UGB106 Management Accounting: Costing, Budgeting, and Analysis
VerifiedAdded on 2023/06/18
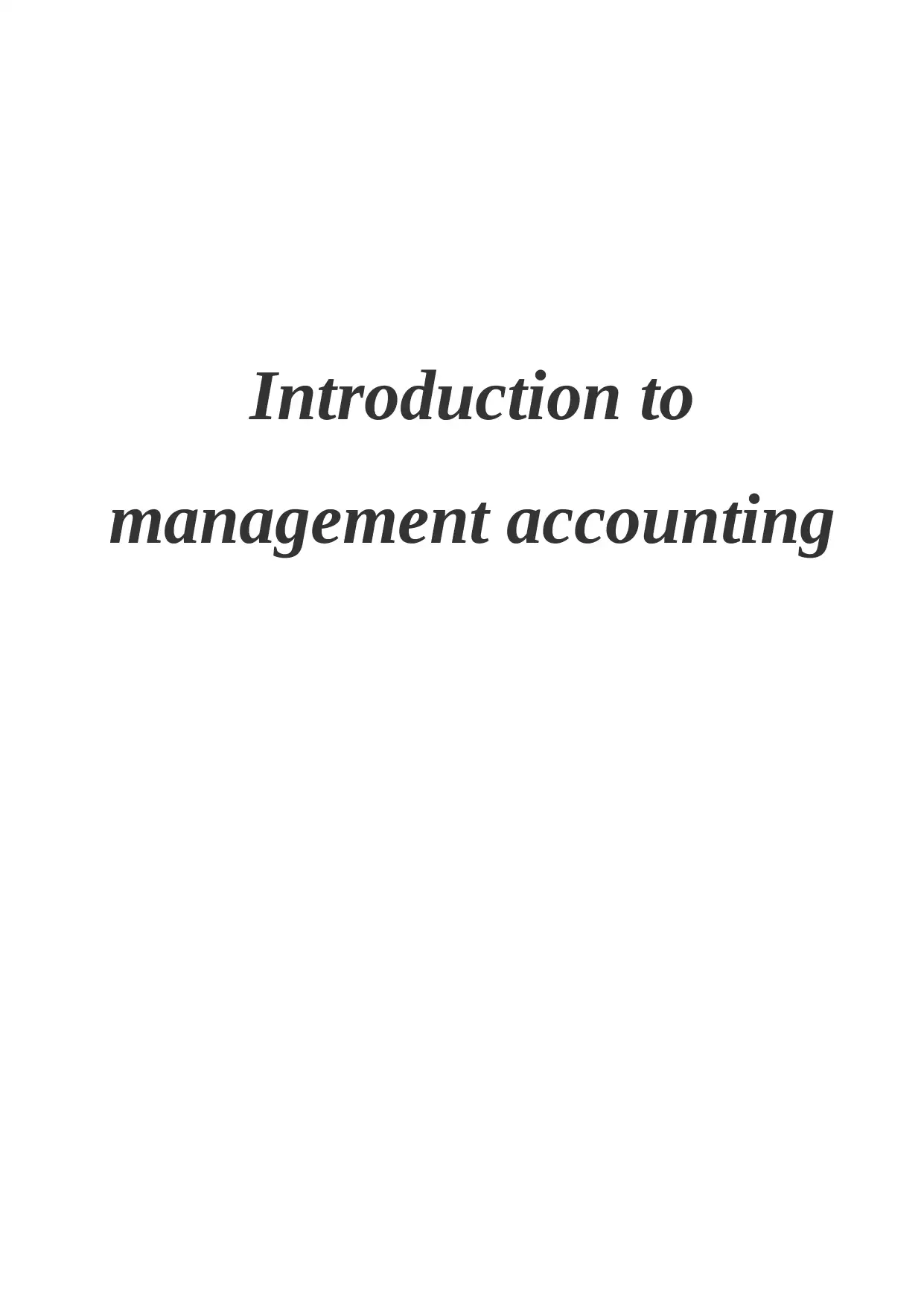
management accounting
Paraphrase This Document

Contents................................................................................................................................................2
Part 1.....................................................................................................................................................3
Question 2: Plaistead Plc..................................................................................................................3
Part 2.....................................................................................................................................................8
Question 3: Crawford Plc.................................................................................................................8
Part 3.....................................................................................................................................................3
Question 4:........................................................................................................................................3
REFERENCES.....................................................................................................................................9
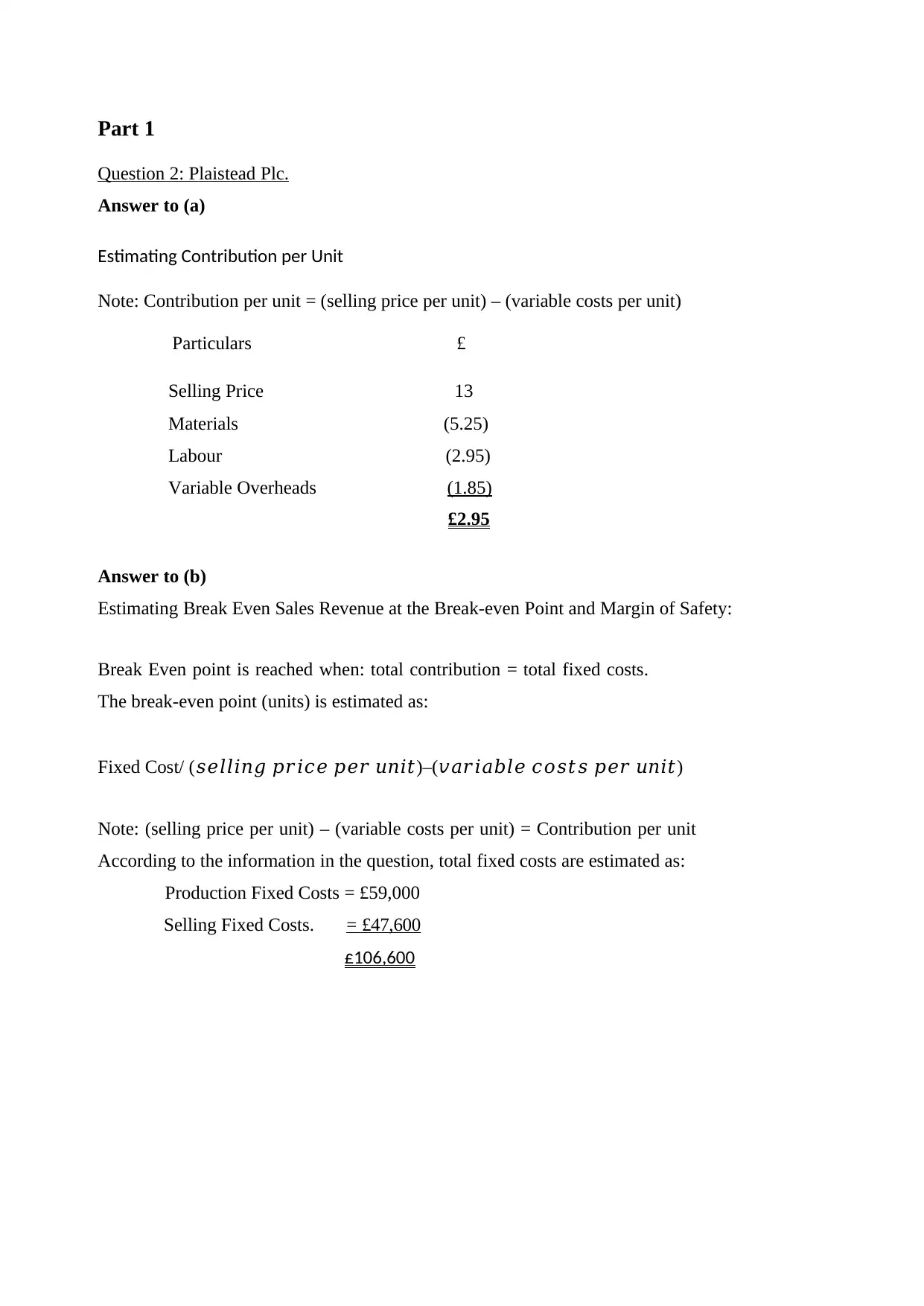
Question 2: Plaistead Plc.
Answer to (a)
Estimating Contribution per Unit
Note: Contribution per unit = (selling price per unit) – (variable costs per unit)
Particulars £
Selling Price 13
Materials (5.25)
Labour (2.95)
Variable Overheads (1.85)
£2.95
Answer to (b)
Estimating Break Even Sales Revenue at the Break-even Point and Margin of Safety:
Break Even point is reached when: total contribution = total fixed costs.
The break-even point (units) is estimated as:
Fixed Cost/ (𝑠𝑒𝑙𝑙𝑖𝑛𝑔 𝑝𝑟𝑖𝑐𝑒 𝑝𝑒𝑟 𝑢𝑛𝑖𝑡)–(𝑣𝑎𝑟𝑖𝑎𝑏𝑙𝑒 𝑐𝑜𝑠𝑡𝑠 𝑝𝑒𝑟 𝑢𝑛𝑖𝑡)
Note: (selling price per unit) – (variable costs per unit) = Contribution per unit
According to the information in the question, total fixed costs are estimated as:
Production Fixed Costs = £59,000
Selling Fixed Costs. = £47,600
£106,600
⊘ This is a preview!⊘
Do you want full access?
Subscribe today to unlock all pages.

Trusted by 1+ million students worldwide
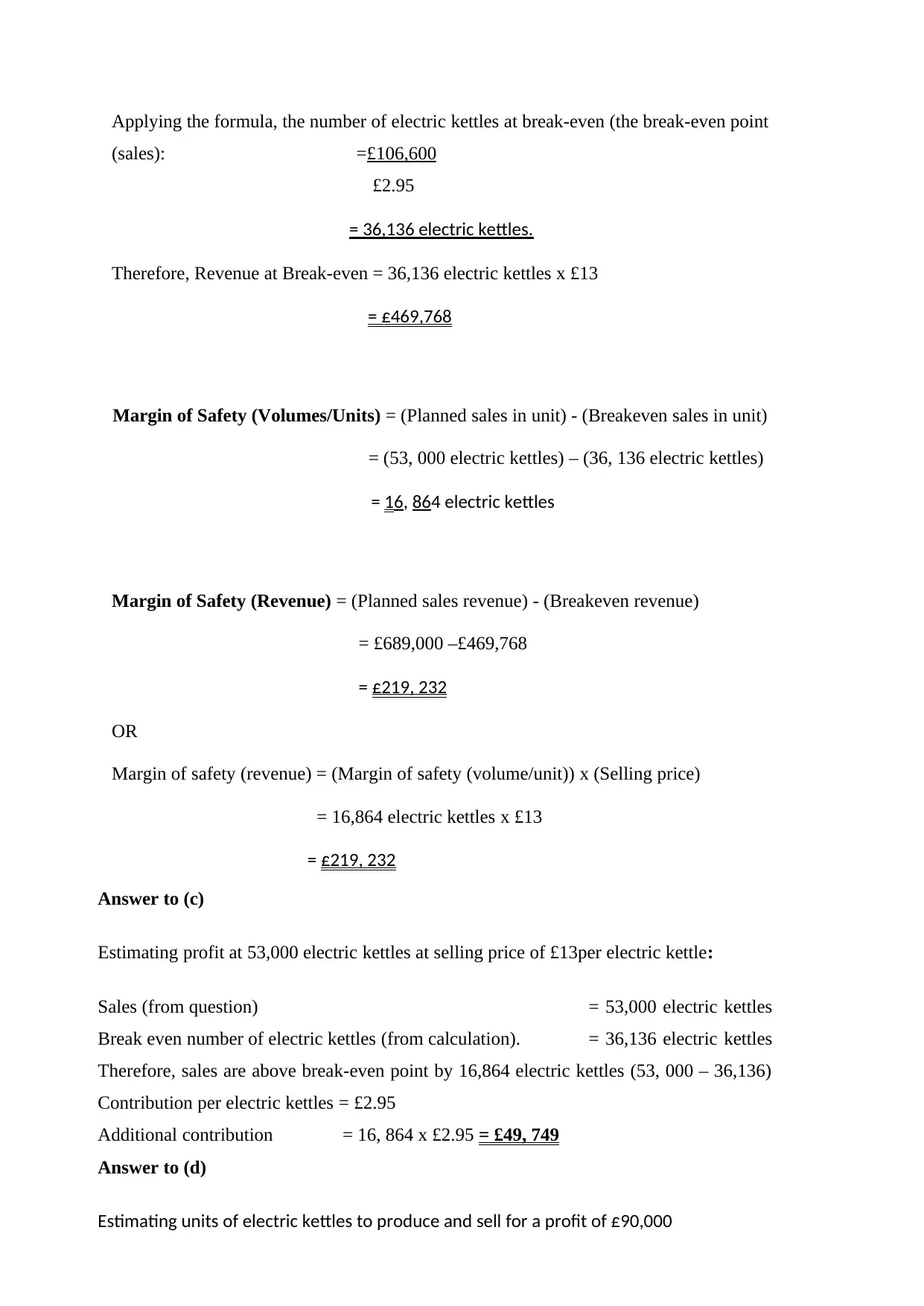
(sales): =£106,600
£2.95
= 36,136 electric kettles.
