Management Accounting Problem (Case Study)
VerifiedAdded on  2023/03/23
|15
|2781
|42
AI Summary
This report discusses the use of job costing system in Connette's Limited and suggests the implementation of activity based costing to overcome its deficiencies. It also provides calculations for work in progress inventory, cost of chairs in finished goods inventory, and over applied or undersupplied overhead.
Contribute Materials
Your contribution can guide someone’s learning journey. Share your
documents today.
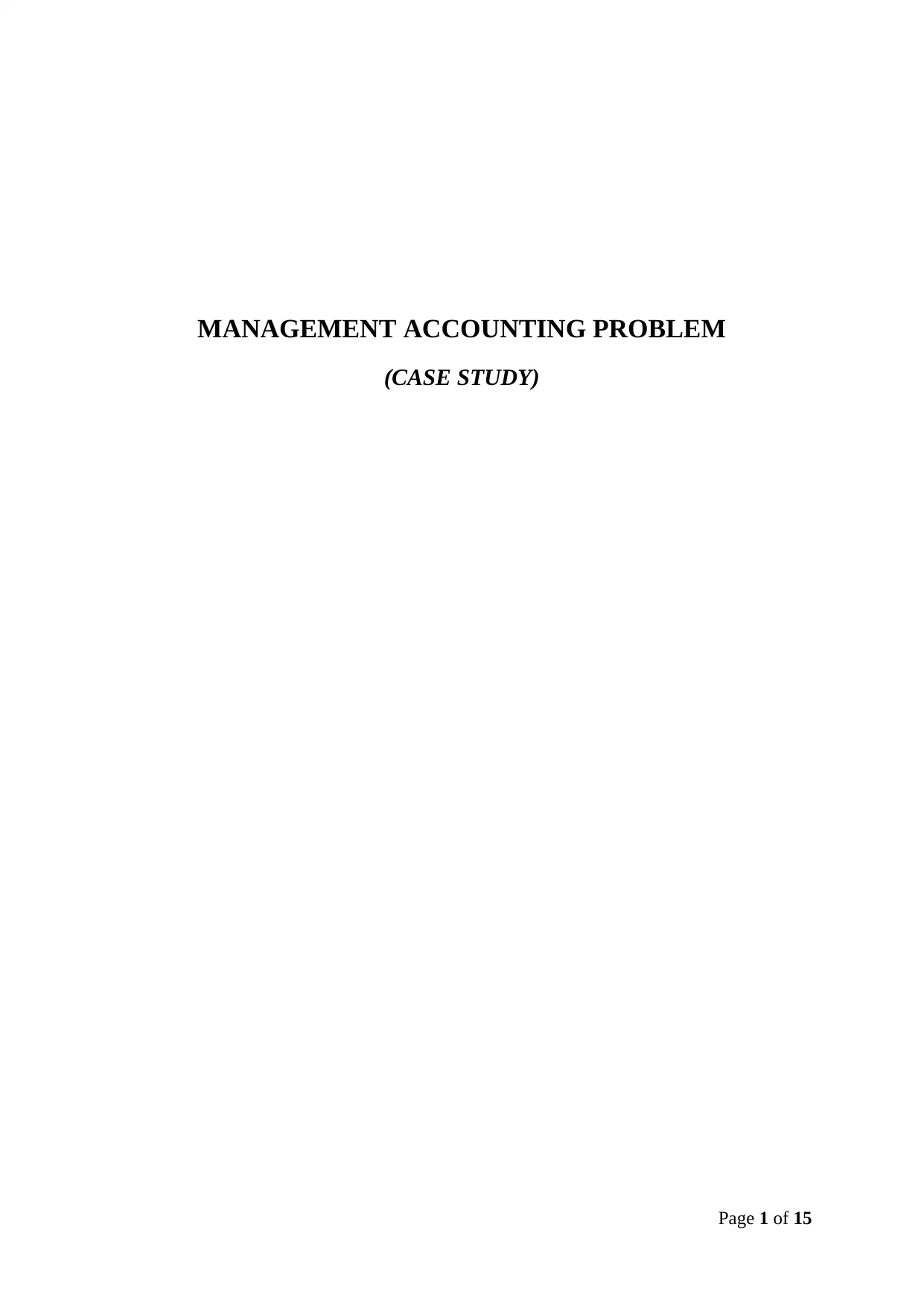
MANAGEMENT ACCOUNTING PROBLEM
(CASE STUDY)
Page 1 of 15
(CASE STUDY)
Page 1 of 15
Secure Best Marks with AI Grader
Need help grading? Try our AI Grader for instant feedback on your assignments.
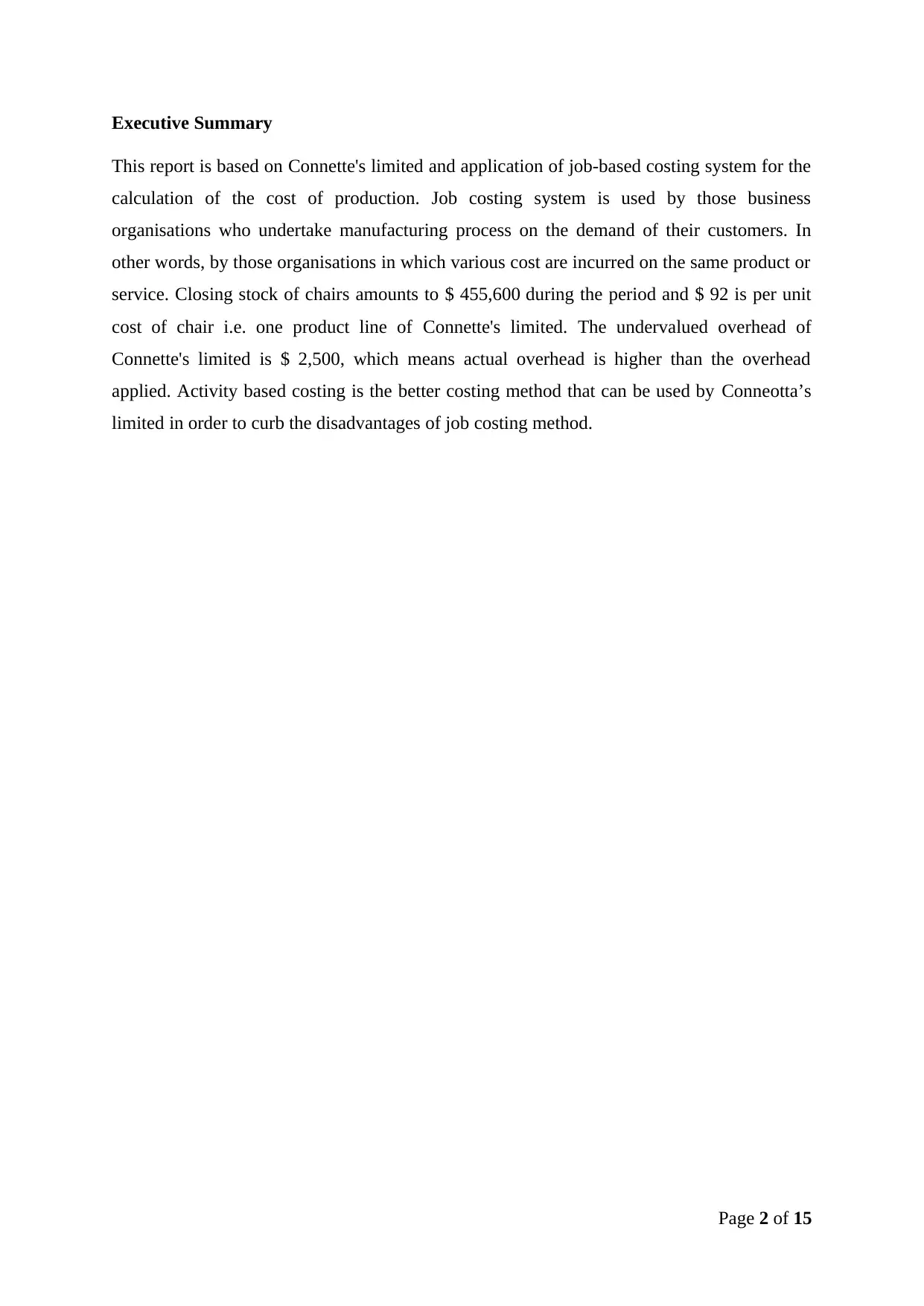
Executive Summary
This report is based on Connette's limited and application of job-based costing system for the
calculation of the cost of production. Job costing system is used by those business
organisations who undertake manufacturing process on the demand of their customers. In
other words, by those organisations in which various cost are incurred on the same product or
service. Closing stock of chairs amounts to $ 455,600 during the period and $ 92 is per unit
cost of chair i.e. one product line of Connette's limited. The undervalued overhead of
Connette's limited is $ 2,500, which means actual overhead is higher than the overhead
applied. Activity based costing is the better costing method that can be used by Conneotta’s
limited in order to curb the disadvantages of job costing method.
Page 2 of 15
This report is based on Connette's limited and application of job-based costing system for the
calculation of the cost of production. Job costing system is used by those business
organisations who undertake manufacturing process on the demand of their customers. In
other words, by those organisations in which various cost are incurred on the same product or
service. Closing stock of chairs amounts to $ 455,600 during the period and $ 92 is per unit
cost of chair i.e. one product line of Connette's limited. The undervalued overhead of
Connette's limited is $ 2,500, which means actual overhead is higher than the overhead
applied. Activity based costing is the better costing method that can be used by Conneotta’s
limited in order to curb the disadvantages of job costing method.
