Macarthur Coal Ltd WHS Audit
VerifiedAdded on 2023/06/10
|26
|7163
|236
AI Summary
This audit investigates the environment the workers of Macarthur Coal Ltd work in and the risks that they are likely to encounter in their undertakings. The company has complied with the Work Health and Safety Act 2011 and the Work Health and Safety Regulation 2011.
Contribute Materials
Your contribution can guide someone’s learning journey. Share your
documents today.
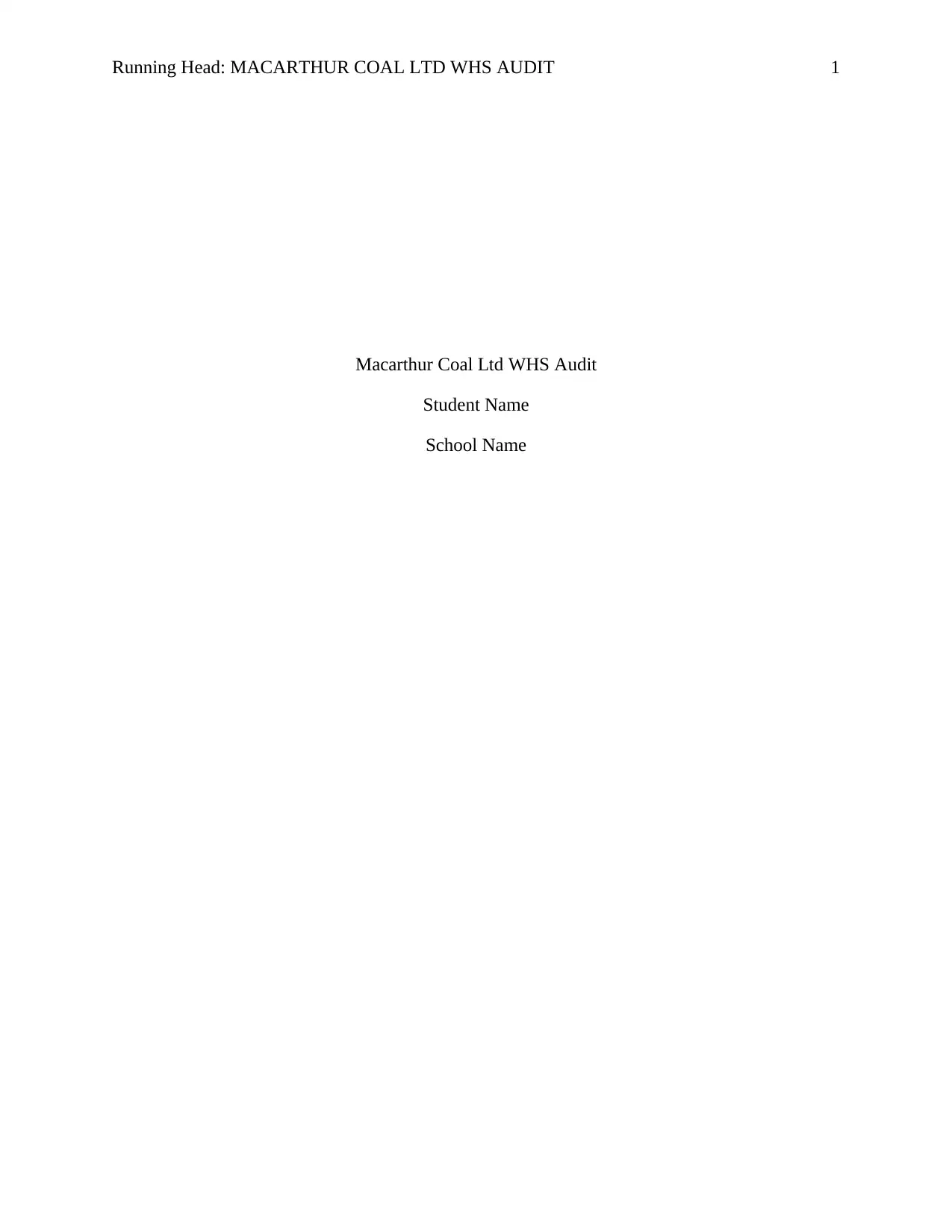
Running Head: MACARTHUR COAL LTD WHS AUDIT 1
Macarthur Coal Ltd WHS Audit
Student Name
School Name
Macarthur Coal Ltd WHS Audit
Student Name
School Name
Secure Best Marks with AI Grader
Need help grading? Try our AI Grader for instant feedback on your assignments.
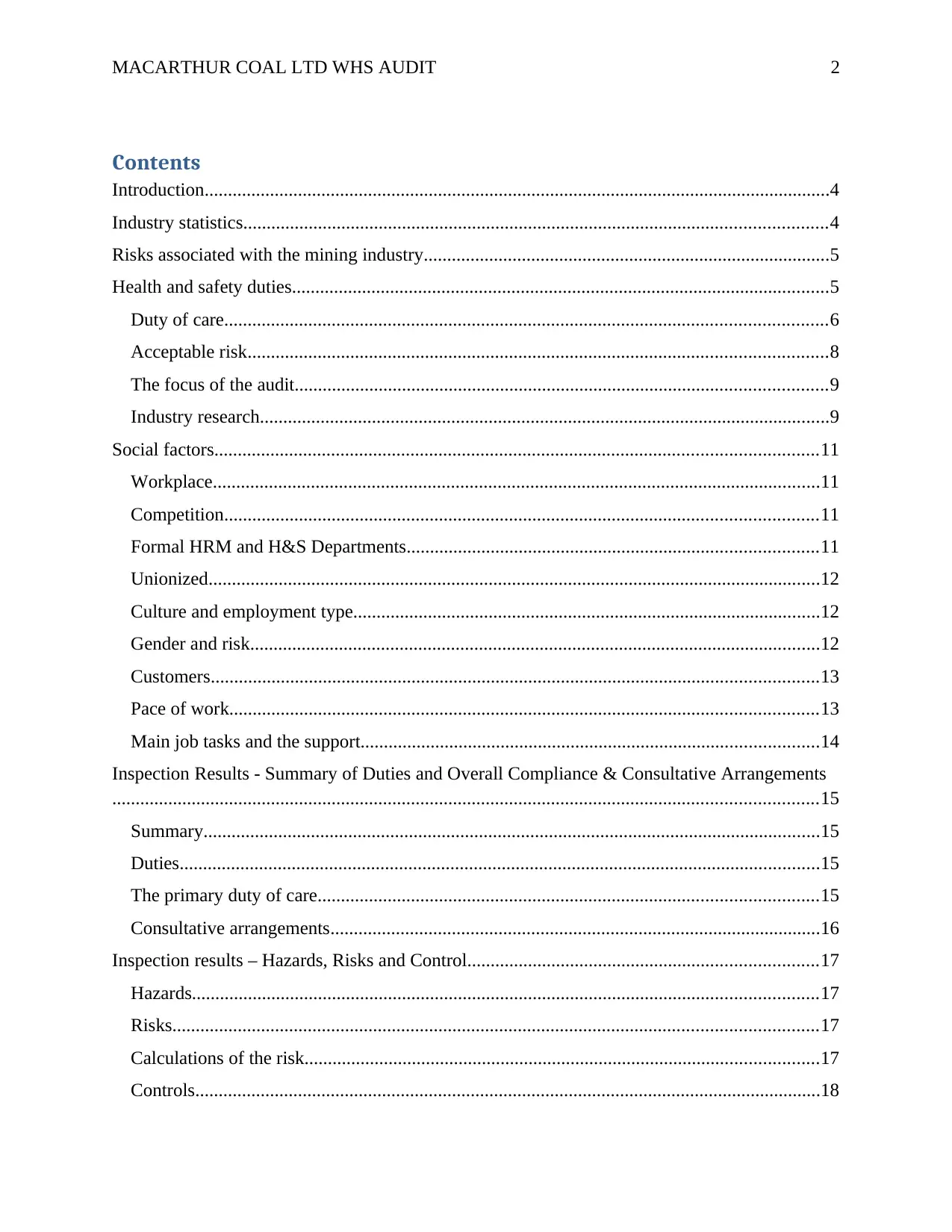
MACARTHUR COAL LTD WHS AUDIT 2
Contents
Introduction......................................................................................................................................4
Industry statistics.............................................................................................................................4
Risks associated with the mining industry.......................................................................................5
Health and safety duties...................................................................................................................5
Duty of care.................................................................................................................................6
Acceptable risk............................................................................................................................8
The focus of the audit..................................................................................................................9
Industry research..........................................................................................................................9
Social factors.................................................................................................................................11
Workplace..................................................................................................................................11
Competition...............................................................................................................................11
Formal HRM and H&S Departments........................................................................................11
Unionized...................................................................................................................................12
Culture and employment type....................................................................................................12
Gender and risk..........................................................................................................................12
Customers..................................................................................................................................13
Pace of work..............................................................................................................................13
Main job tasks and the support..................................................................................................14
Inspection Results - Summary of Duties and Overall Compliance & Consultative Arrangements
.......................................................................................................................................................15
Summary....................................................................................................................................15
Duties.........................................................................................................................................15
The primary duty of care...........................................................................................................15
Consultative arrangements.........................................................................................................16
Inspection results – Hazards, Risks and Control...........................................................................17
Hazards......................................................................................................................................17
Risks..........................................................................................................................................17
Calculations of the risk..............................................................................................................17
Controls......................................................................................................................................18
Contents
Introduction......................................................................................................................................4
Industry statistics.............................................................................................................................4
Risks associated with the mining industry.......................................................................................5
Health and safety duties...................................................................................................................5
Duty of care.................................................................................................................................6
Acceptable risk............................................................................................................................8
The focus of the audit..................................................................................................................9
Industry research..........................................................................................................................9
Social factors.................................................................................................................................11
Workplace..................................................................................................................................11
Competition...............................................................................................................................11
Formal HRM and H&S Departments........................................................................................11
Unionized...................................................................................................................................12
Culture and employment type....................................................................................................12
Gender and risk..........................................................................................................................12
Customers..................................................................................................................................13
Pace of work..............................................................................................................................13
Main job tasks and the support..................................................................................................14
Inspection Results - Summary of Duties and Overall Compliance & Consultative Arrangements
.......................................................................................................................................................15
Summary....................................................................................................................................15
Duties.........................................................................................................................................15
The primary duty of care...........................................................................................................15
Consultative arrangements.........................................................................................................16
Inspection results – Hazards, Risks and Control...........................................................................17
Hazards......................................................................................................................................17
Risks..........................................................................................................................................17
Calculations of the risk..............................................................................................................17
Controls......................................................................................................................................18
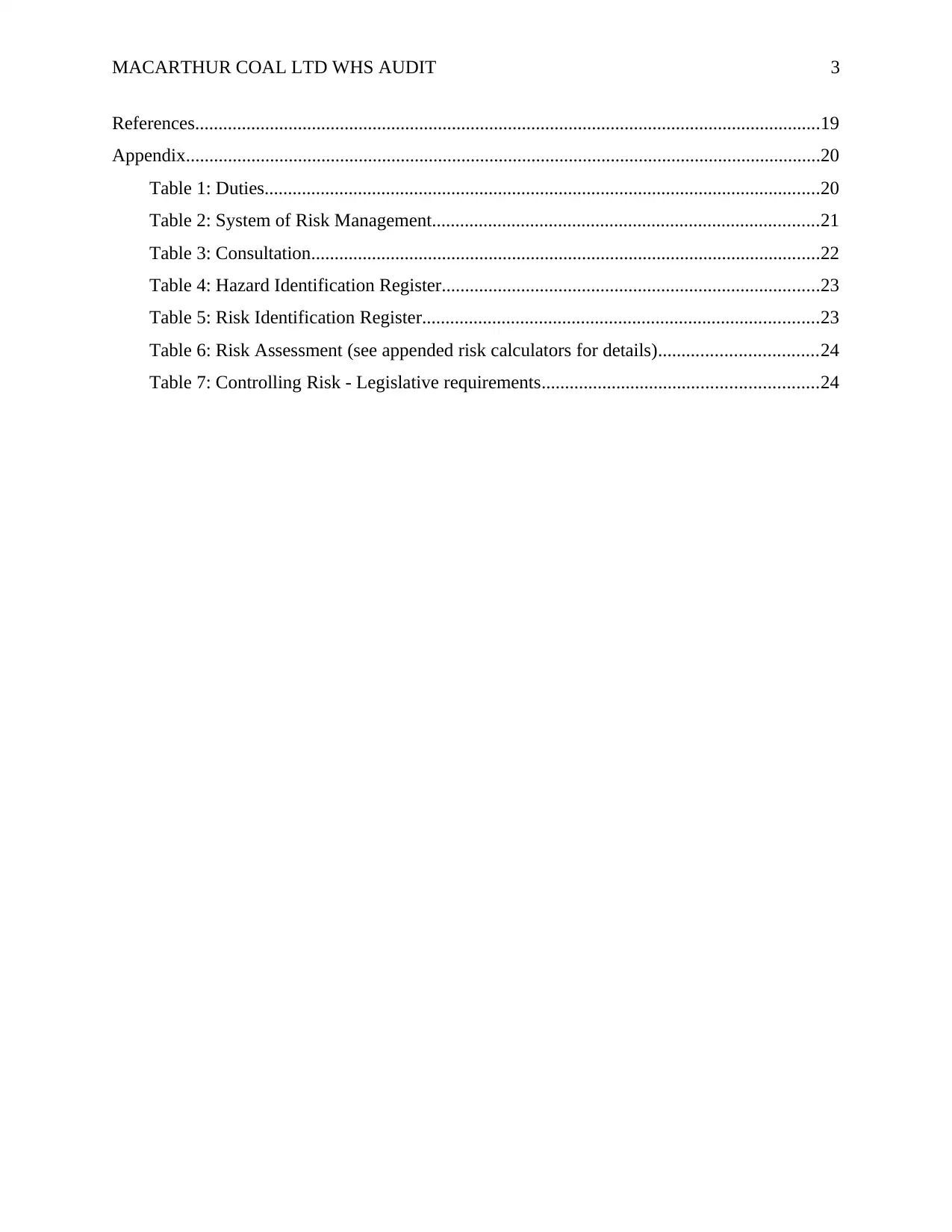
MACARTHUR COAL LTD WHS AUDIT 3
References......................................................................................................................................19
Appendix........................................................................................................................................20
Table 1: Duties.......................................................................................................................20
Table 2: System of Risk Management...................................................................................21
Table 3: Consultation.............................................................................................................22
Table 4: Hazard Identification Register.................................................................................23
Table 5: Risk Identification Register.....................................................................................23
Table 6: Risk Assessment (see appended risk calculators for details)..................................24
Table 7: Controlling Risk - Legislative requirements...........................................................24
References......................................................................................................................................19
Appendix........................................................................................................................................20
Table 1: Duties.......................................................................................................................20
Table 2: System of Risk Management...................................................................................21
Table 3: Consultation.............................................................................................................22
Table 4: Hazard Identification Register.................................................................................23
Table 5: Risk Identification Register.....................................................................................23
Table 6: Risk Assessment (see appended risk calculators for details)..................................24
Table 7: Controlling Risk - Legislative requirements...........................................................24
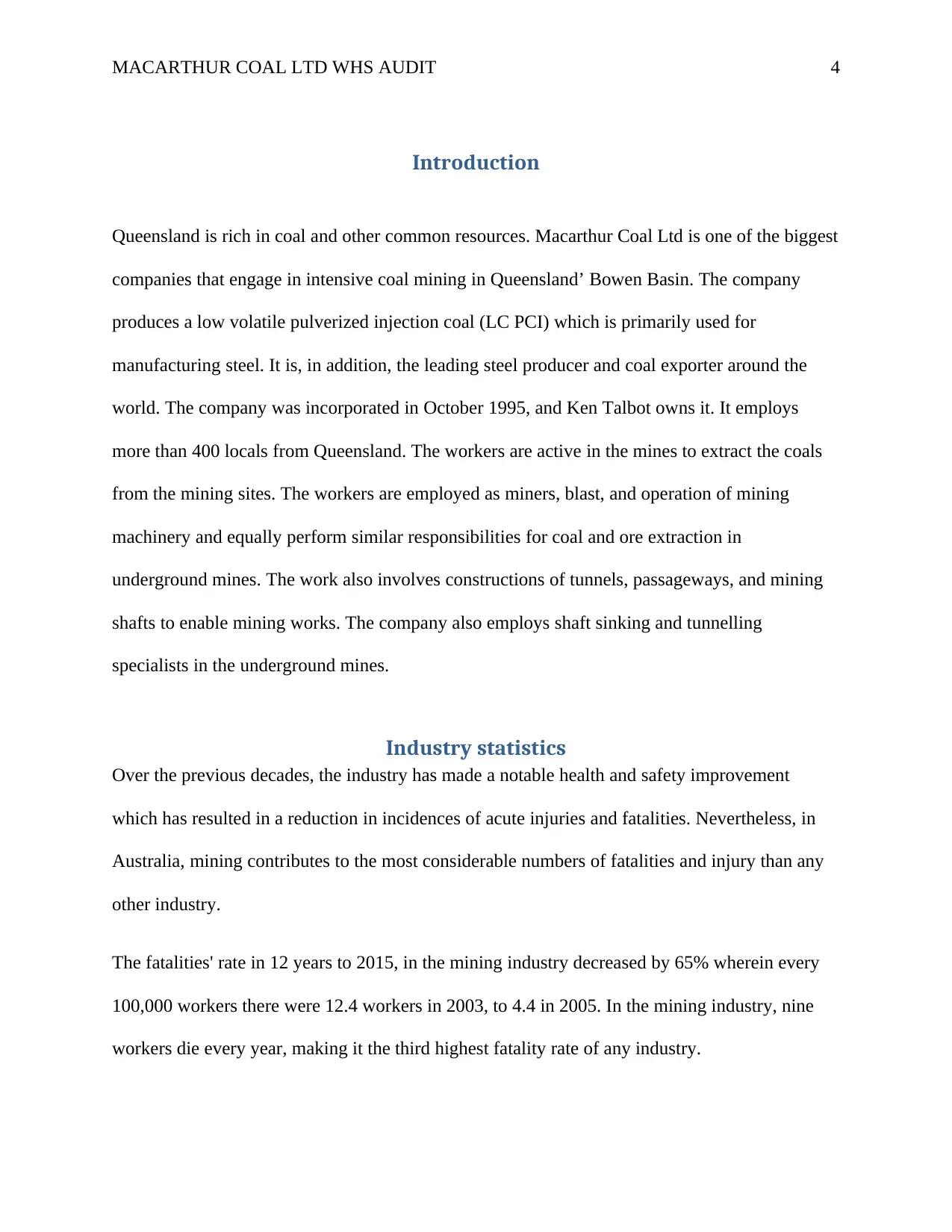
MACARTHUR COAL LTD WHS AUDIT 4
Introduction
Queensland is rich in coal and other common resources. Macarthur Coal Ltd is one of the biggest
companies that engage in intensive coal mining in Queensland’ Bowen Basin. The company
produces a low volatile pulverized injection coal (LC PCI) which is primarily used for
manufacturing steel. It is, in addition, the leading steel producer and coal exporter around the
world. The company was incorporated in October 1995, and Ken Talbot owns it. It employs
more than 400 locals from Queensland. The workers are active in the mines to extract the coals
from the mining sites. The workers are employed as miners, blast, and operation of mining
machinery and equally perform similar responsibilities for coal and ore extraction in
underground mines. The work also involves constructions of tunnels, passageways, and mining
shafts to enable mining works. The company also employs shaft sinking and tunnelling
specialists in the underground mines.
Industry statistics
Over the previous decades, the industry has made a notable health and safety improvement
which has resulted in a reduction in incidences of acute injuries and fatalities. Nevertheless, in
Australia, mining contributes to the most considerable numbers of fatalities and injury than any
other industry.
The fatalities' rate in 12 years to 2015, in the mining industry decreased by 65% wherein every
100,000 workers there were 12.4 workers in 2003, to 4.4 in 2005. In the mining industry, nine
workers die every year, making it the third highest fatality rate of any industry.
