Low Velocity Impact on Compressed Gas Storage Tank
Research on the burst pressure and mechanical behavior of filament wound composite materials used in compressed gas storage tanks.
44 Pages10450 Words2 Views
Added on 2023-01-13
About This Document
This study focuses on the impact and compression after the impact on compressed gas storage tanks. It aims to research the burst pressure and mechanical behavior of filament wound. The study also analyzes the warm and development coefficients for assessing their impact on the burst weight of the composite funnels.
Low Velocity Impact on Compressed Gas Storage Tank
Research on the burst pressure and mechanical behavior of filament wound composite materials used in compressed gas storage tanks.
Added on 2023-01-13
ShareRelated Documents
Low Velocity Impact on Compressed Gas Storage Tank
by
Lawson Onokpasah
1405671
Dissertation submitted in partial fulfilment of
the requirements for the
Bachelor of Engineering (Hons)
Mechanical
MAY 2019
by
Lawson Onokpasah
1405671
Dissertation submitted in partial fulfilment of
the requirements for the
Bachelor of Engineering (Hons)
Mechanical
MAY 2019
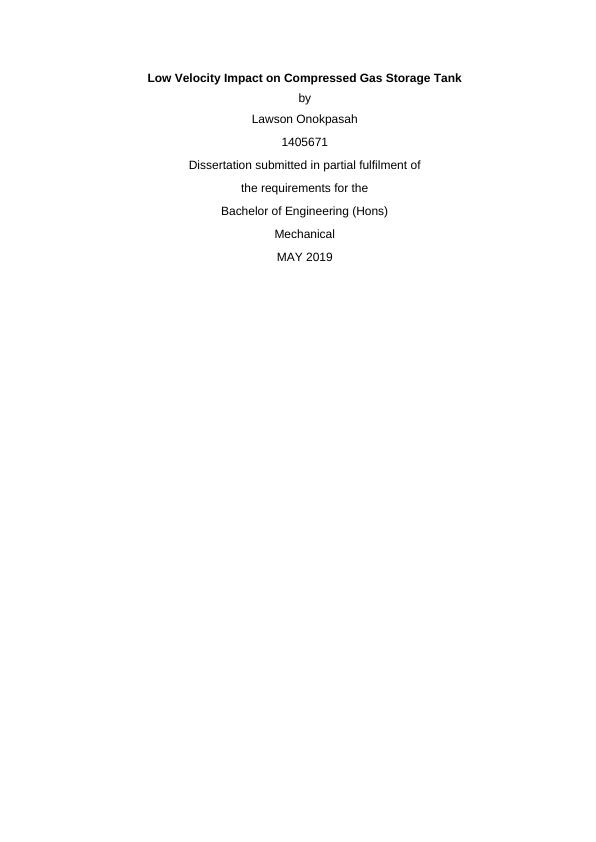
Abstract
Pressure Vessels are normally used in different applications that are indispensable
including automobile, aerospace, vehicles that are used in the underwater,
chemical engineering among other applications. The pressure vessels that are
used in the industries are normally made of ancient metals like aluminum and steel
alloys. This is because the weight of the pressure vessel will affect to great extend
the performance and range of operation. In order to have a better performance,
weight can be effectively reduced in the structure of the shell. The composite
materials are therefore used to increase the strength of the material. The study
aims to research on the burst pressure and mechanical behavior of the filament
wound. Also, the impact and compression after the impact also taken into the
consideration. Likewise, it was resolved the warm and development coefficients for
assess their impact on the burst weight of the composite funnels.
Pressure Vessels are normally used in different applications that are indispensable
including automobile, aerospace, vehicles that are used in the underwater,
chemical engineering among other applications. The pressure vessels that are
used in the industries are normally made of ancient metals like aluminum and steel
alloys. This is because the weight of the pressure vessel will affect to great extend
the performance and range of operation. In order to have a better performance,
weight can be effectively reduced in the structure of the shell. The composite
materials are therefore used to increase the strength of the material. The study
aims to research on the burst pressure and mechanical behavior of the filament
wound. Also, the impact and compression after the impact also taken into the
consideration. Likewise, it was resolved the warm and development coefficients for
assess their impact on the burst weight of the composite funnels.