Page 2 of 15
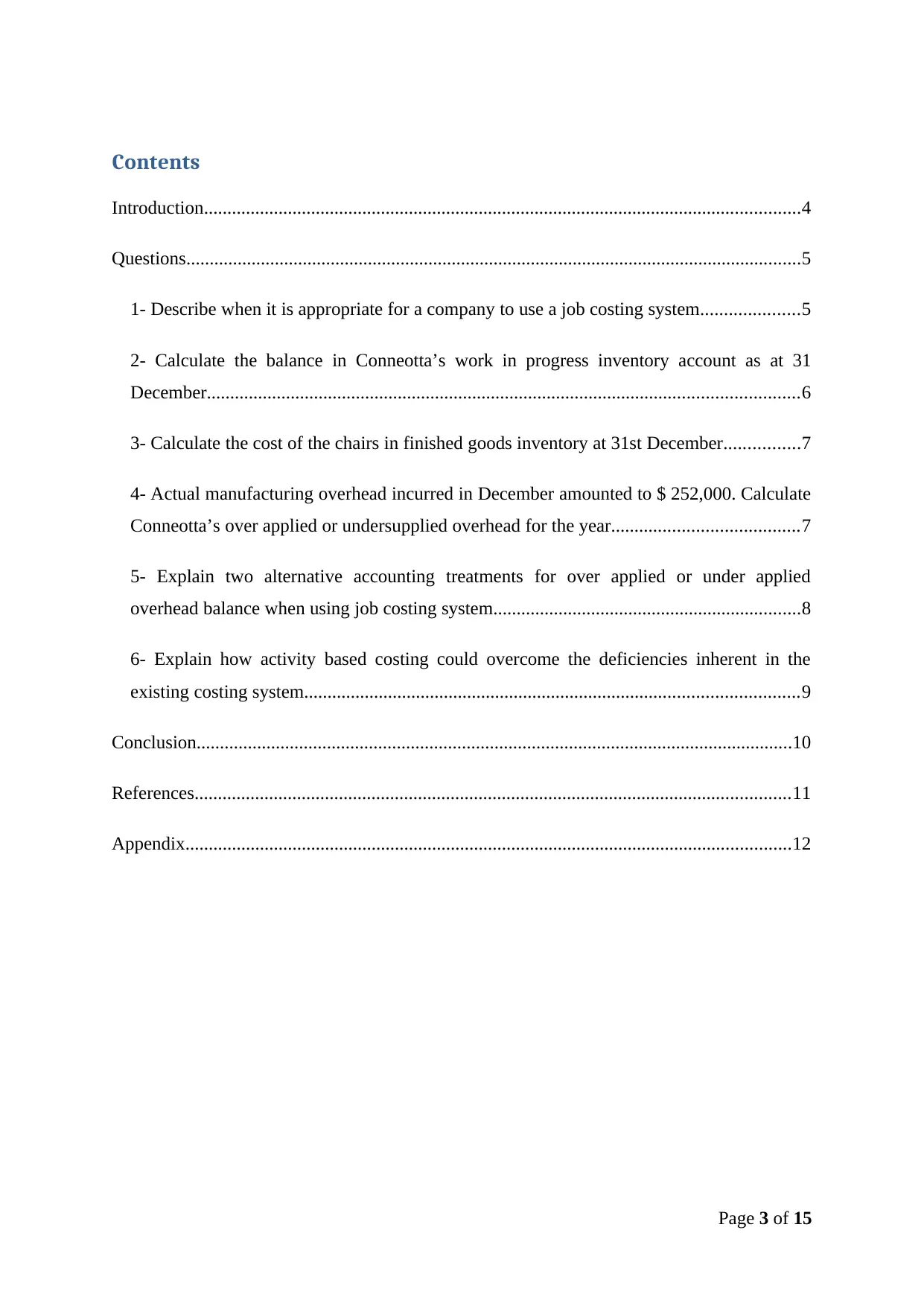
Contents
Introduction................................................................................................................................4
Questions....................................................................................................................................5
1- Describe when it is appropriate for a company to use a job costing system.....................5
2- Calculate the balance in Conneotta’s work in progress inventory account as at 31
December...............................................................................................................................6
3- Calculate the cost of the chairs in finished goods inventory at 31st December................7
4- Actual manufacturing overhead incurred in December amounted to $ 252,000. Calculate
Conneotta’s over applied or undersupplied overhead for the year........................................7
5- Explain two alternative accounting treatments for over applied or under applied
overhead balance when using job costing system..................................................................8
6- Explain how activity based costing could overcome the deficiencies inherent in the
existing costing system..........................................................................................................9
Conclusion................................................................................................................................10
References................................................................................................................................11
Appendix..................................................................................................................................12
Page 3 of 15
Introduction................................................................................................................................4
Questions....................................................................................................................................5
1- Describe when it is appropriate for a company to use a job costing system.....................5
2- Calculate the balance in Conneotta’s work in progress inventory account as at 31
December...............................................................................................................................6
3- Calculate the cost of the chairs in finished goods inventory at 31st December................7
4- Actual manufacturing overhead incurred in December amounted to $ 252,000. Calculate
Conneotta’s over applied or undersupplied overhead for the year........................................7
5- Explain two alternative accounting treatments for over applied or under applied
overhead balance when using job costing system..................................................................8
6- Explain how activity based costing could overcome the deficiencies inherent in the
existing costing system..........................................................................................................9
Conclusion................................................................................................................................10
References................................................................................................................................11
Appendix..................................................................................................................................12
Page 3 of 15
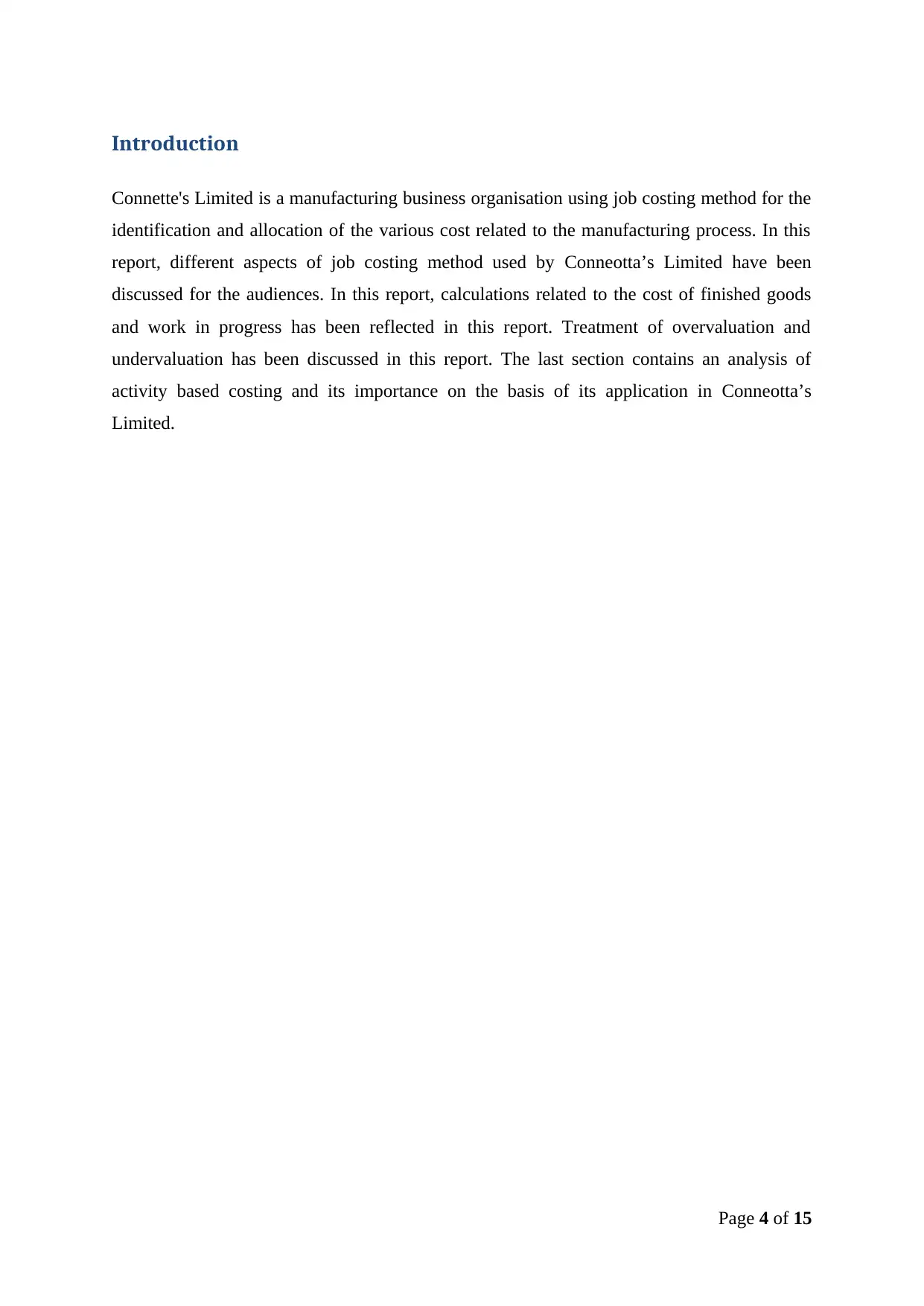
Introduction
Connette's Limited is a manufacturing business organisation using job costing method for the
identification and allocation of the various cost related to the manufacturing process. In this
report, different aspects of job costing method used by Conneotta’s Limited have been
discussed for the audiences. In this report, calculations related to the cost of finished goods
and work in progress has been reflected in this report. Treatment of overvaluation and
undervaluation has been discussed in this report. The last section contains an analysis of
activity based costing and its importance on the basis of its application in Conneotta’s
Limited.
Page 4 of 15
Connette's Limited is a manufacturing business organisation using job costing method for the
identification and allocation of the various cost related to the manufacturing process. In this
report, different aspects of job costing method used by Conneotta’s Limited have been
discussed for the audiences. In this report, calculations related to the cost of finished goods
and work in progress has been reflected in this report. Treatment of overvaluation and
undervaluation has been discussed in this report. The last section contains an analysis of
activity based costing and its importance on the basis of its application in Conneotta’s
Limited.
Page 4 of 15
Secure Best Marks with AI Grader
Need help grading? Try our AI Grader for instant feedback on your assignments.