Introduction
Queensland is rich in coal and other common resources. Macarthur Coal Ltd is one of the biggest
companies that engage in intensive coal mining in Queensland’ Bowen Basin. The company
produces a low volatile pulverized injection coal (LC PCI) which is primarily used for
manufacturing steel. It is, in addition, the leading steel producer and coal exporter around the
world. The company was incorporated in October 1995, and Ken Talbot owns it. It employs
more than 400 locals from Queensland. The workers are active in the mines to extract the coals
from the mining sites. The workers are employed as miners, blast, and operation of mining
machinery and equally perform similar responsibilities for coal and ore extraction in
underground mines. The work also involves constructions of tunnels, passageways, and mining
shafts to enable mining works. The company also employs shaft sinking and tunnelling
specialists in the underground mines.
Industry statistics
Over the previous decades, the industry has made a notable health and safety improvement
which has resulted in a reduction in incidences of acute injuries and fatalities. Nevertheless, in
Australia, mining contributes to the most considerable numbers of fatalities and injury than any
other industry.
The fatalities' rate in 12 years to 2015, in the mining industry decreased by 65% wherein every
100,000 workers there were 12.4 workers in 2003, to 4.4 in 2005. In the mining industry, nine
workers die every year, making it the third highest fatality rate of any industry.
Secure Best Marks with AI Grader
Need help grading? Try our AI Grader for instant feedback on your assignments.
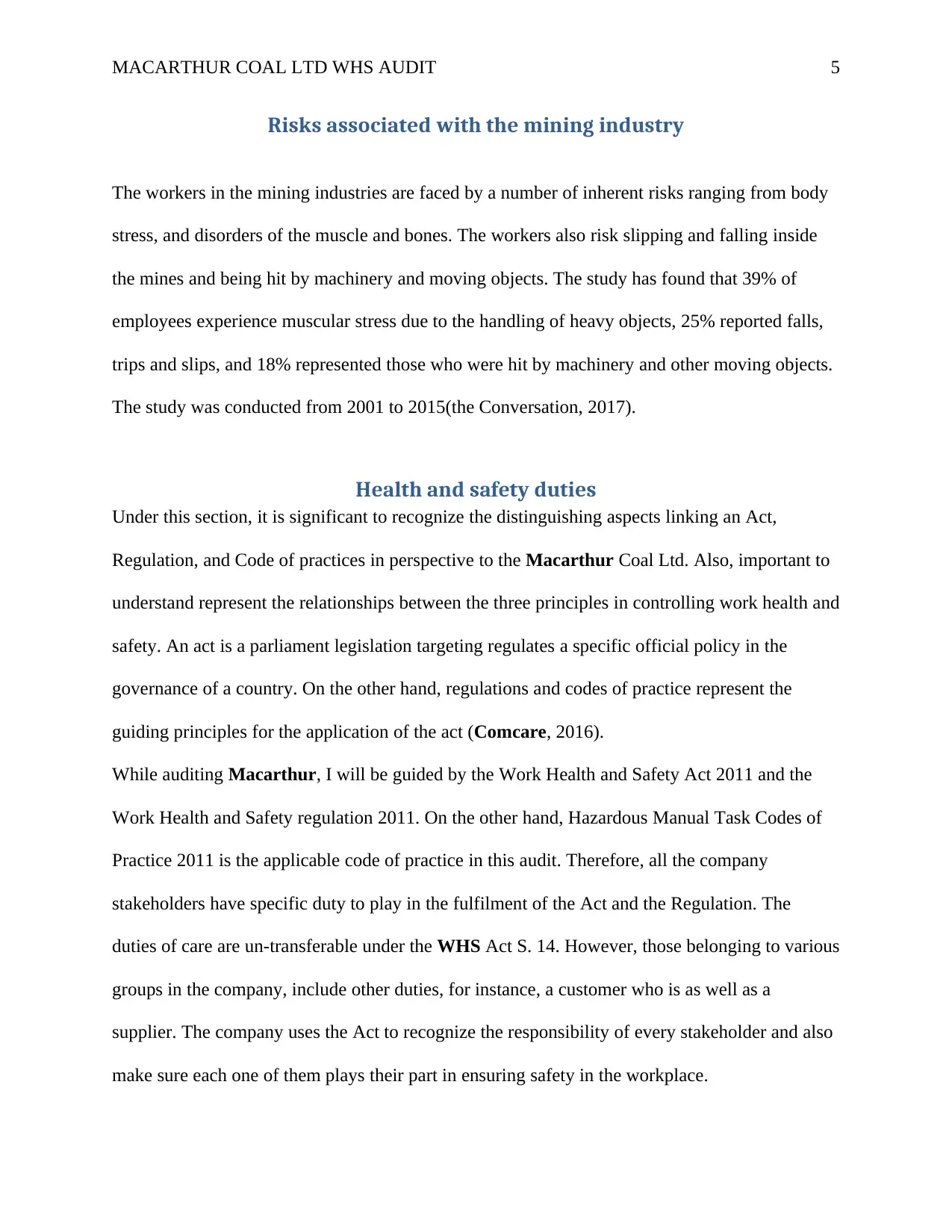
MACARTHUR COAL LTD WHS AUDIT 5
Risks associated with the mining industry
The workers in the mining industries are faced by a number of inherent risks ranging from body
stress, and disorders of the muscle and bones. The workers also risk slipping and falling inside
the mines and being hit by machinery and moving objects. The study has found that 39% of
employees experience muscular stress due to the handling of heavy objects, 25% reported falls,
trips and slips, and 18% represented those who were hit by machinery and other moving objects.
The study was conducted from 2001 to 2015(the Conversation, 2017).
Health and safety duties
Under this section, it is significant to recognize the distinguishing aspects linking an Act,
Regulation, and Code of practices in perspective to the Macarthur Coal Ltd. Also, important to
understand represent the relationships between the three principles in controlling work health and
safety. An act is a parliament legislation targeting regulates a specific official policy in the
governance of a country. On the other hand, regulations and codes of practice represent the
guiding principles for the application of the act (Comcare, 2016).
While auditing Macarthur, I will be guided by the Work Health and Safety Act 2011 and the
Work Health and Safety regulation 2011. On the other hand, Hazardous Manual Task Codes of
Practice 2011 is the applicable code of practice in this audit. Therefore, all the company
stakeholders have specific duty to play in the fulfilment of the Act and the Regulation. The
duties of care are un-transferable under the WHS Act S. 14. However, those belonging to various
groups in the company, include other duties, for instance, a customer who is as well as a
supplier. The company uses the Act to recognize the responsibility of every stakeholder and also
make sure each one of them plays their part in ensuring safety in the workplace.
Risks associated with the mining industry
The workers in the mining industries are faced by a number of inherent risks ranging from body
stress, and disorders of the muscle and bones. The workers also risk slipping and falling inside
the mines and being hit by machinery and moving objects. The study has found that 39% of
employees experience muscular stress due to the handling of heavy objects, 25% reported falls,
trips and slips, and 18% represented those who were hit by machinery and other moving objects.
The study was conducted from 2001 to 2015(the Conversation, 2017).
Health and safety duties
Under this section, it is significant to recognize the distinguishing aspects linking an Act,
Regulation, and Code of practices in perspective to the Macarthur Coal Ltd. Also, important to
understand represent the relationships between the three principles in controlling work health and
safety. An act is a parliament legislation targeting regulates a specific official policy in the
governance of a country. On the other hand, regulations and codes of practice represent the
guiding principles for the application of the act (Comcare, 2016).
While auditing Macarthur, I will be guided by the Work Health and Safety Act 2011 and the
Work Health and Safety regulation 2011. On the other hand, Hazardous Manual Task Codes of
Practice 2011 is the applicable code of practice in this audit. Therefore, all the company
stakeholders have specific duty to play in the fulfilment of the Act and the Regulation. The
duties of care are un-transferable under the WHS Act S. 14. However, those belonging to various
groups in the company, include other duties, for instance, a customer who is as well as a
supplier. The company uses the Act to recognize the responsibility of every stakeholder and also
make sure each one of them plays their part in ensuring safety in the workplace.
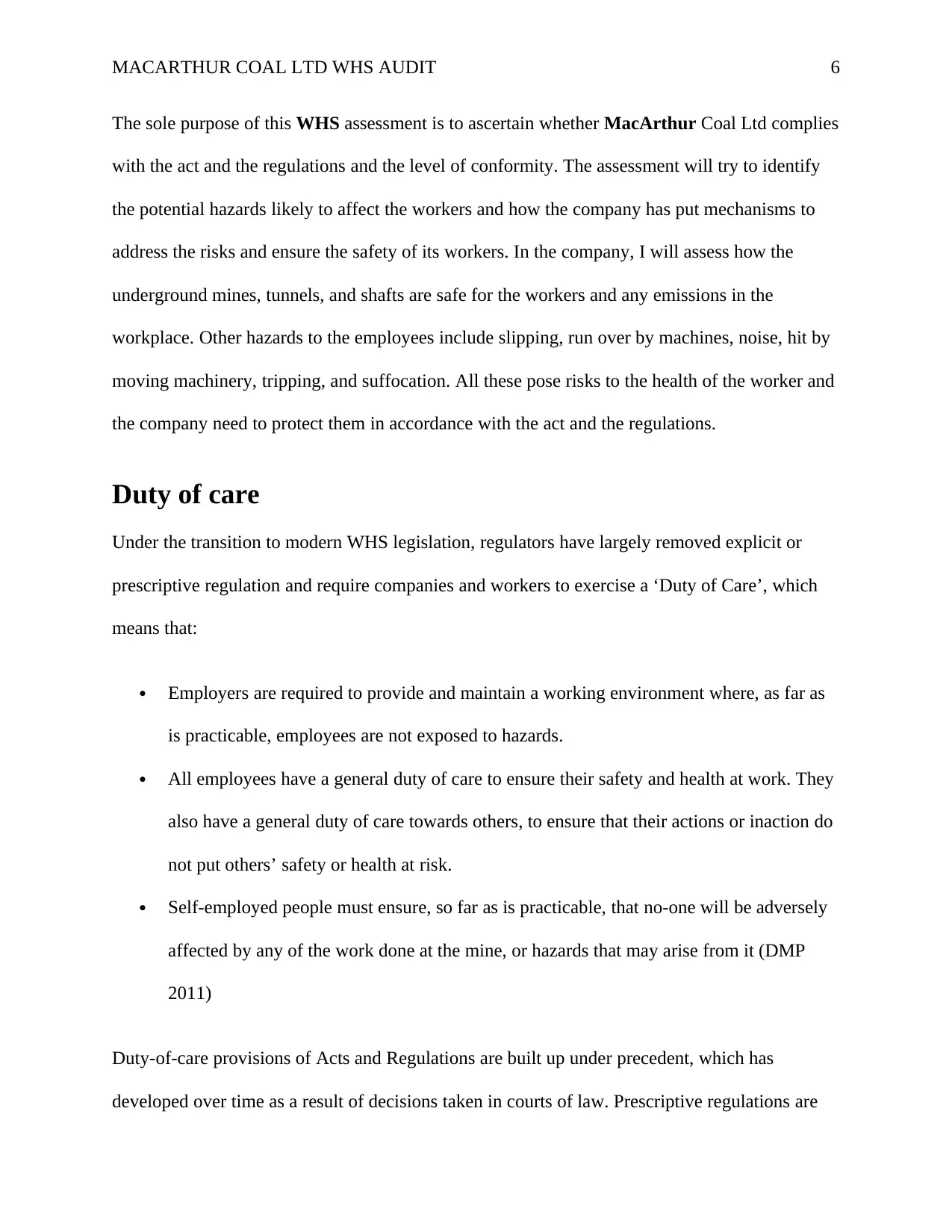
MACARTHUR COAL LTD WHS AUDIT 6
The sole purpose of this WHS assessment is to ascertain whether MacArthur Coal Ltd complies
with the act and the regulations and the level of conformity. The assessment will try to identify
the potential hazards likely to affect the workers and how the company has put mechanisms to
address the risks and ensure the safety of its workers. In the company, I will assess how the
underground mines, tunnels, and shafts are safe for the workers and any emissions in the
workplace. Other hazards to the employees include slipping, run over by machines, noise, hit by
moving machinery, tripping, and suffocation. All these pose risks to the health of the worker and
the company need to protect them in accordance with the act and the regulations.
Duty of care
Under the transition to modern WHS legislation, regulators have largely removed explicit or
prescriptive regulation and require companies and workers to exercise a ‘Duty of Care’, which
means that:
Employers are required to provide and maintain a working environment where, as far as
is practicable, employees are not exposed to hazards.
All employees have a general duty of care to ensure their safety and health at work. They
also have a general duty of care towards others, to ensure that their actions or inaction do
not put others’ safety or health at risk.
Self-employed people must ensure, so far as is practicable, that no-one will be adversely
affected by any of the work done at the mine, or hazards that may arise from it (DMP
2011)
Duty-of-care provisions of Acts and Regulations are built up under precedent, which has
developed over time as a result of decisions taken in courts of law. Prescriptive regulations are
The sole purpose of this WHS assessment is to ascertain whether MacArthur Coal Ltd complies
with the act and the regulations and the level of conformity. The assessment will try to identify
the potential hazards likely to affect the workers and how the company has put mechanisms to
address the risks and ensure the safety of its workers. In the company, I will assess how the
underground mines, tunnels, and shafts are safe for the workers and any emissions in the
workplace. Other hazards to the employees include slipping, run over by machines, noise, hit by
moving machinery, tripping, and suffocation. All these pose risks to the health of the worker and
the company need to protect them in accordance with the act and the regulations.
Duty of care
Under the transition to modern WHS legislation, regulators have largely removed explicit or
prescriptive regulation and require companies and workers to exercise a ‘Duty of Care’, which
means that:
Employers are required to provide and maintain a working environment where, as far as
is practicable, employees are not exposed to hazards.
All employees have a general duty of care to ensure their safety and health at work. They
also have a general duty of care towards others, to ensure that their actions or inaction do
not put others’ safety or health at risk.
Self-employed people must ensure, so far as is practicable, that no-one will be adversely
affected by any of the work done at the mine, or hazards that may arise from it (DMP
2011)
Duty-of-care provisions of Acts and Regulations are built up under precedent, which has
developed over time as a result of decisions taken in courts of law. Prescriptive regulations are
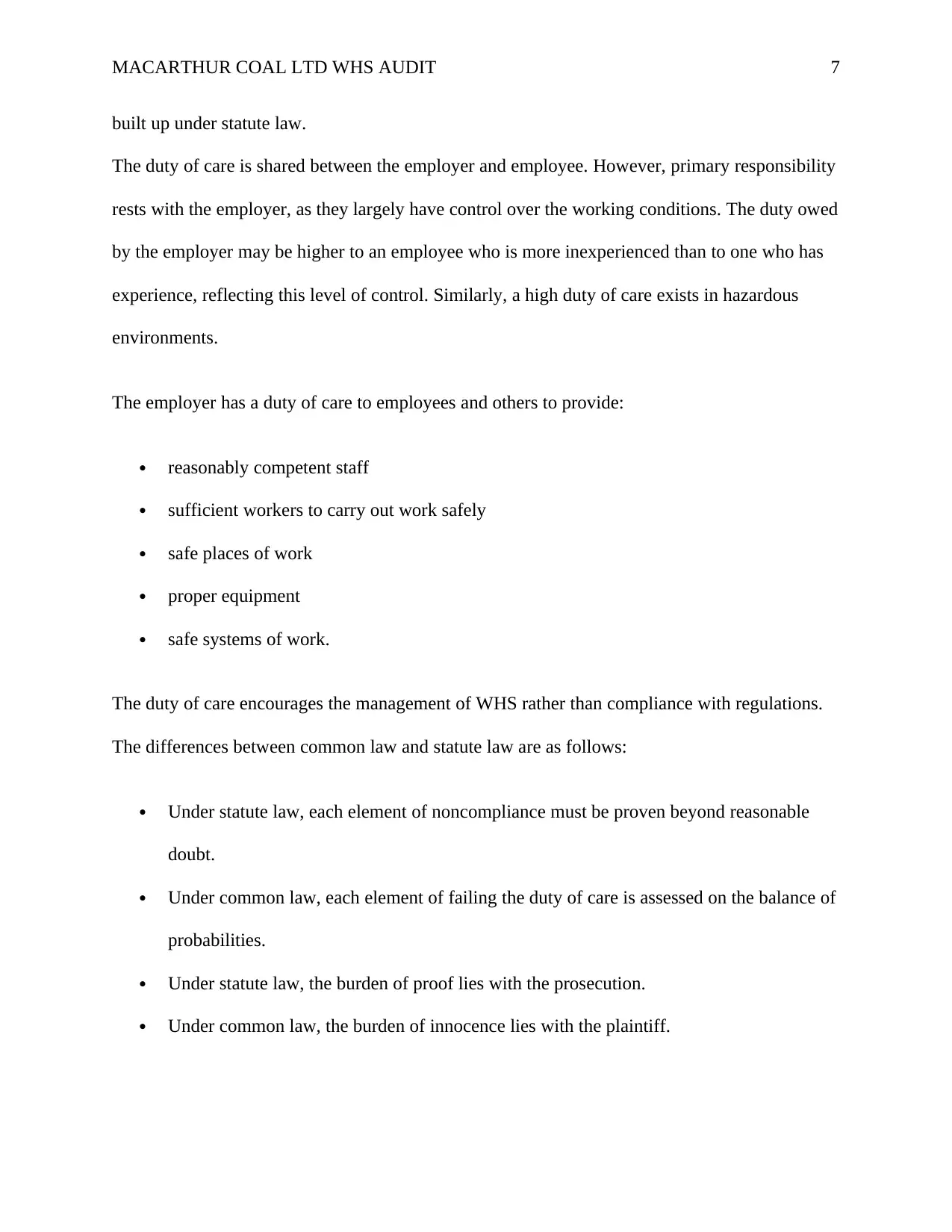
MACARTHUR COAL LTD WHS AUDIT 7
built up under statute law.
The duty of care is shared between the employer and employee. However, primary responsibility
rests with the employer, as they largely have control over the working conditions. The duty owed
by the employer may be higher to an employee who is more inexperienced than to one who has
experience, reflecting this level of control. Similarly, a high duty of care exists in hazardous
environments.
The employer has a duty of care to employees and others to provide:
reasonably competent staff
sufficient workers to carry out work safely
safe places of work
proper equipment
safe systems of work.
The duty of care encourages the management of WHS rather than compliance with regulations.
The differences between common law and statute law are as follows:
Under statute law, each element of noncompliance must be proven beyond reasonable
doubt.
Under common law, each element of failing the duty of care is assessed on the balance of
probabilities.
Under statute law, the burden of proof lies with the prosecution.
Under common law, the burden of innocence lies with the plaintiff.
built up under statute law.
The duty of care is shared between the employer and employee. However, primary responsibility
rests with the employer, as they largely have control over the working conditions. The duty owed
by the employer may be higher to an employee who is more inexperienced than to one who has
experience, reflecting this level of control. Similarly, a high duty of care exists in hazardous
environments.
The employer has a duty of care to employees and others to provide:
reasonably competent staff
sufficient workers to carry out work safely
safe places of work
proper equipment
safe systems of work.
The duty of care encourages the management of WHS rather than compliance with regulations.
The differences between common law and statute law are as follows:
Under statute law, each element of noncompliance must be proven beyond reasonable
doubt.
Under common law, each element of failing the duty of care is assessed on the balance of
probabilities.
Under statute law, the burden of proof lies with the prosecution.
Under common law, the burden of innocence lies with the plaintiff.
