Comparative Analysis of Costing Systems: Traditional vs. ABC
VerifiedAdded on 2021/05/30
|9
|1367
|228
Report
AI Summary
This report provides a comprehensive analysis of product costing using traditional and activity-based costing systems. It begins by outlining the limitations of traditional costing, which often allocates overhead based on volume-based cost drivers like machine or labor hours, potentially distorting produc...
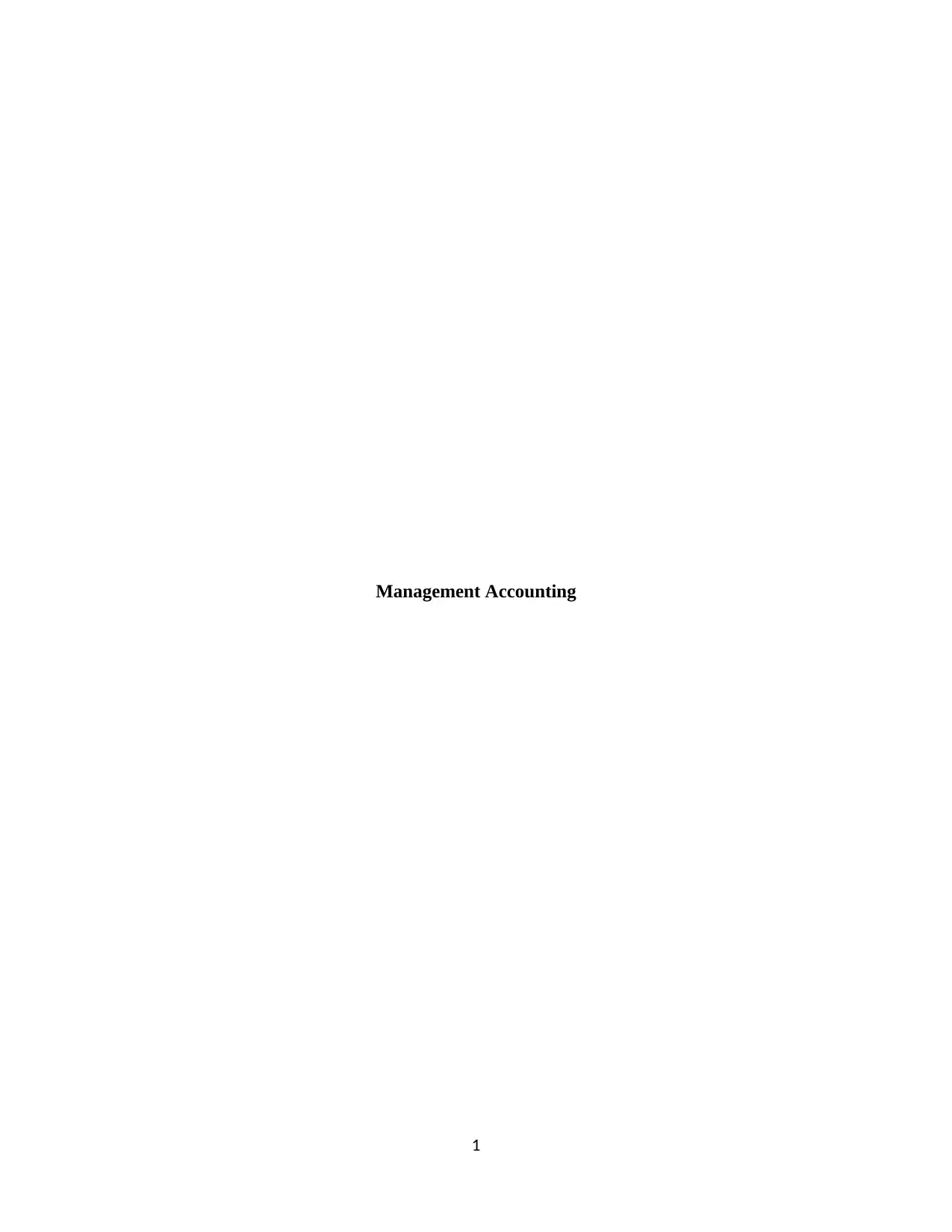
Management Accounting
1
1
Paraphrase This Document
Need a fresh take? Get an instant paraphrase of this document with our AI Paraphraser
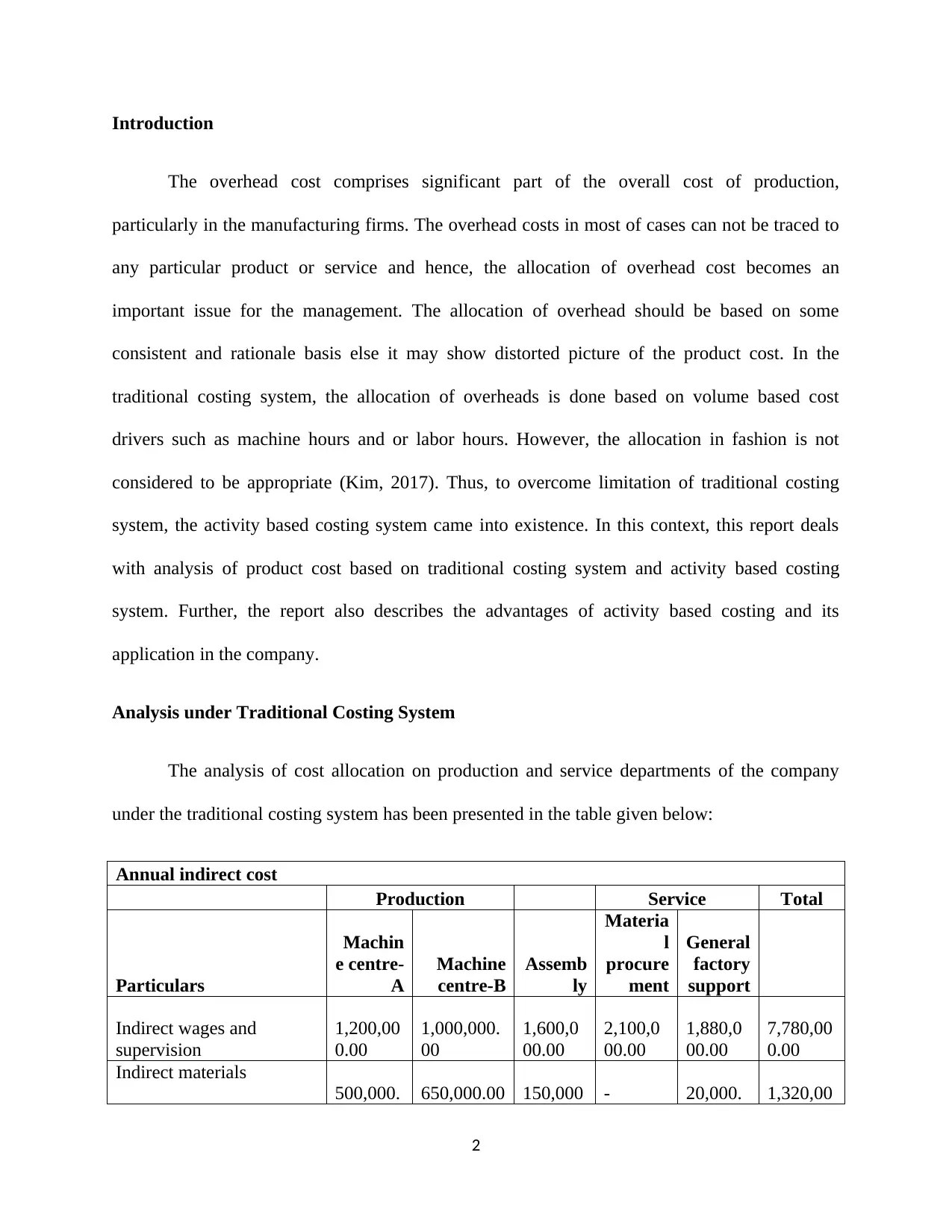
Introduction
The overhead cost comprises significant part of the overall cost of production,
particularly in the manufacturing firms. The overhead costs in most of cases can not be traced to
any particular product or service and hence, the allocation of overhead cost becomes an
important issue for the management. The allocation of overhead should be based on some
consistent and rationale basis else it may show distorted picture of the product cost. In the
traditional costing system, the allocation of overheads is done based on volume based cost
drivers such as machine hours and or labor hours. However, the allocation in fashion is not
considered to be appropriate (Kim, 2017). Thus, to overcome limitation of traditional costing
system, the activity based costing system came into existence. In this context, this report deals
with analysis of product cost based on traditional costing system and activity based costing
system. Further, the report also describes the advantages of activity based costing and its
application in the company.
Analysis under Traditional Costing System
The analysis of cost allocation on production and service departments of the company
under the traditional costing system has been presented in the table given below:
Annual indirect cost
Production Service Total
