Evaluating Costing Systems for Manufacturing Efficiency
VerifiedAdded on 2020/05/08
|11
|1909
|30
AI Summary
The assignment discusses the need for an appropriate costing system to allocate manufacturing overheads effectively among products. Activity-Based Costing (ABC) is highlighted as beneficial in identifying activities directly related to organizational performance, thereby enhancing cost data reliability. The analysis reveals that while ABC improves indirect cost allocation accuracy, it may not be worthwhile if costs are generalized across activities. Furthermore, departmental based overhead rates offer a refined approach for organizations like PW, which manufactures car parts. This system allocates variable manufacturing overheads among departments and products accurately, aiding in better product pricing strategies. The assignment also suggests productivity enhancements in the engineering department by reducing idle hours and ensuring proper machine maintenance. Ultimately, adopting suitable costing systems is crucial for precise expenditure allocation and competitive product pricing.
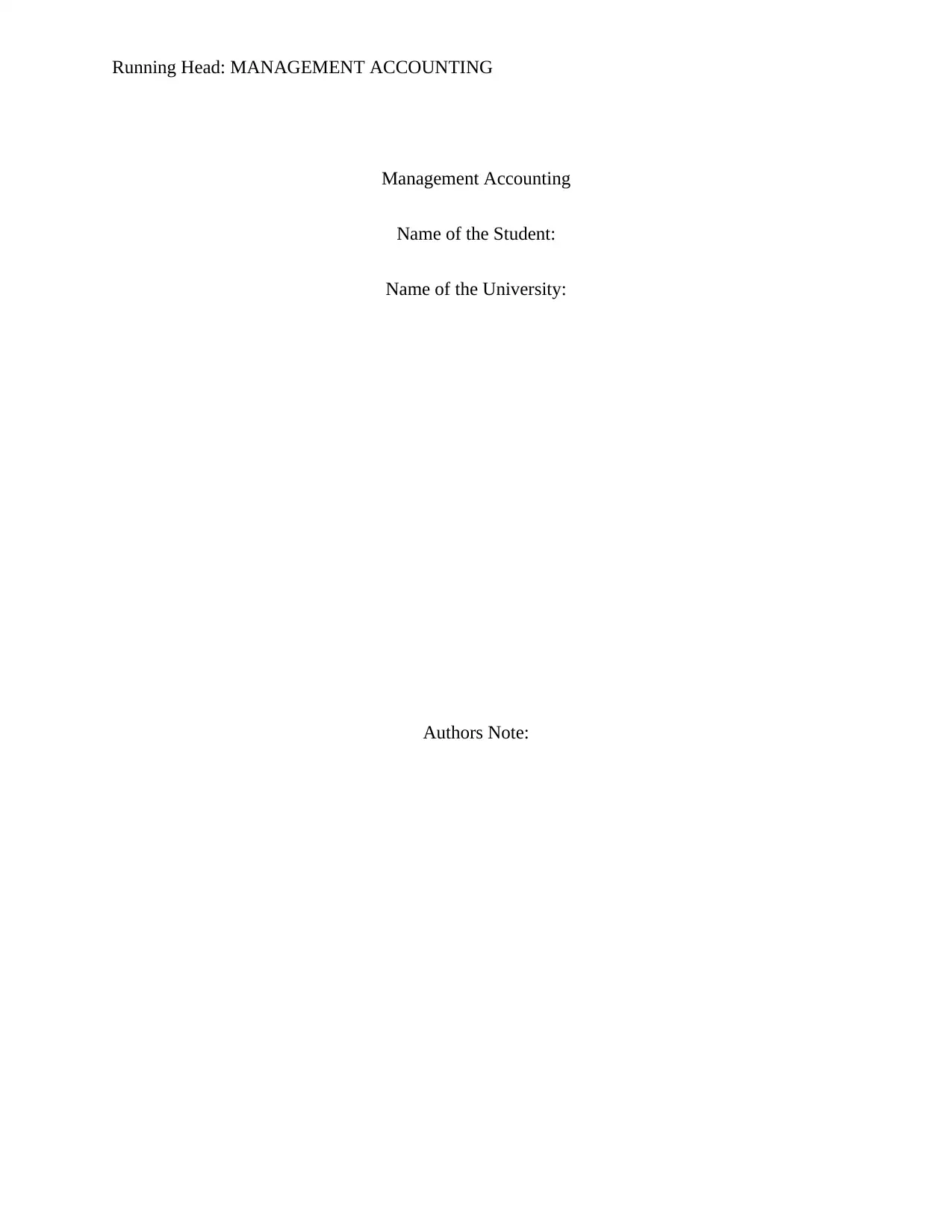
Running Head: MANAGEMENT ACCOUNTING
Management Accounting
Name of the Student:
Name of the University:
Authors Note:
Management Accounting
Name of the Student:
Name of the University:
Authors Note:
Paraphrase This Document
Need a fresh take? Get an instant paraphrase of this document with our AI Paraphraser

1MANAGEMENT ACCOUNTING
Executive summary:
Costing system is a method used by a manufacturing organization to record its costs and
expenditures to allocate these properly to the manufacturing products. In this document, a detail
discussion shall be made with a practical solution to see the importance of using a proper costing
system for appropriate allocation of overheads and other expenditures associated with process of
manufacturing and production of different goods.
Executive summary:
Costing system is a method used by a manufacturing organization to record its costs and
expenditures to allocate these properly to the manufacturing products. In this document, a detail
discussion shall be made with a practical solution to see the importance of using a proper costing
system for appropriate allocation of overheads and other expenditures associated with process of
manufacturing and production of different goods.