Paraphrase This Document
Need a fresh take? Get an instant paraphrase of this document with our AI Paraphraser
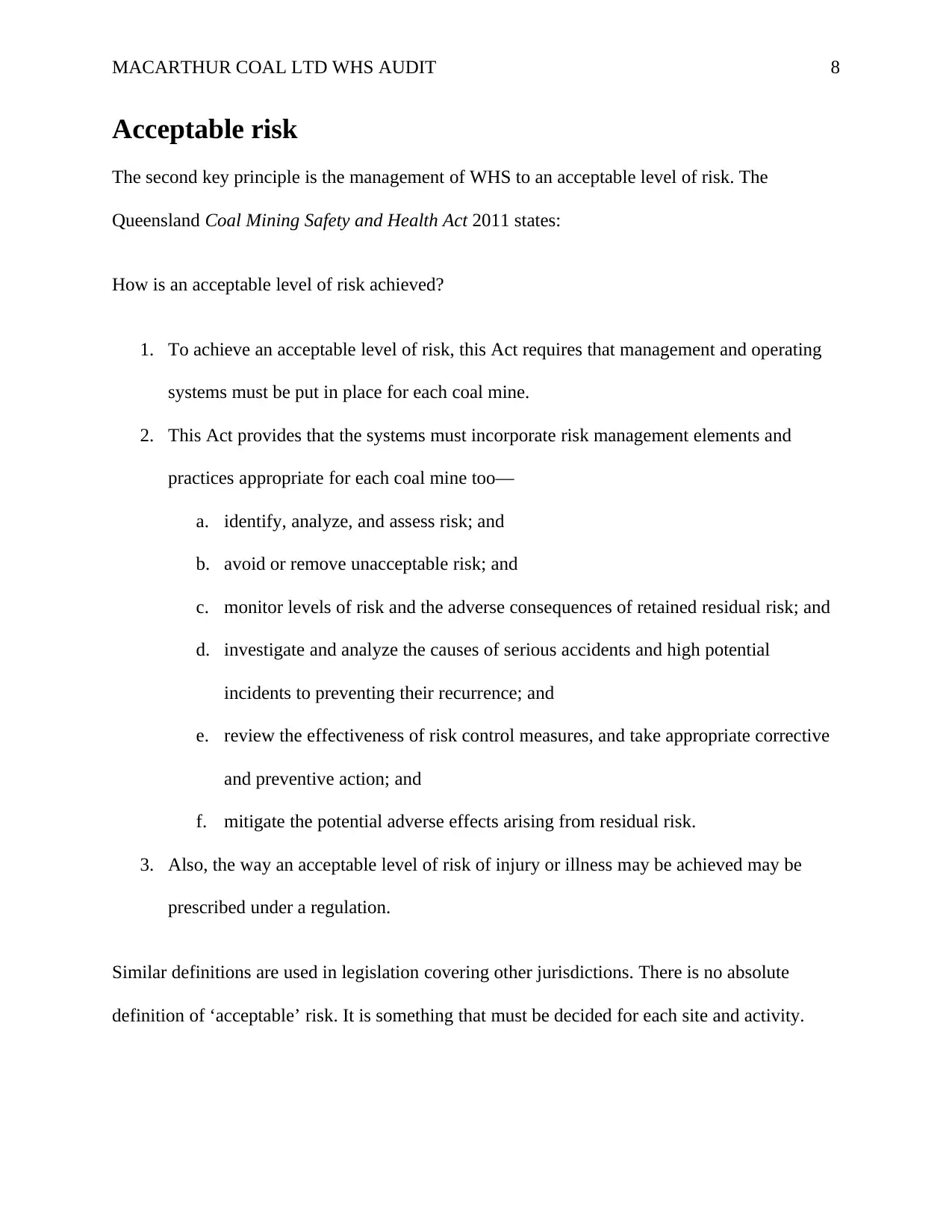
MACARTHUR COAL LTD WHS AUDIT 8
Acceptable risk
The second key principle is the management of WHS to an acceptable level of risk. The
Queensland Coal Mining Safety and Health Act 2011 states:
How is an acceptable level of risk achieved?
1. To achieve an acceptable level of risk, this Act requires that management and operating
systems must be put in place for each coal mine.
2. This Act provides that the systems must incorporate risk management elements and
practices appropriate for each coal mine too—
a. identify, analyze, and assess risk; and
b. avoid or remove unacceptable risk; and
c. monitor levels of risk and the adverse consequences of retained residual risk; and
d. investigate and analyze the causes of serious accidents and high potential
incidents to preventing their recurrence; and
e. review the effectiveness of risk control measures, and take appropriate corrective
and preventive action; and
f. mitigate the potential adverse effects arising from residual risk.
3. Also, the way an acceptable level of risk of injury or illness may be achieved may be
prescribed under a regulation.
Similar definitions are used in legislation covering other jurisdictions. There is no absolute
definition of ‘acceptable’ risk. It is something that must be decided for each site and activity.
Acceptable risk
The second key principle is the management of WHS to an acceptable level of risk. The
Queensland Coal Mining Safety and Health Act 2011 states:
How is an acceptable level of risk achieved?
1. To achieve an acceptable level of risk, this Act requires that management and operating
systems must be put in place for each coal mine.
2. This Act provides that the systems must incorporate risk management elements and
practices appropriate for each coal mine too—
a. identify, analyze, and assess risk; and
b. avoid or remove unacceptable risk; and
c. monitor levels of risk and the adverse consequences of retained residual risk; and
d. investigate and analyze the causes of serious accidents and high potential
incidents to preventing their recurrence; and
e. review the effectiveness of risk control measures, and take appropriate corrective
and preventive action; and
f. mitigate the potential adverse effects arising from residual risk.
3. Also, the way an acceptable level of risk of injury or illness may be achieved may be
prescribed under a regulation.
Similar definitions are used in legislation covering other jurisdictions. There is no absolute
definition of ‘acceptable’ risk. It is something that must be decided for each site and activity.
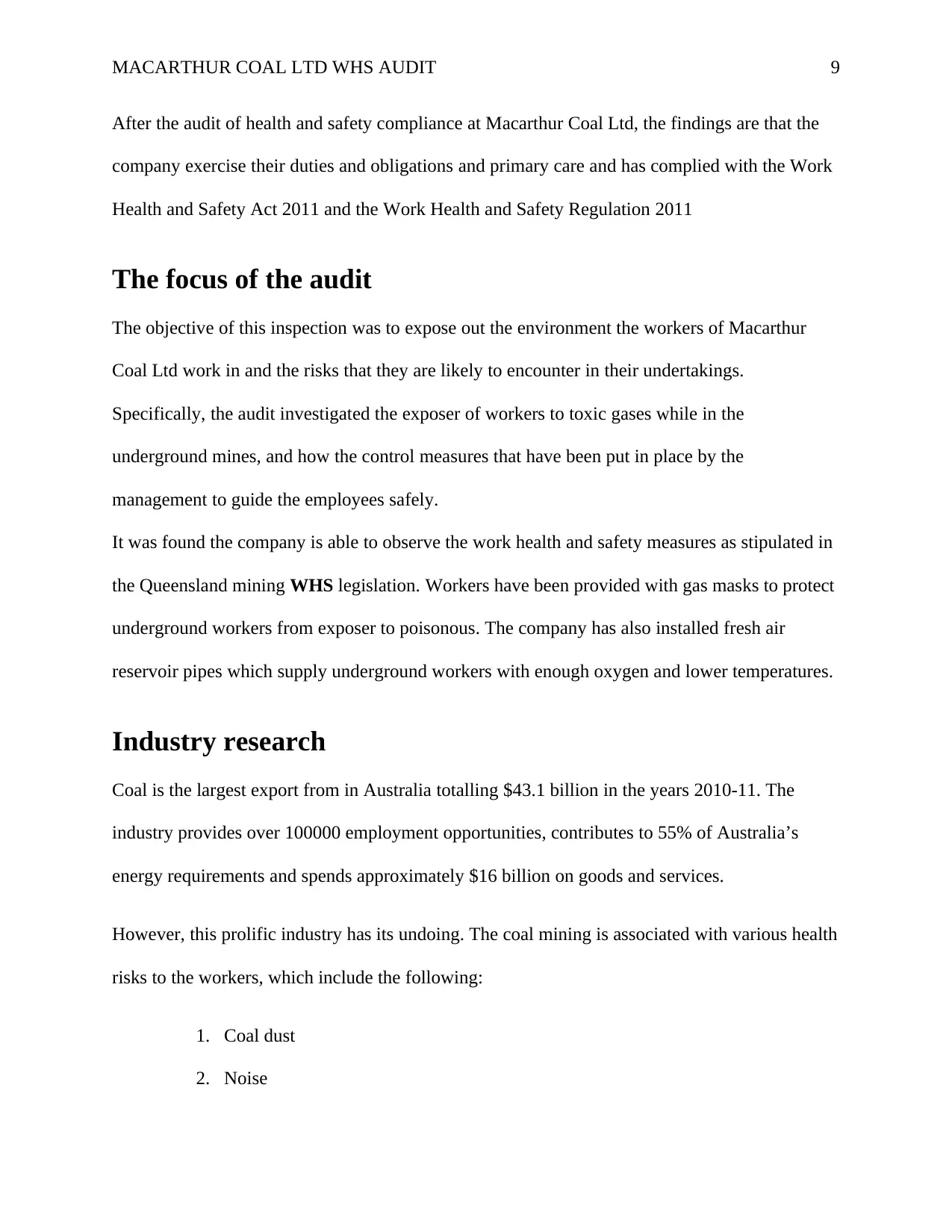
MACARTHUR COAL LTD WHS AUDIT 9
After the audit of health and safety compliance at Macarthur Coal Ltd, the findings are that the
company exercise their duties and obligations and primary care and has complied with the Work
Health and Safety Act 2011 and the Work Health and Safety Regulation 2011
The focus of the audit
The objective of this inspection was to expose out the environment the workers of Macarthur
Coal Ltd work in and the risks that they are likely to encounter in their undertakings.
Specifically, the audit investigated the exposer of workers to toxic gases while in the
underground mines, and how the control measures that have been put in place by the
management to guide the employees safely.
It was found the company is able to observe the work health and safety measures as stipulated in
the Queensland mining WHS legislation. Workers have been provided with gas masks to protect
underground workers from exposer to poisonous. The company has also installed fresh air
reservoir pipes which supply underground workers with enough oxygen and lower temperatures.
Industry research
Coal is the largest export from in Australia totalling $43.1 billion in the years 2010-11. The
industry provides over 100000 employment opportunities, contributes to 55% of Australia’s
energy requirements and spends approximately $16 billion on goods and services.
However, this prolific industry has its undoing. The coal mining is associated with various health
risks to the workers, which include the following:
1. Coal dust
2. Noise
After the audit of health and safety compliance at Macarthur Coal Ltd, the findings are that the
company exercise their duties and obligations and primary care and has complied with the Work
Health and Safety Act 2011 and the Work Health and Safety Regulation 2011
The focus of the audit
The objective of this inspection was to expose out the environment the workers of Macarthur
Coal Ltd work in and the risks that they are likely to encounter in their undertakings.
Specifically, the audit investigated the exposer of workers to toxic gases while in the
underground mines, and how the control measures that have been put in place by the
management to guide the employees safely.
It was found the company is able to observe the work health and safety measures as stipulated in
the Queensland mining WHS legislation. Workers have been provided with gas masks to protect
underground workers from exposer to poisonous. The company has also installed fresh air
reservoir pipes which supply underground workers with enough oxygen and lower temperatures.
Industry research
Coal is the largest export from in Australia totalling $43.1 billion in the years 2010-11. The
industry provides over 100000 employment opportunities, contributes to 55% of Australia’s
energy requirements and spends approximately $16 billion on goods and services.
However, this prolific industry has its undoing. The coal mining is associated with various health
risks to the workers, which include the following:
1. Coal dust
2. Noise
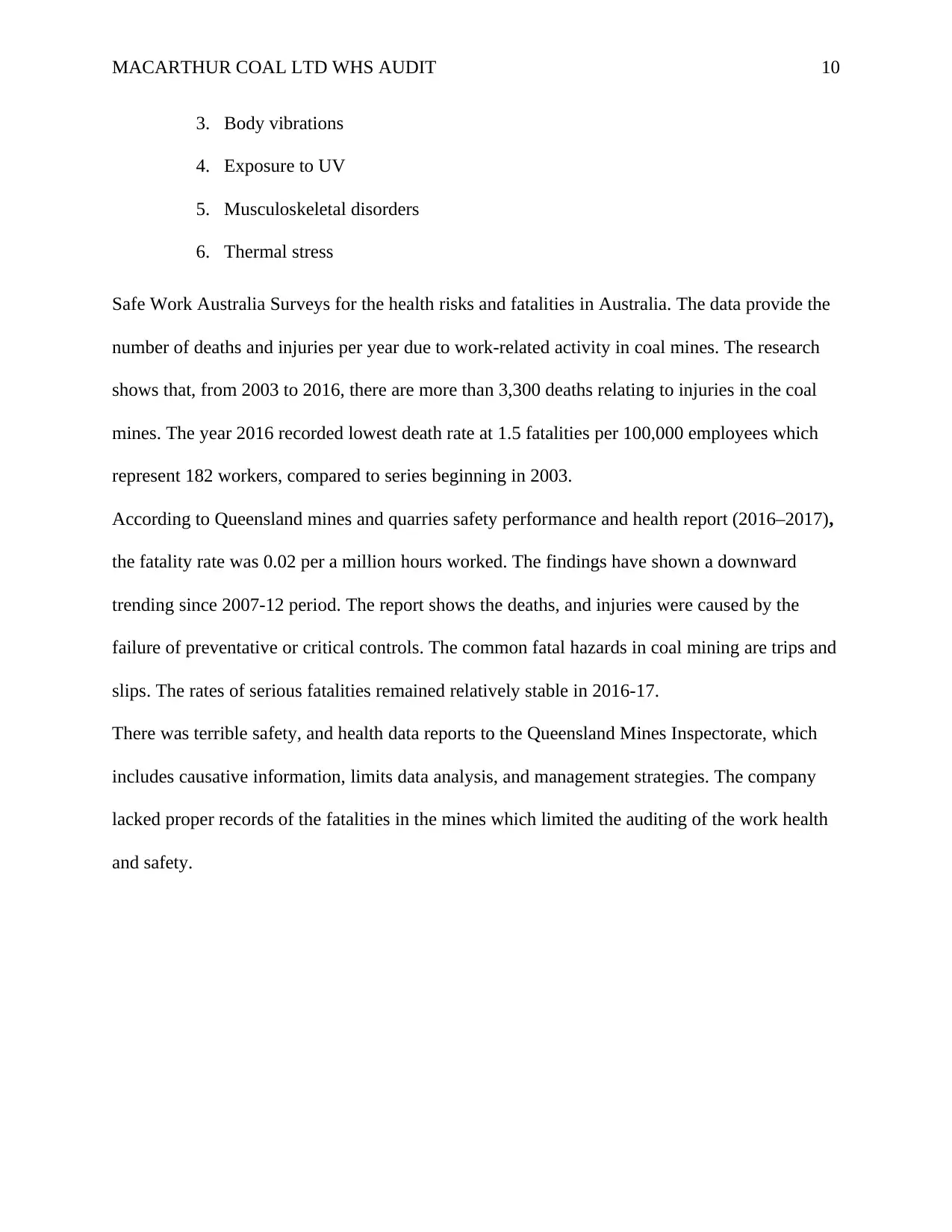
MACARTHUR COAL LTD WHS AUDIT 10
3. Body vibrations
4. Exposure to UV
5. Musculoskeletal disorders
6. Thermal stress
Safe Work Australia Surveys for the health risks and fatalities in Australia. The data provide the
number of deaths and injuries per year due to work-related activity in coal mines. The research
shows that, from 2003 to 2016, there are more than 3,300 deaths relating to injuries in the coal
mines. The year 2016 recorded lowest death rate at 1.5 fatalities per 100,000 employees which
represent 182 workers, compared to series beginning in 2003.
According to Queensland mines and quarries safety performance and health report (2016–2017),
the fatality rate was 0.02 per a million hours worked. The findings have shown a downward
trending since 2007-12 period. The report shows the deaths, and injuries were caused by the
failure of preventative or critical controls. The common fatal hazards in coal mining are trips and
slips. The rates of serious fatalities remained relatively stable in 2016-17.
There was terrible safety, and health data reports to the Queensland Mines Inspectorate, which
includes causative information, limits data analysis, and management strategies. The company
lacked proper records of the fatalities in the mines which limited the auditing of the work health
and safety.
3. Body vibrations
4. Exposure to UV
5. Musculoskeletal disorders
6. Thermal stress
Safe Work Australia Surveys for the health risks and fatalities in Australia. The data provide the
number of deaths and injuries per year due to work-related activity in coal mines. The research
shows that, from 2003 to 2016, there are more than 3,300 deaths relating to injuries in the coal
mines. The year 2016 recorded lowest death rate at 1.5 fatalities per 100,000 employees which
represent 182 workers, compared to series beginning in 2003.
According to Queensland mines and quarries safety performance and health report (2016–2017),
the fatality rate was 0.02 per a million hours worked. The findings have shown a downward
trending since 2007-12 period. The report shows the deaths, and injuries were caused by the
failure of preventative or critical controls. The common fatal hazards in coal mining are trips and
slips. The rates of serious fatalities remained relatively stable in 2016-17.
There was terrible safety, and health data reports to the Queensland Mines Inspectorate, which
includes causative information, limits data analysis, and management strategies. The company
lacked proper records of the fatalities in the mines which limited the auditing of the work health
and safety.
Secure Best Marks with AI Grader
Need help grading? Try our AI Grader for instant feedback on your assignments.
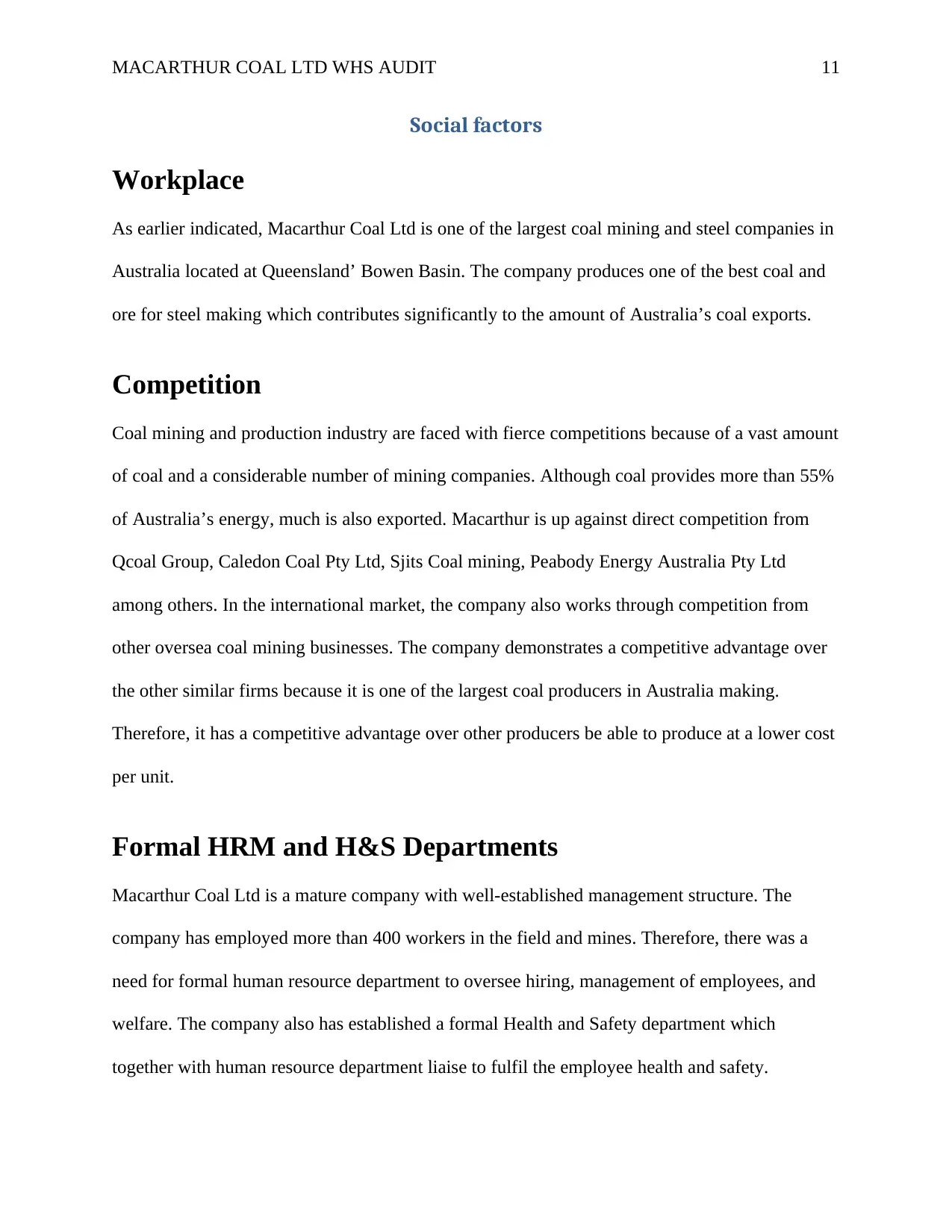
MACARTHUR COAL LTD WHS AUDIT 11
Social factors
Workplace
As earlier indicated, Macarthur Coal Ltd is one of the largest coal mining and steel companies in
Australia located at Queensland’ Bowen Basin. The company produces one of the best coal and
ore for steel making which contributes significantly to the amount of Australia’s coal exports.