Therefore, Revenue at Break-even = 36,136 electric kettles x £13
= £469,768
Margin of Safety (Volumes/Units) = (Planned sales in unit) - (Breakeven sales in unit)
= (53, 000 electric kettles) – (36, 136 electric kettles)
= 16, 864 electric kettles
Margin of Safety (Revenue) = (Planned sales revenue) - (Breakeven revenue)
= £689,000 –£469,768
= £219, 232
OR
Margin of safety (revenue) = (Margin of safety (volume/unit)) x (Selling price)
= 16,864 electric kettles x £13
= £219, 232
Answer to (c)
Estimating profit at 53,000 electric kettles at selling price of £13per electric kettle:
Sales (from question) = 53,000 electric kettles
Break even number of electric kettles (from calculation). = 36,136 electric kettles
Therefore, sales are above break-even point by 16,864 electric kettles (53, 000 – 36,136)
Contribution per electric kettles = £2.95
Additional contribution = 16, 864 x £2.95 = £49, 749
Answer to (d)
Estimating units of electric kettles to produce and sell for a profit of £90,000
Paraphrase This Document
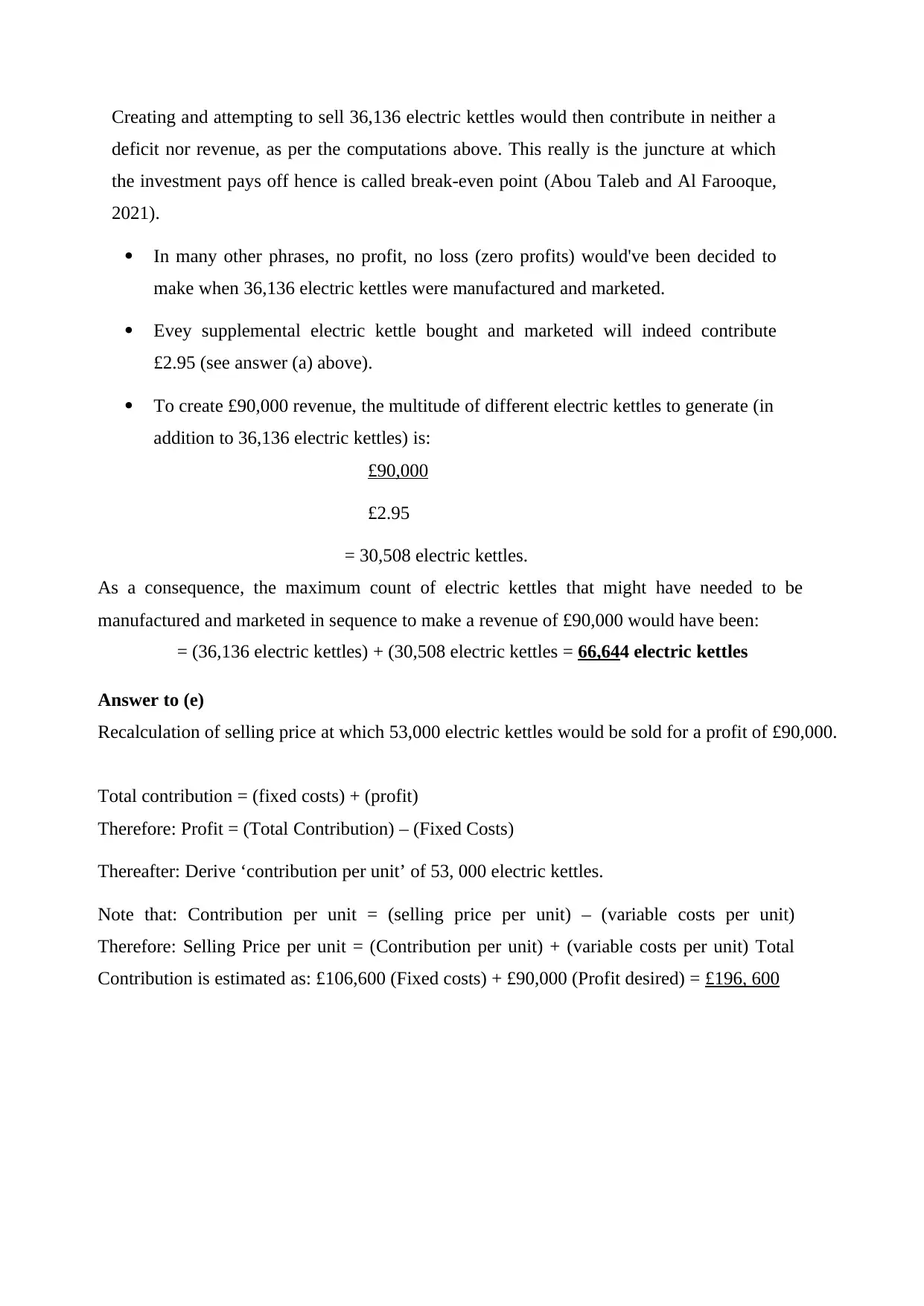
deficit nor revenue, as per the computations above. This really is the juncture at which
the investment pays off hence is called break-even point (Abou Taleb and Al Farooque,
2021).
In many other phrases, no profit, no loss (zero profits) would've been decided to
make when 36,136 electric kettles were manufactured and marketed.
Evey supplemental electric kettle bought and marketed will indeed contribute
£2.95 (see answer (a) above).
To create £90,000 revenue, the multitude of different electric kettles to generate (in
addition to 36,136 electric kettles) is:
£90,000
£2.95
= 30,508 electric kettles.
As a consequence, the maximum count of electric kettles that might have needed to be
manufactured and marketed in sequence to make a revenue of £90,000 would have been:
= (36,136 electric kettles) + (30,508 electric kettles = 66,644 electric kettles
Answer to (e)
Recalculation of selling price at which 53,000 electric kettles would be sold for a profit of £90,000.
Total contribution = (fixed costs) + (profit)
Therefore: Profit = (Total Contribution) – (Fixed Costs)
Thereafter: Derive ‘contribution per unit’ of 53, 000 electric kettles.
Note that: Contribution per unit = (selling price per unit) – (variable costs per unit)
Therefore: Selling Price per unit = (Contribution per unit) + (variable costs per unit) Total
Contribution is estimated as: £106,600 (Fixed costs) + £90,000 (Profit desired) = £196, 600
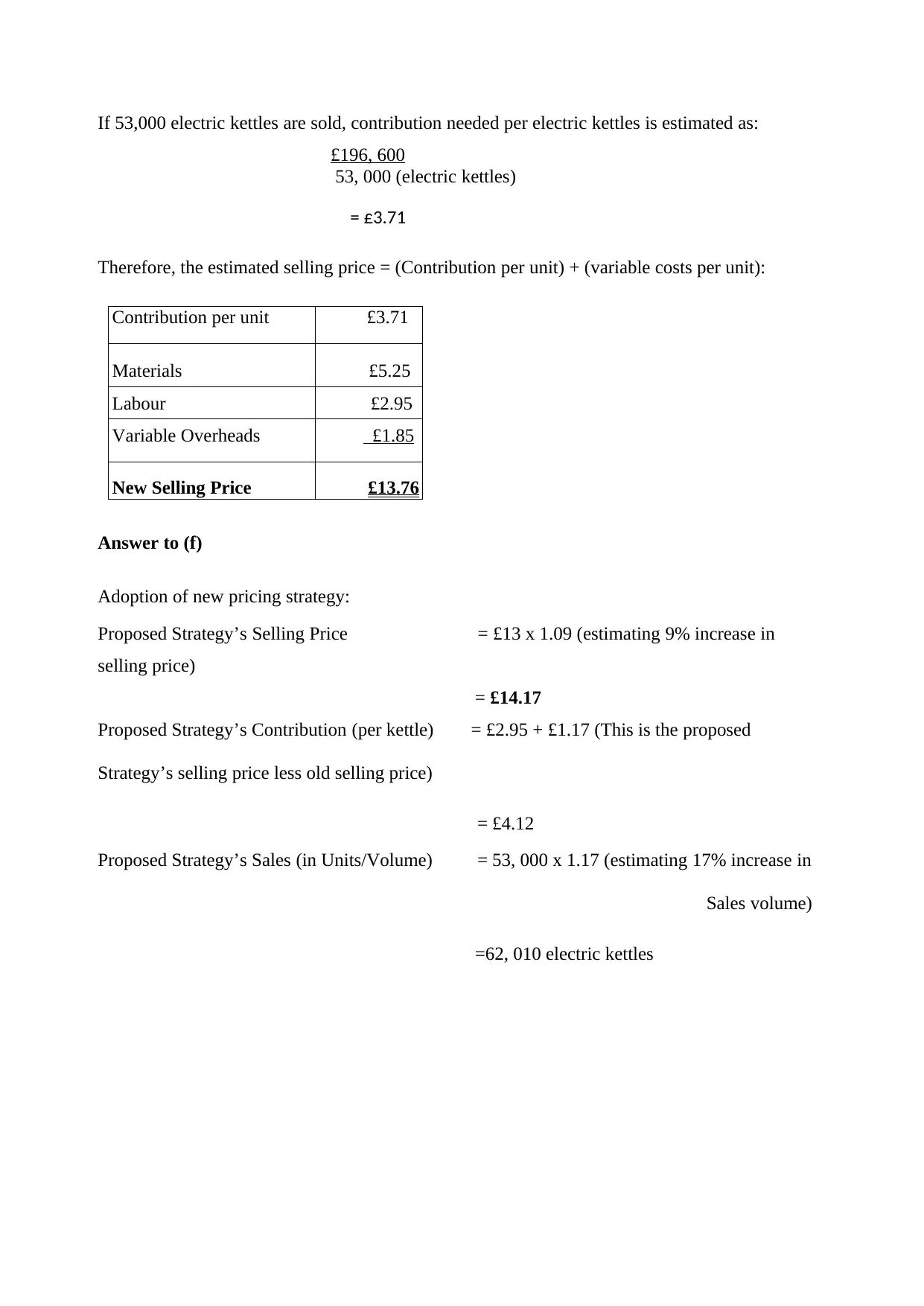
£196, 600
53, 000 (electric kettles)
= £3.71
Therefore, the estimated selling price = (Contribution per unit) + (variable costs per unit):
Contribution per unit £3.71
Materials £5.25
Labour £2.95
Variable Overheads £1.85
New Selling Price £13.76
Answer to (f)
Adoption of new pricing strategy:
Proposed Strategy’s Selling Price = £13 x 1.09 (estimating 9% increase in
selling price)
= £14.17
Proposed Strategy’s Contribution (per kettle) = £2.95 + £1.17 (This is the proposed
Strategy’s selling price less old selling price)
= £4.12
Proposed Strategy’s Sales (in Units/Volume) = 53, 000 x 1.17 (estimating 17% increase in
Sales volume)
=62, 010 electric kettles
⊘ This is a preview!⊘
Do you want full access?
