Management Accounting Case Study: Voltus Overhead Allocation Analysis
VerifiedAdded on 2022/11/19
|12
|2903
|500
Homework Assignment
AI Summary
This document provides a comprehensive solution to a management accounting case study focused on Voltus. It begins by explaining prime costs, overhead, and the traditional volume-based overhead allocation method, calculating a predetermined overhead rate of $45 per machine hour. T...
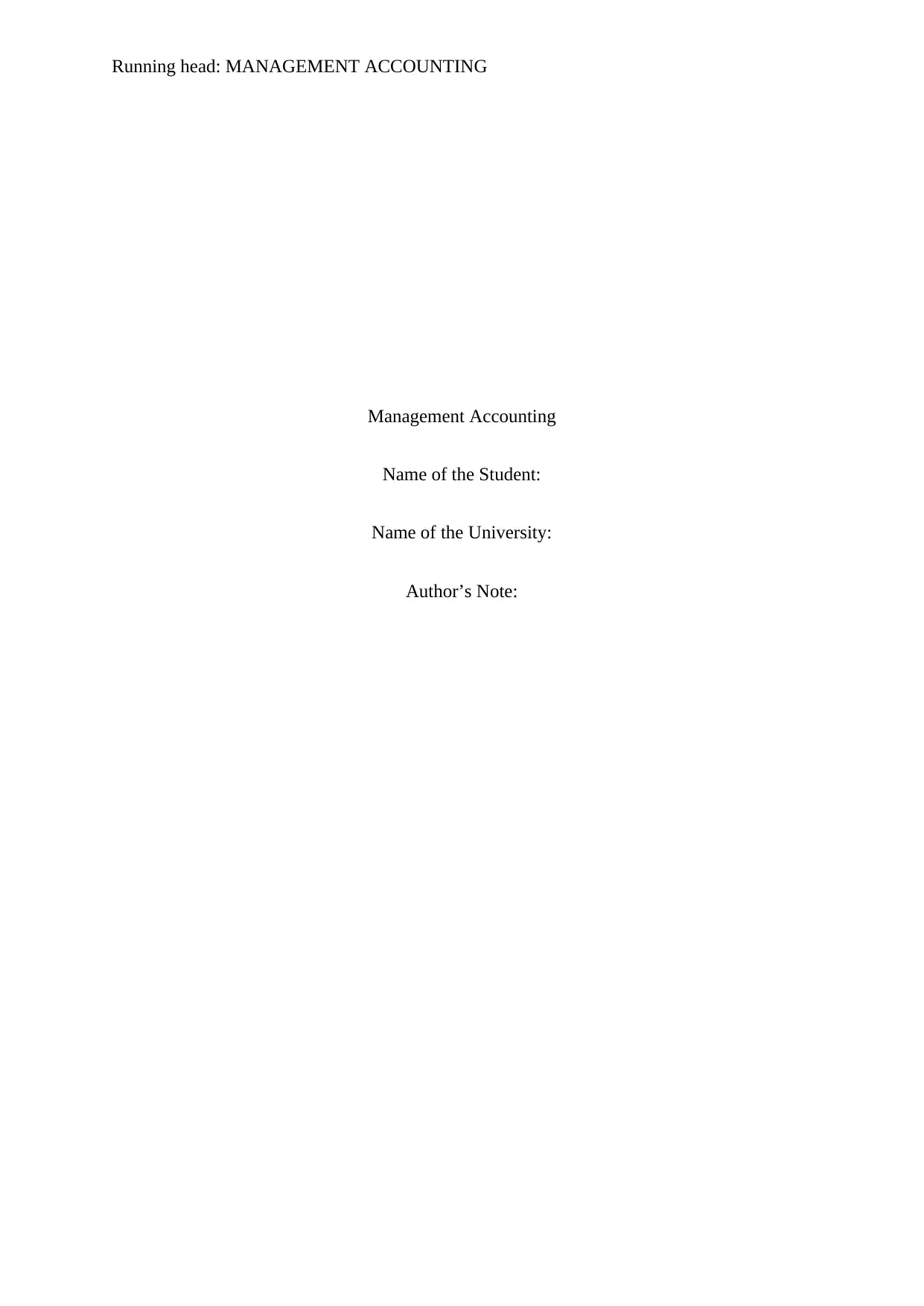
Running head: MANAGEMENT ACCOUNTING
Management Accounting
Name of the Student:
Name of the University:
Author’s Note:
Management Accounting
Name of the Student:
Name of the University:
Author’s Note:
Paraphrase This Document
Need a fresh take? Get an instant paraphrase of this document with our AI Paraphraser
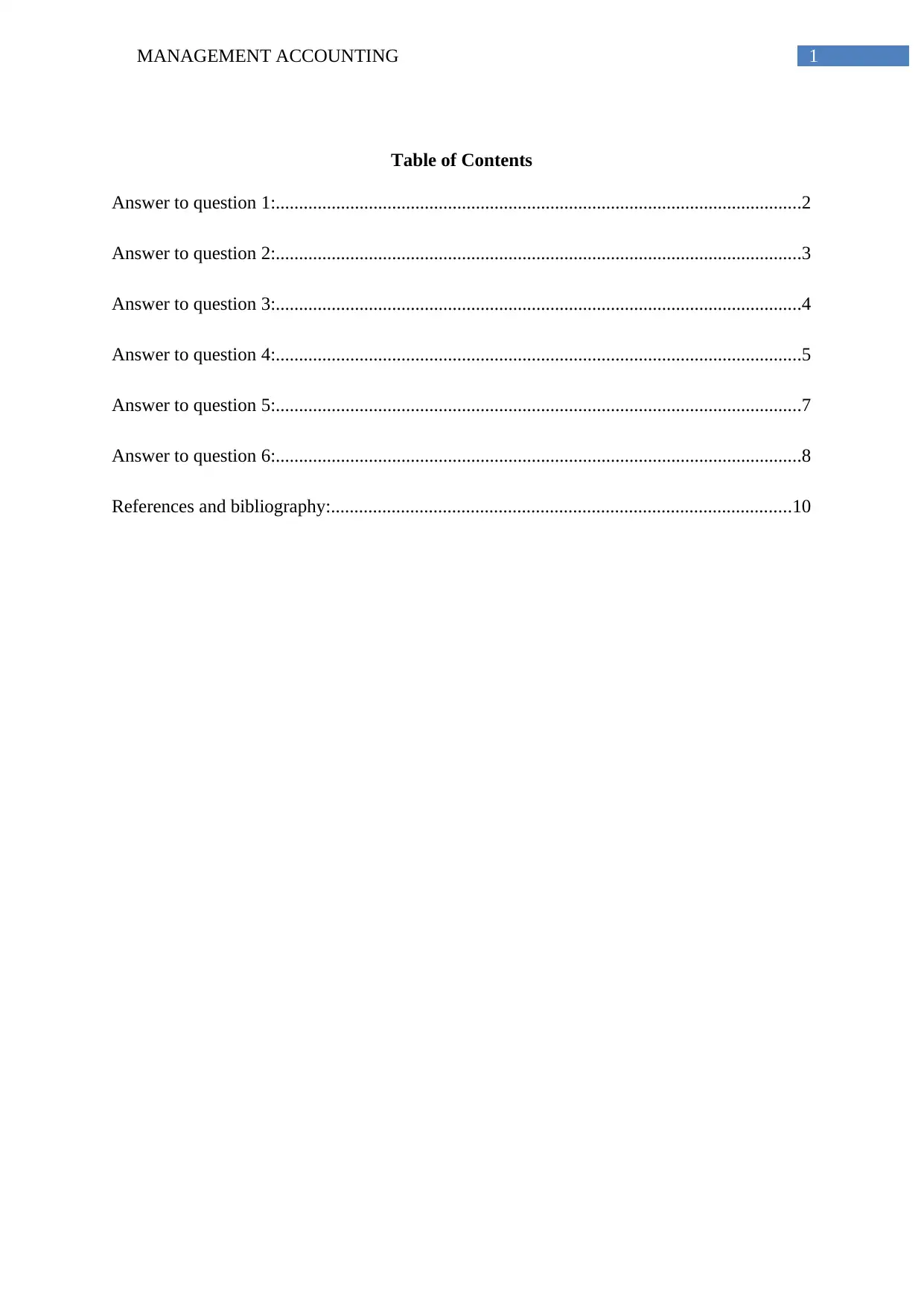
1MANAGEMENT ACCOUNTING
Table of Contents
Answer to question 1:.................................................................................................................2
Answer to question 2:.................................................................................................................3
Answer to question 3:.................................................................................................................4
Answer to question 4:.................................................................................................................5
Answer to question 5:.................................................................................................................7
Answer to question 6:.................................................................................................................8
References and bibliography:...................................................................................................10
Table of Contents
Answer to question 1:.................................................................................................................2
Answer to question 2:.................................................................................................................3
Answer to question 3:.................................................................................................................4
Answer to question 4:.................................................................................................................5
Answer to question 5:.................................................................................................................7
Answer to question 6:.................................................................................................................8
References and bibliography:...................................................................................................10
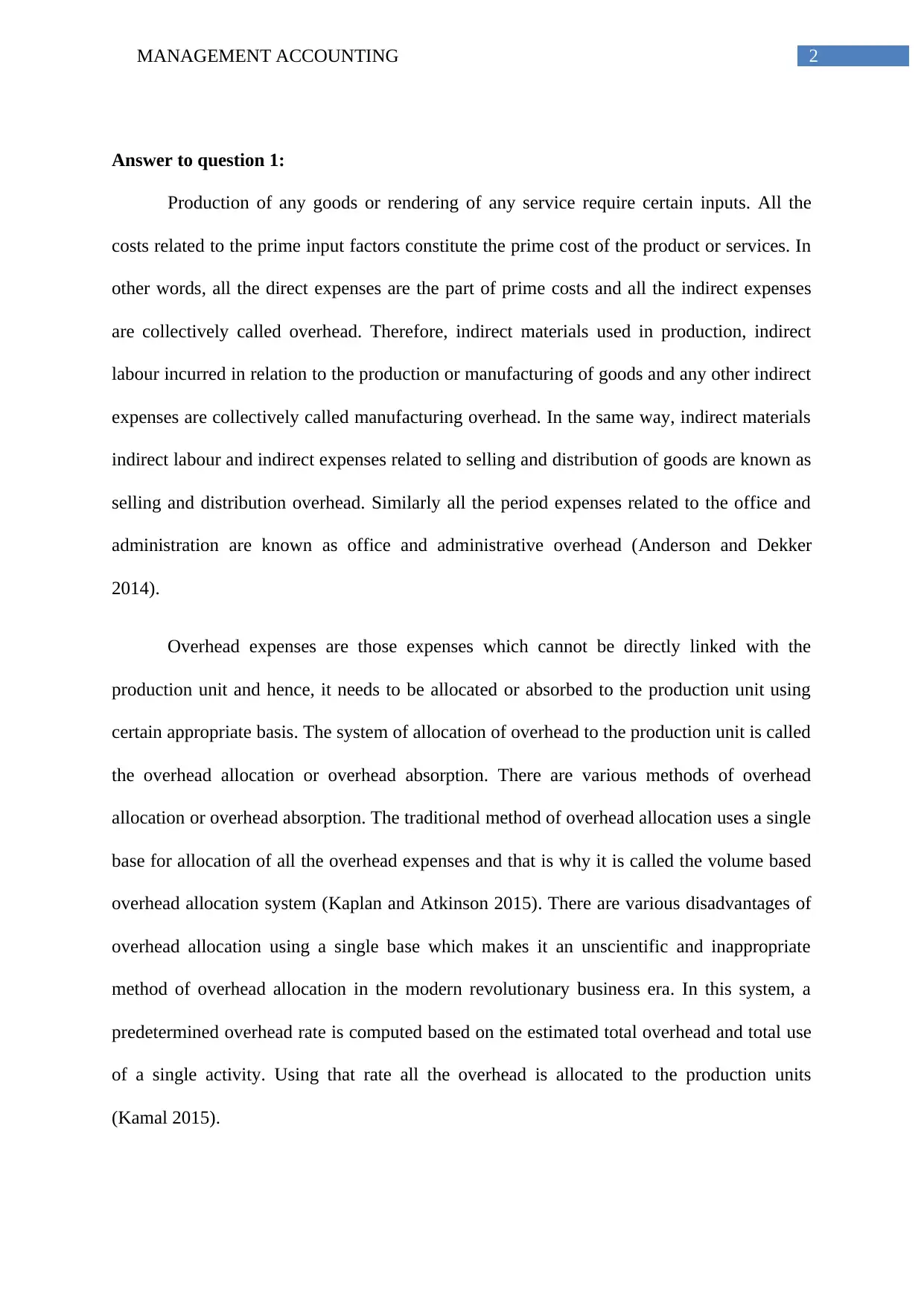
2MANAGEMENT ACCOUNTING
Answer to question 1:
Production of any goods or rendering of any service require certain inputs. All the
costs related to the prime input factors constitute the prime cost of the product or services. In
other words, all the direct expenses are the part of prime costs and all the indirect expenses
are collectively called overhead. Therefore, indirect materials used in production, indirect
labour incurred in relation to the production or manufacturing of goods and any other indirect
expenses are collectively called manufacturing overhead. In the same way, indirect materials
