Managerial Accounting
VerifiedAdded on 2023/04/22
|13
|3101
|254
AI Summary
The study has shown that the typical issues associated with KF’s costing system may also mislead the investors and management of the company. The breakdown of the product cost has shown direct cost per unit may be inferred with $ 50 for Expert fitters and $ 30 for Junior fitters. The adoption of the alternative job costing approach in this case needs to be proceeding with variable costing. It is recommended for Fred to proceed with direct costing method and adopt variable costing for allocating the manufacturing costs and reporting net income.
Contribute Materials
Your contribution can guide someone’s learning journey. Share your
documents today.
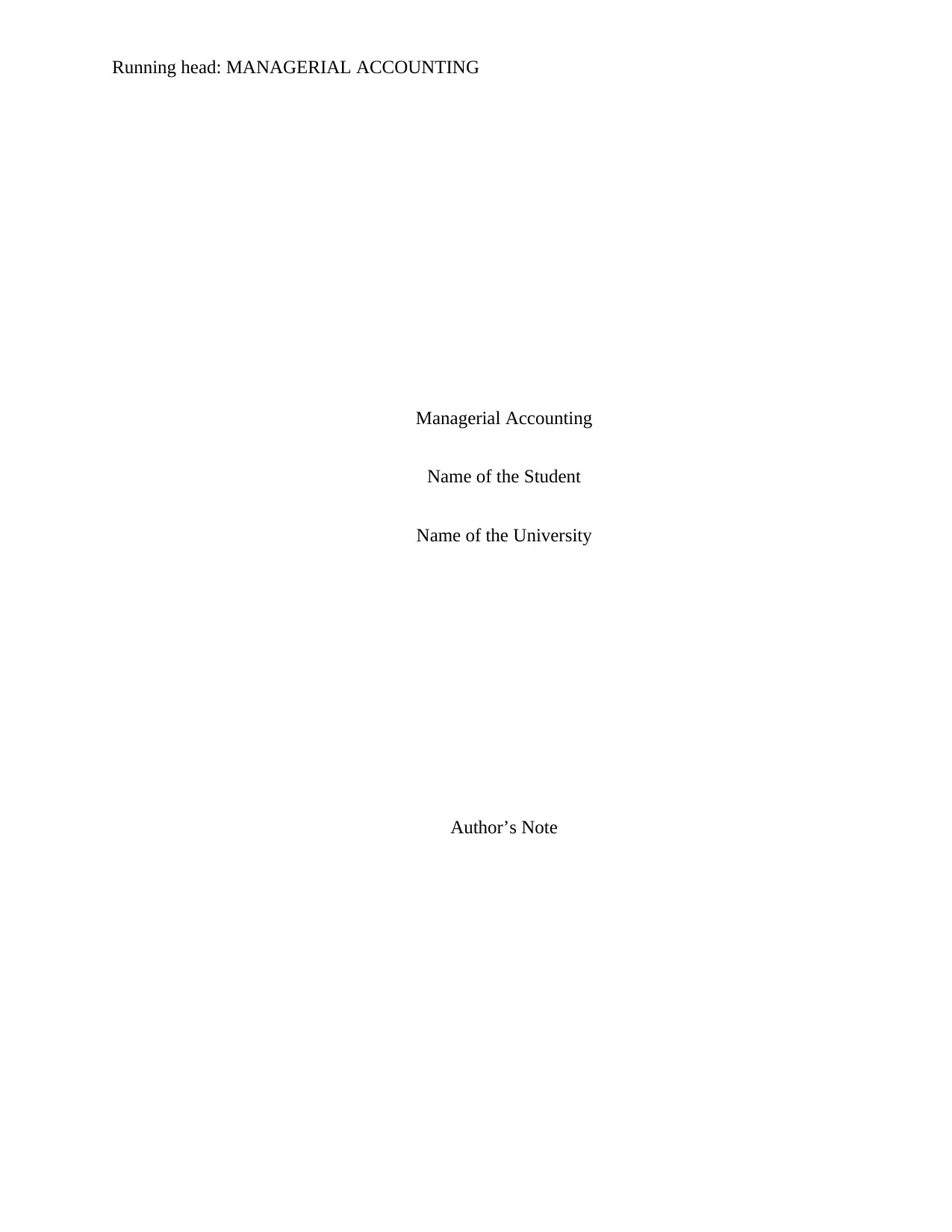
Running head: MANAGERIAL ACCOUNTING
Managerial Accounting
Name of the Student
Name of the University
Author’s Note
Managerial Accounting
Name of the Student
Name of the University
Author’s Note
Secure Best Marks with AI Grader
Need help grading? Try our AI Grader for instant feedback on your assignments.
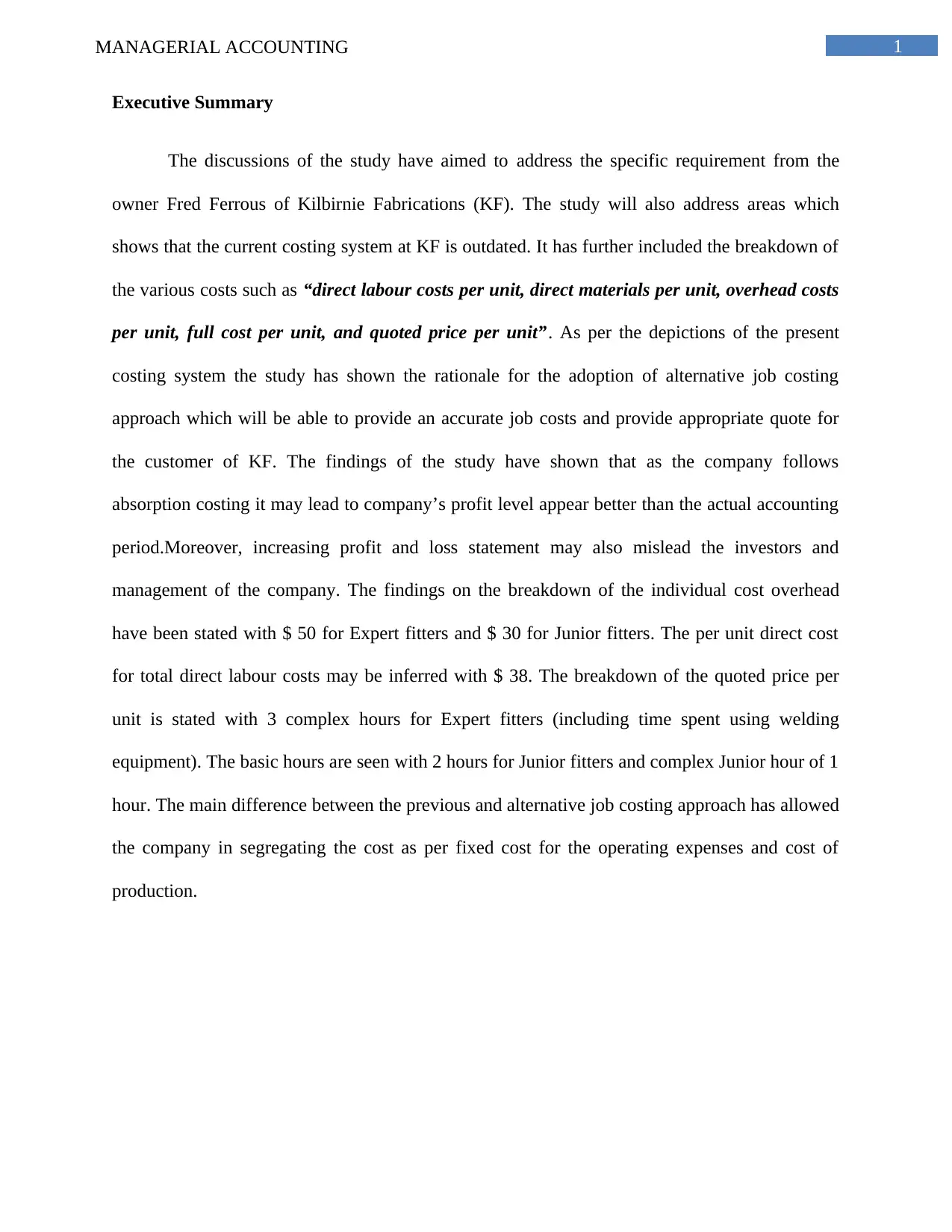
1MANAGERIAL ACCOUNTING
Executive Summary
The discussions of the study have aimed to address the specific requirement from the
owner Fred Ferrous of Kilbirnie Fabrications (KF). The study will also address areas which
shows that the current costing system at KF is outdated. It has further included the breakdown of
the various costs such as “direct labour costs per unit, direct materials per unit, overhead costs
per unit, full cost per unit, and quoted price per unit”. As per the depictions of the present
costing system the study has shown the rationale for the adoption of alternative job costing
approach which will be able to provide an accurate job costs and provide appropriate quote for
the customer of KF. The findings of the study have shown that as the company follows
absorption costing it may lead to company’s profit level appear better than the actual accounting
period.Moreover, increasing profit and loss statement may also mislead the investors and
management of the company. The findings on the breakdown of the individual cost overhead
have been stated with $ 50 for Expert fitters and $ 30 for Junior fitters. The per unit direct cost
for total direct labour costs may be inferred with $ 38. The breakdown of the quoted price per
unit is stated with 3 complex hours for Expert fitters (including time spent using welding
equipment). The basic hours are seen with 2 hours for Junior fitters and complex Junior hour of 1
hour. The main difference between the previous and alternative job costing approach has allowed
the company in segregating the cost as per fixed cost for the operating expenses and cost of
production.