Subscribe today to unlock all pages.

Trusted by 1+ million students worldwide
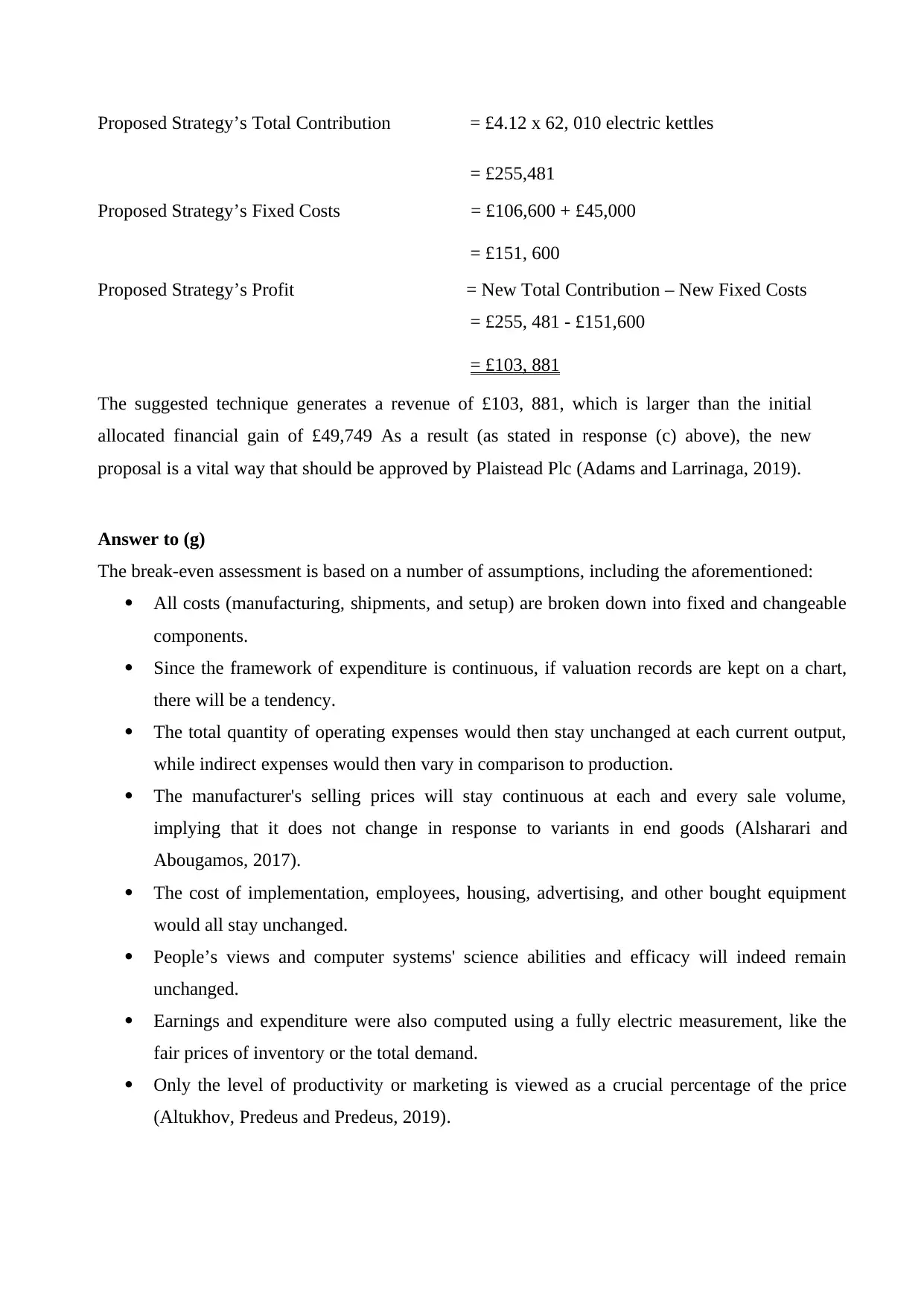
= £255,481
Proposed Strategy’s Fixed Costs = £106,600 + £45,000
= £151, 600
Proposed Strategy’s Profit = New Total Contribution – New Fixed Costs
= £255, 481 - £151,600
= £103, 881
The suggested technique generates a revenue of £103, 881, which is larger than the initial
allocated financial gain of £49,749 As a result (as stated in response (c) above), the new
proposal is a vital way that should be approved by Plaistead Plc (Adams and Larrinaga, 2019).
Answer to (g)
The break-even assessment is based on a number of assumptions, including the aforementioned:
All costs (manufacturing, shipments, and setup) are broken down into fixed and changeable
components.
Since the framework of expenditure is continuous, if valuation records are kept on a chart,
there will be a tendency.
The total quantity of operating expenses would then stay unchanged at each current output,
while indirect expenses would then vary in comparison to production.
The manufacturer's selling prices will stay continuous at each and every sale volume,
implying that it does not change in response to variants in end goods (Alsharari and
Abougamos, 2017).
The cost of implementation, employees, housing, advertising, and other bought equipment
would all stay unchanged.
People’s views and computer systems' science abilities and efficacy will indeed remain
unchanged.
Earnings and expenditure were also computed using a fully electric measurement, like the
fair prices of inventory or the total demand.
Only the level of productivity or marketing is viewed as a crucial percentage of the price
(Altukhov, Predeus and Predeus, 2019).
Paraphrase This Document
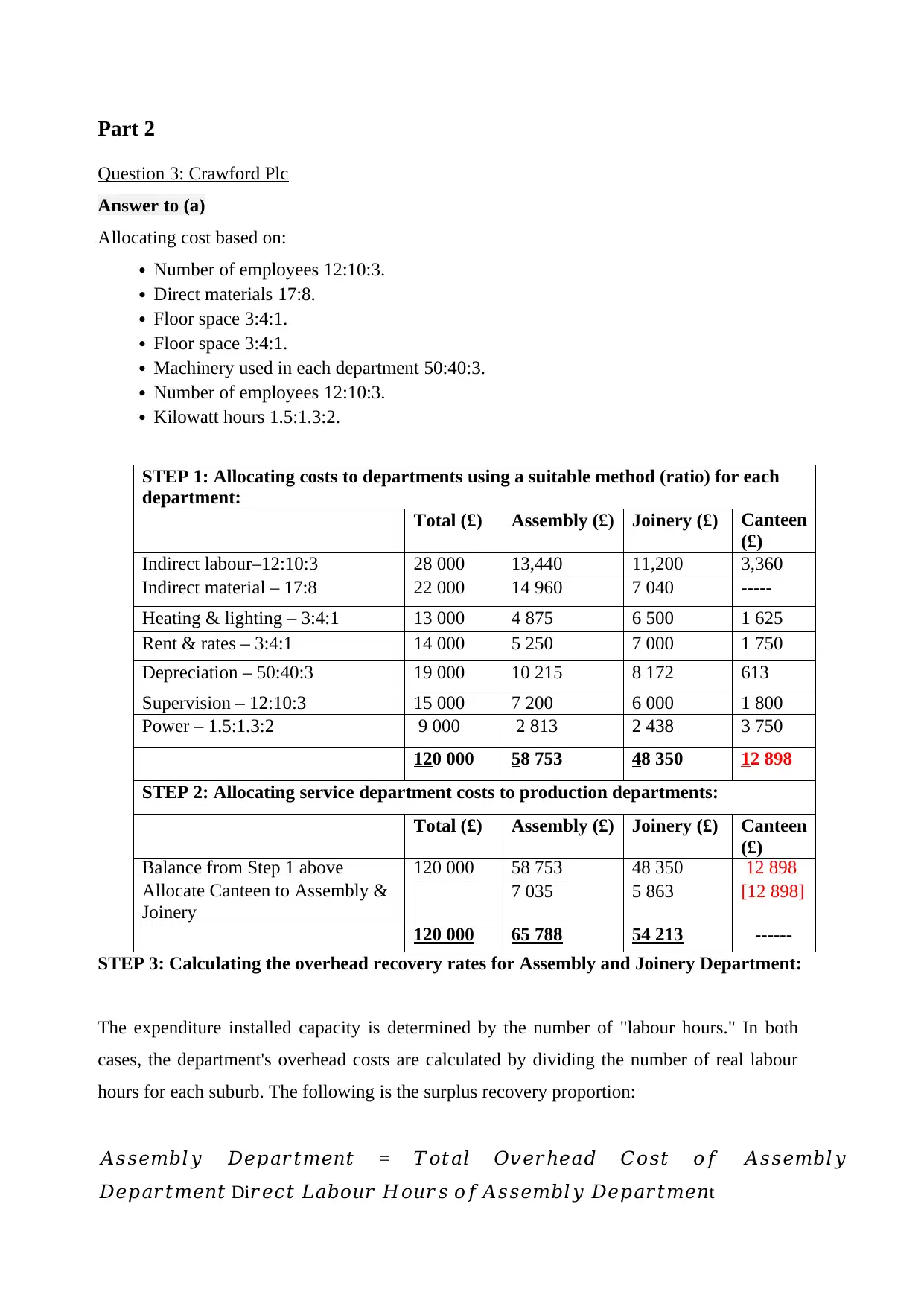
Question 3: Crawford Plc
Answer to (a)
Allocating cost based on:
Number of employees 12:10:3.
Direct materials 17:8.
Floor space 3:4:1.
Floor space 3:4:1.
Machinery used in each department 50:40:3.
Number of employees 12:10:3.
Kilowatt hours 1.5:1.3:2.
