub with the help of LMI. There is a major difference between the LMI and LML
system. The Load Moment Indicator system compares the equipment's rated capacity obtained
by their lifting condition and indicates it to the operator based on the capacity the system is
functioned (Hartani & Miloud, 2010). On the other hand, the Load Moment Limiter system
compares the rated capacity of the equipment along with the lifting condition and immediately
shuts the power off when the significant rated capacity is attained. This could avoid certain
loading severity circumstances such as telescoping out, luffing out, hoisting etc.
2. Typical LMI setup:
Typically, in crane industry, a PAT LMI consists of pressure transducer, anti-two block switches,
length or angle sensors, operating console and a central micro processing unit. The principle of
LMI system operates with the real and reference value comparison, which are obtained with the
geometric sensors and pressure measurement (Mitrovic, Petronijevic, Kostic & Bankovic, 2011).
The reference values are stored in the microprocessor in the central processing memory. The
percentage capacity is denoted in the form of analog indicator in the operator’s end. A warning
signal will be generated when the required limit is reached. Additionally, load severity
parameters such as telescoping out, boom out and hoist down will also be locked out from the
crane movements (Mitrovic, Kostic, Petronijevic & Jeftenić, 2010). The fixed data that includes
the capacity chart, centers of gravity, boom weights and dimensional data are all stored in the
central processing unit memory chip. This crane data will be utilized as the reference values for
the operating conditions. The boom of the crane consists of length or angle sensors, which is
located within the cable reel that promotes the boom angle and the boom length. The cable reel is
used in measuring the boom length that acts as an electric conductor for the anti-two-block
switch. The load of the crane could be measured by the pressure transducer, which is fixed to the
lift cylinder at the side of the piston and rod position (Paul, Banerje, Snatra, & Neogi, 2009). The
operator could select the operating mode and also controls them from their end terminal. Based
on the configuration and the maximum allowable line pull, the system will limits its operation
and acts upon the particular load chart. The complete system will be automatically tested when
the LMI system powers up with the engaged PTO and operating engine. The system will be set
to operation after two successful tests without an error situation. However, an error in the system