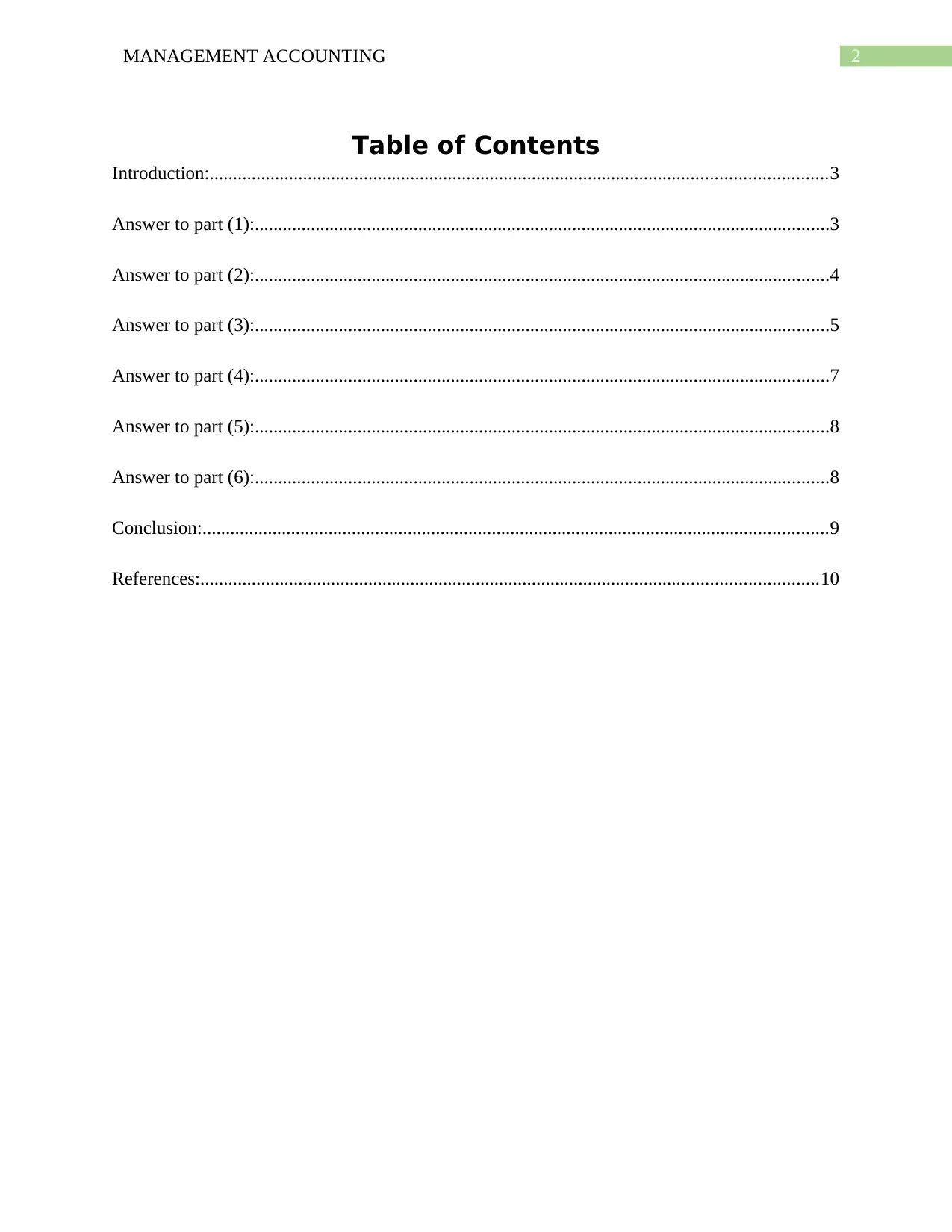
2MANAGEMENT ACCOUNTING
Table of Contents
Introduction:....................................................................................................................................3
Answer to part (1):...........................................................................................................................3
Answer to part (2):...........................................................................................................................4
Answer to part (3):...........................................................................................................................5
Answer to part (4):...........................................................................................................................7
Answer to part (5):...........................................................................................................................8
Answer to part (6):...........................................................................................................................8
Conclusion:......................................................................................................................................9
References:....................................................................................................................................10
Table of Contents
Introduction:....................................................................................................................................3
Answer to part (1):...........................................................................................................................3
Answer to part (2):...........................................................................................................................4
Answer to part (3):...........................................................................................................................5
Answer to part (4):...........................................................................................................................7
Answer to part (5):...........................................................................................................................8
Answer to part (6):...........................................................................................................................8
Conclusion:......................................................................................................................................9
References:....................................................................................................................................10
You're viewing a preview
Unlock full access by subscribing today!
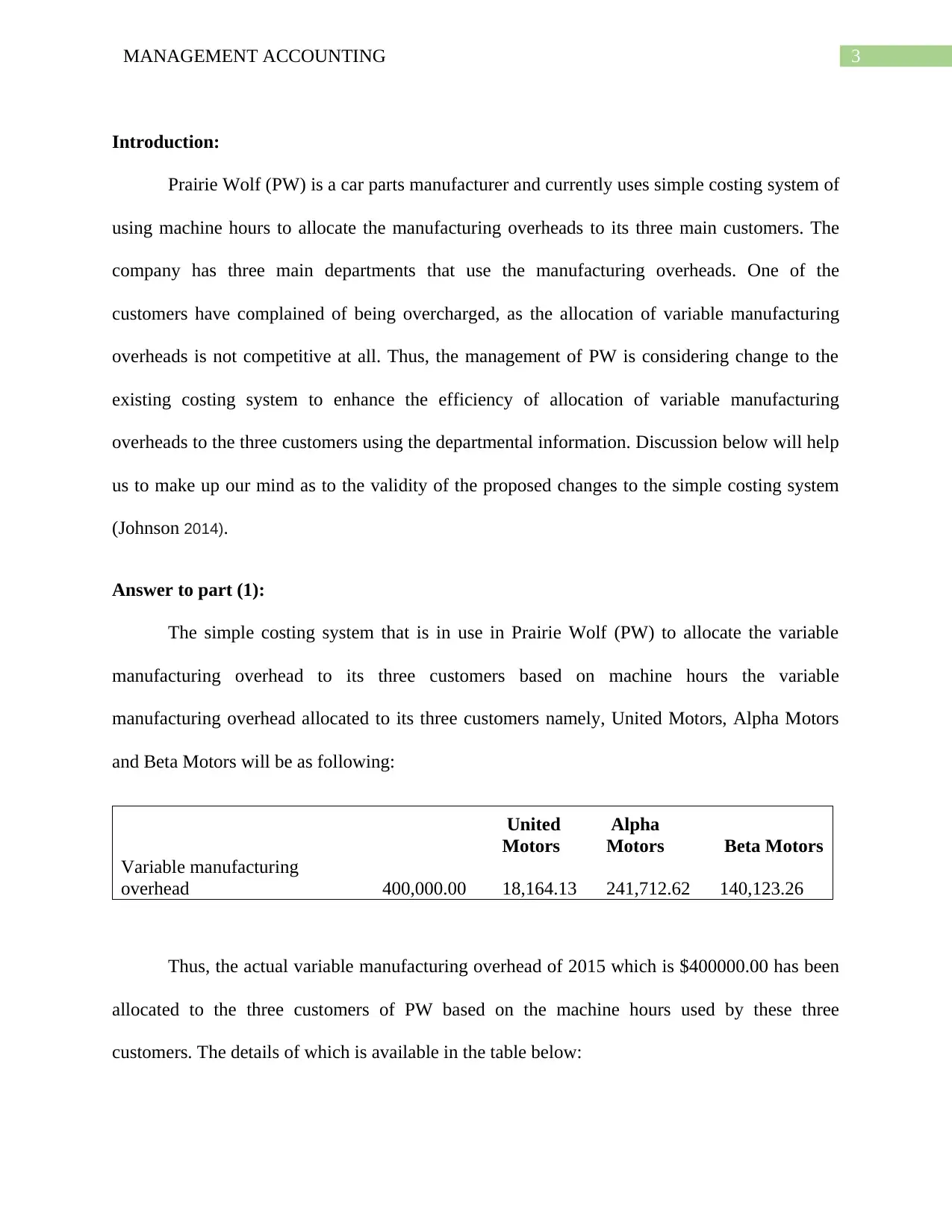
3MANAGEMENT ACCOUNTING
Introduction:
Prairie Wolf (PW) is a car parts manufacturer and currently uses simple costing system of
using machine hours to allocate the manufacturing overheads to its three main customers. The
company has three main departments that use the manufacturing overheads. One of the
customers have complained of being overcharged, as the allocation of variable manufacturing
overheads is not competitive at all. Thus, the management of PW is considering change to the
existing costing system to enhance the efficiency of allocation of variable manufacturing
overheads to the three customers using the departmental information. Discussion below will help
us to make up our mind as to the validity of the proposed changes to the simple costing system
(Johnson 2014).