Competition
Coal mining and production industry are faced with fierce competitions because of a vast amount
of coal and a considerable number of mining companies. Although coal provides more than 55%
of Australia’s energy, much is also exported. Macarthur is up against direct competition from
Qcoal Group, Caledon Coal Pty Ltd, Sjits Coal mining, Peabody Energy Australia Pty Ltd
among others. In the international market, the company also works through competition from
other oversea coal mining businesses. The company demonstrates a competitive advantage over
the other similar firms because it is one of the largest coal producers in Australia making.
Therefore, it has a competitive advantage over other producers be able to produce at a lower cost
per unit.
Formal HRM and H&S Departments
Macarthur Coal Ltd is a mature company with well-established management structure. The
company has employed more than 400 workers in the field and mines. Therefore, there was a
need for formal human resource department to oversee hiring, management of employees, and
welfare. The company also has established a formal Health and Safety department which
together with human resource department liaise to fulfil the employee health and safety.
Social factors
Workplace
As earlier indicated, Macarthur Coal Ltd is one of the largest coal mining and steel companies in
Australia located at Queensland’ Bowen Basin. The company produces one of the best coal and
ore for steel making which contributes significantly to the amount of Australia’s coal exports.
Competition
Coal mining and production industry are faced with fierce competitions because of a vast amount
of coal and a considerable number of mining companies. Although coal provides more than 55%
of Australia’s energy, much is also exported. Macarthur is up against direct competition from
Qcoal Group, Caledon Coal Pty Ltd, Sjits Coal mining, Peabody Energy Australia Pty Ltd
among others. In the international market, the company also works through competition from
other oversea coal mining businesses. The company demonstrates a competitive advantage over
the other similar firms because it is one of the largest coal producers in Australia making.
Therefore, it has a competitive advantage over other producers be able to produce at a lower cost
per unit.
Formal HRM and H&S Departments
Macarthur Coal Ltd is a mature company with well-established management structure. The
company has employed more than 400 workers in the field and mines. Therefore, there was a
need for formal human resource department to oversee hiring, management of employees, and
welfare. The company also has established a formal Health and Safety department which
together with human resource department liaise to fulfil the employee health and safety.
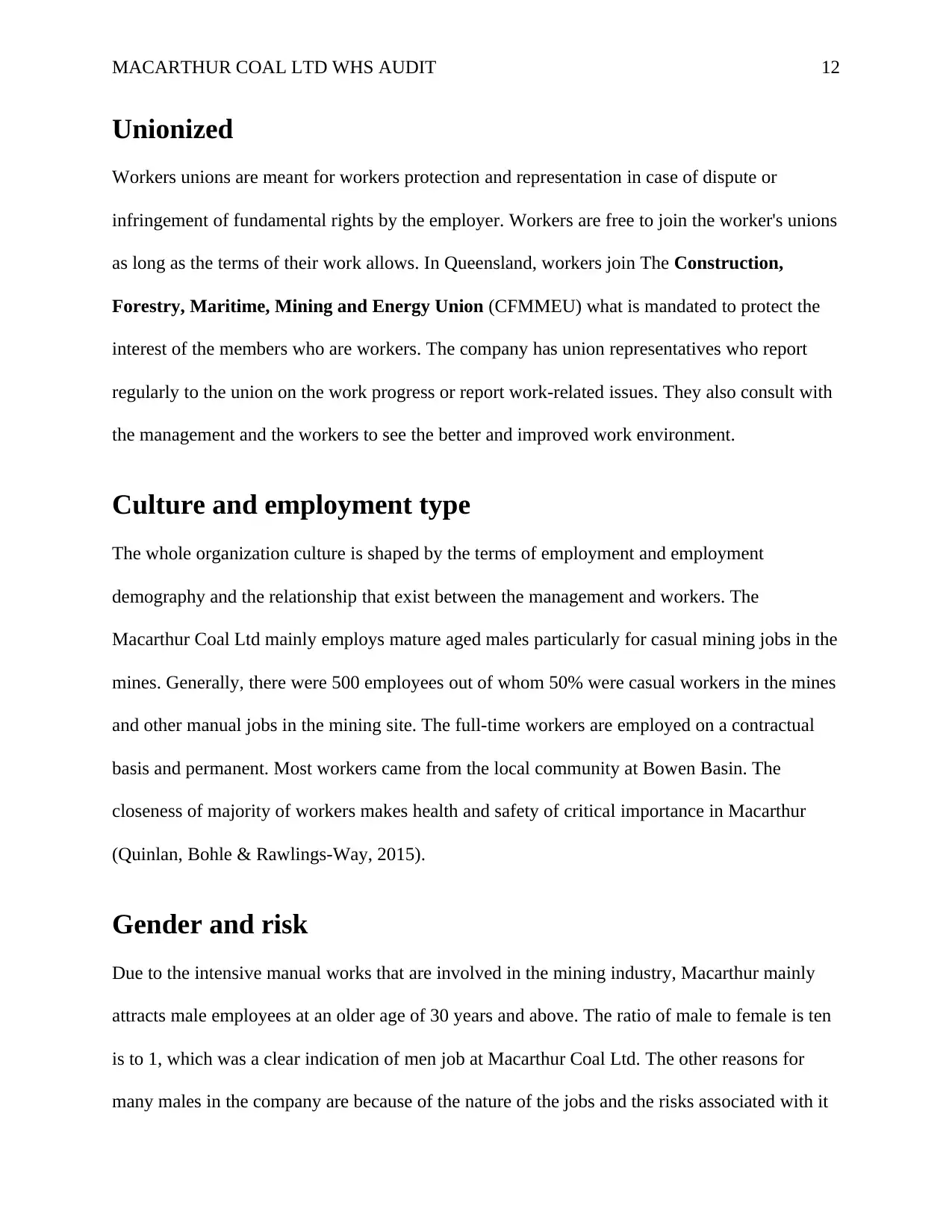
MACARTHUR COAL LTD WHS AUDIT 12
Unionized
Workers unions are meant for workers protection and representation in case of dispute or
infringement of fundamental rights by the employer. Workers are free to join the worker's unions
as long as the terms of their work allows. In Queensland, workers join The Construction,
Forestry, Maritime, Mining and Energy Union (CFMMEU) what is mandated to protect the
interest of the members who are workers. The company has union representatives who report
regularly to the union on the work progress or report work-related issues. They also consult with
the management and the workers to see the better and improved work environment.
Culture and employment type
The whole organization culture is shaped by the terms of employment and employment
demography and the relationship that exist between the management and workers. The
Macarthur Coal Ltd mainly employs mature aged males particularly for casual mining jobs in the
mines. Generally, there were 500 employees out of whom 50% were casual workers in the mines
and other manual jobs in the mining site. The full-time workers are employed on a contractual
basis and permanent. Most workers came from the local community at Bowen Basin. The
closeness of majority of workers makes health and safety of critical importance in Macarthur
(Quinlan, Bohle & Rawlings-Way, 2015).
Gender and risk
Due to the intensive manual works that are involved in the mining industry, Macarthur mainly
attracts male employees at an older age of 30 years and above. The ratio of male to female is ten
is to 1, which was a clear indication of men job at Macarthur Coal Ltd. The other reasons for
many males in the company are because of the nature of the jobs and the risks associated with it
Unionized
Workers unions are meant for workers protection and representation in case of dispute or
infringement of fundamental rights by the employer. Workers are free to join the worker's unions
as long as the terms of their work allows. In Queensland, workers join The Construction,
Forestry, Maritime, Mining and Energy Union (CFMMEU) what is mandated to protect the
interest of the members who are workers. The company has union representatives who report
regularly to the union on the work progress or report work-related issues. They also consult with
the management and the workers to see the better and improved work environment.
Culture and employment type
The whole organization culture is shaped by the terms of employment and employment
demography and the relationship that exist between the management and workers. The
Macarthur Coal Ltd mainly employs mature aged males particularly for casual mining jobs in the
mines. Generally, there were 500 employees out of whom 50% were casual workers in the mines
and other manual jobs in the mining site. The full-time workers are employed on a contractual
basis and permanent. Most workers came from the local community at Bowen Basin. The
closeness of majority of workers makes health and safety of critical importance in Macarthur
(Quinlan, Bohle & Rawlings-Way, 2015).
Gender and risk
Due to the intensive manual works that are involved in the mining industry, Macarthur mainly
attracts male employees at an older age of 30 years and above. The ratio of male to female is ten
is to 1, which was a clear indication of men job at Macarthur Coal Ltd. The other reasons for
many males in the company are because of the nature of the jobs and the risks associated with it
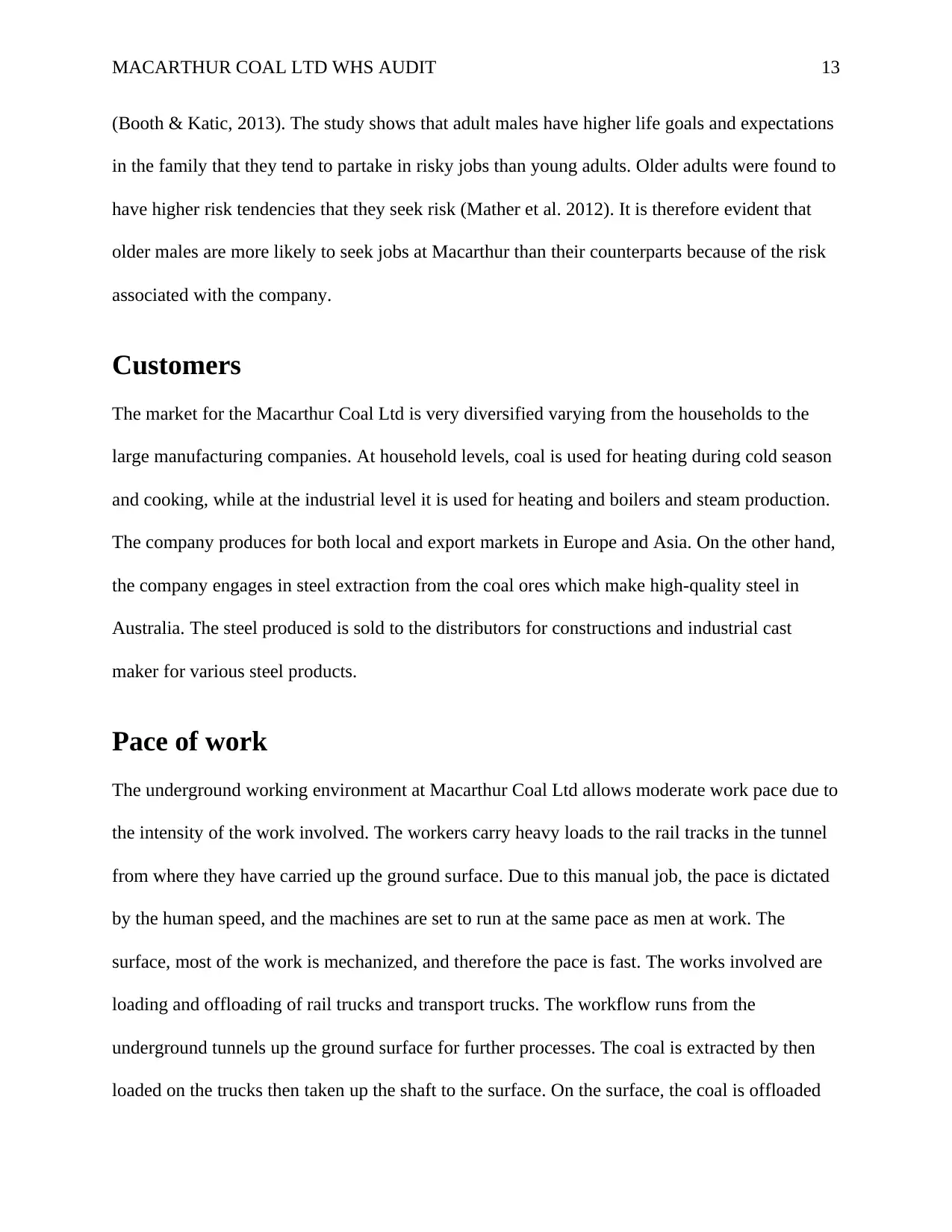
MACARTHUR COAL LTD WHS AUDIT 13
(Booth & Katic, 2013). The study shows that adult males have higher life goals and expectations
in the family that they tend to partake in risky jobs than young adults. Older adults were found to
have higher risk tendencies that they seek risk (Mather et al. 2012). It is therefore evident that
older males are more likely to seek jobs at Macarthur than their counterparts because of the risk
associated with the company.
Customers
The market for the Macarthur Coal Ltd is very diversified varying from the households to the
large manufacturing companies. At household levels, coal is used for heating during cold season
and cooking, while at the industrial level it is used for heating and boilers and steam production.
The company produces for both local and export markets in Europe and Asia. On the other hand,
the company engages in steel extraction from the coal ores which make high-quality steel in
Australia. The steel produced is sold to the distributors for constructions and industrial cast
maker for various steel products.
Pace of work
The underground working environment at Macarthur Coal Ltd allows moderate work pace due to
the intensity of the work involved. The workers carry heavy loads to the rail tracks in the tunnel
from where they have carried up the ground surface. Due to this manual job, the pace is dictated
by the human speed, and the machines are set to run at the same pace as men at work. The
surface, most of the work is mechanized, and therefore the pace is fast. The works involved are
loading and offloading of rail trucks and transport trucks. The workflow runs from the
underground tunnels up the ground surface for further processes. The coal is extracted by then
loaded on the trucks then taken up the shaft to the surface. On the surface, the coal is offloaded
(Booth & Katic, 2013). The study shows that adult males have higher life goals and expectations
in the family that they tend to partake in risky jobs than young adults. Older adults were found to
have higher risk tendencies that they seek risk (Mather et al. 2012). It is therefore evident that
older males are more likely to seek jobs at Macarthur than their counterparts because of the risk
associated with the company.
Customers
The market for the Macarthur Coal Ltd is very diversified varying from the households to the
large manufacturing companies. At household levels, coal is used for heating during cold season
and cooking, while at the industrial level it is used for heating and boilers and steam production.
The company produces for both local and export markets in Europe and Asia. On the other hand,
the company engages in steel extraction from the coal ores which make high-quality steel in
Australia. The steel produced is sold to the distributors for constructions and industrial cast
maker for various steel products.
Pace of work
The underground working environment at Macarthur Coal Ltd allows moderate work pace due to
the intensity of the work involved. The workers carry heavy loads to the rail tracks in the tunnel
from where they have carried up the ground surface. Due to this manual job, the pace is dictated
by the human speed, and the machines are set to run at the same pace as men at work. The
surface, most of the work is mechanized, and therefore the pace is fast. The works involved are
loading and offloading of rail trucks and transport trucks. The workflow runs from the
underground tunnels up the ground surface for further processes. The coal is extracted by then
loaded on the trucks then taken up the shaft to the surface. On the surface, the coal is offloaded
Paraphrase This Document
Need a fresh take? Get an instant paraphrase of this document with our AI Paraphraser
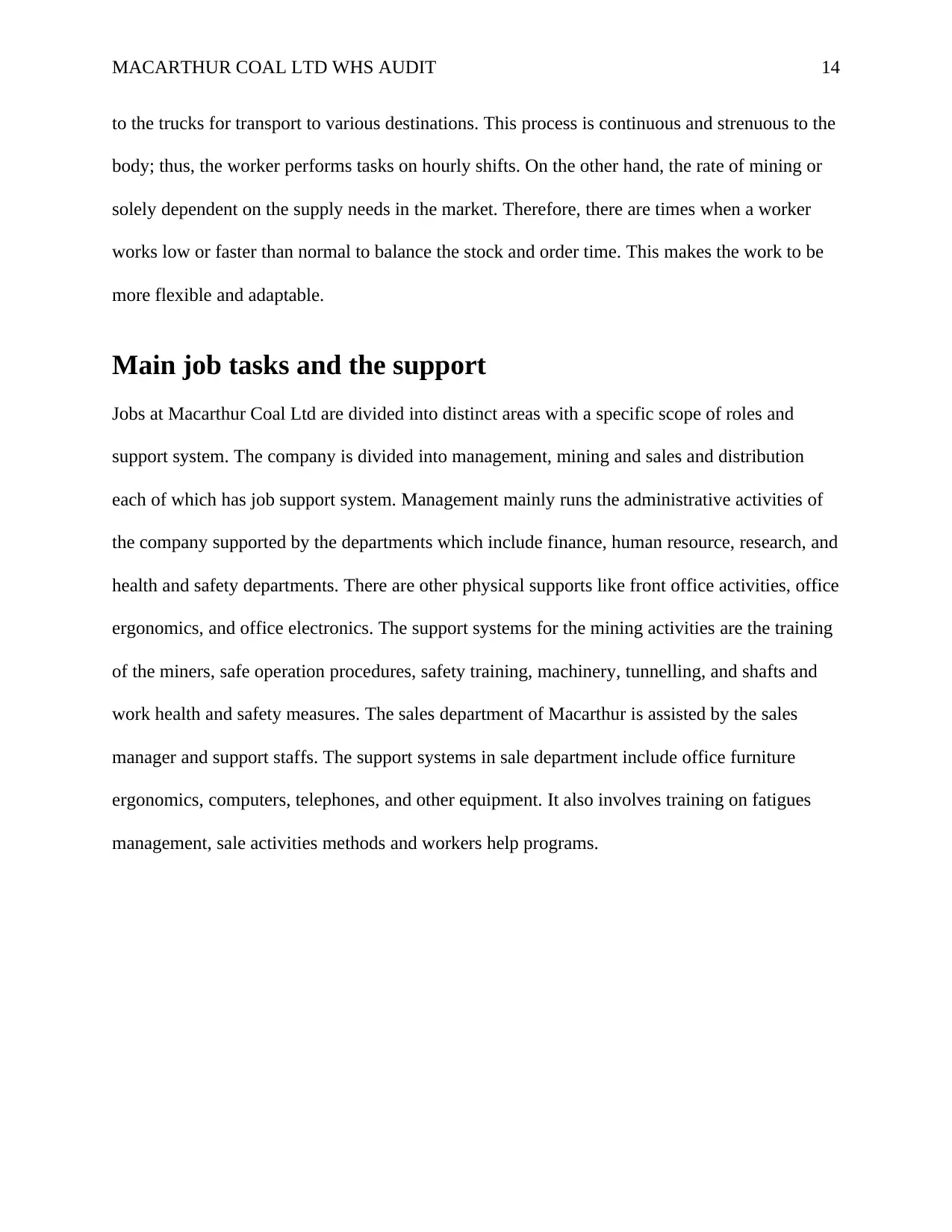
MACARTHUR COAL LTD WHS AUDIT 14
to the trucks for transport to various destinations. This process is continuous and strenuous to the
body; thus, the worker performs tasks on hourly shifts. On the other hand, the rate of mining or
solely dependent on the supply needs in the market. Therefore, there are times when a worker
works low or faster than normal to balance the stock and order time. This makes the work to be
more flexible and adaptable.
Main job tasks and the support
Jobs at Macarthur Coal Ltd are divided into distinct areas with a specific scope of roles and
support system. The company is divided into management, mining and sales and distribution
each of which has job support system. Management mainly runs the administrative activities of
the company supported by the departments which include finance, human resource, research, and
health and safety departments. There are other physical supports like front office activities, office
ergonomics, and office electronics. The support systems for the mining activities are the training
of the miners, safe operation procedures, safety training, machinery, tunnelling, and shafts and
work health and safety measures. The sales department of Macarthur is assisted by the sales
manager and support staffs. The support systems in sale department include office furniture
ergonomics, computers, telephones, and other equipment. It also involves training on fatigues
management, sale activities methods and workers help programs.
to the trucks for transport to various destinations. This process is continuous and strenuous to the
body; thus, the worker performs tasks on hourly shifts. On the other hand, the rate of mining or
solely dependent on the supply needs in the market. Therefore, there are times when a worker
works low or faster than normal to balance the stock and order time. This makes the work to be
more flexible and adaptable.