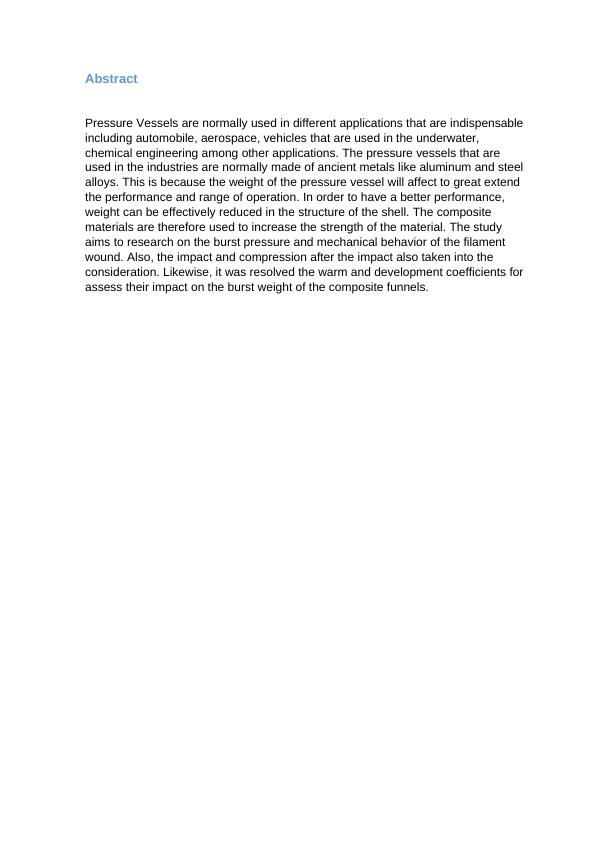
Chapter 1: Introduction
1.1 Rationale/Background
Over the previous four years, using light-weight polymer composite materials for
structural applications has boosted continuously. In addition to the superb quasi-
static mechanical commercial properties such as high rigidity as well as details
longevity, it has actually become critical that these composite frameworks are well
matched to the different kinds of impact loads when they are correctly designed.
Figure 1 Example of Filament Wound Composite Pressure Vessels (1)
1- Ultra-thin-walled aluminium liner
2- Protexal smooth,inert,corrosion resistant internal finish
3- Insulating layer
For instance, fiber-reinforced composite products are utilized in a pressure vessel
or pressed gas storage tanks, modern-day lorries and also lightweight building and
constructions. Pressure vessels consisting of Filament winding have successful
applications, but among the troubles in constructing frameworks as well as the
component of the bodies with carbon-reinforced substances (FCC) is that these
products are prone to small energy impact that can trigger delamination of the
density during the production, operation and maintenance stages. Various low-
velocity impacts might take place in composite pressure vessels. If these
1.1 Rationale/Background
Over the previous four years, using light-weight polymer composite materials for
structural applications has boosted continuously. In addition to the superb quasi-
static mechanical commercial properties such as high rigidity as well as details
longevity, it has actually become critical that these composite frameworks are well
matched to the different kinds of impact loads when they are correctly designed.
Figure 1 Example of Filament Wound Composite Pressure Vessels (1)
1- Ultra-thin-walled aluminium liner
2- Protexal smooth,inert,corrosion resistant internal finish
3- Insulating layer
For instance, fiber-reinforced composite products are utilized in a pressure vessel
or pressed gas storage tanks, modern-day lorries and also lightweight building and
constructions. Pressure vessels consisting of Filament winding have successful
applications, but among the troubles in constructing frameworks as well as the
component of the bodies with carbon-reinforced substances (FCC) is that these
products are prone to small energy impact that can trigger delamination of the
density during the production, operation and maintenance stages. Various low-
velocity impacts might take place in composite pressure vessels. If these
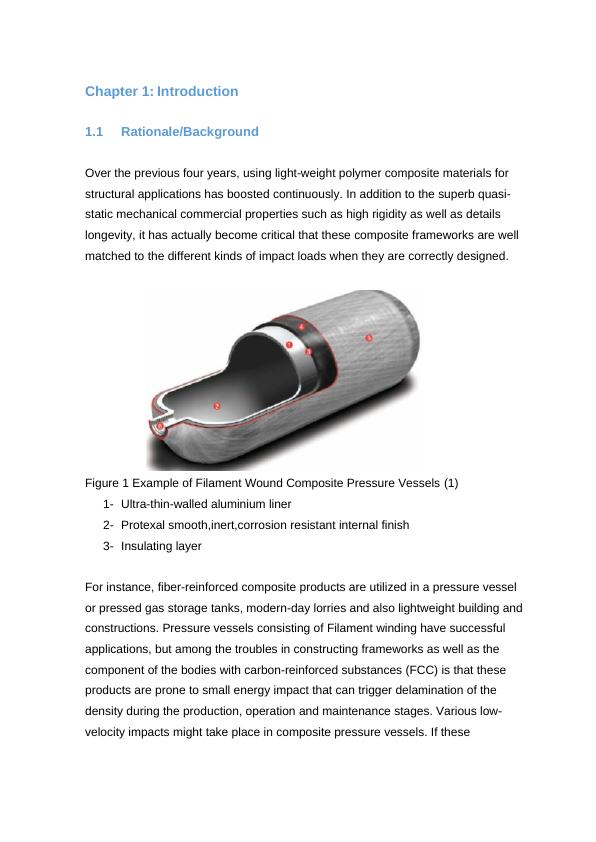
frameworks are influenced at a reduced rate, there is an opportunity for substantial
material damages that can dramatically lower structural performance.
