Operations Management in Abbott's Bakery and Queensland Railway
VerifiedAdded on  2023/04/24
|15
|3912
|303
AI Summary
This document discusses the operations management processes in Abbott's Bakery and Queensland Railway. It covers the tasks of the operations manager, logistics, capacity measurement, and production planning.
Contribute Materials
Your contribution can guide someone’s learning journey. Share your
documents today.

MANAGEMENT 1
INNOVATION AND OPERATIONS MANAGEMENT
Name of student
Name of institution
Name of instructor
Course code
Date
INNOVATION AND OPERATIONS MANAGEMENT
Name of student
Name of institution
Name of instructor
Course code
Date
Secure Best Marks with AI Grader
Need help grading? Try our AI Grader for instant feedback on your assignments.

MANAGEMENT 2
TASK 1
Question 1
Abbott’s bread manufacturer
12/03/2019
Abbott’s village bakery deals in the manufacture of white bread in Australia. The
manufacture of bread requires various operations management stages including the input,
transformational processes and the final output stage (Christopher, 2018). Abbot’s inputs
include raw wheat from the farm, bakers to make bread and machinery such as ovens to cook
the bread.
Furthermore, the transformational stage includes milling of the wheat to get flour, baking the
bread, and finally packing the bread in Abbott’s branded packages. The final process includes
the output stage where the company achieves baked bread in packages. The output stage
requires the distribution of the product to consumers through wholesalers and retailers.
Railway station
INPUTS
Wheat
Bakers
Machinery
TRANSFORMATIONAL
PROCESSES
Wheat milling
Baking
Packing
OUTPUT
White bread
TASK 1
Question 1
Abbott’s bread manufacturer
12/03/2019
Abbott’s village bakery deals in the manufacture of white bread in Australia. The
manufacture of bread requires various operations management stages including the input,
transformational processes and the final output stage (Christopher, 2018). Abbot’s inputs
include raw wheat from the farm, bakers to make bread and machinery such as ovens to cook
the bread.
Furthermore, the transformational stage includes milling of the wheat to get flour, baking the
bread, and finally packing the bread in Abbott’s branded packages. The final process includes
the output stage where the company achieves baked bread in packages. The output stage
requires the distribution of the product to consumers through wholesalers and retailers.
Railway station
INPUTS
Wheat
Bakers
Machinery
TRANSFORMATIONAL
PROCESSES
Wheat milling
Baking
Packing
OUTPUT
White bread

MANAGEMENT 3
Queensland railway station performs various operations management procedures to ensure
that customers get the best services (Mark, 2018). The railway services involve three stages
including the input stage that consists of trains to carry passengers and load, the railway and
the train crew to attend to the passengers. The second stage includes the transformational
processes such as check-in the passengers, helping customers board the right train to various
destinations and riding the passengers to actual destinations. The final stage includes the
output stage that involves satisfied customers safely transported to final destinations.
Question 2
The tasks of the operations manager at Abbott’s bakery
One of the tasks performed in the bread factory includes directing the overall process of
bread making. The activities include ensuring the availability of all materials necessary and
overseeing that the bread achieves the quality standards set by the company to meet customer
expectations (Nigel, 2013).
The other task includes designing the procedures at the factory. For example, the operations
manager sets the requirements of the physical appearance, composition and workflow at the
factory. Furthermore, the operations manager involves in developing the capabilities of the
factory to allow sustainability in the face of competition or changes in the market patterns
(Olsen, 2018). The other task includes delivery, which involves ensuring that the customers
get the goods in the right quality, quantity, time and price.
The tasks of the operations manager at Queensland railway
INPUTS
Trains
Railway
Traincrew
TRANSFORMATIONAL
PROCESS
Check-in passengers
Board passengers
Riding passengers to
destinations
OUTPUT
Transported passengers
Queensland railway station performs various operations management procedures to ensure
that customers get the best services (Mark, 2018). The railway services involve three stages
including the input stage that consists of trains to carry passengers and load, the railway and
the train crew to attend to the passengers. The second stage includes the transformational
processes such as check-in the passengers, helping customers board the right train to various
destinations and riding the passengers to actual destinations. The final stage includes the
output stage that involves satisfied customers safely transported to final destinations.
Question 2
The tasks of the operations manager at Abbott’s bakery
One of the tasks performed in the bread factory includes directing the overall process of
bread making. The activities include ensuring the availability of all materials necessary and
overseeing that the bread achieves the quality standards set by the company to meet customer
expectations (Nigel, 2013).
The other task includes designing the procedures at the factory. For example, the operations
manager sets the requirements of the physical appearance, composition and workflow at the
factory. Furthermore, the operations manager involves in developing the capabilities of the
factory to allow sustainability in the face of competition or changes in the market patterns
(Olsen, 2018). The other task includes delivery, which involves ensuring that the customers
get the goods in the right quality, quantity, time and price.
The tasks of the operations manager at Queensland railway
INPUTS
Trains
Railway
Traincrew
TRANSFORMATIONAL
PROCESS
Check-in passengers
Board passengers
Riding passengers to
destinations
OUTPUT
Transported passengers

MANAGEMENT 4
The operations manager oversees various activities at the railway station to ensure customer
satisfaction (Boyer, 2018). The manager directs the activities at the railway such as ensuring
that the customers get tickets to the right destination, and get transportation to exact places
safely and without delay. In addition to that, the operations manager designs the procedures at
the railway such as putting up clear ticket paying points and proper labeling of trains for
customers to board. The other activity includes developing strategies for the train station to
ensure sustainability in the future (Boyer, 2018). The operations manager develops plans to
ensure that the station survives during uncertainties such as reduction in the number of
customers or stiff competition from other modes of transport. Furthermore, the operations
manager ensures the delivery of high-quality services to the customers. For example,
ensuring that the customers safely arrive at destinations at the right time having paid
reasonable prices.
Question 3
Abbott’s bakery
The costs at the bakery should remain low to allow realization of profits. The bakery should
ensure low production costs to enable selling the products at low prices in the market.
However, the low production costs should not lead to the sale of low-quality bread. The
bakery should ensure that the customers get sweet and fresh bread in the market at affordable
prices (Rebecca, 2018).
The other aspect includes quality that involves ensuring that the bread meets the customer
expectations in terms of taste, size, color, and packaging (Suzanne de Treville, 2018).
Customers require food products that meet high-quality standards to avoid health
complications.
Furthermore, the bakery should ensure speed in delivering the bread to the market. The
customers should not experience shortages in the market to prevent from buying competitor’s
The operations manager oversees various activities at the railway station to ensure customer
satisfaction (Boyer, 2018). The manager directs the activities at the railway such as ensuring
that the customers get tickets to the right destination, and get transportation to exact places
safely and without delay. In addition to that, the operations manager designs the procedures at
the railway such as putting up clear ticket paying points and proper labeling of trains for
customers to board. The other activity includes developing strategies for the train station to
ensure sustainability in the future (Boyer, 2018). The operations manager develops plans to
ensure that the station survives during uncertainties such as reduction in the number of
customers or stiff competition from other modes of transport. Furthermore, the operations
manager ensures the delivery of high-quality services to the customers. For example,
ensuring that the customers safely arrive at destinations at the right time having paid
reasonable prices.
Question 3
Abbott’s bakery
The costs at the bakery should remain low to allow realization of profits. The bakery should
ensure low production costs to enable selling the products at low prices in the market.
However, the low production costs should not lead to the sale of low-quality bread. The
bakery should ensure that the customers get sweet and fresh bread in the market at affordable
prices (Rebecca, 2018).
The other aspect includes quality that involves ensuring that the bread meets the customer
expectations in terms of taste, size, color, and packaging (Suzanne de Treville, 2018).
Customers require food products that meet high-quality standards to avoid health
complications.
Furthermore, the bakery should ensure speed in delivering the bread to the market. The
customers should not experience shortages in the market to prevent from buying competitor’s
Secure Best Marks with AI Grader
Need help grading? Try our AI Grader for instant feedback on your assignments.

MANAGEMENT 5
bread (Wagner, 2018). Therefore, the bakery should ensure nearness to the market to reduce
the time taken during distribution.
Additionally, the bakery should consider flexibility to enable alignment to the customer
demands. The bakery should have the ability to alter such as price and bread ingredients
depending on the customer demands. The flexibility allows the bakery to adequately meet the
customer demands (Rouse, 2019).