indirect labour and indirect expenses related to selling and distribution of goods are known as
selling and distribution overhead. Similarly all the period expenses related to the office and
administration are known as office and administrative overhead (Anderson and Dekker
2014).
Overhead expenses are those expenses which cannot be directly linked with the
production unit and hence, it needs to be allocated or absorbed to the production unit using
certain appropriate basis. The system of allocation of overhead to the production unit is called
the overhead allocation or overhead absorption. There are various methods of overhead
allocation or overhead absorption. The traditional method of overhead allocation uses a single
base for allocation of all the overhead expenses and that is why it is called the volume based
overhead allocation system (Kaplan and Atkinson 2015). There are various disadvantages of
overhead allocation using a single base which makes it an unscientific and inappropriate
method of overhead allocation in the modern revolutionary business era. In this system, a
predetermined overhead rate is computed based on the estimated total overhead and total use
of a single activity. Using that rate all the overhead is allocated to the production units
(Kamal 2015).
Answer to question 1:
Production of any goods or rendering of any service require certain inputs. All the
costs related to the prime input factors constitute the prime cost of the product or services. In
other words, all the direct expenses are the part of prime costs and all the indirect expenses
are collectively called overhead. Therefore, indirect materials used in production, indirect
labour incurred in relation to the production or manufacturing of goods and any other indirect
expenses are collectively called manufacturing overhead. In the same way, indirect materials
indirect labour and indirect expenses related to selling and distribution of goods are known as
selling and distribution overhead. Similarly all the period expenses related to the office and
administration are known as office and administrative overhead (Anderson and Dekker
2014).
Overhead expenses are those expenses which cannot be directly linked with the
production unit and hence, it needs to be allocated or absorbed to the production unit using
certain appropriate basis. The system of allocation of overhead to the production unit is called
the overhead allocation or overhead absorption. There are various methods of overhead
allocation or overhead absorption. The traditional method of overhead allocation uses a single
base for allocation of all the overhead expenses and that is why it is called the volume based
overhead allocation system (Kaplan and Atkinson 2015). There are various disadvantages of
overhead allocation using a single base which makes it an unscientific and inappropriate
method of overhead allocation in the modern revolutionary business era. In this system, a
predetermined overhead rate is computed based on the estimated total overhead and total use
of a single activity. Using that rate all the overhead is allocated to the production units
(Kamal 2015).
You're viewing a preview
Unlock full access by subscribing today!
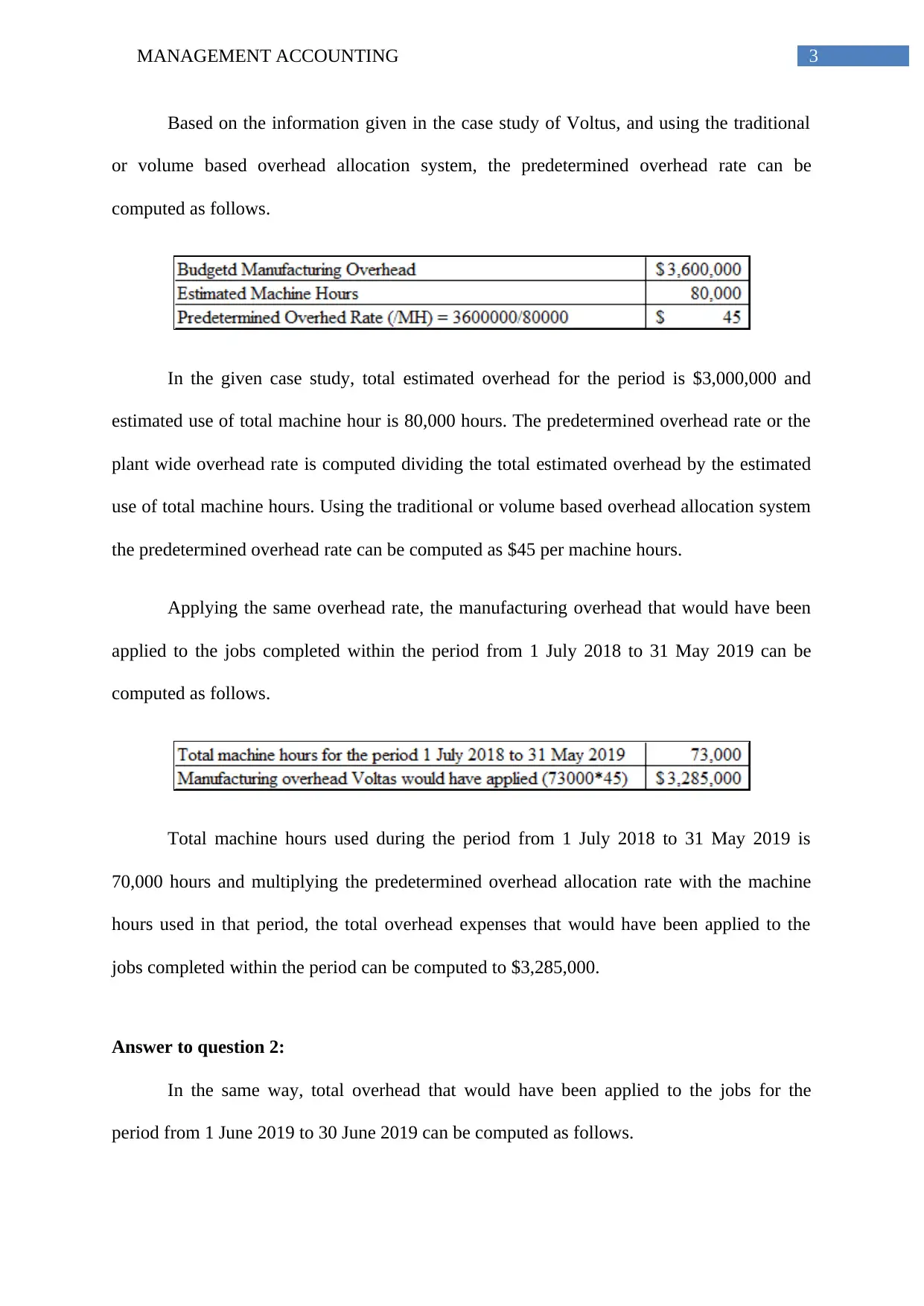
3MANAGEMENT ACCOUNTING
Based on the information given in the case study of Voltus, and using the traditional
or volume based overhead allocation system, the predetermined overhead rate can be
computed as follows.