Secure Best Marks with AI Grader
Need help grading? Try our AI Grader for instant feedback on your assignments.
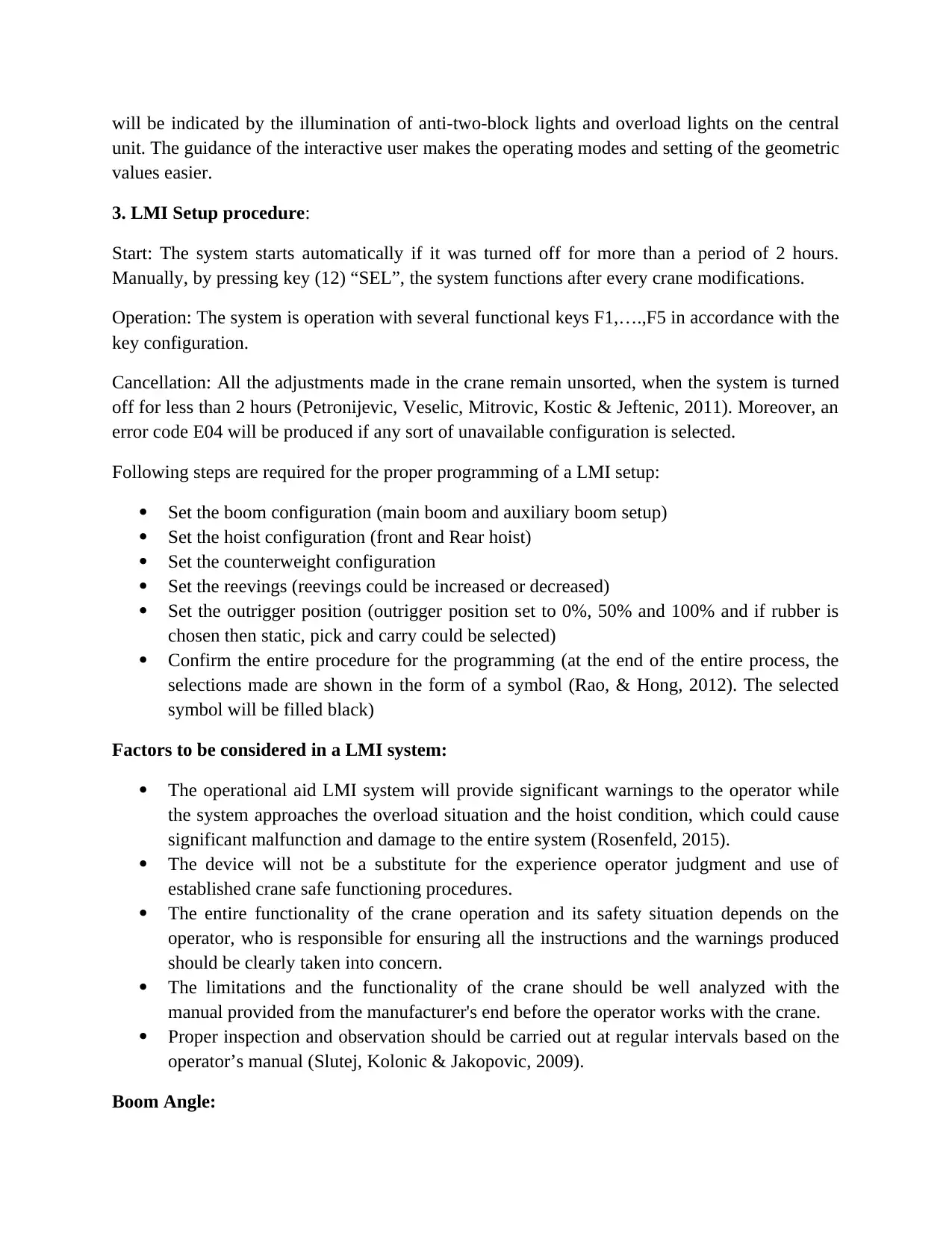
will be indicated by the illumination of anti-two-block lights and overload lights on the central
unit. The guidance of the interactive user makes the operating modes and setting of the geometric
values easier.
3. LMI Setup procedure:
Start: The system starts automatically if it was turned off for more than a period of 2 hours.
Manually, by pressing key (12) “SEL”, the system functions after every crane modifications.
Operation: The system is operation with several functional keys F1,….,F5 in accordance with the
key configuration.
Cancellation: All the adjustments made in the crane remain unsorted, when the system is turned
off for less than 2 hours (Petronijevic, Veselic, Mitrovic, Kostic & Jeftenic, 2011). Moreover, an
error code E04 will be produced if any sort of unavailable configuration is selected.
Following steps are required for the proper programming of a LMI setup:
Set the boom configuration (main boom and auxiliary boom setup)
Set the hoist configuration (front and Rear hoist)
Set the counterweight configuration
Set the reevings (reevings could be increased or decreased)
Set the outrigger position (outrigger position set to 0%, 50% and 100% and if rubber is
chosen then static, pick and carry could be selected)
Confirm the entire procedure for the programming (at the end of the entire process, the
selections made are shown in the form of a symbol (Rao, & Hong, 2012). The selected
symbol will be filled black)
Factors to be considered in a LMI system:
The operational aid LMI system will provide significant warnings to the operator while
the system approaches the overload situation and the hoist condition, which could cause
significant malfunction and damage to the entire system (Rosenfeld, 2015).
The device will not be a substitute for the experience operator judgment and use of
established crane safe functioning procedures.
The entire functionality of the crane operation and its safety situation depends on the
operator, who is responsible for ensuring all the instructions and the warnings produced
should be clearly taken into concern.
The limitations and the functionality of the crane should be well analyzed with the
manual provided from the manufacturer's end before the operator works with the crane.
Proper inspection and observation should be carried out at regular intervals based on the
operator’s manual (Slutej, Kolonic & Jakopovic, 2009).
