Detailed Management Accounting Report: Jeffrey & Son's Ltd Analysis
VerifiedAdded on 2019/12/28
|21
|6431
|412
Report
AI Summary
This management accounting report for Jeffrey & Son's Ltd. covers a range of topics, including cost classification (direct, indirect, fixed, variable), job costing, and absorption costing methods to determine product costs. It analyzes cost data using various techniques and prepares a cost report for September, including variance analysis. The report also addresses budgeting processes, proposes appropriate budgeting methods, and creates production, material purchase, and cash budgets. Furthermore, it examines variance computation, identifies causes, and suggests corrective actions. The report concludes with an operating statement reconciling budgeted and actual results and provides recommendations to responsibility centers, offering insights into cost reduction, value enhancement, and quality improvement.
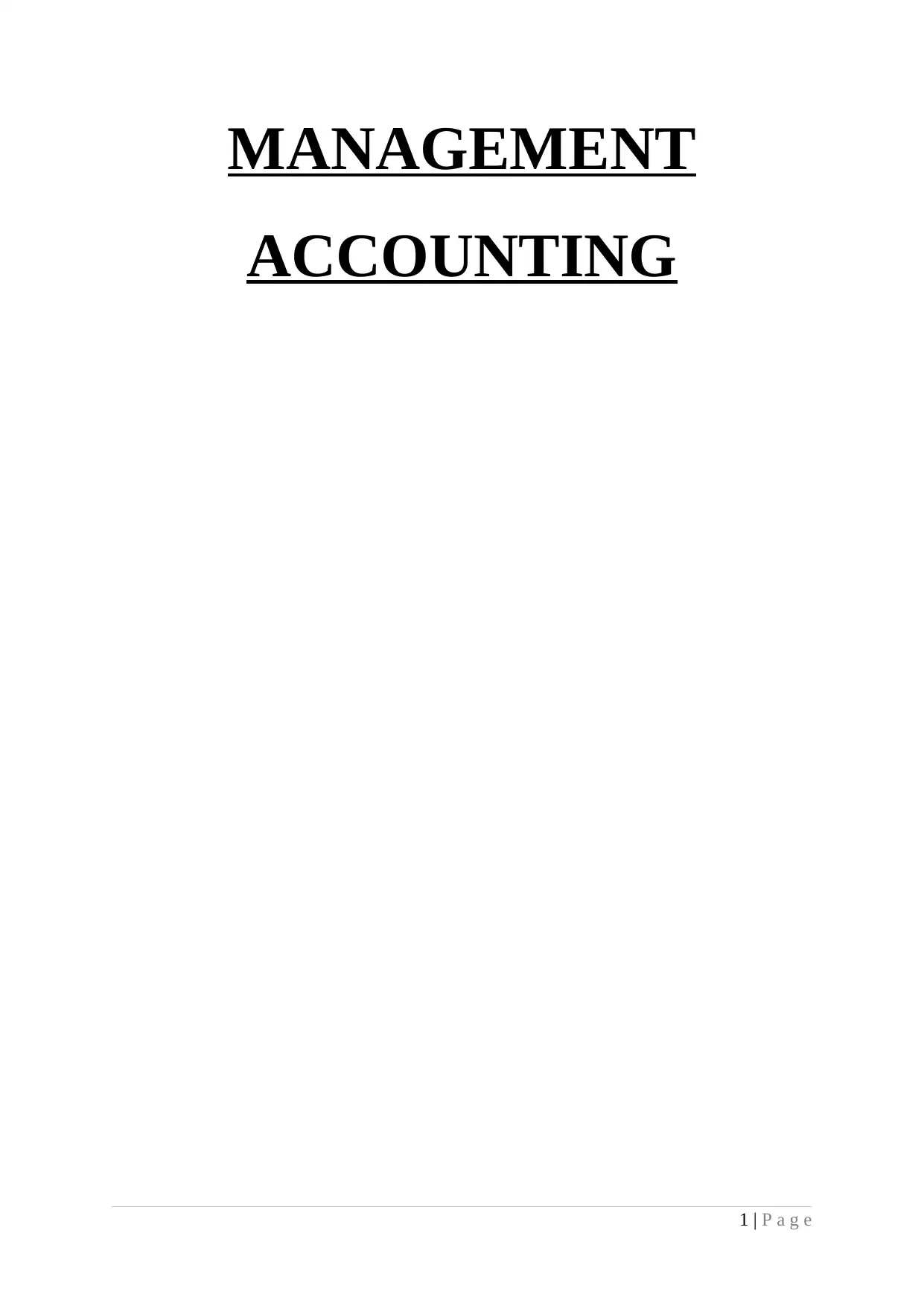
MANAGEMENT
ACCOUNTING
1 | P a g e
ACCOUNTING
1 | P a g e
Paraphrase This Document
Need a fresh take? Get an instant paraphrase of this document with our AI Paraphraser
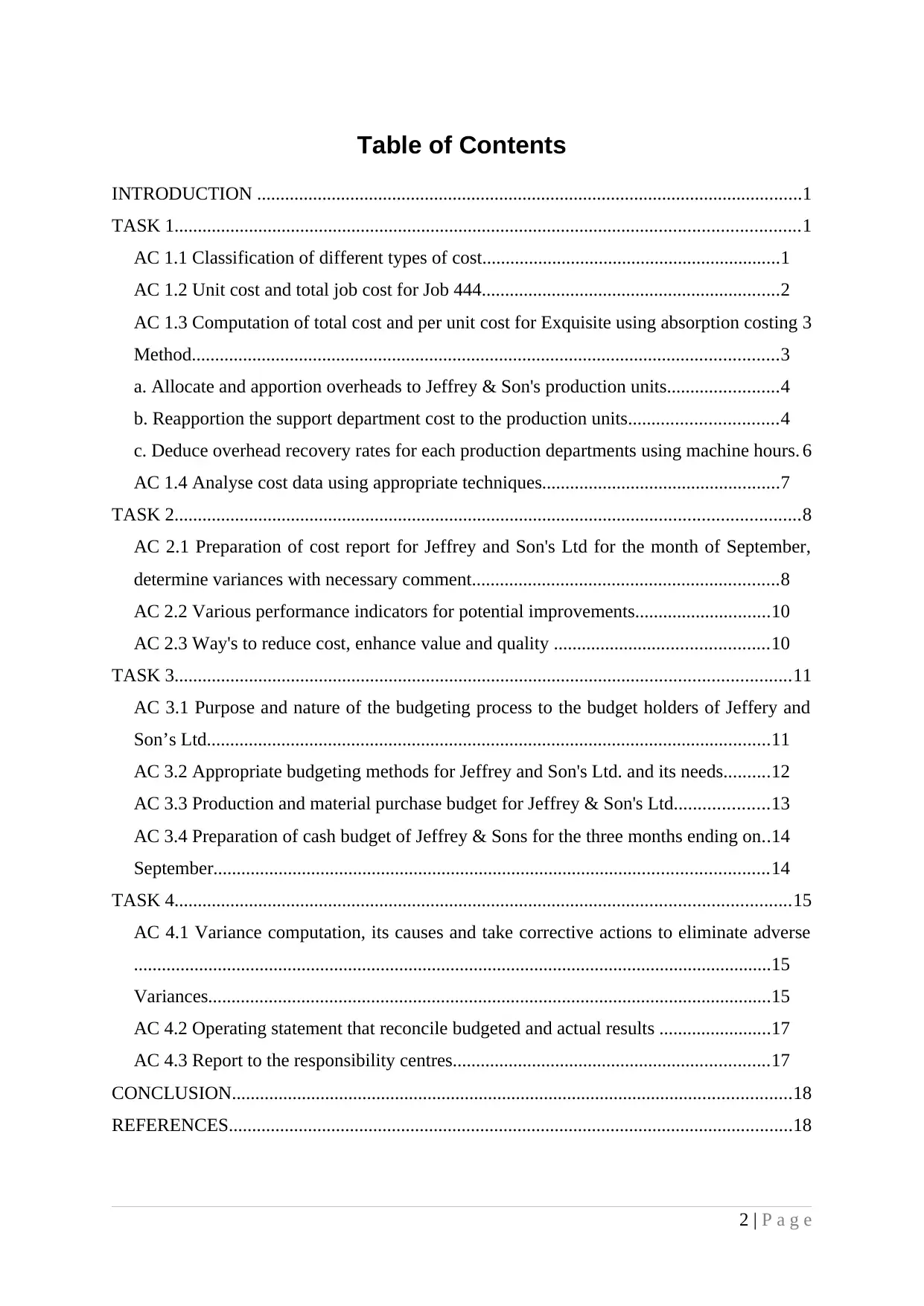
Table of Contents
INTRODUCTION .....................................................................................................................1
TASK 1......................................................................................................................................1
AC 1.1 Classification of different types of cost................................................................1
AC 1.2 Unit cost and total job cost for Job 444................................................................2
AC 1.3 Computation of total cost and per unit cost for Exquisite using absorption costing 3
Method..............................................................................................................................3
a. Allocate and apportion overheads to Jeffrey & Son's production units........................4
b. Reapportion the support department cost to the production units................................4
c. Deduce overhead recovery rates for each production departments using machine hours. 6
AC 1.4 Analyse cost data using appropriate techniques...................................................7
TASK 2......................................................................................................................................8
AC 2.1 Preparation of cost report for Jeffrey and Son's Ltd for the month of September,
determine variances with necessary comment..................................................................8
AC 2.2 Various performance indicators for potential improvements.............................10
AC 2.3 Way's to reduce cost, enhance value and quality ..............................................10
TASK 3....................................................................................................................................11
AC 3.1 Purpose and nature of the budgeting process to the budget holders of Jeffery and
Son’s Ltd.........................................................................................................................11
AC 3.2 Appropriate budgeting methods for Jeffrey and Son's Ltd. and its needs..........12
AC 3.3 Production and material purchase budget for Jeffrey & Son's Ltd....................13
AC 3.4 Preparation of cash budget of Jeffrey & Sons for the three months ending on..14
September.......................................................................................................................14
TASK 4....................................................................................................................................15
AC 4.1 Variance computation, its causes and take corrective actions to eliminate adverse
.........................................................................................................................................15
Variances.........................................................................................................................15
AC 4.2 Operating statement that reconcile budgeted and actual results ........................17
AC 4.3 Report to the responsibility centres....................................................................17
CONCLUSION........................................................................................................................18
REFERENCES.........................................................................................................................18
2 | P a g e
INTRODUCTION .....................................................................................................................1
TASK 1......................................................................................................................................1
AC 1.1 Classification of different types of cost................................................................1
AC 1.2 Unit cost and total job cost for Job 444................................................................2
AC 1.3 Computation of total cost and per unit cost for Exquisite using absorption costing 3
Method..............................................................................................................................3
a. Allocate and apportion overheads to Jeffrey & Son's production units........................4
b. Reapportion the support department cost to the production units................................4
c. Deduce overhead recovery rates for each production departments using machine hours. 6
AC 1.4 Analyse cost data using appropriate techniques...................................................7
TASK 2......................................................................................................................................8
AC 2.1 Preparation of cost report for Jeffrey and Son's Ltd for the month of September,
determine variances with necessary comment..................................................................8
AC 2.2 Various performance indicators for potential improvements.............................10
AC 2.3 Way's to reduce cost, enhance value and quality ..............................................10
TASK 3....................................................................................................................................11
