Principles of Logistic Management: A Case Study of Toyota Motors
VerifiedAdded on 2023/06/07
|14
|4388
|354
AI Summary
This assignment provides a detailed understanding of logistics management and its contribution towards organizational growth. It includes a case study of Toyota Motors and sheds light on how their logistics management process is influencing other business functionalities. The order cycle process and inventory management process at Toyota Motors are also explained in detail.
Contribute Materials
Your contribution can guide someone’s learning journey. Share your
documents today.
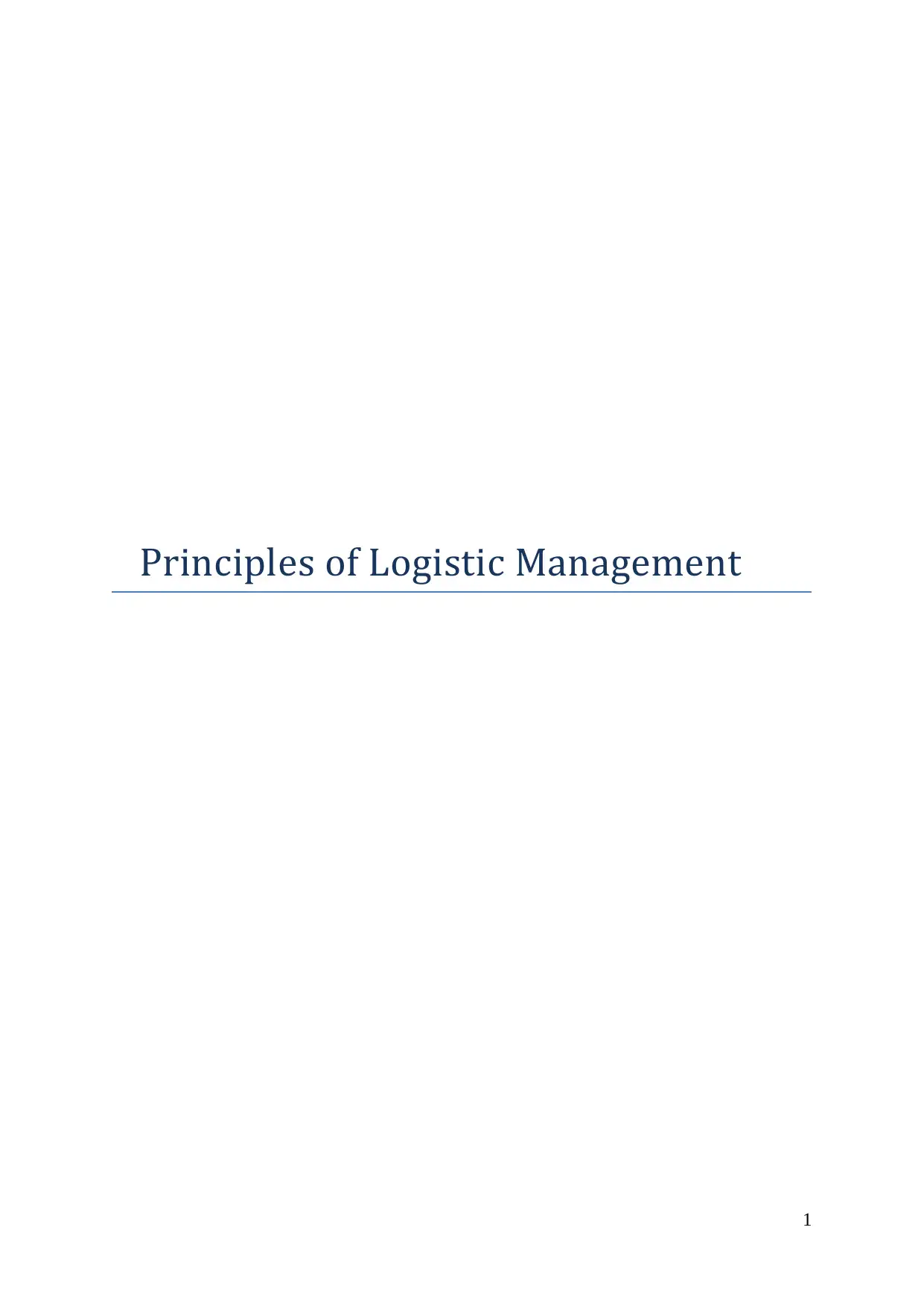
Principles of Logistic Management
1
1
Secure Best Marks with AI Grader
Need help grading? Try our AI Grader for instant feedback on your assignments.
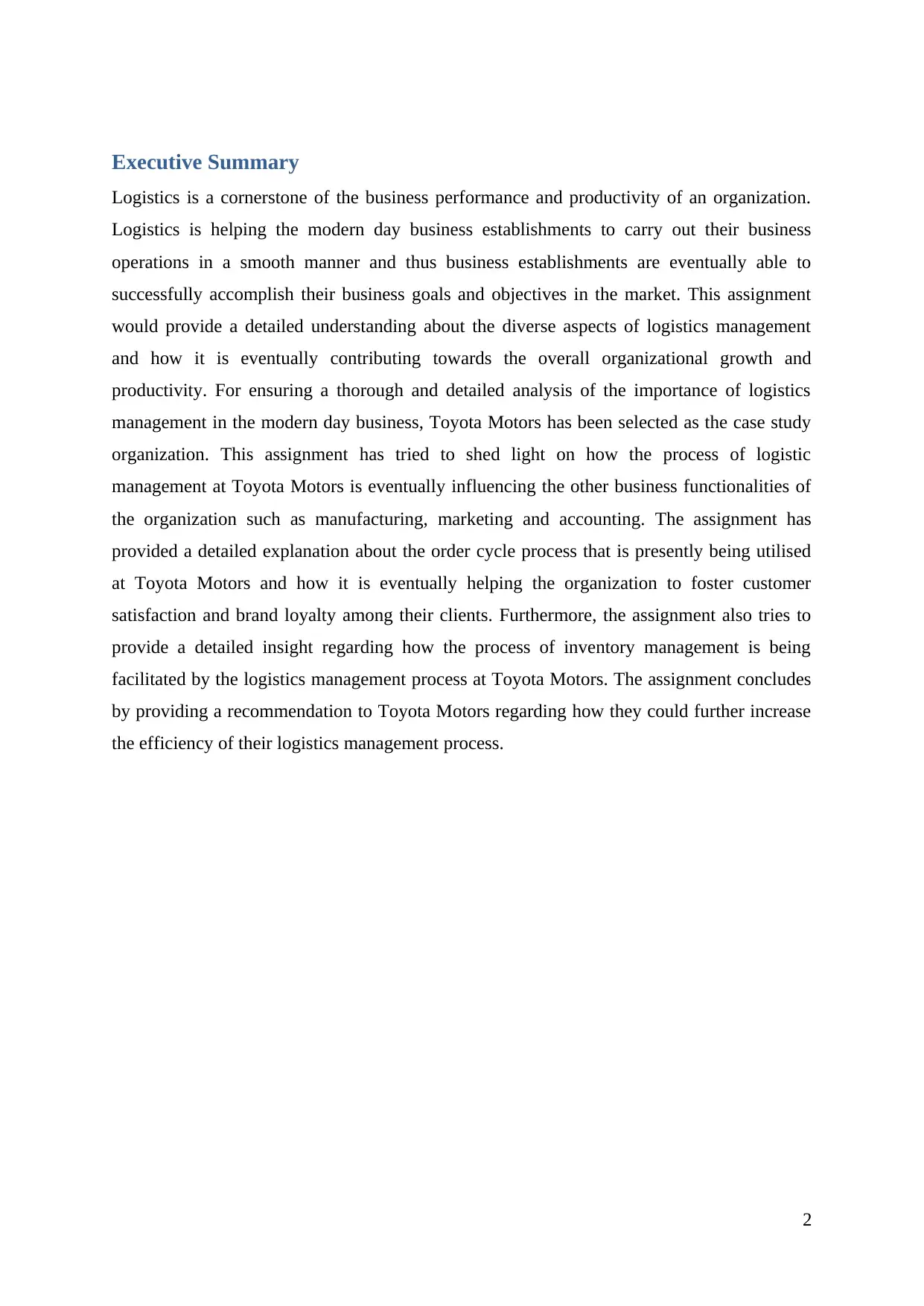
Executive Summary
Logistics is a cornerstone of the business performance and productivity of an organization.
Logistics is helping the modern day business establishments to carry out their business
operations in a smooth manner and thus business establishments are eventually able to
successfully accomplish their business goals and objectives in the market. This assignment
would provide a detailed understanding about the diverse aspects of logistics management
and how it is eventually contributing towards the overall organizational growth and
productivity. For ensuring a thorough and detailed analysis of the importance of logistics
management in the modern day business, Toyota Motors has been selected as the case study
organization. This assignment has tried to shed light on how the process of logistic
management at Toyota Motors is eventually influencing the other business functionalities of
the organization such as manufacturing, marketing and accounting. The assignment has
provided a detailed explanation about the order cycle process that is presently being utilised
at Toyota Motors and how it is eventually helping the organization to foster customer
satisfaction and brand loyalty among their clients. Furthermore, the assignment also tries to
provide a detailed insight regarding how the process of inventory management is being
facilitated by the logistics management process at Toyota Motors. The assignment concludes
by providing a recommendation to Toyota Motors regarding how they could further increase
the efficiency of their logistics management process.
2
Logistics is a cornerstone of the business performance and productivity of an organization.
Logistics is helping the modern day business establishments to carry out their business
operations in a smooth manner and thus business establishments are eventually able to
successfully accomplish their business goals and objectives in the market. This assignment
would provide a detailed understanding about the diverse aspects of logistics management
and how it is eventually contributing towards the overall organizational growth and
productivity. For ensuring a thorough and detailed analysis of the importance of logistics
management in the modern day business, Toyota Motors has been selected as the case study
organization. This assignment has tried to shed light on how the process of logistic
management at Toyota Motors is eventually influencing the other business functionalities of
the organization such as manufacturing, marketing and accounting. The assignment has
provided a detailed explanation about the order cycle process that is presently being utilised
at Toyota Motors and how it is eventually helping the organization to foster customer
satisfaction and brand loyalty among their clients. Furthermore, the assignment also tries to
provide a detailed insight regarding how the process of inventory management is being
facilitated by the logistics management process at Toyota Motors. The assignment concludes
by providing a recommendation to Toyota Motors regarding how they could further increase
the efficiency of their logistics management process.
