Management Accounting for Costs and Controls Homework Assignment
VerifiedAdded on 2020/04/07
|17
|1221
|42
Homework Assignment
AI Summary
This document presents a comprehensive solution to a management accounting assignment, addressing key concepts in cost and control. The assignment delves into job costing, exploring its application and constraints in historical construction projects like the Great Pyramid of Giza. Process costing ...
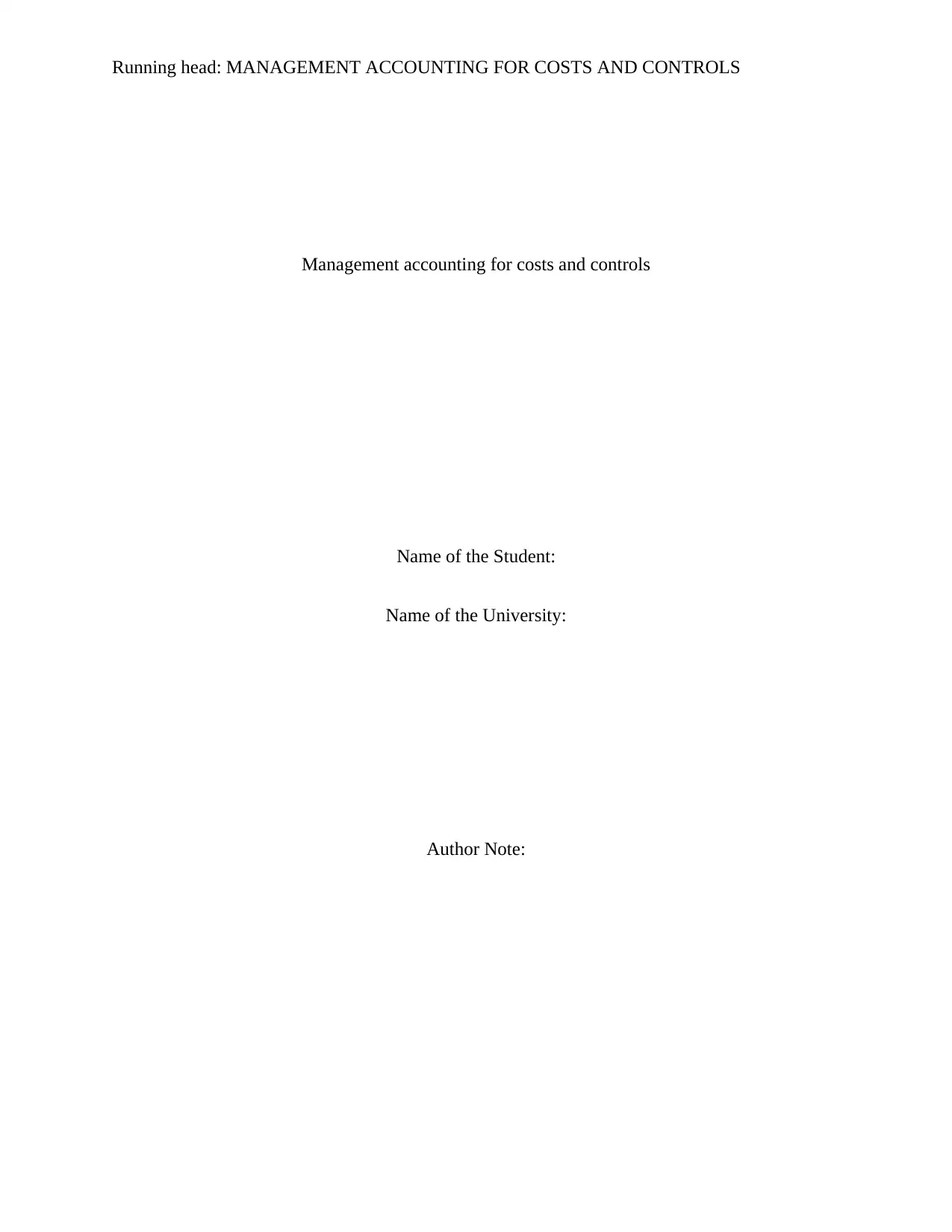
Running head: MANAGEMENT ACCOUNTING FOR COSTS AND CONTROLS
Management accounting for costs and controls
Name of the Student:
Name of the University:
Author Note:
Management accounting for costs and controls
Name of the Student:
Name of the University:
Author Note:
Paraphrase This Document
Need a fresh take? Get an instant paraphrase of this document with our AI Paraphraser
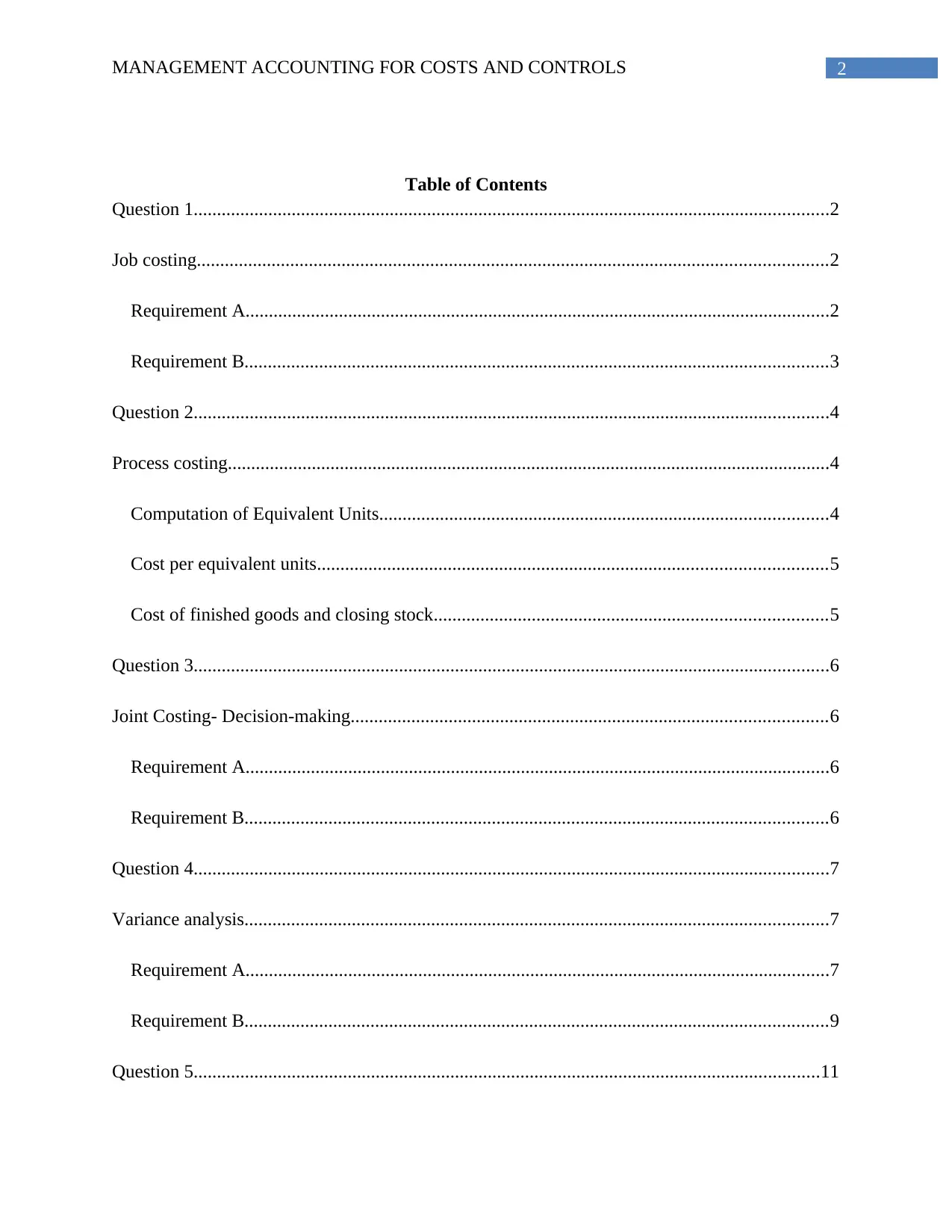
2MANAGEMENT ACCOUNTING FOR COSTS AND CONTROLS
Table of Contents
Question 1........................................................................................................................................2
Job costing.......................................................................................................................................2
Requirement A.............................................................................................................................2
Requirement B.............................................................................................................................3
Question 2........................................................................................................................................4
Process costing.................................................................................................................................4
Computation of Equivalent Units................................................................................................4
Cost per equivalent units.............................................................................................................5
Cost of finished goods and closing stock....................................................................................5
Question 3........................................................................................................................................6
Joint Costing- Decision-making......................................................................................................6
Requirement A.............................................................................................................................6
Requirement B.............................................................................................................................6
Question 4........................................................................................................................................7
Variance analysis.............................................................................................................................7
Requirement A.............................................................................................................................7
Requirement B.............................................................................................................................9
Question 5......................................................................................................................................11
Table of Contents
Question 1........................................................................................................................................2
Job costing.......................................................................................................................................2
Requirement A.............................................................................................................................2
Requirement B.............................................................................................................................3
Question 2........................................................................................................................................4
Process costing.................................................................................................................................4
Computation of Equivalent Units................................................................................................4
Cost per equivalent units.............................................................................................................5
Cost of finished goods and closing stock....................................................................................5
Question 3........................................................................................................................................6
Joint Costing- Decision-making......................................................................................................6
Requirement A.............................................................................................................................6
Requirement B.............................................................................................................................6
Question 4........................................................................................................................................7
Variance analysis.............................................................................................................................7
Requirement A.............................................................................................................................7
Requirement B.............................................................................................................................9
Question 5......................................................................................................................................11
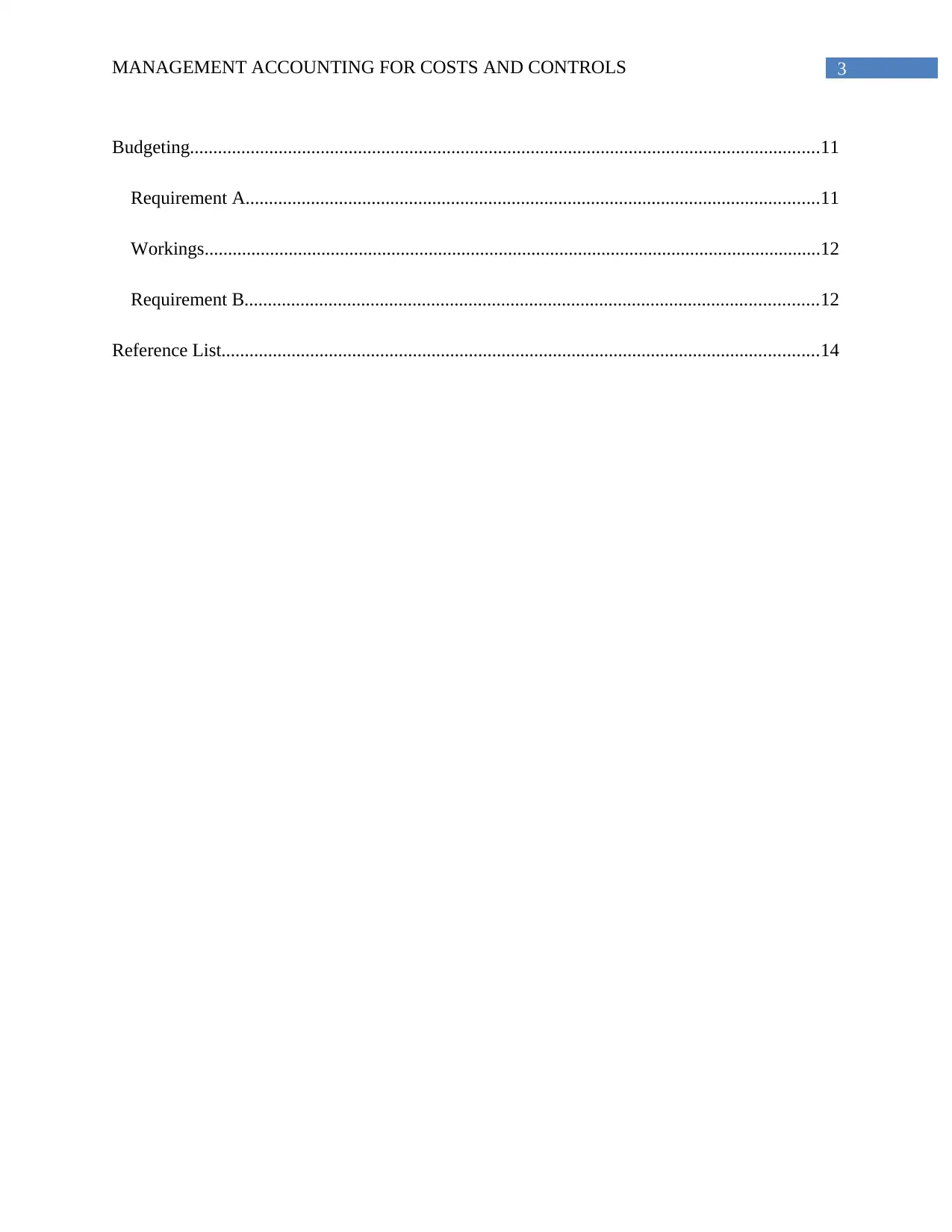
3MANAGEMENT ACCOUNTING FOR COSTS AND CONTROLS
Budgeting.......................................................................................................................................11
Requirement A...........................................................................................................................11
Workings....................................................................................................................................12
Requirement B...........................................................................................................................12
Reference List................................................................................................................................14
Budgeting.......................................................................................................................................11
Requirement A...........................................................................................................................11
Workings....................................................................................................................................12
Requirement B...........................................................................................................................12
Reference List................................................................................................................................14
⊘ This is a preview!⊘
Do you want full access?