AC 3.1 Purpose and nature of the budgeting process to the budget holders of Jeffery and
Son’s Ltd.........................................................................................................................11
AC 3.2 Appropriate budgeting methods for Jeffrey and Son's Ltd. and its needs..........12
AC 3.3 Production and material purchase budget for Jeffrey & Son's Ltd....................13
AC 3.4 Preparation of cash budget of Jeffrey & Sons for the three months ending on..14
September.......................................................................................................................14
TASK 4....................................................................................................................................15
AC 4.1 Variance computation, its causes and take corrective actions to eliminate adverse
.........................................................................................................................................15
Variances.........................................................................................................................15
AC 4.2 Operating statement that reconcile budgeted and actual results ........................17
AC 4.3 Report to the responsibility centres....................................................................17
CONCLUSION........................................................................................................................18
REFERENCES.........................................................................................................................18
2 | P a g e
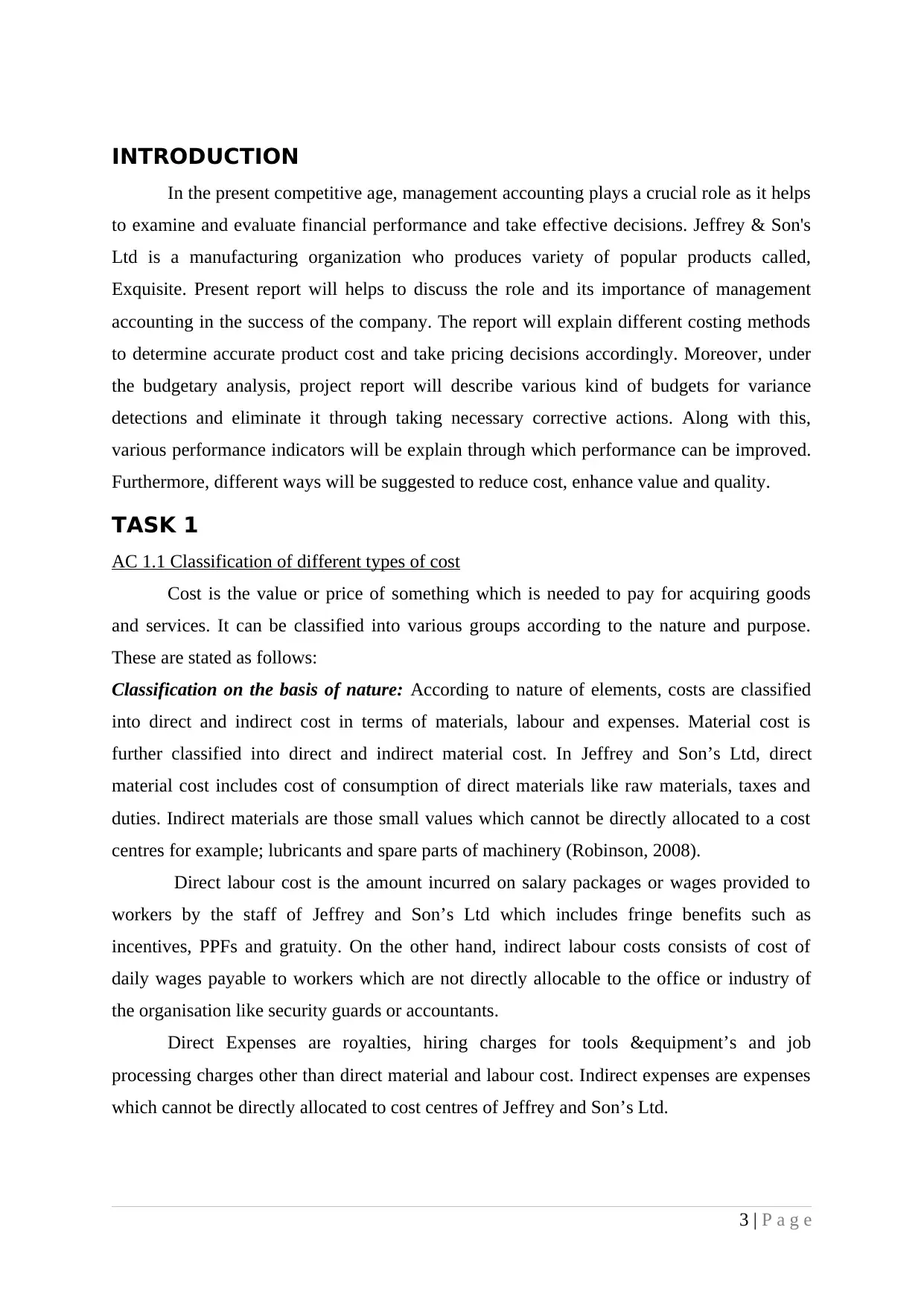
INTRODUCTION
In the present competitive age, management accounting plays a crucial role as it helps
to examine and evaluate financial performance and take effective decisions. Jeffrey & Son's
Ltd is a manufacturing organization who produces variety of popular products called,
Exquisite. Present report will helps to discuss the role and its importance of management
accounting in the success of the company. The report will explain different costing methods
to determine accurate product cost and take pricing decisions accordingly. Moreover, under
the budgetary analysis, project report will describe various kind of budgets for variance
detections and eliminate it through taking necessary corrective actions. Along with this,
various performance indicators will be explain through which performance can be improved.
Furthermore, different ways will be suggested to reduce cost, enhance value and quality.
TASK 1
AC 1.1 Classification of different types of cost
Cost is the value or price of something which is needed to pay for acquiring goods
and services. It can be classified into various groups according to the nature and purpose.
These are stated as follows:
Classification on the basis of nature: According to nature of elements, costs are classified
into direct and indirect cost in terms of materials, labour and expenses. Material cost is
further classified into direct and indirect material cost. In Jeffrey and Son’s Ltd, direct
material cost includes cost of consumption of direct materials like raw materials, taxes and
duties. Indirect materials are those small values which cannot be directly allocated to a cost
centres for example; lubricants and spare parts of machinery (Robinson, 2008).
Direct labour cost is the amount incurred on salary packages or wages provided to
workers by the staff of Jeffrey and Son’s Ltd which includes fringe benefits such as
incentives, PPFs and gratuity. On the other hand, indirect labour costs consists of cost of
daily wages payable to workers which are not directly allocable to the office or industry of
the organisation like security guards or accountants.
Direct Expenses are royalties, hiring charges for tools &equipment’s and job
processing charges other than direct material and labour cost. Indirect expenses are expenses
which cannot be directly allocated to cost centres of Jeffrey and Son’s Ltd.
3 | P a g e
In the present competitive age, management accounting plays a crucial role as it helps
to examine and evaluate financial performance and take effective decisions. Jeffrey & Son's
Ltd is a manufacturing organization who produces variety of popular products called,
Exquisite. Present report will helps to discuss the role and its importance of management
accounting in the success of the company. The report will explain different costing methods
to determine accurate product cost and take pricing decisions accordingly. Moreover, under
the budgetary analysis, project report will describe various kind of budgets for variance
detections and eliminate it through taking necessary corrective actions. Along with this,
various performance indicators will be explain through which performance can be improved.
Furthermore, different ways will be suggested to reduce cost, enhance value and quality.
TASK 1
AC 1.1 Classification of different types of cost
Cost is the value or price of something which is needed to pay for acquiring goods
and services. It can be classified into various groups according to the nature and purpose.
These are stated as follows:
Classification on the basis of nature: According to nature of elements, costs are classified
into direct and indirect cost in terms of materials, labour and expenses. Material cost is
further classified into direct and indirect material cost. In Jeffrey and Son’s Ltd, direct
material cost includes cost of consumption of direct materials like raw materials, taxes and
duties. Indirect materials are those small values which cannot be directly allocated to a cost
centres for example; lubricants and spare parts of machinery (Robinson, 2008).
Direct labour cost is the amount incurred on salary packages or wages provided to
workers by the staff of Jeffrey and Son’s Ltd which includes fringe benefits such as
incentives, PPFs and gratuity. On the other hand, indirect labour costs consists of cost of
daily wages payable to workers which are not directly allocable to the office or industry of
the organisation like security guards or accountants.
Direct Expenses are royalties, hiring charges for tools &equipment’s and job
processing charges other than direct material and labour cost. Indirect expenses are expenses
which cannot be directly allocated to cost centres of Jeffrey and Son’s Ltd.
3 | P a g e
⊘ This is a preview!⊘
Do you want full access?
Subscribe today to unlock all pages.