Boom Angle:
unit. The guidance of the interactive user makes the operating modes and setting of the geometric
values easier.
3. LMI Setup procedure:
Start: The system starts automatically if it was turned off for more than a period of 2 hours.
Manually, by pressing key (12) “SEL”, the system functions after every crane modifications.
Operation: The system is operation with several functional keys F1,….,F5 in accordance with the
key configuration.
Cancellation: All the adjustments made in the crane remain unsorted, when the system is turned
off for less than 2 hours (Petronijevic, Veselic, Mitrovic, Kostic & Jeftenic, 2011). Moreover, an
error code E04 will be produced if any sort of unavailable configuration is selected.
Following steps are required for the proper programming of a LMI setup:
Set the boom configuration (main boom and auxiliary boom setup)
Set the hoist configuration (front and Rear hoist)
Set the counterweight configuration
Set the reevings (reevings could be increased or decreased)
Set the outrigger position (outrigger position set to 0%, 50% and 100% and if rubber is
chosen then static, pick and carry could be selected)
Confirm the entire procedure for the programming (at the end of the entire process, the
selections made are shown in the form of a symbol (Rao, & Hong, 2012). The selected
symbol will be filled black)
Factors to be considered in a LMI system:
The operational aid LMI system will provide significant warnings to the operator while
the system approaches the overload situation and the hoist condition, which could cause
significant malfunction and damage to the entire system (Rosenfeld, 2015).
The device will not be a substitute for the experience operator judgment and use of
established crane safe functioning procedures.
The entire functionality of the crane operation and its safety situation depends on the
operator, who is responsible for ensuring all the instructions and the warnings produced
should be clearly taken into concern.
The limitations and the functionality of the crane should be well analyzed with the
manual provided from the manufacturer's end before the operator works with the crane.
Proper inspection and observation should be carried out at regular intervals based on the
operator’s manual (Slutej, Kolonic & Jakopovic, 2009).
Boom Angle:
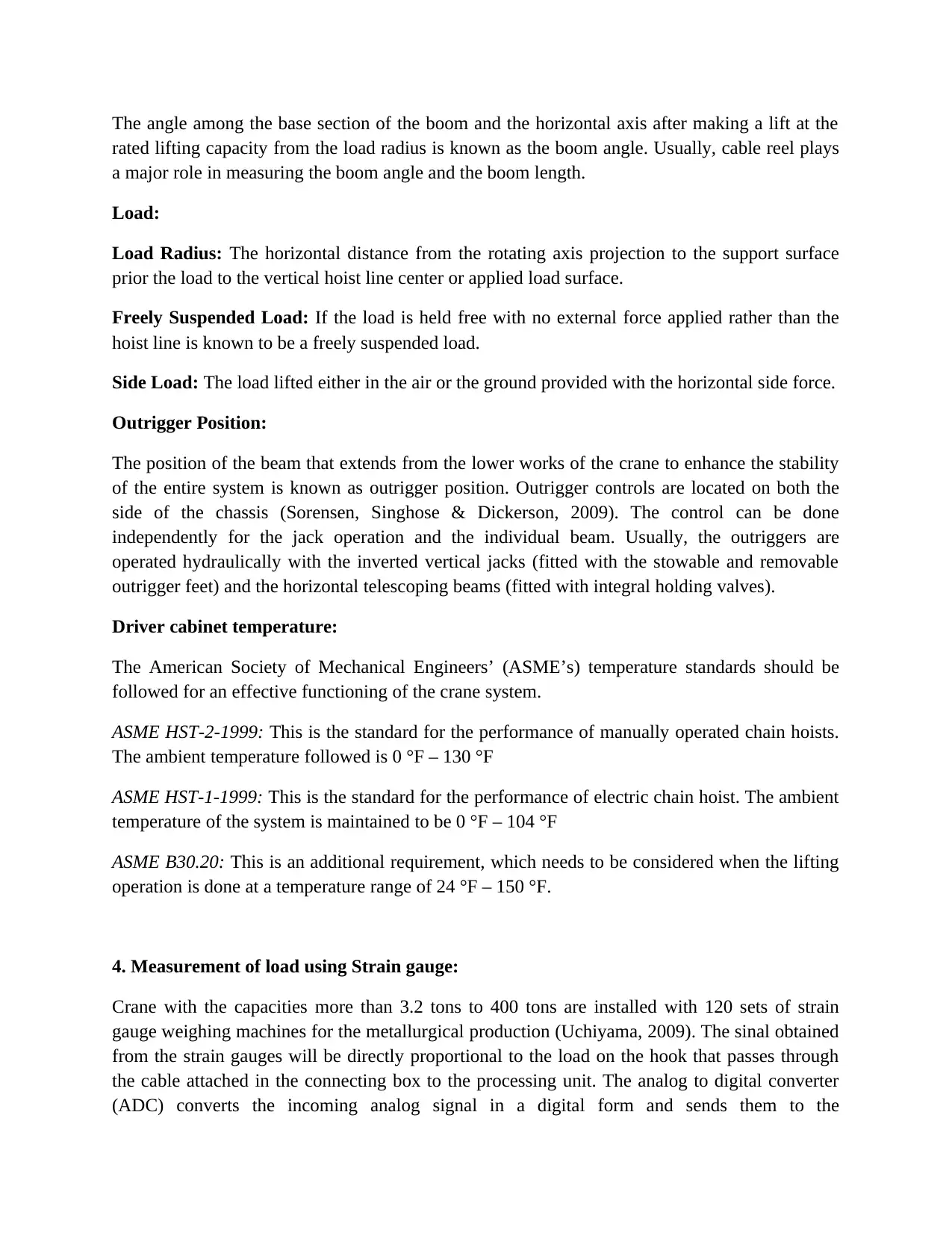
The angle among the base section of the boom and the horizontal axis after making a lift at the
rated lifting capacity from the load radius is known as the boom angle. Usually, cable reel plays