Executive Summary
The discussions of the study have aimed to address the specific requirement from the
owner Fred Ferrous of Kilbirnie Fabrications (KF). The study will also address areas which
shows that the current costing system at KF is outdated. It has further included the breakdown of
the various costs such as “direct labour costs per unit, direct materials per unit, overhead costs
per unit, full cost per unit, and quoted price per unit”. As per the depictions of the present
costing system the study has shown the rationale for the adoption of alternative job costing
approach which will be able to provide an accurate job costs and provide appropriate quote for
the customer of KF. The findings of the study have shown that as the company follows
absorption costing it may lead to company’s profit level appear better than the actual accounting
period.Moreover, increasing profit and loss statement may also mislead the investors and
management of the company. The findings on the breakdown of the individual cost overhead
have been stated with $ 50 for Expert fitters and $ 30 for Junior fitters. The per unit direct cost
for total direct labour costs may be inferred with $ 38. The breakdown of the quoted price per
unit is stated with 3 complex hours for Expert fitters (including time spent using welding
equipment). The basic hours are seen with 2 hours for Junior fitters and complex Junior hour of 1
hour. The main difference between the previous and alternative job costing approach has allowed
the company in segregating the cost as per fixed cost for the operating expenses and cost of
production.
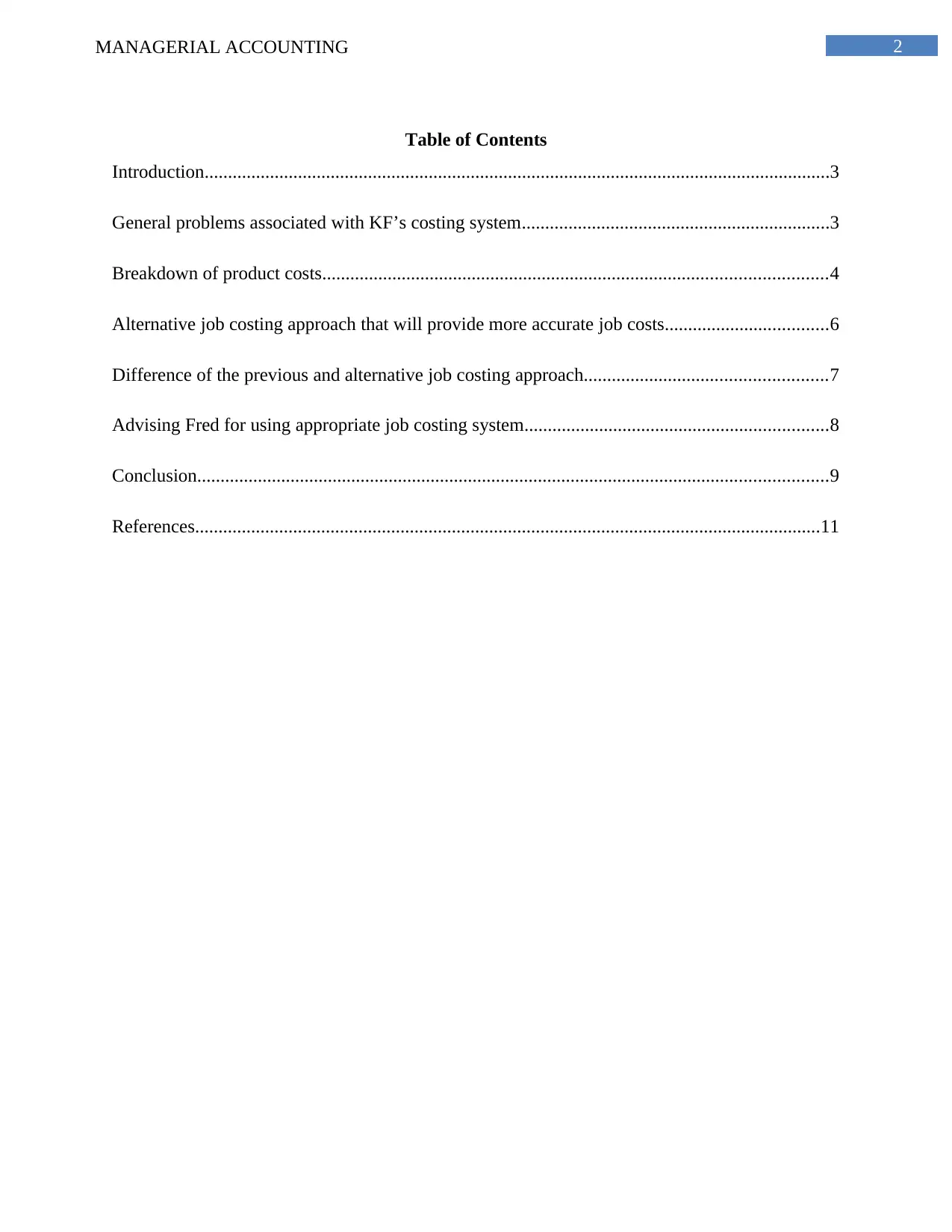
2MANAGERIAL ACCOUNTING
Table of Contents
Introduction......................................................................................................................................3
General problems associated with KF’s costing system..................................................................3
Breakdown of product costs............................................................................................................4
Alternative job costing approach that will provide more accurate job costs...................................6
Difference of the previous and alternative job costing approach....................................................7
Advising Fred for using appropriate job costing system.................................................................8
Conclusion.......................................................................................................................................9
References......................................................................................................................................11
Table of Contents
Introduction......................................................................................................................................3
General problems associated with KF’s costing system..................................................................3
Breakdown of product costs............................................................................................................4
Alternative job costing approach that will provide more accurate job costs...................................6
Difference of the previous and alternative job costing approach....................................................7
Advising Fred for using appropriate job costing system.................................................................8
Conclusion.......................................................................................................................................9
References......................................................................................................................................11
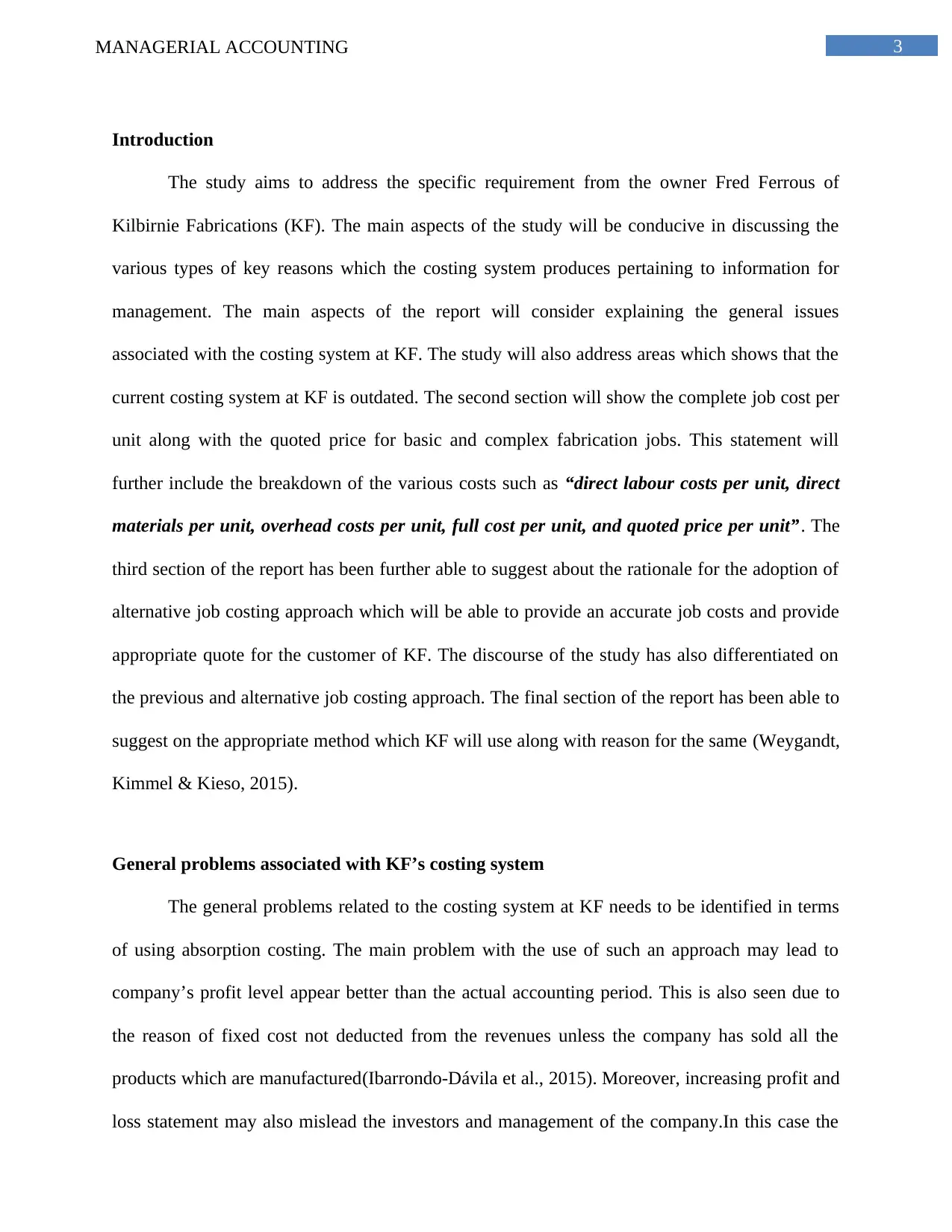
3MANAGERIAL ACCOUNTING
Introduction
The study aims to address the specific requirement from the owner Fred Ferrous of
Kilbirnie Fabrications (KF). The main aspects of the study will be conducive in discussing the
various types of key reasons which the costing system produces pertaining to information for
management. The main aspects of the report will consider explaining the general issues
associated with the costing system at KF. The study will also address areas which shows that the
current costing system at KF is outdated. The second section will show the complete job cost per
unit along with the quoted price for basic and complex fabrication jobs. This statement will
further include the breakdown of the various costs such as “direct labour costs per unit, direct
materials per unit, overhead costs per unit, full cost per unit, and quoted price per unit”. The
third section of the report has been further able to suggest about the rationale for the adoption of
alternative job costing approach which will be able to provide an accurate job costs and provide
appropriate quote for the customer of KF. The discourse of the study has also differentiated on
the previous and alternative job costing approach. The final section of the report has been able to
suggest on the appropriate method which KF will use along with reason for the same (Weygandt,
Kimmel & Kieso, 2015).