Subscribe today to unlock all pages.

Trusted by 1+ million students worldwide
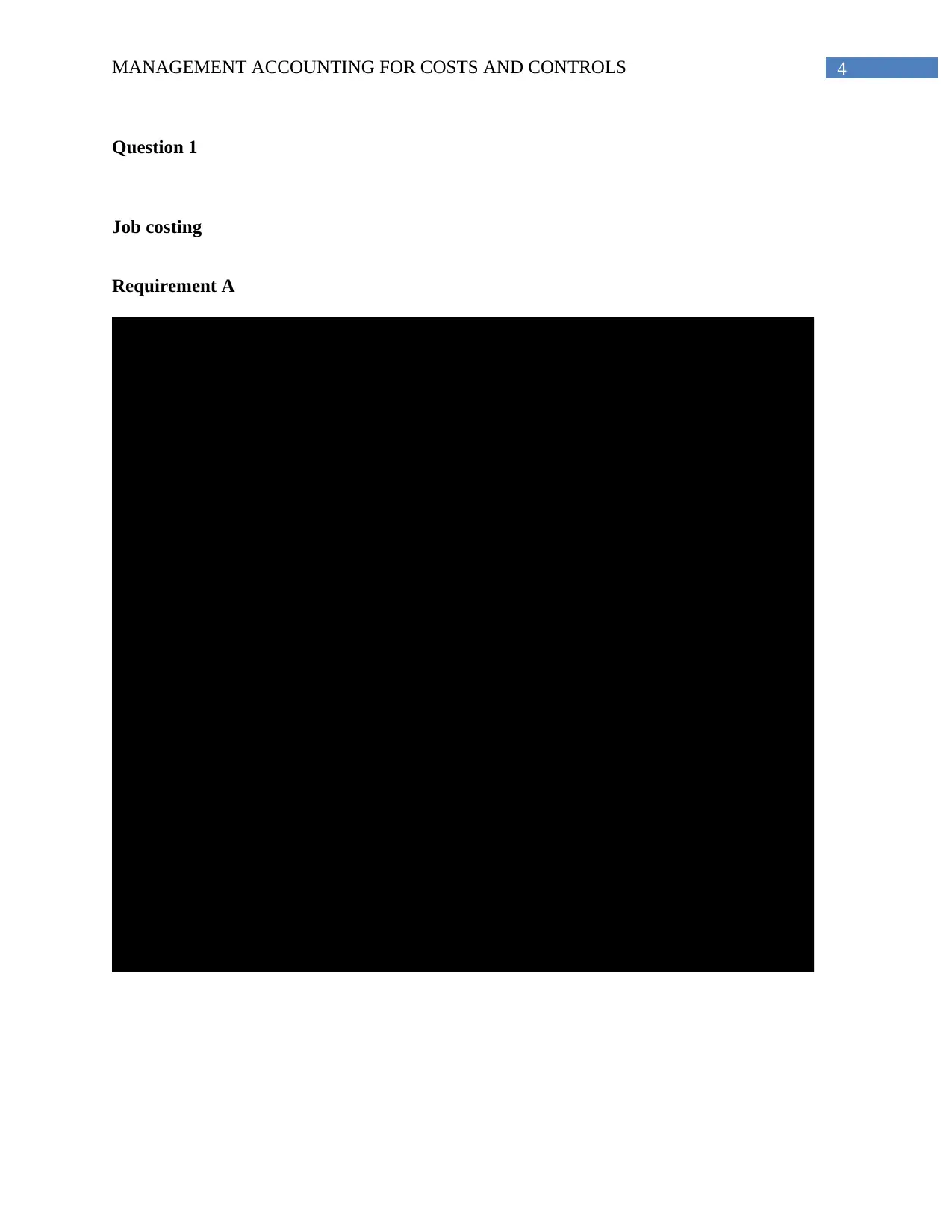
4MANAGEMENT ACCOUNTING FOR COSTS AND CONTROLS
Question 1
Job costing
Requirement A
DR. CR.
Date Particulars Amount Date Particulars Amount
To, Balance b/d. 24855 31/8/14 By, Work-in-Process A/c. 6010
To, Accounts Payable A/c. 6155 By, Balance c/d 25000
31010 31010
DR. CR.
Date Particulars Amount Date Particulars Amount
1/8/X4 To, Balance b/d 8790 31/8/X4 By, Cost of Goods Sold A/c. 30000
31/8/X4 To, Work-in-Process A/c. 30110 By,Balance c/d 8900
38900 38900
DR. CR.
Date Particulars Amount Date Particulars Amount
31/8/X4 To, Finished Goods A/c. 30000 31/8/X4 By, Profit & Loss A/c. 32800
To, Manufacturing
Overhead A/c. 2800
32800 32800
Direct Material Account
Finished Goods
Cost of Goods Sold
Question 1
Job costing
Requirement A
DR. CR.
Date Particulars Amount Date Particulars Amount
To, Balance b/d. 24855 31/8/14 By, Work-in-Process A/c. 6010
To, Accounts Payable A/c. 6155 By, Balance c/d 25000
31010 31010
DR. CR.
Date Particulars Amount Date Particulars Amount
1/8/X4 To, Balance b/d 8790 31/8/X4 By, Cost of Goods Sold A/c. 30000
31/8/X4 To, Work-in-Process A/c. 30110 By,Balance c/d 8900
38900 38900
DR. CR.
Date Particulars Amount Date Particulars Amount
31/8/X4 To, Finished Goods A/c. 30000 31/8/X4 By, Profit & Loss A/c. 32800
To, Manufacturing
Overhead A/c. 2800
32800 32800
Direct Material Account
Finished Goods
Cost of Goods Sold
Paraphrase This Document
Need a fresh take? Get an instant paraphrase of this document with our AI Paraphraser
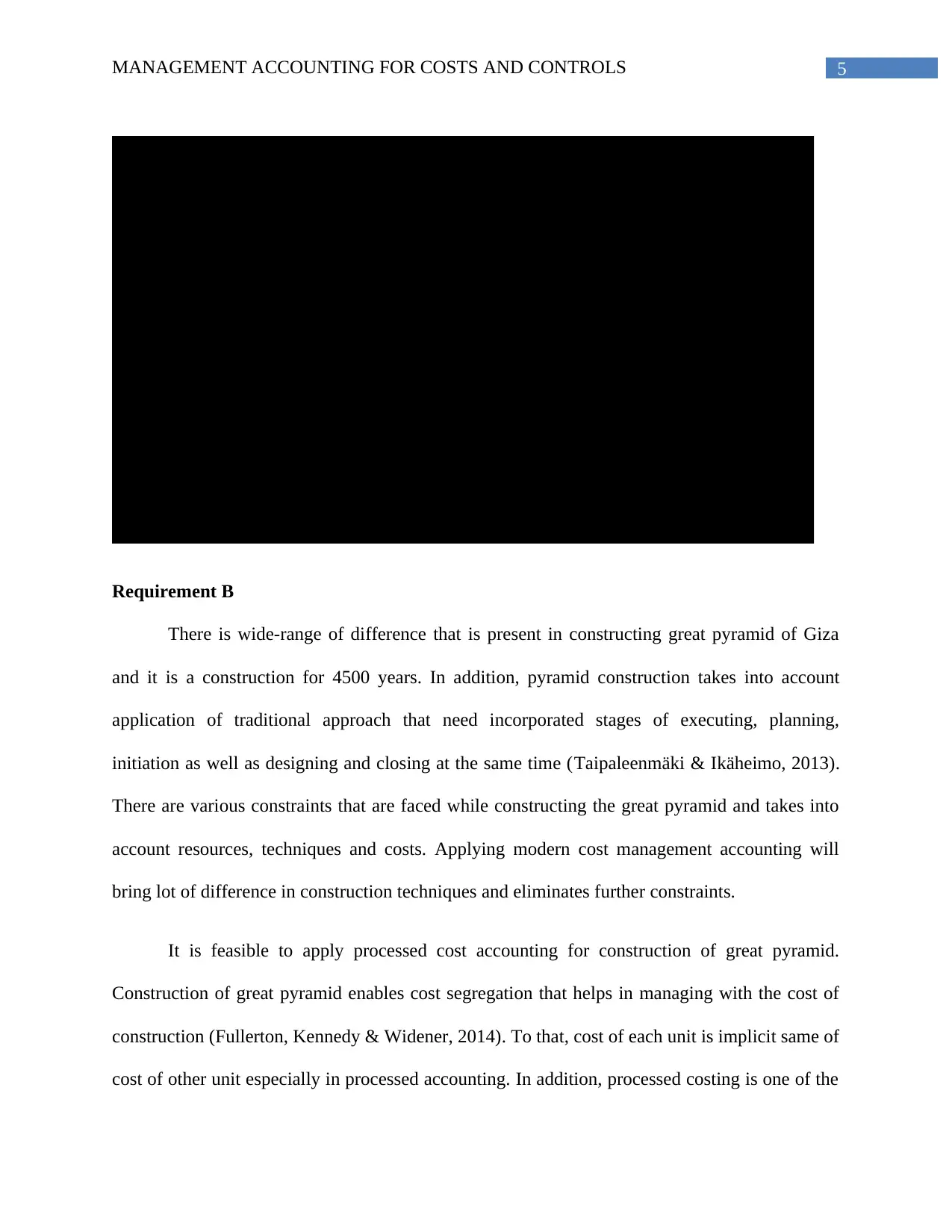
5MANAGEMENT ACCOUNTING FOR COSTS AND CONTROLS
DR. CR.
Date Particulars Amount Date Particulars Amount
1/8/X4 To, Balance b/d 6700 31/8/X4 By, Finished Goods A/c. 30110
To, Direct Labor A/c. 14800 By, Balance c/d 9400
To, Manufacturing Overhead A/c. 12000
To, Direct Material A/c. 6010
39510 39510
DR. CR.
