Maintenance Planning and Scheduling at Centrica
Added on 2021-04-21
17 Pages3403 Words68 Views
MAINTENANCE PLANNING AND SCHEDULING IN CENTRICABy < Name > <University><Date>
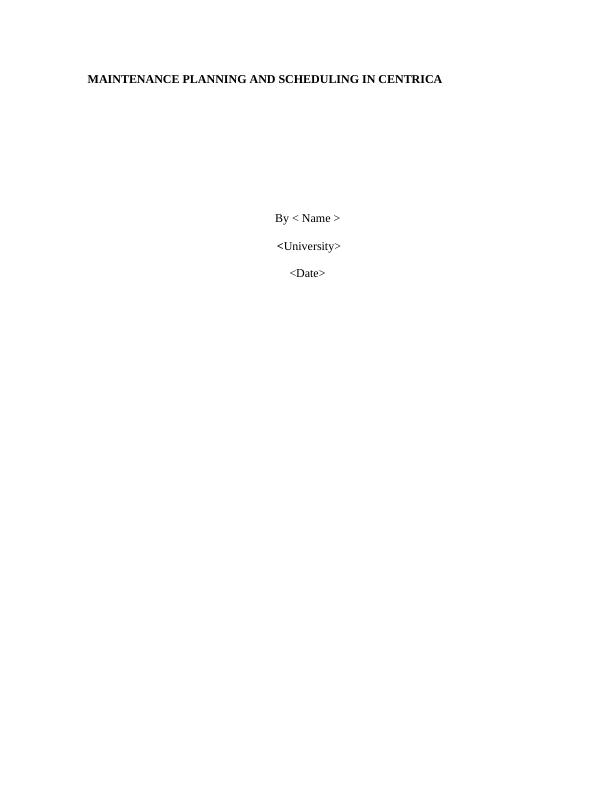
AbstractThe purpose of this project was to establish the maintenance planning and scheduling atCentrica. Centrica is a British multinational utility company with its headquarter in Berkshire.The case study was done with a target population of all the three operational areas withdifferent generation technology of hydro, thermal and geothermal. The study used primary datawhich was gathered by means of a self-administered questionnaire issued to respondents andsecondary data which was extracted from internal operational reports in Eastern hydro powerstations. The average of each aspect was calculated and the quantity identified to evaluate themaintenance practices at Centrica and to benchmark with the world best practices. The studyrecommended that for reliable and competitively priced electric power in UK, there is need tohave the power utilities enhance their maintenance planning and scheduling practices foreffective and efficient generation and distribution of power to meet the customers’ expectations.IntroductionMaintenance planning and scheduling is defined as “The combination of all technical andassociated administrative actions intended to retain an item in, or restore it to, a state inwhich it can perform its required function” by British standard 3811. It includes inspection,testing, servicing, repair and reclamation. In sum maintenance encompasses all workscarried out on a plant or a facility with the view to rectifying a defect or failure in itsfunctioning or performance; preventing failure in its functioning and/or improving the stateof the facility so as to sustain its utilization and value. In a production facility, maintenanceacts as a support for the production process, where the production input is converted into
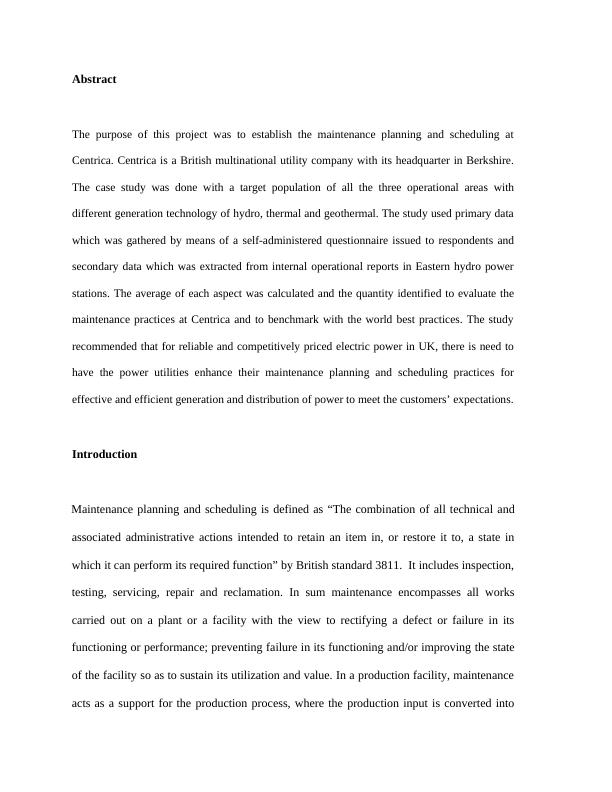
specified production output. Industrial maintenance comes as a secondary process, whichhas to contribute for obtaining the objectives of production. Maintenance must be able toretain or restore the systems for carrying out a perfect production function. (Gits, 2010).There exists asset management software’s in the market and established best world practicebenchmarks which if well utilized could reduce maintenance costs to a great extent.Consequently, a number of surveys conducted in industries throughout the UK have foundthat 70% of equipment failures are self-induced. Maintenance personnel who are notfollowing what is termed as „Best Maintenance Repair Practices‟ substantially affect thesefailures. Between 30% and 50% of the self-induced failures are as a result of maintenancepersonnel not knowing the basics of maintenance. Maintenance personnel, who, althoughskilled, choose not to follow best maintenance repair practices, potentially cause another20% to 30% of those failures (Smith, 2000). Bestmaintenanceplanning and scheduling practicesare defined in two categories:standards and methods. Standards are the measurable performance levels (benchmarking) ofmaintenance execution; methods and strategies must be practiced in order to meet thestandards. The combination of standards with methods and strategies provides the elementsof an integrated planned maintenance system. Achievement of the best maintenancepractice standards (maintenance excellence) is accomplished through an interactive andintegrated series of links with an array of methods and strategies. Maintenance planningand scheduling is an essential part of effective maintenance. Planners must develop andimplement both preventive and corrective maintenance tasks that achieve maximum use ofmaintenance resources and the production capacity of plant systems.