2
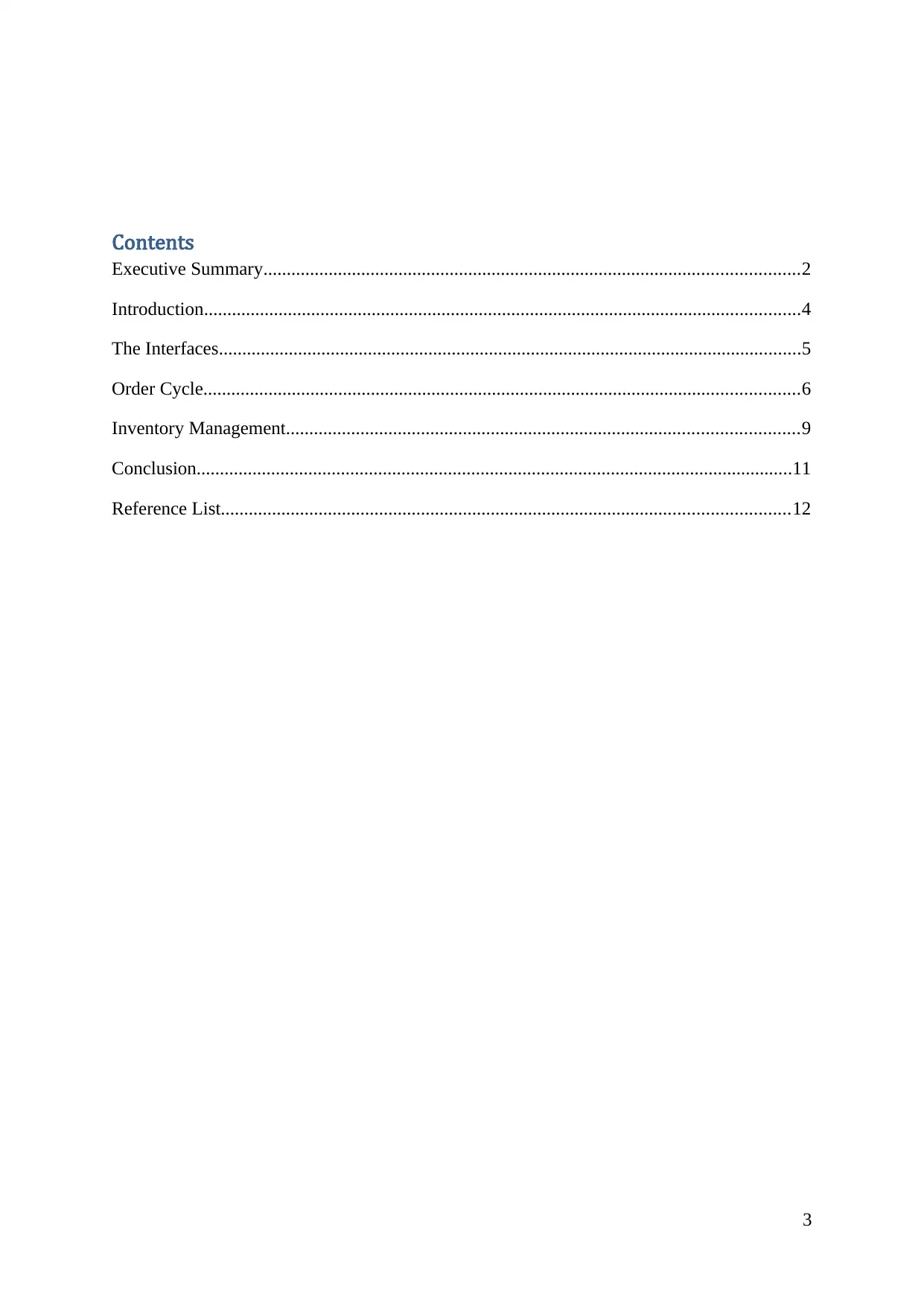
Contents
Executive Summary...................................................................................................................2
Introduction................................................................................................................................4
The Interfaces.............................................................................................................................5
Order Cycle................................................................................................................................6
Inventory Management..............................................................................................................9
Conclusion................................................................................................................................11
Reference List..........................................................................................................................12
3
Executive Summary...................................................................................................................2
Introduction................................................................................................................................4
The Interfaces.............................................................................................................................5
Order Cycle................................................................................................................................6
Inventory Management..............................................................................................................9
Conclusion................................................................................................................................11
Reference List..........................................................................................................................12
3
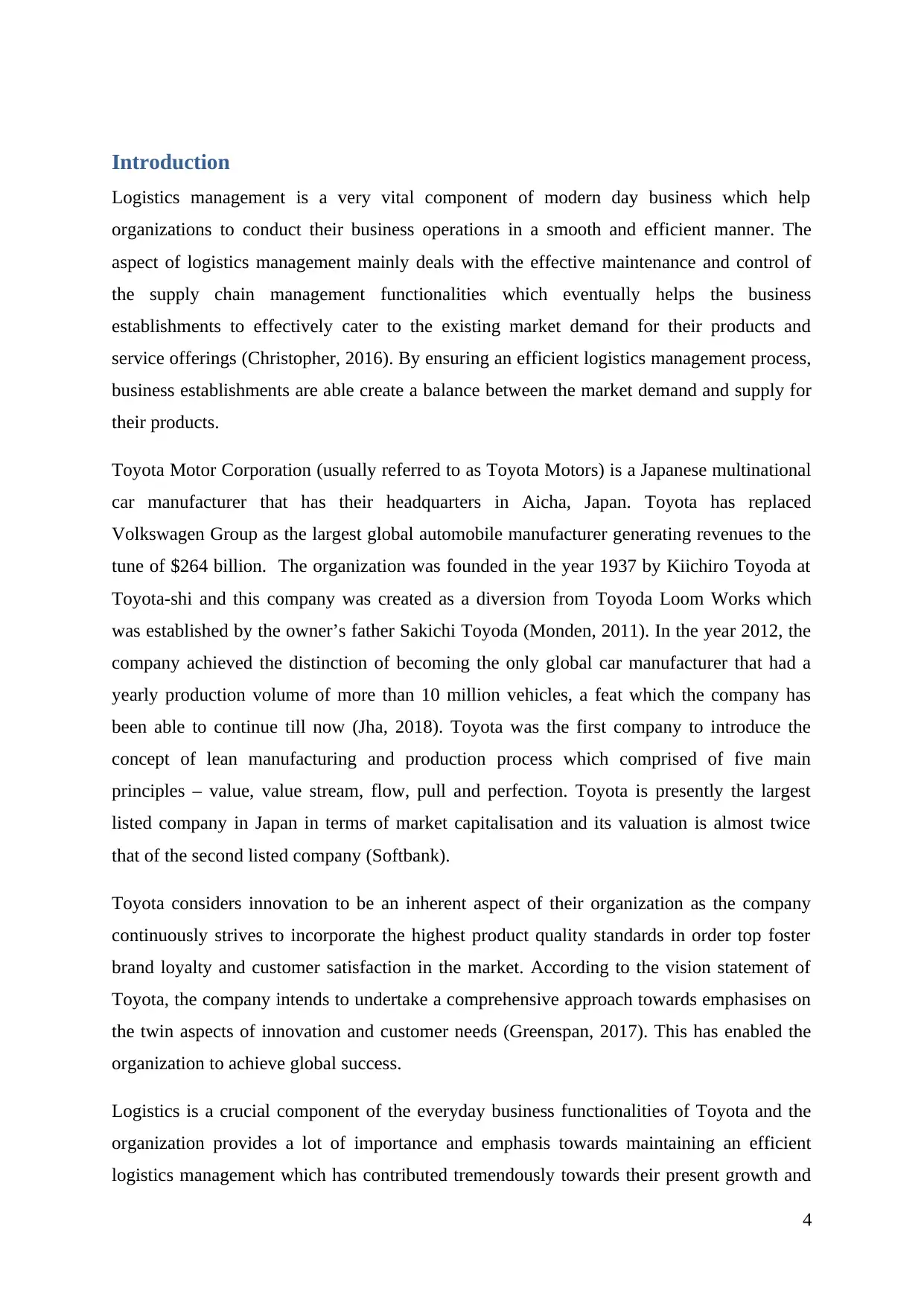
Introduction
Logistics management is a very vital component of modern day business which help
organizations to conduct their business operations in a smooth and efficient manner. The
aspect of logistics management mainly deals with the effective maintenance and control of
the supply chain management functionalities which eventually helps the business
establishments to effectively cater to the existing market demand for their products and
service offerings (Christopher, 2016). By ensuring an efficient logistics management process,
business establishments are able create a balance between the market demand and supply for
their products.
Toyota Motor Corporation (usually referred to as Toyota Motors) is a Japanese multinational
car manufacturer that has their headquarters in Aicha, Japan. Toyota has replaced
Volkswagen Group as the largest global automobile manufacturer generating revenues to the
tune of $264 billion. The organization was founded in the year 1937 by Kiichiro Toyoda at
Toyota-shi and this company was created as a diversion from Toyoda Loom Works which
was established by the owner’s father Sakichi Toyoda (Monden, 2011). In the year 2012, the
company achieved the distinction of becoming the only global car manufacturer that had a
yearly production volume of more than 10 million vehicles, a feat which the company has
been able to continue till now (Jha, 2018). Toyota was the first company to introduce the
concept of lean manufacturing and production process which comprised of five main
principles – value, value stream, flow, pull and perfection. Toyota is presently the largest
listed company in Japan in terms of market capitalisation and its valuation is almost twice
that of the second listed company (Softbank).
Toyota considers innovation to be an inherent aspect of their organization as the company
continuously strives to incorporate the highest product quality standards in order top foster
brand loyalty and customer satisfaction in the market. According to the vision statement of
Toyota, the company intends to undertake a comprehensive approach towards emphasises on
the twin aspects of innovation and customer needs (Greenspan, 2017). This has enabled the
organization to achieve global success.
Logistics is a crucial component of the everyday business functionalities of Toyota and the
organization provides a lot of importance and emphasis towards maintaining an efficient
logistics management which has contributed tremendously towards their present growth and
4
Logistics management is a very vital component of modern day business which help
organizations to conduct their business operations in a smooth and efficient manner. The
aspect of logistics management mainly deals with the effective maintenance and control of
the supply chain management functionalities which eventually helps the business
establishments to effectively cater to the existing market demand for their products and
service offerings (Christopher, 2016). By ensuring an efficient logistics management process,
business establishments are able create a balance between the market demand and supply for
their products.
Toyota Motor Corporation (usually referred to as Toyota Motors) is a Japanese multinational
car manufacturer that has their headquarters in Aicha, Japan. Toyota has replaced
Volkswagen Group as the largest global automobile manufacturer generating revenues to the
tune of $264 billion. The organization was founded in the year 1937 by Kiichiro Toyoda at
Toyota-shi and this company was created as a diversion from Toyoda Loom Works which
was established by the owner’s father Sakichi Toyoda (Monden, 2011). In the year 2012, the
company achieved the distinction of becoming the only global car manufacturer that had a
yearly production volume of more than 10 million vehicles, a feat which the company has
been able to continue till now (Jha, 2018). Toyota was the first company to introduce the
concept of lean manufacturing and production process which comprised of five main
principles – value, value stream, flow, pull and perfection. Toyota is presently the largest
listed company in Japan in terms of market capitalisation and its valuation is almost twice
that of the second listed company (Softbank).
Toyota considers innovation to be an inherent aspect of their organization as the company
continuously strives to incorporate the highest product quality standards in order top foster
brand loyalty and customer satisfaction in the market. According to the vision statement of
Toyota, the company intends to undertake a comprehensive approach towards emphasises on
the twin aspects of innovation and customer needs (Greenspan, 2017). This has enabled the
organization to achieve global success.
Logistics is a crucial component of the everyday business functionalities of Toyota and the
organization provides a lot of importance and emphasis towards maintaining an efficient
logistics management which has contributed tremendously towards their present growth and
4
Secure Best Marks with AI Grader
Need help grading? Try our AI Grader for instant feedback on your assignments.