The order winning aspect of the bakery is quality (Olsen, 2018). The reason for selecting
quality lies in the fact that customers shop for food products that meet high-quality standards
to avoid health issues. Therefore, ensuring quality in the bread enables the customers to
consider the bread in the market.
Queensland railway
The station considers reducing the fares charged to the customers to increase usage. The
railway charges affordable fares while also giving high-quality services to the customers. The
railway services realise that most customers prefer the train due to the low fares compared to
other modes of transportation (Smith, 2018).
The other aspect includes quality of services offered at the station. The station should
maintain high-quality standards to ensure customers arrive safely to the destinations.
Additionally, other quality standards involve no breakdowns during transportation and
comfort in the train (Smith, 2018).
In addition to that, the train station considers the speed of delivering the passengers to the
desired destinations. The station understands that the customers need to travel fast without
experiencing delays on the journey (Perks, 2017). Therefore, Queensland railway has
introduced electric trains that travel at very high speeds.
The other aspect includes flexibility of transportation (Perks, 2017). For example, the ability
to cover more destinations and increased departures from the train station. The customers
bread (Wagner, 2018). Therefore, the bakery should ensure nearness to the market to reduce
the time taken during distribution.
Additionally, the bakery should consider flexibility to enable alignment to the customer
demands. The bakery should have the ability to alter such as price and bread ingredients
depending on the customer demands. The flexibility allows the bakery to adequately meet the
customer demands (Rouse, 2019).
The order winning aspect of the bakery is quality (Olsen, 2018). The reason for selecting
quality lies in the fact that customers shop for food products that meet high-quality standards
to avoid health issues. Therefore, ensuring quality in the bread enables the customers to
consider the bread in the market.
Queensland railway
The station considers reducing the fares charged to the customers to increase usage. The
railway charges affordable fares while also giving high-quality services to the customers. The
railway services realise that most customers prefer the train due to the low fares compared to
other modes of transportation (Smith, 2018).
The other aspect includes quality of services offered at the station. The station should
maintain high-quality standards to ensure customers arrive safely to the destinations.
Additionally, other quality standards involve no breakdowns during transportation and
comfort in the train (Smith, 2018).
In addition to that, the train station considers the speed of delivering the passengers to the
desired destinations. The station understands that the customers need to travel fast without
experiencing delays on the journey (Perks, 2017). Therefore, Queensland railway has
introduced electric trains that travel at very high speeds.
The other aspect includes flexibility of transportation (Perks, 2017). For example, the ability
to cover more destinations and increased departures from the train station. The customers
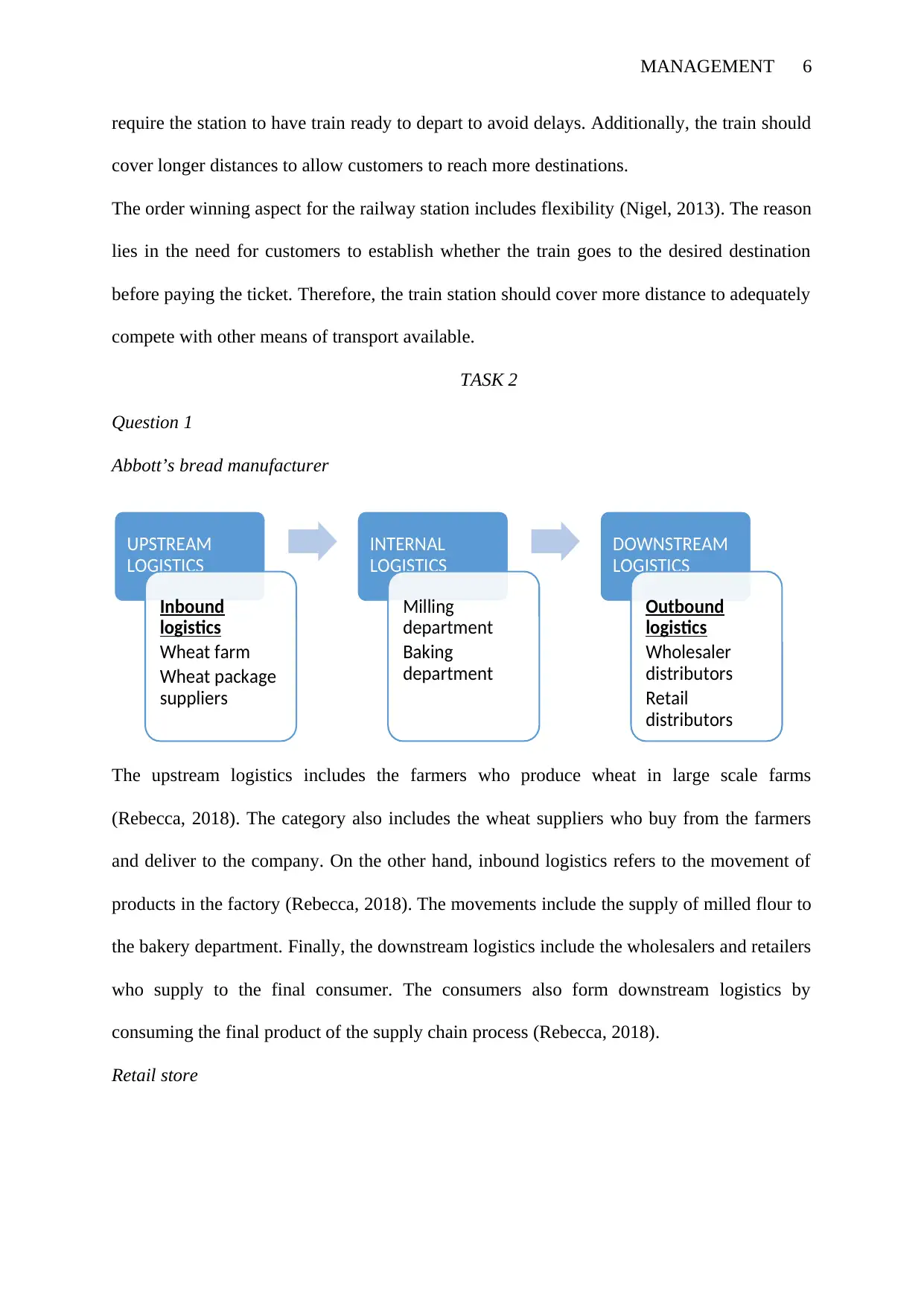
MANAGEMENT 6
require the station to have train ready to depart to avoid delays. Additionally, the train should
cover longer distances to allow customers to reach more destinations.
The order winning aspect for the railway station includes flexibility (Nigel, 2013). The reason
lies in the need for customers to establish whether the train goes to the desired destination
before paying the ticket. Therefore, the train station should cover more distance to adequately
compete with other means of transport available.
TASK 2
Question 1
Abbott’s bread manufacturer
The upstream logistics includes the farmers who produce wheat in large scale farms
(Rebecca, 2018). The category also includes the wheat suppliers who buy from the farmers
and deliver to the company. On the other hand, inbound logistics refers to the movement of
products in the factory (Rebecca, 2018). The movements include the supply of milled flour to
the bakery department. Finally, the downstream logistics include the wholesalers and retailers
who supply to the final consumer. The consumers also form downstream logistics by
consuming the final product of the supply chain process (Rebecca, 2018).
Retail store
UPSTREAM
LOGISTICS
Inbound
logistics
Wheat farm
Wheat package
suppliers
INTERNAL
LOGISTICS
Milling
department
Baking
department
DOWNSTREAM
LOGISTICS
Outbound
logistics
Wholesaler
distributors
Retail
distributors
require the station to have train ready to depart to avoid delays. Additionally, the train should
cover longer distances to allow customers to reach more destinations.
The order winning aspect for the railway station includes flexibility (Nigel, 2013). The reason
lies in the need for customers to establish whether the train goes to the desired destination
before paying the ticket. Therefore, the train station should cover more distance to adequately
compete with other means of transport available.