Date Particulars Amount Date Particulars Amount
31/8/X4 To, Bank A/c. 6700 1/8/X4 By, Balance b/d 2345
31/8/X4 To, Balance c/d 1800 By, Direct Material A/c. 6155
8500 8500
Work-in-Process
Accounts Payable
Requirement B
There is wide-range of difference that is present in constructing great pyramid of Giza
and it is a construction for 4500 years. In addition, pyramid construction takes into account
application of traditional approach that need incorporated stages of executing, planning,
initiation as well as designing and closing at the same time (Taipaleenmäki & Ikäheimo, 2013).
There are various constraints that are faced while constructing the great pyramid and takes into
account resources, techniques and costs. Applying modern cost management accounting will
bring lot of difference in construction techniques and eliminates further constraints.
It is feasible to apply processed cost accounting for construction of great pyramid.
Construction of great pyramid enables cost segregation that helps in managing with the cost of
construction (Fullerton, Kennedy & Widener, 2014). To that, cost of each unit is implicit same of
cost of other unit especially in processed accounting. In addition, processed costing is one of the
DR. CR.
Date Particulars Amount Date Particulars Amount
1/8/X4 To, Balance b/d 6700 31/8/X4 By, Finished Goods A/c. 30110
To, Direct Labor A/c. 14800 By, Balance c/d 9400
To, Manufacturing Overhead A/c. 12000
To, Direct Material A/c. 6010
39510 39510
DR. CR.
Date Particulars Amount Date Particulars Amount
31/8/X4 To, Bank A/c. 6700 1/8/X4 By, Balance b/d 2345
31/8/X4 To, Balance c/d 1800 By, Direct Material A/c. 6155
8500 8500
Work-in-Process
Accounts Payable
Requirement B
There is wide-range of difference that is present in constructing great pyramid of Giza
and it is a construction for 4500 years. In addition, pyramid construction takes into account
application of traditional approach that need incorporated stages of executing, planning,
initiation as well as designing and closing at the same time (Taipaleenmäki & Ikäheimo, 2013).
There are various constraints that are faced while constructing the great pyramid and takes into
account resources, techniques and costs. Applying modern cost management accounting will
bring lot of difference in construction techniques and eliminates further constraints.
It is feasible to apply processed cost accounting for construction of great pyramid.
Construction of great pyramid enables cost segregation that helps in managing with the cost of
construction (Fullerton, Kennedy & Widener, 2014). To that, cost of each unit is implicit same of
cost of other unit especially in processed accounting. In addition, processed costing is one of the
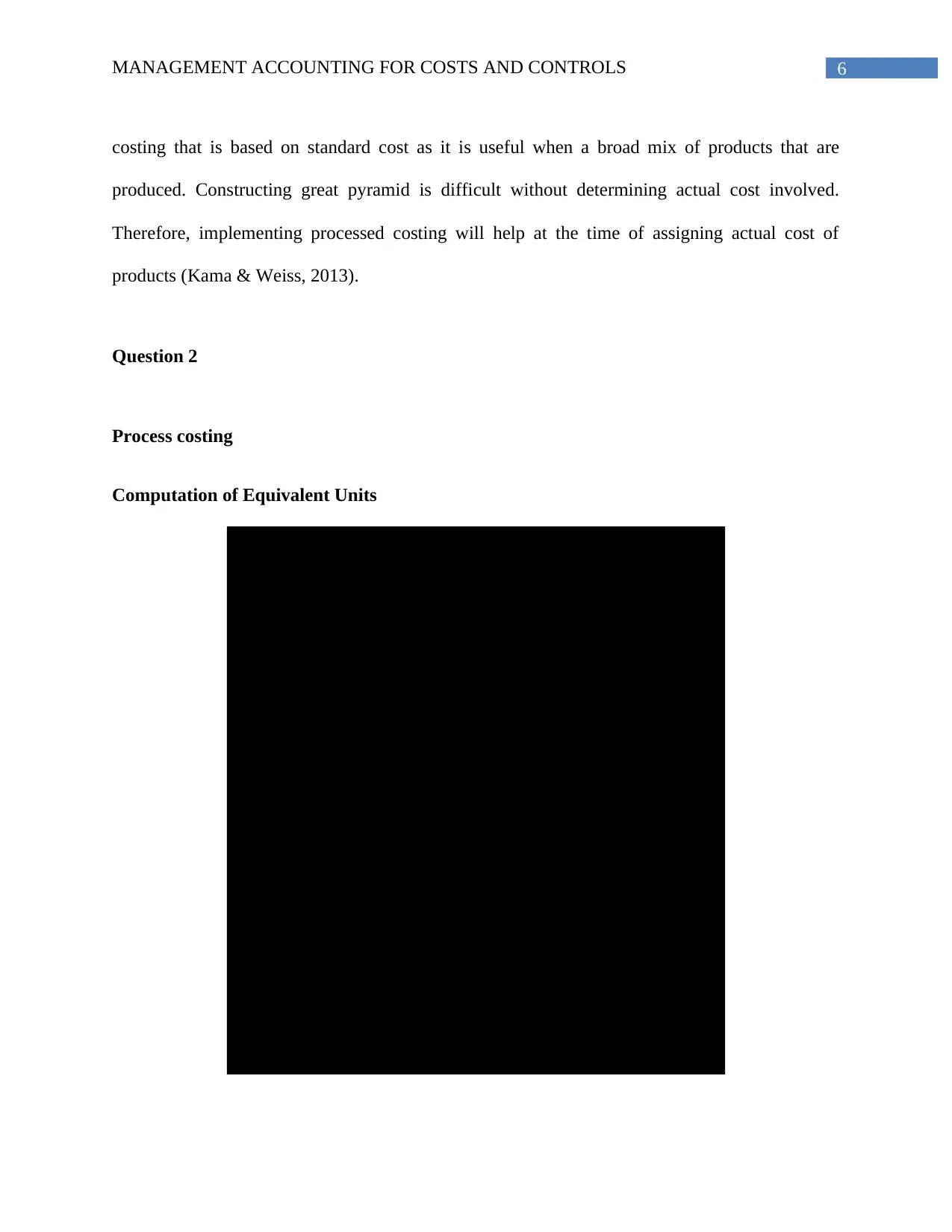
6MANAGEMENT ACCOUNTING FOR COSTS AND CONTROLS
costing that is based on standard cost as it is useful when a broad mix of products that are
produced. Constructing great pyramid is difficult without determining actual cost involved.
Therefore, implementing processed costing will help at the time of assigning actual cost of
products (Kama & Weiss, 2013).
Question 2
Process costing
Computation of Equivalent Units
Process 1 Physical Flow
Material Conversion
O/WIP 2000 0 1400
Started in May 6000
Total Production 8000
Completed in Process 7000 7000 7000
C/WIP 1000 1000 500
Total Equivalent Units 8000 7500
Process 2 Physical Flow
Material Conversion
O/WIP 1000 0 500
Started in May 7000
Total Production 8000
C/WIP 750 0 225
Completed I Process 7250 7250 7250
Total Equivalent Units 7250 7975
Equivalent Units
Equivalent Units
costing that is based on standard cost as it is useful when a broad mix of products that are
produced. Constructing great pyramid is difficult without determining actual cost involved.
Therefore, implementing processed costing will help at the time of assigning actual cost of
products (Kama & Weiss, 2013).
Question 2
Process costing
Computation of Equivalent Units
Process 1 Physical Flow
Material Conversion
O/WIP 2000 0 1400
Started in May 6000
Total Production 8000
Completed in Process 7000 7000 7000
C/WIP 1000 1000 500
Total Equivalent Units 8000 7500
Process 2 Physical Flow
Material Conversion
O/WIP 1000 0 500
Started in May 7000
Total Production 8000
C/WIP 750 0 225
Completed I Process 7250 7250 7250
Total Equivalent Units 7250 7975
Equivalent Units
Equivalent Units
⊘ This is a preview!⊘
Do you want full access?
Subscribe today to unlock all pages.