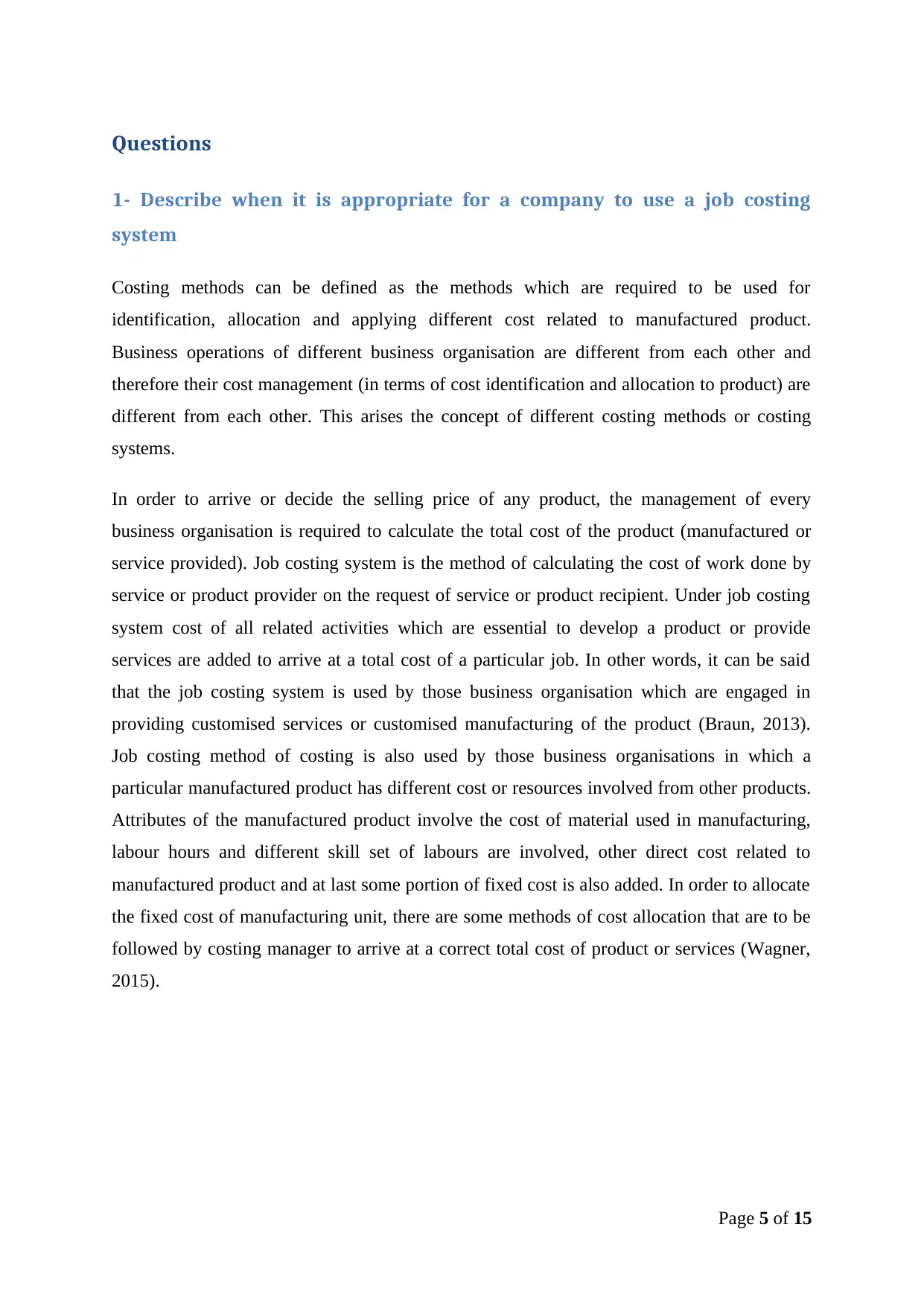
Questions
1- Describe when it is appropriate for a company to use a job costing
system
Costing methods can be defined as the methods which are required to be used for
identification, allocation and applying different cost related to manufactured product.
Business operations of different business organisation are different from each other and
therefore their cost management (in terms of cost identification and allocation to product) are
different from each other. This arises the concept of different costing methods or costing
systems.
In order to arrive or decide the selling price of any product, the management of every
business organisation is required to calculate the total cost of the product (manufactured or
service provided). Job costing system is the method of calculating the cost of work done by
service or product provider on the request of service or product recipient. Under job costing
system cost of all related activities which are essential to develop a product or provide
services are added to arrive at a total cost of a particular job. In other words, it can be said
that the job costing system is used by those business organisation which are engaged in
providing customised services or customised manufacturing of the product (Braun, 2013).
Job costing method of costing is also used by those business organisations in which a
particular manufactured product has different cost or resources involved from other products.
Attributes of the manufactured product involve the cost of material used in manufacturing,
labour hours and different skill set of labours are involved, other direct cost related to
manufactured product and at last some portion of fixed cost is also added. In order to allocate
the fixed cost of manufacturing unit, there are some methods of cost allocation that are to be
followed by costing manager to arrive at a correct total cost of product or services (Wagner,
2015).
Page 5 of 15
1- Describe when it is appropriate for a company to use a job costing
system
Costing methods can be defined as the methods which are required to be used for
identification, allocation and applying different cost related to manufactured product.
Business operations of different business organisation are different from each other and
therefore their cost management (in terms of cost identification and allocation to product) are
different from each other. This arises the concept of different costing methods or costing
systems.
In order to arrive or decide the selling price of any product, the management of every
business organisation is required to calculate the total cost of the product (manufactured or
service provided). Job costing system is the method of calculating the cost of work done by
service or product provider on the request of service or product recipient. Under job costing
system cost of all related activities which are essential to develop a product or provide
services are added to arrive at a total cost of a particular job. In other words, it can be said
that the job costing system is used by those business organisation which are engaged in
providing customised services or customised manufacturing of the product (Braun, 2013).
Job costing method of costing is also used by those business organisations in which a
particular manufactured product has different cost or resources involved from other products.
Attributes of the manufactured product involve the cost of material used in manufacturing,
labour hours and different skill set of labours are involved, other direct cost related to
manufactured product and at last some portion of fixed cost is also added. In order to allocate
the fixed cost of manufacturing unit, there are some methods of cost allocation that are to be
followed by costing manager to arrive at a correct total cost of product or services (Wagner,
2015).
Page 5 of 15
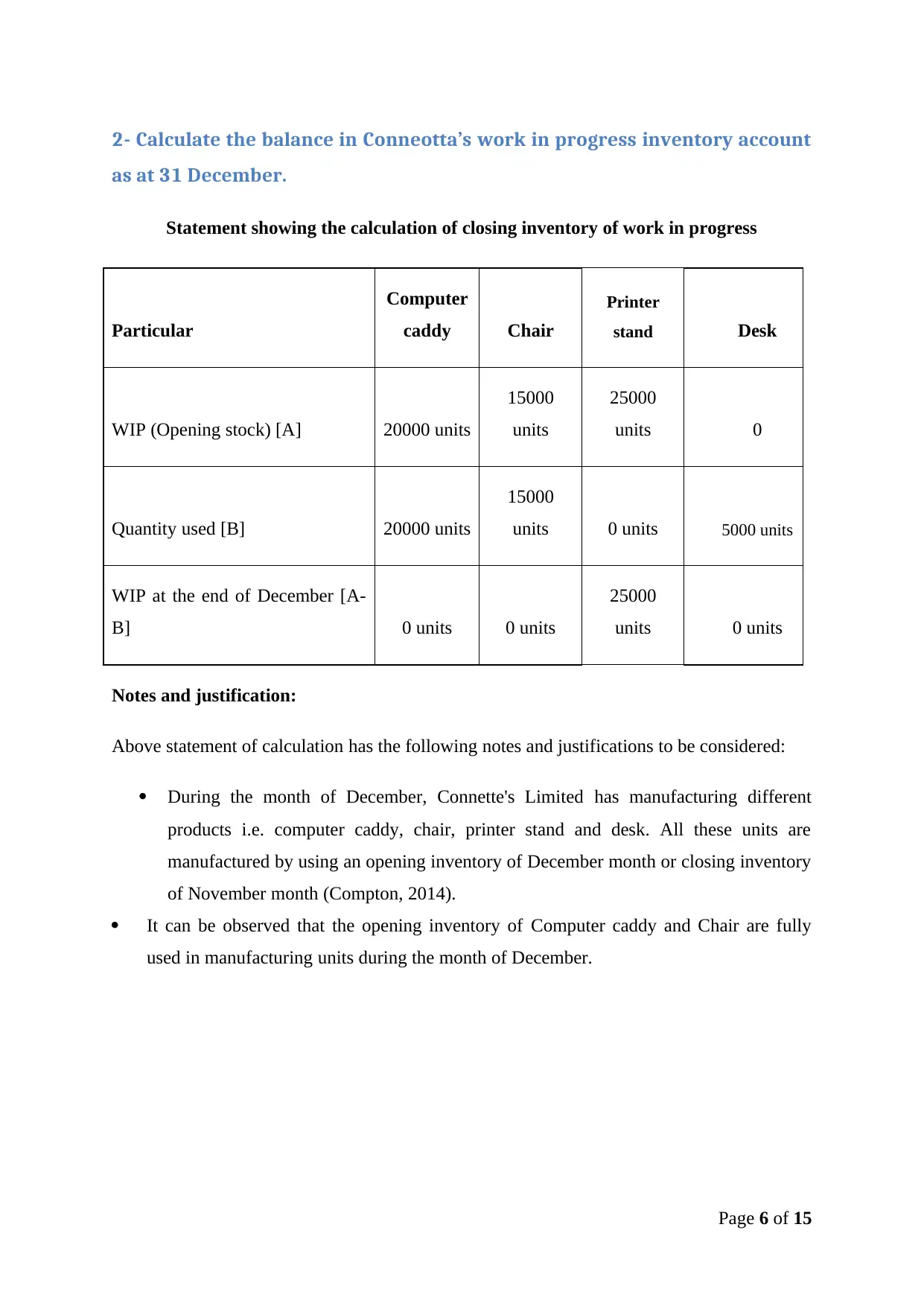
2- Calculate the balance in Conneotta’s work in progress inventory account
as at 31 December.
Statement showing the calculation of closing inventory of work in progress
Particular
Computer
caddy Chair
Printer
stand Desk
WIP (Opening stock) [A] 20000 units
15000
units
25000
units 0
Quantity used [B] 20000 units
15000
units 0 units 5000 units
WIP at the end of December [A-
B] 0 units 0 units
25000
units 0 units
Notes and justification:
Above statement of calculation has the following notes and justifications to be considered:
ï‚· During the month of December, Connette's Limited has manufacturing different
products i.e. computer caddy, chair, printer stand and desk. All these units are
manufactured by using an opening inventory of December month or closing inventory
of November month (Compton, 2014).
ï‚· It can be observed that the opening inventory of Computer caddy and Chair are fully
used in manufacturing units during the month of December.
Page 6 of 15
as at 31 December.
Statement showing the calculation of closing inventory of work in progress
Particular
Computer
caddy Chair
Printer
stand Desk
WIP (Opening stock) [A] 20000 units
15000
units
25000
units 0
Quantity used [B] 20000 units
15000
units 0 units 5000 units
WIP at the end of December [A-
B] 0 units 0 units
25000
units 0 units
Notes and justification:
Above statement of calculation has the following notes and justifications to be considered:
ï‚· During the month of December, Connette's Limited has manufacturing different
products i.e. computer caddy, chair, printer stand and desk. All these units are
manufactured by using an opening inventory of December month or closing inventory
of November month (Compton, 2014).
ï‚· It can be observed that the opening inventory of Computer caddy and Chair are fully
used in manufacturing units during the month of December.