Particulars
Machin
e centre-
A
Machine
centre-B
Assemb
ly
Materia
l
procure
ment
General
factory
support
Indirect wages and
supervision
1,200,00
0.00
1,000,000.
00
1,600,0
00.00
2,100,0
00.00
1,880,0
00.00
7,780,00
0.00
Indirect materials
500,000. 650,000.00 150,000 - 20,000. 1,320,00
2
The overhead cost comprises significant part of the overall cost of production,
particularly in the manufacturing firms. The overhead costs in most of cases can not be traced to
any particular product or service and hence, the allocation of overhead cost becomes an
important issue for the management. The allocation of overhead should be based on some
consistent and rationale basis else it may show distorted picture of the product cost. In the
traditional costing system, the allocation of overheads is done based on volume based cost
drivers such as machine hours and or labor hours. However, the allocation in fashion is not
considered to be appropriate (Kim, 2017). Thus, to overcome limitation of traditional costing
system, the activity based costing system came into existence. In this context, this report deals
with analysis of product cost based on traditional costing system and activity based costing
system. Further, the report also describes the advantages of activity based costing and its
application in the company.
Analysis under Traditional Costing System
The analysis of cost allocation on production and service departments of the company
under the traditional costing system has been presented in the table given below:
Annual indirect cost
Production Service Total
Particulars
Machin
e centre-
A
Machine
centre-B
Assemb
ly
Materia
l
procure
ment
General
factory
support
Indirect wages and
supervision
1,200,00
0.00
1,000,000.
00
1,600,0
00.00
2,100,0
00.00
1,880,0
00.00
7,780,00
0.00
Indirect materials
500,000. 650,000.00 150,000 - 20,000. 1,320,00
2
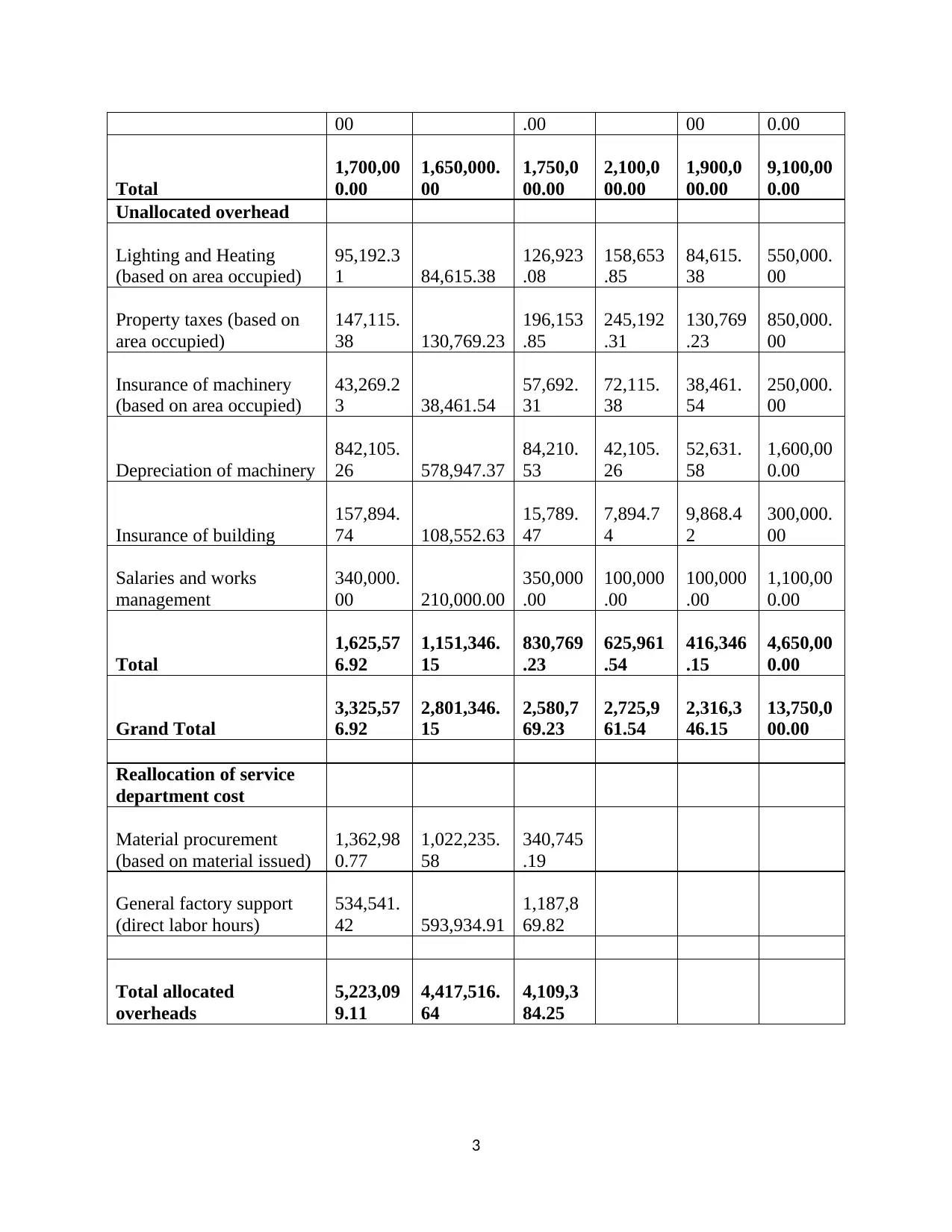
00 .00 00 0.00
Total
1,700,00
0.00
1,650,000.