In the given case study, total estimated overhead for the period is $3,000,000 and
estimated use of total machine hour is 80,000 hours. The predetermined overhead rate or the
plant wide overhead rate is computed dividing the total estimated overhead by the estimated
use of total machine hours. Using the traditional or volume based overhead allocation system
the predetermined overhead rate can be computed as $45 per machine hours.
Applying the same overhead rate, the manufacturing overhead that would have been
applied to the jobs completed within the period from 1 July 2018 to 31 May 2019 can be
computed as follows.
Total machine hours used during the period from 1 July 2018 to 31 May 2019 is
70,000 hours and multiplying the predetermined overhead allocation rate with the machine
hours used in that period, the total overhead expenses that would have been applied to the
jobs completed within the period can be computed to $3,285,000.
Answer to question 2:
In the same way, total overhead that would have been applied to the jobs for the
period from 1 June 2019 to 30 June 2019 can be computed as follows.
Based on the information given in the case study of Voltus, and using the traditional
or volume based overhead allocation system, the predetermined overhead rate can be
computed as follows.
In the given case study, total estimated overhead for the period is $3,000,000 and
estimated use of total machine hour is 80,000 hours. The predetermined overhead rate or the
plant wide overhead rate is computed dividing the total estimated overhead by the estimated
use of total machine hours. Using the traditional or volume based overhead allocation system
the predetermined overhead rate can be computed as $45 per machine hours.
Applying the same overhead rate, the manufacturing overhead that would have been
applied to the jobs completed within the period from 1 July 2018 to 31 May 2019 can be
computed as follows.
Total machine hours used during the period from 1 July 2018 to 31 May 2019 is
70,000 hours and multiplying the predetermined overhead allocation rate with the machine
hours used in that period, the total overhead expenses that would have been applied to the
jobs completed within the period can be computed to $3,285,000.
Answer to question 2:
In the same way, total overhead that would have been applied to the jobs for the
period from 1 June 2019 to 30 June 2019 can be computed as follows.
Paraphrase This Document
Need a fresh take? Get an instant paraphrase of this document with our AI Paraphraser
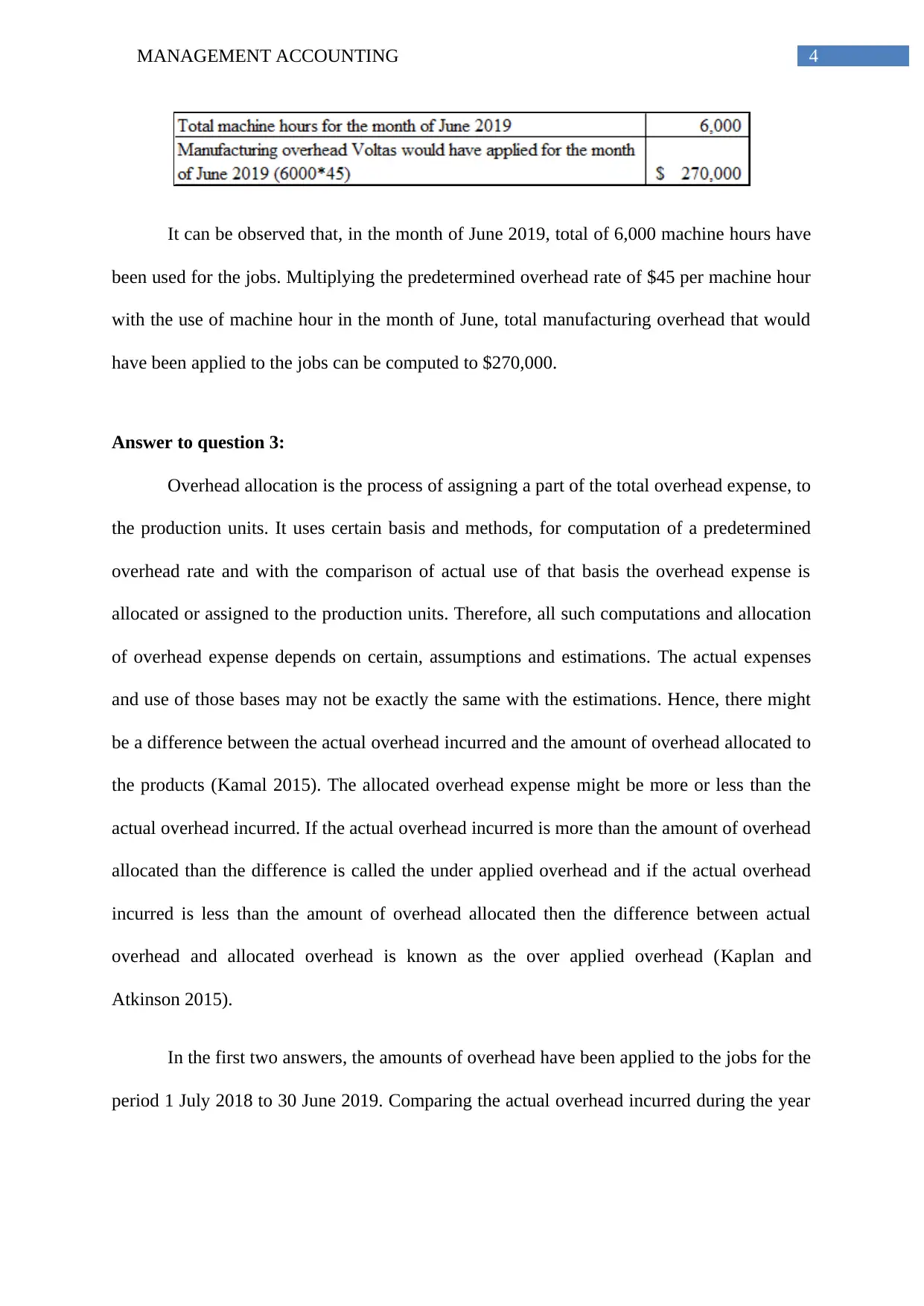
4MANAGEMENT ACCOUNTING
It can be observed that, in the month of June 2019, total of 6,000 machine hours have
been used for the jobs. Multiplying the predetermined overhead rate of $45 per machine hour
with the use of machine hour in the month of June, total manufacturing overhead that would
have been applied to the jobs can be computed to $270,000.
Answer to question 3:
Overhead allocation is the process of assigning a part of the total overhead expense, to
the production units. It uses certain basis and methods, for computation of a predetermined
overhead rate and with the comparison of actual use of that basis the overhead expense is
allocated or assigned to the production units. Therefore, all such computations and allocation
of overhead expense depends on certain, assumptions and estimations. The actual expenses
and use of those bases may not be exactly the same with the estimations. Hence, there might
be a difference between the actual overhead incurred and the amount of overhead allocated to
the products (Kamal 2015). The allocated overhead expense might be more or less than the
actual overhead incurred. If the actual overhead incurred is more than the amount of overhead
allocated than the difference is called the under applied overhead and if the actual overhead
incurred is less than the amount of overhead allocated then the difference between actual
overhead and allocated overhead is known as the over applied overhead (Kaplan and
Atkinson 2015).
In the first two answers, the amounts of overhead have been applied to the jobs for the
period 1 July 2018 to 30 June 2019. Comparing the actual overhead incurred during the year
It can be observed that, in the month of June 2019, total of 6,000 machine hours have
been used for the jobs. Multiplying the predetermined overhead rate of $45 per machine hour
with the use of machine hour in the month of June, total manufacturing overhead that would
have been applied to the jobs can be computed to $270,000.