Trusted by 1+ million students worldwide
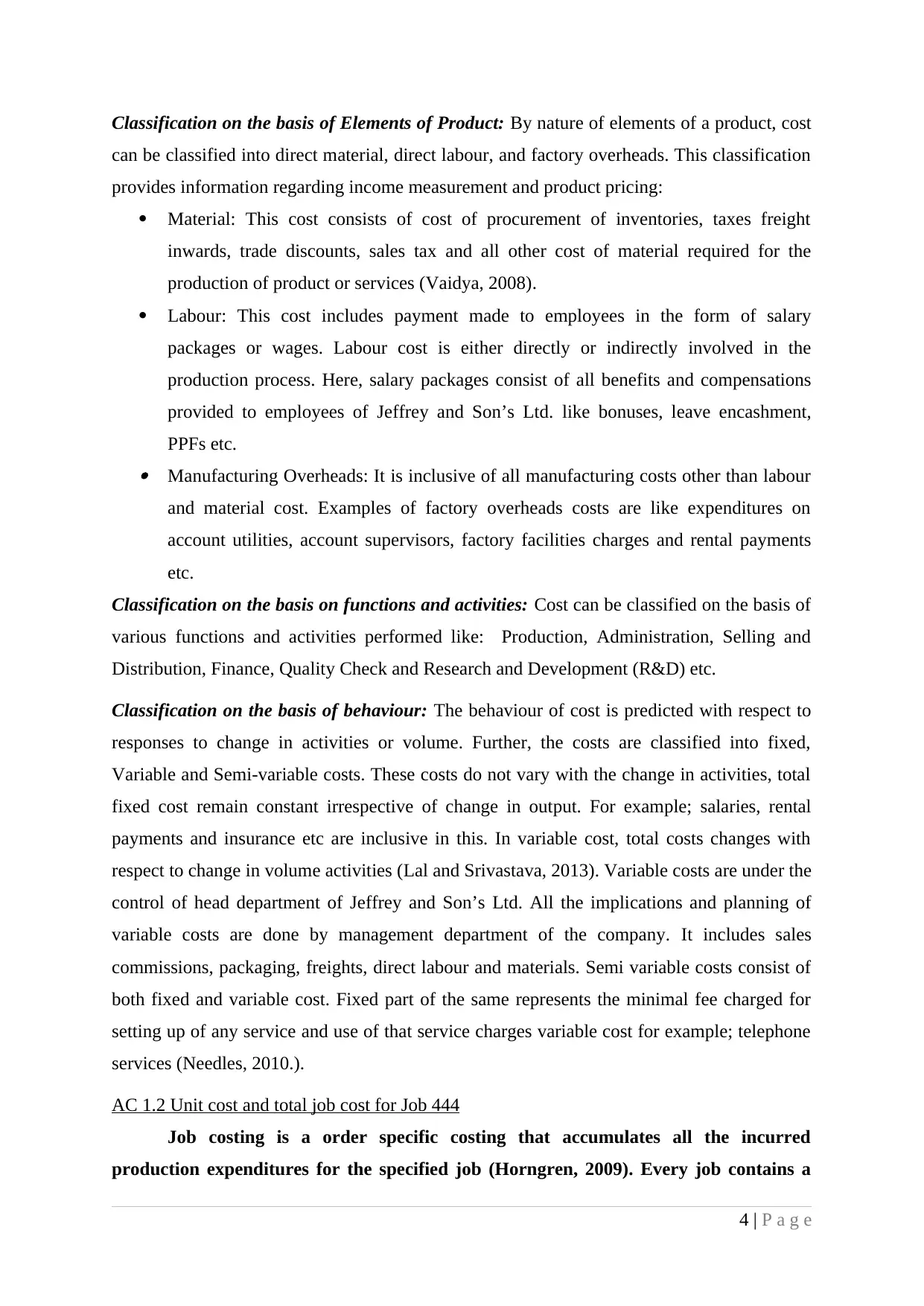
Classification on the basis of Elements of Product: By nature of elements of a product, cost
can be classified into direct material, direct labour, and factory overheads. This classification
provides information regarding income measurement and product pricing:
Material: This cost consists of cost of procurement of inventories, taxes freight
inwards, trade discounts, sales tax and all other cost of material required for the
production of product or services (Vaidya, 2008).
Labour: This cost includes payment made to employees in the form of salary
packages or wages. Labour cost is either directly or indirectly involved in the
production process. Here, salary packages consist of all benefits and compensations
provided to employees of Jeffrey and Son’s Ltd. like bonuses, leave encashment,
PPFs etc. Manufacturing Overheads: It is inclusive of all manufacturing costs other than labour
and material cost. Examples of factory overheads costs are like expenditures on
account utilities, account supervisors, factory facilities charges and rental payments
etc.
Classification on the basis on functions and activities: Cost can be classified on the basis of
various functions and activities performed like: Production, Administration, Selling and
Distribution, Finance, Quality Check and Research and Development (R&D) etc.
Classification on the basis of behaviour: The behaviour of cost is predicted with respect to
responses to change in activities or volume. Further, the costs are classified into fixed,
Variable and Semi-variable costs. These costs do not vary with the change in activities, total
fixed cost remain constant irrespective of change in output. For example; salaries, rental
payments and insurance etc are inclusive in this. In variable cost, total costs changes with
respect to change in volume activities (Lal and Srivastava, 2013). Variable costs are under the
control of head department of Jeffrey and Son’s Ltd. All the implications and planning of
variable costs are done by management department of the company. It includes sales
commissions, packaging, freights, direct labour and materials. Semi variable costs consist of
both fixed and variable cost. Fixed part of the same represents the minimal fee charged for
setting up of any service and use of that service charges variable cost for example; telephone
services (Needles, 2010.).
AC 1.2 Unit cost and total job cost for Job 444
Job costing is a order specific costing that accumulates all the incurred
production expenditures for the specified job (Horngren, 2009). Every job contains a
4 | P a g e
can be classified into direct material, direct labour, and factory overheads. This classification
provides information regarding income measurement and product pricing:
Material: This cost consists of cost of procurement of inventories, taxes freight
inwards, trade discounts, sales tax and all other cost of material required for the
production of product or services (Vaidya, 2008).
Labour: This cost includes payment made to employees in the form of salary
packages or wages. Labour cost is either directly or indirectly involved in the
production process. Here, salary packages consist of all benefits and compensations
provided to employees of Jeffrey and Son’s Ltd. like bonuses, leave encashment,
PPFs etc. Manufacturing Overheads: It is inclusive of all manufacturing costs other than labour
and material cost. Examples of factory overheads costs are like expenditures on
account utilities, account supervisors, factory facilities charges and rental payments
etc.
Classification on the basis on functions and activities: Cost can be classified on the basis of
various functions and activities performed like: Production, Administration, Selling and
Distribution, Finance, Quality Check and Research and Development (R&D) etc.
Classification on the basis of behaviour: The behaviour of cost is predicted with respect to
responses to change in activities or volume. Further, the costs are classified into fixed,
Variable and Semi-variable costs. These costs do not vary with the change in activities, total
fixed cost remain constant irrespective of change in output. For example; salaries, rental
payments and insurance etc are inclusive in this. In variable cost, total costs changes with
respect to change in volume activities (Lal and Srivastava, 2013). Variable costs are under the
control of head department of Jeffrey and Son’s Ltd. All the implications and planning of
variable costs are done by management department of the company. It includes sales
commissions, packaging, freights, direct labour and materials. Semi variable costs consist of
both fixed and variable cost. Fixed part of the same represents the minimal fee charged for
setting up of any service and use of that service charges variable cost for example; telephone
services (Needles, 2010.).
AC 1.2 Unit cost and total job cost for Job 444
Job costing is a order specific costing that accumulates all the incurred
production expenditures for the specified job (Horngren, 2009). Every job contains a
4 | P a g e
Paraphrase This Document
Need a fresh take? Get an instant paraphrase of this document with our AI Paraphraser
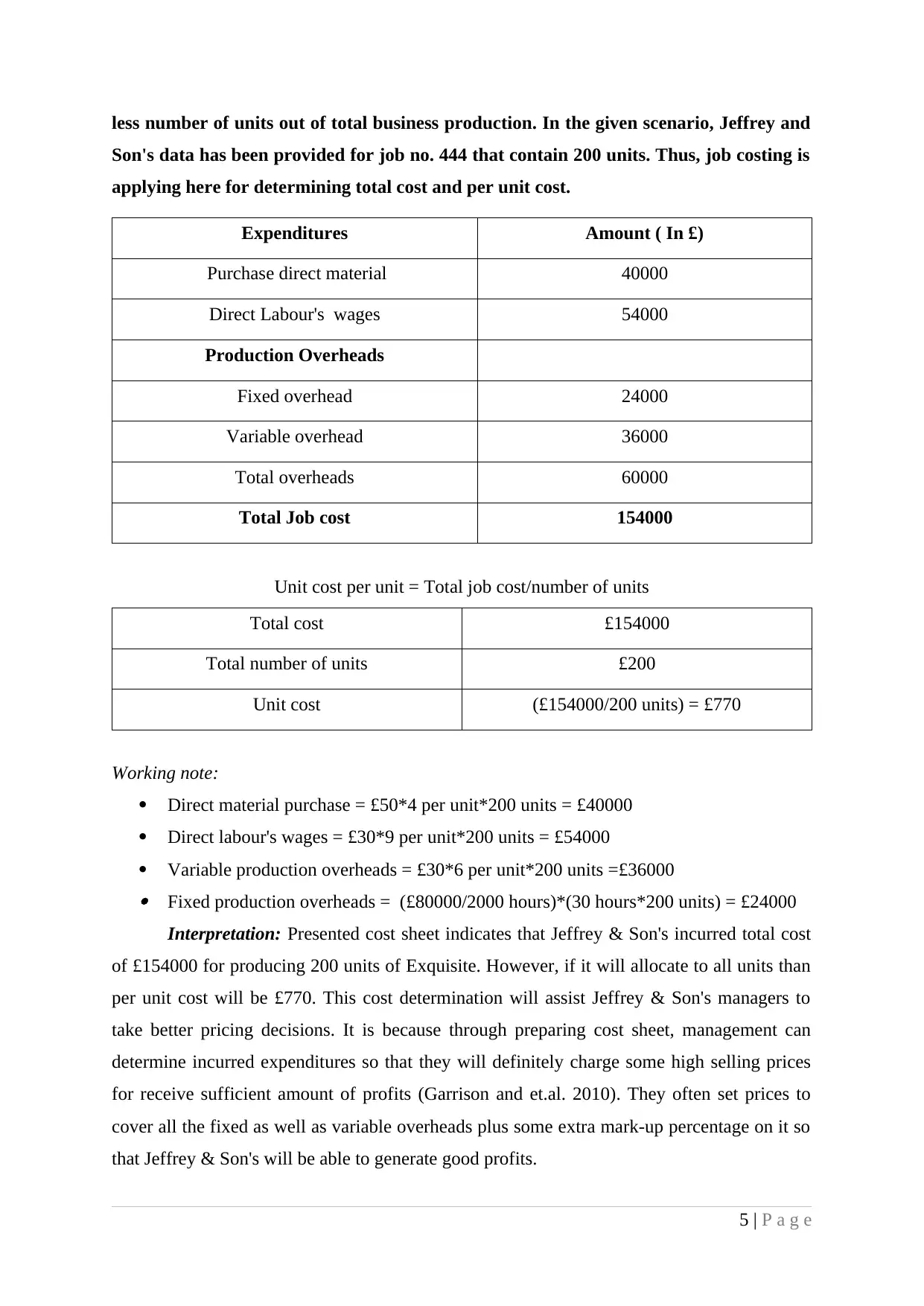
less number of units out of total business production. In the given scenario, Jeffrey and
Son's data has been provided for job no. 444 that contain 200 units. Thus, job costing is
applying here for determining total cost and per unit cost.