TASK 2
Question 1
Abbott’s bread manufacturer
The upstream logistics includes the farmers who produce wheat in large scale farms
(Rebecca, 2018). The category also includes the wheat suppliers who buy from the farmers
and deliver to the company. On the other hand, inbound logistics refers to the movement of
products in the factory (Rebecca, 2018). The movements include the supply of milled flour to
the bakery department. Finally, the downstream logistics include the wholesalers and retailers
who supply to the final consumer. The consumers also form downstream logistics by
consuming the final product of the supply chain process (Rebecca, 2018).
Retail store
UPSTREAM
LOGISTICS
Inbound
logistics
Wheat farm
Wheat package
suppliers
INTERNAL
LOGISTICS
Milling
department
Baking
department
DOWNSTREAM
LOGISTICS
Outbound
logistics
Wholesaler
distributors
Retail
distributors

MANAGEMENT 7
Explanation
The upstream level of Aldi retail store logistics includes farmers who grow vegetables and
fruits for sale (Wagner, 2018). Additionally, the wholesalers who buy from the farmers and
supply to the retail store also form upstream logistics. The inbound logistics includes the
internal movement of the products for example, from the store to the shelves for customers to
access (Nigel, 2013). Finally, the downstream logistics include the customers who buy the
products for consumption.
Question 2
Bread manufacture
The selection of a suitable location should consider the following factors in order of
importance.
1. Availability of raw materials- the location of the bread factory should have an adequate
supply of wheat, which makes the main ingredient for making bread. The raw material factor
ranks first since the factory cannot operate without proper access to the basic requirement
(Cole-Ingait, 2018).
2. The availability of employees- the factory’s location should have available skilled and
unskilled employees. The employees allow the running of activities at the company without
failure (Cole-Ingait, 2018).
Upstream logistics
Inbound logistics
vegetable
farmers
Vegetable
package suppliers
Internal logistics
Departmental
movement
Downstream
logistics
Outbound
logistics
National
Distribution
Centre
Shops and
supermarkets
Explanation
The upstream level of Aldi retail store logistics includes farmers who grow vegetables and
fruits for sale (Wagner, 2018). Additionally, the wholesalers who buy from the farmers and
supply to the retail store also form upstream logistics. The inbound logistics includes the
internal movement of the products for example, from the store to the shelves for customers to
access (Nigel, 2013). Finally, the downstream logistics include the customers who buy the
products for consumption.
Question 2
Bread manufacture
The selection of a suitable location should consider the following factors in order of
importance.
1. Availability of raw materials- the location of the bread factory should have an adequate
supply of wheat, which makes the main ingredient for making bread. The raw material factor
ranks first since the factory cannot operate without proper access to the basic requirement
(Cole-Ingait, 2018).
2. The availability of employees- the factory’s location should have available skilled and
unskilled employees. The employees allow the running of activities at the company without
failure (Cole-Ingait, 2018).
Upstream logistics
Inbound logistics
vegetable
farmers
Vegetable
package suppliers
Internal logistics
Departmental
movement
Downstream
logistics
Outbound
logistics
National
Distribution
Centre
Shops and
supermarkets
Paraphrase This Document
Need a fresh take? Get an instant paraphrase of this document with our AI Paraphraser

MANAGEMENT 8
3. Cost of transport- the third factor refers to the costs incurred in distributing the product to the
market. The factory should ensure low transport costs with the bid to reduce the final price of
the products (Cole-Ingait, 2018).
Retail store
The selection of a suitable location should consider the following factors in order of
importance.
1. Availability of customers- the location should promise a high number of customers since the
store sells to walk-in customers (Wagner, 2018). Therefore, the location should have a wide
population to ensure that more customers visit the shop for purchases. The retail store owners
should first consider the location to allow the selection of a region with a high population.
2. Operating costs- the location should also promise low costs in the course of operations
(Christopher, 2018). The costs include low transportation charges and reduced legal fees to
allow selling products at low prices. The factor plays an important role in the selection of a
good retail store location.
3. Presence of competitors- the presence of other competitors enables understanding whether a
certain location suits the opening of the business (Juneja, 2018). For example, the
performance of other competitors in a location will help make a decision about whether to
select the region. A competitor thriving and making profit from a certain location means that
the area has favorable conditions for the success of the retail store.
Question 3
Abbott’s bakery measures capacity through operating equipment effectiveness. The method
refers to multiplying the availability of machinery by a performance rate. The formula helps
to identify the capacity during setup time or during repairs. The formula suits the factory due
to the use of machinery to mill wheat, bake and pack bread (Boyer, 2018).
3. Cost of transport- the third factor refers to the costs incurred in distributing the product to the
market. The factory should ensure low transport costs with the bid to reduce the final price of
the products (Cole-Ingait, 2018).
Retail store
The selection of a suitable location should consider the following factors in order of
importance.
1. Availability of customers- the location should promise a high number of customers since the
store sells to walk-in customers (Wagner, 2018). Therefore, the location should have a wide
population to ensure that more customers visit the shop for purchases. The retail store owners
should first consider the location to allow the selection of a region with a high population.
2. Operating costs- the location should also promise low costs in the course of operations
(Christopher, 2018). The costs include low transportation charges and reduced legal fees to
allow selling products at low prices. The factor plays an important role in the selection of a
good retail store location.
3. Presence of competitors- the presence of other competitors enables understanding whether a
certain location suits the opening of the business (Juneja, 2018). For example, the
performance of other competitors in a location will help make a decision about whether to
select the region. A competitor thriving and making profit from a certain location means that
the area has favorable conditions for the success of the retail store.
Question 3
Abbott’s bakery measures capacity through operating equipment effectiveness. The method
refers to multiplying the availability of machinery by a performance rate. The formula helps
to identify the capacity during setup time or during repairs. The formula suits the factory due
to the use of machinery to mill wheat, bake and pack bread (Boyer, 2018).

MANAGEMENT 9
Aldi retail store uses forecasting method to measure capacity. The method refers to the study
of market patterns to establish the number of customers who will buy from the shop. The
forecasts give an estimate of how the demand will be in the future, which enables proper
planning (Nigel, 2013). The formulae suits the retail store due to the inability to adequately
come up with a fixed number of customers who will buy the products.
TASK 3
Month Forecaste
d sales Sales
in
worke
r
hours
Worker
s
needed
to meet
sales
Actual
worker
s
Actual
productio
n
Layoff
s Hirin
g Ending
inventor
y
50 10,000
Sep
2013 30000 7500 47 50 31501 0.78 0 11501
Oct 31500 7875 50 50 31501 0 0 11502
Nov 35000 8750 55 50 31501 0 0 8002
Dec 37000 9250 58 50 31501 0 0 2503
Jan
2014 22000 5500 35 50 31501 0 0 12004
Feb 18000 4500 29 50 31501 0 0 25505
March 17500 4375 28 50 31501 0 0 39506
April 27000 6750 43 50 31501 0 0 44006
May 38000 9500 60 50 31501 0 0 37507
June 40000 10000 63 50 31501 0 0 29008
July 42000 10500 66 50 31501 0 0 18,509
Aug 40000 10000 63 50 31501 0 0 10010
50 0.78
TOTAL
S 378,010 249562
Advantages of a level production plan
The level production plan allows Covolo to understand the exact number of employees
needed to accomplish a particular project (Perks, 2017). Therefore, the company has the
ability to plan in advance on the number of employees to hire for a project. Additionally, the
company has the ability to predict the expenses that will adequately cover the expenses in
advance.
Aldi retail store uses forecasting method to measure capacity. The method refers to the study
of market patterns to establish the number of customers who will buy from the shop. The
forecasts give an estimate of how the demand will be in the future, which enables proper
planning (Nigel, 2013). The formulae suits the retail store due to the inability to adequately
come up with a fixed number of customers who will buy the products.
TASK 3
Month Forecaste
d sales Sales
in
worke
r
hours
Worker
s
needed
to meet
sales
Actual
worker
s
Actual
productio
n
Layoff
s Hirin
g Ending
inventor
y
50 10,000
Sep
2013 30000 7500 47 50 31501 0.78 0 11501
Oct 31500 7875 50 50 31501 0 0 11502
Nov 35000 8750 55 50 31501 0 0 8002
Dec 37000 9250 58 50 31501 0 0 2503
Jan
2014 22000 5500 35 50 31501 0 0 12004
Feb 18000 4500 29 50 31501 0 0 25505
March 17500 4375 28 50 31501 0 0 39506
April 27000 6750 43 50 31501 0 0 44006
May 38000 9500 60 50 31501 0 0 37507
June 40000 10000 63 50 31501 0 0 29008
July 42000 10500 66 50 31501 0 0 18,509
Aug 40000 10000 63 50 31501 0 0 10010
50 0.78
TOTAL
S 378,010 249562
Advantages of a level production plan
The level production plan allows Covolo to understand the exact number of employees
needed to accomplish a particular project (Perks, 2017). Therefore, the company has the
ability to plan in advance on the number of employees to hire for a project. Additionally, the
company has the ability to predict the expenses that will adequately cover the expenses in
advance.