Answer to part (1):
The simple costing system that is in use in Prairie Wolf (PW) to allocate the variable
manufacturing overhead to its three customers based on machine hours the variable
manufacturing overhead allocated to its three customers namely, United Motors, Alpha Motors
and Beta Motors will be as following:
United
Motors
Alpha
Motors Beta Motors
Variable manufacturing
overhead 400,000.00 18,164.13 241,712.62 140,123.26
Thus, the actual variable manufacturing overhead of 2015 which is $400000.00 has been
allocated to the three customers of PW based on the machine hours used by these three
customers. The details of which is available in the table below:
Introduction:
Prairie Wolf (PW) is a car parts manufacturer and currently uses simple costing system of
using machine hours to allocate the manufacturing overheads to its three main customers. The
company has three main departments that use the manufacturing overheads. One of the
customers have complained of being overcharged, as the allocation of variable manufacturing
overheads is not competitive at all. Thus, the management of PW is considering change to the
existing costing system to enhance the efficiency of allocation of variable manufacturing
overheads to the three customers using the departmental information. Discussion below will help
us to make up our mind as to the validity of the proposed changes to the simple costing system
(Johnson 2014).
Answer to part (1):
The simple costing system that is in use in Prairie Wolf (PW) to allocate the variable
manufacturing overhead to its three customers based on machine hours the variable
manufacturing overhead allocated to its three customers namely, United Motors, Alpha Motors
and Beta Motors will be as following:
United
Motors
Alpha
Motors Beta Motors
Variable manufacturing
overhead 400,000.00 18,164.13 241,712.62 140,123.26
Thus, the actual variable manufacturing overhead of 2015 which is $400000.00 has been
allocated to the three customers of PW based on the machine hours used by these three
customers. The details of which is available in the table below:
Paraphrase This Document
Need a fresh take? Get an instant paraphrase of this document with our AI Paraphraser
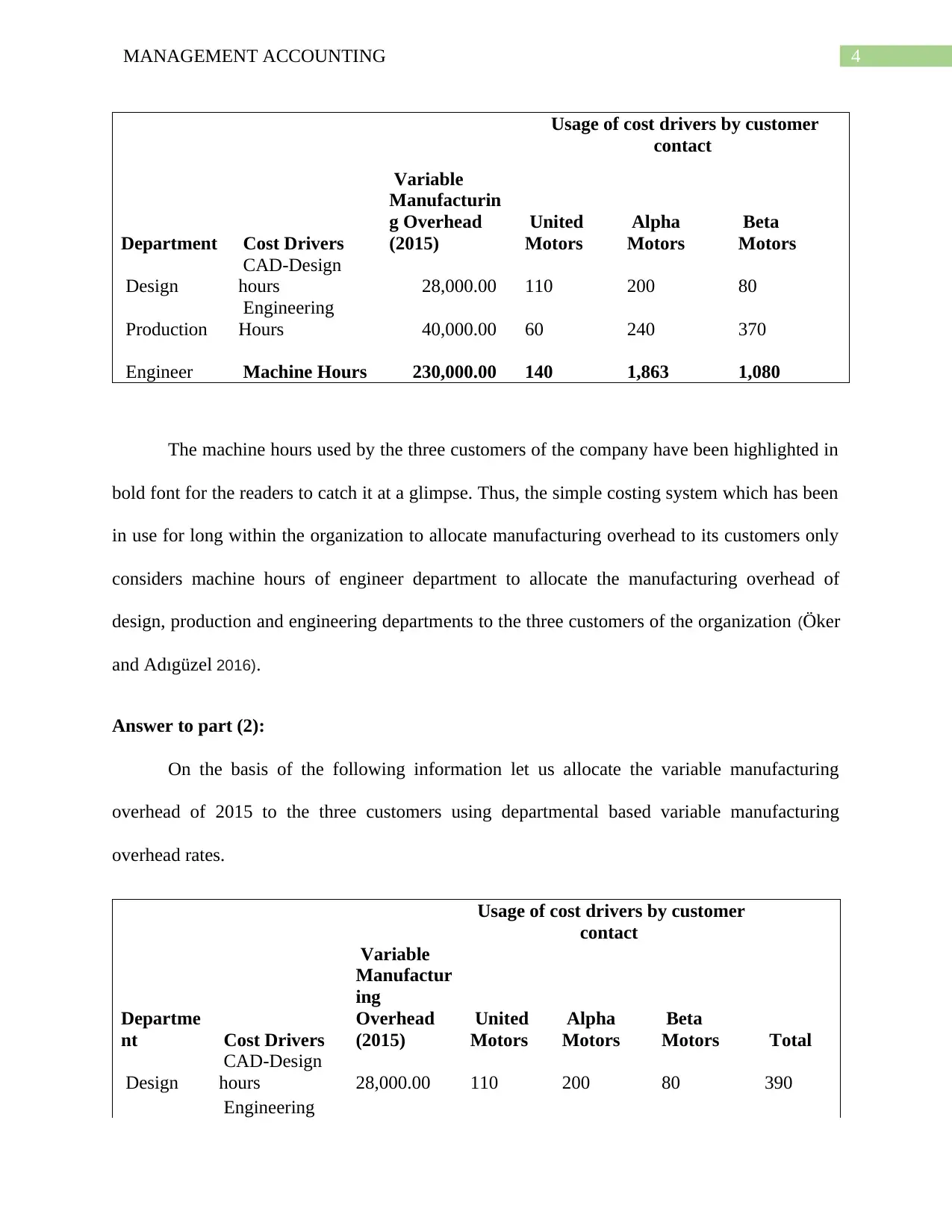
4MANAGEMENT ACCOUNTING
Usage of cost drivers by customer
contact
Department Cost Drivers
Variable
Manufacturin
g Overhead
(2015)
United
Motors
Alpha
Motors
Beta
Motors
Design
CAD-Design
hours 28,000.00 110 200 80
Production
Engineering
Hours 40,000.00 60 240 370
Engineer Machine Hours 230,000.00 140 1,863 1,080
The machine hours used by the three customers of the company have been highlighted in
bold font for the readers to catch it at a glimpse. Thus, the simple costing system which has been
in use for long within the organization to allocate manufacturing overhead to its customers only
considers machine hours of engineer department to allocate the manufacturing overhead of
design, production and engineering departments to the three customers of the organization (Öker
and Adıgüzel 2016).
Answer to part (2):
On the basis of the following information let us allocate the variable manufacturing
overhead of 2015 to the three customers using departmental based variable manufacturing
overhead rates.
Usage of cost drivers by customer
contact
Departme
nt Cost Drivers
Variable
Manufactur
ing
Overhead
(2015)
United
Motors
Alpha
Motors
Beta
Motors Total
Design
CAD-Design
hours 28,000.00 110 200 80 390
Engineering
Usage of cost drivers by customer
contact
Department Cost Drivers
Variable
Manufacturin
g Overhead
(2015)
United
Motors
Alpha
Motors
Beta
Motors
Design
CAD-Design
hours 28,000.00 110 200 80
Production
Engineering
Hours 40,000.00 60 240 370
Engineer Machine Hours 230,000.00 140 1,863 1,080
The machine hours used by the three customers of the company have been highlighted in
bold font for the readers to catch it at a glimpse. Thus, the simple costing system which has been
in use for long within the organization to allocate manufacturing overhead to its customers only
considers machine hours of engineer department to allocate the manufacturing overhead of
design, production and engineering departments to the three customers of the organization (Öker
and Adıgüzel 2016).
Answer to part (2):
On the basis of the following information let us allocate the variable manufacturing
overhead of 2015 to the three customers using departmental based variable manufacturing
overhead rates.