00
1,750,0
00.00
2,100,0
00.00
1,900,0
00.00
9,100,00
0.00
Unallocated overhead
Lighting and Heating
(based on area occupied)
95,192.3
1 84,615.38
126,923
.08
158,653
.85
84,615.
38
550,000.
00
Property taxes (based on
area occupied)
147,115.
38 130,769.23
196,153
.85
245,192
.31
130,769
.23
850,000.
00
Insurance of machinery
(based on area occupied)
43,269.2
3 38,461.54
57,692.
31
72,115.
38
38,461.
54
250,000.
00
Depreciation of machinery
842,105.
26 578,947.37
84,210.
53
42,105.
26
52,631.
58
1,600,00
0.00
Insurance of building
157,894.
74 108,552.63
15,789.
47
7,894.7
4
9,868.4
2
300,000.
00
Salaries and works
management
340,000.
00 210,000.00
350,000
.00
100,000
.00
100,000
.00
1,100,00
0.00
Total
1,625,57
6.92
1,151,346.
15
830,769
.23
625,961
.54
416,346
.15
4,650,00
0.00
Grand Total
3,325,57
6.92
2,801,346.
15
2,580,7
69.23
2,725,9
61.54
2,316,3
46.15
13,750,0
00.00
Reallocation of service
department cost
Material procurement
(based on material issued)
1,362,98
0.77
1,022,235.
58
340,745
.19
General factory support
(direct labor hours)
534,541.
42 593,934.91
1,187,8
69.82
Total allocated
overheads
5,223,09
9.11
4,417,516.
64
4,109,3
84.25
3
Total
1,700,00
0.00
1,650,000.
00
1,750,0
00.00
2,100,0
00.00
1,900,0
00.00
9,100,00
0.00
Unallocated overhead
Lighting and Heating
(based on area occupied)
95,192.3
1 84,615.38
126,923
.08
158,653
.85
84,615.
38
550,000.
00
Property taxes (based on
area occupied)
147,115.
38 130,769.23
196,153
.85
245,192
.31
130,769
.23
850,000.
00
Insurance of machinery
(based on area occupied)
43,269.2
3 38,461.54
57,692.
31
72,115.
38
38,461.
54
250,000.
00
Depreciation of machinery
842,105.
26 578,947.37
84,210.
53
42,105.
26
52,631.
58
1,600,00
0.00
Insurance of building
157,894.
74 108,552.63
15,789.
47
7,894.7
4
9,868.4
2
300,000.
00
Salaries and works
management
340,000.
00 210,000.00
350,000
.00
100,000
.00
100,000
.00
1,100,00
0.00
Total
1,625,57
6.92
1,151,346.
15
830,769
.23
625,961
.54
416,346
.15
4,650,00
0.00
Grand Total
3,325,57
6.92
2,801,346.
15
2,580,7
69.23
2,725,9
61.54
2,316,3
46.15
13,750,0
00.00
Reallocation of service
department cost
Material procurement
(based on material issued)
1,362,98
0.77
1,022,235.
58
340,745
.19
General factory support
(direct labor hours)
534,541.
42 593,934.91
1,187,8
69.82
Total allocated
overheads
5,223,09
9.11
4,417,516.
64
4,109,3
84.25
3
⊘ This is a preview!⊘
Do you want full access?
Subscribe today to unlock all pages.