Trusted by 1+ million students worldwide
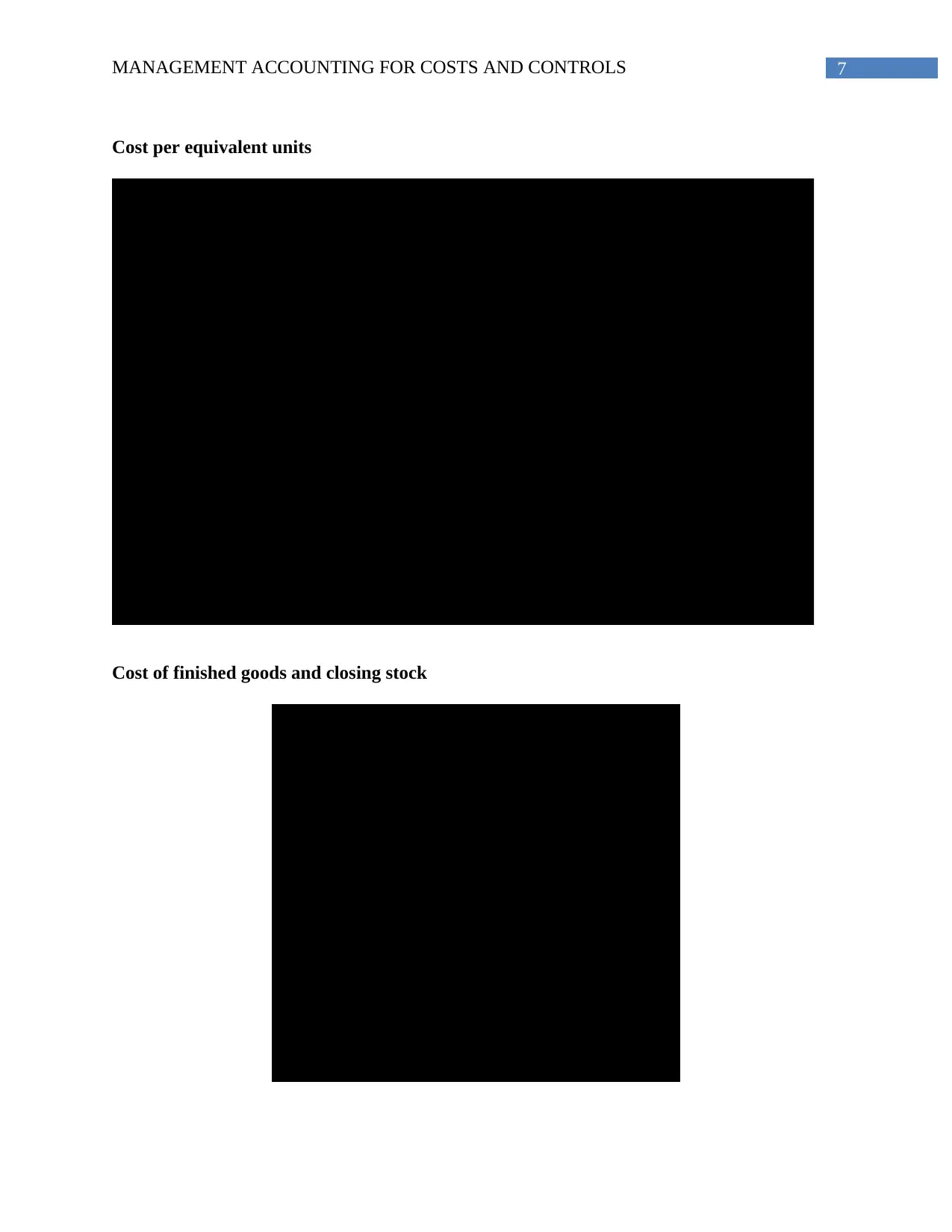
7MANAGEMENT ACCOUNTING FOR COSTS AND CONTROLS
Cost per equivalent units
Particulars Material Coversion Transferred-in Total
Process 1:
O/WIP Cost $3,000 $2,000 $5,000
Current Cost $30,000 $60,000 $90,000
Total Production Cost of Process 1 $33,000 $62,000 $95,000
Total Equivalent Units 8000 7500
Cost per Equivalent Units of Process 1 $4.13 $8.27 $12.39
Process 2:
O/WIP Cost $3,000 $4,000 $8,000 $15,000
Current Cost $35,000 $45,000 $86,742 $166,742
Total Production Cost of Process 2 $38,000 $49,000 $94,742 $181,742
Total Equivalent Units 7250 7975 7000
Cost per Equivalent Units of Process 2 $5.24 $6.14 $13.53 $25
Cost of finished goods and closing stock
Particulars Amount
Finished Goods Completed during May 7250
Cost per Equivalent Units $25
Cost of Finished Goods Completed $180,671
Closing Stock in Process 1 1000
Cost per Equivalent Units for Process 1 $12.39
Cost of Closing Stock in Process 1 $12,391.67
Closing Stock in Process 2 750
Cost per Equivalent Units for Process 1 $24.92
Cost of Closing Stock in Process 2 $18,690.08
Cost per equivalent units
Particulars Material Coversion Transferred-in Total
Process 1:
O/WIP Cost $3,000 $2,000 $5,000
Current Cost $30,000 $60,000 $90,000
Total Production Cost of Process 1 $33,000 $62,000 $95,000
Total Equivalent Units 8000 7500
Cost per Equivalent Units of Process 1 $4.13 $8.27 $12.39
Process 2:
O/WIP Cost $3,000 $4,000 $8,000 $15,000
Current Cost $35,000 $45,000 $86,742 $166,742
Total Production Cost of Process 2 $38,000 $49,000 $94,742 $181,742
Total Equivalent Units 7250 7975 7000
Cost per Equivalent Units of Process 2 $5.24 $6.14 $13.53 $25
Cost of finished goods and closing stock
Particulars Amount
Finished Goods Completed during May 7250
Cost per Equivalent Units $25
Cost of Finished Goods Completed $180,671
Closing Stock in Process 1 1000
Cost per Equivalent Units for Process 1 $12.39
Cost of Closing Stock in Process 1 $12,391.67
Closing Stock in Process 2 750
Cost per Equivalent Units for Process 1 $24.92
Cost of Closing Stock in Process 2 $18,690.08
Paraphrase This Document
Need a fresh take? Get an instant paraphrase of this document with our AI Paraphraser
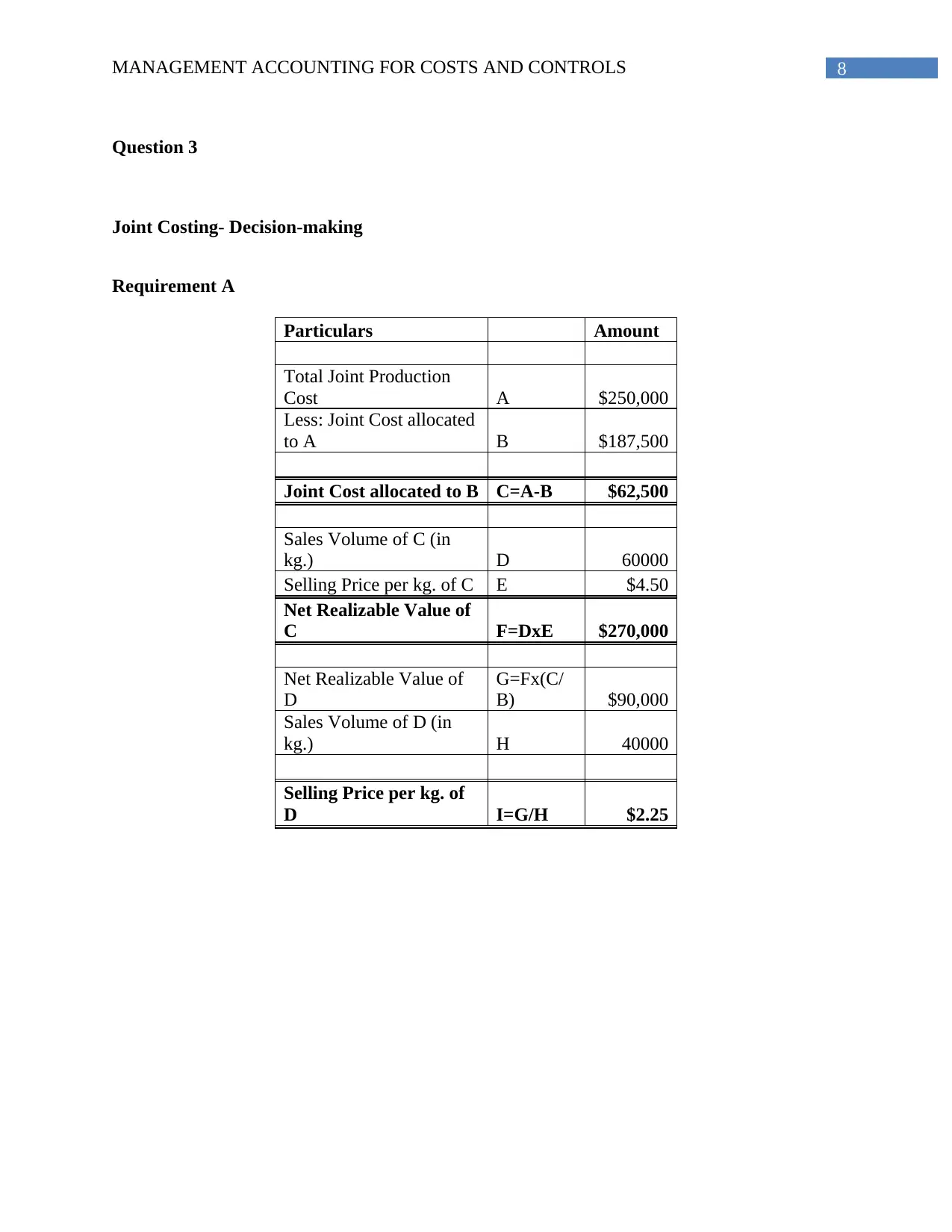
8MANAGEMENT ACCOUNTING FOR COSTS AND CONTROLS
Question 3
Joint Costing- Decision-making
Requirement A
Particulars Amount
Total Joint Production
Cost A $250,000
Less: Joint Cost allocated
to A B $187,500
Joint Cost allocated to B C=A-B $62,500
Sales Volume of C (in
kg.) D 60000
Selling Price per kg. of C E $4.50
Net Realizable Value of
C F=DxE $270,000
Net Realizable Value of
D
G=Fx(C/
B) $90,000
Sales Volume of D (in
kg.) H 40000
Selling Price per kg. of
D I=G/H $2.25
Question 3
Joint Costing- Decision-making
Requirement A
Particulars Amount
Total Joint Production
Cost A $250,000
Less: Joint Cost allocated
to A B $187,500
Joint Cost allocated to B C=A-B $62,500
Sales Volume of C (in
kg.) D 60000
Selling Price per kg. of C E $4.50
Net Realizable Value of
C F=DxE $270,000
Net Realizable Value of
D
G=Fx(C/
B) $90,000
Sales Volume of D (in
kg.) H 40000
Selling Price per kg. of
D I=G/H $2.25
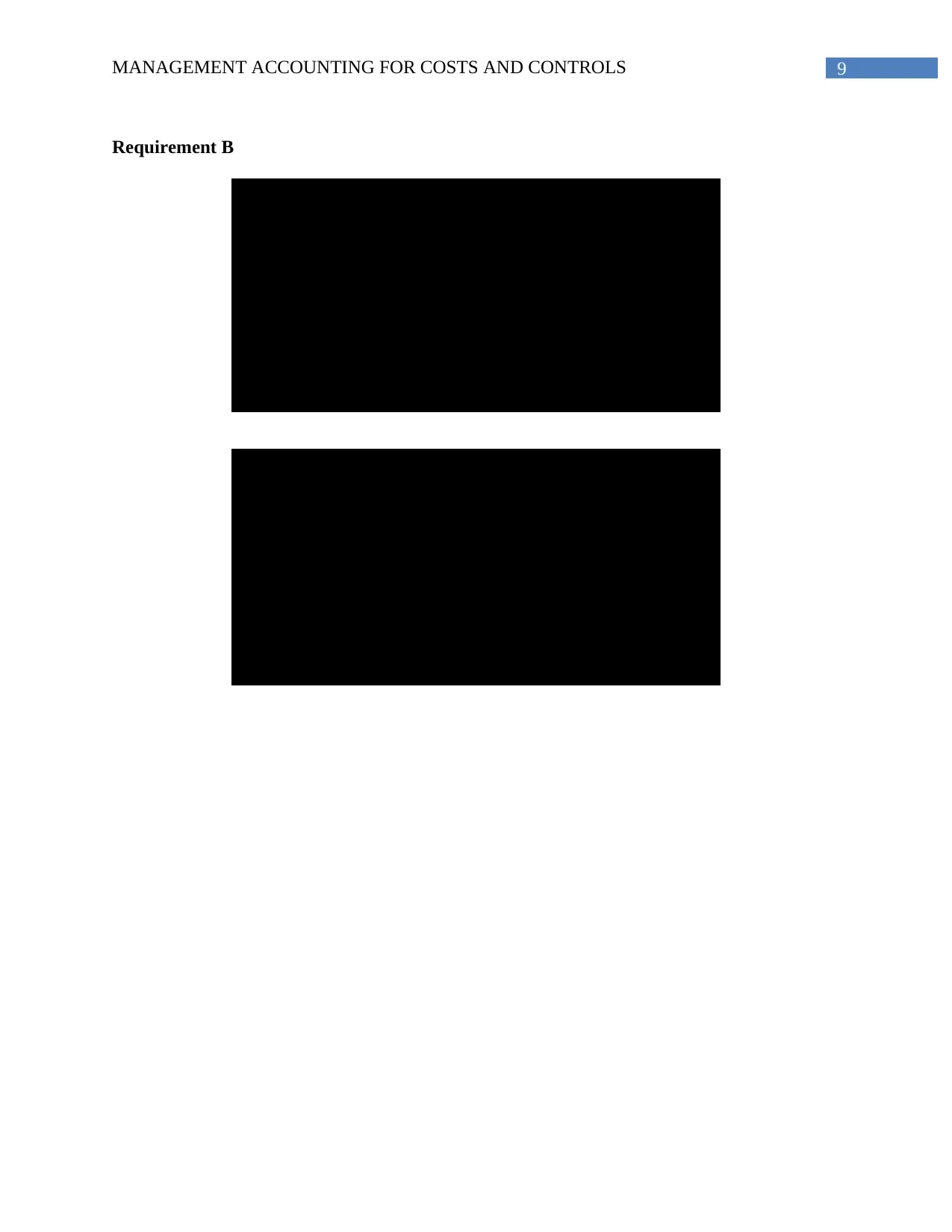
9MANAGEMENT ACCOUNTING FOR COSTS AND CONTROLS
Requirement B
Particulars A B Total
Selling Price per unit $4.50 $2.25
Sales Volume 60000 40000 100000
Total Sale Revenue $270,000 $90,000 $360,000
Joint Cost Allocation ($187,500) ($62,500) ($250,000)
Further Processing Cost ($45,000) ($25,000) ($70,000)
Net Profit $37,500 $2,500 $40,000
Particulars A B Total
Selling Price per unit $2.00 $2.25
Sales Volume 60000 40000 100000
Total Sale Revenue $120,000 $90,000 $210,000
Joint Cost Allocation ($142,857) ($107,143) ($250,000)
Further Processing Cost ($25,000) ($25,000)
Net Profit ($22,857) ($42,143) ($65,000)
Requirement B
Particulars A B Total
Selling Price per unit $4.50 $2.25
Sales Volume 60000 40000 100000
Total Sale Revenue $270,000 $90,000 $360,000
Joint Cost Allocation ($187,500) ($62,500) ($250,000)
Further Processing Cost ($45,000) ($25,000) ($70,000)
Net Profit $37,500 $2,500 $40,000
Particulars A B Total
Selling Price per unit $2.00 $2.25
Sales Volume 60000 40000 100000
Total Sale Revenue $120,000 $90,000 $210,000
Joint Cost Allocation ($142,857) ($107,143) ($250,000)
Further Processing Cost ($25,000) ($25,000)
Net Profit ($22,857) ($42,143) ($65,000)
⊘ This is a preview!⊘
Do you want full access?