a major role in measuring the boom angle and the boom length.
Load:
Load Radius: The horizontal distance from the rotating axis projection to the support surface
prior the load to the vertical hoist line center or applied load surface.
Freely Suspended Load: If the load is held free with no external force applied rather than the
hoist line is known to be a freely suspended load.
Side Load: The load lifted either in the air or the ground provided with the horizontal side force.
Outrigger Position:
The position of the beam that extends from the lower works of the crane to enhance the stability
of the entire system is known as outrigger position. Outrigger controls are located on both the
side of the chassis (Sorensen, Singhose & Dickerson, 2009). The control can be done
independently for the jack operation and the individual beam. Usually, the outriggers are
operated hydraulically with the inverted vertical jacks (fitted with the stowable and removable
outrigger feet) and the horizontal telescoping beams (fitted with integral holding valves).
Driver cabinet temperature:
The American Society of Mechanical Engineers’ (ASME’s) temperature standards should be
followed for an effective functioning of the crane system.
ASME HST-2-1999: This is the standard for the performance of manually operated chain hoists.
The ambient temperature followed is 0 °F – 130 °F
ASME HST-1-1999: This is the standard for the performance of electric chain hoist. The ambient
temperature of the system is maintained to be 0 °F – 104 °F
ASME B30.20: This is an additional requirement, which needs to be considered when the lifting
operation is done at a temperature range of 24 °F – 150 °F.
4. Measurement of load using Strain gauge:
Crane with the capacities more than 3.2 tons to 400 tons are installed with 120 sets of strain
gauge weighing machines for the metallurgical production (Uchiyama, 2009). The sinal obtained
from the strain gauges will be directly proportional to the load on the hook that passes through
the cable attached in the connecting box to the processing unit. The analog to digital converter
(ADC) converts the incoming analog signal in a digital form and sends them to the
rated lifting capacity from the load radius is known as the boom angle. Usually, cable reel plays
a major role in measuring the boom angle and the boom length.
Load:
Load Radius: The horizontal distance from the rotating axis projection to the support surface
prior the load to the vertical hoist line center or applied load surface.
