MIS713: Domino's Pizza Supply Chain, Sourcing & CSR Metrics
VerifiedAdded on 2023/06/07
|17
|3711
|162
Case Study
AI Summary
This case study report examines the supply chain management and corporate social responsibility (CSR) practices of Domino's Pizza in Wheelers Hill, Australia, focusing on the sourcing of veggies, meat, and beverages. It identifies buyer behavior segments, key decision factors, and the environmental impact of sourcing activities. The report applies the SCOR model to analyze sourcing tasks and proposes a CSR metric based on air quality and waste, evaluating its implications for Domino's. It also references a case study report of Phantom India Restaurant with focus on the company’s business goals, strategies, buyer behaviour segments and supply chain. The analysis includes a discussion of the feasibility of collecting data for the metric and the potential positive and negative impacts of its implementation. Desklib provides access to similar case studies and solved assignments for students.
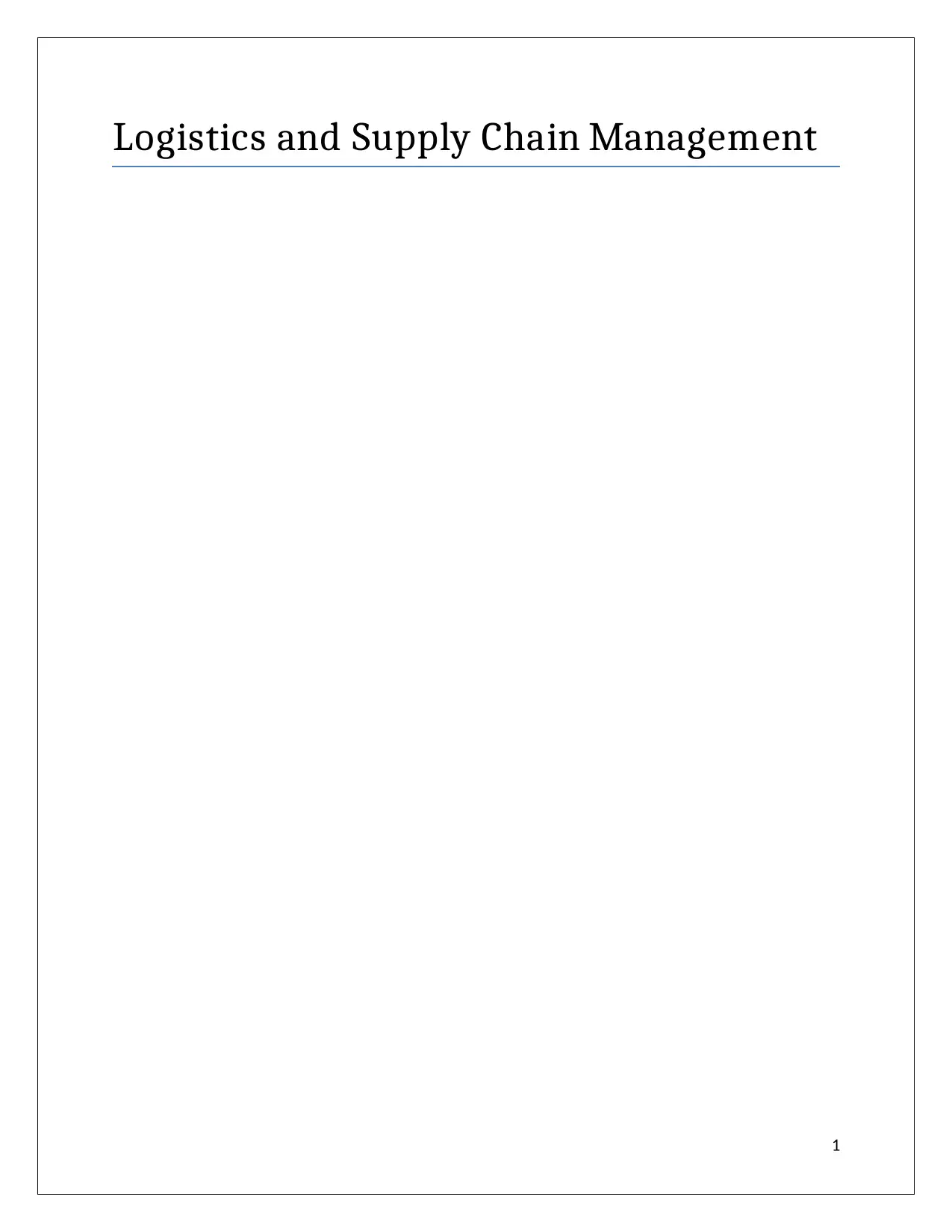
Logistics and Supply Chain Management
1
1
Paraphrase This Document
Need a fresh take? Get an instant paraphrase of this document with our AI Paraphraser
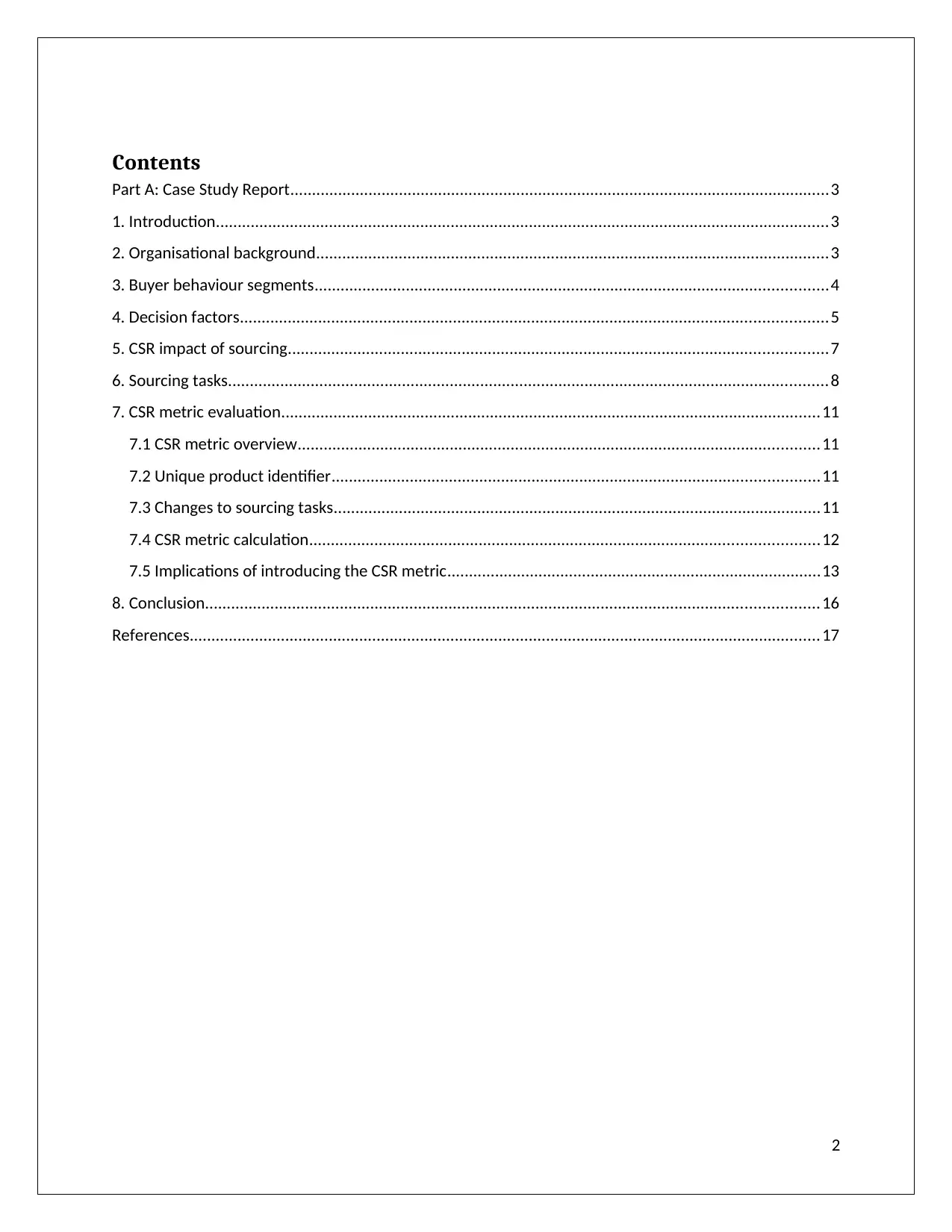
Contents
Part A: Case Study Report............................................................................................................................3
1. Introduction.............................................................................................................................................3
2. Organisational background......................................................................................................................3
3. Buyer behaviour segments......................................................................................................................4
4. Decision factors.......................................................................................................................................5
5. CSR impact of sourcing............................................................................................................................7
6. Sourcing tasks..........................................................................................................................................8
7. CSR metric evaluation............................................................................................................................11
7.1 CSR metric overview........................................................................................................................11
7.2 Unique product identifier................................................................................................................11
7.3 Changes to sourcing tasks................................................................................................................11
7.4 CSR metric calculation.....................................................................................................................12
7.5 Implications of introducing the CSR metric......................................................................................13
8. Conclusion.............................................................................................................................................16
References.................................................................................................................................................17
2
Part A: Case Study Report............................................................................................................................3