STEP 1: Allocating costs to departments using a suitable method (ratio) for each
department:
Total (£) Assembly (£) Joinery (£) Canteen
(£)
Indirect labour–12:10:3 28 000 13,440 11,200 3,360
Indirect material – 17:8 22 000 14 960 7 040 -----
Heating & lighting – 3:4:1 13 000 4 875 6 500 1 625
Rent & rates – 3:4:1 14 000 5 250 7 000 1 750
Depreciation – 50:40:3 19 000 10 215 8 172 613
Supervision – 12:10:3 15 000 7 200 6 000 1 800
Power – 1.5:1.3:2 9 000 2 813 2 438 3 750
120 000 58 753 48 350 12 898
STEP 2: Allocating service department costs to production departments:
Total (£) Assembly (£) Joinery (£) Canteen
(£)
Balance from Step 1 above 120 000 58 753 48 350 12 898
Allocate Canteen to Assembly &
Joinery
7 035 5 863 [12 898]
120 000 65 788 54 213 ------
STEP 3: Calculating the overhead recovery rates for Assembly and Joinery Department:
The expenditure installed capacity is determined by the number of "labour hours." In both
cases, the department's overhead costs are calculated by dividing the number of real labour
hours for each suburb. The following is the surplus recovery proportion:
𝐴𝑠𝑠𝑒𝑚𝑏𝑙𝑦 𝐷𝑒𝑝𝑎𝑟𝑡𝑚𝑒𝑛𝑡 = 𝑇𝑜𝑡𝑎𝑙 𝑂𝑣𝑒𝑟ℎ𝑒𝑎𝑑 𝐶𝑜𝑠𝑡 𝑜𝑓 𝐴𝑠𝑠𝑒𝑚𝑏𝑙𝑦
𝐷𝑒𝑝𝑎𝑟𝑡𝑚𝑒𝑛𝑡 Di𝑟𝑒𝑐𝑡 𝐿𝑎𝑏𝑜𝑢𝑟 𝐻𝑜𝑢𝑟𝑠 𝑜𝑓𝐴𝑠𝑠𝑒𝑚𝑏𝑙𝑦 𝐷𝑒𝑝𝑎𝑟𝑡𝑚𝑒𝑛t
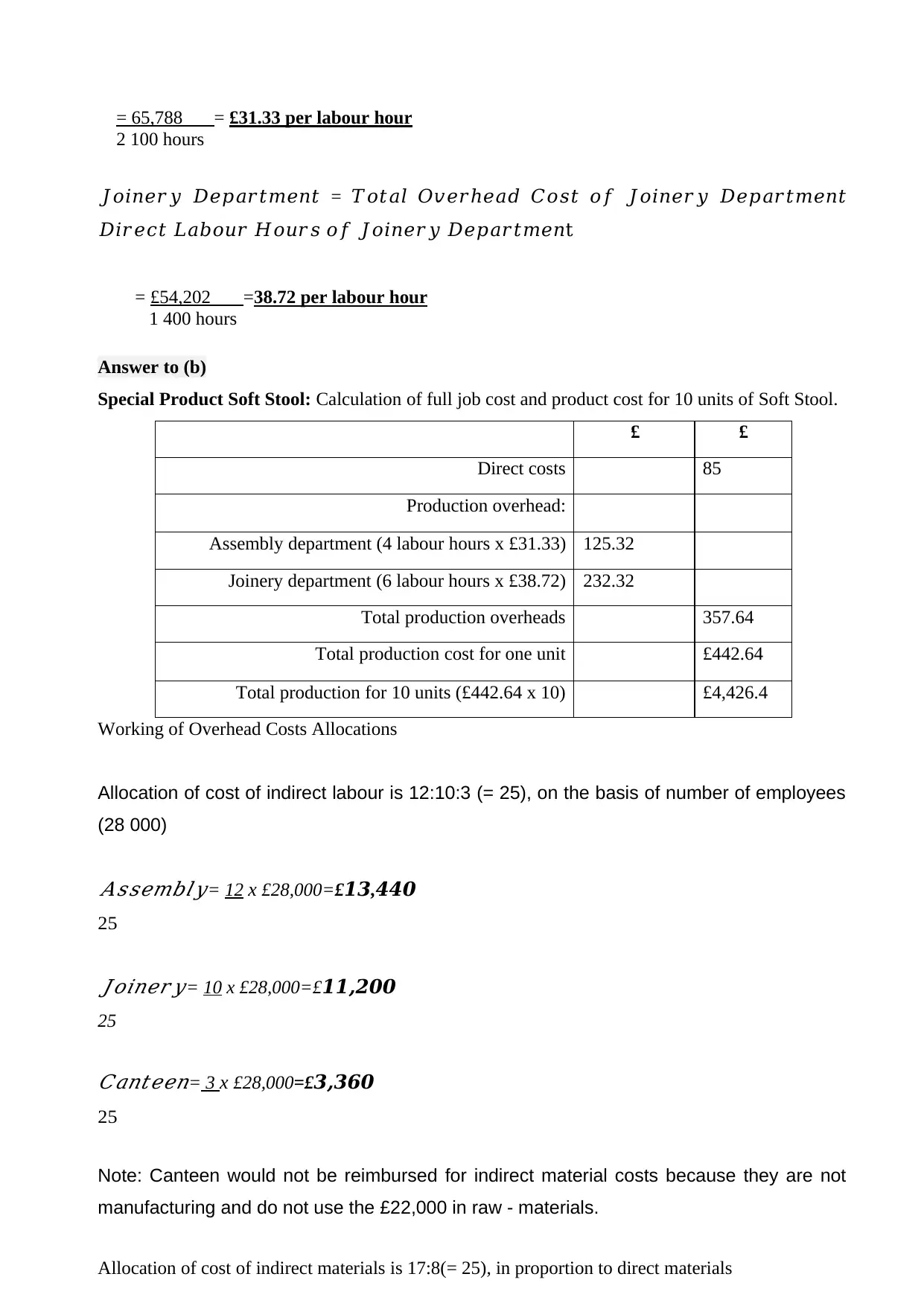
2 100 hours
𝐽𝑜𝑖𝑛𝑒𝑟𝑦 𝐷𝑒𝑝𝑎𝑟𝑡𝑚𝑒𝑛𝑡 = 𝑇𝑜𝑡𝑎𝑙 𝑂𝑣𝑒𝑟ℎ𝑒𝑎𝑑 𝐶𝑜𝑠𝑡 𝑜𝑓 𝐽𝑜𝑖𝑛𝑒𝑟𝑦 𝐷𝑒𝑝𝑎𝑟𝑡𝑚𝑒𝑛𝑡
𝐷𝑖𝑟𝑒𝑐𝑡 𝐿𝑎𝑏𝑜𝑢𝑟 𝐻𝑜𝑢𝑟𝑠 𝑜𝑓 𝐽𝑜𝑖𝑛𝑒𝑟𝑦 𝐷𝑒𝑝𝑎𝑟𝑡𝑚𝑒𝑛t
= £54,202 =38.72 per labour hour
1 400 hours
Answer to (b)
Special Product Soft Stool: Calculation of full job cost and product cost for 10 units of Soft Stool.
£ £
Direct costs 85
Production overhead:
Assembly department (4 labour hours x £31.33) 125.32
Joinery department (6 labour hours x £38.72) 232.32
Total production overheads 357.64
Total production cost for one unit £442.64
Total production for 10 units (£442.64 x 10) £4,426.4
Working of Overhead Costs Allocations
Allocation of cost of indirect labour is 12:10:3 (= 25), on the basis of number of employees
(28 000)
𝐴𝑠𝑠𝑒𝑚𝑏𝑙𝑦= 12 x £28,000=£13,440
25
𝐽𝑜𝑖𝑛𝑒𝑟𝑦= 10 x £28,000=£11,200
25
𝐶𝑎𝑛𝑡𝑒𝑒𝑛= 3 x £28,000=£3,360
25
Note: Canteen would not be reimbursed for indirect material costs because they are not
manufacturing and do not use the £22,000 in raw - materials.
Allocation of cost of indirect materials is 17:8(= 25), in proportion to direct materials
⊘ This is a preview!⊘
Do you want full access?
Subscribe today to unlock all pages.

Trusted by 1+ million students worldwide
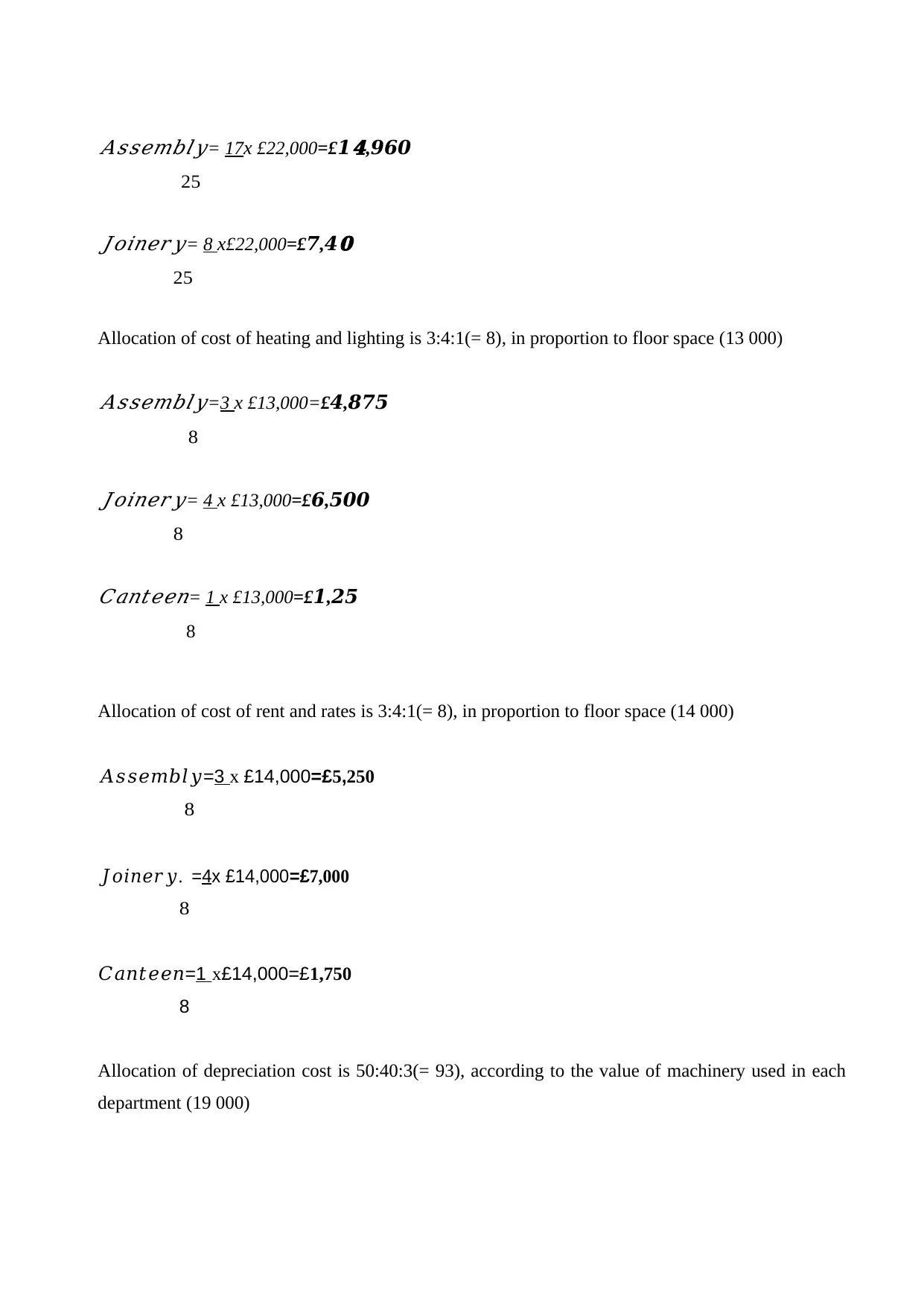
𝟒,960
25
𝐽𝑜𝑖𝑛𝑒𝑟𝑦= 8 x£22,000=£7,4
𝟎
25
Allocation of cost of heating and lighting is 3:4:1(= 8), in proportion to floor space (13 000)