Freely Suspended Load: If the load is held free with no external force applied rather than the
hoist line is known to be a freely suspended load.
Side Load: The load lifted either in the air or the ground provided with the horizontal side force.
Outrigger Position:
The position of the beam that extends from the lower works of the crane to enhance the stability
of the entire system is known as outrigger position. Outrigger controls are located on both the
side of the chassis (Sorensen, Singhose & Dickerson, 2009). The control can be done
independently for the jack operation and the individual beam. Usually, the outriggers are
operated hydraulically with the inverted vertical jacks (fitted with the stowable and removable
outrigger feet) and the horizontal telescoping beams (fitted with integral holding valves).
Driver cabinet temperature:
The American Society of Mechanical Engineers’ (ASME’s) temperature standards should be
followed for an effective functioning of the crane system.
ASME HST-2-1999: This is the standard for the performance of manually operated chain hoists.
The ambient temperature followed is 0 °F – 130 °F
ASME HST-1-1999: This is the standard for the performance of electric chain hoist. The ambient
temperature of the system is maintained to be 0 °F – 104 °F
ASME B30.20: This is an additional requirement, which needs to be considered when the lifting
operation is done at a temperature range of 24 °F – 150 °F.
4. Measurement of load using Strain gauge:
Crane with the capacities more than 3.2 tons to 400 tons are installed with 120 sets of strain
gauge weighing machines for the metallurgical production (Uchiyama, 2009). The sinal obtained
from the strain gauges will be directly proportional to the load on the hook that passes through
the cable attached in the connecting box to the processing unit. The analog to digital converter
(ADC) converts the incoming analog signal in a digital form and sends them to the
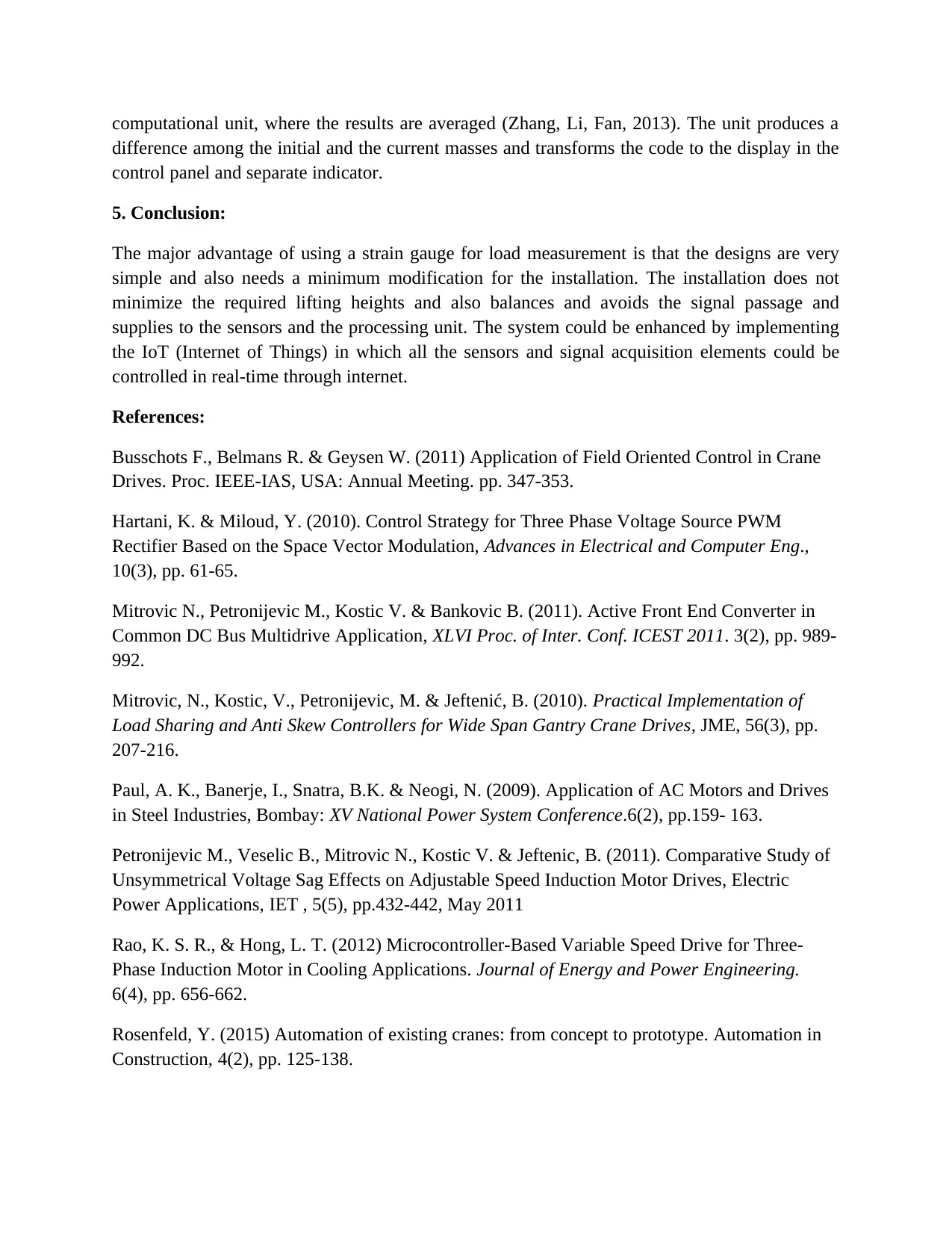
computational unit, where the results are averaged (Zhang, Li, Fan, 2013). The unit produces a
difference among the initial and the current masses and transforms the code to the display in the