Answer to question 3:
Overhead allocation is the process of assigning a part of the total overhead expense, to
the production units. It uses certain basis and methods, for computation of a predetermined
overhead rate and with the comparison of actual use of that basis the overhead expense is
allocated or assigned to the production units. Therefore, all such computations and allocation
of overhead expense depends on certain, assumptions and estimations. The actual expenses
and use of those bases may not be exactly the same with the estimations. Hence, there might
be a difference between the actual overhead incurred and the amount of overhead allocated to
the products (Kamal 2015). The allocated overhead expense might be more or less than the
actual overhead incurred. If the actual overhead incurred is more than the amount of overhead
allocated than the difference is called the under applied overhead and if the actual overhead
incurred is less than the amount of overhead allocated then the difference between actual
overhead and allocated overhead is known as the over applied overhead (Kaplan and
Atkinson 2015).
In the first two answers, the amounts of overhead have been applied to the jobs for the
period 1 July 2018 to 30 June 2019. Comparing the actual overhead incurred during the year
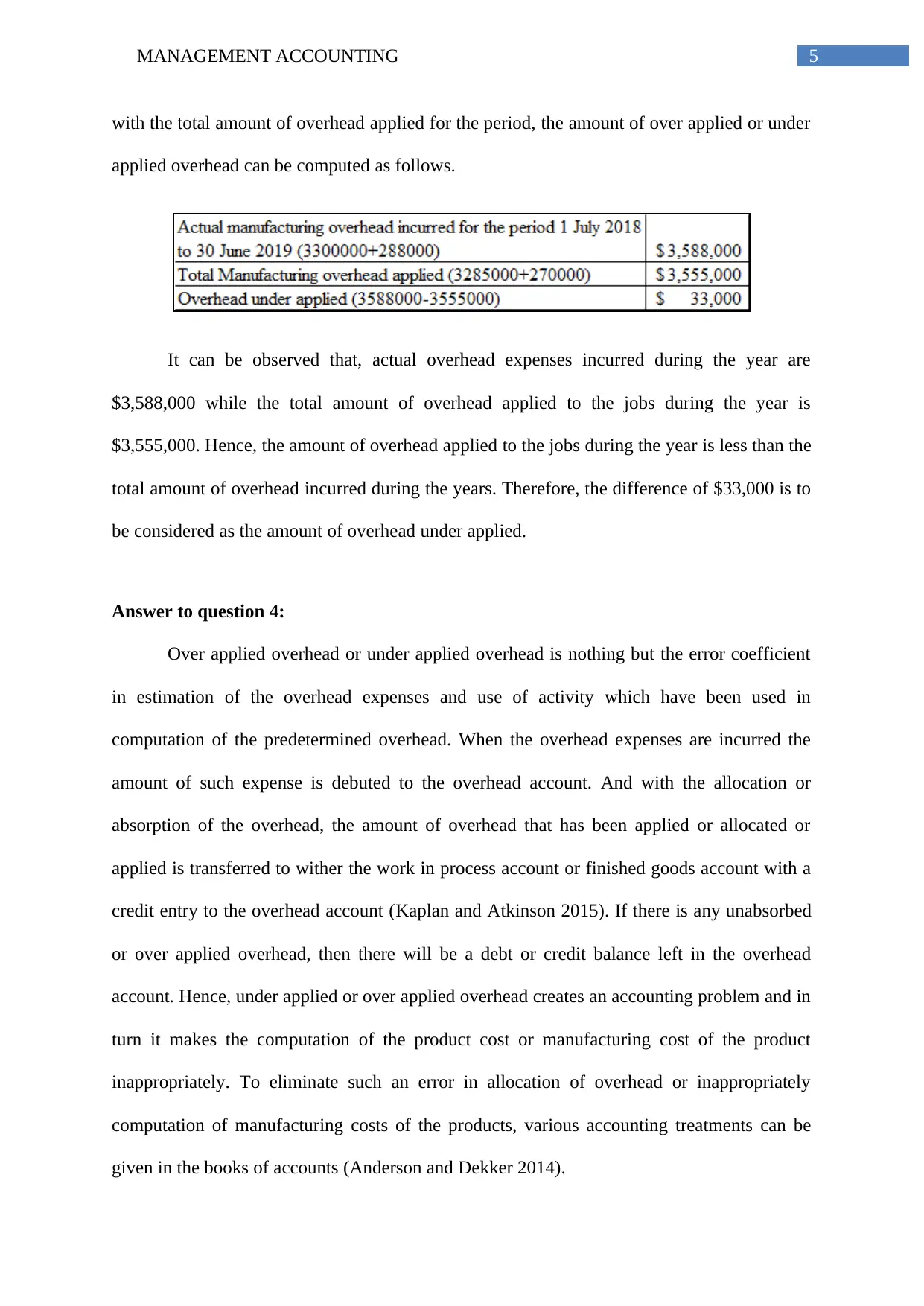
5MANAGEMENT ACCOUNTING
with the total amount of overhead applied for the period, the amount of over applied or under
applied overhead can be computed as follows.
It can be observed that, actual overhead expenses incurred during the year are
$3,588,000 while the total amount of overhead applied to the jobs during the year is
$3,555,000. Hence, the amount of overhead applied to the jobs during the year is less than the
total amount of overhead incurred during the years. Therefore, the difference of $33,000 is to
be considered as the amount of overhead under applied.
Answer to question 4:
Over applied overhead or under applied overhead is nothing but the error coefficient
in estimation of the overhead expenses and use of activity which have been used in
computation of the predetermined overhead. When the overhead expenses are incurred the
amount of such expense is debuted to the overhead account. And with the allocation or
absorption of the overhead, the amount of overhead that has been applied or allocated or
applied is transferred to wither the work in process account or finished goods account with a
credit entry to the overhead account (Kaplan and Atkinson 2015). If there is any unabsorbed
or over applied overhead, then there will be a debt or credit balance left in the overhead
account. Hence, under applied or over applied overhead creates an accounting problem and in
turn it makes the computation of the product cost or manufacturing cost of the product
inappropriately. To eliminate such an error in allocation of overhead or inappropriately
computation of manufacturing costs of the products, various accounting treatments can be
given in the books of accounts (Anderson and Dekker 2014).
with the total amount of overhead applied for the period, the amount of over applied or under
applied overhead can be computed as follows.
It can be observed that, actual overhead expenses incurred during the year are
$3,588,000 while the total amount of overhead applied to the jobs during the year is
$3,555,000. Hence, the amount of overhead applied to the jobs during the year is less than the
total amount of overhead incurred during the years. Therefore, the difference of $33,000 is to
be considered as the amount of overhead under applied.
Answer to question 4:
Over applied overhead or under applied overhead is nothing but the error coefficient
in estimation of the overhead expenses and use of activity which have been used in
computation of the predetermined overhead. When the overhead expenses are incurred the
amount of such expense is debuted to the overhead account. And with the allocation or
absorption of the overhead, the amount of overhead that has been applied or allocated or
applied is transferred to wither the work in process account or finished goods account with a
credit entry to the overhead account (Kaplan and Atkinson 2015). If there is any unabsorbed
or over applied overhead, then there will be a debt or credit balance left in the overhead
account. Hence, under applied or over applied overhead creates an accounting problem and in
turn it makes the computation of the product cost or manufacturing cost of the product
inappropriately. To eliminate such an error in allocation of overhead or inappropriately
computation of manufacturing costs of the products, various accounting treatments can be
given in the books of accounts (Anderson and Dekker 2014).
You're viewing a preview
Unlock full access by subscribing today!