𝐴𝑠𝑠𝑒𝑚𝑏𝑙𝑦=3 x £13,000=£4,875
8
𝐽𝑜𝑖𝑛𝑒𝑟𝑦= 4 x £13,000=£6,500
8𝐶𝑎𝑛𝑡𝑒𝑒𝑛= 1 x £13,000=£1,25
8
Allocation of cost of rent and rates is 3:4:1(= 8), in proportion to floor space (14 000)
𝐴𝑠𝑠𝑒𝑚𝑏𝑙𝑦=3 x £14,000=£5,250
8
𝐽𝑜𝑖𝑛𝑒𝑟𝑦. =4x £14,000=£7,000
8
𝐶𝑎𝑛𝑡𝑒𝑒𝑛=1 x£14,000=£1,750
8
Allocation of depreciation cost is 50:40:3(= 93), according to the value of machinery used in each
department (19 000)
Paraphrase This Document
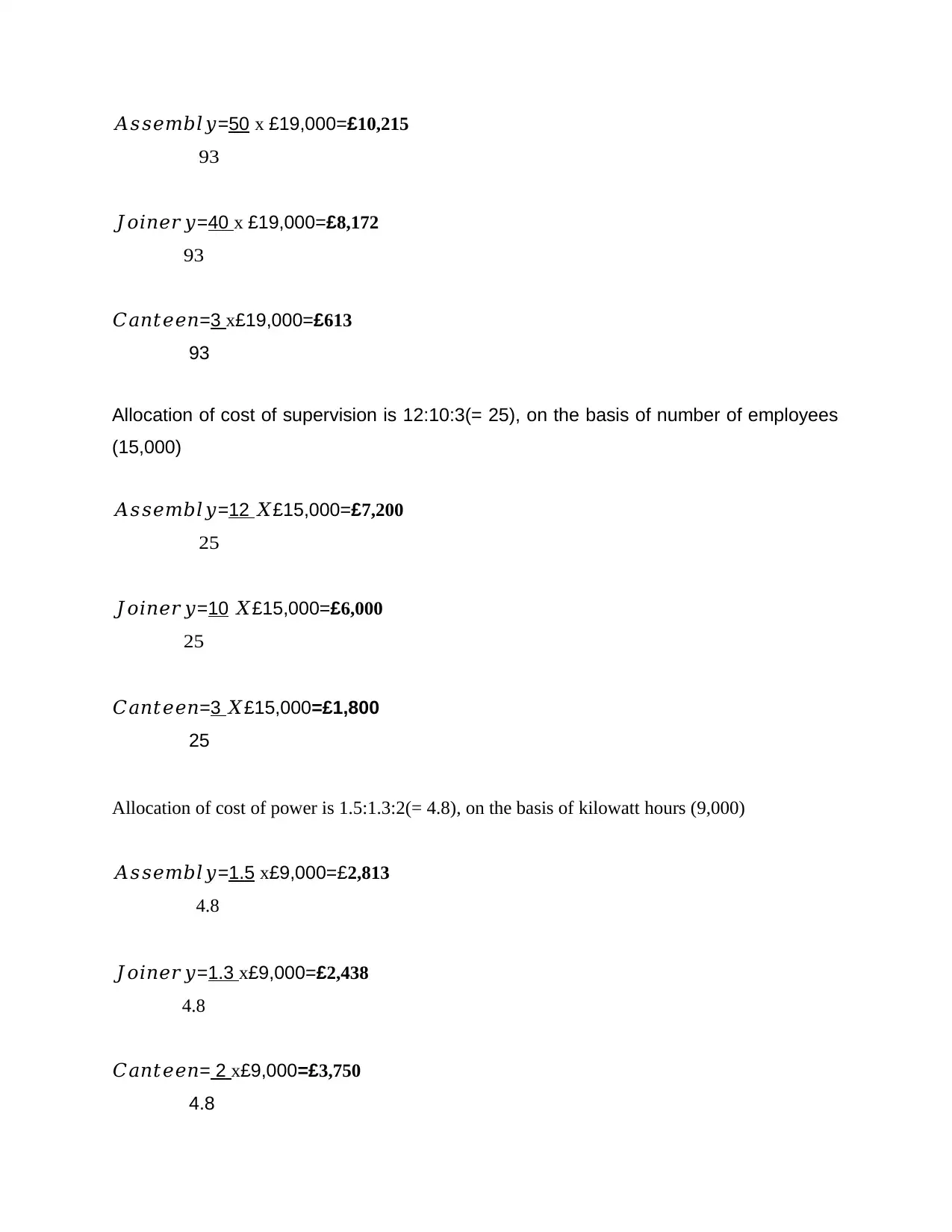
93
𝐽𝑜𝑖𝑛𝑒𝑟𝑦=40 x £19,000=£8,172
93
𝐶𝑎𝑛𝑡𝑒𝑒𝑛=3 x£19,000=£613
93
Allocation of cost of supervision is 12:10:3(= 25), on the basis of number of employees
(15,000)
𝐴𝑠𝑠𝑒𝑚𝑏𝑙𝑦=12 𝑋£15,000=£7,200
25
𝐽𝑜𝑖𝑛𝑒𝑟𝑦=10 𝑋£15,000=£6,000
25
𝐶𝑎𝑛𝑡𝑒𝑒𝑛=3 𝑋£15,000=£1,800
25
Allocation of cost of power is 1.5:1.3:2(= 4.8), on the basis of kilowatt hours (9,000)
𝐴𝑠𝑠𝑒𝑚𝑏𝑙𝑦=1.5 x£9,000=£2,813
4.8
𝐽𝑜𝑖𝑛𝑒𝑟𝑦=1.3 x£9,000=£2,438
4.8
𝐶𝑎𝑛𝑡𝑒𝑒𝑛= 2 x£9,000=£3,750
4.8
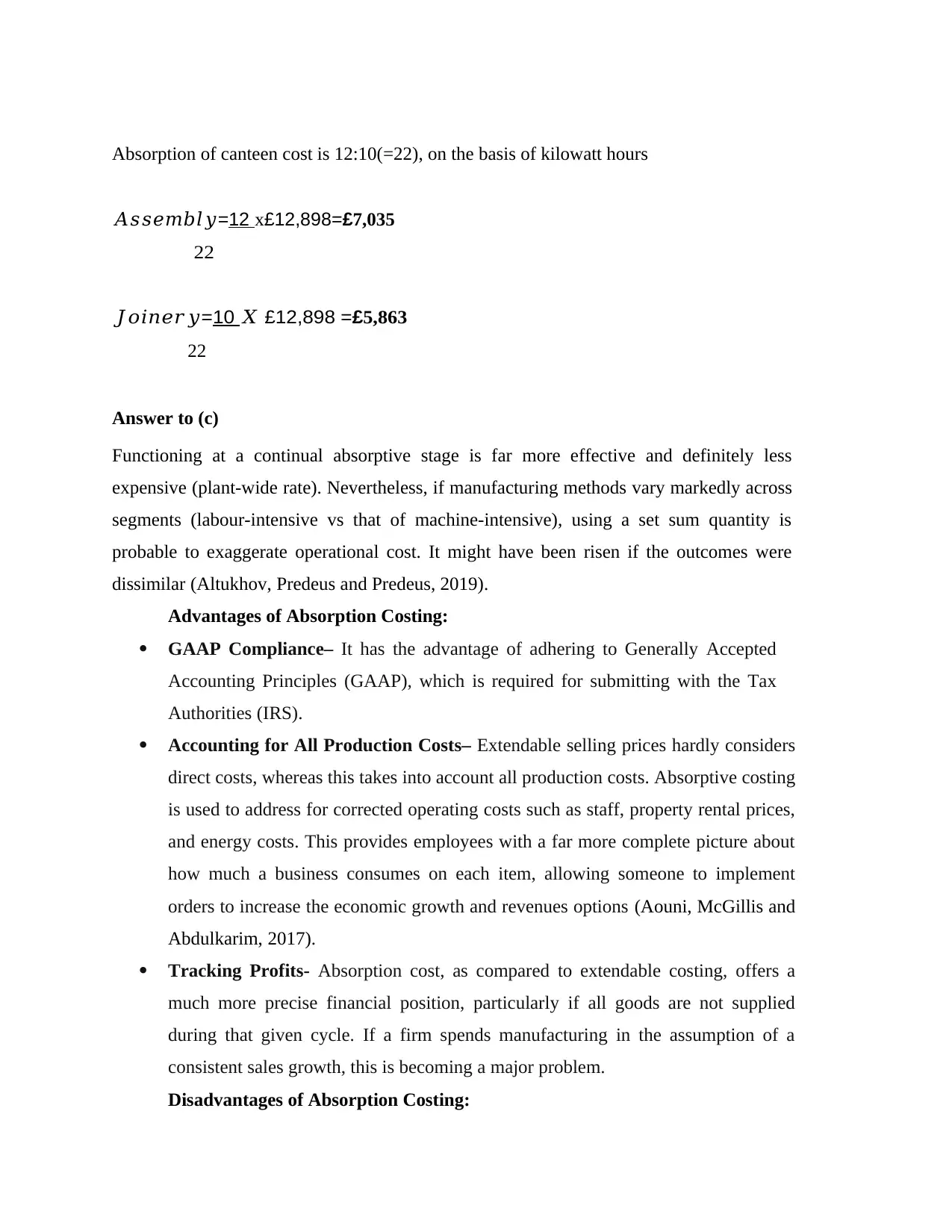
𝐴𝑠𝑠𝑒𝑚𝑏𝑙𝑦=12 x£12,898=£7,035
22
𝐽𝑜𝑖𝑛𝑒𝑟𝑦=10 𝑋 £12,898 =£5,863
22
Answer to (c)
Functioning at a continual absorptive stage is far more effective and definitely less
expensive (plant-wide rate). Nevertheless, if manufacturing methods vary markedly across
segments (labour-intensive vs that of machine-intensive), using a set sum quantity is
probable to exaggerate operational cost. It might have been risen if the outcomes were
dissimilar (Altukhov, Predeus and Predeus, 2019).
Advantages of Absorption Costing:
GAAP Compliance– It has the advantage of adhering to Generally Accepted
Accounting Principles (GAAP), which is required for submitting with the Tax
Authorities (IRS).
Accounting for All Production Costs– Extendable selling prices hardly considers
direct costs, whereas this takes into account all production costs. Absorptive costing
is used to address for corrected operating costs such as staff, property rental prices,
and energy costs. This provides employees with a far more complete picture about
how much a business consumes on each item, allowing someone to implement
orders to increase the economic growth and revenues options (Aouni, McGillis and
Abdulkarim, 2017).
Tracking Profits- Absorption cost, as compared to extendable costing, offers a
much more precise financial position, particularly if all goods are not supplied
during that given cycle. If a firm spends manufacturing in the assumption of a
consistent sales growth, this is becoming a major problem.
Disadvantages of Absorption Costing:
⊘ This is a preview!⊘
Do you want full access?
Subscribe today to unlock all pages.