General problems associated with KF’s costing system
The general problems related to the costing system at KF needs to be identified in terms
of using absorption costing. The main problem with the use of such an approach may lead to
company’s profit level appear better than the actual accounting period. This is also seen due to
the reason of fixed cost not deducted from the revenues unless the company has sold all the
products which are manufactured(Ibarrondo-Dávila et al., 2015). Moreover, increasing profit and
loss statement may also mislead the investors and management of the company.In this case the
Introduction
The study aims to address the specific requirement from the owner Fred Ferrous of
Kilbirnie Fabrications (KF). The main aspects of the study will be conducive in discussing the
various types of key reasons which the costing system produces pertaining to information for
management. The main aspects of the report will consider explaining the general issues
associated with the costing system at KF. The study will also address areas which shows that the
current costing system at KF is outdated. The second section will show the complete job cost per
unit along with the quoted price for basic and complex fabrication jobs. This statement will
further include the breakdown of the various costs such as “direct labour costs per unit, direct
materials per unit, overhead costs per unit, full cost per unit, and quoted price per unit”. The
third section of the report has been further able to suggest about the rationale for the adoption of
alternative job costing approach which will be able to provide an accurate job costs and provide
appropriate quote for the customer of KF. The discourse of the study has also differentiated on
the previous and alternative job costing approach. The final section of the report has been able to
suggest on the appropriate method which KF will use along with reason for the same (Weygandt,
Kimmel & Kieso, 2015).
General problems associated with KF’s costing system
The general problems related to the costing system at KF needs to be identified in terms
of using absorption costing. The main problem with the use of such an approach may lead to
company’s profit level appear better than the actual accounting period. This is also seen due to
the reason of fixed cost not deducted from the revenues unless the company has sold all the
products which are manufactured(Ibarrondo-Dávila et al., 2015). Moreover, increasing profit and
loss statement may also mislead the investors and management of the company.In this case the
Secure Best Marks with AI Grader
Need help grading? Try our AI Grader for instant feedback on your assignments.
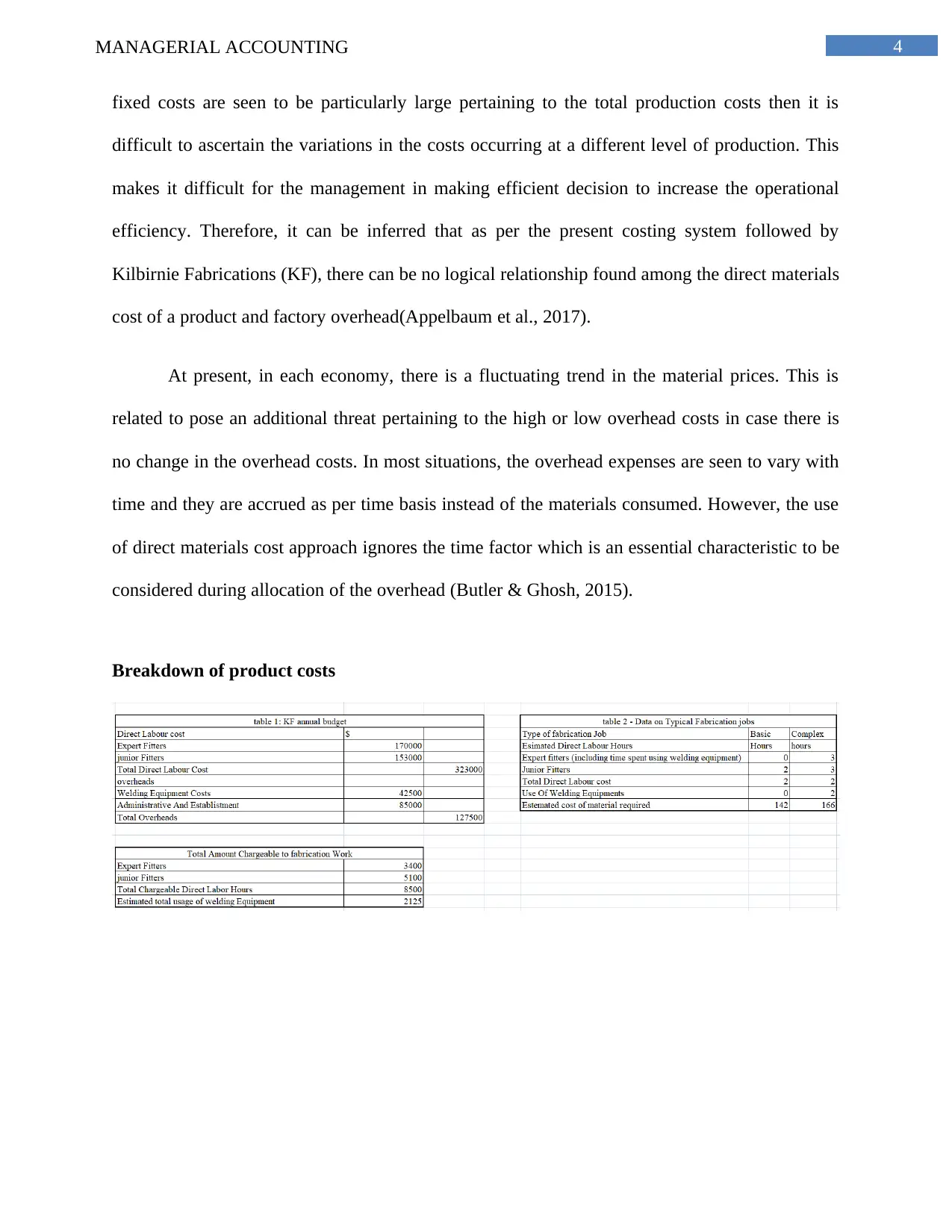
4MANAGERIAL ACCOUNTING
fixed costs are seen to be particularly large pertaining to the total production costs then it is
difficult to ascertain the variations in the costs occurring at a different level of production. This
makes it difficult for the management in making efficient decision to increase the operational
efficiency. Therefore, it can be inferred that as per the present costing system followed by
Kilbirnie Fabrications (KF), there can be no logical relationship found among the direct materials
cost of a product and factory overhead(Appelbaum et al., 2017).
At present, in each economy, there is a fluctuating trend in the material prices. This is
related to pose an additional threat pertaining to the high or low overhead costs in case there is
no change in the overhead costs. In most situations, the overhead expenses are seen to vary with
time and they are accrued as per time basis instead of the materials consumed. However, the use
of direct materials cost approach ignores the time factor which is an essential characteristic to be
considered during allocation of the overhead (Butler & Ghosh, 2015).
Breakdown of product costs
fixed costs are seen to be particularly large pertaining to the total production costs then it is
difficult to ascertain the variations in the costs occurring at a different level of production. This
makes it difficult for the management in making efficient decision to increase the operational
efficiency. Therefore, it can be inferred that as per the present costing system followed by
Kilbirnie Fabrications (KF), there can be no logical relationship found among the direct materials
cost of a product and factory overhead(Appelbaum et al., 2017).
At present, in each economy, there is a fluctuating trend in the material prices. This is
related to pose an additional threat pertaining to the high or low overhead costs in case there is
no change in the overhead costs. In most situations, the overhead expenses are seen to vary with
time and they are accrued as per time basis instead of the materials consumed. However, the use
of direct materials cost approach ignores the time factor which is an essential characteristic to be
considered during allocation of the overhead (Butler & Ghosh, 2015).