Trusted by 1+ million students worldwide
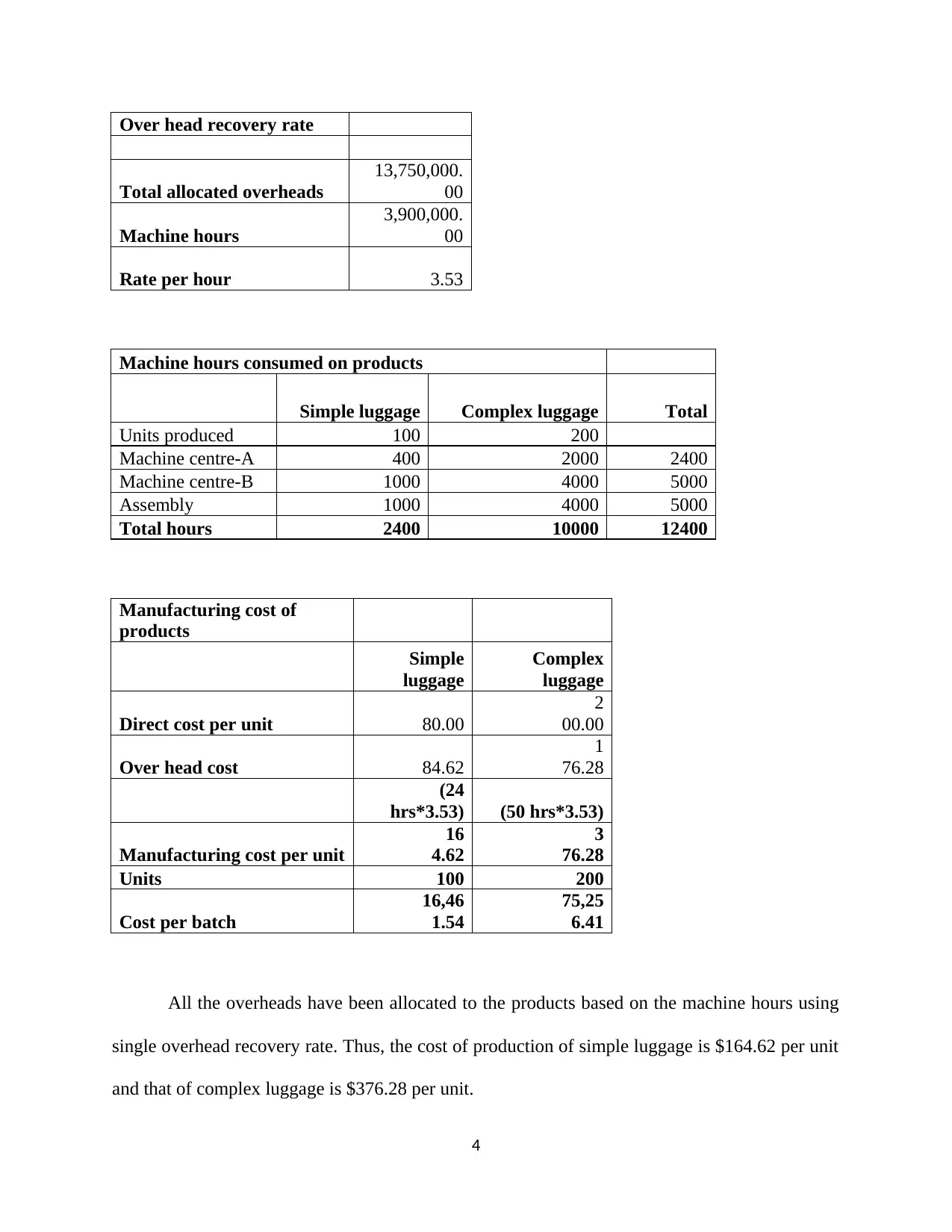
Over head recovery rate
Total allocated overheads
13,750,000.
00
Machine hours
3,900,000.
00
Rate per hour 3.53
Machine hours consumed on products
Simple luggage Complex luggage Total
Units produced 100 200
Machine centre-A 400 2000 2400
Machine centre-B 1000 4000 5000
Assembly 1000 4000 5000
Total hours 2400 10000 12400
Manufacturing cost of
products
Simple
luggage
Complex
luggage
Direct cost per unit 80.00
2
00.00
Over head cost 84.62
1
76.28
(24
hrs*3.53) (50 hrs*3.53)
Manufacturing cost per unit
16
4.62
3
76.28
Units 100 200
Cost per batch
16,46
1.54
75,25
6.41
All the overheads have been allocated to the products based on the machine hours using
single overhead recovery rate. Thus, the cost of production of simple luggage is $164.62 per unit
and that of complex luggage is $376.28 per unit.
4
Total allocated overheads
13,750,000.
00
Machine hours
3,900,000.
00
Rate per hour 3.53
Machine hours consumed on products
Simple luggage Complex luggage Total
Units produced 100 200
Machine centre-A 400 2000 2400
Machine centre-B 1000 4000 5000
Assembly 1000 4000 5000
Total hours 2400 10000 12400
Manufacturing cost of
products
Simple
luggage
Complex
luggage
Direct cost per unit 80.00
2
00.00
Over head cost 84.62
1
76.28
(24
hrs*3.53) (50 hrs*3.53)
Manufacturing cost per unit
16
4.62
3
76.28
Units 100 200
Cost per batch
16,46
1.54
75,25
6.41
All the overheads have been allocated to the products based on the machine hours using
single overhead recovery rate. Thus, the cost of production of simple luggage is $164.62 per unit
and that of complex luggage is $376.28 per unit.
4
Paraphrase This Document
Need a fresh take? Get an instant paraphrase of this document with our AI Paraphraser
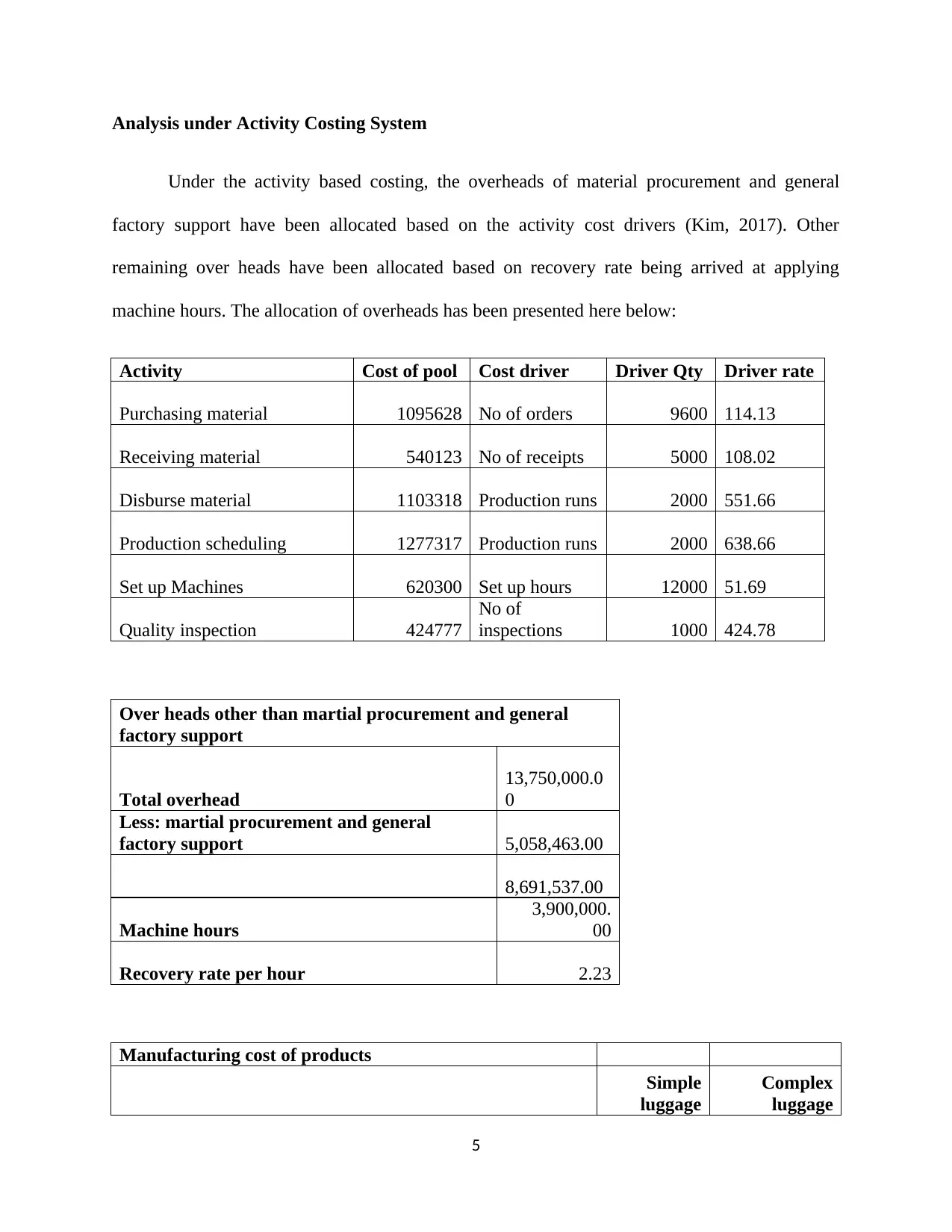
Analysis under Activity Costing System
Under the activity based costing, the overheads of material procurement and general
factory support have been allocated based on the activity cost drivers (Kim, 2017). Other