Expenditures Amount ( In £)
Purchase direct material 40000
Direct Labour's wages 54000
Production Overheads
Fixed overhead 24000
Variable overhead 36000
Total overheads 60000
Total Job cost 154000
Unit cost per unit = Total job cost/number of units
Total cost £154000
Total number of units £200
Unit cost (£154000/200 units) = £770
Working note:
Direct material purchase = £50*4 per unit*200 units = £40000
Direct labour's wages = £30*9 per unit*200 units = £54000
Variable production overheads = £30*6 per unit*200 units =£36000 Fixed production overheads = (£80000/2000 hours)*(30 hours*200 units) = £24000
Interpretation: Presented cost sheet indicates that Jeffrey & Son's incurred total cost
of £154000 for producing 200 units of Exquisite. However, if it will allocate to all units than
per unit cost will be £770. This cost determination will assist Jeffrey & Son's managers to
take better pricing decisions. It is because through preparing cost sheet, management can
determine incurred expenditures so that they will definitely charge some high selling prices
for receive sufficient amount of profits (Garrison and et.al. 2010). They often set prices to
cover all the fixed as well as variable overheads plus some extra mark-up percentage on it so
that Jeffrey & Son's will be able to generate good profits.
5 | P a g e
Son's data has been provided for job no. 444 that contain 200 units. Thus, job costing is
applying here for determining total cost and per unit cost.
Expenditures Amount ( In £)
Purchase direct material 40000
Direct Labour's wages 54000
Production Overheads
Fixed overhead 24000
Variable overhead 36000
Total overheads 60000
Total Job cost 154000
Unit cost per unit = Total job cost/number of units
Total cost £154000
Total number of units £200
Unit cost (£154000/200 units) = £770
Working note:
Direct material purchase = £50*4 per unit*200 units = £40000
Direct labour's wages = £30*9 per unit*200 units = £54000
Variable production overheads = £30*6 per unit*200 units =£36000 Fixed production overheads = (£80000/2000 hours)*(30 hours*200 units) = £24000
Interpretation: Presented cost sheet indicates that Jeffrey & Son's incurred total cost
of £154000 for producing 200 units of Exquisite. However, if it will allocate to all units than
per unit cost will be £770. This cost determination will assist Jeffrey & Son's managers to
take better pricing decisions. It is because through preparing cost sheet, management can
determine incurred expenditures so that they will definitely charge some high selling prices
for receive sufficient amount of profits (Garrison and et.al. 2010). They often set prices to
cover all the fixed as well as variable overheads plus some extra mark-up percentage on it so
that Jeffrey & Son's will be able to generate good profits.
5 | P a g e
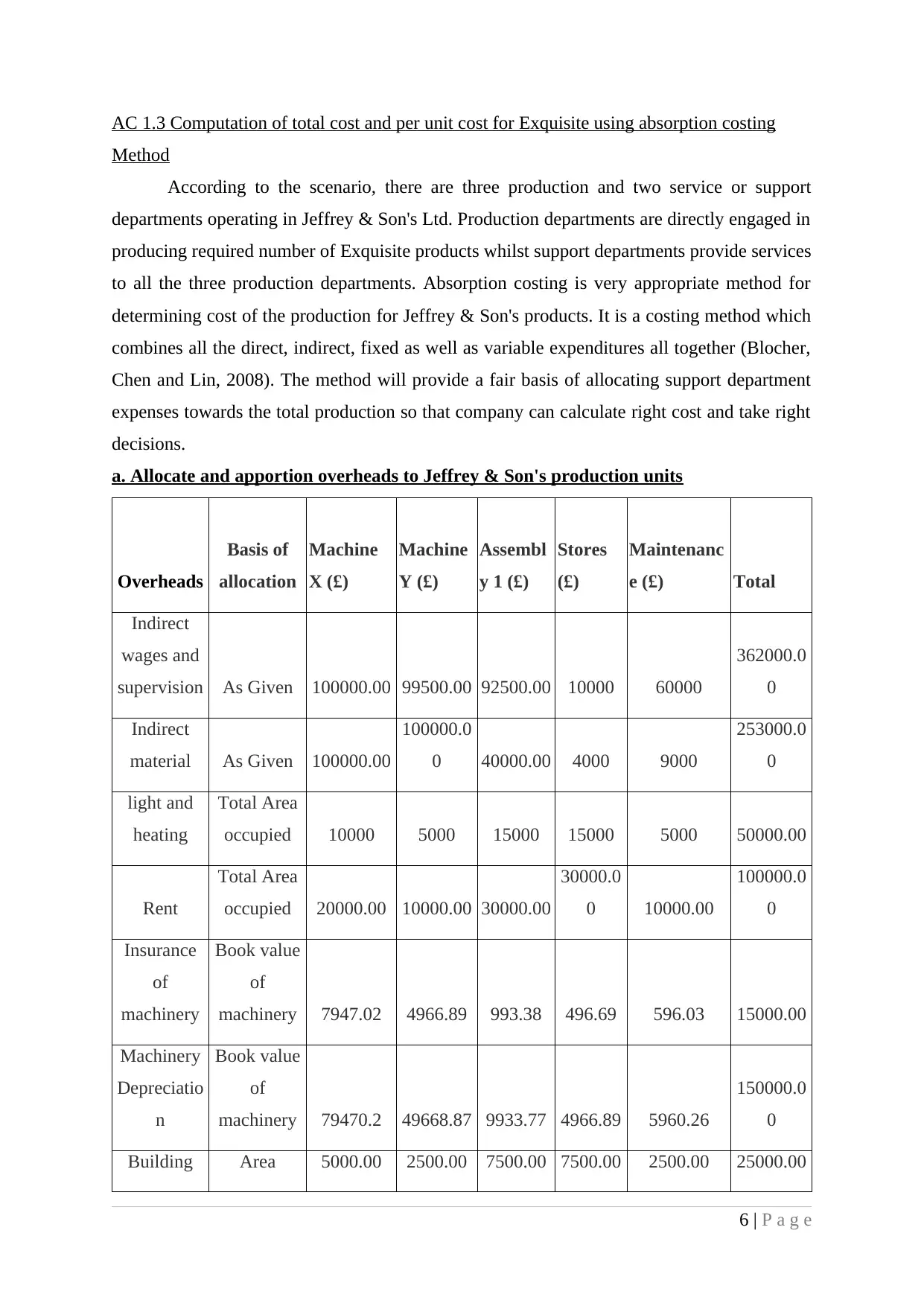
AC 1.3 Computation of total cost and per unit cost for Exquisite using absorption costing
Method
According to the scenario, there are three production and two service or support
departments operating in Jeffrey & Son's Ltd. Production departments are directly engaged in
producing required number of Exquisite products whilst support departments provide services
to all the three production departments. Absorption costing is very appropriate method for
determining cost of the production for Jeffrey & Son's products. It is a costing method which
combines all the direct, indirect, fixed as well as variable expenditures all together (Blocher,
Chen and Lin, 2008). The method will provide a fair basis of allocating support department
expenses towards the total production so that company can calculate right cost and take right
decisions.
a. Allocate and apportion overheads to Jeffrey & Son's production units
Overheads
Basis of
allocation
Machine
X (£)
Machine
Y (£)
Assembl
y 1 (£)
Stores
(£)
Maintenanc
e (£) Total
Indirect
wages and
supervision As Given 100000.00 99500.00 92500.00 10000 60000
362000.0
0
Indirect
material As Given 100000.00
100000.0
0 40000.00 4000 9000
253000.0
0
light and
heating
Total Area
occupied 10000 5000 15000 15000 5000 50000.00
Rent
Total Area
occupied 20000.00 10000.00 30000.00
30000.0
0 10000.00
100000.0
0
Insurance
of
machinery
Book value
of
machinery 7947.02 4966.89 993.38 496.69 596.03 15000.00
Machinery
Depreciatio
n
Book value
of
machinery 79470.2 49668.87 9933.77 4966.89 5960.26
150000.0
0
Building Area 5000.00 2500.00 7500.00 7500.00 2500.00 25000.00
6 | P a g e
Method
According to the scenario, there are three production and two service or support
departments operating in Jeffrey & Son's Ltd. Production departments are directly engaged in
producing required number of Exquisite products whilst support departments provide services
to all the three production departments. Absorption costing is very appropriate method for
determining cost of the production for Jeffrey & Son's products. It is a costing method which
combines all the direct, indirect, fixed as well as variable expenditures all together (Blocher,
Chen and Lin, 2008). The method will provide a fair basis of allocating support department
expenses towards the total production so that company can calculate right cost and take right
decisions.
a. Allocate and apportion overheads to Jeffrey & Son's production units
Overheads
Basis of
allocation
Machine
X (£)
Machine
Y (£)
Assembl
y 1 (£)
Stores
(£)
Maintenanc
e (£) Total
Indirect
wages and
supervision As Given 100000.00 99500.00 92500.00 10000 60000
362000.0
0
Indirect
material As Given 100000.00
100000.0
0 40000.00 4000 9000
253000.0
0
light and
heating
Total Area
occupied 10000 5000 15000 15000 5000 50000.00
Rent
Total Area
occupied 20000.00 10000.00 30000.00
30000.0
0 10000.00
100000.0
0
Insurance
of
machinery
Book value
of
machinery 7947.02 4966.89 993.38 496.69 596.03 15000.00
Machinery
Depreciatio
n
Book value
of
machinery 79470.2 49668.87 9933.77 4966.89 5960.26
150000.0
0
Building Area 5000.00 2500.00 7500.00 7500.00 2500.00 25000.00
6 | P a g e
⊘ This is a preview!⊘
Do you want full access?
Subscribe today to unlock all pages.