For that reason, it is essential to recognize the efficiency as well as mechanical
behaviours of composite pressure vessels in low-velocity impact scenarios as well
as recurring burst pressure in order to safely distribute these structures in the
location of the application. Hence, an efficient approach of analysis is called for to
anticipate impact damages and also residual burst pressure of compressed gas
cylindrical tubes at the design phase. This research study will certainly concentrate
on the impact-resistant section.
The evolution of vessels and storage made to hold fluids under pressure has
proceeded through four distinctive stages: all-metal storage tanks (Type I), steel
hoop-wrapped composite storage tanks (Type II), metal-lined composite
containers (Type III) and plastic-lined composite tanks (Type IV)(2). Composite
overwrapped pressure vessel is classified under type 3. There presently are 4
types of cylinders established for the compressed gas in the market today see
appendix A.
Impact Test is utilized to examine dynamic disfigurement and failure methods of
materials. Low-velocity affect systems can be characterized as plate-on-plate, pole
on-plate, plate-on rod, or on the other hand pole on-pole tests. Two kinds of plate-
on-plate affect tests have been produced: wave generation tests and thin-layer
high-strain-rate tests. The plate-on-plate tests are additionally characterized as
non- recovery or recuperation tests(3).
1.2 Project Aim and Objectives
The aim of this study is to analyse and evaluate a low velocity impact and residual
burst-pressure analysis of a cylindrical composite pressure vessel made of food
grade high density polyethylene (HDPE) winded with a fibreglass filament. The
aim would focus the investigation on a set of standardized tests American Society
for Testing and Materials (ASTM D6264 and D7137) to assess the impact
tolerance of fiber reinforced polymer matrix composites and Standard Test
Method for Compressive Properties of Unidirectional Polymer Matrix Composite
Materials Using a Sandwich Beam.(4).
To attain the task aims, the objectives are:
material damages that can dramatically lower structural performance.
For that reason, it is essential to recognize the efficiency as well as mechanical
behaviours of composite pressure vessels in low-velocity impact scenarios as well
as recurring burst pressure in order to safely distribute these structures in the
location of the application. Hence, an efficient approach of analysis is called for to
anticipate impact damages and also residual burst pressure of compressed gas
cylindrical tubes at the design phase. This research study will certainly concentrate
on the impact-resistant section.
The evolution of vessels and storage made to hold fluids under pressure has
proceeded through four distinctive stages: all-metal storage tanks (Type I), steel
hoop-wrapped composite storage tanks (Type II), metal-lined composite
containers (Type III) and plastic-lined composite tanks (Type IV)(2). Composite
overwrapped pressure vessel is classified under type 3. There presently are 4
types of cylinders established for the compressed gas in the market today see
appendix A.
Impact Test is utilized to examine dynamic disfigurement and failure methods of
materials. Low-velocity affect systems can be characterized as plate-on-plate, pole
on-plate, plate-on rod, or on the other hand pole on-pole tests. Two kinds of plate-
on-plate affect tests have been produced: wave generation tests and thin-layer
high-strain-rate tests. The plate-on-plate tests are additionally characterized as
non- recovery or recuperation tests(3).