Main job tasks and the support
Jobs at Macarthur Coal Ltd are divided into distinct areas with a specific scope of roles and
support system. The company is divided into management, mining and sales and distribution
each of which has job support system. Management mainly runs the administrative activities of
the company supported by the departments which include finance, human resource, research, and
health and safety departments. There are other physical supports like front office activities, office
ergonomics, and office electronics. The support systems for the mining activities are the training
of the miners, safe operation procedures, safety training, machinery, tunnelling, and shafts and
work health and safety measures. The sales department of Macarthur is assisted by the sales
manager and support staffs. The support systems in sale department include office furniture
ergonomics, computers, telephones, and other equipment. It also involves training on fatigues
management, sale activities methods and workers help programs.
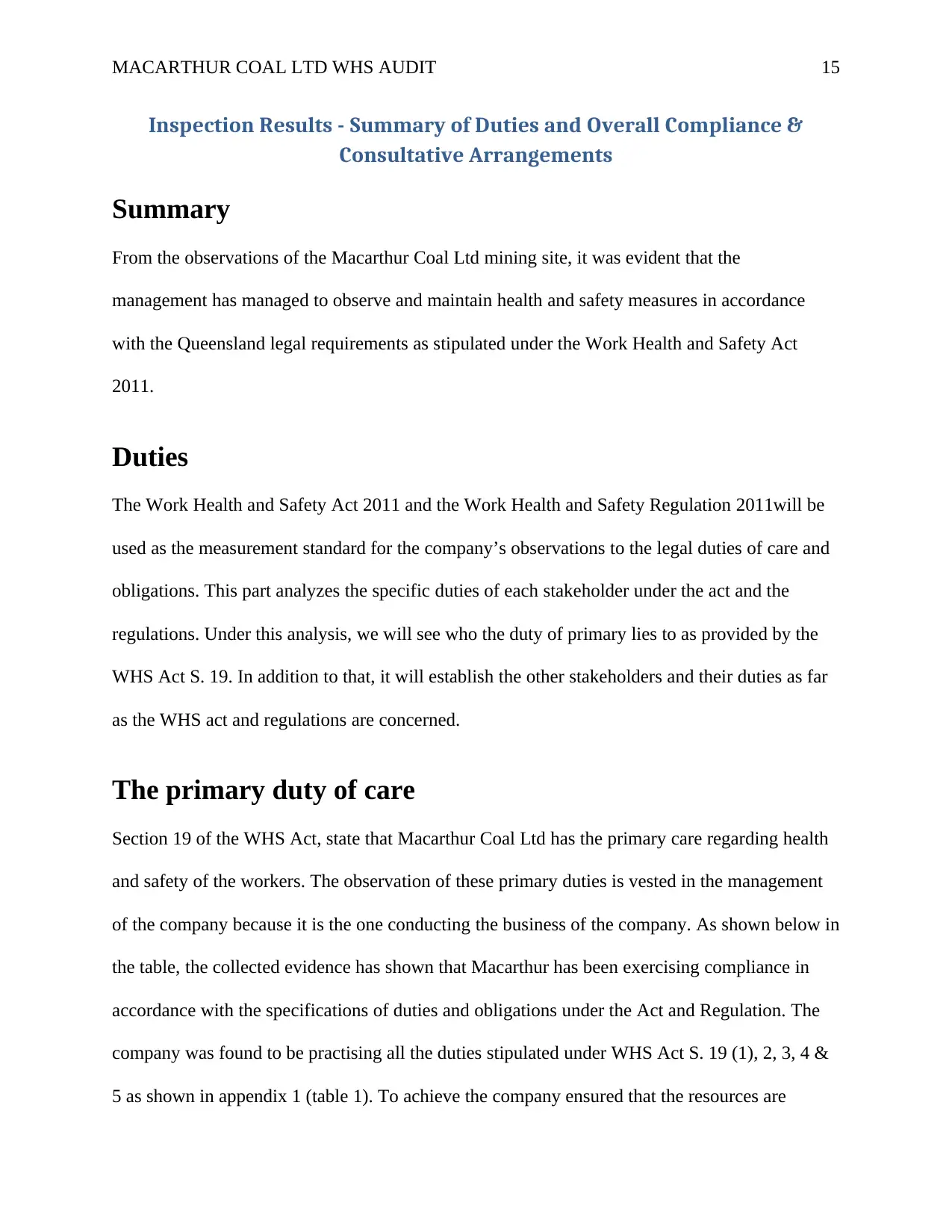
MACARTHUR COAL LTD WHS AUDIT 15
Inspection Results - Summary of Duties and Overall Compliance &
Consultative Arrangements
Summary
From the observations of the Macarthur Coal Ltd mining site, it was evident that the
management has managed to observe and maintain health and safety measures in accordance
with the Queensland legal requirements as stipulated under the Work Health and Safety Act
2011.
Duties
The Work Health and Safety Act 2011 and the Work Health and Safety Regulation 2011will be
used as the measurement standard for the company’s observations to the legal duties of care and
obligations. This part analyzes the specific duties of each stakeholder under the act and the
regulations. Under this analysis, we will see who the duty of primary lies to as provided by the
WHS Act S. 19. In addition to that, it will establish the other stakeholders and their duties as far
as the WHS act and regulations are concerned.
The primary duty of care
Section 19 of the WHS Act, state that Macarthur Coal Ltd has the primary care regarding health
and safety of the workers. The observation of these primary duties is vested in the management
of the company because it is the one conducting the business of the company. As shown below in
the table, the collected evidence has shown that Macarthur has been exercising compliance in
accordance with the specifications of duties and obligations under the Act and Regulation. The
company was found to be practising all the duties stipulated under WHS Act S. 19 (1), 2, 3, 4 &
5 as shown in appendix 1 (table 1). To achieve the company ensured that the resources are
Inspection Results - Summary of Duties and Overall Compliance &
Consultative Arrangements
Summary
From the observations of the Macarthur Coal Ltd mining site, it was evident that the
management has managed to observe and maintain health and safety measures in accordance
with the Queensland legal requirements as stipulated under the Work Health and Safety Act
2011.
Duties
The Work Health and Safety Act 2011 and the Work Health and Safety Regulation 2011will be
used as the measurement standard for the company’s observations to the legal duties of care and
obligations. This part analyzes the specific duties of each stakeholder under the act and the
regulations. Under this analysis, we will see who the duty of primary lies to as provided by the
WHS Act S. 19. In addition to that, it will establish the other stakeholders and their duties as far
as the WHS act and regulations are concerned.
The primary duty of care
Section 19 of the WHS Act, state that Macarthur Coal Ltd has the primary care regarding health
and safety of the workers. The observation of these primary duties is vested in the management
of the company because it is the one conducting the business of the company. As shown below in
the table, the collected evidence has shown that Macarthur has been exercising compliance in
accordance with the specifications of duties and obligations under the Act and Regulation. The
company was found to be practising all the duties stipulated under WHS Act S. 19 (1), 2, 3, 4 &
5 as shown in appendix 1 (table 1). To achieve the company ensured that the resources are
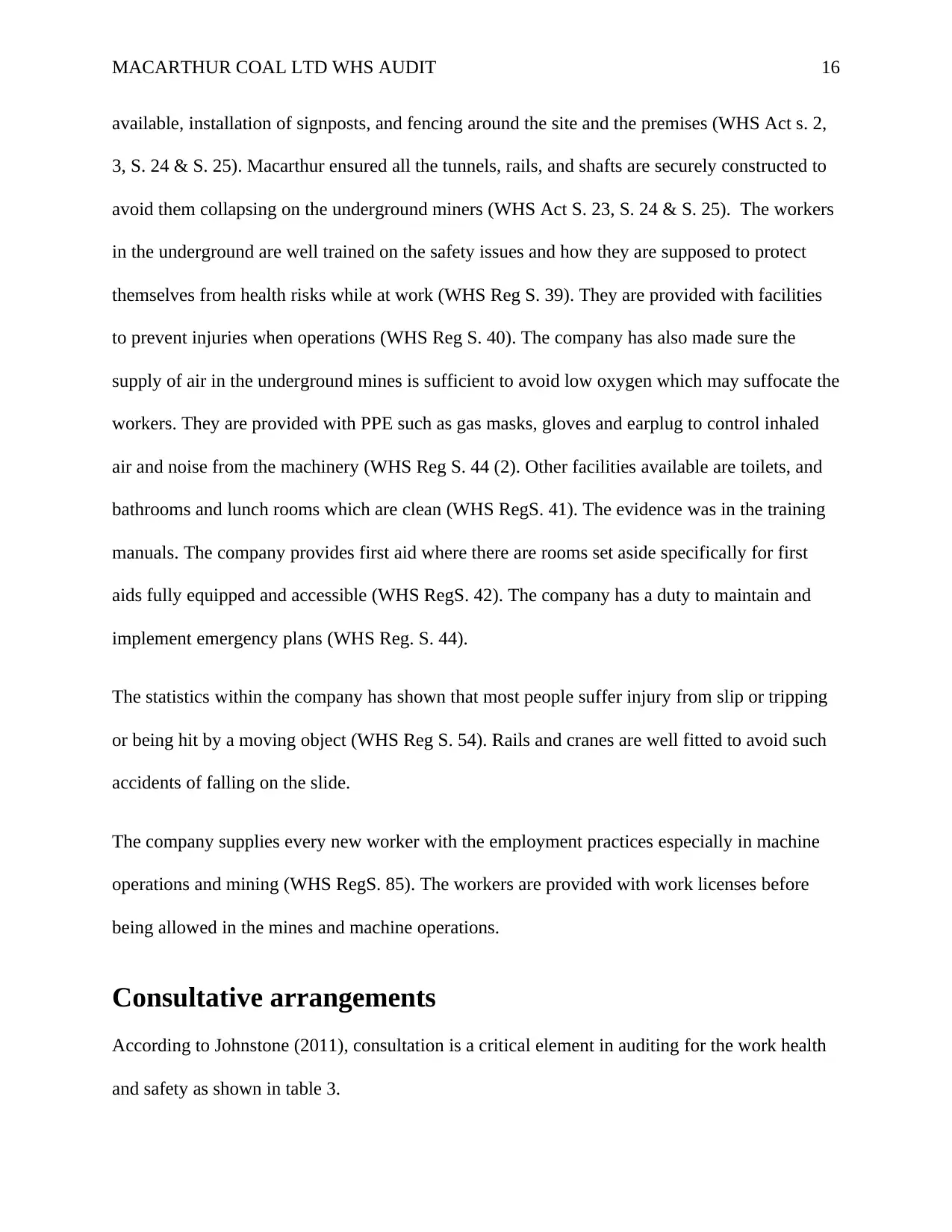
MACARTHUR COAL LTD WHS AUDIT 16
available, installation of signposts, and fencing around the site and the premises (WHS Act s. 2,
3, S. 24 & S. 25). Macarthur ensured all the tunnels, rails, and shafts are securely constructed to
avoid them collapsing on the underground miners (WHS Act S. 23, S. 24 & S. 25). The workers
in the underground are well trained on the safety issues and how they are supposed to protect
themselves from health risks while at work (WHS Reg S. 39). They are provided with facilities
to prevent injuries when operations (WHS Reg S. 40). The company has also made sure the
supply of air in the underground mines is sufficient to avoid low oxygen which may suffocate the
workers. They are provided with PPE such as gas masks, gloves and earplug to control inhaled
air and noise from the machinery (WHS Reg S. 44 (2). Other facilities available are toilets, and
bathrooms and lunch rooms which are clean (WHS RegS. 41). The evidence was in the training
manuals. The company provides first aid where there are rooms set aside specifically for first
aids fully equipped and accessible (WHS RegS. 42). The company has a duty to maintain and
implement emergency plans (WHS Reg. S. 44).
The statistics within the company has shown that most people suffer injury from slip or tripping
or being hit by a moving object (WHS Reg S. 54). Rails and cranes are well fitted to avoid such
accidents of falling on the slide.
The company supplies every new worker with the employment practices especially in machine
operations and mining (WHS RegS. 85). The workers are provided with work licenses before
being allowed in the mines and machine operations.
Consultative arrangements
According to Johnstone (2011), consultation is a critical element in auditing for the work health
and safety as shown in table 3.
available, installation of signposts, and fencing around the site and the premises (WHS Act s. 2,
3, S. 24 & S. 25). Macarthur ensured all the tunnels, rails, and shafts are securely constructed to
avoid them collapsing on the underground miners (WHS Act S. 23, S. 24 & S. 25). The workers
in the underground are well trained on the safety issues and how they are supposed to protect
themselves from health risks while at work (WHS Reg S. 39). They are provided with facilities
to prevent injuries when operations (WHS Reg S. 40). The company has also made sure the
supply of air in the underground mines is sufficient to avoid low oxygen which may suffocate the
workers. They are provided with PPE such as gas masks, gloves and earplug to control inhaled
air and noise from the machinery (WHS Reg S. 44 (2). Other facilities available are toilets, and
bathrooms and lunch rooms which are clean (WHS RegS. 41). The evidence was in the training
manuals. The company provides first aid where there are rooms set aside specifically for first
aids fully equipped and accessible (WHS RegS. 42). The company has a duty to maintain and
implement emergency plans (WHS Reg. S. 44).
The statistics within the company has shown that most people suffer injury from slip or tripping
or being hit by a moving object (WHS Reg S. 54). Rails and cranes are well fitted to avoid such
accidents of falling on the slide.
The company supplies every new worker with the employment practices especially in machine
operations and mining (WHS RegS. 85). The workers are provided with work licenses before
being allowed in the mines and machine operations.
Consultative arrangements
According to Johnstone (2011), consultation is a critical element in auditing for the work health
and safety as shown in table 3.
Secure Best Marks with AI Grader
Need help grading? Try our AI Grader for instant feedback on your assignments.
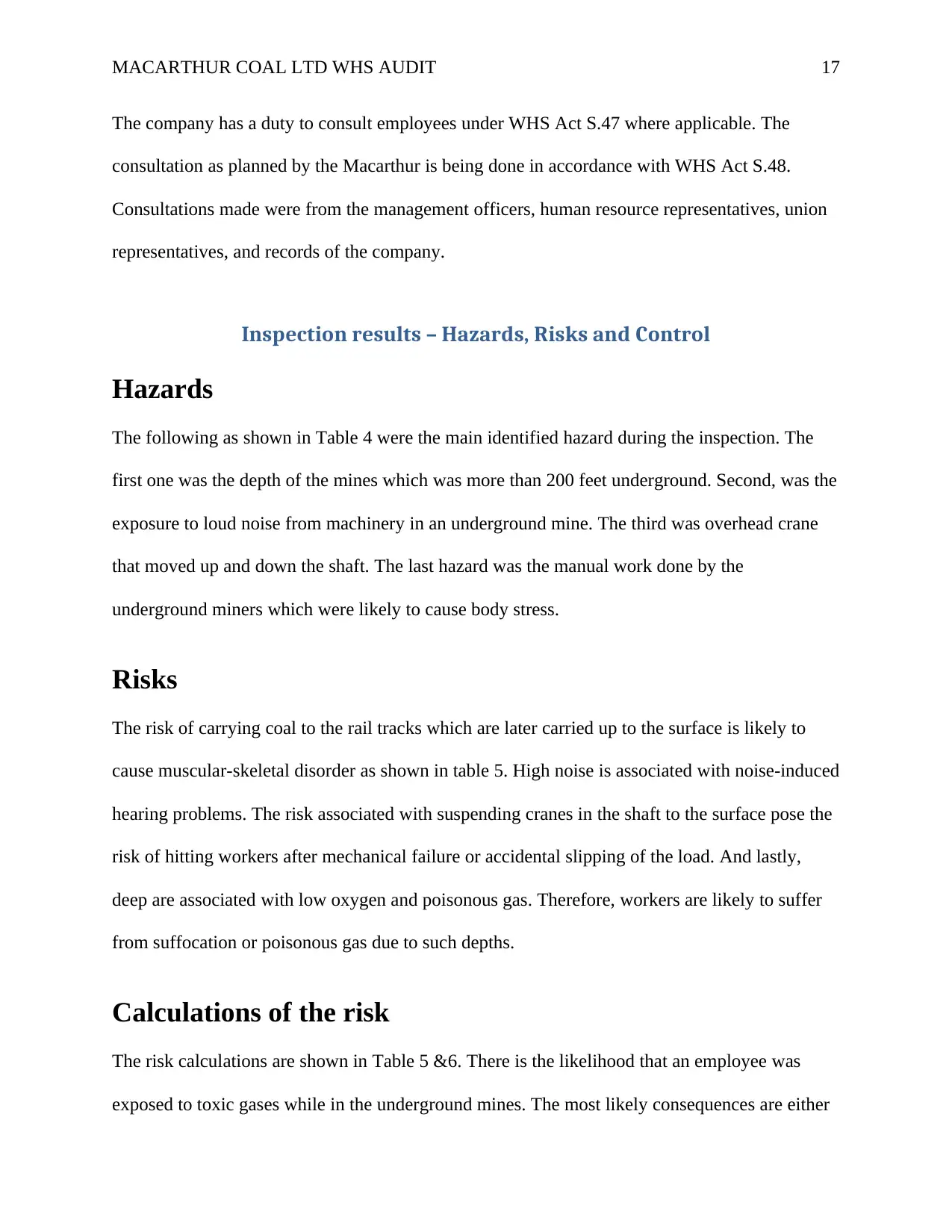
MACARTHUR COAL LTD WHS AUDIT 17
The company has a duty to consult employees under WHS Act S.47 where applicable. The
consultation as planned by the Macarthur is being done in accordance with WHS Act S.48.
Consultations made were from the management officers, human resource representatives, union
representatives, and records of the company.
Inspection results – Hazards, Risks and Control
Hazards
The following as shown in Table 4 were the main identified hazard during the inspection. The
first one was the depth of the mines which was more than 200 feet underground. Second, was the
exposure to loud noise from machinery in an underground mine. The third was overhead crane
that moved up and down the shaft. The last hazard was the manual work done by the
underground miners which were likely to cause body stress.
Risks
The risk of carrying coal to the rail tracks which are later carried up to the surface is likely to
cause muscular-skeletal disorder as shown in table 5. High noise is associated with noise-induced
hearing problems. The risk associated with suspending cranes in the shaft to the surface pose the
risk of hitting workers after mechanical failure or accidental slipping of the load. And lastly,
deep are associated with low oxygen and poisonous gas. Therefore, workers are likely to suffer
from suffocation or poisonous gas due to such depths.
Calculations of the risk
The risk calculations are shown in Table 5 &6. There is the likelihood that an employee was
exposed to toxic gases while in the underground mines. The most likely consequences are either
The company has a duty to consult employees under WHS Act S.47 where applicable. The
consultation as planned by the Macarthur is being done in accordance with WHS Act S.48.
Consultations made were from the management officers, human resource representatives, union
representatives, and records of the company.
Inspection results – Hazards, Risks and Control
Hazards
The following as shown in Table 4 were the main identified hazard during the inspection. The
first one was the depth of the mines which was more than 200 feet underground. Second, was the
exposure to loud noise from machinery in an underground mine. The third was overhead crane
that moved up and down the shaft. The last hazard was the manual work done by the
underground miners which were likely to cause body stress.
Risks
The risk of carrying coal to the rail tracks which are later carried up to the surface is likely to
cause muscular-skeletal disorder as shown in table 5. High noise is associated with noise-induced
hearing problems. The risk associated with suspending cranes in the shaft to the surface pose the
risk of hitting workers after mechanical failure or accidental slipping of the load. And lastly,
deep are associated with low oxygen and poisonous gas. Therefore, workers are likely to suffer
from suffocation or poisonous gas due to such depths.
