Make or Buy Decision Analysis
VerifiedAdded on 2020/02/24
|7
|1266
|42
AI Summary
This assignment presents a case study of Playdough Company facing a make-or-buy decision for coffee cups and canisters. Students are tasked with analyzing the cost structure of both options, calculating profit per unit, and recommending the most profitable course of action based on provided financial data. The analysis highlights key factors influencing such decisions, including production costs, quality considerations, and quantity requirements.
Contribute Materials
Your contribution can guide someone’s learning journey. Share your
documents today.
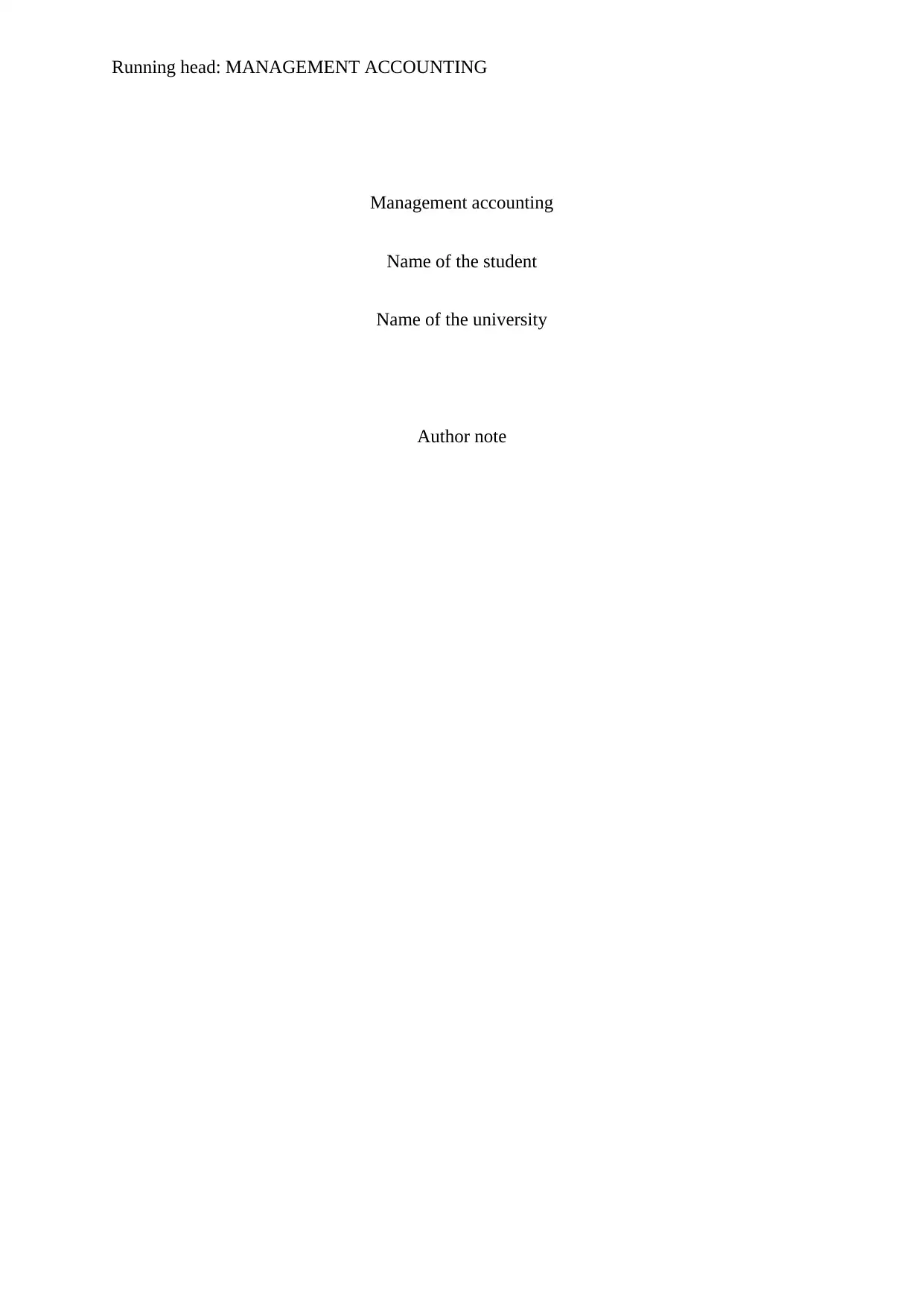
Running head: MANAGEMENT ACCOUNTING
Management accounting
Name of the student
Name of the university
Author note
Management accounting
Name of the student
Name of the university
Author note
Secure Best Marks with AI Grader
Need help grading? Try our AI Grader for instant feedback on your assignments.