remaining over heads have been allocated based on recovery rate being arrived at applying
machine hours. The allocation of overheads has been presented here below:
Activity Cost of pool Cost driver Driver Qty Driver rate
Purchasing material 1095628 No of orders 9600 114.13
Receiving material 540123 No of receipts 5000 108.02
Disburse material 1103318 Production runs 2000 551.66
Production scheduling 1277317 Production runs 2000 638.66
Set up Machines 620300 Set up hours 12000 51.69
Quality inspection 424777
No of
inspections 1000 424.78
Over heads other than martial procurement and general
factory support
Total overhead
13,750,000.0
0
Less: martial procurement and general
factory support 5,058,463.00
8,691,537.00
Machine hours
3,900,000.
00
Recovery rate per hour 2.23
Manufacturing cost of products
Simple
luggage
Complex
luggage
5
Under the activity based costing, the overheads of material procurement and general
factory support have been allocated based on the activity cost drivers (Kim, 2017). Other
remaining over heads have been allocated based on recovery rate being arrived at applying
machine hours. The allocation of overheads has been presented here below:
Activity Cost of pool Cost driver Driver Qty Driver rate
Purchasing material 1095628 No of orders 9600 114.13
Receiving material 540123 No of receipts 5000 108.02
Disburse material 1103318 Production runs 2000 551.66
Production scheduling 1277317 Production runs 2000 638.66
Set up Machines 620300 Set up hours 12000 51.69
Quality inspection 424777
No of
inspections 1000 424.78
Over heads other than martial procurement and general
factory support
Total overhead
13,750,000.0
0
Less: martial procurement and general
factory support 5,058,463.00
8,691,537.00
Machine hours
3,900,000.
00
Recovery rate per hour 2.23
Manufacturing cost of products
Simple
luggage
Complex
luggage
5
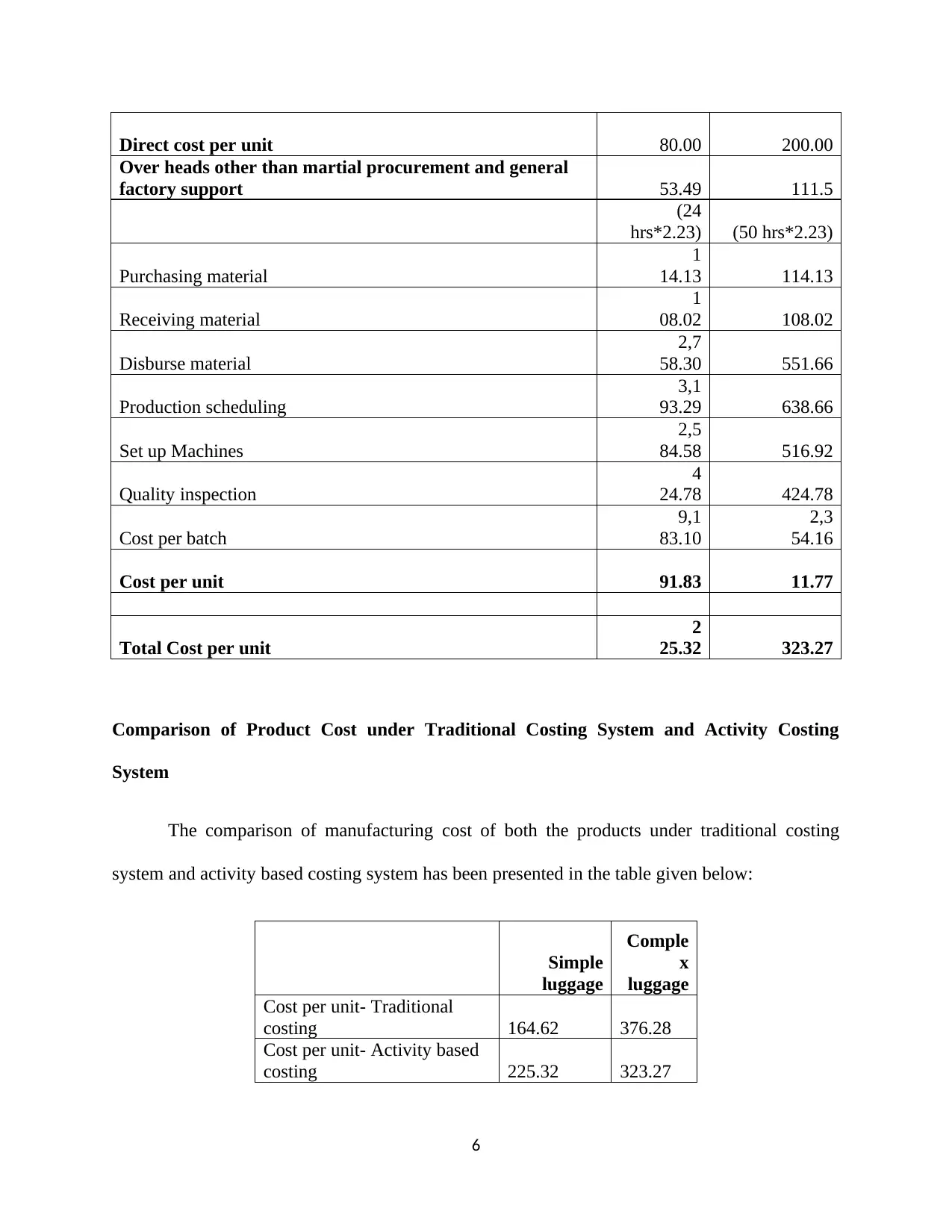
Direct cost per unit 80.00 200.00
Over heads other than martial procurement and general