Trusted by 1+ million students worldwide
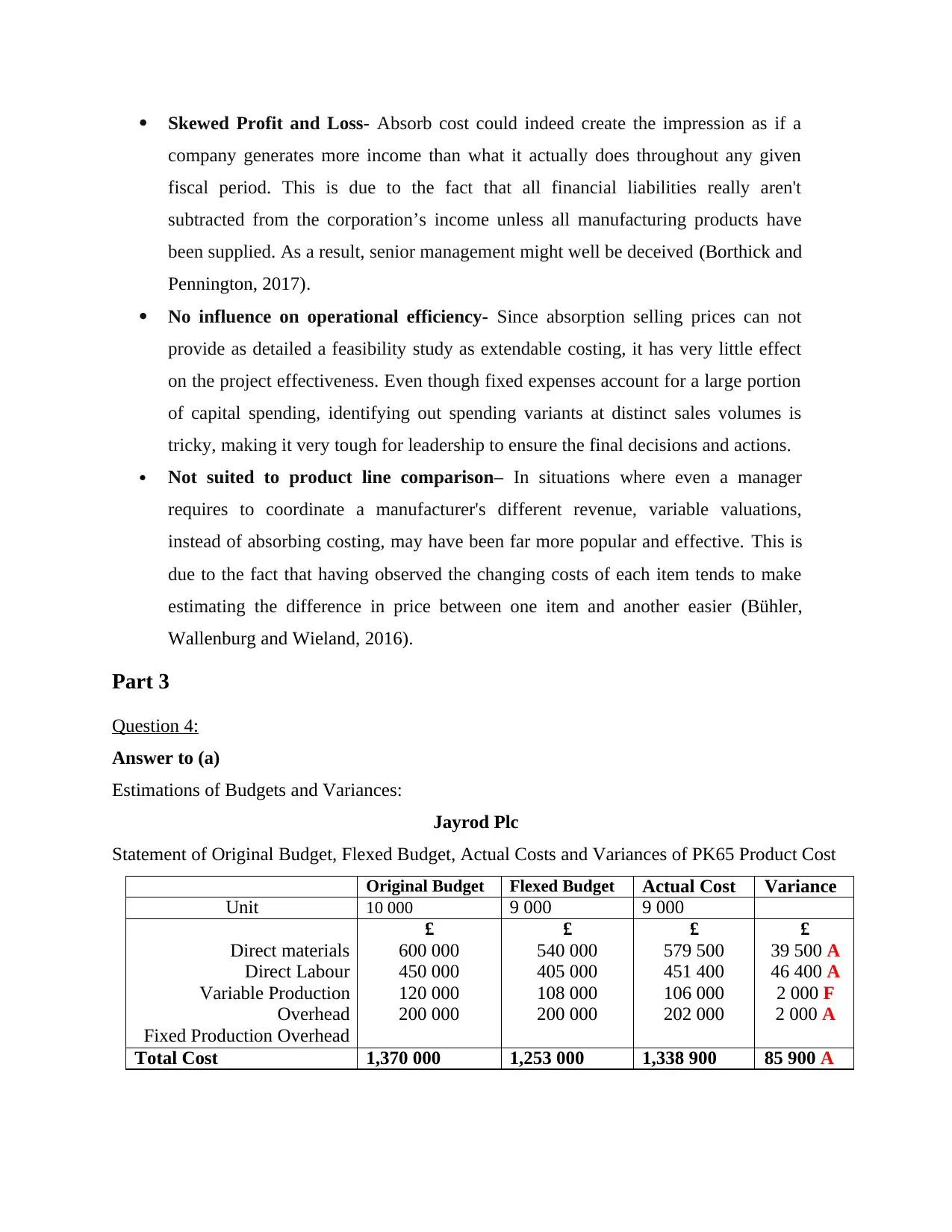
company generates more income than what it actually does throughout any given
fiscal period. This is due to the fact that all financial liabilities really aren't
subtracted from the corporation’s income unless all manufacturing products have
been supplied. As a result, senior management might well be deceived (Borthick and
Pennington, 2017).
No influence on operational efficiency- Since absorption selling prices can not
provide as detailed a feasibility study as extendable costing, it has very little effect
on the project effectiveness. Even though fixed expenses account for a large portion
of capital spending, identifying out spending variants at distinct sales volumes is
tricky, making it very tough for leadership to ensure the final decisions and actions.
Not suited to product line comparison– In situations where even a manager
requires to coordinate a manufacturer's different revenue, variable valuations,
instead of absorbing costing, may have been far more popular and effective. This is
due to the fact that having observed the changing costs of each item tends to make
estimating the difference in price between one item and another easier (Bühler,
Wallenburg and Wieland, 2016).
Part 3
Question 4:
Answer to (a)
Estimations of Budgets and Variances:
Jayrod Plc
Statement of Original Budget, Flexed Budget, Actual Costs and Variances of PK65 Product Cost
Original Budget Flexed Budget Actual Cost Variance
Unit 10 000 9 000 9 000
£ £ £ £
Direct materials 600 000 540 000 579 500 39 500 A
Direct Labour 450 000 405 000 451 400 46 400 A
Variable Production 120 000 108 000 106 000 2 000 F
Overhead 200 000 200 000 202 000 2 000 A
Fixed Production Overhead
Total Cost 1,370 000 1,253 000 1,338 900 85 900 A
Paraphrase This Document
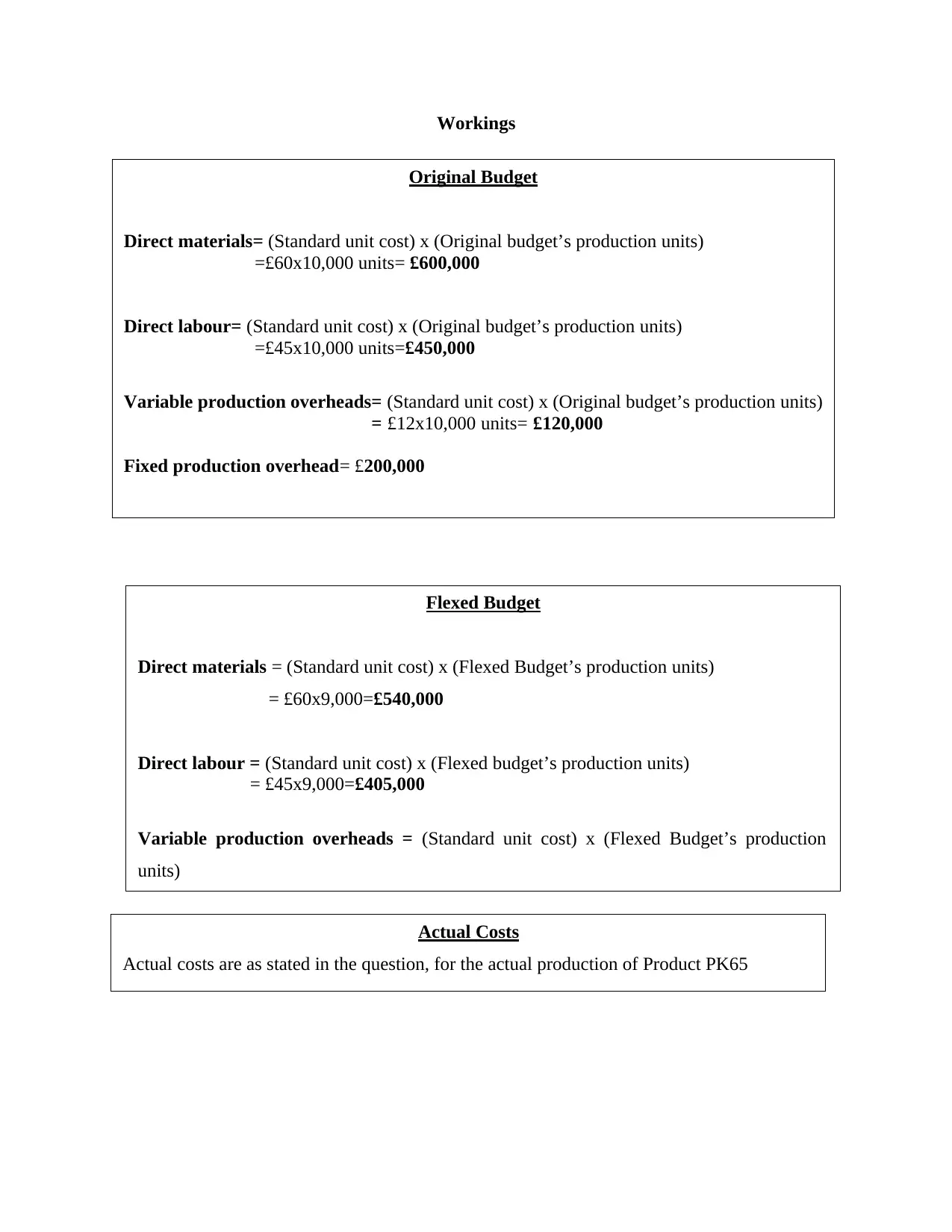
Direct materials= (Standard unit cost) x (Original budget’s production units)
=£60x10,000 units= £600,000
Direct labour= (Standard unit cost) x (Original budget’s production units)
=£45x10,000 units=£450,000
Variable production overheads= (Standard unit cost) x (Original budget’s production units)
= £12x10,000 units= £120,000
Fixed production overhead= £200,000
Actual Costs
Actual costs are as stated in the question, for the actual production of Product PK65
Workings
Flexed Budget
Direct materials = (Standard unit cost) x (Flexed Budget’s production units)
= £60x9,000=£540,000
Direct labour = (Standard unit cost) x (Flexed budget’s production units)
= £45x9,000=£405,000
Variable production overheads = (Standard unit cost) x (Flexed Budget’s production
units)
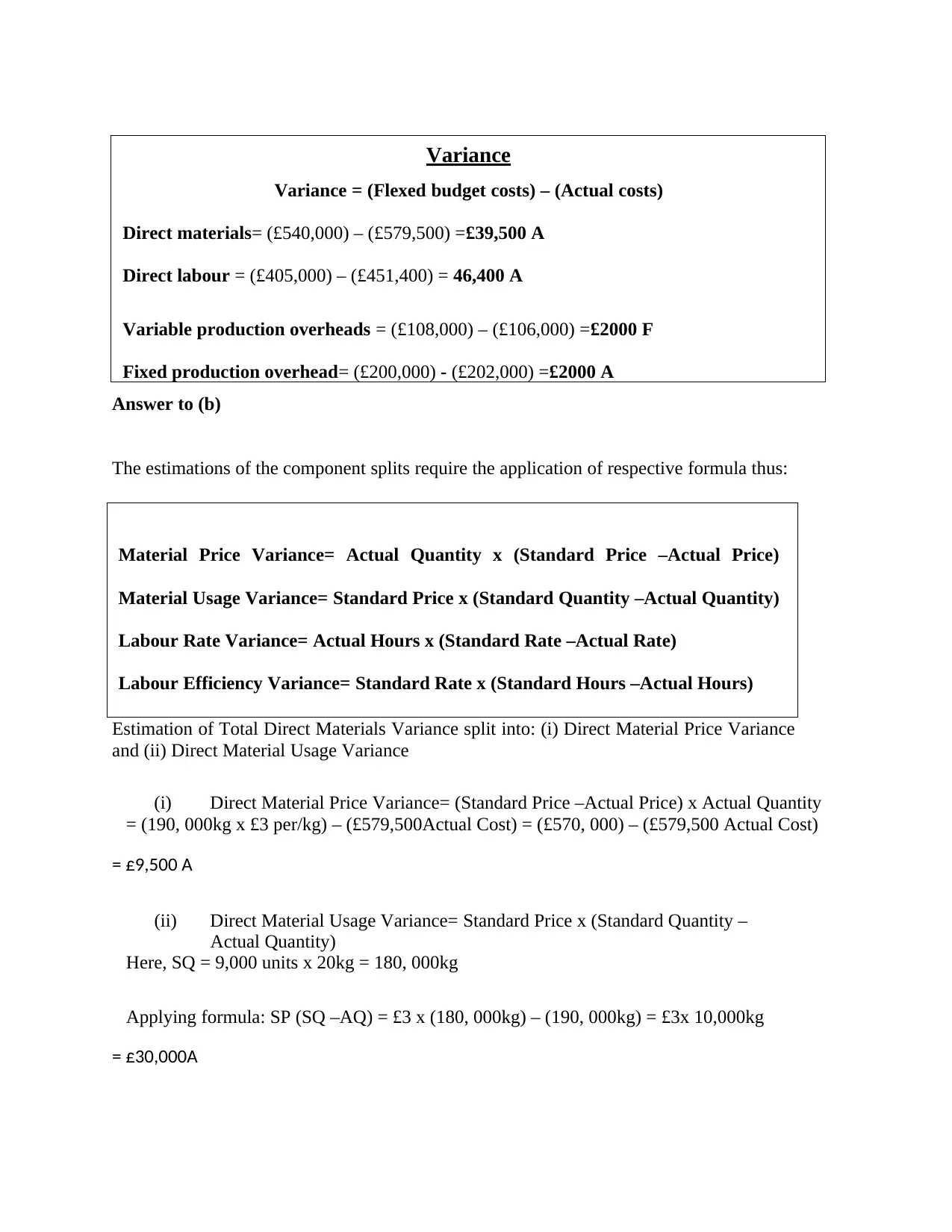
Variance = (Flexed budget costs) – (Actual costs)
Direct materials= (£540,000) – (£579,500) =£39,500 A
Direct labour = (£405,000) – (£451,400) = 46,400 A
Variable production overheads = (£108,000) – (£106,000) =£2000 F
Fixed production overhead= (£200,000) - (£202,000) =£2000 A
Material Price Variance= Actual Quantity x (Standard Price –Actual Price)
Material Usage Variance= Standard Price x (Standard Quantity –Actual Quantity)
Labour Rate Variance= Actual Hours x (Standard Rate –Actual Rate)
Labour Efficiency Variance= Standard Rate x (Standard Hours –Actual Hours)
Answer to (b)
The estimations of the component splits require the application of respective formula thus:
Estimation of Total Direct Materials Variance split into: (i) Direct Material Price Variance
and (ii) Direct Material Usage Variance
(i) Direct Material Price Variance= (Standard Price –Actual Price) x Actual Quantity
= (190, 000kg x £3 per/kg) – (£579,500Actual Cost) = (£570, 000) – (£579,500 Actual Cost)
= £9,500 A
(ii) Direct Material Usage Variance= Standard Price x (Standard Quantity –
Actual Quantity)
Here, SQ = 9,000 units x 20kg = 180, 000kg
Applying formula: SP (SQ –AQ) = £3 x (180, 000kg) – (190, 000kg) = £3x 10,000kg
= £30,000A
⊘ This is a preview!⊘
Do you want full access?