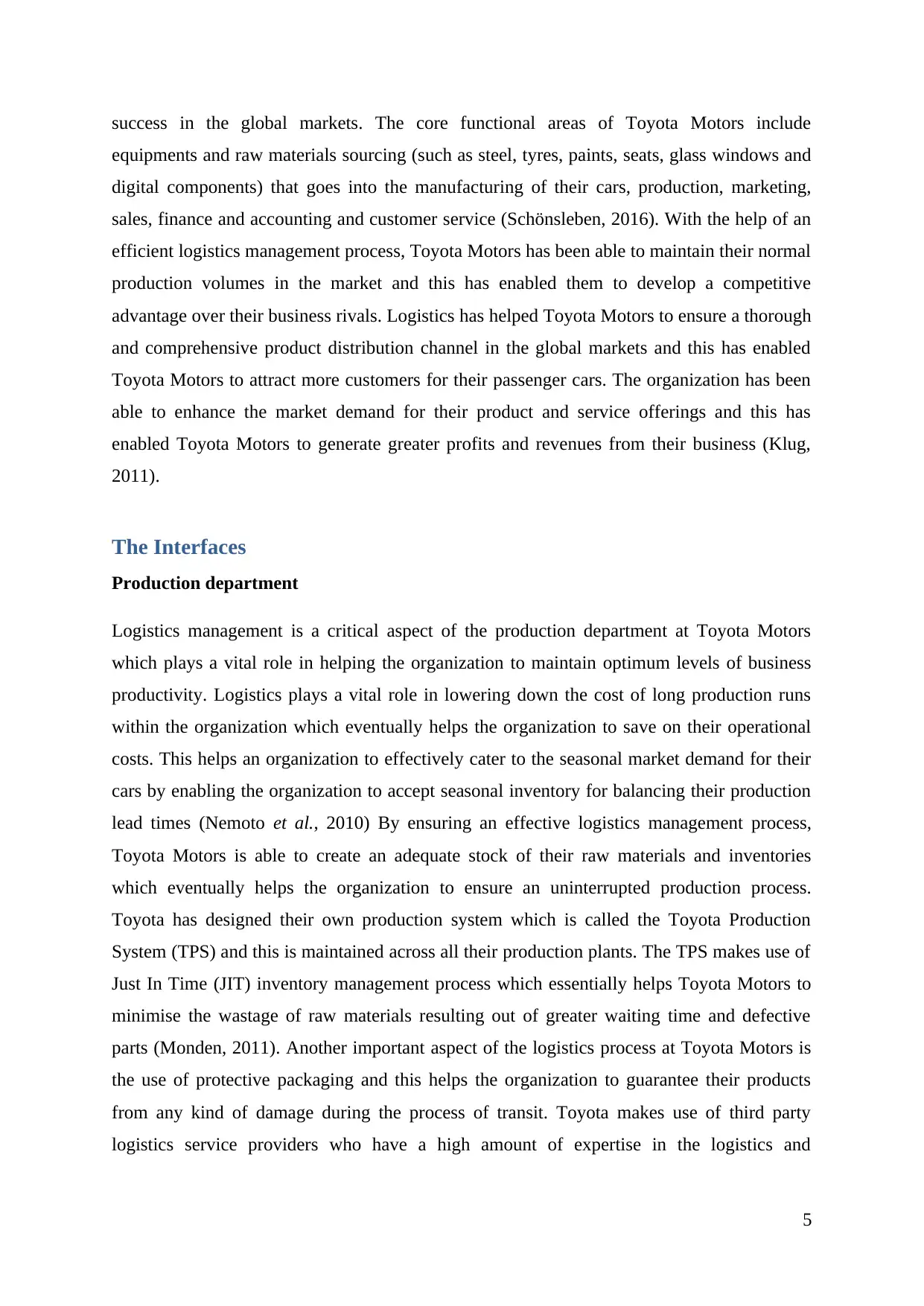
success in the global markets. The core functional areas of Toyota Motors include
equipments and raw materials sourcing (such as steel, tyres, paints, seats, glass windows and
digital components) that goes into the manufacturing of their cars, production, marketing,
sales, finance and accounting and customer service (Schönsleben, 2016). With the help of an
efficient logistics management process, Toyota Motors has been able to maintain their normal
production volumes in the market and this has enabled them to develop a competitive
advantage over their business rivals. Logistics has helped Toyota Motors to ensure a thorough
and comprehensive product distribution channel in the global markets and this has enabled
Toyota Motors to attract more customers for their passenger cars. The organization has been
able to enhance the market demand for their product and service offerings and this has
enabled Toyota Motors to generate greater profits and revenues from their business (Klug,
2011).
The Interfaces
Production department
Logistics management is a critical aspect of the production department at Toyota Motors
which plays a vital role in helping the organization to maintain optimum levels of business
productivity. Logistics plays a vital role in lowering down the cost of long production runs
within the organization which eventually helps the organization to save on their operational
costs. This helps an organization to effectively cater to the seasonal market demand for their
cars by enabling the organization to accept seasonal inventory for balancing their production
lead times (Nemoto et al., 2010) By ensuring an effective logistics management process,
Toyota Motors is able to create an adequate stock of their raw materials and inventories
which eventually helps the organization to ensure an uninterrupted production process.
Toyota has designed their own production system which is called the Toyota Production
System (TPS) and this is maintained across all their production plants. The TPS makes use of
Just In Time (JIT) inventory management process which essentially helps Toyota Motors to
minimise the wastage of raw materials resulting out of greater waiting time and defective
parts (Monden, 2011). Another important aspect of the logistics process at Toyota Motors is
the use of protective packaging and this helps the organization to guarantee their products
from any kind of damage during the process of transit. Toyota makes use of third party
logistics service providers who have a high amount of expertise in the logistics and
5
equipments and raw materials sourcing (such as steel, tyres, paints, seats, glass windows and
digital components) that goes into the manufacturing of their cars, production, marketing,
sales, finance and accounting and customer service (Schönsleben, 2016). With the help of an
efficient logistics management process, Toyota Motors has been able to maintain their normal
production volumes in the market and this has enabled them to develop a competitive
advantage over their business rivals. Logistics has helped Toyota Motors to ensure a thorough
and comprehensive product distribution channel in the global markets and this has enabled
Toyota Motors to attract more customers for their passenger cars. The organization has been
able to enhance the market demand for their product and service offerings and this has
enabled Toyota Motors to generate greater profits and revenues from their business (Klug,
2011).
The Interfaces
Production department
Logistics management is a critical aspect of the production department at Toyota Motors
which plays a vital role in helping the organization to maintain optimum levels of business
productivity. Logistics plays a vital role in lowering down the cost of long production runs
within the organization which eventually helps the organization to save on their operational
costs. This helps an organization to effectively cater to the seasonal market demand for their
cars by enabling the organization to accept seasonal inventory for balancing their production
lead times (Nemoto et al., 2010) By ensuring an effective logistics management process,
Toyota Motors is able to create an adequate stock of their raw materials and inventories
which eventually helps the organization to ensure an uninterrupted production process.
Toyota has designed their own production system which is called the Toyota Production
System (TPS) and this is maintained across all their production plants. The TPS makes use of
Just In Time (JIT) inventory management process which essentially helps Toyota Motors to
minimise the wastage of raw materials resulting out of greater waiting time and defective
parts (Monden, 2011). Another important aspect of the logistics process at Toyota Motors is
the use of protective packaging and this helps the organization to guarantee their products
from any kind of damage during the process of transit. Toyota makes use of third party
logistics service providers who have a high amount of expertise in the logistics and
5
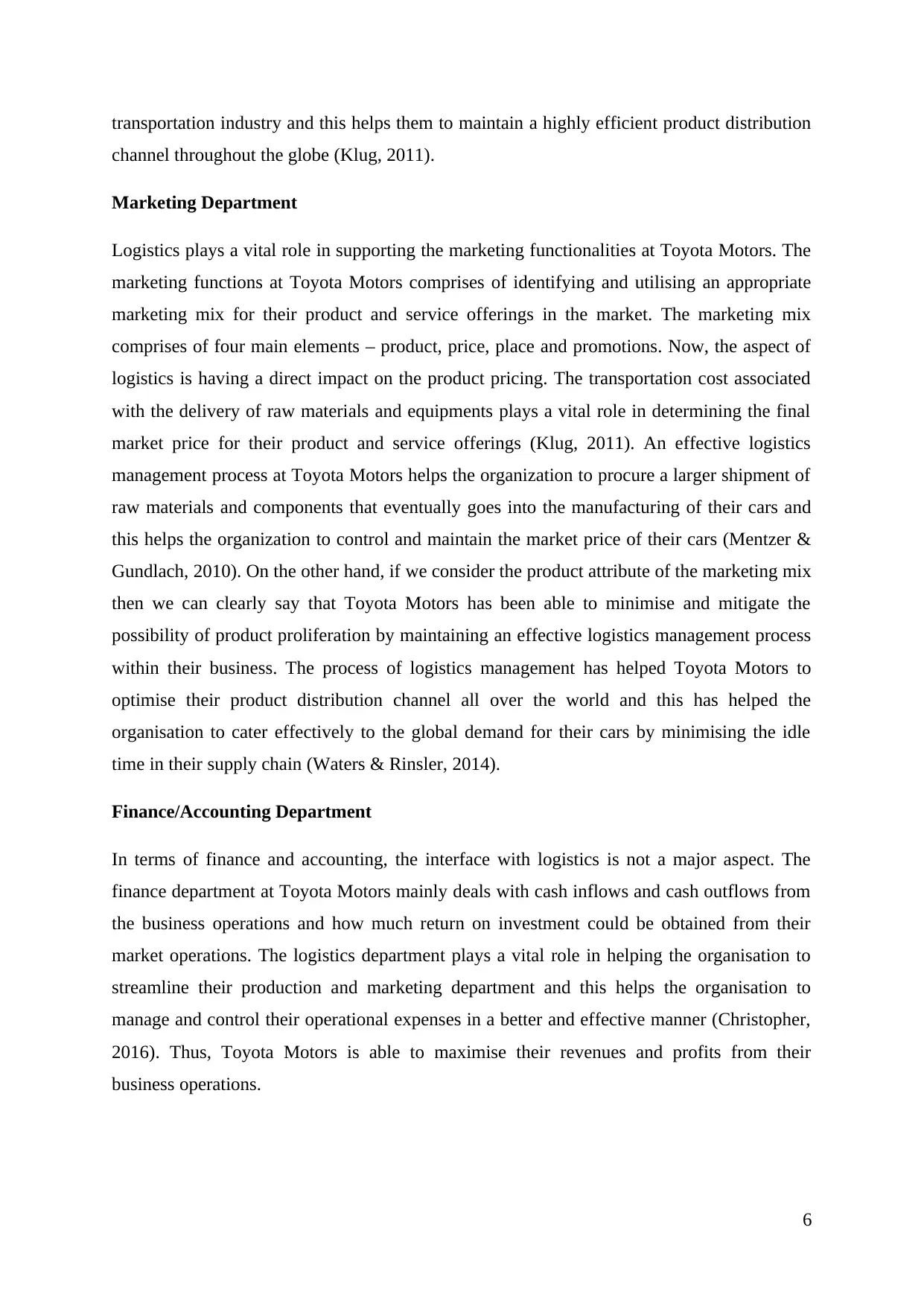
transportation industry and this helps them to maintain a highly efficient product distribution
channel throughout the globe (Klug, 2011).
Marketing Department
Logistics plays a vital role in supporting the marketing functionalities at Toyota Motors. The
marketing functions at Toyota Motors comprises of identifying and utilising an appropriate
marketing mix for their product and service offerings in the market. The marketing mix
comprises of four main elements – product, price, place and promotions. Now, the aspect of
logistics is having a direct impact on the product pricing. The transportation cost associated
with the delivery of raw materials and equipments plays a vital role in determining the final
market price for their product and service offerings (Klug, 2011). An effective logistics
management process at Toyota Motors helps the organization to procure a larger shipment of
raw materials and components that eventually goes into the manufacturing of their cars and
this helps the organization to control and maintain the market price of their cars (Mentzer &
Gundlach, 2010). On the other hand, if we consider the product attribute of the marketing mix
then we can clearly say that Toyota Motors has been able to minimise and mitigate the
possibility of product proliferation by maintaining an effective logistics management process
within their business. The process of logistics management has helped Toyota Motors to
optimise their product distribution channel all over the world and this has helped the
organisation to cater effectively to the global demand for their cars by minimising the idle
time in their supply chain (Waters & Rinsler, 2014).