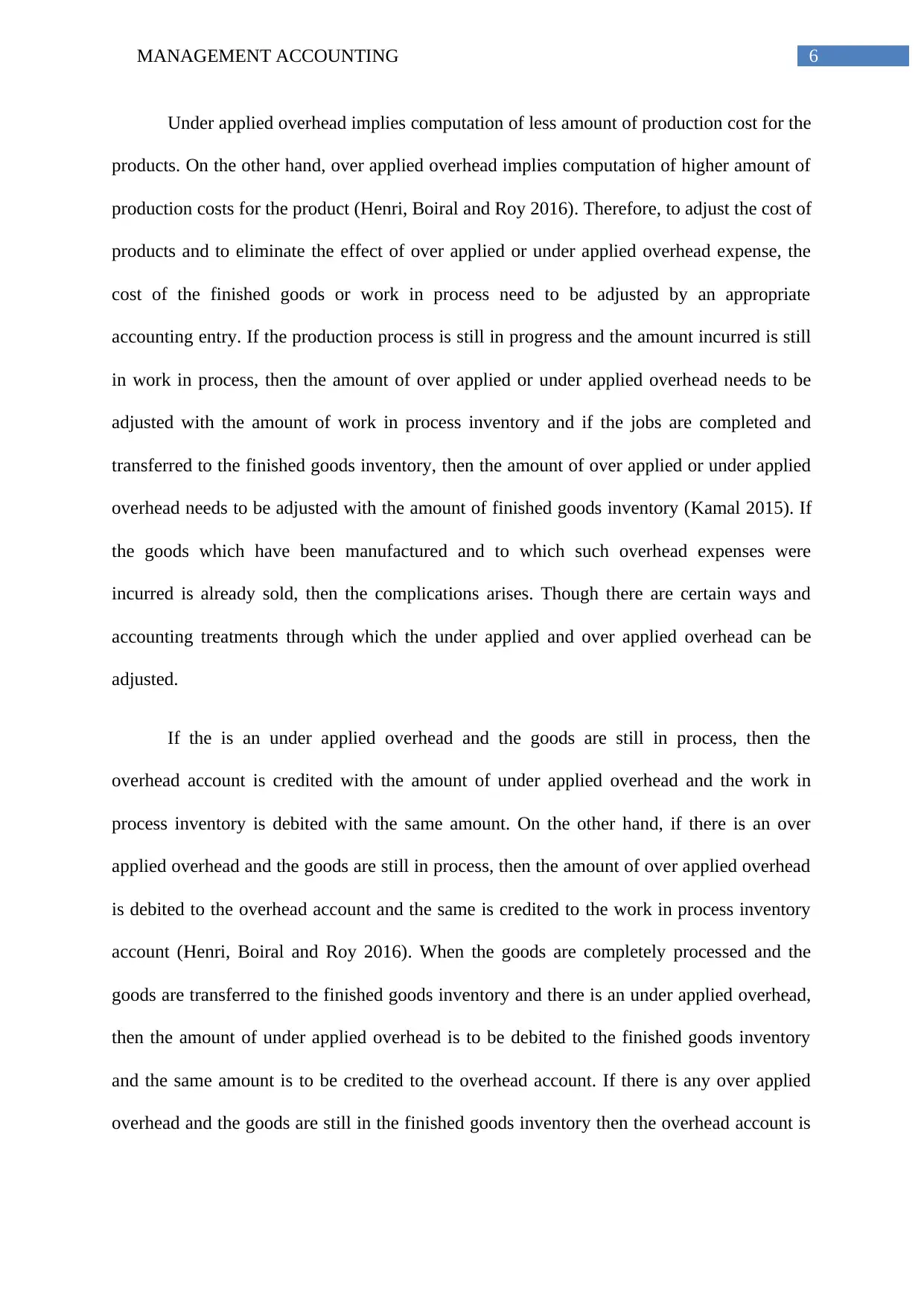
6MANAGEMENT ACCOUNTING
Under applied overhead implies computation of less amount of production cost for the
products. On the other hand, over applied overhead implies computation of higher amount of
production costs for the product (Henri, Boiral and Roy 2016). Therefore, to adjust the cost of
products and to eliminate the effect of over applied or under applied overhead expense, the
cost of the finished goods or work in process need to be adjusted by an appropriate
accounting entry. If the production process is still in progress and the amount incurred is still
in work in process, then the amount of over applied or under applied overhead needs to be
adjusted with the amount of work in process inventory and if the jobs are completed and
transferred to the finished goods inventory, then the amount of over applied or under applied
overhead needs to be adjusted with the amount of finished goods inventory (Kamal 2015). If
the goods which have been manufactured and to which such overhead expenses were
incurred is already sold, then the complications arises. Though there are certain ways and
accounting treatments through which the under applied and over applied overhead can be
adjusted.
If the is an under applied overhead and the goods are still in process, then the
overhead account is credited with the amount of under applied overhead and the work in
process inventory is debited with the same amount. On the other hand, if there is an over
applied overhead and the goods are still in process, then the amount of over applied overhead
is debited to the overhead account and the same is credited to the work in process inventory
account (Henri, Boiral and Roy 2016). When the goods are completely processed and the
goods are transferred to the finished goods inventory and there is an under applied overhead,
then the amount of under applied overhead is to be debited to the finished goods inventory
and the same amount is to be credited to the overhead account. If there is any over applied
overhead and the goods are still in the finished goods inventory then the overhead account is
Under applied overhead implies computation of less amount of production cost for the
products. On the other hand, over applied overhead implies computation of higher amount of
production costs for the product (Henri, Boiral and Roy 2016). Therefore, to adjust the cost of
products and to eliminate the effect of over applied or under applied overhead expense, the
cost of the finished goods or work in process need to be adjusted by an appropriate
accounting entry. If the production process is still in progress and the amount incurred is still
in work in process, then the amount of over applied or under applied overhead needs to be
adjusted with the amount of work in process inventory and if the jobs are completed and
transferred to the finished goods inventory, then the amount of over applied or under applied
overhead needs to be adjusted with the amount of finished goods inventory (Kamal 2015). If
the goods which have been manufactured and to which such overhead expenses were
incurred is already sold, then the complications arises. Though there are certain ways and
accounting treatments through which the under applied and over applied overhead can be
adjusted.
If the is an under applied overhead and the goods are still in process, then the
overhead account is credited with the amount of under applied overhead and the work in
process inventory is debited with the same amount. On the other hand, if there is an over
applied overhead and the goods are still in process, then the amount of over applied overhead
is debited to the overhead account and the same is credited to the work in process inventory
account (Henri, Boiral and Roy 2016). When the goods are completely processed and the
goods are transferred to the finished goods inventory and there is an under applied overhead,
then the amount of under applied overhead is to be debited to the finished goods inventory
and the same amount is to be credited to the overhead account. If there is any over applied
overhead and the goods are still in the finished goods inventory then the overhead account is
Paraphrase This Document
Need a fresh take? Get an instant paraphrase of this document with our AI Paraphraser
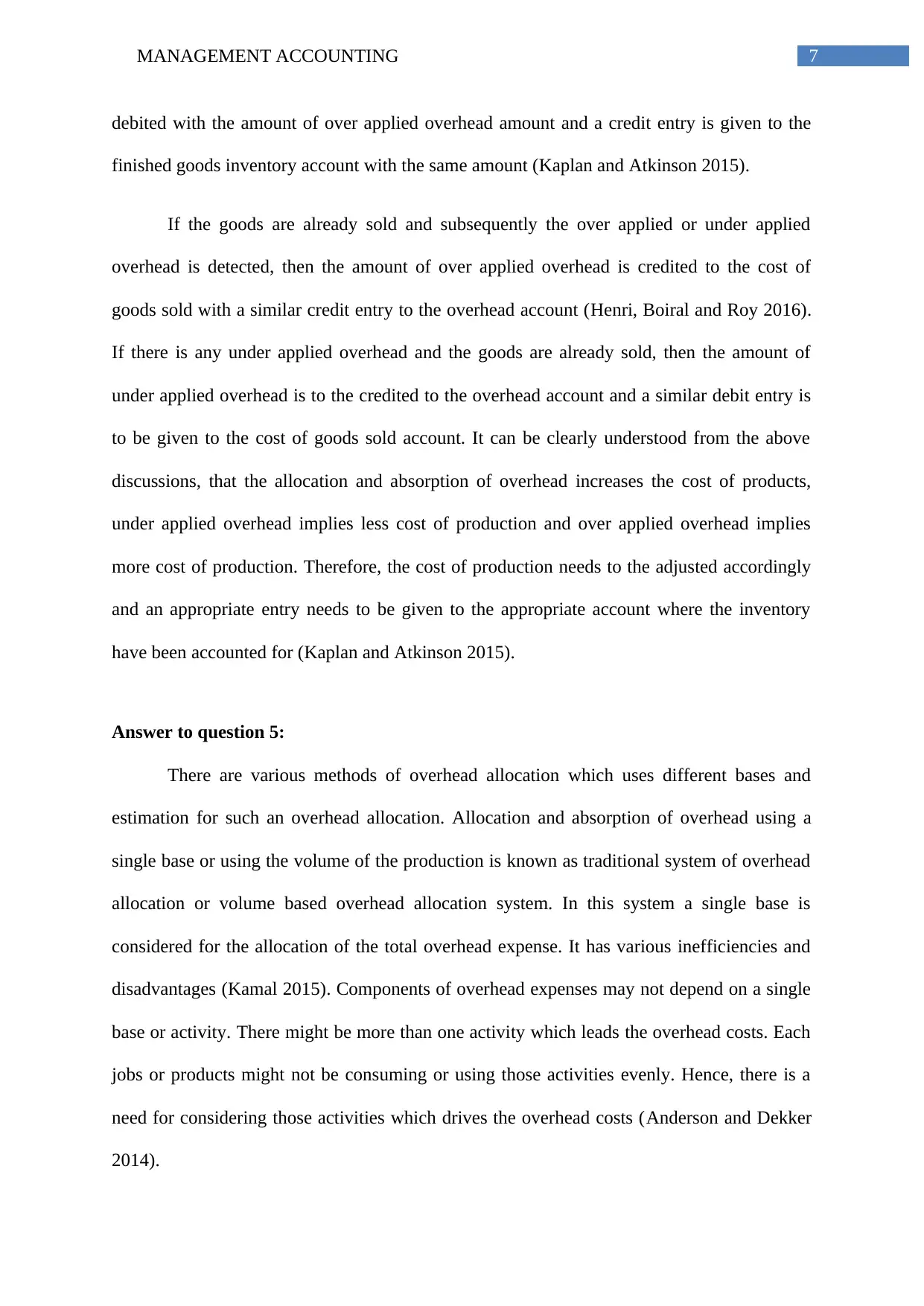
7MANAGEMENT ACCOUNTING
debited with the amount of over applied overhead amount and a credit entry is given to the
finished goods inventory account with the same amount (Kaplan and Atkinson 2015).
If the goods are already sold and subsequently the over applied or under applied
overhead is detected, then the amount of over applied overhead is credited to the cost of
goods sold with a similar credit entry to the overhead account (Henri, Boiral and Roy 2016).