Subscribe today to unlock all pages.

Trusted by 1+ million students worldwide
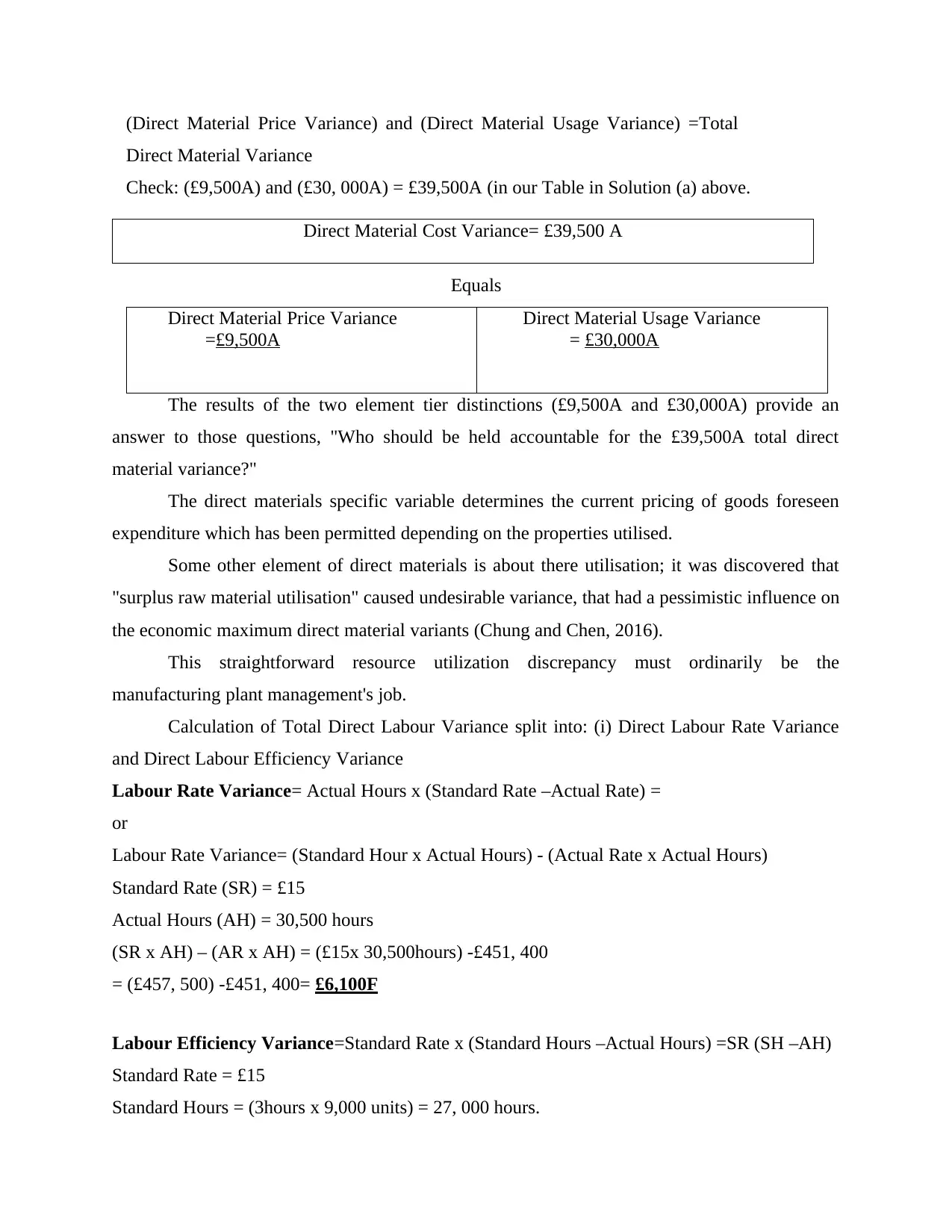
(Direct Material Price Variance) and (Direct Material Usage Variance) =Total
Direct Material Variance
Check: (£9,500A) and (£30, 000A) = £39,500A (in our Table in Solution (a) above.
Equals
Direct Material Price Variance
=£9,500A
Direct Material Usage Variance
= £30,000A
The results of the two element tier distinctions (£9,500A and £30,000A) provide an
answer to those questions, "Who should be held accountable for the £39,500A total direct
material variance?"
The direct materials specific variable determines the current pricing of goods foreseen
expenditure which has been permitted depending on the properties utilised.
Some other element of direct materials is about there utilisation; it was discovered that
"surplus raw material utilisation" caused undesirable variance, that had a pessimistic influence on
the economic maximum direct material variants (Chung and Chen, 2016).
This straightforward resource utilization discrepancy must ordinarily be the
manufacturing plant management's job.
Calculation of Total Direct Labour Variance split into: (i) Direct Labour Rate Variance
and Direct Labour Efficiency Variance
Labour Rate Variance= Actual Hours x (Standard Rate –Actual Rate) =
or
Labour Rate Variance= (Standard Hour x Actual Hours) - (Actual Rate x Actual Hours)
Standard Rate (SR) = £15
Actual Hours (AH) = 30,500 hours
(SR x AH) – (AR x AH) = (£15x 30,500hours) -£451, 400
= (£457, 500) -£451, 400= £6,100F
Labour Efficiency Variance=Standard Rate x (Standard Hours –Actual Hours) =SR (SH –AH)
Standard Rate = £15
Standard Hours = (3hours x 9,000 units) = 27, 000 hours.
Paraphrase This Document
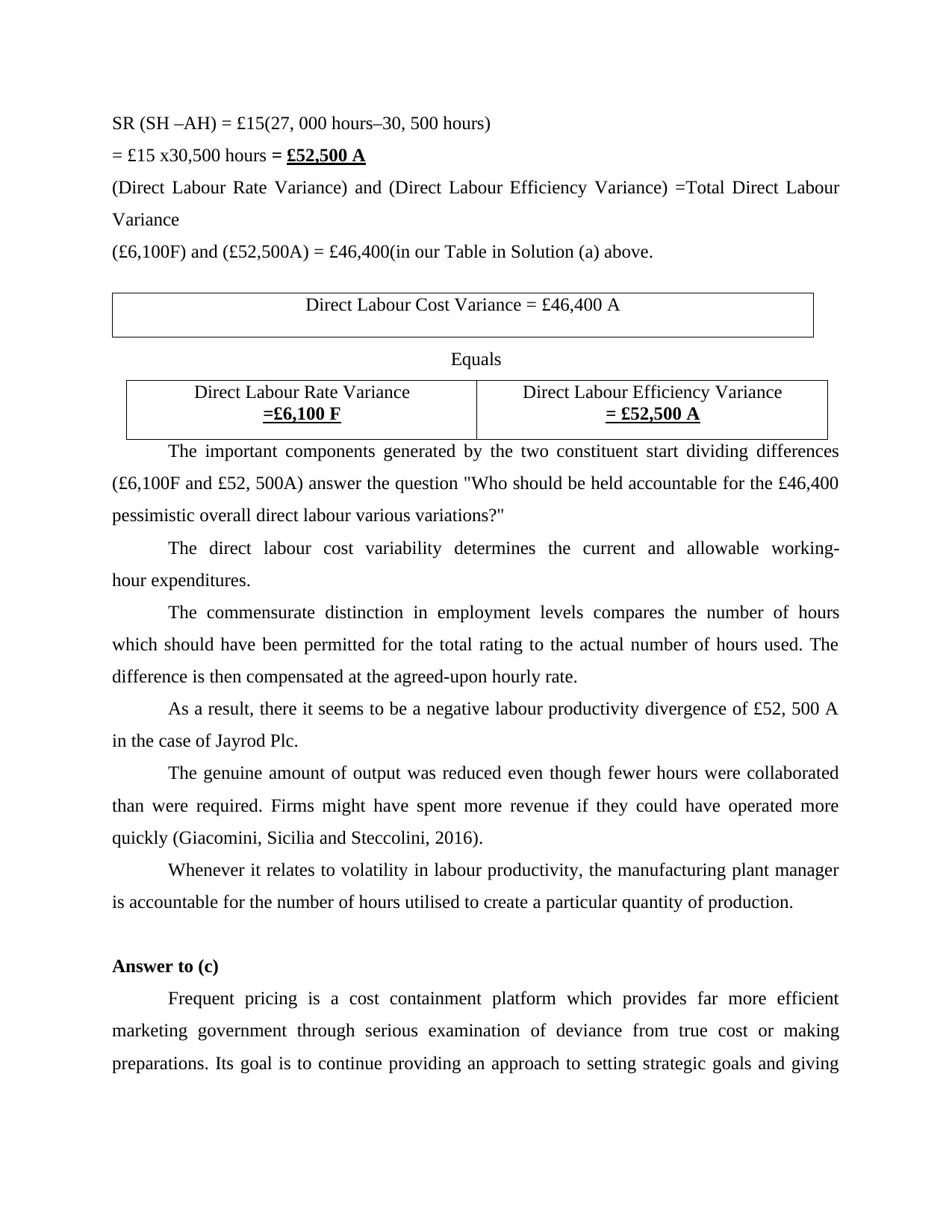
SR (SH –AH) = £15(27, 000 hours–30, 500 hours)
= £15 x30,500 hours = £52,500 A
(Direct Labour Rate Variance) and (Direct Labour Efficiency Variance) =Total Direct Labour
Variance
(£6,100F) and (£52,500A) = £46,400(in our Table in Solution (a) above.
Equals
Direct Labour Rate Variance
=£6,100 F
Direct Labour Efficiency Variance
= £52,500 A
The important components generated by the two constituent start dividing differences
(£6,100F and £52, 500A) answer the question "Who should be held accountable for the £46,400
pessimistic overall direct labour various variations?"
The direct labour cost variability determines the current and allowable working-
hour expenditures.
The commensurate distinction in employment levels compares the number of hours
which should have been permitted for the total rating to the actual number of hours used. The
difference is then compensated at the agreed-upon hourly rate.
As a result, there it seems to be a negative labour productivity divergence of £52, 500 A
in the case of Jayrod Plc.
The genuine amount of output was reduced even though fewer hours were collaborated
than were required. Firms might have spent more revenue if they could have operated more
quickly (Giacomini, Sicilia and Steccolini, 2016).
Whenever it relates to volatility in labour productivity, the manufacturing plant manager
is accountable for the number of hours utilised to create a particular quantity of production.