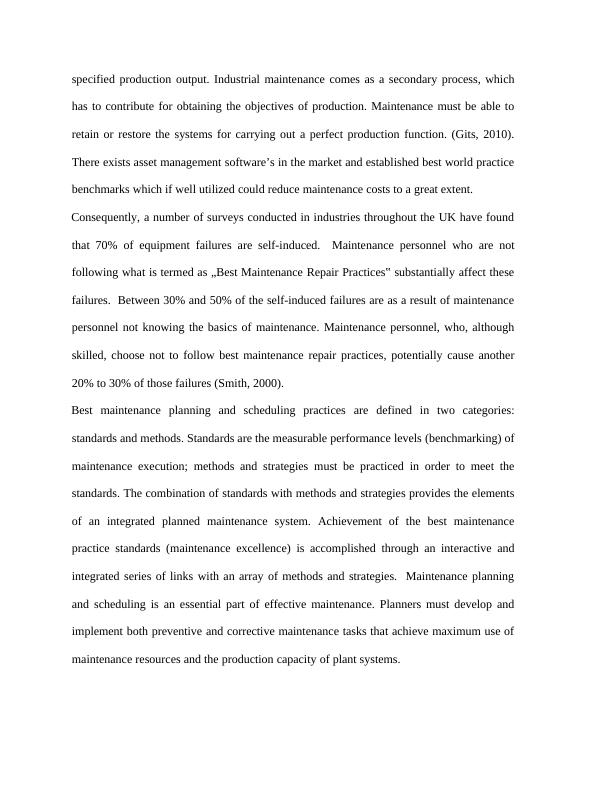
Operation and Maintenance Planning Visser (1998) modeled maintenance as a transformation process encapsulated in anenterprise system. The way maintenance is performed will influence the availability ofproduction facilities, the rate of production, quality of end product and cost of production,as well as the safety of the operation. These factors in turn will determine the profitabilityof the enterprise. Generally, there are four strategic dimensions of maintenance (Tsang,2002). The dimensions start with Service-delivery options which are related with the inputsome are labor, material, spares and external services. This explains the choice within theinside capability and outsourcing. The second and third dimensions are related to the designand selection of maintenance methodologies. The performance will play a major role on theoutput, in which some are productivity output, safety, maintainability and the profit of thewhole enterprise. The last and final dimension is related to the support system which isexplained as the design that is supporting maintenance (Tsang, 2002). The cost of inventory is almost always an area where cost reduction can be substantial. With the help of suppliers and equipment vendors, purchasing usually can place contracts or service level agreement that guarantee delivery lead time for designated inventory items. It just makes sense that your facility should shift the bulk of the cost of maintaining inventory to the suppliers.Conceptual Model Reliability is the probability that an engineering system will perform its intended functionsatisfactorily (from the viewpoint of the customer) for its intended life under specified
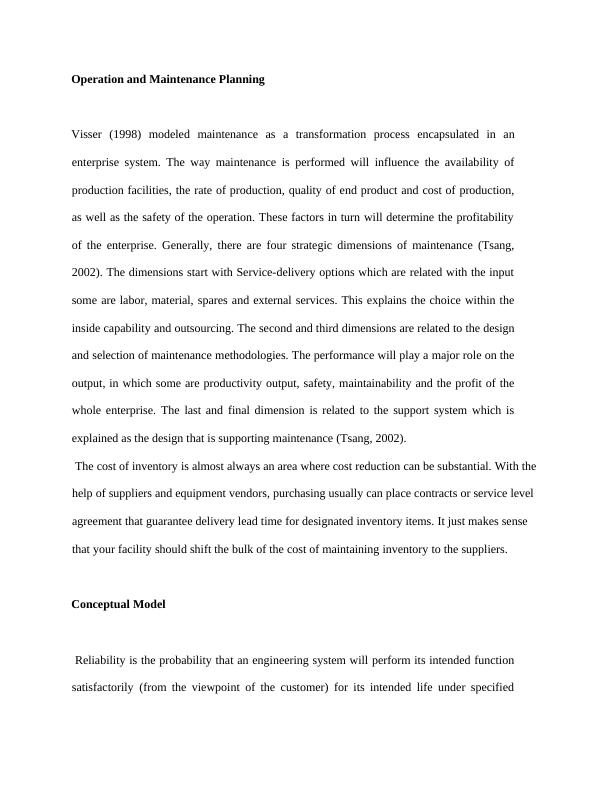
End of preview
Want to access all the pages? Upload your documents or become a member.
Related Documents
Workforce Planning at British Gas: A Study on Human Resource Managementlg...
|17
|3717
|369