1. Introduction.............................................................................................................................................3
2. Organisational background......................................................................................................................3
3. Buyer behaviour segments......................................................................................................................4
4. Decision factors.......................................................................................................................................5
5. CSR impact of sourcing............................................................................................................................7
6. Sourcing tasks..........................................................................................................................................8
7. CSR metric evaluation............................................................................................................................11
7.1 CSR metric overview........................................................................................................................11
7.2 Unique product identifier................................................................................................................11
7.3 Changes to sourcing tasks................................................................................................................11
7.4 CSR metric calculation.....................................................................................................................12
7.5 Implications of introducing the CSR metric......................................................................................13
8. Conclusion.............................................................................................................................................16
References.................................................................................................................................................17
2
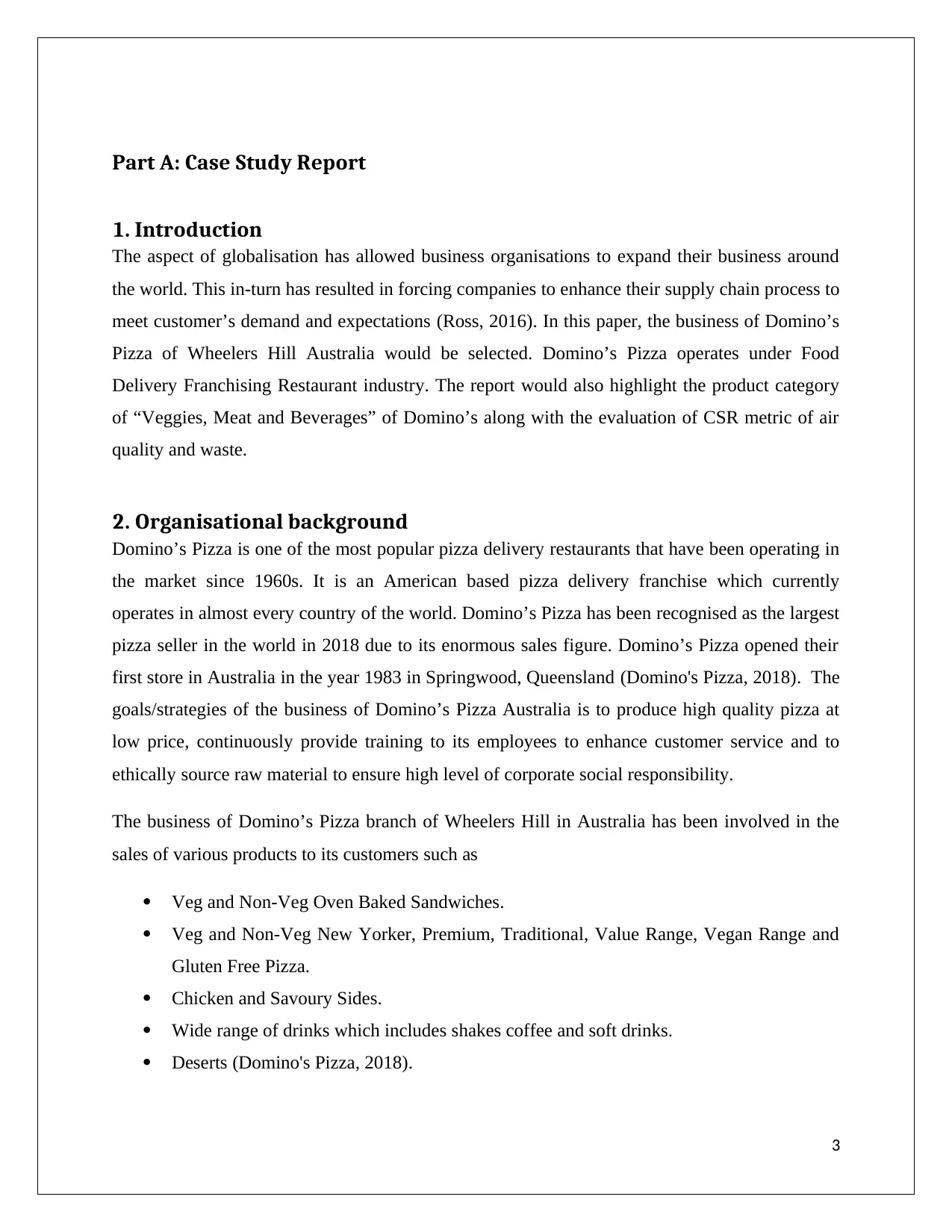
Part A: Case Study Report
1. Introduction
The aspect of globalisation has allowed business organisations to expand their business around
the world. This in-turn has resulted in forcing companies to enhance their supply chain process to
meet customer’s demand and expectations (Ross, 2016). In this paper, the business of Domino’s
Pizza of Wheelers Hill Australia would be selected. Domino’s Pizza operates under Food
Delivery Franchising Restaurant industry. The report would also highlight the product category
of “Veggies, Meat and Beverages” of Domino’s along with the evaluation of CSR metric of air
quality and waste.
2. Organisational background
Domino’s Pizza is one of the most popular pizza delivery restaurants that have been operating in
the market since 1960s. It is an American based pizza delivery franchise which currently
operates in almost every country of the world. Domino’s Pizza has been recognised as the largest
pizza seller in the world in 2018 due to its enormous sales figure. Domino’s Pizza opened their
first store in Australia in the year 1983 in Springwood, Queensland (Domino's Pizza, 2018). The
goals/strategies of the business of Domino’s Pizza Australia is to produce high quality pizza at
low price, continuously provide training to its employees to enhance customer service and to
ethically source raw material to ensure high level of corporate social responsibility.