1.2 Project Aim and Objectives
The aim of this study is to analyse and evaluate a low velocity impact and residual
burst-pressure analysis of a cylindrical composite pressure vessel made of food
grade high density polyethylene (HDPE) winded with a fibreglass filament. The
aim would focus the investigation on a set of standardized tests American Society
for Testing and Materials (ASTM D6264 and D7137) to assess the impact
tolerance of fiber reinforced polymer matrix composites and Standard Test
Method for Compressive Properties of Unidirectional Polymer Matrix Composite
Materials Using a Sandwich Beam.(4).
To attain the task aims, the objectives are:
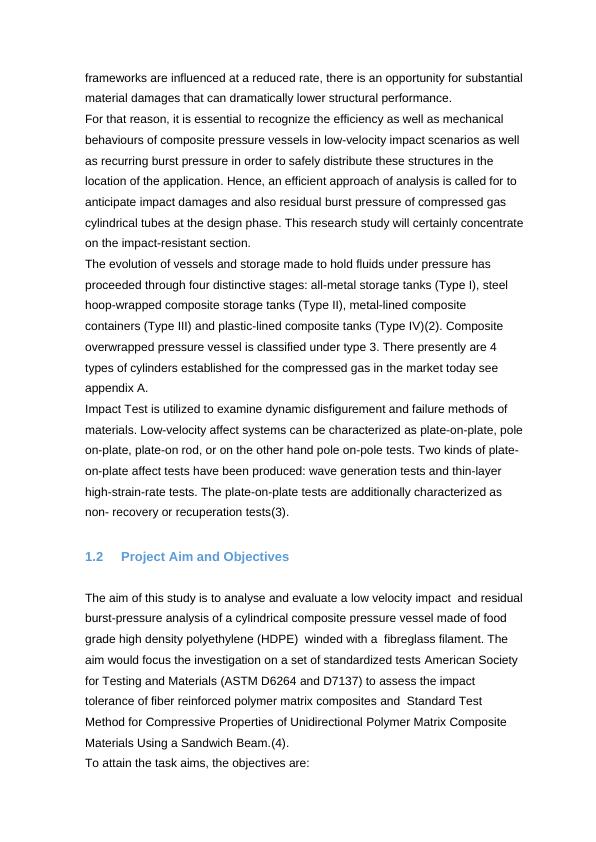
1. To conduct a literature review concentrating on the current state of production,
filament winding, impact, and ruptured analysis researches and also suitable
engineering criteria.
2. To carry out mathematical analysis (FEA and/or hand estimations).
3. To ascertain as well as develop impact testing set up.
4. To accomplish an effective examination at the determined low-velocity
informed by literature.
5. To examine damages characterization of examination samples prior to and
after impact testing.
6. To review the efficiency and compare speculative results with numerical
outcomes.
1.3 Motivation
As a result of incidental loading in the radial direction due to low-velocity impact
(LVI) damages in the internal structure of the vessel can occur and can remain
unseen by the naked eye. This is of worry for subsequent structural stability.
Getting a higher understanding of the impact response as well as the post-impact
performance of such composite structures is a vital challenge, with reasonably few
evaluations reported. The Materials Engineering department at Robert Gordon
University Aberdeen, currently does not have the capability to conduct impact
testing on polymer matrix composite materials. There are two main goals of this
project. The first is to establish a method to test for the effect of low velocity impact
on a cylindrical composite pressure vessel in this instance a quasi-static
indentation test on an Instron 3382 was chosen. Success means the Instron 3382
will be able to perform quasi-static tests according to the American Society for
Testing and Materials (ASTM D6264) standard and achieve a clearly visible effect
of this impact on the material. The second is to perform a compression test on a
pressure vessel on the Instron 3382 which has the potential to except up to 10
metric tonnes load. Success means the testing meets the standard compression
test according to ASTM Standard D5467/D5467M and a clearly visible effect of the
applied load. At this point some clarification is needed the pressure vessel was
not pressurized during the test that is inner pressure was zero and only the
cylinder body of the pressure vessel was used.
filament winding, impact, and ruptured analysis researches and also suitable
engineering criteria.
2. To carry out mathematical analysis (FEA and/or hand estimations).
3. To ascertain as well as develop impact testing set up.
4. To accomplish an effective examination at the determined low-velocity
informed by literature.