Subscribe today to unlock all pages.

Trusted by 1+ million students worldwide
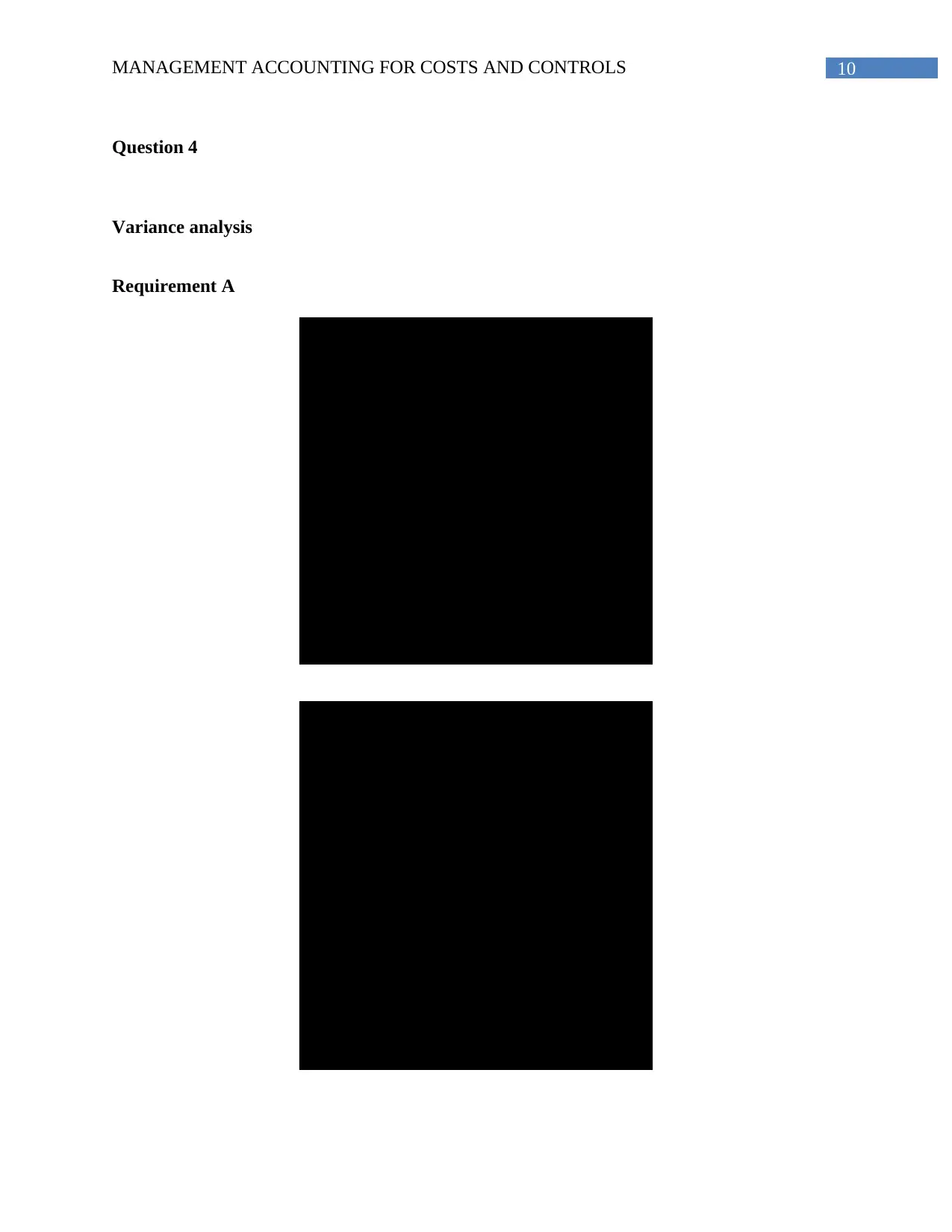
10MANAGEMENT ACCOUNTING FOR COSTS AND CONTROLS
Question 4
Variance analysis
Requirement A
Particulars Amount
Material Purchased (in units) 220000
Standard Price per kg $6
Standard Cost for Actual Material
Purchased $1,320,000
Actual Cost of Actual Material
Purchased $1,364,000
Material Price Variance ($44,000)
Remarks Unfavorable
Material Price Variance:
Particulars Amount
Units Produced 19500
Standard Usage per unit of
production 11
Standard Usage for Actual
Production 214500
Actual Material Usage 197000
Standard price per kg. $6
Material Usage Variance $105,000
Remarks Favorable
Material Usage Variance:
Question 4
Variance analysis
Requirement A
Particulars Amount
Material Purchased (in units) 220000
Standard Price per kg $6
Standard Cost for Actual Material
Purchased $1,320,000
Actual Cost of Actual Material
Purchased $1,364,000
Material Price Variance ($44,000)
Remarks Unfavorable
Material Price Variance:
Particulars Amount
Units Produced 19500
Standard Usage per unit of
production 11
Standard Usage for Actual
Production 214500
Actual Material Usage 197000
Standard price per kg. $6
Material Usage Variance $105,000
Remarks Favorable
Material Usage Variance:
Paraphrase This Document
Need a fresh take? Get an instant paraphrase of this document with our AI Paraphraser
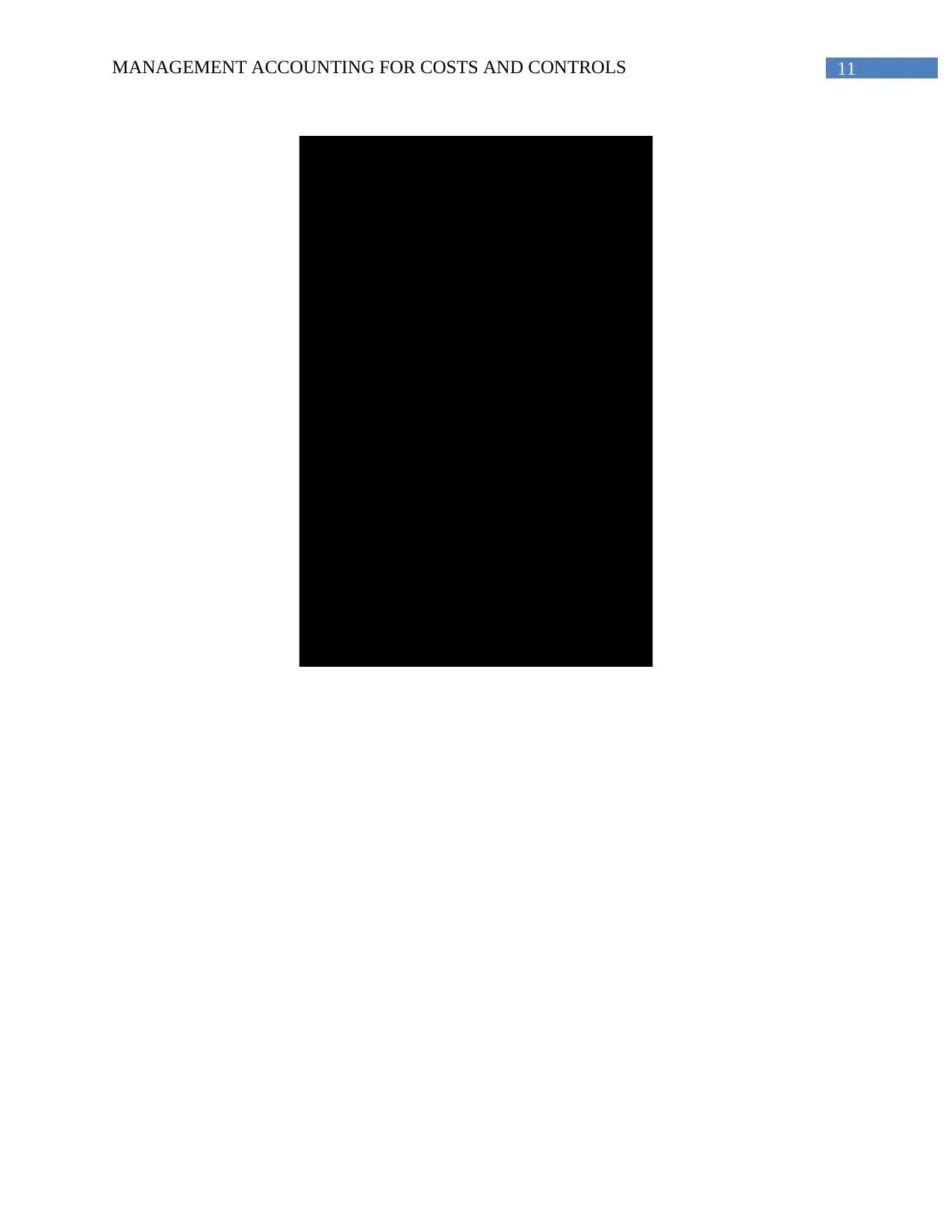
11MANAGEMENT ACCOUNTING FOR COSTS AND CONTROLS
Particulars Amount
Actual Production 19500
Standard Labor hour per unit 2
Standard Labor Hour for Actual
Production 39000
Actual Labor Hours 40000
Standard Labor Rate per hour $20
Direct Labor Efficiency Variance ($20,000)
Total Direct Labor Variance ($1,650)
Direct Labor Rate Variace $18,350
Standard Labor Cost for Actual
Labor Hours $800,000
Actual Labor Cost $781,650
Actual Direct Labor Rate per hour $19.54
Actual Direct Labor Rate per hour:
Particulars Amount
Actual Production 19500
Standard Labor hour per unit 2
Standard Labor Hour for Actual
Production 39000
Actual Labor Hours 40000
Standard Labor Rate per hour $20
Direct Labor Efficiency Variance ($20,000)
Total Direct Labor Variance ($1,650)
Direct Labor Rate Variace $18,350
Standard Labor Cost for Actual
Labor Hours $800,000
Actual Labor Cost $781,650
Actual Direct Labor Rate per hour $19.54
Actual Direct Labor Rate per hour:
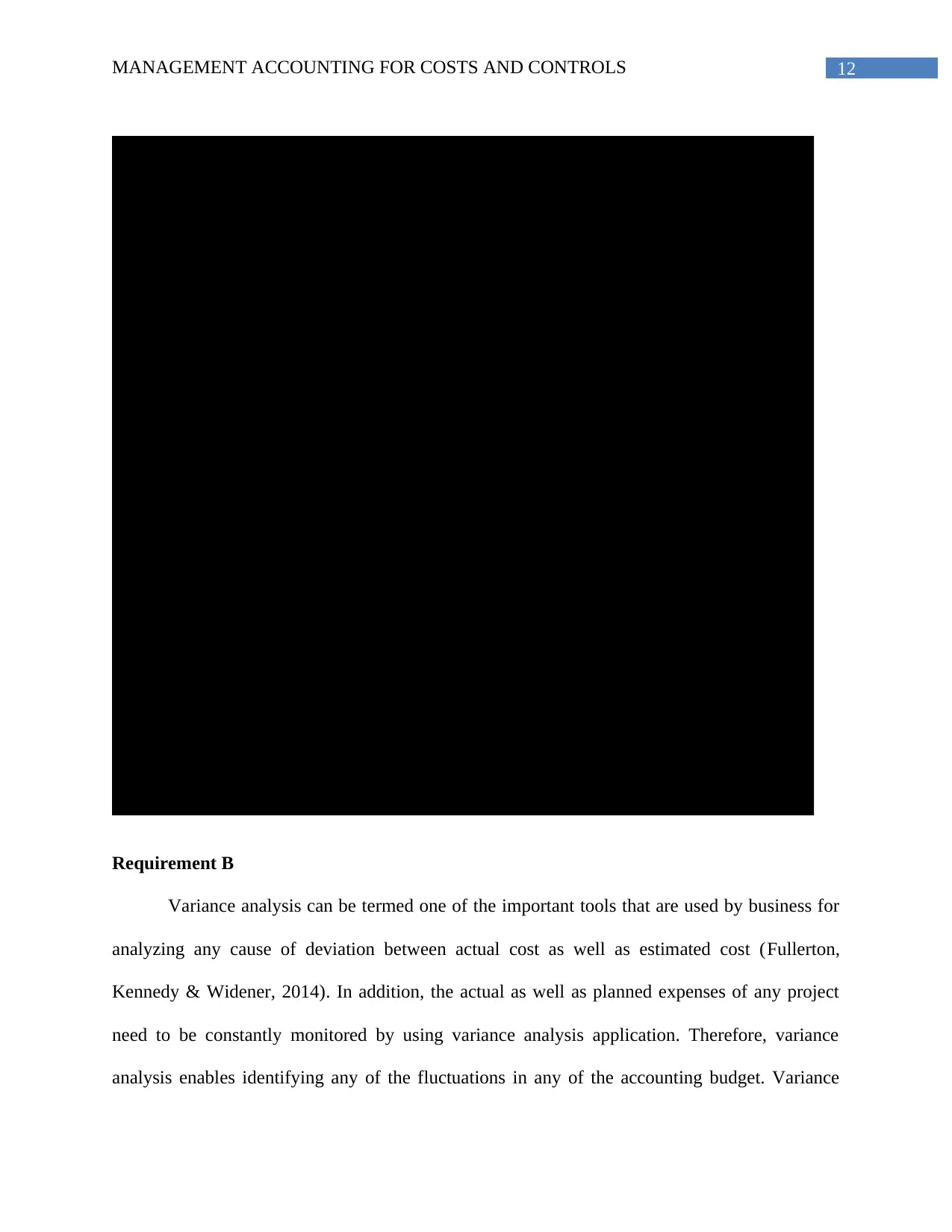
12MANAGEMENT ACCOUNTING FOR COSTS AND CONTROLS
Dr. Cr.