Page 6 of 15
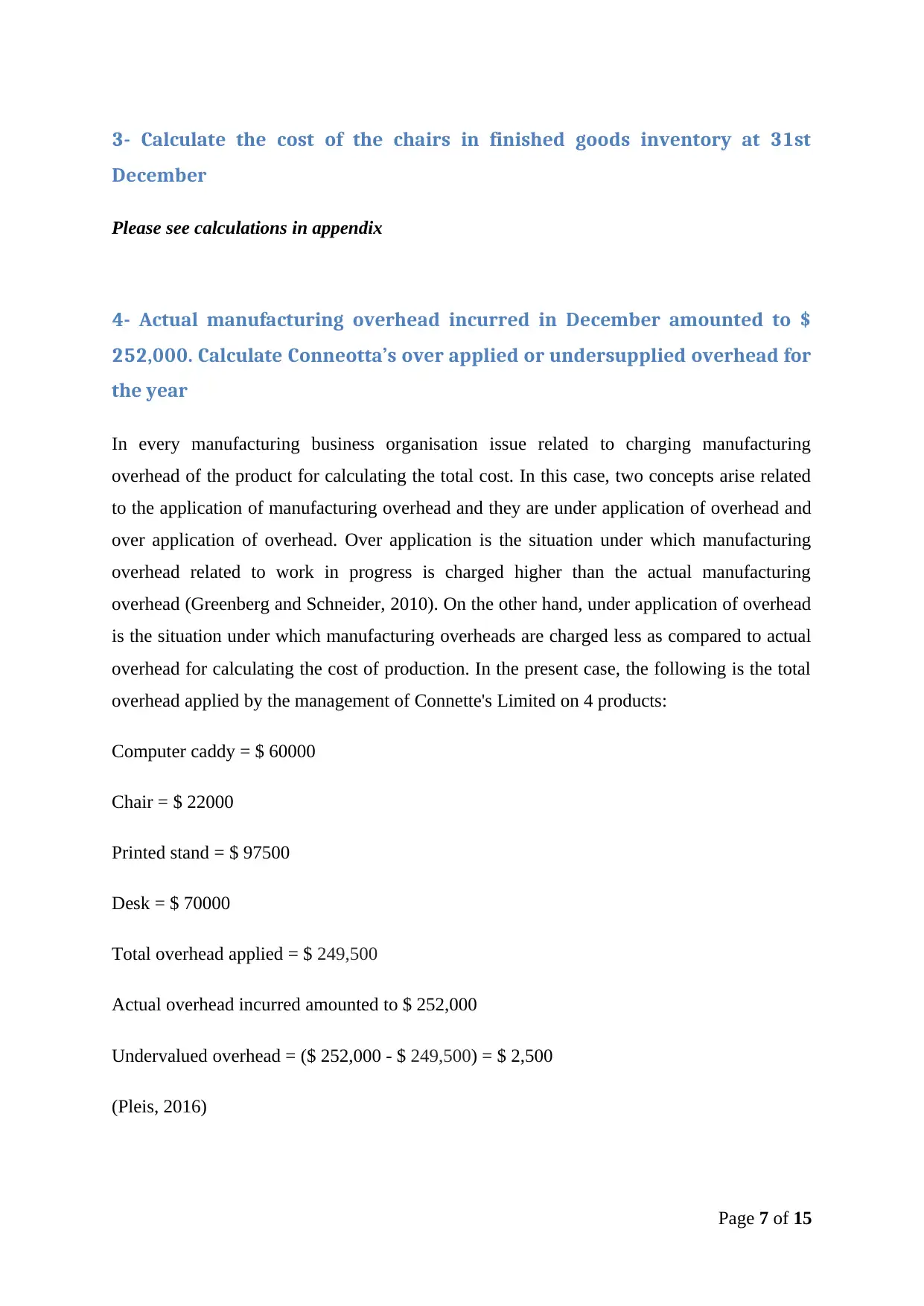
3- Calculate the cost of the chairs in finished goods inventory at 31st
December
Please see calculations in appendix
4- Actual manufacturing overhead incurred in December amounted to $
252,000. Calculate Conneotta’s over applied or undersupplied overhead for
the year
In every manufacturing business organisation issue related to charging manufacturing
overhead of the product for calculating the total cost. In this case, two concepts arise related
to the application of manufacturing overhead and they are under application of overhead and
over application of overhead. Over application is the situation under which manufacturing
overhead related to work in progress is charged higher than the actual manufacturing
overhead (Greenberg and Schneider, 2010). On the other hand, under application of overhead
is the situation under which manufacturing overheads are charged less as compared to actual
overhead for calculating the cost of production. In the present case, the following is the total
overhead applied by the management of Connette's Limited on 4 products:
Computer caddy = $ 60000
Chair = $ 22000
Printed stand = $ 97500
Desk = $ 70000
Total overhead applied = $ 249,500
Actual overhead incurred amounted to $ 252,000
Undervalued overhead = ($ 252,000 - $ 249,500) = $ 2,500
(Pleis, 2016)
Page 7 of 15
December
Please see calculations in appendix
4- Actual manufacturing overhead incurred in December amounted to $
252,000. Calculate Conneotta’s over applied or undersupplied overhead for
the year
In every manufacturing business organisation issue related to charging manufacturing
overhead of the product for calculating the total cost. In this case, two concepts arise related
to the application of manufacturing overhead and they are under application of overhead and
over application of overhead. Over application is the situation under which manufacturing
overhead related to work in progress is charged higher than the actual manufacturing
overhead (Greenberg and Schneider, 2010). On the other hand, under application of overhead
is the situation under which manufacturing overheads are charged less as compared to actual
overhead for calculating the cost of production. In the present case, the following is the total
overhead applied by the management of Connette's Limited on 4 products:
Computer caddy = $ 60000
Chair = $ 22000
Printed stand = $ 97500
Desk = $ 70000
Total overhead applied = $ 249,500
Actual overhead incurred amounted to $ 252,000
Undervalued overhead = ($ 252,000 - $ 249,500) = $ 2,500
(Pleis, 2016)
Page 7 of 15
Paraphrase This Document
Need a fresh take? Get an instant paraphrase of this document with our AI Paraphraser
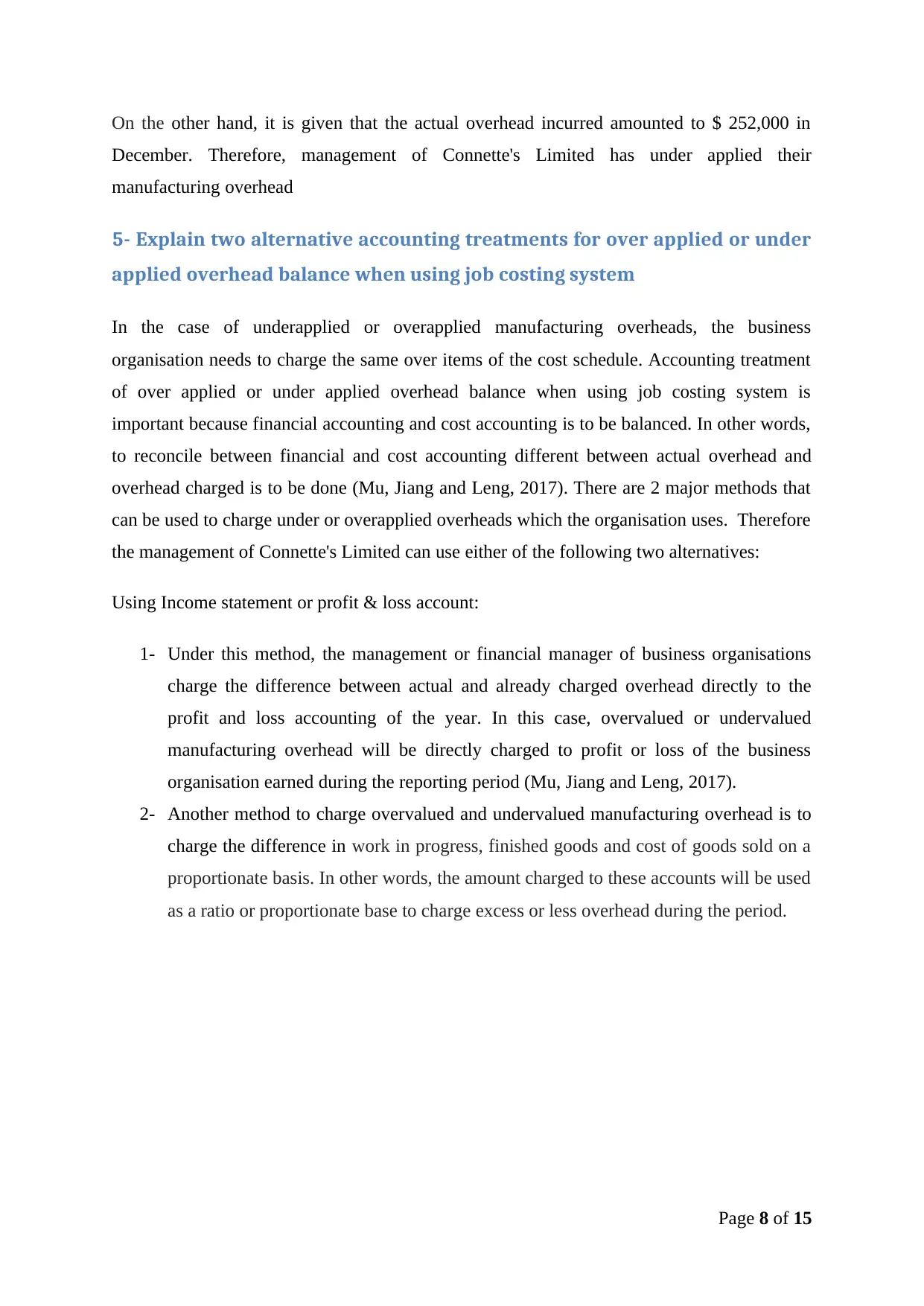
On the other hand, it is given that the actual overhead incurred amounted to $ 252,000 in
December. Therefore, management of Connette's Limited has under applied their
manufacturing overhead
5- Explain two alternative accounting treatments for over applied or under
applied overhead balance when using job costing system
In the case of underapplied or overapplied manufacturing overheads, the business
organisation needs to charge the same over items of the cost schedule. Accounting treatment
of over applied or under applied overhead balance when using job costing system is
important because financial accounting and cost accounting is to be balanced. In other words,
to reconcile between financial and cost accounting different between actual overhead and
overhead charged is to be done (Mu, Jiang and Leng, 2017). There are 2 major methods that
can be used to charge under or overapplied overheads which the organisation uses. Therefore
the management of Connette's Limited can use either of the following two alternatives:
Using Income statement or profit & loss account:
1- Under this method, the management or financial manager of business organisations
charge the difference between actual and already charged overhead directly to the
profit and loss accounting of the year. In this case, overvalued or undervalued
manufacturing overhead will be directly charged to profit or loss of the business
organisation earned during the reporting period (Mu, Jiang and Leng, 2017).