5. To examine damages characterization of examination samples prior to and
after impact testing.
6. To review the efficiency and compare speculative results with numerical
outcomes.
1.3 Motivation
As a result of incidental loading in the radial direction due to low-velocity impact
(LVI) damages in the internal structure of the vessel can occur and can remain
unseen by the naked eye. This is of worry for subsequent structural stability.
Getting a higher understanding of the impact response as well as the post-impact
performance of such composite structures is a vital challenge, with reasonably few
evaluations reported. The Materials Engineering department at Robert Gordon
University Aberdeen, currently does not have the capability to conduct impact
testing on polymer matrix composite materials. There are two main goals of this
project. The first is to establish a method to test for the effect of low velocity impact
on a cylindrical composite pressure vessel in this instance a quasi-static
indentation test on an Instron 3382 was chosen. Success means the Instron 3382
will be able to perform quasi-static tests according to the American Society for
Testing and Materials (ASTM D6264) standard and achieve a clearly visible effect
of this impact on the material. The second is to perform a compression test on a
pressure vessel on the Instron 3382 which has the potential to except up to 10
metric tonnes load. Success means the testing meets the standard compression
test according to ASTM Standard D5467/D5467M and a clearly visible effect of the
applied load. At this point some clarification is needed the pressure vessel was
not pressurized during the test that is inner pressure was zero and only the
cylinder body of the pressure vessel was used.
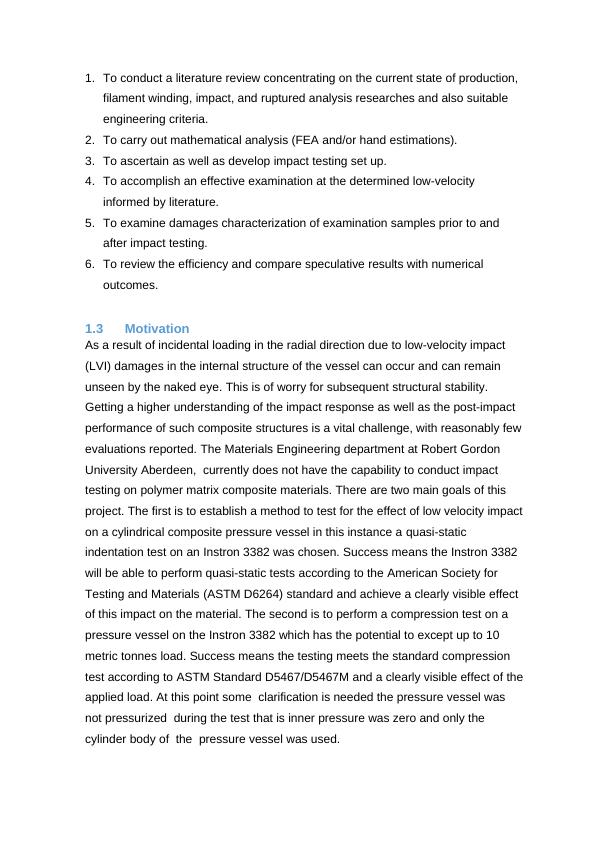
1.4 Methodology overview
To satisfy the purposes and goals detailed above, Composite Overwrapped
Pressure Vessel(COPV) samples need to be manufactured and also examined to
a standard to produce results for evaluation. The composite pressure vessel was
an industrial product produced utilizing a thermosetting orthophthalic unsaturated
polyester material matrix that has been enhanced with a portion weight of 70% of
Tex type E utilizing constant glass fiber as well as the chosen fiber was laminate.
The vessels measured an outer and inner diameter of 155mm, and 147mm
respectively and a 457.2 mm length, and had an average wall thickness of about 8
mm. They were lined internally with a layer of high-density polyethylene (HDPE)
to give, among other objectives, a barrier against diffusion of gas. The samples
should be thoroughly looked for imperfections as well as disparities prior to testing.