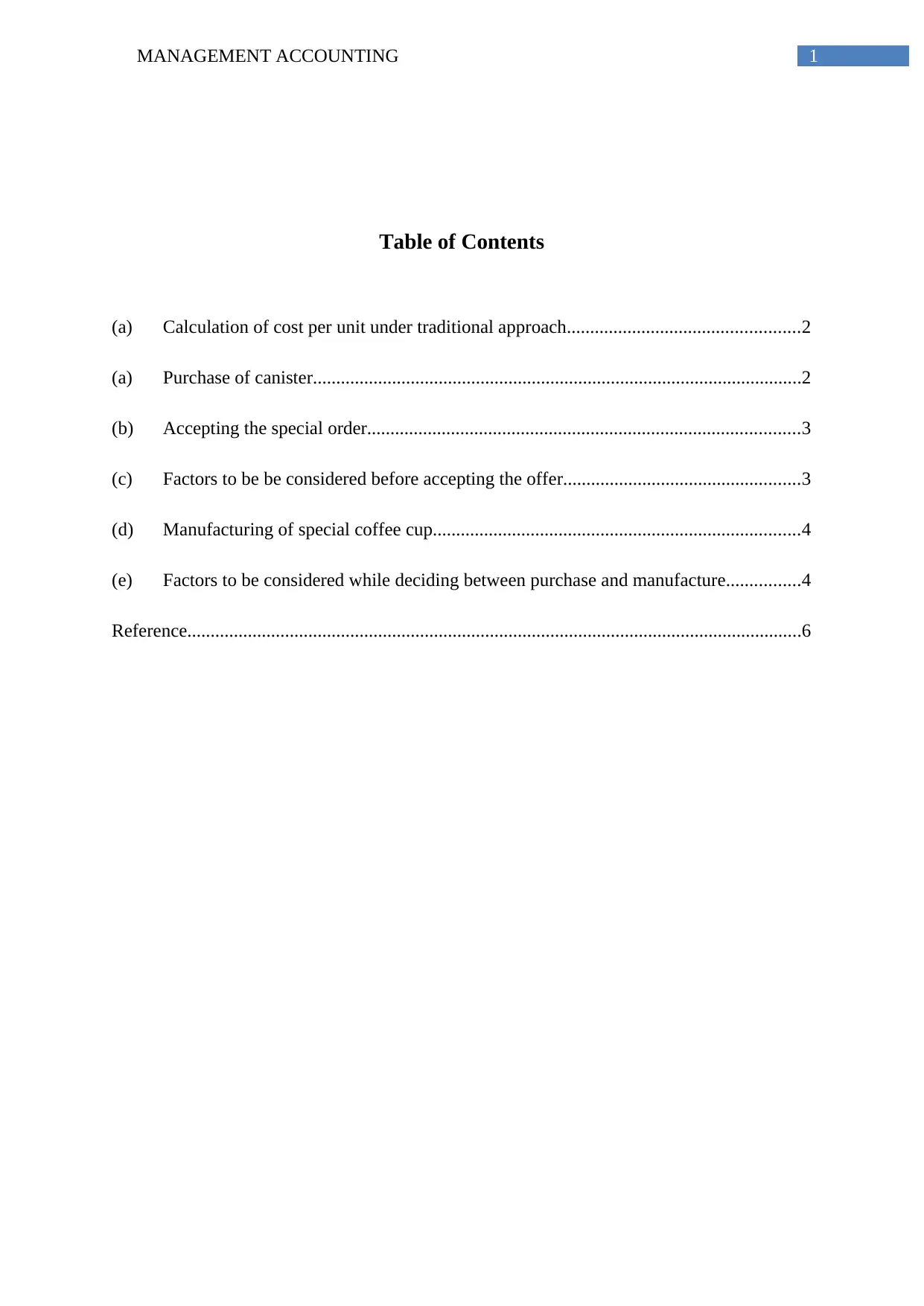
1MANAGEMENT ACCOUNTING
Table of Contents
(a) Calculation of cost per unit under traditional approach..................................................2
(a) Purchase of canister.........................................................................................................2
(b) Accepting the special order.............................................................................................3
(c) Factors to be be considered before accepting the offer...................................................3
(d) Manufacturing of special coffee cup...............................................................................4
(e) Factors to be considered while deciding between purchase and manufacture................4
Reference....................................................................................................................................6
Table of Contents
(a) Calculation of cost per unit under traditional approach..................................................2
(a) Purchase of canister.........................................................................................................2
(b) Accepting the special order.............................................................................................3
(c) Factors to be be considered before accepting the offer...................................................3
(d) Manufacturing of special coffee cup...............................................................................4
(e) Factors to be considered while deciding between purchase and manufacture................4