2- Another method to charge overvalued and undervalued manufacturing overhead is to
charge the difference in work in progress, finished goods and cost of goods sold on a
proportionate basis. In other words, the amount charged to these accounts will be used
as a ratio or proportionate base to charge excess or less overhead during the period.
Page 8 of 15
December. Therefore, management of Connette's Limited has under applied their
manufacturing overhead
5- Explain two alternative accounting treatments for over applied or under
applied overhead balance when using job costing system
In the case of underapplied or overapplied manufacturing overheads, the business
organisation needs to charge the same over items of the cost schedule. Accounting treatment
of over applied or under applied overhead balance when using job costing system is
important because financial accounting and cost accounting is to be balanced. In other words,
to reconcile between financial and cost accounting different between actual overhead and
overhead charged is to be done (Mu, Jiang and Leng, 2017). There are 2 major methods that
can be used to charge under or overapplied overheads which the organisation uses. Therefore
the management of Connette's Limited can use either of the following two alternatives:
Using Income statement or profit & loss account:
1- Under this method, the management or financial manager of business organisations
charge the difference between actual and already charged overhead directly to the
profit and loss accounting of the year. In this case, overvalued or undervalued
manufacturing overhead will be directly charged to profit or loss of the business
organisation earned during the reporting period (Mu, Jiang and Leng, 2017).
2- Another method to charge overvalued and undervalued manufacturing overhead is to
charge the difference in work in progress, finished goods and cost of goods sold on a
proportionate basis. In other words, the amount charged to these accounts will be used
as a ratio or proportionate base to charge excess or less overhead during the period.
Page 8 of 15
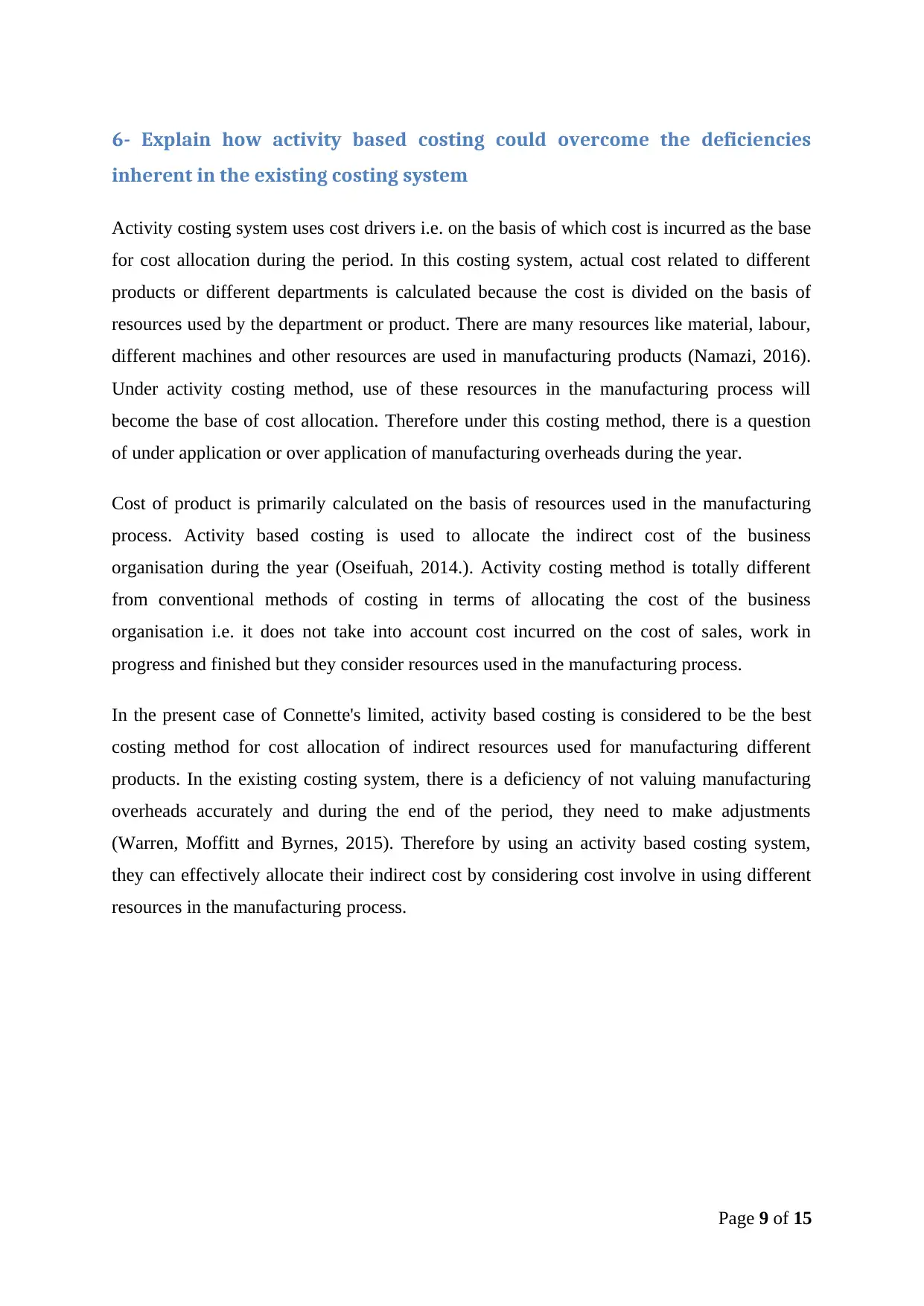
6- Explain how activity based costing could overcome the deficiencies
inherent in the existing costing system
Activity costing system uses cost drivers i.e. on the basis of which cost is incurred as the base
for cost allocation during the period. In this costing system, actual cost related to different
products or different departments is calculated because the cost is divided on the basis of
resources used by the department or product. There are many resources like material, labour,
different machines and other resources are used in manufacturing products (Namazi, 2016).
Under activity costing method, use of these resources in the manufacturing process will
become the base of cost allocation. Therefore under this costing method, there is a question
of under application or over application of manufacturing overheads during the year.
Cost of product is primarily calculated on the basis of resources used in the manufacturing
process. Activity based costing is used to allocate the indirect cost of the business
organisation during the year (Oseifuah, 2014.). Activity costing method is totally different
from conventional methods of costing in terms of allocating the cost of the business
organisation i.e. it does not take into account cost incurred on the cost of sales, work in
progress and finished but they consider resources used in the manufacturing process.
In the present case of Connette's limited, activity based costing is considered to be the best
costing method for cost allocation of indirect resources used for manufacturing different
products. In the existing costing system, there is a deficiency of not valuing manufacturing
overheads accurately and during the end of the period, they need to make adjustments
(Warren, Moffitt and Byrnes, 2015). Therefore by using an activity based costing system,
they can effectively allocate their indirect cost by considering cost involve in using different
resources in the manufacturing process.
Page 9 of 15
inherent in the existing costing system
Activity costing system uses cost drivers i.e. on the basis of which cost is incurred as the base
for cost allocation during the period. In this costing system, actual cost related to different
products or different departments is calculated because the cost is divided on the basis of
resources used by the department or product. There are many resources like material, labour,
different machines and other resources are used in manufacturing products (Namazi, 2016).
Under activity costing method, use of these resources in the manufacturing process will
become the base of cost allocation. Therefore under this costing method, there is a question
of under application or over application of manufacturing overheads during the year.
Cost of product is primarily calculated on the basis of resources used in the manufacturing
process. Activity based costing is used to allocate the indirect cost of the business
organisation during the year (Oseifuah, 2014.). Activity costing method is totally different
from conventional methods of costing in terms of allocating the cost of the business
organisation i.e. it does not take into account cost incurred on the cost of sales, work in
progress and finished but they consider resources used in the manufacturing process.
In the present case of Connette's limited, activity based costing is considered to be the best
costing method for cost allocation of indirect resources used for manufacturing different
products. In the existing costing system, there is a deficiency of not valuing manufacturing
overheads accurately and during the end of the period, they need to make adjustments
(Warren, Moffitt and Byrnes, 2015). Therefore by using an activity based costing system,
they can effectively allocate their indirect cost by considering cost involve in using different
resources in the manufacturing process.