The business of Domino’s Pizza branch of Wheelers Hill in Australia has been involved in the
sales of various products to its customers such as
Veg and Non-Veg Oven Baked Sandwiches.
Veg and Non-Veg New Yorker, Premium, Traditional, Value Range, Vegan Range and
Gluten Free Pizza.
Chicken and Savoury Sides.
Wide range of drinks which includes shakes coffee and soft drinks.
Deserts (Domino's Pizza, 2018).
3
1. Introduction
The aspect of globalisation has allowed business organisations to expand their business around
the world. This in-turn has resulted in forcing companies to enhance their supply chain process to
meet customer’s demand and expectations (Ross, 2016). In this paper, the business of Domino’s
Pizza of Wheelers Hill Australia would be selected. Domino’s Pizza operates under Food
Delivery Franchising Restaurant industry. The report would also highlight the product category
of “Veggies, Meat and Beverages” of Domino’s along with the evaluation of CSR metric of air
quality and waste.
2. Organisational background
Domino’s Pizza is one of the most popular pizza delivery restaurants that have been operating in
the market since 1960s. It is an American based pizza delivery franchise which currently
operates in almost every country of the world. Domino’s Pizza has been recognised as the largest
pizza seller in the world in 2018 due to its enormous sales figure. Domino’s Pizza opened their
first store in Australia in the year 1983 in Springwood, Queensland (Domino's Pizza, 2018). The
goals/strategies of the business of Domino’s Pizza Australia is to produce high quality pizza at
low price, continuously provide training to its employees to enhance customer service and to
ethically source raw material to ensure high level of corporate social responsibility.
The business of Domino’s Pizza branch of Wheelers Hill in Australia has been involved in the
sales of various products to its customers such as
Veg and Non-Veg Oven Baked Sandwiches.
Veg and Non-Veg New Yorker, Premium, Traditional, Value Range, Vegan Range and
Gluten Free Pizza.
Chicken and Savoury Sides.
Wide range of drinks which includes shakes coffee and soft drinks.
Deserts (Domino's Pizza, 2018).
3
⊘ This is a preview!⊘
Do you want full access?
Subscribe today to unlock all pages.

Trusted by 1+ million students worldwide
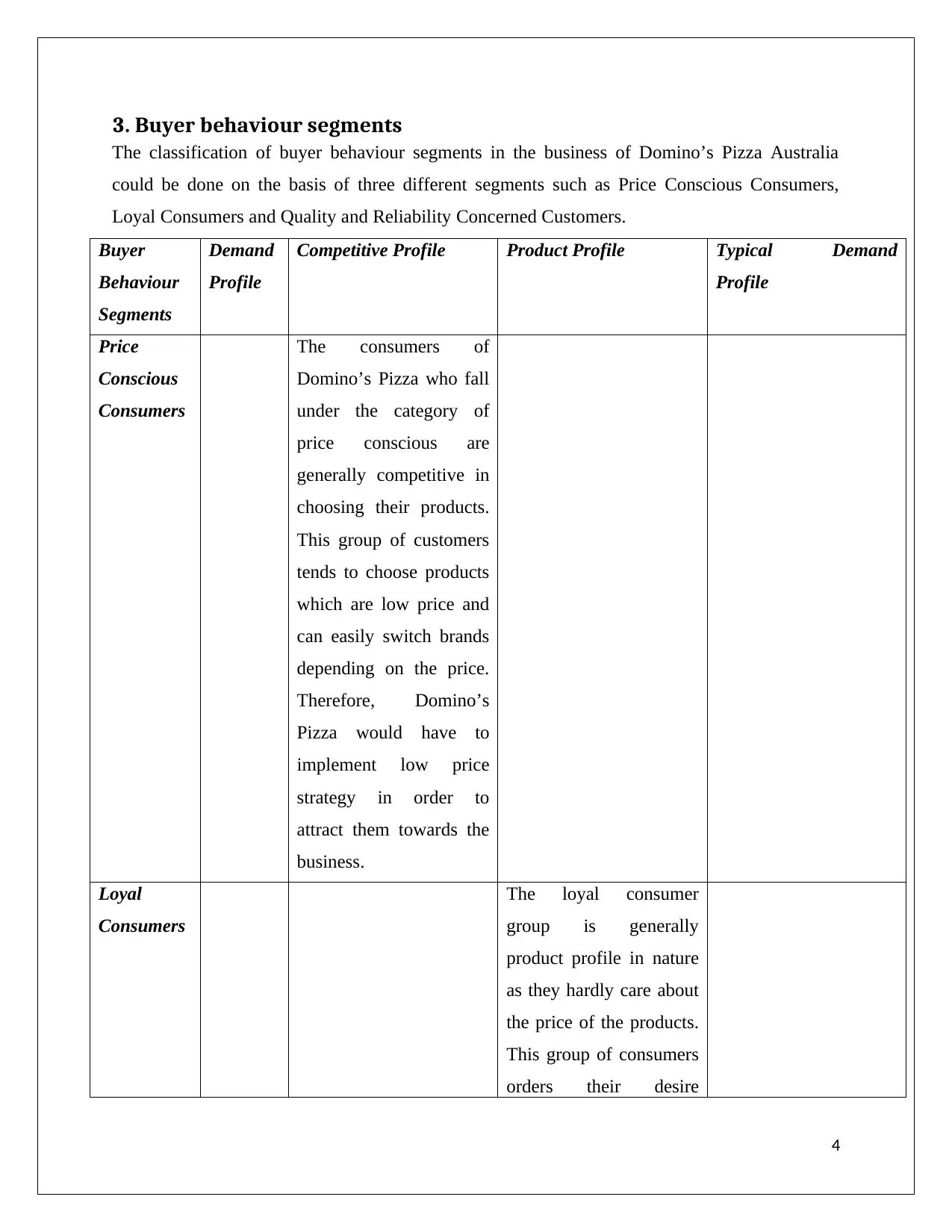
3. Buyer behaviour segments
The classification of buyer behaviour segments in the business of Domino’s Pizza Australia
could be done on the basis of three different segments such as Price Conscious Consumers,
Loyal Consumers and Quality and Reliability Concerned Customers.
Buyer
Behaviour
Segments
Demand
Profile
Competitive Profile Product Profile Typical Demand
Profile
Price
Conscious
Consumers
The consumers of
Domino’s Pizza who fall
under the category of
price conscious are
generally competitive in
choosing their products.
This group of customers
tends to choose products
which are low price and
can easily switch brands
depending on the price.
Therefore, Domino’s
Pizza would have to
implement low price
strategy in order to
attract them towards the
business.
Loyal
Consumers
The loyal consumer
group is generally
product profile in nature
as they hardly care about
the price of the products.
This group of consumers
orders their desire
4
The classification of buyer behaviour segments in the business of Domino’s Pizza Australia
could be done on the basis of three different segments such as Price Conscious Consumers,
Loyal Consumers and Quality and Reliability Concerned Customers.