Finance/Accounting Department
In terms of finance and accounting, the interface with logistics is not a major aspect. The
finance department at Toyota Motors mainly deals with cash inflows and cash outflows from
the business operations and how much return on investment could be obtained from their
market operations. The logistics department plays a vital role in helping the organisation to
streamline their production and marketing department and this helps the organisation to
manage and control their operational expenses in a better and effective manner (Christopher,
2016). Thus, Toyota Motors is able to maximise their revenues and profits from their
business operations.
6
channel throughout the globe (Klug, 2011).
Marketing Department
Logistics plays a vital role in supporting the marketing functionalities at Toyota Motors. The
marketing functions at Toyota Motors comprises of identifying and utilising an appropriate
marketing mix for their product and service offerings in the market. The marketing mix
comprises of four main elements – product, price, place and promotions. Now, the aspect of
logistics is having a direct impact on the product pricing. The transportation cost associated
with the delivery of raw materials and equipments plays a vital role in determining the final
market price for their product and service offerings (Klug, 2011). An effective logistics
management process at Toyota Motors helps the organization to procure a larger shipment of
raw materials and components that eventually goes into the manufacturing of their cars and
this helps the organization to control and maintain the market price of their cars (Mentzer &
Gundlach, 2010). On the other hand, if we consider the product attribute of the marketing mix
then we can clearly say that Toyota Motors has been able to minimise and mitigate the
possibility of product proliferation by maintaining an effective logistics management process
within their business. The process of logistics management has helped Toyota Motors to
optimise their product distribution channel all over the world and this has helped the
organisation to cater effectively to the global demand for their cars by minimising the idle
time in their supply chain (Waters & Rinsler, 2014).
Finance/Accounting Department
In terms of finance and accounting, the interface with logistics is not a major aspect. The
finance department at Toyota Motors mainly deals with cash inflows and cash outflows from
the business operations and how much return on investment could be obtained from their
market operations. The logistics department plays a vital role in helping the organisation to
streamline their production and marketing department and this helps the organisation to
manage and control their operational expenses in a better and effective manner (Christopher,
2016). Thus, Toyota Motors is able to maximise their revenues and profits from their
business operations.
6
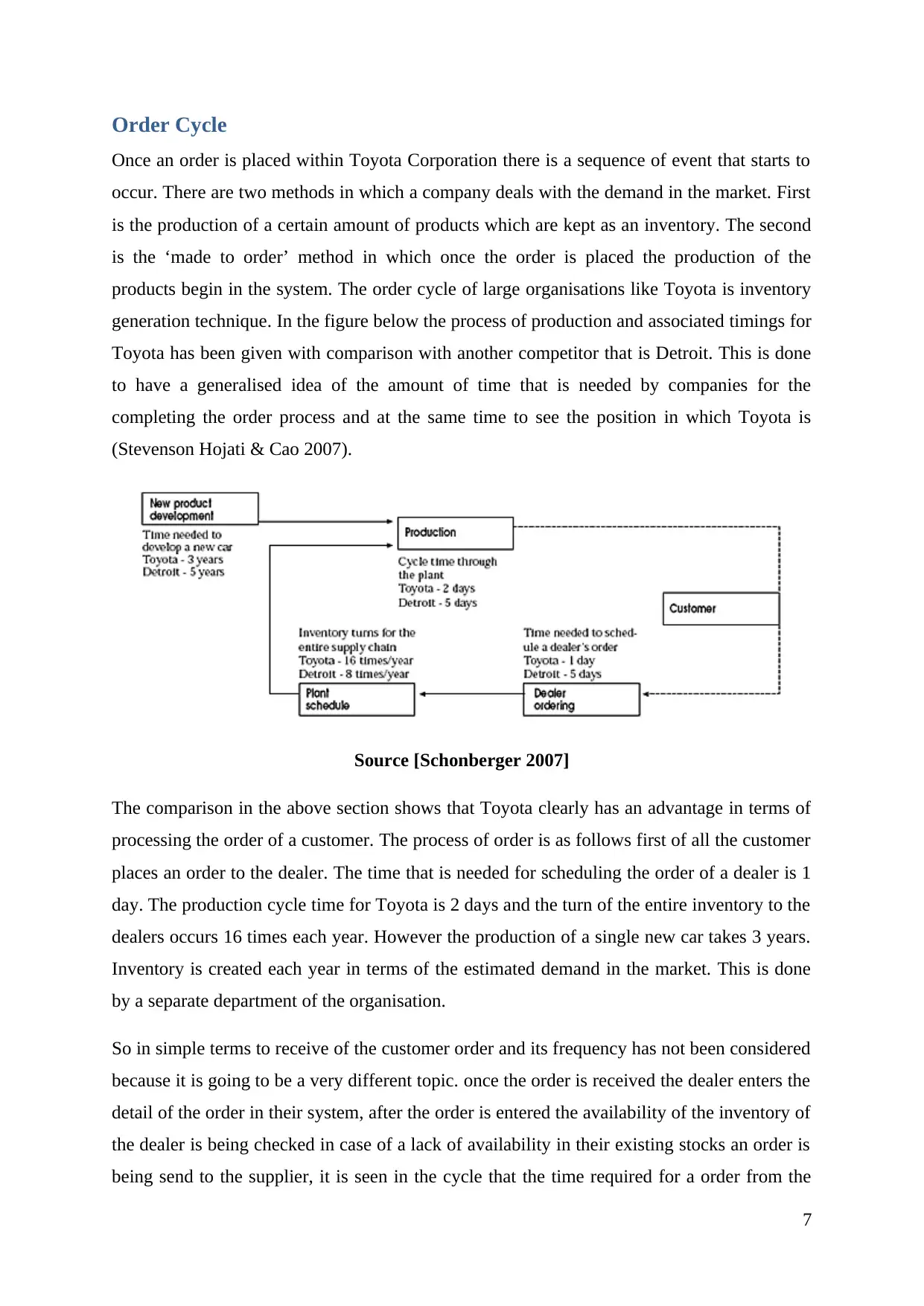
Order Cycle
Once an order is placed within Toyota Corporation there is a sequence of event that starts to
occur. There are two methods in which a company deals with the demand in the market. First
is the production of a certain amount of products which are kept as an inventory. The second
is the ‘made to order’ method in which once the order is placed the production of the
products begin in the system. The order cycle of large organisations like Toyota is inventory
generation technique. In the figure below the process of production and associated timings for
Toyota has been given with comparison with another competitor that is Detroit. This is done
to have a generalised idea of the amount of time that is needed by companies for the
completing the order process and at the same time to see the position in which Toyota is
(Stevenson Hojati & Cao 2007).
Source [Schonberger 2007]
The comparison in the above section shows that Toyota clearly has an advantage in terms of
processing the order of a customer. The process of order is as follows first of all the customer
places an order to the dealer. The time that is needed for scheduling the order of a dealer is 1
day. The production cycle time for Toyota is 2 days and the turn of the entire inventory to the
dealers occurs 16 times each year. However the production of a single new car takes 3 years.
Inventory is created each year in terms of the estimated demand in the market. This is done
by a separate department of the organisation.
So in simple terms to receive of the customer order and its frequency has not been considered
because it is going to be a very different topic. once the order is received the dealer enters the
detail of the order in their system, after the order is entered the availability of the inventory of
the dealer is being checked in case of a lack of availability in their existing stocks an order is
being send to the supplier, it is seen in the cycle that the time required for a order from the
7
Once an order is placed within Toyota Corporation there is a sequence of event that starts to
occur. There are two methods in which a company deals with the demand in the market. First
is the production of a certain amount of products which are kept as an inventory. The second
is the ‘made to order’ method in which once the order is placed the production of the
products begin in the system. The order cycle of large organisations like Toyota is inventory
generation technique. In the figure below the process of production and associated timings for
Toyota has been given with comparison with another competitor that is Detroit. This is done
to have a generalised idea of the amount of time that is needed by companies for the
completing the order process and at the same time to see the position in which Toyota is
(Stevenson Hojati & Cao 2007).
Source [Schonberger 2007]
The comparison in the above section shows that Toyota clearly has an advantage in terms of
processing the order of a customer. The process of order is as follows first of all the customer
places an order to the dealer. The time that is needed for scheduling the order of a dealer is 1
day. The production cycle time for Toyota is 2 days and the turn of the entire inventory to the
dealers occurs 16 times each year. However the production of a single new car takes 3 years.
Inventory is created each year in terms of the estimated demand in the market. This is done
by a separate department of the organisation.
So in simple terms to receive of the customer order and its frequency has not been considered
because it is going to be a very different topic. once the order is received the dealer enters the
detail of the order in their system, after the order is entered the availability of the inventory of
the dealer is being checked in case of a lack of availability in their existing stocks an order is
being send to the supplier, it is seen in the cycle that the time required for a order from the
7
Paraphrase This Document
Need a fresh take? Get an instant paraphrase of this document with our AI Paraphraser
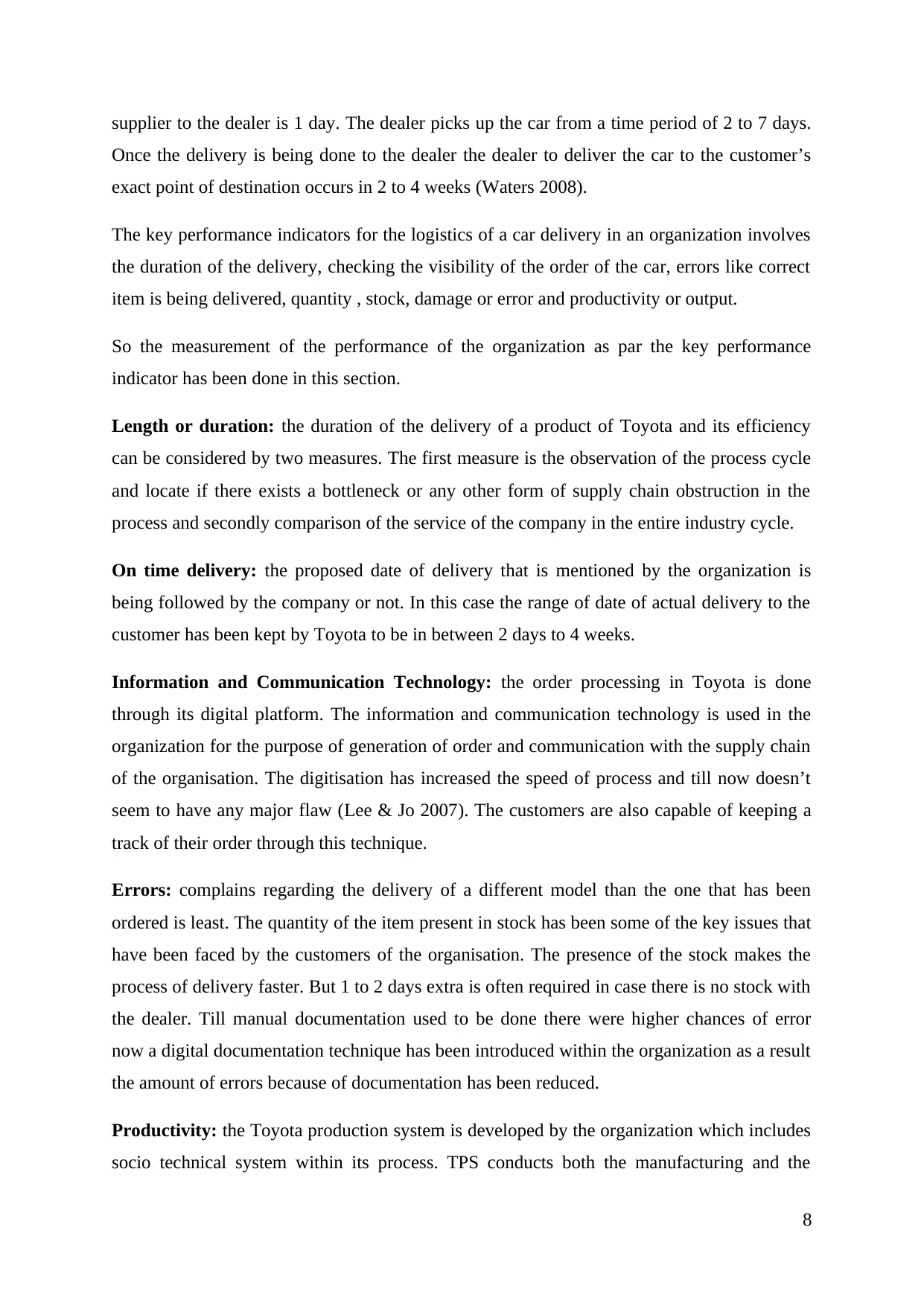
supplier to the dealer is 1 day. The dealer picks up the car from a time period of 2 to 7 days.