If there is any under applied overhead and the goods are already sold, then the amount of
under applied overhead is to the credited to the overhead account and a similar debit entry is
to be given to the cost of goods sold account. It can be clearly understood from the above
discussions, that the allocation and absorption of overhead increases the cost of products,
under applied overhead implies less cost of production and over applied overhead implies
more cost of production. Therefore, the cost of production needs to the adjusted accordingly
and an appropriate entry needs to be given to the appropriate account where the inventory
have been accounted for (Kaplan and Atkinson 2015).
Answer to question 5:
There are various methods of overhead allocation which uses different bases and
estimation for such an overhead allocation. Allocation and absorption of overhead using a
single base or using the volume of the production is known as traditional system of overhead
allocation or volume based overhead allocation system. In this system a single base is
considered for the allocation of the total overhead expense. It has various inefficiencies and
disadvantages (Kamal 2015). Components of overhead expenses may not depend on a single
base or activity. There might be more than one activity which leads the overhead costs. Each
jobs or products might not be consuming or using those activities evenly. Hence, there is a
need for considering those activities which drives the overhead costs (Anderson and Dekker
2014).
debited with the amount of over applied overhead amount and a credit entry is given to the
finished goods inventory account with the same amount (Kaplan and Atkinson 2015).
If the goods are already sold and subsequently the over applied or under applied
overhead is detected, then the amount of over applied overhead is credited to the cost of
goods sold with a similar credit entry to the overhead account (Henri, Boiral and Roy 2016).
If there is any under applied overhead and the goods are already sold, then the amount of
under applied overhead is to the credited to the overhead account and a similar debit entry is
to be given to the cost of goods sold account. It can be clearly understood from the above
discussions, that the allocation and absorption of overhead increases the cost of products,
under applied overhead implies less cost of production and over applied overhead implies
more cost of production. Therefore, the cost of production needs to the adjusted accordingly
and an appropriate entry needs to be given to the appropriate account where the inventory
have been accounted for (Kaplan and Atkinson 2015).
Answer to question 5:
There are various methods of overhead allocation which uses different bases and
estimation for such an overhead allocation. Allocation and absorption of overhead using a
single base or using the volume of the production is known as traditional system of overhead
allocation or volume based overhead allocation system. In this system a single base is
considered for the allocation of the total overhead expense. It has various inefficiencies and
disadvantages (Kamal 2015). Components of overhead expenses may not depend on a single
base or activity. There might be more than one activity which leads the overhead costs. Each
jobs or products might not be consuming or using those activities evenly. Hence, there is a
need for considering those activities which drives the overhead costs (Anderson and Dekker
2014).
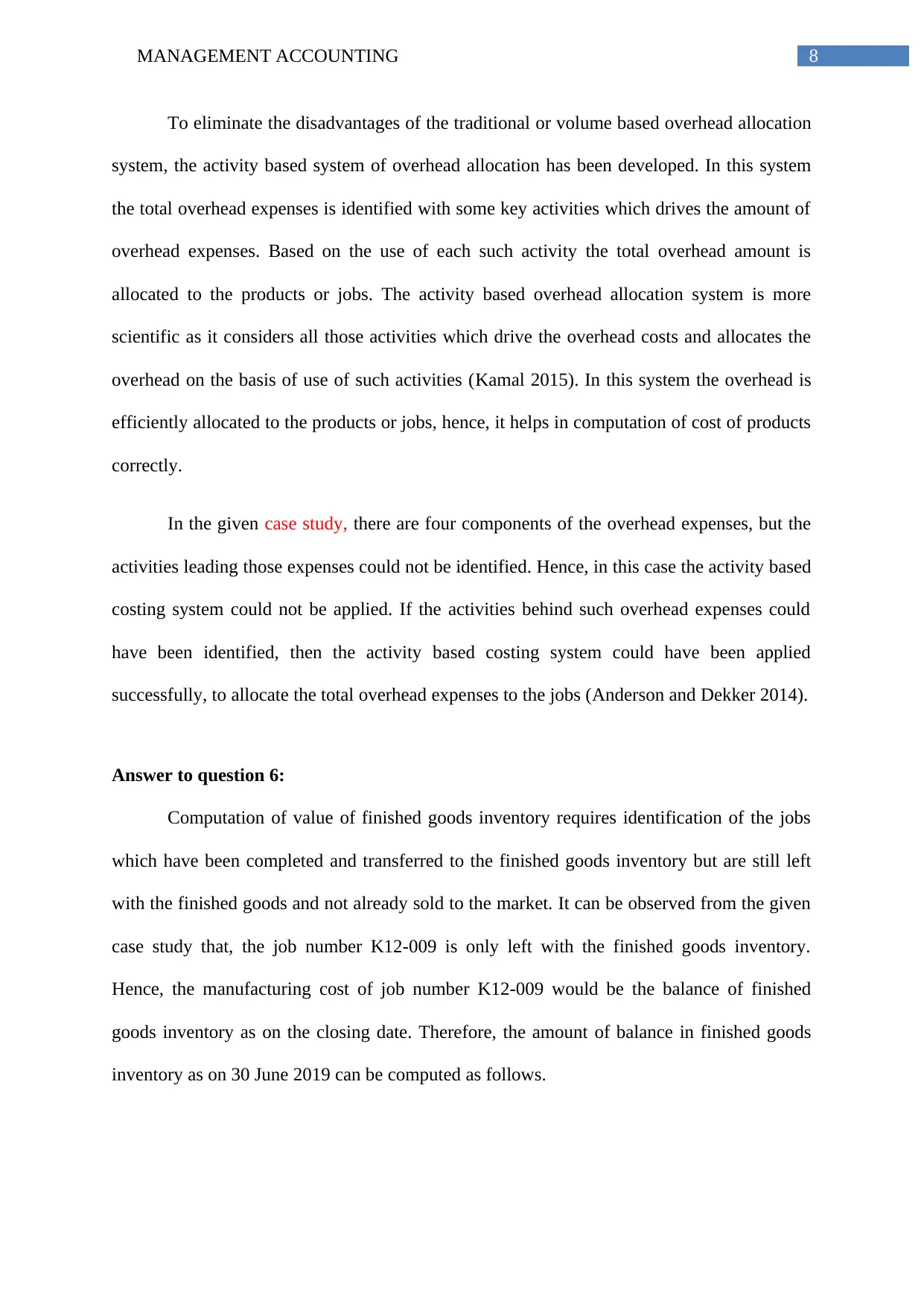
8MANAGEMENT ACCOUNTING
To eliminate the disadvantages of the traditional or volume based overhead allocation
system, the activity based system of overhead allocation has been developed. In this system
the total overhead expenses is identified with some key activities which drives the amount of
overhead expenses. Based on the use of each such activity the total overhead amount is
allocated to the products or jobs. The activity based overhead allocation system is more
scientific as it considers all those activities which drive the overhead costs and allocates the
overhead on the basis of use of such activities (Kamal 2015). In this system the overhead is
efficiently allocated to the products or jobs, hence, it helps in computation of cost of products
correctly.
In the given case study, there are four components of the overhead expenses, but the
activities leading those expenses could not be identified. Hence, in this case the activity based
costing system could not be applied. If the activities behind such overhead expenses could
have been identified, then the activity based costing system could have been applied
successfully, to allocate the total overhead expenses to the jobs (Anderson and Dekker 2014).
Answer to question 6:
Computation of value of finished goods inventory requires identification of the jobs
which have been completed and transferred to the finished goods inventory but are still left
with the finished goods and not already sold to the market. It can be observed from the given
case study that, the job number K12-009 is only left with the finished goods inventory.
Hence, the manufacturing cost of job number K12-009 would be the balance of finished
goods inventory as on the closing date. Therefore, the amount of balance in finished goods
inventory as on 30 June 2019 can be computed as follows.
To eliminate the disadvantages of the traditional or volume based overhead allocation
system, the activity based system of overhead allocation has been developed. In this system
the total overhead expenses is identified with some key activities which drives the amount of
overhead expenses. Based on the use of each such activity the total overhead amount is
allocated to the products or jobs. The activity based overhead allocation system is more
scientific as it considers all those activities which drive the overhead costs and allocates the
overhead on the basis of use of such activities (Kamal 2015). In this system the overhead is
efficiently allocated to the products or jobs, hence, it helps in computation of cost of products
correctly.
In the given case study, there are four components of the overhead expenses, but the
activities leading those expenses could not be identified. Hence, in this case the activity based
costing system could not be applied. If the activities behind such overhead expenses could
have been identified, then the activity based costing system could have been applied
successfully, to allocate the total overhead expenses to the jobs (Anderson and Dekker 2014).
Answer to question 6:
Computation of value of finished goods inventory requires identification of the jobs
which have been completed and transferred to the finished goods inventory but are still left
with the finished goods and not already sold to the market. It can be observed from the given
case study that, the job number K12-009 is only left with the finished goods inventory.
Hence, the manufacturing cost of job number K12-009 would be the balance of finished
goods inventory as on the closing date. Therefore, the amount of balance in finished goods
inventory as on 30 June 2019 can be computed as follows.
You're viewing a preview
Unlock full access by subscribing today!