Breakdown of product costs
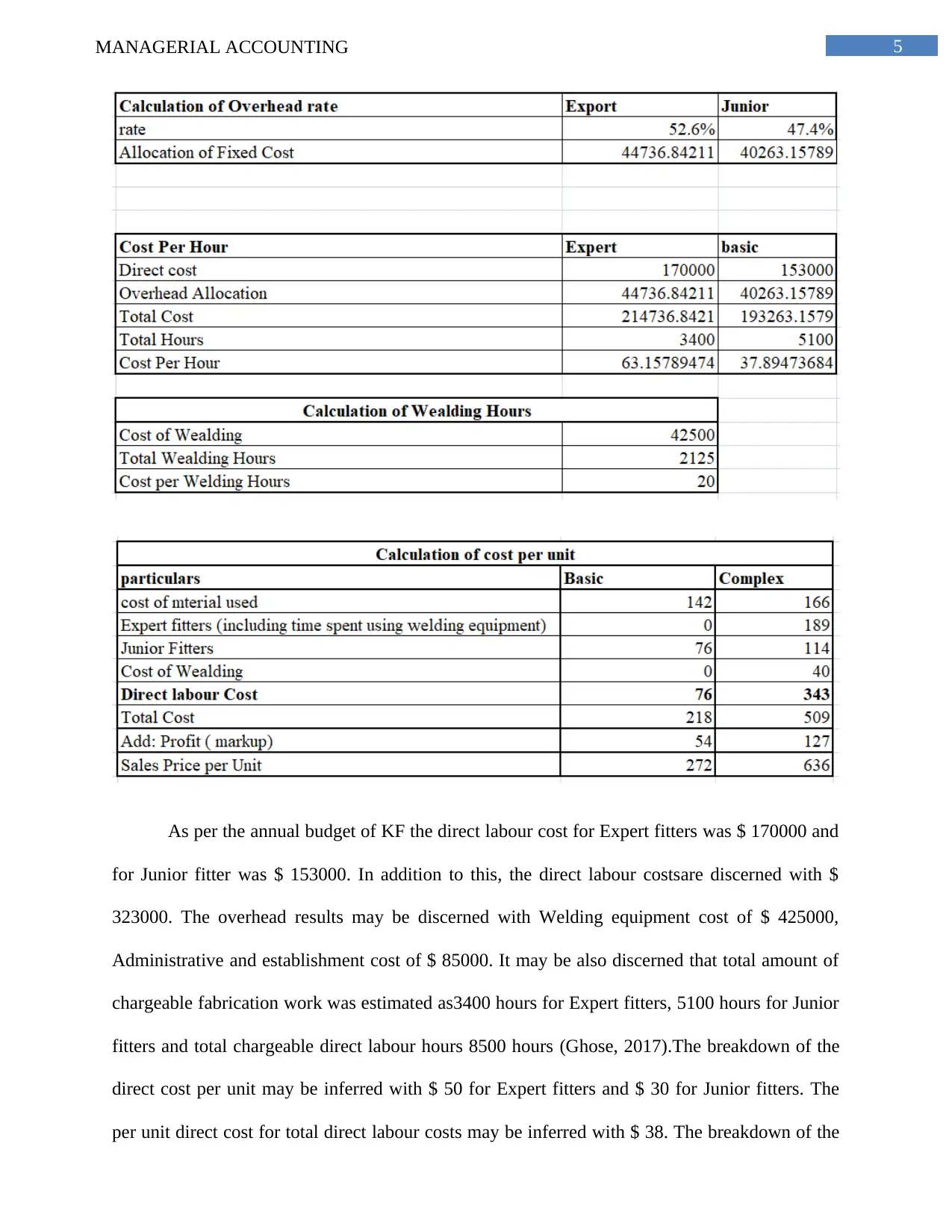
5MANAGERIAL ACCOUNTING
As per the annual budget of KF the direct labour cost for Expert fitters was $ 170000 and
for Junior fitter was $ 153000. In addition to this, the direct labour costsare discerned with $
323000. The overhead results may be discerned with Welding equipment cost of $ 425000,
Administrative and establishment cost of $ 85000. It may be also discerned that total amount of
chargeable fabrication work was estimated as3400 hours for Expert fitters, 5100 hours for Junior
fitters and total chargeable direct labour hours 8500 hours (Ghose, 2017).The breakdown of the
direct cost per unit may be inferred with $ 50 for Expert fitters and $ 30 for Junior fitters. The
per unit direct cost for total direct labour costs may be inferred with $ 38. The breakdown of the
As per the annual budget of KF the direct labour cost for Expert fitters was $ 170000 and
for Junior fitter was $ 153000. In addition to this, the direct labour costsare discerned with $
323000. The overhead results may be discerned with Welding equipment cost of $ 425000,
Administrative and establishment cost of $ 85000. It may be also discerned that total amount of
chargeable fabrication work was estimated as3400 hours for Expert fitters, 5100 hours for Junior
fitters and total chargeable direct labour hours 8500 hours (Ghose, 2017).The breakdown of the
direct cost per unit may be inferred with $ 50 for Expert fitters and $ 30 for Junior fitters. The
per unit direct cost for total direct labour costs may be inferred with $ 38. The breakdown of the
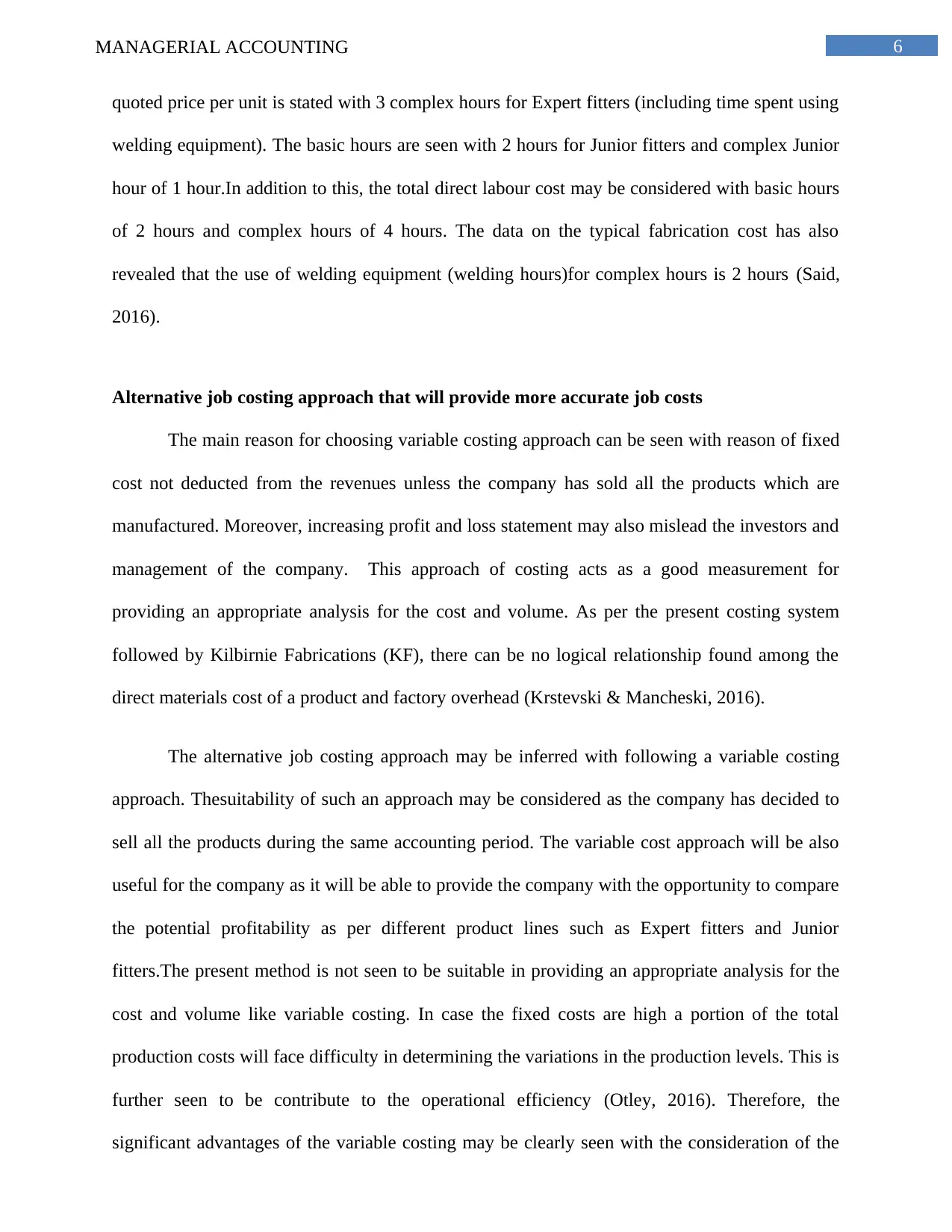
6MANAGERIAL ACCOUNTING
quoted price per unit is stated with 3 complex hours for Expert fitters (including time spent using
welding equipment). The basic hours are seen with 2 hours for Junior fitters and complex Junior
hour of 1 hour.In addition to this, the total direct labour cost may be considered with basic hours
of 2 hours and complex hours of 4 hours. The data on the typical fabrication cost has also
revealed that the use of welding equipment (welding hours)for complex hours is 2 hours (Said,
2016).
Alternative job costing approach that will provide more accurate job costs
The main reason for choosing variable costing approach can be seen with reason of fixed
cost not deducted from the revenues unless the company has sold all the products which are
manufactured. Moreover, increasing profit and loss statement may also mislead the investors and
management of the company. This approach of costing acts as a good measurement for
providing an appropriate analysis for the cost and volume. As per the present costing system
followed by Kilbirnie Fabrications (KF), there can be no logical relationship found among the
direct materials cost of a product and factory overhead (Krstevski & Mancheski, 2016).
The alternative job costing approach may be inferred with following a variable costing
approach. Thesuitability of such an approach may be considered as the company has decided to
sell all the products during the same accounting period. The variable cost approach will be also
useful for the company as it will be able to provide the company with the opportunity to compare
the potential profitability as per different product lines such as Expert fitters and Junior
fitters.The present method is not seen to be suitable in providing an appropriate analysis for the
cost and volume like variable costing. In case the fixed costs are high a portion of the total
production costs will face difficulty in determining the variations in the production levels. This is
further seen to be contribute to the operational efficiency (Otley, 2016). Therefore, the
significant advantages of the variable costing may be clearly seen with the consideration of the
quoted price per unit is stated with 3 complex hours for Expert fitters (including time spent using
welding equipment). The basic hours are seen with 2 hours for Junior fitters and complex Junior
hour of 1 hour.In addition to this, the total direct labour cost may be considered with basic hours
of 2 hours and complex hours of 4 hours. The data on the typical fabrication cost has also
revealed that the use of welding equipment (welding hours)for complex hours is 2 hours (Said,
2016).