Calculations of the risk
The risk calculations are shown in Table 5 &6. There is the likelihood that an employee was
exposed to toxic gases while in the underground mines. The most likely consequences are either
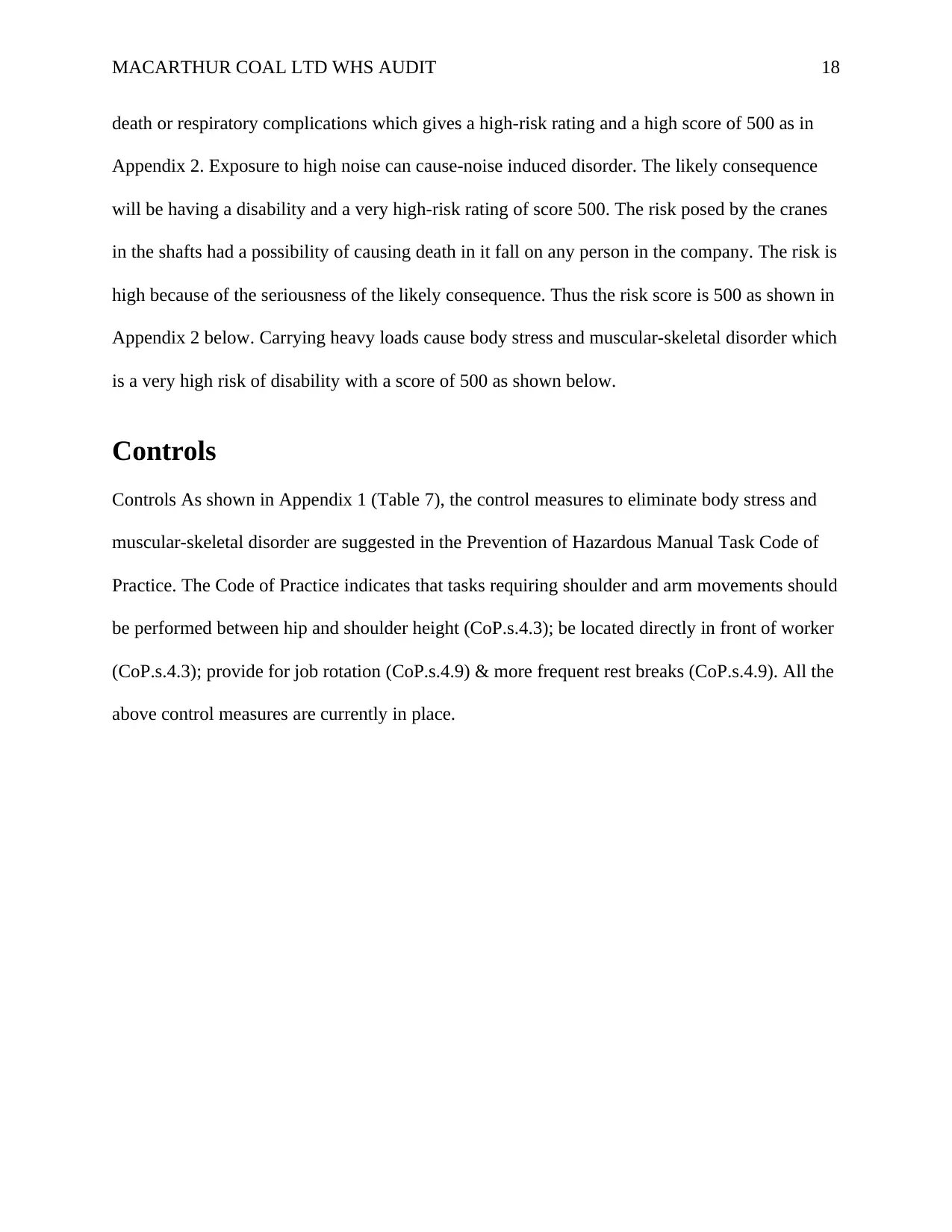
MACARTHUR COAL LTD WHS AUDIT 18
death or respiratory complications which gives a high-risk rating and a high score of 500 as in
Appendix 2. Exposure to high noise can cause-noise induced disorder. The likely consequence
will be having a disability and a very high-risk rating of score 500. The risk posed by the cranes
in the shafts had a possibility of causing death in it fall on any person in the company. The risk is
high because of the seriousness of the likely consequence. Thus the risk score is 500 as shown in
Appendix 2 below. Carrying heavy loads cause body stress and muscular-skeletal disorder which
is a very high risk of disability with a score of 500 as shown below.
Controls
Controls As shown in Appendix 1 (Table 7), the control measures to eliminate body stress and
muscular-skeletal disorder are suggested in the Prevention of Hazardous Manual Task Code of
Practice. The Code of Practice indicates that tasks requiring shoulder and arm movements should
be performed between hip and shoulder height (CoP.s.4.3); be located directly in front of worker
(CoP.s.4.3); provide for job rotation (CoP.s.4.9) & more frequent rest breaks (CoP.s.4.9). All the
above control measures are currently in place.
death or respiratory complications which gives a high-risk rating and a high score of 500 as in
Appendix 2. Exposure to high noise can cause-noise induced disorder. The likely consequence
will be having a disability and a very high-risk rating of score 500. The risk posed by the cranes
in the shafts had a possibility of causing death in it fall on any person in the company. The risk is
high because of the seriousness of the likely consequence. Thus the risk score is 500 as shown in
Appendix 2 below. Carrying heavy loads cause body stress and muscular-skeletal disorder which
is a very high risk of disability with a score of 500 as shown below.
Controls
Controls As shown in Appendix 1 (Table 7), the control measures to eliminate body stress and
muscular-skeletal disorder are suggested in the Prevention of Hazardous Manual Task Code of
Practice. The Code of Practice indicates that tasks requiring shoulder and arm movements should
be performed between hip and shoulder height (CoP.s.4.3); be located directly in front of worker
(CoP.s.4.3); provide for job rotation (CoP.s.4.9) & more frequent rest breaks (CoP.s.4.9). All the
above control measures are currently in place.
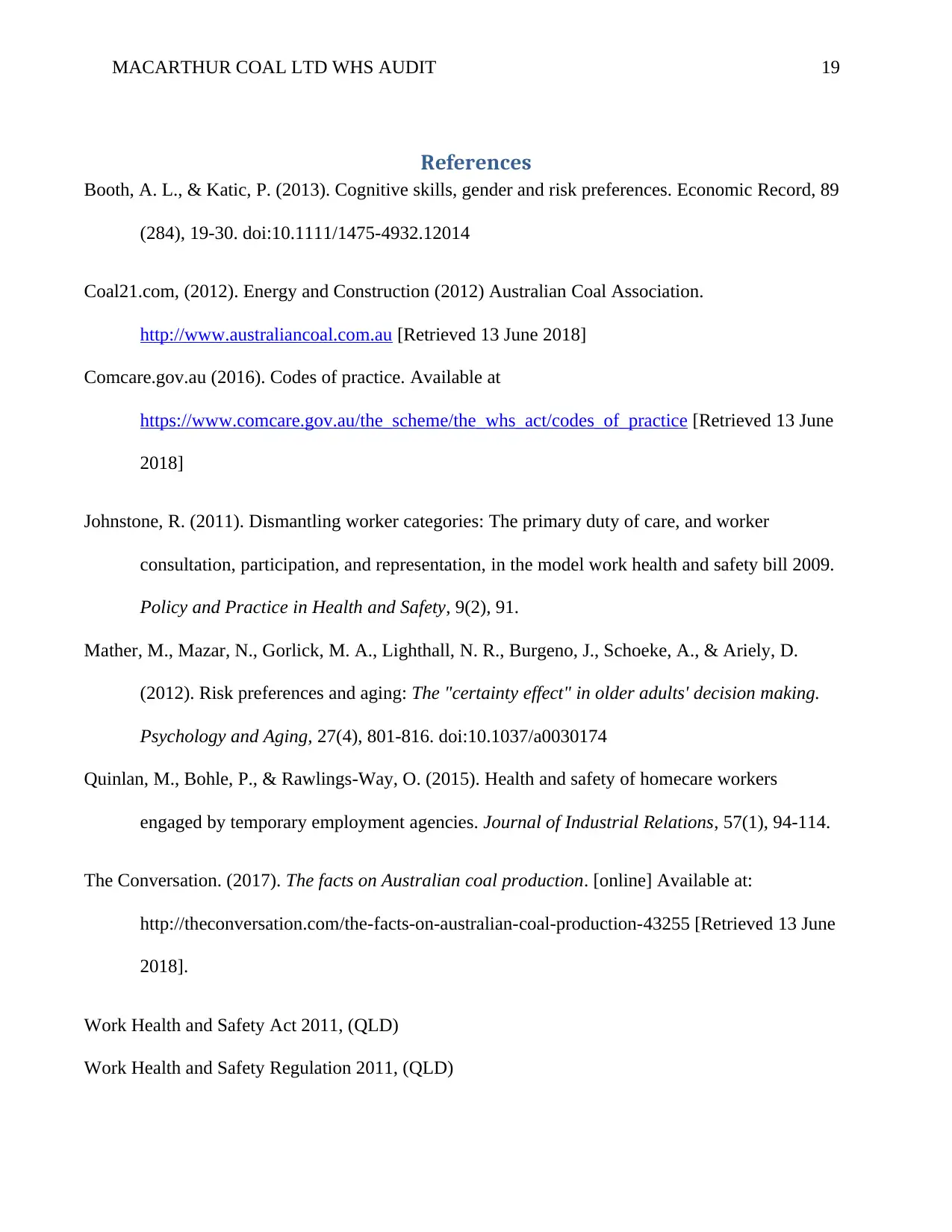
MACARTHUR COAL LTD WHS AUDIT 19
References
Booth, A. L., & Katic, P. (2013). Cognitive skills, gender and risk preferences. Economic Record, 89
(284), 19-30. doi:10.1111/1475-4932.12014
Coal21.com, (2012). Energy and Construction (2012) Australian Coal Association.
http://www.australiancoal.com.au [Retrieved 13 June 2018]
Comcare.gov.au (2016). Codes of practice. Available at
https://www.comcare.gov.au/the_scheme/the_whs_act/codes_of_practice [Retrieved 13 June
2018]
Johnstone, R. (2011). Dismantling worker categories: The primary duty of care, and worker
consultation, participation, and representation, in the model work health and safety bill 2009.
Policy and Practice in Health and Safety, 9(2), 91.
Mather, M., Mazar, N., Gorlick, M. A., Lighthall, N. R., Burgeno, J., Schoeke, A., & Ariely, D.
(2012). Risk preferences and aging: The "certainty effect" in older adults' decision making.
Psychology and Aging, 27(4), 801-816. doi:10.1037/a0030174
Quinlan, M., Bohle, P., & Rawlings-Way, O. (2015). Health and safety of homecare workers
engaged by temporary employment agencies. Journal of Industrial Relations, 57(1), 94-114.
The Conversation. (2017). The facts on Australian coal production. [online] Available at:
http://theconversation.com/the-facts-on-australian-coal-production-43255 [Retrieved 13 June
2018].
Work Health and Safety Act 2011, (QLD)
Work Health and Safety Regulation 2011, (QLD)
References
Booth, A. L., & Katic, P. (2013). Cognitive skills, gender and risk preferences. Economic Record, 89
(284), 19-30. doi:10.1111/1475-4932.12014
Coal21.com, (2012). Energy and Construction (2012) Australian Coal Association.
http://www.australiancoal.com.au [Retrieved 13 June 2018]
Comcare.gov.au (2016). Codes of practice. Available at
https://www.comcare.gov.au/the_scheme/the_whs_act/codes_of_practice [Retrieved 13 June
2018]
Johnstone, R. (2011). Dismantling worker categories: The primary duty of care, and worker
consultation, participation, and representation, in the model work health and safety bill 2009.
Policy and Practice in Health and Safety, 9(2), 91.
Mather, M., Mazar, N., Gorlick, M. A., Lighthall, N. R., Burgeno, J., Schoeke, A., & Ariely, D.
(2012). Risk preferences and aging: The "certainty effect" in older adults' decision making.
Psychology and Aging, 27(4), 801-816. doi:10.1037/a0030174
Quinlan, M., Bohle, P., & Rawlings-Way, O. (2015). Health and safety of homecare workers
engaged by temporary employment agencies. Journal of Industrial Relations, 57(1), 94-114.
The Conversation. (2017). The facts on Australian coal production. [online] Available at:
http://theconversation.com/the-facts-on-australian-coal-production-43255 [Retrieved 13 June
2018].
Work Health and Safety Act 2011, (QLD)
Work Health and Safety Regulation 2011, (QLD)
Paraphrase This Document
Need a fresh take? Get an instant paraphrase of this document with our AI Paraphraser
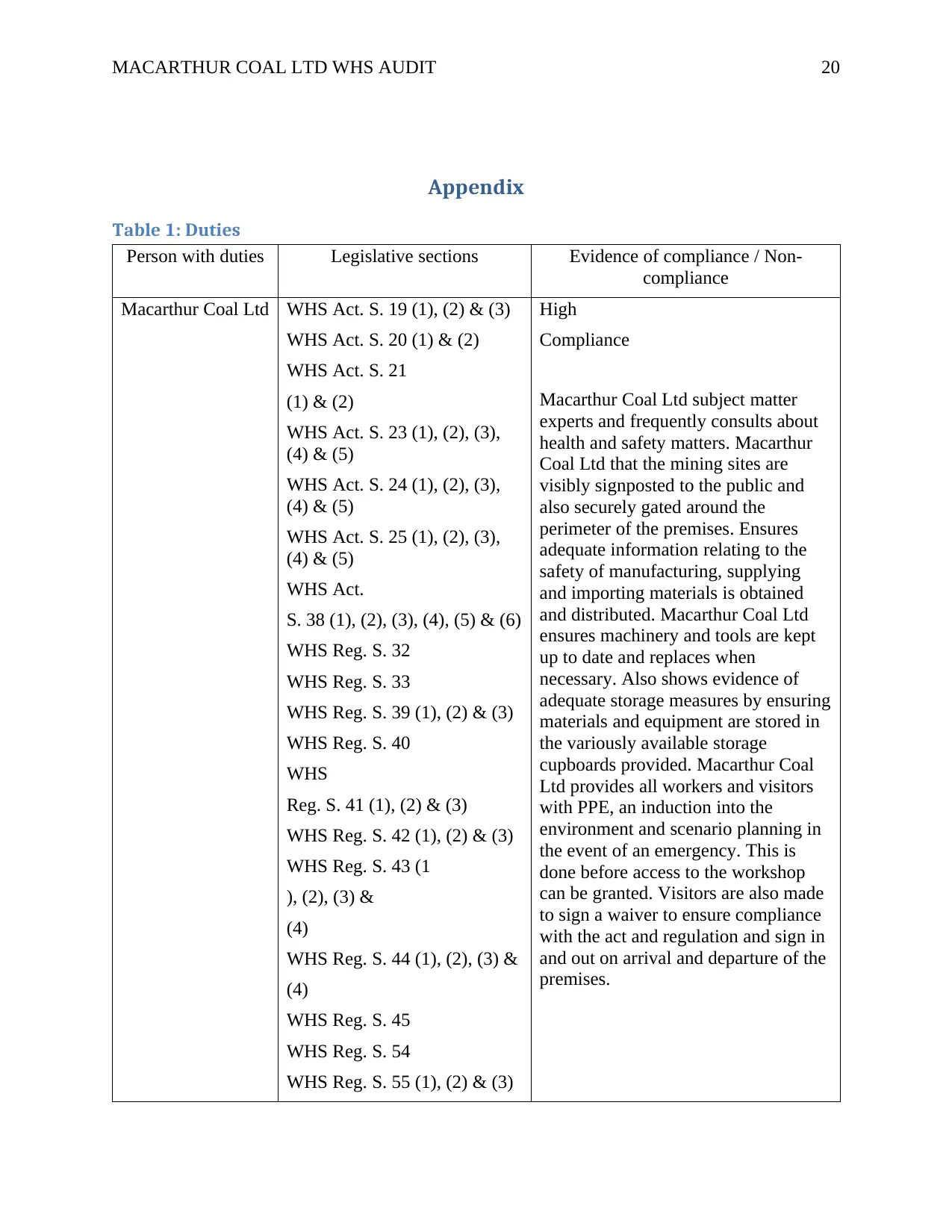
MACARTHUR COAL LTD WHS AUDIT 20
Appendix
Table 1: Duties
Person with duties Legislative sections Evidence of compliance / Non-
compliance
Macarthur Coal Ltd WHS Act. S. 19 (1), (2) & (3)
WHS Act. S. 20 (1) & (2)
WHS Act. S. 21
(1) & (2)
WHS Act. S. 23 (1), (2), (3),
(4) & (5)
WHS Act. S. 24 (1), (2), (3),
(4) & (5)
WHS Act. S. 25 (1), (2), (3),
(4) & (5)
WHS Act.
S. 38 (1), (2), (3), (4), (5) & (6)
WHS Reg. S. 32
WHS Reg. S. 33
WHS Reg. S. 39 (1), (2) & (3)
WHS Reg. S. 40
WHS
Reg. S. 41 (1), (2) & (3)
WHS Reg. S. 42 (1), (2) & (3)
WHS Reg. S. 43 (1
), (2), (3) &
(4)
WHS Reg. S. 44 (1), (2), (3) &
(4)
WHS Reg. S. 45
WHS Reg. S. 54
WHS Reg. S. 55 (1), (2) & (3)
High
Compliance
Macarthur Coal Ltd subject matter
experts and frequently consults about
health and safety matters. Macarthur
Coal Ltd that the mining sites are
visibly signposted to the public and
also securely gated around the
perimeter of the premises. Ensures
adequate information relating to the
safety of manufacturing, supplying
and importing materials is obtained
and distributed. Macarthur Coal Ltd
ensures machinery and tools are kept
up to date and replaces when
necessary. Also shows evidence of
adequate storage measures by ensuring
materials and equipment are stored in
the variously available storage
cupboards provided. Macarthur Coal
Ltd provides all workers and visitors
with PPE, an induction into the
environment and scenario planning in
the event of an emergency. This is
done before access to the workshop
can be granted. Visitors are also made
to sign a waiver to ensure compliance
with the act and regulation and sign in
and out on arrival and departure of the
premises.
Appendix
Table 1: Duties
Person with duties Legislative sections Evidence of compliance / Non-
compliance
Macarthur Coal Ltd WHS Act. S. 19 (1), (2) & (3)
WHS Act. S. 20 (1) & (2)
WHS Act. S. 21
(1) & (2)
WHS Act. S. 23 (1), (2), (3),
(4) & (5)
WHS Act. S. 24 (1), (2), (3),
(4) & (5)
WHS Act. S. 25 (1), (2), (3),
(4) & (5)
WHS Act.
S. 38 (1), (2), (3), (4), (5) & (6)
WHS Reg. S. 32
WHS Reg. S. 33
WHS Reg. S. 39 (1), (2) & (3)
WHS Reg. S. 40
WHS
Reg. S. 41 (1), (2) & (3)
WHS Reg. S. 42 (1), (2) & (3)
WHS Reg. S. 43 (1
), (2), (3) &
(4)
WHS Reg. S. 44 (1), (2), (3) &
(4)
WHS Reg. S. 45
WHS Reg. S. 54
WHS Reg. S. 55 (1), (2) & (3)
High
Compliance
Macarthur Coal Ltd subject matter
experts and frequently consults about
health and safety matters. Macarthur
Coal Ltd that the mining sites are
visibly signposted to the public and
also securely gated around the
perimeter of the premises. Ensures
adequate information relating to the
safety of manufacturing, supplying
and importing materials is obtained
and distributed. Macarthur Coal Ltd
ensures machinery and tools are kept
up to date and replaces when
necessary. Also shows evidence of
adequate storage measures by ensuring
materials and equipment are stored in
the variously available storage
cupboards provided. Macarthur Coal
Ltd provides all workers and visitors
with PPE, an induction into the
environment and scenario planning in
the event of an emergency. This is
done before access to the workshop
can be granted. Visitors are also made
to sign a waiver to ensure compliance
with the act and regulation and sign in
and out on arrival and departure of the
premises.