Usage of cost drivers by customer
contact
Departme
nt Cost Drivers
Variable
Manufactur
ing
Overhead
(2015)
United
Motors
Alpha
Motors
Beta
Motors Total
Design
CAD-Design
hours 28,000.00 110 200 80 390
Engineering
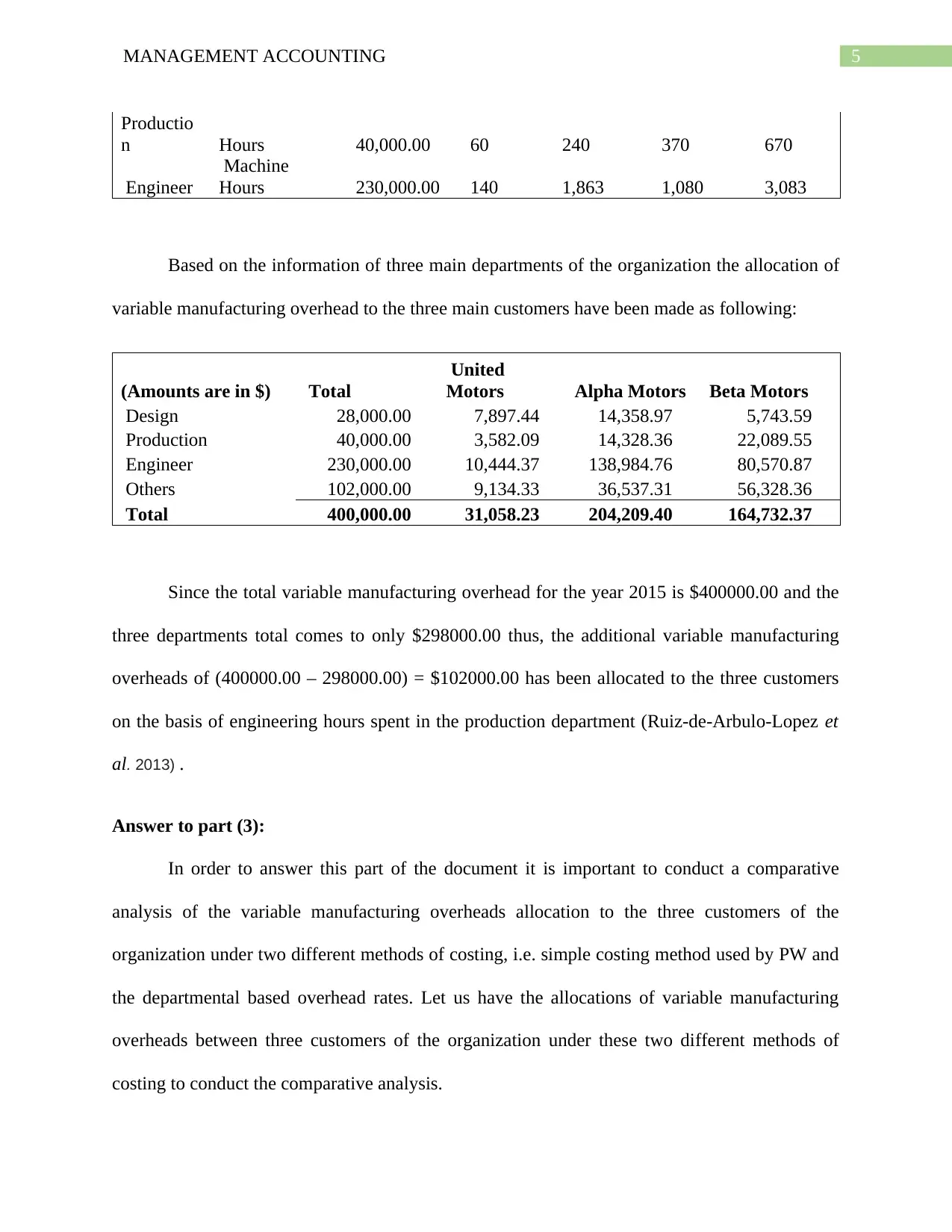
5MANAGEMENT ACCOUNTING
Productio
n Hours 40,000.00 60 240 370 670
Engineer
Machine
Hours 230,000.00 140 1,863 1,080 3,083
Based on the information of three main departments of the organization the allocation of
variable manufacturing overhead to the three main customers have been made as following:
(Amounts are in $) Total
United
Motors Alpha Motors Beta Motors
Design 28,000.00 7,897.44 14,358.97 5,743.59
Production 40,000.00 3,582.09 14,328.36 22,089.55
Engineer 230,000.00 10,444.37 138,984.76 80,570.87
Others 102,000.00 9,134.33 36,537.31 56,328.36
Total 400,000.00 31,058.23 204,209.40 164,732.37
Since the total variable manufacturing overhead for the year 2015 is $400000.00 and the
three departments total comes to only $298000.00 thus, the additional variable manufacturing
overheads of (400000.00 – 298000.00) = $102000.00 has been allocated to the three customers
on the basis of engineering hours spent in the production department (Ruiz-de-Arbulo-Lopez et
al. 2013) .
Answer to part (3):
In order to answer this part of the document it is important to conduct a comparative
analysis of the variable manufacturing overheads allocation to the three customers of the
organization under two different methods of costing, i.e. simple costing method used by PW and
the departmental based overhead rates. Let us have the allocations of variable manufacturing
overheads between three customers of the organization under these two different methods of
costing to conduct the comparative analysis.
Productio
n Hours 40,000.00 60 240 370 670
Engineer
Machine
Hours 230,000.00 140 1,863 1,080 3,083
Based on the information of three main departments of the organization the allocation of
variable manufacturing overhead to the three main customers have been made as following:
(Amounts are in $) Total
United
Motors Alpha Motors Beta Motors
Design 28,000.00 7,897.44 14,358.97 5,743.59
Production 40,000.00 3,582.09 14,328.36 22,089.55
Engineer 230,000.00 10,444.37 138,984.76 80,570.87
Others 102,000.00 9,134.33 36,537.31 56,328.36
Total 400,000.00 31,058.23 204,209.40 164,732.37
Since the total variable manufacturing overhead for the year 2015 is $400000.00 and the
three departments total comes to only $298000.00 thus, the additional variable manufacturing
overheads of (400000.00 – 298000.00) = $102000.00 has been allocated to the three customers
on the basis of engineering hours spent in the production department (Ruiz-de-Arbulo-Lopez et
al. 2013) .
Answer to part (3):
In order to answer this part of the document it is important to conduct a comparative
analysis of the variable manufacturing overheads allocation to the three customers of the
organization under two different methods of costing, i.e. simple costing method used by PW and
the departmental based overhead rates. Let us have the allocations of variable manufacturing
overheads between three customers of the organization under these two different methods of
costing to conduct the comparative analysis.
You're viewing a preview
Unlock full access by subscribing today!