control panel and separate indicator.
5. Conclusion:
The major advantage of using a strain gauge for load measurement is that the designs are very
simple and also needs a minimum modification for the installation. The installation does not
minimize the required lifting heights and also balances and avoids the signal passage and
supplies to the sensors and the processing unit. The system could be enhanced by implementing
the IoT (Internet of Things) in which all the sensors and signal acquisition elements could be
controlled in real-time through internet.
References:
Busschots F., Belmans R. & Geysen W. (2011) Application of Field Oriented Control in Crane
Drives. Proc. IEEE-IAS, USA: Annual Meeting. pp. 347-353.
Hartani, K. & Miloud, Y. (2010). Control Strategy for Three Phase Voltage Source PWM
Rectifier Based on the Space Vector Modulation, Advances in Electrical and Computer Eng.,
10(3), pp. 61-65.
Mitrovic N., Petronijevic M., Kostic V. & Bankovic B. (2011). Active Front End Converter in
Common DC Bus Multidrive Application, XLVI Proc. of Inter. Conf. ICEST 2011. 3(2), pp. 989-
992.
Mitrovic, N., Kostic, V., Petronijevic, M. & Jeftenić, B. (2010). Practical Implementation of
Load Sharing and Anti Skew Controllers for Wide Span Gantry Crane Drives, JME, 56(3), pp.
207-216.
Paul, A. K., Banerje, I., Snatra, B.K. & Neogi, N. (2009). Application of AC Motors and Drives
in Steel Industries, Bombay: XV National Power System Conference.6(2), pp.159- 163.
Petronijevic M., Veselic B., Mitrovic N., Kostic V. & Jeftenic, B. (2011). Comparative Study of
Unsymmetrical Voltage Sag Effects on Adjustable Speed Induction Motor Drives, Electric
Power Applications, IET , 5(5), pp.432-442, May 2011
Rao, K. S. R., & Hong, L. T. (2012) Microcontroller-Based Variable Speed Drive for Three-
Phase Induction Motor in Cooling Applications. Journal of Energy and Power Engineering.
6(4), pp. 656-662.
Rosenfeld, Y. (2015) Automation of existing cranes: from concept to prototype. Automation in
Construction, 4(2), pp. 125-138.
difference among the initial and the current masses and transforms the code to the display in the
control panel and separate indicator.