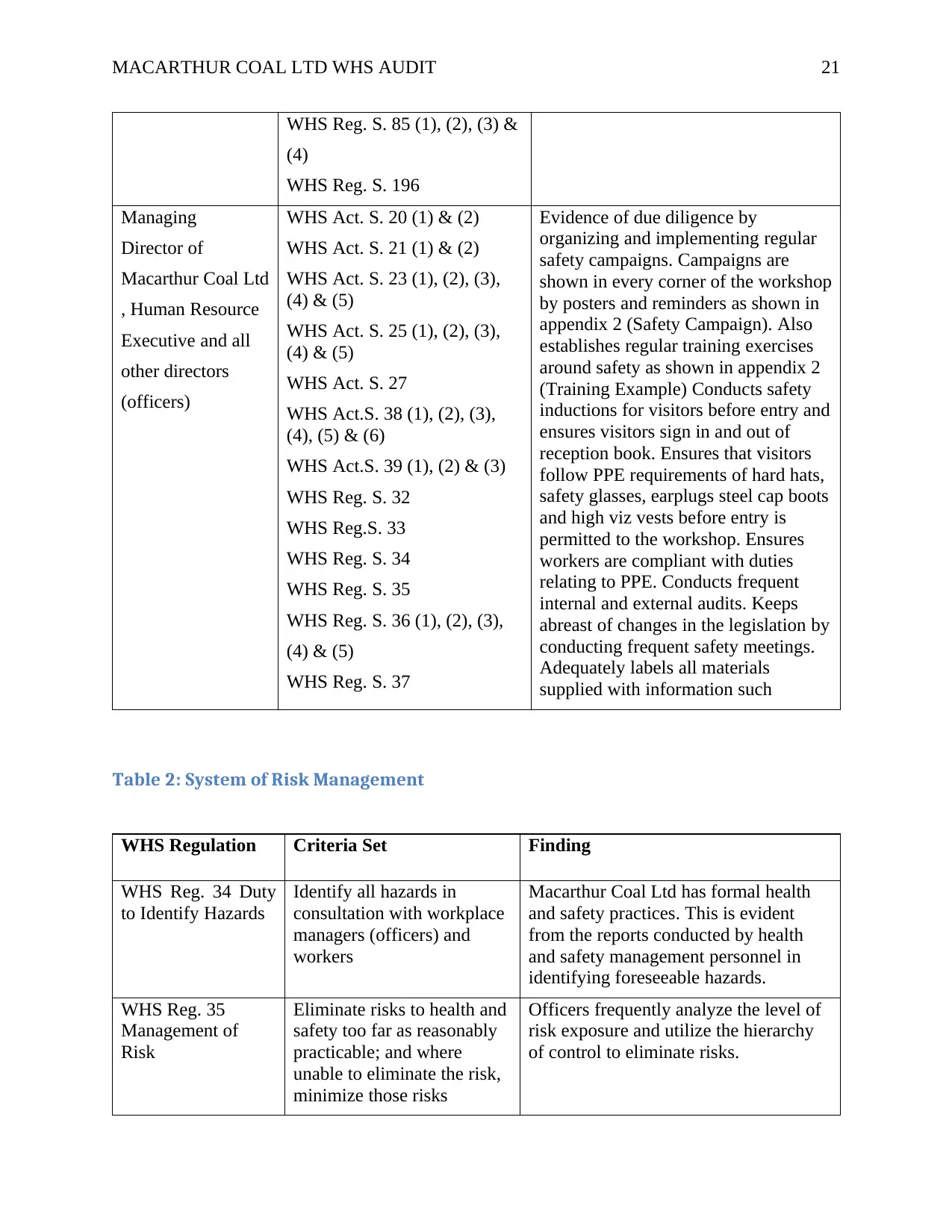
MACARTHUR COAL LTD WHS AUDIT 21
WHS Reg. S. 85 (1), (2), (3) &
(4)
WHS Reg. S. 196
Managing
Director of
Macarthur Coal Ltd
, Human Resource
Executive and all
other directors
(officers)
WHS Act. S. 20 (1) & (2)
WHS Act. S. 21 (1) & (2)
WHS Act. S. 23 (1), (2), (3),
(4) & (5)
WHS Act. S. 25 (1), (2), (3),
(4) & (5)
WHS Act. S. 27
WHS Act.S. 38 (1), (2), (3),
(4), (5) & (6)
WHS Act.S. 39 (1), (2) & (3)
WHS Reg. S. 32
WHS Reg.S. 33
WHS Reg. S. 34
WHS Reg. S. 35
WHS Reg. S. 36 (1), (2), (3),
(4) & (5)
WHS Reg. S. 37
Evidence of due diligence by
organizing and implementing regular
safety campaigns. Campaigns are
shown in every corner of the workshop
by posters and reminders as shown in
appendix 2 (Safety Campaign). Also
establishes regular training exercises
around safety as shown in appendix 2
(Training Example) Conducts safety
inductions for visitors before entry and
ensures visitors sign in and out of
reception book. Ensures that visitors
follow PPE requirements of hard hats,
safety glasses, earplugs steel cap boots
and high viz vests before entry is
permitted to the workshop. Ensures
workers are compliant with duties
relating to PPE. Conducts frequent
internal and external audits. Keeps
abreast of changes in the legislation by
conducting frequent safety meetings.
Adequately labels all materials
supplied with information such
Table 2: System of Risk Management
WHS Regulation Criteria Set Finding
WHS Reg. 34 Duty
to Identify Hazards
Identify all hazards in
consultation with workplace
managers (officers) and
workers
Macarthur Coal Ltd has formal health
and safety practices. This is evident
from the reports conducted by health
and safety management personnel in
identifying foreseeable hazards.
WHS Reg. 35
Management of
Risk
Eliminate risks to health and
safety too far as reasonably
practicable; and where
unable to eliminate the risk,
minimize those risks
Officers frequently analyze the level of
risk exposure and utilize the hierarchy
of control to eliminate risks.
WHS Reg. S. 85 (1), (2), (3) &
(4)
WHS Reg. S. 196
Managing
Director of
Macarthur Coal Ltd
, Human Resource
Executive and all
other directors
(officers)
WHS Act. S. 20 (1) & (2)
WHS Act. S. 21 (1) & (2)
WHS Act. S. 23 (1), (2), (3),
(4) & (5)
WHS Act. S. 25 (1), (2), (3),
(4) & (5)
WHS Act. S. 27
WHS Act.S. 38 (1), (2), (3),
(4), (5) & (6)
WHS Act.S. 39 (1), (2) & (3)
WHS Reg. S. 32
WHS Reg.S. 33
WHS Reg. S. 34
WHS Reg. S. 35
WHS Reg. S. 36 (1), (2), (3),
(4) & (5)
WHS Reg. S. 37
Evidence of due diligence by
organizing and implementing regular
safety campaigns. Campaigns are
shown in every corner of the workshop
by posters and reminders as shown in
appendix 2 (Safety Campaign). Also
establishes regular training exercises
around safety as shown in appendix 2
(Training Example) Conducts safety
inductions for visitors before entry and
ensures visitors sign in and out of
reception book. Ensures that visitors
follow PPE requirements of hard hats,
safety glasses, earplugs steel cap boots
and high viz vests before entry is
permitted to the workshop. Ensures
workers are compliant with duties
relating to PPE. Conducts frequent
internal and external audits. Keeps
abreast of changes in the legislation by
conducting frequent safety meetings.
Adequately labels all materials
supplied with information such
Table 2: System of Risk Management
WHS Regulation Criteria Set Finding
WHS Reg. 34 Duty
to Identify Hazards
Identify all hazards in
consultation with workplace
managers (officers) and
workers
Macarthur Coal Ltd has formal health
and safety practices. This is evident
from the reports conducted by health
and safety management personnel in
identifying foreseeable hazards.
WHS Reg. 35
Management of
Risk
Eliminate risks to health and
safety too far as reasonably
practicable; and where
unable to eliminate the risk,
minimize those risks
Officers frequently analyze the level of
risk exposure and utilize the hierarchy
of control to eliminate risks.
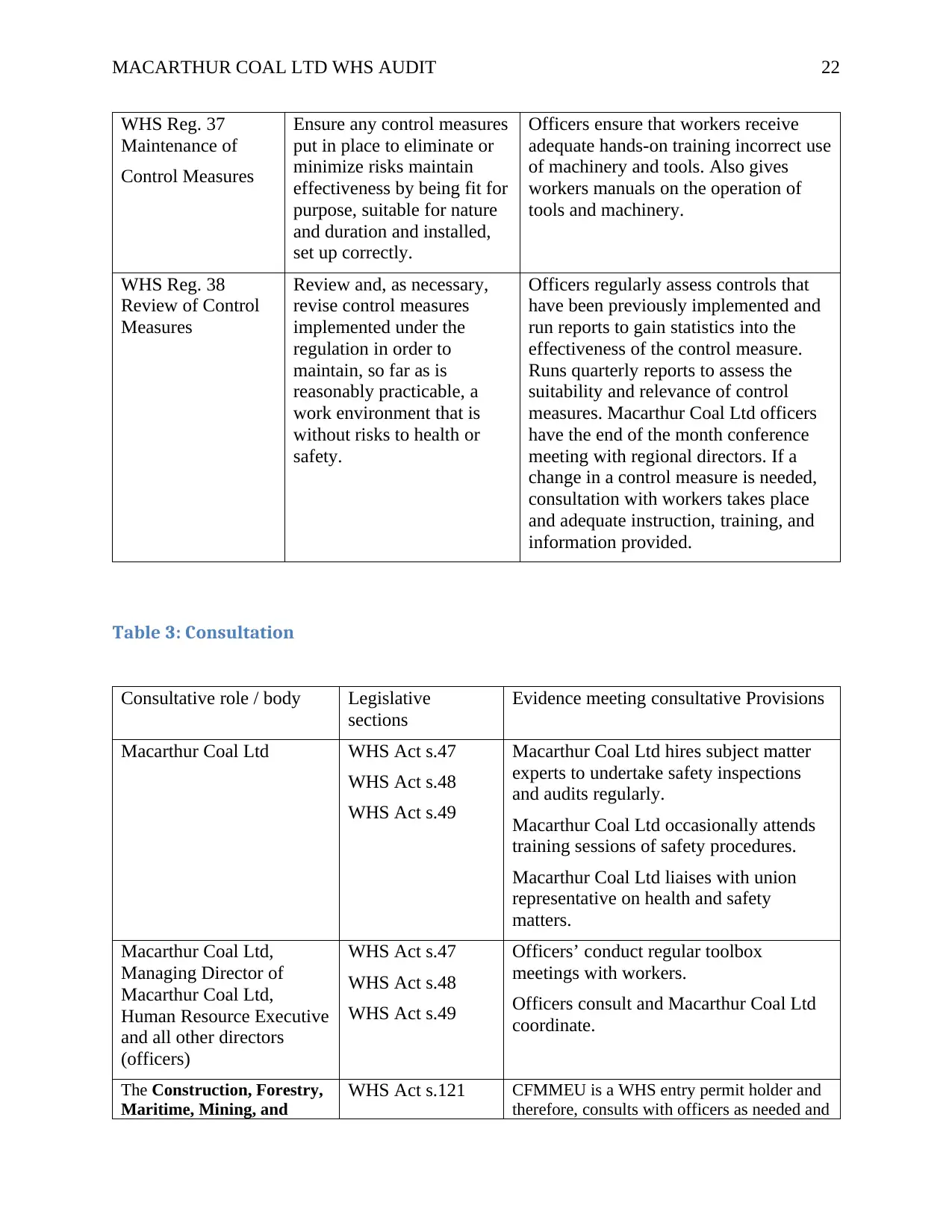
MACARTHUR COAL LTD WHS AUDIT 22
WHS Reg. 37
Maintenance of
Control Measures
Ensure any control measures
put in place to eliminate or
minimize risks maintain
effectiveness by being fit for
purpose, suitable for nature
and duration and installed,
set up correctly.
Officers ensure that workers receive
adequate hands-on training incorrect use
of machinery and tools. Also gives
workers manuals on the operation of
tools and machinery.
WHS Reg. 38
Review of Control
Measures
Review and, as necessary,
revise control measures
implemented under the
regulation in order to
maintain, so far as is
reasonably practicable, a
work environment that is
without risks to health or
safety.
Officers regularly assess controls that
have been previously implemented and
run reports to gain statistics into the
effectiveness of the control measure.
Runs quarterly reports to assess the
suitability and relevance of control
measures. Macarthur Coal Ltd officers
have the end of the month conference
meeting with regional directors. If a
change in a control measure is needed,
consultation with workers takes place
and adequate instruction, training, and
information provided.
Table 3: Consultation
Consultative role / body Legislative
sections
Evidence meeting consultative Provisions
Macarthur Coal Ltd WHS Act s.47
WHS Act s.48
WHS Act s.49
Macarthur Coal Ltd hires subject matter
experts to undertake safety inspections
and audits regularly.
Macarthur Coal Ltd occasionally attends
training sessions of safety procedures.
Macarthur Coal Ltd liaises with union
representative on health and safety
matters.
Macarthur Coal Ltd,
Managing Director of
Macarthur Coal Ltd,
Human Resource Executive
and all other directors
(officers)
WHS Act s.47
WHS Act s.48
WHS Act s.49
Officers’ conduct regular toolbox
meetings with workers.
Officers consult and Macarthur Coal Ltd
coordinate.
The Construction, Forestry,
Maritime, Mining, and
WHS Act s.121 CFMMEU is a WHS entry permit holder and
therefore, consults with officers as needed and
WHS Reg. 37
Maintenance of
Control Measures
Ensure any control measures
put in place to eliminate or
minimize risks maintain
effectiveness by being fit for
purpose, suitable for nature
and duration and installed,
set up correctly.
Officers ensure that workers receive
adequate hands-on training incorrect use
of machinery and tools. Also gives
workers manuals on the operation of
tools and machinery.
WHS Reg. 38
Review of Control
Measures
Review and, as necessary,
revise control measures
implemented under the
regulation in order to
maintain, so far as is
reasonably practicable, a
work environment that is
without risks to health or
safety.
Officers regularly assess controls that
have been previously implemented and
run reports to gain statistics into the
effectiveness of the control measure.
Runs quarterly reports to assess the
suitability and relevance of control
measures. Macarthur Coal Ltd officers
have the end of the month conference
meeting with regional directors. If a
change in a control measure is needed,
consultation with workers takes place
and adequate instruction, training, and
information provided.
Table 3: Consultation
Consultative role / body Legislative
sections
Evidence meeting consultative Provisions
Macarthur Coal Ltd WHS Act s.47
WHS Act s.48
WHS Act s.49
Macarthur Coal Ltd hires subject matter
experts to undertake safety inspections
and audits regularly.
Macarthur Coal Ltd occasionally attends
training sessions of safety procedures.
Macarthur Coal Ltd liaises with union
representative on health and safety
matters.
Macarthur Coal Ltd,
Managing Director of
Macarthur Coal Ltd,
Human Resource Executive
and all other directors
(officers)
WHS Act s.47
WHS Act s.48
WHS Act s.49
Officers’ conduct regular toolbox
meetings with workers.
Officers consult and Macarthur Coal Ltd
coordinate.
The Construction, Forestry,
Maritime, Mining, and
WHS Act s.121 CFMMEU is a WHS entry permit holder and
therefore, consults with officers as needed and
Secure Best Marks with AI Grader
Need help grading? Try our AI Grader for instant feedback on your assignments.
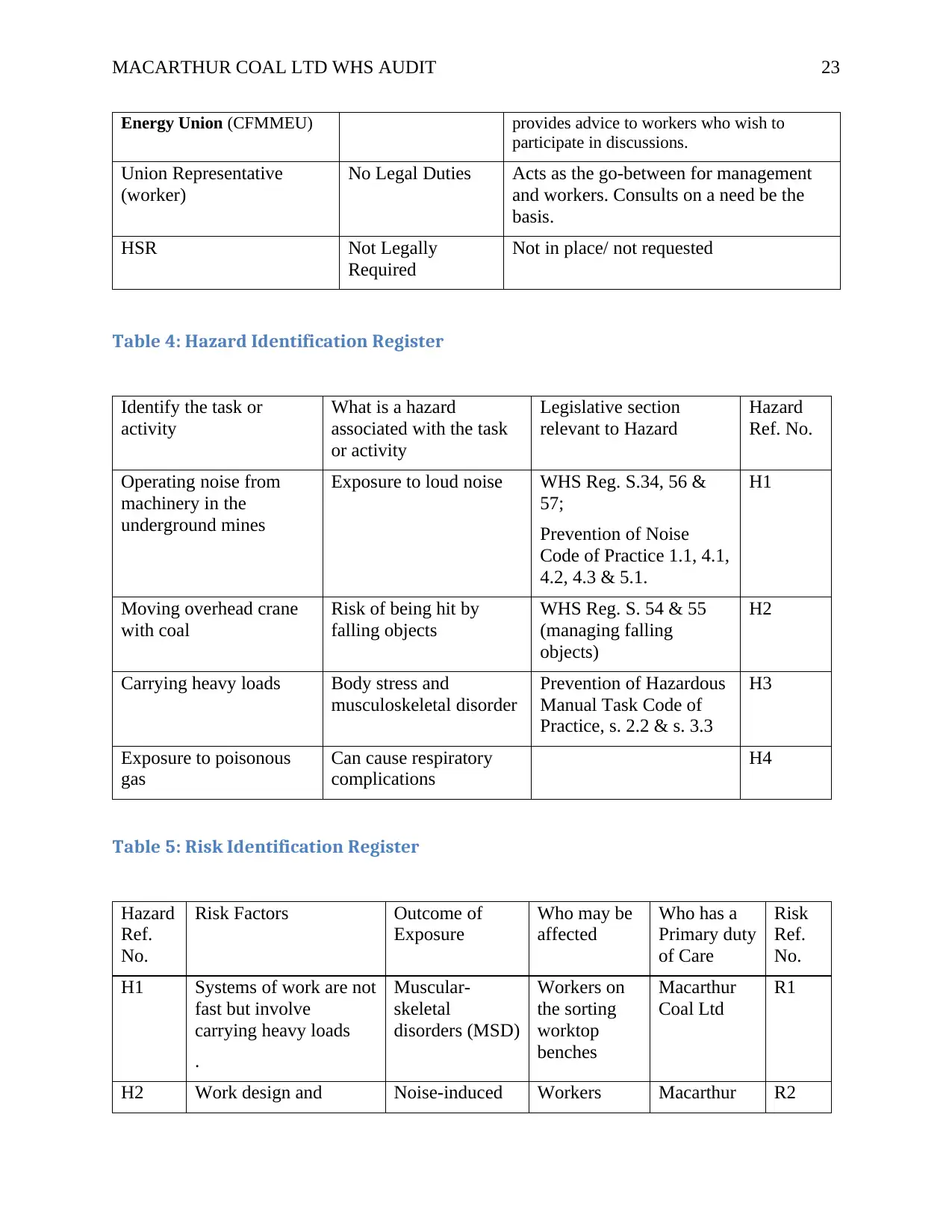
MACARTHUR COAL LTD WHS AUDIT 23
Energy Union (CFMMEU) provides advice to workers who wish to
participate in discussions.
Union Representative
(worker)
No Legal Duties Acts as the go-between for management
and workers. Consults on a need be the
basis.
HSR Not Legally
Required
Not in place/ not requested
Table 4: Hazard Identification Register
Identify the task or
activity
What is a hazard
associated with the task
or activity
Legislative section
relevant to Hazard
Hazard
Ref. No.
Operating noise from
machinery in the
underground mines
Exposure to loud noise WHS Reg. S.34, 56 &
57;
Prevention of Noise
Code of Practice 1.1, 4.1,
4.2, 4.3 & 5.1.
H1
Moving overhead crane
with coal
Risk of being hit by
falling objects
WHS Reg. S. 54 & 55
(managing falling
objects)
H2
Carrying heavy loads Body stress and
musculoskeletal disorder
Prevention of Hazardous
Manual Task Code of
Practice, s. 2.2 & s. 3.3
H3
Exposure to poisonous
gas
Can cause respiratory
complications
H4
Table 5: Risk Identification Register
Hazard
Ref.
No.
Risk Factors Outcome of
Exposure
Who may be
affected
Who has a
Primary duty
of Care
Risk
Ref.
No.
H1 Systems of work are not
fast but involve
carrying heavy loads
.
Muscular-
skeletal
disorders (MSD)
Workers on
the sorting
worktop
benches
Macarthur
Coal Ltd
R1
H2 Work design and Noise-induced Workers Macarthur R2
Energy Union (CFMMEU) provides advice to workers who wish to
participate in discussions.
Union Representative
(worker)
No Legal Duties Acts as the go-between for management
and workers. Consults on a need be the
basis.
HSR Not Legally
Required
Not in place/ not requested
Table 4: Hazard Identification Register
Identify the task or
activity
What is a hazard
associated with the task
or activity
Legislative section
relevant to Hazard
Hazard
Ref. No.
Operating noise from
machinery in the
underground mines
Exposure to loud noise WHS Reg. S.34, 56 &
57;
Prevention of Noise
Code of Practice 1.1, 4.1,
4.2, 4.3 & 5.1.
H1
Moving overhead crane
with coal
Risk of being hit by
falling objects
WHS Reg. S. 54 & 55
(managing falling
objects)
H2
Carrying heavy loads Body stress and
musculoskeletal disorder
Prevention of Hazardous
Manual Task Code of
Practice, s. 2.2 & s. 3.3
H3
Exposure to poisonous
gas
Can cause respiratory
complications
H4
Table 5: Risk Identification Register
Hazard
Ref.
No.
Risk Factors Outcome of
Exposure
Who may be
affected
Who has a
Primary duty
of Care
Risk
Ref.