Trusted by 1+ million students worldwide
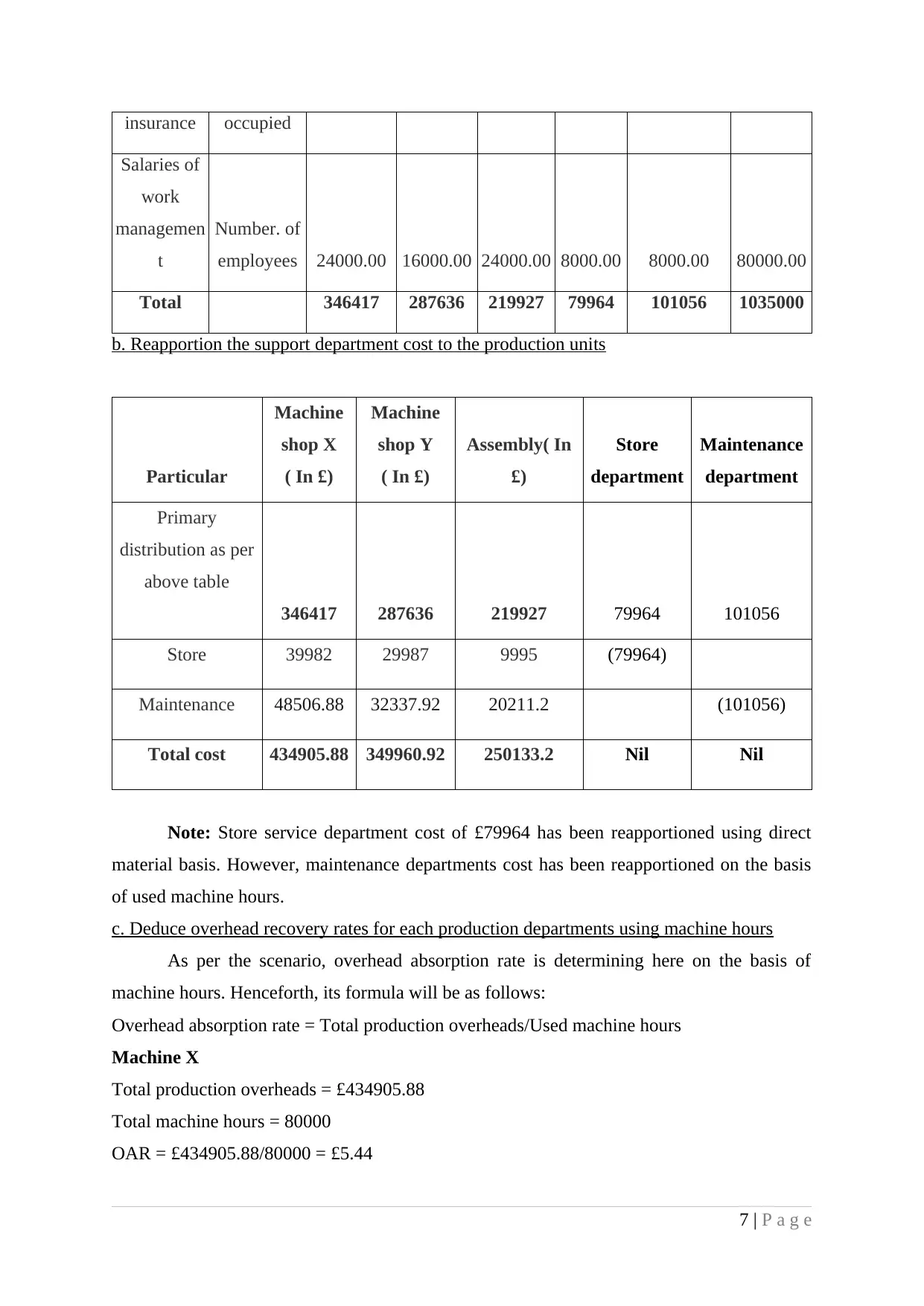
insurance occupied
Salaries of
work
managemen
t
Number. of
employees 24000.00 16000.00 24000.00 8000.00 8000.00 80000.00
Total 346417 287636 219927 79964 101056 1035000
b. Reapportion the support department cost to the production units
Particular
Machine
shop X
( In £)
Machine
shop Y
( In £)
Assembly( In
£)
Store
department
Maintenance
department
Primary
distribution as per
above table
346417 287636 219927 79964 101056
Store 39982 29987 9995 (79964)
Maintenance 48506.88 32337.92 20211.2 (101056)
Total cost 434905.88 349960.92 250133.2 Nil Nil
Note: Store service department cost of £79964 has been reapportioned using direct
material basis. However, maintenance departments cost has been reapportioned on the basis
of used machine hours.
c. Deduce overhead recovery rates for each production departments using machine hours
As per the scenario, overhead absorption rate is determining here on the basis of
machine hours. Henceforth, its formula will be as follows:
Overhead absorption rate = Total production overheads/Used machine hours
Machine X
Total production overheads = £434905.88
Total machine hours = 80000
OAR = £434905.88/80000 = £5.44
7 | P a g e
Salaries of
work
managemen
t
Number. of
employees 24000.00 16000.00 24000.00 8000.00 8000.00 80000.00
Total 346417 287636 219927 79964 101056 1035000
b. Reapportion the support department cost to the production units
Particular
Machine
shop X
( In £)
Machine
shop Y
( In £)
Assembly( In
£)
Store
department
Maintenance
department
Primary
distribution as per
above table
346417 287636 219927 79964 101056
Store 39982 29987 9995 (79964)
Maintenance 48506.88 32337.92 20211.2 (101056)
Total cost 434905.88 349960.92 250133.2 Nil Nil
Note: Store service department cost of £79964 has been reapportioned using direct
material basis. However, maintenance departments cost has been reapportioned on the basis
of used machine hours.
c. Deduce overhead recovery rates for each production departments using machine hours
As per the scenario, overhead absorption rate is determining here on the basis of
machine hours. Henceforth, its formula will be as follows:
Overhead absorption rate = Total production overheads/Used machine hours
Machine X
Total production overheads = £434905.88
Total machine hours = 80000
OAR = £434905.88/80000 = £5.44
7 | P a g e
Paraphrase This Document
Need a fresh take? Get an instant paraphrase of this document with our AI Paraphraser
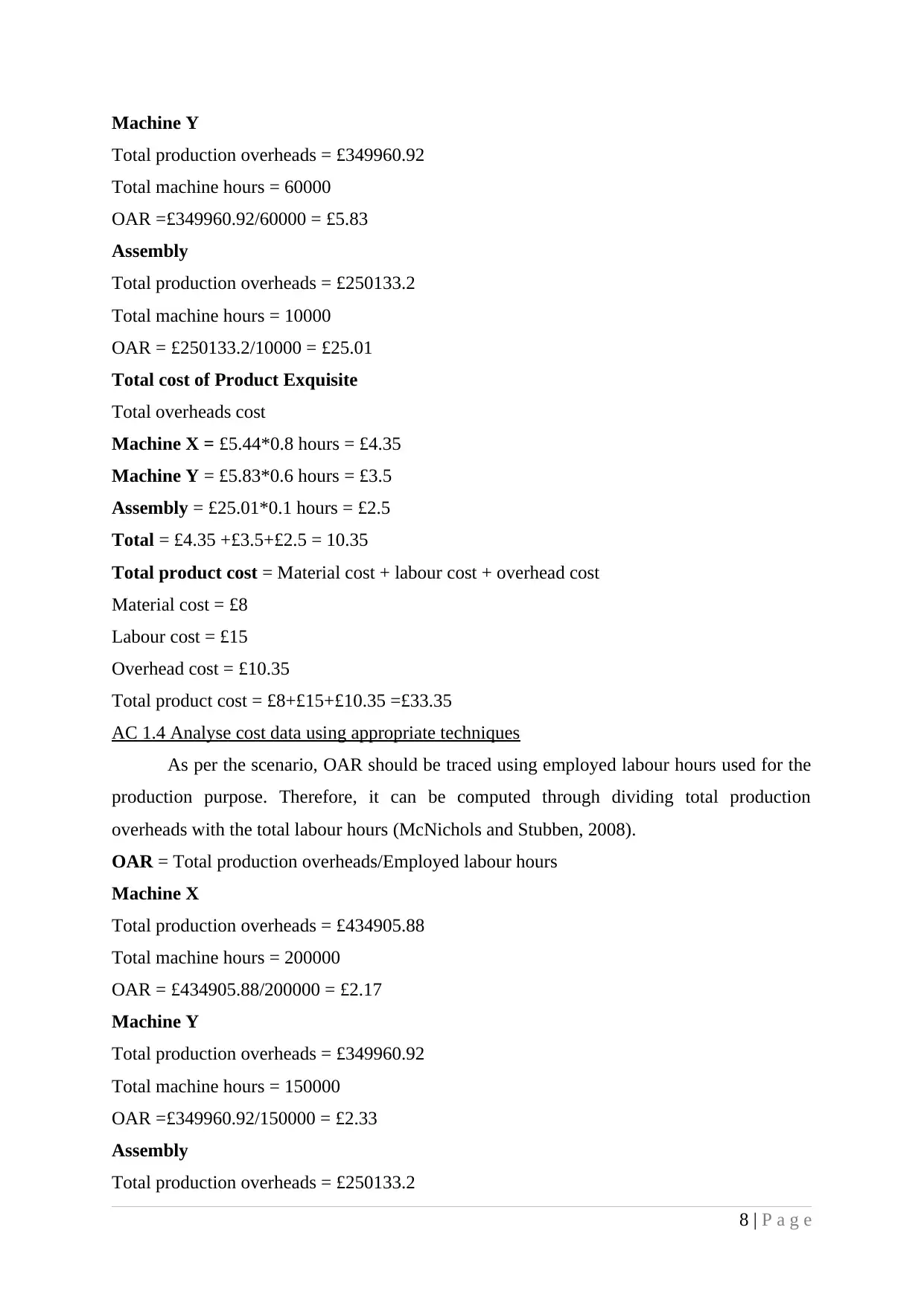
Machine Y
Total production overheads = £349960.92
Total machine hours = 60000
OAR =£349960.92/60000 = £5.83
Assembly
Total production overheads = £250133.2
Total machine hours = 10000
OAR = £250133.2/10000 = £25.01
Total cost of Product Exquisite
Total overheads cost
Machine X = £5.44*0.8 hours = £4.35
Machine Y = £5.83*0.6 hours = £3.5
Assembly = £25.01*0.1 hours = £2.5
Total = £4.35 +£3.5+£2.5 = 10.35
Total product cost = Material cost + labour cost + overhead cost
Material cost = £8
Labour cost = £15
Overhead cost = £10.35
Total product cost = £8+£15+£10.35 =£33.35
AC 1.4 Analyse cost data using appropriate techniques
As per the scenario, OAR should be traced using employed labour hours used for the
production purpose. Therefore, it can be computed through dividing total production
overheads with the total labour hours (McNichols and Stubben, 2008).