Once the delivery is being done to the dealer the dealer to deliver the car to the customer’s
exact point of destination occurs in 2 to 4 weeks (Waters 2008).
The key performance indicators for the logistics of a car delivery in an organization involves
the duration of the delivery, checking the visibility of the order of the car, errors like correct
item is being delivered, quantity , stock, damage or error and productivity or output.
So the measurement of the performance of the organization as par the key performance
indicator has been done in this section.
Length or duration: the duration of the delivery of a product of Toyota and its efficiency
can be considered by two measures. The first measure is the observation of the process cycle
and locate if there exists a bottleneck or any other form of supply chain obstruction in the
process and secondly comparison of the service of the company in the entire industry cycle.
On time delivery: the proposed date of delivery that is mentioned by the organization is
being followed by the company or not. In this case the range of date of actual delivery to the
customer has been kept by Toyota to be in between 2 days to 4 weeks.
Information and Communication Technology: the order processing in Toyota is done
through its digital platform. The information and communication technology is used in the
organization for the purpose of generation of order and communication with the supply chain
of the organisation. The digitisation has increased the speed of process and till now doesn’t
seem to have any major flaw (Lee & Jo 2007). The customers are also capable of keeping a
track of their order through this technique.
Errors: complains regarding the delivery of a different model than the one that has been
ordered is least. The quantity of the item present in stock has been some of the key issues that
have been faced by the customers of the organisation. The presence of the stock makes the
process of delivery faster. But 1 to 2 days extra is often required in case there is no stock with
the dealer. Till manual documentation used to be done there were higher chances of error
now a digital documentation technique has been introduced within the organization as a result
the amount of errors because of documentation has been reduced.
Productivity: the Toyota production system is developed by the organization which includes
socio technical system within its process. TPS conducts both the manufacturing and the
8
Once the delivery is being done to the dealer the dealer to deliver the car to the customer’s
exact point of destination occurs in 2 to 4 weeks (Waters 2008).
The key performance indicators for the logistics of a car delivery in an organization involves
the duration of the delivery, checking the visibility of the order of the car, errors like correct
item is being delivered, quantity , stock, damage or error and productivity or output.
So the measurement of the performance of the organization as par the key performance
indicator has been done in this section.
Length or duration: the duration of the delivery of a product of Toyota and its efficiency
can be considered by two measures. The first measure is the observation of the process cycle
and locate if there exists a bottleneck or any other form of supply chain obstruction in the
process and secondly comparison of the service of the company in the entire industry cycle.
On time delivery: the proposed date of delivery that is mentioned by the organization is
being followed by the company or not. In this case the range of date of actual delivery to the
customer has been kept by Toyota to be in between 2 days to 4 weeks.
Information and Communication Technology: the order processing in Toyota is done
through its digital platform. The information and communication technology is used in the
organization for the purpose of generation of order and communication with the supply chain
of the organisation. The digitisation has increased the speed of process and till now doesn’t
seem to have any major flaw (Lee & Jo 2007). The customers are also capable of keeping a
track of their order through this technique.
Errors: complains regarding the delivery of a different model than the one that has been
ordered is least. The quantity of the item present in stock has been some of the key issues that
have been faced by the customers of the organisation. The presence of the stock makes the
process of delivery faster. But 1 to 2 days extra is often required in case there is no stock with
the dealer. Till manual documentation used to be done there were higher chances of error
now a digital documentation technique has been introduced within the organization as a result
the amount of errors because of documentation has been reduced.
Productivity: the Toyota production system is developed by the organization which includes
socio technical system within its process. TPS conducts both the manufacturing and the
8
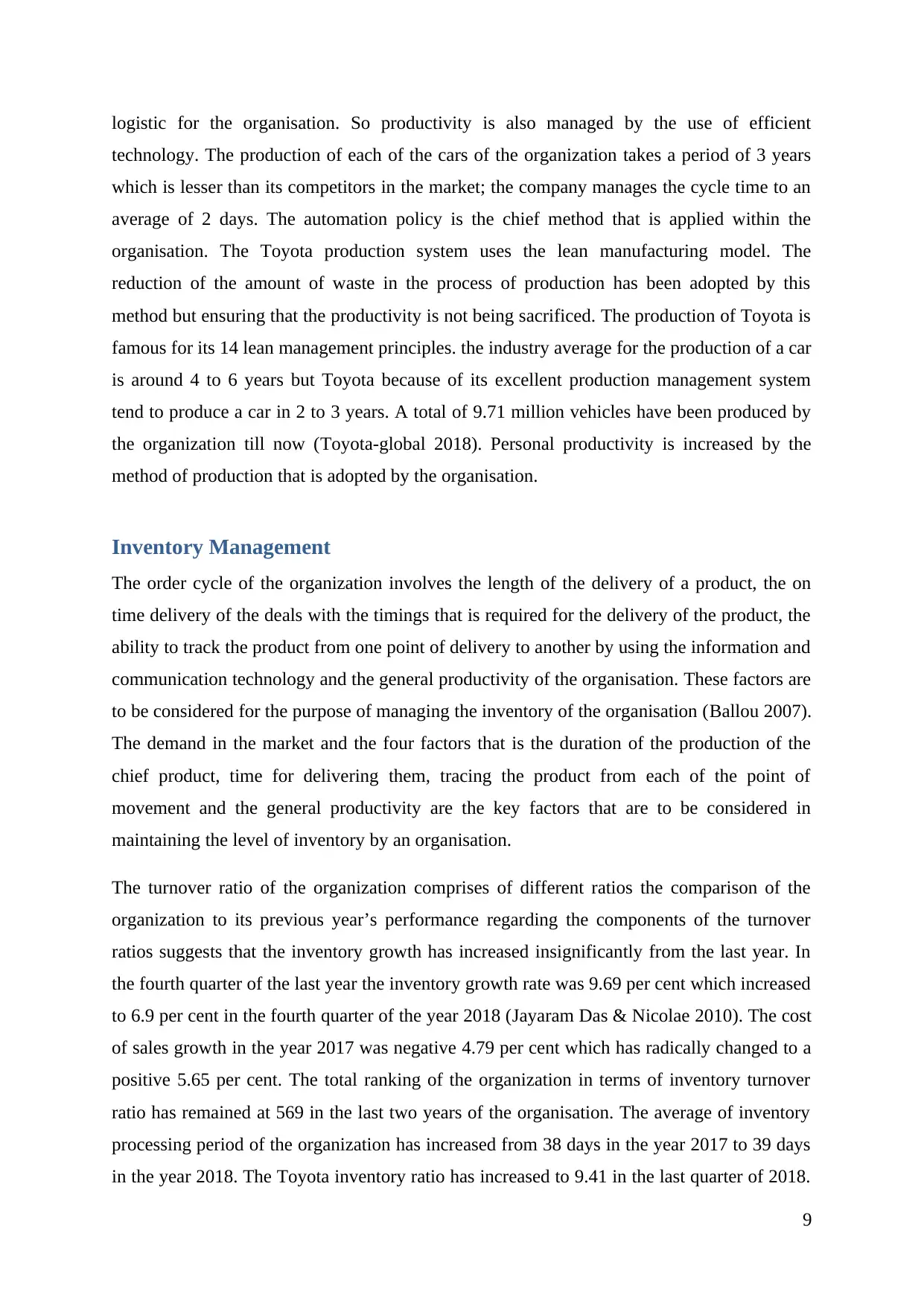
logistic for the organisation. So productivity is also managed by the use of efficient
technology. The production of each of the cars of the organization takes a period of 3 years
which is lesser than its competitors in the market; the company manages the cycle time to an
average of 2 days. The automation policy is the chief method that is applied within the
organisation. The Toyota production system uses the lean manufacturing model. The
reduction of the amount of waste in the process of production has been adopted by this
method but ensuring that the productivity is not being sacrificed. The production of Toyota is
famous for its 14 lean management principles. the industry average for the production of a car
is around 4 to 6 years but Toyota because of its excellent production management system
tend to produce a car in 2 to 3 years. A total of 9.71 million vehicles have been produced by
the organization till now (Toyota-global 2018). Personal productivity is increased by the
method of production that is adopted by the organisation.
Inventory Management
The order cycle of the organization involves the length of the delivery of a product, the on
time delivery of the deals with the timings that is required for the delivery of the product, the
ability to track the product from one point of delivery to another by using the information and
communication technology and the general productivity of the organisation. These factors are
to be considered for the purpose of managing the inventory of the organisation (Ballou 2007).
The demand in the market and the four factors that is the duration of the production of the
chief product, time for delivering them, tracing the product from each of the point of
movement and the general productivity are the key factors that are to be considered in
maintaining the level of inventory by an organisation.
The turnover ratio of the organization comprises of different ratios the comparison of the
organization to its previous year’s performance regarding the components of the turnover
ratios suggests that the inventory growth has increased insignificantly from the last year. In
the fourth quarter of the last year the inventory growth rate was 9.69 per cent which increased
to 6.9 per cent in the fourth quarter of the year 2018 (Jayaram Das & Nicolae 2010). The cost
of sales growth in the year 2017 was negative 4.79 per cent which has radically changed to a
positive 5.65 per cent. The total ranking of the organization in terms of inventory turnover
ratio has remained at 569 in the last two years of the organisation. The average of inventory
processing period of the organization has increased from 38 days in the year 2017 to 39 days
in the year 2018. The Toyota inventory ratio has increased to 9.41 in the last quarter of 2018.
9
technology. The production of each of the cars of the organization takes a period of 3 years
which is lesser than its competitors in the market; the company manages the cycle time to an
average of 2 days. The automation policy is the chief method that is applied within the
organisation. The Toyota production system uses the lean manufacturing model. The
reduction of the amount of waste in the process of production has been adopted by this
method but ensuring that the productivity is not being sacrificed. The production of Toyota is
famous for its 14 lean management principles. the industry average for the production of a car
is around 4 to 6 years but Toyota because of its excellent production management system
tend to produce a car in 2 to 3 years. A total of 9.71 million vehicles have been produced by
the organization till now (Toyota-global 2018). Personal productivity is increased by the
method of production that is adopted by the organisation.