Alternative job costing approach that will provide more accurate job costs
The main reason for choosing variable costing approach can be seen with reason of fixed
cost not deducted from the revenues unless the company has sold all the products which are
manufactured. Moreover, increasing profit and loss statement may also mislead the investors and
management of the company. This approach of costing acts as a good measurement for
providing an appropriate analysis for the cost and volume. As per the present costing system
followed by Kilbirnie Fabrications (KF), there can be no logical relationship found among the
direct materials cost of a product and factory overhead (Krstevski & Mancheski, 2016).
The alternative job costing approach may be inferred with following a variable costing
approach. Thesuitability of such an approach may be considered as the company has decided to
sell all the products during the same accounting period. The variable cost approach will be also
useful for the company as it will be able to provide the company with the opportunity to compare
the potential profitability as per different product lines such as Expert fitters and Junior
fitters.The present method is not seen to be suitable in providing an appropriate analysis for the
cost and volume like variable costing. In case the fixed costs are high a portion of the total
production costs will face difficulty in determining the variations in the production levels. This is
further seen to be contribute to the operational efficiency (Otley, 2016). Therefore, the
significant advantages of the variable costing may be clearly seen with the consideration of the
Paraphrase This Document
Need a fresh take? Get an instant paraphrase of this document with our AI Paraphraser
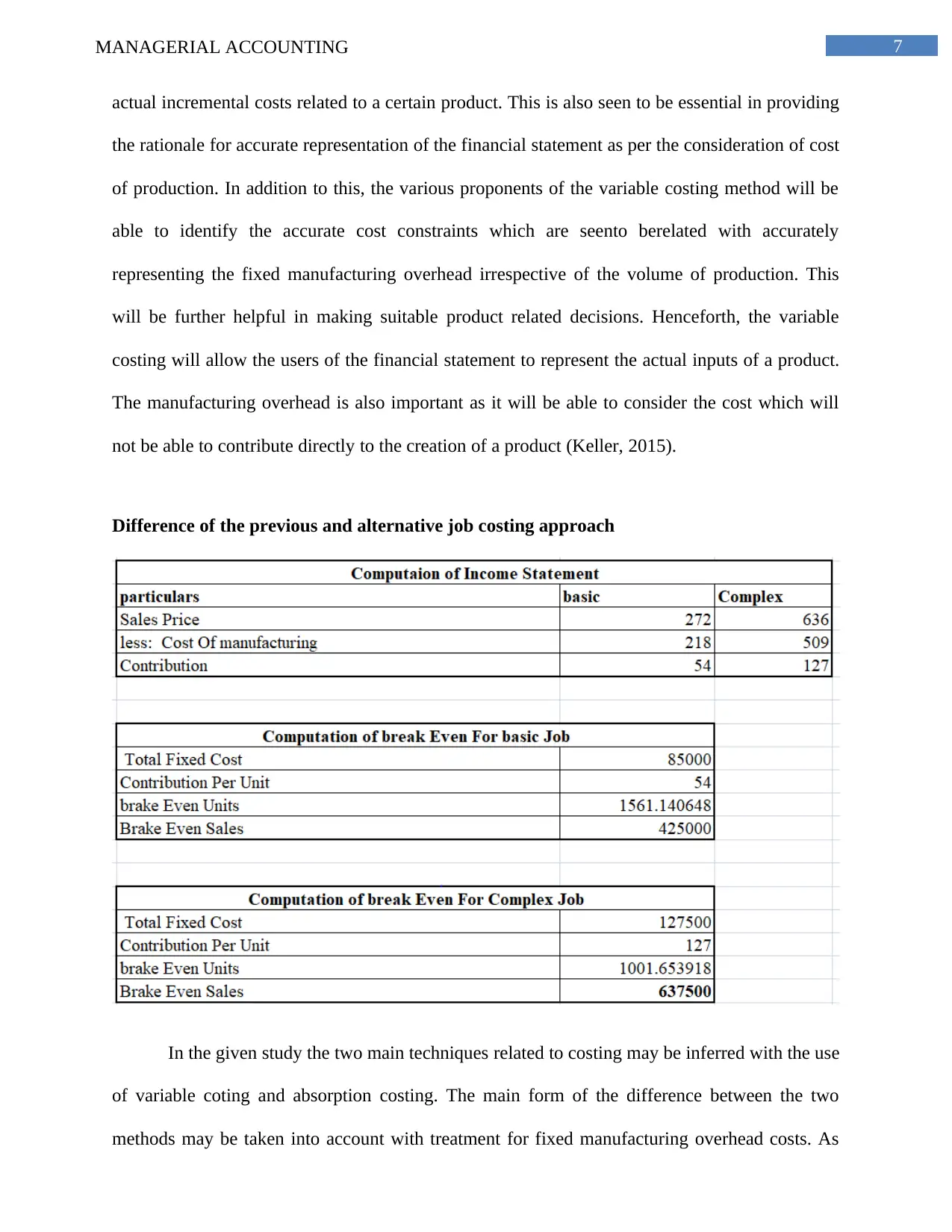
7MANAGERIAL ACCOUNTING
actual incremental costs related to a certain product. This is also seen to be essential in providing
the rationale for accurate representation of the financial statement as per the consideration of cost
of production. In addition to this, the various proponents of the variable costing method will be
able to identify the accurate cost constraints which are seento berelated with accurately
representing the fixed manufacturing overhead irrespective of the volume of production. This
will be further helpful in making suitable product related decisions. Henceforth, the variable
costing will allow the users of the financial statement to represent the actual inputs of a product.
The manufacturing overhead is also important as it will be able to consider the cost which will
not be able to contribute directly to the creation of a product (Keller, 2015).
Difference of the previous and alternative job costing approach
In the given study the two main techniques related to costing may be inferred with the use
of variable coting and absorption costing. The main form of the difference between the two
methods may be taken into account with treatment for fixed manufacturing overhead costs. As
actual incremental costs related to a certain product. This is also seen to be essential in providing
the rationale for accurate representation of the financial statement as per the consideration of cost
of production. In addition to this, the various proponents of the variable costing method will be
able to identify the accurate cost constraints which are seento berelated with accurately
representing the fixed manufacturing overhead irrespective of the volume of production. This
will be further helpful in making suitable product related decisions. Henceforth, the variable
costing will allow the users of the financial statement to represent the actual inputs of a product.
The manufacturing overhead is also important as it will be able to consider the cost which will
not be able to contribute directly to the creation of a product (Keller, 2015).
Difference of the previous and alternative job costing approach
In the given study the two main techniques related to costing may be inferred with the use
of variable coting and absorption costing. The main form of the difference between the two
methods may be taken into account with treatment for fixed manufacturing overhead costs. As
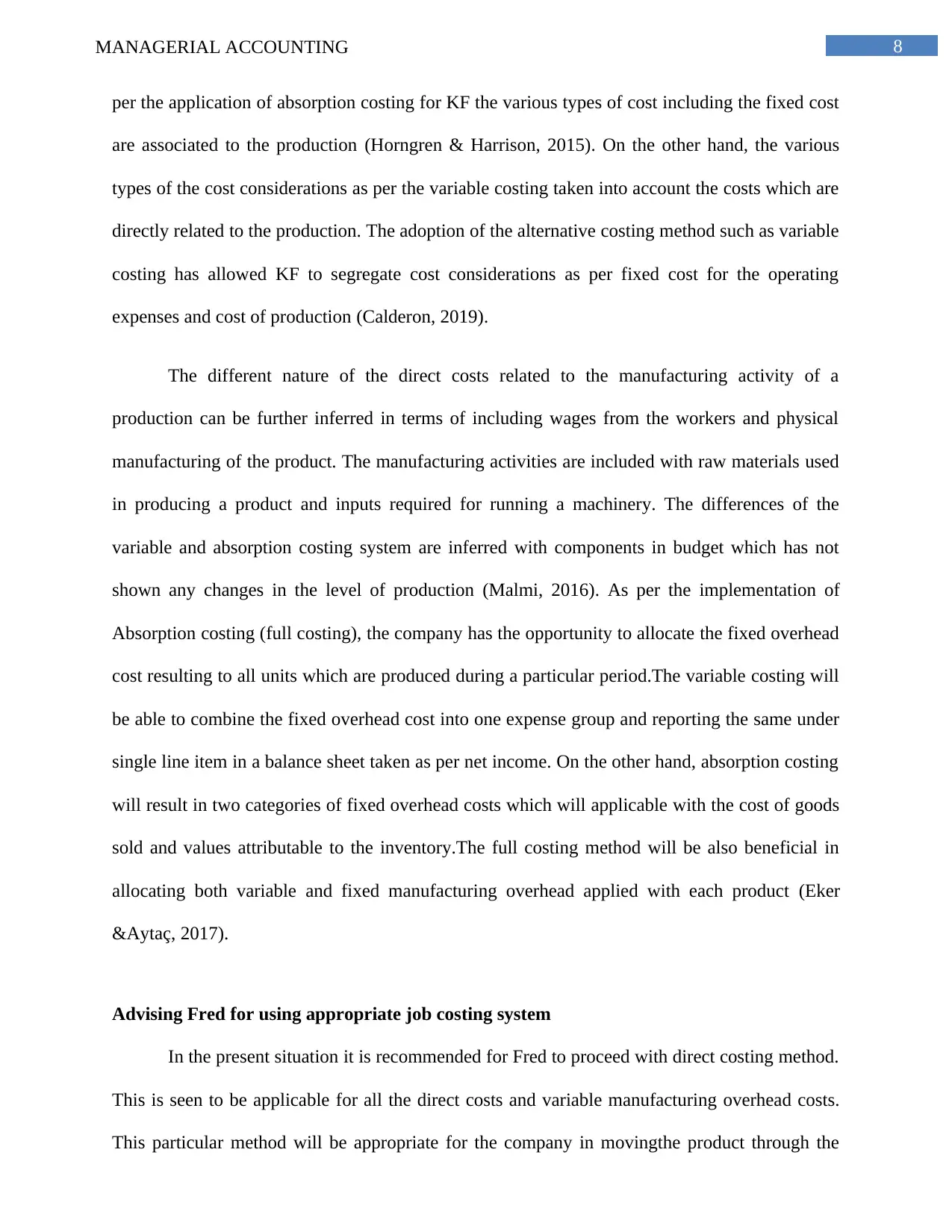
8MANAGERIAL ACCOUNTING
per the application of absorption costing for KF the various types of cost including the fixed cost
are associated to the production (Horngren & Harrison, 2015). On the other hand, the various
types of the cost considerations as per the variable costing taken into account the costs which are
directly related to the production. The adoption of the alternative costing method such as variable
costing has allowed KF to segregate cost considerations as per fixed cost for the operating
expenses and cost of production (Calderon, 2019).