Reference....................................................................................................................................6
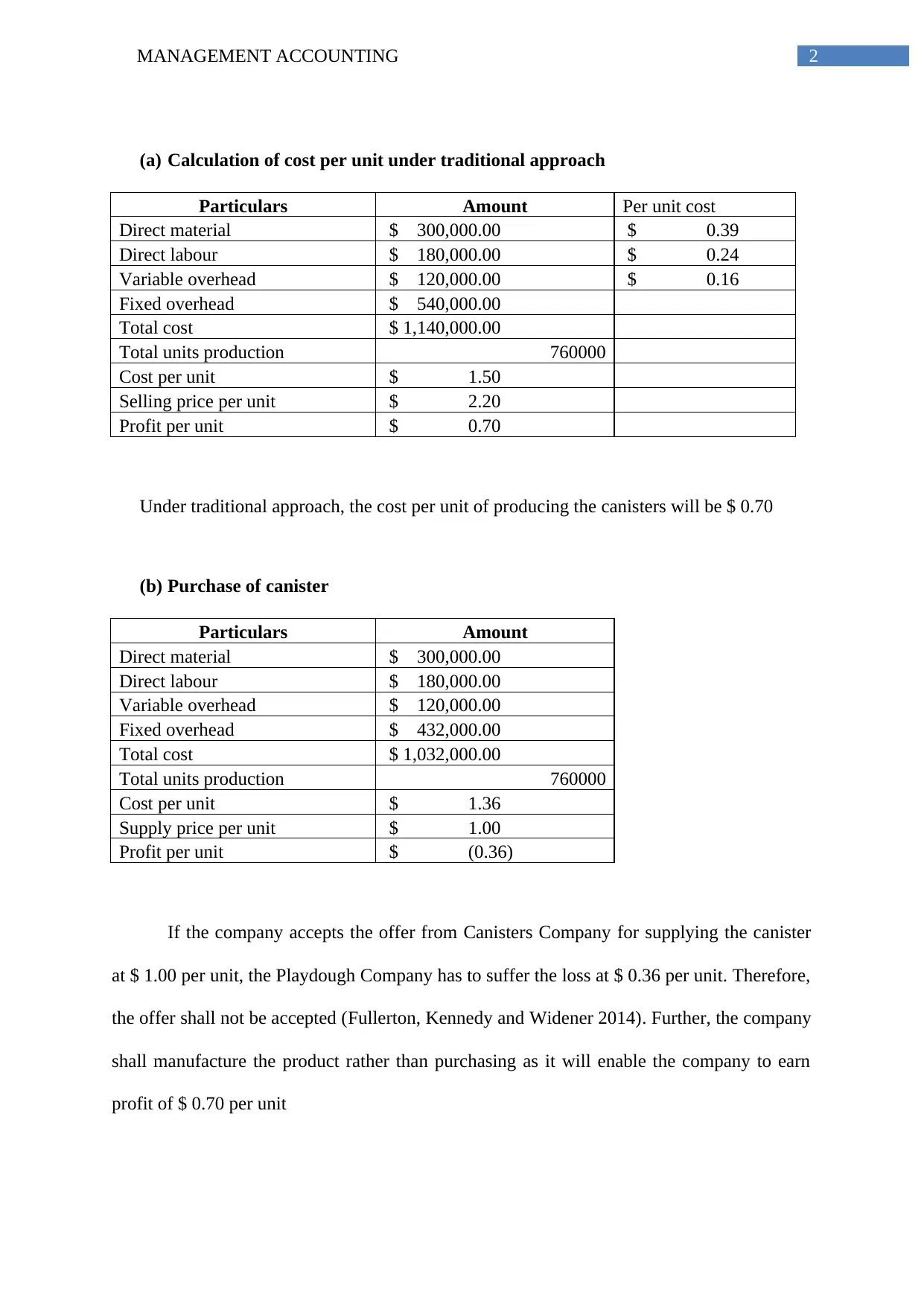
2MANAGEMENT ACCOUNTING
(a) Calculation of cost per unit under traditional approach
Particulars Amount Per unit cost
Direct material $ 300,000.00 $ 0.39
Direct labour $ 180,000.00 $ 0.24
Variable overhead $ 120,000.00 $ 0.16
Fixed overhead $ 540,000.00
Total cost $ 1,140,000.00
Total units production 760000
Cost per unit $ 1.50
Selling price per unit $ 2.20
Profit per unit $ 0.70
Under traditional approach, the cost per unit of producing the canisters will be $ 0.70
(b) Purchase of canister
Particulars Amount
Direct material $ 300,000.00
Direct labour $ 180,000.00
Variable overhead $ 120,000.00
Fixed overhead $ 432,000.00
Total cost $ 1,032,000.00
Total units production 760000
Cost per unit $ 1.36
Supply price per unit $ 1.00
Profit per unit $ (0.36)
If the company accepts the offer from Canisters Company for supplying the canister
at $ 1.00 per unit, the Playdough Company has to suffer the loss at $ 0.36 per unit. Therefore,
the offer shall not be accepted (Fullerton, Kennedy and Widener 2014). Further, the company
shall manufacture the product rather than purchasing as it will enable the company to earn
profit of $ 0.70 per unit
(a) Calculation of cost per unit under traditional approach
Particulars Amount Per unit cost
Direct material $ 300,000.00 $ 0.39
Direct labour $ 180,000.00 $ 0.24
Variable overhead $ 120,000.00 $ 0.16
Fixed overhead $ 540,000.00
Total cost $ 1,140,000.00
Total units production 760000
Cost per unit $ 1.50
Selling price per unit $ 2.20
Profit per unit $ 0.70