Inventory Management
The order cycle of the organization involves the length of the delivery of a product, the on
time delivery of the deals with the timings that is required for the delivery of the product, the
ability to track the product from one point of delivery to another by using the information and
communication technology and the general productivity of the organisation. These factors are
to be considered for the purpose of managing the inventory of the organisation (Ballou 2007).
The demand in the market and the four factors that is the duration of the production of the
chief product, time for delivering them, tracing the product from each of the point of
movement and the general productivity are the key factors that are to be considered in
maintaining the level of inventory by an organisation.
The turnover ratio of the organization comprises of different ratios the comparison of the
organization to its previous year’s performance regarding the components of the turnover
ratios suggests that the inventory growth has increased insignificantly from the last year. In
the fourth quarter of the last year the inventory growth rate was 9.69 per cent which increased
to 6.9 per cent in the fourth quarter of the year 2018 (Jayaram Das & Nicolae 2010). The cost
of sales growth in the year 2017 was negative 4.79 per cent which has radically changed to a
positive 5.65 per cent. The total ranking of the organization in terms of inventory turnover
ratio has remained at 569 in the last two years of the organisation. The average of inventory
processing period of the organization has increased from 38 days in the year 2017 to 39 days
in the year 2018. The Toyota inventory ratio has increased to 9.41 in the last quarter of 2018.
9
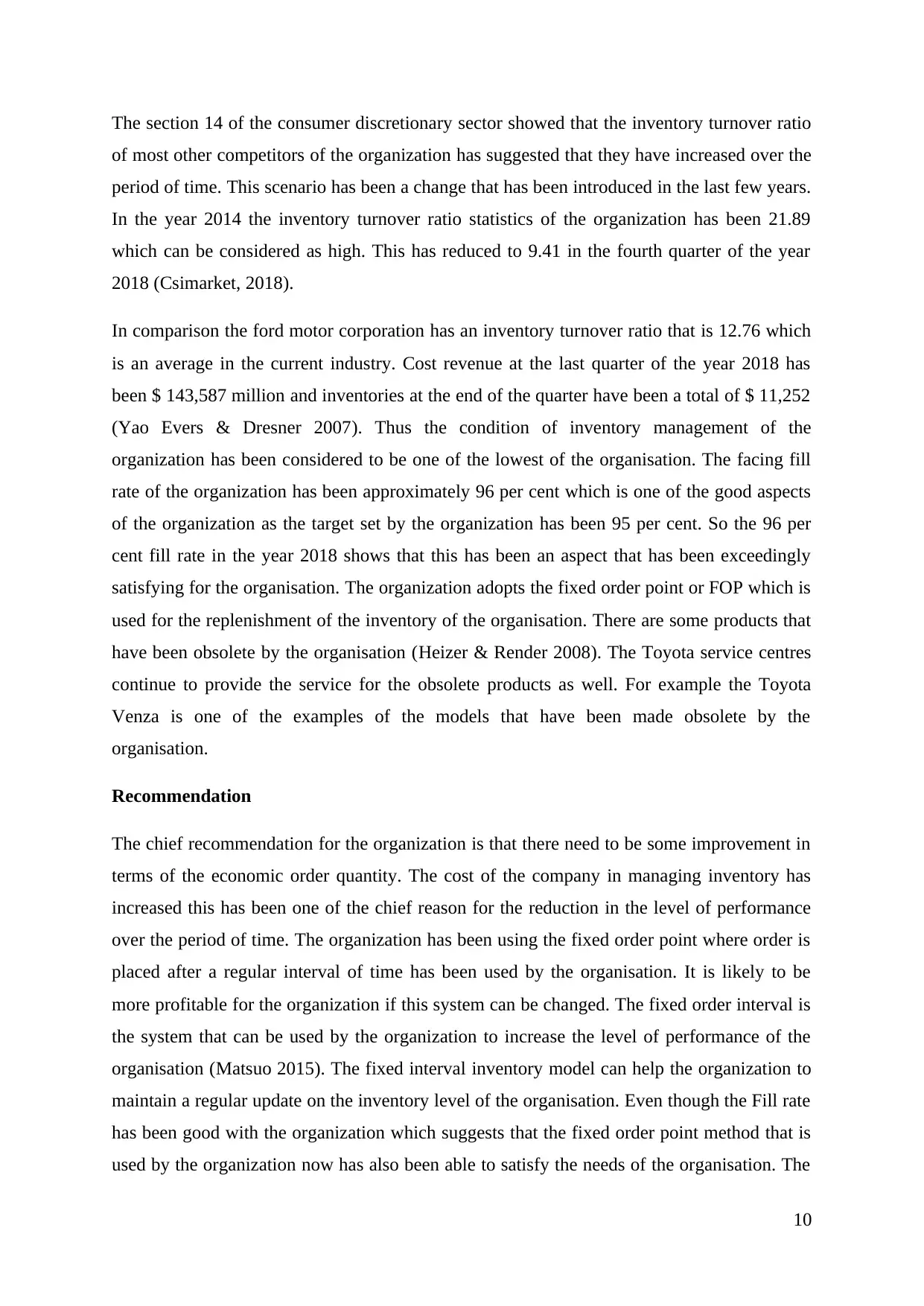
The section 14 of the consumer discretionary sector showed that the inventory turnover ratio
of most other competitors of the organization has suggested that they have increased over the
period of time. This scenario has been a change that has been introduced in the last few years.
In the year 2014 the inventory turnover ratio statistics of the organization has been 21.89
which can be considered as high. This has reduced to 9.41 in the fourth quarter of the year
2018 (Csimarket, 2018).
In comparison the ford motor corporation has an inventory turnover ratio that is 12.76 which
is an average in the current industry. Cost revenue at the last quarter of the year 2018 has
been $ 143,587 million and inventories at the end of the quarter have been a total of $ 11,252
(Yao Evers & Dresner 2007). Thus the condition of inventory management of the
organization has been considered to be one of the lowest of the organisation. The facing fill
rate of the organization has been approximately 96 per cent which is one of the good aspects
of the organization as the target set by the organization has been 95 per cent. So the 96 per
cent fill rate in the year 2018 shows that this has been an aspect that has been exceedingly
satisfying for the organisation. The organization adopts the fixed order point or FOP which is
used for the replenishment of the inventory of the organisation. There are some products that
have been obsolete by the organisation (Heizer & Render 2008). The Toyota service centres
continue to provide the service for the obsolete products as well. For example the Toyota
Venza is one of the examples of the models that have been made obsolete by the
organisation.
Recommendation
The chief recommendation for the organization is that there need to be some improvement in
terms of the economic order quantity. The cost of the company in managing inventory has
increased this has been one of the chief reason for the reduction in the level of performance
over the period of time. The organization has been using the fixed order point where order is
placed after a regular interval of time has been used by the organisation. It is likely to be
more profitable for the organization if this system can be changed. The fixed order interval is
the system that can be used by the organization to increase the level of performance of the
organisation (Matsuo 2015). The fixed interval inventory model can help the organization to
maintain a regular update on the inventory level of the organisation. Even though the Fill rate
has been good with the organization which suggests that the fixed order point method that is
used by the organization now has also been able to satisfy the needs of the organisation. The
10
of most other competitors of the organization has suggested that they have increased over the
period of time. This scenario has been a change that has been introduced in the last few years.
In the year 2014 the inventory turnover ratio statistics of the organization has been 21.89
which can be considered as high. This has reduced to 9.41 in the fourth quarter of the year
2018 (Csimarket, 2018).
In comparison the ford motor corporation has an inventory turnover ratio that is 12.76 which
is an average in the current industry. Cost revenue at the last quarter of the year 2018 has
been $ 143,587 million and inventories at the end of the quarter have been a total of $ 11,252
(Yao Evers & Dresner 2007). Thus the condition of inventory management of the
organization has been considered to be one of the lowest of the organisation. The facing fill
rate of the organization has been approximately 96 per cent which is one of the good aspects
of the organization as the target set by the organization has been 95 per cent. So the 96 per
cent fill rate in the year 2018 shows that this has been an aspect that has been exceedingly
satisfying for the organisation. The organization adopts the fixed order point or FOP which is
used for the replenishment of the inventory of the organisation. There are some products that
have been obsolete by the organisation (Heizer & Render 2008). The Toyota service centres
continue to provide the service for the obsolete products as well. For example the Toyota
Venza is one of the examples of the models that have been made obsolete by the
organisation.
Recommendation
The chief recommendation for the organization is that there need to be some improvement in
terms of the economic order quantity. The cost of the company in managing inventory has
increased this has been one of the chief reason for the reduction in the level of performance
over the period of time. The organization has been using the fixed order point where order is
placed after a regular interval of time has been used by the organisation. It is likely to be
more profitable for the organization if this system can be changed. The fixed order interval is
the system that can be used by the organization to increase the level of performance of the
organisation (Matsuo 2015). The fixed interval inventory model can help the organization to
maintain a regular update on the inventory level of the organisation. Even though the Fill rate
has been good with the organization which suggests that the fixed order point method that is
used by the organization now has also been able to satisfy the needs of the organisation. The
10
Secure Best Marks with AI Grader
Need help grading? Try our AI Grader for instant feedback on your assignments.