factory support 53.49 111.5
(24
hrs*2.23) (50 hrs*2.23)
Purchasing material
1
14.13 114.13
Receiving material
1
08.02 108.02
Disburse material
2,7
58.30 551.66
Production scheduling
3,1
93.29 638.66
Set up Machines
2,5
84.58 516.92
Quality inspection
4
24.78 424.78
Cost per batch
9,1
83.10
2,3
54.16
Cost per unit 91.83 11.77
Total Cost per unit
2
25.32 323.27
Comparison of Product Cost under Traditional Costing System and Activity Costing
System
The comparison of manufacturing cost of both the products under traditional costing
system and activity based costing system has been presented in the table given below:
Simple
luggage
Comple
x
luggage
Cost per unit- Traditional
costing 164.62 376.28
Cost per unit- Activity based
costing 225.32 323.27
6
Over heads other than martial procurement and general
factory support 53.49 111.5
(24
hrs*2.23) (50 hrs*2.23)
Purchasing material
1
14.13 114.13
Receiving material
1
08.02 108.02
Disburse material
2,7
58.30 551.66
Production scheduling
3,1
93.29 638.66
Set up Machines
2,5
84.58 516.92
Quality inspection
4
24.78 424.78
Cost per batch
9,1
83.10
2,3
54.16
Cost per unit 91.83 11.77
Total Cost per unit
2
25.32 323.27
Comparison of Product Cost under Traditional Costing System and Activity Costing
System
The comparison of manufacturing cost of both the products under traditional costing
system and activity based costing system has been presented in the table given below:
Simple
luggage
Comple
x
luggage
Cost per unit- Traditional
costing 164.62 376.28
Cost per unit- Activity based
costing 225.32 323.27
6
⊘ This is a preview!⊘
Do you want full access?
Subscribe today to unlock all pages.

Trusted by 1+ million students worldwide
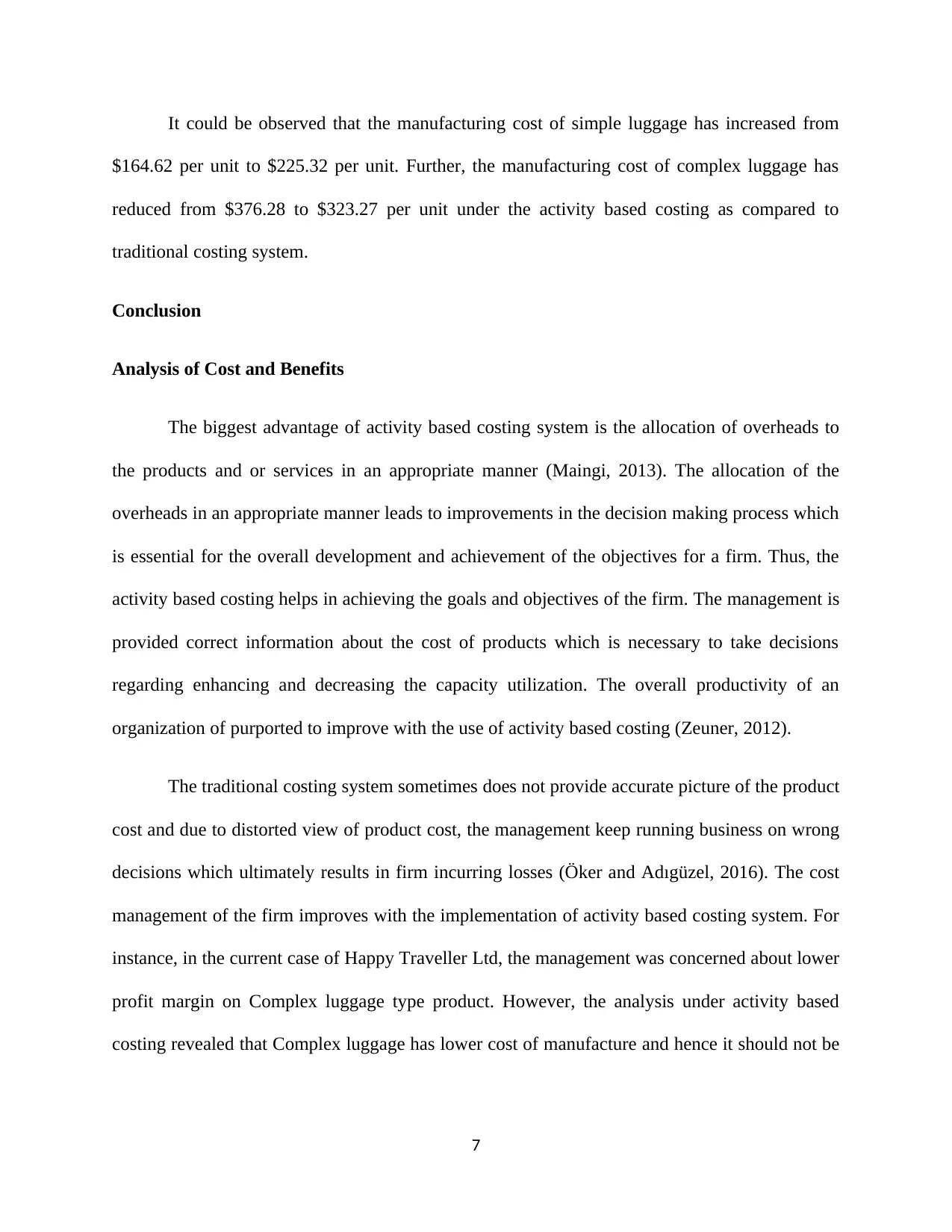
It could be observed that the manufacturing cost of simple luggage has increased from
$164.62 per unit to $225.32 per unit. Further, the manufacturing cost of complex luggage has
reduced from $376.28 to $323.27 per unit under the activity based costing as compared to
traditional costing system.