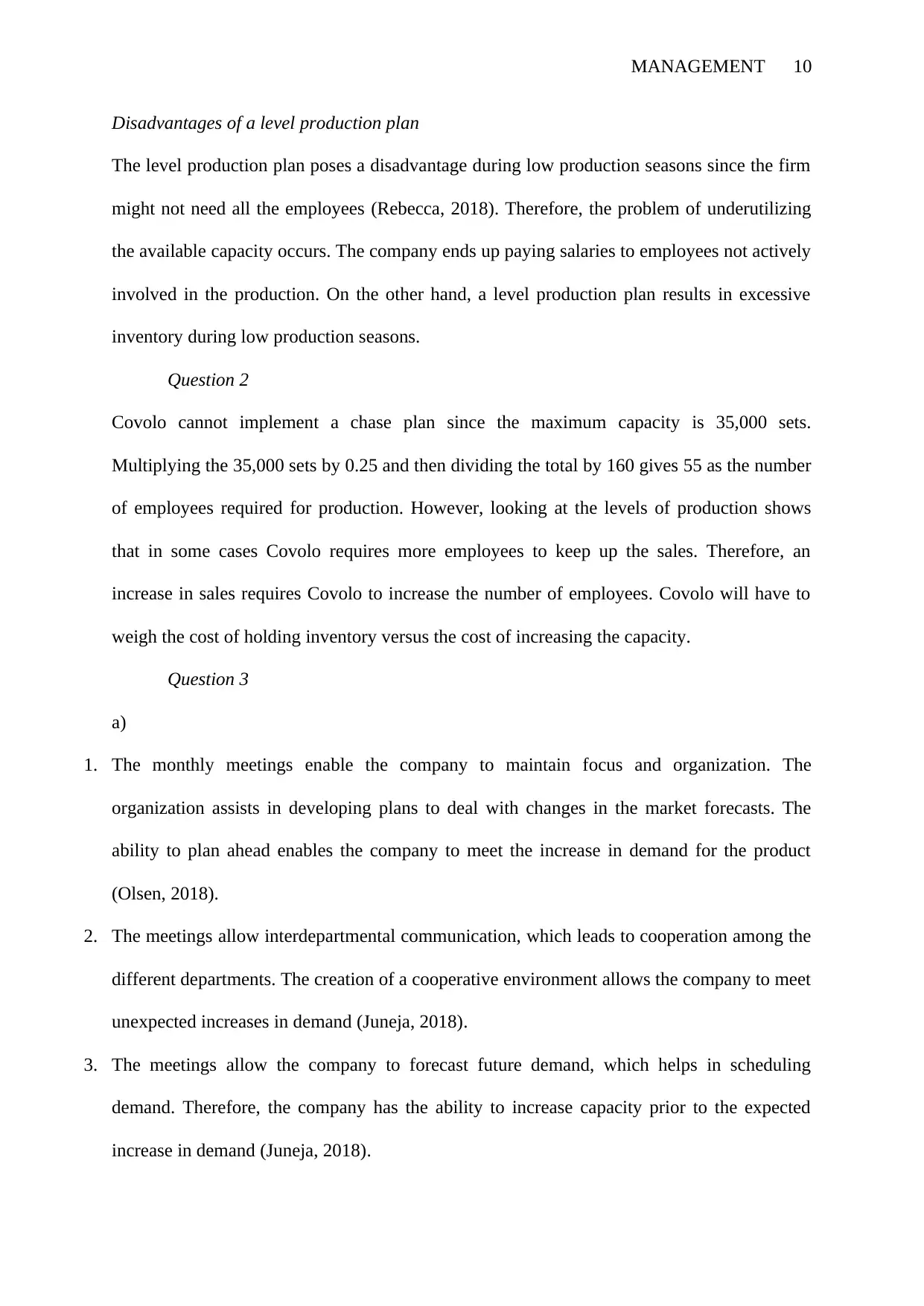
MANAGEMENT 10
Disadvantages of a level production plan
The level production plan poses a disadvantage during low production seasons since the firm
might not need all the employees (Rebecca, 2018). Therefore, the problem of underutilizing
the available capacity occurs. The company ends up paying salaries to employees not actively
involved in the production. On the other hand, a level production plan results in excessive
inventory during low production seasons.
Question 2
Covolo cannot implement a chase plan since the maximum capacity is 35,000 sets.
Multiplying the 35,000 sets by 0.25 and then dividing the total by 160 gives 55 as the number
of employees required for production. However, looking at the levels of production shows
that in some cases Covolo requires more employees to keep up the sales. Therefore, an
increase in sales requires Covolo to increase the number of employees. Covolo will have to
weigh the cost of holding inventory versus the cost of increasing the capacity.
Question 3
a)
1. The monthly meetings enable the company to maintain focus and organization. The
organization assists in developing plans to deal with changes in the market forecasts. The
ability to plan ahead enables the company to meet the increase in demand for the product
(Olsen, 2018).
2. The meetings allow interdepartmental communication, which leads to cooperation among the
different departments. The creation of a cooperative environment allows the company to meet
unexpected increases in demand (Juneja, 2018).
3. The meetings allow the company to forecast future demand, which helps in scheduling
demand. Therefore, the company has the ability to increase capacity prior to the expected
increase in demand (Juneja, 2018).
Disadvantages of a level production plan
The level production plan poses a disadvantage during low production seasons since the firm
might not need all the employees (Rebecca, 2018). Therefore, the problem of underutilizing
the available capacity occurs. The company ends up paying salaries to employees not actively
involved in the production. On the other hand, a level production plan results in excessive
inventory during low production seasons.
Question 2
Covolo cannot implement a chase plan since the maximum capacity is 35,000 sets.
Multiplying the 35,000 sets by 0.25 and then dividing the total by 160 gives 55 as the number
of employees required for production. However, looking at the levels of production shows
that in some cases Covolo requires more employees to keep up the sales. Therefore, an
increase in sales requires Covolo to increase the number of employees. Covolo will have to
weigh the cost of holding inventory versus the cost of increasing the capacity.
Question 3
a)
1. The monthly meetings enable the company to maintain focus and organization. The
organization assists in developing plans to deal with changes in the market forecasts. The
ability to plan ahead enables the company to meet the increase in demand for the product
(Olsen, 2018).
2. The meetings allow interdepartmental communication, which leads to cooperation among the
different departments. The creation of a cooperative environment allows the company to meet
unexpected increases in demand (Juneja, 2018).
3. The meetings allow the company to forecast future demand, which helps in scheduling
demand. Therefore, the company has the ability to increase capacity prior to the expected
increase in demand (Juneja, 2018).
Secure Best Marks with AI Grader
Need help grading? Try our AI Grader for instant feedback on your assignments.