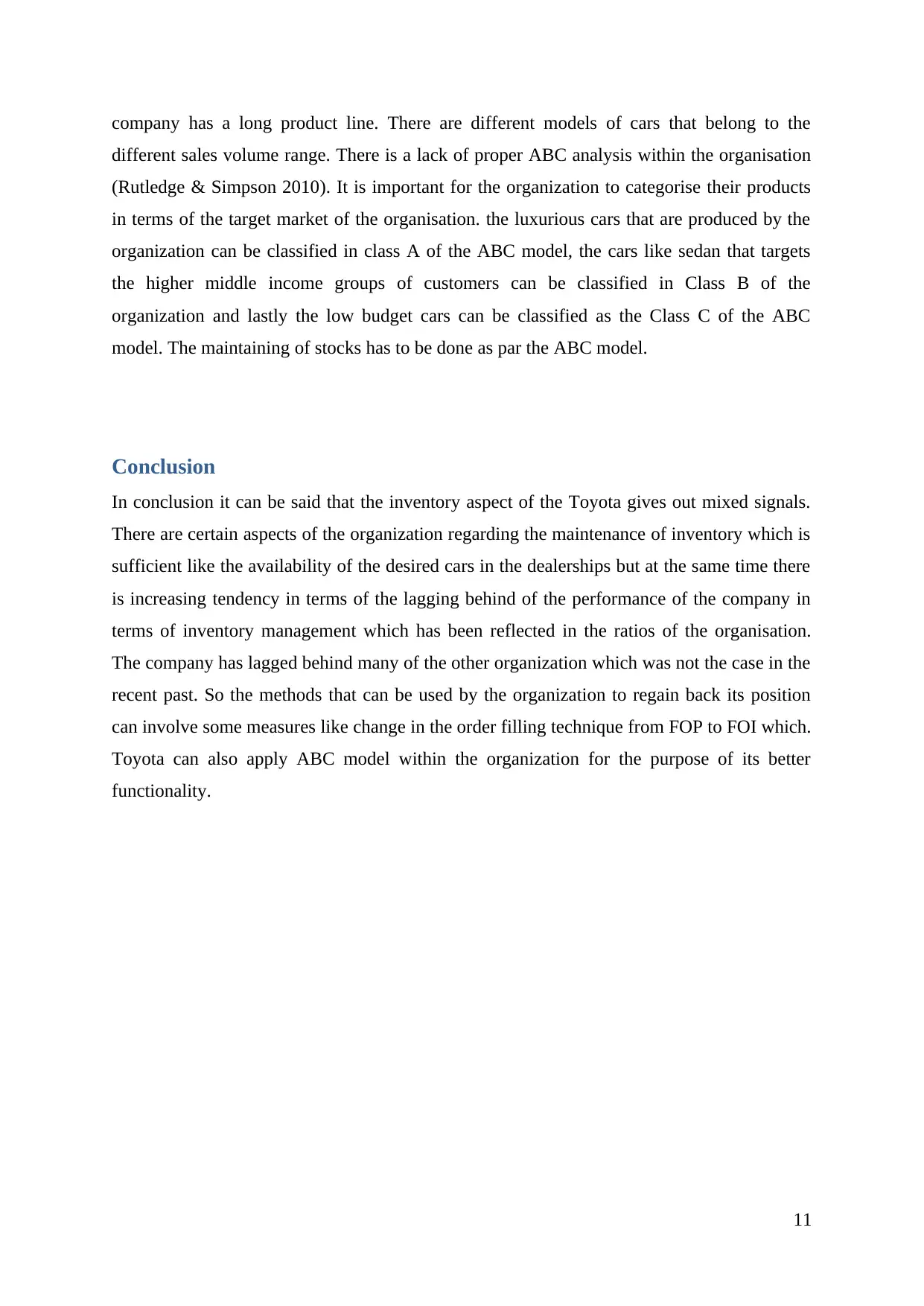
company has a long product line. There are different models of cars that belong to the
different sales volume range. There is a lack of proper ABC analysis within the organisation
(Rutledge & Simpson 2010). It is important for the organization to categorise their products
in terms of the target market of the organisation. the luxurious cars that are produced by the
organization can be classified in class A of the ABC model, the cars like sedan that targets
the higher middle income groups of customers can be classified in Class B of the
organization and lastly the low budget cars can be classified as the Class C of the ABC
model. The maintaining of stocks has to be done as par the ABC model.
Conclusion
In conclusion it can be said that the inventory aspect of the Toyota gives out mixed signals.
There are certain aspects of the organization regarding the maintenance of inventory which is
sufficient like the availability of the desired cars in the dealerships but at the same time there
is increasing tendency in terms of the lagging behind of the performance of the company in
terms of inventory management which has been reflected in the ratios of the organisation.
The company has lagged behind many of the other organization which was not the case in the
recent past. So the methods that can be used by the organization to regain back its position
can involve some measures like change in the order filling technique from FOP to FOI which.
Toyota can also apply ABC model within the organization for the purpose of its better
functionality.
11
different sales volume range. There is a lack of proper ABC analysis within the organisation
(Rutledge & Simpson 2010). It is important for the organization to categorise their products
in terms of the target market of the organisation. the luxurious cars that are produced by the
organization can be classified in class A of the ABC model, the cars like sedan that targets
the higher middle income groups of customers can be classified in Class B of the
organization and lastly the low budget cars can be classified as the Class C of the ABC
model. The maintaining of stocks has to be done as par the ABC model.
Conclusion
In conclusion it can be said that the inventory aspect of the Toyota gives out mixed signals.
There are certain aspects of the organization regarding the maintenance of inventory which is
sufficient like the availability of the desired cars in the dealerships but at the same time there
is increasing tendency in terms of the lagging behind of the performance of the company in
terms of inventory management which has been reflected in the ratios of the organisation.
The company has lagged behind many of the other organization which was not the case in the
recent past. So the methods that can be used by the organization to regain back its position
can involve some measures like change in the order filling technique from FOP to FOI which.
Toyota can also apply ABC model within the organization for the purpose of its better
functionality.
11
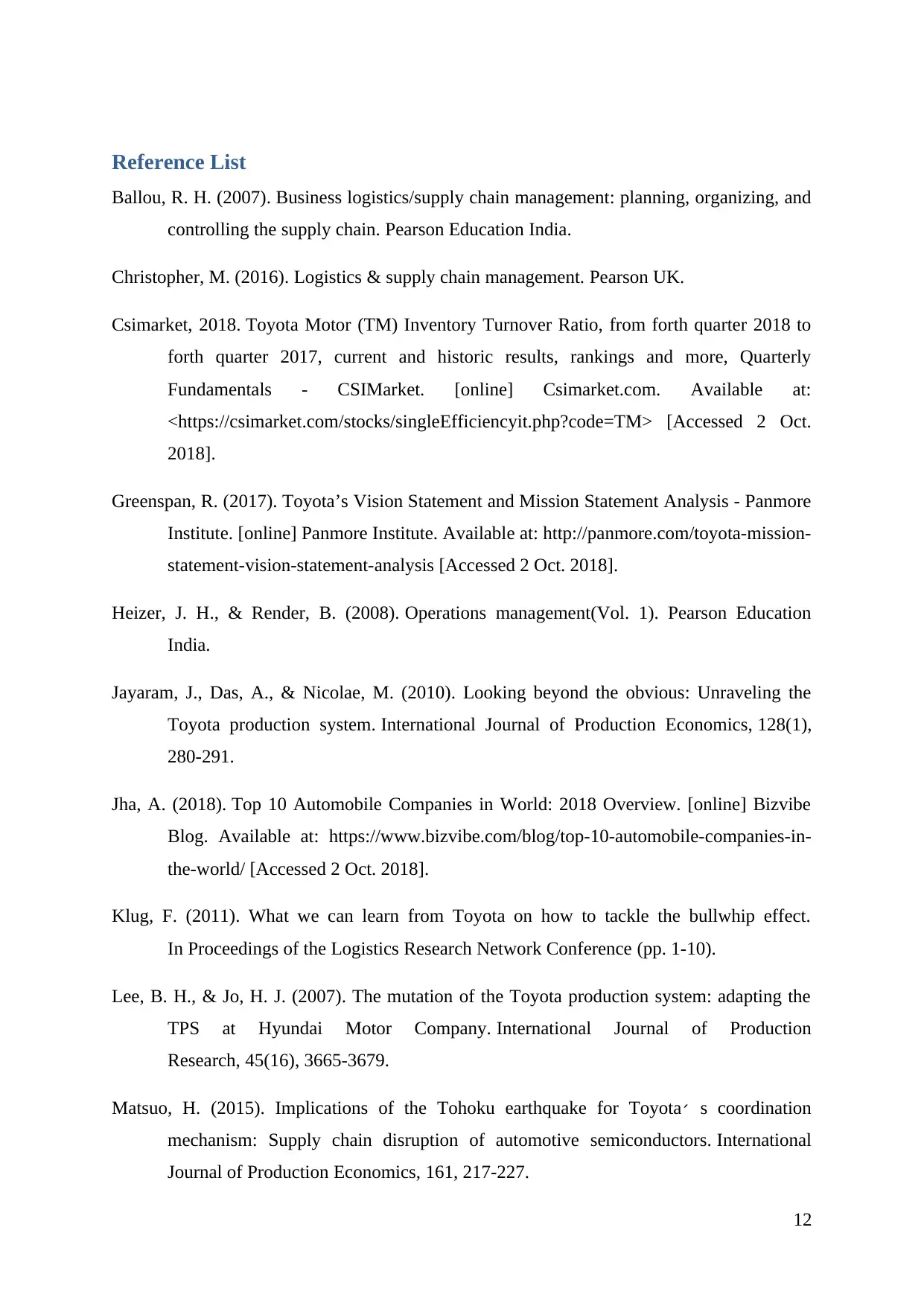
Reference List
Ballou, R. H. (2007). Business logistics/supply chain management: planning, organizing, and
controlling the supply chain. Pearson Education India.
Christopher, M. (2016). Logistics & supply chain management. Pearson UK.
Csimarket, 2018. Toyota Motor (TM) Inventory Turnover Ratio, from forth quarter 2018 to
forth quarter 2017, current and historic results, rankings and more, Quarterly
Fundamentals - CSIMarket. [online] Csimarket.com. Available at:
<https://csimarket.com/stocks/singleEfficiencyit.php?code=TM> [Accessed 2 Oct.
2018].
Greenspan, R. (2017). Toyota’s Vision Statement and Mission Statement Analysis - Panmore
Institute. [online] Panmore Institute. Available at: http://panmore.com/toyota-mission-
statement-vision-statement-analysis [Accessed 2 Oct. 2018].
Heizer, J. H., & Render, B. (2008). Operations management(Vol. 1). Pearson Education
India.
Jayaram, J., Das, A., & Nicolae, M. (2010). Looking beyond the obvious: Unraveling the
Toyota production system. International Journal of Production Economics, 128(1),
280-291.
Jha, A. (2018). Top 10 Automobile Companies in World: 2018 Overview. [online] Bizvibe
Blog. Available at: https://www.bizvibe.com/blog/top-10-automobile-companies-in-
the-world/ [Accessed 2 Oct. 2018].
Klug, F. (2011). What we can learn from Toyota on how to tackle the bullwhip effect.
In Proceedings of the Logistics Research Network Conference (pp. 1-10).
Lee, B. H., & Jo, H. J. (2007). The mutation of the Toyota production system: adapting the
TPS at Hyundai Motor Company. International Journal of Production
Research, 45(16), 3665-3679.
Matsuo, H. (2015). Implications of the Tohoku earthquake for Toyota׳ s coordination
mechanism: Supply chain disruption of automotive semiconductors. International
Journal of Production Economics, 161, 217-227.
12
Ballou, R. H. (2007). Business logistics/supply chain management: planning, organizing, and
controlling the supply chain. Pearson Education India.
Christopher, M. (2016). Logistics & supply chain management. Pearson UK.
Csimarket, 2018. Toyota Motor (TM) Inventory Turnover Ratio, from forth quarter 2018 to
forth quarter 2017, current and historic results, rankings and more, Quarterly
Fundamentals - CSIMarket. [online] Csimarket.com. Available at:
<https://csimarket.com/stocks/singleEfficiencyit.php?code=TM> [Accessed 2 Oct.
2018].
Greenspan, R. (2017). Toyota’s Vision Statement and Mission Statement Analysis - Panmore
Institute. [online] Panmore Institute. Available at: http://panmore.com/toyota-mission-
statement-vision-statement-analysis [Accessed 2 Oct. 2018].
Heizer, J. H., & Render, B. (2008). Operations management(Vol. 1). Pearson Education
India.
Jayaram, J., Das, A., & Nicolae, M. (2010). Looking beyond the obvious: Unraveling the
Toyota production system. International Journal of Production Economics, 128(1),
280-291.
Jha, A. (2018). Top 10 Automobile Companies in World: 2018 Overview. [online] Bizvibe
Blog. Available at: https://www.bizvibe.com/blog/top-10-automobile-companies-in-
the-world/ [Accessed 2 Oct. 2018].
Klug, F. (2011). What we can learn from Toyota on how to tackle the bullwhip effect.
In Proceedings of the Logistics Research Network Conference (pp. 1-10).
Lee, B. H., & Jo, H. J. (2007). The mutation of the Toyota production system: adapting the
TPS at Hyundai Motor Company. International Journal of Production
Research, 45(16), 3665-3679.
Matsuo, H. (2015). Implications of the Tohoku earthquake for Toyota׳ s coordination
mechanism: Supply chain disruption of automotive semiconductors. International
Journal of Production Economics, 161, 217-227.