Conclusion
Analysis of Cost and Benefits
The biggest advantage of activity based costing system is the allocation of overheads to
the products and or services in an appropriate manner (Maingi, 2013). The allocation of the
overheads in an appropriate manner leads to improvements in the decision making process which
is essential for the overall development and achievement of the objectives for a firm. Thus, the
activity based costing helps in achieving the goals and objectives of the firm. The management is
provided correct information about the cost of products which is necessary to take decisions
regarding enhancing and decreasing the capacity utilization. The overall productivity of an
organization of purported to improve with the use of activity based costing (Zeuner, 2012).
The traditional costing system sometimes does not provide accurate picture of the product
cost and due to distorted view of product cost, the management keep running business on wrong
decisions which ultimately results in firm incurring losses (Öker and Adıgüzel, 2016). The cost
management of the firm improves with the implementation of activity based costing system. For
instance, in the current case of Happy Traveller Ltd, the management was concerned about lower
profit margin on Complex luggage type product. However, the analysis under activity based
costing revealed that Complex luggage has lower cost of manufacture and hence it should not be
7
$164.62 per unit to $225.32 per unit. Further, the manufacturing cost of complex luggage has
reduced from $376.28 to $323.27 per unit under the activity based costing as compared to
traditional costing system.
Conclusion
Analysis of Cost and Benefits
The biggest advantage of activity based costing system is the allocation of overheads to
the products and or services in an appropriate manner (Maingi, 2013). The allocation of the
overheads in an appropriate manner leads to improvements in the decision making process which
is essential for the overall development and achievement of the objectives for a firm. Thus, the
activity based costing helps in achieving the goals and objectives of the firm. The management is
provided correct information about the cost of products which is necessary to take decisions
regarding enhancing and decreasing the capacity utilization. The overall productivity of an
organization of purported to improve with the use of activity based costing (Zeuner, 2012).
The traditional costing system sometimes does not provide accurate picture of the product
cost and due to distorted view of product cost, the management keep running business on wrong
decisions which ultimately results in firm incurring losses (Öker and Adıgüzel, 2016). The cost
management of the firm improves with the implementation of activity based costing system. For
instance, in the current case of Happy Traveller Ltd, the management was concerned about lower
profit margin on Complex luggage type product. However, the analysis under activity based
costing revealed that Complex luggage has lower cost of manufacture and hence it should not be
7
Paraphrase This Document
Need a fresh take? Get an instant paraphrase of this document with our AI Paraphraser
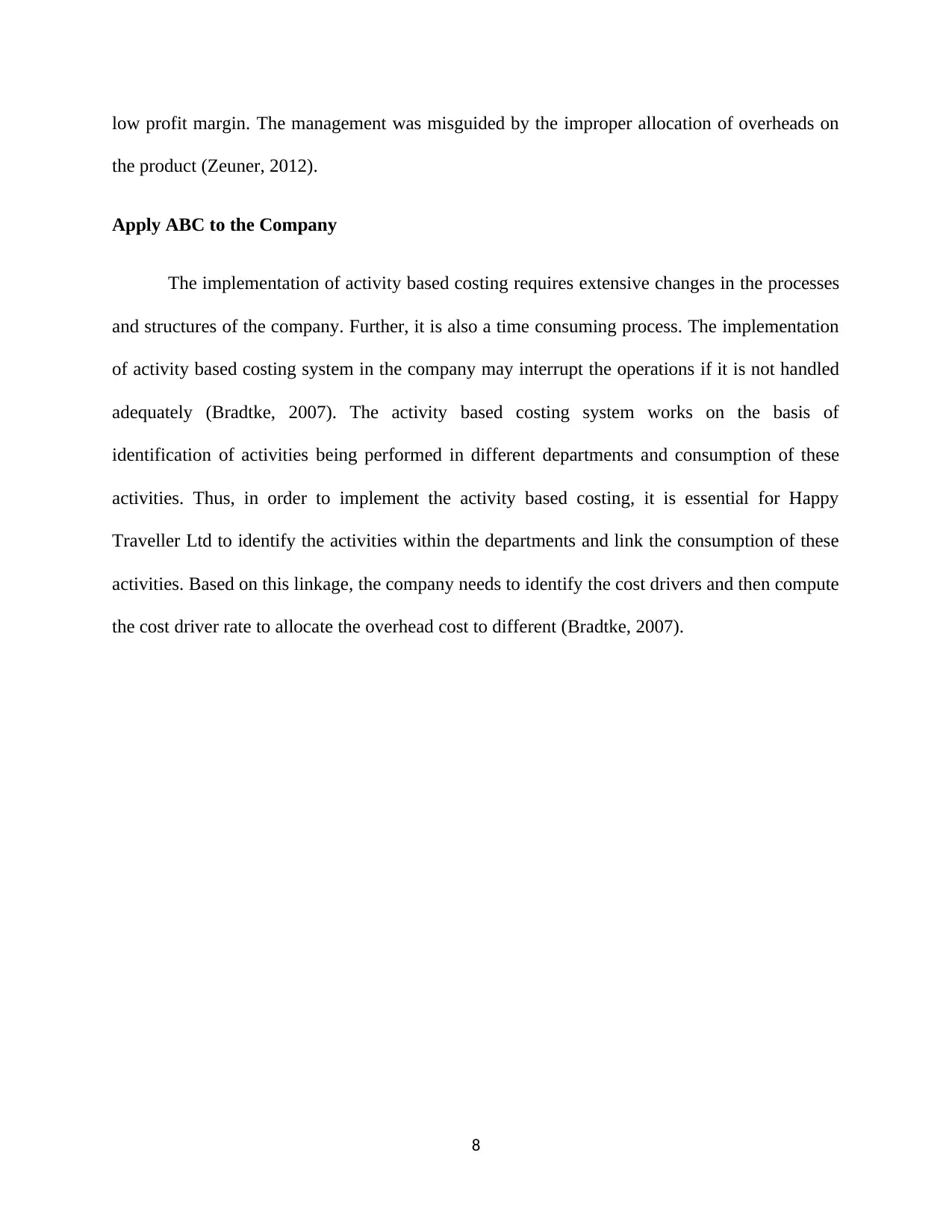
low profit margin. The management was misguided by the improper allocation of overheads on
the product (Zeuner, 2012).