Buyer
Behaviour
Segments
Demand
Profile
Competitive Profile Product Profile Typical Demand
Profile
Price
Conscious
Consumers
The consumers of
Domino’s Pizza who fall
under the category of
price conscious are
generally competitive in
choosing their products.
This group of customers
tends to choose products
which are low price and
can easily switch brands
depending on the price.
Therefore, Domino’s
Pizza would have to
implement low price
strategy in order to
attract them towards the
business.
Loyal
Consumers
The loyal consumer
group is generally
product profile in nature
as they hardly care about
the price of the products.
This group of consumers
orders their desire
4
Paraphrase This Document
Need a fresh take? Get an instant paraphrase of this document with our AI Paraphraser

products from Domino’s
quickly and efficiently.
Quality and
Reliability
Concerned
Customers
Quality and Reliability
concerned consumers
are an important factor
for the business of
Domino’s as they could
either positively or
negatively impact the
market image of the
company. Therefore, it
becomes important for
the supply chain
management of
Domino’s to focus on
sourcing high quality
raw materials to attract
health and quality
conscious consumers in
Wheelers branch of
Australia.
4. Decision factors
Key Decision Factors Changes or No-Changes
Flexible Work Timings The management of Domino’s Pizza of
Wheelers branch should look to keep their
workforce motivated by providing them with
the opportunity to select their work timings as
per their preferences (Altindag & Siller, 2014).
5
quickly and efficiently.
Quality and
Reliability
Concerned
Customers
Quality and Reliability
concerned consumers
are an important factor
for the business of
Domino’s as they could
either positively or
negatively impact the
market image of the
company. Therefore, it
becomes important for
the supply chain
management of
Domino’s to focus on
sourcing high quality
raw materials to attract
health and quality
conscious consumers in
Wheelers branch of
Australia.
4. Decision factors
Key Decision Factors Changes or No-Changes
Flexible Work Timings The management of Domino’s Pizza of
Wheelers branch should look to keep their
workforce motivated by providing them with
the opportunity to select their work timings as
per their preferences (Altindag & Siller, 2014).
5

It should be taken into consideration that a
motivated employee would be beneficial in
enhancing productivity of the business by
enhancing customer service in the store. This
would benefit in achieving the goals and
strategies of the company.
Weekly or Monthly Training The top management authorities of Domino’s
Pizza in order to fulfil the aims and objectives
of the business would have to indulge its staffs
into regular training (Persaud, 2005). The
company would have to organize weekly
training sessions for its employees who would
focus on overcoming issues related to customer
service, customer handling techniques, phone
etiquettes and development of professional
relationship with the guests. These sessions
would help in improving customer service and
thus achieving its goals and objectives.
Technological Adaptations The employees of Domino’s Pizza in Wheelers
branch should be provided training and
guidance to adapt them towards latest
technological advancement in the company.
The in-house staffs are required to be
technologically advanced in order to solve
queries of consumers easily and effectively