5. Conclusion:
The major advantage of using a strain gauge for load measurement is that the designs are very
simple and also needs a minimum modification for the installation. The installation does not
minimize the required lifting heights and also balances and avoids the signal passage and
supplies to the sensors and the processing unit. The system could be enhanced by implementing
the IoT (Internet of Things) in which all the sensors and signal acquisition elements could be
controlled in real-time through internet.
References:
Busschots F., Belmans R. & Geysen W. (2011) Application of Field Oriented Control in Crane
Drives. Proc. IEEE-IAS, USA: Annual Meeting. pp. 347-353.
Hartani, K. & Miloud, Y. (2010). Control Strategy for Three Phase Voltage Source PWM
Rectifier Based on the Space Vector Modulation, Advances in Electrical and Computer Eng.,
10(3), pp. 61-65.
Mitrovic N., Petronijevic M., Kostic V. & Bankovic B. (2011). Active Front End Converter in
Common DC Bus Multidrive Application, XLVI Proc. of Inter. Conf. ICEST 2011. 3(2), pp. 989-
992.
Mitrovic, N., Kostic, V., Petronijevic, M. & Jeftenić, B. (2010). Practical Implementation of
Load Sharing and Anti Skew Controllers for Wide Span Gantry Crane Drives, JME, 56(3), pp.
207-216.
Paul, A. K., Banerje, I., Snatra, B.K. & Neogi, N. (2009). Application of AC Motors and Drives
in Steel Industries, Bombay: XV National Power System Conference.6(2), pp.159- 163.
Petronijevic M., Veselic B., Mitrovic N., Kostic V. & Jeftenic, B. (2011). Comparative Study of
Unsymmetrical Voltage Sag Effects on Adjustable Speed Induction Motor Drives, Electric
Power Applications, IET , 5(5), pp.432-442, May 2011
Rao, K. S. R., & Hong, L. T. (2012) Microcontroller-Based Variable Speed Drive for Three-
Phase Induction Motor in Cooling Applications. Journal of Energy and Power Engineering.
6(4), pp. 656-662.
Rosenfeld, Y. (2015) Automation of existing cranes: from concept to prototype. Automation in