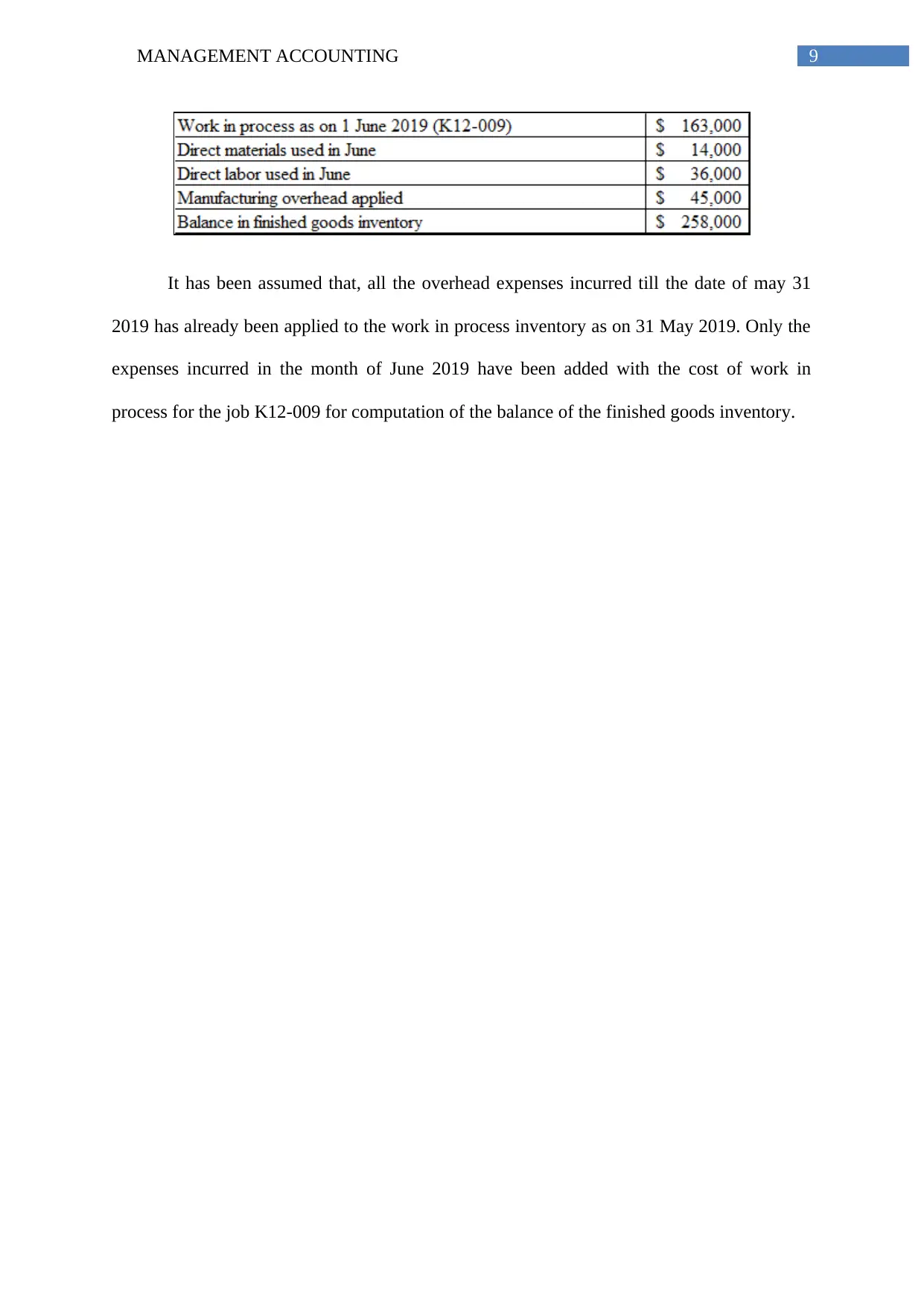
9MANAGEMENT ACCOUNTING
It has been assumed that, all the overhead expenses incurred till the date of may 31
2019 has already been applied to the work in process inventory as on 31 May 2019. Only the
expenses incurred in the month of June 2019 have been added with the cost of work in
process for the job K12-009 for computation of the balance of the finished goods inventory.
It has been assumed that, all the overhead expenses incurred till the date of may 31
2019 has already been applied to the work in process inventory as on 31 May 2019. Only the
expenses incurred in the month of June 2019 have been added with the cost of work in
process for the job K12-009 for computation of the balance of the finished goods inventory.
Paraphrase This Document
Need a fresh take? Get an instant paraphrase of this document with our AI Paraphraser
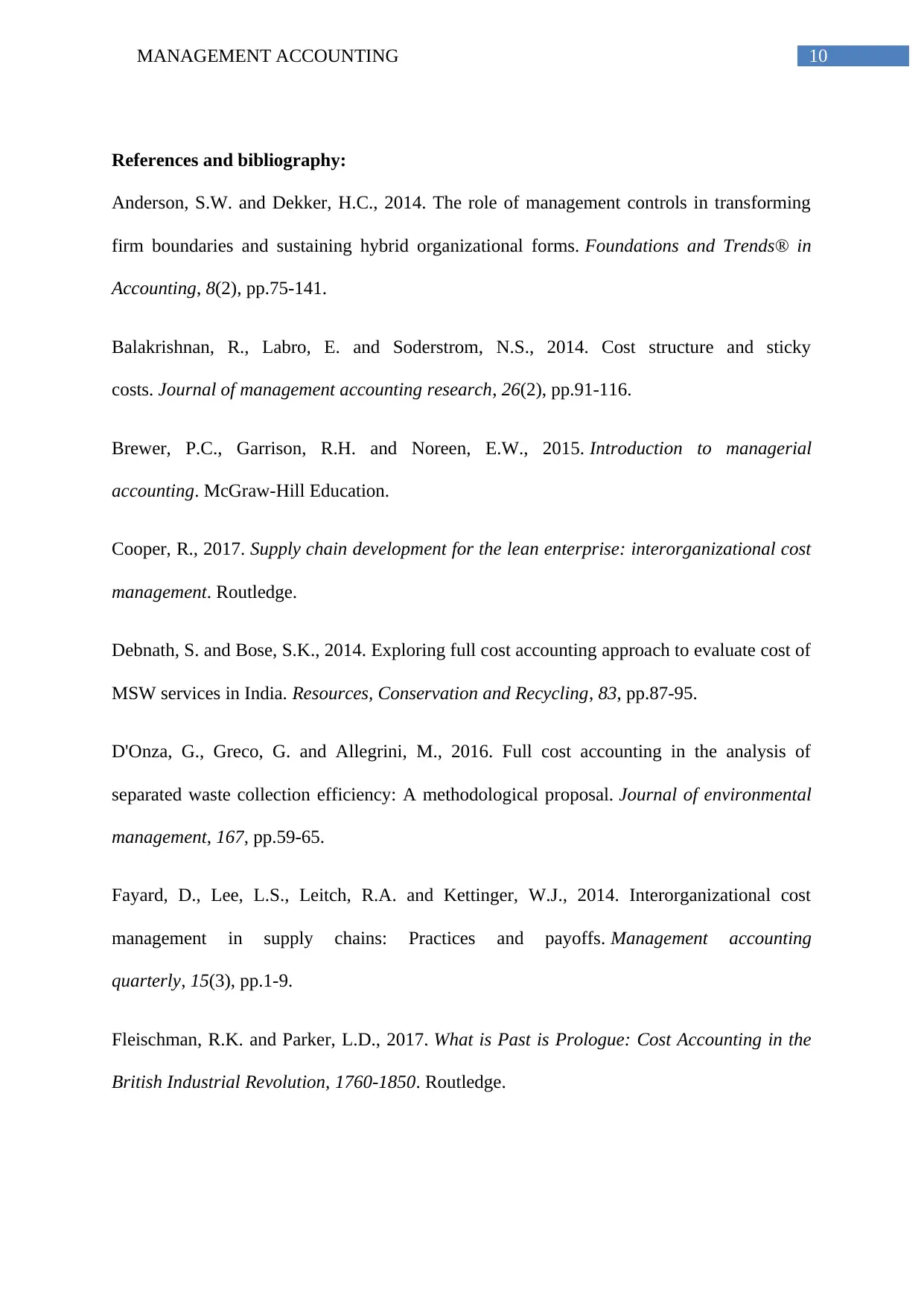
10MANAGEMENT ACCOUNTING
References and bibliography:
Anderson, S.W. and Dekker, H.C., 2014. The role of management controls in transforming
firm boundaries and sustaining hybrid organizational forms. Foundations and Trends® in
Accounting, 8(2), pp.75-141.
Balakrishnan, R., Labro, E. and Soderstrom, N.S., 2014. Cost structure and sticky
costs. Journal of management accounting research, 26(2), pp.91-116.
Brewer, P.C., Garrison, R.H. and Noreen, E.W., 2015. Introduction to managerial
accounting. McGraw-Hill Education.
Cooper, R., 2017. Supply chain development for the lean enterprise: interorganizational cost
management. Routledge.
Debnath, S. and Bose, S.K., 2014. Exploring full cost accounting approach to evaluate cost of
MSW services in India. Resources, Conservation and Recycling, 83, pp.87-95.