Date Amount Amount
Direct Material A/c. Dr. $1,364,000
To, Accounts Payable A/c. $1,364,000
Work-in-Progress A/c. Dr. 1287000
To, Direct Material A/c. 1287000
Material Price Variance A/c. Dr. $44,000
To, Direct Material A/c. $44,000
Direct Material A/c. Dr. $105,000
To, Material Usage Variance A/c. $105,000
Direct Labor Cost A/c. Dr. $781,650
To, Accrued Payroll A/c. $781,650
Work-in-Progress A/c. Dr. 780000
To, Direct Labor Cost A/c. 780000
Direct Labor Cost A/c. Dr. $18,350
To, Direct Labor Rate Variance A/c. $18,350
Direct Labor Efficiency Variance A/c. Dr. $20,000
To, Direct Labor Cost A/c. $20,000
Material Usage Variance A/c. Dr. $105,000
Direct Labor Rate Variance A/c. Dr. $18,350
To, Cost of Goods Sold A/c. $59,350
To, Direct Labor Efficiency Variance A/c. $20,000
To, Material Price Variance A/c. $44,000
Particulars
Requirement B
Variance analysis can be termed one of the important tools that are used by business for
analyzing any cause of deviation between actual cost as well as estimated cost (Fullerton,
Kennedy & Widener, 2014). In addition, the actual as well as planned expenses of any project
need to be constantly monitored by using variance analysis application. Therefore, variance
analysis enables identifying any of the fluctuations in any of the accounting budget. Variance
Dr. Cr.
Date Amount Amount
Direct Material A/c. Dr. $1,364,000
To, Accounts Payable A/c. $1,364,000
Work-in-Progress A/c. Dr. 1287000
To, Direct Material A/c. 1287000
Material Price Variance A/c. Dr. $44,000
To, Direct Material A/c. $44,000
Direct Material A/c. Dr. $105,000
To, Material Usage Variance A/c. $105,000
Direct Labor Cost A/c. Dr. $781,650
To, Accrued Payroll A/c. $781,650
Work-in-Progress A/c. Dr. 780000
To, Direct Labor Cost A/c. 780000
Direct Labor Cost A/c. Dr. $18,350
To, Direct Labor Rate Variance A/c. $18,350
Direct Labor Efficiency Variance A/c. Dr. $20,000
To, Direct Labor Cost A/c. $20,000
Material Usage Variance A/c. Dr. $105,000
Direct Labor Rate Variance A/c. Dr. $18,350
To, Cost of Goods Sold A/c. $59,350
To, Direct Labor Efficiency Variance A/c. $20,000
To, Material Price Variance A/c. $44,000
Particulars
Requirement B
Variance analysis can be termed one of the important tools that are used by business for
analyzing any cause of deviation between actual cost as well as estimated cost (Fullerton,
Kennedy & Widener, 2014). In addition, the actual as well as planned expenses of any project
need to be constantly monitored by using variance analysis application. Therefore, variance
analysis enables identifying any of the fluctuations in any of the accounting budget. Variance
⊘ This is a preview!⊘
Do you want full access?
Subscribe today to unlock all pages.

Trusted by 1+ million students worldwide
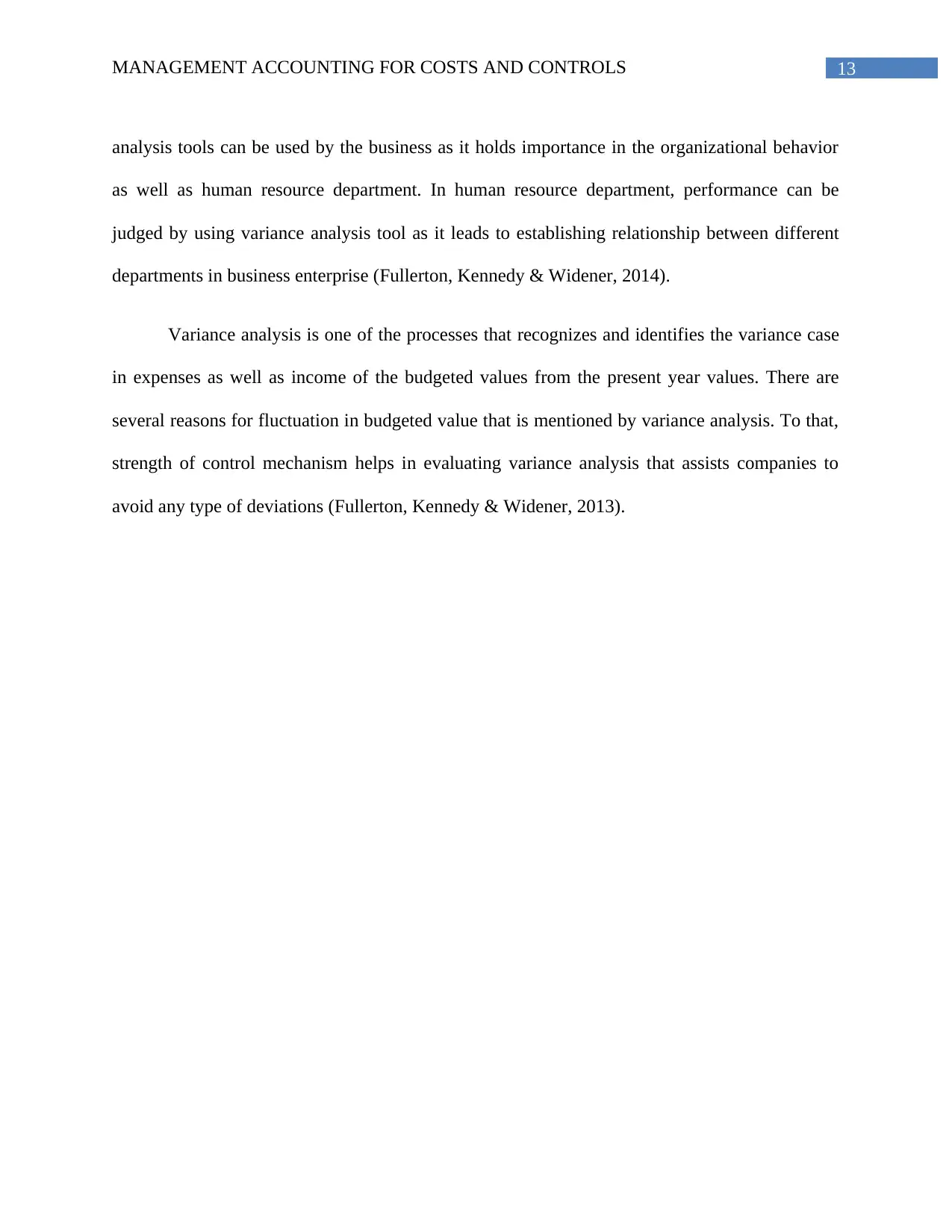
13MANAGEMENT ACCOUNTING FOR COSTS AND CONTROLS
analysis tools can be used by the business as it holds importance in the organizational behavior
as well as human resource department. In human resource department, performance can be
judged by using variance analysis tool as it leads to establishing relationship between different
departments in business enterprise (Fullerton, Kennedy & Widener, 2014).
Variance analysis is one of the processes that recognizes and identifies the variance case
in expenses as well as income of the budgeted values from the present year values. There are
several reasons for fluctuation in budgeted value that is mentioned by variance analysis. To that,
strength of control mechanism helps in evaluating variance analysis that assists companies to
avoid any type of deviations (Fullerton, Kennedy & Widener, 2013).
analysis tools can be used by the business as it holds importance in the organizational behavior
as well as human resource department. In human resource department, performance can be
judged by using variance analysis tool as it leads to establishing relationship between different
departments in business enterprise (Fullerton, Kennedy & Widener, 2014).
Variance analysis is one of the processes that recognizes and identifies the variance case
in expenses as well as income of the budgeted values from the present year values. There are
several reasons for fluctuation in budgeted value that is mentioned by variance analysis. To that,
strength of control mechanism helps in evaluating variance analysis that assists companies to
avoid any type of deviations (Fullerton, Kennedy & Widener, 2013).