No.
H1 Systems of work are not
fast but involve
carrying heavy loads
.
Muscular-
skeletal
disorders (MSD)
Workers on
the sorting
worktop
benches
Macarthur
Coal Ltd
R1
H2 Work design and Noise-induced Workers Macarthur R2
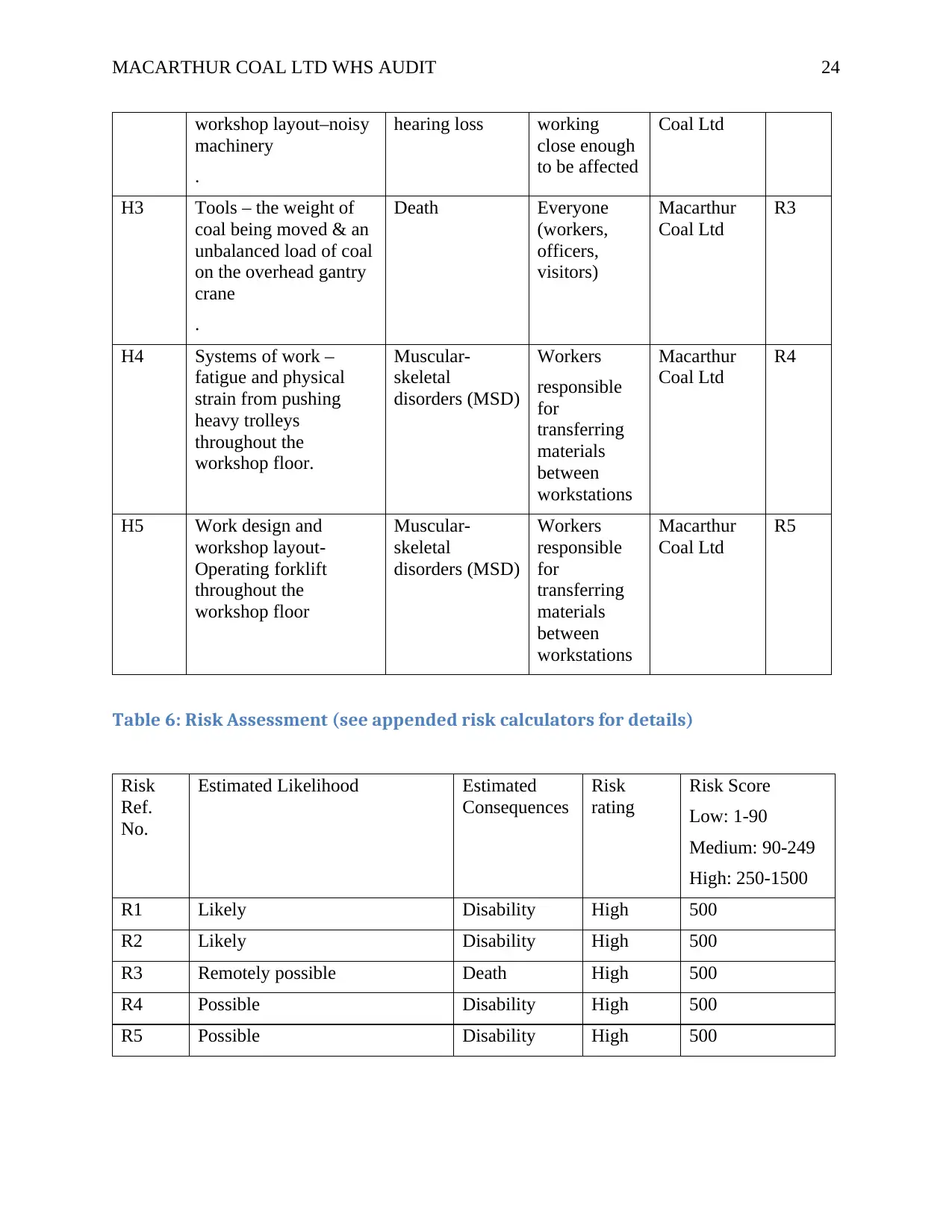
MACARTHUR COAL LTD WHS AUDIT 24
workshop layout–noisy
machinery
.
hearing loss working
close enough
to be affected
Coal Ltd
H3 Tools – the weight of
coal being moved & an
unbalanced load of coal
on the overhead gantry
crane
.
Death Everyone
(workers,
officers,
visitors)
Macarthur
Coal Ltd
R3
H4 Systems of work –
fatigue and physical
strain from pushing
heavy trolleys
throughout the
workshop floor.
Muscular-
skeletal
disorders (MSD)
Workers
responsible
for
transferring
materials
between
workstations
Macarthur
Coal Ltd
R4
H5 Work design and
workshop layout-
Operating forklift
throughout the
workshop floor
Muscular-
skeletal
disorders (MSD)
Workers
responsible
for
transferring
materials
between
workstations
Macarthur
Coal Ltd
R5
Table 6: Risk Assessment (see appended risk calculators for details)
Risk
Ref.
No.
Estimated Likelihood Estimated
Consequences
Risk
rating
Risk Score
Low: 1-90
Medium: 90-249
High: 250-1500
R1 Likely Disability High 500
R2 Likely Disability High 500
R3 Remotely possible Death High 500
R4 Possible Disability High 500
R5 Possible Disability High 500
workshop layout–noisy
machinery
.
hearing loss working
close enough
to be affected
Coal Ltd
H3 Tools – the weight of
coal being moved & an
unbalanced load of coal
on the overhead gantry
crane
.
Death Everyone
(workers,
officers,
visitors)
Macarthur
Coal Ltd
R3
H4 Systems of work –
fatigue and physical
strain from pushing
heavy trolleys
throughout the
workshop floor.
Muscular-
skeletal
disorders (MSD)
Workers
responsible
for
transferring
materials
between
workstations
Macarthur
Coal Ltd
R4
H5 Work design and
workshop layout-
Operating forklift
throughout the
workshop floor
Muscular-
skeletal
disorders (MSD)
Workers
responsible
for
transferring
materials
between
workstations
Macarthur
Coal Ltd
R5
Table 6: Risk Assessment (see appended risk calculators for details)
Risk
Ref.
No.
Estimated Likelihood Estimated
Consequences
Risk
rating
Risk Score
Low: 1-90
Medium: 90-249
High: 250-1500
R1 Likely Disability High 500
R2 Likely Disability High 500
R3 Remotely possible Death High 500
R4 Possible Disability High 500
R5 Possible Disability High 500
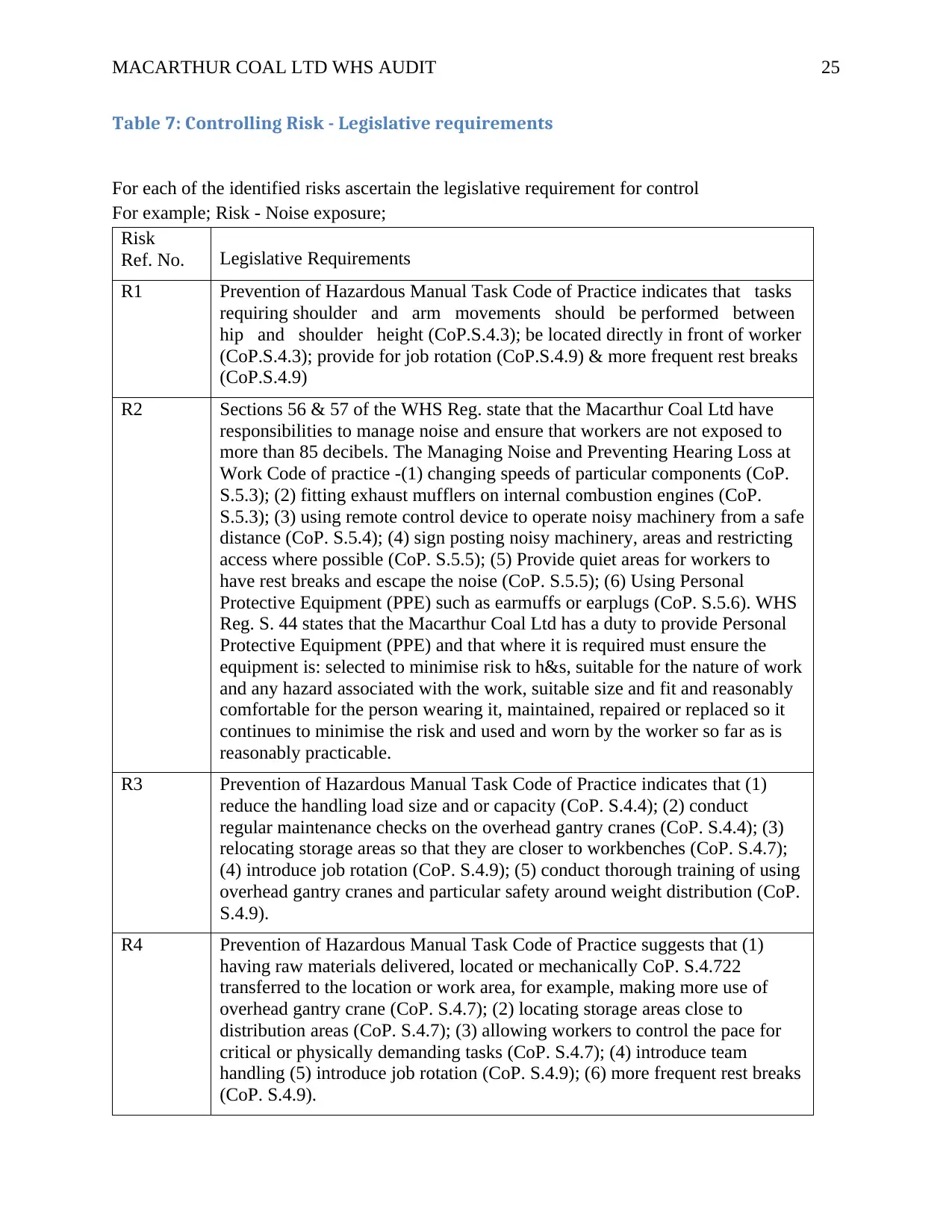
MACARTHUR COAL LTD WHS AUDIT 25
Table 7: Controlling Risk - Legislative requirements
For each of the identified risks ascertain the legislative requirement for control
For example; Risk - Noise exposure;
Risk
Ref. No. Legislative Requirements
R1 Prevention of Hazardous Manual Task Code of Practice indicates that tasks
requiring shoulder and arm movements should be performed between
hip and shoulder height (CoP.S.4.3); be located directly in front of worker
(CoP.S.4.3); provide for job rotation (CoP.S.4.9) & more frequent rest breaks
(CoP.S.4.9)
R2 Sections 56 & 57 of the WHS Reg. state that the Macarthur Coal Ltd have
responsibilities to manage noise and ensure that workers are not exposed to
more than 85 decibels. The Managing Noise and Preventing Hearing Loss at
Work Code of practice -(1) changing speeds of particular components (CoP.
S.5.3); (2) fitting exhaust mufflers on internal combustion engines (CoP.
S.5.3); (3) using remote control device to operate noisy machinery from a safe
distance (CoP. S.5.4); (4) sign posting noisy machinery, areas and restricting
access where possible (CoP. S.5.5); (5) Provide quiet areas for workers to
have rest breaks and escape the noise (CoP. S.5.5); (6) Using Personal
Protective Equipment (PPE) such as earmuffs or earplugs (CoP. S.5.6). WHS
Reg. S. 44 states that the Macarthur Coal Ltd has a duty to provide Personal
Protective Equipment (PPE) and that where it is required must ensure the
equipment is: selected to minimise risk to h&s, suitable for the nature of work
and any hazard associated with the work, suitable size and fit and reasonably
comfortable for the person wearing it, maintained, repaired or replaced so it
continues to minimise the risk and used and worn by the worker so far as is
reasonably practicable.
R3 Prevention of Hazardous Manual Task Code of Practice indicates that (1)
reduce the handling load size and or capacity (CoP. S.4.4); (2) conduct
regular maintenance checks on the overhead gantry cranes (CoP. S.4.4); (3)
relocating storage areas so that they are closer to workbenches (CoP. S.4.7);
(4) introduce job rotation (CoP. S.4.9); (5) conduct thorough training of using
overhead gantry cranes and particular safety around weight distribution (CoP.
S.4.9).
R4 Prevention of Hazardous Manual Task Code of Practice suggests that (1)
having raw materials delivered, located or mechanically CoP. S.4.722
transferred to the location or work area, for example, making more use of
overhead gantry crane (CoP. S.4.7); (2) locating storage areas close to
distribution areas (CoP. S.4.7); (3) allowing workers to control the pace for
critical or physically demanding tasks (CoP. S.4.7); (4) introduce team
handling (5) introduce job rotation (CoP. S.4.9); (6) more frequent rest breaks
(CoP. S.4.9).
Table 7: Controlling Risk - Legislative requirements
For each of the identified risks ascertain the legislative requirement for control
For example; Risk - Noise exposure;
Risk
Ref. No. Legislative Requirements
R1 Prevention of Hazardous Manual Task Code of Practice indicates that tasks
requiring shoulder and arm movements should be performed between
hip and shoulder height (CoP.S.4.3); be located directly in front of worker
(CoP.S.4.3); provide for job rotation (CoP.S.4.9) & more frequent rest breaks
(CoP.S.4.9)
R2 Sections 56 & 57 of the WHS Reg. state that the Macarthur Coal Ltd have
responsibilities to manage noise and ensure that workers are not exposed to
more than 85 decibels. The Managing Noise and Preventing Hearing Loss at
Work Code of practice -(1) changing speeds of particular components (CoP.
S.5.3); (2) fitting exhaust mufflers on internal combustion engines (CoP.
S.5.3); (3) using remote control device to operate noisy machinery from a safe
distance (CoP. S.5.4); (4) sign posting noisy machinery, areas and restricting
access where possible (CoP. S.5.5); (5) Provide quiet areas for workers to
have rest breaks and escape the noise (CoP. S.5.5); (6) Using Personal
Protective Equipment (PPE) such as earmuffs or earplugs (CoP. S.5.6). WHS
Reg. S. 44 states that the Macarthur Coal Ltd has a duty to provide Personal
Protective Equipment (PPE) and that where it is required must ensure the
equipment is: selected to minimise risk to h&s, suitable for the nature of work
and any hazard associated with the work, suitable size and fit and reasonably
comfortable for the person wearing it, maintained, repaired or replaced so it
continues to minimise the risk and used and worn by the worker so far as is
reasonably practicable.
R3 Prevention of Hazardous Manual Task Code of Practice indicates that (1)
reduce the handling load size and or capacity (CoP. S.4.4); (2) conduct
regular maintenance checks on the overhead gantry cranes (CoP. S.4.4); (3)
relocating storage areas so that they are closer to workbenches (CoP. S.4.7);
(4) introduce job rotation (CoP. S.4.9); (5) conduct thorough training of using
overhead gantry cranes and particular safety around weight distribution (CoP.
S.4.9).
R4 Prevention of Hazardous Manual Task Code of Practice suggests that (1)
having raw materials delivered, located or mechanically CoP. S.4.722
transferred to the location or work area, for example, making more use of
overhead gantry crane (CoP. S.4.7); (2) locating storage areas close to
distribution areas (CoP. S.4.7); (3) allowing workers to control the pace for
critical or physically demanding tasks (CoP. S.4.7); (4) introduce team
handling (5) introduce job rotation (CoP. S.4.9); (6) more frequent rest breaks
(CoP. S.4.9).
Paraphrase This Document
Need a fresh take? Get an instant paraphrase of this document with our AI Paraphraser
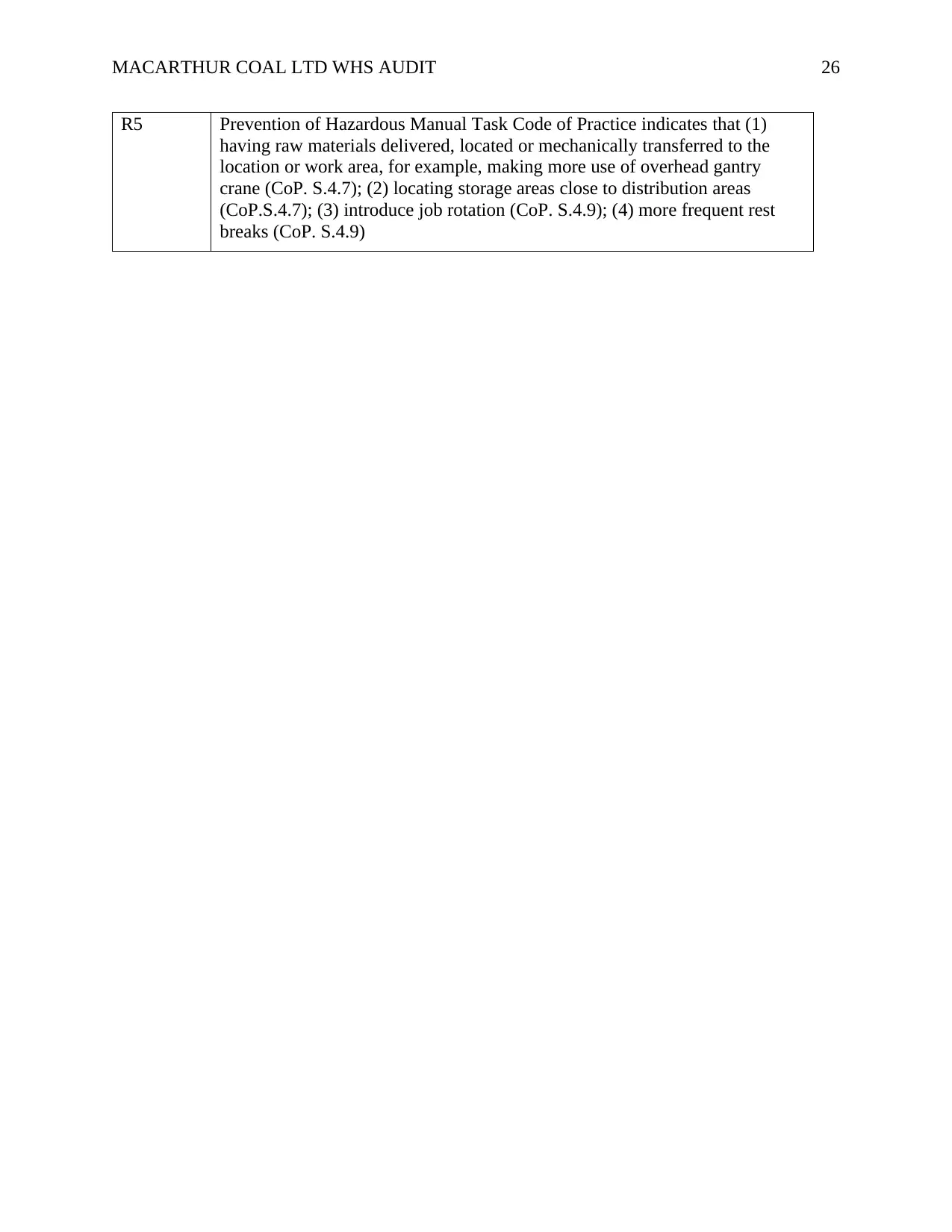
MACARTHUR COAL LTD WHS AUDIT 26
R5 Prevention of Hazardous Manual Task Code of Practice indicates that (1)
having raw materials delivered, located or mechanically transferred to the
location or work area, for example, making more use of overhead gantry
crane (CoP. S.4.7); (2) locating storage areas close to distribution areas
(CoP.S.4.7); (3) introduce job rotation (CoP. S.4.9); (4) more frequent rest
breaks (CoP. S.4.9)
R5 Prevention of Hazardous Manual Task Code of Practice indicates that (1)
having raw materials delivered, located or mechanically transferred to the
location or work area, for example, making more use of overhead gantry
crane (CoP. S.4.7); (2) locating storage areas close to distribution areas
(CoP.S.4.7); (3) introduce job rotation (CoP. S.4.9); (4) more frequent rest
breaks (CoP. S.4.9)
1 out of 26
![[object Object]](/_next/image/?url=%2F_next%2Fstatic%2Fmedia%2Flogo.6d15ce61.png&w=640&q=75)
Your All-in-One AI-Powered Toolkit for Academic Success.
+13062052269
info@desklib.com
Available 24*7 on WhatsApp / Email
Unlock your academic potential
© 2024 | Zucol Services PVT LTD | All rights reserved.