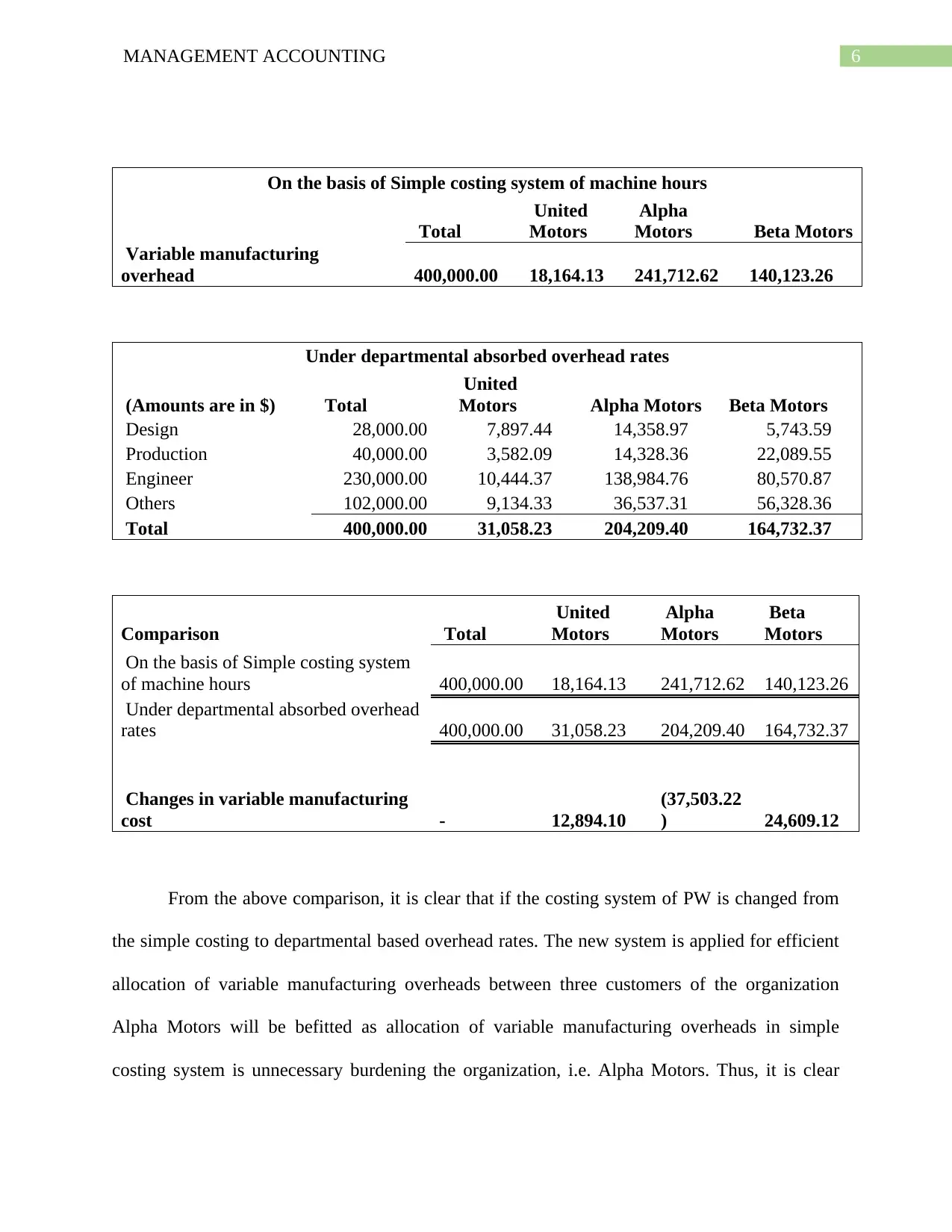
6MANAGEMENT ACCOUNTING
On the basis of Simple costing system of machine hours
Total
United
Motors
Alpha
Motors Beta Motors
Variable manufacturing
overhead 400,000.00 18,164.13 241,712.62 140,123.26
Under departmental absorbed overhead rates
(Amounts are in $) Total
United
Motors Alpha Motors Beta Motors
Design 28,000.00 7,897.44 14,358.97 5,743.59
Production 40,000.00 3,582.09 14,328.36 22,089.55
Engineer 230,000.00 10,444.37 138,984.76 80,570.87
Others 102,000.00 9,134.33 36,537.31 56,328.36
Total 400,000.00 31,058.23 204,209.40 164,732.37
Comparison Total
United
Motors
Alpha
Motors
Beta
Motors
On the basis of Simple costing system
of machine hours 400,000.00 18,164.13 241,712.62 140,123.26
Under departmental absorbed overhead
rates 400,000.00 31,058.23 204,209.40 164,732.37
Changes in variable manufacturing
cost - 12,894.10
(37,503.22
) 24,609.12
From the above comparison, it is clear that if the costing system of PW is changed from
the simple costing to departmental based overhead rates. The new system is applied for efficient
allocation of variable manufacturing overheads between three customers of the organization
Alpha Motors will be befitted as allocation of variable manufacturing overheads in simple
costing system is unnecessary burdening the organization, i.e. Alpha Motors. Thus, it is clear
On the basis of Simple costing system of machine hours
Total
United
Motors
Alpha
Motors Beta Motors
Variable manufacturing
overhead 400,000.00 18,164.13 241,712.62 140,123.26
Under departmental absorbed overhead rates
(Amounts are in $) Total
United
Motors Alpha Motors Beta Motors
Design 28,000.00 7,897.44 14,358.97 5,743.59
Production 40,000.00 3,582.09 14,328.36 22,089.55
Engineer 230,000.00 10,444.37 138,984.76 80,570.87
Others 102,000.00 9,134.33 36,537.31 56,328.36
Total 400,000.00 31,058.23 204,209.40 164,732.37
Comparison Total
United
Motors
Alpha
Motors
Beta
Motors
On the basis of Simple costing system
of machine hours 400,000.00 18,164.13 241,712.62 140,123.26
Under departmental absorbed overhead
rates 400,000.00 31,058.23 204,209.40 164,732.37
Changes in variable manufacturing
cost - 12,894.10
(37,503.22
) 24,609.12
From the above comparison, it is clear that if the costing system of PW is changed from
the simple costing to departmental based overhead rates. The new system is applied for efficient
allocation of variable manufacturing overheads between three customers of the organization
Alpha Motors will be befitted as allocation of variable manufacturing overheads in simple
costing system is unnecessary burdening the organization, i.e. Alpha Motors. Thus, it is clear
Paraphrase This Document
Need a fresh take? Get an instant paraphrase of this document with our AI Paraphraser
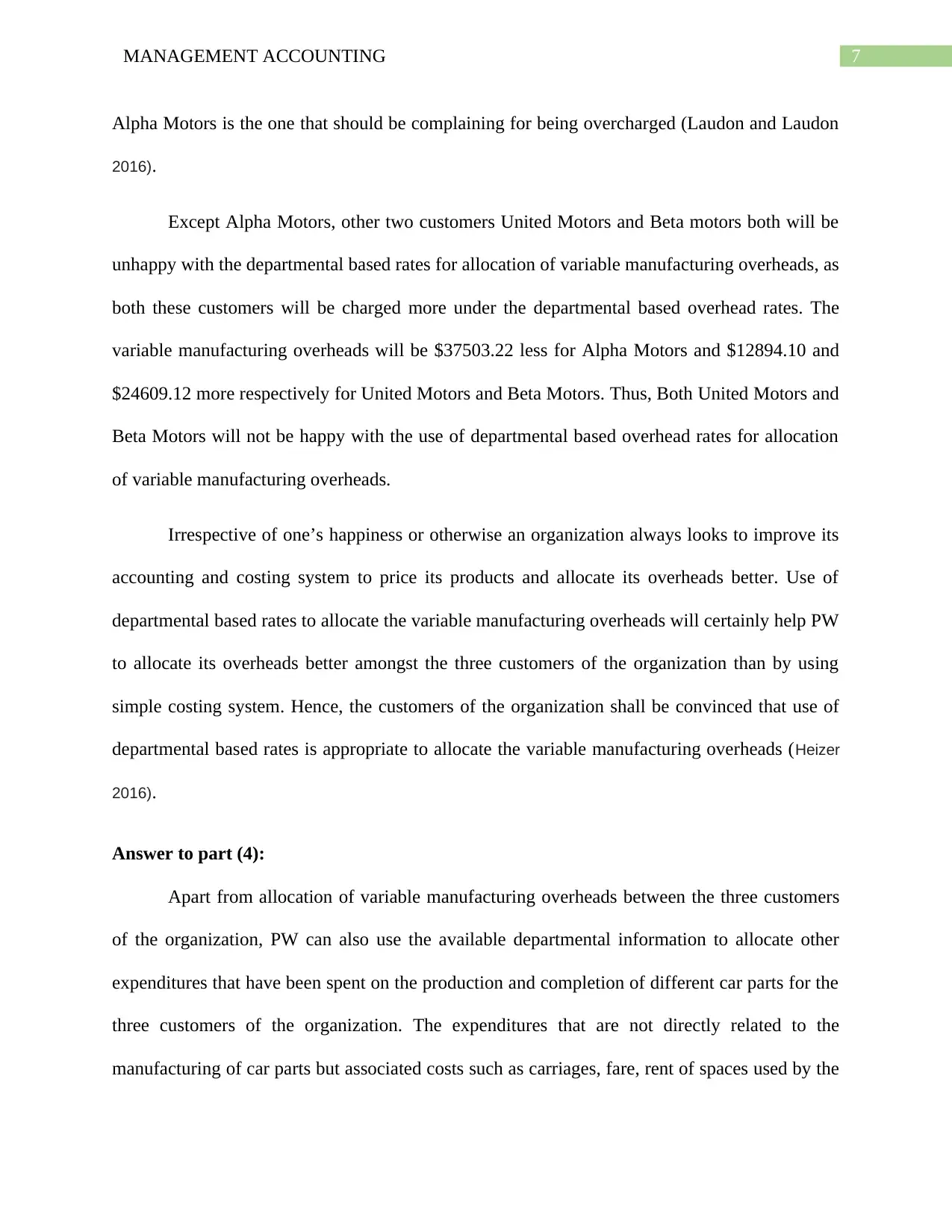
7MANAGEMENT ACCOUNTING
Alpha Motors is the one that should be complaining for being overcharged (Laudon and Laudon
2016).
Except Alpha Motors, other two customers United Motors and Beta motors both will be
unhappy with the departmental based rates for allocation of variable manufacturing overheads, as
both these customers will be charged more under the departmental based overhead rates. The
variable manufacturing overheads will be $37503.22 less for Alpha Motors and $12894.10 and