Under traditional approach, the cost per unit of producing the canisters will be $ 0.70
(b) Purchase of canister
Particulars Amount
Direct material $ 300,000.00
Direct labour $ 180,000.00
Variable overhead $ 120,000.00
Fixed overhead $ 432,000.00
Total cost $ 1,032,000.00
Total units production 760000
Cost per unit $ 1.36
Supply price per unit $ 1.00
Profit per unit $ (0.36)
If the company accepts the offer from Canisters Company for supplying the canister
at $ 1.00 per unit, the Playdough Company has to suffer the loss at $ 0.36 per unit. Therefore,
the offer shall not be accepted (Fullerton, Kennedy and Widener 2014). Further, the company
shall manufacture the product rather than purchasing as it will enable the company to earn
profit of $ 0.70 per unit
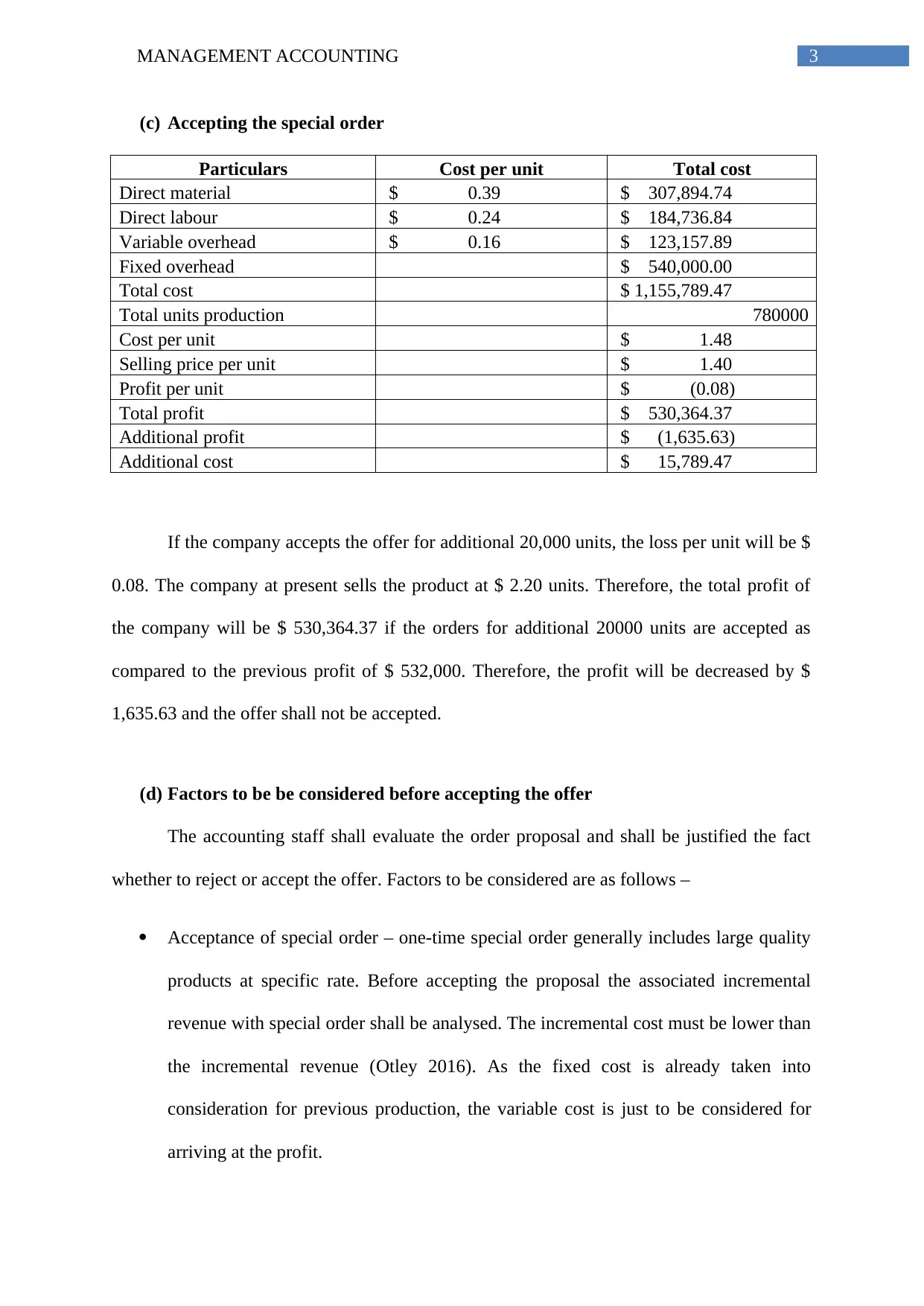
3MANAGEMENT ACCOUNTING
(c) Accepting the special order
Particulars Cost per unit Total cost
Direct material $ 0.39 $ 307,894.74
Direct labour $ 0.24 $ 184,736.84
Variable overhead $ 0.16 $ 123,157.89
Fixed overhead $ 540,000.00
Total cost $ 1,155,789.47
Total units production 780000
Cost per unit $ 1.48
Selling price per unit $ 1.40
Profit per unit $ (0.08)
Total profit $ 530,364.37
Additional profit $ (1,635.63)
Additional cost $ 15,789.47
If the company accepts the offer for additional 20,000 units, the loss per unit will be $
0.08. The company at present sells the product at $ 2.20 units. Therefore, the total profit of
the company will be $ 530,364.37 if the orders for additional 20000 units are accepted as
compared to the previous profit of $ 532,000. Therefore, the profit will be decreased by $
1,635.63 and the offer shall not be accepted.