(Domino's Pizza, 2018). This would lead in the
enhancement of customer service and would
also help in gaining competitive advantage in
Australia.
6
motivated employee would be beneficial in
enhancing productivity of the business by
enhancing customer service in the store. This
would benefit in achieving the goals and
strategies of the company.
Weekly or Monthly Training The top management authorities of Domino’s
Pizza in order to fulfil the aims and objectives
of the business would have to indulge its staffs
into regular training (Persaud, 2005). The
company would have to organize weekly
training sessions for its employees who would
focus on overcoming issues related to customer
service, customer handling techniques, phone
etiquettes and development of professional
relationship with the guests. These sessions
would help in improving customer service and
thus achieving its goals and objectives.
Technological Adaptations The employees of Domino’s Pizza in Wheelers
branch should be provided training and
guidance to adapt them towards latest
technological advancement in the company.
The in-house staffs are required to be
technologically advanced in order to solve
queries of consumers easily and effectively
(Domino's Pizza, 2018). This would lead in the
enhancement of customer service and would
also help in gaining competitive advantage in
Australia.
6
⊘ This is a preview!⊘
Do you want full access?
Subscribe today to unlock all pages.

Trusted by 1+ million students worldwide
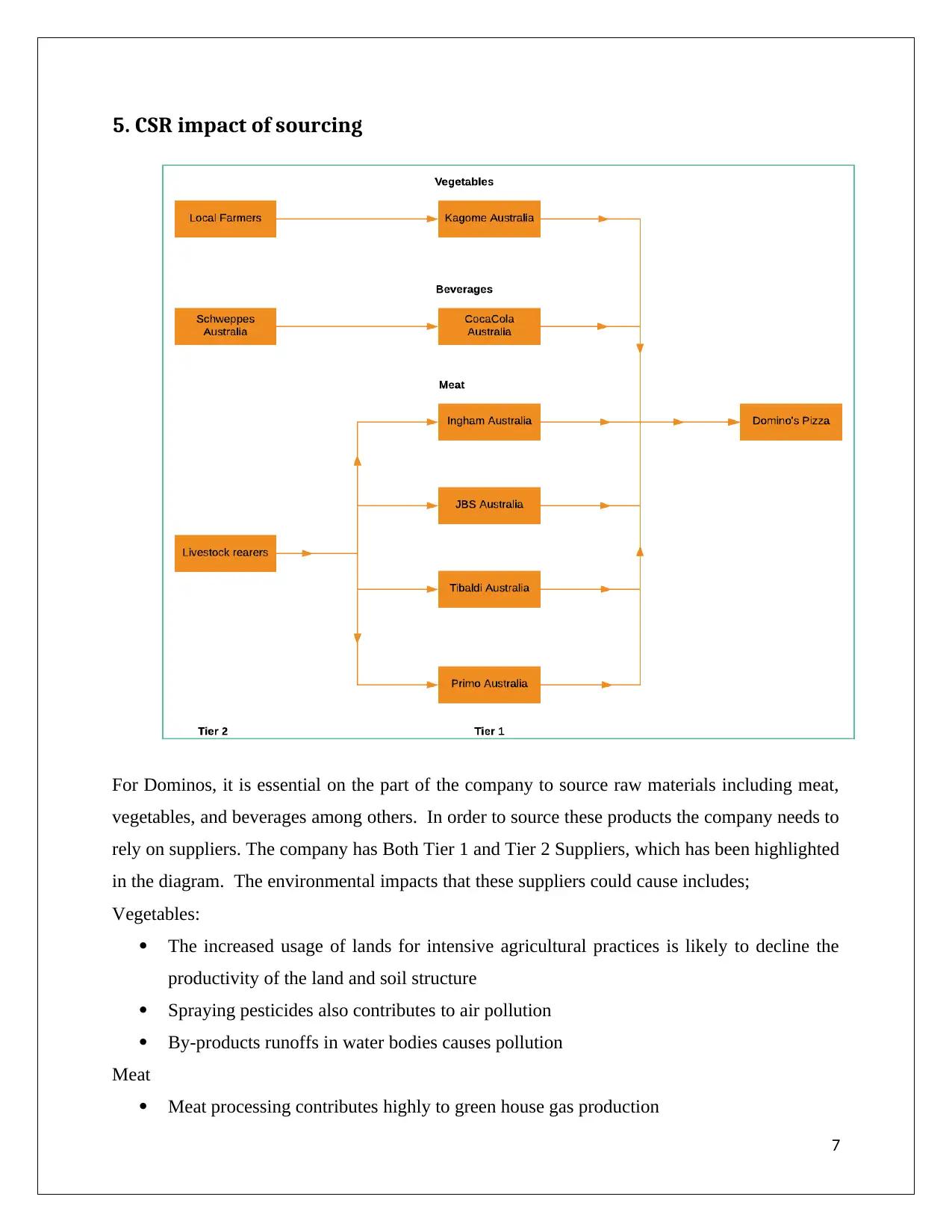
5. CSR impact of sourcing
For Dominos, it is essential on the part of the company to source raw materials including meat,
vegetables, and beverages among others. In order to source these products the company needs to
rely on suppliers. The company has Both Tier 1 and Tier 2 Suppliers, which has been highlighted
in the diagram. The environmental impacts that these suppliers could cause includes;
Vegetables:
The increased usage of lands for intensive agricultural practices is likely to decline the
productivity of the land and soil structure
Spraying pesticides also contributes to air pollution
By-products runoffs in water bodies causes pollution
Meat
Meat processing contributes highly to green house gas production
7
For Dominos, it is essential on the part of the company to source raw materials including meat,
vegetables, and beverages among others. In order to source these products the company needs to
rely on suppliers. The company has Both Tier 1 and Tier 2 Suppliers, which has been highlighted
in the diagram. The environmental impacts that these suppliers could cause includes;
Vegetables:
The increased usage of lands for intensive agricultural practices is likely to decline the
productivity of the land and soil structure
Spraying pesticides also contributes to air pollution
By-products runoffs in water bodies causes pollution
Meat
Meat processing contributes highly to green house gas production
7
Paraphrase This Document
Need a fresh take? Get an instant paraphrase of this document with our AI Paraphraser
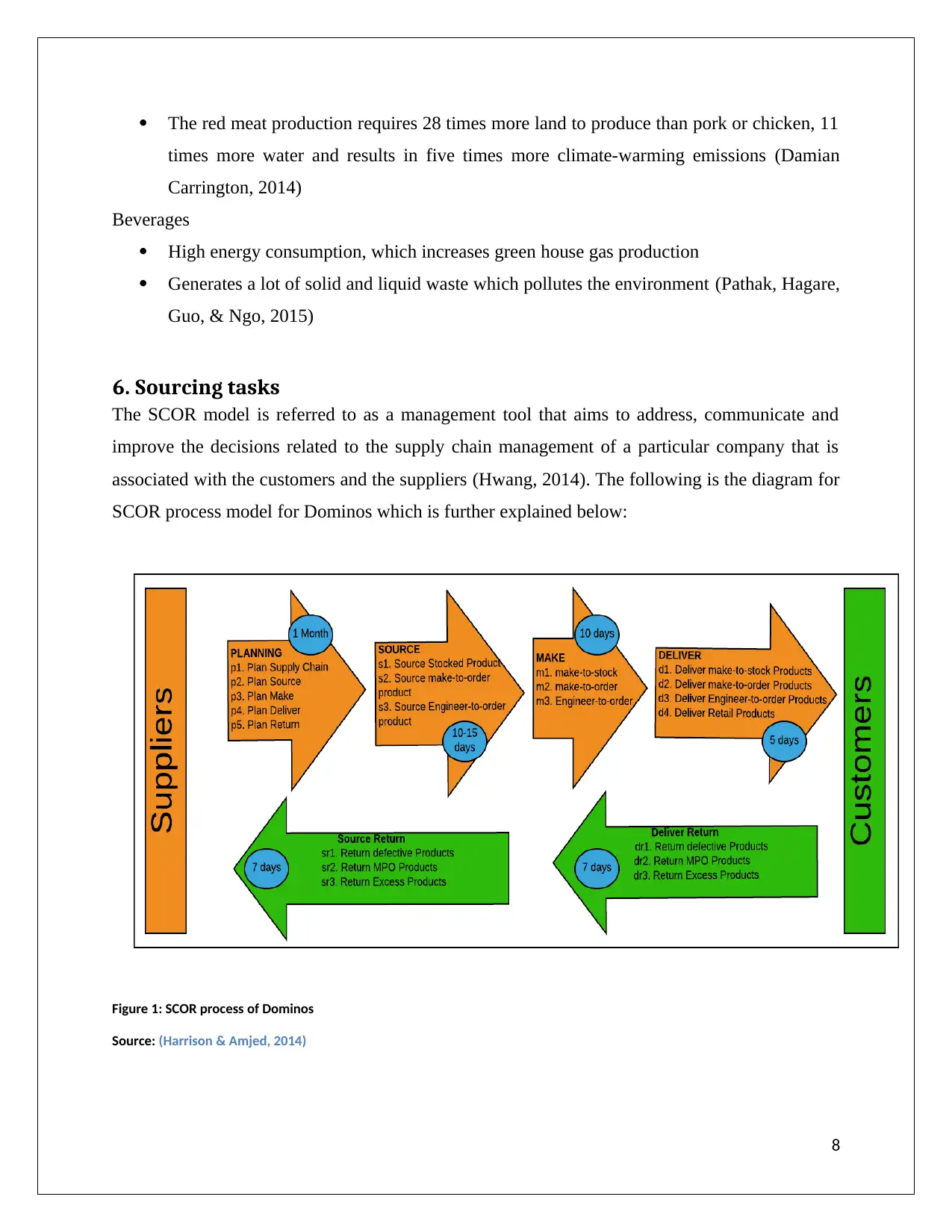
The red meat production requires 28 times more land to produce than pork or chicken, 11
times more water and results in five times more climate-warming emissions (Damian
Carrington, 2014)
Beverages
High energy consumption, which increases green house gas production