Construction, 4(2), pp. 125-138.
Paraphrase This Document
Need a fresh take? Get an instant paraphrase of this document with our AI Paraphraser
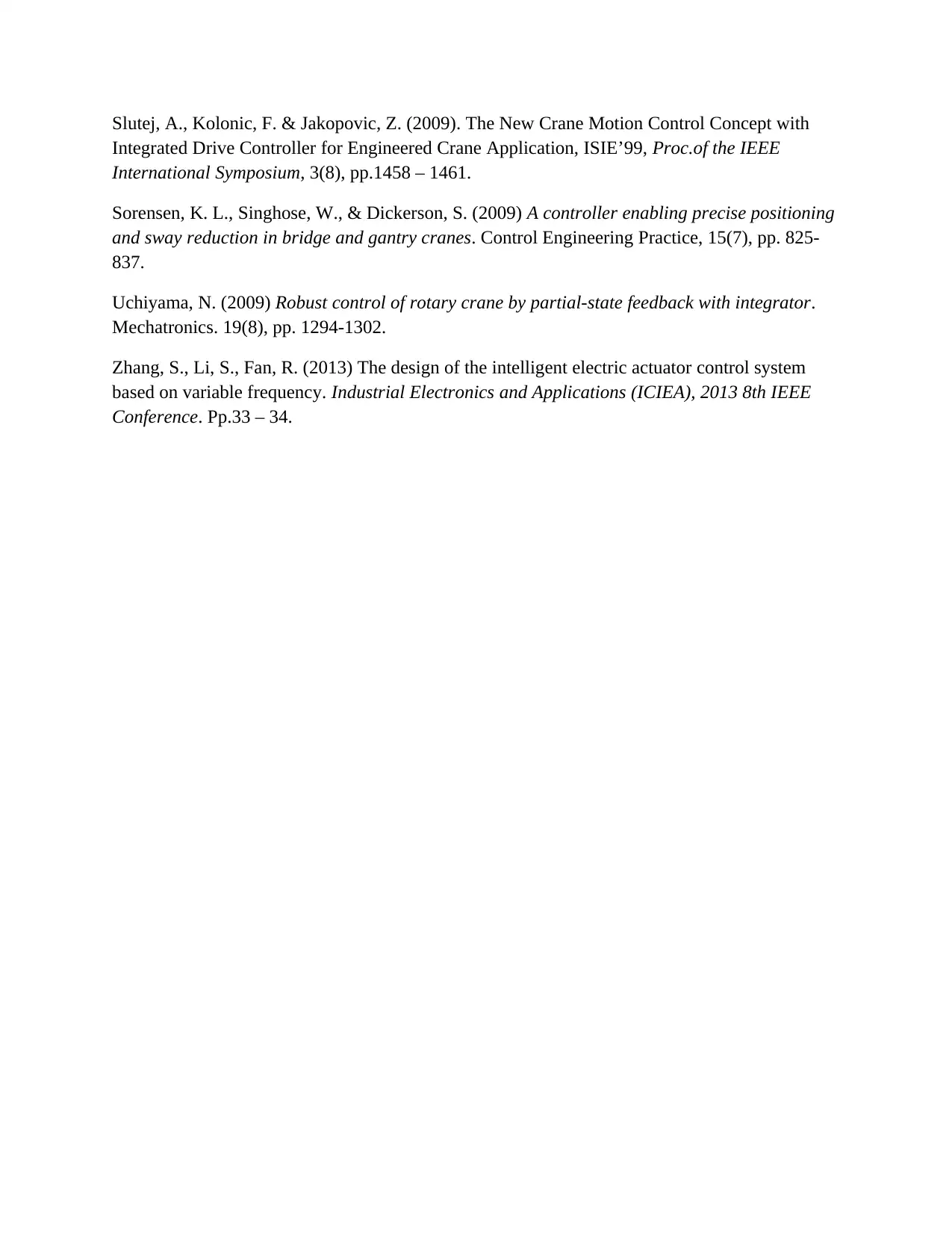
Slutej, A., Kolonic, F. & Jakopovic, Z. (2009). The New Crane Motion Control Concept with
Integrated Drive Controller for Engineered Crane Application, ISIE’99, Proc.of the IEEE
International Symposium, 3(8), pp.1458 – 1461.
Sorensen, K. L., Singhose, W., & Dickerson, S. (2009) A controller enabling precise positioning
and sway reduction in bridge and gantry cranes. Control Engineering Practice, 15(7), pp. 825-
837.
Uchiyama, N. (2009) Robust control of rotary crane by partial-state feedback with integrator.
Mechatronics. 19(8), pp. 1294-1302.
Zhang, S., Li, S., Fan, R. (2013) The design of the intelligent electric actuator control system
based on variable frequency. Industrial Electronics and Applications (ICIEA), 2013 8th IEEE
Conference. Pp.33 – 34.
Integrated Drive Controller for Engineered Crane Application, ISIE’99, Proc.of the IEEE
International Symposium, 3(8), pp.1458 – 1461.
Sorensen, K. L., Singhose, W., & Dickerson, S. (2009) A controller enabling precise positioning
and sway reduction in bridge and gantry cranes. Control Engineering Practice, 15(7), pp. 825-
837.
Uchiyama, N. (2009) Robust control of rotary crane by partial-state feedback with integrator.
Mechatronics. 19(8), pp. 1294-1302.
Zhang, S., Li, S., Fan, R. (2013) The design of the intelligent electric actuator control system
based on variable frequency. Industrial Electronics and Applications (ICIEA), 2013 8th IEEE
Conference. Pp.33 – 34.
1 out of 8
Related Documents
![[object Object]](/_next/image/?url=%2F_next%2Fstatic%2Fmedia%2Flogo.6d15ce61.png&w=640&q=75)
Your All-in-One AI-Powered Toolkit for Academic Success.
+13062052269
info@desklib.com
Available 24*7 on WhatsApp / Email
Unlock your academic potential
© 2024 | Zucol Services PVT LTD | All rights reserved.