Answer to (c)
Frequent pricing is a cost containment platform which provides far more efficient
marketing government through serious examination of deviance from true cost or making
preparations. Its goal is to continue providing an approach to setting strategic goals and giving
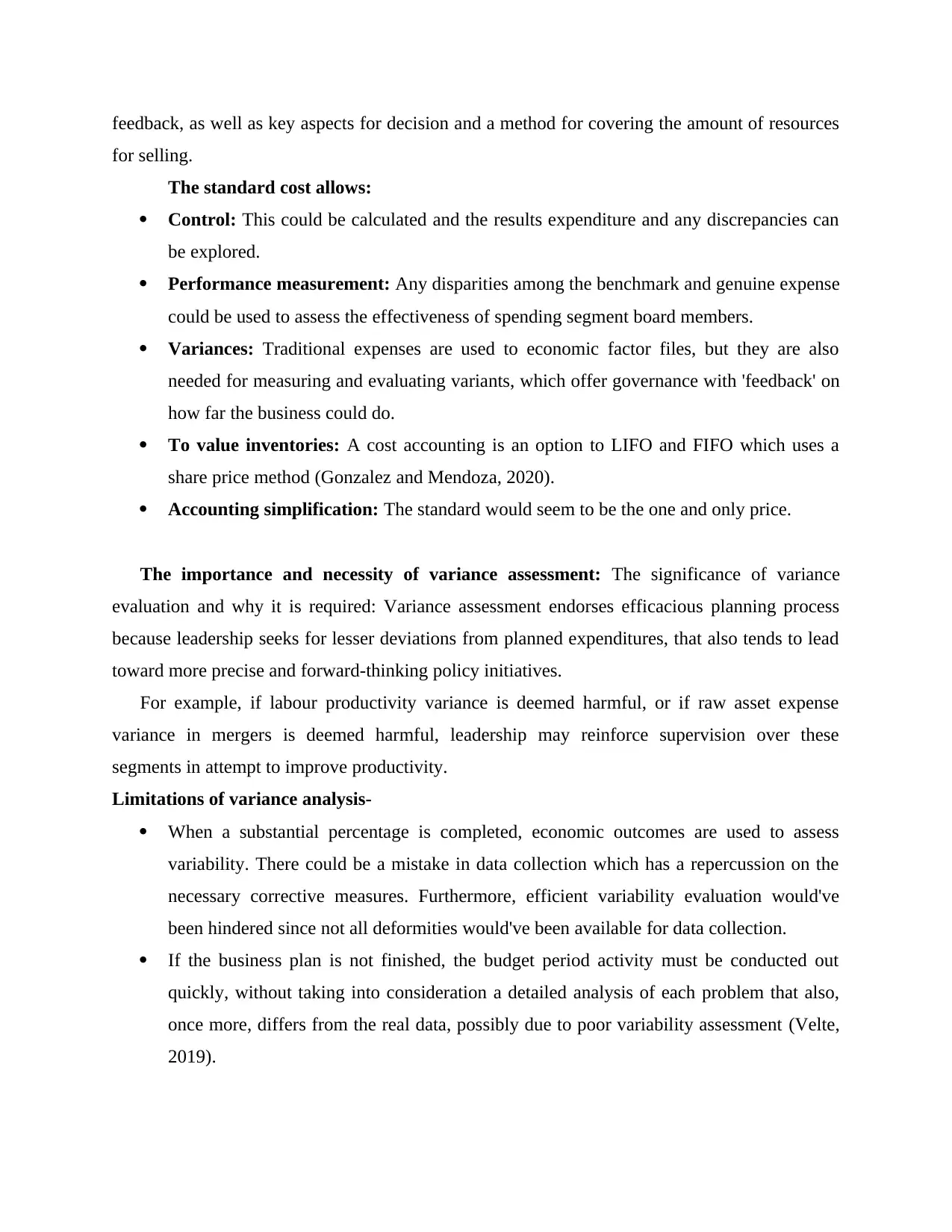
for selling.
The standard cost allows:
Control: This could be calculated and the results expenditure and any discrepancies can
be explored.
Performance measurement: Any disparities among the benchmark and genuine expense
could be used to assess the effectiveness of spending segment board members.
Variances: Traditional expenses are used to economic factor files, but they are also
needed for measuring and evaluating variants, which offer governance with 'feedback' on
how far the business could do.
To value inventories: A cost accounting is an option to LIFO and FIFO which uses a
share price method (Gonzalez and Mendoza, 2020).
Accounting simplification: The standard would seem to be the one and only price.
The importance and necessity of variance assessment: The significance of variance
evaluation and why it is required: Variance assessment endorses efficacious planning process
because leadership seeks for lesser deviations from planned expenditures, that also tends to lead
toward more precise and forward-thinking policy initiatives.
For example, if labour productivity variance is deemed harmful, or if raw asset expense
variance in mergers is deemed harmful, leadership may reinforce supervision over these
segments in attempt to improve productivity.
Limitations of variance analysis-
When a substantial percentage is completed, economic outcomes are used to assess
variability. There could be a mistake in data collection which has a repercussion on the
necessary corrective measures. Furthermore, efficient variability evaluation would've
been hindered since not all deformities would've been available for data collection.
If the business plan is not finished, the budget period activity must be conducted out
quickly, without taking into consideration a detailed analysis of each problem that also,
once more, differs from the real data, possibly due to poor variability assessment (Velte,
2019).
⊘ This is a preview!⊘
Do you want full access?
Subscribe today to unlock all pages.

Trusted by 1+ million students worldwide
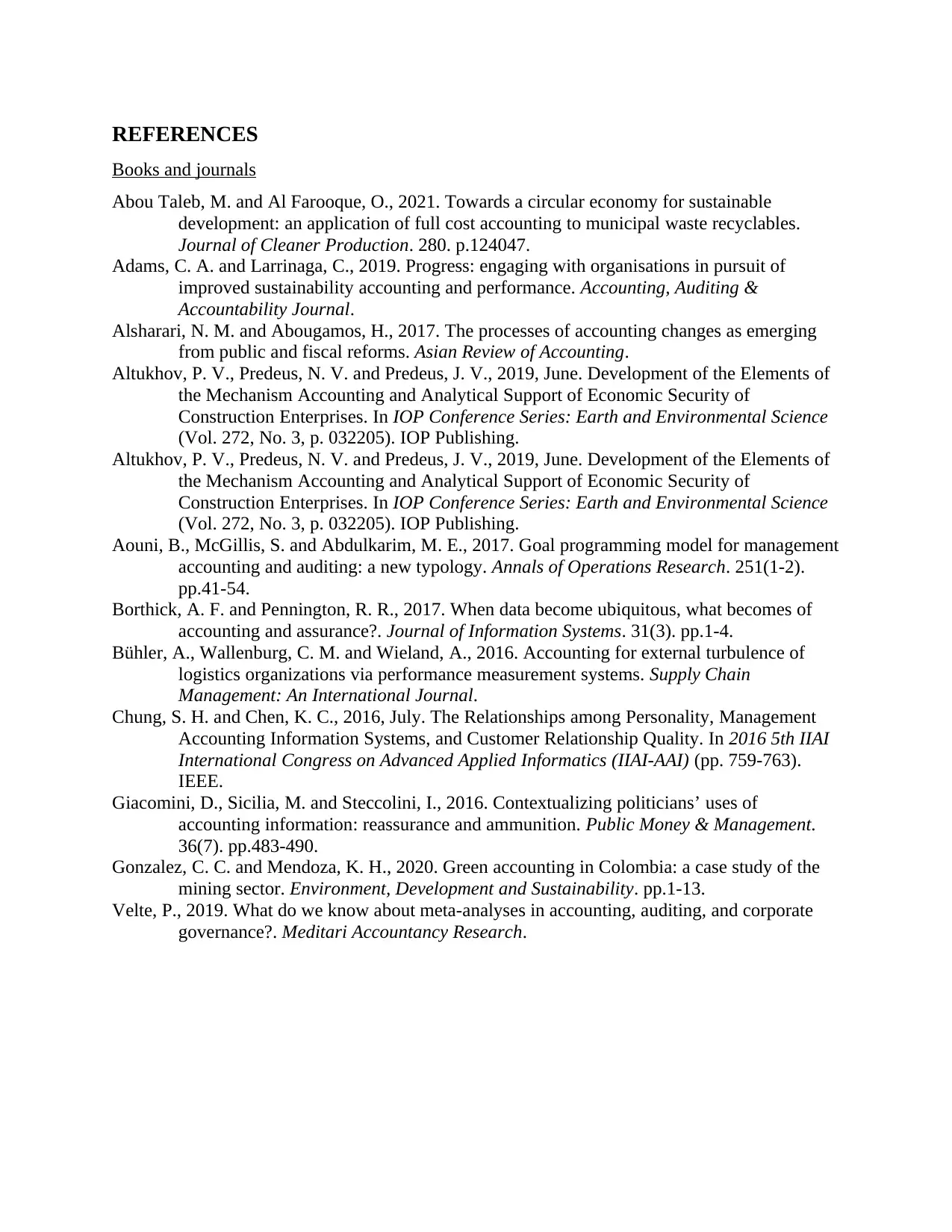
Books and journals
Abou Taleb, M. and Al Farooque, O., 2021. Towards a circular economy for sustainable
development: an application of full cost accounting to municipal waste recyclables.
Journal of Cleaner Production. 280. p.124047.
Adams, C. A. and Larrinaga, C., 2019. Progress: engaging with organisations in pursuit of
improved sustainability accounting and performance. Accounting, Auditing &
Accountability Journal.
Alsharari, N. M. and Abougamos, H., 2017. The processes of accounting changes as emerging
from public and fiscal reforms. Asian Review of Accounting.
Altukhov, P. V., Predeus, N. V. and Predeus, J. V., 2019, June. Development of the Elements of
the Mechanism Accounting and Analytical Support of Economic Security of
Construction Enterprises. In IOP Conference Series: Earth and Environmental Science
(Vol. 272, No. 3, p. 032205). IOP Publishing.
Altukhov, P. V., Predeus, N. V. and Predeus, J. V., 2019, June. Development of the Elements of
the Mechanism Accounting and Analytical Support of Economic Security of
Construction Enterprises. In IOP Conference Series: Earth and Environmental Science
(Vol. 272, No. 3, p. 032205). IOP Publishing.
Aouni, B., McGillis, S. and Abdulkarim, M. E., 2017. Goal programming model for management
accounting and auditing: a new typology. Annals of Operations Research. 251(1-2).
pp.41-54.
Borthick, A. F. and Pennington, R. R., 2017. When data become ubiquitous, what becomes of
accounting and assurance?. Journal of Information Systems. 31(3). pp.1-4.
Bühler, A., Wallenburg, C. M. and Wieland, A., 2016. Accounting for external turbulence of
logistics organizations via performance measurement systems. Supply Chain
Management: An International Journal.
Chung, S. H. and Chen, K. C., 2016, July. The Relationships among Personality, Management
Accounting Information Systems, and Customer Relationship Quality. In 2016 5th IIAI
International Congress on Advanced Applied Informatics (IIAI-AAI) (pp. 759-763).
IEEE.
Giacomini, D., Sicilia, M. and Steccolini, I., 2016. Contextualizing politicians’ uses of
accounting information: reassurance and ammunition. Public Money & Management.
36(7). pp.483-490.
Gonzalez, C. C. and Mendoza, K. H., 2020. Green accounting in Colombia: a case study of the
mining sector. Environment, Development and Sustainability. pp.1-13.
Velte, P., 2019. What do we know about meta-analyses in accounting, auditing, and corporate
governance?. Meditari Accountancy Research.
Related Documents

Your All-in-One AI-Powered Toolkit for Academic Success.
+13062052269
info@desklib.com
Available 24*7 on WhatsApp / Email
© 2024 | Zucol Services PVT LTD | All rights reserved.