Generates a lot of solid and liquid waste which pollutes the environment (Pathak, Hagare,
Guo, & Ngo, 2015)
6. Sourcing tasks
The SCOR model is referred to as a management tool that aims to address, communicate and
improve the decisions related to the supply chain management of a particular company that is
associated with the customers and the suppliers (Hwang, 2014). The following is the diagram for
SCOR process model for Dominos which is further explained below:
Figure 1: SCOR process of Dominos
Source: (Harrison & Amjed, 2014)
8
times more water and results in five times more climate-warming emissions (Damian
Carrington, 2014)
Beverages
High energy consumption, which increases green house gas production
Generates a lot of solid and liquid waste which pollutes the environment (Pathak, Hagare,
Guo, & Ngo, 2015)
6. Sourcing tasks
The SCOR model is referred to as a management tool that aims to address, communicate and
improve the decisions related to the supply chain management of a particular company that is
associated with the customers and the suppliers (Hwang, 2014). The following is the diagram for
SCOR process model for Dominos which is further explained below:
Figure 1: SCOR process of Dominos
Source: (Harrison & Amjed, 2014)
8
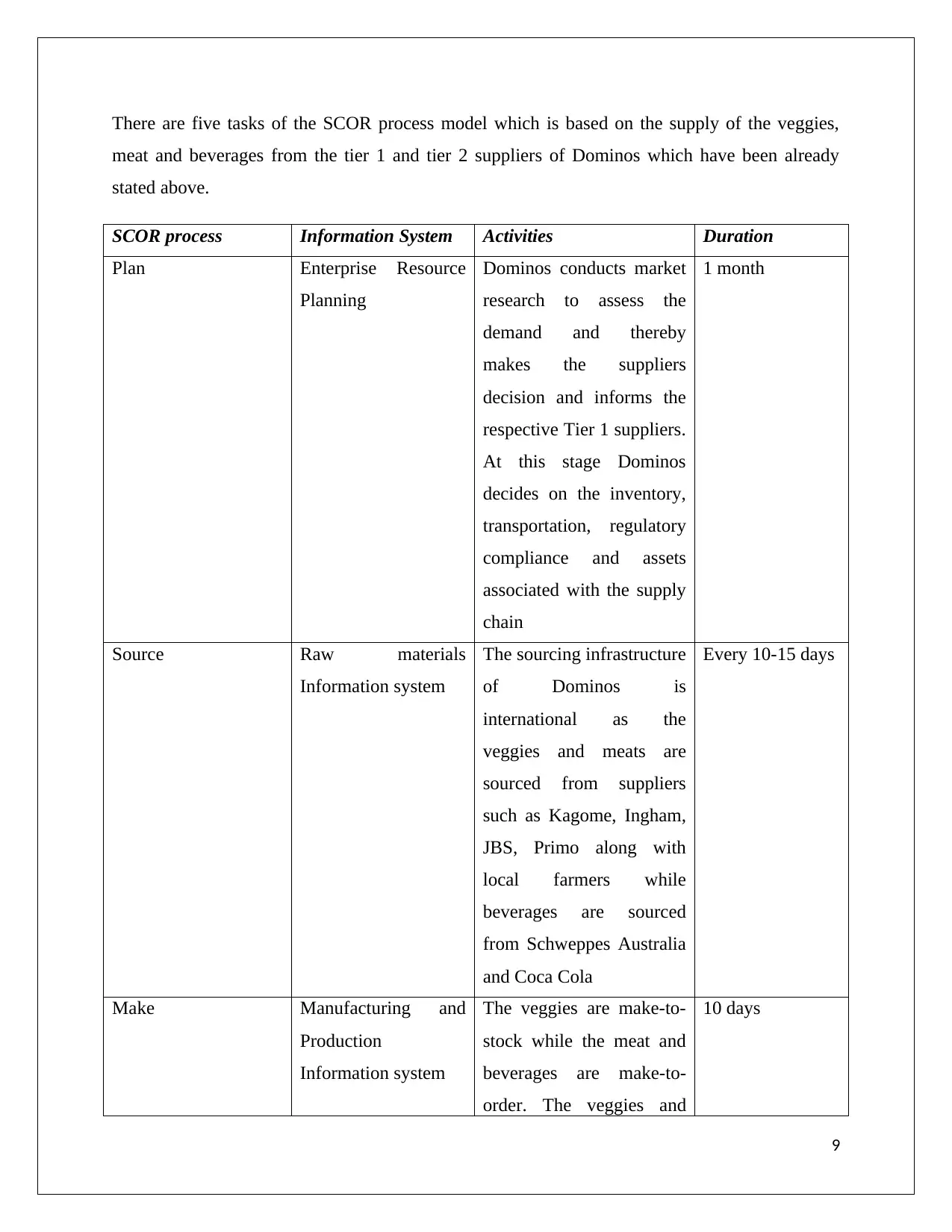
There are five tasks of the SCOR process model which is based on the supply of the veggies,
meat and beverages from the tier 1 and tier 2 suppliers of Dominos which have been already
stated above.
SCOR process Information System Activities Duration
Plan Enterprise Resource
Planning
Dominos conducts market
research to assess the
demand and thereby
makes the suppliers
decision and informs the
respective Tier 1 suppliers.
At this stage Dominos
decides on the inventory,
transportation, regulatory
compliance and assets
associated with the supply
chain
1 month
Source Raw materials
Information system
The sourcing infrastructure
of Dominos is
international as the
veggies and meats are
sourced from suppliers
such as Kagome, Ingham,
JBS, Primo along with
local farmers while
beverages are sourced
from Schweppes Australia
and Coca Cola
Every 10-15 days
Make Manufacturing and
Production
Information system
The veggies are make-to-
stock while the meat and
beverages are make-to-
order. The veggies and
10 days
9
meat and beverages from the tier 1 and tier 2 suppliers of Dominos which have been already
stated above.
SCOR process Information System Activities Duration
Plan Enterprise Resource
Planning
Dominos conducts market
research to assess the
demand and thereby
makes the suppliers
decision and informs the
respective Tier 1 suppliers.
At this stage Dominos
decides on the inventory,
transportation, regulatory
compliance and assets
associated with the supply
chain
1 month
Source Raw materials
Information system
The sourcing infrastructure
of Dominos is
international as the
veggies and meats are
sourced from suppliers
such as Kagome, Ingham,
JBS, Primo along with
local farmers while
beverages are sourced
from Schweppes Australia
and Coca Cola
Every 10-15 days
Make Manufacturing and
Production
Information system
The veggies are make-to-
stock while the meat and
beverages are make-to-
order. The veggies and
10 days
9
⊘ This is a preview!⊘
Do you want full access?
Subscribe today to unlock all pages.

Trusted by 1+ million students worldwide
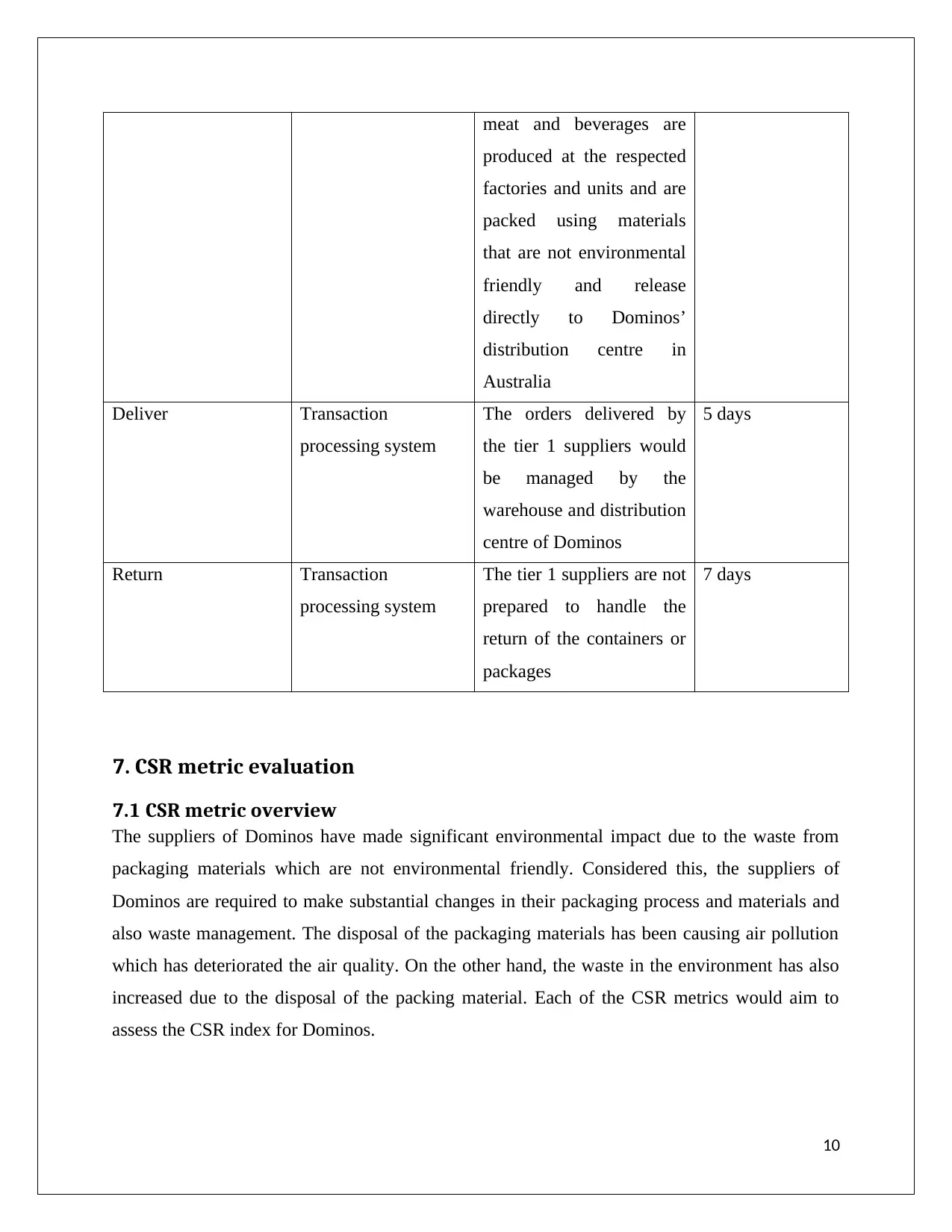
meat and beverages are
produced at the respected
factories and units and are