$24609.12 more respectively for United Motors and Beta Motors. Thus, Both United Motors and
Beta Motors will not be happy with the use of departmental based overhead rates for allocation
of variable manufacturing overheads.
Irrespective of one’s happiness or otherwise an organization always looks to improve its
accounting and costing system to price its products and allocate its overheads better. Use of
departmental based rates to allocate the variable manufacturing overheads will certainly help PW
to allocate its overheads better amongst the three customers of the organization than by using
simple costing system. Hence, the customers of the organization shall be convinced that use of
departmental based rates is appropriate to allocate the variable manufacturing overheads (Heizer
2016).
Answer to part (4):
Apart from allocation of variable manufacturing overheads between the three customers
of the organization, PW can also use the available departmental information to allocate other
expenditures that have been spent on the production and completion of different car parts for the
three customers of the organization. The expenditures that are not directly related to the
manufacturing of car parts but associated costs such as carriages, fare, rent of spaces used by the
Alpha Motors is the one that should be complaining for being overcharged (Laudon and Laudon
2016).
Except Alpha Motors, other two customers United Motors and Beta motors both will be
unhappy with the departmental based rates for allocation of variable manufacturing overheads, as
both these customers will be charged more under the departmental based overhead rates. The
variable manufacturing overheads will be $37503.22 less for Alpha Motors and $12894.10 and
$24609.12 more respectively for United Motors and Beta Motors. Thus, Both United Motors and
Beta Motors will not be happy with the use of departmental based overhead rates for allocation
of variable manufacturing overheads.
Irrespective of one’s happiness or otherwise an organization always looks to improve its
accounting and costing system to price its products and allocate its overheads better. Use of
departmental based rates to allocate the variable manufacturing overheads will certainly help PW
to allocate its overheads better amongst the three customers of the organization than by using
simple costing system. Hence, the customers of the organization shall be convinced that use of
departmental based rates is appropriate to allocate the variable manufacturing overheads (Heizer
2016).
Answer to part (4):
Apart from allocation of variable manufacturing overheads between the three customers
of the organization, PW can also use the available departmental information to allocate other
expenditures that have been spent on the production and completion of different car parts for the
three customers of the organization. The expenditures that are not directly related to the
manufacturing of car parts but associated costs such as carriages, fare, rent of spaces used by the
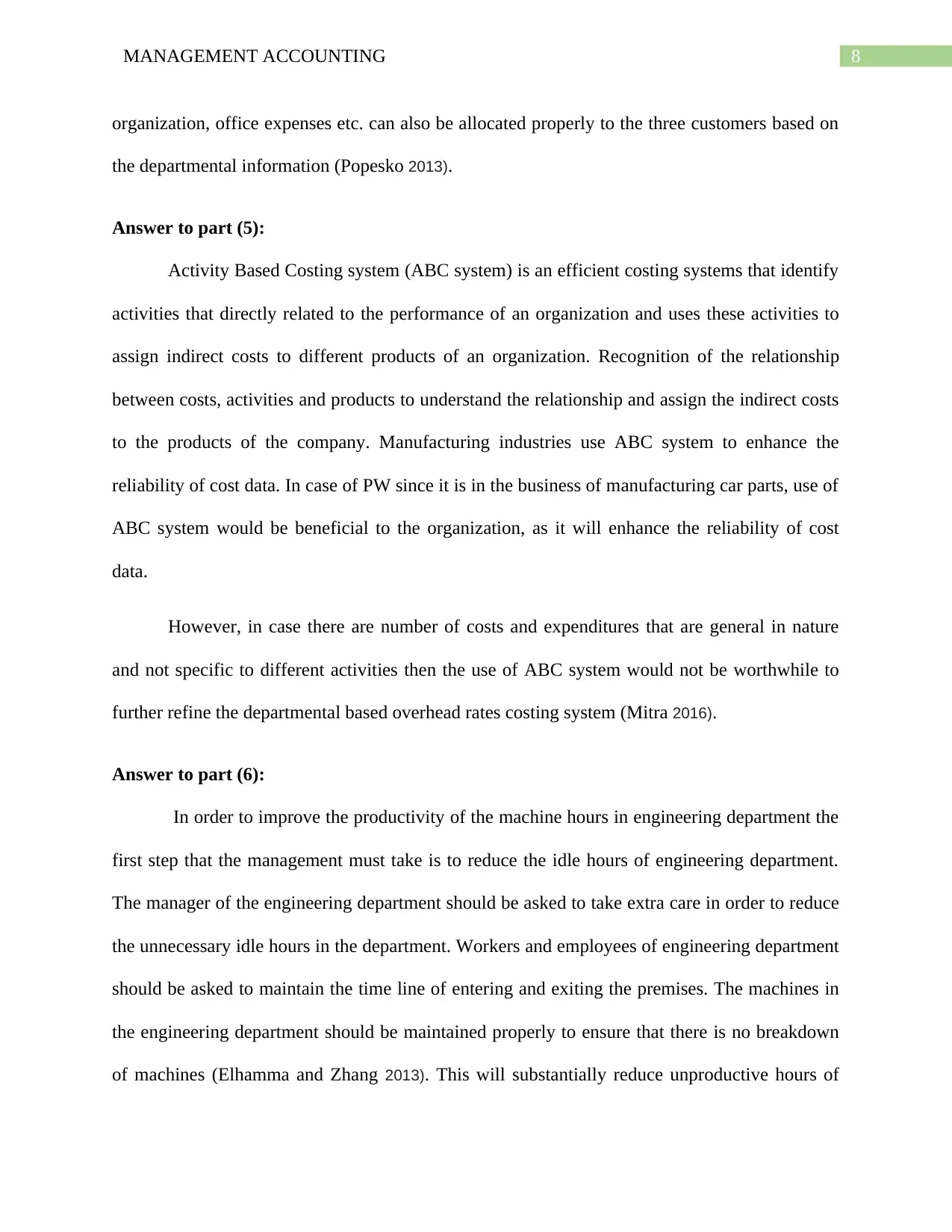
8MANAGEMENT ACCOUNTING
organization, office expenses etc. can also be allocated properly to the three customers based on
the departmental information (Popesko 2013).