Page 9 of 15
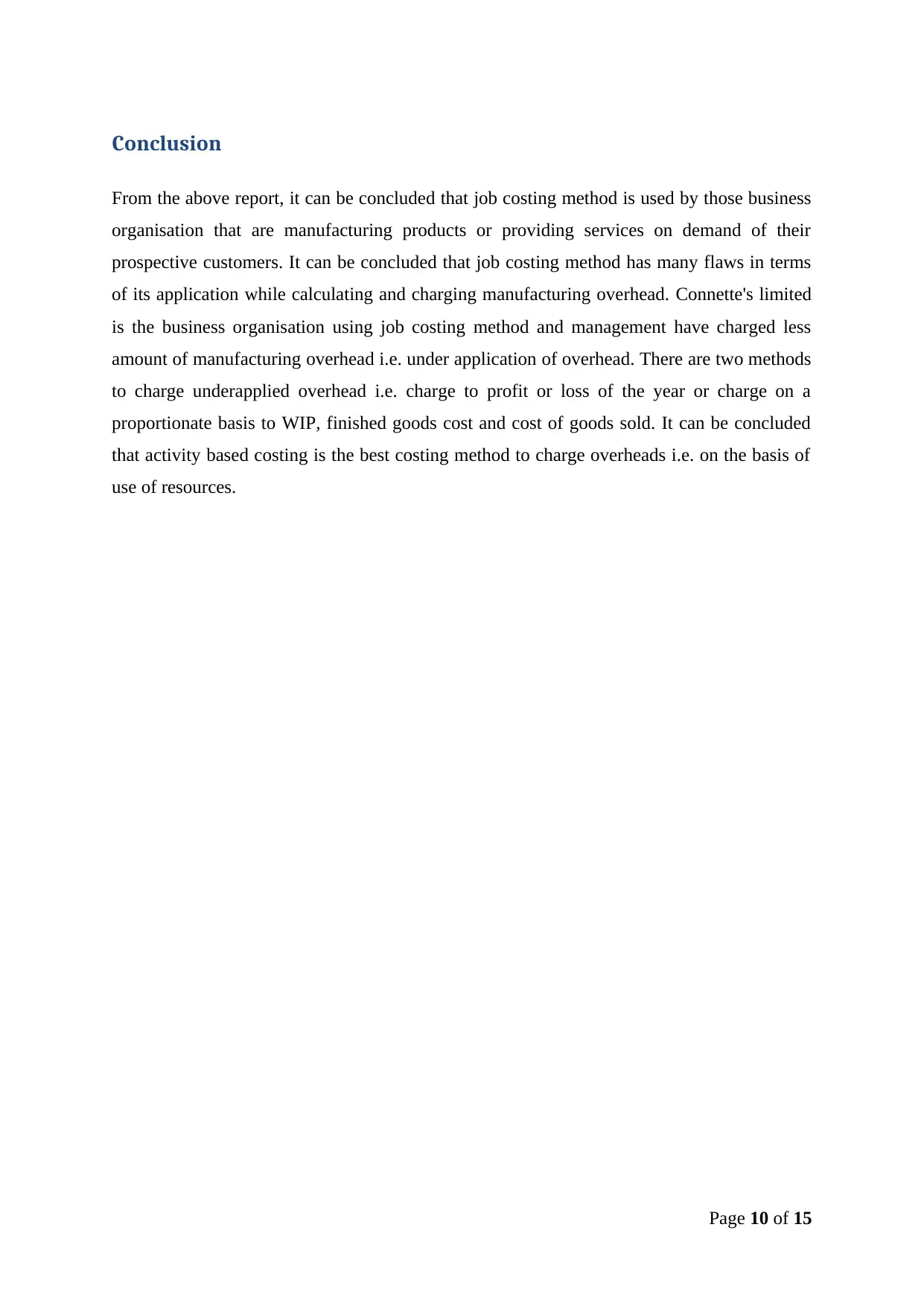
Conclusion
From the above report, it can be concluded that job costing method is used by those business
organisation that are manufacturing products or providing services on demand of their
prospective customers. It can be concluded that job costing method has many flaws in terms
of its application while calculating and charging manufacturing overhead. Connette's limited
is the business organisation using job costing method and management have charged less
amount of manufacturing overhead i.e. under application of overhead. There are two methods
to charge underapplied overhead i.e. charge to profit or loss of the year or charge on a
proportionate basis to WIP, finished goods cost and cost of goods sold. It can be concluded
that activity based costing is the best costing method to charge overheads i.e. on the basis of
use of resources.
Page 10 of 15
From the above report, it can be concluded that job costing method is used by those business
organisation that are manufacturing products or providing services on demand of their
prospective customers. It can be concluded that job costing method has many flaws in terms
of its application while calculating and charging manufacturing overhead. Connette's limited
is the business organisation using job costing method and management have charged less
amount of manufacturing overhead i.e. under application of overhead. There are two methods
to charge underapplied overhead i.e. charge to profit or loss of the year or charge on a
proportionate basis to WIP, finished goods cost and cost of goods sold. It can be concluded
that activity based costing is the best costing method to charge overheads i.e. on the basis of
use of resources.
Page 10 of 15
Secure Best Marks with AI Grader
Need help grading? Try our AI Grader for instant feedback on your assignments.
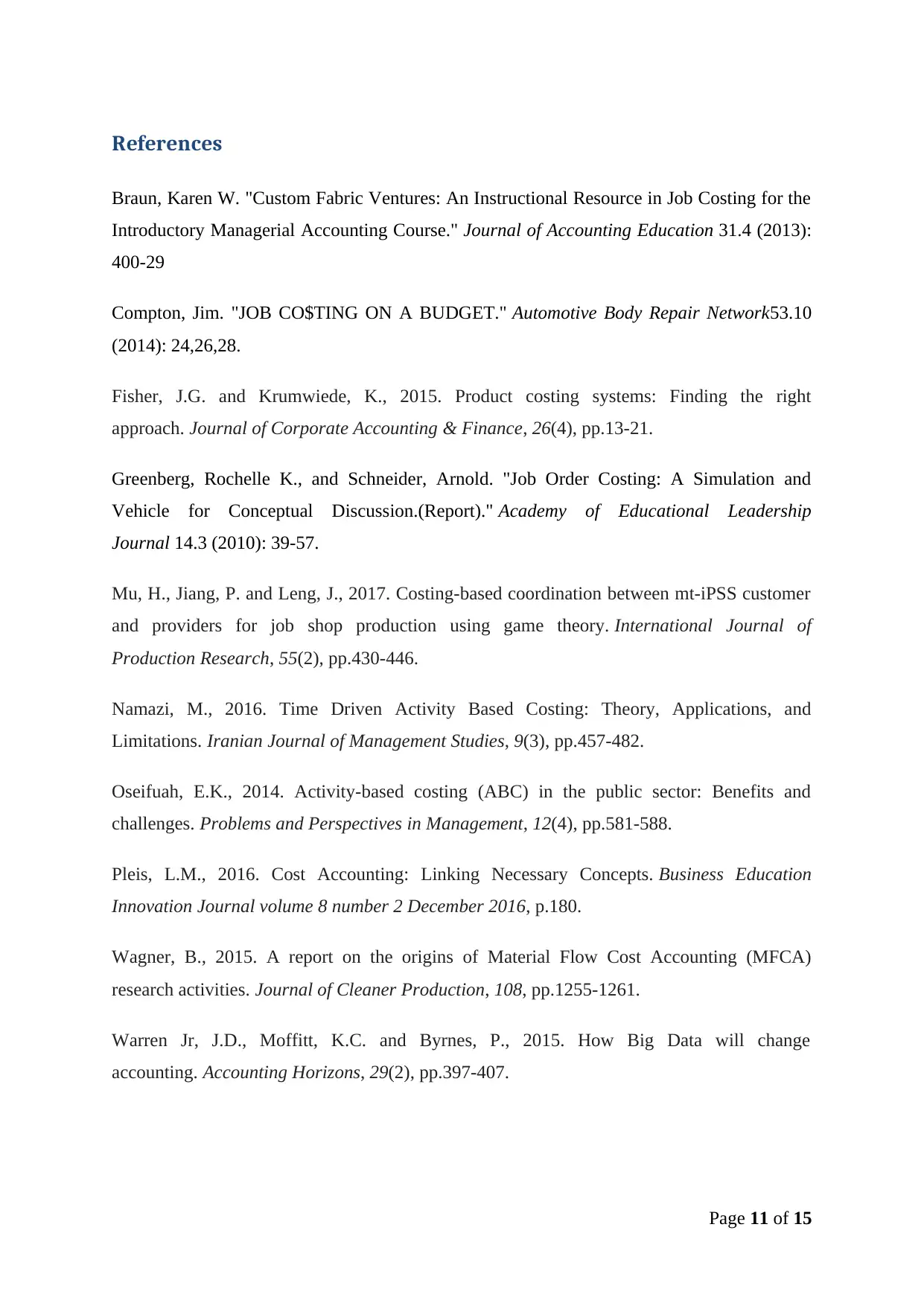
References
Braun, Karen W. "Custom Fabric Ventures: An Instructional Resource in Job Costing for the
Introductory Managerial Accounting Course." Journal of Accounting Education 31.4 (2013):
400-29
Compton, Jim. "JOB CO$TING ON A BUDGET." Automotive Body Repair Network53.10
(2014): 24,26,28.
Fisher, J.G. and Krumwiede, K., 2015. Product costing systems: Finding the right
approach. Journal of Corporate Accounting & Finance, 26(4), pp.13-21.
Greenberg, Rochelle K., and Schneider, Arnold. "Job Order Costing: A Simulation and
Vehicle for Conceptual Discussion.(Report)." Academy of Educational Leadership
Journal 14.3 (2010): 39-57.
Mu, H., Jiang, P. and Leng, J., 2017. Costing-based coordination between mt-iPSS customer
and providers for job shop production using game theory. International Journal of
Production Research, 55(2), pp.430-446.
Namazi, M., 2016. Time Driven Activity Based Costing: Theory, Applications, and
Limitations. Iranian Journal of Management Studies, 9(3), pp.457-482.
Oseifuah, E.K., 2014. Activity-based costing (ABC) in the public sector: Benefits and
challenges. Problems and Perspectives in Management, 12(4), pp.581-588.
Pleis, L.M., 2016. Cost Accounting: Linking Necessary Concepts. Business Education
Innovation Journal volume 8 number 2 December 2016, p.180.
Wagner, B., 2015. A report on the origins of Material Flow Cost Accounting (MFCA)
research activities. Journal of Cleaner Production, 108, pp.1255-1261.
Warren Jr, J.D., Moffitt, K.C. and Byrnes, P., 2015. How Big Data will change
accounting. Accounting Horizons, 29(2), pp.397-407.
Page 11 of 15
Braun, Karen W. "Custom Fabric Ventures: An Instructional Resource in Job Costing for the
Introductory Managerial Accounting Course." Journal of Accounting Education 31.4 (2013):
400-29
Compton, Jim. "JOB CO$TING ON A BUDGET." Automotive Body Repair Network53.10
(2014): 24,26,28.
Fisher, J.G. and Krumwiede, K., 2015. Product costing systems: Finding the right
approach. Journal of Corporate Accounting & Finance, 26(4), pp.13-21.
Greenberg, Rochelle K., and Schneider, Arnold. "Job Order Costing: A Simulation and
Vehicle for Conceptual Discussion.(Report)." Academy of Educational Leadership
Journal 14.3 (2010): 39-57.
Mu, H., Jiang, P. and Leng, J., 2017. Costing-based coordination between mt-iPSS customer
and providers for job shop production using game theory. International Journal of
Production Research, 55(2), pp.430-446.
Namazi, M., 2016. Time Driven Activity Based Costing: Theory, Applications, and
Limitations. Iranian Journal of Management Studies, 9(3), pp.457-482.
Oseifuah, E.K., 2014. Activity-based costing (ABC) in the public sector: Benefits and
challenges. Problems and Perspectives in Management, 12(4), pp.581-588.
Pleis, L.M., 2016. Cost Accounting: Linking Necessary Concepts. Business Education
Innovation Journal volume 8 number 2 December 2016, p.180.
Wagner, B., 2015. A report on the origins of Material Flow Cost Accounting (MFCA)
research activities. Journal of Cleaner Production, 108, pp.1255-1261.
Warren Jr, J.D., Moffitt, K.C. and Byrnes, P., 2015. How Big Data will change
accounting. Accounting Horizons, 29(2), pp.397-407.