Paraphrase This Document
Need a fresh take? Get an instant paraphrase of this document with our AI Paraphraser
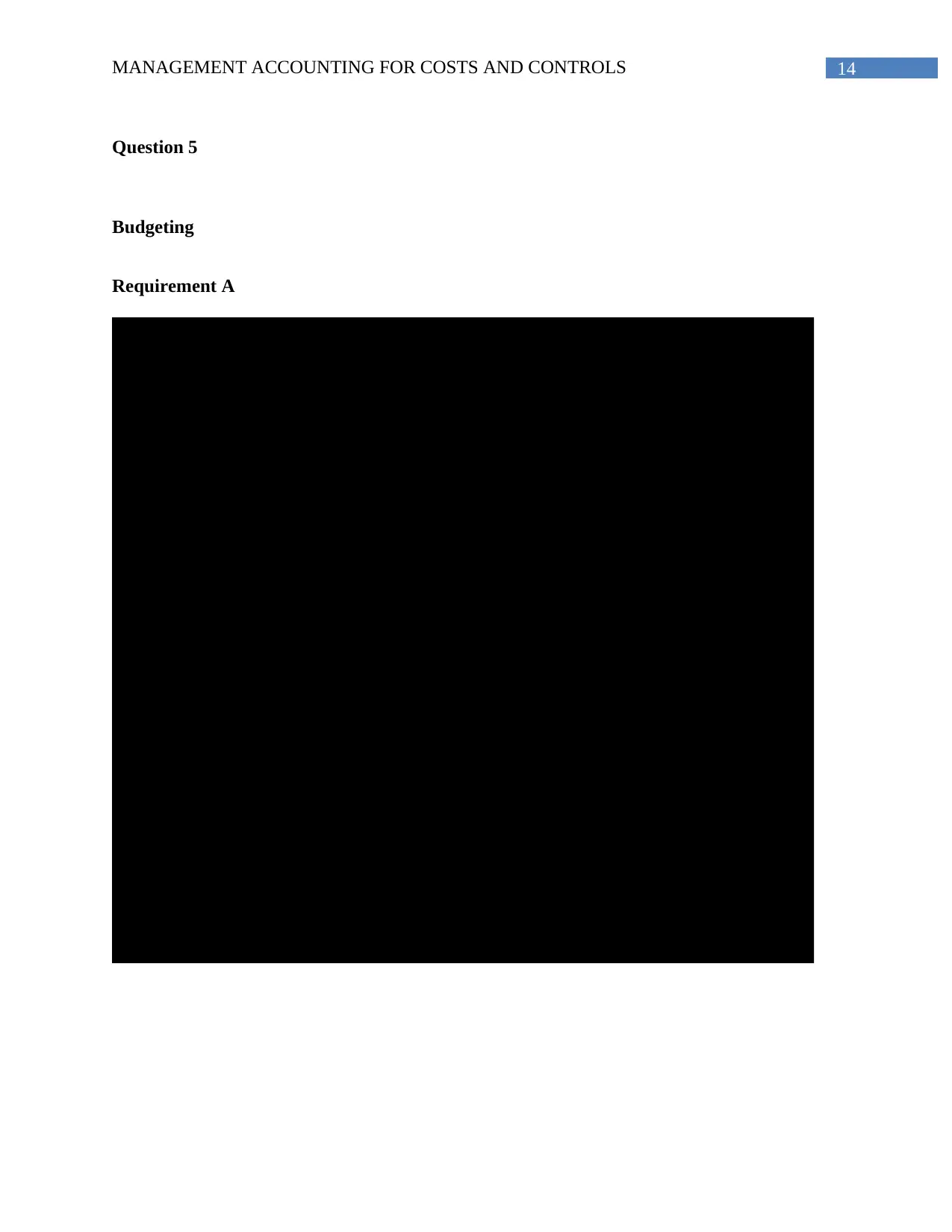
14MANAGEMENT ACCOUNTING FOR COSTS AND CONTROLS
Question 5
Budgeting
Requirement A
Particulars 20X2 20X3 20X4 20X5 20X6
Sales Volume 32400 34992 37791 40000 40000
Selling Price per unit $6.63 $6.97 $7.38 $8.13 $8.78
Total Sales Revenue $214,812 $243,824 $279,051 $325,080 $351,000
Cost of Goods Sold ($164,520) ($186,192) ($212,841) ($238,760) ($257,120)
Gross Profit $50,292 $57,632 $66,210 $86,320 $93,880
General & Administrative
Expenses ($30,074) ($34,135) ($39,067) ($45,511) ($49,140)
Net Profit before Tax $20,218 $23,496 $27,143 $40,809 $44,740
Less: Income Tax @40% ($8,087) ($9,399) ($10,857) ($16,324) ($17,896)
Net Profit after Tax $12,131 $14,098 $16,286 $24,485 $26,844
Particulars 20X2 20X3 20X4 20X5 20X6
Opening Balance of Retained
Earnings $3,500 $3,780 $4,082 $4,409 $4,762
Net Profit for the period $12,131 $14,098 $16,286 $24,485 $26,844
$15,631 $17,878 $20,368 $28,894 $31,606
Less: Dividends Payable ($7,885) ($9,164) ($10,586) ($15,915) ($17,449)
Closing Balance of Retained
Earnings $3,780 $8,714 $9,782 $12,979 $14,157
Budgeted Income Statement:
Budgeted Statement of Retained Earnings:
Question 5
Budgeting
Requirement A
Particulars 20X2 20X3 20X4 20X5 20X6
Sales Volume 32400 34992 37791 40000 40000
Selling Price per unit $6.63 $6.97 $7.38 $8.13 $8.78
Total Sales Revenue $214,812 $243,824 $279,051 $325,080 $351,000
Cost of Goods Sold ($164,520) ($186,192) ($212,841) ($238,760) ($257,120)
Gross Profit $50,292 $57,632 $66,210 $86,320 $93,880
General & Administrative
Expenses ($30,074) ($34,135) ($39,067) ($45,511) ($49,140)
Net Profit before Tax $20,218 $23,496 $27,143 $40,809 $44,740
Less: Income Tax @40% ($8,087) ($9,399) ($10,857) ($16,324) ($17,896)
Net Profit after Tax $12,131 $14,098 $16,286 $24,485 $26,844
Particulars 20X2 20X3 20X4 20X5 20X6
Opening Balance of Retained
Earnings $3,500 $3,780 $4,082 $4,409 $4,762
Net Profit for the period $12,131 $14,098 $16,286 $24,485 $26,844
$15,631 $17,878 $20,368 $28,894 $31,606
Less: Dividends Payable ($7,885) ($9,164) ($10,586) ($15,915) ($17,449)
Closing Balance of Retained
Earnings $3,780 $8,714 $9,782 $12,979 $14,157
Budgeted Income Statement:
Budgeted Statement of Retained Earnings:
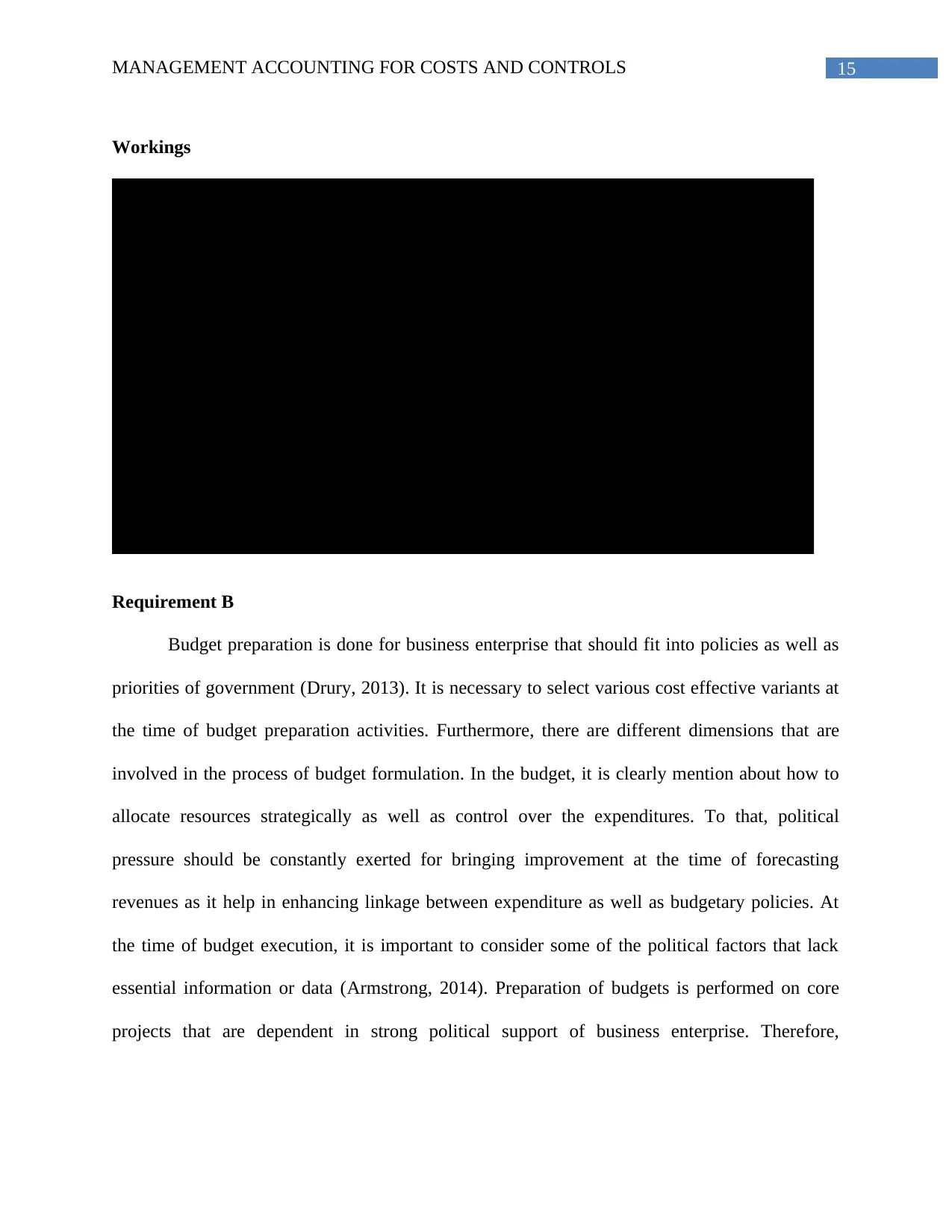
15MANAGEMENT ACCOUNTING FOR COSTS AND CONTROLS
Workings
Particulars 20X1 20X2 20X3 20X4 20X5 20X6 20X7
Sales 30000 32400 34992 37791 40000 40000 40000
Add: Closing Stock 3600 5249 5669 6000 6000 6000
37649 40661 43791 46000 46000
Less: Opening Stock 3600 5249 5669 6000 6000
Total Purchase 34049 35412 38123 40000 40000
Units Purchase Cost $5.10 $5.36 $5.68 $6.02 $6.50
Total Purchase Cost $173,649 $189,808 $216,537 $240,800 $260,000
Add: Opening Stock Value $17,640 $26,769 $30,384 $34,080 $36,120
$191,289 $216,577 $246,921 $274,880 $296,120
Less: Closing Stock Value $26,769 $30,384 $34,080 $36,120 $39,000
Total Cost of Goods Sold $164,520 $186,192 $212,841 $238,760 $257,120
Cost of Goods Sold Schedule:
Requirement B
Budget preparation is done for business enterprise that should fit into policies as well as
priorities of government (Drury, 2013). It is necessary to select various cost effective variants at
the time of budget preparation activities. Furthermore, there are different dimensions that are
involved in the process of budget formulation. In the budget, it is clearly mention about how to
allocate resources strategically as well as control over the expenditures. To that, political
pressure should be constantly exerted for bringing improvement at the time of forecasting
revenues as it help in enhancing linkage between expenditure as well as budgetary policies. At
the time of budget execution, it is important to consider some of the political factors that lack
essential information or data (Armstrong, 2014). Preparation of budgets is performed on core
projects that are dependent in strong political support of business enterprise. Therefore,
Workings
Particulars 20X1 20X2 20X3 20X4 20X5 20X6 20X7
Sales 30000 32400 34992 37791 40000 40000 40000
Add: Closing Stock 3600 5249 5669 6000 6000 6000
37649 40661 43791 46000 46000
Less: Opening Stock 3600 5249 5669 6000 6000
Total Purchase 34049 35412 38123 40000 40000
Units Purchase Cost $5.10 $5.36 $5.68 $6.02 $6.50
Total Purchase Cost $173,649 $189,808 $216,537 $240,800 $260,000
Add: Opening Stock Value $17,640 $26,769 $30,384 $34,080 $36,120
$191,289 $216,577 $246,921 $274,880 $296,120
Less: Closing Stock Value $26,769 $30,384 $34,080 $36,120 $39,000
Total Cost of Goods Sold $164,520 $186,192 $212,841 $238,760 $257,120
Cost of Goods Sold Schedule:
Requirement B
Budget preparation is done for business enterprise that should fit into policies as well as
priorities of government (Drury, 2013). It is necessary to select various cost effective variants at
the time of budget preparation activities. Furthermore, there are different dimensions that are
involved in the process of budget formulation. In the budget, it is clearly mention about how to
allocate resources strategically as well as control over the expenditures. To that, political
pressure should be constantly exerted for bringing improvement at the time of forecasting
revenues as it help in enhancing linkage between expenditure as well as budgetary policies. At
the time of budget execution, it is important to consider some of the political factors that lack
essential information or data (Armstrong, 2014). Preparation of budgets is performed on core
projects that are dependent in strong political support of business enterprise. Therefore,
⊘ This is a preview!⊘
Do you want full access?