The different nature of the direct costs related to the manufacturing activity of a
production can be further inferred in terms of including wages from the workers and physical
manufacturing of the product. The manufacturing activities are included with raw materials used
in producing a product and inputs required for running a machinery. The differences of the
variable and absorption costing system are inferred with components in budget which has not
shown any changes in the level of production (Malmi, 2016). As per the implementation of
Absorption costing (full costing), the company has the opportunity to allocate the fixed overhead
cost resulting to all units which are produced during a particular period.The variable costing will
be able to combine the fixed overhead cost into one expense group and reporting the same under
single line item in a balance sheet taken as per net income. On the other hand, absorption costing
will result in two categories of fixed overhead costs which will applicable with the cost of goods
sold and values attributable to the inventory.The full costing method will be also beneficial in
allocating both variable and fixed manufacturing overhead applied with each product (Eker
&Aytaç, 2017).
Advising Fred for using appropriate job costing system
In the present situation it is recommended for Fred to proceed with direct costing method.
This is seen to be applicable for all the direct costs and variable manufacturing overhead costs.
This particular method will be appropriate for the company in movingthe product through the
per the application of absorption costing for KF the various types of cost including the fixed cost
are associated to the production (Horngren & Harrison, 2015). On the other hand, the various
types of the cost considerations as per the variable costing taken into account the costs which are
directly related to the production. The adoption of the alternative costing method such as variable
costing has allowed KF to segregate cost considerations as per fixed cost for the operating
expenses and cost of production (Calderon, 2019).
The different nature of the direct costs related to the manufacturing activity of a
production can be further inferred in terms of including wages from the workers and physical
manufacturing of the product. The manufacturing activities are included with raw materials used
in producing a product and inputs required for running a machinery. The differences of the
variable and absorption costing system are inferred with components in budget which has not
shown any changes in the level of production (Malmi, 2016). As per the implementation of
Absorption costing (full costing), the company has the opportunity to allocate the fixed overhead
cost resulting to all units which are produced during a particular period.The variable costing will
be able to combine the fixed overhead cost into one expense group and reporting the same under
single line item in a balance sheet taken as per net income. On the other hand, absorption costing
will result in two categories of fixed overhead costs which will applicable with the cost of goods
sold and values attributable to the inventory.The full costing method will be also beneficial in
allocating both variable and fixed manufacturing overhead applied with each product (Eker
&Aytaç, 2017).
Advising Fred for using appropriate job costing system
In the present situation it is recommended for Fred to proceed with direct costing method.
This is seen to be applicable for all the direct costs and variable manufacturing overhead costs.
This particular method will be appropriate for the company in movingthe product through the
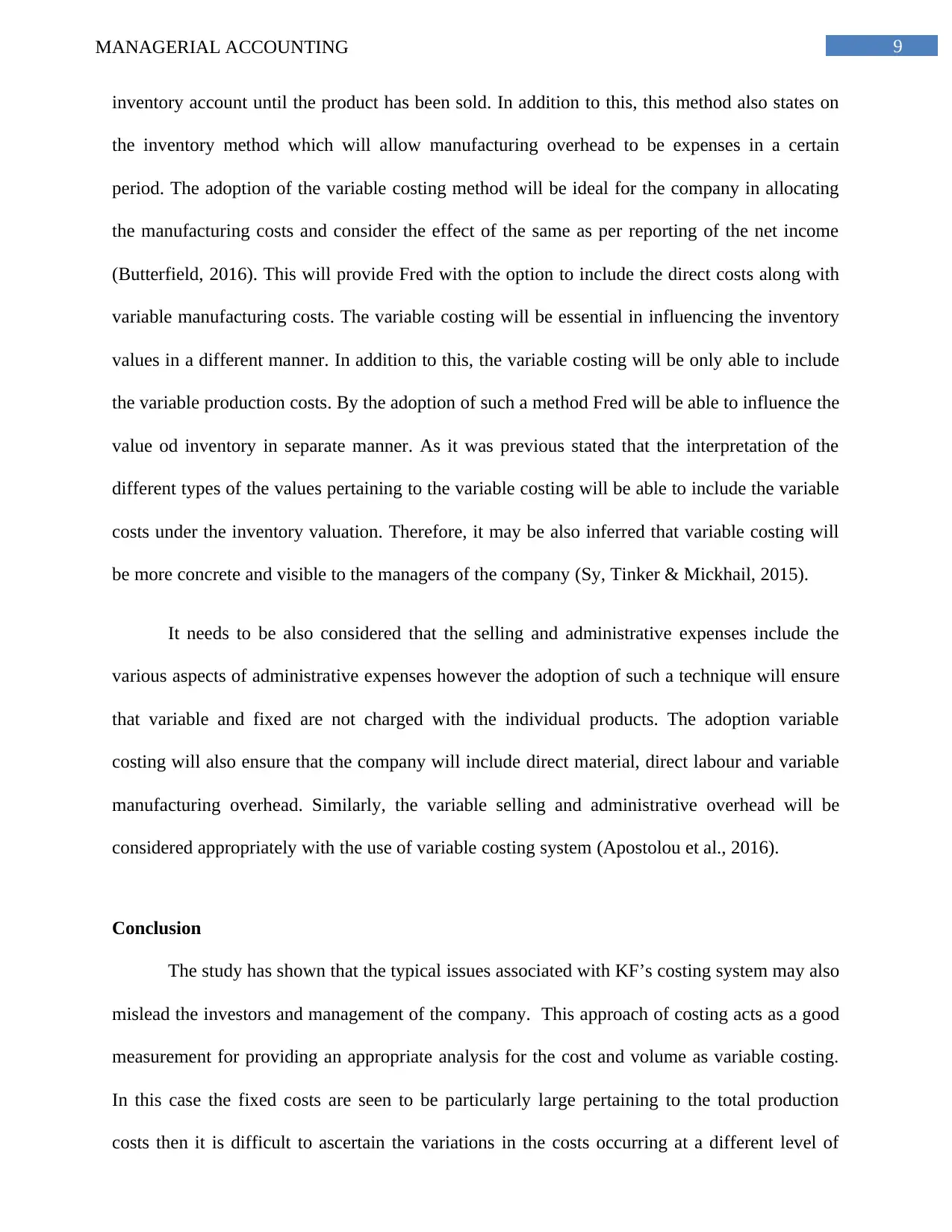
9MANAGERIAL ACCOUNTING
inventory account until the product has been sold. In addition to this, this method also states on
the inventory method which will allow manufacturing overhead to be expenses in a certain
period. The adoption of the variable costing method will be ideal for the company in allocating
the manufacturing costs and consider the effect of the same as per reporting of the net income
(Butterfield, 2016). This will provide Fred with the option to include the direct costs along with
variable manufacturing costs. The variable costing will be essential in influencing the inventory
values in a different manner. In addition to this, the variable costing will be only able to include
the variable production costs. By the adoption of such a method Fred will be able to influence the
value od inventory in separate manner. As it was previous stated that the interpretation of the
different types of the values pertaining to the variable costing will be able to include the variable
costs under the inventory valuation. Therefore, it may be also inferred that variable costing will
be more concrete and visible to the managers of the company (Sy, Tinker & Mickhail, 2015).
It needs to be also considered that the selling and administrative expenses include the
various aspects of administrative expenses however the adoption of such a technique will ensure
that variable and fixed are not charged with the individual products. The adoption variable
costing will also ensure that the company will include direct material, direct labour and variable
manufacturing overhead. Similarly, the variable selling and administrative overhead will be
considered appropriately with the use of variable costing system (Apostolou et al., 2016).
Conclusion
The study has shown that the typical issues associated with KF’s costing system may also
mislead the investors and management of the company. This approach of costing acts as a good
measurement for providing an appropriate analysis for the cost and volume as variable costing.