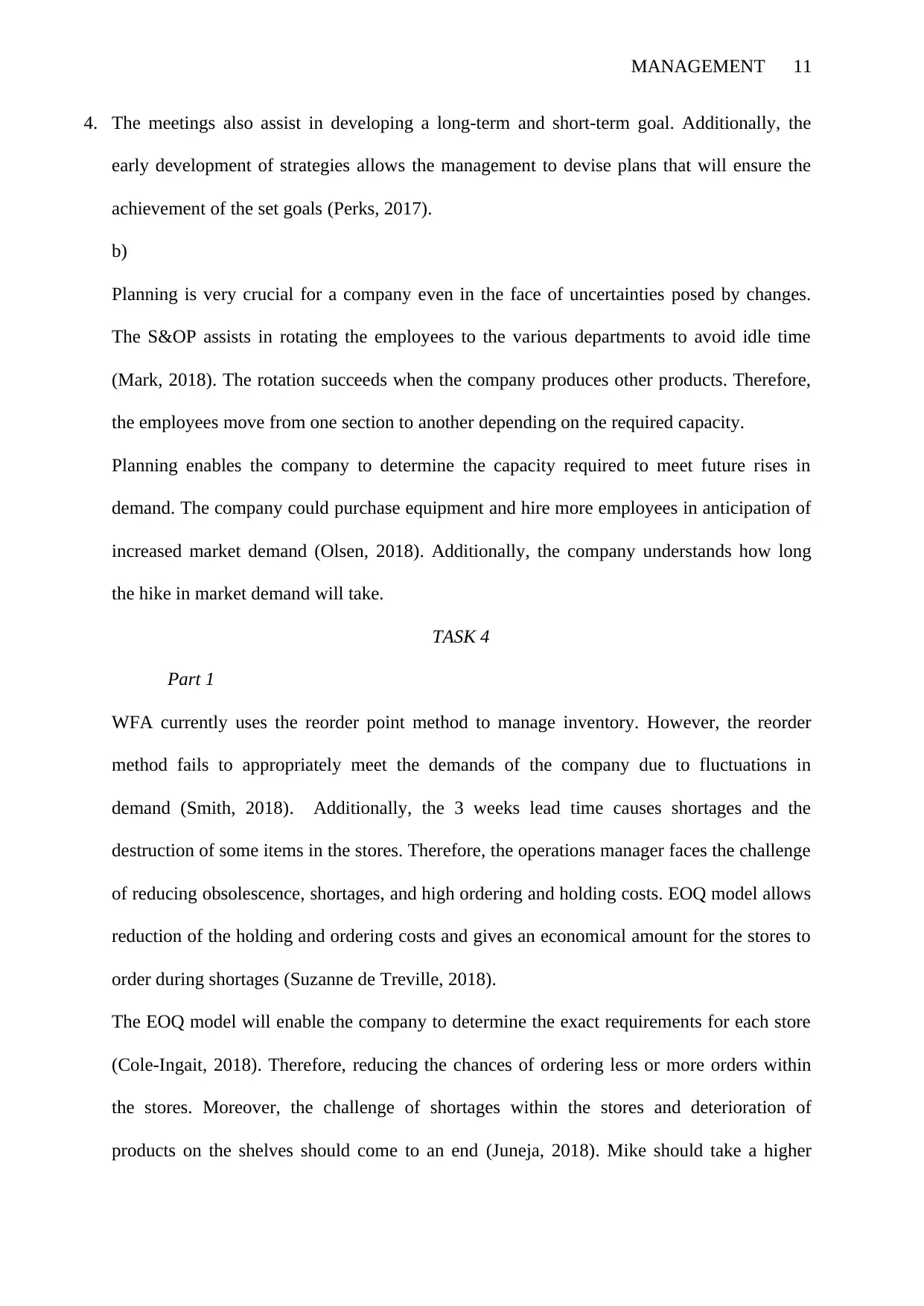
MANAGEMENT 11
4. The meetings also assist in developing a long-term and short-term goal. Additionally, the
early development of strategies allows the management to devise plans that will ensure the
achievement of the set goals (Perks, 2017).
b)
Planning is very crucial for a company even in the face of uncertainties posed by changes.
The S&OP assists in rotating the employees to the various departments to avoid idle time
(Mark, 2018). The rotation succeeds when the company produces other products. Therefore,
the employees move from one section to another depending on the required capacity.
Planning enables the company to determine the capacity required to meet future rises in
demand. The company could purchase equipment and hire more employees in anticipation of
increased market demand (Olsen, 2018). Additionally, the company understands how long
the hike in market demand will take.
TASK 4
Part 1
WFA currently uses the reorder point method to manage inventory. However, the reorder
method fails to appropriately meet the demands of the company due to fluctuations in
demand (Smith, 2018). Additionally, the 3 weeks lead time causes shortages and the
destruction of some items in the stores. Therefore, the operations manager faces the challenge
of reducing obsolescence, shortages, and high ordering and holding costs. EOQ model allows
reduction of the holding and ordering costs and gives an economical amount for the stores to
order during shortages (Suzanne de Treville, 2018).
The EOQ model will enable the company to determine the exact requirements for each store
(Cole-Ingait, 2018). Therefore, reducing the chances of ordering less or more orders within
the stores. Moreover, the challenge of shortages within the stores and deterioration of
products on the shelves should come to an end (Juneja, 2018). Mike should take a higher
4. The meetings also assist in developing a long-term and short-term goal. Additionally, the
early development of strategies allows the management to devise plans that will ensure the
achievement of the set goals (Perks, 2017).
b)
Planning is very crucial for a company even in the face of uncertainties posed by changes.
The S&OP assists in rotating the employees to the various departments to avoid idle time
(Mark, 2018). The rotation succeeds when the company produces other products. Therefore,
the employees move from one section to another depending on the required capacity.
Planning enables the company to determine the capacity required to meet future rises in
demand. The company could purchase equipment and hire more employees in anticipation of
increased market demand (Olsen, 2018). Additionally, the company understands how long
the hike in market demand will take.
TASK 4
Part 1
WFA currently uses the reorder point method to manage inventory. However, the reorder
method fails to appropriately meet the demands of the company due to fluctuations in
demand (Smith, 2018). Additionally, the 3 weeks lead time causes shortages and the
destruction of some items in the stores. Therefore, the operations manager faces the challenge
of reducing obsolescence, shortages, and high ordering and holding costs. EOQ model allows
reduction of the holding and ordering costs and gives an economical amount for the stores to
order during shortages (Suzanne de Treville, 2018).
The EOQ model will enable the company to determine the exact requirements for each store
(Cole-Ingait, 2018). Therefore, reducing the chances of ordering less or more orders within
the stores. Moreover, the challenge of shortages within the stores and deterioration of
products on the shelves should come to an end (Juneja, 2018). Mike should take a higher
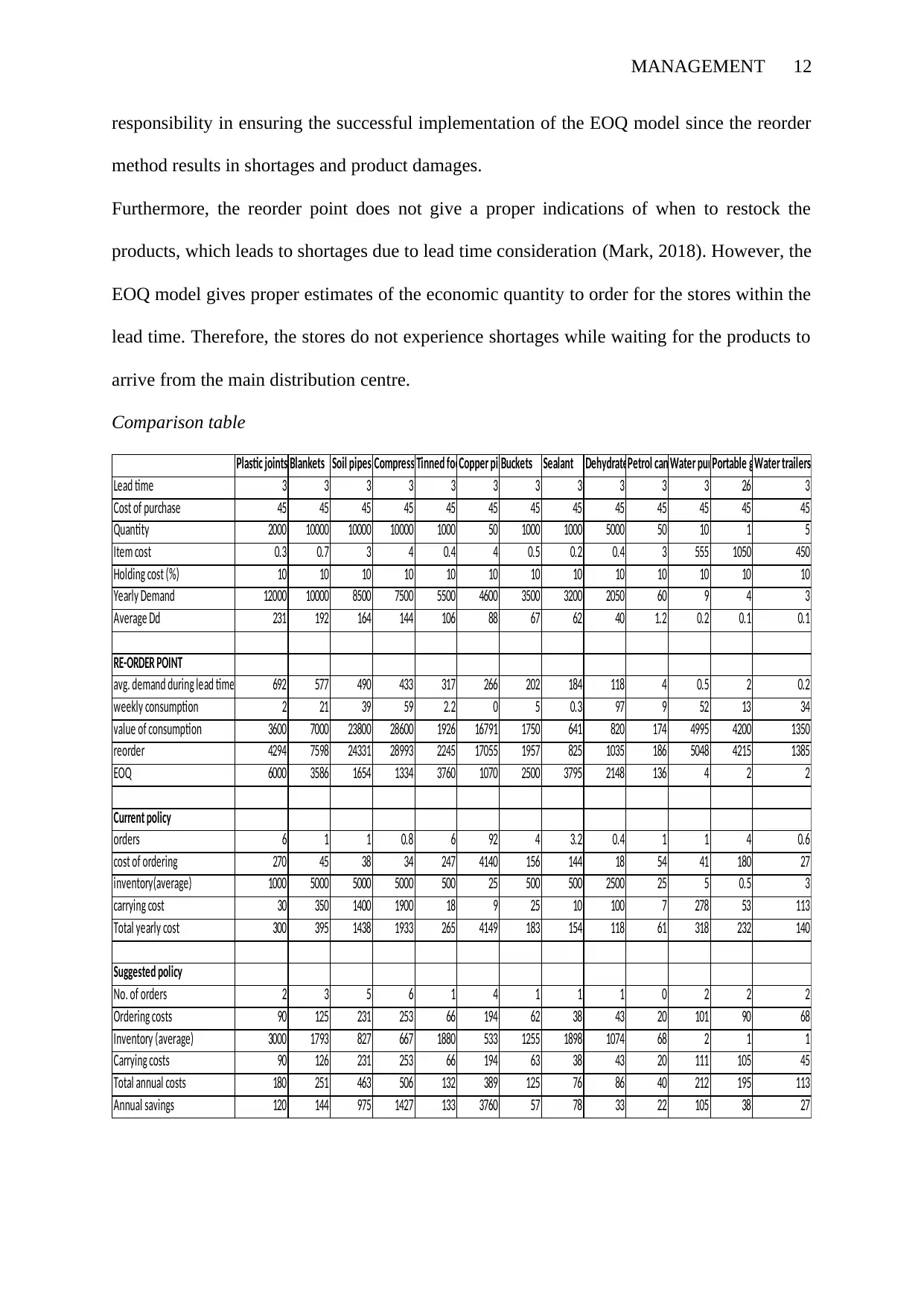
MANAGEMENT 12
responsibility in ensuring the successful implementation of the EOQ model since the reorder
method results in shortages and product damages.