(d) Factors to be be considered before accepting the offer
The accounting staff shall evaluate the order proposal and shall be justified the fact
whether to reject or accept the offer. Factors to be considered are as follows –
Acceptance of special order – one-time special order generally includes large quality
products at specific rate. Before accepting the proposal the associated incremental
revenue with special order shall be analysed. The incremental cost must be lower than
the incremental revenue (Otley 2016). As the fixed cost is already taken into
consideration for previous production, the variable cost is just to be considered for
arriving at the profit.
(c) Accepting the special order
Particulars Cost per unit Total cost
Direct material $ 0.39 $ 307,894.74
Direct labour $ 0.24 $ 184,736.84
Variable overhead $ 0.16 $ 123,157.89
Fixed overhead $ 540,000.00
Total cost $ 1,155,789.47
Total units production 780000
Cost per unit $ 1.48
Selling price per unit $ 1.40
Profit per unit $ (0.08)
Total profit $ 530,364.37
Additional profit $ (1,635.63)
Additional cost $ 15,789.47
If the company accepts the offer for additional 20,000 units, the loss per unit will be $
0.08. The company at present sells the product at $ 2.20 units. Therefore, the total profit of
the company will be $ 530,364.37 if the orders for additional 20000 units are accepted as
compared to the previous profit of $ 532,000. Therefore, the profit will be decreased by $
1,635.63 and the offer shall not be accepted.
(d) Factors to be be considered before accepting the offer
The accounting staff shall evaluate the order proposal and shall be justified the fact
whether to reject or accept the offer. Factors to be considered are as follows –
Acceptance of special order – one-time special order generally includes large quality
products at specific rate. Before accepting the proposal the associated incremental
revenue with special order shall be analysed. The incremental cost must be lower than
the incremental revenue (Otley 2016). As the fixed cost is already taken into
consideration for previous production, the variable cost is just to be considered for
arriving at the profit.
Secure Best Marks with AI Grader
Need help grading? Try our AI Grader for instant feedback on your assignments.
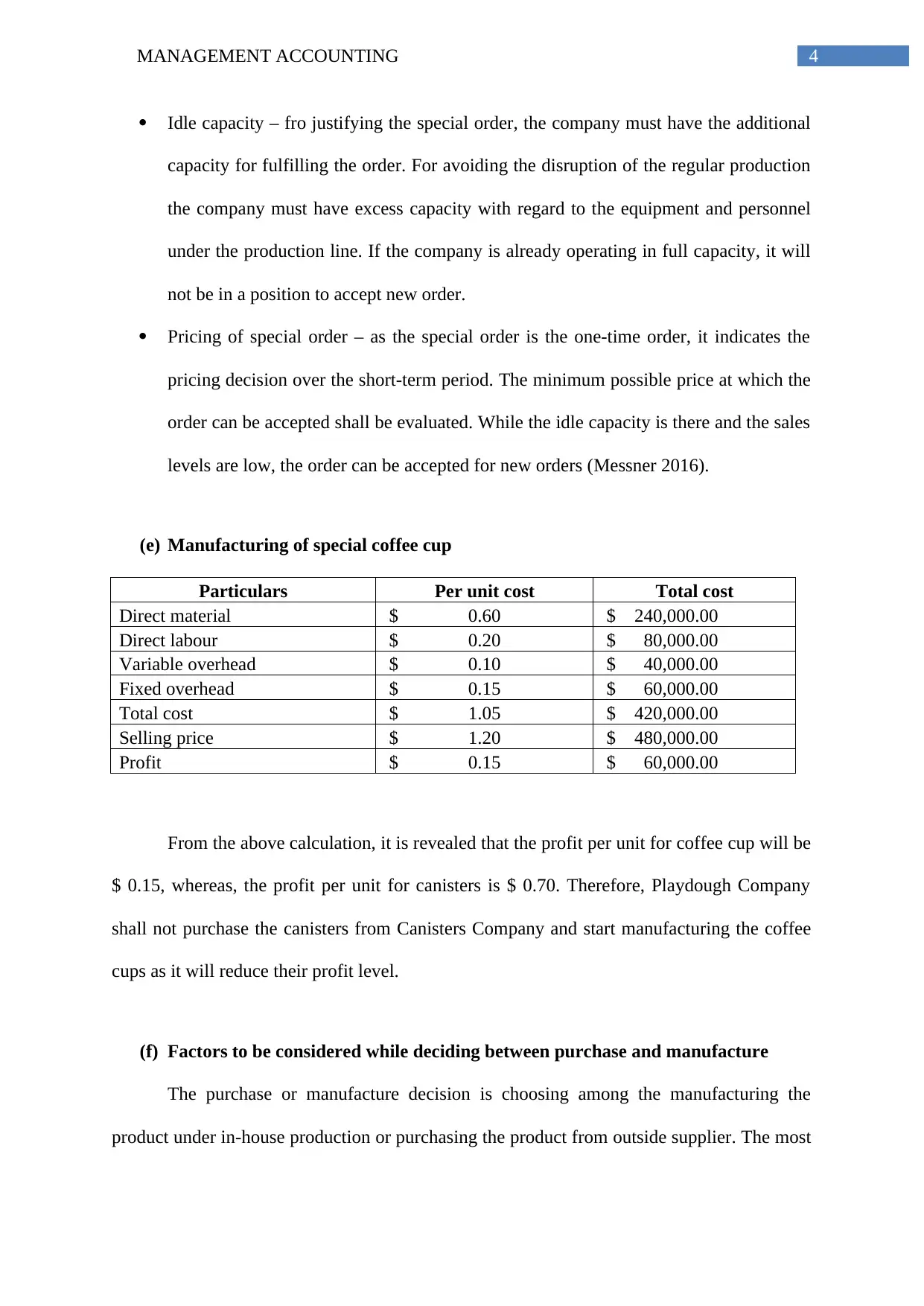
4MANAGEMENT ACCOUNTING
Idle capacity – fro justifying the special order, the company must have the additional
capacity for fulfilling the order. For avoiding the disruption of the regular production
the company must have excess capacity with regard to the equipment and personnel
under the production line. If the company is already operating in full capacity, it will
not be in a position to accept new order.