packed using materials
that are not environmental
friendly and release
directly to Dominos’
distribution centre in
Australia
Deliver Transaction
processing system
The orders delivered by
the tier 1 suppliers would
be managed by the
warehouse and distribution
centre of Dominos
5 days
Return Transaction
processing system
The tier 1 suppliers are not
prepared to handle the
return of the containers or
packages
7 days
7. CSR metric evaluation
7.1 CSR metric overview
The suppliers of Dominos have made significant environmental impact due to the waste from
packaging materials which are not environmental friendly. Considered this, the suppliers of
Dominos are required to make substantial changes in their packaging process and materials and
also waste management. The disposal of the packaging materials has been causing air pollution
which has deteriorated the air quality. On the other hand, the waste in the environment has also
increased due to the disposal of the packing material. Each of the CSR metrics would aim to
assess the CSR index for Dominos.
10
produced at the respected
factories and units and are
packed using materials
that are not environmental
friendly and release
directly to Dominos’
distribution centre in
Australia
Deliver Transaction
processing system
The orders delivered by
the tier 1 suppliers would
be managed by the
warehouse and distribution
centre of Dominos
5 days
Return Transaction
processing system
The tier 1 suppliers are not
prepared to handle the
return of the containers or
packages
7 days
7. CSR metric evaluation
7.1 CSR metric overview
The suppliers of Dominos have made significant environmental impact due to the waste from
packaging materials which are not environmental friendly. Considered this, the suppliers of
Dominos are required to make substantial changes in their packaging process and materials and
also waste management. The disposal of the packaging materials has been causing air pollution
which has deteriorated the air quality. On the other hand, the waste in the environment has also
increased due to the disposal of the packing material. Each of the CSR metrics would aim to
assess the CSR index for Dominos.
10
Paraphrase This Document
Need a fresh take? Get an instant paraphrase of this document with our AI Paraphraser
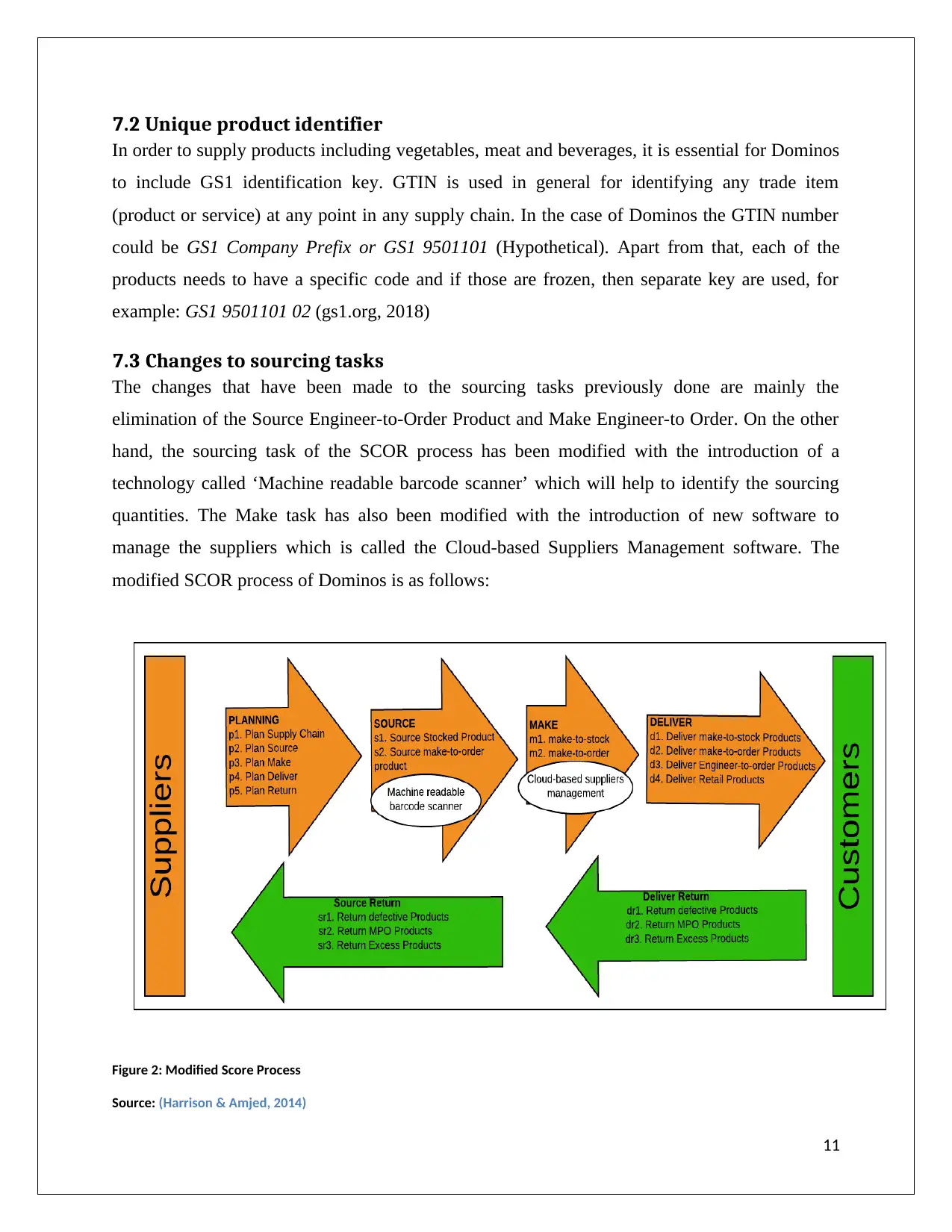
7.2 Unique product identifier
In order to supply products including vegetables, meat and beverages, it is essential for Dominos
to include GS1 identification key. GTIN is used in general for identifying any trade item
(product or service) at any point in any supply chain. In the case of Dominos the GTIN number
could be GS1 Company Prefix or GS1 9501101 (Hypothetical). Apart from that, each of the
products needs to have a specific code and if those are frozen, then separate key are used, for
example: GS1 9501101 02 (gs1.org, 2018)
7.3 Changes to sourcing tasks
The changes that have been made to the sourcing tasks previously done are mainly the
elimination of the Source Engineer-to-Order Product and Make Engineer-to Order. On the other
hand, the sourcing task of the SCOR process has been modified with the introduction of a
technology called ‘Machine readable barcode scanner’ which will help to identify the sourcing
quantities. The Make task has also been modified with the introduction of new software to
manage the suppliers which is called the Cloud-based Suppliers Management software. The