Page 11 of 15
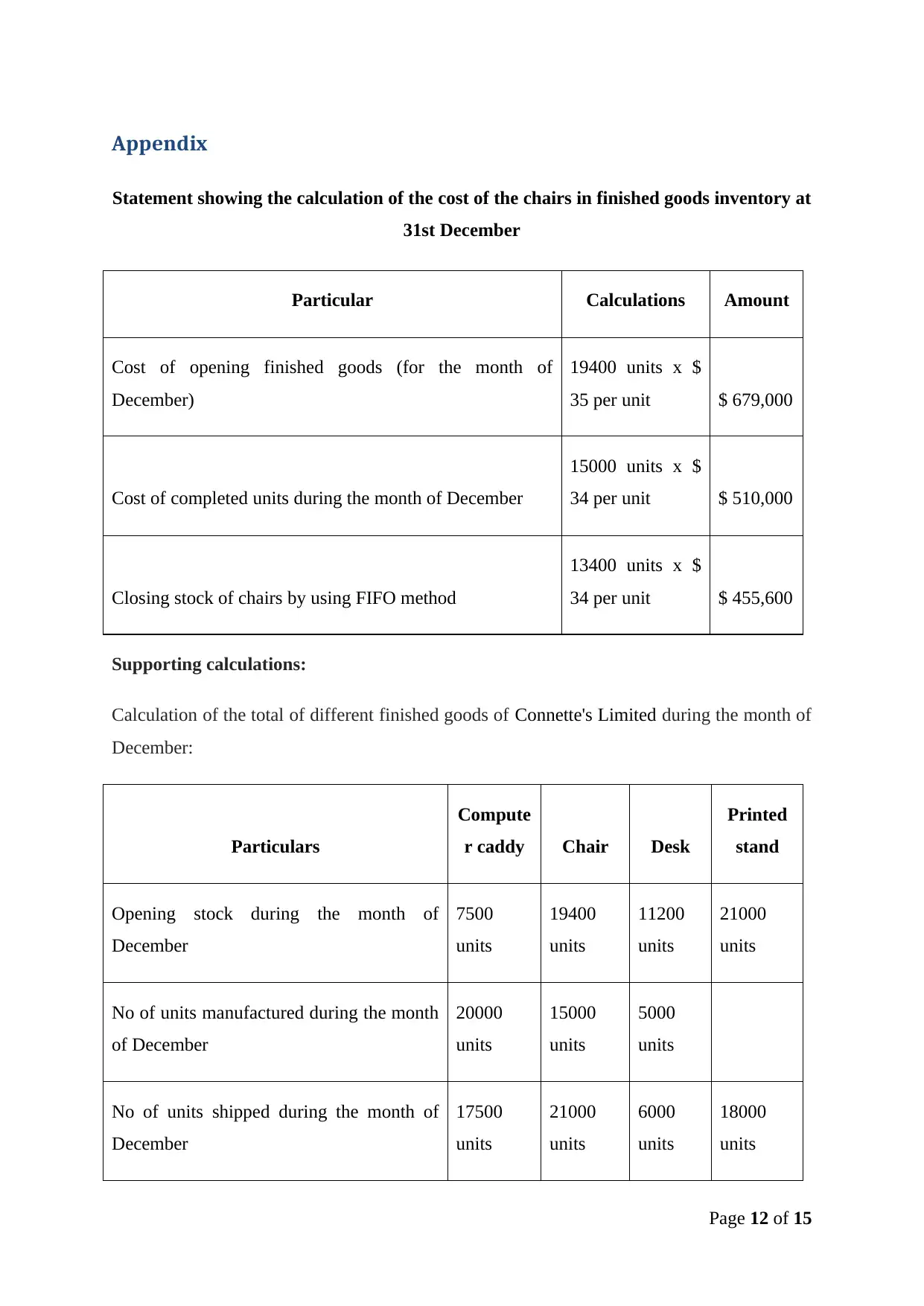
Appendix
Statement showing the calculation of the cost of the chairs in finished goods inventory at
31st December
Particular Calculations Amount
Cost of opening finished goods (for the month of
December)
19400 units x $
35 per unit $ 679,000
Cost of completed units during the month of December
15000 units x $
34 per unit $ 510,000
Closing stock of chairs by using FIFO method
13400 units x $
34 per unit $ 455,600
Supporting calculations:
Calculation of the total of different finished goods of Connette's Limited during the month of
December:
Particulars
Compute
r caddy Chair Desk
Printed
stand
Opening stock during the month of
December
7500
units
19400
units
11200
units
21000
units
No of units manufactured during the month
of December
20000
units
15000
units
5000
units
No of units shipped during the month of
December
17500
units
21000
units
6000
units
18000
units
Page 12 of 15
Statement showing the calculation of the cost of the chairs in finished goods inventory at
31st December
Particular Calculations Amount
Cost of opening finished goods (for the month of
December)
19400 units x $
35 per unit $ 679,000
Cost of completed units during the month of December
15000 units x $
34 per unit $ 510,000
Closing stock of chairs by using FIFO method
13400 units x $
34 per unit $ 455,600
Supporting calculations:
Calculation of the total of different finished goods of Connette's Limited during the month of
December:
Particulars
Compute
r caddy Chair Desk
Printed
stand
Opening stock during the month of
December
7500
units
19400
units
11200
units
21000
units
No of units manufactured during the month
of December
20000
units
15000
units
5000
units
No of units shipped during the month of
December
17500
units
21000
units
6000
units
18000
units
Page 12 of 15
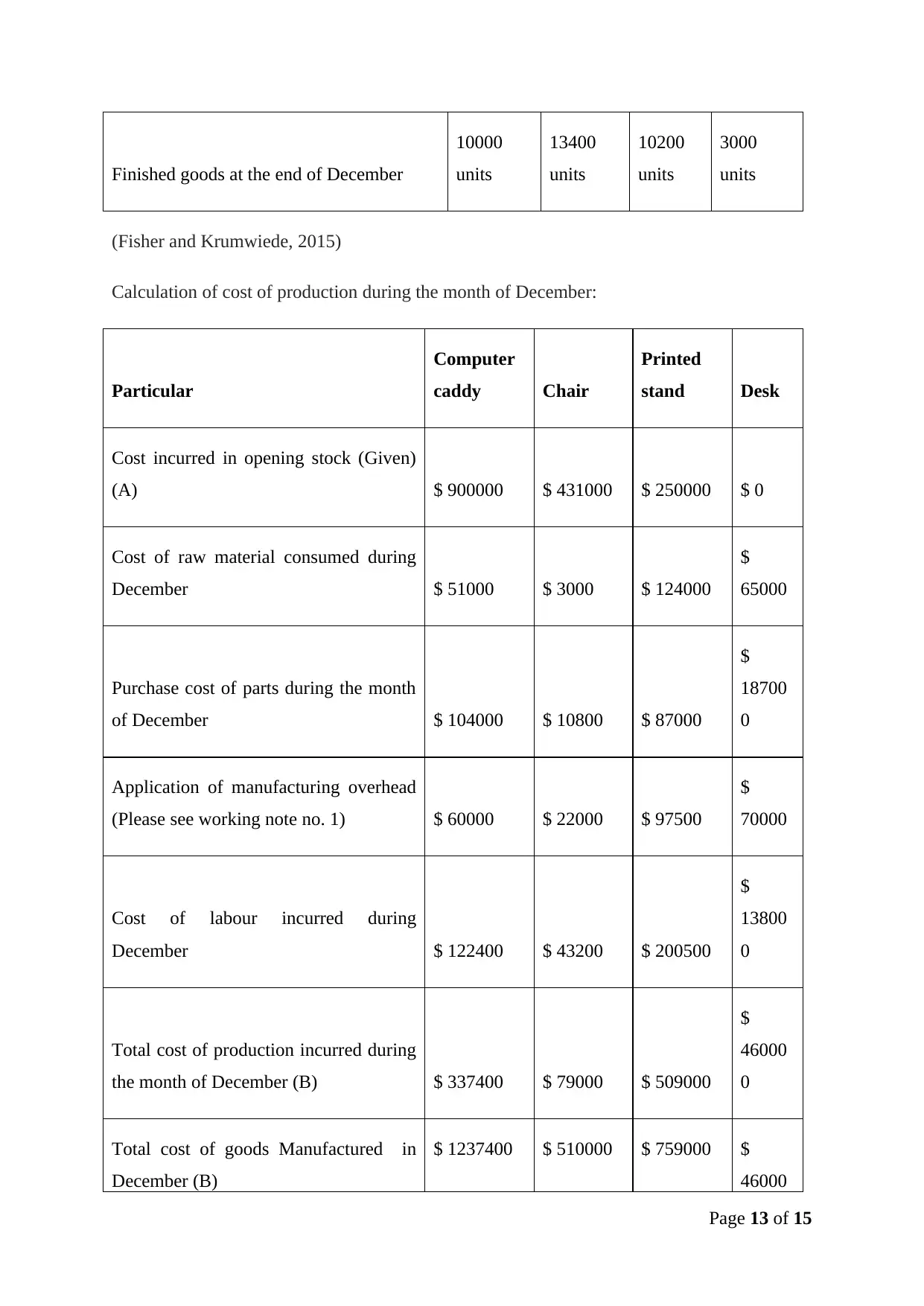
Finished goods at the end of December
10000
units
13400
units
10200
units
3000
units
(Fisher and Krumwiede, 2015)
Calculation of cost of production during the month of December:
Particular
Computer
caddy Chair
Printed
stand Desk
Cost incurred in opening stock (Given)
(A) $ 900000 $ 431000 $ 250000 $ 0
Cost of raw material consumed during
December $ 51000 $ 3000 $ 124000
$
65000
Purchase cost of parts during the month
of December $ 104000 $ 10800 $ 87000
$
18700
0
Application of manufacturing overhead
(Please see working note no. 1) $ 60000 $ 22000 $ 97500
$
70000
Cost of labour incurred during
December $ 122400 $ 43200 $ 200500
$
13800
0
Total cost of production incurred during
the month of December (B) $ 337400 $ 79000 $ 509000
$
46000
0
Total cost of goods Manufactured in
December (B)
$ 1237400 $ 510000 $ 759000 $
46000
Page 13 of 15
10000
units
13400
units
10200
units
3000
units
(Fisher and Krumwiede, 2015)