In this case the fixed costs are seen to be particularly large pertaining to the total production
costs then it is difficult to ascertain the variations in the costs occurring at a different level of
inventory account until the product has been sold. In addition to this, this method also states on
the inventory method which will allow manufacturing overhead to be expenses in a certain
period. The adoption of the variable costing method will be ideal for the company in allocating
the manufacturing costs and consider the effect of the same as per reporting of the net income
(Butterfield, 2016). This will provide Fred with the option to include the direct costs along with
variable manufacturing costs. The variable costing will be essential in influencing the inventory
values in a different manner. In addition to this, the variable costing will be only able to include
the variable production costs. By the adoption of such a method Fred will be able to influence the
value od inventory in separate manner. As it was previous stated that the interpretation of the
different types of the values pertaining to the variable costing will be able to include the variable
costs under the inventory valuation. Therefore, it may be also inferred that variable costing will
be more concrete and visible to the managers of the company (Sy, Tinker & Mickhail, 2015).
It needs to be also considered that the selling and administrative expenses include the
various aspects of administrative expenses however the adoption of such a technique will ensure
that variable and fixed are not charged with the individual products. The adoption variable
costing will also ensure that the company will include direct material, direct labour and variable
manufacturing overhead. Similarly, the variable selling and administrative overhead will be
considered appropriately with the use of variable costing system (Apostolou et al., 2016).
Conclusion
The study has shown that the typical issues associated with KF’s costing system may also
mislead the investors and management of the company. This approach of costing acts as a good
measurement for providing an appropriate analysis for the cost and volume as variable costing.
In this case the fixed costs are seen to be particularly large pertaining to the total production
costs then it is difficult to ascertain the variations in the costs occurring at a different level of
Secure Best Marks with AI Grader
Need help grading? Try our AI Grader for instant feedback on your assignments.
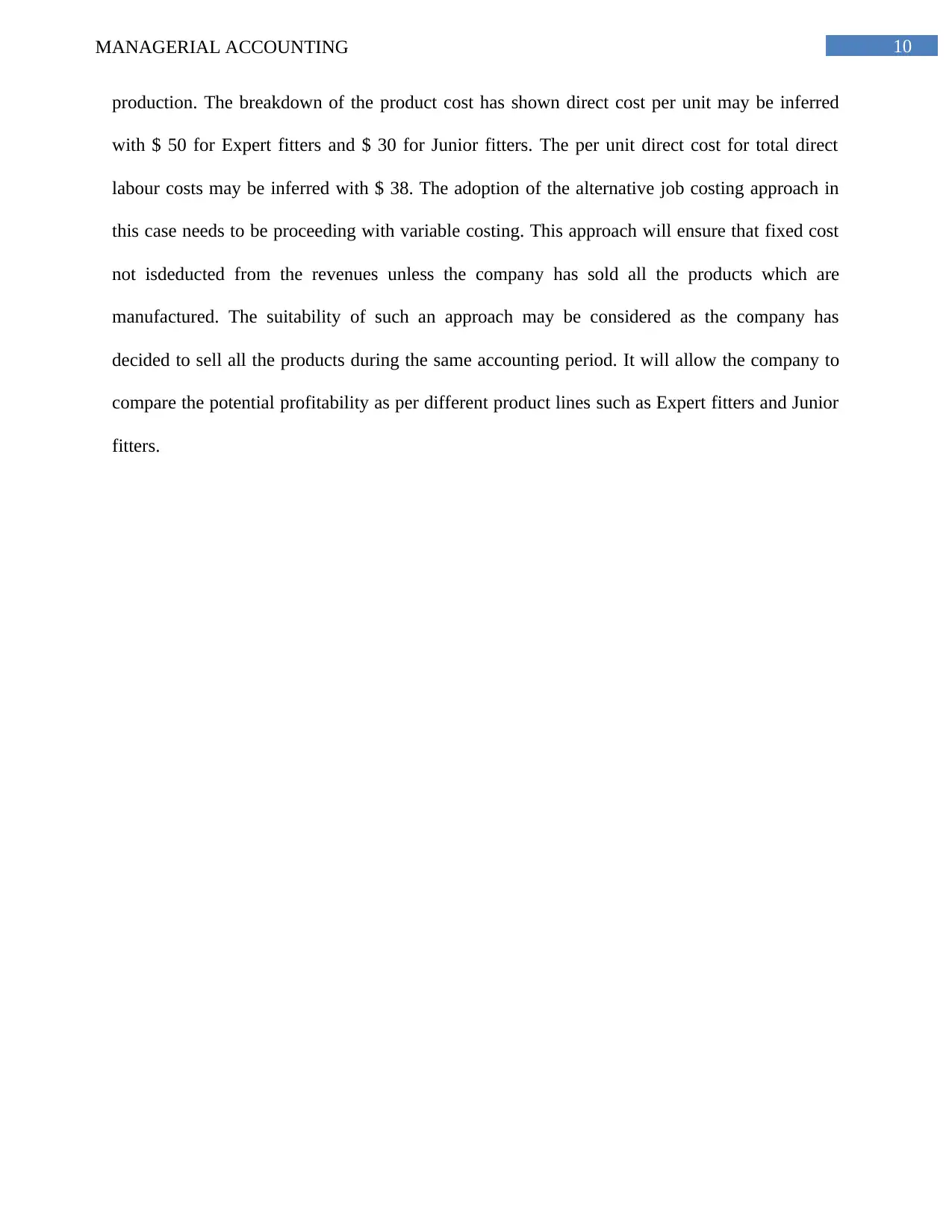
10MANAGERIAL ACCOUNTING
production. The breakdown of the product cost has shown direct cost per unit may be inferred
with $ 50 for Expert fitters and $ 30 for Junior fitters. The per unit direct cost for total direct
labour costs may be inferred with $ 38. The adoption of the alternative job costing approach in
this case needs to be proceeding with variable costing. This approach will ensure that fixed cost
not isdeducted from the revenues unless the company has sold all the products which are
manufactured. The suitability of such an approach may be considered as the company has
decided to sell all the products during the same accounting period. It will allow the company to
compare the potential profitability as per different product lines such as Expert fitters and Junior
fitters.
production. The breakdown of the product cost has shown direct cost per unit may be inferred
with $ 50 for Expert fitters and $ 30 for Junior fitters. The per unit direct cost for total direct
labour costs may be inferred with $ 38. The adoption of the alternative job costing approach in
this case needs to be proceeding with variable costing. This approach will ensure that fixed cost
not isdeducted from the revenues unless the company has sold all the products which are
manufactured. The suitability of such an approach may be considered as the company has
decided to sell all the products during the same accounting period. It will allow the company to
compare the potential profitability as per different product lines such as Expert fitters and Junior
fitters.
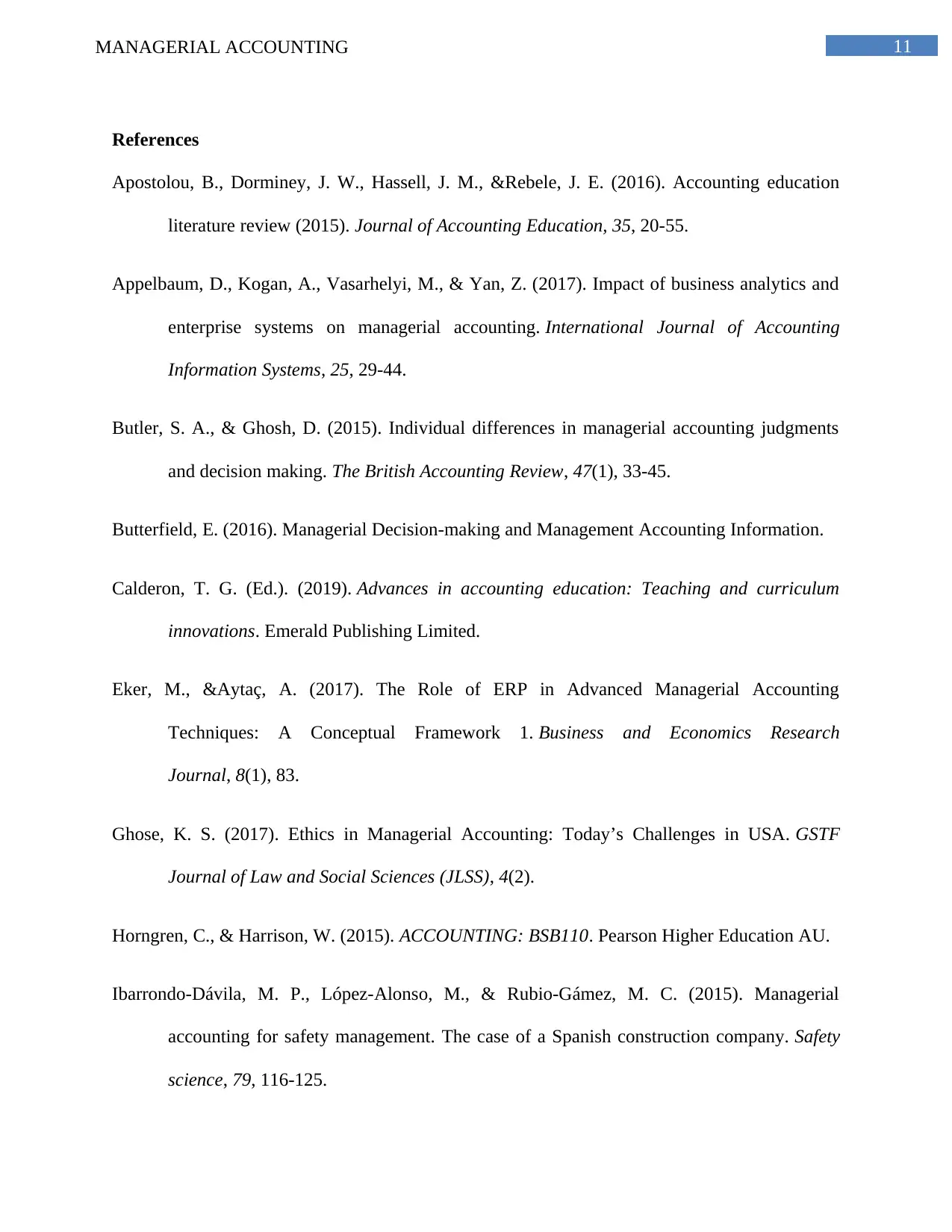
11MANAGERIAL ACCOUNTING
References
Apostolou, B., Dorminey, J. W., Hassell, J. M., &Rebele, J. E. (2016). Accounting education
literature review (2015). Journal of Accounting Education, 35, 20-55.