modified SCOR process of Dominos is as follows:
Figure 2: Modified Score Process
Source: (Harrison & Amjed, 2014)
11
In order to supply products including vegetables, meat and beverages, it is essential for Dominos
to include GS1 identification key. GTIN is used in general for identifying any trade item
(product or service) at any point in any supply chain. In the case of Dominos the GTIN number
could be GS1 Company Prefix or GS1 9501101 (Hypothetical). Apart from that, each of the
products needs to have a specific code and if those are frozen, then separate key are used, for
example: GS1 9501101 02 (gs1.org, 2018)
7.3 Changes to sourcing tasks
The changes that have been made to the sourcing tasks previously done are mainly the
elimination of the Source Engineer-to-Order Product and Make Engineer-to Order. On the other
hand, the sourcing task of the SCOR process has been modified with the introduction of a
technology called ‘Machine readable barcode scanner’ which will help to identify the sourcing
quantities. The Make task has also been modified with the introduction of new software to
manage the suppliers which is called the Cloud-based Suppliers Management software. The
modified SCOR process of Dominos is as follows:
Figure 2: Modified Score Process
Source: (Harrison & Amjed, 2014)
11
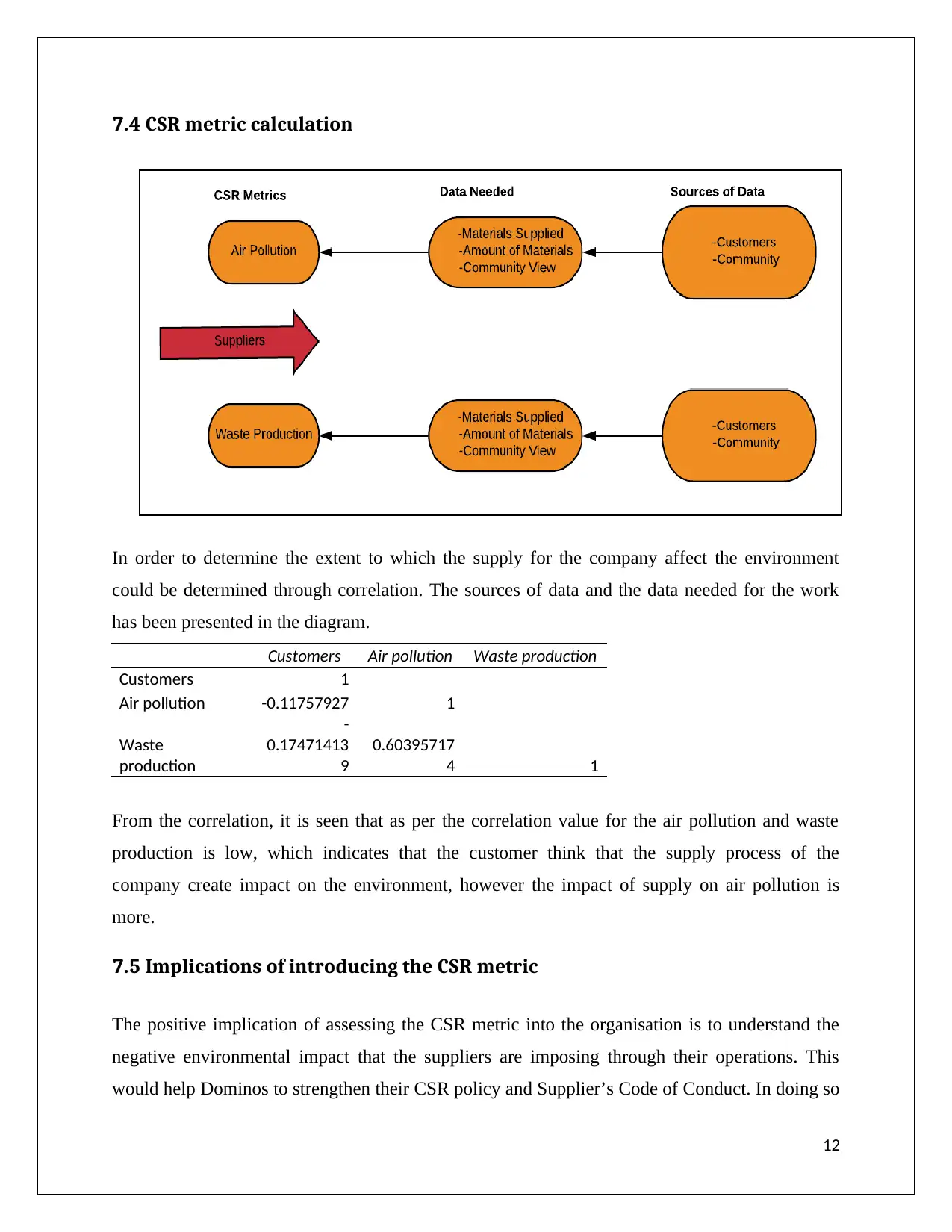
7.4 CSR metric calculation
In order to determine the extent to which the supply for the company affect the environment
could be determined through correlation. The sources of data and the data needed for the work
has been presented in the diagram.
Customers Air pollution Waste production
Customers 1
Air pollution -0.11757927 1
Waste
production
-
0.17471413
9
0.60395717
4 1
From the correlation, it is seen that as per the correlation value for the air pollution and waste
production is low, which indicates that the customer think that the supply process of the
company create impact on the environment, however the impact of supply on air pollution is
more.
7.5 Implications of introducing the CSR metric
The positive implication of assessing the CSR metric into the organisation is to understand the
negative environmental impact that the suppliers are imposing through their operations. This
would help Dominos to strengthen their CSR policy and Supplier’s Code of Conduct. In doing so
12
In order to determine the extent to which the supply for the company affect the environment
could be determined through correlation. The sources of data and the data needed for the work
has been presented in the diagram.
Customers Air pollution Waste production
Customers 1
Air pollution -0.11757927 1
Waste
production
-
0.17471413
9
0.60395717
4 1
From the correlation, it is seen that as per the correlation value for the air pollution and waste
production is low, which indicates that the customer think that the supply process of the
company create impact on the environment, however the impact of supply on air pollution is
more.
7.5 Implications of introducing the CSR metric
The positive implication of assessing the CSR metric into the organisation is to understand the
negative environmental impact that the suppliers are imposing through their operations. This
would help Dominos to strengthen their CSR policy and Supplier’s Code of Conduct. In doing so
12
⊘ This is a preview!⊘
Do you want full access?
Subscribe today to unlock all pages.

Trusted by 1+ million students worldwide
1 out of 17