Furthermore, the reorder point does not give a proper indications of when to restock the
products, which leads to shortages due to lead time consideration (Mark, 2018). However, the
EOQ model gives proper estimates of the economic quantity to order for the stores within the
lead time. Therefore, the stores do not experience shortages while waiting for the products to
arrive from the main distribution centre.
Comparison table
Plastic joints Blankets Soil pipes Compression jointsTinned foodCopper pipeBuckets Sealant Dehydrated food packsPetrol cansWater pumpsPortable generatorsWater trailers
Lead time 3 3 3 3 3 3 3 3 3 3 3 26 3
Cost of purchase 45 45 45 45 45 45 45 45 45 45 45 45 45
Quantity 2000 10000 10000 10000 1000 50 1000 1000 5000 50 10 1 5
Item cost 0.3 0.7 3 4 0.4 4 0.5 0.2 0.4 3 555 1050 450
Holding cost (%) 10 10 10 10 10 10 10 10 10 10 10 10 10
Yearly Demand 12000 10000 8500 7500 5500 4600 3500 3200 2050 60 9 4 3
Average Dd 231 192 164 144 106 88 67 62 40 1.2 0.2 0.1 0.1
RE-ORDER POINT
avg. demand during lead time 692 577 490 433 317 266 202 184 118 4 0.5 2 0.2
weekly consumption 2 21 39 59 2.2 0 5 0.3 97 9 52 13 34
value of consumption 3600 7000 23800 28600 1926 16791 1750 641 820 174 4995 4200 1350
reorder 4294 7598 24331 28993 2245 17055 1957 825 1035 186 5048 4215 1385
EOQ 6000 3586 1654 1334 3760 1070 2500 3795 2148 136 4 2 2
Current policy
orders 6 1 1 0.8 6 92 4 3.2 0.4 1 1 4 0.6
cost of ordering 270 45 38 34 247 4140 156 144 18 54 41 180 27
inventory(average) 1000 5000 5000 5000 500 25 500 500 2500 25 5 0.5 3
carrying cost 30 350 1400 1900 18 9 25 10 100 7 278 53 113
Total yearly cost 300 395 1438 1933 265 4149 183 154 118 61 318 232 140
Suggested policy
No. of orders 2 3 5 6 1 4 1 1 1 0 2 2 2
Ordering costs 90 125 231 253 66 194 62 38 43 20 101 90 68
Inventory (average) 3000 1793 827 667 1880 533 1255 1898 1074 68 2 1 1
Carrying costs 90 126 231 253 66 194 63 38 43 20 111 105 45
Total annual costs 180 251 463 506 132 389 125 76 86 40 212 195 113
Annual savings 120 144 975 1427 133 3760 57 78 33 22 105 38 27
responsibility in ensuring the successful implementation of the EOQ model since the reorder
method results in shortages and product damages.
Furthermore, the reorder point does not give a proper indications of when to restock the
products, which leads to shortages due to lead time consideration (Mark, 2018). However, the
EOQ model gives proper estimates of the economic quantity to order for the stores within the
lead time. Therefore, the stores do not experience shortages while waiting for the products to
arrive from the main distribution centre.
Comparison table
Plastic joints Blankets Soil pipes Compression jointsTinned foodCopper pipeBuckets Sealant Dehydrated food packsPetrol cansWater pumpsPortable generatorsWater trailers
Lead time 3 3 3 3 3 3 3 3 3 3 3 26 3
Cost of purchase 45 45 45 45 45 45 45 45 45 45 45 45 45
Quantity 2000 10000 10000 10000 1000 50 1000 1000 5000 50 10 1 5
Item cost 0.3 0.7 3 4 0.4 4 0.5 0.2 0.4 3 555 1050 450
Holding cost (%) 10 10 10 10 10 10 10 10 10 10 10 10 10
Yearly Demand 12000 10000 8500 7500 5500 4600 3500 3200 2050 60 9 4 3
Average Dd 231 192 164 144 106 88 67 62 40 1.2 0.2 0.1 0.1
RE-ORDER POINT
avg. demand during lead time 692 577 490 433 317 266 202 184 118 4 0.5 2 0.2
weekly consumption 2 21 39 59 2.2 0 5 0.3 97 9 52 13 34
value of consumption 3600 7000 23800 28600 1926 16791 1750 641 820 174 4995 4200 1350
reorder 4294 7598 24331 28993 2245 17055 1957 825 1035 186 5048 4215 1385
EOQ 6000 3586 1654 1334 3760 1070 2500 3795 2148 136 4 2 2
Current policy
orders 6 1 1 0.8 6 92 4 3.2 0.4 1 1 4 0.6
cost of ordering 270 45 38 34 247 4140 156 144 18 54 41 180 27
inventory(average) 1000 5000 5000 5000 500 25 500 500 2500 25 5 0.5 3
carrying cost 30 350 1400 1900 18 9 25 10 100 7 278 53 113