Pricing of special order – as the special order is the one-time order, it indicates the
pricing decision over the short-term period. The minimum possible price at which the
order can be accepted shall be evaluated. While the idle capacity is there and the sales
levels are low, the order can be accepted for new orders (Messner 2016).
(e) Manufacturing of special coffee cup
Particulars Per unit cost Total cost
Direct material $ 0.60 $ 240,000.00
Direct labour $ 0.20 $ 80,000.00
Variable overhead $ 0.10 $ 40,000.00
Fixed overhead $ 0.15 $ 60,000.00
Total cost $ 1.05 $ 420,000.00
Selling price $ 1.20 $ 480,000.00
Profit $ 0.15 $ 60,000.00
From the above calculation, it is revealed that the profit per unit for coffee cup will be
$ 0.15, whereas, the profit per unit for canisters is $ 0.70. Therefore, Playdough Company
shall not purchase the canisters from Canisters Company and start manufacturing the coffee
cups as it will reduce their profit level.
(f) Factors to be considered while deciding between purchase and manufacture
The purchase or manufacture decision is choosing among the manufacturing the
product under in-house production or purchasing the product from outside supplier. The most
Idle capacity – fro justifying the special order, the company must have the additional
capacity for fulfilling the order. For avoiding the disruption of the regular production
the company must have excess capacity with regard to the equipment and personnel
under the production line. If the company is already operating in full capacity, it will
not be in a position to accept new order.
Pricing of special order – as the special order is the one-time order, it indicates the
pricing decision over the short-term period. The minimum possible price at which the
order can be accepted shall be evaluated. While the idle capacity is there and the sales
levels are low, the order can be accepted for new orders (Messner 2016).
(e) Manufacturing of special coffee cup
Particulars Per unit cost Total cost
Direct material $ 0.60 $ 240,000.00
Direct labour $ 0.20 $ 80,000.00
Variable overhead $ 0.10 $ 40,000.00
Fixed overhead $ 0.15 $ 60,000.00
Total cost $ 1.05 $ 420,000.00
Selling price $ 1.20 $ 480,000.00
Profit $ 0.15 $ 60,000.00
From the above calculation, it is revealed that the profit per unit for coffee cup will be
$ 0.15, whereas, the profit per unit for canisters is $ 0.70. Therefore, Playdough Company
shall not purchase the canisters from Canisters Company and start manufacturing the coffee
cups as it will reduce their profit level.
(f) Factors to be considered while deciding between purchase and manufacture
The purchase or manufacture decision is choosing among the manufacturing the
product under in-house production or purchasing the product from outside supplier. The most
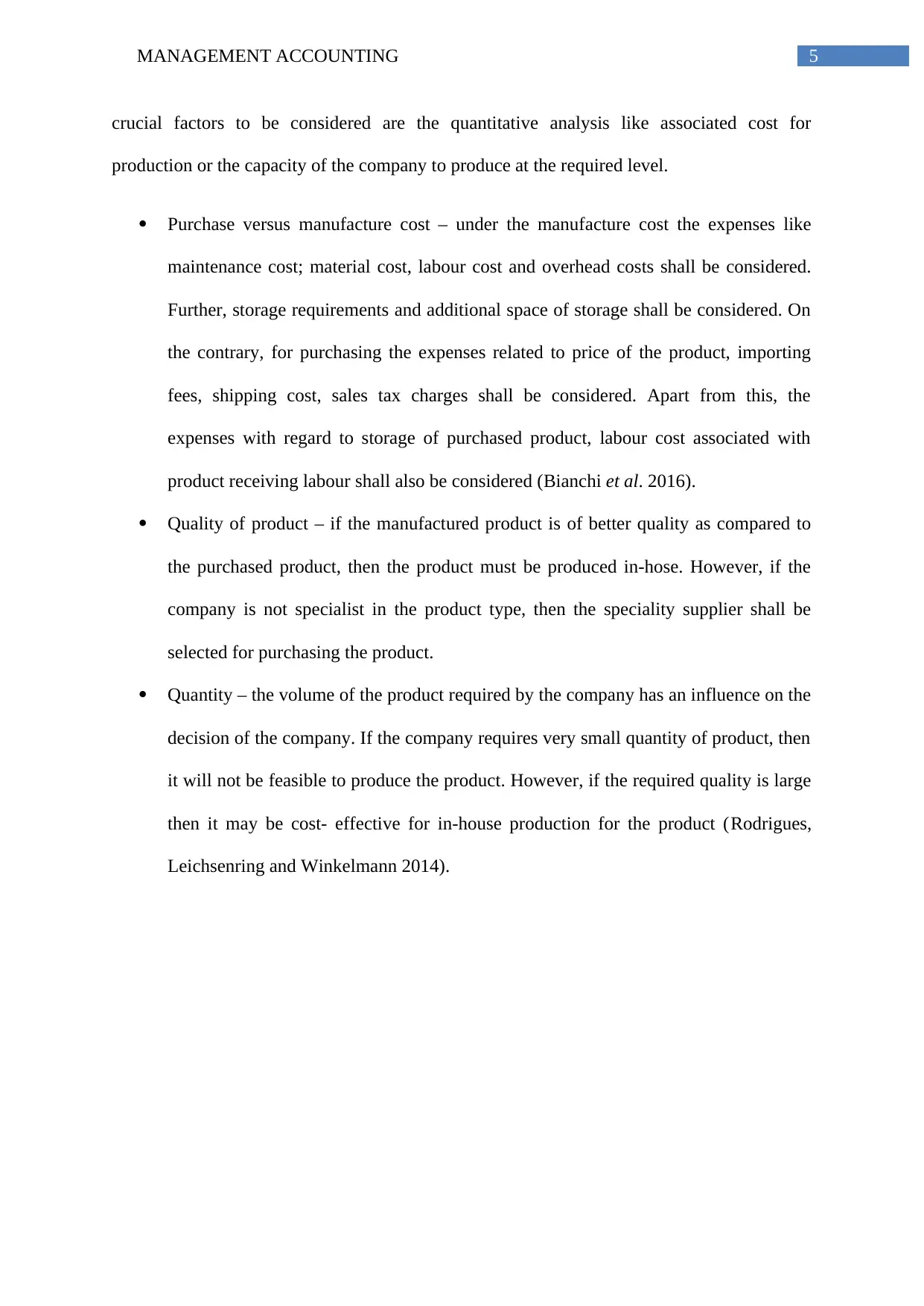