A quasi-static indentation, were performed on filament-wound glass fibre
reinforced polymer (GFRP) composite pressure vessels, using solidified steel
indenter with either a round or a wedge-shaped nose. Added test such as
compression after damage strength test was performed on the impacted as well as
unimpacted composite pressure vessels to identify the vessel strength/burst
pressure reduction as an outcome of the impacted load. The results of all indented
composites pressure vessels shall be compared to each other taking into
consideration damages from the dome nosed colliding indentor, visible damage
around the impacted site, microtomic inspection of the damages which will lead to
interesting discussion considering the impact loading. Additionally, an analysis of
just how the impacted vessel burst pressure or strength was affected as a result of
the impact loading. Figure 2 shows the work flow in attaining the aims and
objectives for this thesis.
To satisfy the purposes and goals detailed above, Composite Overwrapped
Pressure Vessel(COPV) samples need to be manufactured and also examined to
a standard to produce results for evaluation. The composite pressure vessel was
an industrial product produced utilizing a thermosetting orthophthalic unsaturated
polyester material matrix that has been enhanced with a portion weight of 70% of
Tex type E utilizing constant glass fiber as well as the chosen fiber was laminate.
The vessels measured an outer and inner diameter of 155mm, and 147mm
respectively and a 457.2 mm length, and had an average wall thickness of about 8
mm. They were lined internally with a layer of high-density polyethylene (HDPE)
to give, among other objectives, a barrier against diffusion of gas. The samples
should be thoroughly looked for imperfections as well as disparities prior to testing.
A quasi-static indentation, were performed on filament-wound glass fibre
reinforced polymer (GFRP) composite pressure vessels, using solidified steel
indenter with either a round or a wedge-shaped nose. Added test such as
compression after damage strength test was performed on the impacted as well as
unimpacted composite pressure vessels to identify the vessel strength/burst
pressure reduction as an outcome of the impacted load. The results of all indented
composites pressure vessels shall be compared to each other taking into
consideration damages from the dome nosed colliding indentor, visible damage
around the impacted site, microtomic inspection of the damages which will lead to
interesting discussion considering the impact loading. Additionally, an analysis of
just how the impacted vessel burst pressure or strength was affected as a result of
the impact loading. Figure 2 shows the work flow in attaining the aims and
objectives for this thesis.

Fi
gure 2: Project Flow Diagram
gure 2: Project Flow Diagram
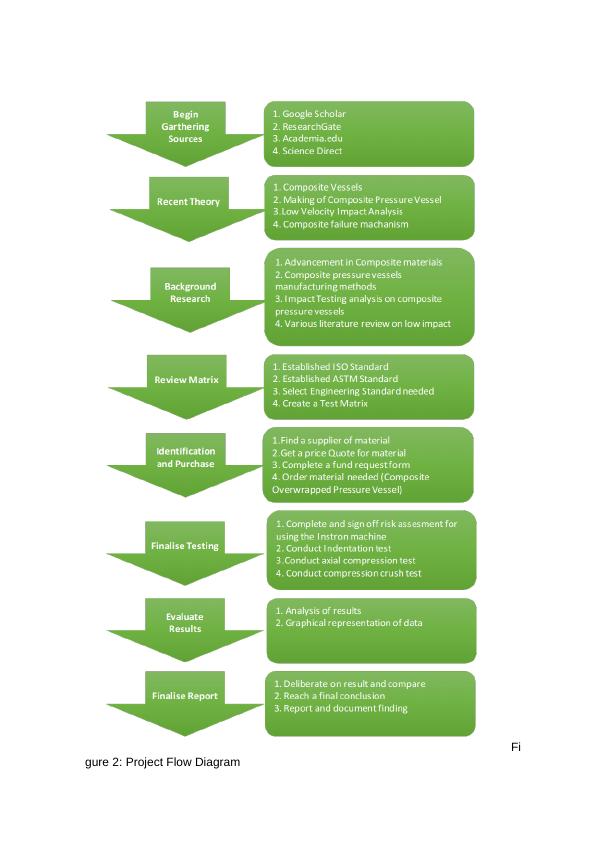
Chapter 2: LITERATURE REVIEW
2.1 Introduction
This chapter presents an introduction of the basics of a composite overwrapped
pressure vessel (COPV), what are they, exactly how they are used and also types.
The section will examine various low-velocity impact tests on composite
overwrapped pressure vessel (COPV) and composite material which have actually
been researched in current times.
2.2 Introduction to Composite Overwrapped Pressure Vessels
A composite material is made by integrating 2 or even more materials to offer a
one-of-a-kind mix of properties(5). The above definition is a lot more basic as well
as can include metals alloys, plastic copolymers, minerals, as well as wood.