Total yearly cost 300 395 1438 1933 265 4149 183 154 118 61 318 232 140
Suggested policy
No. of orders 2 3 5 6 1 4 1 1 1 0 2 2 2
Ordering costs 90 125 231 253 66 194 62 38 43 20 101 90 68
Inventory (average) 3000 1793 827 667 1880 533 1255 1898 1074 68 2 1 1
Carrying costs 90 126 231 253 66 194 63 38 43 20 111 105 45
Total annual costs 180 251 463 506 132 389 125 76 86 40 212 195 113
Annual savings 120 144 975 1427 133 3760 57 78 33 22 105 38 27
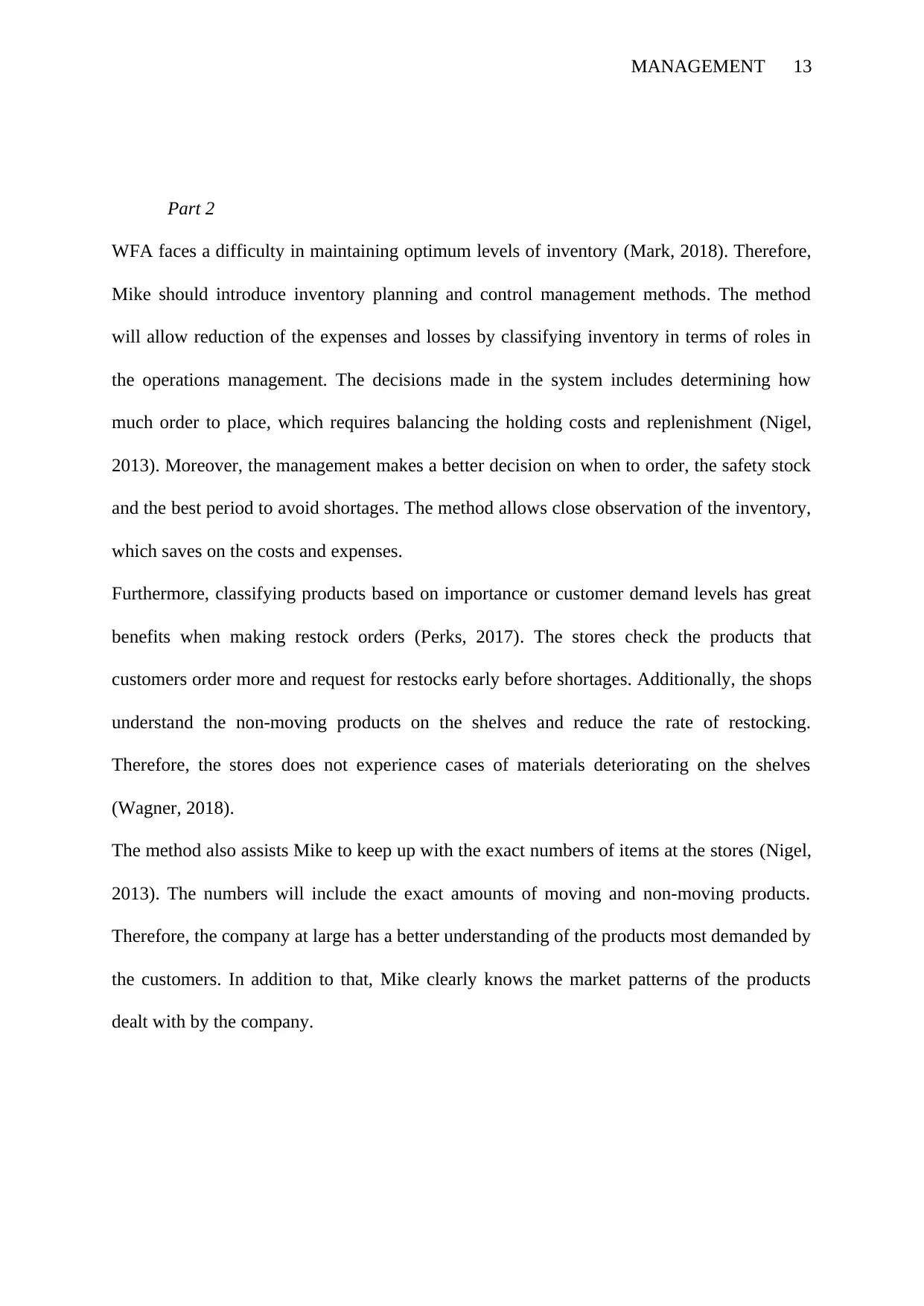
MANAGEMENT 13
Part 2
WFA faces a difficulty in maintaining optimum levels of inventory (Mark, 2018). Therefore,
Mike should introduce inventory planning and control management methods. The method
will allow reduction of the expenses and losses by classifying inventory in terms of roles in
the operations management. The decisions made in the system includes determining how
much order to place, which requires balancing the holding costs and replenishment (Nigel,
2013). Moreover, the management makes a better decision on when to order, the safety stock
and the best period to avoid shortages. The method allows close observation of the inventory,
which saves on the costs and expenses.
Furthermore, classifying products based on importance or customer demand levels has great
benefits when making restock orders (Perks, 2017). The stores check the products that
customers order more and request for restocks early before shortages. Additionally, the shops
understand the non-moving products on the shelves and reduce the rate of restocking.
Therefore, the stores does not experience cases of materials deteriorating on the shelves
(Wagner, 2018).
The method also assists Mike to keep up with the exact numbers of items at the stores (Nigel,
2013). The numbers will include the exact amounts of moving and non-moving products.
Therefore, the company at large has a better understanding of the products most demanded by
the customers. In addition to that, Mike clearly knows the market patterns of the products
dealt with by the company.
Part 2
WFA faces a difficulty in maintaining optimum levels of inventory (Mark, 2018). Therefore,
Mike should introduce inventory planning and control management methods. The method
will allow reduction of the expenses and losses by classifying inventory in terms of roles in
the operations management. The decisions made in the system includes determining how
much order to place, which requires balancing the holding costs and replenishment (Nigel,
2013). Moreover, the management makes a better decision on when to order, the safety stock
and the best period to avoid shortages. The method allows close observation of the inventory,
which saves on the costs and expenses.
Furthermore, classifying products based on importance or customer demand levels has great
benefits when making restock orders (Perks, 2017). The stores check the products that
customers order more and request for restocks early before shortages. Additionally, the shops
understand the non-moving products on the shelves and reduce the rate of restocking.
Therefore, the stores does not experience cases of materials deteriorating on the shelves
(Wagner, 2018).
The method also assists Mike to keep up with the exact numbers of items at the stores (Nigel,
2013). The numbers will include the exact amounts of moving and non-moving products.
Therefore, the company at large has a better understanding of the products most demanded by
the customers. In addition to that, Mike clearly knows the market patterns of the products
dealt with by the company.
Paraphrase This Document
Need a fresh take? Get an instant paraphrase of this document with our AI Paraphraser
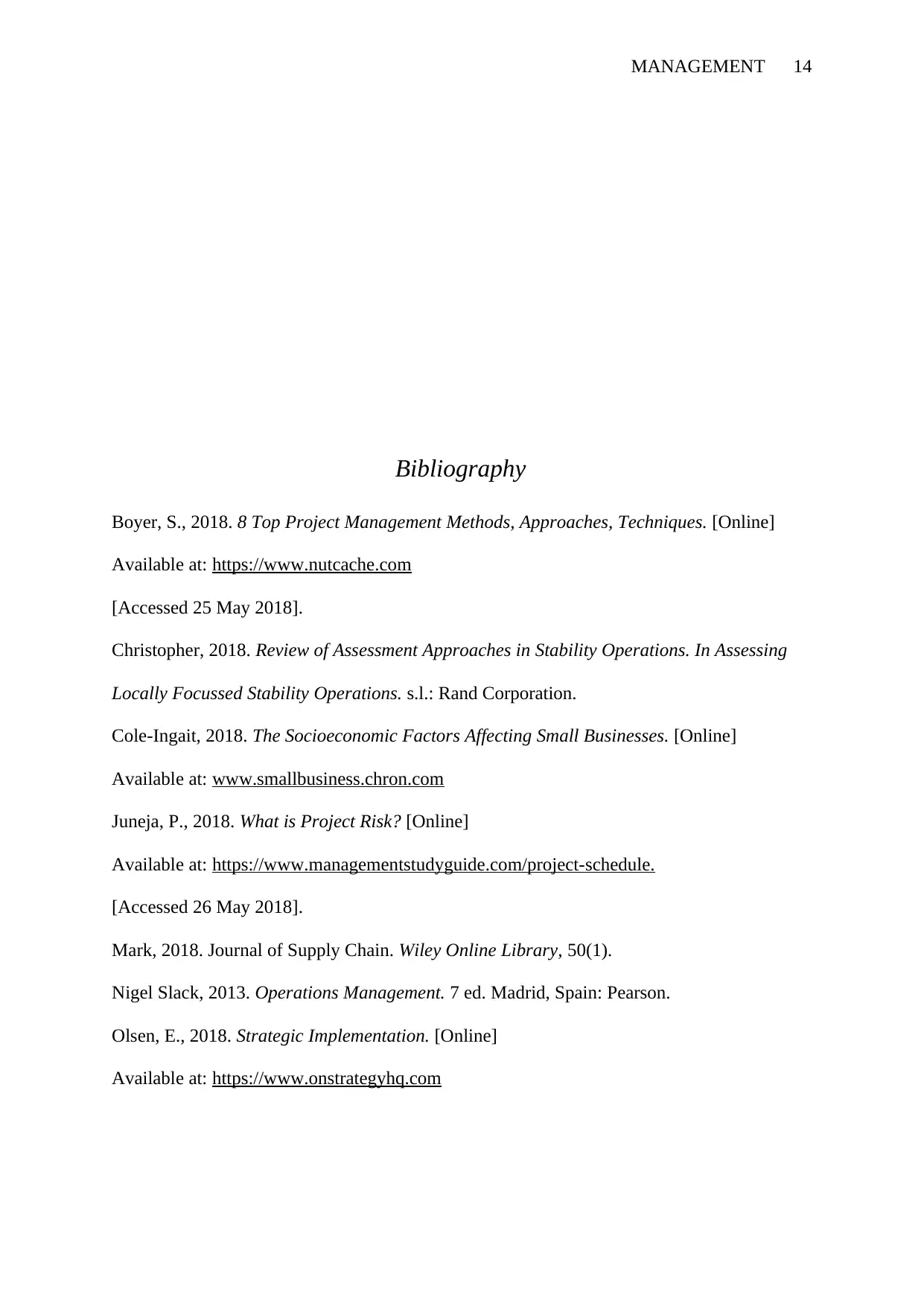
MANAGEMENT 14
Bibliography
Boyer, S., 2018. 8 Top Project Management Methods, Approaches, Techniques. [Online]
Available at: https://www.nutcache.com
[Accessed 25 May 2018].