Apply ABC to the Company
The implementation of activity based costing requires extensive changes in the processes
and structures of the company. Further, it is also a time consuming process. The implementation
of activity based costing system in the company may interrupt the operations if it is not handled
adequately (Bradtke, 2007). The activity based costing system works on the basis of
identification of activities being performed in different departments and consumption of these
activities. Thus, in order to implement the activity based costing, it is essential for Happy
Traveller Ltd to identify the activities within the departments and link the consumption of these
activities. Based on this linkage, the company needs to identify the cost drivers and then compute
the cost driver rate to allocate the overhead cost to different (Bradtke, 2007).
8
the product (Zeuner, 2012).
Apply ABC to the Company
The implementation of activity based costing requires extensive changes in the processes
and structures of the company. Further, it is also a time consuming process. The implementation
of activity based costing system in the company may interrupt the operations if it is not handled
adequately (Bradtke, 2007). The activity based costing system works on the basis of
identification of activities being performed in different departments and consumption of these
activities. Thus, in order to implement the activity based costing, it is essential for Happy
Traveller Ltd to identify the activities within the departments and link the consumption of these
activities. Based on this linkage, the company needs to identify the cost drivers and then compute
the cost driver rate to allocate the overhead cost to different (Bradtke, 2007).
8
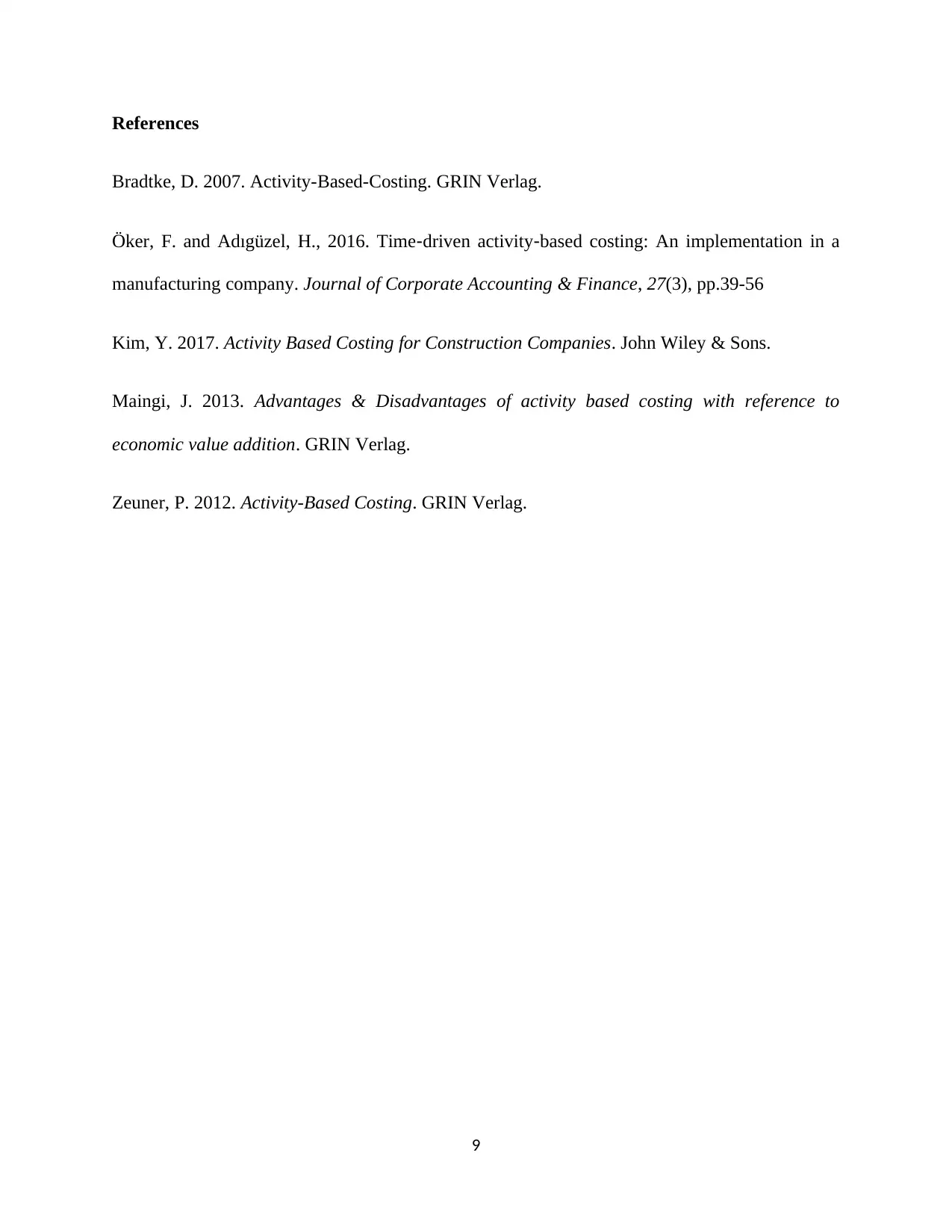
References
Bradtke, D. 2007. Activity-Based-Costing. GRIN Verlag.
Öker, F. and Adıgüzel, H., 2016. Time‐driven activity‐based costing: An implementation in a
manufacturing company. Journal of Corporate Accounting & Finance, 27(3), pp.39-56
Kim, Y. 2017. Activity Based Costing for Construction Companies. John Wiley & Sons.
Maingi, J. 2013. Advantages & Disadvantages of activity based costing with reference to
economic value addition. GRIN Verlag.
Zeuner, P. 2012. Activity-Based Costing. GRIN Verlag.
9
Bradtke, D. 2007. Activity-Based-Costing. GRIN Verlag.
Öker, F. and Adıgüzel, H., 2016. Time‐driven activity‐based costing: An implementation in a
manufacturing company. Journal of Corporate Accounting & Finance, 27(3), pp.39-56
Kim, Y. 2017. Activity Based Costing for Construction Companies. John Wiley & Sons.
Maingi, J. 2013. Advantages & Disadvantages of activity based costing with reference to
economic value addition. GRIN Verlag.
Zeuner, P. 2012. Activity-Based Costing. GRIN Verlag.
9
⊘ This is a preview!⊘
Do you want full access?
Subscribe today to unlock all pages.

Trusted by 1+ million students worldwide
1 out of 9
Related Documents

Your All-in-One AI-Powered Toolkit for Academic Success.
+13062052269
info@desklib.com
Available 24*7 on WhatsApp / Email
Unlock your academic potential
© 2024 | Zucol Services PVT LTD | All rights reserved.