Subscribe today to unlock all pages.

Trusted by 1+ million students worldwide
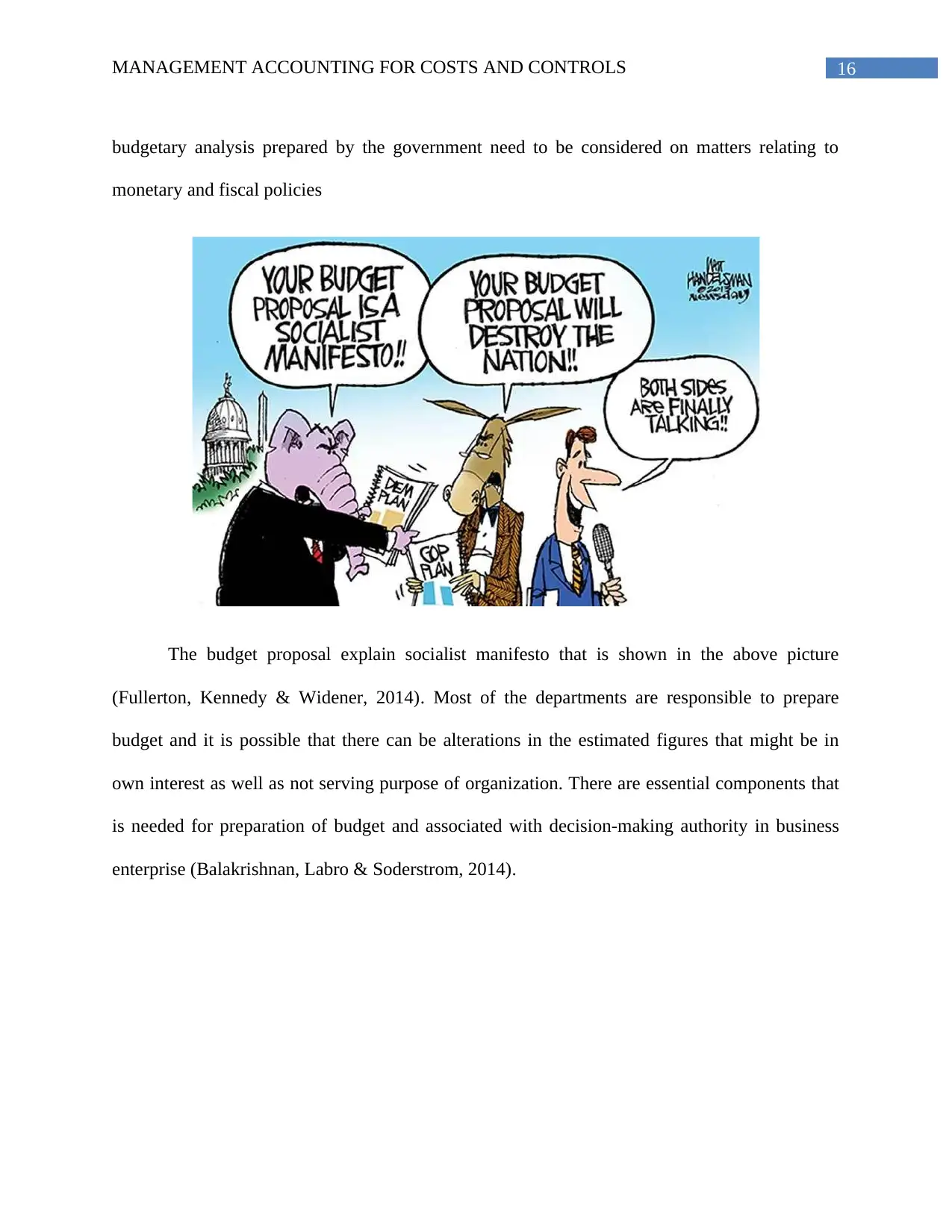
16MANAGEMENT ACCOUNTING FOR COSTS AND CONTROLS
budgetary analysis prepared by the government need to be considered on matters relating to
monetary and fiscal policies
The budget proposal explain socialist manifesto that is shown in the above picture
(Fullerton, Kennedy & Widener, 2014). Most of the departments are responsible to prepare
budget and it is possible that there can be alterations in the estimated figures that might be in
own interest as well as not serving purpose of organization. There are essential components that
is needed for preparation of budget and associated with decision-making authority in business
enterprise (Balakrishnan, Labro & Soderstrom, 2014).
budgetary analysis prepared by the government need to be considered on matters relating to
monetary and fiscal policies
The budget proposal explain socialist manifesto that is shown in the above picture
(Fullerton, Kennedy & Widener, 2014). Most of the departments are responsible to prepare
budget and it is possible that there can be alterations in the estimated figures that might be in
own interest as well as not serving purpose of organization. There are essential components that
is needed for preparation of budget and associated with decision-making authority in business
enterprise (Balakrishnan, Labro & Soderstrom, 2014).
Paraphrase This Document
Need a fresh take? Get an instant paraphrase of this document with our AI Paraphraser
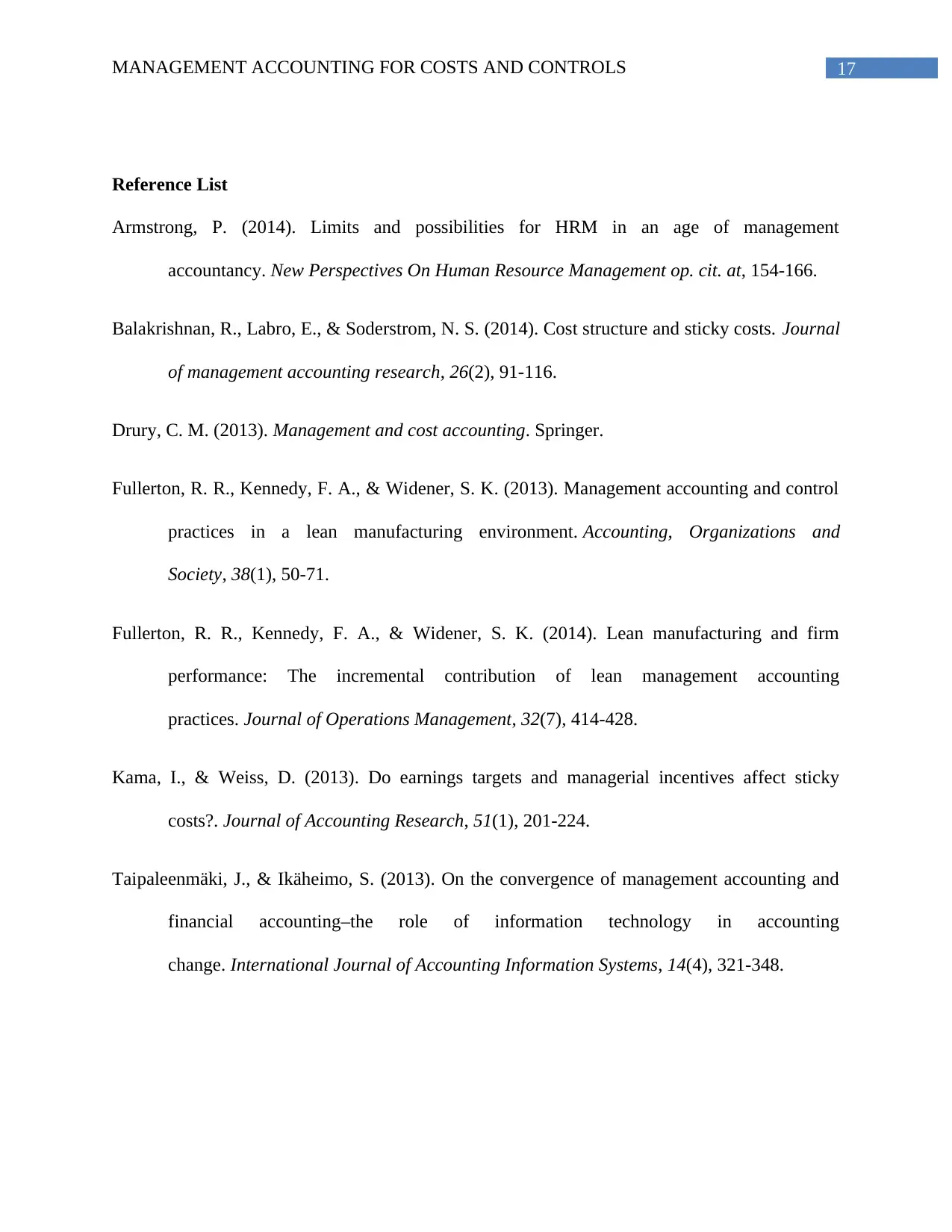
17MANAGEMENT ACCOUNTING FOR COSTS AND CONTROLS
Reference List
Armstrong, P. (2014). Limits and possibilities for HRM in an age of management
accountancy. New Perspectives On Human Resource Management op. cit. at, 154-166.
Balakrishnan, R., Labro, E., & Soderstrom, N. S. (2014). Cost structure and sticky costs. Journal
of management accounting research, 26(2), 91-116.
Drury, C. M. (2013). Management and cost accounting. Springer.
Fullerton, R. R., Kennedy, F. A., & Widener, S. K. (2013). Management accounting and control
practices in a lean manufacturing environment. Accounting, Organizations and
Society, 38(1), 50-71.
Fullerton, R. R., Kennedy, F. A., & Widener, S. K. (2014). Lean manufacturing and firm
performance: The incremental contribution of lean management accounting
practices. Journal of Operations Management, 32(7), 414-428.
Kama, I., & Weiss, D. (2013). Do earnings targets and managerial incentives affect sticky
costs?. Journal of Accounting Research, 51(1), 201-224.
Taipaleenmäki, J., & Ikäheimo, S. (2013). On the convergence of management accounting and
financial accounting–the role of information technology in accounting
change. International Journal of Accounting Information Systems, 14(4), 321-348.
Reference List
Armstrong, P. (2014). Limits and possibilities for HRM in an age of management
accountancy. New Perspectives On Human Resource Management op. cit. at, 154-166.
Balakrishnan, R., Labro, E., & Soderstrom, N. S. (2014). Cost structure and sticky costs. Journal
of management accounting research, 26(2), 91-116.
Drury, C. M. (2013). Management and cost accounting. Springer.
Fullerton, R. R., Kennedy, F. A., & Widener, S. K. (2013). Management accounting and control
practices in a lean manufacturing environment. Accounting, Organizations and
Society, 38(1), 50-71.
Fullerton, R. R., Kennedy, F. A., & Widener, S. K. (2014). Lean manufacturing and firm
performance: The incremental contribution of lean management accounting
practices. Journal of Operations Management, 32(7), 414-428.
Kama, I., & Weiss, D. (2013). Do earnings targets and managerial incentives affect sticky
costs?. Journal of Accounting Research, 51(1), 201-224.
Taipaleenmäki, J., & Ikäheimo, S. (2013). On the convergence of management accounting and
financial accounting–the role of information technology in accounting
change. International Journal of Accounting Information Systems, 14(4), 321-348.
1 out of 17
Related Documents

Your All-in-One AI-Powered Toolkit for Academic Success.
+13062052269
info@desklib.com
Available 24*7 on WhatsApp / Email
Unlock your academic potential
© 2024 | Zucol Services PVT LTD | All rights reserved.