Christopher, 2018. Review of Assessment Approaches in Stability Operations. In Assessing
Locally Focussed Stability Operations. s.l.: Rand Corporation.
Cole-Ingait, 2018. The Socioeconomic Factors Affecting Small Businesses. [Online]
Available at: www.smallbusiness.chron.com
Juneja, P., 2018. What is Project Risk? [Online]
Available at: https://www.managementstudyguide.com/project-schedule.
[Accessed 26 May 2018].
Mark, 2018. Journal of Supply Chain. Wiley Online Library, 50(1).
Nigel Slack, 2013. Operations Management. 7 ed. Madrid, Spain: Pearson.
Olsen, E., 2018. Strategic Implementation. [Online]
Available at: https://www.onstrategyhq.com
Bibliography
Boyer, S., 2018. 8 Top Project Management Methods, Approaches, Techniques. [Online]
Available at: https://www.nutcache.com
[Accessed 25 May 2018].
Christopher, 2018. Review of Assessment Approaches in Stability Operations. In Assessing
Locally Focussed Stability Operations. s.l.: Rand Corporation.
Cole-Ingait, 2018. The Socioeconomic Factors Affecting Small Businesses. [Online]
Available at: www.smallbusiness.chron.com
Juneja, P., 2018. What is Project Risk? [Online]
Available at: https://www.managementstudyguide.com/project-schedule.
[Accessed 26 May 2018].
Mark, 2018. Journal of Supply Chain. Wiley Online Library, 50(1).
Nigel Slack, 2013. Operations Management. 7 ed. Madrid, Spain: Pearson.
Olsen, E., 2018. Strategic Implementation. [Online]
Available at: https://www.onstrategyhq.com
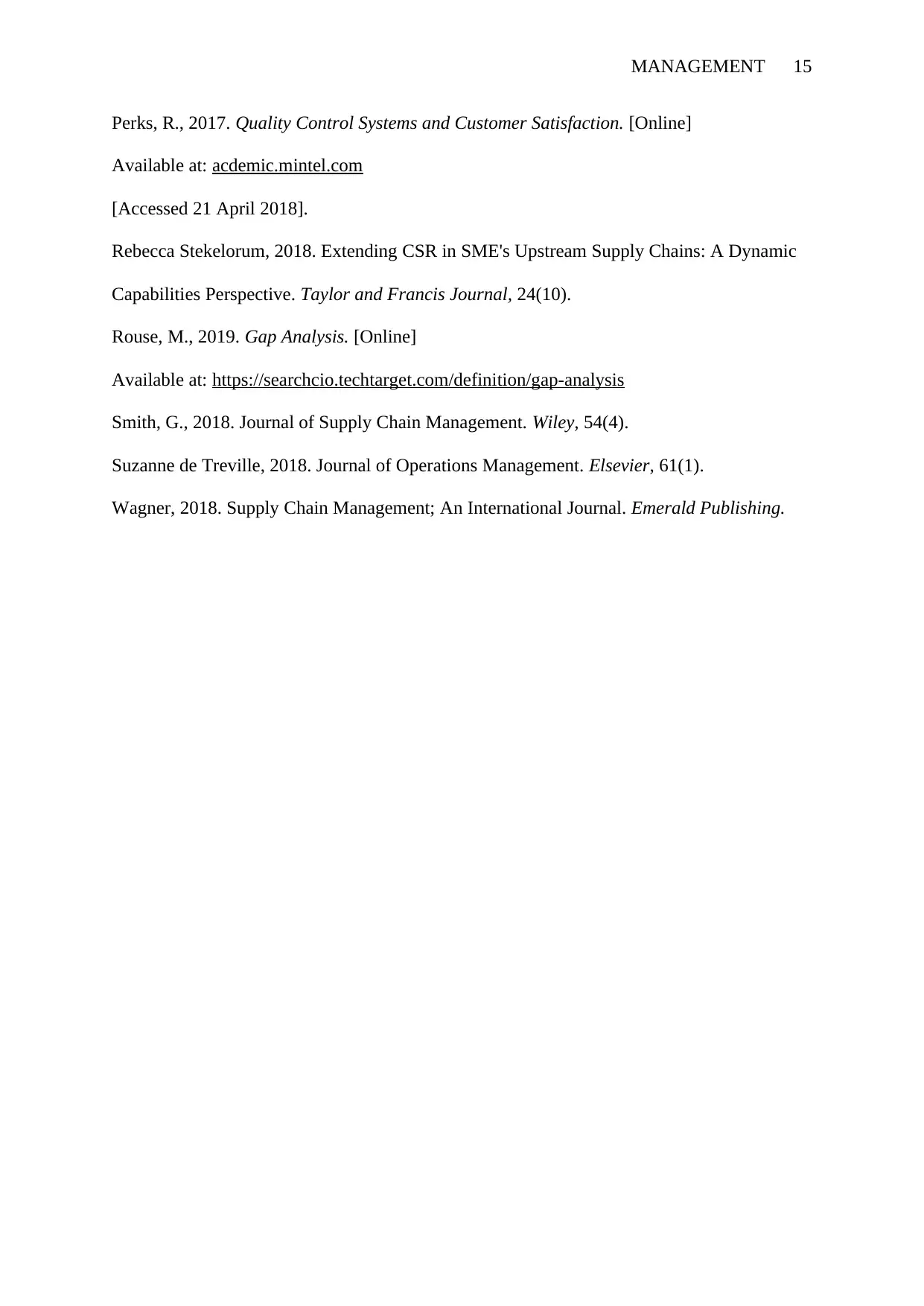
MANAGEMENT 15
Perks, R., 2017. Quality Control Systems and Customer Satisfaction. [Online]
Available at: acdemic.mintel.com
[Accessed 21 April 2018].
Rebecca Stekelorum, 2018. Extending CSR in SME's Upstream Supply Chains: A Dynamic
Capabilities Perspective. Taylor and Francis Journal, 24(10).
Rouse, M., 2019. Gap Analysis. [Online]
Available at: https://searchcio.techtarget.com/definition/gap-analysis
Smith, G., 2018. Journal of Supply Chain Management. Wiley, 54(4).
Suzanne de Treville, 2018. Journal of Operations Management. Elsevier, 61(1).
Wagner, 2018. Supply Chain Management; An International Journal. Emerald Publishing.
Perks, R., 2017. Quality Control Systems and Customer Satisfaction. [Online]
Available at: acdemic.mintel.com
[Accessed 21 April 2018].
Rebecca Stekelorum, 2018. Extending CSR in SME's Upstream Supply Chains: A Dynamic
Capabilities Perspective. Taylor and Francis Journal, 24(10).
Rouse, M., 2019. Gap Analysis. [Online]
Available at: https://searchcio.techtarget.com/definition/gap-analysis
Smith, G., 2018. Journal of Supply Chain Management. Wiley, 54(4).
Suzanne de Treville, 2018. Journal of Operations Management. Elsevier, 61(1).
Wagner, 2018. Supply Chain Management; An International Journal. Emerald Publishing.
1 out of 15
![[object Object]](/_next/image/?url=%2F_next%2Fstatic%2Fmedia%2Flogo.6d15ce61.png&w=640&q=75)
Your All-in-One AI-Powered Toolkit for Academic Success.
 +13062052269
info@desklib.com
Available 24*7 on WhatsApp / Email
Unlock your academic potential
© 2024  |  Zucol Services PVT LTD  |  All rights reserved.