12
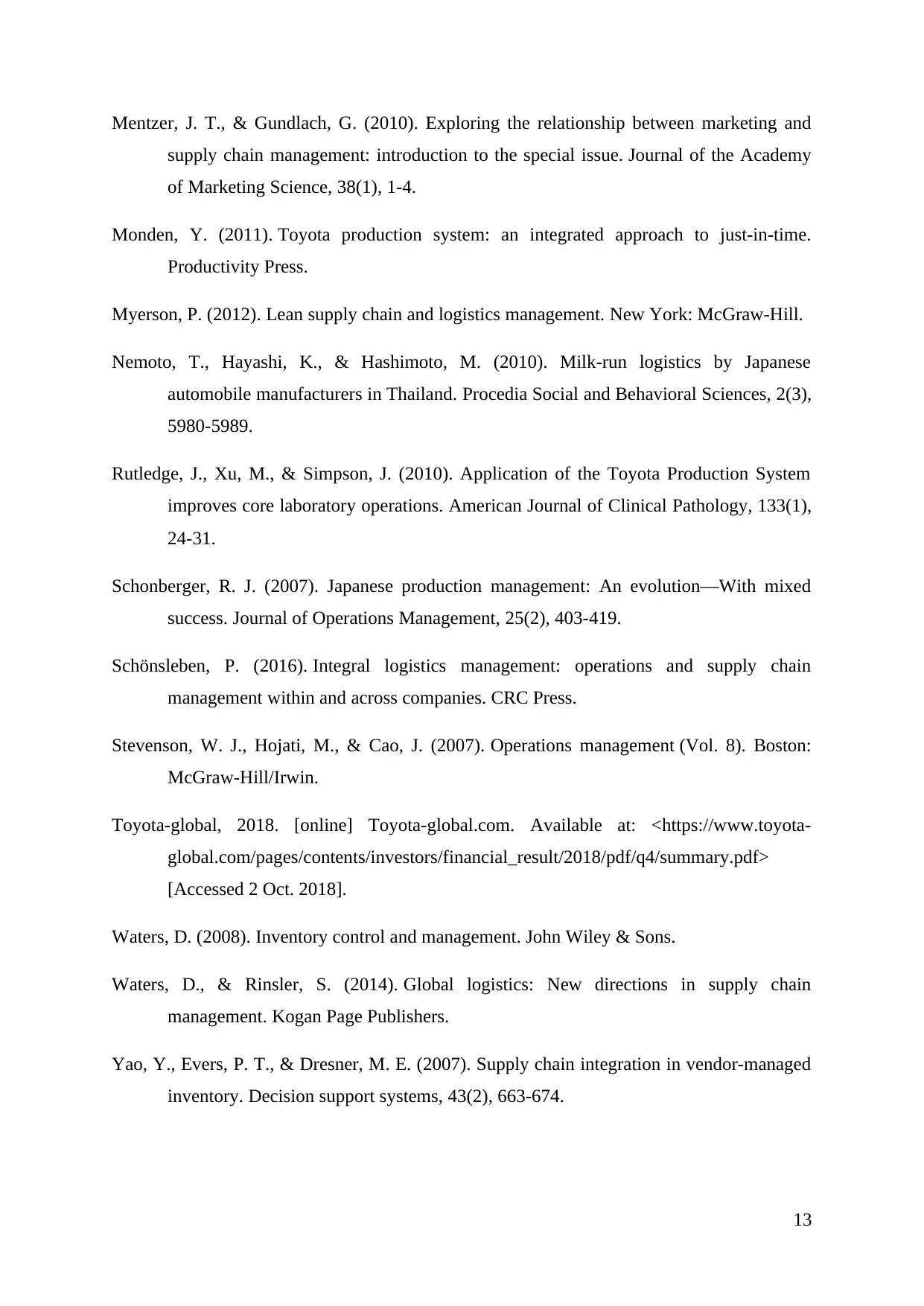
Mentzer, J. T., & Gundlach, G. (2010). Exploring the relationship between marketing and
supply chain management: introduction to the special issue. Journal of the Academy
of Marketing Science, 38(1), 1-4.
Monden, Y. (2011). Toyota production system: an integrated approach to just-in-time.
Productivity Press.
Myerson, P. (2012). Lean supply chain and logistics management. New York: McGraw-Hill.
Nemoto, T., Hayashi, K., & Hashimoto, M. (2010). Milk-run logistics by Japanese
automobile manufacturers in Thailand. Procedia Social and Behavioral Sciences, 2(3),
5980-5989.
Rutledge, J., Xu, M., & Simpson, J. (2010). Application of the Toyota Production System
improves core laboratory operations. American Journal of Clinical Pathology, 133(1),
24-31.
Schonberger, R. J. (2007). Japanese production management: An evolution—With mixed
success. Journal of Operations Management, 25(2), 403-419.
Schönsleben, P. (2016). Integral logistics management: operations and supply chain
management within and across companies. CRC Press.
Stevenson, W. J., Hojati, M., & Cao, J. (2007). Operations management (Vol. 8). Boston:
McGraw-Hill/Irwin.
Toyota-global, 2018. [online] Toyota-global.com. Available at: <https://www.toyota-
global.com/pages/contents/investors/financial_result/2018/pdf/q4/summary.pdf>
[Accessed 2 Oct. 2018].
Waters, D. (2008). Inventory control and management. John Wiley & Sons.
Waters, D., & Rinsler, S. (2014). Global logistics: New directions in supply chain
management. Kogan Page Publishers.
Yao, Y., Evers, P. T., & Dresner, M. E. (2007). Supply chain integration in vendor-managed
inventory. Decision support systems, 43(2), 663-674.
13
supply chain management: introduction to the special issue. Journal of the Academy
of Marketing Science, 38(1), 1-4.
Monden, Y. (2011). Toyota production system: an integrated approach to just-in-time.
Productivity Press.
Myerson, P. (2012). Lean supply chain and logistics management. New York: McGraw-Hill.
Nemoto, T., Hayashi, K., & Hashimoto, M. (2010). Milk-run logistics by Japanese
automobile manufacturers in Thailand. Procedia Social and Behavioral Sciences, 2(3),
5980-5989.
Rutledge, J., Xu, M., & Simpson, J. (2010). Application of the Toyota Production System
improves core laboratory operations. American Journal of Clinical Pathology, 133(1),
24-31.
Schonberger, R. J. (2007). Japanese production management: An evolution—With mixed
success. Journal of Operations Management, 25(2), 403-419.
Schönsleben, P. (2016). Integral logistics management: operations and supply chain
management within and across companies. CRC Press.
Stevenson, W. J., Hojati, M., & Cao, J. (2007). Operations management (Vol. 8). Boston:
McGraw-Hill/Irwin.
Toyota-global, 2018. [online] Toyota-global.com. Available at: <https://www.toyota-
global.com/pages/contents/investors/financial_result/2018/pdf/q4/summary.pdf>
[Accessed 2 Oct. 2018].
Waters, D. (2008). Inventory control and management. John Wiley & Sons.
Waters, D., & Rinsler, S. (2014). Global logistics: New directions in supply chain
management. Kogan Page Publishers.
Yao, Y., Evers, P. T., & Dresner, M. E. (2007). Supply chain integration in vendor-managed
inventory. Decision support systems, 43(2), 663-674.
13
Paraphrase This Document
Need a fresh take? Get an instant paraphrase of this document with our AI Paraphraser
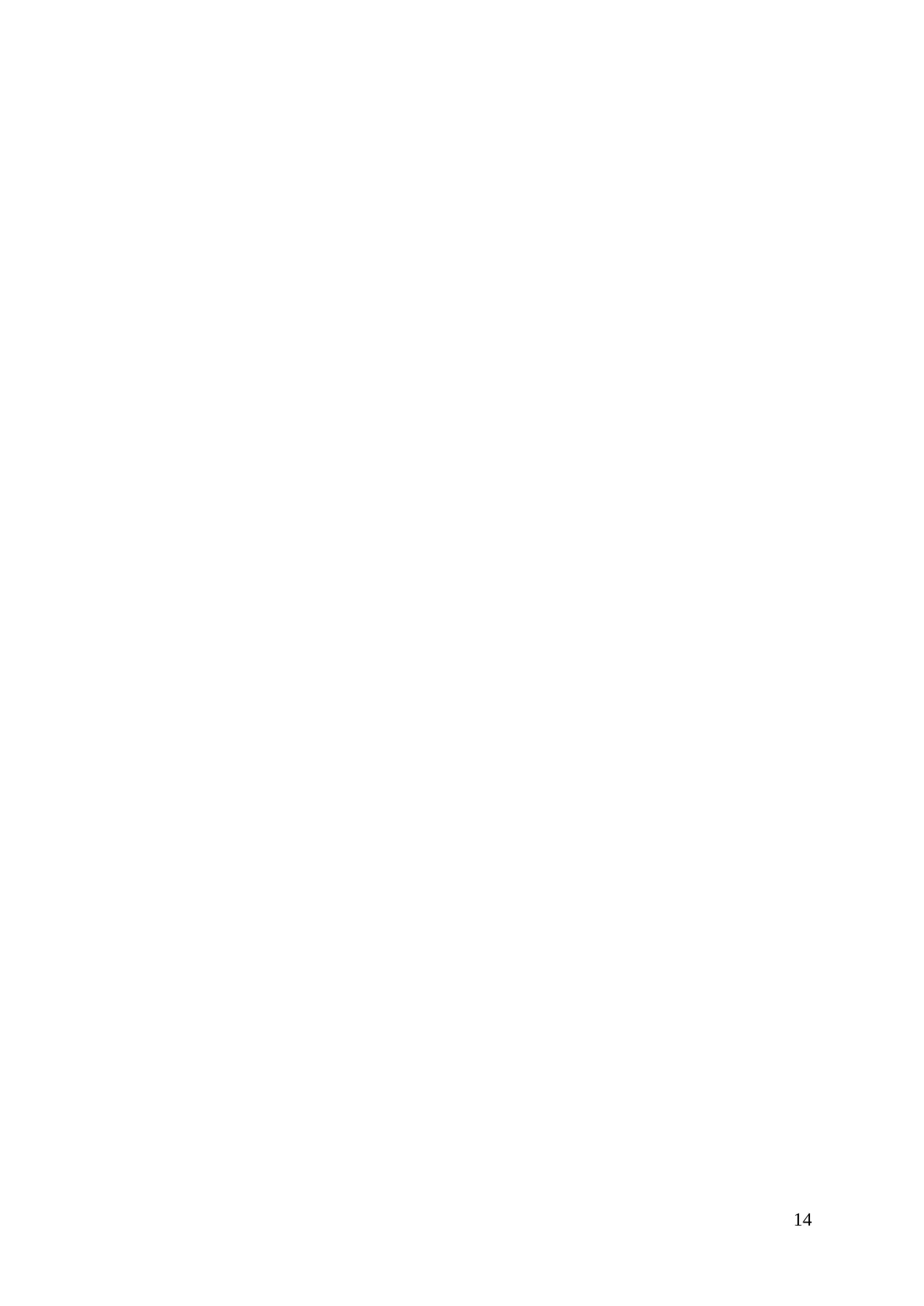
14
1 out of 14
Related Documents
![[object Object]](/_next/image/?url=%2F_next%2Fstatic%2Fmedia%2Flogo.6d15ce61.png&w=640&q=75)
Your All-in-One AI-Powered Toolkit for Academic Success.
+13062052269
info@desklib.com
Available 24*7 on WhatsApp / Email
Unlock your academic potential
© 2024 | Zucol Services PVT LTD | All rights reserved.