D'Onza, G., Greco, G. and Allegrini, M., 2016. Full cost accounting in the analysis of
separated waste collection efficiency: A methodological proposal. Journal of environmental
management, 167, pp.59-65.
Fayard, D., Lee, L.S., Leitch, R.A. and Kettinger, W.J., 2014. Interorganizational cost
management in supply chains: Practices and payoffs. Management accounting
quarterly, 15(3), pp.1-9.
Fleischman, R.K. and Parker, L.D., 2017. What is Past is Prologue: Cost Accounting in the
British Industrial Revolution, 1760-1850. Routledge.
References and bibliography:
Anderson, S.W. and Dekker, H.C., 2014. The role of management controls in transforming
firm boundaries and sustaining hybrid organizational forms. Foundations and Trends® in
Accounting, 8(2), pp.75-141.
Balakrishnan, R., Labro, E. and Soderstrom, N.S., 2014. Cost structure and sticky
costs. Journal of management accounting research, 26(2), pp.91-116.
Brewer, P.C., Garrison, R.H. and Noreen, E.W., 2015. Introduction to managerial
accounting. McGraw-Hill Education.
Cooper, R., 2017. Supply chain development for the lean enterprise: interorganizational cost
management. Routledge.
Debnath, S. and Bose, S.K., 2014. Exploring full cost accounting approach to evaluate cost of
MSW services in India. Resources, Conservation and Recycling, 83, pp.87-95.
D'Onza, G., Greco, G. and Allegrini, M., 2016. Full cost accounting in the analysis of
separated waste collection efficiency: A methodological proposal. Journal of environmental
management, 167, pp.59-65.
Fayard, D., Lee, L.S., Leitch, R.A. and Kettinger, W.J., 2014. Interorganizational cost
management in supply chains: Practices and payoffs. Management accounting
quarterly, 15(3), pp.1-9.
Fleischman, R.K. and Parker, L.D., 2017. What is Past is Prologue: Cost Accounting in the
British Industrial Revolution, 1760-1850. Routledge.
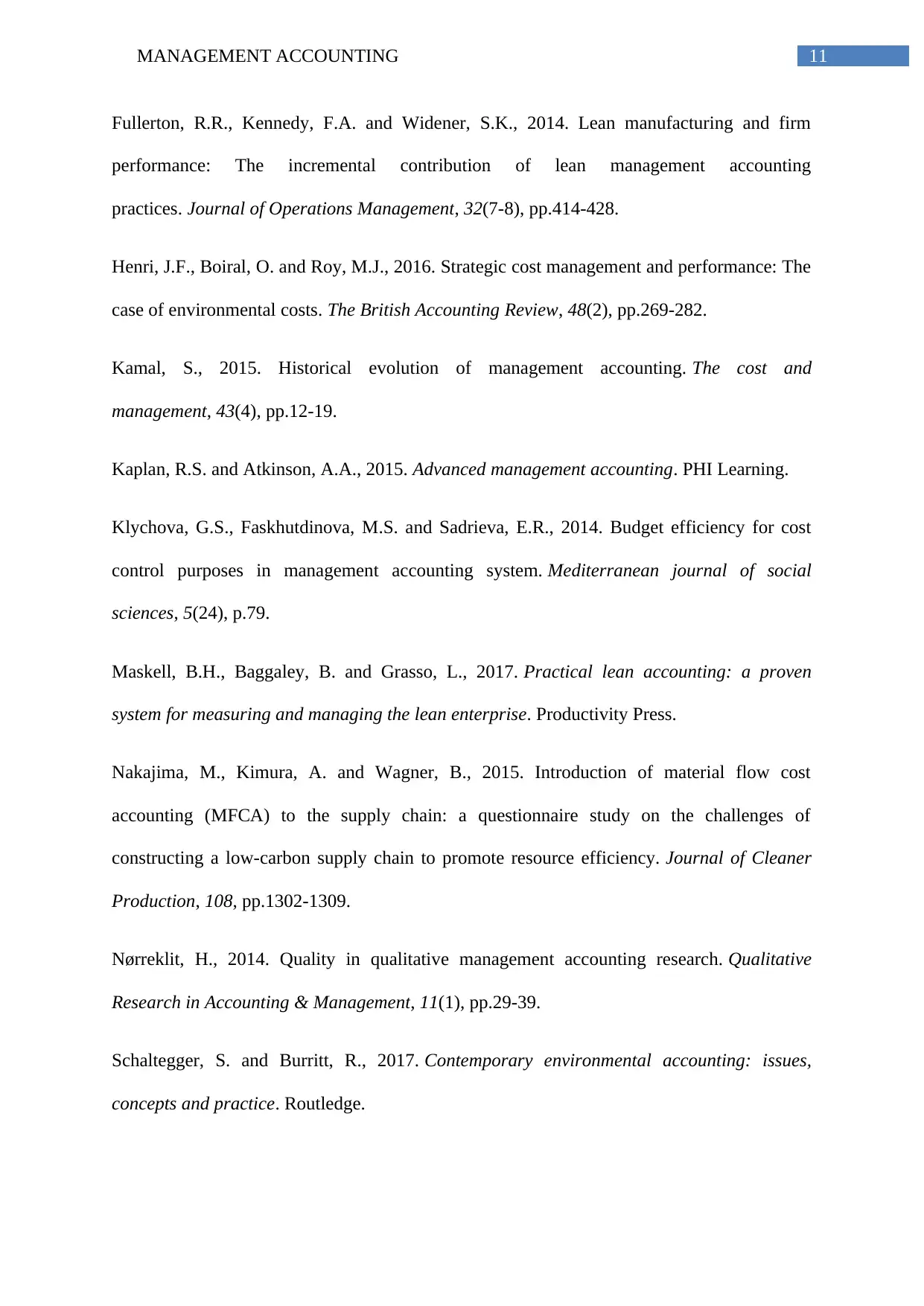
11MANAGEMENT ACCOUNTING
Fullerton, R.R., Kennedy, F.A. and Widener, S.K., 2014. Lean manufacturing and firm
performance: The incremental contribution of lean management accounting
practices. Journal of Operations Management, 32(7-8), pp.414-428.
Henri, J.F., Boiral, O. and Roy, M.J., 2016. Strategic cost management and performance: The
case of environmental costs. The British Accounting Review, 48(2), pp.269-282.
Kamal, S., 2015. Historical evolution of management accounting. The cost and
management, 43(4), pp.12-19.
Kaplan, R.S. and Atkinson, A.A., 2015. Advanced management accounting. PHI Learning.
Klychova, G.S., Faskhutdinova, М.S. and Sadrieva, E.R., 2014. Budget efficiency for cost
control purposes in management accounting system. Mediterranean journal of social
sciences, 5(24), p.79.
Maskell, B.H., Baggaley, B. and Grasso, L., 2017. Practical lean accounting: a proven
system for measuring and managing the lean enterprise. Productivity Press.
Nakajima, M., Kimura, A. and Wagner, B., 2015. Introduction of material flow cost
accounting (MFCA) to the supply chain: a questionnaire study on the challenges of
constructing a low-carbon supply chain to promote resource efficiency. Journal of Cleaner
Production, 108, pp.1302-1309.
Nørreklit, H., 2014. Quality in qualitative management accounting research. Qualitative
Research in Accounting & Management, 11(1), pp.29-39.
Schaltegger, S. and Burritt, R., 2017. Contemporary environmental accounting: issues,
concepts and practice. Routledge.
Fullerton, R.R., Kennedy, F.A. and Widener, S.K., 2014. Lean manufacturing and firm
performance: The incremental contribution of lean management accounting
practices. Journal of Operations Management, 32(7-8), pp.414-428.
Henri, J.F., Boiral, O. and Roy, M.J., 2016. Strategic cost management and performance: The
case of environmental costs. The British Accounting Review, 48(2), pp.269-282.
Kamal, S., 2015. Historical evolution of management accounting. The cost and
management, 43(4), pp.12-19.
Kaplan, R.S. and Atkinson, A.A., 2015. Advanced management accounting. PHI Learning.
Klychova, G.S., Faskhutdinova, М.S. and Sadrieva, E.R., 2014. Budget efficiency for cost
control purposes in management accounting system. Mediterranean journal of social
sciences, 5(24), p.79.
Maskell, B.H., Baggaley, B. and Grasso, L., 2017. Practical lean accounting: a proven
system for measuring and managing the lean enterprise. Productivity Press.
Nakajima, M., Kimura, A. and Wagner, B., 2015. Introduction of material flow cost
accounting (MFCA) to the supply chain: a questionnaire study on the challenges of
constructing a low-carbon supply chain to promote resource efficiency. Journal of Cleaner
Production, 108, pp.1302-1309.
Nørreklit, H., 2014. Quality in qualitative management accounting research. Qualitative
Research in Accounting & Management, 11(1), pp.29-39.
Schaltegger, S. and Burritt, R., 2017. Contemporary environmental accounting: issues,
concepts and practice. Routledge.
You're viewing a preview
Unlock full access by subscribing today!
1 out of 12
Related Documents

Your All-in-One AI-Powered Toolkit for Academic Success.
+13062052269
info@desklib.com
Available 24*7 on WhatsApp / Email
Unlock your academic potential
© 2024 | Zucol Services PVT LTD | All rights reserved.