OAR = Total production overheads/Employed labour hours
Machine X
Total production overheads = £434905.88
Total machine hours = 200000
OAR = £434905.88/200000 = £2.17
Machine Y
Total production overheads = £349960.92
Total machine hours = 150000
OAR =£349960.92/150000 = £2.33
Assembly
Total production overheads = £250133.2
8 | P a g e
Total production overheads = £349960.92
Total machine hours = 60000
OAR =£349960.92/60000 = £5.83
Assembly
Total production overheads = £250133.2
Total machine hours = 10000
OAR = £250133.2/10000 = £25.01
Total cost of Product Exquisite
Total overheads cost
Machine X = £5.44*0.8 hours = £4.35
Machine Y = £5.83*0.6 hours = £3.5
Assembly = £25.01*0.1 hours = £2.5
Total = £4.35 +£3.5+£2.5 = 10.35
Total product cost = Material cost + labour cost + overhead cost
Material cost = £8
Labour cost = £15
Overhead cost = £10.35
Total product cost = £8+£15+£10.35 =£33.35
AC 1.4 Analyse cost data using appropriate techniques
As per the scenario, OAR should be traced using employed labour hours used for the
production purpose. Therefore, it can be computed through dividing total production
overheads with the total labour hours (McNichols and Stubben, 2008).
OAR = Total production overheads/Employed labour hours
Machine X
Total production overheads = £434905.88
Total machine hours = 200000
OAR = £434905.88/200000 = £2.17
Machine Y
Total production overheads = £349960.92
Total machine hours = 150000
OAR =£349960.92/150000 = £2.33
Assembly
Total production overheads = £250133.2
8 | P a g e
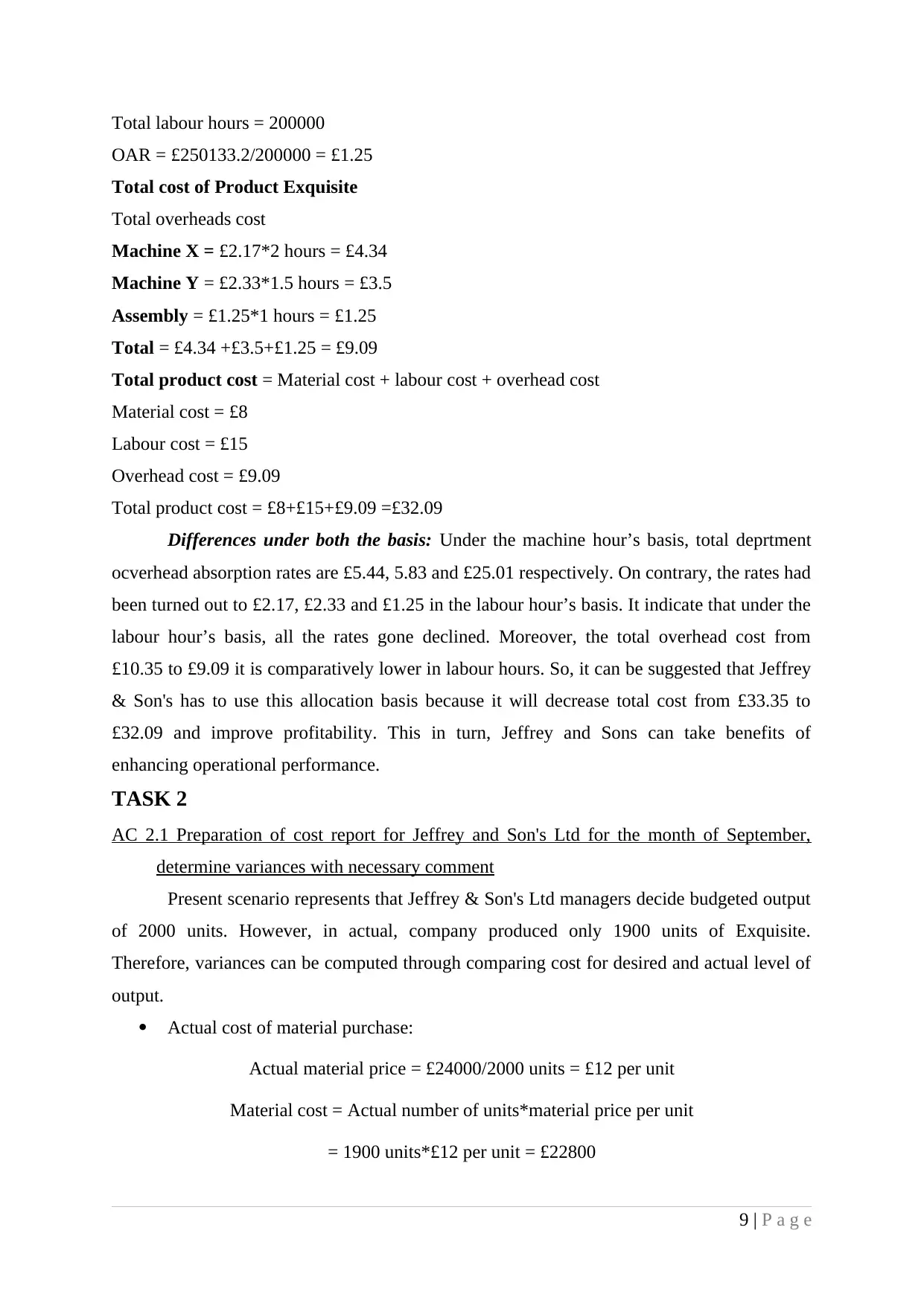
Total labour hours = 200000
OAR = £250133.2/200000 = £1.25
Total cost of Product Exquisite
Total overheads cost
Machine X = £2.17*2 hours = £4.34
Machine Y = £2.33*1.5 hours = £3.5
Assembly = £1.25*1 hours = £1.25
Total = £4.34 +£3.5+£1.25 = £9.09
Total product cost = Material cost + labour cost + overhead cost
Material cost = £8
Labour cost = £15
Overhead cost = £9.09
Total product cost = £8+£15+£9.09 =£32.09
Differences under both the basis: Under the machine hour’s basis, total deprtment
ocverhead absorption rates are £5.44, 5.83 and £25.01 respectively. On contrary, the rates had
been turned out to £2.17, £2.33 and £1.25 in the labour hour’s basis. It indicate that under the
labour hour’s basis, all the rates gone declined. Moreover, the total overhead cost from
£10.35 to £9.09 it is comparatively lower in labour hours. So, it can be suggested that Jeffrey
& Son's has to use this allocation basis because it will decrease total cost from £33.35 to
£32.09 and improve profitability. This in turn, Jeffrey and Sons can take benefits of
enhancing operational performance.
TASK 2
AC 2.1 Preparation of cost report for Jeffrey and Son's Ltd for the month of September,
determine variances with necessary comment
Present scenario represents that Jeffrey & Son's Ltd managers decide budgeted output
of 2000 units. However, in actual, company produced only 1900 units of Exquisite.
Therefore, variances can be computed through comparing cost for desired and actual level of
output.
Actual cost of material purchase:
Actual material price = £24000/2000 units = £12 per unit
Material cost = Actual number of units*material price per unit
= 1900 units*£12 per unit = £22800
9 | P a g e
OAR = £250133.2/200000 = £1.25
Total cost of Product Exquisite
Total overheads cost
Machine X = £2.17*2 hours = £4.34
Machine Y = £2.33*1.5 hours = £3.5
Assembly = £1.25*1 hours = £1.25
Total = £4.34 +£3.5+£1.25 = £9.09
Total product cost = Material cost + labour cost + overhead cost
Material cost = £8
Labour cost = £15
Overhead cost = £9.09
Total product cost = £8+£15+£9.09 =£32.09
Differences under both the basis: Under the machine hour’s basis, total deprtment
ocverhead absorption rates are £5.44, 5.83 and £25.01 respectively. On contrary, the rates had
been turned out to £2.17, £2.33 and £1.25 in the labour hour’s basis. It indicate that under the
labour hour’s basis, all the rates gone declined. Moreover, the total overhead cost from
£10.35 to £9.09 it is comparatively lower in labour hours. So, it can be suggested that Jeffrey
& Son's has to use this allocation basis because it will decrease total cost from £33.35 to
£32.09 and improve profitability. This in turn, Jeffrey and Sons can take benefits of
enhancing operational performance.
TASK 2
AC 2.1 Preparation of cost report for Jeffrey and Son's Ltd for the month of September,
determine variances with necessary comment
Present scenario represents that Jeffrey & Son's Ltd managers decide budgeted output
of 2000 units. However, in actual, company produced only 1900 units of Exquisite.
Therefore, variances can be computed through comparing cost for desired and actual level of
output.
Actual cost of material purchase:
Actual material price = £24000/2000 units = £12 per unit
Material cost = Actual number of units*material price per unit
= 1900 units*£12 per unit = £22800
9 | P a g e
⊘ This is a preview!⊘
Do you want full access?
Subscribe today to unlock all pages.