5MANAGEMENT ACCOUNTING
crucial factors to be considered are the quantitative analysis like associated cost for
production or the capacity of the company to produce at the required level.
Purchase versus manufacture cost – under the manufacture cost the expenses like
maintenance cost; material cost, labour cost and overhead costs shall be considered.
Further, storage requirements and additional space of storage shall be considered. On
the contrary, for purchasing the expenses related to price of the product, importing
fees, shipping cost, sales tax charges shall be considered. Apart from this, the
expenses with regard to storage of purchased product, labour cost associated with
product receiving labour shall also be considered (Bianchi et al. 2016).
Quality of product – if the manufactured product is of better quality as compared to
the purchased product, then the product must be produced in-hose. However, if the
company is not specialist in the product type, then the speciality supplier shall be
selected for purchasing the product.
Quantity – the volume of the product required by the company has an influence on the
decision of the company. If the company requires very small quantity of product, then
it will not be feasible to produce the product. However, if the required quality is large
then it may be cost- effective for in-house production for the product (Rodrigues,
Leichsenring and Winkelmann 2014).
crucial factors to be considered are the quantitative analysis like associated cost for
production or the capacity of the company to produce at the required level.
Purchase versus manufacture cost – under the manufacture cost the expenses like
maintenance cost; material cost, labour cost and overhead costs shall be considered.
Further, storage requirements and additional space of storage shall be considered. On
the contrary, for purchasing the expenses related to price of the product, importing
fees, shipping cost, sales tax charges shall be considered. Apart from this, the
expenses with regard to storage of purchased product, labour cost associated with
product receiving labour shall also be considered (Bianchi et al. 2016).
Quality of product – if the manufactured product is of better quality as compared to
the purchased product, then the product must be produced in-hose. However, if the
company is not specialist in the product type, then the speciality supplier shall be
selected for purchasing the product.
Quantity – the volume of the product required by the company has an influence on the
decision of the company. If the company requires very small quantity of product, then
it will not be feasible to produce the product. However, if the required quality is large
then it may be cost- effective for in-house production for the product (Rodrigues,
Leichsenring and Winkelmann 2014).