Answer to part (5):
Activity Based Costing system (ABC system) is an efficient costing systems that identify
activities that directly related to the performance of an organization and uses these activities to
assign indirect costs to different products of an organization. Recognition of the relationship
between costs, activities and products to understand the relationship and assign the indirect costs
to the products of the company. Manufacturing industries use ABC system to enhance the
reliability of cost data. In case of PW since it is in the business of manufacturing car parts, use of
ABC system would be beneficial to the organization, as it will enhance the reliability of cost
data.
However, in case there are number of costs and expenditures that are general in nature
and not specific to different activities then the use of ABC system would not be worthwhile to
further refine the departmental based overhead rates costing system (Mitra 2016).
Answer to part (6):
In order to improve the productivity of the machine hours in engineering department the
first step that the management must take is to reduce the idle hours of engineering department.
The manager of the engineering department should be asked to take extra care in order to reduce
the unnecessary idle hours in the department. Workers and employees of engineering department
should be asked to maintain the time line of entering and exiting the premises. The machines in
the engineering department should be maintained properly to ensure that there is no breakdown
of machines (Elhamma and Zhang 2013). This will substantially reduce unproductive hours of
organization, office expenses etc. can also be allocated properly to the three customers based on
the departmental information (Popesko 2013).
Answer to part (5):
Activity Based Costing system (ABC system) is an efficient costing systems that identify
activities that directly related to the performance of an organization and uses these activities to
assign indirect costs to different products of an organization. Recognition of the relationship
between costs, activities and products to understand the relationship and assign the indirect costs
to the products of the company. Manufacturing industries use ABC system to enhance the
reliability of cost data. In case of PW since it is in the business of manufacturing car parts, use of
ABC system would be beneficial to the organization, as it will enhance the reliability of cost
data.
However, in case there are number of costs and expenditures that are general in nature
and not specific to different activities then the use of ABC system would not be worthwhile to
further refine the departmental based overhead rates costing system (Mitra 2016).
Answer to part (6):
In order to improve the productivity of the machine hours in engineering department the
first step that the management must take is to reduce the idle hours of engineering department.
The manager of the engineering department should be asked to take extra care in order to reduce
the unnecessary idle hours in the department. Workers and employees of engineering department
should be asked to maintain the time line of entering and exiting the premises. The machines in
the engineering department should be maintained properly to ensure that there is no breakdown
of machines (Elhamma and Zhang 2013). This will substantially reduce unproductive hours of
You're viewing a preview
Unlock full access by subscribing today!
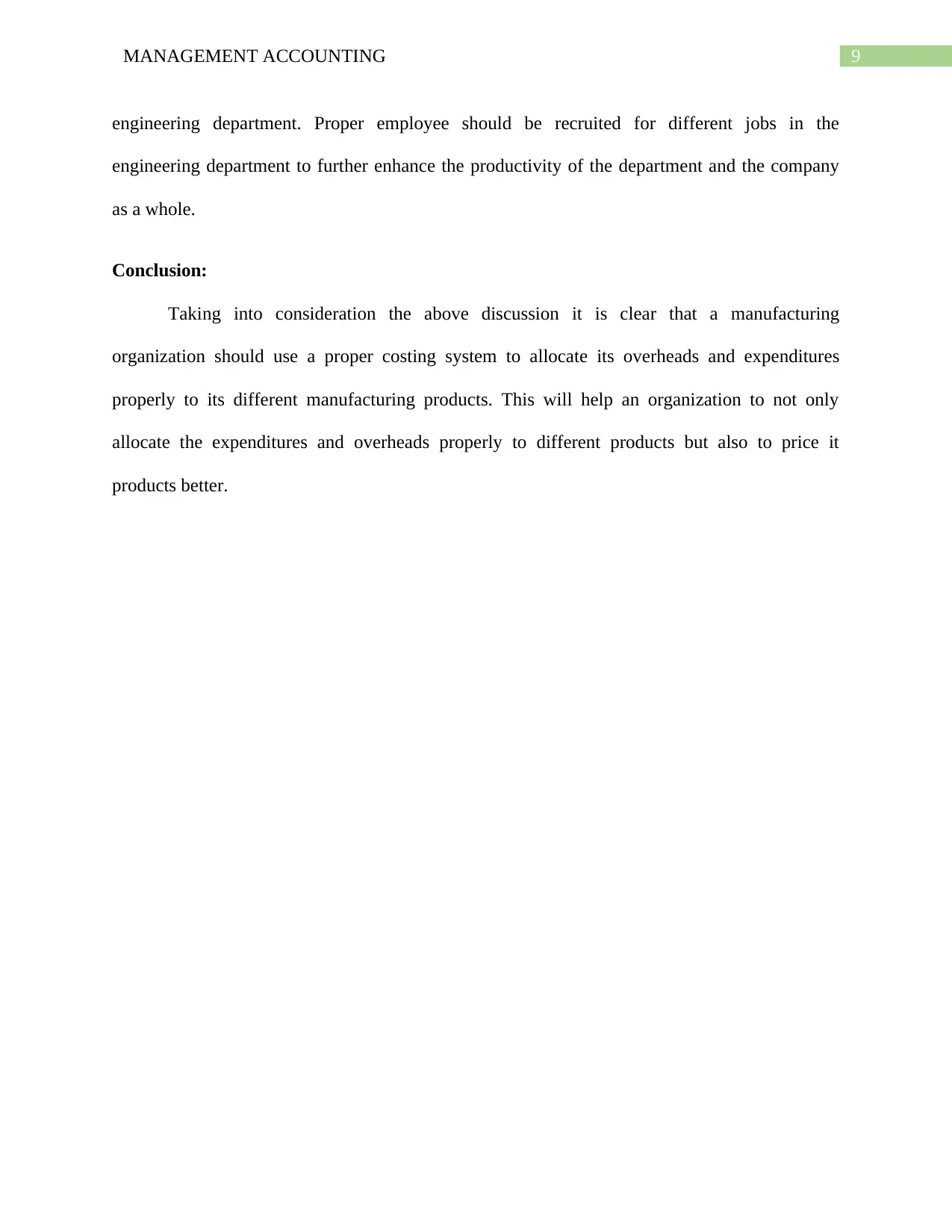
9MANAGEMENT ACCOUNTING
engineering department. Proper employee should be recruited for different jobs in the
engineering department to further enhance the productivity of the department and the company
as a whole.