Trusted by 1+ million students worldwide
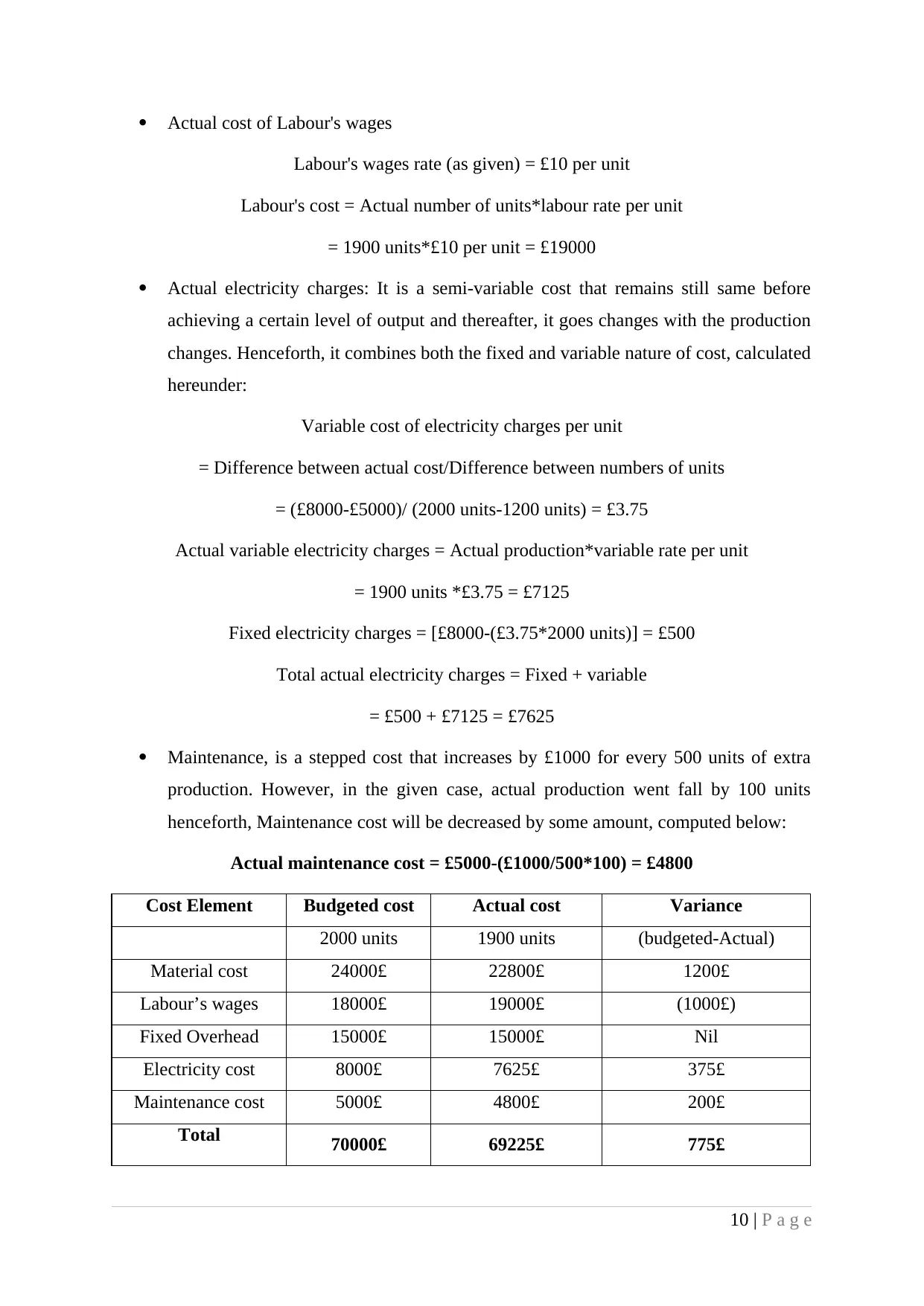
Actual cost of Labour's wages
Labour's wages rate (as given) = £10 per unit
Labour's cost = Actual number of units*labour rate per unit
= 1900 units*£10 per unit = £19000
Actual electricity charges: It is a semi-variable cost that remains still same before
achieving a certain level of output and thereafter, it goes changes with the production
changes. Henceforth, it combines both the fixed and variable nature of cost, calculated
hereunder:
Variable cost of electricity charges per unit
= Difference between actual cost/Difference between numbers of units
= (£8000-£5000)/ (2000 units-1200 units) = £3.75
Actual variable electricity charges = Actual production*variable rate per unit
= 1900 units *£3.75 = £7125
Fixed electricity charges = [£8000-(£3.75*2000 units)] = £500
Total actual electricity charges = Fixed + variable
= £500 + £7125 = £7625
Maintenance, is a stepped cost that increases by £1000 for every 500 units of extra
production. However, in the given case, actual production went fall by 100 units
henceforth, Maintenance cost will be decreased by some amount, computed below:
Actual maintenance cost = £5000-(£1000/500*100) = £4800
Cost Element Budgeted cost Actual cost Variance
2000 units 1900 units (budgeted-Actual)
Material cost 24000£ 22800£ 1200£
Labour’s wages 18000£ 19000£ (1000£)
Fixed Overhead 15000£ 15000£ Nil
Electricity cost 8000£ 7625£ 375£
Maintenance cost 5000£ 4800£ 200£
Total 70000£ 69225£ 775£
10 | P a g e
Labour's wages rate (as given) = £10 per unit
Labour's cost = Actual number of units*labour rate per unit
= 1900 units*£10 per unit = £19000
Actual electricity charges: It is a semi-variable cost that remains still same before
achieving a certain level of output and thereafter, it goes changes with the production
changes. Henceforth, it combines both the fixed and variable nature of cost, calculated
hereunder:
Variable cost of electricity charges per unit
= Difference between actual cost/Difference between numbers of units
= (£8000-£5000)/ (2000 units-1200 units) = £3.75
Actual variable electricity charges = Actual production*variable rate per unit
= 1900 units *£3.75 = £7125
Fixed electricity charges = [£8000-(£3.75*2000 units)] = £500
Total actual electricity charges = Fixed + variable
= £500 + £7125 = £7625
Maintenance, is a stepped cost that increases by £1000 for every 500 units of extra
production. However, in the given case, actual production went fall by 100 units
henceforth, Maintenance cost will be decreased by some amount, computed below:
Actual maintenance cost = £5000-(£1000/500*100) = £4800
Cost Element Budgeted cost Actual cost Variance
2000 units 1900 units (budgeted-Actual)
Material cost 24000£ 22800£ 1200£
Labour’s wages 18000£ 19000£ (1000£)
Fixed Overhead 15000£ 15000£ Nil
Electricity cost 8000£ 7625£ 375£
Maintenance cost 5000£ 4800£ 200£
Total 70000£ 69225£ 775£
10 | P a g e
Paraphrase This Document
Need a fresh take? Get an instant paraphrase of this document with our AI Paraphraser
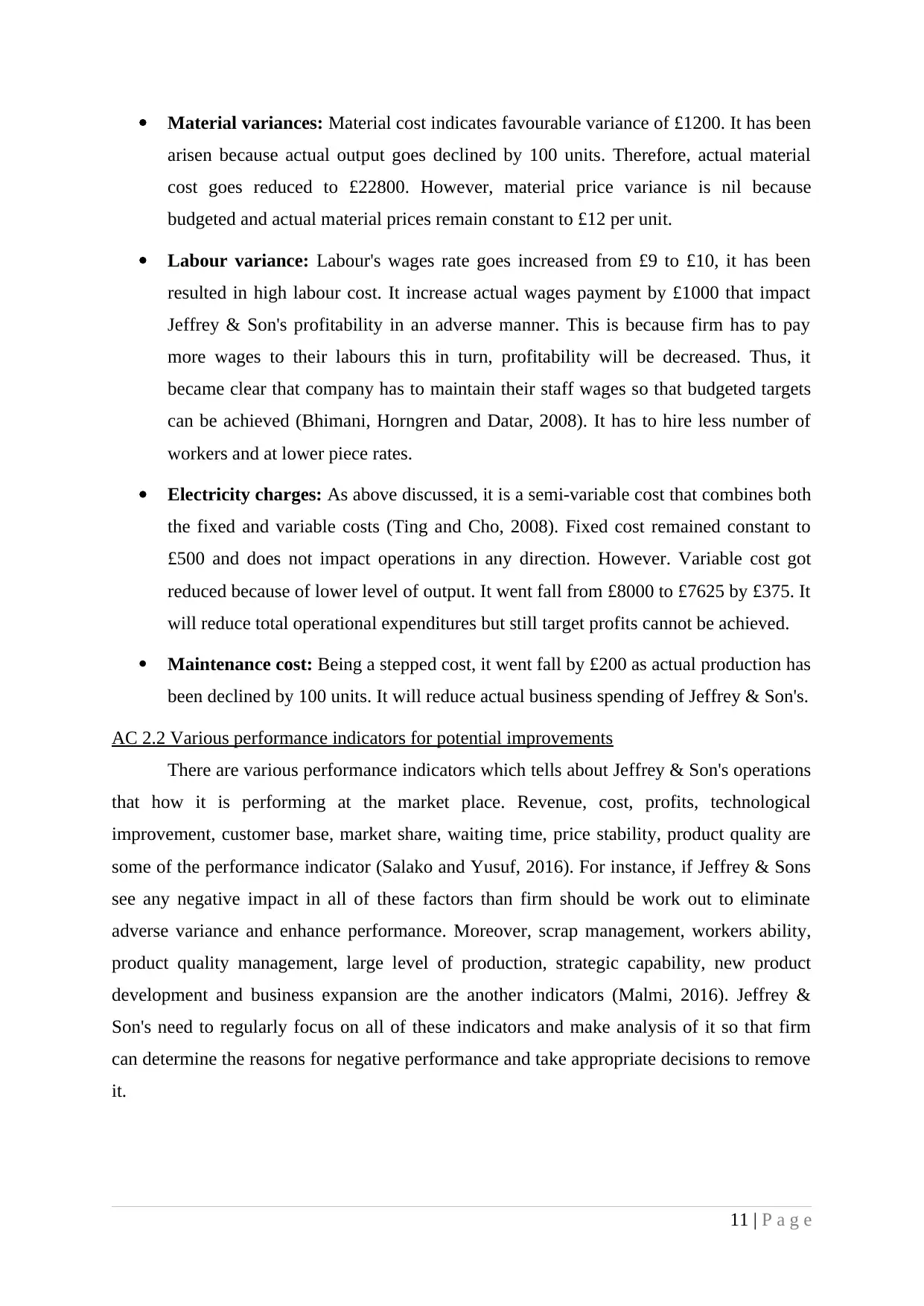
Material variances: Material cost indicates favourable variance of £1200. It has been
arisen because actual output goes declined by 100 units. Therefore, actual material
cost goes reduced to £22800. However, material price variance is nil because
budgeted and actual material prices remain constant to £12 per unit.
Labour variance: Labour's wages rate goes increased from £9 to £10, it has been
resulted in high labour cost. It increase actual wages payment by £1000 that impact
Jeffrey & Son's profitability in an adverse manner. This is because firm has to pay
more wages to their labours this in turn, profitability will be decreased. Thus, it
became clear that company has to maintain their staff wages so that budgeted targets
can be achieved (Bhimani, Horngren and Datar, 2008). It has to hire less number of
workers and at lower piece rates.