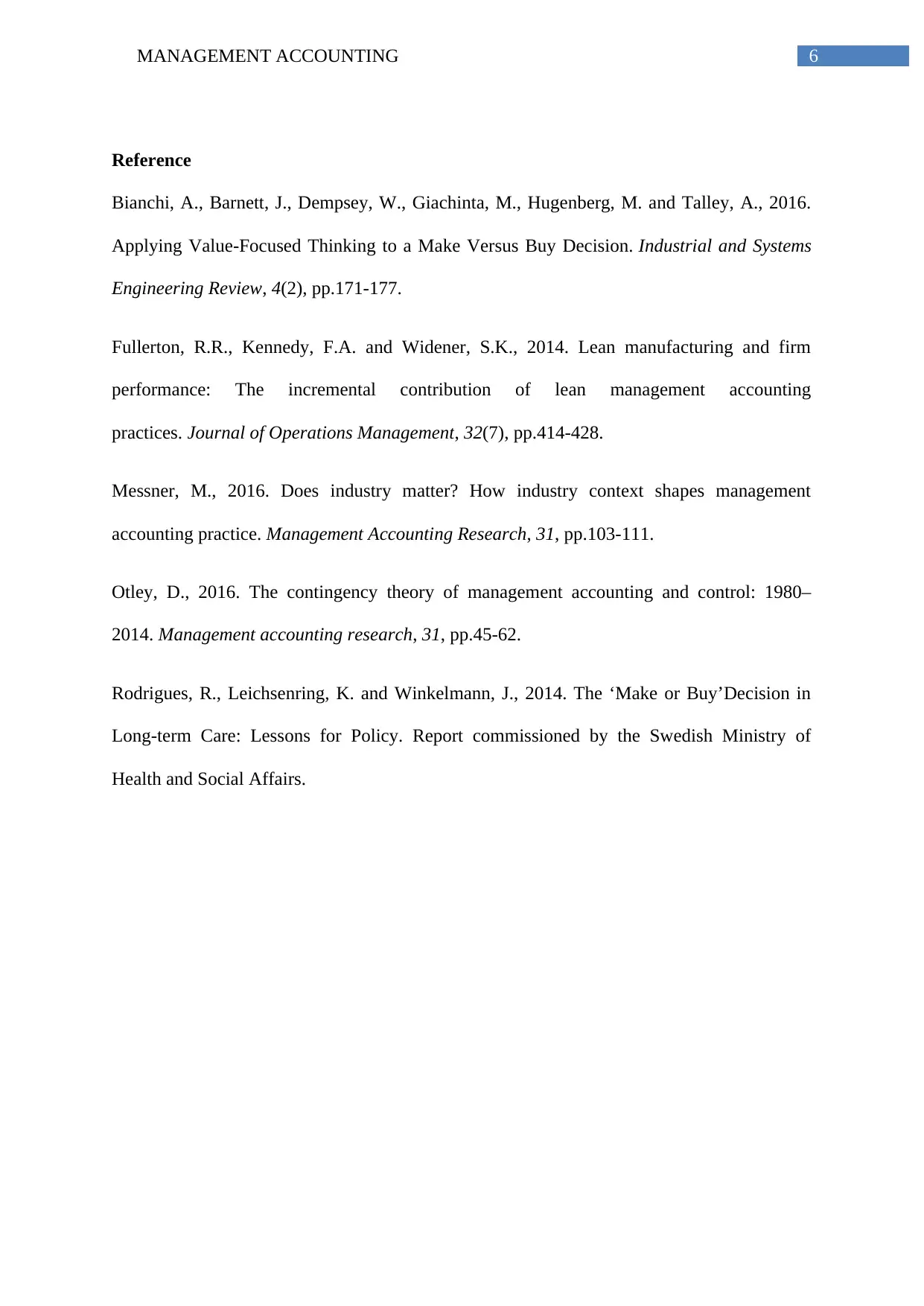
6MANAGEMENT ACCOUNTING
Reference
Bianchi, A., Barnett, J., Dempsey, W., Giachinta, M., Hugenberg, M. and Talley, A., 2016.
Applying Value-Focused Thinking to a Make Versus Buy Decision. Industrial and Systems
Engineering Review, 4(2), pp.171-177.
Fullerton, R.R., Kennedy, F.A. and Widener, S.K., 2014. Lean manufacturing and firm
performance: The incremental contribution of lean management accounting
practices. Journal of Operations Management, 32(7), pp.414-428.
Messner, M., 2016. Does industry matter? How industry context shapes management
accounting practice. Management Accounting Research, 31, pp.103-111.
Otley, D., 2016. The contingency theory of management accounting and control: 1980–
2014. Management accounting research, 31, pp.45-62.
Rodrigues, R., Leichsenring, K. and Winkelmann, J., 2014. The ‘Make or Buy’Decision in
Long-term Care: Lessons for Policy. Report commissioned by the Swedish Ministry of
Health and Social Affairs.
Reference
Bianchi, A., Barnett, J., Dempsey, W., Giachinta, M., Hugenberg, M. and Talley, A., 2016.
Applying Value-Focused Thinking to a Make Versus Buy Decision. Industrial and Systems
Engineering Review, 4(2), pp.171-177.
Fullerton, R.R., Kennedy, F.A. and Widener, S.K., 2014. Lean manufacturing and firm
performance: The incremental contribution of lean management accounting
practices. Journal of Operations Management, 32(7), pp.414-428.
Messner, M., 2016. Does industry matter? How industry context shapes management
accounting practice. Management Accounting Research, 31, pp.103-111.
Otley, D., 2016. The contingency theory of management accounting and control: 1980–
2014. Management accounting research, 31, pp.45-62.
Rodrigues, R., Leichsenring, K. and Winkelmann, J., 2014. The ‘Make or Buy’Decision in
Long-term Care: Lessons for Policy. Report commissioned by the Swedish Ministry of
Health and Social Affairs.
1 out of 7
Related Documents
![[object Object]](/_next/image/?url=%2F_next%2Fstatic%2Fmedia%2Flogo.6d15ce61.png&w=640&q=75)
Your All-in-One AI-Powered Toolkit for Academic Success.
+13062052269
info@desklib.com
Available 24*7 on WhatsApp / Email
Unlock your academic potential
© 2024 | Zucol Services PVT LTD | All rights reserved.