Advanced composites have high-performance fiber reinforcements in a polymer
matrix product such as epoxy(6). The categories according to kinds of
reinforcement are particulate composites (composed of particles), fibrous
composites (composed of fibres), and also laminate composites (composed of
laminates) as displayed in Fig. 3(7).Fiber-reinforced composite products vary from
the above materials in that the basic products are different at the molecular level
as well as are mechanically separable(8). In bulk form, the constituent materials
collaborate yet stay in their original form. The final properties of composite
products are much better than basic material properties. The goals of
reinforcements in composites are to get strength, stiffness and also various other
mechanical properties, control other properties as a coefficient of thermal
extension, conductivity and thermal transportation(9).
2.1 Introduction
This chapter presents an introduction of the basics of a composite overwrapped
pressure vessel (COPV), what are they, exactly how they are used and also types.
The section will examine various low-velocity impact tests on composite
overwrapped pressure vessel (COPV) and composite material which have actually
been researched in current times.
2.2 Introduction to Composite Overwrapped Pressure Vessels
A composite material is made by integrating 2 or even more materials to offer a
one-of-a-kind mix of properties(5). The above definition is a lot more basic as well
as can include metals alloys, plastic copolymers, minerals, as well as wood.
Advanced composites have high-performance fiber reinforcements in a polymer
matrix product such as epoxy(6). The categories according to kinds of
reinforcement are particulate composites (composed of particles), fibrous
composites (composed of fibres), and also laminate composites (composed of
laminates) as displayed in Fig. 3(7).Fiber-reinforced composite products vary from
the above materials in that the basic products are different at the molecular level
as well as are mechanically separable(8). In bulk form, the constituent materials
collaborate yet stay in their original form. The final properties of composite
products are much better than basic material properties. The goals of
reinforcements in composites are to get strength, stiffness and also various other
mechanical properties, control other properties as a coefficient of thermal
extension, conductivity and thermal transportation(9).
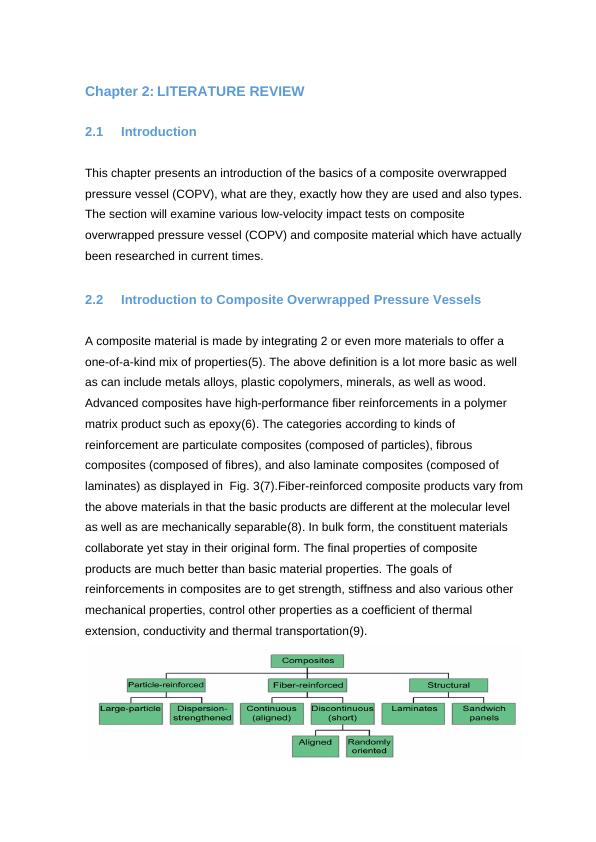
End of preview
Want to access all the pages? Upload your documents or become a member.
Related Documents
Computation of Deformation and Burst Pressure of Cylindrical Composite Pressure Vessels under Low Impact Velocitylg...
|10
|1332
|190
Mechanical Design and Developmentlg...
|29
|4365
|177
Low-Velocity Impact on Compressed Gas Storage Tank: Assessing Damage and Impact Behaviorlg...
|4
|1095
|307
The Essence of Materials for Engineers - PDFlg...
|6
|1617
|221
Presentation on.lg...
|17
|1104
|4
Analysis and optimization of a composite leaf springlg...
|9
|6745
|454