Conclusion:
Taking into consideration the above discussion it is clear that a manufacturing
organization should use a proper costing system to allocate its overheads and expenditures
properly to its different manufacturing products. This will help an organization to not only
allocate the expenditures and overheads properly to different products but also to price it
products better.
engineering department. Proper employee should be recruited for different jobs in the
engineering department to further enhance the productivity of the department and the company
as a whole.
Conclusion:
Taking into consideration the above discussion it is clear that a manufacturing
organization should use a proper costing system to allocate its overheads and expenditures
properly to its different manufacturing products. This will help an organization to not only
allocate the expenditures and overheads properly to different products but also to price it
products better.
Paraphrase This Document
Need a fresh take? Get an instant paraphrase of this document with our AI Paraphraser
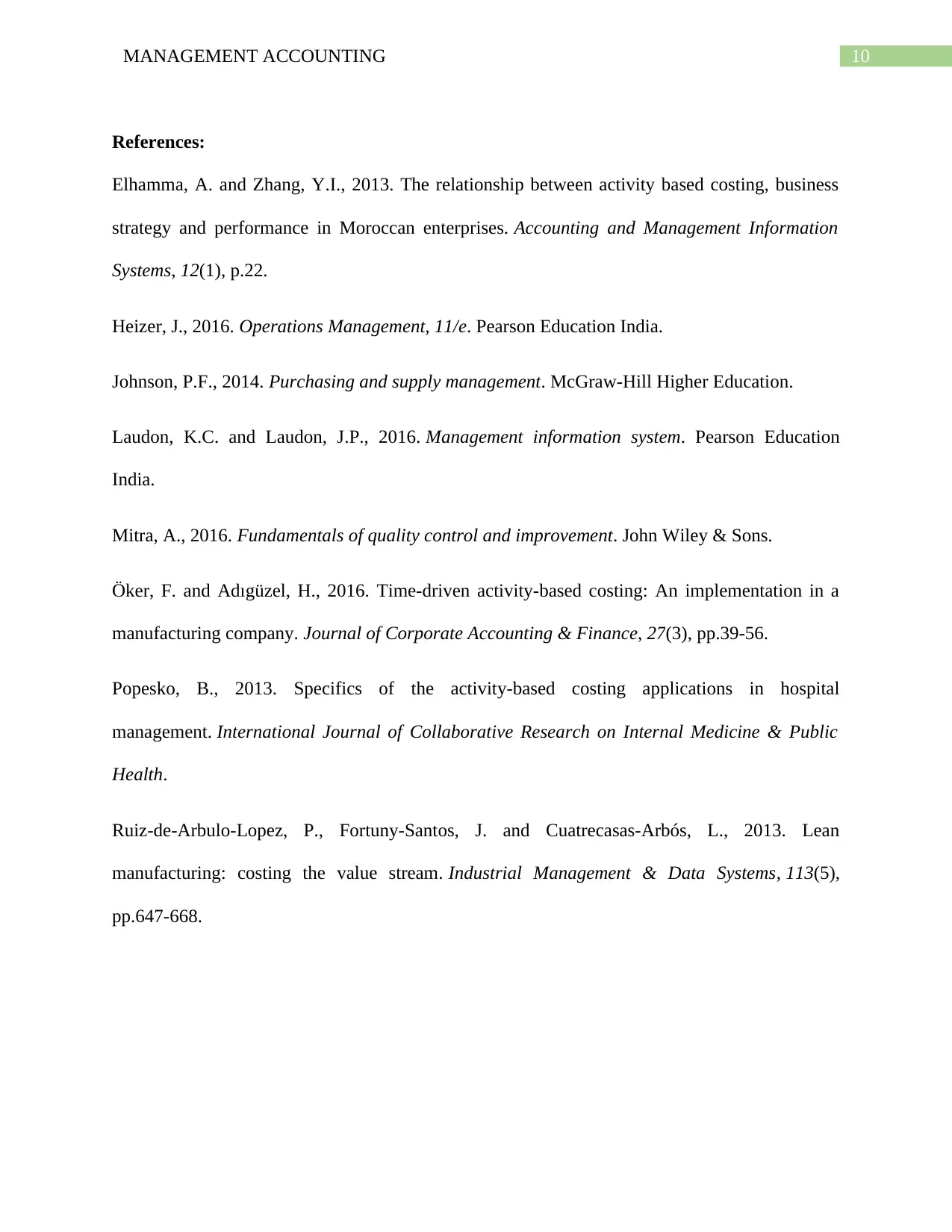
10MANAGEMENT ACCOUNTING
References:
Elhamma, A. and Zhang, Y.I., 2013. The relationship between activity based costing, business
strategy and performance in Moroccan enterprises. Accounting and Management Information
Systems, 12(1), p.22.
Heizer, J., 2016. Operations Management, 11/e. Pearson Education India.
Johnson, P.F., 2014. Purchasing and supply management. McGraw-Hill Higher Education.
Laudon, K.C. and Laudon, J.P., 2016. Management information system. Pearson Education
India.
Mitra, A., 2016. Fundamentals of quality control and improvement. John Wiley & Sons.
Öker, F. and Adıgüzel, H., 2016. Time‐driven activity‐based costing: An implementation in a
manufacturing company. Journal of Corporate Accounting & Finance, 27(3), pp.39-56.
Popesko, B., 2013. Specifics of the activity-based costing applications in hospital
management. International Journal of Collaborative Research on Internal Medicine & Public
Health.
Ruiz-de-Arbulo-Lopez, P., Fortuny-Santos, J. and Cuatrecasas-Arbós, L., 2013. Lean
manufacturing: costing the value stream. Industrial Management & Data Systems, 113(5),
pp.647-668.
References:
Elhamma, A. and Zhang, Y.I., 2013. The relationship between activity based costing, business
strategy and performance in Moroccan enterprises. Accounting and Management Information
Systems, 12(1), p.22.
Heizer, J., 2016. Operations Management, 11/e. Pearson Education India.
Johnson, P.F., 2014. Purchasing and supply management. McGraw-Hill Higher Education.
Laudon, K.C. and Laudon, J.P., 2016. Management information system. Pearson Education
India.
Mitra, A., 2016. Fundamentals of quality control and improvement. John Wiley & Sons.
Öker, F. and Adıgüzel, H., 2016. Time‐driven activity‐based costing: An implementation in a
manufacturing company. Journal of Corporate Accounting & Finance, 27(3), pp.39-56.
Popesko, B., 2013. Specifics of the activity-based costing applications in hospital
management. International Journal of Collaborative Research on Internal Medicine & Public
Health.
Ruiz-de-Arbulo-Lopez, P., Fortuny-Santos, J. and Cuatrecasas-Arbós, L., 2013. Lean
manufacturing: costing the value stream. Industrial Management & Data Systems, 113(5),
pp.647-668.
1 out of 11
Related Documents

Your All-in-One AI-Powered Toolkit for Academic Success.
+13062052269
info@desklib.com
Available 24*7 on WhatsApp / Email
Unlock your academic potential
© 2024 | Zucol Services PVT LTD | All rights reserved.