Appelbaum, D., Kogan, A., Vasarhelyi, M., & Yan, Z. (2017). Impact of business analytics and
enterprise systems on managerial accounting. International Journal of Accounting
Information Systems, 25, 29-44.
Butler, S. A., & Ghosh, D. (2015). Individual differences in managerial accounting judgments
and decision making. The British Accounting Review, 47(1), 33-45.
Butterfield, E. (2016). Managerial Decision-making and Management Accounting Information.
Calderon, T. G. (Ed.). (2019). Advances in accounting education: Teaching and curriculum
innovations. Emerald Publishing Limited.
Eker, M., &Aytaç, A. (2017). The Role of ERP in Advanced Managerial Accounting
Techniques: A Conceptual Framework 1. Business and Economics Research
Journal, 8(1), 83.
Ghose, K. S. (2017). Ethics in Managerial Accounting: Today’s Challenges in USA. GSTF
Journal of Law and Social Sciences (JLSS), 4(2).
Horngren, C., & Harrison, W. (2015). ACCOUNTING: BSB110. Pearson Higher Education AU.
Ibarrondo-Dávila, M. P., López-Alonso, M., & Rubio-Gámez, M. C. (2015). Managerial
accounting for safety management. The case of a Spanish construction company. Safety
science, 79, 116-125.
References
Apostolou, B., Dorminey, J. W., Hassell, J. M., &Rebele, J. E. (2016). Accounting education
literature review (2015). Journal of Accounting Education, 35, 20-55.
Appelbaum, D., Kogan, A., Vasarhelyi, M., & Yan, Z. (2017). Impact of business analytics and
enterprise systems on managerial accounting. International Journal of Accounting
Information Systems, 25, 29-44.
Butler, S. A., & Ghosh, D. (2015). Individual differences in managerial accounting judgments
and decision making. The British Accounting Review, 47(1), 33-45.
Butterfield, E. (2016). Managerial Decision-making and Management Accounting Information.
Calderon, T. G. (Ed.). (2019). Advances in accounting education: Teaching and curriculum
innovations. Emerald Publishing Limited.
Eker, M., &Aytaç, A. (2017). The Role of ERP in Advanced Managerial Accounting
Techniques: A Conceptual Framework 1. Business and Economics Research
Journal, 8(1), 83.
Ghose, K. S. (2017). Ethics in Managerial Accounting: Today’s Challenges in USA. GSTF
Journal of Law and Social Sciences (JLSS), 4(2).
Horngren, C., & Harrison, W. (2015). ACCOUNTING: BSB110. Pearson Higher Education AU.
Ibarrondo-Dávila, M. P., López-Alonso, M., & Rubio-Gámez, M. C. (2015). Managerial
accounting for safety management. The case of a Spanish construction company. Safety
science, 79, 116-125.
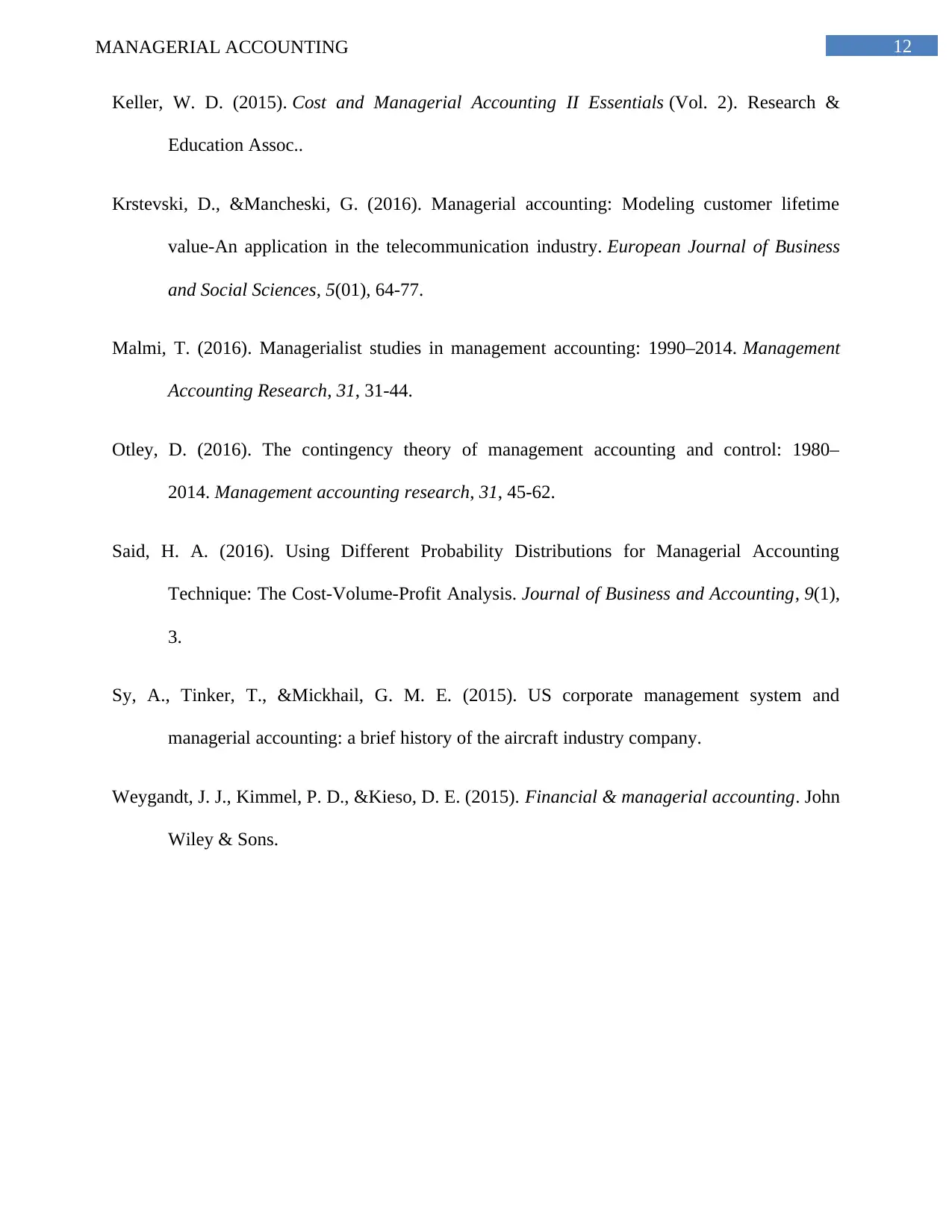
12MANAGERIAL ACCOUNTING
Keller, W. D. (2015). Cost and Managerial Accounting II Essentials (Vol. 2). Research &
Education Assoc..
Krstevski, D., &Mancheski, G. (2016). Managerial accounting: Modeling customer lifetime
value-An application in the telecommunication industry. European Journal of Business
and Social Sciences, 5(01), 64-77.
Malmi, T. (2016). Managerialist studies in management accounting: 1990–2014. Management
Accounting Research, 31, 31-44.
Otley, D. (2016). The contingency theory of management accounting and control: 1980–
2014. Management accounting research, 31, 45-62.
Said, H. A. (2016). Using Different Probability Distributions for Managerial Accounting
Technique: The Cost-Volume-Profit Analysis. Journal of Business and Accounting, 9(1),
3.
Sy, A., Tinker, T., &Mickhail, G. M. E. (2015). US corporate management system and
managerial accounting: a brief history of the aircraft industry company.
Weygandt, J. J., Kimmel, P. D., &Kieso, D. E. (2015). Financial & managerial accounting. John
Wiley & Sons.
Keller, W. D. (2015). Cost and Managerial Accounting II Essentials (Vol. 2). Research &
Education Assoc..
Krstevski, D., &Mancheski, G. (2016). Managerial accounting: Modeling customer lifetime
value-An application in the telecommunication industry. European Journal of Business
and Social Sciences, 5(01), 64-77.
Malmi, T. (2016). Managerialist studies in management accounting: 1990–2014. Management
Accounting Research, 31, 31-44.
Otley, D. (2016). The contingency theory of management accounting and control: 1980–
2014. Management accounting research, 31, 45-62.
Said, H. A. (2016). Using Different Probability Distributions for Managerial Accounting
Technique: The Cost-Volume-Profit Analysis. Journal of Business and Accounting, 9(1),
3.
Sy, A., Tinker, T., &Mickhail, G. M. E. (2015). US corporate management system and
managerial accounting: a brief history of the aircraft industry company.
Weygandt, J. J., Kimmel, P. D., &Kieso, D. E. (2015). Financial & managerial accounting. John
Wiley & Sons.
1 out of 13
Related Documents
![[object Object]](/_next/image/?url=%2F_next%2Fstatic%2Fmedia%2Flogo.6d15ce61.png&w=640&q=75)
Your All-in-One AI-Powered Toolkit for Academic Success.
+13062052269
info@desklib.com
Available 24*7 on WhatsApp / Email
Unlock your academic potential
© 2024 | Zucol Services PVT LTD | All rights reserved.