Electricity charges: As above discussed, it is a semi-variable cost that combines both
the fixed and variable costs (Ting and Cho, 2008). Fixed cost remained constant to
£500 and does not impact operations in any direction. However. Variable cost got
reduced because of lower level of output. It went fall from £8000 to £7625 by £375. It
will reduce total operational expenditures but still target profits cannot be achieved.
Maintenance cost: Being a stepped cost, it went fall by £200 as actual production has
been declined by 100 units. It will reduce actual business spending of Jeffrey & Son's.
AC 2.2 Various performance indicators for potential improvements
There are various performance indicators which tells about Jeffrey & Son's operations
that how it is performing at the market place. Revenue, cost, profits, technological
improvement, customer base, market share, waiting time, price stability, product quality are
some of the performance indicator (Salako and Yusuf, 2016). For instance, if Jeffrey & Sons
see any negative impact in all of these factors than firm should be work out to eliminate
adverse variance and enhance performance. Moreover, scrap management, workers ability,
product quality management, large level of production, strategic capability, new product
development and business expansion are the another indicators (Malmi, 2016). Jeffrey &
Son's need to regularly focus on all of these indicators and make analysis of it so that firm
can determine the reasons for negative performance and take appropriate decisions to remove
it.
11 | P a g e
arisen because actual output goes declined by 100 units. Therefore, actual material
cost goes reduced to £22800. However, material price variance is nil because
budgeted and actual material prices remain constant to £12 per unit.
Labour variance: Labour's wages rate goes increased from £9 to £10, it has been
resulted in high labour cost. It increase actual wages payment by £1000 that impact
Jeffrey & Son's profitability in an adverse manner. This is because firm has to pay
more wages to their labours this in turn, profitability will be decreased. Thus, it
became clear that company has to maintain their staff wages so that budgeted targets
can be achieved (Bhimani, Horngren and Datar, 2008). It has to hire less number of
workers and at lower piece rates.
Electricity charges: As above discussed, it is a semi-variable cost that combines both
the fixed and variable costs (Ting and Cho, 2008). Fixed cost remained constant to
£500 and does not impact operations in any direction. However. Variable cost got
reduced because of lower level of output. It went fall from £8000 to £7625 by £375. It
will reduce total operational expenditures but still target profits cannot be achieved.
Maintenance cost: Being a stepped cost, it went fall by £200 as actual production has
been declined by 100 units. It will reduce actual business spending of Jeffrey & Son's.
AC 2.2 Various performance indicators for potential improvements
There are various performance indicators which tells about Jeffrey & Son's operations
that how it is performing at the market place. Revenue, cost, profits, technological
improvement, customer base, market share, waiting time, price stability, product quality are
some of the performance indicator (Salako and Yusuf, 2016). For instance, if Jeffrey & Sons
see any negative impact in all of these factors than firm should be work out to eliminate
adverse variance and enhance performance. Moreover, scrap management, workers ability,
product quality management, large level of production, strategic capability, new product
development and business expansion are the another indicators (Malmi, 2016). Jeffrey &
Son's need to regularly focus on all of these indicators and make analysis of it so that firm
can determine the reasons for negative performance and take appropriate decisions to remove
it.
11 | P a g e
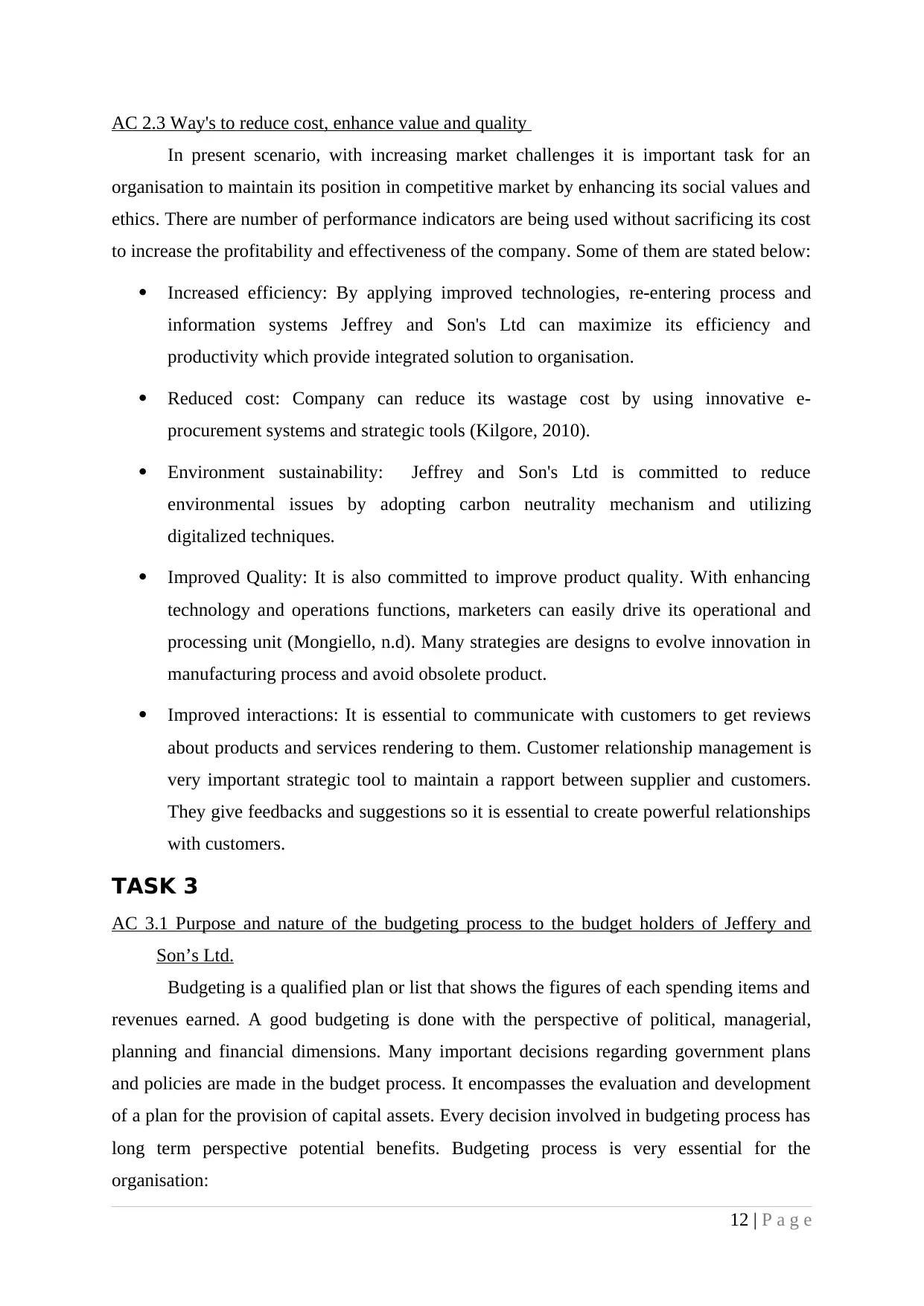
AC 2.3 Way's to reduce cost, enhance value and quality
In present scenario, with increasing market challenges it is important task for an
organisation to maintain its position in competitive market by enhancing its social values and
ethics. There are number of performance indicators are being used without sacrificing its cost
to increase the profitability and effectiveness of the company. Some of them are stated below:
Increased efficiency: By applying improved technologies, re-entering process and
information systems Jeffrey and Son's Ltd can maximize its efficiency and
productivity which provide integrated solution to organisation.
Reduced cost: Company can reduce its wastage cost by using innovative e-
procurement systems and strategic tools (Kilgore, 2010).
Environment sustainability: Jeffrey and Son's Ltd is committed to reduce
environmental issues by adopting carbon neutrality mechanism and utilizing
digitalized techniques.
Improved Quality: It is also committed to improve product quality. With enhancing
technology and operations functions, marketers can easily drive its operational and
processing unit (Mongiello, n.d). Many strategies are designs to evolve innovation in
manufacturing process and avoid obsolete product.
Improved interactions: It is essential to communicate with customers to get reviews
about products and services rendering to them. Customer relationship management is
very important strategic tool to maintain a rapport between supplier and customers.
They give feedbacks and suggestions so it is essential to create powerful relationships
with customers.
TASK 3
AC 3.1 Purpose and nature of the budgeting process to the budget holders of Jeffery and
Son’s Ltd.
Budgeting is a qualified plan or list that shows the figures of each spending items and
revenues earned. A good budgeting is done with the perspective of political, managerial,
planning and financial dimensions. Many important decisions regarding government plans
and policies are made in the budget process. It encompasses the evaluation and development
of a plan for the provision of capital assets. Every decision involved in budgeting process has
long term perspective potential benefits. Budgeting process is very essential for the
organisation:
12 | P a g e
In present scenario, with increasing market challenges it is important task for an
organisation to maintain its position in competitive market by enhancing its social values and
ethics. There are number of performance indicators are being used without sacrificing its cost
to increase the profitability and effectiveness of the company. Some of them are stated below:
Increased efficiency: By applying improved technologies, re-entering process and
information systems Jeffrey and Son's Ltd can maximize its efficiency and
productivity which provide integrated solution to organisation.
Reduced cost: Company can reduce its wastage cost by using innovative e-
procurement systems and strategic tools (Kilgore, 2010).
Environment sustainability: Jeffrey and Son's Ltd is committed to reduce
environmental issues by adopting carbon neutrality mechanism and utilizing
digitalized techniques.
Improved Quality: It is also committed to improve product quality. With enhancing
technology and operations functions, marketers can easily drive its operational and
processing unit (Mongiello, n.d). Many strategies are designs to evolve innovation in
manufacturing process and avoid obsolete product.
Improved interactions: It is essential to communicate with customers to get reviews
about products and services rendering to them. Customer relationship management is
very important strategic tool to maintain a rapport between supplier and customers.
They give feedbacks and suggestions so it is essential to create powerful relationships
with customers.
TASK 3
AC 3.1 Purpose and nature of the budgeting process to the budget holders of Jeffery and
Son’s Ltd.
Budgeting is a qualified plan or list that shows the figures of each spending items and
revenues earned. A good budgeting is done with the perspective of political, managerial,
planning and financial dimensions. Many important decisions regarding government plans
and policies are made in the budget process. It encompasses the evaluation and development
of a plan for the provision of capital assets. Every decision involved in budgeting process has
long term perspective potential benefits. Budgeting process is very essential for the
organisation:
12 | P a g e
⊘ This is a preview!⊘
Do you want full access?
Subscribe today to unlock all pages.

Trusted by 1+ million students worldwide
1 out of 21