Calculation of cost of production during the month of December:
Particular
Computer
caddy Chair
Printed
stand Desk
Cost incurred in opening stock (Given)
(A) $ 900000 $ 431000 $ 250000 $ 0
Cost of raw material consumed during
December $ 51000 $ 3000 $ 124000
$
65000
Purchase cost of parts during the month
of December $ 104000 $ 10800 $ 87000
$
18700
0
Application of manufacturing overhead
(Please see working note no. 1) $ 60000 $ 22000 $ 97500
$
70000
Cost of labour incurred during
December $ 122400 $ 43200 $ 200500
$
13800
0
Total cost of production incurred during
the month of December (B) $ 337400 $ 79000 $ 509000
$
46000
0
Total cost of goods Manufactured in
December (B)
$ 1237400 $ 510000 $ 759000 $
46000
Page 13 of 15
Paraphrase This Document
Need a fresh take? Get an instant paraphrase of this document with our AI Paraphraser
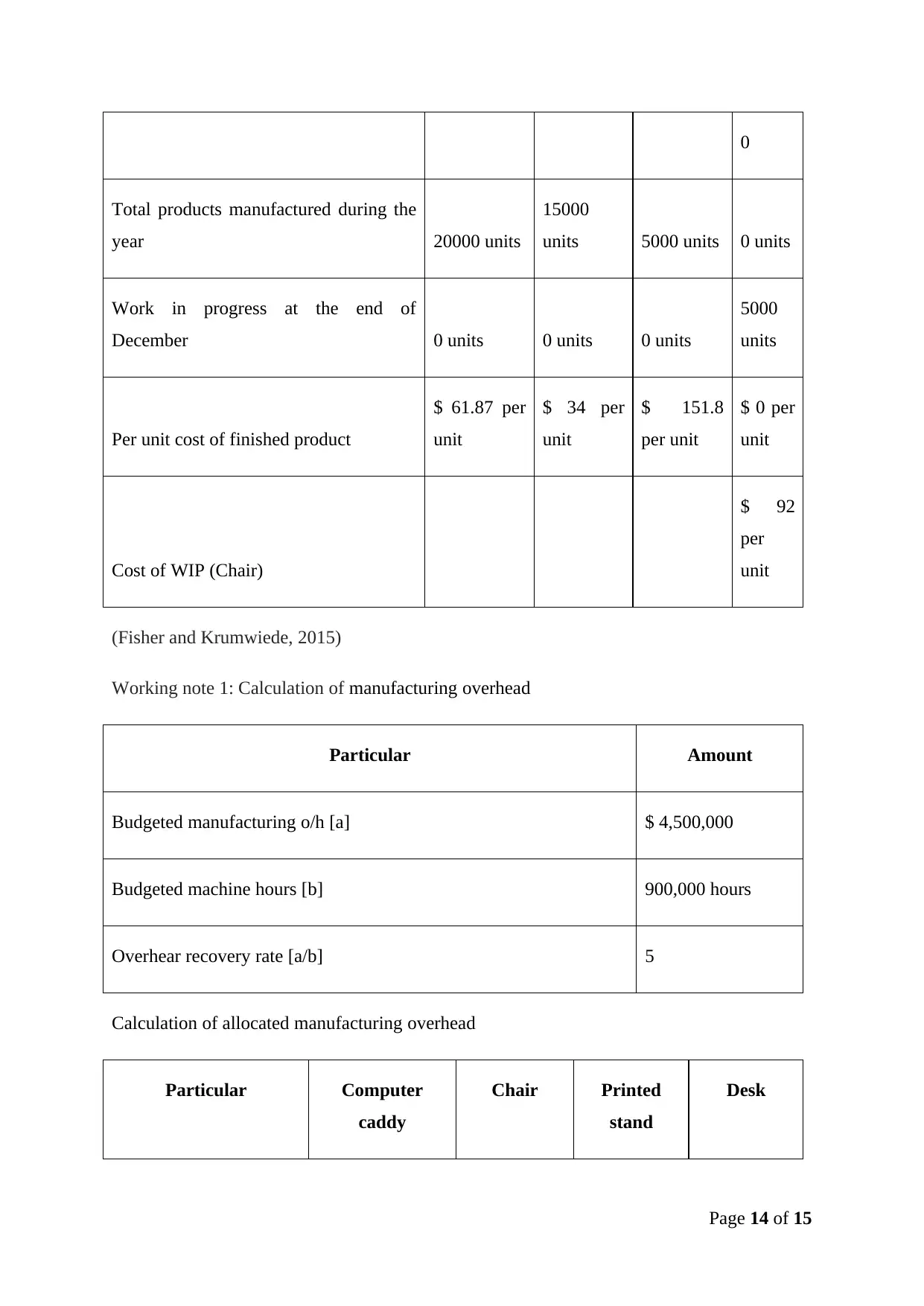
0
Total products manufactured during the
year 20000 units
15000
units 5000 units 0 units
Work in progress at the end of
December 0 units 0 units 0 units
5000
units
Per unit cost of finished product
$ 61.87 per
unit
$ 34 per
unit
$ 151.8
per unit
$ 0 per
unit
Cost of WIP (Chair)
$ 92
per
unit
(Fisher and Krumwiede, 2015)
Working note 1: Calculation of manufacturing overhead
Particular Amount
Budgeted manufacturing o/h [a] $ 4,500,000
Budgeted machine hours [b] 900,000 hours
Overhear recovery rate [a/b] 5
Calculation of allocated manufacturing overhead
Particular Computer
caddy
Chair Printed
stand
Desk
Page 14 of 15
Total products manufactured during the
year 20000 units
15000
units 5000 units 0 units
Work in progress at the end of
December 0 units 0 units 0 units
5000
units
Per unit cost of finished product
$ 61.87 per
unit
$ 34 per
unit
$ 151.8
per unit
$ 0 per
unit
Cost of WIP (Chair)
$ 92
per
unit
(Fisher and Krumwiede, 2015)
Working note 1: Calculation of manufacturing overhead
Particular Amount
Budgeted manufacturing o/h [a] $ 4,500,000
Budgeted machine hours [b] 900,000 hours
Overhear recovery rate [a/b] 5
Calculation of allocated manufacturing overhead
Particular Computer
caddy
Chair Printed
stand
Desk
Page 14 of 15
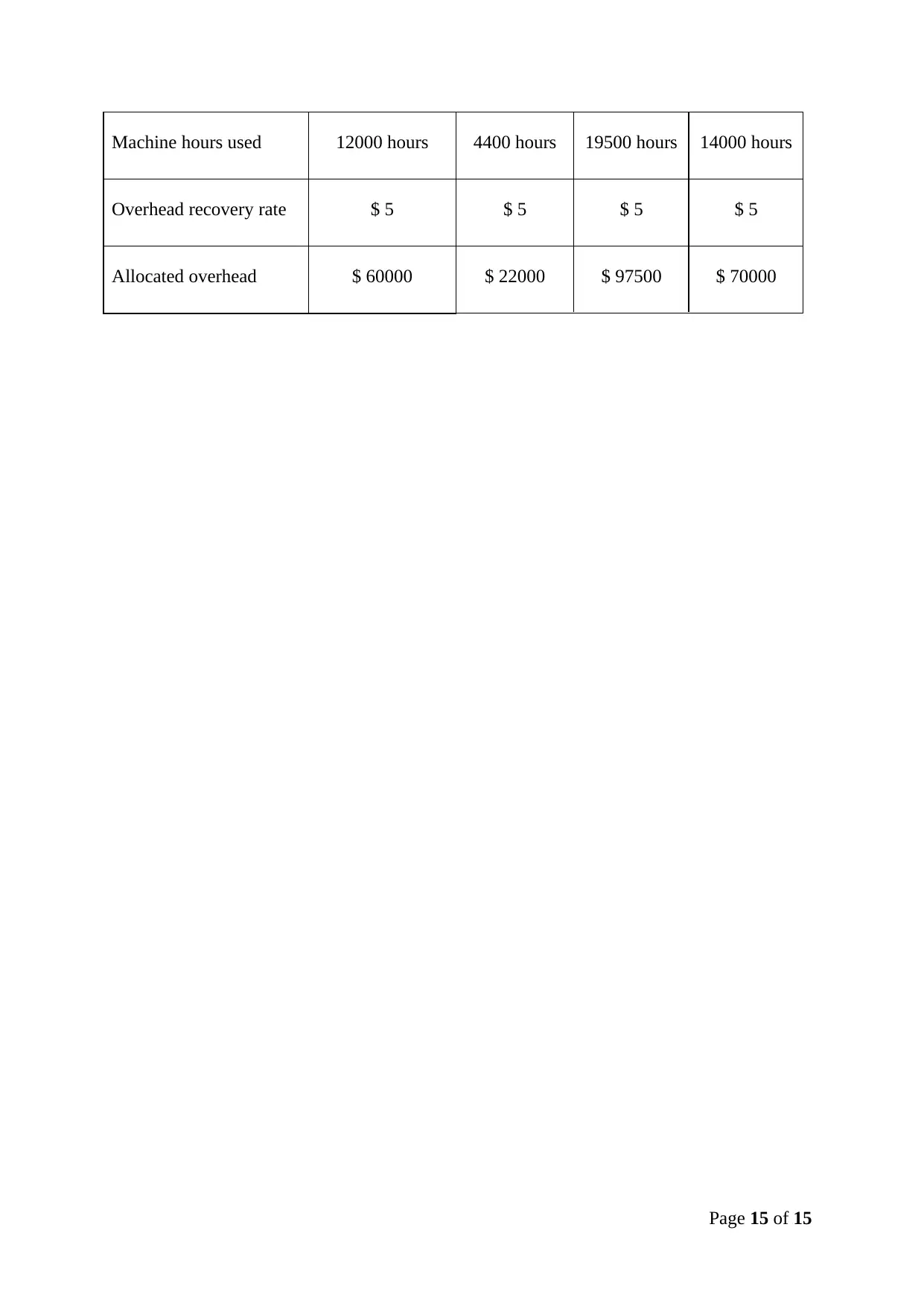
Machine hours used 12000 hours 4400 hours 19500 hours 14000 hours
Overhead recovery rate $ 5 $ 5 $ 5 $ 5
Allocated overhead $ 60000 $ 22000 $ 97500 $ 70000
Page 15 of 15
Overhead recovery rate $ 5 $ 5 $ 5 $ 5
Allocated overhead $ 60000 $ 22000 $ 97500 $ 70000
Page 15 of 15
1 out of 15
Related Documents
![[object Object]](/_next/image/?url=%2F_next%2Fstatic%2Fmedia%2Flogo.6d15ce61.png&w=640&q=75)
Your All-in-One AI-Powered Toolkit for Academic Success.
 +13062052269
info@desklib.com
Available 24*7 on WhatsApp / Email
Unlock your academic potential
© 2024  |  Zucol Services PVT LTD  |  All rights reserved.